Приготовление асфальтобетонной смеси, расчет
Для того чтобы обеспечить получение доброкачественного асфальтобетона, необходимо установить правильное количественное соотношение составляющих его материалов. Одним из условий, обеспечивающих механическую прочность асфальтобетона, является плотность его каменного остова.
Существует несколько методов подбора или проектирования состава асфальтобетона. В настоящее время чаще всего пользуются методом подбора по кривым плотных смесей.
На основании теоретических расчетов установлено, что плотные минеральные смеси получаются при определенном весовом соотношении частиц, диаметры которых относятся как 2 : 1 (например, фракции 16—8 мм, 8—4 мм, 4—2 мм и т. д.).
На рис. 1. Кривые оптимальных смесей.
При подборе состава определяется прежде всего гранулометрический (зерновой) состав всех составляющих: щебня (или гравия), песка и минерального порошка.
Так как особенно важное значение имеет содержание в смеси наиболее мелкой фракции (размером 0,074 мм), то прежде всего устанавливается соотношение исходных материалов, обеспечивающее нужное количество этой фракции.
Предположим, что требуется подобрать мелкозернистый асфальтобетон из материалов, имеющих следующий гранулометрический состав:
Таблица 1.
№№ | Наименование материалов | Частные остатки на ситах, % | |||||||
5 | 2 | 1 | 0,5 | 0,25 | 0,15 | 0,074 | меньше 0,074 мм | ||
1 | Щебень | 60 | 20 | 10 | 5 | 3 | 2 | — | — |
2 | Песок | — | 1,5 | 50 | 30 | 15 | 3,5 | — | — |
3 | Минеральный порошок | — | — | — | — | — | — | 40 | 60 |
Расчет состава каменных материалов для асфальтобетона состоит в нахождении такого весового соотношения имеющихся каменных материалов, при котором одноразмерные фракции в сумме дают требуемое количество данной фракции в смеси, согласно кривым наиболее плотных составов (график 3, рис. 1).
Назначение необходимого количества материалов производится из следующих соображений.
1) Фракция мельче 0,074 мм содержится только в минеральном порошке. Поэтому мы должны взять такое количество минерального порошка, чтобы данной фракции было около 15%:
15X100/ 60 = 25%.
2) Так же рассчитаем количество щебня. Фракция 5 мм содержится в щебне в количестве 60%. В смеси ее должно быть около 25%. Следовательно, для этого потребуется щебня:
25 х 100/ 60 = 42%.
Далее подсчитывается содержание каждой фракции щебня в этой доле, т. е. в 42%.
Содержание этих фракций определяется делением 42% пропорционально частным остаткам:
42/100 Х 60=25,2%; 42/100 X 20 = 8,4%;
42/100 Х 10 ==4,2%; 42/100 Х 5=2,1 % и т, д.
3) Следовательно, песка потребуется:
100—25 — 42 = 33%.
Для проверки правильности произведенного подбора суммируем одноразмерные фракции и наносим на график 3 рис. 1.
Если кривая при этом получается плавная и не выходит за пределы кривых плотных смесей, то при полученном соотношении будем иметь наилучшую смесь. Если кривая получается ломаная и отдельные точки ее выходят за пределы кривых, это указывает на недостаток или избыток соответствующей фракции. Изменив соотношение исходных материалов (но так, чтобы количество фракций 0,074 мм не выходило за пределы плотных смесей), можно улучшить состав. Если же отклонение слишком большое, следует добавить другого материала.
При подборе необходимо учитывать, что при применении гравийного материала и щебня мягких пород следует придерживаться верхнего предела кривых. При твердом и хорошо уплотняющемся дробленом каменном материале можно брать меньшее количество фракций размером 0,074 мм. Оптимальное количество битума определяется по величине временного сопротивления сжатию с проверкой процента объемного водонасыщения.
Для этого изготовляют несколько пробных смесей с различным содержанием битума и определяют временное сопротивление сжатию. При недостаточном количестве битума асфальтобетон получается малосвязный, с низким сопротивлением сжатию вследствие слабого сцепления частиц.
С увеличением количества битума сопротивление сжатию возрастает до известного предела. При избытке битума асфальтобетон становится излишне пластичным и сопротивление сжатию снова уменьшается. За оптимальное количество битума принимается то, при котором получается наибольшее сопротивление сжатию.
Расчет асфальтобетонной смеси
Правильное дозирование материалов имеет большое значение для получения доброкачественного асфальтобетона. Дозирование может производиться по весу (у смесителей типа Д-152 и Д-225) и по объему (у смесителя типа Г-1).
Во втором случае должны быть определены объемные веса всех материалов, входящих в состав асфальтобетона. Зная объемный вес материалов, легко перейти к нужным соотношениям, отвечающим запроектированным в процентах по весу Приведем пример: запроектирован следующий состав асфальтобетонной смеси для приготовления в смесителе Г-1: 50% щебня, 30% песка, 20% минерального порошка, 7% битума.
Полная загрузка смесителя 3 т.
При подборе состава количество каменных материалов принимается за 100%, а битум берется сверх 100%. Следовательно, в 3 т смеси битума должно быть:
Общее количество каменных материалов 3000 — 196 = 2804 кг.
Запроектированное количество щебня
50 X 2804/ 100 = 1402 кг.
Объем щебня будет равняться 1402/ объемный вес
Так же производится расчет и остальных материалов.
При весовой дозировке необходимо учитывать влажность материала.
Расчет производится следующим образом: предположим, что влажность песка 5%.
Весовое количество сухого песка подсчитывается так же, как и в приведенном выше примере, т. е.
25 X 2804 /100 = 701 кг.
Так как во влажном песке содержится 95% сухого песка и 5% воды, т. е 701 х 5/ 95 = 37,9, или, округляя, 38 кг.
Следовательно, влажного песка нужно взять 701 кг+38 кг=739 кг.
При объемном способе получается менее точная дозировка, поэтому предпочтение следует отдавать весовому способу.
Асфальтовое вяжущее вещество и мастика
Асфальтовая мастика представляет собой твердое вещество темно-бурого или черного цвета
Асфальтовый порошок
Асфальтовый порошок получается в результате тонкого помола асфальтовых известняков или доломитов, содержащих обычно от 4 до 8% твердого тугоплавкого битума. Из-за низкого содержания битума порошок без добавки битума в строительствe не применяется; его смешивают с битумом на заводе или на стройке и получают асфальтовое вяжущее вещество.
Асфальтовая мастика
Асфальтовая мастика представляет собой (при нормальной температуре) твердое вещество темно-бурого или черного цвета. Она выпускается заводами в виде квадратных плит толщиной 10-12 см и весом 32 кг. Изготовляют ее, смешивая в определенном соотношении молотую асфальтовую породу с расплавленным нефтяным битумом. Однородную расплавленную смесь разливают в формы, где она и застывает.
Мастика должна удовлетворять следующим требованиям:
- быть однородной;
- содержать битума не менее 13% от общего веса;
- обладать водонепроницаемостью: при слое толщиной 2 см не пропускать воду под давлением в 3 ати в течении час;
- предел прочности при растяжении трамбования образцов — восьмерок — должен быть не менее 30 кг/см2.
Альтовая мастика называется также асфальтовым вяжущим веществом и применяется для изготовления литых асфальтовых растворов.
Классификация и состав асфальта: Основные типы битумных смесей
Дата публикации: 07.10.2016 15:16
Состав и классификация асфальта (по содержанию основных элементов)Асфальтобетон — вещество, имеющее много разновидностей, отличающихся друг от друга в первую очередь составом. Состав асфальта определяет в том числе сферу его применения: дороги, которые используются с различной степенью интенсивности, имеют различные покрытия.
Общеизвестно, что в состав асфальта (битумной смеси) входят песок, щебень, битум и минеральные порошки.
Щебень и гравий могут состоять из частичек различного диаметра, быть однородными и неоднородными. Возможно изготовление асфальтовой битумной смеси без крупного заполнителя из щебня или гравия — так называемая песчано-битумная смесь.
Битум бывает натуральным и искусственным. В производстве асфальта используется искусственный битум, который получают при нефтепереработке.
Наконец, минеральные порошки в мелкозернистом асфальтобетоне — это продукт помола карбонатных горных пород (известняк, доломит и др.) Эти добавки используются для повышения прочности асфальтобетона, так как увеличивают вязкость. Вместе с тем, стоит отметить, что если минеральных порошков будет слишком много, асфальтобетон будет хрупким. Максимально допустимый процент порошков — 12% от общей массы, чаще встречаются смеси с 6-10 процентами минеральных элементов состава асфальта.
Кроме того, асфальтобетон часто включает в себя добавки:
вещества естественного и искусственного происхождения и различных свойств. К естественным добавкам могут относиться сера или сажа, к добавкам искусственного происхождения — к примеру, латексы на основе синтетического каучука.
Добавки улучшают полезные свойства материалов:
могут делать асфальтболее шероховатым (и, соответственно, более безопасным для езды, благодаря улучшению сцепления с шинами), более морозостойким, способствовать тому, что езда по асфальту будет сопровождаться меньшим шумом.
По составу асфальта (наличию битума и минеральной составляющей) выделяют следующие группы:
- Песчаные. Самая непрочная смесь, может использоваться для пешеходной дорожки либо тротуара.
- Резиново-битумные. Основная сфера их использования — строительство спортивных сооружений.
- Мелкозернистый асфальтобетон. Используется для производства междугородних трасс, а также проезжей части в городе.
- Крупнозернистый. В отличие от мелкозернистого асфальтобетона, используется как нижний слой в двуслойном покрытии.
- Полимерно битумные смеси. Достаточно долговечны. Широко применяются при устройстве мостовых конструкций, стоянок, паркингов.
- Щебёночно-мастичные. Особенно долговечны и прочны. Активно используются при строительстве городских дорог (с интенсивным движением), могут использоваться в строительстве аэродромов.
Мы перечислили основные типы асфальтобетона по содержанию основных компонентов. Узнать, по какому принципу асфальтобетон делится на марки, можно из соответствующей статьи Асфальт: марки и типы.
Асфальтобетонная смесь мелкозернистая
Наименование | ед | цена | условия |
Асфальт мелкозернистый тип А марка 1 — МА1 | тонна | 2750 | самовывоз |
Асфальт мелкозернистый тип Б марка 1 — МБ1 | тонна | 2750 | самовывоз |
Асфальт мелкозернистый тип Б марка 2 — МБ2 | тонна | 2750 | самовывоз |
Асфальт мелкозернистый тип В марка 2 — МВ2 | тонна | 2750 | самовывоз |
При заказе партии свыше 1000 тонн — цена договорная
Вы можете купить асфальтобетон мелкозернистый с доставкой в Москве и области.
.
Мелкозернистый асфальтобетон – производство и продажа смесей от производителя с доставкой по Москве и Московской области.
Цена на нашу продукцию на условиях самовывоза указана в прайс-листе. Стоимость асфальта с доставкой вы можете уточнить, позвонив нам по телефонам:
☎ +7(965)139-93-93
☎ +7(495)235-05-04
Мелкозернистый асфальт – это асфальтобетонная смесь, замешанная на основе песка и щебня размером 5-20, с добавлением битума и минерального порошка. Такую смесь часто используют при укладке дорог.
Состав мелкозернистой асфальтобетонной смеси.Для придания большого запаса прочности в мелкозернистом асфальте используется щебень размером от 5 до 20 мм. в больших пропорциях. Далее добавляют битум марки бнд. При затвердевании смесь битума с щебнем и другими компонентами превращается в прочное дорожное полотно. Битум при застывании дает возможность получить однородное, прочное покрытие. При замешивании смеси, нагретый до высокой температуры способствует легкому перемешиванию составляющих компонентов асфальта и облегчает проведение работ по укладке, асфальтировке территорий.
Используя щебень малой фракции, достигается необходимая плотность мелкозернистой асфальтобетонной смеси и при асфальтировании дорог мы получаем покрытие с остатком пор не более 4 %. Большую часть в мелкозернистом асфальте занимает щебень, и его содержание в такой смеси варьируется от 30% и до 60%, в зависимости от марки и типа асфальтобетона. Чем больше щебня в составе мелкозернистого асфальта, тем он крепче.
Асфальтобетон ➤ состав, свойства, требования к асфальтобетонной смеси
Дата публикации: 08.04.2020
На самом деле асфальт и асфальтобетон – разные вещи, которые часто путают. Асфальтобетон – это скорее модифицированный вариант асфальта, несмотря на то, что у них много схожих характеристик, сфер применения и свойств.
Разница в том, что асфальт – более природный материал, который получается смешением битумов, песка и гравия. А асфальтобетонная смесь – это микс из битумов, дополнительных компонентов (которые мы знаем, как обычный асфальт) и различных веществ, в том числе химических, для получения совершенно других, улучшенных, свойств.
Состав асфальтобетона позволяет получить более высокую прочность, твердость, увеличенные показатели по износостойкости, термостойкости и нагрузке. Физико механические свойства асфальтобетона позволяют применять его для покрытия дорог с повышенным трафиком, аэродромов, полов хозяйственных и производственных помещений.
Классификация асфальтобетона
Тип асфальтобетона полностью зависит от его характеристик и компонентов, которые применяются в его составе. В первую очередь от размера наполнителя.
Так, асфальтобетон бывает:
- Крупнозернистым составом, с размерами фракций элементов наполнителя до 40 мм
- Мелкозернистым асфальтобетоном, если размер фракции не превышает 20 мм
- Песчаный асфальтобетон – с фракциями до 5 мм.
Кроме того, разновидности асфальтобетона делятся по проценту минерального наполнителя (щебня/гравия) в нем:
- Высокоплотный асфальтобетон с % наполнителя от 60%
- Асфальтобетон А-категории с 50-60% минерального наполнителя
- Асфальтобетон Б-категории – когда процент наполнителя составляет 40-50%
- Асфальтобетон В-категории, если процент наполнителя не больше 40%
Различают так же асфальтобетоны по типу основного каменного составляющего элемента (минерального заполнителя):
- Гравийные
- Щебеночные
- Песчаные
И еще одна классификация асфальтобетонных смесей зависит от остаточной его пористости:
- Высокоплотные, когда остаточная пористость не превышает 2%
- Плотные, с пористостью от 2 до 7%
- Пористые, если пористость превышает 7% и до 12%
- Высокопористые смеси – с пористостью 12-18%
Кроме того, бывает холодный, теплый и горячий асфальтобетон, который различают по типу вяжущего битумного компонента и температуре, которая требуется для укладки смеси.
- Горячий асфальтобетон укладывается при 120 °С (важно – не ниже этой температуры), сразу же после приготовления
- Теплый асфальтобетон изготавливают и сразу укладывают при температуре от 70 °С
- Холодный асфальтобетон может использоваться для укладки при температуре от -5 °С
Из чего состоит асфальтобетон
Состав асфальтобетонной смеси чаще всего самый стандартный, когда для основы берется битум (его используют в качестве вяжущего вещества) и минеральный заполнитель. В качестве заполнителя используется песок, минеральные порошки и гравий или щебень.
Задача гравия служить наикрупнейшим заполнителем, создать остов будущего покрытия, а минеральные порошки заполняют получившиеся пустоты, созданные щебнем и песком. Помимо чистых фракций щебня в производстве асфальтобетона часто используются смеси различных фракций – можно встретить комплекс и асфальтобетона категории В, и категории Б, и асфальтобетона высокоплотного. Так обычно получается самый распространенный асфальтобетон. Состав обязательно дополняется минеральными порошками, которые получают при дроблении горной породы, например, доломита или известняка.
Так же асфальтобетон состоит из смеси битума и различных компонентов, которые улучают свойства битума и улучшают общие физические и механические свойства асфальтобетона. Это могут быть как специально изготовленные добавки, так и различное сырье, например, резина в гранулах.
Чаще всего состав смеси определяется индивидуально для каждой задачи, так как для изготовления смеси асфальтобетона требуется понимать условия его будущей эксплуатации и различные погодные и нагрузочные характеристики места укладки покрытия.
Требования к асфальтобетону
Основные требования, которые выдвигают к асфальтобетону, зависят от его прочности. Так, предел прочности асфальтобетонной смеси к усилию его сжатия должен составлять не меньше 10 при температуре +50°.
Коэффициент теплоустойчивости асфальтобетона должен не превышать 3,0. Водостойкость (или отношение предела прочности смеси к усилию сжатия водонасыщенного и сухого образца конкретной смеси асфальтобетона) – не меньше 0,9. А водонасыщение по объему – 1-3% и не больше.
Все эти свойства асфальтобетона напрямую зависят от качества вяжущего составляющего и различных заполнителей, которые влияют на прочность, плотность, водо- и термостойкость асфальтобетона.
Механические свойства асфальтобетона
Основные механические и физические свойства асфальтобетона зависят от условий, в которых он будет эксплуатироваться. Кроме механического воздействия от проезжающих автомобилей, асфальтобетон подвергается воздействию атмосферных осадков, талых вод, солевых смесей от наледи, смене температуры окружающей среды.
Основное свойство асфальтобетона, на которое обращают внимание при проектировании смеси – это его прочность. Это прочность при сжатии при температуре +50°С, прочность при сжатии при температуре +20°С, прочность при сжатии при температуре в 0 градусов. Для каждого из этих температурных режимов асфальтобетон должен показывать определенную прочность.
Кроме того, для асфальтобетона важны:
- Сдвигоустойчивость, которая влияет на долговечность уложенного покрытия. Должна составлять от 0,66 до 0,91 при оценке по коэффициенту трения
- Сцепление при сдвиге, которое указывает на плотность, с которой будет сцепляться колесо и дорожное покрытие (показатели должны варьироваться в пределах 0,6 – 0,95)
- Водостойкость – это соотношение между прочностями сухого образца и такого же, но напитавшегося водой.
- Износостойкость – она же долговечность. Для асфальтобетонных смесей стандарт износа не должен превышать 0,3-1,0 мм в год.
Средняя плотность асфальтобетона
Для выполнения укладочных работ нужно понимать, какой расход потребует асфальтобетон. Вес смеси в килограммах необходимо разделить на асфальтобетон удельный вес. Так мы сможем узнать цифру расхода асфальтобетонной смеси. Показатели смеси для расчета можно узнать у производителя или из технических таблиц.
Эти расчеты позволят составить смету расходов.
Плотность асфальтобетонной смеси рассчитывается из его остаточной пористости. Типы пористости мы уже описывали ранее. Средняя плотность смеси зависит от фракции, которая используется в его составе: крупнозернистый асфальтобетон 2100 кг/м³, асфальтобетон на шлаковом и кварцевом песке 2350 кг/м³ и 2200 кг/м³ соответственно.
Асфальтобетонные смеси Суперпейв → АБЗ «Бетас»
На многие участки отечественных шоссейных и городских дорог приходится повышенная нагрузка – в силу популярности этих трасс, а также из-за особенностей их расположения и эксплуатации. Обычное асфальтовое покрытие в подобных случаях деформируется и изнашивается очень быстро. Его приходится заменять, что приводит к неоправданно высоким затратам на ремонт.
Выходом из сложившейся ситуации становится применение для укладки асфальтобетонных смесей, эксплуатационные характеристики которых выше стандартных. Технологию изготовления таких материалов называют Суперпейв, что дословно переводится как “асфальт в супер исполнении”.
Разработки данных составов асфальтобетона велись долгие годы. Полученные исследователями данные активно применяются проектировщиками. При подборе смеси для укладки на конкретном участке учитывается множество факторов, включая местные климатические условия, уровень и характер деформационных сил, воздействующих на дорожное полотно. Когда необходимый состав асфальтобетона подобран, его тестируют с помощью специального оборудования, и лишь затем применяют на практике.
Критерии подбора и испытания вяжущегоСуществует особая шкала (ее называют PG Grade), с помощью которой рассчитывается взаимосвязь между деформационными свойствами битумного вяжущего материала и температурными условиями его эксплуатации. Когда подобные исследования проведены, становится понятно, какой битум будет вести себя наилучшим образом на конкретной дороге. При этом подбирается не марка данного материала, а его точный химический состав.
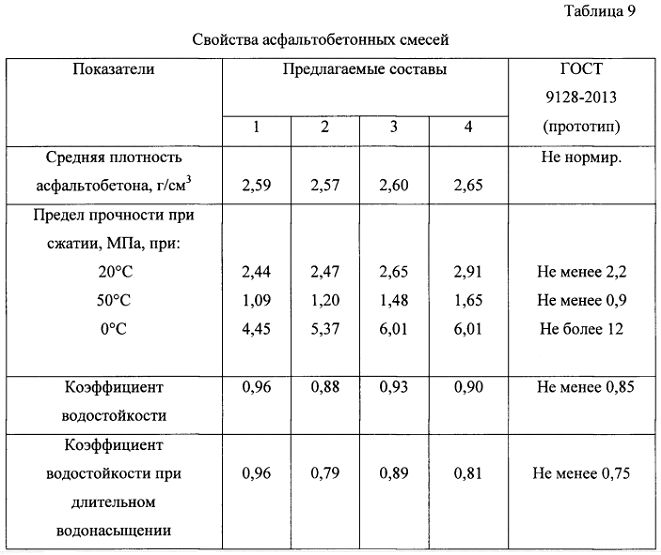
В результате такого подбора сроки эксплуатации дорожного покрытия существенно возрастают. При определении необходимой PG-марки исследователи учитывают полный диапазон температур, в которых будет эксплуатироваться дорожное покрытие.Критерии подбора и испытания каменного материала
Используемая методика позволяет безошибочно определить все важные характеристики щебня. А именно: стойкость к механическому износу и к низким температурам, содержание частиц пыли и глины, средние размеры дробленых, игловатых и лещадных зерен и их процентное соотношение в общей массе материала.
Лабораторные испытания позволяют получить информацию о том, каким способом лучше просеивать каменный материал, чтобы получить его оптимальную плотность в составе смеси асфальтобетона. Кроме того, готовый состав будет обладать наилучшей сопротивляемостью к пластической деформации и к разрушению в результате накопления усталости.Объемное проектирование асфальтобетонной смеси и прогноз ее поведения
Метод Суперпейв позволяет проектировщикам определить наилучшее сочетание массовых долей щебня и битума в составе готовой смеси.
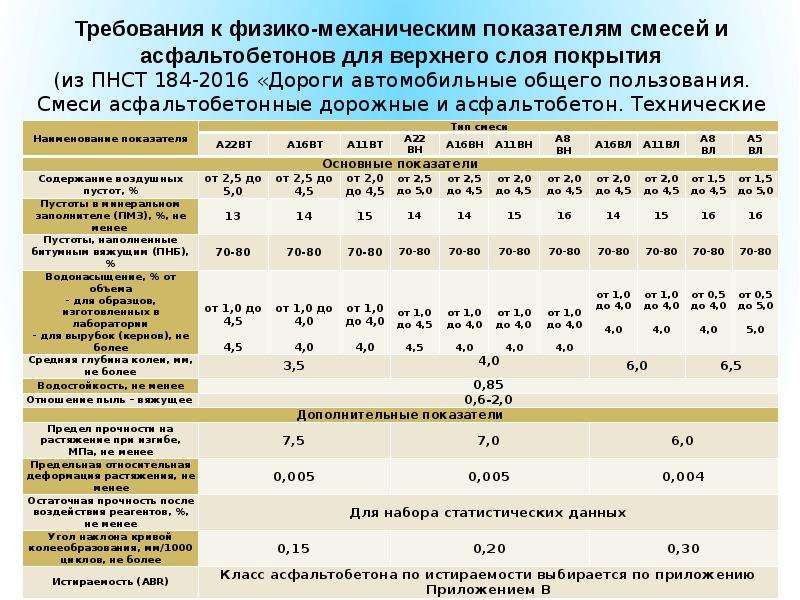
Значение сведений о количестве пор в асфальтобетонном покрытии очень велико. Плохо уплотняющийся материал может быть пригоден лишь для пешеходных тротуаров, но выдержать тяжелые грузовики сможет лишь поверхностный слой с высоким показателем уплотнения.Лучшее основание для укладки асфальтобетона по методу Суперпейв
Метод обустройства оснований сверхпрочных асфальтобетонных покрытий называют холодным ресайклингом. На нижнем слое дороги вероятность возникновения трещин из-за усталости материала окажется минимальной. Дополнительную прочность дорожному полотну придают, в частности, ровно лежащие слои покрытия.
Данная методика предусматривает использование рециклеров – особых машин с фрезерными барабанами, которые перерабатывают старое дорожное полотно и вносят в состав модифицирующие добавки.
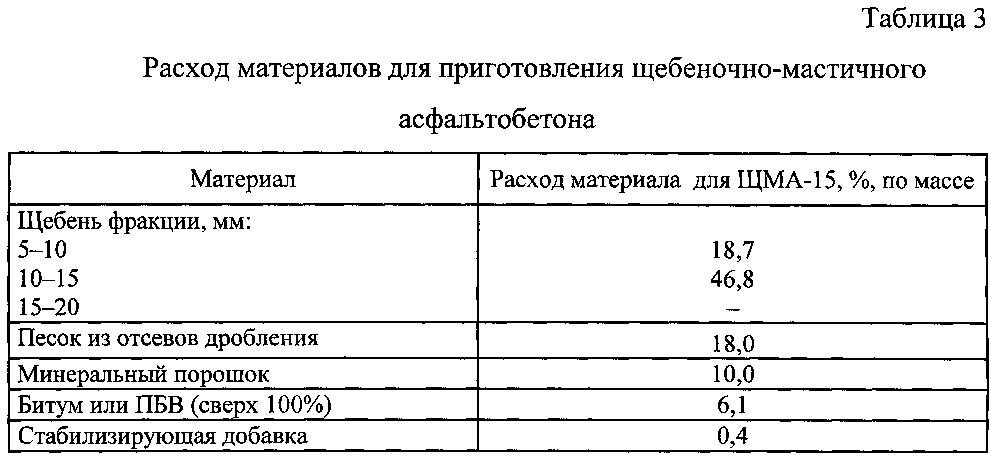
Расчеты, которыми по методу Суперпейв определяются составы асфальтобетонных смесей, не противоречат действующим в России ГОСТам – они их дополняют. Методика позволяет определить необходимое процентное содержание в смеси вяжущей компоненты, а также параметры гранул щебня в ней.
Готовый асфальтобетон окажется идеально пригодным к эксплуатации на конкретной трассе, в существующих на этой территории климатических условиях. Такие результаты метод демонстрирует благодаря точному подбору материалов. Еще до того, как будут уложены первые квадратные метры состава, проектировщики точно определят его параметры, включая остаточную и минеральную пористость, значение плотности, деформацию в результате сжатия при различных температурах, устойчивость к сдвигам и к появлению трещин.

Состав асфальтобетона
Изобретение относится к области строительного производства в автодорожной отросли и может быть применено при изготовлении асфальтобетона, в том числе с использованием нанотехнологий. Состав асфальтобетона включает щебень, кварц-полевошпатовый песок, минеральный порошок, битум и углеродную добавку, в качестве углеродной добавки содержит фуллереновую смесь, полученную при синтезе в электродуговом плазмохимическом реакторе, при следующем соотношении компонентов, мас.%: щебень — 42-44, кварц-полевошпатовый песок с модулем крупности Мкр=3 — 48-50, минеральный порошок МП-1 — 8-9, при этом битум БНД 90/130 берут в количестве 5,4-5,6 мас.% сверх минеральной части, фуллереновую смесь берут в количестве 0,03-0,06 мас.% от массы асфальтобетона, а для равномерного распределения фуллереновой смеси в битуме используется нагрев битума до температуры 130-140°C. Техническим результатом является повышение прочности асфальтобетона на сжатие при 20°C и при 50°C и снижение расхода углеродной добавки. 3 табл., 3 пр.
Изобретение относится к области строительного производства в автодорожной отрасли и может быть применено при изготовлении асфальтобетона, в том числе с использованием нанотехнологий.
Известна асфальтобетонная смесь по способу упрочнения асфальтового дорожного покрытия углеродным наноматериалом, содержащая щебень, отсев щебня, песок и нефтяной битум марки БНД 90/130 с модифицирующей добавкой «Таунит». Нефтяной битум модифицирован углеродными наноматериалами в количестве 0,01-0,005% от массы битума при ультразвуковом воздействии в ультразвуковой мешалке в течение 6 часов. Результатом данного способа модифицирования битума является улучшение прочности и упругости получаемого асфальтобетонного покрытия, а также повышение водостойкости, теплостойкости и морозостойкости и расширение температурного диапазона его укладки в области отрицательных температур (см. патент РФ №2515007, МПК C08L 95/00, С04В 26/26, В82В 1/00, опубл. 10.05.2014).
Недостатками асфальтобетонной смеси по известному способу являются использование продолжительной ультразвуковой обработки, в течение 6 часов, для равномерного распределения и модификации битума ультразвуком, а так же трудоемкий и технологически сложный процесс получения модафицирующей добавки «Таунит», получение которой происходит за счет газофазного химического осаждения (каталитический пиролиз-CVD) углеводородов (CxHy) на катализаторах (Ni/Mg) при атмосферном давлении и температуре 580÷650°C.
Наиболее близким по технической сущности к заявляемому изобретению является состав асфальтобетона с наноструктурирующим модификатором, при применении которого достигается более высокая износостойкость асфальтобетона за счет улучшения свойств не только битумной основы, но и повышения адгезии между компонентами асфальтобетона. Модифицирующее действие такого материала достигается за счет того, что модификатор представляет собой структуру из равномерно распределенных в битумной основе углеродных нанотрубок в количестве 0,2-10 масс. %, технического углерода в количестве 10-20 масс. % и органоглины в количестве 1-20 масс. % путем диспергирования добавки в расплаве битума при ультразвуковом воздействии (см. патент РФ №2412126, МПК С04В 24/36, С04В 20/10, В82В 3/00, опубл. 20.02.2011, бюл. №5).
Недостатками известного состава являются высокое содержание модификатора, в количестве 0,1% от массы асфальтобетонной смеси, а так же использование ультразвуковой обработки для равномерного распределения добавки в битуме.
Задачей, на решение которой направлено изобретение, является разработка состава асфальтобетона для дорожных покрытий с возможностью упрощения технологического процесса подготовки асфальтобетонной смеси.
Технический результат изобретения заключается в повышении прочности асфальтобетона на сжатие при 50°C, повышении прочности на сжатие при 20°C, снижении расхода углеродной добавки.
Технический результат достигается тем, что в составе асфальтобетона, включающем щебень, песок, минеральный порошок, битум и углеродную добавку, согласно изобретению, в качестве углеродной добавки используется фуллереновая смесь, получаемая при синтезе в электродуговом плазмохимическом реакторе, при следующем соотношении компонентов, масс. %:
Щебень | 42-44 |
Кварц-полевошпатовый песок с модулем крупности Мкр=3 | 48-50 |
Минеральный порошок МП-1 | 8-9, |
при этом битум БНД 90/130 берут в количестве 5,4-5,6 масс. % сверх минеральной части, фуллереновую смесь берут в количестве 0,03-0,06 масс. % от массы асфальтобетонной смеси, а для равномерного распределения фуллереновой смеси в битуме используется нагрев битума до температуры 130-140°C.
Отличительной особенностью предлагаемого состава асфальтобетонной смеси является использование в качестве углеродной добавки фуллереновой смеси, применение которой для модификации битума способствует повышению пределов прочности асфальтобетона при сжатии при температурах 50°C и 20°C.
В ходе проведения экспериментов установлено, что для равномерного распределения фуллереновой смеси в общем составе смеси, исключения возможности ее агрегации и седиментации при введении в состав асфальтобетона сверхмалых количеств, битум при добавлении фуллереновой смеси подвергают нагреву до рабочей температуры приготовления асфальтобетонной смеси, равной 130-140°C. Нагревание битума, содержащего фуллереновую смесь, достаточно для обеспечения однородного ее распределения в среде-носителе.
В качестве углеродной добавки в предлагаемом изобретении используется фуллереновая смесь, получаемая при синтезе в электродуговом плазмохимическом реакторе. В основе работы реактора лежит эрозия графитовых электродов в плазме дугового разряда. Разряд инициируется при давлении 105 Па путем пропускания через электроды тока частотой 44 либо 66 кГц. Эрозия стержней (графитовых электродов) происходит в замкнутом герметичном объеме, заполненном гелием.
Хроматографическое исследование фуллереновой смеси методом жидкостной хроматографии путем растворения исследуемого вещества в толуоле и разделение на колонке Cosmosil «Buckyprepwaters» показало выделение из фуллереновой смеси С60 и С70 [см. патент РФ №2320536, МПК С01В 31/00, В82В 3/00, опубл. 27.03.2008, бюл. №9]. Данный способ позволяет получать фуллереновую смесь с высоким содержанием фуллеренов — 10-12%.
Предлагаемый состав асфальтобетона содержит компоненты при следующем соотношении, масс. %: щебень — 42-44; кварц-полевошпатовый песок с модулем крупности Мкр=3 — 48-50; минеральный порошок МП-1 — 8-9; при этом битум берут в количестве — 5,4-5,6 сверх минеральной части; фуллереновую смесь берут в количестве — 0,03-0,06 от массы асфальтобетонной смеси. В ходе проведения экспериментов установлено, что именно такой состав смеси асфальтобетона обеспечивает достижение технического результата, заключающегося в повышении прочностных показателей на сжатие при температурах: 20°C и 50°C, превышающих показатели прочности бездобавочного асфальтобетона в среднем на 55-70% и на 60-75% соответственно и прототипа при температурах: 20°C и 50°C, в среднем на 10-15% и на 5-15% соответственно, уменьшении расхода углеродных материалов. Повышение прочности объясняется улучшением структурирования модифицированного битума фуллереновой смесью, следовательно, вяжущее эффективнее переводится из объемного в пленочное состояние, из-за чего происходит рост прочности асфальтобетона при 20°C и 50°C.
Экспериментально установлено, что при введении в состав смеси для асфальтобетона фуллереновой смеси в количестве менее 0,03 масс. % от массы асфальтобетонной смеси наблюдается незначительное повышение прочностных показателей по сравнению с контрольным бездобавочным составом, а введение фуллереновой смеси в количестве более 0,06 масс. % от массы асфальтобетонной смеси является нецелесообразным, так как ведет к удорожанию конечной стоимости готового продукта — асфальтобетона. При этом введение фуллереновой смеси в указанном интервале позволяет получить параметры прочности при сжатии, превышающие показатели прочности бездобавочного асфальтобетона при температурах: 20°C и 50°C, в среднем на 55-70% и на 60-75% соответственно и прототипа при температурах: 20°C и 50°C, в среднем на 10-15% и на 5-15% соответственно.
Экспериментальные исследования показали, что количественное изменение соотношения компонентов состава асфальтобетонной смеси, масс. %: щебень — 42-44; кварц-полевошпатовый песок с модулем крупности Мкр=3 — 48-50; минеральный порошок МП-1 — 8-9; при этом битум берут в количестве — 5,4-5,6 сверх минеральной части; фуллереновую смесь берут в количестве — 0,03-0,06 от массы асфальтобетонной смеси позволяет варьировать состав асфальтобетона без ощутимого изменения прочностных показателей.
Компоненты состава асфальтобетонной смеси подобраны таким образом, чтобы получаемые образцы имели максимальные прочностные показатели.
Для получения предлагаемого состава асфальтобетонной смеси использовались следующие материалы: щебень фракции 5-15 мм, соответствующий требованиям ГОСТ 8267-82, ГОСТ 10260-82, ГОСТ 8268-82; кварц-полевошпатовый песок с модулем крупности Мкр=3, отвечающий требованиям ГОСТ 8736-85; минеральный порошок МП-1 — молотый известняк/мрамор, битум марки БНД90/130 производства Ангарского нефтеперерабатывающего завода Иркутской области.
Были приготовлены три смеси компонентов, масс. %: щебень — 42-44; кварц-полевошпатовый песок с модулем крупности Мкр=3 — 48-50; минеральный порошок МП-1 — 8-9; при этом битум берут в количестве — 5,4-5,6 сверх минеральной части; фуллереновую смесь берут в количестве — 0,03-0,06 от массы асфальтобетонной смеси (составы 1-3, табл. 1). Одновременно готовят контрольный бездобавочный состав асфальтобетона (состав 4, табл. 1). Кроме того, готовят два известных состава асфальтобетона с использованием щебня, песка, минерального порошка, битума и наноструктурирующих модификаторов на основе битума (соответственно составы 5 и 6 по прототипу, табл. 1).
Смеси для составов 1-3 готовят следующим образом: фуллереновую смесь добавляют в предварительно обезвоженный и разогретый до 130-140°C битум и перемешивают с целью равномерного распределения. Минеральные материалы (щебень, кварц-полевошпатовый песок, минеральный порошок МП-1) предварительно высушивают. Кварц-полевошпатовый песок с модулем крупности Мкр=3 и щебень нагревают, периодически помешивая, до температуры 160-170°C, затем добавляют ненагретый минеральный порошок МП-1 и нагретый в отдельной емкости модифицированный битум. Смеси минеральных материалов с модифицированным битумом окончательно перемешивают в лабораторном смесителе до полного и равномерного объединения всех компонентов в течение 4-5 минут, до равномерного покрытия всех минеральных зерен битумом. При изготовлении образцов формы и вкладыши нагревают до температуры 90-100°C. Смесь полученного состава равномерно распределяют в форме штыкованием ножом. Формы с асфальтобетонной смесью ставят на нижнюю плиту пресса для уплотнения. Давление на уплотняемую смесь доводят до 40 МПа, время нагружения составляет 3 мин. Затем образцы извлекают из формы выжимным приспособлением. Аналогичным образом готовят образцы из контрольной смеси компонентов (состав 4, табл. 1): минеральные материалы (щебень, кварц-полевошпатовый песок, минеральный порошок МП-1) предварительно высушивают. Кварц-полевошпатовый песок с модулем крупности Мкр=3 и щебень нагревают, периодически помешивая, до температуры 160-170°C, затем добавляют ненагретый минеральный порошок и нагретый в отдельной емкости битум. Смеси минеральных материалов с битумом окончательно перемешивают в лабораторном смесителе до полного и равномерного объединения всех компонентов в течение 4-5 минут, до равномерного покрытия всех минеральных зерен битумом.
При изготовлении образцов формы и вкладыши нагревают до температуры 90-100°C. Смесь равномерно распределяют в форме штыкованием ножом. Формы с асфальтобетонной смесью ставят на нижнюю плиту пресса для уплотнения. Давление на уплотняемую смесь доводят до 40 МПа, время нагружения составляет 3 мин. Затем образцы извлекают из форм выжимным приспособлением. Известные смеси компонентов (составы 5, 6 — по прототипу, табл. 1; варианты состава добавок представлены в табл. 2), наноструктурирующий модификатор готовят следующим образом: технический углерод — 10-20%, органоглину (межплоскостное расстояние 3 нм) — 1-20%, углеродные нанотрубки (длинна 0,2-10 мкм, диаметр 1,0 — 7,0 нм, число графеновых слоев от 1 до 5) — 0,2-10% и битум 50,0-88,8% диспергируют в ультазвуковой ванне типа «Сапфир» в течение 10 минут при температуре 180°C. Затем полученный модификатор в количестве 0,1% от общей массы асфальтобетонной смеси добавляют в битум и перемешивают с целью равномерного распределения углеродного наномодификатора.
Минеральные материалы (щебень, кварц-полевошпатовый песок, минеральный порошок МП-1) предварительно высушивают. Кварц-полевошпатовый песок с модулем крупности Мкр=3 и щебень нагревают, периодически помешивая, до температуры 160-170°C, затем добавляют ненагретый минеральный порошок и нагретый в отдельной емкости модифицированный битум. Смеси минеральных материалов с модифицированным битумом окончательно перемешивают в лабораторном смесителе до полного и равномерного объединения всех компонентов в течение 4-5 минут, до равномерного покрытия всех минеральных зерен битумом. При изготовлении образцов формы и вкладыши нагревают до температуры 90-100°C. Смесь равномерно распределяют в форме штыкованием ножом. Формы с асфальтобетонной смесью ставят на нижнюю плиту пресса для уплотнения. Давление на уплотняемую смесь доводят до 40 МПа, время нагружения составляет 3 мин. Затем образцы извлекают из форм выжимным приспособлением.
Исследуемые образцы испытывают на прочность при сжатии при 50°C и при 20°C. Испытания проводятся по стандартным методикам и для каждого вида испытаний изготавливаются образцы в соответствии с требованиями ГОСТ 12801-98 — «Материалы на основе органических вяжущих веществ, для дорожного и аэродромного строительства». В таблице 3 представлены прочностные показатели составов 1-6 исследуемых асфальтобетонов.
Анализ полученных результатов (табл. 3) позволяет сделать следующие выводы:
— прочность асфальтобетона при температуре 20°C с использованием фуллереновой смеси лежит в пределах 3,9-4,3 МПа, что превышает прочность асфальтобетона без добавок в среднем на 55-70% и прочность асфальтобетона по прототипу на 5-15%;
— прочность асфальтобетона при температуре 50°C с использованием фуллереновой смеси лежит в пределах 1,6-1,75 МПа, что превышает прочность асфальтобетона без добавок в среднем на 60-75% и прочность по прототипу на 10-15%;
— в составе смеси для асфальтобетона используется фуллереновая смесь с высоким процентным содержанием фуллеренов;
— введение фуллереновой смеси в разогретый до 130-140°C битум не требует распределения с помощью ультразвука, что упрощает технологический процесс подготовки асфальтобетонной смеси.
Предлагаемый состав асфальтобетонной смеси готовят следующим образом: берут фуллереновую смесь в количестве 0,03-0,06 масс. % от массы асфальтобетонной смеси и добавляют в предварительно обезвоженный и разогретый до 130-140°C битум марки БНД 90/130 производства Ангарского нефтеперерабатывающего завода Иркутской области, который берут в количестве — 5,4-5,6 масс. % сверх минеральной части и перемешивают с целью равномерного распределения. Минеральные материалы (щебень, кварц-полевошпатовый песок, минеральный порошок МП-1) предварительно высушивают. Кварц-полевошпатовый песок с модулем крупности Мкр=3 — 48-50 масс. % и щебень фракции 5-15 мм 42-44 масс. % нагревают, периодически помешивая, до температуры 160-170°C, затем добавляют ненагретый минеральный порошок МП-1 — молотый известняк/мрамор 8-9 масс. % и нагретый в отдельной емкости модафицированный битум. Смеси минеральных материалов с модифицированным битумом окончательно перемешивают в лабораторном смесителе до полного и равномерного объединения всех компонентов в течение 4-5 минут до равномерного покрытия всех минеральных зерен битумом. При изготовлении образцов формы и вкладыши нагревают до температуры 90-100°C. Смесь равномерно распределяют в форме штыкованием ножом. Формы с асфальтобетонной смесью ставят на нижнюю плиту пресса для уплотнения. Давление на уплотняемую смесь доводят до 40 МПа, время нагружения составляет 3 мин. Затем образцы извлекают из форм выжимным приспособлением.
Примеры, подтверждающие получение асфальтобетонной смеси с использованием в качестве углеродной добавки — фуллереновой смеси.
Пример 1: в качестве углеродной добавки используется фуллереновая смесь, которая получена при синтезе в электродуговом плазмохимическом реакторе. В основе работы реактора лежит эрозия графитовых электродов в плазме дугового разряда. Разряд инициируется при давлении 105 Па путем пропускания через электроды тока частотой 44 либо 66 кГц. Эрозия стержней (графитовых электродов) происходит в замкнутом герметичном объеме, заполненным гелием.
Хроматографическое исследование углеродного наноматериала методом жидкостной хроматографии путем растворения исследуемого вещества в толуоле и разделение на колонке Cosmosil «Buckyprepwaters» показало выделение из фуллереновой смеси С60 и С70.
Фуллереновую смесь берут в количестве 0,03% от общей массы асфальтобетонной смеси и добавляют в предварительно обезвоженный и разогретый до 140°C битум марки БНД 90/130 производства Ангарского нефтеперерабатывающего завода, которого берут — 5,6 масс. % сверх минеральной части с целью равномерного распределения. Минеральные материалы (щебень, кварц-полевошпатовый песок, минеральный порошок МП-1) предварительно высушивают. Кварц-полевошпатовый песок с модулем крупности Мкр=3-50 масс. % и щебень фракции 5-15 мм 42 масс. % нагревают, периодически помешивая, до температуры 170°C, затем добавляют ненагретый минеральный порошок МП-1 — молотый известняк/мрамор 8 масс. % и нагретый в отдельной емкости модифицированный битум. Смеси минеральных материалов с модифицированным битумом окончательно перемешивают в лабораторном смесителе до полного и равномерного объединения всех компонентов в течение 5 минут, до равномерного покрытия всех минеральных зерен битумом. При изготовлении образцов формы и вкладыши нагревают до температуры 100°C. Смесь равномерно распределяют в форме штыкованием ножом. Формы с асфальтобетонной смесью ставят на нижнюю плиту пресса для уплотнения. Давление на уплотняемую смесь доводят до 40 МПа, время нагружения составляет 3 мин. Затем образцы извлекают из форм выжимным приспособлением.
Предел прочности на сжатие при 50°C горячего, плотного, мелкозернистого асфальтобетона типа «Б», марки II составляет 1,6 МПа, предел прочности на сжатие при 20°C составляет 3,9 МПа.
Пример 2: проводят аналогично примеру 1, при следующем соотношении компонентов: фуллереновую смесь берут в количестве 0,045% от общей массы асфальтобетонной смеси; битум марки БНД 90/130 производства Ангарского нефтеперерабатывающего завода берут в количестве — 5,5 масс. % сверх минеральной части; кварц-полевошпатовый песок с модулем крупности Мкр=3-49 масс. %; щебень фракции 5-15 мм 43 масс. %; минеральный порошок МП-1 — молотый известняк/мрамор 8 масс. %
Предел прочности на сжатие при 50°C горячего, плотного, мелкозернистого асфальтобетона типа «Б», марки II составляет 1,75 МПа, предел прочности на сжатие при 20°C составляет 4,3 МПа.
Пример 3: проводят аналогично примеру 1, при следующем соотношении компонентов: фуллереновую смесь берут в количестве 0,06% от общей массы асфальтобетонной смеси; битум марки БНД 90/130 производства Ангарского нефтеперерабатывающего завода берут в количестве 5,4 масс. % сверх минеральной части; кварц-полевошпатовый песок с модулем крупности Мкр=3-48 масс. %; щебень фракции 5-15 мм 44 масс. %; минеральный порошок МП-1 — молотый известняк/мрамор 8 масс. %.
Предел прочности на сжатие при 50°C горячего, плотного, мелкозернистого асфальтобетона типа «Б», марки II составляет 1,65 МПа, предел прочности на сжатие при 20°C составляет 4,0 МПа.
Предлагаемое изобретение по сравнению с прототипом (см. патент РФ №2414126, МПК С04В 24/36, С04В 20/10, В82В 3/00, опубл. 20.02.2011, бюл. №5) позволяет получить следующие преимущества:
— уменьшение расхода углеродных наноматериалов; использование в качестве углеродных наноматериалов — фуллереновой смеси с выскоми содеджанием фуллеренов;
— исключение распределения добавки в битуме ультразвуком, применение которого требует значительных затрат энергии, передача которой посредством звукового поля затруднительна;
— повышение пределов прочности на сжатие при температурах 50°C и 20°C при использовании в качестве углеродной добавки — фуллереновой смеси.
Предлагаемый состав асфальтобетонной смеси на основе щебня, песка, минерального порошка, битума и фуллереновой смеси может быть использован в дорожном строительстве для дорожных покрытий.
Состав асфальтобетона, включающий щебень, песок, минеральный порошок, битум и углеродную добавку, отличающийся тем, что в качестве углеродной добавки содержит фуллереновую смесь, полученную при синтезе в электродуговом плазмохимическом реакторе, при следующем соотношении компонентов, мас.%:
щебень | 42-44 |
кварц-полевошпатовый песок с модулем крупности Mкр=3 | 48-50 |
минеральный порошок МП-1 | 8-9, |
при этом битум БНД 90/130 берут в количестве 5,4-5,6 мас.% сверх минеральной части, фуллереновую смесь берут в количестве 0,03-0,06 мас.% от массы асфальтобетона, а для равномерного распределения фуллереновой смеси в битуме используется нагрев битума до температуры 130-140°C.

Отличия асфальта и асфальтобетона, их состав
Анастасия
Специалист примет заявку и ответит на ваши вопросы!
8 (800) 700-97-90
Содержание страницы
В дорожном строительстве используются многочисленные виды асфальтобетонных смесей. На их выбор оказывают влияние различные факторы. Основные из них – характеристика режима движения автотранспорта и климатические условия в регионе строительства. Кроме этого, выбор материала (асфальт или асфальтобетон) зависит от способа его укладки и применяемого для дорожных работ оборудования.
Асфальт – его особенности
По происхождению асфальт бывает природный и созданный искусственно путем смешивания гравия, песка с битумом, минеральным порошком. Природный материал получается из тяжелых нефтяных фракций при испарении из них наиболее легких компонентов. Добыча асфальта осуществляется из пластовых жильных залежей, а также там, где нефть имеет естественный выход нефти на поверхность.
В природном асфальте количество смолисто-асфальтеновых веществ может достигать до 75 процентов, масел – до 40 процентов. Масла придают битуму подвижность и текучесть. Сравнивая между собой асфальт и асфальтобетон в чем разница между ними, следует обратить внимание, что внешне природный асфальт трудно отличить от обычной смолы. Поэтому его называют горной смолой. Асфальтобетонная смесь часто содержит в своем составе крупные фракции щебня, гравий.
Выбирая асфальтобетон или асфальт, сравнивая их характеристики, отмечены положительные качества искусственного материала. Он выдерживает большие нагрузки, обладает лучшей демпфирующей способностью. В зависимости от процентного содержания битума, щебня, минерального порошка, песка производится асфальт следующих марок: 1, 2, 3.
Асфальтобетон – его разновидности и свойства
Получаемый в результате уплотнения асфальтобетонной смеси и включения в ее состав других добавок материал называется асфальтобетоном. Для его изготовления применяется смесь следующего состава:
- Минеральный заполнитель (щебень и гравий из высокопрочных горных пород, природный или дробленый песок). В качестве структурообразующего компонента также используется минеральный порошок, который производится путем измельчения доломита, битуминозного известняка, доменных шлаков. Он необходим для заполнения пор между гравием (щебнем), а также для увеличения прочности битума.
- Битумное вяжущее. В эту категорию входят битумы, а также их модифицированные разновидности. Класс и марка битума выбирается с учетом особенностей климата в местах использования асфальтобетона, категории дорожного покрытия. Требования к дорожным нефтяным битумам содержатся в ГОСТ 22245-90.
Перемешиваются компоненты в нагретом состоянии и при определенной температуре. Вид используемых добавок оказывает влияние на свойства асфальта или асфальтобетона, который подразделяется на следующие виды:
- Щебеночный.
- Гравийный.
- Песчаный.
По типу вяжущего вещества и способу укладки асфальтобетонные смеси бывают:
- Холодные. Для них применяются жидкие нефтяные дорожные битумы. Укладывается смесь при температуре не менее 5°C. Асфальтобетон, одним из компонентов которого является полимермодифицированное битумное вяжущее, и приготовленный без нагревания, может использоваться при температуре от +5 до -5 °C. Одно из главных свойств, чем асфальт отличается от асфальтобетона, это способность последнего после приготовления долго находиться в рыхлом состоянии. Составы холодных асфальтобетонных смесей отличаются от горячих тем, что в холодных составах содержится большее количество минерального порошка (до 20%), а щебня – не более 50%.
- Теплые. Производятся на вязких и жидких нефтяных битумах. Укладываются при температуре смеси не менее 70°C.
- Горячие. Готовятся на дорожных нефтяных битумах (вязких и жидких). Применяются сразу после изготовления смеси, температура которой должна быть равной или выше 120°C.
К основным характеристикам, определяющим свойства и отличие асфальта от асфальтобетона, относятся:
- прочность;
- водостойкость;
- плотность.
Их значения указаны в ГОСТ 9128-2013 и других нормативных документах.
Выбор сферы применения
Асфальт или асфальтобетонная смесь – что выбрать? Это зависит от областей применения, главной из которых является дорожное строительство. Асфальтобетон находит широкое применение при создании монолитных слоев дорожного покрытия, где ценится высокая механическая прочность, технологичность, более низкая стоимость по сравнению с природным асфальтом. Асфальтобетонные смеси незаменимы при строительстве:
- автомобильных дорог различных категорий;
- взлетных полос на аэродромах;
- автостоянок;
- торговых площадок;
- улиц, тротуаров в населенных пунктах, пр.
В чем разница между асфальтом и асфальтобетоном, из-за которой асфальтобетонная смесь может использоваться для ремонта дорог даже в холодное время года? Различие заключается в том, что смесь не замерзает при температуре до -5°C. Благодаря этому можно увеличить промежуток времени, необходимого для проведения ремонтных работ. Работы с асфальтом можно осуществлять при плюсовых температурах. Зная, чем асфальт отличается от
Как делают асфальт? | Санленд Асфальт
Как производится асфальт?
10 января, 18 / Ремонт асфальта
Люди ездят и ходят по асфальту каждый день, даже не задумываясь об этом. Асфальтовое покрытие покрывает дороги, взлетно-посадочные полосы и автостоянки, чтобы люди во всем мире могли добраться туда, куда им нужно. Это один из наиболее часто используемых материалов для дорожного покрытия, потому что он прочный, его можно быстро отремонтировать и повторно использовать в других проектах дорожного покрытия.
Какие ингредиенты входят в состав асфальтового покрытия?
Два основных ингредиента, смешанных вместе, чтобы сделать асфальтовое покрытие, — это асфальтовый цемент и заполнитель. Асфальтовый цемент — это высоковязкая жидкая форма нефти. Он действует как клей, который связывает совокупность (небольшие камни) вместе, чтобы создать жесткий и гибкий материал. Асфальтовое покрытие обычно состоит из 5% асфальтобетона и 95% заполнителя. Как правило, на нижних уровнях слоя дорожного покрытия частицы заполнителя более крупные и немного менее угловатые; на поверхностных уровнях частицы более мелкие и более угловатые.Для продления срока службы дорожного покрытия могут быть добавлены очень мелкие частицы заполнителя, называемые «мелкими частицами». Помимо асфальтового цемента и заполнителя, компании-производители могут добавлять в смесь определенные химические вещества, такие как гашеная известь для более плотного сцепления или полимеры для повышения гибкости. Состав может несколько отличаться в зависимости от климата места, где будет укладываться асфальтовое покрытие. Асфальт для участков с более теплым климатом становится более твердым, чтобы выдерживать более высокие температуры, а асфальт для участков с более холодным климатом — более мягким.
Как производится смесь для асфальтового покрытия?
Смеси для асфальтовых покрытий обычно производятся на заводе. Все ингредиенты должны быть точно отмерены, чтобы соответствовать типу проекта и климату объекта. Затем толстый битумный цемент необходимо сделать более жидким, чтобы его можно было смешать с заполнителем и другими компонентами. Методы разбавления асфальта включают разбавление путем применения растворителя, эмульгирование в воде или нагревание. Отопление — самый распространенный метод.Заполнитель необходимо очистить, просушить и прогреть. Когда и заполнитель, и асфальт нагреваются до нужной температуры, они смешиваются вместе в барабане или толкательной мельнице, которые представляют собой разные типы смесительных машин, которые производят гомогенную смесь. Выбор правильной температуры для процесса имеет решающее значение — производители должны регулировать температуру в зависимости от времени, которое потребуется для транспортировки смеси для дорожного покрытия с завода на строительную площадку, от толщины асфальтового цемента в начале и того, сколько времени потребуется на уплотните смесь после нанесения.
В чем разница между горячим асфальтом и теплым асфальтом?
Горячий асфальт в настоящее время является наиболее часто используемой формой асфальтового покрытия, но теплый асфальт все чаще используется в строительных проектах. HMA требует, чтобы заполнитель был высушен и нагрет, а битумный цемент был нагрет до очень высокой температуры перед их смешиванием. Кроме того, HMA необходимо поддерживать при высоких температурах во время его нанесения и уплотнения.Чтобы сделать WMA, определенные эмульсии, цеолиты, воски или вода добавляются в асфальтовый цемент перед его смешиванием с заполнителем. Этот метод позволяет производить продукцию при гораздо более низких температурах, что снижает потребление энергии, использование нефти и выбросы вредных газов.
Производство асфальта — это разнообразный, но точный процесс. При применении обученными профессионалами и надлежащем обслуживании он может прослужить десятилетия.
HMA Mix Основы дизайна — интерактивное покрытие
HMA состоит из двух основных ингредиентов: заполнителя и асфальтового связующего. Разработка смеси HMA — это процесс определения того, какой заполнитель использовать, какое асфальтовое вяжущее использовать и какой должна быть оптимальная комбинация этих двух ингредиентов.
Когда заполнитель и асфальтовое связующее объединяются для получения однородного вещества, это вещество, HMA, приобретает новые физические свойства, которые связаны, но не идентичны физическим свойствам его компонентов. Механические лабораторные испытания могут использоваться для характеристики основной смеси или прогнозирования свойств смеси.Дизайн смеси HMA развился как лабораторная процедура, которая использует несколько критических тестов для определения ключевых характеристик каждой пробной смеси HMA. Хотя эти характеристики не являются исчерпывающими, они могут дать разработчику смеси хорошее представление о том, как конкретная смесь будет работать в полевых условиях во время строительства и при последующей загрузке трафика.
В этом разделе рассматриваются основы проектирования смесей, общие для всех методов проектирования смесей. Во-первых, обсуждаются две основные концепции (дизайн смеси как моделирование, а также термины и отношения веса и объема), которые задают основу для последующего обсуждения.Во-вторых, представлены переменные, которыми может манипулировать дизайн микса. В-третьих, представлены основные цели дизайна миксов. Наконец, представлена общая процедура расчета смеси (которую используют все методы Hveem, Marshall и Superpave).
Концепции
Перед тем, как обсуждать какие-либо особенности проектирования смесей, важно понять пару основных концепций проектирования смесей:
- Смесь представляет собой симуляцию
- Термины и отношения массы и объема HMA
Mix Design — это моделирование
Прежде всего, дизайн смеси — это лабораторное моделирование.Дизайн смеси предназначен для имитации фактического производства, конструкции и производительности HMA в максимально возможной степени. Затем на основе этого моделирования мы можем предсказать (с достаточной уверенностью), какой тип дизайна смеси лучше всего подходит для конкретного рассматриваемого приложения и как он будет работать.
Поскольку это моделирование, микширование имеет свои ограничения. В частности, существуют существенные различия между лабораторными и полевыми условиями. Конечно, небольшая лабораторная установка, состоящая из нескольких образцов размером 100–150 мм (4–6 дюймов), машины для уплотнения и пары испытательных устройств, не может полностью воссоздать фактические условия производства, конструкции и производительности.Например, уплотнение конструкции смеси должно создавать такую же общую плотность (пустотное содержимое), до которой трафик окончательно уплотняет смесь в полевых условиях в условиях эксплуатации (Roberts et al., 1996 [1] ). Однако трудно откалибровать количество тамперных ударов (лабораторное уплотнение) для конкретного уплотнения конструкции и последующей нагрузки от движения (уплотнение в поле). Используемые в настоящее время корреляции между этими плотностями носят эмпирический характер и чрезвычайно приблизительны (например, категории высокого, среднего и низкого трафика). Однако, несмотря на ограничения, такие как предыдущие, процедуры проектирования смесей могут обеспечить рентабельное и достаточно точное моделирование, которое полезно при принятии решений по проектированию смесей.
Термины и взаимосвязи веса и объема HMA
Конструкция смеси, в частности конструкция смеси Superpave, по своей природе является объемной. То есть он стремится объединить заполнитель и асфальт на основе объема (в отличие от веса). Измерения объема обычно производятся косвенно, путем определения веса и удельного веса материала, а затем вычисления его объема.Таким образом, конструкция смеси включает в себя несколько различных измерений пустот и удельного веса. Прежде чем продолжить, важно четко понимать эти термины.
Переменные
HMA — довольно сложный материал, к которому предъявляется множество различных, а иногда и противоречивых требований к производительности. Он должен противостоять деформации и растрескиванию, быть долговечным, устойчивым к повреждениям водой, обеспечивать хорошее сцепление с поверхностью и при этом быть недорогим, легко производимым и легко размещаемым. Чтобы удовлетворить эти требования, разработчик микса может управлять всеми тремя переменными:
- Совокупность . Такие параметры, как тип (источник), градация и размер, прочность и сопротивление истиранию, долговечность и прочность, форма и текстура, а также чистота могут быть измерены, оценены и в некоторой степени изменены.
- Вяжущее асфальтовое . Такие параметры, как тип, долговечность, реология, чистота, а также дополнительные модифицирующие агенты могут быть измерены, оценены и в некоторой степени изменены.
- Отношение асфальтового вяжущего к заполнителю . Обычно выражаемое в процентах асфальтового вяжущего от общей массы HMA, это соотношение оказывает сильное влияние на характеристики дорожного покрытия HMA. Из-за больших различий в удельном весе заполнителя доля асфальтового вяжущего , выраженная в процентах от общего веса , может широко варьироваться, даже если объем асфальтового вяжущего в процентах от общего объема остается довольно постоянным.
Цели
Перед тем, как приступить к процедуре составления смеси, важно понять, каковы ее цели.В этом разделе представлены типичные качества хорошо сделанной смеси HMA. Манипулируя переменными заполнителя, битумного вяжущего и соотношением между ними, дизайн смеси стремится достичь следующих качеств в конечном продукте HMA (Roberts et al., 1996 [1] ):
- Сопротивление деформации (стабильность) . HMA не должен искажаться (рутиться) или деформироваться (пихаться) под нагрузкой трафика. Деформация HMA связана с одним или несколькими из следующих факторов:
- Общая поверхность и характеристики истирания .Округлые частицы имеют тенденцию скользить друг относительно друга, вызывая деформацию HMA под нагрузкой, в то время как угловатые частицы сцепляются друг с другом, обеспечивая хорошую стойкость к деформации. Хрупкие частицы вызывают деформацию смеси, потому что они имеют тенденцию разрушаться при перемешивании или под нагрузкой.
Тесты на форму и текстуру частиц, а также на прочность и прочность могут выявить источники проблемных агрегатов. Этих источников можно избежать или, как минимум, можно смешать заполнитель с хорошей поверхностью и абразивными характеристиками, чтобы обеспечить лучшие общие характеристики.
- Агрегированная градация . Градации с чрезмерной мелкостью (естественной или вызванной чрезмерным истиранием) вызывают деформацию, поскольку большое количество мелких частиц имеет тенденцию раздвигать более крупные частицы и действовать как смазка шарикоподшипников между этими более крупными частицами. Такой же эффект может иметь градация, приводящая к низкому VMA или чрезмерному содержанию битумного вяжущего. Спецификации градации используются для обеспечения приемлемой градации агрегатов.
- Содержание асфальтового вяжущего .Избыточное содержание битумного вяжущего имеет тенденцию смазывать и раздвигать частицы заполнителя, облегчая их перегруппировку под нагрузкой.
Оптимальное содержание битумного вяжущего, определяемое конструкцией смеси, должно предотвратить это.
- Вязкость битумного вяжущего при высоких температурах . В жаркие летние месяцы вязкость асфальтового вяжущего минимальна, и дорожное покрытие легче деформируется под нагрузкой. Указание асфальтового вяжущего с минимальной высокотемпературной вязкостью (как это можно сделать в процессе выбора битумного вяжущего Superpave) обеспечивает адекватную высокотемпературную вязкость.
- Общая поверхность и характеристики истирания .Округлые частицы имеют тенденцию скользить друг относительно друга, вызывая деформацию HMA под нагрузкой, в то время как угловатые частицы сцепляются друг с другом, обеспечивая хорошую стойкость к деформации. Хрупкие частицы вызывают деформацию смеси, потому что они имеют тенденцию разрушаться при перемешивании или под нагрузкой.
- Сопротивление усталости . HMA не должен трескаться при многократных нагрузках с течением времени. Усталостное растрескивание HMA связано с содержанием и жесткостью битумного вяжущего. Более высокое содержание битумного вяжущего приведет к тому, что смесь будет иметь большую тенденцию к упругой деформации (или, по крайней мере, к деформации), а не к разрушению при повторяющейся нагрузке. Оптимальное содержание битумного вяжущего, определяемое конструкцией смеси, должно быть достаточно высоким, чтобы предотвратить чрезмерное усталостное растрескивание.
Использование битумного вяжущего с более низкой жесткостью увеличит усталостную долговечность смеси за счет большей гибкости.Однако при выборе асфальтового вяжущего необходимо также учитывать возможность образования колей. Обратите внимание, что сопротивление усталости также сильно зависит от соотношения между толщиной структурного слоя и нагрузкой. Однако в этом разделе рассматриваются только проблемы дизайна смеси.
- Устойчивость к низкотемпературному растрескиванию . HMA не должен давать трещин при воздействии низких температур окружающей среды. Низкотемпературное растрескивание в первую очередь является функцией низкотемпературной жесткости битумного вяжущего.Определение асфальтового вяжущего с адекватными низкотемпературными свойствами (как это можно сделать в процессе выбора битумного вяжущего Superpave) должно предотвратить или, по крайней мере, ограничить низкотемпературное растрескивание.
- Прочность . HMA не должен подвергаться чрезмерному старению в процессе производства и эксплуатации.
Долговечность HMA связана с одним или несколькими из следующих факторов:
- Толщина пленки асфальтового вяжущего вокруг каждой частицы заполнителя . Если толщина пленки, окружающей частицы заполнителя, недостаточна, возможно, что заполнитель станет доступным для воды через отверстия в пленке.Если заполнитель является гидрофильным, вода вытесняет асфальтовую пленку, и сцепление асфальта с заполнителем будет потеряно. Этот процесс обычно называют зачисткой. Оптимальное содержание битумного вяжущего, определяемое конструкцией смеси, должно обеспечивать адекватную толщину пленки.
- Воздушные пустоты . Избыточные воздушные пустоты (порядка 8 процентов или более) увеличивают проницаемость HMA и облегчают доступ кислорода к большему количеству битумного вяжущего, тем самым ускоряя окисление и улетучивание. Чтобы решить эту проблему, конструкция смеси HMA стремится отрегулировать такие элементы, как содержание асфальта и градацию агрегата, чтобы создать расчетные воздушные пустоты около 4 процентов.
Избыточные воздушные пустоты могут быть либо проблемой конструкции смеси, либо проблемой конструкции, и в этом разделе рассматривается только проблема конструкции смеси.
- Устойчивость к повреждениям от влаги . HMA не должен существенно разлагаться из-за попадания влаги в смесь. Устойчивость к повреждениям от влаги связана с одним или несколькими из следующих факторов:
- Сводные минеральные и химические свойства . Некоторые заполнители притягивают влагу к своим поверхностям, что может вызвать их отслоение.Чтобы решить эту проблему, можно либо избежать отслаивания заполнителей, либо использовать модификатор асфальтового связующего, препятствующий отслаиванию.
- Воздушные пустоты . Когда воздушные пустоты HMA превышают примерно 8 процентов по объему, они могут стать взаимосвязанными и позволить воде легко проникнуть в HMA и вызвать повреждение влаги из-за порового давления или расширения льда. Чтобы решить эту проблему, конструкция смеси HMA регулирует содержание битумного вяжущего и градацию заполнителя для создания проектных воздушных пустот около 4 процентов.
Избыточные воздушные пустоты могут быть либо проблемой конструкции смеси, либо проблемой конструкции, и в этом разделе рассматривается только проблема конструкции смеси.
- Сопротивление скольжению . HMA, размещенный как поверхностный слой, должен обеспечивать достаточное трение при контакте с шиной транспортного средства. Низкое сопротивление скольжению обычно связано с одним или несколькими из следующих факторов:
- Совокупные характеристики, такие как текстура, форма, размер и стойкость к полировке . Гладкие, округлые или полируемые заполнители менее устойчивы к скольжению.Тесты формы и текстуры частиц могут выявить источники проблемных агрегатов. Этих источников можно избежать или, как минимум, можно смешать заполнитель с хорошей поверхностью и абразивными характеристиками, чтобы обеспечить лучшие общие характеристики.
- Содержание асфальтового вяжущего . Чрезмерное количество битумного вяжущего может вызвать кровотечение HMA.
Использование оптимального содержания битумного вяжущего, определенного конструкцией смеси, должно предотвратить просачивание.
- Технологичность . HMA должен быть уложен и уплотнен с разумными усилиями.Работоспособность обычно связана с одним или обоими из следующих факторов:
- Текстура, форма и размер агрегата . Плоские, удлиненные или угловатые частицы имеют тенденцию сцепляться друг с другом, а не соскальзывать друг с другом, что затрудняет их размещение и уплотнение (обратите внимание, что это почти прямо противоречит желаемым свойствам агрегата для сопротивления деформации). Несмотря на то, что для количественной оценки удобоукладываемости не существует специальных тестов на дизайн смеси, тесты на форму и текстуру частиц могут выявить возможные проблемы с удобоукладываемостью.
- Агрегированная градация . Градации с избытком мелочи (особенно в диапазоне размеров от 0,60 до 0,30 мм (№ 30–50) при использовании натурального окатанного песка) могут привести к тому, что смесь станет нежной.
Такой же эффект может иметь градация, приводящая к низкому VMA или избыточному содержанию битумного вяжущего. Спецификации градации используются для обеспечения приемлемой градации агрегатов.
- Содержание асфальтового вяжущего . При температуре укладки (выше примерно 120 ° C (250 ° F)) асфальтовое вяжущее действует как смазка между частицами заполнителя, когда они уплотняются.Следовательно, низкое содержание битумного вяжущего снижает эту смазку, что приводит к менее технологичной смеси. Обратите внимание, что более высокое содержание битумного вяжущего обычно хорошо для удобоукладываемости, но, как правило, плохо для сопротивления деформации.
- Вязкость битумного вяжущего при температурах смешивания / укладки . Если вязкость битумного вяжущего слишком высока при температурах перемешивания и укладки, HMA становится трудно выгружать, растекать и уплотнять. Ротационный вискозиметр Superpave специально проверяет вязкость асфальтового вяжущего при температуре перемешивания / укладки.
Зная эти цели, задача при проектировании смеси состоит в том, чтобы разработать относительно простую процедуру с минимальным количеством тестов и образцов, которая позволит получить смесь со всеми вышеуказанными качествами HMA.
Основная процедура
Разработка смесиHMA — это процесс определения, какой заполнитель использовать, какое асфальтовое вяжущее использовать и какова должна быть оптимальная комбинация этих двух ингредиентов. Чтобы удовлетворить требования, предъявляемые к предыдущим желательным свойствам HMA, все процессы проектирования смесей включают три основных этапа:
- Совокупный выбор .Независимо от конкретного метода, общая процедура проектирования смеси начинается с оценки и выбора источников заполнителя и асфальтового вяжущего. Разные органы определяют разные методы приема агрегатов. Обычно группа совокупных физических тестов периодически запускается на каждом конкретном совокупном источнике.
Затем для каждого дизайна смеси проверяются требования к градации и размеру. Обычно для соответствия требованиям градации требуется агрегат из более чем одного источника.
- Выбор битумного вяжущего .Несмотря на то, что разные органы могут определять и определяют разные методы оценки асфальтового вяжущего, спецификация на асфальтовое вяжущее Superpave была или будет принята большинством государственных служб в качестве стандарта (NHI, 2000 [2] ).
- Определение оптимального содержания битумного вяжущего . Методы проектирования смесей обычно различаются по методу, с помощью которого они определяют оптимальное содержание асфальтового вяжущего. Этот процесс можно подразделить следующим образом:
- Сделайте несколько пробных смесей с разным содержанием битумного вяжущего.
- Уплотните эти пробные смеси в лаборатории. Важно понимать, что этот шаг в лучшем случае является грубым моделированием полевых условий.
- Проведите несколько лабораторных тестов для определения основных характеристик образца.
Эти испытания представляют собой отправную точку для определения свойств смеси, но они не являются исчерпывающими и не являются точным воспроизведением реальных полевых условий.
- Выберите содержание битумного вяжущего, которое наилучшим образом соответствует целям конструкции смеси.
Формула смешивания рабочих мест
Конечным результатом удачного дизайна смеси является рекомендуемая смесь заполнителя и асфальтового вяжущего. Эту рекомендуемую смесь, которая также включает градацию заполнителя и тип асфальтового вяжущего, часто называют формулой рабочей смеси (JMF) или рецептом.
Сводка
Разработка смеси HMA — это лабораторный процесс, используемый для определения подходящего заполнителя, асфальтового вяжущего и их пропорций для использования в HMA. Конструирование смеси — это процесс управления тремя переменными: (1) заполнителем, (2) содержанием асфальтового связующего и (3) соотношением заполнителя к асфальтовому вяжущему с целью получения HMA, устойчивого к деформации, усталости, низкотемпературного растрескивания. устойчивый, прочный, устойчивый к влаге, скольжению и работоспособный.Хотя конструкция смеси имеет множество ограничений, она оказалась экономически эффективным методом предоставления важной информации, которая может быть использована для создания высокопроизводительного HMA.
Что такое горячее асфальтовое покрытие?
Асфальтовое покрытие — любая дорога с асфальтовым покрытием. Горячий асфальт (HMA) представляет собой смесь примерно 95% камня, песка или гравия, связанных вместе асфальтовым цементом, продуктом сырой нефти. Асфальтовый цемент нагревается, комбинируется и смешивается с заполнителем на установке HMA.Полученный горячий асфальт загружается в грузовики для транспортировки к месту мощения. Самосвалы выгружают горячую асфальтобетонную смесь в бункеры, расположенные в передней части асфальтоукладчиков. Асфальт укладывается, а затем уплотняется тяжелым катком, который перемещается по асфальту. Как правило, движение по тротуару разрешается, как только оно остынет.
HMA Ultra-Thin предлагает простой и экономичный способ ухода за дорогами и улицами, поскольку он защищает ваши вложения в них.HMA Ultra-Thin — это горячая асфальтобетонная смесь, разработанная специально для укладки тонких слоев (3/4 дюйма), для структурно прочных дорожных покрытий с признаками старения, окисления или незначительного разрушения поверхности. В результате вы получаете более прочное и красивое покрытие, которое улучшает качество езды для водителей и снижает уровень шума транспорта для населения. Сочетание хорошо задокументированных преимуществ асфальта в гладкости и безопасности с передовым процессом проектирования многослойного покрытия… Perpetual Pavement сочетает в себе хорошо задокументированные преимущества асфальта в гладкости и безопасности с усовершенствованным процессом проектирования многослойного покрытия, который при регулярном техническом обслуживании продлевает срок службы проезжей части до полувека и более.
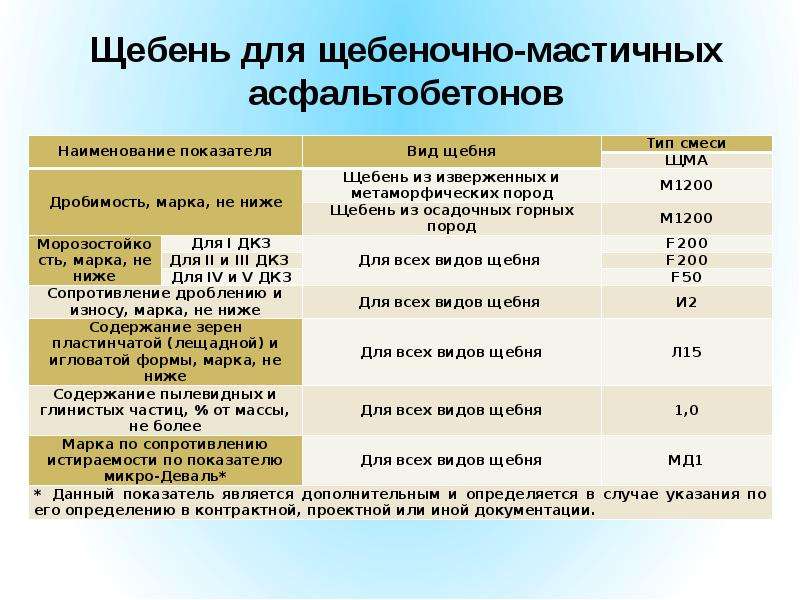
Руббилизация
Руббилизация — это проверенный метод строительства, который превращает разрушенную бетонную дорогу в основание для создания гладкого, безопасного, бесшумного и прочного покрытия, построенного из горячего асфальта (HMA).Это сводит к минимуму задержки для автомобилистов и позволяет строить в «непиковые» часы. Обработка асфальтом — очень рентабельный метод восстановления.
Стоимость жизненного цикла
При начальном строительстве и в долгосрочной перспективе асфальтовое покрытие экономит деньги на строительстве и обслуживании. К такому выводу пришли дорожные инженеры и отделы транспорта всей страны. «Затраты на жизненный цикл» — деньги, потраченные на строительство и обслуживание дороги в течение ее срока службы — значительно ниже при использовании горячего асфальта (HMA), чем при использовании бетона.
Ваше экономичное решение
Тонкие покрытия HMA, 1 ½ дюйма или меньше, являются экономически эффективным решением для сохранения дорожного покрытия, прежде всего благодаря их способности:
Гладкости
Забота автомобилистов о гладком асфальте. Асфальт будет обеспечивать водителям плавную и тихую езду, которую они привыкли ожидать. Гладкое покрытие позволяет сэкономить топливо. Гладкое покрытие снижает эксплуатационные расходы автомобиля.Гладкие тротуары служат дольше. Асфальтовое покрытие более гладкое, и его легче поддерживать, чем бетонное.
Управляемость автомобиля
Национальное исследование показало, что водители предпочитают ухоженные, безопасные и ровные дороги; более того, они понимают, что эти качества требуют периодического обслуживания и финансовых вложений.
Что такое асфальт?
Едем на нем, ходим по нему, играем и ездим на велосипеде. На него садятся даже наши самолеты, но мы редко останавливаемся и думаем о том, что такое асфальт и как за ним ухаживать.Во-первых, давайте взглянем на ингредиенты асфальта.
Состав асфальта
Так что же такое асфальт и его ингредиенты? На самом деле асфальт состоит из двух основных ингредиентов. Первые агрегаты ; это смесь щебня, гравия и песка. Заполнители составляют около 95% горячего асфальта.
Остальные 5% — это битум . Битум — это черный или темный вязкий материал, который скрепляет агрегаты и состоит из полициклических углеводородов (побочный продукт нефти).
Для более глубокого понимания ингредиентов асфальта, элементарные компоненты асфальта включают углерод, водород, серу, кислород, азот и следовые количества железа, никеля и ванадия.
На самом деле существует несколько различных типов асфальта, и они подразделяются на категории в зависимости от процесса, используемого для связывания заполнителя с битумом.
Типы асфальта
- Горячий асфальтобетон образуется при высоких температурах и является наиболее прочным из всех видов асфальта.Обычно он используется в приложениях с интенсивным движением, таких как шоссе и взлетно-посадочные полосы аэропортов.
- Теплый асфальтобетон не требует высоких температур для производства из-за добавления эмульсий, парафинов и цеолитов. Хотя он более безопасен для окружающей среды и рабочих и использует меньше ископаемого топлива при производстве, он не обеспечивает такой же уровень долговечности, как горячий асфальтобетон. Таким образом, он в основном используется для районов с низкой проходимостью или для исправления ошибок.
- Мастичный асфальт имеет меньшее содержание битума, чем горячий асфальтобетон, и обычно используется для изготовления дорог, пешеходных дорожек, игровых площадок и кровли.
Независимо от типа, любой асфальт требует определенного ухода для обеспечения дополнительной защиты и долговечности.
Прочность асфальта
Если вы когда-либо сталкивались с трещиной на асфальтовой дороге, вы знаете, что материал не вечен. Характеристики асфальта могут широко варьироваться в зависимости от ряда переменных, включая наличие влаги, колебания температуры, интенсивность движения и воздействие определенных химикатов. Даже различные ингредиенты асфальта могут определить его долговечность.
Поскольку асфальт может выдерживать вес транспортных средств, он является предпочтительным материалом для дорог, парковок и проездов. Его можно быстро нанести и легко залатать, вдавив его прямо в трещины и выбоины.
Со временем компоненты асфальта могут начать разрушаться и разлагаться в результате интенсивного движения, воздействия элементов, расширения и сжатия. По этой причине использование герметика абсолютно необходимо для надлежащего ухода за любой асфальтированной поверхностью.Несмотря на то, что на рынке имеется ряд герметиков, мы рекомендуем использовать только битумный герметик из каменноугольной смолы из-за его способности создавать эффективный буфер против движения транспорта, воды, масляной соли и других окрашивающих веществ.
Если компоненты асфальта не защищены слоем герметика, они неизбежно треснут. Если оставить открытыми и не ремонтировать даже небольшие трещины и трещины, это определенно приведет к более серьезным повреждениям, таким как выбоины, крошащийся асфальт и повреждение фундамента.В конечном итоге это приводит к необходимости дорогостоящей замены асфальта.
Какова наиболее эффективная стратегия обслуживания асфальта?
Домовладельцам важно понимать состав асфальта, потому что его нужно регулярно обслуживать. Подъездная дорога с асфальтовым покрытием может оставаться в хорошем состоянии десятилетиями, если за ней правильно ухаживать.
Также важно знать, что может негативно повлиять на состав асфальта. Поскольку масло, смазка, газ, соль и трансмиссионная жидкость могут ухудшить качество асфальта и, в конечном итоге, привести к растрескиванию и крошению, эти вещества следует быстро удалить, если они пролились на асфальт.
Заполнение трещин
В рамках профилактического обслуживания необходимо проверить асфальт на наличие трещин. Даже небольшие, незатронутые или незаполненные микротрещины могут привести к порче компонентов асфальта. Со всеми типами асфальта неизбежно образование трещин. Секрет заключается в том, чтобы заполнить трещины до того, как они разовьются и превратятся в выбоины или большие участки осыпающегося покрытия. Есть два типа заполнителей трещин, которые можно использовать на любой асфальтовой или бетонной поверхности.Заливка трещин в асфальте холодной жидкостью очень эффективна при заделке трещин шириной до ½ дюйма. Продукт прост в использовании и сохраняет трещины на всех типах асфальта заделанными в течение нескольких лет.
Горячий заполнитель для трещин — это прорезиненный асфальтный герметик промышленного качества, предназначенный для заделки трещин шириной до 1 дюйма. Его можно безопасно нагреть в чайнике или расплавителе для заливки трещин и заливать в трещины, чтобы защитить от воды, льда и мусора. Он будет держать трещины заделанными до четырех лет.
Уплотнительное покрытие
Все типы асфальта требуют надлежащего ухода и профилактического ремонта для сохранения их внешнего вида и общего состояния.Из-за характера ингредиентов асфальта подъездные пути следует герметизировать каждые два-три года, чтобы предотвратить окисление, потерю гибкости, растрескивание и рассыпание. В Asphalt Kingdom мы рекомендуем использовать герметик из каменноугольной смолы, который защищает битум от окисления, хрупкости и растрескивания. Его легко наносить с помощью распылителя или ракеля, и он быстро сохнет за три-четыре часа.
Независимо от того, есть ли у вас подъездная дорога или парковка для вашего бизнеса, асфальтовое покрытие должно быть приоритетом.
Бесплатное асфальтовое покрытие
Чтобы узнать, как ухаживать за асфальтом, пройдите бесплатный 4-дневный электронный курс по уходу за асфальтом от Asphalt Kingdom AKPRO. С курсом вы можете узнать все, что вам нужно знать, чтобы защитить свои вложения в асфальт.
ГОРЯЧАЯ СМЕСЬ АСФАЛЬТА — McAsphalt
Комбинация однородно смешанного заполнителя, покрытого асфальтовым цементом.
Горячая асфальтовая смесь (HMA) состоит из смеси заполнителя, равномерно перемешанного и покрытого асфальтовым цементом.Чтобы высушить заполнители и получить достаточную текучесть асфальтобетона для надлежащего перемешивания и удобоукладываемости, и заполнитель, и асфальт должны быть нагреты перед смешиванием — отсюда и термин «горячая смесь».
Заполнители и асфальт смешиваются в смесительной установке, в которой все составляющие материалы нагреваются, дозируются и смешиваются для получения желаемой смеси для дорожного покрытия. После того, как смешивание растений завершено, горячая смесь транспортируется к месту мощения и распределяется асфальтоукладчиком рыхлым слоем до однородной, ровной поверхности.Пока смесь для дорожного покрытия еще горячая, материал дополнительно уплотняется тяжелыми роликами с приводом от двигателя для получения гладкого, хорошо уплотненного слоя дорожного покрытия.
Горячие асфальтовые смеси для дорожного покрытия могут производиться из широкого диапазона комбинаций заполнителей, каждая из которых имеет свои особые характеристики, подходящие для конкретных целей проектирования и строительства. В дополнение к количеству и качеству используемого асфальта, основные характеристики смеси определяются относительными количествами заполнителя, мелкого заполнителя и минерального наполнителя.
Основы дизайна 101
Горячая асфальтовая смесь (HMA) состоит из двух основных ингредиентов: заполнителя и асфальтового связующего. Дизайн HMA — это процесс определения того, какой заполнитель использовать, какое асфальтовое вяжущее использовать и какой должна быть оптимальная комбинация этих двух ингредиентов.
Асфальтовые цементы
Асфальтовый цемент — это прочный, универсальный и устойчивый к атмосферным воздействиям и химическим веществам вяжущий материал, который адаптируется к различным областям применения, возможно, чаще всего для связывания щебня и агрегатирования в твердую, жесткую поверхность дорог, улиц и взлетно-посадочных полос аэропортов.
Адгезивные / липкие покрытия и грунтовки
Связующее покрытие — это нанесение битумной эмульсии распылением. Он наносится на существующую асфальтовую или портландцементную бетонную поверхность перед новым асфальтовым покрытием или ямочным ремонтом.
Добавки и модификаторы для асфальта
McAsphalt обеспечивает дорожно-строительную промышленность высококачественными добавками для асфальта, которые увеличивают адгезию между асфальтовым вяжущим и заполнителями и улучшают характеристики покрытия за счет уменьшения образования колей и повреждений, вызванных влажностью.
Уход за дорожной одеждой
Сохранение дорожного покрытия — это стратегия, в которой используется «правильное обращение, правильная дорога в нужное время». Консервация дорожного покрытия позволяет использовать скудные доллары еще больше — каждый потраченный доллар сводит к минимуму дорогостоящие затраты на восстановление и реконструкцию в будущем.
границ | Оптимизация состава и области применения цветной эмульгированной асфальтовой смеси
Введение
Цветное покрытие имеет широкие перспективы применения, например, для стимулирования движения, повышения безопасности вождения и плавности движения (Ando et al., 2011; Xu et al., 2012). Такое покрытие может служить разделителем дорог, украшать окружающую среду и способствовать уменьшению тепловых островов (Synnefa et al., 2011). Кроме того, окрашенное дорожное покрытие, приготовленное с использованием эмульгированного асфальта в качестве связующего, имеет ряд преимуществ, таких как низкая стоимость, удобная конструкция, а также широкая доступность сырья и диапазон применения. Тем не менее, влияние окружающей среды и движущих нагрузок приводит к потере цвета и появлению трещин на начальных или недавних проектах цветного покрытия (Zhang et al., 2019а, б, в). Недостатки цветного покрытия, такие как низкая стойкость цвета, сложность контроля цвета покрытия и серьезное загрязнение цвета, ограничивают его продвижение и применение. Кроме того, не были эффективно решены начальные проблемы цветного покрытия, такие как его плохие характеристики противоскольжения и недостаточная устойчивость к высоким температурам. Наконец, для ухода за цветным покрытием можно использовать несколько материалов. Поэтому содержание и ремонт цветных тротуаров постепенно становятся актуальными проблемами, требующими решения.
Несколько исследователей провели соответствующие исследования цветного покрытия в связи с его все более широким применением в дорожном строительстве. Bocci et al. (2012) изучили механические и фотометрические свойства цветных дорожных покрытий и показали, что они обладают хорошей износостойкостью, но плохой стойкостью к остаточной деформации при высоких температурах. Его замечательные фотометрические свойства могут улучшить дизайн освещения туннелей, что снижает затраты на осветительное оборудование и потребление энергии. Сдвиг, колейность, рыхлое отслаивание и плохая стойкость окраски цветного покрытия по-прежнему являются основными типами проблем при длительном использовании (Lee and Kim, 2007).Tang et al. (2015) смешали ароматическое масло с нефтяной смолой и функциональными полимерами для получения цветного связующего. Затем окрашенное связующее смешивали с пигментом, заполнителями и добавками для приготовления цветных асфальтовых смесей. Светлоокрашенные связующие на основе синтетического асфальта (LCSA) были приготовлены с использованием ароматического масла, нефтяной смолы и различных модификаторов полимеров. Результаты испытаний изгибающей балки (BBR) показывают, что связующее, приготовленное с использованием SBS, EVA и SBS + EVA, имело лучшие характеристики при низких температурах с лучшей устойчивостью к старению в уплотненном покрытии (Sengoz and Isikyakar, 2008; Tang et al., 2018; Чжоу и др., 2020). Он (2013) и Джин (2015) указали, что сетчатая структура может быть сформирована полимерными модификаторами в связующем LCSA, что значительно влияет на характеристики как при высоких, так и при низких температурах. Линь и Луо (2004) обнаружили, что выцветание цветного асфальта зависит от типа и дозировки красителя, а также от продолжительности выдержки. Результаты также показали, что красные красители всегда имели лучшую стойкость к выцветанию, чем зеленые при воздействии ультрафиолетового света. Gao et al. (2005) обнаружили, что состаренный цветной асфальт с повышенным содержанием асфальтенов снижает содержание коллоидов, ароматического фенола и насыщенного фенола, а исходная сбалансированная система коллоидов асфальта разрушается, что приводит к ухудшению характеристик асфальта.
Как уже упоминалось, болезни цветного асфальтового покрытия и приготовление цветного асфальтового вяжущего широко изучены. Однако сложные компоненты и различное сырье цветного асфальта оставили несколько проблем, которые необходимо решить для подготовленных цветных асфальтов и их смесей, особенно в отношении его низкой стойкости цвета и стабильности при хранении. Поэтому здесь был принят единый метод проектирования. Эмульгированный асфальт был модифицирован добавлением неорганических материалов, таких как глина и микрокремнезем.Пропорции его смеси и характеристики дорожного покрытия были изучены в сочетании с соответствующими испытаниями для получения CEASM с хорошей стойкостью окраски и высокой стабильностью при хранении.
Материалы и испытания
Сырье
В данном исследовании использовался самодельный светлый эмульгированный асфальт, его конкретные технические характеристики показаны в таблице 1. Как было предложено Ouyang et al. (2006) и Sasanipour et al. (2019), в качестве функциональных наполнителей были выбраны глина с размером ячеек 325 меш и полузамещенный микрокремнезем D920.Технические показатели микрокремнезема приведены в таблице 2. Был выбран композитный неорганический пигмент титанового красного, технические показатели которого показаны в таблице 3. Используемые минеральные компоненты и пропорции смеси приведены в таблице 4.
Таблица 1. Условные технические показатели светлого эмульгированного асфальта.
Таблица 2. Технические показатели микрокремнезема.
Таблица 3. Технические показатели техники композитного красного пигмента титана.
Таблица 4. Процент каждого компонента минерального заполнителя, проходящего через отверстие сита, и пропорция каждого смешивания.
Процесс подготовки
Процесс подготовки CEASM выглядит следующим образом:
(1) Взвесьте 1000 г глины, 1000 г микрокремнезема, 100 г пигмента, 2000 г минерального заполнителя и 1500 г эмульгированного асфальта для использования.
(2) Добавьте водопроводную воду в резервуар с мешалкой в количестве 11% от общей массы глины, микрокремнезема, пигментов и минерального заполнителя.
(3) Поместите перемешиваемый резервуар с добавленной водой под разбрасыватель и постепенно увеличивайте скорость отлаженного разбрасывателя до 500–800 об / мин.
(4) Взвесьте глину, микрокремнезем и пигмент, добавьте их в емкость с мешалкой и равномерно перемешайте со скоростью 500–800 об / мин в течение 3–4 минут.
(5) Взвесьте пигмент, добавьте его в емкость с мешалкой и равномерно перемешайте при 500–800 об / мин в течение 3–4 мин.
(6) Взвесьте эмульгированный асфальт и добавьте его в резервуар с мешалкой. Установите скорость 1500–1600 об / мин (конкретная скорость зависит от мощности машины и размера разбрасывателя) и перемешивайте в течение 10–15 минут.
(7) Взвесьте минеральные агрегаты и порциями добавьте их в резервуар с мешалкой. Установите скорость 1500–2500 об / мин и перемешивайте в течение 5 минут.
(8) Поместите произведенные материалы в маркированный контейнер для хранения.
Методы испытаний
Учитывая, что CEASM имеет множество компонентов с различными диапазонами содержания, изучение его характеристик дорожного покрытия отнимает много времени и средств. Поэтому для исследования влияния дозировки каждого компонента, в том числе глины, микрокремнезема, пигмента, минерального заполнителя и эмульгированного асфальта, использовался единый метод дизайна испытаний, предложенный Кайтаем и Юань.Этот метод рассматривает равномерно распределенные значения по всему диапазону испытаний и представляет собой приложение квази-метода Монте-Карло из нескольких теоретических подходов (Fang, 1994; Fang and Wang, 1994). По сравнению с «всесторонними испытаниями» и «ортогональным дизайном» количество испытаний унифицированного дизайна значительно сокращается.
Таблица U ∗ 10 (10 8 ) использовалась для единого дизайна (см. Таблицу 5). Согласно правилам таблицы, факторы были помещены в столбцы 1, 2, 4, 5 и 7.После проведения нескольких экспериментов было обнаружено, что при содержании глины 65 г содержание микрокремнезема, пигмента, минерального заполнителя и эмульгированного асфальта составляло 50 г, 50 г, 110 г и 110 г соответственно. Приготовленная уплотнительная смесь имела преимущества простоты хранения и стабильности. Таким образом, исходя из инженерного опыта, было принято 10 уровней для каждого фактора в верхнем и нижнем интервалах этих пяти значений. Конкретный план приведен в таблице 6. Количество каждого компонента выражается в процентах от общей массы.Повторяемые тесты были выполнены для каждого номера теста, включенного в Таблицу 6. Если ошибка для каждого повторного результата теста не превышала ± 5%, результаты теста принимались, поскольку они считались надежными.
Таблица 5. U ∗ 10 (10 8 ) единый дизайн теста.
Таблица 6. Единый проектный план испытаний.
Стабильность при хранении, износостойкость, противоскользящие свойства и стойкость цвета являются ключевыми показателями, которые можно использовать для оценки эффективности CEASM (Fu et al., 2007; Лян и др., 2015; Ю. и др., 2018). Здесь были проведены лабораторные испытания, испытания на стабильность при хранении и износостойкость для изучения свойств CEASM. Характеристики противоскольжения и стойкость цвета были исследованы на пробном участке дороги, проложенном в провинции Гуандун.
Тесты на стабильность при хранении в течение 5 дней
Примерно 300 мл однородной пробы CEASM фильтруют через сетчатый фильтр 1,18 мм в пробирку для определения стабильности асфальтовой эмульсии. Хранится 5 суток при комнатной температуре.Для каждого образца проводят три параллельных теста, чтобы проверить стабильность CEASM при хранении в течение 5 дней.
Тесты на остатки грохота
Образец CEASM хранится в течение 10 дней, а затем 500 г однородного образца CEASM фильтруют через сетчатый фильтр 1,18 мм при комнатной температуре. Тест используется для определения остатка CEASM на экране.
Испытания на износостойкость
Износостойкость смеси может быть определена тестом на истирание на мокрой дорожке (WTAT). Индексы оценки — это значения WTAT за 1 час и 6 дней.Инструмент, используемый в этом испытании, представляет собой тестер на истирание мокрых дорожек.
Тесты против скольжения
Маятниковый тестер для определения коэффициента трения дорожного покрытия используется в качестве метода проверки антискользящих характеристик. Это полевые испытания. Индекс оценки — это значение коэффициента трения маятника BPN. Каждое тестовое положение необходимо измерять параллельно в 3 точках, и за результат теста принимается среднее значение результатов измерения в 3 тестовых точках.
Тесты на стойкость цвета
На ослабление цвета окрашенного покрытия влияет множество факторов.Трудно точно смоделировать скорость затухания цвета и изменение условий эксплуатации цветного покрытия в лаборатории. Таким образом, при укладке пробного участка дороги Хуандао в городе Чжуншань, провинция Гуандун, стойкость цвета оценивается путем наблюдения за изменением цвета покрытия после открытия для движения в течение 6 месяцев.
Результаты и обсуждение
Стабильность при хранении
5-дневная стабильность при хранении
В соответствии с требованиями Технических условий для строительства асфальтовых покрытий для автомагистралей (JTG F40-2004) в Китае, индекс стабильности при 5-дневном хранении не должен превышать 5%.Чем выше значение 5-дневной стабильности при хранении, тем хуже 5-дневная стабильность. На рис. 1 показано влияние различных факторов испытаний на стабильность смеси при хранении в течение 5 дней. Из рисунка 1А видно, что с повышенным содержанием глины 5-дневная стабильность при хранении постепенно увеличивалась до стабильного значения, но имела тенденцию к снижению, когда содержание глины достигало приблизительно 21%. Поэтому предпочтительное количество глины для смешивания было в пределах 15–20%. Как показано на Рисунке 1B, содержание микрокремнезема мало повлияло на 5-дневную стабильность при хранении, поэтому рекомендуется содержание 12–20%.Как показано на Рисунке 1C, дополнительное количество эмульгированного асфальта привело к лучшей стабильности при хранении в течение 5 дней с предпочтительным количеством смеси более 20%. Рисунки 1D, E показывают, что с увеличением количества пигмента и минерального агрегата 5-дневная стабильность при хранении имела тенденцию к снижению. Содержание пигмента должно соответствовать требованиям к цвету после формования с предпочтительным диапазоном смешивания 10–14%. Кроме того, в соответствии с требованиями к характеристикам противоскольжения дорожного покрытия после формования предпочтительное количество смешанного минерального заполнителя составляет от 28 до 38%.
Рис. 1. Влияние различных факторов испытаний на 5-дневную стабильность смесей при хранении. (A) Количество смешанной глины. (B) Количество смешанного микрокремнезема. (C) Количество смешанного эмульгированного асфальта. (D) Количество смешанного пигмента. (E) Количество смешанного минерального заполнителя.
Остаток экрана
Для CEASM важно убедиться, что частицы эмульгированного асфальта не сильно конденсируются с функциональными наполнителями после длительного хранения.Остатки грохота являются ключевым фактором, позволяющим оценить стабильность асфальтобетонных смесей при хранении.
В соответствии с требованиями Технических условий для строительства асфальтовых покрытий для автомобильных дорог (JTG F40-2004), остаточное количество модифицированного эмульгированного асфальта на сите не должно превышать 0,1%. Как показано на рисунке 2, остаток сита в смеси для каждого плана испытаний составлял менее 0,1%, и агломерированные частицы эмульгированного асфальта не образовывались. Таким образом, приготовленная эмульгированная асфальтобетонная смесь имеет хорошую стабильность при хранении.
Рис. 2. Количество остатков на экране CEASM после хранения в течение 10 дней.
Показатели износостойкости
Мощеный CEASM подвергается непосредственно различным нагрузкам, поэтому он должен обладать хорошей износостойкостью. На рисунке 3 показано влияние различных факторов испытаний на значение WTAT смесей. Как показано на Фигуре 3A, по мере увеличения глины значения WTAT за 1 час и 6 дней не менялись регулярно, а результаты испытаний имели большой разброс. Влияние содержания глины на значения WTAT было незаметным, что указывало на то, что эмульсия с высоким коэффициентом вязкости, образованная из глины, и эмульгированный асфальт имели ограниченное влияние на сформированную структуру смеси.Учитывая характеристики износостойкости, предпочтительное содержание глины в смеси составляло от 9 до 17%.
Рис. 3. Влияние различных факторов испытаний на значение WTAT смесей. (A) Количество смешанной глины. (B) Количество смешанного микрокремнезема. (C) Количество смешанного пигмента. (D) Количество смешанного минерального заполнителя. (E) Количество смешанного эмульгированного асфальта.
Из рисунка 3B видно, что существует хорошая корреляция между количеством смешанного микрокремнезема и значениями WTAT.При более высоком содержании микрокремнезема значения WTAT в течение 1 часа и 6 дней увеличивались, в то время как характеристики износостойкости смеси значительно снижались. В сочетании с требованиями индексов испытаний предпочтительное содержание в смеси микрокремнезема составляло от 10 до 16%.
Рисунок 3C показывает, что по мере увеличения пигмента значения 1-часового и 6-дневного WTAT сначала увеличивались, а затем постепенно стабилизировались. Когда количество смешанного пигмента составляло более 15%, эти значения быстро увеличивались. Это указывает на то, что пигмент является не только источником цвета, но и увеличивает компактность смеси после формования.Кроме того, когда содержание пигмента было менее 8%, цвет после формования немного светелся. В сочетании с приведенным выше анализом предпочтительное количество смешанного пигмента составляло от 8 до 15%.
Рисунок 3D показывает, что по мере увеличения содержания минеральных заполнителей значения WTAT за 1 и 6 дней сильно различались. Значительные изменения значений WTAT были вызваны смешанными пропорциями минерального заполнителя и эмульгированного асфальта, что отражает влияние эмульгированного асфальта на устойчивость смеси к повреждениям от влаги.Это также указывает на то, что качество структурной системы минерального заполнителя может сильно зависеть от количества смешанного эмульгированного асфальта. Согласно комплексному анализу, предпочтительное количество смешанного минерального заполнителя составляло от 28 до 32%.
Как показано на Рисунке 3E, эмульгированный асфальт сильно влиял на значения WTAT за 1 и 6 дней. При повышенном содержании эмульгированного асфальта значения WTAT, очевидно, снизились, что указывает на то, что эмульгированный асфальт влияет на сопротивление влагостойкости и износостойкость CEASM.Следовательно, предпочтительное количество смешанного светлого эмульгированного асфальта было в пределах 25–32%.
Противоскользящие характеристики
Устройство CEASM, проложенное на оригинальной дороге, уменьшает глубину конструкции дорожного покрытия. Чтобы изучить влияние различных методов обработки дорожного покрытия и количества смешанного заполнителя на фрикционный маятник, был выбран план испытаний № 7 в единой расчетной таблице, где содержание всех компонентов было в пределах предложенных диапазонов, а также противоскользящие характеристики. были проведены тесты.В качестве заполнителя для асфальтобетонной смеси была выбрана базальтовая порода с размером отдельных зерен 1,18 мм.
Как видно на рисунке 4, значение маятника трения CEASM было больше, чем требуется в спецификации (BPN ≥ 32). Следовательно, можно сделать вывод, что антискользящие характеристики исходной дороги могут быть восстановлены, что улучшается за счет увеличения совокупного содержания. При увеличении содержания заполнителя BPN начал быстро увеличиваться, но замедлился, когда количество смешанного заполнителя стало более 10%.Поэтому предлагается, чтобы на пробном участке дороги был установлен строгий индекс противоскольжения, количество смешанного заполнителя должно составлять 10%.
Рис. 4. Влияние количества смешанного заполнителя на величину маятника трения уплотнительного покрытия.
Стойкость цвета
Цвет дорожного покрытия быстро тускнеет через некоторое время. Поскольку на ослабление цвета влияют несколько сложных факторов, таких как взаимодействие с солнечным светом, мытье под дождем, вождение автомобиля и наземная пыль, трудно точно смоделировать скорость ослабления цвета и изменения цветного покрытия с помощью лабораторных испытаний (Autelitano and Giuliani, 2019).
Исследование дорожного покрытия из пробного раздела седьмого плана единого дизайна было выполнено для дальнейшего изучения стойкости цвета CEASM. Выцветание дорожного покрытия является значительным из-за жаркой погоды и обильных дождей в провинции Гуандун. Поэтому был выбран пробный участок дороги на Хуандао-роуд, Чжуншань, Китай, как показано на Рисунке 5. После того, как пробный участок находился под воздействием окружающей среды и вождения в течение более 6 месяцев, на тротуаре почти не было выцветания цвета и заполнитель сохранил хорошую структуру и форму, как показано на Рисунке 6.Таким образом, CEASM, приготовленный в этом исследовании, показал хорошую стойкость цвета.
Рис. 5. CEASM после формования.
Рис. 6. CEASM после использования в течение 6 месяцев.
План приложения
В инженерных приложениях для CEASM требуются хорошая конструкционная технологичность и стабильность при хранении (Zani et al., 2017). В сочетании с результатами по стабильности при хранении и износостойкости состав смеси, удовлетворяющий требованиям технических приложений, показан в таблице 7.Когда к дорожному покрытию предъявляются строгие требования против скольжения, могут быть добавлены базальтовые горные породы с размером зерна от 0,6 до 1,18 мм. Общее правило добавления составляет 10%, которое было записано от массового процента CEASM.
Таблица 7. План применения CEASM.
Заключение
CEASM был приготовлен путем смешивания глины, микрокремнезема, пигмента и минерального заполнителя. Было изучено влияние содержания каждого компонента на стабильность при хранении, характеристики износостойкости, противоскользящие свойства и стойкость цвета.Противоскользящие свойства и стойкость цвета CEASM были протестированы на пробном участке дороги в Чжуншане. Эти результаты показали, что существует оптимальный состав смеси. Основные выводы сводятся к следующему.
(1) Учитывая стабильность при хранении, износостойкость, противоскользящие свойства и стойкость цвета, рекомендуется, чтобы содержание глины, микрокремнезема, пигмента, минерального заполнителя и эмульгированного асфальта в приготовленной смеси находилось в пределах 15 –17, 12–16, 10–14, 28–32 и 25–32% соответственно.
(2) Учитывая, что CEASM может уменьшить структурную глубину покрытия, антискользящие характеристики покрытия были протестированы после укладки с помощью CEASM. Было обнаружено, что значение маятникового трения покрытия с CEASM было больше 32 (выше требований спецификации). Таким образом, добавление заполнителей может улучшить маятниковую характеристику трения окрашенных покрытий с уплотнением. Кроме того, тест на ходовые качества с CEASM показал, что он обладает хорошими противоскользящими характеристиками и стойкостью окраски.
(3) Когда к дорожному покрытию предъявлялись строгие требования против скольжения, рекомендуется использовать базальтовые горные породы с размером зерна от 0,6 до 1,18 мм. Было зарегистрировано общее добавление 10% в расчете на массовый процент CEASM.
Заявление о доступности данныхНеобработанные данные, подтверждающие выводы этой статьи, будут предоставлены авторами без излишних оговорок.
Авторские взносы
ZS организовал исследование.ZZ и CW выполнили все тесты. З.С. и З.З. написали рукопись. ZS, ZZ и JZ проверили рукопись. Все авторы внесли свой вклад в статью и одобрили представленную версию.
Финансирование
Авторы выражают признательность за финансовую поддержку, предложенную Национальным фондом естественных наук Китая (№№ 51878078 и 51
Конфликт интересов
Авторы заявляют, что исследование проводилось при отсутствии каких-либо коммерческих или финансовых отношений, которые могут быть истолкованы как потенциальный конфликт интересов.
Список литературы
Андо Р., Инагаки Т. и Мимура Ю. (2011). Делает ли цветное покрытие безопаснее несигнализованные перекрестки? Пример из Японии. Процедуры Soc. Behav. Sci. 20, 741–751. DOI: 10.1016 / j.sbspro.2011.08.082
CrossRef Полный текст | Google Scholar
Autelitano, F., и Джулиани, Ф. (2019). Внешний вид окрашенного асфальтового покрытия в дневное и ночное время суток. Констр. Строить. Матер. 207, 98–107. DOI: 10.1016 / j.conbuildmat.2019.02.100
CrossRef Полный текст | Google Scholar
Боччи М., Грилли А., Кардоне Ф. и Вирджили А. (2012). Бесцветная асфальтовая смесь для покрытия туннелей: экспериментальное применение в провинции Больцано. Процедуры Soc. Behav. Sci. 53, 115–124. DOI: 10.1016 / j.sbspro.2012.09.865
CrossRef Полный текст | Google Scholar
Фанг, К. Т. (1994). Единый дизайн и таблица унифицированного дизайна. Пекин: Science Press. (на китайском языке).
Google Scholar
Фанг, К. Т., и Ван, Ю. (1994). Теоретико-числовые методы в статистике. Лондон: Чепмен и Холл.
Google Scholar
Fu, H. Y., Xie, L. D., Dou, D. Y., Li, L. F., Yu, M., and Yao, S. D. (2007). Стабильность при хранении и совместимость битумного вяжущего, модифицированного привитым сополимером SBS. Констр. Строить. Матер. 21, 1528–1533. DOI: 10.1016 / j.conbuildmat.2006.03.008
CrossRef Полный текст | Google Scholar
Гао, М., Сяо, Б., Ляо, К., и Дай, Ю. (2005). Исследование старения цветного асфальта. Sci. Tech. Engng. 5, 401–405. (на китайском языке) doi: 10.3969 / j.issn.1671-1815.2005.07.005
CrossRef Полный текст | Google Scholar
He, X. (2013). Исследование экономичного цветного асфальтового вяжущего и характеристик дорожной смеси. Магистерская диссертация, Университет Чанъань, Шэньси. DOI: 10.7666 / d.D407999.
CrossRef Полный текст | Google Scholar
Джин, Н. С. (2015). Исследование характеристик дорожного покрытия из цветного асфальта и его смеси. Петро. Асфальт. 29, 48–51. (на китайском языке), Google Scholar
Ли, Х. и Ким, Ю. (2007). Лабораторная оценка покрытия из цветного полимербетона со связующим из синтетической смолы для эксклюзивных автобусных полос. Транспорт. Res. Рек. 1991, 124–132.DOI: 10.3141 / 1991-15
PubMed Аннотация | CrossRef Полный текст | Google Scholar
Лян, М., Синь, X., Фань, В., Ло, Х., Ван, X., и Син, Б. (2015). Исследование реологических свойств и стабильности при хранении асфальта, модифицированного CR / SBS. Констр. Строить. Матер. 74, 235–240. DOI: 10.1016 / j.conbuildmat.2014.10.022
CrossRef Полный текст | Google Scholar
Лин, Д. Ф., и Луо, Х. Л. (2004). Выцветание и изменение цвета цветного асфальта количественно определено методом анализа изображений. Констр. Строить. Матер. 18, 255–261. DOI: 10.1016 / j.conbuildmat.2004.01.004
CrossRef Полный текст | Google Scholar
Оуян, К. Ф., Ван, С. Ф., Чжан, Ю. и Чжан, Ю. Х (2006). Термореологические свойства и стабильность при хранении асфальтов, модифицированных SEBS / каолинитовой глиной. Eur. Polym. J. 42, 446–457. DOI: 10.1016 / j.eurpolymj.2005.07.004
CrossRef Полный текст | Google Scholar
Сасанипур, Х., Аслани, Ф., и Тахеринежад, Дж.(2019). Влияние микрокремнезема на долговечность самоуплотняющегося бетона из переработанных заполнителей бетона. Констр. Строить. Матер. 227, 116598. DOI: 10.1016 / j.conbuildmat.2019.07.324
CrossRef Полный текст | Google Scholar
Сенгоз Б., Исикьякар Г. (2008). Оценка свойств и микроструктуры асфальта, модифицированного полимерами SBS и EVA. Констр. Строить. Матер. 22, 1897–1905. DOI: 10.1016 / j.conbuildmat.2007.07.013
CrossRef Полный текст | Google Scholar
Синнефа, А., Карлесси Т., Гайтани Н., Сантамурис М., Ассимакопулос Д. Н. и Папакацикас К. (2011). Экспериментальные испытания тонкослойного асфальта холодного цвета и оценка его возможностей для улучшения городского микроклимата. Сборка. Environ. 46, 38–44. DOI: 10.1016 / j.buildenv.2010.06.014
CrossRef Полный текст | Google Scholar
Тан П., Мо, Л. Т., Пан, К. Л., Фанг, Х., Хавилла, Б., и Риара, М. (2018). Исследование реологических свойств светлых синтетических битумных вяжущих, содержащих различные полимерные модификаторы. Констр. Строить. Матер. 161, 175–185. DOI: 10.1016 / j.conbuildmat.2017.11.098
CrossRef Полный текст | Google Scholar
Тан X. Д., Конг, К., Тиан, Дж., Ли, Ю., Цзинь, З. Т., и Бай, Х. Ю. (2015). Подготовка и укладка цветного асфальта. Заявл. Мех. Матер. 727–728, 362–365. DOI: 10.4028 / 727-728.362
CrossRef Полный текст | Google Scholar
Сюй, М., Пан, X., и Дэн, Q. (2012). «Метод укладки тонкослойного противоскользящего цветного покрытия в тоннеле, основанный на увеличении яркости покрытия».in Proceedings of the 25th COTA International Conference of Transportation Professionals , Columbus, OH: COTA), 3073–3083. DOI: 10.1061 / 9780784412442.313
PubMed Аннотация | CrossRef Полный текст | Google Scholar
Ю, Р. Э., Чжу, Х. Дж., Чжоу, Х., Коу, Ю. Ф., Чжан, М. Р., и Фанг, К. К. (2018). Реологические свойства и стабильность при хранении асфальта, модифицированного наноразмерной полиуретановой эмульсией. Бензин. Sci. Technol. 36, 85–90. DOI: 10.1080 / 106.2017.1405028
CrossRef Полный текст | Google Scholar
Зани Л., Джустоцци Ф. и Харви Дж. (2017). Влияние стабильности при хранении на химические и реологические свойства полимерно-модифицированных асфальтовых вяжущих для строительства дорожных покрытий. Констр. Строить. Матер. 145, 326–335. DOI: 10.1016 / j.conbuildmat.2017.04.014
CrossRef Полный текст | Google Scholar
Чжан, Дж. Х., Пэн, Дж. Х., Лю, В. З. и Лу, В. Х. (2019a). Прогнозирование модуля упругости мелкозернистых грунтов земляного полотна с учетом относительного уплотнения и механического всасывания. Road Mater. Тротуар Des. 1–13. DOI: 10.1080 / 14680629.2019.1651756
CrossRef Полный текст | Google Scholar
Чжан, Дж. Х., Пэн, Дж. Х., Цзэн, Л., Ли, Дж. И Ли, Ф. (2019b). Быстрая оценка модуля упругости грунтов земляного полотна с использованием свойств грунта, связанных с эксплуатационными характеристиками. Внутр. J. Pavement Eng. 1–8. DOI: 10.1080 / 10298436.2019.1643022
CrossRef Полный текст | Google Scholar
Чжан, Дж. П., Тан, Х. К., Пей, Дж. З., Цюй, Т., и Лю, В.Л. (2019c). Оценка трещиностойкости асфальтобетонной смеси на основе существенной энергии разрушения и вязкости разрушения. Внутр. Дж. Геомеч . 19: 06019005. DOI: 10.1061 / (ASCE) GM.1943-5622.0001390
PubMed Аннотация | CrossRef Полный текст | Google Scholar
Zhou, Y., Cai, J. S., Chen, R. X., Hou, D. S., Xu, J., Lv, K., et al. (2020). Разработка и оценка интеллектуального ингибитора переноса жидкостей на полимерной основе. J. Clean. Prod. 257: 120528. DOI: 10.1016 / j.jclepro.2020.120528
CrossRef Полный текст | Google Scholar
Глава 7 — 98042 — Переработка — Устойчивое развитие — Тротуары
Глава 7. Переработка горячего асфальта (материалы и конструкция смеси)
Введение
Рециркуляция горячей смеси — это процесс, в котором регенерированный асфальтный материал дорожного покрытия объединяется с новыми материалами, иногда вместе с рециклирующим агентом, для производства горячих асфальтовых смесей. Как и в случае с обычным HMA, переработанные смеси должны быть правильно спроектированы для обеспечения надлежащих характеристик.При правильном проектировании переработанные смеси могут иметь свойства, аналогичные свойствам новых традиционных горячих асфальтовых смесей. (1)
В рециркуляции горячей смеси есть четыре компонента: регенерированное асфальтовое покрытие (RAP), первичный заполнитель, первичный асфальтный вяжущий и, в некоторых случаях, агент вторичной переработки. Два шага в процедуре проектирования смеси — это оценка материала и проектирование смеси. Целью процесса оценки материалов является определение важных свойств материалов компонентов, чтобы найти оптимальную смесь материалов, отвечающую требованиям к смеси.Целью этапа разработки смеси является определение типа и процентного содержания асфальтового вяжущего с помощью результатов испытаний уплотненных смесей. Конкретные этапы процесса оценки материалов и проектирования смесей заключаются в следующем. (2)
- Получить репрезентативные полевые пробы вторичного материала.
- Провести лабораторный анализ:
- определить состав и свойства RAP
- определить необходимое количество первичных заполнителей для добавления
- выберите тип и количество вяжущего первичного асфальта
- смеси, компактные и тестовые смеси.
- Выберите оптимальную комбинацию компонентов смеси, отвечающую критериям конструкции смеси.
Оценка материалов
Процесс оценки материала состоит из отбора проб и оценки RAP и рециркулирующего агента, если таковой имеется, который будет использоваться в переработанной смеси. RAP, который будет использоваться в переработанной смеси, может поступать из разных слоев HMA с разным составом или складироваться из материалов из разных источников. Следовательно, репрезентативные образцы должны быть получены от существующих покрытий, транспортных средств с RAP или складов RAP, чтобы оценить любые изменения в различных важных свойствах, таких как градация и содержание асфальта.
Отбор проб РАП
Отбор проб с существующих тротуаров: Некоторым дорожным агентствам нравится проводить предварительный отбор проб и программу оценки для включения некоторых важных свойств, таких как градация, содержание асфальта, проникновение и вязкость, смеси на месте в пакет планов, спецификаций и оценок. . (3) Исторические данные, такие как планы строительства, прошлые исследования состояния и записи о техническом обслуживании, могут быть использованы для определения существенных различий в сечении покрытия, повреждений поверхности или повышенной несущей способности конструкции.Эти различия можно использовать для разделения проекта на блоки из разных строительных материалов или разной глубины фрезерования. План случайного отбора проб следует использовать для получения предварительных проб от каждой единицы дорожного покрытия. Рекомендуется следующая процедура предварительного отбора проб. Тротуар будет разделен на строительные блоки аналогичного состава с использованием исторических данных. Каждую строительную единицу следует разделить на шесть-восемь секций равной длины. Из каждого раздела следует случайным образом отбирать по одному образцу.Каждый образец должен быть достаточного размера (минимум 6,8 кг, 15 фунтов) для извлечения, извлечения и испытания битумного вяжущего. Каждый образец следует тестировать индивидуально. Таблица 7-1 (3) показывает частоту и размер выборки для тех государственных дорожных агентств, которые проводят оценку на стадии разработки проекта. Рекомендуется минимум одна проба (состоящая из 3 ядер) на 1,6 км полосы движения (1 милю полосы движения). Несмотря на то, что большинство агентств работают на всю глубину тротуаров, после визуального осмотра керны обрезаются до предполагаемой глубины удаления.Для подробного плана отбора проб можно использовать блок-схему, показанную на рисунке 7-1 (2) , для оценки любых значительных различий в свойствах материала RAP. Особое внимание следует уделять методу случайной выборки, поскольку эта процедура основана на статистических принципах, и с помощью этого метода выборки могут быть сокращены как затраты, так и трудозатраты. (4) AASHTO T168 Отбор проб битумных смесей для дорожных покрытий (относящихся к пробам с проезжей части) можно использовать в качестве руководства для получения сердцевин дорожного покрытия HMA.После проведения тестов на этих образцах (как обсуждается ниже) результаты должны быть проанализированы для определения среднего и стандартного отклонения, а также должны быть обнаружены выбросы, если таковые имеются. Участки дорожного покрытия, соответствующие результатам выбросов, следует рассматривать отдельно.
Отбор проб с грузовиков для перевозки RAP: образцов RAP можно получить с грузовиков, перевозящих RAP с участка измельчения на завод HMA для складирования. Произвольный отбор проб выполняется, как показано на блок-схеме (рисунок 7-1).AASHTO T2, агрегаты для отбора проб (относящиеся к пробам с тягача), можно использовать в качестве руководства для отбора проб RAP с грузовиков.
Отбор проб из складов RAP: Для получения репрезентативных образцов из складов RAP необходимо получить 10 проб из разных мест в штабеле, а для минимизации эффекта сегрегации, по крайней мере, 150 мм (6 дюймов) материала от поверхности перед отбором проб следует удалить из штабеля. (5) Образцы удаляются, а материал, оставшийся на сите 50 мм (2 дюйма), отбрасывается.Рекомендуется, чтобы размер образца после отбора составлял не менее 5 кг (11 фунтов), из которых одна половина должна использоваться для испытания состава смеси, а другая половина — для разработки смеси. Отдельные пробы следует использовать для экстракции градации заполнителей и содержания асфальта. (6) Пять образцов рекомендуются для проведения восстановления Abson и определения свойств битумного вяжущего. Агрегаты отбора проб AASHTO T2 (относящиеся к пробам из хранилища) могут использоваться в качестве руководства для отбора проб RAP из складов RAP.Поскольку дробление или измельчение регенерированного асфальтового покрытия может изменить градацию агрегатной части, следует проверить образцы из складских запасов холодного асфальта на производственной площадке. (4) В дополнение к руководствам, имеющимся в нескольких источниках, для разработки эффективного плана выборочного контроля всегда следует использовать инженерное заключение. После того, как склад RAP создается на заводе HMA, некоторые дорожные агентства присваивают ему номер, например 96-3 (Склад № 3, 1996 год), который затем указывается в проекте смеси для вторичного использования для этого запаса.После окончательного отбора проб для расчета смеси не разрешается добавлять какие-либо другие материалы RAP в этот склад. Как и в случае отбора проб с существующей дороги, результаты испытаний складских запасов ПДП должны быть проанализированы для выявления любых выбросов. Материал из отвалов, соответствующий выбросам, не должен входить в состав смеси.
Состояние | Частота выборки | Размер выборки |
---|---|---|
Аризона | 3 ядра / 1.6 полосных км | Диаметр 150 мм для полной глубины конструкции |
Флорида | 1 комплект из 3 жил / 1,6 линейных км. Минимум 2 набора по 3 ядра на дорожку. | Диаметр 150 мм для полной глубины конструкции |
Канзас | 3 ядра / 1,6 км полосы Минимум 30 ядер. | Диаметр 100 мм для полной глубины структуры |
Невада | 1 ядро / 750 дорожек, м | Диаметр 100 мм для полной глубины структуры |
Техас | 10 ядер на проект | 150 диаметр мм для полной глубины конструкции |
Wisconsin | 1 жила / 800 м | Минимальная площадь поверхности 230 см 2 |
Wyoming | 2 ядра / км | Диаметр 150 мм для полной глубина конструкции |
Рисунок 7-1.Блок-схема планов выборочного контроля. (изменено из 2)
Оценка RAP
Материал RAP необходимо оценить перед фактическим дизайном смеси. Это связано с тем, что при старении и окислении в HMA происходят определенные значительные изменения. Для связующего это включает потерю более легких фракций и соответствующее увеличение доли асфальтенов, твердение (увеличение вязкости) и потерю пластичности. Градация агрегата может измениться из-за деградации, вызванной нагрузкой трафика и окружающей средой.Следовательно, состав ПДП должен быть определен в начале. Большинство агентств определяют градацию заполнителя, содержание асфальта и вязкость асфальта при 60 ° C для восстановленного асфальтового покрытия. Старое асфальтовое вяжущее должно быть извлечено из репрезентативной пробы RAP для определения этих свойств. Следующие рекомендации предлагаются для оценки заполнителя и связующего. (4)
Aggregate Evaluation: AASHTO T30, Механический анализ экстрагированного заполнителя или AASHTO T27, Ситовой анализ мелких и крупных заполнителей, следует использовать для выполнения ситового анализа совокупности, извлеченной из RAP.Любой недостаток можно исправить путем смешивания соответствующих фракций сита первичного и / или регенерированного заполнителя с восстановленным заполнителем асфальтового покрытия. Также рекомендуется проверить угловатость как крупных, так и мелких заполнителей. Экстракция: AASHTO T 164, Количественная экстракция битума из битумных смесей для дорожных покрытий, следует использовать для количественного извлечения асфальтового вяжущего из RAP, если извлеченное вяжущее должно быть извлечено и испытано для дальнейшей оценки. Испытание на воспламенение, проведенное Национальным центром технологии асфальта (NCAT), можно использовать для определения состава RAP (содержание асфальта и градация заполнителя), если асфальтовое вяжущее не предназначено для восстановления.
Оценка битумного вяжущего: Извлеченный асфальт извлекается из раствора с помощью AASHTO T 170. Извлечение асфальта из раствора методом абсона. Компания SHRP разработала улучшенный метод извлечения битумного вяжущего из раствора: SHRP Обозначение B-006 Извлечение и извлечение асфальтового вяжущего для реологических испытаний. Этот метод предпочтительнее AASHTO T170. Затем следует использовать AASHTO T 202 для проверки консистенции восстановленного битумного вяжущего путем измерения его вязкости при 60 ° C, чтобы оценить количество и сорт первичного асфальтового вяжущего, необходимого в повторно используемой смеси.Некоторые агентства также тестируют проникновение восстановленного асфальтового вяжущего при 25 ° C.
Если в переработанной смеси используется не более 15-20 процентов РАП, испытания извлеченного асфальта не требуются многими дорожными агентствами, и качество вяжущего первичного асфальта остается таким же, как и у обычной смеси.
Агенты по переработке
Существует четыре основных цели использования рециклирующих агентов. (7) Это:
- для восстановления характеристик выдержанного асфальтового вяжущего до уровня консистенции, подходящего для строительных целей и конечного использования смеси;
- восстанавливает оптимальные характеристики переработанной смеси HMA для обеспечения долговечности;
- обеспечивает дополнительное связующее, достаточное для покрытия любого первичного заполнителя, добавляемого к переработанной смеси; и
- обеспечивает дополнительное связующее, достаточное для удовлетворения требований к конструкции смеси.
Рециклирующие агенты — это органические материалы с химическими и физическими характеристиками, выбранными для восстановления состаренного асфальта до желаемых характеристик. (4) При выборе рециклирующего агента вязкостные характеристики комбинированного состаренного битумного вяжущего и рециклирующего агента являются определяющими факторами. Эти агенты также известны как смягчающие агенты, регенерирующие агенты, модификаторы, флюсующие масла, масла-наполнители и ароматические масла. (7) Группа потребителей-производителей Тихоокеанского побережья определила рециклирующий агент как углеводородный продукт с физическими характеристиками, выбранными для восстановления старого асфальтового вяжущего в соответствии с требованиями текущих спецификаций асфальтового вяжущего.В соответствии с этим определением более мягкий асфальт и специальные продукты можно отнести к рециркуляционным агентам. (7) Асфальтовые вяжущие могут использоваться, когда требуется увеличение общего содержания вяжущего в повторно используемой смеси, и конкретный сорт может быть смешан со старым асфальтовым вяжущим в RAP, чтобы получить асфальтовое вяжущее, отвечающее желаемым спецификациям. Обычно для этой цели используются асфальтовые вяжущие AC-10, AC-5 или AC 2.5 (85-100, 120-150 или 200-300 пен; AR-4000, AR-2000 или AR-1000). (4) Использование таких мягких сортов асфальтового вяжущего при переработке горячей смеси более распространено в США.S. по сравнению с использованием коммерческих средств рециркуляции. Если состаренное асфальтовое связующее имеет очень высокую вязкость (или низкую проницаемость) или процентное содержание РАП в переработанном ГМА намного превышает 50 процентов, можно использовать относительно небольшое количество коммерческого рециклирующего агента для модификации состаренного асфальтового связующего без изменение желаемого содержания связующего. Затем, если требуется дополнительное связующее, может быть добавлен асфальт обычного сорта для первичной смеси, хотя для этого необходимо, чтобы установка была способна добавлять два связующих материала. (8) Рециклирующие агенты в форме эмульсии обладают потенциальными преимуществами улучшенного флюсования, перемешивания и контроля температуры для предотвращения локального перегрева в барабанных смесителях. Кроме того, состав эмульсии может быть скорректирован для обеспечения расчетной конечной вязкости связующего в повторно используемой смеси ГМА. Недостатком является то, что требуется дополнительное тепло для удаления от 30 до 35 процентов воды, содержащейся в эмульсии. (9) Для обеспечения правильного функционирования модификаторов в целях спецификации предлагаются следующие свойства: (7)
- Легко диспергироваться в переработанной смеси.
- Способен изменять вязкость состаренного асфальтового вяжущего в RAP до желаемого уровня.
- Быть совместимым со старым асфальтовым вяжущим для предотвращения синерезиса (выделения парафинов из асфальта).
- Обладает способностью повторно диспергировать асфальтены в состаренном асфальтовом вяжущем.
- Увеличьте продолжительность жизни переработанной смеси HMA.
- Быть однородным по свойствам от партии к партии.
- Быть стойким к курению и миганию.
Различные агентства провели несколько тестов для оценки рециркулирующих агентов. В Таблице 7-2 показаны физические свойства агентов рециркуляции горячей смеси, содержащиеся в Стандартной практике ASTM D4552 Классификация агентов рециркуляции горячей смеси. (10) Важные упомянутые свойства следующие:
- Вязкость при 60 ° C используется для измерения консистенции битумного вяжущего для оценки материалов и обеспечения однородности.
- Температура вспышки является важным показателем для оценки наличия летучих органических соединений или загрязняющих веществ в рециклирующем агенте.Это важно для безопасности при транспортировке, обращении и хранении агента рециркуляции.
- Весовой процент насыщенных углеводородов указан для обеспечения совместимости.
- Необходимо оценить потерю веса, чтобы свести к минимуму дымообразование и потерю летучих веществ при производстве горячей смеси.
- Испытания на старение необходимы для сведения к минимуму чрезмерного затвердевания средства при горячем перемешивании и обеспечения долговечности.
ТЕСТ | Метод испытания ASTM | RA 1 | RA 5 | RA 25 | RA 75 | RA 250 | RA 500 | |||||||||||||
---|---|---|---|---|---|---|---|---|---|---|---|---|---|---|---|---|---|---|---|---|
Мин. | Макс. | Мин. | Макс. | Мин. | Макс. | Мин. | Макс. | Мин. | Макс. | |||||||||||
Вязкость при 140 ° F, сСт | D 2170 или D 2170 или D 2171 | 50847 | 900 | 901 | 4500 | 4501 | 12500 | 12501 | 37500 | 37501 | 60000 | |||||||||
Точка воспламенения, COC, ° F | 908 47 908.. | 425 | … | 425 | … | 425 | … | 425 | … | 425 | … | |||||||||
Насыщенные вещества, мас.% | D 2007 | … | 30 | … | 30 | … | 30 | … | 30 | … | 30 | … | 30 | |||||||
Тесты остатков из печи RTFO или TFO 325 ° F | D 2872 или D 1754 | 908 908 48 | ||||||||||||||||||
Соотношение вязкости A | — | … | 3 | … | 3 | … | 3 | … | 3 | … | 3 | … | 3 | |||||||
Wt изменение ±% | — | … | 4 | … | 4 | … | 3 | … | 3 | … | 3 | .. . | 3 | |||||||
Удельный вес | D 70 или D 1298 | Отчет | Отчет | Отчет | Отчет | Отчет | Отчет |
Выбор марки Recycling Agent (RA) будет зависеть от количества и твердости асфальта в состаренном покрытии.В общем, типы RA с более низкой вязкостью могут использоваться для восстановления выдержанных битумов с высокой вязкостью и наоборот.
Кроме того, сорта RA 1, RA 5, RA 25 и RA 75 (10) , как правило, будут наиболее подходящими для переработки горячей смеси утилизированного асфальтобетона, когда добавлено не более 30 процентов первичного заполнителя, в то время как марки RA 250 и RA 500 обычно будет наиболее подходящим, когда в смесь включено более 30 процентов первичного заполнителя. (10) Спецификации эмульгированных рециклирующих агентов обычно основаны на спецификациях рециркулирующих агентов с дополнительными испытаниями, которые идентичны или аналогичны испытаниям для асфальтовых эмульсий (таблица 7-3).Стандартную практику классификации эмульгированных рециклирующих агентов ASTM D5505 можно использовать для выбора подходящего эмульгированного рециркулирующего агента. Выбор эмульгированного рециркулирующего агента будет определяться консистенцией связующего в состаренном дорожном покрытии, запланированными методами рециркуляции, количеством новых заполнителей, если таковые имеются, и другими проектными потребностями. (10)
ИСПЫТАНИЯ | Метод тестирования | ER-1 | ER-2 | ER-35 | ||||||||
---|---|---|---|---|---|---|---|---|---|---|---|---|
Мин. | Макс. | Мин. | Макс. эмульсия | |||||||||
Вязкость, 50 ° C, SSF | D 244 | 100 | 908 908 908 908 9048 908 47 908 908 908 908 908 47 908 908 908 | Сито,% | D 244 | 0.1 | 0,1 | 0,1 | ||||
Стабильность при хранении, 24 ч,% | D 244 | 1,5 | 1,5 | 1,5 | ||||||||
D 244 | 65 | 65 | 65 | |||||||||
Разведение | отчет A | 908 908 908 | D 70 | отчет | отчет | отчет | ||||||
Совместимость B | варьируется | отчет | 908 908 908 908 от перегонки | 90 848 | ||||||||
Вязкость, 60 ° C, сСт | D 2170 | 50 | 200 | 30 | 908 D 2007 | 30 | ||||||
Растворимость в трихлорэтилене | D 2042 | 97.5 | 97,5 | 97,5 | ||||||||
На остатке от перегонки после RTFO C | 908 908 50 г 5 с | D 5 | 75 | 200 | 5 | 75 | ||||||
RTFO, изменение веса,% | D 2872 | 4 | 4 | 4 | 4 |
Примечания:
- ЭР-1 должен быть аттестован на разбавление питьевой водой.
- Эта спецификация допускает использование множества эмульсий, включая эмульсии с высоким содержанием флотации и катионные эмульсии. Инженер должен предпринять шаги, необходимые для предотвращения смешивания несовместимых материалов в резервуарах или других сосудах. Было бы разумно иметь сертификат химического состава (плоский тест для эмульсий с высокой плавучестью, тест на заряд частиц для катионных эмульсий или другие тесты, если необходимо), сертифицированный поставщиком.
- RTFO должен быть стандартом. После утверждения инженером, испытание в тонкопленочной печи (Метод испытания D 1754) может быть заменено испытанием на соответствие.
Процедуры проектирования смесей
На рис. 7-2 показана блок-схема, рекомендованная для различных этапов разработки смеси повторно используемых смесей. (4) Сначала будет представлен дизайн обычной смеси из вторичного сырья, а затем — дизайн смеси из вторичного сырья Superpave.
Рисунок 7-2. Блок-схема процедуры расчета смеси.
Для асфальта | ||||||||||||
---|---|---|---|---|---|---|---|---|---|---|---|---|
по весу от всей смеси | по весу заполнителя | |||||||||||
% Новый асфальт, P nb |
| |||||||||||
% РАП, П см |
|
| ||||||||||
% новый заполнитель, P нс | r | |||||||||||
ВСЕГО | 100 | 100 + P b | ||||||||||
% новый асфальт |
Примечания:
P sm | = | Процент утилизируемой смеси (RAP) в переработанной смеси | |
P b | = | Содержание асфальта в переработанной смеси,% | = | Содержание асфальта в утилизированной смеси (RAP),% |
P nb | = | Дополнительный асфальт и / или переработанный агент в повторно используемой смеси,% | |
P 9047 ns ns ns | Процент дополнительного материала заполнителя (новый материал заполнителя) | ||
r | = | Процент нового материала заполнителя к общему количеству заполнителя в повторно используемой смеси | |
R | = | Процент нового заполнителя в процентах к общему количеству / или вторичному реагенту асфальт в рециклированной смеси |
- Комбинированные заполнители в рециклированной смеси — Использование градации агрегата из регенерированного оса При остановке дорожного покрытия и нового заполнителя рассчитывается комбинированная градация, отвечающая требуемым техническим требованиям.После того, как смесь агрегатов (агрегат в RAP и новые агрегаты) установлена, количество нового агрегата выражается как r в процентах. Например, предположим, что для переработанной смеси была создана следующая смесь:
75% новый агрегат
25% RAP агрегат
100% всегоКоличество нового агрегата составляет 75 процентов. Следовательно, r = 75. Таблица 7-4 (4) содержит формулы для дозирования материалов для повторно используемых смесей HMA, в которых смесь заполнителей в смеси поддерживается постоянной.
- Приблизительная потребность в асфальтовом вяжущем для комбинированных заполнителей — Наиболее практичный подход состоит в том, чтобы предположить, что потребность в асфальте для комбинированных заполнителей в предлагаемом переработанном HMA равна оптимальному содержанию асфальта в 100-процентном чистом HMA (без какого-либо RAP). Следовательно, следующая процедура определения приблизительной потребности в асфальте может не потребоваться, если для 100-процентной первичной смеси не существует проекта смеси.
Приблизительная потребность в асфальте для комбинированных заполнителей может быть определена с помощью теста на центрифужный керосиновый эквивалент (CKE), включенного в метод расчета смеси Hveem Института асфальта, или рассчитана по следующей эмпирической формуле:
P = 0.035a + 0,045b + Kc + F
где:
P = приблизительная общая потребность в асфальте переработанной смеси, процент по массе смеси a = процентов минерального заполнителя, оставшегося на сите 2,36 мм, выраженное целым числом b = процентов минерального заполнителя, прошедшего через сито 2,36 мм и оставшегося на сите 75 мкм, выраженного целым числом c = процентов минерального заполнителя, прошедшего через сито 75 мкм К = 0.15 для 11-15 процентов, проходящих через сито 75 мкм, 0,18 для 6-10 процентов, проходящих через сито 75 мкм, и 0,20 для 5 процентов или менее, проходящих через сито 75 мкм F = от 0 до 2,0 процентов. На основе поглощения легкого или тяжелого заполнителя. При отсутствии других данных предлагается значение 0,7 При установленной приблизительной потребности в асфальте это послужит основой для серии пробных смесей для расчета смеси. Пробные смеси будут варьироваться по содержанию асфальта на 0.5 шагов по обе стороны от расчетной приблизительной потребности в асфальте.
Например, предположим, что расчетная потребность в асфальте составила 6,2 процента. Затем серия пробных смесей составляет от 5,0 до 7,0 процентов или от 5,5 до 7,5 процентов.
- Расчетное процентное содержание нового вяжущего асфальта в смеси HMA — Количество нового асфальтового вяжущего, добавляемого к пробным смесям переработанной смеси HMA, выраженное в процентах по массе от общей смеси, рассчитывается по следующей формуле:
P nb = (100 2 — r P sb ) P b — (100 — r) P sb 908 908 100 (100 — П сб ) 100 — П сб где:
P nb = Процент нового асфальтового вяжущего в переработанной смеси (плюс рециклирующий агент, если он используется), выраженный целым числом r = новый заполнитель, выраженный в процентах от общее количество заполнителя в повторно используемой смеси, выраженное в виде целого числа P b = процентов, расчетное содержание асфальта в повторно используемой смеси (предполагается, что такое же, как в 100-процентной смеси первичного HMA, или определяется как примерная потребность в асфальте для комбинированных заполнителей на предыдущем этапе) P sb = процентов, содержание асфальта в восстановленном асфальтовом покрытии (RAP) (плюс рециркулирующий агент, если он используется) Например Предположим, что содержание асфальта P sb RAP равно 4.7 процентов и r = 75 процентов, тогда
34P nb = (100 2 — 75 X 4,7) P b — (100 — 75) 4,7 = 1,01 P b — 1,23 100 (100 — 4,7) 100 — 4,7 Теперь можно легко определить процентное содержание нового асфальтового вяжущего для любого содержания асфальта. Приведенная выше формула рассчитана для содержания асфальта, выраженного в процентах от общей массы смеси.Если содержание асфальта выражено в процентах от массы заполнителя, формула для расчета количества нового асфальтового вяжущего будет:
P nb = P b — (100 — r) P sb 100 - Выбор марки нового асфальтового вяжущего — Используя рисунок 7-3, (4) , выбирается целевая вязкость асфальтовой смеси. Обычно выбираемой целевой точкой является средняя вязкость указанного асфальтового вяжущего с градацией по вязкости.Например, цель для асфальтового вяжущего AC-20 — 2000 пуаз.
Рисунок 7-3. Таблица вязкости асфальта. (4)
Процент нового асфальта, P nb , к общему содержанию асфальта, P b , выражается следующей формулой:
Например, предположим, что смесь, описанная на этапе (3), должна иметь расчетное общее содержание асфальта 6,2 процента. Количество добавляемого нового асфальта (начиная с шага 3):
P nb = 1.01 X 6,2 — 1,23 = 5,0 процента
Тогда:
Сорт нового битумного вяжущего (и / или рециркулирующего агента) определяется с использованием диаграммы зависимости вязкости от процента нового битумного вяжущего, такой как рисунок 7-3. (4) Выбрана целевая вязкость для смеси восстановленного асфальта и нового асфальта (и / или рециркулирующего агента). Как упоминалось ранее, целевая вязкость обычно представляет собой вязкость в среднем диапазоне марки асфальтового вяжущего, обычно используемого в зависимости от типа конструкции, климатических условий, количества и характера движения.
Нанесите вязкость состаренного асфальта в RAP на левой вертикальной шкале, точка A, как показано на рисунке 7-3. Нарисуйте вертикальную линию, представляющую процентное содержание нового асфальтового вяжущего R, рассчитанное выше, и определите ее пересечение с горизонтальной линией, представляющей целевую вязкость (2000 пуазов в этом примере), точку B. Затем проведите прямую линию от точки A до точки. B и продлите ее, чтобы пересечь правую шкалу, точку C. Точка C — это вязкость при 60 ° C (140 ° F) нового асфальтового вяжущего (и / или рециркулирующего агента), необходимая для смешивания с асфальтовым вяжущим в регенерированном асфальтовое покрытие (РАП) для получения заданной вязкости смеси.Выберите марку нового битумного вяжущего, диапазон вязкости которого включает или наиболее близок к вязкости в точке C. Чтобы построить точку с использованием вертикальной шкалы, подумайте о том, чтобы выразить вязкость с помощью 10 в некоторой степени. Например, 75 000 пуазов будут 7,5 X 10 4 . Чтобы нанести точку на вертикальную шкалу, значение 7,5 будет интерполировано на шкале между 10 4 и 10 5 . Предлагается, чтобы при выборе марки асфальтобетона для вторичной переработки использовалось следующее руководство:
RAP до 15 процентов = Нет изменений в классе асфальтового вяжущего (некоторые дорожные агентства используют 20 процентов вместо 15 процентов) 16 процентов RAP или более = Используйте одно асфальтовое вяжущее степень мягкости, чем обычно указывается для 100-процентной чистой смеси HMA.Например, используйте AC-10 вместо AC-20. Не изменяйте более одного класса вязкости, если переработанная смесь HMA не проверена на устойчивость к колейности. - Дизайн пробной смеси — Затем готовятся образцы пробной смеси с использованием метода Маршалла или Хвима. Формулы, приведенные в таблице 7-4, используются для дозирования ингредиентов: новое асфальтовое вяжущее, P nb , процент регенерированного асфальта (RAP), P sm и новый заполнитель, P ns .
- Выбор формулы рабочего смешивания — Оптимальное содержание асфальта выбирается на основе данных испытаний, полученных на предыдущем этапе. Если используется методика расчета смеси Маршалла, оптимальное содержание асфальта выбирается так, чтобы обеспечить содержание пустот по воздуху 4,0 процента. Далее следуют два примера дизайна миксов.
Пример проектирования 1: Восстановленное асфальтовое покрытие имеет содержание асфальта 5,4 процента от общей массы смеси. Вязкость битумного вяжущего, полученного из регенерированного асфальтового покрытия (RAP), составляет 46 000 пуаз при 60 ° C (140 ° F).Обычно используется марка асфальтового цемента AC-20, а целевая вязкость при температуре 60 ° C (140 ° F) составляет 2000 пуаз. Градация ПДП и новый агрегат:
Размер сита Проходящий процент RAP Agg. New Agg. 25,0 мм (1 дюйм) 100 100 19,0 мм (3/4 дюйма) 98 93 9,5 мм (3/847 дюйма) 8553 4.75 мм (№ 4) 65 30 2,36 мм (№ 8) 52 16 300 мкм (№ 50) 22 5 75 мкм (№ 200) 8 1 Примерно 30 процентов RAP было выбрано, потому что
- Серийный завод должен был использоваться для переработки, Влажность RAP
- составляла 5 процентов, а влажность
- это практичный диапазон для поддержания производства смесей на основе процентного содержания RAP и влажности.
Этап 1 — Комбинированные агрегаты в рециклируемой смеси Размер сита Процент прохода 30% RAP Agg. 70% Новый Агг. Комбинированное агг. 25,0 мм (1 дюйм) [100 × 0,3 = 30,0] [100 X 0,7 = 70,0] 100,0 19,0 мм (3/4 дюйма) [98 × 0,3 = 29,4] [93 X 0,7 = 65,1] 94.5 9,5 мм (3/8 дюйма) [85 × 0,3 = 25,5] [53 X 0,7 = 37,1] 62,6 4,75 мм (№ 4) [65 × 0,3 = 19,5] [30 X 0,7 = 21,0] 40,5 2,36 мм (№ 8) [52 × 0,3 = 15,6] [16 X 0,7 = 11,2] 26,8 300 мкм (№ 50) [22 × 0,3 = 6,6] [5 X 0,7 = 3,5] 10,1 75 мкм (№200) [8 × 0,3 = 2,4] [1 X 0,7 = 0,7] 3,1 Тогда: r = 70
Задание на градацию заполнителя (для номинального размера 19 мм):
Размер сита Проход в процентах Макс. Размер% Пройдено Комбинированное Агг. % Проход 25,0 мм (1 дюйм) 100 100,0 19.0 мм (3/4 дюйма) 90-100 94,5 9,5 мм (3/8 дюйма) 56-80 62,6 4,75 мм (№ 4) 35 -65 40,5 2,36 мм (№ 8) 23-49 26,8 300 мкм (№ 50) 5-19 10,1 м 75 № 200) 2-8 3,1 Шаг 2 — Ориентировочная потребность в асфальте комбинированных заполнителей
P = 0.035a + 0,045b + Kc + F = 0,035 × 73,2 + 0,045 × 23,7 + 0,20 x 3,1 + 1,0 = 5,2 процента Шаг 3 — Расчетный процент нового асфальтового вяжущего в смеси
9000 асфальт.2 процента:P nb = = = 1.02 P b — 1.71 P nb = 1,02 (5,2) — 1,71 = 3,6 процента
Процент нового асфальтового вяжущего, P nb , от общего количества асфальта, P b , тогда будет
.R = 100 (3,6) = 69 процентов 5,2 Шаг 4 — Выберите марку нового асфальтового вяжущего
На рисунке 7-4 точка A представляет собой вязкость выдержанного асфальтового вяжущего при 46000 пуаз (4.6 × 10 4 ). Точка B расположена от целевой вязкости 2000 пуаз (2,0 × 10 3 ) и R = 69. Спроектированная линия от точки A через точку B к точке C показывает, что вязкость нового асфальтового вяжущего составляет 7,0 × 10 . 2 (700).
Рисунок 7-4. График смешения вязкости асфальта (пример расчета 1).
Поскольку AC-20 — это обычный асфальтобетон, используемый в строительстве, климате и дорожном движении, для этого проекта будет выбран AC-10.AC-10 при смешивании со старым асфальтовым вяжущим в RAP должен привести к AC-20 в пределах допустимых допусков.
Шаг 5 — Дизайн пробной смеси
Используя смесь 70 процентов нового заполнителя и 30 процентов заполнителя RAP, пробные смеси с различным содержанием асфальта (с шагом 0,5 процента по обе стороны от предполагаемой потребности в асфальте) готовятся в соответствии со стандартными процедурами расчета смесей Marshall или Hveem.
Формулы в таблице 7-4 могут использоваться для расчета процентного содержания каждого ингредиента в пробных смесях.Поскольку формула для P nb была рассчитана на этапе 3, формулы для дозирования P sm и P ns следующие:
P см
= = = 31,91 — 0,32 P b 9048 9048 9048 9048 Содержание асфальта, P b 4.5 5,0 5,5 6,0 6,5 P nb = 1,02 P b — 1,71 2,9 3,0 3,9 4,4 4,9 sm = 31,71 — 0,32 P b 30,3 30,1 29,9 29,8 29,6 P нс = 70 — 0,70 P b 56647 66,2 65,8 65,5 ИТОГО 100,0 100,0 100,0 100,0 100,0 Примечание:
- P нс = процентное содержание нового заполнителя
При приготовлении пробных смесей в лаборатории рекомендуется нагреть РАП до температуры смешивания и поддерживать ее при этой температуре. Новые заполнители обычно нагреваются на 10 ° C (50 ° F) выше температуры смешивания.После взвешивания заполнителя и РАП следует начать сухое перемешивание для тщательного перемешивания материалов перед добавлением нового асфальта. Хранение РАП при повышенных температурах должно быть минимальным (не более одного часа). В противном случае соблюдаются обычные процедуры расчета смеси.
Шаг 6 — Выберите формулу смешивания должностей
Оптимальное содержание нового асфальта и состав смеси определяются в соответствии с установленными стандартными критериями расчета смеси Маршалла или Хвима (как это используется для первичных материалов).
Пример конструкции 2: Восстановленное асфальтовое покрытие имеет содержание асфальта 6,0% с вязкостью 100 000 пуаз. Градация RAP и нового агрегата такая же, как в Примере 1.
Шаги 1 и 2 — такие же, как в примере 1
Этап 3 — Оценить процент нового асфальта в смеси
P nb = = = 1.02 P b — 1,91 Для примерной потребности в асфальте 5,2 процента:
P nb = 1,02 (5,2) — 1,91 = 3,4 процента
Шаг 4 — Выберите марку нового битумного вяжущего
На рисунке 7-5 точка А представляет собой вязкость выдержанного асфальтового вяжущего при 100 000 пуаз (1,0 × 10 5 ). Точка B расположена с использованием значений 2000 пуаз (2,0 X 10 3 ) для целевой вязкости и R = 57, (100P nb / P b = 100 × 3.4 / 6.0) нового вяжущего асфальта. Линия проецируется через эти две точки и пересекает правую ось в 1,8 × 10 2 (180 пуазов), точка C.
Рисунок 7-5. График смешения вязкости асфальта (пример расчета 2).
Это проезжая часть с интенсивным движением, где инженер-проектировщик занимается бороздой и обычно использует AC-20 при проектировании смеси. Рисунок 7-6. (4) можно использовать для определения количества рециклирующего агента, которое нужно смешать с AC-20, чтобы получить кажущуюся вязкость 180 пуаз.
Рисунок 7-6. Сравнение классов пенетрации и классов вязкости асфальтового цемента (на основе остатка RTFOT для марок AR и марок пенетрации; остатка TFOT для марок AC).
Пусть AC-20 будет новым вяжущим асфальтом, и нанесите 2000 пуазов (2,0 × 10 3 ) на левой шкале, точка D (рисунок 7-5). Вязкость рециклирующего агента составляет 1 пуаз. Постройте это как точку E на правой шкале. Соедините точки D и E прямой линией.Теперь определите, какой процент R рециклирующего агента потребуется для получения вязкости 180 пуазов для смеси. Это обозначено точкой F на линии от D до E. Процент R на горизонтальной шкале означает 22 процента. Это означает, что бак AC-20, содержащий 22 процента рециркулирующего агента, должен иметь вязкость примерно 180 пуаз. Когда эта смесь добавляется к смеси до общего содержания асфальта около 5,2 процента, вязкость всего асфальтового связующего в повторно используемой смеси должна составлять 2000 пуаз — в допустимых пределах.
Шаг 5 — Дизайн пробной смеси
Используя смесь 70 процентов нового заполнителя и 30 процентов заполнителя RAP, пробные смеси с различным содержанием асфальта (с шагом 0,5 процента по обе стороны от предполагаемой потребности в асфальте) готовятся в соответствии со стандартными процедурами расчета смесей Marshall или Hveem. Формулы в таблице 7-4 могут использоваться для расчета процентного содержания каждого ингредиента в пробных смесях. Поскольку формула для P nb была рассчитана на этапе 3, формулы для дозирования P sm и P ns следующие:
P см = = = 31.91 — 0,32 P b P нс = Содержание асфальта, P b 4,0 4,5 908 6,04,5 908 6,0P nb = 1,02 P b — 1,91 2,2 2,7 3,2 3,7 4,2 P sm = 31,91 — 0,32 P b6 30,5 30,3 30,1 30,0 P нс = 70 — 0,70 P b 67,2 66,8 6647 66,2 908 908100,0 100,0 100,0 100,0 100,0 Примечание:
- P нс = процентное содержание нового заполнителя
При приготовлении пробных смесей в лаборатории рекомендуется нагревать РАП до температуры смешивания и поддерживать ее.Заполнитель обычно нагревают до температуры смешивания плюс 10 ° C (50 ° F). После взвешивания заполнителя и РАП следует начать сухое перемешивание для тщательного перемешивания материалов перед добавлением нового битумного вяжущего. Хранение РАП при повышенных температурах должно быть минимальным (не более одного часа). В противном случае соблюдаются обычные процедуры расчета смеси.
Шаг 6 — Выберите формулу смешивания работ
Оптимальное содержание нового асфальта и состав смеси определяются в соответствии с установленными стандартными критериями расчета смеси Маршалла или Хвима (как это используется для первичных материалов).Если используется конструкция смеси Маршалла, выберите оптимальное содержание асфальта, которое дает 4,0 процента пустот.
Смесь горячего вторичного использования с технологией Superpave
ТехнологияSuperpave, являющаяся частью Стратегической программы исследований автомобильных дорог (SHRP), разработала спецификации для асфальтовых вяжущих, основанные на характеристиках. (11,12,13) Уровень эксплуатационных характеристик (PG) асфальтового вяжущего разработан для улучшения характеристик дорожных покрытий HMA при трех рабочих температурах.Технические характеристики связующего PG состоят из
- коэффициент колейности (G * / sinδ) для минимизации колейности при высоких температурах дорожного покрытия летом,
- коэффициент усталости (G * sinδ) для минимизации усталостного растрескивания при промежуточных температурах эксплуатации покрытия, а
- — требование максимальной жесткости при ползучести (S) для минимизации низкотемпературного растрескивания при низких температурах эксплуатации дорожного покрытия в зимний период.
Система оценок PG содержит два числа, которые представляют высокие и низкие эксплуатационные температуры, преобладающие на объекте проекта.Например, связующее PG 64-28 предназначено для минимизации образования колеи при высокой температуре покрытия 64 ° C (147 ° F) и для минимизации низкотемпературного растрескивания до -28 ° C (-18 ° F).
Технология Superpave также состоит из объемной системы расчета смеси, в которой используется вращательный уплотнитель Superpave (SGC). (14) Следующие шесть шагов, показанные на рис. 7-7, также используются при приготовлении смеси из горячего вторичного сырья с использованием технологии Superpave. (15)
Рисунок 7-7.Этапы приготовления смеси горячей вторичной переработки с использованием технологии Superpave.
- Комбинированные агрегаты в повторно используемой смеси
Этот шаг точно такой же, как и при проектировании стандартной смеси горячего рециклинга, описанном ранее.
- Ориентировочная потребность в асфальтовом вяжущем для комбинированного заполнителя
Этот шаг аналогичен описанному ранее при проектировании стандартной смеси горячего рециклинга. Альтернативный метод представлен в методе расчета объемной смеси Superpave (16) , который рассчитывает расчетное содержание асфальта на основе комбинированной градации заполнителя.Однако процедура очень утомительна. Рекомендуется принять расчетное содержание асфальта в повторно используемой смеси ГМА равным таковому в 100-процентной смеси первичного ГМА.
- Расчетное процентное содержание нового битумного вяжущего в смеси HMA
Этот шаг аналогичен описанному ранее при проектировании стандартной смеси горячего рециклинга.
- Выберите марку нового асфальтового вяжущего
На основании исследования, проведенного в Национальном центре технологии асфальта, (15) , для выбора марки Superpave PG нового асфальтового вяжущего рекомендуется следующая трехуровневая процедура:
- Уровень 1 (до 15 процентов RAP): Если минимальное количество RAP в рециркулируемой смеси составляет 15 процентов или меньше, используйте ту же марку PG, которая используется в 100-процентной первичной смеси HMA.Например, если дорожное агентство определяет асфальтовое вяжущее PG 64-28 для 100-процентных первичных смесей, тот же сорт может использоваться в переработанных смесях, содержащих до 15 процентов РАП.
- Уровень 2 (от 16 до 25 процентов RAP): Если количество RAP в повторно используемой смеси больше 15 процентов, но равно или меньше 25 процентов, выбранный класс PG первичного асфальтового вяжущего должен быть на один уровень ниже (как высокотемпературный, так и низкотемпературный) для Superpave указан класс PG.Например, если для Superpave указана марка PG 64-22, тогда следует выбрать асфальтовое вяжущее PG 58-28. Использование таблицы смешения (как указано в Уровне 3) для выбора высокотемпературной марки первичного асфальтового вяжущего не является обязательным.
- Уровень 3 (26 процентов или более RAP): Если количество RAP в повторно используемой смеси составляет 26 процентов или более, то рекомендуется использовать диаграмму смешения конкретных марок, показанную на рисунке 7-8. Эта диаграмма смешения может использоваться для определения минимального и максимального количества процентного содержания первичного асфальтового вяжущего (и, наоборот, максимального и минимального количества RAP в повторно используемой смеси), чтобы повторно использованное асфальтовое вяжущее соответствовало определенной марке PG.По оси X в этой таблице смешения отложено процентное содержание первичного асфальтового вяжущего (определено на этапе 3), а по оси Y — коэффициент колейности G * / sinδ, полученный при высокой температуре эксплуатации дорожного покрытия для конкретной марки PG. Например, если дорожное агентство использует вяжущее PG 64-28 для 100-процентных первичных смесей, G * / sinδ состаренного асфальтового вяжущего (восстановленного из RAP) и предлагаемого первичного (нового) асфальтового вяжущего следует определять при 64 ° C. (147 ° F). Если дорожное агентство использует связующее PG 58-28, то G * / sinδ как старого, так и предлагаемого первичного связующего следует определять при 58 ° C (136 ° F).Минимальное и максимальное количество первичного асфальтового вяжущего для получения определенных классов PG получается из двух горизонтальных линий, соответствующих жесткости 1 кПа и 2 кПа (рисунок 7-8). На рис. 7-9 показан пример использования диаграммы смешения конкретных сортов.
Рисунок 7-8. Рекомендуемая диаграмма смешения конкретных марок с линиями жесткости 1,0 и 2,0 кПа.
Рисунок 7-9. Графический метод определения минимального и максимального количества первичного битумного вяжущего в повторно используемом битумном вяжущем. (15)
Предположим, PG 64-28 был указан для проекта мощения. G * / sinδ, измеренные при 64 ° C для состаренного и первичного асфальтового вяжущего (PG 64-28), составили 100 кПа и 1,13 кПа соответственно. Эти значения были нанесены на график как точка A и точка B, как показано на рисунке 7-9. Линия AB пересекла линию жесткости 2,0 кПа на 85%. Следовательно, количество первичного асфальтового связующего PG 64-28, которое может быть добавлено в рециркулируемую смесь, составляло от 85 до 100 процентов (или примерно от 0 до 15 процентов RAP).Предположим, что в качестве вяжущего для первичного асфальта было выбрано асфальтовое связующее PG 58-34. Значение G * / sinδ, измеренное при 64 ° C для PG 58-34, составило 0,65 кПа и обозначено как точка C на рисунке 7-9. Линия AC пересекла линии жесткости 1,0 кПа и 2,0 кПа при 72 процентах и 89 процентах соответственно. Следовательно, количество первичного асфальтового вяжущего PG 58-34, которое может быть использовано в повторно используемой смеси, составляет от 72 до 89 процентов (или примерно от 11 до 28 процентов RAP).
Следует отметить, что низкотемпературная марка выбранного первичного асфальтового вяжущего всегда должна быть по крайней мере на один класс ниже указанной марки PG.Например, если указанный низкотемпературный класс для 100% первичных смесей составляет -28 ° C, то низкотемпературный класс первичного связующего должен быть -34 ° C.
Примечание. В настоящее время (1996 г.) продолжаются исследования по разработке диаграмм смешения Superpave на основе G * sinδ (коэффициент усталости) и низкотемпературных свойств битумного вяжущего в дополнение к G * sinδ (коэффициент колейности), используемому здесь.
- Дизайн пробной смеси
Пробные расчеты смесей выполняются с использованием вращательного уплотнителя Superpave (SGC) в соответствии с процедурами расчета объемных смесей Superpave. (15) Может потребоваться оценить различные градации агрегатов, чтобы получить приемлемую агрегатную структуру, отвечающую критериям Superpave. Приготовление рециркулируемых смесей, таких как нагревание РАП, нового заполнителя и асфальтового связующего, и процедуры смешивания аналогичны тем, которые используются в конструкции обычных рециркулируемых смесей, описанной ранее.
- Выберите формулу смешивания работ
Оптимальное содержание асфальта выбирается на основе данных испытаний, полученных в рамках процедуры расчета объемной смеси Superpave (этап 5).Переработанная смесь должна соответствовать всем критериям, применимым к 100-процентным первичным смесям.
Резюме
Двумя основными этапами разработки системы вторичной переработки горячей смеси являются оценка материала и разработка смеси. Оцениваемые материалы включают RAP и рециркулирующий агент. Для получения репрезентативных образцов ПДП необходимо разработать план случайного отбора проб. План и частота отбора проб должны определяться на основе исторических данных, данных о строительстве и материалах, и, если необходимо, дорожное покрытие может быть разделено на различные подсекции перед отбором проб.Чтобы оценить RAP-материал, который претерпевает изменения со временем и движением, необходимо определить его градацию, содержание асфальта и реологические свойства состаренного асфальтового вяжущего. Рециркулирующий агент должен соответствовать применимым стандартам AASHTO или ASTM. Разработка смеси для горячего вторичного использования включает определение комбинированной градации агрегатов и требуемого количества нового заполнителя для достижения целевой градации. Затем оценивается количество нового (первичного) битумного вяжущего, необходимого в переработанной смеси.Затем используются таблицы смешивания (на основе вязкости или коэффициента колейности G * / sinδ) для выбора марки первичного асфальтового вяжущего. Затем производится серия пробных смесей с различным содержанием асфальта. Оптимальное содержание асфальта для переработанной смеси выбирается на основе процедур расчета объемной смеси Marshall, Hveem или Superpave.
Список литературы
- J.A. Эппс, Д.Н. Литтл, Р.Дж. О’Нил и Б. Галлавей. Свойства смеси переработанных центральных растительных материалов , Американское общество испытаний и материалов (ASTM), STP 662, Филадельфия, 1977.
- Рекомендации по переработке дорожного покрытия для местных органов власти — Справочное руководство , отчет № FHWA-TS-87-230, FHA, Министерство транспорта США, Вашингтон, округ Колумбия, 1987.
- Переработка дорожного покрытия Краткое изложение и отчет , публикация № FHWA-SA-95060, FHA, Министерство транспорта США, Вашингтон, округ Колумбия, 1995.
- Переработка горячей смеси асфальта , Серия руководств Института асфальта № 20 (MS-20), второе издание, 1986 г.
- П.С. Кандал, Э.Р. Браун и С. Кросс. Руководство по переработке горячей смеси в Джорджии , Отчет № FHWA-GA-89-8807, 1987.
- B.F. Kallas. Расчет смеси для гибкой дорожной одежды с использованием регенерированного асфальтобетона , Отчет № FHWA / RD-84/088, Заключительный отчет, 1984.
- J.A. Эппс, Д.Н. Литтл, Р.Дж. Holmgreen и R.L. Terrel. Руководство по переработке материалов дорожного покрытия , Отчет NCHRP № 224, TRB, Национальный исследовательский совет, Вашингтон, округ Колумбия, 1980.
- Pavement Management Systems Limited. Исследование переработки горячей смеси асфальтовых покрытий , Канадская ассоциация автомобильных дорог и транспорта (RTAC), Оттава, Онтарио, 1983.
- C.F. Поттс, Б. Рут, Е. Швейер, К. Мерфи. Проект по переработке битумной эмульсии: анализ и разработка руководящих принципов , Труды AAPT, том 50, 1981.
- Книга стандартов ASTM, Раздел 4, Том. 04.03, Дорожные и тротуарные материалы , 1995.
- Методы испытаний асфальтового вяжущего SHRP: иллюстрированный обзор , Национальный учебный центр по асфальту, демонстрационный проект 101, Федеральное управление автомобильных дорог, Управление технологических приложений, Вашингтон, округ Колумбия, и Исследовательский центр института асфальта, Лексингтон, штат Кентукки, июнь 1993 г.