Марка стали, сплава | Коэффициент линейного расширения α, 10-6 1/ºС, при температуре от 20ºС до, ºС | |||||||||
100 | 200 | 300 | 400 | 500 | 600 | 700 | 800 | 900 | 1000 | |
08кп | 12,5 | 13,4 | 14,0 | 14,5 | 14,9 | 15,1 | 15,3 | 14,7 | 12,7 | 13,8 |
08 | 12,5 | 13,4 | 14,0 | 14,5 | 14,9 | 15,1 | 15,3 | 14,7 | 12,7 | 13,8 |
10кп | 12,4 | 13,2 | 13,9 | 14,5 | 14,9 | 15,1 | 15,3 | 14,7 | 14,8 | 12,6 |
10 | 11,6 | 12,6 | — | 13,0 | — | 14,6 | — | — | — | — |
15кп | 12,4 | 13,2 | 13,9 | 14,5 | 14,8 | 15,1 | 15,3 | 14,1 | 13,2 | 13,3 |
15 | 12,4 | 13,2 | 13,9 | 14,4 | 14,8 | 15,1 | 15,3 | 14,1 | 13,2 | 13,3 |
20кп | 12,3 | 13,1 | 13,8 | 14,3 | 14,8 | 15,1 | 15,2 | — | — | — |
20 | 11,1 | 12,1 | 12,7 | 13,4 | 13,9 | 14,5 | 14,8 | — | — | — |
25 | 12,2 | 13,0 | 13,7 | 14,4 | 14,7 | 15,0 | 15,2 | 12,7 | 12,4 | 13,4 |
30 | 12,1 | 12,9 | 13,6 | 14,2 | 14,7 | 15,0 | 15,2 | — | — | — |
35 | 11,1 | 11,9 | 13,0 | 13,4 | 14,0 | 14,4 | 15,0 | — | — | — |
40 | 11,9 | 12,8 | 13,5 | 14,1 | 14,6 | 14,9 | 15,2 | 12,5 | 13,5 | 14,5 |
45 | 11,9 | 12,7 | 13,4 | 13,7 | 14,3 | 14,9 | 15,2 | — | — | — |
50 | 11,2 | 12,0 | 12,9 | 13,3 | 13,7 | 13,9 | 14,5 | 13,4 | — | — |
55 | 11,0 | 11,8 | 12,6 | 13,4 | 14,0 | 14,5 | 14,8 | 12,5 | 13,5 | 14,4 |
60 | 11,0 | 11,9 | — | 13,5 | 14,6 | — | — | — | — | — |
15К | — | 12,0 | 12,8 | 13,6 | 13,8 | 14,0 | — | — | — | — |
20К | — | 12,0 | 12,8 | 13,6 | 13,8 | 14,2 | — | — | — | — |
22К | 12,6 | 12,9 | 13,3 | 13,9 | — | — | — | — | — | — |
А12 | 11,9 | 12,5 | — | 13,6 | 14,2 | — | — | — | — | — |
15Г | 12,3 | — | 13,2 | — | — | 14,9 | — | — | — | — |
20Г | 12,3 | 13,4 | 14,4 | 15,1 | — | 15,2 | — | — | — | — |
30Г | 12,6 | 13,9 | 14,6 | 15,0 | 15,5 | 15,6 | 14,8 | — | — | — |
40Г | 11,1 | 11,7 | 12,7 | — | 14,3 | — | — | — | — | — |
50Г | 11,8 | 12,5 | 13,2 | 13,8 | 14,3 | 14,8 | 15,1 | 12,3 | — | — |
16ГС | 11,1 | 12,1 | 12,9 | 13,5 | 13,9 | 14,1 | — | — | — | — |
45Г2 | 11,3 | 11,9 | 12,7 | — | 14,7 | — | — | — | — | — |
20Х | 11,3 | 11,6 | 12,5 | 13,2 | 13,7 | — | — | — | — | — |
30Х | 12,4 | 13,0 | 13,4 | 13,8 | 14,2 | 14,6 | 14,8 | 12,0 | 12,8 | 13,8 |
35Х | 11,3 | 12,0 | 12,9 | 13,7 | 14,2 | 14,6 | — | — | — | — |
38ХА | 11,0 | 12,0 | 12,2 | 12,9 | 13,5 | — | — | — | — | — |
40Х | 11,8 | 12,2 | 13,2 | 13,7 | 14,1 | 14,6 | 14,8 | 12,0 | — | — |
45Х | 12,8 | 13,0 | 13,7 | — | — | — | — | — | — | — |
50Х | 12,8 | 13,0 | 13,7 | — | — | — | — | — | — | — |
18ХГТ | 10,0 | 11,5 | 12,3 | 12,8 | 13,3 | 13,6 | — | — | — | — |
30ХГТ | 10,5 | 12,0 | 12,7 | 13,3 | 13,8 | 14,0 | — | — | — | — |
15ХФ | 11,9 | 12,4 | 13,1 | 13,7 | 14,2 | 14,5 | 14,9 | — | — | — |
33ХС | 12,0 | 12,8 | 13,4 | 13,7 | 14,3 | 14,7 | 15,0 | 12,4 | — | — |
38ХС | 12,3 | 13,1 | 13,6 | 14,0 | 14,8 | 14,9 | 15,0 | 12,5 | — | — |
40ХС | 11,7 | 12,7 | 13,4 | 14,0 | 14,4 | 14,8 | — | — | — | — |
30ХМ, 30ХМА | 12,3 | 12,5 | 12,9 | 13,9 | 14,4 | — | — | — | — | — |
35ХМ | 12,3 | 12,5 | 12,9 | 13,9 | 14,4 | — | — | — | — | — |
40ХФА | 12,1 | 12,6 | 13,0 | 13,3 | 13,8 | 14,2 | 14,6 | 11,8 | — | — |
36НХ | 1,6 | 2,8 | 6,6 | — | — | — | — | — | — | — |
40ХН | 11,8 | 12,3 | 13,4 | 13,4 | 14,0 | — | — | — | — | — |
12ХН2 | 10,5 | 11,5 | 11,9 | 12,4 | 12,9 | 13,6 | 13,9 | 11,7 | — | — |
12ХН3А | 11,8 | 13,0 | 14,0 | 14,7 | 15,3 | 15,6 | — | — | — | — |
20ХН3А | 11,5 | 11,7 | 12,0 | 12,6 | 12,8 | 13,2 | 13,6 | 11,2 | — | — |
30ХН3А | 10,8 | 11,5 | 12,2 | 12,8 | 13,2 | 13,5 | — | — | — | — |
15Х2НМФА | 10,5 | 11,2 | 11,9 | 12,6 | — | — | — | — | — | — |
15Х2НМФА-А | 10,8 | 11,6 | 12,2 | 12,8 | — | — | — | — | — | — |
25ХГСА | 12,2 | 13,0 | 13,6 | 14,0 | 14,2 | 14,4 | 14,5 | 12,3 | — | — |
30ХГС, 30ХГСА | 11,0 | — | — | — | — | — | — | — | — | — |
34ХН3М, 34ХН3МА | 10,8 | 11,6 | 12,5 | 13,3 | 13,5 | 13,6 | — | — | — | — |
40ХН2МА (40ХНМА) | 11,6 | 12,1 | 12,7 | 13,2 | 13,6 | 13,9 | — | — | — | — |
30ХН2МФА (30ХН2МВА) | 11,1 | 11,7 | 12,3 | 12,9 | 13,3 | 13,7 | — | — | — | — |
38ХН3МФА | 11,8 | 12,1 | 12,6 | 13,0 | 13,4 | 13,7 | — | — | — | — |
38Х2МЮА (38ХМЮА) | 12,3 | 13,1 | 13,3 | 13,5 | 14,5 | — | — | — | — | — |
12МХ | 11,2 | 12,5 | 12,7 | 12,9 | 13,2 | 13,5 | 13,8 | — | — | — |
15ХМ | 11,9 | 12,6 | 13,2 | 13,7 | 14,0 | 14,3 | — | — | — | — |
20ХМ | 11,9 | 12,6 | 13,2 | 13,7 | 14,0 | 14,3 | — | — | — | — |
12Х1МФ (ЭИ 575) | 10,8 | 11,8 | 12,4 | 12,8 | 13,2 | 13,7 | — | — | — | — |
13Х1МФ (14Х1ГМФ, ЦТ 1) | 9,5 | 10,7 | 11,8 | 12,5 | 13,1 | 13,4 | 13,6 | — | — | — |
15Х1М1Ф | 11,2 | 11,7 | 12,5 | 13,0 | 13,5 | 13,7 | — | — | — | — |
12Х2МФБ (ЭИ 531) | 10,2 | 11,3 | 12,2 | 12,6 | 13,2 | 13,4 | 13,7 | — | — | — |
12Х2МФСР | 11,0 | 12,0 | 12,7 | 13,2 | 13,7 | 14,0 | 14,3 | — | — | — |
25Х1МФ (ЭИ 10) | 10,9 | 12,0 | 12,7 | 13,7 | 13,7 | 13,8 | 14,0 | — | — | — |
25Х2М1Ф (ЭИ 723) | 12,5 | 12,9 | 13,3 | 13,7 | 14,0 | 14,7 | — | — | — | — |
20Х1М1Ф1ТР (ЭП 182) | — | 12,0 | 12,3 | 12,9 | 13,0 | 13,5 | 13,6 | — | — | — |
20Х1М1Ф1БР (ЭП 44) | — | — | — | — | — | 14,5 | — | — | — | — |
20Х3МВФ (ЭИ 415, ЭИ 579) | 10,6 | 11,5 | 11,8 | 12,1 | 12,6 | 13,0 | — | — | — | — |
15Х5М (12Х5МА, Х5М) | 11,3 | 11,6 | 11,9 | 12,2 | 12,3 | 12,5 | 13,1 | — | — | — |
10ГН2МФА, 10ГН2МФА-ВД, 10ГН2МФА-Ш | 11,2 | 11,6 | 12,7 | 13,2 | — | — | — | — | — | — |
65Г | 11,1 | 11,9 | 12,9 | 13,5 | 14,6 | — | — | — | — | — |
50ХФА | 12,4 | 12,8 | 13,4 | 13,9 | 14,2 | 14,5 | 14,7 | — | — | — |
60С2, 60С2А | 12,0 | 12,8 | — | 13,5 | 13,4 | — | — | — | — | — |
ШХ15 | 11,9 | 15,1 | 15,5 | 15,6 | 15,7 | — | — | — | — | — |
ШХ15СГ | — | 13,4 | 13,6 | — | — | — | — | — | — | — |
95Х18 (9Х18, ЭИ 229) | 11,7 | 12,1 | 12,4 | 12,9 | 13,3 | — | — | — | — | — |
10Х9МФБ (ДИ 82) | 10,3 | 10,8 | 11,2 | 11,5 | 11,8 | 12,0 | — | — | — | — |
40Х9С2 (4Х9С2, ЭСХ 8) | 11,1 | 12,7 | — | 14,3 | — | 14,2 | — | 14,0 | — | — |
40Х10С2М (4Х10С2М, ЭИ 107) | 10,0 | 11,0 | 11,0 | 11,0 | — | — | — | 11,0 | — | — |
13Х11Н2В2МФ-Ш (ЭИ 961-Ш) | 11,0 | 11,3 | 11,6 | 12,0 | 12,3 | 12,5 | — | — | — | — |
03Х11Н10М2Т | — | — | — | — | 11,6 | — | — | — | — | — |
10Х11Н20Т3Р (ЭП 696) | 15,9 | 17,4 | 18,8 | 19,9 | 20,3 | 21,1 | — | — | — | — |
15Х11МФ (1Х11МФ) | — | 11,1 | — | 11,3 | 11,7 | 12,0 | 12,2 | 12,4 | — | — |
15Х11МФБ (1Х11МФБ) | 10,0 | 10,4 | 10,8 | 11,3 | 11,5 | 12,0 | 12,2 | 12,4 | — | — |
12Х11В2МФ (типа ЭИ 756) | 10,6 | 11,3 | 12,6 | 12,9 | 13,1 | 13,6 | 14,0 | 14,1 | — | — |
18Х11МНФБ (2Х11МФБН, ЭП291) | 10,3 | 10,6 | 10,8 | 11,3 | 11,7 | 12,0 | 12,4 | 12,8 | — | — |
06Х12Н3Д | 10,8 | 10,8 | 10,9 | 11,0 | — | — | — | — | — | — |
10Х12Н3М2ФА (Ш), 10Х12Н3М2ФА-А (Ш) | 10,7 | 11,1 | 11,3 | 11,7 | 12,0 | 12,1 | — | — | — | — |
18Х12ВМБФР-Ш (ЭИ 993-Ш) | 11,2 | 11,3 | 11,4 | 11,8 | 12,0 | 12,1 | 12,2 | 12,6 | 11,6 | — |
20Х12ВНМФ (ЭП 428) | 10,0 | 10,5 | 10,7 | 11,0 | 11,2 | 11,6 | 11,9 | 12,5 | — | — |
08Х13 (0Х13, ЭИ 496) | 10,5 | 11,1 | 11,4 | 11,8 | 12,1 | 12,3 | 12,5 | 12,8 | — | — |
12Х13 (1Х13) | 10,2 | 11,2 | 11,4 | 11,8 | 12,2 | 12,4 | 12,7 | 13,0 | 10,8 | — |
20Х13 (2Х13) | 10,2 | 11,2 | 11,5 | 11,9 | 12,2 | 12,8 | 12,8 | 13,0 | — | — |
30Х13 (3Х13) | 10,2 | 10,9 | 11,1 | 11,7 | 12,0 | 12,3 | 12,5 | 12,6 | 10,6 | — |
40Х13 (4Х13) | 10,7 | 11,5 | 11,9 | 12,2 | 12,5 | 12,8 | 13,0 | 13,2 | — | — |
25Х13Н2 (2Х14Н2, ЭИ 474) | 11,6 | 12,0 | 12,4 | 12,8 | — | — | — | — | — | — |
12Х13Г12АС2Н2 (ДИ 50) | 15,7 | 17,4 | 18,8 | 20,0 | 21,0 | 21,8 | 22,7 | — | — | — |
10Х13Г12С2Н2Д2Б (ДИ 59) | 16,2 | 17,2 | 18,0 | 18,7 | 19,2 | 18,2 | 18,2 | 17,5 | — | — |
08Х14МФ | 10,1 | 10,9 | 11,5 | 11,9 | 12,3 | 12,5 | — | — | — | — |
10Х14Г14Н4Т (Х14Г14Н3Т, ЭИ 711) | 16,0 | 16,7 | 17,5 | 18,4 | 19,0 | 19,5 | 20,1 | 20,6 | 21,0 | — |
04Х14Н5МГТЮ | 10,6 | 11,7 | 12,0 | 12,5 | 13,2 | 13,5 | 11,8 | — | — | — |
1Х14Н14В2М (ЭИ 257) | 15,6 | 15,7 | 17,3 | 17,3 | 17,3 | 18,2 | 18,4 | — | — | — |
09Х14Н19В2БР1 (ЭИ 726) | 15,2 | 16,3 | 16,9 | 17,5 | 17,8 | 18,1 | 18,6 | 18,6 | 18,9 | — |
45Х14Н14В2М (ЭИ 69) | — | — | 17,0 | — | 18,0 | — | 18,0 | — | 19,0 | — |
08Х15Н24В4ТР (ЭП 164) | 14,5 | 15,5 | 16,3 | 16,8 | 17,2 | 17,4 | 17,5 | 17,8 | 17,9 | — |
07Х16Н6 (Х16Н6, ЭП 288) | 11,3 | 11,7 | 12,1 | 12,5 | 12,9 | — | — | — | — | — |
08Х16Н9М2 (Х16Н9М2) | 17,1 | 17,6 | 18,1 | 18,4 | 19,0 | 19,3 | 19,6 | 19,8 | — | — |
08Х16Н13М2Б (ЭИ 405, ЭИ 680) | — | — | — | 17,1 | 17,4 | 17,8 | 18,2 | 18,6 | — | — |
10Х16Н14В2БР (1Х16Н14В2БР, ЭП 17) | 15,8 | 16,8 | 18,4 | 19,0 | 19,3 | 20,0 | 20,2 | 20,5 | 21,5 | 21,8 |
8Х17Т (0Х17Т, ЭИ 645) | 10,0 | 10,0 | 10,5 | 10,5 | 11,0 | — | — | — | — | — |
12Х17 (Х17, ЭЖ 17) | 10,4 | 10,5 | 10,8 | 11,2 | 11,4 | 11,6 | 11,9 | 12,1 | — | — |
14Х17Н2 (1Х17Н2, ЭИ 268) | 9,8 | 10,6 | 11,8 | 11,0 | 11,1 | 11,3 | 11,0 | 10,7 | 11,4 | — |
02Х17Н11М2 | 16,5 | — | — | 18,0 | — | 18,0 | — | 19,0 | — | — |
08Х17Н13М2Т (0Х17Н13М2Т) | 15,7 | 16,1 | 16,7 | 17,2 | 17,6 | 17,9 | 18,2 | — | — | — |
10Х17Н13М2Т (Х17Н13М2Т, ЭИ 448) | 15,7 | 16,1 | 16,7 | 17,2 | 17,6 | 17,9 | 18,2 | — | — | — |
10Х17Н13М3Т (Х17Н13М3Т, ЭИ 432) | 16,5 | 17,5 | 18,0 | 18,5 | 19,0 | — | — | — | — | — |
015Х18М2Б-ВИ (ЭП 882-ВИ) | 9,9 | 10,3 | 10,8 | 11,0 | 11,3 | 11,4 | 11,3 | 11,6 | 11,7 | — |
12Х18Н9 (Х18Н9) | 16,5 | 17,2 | 17,7 | 18,1 | 18,3 | 18,6 | 18,9 | 19,3 | 19,7 | — |
12Х18Н9Т (Х18Н9Т) | 16,6 | 17,0 | 17,6 | 18,0 | 18,3 | 18,6 | 18,9 | 19,3 | 19,5 | — |
17Х18Н9 (2Х18Н9) | 16,0 | 17,0 | 17,5 | 17,9 | 18,5 | 18,6 | 18,9 | 19,1 | 19,3 | — |
08Х18Н10 (0Х18Н10) | 16,0 | 17,0 | 17,0 | 18,0 | 18,0 | — | — | — | — | — |
08Х18Н10Т (0Х18Н10Т, ЭИ 914) | 16,1 | — | 17,4 | — | 18,2 | — | 19,1 | — | — | — |
12Х18Н12Т (Х18Н12Т) | 16,6 | 17,0 | 17,2 | 17,5 | 17,9 | 18,2 | 18,6 | 18,9 | 19,3 | — |
10Х18Н18Ю4Д (ЭП 841) | 15,5 | 16,5 | 17,0 | 17,4 | 17,7 | 18,2 | 18,4 | 18,8 | 18,6 | — |
36Х18Н25С2 (4Х18Н25С2, ЭЯ 3С) | 13,0 | 13,9 | 14,7 | — | — | 16,1 | — | — | — | — |
01Х19Ю3БЧ-ВИ (02Х18Ю3Б-ВИ, ЭП 904-ВИ) | 10,8 | 11,0 | 11,5 | 11,8 | 12,1 | 12,5 | 12,7 | 13,0 | 13,2 | — |
20Х20Н14С2 (Х20Н14С2, ЭИ 211) | 16,0 | — | — | — | — | 18,1 | 18,3 | 18,5 | 18,8 | — |
08Х21Н6М2Т (0Х21Н6М2Т, ЭП 54) | 9,5 | 13,8 | 16,0 | 16,0 | 16,3 | 16,7 | 17,1 | 17,1 | 17,4 | — |
02Х22Н5АМ3 | 13,0 | 13,5 | 14,0 | 14,5 | — | — | — | — | — | — |
08Х22Н6Т (0Х22Н5Т, ЭП 53) | 9,6 | 13,8 | 16,0 | 16,0 | 16,4 | 16,2 | 16,5 | 16,7 | 17,1 | — |
Х23Ю5Т | — | — | — | — | — | — | — | — | — | 15,0 |
20Х23Н13 (Х23Н13, ЭИ 319) | 14,9 | 15,7 | 16,6 | 17,1 | 17,5 | 17,8 | 18,2 | — | — | — |
20Х23Н18 (Х23Н18, ЭИ 417) | 14,9 | 15,7 | 16,6 | 17,1 | 17,5 | 17,9 | 17,9 | — | — | — |
06ХН28МДТ (0Х23Н28М3Д3Т, ЭИ 943) | 10,9 | 12,9 | 13,6 | 14,4 | 14,9 | 15,3 | 16,8 | 16,3 | 16,8 | — |
03Х24Н6АМ3 (ЗИ 130) | 14,6 | 15,3 | 16,0 | 16,5 | 16,9 | 17,3 | 17,9 | 18,2 | 18,5 | — |
15Х25Т (Х25Т, ЭИ 439) | 10,1 | 10,7 | 11,0 | 11,2 | 11,3 | — | — | — | — | — |
12Х25Н16Г7АР (ЭИ 835) | 16,6 | 16,2 | 16,8 | 17,4 | 18,0 | 18,3 | 18,5 | 18,7 | 18,9 | — |
20Х25Н20С2 (Х25Н20С2, ЭИ 283) | 16,1 | — | — | — | — | 17,8 | 17,8 | 18,1 | 18,5 | — |
03Н18К9М5Т | — | — | — | — | 11,2 | — | — | — | — | — |
ХН32Т (ЭП 670) | 13,7 | 15,6 | 17,2 | 18,0 | 18,0 | 18,4 | 18,9 | 19,0 | 19,0 | — |
ХН45Ю (ЭП 747) | 15,8 | 15,9 | 16,0 | 16,6 | — | 16,6 | 17,7 | 19,0 | 19,7 | — |
06ХН46Б (ЭП 350) | 15,2 | 16,1 | 16,8 | 17,6 | — | — | — | — | — | — |
05ХН46МВБЧ (ДИ 65) | 13,4 | 14,0 | 14,7 | 15,2 | 15,7 | 16,0 | 16,4 | 16,7 | 16,9 | — |
ХН59ВГ-ИД (ЭК 82-ИД) | 12,3 | 12,6 | 13,0 | 13,4 | 13,7 | 14,0 | 14,3 | 14,8 | 15,3 | — |
ХН60Ю (ЭИ 559А) | 12,3 | 13,1 | 13,4 | 14,2 | 14,2 | 14,6 | 15,1 | 15,2 | 15,9 | — |
ХН62МБВЮ (ЭП 709) | 12,0 | 12,8 | 13,3 | 13,5 | 13,8 | 14,5 | 14,8 | 15,5 | 16,4 | 17,3 |
ХН62МВКЮ (ЭИ 867) | 11,5 | 12,6 | 13,0 | 13,4 | 13,7 | 14,0 | 14,3 | 14,8 | 15,6 | — |
ХН65ВМТЮ (ЭИ 893) | 11,3 | — | — | — | — | — | 14,4 | — | — | — |
ХН67МВТЮ (ЭП 202, ЭИ 445 Р) | 12,0 | 12,3 | 13,5 | 13,6 | 13,6 | 14,4 | 14,8 | 15,2 | 16,2 | — |
ХН70Ю (ЭИ 652) | 13,1 | 13,9 | 14,8 | 15,7 | 16,4 | 17,8 | 22,4 | 24,5 | 21,3 | 21,2 |
ХН70БДТ (ЭК 59) | 12,9 | 13,3 | 13,7 | 14,1 | — | — | — | — | — | — |
| ||||||||||
ХН70ВМЮТ (ЭИ 765) | 12,2 | 12,6 | 13,2 | — | — | — | — | — | — | — |
ХН70ВМТЮ (ЭИ 617) | 12,0 | 12,6 | 13,2 | 13,6 | 14,1 | 14,6 | 15,1 | 15,8 | — | — |
ХН70ВМТЮФ (ЭИ 826), ХН70ВМТЮФ-ВД (ЭИ 826-ВД) | 10,4 | 11,7 | 12,7 | 12,9 | 13,2 | 13,6 | 14,0 | 14,5 | 15,0 | — |
ХН73МБТЮ (ЭИ 698) | 12,3 | 13,2 | 14,2 | 15,0 | 16,3 | 17,3 | 18,8 | 21,6 | — | — |
ХН75ВМЮ (ЭИ 827) | 10,2 | 11,3 | 12,0 | 12,2 | 12,4 | 12,6 | 13,1 | 13,2 | 15,1 | — |
ХН80ТБЮ (ЭИ 607) | — | — | 13,1 | 14,0 | 14,4 | 14,9 | 15,6 | 16,4 | — | — |
ХН80ТБЮА (ЭИ 607А) | — | — | 13,1 | 14,0 | 14,4 | 14,9 | 15,6 | 16,4 | — | — |
Х15Н60-Н | — | — | — | — | — | — | — | — | — | 17,0 |
Х20Н80-Н | — | — | — | — | — | — | — | — | — | 18,0 |
У8, У8А | 11,4 | 12,2 | 13,0 | 13,7 | 14,3 | 14,8 | 15,2 | 14,5 | 15,2 | 15,7 |
У9, У9А | 11,0 | 11,6 | 12,4 | 13,2 | — | — | — | — | — | — |
У10, У10А | 11,5 | 11,9 | 12,5 | 13,0 | 13,4 | 13,9 | 14,3 | 14,9 | 15,4 | 13,3 |
У12, У12А | 10,5 | 11,8 | 12,6 | 13,4 | 14,1 | 14,8 | 15,3 | 15,0 | 16,3 | 16,8 |
7Х3 | 10,0 | 14,0 | 15,2 | 15,2 | — | — | — | — | — | — |
5ХНМ | 12,6 | 14,1 | 14,2 | 15,0 | — | 14,2 | — | — | — | — |
3Х3М3Ф | 10,8 | 10,8 | 11,4 | 12,1 | 13,0 | 13,9 | 14,8 | 14,8 | 15,2 | — |
4Х5МФ1С (ЭП 572) | 12,6 | 13,1 | 13,7 | 14,0 | 14,3 | 14,6 | 14,7 | 14,6 | 14,1 | — |
Р6М5 | 9,7 | 10,7 | 10,8 | 11,6 | 13,0 | 13,5 | 13,3 | 13,5 | — | — |
Р18 | 10,6 | 10,8 | 11,3 | 11,0 | 12,6 | 12,8 | 13,2 | 12,7 | — | — |
15Л | 11,9 | 12,5 | — | 13,6 | — | 14,2 | — | — | — | — |
20Л | 11,1 | 12,1 | — | 13,4 | 14,4 | — | — | — | — | — |
25Л | 11,5 | 12,9 | 13,1 | 13,2 | 13,5 | — | — | — | — | — |
30Л | 12,6 | 13,9 | — | 15,0 | 15,6 | — | — | — | — | — |
35Л | 11,1 | 11,9 | — | 13,4 | 14,4 | — | — | — | — | — |
40Л | 12,4 | 12,6 | — | 14,5 | — | 14,6 | — | — | — | — |
45Л | 11,6 | — | — | — | — | — | — | — | — | — |
50Л | 12,0 | 12,4 | — | 13,3 | — | 14,1 | — | — | — | — |
32Х06Л | 12,4 | 12,8 | 13,2 | 13,6 | 14,0 | 14,4 | 14,7 | 12,0 | 12,7 | — |
40ХЛ | 12,2 | 12,7 | 13,1 | 13,4 | 13,8 | 14,2 | 14,6 | 11,8 | 12,6 | — |
20ГСЛ | 11,6 | 12,6 | 13,4 | 13,6 | 14,2 | 14,5 | 14,5 | — | — | — |
15Х1М1ФЛ | 12,4 | 12,8 | 13,3 | 13,7 | 14,0 | 14,1 | — | — | — | — |
20ХМЛ | 10,9 | 12,4 | 12,8 | 13,1 | 13,6 | 13,9 | — | — | — | — |
20ХМФЛ | 10,0 | 11,9 | 12,9 | 13,1 | 13,6 | 13,9 | — | — | — | — |
35ХМЛ | 12,2 | 12,6 | 13,4 | 14,3 | 14,5 | 14,6 | 14,7 | 12,2 | 12,7 | — |
35ХГСЛ | 11,8 | 12,3 | 12,8 | 13,3 | 13,8 | 14,1 | 14,4 | 12,6 | 13,3 | — |
08ГДНФЛ | 10,3 | 11,3 | 12,0 | 13,0 | 13,6 | 14,1 | 14,4 | 12,5 | 13,0 | — |
110Г13Л | 18,0 | 19,4 | — | 21,7 | — | — | — | — | — | — |
10Х12НДЛ | 10,8 | 11,3 | 11,6 | 12,4 | 12,5 | — | — | — | — | — |
06Х12Н3ДЛ | 10,3 | 10,7 | 11,0 | 11,3 | 11,7 | — | — | — | — | — |
10Х13Н3М1Л | 9,8 | 10,8 | 11,0 | 11,4 | 12,0 | 12,1 | 12,1 | — | — | — |
06Х14Н5ДМФЛ | 11,8 | 12,4 | 13,6 | 14,3 | 14,8 | — | — | — | — | — |
10Х18Н3Г3Д2Л | 14,3 | 14,7 | 15,5 | 16,0 | 16,4 | — | — | — | — | — |
10Х18Н9Л | 14,8 | 15,9 | 16,9 | 17,1 | 17,6 | — | — | — | — | — |
40Х24Н12СЛ (ЭИ 316Л) | 18,4 | — | — | — | — | — | — | — | 20,6 | — |
ХН58ВКТЮБЛ (ЦНК 8МП) | — | 12,2 | — | 13,1 | — | 13,8 | — | 14,8 | 16,6 | — |
ХН60КВМЮТЛ (ЦНК 7П) | 11,7 | 12,3 | 12,7 | 13,1 | 13,4 | 13,8 | 14,1 | 14,6 | 16,4 | — |
ХН60КВМЮТБЛ (ЦНК 21П) | — | 11,2 | 11,9 | 12,0 | 12,7 | 12,9 | 13,0 | 14,3 | — | — |
ХН64ВМКЮТЛ (ЗМИ 3) | 12,4 | 12,6 | 12,9 | 13,2 | 13,5 | 13,9 | 14,4 | 15,2 | — | — |
ХН65ВМТЮЛ (ЭИ 893Л) | 11,5 | 11,8 | 12,3 | 12,7 | 13,0 | 13,3 | 14,0 | 14,6 | — | — |
ХН65КМВЮТЛ (ЖС 6К) | 11,8 | 12,0 | 12,4 | 12,8 | 13,1 | 13,3 | 13,7 | 14,2 | — | — |
ХН65ВКМБЮТЛ (ЭИ 539ЛМУ) | 12,4 | 12,6 | 12,7 | 13,0 | 13,3 | 13,7 | 14,2 | 14,9 | 17,2 | — |
|
Версия для печати Таблица 18. Коэффициент линейного расширения
<< назад / в начало / вперед >> 28 Апреля 2012 г. |
Бронза — Коэффициент линейного расширения
При расчете можно принимать для колес бронзу с коэффициентом линейного расширения = 17,5-10 , для червяка сталь с 11,5- 10 для корпуса [c.361]Для расчета можно принимать материал колес—бронза с коэффициентом линейного расширения а = 17,5- 10 б ма-териал червяка—сталь с а = 11,5-10 6 материал корпуса — чугун с о корп = = 10,4-10—6 нагрев корпуса до = = 40° для 1-го и 4-го классов и до 55° для 2-го и 3-го классов нагрев передачи до /j = 55° для 1-го и 4-го классов и до 80° для 2-го и 3-го классов.
Допустим, что соединение при работе подвергается нагреву на 100°С. Коэффициент линейного расширения бронзы = 18-10″ /»О стали 2 = И-10 / С- Температурный натяг Д, = 1000-100-40(18 — 11) 10 = 28 мкм. Натяг в соединении Д = 50 —4,8 Н- 28 = = 73 мкм.
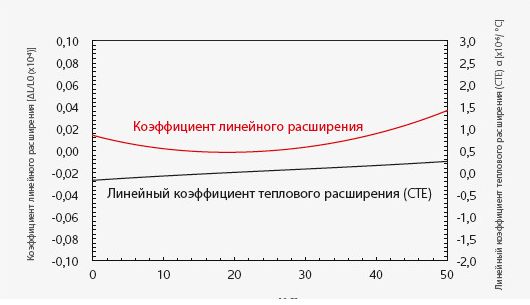
Как изменятся утечки, если вся конструкция охладится до fo = 0° С, и если плунжер выполнен из бронзы (коэффициент линейного расширения а = 17,5-10 Г С), а цилиндр — из стали (а = 11,5-10″ 1/°С). [c.213]
Сжимающие напряжения в камере могут быть получены в том случае, если наибольший коэффициент линейного расширения будет у материала, из которого изготовлен корпус захвата, а наименьший — у материала гайки, соединенной с образцом. Этому требованию отвечают латунь или бронза для корпуса захвата, сталь для гайки и сплав на висмутовой основе. Положительным свойством сплавов на висмутовой основе (например, Л70) является также увеличение объема после затвердевания, что способствует возрастанию сжимающих напряжений в камере захвата. [c.140]
Опасность заедания уменьшается при правильном подборе материалов болта и гайки. С этой целью при температурах до 500 °С и незначительных осевых нагрузках применяют гайки из латуни, бронзы и перлитного чугуна, в более нагруженных резьбовых соединениях — из жаропрочных материалов. При этом материал гайки должен иметь больший коэффициент линейного расширения, чем материал болта.
[c.343]
После некоторого времени работы при высоких температурах наблюдается заедание в резьбе, которое проявляется в том, что гайку не удается отвинтить или она отвинчивается с большим трудом, а резьба портится или разрушается. Для борьбы с заеданием необходимо изготовлять гайки из материалов, обладающих более высоким температурным коэффициентом линейного расширения по сравнению с материалом винта (перлитный чугун, бронза, латунь, жаропрочные стали) применять покрытия — омеднение или хромирование резьбы применять более крупные резьбы с зазором по среднему диаметру.
При работе такого подшипника пористый каркас второго слоя отводит теплоту и воспринимает нагрузку, а поверхностный слой и питающий его фторопласт выполняют роль смазочного материала, уменьшая трение. Если первый слой в отдельных местах по какой-либо причине изнашивается, то начинается трение стали по бронзе, что сопровождается повышением коэффициента трения и температуры.
Во избежание заклинивания при изменениях температуры конус и втулка должны иметь одинаковый коэффициент линейного расширения. В качестве материалов применяются бронза — латунь и сталь ХВ закаленная. [c.494]
У бандажированной конструкции бронзовый венец насажен на стальной или чугунный центр с натягом по посадке Н7/р6 Н7/г6 Н7/56. Эту конструкцию рекомендуется применять для передач с относительно невысоким тепловыделением, так как при значительной разнице в коэффициенте линейного расширения у бронзы и стали или чугуна при высокой температуре натяг уменьшается и надежность соединения снижается. Для предотвращения осевого взаимного смещения венца и ступицы [c.284]
Алюминиевый антифрикционный сплав применяют как заменитель баббита Б16 и оловянных бронз. Иногда эти сплавы являются более пригодными для работы, так как они имеют высокий предел прочности на усталость и высокий коэффициент линейного расширения. Последнее качество является недостатком для работы, где необходима точность.
[c.38]
Задача 230. Решить предыдуш,ую задачу для посадки бронзового венца диаметром 200 лш на стальную ступицу с максимальным натягом 0,15 лш. Коэффициент линейного расширения бронзы принимать 17,5-10- [c.179]
Медь, бронза и латунь обычной дугой и плавящимся электродом свариваются плохо. Это объясняется тем, что в расплавленном состоянии медь и сплавы на ее основе обладают большой жидко-текучестью, хорошо растворяют газы, особенно кислород, легко окисляются. У них большой коэффициент линейного расширения и они подвержены значительным структурным изменениям в зоне сварки. [c.79]
Для уменьшения влияния температуры детали конических опор изготовляются либо из однородных материалов либо из материалов, имеющих почти одинаковые коэффициенты линейного расширения (чугун—сталь латунь—бронза).
[c.69]
Марка бронзы 3 (V) Ё а 3 03 и) 4 0, Коэффициент линейного расширения при 20-100 Л н и о о ° а нЗ [c.75]
При большой разнице температурных коэффициентов линейного расширения материалов цапфы и подшипника изменение температуры может привести к заклиниванию цапфы в подшипнике. Во избежание заклинивания для цапфы и подшипника назначают материалы с близкими коэффициентами линейного расширения, как то латунь—бронза или сталь—чугун. Такое сочетание материалов вполне оправданно, хотя цч чт и противоречит традиционной ком-
Для насосов, работающих в широком диапазоне температур, шестерни в целях сохранения зазоров часто изготавливают из аустенитных сталей или бронз, имеющих коэффициент линейного расширения, более близкий к легким сплавам. К подобным материалам относят сталь ЭИ69, поддающуюся азотированию, а также беррилиевую бронзу, обладающую после термообработки сравнительно высокой твердостью (не менее HR 37).
[c.248]
Перед заливкой антифрикционным сплавом подшипники оцинковываются малолегированным сплавом цинка, содержащего 0,5—1,0% алюминия. Ввиду быстрого затвердевания антифрикционного сплава заливку необходимо производить быстро. Зазор между подшипником и валом делается несколько большим, чем для бронз и баббитов, так как цинковые сплавы имеют более высокий термический коэффициент линейного расширения. [c.273]
Бромбензол — Коэффициент теплопро водности 190 Бронза — К(1чффициеит линейного расширения 17 [c.703]
Размеры накладных направляющих прямолинейного движения из цинкового сплава ЦАМ10-5 и методы их креплспия аналогичны описанным для бронзы Бр. АМц 9-2 (см. рис. 4, а). Длнну пластин следует брать 400—500 мм ввиду значительного коэффициента линейного расширения цинкового сплава. Указанное выше о низкой прочности клеевого вта при склеивапин бронзы Бр. АМц 9-2 с чугуном в значительной мере относится также к цинковому сплаву.
[c.34]
В [6] дополнительного списка литературы приводятся также данные об улучшении некоторых других свойств термопластов при их наполнении. В табл. 1.2 перечислено большинство технически важных термопластов с указанием типичных наполнителей и свойств, которые улучшаются при наполнении. Полиамид 66 является хорошим примером термопласта, практически все свойства которого улучшаются при введении 20—40% стеклянного волокна. Особенно резко возрастают модуль упругости, прочность при растяжении, твердость, устойчивость к ползучести, теплостойкость при изгибе. Термический коэффициент линейного расширения также уменьшается, причем особенно резко в направлении ориентации волокон и становится соизмерим с соответствующими коэффициентами для меди, алюминия, цинка, бронзы и т. п. (В [7] дополнительного списка литературы приведены данные о всех свойствах наполненного и ненаполненного стеклянным волокном полиамида 66). Наполнение полиамидов 30—40% стеклянных микросфер в 8 раз повышает их прочность при сжатии при одновременном возрастании модуля упругости и прочности при растяжении. Эти материалы обладают лучшими технологическими свойствами по сравнению с полиамидами, наполненными стеклянным волокном. Кроме того стеклосферы не разрушаются в процессе переработки. На другие термопласты, такие как полистирол, сополимеры стирола и акри-лонитрила, поликарбонат наполнители оказывают менее упрочняющее влияние по сравнению с полиамидами.
[c.26]
Могут применяться сферические самоориентируюш иеся подшипники скольжения. К материалу подшипников скольжения предъявляются следуюш ие требования минимальные коэффициенты трения и износ материалов в пусковом и установившемся режимах высокие теплостойкость и теплопроводность минимальный коэффициент линейного расширения высокая стабильность свойств технологичность и экономичность. В подшипниках скольжения механизмов управления используют бронзу, фторопласт и композиционные материалы. [c.182]
Теплопроводность бериллиевых бронз составляет порядка 25% теплопроводности технической меди, т. е. 83—108 вт1м-град, плотность 8230 кг/ж , коэффициент линейного расширения при 20—300° С равен 17,6-Ю град , температура литья равна 1030—1060° С. Другие физические и технологические свойства, например, бронзы Бр.Б2 приведены в табл. 49.
[c.137]
Опасность заедания уменьшается прп правильном подборе матерпалов болта п гайкп. С этой целью при температурах до 500° С п незначительных усилиях применяют гайкп из латуни, бронзы п перлитного чугуна, а для более нагруженных соединений — гайкп из жаропрочных матерпалов. Прп этом материал гайки должен иметь больший коэффициент линейного расширения, чем материал болта. [c.152]
Материалом для трубчатых пружин служат сталь, бронза, латунь, нейзильбер. Широко применяются латуни марок Л62, Л68 и фосфористая бронза БР.ОФ4-2,5. Для пружин, работающих при высоких давлениях, применяют легированные стали 50ХФА и 18ХНВА. Для приборов лабораторного назначения, работающих при малых давлениях, трубки изготовляют из кварца и стекла. Материал для трубок должен быть однороден, изотропен, подчиняться закону Гука, обладать наибольшим пределом упругости, иметь небольшой температурный коэффициент линейного расширения, хорошо обрабатываться и иметь небольшую стоимость.
[c.373]
В дальнейшем чистый фторопласт в подшипниках был заменен композицией из смеси фторопласта и свинца, а стальная ленточная основа покрыта слоем олова против коррозии. Такие подшипники в виде втулок, упорных шайб и ленты выпускаются под названием гласир DU. Порошкообразная бронза состоит нз 89% меди и 11% олова, а матрица из этого порошка толщиной 0,25 мм соединяется со стальной основой спеканием. Заполненный фторопластом и свинцом антифрикционный слон имеет 70% бронзы, 25% фторопласта и 5% свинца. На наружной поверхности металлокерамической матрицы образуется слон нз фторопласта и свинца толщиной 0,02 мм, служащий для приработки в начальный период касания. Механизм поступления твердого смазочного материала в зону трения не отличается от описанного ранее для пористых металлокерамических подшипников, пропитанных фторопластом. Основные характеристики подшипникового материала гласир DU имеют следующие значения предел текучести 3100 кгс/см , коэффициент линейного расширения 15-10 1/°С, теплопроводность 0,1 кал/(с-см-°С). Подшипники гласир DU удовлетворительно работают при температурах от —192 до +280 °С. При этом предельно допускаемое давление достигает 300 кгс/см , а скорость скольжения 5 м/с. Рекомендуемый диаметральный зазор равен 0,004—0,014 от диаметра вала. Долговечность подщипников из материала гласир DU зависит от значений pv. Значения pv для минимального срока службы в 1000 и 10 000 ч приведены в табл. 34. Данные таблицы, относящиеся к малоуглеродистой стали, применимы также для чугуна, аустенитной нержавеющей стали и уг леродистых сталей с хромовым и никелевым покрытиями.
[c.127]
Не удается найти страницу | Autodesk Knowledge Network
(* {{l10n_strings.REQUIRED_FIELD}})
{{l10n_strings.CREATE_NEW_COLLECTION}}*
{{l10n_strings. ADD_COLLECTION_DESCRIPTION}}
{{l10n_strings.DRAG_TEXT_HELP}}
{{l10n_strings.LANGUAGE}} {{$select.selected.display}}{{article. content_lang.display}}
{{l10n_strings.AUTHOR_TOOLTIP_TEXT}}
{{$select.selected.display}} {{l10n_strings.CREATE_AND_ADD_TO_COLLECTION_MODAL_BUTTON}} {{l10n_strings.CREATE_A_COLLECTION_ERROR}}Тепловое расширение материалов и клеевое соединение.
При любом соединении деталей, механическом, клеевом, сварном, важно не только получить прочное соединение — не менее важна его долговечность в условиях эксплуатации изделия. Испытать начальную прочность как правило, несложно — устойчивость клеевого соединения к различным типам нагрузки (удары, вибрации, отрыв, расщепление) можно определить испытаниями по стандартным методикам. А вот испытание долговечности соединения представляет собой более сложную и долгую задачу. Необходимо представлять себе условия эксплуатации изделия, собранного с помощью клея, а зная их, оценить поведение соединенных материалов. Так, коррозия под клеевым слоем, встречающаяся при работе клеевого соединения в агрессивных условиях, например, в регионах с морским климатом, в которых сочетается высокая влажность, воздействие мелкодиперсного соляного тумана и, часто, высокие температуры. Это требует длительных испытаний в климатической камере или камере соляного тумана.
Однако существует еще один фактор, который часто упускают из вида, хотя его влияние на надежность, долговечность клеевого соединения очень существенно. Его учет усложняется тем, что протестировать его можно только на полноразмерном изделии точнее — на полноразмерном клеевом соединении. Речь пойдет о различном температурном (или тепловом) расширении материалов. При изменении температуры любой твердый материал сжимается или расширяется. Как правило, при сжатие происходит при охлаждении, а расширение при нагреве (хотя бывают и материалы-исключения, у которых изменение температуры приводит к обратному результату). Для разных материалов одинаковое изменение температуры приводит к различному изменению размера. Поэтому при соединении различных материалов, в тех случаях, когда изделие будет подвергаться температурным перепадам, необходимо учитывать, что изменение температуры приведет к появлению дополнительной сдвиговой нагрузки на клеевой шов.
Насколько велик может быть эффект разницы температурных расширений? Как определить, не опасен ли он для нашего соединения? Как склеить изделие, учитывая этот эффект? На эти вопросы я постараюсь ответить ниже.
Коэффициент теплового (температурного) расширения является характеристикой каждого материала и показывает насколько этот материал увеличивается (уменьшается) в размере при изменении температуры на один градус. Абсолютная величина расширения или сжатия, кроме коэффициента, зависит от размера изделия и изменения температуры.
Из часто используемых материалов, наиболее низким коэффициентом теплового расширения обладает стекло; несколько выше коэффициент расширения у металлов, значительно выше у пластиков. Коэффициенты теплового расширения некоторых материалов приведены в таблице.
Материал | Коэффициент теплового расширения, мм/мм*К |
Стекло | 9 х 10-6 |
Сталь | 12-14 х 10-6 |
Алюминий | 24 х 10-6 |
Полиметилметакрилат (ПММА) | 74 х 10-6 |
Поликарбонат | 68 х 10-6 |
Полипропилен | 86 х 10-6 |
Полиэфир | 120 х 10’6 |
Конечно, каждый металл или сплав, каждый пластик этот параметр имеет свою величину коэффициента. Однако, беря типичные характеристики и температурный перепад 65С (от +25 С при соединении летом до — 40С зимой) можно рассчитать, что одинаковые детали из оргстекла (полиметилметакрилат) и алюминия длиной при соединении 1 метр, зимой будут различаться по длине на 3,5 миллиметра. Жесткое крепление в таком случае неизбежно приведет или к растрескиванию пластика, или к разрушению клеевого соединения, или к деформации (прогибу) пластиковой детали. Конечно, различное расширение материалов необходимо учитывать при любом способе крепления, клеевом или механическом.
Именно зависимость от размера изделия делает сложным лабораторное испытание -стандартные образцы соединения для испытания на сдвиг размером, скажем 25×12 мм могут без потери прочности пройти многократные температурные перепады; но при длине клеевого шва один-два метра, тот же клей на тех же материалах окажется неспособен выдержать типичные для улицы температурные перепады. Впрочем, при использовании жесткого клея разрушение соединения может произойти и на изделиях небольшого размера, особенно если один из соединяемых материалов — стекло. Ввиду хрупкости этого материала, неправильный выбор продукта часто приводит к растрескиванию стекла при охлаждении даже на изделиях небольшого размера. Испытания изделий больших размеров требует использования дорогого и сравнительно редкого оборудования. К счастью, часто оценить воздействие теплового расширения материалов можно и без проведения испытаний. Необходимо учитывать сейчас с использованием клеевых технологий часто собираются изделия большого размера — рекламные вывески, фасадные панели и многие другие. Оценку возможных тепловых расширений соединяемых материалов, по моему мнению, всегда следует проводить если соблюдаются следующие условия:
1. Соединяются различные материалы; такие пары, как стекло-металл, стекло-пластик, металл-пластик наиболее «опасны» с точки зрения расширения.
2. Изделие будет эксплуатироваться на улице или подвергаться нагреву/охлаждению более, чем на 20 С.
3. Максимальный размер изделия более 30 мм.
Как же избежать возникновения критических для клеевого шва нагрузок, вызванных различным тепловым расширением соединенных материалов?
Очевидное решение задачи — использовать эластичный клей. Однако, при выборе продукта нередко забывают вот о чем: во-первых, продукт должен оставаться эластичным при охлаждении. Некоторые клеи и герметики, эластичные при температуре близкой к комнатной, становятся жесткими при охлаждении до -5 — — 10°С, то есть теряют способность компенсировать движение соединенных поверхностей друг относительно друга именно тогда, когда это движение становится значительным. Во-вторых, даже использую эластичный клей или герметик, необходимо создавать клеевой шов достаточной толщины. Например, полиуретановые герметики, безусловно, одни из наиболее эластичных клеевых продуктов — их растяжение до разрыва составляет 500-700%, а у некоторых и несколько больше. Тем не менее, длительно (а расширение/сжатие материалов, связанное, например, с сезонными колебаниями температуры, это именно длительное изменение) они выдерживают сдвиговые деформации 20-25% от толщины. Попробуем оценить, какую толщину должен иметь полиуретановый герметик для соединения стекла и алюминия длиной 1 метр при изменении температуры от +25при склейке до -40.
Расчет с учетом типичных коэффициентов для стекла и алюминия (напомню, точное значение несколько меняется в зависимости от марки стекла или алюминиевого сплава) дает значение примерно 1,4 мм. Для надежного крепления стекла в таком случае потребуется толщина клеевого слоя 5,5-6,0 миллиметров (кстати, именно эту минимальную толщину многие производители полиуретановых герметиков рекомендуют для соединения стекла с металлом).
Отличным решением для соединения материалов с различным тепловым расширением являются ленты ЗМ™ VHB™ — двусторонние монтажные ленты, состоящие только из акрилового полимера. Вязкоупругая основа этих лент, в отличие от герметиков и, тем более, от двухкомпонентных клеев, выдерживает без разрушения сдвиговые деформации до 300% от толщины ленты. Максимальная толщина ленты VHB™ составляет 3 мм, позволяя, таким образом, компенсировать разницу расширений до 15 мм. Акриловый полимер сохраняет эластичность до — 40С, а у некоторых лент VHB™ и при более низких температурах. Ленты ЗМ™ VHB™ успешно используются для соединения стекла с алюминием, в том числе в архитектурных объектах и подтвердили свою работоспособность при соединении самых разных сочетаний материалов в очень широком диапазоне температур.
http://naftaros.ru — Коэффициент линейного расширения базальтопластика
С.П.Оснос, В.Н.Садков, М.Н.Киселев
Тепловое расширение тел характеризуется линейным или объемным коэффициентом расширения.
Истинным коэффициент линейного расширения (истинным КТР) называется отношение увеличения линейного размера базальтопластикового стержня единичной длины к малому изменению температуры, вызвавшему изменение размера. На практике пользуются средним коэффициентом линейного расширения:
Где L0 — длина стержня при начальной температуре Т0;
Lt — длина стержня, нагретого до температуры Т.
В таблице приводятся значения коэффициентов термического расширения некоторых материалов в интервале температур от 15°С до 200°С.
Коэффициенты термического расширения
№ п/п | Материал | a 107град-1 |
1 | 2 | 3 |
1 | Стекло кварцевое | 5,6 |
2 | Стекло листовое оконное | 95 |
3 | Стекло свинцовое (хрусталь) | 120 |
4 | Сталь | 117 |
5 | Медь | 170 |
6 | Серебро | 195 |
7 | Алюминий | 235 |
8 | Свинец | 300 |
9 | Цинк | 358 |
10 | Базальтопластик | 46 |
11 | Стеклопластик | 50 |
12 | Массивное стекло алюмобороси- | 60 |
13 | Стеклянное волокно алюмоборо- | 50 |
14 | Полиэфирные смолы | 800-2000 |
15 | Эпоксидные компаунды | 320-600 |
16 | Кварцевый песок | 5 |
КТР — одно из важнейших эксплуатационных свойств базальтопластика. Правильный подбор КТР для ряда важных областей применения этих материалов определяет не только качество получаемых изделий, но и саму возможность их изготовления.
Так, например, при применении базальтопластика в качестве арматуры бетонных изделий для предотвращения внутреннего растрескивания бетона при больших колебаниях температуры подбирают составляющие с близкими значениями КТР.
КТР базальтопластика определяется методом кварцевого дилатометра, сущность которого заключается в измерении абсолютного удлинения образца при его нагревании.
Измерение КТР образцов проводились на вертикальном кварцевом дилатометре типа ДКВ. Образец пластика длиной 50 мм и диаметром 5 мм, измеренный с точностью до 0,1 мм, помещали в находящуюся в печи кварцевую пробирку и укрепляли между шлифованной цилиндрической пластинкой из кварцевого стекла, покоящейся на сферической опоре, впаянной в дно пробирки, и торцом кварцевого стержня, передающего расширение измерителю — индикатору. Скорость подъема температуры в печи 3-4°С в минуту; температуру в печи измеряли хромель-алюмелевой термопары, ЭДС которой определяли потенциометром.
Коэффициент линейного расширения (a) определяли по формуле:
a — коэффициент линейного расширения в град-1;
Dl — показания индикатора с поправкой на расширение кварца,мк;
Dt — разность конечной и начальной температуры для выбранного при расчете интервала в гард;
l — длина образца в мм.
Коэффициент линейного расширения базальтопластика равен 46*10-7 град-1, стеклопластика 50*10-7 град-1(см.табл.)
В ы в о д
При определении коэффициента термического расширения базальтопластика в сравнении со стеклопластиком на эпоксиполиэфирном связующем установлено, что КТР обоих материалов находится в пределах 45*10-7 50*10-7 град-1 .
Следовательно, изделия из базальтопластика могут применяться также, как и изделия из стеклопластика в качестве арматуры для бетонных изделий.
Тепловое расширение водопроводных труб
Водопроводные трубы, как и большинство материалов меняют свои размеры с изменением температуры. Свойство материала менять свой размер под воздействием изменения температуры характеризуется коэффициентом линейного расширения . У различных материалов коэффициенты линейного расширения могут отличаться на порядок, но в данном случае мы рассматриваем только материалы, из которых изготавливают водопроводные трубы- сталь, медь, полипропилен и металлопластик.
Материал трубы | Коэффициент теплового расширения, мм/мК | Тепловое расширение 1 метра трубы при изменении температуры на 50 градусов, мм |
Полипропилен (не армированный) | 0,1500 | 7,5 |
Армированный полипропилен | 0,03-0,05 | 2,1-3,5 |
Металлопластик | 0,0250 | 1,25 |
Медь | 0,0166 | 0,83 |
Нержавеющая сталь | 0,0165 | 0,825 |
Сталь | 0,0120 | 0,6 |
Из таблицы следует, что наиболее опасно тепловое расширение для полипропиленовых труб — 8 мм на один погонный метр, что необходимо учитывать при замене труб в квартире.
Формула теплового расширения
Тепловое расширение материалов подчиняется линейной формуле
dL=k*L
где L- длина предмета, k -коэффициент теплового расширения, dL-изменение длины предмета
Меры компенсации теплового расширения труб
Для снятия внутренних напряжений от тепловой деформации трубы должны иметь возможность перемещаться на длину своего теплового расширения. Это обеспечивается:
- отсутствием жестких креплений трубы (желательно применение обрезиненных креплений)
- отсутствием ограничителей по торцам трубы (наличие зазоров от торца трубы до препятствия)
- наличие компенсирующих петель
Термопласт ABS (акрилонитрил-бутадиен-стирол) | 72-108 | ||||||||||||||||||||||||||||||||||||||||||||||||||||||||||||||||||||||||||||||||||||||||||||||||||||||||||||||||||||||||||||||||||||||||||||||||||||||||||||||||||||||||||||||||||||||||||||||||||||||||||||||||||||||||||||||||||||||||||||||||||||||||||||||||||||||||||||||||||||||||||||||||||||||||||||||||||||||||||||||||||||||||||||||||||||||||||||||||||||||||||||||||||||||||||||||||||||||||||||||||||||||||||||||||||||||||||||||||||||||||||||||||||||||||||||||||||||||||||||||||||||||||||||||||||||||||||||||||||||||||||||||||||||||||||||||||||||||||||||||||||||||||||||||||||||||||||||||||||||||||||||||||||||||||||||||||||||||||||||||||||||||||||||||||||||||||||||||||||||||||||||||||||||||||||||||||||||||||||||||||||||||||||||||||||||||||||||||||||||||||||||||||||||||||||||||||||||||||||||||||||||||||||||||||||||||||||||||||||||||||||||||||||||||||||||||||||||||||||||||||||||||||||||||||||||||||||||||||||||||||||||||||||||||||||||||||||||||||||||||||||||||||||||||||||||||||||||||||||||||
ABS-стекловолокно, армированное стекловолокном | 31 | ||||||||||||||||||||||||||||||||||||||||||||||||||||||||||||||||||||||||||||||||||||||||||||||||||||||||||||||||||||||||||||||||||||||||||||||||||||||||||||||||||||||||||||||||||||||||||||||||||||||||||||||||||||||||||||||||||||||||||||||||||||||||||||||||||||||||||||||||||||||||||||||||||||||||||||||||||||||||||||||||||||||||||||||||||||||||||||||||||||||||||||||||||||||||||||||||||||||||||||||||||||||||||||||||||||||||||||||||||||||||||||||||||||||||||||||||||||||||||||||||||||||||||||||||||||||||||||||||||||||||||||||||||||||||||||||||||||||||||||||||||||||||||||||||||||||||||||||||||||||||||||||||||||||||||||||||||||||||||||||||||||||||||||||||||||||||||||||||||||||||||||||||||||||||||||||||||||||||||||||||||||||||||||||||||||||||||||||||||||||||||||||||||||||||||||||||||||||||||||||||||||||||||||||||||||||||||||||||||||||||||||||||||||||||||||||||||||||||||||||||||||||||||||||||||||||||||||||||||||||||||||||||||||||||||||||||||||||||||||||||||||||||||||||||||||||||||||||||||||||
армированное стекловолокном | Acetal | ||||||||||||||||||||||||||||||||||||||||||||||||||||||||||||||||||||||||||||||||||||||||||||||||||||||||||||||||||||||||||||||||||||||||||||||||||||||||||||||||||||||||||||||||||||||||||||||||||||||||||||||||||||||||||||||||||||||||||||||||||||||||||||||||||||||||||||||||||||||||||||||||||||||||||||||||||||||||||||||||||||||||||||||||||||||||||||||||||||||||||||||||||||||||||||||||||||||||||||||||||||||||||||||||||||||||||||||||||||||||||||||||||||||||||||||||||||||||||||||||||||||||||||||||||||||||||||||||||||||||||||||||||||||||||||||||||||||||||||||||||||||||||||||||||||||||||||||||||||||||||||||||||||||||||||||||||||||||||||||||||||||||||||||||||||||||||||||||||||||||||||||||||||||||||||||||||||||||||||||||||||||||||||||||||||||||||||||||||||||||||||||||||||||||||||||||||||||||||||||||||||||||||||||||||||||||||||||||||||||||||||||||||||||||||||||||||||||||||||||||||||||||||||||||||||||||||||||||||||||||||||||||||||||||||||||||||||||||||||||||||||||||||||||||||||||||||||||||||||||
Ацетали | 85-110 | ||||||||||||||||||||||||||||||||||||||||||||||||||||||||||||||||||||||||||||||||||||||||||||||||||||||||||||||||||||||||||||||||||||||||||||||||||||||||||||||||||||||||||||||||||||||||||||||||||||||||||||||||||||||||||||||||||||||||||||||||||||||||||||||||||||||||||||||||||||||||||||||||||||||||||||||||||||||||||||||||||||||||||||||||||||||||||||||||||||||||||||||||||||||||||||||||||||||||||||||||||||||||||||||||||||||||||||||||||||||||||||||||||||||||||||||||||||||||||||||||||||||||||||||||||||||||||||||||||||||||||||||||||||||||||||||||||||||||||||||||||||||||||||||||||||||||||||||||||||||||||||||||||||||||||||||||||||||||||||||||||||||||||||||||||||||||||||||||||||||||||||||||||||||||||||||||||||||||||||||||||||||||||||||||||||||||||||||||||||||||||||||||||||||||||||||||||||||||||||||||||||||||||||||||||||||||||||||||||||||||||||||||||||||||||||||||||||||||||||||||||||||||||||||||||||||||||||||||||||||||||||||||||||||||||||||||||||||||||||||||||||||||||||||||||||||||||||||||||||||
Акрил | 68-75 | ||||||||||||||||||||||||||||||||||||||||||||||||||||||||||||||||||||||||||||||||||||||||||||||||||||||||||||||||||||||||||||||||||||||||||||||||||||||||||||||||||||||||||||||||||||||||||||||||||||||||||||||||||||||||||||||||||||||||||||||||||||||||||||||||||||||||||||||||||||||||||||||||||||||||||||||||||||||||||||||||||||||||||||||||||||||||||||||||||||||||||||||||||||||||||||||||||||||||||||||||||||||||||||||||||||||||||||||||||||||||||||||||||||||||||||||||||||||||||||||||||||||||||||||||||||||||||||||||||||||||||||||||||||||||||||||||||||||||||||||||||||||||||||||||||||||||||||||||||||||||||||||||||||||||||||||||||||||||||||||||||||||||||||||||||||||||||||||||||||||||||||||||||||||||||||||||||||||||||||||||||||||||||||||||||||||||||||||||||||||||||||||||||||||||||||||||||||||||||||||||||||||||||||||||||||||||||||||||||||||||||||||||||||||||||||||||||||||||||||||||||||||||||||||||||||||||||||||||||||||||||||||||||||||||||||||||||||||||||||||||||||||||||||||||||||||||||||||||||||||
Глинозем (оксид алюминия, Al 2 O 3 ) | 8.![]() | ||||||||||||||||||||||||||||||||||||||||||||||||||||||||||||||||||||||||||||||||||||||||||||||||||||||||||||||||||||||||||||||||||||||||||||||||||||||||||||||||||||||||||||||||||||||||||||||||||||||||||||||||||||||||||||||||||||||||||||||||||||||||||||||||||||||||||||||||||||||||||||||||||||||||||||||||||||||||||||||||||||||||||||||||||||||||||||||||||||||||||||||||||||||||||||||||||||||||||||||||||||||||||||||||||||||||||||||||||||||||||||||||||||||||||||||||||||||||||||||||||||||||||||||||||||||||||||||||||||||||||||||||||||||||||||||||||||||||||||||||||||||||||||||||||||||||||||||||||||||||||||||||||||||||||||||||||||||||||||||||||||||||||||||||||||||||||||||||||||||||||||||||||||||||||||||||||||||||||||||||||||||||||||||||||||||||||||||||||||||||||||||||||||||||||||||||||||||||||||||||||||||||||||||||||||||||||||||||||||||||||||||||||||||||||||||||||||||||||||||||||||||||||||||||||||||||||||||||||||||||||||||||||||||||||||||||||||||||||||||||||||||||||||||||||||||||||||||||||||||
Алюминий | 21-24 | ||||||||||||||||||||||||||||||||||||||||||||||||||||||||||||||||||||||||||||||||||||||||||||||||||||||||||||||||||||||||||||||||||||||||||||||||||||||||||||||||||||||||||||||||||||||||||||||||||||||||||||||||||||||||||||||||||||||||||||||||||||||||||||||||||||||||||||||||||||||||||||||||||||||||||||||||||||||||||||||||||||||||||||||||||||||||||||||||||||||||||||||||||||||||||||||||||||||||||||||||||||||||||||||||||||||||||||||||||||||||||||||||||||||||||||||||||||||||||||||||||||||||||||||||||||||||||||||||||||||||||||||||||||||||||||||||||||||||||||||||||||||||||||||||||||||||||||||||||||||||||||||||||||||||||||||||||||||||||||||||||||||||||||||||||||||||||||||||||||||||||||||||||||||||||||||||||||||||||||||||||||||||||||||||||||||||||||||||||||||||||||||||||||||||||||||||||||||||||||||||||||||||||||||||||||||||||||||||||||||||||||||||||||||||||||||||||||||||||||||||||||||||||||||||||||||||||||||||||||||||||||||||||||||||||||||||||||||||||||||||||||||||||||||||||||||||||||||||||||||
Нитрид алюминия | 5,3 | ||||||||||||||||||||||||||||||||||||||||||||||||||||||||||||||||||||||||||||||||||||||||||||||||||||||||||||||||||||||||||||||||||||||||||||||||||||||||||||||||||||||||||||||||||||||||||||||||||||||||||||||||||||||||||||||||||||||||||||||||||||||||||||||||||||||||||||||||||||||||||||||||||||||||||||||||||||||||||||||||||||||||||||||||||||||||||||||||||||||||||||||||||||||||||||||||||||||||||||||||||||||||||||||||||||||||||||||||||||||||||||||||||||||||||||||||||||||||||||||||||||||||||||||||||||||||||||||||||||||||||||||||||||||||||||||||||||||||||||||||||||||||||||||||||||||||||||||||||||||||||||||||||||||||||||||||||||||||||||||||||||||||||||||||||||||||||||||||||||||||||||||||||||||||||||||||||||||||||||||||||||||||||||||||||||||||||||||||||||||||||||||||||||||||||||||||||||||||||||||||||||||||||||||||||||||||||||||||||||||||||||||||||||||||||||||||||||||||||||||||||||||||||||||||||||||||||||||||||||||||||||||||||||||||||||||||||||||||||||||||||||||||||||||||||||||||||||||||||||||
Янтарь | 50-60 | ||||||||||||||||||||||||||||||||||||||||||||||||||||||||||||||||||||||||||||||||||||||||||||||||||||||||||||||||||||||||||||||||||||||||||||||||||||||||||||||||||||||||||||||||||||||||||||||||||||||||||||||||||||||||||||||||||||||||||||||||||||||||||||||||||||||||||||||||||||||||||||||||||||||||||||||||||||||||||||||||||||||||||||||||||||||||||||||||||||||||||||||||||||||||||||||||||||||||||||||||||||||||||||||||||||||||||||||||||||||||||||||||||||||||||||||||||||||||||||||||||||||||||||||||||||||||||||||||||||||||||||||||||||||||||||||||||||||||||||||||||||||||||||||||||||||||||||||||||||||||||||||||||||||||||||||||||||||||||||||||||||||||||||||||||||||||||||||||||||||||||||||||||||||||||||||||||||||||||||||||||||||||||||||||||||||||||||||||||||||||||||||||||||||||||||||||||||||||||||||||||||||||||||||||||||||||||||||||||||||||||||||||||||||||||||||||||||||||||||||||||||||||||||||||||||||||||||||||||||||||||||||||||||||||||||||||||||||||||||||||||||||||||||||||||||||||||||||||||||||
Сурьма свинец (твердый свинец) | 0000004 9-11|||||||||||||||||||||||||||||||||||||||||||||||||||||||||||||||||||||||||||||||||||||||||||||||||||||||||||||||||||||||||||||||||||||||||||||||||||||||||||||||||||||||||||||||||||||||||||||||||||||||||||||||||||||||||||||||||||||||||||||||||||||||||||||||||||||||||||||||||||||||||||||||||||||||||||||||||||||||||||||||||||||||||||||||||||||||||||||||||||||||||||||||||||||||||||||||||||||||||||||||||||||||||||||||||||||||||||||||||||||||||||||||||||||||||||||||||||||||||||||||||||||||||||||||||||||||||||||||||||||||||||||||||||||||||||||||||||||||||||||||||||||||||||||||||||||||||||||||||||||||||||||||||||||||||||||||||||||||||||||||||||||||||||||||||||||||||||||||||||||||||||||||||||||||||||||||||||||||||||||||||||||||||||||||||||||||||||||||||||||||||||||||||||||||||||||||||||||||||||||||||||||||||||||||||||||||||||||||||||||||||||||||||||||||||||||||||||||||||||||||||||||||||||||||||||||||||||||||||||||||||||||||||||||||||||||||||||||||||||||||||||||||||||||||||||||||||||||||||||||||
Мышьяк | 4,7 | ||||||||||||||||||||||||||||||||||||||||||||||||||||||||||||||||||||||||||||||||||||||||||||||||||||||||||||||||||||||||||||||||||||||||||||||||||||||||||||||||||||||||||||||||||||||||||||||||||||||||||||||||||||||||||||||||||||||||||||||||||||||||||||||||||||||||||||||||||||||||||||||||||||||||||||||||||||||||||||||||||||||||||||||||||||||||||||||||||||||||||||||||||||||||||||||||||||||||||||||||||||||||||||||||||||||||||||||||||||||||||||||||||||||||||||||||||||||||||||||||||||||||||||||||||||||||||||||||||||||||||||||||||||||||||||||||||||||||||||||||||||||||||||||||||||||||||||||||||||||||||||||||||||||||||||||||||||||||||||||||||||||||||||||||||||||||||||||||||||||||||||||||||||||||||||||||||||||||||||||||||||||||||||||||||||||||||||||||||||||||||||||||||||||||||||||||||||||||||||||||||||||||||||||||||||||||||||||||||||||||||||||||||||||||||||||||||||||||||||||||||||||||||||||||||||||||||||||||||||||||||||||||||||||||||||||||||||||||||||||||||||||||||||||||||||||||||||||||||||||
Бакелит, отбеленный | 22 | ||||||||||||||||||||||||||||||||||||||||||||||||||||||||||||||||||||||||||||||||||||||||||||||||||||||||||||||||||||||||||||||||||||||||||||||||||||||||||||||||||||||||||||||||||||||||||||||||||||||||||||||||||||||||||||||||||||||||||||||||||||||||||||||||||||||||||||||||||||||||||||||||||||||||||||||||||||||||||||||||||||||||||||||||||||||||||||||||||||||||||||||||||||||||||||||||||||||||||||||||||||||||||||||||||||||||||||||||||||||||||||||||||||||||||||||||||||||||||||||||||||||||||||||||||||||||||||||||||||||||||||||||||||||||||||||||||||||||||||||||||||||||||||||||||||||||||||||||||||||||||||||||||||||||||||||||||||||||||||||||||||||||||||||||||||||||||||||||||||||||||||||||||||||||||||||||||||||||||||||||||||||||||||||||||||||||||||||||||||||||||||||||||||||||||||||||||||||||||||||||||||||||||||||||||||||||||||||||||||||||||||||||||||||||||||||||||||||||||||||||||||||||||||||||||||||||||||||||||||||||||||||||||||||||||||||||||||||||||||||||||||||||||||||||||||||||||||||||||||||
Барий | 20,6 | ||||||||||||||||||||||||||||||||||||||||||||||||||||||||||||||||||||||||||||||||||||||||||||||||||||||||||||||||||||||||||||||||||||||||||||||||||||||||||||||||||||||||||||||||||||||||||||||||||||||||||||||||||||||||||||||||||||||||||||||||||||||||||||||||||||||||||||||||||||||||||||||||||||||||||||||||||||||||||||||||||||||||||||||||||||||||||||||||||||||||||||||||||||||||||||||||||||||||||||||||||||||||||||||||||||||||||||||||||||||||||||||||||||||||||||||||||||||||||||||||||||||||||||||||||||||||||||||||||||||||||||||||||||||||||||||||||||||||||||||||||||||||||||||||||||||||||||||||||||||||||||||||||||||||||||||||||||||||||||||||||||||||||||||||||||||||||||||||||||||||||||||||||||||||||||||||||||||||||||||||||||||||||||||||||||||||||||||||||||||||||||||||||||||||||||||||||||||||||||||||||||||||||||||||||||||||||||||||||||||||||||||||||||||||||||||||||||||||||||||||||||||||||||||||||||||||||||||||||||||||||||||||||||||||||||||||||||||||||||||||||||||||||||||||||||||||||||||||||||||
Феррит бария | Бериллий | 12 | |||||||||||||||||||||||||||||||||||||||||||||||||||||||||||||||||||||||||||||||||||||||||||||||||||||||||||||||||||||||||||||||||||||||||||||||||||||||||||||||||||||||||||||||||||||||||||||||||||||||||||||||||||||||||||||||||||||||||||||||||||||||||||||||||||||||||||||||||||||||||||||||||||||||||||||||||||||||||||||||||||||||||||||||||||||||||||||||||||||||||||||||||||||||||||||||||||||||||||||||||||||||||||||||||||||||||||||||||||||||||||||||||||||||||||||||||||||||||||||||||||||||||||||||||||||||||||||||||||||||||||||||||||||||||||||||||||||||||||||||||||||||||||||||||||||||||||||||||||||||||||||||||||||||||||||||||||||||||||||||||||||||||||||||||||||||||||||||||||||||||||||||||||||||||||||||||||||||||||||||||||||||||||||||||||||||||||||||||||||||||||||||||||||||||||||||||||||||||||||||||||||||||||||||||||||||||||||||||||||||||||||||||||||||||||||||||||||||||||||||||||||||||||||||||||||||||||||||||||||||||||||||||||||||||||||||||||||||||||||||||||||||||||||||||||||||||||||||||||||
Висмут | 13 — 13.5 | ||||||||||||||||||||||||||||||||||||||||||||||||||||||||||||||||||||||||||||||||||||||||||||||||||||||||||||||||||||||||||||||||||||||||||||||||||||||||||||||||||||||||||||||||||||||||||||||||||||||||||||||||||||||||||||||||||||||||||||||||||||||||||||||||||||||||||||||||||||||||||||||||||||||||||||||||||||||||||||||||||||||||||||||||||||||||||||||||||||||||||||||||||||||||||||||||||||||||||||||||||||||||||||||||||||||||||||||||||||||||||||||||||||||||||||||||||||||||||||||||||||||||||||||||||||||||||||||||||||||||||||||||||||||||||||||||||||||||||||||||||||||||||||||||||||||||||||||||||||||||||||||||||||||||||||||||||||||||||||||||||||||||||||||||||||||||||||||||||||||||||||||||||||||||||||||||||||||||||||||||||||||||||||||||||||||||||||||||||||||||||||||||||||||||||||||||||||||||||||||||||||||||||||||||||||||||||||||||||||||||||||||||||||||||||||||||||||||||||||||||||||||||||||||||||||||||||||||||||||||||||||||||||||||||||||||||||||||||||||||||||||||||||||||||||||||||||||||||||||||
Латунь | 18 — 19 | ||||||||||||||||||||||||||||||||||||||||||||||||||||||||||||||||||||||||||||||||||||||||||||||||||||||||||||||||||||||||||||||||||||||||||||||||||||||||||||||||||||||||||||||||||||||||||||||||||||||||||||||||||||||||||||||||||||||||||||||||||||||||||||||||||||||||||||||||||||||||||||||||||||||||||||||||||||||||||||||||||||||||||||||||||||||||||||||||||||||||||||||||||||||||||||||||||||||||||||||||||||||||||||||||||||||||||||||||||||||||||||||||||||||||||||||||||||||||||||||||||||||||||||||||||||||||||||||||||||||||||||||||||||||||||||||||||||||||||||||||||||||||||||||||||||||||||||||||||||||||||||||||||||||||||||||||||||||||||||||||||||||||||||||||||||||||||||||||||||||||||||||||||||||||||||||||||||||||||||||||||||||||||||||||||||||||||||||||||||||||||||||||||||||||||||||||||||||||||||||||||||||||||||||||||||||||||||||||||||||||||||||||||||||||||||||||||||||||||||||||||||||||||||||||||||||||||||||||||||||||||||||||||||||||||||||||||||||||||||||||||||||||||||||||||||||||||||||||||||||
Кирпичная кладка | 5 | ||||||||||||||||||||||||||||||||||||||||||||||||||||||||||||||||||||||||||||||||||||||||||||||||||||||||||||||||||||||||||||||||||||||||||||||||||||||||||||||||||||||||||||||||||||||||||||||||||||||||||||||||||||||||||||||||||||||||||||||||||||||||||||||||||||||||||||||||||||||||||||||||||||||||||||||||||||||||||||||||||||||||||||||||||||||||||||||||||||||||||||||||||||||||||||||||||||||||||||||||||||||||||||||||||||||||||||||||||||||||||||||||||||||||||||||||||||||||||||||||||||||||||||||||||||||||||||||||||||||||||||||||||||||||||||||||||||||||||||||||||||||||||||||||||||||||||||||||||||||||||||||||||||||||||||||||||||||||||||||||||||||||||||||||||||||||||||||||||||||||||||||||||||||||||||||||||||||||||||||||||||||||||||||||||||||||||||||||||||||||||||||||||||||||||||||||||||||||||||||||||||||||||||||||||||||||||||||||||||||||||||||||||||||||||||||||||||||||||||||||||||||||||||||||||||||||||||||||||||||||||||||||||||||||||||||||||||||||||||||||||||||||||||||||||||||||||||||||||||||
Бронза | 17,5 — 18 | ||||||||||||||||||||||||||||||||||||||||||||||||||||||||||||||||||||||||||||||||||||||||||||||||||||||||||||||||||||||||||||||||||||||||||||||||||||||||||||||||||||||||||||||||||||||||||||||||||||||||||||||||||||||||||||||||||||||||||||||||||||||||||||||||||||||||||||||||||||||||||||||||||||||||||||||||||||||||||||||||||||||||||||||||||||||||||||||||||||||||||||||||||||||||||||||||||||||||||||||||||||||||||||||||||||||||||||||||||||||||||||||||||||||||||||||||||||||||||||||||||||||||||||||||||||||||||||||||||||||||||||||||||||||||||||||||||||||||||||||||||||||||||||||||||||||||||||||||||||||||||||||||||||||||||||||||||||||||||||||||||||||||||||||||||||||||||||||||||||||||||||||||||||||||||||||||||||||||||||||||||||||||||||||||||||||||||||||||||||||||||||||||||||||||||||||||||||||||||||||||||||||||||||||||||||||||||||||||||||||||||||||||||||||||||||||||||||||||||||||||||||||||||||||||||||||||||||||||||||||||||||||||||||||||||||||||||||||||||||||||||||||||||||||||||||||||||||||||||||||
Cadmium | Каучук66-69 | ||||||||||||||||||||||||||||||||||||||||||||||||||||||||||||||||||||||||||||||||||||||||||||||||||||||||||||||||||||||||||||||||||||||||||||||||||||||||||||||||||||||||||||||||||||||||||||||||||||||||||||||||||||||||||||||||||||||||||||||||||||||||||||||||||||||||||||||||||||||||||||||||||||||||||||||||||||||||||||||||||||||||||||||||||||||||||||||||||||||||||||||||||||||||||||||||||||||||||||||||||||||||||||||||||||||||||||||||||||||||||||||||||||||||||||||||||||||||||||||||||||||||||||||||||||||||||||||||||||||||||||||||||||||||||||||||||||||||||||||||||||||||||||||||||||||||||||||||||||||||||||||||||||||||||||||||||||||||||||||||||||||||||||||||||||||||||||||||||||||||||||||||||||||||||||||||||||||||||||||||||||||||||||||||||||||||||||||||||||||||||||||||||||||||||||||||||||||||||||||||||||||||||||||||||||||||||||||||||||||||||||||||||||||||||||||||||||||||||||||||||||||||||||||||||||||||||||||||||||||||||||||||||||||||||||||||||||||||||||||||||||||||||||||||||||||||||||||||||||||
Серый чугун | 10,8 | ||||||||||||||||||||||||||||||||||||||||||||||||||||||||||||||||||||||||||||||||||||||||||||||||||||||||||||||||||||||||||||||||||||||||||||||||||||||||||||||||||||||||||||||||||||||||||||||||||||||||||||||||||||||||||||||||||||||||||||||||||||||||||||||||||||||||||||||||||||||||||||||||||||||||||||||||||||||||||||||||||||||||||||||||||||||||||||||||||||||||||||||||||||||||||||||||||||||||||||||||||||||||||||||||||||||||||||||||||||||||||||||||||||||||||||||||||||||||||||||||||||||||||||||||||||||||||||||||||||||||||||||||||||||||||||||||||||||||||||||||||||||||||||||||||||||||||||||||||||||||||||||||||||||||||||||||||||||||||||||||||||||||||||||||||||||||||||||||||||||||||||||||||||||||||||||||||||||||||||||||||||||||||||||||||||||||||||||||||||||||||||||||||||||||||||||||||||||||||||||||||||||||||||||||||||||||||||||||||||||||||||||||||||||||||||||||||||||||||||||||||||||||||||||||||||||||||||||||||||||||||||||||||||||||||||||||||||||||||||||||||||||||||||||||||||||||||||||||||||||
Целлулоид | 100 | ||||||||||||||||||||||||||||||||||||||||||||||||||||||||||||||||||||||||||||||||||||||||||||||||||||||||||||||||||||||||||||||||||||||||||||||||||||||||||||||||||||||||||||||||||||||||||||||||||||||||||||||||||||||||||||||||||||||||||||||||||||||||||||||||||||||||||||||||||||||||||||||||||||||||||||||||||||||||||||||||||||||||||||||||||||||||||||||||||||||||||||||||||||||||||||||||||||||||||||||||||||||||||||||||||||||||||||||||||||||||||||||||||||||||||||||||||||||||||||||||||||||||||||||||||||||||||||||||||||||||||||||||||||||||||||||||||||||||||||||||||||||||||||||||||||||||||||||||||||||||||||||||||||||||||||||||||||||||||||||||||||||||||||||||||||||||||||||||||||||||||||||||||||||||||||||||||||||||||||||||||||||||||||||||||||||||||||||||||||||||||||||||||||||||||||||||||||||||||||||||||||||||||||||||||||||||||||||||||||||||||||||||||||||||||||||||||||||||||||||||||||||||||||||||||||||||||||||||||||||||||||||||||||||||||||||||||||||||||||||||||||||||||||||||||||||||||||||||||||||
Ацетат целлюлозы (CA) | 130 | бутылок | |||||||||||||||||||||||||||||||||||||||||||||||||||||||||||||||||||||||||||||||||||||||||||||||||||||||||||||||||||||||||||||||||||||||||||||||||||||||||||||||||||||||||||||||||||||||||||||||||||||||||||||||||||||||||||||||||||||||||||||||||||||||||||||||||||||||||||||||||||||||||||||||||||||||||||||||||||||||||||||||||||||||||||||||||||||||||||||||||||||||||||||||||||||||||||||||||||||||||||||||||||||||||||||||||||||||||||||||||||||||||||||||||||||||||||||||||||||||||||||||||||||||||||||||||||||||||||||||||||||||||||||||||||||||||||||||||||||||||||||||||||||||||||||||||||||||||||||||||||||||||||||||||||||||||||||||||||||||||||||||||||||||||||||||||||||||||||||||||||||||||||||||||||||||||||||||||||||||||||||||||||||||||||||||||||||||||||||||||||||||||||||||||||||||||||||||||||||||||||||||||||||||||||||||||||||||||||||||||||||||||||||||||||||||||||||||||||||||||||||||||||||||||||||||||||||||||||||||||||||||||||||||||||||||||||||||||||||||||||||||||||||||||||||||||||||||||||||||||||||
Нитрат целлюлозы (CN) | 80-120 | ||||||||||||||||||||||||||||||||||||||||||||||||||||||||||||||||||||||||||||||||||||||||||||||||||||||||||||||||||||||||||||||||||||||||||||||||||||||||||||||||||||||||||||||||||||||||||||||||||||||||||||||||||||||||||||||||||||||||||||||||||||||||||||||||||||||||||||||||||||||||||||||||||||||||||||||||||||||||||||||||||||||||||||||||||||||||||||||||||||||||||||||||||||||||||||||||||||||||||||||||||||||||||||||||||||||||||||||||||||||||||||||||||||||||||||||||||||||||||||||||||||||||||||||||||||||||||||||||||||||||||||||||||||||||||||||||||||||||||||||||||||||||||||||||||||||||||||||||||||||||||||||||||||||||||||||||||||||||||||||||||||||||||||||||||||||||||||||||||||||||||||||||||||||||||||||||||||||||||||||||||||||||||||||||||||||||||||||||||||||||||||||||||||||||||||||||||||||||||||||||||||||||||||||||||||||||||||||||||||||||||||||||||||||||||||||||||||||||||||||||||||||||||||||||||||||||||||||||||||||||||||||||||||||||||||||||||||||||||||||||||||||||||||||||||||||||||||||||||||||
Цемент, Портленд | 11 | ||||||||||||||||||||||||||||||||||||||||||||||||||||||||||||||||||||||||||||||||||||||||||||||||||||||||||||||||||||||||||||||||||||||||||||||||||||||||||||||||||||||||||||||||||||||||||||||||||||||||||||||||||||||||||||||||||||||||||||||||||||||||||||||||||||||||||||||||||||||||||||||||||||||||||||||||||||||||||||||||||||||||||||||||||||||||||||||||||||||||||||||||||||||||||||||||||||||||||||||||||||||||||||||||||||||||||||||||||||||||||||||||||||||||||||||||||||||||||||||||||||||||||||||||||||||||||||||||||||||||||||||||||||||||||||||||||||||||||||||||||||||||||||||||||||||||||||||||||||||||||||||||||||||||||||||||||||||||||||||||||||||||||||||||||||||||||||||||||||||||||||||||||||||||||||||||||||||||||||||||||||||||||||||||||||||||||||||||||||||||||||||||||||||||||||||||||||||||||||||||||||||||||||||||||||||||||||||||||||||||||||||||||||||||||||||||||||||||||||||||||||||||||||||||||||||||||||||||||||||||||||||||||||||||||||||||||||||||||||||||||||||||||||||||||||||||||||||||||||||
Церий | 5.![]() | ||||||||||||||||||||||||||||||||||||||||||||||||||||||||||||||||||||||||||||||||||||||||||||||||||||||||||||||||||||||||||||||||||||||||||||||||||||||||||||||||||||||||||||||||||||||||||||||||||||||||||||||||||||||||||||||||||||||||||||||||||||||||||||||||||||||||||||||||||||||||||||||||||||||||||||||||||||||||||||||||||||||||||||||||||||||||||||||||||||||||||||||||||||||||||||||||||||||||||||||||||||||||||||||||||||||||||||||||||||||||||||||||||||||||||||||||||||||||||||||||||||||||||||||||||||||||||||||||||||||||||||||||||||||||||||||||||||||||||||||||||||||||||||||||||||||||||||||||||||||||||||||||||||||||||||||||||||||||||||||||||||||||||||||||||||||||||||||||||||||||||||||||||||||||||||||||||||||||||||||||||||||||||||||||||||||||||||||||||||||||||||||||||||||||||||||||||||||||||||||||||||||||||||||||||||||||||||||||||||||||||||||||||||||||||||||||||||||||||||||||||||||||||||||||||||||||||||||||||||||||||||||||||||||||||||||||||||||||||||||||||||||||||||||||||||||||||||||||||||||
Хлорированный полиэфир | 80 | ||||||||||||||||||||||||||||||||||||||||||||||||||||||||||||||||||||||||||||||||||||||||||||||||||||||||||||||||||||||||||||||||||||||||||||||||||||||||||||||||||||||||||||||||||||||||||||||||||||||||||||||||||||||||||||||||||||||||||||||||||||||||||||||||||||||||||||||||||||||||||||||||||||||||||||||||||||||||||||||||||||||||||||||||||||||||||||||||||||||||||||||||||||||||||||||||||||||||||||||||||||||||||||||||||||||||||||||||||||||||||||||||||||||||||||||||||||||||||||||||||||||||||||||||||||||||||||||||||||||||||||||||||||||||||||||||||||||||||||||||||||||||||||||||||||||||||||||||||||||||||||||||||||||||||||||||||||||||||||||||||||||||||||||||||||||||||||||||||||||||||||||||||||||||||||||||||||||||||||||||||||||||||||||||||||||||||||||||||||||||||||||||||||||||||||||||||||||||||||||||||||||||||||||||||||||||||||||||||||||||||||||||||||||||||||||||||||||||||||||||||||||||||||||||||||||||||||||||||||||||||||||||||||||||||||||||||||||||||||||||||||||||||||||||||||||||||||||||||||||
Хлорированный поливинилхлорид (ХПВХ) | 63-66 | ||||||||||||||||||||||||||||||||||||||||||||||||||||||||||||||||||||||||||||||||||||||||||||||||||||||||||||||||||||||||||||||||||||||||||||||||||||||||||||||||||||||||||||||||||||||||||||||||||||||||||||||||||||||||||||||||||||||||||||||||||||||||||||||||||||||||||||||||||||||||||||||||||||||||||||||||||||||||||||||||||||||||||||||||||||||||||||||||||||||||||||||||||||||||||||||||||||||||||||||||||||||||||||||||||||||||||||||||||||||||||||||||||||||||||||||||||||||||||||||||||||||||||||||||||||||||||||||||||||||||||||||||||||||||||||||||||||||||||||||||||||||||||||||||||||||||||||||||||||||||||||||||||||||||||||||||||||||||||||||||||||||||||||||||||||||||||||||||||||||||||||||||||||||||||||||||||||||||||||||||||||||||||||||||||||||||||||||||||||||||||||||||||||||||||||||||||||||||||||||||||||||||||||||||||||||||||||||||||||||||||||||||||||||||||||||||||||||||||||||||||||||||||||||||||||||||||||||||||||||||||||||||||||||||||||||||||||||||||||||||||||||||||||||||||||||||||||||||||||||
Хром | 6-7 | 9000 Структура плитки12 | |||||||||||||||||||||||||||||||||||||||||||||||||||||||||||||||||||||||||||||||||||||||||||||||||||||||||||||||||||||||||||||||||||||||||||||||||||||||||||||||||||||||||||||||||||||||||||||||||||||||||||||||||||||||||||||||||||||||||||||||||||||||||||||||||||||||||||||||||||||||||||||||||||||||||||||||||||||||||||||||||||||||||||||||||||||||||||||||||||||||||||||||||||||||||||||||||||||||||||||||||||||||||||||||||||||||||||||||||||||||||||||||||||||||||||||||||||||||||||||||||||||||||||||||||||||||||||||||||||||||||||||||||||||||||||||||||||||||||||||||||||||||||||||||||||||||||||||||||||||||||||||||||||||||||||||||||||||||||||||||||||||||||||||||||||||||||||||||||||||||||||||||||||||||||||||||||||||||||||||||||||||||||||||||||||||||||||||||||||||||||||||||||||||||||||||||||||||||||||||||||||||||||||||||||||||||||||||||||||||||||||||||||||||||||||||||||||||||||||||||||||||||||||||||||||||||||||||||||||||||||||||||||||||||||||||||||||||||||||||||||||||||||||||||||||||||||||||||||||||
Бетон | 13-14 | ||||||||||||||||||||||||||||||||||||||||||||||||||||||||||||||||||||||||||||||||||||||||||||||||||||||||||||||||||||||||||||||||||||||||||||||||||||||||||||||||||||||||||||||||||||||||||||||||||||||||||||||||||||||||||||||||||||||||||||||||||||||||||||||||||||||||||||||||||||||||||||||||||||||||||||||||||||||||||||||||||||||||||||||||||||||||||||||||||||||||||||||||||||||||||||||||||||||||||||||||||||||||||||||||||||||||||||||||||||||||||||||||||||||||||||||||||||||||||||||||||||||||||||||||||||||||||||||||||||||||||||||||||||||||||||||||||||||||||||||||||||||||||||||||||||||||||||||||||||||||||||||||||||||||||||||||||||||||||||||||||||||||||||||||||||||||||||||||||||||||||||||||||||||||||||||||||||||||||||||||||||||||||||||||||||||||||||||||||||||||||||||||||||||||||||||||||||||||||||||||||||||||||||||||||||||||||||||||||||||||||||||||||||||||||||||||||||||||||||||||||||||||||||||||||||||||||||||||||||||||||||||||||||||||||||||||||||||||||||||||||||||||||||||||||||||||||||||||||||||
Бетонная конструкция | 9,8 | ||||||||||||||||||||||||||||||||||||||||||||||||||||||||||||||||||||||||||||||||||||||||||||||||||||||||||||||||||||||||||||||||||||||||||||||||||||||||||||||||||||||||||||||||||||||||||||||||||||||||||||||||||||||||||||||||||||||||||||||||||||||||||||||||||||||||||||||||||||||||||||||||||||||||||||||||||||||||||||||||||||||||||||||||||||||||||||||||||||||||||||||||||||||||||||||||||||||||||||||||||||||||||||||||||||||||||||||||||||||||||||||||||||||||||||||||||||||||||||||||||||||||||||||||||||||||||||||||||||||||||||||||||||||||||||||||||||||||||||||||||||||||||||||||||||||||||||||||||||||||||||||||||||||||||||||||||||||||||||||||||||||||||||||||||||||||||||||||||||||||||||||||||||||||||||||||||||||||||||||||||||||||||||||||||||||||||||||||||||||||||||||||||||||||||||||||||||||||||||||||||||||||||||||||||||||||||||||||||||||||||||||||||||||||||||||||||||||||||||||||||||||||||||||||||||||||||||||||||||||||||||||||||||||||||||||||||||||||||||||||||||||||||||||||||||||||||||||||||||||
Константан | 15.2-18,8 | ||||||||||||||||||||||||||||||||||||||||||||||||||||||||||||||||||||||||||||||||||||||||||||||||||||||||||||||||||||||||||||||||||||||||||||||||||||||||||||||||||||||||||||||||||||||||||||||||||||||||||||||||||||||||||||||||||||||||||||||||||||||||||||||||||||||||||||||||||||||||||||||||||||||||||||||||||||||||||||||||||||||||||||||||||||||||||||||||||||||||||||||||||||||||||||||||||||||||||||||||||||||||||||||||||||||||||||||||||||||||||||||||||||||||||||||||||||||||||||||||||||||||||||||||||||||||||||||||||||||||||||||||||||||||||||||||||||||||||||||||||||||||||||||||||||||||||||||||||||||||||||||||||||||||||||||||||||||||||||||||||||||||||||||||||||||||||||||||||||||||||||||||||||||||||||||||||||||||||||||||||||||||||||||||||||||||||||||||||||||||||||||||||||||||||||||||||||||||||||||||||||||||||||||||||||||||||||||||||||||||||||||||||||||||||||||||||||||||||||||||||||||||||||||||||||||||||||||||||||||||||||||||||||||||||||||||||||||||||||||||||||||||||||||||||||||||||||||||||||||
Медь | 16-16,7 | ||||||||||||||||||||||||||||||||||||||||||||||||||||||||||||||||||||||||||||||||||||||||||||||||||||||||||||||||||||||||||||||||||||||||||||||||||||||||||||||||||||||||||||||||||||||||||||||||||||||||||||||||||||||||||||||||||||||||||||||||||||||||||||||||||||||||||||||||||||||||||||||||||||||||||||||||||||||||||||||||||||||||||||||||||||||||||||||||||||||||||||||||||||||||||||||||||||||||||||||||||||||||||||||||||||||||||||||||||||||||||||||||||||||||||||||||||||||||||||||||||||||||||||||||||||||||||||||||||||||||||||||||||||||||||||||||||||||||||||||||||||||||||||||||||||||||||||||||||||||||||||||||||||||||||||||||||||||||||||||||||||||||||||||||||||||||||||||||||||||||||||||||||||||||||||||||||||||||||||||||||||||||||||||||||||||||||||||||||||||||||||||||||||||||||||||||||||||||||||||||||||||||||||||||||||||||||||||||||||||||||||||||||||||||||||||||||||||||||||||||||||||||||||||||||||||||||||||||||||||||||||||||||||||||||||||||||||||||||||||||||||||||||||||||||||||||||||||||||||||
Медь, бериллий 25 | 17,8 | ||||||||||||||||||||||||||||||||||||||||||||||||||||||||||||||||||||||||||||||||||||||||||||||||||||||||||||||||||||||||||||||||||||||||||||||||||||||||||||||||||||||||||||||||||||||||||||||||||||||||||||||||||||||||||||||||||||||||||||||||||||||||||||||||||||||||||||||||||||||||||||||||||||||||||||||||||||||||||||||||||||||||||||||||||||||||||||||||||||||||||||||||||||||||||||||||||||||||||||||||||||||||||||||||||||||||||||||||||||||||||||||||||||||||||||||||||||||||||||||||||||||||||||||||||||||||||||||||||||||||||||||||||||||||||||||||||||||||||||||||||||||||||||||||||||||||||||||||||||||||||||||||||||||||||||||||||||||||||||||||||||||||||||||||||||||||||||||||||||||||||||||||||||||||||||||||||||||||||||||||||||||||||||||||||||||||||||||||||||||||||||||||||||||||||||||||||||||||||||||||||||||||||||||||||||||||||||||||||||||||||||||||||||||||||||||||||||||||||||||||||||||||||||||||||||||||||||||||||||||||||||||||||||||||||||||||||||||||||||||||||||||||||||||||||||||||||||||||||||||
Корунд, спеченный | 6,5 | ||||||||||||||||||||||||||||||||||||||||||||||||||||||||||||||||||||||||||||||||||||||||||||||||||||||||||||||||||||||||||||||||||||||||||||||||||||||||||||||||||||||||||||||||||||||||||||||||||||||||||||||||||||||||||||||||||||||||||||||||||||||||||||||||||||||||||||||||||||||||||||||||||||||||||||||||||||||||||||||||||||||||||||||||||||||||||||||||||||||||||||||||||||||||||||||||||||||||||||||||||||||||||||||||||||||||||||||||||||||||||||||||||||||||||||||||||||||||||||||||||||||||||||||||||||||||||||||||||||||||||||||||||||||||||||||||||||||||||||||||||||||||||||||||||||||||||||||||||||||||||||||||||||||||||||||||||||||||||||||||||||||||||||||||||||||||||||||||||||||||||||||||||||||||||||||||||||||||||||||||||||||||||||||||||||||||||||||||||||||||||||||||||||||||||||||||||||||||||||||||||||||||||||||||||||||||||||||||||||||||||||||||||||||||||||||||||||||||||||||||||||||||||||||||||||||||||||||||||||||||||||||||||||||||||||||||||||||||||||||||||||||||||||||||||||||||||||||||||||||
Алмаз (углерод) | 1,1 — 1,3 | ||||||||||||||||||||||||||||||||||||||||||||||||||||||||||||||||||||||||||||||||||||||||||||||||||||||||||||||||||||||||||||||||||||||||||||||||||||||||||||||||||||||||||||||||||||||||||||||||||||||||||||||||||||||||||||||||||||||||||||||||||||||||||||||||||||||||||||||||||||||||||||||||||||||||||||||||||||||||||||||||||||||||||||||||||||||||||||||||||||||||||||||||||||||||||||||||||||||||||||||||||||||||||||||||||||||||||||||||||||||||||||||||||||||||||||||||||||||||||||||||||||||||||||||||||||||||||||||||||||||||||||||||||||||||||||||||||||||||||||||||||||||||||||||||||||||||||||||||||||||||||||||||||||||||||||||||||||||||||||||||||||||||||||||||||||||||||||||||||||||||||||||||||||||||||||||||||||||||||||||||||||||||||||||||||||||||||||||||||||||||||||||||||||||||||||||||||||||||||||||||||||||||||||||||||||||||||||||||||||||||||||||||||||||||||||||||||||||||||||||||||||||||||||||||||||||||||||||||||||||||||||||||||||||||||||||||||||||||||||||||||||||||||||||||||||||||||||||||||||||
Дюралюминий | 23 | ||||||||||||||||||||||||||||||||||||||||||||||||||||||||||||||||||||||||||||||||||||||||||||||||||||||||||||||||||||||||||||||||||||||||||||||||||||||||||||||||||||||||||||||||||||||||||||||||||||||||||||||||||||||||||||||||||||||||||||||||||||||||||||||||||||||||||||||||||||||||||||||||||||||||||||||||||||||||||||||||||||||||||||||||||||||||||||||||||||||||||||||||||||||||||||||||||||||||||||||||||||||||||||||||||||||||||||||||||||||||||||||||||||||||||||||||||||||||||||||||||||||||||||||||||||||||||||||||||||||||||||||||||||||||||||||||||||||||||||||||||||||||||||||||||||||||||||||||||||||||||||||||||||||||||||||||||||||||||||||||||||||||||||||||||||||||||||||||||||||||||||||||||||||||||||||||||||||||||||||||||||||||||||||||||||||||||||||||||||||||||||||||||||||||||||||||||||||||||||||||||||||||||||||||||||||||||||||||||||||||||||||||||||||||||||||||||||||||||||||||||||||||||||||||||||||||||||||||||||||||||||||||||||||||||||||||||||||||||||||||||||||||||||||||||||||||||||||||||||||
Диспрозий | 9,9 | ||||||||||||||||||||||||||||||||||||||||||||||||||||||||||||||||||||||||||||||||||||||||||||||||||||||||||||||||||||||||||||||||||||||||||||||||||||||||||||||||||||||||||||||||||||||||||||||||||||||||||||||||||||||||||||||||||||||||||||||||||||||||||||||||||||||||||||||||||||||||||||||||||||||||||||||||||||||||||||||||||||||||||||||||||||||||||||||||||||||||||||||||||||||||||||||||||||||||||||||||||||||||||||||||||||||||||||||||||||||||||||||||||||||||||||||||||||||||||||||||||||||||||||||||||||||||||||||||||||||||||||||||||||||||||||||||||||||||||||||||||||||||||||||||||||||||||||||||||||||||||||||||||||||||||||||||||||||||||||||||||||||||||||||||||||||||||||||||||||||||||||||||||||||||||||||||||||||||||||||||||||||||||||||||||||||||||||||||||||||||||||||||||||||||||||||||||||||||||||||||||||||||||||||||||||||||||||||||||||||||||||||||||||||||||||||||||||||||||||||||||||||||||||||||||||||||||||||||||||||||||||||||||||||||||||||||||||||||||||||||||||||||||||||||||||||||||||||||||||||
Эбонит | 70 | 000 | стекловолокно, армированное стекловолокном Эпоксидные, литые смолы и компаунды, ненаполненные45 — 65 | ||||||||||||||||||||||||||||||||||||||||||||||||||||||||||||||||||||||||||||||||||||||||||||||||||||||||||||||||||||||||||||||||||||||||||||||||||||||||||||||||||||||||||||||||||||||||||||||||||||||||||||||||||||||||||||||||||||||||||||||||||||||||||||||||||||||||||||||||||||||||||||||||||||||||||||||||||||||||||||||||||||||||||||||||||||||||||||||||||||||||||||||||||||||||||||||||||||||||||||||||||||||||||||||||||||||||||||||||||||||||||||||||||||||||||||||||||||||||||||||||||||||||||||||||||||||||||||||||||||||||||||||||||||||||||||||||||||||||||||||||||||||||||||||||||||||||||||||||||||||||||||||||||||||||||||||||||||||||||||||||||||||||||||||||||||||||||||||||||||||||||||||||||||||||||||||||||||||||||||||||||||||||||||||||||||||||||||||||||||||||||||||||||||||||||||||||||||||||||||||||||||||||||||||||||||||||||||||||||||||||||||||||||||||||||||||||||||||||||||||||||||||||||||||||||||||||||||||||||||||||||||||||||||||||||||||||||||||||||||||||||||||||||||||||||||||||||||||||||||
Эрбий | 12.2 | ||||||||||||||||||||||||||||||||||||||||||||||||||||||||||||||||||||||||||||||||||||||||||||||||||||||||||||||||||||||||||||||||||||||||||||||||||||||||||||||||||||||||||||||||||||||||||||||||||||||||||||||||||||||||||||||||||||||||||||||||||||||||||||||||||||||||||||||||||||||||||||||||||||||||||||||||||||||||||||||||||||||||||||||||||||||||||||||||||||||||||||||||||||||||||||||||||||||||||||||||||||||||||||||||||||||||||||||||||||||||||||||||||||||||||||||||||||||||||||||||||||||||||||||||||||||||||||||||||||||||||||||||||||||||||||||||||||||||||||||||||||||||||||||||||||||||||||||||||||||||||||||||||||||||||||||||||||||||||||||||||||||||||||||||||||||||||||||||||||||||||||||||||||||||||||||||||||||||||||||||||||||||||||||||||||||||||||||||||||||||||||||||||||||||||||||||||||||||||||||||||||||||||||||||||||||||||||||||||||||||||||||||||||||||||||||||||||||||||||||||||||||||||||||||||||||||||||||||||||||||||||||||||||||||||||||||||||||||||||||||||||||||||||||||||||||||||||||||||||||
Этиленэтилакрилат (EEA) | 205 | ||||||||||||||||||||||||||||||||||||||||||||||||||||||||||||||||||||||||||||||||||||||||||||||||||||||||||||||||||||||||||||||||||||||||||||||||||||||||||||||||||||||||||||||||||||||||||||||||||||||||||||||||||||||||||||||||||||||||||||||||||||||||||||||||||||||||||||||||||||||||||||||||||||||||||||||||||||||||||||||||||||||||||||||||||||||||||||||||||||||||||||||||||||||||||||||||||||||||||||||||||||||||||||||||||||||||||||||||||||||||||||||||||||||||||||||||||||||||||||||||||||||||||||||||||||||||||||||||||||||||||||||||||||||||||||||||||||||||||||||||||||||||||||||||||||||||||||||||||||||||||||||||||||||||||||||||||||||||||||||||||||||||||||||||||||||||||||||||||||||||||||||||||||||||||||||||||||||||||||||||||||||||||||||||||||||||||||||||||||||||||||||||||||||||||||||||||||||||||||||||||||||||||||||||||||||||||||||||||||||||||||||||||||||||||||||||||||||||||||||||||||||||||||||||||||||||||||||||||||||||||||||||||||||||||||||||||||||||||||||||||||||||||||||||||||||||||||||||||||||
Этиленвинилацетат (EVA) | 180 | ||||||||||||||||||||||||||||||||||||||||||||||||||||||||||||||||||||||||||||||||||||||||||||||||||||||||||||||||||||||||||||||||||||||||||||||||||||||||||||||||||||||||||||||||||||||||||||||||||||||||||||||||||||||||||||||||||||||||||||||||||||||||||||||||||||||||||||||||||||||||||||||||||||||||||||||||||||||||||||||||||||||||||||||||||||||||||||||||||||||||||||||||||||||||||||||||||||||||||||||||||||||||||||||||||||||||||||||||||||||||||||||||||||||||||||||||||||||||||||||||||||||||||||||||||||||||||||||||||||||||||||||||||||||||||||||||||||||||||||||||||||||||||||||||||||||||||||||||||||||||||||||||||||||||||||||||||||||||||||||||||||||||||||||||||||||||||||||||||||||||||||||||||||||||||||||||||||||||||||||||||||||||||||||||||||||||||||||||||||||||||||||||||||||||||||||||||||||||||||||||||||||||||||||||||||||||||||||||||||||||||||||||||||||||||||||||||||||||||||||||||||||||||||||||||||||||||||||||||||||||||||||||||||||||||||||||||||||||||||||||||||||||||||||||||||||||||||||||||||||
Европий | 35 | ||||||||||||||||||||||||||||||||||||||||||||||||||||||||||||||||||||||||||||||||||||||||||||||||||||||||||||||||||||||||||||||||||||||||||||||||||||||||||||||||||||||||||||||||||||||||||||||||||||||||||||||||||||||||||||||||||||||||||||||||||||||||||||||||||||||||||||||||||||||||||||||||||||||||||||||||||||||||||||||||||||||||||||||||||||||||||||||||||||||||||||||||||||||||||||||||||||||||||||||||||||||||||||||||||||||||||||||||||||||||||||||||||||||||||||||||||||||||||||||||||||||||||||||||||||||||||||||||||||||||||||||||||||||||||||||||||||||||||||||||||||||||||||||||||||||||||||||||||||||||||||||||||||||||||||||||||||||||||||||||||||||||||||||||||||||||||||||||||||||||||||||||||||||||||||||||||||||||||||||||||||||||||||||||||||||||||||||||||||||||||||||||||||||||||||||||||||||||||||||||||||||||||||||||||||||||||||||||||||||||||||||||||||||||||||||||||||||||||||||||||||||||||||||||||||||||||||||||||||||||||||||||||||||||||||||||||||||||||||||||||||||||||||||||||||||||||||||||||||||
Плавиковый шпат, CaF 2 | 19,5 | ||||||||||||||||||||||||||||||||||||||||||||||||||||||||||||||||||||||||||||||||||||||||||||||||||||||||||||||||||||||||||||||||||||||||||||||||||||||||||||||||||||||||||||||||||||||||||||||||||||||||||||||||||||||||||||||||||||||||||||||||||||||||||||||||||||||||||||||||||||||||||||||||||||||||||||||||||||||||||||||||||||||||||||||||||||||||||||||||||||||||||||||||||||||||||||||||||||||||||||||||||||||||||||||||||||||||||||||||||||||||||||||||||||||||||||||||||||||||||||||||||||||||||||||||||||||||||||||||||||||||||||||||||||||||||||||||||||||||||||||||||||||||||||||||||||||||||||||||||||||||||||||||||||||||||||||||||||||||||||||||||||||||||||||||||||||||||||||||||||||||||||||||||||||||||||||||||||||||||||||||||||||||||||||||||||||||||||||||||||||||||||||||||||||||||||||||||||||||||||||||||||||||||||||||||||||||||||||||||||||||||||||||||||||||||||||||||||||||||||||||||||||||||||||||||||||||||||||||||||||||||||||||||||||||||||||||||||||||||||||||||||||||||||||||||||||||||||||||||||||
Гадолиний | 9 | ||||||||||||||||||||||||||||||||||||||||||||||||||||||||||||||||||||||||||||||||||||||||||||||||||||||||||||||||||||||||||||||||||||||||||||||||||||||||||||||||||||||||||||||||||||||||||||||||||||||||||||||||||||||||||||||||||||||||||||||||||||||||||||||||||||||||||||||||||||||||||||||||||||||||||||||||||||||||||||||||||||||||||||||||||||||||||||||||||||||||||||||||||||||||||||||||||||||||||||||||||||||||||||||||||||||||||||||||||||||||||||||||||||||||||||||||||||||||||||||||||||||||||||||||||||||||||||||||||||||||||||||||||||||||||||||||||||||||||||||||||||||||||||||||||||||||||||||||||||||||||||||||||||||||||||||||||||||||||||||||||||||||||||||||||||||||||||||||||||||||||||||||||||||||||||||||||||||||||||||||||||||||||||||||||||||||||||||||||||||||||||||||||||||||||||||||||||||||||||||||||||||||||||||||||||||||||||||||||||||||||||||||||||||||||||||||||||||||||||||||||||||||||||||||||||||||||||||||||||||||||||||||||||||||||||||||||||||||||||||||||||||||||||||||||||||||||||||||||||||
Немецкое серебро | 18,4 | ||||||||||||||||||||||||||||||||||||||||||||||||||||||||||||||||||||||||||||||||||||||||||||||||||||||||||||||||||||||||||||||||||||||||||||||||||||||||||||||||||||||||||||||||||||||||||||||||||||||||||||||||||||||||||||||||||||||||||||||||||||||||||||||||||||||||||||||||||||||||||||||||||||||||||||||||||||||||||||||||||||||||||||||||||||||||||||||||||||||||||||||||||||||||||||||||||||||||||||||||||||||||||||||||||||||||||||||||||||||||||||||||||||||||||||||||||||||||||||||||||||||||||||||||||||||||||||||||||||||||||||||||||||||||||||||||||||||||||||||||||||||||||||||||||||||||||||||||||||||||||||||||||||||||||||||||||||||||||||||||||||||||||||||||||||||||||||||||||||||||||||||||||||||||||||||||||||||||||||||||||||||||||||||||||||||||||||||||||||||||||||||||||||||||||||||||||||||||||||||||||||||||||||||||||||||||||||||||||||||||||||||||||||||||||||||||||||||||||||||||||||||||||||||||||||||||||||||||||||||||||||||||||||||||||||||||||||||||||||||||||||||||||||||||||||||||||||||||||||||
Германий | 6.![]() | ||||||||||||||||||||||||||||||||||||||||||||||||||||||||||||||||||||||||||||||||||||||||||||||||||||||||||||||||||||||||||||||||||||||||||||||||||||||||||||||||||||||||||||||||||||||||||||||||||||||||||||||||||||||||||||||||||||||||||||||||||||||||||||||||||||||||||||||||||||||||||||||||||||||||||||||||||||||||||||||||||||||||||||||||||||||||||||||||||||||||||||||||||||||||||||||||||||||||||||||||||||||||||||||||||||||||||||||||||||||||||||||||||||||||||||||||||||||||||||||||||||||||||||||||||||||||||||||||||||||||||||||||||||||||||||||||||||||||||||||||||||||||||||||||||||||||||||||||||||||||||||||||||||||||||||||||||||||||||||||||||||||||||||||||||||||||||||||||||||||||||||||||||||||||||||||||||||||||||||||||||||||||||||||||||||||||||||||||||||||||||||||||||||||||||||||||||||||||||||||||||||||||||||||||||||||||||||||||||||||||||||||||||||||||||||||||||||||||||||||||||||||||||||||||||||||||||||||||||||||||||||||||||||||||||||||||||||||||||||||||||||||||||||||||||||||||||||||||||||||
Стекло, твердое | 5,9 | ||||||||||||||||||||||||||||||||||||||||||||||||||||||||||||||||||||||||||||||||||||||||||||||||||||||||||||||||||||||||||||||||||||||||||||||||||||||||||||||||||||||||||||||||||||||||||||||||||||||||||||||||||||||||||||||||||||||||||||||||||||||||||||||||||||||||||||||||||||||||||||||||||||||||||||||||||||||||||||||||||||||||||||||||||||||||||||||||||||||||||||||||||||||||||||||||||||||||||||||||||||||||||||||||||||||||||||||||||||||||||||||||||||||||||||||||||||||||||||||||||||||||||||||||||||||||||||||||||||||||||||||||||||||||||||||||||||||||||||||||||||||||||||||||||||||||||||||||||||||||||||||||||||||||||||||||||||||||||||||||||||||||||||||||||||||||||||||||||||||||||||||||||||||||||||||||||||||||||||||||||||||||||||||||||||||||||||||||||||||||||||||||||||||||||||||||||||||||||||||||||||||||||||||||||||||||||||||||||||||||||||||||||||||||||||||||||||||||||||||||||||||||||||||||||||||||||||||||||||||||||||||||||||||||||||||||||||||||||||||||||||||||||||||||||||||||||||||||||||||
Стекло, пластина | 9,0 | ||||||||||||||||||||||||||||||||||||||||||||||||||||||||||||||||||||||||||||||||||||||||||||||||||||||||||||||||||||||||||||||||||||||||||||||||||||||||||||||||||||||||||||||||||||||||||||||||||||||||||||||||||||||||||||||||||||||||||||||||||||||||||||||||||||||||||||||||||||||||||||||||||||||||||||||||||||||||||||||||||||||||||||||||||||||||||||||||||||||||||||||||||||||||||||||||||||||||||||||||||||||||||||||||||||||||||||||||||||||||||||||||||||||||||||||||||||||||||||||||||||||||||||||||||||||||||||||||||||||||||||||||||||||||||||||||||||||||||||||||||||||||||||||||||||||||||||||||||||||||||||||||||||||||||||||||||||||||||||||||||||||||||||||||||||||||||||||||||||||||||||||||||||||||||||||||||||||||||||||||||||||||||||||||||||||||||||||||||||||||||||||||||||||||||||||||||||||||||||||||||||||||||||||||||||||||||||||||||||||||||||||||||||||||||||||||||||||||||||||||||||||||||||||||||||||||||||||||||||||||||||||||||||||||||||||||||||||||||||||||||||||||||||||||||||||||||||||||||||||
Стекло, Pyrex | 4,0 | ||||||||||||||||||||||||||||||||||||||||||||||||||||||||||||||||||||||||||||||||||||||||||||||||||||||||||||||||||||||||||||||||||||||||||||||||||||||||||||||||||||||||||||||||||||||||||||||||||||||||||||||||||||||||||||||||||||||||||||||||||||||||||||||||||||||||||||||||||||||||||||||||||||||||||||||||||||||||||||||||||||||||||||||||||||||||||||||||||||||||||||||||||||||||||||||||||||||||||||||||||||||||||||||||||||||||||||||||||||||||||||||||||||||||||||||||||||||||||||||||||||||||||||||||||||||||||||||||||||||||||||||||||||||||||||||||||||||||||||||||||||||||||||||||||||||||||||||||||||||||||||||||||||||||||||||||||||||||||||||||||||||||||||||||||||||||||||||||||||||||||||||||||||||||||||||||||||||||||||||||||||||||||||||||||||||||||||||||||||||||||||||||||||||||||||||||||||||||||||||||||||||||||||||||||||||||||||||||||||||||||||||||||||||||||||||||||||||||||||||||||||||||||||||||||||||||||||||||||||||||||||||||||||||||||||||||||||||||||||||||||||||||||||||||||||||||||||||||||||||
Золото | медь | ||||||||||||||||||||||||||||||||||||||||||||||||||||||||||||||||||||||||||||||||||||||||||||||||||||||||||||||||||||||||||||||||||||||||||||||||||||||||||||||||||||||||||||||||||||||||||||||||||||||||||||||||||||||||||||||||||||||||||||||||||||||||||||||||||||||||||||||||||||||||||||||||||||||||||||||||||||||||||||||||||||||||||||||||||||||||||||||||||||||||||||||||||||||||||||||||||||||||||||||||||||||||||||||||||||||||||||||||||||||||||||||||||||||||||||||||||||||||||||||||||||||||||||||||||||||||||||||||||||||||||||||||||||||||||||||||||||||||||||||||||||||||||||||||||||||||||||||||||||||||||||||||||||||||||||||||||||||||||||||||||||||||||||||||||||||||||||||||||||||||||||||||||||||||||||||||||||||||||||||||||||||||||||||||||||||||||||||||||||||||||||||||||||||||||||||||||||||||||||||||||||||||||||||||||||||||||||||||||||||||||||||||||||||||||||||||||||||||||||||||||||||||||||||||||||||||||||||||||||||||||||||||||||||||||||||||||||||||||||||||||||||||||||||||||||||||||||||||||||||
Золото — платина | 15,2 | ||||||||||||||||||||||||||||||||||||||||||||||||||||||||||||||||||||||||||||||||||||||||||||||||||||||||||||||||||||||||||||||||||||||||||||||||||||||||||||||||||||||||||||||||||||||||||||||||||||||||||||||||||||||||||||||||||||||||||||||||||||||||||||||||||||||||||||||||||||||||||||||||||||||||||||||||||||||||||||||||||||||||||||||||||||||||||||||||||||||||||||||||||||||||||||||||||||||||||||||||||||||||||||||||||||||||||||||||||||||||||||||||||||||||||||||||||||||||||||||||||||||||||||||||||||||||||||||||||||||||||||||||||||||||||||||||||||||||||||||||||||||||||||||||||||||||||||||||||||||||||||||||||||||||||||||||||||||||||||||||||||||||||||||||||||||||||||||||||||||||||||||||||||||||||||||||||||||||||||||||||||||||||||||||||||||||||||||||||||||||||||||||||||||||||||||||||||||||||||||||||||||||||||||||||||||||||||||||||||||||||||||||||||||||||||||||||||||||||||||||||||||||||||||||||||||||||||||||||||||||||||||||||||||||||||||||||||||||||||||||||||||||||||||||||||||||||||||||||||||
Гранит | 7,9 — 8,4 | ||||||||||||||||||||||||||||||||||||||||||||||||||||||||||||||||||||||||||||||||||||||||||||||||||||||||||||||||||||||||||||||||||||||||||||||||||||||||||||||||||||||||||||||||||||||||||||||||||||||||||||||||||||||||||||||||||||||||||||||||||||||||||||||||||||||||||||||||||||||||||||||||||||||||||||||||||||||||||||||||||||||||||||||||||||||||||||||||||||||||||||||||||||||||||||||||||||||||||||||||||||||||||||||||||||||||||||||||||||||||||||||||||||||||||||||||||||||||||||||||||||||||||||||||||||||||||||||||||||||||||||||||||||||||||||||||||||||||||||||||||||||||||||||||||||||||||||||||||||||||||||||||||||||||||||||||||||||||||||||||||||||||||||||||||||||||||||||||||||||||||||||||||||||||||||||||||||||||||||||||||||||||||||||||||||||||||||||||||||||||||||||||||||||||||||||||||||||||||||||||||||||||||||||||||||||||||||||||||||||||||||||||||||||||||||||||||||||||||||||||||||||||||||||||||||||||||||||||||||||||||||||||||||||||||||||||||||||||||||||||||||||||||||||||||||||||||||||||||||||
Графит чистый (углерод) | 4-8 | ||||||||||||||||||||||||||||||||||||||||||||||||||||||||||||||||||||||||||||||||||||||||||||||||||||||||||||||||||||||||||||||||||||||||||||||||||||||||||||||||||||||||||||||||||||||||||||||||||||||||||||||||||||||||||||||||||||||||||||||||||||||||||||||||||||||||||||||||||||||||||||||||||||||||||||||||||||||||||||||||||||||||||||||||||||||||||||||||||||||||||||||||||||||||||||||||||||||||||||||||||||||||||||||||||||||||||||||||||||||||||||||||||||||||||||||||||||||||||||||||||||||||||||||||||||||||||||||||||||||||||||||||||||||||||||||||||||||||||||||||||||||||||||||||||||||||||||||||||||||||||||||||||||||||||||||||||||||||||||||||||||||||||||||||||||||||||||||||||||||||||||||||||||||||||||||||||||||||||||||||||||||||||||||||||||||||||||||||||||||||||||||||||||||||||||||||||||||||||||||||||||||||||||||||||||||||||||||||||||||||||||||||||||||||||||||||||||||||||||||||||||||||||||||||||||||||||||||||||||||||||||||||||||||||||||||||||||||||||||||||||||||||||||||||||||||||||||||||||||||
Gunmetal | 180004 Gunmetal | 180004 198 | |||||||||||||||||||||||||||||||||||||||||||||||||||||||||||||||||||||||||||||||||||||||||||||||||||||||||||||||||||||||||||||||||||||||||||||||||||||||||||||||||||||||||||||||||||||||||||||||||||||||||||||||||||||||||||||||||||||||||||||||||||||||||||||||||||||||||||||||||||||||||||||||||||||||||||||||||||||||||||||||||||||||||||||||||||||||||||||||||||||||||||||||||||||||||||||||||||||||||||||||||||||||||||||||||||||||||||||||||||||||||||||||||||||||||||||||||||||||||||||||||||||||||||||||||||||||||||||||||||||||||||||||||||||||||||||||||||||||||||||||||||||||||||||||||||||||||||||||||||||||||||||||||||||||||||||||||||||||||||||||||||||||||||||||||||||||||||||||||||||||||||||||||||||||||||||||||||||||||||||||||||||||||||||||||||||||||||||||||||||||||||||||||||||||||||||||||||||||||||||||||||||||||||||||||||||||||||||||||||||||||||||||||||||||||||||||||||||||||||||||||||||||||||||||||||||||||||||||||||||||||||||||||||||||||||||||||||||||||||||||||||||||||||||||||||||||||||||||||||||
Гафний | 5.9 | ||||||||||||||||||||||||||||||||||||||||||||||||||||||||||||||||||||||||||||||||||||||||||||||||||||||||||||||||||||||||||||||||||||||||||||||||||||||||||||||||||||||||||||||||||||||||||||||||||||||||||||||||||||||||||||||||||||||||||||||||||||||||||||||||||||||||||||||||||||||||||||||||||||||||||||||||||||||||||||||||||||||||||||||||||||||||||||||||||||||||||||||||||||||||||||||||||||||||||||||||||||||||||||||||||||||||||||||||||||||||||||||||||||||||||||||||||||||||||||||||||||||||||||||||||||||||||||||||||||||||||||||||||||||||||||||||||||||||||||||||||||||||||||||||||||||||||||||||||||||||||||||||||||||||||||||||||||||||||||||||||||||||||||||||||||||||||||||||||||||||||||||||||||||||||||||||||||||||||||||||||||||||||||||||||||||||||||||||||||||||||||||||||||||||||||||||||||||||||||||||||||||||||||||||||||||||||||||||||||||||||||||||||||||||||||||||||||||||||||||||||||||||||||||||||||||||||||||||||||||||||||||||||||||||||||||||||||||||||||||||||||||||||||||||||||||||||||||||||||||
Твердый сплав K20 | 6 | ||||||||||||||||||||||||||||||||||||||||||||||||||||||||||||||||||||||||||||||||||||||||||||||||||||||||||||||||||||||||||||||||||||||||||||||||||||||||||||||||||||||||||||||||||||||||||||||||||||||||||||||||||||||||||||||||||||||||||||||||||||||||||||||||||||||||||||||||||||||||||||||||||||||||||||||||||||||||||||||||||||||||||||||||||||||||||||||||||||||||||||||||||||||||||||||||||||||||||||||||||||||||||||||||||||||||||||||||||||||||||||||||||||||||||||||||||||||||||||||||||||||||||||||||||||||||||||||||||||||||||||||||||||||||||||||||||||||||||||||||||||||||||||||||||||||||||||||||||||||||||||||||||||||||||||||||||||||||||||||||||||||||||||||||||||||||||||||||||||||||||||||||||||||||||||||||||||||||||||||||||||||||||||||||||||||||||||||||||||||||||||||||||||||||||||||||||||||||||||||||||||||||||||||||||||||||||||||||||||||||||||||||||||||||||||||||||||||||||||||||||||||||||||||||||||||||||||||||||||||||||||||||||||||||||||||||||||||||||||||||||||||||||||||||||||||||||||||||||||||
Hastelloy C | 11,3 | ||||||||||||||||||||||||||||||||||||||||||||||||||||||||||||||||||||||||||||||||||||||||||||||||||||||||||||||||||||||||||||||||||||||||||||||||||||||||||||||||||||||||||||||||||||||||||||||||||||||||||||||||||||||||||||||||||||||||||||||||||||||||||||||||||||||||||||||||||||||||||||||||||||||||||||||||||||||||||||||||||||||||||||||||||||||||||||||||||||||||||||||||||||||||||||||||||||||||||||||||||||||||||||||||||||||||||||||||||||||||||||||||||||||||||||||||||||||||||||||||||||||||||||||||||||||||||||||||||||||||||||||||||||||||||||||||||||||||||||||||||||||||||||||||||||||||||||||||||||||||||||||||||||||||||||||||||||||||||||||||||||||||||||||||||||||||||||||||||||||||||||||||||||||||||||||||||||||||||||||||||||||||||||||||||||||||||||||||||||||||||||||||||||||||||||||||||||||||||||||||||||||||||||||||||||||||||||||||||||||||||||||||||||||||||||||||||||||||||||||||||||||||||||||||||||||||||||||||||||||||||||||||||||||||||||||||||||||||||||||||||||||||||||||||||||||||||||||||||||||
Гольмий | 11,2 | ||||||||||||||||||||||||||||||||||||||||||||||||||||||||||||||||||||||||||||||||||||||||||||||||||||||||||||||||||||||||||||||||||||||||||||||||||||||||||||||||||||||||||||||||||||||||||||||||||||||||||||||||||||||||||||||||||||||||||||||||||||||||||||||||||||||||||||||||||||||||||||||||||||||||||||||||||||||||||||||||||||||||||||||||||||||||||||||||||||||||||||||||||||||||||||||||||||||||||||||||||||||||||||||||||||||||||||||||||||||||||||||||||||||||||||||||||||||||||||||||||||||||||||||||||||||||||||||||||||||||||||||||||||||||||||||||||||||||||||||||||||||||||||||||||||||||||||||||||||||||||||||||||||||||||||||||||||||||||||||||||||||||||||||||||||||||||||||||||||||||||||||||||||||||||||||||||||||||||||||||||||||||||||||||||||||||||||||||||||||||||||||||||||||||||||||||||||||||||||||||||||||||||||||||||||||||||||||||||||||||||||||||||||||||||||||||||||||||||||||||||||||||||||||||||||||||||||||||||||||||||||||||||||||||||||||||||||||||||||||||||||||||||||||||||||||||||||||||||||||
Ice, 0 o | C water | 11,5 — 12,6 | |||||||||||||||||||||||||||||||||||||||||||||||||||||||||||||||||||||||||||||||||||||||||||||||||||||||||||||||||||||||||||||||||||||||||||||||||||||||||||||||||||||||||||||||||||||||||||||||||||||||||||||||||||||||||||||||||||||||||||||||||||||||||||||||||||||||||||||||||||||||||||||||||||||||||||||||||||||||||||||||||||||||||||||||||||||||||||||||||||||||||||||||||||||||||||||||||||||||||||||||||||||||||||||||||||||||||||||||||||||||||||||||||||||||||||||||||||||||||||||||||||||||||||||||||||||||||||||||||||||||||||||||||||||||||||||||||||||||||||||||||||||||||||||||||||||||||||||||||||||||||||||||||||||||||||||||||||||||||||||||||||||||||||||||||||||||||||||||||||||||||||||||||||||||||||||||||||||||||||||||||||||||||||||||||||||||||||||||||||||||||||||||||||||||||||||||||||||||||||||||||||||||||||||||||||||||||||||||||||||||||||||||||||||||||||||||||||||||||||||||||||||||||||||||||||||||||||||||||||||||||||||||||||||||||||||||||||||||||||||||||||||||||||||||||||||||||||||||||||||
Индий | 33 | ||||||||||||||||||||||||||||||||||||||||||||||||||||||||||||||||||||||||||||||||||||||||||||||||||||||||||||||||||||||||||||||||||||||||||||||||||||||||||||||||||||||||||||||||||||||||||||||||||||||||||||||||||||||||||||||||||||||||||||||||||||||||||||||||||||||||||||||||||||||||||||||||||||||||||||||||||||||||||||||||||||||||||||||||||||||||||||||||||||||||||||||||||||||||||||||||||||||||||||||||||||||||||||||||||||||||||||||||||||||||||||||||||||||||||||||||||||||||||||||||||||||||||||||||||||||||||||||||||||||||||||||||||||||||||||||||||||||||||||||||||||||||||||||||||||||||||||||||||||||||||||||||||||||||||||||||||||||||||||||||||||||||||||||||||||||||||||||||||||||||||||||||||||||||||||||||||||||||||||||||||||||||||||||||||||||||||||||||||||||||||||||||||||||||||||||||||||||||||||||||||||||||||||||||||||||||||||||||||||||||||||||||||||||||||||||||||||||||||||||||||||||||||||||||||||||||||||||||||||||||||||||||||||||||||||||||||||||||||||||||||||||||||||||||||||||||||||||||||||||
Инвар | 1,5 | ||||||||||||||||||||||||||||||||||||||||||||||||||||||||||||||||||||||||||||||||||||||||||||||||||||||||||||||||||||||||||||||||||||||||||||||||||||||||||||||||||||||||||||||||||||||||||||||||||||||||||||||||||||||||||||||||||||||||||||||||||||||||||||||||||||||||||||||||||||||||||||||||||||||||||||||||||||||||||||||||||||||||||||||||||||||||||||||||||||||||||||||||||||||||||||||||||||||||||||||||||||||||||||||||||||||||||||||||||||||||||||||||||||||||||||||||||||||||||||||||||||||||||||||||||||||||||||||||||||||||||||||||||||||||||||||||||||||||||||||||||||||||||||||||||||||||||||||||||||||||||||||||||||||||||||||||||||||||||||||||||||||||||||||||||||||||||||||||||||||||||||||||||||||||||||||||||||||||||||||||||||||||||||||||||||||||||||||||||||||||||||||||||||||||||||||||||||||||||||||||||||||||||||||||||||||||||||||||||||||||||||||||||||||||||||||||||||||||||||||||||||||||||||||||||||||||||||||||||||||||||||||||||||||||||||||||||||||||||||||||||||||||||||||||||||||||||||||||||||||
Иридий | 6,4 | ||||||||||||||||||||||||||||||||||||||||||||||||||||||||||||||||||||||||||||||||||||||||||||||||||||||||||||||||||||||||||||||||||||||||||||||||||||||||||||||||||||||||||||||||||||||||||||||||||||||||||||||||||||||||||||||||||||||||||||||||||||||||||||||||||||||||||||||||||||||||||||||||||||||||||||||||||||||||||||||||||||||||||||||||||||||||||||||||||||||||||||||||||||||||||||||||||||||||||||||||||||||||||||||||||||||||||||||||||||||||||||||||||||||||||||||||||||||||||||||||||||||||||||||||||||||||||||||||||||||||||||||||||||||||||||||||||||||||||||||||||||||||||||||||||||||||||||||||||||||||||||||||||||||||||||||||||||||||||||||||||||||||||||||||||||||||||||||||||||||||||||||||||||||||||||||||||||||||||||||||||||||||||||||||||||||||||||||||||||||||||||||||||||||||||||||||||||||||||||||||||||||||||||||||||||||||||||||||||||||||||||||||||||||||||||||||||||||||||||||||||||||||||||||||||||||||||||||||||||||||||||||||||||||||||||||||||||||||||||||||||||||||||||||||||||||||||||||||||||||
Чугун, литой | 10.4-11 | ||||||||||||||||||||||||||||||||||||||||||||||||||||||||||||||||||||||||||||||||||||||||||||||||||||||||||||||||||||||||||||||||||||||||||||||||||||||||||||||||||||||||||||||||||||||||||||||||||||||||||||||||||||||||||||||||||||||||||||||||||||||||||||||||||||||||||||||||||||||||||||||||||||||||||||||||||||||||||||||||||||||||||||||||||||||||||||||||||||||||||||||||||||||||||||||||||||||||||||||||||||||||||||||||||||||||||||||||||||||||||||||||||||||||||||||||||||||||||||||||||||||||||||||||||||||||||||||||||||||||||||||||||||||||||||||||||||||||||||||||||||||||||||||||||||||||||||||||||||||||||||||||||||||||||||||||||||||||||||||||||||||||||||||||||||||||||||||||||||||||||||||||||||||||||||||||||||||||||||||||||||||||||||||||||||||||||||||||||||||||||||||||||||||||||||||||||||||||||||||||||||||||||||||||||||||||||||||||||||||||||||||||||||||||||||||||||||||||||||||||||||||||||||||||||||||||||||||||||||||||||||||||||||||||||||||||||||||||||||||||||||||||||||||||||||||||||||||||||||||
Кованое железо | 11,3 | ||||||||||||||||||||||||||||||||||||||||||||||||||||||||||||||||||||||||||||||||||||||||||||||||||||||||||||||||||||||||||||||||||||||||||||||||||||||||||||||||||||||||||||||||||||||||||||||||||||||||||||||||||||||||||||||||||||||||||||||||||||||||||||||||||||||||||||||||||||||||||||||||||||||||||||||||||||||||||||||||||||||||||||||||||||||||||||||||||||||||||||||||||||||||||||||||||||||||||||||||||||||||||||||||||||||||||||||||||||||||||||||||||||||||||||||||||||||||||||||||||||||||||||||||||||||||||||||||||||||||||||||||||||||||||||||||||||||||||||||||||||||||||||||||||||||||||||||||||||||||||||||||||||||||||||||||||||||||||||||||||||||||||||||||||||||||||||||||||||||||||||||||||||||||||||||||||||||||||||||||||||||||||||||||||||||||||||||||||||||||||||||||||||||||||||||||||||||||||||||||||||||||||||||||||||||||||||||||||||||||||||||||||||||||||||||||||||||||||||||||||||||||||||||||||||||||||||||||||||||||||||||||||||||||||||||||||||||||||||||||||||||||||||||||||||||||||||||||||||||
Железо чистое | 12,0 | ||||||||||||||||||||||||||||||||||||||||||||||||||||||||||||||||||||||||||||||||||||||||||||||||||||||||||||||||||||||||||||||||||||||||||||||||||||||||||||||||||||||||||||||||||||||||||||||||||||||||||||||||||||||||||||||||||||||||||||||||||||||||||||||||||||||||||||||||||||||||||||||||||||||||||||||||||||||||||||||||||||||||||||||||||||||||||||||||||||||||||||||||||||||||||||||||||||||||||||||||||||||||||||||||||||||||||||||||||||||||||||||||||||||||||||||||||||||||||||||||||||||||||||||||||||||||||||||||||||||||||||||||||||||||||||||||||||||||||||||||||||||||||||||||||||||||||||||||||||||||||||||||||||||||||||||||||||||||||||||||||||||||||||||||||||||||||||||||||||||||||||||||||||||||||||||||||||||||||||||||||||||||||||||||||||||||||||||||||||||||||||||||||||||||||||||||||||||||||||||||||||||||||||||||||||||||||||||||||||||||||||||||||||||||||||||||||||||||||||||||||||||||||||||||||||||||||||||||||||||||||||||||||||||||||||||||||||||||||||||||||||||||||||||||||||||||||||||||||||||
Каптон | 20 | ||||||||||||||||||||||||||||||||||||||||||||||||||||||||||||||||||||||||||||||||||||||||||||||||||||||||||||||||||||||||||||||||||||||||||||||||||||||||||||||||||||||||||||||||||||||||||||||||||||||||||||||||||||||||||||||||||||||||||||||||||||||||||||||||||||||||||||||||||||||||||||||||||||||||||||||||||||||||||||||||||||||||||||||||||||||||||||||||||||||||||||||||||||||||||||||||||||||||||||||||||||||||||||||||||||||||||||||||||||||||||||||||||||||||||||||||||||||||||||||||||||||||||||||||||||||||||||||||||||||||||||||||||||||||||||||||||||||||||||||||||||||||||||||||||||||||||||||||||||||||||||||||||||||||||||||||||||||||||||||||||||||||||||||||||||||||||||||||||||||||||||||||||||||||||||||||||||||||||||||||||||||||||||||||||||||||||||||||||||||||||||||||||||||||||||||||||||||||||||||||||||||||||||||||||||||||||||||||||||||||||||||||||||||||||||||||||||||||||||||||||||||||||||||||||||||||||||||||||||||||||||||||||||||||||||||||||||||||||||||||||||||||||||||||||||||||||||||||||||||
Лантан | 00000000012,1 | Известняк | 8 | ||||||||||||||||||||||||||||||||||||||||||||||||||||||||||||||||||||||||||||||||||||||||||||||||||||||||||||||||||||||||||||||||||||||||||||||||||||||||||||||||||||||||||||||||||||||||||||||||||||||||||||||||||||||||||||||||||||||||||||||||||||||||||||||||||||||||||||||||||||||||||||||||||||||||||||||||||||||||||||||||||||||||||||||||||||||||||||||||||||||||||||||||||||||||||||||||||||||||||||||||||||||||||||||||||||||||||||||||||||||||||||||||||||||||||||||||||||||||||||||||||||||||||||||||||||||||||||||||||||||||||||||||||||||||||||||||||||||||||||||||||||||||||||||||||||||||||||||||||||||||||||||||||||||||||||||||||||||||||||||||||||||||||||||||||||||||||||||||||||||||||||||||||||||||||||||||||||||||||||||||||||||||||||||||||||||||||||||||||||||||||||||||||||||||||||||||||||||||||||||||||||||||||||||||||||||||||||||||||||||||||||||||||||||||||||||||||||||||||||||||||||||||||||||||||||||||||||||||||||||||||||||||||||||||||||||||||||||||||||||||||||||||||||||||||||||||||||||||||||
Литий | 46 | ||||||||||||||||||||||||||||||||||||||||||||||||||||||||||||||||||||||||||||||||||||||||||||||||||||||||||||||||||||||||||||||||||||||||||||||||||||||||||||||||||||||||||||||||||||||||||||||||||||||||||||||||||||||||||||||||||||||||||||||||||||||||||||||||||||||||||||||||||||||||||||||||||||||||||||||||||||||||||||||||||||||||||||||||||||||||||||||||||||||||||||||||||||||||||||||||||||||||||||||||||||||||||||||||||||||||||||||||||||||||||||||||||||||||||||||||||||||||||||||||||||||||||||||||||||||||||||||||||||||||||||||||||||||||||||||||||||||||||||||||||||||||||||||||||||||||||||||||||||||||||||||||||||||||||||||||||||||||||||||||||||||||||||||||||||||||||||||||||||||||||||||||||||||||||||||||||||||||||||||||||||||||||||||||||||||||||||||||||||||||||||||||||||||||||||||||||||||||||||||||||||||||||||||||||||||||||||||||||||||||||||||||||||||||||||||||||||||||||||||||||||||||||||||||||||||||||||||||||||||||||||||||||||||||||||||||||||||||||||||||||||||||||||||||||||||||||||||||||||||
Лютеций | 9,9 | ||||||||||||||||||||||||||||||||||||||||||||||||||||||||||||||||||||||||||||||||||||||||||||||||||||||||||||||||||||||||||||||||||||||||||||||||||||||||||||||||||||||||||||||||||||||||||||||||||||||||||||||||||||||||||||||||||||||||||||||||||||||||||||||||||||||||||||||||||||||||||||||||||||||||||||||||||||||||||||||||||||||||||||||||||||||||||||||||||||||||||||||||||||||||||||||||||||||||||||||||||||||||||||||||||||||||||||||||||||||||||||||||||||||||||||||||||||||||||||||||||||||||||||||||||||||||||||||||||||||||||||||||||||||||||||||||||||||||||||||||||||||||||||||||||||||||||||||||||||||||||||||||||||||||||||||||||||||||||||||||||||||||||||||||||||||||||||||||||||||||||||||||||||||||||||||||||||||||||||||||||||||||||||||||||||||||||||||||||||||||||||||||||||||||||||||||||||||||||||||||||||||||||||||||||||||||||||||||||||||||||||||||||||||||||||||||||||||||||||||||||||||||||||||||||||||||||||||||||||||||||||||||||||||||||||||||||||||||||||||||||||||||||||||||||||||||||||||||||||||
Macor | 9,3 | ||||||||||||||||||||||||||||||||||||||||||||||||||||||||||||||||||||||||||||||||||||||||||||||||||||||||||||||||||||||||||||||||||||||||||||||||||||||||||||||||||||||||||||||||||||||||||||||||||||||||||||||||||||||||||||||||||||||||||||||||||||||||||||||||||||||||||||||||||||||||||||||||||||||||||||||||||||||||||||||||||||||||||||||||||||||||||||||||||||||||||||||||||||||||||||||||||||||||||||||||||||||||||||||||||||||||||||||||||||||||||||||||||||||||||||||||||||||||||||||||||||||||||||||||||||||||||||||||||||||||||||||||||||||||||||||||||||||||||||||||||||||||||||||||||||||||||||||||||||||||||||||||||||||||||||||||||||||||||||||||||||||||||||||||||||||||||||||||||||||||||||||||||||||||||||||||||||||||||||||||||||||||||||||||||||||||||||||||||||||||||||||||||||||||||||||||||||||||||||||||||||||||||||||||||||||||||||||||||||||||||||||||||||||||||||||||||||||||||||||||||||||||||||||||||||||||||||||||||||||||||||||||||||||||||||||||||||||||||||||||||||||||||||||||||||||||||||||||||||||
23000.![]() | |||||||||||||||||||||||||||||||||||||||||||||||||||||||||||||||||||||||||||||||||||||||||||||||||||||||||||||||||||||||||||||||||||||||||||||||||||||||||||||||||||||||||||||||||||||||||||||||||||||||||||||||||||||||||||||||||||||||||||||||||||||||||||||||||||||||||||||||||||||||||||||||||||||||||||||||||||||||||||||||||||||||||||||||||||||||||||||||||||||||||||||||||||||||||||||||||||||||||||||||||||||||||||||||||||||||||||||||||||||||||||||||||||||||||||||||||||||||||||||||||||||||||||||||||||||||||||||||||||||||||||||||||||||||||||||||||||||||||||||||||||||||||||||||||||||||||||||||||||||||||||||||||||||||||||||||||||||||||||||||||||||||||||||||||||||||||||||||||||||||||||||||||||||||||||||||||||||||||||||||||||||||||||||||||||||||||||||||||||||||||||||||||||||||||||||||||||||||||||||||||||||||||||||||||||||||||||||||||||||||||||||||||||||||||||||||||||||||||||||||||||||||||||||||||||||||||||||||||||||||||||||||||||||||||||||||||||||||||||||||||||||||||||||||||||||||||||||||||||||||
Магний | 25 — 26,9 | ||||||||||||||||||||||||||||||||||||||||||||||||||||||||||||||||||||||||||||||||||||||||||||||||||||||||||||||||||||||||||||||||||||||||||||||||||||||||||||||||||||||||||||||||||||||||||||||||||||||||||||||||||||||||||||||||||||||||||||||||||||||||||||||||||||||||||||||||||||||||||||||||||||||||||||||||||||||||||||||||||||||||||||||||||||||||||||||||||||||||||||||||||||||||||||||||||||||||||||||||||||||||||||||||||||||||||||||||||||||||||||||||||||||||||||||||||||||||||||||||||||||||||||||||||||||||||||||||||||||||||||||||||||||||||||||||||||||||||||||||||||||||||||||||||||||||||||||||||||||||||||||||||||||||||||||||||||||||||||||||||||||||||||||||||||||||||||||||||||||||||||||||||||||||||||||||||||||||||||||||||||||||||||||||||||||||||||||||||||||||||||||||||||||||||||||||||||||||||||||||||||||||||||||||||||||||||||||||||||||||||||||||||||||||||||||||||||||||||||||||||||||||||||||||||||||||||||||||||||||||||||||||||||||||||||||||||||||||||||||||||||||||||||||||||||||||||||||||||||||
Магниевый сплав AZ31B | 26 | ||||||||||||||||||||||||||||||||||||||||||||||||||||||||||||||||||||||||||||||||||||||||||||||||||||||||||||||||||||||||||||||||||||||||||||||||||||||||||||||||||||||||||||||||||||||||||||||||||||||||||||||||||||||||||||||||||||||||||||||||||||||||||||||||||||||||||||||||||||||||||||||||||||||||||||||||||||||||||||||||||||||||||||||||||||||||||||||||||||||||||||||||||||||||||||||||||||||||||||||||||||||||||||||||||||||||||||||||||||||||||||||||||||||||||||||||||||||||||||||||||||||||||||||||||||||||||||||||||||||||||||||||||||||||||||||||||||||||||||||||||||||||||||||||||||||||||||||||||||||||||||||||||||||||||||||||||||||||||||||||||||||||||||||||||||||||||||||||||||||||||||||||||||||||||||||||||||||||||||||||||||||||||||||||||||||||||||||||||||||||||||||||||||||||||||||||||||||||||||||||||||||||||||||||||||||||||||||||||||||||||||||||||||||||||||||||||||||||||||||||||||||||||||||||||||||||||||||||||||||||||||||||||||||||||||||||||||||||||||||||||||||||||||||||||||||||||||||||||||||
Марганец | 22 | ||||||||||||||||||||||||||||||||||||||||||||||||||||||||||||||||||||||||||||||||||||||||||||||||||||||||||||||||||||||||||||||||||||||||||||||||||||||||||||||||||||||||||||||||||||||||||||||||||||||||||||||||||||||||||||||||||||||||||||||||||||||||||||||||||||||||||||||||||||||||||||||||||||||||||||||||||||||||||||||||||||||||||||||||||||||||||||||||||||||||||||||||||||||||||||||||||||||||||||||||||||||||||||||||||||||||||||||||||||||||||||||||||||||||||||||||||||||||||||||||||||||||||||||||||||||||||||||||||||||||||||||||||||||||||||||||||||||||||||||||||||||||||||||||||||||||||||||||||||||||||||||||||||||||||||||||||||||||||||||||||||||||||||||||||||||||||||||||||||||||||||||||||||||||||||||||||||||||||||||||||||||||||||||||||||||||||||||||||||||||||||||||||||||||||||||||||||||||||||||||||||||||||||||||||||||||||||||||||||||||||||||||||||||||||||||||||||||||||||||||||||||||||||||||||||||||||||||||||||||||||||||||||||||||||||||||||||||||||||||||||||||||||||||||||||||||||||||||||||||
Марганец | 9000 | 18,1 Марганец | 18,1 | Каменная кладка, кирпич | 4,7 — 9,0 | ||||||||||||||||||||||||||||||||||||||||||||||||||||||||||||||||||||||||||||||||||||||||||||||||||||||||||||||||||||||||||||||||||||||||||||||||||||||||||||||||||||||||||||||||||||||||||||||||||||||||||||||||||||||||||||||||||||||||||||||||||||||||||||||||||||||||||||||||||||||||||||||||||||||||||||||||||||||||||||||||||||||||||||||||||||||||||||||||||||||||||||||||||||||||||||||||||||||||||||||||||||||||||||||||||||||||||||||||||||||||||||||||||||||||||||||||||||||||||||||||||||||||||||||||||||||||||||||||||||||||||||||||||||||||||||||||||||||||||||||||||||||||||||||||||||||||||||||||||||||||||||||||||||||||||||||||||||||||||||||||||||||||||||||||||||||||||||||||||||||||||||||||||||||||||||||||||||||||||||||||||||||||||||||||||||||||||||||||||||||||||||||||||||||||||||||||||||||||||||||||||||||||||||||||||||||||||||||||||||||||||||||||||||||||||||||||||||||||||||||||||||||||||||||||||||||||||||||||||||||||||||||||||||||||||||||||||||||||||||||||||||||||||||||||||||||||||||||||||
Меркурий | 61 | ||||||||||||||||||||||||||||||||||||||||||||||||||||||||||||||||||||||||||||||||||||||||||||||||||||||||||||||||||||||||||||||||||||||||||||||||||||||||||||||||||||||||||||||||||||||||||||||||||||||||||||||||||||||||||||||||||||||||||||||||||||||||||||||||||||||||||||||||||||||||||||||||||||||||||||||||||||||||||||||||||||||||||||||||||||||||||||||||||||||||||||||||||||||||||||||||||||||||||||||||||||||||||||||||||||||||||||||||||||||||||||||||||||||||||||||||||||||||||||||||||||||||||||||||||||||||||||||||||||||||||||||||||||||||||||||||||||||||||||||||||||||||||||||||||||||||||||||||||||||||||||||||||||||||||||||||||||||||||||||||||||||||||||||||||||||||||||||||||||||||||||||||||||||||||||||||||||||||||||||||||||||||||||||||||||||||||||||||||||||||||||||||||||||||||||||||||||||||||||||||||||||||||||||||||||||||||||||||||||||||||||||||||||||||||||||||||||||||||||||||||||||||||||||||||||||||||||||||||||||||||||||||||||||||||||||||||||||||||||||||||||||||||||||||||||||||||||||||||||||
Слюда | 3 | ||||||||||||||||||||||||||||||||||||||||||||||||||||||||||||||||||||||||||||||||||||||||||||||||||||||||||||||||||||||||||||||||||||||||||||||||||||||||||||||||||||||||||||||||||||||||||||||||||||||||||||||||||||||||||||||||||||||||||||||||||||||||||||||||||||||||||||||||||||||||||||||||||||||||||||||||||||||||||||||||||||||||||||||||||||||||||||||||||||||||||||||||||||||||||||||||||||||||||||||||||||||||||||||||||||||||||||||||||||||||||||||||||||||||||||||||||||||||||||||||||||||||||||||||||||||||||||||||||||||||||||||||||||||||||||||||||||||||||||||||||||||||||||||||||||||||||||||||||||||||||||||||||||||||||||||||||||||||||||||||||||||||||||||||||||||||||||||||||||||||||||||||||||||||||||||||||||||||||||||||||||||||||||||||||||||||||||||||||||||||||||||||||||||||||||||||||||||||||||||||||||||||||||||||||||||||||||||||||||||||||||||||||||||||||||||||||||||||||||||||||||||||||||||||||||||||||||||||||||||||||||||||||||||||||||||||||||||||||||||||||||||||||||||||||||||||||||||||||||||
Молибден | 5 | ||||||||||||||||||||||||||||||||||||||||||||||||||||||||||||||||||||||||||||||||||||||||||||||||||||||||||||||||||||||||||||||||||||||||||||||||||||||||||||||||||||||||||||||||||||||||||||||||||||||||||||||||||||||||||||||||||||||||||||||||||||||||||||||||||||||||||||||||||||||||||||||||||||||||||||||||||||||||||||||||||||||||||||||||||||||||||||||||||||||||||||||||||||||||||||||||||||||||||||||||||||||||||||||||||||||||||||||||||||||||||||||||||||||||||||||||||||||||||||||||||||||||||||||||||||||||||||||||||||||||||||||||||||||||||||||||||||||||||||||||||||||||||||||||||||||||||||||||||||||||||||||||||||||||||||||||||||||||||||||||||||||||||||||||||||||||||||||||||||||||||||||||||||||||||||||||||||||||||||||||||||||||||||||||||||||||||||||||||||||||||||||||||||||||||||||||||||||||||||||||||||||||||||||||||||||||||||||||||||||||||||||||||||||||||||||||||||||||||||||||||||||||||||||||||||||||||||||||||||||||||||||||||||||||||||||||||||||||||||||||||||||||||||||||||||||||||||||||||||||
Раствор | 7,3 — 13,5 | ||||||||||||||||||||||||||||||||||||||||||||||||||||||||||||||||||||||||||||||||||||||||||||||||||||||||||||||||||||||||||||||||||||||||||||||||||||||||||||||||||||||||||||||||||||||||||||||||||||||||||||||||||||||||||||||||||||||||||||||||||||||||||||||||||||||||||||||||||||||||||||||||||||||||||||||||||||||||||||||||||||||||||||||||||||||||||||||||||||||||||||||||||||||||||||||||||||||||||||||||||||||||||||||||||||||||||||||||||||||||||||||||||||||||||||||||||||||||||||||||||||||||||||||||||||||||||||||||||||||||||||||||||||||||||||||||||||||||||||||||||||||||||||||||||||||||||||||||||||||||||||||||||||||||||||||||||||||||||||||||||||||||||||||||||||||||||||||||||||||||||||||||||||||||||||||||||||||||||||||||||||||||||||||||||||||||||||||||||||||||||||||||||||||||||||||||||||||||||||||||||||||||||||||||||||||||||||||||||||||||||||||||||||||||||||||||||||||||||||||||||||||||||||||||||||||||||||||||||||||||||||||||||||||||||||||||||||||||||||||||||||||||||||||||||||||||||||||||||||||
Неодим | 9,6 | ||||||||||||||||||||||||||||||||||||||||||||||||||||||||||||||||||||||||||||||||||||||||||||||||||||||||||||||||||||||||||||||||||||||||||||||||||||||||||||||||||||||||||||||||||||||||||||||||||||||||||||||||||||||||||||||||||||||||||||||||||||||||||||||||||||||||||||||||||||||||||||||||||||||||||||||||||||||||||||||||||||||||||||||||||||||||||||||||||||||||||||||||||||||||||||||||||||||||||||||||||||||||||||||||||||||||||||||||||||||||||||||||||||||||||||||||||||||||||||||||||||||||||||||||||||||||||||||||||||||||||||||||||||||||||||||||||||||||||||||||||||||||||||||||||||||||||||||||||||||||||||||||||||||||||||||||||||||||||||||||||||||||||||||||||||||||||||||||||||||||||||||||||||||||||||||||||||||||||||||||||||||||||||||||||||||||||||||||||||||||||||||||||||||||||||||||||||||||||||||||||||||||||||||||||||||||||||||||||||||||||||||||||||||||||||||||||||||||||||||||||||||||||||||||||||||||||||||||||||||||||||||||||||||||||||||||||||||||||||||||||||||||||||||||||||||||||||||||||||||
Никель | 13,0 | ||||||||||||||||||||||||||||||||||||||||||||||||||||||||||||||||||||||||||||||||||||||||||||||||||||||||||||||||||||||||||||||||||||||||||||||||||||||||||||||||||||||||||||||||||||||||||||||||||||||||||||||||||||||||||||||||||||||||||||||||||||||||||||||||||||||||||||||||||||||||||||||||||||||||||||||||||||||||||||||||||||||||||||||||||||||||||||||||||||||||||||||||||||||||||||||||||||||||||||||||||||||||||||||||||||||||||||||||||||||||||||||||||||||||||||||||||||||||||||||||||||||||||||||||||||||||||||||||||||||||||||||||||||||||||||||||||||||||||||||||||||||||||||||||||||||||||||||||||||||||||||||||||||||||||||||||||||||||||||||||||||||||||||||||||||||||||||||||||||||||||||||||||||||||||||||||||||||||||||||||||||||||||||||||||||||||||||||||||||||||||||||||||||||||||||||||||||||||||||||||||||||||||||||||||||||||||||||||||||||||||||||||||||||||||||||||||||||||||||||||||||||||||||||||||||||||||||||||||||||||||||||||||||||||||||||||||||||||||||||||||||||||||||||||||||||||||||||||||||||
Ниобий (Columbium | 90 | ||||||||||||||||||||||||||||||||||||||||||||||||||||||||||||||||||||||||||||||||||||||||||||||||||||||||||||||||||||||||||||||||||||||||||||||||||||||||||||||||||||||||||||||||||||||||||||||||||||||||||||||||||||||||||||||||||||||||||||||||||||||||||||||||||||||||||||||||||||||||||||||||||||||||||||||||||||||||||||||||||||||||||||||||||||||||||||||||||||||||||||||||||||||||||||||||||||||||||||||||||||||||||||||||||||||||||||||||||||||||||||||||||||||||||||||||||||||||||||||||||||||||||||||||||||||||||||||||||||||||||||||||||||||||||||||||||||||||||||||||||||||||||||||||||||||||||||||||||||||||||||||||||||||||||||||||||||||||||||||||||||||||||||||||||||||||||||||||||||||||||||||||||||||||||||||||||||||||||||||||||||||||||||||||||||||||||||||||||||||||||||||||||||||||||||||||||||||||||||||||||||||||||||||||||||||||||||||||||||||||||||||||||||||||||||||||||||||||||||||||||||||||||||||||||||||||||||||||||||||||||||||||||||||||||||||||||||||||||||||||||||||||||||||||||||||||||||||||||||||
Нейлон, армированный стекловолокном | 23 | ||||||||||||||||||||||||||||||||||||||||||||||||||||||||||||||||||||||||||||||||||||||||||||||||||||||||||||||||||||||||||||||||||||||||||||||||||||||||||||||||||||||||||||||||||||||||||||||||||||||||||||||||||||||||||||||||||||||||||||||||||||||||||||||||||||||||||||||||||||||||||||||||||||||||||||||||||||||||||||||||||||||||||||||||||||||||||||||||||||||||||||||||||||||||||||||||||||||||||||||||||||||||||||||||||||||||||||||||||||||||||||||||||||||||||||||||||||||||||||||||||||||||||||||||||||||||||||||||||||||||||||||||||||||||||||||||||||||||||||||||||||||||||||||||||||||||||||||||||||||||||||||||||||||||||||||||||||||||||||||||||||||||||||||||||||||||||||||||||||||||||||||||||||||||||||||||||||||||||||||||||||||||||||||||||||||||||||||||||||||||||||||||||||||||||||||||||||||||||||||||||||||||||||||||||||||||||||||||||||||||||||||||||||||||||||||||||||||||||||||||||||||||||||||||||||||||||||||||||||||||||||||||||||||||||||||||||||||||||||||||||||||||||||||||||||||||||||||||||||||
Нейлон, тип 11, формовочная и экструзионная смесь | 100 | ||||||||||||||||||||||||||||||||||||||||||||||||||||||||||||||||||||||||||||||||||||||||||||||||||||||||||||||||||||||||||||||||||||||||||||||||||||||||||||||||||||||||||||||||||||||||||||||||||||||||||||||||||||||||||||||||||||||||||||||||||||||||||||||||||||||||||||||||||||||||||||||||||||||||||||||||||||||||||||||||||||||||||||||||||||||||||||||||||||||||||||||||||||||||||||||||||||||||||||||||||||||||||||||||||||||||||||||||||||||||||||||||||||||||||||||||||||||||||||||||||||||||||||||||||||||||||||||||||||||||||||||||||||||||||||||||||||||||||||||||||||||||||||||||||||||||||||||||||||||||||||||||||||||||||||||||||||||||||||||||||||||||||||||||||||||||||||||||||||||||||||||||||||||||||||||||||||||||||||||||||||||||||||||||||||||||||||||||||||||||||||||||||||||||||||||||||||||||||||||||||||||||||||||||||||||||||||||||||||||||||||||||||||||||||||||||||||||||||||||||||||||||||||||||||||||||||||||||||||||||||||||||||||||||||||||||||||||||||||||||||||||||||||||||||||||||||||||||||||||
Нейлон, тип 12, формовочная и экструдированная смесь | 80.5 | ||||||||||||||||||||||||||||||||||||||||||||||||||||||||||||||||||||||||||||||||||||||||||||||||||||||||||||||||||||||||||||||||||||||||||||||||||||||||||||||||||||||||||||||||||||||||||||||||||||||||||||||||||||||||||||||||||||||||||||||||||||||||||||||||||||||||||||||||||||||||||||||||||||||||||||||||||||||||||||||||||||||||||||||||||||||||||||||||||||||||||||||||||||||||||||||||||||||||||||||||||||||||||||||||||||||||||||||||||||||||||||||||||||||||||||||||||||||||||||||||||||||||||||||||||||||||||||||||||||||||||||||||||||||||||||||||||||||||||||||||||||||||||||||||||||||||||||||||||||||||||||||||||||||||||||||||||||||||||||||||||||||||||||||||||||||||||||||||||||||||||||||||||||||||||||||||||||||||||||||||||||||||||||||||||||||||||||||||||||||||||||||||||||||||||||||||||||||||||||||||||||||||||||||||||||||||||||||||||||||||||||||||||||||||||||||||||||||||||||||||||||||||||||||||||||||||||||||||||||||||||||||||||||||||||||||||||||||||||||||||||||||||||||||||||||||||||||||||||||||
Нейлон, тип 6, литье | 85 | ||||||||||||||||||||||||||||||||||||||||||||||||||||||||||||||||||||||||||||||||||||||||||||||||||||||||||||||||||||||||||||||||||||||||||||||||||||||||||||||||||||||||||||||||||||||||||||||||||||||||||||||||||||||||||||||||||||||||||||||||||||||||||||||||||||||||||||||||||||||||||||||||||||||||||||||||||||||||||||||||||||||||||||||||||||||||||||||||||||||||||||||||||||||||||||||||||||||||||||||||||||||||||||||||||||||||||||||||||||||||||||||||||||||||||||||||||||||||||||||||||||||||||||||||||||||||||||||||||||||||||||||||||||||||||||||||||||||||||||||||||||||||||||||||||||||||||||||||||||||||||||||||||||||||||||||||||||||||||||||||||||||||||||||||||||||||||||||||||||||||||||||||||||||||||||||||||||||||||||||||||||||||||||||||||||||||||||||||||||||||||||||||||||||||||||||||||||||||||||||||||||||||||||||||||||||||||||||||||||||||||||||||||||||||||||||||||||||||||||||||||||||||||||||||||||||||||||||||||||||||||||||||||||||||||||||||||||||||||||||||||||||||||||||||||||||||||||||||||||||
Нейлон, тип 6/6, формовочная масса | 80 | ||||||||||||||||||||||||||||||||||||||||||||||||||||||||||||||||||||||||||||||||||||||||||||||||||||||||||||||||||||||||||||||||||||||||||||||||||||||||||||||||||||||||||||||||||||||||||||||||||||||||||||||||||||||||||||||||||||||||||||||||||||||||||||||||||||||||||||||||||||||||||||||||||||||||||||||||||||||||||||||||||||||||||||||||||||||||||||||||||||||||||||||||||||||||||||||||||||||||||||||||||||||||||||||||||||||||||||||||||||||||||||||||||||||||||||||||||||||||||||||||||||||||||||||||||||||||||||||||||||||||||||||||||||||||||||||||||||||||||||||||||||||||||||||||||||||||||||||||||||||||||||||||||||||||||||||||||||||||||||||||||||||||||||||||||||||||||||||||||||||||||||||||||||||||||||||||||||||||||||||||||||||||||||||||||||||||||||||||||||||||||||||||||||||||||||||||||||||||||||||||||||||||||||||||||||||||||||||||||||||||||||||||||||||||||||||||||||||||||||||||||||||||||||||||||||||||||||||||||||||||||||||||||||||||||||||||||||||||||||||||||||||||||||||||||||||||||||||||||||||
Дуб, перпендикулярно волокну | 54 | ||||||||||||||||||||||||||||||||||||||||||||||||||||||||||||||||||||||||||||||||||||||||||||||||||||||||||||||||||||||||||||||||||||||||||||||||||||||||||||||||||||||||||||||||||||||||||||||||||||||||||||||||||||||||||||||||||||||||||||||||||||||||||||||||||||||||||||||||||||||||||||||||||||||||||||||||||||||||||||||||||||||||||||||||||||||||||||||||||||||||||||||||||||||||||||||||||||||||||||||||||||||||||||||||||||||||||||||||||||||||||||||||||||||||||||||||||||||||||||||||||||||||||||||||||||||||||||||||||||||||||||||||||||||||||||||||||||||||||||||||||||||||||||||||||||||||||||||||||||||||||||||||||||||||||||||||||||||||||||||||||||||||||||||||||||||||||||||||||||||||||||||||||||||||||||||||||||||||||||||||||||||||||||||||||||||||||||||||||||||||||||||||||||||||||||||||||||||||||||||||||||||||||||||||||||||||||||||||||||||||||||||||||||||||||||||||||||||||||||||||||||||||||||||||||||||||||||||||||||||||||||||||||||||||||||||||||||||||||||||||||||||||||||||||||||||||||||||||||||||
Палладий | 11,8 | ||||||||||||||||||||||||||||||||||||||||||||||||||||||||||||||||||||||||||||||||||||||||||||||||||||||||||||||||||||||||||||||||||||||||||||||||||||||||||||||||||||||||||||||||||||||||||||||||||||||||||||||||||||||||||||||||||||||||||||||||||||||||||||||||||||||||||||||||||||||||||||||||||||||||||||||||||||||||||||||||||||||||||||||||||||||||||||||||||||||||||||||||||||||||||||||||||||||||||||||||||||||||||||||||||||||||||||||||||||||||||||||||||||||||||||||||||||||||||||||||||||||||||||||||||||||||||||||||||||||||||||||||||||||||||||||||||||||||||||||||||||||||||||||||||||||||||||||||||||||||||||||||||||||||||||||||||||||||||||||||||||||||||||||||||||||||||||||||||||||||||||||||||||||||||||||||||||||||||||||||||||||||||||||||||||||||||||||||||||||||||||||||||||||||||||||||||||||||||||||||||||||||||||||||||||||||||||||||||||||||||||||||||||||||||||||||||||||||||||||||||||||||||||||||||||||||||||||||||||||||||||||||||||||||||||||||||||||||||||||||||||||||||||||||||||||||||||||||||||||
Парафин | 106-480 | ||||||||||||||||||||||||||||||||||||||||||||||||||||||||||||||||||||||||||||||||||||||||||||||||||||||||||||||||||||||||||||||||||||||||||||||||||||||||||||||||||||||||||||||||||||||||||||||||||||||||||||||||||||||||||||||||||||||||||||||||||||||||||||||||||||||||||||||||||||||||||||||||||||||||||||||||||||||||||||||||||||||||||||||||||||||||||||||||||||||||||||||||||||||||||||||||||||||||||||||||||||||||||||||||||||||||||||||||||||||||||||||||||||||||||||||||||||||||||||||||||||||||||||||||||||||||||||||||||||||||||||||||||||||||||||||||||||||||||||||||||||||||||||||||||||||||||||||||||||||||||||||||||||||||||||||||||||||||||||||||||||||||||||||||||||||||||||||||||||||||||||||||||||||||||||||||||||||||||||||||||||||||||||||||||||||||||||||||||||||||||||||||||||||||||||||||||||||||||||||||||||||||||||||||||||||||||||||||||||||||||||||||||||||||||||||||||||||||||||||||||||||||||||||||||||||||||||||||||||||||||||||||||||||||||||||||||||||||||||||||||||||||||||||||||||||||||||||||||||||
Фенольная смола без наполнителей | 60-80 | ||||||||||||||||||||||||||||||||||||||||||||||||||||||||||||||||||||||||||||||||||||||||||||||||||||||||||||||||||||||||||||||||||||||||||||||||||||||||||||||||||||||||||||||||||||||||||||||||||||||||||||||||||||||||||||||||||||||||||||||||||||||||||||||||||||||||||||||||||||||||||||||||||||||||||||||||||||||||||||||||||||||||||||||||||||||||||||||||||||||||||||||||||||||||||||||||||||||||||||||||||||||||||||||||||||||||||||||||||||||||||||||||||||||||||||||||||||||||||||||||||||||||||||||||||||||||||||||||||||||||||||||||||||||||||||||||||||||||||||||||||||||||||||||||||||||||||||||||||||||||||||||||||||||||||||||||||||||||||||||||||||||||||||||||||||||||||||||||||||||||||||||||||||||||||||||||||||||||||||||||||||||||||||||||||||||||||||||||||||||||||||||||||||||||||||||||||||||||||||||||||||||||||||||||||||||||||||||||||||||||||||||||||||||||||||||||||||||||||||||||||||||||||||||||||||||||||||||||||||||||||||||||||||||||||||||||||||||||||||||||||||||||||||||||||||||||||||||||||||||
Пластырь | 17 | |||||||
Пластмассы | 40-120 | |||||||
Платина | 9 | |||||||
Плутоний | ||||||||
Плутоний | 47-54 | |||||||
47-54 | ||||||||
Полияллон | 92 | |||||||
Полиамид (PA) | 110 | |||||||
Полибутилен (PB) | 130-139 | |||||||
Поликарбонат (ПК) | 65-70 | армированный стекловолокном | ||||||
21.5 | ||||||||
Полиэстер | 124 | |||||||
Полиэстер — армированный стекловолокном | 25 | |||||||
Полиэтилен (PE) | 108-200 | |||||||
Полиэтилен 9 (PE) — Высокомолекулярный вес 9 (PE) — | ||||||||
Полиэтилентерефталат (ПЭТ) | 59,4 | |||||||
Полифенилен | 54 | |||||||
Полифенилен — армированный стекловолокном | 36 | |||||||
Полипропилен — армированный стекловолокном | 32 | |||||||
Полистирол (ПС) | 70 | |||||||
Полисульфон (ПСО) | 55-60 | |||||||
Политетрафторэтилен | ||||||||
Полиуретан (PUR), жесткий | 57.![]() | |||||||
Поливинилхлорид (ПВХ) | 54-110 | |||||||
Поливинилиденфторид (PVDF) | 128-140 | |||||||
Фарфор, промышленный | 4 | |||||||
Празеодим | 6,7 | |||||||
Прометий | 11 | |||||||
Кварц плавленый | 0,55 | |||||||
Кварц минеральный | 8 — 14 | 7 | ||||||
Родий | 8 | |||||||
Каменная соль | 40,4 | |||||||
Каучук твердый | 80 | |||||||
Рутений | ||||||||
11,6 | ||||||||
Сапфир | 5,3 | |||||||
Скандий | 10,2 | |||||||
Селен | 37 | |||||||
Кремний | Карбид77 | |||||||
Серебро | 19 — 19,7 | |||||||
Ситалл | 0,15 | |||||||
Сланец | 10 | |||||||
Натрий | 70 | |||||||
25 | ||||||||
Металлические зеркала | 19,3 | |||||||
Стеатит | 8,5 | |||||||
Сталь | 10,8 — 12,5 | |||||||
Сталь нержавеющая | .||||||||
Сталь нержавеющая аустенитная (310) | 14,4 | |||||||
Сталь нержавеющая аустенитная (316) | 16,0 | |||||||
Сталь нержавеющая ферритная (410) | 9, | |||||||
9,9 | ||||||||
Тантал | 6,5 | |||||||
Теллур | 36,9 | |||||||
Тербий | 10,3 | |||||||
Терне | 11.6 | |||||||
Таллий | 29,9 | |||||||
Торий | 12 | |||||||
Тулий | 13,3 | |||||||
Олово | 20 — | |||||||
5-8 | ||||||||
Вольфрам | 4,5 | |||||||
Уран | 13,4 | |||||||
Ванадий | 8 | |||||||
6 | ||||||||
Воск | 2-15 | |||||||
Изделия Wedgwood | 8.9 | |||||||
Древесина, перпендикулярно (перпендикулярно) волокнам | 30 | |||||||
Дерево, ель | , параллельно волокну3 | |||||||
Древесина, сосна | 5 | |||||||
Иттербий | 26,3 | |||||||
Иттрий | 10,6 | |||||||
Адмиралтейская латунь | 68 — 572 | 11,2 | |||||
Алюминий | 68 — 212 | 13,1 | Bronze | ||||
Алюминиевый сплав — 2011 | 12,8 | ||||||
Алюминиевый сплав — 2017 | 13,1 | ||||||
Алюминиевый сплав — 2024 | 12.9 | ||||||
Алюминиевый сплав — 3003 | 12,9 | ||||||
Алюминиевый сплав — 5052 | 13,2 | ||||||
Алюминиевый сплав — 5086 | 13,225 | ||||||
Алюминиевый сплав — 7075 | 13,1 | ||||||
Сурьма | 5 | ||||||
Бериллий | 6.7 | ||||||
Бериллий Медь | 68-212 | 9,3 | |||||
Висмут | 7,2 | ||||||
Чугун, серый | 32-212 | 9000% Сталь,32-212 | 9000 C7,0 | ||||
Хром | 3,3 | ||||||
Кобальт | 6,7 | ||||||
Медь | .|||||||
Сплав на медной основе — марганцевая бронза | 11,8 | ||||||
Сплав на медной основе — C1100 (электролитический твердый пек) | 9,8 | ||||||
Медь-14 на основе свободно обрабатываемого сплава | 9,9 | ||||||
Сплав на медной основе — C17200, C17300 (бериллий Cu) | 9,9 | ||||||
Сплав на медной основе — C18200 (Chromium Cu) | 3 | 9,8 9000 — C18700 (свинцовая медь) | 9.8 | ||||
Сплав на основе меди — C22000 (техническая бронза, 90%) | 10,2 | ||||||
Сплав на основе меди — C23000 (красная латунь, 85%) | 10,4 | ||||||
Медь Сплав — C26000 (патронная латунь, 70%) | 11,1 | ||||||
Сплав на медной основе — C27000 (желтая латунь) | 11,3 | ||||||
Сплав на медной основе — C28000 (металл Muntz0005, 60%) 9 | 11.6 | ||||||
Сплав на основе меди — C33000 (латунная трубка с низким содержанием свинца) | 11,2 | ||||||
Сплав на основе меди — C35300 (латунь с высоким содержанием свинца) | 11,3 | ||||||
— C35600 (латунь со сверхвысоким содержанием свинца) | 11,4 | ||||||
Сплав на медной основе — C36000 (латунь без механической обработки) | 11,4 | ||||||
Сплав на основе меди — C36500 (металл Muntz 912 с содержанием свинца) 9000 11.![]() | |||||||
Сплав на основе меди — C46400 (морская латунь) | 11,8 | ||||||
Сплав на основе меди — C51000 (фосфористая бронза, 5% A) | 9,9 | ||||||
9,6 | |||||||
Сплав на основе меди — C62300 (алюминиевая бронза, 9%) | 9,0 | ||||||
Сплав на основе меди — C62400 (алюминиевая бронза, 11%) | 9.2 | ||||||
Сплав на медной основе — C63000 (никель-алюминиевая бронза) | 9,0 | ||||||
Сплав на медной основе — никель-серебро | 9,0 | ||||||
Медно-никелевый сплав | |||||||
Ковкий чугун, A536 (120-90-02) | 5,9 — 6,2 | ||||||
Золото | 7,9 | ||||||
Hastelloy C | 70-200 50005 | 3||||||
Инконель | 68 — 212 | 6,4 | |||||
Инколой | 32 — 212 | 8,0 | |||||
Иридий | 6,5 | ||||||
Железо чистое | 68 — 212 | 6,8 | |||||
Магний | 14 | ||||||
Ковкое железо, A220 (5000512, 60004, 800012)5 | |||||||
Марганец | 12 | ||||||
Марганцевая бронза | 68 — 572 | 11,8 | |||||
Мягкая сталь | 12 | 5.![]() | 000000000000000 | 000000 | 000 | 32 — 212 | 7,8 |
Сплав на основе никеля — никель 200, 201, 205 | 8,5 | ||||||
Сплав на основе никеля — Hastelloy C-22 | 6.9 | ||||||
Сплав на основе никеля — Хастеллой C-276 | 6,2 | ||||||
Сплав на основе никеля — Инконель 718 | 7,2 | ||||||
Сплав на основе никеля 12 9000 9000 | Сплав на основе никеля — Монель 400 | 7,7 | |||||
Сплав на основе никеля — K500 | 7,6 | ||||||
Сплав на основе никеля — R405 | 7,6 | ||||||
7.4 | |||||||
Ниобий (Columbium) | 3,9 | ||||||
Красная латунь | 68 — 572 | 10,4 | |||||
Осмий | 0000004 | ||||||
Плутоний | 19,84 | ||||||
Калий | 46 | ||||||
Родий | 4.![]() | ||||||
Селен | 21 | ||||||
Кремний | 2,8 | ||||||
Серебро | 11 | ||||||
9,4 | |||||||
Нержавеющая сталь — S30200, S30300, S30323 | 9,6 | ||||||
Нержавеющая сталь — S30215 | 9.0 | ||||||
Нержавеющая сталь — S30400, S30500 | 9,6 | ||||||
Нержавеющая сталь — S30430 | 9,6 | ||||||
Нерж. | 8,3 | ||||||
Нержавеющая сталь — S31000, S31008 | 8,8 | ||||||
Нержавеющая сталь — S31600, S31700 | 8.8 | ||||||
Нержавеющая сталь — S31703 | 9.2 | ||||||
Нержавеющая сталь — S32100 | 9.2 | ||||||
Нержавеющая сталь — S34700 | 9.2 | ||||||
000 | |||||||
Нержавеющая сталь — S38400 | 9,6 | ||||||
Нержавеющая сталь — S40300, S41000, S41600, 41623 | 5,5 | ||||||
Нержавеющая сталь — S40500 | 6.![]() | ||||||
Нержавеющая сталь — S41400 | 5,8 | ||||||
Нержавеющая сталь — S42000, S42020 | 5,7 | ||||||
Нержавеющая сталь — S42200 | 0003 | 5,7 | |||||
Нержавеющая сталь — S43000, S43020, S43023 | 5,8 | ||||||
Нержавеющая сталь — S43600 | 5.2 | ||||||
Нержавеющая сталь — S44002, | .7 | ||||||
Нержавеющая сталь — S44003 | 5,6 | ||||||
Нержавеющая сталь — S44600 | 5,8 | ||||||
Нержавеющая сталь — S50100, S50200 | um | 00050005||||||
Торий | 6,7 | ||||||
Олово | 32-212 | 12,8 | |||||
Титан | 68-200 | 4.8 | |||||
Титановый сплав — Ti-5Al-2.5Sn | 5,3 | ||||||
Ti-8Mn | 6,0 | ||||||
Вольфрам | 9,40005 | 9ran0005 | |||||
Ванадий | 4,4 | ||||||
Деформируемая углеродистая сталь | 70-800 | 7,8 | |||||
Желтая латунь | 68-572 | 11.![]() | |||||
Цинк | 19 |
Значения линейного коэффициента теплового расширения при комнатной температуре для металлов | ||
Алюминиевые сплавы | ||
Материал | Коэффициент температурного расширения (CTE) | |
10 -6 (° C) -1 | 10 -6 (° F) -1 | |
Алюминиевый сплав 1100 | 23.6 | 13,1 |
Алюминиевый сплав 2011 | 23,0 | 12,8 |
Алюминиевый сплав 2024 | 22,9 | 12,7 |
Алюминиевый сплав 5086 | 23.![]() | 13,2 |
Алюминиевый сплав 6061 | 23,6 | 13,1 |
Алюминиевый сплав 7075 | 23,4 | 13,0 |
Алюминиевый сплав 356.0 | 21.5 | 11,9 |
Сплавы на медной основе | ||
Материал | Коэффициент теплового расширения | |
10 -6 (° C) -1 | 10 -6 (° F) -1 | |
Медный сплав C11000 (электролитическая вязкая пека) | 17.![]() | 9,4 |
Медный сплав C17200 (бериллий — медь) | 16,7 | 9,3 |
Медный сплав C22000 (техническая бронза, 90%) | 18,4 | 10,2 |
Медный сплав C23000 (красная латунь, 85%) | 18.7 | 10,4 |
Copper Alloy C26000 (патрон латунь) | 19,9 | 11,1 |
Медный сплав C27000 (желтая латунь) | 20,3 | 11,3 |
Медный сплав C36000 (легкая латунь) | 20.![]() | 11,4 |
Медный сплав C51000 (фосфористая бронза, 5% A) | 17,8 | 9,9 |
Медный сплав C62300 (алюминиевая бронза, 9%) | 16,2 | 9,0 |
Медный сплав C71500 (медь — никель, 30%) | 16.2 | 9,0 |
Медный сплав C | (подшипник из бронзы)18,0 | 10,0 |
Чугун | ||
Материал | Коэффициент теплового расширения | |
10 -6 (° C) -1 | 10 -6 (° F) -1 | |
Серый Утюг | ||
Марка G1800 | 11.![]() | 6,3 |
Марка G3000 | 11,4 | 6,3 |
Марка G4000 | 11,4 | 6,3 |
Ковкий чугун | ||
60-40-18 класс | 11.2 | 6,2 |
80-55-06 | марка10,6 | 5,9 |
Драгоценные металлы | ||
Материал | Коэффициент теплового расширения | |
10 -6 (° C) -1 | 10 -6 (° F) -1 | |
Золото (технически чистое) | 14.![]() | 7,9 |
Серебро (технически чистое) | 19,7 | 10,9 |
Стали | ||
Материал | Коэффициент теплового расширения | |
10 -6 (° C) -1 | 10 -6 (° F) -1 | |
Обычная углеродистая и низколегированная сталь | ||
Стальной сплав А36 | 11.7 | 6,5 |
Стальной сплав 1020 | 11,7 | 6,5 |
Стальной сплав 1040 | 11,3 | 6,3 |
Стальной сплав 4140 | 12.![]() | 6,8 |
Стальной сплав 4340 | 12,3 | 6,8 |
Нержавеющая сталь | ||
Нержавеющий сплав 304 | 17,2 | 9,6 |
Нержавеющий сплав 316 | 15.9 | 8,8 |
Нержавеющий сплав 405 | 10,8 | 6.0 |
Нержавеющий сплав 440A | 10,2 | 5,7 |
Нержавеющий сплав 17-7PH | 11.![]() | 6,1 |
Титановые сплавы | ||
Материал | Коэффициент теплового расширения | |
10 -6 (° C) -1 | 10 -6 (° F) -1 | |
Коммерчески чистый (ASTM Grade 1) | 8.6 | 4,8 |
Титановый сплав Ti — 5Al — 2.5Sn | 9,4 | 5,2 |
Титановый сплав Ti — 6Al — 4V | 8,6 | 4,8 |
Титановый сплав Ti-8Mn | 10.![]() | 6.0 |
Различные металлы | ||
Материал | Коэффициент теплового расширения | |
10 -6 (° C) -1 | 10 -6 (° F) -1 | |
Магниевый сплав AZ31B | 26.0 | 14,4 |
Никель 200 | 13,3 | 7,4 |
Инконель 625 | 12,8 | 7,1 |
Инконель 718 | 13.![]() | 7,2 |
Монель | 15,7 | 8,7 |
Монель 400 | 13,9 | 7,7 |
Хейнс Сплав 25 | 12.3 | 6,8 |
Инвар | 1,6 | 0,9 |
Супер Инвар | 0,72 | 0,40 |
Ковар | 5.1 | 2,8 |
Свинец химический | 29,3 | 16,3 |
Сурьма свинец (6%) | 27,2 | 15,1 |
Олово (технически чистое) | 23.![]() | 13,2 |
Свинцово-оловянный припой (60Sn — 40 Pb) | 24,0 | 13,3 |
Цинк (технически чистый) | 23,0 — 32,5 | 12,7 — 18,1 |
Ацеталь | 59.2 |
Акрил экструдированный | 130 |
Акрил, лист, литье | 45 |
Глинозем | 3 |
Алюминий | 13,1 |
Сурьма | 5 |
Мышьяк | 2,6 |
Барий | 11,4 |
Бериллий | 6.![]() |
Бериллий Медь | 9,3 |
висмут | 7,2 |
Латунь | 10,4 |
Латунь, Адмиралтейство | 11,2 |
Латунь, желтый | 11,3 |
бронза | 10 |
Бронза, алюминий | 9 |
Кадмий | 16.8 |
Кальций | 12,4 |
Углерод — алмаз | 0,67 |
Ацетат целлюлозы (CA) | 72,2 |
Бутират ацетата целлюлозы (CAB) | 14 |
Нитрат целлюлозы (CN) | 55,6 |
Цемент | 6 |
Церий | 2,9 |
Хлорированный поливинилхлорид (ХПВХ) | 37 |
Хром | 3.![]() |
Структура глиняной плитки | 3,3 |
Кобальт | 6,7 |
Бетон | 8 |
Бетонная конструкция | 5,5 |
Константан | 10,4 |
Медь | 9,8 |
Медь, бериллий 25 | 9,9 |
Корунд спеченный | 3.6 |
Алмаз | 0,6 |
Диспрозий | 5,5 |
Эбонит | 42,8 |
Эпоксидная смола, литьевые смолы и компаунды, ненаполненные | 31 |
Эрбий | 6,8 |
Этиленэтилакрилат (EEA) | 113,9 |
Этиленвинилацетат (EVA) | 100 |
Европий | 19.4 |
Фторэтиленпропилен (ФЭП) | 75 |
Гадолиний | 5 |
Германий | 3,4 |
Стекло твердое | 3,3 |
Стекло, тарелка | 5 |
Стекло, Pyrex | 2,2 |
Золото | 7,9 |
Гранит | 4.![]() |
Графит | 4,4 |
Гафний | 3,3 |
Твердый сплав K20 | 3,3 |
Хастеллой C | 5,3 |
Гольмий | 6,2 |
Лед | 28,3 |
Инколой | 8 |
Инконель | 6.4 |
Индий | 18,3 |
Инвар | 0,8 |
Иридий | 3,3 |
Утюг | 6,8 |
Чугун литой | 5,9 |
Чугун кованый | 6,3 |
лантан | 6,7 |
Свинец | 15,1 |
Известняк | 4.4 |
Литий | 25,6 |
Лютеций | 5,5 |
Магний | 14 |
Марганец | 12 |
Марганцевая бронза | 11,8 |
Мрамор | 3,1 — 7,9 |
Каменная кладка | 2,6 — 5,0 |
Слюда | 1.![]() |
молибден | 3 |
Монель | 7,8 |
Миномет | 4,1-7,5 |
Неодим | 5,3 |
Никель | 7,2 |
Никель кованый | 7,4 |
Ниобий (Columbium) | 3,9 |
Нейлон общего назначения | 40 |
Нейлон, тип 11, компаунд для формования и экструзии | 55.6 |
Нейлон, тип 12, компаунд для формования и экструзии | 44,7 |
Нейлон, тип 6, литой | 47,2 |
Нейлон, тип 6/6, формовочная масса | 44,4 |
Осмий | 2,8 |
Палладий | 6,6 |
Фенольная смола без наполнителей | 44,4 |
Штукатурка | 9.![]() |
Платина | 5 |
Плутоний | 19,84 |
Полиалломер | 50,8 |
Полиамид (PA) | 61,1 |
Поликарбонат — армированный стекловолокном | 12 |
Поликарбонат (ПК) | 39 |
Полиэстер | 69 |
Полиэстер — армированный стекловолокном | 14 |
Полиэтилен (PE) | 111 |
Полиэтилентерефталат (ПЭТ) | 33 |
Полифенилен — армированный стекловолокном | 20 |
Полипропилен — армированный стекловолокном | 18 |
Полипропилен (ПП) без наполнителя | 50.3 |
Полистирол (ПС) | 38,9 |
Полисульфон (ПСО) | 31 |
Полиуретан (PUR), жесткий | 32 |
Поливинилхлорид (ПВХ) | 28 |
Поливинилиденфторид (ПВДФ) | 71 |
Фарфор | 2 |
Калий | 46 |
празеодим | 3.![]() |
Прометий | 6,1 |
кварцевый | 0,43 — 0,79 |
Красная латунь | 10,4 |
Рений | 3,7 |
Родий | 4,4 |
Твердая резина | 42,8 |
Рутений | 5,1 |
Самарий | 7.1 |
Песчаник | 6,5 |
Скандий | 5,7 |
Селен | 2,1 |
Кремний | 2,8 |
Серебро | 11 |
Сланец | 5,8 |
Натрий | 39 |
Припой 50-50 | 13.4 |
Стеатит | 4,7 |
Сталь | 7,3 |
Сталь нержавеющая аустенитная (304) | 9,6 |
Сталь нержавеющая аустенитная (310) | 8 |
Сталь нержавеющая аустенитная (316) | 8,9 |
Сталь нержавеющая ферритная (410) | 5,5 |
Стронций | 12.![]() |
Тантал | 3,6 |
Теллур | 20,5 |
Тербий | 5,7 |
Терне | 6,5 |
Таллий | 16,6 |
торий | 6,7 |
Тулий | 7,4 |
Олово | 12,8 |
Титан | 4.8 |
Вольфрам | 2,5 |
Уран | 7,4 |
Ванадий | 4,4 |
Виниловый эфир | 8,7 — 12 |
Дерево, ель | 2,1 |
Дерево, дуб | 3 |
Дерево, сосна | 2,8 |
Иттербий | 14.6 |
Иттрий | 5,9 |
цинк | 19 |
Цирконий | 3,2 |
Коэффициент теплового расширения — БЕСПЛАТНАЯ онлайн-таблица
Значения коэффициента линейного теплового расширения для металлов и сплавов
Семья | Материал | CTE (° C) -1 | CTE (° F) -1 |
---|---|---|---|
Алюминиевые сплавы | Алюминиевый сплав 1100 | 0,0000236 | 0,0000131 |
Алюминиевые сплавы | Алюминиевый сплав 2011 | 0,0000230 | 0,0000128 |
Алюминиевые сплавы | Алюминиевый сплав 2024 | 0,0000229 | 0,0000127 |
Алюминиевые сплавы | Алюминиевый сплав 5086 | 0,0000238 | 0,0000132 |
Алюминиевые сплавы | Алюминиевый сплав 6061 | 0,0000236 | 0,0000131 |
Алюминиевые сплавы | Алюминиевый сплав 7075 | 0,0000234 | 0,0000130 |
Алюминиевые сплавы | Алюминиевый сплав 356.![]() | 0,0000215 | 0,0000119 |
Сплавы на основе меди | Медный сплав C11000 (электролитическая вязкая пека) | 0,0000170 | 0,0000094 |
Сплавы на основе меди | Медный сплав C17200 (бериллий — медь) | 0,0000167 | 0,0000093 |
Сплавы на основе меди | Медный сплав C22000 (техническая бронза, 90%) | 0,0000184 | 0,0000102 |
Сплавы на основе меди | Медный сплав C23000 (Красная латунь, 85%) | 0,0000187 | 0,0000104 |
Сплавы на основе меди | Медный сплав C26000 (патрон латунь) | 0,0000199 | 0,0000111 |
Сплавы на основе меди | Медный сплав C27000 (желтая латунь) | 0,0000203 | 0,0000113 |
Сплавы на основе меди | Медный сплав C36000 (легкая латунь) | 0,0000205 | 0,0000114 |
Сплавы на основе меди | Медный сплав C51000 (Фосфорная бронза, 5% A) | 0,0000178 | 0,0000099 |
Сплавы на основе меди | Медный сплав C62300 (алюминиевая бронза, 9%) | 0,0000162 | 0,0000090 |
Сплавы на основе меди | Медный сплав C71500 (медь — никель, 30%) | 0,0000162 | 0,0000090 |
Сплавы на основе меди | Медный сплав C | (подшипник из бронзы)0,0000180 | 0,0000100 |
Чугун | Серый чугун — марка G1800 | 0,0000114 | 0,0000063 |
Чугун | Серый чугун — марка G3000 | 0,0000114 | 0,0000063 |
Чугун | Серый чугун — марка G4000 | 0,0000114 | 0,0000063 |
Чугун | Ковкий чугун — марка 60-40-18 | 0,0000112 | 0,0000062 |
Чугун | Ковкий чугун — марка 80-55-06 | 0,0000106 | 0,0000059 |
Драгоценные металлы | Золото | 0,0000142 | 0,0000079 |
Драгоценные металлы | Серебро | 0,0000197 | 0,0000109 |
Обычная углеродистая и низколегированная сталь | Стальной сплав A36 | 0,0000117 | 0,0000065 |
Обычная углеродистая и низколегированная сталь | Стальной сплав 1020 | 0,0000117 | 0,0000065 |
Обычная углеродистая и низколегированная сталь | Стальной сплав 1040 | 0,0000113 | 0,0000063 |
Обычная углеродистая и низколегированная сталь | Стальной сплав 4140 | 0,0000123 | 0,0000068 |
Обычная углеродистая и низколегированная сталь | Стальной сплав 4340 | 0,0000123 | 0,0000068 |
Нержавеющая сталь | Нержавеющий сплав 304 | 0,0000172 | 0,0000096 |
Нержавеющая сталь | Нержавеющий сплав 316 | 0,0000159 | 0,0000088 |
Нержавеющая сталь | Нержавеющий сплав 405 | 0,0000108 | 0,0000060 |
Нержавеющая сталь | Нержавеющий сплав 440A | 0,0000102 | 0,0000057 |
Нержавеющая сталь | Нержавеющий сплав 17-7PH | 0,0000110 | 0,0000061 |
Титановые сплавы | Коммерчески чистый (ASTM Grade 1) | 0,0000086 | 0,0000048 |
Титановые сплавы | Титановый сплав Ti — 5Al — 2.![]() | 0,0000094 | 0,0000052 |
Титановые сплавы | Титановый сплав Ti — 6Al — 4V | 0,0000086 | 0,0000048 |
Титановые сплавы | Титановый сплав Ti-8Mn | 0,0000108 | 0,0000060 |
Различные металлы | Магниевый сплав AZ31B | 0,0000260 | 0,0000144 |
Различные металлы | Магниевый сплав AZ31B | 0,0000260 | 0,0000144 |
Различные металлы | Никель 200 | 0,0000133 | 0,0000074 |
Различные металлы | Инконель 625 | 0,0000128 | 0,0000071 |
Различные металлы | Инконель 718 | 0,0000130 | 0,0000072 |
Различные металлы | Монель | 0,0000157 | 0,0000087 |
Различные металлы | Монель 400 | 0,0000139 | 0,0000077 |
Различные металлы | Сплав Хейнса 25 | 0,0000123 | 0,0000068 |
Различные металлы | Инвар | 0,0000016 | 0,0000009 |
Различные металлы | Супер Инвар | 0,000000072 | 0,000000040 |
Различные металлы | Ковар | 0,0000051 | 0,0000028 |
Различные металлы | Свинец химический | 0,0000293 | 0,0000163 |
Различные металлы | Сурьма свинец (6%) | 0,0000272 | 0,0000151 |
Различные металлы | Олово | 0,0000238 | 0,0000132 |
Различные металлы | Свинец-оловянный припой (60Sn — 40 Pb) | 0,0000240 | 0,0000133 |
Различные металлы | цинк | 0,0000230 | 0,0000127 |
Семья | Материал | CTE (° C) -1 | CTE (° F) -1 |
Вы можете поделиться этой таблицей через:
Как работает таблица коэффициентов теплового расширения?
В этой таблице представлены значения коэффициента линейного теплового расширения для металлов и сплавов.
Когда объект нагревается или охлаждается, его длина изменяется на величину, пропорциональную исходной длине и изменению температуры.
Другие калькуляторы или статьи, которые могут вас заинтересовать:
Есть вопросы относительно таблицы коэффициентов теплового расширения?
Если у вас есть какие-либо вопросы относительно коэффициента теплового расширения, свяжитесь с нами… В любом случае вы можете заглянуть на нашу страницу часто задаваемых вопросов, там вы найдете ответы на самые распространенные вопросы.
ABS (акрилонитрилбутадиенстирол) термопласт | 73,8 |
АБС-пластик, армированный стекловолокном | 30,4 |
Ацетали | 106.![]() |
Ацеталь — армированный стекловолокном | 39,4 |
Акрил | 75 |
Глинозем (оксид алюминия, Al 2 O 3 ) (Мишень для распыления) (порошки) (Мелющая среда) (Сапфир / Монокристалл) (Планетарные размольные стаканы) (Валковые размольные стаканы) (Высокочистые порошки) | 8,1 |
Алюминий (мишень для распыления) | 21–24 |
Алюминиевый сплав AlSi7Mg (порошок для аддитивного производства / 3D-печати) | 21-22 |
Алюминиевый сплав AlSi10Mg (порошок для аддитивного производства / 3D-печати) | 20 |
Алюминиевый сплав AlSi12 (порошок для аддитивного производства / 3D-печати) | 20 |
Метафосфат алюминия, Al (PO 3 ) 3 (порошок особой чистоты) | 9.6 |
Нитрид алюминия (мишень для распыления) (шаблон AlN на сапфире) | 5,3 |
Янтарь | 50–60 |
Сурьма (мишень для распыления) | 9–11 |
Мышьяк | 4,7 |
Бакелит беленый | 22 |
Барий | 20,6 |
Фторид бария, BaF 2 (порошок высокой чистоты) (монокристаллы и подложки) (мишени для распыления) | 18.![]() |
Феррит бария, | 10 |
Титанат бария, BaTiO 3 (мишень для распыления) (монокристаллическая подложка) | 9,4 |
Бензоциклобутен | 42 |
Бериллий | 11,5 |
Висмут (мишень для распыления) | 13 |
Германат висмута, Bi 4 Ge 3 O 12 (сцинтилляционные кристаллы) | 7 |
Оксид висмута, Bi 2 O 3 (порошок высокой чистоты) (мишень для распыления) | Параллельно А-26.7, б-6.6, в-9.0 |
Карбид бора, B 4 C (мишень для распыления) | 4,5 |
Нитрид бора, BN (мишень для распыления) | 1,0 |
Латунь | 18,7 |
Кирпичная кладка | 5,5 |
бронза | 18,0 |
Кадмий (мишень для распыления) | 30 |
Дифторид кадмия, CdF 2 (мишень для распыления) | 21.![]() |
Селенид кадмия, CdSe (мишень для распыления) | Параллельно А-6.26, С-4.28 |
Сульфид кадмия, CdS (мишень для распыления) | Параллельно А-6.26, С-3.5 |
Теллурид кадмия, CdTe (мишень для распыления) | 4,8 |
Кальций | 22,3 |
Фторид кальция, CaF 2 (монокристалл) (мишень для распыления) (сцинтилляционный кристалл, легированный Eu) | 18.85 |
Фторид кальция, легированный европием, Eu: CaF 2 (сцинтилляционный кристалл, легированный Eu) | 19,5 |
Серый чугун | 10,8 |
Каучук | 66–69 |
Целлулоид | 100 |
Ацетат целлюлозы (CA) | 130 |
Бутинат ацетата целлюлозы (CAB) | 96–171 |
Нитрат целлюлозы (CN) | 80–120 |
Цемент | 10.![]() |
Иодид цезия, CsI (сцинтилляционные кристаллы) | 54 |
Церий (мишень для распыления) | 5,2 |
Диоксид церия, CeO 2 (мишень для распыления) | 11,2 |
Фторид церия, CeF 3 (сцинтилляционный кристалл) (мишень для распыления) | Параллельно а-12,9, с-16,5 |
Оксид церия, Ce 2 O 3 (порошок особой чистоты) | 12 |
Хлорированный полиэфир | 80 |
Хлорированный поливинилхлорид (ХПВХ) | 66.6 |
Хром (мишень для распыления) | 6,2 |
Борид хрома, Cr 5 B 3 (мишень для распыления) | 13,7 |
Карбид хрома, Cr 3 C 2 (мишень для распыления) | 10,3 |
Диборид хрома CrB 2 (мишень для распыления) | 6,2 — 7,5 |
Дисилицид хрома, CrSi 2 (мишень для распыления) | Параллельно А-8.![]() |
Моноборид хрома, CrB | 12,3 |
Нитрид хрома, CrN | 2,3 |
Нитрид хрома, Cr 2 N | 9,4 |
Оксид хрома, Cr 2 O 3 (порошок особой чистоты) (мишень для распыления) | 9,0 |
Структура глиняной плитки | 5,9 |
Кобальт (мишень для распыления) | 12 |
Кобальт-хром-молибденовый сплав, CoCrMo (порошок для аддитивного производства / 3D-печати) | 11.5 |
Кобальт-хром-вольфрамовый сплав, CoCrW (порошок для аддитивного производства / 3D-печати) | 21 |
Дисилицид кобальта, CoSi 2 | 10 |
Бетон | 14,5 |
Бетонная конструкция | 9,8 |
Константан | 18,8 |
Медь (мишень для распыления) | 16,6 |
Медь, бериллий 25 | 17.![]() |
Медно-оловянный сплав, CuSn10 (порошок для аддитивного производства / 3D-печати) | 18 |
Корунд спеченный | 6,5 |
Купроникель 30% | 16,2 |
Алмаз (углерод) | 1,18 |
дюралюминий | 23 |
Диспрозий (мишень для распыления) | 9,9 |
Оксид диспрозия, Dy 2 O 3 (порошок высокой чистоты) (мишени для распыления) | 6.6 |
Эбонит | 76,6 |
Эпоксидные смолы, литые смолы и компаунды, ненаполненные | 45–65 |
Эрбий (мишень для распыления) | 12,2 |
Оксид эрбия, Er 2 O 3 (порошок высокой чистоты) (мишени для распыления) | 6,6 |
Этиленэтилакрилат (EEA) | 205 |
Этиленвинилацетат (EVA) | 180 |
Европий (мишень для распыления) | 35 |
Оксид европия, Eu 2 O 3 (порошок особой чистоты) | 6.![]() |
Фторэтиленпропилен (ФЭП) | 135 |
Плавиковый шпат, CaF 2 (монокристалл) (мишень для распыления) | 19,5 |
Гадолиний (мишень для распыления) | 9 |
Гадолиний-галлий-гранат (GGG), Gd 3 Ga 5 O 12 (монокристалл) (монокристалл, легированный неодимом) | 8 |
Оксид гадолиния, Gd 2 O 3 (порошок особой чистоты) | 7.6 |
Тетраборид гадолиния, GdB 4 | 7,0 |
Галлий | 37 |
Арсенид галлия, GaAs (мишень для распыления) (монокристаллические подложки) | 5,73 |
Оксид галлия, Ga 2 O 3 (монокристаллическая пластина) (высокочистый порошок) (мишень для распыления) | Параллельно а-3,77, б-7,8, в-6,34 |
Нитрид галлия, GaN (монокристалл) | 3.17 |
Германий (мишень для распыления) (монокристалл) | 5,9 |
Оксид германия, GeO 2 (порошок особой чистоты) | 7,5 |
Теллурид германия, GeTe (мишень для распыления) | 11,2 |
Немецкое серебро | 18,4 |
Стекло твердое | 5,9 |
Стекло, Pyrex | 4,0 |
Стекло, тарелка | 9.0 |
Золото (мишень для распыления) | 14,2 |
Золото — медь | 15,5 |
Золото — платина | 15,2 |
Гранит | 7,9 |
Графит чистый (углерод) (мишень для распыления) (материалы анода) | 2–6 |
Gunmetal | 18 |
Гуттаперча | 198 |
Гафний (мишень для распыления) | 5.9 |
Карбид гафния, HfC (мишень для распыления) | 6,9 |
Диоксид гафния, HfO 2 (мишень для распыления) | 6.0 |
Дисилицид гафния, HfSi 2 (мишень для распыления) | 16,4 |
Нитрид гафния, HfN (мишень для распыления) | 6,9 |
Твердый сплав K20 | 6 |
Hastelloy C22 (мишень для распыления) | 12.4 |
Хастеллой C276 (мишень для распыления) | 11,2 |
Hastelloy N (мишень для распыления) | 12,3 |
Гольмий (мишень для распыления) | 11,2 |
Оксид гольмия, Ho 2 O 3 (порошок особой чистоты) (мишени для распыления) | 7,4 |
Лед, 0 o C вода | 51 |
Инконель 625 (порошок для аддитивного производства / 3D-печати) | 13.1 |
Инконель 718 (порошок для аддитивного производства / 3D-печати) | 12,8 |
Индий (мишень для распыления) | 33 |
Антимонид индия, InSb (мишень для распыления) | 5,37 |
Арсинид индия, InAs (монокристалл) (мишень для распыления) | 4,52 |
Оксид индия, галлия, цинка (IGZO), In 2 Ga 2 ZnO 7 (мишень для распыления) | 4.31 |
Оксид индия, In 2 O 3 (порошок особой чистоты) (мишень для распыления) | 7,2 |
Фосфид индия, InP (монокристалл) | 4,5 |
Сульфид индия, дюйм 2 S 3 (мишень для распыления) | Тетрагональная форма: параллельна a-11,7, c-6,7 Тригональная форма: параллельно a-14,1, c-26,7 |
Оксид индия и олова (ITO), In 2 — x Sn x O 3 (Мишень для распыления) (стекло и пленка с покрытием ITO) | 8 |
Инвар | 1.5 |
Иридий (мишень для распыления) | 6,4 |
Железо чистое (мишень для распыления) | 12,0 |
Чугун литой | 10,4 |
Чугун кованый | 11,3 |
Борид железа, FeB (мишень для распыления) | 23 |
(Di) Борид железа Fe 2 B (Мишень для распыления) | 7,65 |
(Tri) Карбид железа, Fe 3 C (мишень для распыления) | 8.6 |
Каптон | 20 |
Лангасит (LGSO), La 3 Ga 5 SiO 14 (монокристалл) | 16 |
Лангатат (LGT), La 3 Gao 5,5 Ta 0,5 O 14 (монокристалл) | 7,65 |
Лантан (мишень для распыления) | 12,1 |
Алюминат лантана, LaAlO 3 (монокристалл) (мишень для распыления) | 9.4 |
Фторид лантана, LaF 3 (мишень для распыления) | Параллельно а-15.8, с-11 |
Гексаборид лантана, LaB 6 (мишень для распыления) | 6,2 |
Манганат лантана, LaMnO 3 (мишень для распыления) | 11,62 |
Оксид лантана, La 2 O 3 (порошок особой чистоты) | 8,6 |
Танталат алюминия-лантана-стронция (LSAT), (La 0.18 Sr 0,82 ) (Al 0,59 Ta 0,41 ) O 3 (монокристалл) | 10 |
Свинец (мишень для распыления) | 28,9 |
Фторид свинца, PbF 2 (монокристалл) (мишень для распыления) | 29 |
Селенид свинца, PbSe (мишень для распыления) | 19 |
Сульфид свинца, PbS (мишень для распыления) | 20,1 |
Теллурид свинца, PbTe (мишень для распыления) | 20.4 |
Вольфрамат свинца, PbWO 4 (монокристалл) | Параллельно А-29,5, С-12,8 |
Известняк | 8 |
Литий (микросхемы для аккумуляторов) | 46 |
Алюминат лития, LiALO 2 (монокристалл) | Параллельно а-10,1, с-16,5 |
Фторид лития, LiF (мишень для распыления) (порошок особой чистоты) (монокристалл) | 37 |
Ниобат лития, LiNbO 3 (монокристалл) (мишень для распыления) | Параллельно А-15.4, с-7,5 |
Танталат лития, LiTaO 3 (монокристаллический) | Параллельно А-16, С-4 |
Лютеций (мишень для распыления) | 9,9 |
Лютеций-алюминиевый гранат (LuAG), Y 3 Al 5 O 12 | 6.0 |
Оксид лютеция, Lu 2 O 3 (порошок особой чистоты) | 7,7 |
Macor | 9.3 |
Магналий | 23,8 |
Магний (мишень для распыления) | 25 |
Алюминат магния, MgAl 2 O 4 (монокристалл) | 6,72 |
Фторид магния, MgF 2 (мишень для распыления) (монокристалл) (порошок высокой чистоты) (монокристаллические подложки) | Параллельно оси C 13,7 Перпендикулярно оси C 8,48 |
Оксид магния, MgO (мишень для распыления) (тигель) (монокристаллический субстрат) (порошок высокой чистоты) | 10.8 |
Марганец (мишень для распыления) | 22 |
Манганин | 18,1 |
Мрамор | 5,5 — 14,1 |
Каменная кладка | 4,7 — 9,0 |
Меркурий | 61 |
Слюда | 3 |
Молибден (мишень для распыления) | 5 |
Борид молибдена, Мо 2 B (мишень для распыления) | 4.78 |
Карбид молибдена, Mo 2 C (мишень для распыления) | 7,8 |
Дисилицид молибдена, MoSi 2 (мишень для распыления) | Параллельно a = 5,6, c = 4,1 |
Оксид молибдена, МоО 3 (мишень для распыления) | 5 |
Металлический монель | 13,5 |
Миномет | 7,3 — 13,5 |
Неодим (мишень для распыления) | 9.6 |
Оксид неодима и меди, Nd 2 CuO 4 (мишень для распыления) | 10,1 |
Фторид неодима, NdF 3 (мишень для распыления) | Параллельно А-17,4, С-14,7 |
Гексаборид неодима, NdB 6 (мишень для распыления) | 7,3 |
Оксид неодима, Nd 2 O 3 (порошок особой чистоты) | 14,7 |
Никель (мишень для распыления) | 13.0 |
Никель Хром (нихром), NiCr (мишень для распыления) | 14 |
Оксид никеля, NiO (мишень для распыления) | 10 |
Ниобий (мишень для распыления) | 7,3 |
Карбид ниобия, NbC (мишень для распыления) | 7,81 |
Дисилицид ниобия, NbSi 2 | Параллельно a = 9,1, c = 8,7 |
Нитрид ниобия, NbN (мишень для распыления) | 10.1 |
Оксид ниобия, Nb 2 O 5 (Мишень для распыления) (Порошок высокой чистоты) | 5,6 |
Селенид ниобия, NbSe 2 (мишень для распыления) | Параллельно a = 6,6, c = 19,9 |
Силицид ниобия, Nb 5 Si 3 (мишень для распыления) | 7,6 |
Нейлон общего назначения | 72 |
Нейлон, тип 11, компаунд для формования и экструзии | 100 |
Нейлон, тип 12, компаунд для формования и экструзии | 80.5 |
Нейлон, тип 6, литой (емкость для планетарного фрезерования) (емкость для роликовой фрезеровки) | 85 |
Нейлон, тип 6/6, формовочная масса | 80 |
Дуб перпендикулярно волокну | 54 |
Осмий | 5 |
Палладий (мишень для распыления) | 11,8 |
Парафин | 106–480 |
Фенольная смола без наполнителей | 60–80 |
Фосфорная бронза | 16.7 |
Штукатурка | 16,4 |
Пластмассы | 40–120 |
Платина (мишень для распыления) | 9,0 |
Плутоний | 54 |
Полиакрилонитрил | 70 |
Полиалломер | 91,5 |
Полиамид (PA) | 110 |
Полибутилен (ПБ) | 130 |
Поликарбонат (ПК) | 70.2 |
Поликарбонат — армированный стекловолокном | 21,5 |
Полиэстер | 123,5 |
Полиэстер — армированный стекловолокном | 25 |
Полиэтилен (PE) | 200 |
Полиэтилен (PE) — высокомолекулярный вес | 108 |
Полиэтилентерефталат (ПЭТ) (Оксид индия и олова на ПЭТ) (Монослойный графен на ПЭТ) | 59.4 |
Полифенилен — армированный стекловолокном | 35,8 |
Полипропилен (ПП), ненаполненный (монокристаллы, футляры с пластинчатыми подложками) | 100–200 |
Полипропилен — армированный стекловолокном | 32 |
Полистирол (ПС) | 70 |
Полисульфон (ПСО) | 55,8 |
Полиуретан (PUR), жесткий (ясы планетарного и роликового фрезерования) | 57.6 |
Поливинилхлорид (ПВХ) | 50,4 |
Поливинилиденфторид (ПВДФ) | 127,8 |
Фарфор промышленный | 6,5 |
Калий | 83 |
Бромид калия, KBr (монокристаллический) | 43 |
Хлорид калия, KCl (монокристалл) | 36 |
Танталат калия, KTaO 3 (монокристалл) | 4.03 |
Празеодим (мишень для распыления) | 6,7 |
Фторид празеодима, PrF 3 (мишень для распыления) | Параллельно а-16.4, с-14 |
Оксид празеодима, Pr 6 O 11 (порошок особой чистоты) (мишени для распыления) | 12 |
Прометий | 11 |
Кварц (монокристаллическая пластина) (монослойный графен на кварце) | 0.77 — 1,4 |
Рений (мишень для распыления) | 6,7 |
Дисилицид рения, ReSi 2 | Параллельно a = 4,2, c = 7,5 |
Родий | 8 |
Каменная соль | 40,4 |
Твердая резина | 77 |
Рутений (мишень для распыления) | 9,1 |
Самарий (мишень для распыления) | 12.7 |
Оксид самария, Sm 2 O 3 (порошок особой чистоты) (мишени для распыления) | 8,5 |
Песчаник | 11,6 |
Сапфир (монокристалл и вафли) | Смотрите эту страницу |
Скандий (мишень для распыления) | 10,2 |
Оксид скандия (порошок особой чистоты) (мишени для распыления) | 6,7 |
Селен (мишень для распыления) | 3.8 |
Кремний (монокристаллическая пластина) (мишень для распыления) (мишень для распыления N-типа) (мишень для распыления P-типа) | Смотрите эту страницу |
Карбид кремния, SiC (монокристаллическая пластина) (мишень для распыления) | Смотрите эту страницу |
Диоксид кремния (плавленый кремний, аморфный), SiO 2 (мишень для распыления) (пластины и подложки) (порошок высокой чистоты) | 5,6 |
Нитрид кремния, Si 3 N 4 (мишень для распыления) | 4.3 |
Серебро (мишень для распыления) | 19,5 |
Ситалл | 0,15 |
Сланец | 10,4 |
Натрий | 70 |
Хлорид натрия, NaCl (монокристалл) | 44 |
Фторид натрия, NaF (мишень для распыления) | 34 |
Свинцово-оловянный припой, 50% — 50% | 24,0 |
Зеркало металлическое | 19.3 |
Стеатит | 8,5 |
Сталь | 12,0 |
Сталь 18 Ni (300) (мартенсит) (порошок для аддитивного производства / 3D-печати) | 10,3 |
Сталь Инвар 36 (порошок для аддитивного производства / 3D-печати) | 1,3 |
Сталь M2 (инструмент) (порошок для аддитивного производства / 3D-печати) | 11 |
Сталь нержавеющая аустенитная (304) (мелющие среды) (стаканы планетарного фрезерования) (стаканы роликового фрезерования) | 17.3 |
Сталь нержавеющая аустенитная (310) | 14,4 |
Сталь Нержавеющая аустенитная (316) (Порошок для аддитивного производства / 3D-печати) (Мелющие среды) (Банки для роликовых фрез) (Банки для планетарного фрезерования) | 16,0 |
Сталь нержавеющая ферритная (410) (порошок для аддитивного производства / 3D-печати) | 9,9 |
Сталь нержавеющая 17-4PH (порошок для аддитивного производства / 3D-печати) | 10,8 |
Нержавеющая сталь 440C (порошок для аддитивного производства / 3D-печати) | 10.2 |
Стронций | 22,5 |
Фторид стронция, SrF 2 (мишень для распыления) | 18,4 |
Титанат стронция, SrTiO 3 (мишень для распыления) (монокристаллические пластины и подложки) (монокристалл, легированный Fe) (монокристалл, легированный Nb) | 9 |
Тантал (мишень для распыления) | 6,5 |
Карбид тантала, TaC (мишень для распыления) | 6.3 |
Диборид тантала, TaB 2 | 8,2 |
Дисилицид тантала, TaSi2 (мишень для распыления) | Параллельно a = 6,8, c = 6,1 |
Нитрид тантала, TaN (мишень для распыления) | 3,6 |
Пятиокись тантала, Ta 2 O 5 (Мишень для распыления) (Порошок высокой чистоты) | 6,7 |
Сульфид тантала, TaS 2 (мишень для распыления) | 12–15 |
Тефлон, (мишень для распыления) (стаканы планетарного фрезерования) (стаканы роликового фрезерования) | 120–170 |
Теллур (мишень для распыления) | 36.9 |
Диоксид теллура, TeO 2 (монокристалл) | Параллельно a = 19,5, c = 6,1 |
Тербий (мишень для распыления) | 10,3 |
Терне | 11,6 |
Таллий | 29,9 |
торий | 12 |
Тулий (мишень для распыления) | 13,3 |
Оксид тулия, Tm 2 O 3 (порошок особой чистоты) (мишени для распыления) | 6.6 |
Олово (мишень для распыления) | 23,4 |
Оксид олова SnO 2 (мишени для распыления) | 4,0 |
Титан (мишень для распыления) | 8,6 |
Титановый сплав Ti-6Al-4v (TC4) (порошок для аддитивного производства / 3D-печати) | 8,7 — 9,1 |
Карбид титана, TiC (мишень для распыления) | 7,4 |
Диборид титана, TiB 2 (мишени для распыления) | 7 |
Диоксид титана (рутил), TiO 2 (монокристалл) (порошок особой чистоты) (мишень для распыления) | Параллельно a = 7.14, с = 9,19 |
Дисилицид титана, TiSi 2 (мишень для распыления) | Параллельно a = 6,9, c = 5,4 |
Окись титана, TiO (мишень для распыления) | 6,6 |
Нитрид титана, TiN (мишень для распыления) | 9,4 |
Оксид титана (III), Ti 2 O 3 (порошок особой чистоты) | 7,6 |
Силицид титана, Ti 5 Si 3 | 7.5 |
Топас | 5–8 |
Вольфрам (мишень для распыления) | 4,4 |
Карбид вольфрама (стабилизированный кобальтом), WC-6% Co (мишень для распыления) (мелющая среда) (планетарные размольные стаканы) (пресс-форма для гранул) | 5,5 (чистый) 4,9 (6% Co) |
Диборид вольфрама, WB 2 | Параллельно А-6.5, С-8.8 |
Диселенид вольфрама, WSe 2 (мишень для распыления) | 7 |
Дисилицид вольфрама, WSi 2 (мишень для распыления) | Параллельно А-6.04, с-9.39 |
Дисульфид вольфрама, WS 2 (мишень для распыления) | 7–10 |
Дителлурид вольфрама, WTe 2 (мишень для распыления) | Параллельно a-10.1, b-7.5, c-4.5 |
Оксид вольфрама (VI), WO 3 (порошок высокой чистоты) (мишень для распыления) | 8–15 |
Уран | 13,9 |
Ванадий (мишень для распыления) | 8 |
Карбид ванадия, VC (мишень для распыления) | 7.3 |
Дисилицид ванадия, VSi 2 (мишень для распыления) | Параллельно a-8.0, c-7.5 |
Нитрид ванадия, ВН | 8,1 |
Оксид ванадия, V 2 O5 (мишень для распыления) | Параллель а-3,3, б- -1,7, в-42,2 |
Виниловый эфир | 16–22 |
Вулканит | 63,6 |
воск | 2–15 |
Изделия Wedgwood | 8.9 |
Дерево, ель | 3,7 |
Дерево параллельно волокну | 3 |
Древесина поперек (перпендикулярно) волокнам | 30 |
Дерево, сосна | 5 |
YCOB, Ca 4 YO (BO 3 ) 3 (кристалл NLO) | Параллель a-9.9, b-8.2, c-12.8 |
Иттербий (мишень для распыления) | 26.3 |
Фторид иттербия, YbF 3 (мишень для распыления) | 8,5 |
Оксид иттербия, Yb 2 O 3 (порошок высокой чистоты) (мишени для распыления) | 8,5 |
Иттрий (мишень для распыления) | 10,6 |
Иттрий-алюминиевый гранат (YAG), Y 3 Al 5 O 3 (Монокристалл YAG) (Монокристалл Ce: YAG) (Монокристалл Er: YAG) (Монокристалл Nd: YAG) (Yb : Монокристалл YAG) (Ce: YAG светодиодный люминофор) | 6.1 (нелегированная) |
Фторид иттрия, YF 3 (мишень для распыления) | 28,5 |
Оксид иттрия, Y 2 O 3 (порошок особой чистоты) (мишени для распыления) | 8,1 |
Ортованадат иттрия, YVO 4 (монокристалл) (монокристалл, легированный неодимом) | Параллельно a = 4,43, c = 11,37 |
Цинк (мишень для распыления) | 29,7 |
Оксид цинка, ZnO (монокристалл) (мишень для распыления) (порошок особой чистоты) | Параллельно a = 6.5, с = 3,7 |
Селенид цинка, ZnSe (мишень для распыления) | 7,1 |
Сульфид цинка, ZnS (мишень для распыления) | 6,5 |
Теллурид цинка, ZnTe (мишень для распыления) | 8,19 |
Цирконий (мишень для распыления) | 5,7 |
Карбид циркония, ZrC (мишень для распыления) | 6,7 |
Диборид циркония, ZrB 2 (мишень для распыления) | Параллельно a = 6.7, с = 6,9 |
Дисилицид циркония, ZrSi 2 (мишень для распыления) | Параллельно a = 1,1, c = 8,6 |
Нитрид циркония, ZrN (мишень для распыления) | 7,2 |
Диоксид циркония, ZrO 2 (порошок особой чистоты) | 7 |
Стабилизированный оксидом иттрия диоксид циркония (YSZ), выход 3-8% 2 O 3 / ZrO 2 (мишень для распыления) (монокристалл) (измельчающая среда) (планетарные размольные стаканы) (порошок высокой чистоты) | 3% = 10.8, 8% = 10,5 |
Термическое расширение — Rolled Alloys, Inc.
Загрузить лист данных (.PDF)«Напряжения (сжимающие, растягивающие или сдвиговые) из-за неравномерного распределения температуры и неоднородной температуры градиенты, вызывают больше отказов в высокотемпературном оборудовании, чем все другие факторы вместе взятые, составляющие примерно 90% от общего количества случаев. Это деструктивно главным образом потому, что инженер не входит в его проектный надлежащий допуск или обеспечение против температурных неравенств или из-за того, что оператор налагает перепады температур, которые вызывают локальные изменения размеров с сопутствующими напряжениями, превышающими упругая прочность сплава при данной температуре.«
— Ф. А. Фаренвальд. Некоторые принципы, лежащие в основе успешного использования металлов при высоких температурах, Proceedings of ASTM, 1924 V. 24
Мало что изменилось за последние 90 лет. Подавляющее большинство отказов, сообщаемых компании Rolled Alloys, включая разрушение или деформацию в процессе эксплуатации, вызваны: ограничение теплового расширения. Для успешного проектирования и монтажа высокотемпературного оборудования очень важно учитывать тепловое расширение, и иметь возможность рассчитать ожидаемую величину расширения.Ниже представлена простая таблица для расчета полного расширения в дюймах на фут длины для заданной температуры.
Тепловое расширение
Полное тепловое расширение, дюйм / фут
Температура, ° F | Углеродистая сталь | 446 | 304 | 309 | 310 | RA 253 MA | RA330 | RA333 | 601 | 600 | RA 602 CA |
70-200 | 0.0139 | 0,00874 | 0,0145 | 0,0137 | 0,0131 | 0,0141 | 0,0129 | 0,0109 | 0,0119 | 0,0115 | 0,0103 |
70-400 | 0,0376 | 0,0225 | 0,0372 | 0,0356 | 0,0348 | 0,0370 | 0,0341 | – | 0,0317 | 0,0305 | 0,0297 |
70-600 | 0.0623 | – | 0,0604 | 0,0591 | 0,0569 | 0,0610 | 0,0566 | – | 0,0516 | 0,0502 | 0,0496 |
70-800 | 0,0885 | 0,0526 | 0,0876 | – | 0,0806 | 0,0859 | 0,0797 | – | 0,0727 | 0,0710 | 0,0710 |
70-1000 | 0.0904 | 0,0681 | 0,115 | 0,108 | 0,106 | 0,111 | 0,104 | 0,0960 | 0,0949 | 0,0937 | 0,0915 |
70-1200 | 0,113 | 0,0854 | 0,144 | – | 0,133 | 0,137 | – | 0,122 | 0,120 | 0,117 | 0,115 |
70-1400 | – | 0.102 | 0,174 | – | 0,160 | 0,164 | – | 0,148 | 0,147 | 0,142 | 0,144 |
70-1600 | – | 0,123 | – | 0,185 | 0,186 | 0,193 | 0,180 | 0,173 | 0,175 | 0,167 | 0,174 |
70-1800 | – | 0,152 | – | – | 0.214 | 0,224 | 0,208 | 0,201 | 0,204 | 0,193 | 0,201 |
70-2000 | – | – | – | – | 0,245 | – | – | – | 0,236 | – | 0,227 |
Чтобы преобразовать эти числа в метрическую систему, умножьте на 83,33, чтобы получить миллиметры расширения на каждый метр длины для заявленной температуры, которая находится в градусах Фаренгейта
В качестве примера использования этой таблицы, рассмотрим муфель длиной 20 футов из RA330, работающий при температуре 1800 ° F.Считайте 0,208 дюйма / фут в таблице выше, умножьте на 20 футов, чтобы получить общее расширение 4,16 дюйма
Более общий способ расчета теплового расширения — использовать средние коэффициенты теплового расширения, например, указанные на следующей странице.
Чтобы использовать таблицу на странице 2, умножьте длину детали в дюймах, умножьте на разницу между комнатной и рабочей температурой и умножьте коэффициент расширения. Обратите внимание, что все эти коэффициенты умножаются на 10-6, что равносильно делению на миллион.
Например, предположим, что муфель длиной 20 футов из RA330, работающий при 1800 ° F:
20 футов X 12 дюймов / фут X (1800-70 ° F) X 10,0×10-6 = 240 дюймов X 1730 ° F X 10×10-6 = 4,152 дюйма.
Средний коэффициент теплового расширения
СПЛАВ | Температура, ° F | ||||||||||||||||||
200 | 300 | 400 | 500 | 600 | 700 | 800 | 900 | 1000 | 1100 | 1200 | 1300 | 1400 | 1500 | 1600 | 1700 | 1800 | 1900 | 2000 | |
304, 316 * | 8.9 | 9,2 | 9,5 | 9,7 | 9,8 | 10,0 | 10,1 | 10,2 | 10,3 | 10,4 | 10,6 | 10,7 | 10,8 | 10,8 | – | – | – | – | – |
2205 | 7,2 | 7,3 | 7,5 | 7.7 | – | – | – | – | – | – | – | – | – | – | – | – | – | – | – |
321 | 9,3 | – | 9,4 | – | 9,5 | – | 10,0 | – | 10.3 | 10,5 | 10,6 | – | 10,9 | – | 11,1 | – | 11,4 | – | – |
309 | 8,8 | 8,9 | 9,0 | 9,2 | 9,3 | 9,4 | – | – | 9,7 | – | – | – | – | 10.0 | 10,1 | – | – | – | – |
310 | 8,4 | 8,6 | 8,8 | – | 8,95 | – | 9,2 | – | 9,5 | – | 9,8 | – | 10,05 | – | 10,15 | – | 10.3 | – | 10,6 |
Углеродистая сталь * | 6,7 | 6,9 | 7,1 | 7,3 | 7,4 | 7,6 | 7,8 | 7,9 | 8,1 | 8,2 | 8,3 | 8,4 | – | – | – | – | – | – | – |
RA 253 MA® | 9.06 | – | 9,34 | – | 9,59 | – | 9,81 | – | 9,97 | – | 10,14 | – | 10,3 | – | 10,5 | – | 10,8 | – | – |
410 | 5,5 | – | – | – | – | – | – | – | – | – | 6.5 | – | – | – | – | – | – | – | – |
RA330® | 8,3 | 8,4 | 8,6 | 8,7 | 8,9 | 9,0 | – | 9,2 | 9,3 | 9,4 | 9,6 | – | – | 9,7 | 9.8 | 9,9 | 10,0 | – | – |
HR-120 ™ | 7,95 | – | 8,29 | – | 8,56 | – | 8,80 | – | 8,98 | – | 9,24 | – | 9,52 | – | 9,72 | – | 9,84 | – | – |
353 MA® | 8.48 | – | 8,68 | – | 8,88 | – | 9,07 | – | 9,27 | – | 9,46 | – | 9,66 | – | 9,86 | – | 10,05 | – | – |
800H / AT | 7,9 | – | 8,8 | – | 9.0 | – | 9,2 | – | 9,4 | – | 9,6 | – | 9,9 | – | 10,2 | – | – | – | – |
446 | 5,6 | – | 5,7 | 5,8 | – | 5,9 | 6.0 | – | 6.1 | – | 6,3 | – | 6,4 | – | 6,7 | 6,9 | 7,3 | – | – |
600 | 7,4 | – | 7,7 | – | 7,9 | – | 8,1 | – | 8,4 | – | 8,6 | – | 8.9 | – | 9,1 | – | 9,3 | – | – |
601 | 7,6 | – | 8,01 | – | 8,11 | – | 8,3 | – | 8,5 | – | 8,87 | – | 9,19 | – | 9,51 | – | 9.82 | – | 10,18 |
RA 602 CA® | 6,6 | – | 7,5 | – | 7,8 | – | 8,1 | – | 8,2 | – | 8,5 | – | 9,0 | – | 9,5 | – | 9,7 | – | 9,8 |
RA333® | 7.0 | – | – | 8,0 | – | – | – | – | 8,6 | – | 9,0 | – | 9,3 | 9,3 | 9,4 | 9,5 | 9,7 | – | – |
HH | – | – | – | – | – | – | – | – | 9.5 | – | 9,7 | – | 9,9 | – | 10,2 | – | 10,5 | – | 10,7 |
HK | – | – | – | – | – | – | – | – | 9,4 | – | 9,6 | – | 9.8 | – | 10,0 | – | 10,2 | – | 10,4 |
HT | 7,9 | – | 8,14 | – | 8,37 | – | 8,61 | – | 8,85 | – | 9,09 | – | 9,33 | – | 9,56 | – | 9.8 | – | 10,04 |
л.с. | – | – | – | – | – | – | – | – | 9,2 | – | 9,5 | – | 9,8 | – | 10,0 | – | 10,3 | – | 10,6 |
825 | 7.8 | – | 8,3 | – | 8,5 | – | 8,7 | – | 8,8 | – | 9,1 | – | 9,5 | – | 9,7 | – | – | – | – |
20Cb-3® | 8,2 | 8,3 | 8,4 | – | 8.65 | – | – | 8,9 | 8,95 | – | 9,15 | – | 9,3 | 9,4 | 9,5 | – | – | – | – |
AL-6XN® | 7,9 | 8,3 | 8,37 | 8,42 | 8,6 | 8,7 | 8,8 | 8.85 | 8,96 | – | 9,3 | – | – | – | – | – | – | – | – |
Ti Gr 2 | 4,8 | – | – | – | 5,1 | – | – | – | 5,4 | – | 5,6 | – | – | – | – | – | – | – | – |