АО КСМ «ЭНЕМСКИЙ» | Керамзитобетонные блоки
Камни керамзитобетонные стеновые далее к/б блоки (ГОСТ 6133 — 99) — это лёгкие стеновые блоки предназначенные для устройства стен (несущих и ограждающих) и перегородок.
Изготавливаются на полуавтоматических линиях методом вибропрессования из жестких керамзитобетонных смесей. Только наше предприятие использует для производства к/блоков, — керамзит, дроблённый керамзит, керамзитовый песок фракций 0-10, 5-10, 0-5, и минимально природный песок (только для подбора прочности), а так же портландцемент М500.
Мы предоставляем клиентам только качественную продукцию, т.к. на предприятие выстроена технологическая линия от производства керамзита и керамзитового песка у=500-700 изготовления к/блоков и набора прочности в пропарочных камерах с по-операционным контролем аттестованной заводской лаборатории строительных материалов. Каждая партия изготовленных к/б блоков проверяется, в т.ч на прочность (разрушение под прессом).
У нас вы можете приобрести к/бетонные блоки при любом виде взаиморасчётов
1. Керамзитобетонные блоки
- 390 х 190 х 188 с круглыми пустотами
- 390 х 190 х 188 с щелевыми пустотами
- 390 х 288 х 188 с квадратными пустотами 35%
- 390 х 288 х 188 с щелевыми пустотами 25 %
2. Полублоки (перегородочные)
390 х 120 х 188 с щелевыми пустотами
390 х 90 х 188 с щелевыми пустотами
3 Также можем изготовить по Вашим размерам керамзитобетонные и бетонные блоки, в соответствии с ГОСТом 6133-99.
Возможна доставка автотранспортом предприятия, условия доставки в зависимости от кол-ва.
КСР-ПР-39 (390х190х188) — камень керамзитобетонный рядовой полнотелый. Является удобным и практичным строительным материалом. Применяется для кладки наружных стен и при строительстве цокольного этажа. Технические характеристики: плотность камня: 1100-1300 кг/м3; марка по прочности: М35-М100; морозостойкость: F25; теплопроводность: 0.291 Вт/м0с; масса: 14-16 кг; расход: 1м2 -13,5 шт.; 1 м3 -71 шт.; на поддоне: 100 шт. |
|
КСР-ПР-ПС-39 (390х190х188) — керамзитобетонный блок пустотелый (три пустоты, пустотность 30% ). Применяется для строительства зданий до 3-х этажей. Наличие пустот облегчает кладочные работы и повышает теплоизоляционные свойства стен. Технические характеристики: плотность камня: 1100 — 1300 кг/м3; марка по прочности: М35-М100; морозостойкость: F25; теплопроводность: 0,335 Вт/м 0с; масса: 11-13 кг; расход: на 1 м2 -12,5 шт.; на 1м3- 62,5 шт.; на поддоне: 100 шт. |
|
КСР-ПР-ПС-39 (390х190х188) — керамзитобетонный блок пустотелый (с щелевыми пустотами). Технические характеристики: плотность камня: 1100 — 1300 кг/м3; марка по прочности: М35-М100; морозостойкость: F25; теплопроводность: 0,335 Вт/м 0с; масса: 9-10,3 кг; расход: на 1 м2 -12,5 шт.; на 1м3-62,5 шт.; на поддоне: 100 шт. |
|
КСР-ПР-ПС-39 (390х288х188) — керамзитобетонный блок пустотелый (с квадратными пустотами 35%). Применяется для строительства зданий до 3-х этажей. Наличие пустот облегчает кладочные работы и повышает теплоизоляционные свойства стен. Технические характеристики: плотность камня: 1100 — 1300 кг/м3; марка по прочности: М35-М100; морозостойкость: F25; теплопроводность: 0,335 Вт/м 0с; масса: 16-17 кг; расход: на 1 м2 -12,5 шт. на поддоне: 60 шт. |
|
КСР-ПР-ПС-39 (390х288х188) — керамзитобетонный блок пустотелый (с квадратными пустотами 25%). Применяется для строительства зданий до 3-х этажей. Наличие пустот облегчает кладочные работы и повышает теплоизоляционные свойства стен. Технические характеристики: плотность камня: 1100 — 1300 кг/м3; марка по прочности: М35-М100; морозостойкость: F25; теплопроводность: 0,335 Вт/м 0с; масса: 18-19,5 кг; расход: на 1 м2 -12,5 шт.; на 1м3-43,4 шт.; на поддоне: 60 шт. |
|
КПР-ПС-39 (390х120х188) — керамзитобетонные блоки перегородочные пустотелые (с щелевыми пустотами). Применяются для кладки внутренних стен и перегородок общественных, производственных зданий с последующей облицовкой. Технические характеристики: плотность камня: 1100-1300 кг/м3; марка по прочности: М35-100; морозостойкость: F25; теплопроводность: 0. масса: 8-9 кг; расход: на 1 м2 -12,5 шт.; на 1м3-104,16 шт.; на поддоне: 140 шт. |
|
КПР-ПС-39 (390х90х188) — керамзитобетонные блоки перегородочные пустотелые (с щелевыми пустотами). Применяются для кладки внутренних стен и перегородок общественных, производственных зданий с последующей облицовкой. Технические характеристики: плотность камня: 1100-1300 кг/м3; марка по прочности: М35-100; морозостойкость: F25; теплопроводность: 0.335 Вт/м0с; масса: 5,5-6,5 кг; расход: на 1 м2 -12,5 шт.; на 1м3-104,16 шт.; на поддоне: 200 шт. |
|
Складируются на поддонах. Хранятся в штабелях не более 2 м высотой. Блоки с несквозными пустотами укладываются пустотами вниз. Погрузка и выгрузка блоков набрасыванием и сбрасыванием не допускается. Срок хранения блоков не регламентируется.
Кладка из всех видов керамзитобетонных блоков производится с применением цементно-песчаного раствора или клея для укладки блоков. Расход раствора: 0,22 м на 1 м3 кладки; 0,022 м3 на 1 м2 перегородки.
Керамзитобетонные блоки приобрели заслуженную репутацию благодаря своим свойствам среди строительных материалов для стен и перегородок:
1. Долговечность
Все компоненты имеют срок более 1000 лет керамика, песок, цемент
2. Экологическая чистота
Основной материал керамзит и керамзитовый песок представляющий собой глину, обожжённую в газовом пламени в связи с оптимальными условиями технологии минимальное кол-во цемента только требуемое для данной марки продукции. Поэтому стены из наших к/блоков не выделяют вредных компонентов, дышат, не тянут тепло.
На все материалы имеются санитарно-гигиенические сертификаты и заключения на радиологическую активность Аэфф= 132 Бк/кг, разрешены к использованию в жилищном строительстве
3. Тепло и звукоизоляция
Применение к/бетонных блоков целесообразно для всех климатических зон, и ограничено только наличием сырья для производства керамзита, т. к. гранулы с закрытыми порами и пористый песок обладает высокой теплоизоляцией ( X = 0,335 вт/ м с°) и звукоизоляцией.
4. Сокращение сроков строительства и снижение себестоимости
1 к/бетонный блок заменяет по объёму 7 глиняных кирпичей, что уменьшает трудоёмкость и расходы на кладку в т.ч. объём раствора. Из-за низкого объёмного веса кладки (в 2 раза легче кирпичной кладки) — дешевле крановые и транспортные работы, и самое главное нагрузка на нижележащие конструкции.
5. Прочность и лёгкость
Керамзитобетонный блок состоящий из керамзитового гравия и пористого песка фр. 0 — 10 используемый при производстве легче воды у=500-700 кг/м и, как следствие, к/бетонный блок весит 11-13 кг, а 7 кирпичей 24,5 кг
6. Пожаробезопастность и биостойкость
Керамзитобетонные блоки не подвержены гниению, огнестойкость выше чем у бетона.
Кладочный раствор М15 | Профессиональная строительная химия Astex
Раствор
М15 предназначен для кладки наружных и внутренних стен с традиционным толстым швом, соединения газобетонных блоков, газобетона, керамзитобетона, пустотелых блоков, керамических материалов, известково-песчаных элементов и других подобных материалов.
- Класс прочности M15
- Для внутренних и наружных работ
- Высокая износостойкость
- Толщина до 40 мм
Площадь покрытия (м 2 )
Средний расход на конкретную площадь:
Вес 25 кг (шт)
Применение 90 Кладочный раствор 002 предназначен для кладки наружных и внутренних стен с традиционный толстый шов, соединяющий газобетонные блоки, газобетон, керамзитобетон, пустотелые блоки, керамические материалы, известково-песчаные элементы и другие подобные материалы.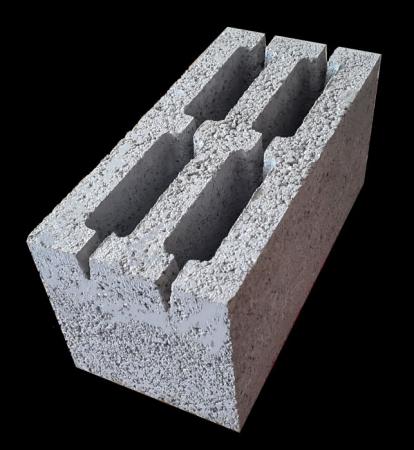
Кладочный раствор представляет собой готовую сухую смесь высшего качества на основе серого цемента класса 52,5 Р, очищенного песка, заполнителей и модифицирующих добавок. Он характеризуется хорошей удобоукладываемостью, пластичностью и адгезией к различным видам строительных материалов, что делает его продуктом с очень универсальным применением и простым в обработке. С очень высокой адгезией к земле. Кладочный раствор является морозостойким и водонепроницаемым продуктом. Он также характеризуется высокой герметичностью. Благодаря своим свойствам предотвращает образование мостиков холода в однослойных и многослойных стенах. Это также влияет на ускорение темпов строительных работ.
Основание должно быть сухим, созревшим, стабильным, ровным и прочным, т.е. достаточно прочным, очищенным от слоев, которые могут ослабить адгезию раствора (пыль, грязь, известь, масла, жиры, воск, остаточное масло и эмульсия). краска). Если необходимо нанести слой раствора на твердые основания с трудно определяемой несущей способностью (например, пыльные, трудно очищаемые), рекомендуется провести испытание на адгезию, состоящее из нанесения контрольного слоя и проверки соединения после минимум 48 часов. Незакрепленные элементы должны быть удалены. Блоки, кирпичи и сильно впитывающие элементы следует смачивать водой перед укладкой в жаркую погоду. Рекомендуется использовать на одном этаже элементы одной разновидности с одинаковым классом прочности и один и тот же тип раствора при работе с несущими стенами.
Приготовление заключается в заливке сухого раствора в емкость с нужным количеством воды (3,5 — 4 л на 25 кг). Затем перемешать массу вручную или механическим способом с помощью тихоходной дрели с миксером или бетономешалкой до получения однородной массы без комков. Оставьте примерно на 5-10 минут и снова перемешайте. При необходимости добавьте небольшое количество воды и снова перемешайте до получения надлежащей консистенции. Приготовленную таким образом массу следует использовать в течение 1-2,5 часов в зависимости от погодных условий. Недопустимо модифицировать раствор добавлением других компонентов строительной химии, т.е. песок, цемент и другие добавки, так как это может привести к потере свойств раствора.
Способ нанесения Кладочный раствор наносится после подготовки основания. Недопустимо однократное нанесение слишком толстого слоя, превышающего стандартные значения в строительстве. После нанесения раствора приступают к первоначальной укладке материала путем вдавливания, а затем сбора излишков раствора с помощью кельмы. Кирпичная кладка с полными швами. При высыхании раствора внутри помещения необходимо обеспечить хорошую вентиляцию. При работе на открытом воздухе защищайте нанесенный слой от прямых солнечных лучей (слишком быстрое высыхание может привести к растрескиванию раствора), а также защищайте поверхность от прямого дождя. Температура воздуха и основания во время работ, а также в процессе схватывания и высыхания должна быть положительной (выше +5°С, но не выше 25°С). Предполагая, что получившаяся стена будет предназначена для оштукатуривания, на наружных гранях оставляют незаполненный шов глубиной 5-10 мм. Помимо приведенных рекомендаций, работы следует проводить в соответствии со строительной практикой и правилами техники безопасности. Производитель гарантирует качество продукта, но не влияет на условия и способ его использования. В случае сомнений проведите испытания на адгезию или обратитесь к производителю.
Свежую грязь после раствора следует промыть чистой водой, а затвердевшую удалить механическим способом. Работать при температуре от +5°С до +25°С. В течение 7 дней после окончания работ температура воздуха должна быть не ниже +5°С, а в течение следующих 21 дня не должна опускаться ниже 0° С.
В среднем расходует от 34 кг/1 м² стены толщиной 1/2 полного кирпича при толщине шва 10 мм. На практике износ зависит от степени толщины сварного шва, а также точности размеров соединяемых элементов. Соотношение смешивания 3,5 — 4 л/25 кг.
Хранение и транспортировка Продукты должны храниться в неповрежденной упаковке и в сухих помещениях на поддонах. Беречь от влаги, намокания при хранении и транспортировке. Срок хранения продукта в условиях, соответствующих приведенным рекомендациям, составляет до 12 месяцев с даты изготовления, указанной на упаковке цифровой печатью. Дата производства, которая размещается на упаковке, также является датой изготовления продукта. Любые изменения, видимые в продукте или структуре упаковки без специальных испытаний, в частности обесцвечивание или смазывание упаковочной графики, нарушение непрерывности упаковки, биологические изменения в структуре продукта, распознаваемые, в частности, как следствие воздействия влаги, могут свидетельствовать о плохом хранении или транспортных условиях и не гарантируют соответствие заявленных эксплуатационных характеристик продукции указанным.
Бумажные мешки по 25 кг. Поддон: 54 мешка по 25 кг, общий вес 1350 кг на поддоне.
Меры предосторожности Продукт содержит цемент, который при смешивании с водой дает щелочную реакцию. Примите меры для предотвращения образования пыли или разбрызгивания раствора. Не вдыхать, защищать глаза и кожу. В случае загрязнения: немедленно промыть глаза большим количеством чистой воды и обратиться к врачу, кожу промыть водой с мылом. Хранить в недоступном для детей месте. При проглатывании немедленно обратиться к врачу и показать контейнер или этикетку.
Температура воздуха от +5ºС до +25ºС. Температура основания от +5ºС до +25ºС. Время работы 1-2,5 часа при определенной температуре и влажности. Класс прочности М15.
Тройные и четвертичные смеси в качестве частичной замены цемента для производства полых пескобетонных блоков
1. Скривенер К., Мартирена Ф., Бишной С., Майти С. Обожженные глинисто-известняковые цементы (LC3) Cem. Конкр. Рез. 2018;114:49–56. [Академия Google]
2. Тенг Ю., Пан В. Систематическая оценка воплощенного углерода и сокращение сборных высотных общественных жилых зданий в Гонконге. Дж. Чистый. Произв. 2019; 238:1–15. [Google Scholar]
3. UN-Environment, Scrivener K., John V., Gartner E. Экологически эффективные цементы: потенциальные экономически выгодные решения для производства материалов на основе цемента с низким содержанием CO 2 . Цем. Конкр. Рез. 2018; 114:2–26. [Google Scholar]
4. Wang X., Chen D., Ren Z. Глобальное потепление и его влияние на стратегии сокращения выбросов для жилых зданий. Строить. Окружающая среда. 2011;46:871–883. [Академия Google]
5. Аволуси Т.Ф., Оке Л., Акинкуролере О.О., Убани Д.П., Бамисайе Р.Т., Алуко О.Г. Применение методологии поверхности отклика для понимания прочности на сжатие и водопоглощающей способности песчано-бетонных блоков. Кремний. 2020: 1–10. [Google Scholar]
6. Чен З., Ли Дж. С., Пун К. С. Комбинированное использование золы осадка сточных вод и переработанного стеклобоя для производства бетонных блоков. Дж. Чистый. Произв. 2018; 171:1447–1459. [Google Scholar]
7. Ченг Х. Повторное использование результатов исследований кирпичных отходов. проц. Окружающая среда. науч. 2016; 31: 218–226. [Академия Google]
8. De Sailva G.H.M.J., Hansamali E. Экологически безопасные обожженные глиняные кирпичи с добавлением фарфоро-керамического шлама. Констр. Строить. Матер. 2019; 228:1–10. [Google Scholar]
9. Filho R.D.T., Goncalves J.P., Americano B.B., Fairbairn E.M.R. Потенциал использования дробленого кирпича из кальцинированной глины в качестве дополнительного вяжущего материала в Бразилии. Цем. Конкр. Рез. 2007; 37: 1357–1365. [Google Scholar]
10. Lee G., Ling T.C., Wong Y.-L., Poon C. Влияние размеров стеклобоя, методов литья и пуццолановых материалов на ASR бетонных блоков. Констр. Строить. Матер. 2011;25:2611–2618. [Академия Google]
11. Мэн Ю., Линг Т.С., Мо К. Переработка отходов для создания добавленной стоимости в бетонных блоках: обзор. Ресурс. Консерв. Реси. 2018; 138: 298–312. [Google Scholar]
12. Акиньеле Дж.О., Игба У.Т., Айоринде Т.О., Джимох П.О. Структурная эффективность обожженных глиняных кирпичей, содержащих отходы дробленого стекла и полипропиленовые гранулы. Кейс Стад. Пост. Матер. 2020; 13:1–11. [Google Scholar]
13. Аль-Тамими А.С., Аль-Амуди О.С.Б., Аль-Оста М. А., Али М.Р., Ахмад А. Влияние изоляционных материалов и расположения полостей на теплопередачу пустотелых блоков бетонной кладки. Констр. Строить. Матер. 2020; 254:1–19. [Google Scholar]
14. Fraile-Garcia E., Ferrero-Cabello J., Mendivil-Giro M., Vicente-Navarro A.S. Тепловые характеристики пустотелых блоков и кирпичей из бетона, легированного резиной из отработанных шин. Констр. Строить. Матер. 2018;176:193–200. [Google Scholar]
15. Gencil O., Erdugmus E., Sutcu M., Oren O.H., Gencil O. Влияние бетонных отходов на характеристики конструкционных обожженных глиняных кирпичей. Констр. Строить. Матер. 2020; 255:1–12. [Google Scholar]
16. Paihte P.L., Lalngaihawma A.C., Saini G. Переработанные пластиковые бутылки, заполненные заполнителями, как замена кирпичам. Матер. Сегодня Продолжить. 2019;15:663–668. [Google Scholar]
17. Секо А., Омер Дж., Марселино С., Эспуэлас С., Прието Э. Экологически безопасное производство необожженного кирпича из отходов строительства и сноса. Констр. Строить. Матер. 2018; 167: 154–165. [Google Scholar]
18. Чидиак С.Э., Михалевич С.Н. Характеристики сухих бетонных блоков, содержащих стеклянный порошок или полиэтиленовые заполнители. Цем. Конкр. Композиции 2011; 33: 855–863. [Google Scholar]
19. СЫН . 2004. Стандарты для песчано-бетонных блоков, Стандартная организация Нигерии, Лагос. [Академия Google]
20. Окафор Ф.О., Эгбе Э.А. Структурные свойства латеритно-цементных блоков из карьерной пыли. J. Arch Civ Eng. 2016;3(3):12–17. [Google Scholar]
21. Акиниеми Б.А., Элайджа А., Олувасегун А., Акпенпуун Д.Т., Глори О. Использование краснозема, латеритных грунтов и карьерной пыли в качестве альтернативного строительного материала в пескобетонных блоках. науч. фр. 2020;7:1–7. [Google Scholar]
22. Попула О.К., Аебокики С.Т., Гамбо М.Д. Исследование характеристик прочности на сжатие пустотелых песчано-бетонных блоков, частично замещенных золой опилок. IOSR Дж. Инж. 2015;5(5):30–34. [Академия Google]
23. Обианё И.И., Онвуалу А.П., Собойджо А.Б.О. Механическое поведение латеритного грунта, стабилизированного костной золой и гашеной известью, для устойчивого строительства. Кейс Стад. Пост. Матер. 2020; 12:1–12. [Google Scholar]
24. ASTM-C90. АСТМ интернэшнл; США: 2009 г. Стандартные технические условия для несущих бетонных блоков кладки. [Google Scholar]
25. IS-2185, Бетонные кладочные блоки. Спецификация (Часть 1) Пустотелые и полнотелые бетонные блоки. Бюро индийских стандартов; Нью-Дели: 2005. [Google Scholar] 9.0005
26. Hu X., Shi C., Shi Z., Tong B., Wang D. Ранняя усадка и теплота гидратации тройных смесей цемента, летучей золы и шлака. Констр. Строить. Матер. 2017; 153: 857–865. [Google Scholar]
27. Розьер Э., Меджигбодо Г., Изорет Л., Лоукили А. Гидратация и долговечность тройных вяжущих на основе метакаолина и известнякового наполнителя. В: Бишной С., редактор. Кальцинированные глины для устойчивого бетона. Спрингер; Сингапур: 2020. [Google Scholar]
28. Юнес М.М., Абдель-Рахман Х.А., Хаттаб М.М. Использование золы рисовой шелухи и отходов стекла в производстве трехкомпонентных смесевых цементных растворов. J. Сборка. англ. 2018;20:42–50. [Академия Google]
29. Рохо-Лопес Г., Нуньес С., Гонсалес-Фонтебоа Б., Мартинес-Абелла Ф. Четвертичные смеси портландцемента, метакаолина, золы биомассы и гранитного порошка для производства самоуплотняющегося бетона. Дж. Чистый. Произв. 2020; 266:1–14. [Google Scholar]
30. Авет Ф., Скривенер К. Исследование содержания кальцинированного каолинита при гидратации известнякового кальцинированного глинистого цемента (LC3) Cem. Конкр. Рез. 2018;107:124–135. [Google Scholar]
31. Лью К.М., Соджоби А.О., Чжан Л.В. Зеленый бетон: перспективы и проблемы. Констр. Строить. Матер. 2017; 156:1063–1095. [Google Scholar]
32. Миллер С.А., Джон В.М., Пакка С.А., Хорват А. Потенциал сокращения выбросов углекислого газа в мировой цементной промышленности к 2050 г. // Cem. Конкр. Рез. 2018;114:115–124. [Google Scholar]
33. Бриендл Л.Г., Миттермайр Ф., Бальдерманн А., Штейндл Ф.Р., Сакопарниг М., Летофски-Папст И., Галан И. Ранняя гидратация вяжущих систем, ускоренная сульфатом алюминия: влияние мелкодисперсного известняка. Цем. Конкр. Рез. 2020; 134:1–14. [Google Scholar]
34. Li C., Jiang L., Li S. Влияние добавления порошка известняка на пороговую концентрацию хлоридов для коррозии стали в железобетоне. Цем. Конкр. Рез. 2020; 131:1–9. [Google Scholar]
35. Надельман Э.И., Куртис К.Е. Стойкость материалов на основе портландцементно-известнякового цемента к физическому солевому воздействию. Цем. Конкр. Рез. 2019; 125:1–11. [Google Scholar]
36. Ши З., Феррейно С., Лотенбах Б., Гейкер М.Р., Кунтер В., Кауфманн Дж., Херфорт Д., Скибстед Дж. Сульфатостойкость кальцинированной глины – известняка – портландцемента. Цем. Конкр. Рез. 2019; 116: 238–251. [Google Scholar]
37. Кришнан С., Бишной С. Численный подход к расчету композиционных цементов с кальцинированной глиной и известняком. Цем. Конкр. Рез. 2020; 138:1–9. [Google Scholar]
38. Сожоби А.О., Аладегбойе О.Дж., Аволуси Т.Ф. Зеленые взаимосвязанные блоки мощения. Констр. Строить. Матер. 2018;173:600–614. [Google Scholar]
39. Дхандапани Ю., Сактхивел Т., Сантанам М., Гетту Р., Пиллаи Р.Г. Механические свойства и показатели долговечности бетонов на известняковом кальцинированном глиняном цементе (LC3) Cem. Конкр. Рез. 2018; 107: 136–151. [Google Scholar]
40. Дхандапани Ю., Сантанам М. Исследование характеристик, связанных с микроструктурой, для выяснения характеристик композиционного цемента с комбинацией известняк-кальцинированная глина. Цем. Конкр. Рез. 2020;129: 1–22. [Google Scholar]
41. Nguyen Q.D., Kim T., Castel A. Смягчение щелочно-кремнеземной реакции с помощью известняково-кальцинированного глиняного цемента (LC3) Cem. Конкр. Рез. 2020; 137:1–14. [Google Scholar]
42. Акино В., Ланге Д.А., Олек Дж. Влияние метакаолина и микрокремнезема на химию продуктов реакции щелочь-кремнезем. Цем. Конкр. Композиции 2001; 23: 485–493. [Google Scholar]
43. Тёрк К., Кина С., Багдикен М. Использование бинарных и тройных вяжущих смесей летучей золы класса F и порошка известняка для снижения риска щелочно-кремнеземной реакции. Констр. Строить. Матер. 2017; 151:422–427. [Академия Google]
44. Джалалян М., Голами С., Рамезанян Р. Анализ компромисса между выбросами CO2 и уровнем обслуживания пассажиров в авиационной отрасли: математическое моделирование и конструктивная эвристика. Дж. Чистый. Произв. 2019; 206: 251–266. [Google Scholar]
45. Чон Б.Дж., Ким Ю.Х., Ли К.С., Ча С.В., Нам Г.Дж., Пак С.Ю., Ли Г.Дж. Расчет параметров процесса изготовления изоляции коаксиального кабеля с использованием аксиоматического проектирования и метода Тагучи. Полим. Пласт. Технол. англ. 2008; 47(8):785–79.0. [Google Scholar]
46. Налбант Н., Гоккая Х., Сур Г. Применение метода Тагучи в оптимизации параметров резания по шероховатости поверхности при точении. Матер. Дес. 2007; 28:1379–1385. [Google Scholar]
47. Субулан К., Чакмакчи М. Технико-экономическое обоснование с использованием оптимизации на основе моделирования и метода экспериментального проектирования Тагучи для системы обработки материалов и перемещения в автомобильной промышленности. Междунар. Дж. Адв. Произв. Технол. 2012;59:433–443. [Google Scholar]
48. Дэйв С.В., Бхогайата А. Ориентированный на прочность расчет смеси для геополимерного бетона с использованием метода Тагучи и индийских норм расчета бетонной смеси. Констр. Строить. Матер. 2020; 262:1–12. [Академия Google]
49. Хоссейнпур-Лонбар М., Алави М.З., Паласси М. Выбор асфальтобетонной смеси с оптимальными свойствами разрушения при промежуточной температуре с использованием метода Тагучи для планирования эксперимента. Констр. Строить. Матер. 2020; 262:1–10. [Google Scholar]
50. Ikeagwuani C.C., Nwonu D.C., Ugwu C.K., Agu C.C. Оптимизация технологических параметров производства экологически чистого высокопрочного песчано-бетонных блоков по методу Тагучи. Гелион. 2020;6 1–14. [Бесплатная статья PMC] [PubMed] [Google Scholar]
51. Джошагани А., Рамезанианпур А., Атаеи О., Голроо А. Оптимизация водопроницаемой бетонной смеси для дорожного покрытия с использованием метода Тагучи. Констр. Строить. Матер. 2015;101:317–325. [Академия Google]
52. Bashar S., Veerendrakumar C., Muhd F. Оптимизация резинобетонной смеси с использованием методологии поверхности отклика. Дж. Чистый. Произв. 2018;171:1605–1621. [Google Scholar]
53. Бетику Э., Аджала С.О. Моделирование и оптимизация синтеза биодизельного топлива из масла Thevetia peruviana (желтый олеандр) с использованием кожуры Musa paradisiacal (подорожник) в качестве гетерогенного базового катализатора: случай искусственной нейронной сети и методология поверхности отклика. Инд. Культуры Прод. 2014;53:314–322. [Академия Google]
54. Мохит Х., Селван В.А.М. Оптимизация прочности на растяжение спеченных нанокомпозитов Al6061/SiC с использованием методологии поверхности отклика. Матер. Сегодня Продолжить. 2020;27:2801–2805. [Google Scholar]
55. Тосун Н., Когун С., Тосун Г. Исследование скорости разреза и съема материала при электроэрозионной обработке проволоки на основе метода Тагучи. Дж. Матер. Процесс. Тех. 2004; 152:316–322. [Google Scholar]
56. Аволуси Т.Ф., Оке О.Л., Акинкуролере О.О., Соджоби А.О. Применение методологии поверхности отклика: прогнозирование и оптимизация свойств бетона, содержащего стальную фибру, извлеченную из отработанных шин с порошком известняка в качестве наполнителя. Кейс Стад. Пост. Матер. 2019;10:1–21. [Google Scholar]
57. Фердосян И., Камоэнс А. Экологически эффективная разработка высокоэффективного бетона с помощью методологии поверхности отклика. Цем. Конкр. Композиции 2017; 84: 146–156. [Google Scholar]
58. Джитендра К., Хед В.К. Оптимизация бетонных блоков с большим объемом летучей золы и литейного песка. Матер. Сегодня Продолжить. 2020;27:1172–1179. [Google Scholar]
59. Nambiar E. K.K., Ramamurthy K. Модели, связывающие состав смеси с плотностью и прочностью пенобетона с использованием методологии поверхности отклика. Цем. Конкр. Композиции 2006; 28: 752–760. [Академия Google]
60. Рухоламини Х., Хассани А., Алиха М.Р.М. Оценка влияния макросинтетического волокна на механические свойства бетонного покрытия, уплотненного роликами, с использованием методологии поверхности отклика. Констр. Строить. Матер. 2018; 159: 517–529. [Google Scholar]
61. Васудеван С., Пурнима В., Балачандран М. Влияние добавок на свойства бетона и оптимизация с использованием методологии поверхности отклика. Матер. Сегодня Продолжить. 2020; 24: 650–661. [Google Scholar]
62. Ашенгроф М., Нахви И., Амини Дж. Применение дизайна Тагучи и методологии поверхности отклика для улучшения превращения изоэвгенола в ванилин покоящимися клетками Psychrobacter sp. CSW4, Иран. Дж. Фарм. Рез. 2013;12(3):411–421. [Бесплатная статья PMC] [PubMed] [Google Scholar]
63. де Фрейтас А. П.Б.Р., де Фрейтас Л.В., Лурес К.С.А., Гонсалвеш Л.Г., Сильва М.Б. Метод поверхности отклика и ортогональная матрица Тагучи применяются к фенольным сточным водам с помощью усовершенствованного процесса окисления (AOP) Am. Дж. Теор. заявл. Стат. 2014;3(6-1):35–41. [Google Scholar]
64. Чжан Л.В., Сожоби А.О., Кодур В.К.Р., Лью К.М. Эффективное использование и переработка смешанных переработанных заполнителей для более экологичной окружающей среды. Дж. Чистый. Произв. 2019; 236:1–27. [Google Scholar]
65. Авойера П.О., Акинмусуру Дж.О., Ндамбуки Дж.М. Производство зеленого бетона с использованием керамических отходов и латерита. Констр. Строить. Матер. 2016;117:29–36. [Google Scholar]
66. Бодиан С., Фэй М., Сене Н., Самбоу В., Лимам О., Тиам А. Термомеханические свойства необожженных кирпичей и обожженных кирпичей, изготовленных из смеси глинистого грунта и латерита. . J. Сборка. англ. 2018;18:172–179. [Google Scholar]
67. Yaragal S.C., Gowda S.N.B., Rajasekaran C. Характеристика и характеристики обработанных латеритных мелких заполнителей в цементных растворах и бетонах. Констр. Строить. Матер. 2019;200:10–25. [Google Scholar]
68. Джон В.М., Даминели Б.Л., Куалтроне М., Пиледжи Р.Г. Наполнители в цементных материалах — опыт, последние достижения и потенциал на будущее. Цем. Конкр. Рез. 2018;115:65–78. [Академия Google]
69. Зунино Ф., Скривенер К. Влияние эффекта наполнителя на потребность в сульфатах цементных смесей. Цем. Конкр. Рез. 2019; 126:1–10. [Google Scholar]
70. Аджао А.М., Огунбайо Б.Ф., Огундипе К.Е., Бамигбой Г.О., Огунде А.О., Тунжи-Олаени П.Ф. Оценка соответствия производителей пескобетонных блоков минимальным стандартным требованиям организацией по стандартизации Нигерии на юго-западе Нигерии. Междунар. Дж. Заявл. англ. Рез. 2018;13(6):4162–4172. [Google Scholar]
71. Амвросий Э.Э., Этим Р.К., Коффи Н.Е. Оценка качества серийно выпускаемых песчано-бетонных блоков в части штата Аква-Ибом, Нигерия. Ниг. Дж. Тех. 2019;38:3. [Google Scholar]
72. Одейеми С.О., Акинпелу М.А., Атоеби О.Д., Орире К.Дж. Оценка качества пескобетонных блоков производится в Адете, штат Квара, Нигерия. Ниг. Дж. Тех. 2018;37(1):53–59. [Google Scholar]
73. ФРН . первое изд. Лексис Нексис, Баттервортс; Южная Африка: 2006 г. Национальный строительный кодекс, Федеративная Республика Нигерия. [Google Scholar]
74. Нзех Р., Нзех Р.Э. Департамент гражданского строительства, Университет Нигерии; Нсукка, Нигерия: 2008 г. Стандартизация прочности песчано-бетонных блоков с помощью математического моделирования и точности. Кандидатская диссертация, кафедра гражданской инженерии, Университет Нигерии, Нсукка. [Академия Google]
75. СЫН . Стандартная организация Нигерии; Лагос, Нигерия: 2007 г. Нигерийский промышленный стандарт: стандарт для пескобетонных блоков, NIS 87. [Google Scholar]
76. Anya C.U., Osadebe N.N. Влияние частичной замены песка карьерной пылью на структурные характеристики пескобетонных кирпичей. Ниг. Дж. Тех. 2015;34(4):679–684. [Google Scholar]
77. Локешвари М., Джагадиш К.С. Экологически безопасное использование отходов гранитной мелочи в строительных блоках. проц. Окружающая среда. науч. 2016; 35: 618–623. [Академия Google]
78. Сингх С., Хан С., Ханделвал Р., Чу А., Нагар Р. Характеристики устойчивого бетона, содержащего отходы резки гранита. Дж. Чистый. Произв. 2016; 119:86–98. [Google Scholar]
79. Lemougna P., Wang K., Tang Q., Kamseu E., Billong N., Melo U., Cui X. Влияние добавления шлака и карбоната кальция на образование геополимера из затвердевшего латерита. . заявл. Глина наук. 2017; 148:109–117. [Google Scholar]
80. Хан К., Улла М.Ф., Шахзада К., Амин М.Н., Биби Т., Вахаб Н., Альжаафари А. Эффективное использование микрокремнезема, извлеченного из золы рисовой шелухи, для производства высокоэффективных производительность и устойчивый цементный раствор. Констр. Строить. Матер. 2020; 258:1–12. [Академия Google]
81. Yaragal S.