ΠΠ»Π°ΡΡΠΈΡΠΈΠΊΠ°ΡΠΈΡ ΡΡΠ³ΡΠ½ΠΎΠ²
Π‘Π΅ΡΡ ΠΏΡΠΎΡΠ΅ΡΡΠΈΠΎΠ½Π°Π»ΡΠ½ΡΡ ΠΊΠΎΠ½ΡΠ°ΠΊΡΠΎΠ² ΡΠΏΠ΅ΡΠΈΠ°Π»ΠΈΡΡΠΎΠ² ΡΠ²Π°ΡΠΊΠΈ
Π§ΡΠ³ΡΠ½ ΠΏΡΠ΅Π΄ΡΡΠ°Π²Π»ΡΠ΅Ρ ΡΠΎΠ±ΠΎΠΉ ΠΌΠ½ΠΎΠ³ΠΎΠΊΠΎΠΌΠΏΠΎΠ½Π΅Π½ΡΠ½ΡΠΉ ΡΠΏΠ»Π°Π² ΠΆΠ΅Π»Π΅Π·Π° Ρ ΡΠ³Π»Π΅ΡΠΎΠ΄ΠΎΠΌ, ΡΠΎΠ΄Π΅ΡΠΆΠ°ΡΠΈΠΉ >2,1% Π‘. ΠΡΠΎΠΌΠ΅ ΡΠ³Π»Π΅ΡΠΎΠ΄Π° Π² ΡΡΠ³ΡΠ½Π΅ ΠΎΠ±ΡΡΠ½ΠΎ ΡΠΎΠ΄Π΅ΡΠΆΠΈΡΡΡ (Π² %): Π΄ΠΎ 4 Si; 2 ΠΠΏ; 0,3 Π ; 0,25 S, Π° ΡΠ°ΠΊΠΆΠ΅ 0,1 Cr, Ni ΠΈΠ»ΠΈ Cu. ΠΠ»Π°ΡΡΠΈΡΠΈΠΊΠ°ΡΠΈΡ ΡΡΠ³ΡΠ½ΠΎΠ² Π² Π·Π°Π²ΠΈΡΠΈΠΌΠΎΡΡΠΈ ΠΎΡ ΡΠΎΡΡΠΎΡΠ½ΠΈΡ ΡΠ³Π»Π΅ΡΠΎΠ΄Π° Π² ΡΠΏΠ»Π°Π²Π΅:
- Π±Π΅Π»ΡΠ΅,
- ΡΠ΅ΡΡΠ΅,
- ΠΊΠΎΠ²ΠΊΠΈΠ΅,
- Π²ΡΡΠΎΠΊΠΎΠΏΡΠΎΡΠ½ΡΠ΅ ΡΡΠ³ΡΠ½Ρ.
Π Π±Π΅Π»ΠΎΠΌ ΡΡΠ³ΡΠ½Π΅ Π²Π΅ΡΡ ΡΠ³Π»Π΅ΡΠΎΠ΄ Π½Π°Ρ ΠΎΠ΄ΠΈΡΡΡ Π² Π²ΠΈΠ΄Π΅ Ρ ΠΈΠΌΠΈΡΠ΅ΡΠΊΠΎΠ³ΠΎ ΡΠΎΠ΅Π΄ΠΈΠ½Π΅Π½ΠΈΡ Ρ ΠΆΠ΅Π»Π΅Π·ΠΎΠΌ — ΡΠ΅ΠΌΠ΅Π½ΡΠΈΡΠ° (FΠ΅3Π‘). Π¦Π΅ΠΌΠ΅Π½ΡΠΈΡ ΠΎΠ±Π»Π°Π΄Π°Π΅Ρ Π²ΡΡΠΎΠΊΠΈΠΌΠΈ ΡΠ²Π΅ΡΠ΄ΠΎΡΡΡΡ (800 ΠΠ) ΠΈ Ρ ΡΡΠΏΠΊΠΎΡΡΡΡ, ΠΏΠΎΡΡΠΎΠΌΡ ΡΡΡΠ΄Π½ΠΎ ΠΏΠΎΠ΄Π΄Π°Π΅ΡΡΡ ΠΌΠ΅Ρ Π°Π½ΠΈΡΠ΅ΡΠΊΠΎΠΉ ΠΎΠ±ΡΠ°Π±ΠΎΡΠΊΠ΅. ΠΠ·-Π·Π° ΡΡΠΎΠ³ΠΎ Π±Π΅Π»ΡΠ΅ ΡΡΠ³ΡΠ½Ρ Π½Π°ΡΠ»ΠΈ ΠΎΠ³ΡΠ°Π½ΠΈΡΠ΅Π½Π½ΠΎΠ΅ ΠΏΡΠΈΠΌΠ΅Π½Π΅Π½ΠΈΠ΅ Π² ΠΊΠ°ΡΠ΅ΡΡΠ²Π΅ ΠΊΠΎΠ½ΡΡΡΡΠΊΡΠΈΠΎΠ½Π½ΡΡ ΠΌΠ°ΡΠ΅ΡΠΈΠ°Π»ΠΎΠ² ΠΈ ΡΠ»ΡΠΆΠ°Ρ Π² ΠΎΡΠ½ΠΎΠ²Π½ΠΎΠΌ Π΄Π»Ρ ΠΏΠΎΠ»ΡΡΠ΅Π½ΠΈΡ ΠΊΠΎΠ²ΠΊΠΈΡ ΡΡΠ³ΡΠ½ΠΎΠ². ΠΡΠΈ Π΄Π»ΠΈΡΠ΅Π»ΡΠ½ΠΎΠΌ ΠΎΠ±ΠΆΠΈΠ³Π΅ Π±Π΅Π»ΠΎΠ³ΠΎ ΡΡΠ³ΡΠ½Π° ΡΠ΅ΠΌΠ΅Π½ΡΠΈΡ Π² Π½Π΅ΠΌ ΡΠ°ΡΠΏΠ°Π΄Π°Π΅ΡΡΡ ΠΈ ΡΠ³Π»Π΅ΡΠΎΠ΄ Π²ΡΠ΄Π΅Π»ΡΠ΅ΡΡΡ Π² ΡΠ²ΠΎΠ±ΠΎΠ΄Π½ΠΎΠ΅ ΡΠΎΡΡΠΎΡΠ½ΠΈΠ΅.
Π‘Π΅ΡΡΠ΅ ΡΡΠ³ΡΠ½Ρ Π² ΠΈΠ·Π»ΠΎΠΌΠ΅ ΠΈΠΌΠ΅ΡΡ ΡΠ΅ΡΠ΅Π±ΡΠΈΡΡΡΠΉ ΡΠ²Π΅Ρ ΠΈΠ·-Π·Π° Π½Π°Π»ΠΈΡΠΈΡ Π² Π½ΠΈΡ
ΠΏΠ»Π°ΡΡΠΈΠ½ΡΠ°ΡΡΡ
Π²ΠΊΠ»ΡΡΠ΅Π½ΠΈΠΉ Π³ΡΠ°ΡΠΈΡΠ°.
ΠΠ°Π»ΠΈΡΠΈΠ΅ ΡΠ²ΠΎΠ±ΠΎΠ΄Π½ΠΎΠ³ΠΎ Π³ΡΠ°ΡΠΈΡΠ° Π² ΡΡΠ³ΡΠ½Π΅ (Π΄ΠΎ 50 % Π‘) ΠΎΠΊΠ°Π·ΡΠ²Π°Π΅Ρ Π²Π»ΠΈΡΠ½ΠΈΠ΅ Π½Π° Π΅Π³ΠΎ ΡΠ²ΠΎΠΉΡΡΠ²Π°. Π£Π²Π΅Π»ΠΈΡΠ΅Π½ΠΈΠ΅ ΠΊΠΎΠ»ΠΈΡΠ΅ΡΡΠ²Π° ΠΈ ΡΠ°Π·ΠΌΠ΅ΡΠΎΠ² Π³ΡΠ°ΡΠΈΡΠΎΠ²ΡΡ Π²ΠΊΠ»ΡΡΠ΅Π½ΠΈΠΉ ΠΈ Π½Π΅ΡΠ°Π²Π½ΠΎΠΌΠ΅ΡΠ½ΠΎΡΡΡ ΠΈΡ ΡΠ°ΡΠΏΡΠ΅Π΄Π΅Π»Π΅Π½ΠΈΡ ΡΠΌΠ΅Π½ΡΡΠ°ΡΡ ΠΏΡΠΎΡΠ½ΠΎΡΡΡ ΡΡΠ³ΡΠ½Π°. ΠΠΌΠ΅ΡΡΠ΅ Ρ ΡΠ΅ΠΌ, ΡΠ²ΠΎΠ±ΠΎΠ΄Π½ΡΠΉ Π³ΡΠ°ΡΠΈΡ ΠΏΡΠΈΠ΄Π°Π΅Ρ ΡΡΠ³ΡΠ½Ρ ΠΈΠ·Π½ΠΎΡΠΎΡΡΠΎΠΉΠΊΠΎΡΡΡ, Π²ΡΡΠΎΠΊΠΈΠ΅ Π»ΠΈΡΠ΅ΠΉΠ½ΡΠ΅ ΡΠ²ΠΎΠΉΡΡΠ²Π°, Ρ ΠΎΡΠΎΡΡΡ ΠΎΠ±ΡΠ°Π±Π°ΡΡΠ²Π°Π΅ΠΌΠΎΡΡΡ ΡΠ΅ΠΆΡΡΠΈΠΌ ΠΈΠ½ΡΡΡΡΠΌΠ΅Π½ΡΠΎΠΌ ΠΈ Π²ΡΡΠΎΠΊΡΡ ΡΠΎΠΏΡΠΎΡΠΈΠ²Π»ΡΠ΅ΠΌΠΎΡΡΡ ΠΏΡΠΈ Π·Π½Π°ΠΊΠΎΠΏΠ΅ΡΠ΅ΠΌΠ΅Π½Π½ΡΡ Π½Π°Π³ΡΡΠ·ΠΊΠ°Ρ . ΠΡΠ΅ ΡΡΠΎ ΠΎΠ±ΡΡΠ»ΠΎΠ²Π»ΠΈΠ²Π°Π΅Ρ ΡΠΈΡΠΎΠΊΠΎΠ΅ ΠΏΡΠΈΠΌΠ΅Π½Π΅Π½ΠΈΠ΅ ΡΠ΅ΡΠΎΠ³ΠΎ ΡΡΠ³ΡΠ½Π° Π² ΠΊΠ°ΡΠ΅ΡΡΠ²Π΅ ΠΊΠΎΠ½ΡΡΡΡΠΊΡΠΈΠΎΠ½Π½ΠΎΠ³ΠΎ ΠΌΠ°ΡΠ΅ΡΠΈΠ°Π»Π°.
Π§ΡΠ³ΡΠ½, ΠΏΠΎΠ»ΡΡΠ΅Π½Π½ΡΠΉ ΠΈΠ· Π±Π΅Π»ΠΎΠ³ΠΎ ΡΡΠ³ΡΠ½Π° ΠΏΡΠΎΠ΄ΠΎΠ»ΠΆΠΈΡΠ΅Π»ΡΠ½ΡΠΌ ΠΎΡΠΆΠΈΠ³ΠΎΠΌ ΠΏΡΠΈ ΡΠ΅ΠΌΠΏΠ΅ΡΠ°ΡΡΡΠ΅ 800…850 oΠ‘, Π½Π°Π·ΡΠ²Π°ΡΡ ΠΊΠΎΠ²ΠΊΠΈΠΌ. Π ΠΎΡΠ»ΠΈΡΠΈΠ΅ ΠΎΡ ΡΠ΅ΡΠΎΠ³ΠΎ ΡΡΠ³ΡΠ½Π° Π² ΠΊΠΎΠ²ΠΊΠΎΠΌ ΡΠ³Π»Π΅ΡΠΎΠ΄ Π½Π°Ρ
ΠΎΠ΄ΠΈΡΡΡ Π½Π΅ Π² Π²ΠΈΠ΄Π΅ ΠΏΠ»Π°ΡΡΠΈΠ½ΡΠ°ΡΠΎΠ³ΠΎ Π³ΡΠ°ΡΠΈΡΠ°, Π° Π² Π²ΠΈΠ΄Π΅ Ρ
Π»ΠΎΠΏΡΠ΅Π²ΠΈΠ΄Π½ΠΎΠ³ΠΎ. ΠΠΎΠ²ΠΊΠΈΠΉ ΡΡΠ³ΡΠ½ ΠΏΠΎ ΡΡΠ°Π²Π½Π΅Π½ΠΈΡ Ρ ΡΠ΅ΡΡΠΌ ΡΡΠ³ΡΠ½ΠΎΠΌ ΠΎΠ±Π»Π°Π΄Π°Π΅Ρ Π±ΠΎΠ»Π΅Π΅ Π²ΡΡΠΎΠΊΠΎΠΉ ΠΏΡΠΎΡΠ½ΠΎΡΡΡΡ (300 … 630 ΠΠΠ°), ΠΏΠ»Π°ΡΡΠΈΡΠ½ΠΎΡΡΡΡ ΠΈ ΡΠ΄Π°ΡΠ½ΠΎΠΉ Π²ΡΠ·ΠΊΠΎΡΡΡΡ. ΠΠΎΠ²ΠΊΠΈΠΉ ΡΡΠ³ΡΠ½ ΠΈΠΌΠ΅Π΅Ρ ΠΎΠ΄Π½ΠΎΡΠΎΠ΄Π½ΡΠ΅ ΡΠ²ΠΎΠΉΡΡΠ²Π° ΠΏΠΎ ΡΠ΅ΡΠ΅Π½ΠΈΡ, Π² Π΅Π³ΠΎ ΠΎΡΠ»ΠΈΠ²ΠΊΠ°Ρ
ΠΎΡΡΡΡΡΡΠ²ΡΡΡ Π½Π°ΠΏΡΡΠΆΠ΅Π½ΠΈΡ, Π΅ΠΌΡ ΠΏΡΠΈ ΡΡΡΠΈ Π²ΡΡΠΎΠΊΠΈΠ΅ ΠΌΠ΅Ρ
Π°Π½ΠΈΡΠ΅ΡΠΊΠΈΠ΅ ΡΠ²ΠΎΠΉΡΡΠ²Π°, ΠΎΠ½ Ρ
ΠΎΡΠΎΡΠΎ ΠΎΠ±ΡΠ°Π±Π°ΡΡΠ²Π°Π΅ΡΡΡ.
Π Π·Π°Π²ΠΈΡΠΈΠΌΠΎΡΡΠΈ ΠΎΡ ΡΠ΅ΠΆΠΈΠΌΠ° ΡΠ΅ΡΠΌΠΎΠΎΠ±ΡΠ°Π±ΠΎΡΠΊΠΈ ΠΎΡΠ½ΠΎΠ²Π° ΠΊΠΎΠ²ΠΊΠΎΠ³ΠΎ ΡΡΠ³ΡΠ½Π° ΠΌΠΎΠΆΠ΅Ρ Π±ΡΡΡ ΡΠ΅ΡΡΠΈΡΠ½ΠΎΠΉ ΠΈΠ»ΠΈ ΠΏΠ΅ΡΠ»ΠΈΡΠ½ΠΎΠΉ. Π‘ΠΎΡΡΠ°Π² ΠΎΡΠ½ΠΎΠ²Π½ΡΡ ΡΠ»Π΅ΠΌΠ΅Π½ΡΠΎΠ² Π² ΠΊΠΎΠ²ΠΊΠΎΠΌ ΡΡΠ³ΡΠ½Π΅ (Π² %): 2,3 …3 Π‘; 0,9 … 16 Si; 0,3 … 1,2 Πn; >0,15 Π ΠΈ S. ΠΡΠ½ΠΎΠ²Π½ΡΠ΅ Ρ Π°ΡΠ°ΠΊΡΠ΅ΡΠΈΡΡΠΈΠΊΠΈ ΠΊΠΎΠ²ΠΊΠΈΡ ΡΡΠ³ΡΠ½ΠΎΠ² ΠΎΠΏΡΠ΅Π΄Π΅Π»Π΅Π½Ρ ΠΠΠ‘Π’ 1215-79. Π€Π΅ΡΡΠΈΡΠ½ΡΠ΅ ΡΡΠ³ΡΠ½Ρ ΠΎΡΠ»ΠΈΡΠ°ΡΡΡΡ Π±ΠΎΠ»Π΅Π΅ Π²ΡΡΠΎΠΊΠΎΠΉ ΠΏΠ»Π°ΡΡΠΈΡΠ½ΠΎΡΡΡΡ, Π° ΠΏΠ΅ΡΠ»ΠΈΡΠ½ΡΠ΅ ΠΎΠ±Π΅ΡΠΏΠ΅ΡΠΈΠ²Π°ΡΡ Π»ΡΡΡΡΡ ΠΈΠ·Π½ΠΎΡΠΎΡΡΠΎΠΉΠΊΠΎΡΡΡ.
Π ΠΏΡΠΎΠΌΡΡΠ»Π΅Π½Π½ΠΎΡΡΠΈ ΠΏΠΎΠ»ΡΡΠΈΠ»ΠΈ ΡΠ°ΡΠΏΡΠΎΡΡΡΠ°Π½Π΅Π½ΠΈΠ΅ Π²ΡΡΠΎΠΊΠΎΠΏΡΠΎΡΠ½ΡΠ΅ ΠΈ Π»Π΅Π³ΠΈΡΠΎΠ²Π°Π½Π½ΡΠ΅ ΡΡΠ³ΡΠ½Ρ. Π Π²ΡΡΠΎΠΊΠΎΠΏΡΠΎΡΠ½ΠΎΠΌ ΡΡΠ³ΡΠ½Π΅ (ΠΠΠ‘Π’ 7293-85) ΡΠ³Π»Π΅ΡΠΎΠ΄ Π½Π°Ρ
ΠΎΠ΄ΠΈΡΡΡ Π² Π²ΠΈΠ΄Π΅ ΡΠ°ΡΠΎΠ²ΠΈΠ΄Π½ΠΎΠ³ΠΎ Π³ΡΠ°ΡΠΈΡΠ°. Π‘ΠΎΠ΄Π΅ΡΠΆΠ°Π½ΠΈΠ΅ ΠΎΡΠ½ΠΎΠ²Π½ΡΡ
ΡΠ»Π΅ΠΌΠ΅Π½ΡΠΎΠ² Π² ΡΠ°ΠΊΠΈΡ
ΡΡΠ³ΡΠ½Π°Ρ
ΡΠΎΡΡΠ°Π²Π»ΡΠ΅Ρ (Π² %): Π΄ΠΎ 38 Π‘; 2.9 Si; 0,9 Πn; 0,1 Π‘Π³; 0,02 S; 0,1 Π ; 0,08 Mg. Π§ΡΠ³ΡΠ½Ρ Ρ ΡΠ°ΡΠΎΠ²ΠΈΠ΄Π½ΡΠΌ Π³ΡΠ°ΡΠΈΡΠΎΠΌ Π·Π½Π°ΡΠΈΡΠ΅Π»ΡΠ½ΠΎ ΠΏΡΠ΅Π²ΠΎΡΡ
ΠΎΠ΄ΡΡ ΠΏΠΎ Ρ
Π°ΡΠ°ΠΊΡΠ΅ΡΠΈΡΡΠΈΠΊΠ°ΠΌ ΡΠ΅ΡΡΠ΅ ΡΡΠ³ΡΠ½Ρ.
ΠΠ΅Π³ΠΈΡΠΎΠ²Π°Π½Π½ΡΠ΅ ΡΡΠ³ΡΠ½Ρ Π²ΡΠΏΡΡΠΊΠ°ΡΡΡΡ ΡΠΎΠ³Π»Π°ΡΠ½ΠΎ ΠΠΠ‘Π’ 7769-82.
ΠΠ»Π°ΡΡΠΈΡΠΈΠΊΠ°ΡΠΈΡ ΡΡΠ³ΡΠ½ΠΎΠ² Π»Π΅Π³ΠΈΡΠΎΠ²Π°Π½Π½ΡΡ :
- ΠΆΠ°ΡΠΎΡΡΠΎΠΉΠΊΠΈΠ΅ Ρ ΡΠΎΠΌΠΎΠ²ΡΠ΅ ΡΡΠ³ΡΠ½Ρ,
- ΠΊΠΎΡΡΠΎΠ·ΠΈΠΎΠ½Π½ΠΎ-ΡΡΠΎΠΉΠΊΠΈΠ΅ ΡΡΠ³ΡΠ½Ρ,
- ΠΈΠ·Π½ΠΎΡΠΎΡΡΠΎΠΉΠΊΠΈΠ΅ ΡΡΠ³ΡΠ½Ρ
- Π΄ΡΡΠ³ΠΈΠ΅.
Π’Π°ΠΊΠΈΠ΅ ΡΡΠ³ΡΠ½Ρ Π»Π΅Π³ΠΈΡΡΡΡΡΡ Ρ ΡΠΎΠΌΠΎΠΌ, Π½ΠΈΠΊΠ΅Π»Π΅ΠΌ, ΠΊΡΠ΅ΠΌΠ½ΠΈΠ΅ΠΌ, ΠΌΠ°Π³Π½ΠΈΠ΅ΠΌ, ΠΌΠ΅Π΄ΡΡ ΠΈ Π΄ΡΡΠ³ΠΈΠΌΠΈ ΡΠ»Π΅ΠΌΠ΅Π½ΡΠ°ΠΌΠΈ. Π Π»Π΅Π³ΠΈΡΠΎΠ²Π°Π½Π½ΡΡ ΡΡΠ³ΡΠ½Π°Ρ Ρ ΡΠΎΠ΄Π΅ΡΠΆΠ°Π½ΠΈΠ΅ΠΌ Π΄ΠΎ 10 % Ni, Π‘r ΠΈ Πn ΠΈ Π±ΠΎΠ»Π΅Π΅ ΠΈΠΌΠ΅ΡΡ ΠΌΠ΅ΡΡΠΎ ΠΏΠ΅ΡΠ»ΠΈΡΠ½ΠΎ-ΠΊΠ°ΡΠ±ΠΈΠ΄Π½ΡΠ΅, Π±Π΅ΠΉΠ½ΠΈΡΠ½ΡΠ΅, ΠΌΠ°ΡΡΠ΅Π½ΡΠΈΡΠ½ΡΠ΅ ΠΈ Π°ΡΡΡΠ΅Π½ΠΈΡΠ½ΡΠ΅ ΠΎΡΠ½ΠΎΠ²Ρ.
ΠΡΡΠ³ΠΈΠ΅ ΡΡΡΠ°Π½ΠΈΡΡ ΠΏΠΎ ΡΠ΅ΠΌΠ΅
:
- ΠΡΠΎΠ±Π΅Π½Π½ΠΎΡΡΠΈ ΡΠ²Π°ΡΠΊΠΈ ΡΡΠ³ΡΠ½Π°.
- ΠΠΎΡΠΎΡΠΊΠΎΠ²Π°Ρ ΠΏΡΠΎΠ²ΠΎΠ»ΠΎΠΊΠ° Π΄Π»Ρ ΡΠ²Π°ΡΠΊΠΈ ΡΡΠ³ΡΠ½Π°.
- Π‘ΠΏΠΎΡΠΎΠ±Ρ ΡΠ²Π°ΡΠΊΠΈ ΡΡΠ³ΡΠ½Π° (ΠΎΡΠ½ΠΎΠ²Π½ΡΠ΅).
- ΠΠ»Π΅ΠΊΡΡΠΎΠ΄Ρ Π΄Π»Ρ ΡΠ²Π°ΡΠΊΠΈ ΠΈ Π½Π°ΠΏΠ»Π°Π²ΠΊΠΈ ΡΡΠ³ΡΠ½Π° — ΡΠΏΠΈΡΠΎΠΊ ΠΌΠ°ΡΠΎΠΊ.
Copyright. ΠΡΠΈ Π»ΡΠ±ΠΎΠΌ ΡΠΈΡΠΈΡΠΎΠ²Π°Π½ΠΈΠΈ ΠΌΠ°ΡΠ΅ΡΠΈΠ°Π»ΠΎΠ² CΠ°ΠΉΡΠ°, Π²ΠΊΠ»ΡΡΠ°Ρ ΡΠΎΠΎΠ±ΡΠ΅Π½ΠΈΡ ΠΈΠ· ΡΠΎΡΡΠΌΠΎΠ², ΠΏΡΡΠΌΠ°Ρ Π°ΠΊΡΠΈΠ²Π½Π°Ρ ΡΡΡΠ»ΠΊΠ° Π½Π° ΠΏΠΎΡΡΠ°Π» weldzone.info ΠΎΠ±ΡΠ·Π°ΡΠ΅Π»ΡΠ½Π°.
ΠΠΈΠ΄Ρ ΡΡΠ³ΡΠ½Π°, ΠΊΠ»Π°ΡΡΠΈΡΠΈΠΊΠ°ΡΠΈΡ, ΡΠΎΡΡΠ°Π², ΡΠ²ΠΎΠΉΡΡΠ²Π°, ΠΌΠ°ΡΠΊΠΈΡΠΎΠ²ΠΊΠ° ΠΈ ΠΏΡΠΈΠΌΠ΅Π½Π΅Π½ΠΈΠ΅
Π‘Π΅Π³ΠΎΠ΄Π½Ρ ΠΏΠΎΡΡΠΈ Π½Π΅Ρ Π½ΠΈ ΠΎΠ΄Π½ΠΎΠΉ ΡΡΠ΅ΡΡ ΠΆΠΈΠ·Π½ΠΈ ΡΠ΅Π»ΠΎΠ²Π΅ΠΊΠ°, Π³Π΄Π΅ Π±Ρ Π½Π΅ ΠΏΡΠΈΠΌΠ΅Π½ΡΠ»ΡΡ ΡΡΠ³ΡΠ½. ΠΡΠΎΡ ΠΌΠ°ΡΠ΅ΡΠΈΠ°Π» ΠΈΠ·Π²Π΅ΡΡΠ΅Π½ ΡΠ΅Π»ΠΎΠ²Π΅ΡΠ΅ΡΡΠ²Ρ ΡΠΆΠ΅ Π΄ΠΎΡΡΠ°ΡΠΎΡΠ½ΠΎ Π΄Π°Π²Π½ΠΎ ΠΈ ΠΏΡΠ΅Π²ΠΎΡΡ
ΠΎΠ΄Π½ΠΎ Π·Π°ΡΠ΅ΠΊΠΎΠΌΠ΅Π½Π΄ΠΎΠ²Π°Π» ΡΠ΅Π±Ρ Ρ ΠΏΡΠ°ΠΊΡΠΈΡΠ΅ΡΠΊΠΎΠΉ ΡΠΎΡΠΊΠΈ Π·ΡΠ΅Π½ΠΈΡ. Π§ΡΠ³ΡΠ½Π½ΠΎΠ΅ Π»ΠΈΡΡΠ΅ β ΠΎΡΠ½ΠΎΠ²Π° Π²Π΅Π»ΠΈΠΊΠΎΠ³ΠΎ ΠΌΠ½ΠΎΠΆΠ΅ΡΡΠ²Π° Π΄Π΅ΡΠ°Π»Π΅ΠΉ, ΡΠ·Π»ΠΎΠ² ΠΈ ΠΌΠ΅Ρ
Π°Π½ΠΈΠ·ΠΌΠΎΠ², Π° Π² Π½Π΅ΠΊΠΎΡΠΎΡΡΡ
ΡΠ»ΡΡΠ°ΡΡ
Π΄Π°ΠΆΠ΅ ΡΠ°ΠΌΠΎΠ΄ΠΎΡΡΠ°ΡΠΎΡΠ½ΠΎΠ΅ ΠΈΠ·Π΄Π΅Π»ΠΈΠ΅, ΡΠΏΠΎΡΠΎΠ±Π½ΠΎΠ΅ Π²ΡΠΏΠΎΠ»Π½ΡΡΡ Π²ΠΎΠ·Π»ΠΎΠΆΠ΅Π½Π½ΡΠ΅ Π½Π° Π½Π΅Π³ΠΎ ΡΡΠ½ΠΊΡΠΈΠΈ. ΠΠΎΡΡΠΎΠΌΡ Π² Π΄Π°Π½Π½ΠΎΠΉ ΡΡΠ°ΡΡΠ΅ ΠΌΡ ΡΠ΄Π΅Π»ΠΈΠΌ ΡΠ°ΠΌΠΎΠ΅ ΠΏΡΠΈΡΡΠ°Π»ΡΠ½ΠΎΠ΅ Π²Π½ΠΈΠΌΠ°Π½ΠΈΠ΅ Π΄Π°Π½Π½ΠΎΠΌΡ ΠΆΠ΅Π»Π΅Π·ΠΎΡΠΎΠ΄Π΅ΡΠΆΠ°ΡΠ΅ΠΌΡ ΡΠΎΠ΅Π΄ΠΈΠ½Π΅Π½ΠΈΡ. Π’Π°ΠΊΠΆΠ΅ Π²ΡΡΡΠ½ΠΈΠΌ, ΠΊΠ°ΠΊΠΈΠ΅ Π±ΡΠ²Π°ΡΡ Π²ΠΈΠ΄Ρ ΡΡΠ³ΡΠ½Π°, ΠΈΡ
ΡΠΈΠ·ΠΈΡΠ΅ΡΠΊΠΈΠ΅ ΠΈ Ρ
ΠΈΠΌΠΈΡΠ΅ΡΠΊΠΈΠ΅ ΠΎΡΠΎΠ±Π΅Π½Π½ΠΎΡΡΠΈ.
ΠΠΏΡΠ΅Π΄Π΅Π»Π΅Π½ΠΈΠ΅
Π§ΡΠ³ΡΠ½ β ΡΡΠΎ ΠΏΠΎΠΈΡΡΠΈΠ½Π΅ ΡΠ½ΠΈΠΊΠ°Π»ΡΠ½ΡΠΉ ΡΠΏΠ»Π°Π² ΠΆΠ΅Π»Π΅Π·Π° ΠΈ ΡΠ³Π»Π΅ΡΠΎΠ΄Π°, Π² ΠΊΠΎΡΠΎΡΠΎΠΌ Fe Π±ΠΎΠ»Π΅Π΅ 90%, Π° C — Π½Π΅ Π±ΠΎΠ»Π΅Π΅ 6,67%, Π½ΠΎ ΠΈ Π½Π΅ ΠΌΠ΅Π½Π΅Π΅ 2,14%. Π’Π°ΠΊΠΆΠ΅ ΡΠ³Π»Π΅ΡΠΎΠ΄ ΠΌΠΎΠΆΠ΅Ρ Π½Π°Ρ ΠΎΠ΄ΠΈΡΡΡΡ Π² ΡΡΠ³ΡΠ½Π΅ Π² Π²ΠΈΠ΄Π΅ ΡΠ΅ΠΌΠ΅Π½ΡΠΈΡΠ° ΠΈΠ»ΠΈ ΠΆΠ΅ Π³ΡΠ°ΡΠΈΡΠ°.
Π£Π³Π»Π΅ΡΠΎΠ΄ Π΄Π°Π΅Ρ ΡΠΏΠ»Π°Π²Ρ Π΄ΠΎΡΡΠ°ΡΠΎΡΠ½ΠΎ Π²ΡΡΠΎΠΊΡΡ ΡΠ²ΡΡΠ΄ΠΎΡΡΡ, ΠΎΠ΄Π½Π°ΠΊΠΎ, Π²ΠΌΠ΅ΡΡΠ΅ Ρ ΡΠ΅ΠΌ, ΠΏΠΎΠ½ΠΈΠΆΠ°Π΅Ρ ΠΊΠΎΠ²ΠΊΠΎΡΡΡ ΠΈ ΠΏΠ»Π°ΡΡΠΈΡΠ½ΠΎΡΡΡ. Π ΡΠ²ΡΠ·ΠΈ Ρ ΡΡΠΈΠΌ ΡΡΠ³ΡΠ½ ΡΠ²Π»ΡΠ΅ΡΡΡ Ρ
ΡΡΠΏΠΊΠΈΠΌ ΠΌΠ°ΡΠ΅ΡΠΈΠ°Π»ΠΎΠΌ. Π’Π°ΠΊΠΆΠ΅ Π² ΠΎΠΏΡΠ΅Π΄Π΅Π»Π΅Π½Π½ΡΠ΅ ΠΌΠ°ΡΠΊΠΈ ΡΡΠ³ΡΠ½Π° Π΄ΠΎΠ±Π°Π²Π»ΡΡΡ ΡΠΏΠ΅ΡΠΈΠ°Π»ΡΠ½ΡΠ΅ ΠΏΡΠΈΡΠ°Π΄ΠΊΠΈ, ΠΊΠΎΡΠΎΡΡΠ΅ ΡΠΏΠΎΡΠΎΠ±Π½Ρ ΠΏΡΠΈΠ΄Π°ΡΡ ΡΠΎΠ΅Π΄ΠΈΠ½Π΅Π½ΠΈΡ ΠΎΠΏΡΠ΅Π΄Π΅Π»Π΅Π½Π½ΡΠ΅ ΡΠ²ΠΎΠΉΡΡΠ²Π°. Π ΡΠΎΠ»ΠΈ Π»Π΅Π³ΠΈΡΡΡΡΠΈΡ
ΡΠ»Π΅ΠΌΠ΅Π½ΡΠΎΠ² ΠΌΠΎΠ³ΡΡ Π²ΡΡΡΡΠΏΠ°ΡΡ: Π½ΠΈΠΊΠ΅Π»Ρ, Ρ
ΡΠΎΠΌ, Π²Π°Π½Π°Π΄ΠΈΠΉ, Π°Π»ΡΠΌΠΈΠ½ΠΈΠΉ. ΠΠΎΠΊΠ°Π·Π°ΡΠ΅Π»Ρ ΠΏΠ»ΠΎΡΠ½ΠΎΡΡΠΈ ΡΡΠ³ΡΠ½Π° ΡΠ°Π²Π΅Π½ 7200 ΠΊΠΈΠ»ΠΎΠ³ΡΠ°ΠΌΠΌ Π½Π° ΠΌΠ΅ΡΡ ΠΊΡΠ±ΠΈΡΠ΅ΡΠΊΠΈΠΉ. ΠΠ· ΡΠ΅Π³ΠΎ ΠΌΠΎΠΆΠ½ΠΎ ΡΠ΄Π΅Π»Π°ΡΡ Π²ΡΠ²ΠΎΠ΄, ΡΡΠΎ Π²Π΅Ρ ΡΡΠ³ΡΠ½Π° β ΠΏΠΎΠΊΠ°Π·Π°ΡΠ΅Π»Ρ, ΠΊΠΎΡΠΎΡΡΠΉ Π½ΠΈΠΊΠ°ΠΊ Π½Π΅Π»ΡΠ·Ρ Π½Π°Π·Π²Π°ΡΡ ΠΌΠ°Π»Π΅Π½ΡΠΊΠΈΠΌ.
ΠΡΡΠΎΡΠΈΡΠ΅ΡΠΊΠ°Ρ ΡΠΏΡΠ°Π²ΠΊΠ°
ΠΡΠΏΠ»Π°Π²ΠΊΠ° ΡΡΠ³ΡΠ½Π° ΡΠΆΠ΅ Π΄ΠΎΡΡΠ°ΡΠΎΡΠ½ΠΎ Π΄Π°Π²Π½ΠΎ ΠΈΠ·Π²Π΅ΡΡΠ½Π° ΡΠ΅Π»ΠΎΠ²Π΅ΠΊΡ. ΠΠ΅ΡΠ²ΡΠ΅ ΡΠΏΠΎΠΌΠΈΠ½Π°Π½ΠΈΡ ΠΎ ΡΠΏΠ»Π°Π²Π΅ Π΄Π°ΡΠΈΡΡΡΡΡΡ ΡΠ΅ΡΡΡΠΌ Π²Π΅ΠΊΠΎΠΌ Π΄ΠΎ Π½Π°ΡΠ΅ΠΉ ΡΡΡ.
Π ΠΠΈΡΠ°Π΅ Π² Π΄ΡΠ΅Π²Π½ΠΈΠ΅ Π²ΡΠ΅ΠΌΠ΅Π½Π° ΠΏΠΎΠ»ΡΡΠ°Π»ΠΈ ΡΡΠ³ΡΠ½ Ρ Π΄ΠΎΠ²ΠΎΠ»ΡΠ½ΠΎ Π½ΠΈΠ·ΠΊΠΎΠΉ ΡΠ΅ΠΌΠΏΠ΅ΡΠ°ΡΡΡΠΎΠΉ ΠΏΠ»Π°Π²Π»Π΅Π½ΠΈΡ. Π ΠΠ²ΡΠΎΠΏΠ΅ ΡΡΠ³ΡΠ½ ΡΡΠ°Π»ΠΈ ΠΏΠΎΠ»ΡΡΠ°ΡΡ ΠΏΡΠΈΠΌΠ΅ΡΠ½ΠΎ Π² 14 Π²Π΅ΠΊΠ΅, ΠΊΠΎΠ³Π΄Π° Π²ΠΏΠ΅ΡΠ²ΡΠ΅ Π½Π°ΡΠ°Π»ΠΈ ΠΈΡΠΏΠΎΠ»ΡΠ·ΠΎΠ²Π°ΡΡ Π΄ΠΎΠΌΠ΅Π½Π½ΡΠ΅ ΠΏΠ΅ΡΠΈ. ΠΠ° ΡΠΎΡ ΠΌΠΎΠΌΠ΅Π½Ρ ΡΠ°ΠΊΠΎΠ΅ ΡΡΠ³ΡΠ½Π½ΠΎΠ΅ Π»ΠΈΡΡΠ΅ ΡΠ»ΠΎ Π½Π° ΠΏΡΠΎΠΈΠ·Π²ΠΎΠ΄ΡΡΠ²ΠΎ ΠΎΡΡΠΆΠΈΡ, ΡΠ½Π°ΡΡΠ΄ΠΎΠ², Π΄Π΅ΡΠ°Π»Π΅ΠΉ Π΄Π»Ρ ΡΡΡΠΎΠΈΡΠ΅Π»ΡΡΡΠ²Π°.
ΠΠ° ΡΠ΅ΡΡΠΈΡΠΎΡΠΈΠΈ Π ΠΎΡΡΠΈΠΈ ΠΏΡΠΎΠΈΠ·Π²ΠΎΠ΄ΡΡΠ²ΠΎ ΡΡΠ³ΡΠ½Π° Π°ΠΊΡΠΈΠ²Π½ΠΎ Π½Π°ΡΠ°Π»ΠΎΡΡ Π² 16 ΡΡΠΎΠ»Π΅ΡΠΈΠΈ ΠΈ Π΄Π°Π»Π΅Π΅ Π±ΡΡΡΡΠΎ ΡΠ°ΡΡΠΈΡΡΠ»ΠΎΡΡ. ΠΠΎ Π²ΡΠ΅ΠΌΠ΅Π½Π° ΠΠ΅ΡΡΠ° I Π ΠΎΡΡΠΈΠΉΡΠΊΠ°Ρ ΠΈΠΌΠΏΠ΅ΡΠΈΡ ΠΏΠΎ ΠΎΠ±ΡΠ΅ΠΌΡ ΠΏΡΠΎΠΈΠ·Π²ΠΎΠ΄ΡΡΠ²Π° ΡΡΠ³ΡΠ½Π° ΡΠΌΠΎΠ³Π»Π° ΠΎΠ±ΠΎΠΉΡΠΈ Π²ΡΠ΅ Π³ΠΎΡΡΠ΄Π°ΡΡΡΠ²Π° ΠΌΠΈΡΠ°, ΠΎΠ΄Π½Π°ΠΊΠΎ ΡΠΆΠ΅ ΡΠ΅ΡΠ΅Π· ΡΡΠΎ Π»Π΅Ρ Π½Π°ΡΠ°Π»Π° ΡΠ½ΠΎΠ²Π° ΡΠ΄Π°Π²Π°ΡΡ ΡΠ²ΠΎΠΈ ΠΏΠΎΠ·ΠΈΡΠΈΠΈ Π½Π° ΡΡΠ½ΠΊΠ΅ ΡΠ΅ΡΠ½ΠΎΠΉ ΠΌΠ΅ΡΠ°Π»Π»ΡΡΠ³ΠΈΠΈ.
Π§ΡΠ³ΡΠ½Π½ΠΎΠ΅ Π»ΠΈΡΡΠ΅ ΠΈΡΠΏΠΎΠ»ΡΠ·ΠΎΠ²Π°Π»ΠΎΡΡ Π΄Π»Ρ ΡΠΎΠ·Π΄Π°Π½ΠΈΡ ΡΠ°Π·Π½ΠΎΠΎΠ±ΡΠ°Π·Π½ΡΡ
Ρ
ΡΠ΄ΠΎΠΆΠ΅ΡΡΠ²Π΅Π½Π½ΡΡ
ΠΏΡΠΎΠΈΠ·Π²Π΅Π΄Π΅Π½ΠΈΠΉ Π΅ΡΡ Π² ΡΠΏΠΎΡ
Ρ Π‘ΡΠ΅Π΄Π½Π΅Π²Π΅ΠΊΠΎΠ²ΡΡ. Π ΡΠ°ΡΡΠ½ΠΎΡΡΠΈ, Π² 10 Π²Π΅ΠΊΠ΅ ΠΊΠΈΡΠ°ΠΉΡΠΊΠΈΠ΅ ΠΌΠ°ΡΡΠ΅ΡΠ° ΠΎΡΠ»ΠΈΠ»ΠΈ ΠΏΠΎΠΈΡΡΠΈΠ½Π΅ ΡΠ½ΠΈΠΊΠ°Π»ΡΠ½ΡΡ ΡΠΈΠ³ΡΡΡ Π»ΡΠ²Π°, Π²Π΅Ρ ΠΊΠΎΡΠΎΡΠΎΠ³ΠΎ ΠΏΡΠ΅Π²ΡΡΠΈΠ» 100 ΡΠΎΠ½Π½. ΠΠ°ΡΠΈΠ½Π°Ρ Ρ 15 Π²Π΅ΠΊΠ° Π½Π° ΡΠ΅ΡΡΠΈΡΠΎΡΠΈΠΈ ΠΠ΅ΡΠΌΠ°Π½ΠΈΠΈ, Π° ΠΏΠΎΡΠ»Π΅ ΠΈ Π² Π΄ΡΡΠ³ΠΈΡ
ΡΡΡΠ°Π½Π°Ρ
Π»ΠΈΡΡΠ΅ ΠΈΠ· ΡΡΠ³ΡΠ½Π° ΠΏΠΎΠ»ΡΡΠΈΠ»ΠΎ ΡΠΈΡΠΎΡΠ°ΠΉΡΠ΅Π΅ ΡΠ°ΡΠΏΡΠΎΡΡΡΠ°Π½Π΅Π½ΠΈΠ΅. ΠΠ· Π½Π΅Π³ΠΎ Π΄Π΅Π»Π°Π»ΠΈ ΠΎΠ³ΡΠ°Π΄ΠΊΠΈ, ΡΠ΅ΡΠ΅ΡΠΊΠΈ, ΠΏΠ°ΡΠΊΠΎΠ²ΡΠ΅ ΡΠΊΡΠ»ΡΠΏΡΡΡΡ, ΡΠ°Π΄ΠΎΠ²ΡΡ ΠΌΠ΅Π±Π΅Π»Ρ, Π½Π°Π΄Π³ΡΠΎΠ±ΠΈΡ.
Π ΠΏΠΎΡΠ»Π΅Π΄Π½ΠΈΠ΅ Π³ΠΎΠ΄Ρ 18 Π²Π΅ΠΊΠ° ΡΡΠ³ΡΠ½Π½ΠΎΠ΅ Π»ΠΈΡΡΠ΅ ΠΌΠ°ΠΊΡΠΈΠΌΠ°Π»ΡΠ½ΠΎ Π·Π°Π΄Π΅ΠΉΡΡΠ²ΠΎΠ²Π°Π½ΠΎ Π² Π°ΡΡ ΠΈΡΠ΅ΠΊΡΡΡΠ΅ Π ΠΎΡΡΠΈΠΈ. Π 19 ΡΡΠΎΠ»Π΅ΡΠΈΠ΅ ΡΠ°ΠΊ ΠΈ Π²ΠΎΠΎΠ±ΡΠ΅ ΠΏΡΠΎΠ·Π²Π°Π»ΠΈ Β«ΡΡΠ³ΡΠ½Π½ΡΠΌ Π²Π΅ΠΊΠΎΠΌΒ», ΡΠ°ΠΊ ΠΊΠ°ΠΊ ΡΠΏΠ»Π°Π² ΠΎΡΠ΅Π½Ρ Π°ΠΊΡΠΈΠ²Π½ΠΎ ΠΈΡΠΏΠΎΠ»ΡΠ·ΠΎΠ²Π°Π»ΡΡ Π² Π·ΠΎΠ΄ΡΠ΅ΡΡΠ²Π΅.
ΠΡΠΎΠ±Π΅Π½Π½ΠΎΡΡΠΈ
Π‘ΡΡΠ΅ΡΡΠ²ΡΡΡ ΡΠ°Π·Π»ΠΈΡΠ½ΡΠ΅ Π²ΠΈΠ΄Ρ ΡΡΠ³ΡΠ½Π°, ΠΎΠ΄Π½Π°ΠΊΠΎ ΡΡΠ΅Π΄Π½ΡΡ ΡΠ΅ΠΌΠΏΠ΅ΡΠ°ΡΡΡΠ° ΠΏΠ»Π°Π²Π»Π΅Π½ΠΈΡ ΡΡΠΎΠ³ΠΎ ΠΌΠ΅ΡΠ°Π»Π»ΠΈΡΠ΅ΡΠΊΠΎΠ³ΠΎ ΡΠΎΠ΅Π΄ΠΈΠ½Π΅Π½ΠΈΡ ΡΠΎΡΡΠ°Π²Π»ΡΠ΅Ρ ΠΏΠΎΡΡΠ΄ΠΊΠ° 1200 Π³ΡΠ°Π΄ΡΡΠΎΠ² Π¦Π΅Π»ΡΡΠΈΡ. ΠΡΠΎΡ ΠΏΠΎΠΊΠ°Π·Π°ΡΠ΅Π»Ρ Π½Π° 250-300 Π³ΡΠ°Π΄ΡΡΠΎΠ² ΠΌΠ΅Π½ΡΡΠ΅, ΡΠ΅ΠΌ ΡΡΠ΅Π±ΡΠ΅ΡΡΡ Π΄Π»Ρ Π²ΡΠΏΠ»Π°Π²Π»Π΅Π½ΠΈΡ ΡΡΠ°Π»ΠΈ. Π’Π°ΠΊΠ°Ρ ΡΠ°Π·Π½ΠΈΡΠ° ΡΠ²ΡΠ·Π°Π½Π° Ρ Π΄ΠΎΡΡΠ°ΡΠΎΡΠ½ΠΎ Π²ΡΡΠΎΠΊΠΈΠΌ ΡΠΎΠ΄Π΅ΡΠΆΠ°Π½ΠΈΠ΅ΠΌ ΡΠ³Π»Π΅ΡΠΎΠ΄Π°, ΡΡΠΎ ΠΏΡΠΈΠ²ΠΎΠ΄ΠΈΡ ΠΊ Π΅Π³ΠΎ ΠΌΠ΅Π½Π΅Π΅ ΡΠ΅ΡΠ½ΡΠΌ ΡΠ²ΡΠ·ΡΠΌ Ρ Π°ΡΠΎΠΌΠ°ΠΌΠΈ ΠΆΠ΅Π»Π΅Π·Π° Π½Π° ΠΌΠΎΠ»Π΅ΠΊΡΠ»ΡΡΠ½ΠΎΠΌ ΡΡΠΎΠ²Π½Π΅.
Π ΠΌΠΎΠΌΠ΅Π½Ρ Π²ΡΠΏΠ»Π°Π²ΠΊΠΈ ΠΈ ΠΏΠΎΡΠ»Π΅Π΄ΡΡΡΠ΅ΠΉ ΠΊΡΠΈΡΡΠ°Π»Π»ΠΈΠ·Π°ΡΠΈΠΈ ΡΠ³Π»Π΅ΡΠΎΠ΄, ΡΠΎΠ΄Π΅ΡΠΆΠ°ΡΠΈΠΉΡΡ Π² ΡΡΠ³ΡΠ½Π΅, Π½Π΅ ΡΡΠΏΠ΅Π²Π°Π΅Ρ ΠΏΠΎΠ»Π½ΠΎΡΡΡΡ ΠΏΡΠΎΠ½ΠΈΠΊΠ½ΡΡΡ Π² ΠΌΠΎΠ»Π΅ΠΊΡΠ»ΡΡΠ½ΡΡ ΡΠ΅ΡΡΡΠΊΡ ΠΆΠ΅Π»Π΅Π·Π°, ΠΈ ΠΏΠΎΡΠΎΠΌΡ ΡΡΠ³ΡΠ½ Π² ΠΈΡΠΎΠ³Π΅ ΠΏΠΎΠ»ΡΡΠ°Π΅ΡΡΡ Π΄ΠΎΠ²ΠΎΠ»ΡΠ½ΠΎ Ρ
ΡΡΠΏΠΊΠΈΠΌ. Π ΡΠ²ΡΠ·ΠΈ Ρ ΡΡΠΈΠΌ ΠΎΠ½ Π½Π΅ ΠΏΡΠΈΠΌΠ΅Π½ΡΠ΅ΡΡΡ ΡΠ°ΠΌ, Π³Π΄Π΅ ΠΈΠΌΠ΅ΡΡ ΠΌΠ΅ΡΡΠΎ ΠΏΠΎΡΡΠΎΡΠ½Π½ΡΠ΅ Π΄ΠΈΠ½Π°ΠΌΠΈΡΠ΅ΡΠΊΠΈΠ΅ Π½Π°Π³ΡΡΠ·ΠΊΠΈ. ΠΠΎ ΠΏΡΠΈ ΡΡΠΎΠΌ ΠΎΠ½ ΠΎΡΠ»ΠΈΡΠ½ΠΎ ΠΏΠΎΠ΄Ρ
ΠΎΠ΄ΠΈΡ Π΄Π»Ρ ΡΠ΅Ρ
Π΄Π΅ΡΠ°Π»Π΅ΠΉ, ΠΊΠΎΡΠΎΡΡΠ΅ ΠΈΠΌΠ΅ΡΡ ΠΏΠΎΠ²ΡΡΠ΅Π½Π½ΡΠ΅ ΡΡΠ΅Π±ΠΎΠ²Π°Π½ΠΈΡ ΠΊ ΠΏΡΠΎΡΠ½ΠΎΡΡΠΈ.
Π’Π΅Ρ Π½ΠΎΠ»ΠΎΠ³ΠΈΡ ΠΏΡΠΎΠΈΠ·Π²ΠΎΠ΄ΡΡΠ²Π°
ΠΠ±ΡΠΎΠ»ΡΡΠ½ΠΎ Π²ΡΠ΅ Π²ΠΈΠ΄Ρ ΡΡΠ³ΡΠ½Π° ΠΏΡΠΎΠΈΠ·Π²ΠΎΠ΄ΡΡΡΡ Π² Π΄ΠΎΠΌΠ΅Π½Π½ΠΎΠΉ ΠΏΠ΅ΡΠΈ. Π‘ΠΎΠ±ΡΡΠ²Π΅Π½Π½ΠΎ, ΡΠ°ΠΌ ΠΏΡΠΎΡΠ΅ΡΡ ΠΏΠ»Π°Π²ΠΊΠΈ β Π΄ΠΎΠ²ΠΎΠ»ΡΠ½ΠΎ ΡΡΡΠ΄ΠΎΠ΅ΠΌΠΊΠ°Ρ Π΄Π΅ΡΡΠ΅Π»ΡΠ½ΠΎΡΡΡ, ΡΡΠ΅Π±ΡΡΡΠ°Ρ ΡΠ΅ΡΡΡΠ·Π½ΡΡ ΠΌΠ°ΡΠ΅ΡΠΈΠ°Π»ΡΠ½ΡΡ Π²Π»ΠΎΠΆΠ΅Π½ΠΈΠΉ. ΠΠ΄Π½Π° ΡΠΎΠ½Π½Π° ΡΡΠ³ΡΠ½Π° ΡΡΠ΅Π±ΡΠ΅Ρ ΠΏΡΠΈΠΌΠ΅ΡΠ½ΠΎ 550 ΠΊΠΈΠ»ΠΎΠ³ΡΠ°ΠΌΠΌ ΠΊΠΎΠΊΡΠ° ΠΈ ΠΏΠΎΡΡΠΈ ΡΠΎΠ½Π½Ρ Π²ΠΎΠ΄Ρ. ΠΠ±ΡΠ΅ΠΌ Π·Π°Π³ΡΡΠΆΠ°Π΅ΠΌΠΎΠΉ Π² ΠΏΠ΅ΡΡ ΡΡΠ΄Ρ Π±ΡΠ΄Π΅Ρ Π·Π°Π²ΠΈΡΠ΅ΡΡ ΠΎΡ ΡΠΎΠ΄Π΅ΡΠΆΠ°Π½ΠΈΡ ΠΆΠ΅Π»Π΅Π·Π°. Π§Π°ΡΠ΅ Π²ΡΠ΅Π³ΠΎ ΠΏΡΠΈΠΌΠ΅Π½ΡΡΡ ΡΡΠ΄Ρ, Π² ΠΊΠΎΡΠΎΡΠΎΠΉ ΠΆΠ΅Π»Π΅Π·Π° Π½Π΅ ΠΌΠ΅Π½Π΅Π΅ 70%. ΠΠ΅Π½ΡΡΠ°Ρ ΠΊΠΎΠ½ΡΠ΅Π½ΡΡΠ°ΡΠΈΡ ΡΠ»Π΅ΠΌΠ΅Π½ΡΠ° Π½Π΅ΠΆΠ΅Π»Π°ΡΠ΅Π»ΡΠ½Π°, ΠΏΠΎΡΠΊΠΎΠ»ΡΠΊΡ Π΅Π΅ Π±ΡΠ΄Π΅Ρ Π½Π΅Π²ΡΠ³ΠΎΠ΄Π½ΠΎ ΡΠΊΠΎΠ½ΠΎΠΌΠΈΡΠ΅ΡΠΊΠΈ ΠΈΡΠΏΠΎΠ»ΡΠ·ΠΎΠ²Π°ΡΡ.
ΠΠ΅ΡΠ²ΡΠΉ ΡΡΠ°ΠΏ ΠΏΡΠΎΠΈΠ·Π²ΠΎΠ΄ΡΡΠ²Π°
ΠΡΠΏΠ»Π°Π²ΠΊΠ° ΡΡΠ³ΡΠ½Π° ΠΏΡΠΎΠΈΡΡ
ΠΎΠ΄ΠΈΡ ΡΠ»Π΅Π΄ΡΡΡΠΈΠΌ ΠΎΠ±ΡΠ°Π·ΠΎΠΌ. Π ΠΏΠ΅ΡΠ²ΡΡ ΠΎΡΠ΅ΡΠ΅Π΄Ρ Π² ΠΏΠ΅ΡΡ Π·Π°ΡΡΠΏΠ°ΡΡ ΡΡΠ΄Ρ, Π° ΡΠ°ΠΊΠΆΠ΅ ΠΊΠΎΠΊΡΡΡΡΠΈΠ΅ΡΡ ΠΌΠ°ΡΠΊΠΈ ΡΠ³Π»Ρ, ΠΊΠΎΡΠΎΡΡΠ΅ ΡΠ»ΡΠΆΠ°Ρ Π΄Π»Ρ Π½Π°Π³Π½Π΅ΡΠ°Π½ΠΈΡ ΠΈ ΠΏΠΎΠ΄Π΄Π΅ΡΠΆΠ°Π½ΠΈΡ ΡΡΠ΅Π±ΡΠ΅ΠΌΠΎΠΉ ΡΠ΅ΠΌΠΏΠ΅ΡΠ°ΡΡΡΡ Π²Π½ΡΡΡΠΈ ΡΠ°Ρ
ΡΡ ΠΏΠ΅ΡΠΈ. ΠΠΎΠΌΠΈΠΌΠΎ ΡΡΠΎΠ³ΠΎ, ΡΡΠΈ ΠΏΡΠΎΠ΄ΡΠΊΡΡ Π² ΠΏΡΠΎΡΠ΅ΡΡΠ΅ Π³ΠΎΡΠ΅Π½ΠΈΡ Π°ΠΊΡΠΈΠ²Π½ΠΎ ΠΏΡΠΈΠ½ΠΈΠΌΠ°ΡΡ ΡΡΠ°ΡΡΠΈΠ΅ Π² ΠΏΡΠΎΡΠ΅ΠΊΠ°ΡΡΠΈΡ
Ρ
ΠΈΠΌΠΈΡΠ΅ΡΠΊΠΈΡ
ΡΠ΅Π°ΠΊΡΠΈΡΡ
Π² ΡΠΎΠ»ΠΈ Π²ΠΎΡΡΡΠ°Π½ΠΎΠ²ΠΈΡΠ΅Π»Π΅ΠΉ ΠΆΠ΅Π»Π΅Π·Π°.
ΠΠ°ΡΠ°Π»Π»Π΅Π»ΡΠ½ΠΎ Π² ΠΏΠ΅ΡΡ ΠΎΡΠ³ΡΡΠΆΠ°Π΅ΡΡΡ ΡΠ»ΡΡ, ΡΠ»ΡΠΆΠ°ΡΠΈΠΉ Π² ΠΊΠ°ΡΠ΅ΡΡΠ²Π΅ ΠΊΠ°ΡΠ°Π»ΠΈΠ·Π°ΡΠΎΡΠ°. ΠΠ½ ΠΏΠΎΠΌΠΎΠ³Π°Π΅Ρ ΠΏΠΎΡΠΎΠ΄Π°ΠΌ Π±ΡΡΡΡΠ΅Π΅ ΡΠ°ΡΠΏΠ»Π°Π²Π»ΡΡΡΡΡ, ΡΡΠΎ ΡΠΎΠ΄Π΅ΠΉΡΡΠ²ΡΠ΅Ρ ΡΠΊΠΎΡΠ΅ΠΉΡΠ΅ΠΌΡ Π²ΡΡΠ²ΠΎΠ±ΠΎΠΆΠ΄Π΅Π½ΠΈΡ ΠΆΠ΅Π»Π΅Π·Π°.
ΠΠ°ΠΆΠ½ΠΎ Π·Π°ΠΌΠ΅ΡΠΈΡΡ, ΡΡΠΎ ΡΡΠ΄Π° ΠΏΠ΅ΡΠ΅Π΄ Π·Π°Π³ΡΡΠ·ΠΊΠΎΠΉ Π² ΠΏΠ΅ΡΡ ΠΏΠΎΠ΄Π²Π΅ΡΠ³Π°Π΅ΡΡΡ ΡΠΏΠ΅ΡΠΈΠ°Π»ΡΠ½ΠΎΠΉ ΠΏΡΠ΅Π΄Π²Π°ΡΠΈΡΠ΅Π»ΡΠ½ΠΎΠΉ ΠΎΠ±ΡΠ°Π±ΠΎΡΠΊΠ΅. ΠΠ΅ ΠΈΠ·ΠΌΠ΅Π»ΡΡΠ°ΡΡ Π½Π° Π΄ΡΠΎΠ±ΠΈΠ»ΡΠ½ΠΎΠΉ ΡΡΡΠ°Π½ΠΎΠ²ΠΊΠ΅ (ΠΌΠ΅Π»ΠΊΠΈΠ΅ ΡΠ°ΡΡΠΈΡΡ Π±ΡΡΡΡΠ΅Π΅ ΠΏΠ»Π°Π²ΡΡΡΡ). ΠΠΎΡΠ»Π΅ ΠΎΠ½Π° ΠΏΡΠΎΠΌΡΠ²Π°Π΅ΡΡΡ Ρ ΡΠ΅Π»ΡΡ ΡΠ΄Π°Π»Π΅Π½ΠΈΡ ΡΠ°ΡΡΠΈΡ, Π½Π΅ ΡΠΎΠ΄Π΅ΡΠΆΠ°ΡΠΈΡ ΠΌΠ΅ΡΠ°Π»Π». ΠΠΎΡΠ»Π΅ ΡΠ΅Π³ΠΎ ΡΡΡΡΠ΅ ΠΎΠ±ΠΆΠΈΠ³Π°ΡΡ, Π·Π° ΡΡΠ΅Ρ ΡΡΠΎΠ³ΠΎ ΠΈΠ· Π½Π΅Π³ΠΎ ΡΠ΄Π°Π»ΡΠ΅ΡΡΡ ΡΠ΅ΡΠ° ΠΈ ΠΏΡΠΎΡΠΈΠ΅ ΡΡΠΆΠ΅ΡΠΎΠ΄Π½ΡΠ΅ ΡΠ»Π΅ΠΌΠ΅Π½ΡΡ.
ΠΡΠΎΡΠΎΠΉ ΡΡΠ°ΠΏ ΠΏΡΠΎΠΈΠ·Π²ΠΎΠ΄ΡΡΠ²Π°
Π Π·Π°Π³ΡΡΠΆΠ΅Π½Π½ΡΡ ΠΈ Π³ΠΎΡΠΎΠ²ΡΡ ΠΊ ΡΠΊΡΠΏΠ»ΡΠ°ΡΠ°ΡΠΈΠΈ ΠΏΠ΅ΡΡ ΠΏΠΎΠ΄Π°ΡΡ ΠΏΡΠΈΡΠΎΠ΄Π½ΡΠΉ Π³Π°Π· ΡΠ΅ΡΠ΅Π· ΡΠΏΠ΅ΡΠΈΠ°Π»ΡΠ½ΡΠ΅ Π³ΠΎΡΠ΅Π»ΠΊΠΈ. ΠΠΎΠΊΡ ΡΠ°Π·ΠΎΠ³ΡΠ΅Π²Π°Π΅Ρ ΡΡΡΡΠ΅. ΠΡΠΈ ΡΡΠΎΠΌ Π²ΡΠ΄Π΅Π»ΡΠ΅ΡΡΡ ΡΠ³Π»Π΅ΡΠΎΠ΄, ΠΊΠΎΡΠΎΡΡΠΉ ΡΠΎΠ΅Π΄ΠΈΠ½ΡΠ΅ΡΡΡ Ρ ΠΊΠΈΡΠ»ΠΎΡΠΎΠ΄ΠΎΠΌ ΠΈ ΠΎΠ±ΡΠ°Π·ΡΠ΅Ρ ΠΎΠΊΡΠΈΠ΄. ΠΡΠΎΡ ΠΎΠΊΡΠΈΠ΄ Π²ΠΏΠΎΡΠ»Π΅Π΄ΡΡΠ²ΠΈΠΈ ΠΏΡΠΈΠ½ΠΈΠΌΠ°Π΅Ρ ΡΡΠ°ΡΡΠΈΠ΅ Π² Π²ΠΎΡΡΡΠ°Π½ΠΎΠ²Π»Π΅Π½ΠΈΠΈ ΠΆΠ΅Π»Π΅Π·Π° ΠΈΠ· ΡΡΠ΄Ρ. ΠΡΠΌΠ΅ΡΠΈΠΌ, ΡΡΠΎ Ρ ΡΠ²Π΅Π»ΠΈΡΠ΅Π½ΠΈΠ΅ΠΌ ΠΊΠΎΠ»ΠΈΡΠ΅ΡΡΠ²Π° Π³Π°Π·Π° Π² ΠΏΠ΅ΡΠΈ ΡΠΊΠΎΡΠΎΡΡΡ ΠΏΡΠΎΡΠ΅ΠΊΠ°Π½ΠΈΡ Ρ ΠΈΠΌΠΈΡΠ΅ΡΠΊΠΎΠΉ ΡΠ΅Π°ΠΊΡΠΈΠΈ ΡΠ½ΠΈΠΆΠ°Π΅ΡΡΡ, Π° ΠΏΡΠΈ Π΄ΠΎΡΡΠΈΠΆΠ΅Π½ΠΈΠΈ ΠΎΠΏΡΠ΅Π΄Π΅Π»ΡΠ½Π½ΠΎΠ³ΠΎ ΡΠΎΠΎΡΠ½ΠΎΡΠ΅Π½ΠΈΡ ΠΈ Π²ΠΎΠ²ΡΠ΅ ΠΎΡΡΠ°Π½Π°Π²Π»ΠΈΠ²Π°Π΅ΡΡΡ.
ΠΠ·Π±ΡΡΠΎΠΊ ΡΠ³Π»Π΅ΡΠΎΠ΄Π° ΠΏΡΠΎΠ½ΠΈΠΊΠ°Π΅Ρ Π² ΡΠ°ΡΠΏΠ»Π°Π² ΠΈ Π²Ρ
ΠΎΠ΄ΠΈΡ Π² ΡΠΎΠ΅Π΄ΠΈΠ½Π΅Π½ΠΈΠ΅ Ρ ΠΆΠ΅Π»Π΅Π·ΠΎΠΌ, ΡΠΎΡΠΌΠΈΡΡΡ Π² ΠΊΠΎΠ½Π΅ΡΠ½ΠΎΠΌ ΡΡΠ΅ΡΠ΅ ΡΡΠ³ΡΠ½. ΠΡΠ΅ ΡΠ΅ ΡΠ»Π΅ΠΌΠ΅Π½ΡΡ, ΠΊΠΎΡΠΎΡΡΠ΅ Π½Π΅ ΡΠ°ΡΠΏΠ»Π°Π²ΠΈΠ»ΠΈΡΡ, ΠΎΠΊΠ°Π·ΡΠ²Π°ΡΡΡΡ Π½Π° ΠΏΠΎΠ²Π΅ΡΡ
Π½ΠΎΡΡΠΈ ΠΈ Π² ΠΈΡΠΎΠ³Π΅ ΡΠ΄Π°Π»ΡΡΡΡΡ. ΠΡΠΈ ΠΎΡΡ
ΠΎΠ΄Ρ ΠΈΠΌΠ΅Π½ΡΡΡ ΡΠ»Π°ΠΊΠΎΠΌ. ΠΠ³ΠΎ ΡΠ°ΠΊΠΆΠ΅ ΠΌΠΎΠΆΠ½ΠΎ ΠΈΡΠΏΠΎΠ»ΡΠ·ΠΎΠ²Π°ΡΡ Π΄Π»Ρ ΠΏΡΠΎΠΈΠ·Π²ΠΎΠ΄ΡΡΠ²Π° Π΄ΡΡΠ³ΠΈΡ
ΠΌΠ°ΡΠ΅ΡΠΈΠ°Π»ΠΎΠ². ΠΠΈΠ΄Ρ ΡΡΠ³ΡΠ½Π°, ΠΏΠΎΠ»ΡΡΠ°Π΅ΠΌΡΠ΅ ΡΠ°ΠΊΠΈΠΌ ΠΎΠ±ΡΠ°Π·ΠΎΠΌ, Π½Π°Π·ΡΠ²Π°ΡΡΡΡ Π»ΠΈΡΠ΅ΠΉΠ½ΡΠΌ ΠΈ ΠΏΠ΅ΡΠ΅Π΄Π΅Π»ΡΠ½ΡΠΌ.
ΠΠΈΡΡΠ΅ΡΠ΅Π½ΡΠΈΠ°ΡΠΈΡ
Π‘ΠΎΠ²ΡΠ΅ΠΌΠ΅Π½Π½Π°Ρ ΠΊΠ»Π°ΡΡΠΈΡΠΈΠΊΠ°ΡΠΈΡ ΡΡΠ³ΡΠ½ΠΎΠ² ΠΏΡΠ΅Π΄ΡΡΠΌΠ°ΡΡΠΈΠ²Π°Π΅Ρ ΡΠ°Π·Π΄Π΅Π»Π΅Π½ΠΈΠ΅ Π΄Π°Π½Π½ΡΡ ΡΠΏΠ»Π°Π²ΠΎΠ² Π½Π° ΡΠ»Π΅Π΄ΡΡΡΠΈΠ΅ ΡΠΈΠΏΡ:
- ΠΠ΅Π»ΡΠ΅.
- ΠΠΎΠ»ΠΎΠ²ΠΈΠ½ΡΠ°ΡΡΠ΅.
- Π‘Π΅ΡΡΠ΅ Ρ ΠΏΠ»Π°ΡΡΠΈΠ½ΡΠ°ΡΡΠΌ Π³ΡΠ°ΡΠΈΡΠΎΠΌ.
- ΠΡΡΠΎΠΊΠΎΠΏΡΠΎΡΠ½ΡΠ΅ Ρ ΡΠ°ΡΠΎΠ²ΠΈΠ΄Π½ΡΠΌ Π³ΡΠ°ΡΠΈΡΠΎΠΌ.
- ΠΠΎΠ²ΠΊΠΈΠ΅.
ΠΠ°Π²Π°ΠΉΡΠ΅ ΡΠ°ΡΡΠΌΠΎΡΡΠΈΠΌ ΠΊΠ°ΠΆΠ΄ΡΠΉ Π²ΠΈΠ΄ ΠΏΠΎ ΠΎΡΠ΄Π΅Π»ΡΠ½ΠΎΡΡΠΈ.
ΠΠ΅Π»ΡΠΉ ΡΡΠ³ΡΠ½
Π’Π°ΠΊΠΈΠΌ ΡΡΠ³ΡΠ½ΠΎΠΌ Π½Π°Π·ΡΠ²Π°Π΅ΡΡΡ ΡΠΎΡ, Ρ ΠΊΠΎΡΠΎΡΠΎΠ³ΠΎ ΠΏΡΠ°ΠΊΡΠΈΡΠ΅ΡΠΊΠΈ Π²Π΅ΡΡ ΡΠ³Π»Π΅ΡΠΎΠ΄ Ρ
ΠΈΠΌΠΈΡΠ΅ΡΠΊΠΈ ΡΠ²ΡΠ·Π°Π½. Π ΠΌΠ°ΡΠΈΠ½ΠΎΡΡΡΠΎΠ΅Π½ΠΈΠΈ ΡΡΠΎΡ ΡΠΏΠ»Π°Π² ΠΏΡΠΈΠΌΠ΅Π½ΡΠ΅ΡΡΡ Π½Π΅ ΠΎΡΠ΅Π½Ρ ΡΠ°ΡΡΠΎ, ΠΏΠΎΡΠΎΠΌΡ ΡΡΠΎ ΠΎΠ½ ΡΠ²ΡΡΠ΄ΡΠΉ, Π½ΠΎ ΠΎΡΠ΅Π½Ρ Ρ
ΡΡΠΏΠΊΠΈΠΉ. Π’Π°ΠΊΠΆΠ΅ ΠΎΠ½ Π½Π΅ ΠΏΠΎΠ΄Π΄Π°Π΅ΡΡΡ ΠΌΠ΅Ρ
Π°Π½ΠΈΡΠ΅ΡΠΊΠΎΠΉ ΠΎΠ±ΡΠ°Π±ΠΎΡΠΊΠ΅ ΡΠ°Π·Π»ΠΈΡΠ½ΡΠΌΠΈ ΡΠ΅ΠΆΡΡΠΈΠΌΠΈ ΠΈΠ½ΡΡΡΡΠΌΠ΅Π½ΡΠ°ΠΌΠΈ, Π° ΠΏΠΎΡΠΎΠΌΡ ΠΈΡΠΏΠΎΠ»ΡΠ·ΡΠ΅ΡΡΡ Π΄Π»Ρ ΠΎΡΠ»ΠΈΠ²Π°Π½ΠΈΡ Π΄Π΅ΡΠ°Π»Π΅ΠΉ, ΠΊΠΎΡΠΎΡΡΠ΅ Π½Π΅ ΡΡΠ΅Π±ΡΡΡ ΠΊΠ°ΠΊΠΎΠΉ-Π»ΠΈΠ±ΠΎ ΠΎΠ±ΡΠ°Π±ΠΎΡΠΊΠΈ. Π₯ΠΎΡΡ ΡΡΠΎΡ Π²ΠΈΠ΄ ΡΡΠ³ΡΠ½Π° Π΄ΠΎΠΏΡΡΠΊΠ°Π΅Ρ ΡΠ»ΠΈΡΠΎΠ²Π°Π½ΠΈΠ΅ Π°Π±ΡΠ°Π·ΠΈΠ²Π½ΡΠΌΠΈ ΠΊΡΡΠ³Π°ΠΌΠΈ. ΠΠ΅Π»ΡΠΉ ΡΡΠ³ΡΠ½ ΠΌΠΎΠΆΠ΅Ρ Π±ΡΡΡ ΠΊΠ°ΠΊ ΠΎΠ±ΡΠΊΠ½ΠΎΠ²Π΅Π½Π½ΡΠΌ, ΡΠ°ΠΊ ΠΈ Π»Π΅Π³ΠΈΡΠΎΠ²Π°Π½Π½ΡΠΌ. ΠΡΠΈ ΡΡΠΎΠΌ ΡΠ²Π°ΡΠΊΠ° Π΅Π³ΠΎ Π²ΡΠ·ΡΠ²Π°Π΅Ρ Π·Π°ΡΡΡΠ΄Π½Π΅Π½ΠΈΡ, ΠΏΠΎΡΠΊΠΎΠ»ΡΠΊΡ ΡΠΎΠΏΡΠΎΠ²ΠΎΠΆΠ΄Π°Π΅ΡΡΡ ΠΎΠ±ΡΠ°Π·ΠΎΠ²Π°Π½ΠΈΠ΅ΠΌ ΡΠ°Π·Π»ΠΈΡΠ½ΡΡ
ΡΡΠ΅ΡΠΈΠ½ Π²ΠΎ Π²ΡΠ΅ΠΌΡ ΠΎΡ
Π»Π°ΠΆΠ΄Π΅Π½ΠΈΡ ΠΈΠ»ΠΈ Π½Π°Π³ΡΠ΅Π²Π°, Π° ΡΠ°ΠΊΠΆΠ΅ ΠΏΠΎ ΠΏΡΠΈΡΠΈΠ½Π΅ Π½Π΅ΠΎΠ΄Π½ΠΎΡΠΎΠ΄Π½ΠΎΡΡΠΈ ΡΡΡΡΠΊΡΡΡΡ, ΡΠΎΡΠΌΠΈΡΡΡΡΠ΅ΠΉΡΡ Π² ΡΠΎΡΠΊΠ΅ ΡΠ²Π°ΡΠΊΠΈ.
ΠΠ΅Π»ΡΠ΅ ΠΈΠ·Π½ΠΎΡΠΎΡΡΠΎΠΉΠΊΠΈΠ΅ ΡΡΠ³ΡΠ½Ρ ΠΏΠΎΠ»ΡΡΠ°ΡΡ Π·Π° ΡΡΠ΅Ρ ΠΏΠ΅ΡΠ²ΠΈΡΠ½ΠΎΠΉ ΠΊΡΠΈΡΡΠ°Π»Π»ΠΈΠ·Π°ΡΠΈΠΈ ΠΆΠΈΠ΄ΠΊΠΎΠ³ΠΎ ΡΠΏΠ»Π°Π²Π° ΠΏΡΠΈ ΡΠΊΠΎΡΠΎΡΠ΅ΡΠ½ΠΎΠΌ ΠΎΡ Π»Π°ΠΆΠ΄Π΅Π½ΠΈΠΈ. Π§Π°ΡΠ΅ Π²ΡΠ΅Π³ΠΎ ΠΎΠ½ΠΈ ΠΈΡΠΏΠΎΠ»ΡΠ·ΡΡΡΡΡ Π΄Π»Ρ ΡΠ°Π±ΠΎΡΡ Π² ΡΡΠ»ΠΎΠ²ΠΈΡΡ ΡΡΡ ΠΎΠ³ΠΎ ΡΡΠ΅Π½ΠΈΡ (Π½Π°ΠΏΡΠΈΠΌΠ΅Ρ, ΡΠΎΡΠΌΠΎΠ·Π½ΡΠ΅ ΠΊΠΎΠ»ΠΎΠ΄ΠΊΠΈ) ΠΈΠ»ΠΈ Π΄Π»Ρ ΠΏΡΠΎΠΈΠ·Π²ΠΎΠ΄ΡΡΠ²Π° Π΄Π΅ΡΠ°Π»Π΅ΠΉ, ΠΎΠ±Π»Π°Π΄Π°ΡΡΠΈΡ ΠΏΠΎΠ²ΡΡΠ΅Π½Π½ΠΎΠΉ ΠΈΠ·Π½ΠΎΡΠΎΡΡΠΎΠΉΠΊΠΎΡΡΡΡ ΠΈ ΠΆΠ°ΡΠΎΡΡΠΎΠΉΠΊΠΎΡΡΡΡ (Π²Π°Π»ΠΊΠΈ ΠΏΡΠΎΠΊΠ°ΡΠ½ΡΡ ΡΡΠ°Π½ΠΎΠ²).
ΠΡΡΠ°ΡΠΈ, Π±Π΅Π»ΡΠΉ ΡΡΠ³ΡΠ½ ΠΏΠΎΠ»ΡΡΠΈΠ» ΡΠ²ΠΎΠ΅ Π½Π°Π·Π²Π°Π½ΠΈΠ΅ Π±Π»Π°Π³ΠΎΠ΄Π°ΡΡ ΡΠΎΠΌΡ, ΡΡΠΎ Π²Π½Π΅ΡΠ½ΠΈΠΉ Π²ΠΈΠ΄ Π΅Π³ΠΎ ΠΈΠ·Π»ΠΎΠΌΠ° β ΡΠ²Π΅ΡΠ»ΠΎ-ΠΊΡΠΈΡΡΠ°Π»Π»ΠΈΡΠ΅ΡΠΊΠ°Ρ, Π»ΡΡΠΈΡΡΠ°Ρ ΠΏΠΎΠ²Π΅ΡΡ Π½ΠΎΡΡΡ. Π‘ΡΡΡΠΊΡΡΡΠ° ΡΡΠΎΠ³ΠΎ ΡΡΠ³ΡΠ½Π° ΠΏΡΠ΅Π΄ΡΡΠ°Π²Π»ΡΠ΅Ρ ΡΠΎΠ±ΠΎΠΉ ΡΠΎΠ²ΠΎΠΊΡΠΏΠ½ΠΎΡΡΡ Π»Π΅Π΄Π΅Π±ΡΡΠΈΡΠ°, ΠΏΠ΅ΡΠ»ΠΈΡΠ° ΠΈ Π²ΡΠΎΡΠΈΡΠ½ΠΎΠ³ΠΎ ΡΠ΅ΠΌΠ΅Π½ΡΠΈΡΠ°. ΠΡΠ»ΠΈ ΠΆΠ΅ Π΄Π°Π½Π½ΡΠΉ ΡΡΠ³ΡΠ½ ΠΏΠΎΠ΄Π²Π΅ΡΠ³Π°ΡΡ Π»Π΅Π³ΠΈΡΠΎΠ²Π°Π½ΠΈΡ, ΡΠΎ ΠΏΠ΅ΡΠ»ΠΈΡ ΡΡΠ°Π½ΡΡΠΎΡΠΌΠΈΡΡΠ΅ΡΡΡ Π² ΡΡΠΎΠΎΡΡΠΈΡ, Π°ΡΡΡΠ΅Π½ΠΈΡ ΠΈΠ»ΠΈ ΠΌΠ°ΡΡΠ΅Π½ΡΠΈΡ.
ΠΠΎΠ»ΠΎΠ²ΠΈΠ½ΡΠ°ΡΡΠΉ ΡΡΠ³ΡΠ½
ΠΠ»Π°ΡΡΠΈΡΠΈΠΊΠ°ΡΠΈΡ ΡΡΠ³ΡΠ½ΠΎΠ² Π±ΡΠ΄Π΅Ρ Π½Π΅ΠΏΠΎΠ»Π½ΠΎΠΉ, Π΅ΡΠ»ΠΈ Π½Π΅ ΡΠΏΠΎΠΌΡΠ½ΡΡΡ ΠΎΠ± ΡΡΠΎΠΉ ΡΠ°Π·Π½ΠΎΠ²ΠΈΠ΄Π½ΠΎΡΡΠΈ ΠΌΠ΅ΡΠ°Π»Π»ΠΈΡΠ΅ΡΠΊΠΎΠ³ΠΎ ΡΠΏΠ»Π°Π²Π°.
ΠΠ»Ρ ΡΠΊΠ°Π·Π°Π½Π½ΠΎΠ³ΠΎ ΡΡΠ³ΡΠ½Π° Ρ Π°ΡΠ°ΠΊΡΠ΅ΡΠ½ΠΎ ΡΠΎΡΠ΅ΡΠ°Π½ΠΈΠ΅ ΠΊΠ°ΡΠ±ΠΈΠ΄Π½ΠΎΠΉ ΡΠ²ΡΠ΅ΠΊΡΠΈΠΊΠΈ ΠΈ Π³ΡΠ°ΡΠΈΡΠ° Π² Π΅Π³ΠΎ ΡΡΡΡΠΊΡΡΡΠ΅. Π ΡΠ΅Π»ΠΎΠΌ ΠΆΠ΅, ΠΏΠΎΠ»Π½ΠΎΡΠ΅Π½Π½Π°Ρ ΡΡΡΡΠΊΡΡΡΠ° ΠΈΠΌΠ΅Π΅Ρ ΡΠ»Π΅Π΄ΡΡΡΠΈΠΉ Π²ΠΈΠ΄: Π³ΡΠ°ΡΠΈΡ, ΠΏΠ΅ΡΠ»ΠΈΡ, Π»Π΅Π΄Π΅Π±ΡΡΠΈΡ. ΠΡΠ»ΠΈ ΠΆΠ΅ ΡΡΠ³ΡΠ½ ΠΏΠΎΠ΄Π²Π΅ΡΠ³Π½ΡΡΡ ΡΠ΅ΡΠΌΠΈΡΠ΅ΡΠΊΠΎΠΉ ΠΎΠ±ΡΠ°Π±ΠΎΡΠΊΠ΅ ΠΈΠ»ΠΈ Π»Π΅Π³ΠΈΡΠΎΠ²Π°Π½ΠΈΡ, ΡΠΎ ΡΡΠΎ ΠΏΡΠΈΠ²Π΅Π΄Π΅Ρ ΠΊ ΠΎΠ±ΡΠ°Π·ΠΎΠ²Π°Π½ΠΈΡ Π°ΡΡΡΠ΅Π½ΠΈΡΠ°, ΠΌΠ°ΡΡΠ΅Π½ΡΠΈΡΠ° ΠΈΠ»ΠΈ ΠΈΠ³ΠΎΠ»ΡΡΠ°ΡΠΎΠ³ΠΎ ΡΡΠΎΠΎΡΡΠΈΡΠ°.
ΠΡΠΎΡ Π²ΠΈΠ΄ ΡΡΠ³ΡΠ½Π° Π΄ΠΎΡΡΠ°ΡΠΎΡΠ½ΠΎ Ρ ΡΡΠΏΠΎΠΊ, ΠΏΠΎΡΡΠΎΠΌΡ Π΅Π³ΠΎ ΠΏΡΠΈΠΌΠ΅Π½Π΅Π½ΠΈΠ΅ Π²Π΅ΡΡΠΌΠ° ΠΎΠ³ΡΠ°Π½ΠΈΡΠ΅Π½ΠΎ. Π‘Π°ΠΌΠΎ ΠΆΠ΅ Π½Π°Π·Π²Π°Π½ΠΈΠ΅ ΡΠΏΠ»Π°Π² ΠΏΠΎΠ»ΡΡΠΈΠ» ΠΏΠΎΡΠΎΠΌΡ, ΡΡΠΎ Π΅Π³ΠΎ ΠΈΠ·Π»ΠΎΠΌ β ΡΠΎΡΠ΅ΡΠ°Π½ΠΈΠ΅ ΡΠ΅ΠΌΠ½ΡΡ ΠΈ ΡΠ²Π΅ΡΠ»ΡΡ ΡΡΠ°ΡΡΠΊΠΎΠ² ΠΊΡΠΈΡΡΠ°Π»Π»ΠΈΡΠ΅ΡΠΊΠΎΠ³ΠΎ ΡΡΡΠΎΠ΅Π½ΠΈΡ.
Π‘Π°ΠΌΡΠΉ ΡΠ°ΡΠΏΡΠΎΡΡΡΠ°Π½Π΅Π½Π½ΡΠΉ ΠΌΠ°ΡΠΈΠ½ΠΎΡΡΡΠΎΠΈΡΠ΅Π»ΡΠ½ΡΠΉ ΠΌΠ°ΡΠ΅ΡΠΈΠ°Π»
Π‘Π΅ΡΡΠΉ ΡΡΠ³ΡΠ½ ΠΠΠ‘Π’ 1412-85 ΡΠΎΠ΄Π΅ΡΠΆΠΈΡ Π² ΡΠ²ΠΎΠ΅ΠΌ ΡΠΎΡΡΠ°Π²Π΅ ΠΎΠΊΠΎΠ»ΠΎ 3,5% ΡΠ³Π»Π΅ΡΠΎΠ΄Π°, ΠΎΡ 1,9 Π΄ΠΎ 2,5% ΠΊΡΠ΅ΠΌΠ½ΠΈΡ, Π΄ΠΎ 0,8% ΠΌΠ°ΡΠ³Π°Π½ΡΠ°, Π΄ΠΎ 0,3% ΡΠΎΡΡΠΎΡΠ° ΠΈ ΠΌΠ΅Π½Π΅Π΅ 0,12% ΡΠ΅ΡΡ.
ΠΡΠ°ΡΠΈΡ Π² ΡΠ°ΠΊΠΎΠΌ ΡΡΠ³ΡΠ½Π΅ ΠΈΠΌΠ΅Π΅Ρ ΠΏΠ»Π°ΡΡΠΈΠ½ΡΠ°ΡΡΡ ΡΠΎΡΠΌΡ. ΠΡΠΈ ΡΡΠΎΠΌ Π½Π΅ ΡΡΠ΅Π±ΡΠ΅ΡΡΡ ΡΠΏΠ΅ΡΠΈΠ°Π»ΡΠ½ΠΎΠ³ΠΎ ΠΌΠΎΠ΄ΠΈΡΠΈΡΠΈΡΠΎΠ²Π°Π½ΠΈΡ.
ΠΠ»Π°ΡΡΠΈΠ½ΠΊΠΈ Π³ΡΠ°ΡΠΈΡΠ° ΠΈΠΌΠ΅ΡΡ ΡΠΈΠ»ΡΠ½ΠΎ ΠΎΡΠ»Π°Π±Π»ΡΡΡΠ΅Π΅ Π΄Π΅ΠΉΡΡΠ²ΠΈΠ΅ ΠΈ ΠΏΠΎΡΠΎΠΌΡ ΡΠ΅ΡΠΎΠΌΡ ΡΡΠ³ΡΠ½Ρ Ρ
Π°ΡΠ°ΠΊΡΠ΅ΡΠ½Ρ ΠΎΡΠ΅Π½Ρ Π½ΠΈΠ·ΠΊΠ°Ρ ΡΠ΄Π°ΡΠ½Π°Ρ Π²ΡΠ·ΠΊΠΎΡΡΡ ΠΈ ΠΏΡΠ°ΠΊΡΠΈΡΠ΅ΡΠΊΠΈ ΠΏΠΎΠ»Π½ΠΎΠ΅ ΠΎΡΡΡΡΡΡΠ²ΠΈΠ΅ ΠΎΡΠ½ΠΎΡΠΈΡΠ΅Π»ΡΠ½ΠΎΠ³ΠΎ ΡΠ΄Π»ΠΈΠ½Π΅Π½ΠΈΡ (ΠΏΠΎΠΊΠ°Π·Π°ΡΠ΅Π»Ρ ΡΠΎΡΡΠ°Π²Π»ΡΠ΅Ρ ΠΌΠ΅Π½Π΅ 0,5%).
Π‘Π΅ΡΡΠΉ ΡΡΠ³ΡΠ½ Ρ ΠΎΡΠΎΡΠΎ ΠΏΠΎΠ΄Π²Π΅ΡΠ³Π°Π΅ΡΡΡ ΠΎΠ±ΡΠ°Π±ΠΎΡΠΊΠ΅. Π‘ΡΡΡΠΊΡΡΡΠ° ΡΠΏΠ»Π°Π²Π° ΠΌΠΎΠΆΠ΅Ρ Π±ΡΡΡ ΡΠ»Π΅Π΄ΡΡΡΠ΅ΠΉ:
- Π€Π΅ΡΡΠΈΡΠΎ-Π³ΡΠ°ΡΠΈΡΠΎΠ²ΠΎΠΉ.
- Π€Π΅ΡΡΠΈΡΠΎ-ΠΏΠ΅ΡΠ»ΠΈΡΠΎ-Π³ΡΠ°ΡΠΈΡΠΎΠ²ΠΎΠΉ.
- ΠΠ΅ΡΠ»ΠΈΡΠΎ-Π³ΡΠ°ΡΠΈΡΠΎΠ²ΠΎΠΉ.
ΠΠ° ΡΠΆΠ°ΡΠΈΠ΅ ΡΠ΅ΡΡΠΉ ΡΡΠ³ΡΠ½ ΡΠ°Π±ΠΎΡΠ°Π΅Ρ Π³ΠΎΡΠ°Π·Π΄ΠΎ Π»ΡΡΡΠ΅, Π½Π΅ΠΆΠ΅Π»ΠΈ Π½Π° ΡΠ°ΡΡΡΠΆΠ΅Π½ΠΈΠ΅. Π’Π°ΠΊΠΆΠ΅ ΠΎΠ½ Π΄ΠΎΠ²ΠΎΠ»ΡΠ½ΠΎ Ρ ΠΎΡΠΎΡΠΎ ΡΠ²Π°ΡΠΈΠ²Π°Π΅ΡΡΡ, Π½ΠΎ Π΄Π»Ρ ΡΡΠΎΠ³ΠΎ ΡΡΠ΅Π±ΡΠ΅ΡΡΡ ΠΏΡΠ΅Π΄Π²Π°ΡΠΈΡΠ΅Π»ΡΠ½ΡΠΉ ΠΏΠΎΠ΄ΠΎΠ³ΡΠ΅Π², Π° Π² ΠΊΠ°ΡΠ΅ΡΡΠ²Π΅ ΠΏΡΠΈΡΠ°Π΄ΠΎΡΠ½ΠΎΠ³ΠΎ ΠΌΠ°ΡΠ΅ΡΠΈΠ°Π»Π° ΡΠ»Π΅Π΄ΡΠ΅Ρ ΠΈΡΠΏΠΎΠ»ΡΠ·ΠΎΠ²Π°ΡΡ ΡΠΏΠ΅ΡΠΈΠ°Π»ΡΠ½ΡΠ΅ ΡΡΠ³ΡΠ½Π½ΡΠ΅ ΡΡΠ΅ΡΠΆΠ½ΠΈ Ρ Π²ΡΡΠΎΠΊΠΈΠΌ ΡΠΎΠ΄Π΅ΡΠΆΠ°Π½ΠΈΠ΅ΠΌ ΠΊΡΠ΅ΠΌΠ½ΠΈΡ ΠΈ ΡΠ³Π»Π΅ΡΠΎΠ΄Π°. ΠΠ΅Π· ΠΏΡΠ΅Π΄Π²Π°ΡΠΈΡΠ΅Π»ΡΠ½ΠΎΠ³ΠΎ ΡΠ°Π·ΠΎΠ³ΡΠ΅Π²Π° ΡΠ²Π°ΡΠΊΠ° Π±ΡΠ΄Π΅Ρ Π·Π°ΡΡΡΠ΄Π½Π΅Π½Π°, ΠΏΠΎΡΠΊΠΎΠ»ΡΠΊΡ Π±ΡΠ΄Π΅Ρ ΠΏΡΠΎΠΈΡΡ ΠΎΠ΄ΠΈΡΡ ΠΎΡΠ±Π΅Π»ΠΈΠ²Π°Π½ΠΈΠ΅ ΡΡΠ³ΡΠ½Π° Π² Π·ΠΎΠ½Π΅ ΡΠ²Π°.
ΠΠ· ΡΠ΅ΡΠΎΠ³ΠΎ ΡΡΠ³ΡΠ½Π° ΠΏΡΠΎΠΈΠ·Π²ΠΎΠ΄ΡΡ Π΄Π΅ΡΠ°Π»ΠΈ, ΡΠ°Π±ΠΎΡΠ°ΡΡΠΈΠ΅ ΠΏΡΠΈ ΠΎΡΡΡΡΡΡΠ²ΠΈΠΈ ΡΠ΄Π°ΡΠ½ΠΎΠΉ Π½Π°Π³ΡΡΠ·ΠΊΠΈ (ΡΠΊΠΈΠ²Ρ, ΠΊΡΡΡΠΊΠΈ, ΡΡΠ°Π½ΠΈΠ½Ρ).
ΠΠ±ΠΎΠ·Π½Π°ΡΠ΅Π½ΠΈΠ΅ Π΄Π°Π½Π½ΠΎΠ³ΠΎ ΡΡΠ³ΡΠ½Π° ΠΏΡΠΎΠΈΡΡ ΠΎΠ΄ΠΈΡ ΠΏΠΎ ΡΠ°ΠΊΠΎΠΌΡ ΠΏΡΠΈΠ½ΡΠΈΠΏΡ: Π‘Π§ 25-52. ΠΠ²Π΅ Π±ΡΠΊΠ²Ρ ΡΠΈΠ³Π½Π°Π»ΠΈΠ·ΠΈΡΡΡΡ ΠΎ ΡΠΎΠΌ, ΡΡΠΎ ΡΡΠΎ ΠΈΠΌΠ΅Π½Π½ΠΎ ΡΠ΅ΡΡΠΉ ΡΡΠ³ΡΠ½, ΡΠΈΡΠ»ΠΎ 25 β ΠΏΠΎΠΊΠ°Π·Π°ΡΠ΅Π»Ρ ΠΏΡΠ΅Π΄Π΅Π»Π° ΠΏΡΠΎΡΠ½ΠΎΡΡΠΈ ΠΏΡΠΈ ΡΠ°ΡΡΡΠΆΠ΅Π½ΠΈΠΈ (Π² ΠΠΏΠ° ΠΈΠ»ΠΈ ΠΊΠ³Ρ/ΠΌΠΌ2), ΡΠΈΡΠ»ΠΎ 52 β ΠΏΡΠ΅Π΄Π΅Π» ΠΏΡΠΎΡΠ½ΠΎΡΡΠΈ Π² ΠΌΠΎΠΌΠ΅Π½Ρ ΠΈΠ·Π³ΠΈΠ±Π°.
ΠΡΡΠΎΠΊΠΎΠΏΡΠΎΡΠ½ΡΠΉ ΡΡΠ³ΡΠ½
Π§ΡΠ³ΡΠ½ Ρ ΡΠ°ΡΠΎΠ²ΠΈΠ΄Π½ΡΠΌ Π³ΡΠ°ΡΠΈΡΠΎΠΌ ΠΏΡΠΈΠ½ΡΠΈΠΏΠΈΠ°Π»ΡΠ½ΠΎ ΠΎΡΠ»ΠΈΡΠ°Π΅ΡΡΡ ΠΎΡ Π΄ΡΡΠ³ΠΈΡ
ΡΠ²ΠΎΠΈΡ
Β«ΡΠΎΠ±ΡΠ°ΡΡΠ΅Π²Β» ΡΠ΅ΠΌ, ΡΡΠΎ Π² Π½Π΅ΠΌ ΡΠΎΠ΄Π΅ΡΠΆΠΈΡΡΡ Π³ΡΠ°ΡΠΈΡ ΡΠ°ΡΠΎΠ²ΠΈΠ΄Π½ΠΎΠΉ ΡΠΎΡΠΌΡ. ΠΠ½Π° ΠΏΠΎΠ»ΡΡΠ°Π΅ΡΡΡ Π·Π° ΡΡΠ΅Ρ Π²Π²Π΅Π΄Π΅Π½ΠΈΡ Π² ΠΆΠΈΠ΄ΠΊΠΈΠΉ ΡΠΏΠ»Π°Π² ΡΠΏΠ΅ΡΠΈΠ°Π»ΡΠ½ΡΡ
ΠΌΠΎΠ΄ΠΈΡΠΈΠΊΠ°ΡΠΎΡΠΎΠ² (Mg, Π‘Π΅). ΠΠΎΠ»ΠΈΡΠ΅ΡΡΠ²ΠΎ Π³ΡΠ°ΡΠΈΡΠ½ΡΡ
Π²ΠΊΠ»ΡΡΠ΅Π½ΠΈΠΉ ΠΈ ΠΈΡ
Π»ΠΈΠ½Π΅ΠΉΠ½ΡΠ΅ ΡΠ°Π·ΠΌΠ΅ΡΡ ΠΌΠΎΠ³ΡΡ Π±ΡΡΡ ΡΠ°Π·Π»ΠΈΡΠ½ΡΠΌΠΈ.
Π§Π΅ΠΌ Ρ ΠΎΡΠΎΡ ΡΠ°ΡΠΎΠ²ΠΈΠ΄Π½ΡΠΉ Π³ΡΠ°ΡΠΈΡ? Π’Π΅ΠΌ, ΡΡΠΎ ΡΠ°ΠΊΠ°Ρ ΡΠΎΡΠΌΠ° ΠΌΠΈΠ½ΠΈΠΌΠ°Π»ΡΠ½ΠΎ ΠΎΡΠ»Π°Π±Π»ΡΠ΅Ρ ΠΌΠ΅ΡΠ°Π»Π»ΠΈΡΠ΅ΡΠΊΡΡ ΠΎΡΠ½ΠΎΠ²Ρ, ΠΊΠΎΡΠΎΡΠ°Ρ, Π² ΡΠ²ΠΎΡ ΠΎΡΠ΅ΡΠ΅Π΄Ρ, ΠΌΠΎΠΆΠ΅Ρ Π±ΡΡΡ ΠΏΠ΅ΡΠ»ΠΈΡΠ½ΠΎΠΉ, ΡΠ΅ΡΡΠΈΡΠ½ΠΎΠΉ ΠΈΠ»ΠΈ ΠΏΠ΅ΡΠ»ΠΈΡΠ½ΠΎ-ΡΠ΅ΡΡΠΈΡΠ½ΠΎΠΉ.
ΠΠ»Π°Π³ΠΎΠ΄Π°ΡΡ ΠΏΡΠΈΠΌΠ΅Π½Π΅Π½ΠΈΡ ΡΠ΅ΡΠΌΠΈΡΠ΅ΡΠΊΠΎΠΉ ΠΎΠ±ΡΠ°Π±ΠΎΡΠΊΠΈ ΠΈΠ»ΠΈ Π»Π΅Π³ΠΈΡΠΎΠ²Π°Π½ΠΈΡ ΠΎΡΠ½ΠΎΠ²Π° ΡΡΠ³ΡΠ½Π° ΠΌΠΎΠΆΠ΅Ρ Π±ΡΡΡ ΠΈΠ³ΠΎΠ»ΡΡΠ°ΡΠΎ-ΡΡΠΎΠΎΡΡΠΈΡΠ½ΠΎΠΉ, ΠΌΠ°ΡΡΠ΅Π½ΡΠΈΡΠ½ΠΎΠΉ, Π°ΡΡΡΠ΅Π½ΠΈΡΠ½ΠΎΠΉ.
ΠΠ°ΡΠΊΠΈ Π²ΡΡΠΎΠΊΠΎΠΏΡΠΎΡΠ½ΠΎΠ³ΠΎ ΡΡΠ³ΡΠ½Π° Π±ΡΠ²Π°ΡΡ ΡΠ°Π·Π»ΠΈΡΠ½Ρ, Π½ΠΎ Π² ΠΎΠ±ΡΠ΅ΠΌ Π²ΠΈΠ΄Π΅ ΠΎΠ±ΠΎΠ·Π½Π°ΡΠ΅Π½ΠΈΠ΅ Π΅Π³ΠΎ ΡΠ°ΠΊΠΎΠ²ΠΎ: ΠΠ§ 40-5. ΠΠ΅Π³ΠΊΠΎ Π΄ΠΎΠ³Π°Π΄Π°ΡΡΡΡ, ΡΡΠΎ ΠΠ§ β ΡΡΠΎ Π²ΡΡΠΎΠΊΠΎΠΏΡΠΎΡΠ½ΡΠΉ ΡΡΠ³ΡΠ½, ΡΠΈΡΠ»ΠΎ 40 β ΠΏΠΎΠΊΠ°Π·Π°ΡΠ΅Π»Ρ ΠΏΡΠ΅Π΄Π΅Π»Π° ΠΏΡΠΎΡΠ½ΠΎΡΡΠΈ ΠΏΡΠΈ ΡΠ°ΡΡΡΠΆΠ΅Π½ΠΈΠΈ (ΠΊΠ³Ρ/ΠΌΠΌ2), ΡΠΈΡΠ»ΠΎ 5 β ΠΎΡΠ½ΠΎΡΠΈΡΠ΅Π»ΡΠ½ΠΎ ΡΠ΄Π»ΠΈΠ½Π΅Π½ΠΈΠ΅, Π²ΡΡΠ°ΠΆΠ°Π΅ΠΌΠΎΠ΅ Π² ΠΏΡΠΎΡΠ΅Π½ΡΠ°Ρ .
ΠΠΎΠ²ΠΊΠΈΠΉ ΡΡΠ³ΡΠ½
Π‘ΡΡΡΠΊΡΡΡΠ° ΠΊΠΎΠ²ΠΊΠΎΠ³ΠΎ ΡΡΠ³ΡΠ½Π° Π·Π°ΠΊΠ»ΡΡΠ°Π΅ΡΡΡ Π² Π½Π°Π»ΠΈΡΠΈΠΈ Π² Π½Π΅ΠΌ Π³ΡΠ°ΡΠΈΡΠ° Π² Ρ
Π»ΠΎΠΏΡΠ΅Π²ΠΈΠ΄Π½ΠΎΠΉ ΠΈΠ»ΠΈ ΡΠ°ΡΠΎΠ²ΠΈΠ΄Π½ΠΎΠΉ ΡΠΎΡΠΌΠ΅. ΠΡΠΈ ΡΡΠΎΠΌ Ρ
Π»ΠΎΠΏΡΠ΅Π²ΠΈΠ΄Π½ΡΠΉ Π³ΡΠ°ΡΠΈΡ ΠΌΠΎΠΆΠ΅Ρ ΠΈΠΌΠ΅ΡΡ ΡΠ°Π·Π»ΠΈΡΠ½ΡΡ Π΄ΠΈΡΠΏΠ΅ΡΡΠ½ΠΎΡΡΡ ΠΈ ΠΊΠΎΠΌΠΏΠ°ΠΊΡΠ½ΠΎΡΡΡ, ΡΡΠΎ, Π² ΡΠ²ΠΎΡ ΠΎΡΠ΅ΡΠ΅Π΄Ρ, ΠΎΠΊΠ°Π·ΡΠ²Π°Π΅Ρ Π½Π΅ΠΏΠΎΡΡΠ΅Π΄ΡΡΠ²Π΅Π½Π½ΠΎΠ΅ Π²Π»ΠΈΡΠ½ΠΈΠ΅ Π½Π° ΠΌΠ΅Ρ
Π°Π½ΠΈΡΠ΅ΡΠΊΠΈΠ΅ ΡΠ²ΠΎΠΉΡΡΠ²Π° ΡΡΠ³ΡΠ½Π°.
Π ΠΏΡΠΎΠΌΡΡΠ»Π΅Π½Π½ΠΎΡΡΠΈ ΠΊΠΎΠ²ΠΊΠΈΠΉ ΡΡΠ³ΡΠ½ ΠΏΡΠΎΠΈΠ·Π²ΠΎΠ΄ΠΈΡΡΡ Π·Π°ΡΠ°ΡΡΡΡ Ρ ΡΠ΅ΡΡΠΈΡΠ½ΠΎΠΉ ΠΎΡΠ½ΠΎΠ²ΠΎΠΉ, ΠΊΠΎΡΠΎΡΠ°Ρ ΠΎΠ±Π΅ΡΠΏΠ΅ΡΠΈΠ²Π°Π΅Ρ Π±ΠΎΠ»ΡΡΡΡ ΠΏΠ»Π°ΡΡΠΈΡΠ½ΠΎΡΡΡ.
ΠΠ½Π΅ΡΠ½ΠΈΠΉ Π²ΠΈΠ΄ ΠΈΠ·Π»ΠΎΠΌΠ° ΡΠ΅ΡΡΠΈΡΠ½ΠΎΠ³ΠΎ ΠΊΠΎΠ²ΠΊΠΎΠ³ΠΎ ΡΡΠ³ΡΠ½Π° ΠΈΠΌΠ΅Π΅Ρ ΡΠ΅ΡΠ½ΠΎ-Π±Π°ΡΡ Π°ΡΠΈΡΡΡΠΉ Π²ΠΈΠ΄. Π§Π΅ΠΌ Π²ΡΡΠ΅ ΠΊΠΎΠ»ΠΈΡΠ΅ΡΡΠ²ΠΎ ΠΏΠ΅ΡΠ»ΠΈΡΠ° Π² ΡΡΡΡΠΊΡΡΡΠ΅, ΡΠ΅ΠΌ ΡΠ²Π΅ΡΠ»Π΅Π΅ Π±ΡΠ΄Π΅Ρ ΡΡΠ°Π½ΠΎΠ²ΠΈΡΡΡΡ ΠΈΠ·Π»ΠΎΠΌ.
Π ΡΠ΅Π»ΠΎΠΌ ΠΆΠ΅, ΠΊΠΎΠ²ΠΊΠΈΠΉ ΡΡΠ³ΡΠ½ ΠΏΠΎΠ»ΡΡΠ°Π΅ΡΡΡ ΠΈΠ· ΠΎΡΠ»ΠΈΠ²ΠΎΠΊ Π±Π΅Π»ΠΎΠ³ΠΎ ΡΡΠ³ΡΠ½Π° Π±Π»Π°Π³ΠΎΠ΄Π°ΡΡ Π΄Π»ΠΈΡΠ΅Π»ΡΠ½ΠΎΠΌΡ ΡΠΎΠΌΠ»Π΅Π½ΠΈΡ Π² ΠΏΠ΅ΡΠ°Ρ , Π½Π°Π³ΡΠ΅ΡΡΡ Π΄ΠΎ ΡΠ΅ΠΌΠΏΠ΅ΡΠ°ΡΡΡΡ 800β950 Π³ΡΠ°Π΄ΡΡΠΎΠ² Π¦Π΅Π»ΡΡΠΈΡ.
ΠΠ° ΡΠ΅Π³ΠΎΠ΄Π½ΡΡΠ½ΠΈΠΉ Π΄Π΅Π½Ρ Π΅ΡΡΡ Π΄Π²Π° ΡΠΏΠΎΡΠΎΠ±Π° ΠΈΠ·Π³ΠΎΡΠΎΠ²Π»Π΅Π½ΠΈΡ ΠΊΠΎΠ²ΠΊΠΎΠ³ΠΎ ΡΡΠ³ΡΠ½Π°: Π΅Π²ΡΠΎΠΏΠ΅ΠΉΡΠΊΠΈΠΉ ΠΈ Π°ΠΌΠ΅ΡΠΈΠΊΠ°Π½ΡΠΊΠΈΠΉ.
ΠΠΌΠ΅ΡΠΈΠΊΠ°Π½ΡΠΊΠΈΠΉ ΠΌΠ΅ΡΠΎΠ΄ Π·Π°ΠΊΠ»ΡΡΠ°Π΅ΡΡΡ Π² ΡΠΎΠΌΠ»Π΅Π½ΠΈΠΈ ΡΠΏΠ»Π°Π²Π° Π² ΠΏΠ΅ΡΠΊΠ΅ ΠΏΡΠΈ ΡΠ΅ΠΌΠΏΠ΅ΡΠ°ΡΡΡΠ΅ 800-850 Π³ΡΠ°Π΄ΡΡΠΎΠ². Π ΡΡΠΎΠΌ ΠΏΡΠΎΡΠ΅ΡΡΠ΅ Π³ΡΠ°ΡΠΈΡ ΡΠ°ΡΠΏΠΎΠ»Π°Π³Π°Π΅ΡΡΡ ΠΌΠ΅ΠΆΠ΄Ρ Π·Π΅ΡΠ½Π°ΠΌΠΈ ΡΠΈΡΡΠ΅ΠΉΡΠ΅Π³ΠΎ ΠΆΠ΅Π»Π΅Π·Π°. Π ΠΈΡΠΎΠ³Π΅ ΡΡΠ³ΡΠ½ ΠΏΡΠΈΠΎΠ±ΡΠ΅ΡΠ°Π΅Ρ Π²ΡΠ·ΠΊΠΎΡΡΡ.
Π Π΅Π²ΡΠΎΠΏΠ΅ΠΉΡΠΊΠΎΠΌ ΠΌΠ΅ΡΠΎΠ΄Π΅ ΠΎΡΠ»ΠΈΠ²ΠΊΠΈ ΡΠΎΠΌΡΡΡΡ Π² ΠΆΠ΅Π»Π΅Π·Π½ΠΎΠΉ ΡΡΠ΄Π΅. Π’Π΅ΠΌΠΏΠ΅ΡΠ°ΡΡΡΠ° ΠΏΡΠΈ ΡΡΠΎΠΌ ΡΠΎΡΡΠ°Π²Π»ΡΠ΅Ρ ΠΎΠΊΠΎΠ»ΠΎ 850-950 Π³ΡΠ°Π΄ΡΡΠΎΠ² Π¦Π΅Π»ΡΡΠΈΡ. Π£Π³Π»Π΅ΡΠΎΠ΄ ΠΏΠ΅ΡΠ΅Ρ
ΠΎΠ΄ΠΈΡ Π² ΠΆΠ΅Π»Π΅Π·Π½ΡΡ ΡΡΠ΄Ρ, Π·Π° ΡΡΠ΅Ρ ΡΠ΅Π³ΠΎ ΠΏΠΎΠ²Π΅ΡΡ
Π½ΠΎΡΡΠ½ΡΠΉ ΡΠ»ΠΎΠΉ ΠΎΡΠ»ΠΈΠ²ΠΎΠΊ ΠΎΠ±Π΅Π·ΡΠ³Π»Π΅ΡΠΎΠΆΠΈΠ²Π°Π΅ΡΡΡ ΠΈ ΡΡΠ°Π½ΠΎΠ²ΠΈΡΡΡ ΠΌΡΠ³ΠΊΠΈΠΌ. Π§ΡΠ³ΡΠ½ ΡΡΠ°Π½ΠΎΠ²ΠΈΡΡΡ ΠΊΠΎΠ²ΠΊΠΈΠΌ, Π° ΡΠ΅ΡΠ΄ΡΠ΅Π²ΠΈΠ½Π° ΡΠΎΡ
ΡΠ°Π½ΡΠ΅Ρ Ρ
ΡΡΠΏΠΊΠΎΡΡΡ.
ΠΠ°ΡΠΊΠΈΡΠΎΠ²ΠΊΠ° ΠΊΠΎΠ²ΠΊΠΎΠ³ΠΎ ΡΡΠ³ΡΠ½Π°: ΠΠ§ 40-6, Π³Π΄Π΅ ΠΠ§ — ΡΡΠΎ, ΡΠ°Π·ΡΠΌΠ΅Π΅ΡΡΡ ΠΊΠΎΠ²ΠΊΠΈΠΉ ΡΡΠ³ΡΠ½; 40 β ΠΏΠΎΠΊΠ°Π·Π°ΡΠ΅Π»Ρ ΠΏΡΠΎΡΠ½ΠΎΡΡΠΈ ΠΏΡΠΈ ΡΠ°ΡΡΡΠΆΠ΅Π½ΠΈΠΈ; 6 β ΠΎΡΠ½ΠΎΡΠΈΡΠ΅Π»ΡΠ½ΠΎΠ΅ ΡΠ΄Π»ΠΈΠ½Π΅Π½ΠΈΠ΅, %.
ΠΡΠΎΡΠΈΠ΅ ΠΏΠΎΠΊΠ°Π·Π°ΡΠ΅Π»ΠΈ
Π§ΡΠΎ ΠΊΠ°ΡΠ°Π΅ΡΡΡ ΡΠ°Π·Π΄Π΅Π»Π΅Π½ΠΈΡ ΡΡΠ³ΡΠ½ΠΎΠ² ΠΏΠΎ ΠΏΡΠΎΡΠ½ΠΎΡΡΠΈ, ΡΠΎ Π·Π΄Π΅ΡΡ ΠΏΡΠΈΠΌΠ΅Π½ΡΠ΅ΡΡΡ ΡΠ»Π΅Π΄ΡΡΡΠ°Ρ ΠΊΠ»Π°ΡΡΠΈΡΠΈΠΊΠ°ΡΠΈΡ:
- ΠΠ±ΡΡΠ½Π°Ρ ΠΏΡΠΎΡΠ½ΠΎΡΡΡ: ΟΠ² Π΄ΠΎ 20 ΠΊΠ³/ΠΌΠΌ2.
- ΠΠΎΠ²ΡΡΠ΅Π½Π½Π°Ρ ΠΏΡΠΎΡΠ½ΠΎΡΡΡ: ΟΠ² = 20 β 38 ΠΊΠ³/ΠΌΠΌ2.
- ΠΡΡΠΎΠΊΠ°Ρ ΠΏΡΠΎΡΠ½ΠΎΡΡΡ: ΟΠ² = 40 ΠΊΠ³/ΠΌΠΌ2 ΠΈ Π²ΡΡΠ΅.
ΠΠΎ ΠΏΠ»Π°ΡΡΠΈΡΠ½ΠΎΡΡΠΈ ΡΡΠ³ΡΠ½Ρ ΡΠ°Π·Π΄Π΅Π»ΡΡΡΡΡ Π½Π°:
- ΠΠ΅ΠΏΠ»Π°ΡΡΠΈΡΠ½ΡΠ΅ β ΠΎΡΠ½ΠΎΡΠΈΡΠ΅Π»ΡΠ½ΠΎΠ΅ ΡΠ΄Π»ΠΈΠ½Π΅Π½ΠΈΠ΅ ΠΌΠ΅Π½Π΅Π΅ 1%.
- ΠΠ°Π»ΠΎΠΏΠ»Π°ΡΡΠΈΡΠ½ΡΠ΅ β ΠΎΡ 1% Π΄ΠΎ 5%.
- ΠΠ»Π°ΡΡΠΈΡΠ½ΡΠ΅ β ΠΎΡ 5% Π΄ΠΎ 10%.
- ΠΠΎΠ²ΡΡΠ΅Π½Π½ΠΎΠΉ ΠΏΠ»Π°ΡΡΠΈΡΠ½ΠΎΡΡΠΈ β Π±ΠΎΠ»Π΅Π΅ 10%.
Π Π·Π°ΠΊΠ»ΡΡΠ΅Π½ΠΈΠ΅ ΡΠ°ΠΊΠΆΠ΅ Ρ ΠΎΡΠ΅Π»ΠΎΡΡ Π±Ρ ΠΎΠ±ΡΠ·Π°ΡΠ΅Π»ΡΠ½ΠΎ ΠΎΡΠΌΠ΅ΡΠΈΡΡ, ΡΡΠΎ Π½Π° ΡΠ²ΠΎΠΉΡΡΠ²Π° Π»ΡΠ±ΠΎΠ³ΠΎ ΡΡΠ³ΡΠ½Π° Π΄ΠΎΠ²ΠΎΠ»ΡΠ½ΠΎ ΡΡΡΠ΅ΡΡΠ²Π΅Π½Π½ΠΎΠ΅ Π²Π»ΠΈΡΠ½ΠΈΠ΅ ΠΎΠΊΠ°Π·ΡΠ²Π°Π΅Ρ Π΄Π°ΠΆΠ΅ ΡΠΎΡΠΌΠ° ΠΈ Ρ Π°ΡΠ°ΠΊΡΠ΅Ρ Π·Π°Π»ΠΈΠ²ΠΊΠΈ.
Π»ΠΈΡΡΠΎΠ²ΡΠ΅ ΡΡΡΠ³ΠΈ ΠΈ ΠΈΡ ΠΊΠ»Π°ΡΡΠΈΡΠΈΠΊΠ°ΡΠΈΡ — Ispatguru
Cast Irons ΠΈ ΠΈΡ ΠΊΠ»Π°ΡΡΠΈΡΠΈΠΊΠ°ΡΠΈΡ
- Satyendra
- 10 ΡΠ½Π²Π°ΡΡ 2016 Π³.
- 0 ΠΠΎΠΌΠΌΠ΅Π½ΡΠ°ΡΠΈΠΈ Π§Π΅ΠΌ -ΠΆΠ΅Π»Π΅Π·ΠΎ, ΡΠ΅ΠΌΠ΅Π½ΡΠΈΡ, ΠΏΡΠΎΠΊΠ°ΡΠ½ΡΠΉ ΠΆΠ΅Π»Π΅Π·ΠΎ, eutectic, ferrite, graphite, ΡΠ΅ΡΠΊΠΈΠΉ. ΡΡΠ³ΡΠ½, ΠΊΠΎΠ²ΠΊΠΈΠΉ ΡΡΠ³ΡΠ½, ΡΡΠ³ΡΠ½ Ρ ΡΠ°ΡΠΎΠ²ΠΈΠ΄Π½ΡΠΌ Π³ΡΠ°ΡΠΈΡΠΎΠΌ, Π±Π΅Π»ΡΠΉ ΡΡΠ³ΡΠ½,
Π§ΡΠ³ΡΠ½Ρ ΠΈ ΠΈΡ ΠΊΠ»Π°ΡΡΠΈΡΠΈΠΊΠ°ΡΠΈΡ
Β Π’Π΅ΡΠΌΠΈΠ½ Β«ΡΡΠ³ΡΠ½Β» ΠΏΡΠ΅Π΄ΡΡΠ°Π²Π»ΡΠ΅Ρ Π±ΠΎΠ»ΡΡΠΎΠ΅ ΡΠ΅ΠΌΠ΅ΠΉΡΡΠ²ΠΎ ΡΠ΅ΡΡΠΎΡΠΏΠ»Π°Π²ΠΎΠ². Π§ΡΠ³ΡΠ½Ρ ΠΏΡΠ΅Π΄ΡΡΠ°Π²Π»ΡΡΡ ΡΠΎΠ±ΠΎΠΉ ΠΌΠ½ΠΎΠ³ΠΎΠΊΠΎΠΌΠΏΠΎΠ½Π΅Π½ΡΠ½ΡΠ΅ ΡΠΏΠ»Π°Π²Ρ ΠΆΠ΅Π»Π΅Π·Π°, Π·Π°ΡΠ²Π΅ΡΠ΄Π΅Π²Π°ΡΡΠΈΠ΅ Ρ ΡΠ²ΡΠ΅ΠΊΡΠΈΠΊΠΎΠΉ. ΠΡΠ½ΠΎΠ²Π½ΡΠΌΠΈ ΡΠ»Π΅ΠΌΠ΅Π½ΡΠ°ΠΌΠΈ ΡΡΠ³ΡΠ½Π° ΡΠ²Π»ΡΡΡΡΡ ΠΆΠ΅Π»Π΅Π·ΠΎ, ΡΠ³Π»Π΅ΡΠΎΠ΄ (2 % ΠΈ Π±ΠΎΠ»Π΅Π΅), ΠΊΡΠ΅ΠΌΠ½ΠΈΠΉ (ΠΎΡ 1 % Π΄ΠΎ 3 %), Π²ΡΠΎΡΠΎΡΡΠ΅ΠΏΠ΅Π½Π½ΡΠ΅ ΡΠ»Π΅ΠΌΠ΅Π½ΡΡ (ΠΌΠ΅Π½Π΅Π΅ 0,1 %) ΠΈ ΡΠ°ΡΡΠΎ Π»Π΅Π³ΠΈΡΡΡΡΠΈΠ΅ ΡΠ»Π΅ΠΌΠ΅Π½ΡΡ (ΠΌΠ΅Π½Π΅Π΅ 0,1 %). Π§ΡΠ³ΡΠ½ ΠΈΠΌΠ΅Π΅Ρ Π±ΠΎΠ»Π΅Π΅ Π²ΡΡΠΎΠΊΠΎΠ΅ ΡΠΎΠ΄Π΅ΡΠΆΠ°Π½ΠΈΠ΅ ΡΠ³Π»Π΅ΡΠΎΠ΄Π° ΠΈ ΠΊΡΠ΅ΠΌΠ½ΠΈΡ, ΡΠ΅ΠΌ ΡΡΠ°Π»Ρ. Π‘ΡΡΡΠΊΡΡΡΠ° ΡΡΠ³ΡΠ½Π° ΡΠΎΠ΄Π΅ΡΠΆΠΈΡ Π±ΠΎΠ»Π΅Π΅ Π±ΠΎΠ³Π°ΡΡΡ ΡΠ³Π»Π΅ΡΠΎΠ΄ΠΎΠΌ ΡΠ°Π·Ρ, ΡΠ΅ΠΌ ΡΡΠ°Π»Ρ, ΠΈΠ·-Π·Π° Π±ΠΎΠ»Π΅Π΅ Π²ΡΡΠΎΠΊΠΎΠ³ΠΎ ΡΠΎΠ΄Π΅ΡΠΆΠ°Π½ΠΈΡ ΡΠ³Π»Π΅ΡΠΎΠ΄Π°. Π§ΡΠ³ΡΠ½ ΠΌΠΎΠΆΠ΅Ρ Π·Π°ΡΠ²Π΅ΡΠ΄Π΅Π²Π°ΡΡ Π² ΡΠΎΠΎΡΠ²Π΅ΡΡΡΠ²ΠΈΠΈ Ρ ΡΠ΅ΡΠΌΠΎΠ΄ΠΈΠ½Π°ΠΌΠΈΡΠ΅ΡΠΊΠΈ ΠΌΠ΅ΡΠ°ΡΡΠ°Π±ΠΈΠ»ΡΠ½ΠΎΠΉ ΡΠΈΡΡΠ΅ΠΌΠΎΠΉ Fe-Fe3C (ΠΊΠ°ΡΠ±ΠΈΠ΄ ΠΆΠ΅Π»Π΅Π·Π°) ΠΈΠ»ΠΈ ΡΡΠ°Π±ΠΈΠ»ΡΠ½ΠΎΠΉ ΡΠΈΡΡΠ΅ΠΌΠΎΠΉ ΠΆΠ΅Π»Π΅Π·ΠΎ-Π³ΡΠ°ΡΠΈΡ, Π² ΠΎΡΠ½ΠΎΠ²Π½ΠΎΠΌ Π² Π·Π°Π²ΠΈΡΠΈΠΌΠΎΡΡΠΈ ΠΎΡ ΡΠΎΡΡΠ°Π²Π°, ΡΠΊΠΎΡΠΎΡΡΠΈ ΠΎΡ Π»Π°ΠΆΠ΄Π΅Π½ΠΈΡ ΠΈ ΠΎΠ±ΡΠ°Π±ΠΎΡΠΊΠΈ ΡΠ°ΡΠΏΠ»Π°Π²Π°.
Π§ΡΠ³ΡΠ½ Π² ΡΠ²ΠΎΠ΅ΠΉ ΠΎΡΠ½ΠΎΠ²Π½ΠΎΠΉ ΡΠΎΡΠΌΠ΅ ΠΏΡΠ΅Π΄ΡΡΠ°Π²Π»ΡΠ΅Ρ ΡΠΎΠ±ΠΎΠΉ Ρ
ΡΡΠΏΠΊΠΈΠΉ ΠΌΠ°ΡΠ΅ΡΠΈΠ°Π» Ρ ΠΎΡΠ΅Π½Ρ Π½ΠΈΠ·ΠΊΠΎΠΉ ΡΠ΄Π°ΡΠ½ΠΎΠΉ Π²ΡΠ·ΠΊΠΎΡΡΡΡ. ΠΠΎ ΡΡΠ°Π²Π½Π΅Π½ΠΈΡ Ρ Π½ΠΈΠ·ΠΊΠΎΡΠ³Π»Π΅ΡΠΎΠ΄ΠΈΡΡΡΠΌΠΈ ΡΡΠ°Π»ΡΠΌΠΈ ΠΎΠ½ ΠΈΠΌΠ΅Π΅Ρ Π½Π΅Π±ΠΎΠ»ΡΡΡΡ ΡΠ΄Π°ΡΠ½ΡΡ Π²ΡΠ·ΠΊΠΎΡΡΡ ΠΈΠ»ΠΈ ΠΏΡΠ°ΠΊΡΠΈΡΠ΅ΡΠΊΠΈ Π½Π΅ ΠΈΠΌΠ΅Π΅Ρ Π΅Π΅. ΠΠ½ ΠΈΠΌΠ΅Π΅Ρ ΡΠ°ΡΡΡ ΠΏΡΠΎΡΠ½ΠΎΡΡΠΈ Π½Π° ΡΠ°ΡΡΡΠΆΠ΅Π½ΠΈΠ΅ Π½ΠΈΠ·ΠΊΠΎΡΠ³Π»Π΅ΡΠΎΠ΄ΠΈΡΡΡΡ
ΡΡΠ°Π»Π΅ΠΉ. ΠΠΎΠ³Π΄Π° ΡΡΠ³ΡΠ½Π½Π°Ρ Π΄Π΅ΡΠ°Π»Ρ Π²ΡΡ
ΠΎΠ΄ΠΈΡ ΠΈΠ· ΡΡΡΠΎΡ, ΠΎΠ½Π° Π½Π΅ Π΄Π΅ΡΠΎΡΠΌΠΈΡΡΠ΅ΡΡΡ Π·Π°ΠΌΠ΅ΡΠ½ΡΠΌ ΠΎΠ±ΡΠ°Π·ΠΎΠΌ ΠΈ ΠΊΠ°ΠΆΠ΅ΡΡΡ, ΡΡΠΎ ΠΎΠ½Π° ΡΠ°ΡΠΊΠ°Π»ΡΠ²Π°Π΅ΡΡΡ ΠΈΠ»ΠΈ Π»ΠΎΠΌΠ°Π΅ΡΡΡ Π² ΠΌΠ°Π½Π΅ΡΠ΅, ΡΠΎΠΎΡΠ²Π΅ΡΡΡΠ²ΡΡΡΠ΅ΠΉ ΡΠ΅Π»ΡΠΊΡ. ΠΠ΅Ρ ΡΠ°Π½Π½Π΅Π³ΠΎ ΠΏΡΠ΅Π΄ΡΠΏΡΠ΅ΠΆΠ΄Π΅Π½ΠΈΡ ΠΎ ΡΠ±ΠΎΠ΅. ΠΡΠ°ΡΠΈΡΠΎΠ²Π°Ρ ΡΠ°Π·Π°, ΠΏΡΠ΅Π΄ΡΡΠ°Π²Π»ΡΡΡΠ°Ρ ΡΠΎΠ±ΠΎΠΉ ΡΠΈΡΡΡΠΉ ΡΠ³Π»Π΅ΡΠΎΠ΄, Π΄Π΅ΠΉΡΡΠ²ΡΠ΅Ρ ΠΊΠ°ΠΊ Π΅ΡΡΠ΅ΡΡΠ²Π΅Π½Π½ΡΠΉ Π΄Π΅ΡΠ΅ΠΊΡ ΠΌΠ°ΡΠ΅ΡΠΈΠ°Π»Π°. ΠΠ΅Π»Π΅Π·ΠΎ Π½Π°ΡΡΠΎΠ»ΡΠΊΠΎ Π½Π°ΡΡΡΠ΅Π½ΠΎ ΡΠ³Π»Π΅ΡΠΎΠ΄ΠΎΠΌ, ΡΡΠΎ ΠΎΠ±ΡΠ°Π·ΡΠ΅ΡΡΡ Π³ΡΠ°ΡΠΈΡ (ΡΠ²ΠΎΠ±ΠΎΠ΄Π½ΡΠΉ ΡΠ³Π»Π΅ΡΠΎΠ΄), ΠΈΠ·-Π·Π° ΡΠ΅Π³ΠΎ ΡΡΠ³ΡΠ½ ΡΡΠ°Π½ΠΎΠ²ΠΈΡΡΡ ΡΠ»Π°Π±Π΅Π΅. ΠΠ½Π°ΡΠΈΡΠ΅Π»ΡΠ½ΠΎ ΠΌΠ΅Π½ΡΡΠ΅Π΅ ΠΊΠΎΠ»ΠΈΡΠ΅ΡΡΠ²ΠΎ ΡΠ³Π»Π΅ΡΠΎΠ΄Π° ΡΠ²ΡΠ·Π°Π½ΠΎ Ρ ΠΆΠ΅Π»Π΅Π·ΠΎΠΌ (Fe) Π² Π²ΠΈΠ΄Π΅ ΠΊΠ°ΡΠ±ΠΈΠ΄Π° ΠΆΠ΅Π»Π΅Π·Π° (Fe3C, ΡΠ΅ΠΌΠ΅Π½ΡΠΈΡ), ΠΊΠΎΡΠΎΡΡΠΉ ΡΠ²Π»ΡΠ΅ΡΡΡ ΡΠ²Π΅ΡΠ΄ΡΠΌ ΠΈ Ρ
ΡΡΠΏΠΊΠΈΠΌ.
ΠΠΎ Π²ΡΠ΅ΠΌΡ ΠΏΡΠΎΡΠ΅ΡΡΠ° Π·Π°ΡΠ²Π΅ΡΠ΄Π΅Π²Π°Π½ΠΈΡ, ΠΊΠΎΠ³Π΄Π° ΠΈΠ΄Π΅Ρ ΠΌΠ΅ΡΠ°ΡΡΠ°Π±ΠΈΠ»ΡΠ½ΡΠΉ ΠΏΡΡΡ, Π±ΠΎΠ³Π°ΡΠ°Ρ ΡΠ³Π»Π΅ΡΠΎΠ΄ΠΎΠΌ ΡΠ°Π·Π° Π² ΡΠ²ΡΠ΅ΠΊΡΠΈΠΊΠ΅ ΠΏΡΠ΅Π΄ΡΡΠ°Π²Π»ΡΠ΅Ρ ΡΠΎΠ±ΠΎΠΉ ΠΊΠ°ΡΠ±ΠΈΠ΄ ΠΆΠ΅Π»Π΅Π·Π°, Π° ΠΊΠΎΠ³Π΄Π° ΠΈΠ΄Π΅Ρ ΡΡΠ°Π±ΠΈΠ»ΡΠ½ΡΠΉ ΠΏΡΡΡ Π·Π°ΡΠ²Π΅ΡΠ΄Π΅Π²Π°Π½ΠΈΡ, Π±ΠΎΠ³Π°ΡΠ°Ρ ΡΠ³Π»Π΅ΡΠΎΠ΄ΠΎΠΌ ΡΠ°Π·Π° ΠΏΡΠ΅Π΄ΡΡΠ°Π²Π»ΡΠ΅Ρ ΡΠΎΠ±ΠΎΠΉ Π³ΡΠ°ΡΠΈΡ. Π§ΡΠΎ ΠΊΠ°ΡΠ°Π΅ΡΡΡ ΡΠΎΠ»ΡΠΊΠΎ Π±ΠΈΠ½Π°ΡΠ½ΠΎΠΉ ΡΠΈΡΡΠ΅ΠΌΡ Fe-Fe3C ΠΈΠ»ΠΈ ΠΆΠ΅Π»Π΅Π·Π°-Π³ΡΠ°ΡΠΈΡΠ°, ΡΡΠ³ΡΠ½ ΠΌΠΎΠΆΠ½ΠΎ ΠΎΠΏΡΠ΅Π΄Π΅Π»ΠΈΡΡ ΠΊΠ°ΠΊ ΡΠΏΠ»Π°Π² ΠΆΠ΅Π»Π΅Π·Π° Ρ ΡΠ³Π»Π΅ΡΠΎΠ΄ΠΎΠΌ Ρ ΡΠΎΠ΄Π΅ΡΠΆΠ°Π½ΠΈΠ΅ΠΌ ΡΠ³Π»Π΅ΡΠΎΠ΄Π° Π±ΠΎΠ»Π΅Π΅ 2 %. ΠΠ΄Π½Π°ΠΊΠΎ ΠΊΡΠ΅ΠΌΠ½ΠΈΠΉ ΠΈ Π΄ΡΡΠ³ΠΈΠ΅ Π»Π΅Π³ΠΈΡΡΡΡΠΈΠ΅ ΡΠ»Π΅ΠΌΠ΅Π½ΡΡ ΠΌΠΎΠ³ΡΡ Π·Π½Π°ΡΠΈΡΠ΅Π»ΡΠ½ΠΎ ΠΈΠ·ΠΌΠ΅Π½ΠΈΡΡ ΠΌΠ°ΠΊΡΠΈΠΌΠ°Π»ΡΠ½ΡΡ ΡΠ°ΡΡΠ²ΠΎΡΠΈΠΌΠΎΡΡΡ ΡΠ³Π»Π΅ΡΠΎΠ΄Π° Π² Π°ΡΡΡΠ΅Π½ΠΈΡΠ΅. ΠΠΎΡΡΠΎΠΌΡ Π² ΠΈΡΠΊΠ»ΡΡΠΈΡΠ΅Π»ΡΠ½ΡΡ
ΡΠ»ΡΡΠ°ΡΡ
Π»Π΅Π³ΠΈΡΠΎΠ²Π°Π½Π½ΡΠΉ ΡΡΠ³ΡΠ½ Ρ ΡΠΎΠ΄Π΅ΡΠΆΠ°Π½ΠΈΠ΅ΠΌ ΡΠ³Π»Π΅ΡΠΎΠ΄Π° ΠΌΠ΅Π½Π΅Π΅ 2 % ΠΌΠΎΠΆΠ΅Ρ Π·Π°ΡΠ²Π΅ΡΠ΄Π΅Π²Π°ΡΡ Ρ ΡΠ²ΡΠ΅ΠΊΡΠΈΡΠ΅ΡΠΊΠΎΠΉ ΡΡΡΡΠΊΡΡΡΠΎΠΉ ΠΈ, ΡΠ»Π΅Π΄ΠΎΠ²Π°ΡΠ΅Π»ΡΠ½ΠΎ, ΠΏΠΎ-ΠΏΡΠ΅ΠΆΠ½Π΅ΠΌΡ ΠΎΡΠ½ΠΎΡΠΈΡΡΡ ΠΊ ΡΠ΅ΠΌΠ΅ΠΉΡΡΠ²Ρ Β«ΡΡΠ³ΡΠ½ΠΎΠ²Β».
ΠΠ±ΡΠ°Π·ΠΎΠ²Π°Π½ΠΈΠ΅ ΡΡΠ°Π±ΠΈΠ»ΡΠ½ΠΎΠΉ ΠΈΠ»ΠΈ ΠΌΠ΅ΡΠ°ΡΡΠ°Π±ΠΈΠ»ΡΠ½ΠΎΠΉ ΡΠ²ΡΠ΅ΠΊΡΠΈΠΊΠΈ Π·Π°Π²ΠΈΡΠΈΡ ΠΎΡ ΠΌΠ½ΠΎΠ³ΠΈΡ ΡΠ°ΠΊΡΠΎΡΠΎΠ², Π²ΠΊΠ»ΡΡΠ°Ρ ΠΏΠΎΡΠ΅Π½ΡΠΈΠ°Π» Π·Π°ΡΠΎΠ΄ΡΡΠ΅ΠΎΠ±ΡΠ°Π·ΠΎΠ²Π°Π½ΠΈΡ ΠΆΠΈΠ΄ΠΊΠΎΡΡΠΈ, Ρ ΠΈΠΌΠΈΡΠ΅ΡΠΊΠΈΠΉ ΡΠΎΡΡΠ°Π² ΠΈ ΡΠΊΠΎΡΠΎΡΡΡ ΠΎΡ Π»Π°ΠΆΠ΄Π΅Π½ΠΈΡ. ΠΠ΅ΡΠ²ΡΠ΅ Π΄Π²Π° ΡΠ°ΠΊΡΠΎΡΠ° ΠΊΠΎΠ½ΡΡΠΎΠ»ΠΈΡΡΡΡ ΠΏΠΎΡΠ΅Π½ΡΠΈΠ°Π» Π³ΡΠ°ΡΠΈΡΠΈΠ·Π°ΡΠΈΠΈ ΠΆΠ΅Π»Π΅Π·Π°. ΠΡΡΠΎΠΊΠΈΠΉ ΠΏΠΎΡΠ΅Π½ΡΠΈΠ°Π» Π³ΡΠ°ΡΠΈΡΠΈΠ·Π°ΡΠΈΠΈ ΠΏΡΠΈΠ²ΠΎΠ΄ΠΈΡ ΠΊ ΠΏΠΎΠ»ΡΡΠ΅Π½ΠΈΡ ΡΡΠ³ΡΠ½ΠΎΠ² Ρ Π³ΡΠ°ΡΠΈΡΠΎΠΌ Π² ΠΊΠ°ΡΠ΅ΡΡΠ²Π΅ Π±ΠΎΠ³Π°ΡΠΎΠΉ ΡΠ³Π»Π΅ΡΠΎΠ΄Π½ΠΎΠΉ ΡΠ°Π·Ρ, ΡΠΎΠ³Π΄Π° ΠΊΠ°ΠΊ Π½ΠΈΠ·ΠΊΠΈΠΉ ΠΏΠΎΡΠ΅Π½ΡΠΈΠ°Π» Π³ΡΠ°ΡΠΈΡΠΈΠ·Π°ΡΠΈΠΈ ΠΏΡΠΈΠ²ΠΎΠ΄ΠΈΡ ΠΊ ΠΏΠΎΠ»ΡΡΠ΅Π½ΠΈΡ ΡΡΠ³ΡΠ½ΠΎΠ² Ρ ΠΊΠ°ΡΠ±ΠΈΠ΄ΠΎΠΌ ΠΆΠ΅Π»Π΅Π·Π°.
ΠΠ²Π° ΠΎΡΠ½ΠΎΠ²Π½ΡΡ
ΡΠΈΠΏΠ° ΡΠ²ΡΠ΅ΠΊΡΠΈΠΊΠΈ, ΡΡΠ°Π±ΠΈΠ»ΡΠ½ΡΠΉ Π°ΡΡΡΠ΅Π½ΠΈΡ-Π³ΡΠ°ΡΠΈΡ ΠΈ ΠΌΠ΅ΡΠ°ΡΡΠ°Π±ΠΈΠ»ΡΠ½ΡΠΉ Π°ΡΡΡΠ΅Π½ΠΈΡ-ΠΊΠ°ΡΠ±ΠΈΠ΄ ΠΆΠ΅Π»Π΅Π·Π°, ΠΈΠΌΠ΅ΡΡ Π±ΠΎΠ»ΡΡΠΈΠ΅ ΡΠ°Π·Π»ΠΈΡΠΈΡ Π² ΡΠ²ΠΎΠΈΡ
ΠΌΠ΅Ρ
Π°Π½ΠΈΡΠ΅ΡΠΊΠΈΡ
ΡΠ²ΠΎΠΉΡΡΠ²Π°Ρ
, ΡΠ°ΠΊΠΈΡ
ΠΊΠ°ΠΊ ΠΏΡΠΎΡΠ½ΠΎΡΡΡ, ΡΠ²Π΅ΡΠ΄ΠΎΡΡΡ, ΡΠ΄Π°ΡΠ½Π°Ρ Π²ΡΠ·ΠΊΠΎΡΡΡ ΠΈ ΠΏΠ»Π°ΡΡΠΈΡΠ½ΠΎΡΡΡ. ΠΠΎΡΡΠΎΠΌΡ ΠΎΡΠ½ΠΎΠ²Π½ΠΎΠΉ ΡΠ΅Π»ΡΡ ΠΌΠ΅ΡΠ°Π»Π»ΡΡΠ³ΠΈΡΠ΅ΡΠΊΠΎΠΉ ΠΎΠ±ΡΠ°Π±ΠΎΡΠΊΠΈ ΡΡΠ³ΡΠ½Π° ΡΠ²Π»ΡΠ΅ΡΡΡ Π²Π»ΠΈΡΠ½ΠΈΠ΅ Π½Π° ΡΠΈΠΏ, ΠΊΠΎΠ»ΠΈΡΠ΅ΡΡΠ²ΠΎ ΠΈ ΠΌΠΎΡΡΠΎΠ»ΠΎΠ³ΠΈΡ ΡΠ²ΡΠ΅ΠΊΡΠΈΠΊΠΈ Π΄Π»Ρ Π΄ΠΎΡΡΠΈΠΆΠ΅Π½ΠΈΡ ΠΆΠ΅Π»Π°Π΅ΠΌΡΡ
ΠΌΠ΅Ρ
Π°Π½ΠΈΡΠ΅ΡΠΊΠΈΡ
ΡΠ²ΠΎΠΉΡΡΠ².
Π‘Π²ΠΎΠΉΡΡΠ²Π° ΡΡΠ³ΡΠ½Π° ΠΌΠΎΠΆΠ½ΠΎ ΡΠΈΡΠΎΠΊΠΎ Π²Π°ΡΡΠΈΡΠΎΠ²Π°ΡΡ ΠΏΡΡΠ΅ΠΌ ΠΈΠ·ΠΌΠ΅Π½Π΅Π½ΠΈΡ ΠΏΡΠΎΡΠ΅Π½ΡΠ½ΠΎΠ³ΠΎ ΡΠΎΠ΄Π΅ΡΠΆΠ°Π½ΠΈΡ ΡΠ³Π»Π΅ΡΠΎΠ΄Π° ΠΈ ΠΊΡΠ΅ΠΌΠ½ΠΈΡ, ΠΏΡΡΠ΅ΠΌ Π»Π΅Π³ΠΈΡΠΎΠ²Π°Π½ΠΈΡ ΡΠ°Π·Π»ΠΈΡΠ½ΡΠΌΠΈ ΠΌΠ΅ΡΠ°Π»Π»ΠΈΡΠ΅ΡΠΊΠΈΠΌΠΈ ΡΠ»Π΅ΠΌΠ΅Π½ΡΠ°ΠΌΠΈ ΠΈ ΠΏΡΡΠ΅ΠΌ ΠΈΠ·ΠΌΠ΅Π½Π΅Π½ΠΈΡ ΠΌΠ΅ΡΠΎΠ΄ΠΎΠ² ΠΏΠ»Π°Π²ΠΊΠΈ, Π»ΠΈΡΡΡ ΠΈ ΡΠ΅ΡΠΌΠΈΡΠ΅ΡΠΊΠΎΠΉ ΠΎΠ±ΡΠ°Π±ΠΎΡΠΊΠΈ.
ΠΠ΅ΡΠ°Π»Π»ΡΡΠ³ΠΈΡ ΡΡΠ³ΡΠ½Π° Π²ΠΎ ΠΌΠ½ΠΎΠ³ΠΎΠΌ ΠΏΠΎΡ ΠΎΠΆΠ° Π½Π° ΠΌΠ΅ΡΠ°Π»Π»ΡΡΠ³ΠΈΡ ΡΡΠ°Π»ΠΈ, Π½ΠΎ ΡΠ°Π·Π»ΠΈΡΠΈΡ Π²Π°ΠΆΠ½Ρ Π΄Π»Ρ ΠΌΠ΅ΡΠ°Π»Π»ΡΡΠ³Π°, ΡΠ°Π±ΠΎΡΠ°ΡΡΠ΅Π³ΠΎ Ρ ΡΡΠ³ΡΠ½ΠΎΠΌ. ΠΠΎΡΠΊΠΎΠ»ΡΠΊΡ ΠΎΠ±ΡΡΠ½ΡΠ΅ ΠΌΠ°ΡΠΊΠΈ ΡΡΠ°Π»ΠΈ ΡΠΎΠ΄Π΅ΡΠΆΠ°Ρ Π½Π΅Π±ΠΎΠ»ΡΡΠΎΠ΅ ΠΊΠΎΠ»ΠΈΡΠ΅ΡΡΠ²ΠΎ Π»Π΅Π³ΠΈΡΡΡΡΠΈΡ ΡΠ»Π΅ΠΌΠ΅Π½ΡΠΎΠ², ΠΈΡ ΠΎΠ±ΡΡΠ½ΠΎ ΡΠ°ΡΡΠΌΠ°ΡΡΠΈΠ²Π°ΡΡ ΠΊΠ°ΠΊ Π±ΠΈΠ½Π°ΡΠ½ΡΠ΅ ΠΆΠ΅Π»Π΅Π·ΠΎ-ΡΠ³Π»Π΅ΡΠΎΠ΄Π½ΡΠ΅ ΡΠΏΠ»Π°Π²Ρ, Π° Π΄ΠΈΠ°Π³ΡΠ°ΠΌΠΌΡ ΠΆΠ΅Π»Π΅Π·ΠΎ-ΡΠ³Π»Π΅ΡΠΎΠ΄ (ΡΠΈΡ. 1) ΠΌΠΎΠΆΠ½ΠΎ ΠΈΡΠΏΠΎΠ»ΡΠ·ΠΎΠ²Π°ΡΡ Π΄Π»Ρ ΠΈΠ½ΡΠ΅ΡΠΏΡΠ΅ΡΠ°ΡΠΈΠΈ ΠΈΡ ΡΡΡΡΠΊΡΡΡΡ Π² ΡΡΠ»ΠΎΠ²ΠΈΡΡ ΠΌΠ΅Π΄Π»Π΅Π½Π½ΠΎΠ³ΠΎ ΠΈΠ»ΠΈ Π±Π»ΠΈΠ·ΠΊΠΎΠ³ΠΎ ΠΊ ΡΠ°Π²Π½ΠΎΠ²Π΅ΡΠΈΡ ΡΡΠ°Π½ΡΡΠΎΡΠΌΠ°ΡΠΈΡ.
Π ΠΈΡ. 1 ΠΠΈΠ°Π³ΡΠ°ΠΌΠΌΠ° ΡΠ³Π»Π΅ΡΠΎΠ΄Π° ΠΆΠ΅Π»Π΅Π·Π°
Π§ΡΠ³ΡΠ½Ρ, ΠΎΠ΄Π½Π°ΠΊΠΎ, ΡΠΎΠ΄Π΅ΡΠΆΠ°Ρ Π·Π½Π°ΡΠΈΡΠ΅Π»ΡΠ½ΠΎΠ΅ ΠΊΠΎΠ»ΠΈΡΠ΅ΡΡΠ²ΠΎ ΠΊΡΠ΅ΠΌΠ½ΠΈΡ Π² Π΄ΠΎΠΏΠΎΠ»Π½Π΅Π½ΠΈΠ΅ ΠΊ Π±ΠΎΠ»Π΅Π΅ Π²ΡΡΠΎΠΊΠΎΠΌΡ ΡΠΎΠ΄Π΅ΡΠΆΠ°Π½ΠΈΡ ΡΠ³Π»Π΅ΡΠΎΠ΄Π°, ΠΏΠΎΡΡΠΎΠΌΡ ΠΈΡ
ΡΠ»Π΅Π΄ΡΠ΅Ρ ΡΠ°ΡΡΠΌΠ°ΡΡΠΈΠ²Π°ΡΡ ΠΊΠ°ΠΊ ΡΡΠΎΠΉΠ½ΡΠ΅ ΡΠΏΠ»Π°Π²Ρ Fe-C-Si. ΠΠΎΠΏΠΎΠ»Π½ΠΈΡΠ΅Π»ΡΠ½ΡΠΉ ΡΠΎΡΡΠ°Π²Π»ΡΡΡΠΈΠΉ ΠΊΡΠ΅ΠΌΠ½ΠΈΠΉ ΠΈΠ·ΠΌΠ΅Π½ΡΠ΅Ρ Π΄ΠΈΠ°Π³ΡΠ°ΠΌΠΌΡ ΠΆΠ΅Π»Π΅Π·ΠΎ-ΡΠ³Π»Π΅ΡΠΎΠ΄. Π Π°Π·ΡΠ΅Π· ΡΡΠΎΠΉΠ½ΠΎΠΉ Π΄ΠΈΠ°Π³ΡΠ°ΠΌΠΌΡ Fe-Fe3C-Si ΠΏΡΠΈ 2 % ΠΊΡΠ΅ΠΌΠ½ΠΈΡ (ΡΡΠΎ ΠΏΡΠΈΠΌΠ΅ΡΠ½ΠΎ ΡΠΎΠΎΡΠ²Π΅ΡΡΡΠ²ΡΠ΅Ρ ΡΠΎΠ΄Π΅ΡΠΆΠ°Π½ΠΈΡ ΠΊΡΠ΅ΠΌΠ½ΠΈΡ Π²ΠΎ ΠΌΠ½ΠΎΠ³ΠΈΡ
ΡΡΠ³ΡΠ½Π°Ρ
) Π΄Π°Π΅Ρ ΡΠ΄ΠΎΠ±Π½ΡΡ ΡΡΡΠ»ΠΊΡ Π΄Π»Ρ ΠΎΠ±ΡΡΠΆΠ΄Π΅Π½ΠΈΡ ΠΌΠ΅ΡΠ°Π»Π»ΡΡΠ³ΠΈΠΈ ΡΡΠ³ΡΠ½Π° (ΡΠΈΡ. 2). ΠΠΈΠ°Π³ΡΠ°ΠΌΠΌΠ° Π½Π°ΠΏΠΎΠΌΠΈΠ½Π°Π΅Ρ Π±ΠΈΠ½Π°ΡΠ½ΡΡ Π΄ΠΈΠ°Π³ΡΠ°ΠΌΠΌΡ Fe-Fe3C, Π½ΠΎ ΠΏΠΎΠΊΠ°Π·ΡΠ²Π°Π΅Ρ Π²Π°ΠΆΠ½ΡΠ΅ ΠΎΡΠ»ΠΈΡΠΈΡ, Ρ
Π°ΡΠ°ΠΊΡΠ΅ΡΠ½ΡΠ΅ Π΄Π»Ρ ΡΡΠΎΠΉΠ½ΡΡ
ΡΠΈΡΡΠ΅ΠΌ. ΠΠ²ΡΠ΅ΠΊΡΠΈΡΠ΅ΡΠΊΠΈΠ΅ ΠΈ ΡΠ²ΡΠ΅ΠΊΡΠΎΠΈΠ΄Π½ΡΠ΅ ΡΠ΅ΠΌΠΏΠ΅ΡΠ°ΡΡΡΡ ΠΈΠ·ΠΌΠ΅Π½ΡΡΡΡΡ ΠΎΡ Π΅Π΄ΠΈΠ½ΠΈΡΠ½ΡΡ
Π·Π½Π°ΡΠ΅Π½ΠΈΠΉ Π² ΡΠΈΡΡΠ΅ΠΌΠ΅ Fe-Fe3C Π΄ΠΎ Π΄ΠΈΠ°ΠΏΠ°Π·ΠΎΠ½ΠΎΠ² ΡΠ΅ΠΌΠΏΠ΅ΡΠ°ΡΡΡ Π² ΡΠΈΡΡΠ΅ΠΌΠ΅ Fe-Fe3C-Si. ΠΠ²ΡΠ΅ΠΊΡΠΈΡΠ΅ΡΠΊΠ°Ρ ΠΈ ΡΠ²ΡΠ΅ΠΊΡΠΎΠΈΠ΄Π½Π°Ρ ΡΠΎΡΠΊΠΈ ΡΠΌΠ΅ΡΠ°ΡΡΡΡ Π² ΡΡΠΎΡΠΎΠ½Ρ ΠΌΠ΅Π½ΡΡΠ΅Π³ΠΎ ΡΠΎΠ΄Π΅ΡΠΆΠ°Π½ΠΈΡ ΡΠ³Π»Π΅ΡΠΎΠ΄Π°. ΠΠ½ ΡΠ°ΠΊΠΆΠ΅ ΠΏΡΠ΅Π΄ΡΡΠ°Π²Π»ΡΠ΅Ρ ΠΌΠ΅ΡΠ°ΡΡΠ°Π±ΠΈΠ»ΡΠ½ΠΎΠ΅ ΡΠ°Π²Π½ΠΎΠ²Π΅ΡΠΈΠ΅ ΠΌΠ΅ΠΆΠ΄Ρ ΠΆΠ΅Π»Π΅Π·ΠΎΠΌ ΠΈ ΠΊΠ°ΡΠ±ΠΈΠ΄ΠΎΠΌ ΠΆΠ΅Π»Π΅Π·Π° (ΡΠ΅ΠΌΠ΅Π½ΡΠΈΡΠΎΠΌ), ΠΌΠ΅ΡΠ°ΡΡΠ°Π±ΠΈΠ»ΡΠ½ΡΡ ΡΠΈΡΡΠ΅ΠΌΡ. ΠΡΠΈΡΡΡΡΡΠ²ΡΡΡΠΈΠΉ ΠΊΡΠ΅ΠΌΠ½ΠΈΠΉ ΠΎΡΡΠ°Π΅ΡΡΡ Π² ΡΠ²Π΅ΡΠ΄ΠΎΠΌ ΡΠ°ΡΡΠ²ΠΎΡΠ΅ Π² ΠΆΠ΅Π»Π΅Π·Π΅, ΠΊΠ°ΠΊ Π² ΡΠ΅ΡΡΠΈΡΠ΅, ΡΠ°ΠΊ ΠΈ Π² Π°ΡΡΡΠ΅Π½ΠΈΡΠ΅, ΠΏΠΎΡΡΠΎΠΌΡ ΠΎΠ½ Π²Π»ΠΈΡΠ΅Ρ ΡΠΎΠ»ΡΠΊΠΎ Π½Π° ΡΡΠ»ΠΎΠ²ΠΈΡ ΠΈ ΠΊΠΈΠ½Π΅ΡΠΈΠΊΡ ΠΊΠ°ΡΠ±ΠΈΠ΄ΠΎΠΎΠ±ΡΠ°Π·ΠΎΠ²Π°Π½ΠΈΡ ΠΏΡΠΈ ΠΎΡ
Π»Π°ΠΆΠ΄Π΅Π½ΠΈΠΈ, Π° Π½Π΅ Π½Π° ΡΠΎΡΡΠ°Π² ΠΊΠ°ΡΠ±ΠΈΠ΄Π½ΠΎΠΉ ΡΠ°Π·Ρ.
Π ΠΈΡ. 2 Π‘Π΅ΡΠ΅Π½ΠΈΠ΅ ΡΡΠ΅Ρ ΠΊΠΎΠΌΠΏΠΎΠ½Π΅Π½ΡΠ½ΠΎΠΉ Π΄ΠΈΠ°Π³ΡΠ°ΠΌΠΌΡ Fe-Fe3C-Si ΠΏΡΠΈ 2 % ΠΊΡΠ΅ΠΌΠ½ΠΈΡ
ΠΠ΅ΠΊΠΎΡΠΎΡΠΎΠ΅ ΠΊΠΎΠ»ΠΈΡΠ΅ΡΡΠ²ΠΎ ΠΊΡΠ΅ΠΌΠ½ΠΈΡ ΠΌΠΎΠΆΠ΅Ρ Π²ΡΠ΄Π΅Π»ΡΡΡΡΡ Π²ΠΌΠ΅ΡΡΠ΅ Ρ ΠΊΠ°ΡΠ±ΠΈΠ΄ΠΎΠΌ, Π½ΠΎ Π΅Π³ΠΎ Π½Π΅Π»ΡΠ·Ρ Π²ΡΠ΄Π΅Π»ΠΈΡΡ ΠΊΠ°ΠΊ Π΄ΡΡΠ³ΡΡ ΡΠ°Π·Ρ. ΠΠ°ΡΠ²Π΅ΡΠ΄Π΅Π²Π°Π½ΠΈΠ΅ Π½Π΅ΠΊΠΎΡΠΎΡΡΡ
ΠΊΠΎΠΌΠΏΠΎΠ·ΠΈΡΠΈΠΉ ΠΏΡΠΎΠΈΡΡ
ΠΎΠ΄ΠΈΡ Π½Π΅ Π² ΠΌΠ΅ΡΠ°ΡΡΠ°Π±ΠΈΠ»ΡΠ½ΠΎΠΉ ΡΠΈΡΡΠ΅ΠΌΠ΅, Π° Π² ΡΡΠ°Π±ΠΈΠ»ΡΠ½ΠΎΠΉ, Π³Π΄Π΅ ΠΏΡΠΎΠ΄ΡΠΊΡΠ°ΠΌΠΈ ΡΠ²Π»ΡΡΡΡΡ ΠΆΠ΅Π»Π΅Π·ΠΎ ΠΈ Π³ΡΠ°ΡΠΈΡ, Π° Π½Π΅ ΠΆΠ΅Π»Π΅Π·ΠΎ ΠΈ ΠΊΠ°ΡΠ±ΠΈΠ΄. ΠΠΎΡΠΎΡΠ΅ Π³ΠΎΠ²ΠΎΡΡ, Π΄ΠΎΠ±Π°Π²Π»Π΅Π½ΠΈΠ΅ ΠΊΡΠ΅ΠΌΠ½ΠΈΡ ΠΊ Π±ΠΈΠ½Π°ΡΠ½ΠΎΠΌΡ ΠΆΠ΅Π»Π΅Π·ΠΎ-ΡΠ³Π»Π΅ΡΠΎΠ΄Π½ΠΎΠΌΡ ΡΠΏΠ»Π°Π²Ρ ΡΠ½ΠΈΠΆΠ°Π΅Ρ ΡΡΠ°Π±ΠΈΠ»ΡΠ½ΠΎΡΡΡ Fe3C, ΠΊΠΎΡΠΎΡΡΠΉ ΡΠΆΠ΅ ΡΠ²Π»ΡΠ΅ΡΡΡ ΠΌΠ΅ΡΠ°ΡΡΠ°Π±ΠΈΠ»ΡΠ½ΡΠΌ, ΠΈ ΡΠ²Π΅Π»ΠΈΡΠΈΠ²Π°Π΅Ρ ΡΡΠ°Π±ΠΈΠ»ΡΠ½ΠΎΡΡΡ ΡΠ΅ΡΡΠΈΡΠ°. Π‘ ΡΠ²Π΅Π»ΠΈΡΠ΅Π½ΠΈΠ΅ΠΌ ΡΠΎΠ΄Π΅ΡΠΆΠ°Π½ΠΈΡ ΠΊΡΠ΅ΠΌΠ½ΠΈΡ Π² ΡΠΈΡΡΠ΅ΠΌΠ΅ Fe-C-Si ΡΠΎΠ΄Π΅ΡΠΆΠ°Π½ΠΈΠ΅ ΡΠ³Π»Π΅ΡΠΎΠ΄Π° Π² ΡΠ²ΡΠ΅ΠΊΡΠΈΠΊΠ΅ ΠΈ ΡΠ²ΡΠ΅ΠΊΡΠΎΠΈΠ΄Π΅ ΡΠΌΠ΅Π½ΡΡΠ°Π΅ΡΡΡ, Π° ΡΠ΅ΠΌΠΏΠ΅ΡΠ°ΡΡΡΠ° ΡΠ²ΡΠ΅ΠΊΡΠΈΠΊΠΈ ΠΈ ΡΠ²ΡΠ΅ΠΊΡΠΎΠΈΠ΄Π° ΡΠ²Π΅Π»ΠΈΡΠΈΠ²Π°Π΅ΡΡΡ.
Π£Π΄ΠΎΠ±Π½ΠΎ ΠΎΠ±ΡΠ΅Π΄ΠΈΠ½ΠΈΡΡ Π²Π»ΠΈΡΠ½ΠΈΠ΅ ΠΊΡΠ΅ΠΌΠ½ΠΈΡ Ρ Π΄Π΅ΠΉΡΡΠ²ΠΈΠ΅ΠΌ ΡΠ³Π»Π΅ΡΠΎΠ΄Π° Π² ΠΎΠ΄ΠΈΠ½ ΠΊΠΎΡΡΡΠΈΡΠΈΠ΅Π½Ρ, ΠΊΠΎΡΠΎΡΡΠΉ Π½Π°Π·ΡΠ²Π°Π΅ΡΡΡ ΡΠ³Π»Π΅ΡΠΎΠ΄Π½ΡΠΌ ΡΠΊΠ²ΠΈΠ²Π°Π»Π΅Π½ΡΠΎΠΌ (Π£Π). CE ΡΡΠ³ΡΠ½Π° ΠΎΠΏΠΈΡΡΠ²Π°Π΅Ρ, Π½Π°ΡΠΊΠΎΠ»ΡΠΊΠΎ Π΄Π°Π½Π½ΡΠΉ Π°Π½Π°Π»ΠΈΠ· Π±Π»ΠΈΠ·ΠΎΠΊ ΠΊ ΡΠ²ΡΠ΅ΠΊΡΠΈΡΠ΅ΡΠΊΠΎΠΌΡ ΡΠΎΡΡΠ°Π²Ρ. ΠΠ ΡΠ²ΡΠ΅ΠΊΡΠΈΠΊΠΈ Π±Π΅Π· ΠΊΡΠ΅ΠΌΠ½ΠΈΡ ΡΠΎΡΡΠ°Π²Π»ΡΠ΅Ρ 4,3 %. ΠΠΎ ΠΌΠ΅ΡΠ΅ ΡΠ²Π΅Π»ΠΈΡΠ΅Π½ΠΈΡ ΡΠΎΠ΄Π΅ΡΠΆΠ°Π½ΠΈΡ ΠΊΡΠ΅ΠΌΠ½ΠΈΡ Π² ΠΆΠ΅Π»Π΅Π·Π΅ ΡΠΎΠ΄Π΅ΡΠΆΠ°Π½ΠΈΠ΅ ΡΠ³Π»Π΅ΡΠΎΠ΄Π° Π² ΡΠ²ΡΠ΅ΠΊΡΠΈΠΊΠ΅ ΡΠΌΠ΅Π½ΡΡΠ°Π΅ΡΡΡ. Π‘ΡΡΠ΅ΡΡΠ²ΡΠ΅Ρ Π»ΠΈΠ½Π΅ΠΉΠ½Π°Ρ Π·Π°Π²ΠΈΡΠΈΠΌΠΎΡΡΡ, ΠΊΠΎΡΠΎΡΡΡ ΠΌΠΎΠΆΠ½ΠΎ Π²ΡΡΠ°Π·ΠΈΡΡ Π² Π²ΠΈΠ΄Π΅ ΠΏΡΠΎΡΡΠΎΠ³ΠΎ ΡΡΠ°Π²Π½Π΅Π½ΠΈΡ, ΠΏΡΠΈΠ²Π΅Π΄Π΅Π½Π½ΠΎΠ³ΠΎ Π½ΠΈΠΆΠ΅.
CE = % C+ 1/3 % Si = 4,3 (ΠΏΡΠΈ 0 % ΠΊΡΠ΅ΠΌΠ½ΠΈΡ)
CE 3,9 ΠΏΡΠ΅Π΄ΡΡΠ°Π²Π»ΡΠ΅Ρ ΡΠΎΠ±ΠΎΠΉ ΡΠΏΠ»Π°Π² Ρ Π±ΠΎΠ»Π΅Π΅ Π½ΠΈΠ·ΠΊΠΈΠΌ ΡΠΎΠ΄Π΅ΡΠΆΠ°Π½ΠΈΠ΅ΠΌ ΡΠ³Π»Π΅ΡΠΎΠ΄Π° ΠΈ ΠΊΡΠ΅ΠΌΠ½ΠΈΡ (Π³ΠΈΠΏΠΎΡΠ²ΡΠ΅ΠΊΡΠΈΡΠ΅ΡΠΊΠΈΠΉ), ΡΠ΅ΠΌ ΡΠ²ΡΠ΅ΠΊΡΠΈΡΠ΅ΡΠΊΠΈΠΉ ΡΠΎΡΡΠ°Π², Π° CE 4,6 ΠΏΡΠ΅Π΄ΡΡΠ°Π²Π»ΡΠ΅Ρ ΡΠΎΠ±ΠΎΠΉ ΡΠΏΠ»Π°Π² Ρ Π±ΠΎΠ»Π΅Π΅ Π²ΡΡΠΎΠΊΠΈΠΌ ΡΠΎΠ΄Π΅ΡΠΆΠ°Π½ΠΈΠ΅ΠΌ ΡΠ³Π»Π΅ΡΠΎΠ΄Π° ΠΈ ΠΊΡΠ΅ΠΌΠ½ΠΈΡ (Π³ΠΈΠΏΠ΅ΡΠ΅ΡΠ²ΡΠ΅ΠΊΡΠΈΡΠ΅ΡΠΊΠΈΠΉ), ΡΠ΅ΠΌ ΡΠ²ΡΠ΅ΠΊΡΠΈΡΠ΅ΡΠΊΠΈΠΉ ΡΠΎΡΡΠ°Π². Π£ΡΡΠ³ΠΈ Ρ ΠΎΠ΄ΠΈΠ½Π°ΠΊΠΎΠ²ΡΠΌ Π·Π½Π°ΡΠ΅Π½ΠΈΠ΅ΠΌ CE ΠΌΠΎΠ³ΡΡ Π±ΡΡΡ ΠΏΠΎΠ»ΡΡΠ΅Π½Ρ Ρ ΡΠ°Π·Π½ΡΠΌΠΈ Π·Π½Π°ΡΠ΅Π½ΠΈΡΠΌΠΈ ΡΠΎΠ΄Π΅ΡΠΆΠ°Π½ΠΈΡ ΡΠ³Π»Π΅ΡΠΎΠ΄Π° ΠΈ ΠΊΡΠ΅ΠΌΠ½ΠΈΡ.
Π’Π°ΠΊΠΆΠ΅ Π±ΡΠ»ΠΈ ΠΏΡΠ΅Π΄Π»ΠΎΠΆΠ΅Π½Ρ Π΄ΡΡΠ³ΠΈΠ΅ Π·Π½Π°ΡΠ΅Π½ΠΈΡ, ΠΏΡΠ΅Π΄ΡΡΠ°Π²Π»ΡΡΡΠΈΠ΅ Π‘Π ΡΡΠ³ΡΠ½ΠΎΠ². ΠΠΎΠ³Π΄Π° Π² ΠΆΠ΅Π»Π΅Π·Π΅ ΠΏΡΠΈΡΡΡΡΡΠ²ΡΠ΅Ρ Π·Π½Π°ΡΠΈΡΠ΅Π»ΡΠ½ΠΎΠ΅ ΠΊΠΎΠ»ΠΈΡΠ΅ΡΡΠ²ΠΎ ΡΠΎΡΡΠΎΡΠ°, ΡΠΎΠ΄Π΅ΡΠΆΠ°Π½ΠΈΠ΅ ΡΠΎΡΡΠΎΡΠ° Π² ΠΆΠ΅Π»Π΅Π·Π΅ Π²ΠΊΠ»ΡΡΠ°Π΅ΡΡΡ Π² ΡΡΠ°Π²Π½Π΅Π½ΠΈΠ΅ CE, ΠΊΠΎΡΠΎΡΠΎΠ΅ Π²ΡΠ³Π»ΡΠ΄ΠΈΡ ΡΠ»Π΅Π΄ΡΡΡΠΈΠΌ ΠΎΠ±ΡΠ°Π·ΠΎΠΌ.
CE = % C+ (% Si+% P)/3
Π’Π°ΠΊΠΈΠΌ ΠΎΠ±ΡΠ°Π·ΠΎΠΌ, ΠΆΠ΅Π»Π΅Π·ΠΎ Ρ 3,2 % C, 2 % Si ΠΈ 0,4 % P ΠΈΠΌΠ΅Π΅Ρ Π·Π½Π°ΡΠ΅Π½ΠΈΠ΅ CE 4,0 ΠΈ ΡΠ²Π»ΡΠ΅ΡΡΡ Π΄ΠΎΡΠ²ΡΠ΅ΠΊΡΠΈΡΠ΅ΡΠΊΠΈΠΌ. ΠΠ΅Π»Π΅Π·ΠΎ Ρ 3,2 % C, 2 % Si ΠΈ 1,3 % P ΠΈΠΌΠ΅Π΅Ρ Π·Π½Π°ΡΠ΅Π½ΠΈΠ΅ CE 4,3 ΠΈ ΡΠ²Π»ΡΠ΅ΡΡΡ ΡΠ²ΡΠ΅ΠΊΡΠΈΡΠ΅ΡΠΊΠΈΠΌ. ΠΠ΅Π»Π΅Π·ΠΎ Ρ 3,2 % C, 2,6 % Si ΠΈ 1,3 % P ΠΈΠΌΠ΅Π΅Ρ Π·Π½Π°ΡΠ΅Π½ΠΈΠ΅ CE 4,5 ΠΈ ΡΠ²Π»ΡΠ΅ΡΡΡ Π·Π°ΡΠ²ΡΠ΅ΠΊΡΠΈΡΠ΅ΡΠΊΠΈΠΌ. ΠΠ±ΡΠ΅Π΅ ΡΠΎΠ΄Π΅ΡΠΆΠ°Π½ΠΈΠ΅ ΡΠ³Π»Π΅ΡΠΎΠ΄Π° ΠΈ ΠΊΡΠ΅ΠΌΠ½ΠΈΡ Π² ΡΠΏΠ»Π°Π²Π΅, ΡΠ²ΡΠ·Π°Π½Π½ΠΎΠ΅ ΡΠΎ Π·Π½Π°ΡΠ΅Π½ΠΈΠ΅ΠΌ CE, Π½Π΅ ΡΠΎΠ»ΡΠΊΠΎ ΠΎΠΏΡΠ΅Π΄Π΅Π»ΡΠ΅Ρ Π΄ΠΈΠ°ΠΏΠ°Π·ΠΎΠ½ ΡΠ΅ΠΌΠΏΠ΅ΡΠ°ΡΡΡ Π·Π°ΡΠ²Π΅ΡΠ΄Π΅Π²Π°Π½ΠΈΡ ΡΠΏΠ»Π°Π²Π°, Π½ΠΎ ΡΠ°ΠΊΠΆΠ΅ ΡΠ²ΡΠ·Π°Π½ΠΎ Ρ Π»ΠΈΡΠ΅ΠΉΠ½ΡΠΌΠΈ Ρ
Π°ΡΠ°ΠΊΡΠ΅ΡΠΈΡΡΠΈΠΊΠ°ΠΌΠΈ ΡΠΏΠ»Π°Π²Π° ΠΈ Π΅Π³ΠΎ ΡΠ²ΠΎΠΉΡΡΠ²Π°ΠΌΠΈ. Π§ΡΠ³ΡΠ½Ρ Ρ ΠΏΠΎΡΡΠΎΡΠ½Π½ΡΠΌ ΠΠ, Π½ΠΎ Ρ Π·Π°ΠΌΠ΅ΡΠ½ΠΎ ΡΠ°Π·Π½ΡΠΌ ΡΠΎΠ΄Π΅ΡΠΆΠ°Π½ΠΈΠ΅ΠΌ ΡΠ³Π»Π΅ΡΠΎΠ΄Π° ΠΈ ΠΊΡΠ΅ΠΌΠ½ΠΈΡ, Π½Π΅ ΠΎΠ±Π»Π°Π΄Π°ΡΡ ΠΎΠ΄ΠΈΠ½Π°ΠΊΠΎΠ²ΡΠΌΠΈ Π»ΠΈΡΠ΅ΠΉΠ½ΡΠΌΠΈ ΡΠ²ΠΎΠΉΡΡΠ²Π°ΠΌΠΈ. Π£Π³Π»Π΅ΡΠΎΠ΄ Π±ΠΎΠ»Π΅Π΅ ΡΠ΅ΠΌ Π² Π΄Π²Π° ΡΠ°Π·Π° Π±ΠΎΠ»Π΅Π΅ ΡΡΡΠ΅ΠΊΡΠΈΠ²Π΅Π½ Π² ΠΏΡΠ΅Π΄ΠΎΡΠ²ΡΠ°ΡΠ΅Π½ΠΈΠΈ ΡΡΠ°Π΄ΠΊΠΈ ΠΏΡΠΈ Π·Π°ΡΠ²Π΅ΡΠ΄Π΅Π²Π°Π½ΠΈΠΈ, ΡΠ΅ΠΌ ΠΏΠΎΠΊΠ°Π·ΡΠ²Π°Π΅Ρ ΡΡΠ°Π²Π½Π΅Π½ΠΈΠ΅ CE. ΠΠ΄Π½Π°ΠΊΠΎ ΠΊΡΠ΅ΠΌΠ½ΠΈΠΉ Π±ΠΎΠ»Π΅Π΅ ΡΡΡΠ΅ΠΊΡΠΈΠ²Π΅Π½ Π² ΠΏΡΠ΅Π΄ΠΎΡΠ²ΡΠ°ΡΠ΅Π½ΠΈΠΈ Π·Π°ΡΠ²Π΅ΡΠ΄Π΅Π²Π°Π½ΠΈΡ ΡΠΎΠ½ΠΊΠΈΡ
ΡΡΠ΅Π·ΠΎΠ². Π‘ΡΡΠ΅ΡΡΠ²ΡΡΡ Π°Π½Π°Π»ΠΎΠ³ΠΈΡΠ½ΡΠ΅ ΡΠ°Π·Π»ΠΈΡΠΈΡ Π² Π½Π΅ΠΊΠΎΡΠΎΡΡΡ
ΡΠ²ΠΎΠΉΡΡΠ²Π°Ρ
ΠΈΡΠΏΠΎΠ»ΡΠ·ΠΎΠ²Π°Π½ΠΈΡ, ΠΊΠΎΡΠΎΡΡΠ΅ ΠΎΠ³ΡΠ°Π½ΠΈΡΠΈΠ²Π°ΡΡ Π·Π½Π°ΡΠ΅Π½ΠΈΠ΅ CE Π² ΡΠΏΠ΅ΡΠΈΡΠΈΠΊΠ°ΡΠΈΡΡ
.
ΠΡΠ½ΠΎΠ²Π½ΡΠΌΠΈ ΡΠ°ΠΊΡΠΎΡΠ°ΠΌΠΈ, Π²Π»ΠΈΡΡΡΠΈΠΌΠΈ Π½Π° ΠΌΠΈΠΊΡΠΎΡΡΡΡΠΊΡΡΡΡ ΡΡΠ³ΡΠ½Π°, ΡΠ²Π»ΡΡΡΡΡ (i) Ρ ΠΈΠΌΠΈΡΠ΅ΡΠΊΠΈΠΉ ΡΠΎΡΡΠ°Π², (ii) ΡΠΊΠΎΡΠΎΡΡΡ ΠΎΡ Π»Π°ΠΆΠ΄Π΅Π½ΠΈΡ, (iii) ΠΎΠ±ΡΠ°Π±ΠΎΡΠΊΠ° ΠΆΠΈΠ΄ΠΊΠΎΡΡΡΡ ΠΈ (iv) ΡΠ΅ΡΠΌΠΈΡΠ΅ΡΠΊΠ°Ρ ΠΎΠ±ΡΠ°Π±ΠΎΡΠΊΠ°. ΠΡΠΎΠΌΠ΅ ΡΠΎΠ³ΠΎ, Π½Π΅ΠΎΠ±Ρ ΠΎΠ΄ΠΈΠΌΠΎ ΡΡΠΈΡΡΠ²Π°ΡΡ ΡΠ»Π΅Π΄ΡΡΡΠΈΠ΅ Π°ΡΠΏΠ΅ΠΊΡΡ ΡΠ²ΡΠ·Π°Π½Π½ΠΎΠ³ΠΎ ΡΠ³Π»Π΅ΡΠΎΠ΄Π° Π² ΡΡΠ³ΡΠ½Π°Ρ .
- ΠΡΠΈ ΠΏΠ΅ΡΠ²ΠΎΠ½Π°ΡΠ°Π»ΡΠ½ΠΎΠΌ ΠΎΡ Π»Π°ΠΆΠ΄Π΅Π½ΠΈΠΈ ΠΈΠ»ΠΈ ΠΏΠΎΡΠ»Π΅Π΄ΡΡΡΠ΅ΠΉ ΡΠ΅ΡΠΌΠΎΠΎΠ±ΡΠ°Π±ΠΎΡΠΊΠ΅ ΠΌΠ°ΡΡΠΈΡΠ° ΠΌΠΎΠΆΠ΅Ρ Π±ΡΡΡ ΠΎΠ±Π΅Π·ΡΠ³Π»Π΅ΡΠΎΠΆΠ΅Π½Π° ΠΈΠ·Π½ΡΡΡΠΈ ΠΈΠ»ΠΈ Π½Π°ΡΠ³Π»Π΅ΡΠΎΠΆΠ΅Π½Π° ΠΏΡΡΠ΅ΠΌ ΠΎΡΠ°ΠΆΠ΄Π΅Π½ΠΈΡ Π³ΡΠ°ΡΠΈΡΠ° Π½Π° ΡΡΡΠ΅ΡΡΠ²ΡΡΡΠΈΡ ΡΡΠ°ΡΡΠΊΠ°Ρ ΠΈΠ»ΠΈ ΠΏΡΡΠ΅ΠΌ ΡΠ°ΡΡΠ²ΠΎΡΠ΅Π½ΠΈΡ ΡΠ³Π»Π΅ΡΠΎΠ΄Π° ΠΈΠ· Π½ΠΈΡ .
- Π Π·Π°Π²ΠΈΡΠΈΠΌΠΎΡΡΠΈ ΠΎΡ ΡΠΎΠ΄Π΅ΡΠΆΠ°Π½ΠΈΡ ΠΊΡΠ΅ΠΌΠ½ΠΈΡ ΠΈ ΡΠΊΠΎΡΠΎΡΡΠΈ ΠΎΡ Π»Π°ΠΆΠ΄Π΅Π½ΠΈΡ ΡΠΎΠ΄Π΅ΡΠΆΠ°Π½ΠΈΠ΅ ΡΠ³Π»Π΅ΡΠΎΠ΄Π° Π² ΠΏΠ΅ΡΠ»ΠΈΡΠ΅ ΠΆΠ΅Π»Π΅Π·Π° ΠΌΠΎΠΆΠ΅Ρ Π²Π°ΡΡΠΈΡΠΎΠ²Π°ΡΡΡΡ. ΠΡΠΎ ΡΡΠΎΠΉΠ½Π°Ρ ΡΠΈΡΡΠ΅ΠΌΠ°, ΠΈ ΡΠΎΠ΄Π΅ΡΠΆΠ°Π½ΠΈΠ΅ ΡΠ³Π»Π΅ΡΠΎΠ΄Π° Π² ΠΏΠ΅ΡΠ»ΠΈΡΠ΅ ΠΌΠΎΠΆΠ΅Ρ ΡΠΎΡΡΠ°Π²Π»ΡΡΡ Π²ΡΠ΅Π³ΠΎ 0,50 % ΠΏΡΠΈ 2,5 % Si.
- ΠΠ° ΠΈΠ·ΠΌΠ΅ΡΠ΅Π½Π½ΡΡ ΡΠ²Π΅ΡΠ΄ΠΎΡΡΡ Π³ΡΠ°ΡΠΈΡΠΎΠ²ΡΡ
ΡΡΠ³ΡΠ½ΠΎΠ² Π²Π»ΠΈΡΠ΅Ρ Π³ΡΠ°ΡΠΈΡ, ΠΎΡΠΎΠ±Π΅Π½Π½ΠΎ Π² ΡΠ΅ΡΠΎΠΌ ΡΡΠ³ΡΠ½Π΅. ΠΠΈΠΊΡΠΎΡΠ²Π΅ΡΠ΄ΠΎΡΡΡ ΠΌΠ°ΡΡΠ΅Π½ΡΠΈΡΠ° ΠΌΠΎΠΆΠ΅Ρ Π΄ΠΎΡΡΠΈΠ³Π°ΡΡ 66 HRC ΠΈΠ»ΠΈ Π²ΡΠ΅Π³ΠΎ 54 HRC Π² ΡΠ΅ΡΠΎΠΌ ΡΡΠ³ΡΠ½Π΅ (58 HRC Π² ΠΊΠΎΠ²ΠΊΠΎΠΌ ΡΡΠ³ΡΠ½Π΅).
- ΠΠ° ΠΊΡΠΈΡΠΈΡΠ΅ΡΠΊΡΡ ΡΠ΅ΠΌΠΏΠ΅ΡΠ°ΡΡΡΡ ΠΆΠ΅Π»Π΅Π·Π° Π²Π»ΠΈΡΠ΅Ρ (ΠΏΠΎΠ²ΡΡΠ°Π΅Ρ) ΡΠΎΠ΄Π΅ΡΠΆΠ°Π½ΠΈΠ΅ ΠΊΡΠ΅ΠΌΠ½ΠΈΡ, Π° Π½Π΅ ΡΠΎΠ΄Π΅ΡΠΆΠ°Π½ΠΈΠ΅ ΡΠ³Π»Π΅ΡΠΎΠ΄Π°.
ΠΠ»Π°ΡΡΠΈΡΠΈΠΊΠ°ΡΠΈΡ ΡΡΠ³ΡΠ½ΠΎΠ²
ΠΡΡΠΎΡΠΈΡΠ΅ΡΠΊΠΈ ΡΠ»ΠΎΠΆΠΈΠ»ΠΎΡΡ ΡΠ°ΠΊ, ΡΡΠΎ ΠΏΠ΅ΡΠ²Π°Ρ ΠΊΠ»Π°ΡΡΠΈΡΠΈΠΊΠ°ΡΠΈΡ ΡΡΠ³ΡΠ½Π° ΠΎΡΠ½ΠΎΠ²ΡΠ²Π°Π»Π°ΡΡ Π½Π° Π΅Π³ΠΎ ΠΈΠ·Π»ΠΎΠΌΠ΅. ΠΠ΅ΡΠ²ΠΎΠ½Π°ΡΠ°Π»ΡΠ½ΠΎ ΡΡΠ³ΡΠ½ Π΄Π΅Π»ΠΈΠ»ΡΡ Π½Π° Π΄Π²Π° ΡΠΈΠΏΠ°, Π° ΠΈΠΌΠ΅Π½Π½ΠΎ Π±Π΅Π»ΡΠΉ ΡΡΠ³ΡΠ½ ΠΈ ΡΠ΅ΡΡΠΉ ΡΡΠ³ΡΠ½, ΠΊΠ°ΠΊ ΡΠΊΠ°Π·Π°Π½ΠΎ Π½ΠΈΠΆΠ΅.
- ΠΠ΅Π»ΡΠΉ ΡΡΠ³ΡΠ½ β ΠΈΠΌΠ΅Π΅Ρ Π±Π΅Π»ΡΡ ΠΊΡΠΈΡΡΠ°Π»Π»ΠΈΡΠ΅ΡΠΊΡΡ ΠΏΠΎΠ²Π΅ΡΡ
Π½ΠΎΡΡΡ ΠΈΠ·Π»ΠΎΠΌΠ°, ΡΠ°ΠΊ ΠΊΠ°ΠΊ ΡΠ°Π·ΡΡΡΠ΅Π½ΠΈΠ΅ Π² ΡΡΠΎΠΌ ΡΡΠ³ΡΠ½Π΅ ΠΏΡΠΎΠΈΡΡ
ΠΎΠ΄ΠΈΡ ΠΏΠΎ ΠΏΠ»Π°ΡΡΠΈΠ½Π°ΠΌ ΠΈΠ· ΠΊΠ°ΡΠ±ΠΈΠ΄Π° ΠΆΠ΅Π»Π΅Π·Π°. ΠΡΠΎ ΡΠ΅Π·ΡΠ»ΡΡΠ°Ρ ΠΌΠ΅ΡΠ°ΡΡΠ°Π±ΠΈΠ»ΡΠ½ΠΎΠ³ΠΎ Π·Π°ΡΠ²Π΅ΡΠ΄Π΅Π²Π°Π½ΠΈΡ (ΡΠ²ΡΠ΅ΠΊΡΠΈΠΊΠ° Fe3C). ΠΠ΅Π»ΡΠΉ ΡΡΠ³ΡΠ½ Π½Π°Π·Π²Π°Π½ ΡΠ°ΠΊ ΠΏΠΎΡΠΎΠΌΡ, ΡΡΠΎ ΡΡΠΎΡ ΡΡΠ³ΡΠ½ ΠΈΠΌΠ΅Π΅Ρ Ρ
Π°ΡΠ°ΠΊΡΠ΅ΡΠ½ΡΡ Π±Π΅Π»ΡΡ ΠΏΠΎΠ²Π΅ΡΡ
Π½ΠΎΡΡΡ ΠΈΠ·Π»ΠΎΠΌΠ°. ΠΡΠΎΡ ΡΡΠ³ΡΠ½ ΠΎΠ±ΡΠ°Π·ΡΠ΅ΡΡΡ, ΠΊΠΎΠ³Π΄Π° ΡΠ³Π»Π΅ΡΠΎΠ΄, ΡΠ°ΡΡΠ²ΠΎΡΠ΅Π½Π½ΡΠΉ Π² ΠΆΠΈΠ΄ΠΊΠΎΠΌ ΡΡΠ³ΡΠ½Π΅, Π½Π΅ ΠΎΠ±ΡΠ°Π·ΡΠ΅Ρ Π³ΡΠ°ΡΠΈΡΠ° ΠΏΡΠΈ Π·Π°ΡΠ²Π΅ΡΠ΄Π΅Π²Π°Π½ΠΈΠΈ, Π° ΠΎΡΡΠ°Π΅ΡΡΡ Π² ΡΠΎΠ΅Π΄ΠΈΠ½Π΅Π½ΠΈΠΈ Ρ ΠΆΠ΅Π»Π΅Π·ΠΎΠΌ, ΡΠ°ΡΡΠΎ Π² Π²ΠΈΠ΄Π΅ ΠΌΠ°ΡΡΠΈΠ²Π½ΡΡ
ΠΊΠ°ΡΠ±ΠΈΠ΄ΠΎΠ². Π£Π³Π»Π΅ΡΠΎΠ΄ ΠΏΡΠΈΡΡΡΡΡΠ²ΡΠ΅Ρ Π² Π²ΠΈΠ΄Π΅ ΠΊΠ°ΡΠ±ΠΈΠ΄ΠΎΠ² ΠΏΡΠ΅ΠΈΠΌΡΡΠ΅ΡΡΠ²Π΅Π½Π½ΠΎ Fe 3C ΠΈ Cr7C3. ΠΠ½ΠΎΠ³Π΄Π° Π² Π±Π΅Π»ΡΡ
ΡΡΠ³ΡΠ½Π°Ρ
ΠΏΡΠΈΡΡΡΡΡΠ²ΡΡΡ ΡΠ»ΠΎΠΆΠ½ΡΠ΅ ΠΊΠ°ΡΠ±ΠΈΠ΄Ρ, ΡΠ°ΠΊΠΈΠ΅ ΠΊΠ°ΠΊ (Fe,Cr)3C ΠΎΡ Π΄ΠΎΠ±Π°Π²ΠΎΠΊ ΠΎΡ 3 Π΄ΠΎ 5 % Ni ΠΈ ΠΎΡ 1,5 Π΄ΠΎ 2,5 % Cr, (Cr,Fe)7C3 ΠΎΡ Π΄ΠΎΠ±Π°Π²ΠΎΠΊ ΠΎΡ 11 Π΄ΠΎ 35 % Cr ΠΈΠ»ΠΈ ΡΠΎΠ΄Π΅ΡΠΆΠ°ΡΠΈΠ΅ Π΄ΡΡΠ³ΠΈΠ΅ ΠΊΠ°ΡΠ±ΠΈΠ΄ΠΎΠΎΠ±ΡΠ°Π·ΡΡΡΠΈΠ΅ ΡΠ»Π΅ΠΌΠ΅Π½ΡΡ.
ΠΠ΅Π»ΡΠΉ ΡΡΠ³ΡΠ½ ΡΠ²Π΅ΡΠ΄ΡΠΉ ΠΈ Ρ ΡΡΠΏΠΊΠΈΠΉ, ΠΏΠΎΠ²Π΅ΡΡ Π½ΠΎΡΡΡ ΠΈΠ·Π»ΠΎΠΌΠ° Π±Π΅Π»Π°Ρ, ΠΊΡΠΈΡΡΠ°Π»Π»ΠΈΡΠ΅ΡΠΊΠ°Ρ. ΠΠ΅Π»ΡΠΉ ΡΡΠ³ΡΠ½ ΠΎΠ±Π»Π°Π΄Π°Π΅Ρ Π²ΡΡΠΎΠΊΠΎΠΉ ΠΏΡΠΎΡΠ½ΠΎΡΡΡΡ Π½Π° ΡΠΆΠ°ΡΠΈΠ΅ (Π±ΠΎΠ»Π΅Π΅ 1380 Π/ΠΊΠ². ΠΌΠΌ) ΠΈ Ρ ΠΎΡΠΎΡΠΈΠΌ ΡΠΎΡ ΡΠ°Π½Π΅Π½ΠΈΠ΅ΠΌ ΠΏΡΠΎΡΠ½ΠΎΡΡΠΈ ΠΈ ΡΠ²Π΅ΡΠ΄ΠΎΡΡΠΈ ΠΏΡΠΈ ΠΏΠΎΠ²ΡΡΠ΅Π½Π½ΠΎΠΉ ΡΠ΅ΠΌΠΏΠ΅ΡΠ°ΡΡΡΠ΅. ΠΠ½ ΠΎΡΠ΅Π½Ρ ΡΠ°ΡΡΠΎ ΠΈΡΠΏΠΎΠ»ΡΠ·ΡΠ΅ΡΡΡ ΠΈΠ·-Π·Π° ΠΎΡΠ»ΠΈΡΠ½ΠΎΠΉ ΡΡΠΎΠΉΠΊΠΎΡΡΠΈ ΠΊ ΠΈΠ·Π½ΠΎΡΡ ΠΈ ΠΈΡΡΠΈΡΠ°Π½ΠΈΡ. ΠΠ° ΡΡΠΈ ΡΠ²ΠΎΠΉΡΡΠ²Π° Π² ΠΎΡΠ½ΠΎΠ²Π½ΠΎΠΌ ΠΎΡΠ²Π΅ΡΡΡΠ²Π΅Π½Π½Ρ ΠΌΠ°ΡΡΠΈΠ²Π½ΡΠ΅ ΠΊΠ°ΡΠ±ΠΈΠ΄Ρ Π² ΠΌΠΈΠΊΡΠΎΡΡΡΡΠΊΡΡΡΠ΅. ΠΠ΅Π»ΡΠ΅ ΡΡΠ³ΡΠ½Ρ ΠΏΠΎΠ»ΡΡΠ°ΡΡ ΠΎΡ Π»Π°ΠΆΠ΄Π΅Π½ΠΈΠ΅ΠΌ Π½Π΅ΠΊΠΎΡΠΎΡΡΡ ΠΏΠΎΠ²Π΅ΡΡ Π½ΠΎΡΡΠ΅ΠΉ Π»ΠΈΡΠ΅ΠΉΠ½ΠΎΠΉ ΡΠΎΡΠΌΡ. ΠΡ Π»Π°ΠΆΠ΄Π΅Π½ΠΈΠ΅ ΠΏΡΠ΅Π΄ΠΎΡΠ²ΡΠ°ΡΠ°Π΅Ρ ΠΎΠ±ΡΠ°Π·ΠΎΠ²Π°Π½ΠΈΠ΅ Π³ΡΠ°ΡΠΈΡΠ° Π²ΠΎ Π²ΡΠ΅ΠΌΡ Π·Π°ΡΠ²Π΅ΡΠ΄Π΅Π²Π°Π½ΠΈΡ ΡΡΠ³ΡΠ½Π°. ΠΡΠΈΠΌΠ΅Π½Π΅Π½ΠΈΠ΅ Π±Π΅Π»ΠΎΠ³ΠΎ ΡΡΠ³ΡΠ½Π° Π²ΠΊΠ»ΡΡΠ°Π΅Ρ Π² ΡΠ΅Π±Ρ ΡΠΎΡΠΌΠΎΠ·Π½ΡΠ΅ ΠΊΠΎΠ»ΠΎΠ΄ΠΊΠΈ, Π΄ΡΠΎΠ±Π΅ΡΡΡΡΠΉΠ½ΡΠ΅ ΡΠΎΠΏΠ»Π°, ΠΌΠ΅Π»ΡΠ½ΠΈΡΠ½ΡΠ΅ ΡΡΡΠ΅ΡΠΎΠ²ΠΊΠΈ, Π΄ΡΠΎΠ±ΠΈΠ»ΠΊΠΈ, ΡΠ°Π±ΠΎΡΠΈΠ΅ ΠΊΠΎΠ»Π΅ΡΠ° Π½Π°ΡΠΎΡΠΎΠ² ΠΈ Π΄ΡΡΠ³ΠΈΠ΅ Π΄Π΅ΡΠ°Π»ΠΈ, ΡΡΡΠΎΠΉΡΠΈΠ²ΡΠ΅ ΠΊ ΠΈΡΡΠΈΡΠ°Π½ΠΈΡ.
- Π‘Π΅ΡΡΠΉ ΡΡΠ³ΡΠ½. ΠΠΎΠ²Π΅ΡΡ
Π½ΠΎΡΡΡ ΠΈΠ·Π»ΠΎΠΌΠ° ΡΠ΅ΡΠΎΠ³ΠΎ ΡΠ²Π΅ΡΠ°, ΡΠΎΡΡΠΎΡΡΠ°Ρ ΠΈΠ· ΡΠ΅ΡΡΠ΅ΠΊ ΡΠ΅ΡΡΠΈΡΠ° ΠΈ ΡΠ°ΡΡΠ΅ΡΠ½Π½ΠΎΠ³ΠΎ Π³ΡΠ°ΡΠΈΡΠ°. ΠΠΎΠ³Π΄Π° ΡΠΎΡΡΠ°Π² ΠΆΠ΅Π»Π΅Π·Π° ΠΈ ΡΠΊΠΎΡΠΎΡΡΡ ΠΎΡ
Π»Π°ΠΆΠ΄Π΅Π½ΠΈΡ ΠΏΡΠΈ Π·Π°ΡΠ²Π΅ΡΠ΄Π΅Π²Π°Π½ΠΈΠΈ ΡΠ²Π»ΡΡΡΡΡ ΠΏΠΎΠ΄Ρ
ΠΎΠ΄ΡΡΠΈΠΌΠΈ, Π·Π½Π°ΡΠΈΡΠ΅Π»ΡΠ½Π°Ρ ΡΠ°ΡΡΡ ΡΠΎΠ΄Π΅ΡΠΆΠ°ΡΠ΅Π³ΠΎΡΡ ΡΠ³Π»Π΅ΡΠΎΠ΄Π° Π²ΡΠ΄Π΅Π»ΡΠ΅ΡΡΡ ΠΈΠ· ΠΆΠΈΠ΄ΠΊΠΎΡΡΠΈ Ρ ΠΎΠ±ΡΠ°Π·ΠΎΠ²Π°Π½ΠΈΠ΅ΠΌ ΡΠ΅ΡΡΠ΅ΠΊ Π³ΡΠ°ΡΠΈΡΠ°. ΠΡΡΡ ΡΠ°Π·ΡΡΡΠ΅Π½ΠΈΡ ΡΠ°ΠΊΠΎΠ³ΠΎ ΠΆΠ΅Π»Π΅Π·Π° ΡΠ»Π΅Π΄ΡΠ΅Ρ Π·Π° ΡΠ΅ΡΡΠΉΠΊΠ°ΠΌΠΈ Π³ΡΠ°ΡΠΈΡΠ°.
ΠΠΎΠ²Π΅ΡΡ Π½ΠΎΡΡΡ ΠΈΠ·Π»ΠΎΠΌΠ° ΡΡΠΎΠ³ΠΎ ΠΆΠ΅Π»Π΅Π·Π° ΠΊΠ°ΠΆΠ΅ΡΡΡ ΡΠ΅ΡΠΎΠΉ ΠΈΠ·-Π·Π° ΠΏΡΠ΅ΠΎΠ±Π»Π°Π΄Π°Π½ΠΈΡ ΠΎΠ±Π½Π°ΠΆΠ΅Π½Π½ΠΎΠ³ΠΎ Π³ΡΠ°ΡΠΈΡΠ°. Π‘Π΅ΡΡΠΉ ΡΡΠ³ΡΠ½ ΡΠ²Π»ΡΠ΅ΡΡΡ ΡΠ΅Π·ΡΠ»ΡΡΠ°ΡΠΎΠΌ ΡΡΡΠΎΠΉΡΠΈΠ²ΠΎΠ³ΠΎ Π·Π°ΡΠ²Π΅ΡΠ΄Π΅Π²Π°Π½ΠΈΡ ΠΏΡΠΈ ΠΌΠ΅Π΄Π»Π΅Π½Π½ΠΎΠΌ ΠΎΡ Π»Π°ΠΆΠ΄Π΅Π½ΠΈΠΈ. ΠΠ½ ΠΎΠ±Π»Π°Π΄Π°Π΅Ρ Π½Π΅ΡΠΊΠΎΠ»ΡΠΊΠΈΠΌΠΈ ΡΠ½ΠΈΠΊΠ°Π»ΡΠ½ΡΠΌΠΈ ΡΠ²ΠΎΠΉΡΡΠ²Π°ΠΌΠΈ, ΠΊΠΎΡΠΎΡΡΠ΅ ΠΎΠ±ΡΡΠ»ΠΎΠ²Π»Π΅Π½Ρ Π½Π°Π»ΠΈΡΠΈΠ΅ΠΌ ΡΠ΅ΡΡΠΉΡΠ°ΡΠΎΠ³ΠΎ Π³ΡΠ°ΡΠΈΡΠ° Π² ΠΌΠΈΠΊΡΠΎΡΡΡΡΠΊΡΡΡΠ΅. ΠΠ½ ΠΎΠ±Π»Π°Π΄Π°Π΅Ρ Π²ΡΡΠΎΠΊΠΎΠΉ ΠΏΡΠΎΡΠ½ΠΎΡΡΡΡ Π½Π° ΡΠΆΠ°ΡΠΈΠ΅, ΡΠΎΠΏΡΠΎΡΠΈΠ²Π»Π΅Π½ΠΈΠ΅ΠΌ ΡΡΡΠ°Π»ΠΎΡΡΠΈ ΠΈ ΠΈΠ·Π½ΠΎΡΠΎΡΡΠΎΠΉΠΊΠΎΡΡΡΡ. ΠΠ½ ΠΎΡΠ½ΠΎΡΠΈΡΠ΅Π»ΡΠ½ΠΎ ΠΌΡΠ³ΠΊΠΈΠΉ ΠΈ Π»Π΅Π³ΠΊΠΎ ΠΏΠΎΠ΄Π΄Π°Π΅ΡΡΡ ΠΌΠ΅Ρ Π°Π½ΠΈΡΠ΅ΡΠΊΠΎΠΉ ΠΎΠ±ΡΠ°Π±ΠΎΡΠΊΠ΅ ΠΈ ΡΠ²Π°ΡΠΊΠ΅. ΠΠ½ ΠΈΠΌΠ΅Π΅Ρ ΡΠ²Π΅ΡΠ΄ΠΎΡΡΡ, ΡΠΏΠΎΡΠΎΠ±ΡΡΠ²ΡΡΡΡΡ Ρ ΠΎΡΠΎΡΠ΅ΠΉ ΠΈΠ·Π½ΠΎΡΠΎΡΡΠΎΠΉΠΊΠΎΡΡΠΈ. ΠΠ½ ΡΡΡΠΎΠΉΡΠΈΠ² ΠΊ ΠΈΡΡΠΈΡΠ°Π½ΠΈΡ Π² ΡΡΠ»ΠΎΠ²ΠΈΡΡ Π³ΡΠ°Π½ΠΈΡΠ½ΠΎΠΉ ΡΠΌΠ°Π·ΠΊΠΈ. ΠΠ½ ΠΎΠ±Π»Π°Π΄Π°Π΅Ρ ΠΎΡΠ΅Π½Ρ Ρ ΠΎΡΠΎΡΠΈΠΌΠΈ ΡΠ²ΠΎΠΉΡΡΠ²Π°ΠΌΠΈ Π΄Π»Ρ ΠΈΡΠΏΠΎΠ»ΡΠ·ΠΎΠ²Π°Π½ΠΈΡ Π² Π΄Π΅ΠΌΠΏΡΠΈΡΡΡΡΠΈΡ Π²ΠΈΠ±ΡΠ°ΡΠΈΡΡ ΠΈΠ»ΠΈ ΡΠΌΠ΅ΡΠ΅Π½Π½ΡΡ ΡΠ΅ΠΏΠ»ΠΎΠ²ΡΡ ΡΠ΄Π°ΡΠ°Ρ . ΠΠ½ ΠΈΡΠΏΠΎΠ»ΡΠ·ΡΠ΅ΡΡΡ Π΄Π»Ρ Π±Π»ΠΎΠΊΠΎΠ² ΡΠΈΠ»ΠΈΠ½Π΄ΡΠΎΠ² Π΄Π²ΠΈΠ³Π°ΡΠ΅Π»Π΅ΠΉ, ΡΠ΅ΡΡΠ΅ΡΠ΅Π½, ΠΌΠ°Ρ ΠΎΠ²ΠΈΠΊΠΎΠ², Π²ΠΎΠ΄ΠΎΠΏΡΠΎΠ²ΠΎΠ΄Π½ΡΡ ΡΡΡΠ±, ΡΠΎΡΠΌΠΎΠ·Π½ΡΡ Π΄ΠΈΡΠΊΠΎΠ², ΠΊΠΎΠ½ΡΡΡΡΠΊΡΠΈΠΉ ΡΡΠ°Π½ΠΊΠΎΠ² ΠΈ Ρ. Π΄.
Π Π½Π°ΡΡΠΎΡΡΠ΅Π΅ Π²ΡΠ΅ΠΌΡ ΠΎΠ±ΡΠ΅ΠΏΡΠΈΠ½ΡΡΠ°Ρ ΡΡ
Π΅ΠΌΠ° ΠΊΠ»Π°ΡΡΠΈΡΠΈΠΊΠ°ΡΠΈΠΈ Π΄Π΅Π»ΠΈΡ ΡΡΠ³ΡΠ½Ρ Π½Π° ΡΠ΅ΡΡΡΠ΅ ΠΎΡΠ½ΠΎΠ²Π½ΡΡ
ΡΠΈΠΏΠ°. ΠΡΠΎ (i) Π±Π΅Π»ΡΠΉ ΡΡΠ³ΡΠ½, (ii) ΡΠ΅ΡΡΠΉ ΡΡΠ³ΡΠ½, (iii) ΠΊΠΎΠ²ΠΊΠΈΠΉ ΡΡΠ³ΡΠ½ ΠΈ (iv) ΠΊΠΎΠ²ΠΊΠΈΠΉ ΡΡΠ³ΡΠ½. Π ΡΠΎ Π²ΡΠ΅ΠΌΡ ΠΊΠ°ΠΊ Π±Π΅Π»ΡΠΉ ΠΈ ΡΠ΅ΡΡΠΉ ΡΡΠ³ΡΠ½ ΠΎΠΏΠΈΡΠ°Π½Ρ Π²ΡΡΠ΅, ΠΊΠΎΠ²ΠΊΠΈΠΉ ΡΡΠ³ΡΠ½ ΠΈ ΠΊΠΎΠ²ΠΊΠΈΠΉ ΡΡΠ³ΡΠ½ ΠΎΠΏΠΈΡΠ°Π½Ρ Π½ΠΈΠΆΠ΅.
- ΠΠΎΠ²ΠΊΠΈΠΉ ΡΡΠ³ΡΠ½ β Π‘Π²ΠΎΠ΅ Π½Π°Π·Π²Π°Π½ΠΈΠ΅ ΠΏΠΎΠ»ΡΡΠΈΠ» ΠΈΠ·-Π·Π° ΡΠΎΠ³ΠΎ, ΡΡΠΎ Π² ΠΎΡΠ»ΠΈΡΠΎΠΌ Π²ΠΈΠ΄Π΅ ΠΎΠ±Π»Π°Π΄Π°Π΅Ρ ΠΈΠ·ΠΌΠ΅ΡΠΈΠΌΠΎΠΉ ΠΏΠ»Π°ΡΡΠΈΡΠ½ΠΎΡΡΡΡ. ΠΠ°ΠΏΡΠΎΡΠΈΠ², Π½ΠΈ Π±Π΅Π»ΡΠΉ, Π½ΠΈ ΡΠ΅ΡΡΠΉ ΡΡΠ³ΡΠ½ Π½Π΅ ΠΏΡΠΎΡΠ²Π»ΡΡΡ Π·Π½Π°ΡΠΈΡΠ΅Π»ΡΠ½ΠΎΠΉ ΠΏΠ»Π°ΡΡΠΈΡΠ½ΠΎΡΡΠΈ ΠΏΡΠΈ ΡΡΠ°Π½Π΄Π°ΡΡΠ½ΠΎΠΌ ΠΈΡΠΏΡΡΠ°Π½ΠΈΠΈ Π½Π° ΡΠ°ΡΡΡΠΆΠ΅Π½ΠΈΠ΅. ΠΠ½ ΡΠ°ΠΊΠΆΠ΅ ΠΈΠ·Π²Π΅ΡΡΠ΅Π½ ΠΊΠ°ΠΊ ΡΡΠ³ΡΠ½ Ρ ΡΠ°ΡΠΎΠ²ΠΈΠ΄Π½ΡΠΌ Π³ΡΠ°ΡΠΈΡΠΎΠΌ ΠΈΠ»ΠΈ ΡΡΠ³ΡΠ½ Ρ ΡΠ°ΡΠΎΠ²ΠΈΠ΄Π½ΡΠΌ Π³ΡΠ°ΡΠΈΡΠΎΠΌ. ΠΠΎ ΡΠΎΡΡΠ°Π²Ρ ΠΎΠ½ ΠΏΠΎΠ΄ΠΎΠ±Π΅Π½ ΡΠ΅ΡΠΎΠΌΡ ΡΡΠ³ΡΠ½Ρ, Π½ΠΎ ΠΏΡΠΈ Π»ΠΈΡΡΠ΅ ΠΊΠΎΠ²ΠΊΠΎΠ³ΠΎ ΡΡΠ³ΡΠ½Π° Π³ΡΠ°ΡΠΈΡ Π·Π°ΡΠΎΠΆΠ΄Π°Π΅ΡΡΡ Π² Π²ΠΈΠ΄Π΅ ΡΡΠ΅ΡΠΈΡΠ΅ΡΠΊΠΈΡ
ΡΠ°ΡΡΠΈΡ, Π° Π½Π΅ ΡΠ΅ΡΡΠ΅ΠΊ. ΠΡΠΎ Π΄ΠΎΡΡΠΈΠ³Π°Π΅ΡΡΡ Π·Π° ΡΡΠ΅Ρ Π΄ΠΎΠ±Π°Π²Π»Π΅Π½ΠΈΡ ΠΎΡΠ΅Π½Ρ Π½Π΅Π±ΠΎΠ»ΡΡΠΎΠ³ΠΎ, Π½ΠΎ ΠΎΠΏΡΠ΅Π΄Π΅Π»Π΅Π½Π½ΠΎΠ³ΠΎ ΠΊΠΎΠ»ΠΈΡΠ΅ΡΡΠ²Π° ΠΌΠ°Π³Π½ΠΈΡ ΠΈ/ΠΈΠ»ΠΈ ΡΠ΅ΡΠΈΡ Π² ΡΠ°ΡΠΏΠ»Π°Π²Π»Π΅Π½Π½ΠΎΠ΅ ΠΆΠ΅Π»Π΅Π·ΠΎ Π½Π° ΡΡΠ°Π΄ΠΈΠΈ ΠΏΡΠΎΡΠ΅ΡΡΠ°, Π½Π°Π·ΡΠ²Π°Π΅ΠΌΠΎΠΉ ΠΎΠ±ΡΠ°Π·ΠΎΠ²Π°Π½ΠΈΠ΅ΠΌ ΠΊΠΎΠΌΠΊΠΎΠ². ΠΠΎΠ²ΠΊΠΈΠΉ ΡΡΠ³ΡΠ½ ΡΠΎΡΡΠΎΠΈΡ ΠΈΠ· ΡΠ°ΡΠΎΠ²ΠΈΠ΄Π½ΡΡ
ΡΠ°ΡΡΠΈΡ ΡΠ°ΡΠΎΠ²ΠΈΠ΄Π½ΠΎΠ³ΠΎ Π³ΡΠ°ΡΠΈΡΠ° Π² ΡΠ΅ΡΡΠΈΡΠ½ΠΎΠΉ ΠΈΠ»ΠΈ ΠΏΠ΅ΡΠ»ΠΈΡΠ½ΠΎΠΉ ΠΌΠ°ΡΡΠΈΡΠ΅. ΠΠ³ΠΎ ΠΏΡΠΎΠΈΠ·Π²ΠΎΠ΄ΡΡ ΠΈΠ· ΡΠΎΠ³ΠΎ ΠΆΠ΅ ΡΡΡΡΡ, ΡΡΠΎ ΠΈ ΡΠ΅ΡΡΠΉ ΡΡΠ³ΡΠ½, Π½ΠΎ ΡΡΠΈ ΠΌΠ°ΡΠ΅ΡΠΈΠ°Π»Ρ Π΄ΠΎΠ»ΠΆΠ½Ρ Π±ΡΡΡ ΡΠΈΡΠ΅, ΠΎΡΠΎΠ±Π΅Π½Π½ΠΎ Π² ΠΎΡΠ½ΠΎΡΠ΅Π½ΠΈΠΈ ΡΠ΅ΡΡ. ΠΠΈΡΠ΅ΠΉΠ½ΡΠ΅ ΡΠ²ΠΎΠΉΡΡΠ²Π° ΠΊΠΎΠ²ΠΊΠΎΠ³ΠΎ ΡΡΠ³ΡΠ½Π°, ΡΠ°ΠΊΠΈΠ΅ ΠΊΠ°ΠΊ ΡΠ΅ΠΊΡΡΠ΅ΡΡΡ ΠΈ Ρ. Π΄., Π°Π½Π°Π»ΠΎΠ³ΠΈΡΠ½Ρ ΡΠ²ΠΎΠΉΡΡΠ²Π°ΠΌ ΡΠ΅ΡΠΎΠ³ΠΎ ΡΡΠ³ΡΠ½Π°. ΠΡΠ½ΠΎΠ²Π½ΡΠΌ ΠΏΡΠ΅ΠΈΠΌΡΡΠ΅ΡΡΠ²ΠΎΠΌ Π²ΡΡΠΎΠΊΠΎΠΏΡΠΎΡΠ½ΠΎΠ³ΠΎ ΡΡΠ³ΡΠ½Π° ΠΏΠ΅ΡΠ΅Π΄ ΡΠ΅ΡΡΠΌ ΡΡΠ³ΡΠ½ΠΎΠΌ ΡΠ²Π»ΡΠ΅ΡΡΡ ΡΠΎΡΠ΅ΡΠ°Π½ΠΈΠ΅ Π²ΡΡΠΎΠΊΠΎΠΉ ΠΏΡΠΎΡΠ½ΠΎΡΡΠΈ Ρ ΠΏΠ»Π°ΡΡΠΈΡΠ½ΠΎΡΡΡΡ.
ΠΠ½ΠΈ ΡΠ°ΠΊΠΆΠ΅ ΠΎΠ±Π»Π°Π΄Π°ΡΡ Ρ ΠΎΡΠΎΡΠ΅ΠΉ ΡΡΡΠ°Π»ΠΎΡΡΠ½ΠΎΠΉ ΠΏΡΠΎΡΠ½ΠΎΡΡΡΡ, ΠΈΠ·Π½ΠΎΡΠΎΡΡΠΎΠΉΠΊΠΎΡΡΡΡ, ΡΠ΄Π°ΡΠΎΠΏΡΠΎΡΠ½ΠΎΡΡΡΡ ΠΈ Π²ΡΡΠΎΠΊΠΈΠΌ ΠΌΠΎΠ΄ΡΠ»Π΅ΠΌ ΡΠΏΡΡΠ³ΠΎΡΡΠΈ. ΠΠ°ΡΡΠ΅Π½ΡΠΈΡΠ½ΡΠ΅ ΠΊΠΎΠ²ΠΊΠΈΠ΅ ΡΡΠ³ΡΠ½Ρ ΠΈ ΠΊΠΎΠ²ΠΊΠΈΠ΅ ΡΡΠ³ΡΠ½Ρ ΠΏΠΎΡΠ»Π΅ ΠΎΡΠΏΡΡΠΊΠ° ΠΎΠ±Π»Π°Π΄Π°ΡΡ Π΅ΡΠ΅ Π»ΡΡΡΠΈΠΌΠΈ ΡΠ²ΠΎΠΉΡΡΠ²Π°ΠΌΠΈ. ΠΡΠΈΠΌΠ΅Π½Π΅Π½ΠΈΠ΅ ΡΡΠ³ΡΠ½ΠΎΠ² Ρ ΡΠ°ΡΠΎΠ²ΠΈΠ΄Π½ΡΠΌ Π³ΡΠ°ΡΠΈΡΠΎΠΌ Π²ΠΊΠ»ΡΡΠ°Π΅Ρ ΠΊΠΎΠ»Π΅Π½ΡΠ°ΡΡΠ΅ Π²Π°Π»Ρ Π°Π²ΡΠΎΠΌΠΎΠ±ΠΈΠ»ΡΠ½ΡΡ Π΄Π²ΠΈΠ³Π°ΡΠ΅Π»Π΅ΠΉ, Π±ΠΎΠ»ΡΡΠ΅Π³ΡΡΠ·Π½ΡΠ΅ ΡΠ΅ΡΡΠ΅ΡΠ½ΠΈ, Π²ΠΎΠ΅Π½Π½ΡΠ΅ Π°Π²ΡΠΎΠΌΠΎΠ±ΠΈΠ»ΠΈ ΠΈ ΠΆΠ΅Π»Π΅Π·Π½ΠΎΠ΄ΠΎΡΠΎΠΆΠ½ΡΠ΅ Π²Π°Π³ΠΎΠ½Ρ.
- ΠΠΎΠ²ΠΊΠΈΠΉ ΡΡΠ³ΡΠ½ β ΠΎΡΠ»ΠΈΠ²Π°Π΅ΡΡΡ ΠΊΠ°ΠΊ Π±Π΅Π»ΡΠΉ ΡΡΠ³ΡΠ½, Π·Π°ΡΠ΅ΠΌ Β«ΠΊΠΎΠ²ΡΠ²Π°Π΅ΡΡΡΒ» (Ρ. Π΅. ΠΏΠΎΠ΄Π²Π΅ΡΠ³Π°Π΅ΡΡΡ ΡΠ΅ΡΠΌΠΈΡΠ΅ΡΠΊΠΎΠΉ ΠΎΠ±ΡΠ°Π±ΠΎΡΠΊΠ΅ Π΄Π»Ρ ΠΏΡΠΈΠ΄Π°Π½ΠΈΡ ΠΏΠ»Π°ΡΡΠΈΡΠ½ΠΎΡΡΠΈ Ρ
ΡΡΠΏΠΊΠΎΠΌΡ ΠΌΠ°ΡΠ΅ΡΠΈΠ°Π»Ρ). ΠΠΈΠΊΡΠΎΡΡΡΡΠΊΡΡΡΠ° ΡΠΎΡΡΠΎΠΈΡ ΠΈΠ· ΡΠ΅ΡΡΠΈΡΠ° ΠΈ ΡΠ°ΡΡΠΈΡ ΡΠ²ΠΎΠ±ΠΎΠ΄Π½ΠΎΠ³ΠΎ Π³ΡΠ°ΡΠΈΡΠ°. ΠΡΠΎΡ ΡΡΠ³ΡΠ½ Π²ΠΊΠ»ΡΡΠ°Π΅Ρ ΡΠΎΡΠΌΡ Π³ΡΠ°ΡΠΈΡΠ°, Π½Π°Π·ΡΠ²Π°Π΅ΠΌΡΡ ΠΎΡΠΏΡΡΠΊΠ½ΡΠΌ ΡΠ³Π»Π΅ΡΠΎΠ΄ΠΎΠΌ. ΠΡΠ° ΡΠΎΡΠΌΠ° Π³ΡΠ°ΡΠΈΡΠ° ΠΏΡΠΎΠΈΠ·Π²ΠΎΠ΄ΠΈΡΡΡ ΡΠ΅ΡΠΌΠΈΡΠ΅ΡΠΊΠΎΠΉ ΠΎΠ±ΡΠ°Π±ΠΎΡΠΊΠΎΠΉ Π±Π΅Π»ΠΎΠ³ΠΎ ΡΡΠ³ΡΠ½Π°. ΠΡΠΈ Π½Π°Π³ΡΠ΅Π²Π°Π½ΠΈΠΈ Π±Π΅Π»ΠΎΠ³ΠΎ ΡΡΠ³ΡΠ½Π° Π² ΡΠ΅ΡΠ΅Π½ΠΈΠ΅ Π΄Π»ΠΈΡΠ΅Π»ΡΠ½ΠΎΠ³ΠΎ Π²ΡΠ΅ΠΌΠ΅Π½ΠΈ (ΠΎΠΊΠΎΠ»ΠΎ 60 ΡΠ°ΡΠΎΠ²) ΠΏΡΠΈ ΡΠ΅ΠΌΠΏΠ΅ΡΠ°ΡΡΡΠ΅ 960Β°Π‘ ΠΏΡΠΎΠΈΡΡ
ΠΎΠ΄ΠΈΡ ΡΠ°ΡΠΏΠ°Π΄ ΡΠ΅ΠΌΠ΅Π½ΡΠΈΡΠ° Π½Π° Π°ΡΡΡΠ΅Π½ΠΈΡ ΠΈ Π³ΡΠ°ΡΠΈΡ. ΠΡΡΠ΅ΠΌ ΠΌΠ΅Π΄Π»Π΅Π½Π½ΠΎΠ³ΠΎ ΠΎΡ
Π»Π°ΠΆΠ΄Π΅Π½ΠΈΡ ΠΎΡ 960Β°Π‘ Π°ΡΡΡΠ΅Π½ΠΈΡ ΠΏΡΠ΅Π²ΡΠ°ΡΠ°Π΅ΡΡΡ Π² ΡΠ΅ΡΡΠΈΡ ΠΈΠ»ΠΈ ΠΏΠ΅ΡΠ»ΠΈΡ Π² Π·Π°Π²ΠΈΡΠΈΠΌΠΎΡΡΠΈ ΠΎΡ ΡΠΊΠΎΡΠΎΡΡΠΈ ΠΎΡ
Π»Π°ΠΆΠ΄Π΅Π½ΠΈΡ ΠΈ ΡΠΊΠΎΡΠΎΡΡΠΈ Π΄ΠΈΡΡΡΠ·ΠΈΠΈ ΡΠ³Π»Π΅ΡΠΎΠ΄Π°.
ΠΠ»Π°ΡΡΠΈΡΠ½ΠΎΡΡΡ ΠΈ ΡΠ΄Π°ΡΠ½Π°Ρ Π²ΡΠ·ΠΊΠΎΡΡΡ ΠΊΠΎΠ²ΠΊΠΎΠ³ΠΎ ΡΡΠ³ΡΠ½Π° Π½Π°Ρ ΠΎΠ΄ΡΡΡΡ ΠΌΠ΅ΠΆΠ΄Ρ ΠΊΠΎΠ²ΠΊΠΈΠΌ ΡΡΠ³ΡΠ½ΠΎΠΌ ΠΈ ΡΠ΅ΡΡΠΌ ΡΡΠ³ΡΠ½ΠΎΠΌ. Π Π½Π°ΡΠΈ Π΄Π½ΠΈ ΠΊΠΎΠ²ΠΊΠΈΠΉ ΡΡΠ³ΡΠ½ Π±ΡΠ» Π·Π°ΠΌΠ΅Π½Π΅Π½ Π±ΠΎΠ»Π΅Π΅ ΡΠΊΠΎΠ½ΠΎΠΌΠΈΡΠ½ΡΠΌ ΠΊΠΎΠ²ΠΊΠΈΠΌ ΡΡΠ³ΡΠ½ΠΎΠΌ, ΠΎΡΠ»ΠΈΡΡΠΌ Π΄Π»Ρ ΠΌΠ½ΠΎΠ³ΠΈΡ ΠΏΡΠΈΠΌΠ΅Π½Π΅Π½ΠΈΠΉ. ΠΠΎΠ²ΠΊΠΈΠ΅ ΡΡΠ³ΡΠ½Ρ ΠΏΠΎΠΌΠΈΠΌΠΎ ΠΏΠ»Π°ΡΡΠΈΡΠ½ΠΎΡΡΠΈ ΠΎΠ±Π»Π°Π΄Π°ΡΡ Ρ ΠΎΡΠΎΡΠ΅ΠΉ ΠΎΠ±ΡΠ°Π±Π°ΡΡΠ²Π°Π΅ΠΌΠΎΡΡΡΡ. Π€Π΅ΡΡΠΈΡΠ½ΡΠ΅ ΠΊΠΎΠ²ΠΊΠΈΠ΅ ΡΡΠ³ΡΠ½Ρ Π±ΠΎΠ»Π΅Π΅ ΠΏΠ»Π°ΡΡΠΈΡΠ½Ρ ΠΈ ΠΌΠ΅Π½Π΅Π΅ ΠΏΡΠΎΡΠ½Ρ ΠΈ ΡΠ²Π΅ΡΠ΄Ρ, ΡΠ΅ΠΌ ΠΏΠ΅ΡΠ»ΠΈΡΠ½ΡΠ΅ ΠΊΠΎΠ²ΠΊΠΈΠ΅ ΡΡΠ³ΡΠ½Ρ. ΠΡΠΈΠΌΠ΅Π½Π΅Π½ΠΈΠ΅ ΠΊΠΎΠ²ΠΊΠΎΠ³ΠΎ ΡΡΠ³ΡΠ½Π° Π²ΠΊΠ»ΡΡΠ°Π΅Ρ Π΄Π΅ΡΠ°Π»ΠΈ ΡΠΈΠ»ΠΎΠ²ΠΎΠΉ ΠΏΠ΅ΡΠ΅Π΄Π°ΡΠΈ ΡΡΠ°Π½ΡΠΏΠΎΡΡΠ½ΡΡ ΡΡΠ΅Π΄ΡΡΠ², ΠΊΡΡΡΠΊΠΈ ΠΏΠΎΠ΄ΡΠΈΠΏΠ½ΠΈΠΊΠΎΠ², ΠΊΠΎΡΠΏΡΡΠ° ΡΡΠ»Π΅Π²ΠΎΠ³ΠΎ ΠΌΠ΅Ρ Π°Π½ΠΈΠ·ΠΌΠ°, ΡΠ΅Π»ΡΡΠΊΠΎΡ ΠΎΠ·ΡΠΉΡΡΠ²Π΅Π½Π½ΠΎΠ΅ ΠΎΠ±ΠΎΡΡΠ΄ΠΎΠ²Π°Π½ΠΈΠ΅ ΠΈ ΠΆΠ΅Π»Π΅Π·Π½ΠΎΠ΄ΠΎΡΠΎΠΆΠ½ΠΎΠ΅ ΠΎΠ±ΠΎΡΡΠ΄ΠΎΠ²Π°Π½ΠΈΠ΅.
Π‘ ΠΏΠΎΡΠ²Π»Π΅Π½ΠΈΠ΅ΠΌ ΠΌΠ΅ΡΠ°Π»Π»ΠΎΠ³ΡΠ°ΡΠΈΠΈ ΠΈ ΠΏΠΎ ΠΌΠ΅ΡΠ΅ ΡΠ²Π΅Π»ΠΈΡΠ΅Π½ΠΈΡ ΠΎΠ±ΡΠ΅ΠΌΠ° Π·Π½Π°Π½ΠΈΠΉ, ΠΎΡΠ½ΠΎΡΡΡΠΈΡ ΡΡ ΠΊ ΡΡΠ³ΡΠ½Ρ, ΡΡΠ°Π»ΠΈ Π²ΠΎΠ·ΠΌΠΎΠΆΠ½ΡΠΌΠΈ Π΄ΡΡΠ³ΠΈΠ΅ ΠΊΠ»Π°ΡΡΠΈΡΠΈΠΊΠ°ΡΠΈΠΈ, ΠΎΡΠ½ΠΎΠ²Π°Π½Π½ΡΠ΅ Π½Π° ΠΌΠΈΠΊΡΠΎΡΡΡΡΠΊΡΡΡΠ½ΡΡ ΠΎΡΠΎΠ±Π΅Π½Π½ΠΎΡΡΡΡ . ΠΡΠΈ ΠΊΠ»Π°ΡΡΠΈΡΠΈΠΊΠ°ΡΠΈΠΈ ΡΠ΄Π΅Π»Π°Π½Ρ ΠΈΠ·-Π·Π° ΡΠΎΡΠΌΡ Π³ΡΠ°ΡΠΈΡΠ° ΠΈΠ»ΠΈ ΠΈΠ·-Π·Π° ΠΌΠ°ΡΡΠΈΡΡ ΡΡΡΡΠΊΡΡΡΡ ΠΈ ΠΏΡΠΈΠ²Π΅Π΄Π΅Π½Ρ Π½ΠΈΠΆΠ΅.
- Π€ΠΎΡΠΌΠ° Π³ΡΠ°ΡΠΈΡΠ°. Π Π·Π°Π²ΠΈΡΠΈΠΌΠΎΡΡΠΈ ΠΎΡ ΡΠΎΡΠΌΡ Π³ΡΠ°ΡΠΈΡΠ° ΡΡΠ³ΡΠ½Ρ ΠΊΠ»Π°ΡΡΠΈΡΠΈΡΠΈΡΡΡΡΡΡ ΠΊΠ°ΠΊ (i) ΠΏΠ»Π°ΡΡΠΈΠ½ΡΠ°ΡΡΠΉ (ΡΠ΅ΡΡΠΉΡΠ°ΡΡΠΉ) Π³ΡΠ°ΡΠΈΡ (FG), (ii) ΡΡΠ΅ΡΠΎΠΈΠ΄Π°Π»ΡΠ½ΡΠΉ (ΡΠ°ΡΠΎΠ²ΠΈΠ΄Π½ΡΠΉ) Π³ΡΠ°ΡΠΈΡ (SG), (iii) ΡΠΏΠ»ΠΎΡΠ½Π΅Π½Π½ΡΠΉ (Π²Π΅ΡΠΌΠΈΠΊΡΠ»ΡΡΠ½ΡΠΉ) Π³ΡΠ°ΡΠΈΡ (CG).
) ΠΈ (iv) ΠΎΡΠΏΡΡΠ΅Π½Π½ΡΠΉ Π³ΡΠ°ΡΠΈΡ (TG). Π’Π΅ΠΌΠΏΠ΅ΡΠΈΡΠΎΠ²Π°Π½Π½ΡΠΉ Π³ΡΠ°ΡΠΈΡ Π²ΠΎΠ·Π½ΠΈΠΊΠ°Π΅Ρ Π² ΡΠ΅Π·ΡΠ»ΡΡΠ°ΡΠ΅ ΡΠ²Π΅ΡΠ΄ΠΎΡΠ°Π·Π½ΠΎΠΉ ΡΠ΅Π°ΠΊΡΠΈΠΈ (ΠΊΠΎΠ²ΠΊΡ).
- ΠΠ°ΡΡΠΈΡΠ° ΡΡΡΡΠΊΡΡΡΡ. ΠΠ·-Π·Π° ΠΌΠ°ΡΡΠΈΡΡ ΡΡΡΡΠΊΡΡΡΡ ΡΡΠ³ΡΠ½Ρ ΠΊΠ»Π°ΡΡΠΈΡΠΈΡΠΈΡΡΡΡΡΡ ΠΊΠ°ΠΊ (i) ΡΠ΅ΡΡΠΈΡΠ½ΡΠ΅, (ii) ΠΏΠ΅ΡΠ»ΠΈΡΠ½ΡΠ΅, (iii) Π°ΡΡΡΠ΅Π½ΠΈΡΠ½ΡΠ΅, (iv) ΠΌΠ°ΡΡΠ΅Π½ΡΠΈΡΠ½ΡΠ΅ ΠΈ (v) Π±Π΅ΠΉΠ½ΠΈΡΠ½ΡΠ΅ (Π°ΡΡΡΠ΅Π½ΠΈΡΠ½ΡΠ΅).
ΠΠΎΠΌΠΈΠΌΠΎ ΡΠ΅ΡΡΡΠ΅Ρ ΠΎΡΠ½ΠΎΠ²Π½ΡΡ ΡΠΈΠΏΠΎΠ², ΡΡΡΠ΅ΡΡΠ²ΡΡΡ ΠΈ Π΄ΡΡΠ³ΠΈΠ΅ ΠΎΡΠΎΠ±ΡΠ΅ ΡΠΎΡΠΌΡ ΡΡΠ³ΡΠ½Π°, ΠΊ ΠΊΠΎΡΠΎΡΡΠΌ ΠΏΡΠΈΠΌΠ΅Π½ΡΡΡΡΡ ΡΠΏΠ΅ΡΠΈΠ°Π»ΡΠ½ΡΠ΅ Π½Π°Π·Π²Π°Π½ΠΈΡ. ΠΠ½ΠΈ ΠΏΡΠΈΠ²Π΅Π΄Π΅Π½Ρ Π½ΠΈΠΆΠ΅.
- ΠΡ Π»Π°ΠΆΠ΄Π΅Π½Π½ΠΎΠ΅ ΠΆΠ΅Π»Π΅Π·ΠΎ β ΡΡΠΎ Π±Π΅Π»ΠΎΠ΅ ΠΆΠ΅Π»Π΅Π·ΠΎ, ΠΏΠΎΠ»ΡΡΠ΅Π½Π½ΠΎΠ΅ ΠΏΡΡΠ΅ΠΌ ΠΎΡΠ΅Π½Ρ Π±ΡΡΡΡΠΎΠ³ΠΎ ΠΎΡ Π»Π°ΠΆΠ΄Π΅Π½ΠΈΡ Π² Π΄ΠΈΠ°ΠΏΠ°Π·ΠΎΠ½Π΅ ΡΠ΅ΠΌΠΏΠ΅ΡΠ°ΡΡΡ Π·Π°ΡΠ²Π΅ΡΠ΄Π΅Π²Π°Π½ΠΈΡ.
- ΠΡΡΠ½ΠΈΡΡΡΠΉ ΡΡΠ³ΡΠ½ β ΡΡΠ°ΡΡΠΎΠΊ ΠΎΡΠ»ΠΈΠ²ΠΊΠΈ, Π·Π°ΡΠ²Π΅ΡΠ΄Π΅Π²Π°ΡΡΠΈΠΉ ΡΠΎ ΡΠΊΠΎΡΠΎΡΡΡΡ, ΠΏΡΠΎΠΌΠ΅ΠΆΡΡΠΎΡΠ½ΠΎΠΉ ΠΌΠ΅ΠΆΠ΄Ρ ΠΎΡΠ±Π΅Π»Π΅Π½Π½ΡΠΌ ΠΈ ΡΠ΅ΡΡΠΌ ΡΡΠ³ΡΠ½ΠΎΠΌ, ΠΈ ΠΈΠΌΠ΅ΡΡΠΈΠΉ ΠΌΠΈΠΊΡΠΎΡΡΡΡΠΊΡΡΡΡ ΠΈ ΠΎΡΠΎΠ±Π΅Π½Π½ΠΎΡΡΠΈ ΠΏΠΎΠ²Π΅ΡΡ Π½ΠΎΡΡΠΈ ΠΈΠ·Π»ΠΎΠΌΠ° ΠΎΠ±ΠΎΠΈΡ ΡΠΈΠΏΠΎΠ².
- Π§ΡΠ³ΡΠ½ Ρ ΡΠΏΠ»ΠΎΡΠ½Π΅Π½Π½ΡΠΌ Π³ΡΠ°ΡΠΈΡΠΎΠΌ β ΡΠ°ΠΊΠΆΠ΅ ΠΈΠ·Π²Π΅ΡΡΠ΅Π½ ΠΊΠ°ΠΊ Π²Π΅ΡΠΌΠΈΠΊΡΠ»ΡΡΠ½ΡΠΉ ΡΡΠ³ΡΠ½. ΠΠ»Ρ Π½Π΅Π³ΠΎ Ρ
Π°ΡΠ°ΠΊΡΠ΅ΡΠ΅Π½ Π³ΡΠ°ΡΠΈΡ, ΡΠ²ΡΠ·Π°Π½Π½ΡΠΉ ΠΌΠ΅ΠΆΠ΄Ρ ΡΠΎΠ±ΠΎΠΉ ΡΠ²ΡΠ΅ΠΊΡΠΈΡΠ΅ΡΠΊΠΈΠΌΠΈ ΡΡΠ΅ΠΉΠΊΠ°ΠΌΠΈ, ΠΊΠ°ΠΊ ΠΈ ΡΠ΅ΡΡΠΉΡΠ°ΡΡΠΉ Π³ΡΠ°ΡΠΈΡ Π² ΡΠ΅ΡΠΎΠΌ ΡΡΠ³ΡΠ½Π΅. ΠΡΠ°ΡΠΈΡ Π² ΡΡΠ³ΡΠ½Π΅ Ρ ΡΠΏΠ»ΠΎΡΠ½Π΅Π½Π½ΡΠΌ Π³ΡΠ°ΡΠΈΡΠΎΠΌ Π±ΠΎΠ»Π΅Π΅ ΠΊΡΡΠΏΠ½ΡΠΉ ΠΈ ΠΎΠΊΡΡΠ³Π»ΡΠΉ, ΡΠ΅ΠΌ Π³ΡΠ°ΡΠΈΡ Π² ΡΠ΅ΡΠΎΠΌ ΡΡΠ³ΡΠ½Π΅.
ΠΠ³ΠΎ ΡΡΡΡΠΊΡΡΡΠ° Π·Π°Π½ΠΈΠΌΠ°Π΅Ρ ΠΏΡΠΎΠΌΠ΅ΠΆΡΡΠΎΡΠ½ΠΎΠ΅ ΠΏΠΎΠ»ΠΎΠΆΠ΅Π½ΠΈΠ΅ ΠΌΠ΅ΠΆΠ΄Ρ ΡΡΡΡΠΊΡΡΡΠ°ΠΌΠΈ ΡΠ΅ΡΠΎΠ³ΠΎ ΡΡΠ³ΡΠ½Π° ΠΈ Π²ΡΡΠΎΠΊΠΎΠΏΡΠΎΡΠ½ΠΎΠ³ΠΎ ΡΡΠ³ΡΠ½Π°. ΠΠ»Π°Π³ΠΎΠ΄Π°ΡΡ ΡΠ½ΠΈΠΊΠ°Π»ΡΠ½ΠΎΠΌΡ ΡΠΎΡΠ΅ΡΠ°Π½ΠΈΡ ΡΠ²ΠΎΠΉΡΡΠ² ΡΠΏΠ»ΠΎΡΠ½Π΅Π½Π½ΠΎΠ³ΠΎ ΡΠ΅ΡΠΎΠ³ΠΎ ΡΡΠ³ΡΠ½Π° ΠΎΠ½ ΠΏΡΠ΅Π²ΠΎΡΡ ΠΎΠ΄ΠΈΡ ΠΊΠ°ΠΊ ΡΠ΅ΡΡΠΉ, ΡΠ°ΠΊ ΠΈ ΠΊΠΎΠ²ΠΊΠΈΠΉ ΡΡΠ³ΡΠ½. ΠΡΠ½ΠΎΠ²Π½ΡΠΌΠΈ ΠΎΠ±Π»Π°ΡΡΡΠΌΠΈ ΠΏΡΠΈΠΌΠ΅Π½Π΅Π½ΠΈΡ ΡΠ²Π»ΡΡΡΡΡ ΡΠΎΡΠΎΡΡ Π΄ΠΈΡΠΊΠΎΠ²ΡΡ ΡΠΎΡΠΌΠΎΠ·ΠΎΠ² ΠΈ Π³ΠΎΠ»ΠΎΠ²ΠΊΠΈ Π΄ΠΈΠ·Π΅Π»ΡΠ½ΡΡ Π΄Π²ΠΈΠ³Π°ΡΠ΅Π»Π΅ΠΉ. Π§ΡΠ³ΡΠ½ Ρ ΡΠΏΠ»ΠΎΡΠ½Π΅Π½Π½ΡΠΌ Π³ΡΠ°ΡΠΈΡΠΎΠΌ ΠΌΠΎΠΆΠ½ΠΎ ΠΏΡΠΎΠΈΠ·Π²ΠΎΠ΄ΠΈΡΡ, ΡΡΠ°ΡΠ΅Π»ΡΠ½ΠΎ ΠΊΠΎΠ½ΡΡΠΎΠ»ΠΈΡΡΡ ΠΊΠΎΠ»ΠΈΡΠ΅ΡΡΠ²ΠΎ ΠΌΠ°Π³Π½ΠΈΡ, Π΄ΠΎΠ±Π°Π²Π»ΡΠ΅ΠΌΠΎΠ³ΠΎ Π² ΠΊΠ°ΡΠ΅ΡΡΠ²Π΅ ΠΌΠΎΠ΄ΠΈΡΠΈΠΊΠ°ΡΠΎΡΠ°, Π² ΠΏΡΠΎΡΠ΅ΡΡΠ΅, ΠΎΡΠ΅Π½Ρ ΠΏΠΎΡ ΠΎΠΆΠ΅ΠΌ Π½Π° ΠΏΡΠΎΡΠ΅ΡΡ, ΠΈΡΠΏΠΎΠ»ΡΠ·ΡΠ΅ΠΌΡΠΉ Π΄Π»Ρ ΠΏΡΠΎΠΈΠ·Π²ΠΎΠ΄ΡΡΠ²Π° ΠΊΠΎΠ²ΠΊΠΎΠ³ΠΎ ΡΡΠ³ΡΠ½Π°.
- ΠΡΡΠΎΠΊΠΎΠ»Π΅Π³ΠΈΡΠΎΠ²Π°Π½Π½ΡΠΉ Π³ΡΠ°ΡΠΈΡΠΎΠ²ΡΠΉ ΡΡΠ³ΡΠ½. ΠΠ½ΠΈ ΠΈΡΠΏΠΎΠ»ΡΠ·ΡΡΡΡΡ Π² ΠΎΡΠ½ΠΎΠ²Π½ΠΎΠΌ Π΄Π»Ρ ΠΏΡΠΈΠΌΠ΅Π½Π΅Π½ΠΈΠΉ, ΡΡΠ΅Π±ΡΡΡΠΈΡ ΠΊΠΎΡΡΠΎΠ·ΠΈΠΎΠ½Π½ΠΎΠΉ ΡΡΠΎΠΉΠΊΠΎΡΡΠΈ ΠΈΠ»ΠΈ ΡΠΎΡΠ΅ΡΠ°Π½ΠΈΡ ΠΏΡΠΎΡΠ½ΠΎΡΡΠΈ ΠΈ ΡΡΠΎΠΉΠΊΠΎΡΡΠΈ ΠΊ ΠΎΠΊΠΈΡΠ»Π΅Π½ΠΈΡ. ΠΠ½ΠΈ ΠΈΠ·Π³ΠΎΡΠ°Π²Π»ΠΈΠ²Π°ΡΡΡΡ ΠΊΠ°ΠΊ ΠΈΠ· ΡΠ΅ΡΡΠΉΡΠ°ΡΠΎΠ³ΠΎ Π³ΡΠ°ΡΠΈΡΠ° (ΡΠ΅ΡΡΠΉ ΡΡΠ³ΡΠ½), ΡΠ°ΠΊ ΠΈ ΠΈΠ· ΡΡΠ΅ΡΠΎΠΈΠ΄Π°Π»ΡΠ½ΠΎΠ³ΠΎ Π³ΡΠ°ΡΠΈΡΠ° (ΠΊΠΎΠ²ΠΊΠΈΠΉ ΡΡΠ³ΡΠ½).
ΠΠ°ΠΊΠΎΠ½Π΅Ρ, ΠΊΠ»Π°ΡΡΠΈΡΠΈΠΊΠ°ΡΠΈΡ, ΡΠ°ΡΡΠΎ ΠΈΡΠΏΠΎΠ»ΡΠ·ΡΠ΅ΠΌΠ°Ρ Π»ΠΈΡΠ΅ΠΉΡΠΈΠΊΠ°ΠΌΠΈ ΠΏΠΎΠ»ΠΎΠ², Π΄Π΅Π»ΠΈΡ ΡΡΠ³ΡΠ½Ρ Π½Π° Π΄Π²Π΅ ΠΊΠ°ΡΠ΅Π³ΠΎΡΠΈΠΈ. ΠΡΠΎ (i) ΠΎΠ±ΡΡΠ½ΡΠ΅ ΡΡΠ³ΡΠ½Ρ, ΠΊΠΎΡΠΎΡΡΠ΅ ΠΈΡΠΏΠΎΠ»ΡΠ·ΡΡΡΡΡ Π΄Π»Ρ ΠΎΠ±ΡΠ΅Π³ΠΎ ΠΏΡΠΈΠΌΠ΅Π½Π΅Π½ΠΈΡ, Π² ΠΎΡΠ½ΠΎΠ²Π½ΠΎΠΌ Π½Π΅Π»Π΅Π³ΠΈΡΠΎΠ²Π°Π½Π½ΡΠ΅ ΠΈΠ»ΠΈ Π½ΠΈΠ·ΠΊΠΎΠ»Π΅Π³ΠΈΡΠΎΠ²Π°Π½Π½ΡΠ΅ ΡΡΠ³ΡΠ½Ρ, ΠΈ (ii) ΡΠΏΠ΅ΡΠΈΠ°Π»ΡΠ½ΡΠ΅ ΡΡΠ³ΡΠ½Ρ, ΠΊΠΎΡΠΎΡΡΠ΅ ΠΈΡΠΏΠΎΠ»ΡΠ·ΡΡΡΡΡ Π΄Π»Ρ ΡΠΏΠ΅ΡΠΈΠ°Π»ΡΠ½ΡΡ
ΠΏΡΠΈΠΌΠ΅Π½Π΅Π½ΠΈΠΉ ΠΈ ΠΎΠ±ΡΡΠ½ΠΎ ΠΏΡΠ΅Π΄ΡΡΠ°Π²Π»ΡΡΡ ΡΠΎΠ±ΠΎΠΉ Π²ΡΡΠΎΠΊΠΎΠ»Π΅Π³ΠΈΡΠΎΠ²Π°Π½Π½ΡΠ΅ ΡΡΠ³ΡΠ½Ρ. Π‘ΠΏΠ΅ΡΠΈΠ°Π»ΡΠ½ΡΠ΅ ΡΡΠ³ΡΠ½Ρ ΠΎΡΠ»ΠΈΡΠ°ΡΡΡΡ ΠΎΡ ΠΎΠ±ΡΡΠ½ΡΡ
ΡΡΠ³ΡΠ½ΠΎΠ² Π³Π»Π°Π²Π½ΡΠΌ ΠΎΠ±ΡΠ°Π·ΠΎΠΌ Π±ΠΎΠ»Π΅Π΅ Π²ΡΡΠΎΠΊΠΈΠΌ ΡΠΎΠ΄Π΅ΡΠΆΠ°Π½ΠΈΠ΅ΠΌ Π»Π΅Π³ΠΈΡΡΡΡΠΈΡ
ΡΠ»Π΅ΠΌΠ΅Π½ΡΠΎΠ² (Π±ΠΎΠ»Π΅Π΅ 3 %), ΡΡΠΎ ΡΠΏΠΎΡΠΎΠ±ΡΡΠ²ΡΠ΅Ρ ΠΏΠΎΠ»ΡΡΠ΅Π½ΠΈΡ ΠΌΠΈΠΊΡΠΎΡΡΡΡΠΊΡΡΡ, ΠΎΠ±Π»Π°Π΄Π°ΡΡΠΈΡ
ΠΎΡΠΎΠ±ΡΠΌΠΈ ΡΠ²ΠΎΠΉΡΡΠ²Π°ΠΌΠΈ Π΄Π»Ρ ΠΏΡΠΈΠΌΠ΅Π½Π΅Π½ΠΈΡ ΠΏΡΠΈ ΠΏΠΎΠ²ΡΡΠ΅Π½Π½ΡΡ
ΡΠ΅ΠΌΠΏΠ΅ΡΠ°ΡΡΡΠ°Ρ
, ΠΊΠΎΡΡΠΎΠ·ΠΈΠΎΠ½Π½ΠΎΠΉ ΡΡΠΎΠΉΠΊΠΎΡΡΡΡ ΠΈ ΠΈΠ·Π½ΠΎΡΠΎΡΡΠΎΠΉΠΊΠΎΡΡΡΡ. ΠΠ»Π°ΡΡΠΈΡΠΈΠΊΠ°ΡΠΈΡ ΠΎΡΠ½ΠΎΠ²Π½ΡΡ
ΡΠΈΠΏΠΎΠ² ΡΠΏΠ΅ΡΠΈΠ°Π»ΡΠ½ΡΡ
Π²ΡΡΠΎΠΊΠΎΠ»Π΅Π³ΠΈΡΠΎΠ²Π°Π½Π½ΡΡ
ΡΡΠ³ΡΠ½ΠΎΠ² ΠΏΡΠ΅Π΄ΡΡΠ°Π²Π»Π΅Π½Π° ββΠ½Π° ΡΠΈΡ. 3.9.0021
Π ΠΈΡ. 3 ΠΡΠ½ΠΎΠ²Π½ΡΠ΅ ΡΠΈΠΏΡ ΡΠΏΠ΅ΡΠΈΠ°Π»ΡΠ½ΡΡ Π²ΡΡΠΎΠΊΠΎΠ»Π΅Π³ΠΈΡΠΎΠ²Π°Π½Π½ΡΡ ΡΡΠ³ΡΠ½ΠΎΠ²
Π’ΠΈΠΏΡ ΡΡΠ³ΡΠ½Π° (ΡΡΡ. 1), ΡΠ΅ΡΡΠΉ ΠΈ ΠΊΠΎΠ²ΠΊΠΈΠΉ ΡΡΠ³ΡΠ½
ΠΠ°ΡΠΊΠΈ ΡΡΠ³ΡΠ½Π°
ΠΠ»Ρ Π±ΠΎΠ»ΡΡΠΈΠ½ΡΡΠ²Π° ΡΠΎΠ²ΡΠ΅ΠΌΠ΅Π½Π½ΡΡ Π°Π²ΡΠΎΠΌΠΎΠ±ΠΈΠ»ΡΠ½ΡΡ ΠΈ ΠΏΠΎΡΡΠ΅Π±ΠΈΡΠ΅Π»ΡΡΠΊΠΈΡ ΠΏΡΠΈΠΌΠ΅Π½Π΅Π½ΠΈΠΉ ΡΡΠ³ΡΠ½ ΠΏΠΎΠ΄ΡΠ°Π·Π΄Π΅Π»ΡΠ΅ΡΡΡ Π½Π° 4 ΠΎΡΠ΄Π΅Π»ΡΠ½ΡΡ ΠΊΠ°ΡΠ΅Π³ΠΎΡΠΈΠΈ:
- Π‘Π΅ΡΡΠΉ ΡΡΠ³ΡΠ½Β (ΡΡΠ° ΡΡΡΠ°Π½ΠΈΡΠ°)
- ΠΡΡΠΎΠΊΠΎΠΏΡΠΎΡΠ½ΡΠΉ ΡΡΠ³ΡΠ½Β (ΡΡΠ° ΡΡΡΠ°Π½ΠΈΡΠ°)
- ΠΡΡΡΠ΅Π½ΠΈΡΠ½ΡΠΉ ΠΊΠΎΠ²ΠΊΠΈΠΉ ΡΡΠ³ΡΠ½ (ΡΡΡΠ°Π½ΠΈΡΠ° 2)
- Π§ΡΠ³ΡΠ½ Ρ ΡΠΏΠ»ΠΎΡΠ½Π΅Π½Π½ΡΠΌ Π³ΡΠ°ΡΠΈΡΠΎΠΌ Π‘ΡΡΠ°Π½ΠΈΡΠ° 2)
Π Π‘Π΅Π²Π΅ΡΠ½ΠΎΠΉ ΠΠΌΠ΅ΡΠΈΠΊΠ΅ Π΅ΡΡΡ 2 ΠΏΡΠΎΠΌΡΡΠ»Π΅Π½Π½ΡΡ ΠΎΠ±ΡΠ΅ΡΡΠ²Π°, ΠΊΠΎΡΠΎΡΡΠ΅ ΠΏΡΠΈΠ½ΠΈΠΌΠ°ΡΡ ΠΎΡΠ²Π΅ΡΡΡΠ²Π΅Π½Π½ΠΎΡΡΡ Π·Π° ΠΎΡΠ³Π°Π½ΠΈΠ·Π°ΡΠΈΡ ΠΈ ΡΠΏΡΠ°Π²Π»Π΅Π½ΠΈΠ΅ ΠΏΡΠΎΠ³ΡΠ°ΠΌΠΌΠ°ΠΌΠΈ ΠΏΠΎ ΡΠ΅Π³ΡΠ»ΠΈΡΠΎΠ²Π°Π½ΠΈΡ ΠΈ ΡΠΎΠ²Π΅ΡΡΠ΅Π½ΡΡΠ²ΠΎΠ²Π°Π½ΠΈΡ ΡΠ΅Ρ Π½ΠΎΠ»ΠΎΠ³ΠΈΡΠ΅ΡΠΊΠΈΡ ΠΏΡΠΎΡΠ΅ΡΡΠΎΠ²:
- ΠΠΌΠ΅ΡΠΈΠΊΠ°Π½ΡΠΊΠΎΠ΅ ΠΎΠ±ΡΠ΅ΡΡΠ²ΠΎ Π»ΠΈΡΠ΅ΠΉΡΠΈΠΊΠΎΠ² (AFS)
- ΠΠ±ΡΠ΅ΡΡΠ²ΠΎ ΠΊΠΎΠ²ΠΊΠΎΠ³ΠΎ ΡΡΠ³ΡΠ½Π° (DIS)
Π‘ΡΠ°Π²Π½Π΅Π½ΠΈΠ΅ Π³ΡΠ°ΡΠΈΡΠ° — ΠΌΠΈΠΊΡΠΎΡΠΎΡΠΎΠ³ΡΠ°ΡΠΈΡΠ΅ΡΠΊΠΈΠ΅ ΠΈΡΡΠ»Π΅Π΄ΠΎΠ²Π°Π½ΠΈΡ
Π‘Π΅ΡΡΠΉ ΡΡΠ³ΡΠ½ — ΠΡΠΈΠΌΠ΅Ρ ΠΌΠΈΠΊΡΠΎΡΠΎΡΠΎΠ³ΡΠ°ΡΠΈΠΈ ΠΠΎΠ²ΠΊΠΈΠΉ ΡΡΠ³ΡΠ½ — ΠΡΠΈΠΌΠ΅Ρ ΠΌΠΈΠΊΡΠΎΡΠΎΡΠΎΠ³ΡΠ°ΡΠΈΠΈ ΠΡΡΠΎΠΊΠΎΠΏΡΠΎΡΠ½ΡΠΉ ΡΡΠ³ΡΠ½ Ρ Π°ΡΡΡΠ΅Π½ΠΈΡΠ½ΡΠΌ ΠΎΡΠΏΡΡΠΊΠΎΠΌ β ΠΌΠΈΠΊΡΠΎΡΠΎΡΠΎΠ³ΡΠ°ΡΠΈΡΠ§ΡΠ³ΡΠ½ Ρ ΡΠΏΠ»ΠΎΡΠ½Π΅Π½Π½ΡΠΌ Π³ΡΠ°ΡΠΈΡΠΎΠΌ β ΠΌΠΈΠΊΡΠΎΡΠΎΡΠΎΠ³ΡΠ°ΡΠΈΡ Π§ΡΠ³ΡΠ½ ΠΏΡΠ΅Π΄ΡΡΠ°Π²Π»ΡΠ΅Ρ ΡΠΎΠ±ΠΎΠΉ ΡΠΏΠ»Π°Π² ΠΆΠ΅Π»Π΅Π·ΠΎ-ΡΠ³Π»Π΅ΡΠΎΠ΄-ΠΊΡΠ΅ΠΌΠ½ΠΈΠΉ, ΡΠΎΠ΄Π΅ΡΠΆΠ°ΡΠΈΠΉ Π±ΠΎΠ»Π΅Π΅ 2% ΡΠ³Π»Π΅ΡΠΎΠ΄Π°, ΠΊΠΎΡΠΎΡΡΠΉ Π·Π°Π»ΠΈΠ²Π°ΡΡ Π² ΡΠΎΡΠΌΡ, ΡΠΎΠ΄Π΅ΡΠΆΠ°ΡΡΡ Π½Π΅Π³Π°ΡΠΈΠ² ΠΆΠ΅Π»Π°Π΅ΠΌΠΎΠΉ ΠΎΠΊΠΎΠ½ΡΠ°ΡΠ΅Π»ΡΠ½ΠΎΠΉ ΡΠΎΡΠΌΡ. ΠΠ΅Ρ
Π°Π½ΠΈΡΠ΅ΡΠΊΠΈΠ΅ ΡΠ²ΠΎΠΉΡΡΠ²Π° ΠΈ ΠΏΠΎΠ²Π΅Π΄Π΅Π½ΠΈΠ΅ ΠΌΠ°ΡΠ΅ΡΠΈΠ°Π»Π° Π·Π°Π²ΠΈΡΡΡ ΠΎΡ ΠΌΠΎΡΡΠΎΠ»ΠΎΠ³ΠΈΠΈ Π³ΡΠ°ΡΠΈΡΠ°, ΠΊΠΎΡΠΎΡΡΠΉ ΠΎΠ±ΡΠ°Π·ΡΠ΅ΡΡΡ Π² ΠΆΠ΅Π»Π΅Π·Π½ΠΎΠΉ ΠΌΠ°ΡΡΠΈΡΠ΅ Π² ΡΠ΅Π·ΡΠ»ΡΡΠ°ΡΠ΅ ΡΠ΅ΡΠΌΠΎΡΠ΅Π³ΡΠ»ΠΈΡΠΎΠ²Π°Π½ΠΈΡ ΠΏΡΠΎΡΠ΅ΡΡΠ° ΠΈ Π΄ΠΎΠ±Π°Π²Π»Π΅Π½ΠΈΡ ΡΠ»Π΅ΠΌΠ΅Π½ΡΠΎΠ² Π΄Π»Ρ ΠΏΠΎΠ»ΡΡΠ΅Π½ΠΈΡ ΠΆΠ΅Π»Π°Π΅ΠΌΠΎΠΉ ΡΠΎΡΠΌΡ Π³ΡΠ°ΡΠΈΡΠ°. ΠΡΠ΅ ΡΡΠ³ΡΠ½Ρ Π·Π°ΡΠ²Π΅ΡΠ΄Π΅Π²Π°ΡΡ Π² ΡΠ΅Π·ΡΠ»ΡΡΠ°ΡΠ΅ ΡΠ»ΠΎΠΆΠ½ΠΎΠΉ ΡΠ²ΡΠ΅ΠΊΡΠΈΡΠ΅ΡΠΊΠΎΠΉ ΡΠ΅Π°ΠΊΡΠΈΠΈ, Π² ΠΊΠΎΡΠΎΡΠΎΠΉ ΡΡΠ°ΡΡΠ²ΡΡΡ Fe, C ΠΈ Si. ΠΡΡΡ ΡΠ°ΠΊΠΆΠ΅ Π²Π»ΠΈΡΠ½ΠΈΠ΅ Cu, Mn, S ΠΈ P.
Π‘Π΅ΡΡΠΉ ΡΡΠ³ΡΠ½
Π‘Π΅ΡΡΠΉ ΡΡΠ³ΡΠ½ β ΡΡΠΎ ΡΠ°ΠΌΠ°Ρ ΠΏΡΠΎΡΡΠ°Ρ, ΡΠ°ΠΌΠ°Ρ ΡΠ°ΡΠΏΡΠΎΡΡΡΠ°Π½Π΅Π½Π½Π°Ρ ΠΈ ΡΠ°ΠΌΠ°Ρ Π΄Π΅ΡΠ΅Π²Π°Ρ ΡΠΎΡΠΌΠ° ΡΡΠ³ΡΠ½Π° Π² ΠΌΠΈΡΠ΅. ΠΠΈΠΊΡΠΎΡΡΡΡΠΊΡΡΡΠ° ΠΆΠ΅Π»Π΅Π·Π° Ρ Π°ΡΠ°ΠΊΡΠ΅ΡΠΈΠ·ΡΠ΅ΡΡΡ ΠΊΠ°ΡΠ΅ΡΡΠ²Π°ΠΌΠΈ Β«ΡΠ΅ΡΡΠΉΡΠ°ΡΠΎΠ³ΠΎ Π³ΡΠ°ΡΠΈΡΠ°Β» Π² Π²ΠΈΠ΄Π΅: Π°) ΡΠΈΠΏΠ°, Π±) ΡΠ°Π·ΠΌΠ΅ΡΠ° ΠΈ Π²) ΠΌΠ°ΡΡΠΈΡΡ.
Π‘Π΅ΡΡΠΉ ΡΡΠ³ΡΠ½ ΠΎΠ±Π»Π°Π΄Π°Π΅Ρ ΠΏΡΠ΅Π²ΠΎΡΡ ΠΎΠ΄Π½ΡΠΌΠΈ Π»ΠΈΡΠ΅ΠΉΠ½ΡΠΌΠΈ ΡΠ²ΠΎΠΉΡΡΠ²Π°ΠΌΠΈ ΠΈ ΠΎΠ±ΡΠ°Π±Π°ΡΡΠ²Π°Π΅ΠΌΠΎΡΡΡΡ, ΡΡΠΎ Π΄Π΅Π»Π°Π΅Ρ Π΅Π³ΠΎ ΠΎΡΠ΅Π½Ρ ΡΠ΅Π½Π½ΡΠΌ Π΄Π»Ρ ΡΡΠΆΠ΅Π»ΡΡ Π΄Π΅ΡΠ°Π»Π΅ΠΉ. ΠΡΠΎΠΌΠ΅ ΡΠΎΠ³ΠΎ, ΡΠ΅ΡΡΠΉ ΡΡΠ³ΡΠ½ ΠΎΠ±Π»Π°Π΄Π°Π΅Ρ ΠΏΡΠ΅Π²ΠΎΡΡ ΠΎΠ΄Π½ΡΠΌΠΈ Π΄Π΅ΠΌΠΏΡΠΈΡΡΡΡΠΈΠΌΠΈ ΠΈ ΡΠ΅ΠΏΠ»ΠΎΠ²ΡΠΌΠΈ ΡΠ²ΠΎΠΉΡΡΠ²Π°ΠΌΠΈ, ΡΡΠΎ Π΄Π΅Π»Π°Π΅Ρ Π΅Π³ΠΎ ΠΈΠ΄Π΅Π°Π»ΡΠ½ΡΠΌ Π΄Π»Ρ Π°Π²ΡΠΎΠΌΠΎΠ±ΠΈΠ»ΡΠ½ΡΡ ΡΠΎΡΠΌΠΎΠ·Π½ΡΡ ΡΠΈΡΡΠ΅ΠΌ. Π₯ΠΎΡΡ ΠΎΠ½ ΠΏΡΠΎΡΠ½ΡΠΉ, ΠΎΠ½ ΡΠ°ΠΊΠΆΠ΅ Ρ ΡΡΠΏΠΊΠΈΠΉ.
Π’ΠΈΠΏΡ ΡΠ΅ΡΡΠΉΡΠ°ΡΠΎΠ³ΠΎ Π³ΡΠ°ΡΠΈΡΠ°
Π‘Π΅ΡΡΠΉ ΡΡΠ³ΡΠ½ Π½Π° ΡΠ΅Π³ΠΎΠ΄Π½ΡΡΠ½ΠΈΠΉ Π΄Π΅Π½Ρ ΡΠ²Π»ΡΠ΅ΡΡΡ Π½Π°ΠΈΠ±ΠΎΠ»Π΅Π΅ ΡΠ°ΡΠΏΡΠΎΡΡΡΠ°Π½Π΅Π½Π½ΡΠΌ ΠΈΠ· ΡΡΠ³ΡΠ½ΠΎΠ². ΠΠ°ΡΡΠ΄Ρ ΡΠΎ ΡΡΠ°Π»ΡΡ ΡΡΠΎ Π½Π°ΠΈΠ±ΠΎΠ»Π΅Π΅ ΡΠΈΡΠΎΠΊΠΎ ΠΈΡΠΏΠΎΠ»ΡΠ·ΡΠ΅ΠΌΡΠΉ ΠΈΠ½ΠΆΠ΅Π½Π΅ΡΠ½ΡΠΉ ΡΠΏΠ»Π°Π². Π 1 Π²Π΅ΠΊΠ΅ Π°Π²ΡΠΎΠΌΠΎΠ±ΠΈΠ»ΡΠ½ΠΎΠΉ ΠΏΡΠΎΠΌΡΡΠ»Π΅Π½Π½ΠΎΡΡΠΈ ΡΡΠΎ Π±ΡΠ» ΠΏΡΠ΅Π΄ΠΏΠΎΡΡΠΈΡΠ΅Π»ΡΠ½ΡΠΉ ΠΌΠ°ΡΠ΅ΡΠΈΠ°Π» Π΄Π»Ρ Π±Π»ΠΎΠΊΠΎΠ² ΡΠΈΠ»ΠΈΠ½Π΄ΡΠΎΠ², Π³ΠΎΠ»ΠΎΠ²ΠΎΠΊ ΠΈ ΠΌΠ½ΠΎΠ³ΠΈΡ
Π΄ΡΡΠ³ΠΈΡ
ΠΊΠΎΠΌΠΏΠΎΠ½Π΅Π½ΡΠΎΠ² ΡΡΠ°Π½ΡΠΌΠΈΡΡΠΈΠΈ. ΠΠ°Π·Π²Π°Π½ΠΈΠ΅ ΠΏΡΠΎΠΈΡΡ
ΠΎΠ΄ΠΈΡ ΠΎΡ Π²Π½Π΅ΡΠ½Π΅Π³ΠΎ Π²ΠΈΠ΄Π° ΠΏΠΎΠ²Π΅ΡΡ
Π½ΠΎΡΡΠΈ ΠΈΠ·Π»ΠΎΠΌΠ°, ΠΊΠΎΡΠΎΡΠ°Ρ ΠΈΠΌΠ΅Π΅Ρ ΡΠ΅ΡΡΠΉ ΡΠ²Π΅Ρ. Π ΡΠ΅ΡΠΎΠΌ ΡΡΠ³ΡΠ½Π΅ Π³ΡΠ°ΡΠΈΡ Π·Π°ΡΠ²Π΅ΡΠ΄Π΅Π²Π°Π΅Ρ Π² Π²ΠΈΠ΄Π΅ Π²Π·Π°ΠΈΠΌΠΎΡΠ²ΡΠ·Π°Π½Π½ΡΡ
ΡΠ΅ΡΡΠ΅ΠΊ, ΠΊΠ°ΠΊ ΠΏΠΎΠΊΠ°Π·Π°Π½ΠΎ Π²ΡΡΠ΅ Π² 3D-ΠΌΠΈΠΊΡΠΎΡΠΊΠΎΠΏΠΈΠΈ Ρ ΠΏΠΎΠΌΠΎΡΡΡ ΡΠΊΠ°Π½ΠΈΡΡΡΡΠ΅Π³ΠΎ ΡΠ»Π΅ΠΊΡΡΠΎΠ½Π½ΠΎΠ³ΠΎ ΠΌΠΈΠΊΡΠΎΡΠΊΠΎΠΏΠ°. Π‘Π³ΡΡΠΏΠΏΠΈΡΠΎΠ²Π°Π½Π½ΡΠ΅ ΡΠΎΡΠΌΡ Π³ΡΠ°ΡΠΈΡΠ° ΡΡΠ°Π²Π½ΠΈΠ²Π°ΡΡ Ρ ΠΊΠ°ΡΡΠΎΡΠ΅Π»ΡΠ½ΡΠΌΠΈ ΡΠΈΠΏΡΠ°ΠΌΠΈ, ΡΠΊΠ»Π΅Π΅Π½Π½ΡΠΌΠΈ Π²ΠΌΠ΅ΡΡΠ΅ Π² ΡΠ΅Π½ΡΡΠ°Π»ΡΠ½ΠΎΠΌ ΠΌΠ΅ΡΡΠ΅. Π¦Π΅Π½ΡΡΠ°Π»ΡΠ½Π°Ρ ΡΠΎΡΠΊΠ° β ΠΈΡΡ
ΠΎΠ΄Π½ΠΎΠ΅ Π³ΡΠ°ΡΠΈΡΠΎΠ²ΠΎΠ΅ ΡΠ΄ΡΠΎ. ΠΠ°ΠΆΠ΄ΡΠΉ ΠΊΠ»Π°ΡΡΠ΅Ρ ΡΠ΅ΡΡΠ΅ΠΊ ΠΎΠΏΡΠ΅Π΄Π΅Π»ΡΠ΅Ρ ΡΠ²ΡΠ΅ΠΊΡΠΈΡΠ΅ΡΠΊΡΡ ΡΡΠ΅ΠΉΠΊΡ Π² ΡΠ΅ΡΠΎΠΌ ΡΡΠ³ΡΠ½Π΅. ΠΠ²ΡΠ΅ΠΊΡΠΈΡΠ΅ΡΠΊΠΈΠ΅ ΡΡΠ΅ΠΉΠΊΠΈ Π½Π΅ΡΠΊΠΎΠ»ΡΠΊΠΎ Π°Π½Π°Π»ΠΎΠ³ΠΈΡΠ½Ρ Π·Π΅ΡΠ½Π°ΠΌ Π² Π΄ΡΡΠ³ΠΈΡ
ΠΌΠ΅ΡΠ°Π»Π»Π°Ρ
. ΠΡΠΎΡΠ½ΠΎΡΡΡ ΠΆΠ΅Π»Π΅Π·Π° ΠΏΠΎΠ²ΡΡΠ°Π΅ΡΡΡ Π·Π° ΡΡΠ΅Ρ Π±ΠΎΠ»Π΅Π΅ ΠΌΠ΅Π»ΠΊΠΈΡ
ΡΠ°Π·ΠΌΠ΅ΡΠΎΠ² ΡΡΠ΅Π΅ΠΊ.
Π€ΠΎΡΠΌΠ° Π³ΡΠ°ΡΠΈΡΠ° Π² ΡΠ΅ΡΠΎΠΌ ΡΡΠ³ΡΠ½Π΅ ΡΠ²Π»ΡΠ΅ΡΡΡ Π²Π°ΠΆΠ½ΡΠΌ ΡΠ°ΠΊΡΠΎΡΠΎΠΌ, ΠΎΠΏΡΠ΅Π΄Π΅Π»ΡΡΡΠΈΠΌ ΡΠ²ΠΎΠΉΡΡΠ²Π° ΡΠΏΠ»Π°Π²Π°. Π€ΠΎΡΠΌΠ° ΠΈ ΡΠ°Π·ΠΌΠ΅Ρ Π³ΡΠ°ΡΠΈΡΠ° ΠΌΠΎΠ³ΡΡ Π·Π°ΠΌΠ΅ΡΠ½ΠΎ ΡΠ°Π·Π»ΠΈΡΠ°ΡΡΡΡ Π² Π·Π°Π²ΠΈΡΠΈΠΌΠΎΡΡΠΈ ΠΎΡ ΡΠΊΠΎΡΠΎΡΡΠΈ ΠΎΡ
Π»Π°ΠΆΠ΄Π΅Π½ΠΈΡ ΠΈ ΡΠΎΠ΄Π΅ΡΠΆΠ°Π½ΠΈΡ ΡΠΏΠ»Π°Π²Π°. ΠΠ°ΠΈΠ±ΠΎΠ»Π΅Π΅ ΡΠ°ΡΠΏΡΠΎΡΡΡΠ°Π½Π΅Π½Π½Π°Ρ ΡΠΎΡΠΌΠ°, ΠΊΠ°ΠΊ ΠΎΠΏΠΈΡΠ°Π½ΠΎ Π² ΠΏΡΠ΅Π΄ΡΠ΄ΡΡΠ΅ΠΌ Π°Π±Π·Π°ΡΠ΅, Π½Π°Π·ΡΠ²Π°Π΅ΡΡΡ Type A . ΠΡΡΡ ΡΠΈΠΏΠΎΠ² Π³ΡΠ°ΡΠΈΡΠ° Π² ΡΠ΅ΡΠΎΠΌ ΡΡΠ³ΡΠ½Π΅ ΠΊΠ»Π°ΡΡΠΈΡΠΈΡΠΈΡΡΡΡΡΡ ΠΊΠ°ΠΊ b ASTM.
Π’ΠΈΠΏ A Π§Π΅ΡΡΠΉΡΠ°ΡΠ°Ρ ΡΡΡΡΠΊΡΡΡΠ°
ΠΡΠ°ΡΠΈΡ ΡΠΈΠΏΠ° A ΠΈΠΌΠ΅Π΅Ρ ΡΠ°Π²Π½ΠΎΠΌΠ΅ΡΠ½ΠΎΠ΅ ΡΠ°ΡΠΏΡΠ΅Π΄Π΅Π»Π΅Π½ΠΈΠ΅ ΠΈ ΡΠ»ΡΡΠ°ΠΉΠ½ΡΡ ΠΎΡΠΈΠ΅Π½ΡΠ°ΡΠΈΡ. ΠΠ°ΠΊ ΠΏΡΠ°Π²ΠΈΠ»ΠΎ, ΠΎΠ½ ΠΎΠ±Π΅ΡΠΏΠ΅ΡΠΈΠ²Π°Π΅Ρ Π½Π°ΠΈΠ»ΡΡΡΠΈΠ΅ ΡΠ²ΠΎΠΉΡΡΠ²Π° ΠΈ ΠΎΠ±ΡΡΠ½ΠΎ ΠΈΡΠΏΠΎΠ»ΡΠ·ΡΠ΅ΡΡΡ Π΄Π»Ρ ΠΊΠΎΠΌΠΏΠΎΠ½Π΅Π½ΡΠΎΠ² ΡΡΠ°Π½ΡΠΌΠΈΡΡΠΈΠΈ.
Π‘Π΅ΡΡΠΉ ΡΡΠ³ΡΠ½ — Π’ΠΈΠΏ ΠΠ‘ΡΡΡΠΊΡΡΡΠ° Ρ Π»ΠΎΠΏΡΠ΅Π² ΡΠΈΠΏΠ° B
ΠΡΠ°ΡΠΈΡ ΡΠΈΠΏΠ° B Π²ΡΠ³Π»ΡΠ΄ΠΈΡ ΠΊΠ°ΠΊ ΡΠΎΠ·Π΅ΡΠΊΠΈ ΡΠΎ ΡΠ»ΡΡΠ°ΠΉΠ½ΠΎΠΉ ΠΎΡΠΈΠ΅Π½ΡΠ°ΡΠΈΠ΅ΠΉ. ΠΡΠΎ ΡΠ°ΡΠ΅ Π²ΡΠ΅Π³ΠΎ ΠΏΡΠΎΠΈΡΡ ΠΎΠ΄ΠΈΡ Π² ΠΏΠΎΡΡΠΈ ΡΠ²ΡΠ΅ΠΊΡΠΈΡΠ΅ΡΠΊΠΈΡ ΡΠΏΠ»Π°Π²Π°Ρ , ΠΊΠΎΡΠΎΡΡΠ΅ Π½Π΅ΠΏΡΠ°Π²ΠΈΠ»ΡΠ½ΠΎ ΠΌΠΎΠ΄ΠΈΡΠΈΡΠΈΡΠΎΠ²Π°Π½Ρ ΠΈ ΡΠΎΠ΄Π΅ΡΠΆΠ°Ρ ΠΎΡΠ΅Π½Ρ ΠΌΠ°Π»ΠΎ Π·Π°ΡΠΎΠ΄ΡΡΠ΅ΠΉ Π³ΡΠ°ΡΠΈΡΠ°. ΠΡΠ°ΡΠΈΡ ΡΠΈΠΏΠ° B ΡΠ°ΡΡΠΎ Π²ΡΡΡΠ΅ΡΠ°Π΅ΡΡΡ Π½Π° ΠΏΠΎΠ²Π΅ΡΡ Π½ΠΎΡΡΠΈ ΠΎΡΠ»ΠΈΠ²ΠΊΠΈ, Π³Π΄Π΅ Π² ΠΎΡΡΠ°Π»ΡΠ½ΠΎΠΌ ΠΎΠ½ ΠΎΡΠ½ΠΎΡΠΈΡΡΡ ΠΊ ΡΠΈΠΏΡ A.
Π‘Π΅ΡΡΠΉ ΡΡΠ³ΡΠ½ — ΡΠΈΠΏ BΠ‘ΡΡΡΠΊΡΡΡΠ° ΡΠ΅ΡΡΠ΅ΠΊ ΡΠΈΠΏΠ° C
ΠΡΠ°ΡΠΈΡ ΡΠΈΠΏΠ° C Π²ΡΡΡΠ΅ΡΠ°Π΅ΡΡΡ Π² Π·Π°ΡΠ²ΡΠ΅ΠΊΡΠΈΡΠ΅ΡΠΊΠΈΡ ΡΡΠ³ΡΠ½Π°Ρ (CE Π±ΠΎΠ»ΡΡΠ΅ 4,3), Π² ΠΊΠΎΡΠΎΡΡΡ Π³ΡΠ°ΡΠΈΡ ΠΎΠ±ΡΠ°Π·ΡΠ΅ΡΡΡ Π² ΠΊΠ°ΡΠ΅ΡΡΠ²Π΅ ΠΏΠ΅ΡΠ²ΠΈΡΠ½ΠΎΠΉ ΡΠ°Π·Ρ. ΠΡΠΎΡ ΠΏΠ΅ΡΠ²ΠΈΡΠ½ΡΠΉ Π³ΡΠ°ΡΠΈΡ Π½Π°Π·ΡΠ²Π°Π΅ΡΡΡ Π³ΡΠ°ΡΠΈΡΠΎΠΌ ΠΠΈΡΠ°. ΠΠ³ΠΎ ΠΏΡΠΈΡΡΡΡΡΠ²ΠΈΠ΅ ΡΠ½ΠΈΠΆΠ°Π΅Ρ ΡΠ²ΠΎΠΉΡΡΠ²Π° ΠΏΡΠΈ ΡΠ°ΡΡΡΠΆΠ΅Π½ΠΈΠΈ, ΡΡΠΎ ΠΌΠΎΠΆΠ΅Ρ Π±ΡΡΡ ΠΆΠ΅Π»Π°ΡΠ΅Π»ΡΠ½ΡΠΌ Π΄Π»Ρ Π½Π΅ΠΊΠΎΡΠΎΡΡΡ ΡΠΏΠ΅ΡΠΈΠ°Π»ΡΠ½ΡΡ ΠΏΡΠΈΠΌΠ΅Π½Π΅Π½ΠΈΠΉ.
Π‘Π΅ΡΡΠΉ ΡΡΠ³ΡΠ½ — Π’ΠΈΠΏ CΠ‘ΡΡΡΠΊΡΡΡΠ° Ρ Π»ΠΎΠΏΡΠ΅Π² ΡΠΈΠΏΠ° D
ΠΡΠ°ΡΠΈΡ ΡΠΈΠΏΠ° D Π²ΠΎΠ·Π½ΠΈΠΊΠ°Π΅Ρ Π² ΡΠ΅Π·ΡΠ»ΡΡΠ°ΡΠ΅ ΠΌΠ΅ΠΆΠ΄Π΅Π½Π΄ΡΠΈΡΠ½ΠΎΠΉ ΡΠ΅Π³ΡΠ΅Π³Π°ΡΠΈΠΈ Π² Π±ΡΡΡΡΠΎ ΠΎΡ
Π»Π°ΠΆΠ΄Π΅Π½Π½ΡΡ
ΡΡΠ³ΡΠ½Π°Ρ
.
Π‘ΡΡΡΠΊΡΡΡΠ° ΡΠ΅ΡΡΠ΅ΠΊ ΡΠΈΠΏΠ° E
ΠΡΠ°ΡΠΈΡ ΡΠΈΠΏΠ° E ΠΏΠΎΡ ΠΎΠΆ Π½Π° ΡΠΈΠΏ D, Π½ΠΎ Ρ ΠΎΡΠΈΠ΅Π½ΡΠΈΡΠΎΠ²Π°Π½Π½ΡΠΌΠΈ ΡΠ΅ΡΡΠΉΠΊΠ°ΠΌΠΈ ΠΌΠ΅ΠΆΠ΄Ρ Π²Π΅ΡΠ²ΡΠΌΠΈ Π°ΡΡΡΠ΅Π½ΠΈΡΠ½ΡΡ Π΄Π΅Π½Π΄ΡΠΈΡΠΎΠ². Π§Π°ΡΠ΅ Π²ΡΠ΅Π³ΠΎ ΡΡΠΎ ΠΏΡΠΎΠΈΡΡ ΠΎΠ΄ΠΈΡ Π² ΡΡΠ³ΡΠ½Π°Ρ Ρ ΠΎΡΠ΅Π½Ρ Π½ΠΈΠ·ΠΊΠΈΠΌ ΡΠ³Π»Π΅ΡΠΎΠ΄Π½ΡΠΌ ΡΠΊΠ²ΠΈΠ²Π°Π»Π΅Π½ΡΠΎΠΌ.
Π‘Π΅ΡΡΠΉ ΡΡΠ³ΡΠ½ — Π’ΠΈΠΏ EΠ Π°Π·ΠΌΠ΅Ρ ΡΠ΅ΡΡΠΉΡΠ°ΡΠΎΠ³ΠΎ Π³ΡΠ°ΡΠΈΡΠ°
Π Π΄ΠΎΠΏΠΎΠ»Π½Π΅Π½ΠΈΠ΅ ΠΊ ΡΠΈΠΏΡ Π³ΡΠ°ΡΠΈΡΠ° ASTM ΡΡΡΠ°Π½ΠΎΠ²ΠΈΠ»Π° ΡΠΏΠ΅ΡΠΈΡΠΈΠΊΠ°ΡΠΈΠΈ Π΄Π»Ρ ΡΠ°Π·ΠΌΠ΅ΡΠ° Π³ΡΠ°ΡΠΈΡΠ°. ΠΡΠΎ ΠΎΠΏΡΠ΅Π΄Π΅Π»ΡΠ΅ΡΡΡ ΠΏΡΡΠ΅ΠΌ ΡΡΠ°Π²Π½Π΅Π½ΠΈΡ ΠΊΠΎΠ»ΠΈΡΠ΅ΡΡΠ²Π° Ρ Π»ΠΎΠΏΡΠ΅Π² Π½Π° ΠΌΠΈΠΊΡΠΎΡΠΎΡΠΎΠ³ΡΠ°ΡΠΈΠΈ ΡΠΎ 100-ΠΊΡΠ°ΡΠ½ΡΠΌ ΡΠ²Π΅Π»ΠΈΡΠ΅Π½ΠΈΠ΅ΠΌ ΡΠΎ ΡΡΠ°Π½Π΄Π°ΡΡΠ½ΠΎΠΉ Π΄ΠΈΠ°Π³ΡΠ°ΠΌΠΌΠΎΠΉ.
ΠΠ΅Ρ Π°Π½ΠΈΡΠ΅ΡΠΊΠΈΠ΅ ΡΠ²ΠΎΠΉΡΡΠ²Π° ΡΠ΅ΡΠΎΠ³ΠΎ ΡΡΠ³ΡΠ½Π° ΠΠ°ΠΊ ΠΏΡΠ°Π²ΠΈΠ»ΠΎ, ΡΠ΅ΡΡΠΉ ΡΡΠ³ΡΠ½ ΠΈΠΌΠ΅Π΅Ρ Π½ΠΈΠ·ΠΊΡΡ ΠΏΡΠΎΡΠ½ΠΎΡΡΡ ΠΈ ΠΎΡΠ΅Π½Ρ Π½ΠΈΠ·ΠΊΡΡ ΠΏΠ»Π°ΡΡΠΈΡΠ½ΠΎΡΡΡ. Π§Π΅ΡΡΠΉΠΊΠΈ Π³ΡΠ°ΡΠΈΡΠ° Π΄Π΅ΠΉΡΡΠ²ΡΡΡ ΠΊΠ°ΠΊ ΠΊΡΠΎΡΠ΅ΡΠ½ΡΠ΅ Π²Π½ΡΡΡΠ΅Π½Π½ΠΈΠ΅ ΡΡΠ΅ΡΠΈΠ½Ρ, ΠΊΠΎΡΠΎΡΡΠ΅ ΡΠΎΠ·Π΄Π°ΡΡ ΡΡΠΈΠ»Π΅Π½ΠΈΠ΅ Π½Π°ΠΏΡΡΠΆΠ΅Π½ΠΈΡ. ΠΡΠΎ ΠΏΠΎΠ·Π²ΠΎΠ»ΡΠ΅Ρ ΡΡΠ΅ΡΠΈΠ½Π°ΠΌ ΠΎΡΠ΅Π½Ρ Π»Π΅Π³ΠΊΠΎ ΡΠ°ΡΠΏΡΠΎΡΡΡΠ°Π½ΡΡΡΡΡ ΠΏΠΎ ΠΌΠ°ΡΠ΅ΡΠΈΠ°Π»Ρ, ΡΡΠΎ ΡΠ½ΠΈΠΆΠ°Π΅Ρ ΠΏΡΠΎΡΠ½ΠΎΡΡΡ, ΠΏΠ»Π°ΡΡΠΈΡΠ½ΠΎΡΡΡ ΠΈ ΡΠ΄Π°ΡΠ½ΡΡ Π²ΡΠ·ΠΊΠΎΡΡΡ (Π²ΡΠ·ΠΊΠΎΡΡΡ ΡΠ°Π·ΡΡΡΠ΅Π½ΠΈΡ). Π‘Π΅ΡΡΠΉ ΡΡΠ³ΡΠ½ ΠΎΠΏΡΠ΅Π΄Π΅Π»ΡΠ΅ΡΡΡ Π½ΠΎΠΌΠ΅ΡΠΎΠΌ ΠΊΠ»Π°ΡΡΠ°, ΠΊΠΎΡΠΎΡΡΠΉ ΡΠΎΠΎΡΠ²Π΅ΡΡΡΠ²ΡΠ΅Ρ Π½ΠΎΠΌΠΈΠ½Π°Π»ΡΠ½ΠΎΠΉ ΠΏΡΠΎΡΠ½ΠΎΡΡΠΈ ΡΠΏΠ»Π°Π²Π° Π½Π° ΡΠ°ΡΡΡΠΆΠ΅Π½ΠΈΠ΅. ΠΠ°ΠΏΡΠΈΠΌΠ΅Ρ, ΡΠ΅ΡΡΠΉ ΡΡΠ³ΡΠ½ ΠΊΠ»Π°ΡΡΠ° 30, ΠΊΠΎΡΠΎΡΡΠΉ Π±ΡΠ» ΡΠΈΠΏΠΈΡΠ½ΡΠΌ Π΄Π»Ρ Π±Π»ΠΎΠΊΠ° ΡΠΈΠ»ΠΈΠ½Π΄ΡΠΎΠ², ΠΈΠΌΠ΅Π΅Ρ Π½ΠΎΠΌΠΈΠ½Π°Π»ΡΠ½ΡΡ ΠΏΡΠΎΡΠ½ΠΎΡΡΡ Π½Π° ΡΠ°ΡΡΡΠΆΠ΅Π½ΠΈΠ΅ 30 000 ΡΡΠ½ΡΠΎΠ² Π½Π° ΠΊΠ²Π°Π΄ΡΠ°ΡΠ½ΡΠΉ Π΄ΡΠΉΠΌ (207 ΠΠΠ°). ΠΠΎΡΠΊΠΎΠ»ΡΠΊΡ ΡΠ΅ΡΡΠΉ ΡΡΠ³ΡΠ½ ΠΈΠΌΠ΅Π΅Ρ ΠΎΡΠ΅Π½Ρ Π½ΠΈΠ·ΠΊΡΡ ΠΏΠ»Π°ΡΡΠΈΡΠ½ΠΎΡΡΡ, ΠΏΡΠ΅Π΄Π΅Π» ΡΠ΅ΠΊΡΡΠ΅ΡΡΠΈ ΠΈ ΠΏΡΠΎΡΠ΅Π½ΡΠ½ΠΎΠ΅ ΡΠ΄Π»ΠΈΠ½Π΅Π½ΠΈΠ΅, ΡΡΠΈ ΡΠ²ΠΎΠΉΡΡΠ²Π° ΡΠ΅Π΄ΠΊΠΎ ΠΈΠ·ΠΌΠ΅ΡΡΡΡΡΡ ΠΈΠ»ΠΈ ΡΠΊΠ°Π·ΡΠ²Π°ΡΡΡΡ. ΠΠΎΡΠΊΠΎΠ»ΡΠΊΡ YTS ΠΈ UTS Π½Π°ΡΡΠΎΠ»ΡΠΊΠΎ Π±Π»ΠΈΠ·ΠΊΠΈ (ΡΠ΄Π»ΠΈΠ½Π΅Π½ΠΈΠ΅ ΠΌΠ΅Π½Π΅Π΅ 1%), ΡΠ΅ΡΡΠΉ ΡΡΠ³ΡΠ½ ΠΊΠ»Π°ΡΡΠΈΡΠΈΡΠΈΡΡΠ΅ΡΡΡ ΠΊΠ°ΠΊ Β«Ρ
ΡΡΠΏΠΊΠΈΠΉ ΠΌΠ°ΡΠ΅ΡΠΈΠ°Π»Β». ΠΡΡΠ³ΠΎΠΉ ΡΠΏΠΎΡΠΎΠ± ΠΎΠΏΡΠ΅Π΄Π΅Π»Π΅Π½ΠΈΡ ΡΠ΅ΡΠΎΠ³ΠΎ ΡΡΠ³ΡΠ½Π° — ΠΏΠΎ ΡΠ²Π΅ΡΠ΄ΠΎΡΡΠΈ ΠΌΠ°ΡΠ΅ΡΠΈΠ°Π»Π°. ΠΠ±ΡΠ΅ΡΡΠ²ΠΎ Π°Π²ΡΠΎΠΌΠΎΠ±ΠΈΠ»ΡΠ½ΡΡ
ΠΈΠ½ΠΆΠ΅Π½Π΅ΡΠΎΠ² (SAE) ΠΎΠΏΡΠ±Π»ΠΈΠΊΠΎΠ²Π°Π»ΠΎ ΡΡΠ°Π½Π΄Π°ΡΡ ΠΌΠ°ΡΠ΅ΡΠΈΠ°Π»Π° Π΄Π»Ρ ΡΡΠ³ΡΠ½Π° SAE J431, ΡΡΠΈΡΡΠ²Π°ΡΡΠΈΠΉ ΠΊΠ°ΠΊ ΡΠ²ΠΎΠΉΡΡΠ²Π° ΠΏΡΠΎΡΠ½ΠΎΡΡΠΈ Π½Π° ΡΠ°ΡΡΡΠΆΠ΅Π½ΠΈΠ΅, ΡΠ°ΠΊ ΠΈ ΡΠ²ΠΎΠΉΡΡΠ²Π° ΡΠ²Π΅ΡΠ΄ΠΎΡΡΠΈ. ΠΡΠΎΠΌΠ΅ ΡΠΎΠ³ΠΎ, ΠΊΠ°ΠΆΠ΄ΡΠΉ Π°Π²ΡΠΎΠΌΠΎΠ±ΠΈΠ»ΡΠ½ΡΠΉ OEM-ΠΏΡΠΎΠΈΠ·Π²ΠΎΠ΄ΠΈΡΠ΅Π»Ρ ΠΈΠΌΠ΅Π΅Ρ ΡΠΎΠ±ΡΡΠ²Π΅Π½Π½ΡΠΉ Π½Π°Π±ΠΎΡ ΡΡΠ°Π½Π΄Π°ΡΡΠΎΠ², ΡΠ΅Π³ΡΠ»ΠΈΡΡΡΡΠΈΡ
ΡΠ²ΠΎΠΉΡΡΠ²Π° ΡΠ΅ΡΠΎΠ³ΠΎ ΡΡΠ³ΡΠ½Π°, ΠΈ ΡΠΏΠ΅ΡΠΈΠ°Π»ΡΠ½ΡΠ΅ ΠΌΠ΅ΡΠΎΠ΄Ρ ΠΈΡΠΏΡΡΠ°Π½ΠΈΠΉ, Π½Π΅ΠΎΠ±Ρ
ΠΎΠ΄ΠΈΠΌΡΠ΅ Π΄Π»Ρ ΠΈΠ·ΠΌΠ΅ΡΠ΅Π½ΠΈΡ ΠΊΠ°ΡΠ΅ΡΡΠ²Π° ΠΌΠ°ΡΠ΅ΡΠΈΠ°Π»Π°.
ΠΡΠΎΡΠ½ΠΎΡΡΡ ΠΈ ΡΠ²Π΅ΡΠ΄ΠΎΡΡΡ
ΠΡΠΎΡΠ½ΠΎΡΡΡ ΠΈ ΡΠ²Π΅ΡΠ΄ΠΎΡΡΡ ΡΠ΅ΡΠΎΠ³ΠΎ ΡΡΠ³ΡΠ½Π° Π·Π°Π²ΠΈΡΠΈΡ ΠΊΠ°ΠΊ ΠΌΠΈΠ½ΠΈΠΌΡΠΌ ΠΎΡ ΡΠ΅ΡΡΡΠ΅Ρ ΠΎΡΠ½ΠΎΠ²Π½ΡΡ ΡΠ°ΠΊΡΠΎΡΠΎΠ²:
- Π£Π³Π»Π΅ΡΠΎΠ΄Π½ΡΠΉ ΡΠΊΠ²ΠΈΠ²Π°Π»Π΅Π½Ρ
- Π‘ΠΎΠ΄Π΅ΡΠΆΠ°Π½ΠΈΠ΅ ΡΠΏΠ»Π°Π²Π°
- ΠΠΎΠ΄ΠΈΡΠΈΠΊΠ°ΡΠΈΡ
- Π‘ΠΊΠΎΡΠΎΡΡΡ Π·Π°ΡΠ²Π΅ΡΠ΄Π΅Π²Π°Π½ΠΈΡ
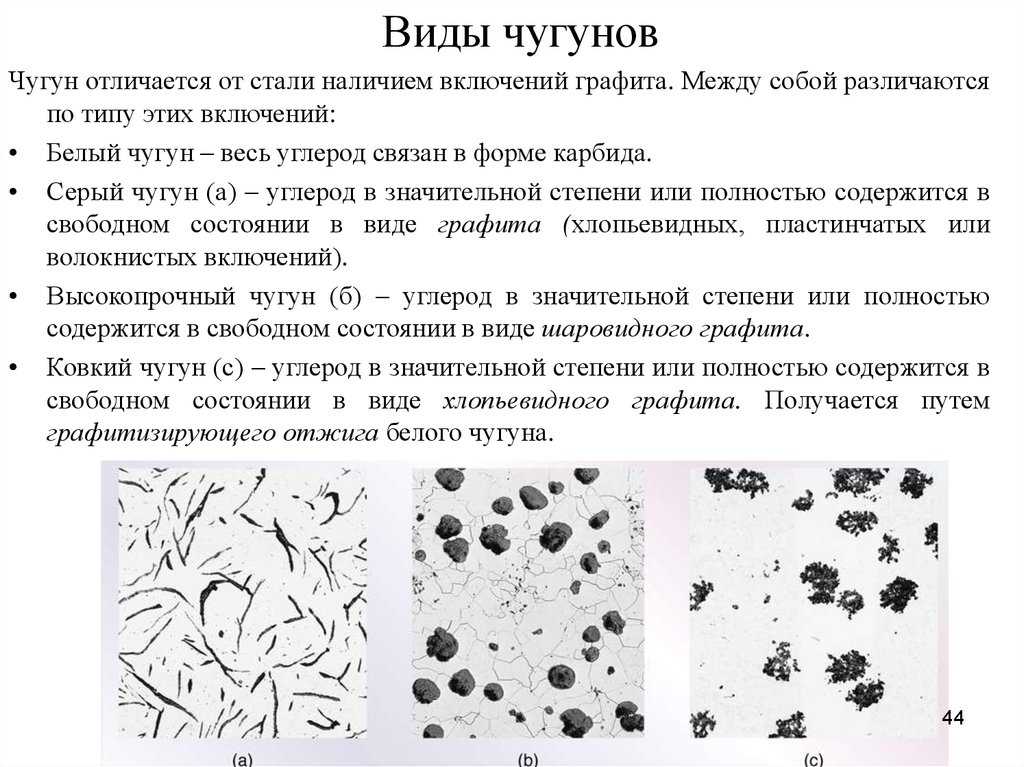
Π£Π³Π»Π΅ΡΠΎΠ΄Π½ΡΠΉ ΡΠΊΠ²ΠΈΠ²Π°Π»Π΅Π½Ρ (CE)
ΠΠ»Ρ ΡΡΠ³ΡΠ½Π° ΡΠΎΡΠΌΡΠ»Π° ΡΠ³Π»Π΅ΡΠΎΠ΄Π½ΠΎΠ³ΠΎ ΡΠΊΠ²ΠΈΠ²Π°Π»Π΅Π½ΡΠ° (CE) ΠΈΡΠΏΠΎΠ»ΡΠ·ΡΠ΅ΡΡΡ Π΄Π»Ρ ΠΏΠΎΠ½ΠΈΠΌΠ°Π½ΠΈΡ ΡΠΎΠ³ΠΎ, ΠΊΠ°ΠΊ Π»Π΅Π³ΠΈΡΡΡΡΠΈΠ΅ ΡΠ»Π΅ΠΌΠ΅Π½ΡΡ Π±ΡΠ΄ΡΡ Π²Π»ΠΈΡΡΡ Π½Π° Ρ Π°ΡΠ°ΠΊΡΠ΅ΡΠΈΡΡΠΈΠΊΠΈ ΠΎΡΠ»ΠΈΠ²ΠΊΠΈ. ΠΠ½ ΠΈΡΠΏΠΎΠ»ΡΠ·ΡΠ΅ΡΡΡ Π² ΠΊΠ°ΡΠ΅ΡΡΠ²Π΅ ΠΏΡΠ΅Π΄ΠΈΠΊΡΠΎΡΠ° ΠΏΡΠΎΡΠ½ΠΎΡΡΠΈ ΡΡΠ³ΡΠ½Π°, ΠΏΠΎΡΠΊΠΎΠ»ΡΠΊΡ Π΄Π°Π΅Ρ ΠΏΡΠΈΠ±Π»ΠΈΠ·ΠΈΡΠ΅Π»ΡΠ½ΡΠΉ Π±Π°Π»Π°Π½Ρ Π°ΡΡΡΠ΅Π½ΠΈΡΠ° ΠΈ Π³ΡΠ°ΡΠΈΡΠ° Π² ΠΊΠΎΠ½Π΅ΡΠ½ΠΎΠΉ ΡΡΡΡΠΊΡΡΡΠ΅.
CE = %C + 0,33 (%Si) + 0,33 (%P) β 0,027 (%Mn) + 0,4 (%S)
CE < 4,3%, Π΄ΠΎΡΠ²ΡΠ΅ΠΊΡΠΈΡΠ΅ΡΠΊΠΎΠ΅ ΠΏΠΎΠ²Π΅Π΄Π΅Π½ΠΈΠ΅ ΠΏΡΠΈ Π·Π°ΡΠ²Π΅ΡΠ΄Π΅Π²Π°Π½ΠΈΠΈ
CE = 4,3, ΡΠ²ΡΠ΅ΠΊΡΠΈΡΠ΅ΡΠΊΠΎΠ΅ ΠΏΠΎΠ²Π΅Π΄Π΅Π½ΠΈΠ΅ ΠΏΡΠΈ Π·Π°ΡΠ²Π΅ΡΠ΄Π΅Π²Π°Π½ΠΈΠΈ
CE > 4,3%, Π·Π°ΡΠ²ΡΠ΅ΠΊΡΠΈΡΠ΅ΡΠΊΠΎΠ΅ ΠΏΠΎΠ²Π΅Π΄Π΅Π½ΠΈΠ΅ Π²ΠΎ Π²ΡΠ΅ΠΌΡ Π·Π°ΡΠ²Π΅ΡΠ΄Π΅Π²Π°Π½ΠΈΡ
Π‘ΠΎΠ΄Π΅ΡΠΆΠ°Π½ΠΈΠ΅ ΡΠΏΠ»Π°Π²Π°
ΠΠ°ΠΈΠ±ΠΎΠ»Π΅Π΅ ΡΡΡΠ΅ΠΊΡΠΈΠ²Π½ΡΠΌΠΈ ΡΠ»Π΅ΠΌΠ΅Π½ΡΠ°ΠΌΠΈ Π΄Π»Ρ ΡΠ΅ΡΠΎΠ³ΠΎ ΡΡΠ³ΡΠ½Π° ΡΠ²Π»ΡΡΡΡΡ ΡΠ³Π»Π΅ΡΠΎΠ΄ ΠΈ ΠΊΡΠ΅ΠΌΠ½ΠΈΠΉ. ΠΠΎΠ³Π΄Π° ΡΠ΅Π»Ρ ΡΠΎΡΡΠΎΠΈΡ Π² ΡΠΎΠΌ, ΡΡΠΎΠ±Ρ ΡΠ°Π·Π»ΠΈΡΡ ΡΡΠ³ΡΠ½ ΠΏΠΎ ΡΠ²ΡΠ΅ΠΊΡΠΈΠΊΠ΅, ΡΡΠΎΠ±Ρ ΠΏΡΠ΅Π΄ΠΎΡΠ²ΡΠ°ΡΠΈΡΡ ΠΎΠ±ΡΠ°Π·ΠΎΠ²Π°Π½ΠΈΠ΅ ΠΊΠ°ΡΠ±ΠΈΠ΄ΠΎΠ² ΠΆΠ΅Π»Π΅Π·Π°, ΠΌΠΎΠΆΠ½ΠΎ ΠΈΡΠΏΠΎΠ»ΡΠ·ΠΎΠ²Π°ΡΡ ΠΊΠΎΠ²ΡΠΎΠ²ΡΠ΅ Π΄ΠΎΠ±Π°Π²ΠΊΠΈ ΠΊΡΠ΅ΠΌΠ½ΠΈΡ Π΄Π»Ρ ΠΌΠΎΠ΄ΠΈΡΠΈΠΊΠ°ΡΠΈΠΈ ΡΠ°ΡΠΏΠ»Π°Π²Π»Π΅Π½Π½ΠΎΠ³ΠΎ ΡΠΏΠ»Π°Π²Π°, ΡΡΠΎΠ±Ρ Π²ΡΠ΅Π³Π΄Π° Π΄ΠΎΡΡΠΈΠ³Π°Π»ΡΡ ΡΠ²ΡΠ΅ΠΊΡΠΈΡΠ΅ΡΠΊΠΈΠΉ ΡΠΊΠ²ΠΈΠ²Π°Π»Π΅Π½Ρ. ΠΡΠΏΠΎΠ»ΡΠ·ΡΡ ΡΠ°ΡΡΠ΅Ρ CE ΠΈ ΠΏΠΎΠ΄ΡΠ²Π΅ΡΠΆΠ΄Π°Ρ ΡΠΎΠΎΡΠ²Π΅ΡΡΡΠ²ΡΡΡΠ΅Π΅ ΠΊΠΎΠ»ΠΈΡΠ΅ΡΡΠ²ΠΎ Π΄ΠΎΠ±Π°Π²ΠΎΠΊ ΡΠ΅ΡΡΠΎΡΠΈΠ»ΠΈΠΊΠ°ΡΠ°, ΠΊΠ»ΠΈΠ½ΠΎΠ²ΠΈΠ΄Π½ΡΠΉ Π±Π»ΠΎΠΊ ΠΈΡΠΏΠΎΠ»ΡΠ·ΡΠ΅ΡΡΡ Π΄Π»Ρ ΠΏΠΎΠ΄ΡΠ²Π΅ΡΠΆΠ΄Π΅Π½ΠΈΡ ΡΠΎΠ³ΠΎ, ΡΡΠΎ ΡΠ΅ΡΡΠΉ ΡΡΠ³ΡΠ½ Π½Π°Ρ
ΠΎΠ΄ΠΈΡΡΡ Π½Π° ΠΆΠ΅Π»Π°Π΅ΠΌΠΎΠΌ ΡΡΠΎΠ²Π½Π΅ CE.
Π£Π³Π»Π΅ΡΠΎΠ΄ ΠΈ ΠΊΡΠ΅ΠΌΠ½ΠΈΠΉ
ΠΠΎ ΡΡΠ°Π²Π½Π΅Π½ΠΈΡ Ρ ΠΎΠ±ΡΡΠ½ΡΠΌΠΈ ΠΌΠ°ΡΠΊΠ°ΠΌΠΈ ΡΡΠ°Π»ΠΈ ΡΠΎΠ΄Π΅ΡΠΆΠ°Π½ΠΈΠ΅ ΡΠ³Π»Π΅ΡΠΎΠ΄Π° Π² ΡΠ΅ΡΠΎΠΌ ΡΡΠ³ΡΠ½Π΅ ΠΏΡΠΈΠΌΠ΅ΡΠ½ΠΎ Π² Π΄Π΅ΡΡΡΡ ΡΠ°Π· Π²ΡΡΠ΅. ΠΠΎΡΠΊΠΎΠ»ΡΠΊΡ ΡΡΠ°Π»ΡΠ½ΠΎΠΉ Π»ΠΎΠΌ ΡΠΎΡΡΠ°Π²Π»ΡΠ΅Ρ Π±ΠΎΠ»ΡΡΡΡ ΡΠ°ΡΡΡ ΡΠΈΡ
ΡΡ ΡΠ°ΡΠΏΠ»Π°Π²Π° Π΄Π»Ρ ΡΡΠ³ΡΠ½ΠΎΠ»ΠΈΡΠ΅ΠΉΠ½ΠΎΠ³ΠΎ ΠΏΡΠΎΠΈΠ·Π²ΠΎΠ΄ΡΡΠ²Π°, ΡΠ³Π»Π΅ΡΠΎΠ΄ ΠΎΠ±ΡΡΠ½ΠΎ ΠΏΡΠΈΡ
ΠΎΠ΄ΠΈΡΡΡ Π΄ΠΎΠ±Π°Π²Π»ΡΡΡ Π² ΠΊΠ°ΠΊΠΎΠΉ-ΡΠΎ ΠΌΠΎΠΌΠ΅Π½Ρ ΠΏΡΠΎΡΠ΅ΡΡΠ° Π»ΠΈΠ±ΠΎ Π² ΠΎΡΠ½ΠΎΠ²Π½ΡΡ ΡΠΈΡ
ΡΡ, Π»ΠΈΠ±ΠΎ ΠΏΠΎΡΠ»Π΅ ΡΠΎΠ³ΠΎ, ΠΊΠ°ΠΊ ΠΆΠ΅Π»Π΅Π·ΠΎ Π½Π°Ρ
ΠΎΠ΄ΠΈΡΡΡ Π² ΡΠ°ΡΠΏΠ»Π°Π²Π»Π΅Π½Π½ΠΎΠΌ ΡΠΎΡΡΠΎΡΠ½ΠΈΠΈ. ΠΠΎΡΠΊΠΎΠ»ΡΠΊΡ Π² ΡΡΠ°Π»ΡΠ½ΠΎΠΌ ΡΠΈΡ
ΡΠΎΠ²ΠΎΠΌ Π»ΠΎΠΌΠ΅ ΠΎΡΠ΅Π½Ρ ΠΌΠ°Π»ΠΎ ΡΠ³Π»Π΅ΡΠΎΠ΄Π°, ΠΌΠ΅ΡΠ°Π»Π»ΡΡΠ³Ρ Π½Π΅ΠΎΠ±Ρ
ΠΎΠ΄ΠΈΠΌΠΎ ΡΡΠΈΡΡΠ²Π°ΡΡ Π²ΡΠ΅ ΠΌΠ΅ΡΠ°Π»Π»ΠΈΡΠ΅ΡΠΊΠΈΠ΅ ΡΠΈΡ
ΡΠΎΠ²ΡΠ΅ ΠΌΠ°ΡΠ΅ΡΠΈΠ°Π»Ρ (ΡΡΠ°Π»Ρ, ΠΆΠ΅Π»Π΅Π·Π½ΡΠΉ Π»ΠΎΠΌ, ΡΡΠ³ΡΠ½) Π² ΠΎΡΠ½ΠΎΠ²Π½ΠΎΠΉ ΠΏΠ΅ΡΠΈ. ΠΠΎΠ±Π°Π²ΠΊΠΈ, ΠΏΠΎΠ²ΡΡΠ°ΡΡΠΈΠ΅ ΡΠΎΠ΄Π΅ΡΠΆΠ°Π½ΠΈΠ΅ ΡΠ³Π»Π΅ΡΠΎΠ΄Π°, Π² Π·Π½Π°ΡΠΈΡΠ΅Π»ΡΠ½ΠΎΠΉ ΡΡΠ΅ΠΏΠ΅Π½ΠΈ Π·Π°Π²ΠΈΡΡΡ ΠΎΡ ΠΌΠ΅ΡΠΎΠ΄Π° ΠΏΠ»Π°Π²ΠΊΠΈ (ΠΏΠ»Π°Π²ΠΊΠ° Π² Π²Π°Π³ΡΠ°Π½ΠΊΠ΅ Ρ ΠΊΠΎΠΊΡΠΎΠΌ ΠΏΡΠΈΠ²ΠΎΠ΄ΠΈΡ ΠΊ ΠΏΠΎΠ²ΡΡΠ΅Π½ΠΈΡ ΡΡΠΎΠ²Π½Ρ ΡΠ³Π»Π΅ΡΠΎΠ΄Π°), ΠΊΠΎΠ»ΠΈΡΠ΅ΡΡΠ²Π° ΠΈΡΠΏΠΎΠ»ΡΠ·ΡΠ΅ΠΌΠΎΠ³ΠΎ ΠΊΡΠ΅ΠΌΠ½ΠΈΡ ΠΈ Π½Π°Π»ΠΈΡΠΈΡ Π΄Π΅ΡΠ΅Π²ΠΎΠ³ΠΎ Π³ΡΠ°ΡΠΈΡΠ°. ΠΠ΄Π½Π°ΠΊΠΎ ΠΏΠΎ ΠΌΠ΅ΡΠ΅ ΠΏΠ΅ΡΠ΅Ρ
ΠΎΠ΄Π° ΡΡΠ³ΡΠ½ΠΎΠ»ΠΈΡΠ΅ΠΉΠ½ΠΎΠΉ ΠΏΡΠΎΠΌΡΡΠ»Π΅Π½Π½ΠΎΡΡΠΈ ΠΎΡ Π²Π°Π³ΡΠ°Π½ΠΊΠΈ ΠΊ ΠΈΠ½Π΄ΡΠΊΡΠΈΠΎΠ½Π½ΠΎΠΉ ΠΏΠ»Π°Π²ΠΊΠ΅ Ρ Π°Π½Π°Π»ΠΎΠ³ΠΈΡΠ½ΡΠΌΠΈ Π²ΡΡΠΎΠΊΠΈΠΌΠΈ Π΄ΠΎΠ±Π°Π²ΠΊΠ°ΠΌΠΈ ΡΡΠ°Π»ΡΠ½ΠΎΠ³ΠΎ Π»ΠΎΠΌΠ° Π² ΡΠΈΡ
ΡΡ ΡΡΠ΅Π±ΡΡΡΡΡ Π°Π»ΡΡΠ΅ΡΠ½Π°ΡΠΈΠ²Π½ΡΠ΅ Π΄ΠΎΠ±Π°Π²ΠΊΠΈ Π² ΠΊΠΎΠ²ΡΠ΅, Π² ΠΏΠΎΡΠΎΠΊΠ΅ ΠΈΠ»ΠΈ Π² Π»ΠΈΡΠ΅ΠΉΠ½ΠΎΠΉ ΡΠΎΡΠΌΠ΅ Π΄Π»Ρ ΠΏΠΎΠ»ΡΡΠ΅Π½ΠΈΡ ΡΠ΅ΡΡΠ΅ΠΊ ΡΠΈΠΏΠ° Π Π² ΡΠ΅ΡΠΎΠΌ ΡΡΠ³ΡΠ½Π΅.
ΠΠ΅ΡΠΎΠ΄Ρ ΠΌΠΎΠ΄ΠΈΡΠΈΡΠΈΡΠΎΠ²Π°Π½ΠΈΡ
Π‘ ΠΏΠ΅ΡΠ΅Ρ ΠΎΠ΄ΠΎΠΌ Π½Π° ΠΈΠ½Π΄ΡΠΊΡΠΈΠΎΠ½Π½ΡΡ ΠΏΠ»Π°Π²ΠΊΡ Π»ΠΈΡΠ΅ΠΉΠ½ΡΠ΅ Π·Π°Π²ΠΎΠ΄Ρ ΡΡΠ°ΡΠ΅Π»ΡΠ½ΠΎ Π·Π°Π³ΡΡΠΆΠ°ΡΡ Π² ΡΠ²ΠΎΠΈ ΠΈΠ½Π΄ΡΠΊΡΠΈΠΎΠ½Π½ΡΠ΅ ΠΊΠΎΠ²ΡΠΈ ΡΡΠ°ΡΠ΅Π»ΡΠ½ΠΎ Π²Π·Π²Π΅ΡΠ΅Π½Π½ΡΠ΅ ΠΊΠΎΠ»ΠΈΡΠ΅ΡΡΠ²Π° ΡΡΠ°Π»ΡΠ½ΠΎΠ³ΠΎ Π»ΠΎΠΌΠ°, Π»ΠΎΠΌΠ° ΠΆΠ΅Π»Π΅Π·Π° ΠΈ Π±ΠΎΠ»Π΅Π΅ Π΄ΠΎΡΠΎΠ³ΠΎΠ³ΠΎ ΡΡΠ³ΡΠ½Π°. Π‘Π΅Π³ΠΎΠ΄Π½Ρ Π±ΠΎΠ»ΡΡΠ΅Π΅ ΠΊΠΎΠ»ΠΈΡΠ΅ΡΡΠ²ΠΎ Π½ΠΈΠ·ΠΊΠΎΡΠ³Π»Π΅ΡΠΎΠ΄ΠΈΡΡΠΎΠΉ ΡΡΠ°Π»ΠΈ ΠΌΠΎΠΆΠ΅Ρ Π±ΡΡΡ ΠΏΠΎΠ»ΡΡΠ΅Π½ΠΎ Π·Π° ΡΡΠ΅Ρ Π΄ΠΎΠ±Π°Π²Π»Π΅Π½ΠΈΡ ΠΌΠΎΠ΄ΠΈΡΠΈΠΊΠ°ΡΠΎΡΠΎΠ² ΡΠ΅ΡΡΠΎΡΠΈΠ»ΠΈΡΠΈΡ (FeSi). ΠΡΠΎΡΠ΅ΡΡ ΠΌΠΎΠ΄ΠΈΡΠΈΡΠΈΡΠΎΠ²Π°Π½ΠΈΡ Π²ΠΊΠ»ΡΡΠ°Π΅Ρ Π΄ΠΎΠ±Π°Π²Π»Π΅Π½ΠΈΠ΅ ΠΎΡ 0,05 Π΄ΠΎ 1% ΡΠΏΠ΅ΡΠΈΠ°Π»ΡΠ½ΠΎΠ³ΠΎ ΡΠΏΠ»Π°Π²Π° FeSi, ΡΠΎΠ΄Π΅ΡΠΆΠ°ΡΠ΅Π³ΠΎ ΠΊΠΎΠ½ΡΡΠΎΠ»ΠΈΡΡΠ΅ΠΌΡΠ΅ ΠΊΠΎΠ»ΠΈΡΠ΅ΡΡΠ²Π° ΠΎΠ΄Π½ΠΎΠ³ΠΎ ΠΈΠ»ΠΈ Π½Π΅ΡΠΊΠΎΠ»ΡΠΊΠΈΡ ΡΡΠ°ΡΠ΅Π»ΡΠ½ΠΎ ΠΎΡΠΎΠ±ΡΠ°Π½Π½ΡΡ ΡΠ»Π΅ΠΌΠ΅Π½ΡΠΎΠ² Π΄Π»Ρ Π΄Π°Π»ΡΠ½Π΅ΠΉΡΠ΅Π³ΠΎ ΡΠ»ΡΡΡΠ΅Π½ΠΈΡ ΠΌΠΎΡΡΠΎΠ»ΠΎΠ³ΠΈΠΈ Π³ΡΠ°ΡΠΈΡΠ°. ΠΠ±ΡΡΡΠ½Π΅Π½ΠΈΠ΅ ΡΠΎΠ³ΠΎ, ΠΊΠ°ΠΊ ΡΡΠΈ ΡΡΠ°ΡΠ΅Π»ΡΠ½ΠΎ ΠΎΡΠΎΠ±ΡΠ°Π½Π½ΡΠ΅ ΡΠ»Π΅ΠΌΠ΅Π½ΡΠ°ΡΠ½ΡΠ΅ Π΄ΠΎΠ±Π°Π²ΠΊΠΈ, Π²ΠΊΠ»ΡΡΠ°Ρ Al, Ca, Ba, Sr, Ce, La, Mn, Bi, S, O ΠΈ Zr, ΠΌΠΎΠΆΠ½ΠΎ Π½Π°ΠΉΡΠΈ Π² Π’Π°Π±Π»ΠΈΡΠ΅ 1.0 Π‘ΡΡΡΠΊΡΡΡΠ½ΡΠ΅ ΡΡΡΠ΅ΠΊΡΡ ΡΠ»Π΅ΠΌΠ΅Π½ΡΠ°ΡΠ½ΡΡ Π΄ΠΎΠ±Π°Π²ΠΎΠΊ ΠΊ ΡΡΠ³ΡΠ½Ρ, ΠΏΠΎΠΊΠ°Π·Π°Π½Π½ΠΎΠΉ Π½ΠΈΠΆΠ΅. . Π Π΄ΠΎΠΏΠΎΠ»Π½Π΅Π½ΠΈΠ΅ ΠΊ ΠΏΠΎΠ²ΡΡΠ΅Π½ΠΈΡ ΡΡΠΎΠ²Π½Ρ ΠΊΡΠ΅ΠΌΠ½ΠΈΡ ΠΌΠΎΠ΄ΠΈΡΠΈΠΊΠ°ΡΠΎΡ ΡΠΎΠ·Π΄Π°Π΅Ρ ΡΠ΅Π½ΡΡΡ Π·Π°ΡΠΎΠ΄ΡΡΠ΅ΠΎΠ±ΡΠ°Π·ΠΎΠ²Π°Π½ΠΈΡ, ΠΊΠΎΡΠΎΡΡΠ΅ ΡΠΏΠΎΡΠΎΠ±ΡΡΠ²ΡΡΡ ΠΎΡΠ°ΠΆΠ΄Π΅Π½ΠΈΡ ΠΈ ΡΠΎΡΡΡ Π³ΡΠ°ΡΠΈΡΠ°, Π° ΡΠ°ΠΊΠΆΠ΅ Π·Π°ΡΠ²Π΅ΡΠ΄Π΅Π²Π°Π½ΠΈΡ ΠΆΠ΅Π»Π΅Π·Π° Π½Π° ΠΎΡΠ½ΠΎΠ²Π΅ ΡΡΠ°Π±ΠΈΠ»ΡΠ½ΠΎΠΉ ΡΠΈΡΡΠ΅ΠΌΡ Fe-C.
ΠΠΎΠ³Π΄Π° Π½Π΅ΠΎΠ±Ρ
ΠΎΠ΄ΠΈΠΌΠΎ ΠΏΡΠΈΠΎΠ±ΡΠ΅ΡΡΠΈ ΡΠ³Π»Π΅ΡΠΎΠ΄ Π΄Π»Ρ Π΄ΠΎΠ±Π°Π²Π»Π΅Π½ΠΈΡ, Π΄ΠΎΠΏΠΎΠ»Π½ΠΈΡΠ΅Π»ΡΠ½ΡΠΉ ΠΌΠ°ΡΠ΅ΡΠΈΠ°Π» ΠΎΠ±ΡΡΠ½ΠΎ ΠΈΠΌΠ΅Π΅Ρ ΡΠΎΡΠΌΡ Π³ΡΠ°ΡΠΈΡΠ°. ΠΠΎΠ±Π°Π²ΠΊΠΈ Π³ΡΠ°ΡΠΈΡΠ° ΡΠ°ΡΡΠΎ ΠΏΠΎΡΡΡΠΏΠ°ΡΡ ΠΈΠ· ΡΠ³ΠΎΠ»ΡΠ½ΡΡ
ΡΠ»Π΅ΠΊΡΡΠΎΠ΄ΠΎΠ², ΡΠ°Π½Π΅Π΅ ΠΈΡΠΏΠΎΠ»ΡΠ·ΠΎΠ²Π°Π²ΡΠΈΡ
ΡΡ Π² ΡΡΠ°Π»Π΅ΠΏΠ»Π°Π²ΠΈΠ»ΡΠ½ΡΡ
ΠΏΠ΅ΡΠ°Ρ
.
Π¦Π΅Π»Ρ ΠΌΠΎΠ΄ΠΈΡΠΈΡΠΈΡΠΎΠ²Π°Π½ΠΈΡ
Π¦Π΅Π»ΡΡ ΠΌΠΎΠ΄ΠΈΡΠΈΡΠΈΡΠΎΠ²Π°Π½ΠΈΡ ΡΠ²Π»ΡΠ΅ΡΡΡ ΡΡΠΈΠΌΡΠ»ΠΈΡΠΎΠ²Π°Π½ΠΈΠ΅ Π³Π΅ΡΠ΅ΡΠΎΠ³Π΅Π½Π½ΠΎΠ³ΠΎ Π·Π°ΡΠΎΠ΄ΡΡΠ΅ΠΎΠ±ΡΠ°Π·ΠΎΠ²Π°Π½ΠΈΡ Π³ΡΠ°ΡΠΈΡΠ° ΠΏΡΡΠ΅ΠΌ Π²Π²Π΅Π΄Π΅Π½ΠΈΡ ΡΠ»Π΅ΠΌΠ΅Π½ΡΠΎΠ², ΠΎΠ±ΡΠ°Π·ΡΡΡΠΈΡ ΠΏΠΎΠ΄Ρ ΠΎΠ΄ΡΡΠΈΠ΅ ΡΡΠ±ΡΡΡΠ°ΡΡ, ΠΊΠΎΡΠΎΡΡΠ΅ Π±ΡΠ΄ΡΡ Π΄Π΅ΠΉΡΡΠ²ΠΎΠ²Π°ΡΡ ΠΊΠ°ΠΊ Π·Π°ΡΠΎΠ΄ΡΡΠΈ ΠΈ ΠΈΠ½ΠΈΡΠΈΠΈΡΠΎΠ²Π°ΡΡ ΠΆΠ΅Π»Π°Π΅ΠΌΠΎΠ΅ ΠΎΠ±ΡΠ°Π·ΠΎΠ²Π°Π½ΠΈΠ΅ Π³ΡΠ°ΡΠΈΡΠ°. Π‘ΠΏΠΎΡΠΎΠ±ΡΡΠ²ΡΡ ΡΡΠ°Π±ΠΈΠ»ΡΠ½ΠΎΠΌΡ Π·Π°ΡΠ²Π΅ΡΠ΄Π΅Π²Π°Π½ΠΈΡ ΡΠ²ΡΠ΅ΠΊΡΠΈΠΊΠΈ, ΠΌΠΎΠ΄ΠΈΡΠΈΡΠΈΡΠΎΠ²Π°Π½ΠΈΠ΅ ΠΏΠΎΠ·Π²ΠΎΠ»ΡΠ΅Ρ C Π²ΡΡ ΠΎΠ΄ΠΈΡΡ ΠΈΠ· ΡΠ°ΡΡΠ²ΠΎΡΠ° Π² ΠΏΠΎΠ΄Ρ ΠΎΠ΄ΡΡΠ΅ΠΉ ΡΠΎΡΠΌΠ΅ Π³ΡΠ°ΡΠΈΡΠ°, Π° Π½Π΅ Π² Π²ΠΈΠ΄Π΅ ΠΊΠ°ΡΠ±ΠΈΠ΄Π° ΠΆΠ΅Π»Π΅Π·Π°.
Π‘ ΡΡΠ°ΡΠ΅Π»ΡΠ½ΡΠΌ ΠΊΠΎΠ½ΡΡΠΎΠ»Π΅ΠΌ ΠΏΡΠΈ ΠΈΡΠΏΠΎΠ»ΡΠ·ΠΎΠ²Π°Π½ΠΈΠΈ ΠΈΠ½ΠΎΠΊΡΠ»ΡΡΠ½ΠΎΠ³ΠΎ Π΄ΠΎΠ±Π°Π²Π»Π΅Π½ΠΈΡ ΠΏΠΎΠΌΠΎΠΆΠ΅Ρ:
- ΠΠ·Π±Π΅Π³Π°ΠΉΡΠ΅ ΠΎΠ±ΡΠ°Π·ΠΎΠ²Π°Π½ΠΈΡ ΠΊΠ°ΡΠ±ΠΈΠ΄ΠΎΠ² (ΡΠ΅ΠΌΠ΅Π½ΡΠΈΡ)
- ΠΠΎΠΎΡΡΠ΅Π½ΠΈΠ΅ ΠΎΠ±ΡΠ°Π·ΠΎΠ²Π°Π½ΠΈΡ Π³ΡΠ°ΡΠΈΡΠ°
- Π£ΠΌΠ΅Π½ΡΡΠΈΡΠ΅ ΡΠ΅Π³ΡΠ΅Π³Π°ΡΠΈΡ
- Π£ΠΌΠ΅Π½ΡΡΠ΅Π½ΠΈΠ΅
- Π£Π»ΡΡΡΠ΅Π½ΠΈΠ΅ ΠΎΠ±ΠΎΡΡΠ΄ΠΎΠ²Π°Π½ΠΈΡ
- . ΠΎΠ΄Π½ΠΎΡΠΎΠ΄Π½Π°Ρ ΡΡΡΡΠΊΡΡΡΠ°
- Π£Π²Π΅Π»ΠΈΡΠ΅Π½ΠΈΠ΅ ΠΏΠ»Π°ΡΡΠΈΡΠ½ΠΎΡΡΠΈ
ΠΡΡΠ΅ΠΊΡ ΠΌΠΎΠ΄ΠΈΡΠΈΡΠΈΡΠΎΠ²Π°Π½ΠΈΡ ΠΏΡΠ΅Π΄ΡΡΠ°Π²Π»Π΅Π½ Π½Π° ΡΠΈΡΡΠ½ΠΊΠ΅ Π½ΠΈΠΆΠ΅ (ΠΡΡΠ΅ΠΊΡ ΠΌΠΎΠ΄ΠΈΡΠΈΡΠΈΡΠΎΠ²Π°Π½ΠΈΡ), Π³Π΄Π΅ ΠΊΡΠΈΠ²ΡΠ΅ ΠΎΡ
Π»Π°ΠΆΠ΄Π΅Π½ΠΈΡ Π΄Π»Ρ Π½Π΅ΠΌΠΎΠ΄ΠΈΡΠΈΡΠΈΡΠΎΠ²Π°Π½Π½ΠΎΠ³ΠΎ ΠΆΠ΅Π»Π΅Π·Π° ΠΎΠ±ΠΎΠ·Π½Π°ΡΠ΅Π½Ρ ΡΠ΅ΡΠ½ΠΎΠΉ ΠΏΡΠ½ΠΊΡΠΈΡΠ½ΠΎΠΉ Π»ΠΈΠ½ΠΈΠ΅ΠΉ, Π° Π΄Π»Ρ ΠΌΠΎΠ΄ΠΈΡΠΈΡΠΈΡΠΎΠ²Π°Π½Π½ΠΎΠ³ΠΎ ΠΆΠ΅Π»Π΅Π·Π° ΡΠΊΠ°Π·Π°Π½Ρ Π² Π²ΠΈΠ΄Π΅ ΡΠΈΠ½Π΅ΠΉ ΡΠΏΠ»ΠΎΡΠ½ΠΎΠΉ Π»ΠΈΠ½ΠΈΠΈ. 9β 0021
ΠΠΎΠ΄ΠΈΡΠΈΡΠΈΡΠΎΠ²Π°Π½ΠΈΠ΅ ΠΌΠΎΠΆΠ΅Ρ ΠΏΡΠΎΠΈΡΡ ΠΎΠ΄ΠΈΡΡ ΠΏΡΠΈ Π²ΡΠΏΡΡΠΊΠ΅, Π² ΠΊΠΎΠ²ΡΠ΅, Π² ΠΏΠΎΡΠΎΠΊΠ΅ Π²ΠΎ Π²ΡΠ΅ΠΌΡ Π»ΠΈΡΡΡ ΠΈΠ»ΠΈ Π΄Π°ΠΆΠ΅ Π²Π½ΡΡΡΠΈ ΡΠΎΡΠΌΡ. ΠΠΎΠ΄ΠΈΡΠΈΡΠΈΡΡΡΡΠΈΠ΅ ΡΠΏΠ»Π°Π²Ρ Π΄ΠΎΡΡΡΠΏΠ½Ρ Π² Π³ΡΠ°Π½ΡΠ»ΠΈΡΠΎΠ²Π°Π½Π½ΠΎΠΉ ΡΠΎΡΠΌΠ΅, ΡΠΏΠ°ΠΊΠΎΠ²Π°Π½Ρ Π² ΠΏΡΠΎΠ²ΠΎΠ»ΠΎΠΊΡ ΠΈΠ»ΠΈ ΠΎΡΠ»ΠΈΡΡ/ΠΏΡΠ΅ΡΡΠΎΠ²Π°Π½Ρ Π² ΡΠ°Π·Π»ΠΈΡΠ½ΡΠ΅ ΡΠΎΡΠΌΡ. Π Π°Π·ΠΌΠ΅Ρ ΡΠ΅Π³ΡΠ»ΠΈΡΡΠ΅ΡΡΡ Π² Π·Π°Π²ΠΈΡΠΈΠΌΠΎΡΡΠΈ ΠΎΡ ΡΠΎΡΠΊΠΈ Π΄ΠΎΠ±Π°Π²Π»Π΅Π½ΠΈΡ, Π²ΡΠ΅ΠΌΠ΅Π½ΠΈ ΠΈ ΡΠ΅ΠΌΠΏΠ΅ΡΠ°ΡΡΡΡ, Π΄ΠΎΡΡΡΠΏΠ½ΡΡ Π΄Π»Ρ ΡΠ°ΡΡΠ²ΠΎΡΠ΅Π½ΠΈΡ Π² ΡΠ°ΡΠΏΠ»Π°Π²Π»Π΅Π½Π½ΠΎΠΌ ΠΆΠ΅Π»Π΅Π·Π΅. ΠΠ°ΠΊ ΠΏΡΠ°Π²ΠΈΠ»ΠΎ, ΠΊΠΎΠ»ΠΈΡΠ΅ΡΡΠ²ΠΎ Π΄ΠΎΠ±Π°Π²ΠΎΠΊ ΠΌΠΎΠΆΠ΅Ρ Π±ΡΡΡ ΡΠΌΠ΅Π½ΡΡΠ΅Π½ΠΎ, Π΅ΡΠ»ΠΈ ΠΌΠΎΠ΄ΠΈΡΠΈΡΠΈΡΠΎΠ²Π°Π½ΠΈΠ΅ ΠΏΡΠΎΠΈΡΡ ΠΎΠ΄ΠΈΡ ΠΊΠ°ΠΊ ΠΌΠΎΠΆΠ½ΠΎ Π±Π»ΠΈΠΆΠ΅ ΠΊ Π·Π°Π»ΠΈΠ²ΠΊΠ΅ ΡΡΠ³ΡΠ½Π° Π² ΡΠΎΡΠΌΡ, ΠΏΠΎΡΡΠΎΠΌΡ ΠΌΠΎΠ΄ΠΈΡΠΈΡΠΈΡΠΎΠ²Π°Π½ΠΈΠ΅ Β«Π² ΠΏΠΎΡΠΎΠΊΠ΅Β» Π³ΡΠ°Π½ΡΠ»Π°ΠΌΠΈ FeSi ΡΠ²Π»ΡΠ΅ΡΡΡ Π½Π°ΠΈΠ±ΠΎΠ»Π΅Π΅ ΡΠ°ΡΠΏΡΠΎΡΡΡΠ°Π½Π΅Π½Π½ΡΠΌ ΠΌΠ΅ΡΠΎΠ΄ΠΎΠΌ Π΄ΠΎΠ±Π°Π²Π»Π΅Π½ΠΈΡ.
ΠΡΡΠ΅ΠΊΡ ΠΌΠΎΠ΄ΠΈΡΠΈΡΠΈΡΠΎΠ²Π°Π½ΠΈΡ
ΠΠ° ΠΊΡΠΈΠ²ΡΡ ΠΎΡ Π»Π°ΠΆΠ΄Π΅Π½ΠΈΡ Π΄Π»Ρ ΠΆΠ΅Π»Π΅Π·Π° Π±Π΅Π· ΠΌΠΎΠ΄ΠΈΡΠΈΡΠΈΡΠΎΠ²Π°Π½ΠΈΡ (ΡΠ΅ΡΠ½Π°Ρ ΠΏΡΠ½ΠΊΡΠΈΡΠ½Π°Ρ Π»ΠΈΠ½ΠΈΡ) ΠΈ ΠΌΠΎΠ΄ΠΈΡΠΈΡΠΈΡΠΎΠ²Π°Π½Π½ΠΎΠ³ΠΎ ΠΆΠ΅Π»Π΅Π·Π° (ΡΠΈΠ½ΡΡ ΡΠΏΠ»ΠΎΡΠ½Π°Ρ Π»ΠΈΠ½ΠΈΡ) Π²Π»ΠΈΡΠ½ΠΈΠ΅ ΠΏΡΠΎΡΠ²Π»ΡΠ΅ΡΡΡ ΠΊΠ°ΠΊ ΡΠ½ΠΈΠΆΠ΅Π½ΠΈΠ΅ ΡΡΠ΅ΠΏΠ΅Π½ΠΈ ΠΏΠ΅ΡΠ΅ΠΎΡ Π»Π°ΠΆΠ΄Π΅Π½ΠΈΡ Π΄ΠΎ ΠΎΠ±ΡΠ°Π·ΠΎΠ²Π°Π½ΠΈΡ Π³ΡΠ°ΡΠΈΡΠ° (ΠΊΡΠ°ΡΠ½Π°Ρ ΡΡΡΠ΅Π»ΠΊΠ°). ). ΠΠΎΠ΄ΠΈΡΠΈΠΊΠ°ΡΠΈΡ ΡΠ°ΠΊΠΆΠ΅ ΠΏΡΠΎΠ΄Π»Π΅Π²Π°Π΅Ρ ΠΎΠ±ΡΠ°Π·ΠΎΠ²Π°Π½ΠΈΠ΅ ΠΈ ΡΠΎΡΡ Π³ΡΠ°ΡΠΈΡΠ°, ΡΠ΅ΠΌ ΡΠ°ΠΌΡΠΌ ΡΠ²Π΅Π»ΠΈΡΠΈΠ²Π°Ρ Π²ΡΠ΅ΠΌΡ Π·Π°ΡΠ²Π΅ΡΠ΄Π΅Π²Π°Π½ΠΈΡ (Π·Π΅Π»Π΅Π½Π°Ρ ΡΡΡΠ΅Π»ΠΊΠ°).
ΠΠ»ΠΈΡΠ½ΠΈΠ΅ ΠΏΡΠΈΠ²ΠΈΠ²ΠΊΠΈ Π½Π° ΠΊΡΠΈΠ²ΡΡ ΠΎΡ Π»Π°ΠΆΠ΄Π΅Π½ΠΈΡ Π€ΠΎΡΠΌΡ ΠΈΡΠΏΡΡΠ°Π½ΠΈΠΉ Π½Π° ΠΎΡ Π»Π°ΠΆΠ΄Π΅Π½ΠΈΠ΅ — ΡΠ΅Π·ΡΠ»ΡΡΠ°ΡΡ ΠΏΠΎΠΊΠ°Π·ΡΠ²Π°ΡΡ ΡΡΠ°Π±ΠΈΠ»ΡΠ½ΠΎΡΡΡ ΡΠΎΡΡΠ°Π²Π° ΠΆΠ΅Π»Π΅Π·Π° ΠΈ ΠΎΠ±ΡΠ°Π±ΠΎΡΠΊΠΈ Π΄Π»Ρ ΠΏΡΠ΅Π΄ΠΎΡΠ²ΡΠ°ΡΠ΅Π½ΠΈΡ ΠΎΠ±ΡΠ°Π·ΠΎΠ²Π°Π½ΠΈΡ ΠΊΠ°ΡΠ±ΠΈΠ΄ΠΎΠ².
ΠΡΠΈ ΠΏΡΠΎΠΌΡΡΠ»Π΅Π½Π½ΠΎΠΌ ΠΏΡΠΎΠΈΠ·Π²ΠΎΠ΄ΡΡΠ²Π΅ ΡΡΠ³ΡΠ½Π° ΠΌΠΎΠ΄ΠΈΡΠΈΡΠΈΡΡΡΡ ΠΊΠ°ΠΊ ΡΠ΅ΡΡΠΉ, ΡΠ°ΠΊ ΠΈ ΠΊΠΎΠ²ΠΊΠΈΠΉ ΡΡΠ³ΡΠ½, Π½ΠΎ ΡΠ΅ΡΡΠΉ ΡΡΠ³ΡΠ½ ΠΎΠ±ΡΡΠ½ΠΎ ΡΡΠ΅Π±ΡΠ΅Ρ ΠΌΠ΅Π½ΡΡΠΈΡ ΠΌΠΎΠ΄ΠΈΡΠΈΡΠΈΡΡΡΡΠΈΡ Π΄ΠΎΠ±Π°Π²ΠΎΠΊ, Π² Π·Π°Π²ΠΈΡΠΈΠΌΠΎΡΡΠΈ ΠΎΡ ΡΠΎΡΡΠ°Π²Π° ΠΆΠ΅Π»Π΅Π·Π½ΠΎΠ³ΠΎ ΡΠΏΠ»Π°Π²Π°, ΠΌΠ΅ΡΠΎΠ΄Π° ΠΏΠ»Π°Π²ΠΊΠΈ ΠΈ ΡΠΎΡΡΠ°Π²Π° ΡΠΈΡ ΡΡ. ΠΠ½Π΅ΡΠ΅Π½ΠΈΠ΅ ΡΠ΅ΡΡΠΎΡΠΈΠ»ΠΈΡΠΈΡ ΠΏΡΠ΅ΠΎΠ±ΡΠ°Π·ΡΠ΅Ρ ΡΡΡΡΠΊΡΡΡΡ ΠΈΠ· ΠΏΠ΅ΡΠ΅ΠΎΡ Π»Π°ΠΆΠ΄Π΅Π½Π½ΠΎΠ³ΠΎ Π³ΡΠ°ΡΠΈΡΠ° (Π³ΡΠ°ΡΠΈΡ ΡΠΈΠΏΠ° E Π² ΡΠ΅ΡΠΎΠΌ ΡΡΠ³ΡΠ½Π΅) Π² ΠΏΠΎΠ»Π½ΠΎΡΡΡΡ ΡΠ΅ΡΡΠΉΡΠ°ΡΡΠΉ ΠΈΠ»ΠΈ ΡΡΠ΅ΡΠΎΠΈΠ΄Π°Π»ΡΠ½ΡΠΉ Π³ΡΠ°ΡΠΈΡ, ΠΊΠ°ΠΊ ΠΏΠΎΠΊΠ°Π·Π°Π½ΠΎ Π½ΠΈΠΆΠ΅.
ΠΠ»ΠΈΡΠ½ΠΈΠ΅ ΠΌΠΎΠ΄ΠΈΡΠΈΡΠΈΡΠΎΠ²Π°Π½ΠΈΡ Π½Π° ΡΡΡΡΠΊΡΡΡΡ Π³ΡΠ°ΡΠΈΡΠ° Π² ΡΠ΅ΡΠΎΠΌ ΠΈ ΠΊΠΎΠ²ΠΊΠΎΠΌ ΡΡΠ³ΡΠ½Π΅ΠΡΡΠ³ΠΈΠ΅ ΡΠ»Π΅ΠΌΠ΅Π½ΡΡ
ΠΠΎΡΠΊΠΎΠ»ΡΠΊΡ ΠΏΡΠΎΡΠ½ΠΎΡΡΡ ΡΡΠ³ΡΠ½ΠΎΠ² Π·Π°Π²ΠΈΡΠΈΡ ΠΎΡ ΡΠΎΠ΄Π΅ΡΠΆΠ°Π½ΠΈΡ ΡΠ΅ΡΡΠΈΡΠ° ΠΏΠΎ ΡΡΠ°Π²Π½Π΅Π½ΠΈΡ Ρ ΡΠΎΠ΄Π΅ΡΠΆΠ°Π½ΠΈΠ΅ΠΌ ΠΏΠ΅ΡΠ»ΠΈΡΠ°, Π΄Π»Ρ ΠΏΠΎΠ²ΡΡΠ΅Π½ΠΈΡ ΠΏΡΠΎΡΠ½ΠΎΡΡΠΈ Π΄ΠΎΠ±Π°Π²Π»ΡΡΡΡΡ Π»Π΅Π³ΠΈΡΡΡΡΠΈΠ΅ ΡΠ»Π΅ΠΌΠ΅Π½ΡΡ, ΠΏΠΎΠ΄Π°Π²Π»ΡΡΡΠΈΠ΅ ΠΎΠ±ΡΠ°Π·ΠΎΠ²Π°Π½ΠΈΠ΅ ΡΠ΅ΡΡΠΈΡΠ° ΠΈ ΡΠ²Π΅Π»ΠΈΡΠΈΠ²Π°ΡΡΠΈΠ΅ ΠΊΠΎΠ»ΠΈΡΠ΅ΡΡΠ²ΠΎ ΠΏΠ΅ΡΠ»ΠΈΡΠ°. ΠΠ»Ρ ΠΈΠ·ΡΡΠ΅Π½ΠΈΡ Π°ΡΡΠ΅ΠΊΡΠΎΠ² Π±ΡΠ» ΠΈΠ·ΡΡΠ΅Π½ ΡΡΠ΄ ΡΠ»Π΅ΠΌΠ΅Π½ΡΠΎΠ² ΠΈ Π΄Π°Π½Ρ ΠΎΠ±ΡΠΈΠ΅ ΠΎΠΏΠΈΡΠ°Π½ΠΈΡ. ΠΠ»Ρ ΡΡΠΎΠΉ ΡΠ΅Π»ΠΈ ΠΈΡΠΏΠΎΠ»ΡΠ·ΡΡΡΡΡ Π»Π΅Π³ΠΈΡΡΡΡΠΈΠ΅ ΡΠ»Π΅ΠΌΠ΅Π½ΡΡ, ΡΠ°ΠΊΠΈΠ΅ ΠΊΠ°ΠΊ Ρ
ΡΠΎΠΌ (Cr), ΠΌΠΎΠ»ΠΈΠ±Π΄Π΅Π½ (Mo) ΠΈ Π²ΠΎΠ»ΡΡΡΠ°ΠΌ (W). ΠΡΠΈ ΡΠ»Π΅ΠΌΠ΅Π½ΡΡ ΡΠΏΠΎΡΠΎΠ±ΡΡΠ²ΡΡΡ ΠΎΠ±ΡΠ°Π·ΠΎΠ²Π°Π½ΠΈΡ ΠΊΠ°ΡΠ±ΠΈΠ΄ΠΎΠ² ΠΈ ΠΏΠΎΠ²ΡΡΠ°ΡΡ ΡΠ²Π΅ΡΠ΄ΠΎΡΡΡ ΠΆΠ΅Π»Π΅Π·Π°. ΠΠΎΠΏΠΎΠ»Π½ΠΈΡΠ΅Π»ΡΠ½ΡΡ ΠΈΠ½ΡΠΎΡΠΌΠ°ΡΠΈΡ ΡΠΌ. Π² Π’Π°Π±Π»ΠΈΡΠ΅ 1.0 Π‘ΡΡΡΠΊΡΡΡΠ½ΡΠ΅ ΡΡΡΠ΅ΠΊΡΡ Π΄ΠΎΠ±Π°Π²ΠΎΠΊ ΡΠ»Π΅ΠΌΠ΅Π½ΡΠΎΠ² ΠΊ ΡΡΠ³ΡΠ½Ρ, ΠΏΡΠΈΠ²Π΅Π΄Π΅Π½Π½ΠΎΠΉ Π½ΠΈΠΆΠ΅.
ΠΠΎΠ²ΠΊΠΈΠΉ ΡΡΠ³ΡΠ½
ΠΠΎΠ²ΠΊΠΈΠΉ (ΡΠ°ΠΊΠΆΠ΅ Π½Π°Π·ΡΠ²Π°Π΅ΠΌΡΠΉ Π³ΡΠ°ΡΠΈΡΠΎΠΌ Ρ ΡΠ°ΡΠΎΠ²ΠΈΠ΄Π½ΡΠΌ Π³ΡΠ°ΡΠΈΡΠΎΠΌ) Π§ΡΠ³ΡΠ½ ΠΏΡΠΎΡΠ½Π΅Π΅ ΡΠ΅ΡΠΎΠ³ΠΎ ΡΡΠ³ΡΠ½Π°, Π±ΠΎΠ»Π΅Π΅ ΠΏΡΠΎΡΠ΅Π½ ΠΈ Π½Π°ΠΌΠ½ΠΎΠ³ΠΎ Π΄Π΅ΡΠ΅Π²Π»Π΅ Π΄Π»Ρ Π»ΠΈΡΡΡ ΡΠ»ΠΎΠΆΠ½ΡΡ Π΄Π΅ΡΠ°Π»Π΅ΠΉ, ΡΠ΅ΠΌ ΡΠΎΡΠΌΠΎΠ²ΠΊΠ° ΡΡΠ°Π»ΠΈ. ΠΠΈΠΊΡΠΎΡΡΡΡΠΊΡΡΡΠ° ΠΆΠ΅Π»Π΅Π·Π° Ρ Π°ΡΠ°ΠΊΡΠ΅ΡΠΈΠ·ΡΠ΅ΡΡΡ ΠΊΠ°ΡΠ΅ΡΡΠ²ΠΎΠΌ Β«Π£Π·Π»ΠΎΠ²Π°ΡΠΎΡΡΡΒ» (ΠΎΠΊΡΡΠ³Π»ΠΎΡΡΡ), ΡΠ°Π·ΠΌΠ΅ΡΠΎΠΌ ΡΠ·Π΅Π»ΠΊΠΎΠ² ΠΈ ΠΏΠ»ΠΎΡΠ½ΠΎΡΡΡΡ ΡΠ·Π»ΠΎΠ² (ΡΠ·Π΅Π»ΠΊΠΎΠ² Π½Π° ΠΌΠΌΒ²).
ΠΠΎΠ²ΠΊΠΈΠΉ ΡΡΠ³ΡΠ½ ΡΡΠΈΡΠ°Π΅ΡΡΡ ΠΏΡΠΎΡΠ½ΡΠΌ ΠΌΠ°ΡΠ΅ΡΠΈΠ°Π»ΠΎΠΌ Π΄Π»Ρ Π΄Π΅ΡΠ°Π»Π΅ΠΉ ΡΠ°ΡΡΠΈ (Π½Π°ΠΏΡΠΈΠΌΠ΅Ρ, ΡΡΠ°Π»Ρ), Π΅ΡΠ»ΠΈ Π΅Π³ΠΎ ΠΌΠΎΡΡΠΎΠ»ΠΎΠ³ΠΈΡ ΡΠ²Π»ΡΠ΅ΡΡΡ ΡΠ΅ΡΡΠΈΡΠ½ΠΎΠΉ. Π ΡΠΎ Π²ΡΠ΅ΠΌΡ ΠΊΠ°ΠΊ ΠΏΡΠΎΡΠ½ΠΎΡΡΡ ΠΌΠΎΠΆΠ΅Ρ Π±ΡΡΡ ΡΠ²Π΅Π»ΠΈΡΠ΅Π½Π° ΠΏΡΡΠ΅ΠΌ ΠΈΡΠΏΠΎΠ»ΡΠ·ΠΎΠ²Π°Π½ΠΈΡ Π΄ΠΎΠ±Π°Π²ΠΎΠΊ ΠΊ ΡΠΏΠ»Π°Π²Ρ Π΄Π»Ρ ΠΏΡΠΎΠ΄Π²ΠΈΠΆΠ΅Π½ΠΈΡ ΠΏΠ΅ΡΠ»ΠΈΡΠ° Π²ΠΎΠΊΡΡΠ³ ΠΊΠΎΠ½ΠΊΡΠ΅ΡΠΈΠΉ, ΡΠ΅Π·ΡΠ»ΡΡΠΈΡΡΡΡΠΈΠΉ % ΡΠ΄Π»ΠΈΠ½Π΅Π½ΠΈΡ ΡΠ½ΠΈΠΆΠ°Π΅ΡΡΡ.
Π Π΅Π·ΡΠΌΠ΅
ΠΠΎΠ²ΠΊΠΈΠΉ ΡΡΠ³ΡΠ½ ΠΏΡΠΎΡΠ½Π΅Π΅ ΠΈ ΠΏΠ»Π°ΡΡΠΈΡΠ½Π΅Π΅ (ΠΆΠ΅ΡΡΡΠ΅), ΡΠ΅ΠΌ ΡΠ΅ΡΡΠΉ ΡΡΠ³ΡΠ½. ΠΠ½ ΠΎΠ±ΡΠ°Π·ΡΠ΅ΡΡΡ ΠΏΡΡΠ΅ΠΌ ΠΎΠ±ΡΠ°Π±ΠΎΡΠΊΠΈ ΠΆΠ΅Π»Π΅Π·Π° Ρ ΠΎΡΠ½ΠΎΡΠΈΡΠ΅Π»ΡΠ½ΠΎ Π²ΡΡΠΎΠΊΠΈΠΌ ΡΠ³Π»Π΅ΡΠΎΠ΄Π½ΡΠΌ ΡΠΊΠ²ΠΈΠ²Π°Π»Π΅Π½ΡΠΎΠΌ ΡΠ·Π΅Π»ΠΊΠΎΠ²ΡΠΌ Π°Π³Π΅Π½ΡΠΎΠΌ, ΡΠ°ΠΊΠΈΠΌ ΠΊΠ°ΠΊ ΠΌΠ°Π³Π½ΠΈΠΉ (Π½Π°ΠΈΠ±ΠΎΠ»Π΅Π΅ ΡΠ°ΡΠΏΡΠΎΡΡΡΠ°Π½Π΅Π½Π½ΡΠΉ) ΠΈΠ»ΠΈ ΡΠ΅ΡΠΈΠΉ, Π΄Π»Ρ ΠΎΠ±ΡΠ°Π·ΠΎΠ²Π°Π½ΠΈΡ Π³ΡΠ°ΡΠΈΡΠΎΠ²ΡΡ
ΡΡΠ΅Ρ, ΠΊΠΎΡΠΎΡΡΠ΅ ΡΠ°ΡΡΡΡ Π²ΠΎ Π²ΡΠ΅ΠΌΡ Π·Π°ΡΠ²Π΅ΡΠ΄Π΅Π²Π°Π½ΠΈΡ. ΠΠ°ΠΈΠ±ΠΎΠ»Π΅Π΅ ΡΠ°ΡΠΏΡΠΎΡΡΡΠ°Π½Π΅Π½Ρ Π°Π²ΡΠΎΠΌΠΎΠ±ΠΈΠ»ΡΠ½ΡΠ΅ Π΄Π΅ΡΠ°Π»ΠΈ, ΡΡΠ΅Π±ΡΡΡΠΈΠ΅ Π²ΡΡΠΎΠΊΠΎΠΉ ΠΏΡΠΎΡΠ½ΠΎΡΡΠΈ ΠΈ ΡΠ΄Π°ΡΠ½ΠΎΠΉ Π²ΡΠ·ΠΊΠΎΡΡΠΈ ΠΏΡΠΈ Π²ΠΎΠ·Π΄Π΅ΠΉΡΡΠ²ΠΈΠΈ Π½Π°Π³ΡΡΠ·ΠΎΠΊ, ΡΠ²ΡΠ·Π°Π½Π½ΡΡ
Ρ ΡΠ΅ΡΠΌΠΎΡΠΈΠΊΠ»ΠΈΡΠΎΠ²Π°Π½ΠΈΠ΅ΠΌ ΠΈΠ»ΠΈ ΡΠ΄Π°ΡΠ°ΠΌΠΈ. Π’ΠΈΠΏΡ Π΄Π΅ΡΠ°Π»Π΅ΠΉ Π²ΠΊΠ»ΡΡΠ°ΡΡ: ΠΊΠΎΠ»Π΅Π½ΡΠ°ΡΡΠ΅ Π²Π°Π»Ρ, ΡΠ°ΡΠΏΡΠ΅Π΄Π΅Π»ΠΈΡΠ΅Π»ΡΠ½ΡΠ΅ Π²Π°Π»Ρ, Π²ΡΠΏΡΡΠΊΠ½ΡΠ΅ ΠΊΠΎΠ»Π»Π΅ΠΊΡΠΎΡΡ, ΠΏΠΎΠ²ΠΎΡΠΎΡΠ½ΡΠ΅ ΠΊΡΠ»Π°ΠΊΠΈ, ΡΡΡΠ°Π³ΠΈ ΠΏΠΎΠ΄Π²Π΅ΡΠΊΠΈ, Π΄Π΅ΡΠΆΠ°ΡΠ΅Π»ΠΈ Π΄ΠΈΡΡΠ΅ΡΠ΅Π½ΡΠΈΠ°Π»Π°, ΠΏΡΡΠΆΠΈΠ½Π½ΡΠ΅ Ρ
ΠΎΠΌΡΡΡ ΠΈ ΡΠΎΠΌΡ ΠΏΠΎΠ΄ΠΎΠ±Π½ΠΎΠ΅. Π ΡΠ°Π½ΡΠ΅Ρ
Π½ΠΈΠΊΠ΅ ΠΈ ΡΡΡΠ±ΠΎΠΏΡΠΎΠ²ΠΎΠ΄Π½ΠΎΠΉ ΠΏΡΠΎΠΌΡΡΠ»Π΅Π½Π½ΠΎΡΡΠΈ ΠΈΡΠΏΠΎΠ»ΡΠ·ΠΎΠ²Π°Π½ΠΈΠ΅ ΠΊΠΎΠ²ΠΊΠΎΠ³ΠΎ ΡΡΠ³ΡΠ½Π° ΡΡΠ°Π»ΠΎ Π±ΠΎΠ»ΡΡΠΈΠΌ Π΄ΠΎΡΡΠΈΠΆΠ΅Π½ΠΈΠ΅ΠΌ Π² ΠΏΡΠΎΠΈΠ·Π²ΠΎΠ΄ΡΡΠ²Π΅ ΡΡΡΠ±, ΡΠΎΠ΅Π΄ΠΈΠ½Π΅Π½ΠΈΠΉ ΠΈ ΠΊΠ»Π°ΠΏΠ°Π½ΠΎΠ², ΠΊΠΎΡΠΎΡΡΠ΅ Π±ΡΠ»ΠΈ ΠΌΠ΅Π½Π΅Π΅ Π΄ΠΎΡΠΎΠ³ΠΈΠΌΠΈ, ΡΠ΅ΠΌ Π°Π»ΡΡΠ΅ΡΠ½Π°ΡΠΈΠ²Π° ΠΈΠ· ΠΊΠΎΠ²ΠΊΠΎΠ³ΠΎ ΡΡΠ³ΡΠ½Π°. ΠΡΠΈ Π²ΡΠ΅Ρ
ΡΡΠΈΡ
ΠΏΡΠΈΠΌΠ΅Π½Π΅Π½ΠΈΡΡ
ΠΊΠΎΠ²ΠΊΠΈΠΉ ΡΡΠ³ΡΠ½ ΠΏΠΎΠ»ΡΡΠ°Π΅Ρ Π²ΡΠ΅ Π±ΠΎΠ»ΡΡΠ΅Π΅ ΠΏΡΠΈΠΌΠ΅Π½Π΅Π½ΠΈΠ΅, ΡΠ°ΡΡΠΎ Π²ΡΡΠ΅ΡΠ½ΡΡ ΠΊΠΎΠ½ΡΡΡΡΠΊΡΠΈΠΈ ΠΈΠ· ΡΠ΅ΡΠΎΠ³ΠΎ ΡΡΠ³ΡΠ½Π°, ΡΠ°ΠΊ ΡΡΠΎ ΠΌΠΎΠΆΠ½ΠΎ Π΄ΠΎΠ±ΠΈΡΡΡΡ ΡΠ½ΠΈΠΆΠ΅Π½ΠΈΡ Π²Π΅ΡΠ° Π·Π° ΡΡΠ΅Ρ ΡΠ»ΡΡΡΠ΅Π½Π½ΡΡ
ΠΌΠ΅Ρ
Π°Π½ΠΈΡΠ΅ΡΠΊΠΈΡ
ΡΠ²ΠΎΠΉΡΡΠ².
ΠΠ° Π΅ΠΆΠ΅Π³ΠΎΠ΄Π½ΠΎΠΉ ΠΊΠΎΠ½ΡΠ΅ΡΠ΅Π½ΡΠΈΠΈ AFS 1948 Π³ΠΎΠ΄Π° ΡΡΠ°ΡΡΠ½ΠΈΠΊΠ°ΠΌ ΠΊΠΎΠ½ΡΠ΅ΡΠ΅Π½ΡΠΈΠΈ Π±ΡΠ»Π° ΠΏΡΠ΅Π΄ΡΡΠ°Π²Π»Π΅Π½Π° ββΠ½ΠΎΠ²Π°Ρ ΠΌΠΎΡΡΠΎΠ»ΠΎΠ³ΠΈΡ ΠΆΠ΅Π»Π΅Π·Π°: ΠΊΠΎΠ²ΠΊΠΈΠΉ ΡΡΠ³ΡΠ½. Π‘ΠΎΠ·Π΄Π°ΡΠ΅Π»Π΅ΠΌ ΡΡΠΎΠ³ΠΎ Π½ΠΎΠ²ΠΎΠ³ΠΎ ΠΌΠ°ΡΠ΅ΡΠΈΠ°Π»Π° ΠΎΠ±ΡΡΠ½ΠΎ ΡΡΠΈΡΠ°Π΅ΡΡΡ ΠΠΈΡ ΠΠΈΠ»Π»Ρ, ΠΎΠ΄Π½Π°ΠΊΠΎ Π² ΠΏΠ΅ΡΠ²ΠΎΠ½Π°ΡΠ°Π»ΡΠ½ΠΎΠΌ ΠΏΠ°ΡΠ΅Π½ΡΠ΅ 1949Β Π³ΠΎΠ΄Π°, ΠΏΠ΅ΡΠ΅Π΄Π°Π½Π½ΠΎΠΌ ΠΠ΅ΠΆΠ΄ΡΠ½Π°ΡΠΎΠ΄Π½ΠΎΠΉ Π½ΠΈΠΊΠ΅Π»Π΅Π²ΠΎΠΉ ΠΊΠΎΠΌΠΏΠ°Π½ΠΈΠΈ (INCO), ΡΠΊΠ°Π·Π°Π½Ρ ΡΡΠΈ ΡΠ΅Π»ΠΎΠ²Π΅ΠΊΠ°: ΠΠΈΡ ΠΡΠ°ΠΉΡ ΠΠΈΠ»Π»ΠΈΡ, ΠΠ»ΡΠ±Π΅ΡΡ ΠΠΎΠ» ΠΠ°Π½Π½Π΅Π±ΠΈΠ½ ΠΈ ΠΠΎΡΠΌΠ°Π½ ΠΠΎΠ΄Π΅Π½ ΠΠΈΠ»Π»ΠΈΠ½Π³. Π ΡΠ²ΠΎΠ΅ΠΌ ΠΏΠ°ΡΠ΅Π½ΡΠ΅ (US 2485760A) ΠΈΠ·ΠΎΠ±ΡΠ΅ΡΠ°ΡΠ΅Π»ΡΠΌ ΠΏΡΠΈΠΏΠΈΡΡΠ²Π°ΡΡ ΠΈΠ·ΠΎΠ±ΡΠ΅ΡΠ΅Π½ΠΈΠ΅ Β«Π»ΠΈΡΠΎΠ³ΠΎ ΡΠ΅ΡΡΠΎΡΠΏΠ»Π°Π²Π° Π΄Π»Ρ ΠΏΡΠΎΠΈΠ·Π²ΠΎΠ΄ΡΡΠ²Π° ΠΊΠΎΠ²ΠΊΠΎΠ³ΠΎ ΡΡΠ³ΡΠ½Π° ΠΏΡΡΠ΅ΠΌ ΠΎΠ±ΡΠ°Π±ΠΎΡΠΊΠΈ ΠΌΠ°Π³Π½ΠΈΠ΅ΠΌΒ».
Π―Π²Π»ΡΡΡΡ ΠΏΠ°ΡΠ΅Π½ΡΠΎΠΎΠ±Π»Π°Π΄Π°ΡΠ΅Π»Π΅ΠΌ ΠΊΠΎΠ²ΠΊΠΎΠ³ΠΎ ΡΡΠ³ΡΠ½Π° Ρ ΠΌΠ°Π³Π½ΠΈΠ΅Π²ΠΎΠΉ ΠΎΠ±ΡΠ°Π±ΠΎΡΠΊΠΎΠΉ, INCO ΠΏΡΠΎΠ΄Π²ΠΈΠ³Π°Π»Π° ΠΏΡΠ΅ΠΈΠΌΡΡΠ΅ΡΡΠ²Π° ΡΠ²ΠΎΠΉΡΡΠ² ΠΌΠ°ΡΠ΅ΡΠΈΠ°Π»Π° ΠΈ ΠΏΡΠ΅Π΄ΡΡΠ°Π²Π»ΡΠ»Π° ΠΊΠΎΠ²ΠΊΠΈΠΉ ΡΡΠ³ΡΠ½ Π΄ΠΈΠ·Π°ΠΉΠ½Π΅ΡΠ°ΠΌ ΠΈ ΠΈΠ½ΠΆΠ΅Π½Π΅ΡΠ°ΠΌ, ΡΠ°ΡΠΏΡΠΎΡΡΡΠ°Π½ΡΡ ΡΠ΅Ρ
Π½ΠΈΡΠ΅ΡΠΊΡΡ Π»ΠΈΡΠ΅ΡΠ°ΡΡΡΡ ΠΈ ΠΏΡΠΎΠ²ΠΎΠ΄Ρ ΡΠ΅ΠΌΠΈΠ½Π°ΡΡ. ΠΠΎ ΠΌΠ΅ΡΠ΅ ΡΠ°ΡΠΏΡΠΎΡΡΡΠ°Π½Π΅Π½ΠΈΡ Π·Π½Π°Π½ΠΈΠΉ ΠΎ ΡΠ²ΠΎΠΉΡΡΠ²Π°Ρ
ΠΈ ΡΠΊΠΎΠ½ΠΎΠΌΠΈΡΠ½ΠΎΡΡΠΈ ΠΊΠΎΠ²ΠΊΠΎΠ³ΠΎ ΡΡΠ³ΡΠ½Π° Π΅Π³ΠΎ ΠΈΡΠΏΠΎΠ»ΡΠ·ΠΎΠ²Π°Π½ΠΈΠ΅ ΡΠ΅Π·ΠΊΠΎ Π²ΠΎΠ·ΡΠΎΡΠ»ΠΎ Π² ΠΏΡΡΠΈΠ΄Π΅ΡΡΡΡΡ
ΠΈ Π½Π°ΡΠ°Π»Π΅ ΡΠ΅ΡΡΠΈΠ΄Π΅ΡΡΡΡΡ
Π³ΠΎΠ΄ΠΎΠ². ΠΠΎΡΠ»Π΅ ΠΏΡΠ΅ΠΊΡΠ°ΡΠ΅Π½ΠΈΡ ΠΏΡΠΎΠ΄Π²ΠΈΠΆΠ΅Π½ΠΈΡ INCO ΠΊΠΎΠ²ΠΊΠΎΠ³ΠΎ ΡΡΠ³ΡΠ½Π° Π² 1966 Π³ΠΎΠ΄Ρ ΡΠΎΡΡ ΡΡΠ½ΠΊΠ° ΠΊΠΎΠ²ΠΊΠΎΠ³ΠΎ ΡΡΠ³ΡΠ½Π° ΠΏΡΠΎΠ΄ΠΎΠ»ΠΆΠ°Π» ΠΎΠΏΠ΅ΡΠ΅ΠΆΠ°ΡΡ ΡΠΎΡΡ ΡΡΠ½ΠΊΠ° Π»ΠΈΡΡΡ Π΄ΡΡΠ³ΠΈΡ
ΡΠ΅ΡΠ½ΡΡ
ΠΌΠ΅ΡΠ°Π»Π»ΠΎΠ², Π½ΠΎ ΠΏΠΎ ΠΌΠ΅ΡΠ΅ ΡΠΎΠ³ΠΎ, ΠΊΠ°ΠΊ ΠΈΠ½ΠΆΠ΅Π½Π΅ΡΡ ΠΈ Π΄ΠΈΠ·Π°ΠΉΠ½Π΅ΡΡ, ΠΊΠΎΡΠΎΡΡΠ΅ ΠΈΠ·Π²Π»Π΅ΠΊΠ»ΠΈ Π²ΡΠ³ΠΎΠ΄Ρ ΠΈΠ· ΠΏΠ΅ΡΠ²ΡΡ
ΡΡΠΈΠ»ΠΈΠΉ INCO ΠΏΠΎ ΠΏΡΠΎΠ΄Π²ΠΈΠΆΠ΅Π½ΠΈΡ, ΡΡΠ»ΠΈ Π½Π° ΠΏΠ΅Π½ΡΠΈΡ, ΠΈΡ
Π·Π°ΠΌΠ΅Π½ΠΈΠ»ΠΎ Π½ΠΎΠ²ΠΎΠ΅ ΠΏΠΎΠΊΠΎΠ»Π΅Π½ΠΈΠ΅, ΠΊΠΎΡΠΎΡΠΎΠ΅ Π½Π΅ Π±ΡΠ»ΠΎ ΠΎΠ·Π½Π°ΠΊΠΎΠΌΠΈΠ»ΠΈΡΡ Ρ ΡΠ΅Ρ
Π½ΠΎΠ»ΠΎΠ³ΠΈΠ΅ΠΉ ΠΏΡΠΎΡΠ΅ΡΡΠ° ΠΈΠ· ΡΠ²ΠΎΠ΅ΠΉ Π°ΠΊΠ°Π΄Π΅ΠΌΠΈΡΠ΅ΡΠΊΠΎΠΉ ΠΏΠΎΠ΄Π³ΠΎΡΠΎΠ²ΠΊΠΈ. ΠΠΎ ΡΡΠΎΠΉ ΠΏΡΠΈΡΠΈΠ½Π΅ Π±ΡΠ»ΠΎ ΡΠΎΠ·Π΄Π°Π½ΠΎ ΠΠ±ΡΠ΅ΡΡΠ²ΠΎ ΠΊΠΎΠ²ΠΊΠΎΠ³ΠΎ ΡΡΠ³ΡΠ½Π° (DIS) Π΄Π»Ρ ΠΎΠ±ΡΡΠ΅Π½ΠΈΡ ΠΈ Π»ΠΈΠΊΠ²ΠΈΠ΄Π°ΡΠΈΠΈ ΡΠ°Π·ΡΡΠ²Π° Π² Π·Π½Π°Π½ΠΈΡΡ
Ρ Π½ΠΎΠ²ΡΠΌΠΈ ΠΏΠΎΠΊΠΎΠ»Π΅Π½ΠΈΡΠΌΠΈ ΠΌΠ΅ΡΠ°Π»Π»ΡΡΠ³ΠΎΠ², ΠΈΠ½ΠΆΠ΅Π½Π΅ΡΠΎΠ²-ΠΊΠΎΠ½ΡΡΡΡΠΊΡΠΎΡΠΎΠ² ΠΈ ΠΈΠ½ΠΆΠ΅Π½Π΅ΡΠΎΠ²-ΡΠ΅Ρ
Π½ΠΎΠ»ΠΎΠ³ΠΎΠ².
ΠΠ΅ΡΡΠ»ΡΡΡΡΠΈΠ·Π°ΡΠΈΡ
ΠΠ±ΡΠ°Π±ΠΎΡΠΊΠ° ΠΊΠΎΠ²ΠΊΠΎΠ³ΠΎ ΡΡΠ³ΡΠ½Π° ΠΈΠΌΠ΅Π΅Ρ ΡΡΠ΅Π·Π²ΡΡΠ°ΠΉΠ½ΠΎ Π²Π°ΠΆΠ½ΠΎΠ΅ Π·Π½Π°ΡΠ΅Π½ΠΈΠ΅ Π΄Π»Ρ ΠΎΠΏΡΠ΅Π΄Π΅Π»Π΅Π½ΠΈΡ Π΅Π³ΠΎ ΡΠ²ΠΎΠΉΡΡΠ². ΠΠ°ΡΠ°Π»ΡΠ½ΡΠΌ ΡΡΠ°ΠΏΠΎΠΌ ΠΏΡΠΎΠΈΠ·Π²ΠΎΠ΄ΡΡΠ²Π° ΠΊΠΎΠ²ΠΊΠΎΠ³ΠΎ ΡΡΠ³ΡΠ½Π° ΡΠ²Π»ΡΠ΅ΡΡΡ ΡΠ΄Π°Π»Π΅Π½ΠΈΠ΅ ΠΈΠ·Π±ΡΡΠΎΡΠ½ΠΎΠΉ ΡΠ΅ΡΡ ΠΈΠ· ΡΠ°ΡΠΏΠ»Π°Π²Π»Π΅Π½Π½ΠΎΠ³ΠΎ ΡΡΠ³ΡΠ½Π°. Π ΡΠ΅ΡΡΠΉ ΡΡΠ³ΡΠ½ ΠΈΠ½ΠΎΠ³Π΄Π° Π΄ΠΎΠ±Π°Π²Π»ΡΡΡ ΡΠ΅ΡΡ, ΠΏΠΎΡΠΊΠΎΠ»ΡΠΊΡ ΠΎΠ½Π° ΡΠΏΠΎΡΠΎΠ±ΡΡΠ²ΡΠ΅Ρ ΠΎΠ±ΡΠ°Π·ΠΎΠ²Π°Π½ΠΈΡ Π³ΡΠ°ΡΠΈΡΠΎΠ²ΡΡ
ΡΠ΅ΡΡΠ΅ΠΊ. ΠΠΎ ΡΡΠΎΠΉ ΠΏΡΠΈΡΠΈΠ½Π΅ ΠΎΠ½ Π΄ΠΎΠ»ΠΆΠ΅Π½ Π±ΡΡΡ ΠΏΡΠ°ΠΊΡΠΈΡΠ΅ΡΠΊΠΈ ΠΈΡΠΊΠ»ΡΡΠ΅Π½ ΠΈΠ· ΡΠ°ΡΠΏΠ»Π°Π²ΠΎΠ² ΠΊΠΎΠ²ΠΊΠΎΠ³ΠΎ ΡΡΠ³ΡΠ½Π°. ΠΡΡΡ Π½Π΅ΠΊΠΎΡΠΎΡΡΠ΅ Π»ΠΈΡΠ΅ΠΉΠ½ΡΠ΅ Π·Π°Π²ΠΎΠ΄Ρ, ΠΊΠΎΡΠΎΡΡΠ΅ ΠΏΠ΅ΡΠ΅ΡΠ°Π±Π°ΡΡΠ²Π°ΡΡ ΠΊΠ°ΠΊ ΡΠ΅ΡΡΠΉ, ΡΠ°ΠΊ ΠΈ ΠΊΠΎΠ²ΠΊΠΈΠΉ ΡΡΠ³ΡΠ½ ΠΈΠ· ΠΎΠ΄Π½ΠΎΠ³ΠΎ ΠΈ ΡΠΎΠ³ΠΎ ΠΆΠ΅ ΡΠΈΡ
ΡΠΎΠ²ΠΎΠ³ΠΎ ΠΌΠ°ΡΠ΅ΡΠΈΠ°Π»Π°, ΠΏΠΎΡΡΠΎΠΌΡ Π»ΡΠ±ΠΎΠΉ Π»ΠΎΠΌ ΡΠ΅ΡΠΎΠ³ΠΎ ΡΡΠ³ΡΠ½Π°, ΠΏΠ΅ΡΠ΅ΡΠ°Π±Π°ΡΡΠ²Π°Π΅ΠΌΡΠΉ Π²Π½ΡΡΡΠΈ ΠΊΠΎΠΌΠΏΠ°Π½ΠΈΠΈ, Π±ΡΠ΄Π΅Ρ ΡΠΎΠ΄Π΅ΡΠΆΠ°ΡΡ ΡΠ΅ΡΡ, ΠΊΠΎΡΠΎΡΡΡ Π½Π΅ΠΎΠ±Ρ
ΠΎΠ΄ΠΈΠΌΠΎ ΡΠ΄Π°Π»ΠΈΡΡ. Π£Π΄Π°Π»Π΅Π½ΠΈΠ΅ ΡΠ΅ΡΡ Π²ΠΊΠ»ΡΡΠ°Π΅Ρ Π΄ΠΎΠ±Π°Π²Π»Π΅Π½ΠΈΠ΅ CaO ΠΈΠ»ΠΈ ΠΊΠ°ΠΊΠΎΠ³ΠΎ-Π»ΠΈΠ±ΠΎ Π΄ΡΡΠ³ΠΎΠ³ΠΎ Π°Π³Π΅Π½ΡΠ°. Π‘Π»Π΅Π΄ΡΠ΅Ρ ΠΎΡΠΌΠ΅ΡΠΈΡΡ, ΡΡΠΎ Π»ΠΈΡΠ΅ΠΉΠ½ΡΠ΅ Π·Π°Π²ΠΎΠ΄Ρ, ΠΊΠΎΡΠΎΡΡΠ΅ ΡΠΏΠ΅ΡΠΈΠ°Π»ΠΈΠ·ΠΈΡΡΡΡΡΡ ΡΠΎΠ»ΡΠΊΠΎ Π½Π° ΠΎΠ±ΡΠ°Π±ΠΎΡΠΊΠ΅ ΠΊΠΎΠ²ΠΊΠΎΠ³ΠΎ ΡΡΠ³ΡΠ½Π°, ΠΌΠΎΠ³ΡΡ ΠΈΠΌΠ΅ΡΡ Π²ΠΎΠ·ΠΌΠΎΠΆΠ½ΠΎΡΡΡ ΠΈΠ·Π±Π΅ΠΆΠ°ΡΡ ΠΎΠ±ΡΠΈΡΠ½ΡΡ
ΠΏΡΠΎΡΠ΅Π΄ΡΡ Π΄Π΅ΡΡΠ»ΡΡΡΡΠ°ΡΠΈΠΈ, Π½ΠΎ ΠΎΠ½ΠΈ Π²ΡΠ΅Π³Π΄Π° Π΄ΠΎΠ»ΠΆΠ½Ρ ΡΠ»Π΅Π΄ΠΈΡΡ Π·Π° ΡΡΠΈΠΌ ΠΏΡΠΈ ΠΈΠ·ΠΌΠ΅ΡΠ΅Π½ΠΈΠΈ Ρ
ΠΈΠΌΠΈΡΠ΅ΡΠΊΠΎΠ³ΠΎ ΡΠΎΡΡΠ°Π²Π°.
ΠΠΎΠ΄ΡΠ»ΡΡΠΈΠ·Π°ΡΠΈΡ Ρ ΠΈΡΠΏΠΎΠ»ΡΠ·ΠΎΠ²Π°Π½ΠΈΠ΅ΠΌ ΠΊΠΎΠ½Π²Π΅ΡΡΠΈΠΈ ΠΌΠ°Π³Π½ΠΈΡ
Π£Π½ΠΈΠΊΠ°Π»ΡΠ½ΠΎΠΉ ΡΡΠ°Π΄ΠΈΠ΅ΠΉ ΠΎΠ±ΡΠ°Π±ΠΎΡΠΊΠΈ ΠΊΠΎΠ²ΠΊΠΎΠ³ΠΎ ΡΡΠ³ΡΠ½Π° ΡΠ²Π»ΡΠ΅ΡΡΡ ΡΠ°ΡΠΎΠΎΠ±ΡΠ°Π·ΠΎΠ²Π°Π½ΠΈΠ΅ Π³ΡΠ°ΡΠΈΡΠ°. ΠΠ° ΡΡΠΎΠΌ ΡΡΠ°ΠΏΠ΅ ΠΊ ΡΠ°ΡΠΏΠ»Π°Π²Π»Π΅Π½Π½ΠΎΠΌΡ ΡΠΏΠ»Π°Π²Ρ Π΄ΠΎΠ±Π°Π²Π»ΡΡΡ ΠΌΠ°Π³Π½ΠΈΠΉ Π΄Π»Ρ ΡΠΎΠ·Π΄Π°Π½ΠΈΡ ΠΎΡΡΠ°ΡΠΎΡΠ½ΠΎΠ³ΠΎ ΡΡΠΎΠ²Π½Ρ Mg ΠΏΡΠΈΠΌΠ΅ΡΠ½ΠΎ 0,03-0,06%, ΡΡΠΎ ΡΠ²Π»ΡΠ΅ΡΡΡ ΠΊΠΎΠ»ΠΈΡΠ΅ΡΡΠ²ΠΎΠΌ, Π½Π΅ΠΎΠ±Ρ ΠΎΠ΄ΠΈΠΌΡΠΌ Π΄Π»Ρ ΠΎΠ±ΡΠ°Π·ΠΎΠ²Π°Π½ΠΈΡ ΡΡΠ΅ΡΠΎΠΈΠ΄ΠΎΠ² ΠΈΠ· Π³ΡΠ°ΡΠΈΡΠ°. Π ΡΠΎΠΆΠ°Π»Π΅Π½ΠΈΡ, Mg ΠΈΡΠΏΠ°ΡΡΠ΅ΡΡΡ ΠΏΡΠΈ ΡΠ΅ΠΌΠΏΠ΅ΡΠ°ΡΡΡΠ΅ Π·Π½Π°ΡΠΈΡΠ΅Π»ΡΠ½ΠΎ Π½ΠΈΠΆΠ΅ ΡΠ΅ΠΌΠΏΠ΅ΡΠ°ΡΡΡΡ ΠΏΠ»Π°Π²Π»Π΅Π½ΠΈΡ ΡΡΠ³ΡΠ½Π° Ρ ΡΠ°ΡΠΎΠ²ΠΈΠ΄Π½ΡΠΌ Π³ΡΠ°ΡΠΈΡΠΎΠΌ, ΠΏΠΎΡΡΠΎΠΌΡ Π΄Π»Ρ Π΄ΠΎΡΡΠΈΠΆΠ΅Π½ΠΈΡ ΡΠ°ΠΊΠΎΠΉ ΠΊΠΎΠ½Π²Π΅ΡΡΠΈΠΈ Π±ΡΠ»ΠΈ ΡΠ°Π·ΡΠ°Π±ΠΎΡΠ°Π½Ρ ΠΈΠ½Π½ΠΎΠ²Π°ΡΠΈΠΎΠ½Π½ΡΠ΅ ΠΌΠ΅ΡΠΎΠ΄Ρ ΠΊΠΎΠ½Π²Π΅ΡΡΠΈΠΈ:
ΠΠΎΠ½Π²Π΅ΡΡΠΈΡ Π² ΠΎΡΠΊΡΡΡΠΎΠΌ ΠΊΠΎΠ²ΡΠ΅
- ΠΠ·Π²Π»Π΅ΡΠ΅Π½ΠΈΠ΅ Mg ΠΏΡΠΈ ΠΊΠΎΠ½Π²Π΅ΡΡΠΈΠΈ = 20-25%
- ΠΠ΅ΡΡΠ»ΡΡΡΡΠΈΠ·Π°ΡΠΈΡ ΠΎΡΠ½ΠΎΠ²Π½ΠΎΠ³ΠΎ ΡΠΏΠ»Π°Π²Π° ΠΏΠ΅ΡΠ΅Π΄ ΠΊΠΎΠ½Π²Π΅ΡΡΠΈΠ΅ΠΉ Π²Π°ΠΆΠ½Π°
- Π Π΅Π°ΠΊΡΠΈΡ Π±ΡΡΠ½Π°Ρ ΠΈ Π½Π΅ ΡΠ΅ΠΊΠΎΠΌΠ΅Π½Π΄ΡΠ΅ΡΡΡ Π΄Π»Ρ ΠΎΠ±Π΅ΡΠΏΠ΅ΡΠ΅Π½ΠΈΡ Π±Π΅Π·ΠΎΠΏΠ°ΡΠ½ΠΎΡΡΠΈ
- ΠΡΠ΅Π½Ρ Π΄ΡΠΌΠ½ΠΎ Π²ΠΎ Π²ΡΠ΅ΠΌΡ ΠΊΠΎΠ½Π²Π΅ΡΡΠΈΠΈ
- ΠΠ·Π²Π»Π΅ΡΠ΅Π½ΠΈΠ΅ ΠΌΠ°Π³Π½ΠΈΡ ΠΏΡΠΈ ΠΊΠΎΠ½Π²Π΅ΡΡΠΈΠΈ = 40-45%
- ΠΠ΅ΡΡΠ»ΡΡΡΡΠ°ΡΠΈΡ ΠΎΡΠ½ΠΎΠ²Π½ΠΎΠ³ΠΎ ΡΠΏΠ»Π°Π²Π° ΠΏΠ΅ΡΠ΅Π΄ ΠΊΠΎΠ½Π²Π΅ΡΡΠΈΠ΅ΠΉ Π²Π°ΠΆΠ½Π°
- Π Π΅Π°ΠΊΡΠΈΡ Π±ΡΡΠ½Π°Ρ, Π½ΠΎ ΡΠ½ΠΈΠΆΠ°Π΅ΡΡΡ, ΠΏΠΎΡΠΊΠΎΠ»ΡΠΊΡ ΠΊΠΎΠ²Ρ Π³Π»ΡΠ±ΠΆΠ΅ ΠΈ ΠΈΠΌΠ΅Π΅Ρ ΠΊΠ°ΡΠΌΠ°Π½ Π΄Π»Ρ ΠΎΠ±ΡΠ°Π±ΠΎΡΠΊΠΈ
- ΠΡΠ΅ Π΅ΡΠ΅ Π΄ΡΠΌΠΈΡΡΡ Π²ΠΎ Π²ΡΠ΅ΠΌΡ ΠΊΠΎΠ½Π²Π΅ΡΡΠΈΠΈ ΠΈ Π½ΡΠΆΠ΄Π°Π΅ΡΡΡ Π² Π²Π΅Π½ΡΠΈΠ»ΡΡΠΈΠΎΠ½Π½ΠΎΠΌ ΠΊΠΎΠ»ΠΏΠ°ΠΊΠ΅
ΠΠΎΠ½Π²Π΅ΡΡΠΈΡ ΠΏΡΠΎΠΌΠ΅ΠΆΡΡΠΎΡΠ½ΠΎΠ³ΠΎ ΠΊΠΎΠ²ΡΠ°
- ΠΠ·Π²Π»Π΅ΡΠ΅Π½ΠΈΠ΅ ΠΌΠ°Π³Π½ΠΈΡ ΠΏΡΠΈ ΠΊΠΎΠ½Π²Π΅ΡΡΠΈΠΈ = 60-65%
- ΠΠ΅ΡΡΠ»ΡΡΡΡΠΈΠ·Π°ΡΠΈΡ ΠΎΡΠ½ΠΎΠ²Π½ΠΎΠ³ΠΎ ΡΠΏΠ»Π°Π²Π° ΠΌΠ΅Π½Π΅Π΅ ΠΊΡΠΈΡΠΈΡΠ½Π° 90% ΠΎΡ ΠΊΠΎΠ½Π²Π΅ΡΡΠΈΠΈ Π² ΠΎΡΠΊΡΡΡΠΎΠΌ ΠΊΠΎΠ²ΡΠ΅
ΠΠΎΠ½Π²Π΅ΡΡΠ΅ΡΠ½ΡΠΉ ΠΌΠ΅ΡΠΎΠ΄ ΠΠΆΠΎΡΠ΄ΠΆΠ° Π€ΠΈΡΠ΅ΡΠ°
- ΠΠ·Π²Π»Π΅ΡΠ΅Π½ΠΈΠ΅ ΠΌΠ°Π³Π½ΠΈΡ = 70% (ΠΈΡΠΏΠΎΠ»ΡΠ·ΡΠ΅ΡΡΡ ΠΌΠ°Π³Π½ΠΈΠ΅Π²Π°Ρ ΡΡΡΡΠΆΠΊΠ°)
- ΠΠ΅ΡΡΠ»ΡΡΡΡΠ°ΡΠΈΡ ΠΎΡΠ½ΠΎΠ²Π½ΠΎΠ³ΠΎ ΡΠΏΠ»Π°Π²Π° ΠΎΠ±ΡΡΠ½ΠΎ Π½Π΅ ΡΡΠ΅Π±ΡΠ΅ΡΡΡ
- ΠΠ°ΠΊΡΡΡΡΠΉ ΠΊΠΎΠ½Π²Π΅ΡΡΠΈΠΎΠ½Π½ΡΠΉ ΡΠΎΡΡΠ΄ ΡΠΎΠ΄Π΅ΡΠΆΠΈΡ ΡΠ΅Π°ΠΊΡΠΈΠΎΠ½Π½ΡΡ ΡΠΌΠ΅ΡΡ
- ΠΠ΅Π·ΠΎΠΏΠ°ΡΠ΅Π½ Π΄Π»Ρ Π±ΠΎΠ»ΡΡΠΈΡ ΠΎΠ±ΡΠ΅ΠΌΠΎΠ² ΠΊΠΎΠ²ΡΠ°
ΠΠΎΠ½Π²Π΅ΡΡΠΈΡ Π² Π»ΠΈΡΠ΅ΠΉΠ½ΠΎΠΉ ΡΠΎΡΠΌΠ΅
- ΠΠ·Π²Π»Π΅ΡΠ΅Π½ΠΈΠ΅ ΠΌΠ°Π³Π½ΠΈΡ ΠΏΡΠΈ ΠΊΠΎΠ½Π²Π΅ΡΡΠΈΠΈ = 70% (ΠΈΡΠΏΠΎΠ»ΡΠ·ΡΠ΅ΡΡΡ ΠΌΠ°Π³Π½ΠΈΠ΅Π²Π°Ρ ΡΡΡΡΠΆΠΊΠ°)
- ΠΠ΅ΡΡΠ»ΡΡΡΡΠ°ΡΠΈΡ ΠΎΡΠ½ΠΎΠ²Π½ΠΎΠ³ΠΎ ΡΠΏΠ»Π°Π²Π° ΠΌΠ΅Π½Π΅Π΅ ΠΊΡΠΈΡΠΈΡΠ½Π° ΡΠ΅Π°ΠΊΡΠΈΡ
- ΠΠ±ΡΡΠ½ΠΎ Π² ΡΠΎΡΠ΅ΡΠ°Π½ΠΈΠΈ Ρ Π°Π²ΡΠΎΠΌΠ°ΡΠΈΡΠ΅ΡΠΊΠΈΠΌ ΡΠ°Π·Π»ΠΈΠ²ΠΎΡΠ½ΡΠΌ ΠΊΠΎΠ²ΡΠΎΠΌ Π΄Π»Ρ ΡΠ΅Π³ΡΠ»ΠΈΡΠΎΠ²Π°Π½ΠΈΡ ΠΏΠΎΡΠΎΠΊΠ°
Β
ΠΡΠ΅ΠΎΠ±ΡΠ°Π·ΠΎΠ²Π°Π½ΠΈΠ΅ ΠΌΠ°Π³Π½ΠΈΡ
ΠΡΠ΅ΠΎΠ±ΡΠ°Π·ΠΎΠ²Π°Π½ΠΈΠ΅ Π² ΡΠ°Π·Π»ΠΈΠ²ΠΎΡΠ½ΠΎΠΌ ΠΊΠΎΠ²ΡΠ΅ ΡΠ²Π»ΡΠ΅ΡΡΡ Π½Π°ΠΈΠ±ΠΎΠ»Π΅Π΅ ΡΠ°ΡΠΏΡΠΎΡΡΡΠ°Π½Π΅Π½Π½ΡΠΌ ΠΌΠ΅ΡΠΎΠ΄ΠΎΠΌ ΠΏΡΠ΅ΠΎΠ±ΡΠ°Π·ΠΎΠ²Π°Π½ΠΈΡ ΠΈ ΡΡΠΈΡΠ°Π΅ΡΡΡ Π±Π΅Π·ΠΎΠΏΠ°ΡΠ½ΡΠΌ:
ΠΠ·Π²Π»Π΅ΡΠ΅Π½ΠΈΠ΅ ΠΌΠ°Π³Π½ΠΈΡ 60-65%, Π½ΠΈΠ·ΠΊΠΎΠ΅ Π²ΡΠ΄Π΅Π»Π΅Π½ΠΈΠ΅ Π΄ΡΠΌΠ°, ΡΠ½ΠΈΠΆΠ΅Π½ΠΈΠ΅ ΠΏΠΎΡΠ΅ΡΡ ΡΠ³Π»Π΅ΡΠΎΠ΄Π°.Π‘ΡΡΠ΅ΡΡΠ²ΡΡΡ ΠΈ Π΄ΡΡΠ³ΠΈΠ΅ ΠΌΠ΅ΡΠΎΠ΄Ρ ΠΊΠΎΠ½Π²Π΅ΡΡΠΈΠΈ Ρ ΡΠ°Π·Π½ΠΎΠΉ ΡΡΠ΅ΠΏΠ΅Π½ΡΡ Π±Π΅Π·ΠΎΠΏΠ°ΡΠ½ΠΎΡΡΠΈ ΠΈ ΡΡΡΠ΅ΠΊΡΠΈΠ²Π½ΠΎΡΡΠΈ ΠΈΠ·Π²Π»Π΅ΡΠ΅Π½ΠΈΡ ΠΌΠ°Π³Π½ΠΈΡ: ΠΊΠΎΠ½Π²Π΅ΡΡΠΈΡ Π² ΠΎΡΠΊΡΡΡΠΎΠΌ ΠΊΠΎΠ²ΡΠ΅ (ΠΈΠ·Π²Π»Π΅ΡΠ΅Π½ΠΈΠ΅ 20β25 % Mg), ΠΊΠΎΠ½Π²Π΅ΡΡΠΈΡ Π² ΡΡΠ½Π΄Π²ΠΈΡ-ΠΊΠΎΠ²ΡΠ΅ (ΠΈΠ·Π²Π»Π΅ΡΠ΅Π½ΠΈΠ΅ 40β45 Mg), ΠΊΠΎΠ½Π²Π΅ΡΡΠ΅Ρ ΠΠΆΠΎΡΠ΄ΠΆΠ° Π€ΠΈΡΠ΅ΡΠ° (ΠΈΠ·Π²Π»Π΅ΡΠ΅Π½ΠΈΠ΅ 70 % Mg), ΠΠΎΠ½Π²Π΅ΡΡΠΈΡ Π² ΡΠΎΡΠΌΠ΅ (ΠΈΠ·Π²Π»Π΅ΡΠ΅Π½ΠΈΠ΅ 75% Mg)
Π Π°Π·Π»ΠΈΠ²ΠΎΡΠ½ΡΠΉ ΠΊΠΎΠ²Ρ — ΠΏΠΎΠΏΠ΅ΡΠ΅ΡΠ½ΠΎΠ΅ ΡΠ΅ΡΠ΅Π½ΠΈΠ΅ΠΠ±Π΅ΡΡΠ²Π΅ΡΠΈΠ²Π°Π½ΠΈΠ΅ ΠΌΠ°Π³Π½ΠΈΡ
ΠΡΠ΅ ΠΎΠ΄Π½Π° ΠΏΡΠΎΠ±Π»Π΅ΠΌΠ°, ΡΠ²ΡΠ·Π°Π½Π½Π°Ρ Ρ ΠΎΠ±ΡΠ°Π·ΠΎΠ²Π°Π½ΠΈΠ΅ΠΌ ΠΊΠΎΠΌΠΊΠΎΠ², Π·Π°ΠΊΠ»ΡΡΠ°Π΅ΡΡΡ Π² ΠΎΠ±Π΅ΡΡΠ²Π΅ΡΠΈΠ²Π°Π½ΠΈΠΈ Mg Ρ ΡΠ΅ΡΠ΅Π½ΠΈΠ΅ΠΌ Π²ΡΠ΅ΠΌΠ΅Π½ΠΈ, ΡΡΠΎ ΠΏΡΠ΅Π΄ΡΡΠ°Π²Π»ΡΠ΅Ρ ΡΠΎΠ±ΠΎΠΉ ΡΠ΅Π½Π΄Π΅Π½ΡΠΈΡ Mg ΠΊ ΠΏΠΎΡΡΠ΅ΠΏΠ΅Π½Π½ΠΎΠΌΡ ΠΈΡΠΏΠ°ΡΠ΅Π½ΠΈΡ (ΠΈΠ»ΠΈ ΠΎΠΊΠΈΡΠ»Π΅Π½ΠΈΡ) ΠΈΠ· ΡΠ°ΡΡΠ²ΠΎΡΠ°, ΠΊΠΎΠ³Π΄Π° ΠΏΠΎΠ²Π΅ΡΡ Π½ΠΎΡΡΡ ΠΊΠΎΠ²ΡΠ° Π½Π°Ρ ΠΎΠ΄ΠΈΡΡΡ Π² ΠΊΠΎΠ½ΡΠ°ΠΊΡΠ΅ Ρ Π²ΠΎΠ·Π΄ΡΡ ΠΎΠΌ. ΠΠΎΠ³Π΄Π° Mg ΠΈΡΡΠ΅Π·Π°Π΅Ρ ΠΈΠ· ΡΠΎΡΡΠ°Π²Π° ΡΠΏΠ»Π°Π²Π°, ΡΠΌΠ΅Π½ΡΡΠ°Π΅ΡΡΡ ΡΠ°ΡΠΎΠ²ΠΈΠ΄Π½ΠΎΡΡΡ, ΠΈ ΠΌΠ΅Ρ Π°Π½ΠΈΡΠ΅ΡΠΊΠΈΠ΅ ΡΠ²ΠΎΠΉΡΡΠ²Π° Π½Π΅ΠΎΠΆΠΈΠ΄Π°Π½Π½ΠΎ ΠΌΠ΅Π½ΡΡΡΡΡ. ΠΠ»Ρ ΠΏΡΠ΅Π΄ΠΎΡΠ²ΡΠ°ΡΠ΅Π½ΠΈΡ Π²ΡΠ³ΠΎΡΠ°Π½ΠΈΡ Π² ΠΎΡΠΊΡΡΡΠΎΠΌ ΠΊΠΎΠ²ΡΠ΅ ΡΠΏΠ»Π°Π² Π½Π΅ΠΎΠ±Ρ ΠΎΠ΄ΠΈΠΌΠΎ ΡΠ°Π·Π»ΠΈΠ²Π°ΡΡ Π² ΡΠ΅ΡΠ΅Π½ΠΈΠ΅ ΡΠΈΠΊΡΠΈΡΠΎΠ²Π°Π½Π½ΠΎΠ³ΠΎ ΠΏΡΠΎΠΌΠ΅ΠΆΡΡΠΊΠ° Π²ΡΠ΅ΠΌΠ΅Π½ΠΈ (ΠΊΠ°ΠΊ ΠΏΡΠ°Π²ΠΈΠ»ΠΎ, 10-12 ΠΌΠΈΠ½ΡΡ). ΠΠ΄Π½Π°ΠΊΠΎ ΠΏΡΠΈ ΠΈΡΠΏΠΎΠ»ΡΠ·ΠΎΠ²Π°Π½ΠΈΠΈ Π·Π°ΠΊΡΡΡΠΎΠΉ Π°Π²ΡΠΎΠΌΠ°ΡΠΈΡΠ΅ΡΠΊΠΎΠΉ ΡΠ°Π·Π»ΠΈΠ²ΠΎΡΠ½ΠΎΠΉ ΡΡΠ°Π½ΡΠΈΠΈ ΡΡΠΎΡ ΡΡΠΎΠΊ ΠΌΠΎΠΆΠ΅Ρ Π±ΡΡΡ ΡΠ²Π΅Π»ΠΈΡΠ΅Π½ Π΄ΠΎ ΡΠ°ΡΠ°, Π΅ΡΠ»ΠΈ ΠΈΡΠΏΠΎΠ»ΡΠ·ΡΠ΅ΡΡΡ ΠΈΠ½Π΅ΡΡΠ½ΡΠΉ Π·Π°ΡΠΈΡΠ½ΡΠΉ Π³Π°Π· Π΄Π»Ρ ΠΏΡΠ΅Π΄ΠΎΡΠ²ΡΠ°ΡΠ΅Π½ΠΈΡ ΠΊΠΎΠ½ΡΠ°ΠΊΡΠ° ΡΠ°ΡΠΏΠ»Π°Π²Π° Ρ Π²ΠΎΠ·Π΄ΡΡ ΠΎΠΌ, ΡΠ΅ΠΌ ΡΠ°ΠΌΡΠΌ ΠΏΡΠ΅Π΄ΠΎΡΠ²ΡΠ°ΡΠ°Ρ ΠΎΠΊΠΈΡΠ»Π΅Π½ΠΈΠ΅ ΠΌΠ°Π³Π½ΠΈΡ.
ΠΠΎΠ΄ΠΈΡΠΈΠΊΠ°ΡΠΈΡ
ΠΠΎΡΠ»Π΅Π΄Π½ΠΈΠΌ ΡΡΠ°ΠΏΠΎΠΌ ΠΏΠ΅ΡΠ΅Π΄ Π·Π°Π»ΠΈΠ²ΠΊΠΎΠΉ ΡΠ²Π»ΡΠ΅ΡΡΡ ΠΌΠΎΠ΄ΠΈΡΠΈΠΊΠ°ΡΠΈΡ, ΠΊΠΎΡΠΎΡΠ°Ρ ΡΠ°ΠΊΠΆΠ΅ Π²ΡΠΏΠΎΠ»Π½ΡΠ΅ΡΡΡ ΡΠ΅ΠΌΠΈ ΠΆΠ΅ ΠΌΠ΅ΡΠΎΠ΄Π°ΠΌΠΈ, ΡΡΠΎ ΠΈ ΡΠ΅ΡΡΠΉ ΡΡΠ³ΡΠ½. ΠΠ°ΠΊ ΠΎΠΏΠΈΡΠ°Π½ΠΎ Π² ΡΠ°Π·Π΄Π΅Π»Π΅, ΠΏΠΎΡΠ²ΡΡΠ΅Π½Π½ΠΎΠΌ ΡΠ΅ΡΠΎΠΌΡ ΡΡΠ³ΡΠ½Ρ, ΡΠΏΠ»Π°Π²Ρ ΡΠ΅ΡΡΠΎΡΠΈΠ»ΠΈΡΠΈΡ ΠΎΠ±ΡΡΠ½ΠΎ Π΄ΠΎΠ±Π°Π²Π»ΡΡΡ Π² ΡΠ°ΡΠΏΠ»Π°Π² Π½Π΅ΠΏΠΎΡΡΠ΅Π΄ΡΡΠ²Π΅Π½Π½ΠΎ ΠΏΠ΅ΡΠ΅Π΄ Π·Π°Π»ΠΈΠ²ΠΊΠΎΠΉ, ΡΡΠΎΠ±Ρ ΠΎΠ±Π΅ΡΠΏΠ΅ΡΠΈΡΡ ΠΌΠ΅ΡΡΠ° Π΄Π»Ρ Π·Π°ΡΠΎΠ΄ΡΡΠ΅ΠΎΠ±ΡΠ°Π·ΠΎΠ²Π°Π½ΠΈΡ Π³ΡΠ°ΡΠΈΡΠ°. ΠΠΎΠ»Π΅Π΅ ΡΠΎΠ²Π΅ΡΡΠ΅Π½Π½ΡΠ΅ ΠΈ Π±ΠΎΠ»Π΅Π΅ ΠΏΠΎΠ·Π΄Π½ΠΈΠ΅ ΠΌΠ΅ΡΠΎΠ΄Ρ ΠΈΠ½ΠΎΠΊΡΠ»ΡΡΠΈΠΈ ΠΎΠ±Π΅ΡΠΏΠ΅ΡΠ°Ρ Π±ΠΎΠ»Π΅Π΅ ΠΌΠ΅Π»ΠΊΠΎΠ΅ ΡΠ°ΡΠΏΡΠ΅Π΄Π΅Π»Π΅Π½ΠΈΠ΅ ΠΊΠΎΠ½ΠΊΡΠ΅ΡΠΈΠΉ ΠΈ Π²ΡΡΠΎΠΊΡΡ ΠΏΠ»ΠΎΡΠ½ΠΎΡΡΡ ΠΊΠΎΠ½ΠΊΡΠ΅ΡΠΈΠΉ (ΠΊΠΎΠ»ΠΈΡΠ΅ΡΡΠ²ΠΎ ΠΊΠΎΠ½ΠΊΡΠ΅ΡΠΈΠΉ Π½Π° ΠΌΠΌΒ²). ΠΠΎΠ»ΠΈΡΠ΅ΡΡΠ²ΠΎ ΡΠ·Π΅Π»ΠΊΠΎΠ² 200 ΠΈ Π±ΠΎΠ»Π΅Π΅ ΡΠ°ΡΡΠΎ ΡΠΊΠ°Π·ΡΠ²Π°Π΅ΡΡΡ Π΄Π»Ρ Π±ΠΎΠ»Π΅Π΅ ΡΠΎΠ½ΠΊΠΈΡ ΡΡΠ΅Π·ΠΎΠ², Π½ΠΎ ΡΠ°ΠΊΠΎΠ³ΠΎ Π±ΠΎΠ»Π΅Π΅ Π²ΡΡΠΎΠΊΠΎΠ³ΠΎ ΠΊΠΎΠ»ΠΈΡΠ΅ΡΡΠ²Π° ΡΡΡΠ΄Π½ΠΎ Π΄ΠΎΡΡΠΈΡΡ Π² ΡΠΎΠ»ΡΡΡΡ ΠΈΠ»ΠΈ ΡΡΠΆΠ΅Π»ΡΡ ΡΡΠ΅Π·Π°Ρ .
Π‘ΡΠ°Π²Π½ΠΈΡΠ΅Π»ΡΠ½Π°Ρ ΡΠ°Π±Π»ΠΈΡΠ° ΠΏΠ»ΠΎΡΠ½ΠΎΡΡΠΈ ΠΊΠΎΠ½ΠΊΡΠ΅ΡΠΈΠΉ ΠΈΠ· ΠΊΠΎΠ²ΠΊΠΎΠ³ΠΎ ΡΡΠ³ΡΠ½Π° (100x)Π€Π΅ΡΡΠΈΡΠ½ΡΠ΅ ΠΈ ΠΏΠ΅ΡΠ»ΠΈΡΠ½ΠΎ-Π³ΡΠ°ΡΠΈΡΠΎΠ²ΡΠ΅ ΠΊΠΎΠ½ΡΡΡΡΠΊΡΠΈΠΈ
ΠΠ·-Π·Π° Π²ΡΡΠΎΠΊΠΈΡ ΡΠΊΠΎΡΠΎΡΡΠ΅ΠΉ ΡΠ΄Π»ΠΈΠ½Π΅Π½ΠΈΡ, Π΄ΠΎΡΡΠΈΠΆΠΈΠΌΡΡ Π΄Π»Ρ Π»ΠΈΡΠΎΠ³ΠΎ ΡΠ΅ΡΡΠΈΡΠ½ΠΎΠ³ΠΎ ΡΠΎΡΡΠ° ΠΊΠΎΠ²ΠΊΠΎΠ³ΠΎ ΡΡΠ³ΡΠ½Π°, Π°Π²ΡΠΎΠΌΠΎΠ±ΠΈΠ»ΡΠ½ΡΠ΅ ΠΊΠΎΠ½ΡΡΡΡΠΊΡΠΎΡΡ, ΠΎΡΠ²Π΅ΡΡΡΠ²Π΅Π½Π½ΡΠ΅ Π·Π° ΠΊΡΠΈΡΠΈΡΠ΅ΡΠΊΠΈ Π²Π°ΠΆΠ½ΡΠ΅ Π΄Π»Ρ Π±Π΅Π·ΠΎΠΏΠ°ΡΠ½ΠΎΡΡΠΈ ΠΊΠΎΠ½ΡΡΡΡΠΊΡΠΈΠΈ ΡΠ°ΡΡΠΈ, ΠΏΡΠ΅Π΄ΠΏΠΎΡΠΈΡΠ°ΡΡ ΠΈΡΠΏΠΎΠ»ΡΠ·ΠΎΠ²Π°ΡΡ ΠΊΠΎΠ²ΠΊΠΈΠΉ ΡΡΠ³ΡΠ½.
ΠΠ»Ρ Π΄ΠΈΠ·Π°ΠΉΠ½Π΅ΡΠΎΠ² Π°Π²ΡΠΎΠΌΠΎΠ±ΠΈΠ»Π΅ΠΉ ΠΊΠΎΠ²ΠΊΠΈΠΉ ΡΡΠ³ΡΠ½ ΡΡΠΈΡΠ°Π΅ΡΡΡ ΡΠ΅Π½Π½ΡΠΌ ΠΌΠ°ΡΠ΅ΡΠΈΠ°Π»ΠΎΠΌ, ΠΏΠΎΡΠΎΠΌΡ ΡΡΠΎ ΠΎΠ½ Π΄Π΅ΡΠ΅Π²Π»Π΅, ΡΠ΅ΠΌ Π°Π»ΡΡΠ΅ΡΠ½Π°ΡΠΈΠ²Ρ, ΡΠ°ΠΊΠΈΠ΅ ΠΊΠ°ΠΊ ΠΊΠΎΠ²Π°Π½Π°Ρ ΡΡΠ°Π»Ρ, ΠΊΠΎΠ²Π°Π½ΡΠΉ Π°Π»ΡΠΌΠΈΠ½ΠΈΠΉ ΠΈΠ»ΠΈ Π΄Π°ΠΆΠ΅ Π°Π»ΡΠΌΠΈΠ½ΠΈΠ΅Π²ΡΠ΅ ΠΎΡΠ»ΠΈΠ²ΠΊΠΈ, ΠΎΠ±ΡΠ°Π±ΠΎΡΠ°Π½Π½ΡΠ΅ ΡΠ°ΡΡΠ²ΠΎΡΠΎΠΌ. ΠΠ»Π°Π³ΠΎΠ΄Π°ΡΡ Π²ΡΡΠΎΠΊΠΈΠΌ ΡΠ²ΠΎΠΉΡΡΠ²Π°ΠΌ ΠΎΡΠ½ΠΎΡΠΈΡΠ΅Π»ΡΠ½ΠΎΠ³ΠΎ ΡΠ΄Π»ΠΈΠ½Π΅Π½ΠΈΡ ΠΈ ΡΠ΄Π°ΡΠ½ΠΎΠΉ Π²ΡΠ·ΠΊΠΎΡΡΠΈ, ΠΏΡΠΈΡΡΡΠΈΠΌ Π»ΠΈΡΡΠΌ ΠΊΠΎΠ½ΡΡΡΡΠΊΡΠΈΠΎΠ½Π½ΡΠΌ Π΄Π΅ΡΠ°Π»ΡΠΌ ΠΈΠ· ΠΊΠΎΠ²ΠΊΠΎΠ³ΠΎ ΡΡΠ³ΡΠ½Π°, ΠΊΠΎΠ½ΡΡΡΡΠΊΡΠΎΡΡ Π°Π²ΡΠΎΠΌΠΎΠ±ΠΈΠ»ΡΠ½ΡΡ ΡΠ°ΡΡΠΈ ΠΈΠΌΠ΅ΡΡ Π½ΠΈΠ·ΠΊΠΎΠ·Π°ΡΡΠ°ΡΠ½ΡΠΉ ΠΏΡΠΎΠΈΠ·Π²ΠΎΠ΄ΡΡΠ²Π΅Π½Π½ΡΠΉ ΠΏΡΠΎΡΠ΅ΡΡ, ΠΊΠΎΡΠΎΡΡΠΉ ΠΏΠΎΠ·Π²ΠΎΠ»ΡΠ΅Ρ ΠΈΡ ΠΊΠΎΠ½ΡΡΡΡΠΊΡΠΈΡΠΌ ΠΏΡΠΎΠΉΡΠΈ ΡΡΡΠΎΠ³ΠΈΠ΅ ΡΡΠ΅Π±ΠΎΠ²Π°Π½ΠΈΡ ΠΊ ΠΊΡΠ°Ρ-ΡΠ΅ΡΡΠ°ΠΌ. ΠΠ΄Π½Π°ΠΊΠΎ, ΠΊΠΎΠ³Π΄Π° ΡΡΠΈ ΠΆΠ΅ ΠΊΠΎΠ½ΡΡΡΡΠΊΡΠΎΡΡ ΡΠ°ΡΡΠΌΠ°ΡΡΠΈΠ²Π°ΡΡ Π²ΠΎΠ·ΠΌΠΎΠΆΠ½ΠΎΡΡΡ ΡΠ½ΠΈΠΆΠ΅Π½ΠΈΡ ΠΎΠ±ΡΠ΅Π³ΠΎ Π²Π΅ΡΠ° Π°Π²ΡΠΎΠΌΠΎΠ±ΠΈΠ»Ρ, ΠΎΠ½ΠΈ Π½Π°ΡΠΈΠ½Π°ΡΡ ΡΠΊΠ°Π·ΡΠ²Π°ΡΡ Π±ΠΎΠ»Π΅Π΅ ΠΏΡΠΎΡΠ½ΡΠ΅ ΠΌΠ°ΡΠΊΠΈ ΠΊΠΎΠ²ΠΊΠΎΠ³ΠΎ ΡΡΠ³ΡΠ½Π°. ΠΠ΄Π½Π°ΠΊΠΎ Π² ΡΠΎ ΠΆΠ΅ Π²ΡΠ΅ΠΌΡ ΠΊΠΎΠ½ΡΡΡΡΠΊΡΠΎΡΡ ΡΠ°ΠΊΠΆΠ΅ ΡΡΠ΅Π±ΡΡΡ Π²ΡΡΠΎΠΊΠΎΠΉ ΠΏΠ»Π°ΡΡΠΈΡΠ½ΠΎΡΡΠΈ, ΠΈΠ·ΠΌΠ΅ΡΡΠ΅ΠΌΠΎΠΉ % ΡΠ΄Π»ΠΈΠ½Π΅Π½ΠΈΡ ΠΏΡΠΈ ΠΎΠ±ΡΡΠ½ΡΡ ΠΏΡΠΎΠΈΠ·Π²ΠΎΠ΄ΡΡΠ²Π΅Π½Π½ΡΡ ΠΈΡΠΏΡΡΠ°Π½ΠΈΡΡ Π½Π° ΡΠ°ΡΡΡΠΆΠ΅Π½ΠΈΠ΅. Π’Π°ΠΊΠΈΠΌ ΠΎΠ±ΡΠ°Π·ΠΎΠΌ, ΡΠ΅ΠΏΠ΅ΡΡ Ρ Π½Π°Ρ Π΅ΡΡΡ ΠΌΠ°ΡΠΊΠΈ ΠΆΠ΅Π»Π΅Π·Π°, ΠΊΠΎΡΠΎΡΡΠ΅ Π·Π°Π²ΠΈΡΡΡ ΠΎΡ Π½Π΅ΠΊΠΎΡΠΎΡΠΎΠ³ΠΎ ΠΊΠΎΠ»ΠΈΡΠ΅ΡΡΠ²Π° ΠΏΠ΅ΡΠ»ΠΈΡΠ° Π² ΠΌΠΎΡΡΠΎΠ»ΠΎΠ³ΠΈΠΈ ΠΆΠ΅Π»Π΅Π·Π° Π΄Π»Ρ ΡΠ²Π΅Π»ΠΈΡΠ΅Π½ΠΈΡ YTS, Π½ΠΎ ΠΏΡΠΈ ΡΡΠΎΠΌ ΡΠΎΡ ΡΠ°Π½ΡΡΡ ΡΠ΄Π»ΠΈΠ½Π΅Π½ΠΈΠ΅ > 8%. ΠΠΎΡΡΠΎΠΌΡ ΡΡΠ°ΡΠ΅Π»ΡΠ½ΡΠΉ Π°Π½Π°Π»ΠΈΠ· ΠΌΠΎΡΡΠΎΠ»ΠΎΠ³ΠΈΠΈ ΠΆΠ΅Π»Π΅Π·Π° Π΄ΠΎΠ»ΠΆΠ΅Π½ ΡΠΎΡΠ΅ΡΠ°ΡΡΡΡ Ρ ΠΏΡΠΎΠ²Π΅ΡΠΊΠΎΠΉ ΠΌΠ΅Ρ Π°Π½ΠΈΡΠ΅ΡΠΊΠΈΡ ΡΠ²ΠΎΠΉΡΡΠ², ΡΡΠΎΠ±Ρ ΠΌΠΎΠΆΠ½ΠΎ Π±ΡΠ»ΠΎ ΡΡΡΠΎΠ³ΠΎ ΠΊΠΎΠ½ΡΡΠΎΠ»ΠΈΡΠΎΠ²Π°ΡΡ Ρ ΠΈΠΌΠΈΡΠ΅ΡΠΊΠΈΠΉ ΡΠΎΡΡΠ°Π² ΡΠΏΠ»Π°Π²Π°, ΡΡΠΎΠ±Ρ ΠΏΠΎΠ»ΡΡΠΈΡΡ ΠΎΠΆΠΈΠ΄Π°Π΅ΠΌΡΠ΅ ΡΠ΅Π·ΡΠ»ΡΡΠ°ΡΡ ΠΏΠΎΡΠ»Π΅ ΠΈΠ·Π²Π»Π΅ΡΠ΅Π½ΠΈΡ ΠΎΠ±ΡΠ°Π·ΡΠΎΠ² ΠΈΠ· Π»ΠΈΡΡΡ Π΄Π΅ΡΠ°Π»Π΅ΠΉ.
Β
ΠΡΠ»ΠΈΠ²ΠΊΠΈ ΠΈΠ· ΠΊΠΎΠ²ΠΊΠΎΠ³ΠΎ ΡΡΠ³ΡΠ½Π°, ΠΈΡΠΏΠΎΠ»ΡΠ·ΡΠ΅ΠΌΡΠ΅ Π΄Π»Ρ ΠΈΠ·Π³ΠΎΡΠΎΠ²Π»Π΅Π½ΠΈΡ Π°Π²ΡΠΎΠΌΠΎΠ±ΠΈΠ»ΡΠ½ΡΡ ΡΠ°ΡΡΠΈ.ΠΠ΅ΡΠ°Π»Π»ΠΎΠ³ΡΠ°ΡΠΈΡΠ΅ΡΠΊΠΈΠΉ Π°Π½Π°Π»ΠΈΠ·
ΠΠΎΠ·ΠΌΠΎΠΆΠ½ΠΎΡΡΡ ΠΎΡΠ΅Π½ΠΊΠΈ ΠΌΠΈΠΊΡΠΎΡΡΡΡΠΊΡΡΡΡ ΠΊΠΎΠ²ΠΊΠΎΠ³ΠΎ ΡΡΠ³ΡΠ½Π° Π² Π»ΠΈΡΠ΅ΠΉΠ½ΠΎΠΌ ΠΏΡΠΎΠΈΠ·Π²ΠΎΠ΄ΡΡΠ²Π΅ ΠΎΡΠΎΠ±Π΅Π½Π½ΠΎ Π²Π°ΠΆΠ½Π° ΠΏΡΠΈ ΠΈΡΠΏΠΎΠ»ΡΠ·ΠΎΠ²Π°Π½ΠΈΠΈ ΡΠΎΡΡΠ°Π²ΠΎΠ² ΡΠΏΠ»Π°Π²ΠΎΠ², Π² ΠΊΠΎΡΠΎΡΡΠ΅ Π² ΡΠΏΠ»Π°Π² Π΄ΠΎΠ±Π°Π²Π»ΡΡΡ ΠΎΠ»ΠΎΠ²ΠΎ (Sn) ΠΈΠ»ΠΈ ΠΌΠ΅Π΄Ρ (Cu) Ρ ΡΠ΅Π»ΡΡ ΠΏΠΎΠ΄Π½ΡΡΠΈΡ ΠΏΠ΅ΡΠ»ΠΈΡΠ½ΡΡ ΠΎΠ±ΡΠ°Π·ΠΎΠ²Π°Π½ΠΈΠΉ Π²ΠΎΠΊΡΡΠ³ Π³ΡΠ°ΡΠΈΡΠΎΠ²ΡΡ ΠΊΠΎΠ½ΠΊΡΠ΅ΡΠΈΠΉ. ΠΠ½ΡΠ΅ΡΠΏΡΠ΅ΡΠ°ΡΠΈΡ ΡΡΠΈΡ ΡΠΈΠΏΠΎΠ² ΠΌΠΈΠΊΡΠΎΡΠΎΡΠΎΠ³ΡΠ°ΡΠΈΠΉ ΠΈ ΠΈΡ ΠΊΠΎΡΡΠ΅Π»ΡΡΠΈΡ Ρ ΠΌΠ΅Ρ Π°Π½ΠΈΡΠ΅ΡΠΊΠΈΠΌΠΈ ΡΠ²ΠΎΠΉΡΡΠ²Π°ΠΌΠΈ ΠΎΡΠ΅Π½Ρ Π²Π°ΠΆΠ½Ρ Π΄Π»Ρ ΡΡΡΠ°Π½ΠΎΠ²Π»Π΅Π½ΠΈΡ Π·Π½Π°ΡΠΈΠΌΡΡ ΠΏΡΠ΅Π΄Π΅Π»ΠΎΠ² Ρ ΠΈΠΌΠΈΡΠ΅ΡΠΊΠΎΠ³ΠΎ ΡΠΎΡΡΠ°Π²Π° ΡΠΏΠ»Π°Π²Π°, ΠΊΠΎΠ³Π΄Π° ΠΆΠ΅Π»Π΅Π·ΠΎ ΠΏΠ»Π°Π²ΠΈΡΡΡ ΠΈ Π·Π°Π»ΠΈΠ²Π°Π΅ΡΡΡ Π½Π° ΠΏΡΠΎΠΈΠ·Π²ΠΎΠ΄ΡΡΠ²Π΅Π½Π½ΡΡ Π»ΠΈΠ½ΠΈΡ.
ΠΠΈΠΊΡΠΎΡΡΡΡΠΊΡΡΡΠ° ΠΏΠ»Π°ΡΡΠΈΠ½ ΡΠΎΠ»ΡΠΈΠ½ΠΎΠΉ 2,5 ΠΌΠΌ: Π½Π΅Π»Π΅Π³ΠΈΡΠΎΠ²Π°Π½Π½Π°Ρ β ΡΠ»Π΅Π²Π°, Π»Π΅Π³ΠΈΡΠΎΠ²Π°Π½Π½Π°Ρ 0,5 % ΠΌΠ΅Π΄ΠΈ β ΡΠΏΡΠ°Π²Π°. ΠΠΈΡΠ°Π» ΡΡΠ°Π²Π»Π΅Π½ΡΠΉ.ΠΠ·ΠΎΠ±ΡΠ°ΠΆΠ΅Π½ΠΈΠ΅ ΠΏΡΠ΅Π΄ΠΎΡΡΠ°Π²Π»Π΅Π½ΠΎ Π΄Π»Ρ ΠΏΡΠΈΠ²Π΅Π΄Π΅Π½Π½ΡΡ Π²ΡΡΠ΅ ΠΈΠ·ΠΎΠ±ΡΠ°ΠΆΠ΅Π½ΠΈΠΉ ΠΌΠΈΠΊΡΠΎΡΡΡΡΠΊΡΡΡΡ:
Π‘ΡΠ΅ΡΠ°Π½Π΅ΡΠΊΡ, ΠΠΎΡΡ Π. ΠΈ Π΄Ρ., Β«ΠΠ΅ΡΠ°Π»Π»ΡΡΠ³ΠΈΡ ΠΈ ΠΌΠ΅Ρ Π°Π½ΠΈΡΠ΅ΡΠΊΠΈΠ΅ ΡΠ²ΠΎΠΉΡΡΠ²Π° ΠΏΡΠΈ ΡΠ°ΡΡΡΠΆΠ΅Π½ΠΈΠΈ ΡΠΎΠ½ΠΊΠΎΡΡΠ΅Π½Π½ΡΡ ΡΡΠ³ΡΠ½ΠΎΠ² Ρ ΡΡΠ΅ΡΠΎΠΈΠ΄Π°Π»ΡΠ½ΡΠΌ Π³ΡΠ°ΡΠΈΡΠΎΠΌΒ», ΠΠ΅ΠΆΠ΄ΡΠ½Π°ΡΠΎΠ΄Π½ΡΠΉ ΠΆΡΡΠ½Π°Π» ΠΈΡΡΠ»Π΅Π΄ΠΎΠ²Π°Π½ΠΈΠΉ Π»ΠΈΡΡΡ ΠΌΠ΅ΡΠ°Π»Π»ΠΎΠ², 2003 Π³., ΡΠΎΠΌ. 16 β 1-3.
https://www.researchgate.net/publication/260037434_The_Metallurgy_and_Tensile_Mechanical_Properties_of_Thin_Wall_Spheroidal_Graphite_IronsΠΠ΅ΡΠ»ΠΈΡΠ½ΡΠΉ ΠΊΠΎΠ²ΠΊΠΈΠΉ ΡΡΠ³ΡΠ½
ΠΠΎΠ³Π΄Π° ΡΠ²ΠΎΠΉΡΡΠ²Π° ΡΠ΄Π»ΠΈΠ½Π΅Π½ΠΈΡ Π½Π΅ ΡΠ°ΠΊ Π²Π°ΠΆΠ½Ρ, ΠΊΠ°ΠΊ YTS ΠΈ UTS, ΠΎΠ±ΡΡΠ½ΠΎ ΠΈΡΠΏΠΎΠ»ΡΠ·ΡΡΡΡΡ ΠΊΠΎΠ½ΡΡΠΎΠ»ΠΈΡΡΠ΅ΠΌΡΠ΅ Π΄ΠΎΠ±Π°Π²ΠΊΠΈ Cu ΠΈ Sn Π΄Π»Ρ ΡΡΠΈΠΌΡΠ»ΠΈΡΠΎΠ²Π°Π½ΠΈΡ ΠΎΠ±ΡΠ°Π·ΠΎΠ²Π°Π½ΠΈΡ ΠΏΠ΅ΡΠ»ΠΈΡΠ° Π²ΠΎΠΊΡΡΠ³ Π³ΡΠ°ΡΠΈΡΠΎΠ²ΡΡ ΠΊΠΎΠ½ΠΊΡΠ΅ΡΠΈΠΉ. ΠΡΠ»ΠΎ ΠΎΠ±Π½Π°ΡΡΠΆΠ΅Π½ΠΎ, ΡΡΠΎ ΠΊΠΎΠ»ΠΈΡΠ΅ΡΡΠ²ΠΎ ΠΎΠ±ΡΠ°Π·ΠΎΠ²Π°Π²ΡΠ΅Π³ΠΎΡΡ ΠΏΠ΅ΡΠ»ΠΈΡΠ° ΠΏΡΠΎΠΏΠΎΡΡΠΈΠΎΠ½Π°Π»ΡΠ½ΠΎ ΡΠ»ΡΡΡΠ΅Π½Π½ΠΎΠΉ ΠΏΡΠΎΡΠ½ΠΎΡΡΠΈ Π½Π° ΡΠ°ΡΡΡΠΆΠ΅Π½ΠΈΠ΅ Ρ ΡΠΊΡΠΏΠΎΠ½Π΅Π½ΡΠΈΠ°Π»ΡΠ½ΡΠΌ ΡΠΌΠ΅Π½ΡΡΠ΅Π½ΠΈΠ΅ΠΌ % ΡΠ΄Π»ΠΈΠ½Π΅Π½ΠΈΡ.
ΠΠ·ΠΎΠ±ΡΠ°ΠΆΠ΅Π½ΠΈΠ΅ ΠΏΡΠ΅Π΄ΠΎΡΡΠ°Π²Π»Π΅Π½ΠΎ:
DIS Π ΠΈΡΡΠ½ΠΎΠΊ 3.16 Π‘Π²ΠΎΠΉΡΡΠ²Π° ΠΏΡΠΈ ΡΠ°ΡΡΡΠΆΠ΅Π½ΠΈΠΈ Π² Π·Π°Π²ΠΈΡΠΈΠΌΠΎΡΡΠΈ ΠΎΡ Π΄ΠΎΠ±Π°Π²ΠΎΠΊ Cu ΠΈ Sn
ΠΠ±ΡΠ΅ΡΡΠ²ΠΎ ΠΊΠΎΠ²ΠΊΠΎΠ³ΠΎ ΡΡΠ³ΡΠ½Π° ΡΠΈΡ. 3.16
https://www.ductile.org/didata/Section3/Figures/pfig3_16.htmΠΡΠΎΠΌΡΡΠ»Π΅Π½Π½ΡΠ΅ ΡΠΏΠ΅ΡΠΈΡΠΈΠΊΠ°ΡΠΈΠΈ
ΠΠ° ΠΏΡΠΈΠ²Π΅Π΄Π΅Π½Π½ΠΎΠΉ Π½ΠΈΠΆΠ΅ Π΄ΠΈΠ°Π³ΡΠ°ΠΌΠΌΠ΅ ΠΠ±ΡΠ΅ΡΡΠ²ΠΎ Π°Π²ΡΠΎΠΌΠΎΠ±ΠΈΠ»ΡΠ½ΡΡ ΠΈΠ½ΠΆΠ΅Π½Π΅ΡΠΎΠ² (SAE) ΠΏΡΠ±Π»ΠΈΠΊΡΠ΅Ρ ΡΠ΄ΠΎΠ±Π½ΡΡ Π΄ΠΈΠ°Π³ΡΠ°ΠΌΠΌΡ, Π² ΠΊΠΎΡΠΎΡΠΎΠΉ Π΄ΠΎΠ±Π°Π²ΠΊΠΈ ΠΊ ΡΠΏΠ»Π°Π²Ρ ΠΈΡΠΏΠΎΠ»ΡΠ·ΡΡΡΡΡ Π΄Π»Ρ ΠΈΠ·ΠΌΠ΅Π½Π΅Π½ΠΈΡ ΡΡΡΡΠΊΡΡΡΡ ΠΎΡ 100% ΡΠ΅ΡΡΠΈΡΠ° Π΄ΠΎ ΠΏΠΎΠ²ΡΡΠ΅Π½ΠΈΡ ΡΡΠΎΠ²Π½Ρ ΠΏΠ΅ΡΠ»ΠΈΡΠ° Π² ΠΌΠΎΡΡΠΎΠ»ΠΎΠ³ΠΈΠΈ ΠΆΠ΅Π»Π΅Π·Π°.
SAE ΠΊΠ»Π°ΡΡΠΈΡΠΈΡΠΈΡΡΠ΅Ρ ΠΌΠ°ΡΠ΅ΡΠΈΠ°Π»Ρ ΠΏΠΎ UTS (ΠΌΠΈΠ½ΠΈΠΌΠ°Π»ΡΠ½ΠΎΠ΅ ΠΎΠΆΠΈΠ΄Π°Π½ΠΈΠ΅) ΠΈ ΠΎΠΆΠΈΠ΄Π°Π΅ΠΌΠΎΠΌΡ % ΡΠ΄Π»ΠΈΠ½Π΅Π½ΠΈΡ. ΠΠ°ΠΊ ΠΏΠΎΠΊΠ°Π·Π°Π½ΠΎ Π½Π° ΡΠΈΡΡΠ½ΠΊΠ΅ 3.16 DIS, % ΡΠ΄Π»ΠΈΠ½Π΅Π½ΠΈΡ ΡΠΌΠ΅Π½ΡΡΠ°Π΅ΡΡΡ ΡΠΊΡΠΏΠΎΠ½Π΅Π½ΡΠΈΠ°Π»ΡΠ½ΠΎ, Π² ΡΠΎ Π²ΡΠ΅ΠΌΡ ΠΊΠ°ΠΊ ΠΌΠ΅Ρ Π°Π½ΠΈΡΠ΅ΡΠΊΠΈΠ΅ ΡΠ²ΠΎΠΉΡΡΠ²Π° ΡΠ²Π΅Π»ΠΈΡΠΈΠ²Π°ΡΡΡΡ Π»ΠΎΠ³Π°ΡΠΈΡΠΌΠΈΡΠ΅ΡΠΊΠΈ.
ΠΠ·ΠΎΠ±ΡΠ°ΠΆΠ΅Π½ΠΈΠ΅ ΠΏΡΠ΅Π΄ΠΎΡΡΠ°Π²Π»Π΅Π½ΠΎ Π΄Π»Ρ Π΄ΠΈΠ°Π³ΡΠ°ΠΌΠΌΡ Π²ΡΡΠ΅:
ΠΠ±ΡΠ΅ΡΡΠ²ΠΎ ΠΊΠΎΠ²ΠΊΠΎΠ³ΠΎ ΡΡΠ³ΡΠ½Π° β Π ΠΠΠΠΠ XII. Π‘ΠΠΠ¦ΠΠ€ΠΠΠΠ¦ΠΠ
https://www.ductile.org/didata/Section12/12intro.htmΠΡΠΏΡΡΠ°Π½ΠΈΡ ΡΠ²ΠΎΠΉΡΡΠ² Π½Π° ΡΠ°ΡΡΡΠΆΠ΅Π½ΠΈΠ΅
ΠΠΈΡΠ΅ΠΉΠ½ΡΠΉ ΡΠ΅Ρ ΠΏΠΎ ΠΏΡΠΎΠΈΠ·Π²ΠΎΠ΄ΡΡΠ²Ρ Π²ΡΡΠΎΠΊΠΎΠΏΡΠΎΡΠ½ΠΎΠ³ΠΎ ΡΡΠ³ΡΠ½Π° Π΄ΠΎΠ»ΠΆΠ΅Π½ ΠΈΠΌΠ΅ΡΡ Π²ΠΎΠ·ΠΌΠΎΠΆΠ½ΠΎΡΡΡ ΠΏΡΠΎΠ²ΠΎΠ΄ΠΈΡΡ Π±ΠΎΠ»Π΅Π΅ ΡΡΠ°ΡΠ΅Π»ΡΠ½ΡΠ΅ ΠΈΡΠΏΡΡΠ°Π½ΠΈΡ ΠΎΠ±ΡΠ°Π·ΡΠΎΠ² Π½Π° ΡΠ°ΡΡΡΠΆΠ΅Π½ΠΈΠ΅, ΡΠ΅ΠΌ Π»ΠΈΡΠ΅ΠΉΠ½ΡΠΉ ΡΠ΅Ρ ΠΏΠΎ ΠΏΡΠΎΠΈΠ·Π²ΠΎΠ΄ΡΡΠ²Ρ ΡΠ΅ΡΠΎΠ³ΠΎ ΡΡΠ³ΡΠ½Π°. ΠΡΠ΅Π½ΠΊΠ° ΠΊΠΎΠ²ΠΊΠΎΠ³ΠΎ ΡΡΠ³ΡΠ½Π° Π² ΡΠΎΠΎΡΠ²Π΅ΡΡΡΠ²ΠΈΠΈ Ρ Π»ΡΠ±ΠΎΠΉ ΠΎΡΠ½ΠΎΠ²Π½ΠΎΠΉ ΡΠ΅Ρ Π½ΠΈΡΠ΅ΡΠΊΠΎΠΉ ΡΠΏΠ΅ΡΠΈΡΠΈΠΊΠ°ΡΠΈΠ΅ΠΉ ΠΏΠΎΡΡΠ΅Π±ΡΠ΅Ρ ΠΈΠ·ΠΌΠ΅ΡΠ΅Π½ΠΈΡ YTS, UTS, % ΡΠ΄Π»ΠΈΠ½Π΅Π½ΠΈΡ, ΠΎΠ±ΡΠ°Π·ΡΠΎΠ² Π΄Π»Ρ ΡΠ΄Π°ΡΠ° ΠΏΠΎ Π¨Π°ΡΠΏΠΈ ΠΈ ΡΠ²Π΅ΡΠ΄ΠΎΡΡΠΈ ΠΏΠΎ ΠΡΠΈΠ½Π΅Π»Π»Ρ. Π’Π°ΠΊΠΈΠΌ ΠΎΠ±ΡΠ°Π·ΠΎΠΌ, Π² Π΄ΠΎΠΏΠΎΠ»Π½Π΅Π½ΠΈΠ΅ ΠΊ ΠΏΡΠΎΠ²Π΅Π΄Π΅Π½ΠΈΡ ΡΠΏΠ΅ΠΊΡΡΠΎΠ³ΡΠ°ΡΠΈΡΠ΅ΡΠΊΠΎΠ³ΠΎ ΠΈ ΠΌΠ΅ΡΠ°Π»Π»ΠΎΠ³ΡΠ°ΡΠΈΡΠ΅ΡΠΊΠΎΠ³ΠΎ Π°Π½Π°Π»ΠΈΠ·Π° Π»ΠΈΡΠ΅ΠΉΠ½ΡΠΉ ΡΠ΅Ρ Π΄ΠΎΠ»ΠΆΠ΅Π½ ΠΈΠΌΠ΅ΡΡ ΡΠΎΡΠ½ΡΠΉ ΠΏΡΠΈΠ±ΠΎΡ Π΄Π»Ρ ΠΈΡΠΏΡΡΠ°Π½ΠΈΠΉ Π½Π° ΡΠ°ΡΡΡΠΆΠ΅Π½ΠΈΠ΅.
ΠΠΏΡΠ΅Π΄Π΅Π»Π΅Π½ΠΈΠ΅ YTS (ΠΏΡΠ΅Π΄Π΅Π»Π° ΡΠ΅ΠΊΡΡΠ΅ΡΡΠΈ ΠΏΡΠΈ ΡΠ°ΡΡΡΠΆΠ΅Π½ΠΈΠΈ)
Π ΡΠ²ΡΠ·ΠΈ Ρ ΡΡΠ΅Π±ΠΎΠ²Π°Π½ΠΈΠ΅ΠΌ Π²ΡΡΠΎΠΊΠΎΠΉ ΠΏΡΠΎΡΠ½ΠΎΡΡΠΈ ΠΏΡΠΈ ΡΠ°ΡΡΡΠΆΠ΅Π½ΠΈΠΈ ΠΈ ΠΌΠΈΠ½ΠΈΠΌΠ°Π»ΡΠ½ΠΎΠΉ ΠΏΠΎΡΠ΅ΡΠΈ ΠΏΠ»Π°ΡΡΠΈΡΠ½ΠΎΡΡΠΈ, ΠΈΠ·ΠΌΠ΅ΡΡΠ΅ΠΌΠΎΠΉ Π² % ΠΎΡΠ½ΠΎΡΠΈΡΠ΅Π»ΡΠ½ΠΎΠ³ΠΎ ΡΠ΄Π»ΠΈΠ½Π΅Π½ΠΈΡ, ΠΎΡΠΎΠ±ΠΎΠ΅ Π²Π½ΠΈΠΌΠ°Π½ΠΈΠ΅ ΡΠ»Π΅Π΄ΡΠ΅Ρ ΡΠ΄Π΅Π»ΠΈΡΡ ΠΈΡΠΏΡΡΠ°Π½ΠΈΡΠΌ Π½Π° ΡΠ°ΡΡΡΠΆΠ΅Π½ΠΈΠ΅ ΠΊΠ°ΠΊ ΡΠ°ΡΡΠΈ ΠΏΡΠΎΠΈΠ·Π²ΠΎΠ΄ΡΡΠ²Π΅Π½Π½ΠΎΠ³ΠΎ ΠΏΡΠΎΡΠ΅ΡΡΠ°.
Π’Π΅ΠΏΠ΅ΡΡ Ρ Π½Π°Ρ Π΅ΡΡΡ ΠΌΠ°ΡΠΊΠΈ ΠΆΠ΅Π»Π΅Π·Π°, ΠΊΠΎΡΠΎΡΡΠ΅ Π·Π°Π²ΠΈΡΡΡ ΠΎΡ Π½Π΅ΠΊΠΎΡΠΎΡΠΎΠ³ΠΎ ΠΊΠΎΠ»ΠΈΡΠ΅ΡΡΠ²Π° ΠΏΠ΅ΡΠ»ΠΈΡΠ° Π² ΠΌΠΎΡΡΠΎΠ»ΠΎΠ³ΠΈΠΈ ΠΆΠ΅Π»Π΅Π·Π° Π΄Π»Ρ ΡΠ²Π΅Π»ΠΈΡΠ΅Π½ΠΈΡ YTS, Π½ΠΎ ΠΏΡΠΈ ΡΡΠΎΠΌ ΡΠΎΡ ΡΠ°Π½ΡΡΡ ΡΠ΄Π»ΠΈΠ½Π΅Π½ΠΈΠ΅ > 8%. ΠΠΎΡΡΠΎΠΌΡ ΡΡΠ°ΡΠ΅Π»ΡΠ½ΡΠΉ Π°Π½Π°Π»ΠΈΠ· ΠΌΠΎΡΡΠΎΠ»ΠΎΠ³ΠΈΠΈ ΠΆΠ΅Π»Π΅Π·Π° Π΄ΠΎΠ»ΠΆΠ΅Π½ ΡΠΎΡΠ΅ΡΠ°ΡΡΡΡ Ρ ΠΏΡΠΎΠ²Π΅ΡΠΊΠΎΠΉ ΠΌΠ΅Ρ Π°Π½ΠΈΡΠ΅ΡΠΊΠΈΡ ΡΠ²ΠΎΠΉΡΡΠ², ΡΡΠΎΠ±Ρ ΠΌΠΎΠΆΠ½ΠΎ Π±ΡΠ»ΠΎ ΡΡΡΠΎΠ³ΠΎ ΠΊΠΎΠ½ΡΡΠΎΠ»ΠΈΡΠΎΠ²Π°ΡΡ Ρ ΠΈΠΌΠΈΡΠ΅ΡΠΊΠΈΠΉ ΡΠΎΡΡΠ°Π² ΡΠΏΠ»Π°Π²Π°, ΡΡΠΎΠ±Ρ ΠΏΠΎΠ»ΡΡΠΈΡΡ ΠΎΠΆΠΈΠ΄Π°Π΅ΠΌΡΠ΅ ΡΠ΅Π·ΡΠ»ΡΡΠ°ΡΡ ΠΏΠΎΡΠ»Π΅ ΠΈΠ·Π²Π»Π΅ΡΠ΅Π½ΠΈΡ ΠΎΠ±ΡΠ°Π·ΡΠΎΠ² ΠΈΠ· Π»ΠΈΡΡΡ Π΄Π΅ΡΠ°Π»Π΅ΠΉ. ΠΠΌΠ΅Ρ ΡΡΠΎ Π² Π²ΠΈΠ΄Ρ, ΠΎΠΏΡΠ΅Π΄Π΅Π»Π΅Π½ΠΈΠ΅ YTS Π½Π° ΠΎΡΠ½ΠΎΠ²Π΅ ΠΌΠ΅ΡΠΎΠ΄Π° ΡΠΌΠ΅ΡΠ΅Π½ΠΈΡ 0,2% Π΄ΠΎΠ»ΠΆΠ½ΠΎ ΠΎΡΠ½ΠΎΠ²ΡΠ²Π°ΡΡΡΡ Π½Π° ΠΈΡΠΏΠΎΠ»ΡΠ·ΠΎΠ²Π°Π½ΠΈΠΈ ΠΏΡΠΈΠ½ΡΡΠΎΠΉ ΠΈΠ½ΡΠ΅ΡΠΏΡΠ΅ΡΠ°ΡΠΈΠΈ Π½Π° ΠΎΡΠ½ΠΎΠ²Π΅ ΠΏΡΠΎΠ³ΡΠ°ΠΌΠΌΠ½ΠΎΠ³ΠΎ ΠΎΠ±Π΅ΡΠΏΠ΅ΡΠ΅Π½ΠΈΡ. ΠΡΠΎΠΌΠ΅ ΡΠΎΠ³ΠΎ, Π²ΡΠ΅ ΠΈΡΠΏΡΡΠ°ΡΠ΅Π»ΡΠ½ΡΠ΅ Π»Π°Π±ΠΎΡΠ°ΡΠΎΡΠΈΠΈ, ΡΠ²ΡΠ·Π°Π½Π½ΡΠ΅ Ρ ΠΈΠ·ΠΌΠ΅ΡΠ΅Π½ΠΈΠ΅ΠΌ ΡΠ²ΠΎΠΉΡΡΠ² ΠΏΡΠΈ ΡΠ°ΡΡΡΠΆΠ΅Π½ΠΈΠΈ Π΄Π»Ρ Π΄Π°Π½Π½ΠΎΠΉ ΠΊΠ°ΡΠ΅Π³ΠΎΡΠΈΠΈ ΠΏΡΠΎΠ΄ΡΠΊΡΠΎΠ², Π΄ΠΎΠ»ΠΆΠ½Ρ ΡΡΠ°Π²Π½ΠΈΠ²Π°ΡΡ ΡΠ΅Π·ΡΠ»ΡΡΠ°ΡΡ Ρ Β«ΡΠΈΠΊΠ»ΠΈΡΠ΅ΡΠΊΠΈΠΌΠΈΒ» ΡΠΎΡΠΌΠ°ΠΌΠΈ ΠΈΡΠΏΡΡΠ°Π½ΠΈΠΉ. ΠΡΠ΅ Π·Π°Π΄Π΅ΠΉΡΡΠ²ΠΎΠ²Π°Π½Π½ΡΠ΅ Π»Π°Π±ΠΎΡΠ°ΡΠΎΡΠΈΠΈ Π΄ΠΎΠ»ΠΆΠ½Ρ Π΄Π΅ΠΌΠΎΠ½ΡΡΡΠΈΡΠΎΠ²Π°ΡΡ ΡΠ°Π·ΡΠΌΠ½ΡΡ Π²Π·Π°ΠΈΠΌΠΎΡΠ²ΡΠ·Ρ ΠΌΠ΅ΠΆΠ΄Ρ ΠΎΠ±ΡΠ΅ΠΊΡΠ°ΠΌΠΈ ΠΈ ΠΎΠΏΠ΅ΡΠ°ΡΠΎΡΠ°ΠΌΠΈ.
ΠΠΎΠΏΠΎΠ»Π½ΠΈΡΠ΅Π»ΡΠ½Π°Ρ ΠΈΠ½ΡΠΎΡΠΌΠ°ΡΠΈΡ:
Π’Π°Π±Π»ΠΈΡΠ° 1.
0 Π‘ΡΡΡΠΊΡΡΡΠ½ΡΠ΅ ΡΡΡΠ΅ΠΊΡΡ ΡΠ»Π΅ΠΌΠ΅Π½ΡΠ½ΡΡ Π΄ΠΎΠ±Π°Π²ΠΎΠΊ ΠΊ ΡΡΠ³ΡΠ½Ρ
ΠΠ»ΡΠΌΠΈΠ½ΠΈΠΉ
.
Π‘ΡΡΡΠΌΠ°
.
.
ΠΠΈΡΠΌΡΡ
.
.
ΠΠΎΡ β€ 0,15%
.
ΠΠΎΡ > 0,15%
.
Π₯ΡΠΎΠΌ
.
.
.
ΠΠ΅Π΄Ρ
.
ΠΠ°ΡΠ³Π°Π½Π΅Ρ
.
ΠΠΎΠ»ΠΈΠ±Π΄Π΅Π½
.
ΠΠΈΠΊΠ΅Π»Ρ
.
ΠΡΠ΅ΠΌΠ½ΠΈΠΉ
.
Π’Π΅Π»Π»Π΅ΡΠΈΡΠΌ
.
.
.
ΠΠ»ΠΎΠ²ΠΎ
.
.
Π’ΠΈΡΠ°Π½ < 0,25%
.
ΠΠ°Π½Π°Π΄ΠΈΠΉΠ‘ΠΈΠ»ΡΠ½ΡΠΉ Π³ΡΠ°ΡΠΈΡΠΈΠ·Π°ΡΠΎΡ
.
ΠΠ°Π»Π΅Π½ΡΠΊΠΈΠΉ ΡΡΡΠ΅ΠΊΡ Π² ΠΈΡΠΏΠΎΠ»ΡΠ·ΠΎΠ²Π°Π½Π½ΠΎΠΌ ΠΊΠΎΠ»ΠΈΡΠ΅ΡΡΠ²Π΅
.
ΠΠ°ΡΠ±ΠΈΠ΄Π½ΡΠΉ ΠΏΡΠΎΠΌΠΎΡΠΎΡ, Π½ΠΎ Π½Π΅ ΠΊΠ°ΡΠ±ΠΈΠ΄Π½ΡΠΉ ΡΠΎΡΠΌΠΈΡΠΎΠ²Π°ΡΠ΅Π»Ρ
.
Π‘ΠΈΠ»ΡΠ½ΡΠΉ Π³ΡΠ°ΡΠΈΡΠΈΠ·Π°ΡΠΎΡ
.
Π’Π²Π΅ΡΠ΄ΠΎΡΠΏΠ»Π°Π²Π½ΡΠΉ ΡΡΠ°Π±ΠΈΠ»ΠΈΠ·Π°ΡΠΎΡ
.
Π‘ΠΈΠ»ΡΠ½ΡΠΉ ΡΠΎΡΠΌΠΈΡΠΎΠ²Π°ΡΠ΅Π»Ρ ΠΊΠ°ΡΠ±ΠΈΠ΄Π°. ΠΠ±ΡΠ°Π·ΡΠ΅Ρ ΡΠ»ΠΎΠΆΠ½ΡΠ΅ ΠΊΠ°ΡΠ±ΠΈΠ΄Ρ, ΠΊΠΎΡΠΎΡΡΠ΅ ΠΎΡΠ΅Π½Ρ ΡΡΠ°Π±ΠΈΠ»ΡΠ½Ρ
.
ΠΡΠ³ΠΊΠΈΠΉ Π³ΡΠ°ΡΠΈΡΠΈΠ·Π°ΡΠΎΡ
.
ΠΡΠ³ΠΊΠΈΠΉ ΡΠ²Π΅ΡΠ΄ΠΎΡΠΏΠ»Π°Π²Π½ΡΠΉ ΡΠΎΡΠΌΠΈΡΠΎΠ²Π°ΡΠ΅Π»Ρ
.
ΠΡΠ³ΠΊΠΈΠΉ ΡΠ²Π΅ΡΠ΄ΠΎΡΠΏΠ»Π°Π²Π½ΡΠΉ ΡΠΎΡΠΌΠΈΡΠΎΠ²Π°ΡΠ΅Π»Ρ
.
ΠΡΠ°ΡΠΈΡΠΈΠ·Π°ΡΠΎΡ
.
Π‘ΠΈΠ»ΡΠ½ΡΠΉ Π³ΡΠ°ΡΠΈΡΠΈΠ·Π°ΡΠΎΡ
.
ΠΡΠ΅Π½Ρ ΡΠΈΠ»ΡΠ½ΡΠΉ ΠΊΠ°ΡΠ±ΠΈΠ΄Π½ΡΠΉ Π°ΠΊΡΠΈΠ²Π°ΡΠΎΡ, Π½ΠΎ Π½Π΅ ΡΡΠ°Π±ΠΈΠ»ΠΈΠ·Π°ΡΠΎΡ
.