Газосиликат или поризованные керамические блоки?
Современный рынок строительных материалов постоянно расширяется. Производители предлагают все новые образцы продукции, используемой для возведения домов. Времена, когда обходились только древесиной или белым силикатным кирпичом, ушли навсегда. Сейчас каждый застройщик имеет возможность для самостоятельного выбора понравившегося материала. К сожалению, далеко не все варианты доступны широкому кругу застройщиков по стоимости. Поэтому люди, планирующие построить частный дом, должны определиться с выбором подходящего варианта еще на стадии разработки проекта.
В последние годы все популярнее и востребованные у различных категорий пользователей новые образцы строительных материалов, используемые для возведения несущих стен и перегородок строящихся загородных домах. Это газобетонные и керамические блоки. Цена у этих материалов, равно как и многие физико-механические параметры и свойства, схожи. Поэтому среднестатистический пользователь, не имеющий достаточного практического опыта по применению тех или иных стройматериалов, затрудняется в выборе.
Информация, представленная ниже, позволит сравнить газосиликатные блоки и аналогичные изделия из керамики, узнать их свойства и некоторые особенности. Ну а после этого можно будет принимать окончательное решение.
Область применения
Если планируется построить жилой дом, общая площадь которого не будет превышать 300 м2, то по мнению специалистов, лучшее решение – использовать газобетонные блоки. Если же общая площадь будет большей, целесообразно применять для возведения стен керамический блок. Важно понимать, что у одинаковых проектов выбор керамических блоков для строительства приведет к удорожанию дома не менее чем на 15%.
В целом, строительные блоки существенно увеличивают производительность труда. Кладка одного такого изделия заменяет 13 кирпичей, экономить не только время, но и раствор.
Еще один важный показатель – снижение общей массы дома, уменьшение нагрузки на цоколь и на фундамент. Все это приводит к повышению надежности и долговечности строения и ничуть не ухудшает такие параметры как прочность, устойчивость к нагрузкам и т.п.
В целом, специалисты рекомендуют использовать газосиликатные блоки для возведения домов высотой в 1, максимум – 2 этажа. Ну а для более высоких конструкций – идеальное решение – керамический блок!
Основные параметры материалов
Керамические блоки
Поризованный блок изготавливается из глины с добавлением тщательно подготовленных, измельченных опилок. В процессе производства смесь перемешивается с водой, доводится до состояния мягкого пластилина, укладывается в специальную форму и отправляется в печь. Здесь при температуре в 1000С происходит обжиг изделия, благодаря чему блок получает привлекательный красный цвет и прочные формы. Одновременно под воздействием высокой температуры в печи опилки, добавленные в смесь, выгорают, образуют многочисленные мельчайшие поры, которые вместе с пустотами, специально сформированными в процессе изготовления блока, придают изделию улучшенные технические характеристики.
Конструкция каждого блока разработана таким образом, чтобы обеспечить за счет вертикально расположенных пазов и специальных гребней плотное соединение между собой. В результате – по бокам во время кладки стены, цементный или клеевой состав не нужен. Гребни легко можно подогнать один к другому с помощью резинового строительного молотка. Кладочный раствор, клей для соединения блоков, используются только при укладке горизонтальных рядов каркаса дома.
Выгодные преимущества материала
Керамоблоки – это высококачественный строительный материал, который становится все более популярным у индивидуальных застройщиков. Оптимальный баланс цены и качества, улучшенные физико-механические параметры и свойства, позволяют активно применять поризованные керамические блоки в процессе возведения загородных домов, дач, коттеджей, различных строений на загородном участке.
Основные достоинства керамических блоков
- Высокая прочность, устойчивость к механической и статической нагрузкам.
Блоки легко выдерживают и кровлю, и балки перекрытия. При этом нагрузка на фундамент по сравнению с кирпичом в 2-2,5 раз меньше.
- Экономичность. Различные строительные материалы: клей, лак, краска и другие, а самое главное – цементный раствор, расходуется в меньших пропорциях, по сравнению с ранее применявшейся традиционной технологии.
- Высокая скорость возведения дома. Керамические блоки позволяют поднимать стены домов в среднем в 2-3 раза.
- Высокие теплоизоляционные свойства, звуконепроницаемость.
- Экологическая безопасность. Материал изготовлен из натуральных природных компонентов, в процессе эксплуатации не выделяет вредных веществ и абсолютно безопасен для жизни и здоровья людей.
- Устойчивость к воздействию внешней агрессивной среды – высокой влажности, перепадам температуры, морозам, солнечному ультрафиолету.
Технология производства газобетонных блоков отличается. Основные компоненты для изготовления здесь – цемент высоких марок прочности, измельченный до состояния пыли песок, вода и специальные газообразующие компоненты. Основные компоненты, позволяющие насыщать состав мельчайшими пузырьками газа – порошкообразный алюминий, а также гипс и известь. В результате простой химической реакции в смеси активно образуется кислород, который и вспучивает раствор. Подготовленный таким способом раствор поступает в дальнейшую обработку, укладывается в форму и доводится до нужной кондиции при поддержании температуры в районе 300С и давления -12 Бар. Далее полуфабрикат нарезается на блоки установленного размера и упаковывается для дальнейшего хранения или транспортировки.
К основным достоинствам газосиликатных блоков следует отнести:
- Высочайшую точность изготовления. Идеальные геометрические формы и размеры позволяют облегчить сам процесс строительства, повысить производительность труда и, естественно, качество!
- Низкая теплопроводность, отличная шумоизоляция.
- Материал не поддерживает горения, устойчив к воздействию открытого огня.
- Легко обрабатывать, придавать блокам определенную форму.
- Экологичность.
- Экономичность. Производство блоков обходится дешевле по сравнению с керамическими изделиями, соответственно и цена для потребителя на материал будет ниже.
На что обратить внимание, выбирая газосиликатные или керамические блоки
Прежде всего, необходимо оценить проект и обратить внимание на этажность дома. Керамоблоки имеют большую прочность на сжатие и их следует использовать при строительстве многоэтажных особняков. Если же кладка стен выполняется из газоблоков, необходимо предусмотреть и исполнить дополнительное армирование.
Морозостойкость, влагостойкость: здесь преимущества однозначно на стороне керамических блоков. Ведь они запекаются в специальных печах при максимально высоких температурах. Результат – каждый блок становится монолитным и практически не подвержен воздействию внешний природных факторов. Газосиликат такими свойствами не обладает.
Газосиликатные блоки имеют более строгие, идеально точные размеры. Поэтому их можно укладывать и отделывать, используя различные строительные материалы: клей, лак, краска и другие. Скорость возведения стен. Керамические блоки в 3 раза быстрее укладываются, а газосиликатные – не менее чем в 5 раз. Газобетон лучше поддается обработке. Соответственно, его применение позволяет принимать и воплощать любые дизайнерские и архитектурные решения. Легче подгонять различные конструктивные элементы, проще и точнее оформляются оконные и дверные проемы.
При проведении внутренних и наружных отделочных работ при использовании керамоблоков, застройщик обязательно столкнется с проблемой пустотелых стен. Сложно установить анкерный болт, сделать штробы под электропроводку, другие коммуникации. Обеспечить прочность и надежность их монтажа. В данном показателе газобетон однозначно выигрывает.
На первый взгляд, теплопроводность газоблока также лучше. Но это только до тех пор, пока материал не намокнет, не впитает в себя влагу, которой в наших географических широтах более чем достаточно.
Подведем итог
Очевидно, что в любом случае, окончательное решение при выборе того или иного строительного материала, остается за заказчиком. Здесь в расчет берутся не только технические параметры и цена, но и личные предпочтения. Тем не менее, следует помнить, что в целом, блоки из газобетона обходятся дешевле, но такой материал по многим параметрам, эксплуатационным показателям, уступает керамике!
Газосиликат или тёплая керамика? — Кирпичев
Рынок строительных материалов расширяется постоянно. Причин тому много: одни ресурсы исчезают, другие вредны, третьи ― непомерно дороги. Всё чаще появляются искусственные стройматериалы, качеством не уступающие натуральным, природным. К ним относятся керамо- и газоблоки. У керамоблоков вообще всё натуральное, искусственно только производство.
Керамоблоки и их характеристики
Керамические блоки изготавливаются из глины, куда добавлены опилки. Процесс компьютеризирован, поэтому в замесе полностью выдерживаются пропорции частей: глины, опилок и воды. Состав хорошо перемешивается, доводится до консистенции пластилина, формуется и отправляется в печь на обжиг. В печи около 1000°С. При такой температуре опилки полностью выгорают, образуя поры. Они-то вместе с формовочными пустотами делают керамику «тёплой».
Каждый керамоблок отформован так, что соседние блоки за счёт вертикальных пазов и гребней плотно смыкаются между собой и кладочный состав не нужен. Для подгонки гребней в пазы можно пользоваться резиновым молотком. Торцовые же грани имеют неглубокие борозды для надёжности оштукатуривания. Между горизонтальными рядами укладывается либо раствор, либо перлитовые смеси.
Размеры могут быть разными, но в одной кладке лучше использовать только одинаковые. Длина их ― 250-510 мм, ширина ― 230-250 мм. Причём кладка производится так, что толщину стены определяет длина блока, то есть он укладывается поперёк стены.
Особенности газоблоков
Газобетонные блоки производятся из цемента, песка, измельчённого до состояния пыли, газообразующей добавки и воды. В газообразующую добавку входят гипс, известь и порошкообразный алюминий. При быстром перемешивании алюминий вступает в химическую реакцию с гипсом и известью. Образуется водород, который вспучивает раствор (аналогично дрожжевому тесту).
Когда растущий блок заполнит форму, она убирается, и сырьё поступает в автоклав. При 300°С и давлении 12 атмосфер газоблок доходит до нужной кондиции. После извлечения полуфабриката из автоклава он нарезается на блоки определенного размера и упаковывается. Газобетон хорошо режется металлической струной.
Из-за воздушных пустот его нередко называют ячеистым бетоном, а из-за песчаной составляющей ― газосиликатным блоком. От количества ячеек зависит плотность. Стройматериал с малой плотностью относится к теплоизоляционным блокам, с большой ― к конструкционным. Наилучшая марка ― D500, считающаяся конструкционно-теплоизоляционной.
Так что же выбрать — керамический блок или газосиликат?
Проведем сравнительный анализ по основным характеристикам этих двух материалов:
Прочность. Газосиликатные блоки имеют марку по прочности М-35, а Теплая керамика в среднем – М-125. Это означает, что на газосиликатные блоки нельзя опирать плиты перекрытия, для этого требуется бетонный армопояс, и вообще из таких блоков здания выше двух этажей не строят. Керамические крупноформатные блоки при своей прочности позволяют опирать плиты перекрытия, а допустимая высота здания из них без применения специального монолитного каркаса – до 9 этажей.
Невысокая прочность на изгиб и низкая эластичность даже при незначительной подвижке фундамента приводят к глубоким трещинам в стенах из газосиликатных блоков. Теплая керамика имеет высокую прочность на изгиб.
Водопоглощение. У газосиликатных блоков высокое водопоглощение, что при эксплуатации здания приводит к адсорбции водяных паров из воздуха и влаги из земли с последующим резким увеличением коэффициента теплопроводности. Это означает, что теплозащитные качества такой стены значительно снижаются. Водопоглощение теплой керамики небольшое, и поэтому не происходит аналогичного насыщения блоков влагой, следовательно термическое сопротивление стены будет в норме.
Принимая во внимание, что в процессе эксплуатации происходит увлажнение газосиликата, и его коэффициент теплопроводности λ значительно увеличивается, стену из такого материала надо строить более толстой, чем из аналогичных (по значению коэффициента теплопроводности) керамических блоков.
Паспортный коэффициент λ измеряют в сухом состоянии. Соответственно, фундамент должен быть более широким и более дорогим по материалам и работе.
При возведении стен из теплых блоков толщиной 38 см, толщиной 44 см или толщиной 51 см утеплитель не требуется, что позволяет сэкономить, а при не очень большой толщине газосиликата утеплитель необходим.
Состав материала. При производстве поризованных керамических блоков используется глина и смешанные с ней опилки, выгорающие в процессе обжига и образующие внутренние поры внутри материала. То есть все используемые материалы экологичны и не вредны. Для производства газосиликата используются алюминиевая пудра, известь и цемент, а в результате химической реакции возникает водород, образующий поры. Алюминиевая пудра никогда не считалась безвредной для здоровья, и после завершения строительства газосиликатные стены еще в течение как минимум пяти лет продолжают выделять токсичные вещества.
Цементосодержащие материалы часто после завершения строительства дают усадку, что приводит к появлению трещин. Керамоблоки за счет низкого влагопоглощения этого недостатка лишены.
Остаточная известь в составе газосиликатных блоков способствует усиленной коррозии металла (арматуры, трубопроводов, монолитного каркаса и т.д.).
Пенобетонные блоки имеют небольшой срок службы и через 15-20 лет требуют полной замены.
При строительстве стены из газосиликата или пенобетона раствор кладется и на вертикальные, и на горизонтальные швы, что приводит к образованию мостиков холода. Крупноформатные керамические блоки имеют на боковых поверхностях пазы и гребни, которые входят друг в друга и не требуют использования раствора в вертикальных швах. Горизонтальные швы предпочтительно делать из теплого раствора с перлитовым наполнителем. Соответственно, не только повышаются теплозащитные свойства стены, но и значительно сокращается расход раствора.
Воздухопроницаемость. Блоки из поризованной керамики отлично дышат и работают наподобие термоса, сохраняя тепло зимой и защищая от излишней жары летом. При этом они отводят избыток влаги из помещения, никогда не покрываясь конденсатом и не провоцируя развитие плесени и грибка. Газосиликатные блоки этими свойствами не обладают и многократно проигрывают теплой керамике в процессе эксплуатации, в том числе и по стоимости отопления здания.
В сравнении со стандартным кирпичом скорость строительства из крупноформатных блоков в 4-5 раз выше, соответственно снижается стоимость работы. Поскольку керамоблоки заменяют 10-15 обычных кирпичей, расход раствора на их укладку сокращается в 3-4 раза по сравнению с кирпичом.
В последние годы в России и Белоруссии появилось много заводов по производству газосиликатных блоков с хорошим импортным оборудованием и соответственно хорошей геометрией и качеством поверхности получаемых блоков.
При этом не всем известно, почему вдруг возникли эти заводы. Ответ прост – газосиликатные блоки запрещены для возведения жилья в Европе, как опасные и вредные, а существовавшие там заводы срочно продают свое оборудование к нам, в Восточную Европу.
Стоимость материала. Средняя стоимость газосиликатного блока в 1,3-1,5 раза меньше, чем стоимость аналогичного блока из теплой керамики, но, учитывая все вышесказанное, не стоит экономить на самих блоках, поскольку использование теплой керамики ведет к сокращению расходов как при строительстве, так и при эксплуатации здания.
В последнее время все больше и больше людей начинают понимать преимущества теплой керамики и переходить на строительство домов из крупноформатных керамоблоков. Но все же очень велико количество тех, кто в погоне за кажущейся сиюминутной выгодой выбирает газосиликатные блоки.
Газобетонный блок — минусы и плюсы по сравнению с керамическим блоком
Сравнение газобетона с керамическим блоком
Сегодня застройщики выбирают современный стеновой материал и чаще всего они сравнивают газоблок (газосиликат, газосиликатный блок) и керамический блок (керамический камень, поризованная керамика, теплая керамика). Оба материала получили широкое распространение в последние 10-15 лет в России и сегодня доступны каждому.
Сравнение характеристик газоблока и керамического блока
У данных материалов есть общее черты – они хорошо держат тепло в доме, производство керамического и газосиликатного блока требует определённых современных технологий и дорогого оборудования. Но есть и различая, касающиеся марки прочности, морозостойкости, метода изготовления, стоимости. Различается также нормативный документ, определяющий основные характеристики продукции. Для керамического блока это ГОСТ 530-2012 «Кирпич и камень керамические», по которому выпускаются керамические полнотелые и облицовочные кирпичи. Для газобетонного блока это ГОСТ 31360-2012 «Изделия стеновые неармированные из ячеистого бетона автоклавного твердения. Технические условия».
Ниже мы сравним стеновые строительные материалы по характеристикам из открытых источников, чтобы вы сформировали своё мнение касательно материалов.
Характеристика сравнения |
Керамический блок |
Газобетон |
Марка прочности |
Керамический блок имеет стандартную марку прочности М100. Марка прочности (М750, М100, М125 и т.д.) показывает, какую нагрузку в кг выдерживает 1 см2 поверхности материала до начала разрушения.
Стандартная для керамических камней марка прочности М100 позволяет укладывать железобетонные плиты перекрытий на блоки, без армопоясов. |
Для бетонов (в том числе и газобетона) используется другая марка прочности, в котором значения определяются через букву В. Так, у газобетона марка прочности составляет от В1,5 и выше, что в переводе на прочность кирпича соответствует марке от М20 и до М50. |
Армирование кладки |
Для строительства индивидуального дома из керамического блока не требуется дорогостоящее армирование.
Марка прочности М100 позволяет укладывать плиты перекрытий в 5 этажей. Керамические камни с М125 применяются при строительстве 9 этажных зданий без монолитного каркаса. |
Для укладки ЖБ плит перекрытия на кладку из газобетона требуется армирующий пост. Данный пояс выполняется из армированного бетона или полнотелого кирпича. По сообщениям специалистов, без использования армирующего существует большая вероятность, что нагрузка будет передана неравномерно и плиту газоблок не выдержит. |
Изменение характеристик |
В кладке керамический блок себя ведёт также, как и сразу после изготовления. Он не меняет прочности, также хорошо паропроницаем, у него нет избыточной влажности и он не даёт усадки. |
После выхода из автоклава газосиликатный блок снижает свою влажность до нормального состояния – то есть продолжает отдавать влагу по чуть-чуть внутрь помещения. |
Морозостойкость |
Морозостойкость керамического блока составляет F50, что гарантирует 50 циклов заморозки и разморозки. Блок насыщают водой, после этого он 50 раз способен противостоять морозам до появления первых признаков разрушения. Такие испытания показывают, что при обычном использовании морозостойкости керамики хватает на 70-90 лет использования. |
Газосиликат гигроскопичен и впитывает влагу. Такой материал специалисты рекомендуют защищать от воздействия влаги, ведь при насыщении блок может впитать до 35% воды от своей массы, что существенно снижает тепловые и прочностные характеристики стены. |
Теплопроводность |
Теплопроводность керамического блока составляет 0,16-0,21 Вт/м*С
Керамический блок обладает высокими показателями теплоемкость – из-за своей плотности 900-1100 кг он накапливает тепло в своей структуре. |
Теплопроводность газосиликата составляет 0,12-0,14 Вт/м*С
Газосиликат обладает малой тепловой инерцией из-за плотности в 400-600 кг. Дом из газосиликата остывает быстрее, так как ячеистый бетон не накапливает тепло, он его просто сдерживает. Подробнее в книге «Строительная физика», В. Блази. |
Необходимость утепления |
При толщине стены в 51 см на территории Поволжья или 38 см южнее, керамический блок не требует утепления и может быть просто оштукатурен и покрашен. |
Из-за своего состава, газобетонные блоки принято обшивать экструдированным пенополистиролом, что придаём такому дому эффект «термоса» и увеличивает стоимость возведения стен. |
Цена за 1 м3 на март 2017 |
3200-3500 |
3200-3500 |
Вывод из сравнения газобетонного блока и керамоблока
Керамический блок и газосиликат являются близкими по характеристикам строительными материалам. У них есть отличия (например, в сырье: один изготавливается из глины, другой из бетона), и похожие моменты (это современные материалы и у них эффективные показатели теплопроводности). Окончательный выбор лежит на покупателе.
5 главных причин выбрать POROTHERM для строительства дома
0 Доступно, хорошо или быстро? Как правило, строя дом мы можем выбрать лишь две опции из перечисленных, особенно – в случае стеновых материалов. До недавнего времени их выбор был невелик – ячеистый бетон (газосиликат), деревянный брус, силикатный либо керамический полнотелый кирпич в сочетании с утеплителем. И правило «двух опций» для них работало всегда. К счастью, прогресс на месте не стоит, и в мире появились и стали широко использоваться крупноформатные керамические блоки или керамоблоки.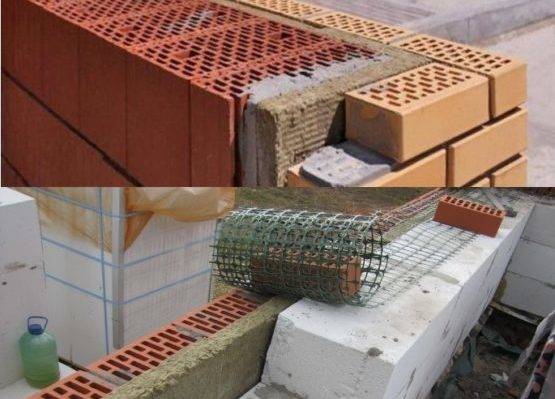
Тепло
Porotherm имеет незаурядные теплотехнические характеристики, превышающие соответствующие параметры у традиционных материалов.

Такими уникальными теплоизоляционными свойствами Porotherm 38 Thermo обладает за счет новой, более эффективной HV формы пустот и повышенной поризации керамического черепка. А собственно поризация появляется благодаря особенностям изготовления Porotherm: в глину добавляются мелкие древесные частицы. Выгорая при обжиге, они образуют сеть замкнутых микрокапилляров, которые не только хранят тепло, но и способствуют улучшению микроклимата – стены «дышат».
Толщина стены которая позволяет достичь сопротивления теплопередачи Ro=3,24(м2*С)/Вт. Данный показатель соответствует требованиям по теплозащите наружных стен практически на всей европейской территории России (в соответствии со СНиП 23-02-2003 «Тепловая защита зданий»).
Доступность и быстрота возведения стен дома
Часто считают, что строительство из керамических блоков – это дорогое удовольствие по сравнению с ячеистым бетоном и традиционным кирпичом. Так происходит потому, что сравнивается лишь стоимость стеновых материалов. Например, розничная цена ячеистого автоклавного бетона варьируется в пределах 3000-4500 руб/м3, а цена теплой керамики – 4000-5000 руб/м3, разница заметна. Однако все дело в деталях, если считать расходы на строительство в целом, то ценовое отличие между этими материалами нивелируется.
Керамические блоки Porotherm VS ячеистый бетон:
- кладка из крупноформатного керамического блока не требует армирования и сооружения монолитных железобетонных поясов, которое занимает не менее 30 дней;
- к отделочным работам можно приступать практически сразу после возведения стен, т.к. не требуют длительного просушивания;
- высокие теплоизоляционные свойства, которые дают возможность обойтись без утепления стен.
Керамические блоки Porotherm VS традиционный кирпич:
- соединение паз-гребень оптимизирует расходы на дополнительные материалы – вертикальные швы не заполняются кладочным раствором и его расход сокращается на 30%;
- один блок заменяет от 10 до 14 кирпичей в кладке, что существенно ускоряет процесс возведения стен;
- снижение трудозатрат по сравнению и экономия на оплате работ – рабочему при кладке кирпича потребуется в три раза больше времени, следовательно, вы заплатите в три раза выше мастерам за работу;
- каркас индивидуального жилого дома из керамических блоков может быть возведён за две недели без применения сложной строительной техники;
- высокие теплоизоляционные свойства, которые дают возможность обойтись без утепления стен.
В итоге, стоимость дома из керамоблока в сравнении с газосиликатом не превышает 5%, при заведомо лучших эксплуатационных качествах. Рассчитать количество блоков и их стоимость под площадь вашего будущего дома можно с помощью калькулятора Porotherm.
Продолжение читайте здесь.
Керамические блоки | Варбус
Керамический блок крупноформатный — это изготовленный из глины в отсутствии вредных примесей, стеновой материал. С его помощью можно возвести стены толщиной от 38 до 64 см, при этом не нужно использовать дополнительное утепление. Легко штукатурится и обкладывается облицовочным кирпичом. Крупноформатность керамического блока облегчает процесс кладки за счет легкости керамики и при этом экономится раствор . Прочность его достигает до 150кг на квадратный сантиметр. При своей высокой теплоизоляции керамический блок защитит жилище от шума. При толщине 12 см коэффициент звукоизоляции не менее 15дБ, а при 38см- 53дБ. Благодаря пустотам керамический блок обеспечивает тепло- и влагообмен. Образование грибка практически невозможно.
Керамические блоки – это экологически чистый стеновой строительный материал, изготовленный из глины. Он имеет широкий спектр применения, а также ряд преимуществ перед другими строительными материалами.
Хотите, чтобы Ваш дом был теплым и уютным, но все еще ищите экономически выгодный и доступный материал? Керамические блоки компании ООО «Варбус» — идеальный вариант!
Вы, несомненно, оцените следующие преимущества использования керамических блоков в качестве строительного материала:
Материал долговечен и прослужит Вам не менее 150 лет
Обладает самыми высокими характеристиками прочности в своем классе
Устойчив к холодам и морозам, что делает его идеальным для постройки сооружений во многих регионах нашей страны
Экологически чистый и безопасный, благодаря своему натуральному составу
Керамические блоки сохраняют тепло, что делает энергоэффективность материала достаточно высокой
Благодаря пористой структуре, материал способен поддерживать естественный комфортный микроклимат в помещении
Эффективно поглощает звук, тем самым снижая уровень шума в постройке
Керамические блоки – это безопасный строительный материал с точки зрения огнестойкисти
Экономически выгодный материал с точки зрения затрат на время строительства и трудозатрат, а также расхода раствора для укладки блоков
Имеет сравнительно небольшой вес, но при этом крупные размеры, что ускоряет и облегчает процесс строительства и снижает нагрузку на фундамент
Керамические блоки обладают гладкой поверхностью, что позволяет не выравнивать стены.
Если Вы еще не определились, где купить керамические блоки, цена на которые не будет завышена, то предлагаем Вам прекратить поиски и обратить свое внимание на наше предложение.
У нас Вас ожидает широкий ассортимент, состоящий из восьми различных модификаций керамических блоков. Материал отличается по размерам, техническим характеристикам и цене. Каждое изделие проходит тщательную проверку, весь строительный материал сертифицирован и соответствует принятым стандартам качества.
Вы легко подберете для себя необходимый вариант, который полностью устроит Вас по цене.
Область применения керамических блоков в строительстве не маленькая, поэтому если Вы ищите материал для постройки жилых или промышленных зданий высотой не более 9-ти этажей, или же выбираете, чем лучше произвести облицовку здания, то знайте, керамоблоки – это именно то, что Вам нужно.
Мы предлагаем Вам лучший материал в Нижнем Новгороде по оптимальной цене. Наши керамические блоки выполнены из натуральной глины и не имеют вредных химических добавок, способных влиять на здоровье человека.
Использование импортного оборудования при производстве блоков позволяет добиться идеальных форм и размеров, что напрямую будет влиять на выравненность Ваших стен.
Мы предлагаем не просто выгодные цены на керамические блоки и другие строительные материалы, мы готовы применять к каждому нашему клиенту индивидуальный подход и предоставлять гибкую систему скидок.
Итак, Вы уже решили приобрести в нашей компании керамические блоки, но у Вас остались вопросы? Заказав звонок на нашем сайте, Вы сможете получить более подробную информацию о качестве, цене, скидках на товары, технических характеристиках строительных материалов. Наши специалисты круглосуточно отвечают на телефонные звонки или перезванивают Вам сами.
После подробной консультации Вы сможете заказать керамические блоки сразу на нашем сайте. При необходимости мы оформляем услугу доставки, или же Вы самостоятельно можете вывезти заказанный материал по указанному адресу.
Наша компания поставляет керамические блоки произведенные на импортном оборудовании обеспечивающим идеальный размер, что дает в последующем ровные стены, а его рифленая поверхность делает возможным экономично штукатурить.
Как построить газосиликатный дом
Газосиликатные блоки – строительный материал с отличными качествами. Здания, возведенные с помощью газосиликата, одновременно сочетают в себе свойства деревянных и кирпичных домов.
Как построить газосиликатный домНеобходимо
- — уровень;
- — лопата;
- — колья деревянные;
- — леска;
- — песок;
- — прутья железные;
- — бетон;
- — блоки бетонные;
- — раствор цементный;
- — балки;
- — пергамент;
- — гидроизоляционный материал;
- — блоки газосиликатные;
- — клей;
- — кирпичи;
- — сетка кладочная;
- — отделочный материал.
Инструкции
Шаг 1
Определите расположение будущих комнат, иначе говоря, мысленно представьте свой уже построенный дом: здесь будет спальня, а будет гостиная, рядом с которой будет располагаться ваш кабинет… Такая планировка крайне необходима, потому что в данный момент создается проект дома.
Шаг 2
Сделать фундамент. Для этого разметьте фундамент, выкопайте траншею, а затем соберите и поставьте опалубку из досок (она крепится саморезами).Поместите песок под фундамент в качестве подушки. Затем установите арматуру и залейте фундамент бетоном (высота должна быть примерно 650 мм).
Шаг 3
Построить цоколь из бетонных блоков, уложенных в три ряда. Скрепите бетонные блоки между собой цементным раствором.
Шаг 4
Уложить двойной слой гидроизоляции на встроенный цоколь, а также предварительно обернутые пергаментом балки.
Шаг 5
Укладка первых газосиликатных блоков на гидроизоляционный слой.Есть два способа построить дом из газосиликата. Первый способ – выложить версту из кирпича, а затем версту из газосиликатных блоков. С помощью армирующей кладочной сетки обвязываются кирпичи с газосиликатными элементами. В этом же случае для утепления стен между кирпичом и газосиликатным блоком укладывают пенополистирольный утеплитель. Второй способ строительства дома из газосиликата предполагает возведение строительной коробки из газосиликатных блоков и последующее производство наружных отделочных работ (сайдинг, штукатурка или другие способы отделки фасада дома).
Силикатный кирпич – обзор
6.8.2 Высокотемпературная карбонизация (ВТК)
Высокотемпературная карбонизация проводится при температуре от 900 до 1200°C. Основной целью этого процесса является получение твердого некреативного кокса, подходящего для металлургических применений. В частности, кокс, полученный при температуре 900°C, подходит для применения в литейном производстве, в то время как кокс доменной печи производится при температуре от 950 до 1050°C. Еще при более высокой температуре 1100–1200 ° C кокс производится методом коксовой печи Beehive Coke и зарезервирован для некоторых специальных применений.В Таблице 6.12 ниже показаны спецификации ISI коксов, полученных в процессе HTC.
Таблица 6.12. Свойства кокса (спецификация ISI)
Walatile Motal | 2,0% |
фосфор в кокса | 0,30% (максимум) |
Пористость | 35 — 48% |
Micum-index на 40 мм | 75% |
Micum-index ниже 10 мм | 14% (максимум) |
Shipping Index на 38 мм | 85 % (максимум) |
Индекс разбитости на 12.![]() | 97 (минимум) |
Коэффициент стабильности по Гавену на 1 дюйм | 40 минимум |
На практике для получения кокса с указанными характеристиками смешивают угли разных сортов. Для этого необходимо знание коксохимических свойств различных углей. Как правило, коксующиеся свойства угля ухудшаются при хранении, и если не принять надлежащих мер предосторожности для предотвращения окисления, то будет установлено, что кокс, полученный в процессе HTC, имеет более низкое качество.
Дилатометрические исследования в постпластической зоне показывают наличие двух пиков скорости сокращения, связанных с первичным и вторичным влиянием, вызывающим трещины. Основная сила, образующая трещины, имеет тенденцию контролировать размер кусков на выходе из коксовой печи. Второе влияет на менее грубую систему трещин, которые проявляются только при более сильных нагрузках на образованные таким образом куски, как, например, при испытании на разрушение; отсюда взаимосвязь между высотой первого и второго пиков на кривой скорости усадки и размером кокса и прочностью на разрушение соответственно. Ни коксовая мелочь, ни антрацит не проявляют сжатия в области первого пика сжатия, в то время как при температуре второго пика или вблизи нее антрацит сжимается. Если вышеуказанное соотношение верно, то добавление антрацита или мелочи к коксующемуся углю должно уменьшить первый пик и увеличить средний размер кокса, получаемого из такой смеси. Точно так же уменьшение второго пика за счет добавления мелкой мелочи должно привести к улучшению индекса разрушения кокса. Однако антрацит, который не может в такой же степени повлиять на второй пик, должен оказывать заметное влияние.Все эти постулаты проверены экспериментально. Кроме того, было показано, что кальцинирование антрацита и снижение содержания в нем летучих веществ постепенно снижает его второй пик скорости усадки. Сравнение коксов, приготовленных без каких-либо добавок, с необработанным антрацитом и с прокаленным антрацитом, показало, что необработанный антрацит влиял только на средний размер, тогда как прокаленный антрацит в большей степени увеличивал средний размер и улучшал ударопрочность, подтверждая тем самым предполагаемую взаимосвязь.
Однако количество бриза и антрацита, которые могут быть включены в смесь, может быть ограничено их влиянием на стойкость к истиранию; оба вызывают ухудшение после определенных уровней добавления, в зависимости также от сортности. При использовании высоколетучих углей компенсировать это могут более текучие низколетучие энергетические угли, и там, где необходим контроль размера, прочности и стойкости к истиранию, эти энергетические угли выполняют важную функцию. Классификация по размеру модификатора коксования важна, и обычно он тонко измельчен.Крупные инертные частицы неправильной формы создают напряжения и распространяют трещины по мере того, как полукокс сжимается вокруг них, ослабляя коксовый продукт и снижая его стойкость к истиранию, тем самым ухудшая фактор, а не улучшая свойства.
Исследование пилотной установки HTC, проведенное Dasgupta et al (CFRI, Dhanbad), выявило критические параметры конструкции и эксплуатации. На рисунках 6.48 и 6.49 показан вид этой пилотной установки, а на рисунке 6. 50 показана схема извлечения побочных продуктов. На этом заводе батарея печей состоит из трех печей 14 в., 16 дюймов и 18 дюймов средней ширины, 4 фута в высоту и 9 футов в длину. Печи построены из чистого силикатного кирпича и имеют емкость 980, 1100 и 1180 кг угля на одну загрузку. Печи по-прежнему комбинированного регенеративного типа с общим газовым обогревом, и каждая печь снабжена 8 нагревательными желобами, 4 на напорной и 4 на коксовой стороне, и 2 самоочищающимися дверцами, 2 загрузочными отверстиями и 1 подъемной трубой (для выхода газообразные продукты). Каждая нагревательная стенка снабжена регенераторной камерой, состоящей из двух частей, для облегчения нагрева как газа, так и воздуха в случае сжигания обедненного газа.Механизм реверсирования нагревательного газа в основном работает, и реверсирование производится каждые 30 мин. Отработанные газы регенераторов поступают в нижеупомянутый дымоход через тепловые коробки и выводятся в атмосферу. Суточная пропускная способность батареи в сухом состоянии составляет около 3500 кг при верхней заправке и 3850 кг при штемпельной заправке с температурой дымовых газов.
1250°С. Время карбонизации для 14-, 16- и 18-дюймовых печей составляет около 14, 17 и 19 часов соответственно. Тележка с электроприводом, снабженная дверным экстрактором, выталкивает шихту из печей на облицованный кирпичом коксовый причал через направляющую для кокса.Раскаленный кокс гасится водой из шланга. Таранная машина также снабжена выравнивателем и устройством для штамповки или сжатия шихты. Штампованная шихта вводится в печь сбоку. Кокс с пристани может быть доставлен в систему просеивания кокса для разделения на фракции размером + 38 мм, 40–13 мм и 18–13 мм или может быть просеян вручную до большего диапазона размеров от 6 до 0,5 дюйма. , как это обычно делается.
6.48. Вид на пилотную батарею со стороны толкателя.
6.49. Побочный завод.
6.50. Технологическая схема секции побочного продукта пилотной установки высокотемпературной карбонизации.
Газообразные продукты карбонизации по чугунному подводу и газопроводам (4 шт.) поступают к первичным охладителям (конденсаторам вертикальным трубчатым диаметром 400 мм, высотой 600 мм и площадью охлаждения 30 м 2 поверхности охлаждения на каждый, с циркуляция материала внутри труб) по одной на каждую печь для конденсации смолы и щелока в газах. Выходящие газы из первичных охладителей смешиваются и проходят через обычный электростатический детарер для удаления смолистого тумана, все еще остающегося в газе. В детарере подается напряжение около 30 000–40 000 В. Затем газы всасываются радиальным дымососом (предусмотрен также один резервный), который подает около 250 мм водяного столба в конечный охладитель (вертикальный трубчатый конденсатор диаметром 4000 мм, высотой 5000 мм и поверхностью охлаждения 25 м 2 ) при газы проходят через аммиачный скруббер с 1 дюйм.берл-седла в двух секциях; вода распыляется сверху со скоростью 25 галлонов/ч (диаметр 400 мм, высота 10 000 мм и площадь поверхности 260 м 90 143 2 90 144).
Содержащиеся в газе NH 3 и часть H 2 S поглощаются водой, и эта вода из скруббера уходит в канализацию. Наконец, газы поступают в газгольдер емкостью 3 объемом 150 м, из которого часть газа возвращается в печи для нагрева. Предусмотрена циркуляция части газа в основной газовый поток перед дымососом для регулирования всасывания дымососа. Конденсированная смола и щелок из газопровода собираются в резервуаре для сбора смолы. Конденсат из охладителей, электродетарера и эксгаустера собирается в низкоуровневой емкости и перекачивается обратно в емкость для улавливания гудрона, откуда поступает в приемную емкость (диаметр 1000 мм, высота 1200 мм) и перекачивается в декантер, в котором деготь и ликер разделяются под действием силы тяжести. Диаметр декантера 800 мм, высота 6500 мм. Густая смола со дна собирается в цилиндрический накопительный бак, а раствор из верхней части декантера переливается в промежуточный сосуд, где постоянный поток возвращается в приемный бак и соединяется с основным потоком конденсата.Избыток жидкости из промежуточного сосуда может быть слит. Часть раствора из верхней части декантера нагревается за счет рециркуляции в конической нижней части перед тем, как перекачивается в восходящие трубы для распыления. На рис. 6.51 показаны результаты карбонизации в трех печах. На прогресс карбонизации указывает зависимость температуры коксовой массы от времени для трех печей при температуре дымовых газов около 1250°С.
Центр коксовой массы остается при температуре около 100°C в течение 4, 6 и 10 ч для 14, 16 и 18 дюймов.широкие печи.
6.51. Скорость карбонизации в трех печах.
Более или менее такая же практика используется в реальной эксплуатации коксовых печей на сталелитейных заводах, но для извлечения побочных продуктов на начальной стадии используется промывочное масло для извлечения «бензольной» или легкой нефтяной фракции (кипящая 170 °С). Эта фракция преобладает в бензоле (70%), толуоле (20%) и ксилоле (4%). и имеют коммерческое значение для извлечения этих химикатов, встречающихся в высоких концентрациях на первой стадии.Промывочное масло обладает свойством растворять BTX, его можно регенерировать и использовать снова. Стандартная промывочная нефть – нефтеперегонный завод, фракция 230–300°С. Для извлечения бензола путем абсорбции были предложены различные типы масел. Так, были предложены тетралин, каменноугольное масло (креозотовая фракция), зеленое антраценовое масло и различные нефтяные фракции, но из них получили повсеместное применение только креозотовое масло и нефтяное масло. Работа в CFRI, Дханбад также привела к выбору выбранных фракций HTC и LTC гудрона для извлечения бензола.Фракции смолистого масла HTC оказались более эффективными, чем нефтяное масло, для поглощения бензолов (90–95% газа) в последних исследованиях. Характеристики низкотемпературного дегтярного масла сравнимы с показателями высокотемпературного дегтярного масла в отношении характеристик поглощения бензола.
ТОП-3 крупнейших покупателей силикатных блоков в 🇰🇪 Кении
Показать все Трейдинг Производство
Товары Блоки силикатные оптом
Торгово-скупочная компания
Вы хотите найти новых клиентов, покупающих силикатные блоки оптом
Blue Nile Rolling Mills Ltd.
Материалы для печей: Блоки силикатно-кальциевые-600х150х40мм- дтлс по инв/пл
Момбаса Цемент Лтд.
Блоки силиката кальция (600x100x100 мм
Transmara Sugar Co.ltd.
Hil производит блок из силиката кальция 1100 град.
класс c (hysil h 1100) размер: 900 x 600 x 25 мм
менеджер по логистике в ЕС, Азию
логистика, сертификат
электронная почта: [email protected]
Крупнейшие производители и экспортеры силикатных блоков
Компания (размер) | Продукт | Страна |
1.🇯🇵 Kubota Matsushita Denko Exterior (2) | Кирпичи, блоки, плитка и другая керамика Good Siliceous Earth | Япония |
2. 🇨🇳 Otto Junker Metallurgical Equipment (2) | ЗАПАСНЫЕ ЧАСТИ ДЛЯ ОДНОГО КОМПЛЕКТА ОБОРУДОВАНИЯ ДЛЯ ТЕРМИЧЕСКОЙ ОБРАБОТКИ НАПРАВЛЯЮЩАЯ ПАРА, АЛЮМИНИЕВОСИЛИКАТНЫЙ ВОЛОКОННЫЙ ТРОС, ВЕНТИЛЯТОРЫ, ШЛАНГИ, ПОДШИПНИКОВЫЕ БЛОКИ, СТАЛЬНЫЕ БЛОКИ , РЕМНИ, ПНЕВМАТИЧЕСКИЕ ЦИЛИНДРЫ, ЭЛЕКТРОМАГНИТНЫЕ КЛАПАНЫ, ОДНОХОДОВЫЕ КЛАПАНЫ | Китай |
3. 🇯🇵 Kubota Matsushitadenko Exterior Works Ltd.(2) | Кирпичи, блоки, плитка Керамика, ископаемые кремнеземы, кирпич | Япония |
4.![]() | Кирпичи, блоки, плитка и другие керамические изделия Керамические, кремнеземные ископаемые Кирпичи, блоки, плитки и другие керамические изделия Плитка А | Бразилия |
5. 🇨🇳 Evergreen Marine Corp. (Taiwan) Ltd. (1) | Без абестос-цемента, других материалов из силиката кальция и блочной изоляции Hs | Китай |
СИЛИКАТНЫЕ БЛОКИ оптовая цена в Кении
Товар | Блоки силикатные цена за кг,т | Масса | |
---|---|---|---|
Известь полировочная технологическая Ту 4422-001-21061342-93 Известь гашеная мелкодисперсная.Порошковый продукт сжигания известь-магресиальные карбонаты Rocks | $ 1 / кг | $ 1 / кг | 10-100 кг |
$ 0.3 на KG | $ 0.3 — 1.000 кг | 100 — 1.000 кг | |
Lime Gunhueed Maerker Super 40 | $ 0.5 / кг | 1.000 — 10.000 кг | |
Известь в MCR ГОСТ 9179-77 (Unextedended) | $ 93,5 за MT | выше 10 мл | |
Аэробрионные бетонные блоки | $ 0,1 за KG | 100 — 1.![]() | |
Настенный газовый блок — это строительный газобетонный блок из сотового бетона unreinforced | $ 0,1 / кг | $ 0,1 / кг | 1.000 — 10.000 кг |
Волоконно-волокна (стекловолокна) | $ 4.1 / кг | 10-100 кг | |
Огнеупорные кирпичи для строительства стеклянных печей: силлиманитный огнеупорный кирпич | $ 10.8 на кг | 100 — 1.000 кг | |
Огнеупорные продукты общего назначения | $ 1.5 / кг | 1.000 — 10.000 кг | |
Огнеупорные кирпичи | 2186 долл. США за тонну | свыше 10 тонн | |
Ситал Силикатный бланки для белого цвета. Стеклокерамические непрозрачные (белые) пористые монолитные цилиндрические блоки (диаметр 30 мм | 917 $/кг | 10-100 кг |
Силикатные блоки Склад
- Склад в Найроби
- Силикатные блоки в Момбасе
- Склад Кисуму
- Накуру Кения
- Склад Элдорет Кения
Просмотрите эту статью:
Лицо: Неглинова Катя 28 января 2022 г.
Образование: Национальный университет Цин Хуа, Тайвань
© Copyright 2016 — 2022 «Экспорт из России».Все права защищены. Сайт не является публичной офертой. Вся информация на сайте носит ознакомительный характер. Все тексты, изображения и товарные знаки на этом веб-сайте являются интеллектуальной собственностью их соответствующих владельцев. Мы не являемся дистрибьютором бренда или компаний, представленных на сайте, Политика конфиденциальности
Форма / Форма: | |||
Ваш выбор… | |||
Футеровка – модульная/секционная | Модульные или секционные системы футеровки состоят из ряда взаимосвязанных компонентов, которые соединяются или складываются вместе, образуя защитную футеровку печи.![]() | ||
Плитка | Плитка состоит из плоской тонкой керамической формы, обычно со скошенными краями для облицовки или покрытия поверхности. Плитка может иметь квадратную, прямоугольную, шестиугольную, треугольную, круглую или нестандартную форму.Плитка часто имеет защитную глазурь для создания водонепроницаемой или водостойкой поверхности.![]() | ||
Держатель / держатель пластин | Держатели и держатели пластин представляют собой специализированные устройства для обработки кремниевых или составных (GaAs) полупроводниковых пластин. Керамика используется для изготовления подложек из-за ее коррозионной стойкости и огнеупорности.Пластины устанавливаются на держатели или удерживаются ими во время нарезки, полировки, притирки, утончения, химико-механической планаризации (ХМП), осмотра или других операций. | ||
Пластина/подложка | Керамические изделия в виде тонких подложек и пластин используются в полупроводниковых технологиях, при осаждении тонких и толстых пленок и в оптоэлектронике.![]() | ||
Стержень | Складские изделия доступны в виде стержня или прутка круглого сечения. | ||
Ролик / Рулон | Валки или ролики представляют собой трубчатые или полые компоненты, используемые в подшипниках, качениях и погрузочно-разгрузочных работах.Керамические ролики являются ключевым компонентом гибридных керамических роликоподшипников. Валики из керамики или плавленого кварца используются в печах для обработки или перемещения горячего листового стекла или других термически обработанных материалов. | ||
Носик/сопло (для заливки/распыления) | Разливочные сопла или отверстия используются для направления или измерения потока расплавленного металла или других расплавленных материалов.![]() | ||
Трубка | Трубная заготовка имеет одно центральное отверстие или внутренний диаметр.Трубки обычно используются в качестве нагревательных элементов, для защиты термопар или для направления расплавленного металла. | ||
Плита/плита (например, ДВП) | Складские продукты доступны в виде сплошной плиты, плиты, доски или подложки.![]() | ||
Порошок/агрегат (зерно/грог) | Складские продукты доступны в форме частиц, такой как порошок, грог, зерно или сплавленный и измельченный заполнитель. | ||
Прекурсор / Золь-гель | Стандартные или стандартные продукты доступны в виде жидкого, твердого или газообразного химического прекурсора или химических компонентов в виде золь-геля. Золь-гель керамика изготавливается с использованием химических веществ-предшественников алкоксидов. | ||
Изготовленная / нестандартная форма | Материалы изготавливаются в форме нестандартной формы или формы для конкретного применения, такой как тигель, седло клапана, лопасть, обожженный кирпич или блок нестандартной формы, плитка с нестандартным контуром, диффузор, футеровка печи, дегазатор и сборный цемент или бетонная конструкционная форма.![]() | ||
Инструменты для литейного производства / плунжера (мешалка, пробка и т. д.) | Литейные или плунжерные инструменты предназначены для погружения в расплавленный металл и помогают в обработке и разливке металлических расплавов. К литейным и плунжерным инструментам относятся стержни для перемешивания, смесительные лопасти, ковши, скиммеры, трубки для дегазации, роторы для дегазации, стояки и стопорные стержни.Плунжерные смесители или стержни для перемешивания погружают в расплавленные материалы для взбалтывания, перемешивания или отбора проб расплава металла или стекла, чтобы обеспечить постоянную однородность. Стопорные стержни используются для контроля потока и перемешивания расплавленного материала в тигле, ковше, котле или печи.![]() | ||
Наконечник / ушко | Наконечники и люверсы представляют собой керамические компоненты цилиндрической формы с центральным отверстием для защиты или прокладки.Огнеупорные втулки обеспечивают наилучшую возможную защиту уязвимых участков входных патрубков котлов и металлических трубных решеток в установках регенерации серы (SRU), установках риформинга метана и котлах-утилизаторах (КУ). Люверсы используются в текстильной промышленности и в направляющих для износа. Керамические наконечники или стойки используются в печатных платах, оптоволоконных и радиочастотных и микроволновых устройствах. Электронные наконечники или стойки требовали хороших диэлектрических свойств. Оптические керамические наконечники используются для выравнивания оптического волокна.![]() | ||
Фильтр/диффузор | Барботеры или диффузоры представляют собой пористую керамику, используемую для вдувания мелких пузырьков газа в расплав металла для удаления примесей, твердых частиц или других вредных газов расплава, раскисления расплавов и обеспечения химических реакций. Фильтры из пористой керамики используются для удаления примесей путем пропускания расплавленных материалов через фильтр. | ||
Пруток | Изделия на складе доступны в виде стержня или стержня, как правило, квадратного сечения. Заготовки могут иметь прямоугольную, овальную, шестиугольную или другую форму. | ||
Трубка/оболочка – погружная (закрытый конец) | Трубки с оболочкой, погружные или закрытые на конце предназначены для защиты нагревательных элементов, горелок или других устройств в высокотемпературных печах от погружения в расплавленные металлы, стекло или другие расплавленные материалы.![]() | ||
Мебель для печи / Опора | Балки, стойки, установщики, опоры, ролики, перегородки, вагонетки, лодки, полки или другие компоненты используются для поддержки, перемещения и обработки продуктов или сырья в печах или печах. | ||
Блок | Блоки — это строительные материалы или блоки кладки, состоящие из обожженных керамических или цементных материалов правильной формы.Блоки обычно имеют прямоугольную форму, хотя специальные формы используются для мощения, огнеупоров, декоративных и других специальных применений. Огнеупорные или шамотные блоки изготавливаются из термостойких материалов. Огнеупорные блоки укладываются друг на друга, образуя изолирующие стенки печи, котла или другого сосуда для термического процесса. Огнеупорные блоки обычно скрепляются огнеупорным раствором.![]() | ||
Логика поиска: | Все продукты с ЛЮБЫМ из выбранных атрибутов будут возвращены как совпадения.Снятие всех флажков не ограничит критерии поиска для этого вопроса; товары со всеми параметрами атрибутов будут возвращены как совпадения. | ||
Полый шток/форма? | Материалы поставляются или доступны в виде полых труб, труб или другого материала с открытым внутренним отверстием. | ||
Логика поиска: | Ограничение критериев «Обязательно» и «Не должно быть» возвращено
соответствует указанному.Товары с необязательными атрибутами
будет возвращен для любого выбора.![]() | ||
Продукция
Кварцевые кирпичи Super Duty
Сверхпрочные кремнеземные кирпичи для стекловаренной печи Firebird изготавливаются из принадлежащего заводу минерала кремнезема высокой чистоты, спеченного в газовой печи с нисходящей тягой.
Кирпичи отличаются высокой чистотой (высокое содержание SiO2, низкое содержание Fe2O3, низкий коэффициент текучести), высокой огнеупорностью под нагрузкой, высоким содержанием тридимита, высокой плотностью и высокой прочностью, низкой истинной плотностью, низким расширением и низкой скоростью ползучести, точными размерами. толерантность.
Типичное применение
Коронка и надстройка стекловаренной ванны и регенераторов.
Типовые индексы
Гарантия | Типичный | Гарантия | Типичный | ||
SiO 2 | ≥ 96 | 96.![]() | ≥ 96 | 96.1 | |
Fe 2 О 3 | ≤ 0,7 | 0,61 | ≤ 1,0 | 0,8 | |
СаО | % | ≤ 2,5 | 2,24 | ≤ 2.5 | 2,35 |
Коэффициент потока AI 2 O 3 +2(K 2 O+Na 2 O) | ≤ 0,5 | 0,44 | ≤ 0,7 | 0,60 | |
Огнеупорность | °С | 1710 | 1710 | 1710 | 1710 |
Кажущаяся пористость | % | ≤ 21 | 18 | ≤ 22 | 20 |
Объемная плотность | г/см 3 | 1.83 | 1,88 | 1,83 | 1,87 |
Истинная плотность | г/см 3 | ≤ 2,34 | 2,32 | ≤ 2,34 | 2,32 |
Прочность на раздавливание в холодном состоянии | МПа | ≥ 35 | 45 | ≥ 30 | 38 |
0.![]() | °С | ≥ 1680 | 1695 | ≥ 1680 | 1690 |
Постоянное линейное изменение (°C x 2 ч) | % | 0~+0,2 1450 | +0,1 | 0~+0,3 1450 | +0.2 |
20-1000°C Тепловое расширение (x10 6 /°C) | % | 1,25 | — | 1,25 | — |
Остаточный кварц | % | ≤ 1 | 0,3 | ≤ 1 | 0.7 |
Корундовые кирпичи
Типовые индексы
Товар | Высокая чистота Корундовый кирпич | 99 Корундовый кирпич | 90 Корундовый кирпич | Корунд-миллит Кирпич | |
Ал 2 О 3 | % | ≥ 99.![]() | ≥ 98,5 | ≥ 90 | ≥ 80 |
SiO2 | % | ≤ 0,15 | ≤ 0,3 | ≤ 8,5 | ≤ 18,5 |
Fe 2 О 3 | % | ≤ 0.1 | ≤ 0,2 | ≤ 0,2 | ≤ 0,3 |
Насыпная плотность | г/см 3 | ≥ 3,25 | ≥ 3,25 | ≥ 3,1 | ≥ 2,9 |
Кажущаяся пористость | % | ≤ 18 | ≤ 18 | ≤ 18 | ≤ 18 |
Прочность на раздавливание в холодном состоянии | МПа | ≥ 100 | ≥ 100 | ≥ 120 | ≥ 120 |
Огнеупорность под нагрузкой (0.2МПа, 0,6%) | °С | ≥ 1700 | ≥ 1700 | ≥ 1700 | ≥ 1700 |
Линейное изменение нагрева (1600°C x 8 ч) | % | -0,2 | -0,2 | 0,2 | 0,2 |
Тепловое расширение x 10 -6 (комнатная температура, до 1300°C) | 8.![]() | 8.1 | 8.1 | 7,6 | |
Типичное применение | В основном используется для ключевых частей промышленных печей из стали, электроники, нефтехимии, удобрений, цветных металлов, огнеупоров и т. д. |
Муллит Силлиманит Андалузит
Кирпич муллитовый, силлиманитовый, андалузитовый серии скрепленный
огнеупорные кирпичи в основном содержат кристаллическую структуру
муллитовая фаза (3Al2O3·2SiO2), стеклофаза (SiO2) и
корундовый фосфат (Al2O3) после высокой температуры
спеченный.Кирпичи обладают характеристиками высокой
огнеупорность под нагрузкой, хороший термоудар
сопротивление, хорошая способность сопротивления эрозии и
малая скорость ползучести и др.
Типичное применение
В основном используется в верхней части стекловаренной печи, регенераторе, оловянной ванне, канале, накладке и копателе. А также сталелитейная промышленность воздухонагревателей, доменных печей и др.
Типовые индексы
Предметы | Муллитовый кирпич | Силлиманитовый кирпич | Андалузитовый кирпич | ||||
класс | МУ-75 | МУ-70 | SIL65 | SIL60 | ХЗ65 | ХЗ60 | |
Ал 2 О 3 | % | 75.3 | 73,8 | 66,8 | 60 | 65 | 60 |
SiO 2 | % | 23.28 | 24,5 | 30,7 | 38 | 33 | 38 |
Fe 2 О 3 | % | 0.12 | 0,17 | 0,31 | 0,6 | 0,9 | 0,8 |
Насыпная плотность | г/см 3 | 2,77 | 2,67 | 2,53 | 2,5 | 2,45 | 2.![]() |
Кажущаяся пористость | % | 15 | 16,3 | 16,8 | 17 | 18 | 19 |
Прочность на раздавливание в холодном состоянии | МПа | 140 | 140 | 140 | 80 | 80 | 80 |
0.2 МПа Огнеупорность под нагрузкой | ℃ | 1700 | 1700 | 1670 | 1600 | 1650 | 1600 |
Линейное изменение нагрева (1600 ℃ × 3 ч) | % | 0,2 | 0,2 | 0.2 | 0,2 | 0,2 | 0,2 |
Ползучесть при сжатии 5-25 часов при 0,2 МПа | % | 0,2 @1600 | 0,2 @1630 | 0,2 @1650 | 0,2 @1600 |
Кирпич из спеченного циркона
Серия кирпичей Firebird Sintered Zircon Brick включает кирпичи Zircon,Спеченные кирпичи AZS и циркониевые муллитовые кирпичи.

Цирконовый кирпич обладает высокой огнеупорностью
под нагрузкой, хорошая термостойкость, хорошая эрозия
способность сопротивления и др.
Цирконий муллитовый кирпич обладает характеристиками высокой прочности,
хорошая стойкость к тепловому удару и отличная стойкость к эрозии.
В основном используется в стекловаренной печи, печи для производства стекловолокна, печи для минеральной ваты, мусоросжигательной печи, печи для глазури из керамической фритты, нагревательной печи и т. д.
Типовые индексы
Предметы | Цирконовый кирпич | Спеченный кирпич AZS | Циркон-муллитовый кирпич | ||||
Код | ЗС-КБЛ | СР-HQ | ЗС-ПТ | СЖ-АЗС | ЗМ-20 | ЗМ-15 | |
Описание | Расщепление Сопротивление | Высокий качество | Обычный Обязанность | АЗС | Циркон Муллит | ||
ZrO 2 | % | ≥ 65 | ≥ 65 | ≥ 63 | ≥ 31 | ≥ 20 | 15-20 |
SiO 2 | % | ≤ 33 | ≤ 33 | ≤ 34 | ≤ 21 | 11 | ≤ 20 |
Ал 2 О 3 | % | / | / | / | ≥ 46 | ≥ 60 | 50-60 |
Fe 2 О 3 | % | ≤ 0.![]() | ≤ 0,3 | ≤ 0,3 | ≤ 0,5 | ≤ 0,5 | ≤ 1,0 |
Насыпная плотность | г/см 3 | 3,84 | 3,7 | 3,65 | 3.2 | 3.2 | 3.1 |
Кажущаяся пористость | % | ≤ 16 | ≤ 18 | ≤ 22 | ≤ 18 | 17 | 17 |
Прочность на раздавливание в холодном состоянии | МПа | ≥ 130 | ≥ 100 | ≥ 90 | ≥ 110 | 150 | 100 |
Рефрактерность под нагрузкой 0.2 МПа, 0,6% | °С | ≥ 1700 | ≥ 1670 | ≥ 1650 | ≥ 1650 | ≥ 1700 | ≥ 1650 |
Линейное изменение повторного нагрева (1600°C × 3 ч) | % | ±0,2 | ±0,3 | ±0.3 | ±0,3 | ±0,3 | ±0,3 |
Ползучесть при сжатии 5-25 часов при 0,2 МПа | % | <0,2 @1500 | <0,2 @1500 |
Кирпичи с высоким содержанием хрома
Серия хромового кирпича изготовлена из оксида хрома, глинозема,.

спечены в высокотемпературной челночной печи.
Кирпичи обладают высокой коррозионной стойкостью к кислоте
или щелочные расплавы, хорошая износостойкость, хорошая термостойкость
Типичное применение
В основном используется в ключевой части углехимической, стекловолоконной печи, печи C-стекла, керамической глазури, мусоросжигателях, печах для плавки цветных металлов и т. д.
Типовые индексы
Предметы | Высокий хром | Середина Хром | 60 Хром Корунд | 30 Хром Корунд | 12 Хромовый корунд | |
класс | HC-93 | МС-86 | СС-60 | СС-30 | CC-12 | |
Кр 2 О 3 | % | 93 | 86 | 60 | 30 | 12 |
Ал 2 О 3 | % | 38 | 68 | 80 | ||
Fe 2 О 3 | % | 0.![]() | 0,2 | 0,5 | ||
Насыпная плотность | г/см 3 | 4.3 | 4.2 | 3,63 | 3,53 | 3.3 |
Кажущаяся пористость | % | 17 | 17 | 14 | 16 | 18 |
Прочность на раздавливание в холодном состоянии | МПа | 100 | 100 | 130 | 130 | 120 |
Рефрактерность под нагрузкой (0.2МПа, 0,6%) | ℃ | 1700 | 1700 | 1700 | 1700 | 1700 |
Кирпич из спеченного плавленого кварца
Керамика из спеченного плавленого кварца Firebird в основном состоит из материалов из плавленого кварца высокой чистоты.Он обладает многими превосходными свойствами, в том числе высокой устойчивостью к термическому воздействию
.
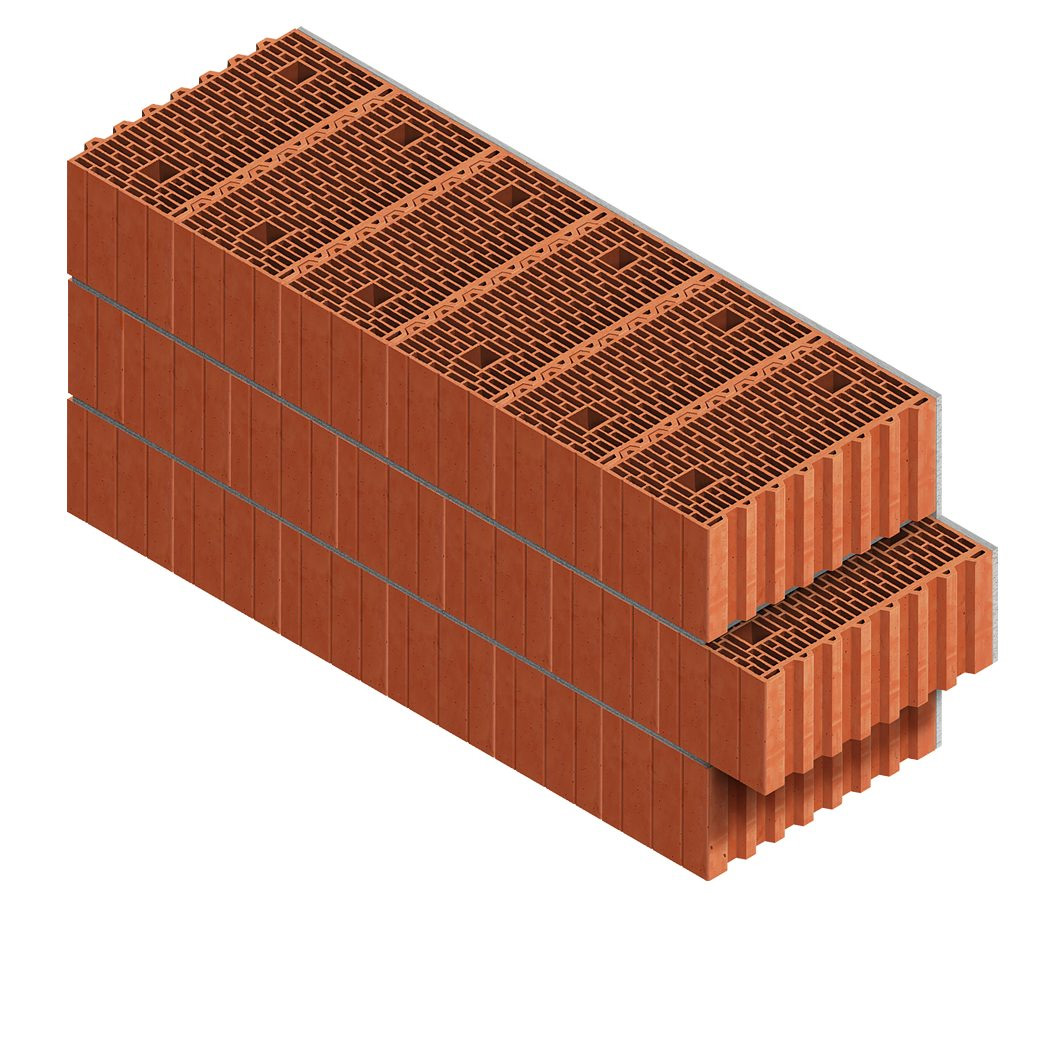
высокая коррозионная стойкость к химическим веществам и расплавленным металлам.Керамика из плавленого кварца
Firebird в основном состоит из материалов из плавленого кварца высокой чистоты.
Он обладает многими превосходными свойствами, в том числе высокой устойчивостью к тепловому удару
.
из-за очень низкой скорости теплового расширения, низкой теплопроводности,
высокая коррозионная стойкость к химическим веществам и расплавленным металлам.
Типичное применение
● Стекло: горячий ремонт короны, конвейерные ролики; Компоненты огнеупоров
● Алюминиевое литье: желоба, чаши фильтров и разливочные желоба
● Коксовая печь, кислотная футеровка химической промышленности, тигель высокотемпературной печи и т. д.
Типовые индексы
Индексы | ФС-а | ФС-б | |
SiO 2 | % | ≥ 99,5 | ≥ 98,5 |
Объемная плотность | г/см 3 | 1.![]() | 1,75-1,80 |
Кажущаяся пористость | % | 8-12 | 16-21 |
Прочность на сжатие | РТ | ≥ 50 | ≥ 35 |
Тепловое расширение (комн. 1000°C)(x10 -6 /°C) | % | 0.6 | 0,6 |
Теплопроводность (500°C) | Вт/м·К | 0,66 | 0,65 |
Стойкость к тепловому удару (1100°C для холодной воды) | циклы | ≥ 30 | ≥ 50 |
Характеристики материала | Однородный, плотный, бездефектный | ||
Использовать эффект | Долгий срок службы, отличная стабильность |
Кирпич из карбида кремния
Типовые индексы
Товар | Оксидная связка SiC-кирпич | Зеленый SiC-кирпич | Кирпич из карбида кремния корундовый | Муллитовый кирпич из карбида кремния | Кирпич SiC с высоким содержанием глинозема | |
карбид кремния | % | ≥ 90 | ≥ 90 | ≥ 70 | ≥ 65 | ≥ 20 |
Ал 2 О 3 | % | — | — | — | ≥ 20 | ≥ 55 |
Fe 2 О 3 | % | ≤ 0.![]() | ≤ 0,6 | ≤ 1,0 | ≤ 1,0 | ≤ 1,5 |
Объемная плотность | г/см 3 | ≥ 2,6 | ≥ 2,6 | ≥ 2,7 | ≥ 2,3 | ≥ 2,5 |
Кажущаяся пористость | % | ≤ 17 | ≤ 17 | ≤ 22 | ≤ 20 | ≤ 20 |
Прочность на раздавливание в холодном состоянии | МПа | ≥ 100 | ≥ 100 | ≥ 100 | ≥ 80 | ≥ 80 |
Рефрактерность под нагрузкой (0.2МПа, 0,6%) | ℃ | ≥ 1650 | ≥ 1650 | ≥ 1700 | ≥ 1600 | ≥ 1600 |
Типичное приложение | В основном используется для футеровки плавки цветных металлов; обжиговую подложку, толкающую доску и тигель из технической керамики; муфельный колпак печи; футеровка и воспламенитель ЦКС; футеровка мусоросжигательных заводов и др.![]() |
Серия мебели для печи
Типовые индексы
Товар | Пластина толкателя корундового муллита | Корунд муллит Sagger | карбид кремния | Sagger из плавленого кварца | ||
Стойка, перегородка | Саггер | |||||
Ал 2 О 3 | % | ≥ 80 | ≥ 75 | — | — | — |
карбид кремния | % | — | — | ≥ 90 | ≥ 86 | — |
SiO 2 | % | ≤ 18 | ≤ 24 | — | — | ≥ 98 |
Fe 2 O3 | % | ≤ 0.![]() | ≤ 0,2 | ≤ 0,5 | ≤ 0,5 | ≤ 0,2 |
Объемная плотность | г/см 3 | ≥ 2,7 | ≥ 2,65 | ≥ 2,55 | ≥ 2,5 | ≥ 1,7 |
Кажущаяся пористость | % | ≤ 22 | ≤ 25 | ≤ 18 | ≤ 18 | ≤ 22 |
Прочность на раздавливание в холодном состоянии | МПа | ≥ 80 | ≥ 50 | ≥ 100 | ≥ 100 | ≥ 30 |
Термостойкость (1100X для холодной воды) | Циклы | ≥ 30 | ≥ 30 | ≥ 30 | ≥ 30 | ≥ 50 |
Типичное применение | В основном используется для толкающей доски, стойкости к высоким температурам sagger, подложки для типичного применения в электронной керамике, конструкционной керамике, промышленности химических или магнитных материалов и т.![]() |
Шамотные нижние блоки
Шамотная глина с низкой пористостью
токопроводящая керамика | Британика
токопроводящая керамика , передовые промышленные материалы, которые благодаря модификации своей структуры служат электрическими проводниками.
Помимо известных физических свойств керамических материалов — твердости, прочности на сжатие, хрупкости — существует свойство удельного электрического сопротивления.Большинство керамических изделий сопротивляются прохождению электрического тока, и по этой причине керамические материалы, такие как фарфор, традиционно используются в качестве электрических изоляторов. Однако некоторые виды керамики являются отличными проводниками электричества. Большинство этих проводников представляют собой передовую керамику, современные материалы, свойства которых изменяются путем точного контроля за их изготовлением из порошков в изделия. Свойства и производство усовершенствованной керамики описаны в статье усовершенствованная керамика. В этой статье предлагается обзор свойств и областей применения нескольких передовых электропроводящих керамических материалов.
Британская викторина
Строительные блоки предметов повседневного обихода
Из чего сделаны сигары? К какому материалу относится стекло? Посмотрите, на что вы действительно способны, ответив на вопросы этого теста.
Причины возникновения удельного сопротивления в большинстве керамических материалов описаны в статье Состав и свойства керамики.Для целей этой статьи можно кратко объяснить происхождение проводимости в керамике. Электропроводность в керамике, как и в большинстве материалов, бывает двух видов: электронная и ионная. Электронная проводимость — это прохождение свободных электронов через материал. В керамике ионные связи, удерживающие атомы вместе, не допускают свободных электронов. Однако в ряде случаев в материал могут входить примеси разной валентности (т. е. обладающие разным числом связывающих электронов), и эти примеси могут действовать как доноры или акцепторы электронов.В других случаях могут быть включены переходные металлы или редкоземельные элементы различной валентности; эти примеси могут действовать как центры для поляронов — видов электронов, которые создают небольшие области локальной поляризации при переходе от атома к атому. Керамика с электронной проводимостью используется в качестве резисторов, электродов и нагревательных элементов.
Ионная проводимость состоит из перехода ионов (атомов с положительным или отрицательным зарядом) из одного места в другое через точечные дефекты, называемые вакансиями в кристаллической решетке.При нормальной температуре окружающей среды происходит очень мало прыжков ионов, поскольку атомы находятся в состояниях с относительно низкой энергией. Однако при высоких температурах вакансии становятся подвижными, и некоторые виды керамики проявляют так называемую быструю ионную проводимость. Эта керамика особенно полезна в газовых датчиках, топливных элементах и батареях.
Толстопленочные и тонкопленочные резисторы и электроды
Полуметаллические керамические проводники имеют самую высокую проводимость из всех, кроме сверхпроводящей керамики (описанной ниже).Примерами полуметаллической керамики являются оксид свинца (PbO), диоксид рутения (RuO 2 ), рутенат висмута (Bi 2 Ru 2 O 7 ) и ирид висмута (Bi 2 2 Ir). 7 ). Подобно металлам, эти материалы имеют перекрывающиеся энергетические зоны электронов и поэтому являются отличными электронными проводниками. Они используются в качестве «чернил» для трафаретной печати резисторов в толстопленочных микросхемах. Краски представляют собой измельченные частицы проводника и глазури, диспергированные в подходящей органике, которые придают свойства текучести, необходимые для трафаретной печати. При обжиге органика выгорает по мере плавления глазури. Варьируя количество частиц проводника, можно получить широкий диапазон сопротивления толстых пленок.
Керамика на основе смесей оксида индия (In 2 O 3 ) и оксида олова (SnO 2 ), называемая в электронной промышленности оксидом индия и олова (ITO), является превосходными электронными проводниками и имеет дополнительное достоинство оптически прозрачно. Проводимость и прозрачность возникают из-за комбинации большой запрещенной зоны и включения достаточного количества доноров электронов.Таким образом, существует оптимальная концентрация электронов для максимизации как электронной проводимости, так и оптического пропускания. ITO находит широкое применение в качестве тонких прозрачных электродов для солнечных элементов и для жидкокристаллических дисплеев, таких как те, которые используются в экранах портативных компьютеров. ITO также используется в качестве тонкопленочного резистора в интегральных схемах. Для этих приложений он применяется стандартными методами осаждения тонких пленок и фотолитографии.
Токопроводящая керамика давно используется в качестве нагревательных элементов для электронагревателей и электропечей.Токопроводящая керамика особенно эффективна при повышенных температурах и в окислительных средах, где устойчивые к окислению металлические сплавы выходят из строя. Примеры электродной керамики и температуры их максимального использования на воздухе показаны в таблице 1. Каждый материал имеет уникальный механизм проводимости. Карбид кремния (SiC) обычно является полупроводником; Однако при соответствующем легировании он является хорошим проводником. Как SiC, так и дисилицид молибдена (MoSi 2 ) образуют защитные поверхностные слои кварцевого стекла, которые предохраняют их от окисления в окислительной атмосфере.MoSi 2 — полуметалл с высокой электропроводностью. Хромит лантана (LaCr 2 O 4 ) представляет собой небольшой поляронный проводник; замена ионов щелочноземельных металлов (, например, кальция или Ca 2+ ) на La 3+ приводит к тому, что равная доля Cr 3+ превращается в Cr 4+ . Прыжки электронов между двумя состояниями ионов Cr обеспечивают высокую проводимость, особенно при повышенных температурах.
керамический материал | температура максимального использования на воздухе | |
---|---|---|
распространенное имя | химическая формула | (°С/°Ф) |
Карбид кремния | карбид кремния | 1500/2730 |
дисилицид молибдена | MoSi 2 | 1800/3270 |
хромит лантана | LaCr 2 O 4 | 1800/3270 |
цирконий | ZrO 2 | 2200/3630 |
Проводимость в диоксиде циркония (ZrO 2 ) ионная, в отличие от электронных механизмов проводимости, описанных выше. При легировании диоксида циркония Ca 2+ или ионами иттрия (Y 3+ ) образуются кислородные вакансии. При температуре выше 600°C (1100°F) ионы кислорода (O 2− ) становятся подвижными и заполняют эти вакансии, и они очень подвижны при более высоких температурах. Нагревательным элементам из диоксида циркония требуется предварительный нагреватель для достижения порога 600 ° C, но их можно использовать для достижения температуры до 2000 ° C (3600 ° F).
Оксид олова (SnO 2 ) имеет очень специфическое применение в качестве предпочтительного электрода для специальных стекловаренных печей (как и для оптического стекла).Это приложение требует высокой проводимости и устойчивости к коррозионным элементам в расплавах стекла; кроме того, корродированный материал электрода не должен обесцвечивать стекло. Оксид олова является единственным материалом, удовлетворяющим этим критериям. Чистый оксид олова представляет собой полупроводник с широкой запрещенной зоной, но присущий ему дефицит кислорода плюс замена олова ионами сурьмы приводят к высокой проводимости.
Произошла ошибка при настройке пользовательского файла cookie
Этот сайт использует файлы cookie для повышения производительности.Если ваш браузер не принимает файлы cookie, вы не можете просматривать этот сайт.
Настройка браузера на прием файлов cookie
Существует множество причин, по которым файл cookie не может быть установлен правильно. Ниже приведены наиболее распространенные причины:
- В вашем браузере отключены файлы cookie. Вам необходимо сбросить настройки браузера, чтобы принять файлы cookie, или спросить вас, хотите ли вы принимать файлы cookie.
- Ваш браузер спрашивает, хотите ли вы принимать файлы cookie, и вы отказались.Чтобы принять файлы cookie с этого сайта, нажмите кнопку «Назад» и примите файл cookie.
- Ваш браузер не поддерживает файлы cookie. Попробуйте другой браузер, если вы подозреваете это.
- Дата на вашем компьютере в прошлом.
Если часы вашего компьютера показывают дату до 1 января 1970 г., браузер автоматически забудет файл cookie. Чтобы это исправить, установите правильное время и дату на своем компьютере.
- Вы установили приложение, которое отслеживает или блокирует установку файлов cookie.Вы должны отключить приложение при входе в систему или проконсультироваться с системным администратором.
Почему этому сайту требуются файлы cookie?
Этот сайт использует файлы cookie для повышения производительности, запоминая, что вы вошли в систему, когда переходите со страницы на страницу. Предоставить доступ без файлов cookie потребует от сайта создания нового сеанса для каждой посещаемой вами страницы, что замедляет работу системы до неприемлемого уровня.
Что сохраняется в файле cookie?
Этот сайт не хранит ничего, кроме автоматически сгенерированного идентификатора сеанса в файле cookie; никакая другая информация не фиксируется.