Газобетон своими руками в домашних условиях: технология
Газобетон – это универсальный материал, который обладает отменными прочностными характеристиками и является простым в монтаже. Поэтому материал широко применяется в строительстве. Для экономии денежных средств на этом процессе рекомендовано изготовление газобетона своими руками в домашних условиях.
Что такое газобетон и каковы его характеристики
Перед применением газобетона для возведения домов и других построек на участке, рекомендовано предварительно определить его характеристики.
Основные свойства и качества
Соответственно мировым стандартам качества и ГОСТу материал должен обладать перечнем определенных качеств. Качественный материал должен выдерживать 35-100 циклов заморозки и разморозки. Показатель теплопроводности газобетона составляет 0,09-0,38. Плотность материала составляет Д300-Д1200. Средний показатель паропроницаемости – 0,2. Усадка газобетона составляет 0,3 миллиметра на квадратный метр.
Виды материала и изделий из него
Соответственно характеристикам газобетона его разделяют на: теплоизоляционный, конструкционный, конструкционно-теплоизоляционный.
Теплоизоляционный газобетон имеет плотность от 300 до 400. Он имеет низкую теплопроводность и характеризуется незначитекльным весом. Применение материала рекомендуется для теплоизоляции помещений.
Конструкционный газобетон обладает отменными прочностными характеристиками и имеет плотность от 1000 до 1200. Благодаря высокому коэффициенту теплопроводности предоставляется возможность его применения в качестве утеплителя.
Наиболее популярным является конструкционно-теплоизоляционный газобетон. Он характеризуется плотностью 400-900. С его применением возводятся стены и перегородки.
Сильные стороны строений возведенных из газобетона
Материал широко применяется в строительстве благодаря наличию большого количества преимуществ:
- Для производства материала используется песок, известь, цемент, алюминиевая пудра и вода, что обеспечивает экологичность материала.
- Газобетон имеет небольшой вес, что упрощает процесс его укладки.
- Благодаря большим размерам газоблоков ускоряется процесс возведения газобетона.
- Материал характеризуется высоким уровнем стойкости к возгоранию.
- Газобетон является стойким к морозам, что позволяет его применять в суровых климатических условиях.
- Благодаря универсальному составу материала предоставляется возможность его распиловки и шлифовки.
- Газобетон позволяет использовать разнообразные материалы для отделки зданий внутри и снаружи.
- Такие показатели, как прочность и теплопроводность, являются оптимальными.
- Производство материала осуществляется различными компаниями, что позволяет клиенту выбрать наиболее приемлемый вариант для себя.
- Материал обладает паропроницаемыми свойствами, что позволяет обеспечить оптимальный микроклимат в помещении.
- Газобетон обладает хорошими звукоизоляционными свойствами, что обеспечивает комфортное пребывание в помещении.
Газобетонный дом имеет высокие эксплуатационные характеристики, что объясняется большим количеством преимуществ материала.
Недостатки изделий и их устранение
Перед тем, как сделать газобетон в домашних условиях, рекомендовано определить его недостатки. Материал является гигроскопичным, что приводит к усиленному водопоглощению. При отрицательных температурах накопленная в блоках влага кристаллизируется, что приводит к их разрушению.
Для того чтобы решить эту проблему нужно стены из газобетонных блоков облицовывать. С этой целью используется кирпич, металлопрофиль, дерево и другие отделочные материалы.
Производство газоблока своими руками
Технология производства газобетона в домашних условиях требует от мастера придерживаться определенных правил. Этот процесс состоит из нескольких этапов.
Необходимый набор оборудования и материалов
Перед тем, как изготавливать газобетон, нужно подготовить материалы и инструменты. Бетон делается из смеси таких материалов:
- Песок. Рекомендуется отдавать предпочтение кварцевому песку, который предварительно проходит процесс промывки и высушивания.
- Цемент. Высокопрочный материал получается при использовании цемента, который имеет марку более 400.
- Чистой воды.
- Негашеной извести.
- Алюминиевой пудры, каустической соды, сульфата натрия.
Формы
Перед тем, как делают газобетон, подготавливают формы. В строительных магазинах можно купить готовые изделия. Для экономии денежных средств их создают самостоятельно. Изначально изготавливают пенал из деревянных досок. В него вставляют перемычки, с помощью которых обеспечивается разделение каркаса на отсеки. Изготовление форм может проводиться из влагонепроницаемой фанеры. Для того чтобы зафиксировать доски, в них предварительно нужно сделать пропилы.
Размеры ячеек должны совпадать с размерами, которые в соответствии с проектом должен иметь готовый блок. Для того чтобы ускорить производственный процесс, рекомендовано провести одновременное сооружение нескольких форм. Для того чтобы исключить возможность прилипания раствора к формам, их нужно предварительно смазать специальным средством. В домашних условиях рекомендовано применение отработанного машинного масла, которое разводится водой в соотношении 1:3.
Для того чтобы ускорить изготовление газобетона можно использовать мобильные установки, которые состоят из компрессора, смесителя и соединительных рукавов. Предварительно подготавливаются приспособления, с помощью которых удаляются излишки бетона.
Приготовление раствора
Процесс изготовления газобетона в домашних условиях начинается с приготовления раствора. Количество используемых компонентов зависит от того, какой плотности материал пользователь хочет получить. Рассмотри вариант приготовления раствора для газобетона, плотностью 1600 килограмм на метр кубический. Для этого понадобится 1100 килограмм песка и 400 килограмм цемента. Компоненты тщательно перемешиваются. К ним нужно добавить 5 кг извести. Также в раствор добавляются такие добавки, как каустическая сода, алюминиевая пудра и сульфат натрия.
После тщательного перемешивания всех сухих компонентов, они заливаются 189 литрами воды. После перемешивания состава до однородности его можно использовать для заливки.
Заливка
После смазывания форм специальным составом, в них заливается раствор. При этом нужно следить, чтобы формы не заливались до краев, так как при застывании смесь вспучивается и излишки будут вылизать наружу. Формы нужно заливать до половины. После заливки материала наблюдается появление процесса газообразования. На следующем этапе проводится удаление излишков смеси с применением металлических струн. Процедура проводиться по истечению 5-6 часов после заливки.
Спустя 18 часов после заливки можно проводить распалубку изделий. Для того чтобы газобетонные блоки лучше отходили, нужно немного постучать по формам. По истечению месяца газобетон обретет техническую прочность. Затвердевание блоков наблюдается не только в помещениях, но и на открытых площадках.
Сравнение изделий самостоятельного и заводского выпуска
При производстве газобетонных блоков своими руками они затвердевают гидратационно, а на производстве – автоклавно. Эти материалы отличаются между собой по техническим и физическим параметрам. На производстве изготавливаются блоки стационарным и конвейерным способом. При использовании второго варианта снижается необходимость в участии человека к минимуму. В домашнем производстве материала человек принимает постоянное и непосредственное участие.
Рентабельность производства
На рентабельность изготовления блоков влияют разнообразные факторы. Она зависит от:
- Стоимости сырья;
- Вложений на покупку оборудования;
- Количества производственных отходов;
- Желаемого объема;
- Цели производства.
Специалисты провели расчеты в соответствии с показателями, в соответствии с которыми было установлено, что сделать газобетонные блоки своими руками дороже, чем приобрести готовый материал. Кроме того, этот процесс требует затрат сил и времени.
Газобетонные блоки – это универсальный строительный материал, который широко применяется для возведения зданий. Приобрести его можно на заводах и в строительных магазинах. Также можно провести изготовление блоков своими руками, предварительно рассчитав рентабельность этого процесса.
1beton.info
Газобетонные блоки своими руками: технология изготовления (видео)
Сегодня для строительства все чаще применяются материалы, которые можно сделать своими руками, закупив только необходимые ингредиенты. Все они характеризуются отличными эксплуатационными особенностями, прочностью; стоимость их выходит в итоге не слишком большая. Одним из таких материалов является газобетон. Укладка блоков простая, а сам материал отличается многочисленными достоинствами включая хорошие теплоизоляционные свойства, важные для строительства дома.
Газобетонные блоки имеют хорошие теплоизоляционные свойства.
Газобетон не является новинкой на рынке, впервые он использовался для строительства еще в начале прошлого века. Активное его применение в сооружении зданий началось около 10 лет назад. Хотя сама технология изготовления газобетона была запатентована Эриксоном, архитектором из Швеции, в далеком 1924 году.
Ранее газобетон изготавливался только в заводских условиях, так как для этого требовалось в точности соблюдать технологию и подбор пропорции для замешивания. Само производство несложное, но вес одного блока, который получается после заливки, не самый малый, поэтому работы надо выполнять хотя бы вдвоем.
Для производства газобетона потребуются:
Таблица производства газобетонных блоков.
- портландцемент;
- кварцевый песок;
- алюминиевая пудра;
- вода;
- известь.
Сам процесс изготовления основан на использовании одного из 2-х методов:
- автоклавного;
- неавтоклавного.
Первый метод применяется в заводских условиях, так как для него необходимо наличие спецоборудования. Блоки после заливки спекаются при специально созданных условиях. Самостоятельно создать их не получится, поэтому практичнее использовать 2-й метод. Бетон заливается в формы и высыхает в естественных условиях. Газобетонный блок затем извлекается и при необходимости разрезается на части. Хотя лучше сразу использовать для заливки формы, которые соответствуют требуемым размерам.
Компоненты для изготовления смеси
Чтобы сделать газобетонные блоки своими руками, необходимо приготовить следующие ингредиенты:
Таблица размеров газобетонных блоков.
- На каждый кубометр готового газобетона (по выходу) требуется примерно 250-300 л воды. Это должна быть чистая питьевая воды. Лучше всего ее брать из поверхностных слоев любых чистых источников.
- На кубометр готового газобетона требуется примерно 260-320 кг цемента. Для самостоятельного изготовления используются марки M500D0, M400D0.
- Карьерный песок, речной, очищенный. Количество его на кубометр готовой смеси составляет 250-350 кг. Лучше всего брать мелкий, размер частиц которого составляет до 2 мм. Ни в коем случае не допускается содержание веток, мусора, глины.
- Специальные добавки для газобетона. Количество 1-3 кг на каждый кубометр готовой смеси.
- Газообразователь, т. е. алюминиевая пудра. Достаточно 0,5-0,7 кг на каждый готовый кубометр бетона. Пудра нужна для того, чтобы в смеси началась реакция, необходимая для газообразования. Во время замешивания начинает выделяться газ, внутри бетона образуются пузырьки, ячейки, которые и придают составу необходимые ему качества.
- Смазка для контейнеров в количестве 0,3-0,5 кг на куб. Перед тем как начать заливку эмульсиями тщательно смазываются формы. Нельзя применять отработанные масла, так как они содержат большое количество сажи.
Сделать газобетон своими руками не так сложно, но важно в точности соблюдать все этапы производства, подобрать ингредиенты для будущей смеси в правильной пропорции.
Список оборудования:
- Формы для заливки будущих газобетонных блоков, которые могут иметь различный размер. Лучше всего приобретать уже готовые контейнеры.
- Струны, которые необходимы для удаления излишков смеси с поверхности форм.
- Бетономешалка, которая будет использована для перемешивания смеси.
Вернуться к оглавлению
Требования к ингредиентам
Таблица сравнения характеристик газобетона и пенобетона.
Самостоятельно сделать большой объем строительного материала не получится, но для сооружения небольшого дома их вполне хватит. Вес одного блока стандартного размера может составлять примерно 650 кг. Поэтому необходимо присутствие нескольких человек не только для выполнения кладки стен, но и для заливки форм, вытаскивания газобетонных блоков из контейнеров. При выполнении всех условий газобетонные блоки получатся прочными и качественными, стоимость их будет меньше, чем при покупке уже готового материала.
Можно использовать специальные установки, которые замешивают газобетон в автоматическом режиме. Их можно арендовать, но зато оборудование самостоятельно дозирует ингредиенты, выполняет замешивание бетона именно того качества, которое необходимо. Расходы на аренду будут оправданы.
Пропорции газобетона могут быть различными, но лучше всего придерживаться следующей формулы (для газобетона D-600):
- портландцемент ПЦ500 D0 — 65%;
- очищенный песок — 30%;
- доломит — 5%;
- В/Т — до 0,48.
Известковая мука, т. е. доломит, может содержать примерно до 10% газобетона, но важно определиться с тем, какой цвет блоков необходим. При большем количестве извести цвет газобетонных блоков будет более светлым. Большое количество пудры также не требуется, она выступает в качестве катализатора реакции газообразования.
Вернуться к оглавлению
Процесс изготовления газобетона
Схема дома из газобетонных блоков.
Чтобы сделать ячеистый бетон, необходимо выполнить несколько этапов, которые включают:
- дозировку ингредиентов, перемешивание сухой смеси;
- добавление воды, замешивание раствора;
- заполнение получившейся массой форм для заливки;
- выдержку смеси для набора прочности, высыхание газобетонных блоков и их извлечение из форм.
Необходимо тщательно отмерить все сухие ингредиенты, нужные для производства газобетонных блоков. Основными материалами являются цемент, известь, песок. Чтобы запустить процесс газообразования, необходимо использовать алюминиевую пудру. После реакции с водой она провоцирует выделение водорода, смесь начинает вспениваться. Пропорции очень важны, так как именно от них зависит прочность, пористость и другие характеристики будущего газобетона.
Схема производства газобетона.
На втором этапе осуществляется перемешивание компонентов. Масса должна получиться однородной. От качества замеса зависит и то, каким будет газобетон после приготовления. Для замешивания необходимо использовать только специальное оборудование. Подойдут бетономешалки, вручную этот процесс не производится.
Когда будущий бетон перемешан, необходимо начинать его заливку по формам.
Формы применяются специальные, лучше всего приобрести уже готовые, которые полностью соответствуют всем требованиям.
Заливка проводится только до половины форм, ни в коем случае нельзя заливать их полностью. Это объясняется тем, что в процессе газообразования смесь сильно увеличивается в объемах, полностью заполняя все формы. После того как увеличение объема закончено, при помощи металлического прута необходимо сверху все излишки смеси убрать, чтобы верхняя часть получилась ровной и гладкой. Производится это примерно через 6 часов после того, как заливка была выполнена.
Вернуться к оглавлению
Как происходит сушка газобетонных блоков?
Правильная и неправильная отделка домов из газобетона.
Далее будущие блоки выдерживаются в формах примерно 12 часов, при этом держать их надо на закрытой площадке. Затем их можно извлекать из контейнеров, далее их на пару суток оставляют на ровной поверхности для набора прочности. Для полного приобретения всех необходимых показателей газобетонный блок надо выдерживать 28 дней.
Во время заливки можно использовать контейнеры различных форм и размеров. Во время планирования надо учесть и то, что некоторое количество материала может уйти на подбор правильной пропорции, так как универсального рецепта нет. Еще некоторое количество может уйти на брак. В любом случае изготовление газобетонных блоков своими руками будет более дешевым, чем покупка уже готовых или использование других материалов для строительства, например, традиционного кирпича.
После того как весь материал готов, может начинаться его укладка. Для этого применяется специальный клеевой раствор, который обеспечивает не такую большую толщину шва, как при цементном растворе. В итоге теплопотери будут меньшие, а прочность выше. Начинается кадка от угла, обязательно надо для каждого ряда соблюдать перевязку, чтобы стена получилась прочной и надежность. Во время кладки необходимо использовать металлические пруты для армирования. Процесс этот несложный, следует заранее проделать в блоках пазы — в них и будут устанавливаться пруты. После этого сверху укладывается слой раствора, начинается кладка следующего ряда.
Газобетонные блоки представляют собой прочный и качественный строительный материал, который используется для различных целей. Сегодня он стал популярен для малоэтажного частного строительства. Некоторые умельцы предпочитают не покупать такие блоки в уже готовом виде, а делать их своими руками. Для этого необходимо в точности соблюдать разработанную технологию изготовления.
Источник
thewalls.ru
Изготовление газобетона своими руками в домашних условиях
Еще больше удешевить строительство собственного дома или дачи можно, если сделать газобетон своими руками. Газобетонные блоки давно стали незаменимым строительным материалом для быстрого и недорогого возведения различных построек.
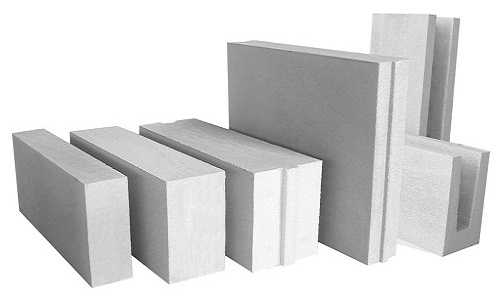
В состав газобетонных блоков входят: цемент, известь, песок кварцевый, камень гипсовый, пудра из алюминия и вода.
В технологии изготовления неавтоклавного пористого бетона нет ничего сложного. В состав входят доступные и широко распространенные материалы, а условия созревания состава нормальные. Все это говорит о том, что сделать газобетон своими руками реально.
Особенности газобетона
Газобетонные блоки представляют собой правильные параллелепипеды из пористого бетона. Сам материал является разновидностью бетона на цементной основе, в котором равномерно распределены воздушные поры размером до 3 мм. В качестве добавки для образования пор обычно используется алюминиевая пудра или паста. В целом бетонная смесь имеет следующий состав: цемент, песок, алюминиевая пудра, вода, а также различные добавки.
Технология производства газобетонных блоков.
По способу изготовления газобетон подразделяется на автоклавный и неавтоклавный. Первый тип материала получают в автоклаве при повышенном давлении и температуре, что реализуется только в промышленных условиях, обеспечивающих должный контроль процесса в экстремальной обстановке.
Неавтоклавный способ изготовления реализуется в естественных условиях, что позволяет применять его самостоятельно. Технология производства основана на том, что при контакте алюминиевого порошка с водой происходит бурная реакция с выделением углекислого газа. Если этот процесс происходит в закрытой форме внутри вязкой массы, то газы образуют поры в объеме этого материала. Даже после того, как газы выйдут за пределы смеси, поры остаются в толще смеси. После затвердения массы в нормальных атмосферных условиях получается газобетон, т. е. бетон с закрытыми порами по форме, близкой к круглой, диаметром в 1-3 мм.
Пористая структура обеспечивает главные преимущества материала, а именно высокие теплоизоляционные свойства в сочетании с низким удельным весом при достаточно высокой прочности на сжатие. Газобетонные блоки имеют плотность от 300 до 1200 кг/м³ в зависимости от количества вводимого порообразующего вещества.
Вернуться к оглавлению
Особенности изготовления
Технология получения неавтоклавного газобетона включает в себя несколько обязательных этапов и условий. Порообразующий компонент добавляется в цементно-песочную смесь и равномерно распределяется по объему. Процесс образования пор происходит достаточно активно с расширением объема при контакте пудры с водой.
Производство неавтоклавного газобетона.
Для удержания пор внутри массы реакция выделения газа должна протекать в формах, имеющих достаточную прочность. Внутренняя полость пресс-формы задает размеры получаемого блока газобетона. Для первичного затвердения массы необходимо не менее 2 часов. После этого бетон может извлекаться из формы, но должен находиться в стационарном состоянии на стеллажах до полного отвердения. Окончательно величина прочности достигается только после 28 дней сушки блоков. Для изготовления газобетона своими руками необходимо обеспечить выполнение основных условий и произвести ряд необходимых работ.
Вернуться к оглавлению
Необходимые инструменты
Для изготовления газобетонных блоков своими руками потребуются следующие инструменты:
- болгарка;
- ножовка;
- рубанок;
- электродрель;
- ножовка по металлу;
- нож;
- молоток;
- лопата;
- миксер;
- линейка;
- фен строительный;
- мастерок;
- шпатель;
- струна стальная;
- стамеска;
- зубило;
- весы;
- ведро мерное.
Вернуться к оглавлению
Приготовление смеси
Состав газобетона.
Стандартная смесь для газобетона содержит цемент, песок, воду и известь. В качестве вещества, образующего поры, применяется алюминиевая пудра. Гашеная известь исполняет роль пластификатора. Для улучшения свойств рекомендуется использовать дополнительные добавки: сульфат натрия (не более 0,5%) и каустическую соду (не более 1,5% по весу).
Основу газобетона составляет цемент. Рекомендуется использовать портландцемент марки М400 или М500. Наполнитель берется в виде кварцевого песка. Его следует тщательно просеять с удалением крупных фракций. Глина в песке может быть только в виде небольших следов и составлять не более 7% от веса песка. Рекомендуются следующий состав и соотношение ингредиентов бетонной смеси:
- цемент — 50-70%;
- песок — 20-40%;
- известь, каустическая сода, сульфат натрия — 1-5%;
- алюминиевая пудра — 0,04-0,09%;
- вода — 0,25-0,8%.
Смесь должна быть тщательно перемешана. Путем изменения содержания цемента и порообразующего состава можно регулировать объем пор в бетоне, то есть изменять плотность материала.
Вернуться к оглавлению
Изготовление формы
Виды газобетонных блоков.
Для того чтобы решить вопрос о том, как сделать газобетон, надо обеспечить изготовление формы для заливки бетонной смеси. Такие формы могут быть двух типов. Первый тип (наиболее простой) представляет собой прямоугольный короб с высотой, равной высоте блока. Площадь короба должна вмещать объем массы, из которого можно сделать несколько (4-9 штук) газобетонных элементов. Если запланирован значительный объем изготовления газоблоков, то форму лучше сделать из стальной полосы толщиной в 4-5 мм. Конструкция должна быть разборной, чтобы облегчить выемку бетонной заготовки. Сверху надо предусмотреть съемную крышку. Целесообразно предусмотреть ее крепление к бортам короба с помощью болтов (винтов) или других зажимов. Упрощенный вариант формы можно сделать из дерева. Для бортов короба следует использовать доску толщиной в 30-40 мм.
Второй тип формы представляет собой решетчатую систему. В такой конструкции полость короба разделена перегородками на ячейки, в которых формируется по одному газоблоку. Такая форма тоже может быть изготовлена из стальной полосы или дерева. Для внутренних перегородок может использоваться фанера толщиной в 12-15 мм.
Вернуться к оглавлению
Изготовление газобетона в домашних условиях
Перед началом работ внутреннюю поверхность формы необходимо тщательно смазать машинным маслом для исключения прилипания массы. Форму рекомендуется прогреть до температуры около 40º С. В равномерно перемешанный бетонный раствор вводится алюминиевая пудра, и он заливается в форму.
Таблица производства газобетонных блоков своими руками.
Заливать надо на высоту, примерно равную половине высоты борта короба, что учитывает расширение массы при прохождении химической реакции с образованием пор.
Бурная реакция с выделением газа протекает в течение 6-8 минут. В это время наблюдается активный рост уровня массы в форме. По окончании реакции расширение состава прекращается, а затем происходит небольшая усадка раствора. После прекращения вертикального перемещения уровня с помощью прочной стальной струны срезаются с поверхности заготовки все неровности (бугры, наплывы). Поверх успокоившейся заготовки блока накладывается теплоизоляционный материал: асбест, пенопласт и т. д. Сверху форма закрывается крышкой.
Производится естественная сушка газобетонных блоков. Минимальное время сушки — 2 часа. После этого монолит можно разрезать на блоки нужного размера. Рекомендуемое время до начала транспортировки на площадку для хранения — 24 часа. В процессе работ необходимо исключить возникновение сквозняков. Работа вентилятора не рекомендуется. Охлаждение массы должно быть медленным и равномерным.
Вернуться к оглавлению
Дополнительные рекомендации
Перед подготовкой бетонной смеси необходимо проверить качество цемента: целостность упаковки, срок изготовления, наличие слипшихся комков и т. д. Следует применять только качественные ингредиенты.
Форму для изготовления блоков надо устанавливать на горизонтальной ровной поверхности (желательно металлической). Одновременно рекомендуется использовать несколько форм, чтобы раствор перемешивать сразу в значительном количестве. Сам процесс изготовления следует осуществлять в теплом помещении. Если формовка блоков производится на открытом воздухе, то следует выбрать теплую погоду, а участок должен быть закрыт от ветра.
Газобетонные блоки рекомендуется выдержать на площадке хранения до полного набора прочности (28 дней).
Прогрев формы надо производить равномерно (по всему ее объему). Если используется несколько форм, то необходимо им всем обеспечить одинаковые температурные режимы.
При выборе размеров форм лучше всего исходить не из стандартных размеров блоков, а из размеров, наиболее подходящих для вашего строения, чтобы в будущем не приходилось часто разрезать элементы. Можно путем вкладок в форму изготавливать некоторые элементы другой конфигурации.
Технология изготовления неавтоклавных газобетонных блоков достаточно проста. При правильной организации работ нужное количество строительных элементов вполне можно сделать своими руками в домашних условиях.
tolkobeton.ru
Как производят газобетон. — Как это сделано, как это работает, как это устроено — LiveJournal
Газобетон — современный энергоэффективный материал для индивидуального строительства. Он относится к ячеистым бетонам т.к. до 85% объема материала занимают пузырьки газа. Газобетон обладает превосходными теплоизоляционными характеристиками, имеет небольшую массу и легко поддается обработке. И самое главное — дом из газобетона можно построить самостоятельно, без посторонней помощи (один человек в день может выложить до 3 кубических метров газобетона). Главное не путать газобетон и пенобетон, это совершенно разные материалы, об этом поговорим в конце репортажа.Чтобы более подробно увидеть процесс производства газобетона я отправился на завод Ytong в Можайске, начавший свою работу в 2008 году. По объемам произодства газобетона, это самый крупный завод в России. Смотрим!
2. Для производства газобетона используется безопасное сырье: цемент (~20%), известь (~20%), кварцевый песок (~60%), алюминиевая паста (~1%) и вода. Все компоненты смешиваются в определённых пропорциях, которая определяется требуемой прочностью готовой продукции.
3. Основу газобетона составляет песок, который нужно предварительно обработать.
4. Для этого используются шаровые мельницы.
5. Внутри барабана находятся вот такие шары, которые измельчают песок до превращения в пыль. Это нужно для того, чтобы после формовки блоки было легче обрабатывать.
6. После этого исходное сырье поступает в накопительные бункера на хранение. Затем в газобетоносмесителе происходит смешивание песка, цемента и извести.
7. А непосредственно перед заливкой к уже смешанным компонентам добавляется вода и суспензия алюминиевой пасты. Готовая смесь заливается в специальную прямоугольную форму (стенки формы не имеют жесткого соединения с дном) примерно на 2/3.
8. Именно на этом этапе происходит самое интересное. Алюминиевая паста вступает в реакцию с известью, в результате получается водород. Он образует в сырьевой массе огромное количество пор размером от 0,5 до 2 мм, разномерно распределённых внутри. Поддоны со смесью медленно продвигаются в герметичном помещении с запредельной влажностью (это единственный кадр, который я успел сделать до того, как запотел объектив) до тех пор, пока смесь не увеличится в объеме до верхней кромки поддона.
9. Через некоторое время (2-3 часа) транспортёр переносит форму с застывшей смесью на следующий этап. Показательно, что подъемник только за счёт ваккуума удерживает поддон без дна.
10. Теперь застывшую форму разрезают на блоки равного размера. Сначала в поперечном, а затем продольном направлениях. На заводе одна линия, которая единовременно может производить блоки только одного размера. Для производства блоков другого типоразмера просто заменяют ножи. Большая площадь для складирования готовой продукции позволяет всегда иметь в наличии полный ассортимент продукции.
11. После этого внешняя проверхность блоков шлифуется и затем они прижимаются друг к другу.
12. Кран захватывает поддон с блоками и переносит их на следующий этап производства.
13. И сразу же укладывается новый поддон в основание для следующей партии блоков. Да, очень важный факт — производство на заводе полностью автоматизировано и практически не требует участия человека. Люди работают только на линии упаковки (она пока еще не настолько автоматизирована), складе и в испытательной лаборатории. Всего на заводе работает менее 80 человек (завод работает круглосуточно).
14. Теперь блоки нужно поместить в автоклав. Слева «сырые» блоки, справа уже «готовые». Здесь хочу упомянуть следующий момент, после автоклавирования блоки имеют влажность порядка 30%, которая постепенно (в течение года) упадёт до 5-10%.
15. Автоклавирование очень важный этап, улучшающий свойства газобетонных блоков.
16. Разрезанные блоки помещают в специальные автоклавные камеры, где они в течение 12 часов при повышенном давлении в 12 кг/кв. см. обрабатываются насыщенным паром при температуре 190°C. При этом температура в начале и конце цикла плавно поднимается и опускается в течение определённого времени.
17. Каждый автоклав имеет длину более 30 метров. Использование автоклавирования позволяет повысить прочность газобетонных блоков и уменьшить его последующую усадку (менее 1 мм/м).
18. Каждая партия блоков после автоклавирования отправляется в лабораторию для проверки на соответствие заданным характеристикам. На этом станке нарезаются кубики правильной формы, которые затем отправятся на испытания.
19. А готовые блоки отправляются на линию упаковки. Здесь их складывают в 2 ряда. Позиционирование рядов блоков производят вручную.
20. Затем их переворачивают на бок под уже установленные деревянные паллеты. После чего блоки запечатываются в плёнку (чтобы защитить их от повреждений) и отправляются на склад.
21. Склад расположен под открытым небом, здесь всегда есть запас всей выпускаемой продукции. Ежедневно с завода отгружается покупателям более 2000 кубометров блоков.
22. Основная продукция завода это блоки толщиной от 50 до 500 мм с плотностью от 400 до 500 кг/куб.м.
И ещё несколько слов про различия газобетона и пенобетона. Понятно, что газобетон материал новый, но очень многие неосознанно их путают даже не понимая, что их характеристики существенно отличаются.
Во-первых, их различие кроется в названии. Для производства пенобетона используется пена, состоящая их вредных химических веществ (канифоль, клей, едкий натр и т.д.). А в производстве газобетона используется газ, образующийся в результате химической реакции извести и алюминиевой пасты, в результате получается просто водород. То есть газобетон является экологически чистым строительным материалом.
Во-вторых, пенобетон имеет очень низкие прочностные характеристики. А здесь, как известно, имеет место быть обратная зависимость. То есть, чем ниже плотность (и соответственно прочность), тем «теплее» материал. Но если газобетон плотностью D400 (400 кг/кв.м) можно использовать для несущих стен в домах до 3 этажей включительно и он будет обладать классом прочности В2,5 и морозстойкостью F100, то из пенобетона плотностью ниже D600 вообще нельзя делать несущие стены. Следовательно и теплопроводность пенобетона D600 будет значительно выше (то есть «холоднее»), чем газобетона D400.
В-третьих, технология производства пенобетона обычно не подразумевает использования автоклавов и нарезки блоков после застывания. Обычно его заливают сразу в готовые формы, а в результате блоки дают большую усадку (3-5 мм/м) после строительства. Не говоря уже о том, что сам процесс автоклавирования повышает прочность блоков в 3-4 раза.
Немного видео с производства:
Взят у victorborisov в Производство газобетонных блоков
Читайте наше сообщество также вконтакте, где огромный выбор видеосюжетов по тематике «как это сделано» и в фейсбуке.
kak-eto-sdelano.livejournal.com
Как сделать газобетонные блоки своими руками
Блоки из газобетона относятся к тем популярным строительным материалам, которые ценятся за прекрасные свойства и надежное качество. В настоящее время газобетонные блоки можно сделать своими руками. При этом, стоимость строительства будет на порядок дешевле, а производство блоков достаточно простое. Изготовить блоки в объеме, необходимом для строительства небольшого жилого дома, вполне реально.
Немного истории
Технология производства газобетона была изобретена еще в начале XX века в Швеции. С тех пор газобетонные блоки стали применяться в строительстве. Однако, не так часто, как теперь. Активно использовать газобетонные блоки стали только в последнее десятилетие. Сначала их изготовлением занимались исключительно промышленные предприятия. А сейчас любому строителю по силам сделать блоки из этого материала самому.
Способы производства газобетона
Процесс изготовления газобетонных блоков нетрудный. Однако, учтите, что из-за их большого веса (примерно 650 кг.) потребуется участие, как минимум, двух человек.
Существуют два способа производства блоков:
- первый способ — «автоклавный». Он применим лишь в заводских условиях, поскольку в этом случае происходит спекание блоков при помощи специального оборудования.
- второй способ заключается в том, что раствор, залитый в форму нужного размера, затвердевает естественным путем. Именно этот способ можно применять при самостоятельном изготовлении газобетонных блоков.
Компоненты газобетона
Для изготовления блоков вам понадобятся:
- песок (карьерный, речной), который должен быть мелким (до 2 мм.) и обязательно чистым, без мусора. На 1 кубометр смеси его потребуется – 250-350 кг.
- цемент (лучше взять марку М500D0 или М400D0). На 1 кубометр смеси его потребуется – 260-320 кг.
- вода, которая также должна быть чистая, лучше питьевая. На 1 кубометр смеси ее потребуется – 250-300 л.
- алюминиевая пудра. Она вступает в реакцию с водой, после чего начинается процесс газообразования. Смесь пенится, а внутри состава формируются пузырьки. На 1 кубометр смеси ее потребуется – 0,5-0,7 кг.
- смазка, которой обрабатывают формы перед заливкой. Потребность масла примерно составляет 0,3-0,5 кг.
Необходимое оборудование
При производстве блоков требуются следующие приспособления:
- контейнеры, необходимые для заливки состава
- металлический прут, с помощью которого удаляют лишний раствор
- бетономешалка (при этом обратите внимание, что выгодно арендовать установку, которая работает автоматически: сама определяет количество ингредиентов, сама перемешивает состав).
Этапы производства газобетона
Далее подробно рассмотрим технологию изготовления блоков, которая состоит из следующих этапов:
- 1 этап — подготовка всех ингредиентов и сухое перемешивание. Нужно тщательно рассчитать правильные пропорции всех входящих в состав газобетона компонентов (о них подробно рассказано выше).
- 2 этап — добавление воды и перемешивание состава. Хороший замес в последствие определит качество готового изделия. После добавления воды начнется вспенивание (газообразование), что придаст бетону нужную пористость.
- 3 этап – заливка смеси в специально предназначенные для этого контейнеры, которые рекомендуем брать сразу нужной формы, чтобы в последствие не разрезать блок. При этом наполнение контейнера проводится только до половины, поскольку в результате газообразования смесь значительно увеличится и заполнит всю форму.
- 4 этап – через 6 часов после заливки нужно выровнять поверхность, убрав лишний объем смеси металлической струной (прутом).
- 5 этап – сушка в течение 12 часов в контейнерах. Потом блоки вынимают и держат примерно двое суток на ровной площадке. Полный цикл выдержки блоков составляет 28 дней. После этого они готовы к работе.
Итак, если вы планируете частное строительство, то вполне можете самостоятельно справиться с изготовлением газобетонных блоков. Этот прочный материал с прекрасными теплоизоляционными свойствами отлично пойдет для сооружения стен вашего дома.
stroi-remontirui.ru
Оборудование для производства газобетонных блоков. Как делают газобетонные блоки
В зависимости от требуемых объемов производства бывают разные виды оборудования.
- Мобильные установки
- Стационарное оборудование
- Мини установки
- Конвейерные установки
Так же сам процесс изготовления блоков может быть полностью автоматизирован либо полуавтоматизирован.
Но независимо от вида установки и процесса производства, оборудование чаще всего состоит из следующих компонентов:
Смесителей-активаторов – емкость с лопастями, в которой смешивают все компоненты для газобетона. Чаще всего используют самоходный или передвижной смеситель. Он сам перемещается от зоны загрузки компонентов до зоны выгрузки смеси в формы. Смесители бывают разных емкостей, соответственно, от его размеров зависит объем производимого газобетона, так же зависят размеры помещения, в котором происходит процесс изготовления блоков.
Производительность смесителей измеряется в м.куб. в сутки, чем больше производительность, тем больше потребляемая мощность электроэнергии. Поэтому смесители с большой производительностью устанавливают только на крупных предприятиях, так как не экономно для маленьких объемов ставить подобный смеситель.
Формы для газобетонных блоков – в них разливается полученная ранее смесь из смесителя. Бывают формы разборные и колпачные. В разборных формах все борта снимаются вручную, а в колпачных только механизировано, так как у них сплошной каркас. Формы могут быть металлическими, деревянными или пластиковыми, но чаще и целесообразней всего используют формы из металла. Емкость форм должна соответствовать емкости смесителя. При выгрузке смеси в форму, они заполняются только на половину, так как спустя несколько часов смесь подымается. Если появляются неровности на поверхности бетона, их необходимо срезать струной.
и выдерживается в них 8-16 часов.
Оборудование для резки блоков – кондуктор для резки блоков, пилы для резки (ручные, сабельные, электропилы). Если получается неровная поверхность блока, можно использовать рубанок для газобетона. С его помощью все грани блока делаются идеально ровными.
Аавтоклавные печи (для автоклавного газобетона). Там происходит сушка блоков на протяжении 12 часов под высоким давлением.
Дозаторы для всех компонентов, транспортеры, подъемники для загрузки сырья, виброустановки для увеличения прочности газобетона.
Популярные производители оборудования для изготовления газобетонных блоков на российском рынке: «ИННТЕХГРУПП», компания «Метем», ООО «Свой дом», промышленная группа «СтройКомплект», «HESS AAC», « China Yanbian Kangrun».
Как делают газобетонные блоки
- Засыпка и смешивание всех компонентов в смеситель. Сначала засыпаю воду, известь, цемент и перемешивают 4-7 мин., потом добавляют раствор воды с алюминиевой стружкой, заранее хорошо размешанной смесителем.
- Заливка форм. Сразу же после добавления суспензии, смесь из смесителя переливается в формы при помощи шланга. В формах раствор выстаивается около 2-4 часа.
- Извлечение блоков или снятие бортов форм. После того, как раствор достиг определенной прочности, борты формы разбирают и готовят газобетон к резке.
- Резка на блоки. Обычно при помощи резочного кондуктора и пилы весь массив режется на части.
- Сушка в автоклаве. При температуре 190°С и давлении 12 атм. блоки сушатся около 12 часов. Если же производится не автоклавный газобетон, то блоки выдерживаются в сухом помещении при температуре 20° С около двух суток.
- Упаковка и хранение. Что бы блоки набрали требуемой прочности, им нужно выстояться в течение 28 дней. Поэтому после их производства, их укладывают на поддон и упаковывают специальной термоусадочной пленкой, а затем отправляют на склад.
kudavlozitdengi.adne.info
Стены из газобетона своими руками | Своими руками
Свойства газобетона
Сырьевыми компонентами для производства газобетона служат песок, известь, цемент, вода и алюминиевая паста. Отформованная масса пропаривается под давлением в автоклавных установках при температуре 180-200 °С, в результате чего твердеет. Материал изготавливают в виде блоков, в том числе крупноформатных и обладающих нестандартной формой.
На нашем рынке он представлен продукцией марок Ytong (Германия), AeroStone, Bonolit, EuroBlock, Poritep, «Грас» (все – Россия) и др. У газобетона целый ряд достоинств, среди которых – высокая прочность на сжатие, хорошая паропроницаемость, экологическая и пожарная безопасность, хорошее звукопоглощение, простота обработки (легко режется специальной ножовкой).
Но главный плюс газобетона – отличные теплозащитные свойства, что позволяет строить из него здания с однослойными наружными стенами малой толщины. То есть не требуется дополнительно утеплять ограждающие конструкции тем или иным теплоизоляционным материалом, срок службы которого будет, скорее всего, меньше срока службы самих конструкций.
При сооружении в средней полосе России коттеджа высотой до 4 этажей большинство производителей рекомендует для наружных стен применять блоки толщиной 375 мм и плотностью марки D500. Теплотехнические свойства ограждающих конструкций из таких блоков в сочетании со штукатурной отделкой почти соответствуют требованиям СНиП 23-02-2003 «Тепловая защита здания» по сопротивлению теплопередаче (R0) стены в этом регионе (не стоит забывать и о том, что те-плопотери через стены значительно меньше, чем через окна, двери, крышу, фундамент, подвал). Некоторые производители выпускают блоки плотностью D400, которые обладают необходимой несущей способностью, но при этом обеспечивают величину R0, превышающую требования СНиПов (чем меньше плотность блока, тем лучше его теплозащитные характеристики).
Читайте также: Строительство дома из керамоблоков
Фундамент для дома из газобетона
Вес здания из газобетона значительно меньше, чем из других каменных материалов (в частности, из крупноформатного кирпича), а потому и нагрузка на фундамент ниже. Понадобится менее массивный фундамент, а значит, расходы на его сооружение также будут меньше. Однако у газобетона сравнительно низкая прочность на изгиб, и, чтобы избежать появления трещин в стенах дома, необходимо создать надёжное основание под кладкой.
Опирание железобетонной плиты на стену из газобетонных блоков:
1. Газобетонный блок
2. Внутренняя отделка
3. Выравнивающий слой из цементнопесчаного раствора
4. Слой эффективной теплоизоляции
5. Монолитная железобетонная плита
6. Доборный газобетонный блок
7. Наружная отделка
Тип и конструктив фундамента выбирают в соответствии с геологическими исследованиями грунта и расчётными нагрузками на основание. Возможно возведение фундаментов любых типов.
Отметим, что самым экономичным и быстро реализуемым решением можно считать сборное основание в виде ленты из блоков ФБС, заложенное на глубину промерзания грунта.
Готовые крупноформатные блоки устанавливают с помощью крана, и сразу после их укладки можно приступать к сооружению стен. Другой сравнительно недорогой и быстровозводимый вариант основания – буронабивные сваи с железобетонным ростверком.
Комментарий
«Среди ошибок, допускаемых при возведении стен из газобетона, – укладка блоков на обычный цементно-песчаный раствор вместо специального клеевого состава, рекомендованного производителем газобетона. Обычный раствор предполагает толстый шов (10-15 мм), что приводит к существенным теплопотерям через кладку (при отсутствии дополнительного утепления). Зачастую на вертикальную часть блока наносят слой клеевого состава меньшей толщины или не наносят его вообще, что ухудшает эксплуатационные свойства стены. Блоки необходимо укладывать с перевязкой размером не менее 110 мм для передачи нагрузки от блока к блоку Отсутствие такой перевязки чревато появлением трещин в стене здания. Притом влага, попадающая в трещины, при замерзании будет увеличиваться в размерах, и они также станут расти. Трещины могут образоваться и из-за отсутствия монолитных обвязочных поясов по периметру дома на уровне перекрытий, а также если не предусмотрено армирование под оконными проёмами».
Опирание стропил на стену из газобетонных блоков:
1. Стропильная нога
2. Металлический уголок
3. Мауэрлат
4. Гидроизоляция
5. Армопояс
6. Шпилька
7. Слой эффективной теплоизоляции
8. Газобетонный блок
Стены и перекрытия из газобетона
Принципиальная разница между кладкой из газобетонных блоков и кладкой из других каменных материалов (крупноформатного кирпича, пенобетонных блоков и др.) заключается в том, что стену из газобетона возводят с использованием специального клеевого раствора на цементно-песчаной основе, толщина которого – всего 1 -3 мм (для сравнения: размер шва в кирпичной кладке – 10-15 мм). Шов – это мостик холода в конструкции стены, поскольку обладает большей теплопроводностью, и чем он тоньше – тем меньше потери тепла.
Столь тонкий шов возможен благодаря тому, что ведущие производители выпускают блоки с очень точной геометрией. Соблюдать толщину шва во время кладки позволяет специальный инструмент – кельма. Клеевым составом фиксируют как горизонтальную, так и вертикальную часть блока. Швы следует заполнять клеем на всю глубину кладки.
Первый ряд блоков укладывают поверх отсечной гидроизоляции (чаще всего рулонной битумной или битумнополимерной). Важный момент: блоки первого ряда фиксируют к основанию с помощью обычного цементно-песчаного раствора.
Дело в том, что верхняя поверхность фундамента не бывает идеально ровной (плоской), а подобный раствор (толщиной не менее 20 мм) позволяет нивелировать незначительные перепады по высоте (их допустимая величина – не более 20 мм). Очень важно добиться ровности первого ряда кладки, поскольку от этого зависит ровность стен всего здания. Небольшие перепады между соседними блоками устраняют с применением рубанка и шлифовальной доски.
Читайте также: Дом из газобетона – плюсы строительства
Для устройства эркеров или криволинейных поверхностей можно либо использовать готовые дугообразные модули, предлагаемые многими изготовителями, либо подрезать углы стандартных блоков ножовками по газобетону, либо – в случае большого радиуса – закруглять кладку за счёт шва.
Ряд производителей рекомендует предусматривать армирующие элементы через каждые 4 ряда блоков для повышения прочности кладки. Армирование можно выполнять с помощью сетки из оцинкованной стали, например, толщиной 3 мм с ячейками 50 х 50 мм. Однако при этом толщина шва будет 5-8 мм, и он станет мостиком холода.
а, б) Блоки укладывают с помощью специального клея на цементно-песчаной основе. Клей наносят на горизонтальную и вертикальную поверхность блока, используя для этого особый инструмент – кельму в) Для распиливания блоков предусмотрены ножовка и угольник. г, д) Поскольку толщина клеевого шва – всего 1 -3 мм, нет возможности выравнивать кладку за счёт него. А значит, надо тщательно выровнять фундамент и первые ряды кладки
е) Блоки легко пилятся, что позволяет получить элементы нужных размеров
Поэтому лучше армировать металлическими прутами диаметром 8-12 мм, уложенными в горизонтальные штрабы, которые проделаны в кладке (на расстоянии не менее 60 мм от боковых граней блоков). Штрабы затем заполняют клеевым раствором. Для блока толщиной 375 мм обычно требуется два арматурных прута. Вместе с тем другие производители газобетона утверждают, что армировать рядовые участки кладки из их блоков не нужно, поскольку сами блоки и предлагаемый для них клеевой раствор обладают высокой прочностью.
Но даже при использовании таких блоков необходимо предусмотреть армирование подоконными проёмами (в предпоследнем ряду блоков, притом длина арматуры должна быть больше проёма не менее чем на 50 см с каждой стороны), а также монолитный обвязочный пояс (связывающий несущие стены) на уровне межэтажных перекрытий. Обвязочный пояс обязательно должен быть замкнутым. Он может представлять собой арматурный каркас, залитый бетоном. Но можно его создать и с помощью U-образных газобетонных блоков, предлагаемых многими производителями.
Комментарий специалиста
«Монолитный железобетонный пояс по периметру здания, связывающий воедино наружные стены, обязателен в сейсмоопасных зонах. Его непременно следует предусматривать и при строительстве на сильно- или среднепучинистых грунтах. Если же грунты слабопучи- нистые или непучинистые, то можно отказаться от него и выполнить распределительный пояс в виде кирпичной кладки, что значительно удешевит, упростит и ускорит процесс сооружения здания. Обычно кирпичную кладку делают высотой в три ряда и затем опирают на неё плиту или балки перекрытия. Толщину кладки подбирают в том числе с учётом того, что по периметру её необходимо закрыть теплоизоляционной вставкой (например, из пенополистирола), чтобы избежать промерзания через стену. А в случае оконного проёма большого размера следует выполнить армирование блоков подоконного ряда с помощью прутов диаметром 10-12 мм (укладывая их в штрабы и заливая цементным раствором), чтобы распределить нагрузку от тяжёлого оконного блока и тем самым предотвратить появление трещин по углам проёма».
Внутрь такого блока укладывают арматуру и заливают её бетоном, притом оболочка из газобетона уменьшает теплопотери через этот пояс. В то же время инженеры-конструкторы напоминают, что необходимость армирования определяется только на основании расчёта нагрузок в соответствии с проектом здания. И некоторые строительные компании после проведения расчётов отказались от применения обвязочного пояса и армирования в подоконных зонах при сооружении малоэтажных загородных домов, полагая, что они неоправданно увеличивают стоимость и сроки возведения здания. Добавим, что для перевязки внешних стен и внутренних перегородок предусматривают анкерные пластины из нержавеющей стали.
Читайте также: Из какого материала лучше строить дом
Существуют разные технологии выполнения перекрытий в доме из газобетона. Наиболее надёжным решением, к тому же подходящим для здания любой геометрии, является устройство монолитной железобетонной плиты (её толщина, как правило, 160 мм).
Однако это самый дорогой и не лишённый недостатков вариант, в частности, придётся долго ждать, пока бетон наберёт прочность, соответственно время строительства увеличится. Не менее надёжным, но более экономичным и быстрым в исполнении решением можно считать сборные железобетонные плиты перекрытия. Это готовые конструкции, поднимаемые с помощью крана.
Их недостаток – стандартные форма и размеры, а значит, в случае сложной геометрии здания (например, с эркерами) или при небольшом расстоянии между плитами понадобится дополнять перекрытие монолитными участками. К тому же такое перекрытие будет потолще – 220 мм.
Обратите внимание: чтобы минимизировать промерзание через перекрытие, обязательно устанавливают слой теплоизоляции (чаще всего из пенополистирола) между плитой и стеновым блоком. Если есть необходимость уложить перекрытие вручную (без применения крана) и в сжатые сроки, тогда можно использовать сборно-монолитное перекрытие, предлагаемое некоторыми производителями газобетона.
В его основе – железобетонные балки, изготавливаемые на заказ, требуемой длины (до 7 м) и небольшого сечения. Их устанавливают с определённым шагом, а между ними (с опорой на них) укладывают Т-образные газобетонные блоки. Далее настилают арматурную сетку и заливают её стяжкой толщиной 40-50 мм. Несущая способность такого перекрытия – до 450 кг/м2. Общая толщина конструкции – порядка 240 мм. Добавим, что в большинстве случаев допустимо опирать перекрытие на газобетонную кладку, поверх которой нанесён цемент-но-песчаный раствор слоем около 50 мм. Реже всего применяют перекрытия по деревянным балкам.
При устройстве оконных и дверных проёмов предусматривают перемычки. Самый дешёвый и простой в исполнении вариант – металлические уголки (обязательно защищённые антикоррозийными составами), на которые опирают обычные блоки.
Также можно устанавливать перемычки из сборных или монолитных железобетонных балок (это самое надёжное решение, но чреватое мостиками холода, поэтому балки нужно закрывать снаружи теплоизоляцией), готовых армированных балок из газобетона, U-образных газобетонных блоков с заполнением арматурой и бетоном и др. Отметим, что U-образные блоки с таким заполнением и закладными анкерами обычно предусматривают и для верхнего ряда кладки, на которую будет опираться мауэрлат – опорный брус для стропильной системы.
Выбирая отделочный материал для фасада, стоит помнить, что газобетон обладает высокой паропроницаемостью, а значит, отделка не должна препятствовать выходу водяного пара из конструкции стены, чтобы исключить накопление влаги в зоне контакта стены и отделки. Так, допустимо применять минеральные штукатурки высокой прочности (возможны тонкослойные и толстослойные варианты их нанесения) с последующей окраской паропроницаемыми красками.
Отделка внешней стены тонкослойной штукатуркой:
1. Газобетонный блок
2. Грунтовочный слой
3. Фасадная стеклосетка
4. Декоративная штукатурка
В случае облицовки лицевым кирпичом следует оставлять вентилируемый зазор около 40 мм между газобетонной стеной и кирпичной кладкой для удаления водяного пара (самонесущую кирпичную стену соединяют с газобетонными блоками при помощи гибких связей). Несмотря на высокие теплотехнические характеристики газобетона, некоторые застройщики предпочитают дополнительно утеплять наружные стены.
Не рекомендуют использовать для этих целей теплоизоляцию с низкой паро-проницаемостью (например, пенополистирол). Лучше применять «дышащие» волокнистые плиты высокой плотности (как правило, 145-150 кг/м3).
Их фиксируют к стене минеральным клеем и тарельчатыми дюбелями, после чего оштукатуривают (в том числе с последующей окраской) паропроницаемыми составами. Или закрывают лицевым кирпичом с обязательным устройством вентзазора.
Читайте также: Веранда своими руками
Комментарий специалиста
Газобетонные блоки толщиной 375 мм, имеющие плотность D500, в сочетании со штукатурной отделкой отвечают требованиям по сопротивлению теплопередаче ограждающих конструкций, предъявляемым СНиП 23-02-2003 «Тепловая защита здания» для средней полосы России. Имеет ли смысл дополнительно утеплять дом из газобетона? Однозначного ответа на этот вопрос нет. Если заказчик с помощью теплоизоляции стремится свести к минимуму затраты на отопление коттеджа, то в этом есть смысл. Однако эффект будет незначительным, если не предусмотрены другие меры по сбережению тепла – качественное утепление крыши и перекрытий на границе с холодными зонами, энергоэффективные окна, теплоизолированные двери и пр. Иными словами, должна быть реализована концепция пассивного дома. Вместе с тем срок службы утеплителя будет значительно меньше, чем срок службы стеновых конструкций, и заказчик должен быть готов к тому, что через несколько десятков лет может понадобиться реконструировать фасад здания».
Автор: Известный строительный журналист А.Левенко. Фото В.Ковалев. Ytong
ИНСТРУМЕНТ ДЛЯ МАСТЕРОВ И МАСТЕРИЦ, И ТОВАРЫ ДЛЯ ДОМА ОЧЕНЬ ДЕШЕВО. БЕСПЛАТНАЯ ДОСТАВКА. РЕКОМЕНДУЕМ — ПРОВЕРЕНО 100% ЕСТЬ ОТЗЫВЫ.
Реклама
Ниже другие записи по теме «Как сделать своими руками — домохозяину!»
Подпишитесь на обновления в наших группах.
Будем друзьями!
kak-svoimi-rukami.com