Изготовление арболита своими руками: технология производства и самостоятельные работы
Поэтапная технология изготовления арболита предвидит подготовку основания, определения компонентов и состава блочного материала. В данной статье рассмотрим особенности производства своими руками с применением необходимого оборудования, расчета массы и заливки.
Оглавление:
- Преимущества и недостатки арболита
- Технология производства арболита
- Подготовка основания для работы
- Компоненты и состав арболита
- Процесс и принципы изготовления
- Оборудование: применение на практике
- Блочные формы для арболита
- Процесс производства своими руками
- Советы экспертов при изготовлении блоков своими руками
Преимущества и недостатки арболита
Для многих строителей арболитные блоки являются ценным и качественным материалом для возведения домов.
1. Прочность материала составляет 600-650 кг/м3, что по компонентной структуре не уступает иному строительному материалу. Главной особенностью является пластичность, что формируется в результате использования древесины, которая качественно армирует блоки. Таким образом, арболит не трескается под тяжестью иных материалов, а может только слегка деформироваться сохраняя общую систему конструкции.
2. Стойкость к низким температурам, что очень важно в процессе возведения дома и его эксплуатации. Дело в том, что если здание нагреется и замерзнет несколько раз, то это не повлияет на качество материала. Фактически дом из арболита может простоять минимум 50 лет в любые погодные условия. Конструкции из пеноблоков не имеют подобных свойств, ведь при постоянном замораживании они быстро потеряют свою функциональность.
3. Арболит не поддается воздействию углекислого газа, так что не стоит беспокоиться о карбонизации блоков, ведь их структура не позволит превратиться материалу в мел.
4. Теплопроводность блоков свидетельствует о популярности материала. Сравнивая показатели, стоит отметить, что стена из арболита в 30 см равняется 1 метру толщины кирпичной кладке. Структура материала позволяет сохранять тепло внутри помещения даже в самые холодные зимы, что весьма экономично при строительстве.
5. Звукоизоляционные свойства свидетельствуют о высоком коэффициенте поглощения арболита, который составляет от 0,7 до 0,6. Для сравнения древесина имеет показатели 0,06 -0,1, а кирпич немного больше около 0,04-0,06.
6. Легкость материала, что позволяет сэкономить средства на заливку фундамента.
7. Арболит является экологически чистым и долговечным строительным материалом, что определяет компонентный состав блоков. После возведения дома он не образует плесень и грибок на стенах.
8. Материал является безопасным, так он не воспламенятся.
9. Арболитные блоки легко применять в строительных работах, поскольку без труда в них можно забить гвозди, просверлить отверстие, использовать шурупы и так далее. Внешняя структура материала позволяет покрывать его штукатуркой без использования специальных сеток и дополнительных утеплителей.
Мы рассмотрели преимущества арболитных блоков, но для полного воссоздания картины о данном строительном материале приведем некоторые недостатки:
1. Стеновая панель может не выделяться точными геометрическими параметрами, от чего для восстановления ровности стены используют вагонку, сайдинг или гипсокартон, а сверху все отделяют штукатуркой.
2. Блоки не являются дешевым строительным материалом, ведь изготовление щепы для арболита требует некоторых затрат. Делая расчеты по сравнению из газобетоном, данный строительный материал обойдется только на 10-15 процентов дороже, что не формирует полное преимущество.
Технология производства арболита
Изготовление арболита требует следованию технологиям производства с расчетом состава и объема для одного блока. Арболитные блоки представляют собой строительный материал простой по компонентному составу, в который входят древесина, вода, опилки, цемент и другие предметы.
Главной основой для производства считается древесная щепа. Составная часть арболитового блока определяет его прочность и устойчивость к повреждениям, что высчитывается высшим уровнем, чем у пено- или газоблоков. Производство в домашних условиях осуществить не сложно, однако необходимо придерживаться распределения массы предмета и следовать инструкции.
Подготовка основания для работы
Основной составляющей для изготовления щепы для арболита является соотношение пропорций стружки и опилок – 1:2 или 1:1. Все предметы хорошо высушивают, для чего их помещают на 3 – 4 месяца на свежий воздух, время от времени обрабатывая известью и переворачивая.
Примерно на 1 кубический метр средства потребуется около 200 литров извести 15-ти процентной. В них помещают все щепы на четыре дня и перемешивают их от 2 до 4 раз на день. Все работы проводятся с целью убрать сахар с древесины, который может спровоцировать гниение блоков. Щепу приобретают в готовом виде, однако, с помощью щепорезов можно сделать самостоятельно.
Компоненты и состав арболита
Компонентный состав арболита является самым важным этапом технологии производства и требует внимательного соотношения всех материалов. При изготовлении блоков важно следить за качеством и разновидностью приобретаемых материалов, которые определяют готовый строительный материал. После процесса изготовления в щепу добавляют следующие материалы, такие как:
- известь гашеную;
- жидкое стекло растворимое;
- портландцемент;
- хлористый калий;
- алюминий и сернокислый кальций.
Производство арболита в пропорциях представлено в таблице 1. Стоит учесть, что для всех компонентов масса рассчитана на четыре процента доли цемента. Данная компоновка помогает сохранить огнеупорность предмета и придает пластичности.
Таблица 1. Состав арболита по объему
Марка арболита | Цемент (М400) | Кол-во извести | Кол-во песка | Кол-во опилок | Получаемая плотность (кг/м3) |
5 | 1 | 1,5 | — | 15 | 300-400 |
10 | 1 | 1 | 1,5 | 12 | 600-700 |
15 | 1 | 0,5 | 2,5 | 9 | 900-1000 |
25 | 1 | — | 3 | 6 | 1200-1300 |
Процесс и принципы изготовления
Оптимальные параметры блоков для технологии производства арболита составляют 25х25х50 сантиметров. Установленные размеры удобны при кладке стен домов, а также в процессе промышленности. Заливка блока состоит из трех рядов смеси и арболита, после каждого этапа необходимо уплотнять раствор молотком, отделанным жестью.
Излишняя масса свертывается при содействии шпателя. Выдерживается блок при температуре 18 градусов тепла на раскрытом воздухе. По истечении суток арболит выстукивается из формы на ровную поверхность, где он скрепляется на протяжении 10 дней.
Оборудование: применение на практике
Для производства необходимо разное снабжение, например, станки для изготовления арболита, которые выбираются в соответствии с объемом продукции и количества сырья. Технология промышленного процесса должна отвечать требованиям и критериям СН 549-82 и ГОСТу 19222-84. В качестве основного материала для выработки выступают хвойные деревья. Раздробление древесины происходит с помощью рубильных машин, таких как РРМ-5, ДУ-2, а более скрупулезное дробление осуществляется на оборудовании ДМ-1.
Арболитовую смесь подготавливают со смесителями и растворителями различного цикличного воздействия на материал. Подвозят большие объемы обработанной смеси к формам с помощью приспособления в качестве бетонораздатчиков или кюбелей. Подъем или опускание машины должно осуществляться при параметрах 15о по верхнему подъему и 10о по нижнему, а скорость оборудования рассчитывается в 1 м/с. Разлив арболитовой смеси по формам делают на высоте до 1 метра.
Уплотнения раствора производят с содействием вибропреса или ручной трамбовки. Для производства небольшого количества блоков нужно применить мини-станок. Изготовление своими руками арболита не представляет особых трудностей, однако на промышленных объектах применяется специальное оборудование по смешиванию, изготовления блоков. На некоторых заводах присутствуют тепловые камеры с ИК-излучением или ТЭНом, что позволяет определить нужную температуру для высыхания блоков.
Блочные формы для арболита
Существуют разные блочные формы для обработки арболита, а примерные величины могут составлять: 20х20х50 см или 30х20х50 см.
В зависимости от класса арболитовые блоки применяют в малоэтажном строительстве для возведения несущих стен, перегородок, а также для теплоизоляциии и звукоизоляции конструктивных элементов здания.
Процесс производства своими руками
Рассмотрев технологию изготовления состава арболита, можно приступать к выполнению работы самостоятельно. Для начала потребуются некоторые материалы и оборудование:
- специальный лоток для смеси;
- падающий и вибрирующий стол;
- стол с ударно-встряхивающим эффектом;
- разъемные формы и подставки;
- поддон из металла для форм.
Производить арболит своими руками очень сложно без использования необходимых инструментов, станков и оборудования. Как правило, на производстве потребуются некоторые приспособления:
1. Для получения качественного раствора необходимо применить бетономешалку. Разумеется, в процессе можно все сделать своими руками, однако придется, много времени потратить на получение раствора необходимой консистенции.
2. Для формирования структуры блоков важно приобрести формы соответствующих размеров. Как правило, арболит имеет прямоугольную форму, а в производстве используются пластиковые формы.
3. При помощи станка вы профессионально измельчите щепу.
4. Используя пресс можно получить хорошую плотность материала при трамбовке, при этом важно убрать воздух из консистенции. В качестве приспособлений применяется вибростол.
5. Обязательное наличие камеры для сушки арболита, что позволит его превратить в твердую однокомпонентную структуру.
6. В домашних условиях понадобится лопата для загрузки смеси в формы, а для скрепления блоков используют армирующую сетку.
При наличии выше перечисленных приспособлений можно производить в день около 350 – 450 м3 строительного раствора в месяц. Места для монтажа потребуется около 500 квадратных метров, а затрат на электроэнергию пойдет 15-45 кВт/ч. Для самостоятельного процесса органические средства заливаются водой, а также цементом до образования однородной смеси. Все пропорции и расчеты отображены в таблице 1, главное чтобы вышедшая смесь была сыпучей.
Перед заливкой раствора в формы, их обмазывают с внутренней стороны молочком известковым. После этого, средство скрупулезно и аккуратно укладывают и утрамбовывают специальными приспособлениями. Верхняя часть блока выравнивается с помощью шпателя или линейки и заливается раствором штукатурки на слой в 2 сантиметра.
После образованной формы арболита его потребуется тщательно уплотнить с помощью деревянной конструкции, оббитой железом. Прочными и надежными считаются блоки, которые выстоялись и схватились на протяжении десяти дней при температуре 15о. Чтобы арболит не пересох, рекомендуется периодически поливать его водой.
Технология изготовления арболита своими руками не представляет определенной сложности, а поэтому все работы провести легко при наличии необходимых инструментов и приспособлений. При соблюдении правил и критериев производства, правильного расчета компонентов строительный материал получится качественным и прочным для применения.
Советы экспертов при изготовлении блоков своими руками
Рекомендации специалистов по производству арболитных блоков основаны на практике их использования и применения. Чтобы достичь высокого качества продукции необходимо следовать некоторым факторам. В производстве рекомендуется применять не только большую щепу, но и использовать опилки, стружку из дерева. Обработка консистенции и выдавливание из него сахара позволяет избежать дальнейшего вспучивания строительного материала, что не приспускается при сооружении дома.
В процессе изготовления раствор следует тщательно перемешивать, чтобы все части оказались в цементе. Это важно для качественного и прочного скрепления древесины и иных материалов в блоке. В производстве не менее важным остается добавление следующих компонентов, таких как алюминий, гашеная известь и так далее. Весь состав образует дополнительные свойства арболита, например жидкое стекло не позволяет впитывать влагу блокам, а известь служит в качестве антисептика.
Хлористый калий способствует уничтожению микроорганизмов и других веществ, что не благотворно влияют на структуру. При добавлении всех компонентов стоит следить за таблицей пропорциональности, чтобы готовый раствор соответствовал требованиям производства арболитных блоков.
Завод, производитель арболита в Новосибирске
Производство арболита в Новосибирске — «Сибирский Арболит».
Арболит завод в Новосибирске на протяжении многих лет специализируется на производстве и продаже арболитовых блоков высшего качества, а также разработке технологий для реализации проектов строительства домов из арболита.
Современное производство арболита в Новосибирске.
Производители арболита для создания строительной продукции в блоках используют натуральный материал из хвойных пород древесины, цемент высшей категории и химические добавки, придающие готовому материалу уникальные функциональные свойства. Производство арболита в Новосибирске рассчитано на различные категории клиентов: частные и физические лица, строительные компании и организации по продаже стройматериалов.Изготовление арболита по всем стандартам позволяет создать стройматериалы для возведения несущих стен, любых перегородок, а также с целью максимальной звукоизоляции и теплоизоляции. Арболит имеет максимальный класс огнестойкости и устойчивости к влиянию биологических факторов: размножению грибков, микроорганизмов и плесени. Благодаря таким качествам арболитовые блоки соответствуют стандартам экологичного строительства.
Где заказать арболитовые блоки?
Прежде чем оформить крупный заказ на поставки строительных блоков из арболита, стоит подробнее узнать, сколько стоит арболитовый блок в Новосибирске. Ознакомиться с ценами можно на страницах сайта, где представлены все виды блоков в различных размерах и конфигурациях. Арболитовые блоки отзывы владельцев получают исключительно положительные не только благодаря высокому качеству стройматериалов, но и по причине отличного сервиса компании:- Наличие собственного мощного производства основных компонентов, а также арболитовых блоков;
- Идеальная геометрия блоков всех размеров;
- Закупки цемента у престижных производителей;
- Строгий контроль всей продукции на соответствие государственным стандартам, наличие сертификатов качества;
- Гарантийные обязательства на все виды продукции.
Производство арболитовых блоков в Новосибирске предлагает не только жителям Новосибирска, но и обитателям всей страны заказать блоки из арболита по выгодной цене.

Читать далее
Технология изготовления арболита блоки
Основой получения качественного арболита является прочное соединение древесной щепы с цементом. Водорастворимые вещества, имеющиеся в древесине, играют отрицательную роль в этом процессе, тормозят твердение цемента и препятствуют прочному соединению цемента с древесной стружкой.
Поэтому древесную щепу перед смешиванием с цементом необходимо освободить от водорастворимых веществ или нейтрализовать их путем химической обработки. Наиболее распространенным химикатом, применяемым для этих целей, является хлористый кальций (плавленый), отвечающий требованиям ГОСТ 450—58. При отсутствии хлористого кальция применяется жидкое стекло, отвечающее требованиям ГОСТ 962—41. Приготовление концентрированного раствора из плавленого хлористого кальция производится в деревянных чанах с перемешивающим устройством при температуре воды 70—80° С. На 1 м3 арболита (плотной массы) расходуется до 8 кг хлористого кальция или 4 кг жидкого стекла с удельным весом 1,5.
Древесная щепа должна быть по возможности однородной по размерам и конфигурации и иметь длину (вдоль волокон) 15—20, толщину 2—3 и ширину 10—12 мм. Приготовление щепы, идущей на изготовление изделий из арболита, производится на рубительных машинах дисковой или другой конструкции, применяемых в целлюлозно-бумажной промышленности или в лесопильной промышленности для дробления отходов. Щепа сортируется на плоских или барабанных сортировках, при этом удаляются вся мелочь и пыль.
После сортировки щепа подвергается обработке (минерализации) 5%-ным раствором хлористого кальция или жидкого стекла при помощи механизмов окунанием щепы в раствор или же обрызгиванием. Расход хлористого кальция — 0,1—0,12 кг сухого вещества на 1 кг щепы. Длительность обработки минерализатором зависит от породы древесины, влажности и других факторов и определяется в каждом отдельном случае опытным путем. При организации пропитки следует предусмотреть возможность повторного использования раствора, стекающего со щепы. Пропитывание щепы раствором считается законченным, как только щепа оказывается равномерно смоченной, на что требуется 2—3 мин. Общее время смачивания и перемешивания составляет от 8 до 12 мин. Механизмами для минерализации щепы могут служить сетчатые транспортеры, мешалки и чаны, если операция производится по способу окунания.
Минерализованная щепа смешивается с портландцементом марки 400 при расходе последнего от 300 до 400 кг на 1 м3 изделий (плотной массы). Дозировка цемента производится по весу и устанавливается опытным путем в зависимости от требований, предъявляемых к физико-механическим свойствам изделий из арболита, и его объемного веса. Смешивание щепы с цементом продолжается 2—3 мин и заканчивается после того, как вся стружка оказывается покрытой цементом, что распознается по однородному серому цвету смеси.
Количество цемента, которое необходимо добавлять во время смешивания, определяется экспериментальным путем. Необходимо следить, чтобы смесь была достаточно смочена и представляла собой мягкую и пластичную массу. В жаркое время массу приготавливают с несколько большим содержанием воды, чем обычно, для компенсации потери воды во время формирования. В среднем на 1 м3 арболита расходуется до 265 л воды, включая и воду химического раствора.
При изготовлении стеновых блоков желательно в массу добавить 10—12% дробленого сланца, что придает массе пластичность и способствует более легкому освобождению изделий из формы.
Формование арболита производится путем заполнения специальных металлических форм на станках, применяемых при изготовлении подобных изделий из бетона, глины и других материалов. Для изготовления стеновых блоков можно приспособить станок, которым пользуются при производстве шлакобетонных камней; для изготовления плитных материалов — прессы, применяемые для изготовления фибролитовых плит, и др.
При ручной работе сначала производится частичное заполнение форм с последующей утрамбовкой краев железным инструментом для получения правильных и прочных граней. Сжатие материала при его нормальном качестве составляет 20%. Эту усадку необходимо учитывать при конструировании и определении размеров форм. Хорошие результаты формования дает также вибрирование, особенно при применении высоких форм.
Изделия из арболита после их формования подвергаются искусственному твердению в специальных камерах при температуре 35° С. Время выдержки —от 12 до 24 ч. При производстве фибролита выявлено, что режим искусственного твердения для цемента разных марок неодинаков и существенно отражается на прочности и качестве плит. Поэтому при организации производства арболита режимы твердения плит в каждом отдельном случае должны устанавливаться опытным путем.
Камеры твердения, в которых происходит термическая обработка изделий, оборудуются продольными и поперечными траверсными узкоколейными путями и механическим устройством для передвижения тележек во время загрузки и разгрузки камер.
Распалубка форм производится в зависимости от конфигурации и размеров изделий вручную или при помощи тельферов.
После выдержки в камерах твердения изделия на тележках по узкоколейным путям направляются в сушильные камеры. Время сушки —от 24 до 30 ч при температуре 60—65° С. Готовые изделия после сушки зачищают от возможных заусенцев и подают на склад готовой продукции, где их укладывают и хранят в штабелях высотой до 2 м.
Технология изготовления арболита. Арболит: технология производства, состав
Производство строительных материалов на сегодняшний день — довольно прибыльная отрасль. Обусловлено это высоким спросом на все, что связано с возведением зданий. Все застройщики стараются применять и проверенные материалы и внедрять новые технологии, которые будут менее затратными в себестоимости и более практичными в применении.
Несмотря на огромный ассортимент строительных блоков, огромной популярностью стал пользоваться и арболит. Технология производства его зависит от того, в каких условиях он изготавливается. Сам материал обладает отличными эксплуатационными свойствами и характеристиками.
Что такое арболит?
Это строительный материал, который выпускается в виде блоков. Они имеют определенные размеры и состав. Благодаря тому, что в его производстве используется натуральное сырье, он обладает отличными техническими характеристиками.
Способы производства арболитовых блоков
Технология изготовления арболита может быть применена:
- в заводском производстве;
- при домашнем изготовлении.
Сырье для производства арболита
Технология изготовления арболита характеризуется применением определенных материалов:
- бетон марки 400 или 500;
- химическая добавка;
- органический заполнитель.
Есть некоторые рекомендации по выбору сырья. Например, бетон нужно покупать тот, который изготавливается на основе вяжущего вещества. Также можно применять бетон более высокой прочности. В качестве химической добавки используют жидкое стекло, хлорид или нитрат кальция. Органические наполнители: древесная стружка, дробленые стебли хлопчатника, дробленая рисовая соломка и многое другое.
Арболит, технология производства которого отличается применением определенных средств, может иметь различный удельный вес. Например, блоки, имеющие плотность менее 500 кг/м3 относят к группе теплоизоляционного арболита. А те, которые имеют плотность более 500 кг/м3, принадлежат уже к группе конструкционных блоков.
Соответственно, первый вариант арболита наиболее часто используется для сооружения межкомнатных перегородок, а вот из второго выстраиваются несущие арболитовые конструкции.
Стадии изготовления материала
Технология изготовления арболита состоит из нескольких этапов:
- подготовка определенного количества органического заполнителя;
- работа по замачиванию древесной щепы в растворе хлорида кальция;
- дозирование определенных составляющих арболита;
- непосредственно изготовление блоков.
Подготовка органического заполнителя
Любое производство строительных материалов характеризуется предварительной подготовкой всего необходимого сырья. Древесина в брусках измельчается и формируется в определенные кучки. Их надо положить под навес и выдержать при оптимальной наружной температуре +15…+25 градусов около 1 месяца. После этого древесина измельчается в специальном оборудовании на щепку.
Только к такому действию нужно подходить ответственно. Щепа имеет свою определенную фракцию. Именно от нее зависит качество арболитовой смеси. Щепка размером в 10-20 мм характеризует фракционный состав в 70%, 5-10 мм уже относят к 30% фракции.
Замачивание древесины и приготовления раствора хлорида кальция
Полученную в ходе дробления щепку необходимо замочить в воде. Температура жидкости при этом должна быть не менее +20 градусов. Весь процесс замачивания длится до 6 часов. Все эти действия помогают увеличить прочность арболитовых блоков. Необходимо постоянно следить за наполняемостью древесины водой. Влажность полученного сырья должна быть не более 30%.
По истечении этого времени в бак с жидкостью выливается заранее приготовленный раствор хлорида кальция. В эту же емкость отправляется и пенообразователь.
Дозирование составляющих будущего строительного материала
Важный этап, которым обладает технология изготовления арболита, является правильное дозирование всех компонентов. Именно от этого зависит качество арболитовых блоков и его показатель прочности. Дозировка дробленой замоченной щепки должна учитывать влажность сырья. Все ингредиенты взвешиваются и дозируются согласно определенным установленным параметрам (ГОСТ). Можно использовать для этого процесса специальное оборудование. Нужно учитывать, что оно достаточно дорого, и в условиях некоммерческого производства покупать его нецелесообразно.
Процесс изготовления блоков
Необходимо подготовить специализированное оборудование для арболита. К нему на этапе смешивания ингредиентов относят бетономешалки и другие приспособления, которые могут качественно перемешивать смеси высокой плотности и доводить их до определенной консистенции.
Большую роль играет очередность закладки составляющих. Изначально засыпается подготовленная древесная щепка. Затем – цемент. После этого заливается вода и химические наполнители. Они могут меняться местами в производстве. Кому как будет удобно. Только подачу всех жидкостей стоит пропускать через специальный расходомер.
Далее происходит смешивание сырья. Мешать нужно до тех пор, пока смесь не станет однородной.
Необходимо заранее изготовить формы для блоков. Как правило, они деревянные, а размеры могут быть любыми. Внутри нее по всему периметру выкладывается линолеум. Он даст возможность после застывания смеси свободно вытащить блок из формы. Также его поверхность промазывается специальным средством.
Довольно часто в домашних условиях изготовления арболитовых блоков применяется вибростол. Он позволяет равномерно распределить смесь. После этого залитые составом формы выставляются под навес и находятся там до полного застывания. В некоторых случаях применяют определенные добавки, которые помогают сократить время отвердения цементного состава.
Строительство из арболита, который сделан в домашних условиях, может проводиться только по истечении определенного срока, обычно через 14-20 дней. За это время блоки полностью отвердеют, высохнут и будут готовы к кладке.
Арболитовые блоки от производителя | Производство арболита в Смоленске
Внимание!
Принимаем заказы на изготовление блоков на строительный сезон 2021-2022 года.
Производство высококачественного арболита осуществляется по ГОСТ-19222-84. Наша
компания выпускает арболитовые блоки в Смоленске, которые полностью отвечают всем требованиям, что подтверждается сертификатом соответствия. Блоки изготавливаются в металлических формах, смазанных изнутри специальной жидкостью для железных опалубок! Называется эта жидкость «эмульсол». Залитая в формы древесно-цементная смесь утрамбовывается вибропрессом и выстаивается 24 часа в тёплом помещении. В первые сутки полуфабрикат теряет до 40% влаги. После выемки из формы блоки просушиваются ещё 26 суток при температуре выше +10°C и достигают прочности 96%.
Для производства качественных строительных блоков большое значение имеет размер древесной щепы. Оптимальная фракция: длина 30-60 мм, ширина 2-10 мм, толщина 1-5 мм. Добавление опилок, соломы, прочих растительных отходов и сторонних включений недопустимо. В нашем составе наших блоков отсутствует кора.
Древесные волокна содержат сахара и смолы, мешающие пропитке наполнителя водным раствором цемента. Для их нейтрализации сухая щепа предварительно минерализуется несколькими химическими соединениями. Компания «АрболитСтройСмоленск» использует для этих целей сернокислый алюминий, который спустя некоторое время разлагается на экологически безопасные составляющие. Подготовленный таким образом наполнитель обладает максимальной адгезией и плотно сливается с жидкой бетонной массой.
Арболитовые блоки называют древобетонными, потому что щепа в них составляет 80-90% от общего объёма. В связи с этим среди потребителей, не уделивших достаточно внимания изучению характеристик и свойств арболита, сложилось необъективное, а порой и предвзятое отношение к нему. Компания «АрболитСтройСмоленск», как производитель качественных арболитовых блоков, считает необходимым развеять все мифы, окружающие этот перспективный строительный материал.
Юрий Смоленский
Исследователи Purdue показывают, что бетон, пропитанный нанокристаллами дерева, прочнее, планируют использовать его на мосту в Калифорнии
ВЕСТ-ЛАФЕЙЕТ, штат Индиана — Исследователи из Университета Пердью, изучающие, стал ли бетон более прочным за счет введения в него нанокристаллов микроскопических размеров из дерева, перемещаются из лаборатории в реальный мир с помощью моста, который будет построен в Калифорнии этой весной.
Исследователи работали с нанокристаллами целлюлозы, побочными продуктами, производимыми в бумажной, биоэнергетической, сельскохозяйственной и целлюлозно-бумажной отраслях, чтобы найти лучшую смесь для укрепления бетона, самого распространенного в мире искусственного материала.
«Я думаю, что просто добраться туда, где люди могут на нем ездить, — это огромный шаг, потому что на данный момент нельзя просто сказать, что это лабораторное любопытство. Это имеет значение для реального мира », — сказал Джеффри Янгблад, профессор материаловедения Purdue.
Укрепление бетона может иметь другие последствия, например, сделать изделия из бетона более тонкими и легкими, сохраняя при этом ту же прочность, с потенциальным побочным эффектом уменьшения выбросов углекислого газа в атмосферу.На цементные заводы приходится около 8 процентов глобальных выбросов углекислого газа, основной причины изменения климата.
Катализатором этого потенциально преобразующего изменения является нанокристалл целлюлозы длиной около 100 нанометров и шириной 5 нанометров, который слишком мал, чтобы его можно было увидеть в обычный микроскоп. Увидеть это можно только с помощью электронного микроскопа. Для сравнения: человеческий волос имеет ширину около 100 000 нанометров. Тем не менее, целлюлоза является наиболее распространенным полимером в мире, поскольку ее можно получить из изделий из древесины, растений, бактерий и водорослей.
Этот просвечивающий электронный микроскоп показывает нанокристаллы целлюлозы, крошечные структуры, полученные из возобновляемых источников, которые могут быть использованы для создания нового класса биоматериалов с множеством потенциальных применений.
Нанокристаллы целлюлозы делают бетон более прочным за счет химической реакции, которая увеличивает гидратацию частиц цемента, делая бетон более прочным, говорят исследователи.«Прочность бетона зависит от степени гидратации. Так что чем больше он гидратирован, тем он сильнее », — сказал Янгблад. «Значит, можно подумать, если добавить больше воды, она будет сильнее. Проблема в том, что вода добавляет поры, которые делают их более слабыми. Но нанокристаллы целлюлозы улучшают гидратацию с меньшим количеством воды, делая бетон более прочным ».
Пабло Заваттьери, профессор Школы гражданского строительства Лайлса, сказал, что нанокристаллы целлюлозы предоставляют воде путь туда, где она необходима.Не все частицы цемента гидратируются при смешивании бетона, что снижает прочность и долговечность бетона.
«Нанокристаллы целлюлозы хороши тем, что они создают барьер, по которому вода попадает в частицы, — сказал Заваттьери.
Джейсон Вайс, профессор Майлза Лоуэлла и Маргарет Уотт Эдвардс, выдающийся заведующий кафедрой инженерии в Университете штата Орегон, который ранее был профессором Purdue, сказал, что нанокристаллы целлюлозы делают бетон более эффективным, поскольку для создания чего-то столь же прочного требуется меньшая масса.
«Так это может быть более экологичным и эффективным», — сказал он.
Youngblood сказал, что еще одним преимуществом является то, что бетон, пропитанный целлюлозой, схватывается быстрее, а это означает, что меньше времени нужно ждать, пока бетон застынет при использовании форм для строительства мостов или при бурении нефтяных скважин.
«Потому что каждый день, когда бригада не качает нефть, — это день потери денег», — сказал Янгблад. На этой фотографии показаны образцы цемента, залитые эпоксидной смолой, готовые для микроскопического анализа. Исследователи из Университета Пердью работают над поиском наилучшего соотношения смешивания нанокристаллов целлюлозы с цементом, чтобы сделать его более прочным.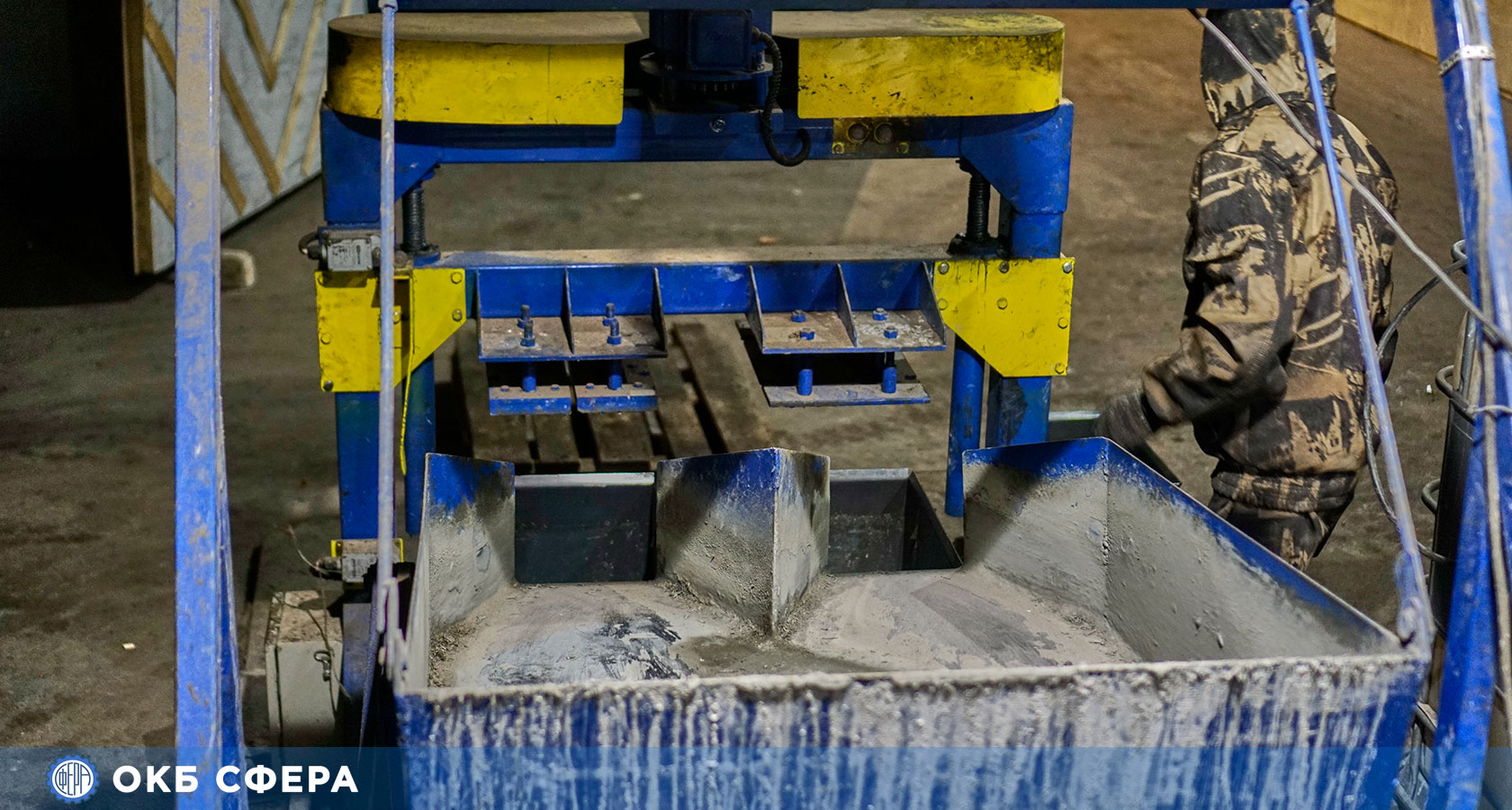
Исследователи говорят, что стоимость использования нанокристаллов целлюлозы может быть компенсирована за счет возможности использовать меньше цемента, но точная стоимость еще не определена. Они говорят, что решающим фактором будет то, насколько широко используются нанокристаллы целлюлозы. Но даже если бы только небольшой процент всего производимого бетона использовал нанокристаллы целлюлозы, это оказало бы большое влияние только потому, что бетон используется повсеместно.
Исследователи говорят, что работа по масштабированию до бетона и подготовка моста в Калифорнии — это сотрудничество между Purdue, Государственным университетом Орегона, P3Nano и другими.P3Nano — это государственно-частное партнерство, направленное на поддержку коммерциализации целлюлозных наноматериалов. P3Nano принимает активное участие в полномасштабных испытаниях и является спонсором проекта в Университете штата Орегон по демонстрации полномасштабного применения нанокристаллов целлюлозы в мостах и плоских плитах. Точный мост в Калифорнии, где будет использоваться бетон, наполненный целлюлозой, еще не определен.
Исследователи Purdue начали изучать целлюлозу десять лет назад в сотрудничестве с Робертом Муном, исследователем из США.Лаборатория лесных товаров S. Forest Service, которая в то время базировалась в Purdue. Лесная служба искала способы использования больных, поврежденных бревен и бревен небольшого диаметра, которых в лесах много.
Youngblood, который работает в основном с пластмассами, сказал, что изначально проблема заключалась в том, чтобы определить, где можно использовать водорастворимые нанокристаллы целлюлозы. Идея использовать его в бетоне пришла ему в голову, когда он копал яму для столба и готовил бетон. Вот где начались исследования.
Янгблад сказал, что исследователи быстро обнаружили, что нанокристаллы целлюлозы делают бетон более прочным, но они не знали почему.
«Я пошел в офис Джейсона Вайса и показал ему данные, и он сказал, что они не должны работать, потому что нанокристаллы целлюлозы слишком малы. Именно тогда мы поняли, что у нас что-то есть, потому что если что-то, основанное на том, как все обычно работает, на теориях или чем-то еще, не должно работать, а оно работает, именно тогда вы обычно находите что-то важное », — сказал Янгблад. «Вот так все и началось».
Исследование частично финансировалось Национальным научным фондом.Вайс сказал, что работа NSF привела к созданию паст, которые были протестированы, что помогло исследователям понять, что нанокристаллы целлюлозы не действуют как обычные волокна, а, скорее, изменяют микроструктуру.
Блейн Канкель, генеральный директор Nano-Green Biorefineries Inc., имеющей лицензионное соглашение с Управлением коммерциализации технологий Purdue Research Foundation на коммерциализацию технологии, сказал, что компания воодушевлена потенциалом нанокристаллов целлюлозы.
«Мы рассматриваем это как трансформационную технологию», — сказал он.
Об управлении коммерциализации технологий Purdue
Управление коммерциализации технологий Purdue управляет одной из самых всеобъемлющих программ передачи технологий среди ведущих исследовательских университетов США. Услуги, предоставляемые этим офисом, поддерживают инициативы экономического развития Университета Пердью и способствуют академической деятельности университета. Офис управляется Исследовательским фондом Purdue, получившим в 2016 году премию университетов за инновации и экономическое процветание от Ассоциации государственных университетов и университетов, получивших земельные гранты.Для получения дополнительной информации о возможностях финансирования и инвестирования в стартапы, основанные на инновациях Purdue, свяжитесь с Purdue Foundry по адресу [email protected]. Для получения дополнительной информации о лицензировании инновации Purdue обращайтесь в Управление коммерциализации технологий по адресу [email protected].
Purdue Research Foundation Контактное лицо: Том Койн, 765-588-1044 , [email protected]
Источники: Джеффри Янгблад, [email protected]
Пабло Заваттьери, zavattie @ purdue.edu
Джейсон Вайс, Jason.Weiss@oregonstate. edu
Бетон должен избавиться от колоссального углеродного следа
На производство цемента (например, на этом заводе в России) приходится 8% мировых выбросов диоксида углерода Фото: Getty
Мокрый бетон заливали здания, дороги, мосты и многое другое на протяжении веков. Конструкции из бетона пережили войны и стихийные бедствия, пережив многие цивилизации, построившие их 1 .Помимо прочности и устойчивости, бетон также является основным элементом строительства, поскольку он относительно дешев и прост в изготовлении. Ежегодно во всем мире используется 30 миллиардов тонн бетона. В расчете на душу населения это в 3 раза больше, чем 40 лет назад, а спрос на бетон растет быстрее, чем спрос на сталь или дерево 2 .
Универсальные и долговечные бетонные здания и сооружения во многих отношениях идеально подходят для строительства, устойчивого к климатическим воздействиям. Но бетон имеет колоссальный углеродный след — не менее 8% глобальных выбросов, вызываемых людьми, приходится на только цементную промышленность 3 .Мы должны обезуглероживать его производство.
Бетон получают путем добавления в цемент песка и гравия, взбивания смеси с водой и заливки ее в формы до высыхания. Изготовление цемента — наиболее углеродоемкая часть: оно включает использование ископаемого топлива для нагрева смеси известняка и глины до температуры более 1400 ° C в печи. Кроме того, когда известняк (карбонат кальция) нагревается с помощью глин, на каждую тонну произведенного цемента выделяется примерно 600 кг углекислого газа (см. Природу.com / 3exhg82).
Существуют альтернативы цементу, но они находятся на ранней стадии разработки, а сам цемент остается высокорентабельным — два сдерживающих фактора для компаний к изменениям.
Альтернативы включают остатки соединений от производства чугуна и стали, известные как шлак, и груды неиспользованной летучей золы, остаточного материала угольных электростанций. Исследователи также экспериментируют с понижением температуры, необходимой в процессе производства цемента, тем самым уменьшая потребление энергии.
С точки зрения учета выбросов углерода, такие замены и изменения в процедурах уменьшат воздействие цемента на окружающую среду, а также воздействие бетона. Но они по-прежнему связаны с выбросами углерода. Уголь постепенно сокращается, поэтому летучая зола не является долгосрочным решением. А альтернативы еще не сертифицированы для использования в строительстве; для этого необходимы долгосрочные исследования их эффективности.
Цемент появится в обозримом будущем, поэтому само производство цемента должно быть обезуглерожено, что может произойти по-разному.Например, низкоуглеродное топливо, такое как водород или биомасса, можно заменить ископаемым топливом при нагревании известняка и глины. И ученые изучают, можно ли использовать электричество вместо сжигания для отопления.
Улавливание углерода может быть частью переходного процесса в цементной промышленности 4 . В Швеции, например, в июле компания объявила, что хочет уловить 1,8 миллиона тонн CO 2 с цементного завода и закопать его в Северном море.Другая возможность — закачать захваченный CO 2 в сам бетон, навсегда заблокировав его, что также может улучшить свойства получаемого материала. Впрыскиваемый CO 2 вступает в реакцию с ионами кальция в цементе, производя больше карбоната кальция и потенциально делая бетон способным выдерживать большие нагрузки.
Технологические изменения могут быть ускорены за счет регулирования и законодательства. Огромная доля бетона используется в проектах общественных зданий.Только в Северной Америке государственные агентства закупают до трети производимого бетона ежегодно. Это означает, что у них есть рычаги воздействия на переход к низкоуглеродным технологиям: они могут работать с исследователями и производителями, чтобы изменить бетонную промышленность.
В Нью-Йорке и Нью-Джерси законодательные органы штатов проходят рассмотрение законопроектом, который, в случае его принятия, обяжет агентства и департаменты штата отдавать приоритет цементу с меньшим углеродным следом.
Другие штаты вводят законодательство, требующее, чтобы в предложениях по строительству декларировалось воздействие цементных смесей на окружающую среду.Некоторые регионы, такие как Гонолулу, Гавайи, добавили требование, согласно которому в городских строительных проектах необходимо учитывать использование бетона, в котором хранится CO 2 .
В Европе Рамочная директива Европейского Союза по отходам требует повторного использования 70% строительных отходов. Другая идея, известная как паспорта материалов, также может помочь. При сносе зданий бетонные отходы разбиваются и выбрасываются или продаются для низкосортного использования, например, для засыпки при строительстве дорог. Но паспорт обеспечит регистрацию бетона «при рождении», а затем отслеживание его жизненного цикла, что сделает его доступным для большего количества видов повторного использования.
Наконец, цементной промышленности необходимо публиковать более точные данные о выбросах, чтобы можно было отслеживать прогресс. В исследовании, опубликованном в прошлом месяце, исследователи из Колумбийского университета в Нью-Йорке сообщают, что некоторые китайские цементные компании стремятся достичь пика выбросов в 2023 году (см. Go.nature.com/39z1sdd). Но только одна из десяти опрошенных компаний представляет данные о выбросах. Китай является крупнейшим производителем цемента в мире (55% мировых мощностей), и на цемент приходится 15% выбросов углерода в стране.Без данных невозможно будет узнать, достигаются ли национальные цели.
В следующем месяце в рамках кампании цементной промышленности под названием «Конкретные действия в интересах климата» будет объявлена дорожная карта по обеспечению углеродной нейтральности к 2050 году. Это просрочено, но дорожная карта также должна объяснять промежуточные шаги, как компании намерены достичь нейтральности и как будет прогресс быть измеренным.
Части древнего мира были сделаны из бетона, и этот материал также использовался для строительства большей части современного мира. Исследователи и правительства должны работать с цементной промышленностью, чтобы сократить ее углеродный след, способствуя созданию экологически безопасного строительства, в котором сейчас остро нуждается мир.
по уровню шума полов поднимает еще один красный флаг, связанный с деревянными конструкциями — бетонные изделия
Новый стандарт ASTM E3207-21 предоставит пользователям официальные рейтинги для шума шагов арендатора или жильца — одного из самых распространенных неудобств многоуровневых деревянных зданий.Новый стандарт Международного комитета ASTM E33 по строительной и экологической акустике устанавливает метрику оценки низкочастотного ударного шума, особенно ударов от шагов, типичных для многоуровневых зданий, построенных из материалов, отличных от монолитного или сборного железобетона. .
«Находясь внутри деревянного каркаса или другого легкого здания, можно услышать тяжелые шаги других людей, которые обычно описываются как глухие удары», — говорит Саманта Роулингс, заместитель директора в Санта-Монике, Калифорния, консультант по акустике Veneklasen Associates and Technical по акустике. свяжитесь с нами, чтобы узнать о новом стандарте ASTM E3207-21, Стандартная классификация для определения характеристик низкочастотного ударного шума. «Использование этого стандарта открывает возможности для проектирования, которых не было более 60 лет, когда проводилась оценка ударного шума от шагов в зданиях.”
E3207 может использоваться вместе с данными, полученными из ASTM E3222-20a, Стандартная классификация для определения характеристик высокочастотного ударного шума. Классификации помогут заинтересованным сторонам на протяжении всей цепочки создания стоимости проекта, от разработчиков, инженеров, архитекторов и подрядчиков до лабораторий, регулирующих органов и субъектов устойчивой рейтинговой системы. Всемирная организация здравоохранения считает, что чрезмерный шум в жилых домах оказывает негативное воздействие. E3207 способствует укреплению общественного здоровья, предоставляя проектировщикам зданий дополнительные инструменты для создания тихой жизни, которая принесет пользу сообществам во всем мире.
ГОСУДАРСТВЕННЫЙ ВЕРХОВНЫЙ СУД ПОДДЕРЖИВАЕТ ЗАЩИТУ ПОДРЯДЧИКА «ДЕФЕКТНЫЙ ДИЗАЙН»
Американская ассоциация Surety & Fidelity (Surety & Fidelity Association) (SFAA) одобряет решение Верховного суда штата Вашингтон отменить решение суда низшей инстанции по делу Lake Hills Investments против Rushforth Construction Co. за ущерб, причиненный дефектной конструкцией, предоставленной владельцем, даже если подрядчик несет ответственность за определенные дефектные работы.Кроме того, подрядчику не запрещается полностью отстаивать эту защиту, если дефекты были вызваны сочетанием ненадлежащих характеристик подрядчика и несовершенного проекта, и должна быть определена пропорциональная ответственность.
Присоединившись к отделению Пьюджет Саунд Национальной ассоциации электротехнических подрядчиков, Ассоциации механических подрядчиков Западного Вашингтона и SMACNA — Западный Вашингтон, SFAA выпустило Amici Curiae в поддержку заявителя AP Rushforth Construction Co., Inc. d / b / a AP Rushforth и Adolfson & Peterson, Inc. (совместно именуемые AP) о дискреционном пересмотре. В кратком изложении они утверждали, что Суд должен удовлетворить ходатайство, потому что решение суда низшей инстанции противоречит прецеденту ограничения ответственности подрядчика, когда дефектные планы и спецификации владельца привели к дефектной работе и нарушают устоявшиеся ожидания распределения риска и ответственности между подрядчики, собственники и архитекторы на строительных объектах. Распределение рисков и принцип ограничения ответственности подрядчика за некорректную работу на основе дефектных планов и спецификаций — давно устоявшаяся доктрина в штате Вашингтон и по всей стране, отражая U.Официальные лица SFAA отмечают, что более 100 лет назад Верховный суд США принял историческое решение по делу США и Спирин.
«Мы смогли работать с нашими партнерами из строительной отрасли в поддержку их усилий, демонстрирующих судам, почему было уместно оставить это устоявшееся распределение рисков без изменений», — говорит вице-президент SFAA по политике и главный юрисконсульт Джули Аллейн. «Решение суда — это здравый смысл. Каждая сторона несет ответственность за свои ошибки ».
Сталь против дерева против бетона
ширина: 80%;}
]]>
Сталь против дерева против бетона
Проектирование конструкций зависит от знания строительных материалов и соответствующих им свойств, чтобы мы могли лучше предсказать поведение различных материалов при их нанесении на конструкцию.Как правило, три (3) наиболее часто используемых материала в строительстве — это сталь, бетон и дерево / древесина. Знание преимуществ и недостатков каждого материала важно для обеспечения безопасного и экономичного подхода к проектированию конструкций. Итак, давайте посмотрим на плюсы и минусы стали, древесины и бетона!
Конструкционная сталь
Сталь — это сплав, состоящий в основном из железа и углерода. Другие элементы также примешиваются к сплаву для получения других свойств.Одним из примеров является добавление хрома и никеля для создания нержавеющей стали. Увеличение содержания углерода в стали имеет предполагаемый эффект увеличения прочности материала на разрыв. Увеличение содержания углерода делает сталь более хрупкой, что нежелательно для конструкционной стали.
Преимущества конструкционной стали
- Сталь имеет высокое соотношение прочности и веса. Таким образом, собственный вес металлоконструкций относительно невелик. Это свойство делает сталь очень привлекательным конструкционным материалом для высотных зданий, длиннопролетных мостов, сооружений, расположенных на земле с низким содержанием грунта и в районах с высокой сейсмической активностью.
- Пластичность. Перед разрушением сталь может подвергаться значительной пластической деформации, что обеспечивает большой резерв прочности.
- Прогнозируемые свойства материала. Свойства стали можно предсказать с высокой степенью уверенности. На самом деле сталь демонстрирует упругие свойства до относительно высокого и обычно четко определенного уровня напряжения.
В отличие от железобетона свойства стали существенно не меняются со временем.
- Скорость возведения. Стальные элементы просто устанавливаются на конструкцию, что сокращает время строительства.Обычно это приводит к более быстрой окупаемости в таких областях, как затраты на рабочую силу.
- Простота ремонта. Металлоконструкции в целом можно отремонтировать быстро и легко.
- Адаптация заводской сборки. Сталь отлично подходит для заводского изготовления и массового производства.
- Многократное использование. Сталь можно повторно использовать после разборки конструкции.
- Расширение существующих структур. Стальные здания можно легко расширить, добавив новые отсеки или флигели. Стальные мосты можно расширять.
- Усталостная прочность. Металлоконструкции обладают относительно хорошей усталостной прочностью.
Недостатки конструкционной стали
- Общие расходы. Сталь очень энергоемкая и, естественно, более дорогая в производстве.
Стальные конструкции могут быть более дорогостоящими в строительстве, чем конструкции других типов.
- Противопожарная защита. Прочность стали существенно снижается при нагревании до температур, обычно наблюдаемых при пожарах в зданиях. Сталь также довольно быстро проводит и передает тепло от горящей части здания.Следовательно, стальные конструкции в зданиях должны иметь соответствующую противопожарную защиту.
- Техническое обслуживание. Сталь, подвергающаяся воздействию окружающей среды, может повредить материал и даже привести к загрязнению конструкции из-за коррозии. Стальные конструкции, подверженные воздействию воздуха и воды, такие как мосты и башни, регулярно окрашиваются. Устранить эту проблему может применение погодоустойчивых и коррозионно-стойких сталей.
- Склонность к короблению. Из-за высокого отношения прочности к весу стальные сжимающие элементы, как правило, более тонкие и, следовательно, более подвержены короблению, чем, скажем, железобетонные сжимающие элементы.
В результате требуется больше конструктивных решений для улучшения сопротивления продольному изгибу тонких стальных компрессионных элементов.
Программное обеспечение SkyCiv Steel Design
Рис. 1. Обзор стальных конструкций
Бетон железобетон
Бетон представляет собой смесь воды, цемента и заполнителей. Пропорция трех основных компонентов важна для создания бетонной смеси желаемой прочности на сжатие. Когда в бетон добавляют арматурные стальные стержни, два материала работают вместе с бетоном, обеспечивающим прочность на сжатие, и сталью, обеспечивающей предел прочности на растяжение.
Преимущества железобетона
- Прочность на сжатие. Железобетон имеет высокую прочность на сжатие по сравнению с другими строительными материалами.
- Предел прочности при растяжении. Благодаря предусмотренной арматуре железобетон также может выдерживать значительную величину растягивающего напряжения.
- Огнестойкость. Бетон обладает хорошей способностью защищать арматурные стержни от огня в течение длительного времени. Это выиграет время для арматурных стержней до тех пор, пока пожар не будет потушен.
- Материалы местного производства. Большинство материалов, необходимых для производства бетона, можно легко найти на месте, что делает бетон популярным и экономичным выбором.
- Прочность. Система здания из железобетона более прочна, чем любая другая система здания.
- Формуемость. Железобетон, будучи изначально жидким материалом, можно экономично формовать в практически неограниченном диапазоне форм.
- Низкие эксплуатационные расходы. Железобетон спроектирован так, чтобы быть прочным, с использованием недорогих материалов, таких как песок и вода, которые не требуют обширного обслуживания.Бетон предназначен для того, чтобы полностью покрыть арматурный стержень, так что арматурный стержень не будет нарушен. Это делает стоимость обслуживания железобетонных конструкций очень низкой.
- В конструкции, такой как фундаменты, плотины, опоры и т. Д., Железобетон является наиболее экономичным строительным материалом.
- Жесткость. Он действует как жесткий элемент с минимальным прогибом. Минимальный прогиб хорош для удобства эксплуатации зданий.
- Удобство в использовании. По сравнению с использованием стали в конструкции, при строительстве железобетонных конструкций может быть задействована менее квалифицированная рабочая сила.
Недостатки железобетона
- Долгосрочное хранение. Бетон нельзя хранить после смешивания, так как цемент вступает в реакцию с водой и смесь затвердевает. Его основные ингредиенты нужно хранить отдельно.
- Время отверждения. Бетон выдерживает тридцать дней. Этот фактор сильно влияет на график строительства здания. Это снижает скорость возведения монолитного бетона по сравнению со сталью, однако ее можно значительно улучшить с помощью сборного железобетона.
- Стоимость форм. Стоимость форм, используемых для отливки ЖБИ, относительно выше.
- Поперечное сечение большее. Для многоэтажного здания секция железобетонной колонны (RCC) больше, чем стальная секция, так как в случае RCC прочность на сжатие ниже.
- Усадка. Усадка вызывает развитие трещин и потерю прочности.
Программное обеспечение SkyCiv RC для проектирования
Рис. 2. Типичный пример железобетона
Древесина
Древесина — это органический, гигроскопичный и анизотропный материал.Его тепловые, акустические, электрические, механические, эстетические, рабочие и т. Д. Свойства очень подходят для использования, можно построить комфортный дом, используя только деревянные изделия. С другими материалами это практически невозможно. Очевидно, что дерево — это и распространенный, и исторический выбор в качестве конструкционного инженерного материала. Однако в последние несколько десятилетий произошел отход от дерева в пользу инженерных изделий или металлов, таких как алюминий.
Преимущества древесины
- Предел прочности при растяжении.Поскольку древесина является относительно легким строительным материалом, она превосходит даже сталь по разрывной длине (или длине самонесущей конструкции). Проще говоря, он может лучше выдерживать собственный вес, что позволяет использовать большие пространства и меньше необходимых опор в некоторых конструкциях зданий.
- Электрическое и тепловое сопротивление. Он обладает естественным сопротивлением электропроводности при сушке до стандартного уровня содержания влаги (MC), обычно от 7% до 12% для большинства пород древесины. Его прочность и размеры также не подвержены значительному влиянию тепла, что обеспечивает устойчивость готового здания и даже безопасность при определенных пожарных ситуациях.
- Звукопоглощение. Его акустические свойства делают его идеальным для минимизации эха в жилых или офисных помещениях. Дерево поглощает звук, а не отражает или усиливает его, и может помочь значительно снизить уровень шума для дополнительного комфорта.
- Из местных источников. Дерево — это строительный материал, который можно выращивать и повторно выращивать с помощью естественных процессов, а также с помощью программ пересадки и лесного хозяйства. Выборочная уборка и другие методы позволяют продолжить рост, пока собираются более крупные деревья.
- Экологически чистый. Одна из самых больших проблем для многих строительных материалов, включая бетон, металл и пластик, заключается в том, что, когда они выброшены, они разлагаются невероятно долго. В естественных климатических условиях древесина разрушается намного быстрее и фактически пополняет почву.
Недостатки бруса
Усадка и разбухание древесины — один из ее основных недостатков.
Дерево — гигроскопичный материал.Это означает, что он будет поглощать окружающие конденсируемые пары и терять влагу в воздух ниже точки насыщения волокна. Еще один недостаток — его износ. Агенты, вызывающие порчу и разрушение древесины, делятся на две категории: биотические (биологические) и абиотические (небиологические). Биотические агенты включают гниющие и плесневые грибы, бактерии и насекомые. К абиотическим агентам относятся солнце, ветер, вода, некоторые химические вещества и огонь.
Программное обеспечение SkyCiv Wood Design
Рисунок 3.Деревянный конструкционный каркас
Сводка
Для лучшего описания стали, бетона и дерева. Обобщим их основные характеристики, чтобы выделить каждый материал.
Сталь очень прочна как на растяжение, так и на сжатие и, следовательно, имеет высокую прочность на сжатие и растяжение. Сталь имеет предел прочности от 400 до 500 МПа (58 — 72,5 ksi). Это также пластичный материал, который поддается или прогибается перед разрушением. Сталь выделяется своей скоростью и эффективностью в строительстве.Относительно легкий вес и простота конструкции позволяют сократить рабочую силу примерно на 10-20% по сравнению с аналогичной строящейся структурой на бетонной основе. Металлоконструкции также обладают отличной прочностью.
Бетон чрезвычайно прочен на сжатие и, следовательно, имеет высокую прочность на сжатие от 17 МПа до 28 МПа. С более высокой прочностью до 70 МПа или более. Бетон позволяет проектировать очень прочные и долговечные здания, а использование его тепловой массы, удерживая его внутри оболочки здания, может помочь регулировать внутреннюю температуру.Также в строительстве все чаще используется сборный железобетон, который дает преимущества с точки зрения воздействия на окружающую среду, стоимости и скорости строительства.
Древесина устойчива к электрическим токам, что делает ее оптимальным материалом для электроизоляции. Прочность на разрыв также является одной из основных причин выбора древесины в качестве строительного материала; его исключительно сильные качества делают его идеальным выбором для тяжелых строительных материалов, таких как конструкционные балки.Дерево намного легче по объему, чем бетон и сталь, с ним легко работать и легко адаптировать на месте. Он прочен, дает меньше тепловых мостиков, чем его аналоги, и легко включает в себя готовые элементы. Его структурные характеристики очень высоки, а его прочность на сжатие аналогична прочности бетона. Несмотря на все это, древесина все шире используется для строительства жилых и малоэтажных построек. Его редко используют в качестве основного материала для высотных конструкций.
Это самые распространенные строительные материалы, используемые для строительства.У каждого материала есть свой уникальный набор достоинств и недостатков. В конце концов, они могут быть заменены материалами, которые практически не имеют ограничений с технологическими достижениями будущего. Тем не менее, наши нынешние строительные материалы будут оставаться актуальными еще многие десятилетия.
Прямое получение фактов о дереве и бетоне
Автор: Уильям Ларсон
Недавний анализ отраслевых тенденций, опубликованный Business Monitor International Ltd по развивающимся технологиям в строительном секторе ( Анализ тенденций в отрасли — Постоянное развитие технологий : Развитие строительного сектора В 2018 г. (6 июля 2018 г.) отметили растущее внимание к вопросам устойчивости в новых зданиях.В статье подчеркиваются нетрадиционные строительные материалы, такие как древесина, которая, по ее словам, дает значительные преимущества по сравнению со сталью и бетоном.
Примечательным заявлением на этот счет было следующее: «Древесина легче без ущерба для прочности, что позволяет снизить стоимость фундамента, а поскольку его компоненты являются сборными, процесс строительства ускоряется. Древесина также предлагает преимущества в области устойчивого развития, поскольку она поступает из возобновляемых источников и сокращает количество отходов на месте по сравнению с цементом.”
BMI Research — уважаемое издание, известное своим превосходным освещением отраслевых тенденций. Вот почему это одностороннее и фактически неполное заявление так необычно. Фактически, цемент — это просто ингредиент бетона, самого устойчивого и эластичного строительного материала на планете, и, как правило, он составляет лишь 10-15% от объема смеси, вместе с заполнителем и водой.
Конечно, некоторые виды древесины легче бетона или стали. Точно так же некоторые строительные изделия из дерева демонстрируют прочностные характеристики, близкие к характеристикам стали или бетона.Но это не означает, что древесина является подходящей заменой для всех видов строительных конструкций. И не всегда это менее затратная форма строительства. Тот факт, что некоторые строительные материалы на основе древесины собираются за пределами строительной площадки, относится не только к древесине. Сборный бетон и сталь используются десятилетиями.
Предполагаемые преимущества древесины благодаря возобновляемому происхождению (например, деревьям) и утвержденной древесине «меньше отходов на месте по сравнению с цементом» — вот где некоторые выводы об устойчивости, сделанные в статье, «не связаны».
Во-первых, недавнее исследование доказывает, что лишь небольшое количество (18-30%) углерода, изначально хранящегося в живом дереве, попадает в долговечные строительные изделия, такие как размерные пиломатериалы или поперечно-клееная древесина. Точно так же, в то время как древесина в зданиях сохраняет небольшую долю этого углерода в течение своего срока службы, древесина на свалках фактически выделяет метан, потенциал глобального потепления которого в 28-36 раз выше, чем у CO2.
Но на этом история не заканчивается. Недавние исследования также показали, что бетон реабсорбирует большую часть углерода, ранее выделявшегося при производстве цемента, посредством процесса, называемого карбонизацией.Проще говоря, бетон также является поглотителем углерода.
Есть много факторов, которые необходимо учитывать перед оценкой утверждений о том, что тот или иной тип здания или продукт обеспечивает лучшую экологическую отдачу. Чтобы понять полное воздействие конструкции на окружающую среду в течение десятилетий использования, необходимо учитывать все этапы, начиная с начала строительства и заканчивая сносом.
Это указывает на то, что всесторонняя оценка жизненного цикла, от колыбели до могилы, является более реалистичной основой для оценки истинных преимуществ устойчивости строительных материалов, и этот момент в статье вполне мог быть подчеркнут более убедительно.
Споры между деревом и бетоном — это утомленный, пронизанный клише аргумент, имеющий небольшую научную ценность. Существует множество факторов, которые определяют, какой строительный материал является наиболее подходящим для данной конструкции, местоположения или цели.
Настоящая проблема — это потребность в более устойчивых зданиях, лучше способных противостоять воздействиям постоянно меняющегося климата. Как отмечает Эван Рейс, глава Совета по устойчивости США, «при оценке истинной устойчивости любого материала мы должны учитывать его устойчивость к окружающей среде в долгосрочной перспективе.В конце концов, это то, что создает более сильные и устойчивые сообщества ».
Уильям Ларсон, вице-президент по маркетингу в CalPortland. Он также был председателем Руководящего комитета, координирующего развитие Коалиции устойчивости зданий северо-западного Тихоокеанского региона с момента ее создания в октябре 2016 года.
Примечание редактора : Коалиция устойчивости строительства северо-западного Тихоокеанского региона выступит спонсором основного выступления Эвана Рейса. , глава Совета по устойчивости США 24 июля на саммите Тихоокеанского Северо-Западного экономического региона 2018 года.Подробнее см. Здесь.
Почему бетон лучше дерева как лучшее здание…
Опубликовано 20 июня 2019 г.
От высотных зданий до загородных домов бетон — строительный материал номер один, который выбирают архитекторы и дизайнеры во всем мире.
Хотя древесина является близким заменителем, бетон имеет множество преимуществ, которые делают его лучшим вариантом для большинства строительных проектов.
Вот несколько причин, по которым бетон превосходит дерево в качестве строительного материала.
Высокая прочность
Одно из главных качеств бетона — его податливость и высокая прочность. Бетон твердый в сухом состоянии и эластичный во влажном состоянии; достаточно, чтобы придать ему любую форму. Это придает ему стабильность размеров, необходимую как для наружных конструкций, так и для установки внутри помещений, и дает возможность для творческого самовыражения.
Бетон со временем становится прочнее, укрепляя конструкцию. Для сравнения, древесина менее плотная и, следовательно, менее прочная.
Еще одно преимущество бетона заключается в том, что его можно довести до любой желаемой прочности и отлить на месте, что делает его экономичным выбором.
Кроме того, он может противостоять ветру до 250 миль в час. Бетонные дома также имеют более глубокий фундамент, что делает их пригодными для зон, уязвимых для торнадо и ураганов.
прочный
Хотя древесина является более дешевой альтернативой бетону, она быстрее стареет и требует более высоких затрат на обслуживание и ремонт.Следовательно, хотя древесина быстро портится, особенно если за ней не ухаживать регулярно, срок службы бетона в два-три раза больше, чем у большинства других строительных материалов.
Кроме того, термиты прекрасно себя чувствуют в деревянных конструкциях и деревянных каркасных домах, а древесина, как правило, страдает от эпидемий и проблем с влажностью. Как органическое соединение, древесина также привлекает такие микроорганизмы, как плесень и грибок, что оказывает неблагоприятное воздействие на внутреннюю среду в замкнутых пространствах. Бетон, с другой стороны, устойчив к образованию термитов и плесени, что со временем снижает его деградацию.
Деревянные конструкции также не устойчивы к повреждениям от воды; даже малейший ливень может привести к утечкам из небольших отверстий. Бетон, напротив, более устойчив к влаге и впитывает воду, что приводит к меньшему повреждению всей конструкции. Точно так же бетон огнестойкий, в отличие от дерева, которое усиливает пламя.
В целом стойкие свойства бетона приводят к снижению затрат на обслуживание в течение всего срока службы конструкции.
Звукоизоляция
Деревянные конструкции имеют плохую репутацию шумных, поскольку они не изолируют шум так же хорошо, как бетон из-за разницы в плотности.
Определенные трещины или протечки в конструкции создают проходы для прохождения шума, что доставляет неудобства тем, кто живет на оживленной улице.
Кроме того, с изменением климата древесина также сжимается и расширяется, что может привести к сужению или расширению дверей и шкафов в их рамах. С другой стороны, бетон предлагает плотное, воздухонепроницаемое и звукоизоляционное решение всех этих проблем.
Энергоэффективность
Бетонные дома менее подвержены утечкам, чем деревянные каркасы.Деревянные стены снабжены различными компонентами, такими как обшивка и изоляция, которые могут образовывать трещины и пропускать воздух.
Молекулярная структураConcrete позволяет создавать воздухонепроницаемую и непрерывную композицию с меньшими шансами на прохождение воздуха через нее. Это предотвращает проникновение тепла в конструкции, сохраняя при этом прохладный воздух внутри.
Современные бетонные дома также имеют более плотную изоляцию и изоляцию, начиная от войлока с фольгой и заканчивая панелями из полистирола.
Короче говоря, в бетонных зданиях обычно меньше холодных или горячих зон, а его компактная конструкция замедляет прохождение тепла через стены. Таким образом, бетон является идеальным выбором для энергоэффективных конструкций и обеспечивает экономичные счета за отопление и охлаждение в течение всего года.
Экономически выгодно
Бетон можно производить партиями в соответствии с потребностями проекта, что приводит к меньшим потерям. Помимо своей рентабельности в долгосрочной перспективе, бетон предлагает существенную разницу в стоимости строительства и страхования — в зависимости от типа жилья, в котором он используется.
Многие исследования показали, что бетон подходит для строительства многоквартирных домов.
Некоторые из его преимуществ включают:
Экономия на страховых расходах
Одно из качеств бетона — негорючесть; это снижает риск возникновения пожара, последствий применения методов локализации пожара и проблем, связанных с возгоранием.
Поскольку бетон является огнестойким материалом, расходы на страхование домов, построенных из бетона, ниже по сравнению с домами, построенными из дерева.
Фактически, исследование, проведенное в нескольких городах США, таких как Лос-Анджелес, Орландо, Даллас, Таусон и Эджуотер, штат Нью-Джерси, показало, что владельцы могут сэкономить на страховых расходах, если выберут бетон.
В исследовании говорится, что экономия составляет от 14% до 65% на коммерческой недвижимости и от 22% до 72% на страховании строительного риска в отношении бетона. Ожидается, что в следующие годы эта разница будет постепенно увеличиваться.
Более низкие начальные затраты на строительство
Качествами, которые делают бетон хорошим выбором для строительных проектов, являются его долговечность и прочность.
Бетон — это экономичный выбор для строительства секционных или многоквартирных домов, таких как кондоминиумы, квартиры и студенческие общежития.
Согласно исследованию Вальтера Г. М. Шнайдера III, строительные проекты с использованием дерева обходятся дороже, чем бетон. Исследование было сосредоточено в основном на трех городах Даллас, Эджуотер и Тоусон — и изучались шесть различных строительных материалов.
Результаты показали, что первоначальные затраты, связанные с бетонными строительными материалами, были не только ниже, чем на материалы на основе древесины, но и на строительство легких стальных конструкций.
Было обнаружено, что другие методы на основе бетона на 20% больше затрат, связанных с традиционным деревянным каркасом — это обычно может быть покрыто за счет непредвиденных расходов на непредвиденные расходы, что делает бетон более эффективным выбором.
Бетонные дома построены на долгий срок, что делает их выгодным вложением средств для современных домовладельцев.
Полученные в результате конструкции не только не требуют особого ухода, но и увеличиваются в цене по сравнению с каждым потраченным долларом.
Если вам нужна дополнительная информация о различных типах бетона, пригодности для строительства и экономической эффективности, обращайтесь к SpecifyConcrete прямо сейчас.
Влияние соотношения цемент / древесина и условий хранения древесины на температуру гидратации, время гидратации и прочность на сжатие древесно-цементных смесей
Влияние соотношения цемент / древесина и условий хранения древесины на температуру гидратации, время гидратации и прочность древесины на сжатие.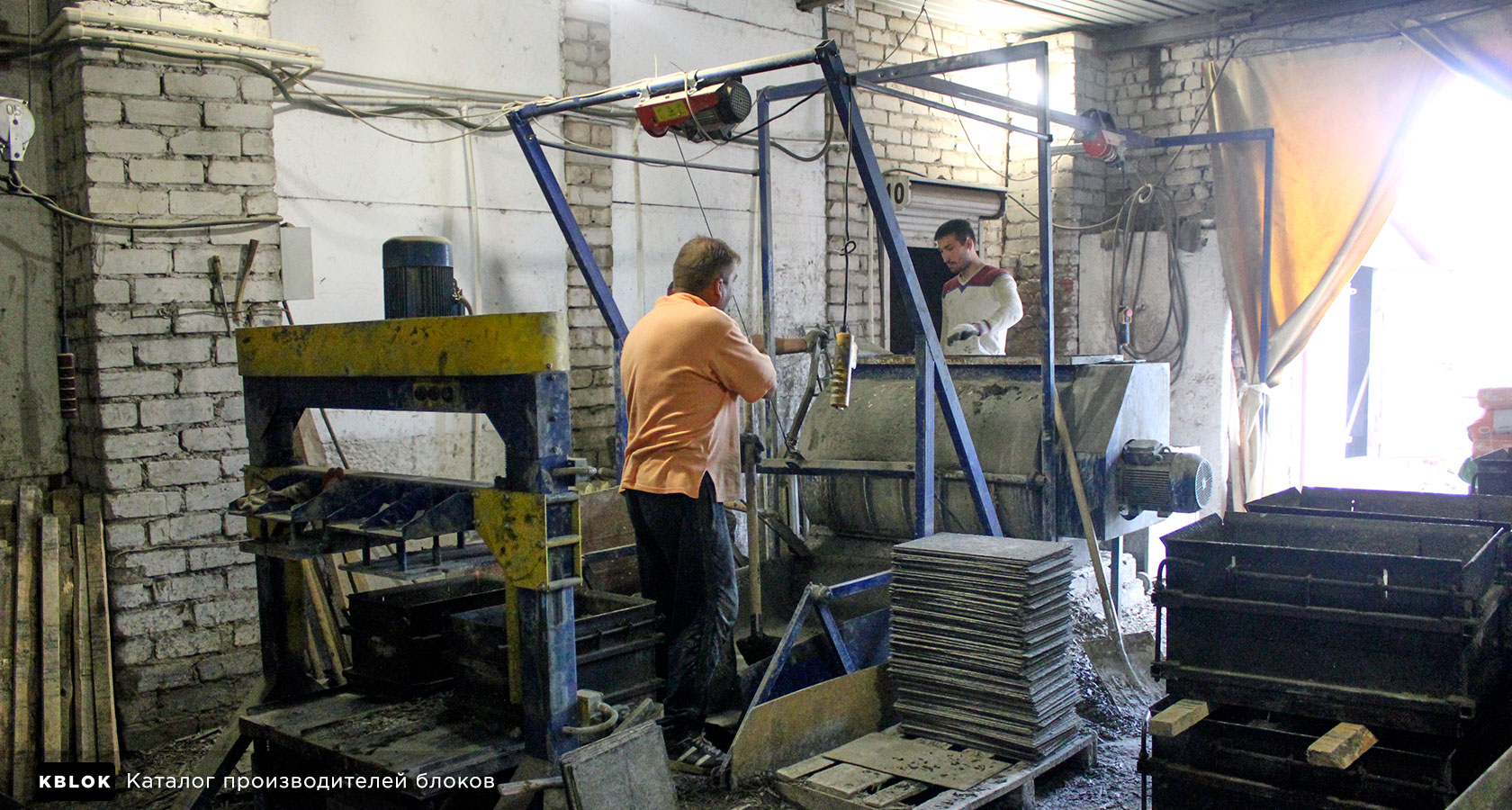
The.gov означает, что это официально.
Веб-сайты федерального правительства часто заканчиваются на .gov или .mil. Прежде чем делиться конфиденциальной информацией, убедитесь, что вы находитесь на сайте федерального правительства.
Сайт безопасен.
https: // гарантирует, что вы подключаетесь к официальному веб-сайту и что любая предоставляемая вами информация шифруется и безопасно передается.
Автор (ы):
Энди В. К. Ли
Чжунли Хун
Дуглас Р. Филлипс
Chung-Yun Hse
Тип публикации:
Научный журнал (JRNL)
Первичная станция (и):
Южная научная станция
Источник:
Наука о древесине и волокне 19 (3): 262-268
Описание
В этом исследовании изучалось влияние соотношения цемент / древесина и условий хранения древесины на температуру гидратации, время гидратации и прочность на сжатие древесно-цементных смесей, изготовленных из шести пород древесины: южной сосны, белого дуба, южного красного дуба, желтого тополя и т. сладкая резинка и гикори.Соотношение цемент / древесина варьировалось от 13/1 до 4/1. Условия хранения древесины: высушенная на воздухе и хранимая в холодильнике. Результаты показывают, что температура гидратации была резко снижена, время гидратации было продлено, а прочность на сжатие снизилась по мере уменьшения отношения цемент / древесина. Этот эффект был более выражен для твердых пород дерева и при более низком соотношении цемент / древесина. Холодное хранение древесины немного повысило температуру гидратации и сократило время гидратации белого дуба и сладкой жевательной резинки, но не имело никакого положительного влияния на другие четыре породы.Результаты также показывают, что смеси с высоким соотношением цемент / древесина, традиционно используемые в лабораториях для исследовательских целей, могут не полностью отражать совместимость древесины и цемента при более низких соотношениях цемент / древесина, используемых в коммерческом производстве.
Цитата
Ли, Энди В.