Презентация по технической механике «Валы и оси»
Инфоурок › Другое › Презентации › Презентация по технической механике «Валы и оси»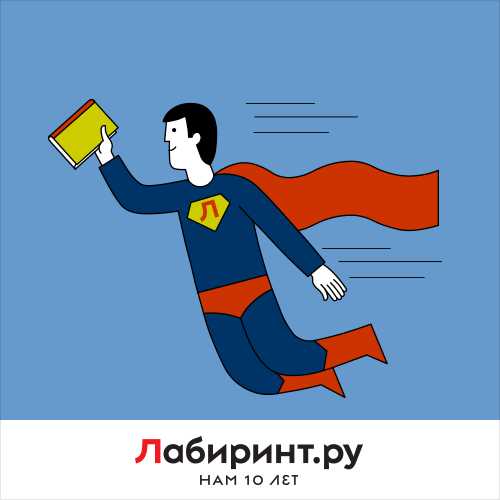
Описание презентации по отдельным слайдам:
1 слайд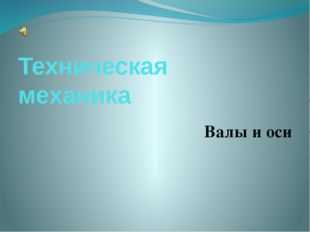
Техническая механика Валы и оси
2 слайд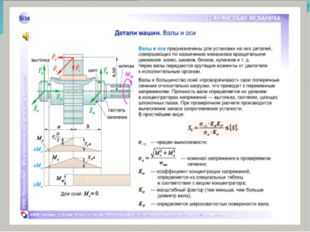
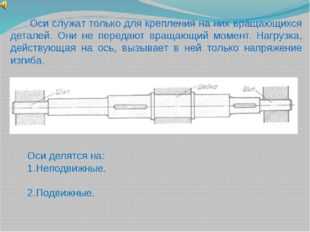
Оси служат только для крепления на них вращающихся деталей. Они не передают вращающий момент. Нагрузка, действующая на ось, вызывает в ней только напряжение изгиба. Оси делятся на: 1.Неподвижные. 2.Подвижные.
4 слайд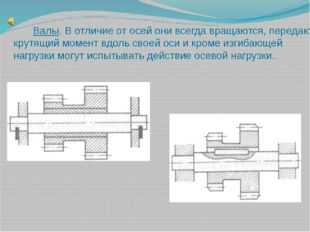
Валы. В отличие от осей они всегда вращаются, передают крутящий момент вдоль своей оси и кроме изгибающей нагрузки могут испытывать действие осевой нагрузки..
5 слайд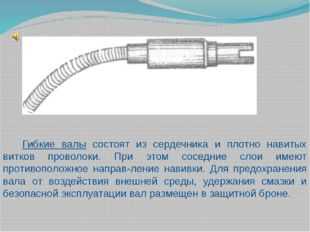
Гибкие валы состоят из сердечника и плотно навитых витков проволоки. При этом соседние слои имеют противоположное направление навивки. Для предохранения вала от воздействия внешней среды, удержания смазки и безопасной эксплуатации вал размещен в защитной броне.
6 слайд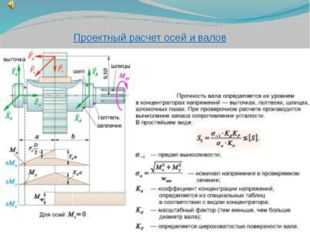
Проектный расчет осей и валов
7 слайд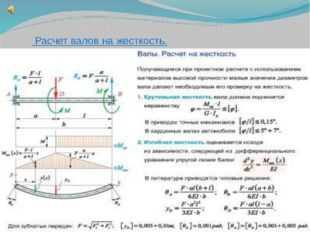
Расчет валов на жесткость.
8 слайд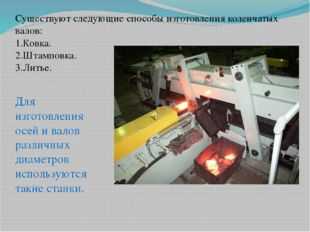
Для изготовления осей и валов различных диаметров используются такие станки. Существуют следующие способы изготовления коленчатых валов: 1.Ковка. 2.Штамповка. 3.Литье.
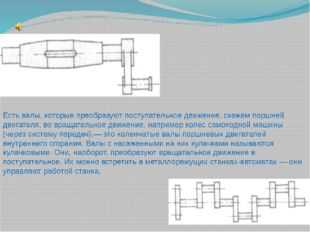
Есть валы, которые преобразуют поступательное движение, скажем поршней двигателя, во вращательное движение, например колес самоходной машины (через систему передач),— это коленчатые валы поршневых двигателей внутреннего сгорания. Валы с насаженными на них кулачками называются кулачковыми. Они, наоборот, преобразуют вращательное движение в поступательное. Их можно встретить в металлорежущих станках-автоматах — они управляют работой станка.
10 слайд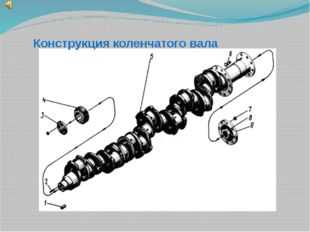
Конструкция коленчатого вала
11 слайд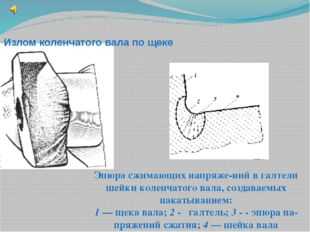
Излом коленчатого вала по щеке Эпюра сжимающих напряжений в галтели шейки коленчатого вала, создаваемых накатыванием: 1 — щека вала; 2 — галтель; 3 — — эпюра напряжений сжатия; 4 — шейка вала
12 слайд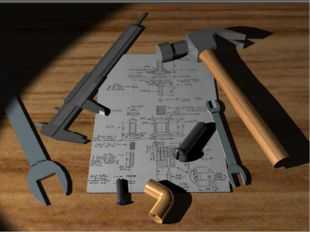
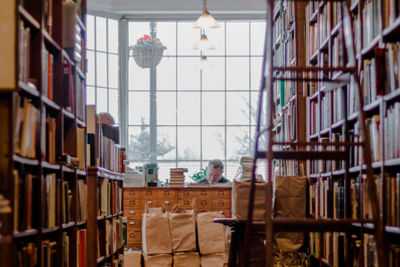
Курс повышения квалификации
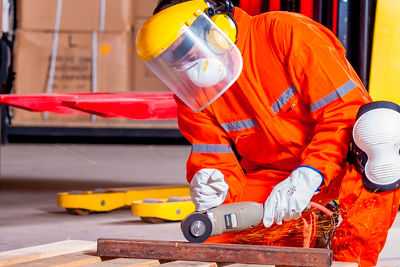
Курс профессиональной переподготовки
Специалист по охране труда
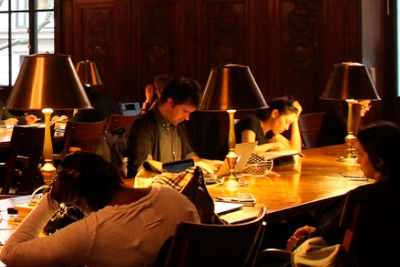
Курс профессиональной переподготовки
Библиотекарь
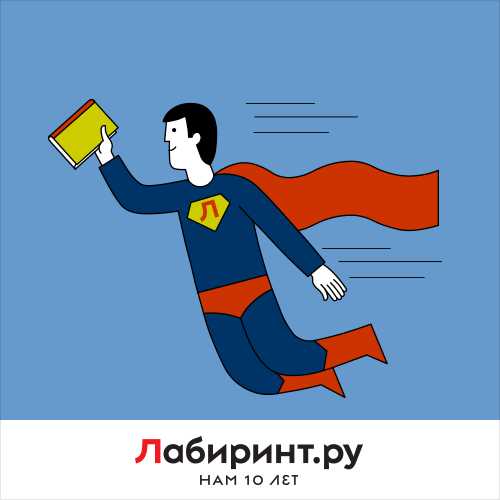
Найдите материал к любому уроку,
указав свой предмет (категорию), класс, учебник и тему:
Выберите категорию: Все категорииАлгебраАнглийский языкАстрономияБиологияВсеобщая историяГеографияГеометрияДиректору, завучуДоп. образованиеДошкольное образованиеЕстествознаниеИЗО, МХКИностранные языкиИнформатикаИстория РоссииКлассному руководителюКоррекционное обучениеЛитератураЛитературное чтениеЛогопедияМатематикаМузыкаНачальные классыНемецкий языкОБЖОбществознаниеОкружающий мирПриродоведениеРелигиоведениеРусский языкСоциальному педагогуТехнологияУкраинский языкФизикаФизическая культураФилософияФранцузский языкХимияЧерчениеШкольному психологуЭкологияДругое
Выберите класс: Все классыДошкольники1 класс2 класс3 класс4 класс5 класс6 класс7 класс8 класс9 класс10 класс11 класс
Выберите учебник: Все учебники
Выберите тему: Все темы
также Вы можете выбрать тип материала:
Общая информация
Номер материала: ДВ-520258
ВНИМАНИЮ ВСЕХ УЧИТЕЛЕЙ: согласно Федеральному закону N273-ФЗ «Об образовании в Российской Федерации» педагогическая деятельность требует от педагога наличия системы специальных знаний в области обучения и воспитания детей с ОВЗ. Поэтому для всех педагогов является актуальным повышение квалификации по этому направлению!Подать заявку на курс
Похожие материалы
Вам будут интересны эти курсы:
Оставьте свой комментарийinfourok.ru
Расчет стального вала | Лекции и примеры решения задач механики
Задача
Стальной вал круглого сплошного и кольцевого сечения нагружен скручивающими моментами m0, m1=3кНм, m2=5кНм, m3=3кНм, m4=4кНм.
Расчетная схема вала:
Требуется спроектировать ступенчатый вал заданной формы (по конструктивным соображениям, диаметр вала на участках 1-3 и 4-5 должен быть одинаков, причем на участке 1-2 вал имеет кольцевое сечение с соотношением внутреннего и наружного диаметров: c=d/D=0,4) и построить эпюры крутящих моментов и углов закручивания сечений.
Показать напряженное состояние по участкам вала.
Принять:
Решение
Посмотреть теорию по теме «Кручение»
Определение неизвестного момента
Определим величину и направление момента m0.
Направим m0 произвольно, например, по ходу часовой стрелки.
находим
Здесь, знак “-” показывает, что направление m0 нужно изменить на противоположное.
Расчет крутящих моментов
Величину крутящих моментов на участках вала определяем методом сечений.
С учетом правила знаков, получаем:
По этим значениям строим эпюру крутящих моментов T:
Расчет диаметров вала
Диаметры вала будем определять из условия прочности.
На участках I, II и IV диаметр вала одинаков.
Наружный диаметр кольцевого (полого) участка:
Сравнивая TII и TIV видим, что TII>TIV, поэтому:
Так как 63,38>58,08 мм, выбираем большее значение.
Окончательно, согласно ГОСТ 6636, принимаем стандартное значение диаметра:
Диаметр вала на III участке (TIII=7кНм)
По ГОСТ, принимаем DIII=80мм.
Расчет геометрических характеристик
Вычислим геометрические характеристики сечений на участках вала.
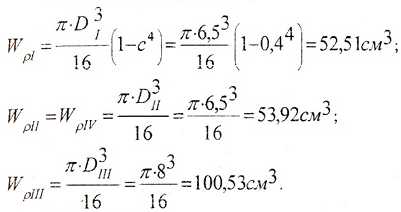
Моменты инерции
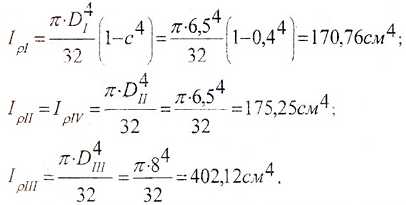
Расчет касательных напряжений
Вычисляем максимальные касательные напряжения на участках по формуле:
Определяем углы закручивания участков:
Построение эпюры перемещений
Рассчитаем углы закручивания характерных сечений.
Примем крайнее левое сечение вала за условно неподвижное.
По этим значениям строим эпюру углов закручивания сечений и вычерчиваем эскиз спроектированного вала.
Другие примеры решения задач >
Лекции по сопромату >
isopromat.ru
Предмет «Техническая механика» Тема урока «Валы и оси»
Материал предназначен для студенов, изучающих предмет «Техническая механика»
Просмотр содержимого документа
«Предмет «Техническая механика» Тема урока «Валы и оси»»
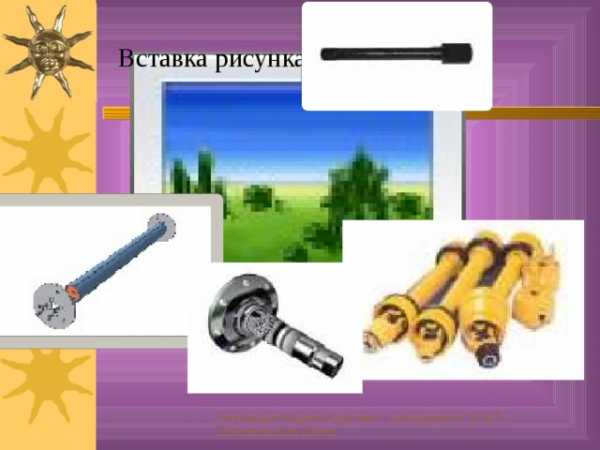
Вставка рисунка
ВАЛЫ И ОСИ
Бобровицкая Марина Борисовна – преподаватель КСМТ г. Комсомольск-на-Амуре
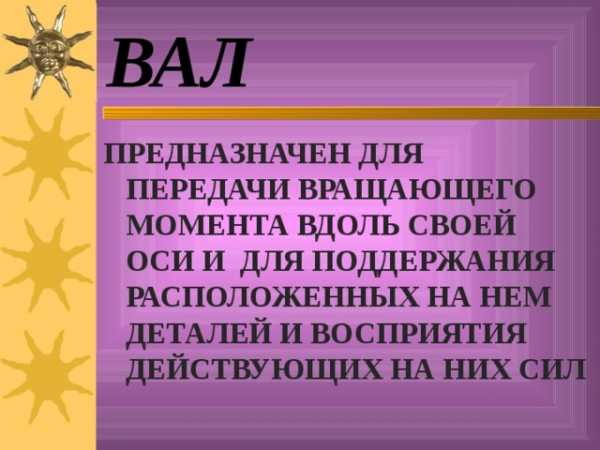
ВАЛ
ПРЕДНАЗНАЧЕН ДЛЯ ПЕРЕДАЧИ ВРАЩАЮЩЕГО МОМЕНТА ВДОЛЬ СВОЕЙ ОСИ И ДЛЯ ПОДДЕРЖАНИЯ РАСПОЛОЖЕННЫХ НА НЕМ ДЕТАЛЕЙ И ВОСПРИЯТИЯ ДЕЙСТВУЮЩИХ НА НИХ СИЛ
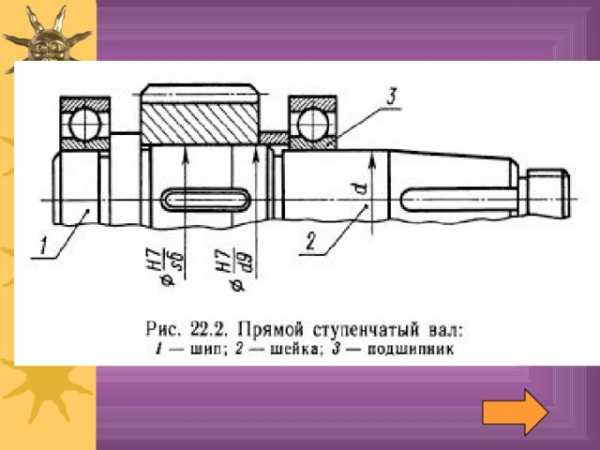
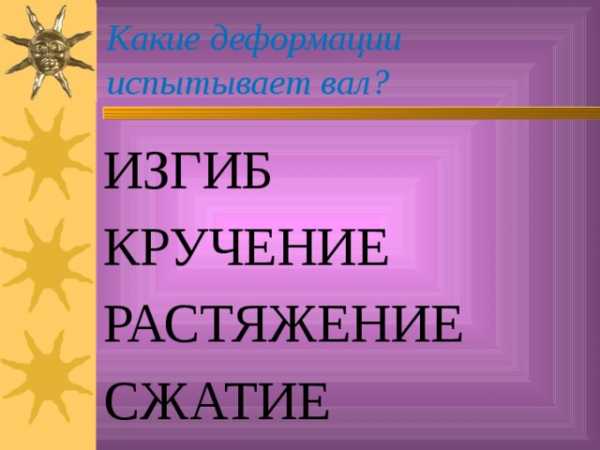
Какие деформации испытывает вал?
ИЗГИБ
КРУЧЕНИЕ
РАСТЯЖЕНИЕ
СЖАТИЕ
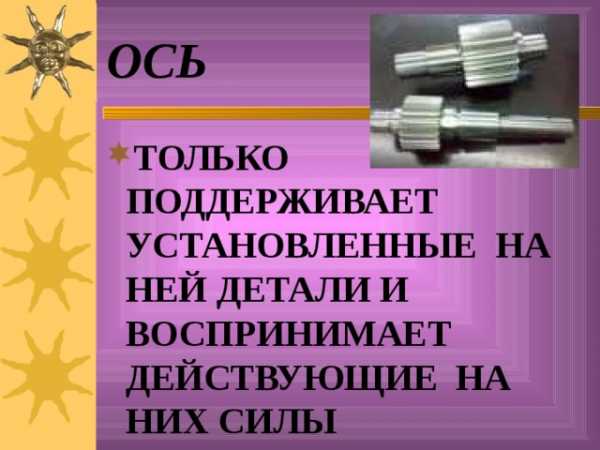
ОСЬ
- ТОЛЬКО ПОДДЕРЖИВАЕТ УСТАНОВЛЕННЫЕ НА НЕЙ ДЕТАЛИ И ВОСПРИНИМАЕТ ДЕЙСТВУЮЩИЕ НА НИХ СИЛЫ
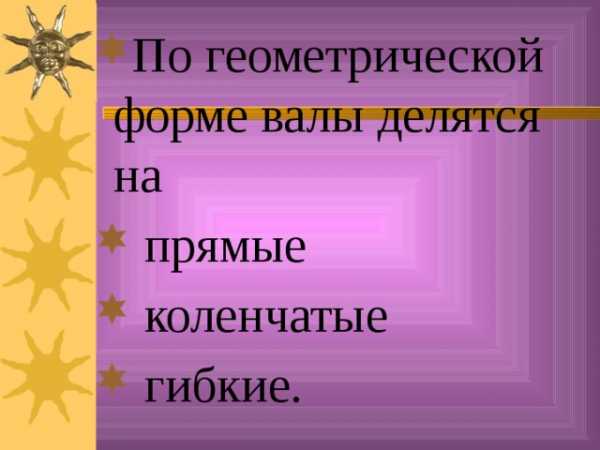
- По геометрической форме валы делятся на
- прямые
- коленчатые
- гибкие.
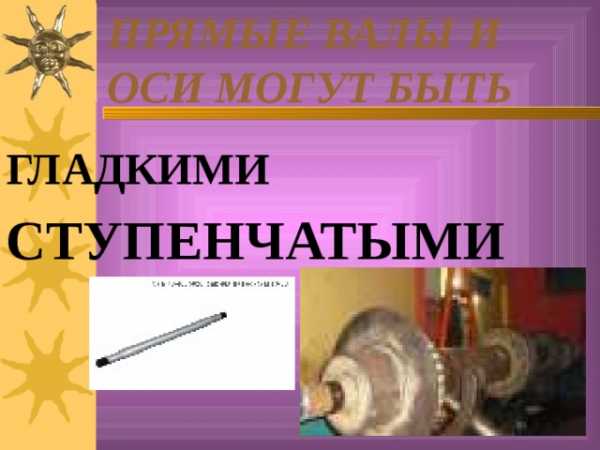
ПРЯМЫЕ ВАЛЫ И ОСИ МОГУТ БЫТЬ
ГЛАДКИМИ
СТУПЕНЧАТЫМИ
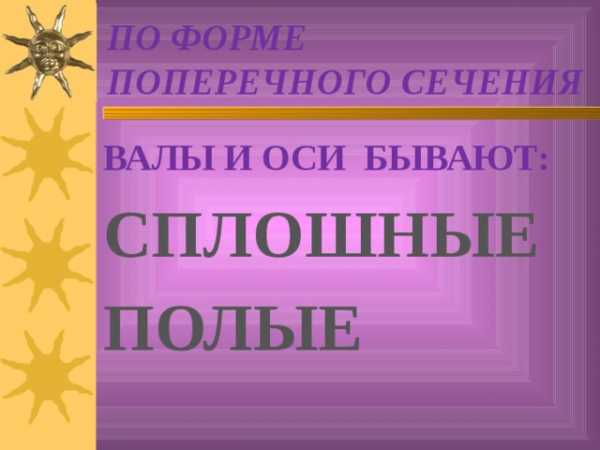
ПО ФОРМЕ ПОПЕРЕЧНОГО СЕЧЕНИЯ
ВАЛЫ И ОСИ БЫВАЮТ:
СПЛОШНЫЕ
ПОЛЫЕ
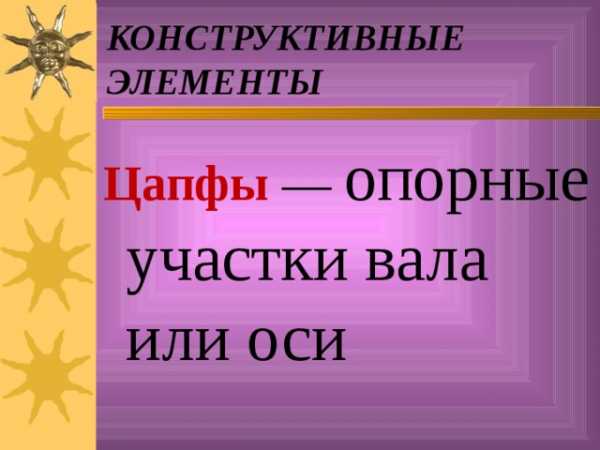
КОНСТРУКТИВНЫЕ ЭЛЕМЕНТЫ
Цапфы — опорные участки вала или оси
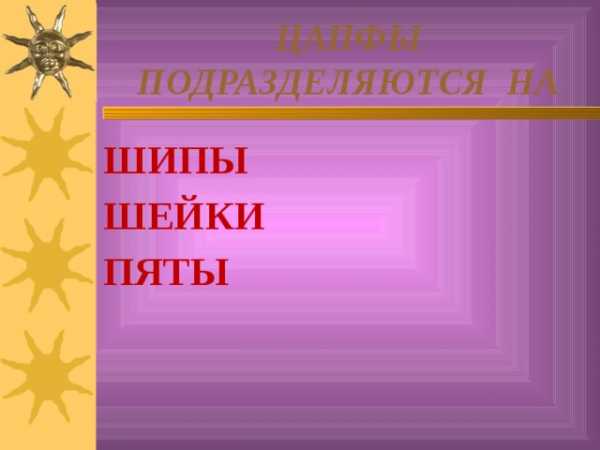
ЦАПФЫ ПОДРАЗДЕЛЯЮТСЯ НА
ШИПЫ
ШЕЙКИ
ПЯТЫ
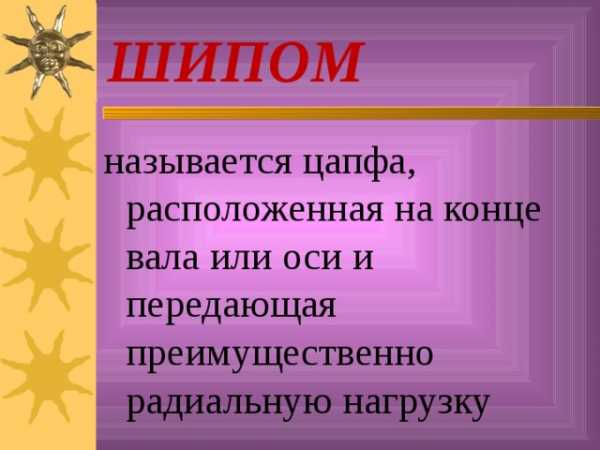
ШИПОМ
называется цапфа, расположенная на конце вала или оси и передающая преимущественно радиальную нагрузку

ШЕЙКОЙ
называется цапфа, расположенная в средней части вала или оси
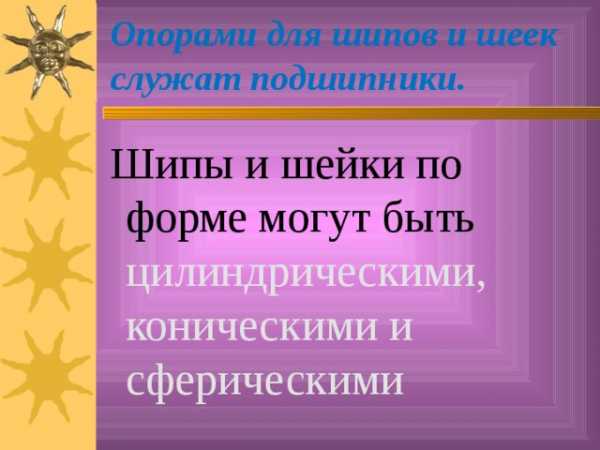
Опорами для шипов и шеек служат подшипники.
Шипы и шейки по форме могут быть цилиндрическими, коническими и сферическими
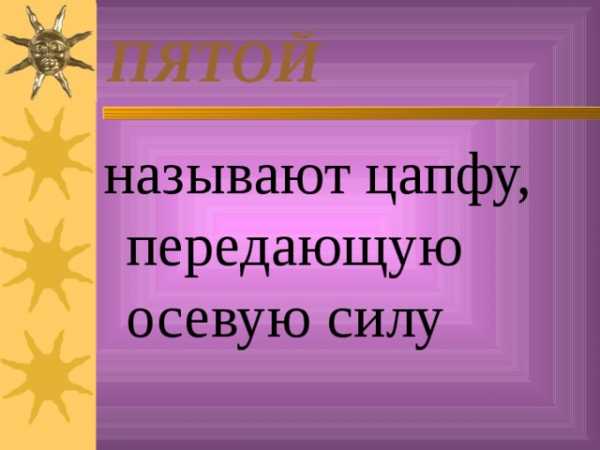
ПЯТОЙ
называют цапфу, передающую осевую силу
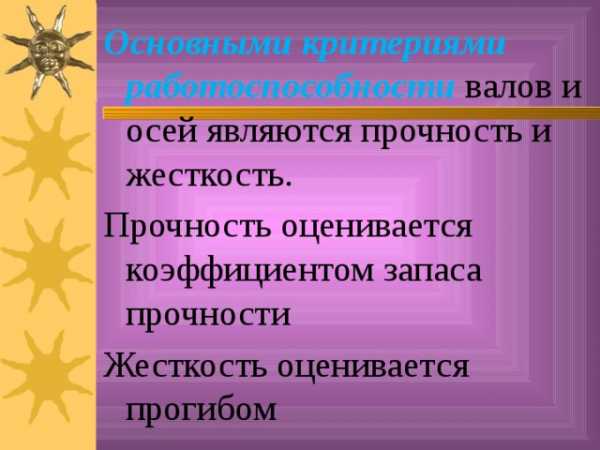
Основными критериями работоспособности валов и осей являются прочность и жесткость.
Прочность оценивается коэффициентом запаса прочности
Жесткость оценивается прогибом
kopilkaurokov.ru
Прикладная механика Расчет вала 6-6.2.4 (2)
6.1 Предварительный расчет тихоходного вала
Расчет выполняется на кручение по пониженным допускаемым напряжениям [k]. Ориентировочно определяем диаметр вала в опасном сечении в мм по формуле
d2===50.31 мм
Т – крутящий момент на валу, [Нм]
Полученный результат округляем до ближайшего значения из стандартного ряда
d2=50
Табл.9 Размеры участков тихоходного вала
№ участка | Диаметр, мм | Длина, мм |
1 | d1=45 | l1=(1,5..2) d1=45*1,5=67,5 |
2 | d2=d1+5=45+5=50 | l2= L2-В-n+ Lк+У=55-21- 7+18+5=50 |
3 | d3= d1+10=45+10=55 | l3=(20..30)+В=20+21=41 |
4 | d4=d3+5=55+5=60 | l4= Lст-2=66-2=64 |
5 | d5= d4+(3…4)С3=60+3*2=66 | L5=12 |
6 | d6=64 | L6=12 |
7 | D7=55 | L7=В=21 |
где С3-фаска посадочного отверстия зубчатого колеса
Табл.10 Размеры фасок отверстия
d,мм | 30 | 30…50 | 50…80 | 80…120 | 120…150 | 150…250 | 250…500 |
С3,мм | 1.0 | 1.6 | 2.0 | 2.5 | 3.0 | 4.0 | 5.0 |
6.1.1 Расчет элементов корпуса редуктора
Толщина стенки корпуса редуктора определяется по формуле
=0.025+1=0.025*140+1=4,58 мм.
=8 мм.
Диаметр фундаментного болта равен dб1=0.036+12=0.036*140+12=17,04.
Выбираем М20Полученное значение округляют до ближайшего большего диаметра болта из ряда в табл11.
Табл.11. Размеры элементов корпуса редуктора
Параметр | Диаметр болта | ||||||
М8 | М10 | М12 | М16 | М20 | М24 | М30 | |
aj | 13 | 15 | 18 | 21 | 25 | 28 | 35 |
bj | 24 | 28 | 33 | 40 | 48 | 55 | 68 |
d0 | 9 | 11 | 13 | 17 | 22 | 26 | 32 |
D0 | 17 | 20 | 25 | 30 | 38 | 45 | 56 |
Диаметры
болтов крепления крышки корпуса к
основанию (рис.2) равны: у подшипников
dб2=(0.7…0.75)
dб1=0.75*20=15
Выбираем М16
на фланцах dб3=(0.5…0.6) dб1=0.5*20=10.
Выбираем М8
Полученные значения округляют до ближайших диаметров болта из ряда в табл.2. В этой же табл. даны диаметры отверстий d0 и диаметры зенковок или бобышек D0 для соответствующих болтов.
Расстояние от внутренней стенки корпуса до края лапы L1=3++b1=3+8+48=59и до оси фундаментного болта Р1=3++a1=3+8+25=36, где a1 и b1 определяются по табл.2 в зависимости от диаметра болта.
Ширина фланцев у подшипников L2=3++t+b2=3+8+4+40=55, где t=4 мм – высота бобышки. Расстояние от внутренней стенки корпуса до оси болта с диаметром d2 равно Р2=3++a2=3+8+21=32.
Ширина боковых фланцев L3=3++b3=3+8+28=39, расстояние от внутренней стенки корпуса до оси болта с диаметром dб3 равно Р3=3++a3=3+8+10=21.
Расстояние от оси болта с диаметром dб2 до оси вала равно Lb2=0,5D2+(1…1,25) dб2, где Dj – наружные диаметры подшипников тихоходного валов. Lb2=0,5*80+16 =56.
Для сравнительно малого межосевого расстояния D1+D2+5dб2 между подшипниками устанавливают один болт, размещая его посредине между расточками в корпусе для подшипников.
Расстояние y от головки болта до границы хвостовика вала зависит от межосевого расстояния и выбирается из диапазона y=10 мм.
Предварительный расчет быстроходного вала
d1===28.19 мм.
d1=28мм
Табл.12. Размеры участков быстроходного вала
№ участка | Диаметр, мм |
1 | d1=23 |
2 | d2=28 |
3 | d3=35 |
4 | d4=43 |
5 | Вал-шестерня |
6 | d6=43 |
7 | D7=35 |
Конструирование цилиндрических зубчатых колес
Основные размеры кованых и штампованных зубчатых колес, представленных на рис.2, определяются следующими зависимостями.
Диаметр
ступицы: стальной DC=1.55•d=1,55*60=93
где d – диаметр посадочного отверстия зубчатого колеса.
Длина ступицы
LC=(1,1…1,5)• d4bw=1,1*60=66
где bw – ширина зубчатого венца колеса.
Толщина обода
A1=(5…6)•m=5*2=10
где m – модуль передачи.
Толщина диска e=0.3•bw=0,3*65=16,8
Диаметр центровой окружности
D0=0.5(da-2A1+dC)=0,5(222,69-2*10+93)=147,845
где da – диаметр окружности вершин зубьев колеса.
Диаметр отверстий d0
d0=0.25(da-2A1-dC)=0,25(222,69-2*10-93)=27,4225
Размер фаски посадочного отверстия определяют по табл.1
Рис.2 Основные размеры зубчатых колес
Табл.13 Размеры фасок отверстия
d,мм | 30 | 30…50 | 50…80 | 80…120 | 120…150 | 150…250 | 250…500 |
| 1.0 | 1.6 | 2.0 | 2.5 | 3.0 | 4.0 | 5.0 |
Размер фаски зубчатого венца определяют по формуле C1=0.5mи округляют до ближайшего значения по табл.13. Размер фаскиC2принимают равным 2…3 мм. РадиусRравен 4…10 мм.
6.2.2
Выбор подшипников
Выбраны подшипники шариковые радиальные однорядные (ГОСТ 8338-75) 212 легкой серии, характеристики которых занесены в таблицу 14.
Таблица 14 – Характеристики подшипников шариковых радиальных однорядных 212, легкой серии
Легкая серия | |||||||
Обозначение | Размеры, мм | Грузоподъемность, кН | |||||
d | D | B | r | С | С0 | ||
211 | 55 | 100 | 21 | 2,5 | 43,6 | 29 |
6.2.3. Выбор крышек подшипниковых узлов.
Будем использовать накладные крышки которые устанавливаются на корпус с помощью болтов.
Размеры выбранных крышек представим в виде таблиц.
Размеры глухих чугунных крышек:[1 табл. 6]
Таблица 15.
D1 | d болта | n кол-во болтов | d0 | d1 | d2 | d3 | d4 | е | C | е1 | R | е 2 |
80м | 8мм | 4 | 9мм | 78.5м | 68мм | 96мм | 116м | 8м | 1.5мм | 10мм | 0,6м | 2м |
100 | 10мм | 6 | 11мм | 98,5м | 85мм | 120мм | 145м | 10мм | 2мм | 12мм | 0,6м | 2м |
lвк — глубина ввинчивания болтов, мм
lвк=(1.35…1.5)dболта=(1.35…1.5)10=13.5…15 мм Принимаем Болт М10-25.36 ГОСТ 7798-70 [7]
Размеры сквозных чугунных крышек. [1 табл.8]
Таблица 16.
d вала | Уплотнение | Крышка | ||||||
d1 | D1 | b1 | d0 | d3 | b0 | S1 | ||
28мм | 28 мм | 47мм | 10мм | 29мм | М8 | 10 мм | 2.5мм | |
50мм | 50 | 72мм | 10мм | 51мм | М8 | 10 мм | 3мм |
Для сквозных крышек подшипниковых узлов быстроходного и тихоходного валов для уплотнения выбираем манжеты армированные резиновые (резина группы 1):
Быстроходный вал: Манжета 1.1-30х52-1 ГОСТ 8752-79 [1]
тихоходный вал: Манжета 1.1-45х65-1 ГОСТ 8752-79 [1]
6.2.4 Крепежные изделия
Диаметр фундаментного болта [1 табл.10]:
М20
d=20мм
Н=13мм
S=30мм
D=33.3мм
L=45мм
L0=40мм
Диаметры болтов крепления у подшипниковых узлов [1 табл.10]:
М16
d=16мм
Н=10мм
S=24мм
D=26,6мм
L=128мм
L0=120мм
Диаметры болтов крепления на фланцах [1 табл.10]:
М10
d=10мм
Н=7мм
S=17мм
D=18,7 мм
L=37мм
L0=20мм
Гайки шестигранные [1 табл.11]:
М10 М16 М20
d=10мм d=16мм d=20мм
Н=8мм Н=13мм Н=16мм
S=17мм S=24мм S=30мм
D=18,7 мм D=26,6мм D=33.3мм
Шайбы пружинные[ 1 табл.11]:
10 1620
b=h=2.5 b=h=4 b=h=5
20
studfiles.net
Лекции и примеры решения задач механики
Кручением называется такой вид деформации бруса, при котором в его поперечных сечениях возникает только один внутренний силовой фактор – крутящий момент T.
Брусья, испытывающие кручение, принято называть валами.
Внутренний крутящий момент
Внутренние скручивающие моменты появляются под действием внешних крутящих моментов mi, расположенных в плоскостях, перпендикулярных к продольной оси бруса.
Скручивающие моменты передаются на вал в местах посадки зубчатых колес, шкивов ременных передач и т.п.
Величина крутящего момента в любом сечении вала определяется методом сечений:
т.е. крутящий момент численно равен алгебраической сумме скручивающих моментов mi, расположенных по одну сторону от рассматриваемого сечения.
Правило знаков внутренних скручивающих моментов:
Положительными принимаются внутренние моменты, стремящиеся повернуть рассматриваемую часть вала против хода часовой стрелки, при рассмотрении со стороны отброшенной части вала.
В технике наиболее широко используются валы круглого поперечного сечения.
Теория кручения круглых валов основана на следующих гипотезах:
- поперечное сечение, плоское до деформации вала, остается плоским и после деформации;
- радиусы, проведенные мысленно в любом поперечном сечении, в процессе деформации вала не искривляются.
Напряжения при кручении
В поперечных сечениях вала при кручении имеют место только касательные напряжения.
Касательные напряжения, направленные перпендикулярно к радиусам, для произвольной точки, отстоящей на расстоянии ρ от центра, вычисляются по формуле:
где Iρ — полярный момент инерции.
Эпюра касательных напряжений при кручении имеет следующий вид:
Касательные напряжения меняются по линейному закону и достигают максимального значения на контуре сечения при ρ= ρmax:
Здесь:
— полярный момент сопротивления.
Геометрические характеристики сечений:
а) для полого вала:
б) для вала сплошного сечения (c=0)
в) для тонкостенной трубы (t0,9)
где
— радиус срединной поверхности трубы.
Деформации
Деформации валов при кручении заключаются в повороте одного сечения относительно другого.
Угол закручивания вала на длине Z определяется по формуле:
Если крутящий момент и величина GIρ, называемая жесткостью поперечного сечения при кручении, постоянны, для участка вала длиной l имеем:
Угол закручивания, приходящийся на единицу длины, называют относительным углом закручивания:
Расчет валов сводится к одновременному выполнению двух условий:
- условию прочности:
- условию жесткости:
Для стальных валов принимается:
- допускаемое касательное напряжение
- допускаемый относительный угол закручивания
Используя условия прочности и жесткости, как и при растяжении – сжатии можно решать три типа задач:
- проверочный расчет, заключающийся в проверке выполнения условий прочности и жесткости при известных значениях крутящего момента, размеров и материала вала.
- Проектировочный расчет, при котором вычисляются диаметры:
при этом берется большее из найденных значений, а затем принимается стандартное значение по ГОСТ. - Определение грузоподъемности вала:
- из условия прочности
- из условия жесткости
Из двух найденных значений крутящего момента необходимо принять меньшее.
- из условия прочности
При кручении, наряду с касательными напряжениями в поперечных сечениях, в соответствии с законом парности, касательные напряжения возникают и в продольных сечениях. Таким образом, во всех точках вала имеет место чистый сдвиг.
Главные напряжения σ1 = τ, σ3 = -τ наклонены под углом α=±45о к образующей.
Потенциальная энергия упругой деформации определяется по формуле
или для участка вала при постоянном T и GIρ
Лекции по сопромату >
Примеры решения задач >
isopromat.ru
Механический вал — Большая Энциклопедия Нефти и Газа, статья, страница 1
Механический вал
Cтраница 1
Механический вал с стопорами и инерционным элементом является ненаправленной нелинейностью, потому что энергия от стопора, обладающего определенной постоянной упругости, может переходить к инерционному элементу и обратно. Механический стопор вносит не только разрывность в скорость, но и резкое изменение упругой постоянной сжатия. Очевидно, упругая постоянная может измениться от значения, близкого к нулю почти до бесконечности. Другим типом нелинейности является ограничитель напряжения, состоящий из диодов в цепи, составленной из активных сопротивлений. В этом случае имеют место скачки сопротивления. [1]
Двухдвигательный асинхронный электропривод с общим механическим валом применяется для крановых механизмов в тех случаях, когда требуется снизить момент инерции или необходимо увеличить вдвое мощность привода при заданной мощности серийного двигателя, а также по различным конструктивным соображениям. [2]
Для синхронного перемещения нескольких механизмов используют механические валы между ними. Некоторые механизмы требуют наряду с синхронным совместным перемещением раздельного управления. [4]
Рассмотрим работу двух асинхронных электродвигателей на общий механический вал. Оба двигателя работают неизменно с одинаковыми скоростями вращения. Двигатели должны иметь одинаковые характеристики. В этом случае обычно ставится требование равномерного распределения нагрузки между обоими двигателями и обязательного одновременного включения и отключения цепей статоров и роторов. [5]
Рассмотрим работу двух асинхронных электродвигателей на общий механический вал. Оба двигателя работают неизменно с одинаковыми скоростями вращения. Двигатели должны иметь одинаковые характеристики. В этом случае обычно ставится требование равномерного распределения нагрузки: между обоими двигателями и обязательного одновременного включения и отключения цепей статоров и роторов. [6]
Таким образом, для равномерного распределения нагрузок между двумя двигателями, работающими на общий механический вал, необходимы мягкие характеристики. Это в одинаковой степени относится как к двигателям переменного, так и постоянного тока. [8]
При наличии момента полезного сопротивления на приемнике появляется угол рассогласования, который соответствует углу закручивания обычного механического вала. [9]
В случаях, когда по условиям работы отдельных элементов системы необходимо обеспечить синхронное вращение двигателей без использования механического вала, применяется многодвигательный привод с соединением двигателей по системе электрического вала, а также синхронно-следящий привод. [11]
В случаях, когда в многодвигательном приводе необходимо строгое поддержание постоянства соотношения скоростей рабочих органов и по тем или иным причинам нежелательно применение механического вала, применяется специальная схема взаимной связи двигателей, называемая схемой электрического вала. [12]
Для получения жестких характеристик при низких скоростях может быть использована схема двухдвига-тельного привода, действие которой состоит в том, что два двигателя работают на общий механический вал, причем одна машина работает в двигательном режиме, а другая — в тормозном — противовключения или динамического торможения. [13]
Для получения жестких характеристик при низких скоростях может быть использована схема двухдвигательного привода, действие которой состоит в том, что два двигателя работают на общий механический вал, причем одна машина работает в двигательном режиме, а другая — в тормозном — противовключения или динамического торможения. На рис. 1 — 44 а приведены схема и характеристики двухдвигательного привода. [15]
Страницы: 1 2
www.ngpedia.ru
Изготовление валов | Технология гидротурбостроения
Вал гидротурбины является одним из наиболее ответственных элементов ротора гидроагрегата. Одним фланцем он жестко крепится к рабочему колесу, другим — соединен с валом или ступицей ротора генератора. Через вал турбины крутящий момент, соответствующий мощности гидроагрегата, передается от рабочего колеса к ротору генератора. Конструктивно вал 1 турбины представляет собой полый цилиндр (тело вала) с двумя фланцами (рис. 7.1). В зоне расположения направляющего подшипника на теле вала имеется направляющий пояс 5 или облицовка 4 из нержавеющей стали (рубашка). Центровка вала турбины с рабочим колесом и ротором генератора 2 осуществляется посредством буртика D1 и выточки D2, сопрягаемым, как правило, по посадке скольжения.
Жесткость соединения деталей, а также передачу осевого усилия и крутящего момента обеспечивают болты 3, центральная часть которых диаметром d припасована в отверстиях с минимальным зазором, соответствующим посадке движения. В соответствии с принятой номенклатурой и ОСТ 24.2Э4.01—74 гидротурбинные валы могут быть диаметром 600—2500 мм массой до 120 т; длина вала 4000—10 000 мм.
Рис. 7.1. Вал турбины и фланцевое соединение.
В настоящее время заготовки валов гидротурбин выполняют либо в виде цельной поковки, либо сварными, состоящими из фланцев и полого тела (трубы), соединенных сваркой (рис. 7.2).
Рис. 7.2. Заготовка цельнокованого (а) и сварного (б) вала.
1 — кольцевые пробы; 2 — кольцевые припуски; 3 — кольца для измерения остаточных напряжений; 4 — литой развитый фланец; 5 — сварные швы; 6 — кованая труба; 7 — кованый фланец; 8 — цилиндрические пояски; 9 — сварной стык-свидетель.
В зависимости от способа получения заготовки выбирают марку стали. Цельнокованые заготовки, как правило, изготавливают из углеродистой стали марки 40. Элементы сварной заготовки выполняют из хорошо сваривающейся низколегированной стали марки 20ГС или 25ГС.
Проверка качества изготовления цельнокованого вала и кованых частей сварного вала изложена в разделе 3.4. Литые развитые фланцы сварных валов дополнительно к обычному контролю отливок (см. раздел 3.2) после предварительной механической обработки подвергают проверке магнитнопорошковой дефектоскопией и травлению галтельных переходов. Зону сварного соединения с трубчатой частью вала на длине 150 мм от торца подвергают контролю ультразвуковой дефектоскопией. Эти меры необходимы для выявления и устранения поверхностных и внутренних дефектов типа трещин, крупных раковин и скоплений неметаллических включений.
Для испытания механических свойств сварных швов изготавливаются специальные контрольные сварные стыки-свидетели (рис. 7.2). Для их сварки служат кольца, отрезаемые от каждого конца трубы и от примыкающих к сварным швам концов фланцев. Кольца имеют те же размеры в сечении, что и сварной вал в зоне сварных швов. На каждый сварной шов вала изготавливается один стык-свидетель. При сварке свидетелей устанавливаются те же режимы сварки и сварочные материалы, которые применяются при сварке стыков заготовки вала.
Испытания на разрыв металла шва производятся на пятикратных образцах (тип II по ГОСТ 6996—66) вдоль оси шва, а сварного соединения — на десятикратных образцах (тип III по ГОСТ 1497—61) поперек шва. Испытания на ударную вязкость проводятся на образцах (тип VI по ГОСТ 6996—66) с надрезом по оси шва и в зоне сплавления. Минимальный уровень механических свойств сварных швов и соединений приведен в табл. 7.1. Сплошность сварных швов контролируется ультразвуковой дефектоскопией и травлением в объеме 100% их протяженности. Нормы допустимых дефектов устанавливаются техническими условиями. Определение уровня остаточных напряжений в сварных валах аналогично проводимому для цельнокованых. Цель контроля — проверка качества термической обработки после сварки.
Испытуемый материал | Предел текучести (условный) σ0,2, кгс/мм2 | Временное сопротивление разрыву σв, кгс/мм2 | Относительное удлинение δ5, % | Относительное сужение ψ, % | Ударная вязкость αн, кгс·м/см* |
Металл сварного шва Сварное соединение |
26 — |
50 50 |
16 — |
30 — |
4 4 |
Для спокойной работы агрегата при вращении ротора необходимо, чтобы между сопрягаемыми деталями ротора отсутствовали линейные и угловые эксцентриситеты. На линейный эксцентриситет влияют: радиальное смещение сопрягаемых деталей в пределах зазоров между ними и несоосность посадочных поверхностей турбинного вала относительно поверхности направляющего пояса. На угловой эксцентриситет влияет неперпендикулярность сопрягаемых торцевых плоскостей фланцев относительно оси, а также отклонение их от плоскостности.
Такое большое количество погрешностей требует максимального ужесточения каждой из них. Особое внимание уделяется ужесточению неперпендикулярности сопрягаемых плоскостей (торцевого биения), так как вызываемый этой погрешностью угловой эксцентриситет возрастает пропорционально длине вала.
Основные технические требования к точности обработки валов указываются в чертежах: 1) диаметральные размеры посадочного буртика фланца выполняются по 2-му классу точности, а выточки — с предельными отклонениями 1-го класса; 2) сопрягаемые поверхности фланцев должны быть плоскими; выпуклость их не допускается, а вогнутость допустима не более 0,03 мм; 3) шероховатость основных поверхностей должна быть не более 1,25 мкм, а поверхности шейки под подшипник — 0,63 мкм; 4) радиальное биение не должно превышать 0,03 мм для шейки вала, базовых поясков на наружной поверхности фланцев или тела вала и для посадочного буртика (выточки) на фланце со стороны генератора; 0,04 мм для посадочного буртика на фланце, сопрягаемом с рабочим колесом; 5) торцевое биение плоскости фланца со стороны генератора, замеренное на периферийном диаметре, — не более 0,03; со стороны рабочего колеса — не более 0,04 мм.
Для обеспечения столь жестких требований даже при использовании уникальных токарно-центровых станков высокой точности технологический процесс должен быть построен таким образом, чтобы все поверхности вала, от которых требуется получить минимальный торцевой и радиальный бой, протачивались с одной установки. Поскольку это требование технологически невыполнимо, то поверхности фланца, сопрягаемого с рабочим колесом, вынужденно обрабатываются с другой установки вала на станке, так как повышенные погрешности обработки этого фланца не сказываются на изломе оси агрегата. Эксцентриситет шейки вала турбины в зоне подшипника
где Δ — суммарный; Δугл — угловой; Δлин — линейный эксцентриситет; ε1, ε2 — торцевые биения сопрягаемых плоскостей фланцев валов турбины и генератора; ε3 — радиальное биение шейки вала турбины; ε4 — радиальное биение буртика (выточки) фланца турбинного вала со стороны генератора; ε5 — радиальное биение выточки (буртика) фланца вала генератора, сопрягаемого с фланцем турбинного вала; δ — максимальное смещение в сопряжении буртик—выточка фланцевого соединения валов; DФ — наружный диаметр сопрягаемых фланцев; L — расстояние от плоскости сопряжения фланцев до шейки турбинного вала.
Если не принять специальных мер, то суммарный эксцентриситет А может оказаться очень большим, что приведет к нестабильной работе агрегата, преждевременному выходу из строя вкладышей турбинного подшипника. Устранение чрезмерно большого излома оси вала агрегата достигается при сборке и рас-центровке валов — операции спаривания.
www.stroitelstvo-new.ru