Заточка инструментов — Заточка инструментов
Заточка инструментов
Категория:
Заточка инструментов
Заточка инструментов
Заточка зубила. Инструмент устанавливают на подручник заточного станка и, слегка нажимая на него, медленно и плавно перемещают по всей ширине заточного круга. В процессе работы зубило следует переворачивать и затачивать то одну, то другую сторону, периодически охлаждая режущую часть в воде.
Режущая кромка зубила после заточки должна иметь одинаковую ширину и наклон к оси с обеих сторон инструмента. Только в этом случае зубило будет заточено правильно.
Для рубки чугуна и бронзы угол заточки, или заострения, зубила делают 70°, для стали средней твердости — 60°, меди и латуни — 45°, алюминия и цинка — 35°. Угол заострения проверяют по шаблону, представляющему собой пластинку с угловыми вырезами в 70°, 60°, 45°, 35° (рис. 2).
Рис. 1. Заточка зубила
Рис.
Рис. 3. Заточка чертилки
После заточки режущую кромку зубила заправляют на абразивном бруске, то есть снимают с нее неровности.
Заточка чертилки. Сначала проверяют установку подручника. Если он расположен правильно, то есть зазор между ним и абразивным кругом не превышает 2—3 мм, можно приступать к работе.
Включают электроточило, берут обеими руками чертилку и, опираясь левой рукой на подручник, прижимают рабочую часть инструмента к боковой поверхности заточного круга под небольшим углом к ней (рис. 2). Чтобы чертилка была заточена ровно и правильно, ее надо все время поворачивать вокруг своей оси.
Заточка кернера. Отрегулировав зазор между подручником и заточным кругом, берут кернер обеими руками и, располагая левую руку на подручнике, устанавливают кернер под углом 30—40° к рабочей поверхности круга (рис. 3).
Включив электроточило, прижимают к нему рабочую часть кернера и затачивают инструмент, поворачивая его вокруг своей оси.
—
С помощью заточки восстанавливают рабочую часть режущего инструмента, т. е. получают оптимальную форму, размеры и шероховатость его режущих кромок. Повторные операции заточки затупленного инструмента называют перетачиванием.
Заточка резцов. Износ по задней поверхности определяется величиной, износ по передней поверхности — шириной В и глубиной Нл лунки. В зависимости от условий обработки износ твердого сплава может происходить только по передней или только по задней поверхности или по обеим поверхностям одновременно.
Рис. 4. Заточка резца на точильно-шлифовальном станке
Если износ резцов не превышает допустимой величины, то припуск на заточку составляет 0,6—0,9 мм.
Заточку резцов производят на точильно-шлифоваль-ных станках (точилах), универсально-заточных станках и специальных резцезаточных станках. Установка резца на подручниках точила при заточке передней поверхности показана на рис. 4, а; при заточке главной задней поверхности — на рис.
При расчетах учитывают, является ли положительным или отрицательным угол Я и подставляют его в формулы соответственно со знаком плюс или минус.
Последовательность операций заточки и доводки твердосплавного резца:
1) заточка передней поверхности;
2) заточка задней главной поверхности по державке;
3) заточка задней вспомогательной поверхности по державке;
4) заточка фаски по передней поверхности;
5) заточка задней главной поверхности по пластине;
6) заточка задней вспомогательной поверхности по пластине;
7) заточка задней поверхности по радиусу вершины;
8) доводка фаски по передней поверхности;
9) доводка ленточки по задней поверхности.
Рис. 5. Схема расчета установочных углов резца при заточке в трех-поворотных тисках на универсально-заточном станке
Рис. 6. Установка резца в трехповоротных тисках при заточке передней (а и б) и задней поверхности (в и г)
Рис. 7. Контроль углов резца угломером, размещенным на стойке
Рис. 8. Схема двухплоскостной заточки сверла
Рис. 9. Характер износа и величина стачивания при заточке незатылованной (а) и затылованной (б) фрезы
Рис. 10. Затачивание незатылованной фрезы по передней (о) и задней (б) поверхностям
Рис. 11. Контроль передних (а) и задних (б) углов фрезы
Реклама:
Читать далее:
Плоскостная разметка по чертежу и обработка по разметке
Статьи по теме:
В помощь будущему автомеханику — рубка
Рубка металла
Общие понятия о рубке. Сущность процесса резания металла
Инструменты для рубки
Техника рубки
Приемы рубки
Механизация рубки
Безопасность труда при рубке
1. Общие понятия о рубке. Сущность процесса резания металла
Рубкой называется слесарная операция, при которой с помощью режущего инструмента (зубила и др.) и ударного инструмента (слесарного молотка) с поверхности заготовки или детали удаляются лишние слои металла или заготовка разрубается на части.
Рубка производится в тех случаях, когда по условиям производства станочная обработка трудно выполнима или нерациональна и когда не требуется высокой точности обработки.
Рубка применяется для удаления (срубания) с заготовки больших неровностей (шероховатостей), снятия твердой корки, окалины, заусенцев, острых углов кромок на литых и штампованных деталях, для вырубания шпоночных пазов, смазочных канавок, для разделки трещин в деталях под сварку (разделка кромок), срубания головок заклепок при их удалении, вырубания отверстий в листовом материале.
Кроме того, рубка применяется тогда, когда необходимо от пруткового, полосового или листового материала отрубить какую-то часть.
Заготовку перед рубкой закрепляют в тиски.
Крупные заготовки рубят на плите или наковальне, а особо крупные — на том месте, где они находятся.
В зависимости от назначения обрабатываемой детали рубка может быть чистовой и черновой.
В первом случае зубилом за один проход снимают слой металла толщиной от 0,5 до 1 мм, во втором — от 1,5 до 2 мм.
Точность обработки, достигаемая при рубке, составляет 0,4-1,0 мм.
Резанием называется процесс удаления с обрабатываемой заготовки (детали) лишнего слоя металла в виде стружки, осуществляемый при помощи режущих инструментов.
Процесс резания осуществляется при выполнении большинства слесарных операций: рубки, резания, опиливания, сверления, шабрения, притирки.
Форма режущей части (лезвия) любого режущего инструмента представляет собой клин с определенными углами (зубило, резец) или несколько клиньев (ножовочное полотно, метчик, плашка, фреза, напильник).
Зубило представляет собой простейший режущий инструмент, в котором форма клина особенно четко выражена.
В зависимости от того, как будет заострен режущий клин, как он будет установлен по отношению к плоскости (поверхности) детали и как будет направлена сила, двигающая клин в слое металла, можно получить наибольший или наименьший выигрыш в затрате труда, в качестве обработки, а также в количестве израсходованных инструментов.
Чем острее клин, т. е. меньше угол, образованный его сторонами, тем меньшее усилие потребуется для его углубления в материал.
Теорией и практикой резания установлены определенные углы заострения режущих инструментов для различных металлов.
На обрабатываемой заготовке различают следующие поверхности: обрабатываемую, обработанную, а также поверхность резания.
Обрабатываемой поверхностью называется поверхность, с которой будет сниматься слой материала (стружка).
Обработанной поверхностью называется поверхность, с которой снят слой металла (стружка).
Грань, по которой сходит стружка при резании, называется передней, а противоположная ей грань, обращенная к обрабатываемой поверхности заготовки, —
Пересечение передней и задней граней образуют режущую кромку, ширина которой у зубила обычно 15 — 25 мм.
Угол заострения β (бэта) — угол, образованный между передней и задней поверхностями инструмента.
Угол резания δ (дельта) — угол между передней гранью и обрабатываемой поверхностью; он равен сумме угла заострения и заднего угла, т. е. δ = β + α.
Передний угол γ (гамма) — угол между передней гранью и плоскостью, проведенной через режущую кромку перпендикулярно обрабатываемой поверхности. Чем больше передний угол у инструмента, тем меньше угол заострения и тем, следовательно, меньше будет усилие резания, но менее прочной и стойкой будет режущая его часть.
Задний угол α (альфа) образуется задней поверхностью (гранью) и поверхностью резания. Задний угол должен быть очень небольшим, чтобы не ослабить режущую часть инструмента. Для зубил он равен 3 — 8°. Если зубило наклонить под большим углом, оно врежется в обрабатываемую поверхность; при меньших углах зубило скользит, не производя резания. Этот угол уменьшает трение задней поверхности инструмента об обработанную поверхность.
Действие клинообразного инструмента на обрабатываемый металл изменяется в зависимости от положения оси клина и направления действия силы Р.
Различают два основных вида работы клина:
ось клина и направление действия силы Р перпендикулярны поверхности заготовки. В этом случае заготовка разрубается;
ось клина и направление действия силы Р образуют с поверхностью заготовки угол меньше 90°. В этом случае с заготовки снимается стружка.
При работе клина при угле менее 90° его передняя поверхность сжимает находящийся перед нею срубаемый слой металла, отдельные его частицы смещаются относительно друг друга; когда напряжение в металле превысит прочность металла, происходит сдвиг или скалывание его частиц, в результате чего образуется стружка.
2. Инструменты для рубки
Слесарное зубило представляет собой стальной стержень, изготовленный из инструментальной углеродистой стали У7А, У8А, 7ХФ, 8Хф.
Зубило состоит из трех частей: рабочей, средней и ударной.
Рабочая часть зубила представляет собой стержень с клиновидной режущей частью (лезвие) на конце, заточенной под определенным углом.
Ударная часть (боек) сделана суживающейся кверху, вершина ее закруглена.
Угол заострения (угол между боковыми гранями) выбирается в зависимости от твердости обрабатываемого металла.
За среднюю часть зубило держат при рубке.
Рекомендуемые углы заострения зубила для рубки некоторых материалов следующие (град):
Для твердых материалов (твердая сталь, бронза, чугун)…. 70
Для материалов средней твердости (сталь) ….. 60
Для мягких материалов (медь, латунь) … 45
Для алюминиевых сплавов …… 35
Зубило изготовляют длиной 100, 125, 160, 200 мм, ширина рабочей части соответственно равна 5, 10, 16, 20 мм.
Рабочая часть зубила на длине 0,3 — 0,5 закаливается и отпускается.
После термической обработки режущая кромка должна иметь твердость HRC 53 — 59, боек — HRC 35 — 45.
При испытании зубила на прочность и стойкость им отрубают зажатую в тиски стальную полосу марки Ст6 толщиной 3 мм и шириной 50 мм.
После испытания на лезвии зубила не должно быть вмятин, выкрошенных мест и заметных следов затупления.
Степень закалки зубила можно определить старым напильником, которым проводят по закаленной части зубила. Если при этом напильник не снимает стружку с закаленной части зубила (на ней остаются лишь едва заметные риски), закалка выполнена хорошо.
Крейцмейсель отличается от зубила более узкой режущей кромкой, предназначен для вырубания узких канавок, шпоночных пазов и т. п.
Однако довольно часто им пользуются для срубания поверхностного слоя с широкой плиты: сначала крейцмейселем прорубают канавки, а оставшиеся выступы срубают зубилом.
Материалы для изготовления крейцмейселя и углы заострения, твердость рабочей и ударных частей те же, что и для зубила.
Для вырубания профильных канавок — полукруглых, двугранных и других применяют специальные крейцмейсели, называемые канавочниками, отличающиеся от крейцмейселя только формой режущей кромки.
Канавочники изготовляют из стали У8А длиной 80, 100, 120, 150, 200, 300 и 350 мм, с радиусом закругления 1; 1,5; 2,0; 2,5 и 3,0 мм.
Заточка зубил на станке вручную.
Заточка зубил и крейцмейселей производится на заточном станке. Для заточки зубило или крейцмейсель накладывают на передвижной подручник и с легким нажимом медленно передвигают по всей ширине шлифовального круга, периодически поворачивая инструмент то одной, то другой стороной.
Не следует допускать сильных нажимов на затачиваемый инструмент, так как это приводит к перегреву режущей кромки, в результате чего лезвие теряет первоначальную твердость.
Перед заточкой инструмента подручник устанавливают как можно ближе к заточному кругу.
Зазор между подручником и заточным кругом должен быть не более 2 — 3 мм, чтобы затачиваемый инструмент не мог попасть между кругом и подручником.
Заточку лучше всего вести с охлаждением водой, в которую добавлено 5% соды, или на мокром круге.
Несоблюдение этого условия вызывает повышенный нагрев, отпуск и уменьшение твердости инструмента, а следовательно, и стойкости в работе.
Боковые грани после заточки должны быть плоскими, одинаковыми по ширине и с одинаковыми углами наклона.
Проверка угла заточки зубила.
После заточки зубила или крейцмейселя с режущих кромок снимают заусенцы.
Величина угла заострения проверяется шаблоном, представляющим собой пластинки с угловыми вырезами 70, 60, 45 и 35°.
Слесарные молотки с круглым бойком изготовляют шести номеров:
молотки №1 массой 200 г рекомендуется применять для инструментальных работ, а также для разметки и правки;
молотки № 2 массой 400 г, № 3 — 500 г и № 4 — 600 г — для слесарных работ;
молотки № 5 — 800 г и № 6 — 1000 г применяются редко (при ремонтных работах).
Слесарные молотки с квадратным бойком изготовляют восьми номеров:
№ 1 массой 50 г, № 2 — 100 г и № 3 — 200 г — для слесарно-инструментальных работ;
№4 — 400 г, №5 — 500 г, №6 — 600 г — для слесарных работ, рубки, гибки, клепки и др.;
№7 — 800 г и №8 — 1000 г применяют редко (при выполнении ремонтных работ).
Для тяжелых работ применяют молотки массой от 4 до 16 кг, называемые кувалдами.
Противоположный бойку конец молотка называется носком.
Носок имеет клинообразную форму, скругленную на конце.
Носком пользуются при правке, расклепывании и т. д.
Бойком наносят удары по зубилу или крейцмейселю.
Изготовляют молотки из стали 50 и 40Х и инструментальной углеродистой стали У7 и У8.
В средней части молотка имеется отверстие овальной формы, служащее для крепления рукоятки.
Рабочие части молотка — боек квадратной или круглой формы и носок клинообразной формы — термически обрабатывают до твердости HRC 49 — 56.
Рукоятку молотка делают из твердых пород дерева (кизила, рябины, дуба, клена, граба, ясеня, березы или из синтетических материалов).
Рукоятка имеет овальное сечение, отношение малого сечения к большому 1:1,5, т. е. свободный конец в 1,5 раза толще конца, на который насаживается молоток.
Конец, на который насаживается молоток, расклинивается деревянным клином, смазанным столярным клеем, или металлическим клином, на котором делают насечки (ерши).
Толщина клиньев в узкой части 0,8 — 1,5 мм, а в широкой — 2,5 — 6 мм.
Если отверстие молотка имеет только боковое расширение, забивают один продольный клин; если расширение идет вдоль отверстия, то забивают два клина, и наконец если расширение отверстия направлено во все стороны, забивают три стальных или три деревянных клина, располагая два параллельно, а третий перпендикулярно к ним.
Правильно насаженным считается молоток, у которого ось рукоятки образует прямой угол с осью молотка.
Помимо обычных стальных молотков в некоторых случаях, например при сборке машин, применяют так называемые мягкие молотки со вставками из меди, фибры, свинца и алюминиевых сплавов.
При ударах, наносимых мягким молотком, поверхность материала заготовки почти не повреждается.
Из-за дефицитности меди, свинца и быстрого износа эти молотки мало эффективны и не всегда удобны в эксплуатации.
В целях экономии металлов медные или свинцовые вставки заменяют резиновыми, более дешевыми и эффективными в работе.
Такой молоток состоит из стального корпуса, на цилиндрические концы которого надеты накостыльники из твердой резины.
Резиновые накостыльники достаточно стойки против ударов и при износе легко заменяются новыми.
Молотки этой конструкции применяют при точных сборочных работах, особенно когда приходится иметь дело с деталями невысокой твердости.
В некоторых случаях, в особенности при изготовлении изделий из тонкого листового железа, применяют деревянные молотки (киянки).
Киянки бывают с круглым и прямоугольным ударниками.
3. Техника рубки
Для рубки используют возможно более прочные и тяжелые тиски (предпочтительно стуловые).
Правильное положение корпуса, держание (хватка) инструмента при рубке — существенные условия высокопроизводительной работы.
Для слесарной рубки используют поворотные и не поворотные параллельные тиски с шириной губок 100 -140 мм.
Для тяжелой кузнечной рубки применяют стуловые тиски с шириной губок от 130 до 150 мм, которые крепят на специальной тумбе.
При рубке металла зубилом решающее значение имеет положение рабочего (установка корпуса и ног), которое должно создавать наибольшую устойчивость центра тяжести тела при ударе.
Положение корпуса и ног.
Установка корпуса рабочего при рубке зубилом будет правильной, если корпус выпрямлен и обращен в пол-оборота (45°) к оси тисков, левая нога выставлена на полшага вперед, а угол, образуемый линиями осей ступней, будет составлять 60 — 75° в зависимости от силы удара.
Держание (хватка) зубила.
Зубило берут в левую руку за среднюю часть на расстоянии 15 — 20 мм от конца ударной части.
Удары наносят правой рукой. Левая рука только держит зубило в определенном положении; сильно сжимать в руке зубило не следует.
При движениях правой руки, наносящей удары по зубилу, левая рука играет роль балансира при последовательных установках инструмента.
Держание (хватка) молотка.
Молоток берут правой рукой за рукоятку на расстоянии 15 — 30 мм от конца, обхватывая четырьмя пальцами и прижимая к ладони, большой палец накладывая на указательный, крепко сжимая всеми пальцами.
Все пальцы остаются в таком положении при замахе и при ударе. Этот способ называется «нанесение кистевого удара без разжатия пальцев».
При другом способе хватки в начале замаха мизинец, безымянный и средний пальцы постепенно разжимают и рукоятку молотка охватывают только указательным и большим пальцами.
Затем разжатые пальцы сжимают и ускоряют движение руки вниз. В результате получается сильный удар молотка. Этот способ называется «нанесение удара с разжатием пальцев».
Существенное влияние на качество и производительность рубки оказывает характер удара (замаха) молотком.
Удар может быть кистевым, локтевым или плечевым.
При кистевом ударе замах осуществляют молотком только за счет изгиба кисти правой руки. При этом замахе сгибают кисть в запястье до отказа, разжав слегка пальцы, кроме большого и указательного, при этом мизинец не должен сходить с рукоятки молотка. Затем пальцы сжимают и наносят удар.
Кистевой удар применяют при выполнении точных работ, легкой рубке, срубании тонких слоев металла и т. д.
Во время рубки смотрят на режущую часть зубила, а не на боек, как это часто делает ученик-слесарь, и следят за правильным положением лезвия зубила.
Удары наносят по центру бойка сильно, уверенно и метко. Этот навык приходит после тренировки.
Массу слесарного молотка выбирают в зависимости от размера зубила и толщины снимаемого слоя металла (обычно толщина стружки составляет 1-2 мм) из расчета 40 г на 1 мм длины лезвия зубила.
При работе крейцмейселем массу молотка принимают из расчета 80 г на 1 мм длины лезвия.
При выборе молотка учитывают также и физическую силу рабочего.
Масса молотка для ученика должна быть около 400 г, для молодого рабочего 16 — 17 лет — 500 г, для взрослого рабочего — 600 — 800 г.
Удар осуществляют не за счет излишних мускульных усилий, ведущих к быстрому утомлению, а за счет ускоренного падения молотка.
В момент нанесения удара рукоятку молотка прочно сжимают пальцами: слабо удерживаемый молоток при неточном ударе может отскочить в сторону, что очень опасно.
При локтевом ударе правую руку сгибают в локте.
При замахе действуют пальцы руки, которые разжимаются и сжимаются, кисть (движение ее вверх, затем вниз) и предплечье.
Для получения сильного удара руку разгибают достаточно быстро.
Этим ударом пользуются при обычной рубке, при срубании слоя металла средней толщины или при прорубании пазов и канавок.
При плечевом ударе рука движется в плече, при этом получается большой замах и максимальной силы удар с плеча.
В этом ударе участвуют плечо, предплечье и кисть.
Плечевым ударом пользуются при снятии толстого слоя металла и обработке больших поверхностей.
Сила удара должна соответствовать характеру работы, а также массе молотка (чем тяжелее молоток, тем сильнее удар), длине рукоятки (чем длиннее рукоятка, тем сильнее удар), длине руки работающего (чем длиннее рука и выше замах, тем сильнее удар).
При рубке действуют обеими руками согласованно (синхронно), метко наносят удары правой рукой, перемещая в определенные промежутки времени зубило левой рукой.
Угол установки зубила при рубке в тисках регулируют так, чтобы лезвие находилось на линии снятия стружки, а продольная ось стержня зубила находилась под углом 30 — 35° к обрабатываемой поверхности заготовки и под углом 45° к продольной оси губок тисков.
При меньшем угле наклона зубило будет соскальзывать, а не срезать, а при большем — излишне углубляться в металл и давать большую неровность.
Угол наклона зубила при рубке не измеряют, опытный слесарь по навыку ощущает наклон и регулирует его положение движением левой руки.
1, 2
Copyright avtomeh.ucoz.net © 2021 |
Как правильно заточить ручной инструмент
Любой режущий инструмент в процессе эксплуатации рано или поздно тупится. Если он «одноразовый», у него одна дорога – на свалку. Если же инструмент реально восстановить, почему бы не воспользоваться такой возможностью? Исходя из этого, мы решили подготовить статью о том, как «приводят в чувство» режущий инструмент.
Уточним терминологию. Режущая кромка инструмента образуется двумя сходящимися плоскостями (или кривыми, как у сверл). Угол заточки есть угол при вершине схождения этих плоскостей. Остроту кромки можно представить как величину, обратную ширине «площадки» на вершине или диаметру вписанного в нее круга. Практически же чем глаже сходящиеся поверхности, тем более острой будет РК. Углы заточки у разных инструментов различаются и в зависимости от качества стали и разрезаемого материала составляют: у стамески – 17–25 градусов, у рубаночного железка – 25–40, у долота – 30–40, у зубила по металлу – до 60, у ножниц – 45–60, у ножей – 20–30 градусов.
Все режущие инструменты с точки зрения приемов заострения можно условно разделить на «ножи» (то есть то, что длиннее ширины точильного камня) и «резцы» (то, что уже камня: пилы, фрезы, резцы и сверла). Приемы заточки последних отличаются от всего остального.
К категории «ножей», кроме собственно ножей, отнесем ножницы, ножи электрофуганков и рейсмусов, а также прочий длинномер. Важное замечание: ножницы и ножи деревообрабатывающего оборудования точатся только с одной стороны. Перед заточкой инструмент надо очистить от грязи, опилок, смолы и прочего, так как эти субстанции легко и необратимо забивают точильный камень.
Заточка ножей
Сначала надо рассмотреть режущую кромку и решить, с какого абразива стартовать. Если нож новый или сильно затупленный, возможно, стоит начать с грубого камня. Хорошая заточка режущего инструмента – это всего лишь умение выдержать один и тот же угол при движениях по камню. Важное замечание: никогда не точите ножи на высокооборотном точильном круге – он мгновенно отпускает и пережигает режущую кромку.
|
Итак, намочим точильный камень водой, положим его на старые газеты или лучше в углубление, выдолбленное в доске по форме камня, и водим ножом вдоль камня, соблюдая угол заточки. Нож должен набегать на камень под углом, как можно более близким к прямому. Но так как камень узкий, придется делать некое наклонное движение, перемещая нож по диагонали, то есть одновременно вдоль камня и вдоль ножа.
Большой ошибкой будет точить режущую кромку участками. Абсолютно точного перехода не получится – образуется ступенька, и нож будет плохо резать. Необходимо точить до тех пор, пока на кромке не появится завернутый вверх заусенец, который выявляется легким движением пальца поперек ножа от обуха к кромке (вдоль делать этого не стоит – можно порезаться). Когда заусенец появится по всей длине, нож нужно перевернуть и точить другую сторону.
Не пытайтесь доточить только те участки, где нет заусенца. Непрерывный заусенец показывает, что одна фаска режущей кромки ножа получила по всей длине плоскость. Когда при заточке второй стороны заусенец появится на уже заточенной, надо опять перевернуть нож и перейти на более мелкий абразив.
Чем меньше зерна абразива, тем более гладкие фаски и острее кромка. После мелкого камня надо перейти к наждачной бумаге, постеленной абразивом вверх на гладкую поверхность, например на кусок стекла или стали либо на ровную часть верстака.
Ножницы следует затачивать только с фаски.
Обычно используют сначала дешевый двухсторонний точильный камень и затем, последовательно, наждачные бумаги с зернистостью 120, 400, 600 (или 800) и иногда 1200. Самое сложное и простое в этом процессе – выдерживать одинаковый угол при всех движениях ножа. Стоит отметить, что постоянная практика лучше всяких хитроумных приспособлений – они ломаются и к тому же стоят намного дороже камня, который, кстати, в них тоже присутствует. Хитрость заключается в том, чтобы двигать затачиваемый инструмент при неподвижном запястье и внимательно смотреть на верхнюю плоскость инструмента. Тогда угол выдерживается весьма точно.
Ножницы точат только с фаски, прилегающую к другой бранше плоскость лишь выравнивают на мелкой наждачке.
Ножи фуганков тоже точат только с фаски. Их особенность в том, что нужно часто прикладывать кромку к линейке или стеклу, чтобы видеть прямизну режущей кромки и избегать ее скругления.
Заточка стамесок и рубаночных железок
Стамески и рубаночные железки имеют много общего. При сильном затуплении или выбоинах на режущей кромке, которые возникают из-за сучков или гвоздей, надо сначала ее спрофилировать. К слову, так же поступают при изготовлении резца по дереву из закаленной заготовки.
Наиболее эффективный способ заточки железко для рубанка – с помощью электроточила.
Здесь нам понадобится высокооборотистое электроточило. Часто макая железко в воду для остывания, нужно сделать фаску с углом немного острее 25 градусов. Ни в коем случае не утончайте кромку железка до появления режущей кромки, так как огромное трение абразива о металл нагревает последний, и при попытке заточки на высокооборотном камне режущая кромка будет немедленно отпущена и инструмент испорчен.
Когда толщина кромки станет около полумиллиметра, надо угольником проверить перпендикулярность режущей кромки оси или боковой стороне рубаночного железка.
Окончательно заострять железко можно двумя способами. Лучше всего – на низкоскоростном электроточиле с мокрым камнем (налив воды в поддон и равномерно прижимая железко к камню). Если ширина последнего недостаточна, то необходимо водить железком из стороны в сторону.
Болт с двумя гайками поможет соблюсти необходимый угол при заточке железко для рубанка.
Если такого точила у вас нет, придется работать вручную на абразивном бруске, смоченном водой. Его лучше положить в углубление в доске – так удобнее держать. Железко ставят на камень под выбранным углом или проще – фаской на камень, покачивая вперед и назад, пока он не встанет всей фаской. Заостряют движениями вдоль камня и обратно, а лучше – описывая будущей режущей кромкой восьмерки, чтобы достичь равномерного износа камня и сохранить его плоскостность. Когда появится заусенец, кладут железко плоскостью на камень и парой движений удаляют его, после чего переходят к более мелкому абразиву, например, перевернув двухсторонний камень.
Окончательная заточка производится положенными на стекло наждачными бумагами разной степени зернистости.
Маленькая хитрость. Болт с гайкой и двумя большими шайбами можно использовать как нехитрое приспособление для держания правильного угла наклона рубаночного железка (см. рисунок).
Заточка пил по дереву
Пилы по дереву, как правило, продаются не всегда достаточно острыми (а крупнозубые в большинстве своем – просто тупыми). Опять возникает необходимость заточки, причем для каждого вида работ она своя.
Если пила недостаточно разведена, сначала ее разводят. Если под рукой нет специализированной разводки, можно обойтись плоскогубцами. Пилу зажимают в тисках зубьями вверх, садятся так, чтобы смотреть вдоль полотна, и отгибают зубья в разные стороны через один, при каждом движении наклоняя плоскогубцы на один и тот же угол. Обычно небольшая разводка всегда есть изначально, и ее надо просто увеличить, если дело имеешь с сырым деревом или большими пилами. Если пила небольшая и для точных работ, вполне можно оставить и заводскую разводку.
При заточке пилы по дереву используется трехгранный напильник.
Для заточки зубьев используется треугольный напильник. Им точат с внутренней (по отношению к разводке) стороны зубьев пилы. Напильник держат так, чтобы угол режущей кромки был 60–45 градусов. На деле легче и быстрее заострить сначала одну сторону зубьев, а потом, перевернув пилу, заточить зубья другой стороны. В этом случае движения более однотипные – пила получается более острой.
При заточке пил лучше работать одному и в тишине, отключив помехи в виде радио и телевизора, так как неосторожное движение либо портит инструмент, либо наносит трудно заживающую рану. Совет: если при резке пила стремится уйти в сторону, это означает, что зубья разведены неравномерно – нужно увеличить их отклонение с той стороны, в которую пилу уводит.
Заточка пильных дисков
Дисковые пилы затачивают с задней поверхности, при работе обращенной к обрабатываемому материалу. Передняя, которая при пилении набегает на материал, остается как есть.
Диск можно точить или прямо в станке (если речь идет об оснастке для станка), или вынув из станка или циркулярной пилы. В первом случае сначала нужно выдернуть вилку из розетки, чтобы избежать случайного пуска станка. Диск следует подклинить, положив с двух сторон от него по тонкой деревяшке и прижав их к зубьям. Зуб, с которого начинается заточка, надо пометить фломастером по боковой стороне, чтобы не ошибиться в работе. Затачивая первый зуб, запоминайте количество движений напильником или алмазным надфилем – все остальные зубья предстоит точить с тем же усилием и тем же количеством движений абразивного инструмента, что и первый.
Если диск был снят со станка, зажмите его в тисках и проделайте те же процедуры, что описаны выше.
Далее диск нужно вернуть в станок и распилить ненужную деревяшку. При сильном шуме или неровной подаче надо проверить, одинакова ли высота зубьев. Для этого к режущему краю подносят фломастер и медленно проворачивают диск рукой на один оборот в сторону, обратную направлению вращения. На каждом зубе останется отметина. Осмотрев диск, можно обнаружить зубья, которые выше или ниже других. Если разница велика, необходимо аккуратно уменьшить высоту слишком длинных зубьев.
Заточка фрез
Заточку фрез ведут по задней или передней поверхности.
Перед заточкой от фрезы необходимо предварительно отделить направляющий подшипник, иначе можно испортить инструмент.
Фасонные концевые фрезы проще затачивать по передней поверхности – либо тонким алмазным бруском, либо (при узкой стружковыводной канавке) наждачной бумагой, обернутой вокруг рейки из твердого дерева или полоски стали. По мере стачивания передней поверхности кромка заострится, а диаметр фрезы уменьшится (незначительно).
С фрез с направляющим подшипником сначала надо снять подшипник и только потом затачивать их. Попытка сэкономить минуту закончится загубленным подшипником и испорченной фрезой.
Заточка токарных резцов
Токарные резцы заостряют со стороны передней и задней поверхностей. Нюанс там только один – резец сужается вниз, поэтому, чтобы его боковые плоскости ни в коем случае не соприкасались с заготовкой, контакт должен быть только по режущей грани.
Резцы из быстрореза и с твердосплавными напайками точат на точильном круге. Если на станке подачи воды не предусмотрено, почаще макайте резец в емкость с водой.
Заточка сверла
При заточке сверла нужно держать его так, чтобы получить желаемый угол схождения режущих граней. При этом режущая кромка должна быть симметричной.
Затачивать сверло необходимо с особой точностью.
Проще всего провести на подручнике электроточила линию фломастером и держать сверло параллельно ей. Однако просто положить сверло по линии недостаточно, следует еще и повернуть его на нужный угол вокруг оси, а потом на 180 градусов относительно первого положения.
Нужен угол между кромкой сверла и плоскостью стола, то есть внешний край должен быть ниже центра, иначе сверло будет не резать материал, а ехать по нему задней поверхностью. Для контроля этого угла есть разные приспособления, но проще стоять или сидеть за столом так, чтобы блик от освещения был на внешней части режущей кромки, а потом, не меняя положения тела, повернуть сверло в пальцах и опять поймать блик – кромки будут заострены под одним углом.
Заточка сверла по задней поверхности называется одинарной, при ней остается довольно большая перемычка в центре, которая не режет, а скоблит металл. Если ее подточить, скорость сверления возрастет. Способов подточки перемычки много. На заводах ее подтачивают тонкими абразивными или алмазными кругами либо на углу широкого камня. Но можно подтачивать перемычку так, как показано на фото. Защитные очки при выполнении заточки строго обязательны.
Электроточила
Для облегчения труда при заточке инструмента существуют различныеэлектроточила и заточные станки.
Выбор электроточила крайне прост. Такой станок состоит из асинхронного двигателя (подобные моторы в совершенстве освоены промышленностью), точильных кругов (они сменные и меняются при помощи гаечного ключа) и кожухов. Если точило берется не для промышленного применения, то марка не имеет такого уж большого значения. Подобное оборудование включают ненадолго, и ресурс его будет расходоваться крайне медленно – даже недорогой станок прослужит много лет.
Диаметр круга прямо влияет на цену точила, поэтому мастеровому-любителю или маленькому предприятию не стоит гнаться за большими диаметрами.
Осматривая электроточило перед покупкой, попробуйте пошевелить вал. Если он не только вращается, но и ходит – перед вами брак. Крутаните камень рукой и посмотрите на свободный конец вала, не вибрирует ли он? Лучше всего, конечно, включить точило, но не во всех магазинах позволяют это сделать.
Заточные станки
Заточные станки делятся на три группы.
Первая – фактически высокоскоростное электроточило (около 3000 об/мин), оборудованное сменными держателями для разных видов инструмента.
|
Вторая – узкоспециализированные станки, например для заточки сверл. Зачастую на них нельзя заточить никакой другой режущий инструмент.
Третья – станки, оборудованные низкоскоростными кругами с водяным охлаждением («мокрые»). Скорость вращения – 80–150 оборотов в минуту. На них можно затачивать и править любой режущий инструмент, от сверл из быстрорежущей стали до ножей из углеродистой стали. Низкая скорость и водяное охлаждение – необходимые условия для выведения тончайшей и острейшей режущей кромки. Часто такие станки имеют и полировальный круг для полировки режущей кромки.
Работа с электроточилом и заточным станком
После работы на станке с «мокрым» кругом не забывайте выливать воду из поддона и не оставляйте камень в воде одним боком на продолжительное время – камень напитывается водой, теряет прочность и превращается в эксцентрик, разбивающий станок.
После работы с мокрым кругом нужно удалять воду из поддона станка.
Абразивные круги всегда должны «набегать» на режущую кромку затачиваемого инструмента, а полировальные (кожаные, войлочные, вулканитовые) – «убегать», то есть вращаться «от рабочего». Не пытайтесь полировать вращением круга «на себя» – обрабатываемый объект врежется в круг, будет им захвачен и выброшен в сторону оператора. Кроме порчи круга, можно получить серьезную травму.
Если вы устанавливаете полировальный круг на высокоскоростное электроточило, поверните кожух на 180 градусов. Для работы на полировальнике либо разверните станок, либо подойдите к нему с другой стороны.
Кернение отверстий. Кернер – чтобы сверло не соскользнуло! Механический пружинный кернер – инструмент для работы без молотка
Заточка инструментов
К атегория:
Заточка инструментов
Заточка инструментов
Заточка зубила. Инструмент устанавливают на подручник заточного станка и, слегка нажимая на него, медленно и плавно перемещают по всей ширине заточного круга. В процессе работы зубило следует переворачивать и затачивать то одну, то другую сторону, периодически охлаждая режущую часть в воде.
Режущая кромка зубила после заточки должна иметь одинаковую ширину и наклон к оси с обеих сторон инструмента. Только в этом случае зубило будет заточено правильно.
Для рубки чугуна и бронзы угол заточки, или заострения, зубила делают 70°, для стали средней твердости — 60°, меди и латуни — 45°, алюминия и цинка — 35°. Угол заострения проверяют по шаблону, представляющему собой пластинку с угловыми вырезами в 70°, 60°, 45°, 35° (рис. 2).
Рис. 1. Заточка зубила
Рис. 2. Шаблон (а) и проверка угла заточки зубила (б)
Рис. 3. Заточка чертилки
После заточки режущую кромку зубила заправляют на абразивном бруске, то есть снимают с нее неровности.
Заточка чертилки. Сначала проверяют установку подручника. Если он расположен правильно, то есть зазор между ним и абразивным кругом не превышает 2-3 мм, можно приступать к работе.
Включают электроточило, берут обеими руками чертилку и, опираясь левой рукой на подручник, прижимают рабочую часть инструмента к боковой поверхности заточного круга под небольшим углом к ней (рис. 2). Чтобы чертилка была заточена ровно и правильно, ее надо все время поворачивать вокруг своей оси.
Заточка кернера. Отрегулировав зазор между подручником и заточным кругом, берут кернер обеими руками и, располагая левую руку на подручнике, устанавливают кернер под углом 30-40° к рабочей поверхности круга (рис. 3).
Включив электроточило, прижимают к нему рабочую часть кернера и затачивают инструмент, поворачивая его вокруг своей оси.
С помощью заточки восстанавливают рабочую часть режущего инструмента, т. е. получают оптимальную форму, размеры и шероховатость его режущих кромок. Повторные операции заточки затупленного инструмента называют перетачиванием.
Заточка резцов. Износ по задней поверхности определяется величиной, износ по передней поверхности — шириной В и глубиной Нл лунки. В зависимости от условий обработки износ твердого сплава может происходить только по передней или только по задней поверхности или по обеим поверхностям одновременно.
Рис. 4. Заточка резца на точильно-шлифовальном станке
Если износ резцов не превышает допустимой величины, то припуск на заточку составляет 0,6-0,9 мм.
Заточку резцов производят на точильно-шлифоваль-ных станках (точилах), универсально-заточных станках и специальных резцезаточных станках. Установка резца на подручниках точила при заточке передней поверхности показана на рис. 4, а; при заточке главной задней поверхности — на рис. 4,б.
При расчетах учитывают, является ли положительным или отрицательным угол Я и подставляют его в формулы соответственно со знаком плюс или минус.
Последовательность операций заточки и доводки твердосплавного резца:
1) заточка передней поверхности;
2) заточка задней главной поверхности по державке;
3) заточка задней вспомогательной поверхности по державке;
4) заточка фаски по передней поверхности;
5) заточка задней главной поверхности по пластине;
6) заточка задней вспомогательной поверхности по пластине;
7) заточка задней поверхности по радиусу вершины;
8) доводка фаски по передней поверхности;
9) доводка ленточки по задней поверхности.
Рис. 5. Схема расчета установочных углов резца при заточке в трех-поворотных тисках на универсально-заточном станке
Заточка инструмента
Всякий режущий инструмент тупится в процессе работы, и поэтому его нужно время от времени затачивать. Эту операцию лучше и легче всего вести на заточном станке или другом механическом точиле.
Заточка зубила на заточном станке
Заточка зубила и крейцмейселя. Взяв зубило в руки, его осторожно прикладывают к вращающемуся кругу и двигают влево и вправо с легким нажимом. Заточке подвергают попеременно обе грани. Угол между ними — угол заточки — может быть различным и изменяется в зависимости от твердости обрабатываемого материала в следующих пределах: для алюминия и цинка — 35°, меди и латуни — 45°, стали — 60°, чугуна и бронзы — 75°. Углы заточки удобнее всего проверять по шаблону.
Правила заточки крейцмейселя те же, что и у зубила.
Заточка сверл. На рисунке ниже изображена передняя часть спирального сверла.
Передняя часть спирального сверла
Винтообразные канавки по оси сверла служат для удаления стружки. Ребро между плоскостью канавки и задней поверхностью является режущей кромкой. Угол между кромками делается обычно в 116-118°, однако он может меняться, в зависимости от твердости обрабатываемого материала, от 90 до 140°. Сверло при заточке держат левой рукой, возможно ближе к передней части, а правой рукой — за хвостовик, покачивая сверло плавным.
Заточка сверла
При этом нужно соблюдать следующие условия: а) режущие кромки должны быть симметричны, иметь одинаковый угол наклона и одинаковую длину; б) поперечная кромка должна составлять с режущей кромкой угол в 55°. Правильность заточки проверяется по шаблону.
Заточка кернера подобна заточке сверл. Инструмент держат левой рукой, прижимая к абразивному кругу, а правой равномерно вращают его для получения ровного конуса. Угол заточки равен 60°, для накернивания центров — 120°.
Помните, что сильно нажимать на инструмент во время заточки нельзя, иначе его рабочий конец нагреется слишком сильно и может отпуститься — потерять закалку. Во время работы от инструмента и абразивного круга отделяются раскаленные частицы, которые могут попасть в глаза. При заточке пользуйтесь защитными очками или защитным экраном!
В случае попадания частичек в глаз немедленно обращайтесь к врачу.
Любой режущий инструмент в процессе эксплуатации рано или поздно тупится. Если он «одноразовый», у него одна дорога – на свалку. Если же инструмент реально восстановить, почему бы не воспользоваться такой возможностью? Исходя из этого, мы решили подготовить статью о том, как «приводят в чувство» режущий инструмент.
Уточним терминологию. Режущая кромка инструмента образуется двумя сходящимися плоскостями (или кривыми, как у сверл). Угол заточки есть угол при вершине схождения этих плоскостей. Остроту кромки можно представить как величину, обратную ширине «площадки» на вершине или диаметру вписанного в нее круга. Практически же чем глаже сходящиеся поверхности, тем более острой будет РК. Углы заточки у разных инструментов различаются и в зависимости от качества стали и разрезаемого материала составляют: у стамески – 17–25 градусов, у рубаночного железка – 25–40, у долота – 30–40, у зубила по металлу – до 60, у ножниц – 45–60, у ножей – 20–30 градусов.
Все режущие инструменты с точки зрения приемов заострения можно условно разделить на «ножи» (то есть то, что длиннее ширины точильного камня) и «резцы» (то, что уже камня: пилы, фрезы, резцы и сверла). Приемы заточки последних отличаются от всего остального.
К категории «ножей», кроме собственно ножей, отнесем ножницы, ножи электрофуганков и рейсмусов, а также прочий длинномер. Важное замечание: ножницы и ножи деревообрабатывающего оборудования точатся только с одной стороны. Перед заточкой инструмент надо очистить от грязи, опилок, смолы и прочего, так как эти субстанции легко и необратимо забивают точильный камень.
Заточка ножейСначала надо рассмотреть режущую кромку и решить, с какого абразива стартовать. Если нож новый или сильно затупленный, возможно, стоит начать с грубого камня. Хорошая заточка режущего инструмента – это всего лишь умение выдержать один и тот же угол при движениях по камню. Важное замечание: никогда не точите ножи на высокооборотном точильном круге – он мгновенно отпускает и пережигает режущую кромку.
Итак, намочим точильный камень водой, положим его на старые газеты или лучше в углубление, выдолбленное в доске по форме камня, и водим ножом вдоль камня, соблюдая угол заточки. Нож должен набегать на камень под углом, как можно более близким к прямому. Но так как камень узкий, придется делать некое наклонное движение, перемещая нож по диагонали, то есть одновременно вдоль камня и вдоль ножа.
Большой ошибкой будет точить режущую кромку участками. Абсолютно точного перехода не получится – образуется ступенька, и нож будет плохо резать. Необходимо точить до тех пор, пока на кромке не появится завернутый вверх заусенец, который выявляется легким движением пальца поперек ножа от обуха к кромке (вдоль делать этого не стоит – можно порезаться). Когда заусенец появится по всей длине, нож нужно перевернуть и точить другую сторону.
Не пытайтесь доточить только те участки, где нет заусенца. Непрерывный заусенец показывает, что одна фаска режущей кромки ножа получила по всей длине плоскость. Когда при заточке второй стороны заусенец появится на уже заточенной, надо опять перевернуть нож и перейти на более мелкий абразив.
Чем меньше зерна абразива, тем более гладкие фаски и острее кромка. После мелкого камня надо перейти к наждачной бумаге, постеленной абразивом вверх на гладкую поверхность, например на кусок стекла или стали либо на ровную часть верстака.
Обычно используют сначала дешевый двухсторонний точильный камень и затем, последовательно, наждачные бумаги с зернистостью 120, 400, 600 (или 800) и иногда 1200. Самое сложное и простое в этом процессе – выдерживать одинаковый угол при всех движениях ножа. Стоит отметить, что постоянная практика лучше всяких хитроумных приспособлений – они ломаются и к тому же стоят намного дороже камня, который, кстати, в них тоже присутствует. Хитрость заключается в том, чтобы двигать затачиваемый инструмент при неподвижном запястье и внимательно смотреть на верхнюю плоскость инструмента. Тогда угол выдерживается весьма точно.
Ножницы точат только с фаски, прилегающую к другой бранше плоскость лишь выравнивают на мелкой наждачке.
Ножи фуганков тоже точат только с фаски. Их особенность в том, что нужно часто прикладывать кромку к линейке или стеклу, чтобы видеть прямизну режущей кромки и избегать ее скругления.
Заточка стамесок и рубаночных железок
Стамески и рубаночные железки имеют много общего. При сильном затуплении или выбоинах на режущей кромке, которые возникают из-за сучков или гвоздей, надо сначала ее спрофилировать. К слову, так же поступают при изготовлении резца по дереву из закаленной заготовки.
Наиболее эффективный способ заточки железко для рубанка – с помощью электроточила.
Здесь нам понадобится высокооборотистое электроточило. Часто макая железко в воду для остывания, нужно сделать фаску с углом немного острее 25 градусов. Ни в коем случае не утончайте кромку железка до появления режущей кромки, так как огромное трение абразива о металл нагревает последний, и при попытке заточки на высокооборотном камне режущая кромка будет немедленно отпущена и инструмент испорчен.
Когда толщина кромки станет около полумиллиметра, надо угольником проверить перпендикулярность режущей кромки оси или боковой стороне рубаночного железка.
Окончательно заострять железко можно двумя способами. Лучше всего – на низкоскоростном электроточиле с мокрым камнем (налив воды в поддон и равномерно прижимая железко к камню). Если ширина последнего недостаточна, то необходимо водить железком из стороны в сторону.
Болт с двумя гайками поможет соблюсти необходимый угол при заточке железко для рубанка.
Если такого точила у вас нет, придется работать вручную на абразивном бруске, смоченном водой. Его лучше положить в углубление в доске – так удобнее держать. Железко ставят на камень под выбранным углом или проще – фаской на камень, покачивая вперед и назад, пока он не встанет всей фаской. Заостряют движениями вдоль камня и обратно, а лучше – описывая будущей режущей кромкой восьмерки, чтобы достичь равномерного износа камня и сохранить его плоскостность. Когда появится заусенец, кладут железко плоскостью на камень и парой движений удаляют его, после чего переходят к более мелкому абразиву, например, перевернув двухсторонний камень.
Окончательная заточка производится положенными на стекло наждачными бумагами разной степени зернистости.
Маленькая хитрость. Болт с гайкой и двумя большими шайбами можно использовать как нехитрое приспособление для держания правильного угла наклона рубаночного железка (см. рисунок).
Заточка пил по дереву
Пилы по дереву, как правило, продаются не всегда достаточно острыми (а крупнозубые в большинстве своем – просто тупыми). Опять возникает необходимость заточки, причем для каждого вида работ она своя.
Если пила недостаточно разведена, сначала ее разводят. Если под рукой нет специализированной разводки, можно обойтись плоскогубцами. Пилу зажимают в тисках зубьями вверх, садятся так, чтобы смотреть вдоль полотна, и отгибают зубья в разные стороны через один, при каждом движении наклоняя плоскогубцы на один и тот же угол. Обычно небольшая разводка всегда есть изначально, и ее надо просто увеличить, если дело имеешь с сырым деревом или большими пилами. Если пила небольшая и для точных работ, вполне можно оставить и заводскую разводку.
Для заточки зубьев используется треугольный напильник. Им точат с внутренней (по отношению к разводке) стороны зубьев пилы. Напильник держат так, чтобы угол режущей кромки был 60–45 градусов. На деле легче и быстрее заострить сначала одну сторону зубьев, а потом, перевернув пилу, заточить зубья другой стороны. В этом случае движения более однотипные – пила получается более острой.
При заточке пил лучше работать одному и в тишине, отключив помехи в виде радио и телевизора, так как неосторожное движение либо портит инструмент, либо наносит трудно заживающую рану. Совет: если при резке пила стремится уйти в сторону, это означает, что зубья разведены неравномерно – нужно увеличить их отклонение с той стороны, в которую пилу уводит.
Заточка пильных дисков
Дисковые пилы затачивают с задней поверхности, при работе обращенной к обрабатываемому материалу. Передняя, которая при пилении набегает на материал, остается как есть.
Диск можно точить или прямо в станке (если речь идет об оснастке для станка), или вынув из станка или циркулярной пилы. В первом случае сначала нужно выдернуть вилку из розетки, чтобы избежать случайного пуска станка. Диск следует подклинить, положив с двух сторон от него по тонкой деревяшке и прижав их к зубьям. Зуб, с которого начинается заточка, надо пометить фломастером по боковой стороне, чтобы не ошибиться в работе. Затачивая первый зуб, запоминайте количество движений напильником или алмазным надфилем – все остальные зубья предстоит точить с тем же усилием и тем же количеством движений абразивного инструмента, что и первый.
Если диск был снят со станка, зажмите его в тисках и проделайте те же процедуры, что описаны выше.
Далее диск нужно вернуть в станок и распилить ненужную деревяшку. При сильном шуме или неровной подаче надо проверить, одинакова ли высота зубьев. Для этого к режущему краю подносят фломастер и медленно проворачивают диск рукой на один оборот в сторону, обратную направлению вращения. На каждом зубе останется отметина. Осмотрев диск, можно обнаружить зубья, которые выше или ниже других. Если разница велика, необходимо аккуратно уменьшить высоту слишком длинных зубьев.
Заточка фрез
Заточку фрез ведут по задней или передней поверхности.
Перед заточкой от фрезы необходимо предварительно отделить направляющий подшипник, иначе можно испортить инструмент.
Фасонные концевые фрезы проще затачивать по передней поверхности – либо тонким алмазным бруском, либо (при узкой стружковыводной канавке) наждачной бумагой, обернутой вокруг рейки из твердого дерева или полоски стали. По мере стачивания передней поверхности кромка заострится, а диаметр фрезы уменьшится (незначительно).
С фрез с направляющим подшипником сначала надо снять подшипник и только потом затачивать их. Попытка сэкономить минуту закончится загубленным подшипником и испорченной фрезой.
Заточка токарных резцов
Токарные резцы заостряют со стороны передней и задней поверхностей. Нюанс там только один – резец сужается вниз, поэтому, чтобы его боковые плоскости ни в коем случае не соприкасались с заготовкой, контакт должен быть только по режущей грани.
Резцы из быстрореза и с твердосплавными напайками точат на точильном круге. Если на станке подачи воды не предусмотрено, почаще макайте резец в емкость с водой.
Заточка сверла
При заточке сверла нужно держать его так, чтобы получить желаемый угол схождения режущих граней. При этом режущая кромка должна быть симметричной.
Проще всего провести на подручнике электроточила линию фломастером и держать сверло параллельно ей. Однако просто положить сверло по линии недостаточно, следует еще и повернуть его на нужный угол вокруг оси, а потом на 180 градусов относительно первого положения.
Нужен угол между кромкой сверла и плоскостью стола, то есть внешний край должен быть ниже центра, иначе сверло будет не резать материал, а ехать по нему задней поверхностью. Для контроля этого угла есть разные приспособления, но проще стоять или сидеть за столом так, чтобы блик от освещения был на внешней части режущей кромки, а потом, не меняя положения тела, повернуть сверло в пальцах и опять поймать блик – кромки будут заострены под одним углом.
Заточка сверла по задней поверхности называется одинарной, при ней остается довольно большая перемычка в центре, которая не режет, а скоблит металл. Если ее подточить, скорость сверления возрастет. Способов подточки перемычки много. На заводах ее подтачивают тонкими абразивными или алмазными кругами либо на углу широкого камня. Но можно подтачивать перемычку так, как показано на фото. Защитные очки при выполнении заточки строго обязательны.
Электроточила
Для облегчения труда при заточке инструмента существуют различныеэлектроточила и заточные станки.
Выбор электроточила крайне прост. Такой станок состоит из асинхронного двигателя (подобные моторы в совершенстве освоены промышленностью), точильных кругов (они сменные и меняются при помощи гаечного ключа) и кожухов. Если точило берется не для промышленного применения, то марка не имеет такого уж большого значения. Подобное оборудование включают ненадолго, и ресурс его будет расходоваться крайне медленно – даже недорогой станок прослужит много лет.
Диаметр круга прямо влияет на цену точила, поэтому мастеровому-любителю или маленькому предприятию не стоит гнаться за большими диаметрами.
Осматривая электроточило перед покупкой, попробуйте пошевелить вал. Если он не только вращается, но и ходит – перед вами брак. Крутаните камень рукой и посмотрите на свободный конец вала, не вибрирует ли он? Лучше всего, конечно, включить точило, но не во всех магазинах позволяют это сделать.
Заточные станки
Заточные станки делятся на три группы.
Первая – фактически высокоскоростное электроточило (около 3000 об/мин), оборудованное сменными держателями для разных видов инструмента.
Вторая – узкоспециализированные станки, например для заточки сверл. Зачастую на них нельзя заточить никакой другой режущий инструмент.
Третья – станки, оборудованные низкоскоростными кругами с водяным охлаждением («мокрые»). Скорость вращения – 80–150 оборотов в минуту. На них можно затачивать и править любой режущий инструмент, от сверл из быстрорежущей стали до ножей из углеродистой стали. Низкая скорость и водяное охлаждение – необходимые условия для выведения тончайшей и острейшей режущей кромки. Часто такие станки имеют и полировальный круг для полировки режущей кромки.
Работа с электроточилом и заточным станком
После работы на станке с «мокрым» кругом не забывайте выливать воду из поддона и не оставляйте камень в воде одним боком на продолжительное время – камень напитывается водой, теряет прочность и превращается в эксцентрик, разбивающий станок.
Абразивные круги всегда должны «набегать» на режущую кромку затачиваемого инструмента, а полировальные (кожаные, войлочные, вулканитовые) – «убегать», то есть вращаться «от рабочего». Не пытайтесь полировать вращением круга «на себя» – обрабатываемый объект врежется в круг, будет им захвачен и выброшен в сторону оператора. Кроме порчи круга, можно получить серьезную травму.
Если вы устанавливаете полировальный круг на высокоскоростное электроточило, поверните кожух на 180 градусов. Для работы на полировальнике либо разверните станок, либо подойдите к нему с другой стороны.
Чертилки (иглы) служат для нанесения линий (рисок) на размечаемую поверхность при помощи линейки, угольника или шаблона. Изготовляют чертилки из инструментальной стали У10 или У12. Для разметки на стальной, хорошо обработанной поверхности применяют чертилки из латуни, а на алюминий риски наносят остро заточенным карандашом.
Широко применяют три вида чертилок: круглую, с отогнутым концом и со вставной иглой.
Круглая чертилка представляет собой стальной стержень длиной 150 — 200 мм и диаметром 4 — 5 мм, один конец которого закален на длине 20 — 30 мм и заострен под углом 15°, а другой согнут в кольцо диаметром 25 — 30 мм (рис. 32, а).
Чертилка с отогнутым концом представляет собой стальной стержень, заостренный с двух сторон, один конец которого отогнут под углом 90° (рис. 32, б). Средняя часть чертилки утолщена и для удобства на ней сделана накатка. Отогнутым концом наносят риски в труднодоступных местах (рис 32, в).
Чертилка со вставной иглой (рис. 32,г) выполнена по типу часовых отверток; в качестве вставной иглы могут быть использованы стальные заточенные и закаленные стержни.
Чертилка карманная разметчика
В. А. Андреева (рис. 32,л) выполнена в виде карандаша с убирающимся острием. Корпус чертилки состоит из двух частей, вращающихся друг относительно друга на четырех шариках, которые заводятся при сборке через продольные пазы. Предусмотрен держатель для крепления чертилки в кармане работающего и для предотвращения скатывания с плиты. На рабочим стержень напаян стержень из твердого сплава ВК6, заточенный на конус с углом 20°. Чертилки должны быть острозаточенными. Коническая поверхность чертилки должна быть хорошо обработанной (гладкой), не царапать линейку, угольник. Чем острее рабочая часть чертилки, тем тоньше будет разметочная риска и тем, следовательно, выше точность разметки. Затачивают чертилки на зоточных станках (рис. 33). Чертилку берут левой рукой за середину, а правой рукой за конец, противоположный затачиваемому. Выдерживая постоянный угол наклона относительно абразивного круга, с легким нажимом прикладывают чертилку конусом к вращающемуся кругу, равномерно вращая ее пальцами правой руки. Во избежание отпуска острие чертилки периодически охлаждают в жидкости.
Кернер-слесарный инструмент, применяется для нанесения углубления (кернов) на предварительно размеченных линиях. Керны делают для того, чтобы риски были отчетливо видны и не стирались в процессе обработки детали. Изготовляют кернеры из инструментальной углеродистой стали У7А, У8А, 7ХФ, 8ХФ. Рабочую часть кернеров (конус) термически обрабатывают на длине 15 — 30 мм до твердости HRC 55 — 59, а ударную часть — на длине 15 — 25 мм до твердости HRC 40 — 45. Средняя часть кернера имеет рифление (накатку) для удобства работы им.
Кернеры бывают обыкновенные, специальные, пружинные (механические) и электрические.
Обыкновенный кернер (рис. 34,а) представляет собой стальной стержень длиной 100, 125 и 160 мм и диаметром 8, 10, 12 мм, боек его имеет сферическую поверхность. Острие кернера затачивают на шлифовальном круге под углом 60° (рис. ЗА,6). При более точной разметке пользуются малыми кернерами с острием, заточенным под углом 30-45°.
Рис. 38. Кернеры: а — пневматический «пистолет», б — пневматический портативный А. Н. Подвысоцкого
У кернеров для разметки центров отверстий, подлежащих сверлению, острие затачивают под углом 75°.
Высокопроизводительными кернерами являются специальные, для шаговой разметки, пружинные, электрические.
Специальные кернеры (рис. 35,а) применяют для накернивания малых отверстий и закруглений небольших радиусов. Применение такого кернера заметно повышает качество разметки и производительность.
Кернер для шаговой разметки (рис. 35,6) состоит из двух кернеров — основного 7″ и вспомогательного 2, скрепленных общей планкой 3. Расстояние между ними регулируется при помощи отверстий в планке 3 в зависимости от шага размечаемых отверстий. Первое углубление накернивают кернером 7. Затем в полученное углубление вставляют кернер 2 и ударом молотка по кернеру 7 накернивают углубление. После этого кернер 2 переставляют в следующее положение. Шаг между отверстиями выдерживается автоматически, чем и достигается точность разметки и повышение производительности.
Кернер с лупой С. М. Ненастьева (рис. 35,в) состоит из двух хомутиков, соединенных винтом 6 и затягиваемых после установки лупы 8 по зрению рабочего. В одном хомутике 7 устанавливается 3 — 5-кратная лупа, другой хомутик 5 служит для установки лупы на кернер 4 по высоте ее крепления.
Пружинный кернер (рис. 36) применяется для точной разметки тонких и ответственных изделий. Принцип его действия основан на сжатии и мгновенном освобождении пружины.
Кернер имеет корпус, свинченный из трех частей 3, 5, 6. В корпусе помещаются две пружины 7, 7 7, стержень 2 с кернером 7, ударник В со смещающимся сухарем 10 и плоская пружина 4. При нажатии на изделие острием кернера внутренний конец стержня 2 упирается в сухарь, в результате чего ударник перемещается вверх и сжимает пружину 7. Упершись в ребро заплечика 9, сухарь сдвигается в сторону и кромка его сходит со стержня 2. В этот момент ударник под действием силы сжатой пружины 7 наносит по концу стержня с кернером удар. Сразу после этого пружиной 7 7 восстанавливается начальное положение кернера. Сила удара 10-15 кгс регулируется ввинчиванием или отвинчиванием упорного колпачка 6. Вместо кернера 7 в стержень 2 можно вставить клеймо и тогда механический кернер можно использовать для клеймения деталей.
Электрический кернер (рис. 37) состоит из корпуса 6, пружин 2 и 5, ударника 3, катушки 4, кернера 7. При нажатии установленным на риске острием кернера электрическая цепь замыкается и ток, проходя через катушку, создает магнитное поле, ударник мгновенно втягивается в катушку и наносит удар по стержню кернера. Во время переноса кернера в другую точку пружина 5 размыкает цепь, а пружина 2 возвращает ударник в исходное положение. Электрический кернер отличается высокой производительностью.
Пневматический «пистолет» (рис. 38,а) применяется для различных керновочных работ. Для удобства он снабжен ручкой 7, расположенной под углом к оси корпуса, и пусковой кнопкой 2.
Пневматический портативный кернер А. Н. Подвысоцкого (рис. 38,6) отличается от других кернеров малыми размерами и отсутствием рукоятки, которой служит сам кернер.
Циркули используют для разметки окружностей и дуг, для деления отрезков, окружностей и для геометрических построений. Циркулями пользуются и для переноса размеров с измерительных линеек на деталь.
Разметочные циркули бывают: простой или с дугой, точный (рис. 39,а) и пружинный (рис. 39,6). Простой циркуль состоит из двух шарнирно соединенных ножек (рис. 39,а), целых или со вставными иглами (рис. 39,а), он позволяет установку нужного раствора ножек фиксировать винтом.
Слесари-новаторы, стремясь повысить точность разметки, совершенствуют конструкции циркулей.
Л. С. Новиков разработал конструкцию циркуля (рис 39,г), состоящего из двух ножек 6, снабженных на концах закаленными иглами 4, и двух разъемных линз 7 с пятикратным увеличением. Линзы установлены так, что концы игл 4 находятся в фокусе. Это дает возможность отчетливо видеть острие иглы и точно совмещать его с делениями масштабной линейки или с рисками размечаемой детали.
Для точной установки размеров циркуль имеет микрометрический винт 2. Преимущества этого циркуля: удобство и высокая точность установки. Однако его детали требуют особо аккуратного обращения и хранения.
Особенностью конструкции циркуля (рис. 39,а) является устройство 3 для установки циркуля непосредственно по его шкале с точностью до 0,2 мм. Микрометрические винты 7 и 2 повышают точность этой установки. Сменные иглы 4 затягиваются гайками 5.
Разметочный штангенциркуль (рис. 40,а) предназначен для точной разметки прямых линий (рис. 40,6) и центров (рис. 40,а).
Разметочный штангенциркуль (рис. 41) служит для разметки окружностей больших диаметров. Он имеет штангу 3 с миллиметровыми делениями и две ножки — неподвижную 2 со стопорным винтом 7 и подвижную 8 с рамкой 5 и нониусом 6, стопорным винтом 4 для закрепления рамки 5. Стопорный винт 7 служит для крепления вставной иглы 9, которая перемещается вниз и вверх и может устанавливаться на разных уровнях.
На рис. 42 показан усовершенствованный разметочный штангенциркуль для разметки плоскостей. Он имеет штангу 9 с утолщенным концом, в который устанавливается резец 2. По штанге перемещается рамка 6 с нониусом 3. В нижней части рамки находится вставка 13, в отверстие которой вставляется сменная центрирующая коническая опора, закрепляемая зажимом 12.
Рамка 6 при помощи микрометрического винта 7 7 соединяется с хомутиком 8. Перемещается рамка 6 по штанге вручную и закрепляется зажимом 4. Микрометрическая подача рамки осуществляется поворотом гайки 10 при закрепленном хомутике винтом 7.
При разметке вначале устанавливают центрирующую опору, соответствующую базовому отверстию, затем на плоскость размечаемой детали устанавливают резец. После этого проверяют горизонтальное положение штангенциркуля по уровню 5, закрепляют резец стопорным зажимом 7 и производят разметку.
Рейсмас является основным инструментом для пространственной разметки. Он служит для нанесения параллельных, вертикальных и горизонтальных линий, а также для проверки установки деталей на плите. Рейсмас состоит из чугунного основания 2 (рис. 43,а), вертикальной стойки (штатива) 5, винта с гайкой 6 для крепления чертилки 4, установочного винта 3 для подводки иглы на точную установку размера, планки 7 и муфты 7. Применение рейсмаса показано на рис. 43,6.
Для более точной разметки применяют рейсмас с микрометрическим винтом.
Штангенрейсмасы для разметки описаны в главе XIX «Основы измерения».
Устанавливают подручник электроточила так, чтобы зазор между ним и абразивным (заточным) кругом не превышал 2 — 3 мм. Включив электроточило, берут обеими руками чертилку и, опираясь левой рукой на подручник, вращают чертилку вокруг своей оси. Затачивают на боковой поверхности абразивного круга под небольшим углом к ней. Рабочую часть чертилки затачивают на длину 15 — 20 мм.
Отрегулировав зазор между подручником и заточным кругом, берут кернер обеими руками и располагают под углом 30 — 40° к периферии, а не к боковой поверхности круга, как при заточке чертилки. Включив электроточило, поворачивают кернер вокруг своей оси, опираясь левой рукой на подручник.
Проверяют углы заточки шаблонами.
Углы заточки для , чугуна, бронзы 60°, для мягких металлов 45°.
Заточка разметочного циркуля
Готовят станок так же, как и при заточке чертилки и кернера. Ножки циркуля затачивают на боковой поверхности абразивного круга. Вместе сведенные ножки циркуля затачивают с четырех сторон на длину 15 — 20 мм так, чтобы острия обеих ножек сходились в одной точке.
Заправляют ножки циркуля на бруске.
При работе на электроточиле надо пользоваться защитным экраном или очками.
Вопросы
- Из каких частей состоит электроточило?
- Перечислите правила безопасной работы на электроточиле.
- На какой поверхности абразивного круга затачивают чертилки?
- Расскажите о последовательности заточки кернера.
- Как затачивают разметочный циркуль?
Упражнения
- Проверьте состояние чертилок, кернеров и заправьте их.
- Проверьте, исправлен ли циркуль, и подготовьте его к работе.
На подготовленной поверхности заготовки чертилкой при помощи линейки проводят произвольную линию (риску) АБ.
а — проведение дуг; б — проведение касательной ВГ к дугам.
Отступив от концов линии АБ на 10 — 15 мм, делают на ней кернером два углубления О и О 1 . Заданным раствором циркуля (в нашем примере 30 мм) устанавливают ножку в углубление О и чертят одну дугу, а из углубления О 1 другую дугу.
Касательно к обеим дугам по линейке проводят чертилкой риску ВГ, которая будет параллельна ранее проведенной риске — АБ. Параллельность рисок проверяют линейкой. Расстояние между рисками в любых точках должно быть одинаково (30 мм).
Вопросы
- Какие линии параллельны между собой?
- Как провести риску параллельно ровной кромке заготовки, пользуясь линейкой и циркулем, если расстояние между кромкой и риской 40 мм?
- Как проверяют параллельность рисок?
Упражнения
- Проведите параллельные риски при помощи линейки и циркуля на расстоянии 20 мм, 40 мм, 65 мм.
- В прямоугольнике со сторонами 60 и 130 мм проведите горизонтальную и вертикальную осевые линии, пользуясь линейкой и циркулем. Определите, какие линии параллельны.
«Слесарное дело», И.Г.Спиридонов,
Г.П.Буфетов, В.Г.Копелевич
При пересечении двух прямых образуется угол; поэтому рассмотрим разметку сопряжением сторон разных углов. На рисунке ниже показаны сопряжения прямого, острого и тупого углов. Сопряжения сторон углов а — прямого; б — острого; в — тупого. Построение сводится к нахождению центра дуги, которая касалась бы обеих сторон угла. Пусть радиус R дуги (сопряжения) окружности равен 40…
Перпендикуляр (рисунок ниже) — это прямая линия, составляющая прямой угол с другой прямой или плоскостью. Перпендикуляры к прямой (а) и плоскости (б) При нарезании метчиком резьбы в отверстии метчик ставят перпендикулярно к поверхности детали (рисунок ниже). Перпендикулярность метчика к нарезаемому отверстию детали Перед сверлением глубоких отверстий в деталях необходимо проверить перпендикулярность сверла, установленного в…
С ученическим транспортиром вы уже работали. Пользуясь им, можно построить любой угол. Вспомним построение угла 45°, которое часто встречается при разметке: Построение угла 45° при помощи транспортира На подготовленной поверхности заготовки проводят прямую риску АБ. Отмечают на этой риске точку и делают кернером метку О. Прикладывают к риске транспортир так, чтобы его начальная точка…
Разметку выполняют не спеша, аккуратно на разметочной плите. Рабочее место разметчика должно быть хорошо освещено. Перед разметкой изучают (читают) чертеж и определяют основные размеры детали (длину, ширину, высоту). У заготовки должен быть припуск на обработку. Проверяют заготовку на обрабатываемость пробным опиливанием, резанием или гибкой. Заготовка должна быть чистой, не иметь заусенцев и наплывов (если это…
К атегория: Слесарные работы
Заточка разметочного инструмента
Чтобы разметка была произведена точно, была хорошо видна и не стиралась, пользуются хорошо заточенным, исправным разметочным инструментом. Поэтому время от времени нужно затачивать чертилки, циркули и кернеры, которые тупятся чаще всего. Заточку производят на шлифовальном абразивном круге, наличие его в каждой домашней мастерской обязательно. Чертилку можно затачивать, определяя угол заточки на глазок: ее нужно расположить под небольшим углом к поверхности шлифовального круга и заточить на длину 12-15 мм. Острие кернера затачивается под углом 60-70°, угол контролируют, измеряя его транспортиром или сравнив с шаблоном. Для того, чтобы наточить ножки циркуля, их сводят вместе и затачивают с четырех сторон на квадрат на длине 15-20 мм, стремясь к тому, чтобы оба острия сошлись в одной точке. Окончательную доводку ножек циркуля нужно сделать, заточив их поочередно на точильном бруске.
Угол заточки сверла по металлу: таблица и рекомендации
Сверла по металлу, как и любой другой режущий инструмент, изнашиваются в процессе эксплуатации, что делает их непригодными к использованию. Между тем в большинстве случаев режущие и другие углы сверла по металлу можно восстановить, выбрав их значения по специальной таблице и выполнив заточку.
Ручная заточка сверла по металлу
Назначение и конструктивные особенности инструмента
Сверла по металлу, для изготовления которых используются стальные сплавы быстрорежущей группы, применяются для создания в металлических деталях как сквозных, так и глухих отверстий. Наиболее распространенными являются спиральные сверла, конструкция которых включает в себя следующие элементы:
- режущую часть;
- рабочее тело;
- хвостовик;
- лапку.
Конструктивные элементы спирального сверла
Если хвостовик, который может быть как цилиндрическим, так и коническим, предназначен для надежной фиксации инструмента в патроне используемого оборудования, то рабочая часть одновременно выполняет сразу несколько важных функций. Именно геометрией сверла определяются его работоспособность и режущие свойства.
Важнейшими элементами рабочей части сверла по металлу являются винтовые канавки. Их задача состоит в том, чтобы выводить из зоны обработки стружку. Геометрия спирального сверла по металлу предусматривает, что передняя сторона спиральной канавки выполняется под определенным углом, величина которого по направлению от оси инструмента к его периферийной части меняется. В процессе изготовления сверла по металлу на боковой области его спиральных элементов формируются узкие ленточки, несколько выступающие над основной поверхностью. Задача таких ленточек состоит в том, чтобы уменьшить величину трения инструмента о стенки формируемого отверстия.
Особенности различных видов заточки сверл
Заточка сверл, как уже говорилось выше, необходима для того, чтобы восстановить их геометрические параметры. Выбор определенного вида заточки сверла зависит от ряда факторов (диаметра инструмента, характеристик обрабатываемого металла и др.).
Наиболее универсальной является нормальная заточка (Н), при выполнении которой на рабочей части сверла формируются одна поперечная и две режущие кромки. Угол заточки сверла в данном случае составляет 118–120°. Выбирая такой вид заточки сверл, следует иметь в виду, что использовать его можно по отношению к инструментам, диаметр которых не превышает 12 мм.
Типы заточек сверл по металлу
Все остальные виды заточки, которые обозначаются буквосочетаниями НП, НПЛ, ДП, ДПЛ, можно применять для инструментов с диаметром до 80 мм. Каждый из указанных типов заточки предполагает доведение геометрии сверла по металлу до требуемых параметров.
Такая заточка подразумевает подточку поперечной кромки, что делается для уменьшения ее длины и, соответственно, для снижения нагрузок, воспринимаемых инструментом в процессе сверления.
НПЛВ данном случае кроме поперечной кромки подточке подвергается и ленточка, что позволяет уменьшить ее ширину в области режущей части. Подточка ленточки помимо уменьшения силы трения, создаваемой при сверлении, позволяет сформировать дополнительный задний угол сверла, что способствует облегчению процесса обработки.
ДПЭто двойная заточка, совмещенная с подточкой поперечной кромки. Выполнение заточки данного вида позволяет сформировать на рабочей части сверла по металлу одну поперечную и четыре режущие кромки, имеющие вид ломаных линий.
ДПЛЭто аналогичный предыдущему вид заточки, при котором дополнительно подтачивают ленточку. Создание четырех режущих кромок при выполнении двойной заточки необходимо для того, чтобы уменьшить угол между периферийными участками режущих кромок. Такой подход позволяет улучшить отвод тепла от режущей части инструмента и, соответственно, значительно повысить его стойкость.
Как правильно выбрать углы заточки
Углы заточки сверла, как уже говорилось выше, выбираются по специальным таблицам, где их значения представлены в зависимости от того, в каком именно материале необходимо сформировать отверстие.
Таблица 1. Углы заточки сверла по металлу для различных материалов
Если неправильно выбрать углы, под которыми будет затачиваться сверло, то это приведет к тому, что оно в процессе работы будет сильно нагреваться. Это в итоге может привести к его поломке. Кроме того, именно неправильно выбранные углы, используемые для заточки сверла по металлу, часто становятся основной причиной некачественно выполненного сверления.
Выполнение операции
Традиционно заточка сверл по металлу спирального типа выполняется на наждачном станке, оснащенном точильным кругом соответствующей твердости. Начинать затачивать их следует с обработки задней поверхности. Прижимая инструмент данной поверхностью к вращающемуся точильному кругу под определенным углом, надо следить за тем, чтобы на ней формировался правильный уклон.
При заточке передней режущей поверхности необходимо контролировать не только угол, под которым выполняется операция, но и размер перемычки. Очень важно, чтобы при заточке на рабочей части сверла по металлу были сформированы режущие кромки равной длины, расположенные под одним углом. Если просверлить отверстие сверлом, при заточке которого не соблюдены эти важные требования, то диаметр такого отверстия будет больше, чем поперечный размер самого инструмента.
Проверка углов заточки с помощью шаблона
Проверить соответствие основных геометрических параметров (в том числе угла заточки) сверла требуемым характеристикам можно при помощи одного шаблона, который несложно приобрести в серийном исполнении или изготовить самостоятельно.
И в заключение небольшой видеоролик о том, как самостоятельно заточить сверло по металлу.
И способы предупреждения
Производство И способы предупреждения
просмотров — 556
Типичные дефекты при рубке, причины их появления
Таблица 3
Дефект | Причина | Способ предупреждения |
Рубка листовой стали в тисках | ||
Обрубленная кромка детали прямолинейна | Деталь слабо зажата в тисках | Прочно закреплять деталь в тисках |
Стороны вырубленной детали непараллельные | Перекос разметочных рисок. Перекос заготовки в тисках | Соблюдать правила разметки, точно устанавливать деталь в тисках по разметочной риске |
«Рваная» кромка детали | Рубка выполнялась слишком сильными ударами или тупым зубилом | Перед рубкой убедиться в правильной заточке зубила.![]() |
Прорубание канавок | ||
«Рваные» кромки канавки | Неправильная заточка крейцмейселя | Крейцмейсель затачивать с поднутрением режущей кромки |
Глубина канавки неодинакова по ее длине | В процессе рубки не производилось регулирование наклона крейцмейселя | При рубке толщину срезаемого слоя материала, а следовательно, и глубину канавки регулировать наклоном крейцмейселя |
Сколы на конце канавки | Не обрублена фаска на детали | Перед началом рубки (особенно хрупких металлов) обязательно срубать фаску на ребре заготовки в месте выхода крейцмейселя |
Срубание слоя металла на широкой поверхности | ||
Грубые завалы и зарубы на обработанной поверхности | Рубка осуществлялась тупым зубилом.![]() | Наиболее рационально производить срубание выступов между прорубленными ранее канавками способом «елочка». Толщину снимаемого слоя регулировать наклоном зубила |
Сколы на кромке детали | Не обрублены фаски на детали | Перед рубкой широкой поверхности детали (особенно хрупкого металла) обязательно срубить фаски со всех ребер детали |
Рубка листовой, полосовой и прутковой стали на плите | ||
Непрямолинейная кромка отрубленной детали | Нарушение правил разметки детали. Рубка велась не по разметочной риске | Следить за прямолинейностью риски разметки. Точно устанавливать зубило на риску |
Кромка отрубленной детали имеет глубокие зарубы и сколы | Неправильная заточка зубила.![]() | Для рубки листового металла зубило следует затачивать слегка закругленно. Рубку производить энергичными ударами без «пристукивания». Прочно удерживать зубило на риске разметки |
Контрольные вопросы:
1. Почему угол заточки зубила, крейцмейселя, канавочника увеличивается по мере увеличения твердости, обрабатываемого материла?
2. Чем можно объяснить, что рабочая и ударная части зубила подвергаются термической обработке, в то время как средняя часть, удерживаемая в руке, остается сырой?
3. Почему при заточке крейцмейселя следует выполнять поднутрение режущей кромки?
4. В каком случае и с какой целью перед началом рубки на кромке детали делают фаски?
5. Почему при рубке листового материала на плите режущая кромка зубила должна иметь криволинейную форму?
Тема 6 Резка металла
Студент должен
знать:
— назначения и способы выполнения операций при резке металла ножовкой и труборезом; ручными и рычажными ножницами; приводными ножовками; электрическими ножницами;
— правила организации рабочего места;
— правила безопасности труда.
уметь:
— отрезать полосовой материал, а также квадратного, круглого и прямоугольного сечения без разметки и по рискам;
— правильно выполнять приемы работы и организовывать рабочее место;
— выполнять требования безопасности труда.
Оснащение рабочего места: тиски слесарные; тиски ручные; угольники-нагубники к тискам; ножницы по металлу; линейки измерительные металлические; чертилки; шаблоны разметочные; ножовки; щетка металлическая; щетка-сметка.
Резка металла – операция разделения на части круглого, полосового, профильного проката͵ а также труб ручным и механическим способом. Ручную резку заготовок в зависимости от профиля и площади сечения производят различными инструментами: ножовками, ножницами (ручными, стуловыми, рычажными), труборезами и газопламенными резаками.
Ручная ножовка – наиболее распространенный инструмент для разрезки толстых листов, полосового и профильного металла, а также для прорезания пазов, шлицев, обрезки и вырезки заготовок по контуру и т. п.
Она состоит из рамки (ножовочного станка) натяжного винта подвижной головки с хвостовиком и ручкой (рис. 6.1, а). Рамки ножовки бывают цельной и раздвижной конструкции. Ножовочное полотно представляет собой тонкую и узкую стальную пластину с зубьями на одном ребре. Каждый зуб ножовочного полотна (рис. 6.1, б, в) имеет форму клина (резца), на котором различают задний угол, угол заострения, передний угол.
Для уменьшения трения ножовочного полотна о стенки разрезаемого металла (пропила) зубья его разводят в разные стороны, увеличивая таким образом толщину полотна n до ширины пропила k.
Зубья с большим шагом отгибают по одному поочередно вправо и влево (рис. 6.1, д), зубья с малым шагом отгибают по 2-3 вправо и по 2-3 влево, при этом образуется волнистая линия (рис. 6.1, г).
| |||||||
|
При резке металла ножовкой корпус слесаря крайне важно развернуть вправо под углом 45о к оси тисков (рис. 6.2, а). Положение ног показано на рис. 6.2, б. Во время разрезки ножовку держат в горизонтальном положении. Двигать ее нужно плавно, без рывков, производя 30-60 двойных ходов за минуту. При движении вперед рамку ножовки нажимать вниз.
Длина хода ножовки должна быть такой, чтобы работало не менее 2/3 ее длины, а не только ее средняя часть.
Тонкий материал для разрезки ножовкой зажимают между деревянными брусками и разрезают вместе с ними. Приемы разрезания металла показаны на рис. 6.3, а … ж.
| |||
Читайте также
… [читать подробенее]
Типичные дефекты при выполнении разметки, причины их появления Правила техники безопасности при плоскостной разметке 1. Не класть чертилку и разметочный циркуль в карман халата; их можно держать только на верстаке. 2. Чтобы не поранить руки, подавать… [читать подробенее]
Правила выполнения работ при ручной гибке металла
* При изгибании листового и полосового материала в тисках разметочную риску необходимо
располагать точно, без перекосов, на уровне губок тисков в сторону изгиба. Полосовой
материал толщиной свыше 3,0мм следует. .. [читать подробенее]
Мм. Раскатанный пласт смазывают еще раз размягченным маслом или маргарином и формуют из него изделия. Температура при слоении и разделке должна быть 20—22°С. После разделки изделия расстаивают 10—12 мин при температуре не выше 35°С, чтобы масло не вытекло. Выпекают… [читать подробенее]
Ассортимент изделий из дрожжевого теста Пирожки печеные.Готовят в основном из опарного теста. На подпыленном мукой столе формуют полуфабрикаты в виде шариков. Через 5 мин шарики раскатывают в виде лепешек толщиной 0,5—1 см. На середину каждой лепешки кладут фарш… [читать подробенее]
Дефект
Причина
Способ предупреждения
Неправильная структура движений при притирке плоских поверхностей.
Несоблюдение правил притирки.
При притирке необходимо использовать всю поверхность притира во избежание
неравномерного его износа и… [читать подробенее]
Правила безопасности труда при клепке · нельзя проверять совпадение отверстий ни чем, кроме бородка; · инструмент, используемый при клепке должен быть исправен и предназначен для этой операции; · необходимо следить, чтобы в процессе нанесения ударов по обжимке было… [читать подробенее]
Дефект
Причина
Способ предупреждения
Перекос отверстия.
Стол станка неперпендикулярен шпинделю. Попадание стружки под нижнюю поверхность заготовки. Неправильные (непараллельные) подкладки. Неправильная установка заготовки
на столе станка. Неисправные. .. [читать подробенее]
Типичные дефекты при развертывании, причины их появления и способы предупреждения Припуски на обработку отверстий Припуск– это слой материала, подлежащий снятию при обработке. Величина этого слоя зависит от требований, предъявляемых к обработанной… [читать подробенее]
Типичные дефекты при выполнении разметки, Таблица 2 Дефект Причина Способ предупреждения Раздвоенная риска Линейка слабо прижималась к детали. Риска проводилась дважды по одному и тому же месту. Разметка проводилась тупой чертилкой. Линейку плотно… [читать подробенее]
Черновая, Чистова, Механическая рубка.
Зубило представляет собой ударный инструмент, который используется при работе с деревом, металлом, бетоном, натуральным, искусственным камнем. С его помощью делают различные пазы, канавки, углубления сложной формы. При работе с металлом острая часть со временем тупится, из-за чего его нужно перетачивать. Провести процедуру можно только учитывая угол заточки зубила, выполняя процедуру в определенном порядке.
Приспособление для заточки угла зубила
Устройство и характеристики
Зубило является слесарным инструментом, которое применяют для рубки, создания углублений в твердых материалах. Оно представляет собой стальной стержень, одна из сторон которого тупая, другая заточенная по двум краям. По тупой стороне (обуху), мастер наносит удары молотком.
В продаже можно найти два вида зубил. Одни предназначены для проведения работ вручную, другие устанавливаются в специальное оборудование.
Материал
Особое внимание при выборе зубила обращают на материал, из которого оно изготавливается. Сплав должен быть устойчивым к ударам, не крошиться от физического воздействия. Существует два варианта изготовления рабочих частей инструмента:
- Инструментальные стали.
- Твердосплавные пластины из конструкционных сталей.
Самым распространенным материалом является углеродистая сталь. Раньше инструменты изготавливались из алюминия, однако, он мягкий, быстро деформируется от ударов.
Размеры и вес
Еще два фактора, на которые покупатель обращает внимание во время выбора — размеры, вес. Размеры:
- Возможные варианты по длине — от 10 до 20 см.
- Разделение по ширине — от 5 до 25 мм.
- Варианты длины рабочей части — 25–60 мм.
На вес влияют не только размеры, но и материал, который использовался при изготовлении инструмента. Вес легких моделей ограничивается 380 граммами, тяжелых — 750 грамм.
§ 3. Инструменты для рубки
Слесарное зубило. Слесарное зубило представляет собой металлический стержень, изготовленный из инструментальной углеродистой стали У7А, иногда из стали У7 и У8А. Зубило состоит из трех частей: рабочей, средней и удар (рис. 90, а). Рабочая часть 2 зубила представляет собой стержень с клиновидной режущей частью 1 на конце, заточенной под определенным углом.
Ударная часть 4 сделана суживающейся кверху, вершина ее закруглена. Угол заострения (угол между боковыми гранями) выбирается в зависимости ог твердости обрабатываемого металла. За среднюю часть 3 зубило держат при рубке.
Рис. 90. Слесарные зубила: а — зубило, б — крейцмейсель, в — канавочник
Рекомендуемые углы заострения зубила для некоторых материалов
Рабочая часть зубила на длине 0,3—0,5 мм L закаливается и отпускается до твердости HRC 52—57, а ударная часть на длине 15—25 мм — до твердости HRC 32—40.
При испытании зубила на прочность и стойкость им отрубают зажатую в тиски стальную полосу марки Ст. 6 толщиной 3 мм и шириной 50 мм. После испытания на лезвии зубила не должно быть вмятин, выкрошенных мест и заметных следов затупления.
Степень закалки зубила можно определить личным напильником, которым проводят по закаленной части зубила. Если при этом напильник не снимает стружку с закаленной части зубила (на ней остаются лишь едва заметные риски), закалка зубила выполнена хорошо.
Крейцмейсель. Крейцмейсель отличается от зубила более узкой режущей кромкой, предназначен для вырубания узких канавок и шпоночных пазов, срубания заклепок и т. п. Однако довольно часто им пользуются для срубания поверхностного слоя с широкой чугунной плиты: сначала крейцмейселем прорубают канавки, а оставшиеся выступы срубают зубилом. Материалы для изготовления крейцмейселя и углы заострения, твердость рабочей и ударных частей те же, что и для зубила.
Для вырубания профильных канавок—полукруглых, двугранных и т. п. применяют специальные крейцмейсели, называемые канавочниками (рис. 90, е), отличающиеся от крейцмейселя только формой режущей кромки. Канавочники изготовляют из стали У8А длиной 80; 100; 120; 150; 200; 300 и 350 мм.
Заточка зубил и крейцмейселей производится на обычном заточном станке (рис. 91). Для заточки зубило или крейцмейсель накладывают на подручник 7 и с легким нажимом медленно передвигают по всей ширине абразивного круга, периодически поворачивая инструмент то одной, то другой стороной. Следует не допускать сильных нажимов на затачиваемый инструмент, так как это приводит к перегреву режущей кромки, в результате чего лезвие теряет первоначальную твердость.
Рис. 91. Заточка зубила (а), зазор между подручником и кругом (б)
Заточку лучше всего вести с охлаждением водой, в которую добавлено 5% соды, или на мокром круге. Несоблюдение этого условия вызывает повышенный нагрев, отпуск и уменьшение твердости инструмента, а следовательно, и стойкости в работе. Боковые грани после заточки должны быть плоскими, одинаковыми по ширине и с одинаковыми углами наклона. Величина угла заострения проверяется шаблоном, представляющим собой пластинку с угловыми вырезами 70; 60; 45°.
Запрещается затачивать на станке инструмент без подручника и с открытым кожухом 3. При заточке защитный экранчик 2 должен быть опущен.
Иногда делают двойную заточку зубила, т. е. одна грань затачивается под углом 35°, а вторая — под углом 70°. При такой заточке можно рубить мягкий и твердый металл.
Закалка зубил и крейцмей-селей, изготовленных из стали У7А, осуществляется нагревом до 780—800° С и с охлаждением в воде или масле; с последующим отпуском при температуре 160—180°С.
Слесарные молотки. Молоток является ударным инструментом для нанесения ударов при рубке, правке, гибке и других слесарных операциях.
Слесарные молотки изготовляются (ГОСТ 2310—54) двух типов: тип А — с квадратным бойком (рис. 92, а) и тип Б — с круглым бойком (рис. 92, б).
Рис. 92. Молотки: а — с квадратным бойком, б — с круглым бойком, в — с вставками из мягкого металла, г — деревянный (княнка), д — расклинивание ручек молотка; 1 — ударная часть (боек), 2 — клин. 3 — носок, 4 — рукоятка
Основной характеристикой молотка является его вес. Молотки типа А изготовляют весом 200; 400; 500; 600; 800 и 1000 г, а молотки типа Б — весом 50; 100; 200; 500; 600; 800 и 1000 г.
При неточных ударах молоток с квадратным бойком оставляет вмятины на поверхности обрабатываемого материала, но изготовление их проще, чем молотков с круглым бойком.
Изготовляются молотки из стали марок 50 и 40Х и инструментальной углеродистой стали марок У7 и У8. В средней части молотка имеется отверстие овальной формы, служащее для крепления рукоятки.
Рабочие части молотка — боек квадратной или круглой формы и носок клинообразной формы термически обрабатывают до твердости HRC 49—56.
Молотки с квадратным бойком 50; 100; 200 г применяются для выполнения разметочных, инструментальных работ, 400 и 500 г — для слесарных работ и 600; 800; 1000 г — для ремонтных работ. Для тяжелых работ применяют молотки весом от 4 до 16 кг, называемые кувалдами.
Рукоятки молотка по ГОСТ 2309—54 делают из наиболее твердых и упругих пород дерева (березы, бука, кизила, рябины, дуба, клена, граба и др.). Рукоятки должны быть без сучков и трещин, а поверхность ручки — гладкой, без бугорков и неровностей.
Рукоятка имеет овальное сечение, отношение малого сечения к большому 1 : 1,5, т. е. свободный конец в 1,5 раза толще конца, на который насаживается молоток.
В зависимости от веса молотка рекомендуются следующие длины рукояток:
- для легких молотков до 400 г: 200; 250; 300 мм.
- для средних молотков 500—600 г; 320; 360 мм.
- для тяжелых молотков 800—1000 г; 360; 400; 500 мм.
Конец, на который насаживается молоток, расклинивается деревянным клином, смазанным столярным клеем, или же металлическим клином, на котором делают насечки (ерши). Толщина клиньев 2—6 мм. Если отверстие молотка имеет только боковое расширение, забивают один продольный клин, если же расширение идет вдоль отверстия, то забивают два клина (рис. 92, д) и, наконец, если расширение отверстия направлено во все стороны, забивают три стальных или три деревянных клина, располагая два параллельно, а третий перпендикулярно к ним. Правильно насаженным считается такой молоток, у которого ручка образует прямой угол с осью молотка.
Виды и назначение
Ручные инструменты классифицируются по различным факторам. Заточка зубила изменяется зависимо от того, какой вид приспособления есть у мастера. К основным разновидностям относятся:
- Классические столярные металлические стержни за острой рабочей частью. Применяются для обработки незакаленных поверхностей.
- Пикообразные металлически стержни, которые используются для дробления камня, бетона. Часто являются насадкой на перфораторы, отбойные молотки.
- Крейцмейсель — канавочный вид зубила, применяемый для изготовления выемок разной формы.
- Слесарный цилиндрический стержень, заточенный с одной стороны.
- Кузнечное зубило. Наличие рукояти позволяет использовать его во время холодной или горячей рубки.
Выбираются инструменты зависимо от того, какую технологическую операцию необходимо провести.
Кузнечное зубило на наковальне
Как пользоваться зубилом?
Чтобы правильно использовать зубило по металлу при обработке заготовок из стали, необходимо учитывать следующие правила:
- Прежде чем начинать работы, проверить целостность рабочей части металлического стержня, надежность крепления рукояти.
- Надеть перчатки, защитные очки, чтобы осколки металла или камня не попали в глаза.
- Легкими ударами молотка по обуху начать обработку.
Инструмент должен быть сухим, чтобы при работе он не вылетел из руки. Опытные слесаря рекомендуют покупать металлические стержни с грибком у обуха. Это обеспечит большую надежность удержания его в руке во время ударов.
Процесс заточки стамески
Перед проведением переточки необходимо узнать насколько испорчена рабочая часть. Для этого можно провести металлом по тыльной стороне ладони. Цепляющийся материал говорит о том, что нужно принять меры.
Правильно переточить зубило можно с помощью заточного станка, абразивных брусков. Пошаговая инструкция:
- Очистить режущие части от грязи, мусора, протереть ацетоном.
- Надеть защитные очки, перчатки, робу.
- Проверить целостность абразивного круга перед запуском станка. Для удобства проведения работы желательно использовать параллельный упор, которые поможет удерживать требуемый угол.
- Включить станок на низких оборотах. Медленно передвигать режущую кромку относительно абразивного круга, удерживая требуемый угол.
При переточке смачивать абразив водой, чтобы избежать перегрева.
Помимо смачивания круга, необходимо охлаждать затачиваемую часть зубила в холодной воде по 1 минуте. Перегрев может привести к потере твердости. Исправить мелкие неровности, заусенцы можно с помощью абразивных брусков. Для этого необходимо применять несколько камней разной зернистости. Последним этапом будет доводка рабочей части с помощью мелкой наждачной бумаги. Если на металлическом стержне есть большие сколы или трещины, его нужно заменить на новый.
Зубило применяется для работы с твердыми материалами. Оно должно быть в любой кузнице. Однако, со временем рабочая часть приходит в негодное состояние, требует переточки. Для этого необходимо подобрать угол заточки, провести обработку с помощью абразивного круга. Довести кромку до финишного состояния с помощью наждачной бумаги или заточных брусков.
Подробные схемы и инструкции, как это сделать своими руками
Мастер должен знать полный технологический процесс, чтобы правильно производить заточку инструмента своими руками.
Технологический процесс
Технологический процесс включает в себя несколько основных моментов:
- Заднюю поверхность обрабатывают под углом равным заднему углу державки.
- На втором этапе происходит обработка самой режущей поверхности.
- Угол заточки должен быть на пару градусов больше, чем задний угол резания на пару градусов.
- Уже на третьем этапе формируется задний угол.
После доводки следует шлифовка, как финальный этап заточки.
Проведение доводки
Доводку следует проводить по выбранной методике. Основные моменты:
- резцы не погружают в воду, поскольку они могут сломаться;
- при доводке обязательно подавать воду для охлаждения;
- сначала обрабатывают заднюю грань, затем главную и вспомогательную.
Шлифовка
Шлифовку проводят с использованием наждачного круга. Оптимальный вариант – мелкозернистая модель.
Заточные долота | Популярный журнал Woodworking
Мы можем получать комиссию, когда вы используете наши партнерские ссылки. Однако это не влияет на наши рекомендации.
Набор зубил для очистки ласточкин хвост от Blue Spruce Toolworks
(www.bluesprucetoolworks.com).
ДОЛОТА СОСТАВЛЯЮТ БОЛЬШУЮ И ВАЖНУЮ часть набора инструментов столяра. Кажущаяся простота стамески — лезвия на палке — опровергает многочисленные вариации на эту тему.По крайней мере, хорошо настроенное долото поможет вам выполнить задуманную работу с минимумом усилий. А хорошо настроенное долото, выполняющее задачу, для которой оно было разработано, — это поистине приятное и вселяющее уверенность занятие.
Правильное хонингование долота зависит от правильного выравнивания тыльной стороны. Как и в случае с плоскими утюгами, для получения острого края необходима плоская полированная задняя часть. Часто используют долото, надев его на плоскую заднюю часть. Кромка может вычистить скол из угла или выровнять поверхность. Если задняя часть долота не плоская, режущая кромка будет дугой вверх и оторваться от поверхности, поэтому, чтобы добраться до последнего кусочка стружки и отрезать ее, вам придется поднять ручку, иначе она будет просто подниматься и преодолевать неровности, которые вы пытаетесь срезать.
Вогнутое или выпуклое долото — обе проблемы, требующие
внимания для правильной работы долота.
Вогнутость на спине не такая серьезная проблема, как выпуклость. Фактически, японские мастера-резчики шлифуют полые выемки на тыльной стороне своих долот, чтобы уменьшить усилие, необходимое для их заточки.Если японский производитель долота пошел на все эти неприятности, самое меньшее, что мы можем сделать, — это использовать только методы ручного хонингования на наших японских долотах. Шлифовальные машины с приводом, безусловно, высокоскоростные, слишком жесткие для стали, которая часто бывает очень твердой и хрупкой.
Японские долота имеют полую шлифовку на тыльной стороне, чтобы на
уменьшить количество стали, которую необходимо удалить во время заточки.
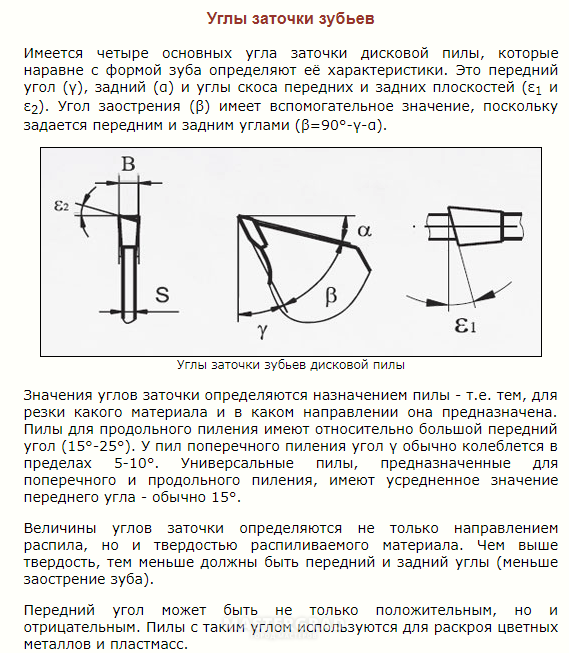
Выпуклую спину исправить гораздо сложнее, чем вогнутую.Существует тенденция раскачивать выпуклость взад и вперед, когда вы скользите по камню, а это означает, что вы либо полируете его как есть, либо фактически усугубите выпуклость. Вам нужно держать долото устойчиво, чтобы ваши усилия на абразиве были постоянными — непоколебимо параллельными камню — без раскачивания, когда вы вращаете лезвие вперед и назад. Это хорошая работа для электроинструментов. Медленный дисковый шлифовальный станок, такой как Lap-Sharp, Veritas или сторона тихоходного колеса в стиле Tormek, может помочь, позволяя вам сосредоточиться на высокой точке, которую вы пытаетесь измельчить.Также можно использовать ручную шлифовальную машину Dremel, позволяющую отшлифовать выпуклости и даже создать вогнутость на тыльной стороне, как японское долото. Используйте маркер, чтобы раскрасить всю заднюю поверхность, чтобы вы могли легко видеть, что шлифуется. Прижмите выступ на лезвии к абразиву, шлифуя его понемногу, часто проверяя свою работу линейкой или протирая лезвие долота о плоский камень. Следы, оставленные камнем, четко укажут на ваш прогресс.
Некоторые новые лезвия будут иметь защитное покрытие, которое необходимо удалить ацетоном или растворителем для лака.После этого новое долото, как правило, требует удаления заводских следов заточки на обратной стороне. Выбор первой, самой крупной зернистости — это вопрос личного суждения, поскольку некоторые заводские следы шлифования более глубокие, чем другие, и требуют более агрессивной обработки. Вы можете понять, что может потребоваться, начав с зернистости 800 или 1000, чтобы увидеть, как идут дела. Если вы просто полируете вершины шлифовальных выступов, вам может потребоваться перейти на более крупную зернистость, чтобы работа была выполнена в разумные сроки.Удаление царапин после хонингования обычно занимает меньше времени с использованием более мелких зерен, чем когда вы делаете все начальное шлифование на слишком мелком камне. Кромка нового долота, вероятно, будет достаточно квадратной, но все равно проверьте ее и исправьте, если она не квадратная, пока вы затачиваете фаску.
Фотография долота, нуждающегося в реставрации, «до». Для спасения сломанного долота требуется аналогичная оценка. Часто тыльная сторона бывших в употреблении долот с барахолки вообще никогда не выравнивалась должным образом.Вам нужно будет пройти тест на зернистость 800, чтобы увидеть, сколько работы вам предстоит сделать, а затем приступить к подготовке спинки. Фаска старого долота, несомненно, испорчена после открытия всех этих банок с краской (или соскребала жевательную резинку с тротуара?), И, возможно, ее нужно правильно заточить.
Удерживайте лезвие долота на камне так, чтобы задняя часть лезвия и рукоятка
свисали с края камня.
ПЛОСКАЯ СПИНКА
Начните с тончайшей зернистости, которая позволит выполнить работу в разумные сроки.Будьте очень осторожны и всегда держите лезвие ровно на абразивной поверхности. Избегайте раскачивания, которое может огибать край или угол. Как только долото станет ровным, вы можете сосредоточиться на режущем конце спины. Поскольку для долота нежелательна даже небольшая обратная фаска, не поддавайтесь соблазну использовать «трюк с линейкой» с помощью плоского железа, чтобы сэкономить время. Позвольте задней части долота соскользнуть со стороны камня во время его заточки, и вы получите отполированную и должным образом острую переднюю часть без необходимости обрабатывать всю заднюю часть.
Очистите лезвие и руки и измените угол наклона инструмента на камне при смене зерен. Когда все царапины старой зернистости заменены царапинами новой зернистости, вы готовы к следующей, более мелкой зернистости. Продолжайте использовать более мелкую крупу, пока задняя часть не будет иметь желаемый полироль. Подготовка спины — это, по большей части, разовая работа, и в зависимости от того, какую часть спины вы полируете, вам не придется снова об этом беспокоиться в течение длительного времени. Так что пройдите через более мелкую зернистость до самого лучшего камня, чтобы получить зеркальную полированную поверхность. Я не рекомендую ремень для стамески, потому что они имеют тенденцию слегка закруглять край.
Эту сплющенную и отполированную заднюю часть
больше не нужно затачивать, если только она не повреждена или не заржавела.
Используйте фломастер, чтобы раскрасить лезвие для разметки. | Нарисуйте квадрат направляющей линии поперек лезвия. |
Отшлифуйте до линии, чтобы удалить зазубрины на кромке. | Кромка отшлифована под квадрат, готова для шлифования под углом. |
ЗАТИФКА ДЛЯ ФАСА
Теперь пора определиться с углом скоса. Для отрезного долота скос может составлять всего 20 ° (некоторым деревообработчикам нравится угол скоса еще меньше, например, 15 °, но вы жертвуете прочностью кромки из-за такой низкой фаски). Стандартные настольные и стыковые долота традиционно шлифуются на заводе до 25 °, и это нормально для большинства работ, но лезвие прослужит дольше, если вы добавите микрокосмический скос 5 °, чтобы получить угол резания 30 °.Некоторые долота будут работать лучше с комбинацией мелкого скоса и микрокоса, например долота для долбления (подробнее позже), но часто микрокосы добавляются только для экономии времени. С большинством мощных систем заточки добавление микрокоса может действительно продлить процесс. Поэтому, если вы не уверены, что инструмент действительно лучше всего работает с микрокосом, просто отключите его при использовании точилки с электроприводом.
Если лезвие остро нуждается в помощи — оно сколотое, ржавое, неквадратное — проще всего провести линию по ширине долота на месте повреждения, а затем затупить кромку. вернитесь к этой линии и измените фаску до выбранного угла.
Установите угол скоса, отрегулировав удлинение лезвия по направляющей для хонингования, установив опору инструмента на правильном расстоянии от шлифовального круга или отрегулировав стол на ленточно-шлифовальном станке.
Низкоскоростные шлифовальные машины, такие как Tormek, Veritas, Work Sharp и Lap-Sharp, имеют специальные державки для инструментов и измерители угла, которые помогают правильно установить угол скоса.
Расстояние от направляющей определяет угол кромки. Это направляющая для хонингования с боковым зажимом в стиле Eclipse. | Для определения угла скоса на шлифовальном станке требуется комбинация удлинения лезвия и шарнирного соединения двух шарниров этого стола шлифовального станка Veritas. |
Избегайте перегрева при шлифовании фаски. | Готовая фаска должна быть ровной и прямой поперек лезвия. |
Зубило справа имеет край в половину от
ширины другого.Требуется лишь половина усилия
, чтобы сделать такой же разрез, как и слева.
Долбежные долота и более прочные долота при резке и взламывании подвергаются значительным ударным нагрузкам — их кромки, как правило, служат дольше с более высоким углом скоса. Отшлифуйте первичный скос 25 ° и добавьте микрокосос 10 ° для прочности. Если кромка держится хорошо, вы сможете уменьшить микрокосмический скос и улучшить режущее действие. Если кажется, что кромка недолговечна, подойдет более высокий скос. Ударяя этим долотом, помните, что по более узким не нужно бить с такой же силой, как по более широким.Концентрация силы, обсуждаемая в первой главе, прекрасно иллюстрируется здесь. Та же сила удара, которую вы прикладываете к 2-дюймовому долоту, преобразуется в силу, в восемь раз большую, когда вы прикладываете ее к четверть-дюймовому долоту. Так что отрегулируйте удары молотка соответствующим образом — ваши долота будут вам благодарны.
Установить фаску проще всего с помощью помощника с электроприводом, но простое руководство по хонингованию позволит вам быстро отшлифовать фаску до нужного угла. Если вы не затачиваете косое долото, вы, вероятно, захотите убедиться, что лезвие имеет прямоугольную форму по бокам.Хотя при использовании стамески нетрудно скомпенсировать край кромки вне квадрата, большинство мастеров по дереву предпочитают, чтобы кромка была квадратной. Косое долото заточено не зря — угол режущей кромки должен быть сохранен. Правильно установленная направляющая для хонингования может помочь при заточке любых долот.
Надежно прижмите край к камню во время хонингования
с помощью направляющей.
Щелкните здесь, чтобы загрузить PDF-файл для этой статьи.
Через непродолжительное время на плоской шлифовальной машине.
Рекомендации по продукту
Вот некоторые расходные материалы и инструменты, которые нам необходимы в повседневной работе в магазине. Мы можем получать комиссию с продаж по нашим ссылкам; однако мы тщательно отбирали эти продукты с учетом их полезности и качества.
Мифы и тайны, окружающие плоские и чизельные фаски
Для получения дополнительной информации о самолетах посетите наш сайт для начинающих Common Woodworking.
Я хочу вернуться к чему-то, что оказалось интересным во время моего турне по США за последние три месяца.Я спрашивал участников на каждом семинаре, под каким углом мы шлифуем фаски долота и рубанки, и все ответили, что 25 градусов. Затем я спросил, под каким углом мы их затачиваем? Ответ был громким: «30 градусов», и я спросил их: «Почему 30?»
На самом деле это утверждение стало более верным только в последние десятилетия. Мы, плотники, на самом деле затачивали то, что нам войлок мы хотели, а не то, что нам сказали точить . Мы, мастера по дереву, решили затачивать долото по задаче, так что если мы работали с одной древесиной или выполняли одну задачу, мы меняли фаску на глаз за доли минуты и продолжали работу.Некоторые долота мы затачивали до 35 градусов, но мы никогда не проверяли угол с помощью транспортира, но вы можете, если хотите, и я думаю, что начинающие плотники должны время от времени проверять себя. Иногда мы меняли его на 25 градусов, и это очень эффективно работало при ручной резке мягкой древесины. Реальность такова, что есть веские и практические причины, по которым мы затачиваем или затачиваем примерно до 30 градусов для обычной обработки дерева, но они могут быть не такими, как вы думаете. По большей части, конечно, на протяжении всей истории, этот 30-градусный скос был просто углом, по которому нужно было стрелять, его редко измеряли, и это не был юридический и жесткий окончательный угол.Как часто мы учим этому как абсолюту так же, как мы говорим, что вы должны затачивать от руки или вы всегда должны использовать руководство по затачиванию. Для меня недостатком использования направляющей для хонингования является то, что вы не можете создать макрос изгиба, который мне нравится, как скос. Преимущество в том, что вы уверены, что получите именно тот скос, который вам нужен. С другой стороны, это может быть немного медленнее, совсем немного и сложнее, но, возможно, не слишком, потому что, как мне сказали, вы можете «быстро справиться с этим». В общем, есть причины как для ручного, так и для ручного методов заточки, так что тогда это вопрос личного выбора.
Эта плоскость имеет рельеф всего на 3 градуса меньше, чем угол наклона панели, и она очень хорошо режет; а также один, заточенный до 30 градусов. Вау! Это освобождение!
Проблема шлифовки или отшлифованной фаски для меня важна, потому что точно так же, как укладывать самолет на бок стало правильным, а оставлять его вертикально на скамейке было неправильным, когда это не было неправильно, и никогда действительно не было, пока кто-нибудь сказал, что это неправильно, поэтому слишком много затачивания рубанка на 36, 29, 33 или 40 градусов может быть сочтено многими как неправильное, хотя на самом деле это совсем не так.
Позвольте задать вам вопрос. Если плоскость со скосом вниз имеет угол наклона 44-45 градусов, как все плоскости скамьи с шаблоном Бейли и многие другие, какая разница для режущей кромки, если плоскость заточена под углом более 30? и меньше 44 до 45 градусов? Конечно, пока фаска находится внизу, это не имеет значения для представления угла резания к поверхности дерева, верно?
На выставках я задавал этот вопрос и действительно ответил.Это демистифицировало, в чем был незаданный вопрос, кто сказал, что он должен быть мертвым при 30 градусах? Как я уже сказал, угол подачи остается идентичным, потому что скос находится на обратной стороне режущего инструмента, а не сверху.
Дело в том, что есть смысл стрелять, а угол 30 градусов — вполне практичный угол для установки. Я никогда не использую руководство для хонингования, если что-то не вышло из строя. С другой стороны, на моих занятиях у меня есть полезные руководства, которые люди могут использовать, поскольку некоторые предпочитают, по крайней мере, начинать с этого пути.В конечном итоге все мои ученики в конечном итоге затачивают вручную из-за скорости, эффективности и действительно вариативности создания, скажем, мгновенного изменения наклона 30 градусов, чтобы сделать его 40 градусов для резки пазов в определенных типах древесины или чего-то в этом роде. угла обрезки руки. У большинства людей есть долота для измельчения, а у других — для очистки, поскольку они накапливают все больше и больше инструментов.
Этот транспортир показывает точный угол, под которым мы шлифуем и шлифуем. Никаких вторичных или микрокаскосок.
Вчера я заточил под углом 42 градуса угол в 42 градуса на плоской старой гладкой плоскости Stanley со скосом вниз и выровнял безупречную отделку на поверхности, которая слегка порвалась, когда плоскость со скосом вверх имела тот же угол, что и Stanley. Я знал это всю свою жизнь, и вчера мы с Филом провели серию стендовых испытаний, чтобы увидеть результаты. Теперь вы можете увидеть последствия этого. Фаска 42 градуса намного прочнее, чем фаска 30 градусов, потому что сразу за режущей кромкой и по всей ширине утюга находится масса стали.Он presto, болтовни тоже нет. Не то, чтобы мой простой, не модернизированный, № 4, Стэнли по образцу Бейли с его оригинальным железом вообще когда-либо болтал.
Прямоугольник, показывающий отшлифованный первичный скос по отношению к подошве и показывающий 3-градусный рельеф на заднем крае скоса.
Результат всего этого — помочь людям понять, что 30-градусный скос — хороший и практичный угол для стрельбы, и когда или если вы все же решите, что заточка от руки — хороший вариант для развития в качестве навыка, Лучше вообще не думать слишком много об угле, даже на скамейке, потому что он не имеет большого значения для фактического разреза.По моему опыту, маловероятно, что кто-то собирается затачивать от руки где-то около 45 градусов. Фаска должна быть примерно на 2 градуса ниже угла опоры утюга для того, что называется рельефом, вот и все. В противном случае, пружина в поверхности древесины заставит рубанок скользить по дереву и подниматься против пропила, в результате чего рубанок не срезается.
Другое дело, что под углом 30 градусов легче затачивать, чем под 40, из-за крутизны и контроля. Если вы затачиваете вручную и находитесь под углом 30-40 градусов, режущая кромка рубанка, конечно же, прослужит дольше, и рубанок будет резать с точно таким же давлением, потому что угол наклона к дереву одинаков, независимо от угла скоса. .То же самое, что и на плоскостях со скосом вверх. Таким образом, это не имеет значения с точки зрения давления и сопротивления. Тем не менее, есть физическая динамика, играющая с плоскостями со скосом вверх, и это связано с выравниванием режущего инструмента для обеспечения большей прямой тяги, так что вы также не можете сбрасывать со счетов эффективность плоскостей со скосом вверх. Не думаю, что это иная ситуация, и мне очень нравятся самолеты со скосом. Вам не нужно увязнуть в бесконечных углах наклона плоскости, и вы должны оставить себе варианты для изменений.Вы можете безгранично разнообразить заточку плоскостей со скосом вниз. При заточке от руки это становится очень важным и мало влияет на работу, которую вы планируете, поэтому наслаждайтесь свободой, используете ли вы направляющую для хонингования или от руки обрабатываете режущие кромки. Попробуйте, дайте мне знать, что вы думаете. Ах да, кстати. Я недавно купил три самолета, которым было по крайней мере 70-80 лет, которые принадлежали мастеру, и у них были макро-изгибы, которые начинались под углом 35 градусов и опускались по эллипсу примерно до 20 градусов.Я вижу это довольно часто. Далее о долотах.
Общие советы по заточке инструментов — Garrett Wade
Пила, которая использовалась в течение длительного времени или использовалась неправильно, потребует доливки, придания формы, настройки или заточки.
Тем не менее, с этим обращаются осторожно, пилу нужно затачивать несколько раз, прежде чем возникнут какие-либо или все из первых трех процессов.
Заточка пилы после освоения становится полезным занятием — нет ничего лучше, чем хорошо отточенная и заточенная пила.Правильно подобранное оборудование упростит работу и даст первоклассный результат.
Топпинг или соединение
Зубья ручной и шиповидной пилы после продолжительного использования становятся нестандартными. Их необходимо выровнять до обычной высоты, прежде чем их можно будет затачивать и устанавливать.
- Поместите пилу в тиски и зафиксируйте напильник в желобчатом зажиме.
- Проведите напильником несколько раз по всей длине пильного диска. С сильно изношенными зубами может потребоваться повторная форма и вершина, чтобы сохранить правильное расстояние между зубами.Не забудьте, что файл должен быть плоским, используя зажим для верхней части.
Формовочный
Специально изготовлены напильники для заточки пил. В прошлом они были двусторонними. Сегодня они имеют треугольную форму и поставляются без ручки во множестве размеров. Напильник стандартного размера для продольной пилы имеет длину 7 дюймов. Сверхтонкие 7 и 6 дюймов и двойные сверхтонкие идеально подходят для пил с разрешением от 11 до 14 точек на дюйм. Используйте сверхтонкие 4 дюйма для меньших зубьев.
Обычно пилы большего размера и пилы для бревен затачиваются напильником, у которого более толстый край закруглен, чтобы можно было подпиливать круглые канавки.У этих файлов есть неразрезанные боковые зубы.
Для придания формы зубьям выберите тонкий напильник с конической пилой, ширина которого примерно вдвое превышает глубину зубьев пилы.
- Поместите пилу в тиски так, чтобы были видны только зубья.
- Поместите напильник между зубами («пищевод») и сильно надавите левой рукой, чтобы напильник занял правильное расстояние между зубьями.
- Нарисуйте его прямо поперек пилы и под прямым углом к зубам
- Тщательно подпилите каждый пищевод, следя за тем, чтобы каждый зуб во время подпиливания имел правильную форму и высоту.
- Любое сглаживание, вызванное топпингом, будет удалено.
Настройка
Для того, чтобы какая-либо пила заработала правильно, ее зубья должны устанавливаться попеременно влево и вправо. Делать это нужно аккуратно, чтобы острия пилы прорезали пропил немного шире, чем толщина полотна, и пила легко проходила по дереву.
Эту задачу выполнит комплект пил. Он оснащен упорной опорой из закаленной стали и установочным винтом с микропроцессором, который регулирует расстояние, на котором может быть установлен каждый зуб.Его действие спускового механизма упрощает использование и означает, что его можно использовать на ручных и дисковых пилах.
Купите набор пил для плоскогубцев, если вы собираетесь использовать его только изредка. Отрегулируйте плоскогубцы, чтобы получить правильный набор, и наденьте их на зуб. Когда вы сжимаете ручки, поршень прижимает зуб к наковальне. Установите чередующиеся зубья таким образом, затем переверните пилу и установите чередующиеся зубья, которые вы проигнорировали в первый раз.
Зубья, установленные вручную, могут иметь небольшие неровности, которые необходимо удалить с помощью боковой повязки.Это делается путем легкого скольжения по сторонам зубьев, удерживая пилу на скамье.
ЗАТОЧКА
Торцовочные пилы
- Используйте напильник для заточки торцовочных пил.
- Поместите пилку для обработки на передний край первого зуба, обращенного к вам.
- Напильник также будет воздействовать на задний край левого зуба, который отклоняется от вас.
- Переместите рукоятку напильника влево, пока она не составит угол 60 градусов с пилой.
- Нанесите несколько ударов по каждому чередующемуся зубу, удерживая пилкой под этим углом.
- Затем каждый раз опиливается передний край зуба, который наклоняется к вам.
- Продолжайте подпиливание до конца пилы, переверните и повторите действие.
RIP-пила
Заточивается так же, как и торцовочная пила, но напильник необходимо держать под углом 90 градусов поперек пилы. Подпилите каждый дополнительный зуб с одной стороны, а затем подпилите каждый дополнительный зуб с обратной стороны.
Шипорезные пилы и пилы типа ласточкин хвост
Заточен так же, как и торцовочные пилы, но требуется большая осторожность для поддержания правильного размера и посадки зуба. Пилы с очень маленькими зубьями, возможно, придется вернуть производителю для настройки и заточки.
После заточки
Слегка обработайте пилу по бокам масляным камнем, чтобы удалить заусенцы.
Ознакомьтесь с нашей коллекцией ручных пил и выберите подходящую для своего следующего проекта.
Уголки и профили режущих кромок
Угол скоса
Угол скоса — это угол между скосом и осью инструмента.Угол скоса имеет ряд эффектов. Он определяет «угол кромки» инструмента (за исключением долот, которые заточены с обеих сторон, так что это сумма углов скоса). Это также угол резания на канавках, когда скос находится в контакте с деревом. Угол скоса определяет прочность кромки — большие углы имеют более сильные кромки. 45-футовая кромка — хорошая прочная кромка. Если угол меньше 30 секунд, кромка немного хрупкая для точения, но может использоваться в особых случаях.
Угол скоса также определяет положение ручки относительно направления резки.Небольшой угол приближает ручку к линии разреза: большой угол уводит ручку дальше от линии разреза.
Когда долота и долота имеют длинные фаски. Я бы порекомендовал использовать дополнительный скос, чтобы улучшить контроль над инструментом.
Матовая поверхность для надежного захвата
Дерево — ясень или аналогичный
Узкий профиль и ручка для удержания и перекатывания инструмента в фиксаторах
Расширяющая секция для ручки poftci
Матепнан, 3amwineHHt »iw aoTopcK
Эффекты углов скоса
60 «
Конечное положение:
Стартовая позиция
30 «
Изменение положения ручки * ое изменение be.эль угол
Место финиша:
Исходное положение
- Слишком * поворот — угол скоса
Угол скоса
Торговля БОВЦЛ
paBOM
Угол профиля
Угол профиля — это угол между скосом и режущей кромкой. Проще говоря, он определяет самую узкую клинку, которую режет инструмент.
Передний угол
Стандартные скребки плоские сверху, что составляет нулевой передний угол. Добавление отрицательного угла наклона режущей кромки может снизить риск закапывания.
- Влияние угла профиля
Передний угол
Шлифовальный скребок с отрицательной передней кромкой
Шлифовальный скребок с отрицательной передней кромкой
Zero rako измельчение icrapcr
Zero rako измельчение icrapcr
Mmepnan, 3amwineHHt »iw aoTopcK
Угол перекоса
Косое долото скребка с перекосом — это зубило, режущая кромка которого находится не под углом 90 дюймов к оси инструмента. Угол перекоса измеряется от режущей кромки к оси инструмента. Основным эффектом перекоса режущей кромки является изменение положение ручки относительно режущей кромки.Это может значительно улучшить контроль tccl и обеспечить доступ в ограниченные пространства. Хороший угол наклона долота должен составлять 60 футов.
Влияние угла наклона на положение рукоятки инструмента
Прямая кромка
Изогнутая кромка
Скребок с перекосом
Угол наклона зубила
Угол наклона зубила
Скребок косой 3nglo
Квадратный
Зубило косое 60®
Изменение положения ручки при изменении угла наклона
Зубило косое 60®
Изменение положения ручки при изменении угла наклона
Квадратные chisci
МаТепнан, 3amnujeHHbifi aoTopc <нМ npaBOM
Заточка ногтей по мелкой канавке (SFG)
Заточка с обратной шлифовкой на канавке с глубокими канавками (DFG}
Формы режущих кромок
Передовые формы — это во многом визуальные определения.Одно время ноготь назывался «женский ноготь». Скошенный край не виден с передней части инструмента. Шлифовка ногтя является традиционной и долгое время использовалась для обработки канавок с мелкими канавками. Шлифовка мелких деталей, используется для обработки мелких деталей.
Заточка с обратной стреловидностью используется на канавках с глубокими канавками, где кромка проходит намного дальше по заготовке, чем при квадратной шлифовке. Некоторая часть скоса будет видна спереди, хотя скользящая кромка будет похожа на шлифовку ногтя.Этот помол был разработан в начале 1980-х годов, когда круглая заготовка из быстрорежущей стали стали использоваться для токарной обработки древесины. Иногда это называют «кельтским» измельчением.
Квадратная шлифовка — это место, где стамеска просто раскатывают по платформе, создавая квадратную форму, как если бы она была заточена точилкой для карандашей. Обычно он используется для черновой строжки шпинделя.
На скребках и долотах форма режущей кромки не зависит от угла наклона и профиля, и любая форма режущей кромки не может быть создана на шлифовальном станке.
Некоторые скребки являются инструментами для формования; это. форма режущей кромки аналогична или точно такая же, как форма, которую он режет. Есть бусинки, бугорки и клиновидные режущие инструменты. Эти формы заостряются на верхней части инструмента, чтобы не менять форму режущей кромки.
Прочтите здесь: Заточка и уход за инструментами
Была ли эта статья полезной?
Как точить стамески и лезвия рубанков | Dubbeld How To
Как точить долота и плоские лезвия | Dubbeld How To
Introduction
Я считаю, что одна из основных причин, по которой многие люди отказываются от деревообработки, заключается в том, что их опыт основан на использовании неострых инструментов.
Самым крутым в деревообработке может быть использование по-настоящему острого инструмента — это чувство расширения возможностей, которое вы испытываете, когда внезапно вам дается сверхъестественная сила, позволяющая почти без усилий направлять инструмент по дереву, опьяняет … никакой пыли, просто стружки и песня стали о дереве.
С другой стороны, работа с тупым инструментом отнимает удовольствие от работы с деревом и может быть весьма обескураживающей, особенно для новичков в этом ремесле. Результаты неизбежно беспорядочные, разочаровывающие, утомительные и потенциально опасные; а кто этого хочет?
Мне не особенно нравится заточка, но мне нравится использовать острые инструменты, поэтому моя цель в этой теме об заточке — как можно лучше объяснить методы, которые я использую для эффективной и быстрой заточки инструментов.
— Joel Dubbeld
Содержание:
- Почему необходимо затачивать?
- Геометрия долота и плоскость
- Шлифовальные станки
- Заточные камни
- Процесс заточки: долота и рубанки
1. Почему необходимо затачивать?
Режущий инструмент — это, по сути, твердый клин, который используется для резки более мягкого материала (в нашем случае дерева).
Режущая кромка этого клина будет изнашиваться, хотя она проталкивается через абразивные минералы, содержащиеся в древесине.По мере затупления кромки площадь поверхности увеличивается, создавая большее сопротивление и сжимая древесные волокна. В результате обычно получается рваный, грубый разрез и повышенный риск травмы из-за повышенного усилия, необходимого для выполнения разрезов.
Следовательно, для сохранения эффективности резания инструмента требуется заточка. Частота этой заточки зависит от разрезаемого материала и состава используемой фрезы. Следовательно, прочность и долговечность кромки становятся наиболее важными факторами при выборе типа инструмента и качества инструментальной стали, наиболее подходящего для решения поставленной задачи.
При покупке ручных инструментов с намерением использовать их часто, важно помнить о различиях в инструментальных сталях. Изучите информацию об известных производителях и получите лучшее качество из того, что вы можете себе позволить.
Примечание об инструментальной стали:
Инструментальная сталь чаще всего используется для изготовления лезвий для деревообработки, потому что она обычно имеет такой баланс прочности и твердости, который дает ей способность сохранять острую и прочную кромку.
Мое простое представление о типах стали, которые мы используем для обработки дерева, говорит мне о том, что инструментальная сталь в основном представляет собой комбинацию железа и углерода с другими элементами (сплавами), добавленными для повышения ее прочности и твердости.Сложность состоит в том, чтобы сделать лезвие одновременно твердым и жестким; по мере увеличения твердости (чтобы лезвие оставалось дольше), вы делаете лезвие менее жестким (более хрупким, менее устойчивым к ударам и ударам). Углерод является наиболее важным упрочняющим элементом, но чем выше содержание углерода, тем сильнее уменьшается ударная вязкость инструмента.
После ковки и формовки инструментальную сталь закаляют, а затем отпускают для получения более прочной кромки. В процессе закалки при высокой температуре (точка где-то около докрасна) углерод растворяется и образует карбид железа (не карбид вольфрама, который представляет собой другой материал).Если с этого момента стали дать стали медленно остыть, она станет отожженной (мягкой). Однако, если в этот момент сталь быстро закалить или охладить, карбид «замерзнет», и сталь станет твердой.
Отпуск, термическая обработка, обычно выполняемая после закалки, снижает твердость и увеличивает ударную вязкость стали. Уровень и температура, до которой это достигается, зависят от смеси сплавов и желаемых характеристик готового продукта.Например, напильник, как правило, не закаляется для сохранения максимальной твердости, но долото быстро сломается, если не будет обладать некоторой пластичностью и упругостью (жесткостью), поэтому закаливают соответствующим образом.
Твердость стали обычно определяют путем измерения ее сопротивления деформации. Во многих описаниях инструментов вы заметите символ «Rc» с последующим номером. Это относится к твердости инструмента, измеренной по шкале твердости С. Роквелла.
Важно знать об этих степенях твердости, потому что для разных задач требуются разные инструменты.
Ручные пилы обычно имеют более мягкую оценку Rc38-42, чем долота или рубанки по Rc58-62. Долото на Rc63 будет удерживать лезвие намного дольше, чем зубило на Rc58, но будет намного легче откалываться.
Эта шкала является лишь одним из факторов способности инструмента удерживать хорошую кромку. Не менее важны используемые стальные сплавы и сам процесс отпуска.
Очень твердые инструменты хрупкие, их труднее затачивать, часто для этого требуется специальное оборудование.Более мягкие инструменты более гибкие и затачиваются быстрее и легче.
Карбид (чаще всего карбид вольфрама в деревообработке), хотя и не является сталью, представляет собой очень твердый состав, получаемый путем нагревания одного или нескольких тяжелых металлов и углерода при очень высоких температурах. Чаще всего он используется в инструментах с механическим приводом, таких как дисковые пилы, фрезы и фрезы. Обычно он не подходит для использования с ручными инструментами, так как он слишком хрупкий, чтобы выдерживать углы менее 45 градусов.Однако он будет оставаться острым в 10-20 раз дольше, чем стальные инструменты, используемые при тех же условиях.
2. Геометрия долота и плоскость
Резкость и острые углы не обязательно одно и то же. Резкость инструментов обычно относится к состоянию кромки инструмента, а не к ее углу.
Давайте посмотрим на это в перспективе; возьмем, например, топор. Топор, используемый для колки дров, не точен так же, как топор, которым рубят дерево.Оба должны быть острыми, но геометрия кромок отличается, чтобы они могли эффективно выполнять свои функции.
То же самое и с долотом; тот, который используется для вырубки пазов каркаса дома в австралийской твердой древесине, не затачивается таким же образом, как тот, который используется для вырезания мелких деталей в мыльном дереве, как Tarzali Silkwood.
В обоих случаях, чем острее угол кромки, тем меньше сопротивление она оказывает, но чем острее становится кромка, тем более хрупкой она становится. Таким образом, углы кромки (или фаски) определяются тем, для чего используется инструмент.
Отполировав 2 пересекающиеся грани этой кромки, мы можем получить более острую и прочную кромку, которая легче прорезает древесные волокна, оставляя гладкую, ровную поверхность.
Идеальный угол инструмента зависит от инструмента и от того, для чего он используется. Долота, толкаемые вручную, можно затачивать до довольно острых углов, потому что они будут испытывать меньшую силу, чем долота, забиваемые молотками. По тем же причинам у инструментов с механическим приводом углы больше или больше тупые.
Типичные углы первичной фаски для долот
Если смотреть спереди, долота обычно отшлифованы под прямым углом к краям.
Плоские ножи можно шлифовать по-разному в зависимости от их использования. Утюги для обработки уступов, ребер и стыков должны шлифоваться под прямым углом, в то время как при работе с поверхностью они намеренно шлифуются с небольшим изгибом. Изгиб помогает предотвратить заедание углов лезвия при строгании плоских поверхностей, а также снижает усилие, необходимое для толкания плоскости при выполнении глубоких пропилов при черновой обработке.
Формы долот и рубанков
3. Шлифовальные станки
Угол резца обычно достигается шлифованием; либо путем выпуклого шлифования, полого шлифования (вогнутого) или плоского шлифования.
Типы заточки
Большой угол выпуклых шлифованных инструментов, таких как топоры, делает режущую кромку очень прочной, но для резки требуется большое усилие. Твердосплавные наконечники на фрезах иногда имеют выпуклую шлифовку, чтобы поддерживать хрупкую вольфрамовую режущую кромку.
Пустотелый шлифовальный станок (достигается за счет использования торца вертикального шлифовального круга) и плоских шлифовальных инструментов (достигается вручную с помощью настольных камней или с помощью механизированных шлифовальных машин, таких как шлифовальные станки с абразивными лентами, горизонтальные шлифовальные круги или кромки вертикальных шлифовальных кругов, таких как как алмазный круг Tormek), их легче шлифовать, и поэтому они более распространены, чем инструменты с выпуклой шлифовкой.
Скорость шлифовальных машин делает этот вариант наиболее популярным. Из них колесные шлифовальные машины наиболее распространены в виде сухих шлифовальных машин и мокрых шлифовальных машин.
Сухие шлифовальные машиныотносительно недороги, что делает их популярным выбором.
Обычная шлифовальная машина, предназначенная для более общего измельчения, работает прибл. 3500 об / мин и чаще всего идет с жесткими, медленно режущими средне-мелкими и средне-крупными кругами. Эти круги не идеальны для шлифования инструментов, потому что их твердость в сочетании с высокой скоростью резания приводит к высокому нагреву от трения, который может легко перегреть и обжечь инструментальную сталь.Замена этих колес на более мягкие белые колеса из оксида алюминия 60–100 грит снизит вероятность перегрева, так как эти колеса будут резать быстрее. Однако они изнашиваются быстрее. Будьте осторожны с переносимой по воздуху пылью от этих шлифовальных машин — вдыхание комбинации оксида алюминия и стали не продлит вашу жизнь. ИСПОЛЬЗУЙТЕ ПЫЛЕВАЮЩУЮ МАСКУ и ЗАЩИТНЫЕ ОЧКИ!
Также важно закаливать лезвие после каждых нескольких проходов по шлифовальному кругу, чтобы предотвратить его перегрев.
Существуют более специализированные сухие шлифовальные машины, которые работают на более низких скоростях, но они также и более дорогие.
Мокрые шлифовальные машины — отличный выбор для заточки инструментов. Их шлифовальные круги проходят через ванну с водой, которая действует как охлаждающая жидкость и сохраняет круг в чистоте, удаляя шлифовальную стружку. Также отсутствует переносимая по воздуху пыль, поэтому нет необходимости носить маску.
Эти типы шлифовальных машин обычно работают на медленных скоростях и удаляют материал медленнее, чем сухие шлифовальные машины, однако после шлифования основных углов скорость теряется незначительно, если используются приспособления для повышения воспроизводимости.
Tormek T-8 Шлифовальный станок для влажного камня
Шлифовальные круги, как и все режущие инструменты, нуждаются в регулярном обслуживании для поддержания их остроты, чистоты и сбалансированности.
Правка — это процесс очистки шлифовальной поверхности путем удаления металла или посторонних частиц и тусклых абразивных зерен. В этом изношенном или затупленном состоянии колесо покрывается лаком и выделяет чрезмерное тепло из-за трения. Правка также исправляет и выравнивает колесо, удаляя канавки и неровности.
Для этого доступны различные типы инструментов для правки колес, и все они работают по одному и тому же основному принципу заточки; используйте более твердый материал, чтобы стереть более мягкий.
Инструменты для правки колес:
Алмазный точильный камень Atoma с зернистостью 600
4. Заточные камни
Заточные камни, вероятно, являются наиболее важными предметами, используемыми при ручной заточке. Материалы, из которых состоят эти камни, могут быть натуральными или синтетическими, и они бывают самых разных форм, размеров и крупности.Камни в основном используются с легким маслом или водой, которые поддерживают чистоту камней, унося стружку. Отличные результаты могут быть достигнуты со всеми следующими точильными камнями:
Абразивные материалы с покрытием (наждачная бумага) недороги и, вероятно, недостаточно используются для заточки инструментов. В них используются абразивные материалы из оксида алюминия и карбида кремния с различной степенью зернистости от 40 до 4000. Листы приклеиваются к субстратам, таким как флоат-стекло или обработанный гранит, и используются в качестве плоских камней или оборачиваются вокруг других форм для изготовления скользящих камней.Для влажной и сухой бумаги из карбида кремния можно использовать воду для удаления стружки. С помощью этих абразивов можно заточить большинство инструментов, за исключением твердосплавных.
Преимущества:
Недостатки:
Листы наждачной бумаги (влажная и сухая)
Абразивная пленка — относительно новый продукт на рынке заточки. Разработанный для промышленного использования, он использует частицы быстрорежущего микрокристаллического алмаза, карбида кремния или оксида хрома, нанесенные на пленочную основу. Эта самоклеящаяся пленка наносится на такие подложки, как флоат-стекло для плоской заточки или на различные формы для заточки профилей.
Легкое масло, такое как масло камелии, лучше всего подходит для удаления стружки.
С помощью этих абразивов можно заточить большинство инструментов, для карбида требуется алмазная пленка.
Сорт:
- 15 микрон для быстрой резки
- 3 микрона для хонингования
- 0,5 и 0,1 для полировки
Преимущества:
- чрезвычайно быстрая резка
- чрезвычайно острая кромка
- соответствует любой форме
- портативность
Недостатки:
- Относительно дорого
- пузырьки могут потенциально образовываться между пленкой и подложкой
Арканзасские камни — это новакулит природного происхождения (разновидность кремня), добываемый в Арканзасе, США.Они делятся на твердые и мягкие, мягкие камни более пористые, чем быстрее огранка. Твердые камни режут медленнее и дают более полированные и острые края.
Масло используется для удаления стружки. Большинство инструментов можно заточить арканзасскими камнями, за исключением карбида.
Классификация:
- Washita (P400-600) бело-фиолетовый, бело-оранжевый
- Soft Arkansas (P600-800) белый, серый черный, зеленый, розовый или их сочетание
- Hard Arkansas (P800-1000) черный, серый, белый и красный или их комбинация
- True Hard Arkansas (P1200 +) черный, серый, белый, красный или комбинация
- Translucent Arkansas (P1200 +) полупрозрачный серый, t желтый, t коричневый, t розовый
- Black Hard Arkansas (P1200 +) черный, сине-черный
Преимущества:
- Долговечность
- Чрезвычайно острая кромка, получаемая на мелких камнях
Недостатки:
- Режет медленно
- Масло притягивает пыль
- Масло может загрязнять деревянные поверхности от до повторно сплющивать после раскатки
Синтетические нефтесодержащие камни — это искусственные камни двух типов: оксид алюминия (Индия) и карбид кремния (Crystolon), связанные смолой и изготовленные из металла. y Norton.Они заправлены маслом от производителя. Большинство инструментов можно заточить с помощью синтетических маслостойких камней, за исключением твердосплавных.
Сорт:
- Coarse India (P100) Коричневый или коричневый
- Coarse Crystolon (P100) Серый или черный
- Medium Crystolon (P180) Серый или черный
- Medium India (P240) Коричневый или коричневый
- Fine India ( P280) Коричневый или желто-коричневый
- Fine Crystolon (P280) Серый или черный
Преимущества:
Недостатки:
- Из-за ограниченной зернистости не получается получить особенно острую кромку
- Масло притягивает пыль
- Масло может загрязнять деревянные поверхности
Водяные камни, точильные камни или японские водные камни являются естественными или искусственными.Искусственные камни состоят из частиц оксида алюминия или карбида кремния, взвешенных в связующем, таком как глина или смола. Как правило, более крупные камни довольно пористые, и перед использованием их необходимо замочить в воде. Мелкие и натуральные камни не нуждаются в подготовке, их достаточно лишь разбрызгать водой. Вода смывает стружку, а также изношенные абразивные зерна, обнажая новые острые кромки и ускоряя процесс заточки резания. Однако, поскольку водные камни режут быстрее, они также быстрее изнашиваются, и их необходимо часто выравнивать, чтобы предотвратить образование выпуклостей.Однако это легко сделать, чаще всего с алмазной пластиной, такой как Atoma Diamond Sharpening Stone 600 зернистостью, или с листом мокрой и сухой наждачной бумаги P240, приклеенной к куску гранита или флоат-стекла. Большинство инструментов можно заточить с помощью водяных камней (мой нынешний фаворит — Shapton), за исключением карбида вольфрама. Камни нагура (что означает «корректирующий») можно использовать, чтобы помочь сгладить и сформировать суспензию на поверхности мелких гидрогелей. Жидкий раствор помогает уменьшить всасывание, возникающее между инструментом и поверхностью камня.
Сортировка:
Преимущества:
- Быстрая резка
- Большой диапазон зернистости
- Кромка с очень острой кромкой
Недостатки:
- Быстро, но легко сглаживается
Waterstone5: Waterstone5: Waterstone Керамический точильный камень зернистостью 12000 (кремовый) Керамические камни изготовлены из частиц оксида алюминия и обожжены при 1650 ° C под давлением в керамическом связующем.Их можно использовать для заточки карбида вольфрама. Для удаления стружки не требуется вода, но они быстро загружаются и требуют очистки под водой с помощью моющего средства и мочалки из стекловолокна. Класс: Преимущества: Недостатки: Алмазные камни, называемые пластинами, изготовлены из микрокристаллических кристаллов алмаза, прикрепленных к перфорированным или прочным стальным или алюминиевым плоским пластинам. Я обнаружил, что с алмазными пластинами вы получаете то, за что платите. Высококачественные японские алмазные точильные камни Atoma не продадут свой алмаз по сравнению с дешевыми альтернативами. Следует отметить одну вещь: первоначальная острота алмаза со временем станет менее агрессивной, поскольку острые нити кристалла алмаза отламываются. Сорт: Преимущества: Недостатки: Tormek DC-250 Diamond Wheel Coarse Напильники разработаны и используются для заточки многих деревообрабатывающих инструментов. Стропы — это пористые поверхности, такие как кожа, бумага или дерево, используемые с очень мелкими абразивами или без них для полировки режущих кромок.Движение, используемое для подгонки, состоит в том, чтобы отвести лезвие от режущей кромки и удерживать его под точно определенным углом скоса. Тщательная зачистка обеспечит хорошую режущую способность кромочного инструмента в течение длительного времени, но, в конечном итоге, правка приведет к образованию тупого угла резания (дублирование), и инструмент необходимо будет переточить. Кожаные ремешки с хвостом кенгуру по своей природе абразивны и не обязательно требуют дополнительных абразивных составов. Они считаются лучшими из кожаных ремешков. К абразивам, используемым для заточки, относятся: Ремешок из кожи хвоста кенгуру Из-за этого камни никогда не отслаиваются и остаются плоскими. Алмаз, самый твердый из известных материалов, затачивает все инструменты и может использоваться для выравнивания любых других камней. Вода не обязательна, но несколько капель могут помочь удалить стружку.
Обычные напильники из закаленной стали, описанные в примечании к инструментальной стали, закалены в большей степени, чем режущие инструменты по дереву, что дает им возможность резать изношенные края более мягкой инструментальной стали таких инструментов, как ручные пилы и сверла. Напильники, предназначенные для заточки, обычно имеют одинарную резку и могут иметь безопасные края или грани (без зубцов). Это становится полезным при заточке режущих кромок без изменения формы прилегающих поверхностей (например, лопата). Алмазные и керамические напильники используются для заточки более твердых материалов, включая твердый сплав
5. Процесс заточки
Я считаю, что процесс заточки должен быть быстрым и в нормальных условиях быть достижимым менее чем за 2 минуты, но для этого необходимо выполнить некоторую подготовку путем Шлифование угла скоса и Хонингование тыльной стороны долот и рубанков до упора.
Процесс шлифования:
В процессе заточки мы обычно используем процесс шлифования, чтобы установить желаемый угол инструмента или первичный скос. Используйте любой предпочитаемый вами тип крупного камня или шлифовальный станок, но помните, что будьте очень осторожны, чтобы не перегреться и не обжечь (или не посинеть) край. Во время шлифования нельзя допускать перегрева инструмента. Если край становится слишком горячим и обесцвечивается, весь этот металл необходимо отшлифовать.
При использовании сухой шлифовальной машины убедитесь, что шлифовальный камень одет и содержится в чистоте, слегка прикоснитесь к нему и закаливайте инструмент в воде после каждых нескольких движений по шлифовальному камню.Может быть полезно подержать палец на задней части инструмента рядом с шлифовальным кругом, чтобы проверить выделяемое тепло и определить, как часто требуется закалка.
Если кромка обгорела, инструмент упал или порезался, форму кромки необходимо отшлифовать. Я обнаружил, что самый простой способ отшлифовать правильную форму — сначала отшлифовать режущую кромку перпендикулярно ее задней части до желаемого угла или формы, а затем отшлифовать фаску до тех пор, пока она не встретится с этой кромкой.
После того, как инструмент заточен, очень важно, чтобы на обратной стороне инструмента был заметен заусенец.
После процесса шлифования, который придает инструменту правильную форму и первичный угол скоса, для получения действительно острого инструмента возникает необходимость заточить режущую кромку.
Хонингование — это процесс использования все более мелкого абразива, чтобы сделать режущую кромку как можно более гладкой. В этом процессе абразивные материалы прорезают небольшие канавки как на передней, так и на задней поверхности. На режущей кромке, где встречаются эти две грани, по мере того, как зерно становится мельче, кромка становится более гладкой. На микроскопическом уровне, чем ближе эта кромка к единой прямой, тем острее будет кромка и тем лучше будет додубливание кромки.
Хотя это и не обязательно, микрокосок может быть полезным.
Микро-фаска или вторичная фаска — это крошечная фаска на острие инструмента, которая усиливает режущую кромку, делая ее более прочной. Поскольку микрокосмическая кромка настолько мала, усилие, необходимое для выполнения разреза, лишь незначительно увеличивается. Вероятно, самым большим преимуществом создания микрокоса является то, что нам не нужно затачивать всю поверхность скоса. Это уменьшает количество металла, которое необходимо удалить, и может ускорить процесс заточки.
Рекомендуемый угол наклона инструмента и микрокос (долота и рубанки) для деревянных работ общего назначения
Рекомендуемый кухонный нож с микрокосом
Большинство зубил и плоскостей имеют фаску и плоскость назад, что делает их одними из самых простых инструментов для заточки.
Инструмент, особенно долото, должен иметь идеально ровную спинку. После того, как обратная сторона будет должным образом сплющена, заточена и отполирована, отпадает необходимость в ее повторном шлифовании на весь срок службы инструмента, за исключением удаления заусенцев, слегка потерев ее о мелкий камень.
Термины, связанные с заточкой стамески и других связанных инструментов с одной скосом, включая плоские инструменты
Процесс хонингования:
Степень резкости, которую вы можете достичь, напрямую зависит от того, насколько плавно скашиваются обе кромки. а тыльную сторону (или в ножах, обе фаски) можно полировать.
Чтобы сплющить заднюю часть верстачного долота или рубанка, начните с довольно крупного точильного камня (P320), убедившись, что камень полностью плоский.При необходимости обработайте камень. Если вы используете водяной камень, это, вероятно, каждые пару минут. Если вы используете наждачную бумагу, убедитесь, что она хорошо приклеена к плоской поверхности, иначе вы будете закатывать края.
Никогда не используйте ленточно-шлифовальные станки на тыльной стороне долота или рубанка — кромки скатываются. Сторона алмазного круга Tormek — очень эффективный инструмент для выравнивания задней поверхности, особенно при работе с крупным зерном, поскольку она остается плоской и может немного ускорить процесс выравнивания.
Прижмите инструмент к камню, покрывая как можно больше камня, и потрите взад и вперед.Продолжайте следить за рисунком царапин, и по мере того, как поверхность, особенно возле режущей кромки, станет однородного тусклого цвета, переходите к более мелкой зернистости. Повторяйте этот процесс до получения однородного зеркального блеска на очень мелком камне (P1200 +). Опять же, убедитесь, что каждый камень ровный и полностью плоский.
В зависимости от исходной плоскостности тыльной стороны инструмента этот процесс может занять некоторое время, даже с новыми высококачественными долотами или рубанками, но это нужно делать только один раз.
Японские инструменты обычно полые. Это позволяет быстро разгладить спинку, ближайшую к режущей кромке.
Одна из самых распространенных ошибок — начать с слишком мелкого абразива. Большую часть работы по выравниванию следует выполнять с помощью крупного камня. Каждый последующий уровень зернистости удаляет более глубокие царапины от предыдущего абразива.
Чтобы сформировать микрокосмический скос, поместите основной скос на тыльную сторону мелкого камня (скажем, зернистостью 2000), чтобы режущая кромка и пятка находились в полном контакте и не качались.Поднимите инструмент (примерно на 2-5 ° для долота или рубанка), зафиксируйте рычаги и отведите инструмент назад. Повторите это для нескольких штрихов, пока микрокосник не станет ровного цвета без зазоров. Если на этом этапе видны какие-либо зазубрины, отшлифуйте заново, затем заточите заново. Повторите этот процесс с более мелкими камнями, скажем, зернистостью 5000 и зернистостью 12000, чтобы отполировать фаску до зеркального блеска. Если вы используете водяные камни, убедитесь, что они регулярно притираются, чтобы они оставались ровными.
В качестве альтернативы можно установить и использовать хонинговальную направляющую. Это может быть полезно для предотвращения раскачивания микрокауса и образования выпуклой формы.
По окончании хонингования заусенец, который образуется и скручивается к задней части лезвия, должен отпасть, если использовался очень мелкий камень.
В завершение процесса хонингования выполните протяжку, чтобы получить невероятно острую кромку. Помните, рисуйте только штрихи и поправляйте только скос, а не заднюю часть.
Проверьте резкость, отрезав бумагу или отрезав тонкие кусочки от волокон мягкой древесины (чем мягче древесина, тем острее должен быть инструмент). Любые следы заусенцев или мелкие царапины на лезвии оставят линии на поверхности среза.
Наилучший способ ухода за кромкой — это чаще полировать или стачивать ее немного, чем сильно и реже затачивать.
Уголки с квадратным шлифованным зубилом
Углы заточки квадратной шлифовальной цепи
Выше представлены четыре угла
диапазоны, которые следует учитывать при заточке цепной пилы с квадратным шлифованным зубилом.
Небольшие изменения этих углов влияют на работу вашей цепи. Там есть
никакой «секретной» комбинации, которая лучше всего работает для каждого профессионала в любом
ситуация.Комбинация, которая лучше всего подходит для вас, зависит от типа
древесины, которую вы режете, ее состояние, а также мощность и скорость
твоя пила.
Внутренняя верхняя пластина
Когда условия резания чистая и мягкая древесина, этот угол может составлять около 40 °. когда лес твердая или замороженная, обычно имеет смысл сделать этот угол более тупым. А более тупой угол снижает эффективность резки, но помогает поддерживать кромку и рабочий уголок для увеличения времени работы между заточками.
Наружная боковая пластина
Этот угол должен быть чуть менее 90 °, но не менее 85 °.После этого предложения будет
небольшой задний наклон в боковой пластине, который показывают наши тесты, помогает цепи
подача. Этот небольшой задний наклон помогает гарантировать, что рабочий угол будет
первая часть режущей кромки соприкасается с деревом. Любой угол до 85 °
градусов обычно слишком большой задний наклон. Это может заставить цепочку цепляться
и еще труднее держать в поле зрения. Некоторые люди также притачивают клювом
эта область зуба. Обычно мы рекомендуем избегать клювов. Увидеть
раздел о клювах для получения дополнительной информации.
Наружная верхняя пластина
Этот угол должен быть примерно 20 °.Некоторые операторы утверждают, что этот угол влияет на «пропил» резать. Говорят, больший угол вытягивает зубы, поэтому они увеличиваются. этот угол по мере того, как зуб изнашивается. Говорят, это помогает восполнить часть «набора», которая теряется при шлифовке зуба. Пока это хорошая теория, наши попытки измерить ее никогда не показали этого быть правдой. Наш совет — шлифуйте около 20 ° и придерживайтесь этого.
Внутренняя боковая пластина
Этот угол должен быть около
45 °. Его можно уменьшить в чистой древесине для большей эффективности резки и
уменьшен, чтобы сохранить остроту при работе в тяжелых или замороженных
древесина.На многих шлифовальных машинах этот угол либо не регулируется, либо
сложно отрегулировать. Даже когда он регулируется, часто бывает сложно
шлифовать острые углы без притирки боковой планки и забивать
ссылка под зуб. Шлифовка этих деталей часто ослабляет их и
цепи могут порваться из-за этого.
Наш совет
Мы находим, что большинство профессиональных пользователей гриндят под углами, приближающимися к указанным в строке с надписью «Более быстрая резка» на диаграмме выше. Причина, по которой они это делают, заключается в том, что большинство профессионалов ищут быстрорежущие цепи и готовы пожертвовать некоторым пребыванием острая способность для эффективности резки.
Есть вопросы про заточку пильной цепи с квадратным зубилом? Позвоните или зайдите.
Сопрягающие долота Narex должны быть в вашем ящике для инструментов
Зубила для обрезки стружки, Кларк Гейбл в мире зубил.
Зубила для чистки — это Кларк Гейбл в мире зубил. Высокий и стройный, грациозный, но мужественный, не идеальный для каждой роли, но когда появляется подходящая роль, они срывают вам носки. Narex производит отличный набор этих не очень распространенных инструментов, и когда дело доходит до точной настройки шипа, достижения плотно закрывающихся дадо или очистки торцевых волокон, эти зубила для обрезки стружки достойны Оскара.
Набор зубил Narex 4-Pc Paring Chisel включает долота размером 1/4 дюйма, 1/2 дюйма, 3/4 дюйма и 1 дюйм, что делает его идеальным набором практически для любой работы.
Есть несколько деталей, которые делают резец великолепным, и Narex прибил их все. Долото для обрезки обрезков должно быть длинным, чтобы можно было дотянуться до глубоких мест, дать вам больший контроль и усилить рычаг. Долота Narex Paring имеют размеры 9-1 / 2 дюйма от режущей кромки до рукоятки и имеют общую длину от 14-1 / 2 до 15 дюймов, в зависимости от ширины. Долота 1/4 и 1/2 дюйма имеют ручку из граба меньшего размера. чем версии 3/4 «и 1», что делает их в целом немного короче.Эта маленькая деталь помогает поддерживать прекрасный баланс во всем наборе, и этот точный баланс является настоящим усилителем уверенности, когда дело доходит до точных разрезов. Стандартное долото для скамейки будет иметь гораздо меньшую общую длину, чем отрезное долото. Большая общая длина обрезного долота позволяет пользователю гораздо легче почувствовать угол атаки долота через разрез, а поскольку ручка находится дальше от режущей кромки, ручка должна перемещаться на большее расстояние, чтобы изменить угол резания до той же степени. .
Разглаживание тыльной стороны и заточка фаски 20 ° были быстрыми и легкими, даже на 1-дюймовом долоте.
И да, размеры этих красавиц соответствуют истинным имперским единицам!
Эти красавицы имеют размер с шагом 1/4 дюйма — 1/4 дюйма, 1/2 дюйма, 3/4 дюйма и 1 дюйм
Хром-марганцевая сталь Narex закалена до Rc 59, ее легко затачивать, но при этом она очень хорошо держит лезвие. Зубило для обрезки стружки должно иметь низкий угол скоса, чтобы уменьшить усилие, необходимое для выполнения чистого реза.Narex не упустил из виду эту деталь, и эти прекрасные инструменты сразу же поставляются со скосом 20 °. Мне удалось сплющить заднюю часть 1-дюймового долота и сделать его острым и готовым к работе в кратчайшие сроки. Многие виды стали могут с трудом удерживать кромку с таким низким углом скоса, потому что на режущей кромке меньше материала позади него и будет иметь тенденцию к скалыванию или быстро затупиться. Я обнаружил, что долота Narex Paring Chisels очень хорошо обрабатывают торцевые волокна клена и тополя и не имеют проблем с удержанием кромки. зерно, где будут выполняться некоторые из ваших самых важных работ по очистке.
Удаление мелкой стружки на концах или точная настройка шипа не проблема для долот Narex Paring благодаря их скосу 20 ° и прекрасному общему балансу.
Нет лучшего инструмента для точной подгонки и отделки множества различных соединений, чем хороший набор чистовых долот. Если вы боретесь с тонкой настройкой столярных изделий, на самом деле вас могут сдерживать ваши инструменты, а не ваш уровень навыков. Качественный набор обрезного долота будет иметь значение днем и ночью в том, насколько быстро и точно будет выполнена задача.Я настоятельно рекомендую попробовать набор этих зубил Narex Paring, потому что они обязательно произведут впечатление.
Связанные .