Набрызг-бетон
НАБРЫЗГ-БЕТОН (а. shotcrete; н. Spritzbeton; ф. gunite, beton projete, beton Torkret; и. hormigon salpicado, hormigon а soplete, torcreto) — искусственный материал (бетон), состоящий из смеси цемента, песка, гравия или щебня и, как правило, добавок — ускорителей схватывания и твердения, и получаемый нанесением этой смеси безопалубочным методом. Получил распространение в горном деле и подземном строительстве как один из основных материалов для крепления и гидроизоляции выработок, ремонта тоннельных обделок. Применяется в широком диапазоне горно-геологических условий в виде самостоятельной конструкции (в скальных и плотных глинистых грунтах с коэффициентом крепости f>4), а также в сочетании с анкерами или арками с покрытием непосредственно по породе или по сетке, используемой в качестве затяжки (при f=2-4).
Первое сообщение о возможности получения бетонного покрытия безопалубочным способом было сделано в 1910 в Нью-Йорке на ежегодном съезде потребителей цемента Д. Л. Прентиссом. Им же в 1914 набрызг-бетон был использован для крепления подземных выработок. В России набрызг-бетон впервые применён в 1916. Создание в 1942 в Швейцарии машин для нанесения смеси с наполнителем крупностью до 30 мм и разработка эффективных ускорителей схватывания и твердения смеси способствовали широкому использованию набрызг-бетона для возведения как временной, так и постоянной крепи подземных выработок.
В технической литературе часто употребляются другие названия набрызг-бетона: торкретбетон, шприц-бетон, пневмобетон. Под этими материалами принято понимать искусственные смеси, применяемые для создания тонких изолирующих покрытий толщиной до 3 см с использованием мелких наполнителей (до 5 мм), в то время как из собственно набрызг-бетона возводятся грузонесущие конструкции крепи толщиной до 15 см и более с использованием наполнителя крупностью до 25 мм.
Различают т.н. сухой (наиболее распространённый) и мокрый способы нанесения набрызг-бетонных покрытий. При сухом способе в специальную машину загружают сухую смесь, выдуваемую сжатым воздухом по шлангу в сопло, перед вылетом смесь смешивается с водой, подводимой к соплу по другому шлангу; при мокром — готовая смесь, загружаемая в герметически закрытый резервуар, наносится на поверхность под действием сжатого воздуха. Состав сухой смеси для набрызг-бетона (% по массе): цемента и песка — 54-58, наполнителя с размерами зёрен от 5 до 10 мм — 24-27, то же от 10 до 20-25 мм — 18-19. На 1 м3 сухой смеси в зависимости от требуемой марки расходуется от 250 до 350 кг цемента при водоцементном отношении от 0,35 до 0,45. Набрызг-бетон обладает более высокими по сравнению с обычным бетоном прочностными свойствами (в 2,75 раза на сжатие, в 1,5 раза на растяжение). Сцепление покрытия с породой 1,5-2,5, с бетоном 1-1,8, с арматурой 2,5-4,5 МПа. Для повышения прочности материала на растяжение в бетонную смесь вводят армирующие элементы в виде стальных обрезков или стеклянных волокон длиной 15-25 мм. Вместе с грунтом набрызг-бетон способен образовывать единую грузонесущую систему. Он также имеет высокую степень водо- и газонепроницаемости, обладает возможностью полной механизации процесса крепления и совмещения его с другими горнопроходческими операциями. Недостатки набрызг-бетона при традиционном (сухом) способе нанесения: высокая запылённость, потери материала при «отскоке» (до 30%), повышенный расход цемента и др. Для устранения этих недостатков шире внедряют мокрый способ набрызг-бетонирования, установки с дистанционно управляемыми соплами.
www.mining-enc.ru
Набрызг бетон
Торкретирование и набрызг-бетон
Способ торкретирования заключается в нанесении на вертикальные, наклонные и горизонтальные поверхности одного или нескольких защитных слоев цементно-песчаного раствора (торкрета) при помощи цемент-пушки или бетонной смеси, нагнетаемой бетон-шприцмашиной. Этот способ применяют для укрепления поверхностей тонкостенных конструкций в односторонней опалубке (куполов, сводов-оболочек, резервуаров), для нанесения плотного и водонепроницаемого защитного слоя подземных сооружений, а также для замоноличивания швов, исправления дефектов в бетоне, при ремонтно-восстановительных работах и для усиления железобетонных конструкций. Для торкретирования применяют высокомарочные цементы. В обычных условиях используют портландцемент марки 500, а для омоноличивания, создания водонепроницаемых облицовок и ремонта быстротвердеющий цемент. Песок должен быть по возможности чистым, сухим и не содержать зерен более 8 мм. Для ускорения схватывания смеси в воду затворения растворяют добавки. Комплект оборудования для торкретирования состоит из цемент-пушки, компрессора, бака для воды, воздушных и материальных шлангов и сопла.
Сухую цементно-иесчаную смесь соответствующего состава, приготовленную в смесителе, загружают в цемент-пушку. Под давлением сжатого воздуха 2—3,5 кг/см2 смесь подается по материальному шлангу в сопло. Одновременно в сопло поступает вода из бака, давление которой должно быть на 1—1,5 кгс/см2 выше, чем в цемент-пушке. Увлажненная смесь, вылетая из сопла со скоростью до 100 м/с, ударяется о торкретируемую поверхность и прилипает к ней. В результате образуется плотный и прочный слой торкрет-бетона. Некоторая часть цементно-песчаной смеси отскакивает от поверхности и падает у места торкретирования. Эти потери называют отскоком.
Для уменьшения отскока в воду затворения добавляют поверхностно-активные вещества (абиетат натрия, мылонафт), которые увеличивают клеящую способность смеси. Перед торкретированием тонкостенных конструкций устанавливают и закрепляют одностороннюю опалубку, оставляя одну сторону открытой для нанесения торкрета, и монтируют арматуру. Перед нанесением защитных обделок, ремонтом и омоноличиванием тщательно очищают и промывают поверхности. Для обеспечения лучшего сцепления слоя торкрета с бетоном на гладких поверхностях делают надсечку. Перед торкретированием проверяют исправность всех механизмов, чистоту и соединения шлангов, а также наносят пробу торкрета на переносной деревянный щит. Для получения плотного торкрета и уменьшения отскока сопло при нанесении следует держать на расстоянии 0,7—1,0 м от торкретируемой поверхности, а струю смеси направляют перпендикулярно ей. Чтобы получить слой торкрета равномерной толщины, сопло в процессе нанесения перемещают круговыми движениями. На вертикальные, наклонные и криволинейные поверхности торкрет наносят снизу вверх. Чтобы свеженанесенный торкрет не сползал с них, регулируют подачу воды в смесь и толщину слоев, которую контролируют по маякам. Оптимальная толщина слоя торкрета, нанесенного за одну проходку, составляет 25—30 мм. Потолки торкретируют в несколько слоев, иолы — сразу на всю толщину. При многослойном торкретировании время между нанесением отдельных слоев устанавливает строительная лаборатория. Это время должно быть таким, чтобы под действием струи смеси не разрушался предыдущий слой торкрета. С другой же стороны, для обеспечения втапливанця свежего слоя в ранее нанесенный и лучшего их сцепления максимальный перерыв не должен превышать времени схватывания цемента. Для получения гладких поверхностей, бетонируемых методом торкретирования, сразу же после нанесения последнего слоя его заглаживают и затирают стальными гладилками или яюлутерками. Затем поверхность железнят. После такой обработки получают конструкции с гладкими поверхностями, отличающимися плотностью, водонепроницаемостью и морозостойкостью. Метод набрызг-бетона применяют для возведения тонкостенных конструкций, обделки туннелей, омоноличивания швов, а также для исправления дефектов бетона и ремонтных работах. В отличие от торкрет-бетона смесь, наносимая набрызгом, содержит помимо цемента и песка также щебень или гравий крупностью до 25 мм. Бетон способом набрызга наносят на вертикальные, наклонные и горизонтальные поверхности. Перед началом работ устанавливают одностороннюю опалубку и арматуру, очищают и промывают поверхности. Комплект оборудования для нанесения набрызг-бетона смонтирован на двухосном прицепе. В него входят бетоносмеситель принудительного действия со скиповым подъемником, многоковшовый элеватор, бункер-накопитель, набрызг-машина тила С-630А, два бака для воды, шланги, сопло и компрессор. Сухую смесь, приготовленную в смесителе, подают элеватором в бункер, а из него загружают набрызг-машину. Под давлением воздуха в 4—5 кгс/см2 смесь по шлангу подается в сопло, в смесительную камеру которого поступает вода. Увлажненная омесь вылетает из сопла со скоростью 120 м/с. Оптимальное расстояние между бетонируемой поверхностью и соплом составляет 1—1,2 м.; Вращательные движения сопла обеспечивают равномерную толщину слоя, которая должна быть 50—70 мм.betony.ru
§ 60. БЕТОНИРОВАНИЕ ОБДЕЛОК В СКАЛЬНЫХ ПОРОДАХ (ч. 5)
Набрызгбетон. В практике современного тоннелестроения получил широкое распространение так называемый набрызгбетон («шприц-бетон») марок 300—400—500, применяемый как для временного крепления, так и для возведения постоянных подземных конструкций. Эту полупластичную смесь портландце
vest-beton.ru
Торкрет, торкрет бетон — Стройфора
Торкрет это механическое нанесение бетонной смеси под давлением сжатого воздуха, создающее высокопрочное покрытие с сильнейшей адгезией, имеет широчайшую область применения. Инновацией данная технология была больше сотни лет тому назад, сейчас торкрет – классика.
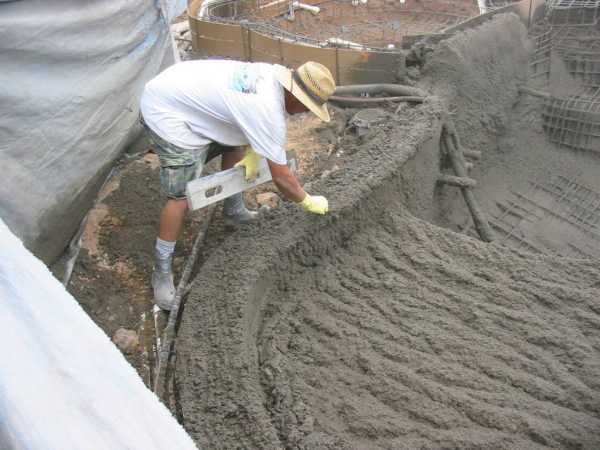
Tor — штукатурка, cret – уплотнить. Сфера применения огромна – тоннелестроение, реконструкция и усиление, гидротехнические сооружения и путепроводы, герметизация и укрепление грунтов, горная отрасль и… искусство. Художественные объекты и отделочные работы в том числе, поскольку торкрет – технологии относятся к универсальным.
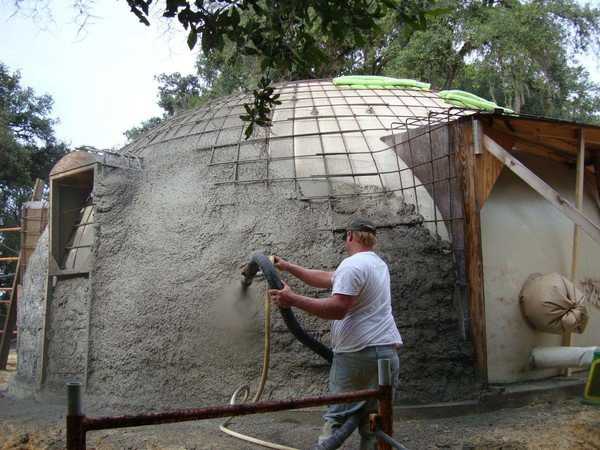
Иногда к торкретированию относят виды нанесения растворных смесей способами набрызга – но это не совсем верно. Торкрет – это уплотнение смеси в поверхности конструкций с ударом. Кроме того, песчано-цементные смеси для торкрета содержат дисперсные включения с наибольшим размером 8мм (набрызг-бетон может иметь в качестве заполнителя зерно фракцией до 25 мм).
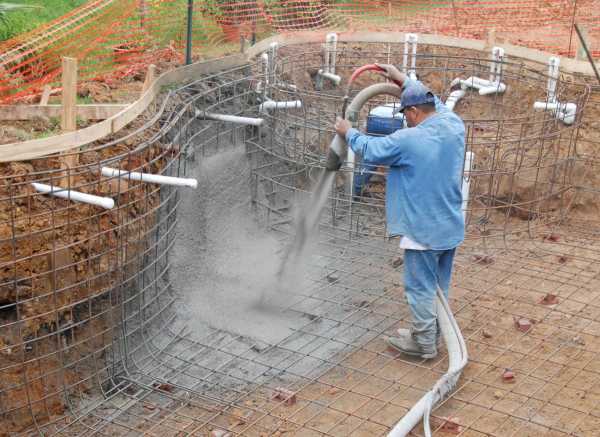
При торкретировании под расчетным пневматическим давлением невозможны остаточные полости и неуплотненные участки за арматурными каркасами и в результате – создается монолитная конструкция высокой прочности.
Торкрет в частном строительстве
В частном строительстве торкрет находит применение в фундаментных работах – усилении, восстановлении и реконструкциях. Торкретом можно укрепить свод, сформировать арку и выполнить практически любую работу, где требуется создать на поверхности конструкции прочный монолитный слой из раствора или бетона. Причем расположение поверхности может быть любым – вертикальным, горизонтальным, наклонным и даже труднодоступным.
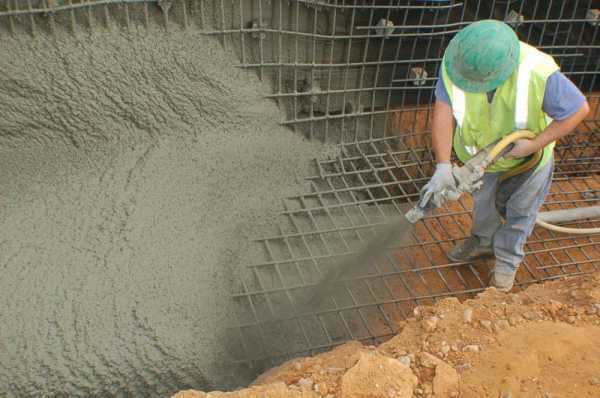
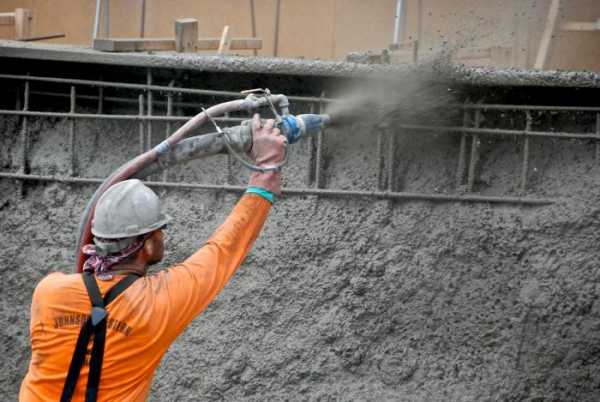
Виды технологии торкретирования
Основные виды технологий – это сухое торкретирование и мокрое.
Специальная техника нужна в обоих случаях, как и умение ей управлять, и конечно, нужен навык работ. И для управления установкой – выбора и настройки давления, контроля подачи составляющих раствора или готовых растворов, и для работы с раствором — регулировки процесса нанесения, толщины слоев и последовательности проходок. Обслуживание торкрет- установок не считают сложным процессом, и обучение не требует много времени, но помощь опытного специалиста на первых порах необходима. Грубые ошибки, часто допускаемые новичками при нанесении растворов, не позволят создать качественный бетон.
Сухое торкретирование
При методе сухого торкретирования непосредственно в сопле специальной торкрет-установки происходит смешивание компонентов бетона в сухом виде с водой. Вода, подаваемая под давлением, и сухая бетонная смесь дают на выходе готовый раствор, который подается на поверхность бетонирования через сопло.
Плюсы сухого торкрета:
- Возможность создать слой значительной толщины — до 60 мм
- Подача растворной смеси на значительное расстояние
- Высокая скорость подачи растворной смеси
- Высокая адгезия полученного раствора
Сухое торкретирование имеет особенность, следующую из его технологии – при неумелом нанесении от поверхности бетонирования может отскакивать до половины подаваемого раствора. Процесс может стать крайне неэффективным, к тому же грязным и пыльным, на рабочем месте без респиратора находиться при таком процессе сложно. Все эти неприятности вполне понятны при обучении работам, поэтому так важен на первых порах контроль специалиста. Навыки в регулировке торкрет-установки, управлении и нанесении растворов необходимы.
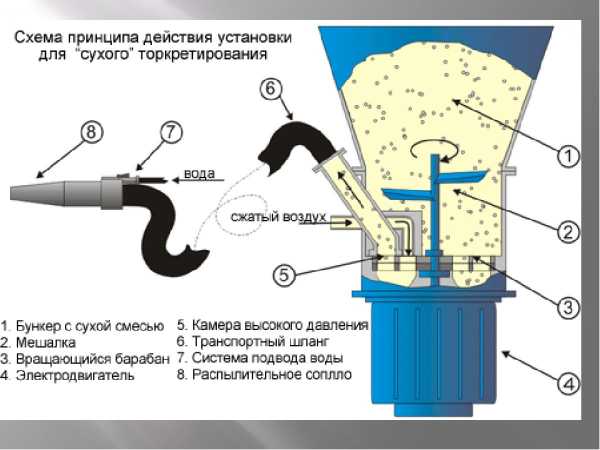
Квалифицированная работа обеспечивает долю отскока до 26% смеси максимально при скорости потока до 180 м/сек. Пылеобразование присутствует всегда, в разной степени, многое зависит от квалификации персонала. Смеси возможны разнородного состава, с кальмафлексом, шлаком или микрокремнеземом. Финишная затирка возможна только после выдержки.
Мокрое торкретирование
Технология мокрого торкретирования – это нагнетание готовой растворной смеси, подача производиться также посредством сжатого воздуха.
Плюсы мокрого торкрета:
- Полная однородность готовой растворной смеси, представляющей собой суспензию. Как следствие, пылеобразование минимальное
- Брызги раствора, грязь и пыль в рабочей зоне практически отсутствуют. Доля отскока смеси от 8 до 20% при скорости потока торкрета от 70 до 100 м/сек
- Поверхность обрабатываемой поверхности более ровная, чем при сухом способе, и годится для финишной затирки сразу после нанесения, без выдержки.
- Процесс не требует высокой квалификации, может выполняться при общем уровне подготовки.
Недостаток мокрого метода – толщина слоя максимум 30 мм, для создания слоя большей толщины нужны еще проходки после схватывания первого слоя. Бетонная смесь при мокром методе распределяется медленнее, и времени нужно значительно больше.
Установка после работы требует тщательной очистки от оставшегося раствора и мытья, что так же требует времени. Износостойкость оборудования низкая. Мокрый торкрет более рационален на небольших участках работ.
Торкрет-бетон своими руками
Требуемое оборудование и инструменты для сухого торкрета:
- Компрессорная установка с баком, предусматривающая использование очищенного воздуха
- Цемент-пушка, имеющая накопительные бункера для сухих смесей, входные и выходные штуцера
- Накопительный бак для воды, имеющий штуцер для забора сжатого воздуха от компрессорной установки и выходной патрубок
- Сопло для смешивания и нанесения растворной смеси на обрабатываемую поверхность
Оборудование для мокрого торкрета:
- Бетоносмеситель для приготовления растворной смеси
- Установка для механизированного просеивания заполнителя (вибросита ячейкой 8 мм) Используются для замеса только определенные фракции заполнителя (до 8 мм или по технической характеристике установки)
- Насос, подающий раствор
- Камера смешивания готового раствора и очищенного сжатого воздуха от компрессорной установки
- Сопло для нанесения растворной смеси на бетонируемую конструкцию
Торкрет- установки могут приобретаться как отдельные аппараты и агрегаты, так и в комплекте. Готовый комплект дает возможность выполнить работы своими силами. Для приготовления растворов возможно как применение готовых сухих смесей, что экономит время и дает хорошее качество, но в то же время весьма недешево, так и собственноручная дозировка смесей взвешиванием.

Иногда для торкрета используют штукатурные хоппер-ковши. Хоппер-ковш представляет собой конусовидную металлическую емкость, имеющую патрубок, посредством которого его подключают к компрессору большой мощности. Для работы требуется давление 4-6 атм. Нижняя часть хоппер-ковша имеет отверстие для сопла. Преимущество – возможна смена сопел разных диаметров, это позволяет наносить слои разной толщины, с последующим выравниванием. Излишки раствора возможно применять вторично.
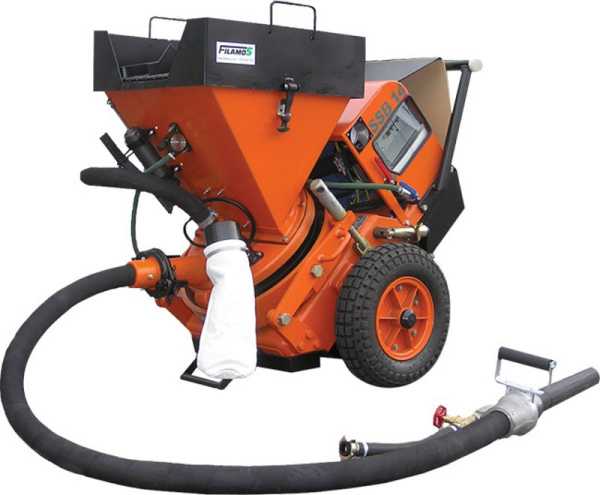
Подготовка для выполнения торкрета
- Для качественного торкрета необходимо обеспечить сцепление раствора с обрабатываемой поверхностью.
- На поверхности бетонирования не должно быть пятен масла и нефтепродуктов. Все загрязненные участки вырубают или выполняют пескоструйную очистку
- Глубокие узкие щели предварительно заделывают раствором, поскольку их надлежащее уплотнение под вопросом. Пустот под торкретом быть не должно.
- Обрубают все выступающие края, кромки, а также раковины до 50 мм, угол скоса делают не менее 45 град. Если на поверхности есть раковины глубже 50 мм и более 100 мм диаметром, их заделывают ремонтной смесью или специальными растворами, предварительно выполнив скосы кромок на угол не менее 45 град
- Если поверхность была обработана железнением, ее делают шероховатой при помощи пескоструйной обработки
- Арматурные сетки и плоские каркасы усиления очищают от загрязнений. Масло, грязь, отслаивающаяся ржавчина на поверхности арматуры не допускается, так как может значительно снизить адгезию. Применяется как пескоструйная, так и кислотная обработка
- Вся поверхность зачищается, удаляется грязь, мусор, старый раствор
- Поверхность тщательно увлажняется большим количеством воды
При мокром способе торкретирования порция приготовленного раствора должна быть выработана за два часа, пока раствор имеет наибольшую подвижность и активность. Раннее схватывание раствора снижает качество работ.

Применение смесей с использованием разных вяжущих и с различными добавками позволяет создавать морозостойкие, негорючие, водонепроницаемые, химически стойкие покрытия. Для применения на частной стройке торкрет-бетон востребован как для реконструкции и усиления несущих конструкций фундаментов, стен и сводов, так и для отделки стен и перекрытий. Торкрет-технология обеспечивает не только армирующий слой, но и возможность придать обработанной поверхности эстетичный внешний вид вместе с повышенной прочностью и износостойкостью.
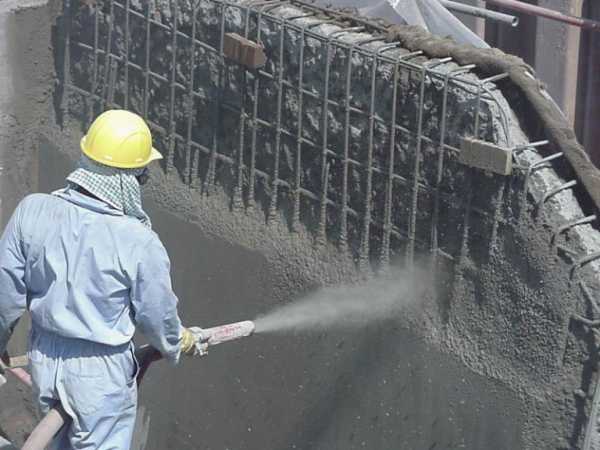
stroyfora.ru
Набрызг-бетон в метрострое: russos — LiveJournal
В последний раз технология набрызг-бетона на Московском Метрострое использовалась давно — около 10-11 лет назад, когда Тоннельный Отряд №6 вел проходку перегонного тоннеля между станциями Киевская и Парк Победы. Тогда комбайном раскрывали сечение тоннеля на полный профиль (так называемый новоавстрийский метод) и делали первичную крепь из набрызг-бетона. Потом обклеивали гидроизоляцией и делали внутренную обделку. На одном участке полностью монолитную, а на другом комбинированную — сборный железобетон и монолитный лоток. После этого эта технология не применялась.Но за прошедшее время много изменилось, и в первую очередь химия, которая добавляется в бетон. Так что было принято решение на шахте №952 применить на опытном участке снова обделку из набрызг-бетона.
Во всем мире она очень много где применяется. Эта технология позволяет весьма быстро строить тоннели, делая только обделку из набрызг-бетона. Причем, в весьма разных геологических условиях. Европейский специалист по этой технологии, который осмотрел строительство станции Петровско-Разумоувская сказал: «У вас нет причин, чтобы не построить такую станцию именно с этой технологией. Вся ваша проблема в головах и традициях, которые ведут к началу строительства метрополитена в Лондоне, где и начали повсеместно применять тюбинги».
1. Для начала схема. Слева ствол №952. От него идет подходная штольня к кресту, где СМУ-6 уже во всю ведет проходку перегонных тоннелей в сторону Фонвизинской. А вот справа ствол №952а, который прошли с помощью ВСМ. От него идет подходная выработка, что по плавной кривой выходит на ось перегонного тоннеля. Именно это и есть опытный участок, где применяется набрызг-бетон.
2. Разработку крепчайшего известняка ведут комбайном. За три-четыре часа он выбирает породу на метр заходки.
3. Евгений Шаймухаметов был моим гидом в хитростях набрызг-бетона и его технологиях применения.
4. С помощью этого метода будет построен конус расширения на шестиметровый диаметр и монтажная камера для блокоукладчика.
5. Забой пока сухой, но в случае появления воды на поверхности есть дополнительное оборудование, чтобы отжать воду. В забой забуриваются скважины и закачивают химию.
6. Толщина набрызг-бетона — 25 см. В качестве связующего элемента используется мелкая нарезка фибры — жесткий пластик.
7. По проекту предусмотрено устройство гидроизоляции методом набрызга мембраны. Это тоже будет проверено на этом участке. Но, так как это первый опыт, в тоннеле потом будет собрана чугунная обделка. На всякий пожарный случай. Хотя тоннель можно идти только набрызгом и гидроизоляцией.
8. Спрей-машина. С помощью сжатого воздуха она набрызгивает бетон на стенки.
9. В сопло подается бетон и химия. За счет силы сжатого воздуха эта смесь утрамбовывается на стенках выработки.
10. Технология в целом проста и не требует большой бригады. Вот сейчас проходку ведет один человек — Дмитрий, оператор комбайна.
11. Потом Сергей садится за рукоятки спрей-машины и наносит набрызг-бетон.
12. Готовая штольня к опытному участку.
13. Слабое место откатка. Пока она делается руками, а в дальнейшем будет использован дизельвоз. Бывают применяют и конвейерную откатку. С помощью комбайна проходка идет быстро. Вагонетка наполняется буквально за 30 секунд. А весь объем породы с метра тоннеля комбайн перекидывает в вагонетки минут за 15. Темпы очень приличные.
14. А это опытный участок опытного тоннеля. Перед боевым применением на перегоне, сначала набрызг-бетон испытали на земле, на полигоне. Потом в самом начале штольни. И только потом, уже на боевом участке в перегонном тоннеле.
15. Низ ствола №952а.
16. Тут стоит специальный бетонный насос, который смешивает смесь с присадками. А сам бетон подается по трубе сверху.
17. Быстро пробежался по шахте — посмотрел как идут дела.
18. Это левый перегонный тоннель в сторону Фонвизинской. Весьма прилично уже прошли. А электровоз К-4 вижу впервые. Обычно К-10 используются.
19. Правый перегонный тоннель. Здесь только начали проходку.
20. Подходная штольня.
21. Руддвор.
22. Ствол №952а и тепляк для миксера. Туда заезжает целая машина и подает бетон вниз.
russos.livejournal.com
Набрызг бетонная крепь
4.3. Набрызгбетонная крепь
Набрызгбетонная крепь (покрытие стенок выработки быстротвердеющей смесью на цементной основе) в последнее время находит все более широкое применение. Она достаточно надежна в работе, позволяет механизировать процесс крепления, что обеспечивает уменьшение сроков сооружения выработки и снижение затрат на проходку.
Набрызгбетонная смесь изготавливается из цемента марок 300-500, песка и заполнителя (щебня) крупностью не более 25 мм. Состав смеси 1:2:2. В качестве ускоряющих твердение добавок в состав смеси вводят тонкомолотый алюминистый спек (2-5% от массы цемента).
Техническая характеристика бетономашин
Таблица 17
Показатели | БМ-60 | БМ-68 | ТП-3 |
Производительность по сух. смеси, м3/ч | 3,0 | 5,0 | 3,0 |
Размеры фракции заполнителя, мм | 20 | 25 | 15 |
Расход сжатого воздуха, м3/мин | 8-14 | 9 | 4-5 |
Давление сжатого воздуха, МПа | 0,15-0,6 | 0,3-0,5 | 0,3-0,5 |
Дальность транспортирования, м: по горизонтали по вертикали | 200 100 | 250 100 | 100 40 |
Мощность привода, кВт | 4,5 | 5,5 | 7,5 |
Габариты, мм: длина высота ширина | 1740 1600 1100 | 1450 1675 836 | 1160 1000 540 |
Масса, кг | 1000 | 780 | 470 |
Расчетное сопротивление набрызгбетона растяжению [p] зависит от марки цемента и при изготовлении смеси на основе цемента марок 300, 400 и 500 соответственно составляет 1,2; 1,4 и 1,6 МПа. Толщина слоя набрызгбетона определяется расчетом и обычно варьирует в пределах от 3 до 15 см.
Набрызгбетонное покрытие наносится на кровлю и стенки выработки с помощью одно- и двухкамерных роторных бетономашин БМ или шнековых бетономашин ТП (табл. 17). На базе двухкамерной машины БМ-60 создан комплекс оборудования «Монолит-1», в состав которого входят вагонетки с лобовой разгрузкой (при помощи опрокида), ленточный перегружатель, гидроцистерна и сместитель с соплом. Техническая характеристика комплекса приведена ниже:
Производительность по бетону, м3/ч . . . . . . . . . . . . . . . . . . . 2,4
Суммарная мощность установленных двигателей, кВт . . . . 6,2
Габариты, мм: длина . . . . . . . . . . . . . . . . . . . . . . . . . . . . . .10000
высота в рабочем положении . . . . . . . . . . 2350
Масса, кг . . . . . . . . . . . . . . . . . . . . . . . . . . . . . . . . . . . . . . . . 4000
Порядок расчета прочных размеров набрызгбетонной крепи рекомендуется следующий:
Выбирается марка цемента, расчетное сопротивление набрызгбетона растяжению, крупность фракции заполнителя и состав бетонной смеси
Коэффициент внутреннего трения пород определяется по формуле (20).
Высота свода естественного равновесия определяется по формуле (38).
Рассчитывается интенсивность нормативной нагрузки (Па)
(49)
где bсв – высота свода естественного равновесия, м; hсв – высота свода выработки, м; ρ – плотность породы кг/м3.
Минимальная толщина слоя набрыгзбетона при отсутствии запаса устойчивости в кровле выработки (при nкр 1) вычисляется по формуле
(50)
а при nкр > 1
(51)
где nп = 1,2 – коэффициент перегрузки от горного давления; mу — коэффициент условий работы, равный 0,8, для неармированного набрыгзбетона и 1,0 для армированного.
Выбираются средства механизации возведения набрызгбетонной крепи и приводится их техническая характеристика.
Определяется расход бетонной смеси на крепление 1 м выработки:
где PЧ — периметр поперечного сечения выработки вчерне, м.
Определяется площадь закрепляемой поверхности, м2/цикл:
где lшп и — глубина и коэффициент использования шпуров.
studfiles.net
Временное крепление тоннельных выработок в устойчивых грунтах
Если при проходке тоннелей в неустойчивых грунтах наиболее широко применяются лишь два вида крепи – веерная деревянная и арочная металлическая, то в устойчивых грунтах разнообразие используемых видов крепи значительно больше. Наибольшее распространение получила анкерная и набрызгбетонная крепь, как в виде самостоятельных конструкций, так и в различных сочетаниях друг с другом. Преимущество такой крепи – включение ее в обделку составной частью или отдельным элементом.
Выбор вида временной крепи обусловливается следующими факторами:
- назначением, формой и размерами выработки;
- физико-механическими свойствами грунтов, обусловливающими устойчивость выработки, величину и характер проявления горного давления. Показатель устойчивости является определяющим исходным фактором при выборе конструкции крепи и паспорта крепления выработки:
- сроком работы временной крепи;
- взаимным расположением выработок;
- экономической целесообразностью.
Временное крепление выработок производится в соответствии с утвержденным проектом и паспортом крепления. Паспорт крепления утверждается главным инженером строительной организации.
Раскрытие калоттного профиля выработок; сооружаемых в скальных грунтах, производится либо за один прием, либо по частям (при пролете выработки свыше 20 м). Разработка грунта в этом случае производится буровзрывным способом. В качестве временной крепи применяется полигональная (контурная) деревянная крепь, которая устанавливается по периметру (контуру) выработки, оставляя свободным внутреннее пространство, что позволяет максимально использовать механизацию всех основных работ.
Полигональная (многоугольная) крепь
Деревянная полигональная крепь (рис. 1.36) состоит из прямоугольных брусьев (косяков) (3) сечением 18×22, 22×24 или 24×26 см длиной 1,5–2 м, соединяемых впритык и опирающихся на прогоны (2), под которые подводят стойки (1), устанавливаемые на лежни (5). В местах стыков элементов устанавливают распорки (4). За элементы
vest-beton.ru
бетон — это… Что такое Набрызг-бетон?
- Набрызг-бетон
- (a. shotcrete; н. Spritzbeton; ф. gunite, beton projete, beton Torkret; и. hormigon salpicado, hormigon a soplete, torcreto) — искусственный материал (бетон), состоящий из смеси цемента, песка, гравия или щебня и, как правило, добавок — ускорителей схватывания и твердения, и получаемый нанесением этой смеси безопалубочным методом. Получил распространение в горн. деле и подземном стр-ве как один из осн. материалов для крепления и гидроизоляции выработок, ремонта тоннельных обделок. Применяется в широком диапазоне горно-геол. условий в виде самостоят. конструкции (в скальных и плотных глинистых грунтах c коэфф. крепости f>4), a также в сочетании c анкерами или арками c покрытием непосредственно по породе или по сетке, используемой в качестве затяжки (при f=2-4).
Первое сообщение o возможности получения бетонного покрытия безопалубочным способом было сделано в 1910 в Нью-Йорке на ежегодном съезде потребителей цемента Д. Л. Прентиссом. Им же в 1914 H.-б. был использован для крепления подземных выработок. B России H.-б. впервые применён в 1916. Создание в 1942 в Швейцарии машин для нанесения смеси c наполнителем крупностью до 30 мм и разработка эффективных ускорителей схватывания и твердения смеси способствовали широкому использованию H.-б. для возведения как временной, так и постоянной крепей подземных выработок.
B техн. литературе часто употребляются др. названия H.-б.: торкретбетон, шприц- бетон, пневмобетон. Под этими материалами принято понимать искусств. смеси, применяемые для создания тонких изолирующих покрытий толщиной до 3 см c использованием мелких наполнителей (до 5 мм), в то время как из собственно H.-б. возводятся грузонесущие конструкции крепи толщиной до 15 см и более c использованием наполнителя крупностью до 25 мм.
Различают т.н. сухой (наиболее распространённый) и мокрый способы нанесения набрызг-бетонных покрытий. При сухом способе в спец. машину загружают сухую смесь, выдуваемую сжатым воздухом по шлангу в сопло, перед вылетом смесь смешивается c водой, подводимой к соплу по др. шлангу; при мокром — готовая смесь, загружаемая в герметически закрытый резервуар, наносится на поверхность под действием сжатого воздуха. Состав сухой смеси для H.-б. (% по массе): цемента и песка — 54-58, наполнителя c размерами зёрен от 5 до 10 мм — 24-27, то же от 10 до 20-25 мм — 18-19. Ha 1 м3 сухой смеси в зависимости от требуемой марки расходуется от 250 до 350 кг цемента при водоцем. отношении от 0,35 до 0,45. H.-б. обладает более высокими по сравнению c обычным бетоном прочностными свойствами (в 2,75 раза на сжатие, в 1,5 раза на растяжение). Сцепление покрытия c породой 1,5-2,5, c бетоном 1-1,8, c арматурой 2,5-4,5 МПa. Для повышения прочности материала на растяжение в бетонную смесь вводят армирующие элементы в виде стальных обрезков или стеклянных волокон дл. 15-25 мм. Вместе c грунтом H.-б. способен образовывать единую грузонесущую систему. Oн также имеет высокую степень водо- и газонепроницаемости, обладает возможностью полной механизации процесса крепления и совмещения его c другими горнопроходч. операциями. Недостатки H.-б. при традиционном (сухом) способе нанесения: высокая запылённость, потери материала при «отскоке» (до 30%), повышенный расход цемента и др. Для устранения этих недостатков шире внедряют мокрый способ набрызг-бетонирования, установки c дистанционно управляемыми соплами. Литература: Воронин B. C., Набрызг-бетонная крепь, M., 1980. B. E. Меркин.
Горная энциклопедия. — М.: Советская энциклопедия. Под редакцией Е. А. Козловского. 1984—1991.
- Наблюдательная скважина
- Навалочная машина
Смотреть что такое «Набрызг-бетон» в других словарях:
Набрызг бетон — – цементобетонная смесь, укладываемая с помощью энергии сжатого воздуха специальным оборудованием (цемент пушки и бетонные шприц машины). [Справочник дорожных терминов, М. 2005 г.] Рубрика термина: Виды бетона Рубрики энциклопедии:… … Энциклопедия терминов, определений и пояснений строительных материалов
набрызг-бетон — набрызг бетон, набрызг бетона … Орфографический словарь-справочник
набрызг-бетон — набры/зг бето/н, набры/зг бето/на … Слитно. Раздельно. Через дефис.
Бетон — (от лат. bitumen горная смола * a. concrete, beton; н. Beton; ф. beton; и. hormigon) искусственный кам. материал из смеси вяжущего вещества с водой, заполнителей и (в нек рых случаях) спец. добавок. Развитие и совершенствование технологии … Геологическая энциклопедия
Набрызг — – нанесение методом распыления жидкого материала, например, строительного раствора, краски и т. п., на подготовленную поверхность для отделки, защиты или изоляции этой поверхности. [Терминологический словарь по строительству на 12 языках… … Энциклопедия терминов, определений и пояснений строительных материалов
Обделка — (a. lining; н. Verkleidung, Verschalung; ф. blindage, chemisage, coffraqe; и. revestimiento, cubierta) строит. конструкция, возводимая в подземных сооружениях для сохранения их размеров и формы, защиты от обрушений и чрезмерных смещений… … Геологическая энциклопедия
Виды бетона — Термины рубрики: Виды бетона Аглопоритобетон Активированная смесь сфб Алб Арболит Арболит конструкционно теплоиз … Энциклопедия терминов, определений и пояснений строительных материалов
Крепь — У этой статьи нет иллюстраций. Вы можете помочь проекту, добавив их (с соблюдением правил использования изображений). Для поиска иллюстраций можно: попробовать воспользоваться инструментом … Википедия
Крепь металлическая податливая — Крепь искусственное сооружение, возводимое для предотвращения возможности обрушения окружающих горных пород в горных выработках, а также при строительстве шахт, тоннелей и метрополитенов и др. подземных объектов. Конструкция крепи зависит от… … Википедия
Тюбинговая крепь — Крепь искусственное сооружение, возводимое для предотвращения возможности обрушения окружающих горных пород в горных выработках, а также при строительстве шахт, тоннелей и метрополитенов и др. подземных объектов. Конструкция крепи зависит от… … Википедия
dic.academic.ru
Торкретирование и набрызг-бетон |
Торкретирование и набрызг-бетон
Способ торкретирования заключается в нанесении на вертикальные, наклонные и горизонтальные поверхности одного или нескольких защитных слоев цементно-песчаного раствора (торкрета) при помощи цемент-пушки или бетонной смеси, нагнетаемой бетон-шприцмашиной.
Этот способ применяют для укрепления поверхностей тонкостенных конструкций в односторонней опалубке (куполов, сводов-оболочек, резервуаров), для нанесения плотного и водонепроницаемого защитного слоя подземных сооружений, а также для замоноличивания швов, исправления дефектов в бетоне, при ремонтно-восстановительных работах и для усиления железобетонных конструкций.
Для торкретирования применяют высокомарочные цементы. В обычных условиях используют портландцемент марки 500, а для омоноличивания, создания водонепроницаемых облицовок и ремонта быстротвердеющий цемент. Песок должен быть по возможности чистым, сухим и не содержать зерен более 8 мм. Для ускорения схватывания смеси в воду затворения растворяют добавки. Комплект оборудования для торкретирования состоит из цемент-пушки, компрессора, бака для воды, воздушных и материальных шлангов и сопла.
Сухую цементно-иесчаную смесь соответствующего состава, приготовленную в смесителе, загружают в цемент-пушку. Под давлением сжатого воздуха 2—3,5 кг/см2 смесь подается по материальному шлангу в сопло. Одновременно в сопло поступает вода из бака, давление которой должно быть на 1—1,5 кгс/см2 выше, чем в цемент-пушке. Увлажненная смесь, вылетая из сопла со скоростью до 100 м/с, ударяется о торкретируемую поверхность и прилипает к ней. В результате образуется плотный и прочный слой торкрет-бетона. Некоторая часть цементно-песчаной смеси отскакивает от поверхности и падает у места торкретирования. Эти потери называют отскоком.
Для уменьшения отскока в воду затворения добавляют поверхностно-активные вещества (абиетат натрия, мылонафт), которые увеличивают клеящую способность смеси.
Перед торкретированием тонкостенных конструкций устанавливают и закрепляют одностороннюю опалубку, оставляя одну сторону открытой для нанесения торкрета, и монтируют арматуру. Перед нанесением защитных обделок, ремонтом и омоноличиванием тщательно очищают и промывают поверхности. Для обеспечения лучшего сцепления слоя торкрета с бетоном на гладких поверхностях делают надсечку. Перед торкретированием проверяют исправность всех механизмов, чистоту и соединения шлангов, а также наносят пробу торкрета на переносной деревянный щит.
Для получения плотного торкрета и уменьшения отскока сопло при нанесении следует держать на расстоянии 0,7—1,0 м от торкретируемой поверхности, а струю смеси направляют перпендикулярно ей. Чтобы получить слой торкрета равномерной толщины, сопло в процессе нанесения перемещают круговыми движениями.
На вертикальные, наклонные и криволинейные поверхности торкрет наносят снизу вверх. Чтобы свеженанесенный торкрет не сползал с них, регулируют подачу воды в смесь и толщину слоев, которую контролируют по маякам. Оптимальная толщина слоя торкрета, нанесенного за одну проходку, составляет 25—30 мм.
Потолки торкретируют в несколько слоев, иолы — сразу на всю толщину.
При многослойном торкретировании время между нанесением отдельных слоев устанавливает строительная лаборатория. Это время должно быть таким, чтобы под действием струи смеси не разрушался предыдущий слой торкрета. С другой же стороны, для обеспечения втапливанця свежего слоя в ранее нанесенный и лучшего их сцепления максимальный перерыв не должен превышать времени схватывания цемента.
Для получения гладких поверхностей, бетонируемых методом торкретирования, сразу же после нанесения последнего слоя его заглаживают и затирают стальными гладилками или яюлутерками. Затем поверхность железнят. После такой обработки получают конструкции с гладкими поверхностями, отличающимися плотностью, водонепроницаемостью и морозостойкостью.
Метод набрызг-бетона применяют для возведения тонкостенных конструкций, обделки туннелей, омоноличивания швов, а также для исправления дефектов бетона и ремонтных работах. В отличие от торкрет-бетона смесь, наносимая набрызгом, содержит помимо цемента и песка также щебень или гравий крупностью до 25 мм.
Бетон способом набрызга наносят на вертикальные, наклонные и горизонтальные поверхности. Перед началом работ устанавливают одностороннюю опалубку и арматуру, очищают и промывают поверхности.
Комплект оборудования для нанесения набрызг-бетона смонтирован на двухосном прицепе. В него входят бетоносмеситель принудительного действия со скиповым подъемником, многоковшовый элеватор, бункер-накопитель, набрызг-машина тила С-630А, два бака для воды, шланги, сопло и компрессор.
Сухую смесь, приготовленную в смесителе, подают элеватором в бункер, а из него загружают набрызг-машину. Под давлением воздуха в 4—5 кгс/см2 смесь по шлангу подается в сопло, в смесительную камеру которого поступает вода. Увлажненная омесь вылетает из сопла со скоростью 120 м/с. Оптимальное расстояние между бетонируемой поверхностью и соплом составляет 1—1,2 м.; Вращательные движения сопла обеспечивают равномерную толщину слоя, которая должна быть 50—70 мм.
Бетонирование методом набрызг-бетона обеспечивает высокое качество поверхностей конструкций. Набрызг-бетон имеет плотную структуру, высокую прочность, водонепроницаем и морозостоек. Сменная производительность установки, обслуживаемой тремя рабочими, достигает 18—21 м3, что обеспечивает весьма высокую выработку на одного человека — 6—7 м3 в смену.
midas-beton.ru