Предел прочности — это… Что такое Предел прочности?
Преде́л про́чности — механическое напряжение , выше которого происходит разрушение материала. Согласно ГОСТу 1497-84 более корректным термином является «Временное сопротивление разрушению», то есть напряжение, соответствующее наибольшему усилию, предшествующему разрыву образца при (статических) механических испытаниях. Термин происходит от того представления, что материал может бесконечно долго выдержать любую статическую нагрузку, если она создаёт напряжения меньшие по величине, чем временное сопротивление. При нагрузке, соответствующей временному сопротивлению (или даже превышающей её — в реальных и квазистатических испытаниях) разрушение материала (разделение образца на несколько частей) произойдёт через какой-то конечный промежуток времени, возможно, что и практически сразу.
В случае динамических испытаний время нагружения образцов часто не превышает нескольких секунд от начала нагружения до момента разрушения, в таком случае соответствующая характеристика называется также условно-мгновенным пределом прочности, или хрупко-кратковременным пределом прочности.
Мерами измерения прочности также могут являться предел текучести, предел пропорциональности, предел упругости, предел выносливости и др, так как для выхода конкретной детали из строя часто достаточно и слишком большого (больше допустимого) изменения размеров детали, а при этом может и не произойти нарушение целостности, лишь только деформация. Эти показатели практически никогда не подразумеваются под термином предел прочности.
Значения предельных напряжений на растяжение и на сжатие обычно различаются. Для композитов предел прочности на растяжение обычно больше предела прочности на сжатие, для керамических (и других хрупких) материалов — наоборот, металлы, сплавы и многие пластики как правило показывают одинаковые свойства. В большей степени эти явления связаны не с какими-то физическими свойствами материалов, а с особенностями нагружения, схемы напряженного состояния при испытаниях и с возможностью пластической деформации перед разрушением.
Некоторые значения прочности на растяжение, , в кгс/мм2 (1 кгс/мм2 = 10 МН/м2 = 10 МПа)
См. также
Ссылки
dic.academic.ru
Пределы прочности материалов
Быстрый поиск
Определённая пороговая величина для конкретного материала, превышение которой приведёт к разрушению объекта под действием механического напряжения. Основные виды пределов прочности: статический, динамический, на сжатие и на растяжение. Например, предел прочности на растяжение — это граничное значение постоянного (статический предел) или переменного (динамический предел) механического напряжения, превышение которого разорвет (или неприемлемо деформирует) изделие. Единица измерения — Паскаль [Па], Н/мм ² = [МПа].
Предел текучести (σт)
Величина механического напряжения, при которой деформация продолжает увеличиваться без увеличения нагрузки; служит для расчётов допустимых напряжений пластичных материалов.
После перехода предела текучести в структуре металла наблюдаются необратимые изменения: кристаллическая решетка перестраивается, появляются значительные пластические деформации. Вместе с тем происходит самоупрочнение металла и после площадки текучести деформация возрастает при увеличении растягивающей силы.
Нередко этот параметр определяют как «напряжение, при котором начинает развиваться пластическая деформация» [1], таким образом, отождествляя пределы текучести и упругости. Однако следует понимать, что это два разных параметра. Значения предела текучести превышают предел упругости ориентировочно на 5%.
Предел выносливости или предел усталости (σR)
Способность материала воспринимать нагрузки, вызывающие циклические напряжения. Этот прочностной параметр определяют как максимальное напряжение в цикле, при котором не происходит усталостного разрушения изделия после неопределенно большого количества циклических нагружений (базовое число циклов для стали Nb = 10 7). Коэффициент R (σR) принимается равным коэффициенту асимметрии цикла. Поэтому предел выносливости материала в случае симметричных циклов нагружения обозначают как σ-1, а в случае пульсационных — как σ0.
Отметим, что усталостные испытания изделий очень продолжительны и трудоёмки, они включают анализ больших объёмов экспериментальных данных при произвольном количестве циклов и существенном разбросе значений. Поэтому чаще всего используют специальные эмпирические формулы, связывающие предел выносливости с другими прочностными параметрами материала. Наиболее удобным параметром при этом считается предел прочности.
Для сталей предел выносливости при изгибе как правило составляет половину от предела прочности: Для высокопрочных сталей можно принять:
Для обычных сталей при кручении в условиях циклически изменяющихся напряжений можно принять:
Приведённые выше соотношения стоит применять осмотрительно, потому что они получены при конкретных режимах нагружения, т.е. при изгибе и при кручении. Однако, при испытании на растяжение-сжатие предел выносливости становится примерно на 10—20% меньше, чем при изгибе.
Предел пропорциональности (σ)
Максимальная величина напряжения для конкретного материала, при которой ещё действует закон Гука, т.е. деформация тела прямо пропорционально зависит от прикладываемой нагрузки (силы). Обратите внимание, что для множества материалов достижение (но не превышение!) предела упругости приводит к обратимым (упругим) деформациям, которые, впрочем, уже не прямо пропорциональны напряжениям. При этом такие деформации могут несколько «запаздывать» относительно роста или снижения нагрузки.
Диаграмма деформации металлического образца при растяжении в координатах удлинение (Є) — напряжение (σ).
1:Предел абсолютной упругости.
2:Предел пропорциональности.
3:Предел упругости.
4:Предел текучести. (σ 0.2)
www.smalley.ru
Материал | σв | ||
---|---|---|---|
кгс/мм2 | 107 Н/м2 | МПа | |
Металлы | |||
Алюминий | 8-11 | 7,8-10,8 | 78-108 |
Алюминий отожженный | 9,1-10,95 | 89-108 | |
Бериллий | 14 | 13,8 | 138 |
Бронза (91 % Cu + 6 % Sn + 3 % Zn) | 20-38 | 19,6-37,3 | 196-373 |
Ванадий | 18-45 | 17,6-44,2 | 176-442 |
Вольфрам | 120-140 | 118,0-137,5 | 1180-1375 |
Вольфрам отожженный | 71,3-82,5 | 69,9-80,9 | 699-809 |
Дюраль | 40-50 | 39,2-49,1 | 392-491 |
Железо кованное | 40-60 | 39,2-58,9 | 392-589 |
Гафний | 35-45 | 34,5-44,2 | 345-442 |
Золото | 14-16 | 13,8-15,7 | 138-157 |
Золото отожженное | 12,6 | 12,4 | 124 |
Инвар | 78 | 76,5 | 765 |
Индий | 5,1 | 5,05 | 50,5 |
Кадмий | 6,4 | 6,3 | 63 |
Кальций | 6,1 | 6 | 60 |
Кобальт отожженный | 49,8 | 48,9 | 489 |
Константан (60 % Cu + 40 % Ni) | 32 | 31,4 | 314 |
Латунь (66 % Cu + 34 % Zn) | 10-20 | 9,8-19,6 | 98-196 |
Магний | 18-25 | 17,6-24,5 | 176-245 |
Магний литой | 30 | 29,4 | 294 |
Медь | 22-24 | 21,6-23,5 | 216-235 |
Медь деформированная | 20,4-25,5 | 20-25 | 200-250 |
Молибден | 40-70 | 39,3-68,6 | 393-686 |
Молибден литой | 31,4 | 30,8 | 308 |
Никель | 40-50 | 39,3-49,1 | 393-491 |
Ниобий | 35-50 | 34,5-49,1 | 345-491 |
Ниобий отожженный | 32,8-41,4 | 32,2-40,6 | 320-406 |
Олово | 1,7-2,5 | 1,7-2,5 | 17-25 |
Олово литое | 1,5-2,5 | 1,5-2,4 | 15-24 |
Палладий | 18-20 | 17,6-19,6 | 176-196 |
Палладий литой | 18,6 | 18,2 | 182 |
Платина | 24-34 | 23,5-34,0 | 235-34 |
Родий отожженный | 56 | 55 | 550 |
Свинец | 1,1-1,3 | 1,1-1,3 | 10,8-12,7 |
Серебро | 10-15 | 9,8-14,7 | 98-147 |
Серебро отожженное | 13,8 | 13,5 | 135 |
Сталь инструментальная | 45-60 | 44,1-58,9 | 441-589 |
Сталь кремнехромомарганцовистая | 155 | 152 | 1520 |
Сталь специальная | 50-160 | 49-157 | 491-1570 |
Сталь рельсовая | 70-80 | 68-78 | 687-785 |
Сталь углеродистая | 32-80 | 31,4-78,5 | 314-785 |
Тантал | 20-45 | 19,6-44,2 | 196-442 |
Титан | 25-35 | 24,5-34,5 | 245-345 |
Титан отожженный | 30 | 29,6 | 296 |
Хром | 30-70 | 29-69 | 294-686 |
Цинк | 11-15 | 10,8-14,7 | 108-147 |
Цирконий | 25-40 | 24,5-39,3 | 245-393 |
Чугун | 10-12 | 9,8-11,8 | 98-118 |
Чугун ковкий | 20 | 19,6 | 196 |
Чугун серый мелкозернистый | 21-25 | 20,6-24,5 | 206-245 |
Чугун серый обыкновенный | 14-18 | 13,7-17,7 | 137-177 |
Пластмассы | |||
Аминопласт слоистый | 8 | 7,8 | 78 |
Асботекстолит | 6,5-11,9 | 6,4-11,7 | 64-117 |
Винипласт | 4-6 | 3,9-5,9 | 39-59 |
Гетинакс | 15-17 | 14,7-16,7 | 147-167 |
Гранулированный сополимер | 4 | 3,9 | 39 |
Древесно-слоистый пластик ДСП-Б (длинный лист) | 22 | 21,6 | 216 |
Древесный коротковолнистый волокнит К-ФВ25 | 3 | 2,94 | 29,4 |
Капрон стеклонаполненный | 15-18 | 14,7-17,6 | 147-176 |
Пенопласт плиточный | 0,06 | 0,06 | 0,59 |
Пенопласт ФК-20 | 0,17 | 0,17 | 1,7 |
Полиакрилат (оргстекло) | 5 | 4,9 | 49 |
Полиамид наполненный П-68 | 5-6 | 4,9-5,9 | 49-59 |
Полиамид стеклонаполненный СП-68 | 7,4-8,5 | 7,3-8,3 | 73-83 |
Поливинилхлорид неориентированный | 3-5 | 2,9-4,9 | 29-49 |
Поликапроамид | 6,0-6,5 | 5,9-6,4 | 59-64 |
Поликапроамид стеклонаполненный | 12,9-15,0 | 12,7-14,7 | 127-147 |
Поликарбонат (дифион) | 6,0-8,9 | 5,9-8,7 | 59-87 |
Поликарбонат стеклонаполненный | 12,5-15,0 | 12,3-14,8 | 123-148 |
Полипропилен ПП-1 | 2,5 | 2,5 | 25 |
Полипропилен стеклонаполненный | 5,6 | 5,5 | 55 |
Полистирол стеклонаполненный | 7,4-10,5 | 7,3-10,3 | 73-103 |
Полистирол суспензионный ПС-С | 4,0 | 3,9 | 39 |
Полистирол эмульсионный А | 3,5-4,0 | 3,4-3,9 | 34-39 |
Полиформальдегид стабилизированный | 6-7 | 5,9-6,9 | 59-69 |
Полиэтилен высокого давления кабельный П-2003-5 | 1,20-1,39 | 1,18-1,37 | 11,8-13,7 |
Полиэтилен высокого давления П-2006-Т | 1,39 | 1,37 | 13,7 |
Полиэтилен низкого давления П-4007-Э | 2,20 | 2,16 | 21,6 |
Полиэтилен среднего давления | 2,70-3,29 | 2,65-3,23 | 26,5-32,3 |
Стекло органическое ПА, ПБ, ПВ | 5 | 4,9 | 49 |
Стеклотекстолит | 30 | 29,4 | 294 |
Текстолит графитированный | 9 | 8,8 | 88 |
Текстолит поделочный ПТК | 10 | 9,8 | 98 |
Фаолит А | 1,73 | 1,7 | 17 |
Фенопласт текстолитовый | 8-10 | 7,8-9,8 | 78-98 |
Фторопласт 3 | 3-4 | 2,9-3,9 | 29-39 |
Фторопласт 4 | 2 | 1,96 | 19,6 |
Целлон | 4 | 3,9 | 39 |
Дерево | |||
Бамбук | 22 | 21,6 | 216 |
Береза | 7 | 6,9 | 69 |
Бук | 8 | 7,8 | 78 |
Дуб | 8 | 7,8 | 78 |
Дуб (при 15 % влажности) вдоль волокон | 9,5 | 9,3 | 93 |
Ель | 5 | 4,9 | 49 |
Железное дерево | 22 | 21,6 | 216 |
Сосна | 5 | 4,9 | 49 |
Сосна (при 15 % влажности) вдоль волокон | 8 | 7,8 | 78 |
Минералы | |||
Графит | 0,5-1,0 | 0,5-0,9 | 4,9-9,8 |
Различные материалы | |||
Бакелит | 2-3 | 1,96-2,94 | 19,6-29,4 |
Гранит | 0,3 | 0,29 | 2,9 |
Кетгут | 42 | 41,2 | 412 |
Лед (0 °С) | 0,1 | 0,098 | 0,98 |
Нити кварцевые | 90 | 88,3 | 883 |
Нити шелковые | 26 | 25,5 | 255 |
Паутина | 18 | 17,6 | 176 |
Стекло органическое | 4 | 3,9 | 39 |
weldworld.ru
Единицы измерения прочности
Единицы измерения прочности (единицы давления):
Кгс/см2 и МПа — это единицы измерения давления. Для перевода из одной системы измерения в другую необходимо знать следующее — 1 кгс/см2 = 0,098066 МПа. Т.е. давление в 100 кгс/см2 соответствует 9,8066 МПа (≈10 МПа).
1МПа = 1000000 Па=1*106 Н/м2
1МПа = 1000 кПа
1 МПа = 10,19716 кгс/см2 ≈ 10 кгс/см2
1кгс/см2 = 0,0980665 МПа
1кгс/см2 = 98,0665 кПа
1 кгс/см2= 0,0980665 МПа
1 кгс/см2= 10000 кгс/м2
Соотношение кгс/см2 и МПа такое:
1 кгс/см2 = 0,098066 МПа ≈0,1 МПа
т.е. давление в 100 кгс/см2 соответствует 9,8066 МПа. На практике, как правило, можно округлить до 10 и, в итоге получим
100 кгс/см2 = 10 МПа
т.е. Для марки бетона M250 прочность в кгс/см2 — 261,9 в МПа мы можем принять ~26,2 МПа
Единицы измерения прочности (единицы давления):
Кгс/см2 и МПа — это единицы измерения давления. Для перевода из одной системы измерения в другую необходимо знать следующее — 1 кгс/см2 = 0,098066 МПа. Т.е. давление в 100 кгс/см2 соответствует 9,8066 МПа (≈10 МПа).
1МПа = 1000000 Па=1*106 Н/м2
1МПа = 1000 кПа
1 МПа = 10,19716 кгс/см2 ≈ 10 кгс/см2
1кгс/см2 = 0,0980665 МПа
1кгс/см2 = 98,0665 кПа
1 кгс/см2= 0,0980665 МПа
1 кгс/см2= 10000 кгс/м2
Соотношение кгс/см2 и МПа такое:
1 кгс/см2 = 0,098066 МПа ≈ 10 МПа
т.е. давление в 100 кгс/см2 соответствует 9,8066 МПа. На практике, как правило, можно округлить до 10 и, в итоге получим
100 кгс/см2 = 10 МПа
т.е. Для марки бетона M250 прочность в кгс/см2 — 261,9 в МПа мы можем принять ~26,2 МПа
studfiles.net
Предел прочности стали при сжатии и растяжении
Прочность металлических конструкций – один из важнейших параметров, определяющих их надежность и безопасность. Издревле вопросы прочности решались опытным путем — если какое-либо изделие ломалось — то следующее делали толще и массивнее. С 17 века ученые начали планомерное исследование проблемы, прочностные параметры материалов и конструкций из них можно рассчитать заранее, на этапе проектирования. Металлурги разработали добавки, влияющие на прочность стальных сплавов.
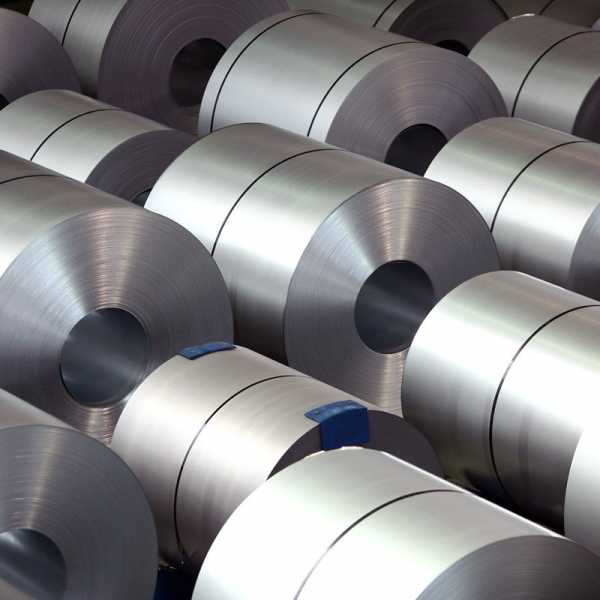
Предел прочности
Предел прочности — это максимальное значение напряжений, испытываемых материалом до того, как он начнет разрушаться. Его физический смысл определяет усилие растяжения, которое нужно приложить к стрежневидному образцу определенного сечения, чтобы разорвать его.
Каким образом производится испытание на прочность
Прочностные испытания на сопротивление разрыву проводятся на специальных испытательных стендах. В них неподвижно закрепляется один конец испытываемого образца, а к другому присоединяют крепление привода, электромеханического или гидравлического. Этот привод создает плавно увеличивающее усилие, действующее на разрыв образца, или же на его изгиб или скручивание.

Испытание на разрыв
Электронная система контроля фиксирует усилие растяжения и относительное удлинение, и другие виды деформации образца.
Виды пределов прочности
Предел прочности — один из главных механических параметров стали, равно как и любого другого конструкционного материала.
Эта величина используется при прочностных расчетах деталей и конструкций, судя по ней, решают, применим ли данный материал в конкретной сфере или нужно подбирать более прочный.
Различают следующие виды предела прочности при:
- сжатии — определяет способность материала сопротивляться давлению внешней силы;
- изгибе — влияет на гибкость деталей;
- кручении – показывает, насколько материал пригоден для нагруженных приводных валов, передающих крутящий момент;
- растяжении.

Виды испытаний прочности материалов
Научное название параметра, используемое в стандартах и других официальных документах — временное сопротивление разрыву.
Предел прочности стали
На сегодняшний день сталь все еще является наиболее применяемым конструкционным материалом, понемногу уступая свои позиции различным пластмассам и композитным материалам. От корректного расчета пределов прочности металла зависит его долговечность, надежность и безопасность в эксплуатации.
Предел прочности стали зависит от ее марки и изменяется в пределах от 300 Мпа у обычной низкоуглеродистой конструкционной стали до 900 Мпа у специальных высоколегированных марок.
На значение параметра влияют:
- химический состав сплава;
- термические процедуры, способствующие упрочнению материалов: закалка, отпуск, отжиг и т.д.
Некоторые примеси снижают прочность, и от них стараются избавляться на этапе отливки и проката, другие, наоборот, повышают. Их специально добавляют в состав сплава.
Условный предел текучести
Кроме предела прочности, в инженерных расчетах широко применяется связанное с ним понятие-предел текучести, обозначаемый σт. Он равен величине напряжения сопротивления разрыву, которое необходимо создать в материале, для того, чтобы деформация продолжала расти без наращивания нагрузки. Это состояние материала непосредственно предшествует его разрушению.
На микроуровне при таких напряжениях начинают рваться межатомные связи в кристаллической решетке, а на оставшиеся связи увеличивается удельная нагрузка.
Общие сведения и характеристики сталей
С точки зрения конструктора, наибольшую важность для сплавов, работающих в обычных условиях, имеют физико-механические параметры стали. В отдельных случаях, когда изделию предстоит работать в условиях экстремально высоких или низких температур, высокого давления, повышенной влажности, под воздействием агрессивных сред — не меньшую важность приобретают и химические свойства стали. Как физико-механические, так и химические свойства сплавов во многом определяются их химическим составом.
Влияние содержание углерода на свойства сталей
По мере увеличения процентной доли углерода происходит снижение пластичности вещества с одновременным ростом прочности и твердости. Этот эффект наблюдается до приблизительно 1% доли, далее начинается снижение прочностных характеристик.
Повышение доли углерода также повышает порог хладоемкости, это используется при создании морозоустойчивых и криогенных марок.
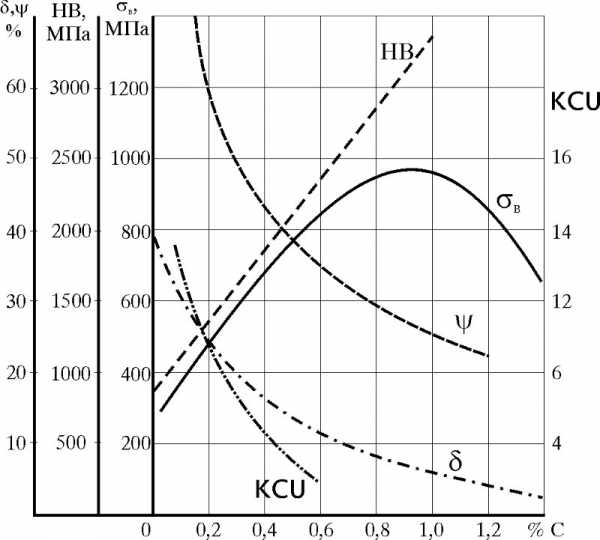
Влияние углерода на механические свойства стали
Рост содержания С приводит к ухудшению литейных свойств, отрицательно влияет на способность материала к механической обработке.
Добавки марганца и кремния
Mn содержится в большинстве марок стали. Его применяют для вытеснения из расплава кислорода и серы. Рост содержания Mn до определенного предела (2%) улучшает такие параметры обрабатываемости, как ковкость и свариваемость. После этого предела дальнейшее увеличение содержания ведет к образованию трещин при термообработке.
Влияние кремния на свойства сталей
Si применяется в роли раскислителя, используемого при выплавке стальных сплавов и определяет тип стали. В спокойных высокоуглеродистых марках должно содержаться не более 0,6% кремния. Для полуспокойных марок этот предел еще ниже — 0,1 %.
При производстве ферритов кремний увеличивает их прочностные параметры, не понижая пластичности. Этот эффект сохраняется до порогового содержания в 0,4%.

Влияние легирующих добавок на свойства стали
В сочетании с Mn или Mo кремний способствует росту закаливаемости, а вместе с Сг и Ni повышает коррозионную устойчивость сплавов.
Азот и кислород в сплаве
Эти самые распространенные в земной атмосфере газы вредно влияют на прочностные свойства. Образуемые ими соединения в виде включений в кристаллическую структуру существенно снижают прочностные параметры и пластичность.
Легирующие добавки в составе сплавов
Это вещества, намеренно добавляемые в расплав для улучшения свойств сплава и доведения его параметров до требуемых. Одни из них добавляются в больших количествах (более процента), другие — в очень малых. Наиболее часто применяю следующие легирующие добавки:
- Хром. Применяется для повышения прокаливаемости и твердости. Доля – 0,8-0,2%.
- Бор. Улучшает хладноломкость и радиационную стойкость. Доля – 0,003%.
- Титан. Добавляется для улучшения структуры Cr-Mn сплавов. Доля – 0,1%.
- Молибден. Повышает прочностные характеристики и коррозионную стойкость, снижает хрупкость. Доля – 0,15-0,45%.
- Ванадий. Улучшает прочностные параметры и упругость. Доля – 0,1-0,3%.
- Никель. Способствует росту прочностных характеристик и прокаливаемости, однако при этом ведет к увеличению хрупкости. Этот эффект компенсируют одновременным добавлением молибдена.
Металлурги используют и более сложные комбинации легирующих добавок, добиваясь получения уникальных сочетаний физико-механических свойств стали. Стоимость таких марок в несколько раз (а то и десятков раз) превышает стоимость обычных низкоуглеродистых сталей. Применяются они для особо ответственных конструкций и узлов.
Если вы нашли ошибку, пожалуйста, выделите фрагмент текста и нажмите Ctrl+Enter.
stankiexpert.ru
Измерение — предел — прочность
Измерение — предел — прочность
Cтраница 1
Измерения предела прочности относятся к системам, тиксотропно восстановленным после полного механического разрушения. [1]
Измерение предела прочности и относительного удлинения производят по ГОСТ 10446 — 63 или по ГОСТ 1497 — 61 на образцах с расчетной длиной 200 мм, отобранных на расстоянии не менее 1 м от начала или конца бухты. [2]
Для измерения предела прочности при статическом изгибе а пластмасс используют образцы, представляющие собой бруски длиной I 120 мм, шириной 615 мм и толщиной h 10 мм. Изгибающее усилие Р прикладывают к стальному пестику 1, располагаемому на середине образца. [4]
При измерении предела прочности гранулу равномерно сжимают вдоль одной оси. Давление увеличивают до разрушения гранулы. Предел прочности находят как а — Р / А, где Р — нагрузка, а А — площадь поперечного сечения. Дефекты поверхности сильно снижают прочность материалов. Не следует упускать из виду чистоту поверхности, так как трещины могут начать распространяться от частиц примеси к чистой поверхности. Напряжения, возникающие при охлаждении порошков и гранул после прокаливания, могут привести к образованию микротрещин, которые затем увеличиваются в условиях реакции. Если возможно, то нужно избегать быстрого охлаждения и циклических изменений температуры. Как указывалось ранее, микротрещины образуются также при дроблении. Пластическая деформация вязких металлов предотвращает развитие трещин в них. В поликристаллической керамике аналогичные процессы поглощения энергии не происходят, и образование трещин продолжается до разрушения. Поры могут предотвращать развитие трещин, поэтому оптимальная пористость желательна и с этой точки зрения. [5]
При измерении пределов прочности у пластичных систем при очень низких скоростях даже при сравнительно высоких степенях однородности напряженного состояния обычно бывает трудно установить, распространяется сдвиг равномерно по всему зазору или зона разрушения структурного каркаса локализуется в более или менее узком участке, прилегающем к измерительной поверхности, на которой действует наивысшее напряжение. [6]
На основе измерений предела прочности на растяжение, относительного удлинения и твердости Харрингтон [49] делает следующие выводы о влиянии акрилонитрила. [7]
Стандартная методика измерения предела прочности на сжатие не позволяет устанавливать одновременно и характеристики деформативности тампонажного камня, поскольку датчики можно прикрепить только к образцу с одним из размеров сечения не более 10 мм. [8]
Метод основан на измерении предела прочности на разрыв после разрушения и при последующем отдыхе. Установлено, что с увеличением концентрации нафтената алюминия улучшается механическая стабильность смазок. [9]
Механические свойства пленок определяются измерением предела прочности при растяжении, относительным удлинением при разрыве и модулем упругости. [10]
В табл. 36 представлены результаты измерения предела прочности однонаправленного материала при растяжении в направлении армирования. [12]
Таким образом, оказывается, что измерения предела прочности не характеризуют в достаточной мере условий разрушения материала, которые определяются структурными изменениями при предшествующем разрыву нагружении. Известно лишь очень ограниченное число экспериментов, в которых изучалось изменение вязкоупругих свойств полимера при нагружении до разрушения. Тем не менее имеющиеся результаты весьма интересны. Так, Нильсен [3] при исследовании образцов армированного стекловолокном полиамида обнаружил, что при деформациях, предшествующих разрушению, происходит заметное увеличение тангенса угла механических потерь и снижение модуля упругости. Поскольку частично кристаллические полимеры можно рассматривать как двухфазные системы, естественно предположить, что аналогичные изменения механических характеристик должны наблюдаться также в неармированных частично-кристаллических полимерных волокнах. [13]
Из-за различной плотности пропитываемых материалов изменчивость результатов измерения предела прочности на растяжение при изгибе проявляется по-разному, однако для всех пропитанных изделий она ниже, чем у непропитанных образцов. Снижение изменчивости объясняется меньшей дефектностью структуры материалов после пропитки, причем заметнее это проявляется у фибролита. [14]
Страницы: 1 2 3
www.ngpedia.ru
Понятие предела прочности
Контрольная работа № 1
Преде́л про́чности — механическое напряжение σ0, выше которого происходит разрушение материала. Поскольку при оценке прочности время нагружения образцов часто не превышает нескольких секунд от начала нагружения до момента разрушения, то его также называют условно-мгновенным пределом прочности, или хрупко-кратковременным пределом прочности.
Мерами измерения прочности также являются предел текучести, предел усталости.
Значения предельных напряжений на растяжение и на сжатие обычно различаются. Для металлов предел прочности на сжатие обычно больше предела прочности на растяжение, для композитных материалов наоборот.
Относительное удлинение – представляет собой отношение приращения длины образца после его разрыва к первоначальной расчетной длине
и выражается в процентах:где
– длина образца после разрыва.Перлит – это эвтектоид, состоящий из двух фаз феррита и цементита. Образуется перлит при температуре ниже 727
в результате разложения аустенита на феррит и цементит. Содержание углерода в нем равно 0,8%Горячая пластическая деформация – Это деформация, которая осуществляется при температуре рекристализации. Такая деформация сопровождается реклистализацией в результате которой наклёп ускоряется.
2. Диаграмма железо- цементит
Диаграмма железо- цементит

Аустенит (-фаза) — высокотемпературная гранецентрированная модификация железа и его сплавов.
В углеродистых сталях аустенит — это твёрдый раствор внедрения, в котором атомы углерода входят внутрь элементарной ячейки -железа во время конечной термообработки. В сталях, содержащих другие металлы (кроме железа, легированные стали), атомы металлов замещают атомы железа в кристаллической решетке и возникает твердый раствор замещения. В чистом железе существует в интервале температур 910—1401°C; в углеродистых сталях аустенит существует при температурах не ниже 723°C (1333°F). Фаза названа в честь сэра Уильяма Чандлера Робертс-Остина. В легированных сталях аустенит может существовать и при гораздо более низких температурах. Такие элементы, как никель стабилизируют аустенитную фазу. Нержавеющие стали, такие как 08Х18Н10Т. относятся к аустенитному классу. Присутствие никеля в количестве 8—10% приводит к тому, что аустенитная фаза сохраняется и при комнатной температуре. Мартенситно-стареющие нержавеющие стали типа 08Х15Н2ДТ или Ph 17-4 могут содержать некоторое количество остаточного аустенита. Оптическая металлография во многих случаях не позволяет выявить присутствие аустенита, расположенного, как правило, по границам мартенситных пакетов. Основными способами определения количества остаточного аустенита являются рентгеноструктурный анализ и просвечивающая электронная микроскопия.
Перлит (от фр. perle — жемчужина) — одна из структурных составляющих железоуглеродистых сплавов — сталей и чугунов: представляет собой эвтектоидную смесь двух фаз — феррита и цементита (в легированных сталях — карбидов). Перлит — продукт эвтектоидного распада аустенита при сравнительно медленном охлаждении железоуглеродистых сплавов ниже 727 °C. При этом γ-железо переходит в α-железо, растворимость углерода в котором составляет от 0,006 до 0,025%; избыточный углерод выделяется в форме цементита или карбидов. В зависимости от формы различают перлит пластинчатый (основной вид перлита; обе фазы имеют форму пластинок) и зернистый (округлые зёрнышки, или глобули, цементита располагаются на фоне зёрен феррита). С увеличением переохлаждения растёт число колоний перлита, то есть участков с однообразной ориентацией пластинок феррита и цементита (карбидов), а сами пластинки становятся более тонкими. Механические свойства перлита зависят в первую очередь от межпластиночного расстояния (суммарная толщина пластинок обеих фаз): чем оно меньше, тем выше значение предела прочности и предела текучести и ниже критическая температура хладноломкости. При перлитной структуре облегчается механическая обработка стали. Дисперсные разновидности перлита иногда называют сорбитом и трооститом.
Ледебурит — структурная составляющая железоуглеродистых сплавов, главным образом чугунов, представляющая собой эвтектическую смесь аустенита и цементита в интервале температур 723—1147 °C, или феррита и цементита ниже 723 °C. Назван в честь немецкого металлурга Карла Генриха Адольфа Ледебура
Феррит (лат. ferrum — железо), фазовая составляющая сплавов железа, представляющая собой твёрдый раствор углерода и легирующих элементов в α-железе (α-феррит). Имеет объемноцентированную кубическую кристаллическую решётку. Является фазовой составляющей других структур, например, перлита, состоящего из феррита и цементита.
При температурах выше 1401 °С в железоуглеродистых сплавах образуется твёрдый раствор углерода в δ-железе (δ-феррит), который можно рассматривать как высокотемпературный феррит.
Цементит — карбид железа, химическое соединение. Концентрация углерода 6,67% по массе — предельная для железоуглеродистых сплавов. Цементит — метастабильная фаза; образование стабильной фазы — графита во многих случаях затруднено. Цементит имеет орторомбическую кристаллическую решётку, очень тверд и хрупок, слабо магнитен до 210 °С.
В зависимости от условий кристаллизации и последующей обработки цементит может иметь различную форму — равноосных зёрен, сетки по границам зёрен, пластин, а также видманштеттову структуру.
Цементит в разных количествах, в зависимости от концентрации, присутствует в железоуглеродистых сплавах уже при малых содержаниях углерода. Формируется в процессе кристаллизации из расплава чугуна. В сталях выделяется при охлаждении аустенита или при нагреве мартенсита. Цементит является фазовой и структурной составляющей железоуглеродистых сплавов, составной частью ледебурита, перлита, сорбита и троостита. Цементит — представитель так называемых фаз внедрения, соединений переходных металлов с легкими металлоидами. В фазах внедрения велики доля как ковалентной, так и металлической связи. Прочность-8500 МПА.
3. Сталь 15Х Сталь конструкционная легированная; качественная; 0.15% содержания углерода, низко – углеродистая; около 1% содержания хрома, низко – легированная. Применение, втулки, пальцы, шестерни, валики, толкатели и другие цементуемые детали, к которым предъявляется требование высокой поверхностной твердости при высокой прочности сердцевины, детали, работающие в условиях износа при трении.
Сталь 12Х17 Сталь конструкционная легированная; 0.12% содержания углерода, низко – углеродистая; 17% содержания хрома, высоко – легированная; коррозийно-стойкая жаропрочная. Применяется крепежные детали, валики, втулки и другие детали аппаратов и сосудов, работающих в разбавленных растворах азотной, уксусной, лимонной кислоты, в растворах солей, обладающих окислительными свойствами; сталь ферритного класса.
Нихром Х20Н80 Углеродистый сплав нихрома; 20% хрома, 80% никеля. Обладает повышенной жаропрочностью, крипоустойчивостью, пластичностью и стабильностью формы. Широко используется в высокотемпературных электропечах, печах обжига и сушки, различных электрических аппаратах теплового действия.
Сплав ЕХ5К5 Сплав прецизионный магнитно-твердый; Около 1% содержания углерода, 5% хрома, 5% кобальта. для изготовления магнитов неответственного назначения.
11ХФ Сталь инструментальная легированная содержание углерода 0,11%; Низко – углеродистая, 1% хрома, 1% ванадия. Низко – легированная. Применяется для метчиков и другого режущего инструмента диаметром до 30 мм, закаливаемого с охлаждением в горячих средах.
БРОЦС5-5-5 Сплав бронзы, 5% содержания олова, 5% содержания цинка, 5 % содержания Свинца. Обладает хорошими литейными и декоративными свойствами. Применяется для декоративно – художественных отливок.
Стеклопластик , (другие названия – фибергласс композит (fiber glass composite), более привычное в России название – стеклокомпозит), многие годы использовался в оборонной промышленности, самолетостроении, кораблестроении и других областях, где к материалу предъявлялись повышенные требования по прочностным характеристикам, теплосбережению, устойчивости к агрессивным средам, сохранению свойств при резких колебаниях температур, долговечность, экологичность, словом, все требования, которые мы предъявляем к современным материалам.
Стеклопластик- стеклонаполненный материал (70% стекловолокна) на основе полиэфирных смол, обладает прочностью и долговечностью металла,биологической стойкостью полимера (не гниёт, не меняет цвет, не становится хрупким).
Прочность в 9 раз выше ,чем у ПВХ и в 2-4 раза выше, чем у алюминия, термическое расширение и сжатие стекла, поэтому нет деформаций.
4. Строительная арматура
Предъявляемые требования:
· высокие прочностные и пластические механические свойства;
· прочность и жесткость сцепления с бетоном;
· низкая распорность в бетоне;
· хорошая свариваемость;
· коррозионная стойкость и усталостная прочность
Сталь углеродистые стали Ст3-Ст5пс а также легированный стали 35ГС, 25Г2С
Подшипник скольжения тяжело нагруженных машин
· Широкий интервал рабочих температур то 0 до 1000 C
· Устойчивость к трению
Применяемые марки стали ШХ15, ШХ15СГ, ШХ20СГ, 11Х18М-ШД, 8Х4В9Ф2-Ш
Мечик – Применяемая марка стали 9ХС, 11ХФ, быстрорежущая сталь Р6М5, Р18 или Р9.
mirznanii.com