антигрибковый, проникающий и укрепляющий составы, акриловая грунтовка для стен и бетонного пола
Любые отделочные работы начинаются с грунтовки. Каждому материалу требуется свое покрытие, благодаря которому дальнейшие работы пройдут успешно. Для бетона выпускаются специальные грунтовки глубокого проникновения, которые имеют особенности применения.
Особенности и предназначение
Любые поверхности, какими прочными бы они ни были, время от времени нуждаются в ремонте, поскольку внутренняя структура разрушается, от чего портится и внешний вид. Покрытия глубокого проникновения способны это предотвратить и увеличить срок эксплуатации поверхности.
Грунтовка глубокого проникновения может использоваться для наружных и внутренних работ.
Благодаря применению грунтовки возрастает прочность покрытия, появляется необходимая защита от влаги. После ее использования хорошо ложится штукатурка и другие материалы, предназначенные для дальнейшей обработки поверхности. И, кроме того, любое декоративное покрытие будет держаться лучше и прослужит дольше.
Благодаря грунтовке можно сэкономить на других материалах. Это происходит за счет того, что она хорошо впитается внутрь, а краска ложится на поверхность. За счет грунтовки на поверхность хорошо наносится и шпатлевка, становясь более эластичной.
Характеристики
Глубокопроникающая основа является водорастворимым составом, в который входит латексная смесь и акриловая краска.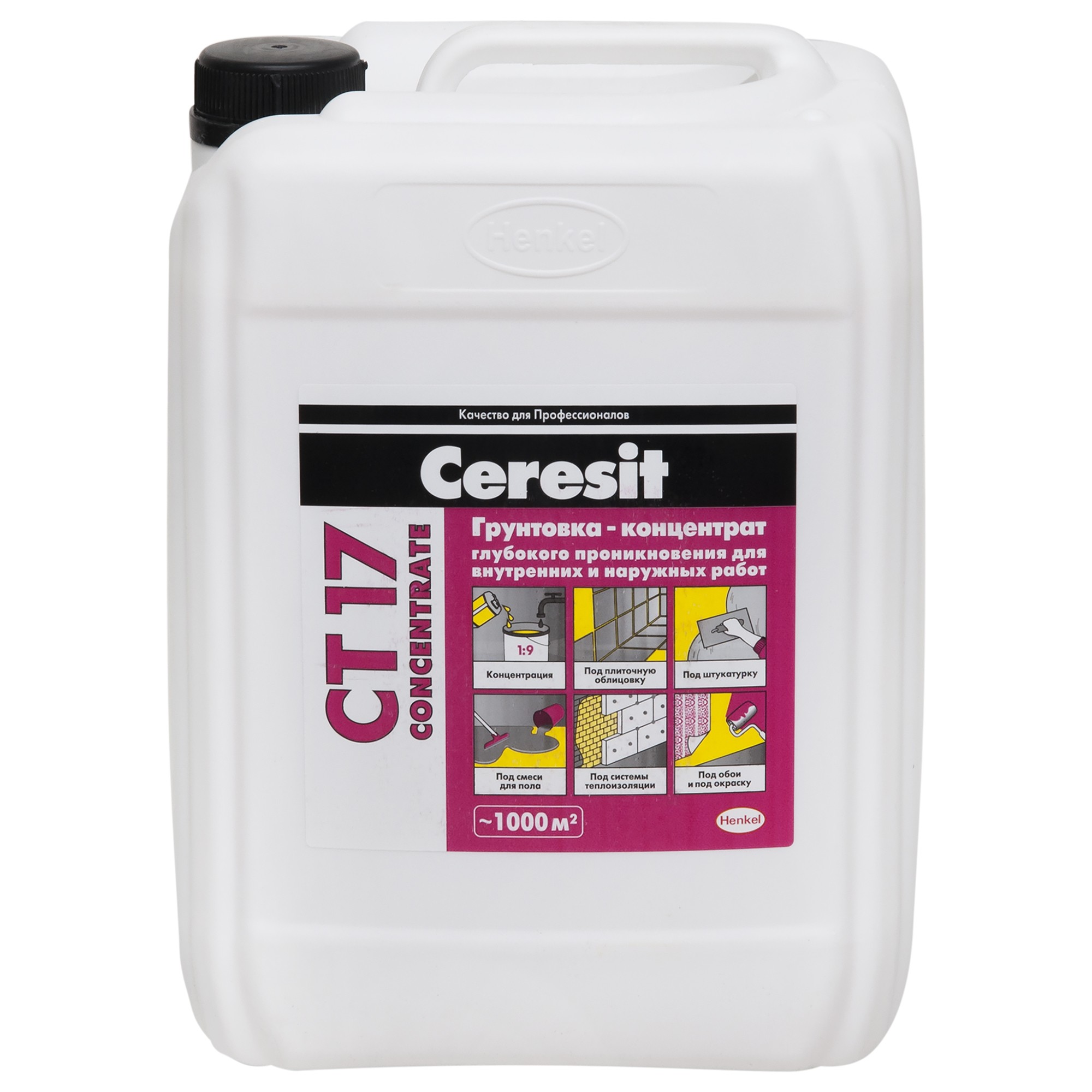
У грунтовок разных производителей есть дополнительные качества и характеристики, но суть остается одна – это основа, защищающая и укрепляющая стены, полы и потолки.
Виды
- Акриловая. Она относится к разряду тех, что очень быстро сохнут. К преимуществам можно отнести и то, что она не имеет неприятного запаха. Такой грунтовкой лучше обрабатывать бетонный пол и стены в помещении.
- Полистирольная. Этот вид содержит растворители с токсичными составляющими, поэтому его рекомендуется использовать на открытом пространстве. Закрытые помещения не подходят. Прежде чем наносить полистирольную грунтовку, поверхность нужно оштукатурить.
- Поливинилацетатная. Идеально подходит для работы в помещениях. Время высыхания составляет тридцать минут. После можно красить соответствующими красками.
Грунтовки могут различаться и по воздействию на поверхность.
- Проникающая с содержанием клея. Она проникает достаточно глубоко в основание, тем самым увеличивая прочность. Это очень хороший вариант, когда требуется восстановить старую поверхность, чтобы впоследствии придать ей должный вид. Благодаря такому составу все мелкие трещины будут заполнены, что предотвратит дальнейшее разрушение. Грунтовка глубокого проникновения способна укрепить пористую поверхность, но не рыхлую.
Латексные частицы способствуют созданию прочной пленки.
- Адгезионная. Этот вариант отличается тем, что он способен образовать непроницаемую пленку. Это качество незаменимо, когда приходится обрабатывать уже окрашенную поверхность с целью обновления стен. Потом можно класть цементный раствор и наносить свежую краску.
Но всегда следует учитывать, что после использования той или иной грунтовки нужно наносить составы схожие по наличию компонентов. Краска или шпатлевка должны быть совместимыми с грунтовкой.
Как выбрать?
Когда предстоит выбрать подходящий состав, нужно учитывать, где будет эксплуатироваться поверхность и какими свойствами обладает. Один из важных факторов – это место проведения работ, поскольку грунтовка может применяться как для внутренних, так и для наружных. Если помещение отличается повышенной влажностью, то и средство для грунтования нужно с соответствующей защитой. Кроме того, нужно обращать внимание на то, какие дальше будут производиться отделочные работы.
Будет полезным ознакомиться с некоторыми производителями и их продукцией, чтобы легче было ориентироваться при выборе подходящей грунтовки. В продаже представлена отечественная продукция по невысокой цене, а есть грунтовки от импортных производителей, цена на которые может быть значительно выше.
Производители
Для непрочной поверхности, которой нужна глубокая обработка, подойдет грунтовка «Старатели». Она выровняет поверхность и отлично подготовит ее для нанесения последующих материалов. Данный вариант относится к числу самых дешевых.
Грунтовка «Ceresin CT 17» хорошо пропитывает любое бетонное основание.
Большой спектр работ можно выполнить с помощью полиуретановой грунтовки «Лакра». С ней удастся избежать появления на поверхности грибка и плесени. Антисептическая добавка, которая входит в этот вид грунтовки, позволяет использовать ее в помещениях с высокой влажностью.
Раствор, который быстро сохнет и глубоко проникает, в некоторых случаях бывает просто незаменим. Большой популярностью пользуется грунтовка «Knauf Tiefengrand». Если предстоит произвести шпаклевание, укладку кафельной плитки, покраску, приклеивание обоев, то это средство подходит идеально.
«Knauf Бетоконтакт» – это полимерная дисперсионная грунтовка, содержащая по большей части кварцевый песок. Она идеальна для работ в комнатах. С ее помощью хорошо обрабатывать стены и потолки, причем даже в тех случаях, где потом планируются сложные работы. Например, нанесение декоративной штукатурки или гипсовой лепнины. Сразу стоит отметить, что это дорогостоящий вариант покрытия.
Если в работе наиболее важны адгезионные характеристики, то лучше использовать акриловую грунтовку «Бетон-Контакт». После ее нанесения поверхность становится шероховатой, при этом на нее хорошо ложится штукатурка, клеевой состав. Соответственно, хорошо держатся и все материалы, которые потом крепятся на эту поверхность. Такими же свойствами обладают и такие продукты, как «Бетон-Контакт Лакра» и «Cerfecit CT19».
Как правильно наносить?
Специалисты рекомендуют производить нанесение грунтовки глубокого проникновения для бетона следующим образом:- бетонная поверхность должна быть абсолютно сухой и чистой;
- если на стене есть трещины и неровности, их надо устранить;
- раствор готовится согласно инструкции на упаковке, чаще всего сухую смесь с водой разводят в пропорциях один к одному;
- грунтовку распределяют по поверхности валиком или кистью, большие площади лучше обрабатывать краскопультом;
- при использовании составом с резким запахом рекомендуется защитить дыхательные пути с помощью респиратора.
Если производятся наружные работы, то нужно придерживаться температуры от +5 до +30.
Прежде чем продолжить работы по декоративной отделке стен, потолка или пола,
Придерживаясь этих несложных правил и знаний о том, какие виды грунтовок существуют и как применяются, можно без особых сложностей справиться с ремонтными работами, в частности с нанесением грунтовки на бетонную поверхность.
О том, как правильно грунтовать бетонный пол, смотрите далее.
технические характеристики, расход и цена
Домашним мастерам хорошо известно, что перед началом отделочных работ любую поверхность необходимо обрабатывать грунтом. Для каждого вида основного материала промышленность выпускает составы специального назначения. Плоскость из бетона рекомендуется покрывать грунтовкой глубокого проникновения. Прежде чем купить необходимое средство, специалисты рекомендуют ознакомиться с особенностями, характеристиками и правилами его нанесения. Полезные знания помогут выбрать оптимальный вид грунта и определить предстоящие расходы.
Оглавление:
- Для чего применяется?
- Принцип действия
- Обзор популярных марок
- Технология нанесения и расход
Для чего нужны такие составы?
Плоскости различных конструкций, содержащих бетон, в процессе длительной эксплуатации постепенно приходят в негодность. Разрушениям способствуют многочисленные агрессивные вещества, содержащиеся в атмосфере и промышленных выбросах. Образовавшиеся в результате химических реакций водорастворимые соли постепенно расширяются, что приводит к разрывам бетонных оснований.
Для изоляции конструктивных поверхностей от внешней среды были разработаны специальные растворы глубокого проникновения. Они предназначаются для наружных работ и внутренней отделки помещений. Целью обработки такими составами является изменение технических характеристик различных плоскостей (газобетон, гипсокартон, кирпич, пенобетон, железобетон, бетонная плита):
- увеличение прочности;
- снижение впитывающей способности;
- усиление адгезии со штукатуркой, клеями и ровнителями;
- защита от биологического разрушения;
- выравнивание;
- уменьшение расходов отделочных материалов.
Грунтовка глубокой инфильтрации по бетону представляет собой своеобразную прокладку между строительным основанием и внешним покрытием. Она обеспечивает надлежащее качество последующих малярных работ и долговечность облицовки.
Технические характеристики акриловой грунтовки
Глубоко проникающие средства по бетону представляют собой водорастворимые составы на основе латексных смесей и акриловой краски. Отличаются большой текучестью, повышенными проникающим и вяжущим параметрами. Эти качества способствуют глубокой диффузии (до 100 мм) и максимальному упрочению бетона. Такие возможности достигаются благодаря дисперсиям с латексными частицами сверхмалых размеров – мицеллами.
После обработки на плоскости образуется тонкая защитная пленка, похожая на матовый лак. Она хорошо отталкивает влагу и выдерживает более пяти циклов заморозки-оттаивания. Антисептические свойства грунтовки глубокого проникновения не допускают на поверхностях из бетона появления грибка и плесени. Кроме того, защитные составы не закрывают поры основания, способствуя нормальной циркуляции воздуха.
Дополнительные качества и эксплуатационные характеристики грунтовок для наружных и внутренних работ обусловлены техническими условиями марки и компанией производителем.
Потребительский рейтинг
Большое разнообразие пропиточных составов для бетона может затруднить выбор покупателей. Какая грунтовка лучше: импортный товар с громким именем и высокой ценой или недорогое средство отечественного производства? Чтобы ответить на эти вопросы, рассмотрим несколько видов популярных изделий.
1. Старатели – недорогая грунтовка по бетону для наружных работ. Имеет смысл купить в том случае, когда требуется глубокая обработка и укрепление непрочных поверхностей. Она также способствует выравниванию бетонных оснований и усилению сцепления с отделочными материалами.
2. Ceresit CT 17 – пропитывающий грунт широкого назначения. Благодаря ультрамелким частицам глубоко проникает в самые узкие поры, не препятствуя паро- и газообмену. Выпускается в летней и зимней морозостойкой версиях. Содержание красящего пигмента позволяет легко отличать обработанную плоскость.
3. Лакра – полиуретановая грунтовка универсального назначения. Пропитывающий состав лучше других справляется с защитой бетона от плесени, бактерий и грибков. Наличие антисептических добавок делает грунт пригодным для использования в помещениях с повышенной влажностью: санузле, бане, лоджии, зимнем саду.
4. Knauf Tiefengrund – универсальный быстросохнущий раствор глубокого проникновения. Предназначается для предварительной обработки поверхностей под шпатлевку, укладку керамической плитки, малярные работы, оклеивание обоями. Благодаря высокой проникающей способности грунт лучше всего подходит для сверхгигроскопичных оснований.
5. Knauf Бетоконтакт – полимерная дисперсия из кварцевого песка. Отлично подходит для гладких, плотных поверхностей из бетона и различных слабо впитывающих. Такой грунт следует выбрать, если планируются внутренние работы. Это оптимальный вариант при подготовке стен и потолка к гипсовой лепнине. Единственный недостаток материалов этой марки – высокая цена.
6. Бетон-Контакт – адгезионная акриловая дисперсия. После ее нанесения образуется шероховатая пленка, сходная с наждачной бумагой. Рельефная фактура Бетон-Контакт лучше других видов скрепляет основание с различными штукатурными растворами и плиточными клеями. Благодаря введению дополнительных присадок адгезионный грунт имеет повышенную стоимость относительно других пропиток. На рынке также широко известна акриловая грунтовка Бетон-Контакт Лакра. Аналогичными адгезионными характеристиками обладает и Ceresit СТ 19.
Техника нанесения и расход
Перед пропиткой основание необходимо подготовить. Хорошо просушенную поверхность из бетона зачищают от пыли и сора, удаляют заусенцы, заделывают трещины. Смесь приготавливают, следуя инструкции на упаковке. Чаще всего рекомендуется соотношение порошка и воды 1:1. Грунтовку для бетона наносят вручную равномерно сплошным слоем с помощью валика или малярной кисти. Большую площадь удобно обрабатывать из краскопульта.
Важным условием качественного покрытия бетона является соблюдение температурного режима окружающей среды от +5 до +30 °С. Приступать к отделке можно только после его полного высыхания.
Теоретический расход глубокого бетонного грунта производители обязательно указывают на упаковке. Фактический объем затраченного средства зависит от состояния поверхности. Для наружных работ средний расход на 1 м2 составляет от 100 до 200 мл. При обработке пола большое значение имеет его рельеф и марка бетона. Плоскость с рыхлой структурой прокатывают грунтовкой дважды. При этом расход может увеличиться до 500 мл/кв.м.
Название | Страна-производитель | Цена за 1 кг, рубли |
DecoTech Eco | Россия | 30-42 |
Krafor | 50-65 | |
RDS Decore универсальная | 40-55 | |
UNIS | 37-50 | |
Лакра | 44-48 | |
Лакра Бетон-Контакт | 77-80 | |
Оптимист | 40-50 | |
Старатели | 48-55 | |
Старатели Бетон-Контакт | 57-70 | |
Текс Универсал | 62-80 | |
Bergauf Tiefgrunt | Германия-Россия | 42-60 |
Ceresit CT 17 | Германия | 47-59 |
Ceresit CT 19 Бетон-Контакт | 70-100 | |
Кнауф Tiefengrund | 60-95 | |
Кнауф Бетоконтакт | 107-170 | |
Litokol Primer C | Италия | 95-155 |
Marshall Export Base | Турция | 76-93 |
Тиккурила Евро Праймер | Финляндия | 120-167 |
Tikkurila Euro Primer | 100-110 |
Свойства и преимущества грунтовок глубокого проникновения
Основная задача, которая решается за счет использования составов для грунтования – повышение прочности поверхностей, улучшение их адгезивных качеств (то есть сцепления с клеем, штукатуркой, краской), придание антисептических свойств и т.д. сегодня грунтовки производятся на разной химической основе – акриловой, алкидной, минеральной. Причем первые позволяют работать практически со всеми видами поверхностей, от стекловолокна до дерева и бетона (кроме металла). СвойстваГлавное отличие грунтовок глубокого проникновения от универсальных составов выражено в их названии. «Глубокий грунт», как его нередко называют, является очень мелкодисперсным, поэтому глубина пропитки обрабатываемой достигает 20 мм. После этого пористый и неровный материал (к примеру, кирпич, бетон, штукатурка) гораздо лучше удерживает на себе клеящие и красящие составы. Еще один результат применения глубоких грунтовок – заметное уменьшение расхода отделочных материалов. Каждый, кто когда-либо клеил обои на оштукатуренную стену, знает, сколько времени надо потратить, чтобы как следует промазать осыпающуюся поверхность, куда клей уходит, как вода в песок. Однако если предварительно ее загрунтовать, то она, во-первых, станет крепче, во-вторых, уже не потребует такого количества краски или клея, так как пористая структура поверхности заполнена частицами грунтовки. Глубокопроникающие составы для грунтования имеют еще один плюс – после их применения на стене уже не заведется плесень и гниль, поскольку микроорганизмам становится негде размножаться. А, значит, оклеенные обои не покроются серо-желтыми разводами, и воздух в помещении будет более здоровым. Задел на будущееЛюбой ремонт – довольно дорогое мероприятие, и естественным при его проведении является стремление сэкономить. Конечно, отделку можно провести и без загрунтовывания стен, однако при каких-либо последующих переменах в интерьере это чревато проблемами. Например, при снятии старых обоев вслед за ними может вывалиться кусок штукатурки, так что придется тратить финансы еще и на выравнивание стен. Если же использовать глубокую грунтовку сейчас, это позволит существенно облегчить и, в конечном счете, удешевить будущие переделки. Еще один подводный камень ремонта – поиск самых низких цен. Безусловно, вряд ли стоит переплачивать, закупая товары на дорогих рынках, однако желание минимизировать расходы должно находить в подчинении у здравого смысла, чтобы потом работу не пришлось переделывать. Поэтому во главу угла следует ставить качество отделочных материалов и репутацию продавца. Как избежать ошибки?Первый шаг при выборе глубокой грунтовки — визуальное оценивание. Помимо этого, нужно оценить соотношение твердого вещества и воды — эта информация должна быть указана на фасовочной емкости. «Сухой остаток» должен быть примерно равен 12 %. Если эта цифра больше, то грунтовка не сумеет достаточно глубоко пропитать поверхность, а, значит, ее следует отнести к укрепляющим составам. Еще один критерий – вид обработанной поверхности: как ни непривычно это звучит, но после пропитки глубокой грунтовкой покрытие внешне остается прежним. А вот если после высыхания образовалась пленка, значит, для грунтования был выбран не тот состав, который следовало применить. Общие рекомендацииНесмотря на то, что есть разные по составу и назначению грунтовки, работа с ними подчиняется общим правилам: выбор раствора в соответствии с типом поверхности, тщательная очистка ее от пыли, при необходимости обезжиривание. Только после этого можно приступать к обработке. Выполнение этих правил в сочетании с качественными материалами позволит получить прочное и химически стойкое покрытие. |
Акриловая грунтовка глубокого проникновения ПЛИТОНИТ Грунт Упрочняющий для наружных и внутренних работ по бетону
Ленинградская область
Санкт-Петербург
Бокситогорск
Васкелово
Волосово
Волхов
Всеволожск
Выборг
Выра
Вырица
Гатчина
Грузино
Дранишники
Заполье
Зеленогорск
Кингисепп
Кириши
Кировск
Колпино
Колтуши
Коммунар
Лодейное поле
Ломоносов
Лосево
Луга
Мичуринское
Мурино
Ново-Токсово
Отрадное
Павлово
Песочный
Пикалево
Приозерск
Псков
Романовка
Ропша
Рощино
Сестрорецк
Сиверский
Сланцы
Сосново
Сосновый Бор
Тихвин
Токсово
Тосно
Ульяновка
Черемыкино
Москва и Московская область
Москва
Алтуфьево
Видное
Владимир
Дмитров
Дубино
Дубна
Егорьевск
Зеленоград
Иваново
Истра
Климовск
Клин
Коломна
Кострома
Красногорск
Кубинка
Лосино-Петровский
Люберцы
Меличкино
Можайск
Мытищи
Ногинск
Одинцово
Орехово-Зуево
п. Соболиха
Павловский Посад
пгт. Белоозерский
Подольск
Пушкино
Раменское
Сергиев Посад
Серпухов
Сокольники
Старая Купавна
Тарасовка
Химки
Хотьково
Шолохово
Шуя
Щелково
Электросталь
Юдино
Ям
Ярославль
Алтайский край
Барнаул
Амурская область
Благовещенск
Архангельская область
Архангельск
Новодвинск
Северодвинск
Брянская область
Брянск
Волгоградская область
Волгоград
Волжский
Вологодская область
Белозерск
Великий Устюг
Вологда
Воронеж
п. Кадуй
п. Шексна
Тотьма
Череповец
Воронежская область
Воронеж
Забайкальский край
Чита
Ивановская область
Иваново
Шуя
Иркутская область
Ангарск
Иркутск
Шелехов
Кабардино-Балкаарская Республика
Баксан
Нальчик
Калининградская область
Калининград
Калужская область
Кемеровская область
Кемерово
Новокузнецк
Кировская область
Киров
Кирово-Чепецк
Костромская область
Кострома
Краснодарский край
Адлер
Адыгея
Краснодар
Курганинск
Сочи
Красноярский край
Красноярск
Курганская область
Курган
Шадринск
Курская область
Курск
Мурманская область
Апатиты
Кандалакша
Мурманск
Нижегородская область
Нижний Новгород
Новгородская область
Боровичи
Великий Новгород
Старая Русса
Новосибирская область
Новосибирск
Омская область
Омск
Оренбургская область
Бузулук
Новотроицк
Оренбург
Орск
Пензенская область
Пенза
Пермский край
Пермь
Приморский край
Артем
Владивосток
Находка
Псковская область
Великие Луки
Псков
Республика Башкортостан
Бирск
Красноусольский
Кумертау
Нефтекамск
Октябрьский
Салават
Стерлитамак
Уфа
Республика Беларусь
Минск
Республика Бурятия
Улан-Удэ
Республика Дагестан
Махачкала
Республика Казахстан
Астана
Республика Карелия
Костомукша
Петрозаводск
Сегежа
Сортавала
Республика Коми
Сыктывкар
Республика Крым
Севастополь
Симферополь
Республика Мордовия
Саранск
Республика Татарстан
Казань
Набережные Челны
Республика Чувашия
Чебоксары
Ростовская область
Аксай
Батайск
г. Каменск-Шахтинский
Новочеркасск
Ростов-на-Дону
Рязанская область
Рязань
Самарская область
Кинель
п. Волжский (Царевщина)
п. Стройкерамика
Похвистнево
Самара
Тольятти
Ульяновск
Саратовская область
Саратов
Сахалинская область
Южно-Сахалинск
Свердловская область
Екатеринбург
Нижний Тагил
Ставропольский край
Михайловск
Невинномысск
Ставрополь
Тверская область
Тверь
Тульская область
Тула
Тюменская область
Тобольск
Тюмень
Ялуторовск
Ульяновская область
Ульяновск
Хабаровский край
Хабаровск
Ханты-Мансийский АО (Югра)
Лангепас
Мегион
Нефтеюганск
Нижневартовск
Сургут
Челябинская область
Челябинск
Читинская область
Чита
Ярославская область
Ярославль
Грунтовка глубокого проникновения 2 в 1 Текс Универсал, 2,5 л цена
Укрепляет бетонные и деревянные поверхности
Одно из универсальных средств, позволяющих выровнять впитывающую способность основы из кирпича, бетона, гипсокартонных плит, оштукатуренных плоскостей или древесины, предлагаемая компанией Текс пропиточная грунтовка Универсал.
Грунтовка Текс Универсал 2 в 1 – это пропитка глубокого проникновения, которая укрепляет мелящие и неустойчивые поверхности, обеспечивая скрепление частиц основы с целью надежного крепления покрывных материалов.
Снижает расход покрывных материалов
К преимуществам пропиточной грунтовки Универсал Текс можно отнести способность пропитывать основу на глубину до 6 мм, чем усиливать адгезию с наносимыми впоследствии покрытиями. Расход финишных материалов сокращается, так как пропитка способствует изменению впитывающей способности плоскостей. После обработки степень этого показателя значительно снижается.Сокращение расходной части в отношении декоративных покрытий выгодно при выборе в качестве таковых дорогих рельефных красок или составов, которые лучше наносятся на основу с равномерным коэффициентом поглощения. Поэтому лучше не экономить на пропиточной грунтовке Универсал Текс, цена которой ниже, чем, например, текстурной краски Универсал, чтобы не столкнуться с неприятными последствиями в виде трещин или облупливания.
На что обратить внимание?
Поскольку предлагаемое средство применяется для обработки пористых материалов разной плотности, то и расход может сильно отличаться в зависимости от характеристик основания, на которое наносится пропитка. Одного литра состава может хватить, чтобы обработать плоскость площадью 5-14 кв. м. Такой разброс говорит о том, что расход средства сильно зависит от впитывающей способности материала.Покупая грунтовку глубокого проникновения 2 в 1 Универсал Текс, рассчитайте необходимое количество в зависимости от тех поверхностей, на которые она будет наноситься. В любом случае вы можете проконсультироваться у нашего менеджера и получить консультацию компетентного специалиста.
антигрибковые составы для бетонных полов, проникающий акриловый грунт
Сегодня для выполнения отделочных работ в помещении применяется множество разнообразных материалов, и особое место в этом списке занимает грунтовка глубокого проникновения. Благодаря использованию данного состава, ремонтный процесс можно произвести на довольно качественном уровне.
Сегодня грунтовка представлена в нескольких видах, которые подходят для разных типов работ. Но сначала необходимо ознакомиться с особенностями данного материала.
Особенности
Перед тем как ознакомиться с основными видами грунтовок глубокого проникновения, необходимо понять, что представляет собой этот материал и чем он отличается от других составов.
Этот вариант является своеобразной пропиткой для бетонной поверхности. Грунтовка способна проникать на глубину от 5 до 10 мм в зависимости от используемого вида.
Благодаря применению этого состава можно обеспечить максимальное сцепление бетона и материала для отделки. Проникающая грунтовка отличается высокой степенью влагостойкости и к тому же обладает паропроницаемыми свойствами.
Кроме этого, она имеет высокие антисептические свойства, не позволяющие развиваться грибку и плесени на бетонной поверхности.
Еще одна особенность проникающей грунтовки заключается в том, что она способна снизить расход тех отделочных материалов, которые будут использоваться в дальнейшем.
Применение состава положительно влияет на воздухообмен в помещении. При этом грунтовка выполняет изолирующую функцию внутри материала.
После обработки проникающим составом поверхность становится более устойчивой к различным внешним воздействиям. К примеру, это касается применения химических веществ, которые нередко приводят к истиранию.
Сфера применения
Как уже было отмечено выше, грунтовка применяется в процессе подготовки стен. Состав используется, если существует риск того, что материал для отделки слабо зафиксируется на бетонной поверхности.
Грунтовка глубокого проникновения значительно улучшает адгезию основания, что исключает возникновение подобной проблемы во время работы.
Нередко состав используется при отсутствии утепления монолита. На основании с большим количеством пор отделочные материалы фиксируются не лучшим образом. Именно поэтому специалисты рекомендуют использовать грунтовку глубокого проникновения, которая «запечатывает» все каналы. Состав препятствует быстрому впитыванию различных веществ, что позволяет надежно зафиксировать отделку.
Грунтовка глубокого проникновения используется как для внутренних, так и для фасадных работ. Она хорошо защищает бетонные поверхности от влияния агрессивных веществ, присутствующих в атмосфере.
Основные виды
Строительный рынок богат различными видами грунтовок глубокого проникновения. Чтобы понять, какой из вариантов лучше всего использовать для подготовки бетонной поверхности, необходимо ознакомиться со свойствами каждого отдельного состава.
Первым и одним из наиболее распространенных видов является универсальная грунтовка. Чаще всего состав используется для проведения внутренних работ. Нередко универсальные проникающие варианты применяются для наружных облицовочных ремонтных процессов.
Грунтовки подходят как для вертикальных, так и для горизонтальных поверхностей.
Что же касается стоимости универсальных вариантов, то она относительно невысокая. Кроме того, расход грунтовки во время работы небольшой, что является одним из весомых преимуществ. Универсальные варианты рекомендуется хранить при температуре от 5 до 35 градусов.
После обработки проникающей грунтовкой бетонную поверхность необходимо оставить на 4-5 часов, чтобы она полностью просохла.
Как утверждают сами производители, универсальные составы относятся к экологически безопасным группам строительных товаров. После обработки поверхность будет хорошо укреплена и подготовлена для дальнейших манипуляций. Нередко универсальная грунтовка применяется на стяжке с подогревом.
Следующий вид – акриловые составы. Этот вариант можно применять для обработки любых оснований, начиная от дерева и заканчивая бетоном. Многие специалисты относят акриловую грунтовку к универсальным видам. Главной особенностью состава является глубокое проникновение в основание, что значительно упрощает весь ремонтный процесс в дальнейшем.
Нередко производители дополняют основу грунтовки различными добавками, что повышает ее эксплуатационные характеристики. Чаще всего состав сочетают с антисептическими компонентами, благодаря чему пропитку можно применять для подготовки поверхностей в санузле.
Грунтовка предотвращает появление плесени, которая возникает при воздействии сильной влажности.
Отдельным видом являются антигрибковые составы. Эта проникающая грунтовка подходит для разных поверхностей, в том числе и для бетона. Отличительной особенностью данного вида является наличие фунгицидов в основе – компонентов, которые способны быстро уничтожать грибковые споры. Кроме этого, пропитка препятствует развитию вредной микрофлоры в помещении.
Антригрибковые грунтовки могут иметь разную основу, что является их главным плюсом. Для подготовки бетонных поверхностей применяются разные типы составов. Стоит отметить, что использовать такие пропитки рекомендуется для обработки тех поверхностей, которые уже подверглись поражению плесенью.
Обратите внимание и на то, что антигрибковые составы используются исключительно для подготовки основания под обои. Кроме этого, пропитка имеет довольно резкий запах.
Другим видом является антисептическая проникающая грунтовка. В отличие от предыдущего варианта эти составы используются для предупреждения развития вредной микрофлоры. Грунтовка применяется для обработки еще непораженных поверхностей.
Чаще всего антисептические составы используются для подготовки стен и пола в туалете и ванной. Применяется грунтовка перед укладкой напольного материала. В основе качественной антисептической пропитки всегда присутствуют фунгициды. Преимущество грунтовок заключается в том, что они выполняют укрепляющую функцию в работе с рыхлыми основаниями.
Для устранения недостатков на поверхности используются латексные пропитки глубокого проникновения. В их основу входят вода и полимеры, обеспечивающие достойные технические свойства данному виду. Эти составы незаменимы для обработки металла, бетона и древесины. Нередко этот вид грунтовки сочетают с алкидными вариантами.
Универсальность составов заключается в том, что их можно использовать для внутренних и наружных работ. Латексная грунтовка хорошо укрепляет основания, которые сильно впитывают в себя различные вещества.
Отдельным видом являются фасадные пропитки. Силиконовые и силикатные составы являются идеальным решением для проведения наружных работ. С помощью таких вариантов можно произвести обработку трещин перед заполнением.
Как выбрать?
Выбирая качественную пропитку для бетонной поверхности, следует обратить внимание на несколько важных моментов.
- Тип работы. Если вы намерены использовать грунтовку для наружных работ, лучше всего выбирать акриловые или силикатные составы, которые отличаются высокой устойчивостью к низким температурам. Латексные или акриловые пропитки – идеальный выбор для обработки стен внутри помещения.
- Материал. Для бетонных поверхностей рекомендуется использовать алкидные или акриловые составы, которые надежно укрепят основание и качественно подготовят его к дальнейшим манипуляциям.
- Отделка. Заранее определитесь с тем, какой материал вы будете использовать после подготовки поверхности. Для обоев, штукатурки или краски применяются разные виды пропиток.
Еще один значимый критерий – время высыхания. Если грунтовка применяется для внутренних работ, то лучше всего использовать составы, которым требуется 2-3 часа. Обусловлено это тем, что грунтовку наносят в несколько слоев, и длительное высыхание значительно замедляет ремонтный процесс.
Также следует обратить внимание на производителя и стоимость проникающего состава. Лучше всего выбирать товар от известной марки, которая успела хорошо себя зарекомендовать.
Как наносить?
Работая с пропиткой глубокого проникновения для бетона, следует учесть несколько важных правил. Перед нанесением состава необходимо тщательно подготовить основание. Нужно очистить поверхность от загрязнений, трещины зашпатлевать, а пятна устранить специальным раствором. Бетонное основание должно быть чистым и сухим.
Далее нужно приготовить строительную смесь, ориентируясь на инструкцию от производителя. Чаще всего состав замешивают в соотношении 1: 1 (грунтовка и вода). Для нанесения готовой смеси используют кисть или валик. Ускорить процесс подготовки поверхности поможет краскопульт.
Обратите внимание на то, что перед началом работы рекомендуется надеть резиновые перчатки. Это защитит кожу от попадания состава. После этого проникающую пропитку наносят равномерно распределяя по всей поверхности. Если основание отличается быстрой впитываемостью, понадобится 2 слоя.
Что же касается расхода проникающей грунтовки, то здесь все зависит от самой поверхности. Средние показатели составляют 80-120 г на 1 м². Специалисты рекомендуют оставить поверхность на 24 часа, чтобы она полностью была готова к дальнейшим манипуляциям.
О том, как выбрать грунтовку, смотрите в следующем видео.
Грунтовка укрепляющая глубокого проникновения «Oscar» 10 кг
Грунтовка укрепляющая глубокого проникновения «Oscar» в герметичном ведре. Вес нетто 10 кг. Идеальная формула для профессиональной подготовки поверхности. Позволяет обработать до 100 кв.м. поверхности.
Свойства
- Надёжно укрепляет осыпающиеся поверхности, улучшает адгезию финишных покрытий (краска, обои, стеклообои, малярные стеклохолсты и флизелины, декоративные штукатурки, шпатлёвки, облицовочная плитка), заметно уменьшает повышенную впитываемость пористых поверхностей.
- Обладает повышенной проникающей способностью, благодаря мелкодисперсному составу.
- Придаёт покрытию дополнительную влагостойкость и износостойкость.
- Сохраняет паро и воздухопроницаемость поверхностей.
- Эффективно препятствует росту бактерий, грибка и плесени.
- Идеально подходит для любых внутренних и внешних работ.
- Морозостойкая. Допускается многократное замораживание.
- Проверенная формула на основе латекса, не содержит поливинилацетат (ПВА).
- За счёт латексной основы может применяться на стяжках с подогревом.
- Без резкого запаха, легко наносится валиком или кистью, не разбрызгивается.
- Экономичный расход: от 100 до 250 г/м2 в зависимости от типа поверхности и температурно-влажностных условий нанесения.
- Экологически чистый и полностью безопасный для людей и домашних животных состав.
Область применения
Применяется для обработки поверхностей потолков, стен и полов, устроенных из бетона, гипсовых и цементных штукатурок и стяжек, гипсокартонных и гипсоволоконных листов, пазогребневых и цементностружечных, древесностружечных и древесноволоконных плит, кирпича, лёгкого и ячеистого бетона, ангидритных стяжек, кладок из натурального камня и т. д.
Благодаря мелкодисперсному составу обладает повышенной проникающей способностью, снижает впитывающую способность оснований, связывает пыль, укрепляет поверхность, предотвращает пересыхание тонкослойных выравнивающих смесей, повышает адгезию материалов к основанию, повышает растекаемость напольных смесей и предотвращает появление пузырьков воздуха на выравнивающем слое, повышает влагостойкость и износостойкость поверхностей, содержит противоплесневые, противогрибковые и антибактериальные добавки.
Подготовка основания
Основание должно быть сухим и очищенным от любых загрязнений и воздухонепроницаемых материалов (пыль, жировые и масляные пятна, масляная краска и т.п.). Осыпающиеся и непрочные участки основания, ослабленный поверхностный слой, выделения из водно-цементной смеси следует удалить. Конструктивные элементы, не подлежащие грунтованию (дверные полотна, коробки, наличники, оконные рамы, напольные покрытия и пр.) следует укрыть водонепроницаемым материалом и защитить малярной лентой.
Выполнение работ
Грунтовку наносят кистью или малярным валиком, не допуская скопления большого количества грунтовочного состава на поверхности. Время высыхания грунтовки составляет до 2 часов в зависимости от температуры, влажности воздуха, количества нанесённой грунтовки и впитывающей способности основания. После высыхания грунтовки проверить основание на впитывающую способность и, при необходимости, обработать поверхность ещё раз.
Сильновпитывающие основания, например, ячеистый бетон, рекомендуется грунтовать не менее двух раз. Второй слой грунтовки наносят после полного высыхания первого. Свежие пятна грунтовки можно удалить водой, засохшие удаляются при помощи бытовых растворителей.
Рекомендации
Внутренние и внешние работы следует выполнять в сухих условиях, при температуре воздуха и основания от +5 до +35°C и относительной влажности воздуха не выше 80%.
Срок хранения
В оригинальной герметичной упаковке, при температуре от +5 до +35°C — не более 12 месяцев со дня изготовления. Допускается многократное замораживание при температуре до –40°C.
Упаковка
Грунтовка поставляется в герметичных пластиковых 10-килограммовых вёдрах.
Технические характеристики
- Область применения: для внутренних и наружных работ.
- Состав: латекс, вода, антисептик, поверхностно-активные вещества (ПАВ), пеногаситель, противогрибковые добавки.
- Цвет плёнки: молочно-прозрачный.
- Массовая доля сухого остатка, %, не менее: 6,5.
- Условная вязкость по стандартной кружке ВМС, с: 2 – 10.
- Показатель концентрации водородных ионов, pH : 6 – 8.
- Время высыхания: 2 – 4 часа.
- Температура транспортировки и хранения: от +5°С до +35°С (допускается не менее 4 циклов замораживания-оттаивания при температуре –40°C).
- Температура применения: от +5°С до +35°С.
- Расход: 0,1–0,25 л/м2 при однократном нанесении в зависимости от впитывающей способности основания (одна упаковка 10 кг – на 100 м2 поверхности).
обзоров, описание, виды и отзывы. Грунтовка для глубокого проникновения по бетону
Перед началом работ, связанных с отделкой поверхностей зданий из бетона, их необходимо загрунтовать, для чего используются разные типы грунтовок.
Грунтовка для бетона и штукатурки: назначение
Основное назначение грунтовки — укрепление оснований, а также их защита от различных негативных атмосферных воздействий. Стоимость этого материала невысока, несмотря на то, что он выполняет важную функцию.
Плюсы использования грунтовки
Из положительных сторон грунтовочного материала по отзывам пользователей можно выделить следующие:
- свойства обрабатываемой поверхности остаются неизменными;
- продлен срок службы фундамента;
- при ремонте крепится фундамент и отделочные материалы;
- грунтовка для бетона служит изолятором, исключающим возможность контакта с непригодными материалами.
Рекомендации : некоторые разновидности грунтовок могут использоваться в качестве материала, подходящего для завершающей стадии при отделке поверхностей.
Подготовка основания
Поверхность, на которую был нанесен бетон надлежащего качества, характеризующийся мелкодисперсной структурой, за счет чего отличается идеальной гладкостью (например, полы из бетонных плит, а также панельные дома) . Однако следует отметить, что на такой основе клей и шпатлевка просто не цепляются, плохо ложатся.
Со временем:
- обои быстро начинают отслаиваться;
- шпатлевка подверженная отслаиванию;
- На штукатурке появляются трещины.
Если отделку проводят высококвалифицированные специалисты, то перед началом ремонтных работ определяют характеристики поверхностей.
Если на старой отделке имеется большое количество разного рода повреждений, это говорит о том, что стены не подвергались необходимой обработке, не проводились предварительные подготовительные работы, включающие очистку поверхности и грунтовку по бетону.
Этапы очистки поверхности и грунтовки
1. Перед нанесением грунтовки на основание рекомендуется тщательно очистить его оригинальным покрытием, где, скорее всего, скопилась ненужная пыль.
2. Все имеющиеся дефекты (трещины, неровности) на поверхности должны быть полностью устранены.
3. Далее на основание нанести грунтовку глубокого проникновения для бетона, которая поможет укрепить поврежденные участки.
4. После выполнения вышеуказанных действий основание должно быть выровнено.
Перед покраской стен также рекомендуется их покрасить. Для этого также используется грунтовка для глубокого проникновения по бетону.
Рекомендации : Для защиты поверхности от микроорганизмов необходимо нанести в состав грунтовку, содержащую антисептик. Применяется при обработке наружных стен зданий, а также в помещениях с повышенным уровнем влажности.
Нанесение грунтовки
Наносите этот материал валиком или кистью.
Кроме того, не забываем о рекомендациях по расходу средства, которые имеются на упаковке:
- В силу своих свойств поверхность не способна впитывать количество грунтовки, превышающее обозначенный объем.
Излишки материала просто высохнут, что не принесет никакой пользы.
- Если праймера нанести меньше необходимого количества, то и от этого толку не будет, так как в подвал не проникнет, соответственно, укрепить не может.
Рекомендации : Перед нанесением грунтовки необходимо завершить работы с основанием и стенами.
Виды грунтовки
Материал предназначен для обработки внутренних и внешних поверхностей. Грунтовка для бетона для наружных работ с таким же успехом может применяться и для внутренних работ. Однако из-за того, что в состав входят опасные для дыхательной системы компоненты, необходимо после использования проветривать помещения.
Существуют следующие разновидности:
- Грунтовка для армирования бетона, с глубоким проникновением.
- Текстура, включающая наполнители. Их используют для последующей работы с поверхностями (например, акриловой грунтовкой по бетону).
- Изолирующий. Защищают от неблагоприятного воздействия климатических условий, химикатов, механических воздействий (в их состав входит силикон, полиуретан и эпоксидная грунтовка для бетона).
- Грунтовки с антисептиками: защищают от плесени и грибка.
В зависимости от типа поверхности грунтовки делятся на:
- Грунтовки, предназначенные для гладкой поверхности (выполняют функцию защиты от влаги, используются для окраски или оштукатуривания).
- Грунтовки для ячеистого бетона (характеризуются хорошей вязкостью, в их состав входят силикатные наполнители, предназначенные для заполнения пор). Они отлично впитывают, но плохо укрепляют бетон.
В инструкции на упаковке материала указано, для какой поверхности предназначена грунтовка по бетону — для наружных работ или для внутренних.
Советы специалистов
При выборе грунта:
1. Необходимо выяснить, для чего предназначен состав (для подготовки поверхности к штукатурке или покраске, для гидроизоляции).
2. Необходимо знать, из какого материала выполнено основание (бетон свежий или старый, плотный или ячеистый). Исходя из этого и следует выбирать грунтовку с соответствующими характеристиками.
3. Необходимо рассчитать расход грунтовки.
Рекомендации : необходимо помнить, что состав не способен укреплять бетон, потому что его нельзя добавлять в раствор.
Глубина максимального проникновения 70 мм, создается защитный слой. Этот материал, как бампер, принимает на себя весь удар, выполняя функцию защиты основания.
Основа, обработанная грунтовкой, сохранит свои свойства намного дольше и лучше. Но если этот материал добавить в раствор, он от этого не станет прочнее без применения специально предназначенных для этих целей добавок.
Рекомендации : нецелевое использование грунта в бетоне может снизить прочностные характеристики.
Для добавления в бетонный раствор специальных компонентов, повышающих его прочность, необходимо специальное строительное или инженерное образование.
Заключение
Грунтовка поверхностей из бетона позволяет использовать их для последующих отделочных работ, а также способствует их укреплению, защищает от грибка. Перед приобретением необходимого материала необходимо выяснить структуру основания, которая поможет подготовить его наилучшим образом.
Грунтовка по бетону, цена которой от 450 руб. — качественный и экологически чистый материал без специфического запаха. Реализуется в различной вместимости и имеет различную упаковку.
Глава 2 — Комплексные системы защиты от коррозии для компонентов железобетонных мостов, ноябрь 2011 г.
ГЛАВА 2. ЭКСПЕРИМЕНТАЛЬНЫЕ РАБОТЫ
СИСТЕМЫ ЗАЩИТЫ ОТ КОРРОЗИИ
Это исследование включало оценку 11 систем, в которых ECR сочеталась с другой системой защиты от коррозии.Исследование включало семь типов стержней: один без покрытия и шесть с наплавленным эпоксидным покрытием, изготовленным из стали той же плавки. Обычная арматурная сталь без покрытия и обычная ЭКР служили в качестве контроля. Множественные системы защиты от коррозии включали обычный ECR в сочетании с одним из трех ингибиторов коррозии; бруски, которые были обработаны грунтовочным покрытием, содержащим микрокапсулированный нитрит кальция (ингибитор коррозии), перед покрытием обычной эпоксидной смолой; стержни с улучшенной адгезией между эпоксидной смолой и армирующей сталью, полученные за счет использования предварительной обработки хроматом цинка или специальных эпоксидных смол с более высокой адгезией; сочетание брусков с эпоксидной смолой с улучшенной адгезией и добавкой нитрита кальция в раствор или бетон; и стержни с несколькими покрытиями, состоящими из слоя толщиной 50 м (2 мил), состоящего из 98 процентов цинка и 2 процентов алюминия, который, в свою очередь, был покрыт обычной эпоксидной смолой. Кроме того, вторая плавка обычной арматуры была использована для оценки коррозионных характеристик стального литья без покрытия в бетоне, содержащем один из трех ингибиторов коррозии, использованных в исследовании. Системы перечислены в таблице 1 вместе с сокращенными обозначениями, используемыми в этом отчете.
Таблица 1. Исследуемые системы.
Ингибиторы коррозии
Прутки без покрытия с Ca (NO 2 ) 2
901 ECR (HY)03 901 222 +
22 Эпоксидные смолы с повышенной адгезией плюс нитрит кальция в строительном растворе или бетоне ECR (Valspar) с несколькими покрытиямиСистема | Сокращение | |
Control | ||
Обычные непокрытые арматурные стержни 9152.и Conv.2 | ||
Обычный ECR | ECR | |
Эпоксидные смолы с повышенной адгезией | ||
Предварительная обработка хроматом 9603 Покрытие DuPont ™ | ECR (DuPont) | |
Покрытие Valspar ® | ECR (Valspar) | |
Конв. | ||
Стержни без покрытия с Hycrete | Conv.2 (HY) | |
Стержни без покрытия с Rheocrete 3 222 8 (RH) | ||
ECR с нитритом кальция | ECR (DCI) | |
ECR с Hycrete ™ | ECR (HY) 03 | ECR (RH) |
Грунтовка 3M ™, содержащая нитрит кальция | ECR (праймер / Ca (NO 2 ) 2 | |
Предварительная обработка хроматом | ECR (Хромат) -D CI | |
Покрытие DuPont ™ | ECR (DuPont) -DCI | |
Valspar ® с покрытием | ||
MC |
Системы управления
Обычная сталь без покрытия (конв. )
За исключением испытаний для оценки непокрытых стержней в бетоне, содержащих ингибиторы коррозии, все испытания стержней без покрытия и с покрытием включали использование однократной плавки № 16 (№ 5) класса 420 (60). Арматурная сталь ASTM A615, обозначенная как «Конв.» (12) Арматура без покрытия, использованная в испытаниях ингибитором коррозии, обозначается как «Conv.2». Химический анализ представлен в таблице 2.
Таблица 2. Химический анализ стали в процентах.
16 (5)
Сталь | Размер стержня No. | Число плавок | C | Mn | Si | пол | пол | Cr | Ni | Пн | Cu | B | ||||||||||||||
---|---|---|---|---|---|---|---|---|---|---|---|---|---|---|---|---|---|---|---|---|---|---|---|---|---|---|
Конв.![]() | 16 (5) | 231159 | 0,43 | 0,95 | 0,21 | 0,014 | 0,046 | 0,20 | 0,17 | 0,038 | 42 0,49 | 42 0,49 | 42 0,49 | Нет | Нет | Нет | Нет | Нет | НЕТ | НЕТ | НЕТ | НЕТ | НЕТ |
C = Углерод; Mn = марганец; Si = Кремний; P = фосфор; S = сера; Cr = хром; Мо = молибден;
Cu = медь; N = азот; B = бор.
N / A означает, что химический анализ недоступен.
Обычный ECR
Обычная арматура, покрытая термореактивной эпоксидной смолой, склеенной плавлением, использованная в качестве контроля, была покрыта Scotchkote ™ 413, производимой 3M ™.
Эпоксиды с повышенной адгезией
Был использован ряд методов для улучшения адгезии эпоксидных покрытий к стали. В этом исследовании оценивались три системы. Первый заключался в предварительной обработке стали без покрытия хроматом цинка перед нанесением эпоксидного покрытия.Эта процедура используется в Канаде для всех ECR, но поскольку она включает использование шестивалентного хромата, что представляет серьезную проблему для окружающей среды, она не получила широкого распространения в Соединенных Штатах. В качестве альтернативы DuPont ™ и Valspar ® разработали эпоксидные порошки с улучшенной адгезией к арматурной стали, которые не требуют предварительной обработки стержней. Эти три системы обозначаются как ECR (Chromate), ECR (DuPont) и ECR (Valspar).
Ингибиторы коррозии
Были исследованы три ингибитора коррозии, один неорганический и два органических.Нитрит кальция является наиболее широко используемым неорганическим ингибитором коррозии в практике США. Поскольку нитрит кальция действует как ускоритель схватывания, в этом исследовании использовалась смесь dci ® s, производимая Grace Construction Products и содержащая замедлитель схватывания. Ингибиторами органической коррозии были Rheocrete ® 222 + , комбинация аминов и сложных эфиров на водной основе, производимая BASF Admixtures, и Hycrete ™, соль алкенилзамещенной янтарной кислоты, производимая Broadview Technologies для этого исследования и производимая в настоящее время. компании Hycrete, Inc.Четвертая система, в которой эпоксидное покрытие Scotchkote ™ 413 было нанесено на стержни после нанесения грунтовочного покрытия, содержащего микрокапсулированный нитрит кальция, также была оценена. Согласно 3M ™, система обеспечивает защиту, выделяя нитрит кальция при повреждении эпоксидного покрытия. Системы обозначены, соответственно, как ECR (DCI), ECR (HY), ECR (RH) и ECR (праймер / Ca (NO 2 ) 2 ). Три ингибитора коррозии (DCI ® S, Hycrete ™ и Rheocrete ® ) также были изучены в сочетании с обычной арматурой без покрытия и обозначены как Conv.
2 (DCI), Conv.2 (HY) и Conv.2 (RH), соответственно.
Эпоксиды с повышенной адгезией плюс нитрит кальция
Три типа ЭЦР с улучшенной адгезией были также испытаны для строительного раствора и бетона, содержащих ингибитор коррозии нитрит кальция. Системы обозначены как ECR (Chromate) -DCI, ECR (DuPont) -DCI и ECR (Valspar) -DCI.
Multiple Coatings
Western Coating разработала запатентованный процесс для прутков с многослойным покрытием (MC), который включает нанесение слоя 98% цинка и 2% алюминия на арматурную сталь с использованием процесса термического напыления до нанесения эпоксидной смолы. покрытие.Слой цинка имеет номинальную толщину 50 м (2 мил). После нанесения цинка стержни в этом исследовании были покрыты DuPont ™ 8-2739 Flex West Blue, обычной эпоксидной смолой.
Один аппликатор нанес эпоксидную смолу на обычные стержни ECR и ECR (Valspar). Второй аппликатор обрабатывал стержни MC и ECR (DuPont), в то время как два других аппликатора отдельно обрабатывали стержни ECR (Хромат) и ECR (праймер / Ca (NO 2 ) 2 ).
ПРЕДВАРИТЕЛЬНАЯ ОЦЕНКА БРУСОВ С ЭПОКСИДНЫМ ПОКРЫТИЕМ
Перед испытанием на коррозию стержни, использованные в этом исследовании, были оценены на предмет толщины покрытия и количества пропусков.Стержни также оценивали на адгезию покрытия с использованием испытания на катодное отслоение в соответствии с ASTM A775-04a и ASTM G8-96 (далее именуемые ASTM A775 и ASTM G8, соответственно). (13,14)
Оценка толщины покрытия и пропусков
Шесть типов стержней ECR, использованных в этом исследовании, были оценены на предмет толщины покрытия и количества пропусков. Результаты приведены в таблице 3. Все стержни соответствуют требованиям к толщине покрытия ASTM A775, за исключением стержней с грунтовочным покрытием из нитрита кальция, которые, как правило, имеют больший процент измерений покрытия ниже 175 и 125 мкм (6.89 и 4,92 мил), чем максимально допустимые значения на 10 и 5 процентов соответственно. [1] (13) Только бруски с грунтовочным покрытием из нитрита кальция имели выходы, хотя количество выходов было ниже максимально допустимого значения 3 выходных / м (1 выходных / фут), указанного в ASTM A775. Остальные пять типов столбцов не показали измеримых выходных на полноразмерных столбцах. Однако дополнительные испытания образцов небольших стержней показали наличие небольшого количества выходных дней на всех типах стержней.
Таблица 3.Толщина покрытия.
46 Среднее значение ( 46 из ВариантТип стержня | Количество измерений a | Максимум ( ) | Минимум ( ) | |||||||||||||||||||||||||||||||||||||||||||||||||||||||||||||||||||||||||||||||||||||||||||||||||||||||||||||||||||||||||||||||||||||||||||||||||||||||||||||||||||||||||||||||||||||||||||||||||||||||||||||||||||||||||||||||||||||||||||||||||||||||||||||||||||||||||||||||||||||||||||||||||||||||||||||||||||||||||||||||||||||||||||||||||||||||||||||||||||||||||||||||||||||||||||||||||||||||||||||||||||||||||||||||||||||||||||||||||||||||||||||||||||||||||||||||||||||||||||||||||||||||||||||||||||||||||||||||||||||||||||||||||||||||||||||||||||||||||||||||||||||||||||||||||||||||||||||||||||||||||||||||||||||||||||||||||||||||||||||||||||||||||||||||||||||||||||||||||||||||||||||||||||||||||||||||||||||||||||||||||||||||||||||||||||||||||||||||||||||||||||||||||||||||||||||||||||||
---|---|---|---|---|---|---|---|---|---|---|---|---|---|---|---|---|---|---|---|---|---|---|---|---|---|---|---|---|---|---|---|---|---|---|---|---|---|---|---|---|---|---|---|---|---|---|---|---|---|---|---|---|---|---|---|---|---|---|---|---|---|---|---|---|---|---|---|---|---|---|---|---|---|---|---|---|---|---|---|---|---|---|---|---|---|---|---|---|---|---|---|---|---|---|---|---|---|---|---|---|---|---|---|---|---|---|---|---|---|---|---|---|---|---|---|---|---|---|---|---|---|---|---|---|---|---|---|---|---|---|---|---|---|---|---|---|---|---|---|---|---|---|---|---|---|---|---|---|---|---|---|---|---|---|---|---|---|---|---|---|---|---|---|---|---|---|---|---|---|---|---|---|---|---|---|---|---|---|---|---|---|---|---|---|---|---|---|---|---|---|---|---|---|---|---|---|---|---|---|---|---|---|---|---|---|---|---|---|---|---|---|---|---|---|---|---|---|---|---|---|---|---|---|---|---|---|---|---|---|---|---|---|---|---|---|---|---|---|---|---|---|---|---|---|---|---|---|---|---|---|---|---|---|---|---|---|---|---|---|---|---|---|---|---|---|---|---|---|---|---|---|---|---|---|---|---|---|---|---|---|---|---|---|---|---|---|---|---|---|---|---|---|---|---|---|---|---|---|---|---|---|---|---|---|---|---|---|---|---|---|---|---|---|---|---|---|---|---|---|---|---|---|---|---|---|---|---|---|---|---|---|---|---|---|---|---|---|---|---|---|---|---|---|---|---|---|---|---|---|---|---|---|---|---|---|---|---|---|---|---|---|---|---|---|---|---|---|---|---|---|---|---|---|---|---|---|---|---|---|---|---|---|---|---|---|---|---|---|---|---|---|---|---|---|---|---|---|---|---|---|---|---|---|---|---|---|---|---|---|---|---|---|---|---|---|---|---|---|---|---|---|---|---|---|---|---|---|---|---|---|---|---|---|---|---|---|---|---|---|---|---|---|---|---|---|---|---|---|---|---|---|---|---|---|---|---|---|---|---|---|---|---|---|---|---|---|---|---|---|---|---|---|---|---|---|---|---|---|---|---|---|---|---|---|---|---|---|---|---|---|---|---|---|---|---|---|---|---|---|---|---|---|---|---|---|---|---|---|---|---|---|---|---|---|---|---|---|---|---|---|---|---|---|---|---|---|---|---|---|---|---|---|---|---|---|---|---|---|---|---|---|---|---|---|---|---|---|---|---|---|---|---|---|---|---|---|---|---|---|---|---|---|---|---|---|---|---|---|---|---|---|---|---|---|---|---|---|---|---|---|---|---|---|---|---|---|---|---|---|---|---|---|---|---|---|---|---|---|---|---|---|---|---|---|---|---|---|---|---|---|---|---|---|---|---|---|---|---|---|---|---|---|---|---|---|---|---|---|---|---|---|---|---|---|---|---|---|---|---|---|---|---|---|---|---|---|---|---|---|---|---|---|---|---|---|---|---|---|---|---|---|---|---|---|---|---|---|---|---|---|---|---|---|---|---|---|---|---|---|---|---|---|---|---|---|---|---|---|---|---|---|---|---|---|---|---|---|---|---|---|---|---|---|---|---|---|---|---|---|---|---|---|---|---|---|---|---|---|---|---|---|---|---|---|---|---|---|---|---|---|---|---|---|---|---|---|---|---|---|---|---|---|---|---|---|---|---|---|---|---|---|---|---|---|---|---|---|---|---|---|---|---|---|---|---|---|---|---|---|---|---|---|---|---|---|---|---|---|---|---|---|---|---|---|---|---|---|---|---|---|---|---|
ECR | 4 бара, 144 точки | 307 | 175 | 244 | 0.10 | |||||||||||||||||||||||||||||||||||||||||||||||||||||||||||||||||||||||||||||||||||||||||||||||||||||||||||||||||||||||||||||||||||||||||||||||||||||||||||||||||||||||||||||||||||||||||||||||||||||||||||||||||||||||||||||||||||||||||||||||||||||||||||||||||||||||||||||||||||||||||||||||||||||||||||||||||||||||||||||||||||||||||||||||||||||||||||||||||||||||||||||||||||||||||||||||||||||||||||||||||||||||||||||||||||||||||||||||||||||||||||||||||||||||||||||||||||||||||||||||||||||||||||||||||||||||||||||||||||||||||||||||||||||||||||||||||||||||||||||||||||||||||||||||||||||||||||||||||||||||||||||||||||||||||||||||||||||||||||||||||||||||||||||||||||||||||||||||||||||||||||||||||||||||||||||||||||||||||||||||||||||||||||||||||||||||||||||||||||||||||||||||||||||||||||||||||||
ECR (хромат) | 1 бар, 36 точек | 241 | 175 | 213 | 1 бар, 36 точек | 249 | 160 | 213 | 0,08 | |||||||||||||||||||||||||||||||||||||||||||||||||||||||||||||||||||||||||||||||||||||||||||||||||||||||||||||||||||||||||||||||||||||||||||||||||||||||||||||||||||||||||||||||||||||||||||||||||||||||||||||||||||||||||||||||||||||||||||||||||||||||||||||||||||||||||||||||||||||||||||||||||||||||||||||||||||||||||||||||||||||||||||||||||||||||||||||||||||||||||||||||||||||||||||||||||||||||||||||||||||||||||||||||||||||||||||||||||||||||||||||||||||||||||||||||||||||||||||||||||||||||||||||||||||||||||||||||||||||||||||||||||||||||||||||||||||||||||||||||||||||||||||||||||||||||||||||||||||||||||||||||||||||||||||||||||||||||||||||||||||||||||||||||||||||||||||||||||||||||||||||||||||||||||||||||||||||||||||||||||||||||||||||||||||||||||||||||||||||||||||||||||||||||||||||||
ECR 9 (Valspar) 9 (Valspar) | 262 | 175 | 226 | 0. | ||||||||||||||||||||||||||||||||||||||||||||||||||||||||||||||||||||||||||||||||||||||||||||||||||||||||||||||||||||||||||||||||||||||||||||||||||||||||||||||||||||||||||||||||||||||||||||||||||||||||||||||||||||||||||||||||||||||||||||||||||||||||||||||||||||||||||||||||||||||||||||||||||||||||||||||||||||||||||||||||||||||||||||||||||||||||||||||||||||||||||||||||||||||||||||||||||||||||||||||||||||||||||||||||||||||||||||||||||||||||||||||||||||||||||||||||||||||||||||||||||||||||||||||||||||||||||||||||||||||||||||||||||||||||||||||||||||||||||||||||||||||||||||||||||||||||||||||||||||||||||||||||||||||||||||||||||||||||||||||||||||||||||||||||||||||||||||||||||||||||||||||||||||||||||||||||||||||||||||||||||||||||||||||||||||||||||||||||||||||||||||||||||||||||||||||||||||
ECR (праймер / Ca (NO 2 ) 2 ) | 4 бара, 126 точек | 264 | 52 102438 0,16 | |||||||||||||||||||||||||||||||||||||||||||||||||||||||||||||||||||||||||||||||||||||||||||||||||||||||||||||||||||||||||||||||||||||||||||||||||||||||||||||||||||||||||||||||||||||||||||||||||||||||||||||||||||||||||||||||||||||||||||||||||||||||||||||||||||||||||||||||||||||||||||||||||||||||||||||||||||||||||||||||||||||||||||||||||||||||||||||||||||||||||||||||||||||||||||||||||||||||||||||||||||||||||||||||||||||||||||||||||||||||||||||||||||||||||||||||||||||||||||||||||||||||||||||||||||||||||||||||||||||||||||||||||||||||||||||||||||||||||||||||||||||||||||||||||||||||||||||||||||||||||||||||||||||||||||||||||||||||||||||||||||||||||||||||||||||||||||||||||||||||||||||||||||||||||||||||||||||||||||||||||||||||||||||||||||||||||||||||||||||||||||||||||||||||||||||||||||||
MC | 1 бар, 36 точек | 251 | 213 | 236 | 52 0,04 0394 мил Испытания на катодное расслоение Испытания на катодное отсоединение включают проникновение эпоксидного покрытия на испытуемый образец с помощью сверла диаметром 3 мм (0,12 дюйма). Затем образец погружают на 168 часов в раствор электролита (3% хлорида натрия) при температуре 24 ± 2 ° C (75 ± 3,6 ° F) и выдерживают при разности потенциалов -1,5 В с анодом, измеренной относительно насыщенного каломельный электрод (SCE).Схема испытаний, описанная в ASTM A775, показана на рисунке 1. Рисунок 1. Иллюстрация. Установка для испытания катодного отслаивания (после ссылки 13). Обследование проводится сразу по окончании испытания. По окончании периода испытаний зону испытания ополаскивают теплой водопроводной водой. Образец сразу вытирают насухо и визуально исследуют всю площадь покрытия по краю умышленного дефекта. Новый дефект, который может служить ориентиром, просверливается в части покрытой области, которая не была погружена.Два радиальных разреза под углом 90 градусов друг к другу и под углом 45 градусов относительно продольной оси стержня выполняются через покрытие, пересекая центр обоих намеренных дефектов, с помощью острого ножа с тонким лезвием. Затем делается попытка поднять покрытие острием ножа как на эталонном дефекте, так и на затопленном дефекте. Связка на эталонном дефекте затем используется для оценки качества связи при затопленном отпуске. Наконец, измеряются и регистрируются увеличение радиальной площади и общей площади отслоившегося покрытия на затопленном дефекте. В этом исследовании было проведено три цикла испытаний на катодное отслоение, по одному образцу на цикл для каждого из шести типов ЭЦР. Испытания также проводились на обычных стержнях с эпоксидным покрытием, которые использовались в предыдущем исследовании. В соответствии со стандартом ASTM A775 были проведены четыре радиальных измерения области отслоения под углом 0, 90, 180 и 270 градусов по отношению к продольной оси стержня, и значения были усреднены. (13) Испытания на катодное отслоение регистрировали как по площади отслоившегося покрытия (в соответствии с ASTM G8), так и по среднему радиусу отслоения покрытия (четыре измерения). (14) Результаты приведены в таблице 4. Площадь отслоившегося покрытия и радиус не включают первоначальное проникновение через покрытие. Как показано в таблице 4, средний радиус отслоения покрытия был выше 4 мм (0,16 дюйма), максимально разрешенный в приложении A1 к ASTM A775, для обычных стержней ECR и ECR (Valspar), что указывает на то, что эти стержни не соответствовали требованиям к отслоению покрытия. Таблица 4. Результаты катодного отслоения 0,5279 9000Pont 2 909 90965 909909Ca 2 )
1 м = 0,0394 мил Критерии в приложении A1 к ASTM A775 являются квалификационными требованиями для самого эпоксидного покрытия и не предназначены для применения к производственным стержням, таким как те, которые использовались в этом исследовании. ПРОЦЕДУРЫ ИСПЫТАНИЙ НА КОРРОЗИЮСистемы защиты от коррозии в этом исследовании были оценены с использованием комбинации лабораторных и полевых испытаний. Производительность каждой системы сравнивалась с характеристиками обычной арматуры из углеродистой стали без покрытия и без покрытия. Тесты включали экспресс-тесты макроячеек, стендовые тесты, линейное сопротивление поляризации и полевые тесты. Экспресс-тесты макроячеекКраткое описание метода Реакция нескольких систем защиты от коррозии была сначала оценена с помощью быстрого теста макроэлементов, первоначально разработанного в Канзасском университете в рамках программы стратегических исследований автомобильных дорог и с тех пор обновленного. Рисунок 2. Иллюстрация. Макроэлементный тест с образцами без покрытия. Рисунок 3. Иллюстрация. Макроэлементный тест с образцами, покрытыми строительным раствором. Рисунок 4. Тесты макроячейки, показанные на рисунках 2 и 3, требуют двух контейнеров.Образец для испытаний, брусок № 16 (№ 5) без покрытия или обернутый ступкой, помещают в контейнер объемом 1,5 л (1,6 кварты) вместе с имитирующим поровым раствором, содержащим предварительно выбранную концентрацию хлорида натрия (1,6 или 6,04). моль / кг (0,73 или 2,74 моль / фунт) концентрации иона растворителя (4,68 или 15 процентов)). Два образца помещают во второй контейнер и погружают в раствор с имитацией пор без добавления хлоридов. Для образцов, обернутых строительным раствором, в контейнеры добавляется измельченный раствор для более точного моделирования среды бетона.Глубина раствора дает 76 мм (3,0 дюйма) стержня (включая 13-мм (0,5 дюйма) пластмассовый колпачок, используемый для защиты конца стержней с эпоксидным покрытием) ниже уровня раствора. Два контейнера соединены солевым мостиком, и испытуемый образец в поровом растворе, содержащем хлорид натрия (анод), электрически соединен через единственный резистор сопротивлением 10 Ом с двумя образцами в имитирующем поровом растворе (катод). Скорость коррозии и потери от коррозии Скорость коррозии арматурной стали (измеренная в лабораторных и полевых испытаниях, а также в экспресс-тестах с использованием микроячеек) показывает, насколько быстро арматурная сталь окисляется.Его можно выразить как плотность тока в микроампер на квадратный сантиметр (А / см 2 ), которая получается путем измерения скорости потока электронов от анодов к катодам. Основываясь на законе Фарадея, плотность тока можно преобразовать в другое выражение для скорости коррозии — скорость потери металла с поверхности стали в м / год. Рисунок 5. Уравнение. Скорость коррозии железа. Где: R = Скорость коррозии, выраженная как скорость потери металла, м / год. i = Скорость коррозии, выраженная как плотность тока, А / см 2 . k = Коэффициент пересчета = 31,5 ’10 4 ампер ∙ м с / А см ∙ год. (30) a = Атомный вес металла = 55,8 г / моль для железа. n = Количество перенесенных электронов = 2 для железа. F = постоянная Фарадея = 96 500 кулонов / эквивалент. = Плотность металла, г / см 3 = 7,87 г / см 3 для железа. Например, при расчете потерь от коррозии для обычного стержня без покрытия, падение напряжения 0,70 мВ на резисторе 10 Ом представляет собой общий ток 70,0 А. Рисунок 6. Уравнение. Пример скорости коррозии железа. Для цинка, первого слоя покрытия стержней MC, уравнение на рисунке 5 становится уравнением на рисунке 7. Рисунок 7. Уравнение. Скорость коррозии цинка. Где: a = Атомный вес металла = 65,38 г / моль для цинка. n = Число перенесенных электронов = 2 для цинка. = Плотность металла, г / см 3 = 7,14 г / см 3 для цинка. Для железобетонных мостовых настилов измерение тока макроячейки, как правило, невозможно, поскольку верхний и нижний маты из арматурной стали обычно соединяются стальными проволочными стяжками и опорами стержней в бетонной плите.Однако в лабораторных испытаниях, имитирующих коррозию стали в настилах мостов, стяжки и стержневые опоры не используются, а ток макроячейки можно определить путем измерения падения напряжения на резисторе, который электрически соединяет анод и катод через внешнюю цепь. , как показано в уравнении на рисунке 8. Рисунок 8. Уравнение. Плотность тока коррозии. Где: i = Плотность тока коррозии, мА / см 2 . В = Падение напряжения на резисторе, мВ. R = Сопротивление резистора, кОм. A = Площадь оголенного металла на стержне анода, см 2 . На измеренную плотность тока макроячейки и рассчитанную скорость коррозии могут существенно повлиять методы испытаний и детали конфигурации испытания, такие как соотношение площадей анода и катода и размер резистора, соединяющего анод и катод. Коррозионные потери представляют собой совокупные потери металла, выраженные в микрометрах, и рассчитываются путем численного интегрирования скорости коррозии. Образцы для испытаний Образцы в экспресс-тесте макроячеек состоят из 127-мм (5-дюймовой) длины No.16 (№ 5) арматурных стержней, голые или залитые в строительный раствор, как показано на рисунке 9 для стержней с эпоксидным покрытием. Рисунок 9. Иллюстрация. Открытые бруски и образцы быстрых макроячеек, обернутые строительным раствором, с крышкой для защиты открытого конца брусков с эпоксидным покрытием. Для изготовления образцов используется следующая процедура:
Испытательные материалы В быстрых тестах макроячеек используются следующие материалы:
Сбор данных Вольтметр с разрешением 0,001 мВ используется для измерения коррозии.
потенциал анода и катода и
падение напряжения на резисторе 10 Ом. В типичном тесте падение напряжения
имеет тенденцию колебаться между -0.003 и 0,003 мВ при коррозии
ток близок к нулю. Только значения падения напряжения за пределами этого региона являются
используется для оценки эффективности систем защиты от коррозии. Стендовые испытанияВ течение последних двух десятилетий такие стендовые испытания, как южный воздействие, треснувший луч и испытания ASTM G109 часто используются для оценки коррозионных характеристик арматуры. стали. (31,35,36) Из этих испытаний южная экспозиция и трещины Испытания на пучке доказали, что дают полезные данные за относительно короткий период времени. Все В этом исследовании использовались три метода испытаний, но только результаты для первого два сообщаются, потому что они дали полезные данные. В тесте ASTM G109 используются только 3-процентный раствор хлорида натрия и обеспечивает гораздо более мягкую степень воздействие на образцы. Он не дал полезной информации за 4 года период, вдвое больший, чем для южной экспозиции и треснувшей балки тесты. Южный тест экспозиции Образец, использованный в испытании на южную экспозицию, состоит из
небольшая плита с двумя матами из арматурной стали (см. Рис. 10. Иллюстрация. Образец для испытаний на южную экспозицию. Бетон отверждается влажным способом в течение 3 дней, а затем выдерживается на воздухе до
тест начинается в 28 дней. Верхний коврик состоит из двух стержней № 16 (№ 5),
а нижний коврик состоит из четырех No.16 (№ 5) стержней. Коврики связаны
электрически через резистор 10 Ом, по краю
верхняя поверхность (отлита как единое целое с образцом) и боковые стороны бетона
заделаны эпоксидной смолой. 15-процентный (6,04 моль иона) раствор хлорида натрия
помещается внутри дамбы, позволяя хлоридам проникать в бетон. В
плиты подвергаются 7-дневному чередующемуся режиму выдержки и сушки с выдержкой при 23 ± 2 ° C (73 ± 3 ° F) в течение 4 дней и сушкой при 38 ° C (100 ° F).
(отсюда и название южная экспозиция) на 3 дня.Перед сушкой раствор
удаляется с верхней поверхности промышленным пылесосом. Пруд
и режим сушки продолжался 12 недель. При возникновении коррозии и по завершении испытаний, Образцы южной экспозиции отбираются на содержание хлоридов с использованием процедур описано в разделе, посвященном анализу хлоридов, далее в этой главе. Испытание балки с трещинами Образец балки с трещиной
используется для моделирования коррозии арматурной стали, в которой трещины непосредственно
подвергните сталь воздействию химикатов для борьбы с обледенением (см. Рисунок 11. Иллюстрация. Испытательный образец с трещинами на балке. Трещина моделируется параллельно и выше вершины арматурный стержень путем вставки 0.3 ‑ мм (12 ‑ мил) при изготовлении образца прокладку из нержавеющей стали. Прокладка снята в течение 12 часов после заливки, оставляя прямой путь для хлоридов к арматуре сталь и моделирование эффекта трещины оседания на стержне. An интегральная плотина используется аналогично тому, что использовалось для образца южной экспозиции вокруг верхнего поверхность образца. Как и образец южной экспозиции, образец балки с трещинами подвергается циклам смачивания и сушки при 15 ° C. процентный раствор натрия хлорида, продолжающийся до 96 недель. Изготовление образцов Следующий процесс для изготовления образцов южной экспозиции и треснувшей балки:
Испытательные материалы Свойства материалов были следующим образом:
15-процентный раствор хлорида натрия (6.04 моль ион концентрация) использовалась для пруда испытуемых образцов: 600 мл (20,3 жидких унций) в пруд один образец для южной экспозиции и 300 мл (10,1 жидких унций) для пруда одной треснувшей балки образец. Сбор данных Тот же вольтметр и правила преобразования данных описаны
для быстрых тестов макроячеек использовались для стендовых испытаний. Испытание пучком инициирования коррозии используется для определения критический порог хлоридной коррозии антикоррозийной защиты система.Хотя эти данные также получены на образцах с южной экспозицией, испытания на начало коррозии заканчиваются в начало коррозии, что позволяет подвергнуть большее количество образцов собраны. Этот тест использовался в этом исследовании для оценки обычного армирования. стальное литье в бетоне, содержащем ингибиторы коррозии. Образец идентичен образцу балки с трещинами, за исключением того, что нет намеренной трещины. размещается над арматурой. Показан образец пучка инициирования коррозии. на рисунке 12. Рис. 12. Иллюстрация. Образец для испытаний пучком инициирования коррозии. Материалы, изготовление и процедуры испытаний, используемые в
испытания на начало коррозии идентичны испытаниям, используемым для южных
испытания на экспозицию и балку с трещиной, за исключением продолжительности испытания. Для обычной арматурной стали учитывается начало коррозии. возникать при коррозии макроэлементов скорость сначала достигает значения больше или равного 0.3 м / год (0,01 млн / год) или при коррозии потенциал верхнего мата из стали сначала смещается к значению более отрицательному, чем –0,350 V по отношению к CSE. Для оцинкованной стали инициация коррозии основана на при скорости коррозии 0,3 м / год (0,01 мил / год) или при резком наблюдается изменение потенциала коррозии, причем первый служит основное руководство. Как только возникает коррозия, испытания останавливаются и бетон
отбираются пробы для анализа хлоридов.Всего отобрано 20 проб из
каждый инициирующий луч, по 10 с каждой стороны луча, начиная с 40 мм (1,5 дюйма)
от края и с интервалом в 25 мм (1 дюйм), как показано на виде сбоку образца на рис.13.
Для каждого образца просверленные отверстия располагаются так, чтобы верх отверстий и верхняя поверхность арматуры
бар находятся на одном уровне. Рис. 13. Иллюстрация. Места отбора проб для испытаний инициирующим пучком. Тест на сопротивление линейной поляризацииИзмерение обоих микроэлементов а коррозия макроэлементов может быть получена с помощью теста на сопротивление поляризации, в котором используется некорродирующий счетчик. электрод и электрод сравнения, чтобы установить кривую поляризации путем наложение на металл диапазона потенциалов и измерение соответствующей коррозии токи с помощью потенциостата.Были получены измерения сопротивления поляризации. от выбранных лабораторных образцов на протяжении всего периода испытаний. В данном исследовании использовалось тестов на сопротивление поляризации, чтобы
получить общую скорость коррозии для лабораторных
образцы. В тестах текущие показания снимаются во время короткой медленной развертки. Рисунок 14. Уравнение. Плотность тока коррозии. Где: i = Ток коррозии плотность (А / см 2 ). B = Константа Штерна-Гири (обычно принимается равным 26 мВ как для арматурной стали, так и для цинка в бетоне). R p = Наклон определяется по поляризации кривая (килом · см 2 ). Общая скорость коррозии в м / год рассчитывается с использованием
уравнения на рисунках 5 и 7 для железа и цинка соответственно. В этом
исследования, испытания проводятся с использованием потенциостата PC4 / 750 и DC105. Испытания стендовых образцов проводились каждые 4 недель, чтобы получить общую скорость коррозии верхних матов с нижними матами отключен.При испытаниях верхний мат из арматурной стали используется в качестве рабочий электрод, на поверхность образца помещается ГЭП, погруженный в солевой раствор. используется в качестве электрода сравнения, а платиновая полоска, погруженная в соль раствор используется в качестве противоэлектрода. Файл данных из
тест поляризационного сопротивления анализируется с помощью пакета анализа данных
поставляется с DC105. Это программное обеспечение для анализа может читать файл данных
и построить график на основе данных в файле.Когда новый график создается в
В этом пакете пользователь выбирает диапазон напряжения на графике, а программное обеспечение
автоматически использует линейную аппроксимацию данных в выбранном диапазоне для расчета
сопротивление поляризации. Плотность тока коррозии и скорость коррозии
затем можно определить, используя сопротивление поляризации. Поле ТестыИспользование образцов для испытаний бетонных плит, хранящихся на открытом воздухе, в полевых условиях. Испытание предназначено для определения эффективности защиты от коррозии. системы в реальных условиях воздействия.Подобно лабораторным образцам, некоторые образцы для полевых испытаний не имеют трещин, а некоторые имеют прямую имитацию трещин выше и параллельно выбранным арматурным стержням. Плотина из уплотнителя прикрепляется к верхней бетонной поверхности, чтобы удерживать солевой раствор, который разводили образцы каждые 4 недели. Получены измерения скорости коррозии. минимум 250 недель. Образцы для полевых испытаний
состояла из бетонных плит размером 1219 x 1219 x 165 мм (48 x 48 x 6,5 дюйма) с двумя
маты No.16 (№ 5) арматурных стержней (см. Рисунки с 15 по 18). Каждый
мат содержит семь стержней как в продольном, так и в поперечном направлениях с
прозрачные бетонные покрытия 25 мм (1 дюйм)
сверху и снизу и 76 мм (3 дюйма) от концов. Рисунок 15. Иллюстрация. Образцы для полевых испытаний, верхняя плита без трещин. Рисунок 16.Иллюстрация. Образцы для полевых испытаний, верхняя плита с трещинами. Рисунок 17. Иллюстрация. Образцы для полевых испытаний, нижняя плита. Рисунок 18. Иллюстрация. Образцы для полевых испытаний, вид спереди и сбоку. Образцы для испытаний перемещены в кампус Адамса
Университет Канзаса за 7 дней до тестирования. Расстояние между образцами 0,914 м (3
футов) друг от друга и размещены на высоте 203 мм (8 дюймов) над землей, используя размер 203 x 203 x 406 мм. Плотина из уплотнительной ленты толщиной 9,5 мм (0,375 дюйма) прикреплен к верхней бетонной поверхности по краям и герметизирован силиконом герметик, чтобы предотвратить утечку. Образцы заполнены 3,3 л (0,87 галлона) 10 раствор каменной соли, содержащий 0,30 кг (0,66 фунта) каменной соли, каждые 4 недели. Иногда зимой используют только каменную соль. Программа воздействия соли была основана на использовании соли Канзаса. история с 1998 по 2002 год, как показано в таблице 6. (40) Средняя норма внесения основана на общей длине все полосы движения протяженностью 33 742 км (20 967 миль) со средней шириной полосы 3,7 м (12 футов). Среднегодовая норма внесения соли составила 0,66 кг / м3 2 (0,13 фунт / фут 2 ). Таблица 6. История использования соли Министерством транспорта Канзаса (KDOT). (40)
Техническое обслуживание KDOT
В руководстве приведены общие рекомендации по внесению соли в снежный сезон. (41) По данным персонала КДОТ, мост
настилы получают в четыре-пять раз больше соли, нанесенной на прилегающее покрытие, чтобы учесть более низкие температуры
на мостовых настилах. Медные провода калибра 16 от верхних планок мата соединены к красным клеммам, а провода от нижних стержней коврика подключаются к парные черные переплетные столбы. К красной обвязке был подключен выключатель. через резистор 10 Ом. Переключатели включаются и выключаются для управления электрические схемы. Связующие столбики нескольких экземпляров центрируются вместе. в клеммной коробке для удобства тестирования. В испытуемые образцы помещают 3,3 л (0,87 галлона) 10
процентный раствор каменной соли в первые сутки.
Через две недели измеряются падения напряжения на резисторах сопротивлением 10 Ом. Потенциал коррозии варьируется с температурой, и температуры колеблются в поле. (42) Следовательно, необходимо применять поправочный коэффициент для преобразования потенциала измерения, сделанные в полевых условиях, до значения, соответствующего 22 ° C (72 ° F). За CSE, поправка показана на рисунках 19 и 20. Рисунок 19.Уравнение. Температурная поправка в градусах Цельсия. Рисунок 20. Где: T = Температура, ° C или ° F. E o = Не исправлено Показание потенциала коррозии, мВ. E = Показание потенциала коррозии с поправкой на температуру, мВ. Цикл проверки повторяется каждые 4 недели. Образцы помещаются в воду при одновременном снятии показаний. взятый.После того, как образцы достигают примерно 96 недель, показания снимаются каждые 8 недель. но цикл прудирования поддерживается на уровне 4 недель. Потенциалы коррозии измеряются в фиксированных точках сетки на верхняя поверхность образца, как показано на рисунках с 21 по 23. Рисунок 21. Иллюстрация. Возможные контрольные точки для обычные стальные образцы. Рисунок 22. Иллюстрация. Возможные контрольные точки для образцов стержней с эпоксидным покрытием с четырьмя
тестовые бары. Рисунок 23. Иллюстрация. Возможные контрольные точки для образцов стержней с эпоксидным покрытием с двумя тестовые бары. Изготовление образцов Следующий процесс использованы для изготовления образцов для полевых испытаний:
Анализ хлоридов Процедуры отбора проб и испытаний для определения хлорид-иона
концентрации в лабораторных образцах и образцах начала коррозии были такими
принят Ji et al. (26) Образцы порошкообразного бетона получены
просверливание отверстий диаметром 6,4 мм (0,25 дюйма) сбоку образца с помощью
дрель ударно-роторного типа. Перед отбором проб просверленная бетонная поверхность
промыли три раза, сначала водой с мылом, затем водой из-под крана и
наконец, используя деионизированную воду. Затем поверхность сушат бумажными полотенцами. Позиции сверления измерены
и отмечен. Длина 152 мм (6 дюймов), диаметр 6,4 мм (0,25 дюйма)
сверло устанавливается на сверхмощную дрель.Образец просверлен
перпендикулярно арматурной стали, параллельно верхней поверхности
образец. Образец, полученный с первой глубины 13 мм (0,5 дюйма), содержит
эпоксидное покрытие с внешней стороны образца и выбрасывается. Четыре ядра взяты из большинства
образцы для полевых испытаний в конце срока службы с использованием сердечника диаметром 89 мм (3,5 дюйма)
сверло и корончатое сверло для определения концентрации хлорид-ионов. Ядра
берутся по углам образца, 230
мм (9 дюймов) от краев. Сердечники, включающие арматуру, не
проанализированы, чтобы избежать измерения эффекта скопления хлоридов на стержнях.После отбора керна керны хранятся при -18 ○ ° C (0 ○ ° F), чтобы минимизировать миграцию хлорид-ионов перед отбором проб.
Бетонный порошок для отбора проб получают из кернов на фрезерном станке. Бетонные образцы
анализировали на содержание водорастворимых хлоридов с использованием процедуры A из AASHTO T 260-94. Средняя скорость коррозии, основанная на потерях после начала коррозии Системы защиты от коррозии обычно сравниваются на основе
средние потери металла с поверхности (выраженные в м) с течением времени для
данный метод испытаний. Для иллюстрации процесса приведены графики коррозии макроэлементов. 1 м = 0,0394 мил Рисунок 27. График. Индивидуальные потери от коррозии на основе
общая площадь верхних планок
для образцов для полевых испытаний, содержащих Rheocrete ® без трещин
конкретный,
с отмеченным началом коррозии. 1 м = 0,0394 мил Рисунок 28. График. Индивидуальные потери от коррозии на основе общая площадь верхних планок для образцов для полевых испытаний, содержащих Rheocrete ® без трещин конкретный, с линиями, соединяющими потери от коррозии в начале с потерей от коррозии при 250 недели. Как показано на рисунке 29 для трех образцы южной экспозиции, содержащие стержни с эпоксидным покрытием (с четырьмя отверстиями через эпоксидную смолу), залитый в бетон с соотношением вода / цемент 0,45, содержащий ингибитор коррозии DCI, некоторые образцы проявлять потери от коррозии (результат коротких периодов измерения коррозии) и длительные периоды без коррозии без измеримого скорость коррозии с течением времени. На рисунке 29 скорость коррозии после коррозии инициирование можно измерить только для одного из трех образцов (ECR-DCI-4h-45-2). 1 м = 0,0394 мил Рисунок 29. ТЕСТОВАЯ ПРОГРАММА Тест
программа, обобщенная в таблице 8, сравнила коррозионные характеристики 11
несколько систем защиты от коррозии с традиционным армированием
стали и обычных ECR и сравнили эффективность коррозии
ингибиторы при использовании с обычной арматурной сталью.Как показано в таблице,
быстрые макроячейки и стендовые испытания были использованы для всех множественных антикоррозионных защит
систем, но не для каждой системы использовались все версии тестов. В целом,
Работа включала 126 испытаний макроэлементов, 117 испытаний южной экспозиции, 93 испытания с трещинами.
балочные испытания,
30 балок инициирования коррозии, 42 полевых испытания и 32 бетона с потерей коррозии до трещин
тесты. Таблица 8. Количество образцов для испытаний в программе испытаний.
SE = южная экспозиция; CB = треснувший
луч; FTS = образец для полевых испытаний Rapid Тестовая программа Macrocell Как показано в таблице 8, экспресс-тест макроячейки с
обернутые минометом образцы использовались для всех множественных систем защиты, в то время как
Тест макроячейки с голыми стержнями не использовался для оценки эффектов ингибиторов коррозии. Настольные весы и программы испытаний на начало коррозии Южная экспозиция, треснувшая балка и начало коррозии
были проведены испытания для сравнения характеристик литых систем защиты от коррозии.
в бетоне.Во всех случаях использовалось водно-солевое соотношение 0,45. Кроме того, бетон
с отношением в / ц 0,35 использовался для оценки эффективности коррозии.
ингибиторы (а также контрольные образцы), потому что защита от коррозии
обеспечивается нитритом кальция по сравнению с другими ингибиторами коррозии. Программа испытаний сопротивления линейной поляризацииИзмерения сопротивления линейной поляризации проводились на один образец южной экспозиции и образец балки с трещинами для каждой конфигурации и система защиты от коррозии в исследовании (см. таблицу 8). Результаты были использованы в сочетании с показаниями макроячейки, лабораторных весов и полевые испытания для определения характеристик защиты от коррозии системы. Программа полевых испытаний образцов для полевых испытаний были использованы для сравнения традиционных
армирующая сталь и обычная сталь ECR для стержней с эпоксидным покрытием с
повышенная адгезия, стержни с эпоксидным покрытием с ингибиторами коррозии и стержни MC с проникающими в них обоими слоями. После экспресс-макроячейки, лабораторных и полевых испытаний, образцы были сфотографированы, чтобы зафиксировать видимые продукты растрескивания и коррозии. на внешней стороне бетона или раствора, а также на арматурной стали и окружающей среде вяжущие материалы после снятия бетона или раствора. По стендовой шкале и полевые испытания, покрытия были оценены на отслоение, и образцы бетона были взяты для анализа на содержание хлоридов. Праймер для углеродного волокна для усиления FRP Horse HM-180 Видео по нанесению грунтовки из углеродного волокна Видео по усилению углеродного волокна (щелкните) >> Обработка бетонной поверхности , бетонные детали следует обрабатывать путем снятия фаски на углу, пыль сдувается сжатым воздухом после завершения полировки и, наконец, поверхность протирали хлопчатобумажной тканью, смоченной ацетоном, и оставляли сухой для использования.Если бетон необходимо для укрепления существующих трещин, сначала выберите перфузионный клей HM-120M или HM-120L для заливки трещин в соответствии с размером трещины >> Строительный грунт вылили в чистую емкость и перемешали до однородности (при перемешивании лучше всего перемешать в том же направлении, чтобы воздух не образовывал пузырьков воздуха.) Кисть или роликовая щетка использовалась для равномерного нанесения кистью на бетонную поверхность, после высыхания поверхностного слоя клея его следует очистить щеткой несколько раз в зависимости от конкретных обстоятельств, но толщина покрытия не должна превышать 0,4 мм, и она должна быть это было уместно, когда палец был сухим на ощупь, обычно не менее 2 часов), затем был следующий процесс продолжился. каждый раз следует использовать один раз в течение всего срока действия клея. >> Выравнивающая конструкция использовался для ремонта и заполнения посредством заделки и соскабливания скребка. , то место, где возникает разница высот, такая как стык шаблонов , должен быть заполнен выравнивающим клеем, который пытается минимизировать разницу в высоте.Обработка угла заключалась в том, что отремонтирован для сглаживания дуги с помощью выравнивающего клея, его радиус не более 20мм. После отверждения выравнивающего клея (время отверждения . >> Паста из углеродного волокна обертка Клей HM-180C3P, пропитанный углеродным волокном, был нанесен на приклеиваемую поверхность равномерно, угловой участок был более смазан соответствующим образом. после перетягивания углеродного волокна плотно и ровно, используйте пластиковый скребок или валик (малярный валик, с которого была удалена ворсинка), чтобы прокатить несколько раз в том же направлении, пока не начнет выделяться клеевой состав. Затем равномерно нанесите пропитанный клей на внешнюю поверхность обертки из углеродного волокна и прокатите несколько раз, чтобы пропитанный клей мог погружать пленку из углеродного волокна двумя способами, , если это мульти-паста, до тех пор, пока ваши пальцы не высохнут, следующий слой пасты может быть новичком.Если пленка из углеродного волокна требует нахлеста , ударившего о поверхность конструкции. При средней температуре воздуха 20, 25 ℃ время отверждения составляет не менее 3 дней; при средняя температура воздуха 10 ℃, время отверждения составляет не менее 7 дней. Грунтовка для глубокого проникновения.Технические характеристики, типы, назначениеЕсли вы столкнулись с проблемой отделки рыхлой и пористой основы, то вам понадобится грунтовка глубокого проникновения. Технические характеристики, состав и назначение этих видов отделочных решений — вот о чем пойдет речь. Использование по назначению раствора для глубокого проникновенияС помощью растворов для глубокого проникновения этого типа можно качественно соединить и укрепить даже самые капризные поверхности.Акриловый полимер, входящий в состав механической смеси, надежно склеивает материал и делает его очень прочным. Основной компонент состоит из мелких частиц, которые выполняют основную функцию, проникая на самую глубину основы, обеспечивая 100% сцепление и сцепление. К тому же после обработки поверхности раствором глубокого проникновения можно сэкономить на краске и штукатурке. Грунтовка глубокого проникновения, технические характеристики которой просто поражают, отличается антисептическими качествами. Характеристики раствора глубокого проникновенияЗащита основания, укрепление, влагостойкость — все это грунтовка глубокого проникновения.Технические характеристики определяются его внешним видом. Например, композиция характеризуется размерами частиц акрилового полимера или уровнем водородного индекса (ph). Однако есть особенности, сочетающие в себе все виды глубокопроникающего отделочного материала:
Раствор для глубокого проникновения «Боларс» Подготовка поверхности, укрепление, сцепление — все это грунтовка для глубокого проникновения «Боларс». Такие отделочные материалы идеально подходят для подготовки основания под укладку цемента, гипса, полимера, плитки или обоев.Материал подходит для работы с бетоном, газосиликатом, кирпичом, штукатуркой и др. Кроме того, состав отлично подходит для обработки старых деревянных досок, покрытых воском. С его помощью можно выполнять внешние и внутренние работы. Он прочно склеивает поверхности и укрепляет их. Смесь состоит из акрилового полимера, мелкие частицы которого впитываются в основу на глубине около 6 мм. Технические данные раствора Болар:
Смесь хранить в плотно закрытой емкости при температуре от + 6º до + 28º в темном месте. Раствор глубокого проникновения «Ceresite ST 17»Грунтовка «Ceresite CT 17» — грунтовка глубокого проникновения, укрепляющая и защищающая основания. Этот глубокий состав отличается высокими пропитывающими качествами и полностью повторяет форму основы. Смесь защищает поверхность от проникновения влаги и сводит к минимуму использование отделочных материалов. Механический раствор подходит для работы с гипсом, цементом, деревом, бетоном, гипсокартоном, керамикой и кирпичом.С его помощью подготовьте пол и стены перед укладкой паркета, плитки, обоев и т. Д. Технические данные композиции «Церезит»:
Состав следует хранить в плотно закрытой таре в прохладном помещении без доступа солнечных лучей. Акриловый раствор глубокого проникновенияАкриловый грунт глубокого проникновения — это интерьерная смесь с адгезионными функциями. Акриловый состав защищает основание от впитывания влаги, сохраняет воду в отделках (штукатурка, штукатурка, клеевой раствор). Раствор подходит для работы с гипсом, цементом, керамикой, деревом, гипсокартоном и т. Д.Применяется для подготовки поверхности перед укладкой плитки, паркета и перед оклейкой стен обоями. Укрепляет основания, обладает высокими износостойкими и адгезионными качествами, не пропускает влагу. Акриловый состав применяется как для внутренних, так и для наружных работ. Технические данные акриловой грунтовки:
Хранить состав в закрытой таре в темном прохладном месте при температуре от + 4º до + 38º. Универсальный раствор глубокого проникновения Универсальный грунт глубокого проникновения — это механический раствор, созданный на основе синтетических смол. Универсальная смесь достаточно пористая и быстро впитывает жидкие отделочные материалы.Для надежного склеивания бетонных и цементных оснований грунтовку необходимо аккуратно втереть в поверхность до появления белой пены. Таким образом, можно качественно совместить бетон и цемент и очистить поверхности от пыли и мелких зерен. Универсальное решение, подходящее для работы с любым материалом. Состав идеален для работы на улице и в помещении. Кроме того, универсальная грунтовка обладает высокой устойчивостью к влаге и механическим воздействиям.Раствор не мешает нормальному газообмену в помещении и экологически безопасен. Качественная адгезия, защита стен, долговечность и безопасность для здоровья — все это грунтовка глубокого проникновения. Технические характеристики всевозможных растворов глубокого проникновения убеждают в надежности и высоком качестве отделочных материалов. Влияние волокон на долговечность бетона: практический обзорAbstract В этой статье приводится обзор литературы, относящейся к характеристикам фибробетона (FRC) в контексте долговечности бетонных инфраструктур.Долговечность бетонной инфраструктуры определяется ее способностью поддерживать надежные уровни эксплуатационной пригодности и структурной целостности в условиях воздействия окружающей среды, которое может быть суровым без какой-либо серьезной потребности в ремонте на протяжении всего расчетного срока службы. Обычный бетон имеет относительно низкую прочность на растяжение и пластичность, поэтому он подвержен растрескиванию. Трещины считаются путями проникновения газов, жидкостей и вредных растворенных веществ в бетон, что приводит к раннему началу процессов разрушения бетона или арматурной стали.Водный раствор хлоридов может быстро достигнуть заделанной стали после того, как области с трещинами подвергаются воздействию соли или брызг против обледенения в прибрежных регионах, что деструктурирует защитную пленку, в результате чего начало коррозии происходит на десятилетия раньше, чем когда хлориды должны были бы постепенно проникать в бетонное покрытие без трещин. Ключевые слова: фибробетон (FRC), долговечность, применение FRC, тематические исследования 1. Введение Бетонная конструкция может подвергаться воздействию различных условий окружающей среды на протяжении всего срока службы. Фибробетон (FRC) — это особый класс бетона, в состав которого входят волокна для повышения его сопротивления (растягивающим) нагрузкам.Были разработаны различные классы FRC с различными преимуществами. Использовались волокна разного поперечного сечения (плоские, круглые, прямоугольные и др.). Традиционно волокна классифицируются по материалам: обычно используются металлические, стеклянные, синтетические и натуральные волокна. Дальнейшее различие может быть проведено на основе размера волокна: мы различаем микроволокна (короче 20 мм с эквивалентным диаметром 5–200 мкм) и макроволокна (обычно длиной 20–80 мм с отношением длины к диаметру 40–2). 120).Физические свойства обычно используемых типов волокон суммированы в. Таблица 1Физические свойства обычно используемых типов волокон в FRC. (%) –50 –3
Непрерывное развитие волокон привело к появлению многих классов передовых FRC. Спроектированные цементирующие материалы с деформационным упрочнением (ECC / SHCC) [1,2,3] характеризуются высокой пластичностью при растяжении и множественными мелкими трещинами, которые контролируются за счет образования перемычек между волокнами. С другой стороны, сверхвысокая прочность на растяжение и сжатие являются основными характеристиками сверхвысококачественного фибробетона (UHPFRC) [4,5].Поведение FRC зависит от многих факторов, таких как соотношение сторон волокна (длина / диаметр), модуль упругости, объемный процент, включенный в композит, ориентация волокон, удобоукладываемость бетона через его влияние на дисперсию и ориентацию волокон, а также размер крупных агрегатов. . Таким образом, чтобы получить максимальную пользу от использования волокон, все эти факторы должны быть учтены и тщательно учтены при проектировании материала и конструкции бетона. Некоторые преимущества использования различных типов FRC описаны в [6,7,8,9].По сравнению с обычным бетоном (NC) и FRC, замечательные свойства материала UHPFRC приводят к высоким показателям деформации при растяжении и прочности, а также к развитию псевдопластической фазы (деформационное упрочнение) перед размягчением бетона, что отвечает за высокое поглощение энергии ( вязкость) до разрушения [10]. Энергия разрушения UHPFRC также может быть значительно выше (примерно в пять раз), чем FRC [10]. Преимущество использования фибры в бетоне ( a ) сравнение различных типов бетона по растягивающим напряжениям и деформации, ( b ) трещинам в SHCC, ( c ) раскрытие устья трещины в балке с надрезом для различного объема стальные фибровые волокна и ( d ) FRC повреждены в испытании на расщепление [6,7,8,9]. Оптимальное содержание волокна в FRC зависит от класса FRC, а также от типа волокна и соотношения сторон. Для микроволокон, таких как поливиниловый спирт (ПВС) и полиэтилен (ПЭ), было обнаружено, что оптимальное содержание в SHCC находится в диапазоне 1-2% [11,12]. В случае стальной фибры этот диапазон составляет от 1,5 до 2,5% в HPFRC [13,14,15]. Различия в оптимальном уровне между исследованиями можно объяснить разным соотношением сторон используемых волокон. Аналогичным образом, для макроволокон из полипропилена (длиной до 70 мм) этот оптимум оказался между 0.От 5 до 1% для деформационного разупрочнения FRC [16,17], в то время как до 0,5% стального макроволокна типично для традиционных плит FRC с грунтовкой [18]. Благодаря своим многочисленным преимуществам — хорошей прочности на разрыв, пластичности, сопротивлению усталости — FRC использовались в широком диапазоне применений, включая тротуары, промышленные полы, облицовку туннелей, стабилизацию откосов и ударопрочные конструкции, среди прочего [19] . Соответствующее использование FRC может увеличить долговечность и срок службы структурного элемента, тем самым также снизив общее воздействие элемента на окружающую среду на протяжении всего его жизненного цикла.Поскольку FRC имеет высокую ударную вязкость и устойчивость к ударам, его использование может быть выгодным в производстве сборных железобетонных изделий из-за снижения подверженности повреждениям во время транспортировки и погрузочно-разгрузочных работ. Кроме того, было показано, что использование стальной фибры приводит к более высокому сопротивлению разрушению при сдвиге железобетонных балок, тем самым снижая потребность в хомутах [20,21,22]. В сжатых элементах обычную арматуру (например, арматуру) можно заменить армированием волокном [23]. В балочных элементах бетон, армированный фиброй, также использовался в гибридных бетонных конструкциях в качестве поверхностного слоя для контроля ширины трещин [24,25].Фибробетоны различных типов успешно использовались в качестве ремонтных материалов в нескольких реальных проектах, включая мостовые настилы, бетонные плотины, туннели, соединительные балки в высотных зданиях в США, Японии и Германии [26,27]. FRC также используется для усиления конструкций, чувствительных к землетрясениям [28]. Более высокая пластичность и характеристики разрушения FRC также могут снизить риск повреждения конструкции RC из-за сейсмической нагрузки. Благодаря своим лучшим механическим характеристикам и долговечности, FRC также стали популярными для подземных сооружений в сейсмически активных районах [29].Несколько исследований также были сосредоточены на анализе чувствительности реакции конструкции во время сейсмической нагрузки по отношению к изменению механических параметров [30,31]. Для практического использования фибробетона важно понимать его долговечность в различных условиях окружающей среды. По сравнению с обычным бетоном, область применения фибробетона менее развита. Следовательно, в последние годы были предприняты значительные усилия по исследованию, чтобы лучше понять долговечность FRC.Эта статья направлена на обзор существующей литературы, относящейся к долговечности FRC с точки зрения различных механизмов разрушения, включая коррозию, вызванную хлоридом и карбонизацией, циклы замораживания / оттаивания и щелочно-кремнеземную реакцию. Также обсуждаются некоторые практические применения. Этот обзор может стать основой для практического использования FRC в инфраструктурах, а также предоставить исследователям базовую информацию перед тем, как приступить к исследованиям в области долговечности FRC. 2. Процессы износа, влияющие на бетон, армированный волокномВ общем, ухудшение состояния бетона может быть вызвано множеством физических, химических или механических процессов, которые обычно действуют в сочетании [32].Одним из наиболее распространенных механизмов разрушения железобетонных инфраструктур является коррозия стальной арматуры. Коррозия — это электрохимический процесс, при котором заряд (электроны и ионы) перетекает от анода к катоду. Как правило, пассивная пленка самопроизвольно образуется на стальной поверхности в щелочной среде гидратирующего бетона [33], защищая ее от коррозии. Однако эта пассивная пленка может разрушиться из-за попадания хлоридов [34,35] или карбонизации [36,37], что приведет к активной коррозии [38,39,40].Кроме того, в бетоне на процесс коррозии (как начало [41], так и период распространения [42]) сильно влияет наличие трещин. Поскольку процесс растрескивания в FRC фундаментально отличается от обычного бетона, разумно ожидать, что процессы разрушения также будут другими. Краткий обзор существующей литературы, относящейся к влиянию волокон на коррозию стальной арматуры в бетоне с трещинами, дается в, а подробности обсуждаются в следующих разделах. Таблица 2Общий обзор влияния трещин в FRC на коррозию арматурной стали. Обратите внимание, что W cr, ave — это средняя ширина трещины, а W cr, total — общая ширина трещины. 37 Коррозионное повреждение997 –0,26 Потеря массы 8%
2.1. Бетон, армированный волокном, подверженный воздействию хлоридовКак описано, ионы хлора могут вызывать коррозию арматурной стали в бетоне.Хотя иногда они присутствуют в бетонной смеси — как часть загрязненного заполнителя или использовались в прошлом в качестве ускорителей схватывания — обычно хлориды из окружающей среды проникают через бетонное покрытие и медленно достигают стали. Основное последствие попадания хлоридов — коррозия арматуры. Точечная коррозия — это типичная форма коррозии, вызванной хлоридом [39]. Поскольку для инициирования коррозии необходимо определенное количество хлоридов на уровне арматуры, период, необходимый для возникновения коррозии, в значительной степени зависит от целостности бетонного покрытия.Кроме того, хлориды могут присутствовать в бетоне в виде свободных или связанных хлоридов, и только свободные хлориды способствуют коррозии арматуры. Связывание хлоридов с цементным матриксом — сложный процесс, зависящий от многих факторов [48]. Присутствие химических соединений цемента, таких как трикальцийалюминат (C 3 A) и феррит тетракальциевого оксида алюминия (C 4 AF), вместе со связанными хлорид-ионами образуют соль Фриделя, которая имеет менее пористую структуру и замедляет вниз транспорт хлорид-ионов [49].В целом, хлоридсвязывающая способность бетона зависит от C 3 A, C 4 AF, силиката кальция (C 3 S), отношения вода / цемент, из которых C 3 A имеет наиболее доминирующее значение. эффект [50]. Следовательно, связывание хлоридов в FRC будет зависеть в основном от компонентов матрицы. Как уже упоминалось, проблемы, связанные с проникновением хлоридов, могут быть еще более заметными при наличии трещин. Поэтому в этом разделе основное внимание уделяется исследованиям, связанным с характеристиками FRC при одновременном воздействии растрескивания и проникновения хлоридов. Хлоридостойкость образцов FRC и RC из стальной фибры без трещин была исследована Аббасом и др. [51] с помощью быстрого теста на миграцию хлоридов (RCPT) в соответствии с рекомендациями ASTM C1202-10. Коэффициент диффузии хлоридов также был рассчитан с использованием второго закона Фика. Было обнаружено, что коэффициент диффузии хлоридов и заряд, прошедший через образцы FRC, были ниже, чем у RC. Это было связано со способностью FRC задерживать микротрещины на волокнах (смесь стали и полипропилена) во время отверждения и обработки [52].В общем, начало растрескивания, вызванного коррозией арматуры, задерживается армированием волокном [53,54,55]. В этом процессе интерфейс волокно-матрица может играть важную роль в FRC без трещин. Как правило, улучшенная поверхность раздела волокон с матрицей снижает расширение продуктов коррозии в стальных стержнях. Считается, что граница раздела волокно-матрица более плотная и однородная из-за богатого гидроксида кальция, чем граница раздела между обычной стальной арматурой и матрицей, что предотвращает попадание вредных растворенных веществ в FRC [56,57].Высокое содержание гидроксида кальция, присутствующего на границе раздела волокно-матрица, может увеличивать связывание хлоридов [58]. Тем не менее, чрезмерное повреждение границы раздела волокно-матрица приведет к постепенному и локализованному уменьшению поперечного сечения волокна из-за коррозии. Превосходная способность перекрывать трещины и образование множественных мелких трещин в SHCC приводит к хорошей стойкости к проникновению хлоридов, что может замедлить процесс инициирования коррозии в железобетоне [12,44].показывает проникновение как общего, так и свободного хлорида в образцы с множественными трещинами SHCC (средняя ширина трещины менее 50 мкм) с 2% ПВС-волокнами при испытании на ускоренную коррозию, вызванную хлоридом [59,60]. Обратите внимание, что пунктирная линия на рисунке показывает критическое содержание хлоридов для бетона (минимальная прочность на сжатие 17 МПа) без каких-либо волокон, подверженных воздействию влаги, но не внешних источников хлоридов, как рекомендовано Строительными нормами ACI 318 [61]. На рисунке глубина проникновения хлоридов (без трещин) строительного раствора и образцов SHCC (2% ПВС-волокон) показана после теста на быструю миграцию хлоридов (NT Build 492).В неповрежденном состоянии в образцах SHCC было обнаружено несколько меньшее проникновение хлоридов по сравнению с образцами строительного раствора. Проникновение хлоридов на разную глубину в образцы SHCC с множественными трещинами (средняя ширина трещины менее 50 мкм) с 2% ПВС-волокнами. Черные ромбы и красные квадраты относятся к общему и свободному хлоридам соответственно. Глубина проникновения хлоридов в раствор ( a ) и образцы SHCC ( b ) после теста быстрой миграции хлоридов (примечание: стрелки указывают направление проникновения хлоридов). Стойкость к коррозии стали в высокоэффективном цементирующем композите, армированном волокном (HPFRCC), сделанном с 1,5% объемных ПЭ-волокон с трещинами изгиба, была исследована Миядзато и Хираиши [45]. В их исследовании образцы, армированные сталью, изготовленные с использованием как HPFRCC, так и стандартного раствора, сначала подвергались изгибу при постоянной нагрузке 20 кН для образования трещин. Затем потрескавшиеся поверхности образцов подвергали еженедельным циклам смачивания / сушки 3% -ным раствором NaCl в течение 28 дней (2 дня смачивания, 5 дней сушки).Сопротивление линейной поляризации использовалось для измерения скорости коррозии стальных стержней. Глубину проникновения хлоридов измеряли путем распыления на поверхность образца после его продольного разрушения. Глубина проникновения хлоридов в образце с трещинами HPFRCC была на 25% ниже, чем в эталонном образце раствора. Аналогичным образом, скорость коррозии в HPFRCC также была на 10% ниже, чем в образце строительного раствора [45]. Был сделан вывод, что долговечность FRC с трещинами зависит не только от ширины трещины, но и от структуры трещин, которая контролирует коррозию макро- и микроячеек.Как правило, большее расстояние между трещинами приводит к образованию ячеек макрокоррозии между анодной и катодной областями, и, таким образом, могут происходить более высокие скорости коррозии и потеря массы стали [42]. С другой стороны, при меньшем расстоянии между трещинами движение ионов или заряда происходит медленно, что приводит к образованию микроячеек между анодной и катодной областями, что приводит к меньшей коррозии или потере массы стальных стержней. Эта гипотеза была подтверждена Полом и ван Зейлом для образцов SHCC [62]. Коррозионная стойкость HPFRCC в качестве материала для ремонта заплат и поверхностного покрытия была исследована Kobayashi et al.[63]. Полиэтиленовые (PE) волокна в дозировках 0,75%, 1% и 1,5% по объему использовали для приготовления HPFRCC. Три типа железобетонных (ЖБИ) балок: монолитная балка из обычного бетона, балка с HPFRCC в качестве покрытия поверхности (в этом случае стальные стержни находились внутри нормальной RC-балки) и балка с HPFRCC в качестве материала заплаты (здесь использовались стальные стержни. внедренные в HPFRCC) были подготовлены и испытаны на коррозию, вызванную хлоридом. Трещины возникли во всех образцах путем вытягивания стальных стержней с помощью гидравлических домкратов с обоих концов балок.В балке RC максимальная ширина трещины составляла от 0,36 мм до 0,65 мм. С другой стороны, в образцах HPFRCC с поверхностным покрытием и заплатами образовывались множественные трещины, а максимальная ширина составляла от 0,01 мм до 0,12 мм. Затем все образцы подвергались воздействию 3% раствора NaCl в течение 60 дней путем распыления на поверхность с трещинами образцов в течение 5 минут каждые 6 часов. Затем измеряли проникновение хлоридов и площадь коррозии стальных стержней. Никакой коррозии не наблюдалось в балках с HPFRCC в качестве материала заплаты даже при меньшем объеме волокна (0.75%). Кроме того, проникновение хлоридов было ниже, чем в других случаях. Балки с HPFRCC в качестве материала покрытия также показали улучшение по сравнению с балками RC. Множественные мелкие трещины, которые образовались в этих образцах HPFRCC, привели к значительному улучшению как коррозионной стойкости, так и сопротивления проникновению хлоридов по сравнению с образцами RC. Shaikh et al. [64] показали, что устойчивость HPFRCC к коррозии, вызванной хлоридом, может быть дополнительно улучшена при использовании гибридной смеси волокон металлокорда и волокон PE.В этом случае коррозионная потеря массы и продольное растрескивание, вызванное коррозией, были ниже, чем в образцах HPFRCC, содержащих только волокна PE. Следует также отметить, что накопленные хлориды в трещинах из-за циклов «влажный-сухой», испарения и ограниченного вымывания увеличивают концентрацию хлоридов внутри трещины. Это может привести к аналогичным концентрациям хлоридов внутри берегов трещины по сравнению с внешними открытыми поверхностями, т. Е. Грани трещины действуют как свободные поверхности [65]. С точки зрения практического применения, в настоящее время нет согласия относительно допустимого порога ширины трещины для ограничения хлорид-индуцированной коррозии в FRC.Бернерд [66] пришел к выводу, что ширина трещин более 0,10 мм приводит к более быстрому началу коррозии, чем ухудшение состояния без трещин. Аналогичный вывод был сделан в исследовании Granju и Balouch [67], поскольку они не обнаружили признаков коррозии для образцов с шириной трещин менее 0,1 мм даже после одного года воздействия морской среды. Самозаживление трещин может иметь значение, поскольку известно, что небольшие трещины обладают способностью к самовосстановлению за счет так называемого аутогенного самовосстановления (т.е., без какого-либо внешнего вмешательства или специальных добавок) [68,69,70]. С другой стороны, Mangat & Gurusamy [71] пришли к выводу, что допустимая ширина трещины в FRC составляет 0,20 мм. По мере увеличения ширины трещины в FRC наблюдалась тенденция к более высокой коррозионной активности. Однако Berrocal et al. [72] сообщили, что начало коррозии несколько задерживается для FRC, сделанного как из стали, так и из ПВС-волокон, по сравнению с железобетоном с такой же шириной поверхностной трещины. Напротив, удельное электрическое сопротивление бетона было снижено как для стали, так и для волокна ПВС FRC по сравнению с RC.Это, конечно, серьезная проблема, поскольку более низкое электрическое сопротивление может в конечном итоге привести к более высокой скорости коррозии [39]. Следовательно, необходимы дальнейшие исследования для решения этой проблемы. Следует отметить, что процесс разрушения (проникновение хлоридов и коррозия) в FRC в значительной степени зависит от типа волокна. Некоторые авторы предполагают, что, хотя сами стальные волокна, безусловно, подвержены коррозии, они обладают более высокой коррозионной стойкостью из-за наличия на поверхности окалины [73].Прочность FRC со сталью и макросинтетическими волокнами была исследована на образцах с предварительным растрескиванием, подвергшихся воздействию прибрежных и внутренних сред в течение продолжительности от 7 до 24 месяцев [66]. Было обнаружено, что синтетические волокна сами по себе обладают отличной износостойкостью как в прибрежных водах, так и на суше. В образцах с шириной трещины 0,20 мм стальные волокна были значительно повреждены коррозией. Образование ямок в области перекрытия трещин в стальных волокнах и деформированных областях приводит к значительному уменьшению поперечного сечения волокна и вызывает заметное снижение остаточной прочности на растяжение.Некоторые исследования также показали, что стальные волокна с ингибитором, таким как триэтаноламин, могут быть использованы для решения проблемы коррозии стального волокна, связанной с FRC [74]. Кроме того, в морской среде образцы FRC, изготовленные из стальных волокон с шириной трещин менее 0,1 мм, были менее уязвимы к коррозии [67]. В другом исследовании коррозионные характеристики FRC были исследованы для трех различных типов волокон: экстракта расплава (изготовленного из нержавеющей стали), коррозионно-стойкой и низкоуглеродистой стали [75].После одного года воздействия на море FRC с экстрактом расплава и коррозионно-стойкими волокнами не показал признаков коррозии, в то время как значительная коррозия была замечена в FRC из низкоуглеродистой стали. Причиной лучшей коррозионной стойкости экстракта расплава и коррозионно-стойкого волокна может быть также их оцинкованная поверхность. Коррозия стальных волокон в FRC также может увеличивать шероховатость волокон, что также может увеличивать фрикционную связь в матрице волокна, тем самым улучшая остаточную прочность на разрыв FRC [67]. В целом, улучшенные характеристики FRC можно приписать образованию более равномерной диффузии хлоридов в армированных сталью элементах и структурах с множественными трещинами и более равномерному формированию реакции анод / катод меньшего размера по сравнению с обычным RC [76 ]. Однако большие количественные различия в результатах исследований прочности FRC, о которых сообщают разные авторы, можно объяснить различным содержанием волокон, шириной трещин, условиями и продолжительностью воздействия, свойствами волокон, качеством бетона и т. Д.которые могут быть сокращены за счет систематических сравнительных исследований. Влияние размера волокна на коррозию неясно, поскольку было высказано предположение, что влиянием длины проволоки в диапазоне от 0 до 160 мм можно пренебречь [77]. Более того, контроль ширины трещины как в NC, так и в FRC имеет решающее значение для задержки начала коррозии [78]. 2.2. Бетон, армированный волокном, подвергнутый карбонизацииКарбонизация вызывает химико-механические изменения в бетоне, в частности, изменения прочности, проницаемости, распределения пор по размерам и химического состава.Кроме того, хорошо известно, что карбонизация может вызвать усадку и, как следствие, возможное растрескивание бетона [36]. Это также один из основных факторов износа, который приводит к коррозии стали в железобетонных конструкциях [39]. В этом разделе рассматриваются имеющиеся данные исследований эффективности FRC при карбонизации. Из литературы очевидно, что соответствующее количество волокон может замедлить скорость карбонизации в FRC по сравнению с бетоном без волокон. Поскольку карбонизация связана с пористостью матрицы, структурой пор и проницаемостью, оптимальное содержание волокон играет важную роль в карбонизации.Роль различных процентных соотношений стальных волокон (0,0, 0,5, 1,0, 1,5 и 2%) на глубину карбонизации FRC без трещин была исследована Wang et al. [79]. Они сообщили, что содержание волокна до 1,5% может снизить скорость карбонизации, в то время как более быстрая карбонизация сообщается при содержании волокна 2%. В другом исследовании также было обнаружено, что 2% содержания стальной фибры приводит к более высокой пористости и проницаемости FRC [80]. Следует также отметить, что более высокая пористость не всегда приводит к более высокой проницаемости.Взаимосвязь пор более важна [36,81]. Однако независимо от содержания волокна в FRC увеличиваются как коэффициент водопроницаемости, так и коэффициент газопроницаемости [80]. Характеристики образцов FRC без трещин, изготовленных из стальных волокон, подвергнутых карбонизации, были признаны хорошими, но в некоторых исследованиях также сообщалось о серьезных коррозионных повреждениях волокна в области мостиковых трещин, что привело к значительному снижению остаточной прочности на разрыв FRC [82,83] . В взломанном FRC, содержащем 0.5% полипропиленовое волокно, самозаживление более мелких трещин в течение периода испытаний также привело к снижению проникновения CO 2 . Хотя не было обнаружено никакой связи между шириной трещины и временем начала коррозии, было обнаружено положительное влияние добавления волокна на скорость коррозии, вызванной карбонизацией [84]. Аналогичным образом, в другом исследовании FRC с трещинами с низким объемом стального волокна (0,6%) и полиэфирных волокон (POL) (0,9%) было обнаружено, что глубина карбонизации на 24–36% ниже, чем у контрольных балок, которые были растресканы при том же уровне. уровень приложенной нагрузки [43].Обратите внимание, что, как и ожидалось, ширина трещин в контрольных балках и балках из FRC была разной (0,24 мм для контроля и 0,10 мм для FRC), что подтверждает роль волокон в уменьшении ширины трещин и тем самым снижении глубины карбонизации в FRC. Устойчивость к карбонизации образцов HPFRCC, изготовленных из 1,5% полиэтиленового волокна и двух различных водоцементных соотношений (в / ц) (0,30 и 0,60), также была исследована и сравнена с образцами нормальных строительных растворов в треснувшем и без трещин [45]. Все образцы подвергались воздействию 5% CO 2 и относительной влажности 60% в течение 4 дней, а затем последующей влажной среде в течение 10 дней с относительной влажностью 90% для завершения одного цикла.Таким образом, перед измерением глубины карбонизации для образцов было выполнено в общей сложности 6,5 циклов (около 91 дня). При более низком значении w / c (0,30) глубина карбонизации как в образцах HPFRCC без трещин, так и в образцах нормальных строительных растворов была почти одинаковой (почти нулевой). Однако при более высоком значении w / c (0,6) карбонизация в образцах HPFRCC была более чем вдвое выше, чем в образцах из строительного раствора. Противоположная тенденция была отмечена для образцов с трещинами. При этом глубина проникновения в образцы раствора оказалась в три раза выше, чем в образцах HPFRCC.Следует отметить, что остаточная ширина трещины в образцах раствора составляла 0,3–0,4 мм, тогда как в образцах HPFRCC она составляла 0,10 мм и менее. Кроме того, в образцах строительного раствора образовалась только одна трещина, в отличие от образцов HPFRCC, где образовывались множественные трещины. Следовательно, более высокая глубина карбонизации образцов строительных растворов может быть объяснена наличием более глубоких и широких трещин по сравнению с образцами HPFRCC. Обычно карбонизация развивается быстрее в области трещин, а коррозия стальной арматуры в областях с трещинами выше [26].Кроме того, в отличие от коррозии микроэлементов при коррозии, вызванной хлоридом, заметная коррозия макроэлементов преобладала при коррозии, вызванной карбонизацией [59]. Локальная коррозия обычно бывает быстрой при коррозии макроячеек, в то время как при коррозии микроэлементов эта скорость коррозии мала [85]. Тем не менее, опубликованные данные о коррозии, вызванной карбонизацией, в FRC ограничены. Плотная и однородная поверхность раздела волокно-матрица FRC без трещин создает однородное покрытие, окружающее волокна, которое может ограничивать доступ кислорода и, таким образом, отделять электролит стальной арматуры (ограничивая диффузию ионов на поверхности арматурного стержня).Это может в конечном итоге задержать процесс карбонизации на границе раздела стали и бетона [86]. В случае FRC с трещинами граница раздела волокно-матрица может разорваться, позволяя переносить кислород и ионы к поверхности стали. В этом случае стальные волокна, перекрывающие трещину (трещины), действуют как аноды, а встроенные стальные стержни действуют как катод из-за градиента pH в области трещины [87]. На поверхности трещины pH ниже, так как это обеспечивает доступ воды. Если ширина трещины ниже порогового уровня, может произойти самовосстановление, что препятствует переносу кислорода и ионов.Трещины могут залечивать из-за негидратированных частиц цемента или блокироваться продуктами коррозии и т. Д. В области трещины, что дополнительно ограничивает диффузию кислорода и CO 2 . Кроме того, если цементирующая матрица богата Ca (OH) 2 , это может ограничить снижение pH и репассивацию анодной области [61]. 2.3. Бетон, армированный волокном, подвергается щелочно-кремнеземной реакции (ASR)Щелочно-кремнеземная реакция (ASR) — это реакция набухания, происходящая между сильно щелочным цементным тестом и аморфным кремнеземом, который может присутствовать в заполнителях [88].Для ASR достаточное количество влаги (более 80%) может также присутствовать в некоторых типах заполнителей [89]. Обычно ASR производит гель (также называемый гелем ASR), который является мягким, вязким и расширяющимся по своей природе, полученный из силиката натрия [90]. Гель ASR расширяется в присутствии воды, вызывая давление внутри и вокруг кремнистого заполнителя, что может привести к растрескиванию и растрескиванию, вызывая ухудшение жесткости и прочности бетона [91,92]. Встроенные волокна обладают способностью перекрывать трещины в бетоне, что побудило нескольких исследователей изучить поведение ASR в FRC.В этом разделе обсуждается литература, относящаяся к ASR в FRC. Несколько исследователей исследовали влияние включения волокон в борьбе с растрескиванием бетона, вызванным ASR [93,94,95]. Большинство отчетов согласны с тем, что расширение ASR в FRC ниже, чем у обычного бетона без волокон (см.). Было обнаружено, что расширение уменьшается с увеличением содержания волокна [93,96]. В строительных смесях из FRC использовались микростальные волокна в количестве 0, 1, 3, 5 и 7% об. цемента, соответственно, и расширение измеряли каждые 24 часа в течение 30 дней в соответствии с ASTM C-1260 [96].После 30 дней испытаний было обнаружено, что расширение (%) составляет от 0,80 до 0,70, 0,55, 0,30 и 0,19 для содержания волокна 0%, 1%, 3%, 5% и 7% соответственно (см.). Уменьшение расширения было еще более выраженным при увеличении времени отверждения, что объясняется тем фактом, что прочность связи между волокнами и матрицей увеличивалась. Никакого влияния продолжительности отверждения на характеристики контрольного образца не наблюдалось. Более высокая прочность на разрыв и небольшое раскрытие трещин в волокнах из микростали, содержащих FRC, не только ограничивают расширение продукта ASR, но также ограничивают миграцию геля ASR от места реакции [97].Аналогичный вывод о лучшем расширении FRC с увеличенным периодом отверждения и микроволокон был также сделан в исследовании Andic et al. [93]. Кроме того, распространение трещин ASR в FRC зависит от типа волокна, содержания и возраста образцов, как показано на. Пунктирной линией показан максимальный предел расширения заполнителей при одногодичном испытании бетонной призмой, как рекомендовано ASTM C 1293 [98]. Выше этого расширения считается, что агрегаты очень реакционноспособны по своей природе. Расширение ASR в FRC, измеренное в разные дни для разных типов волокон и их содержания (примечание: SF, CF и PVA означают стальное волокно, углеродное волокно и волокна PVA) [88,93,95,96]. Об эффективном контроле ASR в FRC также сообщалось при низком объемном содержании стальной фибры (1-2%) [88]. После погружения образцов на 120 дней в раствор NaOH при 80 ° C, было обнаружено, что для 1% и 2% микростальной фибры FRC расширение примерно на 12% и 35% ниже, соответственно, по сравнению с эталонными образцами бетона. Сканирующая электронная микроскопия (SEM) использовалась для выявления продуктов ASR (диоксид кремния, кальций и богатая щелочь) и их морфологии (полуорганизованный, волокнистый, розеточный и т.д.) в трещинах FRC, как показано в [88].Энергодисперсионный рентгеновский анализ (EDX) показал, что отношение кальция к силикату (Ca / Si) и отношение натрия к силикату (Na / Si) в этих продуктах было выше, что определяет прочность цементного теста. Это уменьшило внутренний износ растрескавшихся стальных волокон в FRC, пораженном ASR. Кроме того, микроволокна также эффективны в ограничении ухудшения механических свойств, вызванного ASR. В целом использование FRC выгодно для продления срока службы конструкций из-за его способности сохранять остаточные механические свойства и способность контролировать трещины, даже если имеют место процессы значительного повреждения [99,100,101]. СЭМ-изображение ( a ) продукта ASR, ( b ) полуорганизованных продуктов, заполняющих поры в цементном тесте, ( c ) продуктов с трещинами, имеющих волокнистую морфологию и ( d ) розеточного типа морфология (адаптировано из [88]). 2.4. Бетон, армированный волокном, подвергающийся воздействию высоких температурВ целом бетон относительно хорошо реагирует на высокие температуры из-за его негорючести и низкой температуропроводности [102]. Однако высокие температуры в бетоне действительно изменяют его физические и химические свойства и влияют на остаточную прочность и механизм переноса жидкости [103,104].При высокой температуре (более 1000 ° C) физико-химические изменения бетона могут вызвать расширение заполнителя, разрушение их кристаллической микроструктуры и даже плавление [102]. Однако ухудшение свойств бетона напрямую связано с факторами, связанными с материалом и окружающей средой, такими как типы заполнителя и цемента, соотношение воды и цемента, наличие волокна, время воздействия, скорость нагрева и т. Д. [102,105]. При высоких температурах (выше 400 ° C) гидроксид кальция и карбонат кальция начинают распадаться.Точно так же гидраты силиката кальция также разлагаются после 500 ° C и образуют поры в микроструктурах [106,107]. Прочность на сжатие FRC со стальной фиброй постепенно увеличивается при нагревании материала до 200–300 ° C, но начинает уменьшаться при дальнейшем повышении температуры [108]. Это объясняется улучшенной гидратацией негидратированных зерен цемента из-за условий внутреннего автоклавирования и испарения воды при высокой температуре [109]. Образцы FRC с 2% ПВС подвергались воздействию различных уровней температуры (20, 100, 200, 300, 400 и 600 ° C) в течение 2 и 6 часов соответственно, прежде чем они были испытаны на прочность при растяжении и сжатии после охлаждения. до комнатной температуры [110].Выявлено, что в образцах FRC не происходит выкрашивания даже после 6 часов постоянной выдержки при 600 ° C (хотя их пластичность значительно снизилась). В контрольных образцах (образцы раствора без волокон), подвергшихся воздействию той же среды, сильное растрескивание произошло через 35–70 мин. Лучшие характеристики FRC объясняются его более высокой прочностью на растяжение, а также увеличением пористости из-за плавления волокон. Образование микротрещин было подтверждено на микроструктуре с помощью СЭМ.Относительно низкая температура плавления синтетических волокон (ПП, ПВС, ПЭ) может играть важную роль в повторном отверждении после воздействия высокой температуры. Волокна создают микроканалы в бетоне, которые могут увеличивать скорость диффузии воды в процессе повторного отверждения водой [111]. Однако стальные волокна имеют высокую температуру плавления и могут влиять на механические свойства FRC после нагрева. Положительный эффект стальной фибры, замеченный сразу после охлаждения от высокой температуры, повторное отверждение FRC на воздухе может ограничивать образование новых трещин и расширение Ca (OH) 2 [111].В зависимости от типа волокна, механические свойства FRC увеличиваются с повышением температуры до определенного предела (например, стальная фибра 200–300 ° C) из-за того, что волокна препятствуют росту трещин в бетоне при повышенной температуре. Оптимальный предел температуры варьируется в зависимости от типа волокна и состава смеси. Комбинация стального и полипропиленового волокна (75% + 25%) также показала лучшие характеристики, чем другие комбинации (50% + 50%) и (25% + 75%) [112]. В другом исследовании FRC был изготовлен из трех различных типов волокна (сталь, полипропилен и полиэтилен) при 0.5 и 1,0 об.% [113]. Перед испытанием на изгиб образцы подвергали воздействию высоких температур 400, 600 и 800 ° C в печи в соответствии с ASTM E119-98. До 400 ° C все образцы показали повышенную прочность на изгиб и вязкость. Для образцов из синтетических или пластиковых волокон (ПП и ПЭ) при 800 ° C была отмечена значительная разница по сравнению с образцами из стального волокна. Плотность FRC, измеренная с помощью скорости ультразвукового импульса (UPV), также показала, что потеря массы в образцах стальных волокон ниже, чем в образцах волокон из полипропилена и полиэтилена [113].Хаддад и др. Также сообщили о значительном ухудшении качества образцов FRC, изготовленных из стальной фибры, подвергшихся воздействию температуры свыше 600 ° C. [114]. При высокой температуре FRC со стальной фиброй также может изменить свое поведение с хрупкого на псевдовязкое и, таким образом, образовать множественные трещины в конструкции до того, как произойдет разрушение [115]. 2,5. Бетон, армированный волокном, подверженный циклам замораживания / оттаиванияВ этом разделе обсуждается влияние добавления волокна в бетон на снижение деградации при замерзании-оттаивании в FRC.Допустимая потеря массы образцов бетона (размером 150 × 140 × 50 мм) в испытании CDF (капиллярное всасывание химикатов для борьбы с обледенением и испытание на замораживание-оттаивание) после 28 циклов замораживания-оттаивания составляет <1500 г / м 2 , как рекомендовано Комитет RILEM TC 117-FDC45 [116]. Аналогичным образом, для испытания, включающего 56 циклов замораживания-оттаивания в кубах размером 100 мм, критерий приемлемости составляет <3% от веса материала с накипью, как рекомендовано в [117]. Несколько исследователей изучали процент потери веса образцов FRC с различным содержанием стальной фибры и растворов (вода и NaCl) под воздействием замораживания-оттаивания (см.).Потеря веса образцов FRC была уменьшена по мере увеличения содержания стальной фибры (см. А). Было также обнаружено, что в / к влияет на потерю веса образцов [118,119]. Было обнаружено, что окончательные циклы замораживания-оттаивания (т. Е. Образцы растрескались и были извлечены из камеры замораживания-оттаивания) в образцах FRC с более низким значением w / c (0,26) составили 1900, в то время как образцы с w / c 0,32 и 0,44 выдержали (до того, как они были удалены из испытательной камеры) всего 780 и 260 циклов соответственно. Даже потеря массы была значительно ниже при низкой в / ц по сравнению с более высокой в / ц.Снижение динамического модуля упругости в образцах FRC происходило медленнее, чем в контрольном образце. Это объясняется способностью FRC задерживать трещины. Повреждение образцов бетона зависит от их способности размещать увеличенный объем застывшего раствора в порах. Типы волокон также играют важную роль, как показано на b. Для полипропилена и стекловолокна (GF) оптимальный предел содержания волокна составляет менее 2%. Потеря массы ( a ) образцов FRC из стального волокна и ( b ) раствора образцов полипропилена (PP) и стекловолокна (GF) при различных циклах замораживания-оттаивания (адаптировано из [120,121,122,123,124]). Об отличной устойчивости FRC с синтетическими волокнами к замораживанию и оттаиванию также сообщалось во многих исследованиях [3]. Инь и др. [125] сообщили, что FRC с волокнами ПВС не имеет заметной потери массы даже после 500 циклов замораживания-оттаивания. Однако прочность на изгиб FRC действительно уменьшалась с количеством циклов. Анализ микроструктуры с помощью SEM показал, что, хотя игольчатые кристаллы эттрингита можно найти в образцах FRC до циклов замораживания-оттаивания, они постепенно исчезли, и внутренняя структура FRC стала более компактной при воздействии замораживания-оттаивания.Однако внутренняя структура была повреждена из-за атаки замораживания-оттаивания, и постепенно образовались микротрещины, что привело к снижению прочности на изгиб по мере увеличения количества циклов замораживания-оттаивания [93]. Способность микроволоконных образцов FRC перекрывать трещины также может минимизировать количество соединительных пор в матрице и, таким образом, остановить образование льда в порах, что приведет к меньшему повреждению образцов. В целом циклы замораживания-оттаивания ухудшают и ослабляют поверхность раздела волокно-матрица в FRC [126]. Лучшее сопротивление FRC с низким объемом (0.1%) ПП по сравнению с контрольной смесью также обнаружили Ван и Чен [127]. Что касается стальных волокон, потеря массы в синтетических образцах FRC из-за циклов замораживания / оттаивания также была снижена по мере увеличения содержания волокна [122]. показывает сравнение характеристик SHCC с 2% ПВС и образцов строительного раствора после 28 циклов замораживания-оттаивания. Значительно более высокая потеря массы была измерена в строительном растворе (прочность на сжатие за 28 дней 62 МПа) по сравнению с SHCC со значительно более низкой прочностью на сжатие (прочность на сжатие 30 МПа). Повреждение поверхности ( a ) FRC с ПВС волокном и ( b ) образца высокопрочного раствора после 28 циклов замораживания-оттаивания. По сравнению с синтетическими, стальные волокна оказались более эффективными в плане сопротивления замораживанию-оттаиванию. Кроме того, прямые короткие волокна показали лучшую эффективность, чем волокна с более длинными крючковатыми концами [120]. Это можно объяснить количеством волокон в единице объема материалов и в поверхностном слое. Как правило, количество более длинных волокон с загнутыми концами на объем меньше по сравнению с прямыми волокнами.Следовательно, правильный выбор типа, размера и содержания волокна может сыграть важную роль в повреждении бетона из-за воздействия мороза. 3. Оставшийся срок службы инфраструктуры FRCВ этом разделе обсуждаются существующие модели, которые имеют дело с FRC, особенно в области коррозии. В исследовании Wang et al. [128], время до начала коррозии FRC оценивалось с использованием второго закона Фика, как показано на рис. Авторы отмечают, что, хотя второй закон Фика не может физически представить различные механизмы, которые приводят к проникновению хлоридов в бетон (например,g., капиллярное всасывание, действие фитиля, циклы смачивания и сушки и т. д.), это наиболее широко используемый подход в научной литературе и инженерной практике из-за своей простоты [41]. Было обнаружено, что преимущество FRC перед RC в условиях разгрузки неочевидно, так как разница в результатах была незначительной. Однако при тех же условиях нагружения (изгибающей нагрузки) время до начала коррозии в FRC было увеличено примерно в 2,2–3,6 раза; варьируется в зависимости от содержания волокна и толщины покрытия (см.).В исследовании Dhinakaran et al. [129] было выполнено сравнение стоимости жизненного цикла армированного стекловолокном полимера (GFRP) и обычных RC-балок. Сделан вывод, что балка, изготовленная из стеклопластика, примерно на 40% экономичнее, а также имеет в два раза больший срок службы по сравнению с балкой RC. Улучшенные характеристики FRC можно отнести к его перекрытию трещин и множественному растрескиванию, которые контролируют макро- и микрокоррозию. Прогнозируемое начало коррозии FRC и простого бетона при различной глубине покрытия (адаптировано из [128]). Ожидаемый срок службы образцов FRC, изготовленных из различных процентных соотношений волокон мягкой древесины (0,1, 0,3 и 0,5%) с и без приложенного напряжения сжатия, был спрогнозирован для коэффициентов диффузии хлоридов, как показано в [130]. Коэффициент диффузии был оценен с помощью эмпирического соотношения [131], а затем использован для оценки срока службы. Наконец, коэффициент долговечности D для данного бетона был определен как отношение его ожидаемого срока службы к аналогичному обычному бетону при нулевом напряжении.Фактор долговечности оказался наивысшим при уровне сжимающего напряжения, равном 0,3 от предела прочности на сжатие (0,3 f u ). В другом исследовании [132] срок службы SHCC был предсказан на основе испытаний на ускоренную коррозию потери массы для различной глубины покрытия (15, 25 и 35 мм). Здесь коррозионная потеря массы стальной арматуры определялась путем приложения различных напряжений (10, 20 и 30 В) до определенного периода времени, пока образцы подвергались воздействию хлоридного раствора. Коррозионная потеря массы была преобразована в фактическую потерю сопротивления для оценки срока службы путем определения распределения потери массы.Коэффициенты ускорения, которые определяют время разрушения образцов SHCC для разной глубины покрытия, затем были определены из соотношения типа Аррениуса. Влияние содержания волокна и уровня напряжений на коэффициент долговечности простых и FRC образцов. Здесь f u представляют предел прочности бетона на сжатие (адаптировано из [130]). Исследования были также посвящены разработке моделей срока службы FRC для температур и замораживания-оттаивания, и в обоих случаях было обнаружено увеличение срока службы FRC по сравнению с обычным бетоном [133,134].При тех же условиях испытаний на замораживание-оттаивание, срок службы образцов FRC (с 1% волокна) был на 11 лет дольше, чем у обычного бетона [133]. Предложенные модели могут быть полезны при проектировании таких конструкций, как резервуары для воды, настилы мостов и морские сооружения [130]. Тем не менее, недостатком всех прогнозов срока службы является то, что они основаны на лабораторных испытаниях, а реальные условия разрушения могут сильно отличаться. Следовательно, для калибровки коэффициентов ускорения, определенных на более ранней стадии, требуется мониторинг долговременного износа в естественных условиях [135].Кроме того, модели прогнозирования срока службы могут быть обновлены путем получения большего количества полевых данных с использованием датчиков или исследований коррозии на месте, которые вводятся в модели вероятностного прогнозирования, а не на основе лабораторных экспериментов [136]. 4. Долговечность существующей инфраструктуры FRCВ традиционных приложениях FRC наблюдается различие между использованием микроволоконных и макроволоконных FRC. FRC из микроволокна широко используются для контроля пластической усадки [137,138], ударопрочности [139,140,141,142] и огнестойкости [143,144].FRC из макроволокна применялись в конструкционных материалах, таких как плиты на грунте в качестве промышленных полов и дорожных покрытий [145], в меньшей степени в подвесных плитах [146,147] и футеровке туннелей [148,149]. Недавняя разработка усовершенствованных классов FRC также привела к использованию коротких тонких микроволокон в конструкционных приложениях. В этом разделе сообщается о долговечности различных инфраструктур FRC, сначала в обычных приложениях, а затем при модернизации / восстановлении инфраструктуры с использованием расширенных классов FRC. 4.1. Характеристики традиционных инфраструктур FRC — грунтовые и подвесные плитыСообщалось, что преобладающим традиционным применением FRC были плиты на уровне земли или так называемые грунтовые плиты в виде промышленных полов и дорожных покрытий [150], которые составляли около 60% Приложения FRC. Волокна в основном используются для контроля трещин в качестве вторичного армирования [145], что может привести к значительной экономии затрат в течение жизненного цикла за счет снижения затрат на техническое обслуживание и ремонт из-за ударов колес и выкрашивания стыков полов и тротуаров или усадочных трещин в бесшовных плитах.Эти типы приложений также эволюционировали в руководящие принципы проектирования, например, Технический отчет 34 Общества бетона [151], Код модели fib [152], ACI 360 [153], хотя стандартизованный дизайн еще не включен в нормы Еврокода или ACI для бетона. . В подвесных плитах волокна способствуют уменьшению ширины трещин и контролю расстояния между ними, что улучшает удобство эксплуатации и долговечность [152]. Однако использование волокон в качестве единственной арматуры (то есть без обычной стальной арматуры) в подвесных плитах было ограничено.Общее мнение состоит в том, что для надежного поведения конструкции требуется комбинация традиционной стальной арматуры и волокон, и недавно было высказано предположение, что соответствующая комбинация арматурных стержней и волокон может дать самый низкий общий коэффициент армирования [154]. Тем не менее, подвесные плиты, армированные только волокнами, были построены в ряде коммерческих и жилых зданий в странах Балтии, континентальной Европы и Великобритании, включая пятиэтажное офисное здание и шестнадцатиэтажную офисную башню [146,147].Тонкие плиты простираются на 5–8 м и содержат стальную фибру в объемном процентном соотношении в диапазоне 0,6–1,2% (45–100 кг / м 3 ). Тем не менее, стальная арматура была встроена в полосы, проходящие между колоннами, чтобы снизить риск прогрессирующего обрушения. На момент публикации отчетов о характеристиках этих плит от авторов не поступало. Однако сообщалось об успешном и регулярном использовании подвесных плит FRC (только) с более коротким пролетом (3-5 м) в течение 15 лет [146].Считается, что в помещениях основным механизмом разрушения плит FRC является карбонизация и коррозия, вызванная карбонизацией, из-за воздействия на людей или промышленных источников CO 2 . Как сообщалось в разделе 2.2, оптимальная конструкция смеси FRC может снизить скорость, с которой фронт карбонизации углубляется в бетон. Однако сообщений о таком ухудшении, связанном с практическим применением FRC, не поступало. 4.2. Характеристики традиционной инфраструктуры FRC — облицовка туннелейХотя облицовка туннелей из FRC была представлена в 1980-х годах [155], первым руководством по проектированию футеровки туннелей из FRC является ACI 544.7R [153] от 2016 г. Используются все футеровки туннелей из торкрет-бетона, сборные железобетонные или монолитные из FRC. Сообщается, что процессы износа футеровки туннелей включают коррозию, вызванную хлоридом и карбонизацией, сульфатное и кислотное воздействие, замораживание-оттаивание, ASR и коррозию в железнодорожных туннелях от паразитных токов [156, 157]. Дискретные стальные волокна в FRC менее подвержены паразитной коррозии, чем RC, в основном из-за прерывистой природы диспергированных волокон [142]. Эксплуатационные характеристики футеровок из FRC, подверженных усталостным нагрузкам из-за повторяющихся нагрузок за счет давления воздуха и всасывания от проходящих поездов, зависят от предотвращения образования трещин.При отсутствии трещин усталостная долговечность футеровки из FRC выше, чем у простого бетона, но в случаях, когда ограниченная усадка действительно приводит к образованию трещин, циклическое нагружение может вызвать широкие трещины с высоким риском снижения усталостной долговечности [158]. Вызванная хлоридом коррозия самих стальных волокон, как сообщается в разделе 2.1, менее значительна для стальных FRC с трещинами, чем для стальных стержней, при отсутствии или незначительной коррозии волокон, перекрывающих трещины шириной менее 0,1 мм, и легкой коррозии без потерь в поперечном сечении. сечение волокон шире (0.5 мм) трещины [67]. 4.3. Инфраструктура, модифицированная с помощью FRCСтарение инфраструктуры, повреждение землетрясениями и преждевременная коррозия арматуры в прибрежных районах и регионах, где используются противообледенительные соли, привели к использованию FRC для укрепления и модернизации дорожной инфраструктуры. Здесь сообщается о характеристиках модифицированной инфраструктуры для повышения устойчивости к проникновению воды и вредных веществ за счет использования FRC высокой плотности, а также там, где были обеспечены более высокая деформируемость и пластичность. Сверхвысокая прочность (прочность на сжатие 180–200 МПа и растяжение 7–15 МПа) UHPFRC с низкой водопроницаемостью применяется при частичной замене изношенных настилов и плит некоторых дорожных и железнодорожных инфраструктур и зданий с 2004 г. [159]. Высокая прочность и низкая проницаемость этих материалов сочетают в себе функции упрочнения и устойчивости к проникновению вредных веществ, тем самым нарушая процессы разрушения [5]. Как правило, после удаления разрушенного бетона наносятся клееные перекрытия из UHPFRC, содержащие высокопрочные стальные волокна или волокна HMPE.Тонкие накладки восстанавливали или увеличивали сопротивление надстроек без значительного увеличения веса и необходимости усиления подконструкций. Вмешательства заключались в разрушении инфраструктуры в возрасте 50–70 лет, с восстановлением ожидаемого срока службы до 100 лет, типичных для такой инфраструктуры. Для повышения сейсмостойкости и снижения требований к техническому обслуживанию деформационных швов на автомобильных мостах была разработана система соединения плит [160,161]. Концепция проиллюстрирована в.Для соединительной плиты был использован высокопластичный SHCC с номинальной прочностью на сжатие 30 МПа и модулем упругости 15–20 ГПа. Пластичность была разработана для образования множественных трещин в соединительной плите, которые могут возникнуть из-за усадки или землетрясения, в результате чего компенсируется относительное движение между двумя балками. Поверх соединительной плиты кладут гидроизоляцию и асфальт для обеспечения геометрической непрерывности. Это означает, что состояние соединительной плиты R / SHCC невозможно проверить визуально.Однако он выглядит в хорошем состоянии из-за отсутствия видимых трещин или выбоин на асфальте с момента его установки в 2011 году. Схема соединительной плиты настила моста (адаптировано из [160]). В рамках еще одной модификации для повышения надежности инфраструктуры с помощью FRC, Ishikawa et al. [162] разработали соединение упор-плита, проиллюстрированное на. Значительная утечка и связанная с ней коррозия железобетона в опоре и плитах под традиционными швами на автомобильных мостах послужили причиной этого вмешательства.Ishikawa et al. [162] сообщили о выполнении 85 замен суставов с использованием этого подхода. Кроме того, этот подход позволяет непрерывно укладывать гидроизоляцию и асфальт на стык FRC. При осмотре в трех случаях было обнаружено расслоение, которое привело к утечке, но, помимо значительного уменьшения утечки, это бесшарнирное соединение также снижает удар колес транспортного средства по сравнению с традиционными соединениями. Таким образом, помимо повышения долговечности, вмешательство привело к повышению комфорта вождения и увеличению усталостной долговечности этих мостов. Схема соединения ( a ) FRC абатмент-плита для предотвращения утечки и коррозии в инфраструктуре шоссе, и ( b ) отливка FRC [162]. иллюстрирует третье мероприятие по повышению долговечности автомобильных мостов путем модернизации FRC, так называемую концепцию перемычек [163,164]. Традиционные деформационные швы, допускающие утечку воды и противообледенительных солей и связанные с этим коррозионные повреждения основания или палубы, заменяются высокопластичными, армированными сталью SHCC.Замены традиционных деформационных шарниров производились каждые три года. Однако, согласно сообщениям, соединительная плита, построенная в 2005 году, все еще находится в рабочем состоянии и функционирует нормально. Множественные трещины видны на поверхности соединительной плиты на регулярном расстоянии, но контролируются армированием волокном, чтобы предотвратить локализацию в широких трещинах и связанное с этим ускоренное разрушение. Схема соединительной плиты, заменяющей проблемный деформационный шов в многопролетных автодорожных мостах, подверженных разложению противообледенительной соли (адаптировано из [163]). Грунтовка глубокопроникающая | Жидкие фасадные краски и покрытия | ПродукцияОписание товараFescon Deeply Penetrating Primer — водорастворимая, не содержащая растворителей, почти без запаха, бесцветная грунтовка со связующим из акриловой полимерной смолы для внутреннего и наружного применения.Может использоваться как грунтовка под различные краски и штукатурки.
Приложения
Обращение с отходамиХранение и обращение с отходами. См. Отдельные инструкции по хранению и утилизации https://www.fescon.fi/en/material-bank .
Информация основана на тестах и практическом опыте. Мы не можем повлиять на условия на рабочем месте, поэтому мы не можем нести ответственность за конечный результат, на который влияют местные условия. Эпоксидная смола для инъекций | CTech-LLCEIR ™ — это двухкомпонентная высокопрочная, не содержащая растворителей двухкомпонентная эпоксидная смола, содержащая 100% твердых веществ, для инъекции трещин.Благодаря высокой скорости проникновения в пористые основания и отличной адгезии к бетону и каменной кладке, EIR ™ обеспечивает прочное склеивание даже самых мелких трещин и восстанавливает структурную целостность. Основные характеристики
Приложения
Условия храненияСмолуCTech-LLC ® EIR ™ следует хранить в сухом и прохладном месте при температуре от 4 ° до 40 ° C. Избегайте замораживания продукта и храните его вдали от прямых солнечных лучей, пламени и других опасностей. Срок годностиПри правильном хранении EIR ™ может храниться в течение трех лет в оригинальной упаковке. ОпцииУпаковка / Вес:
*** Примечание: также доступна индивидуальная упаковка. Коды и стандартыASTM, 2013, Стандартные спецификации для эпоксидных смол, ASTM D1763–00, Американское общество испытаний и материалов. ASTM, 2017, Стандартное руководство по испытаниям эпоксидных смол, ASTM D4142-89, Американское общество испытаний и материалов. ISO, 2010, Пластмассы — Эпоксидные смолы — Методы испытаний, ISO 18280, Международная организация по стандартизации. |