Сухая смесь полистиролбетона Пластблок Унбетформ легкая 19 кг, цена
Сухая смесь полистиролбетона Пластблок Унбетформ легкая 19 кг Пластблок Унбетформ — это сухая полистиролбетонная смесь, используемая в строительстве. Область применения ее очень обширна. Это и выполнение долговечной и бесшумной стяжки пола с утеплением, и устройство отмостки дома, и утепление межэтажных перекрытий и кровли (если на чердаке предусмотрена пешеходная нагрузка). Однако стоит отметить, что данная смесь не является финишным покрытием. Преимущества строительной смеси Пла…
Читать далее- Бренд
- Пластблок
- Жизнеспособность раствора
?
- 180 мин.
- Морозостойкость
?
Морозостойкость — способность материала в насыщенном водой состоянии выдерживать многократное попеременное замораживание и оттаивание без видимых признаков разрушения и без значительного понижения прочности. Основная причина разрушения материала под действием низких температур — расширение воды, заполняющей поры материала, при замерзании.
- 150 циклов
- Основа
- Полистиролбетон
- Помещение
- Для мансарды, Для чердака
- Тип применения
?
По типу применения можно выделить материалы для внутреннего (внутри помещения) и наружного (снаружи помещения) использования.
- Для внутреннего применения
Армированная полистиролбетонная смесь, способ приготовления смеси, способ изготовления теплоизоляционных изделий, панель и блок (варианты)
Изобретения относятся к производству строительных материалов и изделий. В состав для получения армированной полистиролбетонной смеси входит, кГ/м3: портландцемент — 160-170, вспененный гранулированный полистирол — 15-17, базальтовое волокно — 0,50-0,70, смола древесная омыленная — 0,35-0,50, пластифицирующая добавка — С-3 — 1,50-2,50, гидрофобизирующая добавка — 0,4-0,5, полиакриламид — 0,40-0,60, лигнопан Б-2 — 0,35-0,50, вода — 50-55. Способ приготовления армированной полистиролбетонной смеси включает смешивание компонентов состава для ее получения. При этом предварительно перемешивают пенополистирол, базальтовое волокно и добавки, введенные совместно с частью воды затворения. Затем при перемешивании вводят портландцемент, продолжают перемешивать в течение 5-15 сек, после чего добавляют воду и перемешивают 25-40 сек. Изготовление изделий из полистиролбетонной смеси осуществляют объемным вибропрессованием при величине уплотнения 8-15 кГ/см 2. Технический результат заключается в упрощении способа приготовления смеси, высокой прочности изделий, улучшении теплоизоляционных свойств, высокой морозостойкости низкой паропроницаемости и низком водопоглощении. 6 н. и 3 з.п. ф-лы, 3 ил.
Изобретения относятся к производству строительных материалов и изделий, в частности, к теплоизоляционно-конструкционным материалам и изделиям на основе цементного вяжущего, вспененного полистрольного заполнителя и минеральных волокон.
Известны состав сырьевой смеси, способ ее приготовления и способ изготовления армированных полистиролбетонных изделий (патент РФ 2223931, кл.
Армирующий материал в известном способе /1/ не перемешивают с другими компонентами сырьевой смеси.
Известна панель из полистиролбетона, выполненная в виде прямоугольной монолитной плиты с пазами и гребнями — выступами по торцам (свидетельство на полезную модель РФ 17329, кл. Е04С 2/00, 27.03.2001 /2/).
Известен строительный блок, выполненный из полистиролбетона в виде замкнутой оболочки с продольными и поперечными перемычками, которые образуют сквозные каналы; по крайней мере, на одной боковой стороне блока расположены дистанцирующие выступы, а на верхних гранях перемычек выполнен продольный паз (свидетельство на полезную модель РФ 22490, кл. Е04С 1/00, 10.
Физико-механические свойства известных изделий определяются, наряду с другими характеристиками, свойствами полистиролбетонной смеси. Такие характеристики, как, например, прочность при сжатии и изгибе для таких изделий ниже, чем могут быть обеспечены при наличии армирующих элементов.
Наиболее близким аналогом является состав армированной полистиролбетонной смеси, способ ее приготовления и способ изготовления изделий, описанные в патенте РФ 2150446, кл. С04В 38/08, 10.06.2000 /4/.
Известный состав для приготовления сырьевой смеси включает, мас.%: минеральное вяжущее (цемент) 68-90, полистирольный заполнитель (смесь частиц из вспененных полистирольных гранул фракции 0,04-1,25 мм и частицы рваного пенополистирола) 0,7-2,3, щелочестойкое минеральное волокно (стекловолокно или минеральная вата) 1,4-5,2, воздухововлекающая добавка — (СДО) или смола нейтрализованная воздухововлекающая 0,3-0,7, пластифицирующая добавка С-3 0,25-0,55, вода остальное. При приготовлении смеси полистирольный заполнитель смачивают в смесителе частью воды затворения, затем подают цемент, волокнистый материал, оставшуюся часть воды затворения, пластифицирующую и воздухововлекающую добавки и перемешивают до получения однородной смеси.
Получаемые изделия характеризуются плотностью 850-1120 кГ/м3, прочностью при сжатии 19,5-27,2 МПа, прочностью при изгибе 6,4-9,3 МПа, коэффициентом теплопроводности 0,226-0,273 Вт/м·К, водопоглощением 7,7-10,2 мас.%.
Задачей данного изобретения является создание состава для получения армированной полистиролбетонной смеси достаточно простым методом ее приготовления, а также способа изготовления изделий из этой смеси, характеризующихся при низкой плотности достаточно высокой прочностью при сжатии и изгибе, хорошими теплоизоляционными свойствами, высокой морозостойкостью, паро проницаемостью и низким водопоглощением.
Сформулированная задача решается за счет того, что состав для получения армированной полистиролбетонной смеси, включающий портландцемент, полистирольный заполнитель, щелочестойкое минеральное волокно, воздухововолекающую добавку — смолу древесную омыленную, пластифицирующую добавку — С-3 и воду, дополнительно содержит гидрофобизирующую добавку — ГКЖ-94, структурообразующую добавку — полиакриламид, и регулятор твердения — Лигнопан Б-2, а в качестве полистирольного заполнителя — предварительно вспененный гранулированный полистирол с размером гранул 2,8-3,0 мм и в качестве щелочестойкого минерального волокна — базальтовое волокно с длиной волокон 15-20 мм и диаметром 12-15 мкм, при следующем соотношении компонентов, кг/м 3:
портландцемент | 160-170 |
указанный полистирол | 15-17 |
указанное базальтовое волокно | 0,50-0,70 |
смола древесная смыленная (50%-ный раствор) | 0,35-0,50 |
С-3 (на сухое) | 1,50-2,50 |
ГКЖ-94 (50%-ной концентрации) | 0,40-0,50 |
полиакриламид (10%-ный раствор) | 0,40-0,60 |
Лигнопан Б-2 | 0,35-0,50 |
Вода | 50-55 |
Сформулированная задача решается также за счет того, что в способе приготовления армированной полистролбетонной смеси, включающем смешивание компонентов состава для ее получения, при смешивании компонентов вышеприведенного состава предварительно перемешивают пенополистирол, базальтовое волокно и добавки, введенные совместно с частью воды затворения, затем при перемешивании вводят портландцемент, продолжают перемешивать в течение 5-15 сек, после чего добавляют воду и перемешивают 25-40 сек.
Сформулированная задача решается также за счет того, что в способе изготовления изделий из полистиролбетонной смеси, включающем приготовление смеси путем смешивания компонентов состава для ее получения, формование и отверждение, формование приготовленной вышеприведенным способом армированной полистролбетонной смеси из компонентов указанного ранее состава осуществляют объемным вибропрессованием при величине уплотнения 8-15 кг/см2.
Формование может быть осуществлено с использованием пустотообразователей.
Панель армированную полистролбетонную изготавливают указанным ранее способом в виде прямоугольной монолитной плиты с гребнем или выступом, по крайней мере, на одном торце и с, по крайней мере, одним пазом — на другом.
Блок армированный полистиролбетонный изготавливают указанным ранее способом монолитным с, по крайней мере, одним пазом на одной его боковой стороне и с, по крайней мере, одним выступом — на другой.
Блок армированный полистиролбетонный изготавливают указанным ранее способом в виде замкнутой оболочки, содержащей продольные и/или поперечные перемычки, которые образуют полости или сквозные каналы. Такой блок может быть выполнен с пазом или пазами, по крайней мере, на одной его боковой стороне, и с соответствующим выступом или выступами — на другой. На верхних гранях перемычек и боковых сторон может быть выполнен продольный паз.
Именно указанный качественный и количественный состав обеспечивает получение достаточно простым способом армированной полистиролбетонной смеси, характеризующейся равномерным распределением по объему гранул вспененного полистирола и базальтовых волокон, не расслаивающейся в течение времени (не менее часа), достаточного для ее транспортировки на производственной территории или для доставки на стройплощадки.
При содержании компонентов в составе выше или ниже указанных в формуле значений изменяются нежелательным образом такие характеристики смеси, как устойчивость к расслаиванию, однородность смеси, формуемость, а также характеристики изготавливаемых изделий: плотность, прочность, теплопроводность, морозостойкость, водопоглощение.
Именно указанные в формуле сочетания размеров гранул пенополистирола (2,8-3,0 мм) и базальтовых волокон (длина 15-20 мм и диаметр 12-15 мкм) необходимы для равномерного их распределения в смеси и повышения устойчивости смеси к расслаиванию. При длине волокон свыше 20 мм и их диаметре меньше 12 мкм отмечено скручивание волокон или их измельчение, что приводит к ухудшению перемешиваемости смеси, неравномерному распределению волокон, ухудшению физико-механических характеристик получаемых из такой смеси изделий. При увеличении размера гранул пенополистирола повышается склонность смеси к расслаиванию. При уменьшении размеров гранул пенополистирола и длины волокон и увеличении их диаметра увеличивается плотность смеси и плотность формуемых из нее изделий.
В способе приготовления смеси порядок подачи компонентов на смешивание и продолжительность отдельных этапов перемешивания подобраны экспериментально. При больших продолжительностях перемешивания наблюдается скручивание базальтовых волокон, их дробление, а также дробление пенополистирольных гранул. При меньших продолжительностях не достигается равномерного распределения гранул пенополистирола и базальтовых волокон в смеси.
Используемые материалы:
— портландцемент по ГОСТ 10178-85;
— вспененный гранулированный полистирол с размером гранул 2,8-3,0 мм, полученный одно- или многоступенчатым вспениванием суспензионного вспенивающегося полистирола по ОСТ 301-05-202-92Е или марок R, SEPS, ZKF;
— пластификатор С-3 по ТУ 6-36-0204229-625;
— смола древесная омыленная — СДО по ТУ 13-02-81078-02-93;
— ГКЖ-94 — гидрофобизирующая жидкость [-C2H5Si(H)O-]n, где n=9÷14;
— Лигнопан Б-2 — модифицированные электролитами лигносульфонаты с молекулярной массой 10-50;
— Полиакриламид, например, по ТУ 6-02-00209912-41-94 или ТУ 6-10-1049-92.
Реализация заявленных изобретений подтверждается примерами.
На фиг.1 представлено изделие из описанного выше конструкционно-теплоизоляционного материала, выполненное в виде имеющего несколько расположенных рядами пустот блока, используемого, например, для стен.
На фиг.2 представлен блок (узкий) из того же материала, используемый, например, в качестве кладочных изделий для перегородок или в качестве утеплителя при укладке его параллельно несущей или ограждающей конструкции здания или сооружения.
На фиг.3 представлено изделие, выполненное из конструкционно-теплоизоляционного материала, в виде имеющего расположенные рядом пустоты блока, используемого, например, для стен.
Пример 1. В герметичный баросмеситель загружают 16 кг вспененного гранулированного полистирола с размером гранул 2,8-3,0 мм, 0,6 кг базальтового волокна с длиной волокна 18 мм и диаметром 13 мкм, 0,35 кг смолы древесной омыленной, разбавленной частью воды затворения, 2 кг С-3, 0,5 кг полиакриламида, разбавленного частью воды затворения до 10%-ной концентрации, 0,4 кг ГКЖ-94 в виде 50%-ной эмульсии, 0,4 кг Лигнопана Б-2, перемешивают до однородной массы, затем при перемешивании вводят 160 кг портландцемента М-500, продолжают перемешивать в течение 10 сек, после чего добавляют остаток воды затворения (общее ее содержание 55 кг) и перемешивают 30 сек.
Полученную однородную смесь пневмотранспортом подают к дозаторам линии формования для изготовления монолитных блоков с пазом на одной боковой стороне и выступом — на другой. Размещенную в формах смесь подвергают объемному вибропрессованию при наложении колебаний от ИВ-99Е снизу и уплотнении сверху при давлении 10 кг/см2. После формования блоки на поддонах ставят на сушку.
Полученные блоки характеризуются плотностью 220 кг/м3, прочностью при сжатии 0,95 МПа, прочностью при изгибе 0,4 МПа, коэффициентом теплопроводности 0,078 Вт/м·К, водопоглощением при полном погружении 1,4% по объему, паропроницаемостью 0,85 мг/м·ч·Па, морозостойкостью (по ГОСТ 10060.2-95) F70.
Пример 2. В герметичный баросмеситель загружают 15 кг вспененного гранулированного полистирола с размером гранул 2,8-3,0 мм, 0,7 кг базальтового волокна с длиной волокна 18 мм и диаметром 13 мкм, 0,45 кг смолы древесной омыленной, разбавленной частью воды затворения, 2,5 кг С-3, 0,45 кг полиакриламида, разбавленного частью воды затворения до 10%-ной концентрации, 0,4 кг ГКЖ-94 в виде 50%-ной эмульсии, 0,35 кг Лигнопана Б-2, перемешивают до однородной массы, затем при перемешивании вводят 170 кг портландцемента М-500, продолжают перемешивать в течение 15 сек, после чего добавляют остаток воды затворения (общее ее содержание 53 кг) и перемешивают 40 сек.
Полученную однородную смесь пневмотранспортом подают к дозаторам линии формования для изготовления монолитных панелей с пазом на одной боковой стороне и выступом — на другой. Размещенную в формах смесь подвергают объемному вибропрессованию при наложении колебаний от ИВ-99Е снизу и уплотнении сверху при давлении 12 кг/см2. После формования панели на поддонах ставят на сушку.
Формуют прямоугольную монолитную панель с выступом на одном торце и пазом на другом.
Пример 3. В герметичный баросмеситель загружают 17 кг вспененного гранулированного полистирола с размером гранул 2,8-3,0 мм, 0,5 кг базальтового волокна с длиной волокна 18 мм и диаметром 13 мкм, 0,50 кг смолы древесной омыленной, разбавленной частью воды затворения, 2,3 кг С-3, 0,55 кг полиакриламида, разбавленного частью воды затворения до 10%-ной концентрации, 0,45 кг ГКЖ-94 в виде 50%-ной эмульсии, 0,35 кг Лигнопана Б-2, перемешивают до однородной массы, затем при перемешивании вводят 165 кг портландцемента М-500, продолжают перемешивать в течение 12 сек, после чего добавляют остаток воды затворения (общее ее содержание 50 кг) и перемешивают 35 сек.
В формы для получения блоков размещают 4 пустотообразователя, имеющих в горизонтальном сечении форму близкую прямоугольной, подают приготовленную смесь и формуют объемным вибропрессованием при давлении сверху 15 кг/см2 блок в виде замкнутой оболочки 1, содержащей продольную 2 и поперечную 3 перемычки (фиг.1). Пазы 4 на боковых сторонах и перемычке могут быть образованы размещением, после загрузки смеси в форму, соответствующего протяженного формообразующего элемента.
Получаемые по изобретениям изделия характеризуются следующими показателями:
Плотность, кг/м3 | 175-425 |
прочность при сжатии, МПа | 0,35-1,8 |
прочность при изгибе, МПа | 0,15-0,6 |
коэффициент теплопроводности, Вт/мК | 0,065-0,10 |
водопоглощение при полном погружении, % по объему | 1-2 |
морозостойкость | F50-F100 (ГОСТ 10060.2-95) |
паропроницаемость, мГ/м·ч·Па | 0,85-0,90 |
потеря прочности при 50-кратном | |
замерзании до -50°С, % | 1,5-1,8.![]() |
1. Состав для получения армированной полистиролбетонной смеси, включающий портландцемент, полистирольный заполнитель, щелочестойкое минеральное волокно, воздухововлекающую добавку — смолу древесную омыленную, пластифицирующую добавку — С-3 и воду, отличающийся тем, что он дополнительно содержит гидрофобизирующую добавку — ГКЖ-94, структурообразующую добавку — полиакриламид и регулятор твердения — Лигнопан Б-2, а в качестве полистирольного заполнителя — предварительно вспененный гранулированный полистирол с размером гранул 2,8-3,0 мм и в качестве щелочестойкого минерального волокна — базальтовое волокно с длиной волокон 15-20 мм и диаметром 12-15 мкм, при следующем соотношении компонентов, кг/м3:
портландцемент | 160-170 |
указанный полистирол | 15-17 |
указанное базальтовое волокно | 0,50-0,70 |
смола древесная омыленная (50%-ный раствор) | 0,35-0,50 |
С-3 (на сухое) | 1,50-2,50 |
ГКЖ-94 (50%-ной концентрации) | 0,4-0,5 |
полиакриламид (10%-ный раствор) | 0,40-0,60 |
Лигнопан Б-2 | 0,35-0,50 |
вода | 50-55 |
2. Способ приготовления армированной полистиролбетонной смеси, включающий смешивание компонентов состава для ее получения, отличающийся тем, что при смешивании компонентов состава по п.1 предварительно перемешивают пенополистирол, базальтовое волокно и добавки, введенные совместно с частью воды затворения, затем при перемешивании вводят портландцемент, продолжают перемешивать в течение 5-15 с, после чего добавляют воду и перемешивают 25-40 с.
3. Способ изготовления изделий из полистиролбетонной смеси, включающий приготовление смеси путем смешивания компонентов состава для ее получения, формование и отверждение, отличающийся тем, что формование приготовленной способом по п.2 армированной полистиролбетонной смеси из компонентов состава по п.1 осуществляют объемным вибропрессованием при величине уплотнения 8-15 кг/см2.
4. Способ изготовления изделий по п.3, отличающийся тем, что формование осуществляют с использованием пустотообразователей.
5. Панель армированная полистиролбетонная, изготовленная способом по п. 3, характеризующаяся тем, что она выполнена в виде прямоугольной монолитной плиты с гребнем или выступом, по крайней мере, на одном торце и с, по крайней мере, одним пазом — на другом.
6. Блок армированный полистиролбетонный, изготовленный способом по п.3, характеризующийся тем, что он выполнен монолитным с, по крайней мере, одним пазом на одной его боковой стороне и с, по крайней мере, одним выступом — на другой.
7. Блок армированный полистиролбетонный, изготовленный способом по п.4, характеризующийся тем, что он выполнен в виде замкнутой оболочки, содержащей продольные и/или поперечные перемычки, которые образуют полости или сквозные каналы.
8. Блок по п.7, отличающийся тем, что, по крайней мере, на одной его боковой стороне выполнен паз и/или пазы, а на другой — соответствующие выступ или выступы.
9. Блок по п.8, отличающийся тем, что на верхних гранях перемычек и боковых сторон выполнен продольный паз.
Мы на You TubeУслуги предприятияСамое популярноеНовости
|
youtube.com/embed/uQW8_0csmNQ» frameborder=»0″ allow=»accelerometer; autoplay; encrypted-media; gyroscope; picture-in-picture» allowfullscreen=»»/>
|
Пазогребневые блоки из полистиролбетона | Polimerbeton —
1.

2. Область применения полистиролбетона
3. Преимущества пазогребневых блоков из полистиролбетона
1. Что такое полистиролбетон
В состав полистиролбетона входят: цемент, вспененный полистирол (шарики пенопласта), вода и воздухововлекающие добавки. Все компоненты проходят испытания на безопасность для здоровья человека, что подтверждается соответствующими сертификатами СЭС. К цементу, воде и добавкам вопросов не у кого из потребителей не возникает. Главный миф вызывающий настороженность потребителей – это использование вспененного полистирола в составе бетона. На самом деле бояться этого компонента полистиролбетонной смеси стоит не больше чем всех остальных составляющих.
Для получения гигиенического сертификата на полистиролбетон производитель предоставляет не только образец полистиролбетона в испытательную лабораторию, но и отдельно само сырьё, гранулы полистирола из которого при температурной обработке получаются шарики пенопласта. Там его помещают в камеру с датчиками, определяющими содержание газов в испытуемом веществе. Показания снимают три раза нагревая вещество до максимальной температуры в 60 градусов. Если у образца превышены показатели по стиролу или ещё каким-либо предельно допустимым веществам, то сертификат СЭС производитель не получит.
Для изготовления полистиролбетона нет специальных сортов полистирола. Из этих же гранул производят подложки для продуктов питания, которые мы ежедневно видим в наших магазинах. Емкости для лапши быстрого приготовления в которых она заваривается при помощи кипятка. И наконец всем знакомые потолочная плитка и плинтуса из пенопласта, где пенопласт находится в открытом виде и каждый шарик не замурован в раствор, как в это происходит в полистиролбетоне.
2. Область применения полистиролбетона
В зависимости от изготавливаемой марки данный ячеистый бетон может быть конструкционным, самонесущим или использоваться в качестве монолитного утепления. Из него изготавливают такие штучные изделия как стеновые блоки, межкомнатные перегородки. Блоки производят двумя способами распиловкой предварительно изготовленного массива или заливкой полистиролбетонной смеси в формы.
Благодаря своим повышенным показателям прочности на растяжение при изгибе, 60% от прочности на сжатие, из армированного полистиролбетона в специальных формах производят «тёплые» перемычки и плиты перекрытия. Такие перемычки не нуждаются в дополнительном утеплении и могут быть использованы при строительстве зданий из любых ячеистых бетонов.
Небольшой вес перемычек позволяет монтировать их без помощи подъёмных механизмов. К примеру вес перемычки из полистиролбетона размерами 200х300х1500 мм составляет около 60 кг, что вполне по силам двум каменщикам.
Низкие марки полистиролбетона сравнимы по теплотехническим характеристикам с минераловатной плитой. Так марка бетона Д200 имеет такие – же показатели теплопроводности, как и минераловатная плита ППЖ-200 — 0,07 Вт/м°С. В отличии от применения минплиты утепление монолитным полистиролбетоном позволяет получить следующие преимущества:
- плотное прилегание утеплителя к основанию без образования пустот, как это не редко происходит при использовании минплиты
- нет потери тепла по стыковочным швам между рулонами утеплителя.
- после того как полистиролбетон «схватился» на него можно стелить ламинат или клеить плитку в отличии от утепления минплитой, где на поверхности утеплителя необходимо вначале устраивать цементно-песчаную стяжку.
- при попадании влаги он не накапливает влагу как минераловатная плита и легко её «отдаёт»
При монолитном строительстве полистиролбетон укладывают в несъёмную опалубку или он служит монолитным утеплителем в колодезной кладке.
3. Преимущества пазогребневых блоков из полистиролбетона
Блоки данного вида отливаются в специальных металлических формах, изготовленных на современном импортном оборудовании и имеют точные геометрические размеры с разницей по сторонам + 1 мм. Как правило формы делятся на два вида, для рядовых и угловых блоков.
Основным преимуществом таких пазогребневых блоков является возможность возводить однослойную конструкцию наружных стен здания без дополнительного утепления снаружи. Ведь не малых денег стоит сам утеплитель, а ещё нужно заплатить за клей, крепёж и сами работы по монтажу утепления. Полистиролбетон теплее на 20 – 25 %, чем аналогичные марки пенобетона или газобетона. Пазогребневая конструкция блоков позволяет избежать потери тепла по вертикальным и горизонтальным швам кладки.
Последние годы набирает популярность строительство домов из полистиролбетонных панелей. Заказчик выбирает проект и ему привозят готовый «домокомплект» из полистиролбетонных панелей различных размеров. Монтаж такого дома осуществляется при помощи крана и занимает не более недели. Это позволяет получать значительную экономию не только времени, но и средств на возведение «коробки».
Важным моментом в строительстве таких домов является конструкция самой панели. Чтобы здание не получилась не только крупнопанельным, но и «крупнощелевым» для изготовления применяются формы для панелей с пазогребневым профилем.
Какую бы конструкцию дома вы для себя не выбрали из полистиролбетонных пазогребневых блоков или панелей она будет менее затратной чем многослойная из других материалов с дополнительным утеплением. Строительство займёт значительно меньше времени, а качество будет только радовать.
Живите в комфорте.
Полистиролбетон производить получится?
Производство полистиролбетона и полистиролбетонных блоков
Нас часто спрашивают — как производить монолитный полистиролбетон или полистиролбетонные блоки? Какие при этом существуют особенности производства полистиролбетона и на какие особенности технологии стоит обратить внимание?
Себестоимость полистиролбетона
Во первых хотелось бы обратить внимание на экономическую составляющую при производстве полистиролбетона.
Себестоимость любого строительного материала помимо стоимости работ складывается так же из стоимости исходных материалов затрачиваемых на его производство.
Так же и в случае с полистиролбетоном часть его себестоимости состоит из стоимости закупаемого полистирола или пенополистирола. Чем ниже его стоимость тем ниже будет стоимость получаемого на выходе полистиролбетона.
Наиболее выгодным производство полистиролбетона становится тогда, когда у вас есть источник дешевого сырья в виде полистирола или пенополистирола. Одним из путей для достижения этого является переработка отходов пенопласта или пенополистирола. Для этих целей можно собрать нехитрую дробилку которая поможет вам получать пенополистирольную крошку. Иногда для этого используют даже отходы в виде строительной пены, или отходы от производства наполнителя сэндвич-панелей.
Если же у вас нет источника подобного рода отходов то полистирольные гранулы нужно будет закупать у производителя или продавца в вашем регионе.
Технология производства полистиролбетона
Для производства полистиролбетона применяются следующие компоненты:
- цемент
- песок
- пенообразователь
- пластификатор
- полистирольные гранулы или пенополистирольная крошка
- фибра (опционально)
Сам процесс производства полистиролбетона не многим отличается от производства обычного пенобетона. Есть конечно свои тонкости. Но в целом процессы схожи.
Состав смеси отличается уменьшенным количеством пенообразователя и добавлением полистирольных шариков или полистирольной крошки.
На видео выше показан процесс производства монолитного полистиролбетона на установке для пенобетона БАС350 присланный нашими клиентами. Он несколько отличается от рекомендуемой нами методики но в целом даёт понятие того как делать полистиролбетон на установке для пенобетона.
При заказе оборудования мы даём базовую рецептуру производства полистиролбетона и методологию процесса. А так же осуществляем технологическую поддержку в дальнейшем.
И на последок — если вы планируете заниматься производством полистиролбетона на нашем оборудовании, то оформляя заказ сообщите нам об этом. По вашему желанию мы можем изготовить увеличенный диаметр выходного коллектора для улучшенной выгрузки смеси из установки.
Легкий заполнитель бетона | Энстайро Шред
Enstyro Shred
Бетонный заполнитель
Пенополистиролсуществует уже более пятидесяти лет, почему сейчас его не используют в бетоне?
EPS (пенополистирол) был использован в бетоне. Новые шарики из пенополистирола в настоящее время продаются как заполнитель для бетона, и несколько университетов изучали измельченный вторичный пенопласт в качестве заполнителя для бетона. Оба метода малоэффективны по разным причинам.
Новые валики круглые и гладкие, что является худшей формой и поверхностью для заполнителя бетона.Когда в смесь добавляется слишком много воды, шарики в форме пузырей всплывают вверх и портят работу. Подрядчики, которым приходится срывать новую работу из-за того, что это происходит, отказываются когда-либо снова пробовать EPS. Новые бусинки и молва сделали EPS плохой репутацией в бетоне.
Измельченный EPS не прижился по совершенно другой причине. Он не всплывает наверх, потому что имеет большую шероховатость поверхности. Однако он содержит очень мелкие частицы, которые, будучи разорванной пеной, имеют огромную площадь поверхности.Эта огромная площадь поверхности из мельчайших частиц требует слишком много воды, чтобы бетон хорошо растекался и быстро застывал. Слишком большое количество воды снижает прочность бетона на сжатие.
Оборудование Enstyro решает проблемы путем измельчения до точного диапазона размеров и последующего удаления мельчайших частиц за один простой шаг. Этот метод обеспечивает шероховатость поверхности и изменение формы, чтобы она не всплыла даже при сильной вибрации. Удаление мельчайших частиц упрощает процесс смешивания.Влажный цемент, который легко течет и имеет высокую прочность, теперь используется вместе с переработанным пенополистиролом.
Enstyro Shred действительно лучший из всех миров, когда дело касается заполнителя EPS. Если вы пробовали EPS в прошлом, дайте ему еще один шанс. Enstyro потратила много времени на то, чтобы сделать это правильно, и теперь каждый может пожинать плоды изоляции трещиностойкого бетона.
Синтетические легкие добавки Advance Concrete | Журнал Concrete Construction
Благодаря высокой прочности на сжатие и способности принимать бесчисленные формы бетон является одним из самых полезных строительных продуктов человечества. Однако производители бетона знают, что большой вес материала создает множество проблем, таких как высокие затраты на транспортировку и установку, а также усталость рабочих.
Чтобы преодолеть эти и другие проблемы, люди на протяжении всей истории стремились уменьшить вес бетона без отрицательного воздействия на его характеристики. Одним из первых примеров является добавление древними римлянами пемзы и наполненных воздухом глиняных горшков на бетонную крышу Пантеона с куполом. В последние годы присадки стали намного более сложными, особенно с появлением сверхлегких синтетических заполнителей.
Среди них — шарики из легкого полистирола и пенополистирола (EPS). Эти маленькие шарики из пенопласта иногда ошибочно называют «пенополистиролом», но это другой материал.
CityMix Легкие добавки на основе полистирола уменьшают вес бетона, сохраняя при этом полезные механические свойства.Преимущества легких добавок к полистиролу
Сверхлегкие добавки на основе полистирола служат частичным объемным заменителем тяжелых песков и гравия в бетоне. Такие добавки снижают удельный вес бетона, что, в свою очередь, снижает вес конструкций, снижает затраты на транспортировку и снижает утомляемость рабочих, что приводит к снижению затрат и потенциально более высокой прибыли производителей бетона. Возможное снижение веса зависит от производимого бетонного продукта — порядка 5-15% для структурных бетонных строительных панелей, но потенциально до 80% для неструктурных бетонных объектов, таких как фанерный камень, декоративные молдинги. и ландшафтный блок.
Помимо снижения веса бетонных изделий, добавки на основе полистирола также могут улучшить характеристики бетона в нескольких ключевых областях. Основными среди этих свойств являются повышенная гибкость и упругость, улучшенная трещиностойкость и устойчивость к замерзанию / оттаиванию, а также улучшенные огнестойкие и термические характеристики.
В зависимости от добавки, заполнители на основе полистирола могут использоваться в различных конструкционных и неструктурных областях, в том числе:
- Штукатурка
- Шпонированный камень
- Цементная плита
- Архитектурный и промышленный сборный железобетон
- Прокачиваемый легкий пол
- Сборный
- Ландшафтный блок
- Добавки для почвы
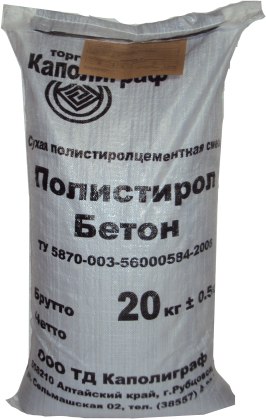
Проблемы, связанные с добавками к полистиролу
Хотя сверхлегкие добавки на основе полистирола обладают множеством преимуществ, до недавнего времени они имели ряд недостатков, таких как:
- Сверхлегкие шарики могут разлетаться по воздуху на ветру или при общем перемешивании, что может затруднить обращение с ними и их смешивание в полевых условиях или на фабрике.
- Из-за присущего ему высокого статического заряда шарики цепляются за кожу, одежду и другие поверхности, что может затруднить работу с добавкой
- Слипание шариков в бетонной смеси, или тенденция всплывать на поверхность, что препятствует равномерному распределению добавки по бетону.
- Использование первичного пенопласта в некоторых добавках может как увеличить стоимость добавки, так и нанести вред окружающей среде.
Появляется новая технология
Строительство промышленные ученые недавно разработали новый класс добавок на основе полистирола, который обеспечивает все легкие легкие и механические преимущества обсуждались выше, при устранении недостатков. В этой уникальной запатентованной добавке, которая в настоящее время производится Insulfoam для CityMix, используются переработанные частицы EPS, заключенные во внешнюю оболочку, улучшающую рабочие характеристики. В этом экономичном и сверхлегком продукте статическое электричество устранено, и добавлен вес частиц, достаточный для того, чтобы материал можно было легко обрабатывать и смешивать.
R Эциклированный и чистый EPS
Частицы EPS, используемые в этой новой легкой добавке, могут быть либо из первичного материала, либо переработаны из других продуктов EPS (таких как изоляция зданий, геопена, используемая в строительных работах, или упаковка продукции) , что позволяет отводить большие объемы отработанной пены с общественных свалок.
Бетон часто считают первым композитным строительным материалом человечества. Путем проб и ошибок древние цивилизации выяснили, как комбинировать песок, заполнители и цемент для получения исключительно прочного, но при этом адаптируемого строительного материала. Сегодня наука открыла способы дальнейшего улучшения бетона с помощью синтетических легких добавок, которые продолжают улучшаться год за годом.
Легкие стеновые панели из цемента, также известные как бетонные стеновые панели из пенополистирола (EPS), представляют собой экологически чистый строительный материал, используемый для экологически чистых домов.Эта бетонная легкая стеновая панель производится путем смешивания цемента и небольших пенополистирольных шариков в качестве легкого заполнителя вместо щебня, используемого в обычном бетоне.
Легкие стеновые панели из пенополистирола, изготовленные из цемента с теплоизоляцией (вспененные частицы пенополистирола), имеют ряд преимуществ по сравнению с более традиционной смесью для бетонных блоков. Бетон из пенополистирола имеет улучшенные изоляционные свойства, особенно для теплоизоляции, и, поскольку он на 1/6 легче, чем бетонный блок на каменной основе, он может уменьшить занимаемое пространство стены, увеличить коэффициент использования жилого пространства, снизить нагрузку на конструкцию и уменьшить полная стоимость.
Шарики из пенополистирола добавляют изоляционные свойства и облегчают вес бетона, поэтому использование EPS для смешивания цемента для изготовления бетона позволяет получить легкие легкие стеновые панели. Здесь вы узнаете, как сделать легкие цементные стеновые панели из пенополистирола EPS.
Шаг 1
Залейте воду в бетономешалку Hongfa. Количество воды зависит от размера бетоносмесителя, который вы выбираете, доступны смесители объемом 1 м3, 2 м3, 3 м3, 4 м3 или 5 м3.Добавьте любую добавку, которую вы хотите использовать в бетоне, и тщательно смешайте добавки с водой.
Шаг 2
Добавьте портландцемент автоматически с помощью винтового конвейера. Если вы хотите смешать с песком или летучей золой, вы можете добавить песок и летучую золу во время процесса. Тщательно перемешайте с водой, чтобы получилась жидкая консистенция.
Шаг 3
Для изготовления стеновой панели из бетона EPS очень важны шарики из пенополистирола. В этом процессе поместите определенные частицы EPS после точного взвешивания с помощью весов Hongfa EPS рядом с трубами EPS. Перед добавлением дополнительных ведер пенополистирола перемешивайте в течение минуты, чтобы шарики впитали воду.
Шаг 4
Продолжайте добавлять пенополистирол EPS, выдерживая время для перемешивания в бетономешалке после добавления в цементную смесь. Пенополистирол быстро впитает воду из смеси. Если смесь станет слишком густой для включения шариков, при необходимости добавьте воды.
Шаг 5
Когда пенополистирол впитался и равномерно перемешался, он должен прекратить перемешивание бетона. Смесь должна быть легкой, текучей, но не слишком жидкой.
Шаг 6
Заполнение готового бетонного пенополистирола к машинам для производства стеновых панелей Hongfa. Есть три типа станков для производства цементных стеновых панелей Hongfa. Различные типы вагонеток для формования стеновых панелей имеют разные способы наполнения. Этот бетонный EPS будет использоваться в качестве материала для плиты или стены, поэтому после заливки готового бетонного EPS непосредственно в оборудование для стеновых панелей Hongfa его можно разместить и оставить для отверждения.Чтобы узнать больше, пожалуйста, ознакомьтесь с тем, как производить цементные стеновые панели на заводах и оборудовании Hongfa.
Шаг 7
Снимите цементную стеновую панель с машины Hongfa Mold через 4-8 часов в зависимости от технологии отверждения. Этот процесс также называется извлечением стеновых панелей из цементной стали.
Step 8
Затем, через определенные дни, бетонные стеновые панели EPS можно транспортировать на строительные площадки для строительства легких внутренних или внешних стен.
Зеленые бетонные стеновые панели из пенополистирола, производимые эксклюзивным заводом и оборудованием для производства цементных стеновых панелей Hongfa, становятся все более популярными в строительной сфере. Пожалуйста, свяжитесь с [email protected] или Whatsapp 0086 18378813711, чтобы узнать больше о стеновых панелях типа сэндвич EPS easy, а также о заводе и оборудовании для производства цементных стеновых панелей.
(PDF) Прочность модифицированного пенополистиролбетона после динамического циклического нагружения
Удар и вибрация
0203040
Пропорция смеси EPS (%)
Перед испытанием на усталость
Испытание на усталость по Ашеру
Прочность на сжатие )
60
50
40
30
20
10
0
F : Последующая сила циклической нагрузки кН.
030
Соотношение смешивания EPS (%)
Перед испытанием на усталость
Испытание на усталость
Прочность на сжатие (МПа)
60
50
40
30
10
000 0F : Более поздняя сила циклической нагрузки KN time.
тест. Прочность на сжатие пенополистирола с
объемным соотношением частиц на% была увеличена после
приложения циклической динамической нагрузки кН и кН, а
— относительного отношения объема частиц EPS к
при испытании на пониженную долговечность; в то же время степень снижения прочности на сжатие
была обратно пропорциональна доле
по отношению к объему частиц EPS. Кроме того,
больше прикладывала динамическую циклическую нагрузку,
больше разрыв прочности на сжатие между до
и испытанием на долговечность. % упадет, когда динамическая циклическая нагрузка составит
приложенных раз, а уменьшение прочности на сжатие матрицы
было намного больше, чем соотношение объема частиц бетона EPS
, равное% по сравнению с
, применяемым динамически. вибрационная нагрузка раз.
() По результатам испытаний на долговечность
было доказано, что легкий бетон из пенополистирола имеет хорошую прочность
и очень хорошо используется на практике
инженерное дело, которое имеет определенные сейсмические требования
и применяется циклическая нагрузка.
Конфликт интересов
Авторы заявляют об отсутствии конфликта интересов
относительно публикации данной статьи.
Ссылки
[] Y.Сюй, Л. Цзян, Дж. Сюй и Ю. Ли, «Механические свойства
пенополистирольного легкого заполнителя и кирпича
», Строительные и строительные материалы, том no, № pp, стр.
– -, .
[] Б. Чен и Дж. Лю, «Вклад гибридных аберов в свойства
высокопрочного легкого бетона, имеющего хорошую обрабатываемость
», Cement and Concrete Research, vol., no.
, стр. – , .
[] Д. Дж. Кук, Шарики из пенополистирола как легкий заполнитель
для бетона, Школа гражданского строительства, Университет Нью-Йорка
Южный Уэльс, .
[] К.Милд, К.Саб, Р.Лерой, «Particlesizeeecton
EPS легкого бетона на сжатие: экспериментальный
исследование и моделирование», «Механика материалов», том №,
№. , стр. – , .
[] Р. Ле Рой, Э. Парант и К. Буле, «Принимая во внимание размер включений
в легком бетоне, прочность на сжатие
прогноз», Исследование цемента и бетона, т., № ., стр.
– , .
[] C.Багон и С. Фрондисту-Яннас, «Морской бетон
, сделанный из вспененного полистирола», Журнал Concrete
Research, том , №, стр. – , .
[] Р. Шри Равиндрараджах и А. Дж. Так, «Свойства твердого бетона
, содержащего обработанные шарики из пенополистирола»,
Цементные и бетонные композиты, том , № , стр. –,
.
[] Г. К. Хо, «Новые приложения для бетонов с низкой плотностью», т.,
Специальная публикация ACI,.
[] A.Laukaitis, R.
ˇ
Зураускас и Й. Кериене, «Эффект пенополистирола
на свойствах цементного композита», Цемент
и бетонные композиты, том, №, стр. , .
[] Э. Парант и Р. Ле Рой, «Оптимизация по
´
этонов по плотности
´
e
inf
´
erieure
`
Tech. Rep., Laboratoire Central des Ponts et
Chauss
´
ees, Париж, Франция, .
[] Б. Чен и Дж. Лю, «Механические свойства модифицированных полимером бетонов
, содержащих гранулы пенополистирола», Construc-
и строительные материалы, т. , нет. , стр. – , .
[] Д.С. Бабу, К. Ганеш Бабу и Т.Х. Ви, «Свойства
легких бетонов из пенополистирола, содержащих —
золы», Исследование цемента и бетона, т., №. , стр.
-, .
[] K.G.Бабу и Д.С. Бабу, «Поведение легковесовспененного полистиролбетона
, содержащего микрокремнезем», Cement and Con-
crete Research, vol. , нет. , стр. – , .
(PDF) Влияние соотношения цемента и шариков пенополистирола на прочность на сжатие и плотность легкого бетона
INDIAN J. ENG. МАТЕР. SCI., АПРЕЛЬ 2007
162
Изменение прочности бетона при использовании валиков из поликарбоната и пенополистирола
может быть в основном из-за незначительной прочности валиков из
пенополистирола.Кроме того, для бетона с легким заполнителем
более актуально для целей расчета смеси, чтобы
соотносило прочность с содержанием цемента 3.
Связь между соотношением PC / EPS и прочностью на сжатие
была линейной, и коэффициент определения
был 0,998, когда значение контрольного образца, что
состояло из 10% портландцемента, было исключено
(см. Рис. 3).
Плотность бетона можно контролировать с помощью
, изменяя объем PC в смеси.Прочность бетона
EPS увеличивается линейно с увеличением плотности бетона на
или с увеличением объема
PC.
Плотность — один из важных параметров, который
может контролировать многие физические свойства легкого бетона
, и он в основном контролируется количеством и плотностью
легкого заполнителя6. Предыдущие исследования
показывают, что плотность бетона EPS
уменьшается с увеличением объема заполнителя EPS
и, следовательно, приводит к снижению прочности бетона на сжатие
2,3,16,17.Зависимость
между прочностью на сжатие и затвердевшим бетоном
Плотность бетона из пенополистирола показана на рис. 4.
Прочность бетона из пенополистирола оказалась равной
, прямо пропорциональной плотности бетона. Соотношение
между плотностью бетона и прочностью на сжатие
, основанное на результатах для бетонов EPS
с плотностью от 464 до 1940 кг / м3, может быть
, предложенным как:
(fc).
fc = 2.10-12.γ 4.1021… (2)
Где fc — прочность на сжатие (МПа), а γ —
— плотность (кг / м3) пенополистирола.
В результате этого исследования, за счет включения
валиков EPS в различных объемных процентах в бетон, раствор или цементное тесто
, можно получить широкий диапазон плотностей бетона
.
Выводы
На основании экспериментального исследования, проведенного на бетоне с шариками из
EPS, можно сделать следующие выводы
:
(i) Плотность бетона из пенополистирола
существенно зависит от соотношения PC / EPS.
(ii) Плотности более чувствительны к изменению значения осадки
, чем соотношение воды и воды.
(iii) Шарики из пенополистирола имеют замкнутую ячеистую структуру,
увеличение их объемной доли в смесях
заметно снижает прочность на сжатие
.
(iv) Было замечено, что увеличение продолжительности вибрации
вызывает накопление шариков на форме.
(v) Суперпластификатор повышает удобоукладываемость всей бетонной смеси
.
(vi) 28-дневная прочность на сжатие и плотность сухого бетона
варьировались от 0,11 до 38,50 МПа
и от 464 до 1940 кг / м3 соответственно
Ссылки
1 Miled K, Roy RL, Sab K & Boulay C, Mech Mater, 36
(2004) 1031-1046
2 Babu KG & Babu DS, Cem Concr Res, 33 (2003) 755–762
3 Sabaa B & Ravindrarajah RS, Оценка пригодности к применению для
бетон из полистирольного заполнителя, доклад, представленный на 7-м Конгрессе по контролю качества
, Монтевидео, Уругвай, 1999 г.
4 Tang S, Colloids Surf A: Physicochem Eng Aspects, 157
(1999) 185-192
5 Ravindrarajah RS & Collins J , Развитие температуры в бетоне
с валиками EPS, доклад, представленный на AUSTCERM
98, Мельбурн, Австралия, 1998
6 Demirboga R & Gül R, Indian J Eng Mater Sci, 11 (2004)
201-206
7 Международный веб-сайт EPS: «Recycle», доступно по адресу: http:
www. epsrecycling. Org / recycling / index. html, по состоянию на 1
марта 2006 г.
8 Laukaitis A, Zurauskas R & Keriene J, Cem Concr Compos,
27 (2005) 41-47
9 Choi NW & Ohama Y, Construct Build Mater, 18 (2004 г.) )
235–241
10 Husem M, Mater Sci Eng A, 363 (2003) 152-158
11 Lo Y, Gao XF & Jeary AP, Build Environ, 34 (1999) 759-
764)
12 ASTM C 332-98: Стандартные спецификации для легких
заполнителейдля изоляционного бетона1, Ежегодный свод стандартов ASTM
, Истон, Мэриленд, США, 1998
13 ASTM – C 109-98: Испытание на прочность на сжатие
Гидравлические цементные растворы (2 дюйма или 50 мм.Куб
экз.). Annual Book of ASTM Standards, Easton, MD,
USA, 1998
14 Beecrof G.W, Highway Res Board, Bull, 307 (1992) 26-41
15 Ravindrarajah SR, Несущая способность бетона, содержащего полистирол
совокупный, Proc. RILEM 8th
Int Conf
Durability of Building Materials and Components,
Vancouver, Canada, 1 (1999) 505-514
16 Perry SH, Bischoff PH & Yamura K, Mag Concr Res, 6
(1991 ) 43.
17 Babu DS, Babu KG & Tiong-Huan W, Cem Concr Compos,
28 (2006) 520-527
EPS бетон — ARQUIPANEL
Пенополистирольный заполнитель был первоначально разработан BASF в Европе в 1950-х годах. s, вскоре после создания пенополистирола. BASF занималась разработкой приложений для бетона, проверила его физические свойства и опубликовала передовой опыт для ряда строительных приложений. Эта дальновидность со стороны BASF привела к значительному использованию пенополистирола по всей Европе, и сегодня пенополистирол больше не является новым материалом для строительства или строительства.
Европейские строительные нормы и правила и методы строительства включают материал свободно там, где его использование лучше всего подходит для применения, иногда исключая любой другой продукт. В этом отношении Соединенные Штаты отстают в лучшем случае на двадцать лет, а в худшем — на сорок лет в использовании и принятии бетонов из EPS. Из-за широкого использования в Европе физические свойства бетонных смесей EPS были тщательно протестированы, и формулы смесей были разработаны для различных областей применения. Параллельно с этим была создана целая строительная практика по использованию бетона.
Испытания, проводимые в Европе, и / или используемые строительные практики обычно соответствуют «Стандартам DIN». Эти стандарты наиболее близки к «Стандартам ASTM», принятым в США. Фактически, в некоторых случаях ASTM приходилось полагаться на DIN, чтобы предоставить методы испытаний, необходимые для испытания легких бетонов, чтобы эти методы могли быть включены в стандарты ASTM.
Многие результаты испытаний и методы строительства, показанные в этом разделе, относятся к DIN как к органу по стандартизации, если в США нет аналогичных методов испытаний или стандартов строительных практик.
Производственный процесс, ч Время изготовления
Бетон представляет собой сухой предварительно смешанный материал, содержащий портландцемент, пуццоланы и шарики пенополистирола (EPS) в качестве заполнителей. Портландцемент и пуццоланы — обычные ингредиенты современных цементных паст, которые смешиваются с песком и каменными заполнителями для получения стандартного бетона. Шарики из вспененного полистирола в качестве основного заполнителя, а не камня, используются для изготовления легкого бетона.
Пенополистирол наиболее широко известен как материал, используемый для изготовления пенопласта, стаканов Styropor® / Styrofoam® и упаковки из пенопласта. В первоначальном виде полистирол образуется в результате ряда сложных химических реакций в результате жидких непредельных углеводородов. В результате получаются очень маленькие шарики из пенопласта. Эти шарики имеют среднюю молекулярную массу от 160 000 до 260 000.Вспенивающий агент обычно составляет около 2-5% веса и используется для расширения гранул. Этот вспенивающий агент обычно представляет собой пентан или бутан. Бусинки обычно имеют диаметр от 0,007 до 0,12 дюйма.
Пенополистирол получают путем нагрева гранул полистирола. В зависимости от используемой формулы расширенная бусина может быть в 40 раз больше, чем исходная бусина. Для пенополистирола характерна номинальная плотность от 1 до 1,5 пкф.
Смесь сухих портландцементов, сухого песка, пуццоланов и шариков из пенополистирола различного размера для использования при изготовлении легкого бетона.Смесь очень точная, чтобы получить желаемый конечный продукт по характеристикам; прочность, удобоукладываемость, отделка и т. д.
Легкий бетон может быть чрезвычайно легким, он может быть до 88% легче традиционного бетона. Как? Мы используем пенополистирол (похожий на маленькие шарики из пенополистирола) в качестве заполнителя вместо песка и гравия. Бетон с использованием пенополистирола (eps) известен как бетон epscrete или eps. ASTM определяет легкие бетоны как имеющие диапазон плотности от 60 до 100 фунтов на кубический фут (pcf).Бетоны Eps относятся к классу сверхлегких бетонов, когда верхний диапазон плотности этих бетонов обычно составляет менее 60 фунтов на фут (всего 18 фунтов на фут или 635 фунтов на квадратный дюйм).
Пример использования:
Бетон образуется при смешивании сухой смеси с водой. Во время гидратации воды происходят химические реакции, отверждение цементной базовой пасты вокруг заполнителей пенополистирола с образованием легкого бетона. Различные добавки используются для изменения свойств бетона для конкретных целей.Самым важным является суспендирующий агент, необходимый для компенсации отвращения EPS к водопоглощению.
Без суспендирующего агента устойчивость eps к водопоглощению приведет к его расслоению в бетонной смеси, что приведет к получению ненадежной бетонной смеси. Добавки суспендирующих агентов также могут эффективно увеличивать плотность пенополистирола, предотвращая всплытие гранул на поверхность бетонной смеси. Для этого в легких бетонах используются запатентованные суспендирующие агенты и соответствующая процедура смешивания.
Как правило, бетонные панели из армированного пенополистирола могут быть установлены в течение 2–3 дней. Легкие бетоны достигают большей части своей окончательной прочности через 7-10 дней, если их нагнетать ускорителем. Лучше всего держать любой бетон защищенным и влажным в течение семи дней. По сравнению с обычным временем отверждения бетона, составляющим 28 дней, бетон LW будет продолжать гидратировать и отверждаться в течение 90 дней, в зависимости от состава. Сегодня производители, подрядчики, строители, ремесленники и частные лица используют LW-бетон для зданий, домов, стен, водных объектов, архитектурных элементов, скульптур, тематических структур, изоляционного заполнения для стандартных бетонных блоков и экологически чистых строительных объектов.Новые применения LW-бетонов постоянно развиваются.
IRJET-Запрошенная вами страница не найдена на нашем сайте
IRJET приглашает статьи из различных инженерных и технологических дисциплин для Тома 8, выпуск 5 (май-2021)
Отправить сейчас
IRJET Vol -8 Выпуск 5, май 2021 г. Публикация продолжается …
Обзор статей
IRJET получил «Импакт-фактор научного журнала: 7,529» за 2020 год.
Проверить здесь
IRJET получил сертификат регистрации ISO 9001: 2008 для своей системы менеджмента качества.
IRJET приглашает специалистов по различным инженерным и технологическим дисциплинам, научным дисциплинам для Тома 8, выпуск 5 (май 2021 г.)
Отправить сейчас
IRJET Vol-8, выпуск 5, май 2021 г. Публикация в процессе …
Просмотр Статьи
IRJET получил «Импакт-фактор научного журнала: 7,529» за 2020 год.
Проверить здесь
IRJET получил сертификат регистрации ISO 9001: 2008 для своей системы менеджмента качества.
IRJET приглашает специалистов по различным инженерным и технологическим дисциплинам, научным дисциплинам для Тома 8, выпуск 5 (май 2021 г.)
Отправить сейчас
IRJET Vol-8, выпуск 5, май 2021 г. Публикация в процессе …
Просмотр Статьи
IRJET получил «Импакт-фактор научного журнала: 7,529» за 2020 год.
Проверить здесь
IRJET получил сертификат регистрации ISO 9001: 2008 для своей системы менеджмента качества.
IRJET приглашает специалистов по различным инженерным и технологическим дисциплинам, научным дисциплинам для Тома 8, выпуск 5 (май 2021 г.)
Отправить сейчас
IRJET Vol-8, выпуск 5, май 2021 г. Публикация в процессе …
Просмотр Статьи
IRJET получил «Импакт-фактор научного журнала: 7,529» за 2020 год.
Проверить здесь
IRJET получил сертификат регистрации ISO 9001: 2008 для своей системы менеджмента качества.
IRJET приглашает специалистов по различным инженерным и технологическим дисциплинам, научным дисциплинам для Тома 8, выпуск 5 (май 2021 г.)
Отправить сейчас
IRJET Vol-8, выпуск 5, май 2021 г. Публикация в процессе …
Просмотр Статьи
IRJET получил «Импакт-фактор научного журнала: 7,529» за 2020 год.
Проверить здесь
IRJET получил сертификат регистрации ISO 9001: 2008 для своей системы менеджмента качества.
IRJET приглашает специалистов по различным инженерным и технологическим дисциплинам, научным дисциплинам для Тома 8, выпуск 5 (май 2021 г.)
Отправить сейчас
IRJET Vol-8, выпуск 5, май 2021 г. Публикация в процессе …
Просмотр Статьи
IRJET получил «Импакт-фактор научного журнала: 7,529» за 2020 год.
Проверить здесь
IRJET получил сертификат регистрации ISO 9001: 2008 для своей системы менеджмента качества.
IRJET приглашает специалистов по различным инженерным и технологическим дисциплинам, научным дисциплинам для Тома 8, выпуск 5 (май 2021 г.)
Отправить сейчас
IRJET Vol-8, выпуск 5, май 2021 г. Публикация в процессе …
Просмотр Статьи
IRJET получил «Импакт-фактор научного журнала: 7,529» за 2020 год.