Гидротехнический бетон, Дорожный, Декоративный, Жаростойкий и Бетонополимеры
Специальные виды бетона
Бетоны повышенной прочности чаще всего являются быстротвердеющими, но для того, чтобы быстрее получить прочное изделие, термическую обработку проводят в ускоренном темпе. Данную обработку избегают вовсе, производя бетонные изделия из новейших цементов с высокой скоростью затвердевания. Тяжёлый бетон прекрасно морозоустойчив и имеет повышенную сопротивляемость износу и растяжению.
Изготовление высокопрочного бетона — занятие трудоёмкое. Используются суперпластификаторы и особо прочный цемент, старательно перемешивают и уплотняют бетонную смесь, принимают наиболее низкое водоцементное соотношение, ну и, конечно, нельзя забывать о тщательном уходе за бетоном.
В мелкозернистом бетоне значительно присутствие цементного камня, вследствие чего ненамного увеличена его ползучесть и усадка. Подобный бетон применяют в нескольких случаях: при отсутствии крупного заполнителя, а также в процессе изготовления тонкостенных, в частности армоцементных изделий. В принципе, мелкозернистый бетон мало чем отличается от обычного, однако неимение заполнителя приходится компенсировать расходом цемента на 20-40%, кроме того, увеличивается потребность воды для бетонной смеси. Сократить расход цемента помогают различные пески высокого качества и пластифицирующие добавки, а также суперпластификаторы. Стоит отметить отличную водонепроницаемость мелкозернистого бетона.
Кислотоупорный бетон имеют увеличенную сопротивляемость различным концентрированным кислотам (соляной, азотной, серной), но вот под воздействием слабых кислот, воды и растворов щелочей начинают происходить необратимые разрушения. Уровень прочности при сжатии составляет 11-12 МПа через 3 суток и 15 МПа — через 28. Подобный бетон заменяет дорогой листовой свинец и тесаный камень при облицовке различных агрегатов в хим. промышленности.
Жаростойкий бетон отличается способностью выдерживать огромные температуры, не теряя при этом своих физико-химических свойств. Виды такого бетона отличаются и зависят от применяемого вяжущего: шлакопортландцемента, на портландцементе, на глиноземистом цементе и на жидком стекле. Увеличения стойкости добиваются, добавляя шамотный бой, хромитовую руду, магнезитовый кирпич, гранулированный доменный шлак и т.п. Также хромит, шамот, базальт, диабаз и др. используются как мелкие и крупные заполнители. Если правильно подобрать все компоненты, то жаростойкий бетон с лёгкостью выдерживает температуру в 1200 градусов. Материалы подбираются строго в соответствии с условиями эксплуатации изделия. Например, бетоны на жидком стекле нельзя использовать при частом воздействии воды, а вот при наличии кислой агрессивной среды нежелателен бетон на портландцементе.
Свойства жаростойкого бетона: способность сохранять свои свойства при длительном воздействии высоких температур.
Компоненты жаростойкого бетона: вяжущее — глиноземистый цемент, шлакопортландцемент, жидкое стекло, кремнефтористый натрий. Заполнители — шлак, бой керамических материалов, базальт.
Применение жаростойкого бетона: выполняют футеровку промышленных печей.
Существует определенный порядок приготовления бетонной смеси на глиноземистом цементе и портландцементе. Для начала в смеситель заливается энное количество воды, затем начинают 2-3 минутное перемешивание, в ходе которого добавляют остальные составляющие части. А вот изготовляя газобетон, в котором нет заполнителей, перемешав, вводят водно-алюминиевую суспензию, и перемешивают еще порядка 1-2 минут.
Бетонные смеси на силикат глыбе производятся в шламбассейне, куда добавляют едкий натр, силикат-глыбу, тонкомолотую добавку и воду в строго определенных пропорциях. Получившийся шлам перекачивается и подогревается до 35 градусов, после чего в смесителе на 2-3 минуты включают перемешивающий механизм и загружают нефелиновый шлам, водно-алюминиевую суспензию и заполнитель. Формование продуктов из ячеистого бетона занимает 2-3 часа и происходит в специальных металлических формах.
Существуют различия между твердением изделий из глиноземистого цемента, портландцемента и силикат-глыбы. В первом случае требуется температура 18-20 градусов и влажность порядка 90-100%, во втором – 80-90 градусов и 90-100% влажности, а в третьем случае вообще используется автоклав. Есть особенность в приготовлении жаростойкого бетона — по минимуму прибегают к «помощи» жидкого стекла и воды. Разные составы бетона на портландцементе выдерживают односторонний нагрев до 1700 градусов, а бетон на жидком стекле и глиноземистом цементе – до 1400.
Декоративные бетоны получаются при введении различных цветных цементов или же светостойких пигментов (охра, сурик и т.д.) в массе 8-10% от общей массы цемента. Иногда прибегают к специальным заполнителям — окрашенным горным породам типа мрамора или красных кварцитов. Такого рода бетоны применяются при сооружении зданий, пешеходных переходов и парковых дорожек.
Свойства декоративного бетона: предъявляются повышенные требования к прочности, плотности и долговечности.
Компоненты декоративного бетона: белый или цветной цемент, щелочестойкие пигменты, заполнители из цветных горных пород. Важен красивый внешний вид.
Применение декоративного бетона: наружный слой бетонных конструкций, декоративных плит, элементов фасада.
Дорожный и аэродромный бетон. Такой бетон подвергается жестким испытаниям — неоднократно увлажняется и высыхает, замерзает и оттаивает, постоянная нагрузка от различного транспорта. К нему предъявляются совсем другие требования. Дорожный бетон должен обладать огромной устойчивостью к морозам, стойко сопротивляться износу и влиянию воздуха. Но мало грамотно подобрать необходимые материалы — следует верно выполнять порядок выполнения работ. Портландцемент высоких марок, заполнители в виде щебня из гранита, кварцевого песка и известняка являются главными компонентами высококачественного дорожного бетона.
Свойства дорожного бетона: повышенная прочность, плотность, износостойкость и морозостойкость.
Компоненты дорожного бетона: пластифицированный и гидрофобный цемент, заполнитель — очищенный песок, щебень.
Применение дорожного бетона: покрытия автомагистралей, дорог.
Бетон, защищающий от радиации, в своем составе имеет заполнители с огромной плотностью (лимонит, барий, металлическая стружка, обрезки арматурного металла и т.д.). Чем больше плотность заполнителя — тем больше защита от различных радиоактивных воздействий. Такой бетон необходим на АЭС и других сооружений подобного типа, ведь только с его помощью можно обезопасить персонал от влияния нейтронного излучения.
Портландцемент, а также шлакопортландцемент и глиноземистый цемент являются вяжущими в тяжелом защитном бетоне особой прочности. Но в специальных бетонах другая технология — там нужно вяжущее, которое при затвердевании увеличивает количество водорода путем присоединения значительного количества воды. В качестве такого вещества известен гидросульфоалюминат кальция, получающийся реакцией трехкальциевого алюмината с гипсом, что является причиной повышенного содержания данных элементов в некоторых видах специального бетона. Чтобы исключить возможность его саморазрушения, часто вводят добавки в виде трепела или диатомита. Допускается использование расширяющихся и безусадочных цементов вместо портландцемента, но их себе стоимость слишком высока.
Гидратные бетоны, имеющие достаточно воды в своем составе, модернизируются и их защитные характеристики улучшаются путем введения добавок, увеличивающих количество водорода, бора и борсодержащих веществ, а также карбида и хлористого лития в бетоне. Свойства гидротехнического бетона: повышенная плотность, водонепроницаемость, морозостойкость, низкое тепловыделение, стойкий против воздействия агрессивных сред.
Компоненты гидротехнического бетона: Сульфатостойкий и пуццолановый цементы, заполнители с хорошо подобранным зерновым составом, тонкомолотые гидравлические и инертные добавки. Обязательное присутствие пластифицирующих и гиброфобных добавок.
Применение гидротехнического бетона: гидротехнические сооружения.
Особо тяжелый бетон
Свойства особо тяжелого бетона: высокая плотность.
Компоненты особо тяжелого бетона: заполнители — чугунная дробь, магнезит, портландцемент или шлакопортландцемент.
Применение особо тяжелого бетона: защитные сооружения от радиоактивных излучений.
Бетонополимеры
Свойства бетонополимера: повышенная прочность, водонепроницаемость, морозостойкость, долговечность.
Компоненты бетонополимера: поры заполнены полимерами, бетон пропитан смолами, битумом.
Применение бетонополимера: бетонные изделия, работающие в суровых природно-климатических условиях с агрессивными средами.
Купить бетон М100 с доставкой.
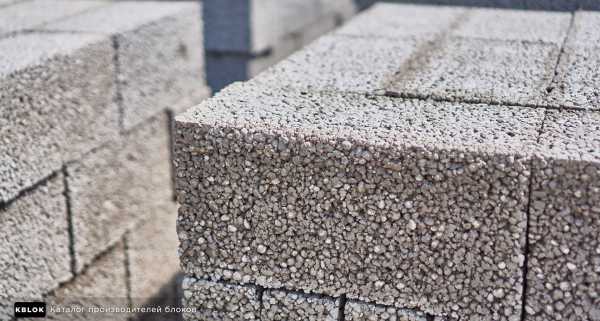
Жаростойкие бетоны — Статьи — М350
Для футеровки топок в конструкциях газоходов, дымовых труб при строительстве тепловых электростанций, в элементах защитных стен и перекрытий АЭС применяют жаростойкие бетоны. Обычный тяжелый цементный бетон пригоден для изготовления строительных конструкций, подвергающихся длительному воздействию температуры лишь до 200° С. В зависимости от предельно допустимой температуры применения жаростойкие бетоны разделяют на классы — от 3 до 16 (предельная температура применения соответственно от 300 до 1600). Их также классифицируют:
— по огнеупорности — на жароупорные с огнеупорностью ниже 158СС, огнеупорные — от 1580 до 1770°С и высокоогнеупорные — свыше 1770°С;
по плотности в высушенном состоянии — на тяжелые с ро> 1500 кг/м3 и легкие- ро< 1500 кг/м3;
по виду применяемого вяжущего — на портландцементе, шла-копортландцементе, глиноземистом цементе, жидком стекле, периклазовом цементе, алюмофосфатной связке и др. На портландцементе, быстротвердеющем цементе и шлако-портландцементе изготавливают бетоны классов от 3 до 12 в зависимости от вида заполнителей и тонкомолотых добавок.
Огнеупорность портландцемента в зависимости от минералогического состава находится в интервале 1700- 1750°С. Введение тонкомолотых добавок приводит к значительному снижению огнеупорности за счет образования эвтектик. Только такие добавки как тонкомолотый хромит не образуют эвтектик и повышают огнеупорность.
Предельная рабочая температура жаростойких бетонов определяется температурой деформации (размягчения) под нагрузкой 0,2 МПа. Температура начала размягчения портландцемента без тонкомолотых добавок находится в пределах от 970 до 1130°С, а температура 40%-ной деформации от 1370 до 1480°С. Тонкомолотые добавки повышают температуру размягчения, если образуют при нагревании с цементом соединения, обладающие высокой огнеупорностью и незначительной растворимостью в расплаве. К таким добавкам относятся хромит и магнезит. Цементный камень без тонкомолотой добавки разрушается под действием нагрузки 0,2 МПа при температуре 1460°С, тогда как образцы с 3 мае.ч. магнезита при температуре более 1700°С.
При нагревании обычных цементных бетонов деструктивные процессы происходят не только в цементном камне, но и в заполнителях. Такие процессы обусловлены неравномерным температурным расширением полиминеральных кристаллических пород, каковыми являются, например, граниты. Непригодны в качестве заполнителей бетонов, работающих в условиях нагревания, материалы, содержащие свободный кварц (песчаник, кварцевые пески, кварциты и др.). Наиболее опасным является превращение (3-кварца в а-кварц при 573 °С, связанное с уменьшением плотности зерен и, соответственно, эффектом объемного расширения.
Обычные заполнители используют при температуре до 200″С. Известняки и доломиты, широко применяемые как заполнители для тяжелого бетона, начинают разлагаться примерно при 600°С, однако их нагрев уже до 200″С приводит к снижению прочностных характеристик бетона.
Выбор заполнителей для жаростойких бетонов зависит от максимальной температуры их эксплуатации. Заполнители из таких излившихся изверженных пород, не содержащих свободного кварца, как андезиты, диабазы, базальты, вулканические лавы, туфы, пеплы, пемза при введении в бетонные смеси тонкомолотых добавок могут использоваться в условиях температуры до 700 — 800°С. В таком же диапазоне температуры используются нераспадающиеся доменные отвальные шлаки с модулем основности не более 1, а также топливные шлаки и бой обыкновенного глиняного кирпича.
Для легких жаростойких бетонов используют в качестве заполнителей керамзит, перлит, вермикулит.
Наибольшее распространение как заполнитель жаростойких бетонов получил шамот. К шамотным относятся материалы с содержанием А12О3+ТЮ2 от 30 до 45%. Их получают обжигом огнеупорных глин и каолинов до спекания. Обожженный продукт сортируют, измельчают и рассеивают по фракциям.
Для жаростойких бетонов с наиболее высокой температурой применения в качестве заполнителей используют бой магнезитовых, хромомагнезитовых, корундовых и других огнеупоров.
Тяжелые жаростойкие бетоны на портландцементе изготавливают обычно классов В15 — В40.
Легкие жаростойкие бетоны имеют прочность, соответствующую классам В2,5 — В15 и плотность 500 — 1200 кг/м3. Минимально допустимая остаточная прочность бетонов после нагревания до 800°С составляет 30 — 50% начальной прочности.
При работе тепловых агрегатов жаростойкие бетоны подвергаются резким колебаниям температуры, что является одной из основных причин появления трещин и отколов на футеровке. Термическая стойкость бетонов зависит от вида вяжущих, заполнителей и тонкомолотых добавок, водовяжущего отношения. Для пор-тландцементных бетонов с шамотным заполнителем при нагреве до 800°С уже через 10- 15 циклов появляется волосяные, а 20- 25 циклов открытые трещины. Для повышения термостойкости бетонов применяют дисперсное армирование температуростойкими волокнами из асбеста, базальта и др. Для повышения термической трещиностойкости необходимо подбирать состав бетона с минимальным различием температурных деформаций крупного заполнителя и растворной части. Нагрев жаростойкого бетона на портландцементе желателен не ранее чем через 7 суток нормального твердения.
Важным показателем трещиностойкости жаростойких бетонов является усадка. Она обусловлена в основном усадкой цементного камня, которая возрастает не только с увеличением водоцемент-ного отношения, но и с повышением температуры нагрева. Усадка бетонов при сушке составляет 0,04-0,07%. При 800- 1100″С линейная усадка жаростойкого бетона возрастает до 0,2 — 0,7%. Величина усадки увеличивается с повышением расходов цемента и тонкомолотой добавки.
Коэффициент термического расширения жаростойкого бетона в основном зависит от расширения заполнителя и колеблется в интервале 4-11106. Качество жаростойких бетонов в значительной мере зависит от режима сушки и первого нагрева.
Жидкое стекло в качестве вяжущего для жаростойких бетонов применяют с модулем от 2,4 до 3,0 и плотностью от 1,36 до 38 г/см3. Ускорение твердения жидкого стекла и повышение прочности бетонов достигается введением добавки отвердителя — кремнефтористого натрия. Отвердителями жидкого стекла служат также нефелиновый шлам, феррохромовый шлак, технический глинозем, глиноземистый шлак, клинкерный портландцемент.
Бетоны на основе жидкого стекла используют при температурах 600 — 1600 °С, начальная прочность их на сжатие обычно не превышает 10 — 20 МПа, однако остаточная прочность после нагревания до 800°С значительно выше, чем для портландцементных бетонов — 50 — 90%. Эти бетоны при применении соответствующих заполнителей в условиях высоких температур стойки к кислотам (кроме НР), расплавам солей, другим агрессивным средам. Однако для ряда составов не допускается воздействие пара и воды.
Бетоны на основе глиноземистого и высокоглиноземистого (не менее 75% А12О3) цементов эксплуатируются при температурах 1300- 1700°С. При их изготовлении не требуются тонкомолотые добавки, заполнителями служат обычно хромит, электрокорунд и другие высокоглиноземистые материалы. Поскольку твердение глиноземистого цемента характеризуется высокой экзотермией при применении его в конструкциях, толщина которых превышает 400 мм, необходим интенсивный отвод тепла. Температура в толще бетона в первые сутки твердения не должна превышать 40°С, прочность бетонов на глиноземистом цементе соответствует классам В20 — В40 и достигается через 3 суток нормального твердения.
Огнеупорные бетоны, обладающие высокой термической стойкостью и сопротивляемостью истирающим воздействиям, получают с применением фосфатных вяжущих. Ими служит ортофос-форная кислота или ортофосфаты различной степени замещения. Тонкомолотыми добавками в таких бетонах являются обычно высокоглиноземистые (не менее 62% АI2О3) порошки. При нагревании ортофосфорная кислота вступает в реакцию с АI2О3, образуя высокоогнеупорные алюмофосфатные связки. Бетоны на алю-мофосфатных связках применяют при температурах нагрева до 1600 — 1800°С. Их прочность на сжатие достигает 70 МПа. После нагревания до 800 °С снижения прочности не наблюдается. Термическая стойкость — 39 — 60 водных теплосмен при начальной температуре 800″С. В отличие от жаростойких бетонов на других вяжущих алюмофосфатные бетоны вместо огневой усадки после нагревания до максимальной температуры характеризуются расширением (до 0,2%).
Авторы: Л. И. Дворкин, О. Л. Дворкин
m350.ru
Жаростойкий бетон | Новости в строительстве
Жаростойкий бетон предназначается для промышленных агрегатов ( футеровка печей, облицовка котлов и т. п.) и строительных конструкций, подверженных нагреванию ( например для дымовых труб).
В зависимости от применяемого вяжущего жаростойкие бетоны бывают следующих видов: бетоны на портландцементе, шлакопортландцемента, на глиноземистом цементе и жаростойкие бетоны на жидком стекле. Для повышения стойкости бетона при нагревании в его состав вводят тонкомолотые добавки из хромитовой руды, шамотного боя, магнезитового кирпича, андезита, гранулированного доменного шлака и др.
Тонкость помола добавки для бетона на портландцементе должна быть такой, чтобы через сито № 009 проходило не менее 70%, а для бетона на жидком стекле — не менее 50%, В качестве мелкого и крупного заполнителя применяют хромит, шамот, бой глиняного кирпича, базальт, диабаз, андезит и др. При правильно выбранных вяжущих и заполнителях бетон может длительное время выдерживать, не разрушаясь, действие температуры до 1200°С.
Выбор материалов производят в зависимости от условий и температуры его эксплуатации. Жаростойкие бетоны на портландцементе и глиноземистом цементе производят класса (марки) не менее В20 (250), а на жидком стекле — В12,5 (150). Бетоны на жидком стекле не применяют в условиях частого воздействия воды, а на портландцементе — в условиях кислой агрессивной среды.
При приготовлении бетонных смесей на портландцементе или глиноземистом цементе соблюдается такая последовательность:
в смеситель заливают заданное количество воды, при включенном перемешивании загружают другие компоненты и перемешивают 2…3 мин. При изготовлении газобетона, в котором заполнители отсутствуют, после перемешивания загружают водно-алюминиевую суспензию и перемешивают дополнительно 1…2 мин.
Приготовление бетонных смесей на силикат-глыбепроизводят в шламбассейне, куда загружают дозированные по массе силикат глыбу, тонкомолотую добавку, едкий натр и воду. Полученный шлам перекачивают в ванну, подогревают до 30…35°С и подают в с меситель, в который при включенном перемешивающем механизме вводят дозированные по массе заполнитель, водо-алюминиевую суспензию и нефелиновый шлам. Смесь перемешивают 2…3 мин. Для формования изделий из ячеистого бетона применяют металлические формы. В форме смесь выдерживают 2…3 ч.
Твердение изделий на глиноземистом цементе происходит в течение 1 сут при температуре 18…20°С и влажности 90…100%,
на портландцементе твердение изделий проходит при температуре 80…90°С и влажности 90… 100%, а изделия на силикатглыбе твердеют в автоклаве. При приготовлении жаростойких бетонов стремятся ограничить количество воды и жидкого стекла. Осадка конуса должна быть не более 2 см, а жесткость — не менее 10 с.
Бетоны на портландцементе разных составов используются при одностороннем нагреве с предельной температурой 1700°С, на глиноземистом цементе и на жидком стекле — до 1400°С.
♦При действии высокой температуры на цементный камень происходит обезвоживание кристаллогидратов и разложение гидрата окиси кальция с образованием СаО. Окись кальция при воздействии влаги гидратируется с увеличением объема и вызывает растрескивание бетона. Поэтому в жаростойкий бетон на портландцементе вводят тонко измельченные материалы, содержащие активный кремнезем SiO2, который реагирует с СаО при температуре 700 — 900°С и в результате химических реакций, протекающих в твердом состоянии, связывает окись кальция.
Цементы
Жаростойкий бетон изготовляют на портландцементе с активной минеральной добавкой (пемзы, золы, доменного гранулированного шлака, шамота). Шлакопортландцемент уже содержит добавку доменного гранулированного шлака и может успешно применяться при температурах до 700°С. Портландцемент и шлакопортландцемент нельзя применять для жаростойкого бетона, подвергающегося кислой коррозии (например, действию сернистого ангидрида в дымовых трубах). В этом случае следует применить бетон на жидком стекле. Он хорошо противостоит кислотной коррозии и сохраняет свою прочность при нагреве до 1000°С.
Глиноземистый цемент можно применять без тонкомолотой добавки, поскольку при его твердении не образуется гидрат окиси кальция. Еще большей огнеупорностью (не ниже 1580°С) обладает высокоглиноземистый цемент с содержанием глинозема 65 — 80%; в сочетании с высокоогнеупорным заполнителем его применяют при температурах до 1700°С.
Столь же высокой огнеупорности позволяют достигнуть фосфатные и алюмофосфатные связующие: фосфорная кислота (Н3РО4), алюмофосфаты Аl(Н2P04)з и магнийфосфаты Mg(h3P04)2. Жаростойкие бетоны на фосфатных связующих можно применять при температурах до 1700°С, они имеют небольшую огневую усадку, термически стойки, хорошо сопротивляются истиранию.
Заполнитель
Заполнитель для жаростойкого бетона должен быть не только стойким при высоких температурах, но и обладать равномерным температурным расширением. Бескварцевые изверженные горные породы как плотные (сиенит, диорит, диабаз, габбро), так и пористые (пемза, вулканические туфы, пеплы) можно использовать для жаростойкого бетона, применяемого при температурах до 700°С.
Для бетона, работающего при температурах 700 — 900°С, целесообразно применять бой обычного глиняного кирпича и доменные отвальные шлаки с модулем основности не более 1, не подверженные распаду. При более высоких температурах заполнителем служат огнеупорные материалы: кусковой шамот, хромитовая руда, бой шамотных, хроммагнезитовых и других огнеупорных изделий.
Легкий жаростойкий бетон
Легкий жаростойкий бетон на пористом заполнителе имеет объемную массу менее 2100 кг/м3, его теплопроводность в 1,5 — 2 раза меньше, чем у тяжелого бетона. Применяют пористые заполнители, выдерживающие действие высоких температур (700 — 1000°С): керамзит, вспученный перлит, вермикулит, вулканический туф.
Ячеистый жаростойкий бетон отличается небольшой массой (500 — 1200 кг/м3) и малой теплопроводностью.
Сборные элементы и монолитные конструкции из жаростойкого бетона широко применяют в различных отраслях промышленности: энергетической, черной и цветной металлургии, в химической и нефтеперерабатывающей, в производстве строительных материалов. Жаростойкие ячеистые бетоны используют взамен полукислых и шамотных изделий, предназначенных для температур 800 — 1400°С, а также вместо высокоогнеупорных изделий при температуре выше 1400°С.
Замена только 150 тыс. м³ огнеупорной кладки жаростойким бетоном и железобетоном дает значительную экономию .
Большие работы по жаростойким бетонам проводятся под руководством Ю. П. Горлова, К. Д. Некрасова и др.
В МИСИ им. В.В. Куйбышева разработаны алюмосиликатные вяжущие цеолитовой структуры путем гидротермального омоноличивания кислых вулканических стекол: перлитов, обсидианов, липаритов, литоидной пемзы и других видов материалов а также жароупорные бетоны на их основе. Природные высококремнеземистые стекла по своему химическому составу (смотри таблицу №1) можно отнести к алюмосиликатным системам.
Читать далее на http://stroivagon.ru жаростойкий шлакощелочной бетон
Таблица №1. Химический состав перлитов, %.
При дисперсности S уд=450 м² /кг перлитовые породы проявляют химическую активность вяжущего компонента. Такие виды вяжущих возможно легировать путем добавления в них микро наполнителей, такие как корунд, тонкомолотый шамот, технический глинозем и другие виды. Это позволяет в широких пределах изменить химический и фазовый состав вяжущего, в частности соотношение основных оксидов SiO2 и Al2O3 а также соответственно термические свойства изделий.
Алюмосиликатные вяжущие обладают рядом существенных достоинств, обуславливающих техническую и экономическую целесообразность их применения при изготовлении жаростойких бетонов. Такие как:
1. Повышение прочности бетонов после нагрева на рабочую температуру.
2. Высокая реакционная способность при нагреве, позволяющая за счет использования специальных добавок управлять структурой синтезируемого вяжущего.
3. Возможность регулирования огнеупорности и термомеханических характеристик вяжущего изменения содержания щелочного и кремнеземистого компонентов.
На основе вяжущего (алюмосиликатное вяжущее, силикатно-натриевом композиционном вяжущем) и использования различных видов огнеупорных заполнителей получены огнеупорные и жаростойкие бетоны с температурой использования до 1550 °С. Для приготовления жаростойкого бетона используют шамот, перлит, керамзит и другие виды (шамотный перлитобетон, легкий шамотный керамзито-перлитобетон, ячеистые виды бетонов, цирконовые, корундовые и другие виды бетонов).
Такие виды жаростойких бетонов характеризуются несложностью технологии изготовления, низкой себестоимостью и энергоемкостью производства а также высокими термомеханическими эксплуатационными показателями. Достоинства таких видов бетонов являются:
1. Возможность форсированного первого разогрева на рабочую температуру со скоростью до 500 °С в час.
2. Отказ от предварительной сушки перед началом монтажа. Отказ обуславливается низкой влажностью изделий после автоклавной обработки.
3. Отсутствие снижения прочности для большинства изделий в интервале температур 600…900 °С.
4. Высокая прочность после разогрева на рабочую температуру.
Поэтому при получении алюмосиликатных жаростойких и огнеупорных бетонов применение природных вулканических стекол в качестве компонента вяжущего наиболее предпочтительно. Такие материалы приобретают эксплуатационные свойства в процессе первого разогрева на рабочую температуру когда происходит перерождение вяжущего в керамический черепок.
Жаростойкий шамотный перлитобетон
Получают из гидроалюмосиликатного вяжущего на основе кислых вулканических стекол и шамота ( смотри таблицу №2).
Таблица №2. Состав шамотных перлитобетонов, % по массе
Основные физико-механические показатели жаростойкого шамотного перлитобетона изготовленного на основе сырьевой шихты оптимального состава при использовании в качестве затворителя 8 % -ного раствора NaOH и раствора силиката натрия Мс=2,8 приведены в таблицу №3.
Таблица № 3. Физико-механические свойства шамотных перлитобетонов.
Из приведенных в таблицу данных следует что жаростойкий шамотный перлитобетон по всем показателям превосходит мелкоштучные керамические изделия (ГОСТ 390-83), которые применяют в качестве футеровки обжиговых вагонеток предприятий строительной керамики.
Мелкозернистый циркониевый перлитобетон
Получают такой бетон на основе циркониевого концентрата, которого используют как заполнитель , а также молотой перлитовой породы в количестве 8 % и обезжелезненного циркона в качестве добавки. В качестве затворителя используют раствор
stroivagon.ru
состав, применение и способы приготовления
В процессе строительства возникают ситуации, когда обычный бетон идеально не подходит, оставляя дырки в конструкциях. Целесообразней использовать смеси с мелкофракционной структурой. Изготовление тонкостенных армированных конструкций, заполнение стыков между элементами, формирование гидроизоляции — неполный перечень процессов, в которых используют бетон с мелкими зерновыми частицами.
Понятие о материале
Мелкозернистый бетон — искусственный камень, который производится с помощью частиц песка разных фракций, цемента, воды. Другое, не менее известное название, — песчаный бетон. Довольно распространенный строительный материал, относящийся к категории тяжелого бетона. Величина фракций, входящих в состав, не превышает 2 мм. При соединении песка, цемента, воды происходит химическая реакция, превращающая составляющие в цементный камень. Мелкозернистый бетон отличается морозостойкостью, водонепроницаемостью, прочностью, плотностью.
Вернуться к оглавлениюОсобенности
В производстве искусственного камня задействованы элементы с определенными параметрами. Как правило, песок, входящий в состав, имеет размер фракций до 2,5 мм. Кроме наполнителей в состав входят базовые компоненты: вода, цемент, добавки.
Характеризуется материал следующими особенностями:
- Однородность состава позволяет достичь максимальной плотности раствора, а значит, высокой прочности конструкций.
- Отсутствие крупных частей придает раствору подвижность, позволяя свободно заливать его в труднодоступные места, придерживаясь различных форм строений.
- Во избежание проникновения воздуха в массу, уплотнение при помощи вибропресса не рекомендуется. Во время процесса в смесь попадает воздух, образуя пузырьки, которые отрицательно влияют прочность материала.
- Присутствие пористости положительно сказывается на сохранении тепла.
- Небольшая стоимость материала, причем комбинация компонентов, изменение пропорций, позволяет в результате получать различные технические характеристики растворов.
Свойства песчано-цементного бетона схожи по параметрам с классическим бетоном. Только согласно необычной структуре песчаного состава, выделяются некоторые отличия:
- удвоенное содержание цемента;
- наличие мелкозернистого компонента;
- отсутствие крупных частиц.
Соединение компонентов
Составляющие, входящие в состав раствора, подбираются с соблюдением стандартов. Так как раствор содержит компоненты с разными техническими характеристиками, каждый элемент поддается испытанию на надежность. Строительные нормативы регулируют использование, расщепление песка на размеры. Для начала песок просеивают сквозь сетку с отсеками размером в 2,5 мм, получая первую фракцию песка. Затем берут сетку с размером ячеек в 1,2 мм, после ячейки уменьшают, соответствуют размеру в 0,135 мм. Все, что пройдет через сетку в последний раз. и будет использовано в качестве заполнителя.
При производстве мелкозернистых бетонов, первая группа песка составляет от 20 до 50% общей массы, оставшееся количество составляет вторая, мелкая фракция. Важно знать, что цемент в растворе играет не только соединяющую, но и несущую роль, чтобы крепко «связать» частицы песка, количество цемента берут больше нормы. Марку цемента лучше использовать м400 или м500. Дополнительное применение добавок, существенно увеличит стоимость, но увеличит прочность и качество.
К особенностям мелкозернистой смеси можно отнести:
- простую технологию изготовления, очень легко готовить раствор своими руками;
- удобство транспортировки, не расслаивается;
- специфическая структура компонентов позволяет получить высокой плотности однородную структуру;
- четкое соблюдение технологий гарантирует получение продукта, который подходит для строительства любых форм, любой прочности.
Область применения
Чаще всего мелкозернистые растворы используются при производстве армированных конструкций. Частота расположения арматуры не дает возможности проникновению классическому раствору, а мелкозернистые бетоны с легкостью проникнут в недоступное место.
Мелкофракционный раствор, благодаря своей главной характеристике – подвижности, с легкостью используется в ремонте трещин, заполнении соединительных швов. Перед гидроизоляционными работами стяжку подготавливают мелкозернистыми элементами.
В дорожном строительстве не обойтись без раствора, мелкозернистым бетоном выстилают дорожное полотно. Идеально подходит для производства тротуарной плитки, бордюров. В районах, где отсутствуют залежи природного камня, доставка из других районов может быть экономически не выгодной. Идеальным заменителем в любой строительной, ремонтной работе выступает мелкозернистый бетон.
Вернуться к оглавлениюПроцесс приготовления
Соблюдение определенных требований обеспечит необходимое качество цементной смеси:
- внимательно проверяйте дату производства, срок службы цемента, не должно быть просроченного периода;
- контролируйте раствор на наличие затвердевших кусочков, их не должно быть;
- компоненты-заполнители очищены от глины, грязи и других примесей.
Распределение этапов подготовки бетона выглядит следующим образом.
Вернуться к оглавлениюРаспределение песка на фракции
Первоначально подготавливается сухой компонент. Подготовленный чистый, просеянный в три стадии песок, смешивается между собой в процентном соотношении:
- крупная часть в количестве 50 -60% от всего объема;
- остальной объем занимают средняя и мелкая часть в равных долях.
Соединение с вяжущим веществом
Недавно появившийся метод пневмонабрызг — под давлением с использованием пневматического оборудования.Следующим этапом идет смешение наполнителя и вяжущего вещества. В данном промежутке процесса учитываются требования к использованию, назначению, эксплуатации. Исходя из этого, составляющие в бетоне могут изменяться. Соотношение компонентов прочной структуры соответствуют пропорции 1:1,5 (цемент/песок), для более слабой 1:1,35. Всегда стоит помнить, что при соотношении цемента больше чем 1 к 3, в растворе не будет доставать цементного клея для окутывания частиц песка и заполнения пустоты. Прочность материала нарушается.
Вернуться к оглавлениюОтмеривание воды
На долю воды и добавок в растворе влияют индивидуальные обстоятельства, учитывается каждый определенный случай. При использовании пластификаторов, последний добавляется в уже отмерянную воду. Единственное, самое главное, учитывается всегда обеспечение плотности, текучести, прочности бетона при затвердевании.
Вернуться к оглавлениюСоединение компонентов
Заключительный этап — соединение компонентов в бетономешалке, где происходит окончательное приготовление раствора, утрамбовка смеси. В процессе приготовления смеси важно всегда выдерживать правильные пропорции, результатом является лучшая плотность, прочность. При повышенном содержании цемента, стоит добавлять и больше воды, но это снизит прочность и увеличит пористость. Пониженное содержание цемента затрудняет укладку раствора, что тоже приводит к нарушению прочности конструкций.
Вернуться к оглавлениюПневмонабрызг
Увеличивающаяся популярность продуктов, выполненных по технологии пневмонабрызга, объясняется высокой эксплуатационной оценкой. Технические параметры мелкозернистого бетона отлично подходят для применения при специфической укладке.
Пневмонабрызг — процедура, при которой одновременно наносится раствор песка, цемента и стекловолокна.
Процедуру проводят при помощи специального строительного пистолета. В аппарат подаются сразу все компоненты, внутри перемешиваются и передаются в трубу, где добавляется сжатый воздух. На выходе получается волокно с раствором, которым заполняется подготовленная форма, материал укатывается валиком.
Отличительная особенность процедуры состоит в постоянном воздействии на составляющие смеси сжатого воздуха, даже при транспортировке. По результатам исследования, новая технология улучшает качество мелкозернистого бетона путем вытеснения воды. Полученные на выходе свойства материала отличаются (в лучшую сторону) от первоначального песчано-цементного материала.
Вернуться к оглавлениюЗаключение
Мелкозернистые фракции в структуре бетона наделяют материал особенными свойствами, которые выделяют раствор из ряда классических бетонов. Именно благодаря отличительным параметрам его использование в некоторых случаях предпочтительней.
Важно помнить, что в процессе приготовления стоит уделить внимание правильности пропорций и качеству составляющих.
—
kladembeton.ru
Специальные бетоны — ТехЛиб СПБ УВТ
Высокопрочные бетоны — это бетоны с пределом прочности при сжатии 50 МПа и более. Однако пределы прочностных характеристик таких бетонов чисто условны, поскольку больше связаны с уровнем развития науки и техники в области производства цемента, бетона и химических добавок. Уже сегодня возможно получение бетонов прочностью более 150 МПа.
Достигается высокая прочность бетонов различными приемами. Основными условиями получения высокопрочных бетонов являются применение высокоактивных цементов, низких водоцементных отношений (0,20…0,30), использование плотных высокопрочных заполнителей, химических добавок пластификаторов и, в частности, суперпластификаторов и комплексных добавок, тщательное перемешивание и уплотнение бетонной смеси, создание наиболее благоприятных условий твердения и др. Способствует повышению прочности бетона также высокий предельно допустимый расход цемента, максимально возможное насыщение его крупным заполнителем за счет подбора оптимального зернового состава и уменьшения доли песка. Высокая прочность таких бетонов часто достигается за счет применения специальных технологических приемов, например сухого бетонирования, сущность которого заключается в укладке в опалубку или форму сухой смеси вяжущего и заполнителей с последующим ее увлажнением.
Таким способом на рядовых материалах возможно получить бетон прочностью до 100 МПа. Основу подобного уровня характеристик бетона составляют повышенная плотность его структуры и низкое (0,15…0,25) водоцементное отношение, которое соотносится с теоретически необходимым для реакций гидратации цемента количеством воды.
Поскольку высокопрочные бетоны получают на цементе высокой активности и при низких значениях В/Ц, они одновременно являются и быстротвердеющими. Это позволяет значительно сократить длительность тепловой обработки или вовсе отказаться от нее. Такие бетоны отличаются высокой плотностью и являются более долговечными и стойкими к агрессивным средам, что увеличивает срок их службы и позволяет применять в тяжелых условиях эксплуатации. В настоящее время возможно получение супердолговечных бетонов со сроками службы до 500 лет. Применение высокопрочных бетонов способствует также уменьшению массы конструкций.
Особо тяжелые бетоны называют еще гидратными (из-за большого содержания в них химически связанной воды) и бетонами для защиты от радиоактивного воздействия. Применяют их в качестве защитных экранов ядерных реакторов. Из всех радиоактивных излучений наибольшей проникающей способностью обладают протоны и нейтроны. Способность материала поглощать излучение — пропорциональна его плотности.
Для ослабления потока нейтронов в материале наоборот должны присутствовать элементы с малой атомной плотностью, как, например, водород. Бетон является как раз эффективным материалом для биологической защиты ядерных реакторов, поскольку в нем удачно сочетаются при сравнительно низкой стоимости высокая плотность и содержание достаточно большого количества водорода в химически связанной воде.
Характерным свойством таких бетонов является большая средняя плотность, которая составляет 2500…6000 кг/м3. Они отличаются также повышенным количеством химически связанной воды — более 30 % по массе, а следовательно, и ядер водорода. Вследствие этого водород, обладая малой молекулярной массой, способствует захвату потока горячих нейтронов.
В качестве вяжущего в особо тяжелых бетонах используют портландцемент, глиноземистый и гипсоглиноземистый цемент, расширяющийся, напрягающий и др. Все они в той или иной мере способствуют максимальному химическому и адсорбционному удержанию воды в цементном камне и бетоне. Заполнителями в таких бетонах служат весьма тяжелые (с высокой плотностью) породы: ильменит, магнетит, гематит, барит, металлический скрап, обрезки железа и т. п. Мелкий заполнитель обычно составляют дробленный бурый железняк, кварцитовые «хвосты», чугунная дробь и др. Например, насыпная плотность ильменитового песка составляет 4620 кг/м3 , щебня — 4760 кг/м3 , а средняя плотность бетона на таких заполнителях превышает 4000 кг/м3. Для улучшения защитных свойств особо тяжелых бетонов от нейтронного потока в них вводят также добавки, содержащие легкие элементы, например карбид бора, хлористый литий, сернокислый кадмий и др.
Мелкозернистый цемент и армоцемент. Для производства крупноразмерных пространственных конструкций (таких, как своды, оболочки, купольные и складчатые конструкции) с толщиной стенок 20…30 мм и других тонкостенных изделий необходимо применять мелкозернистый бетон с наибольшей крупностью заполнителя, не превышающей 10 мм (в среднем 5…7 мм). Для армоцементных конструкций крупность заполнителя не превышает даже 3 мм.
Бетоны мелкозернистого строения характеризуются более высокой удельной поверхностью заполнителя, а иногда повышенным объемом межзерновой пустотности, и поэтому нуждаются в увеличенном содержании цементного теста (на 20…40 %) по сравнению с обычным крупнозернистым бетоном. Вместе с тем мелкозернистые бетоны отличаются более однородным строением.
Для сокращения расхода цемента необходимо применять высококачественные пески, пластифицирующие добавки, суперпластификаторы, производить хорошее уплотнение смеси.
Мелкозернистый бетон обладает повышенной прочностью на изгиб, хорошими водонепроницаемостью и морозостойкостью.
Армоцемент как разновидность мелкозернистого бетона представляет собой особо мелкозернистый бетон, армированный по всему сечению расположенными в несколько рядов по толщине ткаными металлическими сетками. Он обладает высокой прочностью не только на сжатие, но и на растяжение. Армоцемент используется в весьма тонкостенных пространственных конструкциях сложного очертания и благодаря жесткости сечения элементов обладает высокой несущей способностью.
Гидротехнический бетон должен обеспечить длительную эксплуатацию конструкций, постоянно или периодически омываемых водой. По условиям эксплуатации делится на следующие разновидности: подводный постоянно находящийся в воде; надводный подвергаемый лишь периодическому воздействию воды и расположенный в зоне переменного горизонта воды. Кроме того, различают массивный и немассивный бетон и бетон напорных и безнапорных конструкций, поэтому в зависимости от условий эксплуатации к гидротехническому бетону помимо требований прочности предъявляются также требования по водонепроницаемости, морозостойкости и др.
Прочность на сжатие и водонепроницаемость гидротехнического бетона определяется в возрасте 180 сут. По прочности на сжатие он подразделяется на классы В10…В40; по водонепроницаемости — на марки W2…W8. Требования по морозостойкости предъявляются к тем гидротехническим бетонам, конструкции из которых подвергаются совместному действию воды и мороза. По морозостойкости такие бетоны делят на пять марок: F50, F100, F150, F200 и F300.
В зависимости от условий эксплуатации для приготовления гидротехнического бетона допускается применение портландцемента, пластифицированного и гидрофобного цементов, пуццоланового и шлакового, а в некоторых случаях и сульфатостойкого цемента. Так, для зоны сооружений на уровне переменного горизонта воды в суровых климатических условиях используется пластифицированный или обычный портландцемент. Они позволяют получить водонепроницаемые и морозостойкие бетоны, а также несколько уменьшить расход цемента и тем самым тепловыделение бетона при твердении в случае массивных конструкций. Для особо тяжелых условий при наличии агрессивной среды применяют сульфатостойкие цементы.
Для повышения водонепроницаемости и морозостойкости такого бетона применяют химические добавки и в первую очередь СДБ и СНВ. Для уменьшения расхода цемента, а следовательно, тепловыделения и объемных деформаций бетона при сохранении необходимой подвижности бетонной смеси и плотности бетона в него вводят различные микронаполнители, например золу-унос и др.
Заполнители для гидротехнического бетона должны обеспечивать его водостойкость и морозостойкость. Допускается применение только крупных и средних песков, а зерновой состав заполнителей подбирается таким образом, чтобы получался минимальный объем пустот при возможно большей крупности максимальных по размеру зерен. Применение таких заполнителей снижает расход цемента и уменьшает выделение теплоты при твердении бетона. Расход цемента должен быть больше минимальных значений, обеспечивающих получение плотного бетона, и в то же время по условиям тепловыделения его не должно быть для массивных конструкций более 350 кг/м3, а немассивных — 400 кг/м3. Для получения требуемой водонепроницаемости такого бетона содержание песка в смеси заполнителей должно быть несколько увеличено по сравнению с обычными значениями.
Бетонную смесь необходимо укладывать с максимальным уплотнением, а за твердеющим бетоном наладить тщательный уход, обеспечивающий необходимый влажностный и температурный режимы, при которых предотвращаются объемные деформации.
Бетонные конструкции в современных гидротехнических сооружениях имеют своими основными характеристиками значения прочности на сжатие-растяжение, а сам предел прочности бетона будет определяться в следующие периоды: 28, 60, 180 суток – в зависимости от времени строительства.
Показатели величины предела растяжимости, набухания и усадки бетона должны быть:
— предельная растяжимость для бетона в возрасте 180 суток: не ниже 5-10-5 – для бетона внутренних зон, не ниже 7-10~5 – для бетона наружных зон сооружений. Этот показатель будет тем лучше, чем выше прочность бетона при использовании цемента без минеральных добавок и введением полимеров в бетонные смеси.
— линейная усадка для бетона в условиях относительной влажности 60% и температуре воздуха 18 С: для бетона с возрастом в 28 суток – не выше 0,3 мм/м, в возрасте 180 суток – до 0,7 мм/м относительно первоначальной длины.
— набухание бетона относительно размеров высушенных конструкций не должно превышать 0,1 мм/м для бетона в возрасте 28 суток, и 0,3 мм/м – для бетона в возрасте 180 суток.
Негативное проявление имеет усадка бетонной смеси при строительстве резервуаров и водоемов из напряженного железобетонного материала, во время ремонта конструкций и работ по гидроизоляции конструкций.
Такой показатель прочности бетона, как трещинностойкость, в массивных конструкциях имеет прямую зависимость от температурных напряжений, что обусловлено количеством тепловыделений в результате гидратации цемента в процессе застывания бетонной смеси.
Для бетонов специального назначения к числу наиболее важных показателей свойств, характеризующих долговечность, относятся морозостойкость, водонепроницаемость, стойкость к химической коррозии в водной среде. Кроме этого, на гидротехнические бетонные сооружения агрессивное влияние оказывают абразивное действие наносов, взвешенных в воде, и кавитация.
Негативное воздействие от абразивных наносов может повлечь за собой разрушение конструкции, а чтобы увеличить устойчивость бетона к данному воздействию, можно снизить содержание таких составляющих, как вода и цемент, и использовать в виде добавок алитовые цементы, имеющие высокую удельную поверхность, а также увеличить расход цемента, количество заполнителя крупных размеров.
Помимо абразивного разрушения, при наличии высокоскоростного потока воды может наступить кавитационное разрушение бетонной конструкции. При этом нарушается сплошность внутри текущей жидкости, образуются пузыри, которые разрываясь, образуют гидравлические удары.
Кавитационная стойкость бетонов, так же как и износостойкость, достаточно хорошо характеризуется прочностью на сжатие. Для бетонных обделок водопроводящих сооружений следует применять бетоны с прочностью при сжатии 45— 50 МПа. Дальнейшее повышение прочности уже незначительно увеличивает кавитационную стойкость.
Для защиты от наносов и кавитации применяют защитные облицовки; в зависимости от условий могут быть использованы чугуно- и сталебетон, камень, металл, резина, полимерные бетоны. Особенно эффективными являются полимербетонные облицовки, стойкость к износу и кавитации которых в несколько раз выше, чем высокопрочных цементных бетонов.
Чтобы избежать (или снизить) воздействие кавитации, в работе с бетоном используют создание таких форм, которые обеспечили бы обтекание потоком конструкции – например, плавных линий параболы.
Декоративные бетоны. В зависимости от состава и назначения декоративные бетоны можно подразделить на цветные и бетоны, имитирующие природные камни или сами по себе обладающие выразительной структурой. При необходимости поверхность бетона подвергают специальной обработке или формуют изделия с рельефной поверхностью.
Для получения цветных бетонов применяют белые и цветные цементы, различные минеральные и органические пигменты. Пигменты должны обладать высокой свето-, атмосфере- и щелочестойкостью. В качестве пигментов используют: мел природный молотый, известь гашеную (белый цвет), охру сухую (желтый цвет), сурик железный (красно-коричневый цвет), марганцевый черный, белила титановые, ультрамарин (синий цвет), оксид хрома (зеленый цвет) и др. В качестве дробленого декоративного материала применяют щебень и гравий из плотных горных пород, цветные шлаки, цветное кусковое стекло (эрклез).
Наиболее часто применяют минеральные пигменты и вводят их в количестве 1…5 % от массы цемента в зависимости от их укрывистости, плотности и других свойств.
Расход цемента в цветных бетонах по сравнению с обычными следует принимать несколько выше. При крупности заполнителя до 10 мм он составляет 450…500 кг/м3. Это позволяет повысить плотность и улучшить цветовую выразительность поверхности бетона. Целесообразно в этом случае использовать мелкозернистые бетоны. Оптимальными с точки зрения получения хороших декоративных качеств являются составы 1:2… 1:3. Расход воды в цветных бетонах определяется, как правило, предварительным испытанием и затем постоянно контролируется, поскольку даже небольшие изменения в расходе воды влекут за собой заметные изменения цвета бетона. Для формования изделий используются достаточно пластичные, жирные бетонные смеси, которые хорошо формуются и мало подвержены расслоению.
В цветных бетонах следует использовать чистые кварцевые пески светлых оттенков без примесей, окрашивающих их в серый цвет. В качестве крупных и мелких заполнителей могут применяться светлый известняк и доломит, отходы камнедробления, дробленые пески и щебень из мрамора, высевки гранита, туфа и др. Крупный заполнитель, как правило, не придает определенный цвет бетону. Больше всего на цвет бетона влияют мелкие частицы заполнителя — до 0?3 мм.
Марка декоративного бетона должна быть не менее М150 (В 10), морозостойкость — F50. Для повышения художественной выразительности декоративных бетонов применяют специальные приемы, позволяющие обнажить заполнители и выявить структуру бетона. Для выявления структуры бетона его поверхность подвергают шлифовке и полировке, обрабатывают бучардой или пневматическим молотком, с помощью пескоструйного аппарата и т. п. Для обнажения заполнителя используют различные замедлители твердения. Декоративные бетоны применяются в ограждающих конструкциях общественных и жилых зданий, для изготовления элементов фасада, декоративных плит для наружных и внутренних стен зданий, для лестничных маршей и деталей малых архитектурных форм, для барельефов, скульптур и других изделий специального назначения.
Жаростойкий бетон. Жаростойкий бетон изготовляют из вяжущего, тонкомолотой минеральной добавки, жаростойких заполнителей и воды (или другого затворителя, например ортофосфорной кислоты).
В качестве вяжущих в жаростойком бетоне применяют портландцемент, шлакопортландцемент, глиноземистый цемент или жидкое стекло. Жидкое стекло должно иметь модуль от 2,4 до 3,0 и плотность от 1,36 до 1,38 г/см3 и применяется вместе с отвердителем — кремнефтористым натрием. Для улучшения структуры цементного камня и сохранения прочности при нагреве в вяжущее вводят минеральные добавки (хромитовую руду, бой шамотного, магнезитового или обычного кирпича, андезит, пемзу, лессовидный суглинок, гранулированный доменный шлак, топливный шлак и золу-унос). Тонкость помола добавок должна быть такой, чтобы через сито N 008 проходило не менее 70 % добавок для бетонов на портландцементе и не менее 50 % — для бетонов на жидком стекле.
В качестве мелкого и крупного заполнителей в жаростойком бетоне применяют следующие дробленые материалы: бой магнезитового, шамотного и обыкновенного глиняного кирпича, кусковый шамот, доменный отвальный шлак, базальт, диабаз, лом и бой жаростойких бетонов или огнеупорных изделий. Максимальная крупность щебня составляет обычно 20 мм, а мелких частиц размером менее 0,14 мм в заполнителях должно быть не более 15 % по массе.
Материалы и состав жаростойкого бетона выбирают в зависимости от требуемой марки по прочности, температуры и условий службы в конструкции. Смеси готовят в бетоносмесителях принудительного действия; укладку ведут при температуре не ниже +15 °С. Время твердения жаростойкого бетона зависит от вида вяжущего и составляет 0,5…1 сут. для бетона на ортофосфорной кислоте и 3…7сут. — для бетонов на глиноземистом и портландцементе.
Жаростойкий бетон на портландцементе и цементном клинкере в качестве заполнителя может использоваться при температуре до 250°С. Он применяется, например, для футеровки холодного конца вращающихся печей по производству цемента и извести по мокрому способу. Бетон на глиноземистом цементе используется в условиях более высоких температур — порядка 1200°С (например, для изготовления стеновых панелей туннельных печей для обжига керамического кирпича). Еще более высокой огнеупорностью (до 1350 °С) при одновременно высокой термостойкости обладает бетон на фосфатных связующих — фосфорной кислоте, алюмофосфатной и алюмохромфосфатной связках. Указанные значения огнеупорности соответствуют температуре деформации под нагрузкой, которая всегда на 200…300°С ниже так называемой конусной или просто огнеупорности.
Читать по теме:
К разделу
Строительные материалы
tehlib.com
Особые виды бетона
СТРОИТЕЛЬНЫЕ МАТЕРИАЛЫ
Высокопрочный бетон
Высокопрочный бетон классов по прочности на сжатие В 80, В115 (Ml000, Ml500) получают на основе высокопрочного портландцемента, промытого песка и щебня[11].
Малоподвижные и жесткие смеси приготовляют с низкими В/Ц = 0,27-0,45 в бетоносмесителях принудительного действия (например, турбинных). Для плотной укладки этих смесей при формовании изделий и конструкций используют интенсивное уплотнение: вибрирование с пригрузом, двойное вибрирование, сильное прессование. Значительно облегчают уплотнение суперпластификаторы, не понижающие прочности бетона.
Высокопрочные бетоны являются, как правило, и быстротвер — деющими. Однако для ускоренного достижения отпускной прочности бетона в изделиях обычно требуется тепловая обработка, которая может проводиться по сокращенному режиму. Новые особобыстрот — вердеющие цементы дают возможность обойтись без тепловой обработки, так как бетон достигает нужной прочности в «естественных» условиях твердения при температуре 20-25 °С. Применение высокопрочных бетонов взамен бетона М400 дает возможность уменьшить расход арматурной стали на 10-12% и сократить объем бетона на 10-30%.
Гидротехнический бетон предназначается для конструкций, находящихся в воде или периодически соприкасающихся с водой, поэтому он должен обладать свойствами, необходимыми для длительной нормальной службы этих конструкций в данных климатических и эксплуатационных условиях.
Гидротехнический бетон должен иметь минимальную стоимость и удовлетворять требованиям по прочности, долговечности, водостойкости, водонепроницаемости, морозостойкости, тепловыделению при твердении, усадке и трещиностойкости. Противоречивые на первый взгляд требования высокого качества и низкой стоимости можно выполнить, если выделить наружную зону массивного сооружения, подвергающуюся непосредственному влиянию среды, и внутреннюю зону.
Бетон наружной зоны в зависимости от расположения в сооружении по отношению к уровню воды делят на бетон подводный (находящийся постоянно в воде), переменного уровня воды и надводный, находящийся выше уровня воды.
В самых суровых условиях находится бетон, расположенный в области переменного уровня воды. Он многократно замерзает и оттаивает, находясь все время во влажном состоянии. Это же относится к бетону водосливной грани плотин, морских сооружений (причалов, пирсов, молов и т. д.), градирен, служащих для охлаждения оборотной воды на тепловых электростанциях, предприятиях металлургической и химической промышленности. Этот бетон должен обладать высокой плотностью и морозостойкостью. Правильный выбор цемента, применение морозостойких заполнителей, подбор состава плотного бетона и тщательное производство бетонных работ обеспечивают получение долговечного бетона.
10 Строительные материалы |
Бетон внутренней зоны массивных конструкций защищен наружным бетоном от непосредственного воздействия среды. Главное требование к этому бетону — минимальная величина тепловыделения при твердении, так как неравномерный разогрев массива может вызвать образование трещин. Малое тепловыделение имеет шлакопортландцемент, поэтому его и применяют для внутримассивного бетона наряду с пуццолановым портландцементом; эти цементы экономичнее портландцемента и к тому же хорошо противостоят выщелачиванию Са(ОН)2. Требования к физико-механическим свойствам бетона внутренней зоны не столь высоки: марки по прочности Ml00, Ml50, по водонепроницаемости W2, W4.
Марку бетона по водонепроницаемости назначают в зависимости от напорного градиента, равного отношению максимального напора к толщине конструкций или к толщине бетона наружной зоны конструкции (при наличии зональной разрезки):
Напорный градиент | до 5 | 5-10 | 10-12 | 12 и более |
Марка бетона по водонепроницаемости | W4 | W6 | W8 | W12 |
Для конструкций с напорным градиентом более 12 на основании опытов могут назначаться марки по водонепроницаемости выше W12.
Стойкость бетона к воздействиям среды определяется комплексом его свойств: морозостойкостью, малым водопоглощением, небольшими деформациями усадки.
Марку бетона по морозостойкости назначают в зависимости от климатических условий и числа расчетных циклов попеременного замораживания и оттаивания в течение года. Установлены следующие марки гидротехнического бетона по морозостойкости: F100, F150, F200, F300, F400, F500.
Водопоглощение гидротехнического бетона характеризуется величиной капиллярного всасывания при погружении в воду образцов 28-суточного возраста, высушенных до постоянной массы при температуре 105 °С. Водопоглощение бетона зоны переменного уровня воды не должно превышать 5% (от массы высушенных образцов), для бетонов других зон — не более 7%.
Линейная усадка бетона при относительной влажности воздуха 60% и температуре 18 °С в возрасте 28 сут не должна превышать 0,3 мм/м, в возрасте 180 сут — 0,7 мм/м. Предельно допустимые величины набухания установлены: в возрасте 28 сут — 0,1 мм/м, 180 сут — 0,3 мм/м (по сравнению с высушенными до постоянной массы при 60 °С эталонными образцами).
Дорожный бетон
Дорожный бетон предназначен для оснований и покрытий автомобильных дорог и аэродромов. Покрытие работает на изгиб как плита на упругом основании, поэтому основной прочностной характеристикой бетона является проектная марка на растяжение при изгибе.
Крупный заполнитель (щебень, гравий, щебень из шлака) обязательно проверяют на износостойкость в полочном барабане: она нормируется в соответствии с назначением бетона.
Бетон дорожных покрытий подвергается совместному действию воды и мороза при одновременном влиянии солей, использующихся для предотвращения обледенения и облегчения очистки дорог от льда. Поэтому бетон однослойных покрытий и верхнего слоя двухслойных покрытий должен иметь необходимую морозостойкость: в суровом климате — не ниже 200; в умеренном — 150; в мягком — 100.
Чтобы получить морозостойкий бетон, применяют портландцемент М500 с содержанием трехкальциевого алюмината не более 10%, гидрофобный и пластифицированный портландцементы, а В/Ц бетона ограничивают пределом 0,5-0,55. Бетон оснований дорожных покрытий изготовляют на портландцементе М300 и М400 и шлакопортландцементе. Начало схватывания цемента должно быть не ранее 2 ч, поскольку дорожный бетон нередко приходится перевозить на большие расстояния.
Для декоративных целей при устройстве пешеходных переходов, разделительных полос на дорожных покрытиях, парковых дорожек, а также изготовлении элементов городского благоустройства используют цветные бетоны. Такие бетоны получают при введении в бетонную смесь щелоче — и светостойких пигментов в количестве
8.. . 10% от массы цемента (охра, мумия, сурик и др.) или применении цветных цементов. В отдельных случаях используют заполнители, обладающие необходимым цветом, например туфы, красные кварциты, мрамор и другие окрашенные горные породы.
Жаростойкий бетон
Жаростойкий бетон предназначается для промышленных агрегатов (облицовки котлов, футеровки печей и т. п.) и строительных конструкций, подверженных нагреванию (например, для дымовых труб). При действии высокой температуры на цементный камень происходит обезвоживание кристаллогидратов и разложение гидроксида кальция с образованием СаО. Оксид кальция при воздействии влаги гидратируется с увеличением объема и вызывает растрескивание бетона. Поэтому в жаростойкий бетон на портландцементе вводят тонко измельченные материалы, содержащие активный кремнезем Si02, который реагирует с СаО при температуре 700-900 °С и в результате химических реакций, протекающих в твердом состоянии, связывает оксид кальция.
Жаростойкий бетон изготовляют на портландцементе с активной минеральной добавкой (пемзы, золы, доменного гранулированного шлака, шамота). Шлакопортландцемент уже содержит добавку доменного гранулированного шлака и может успешно применяться при температурах до 700 °С. Портландцемент и шлакопортландцемент нельзя применять для жаростойкого бетона, подвергающегося кислой коррозии (например, действию сернистого ангидрида в дымовых трубах). В этом случае следует применить бетон на жидком стекле. Он хорошо противостоит кислотной коррозии и сохраняет свою прочность при нагреве до 1000 °С.
Глиноземистый цемент можно применять без тонкомолотой добавки, поскольку при его твердении не образуется гидроксид кальция. Еще большей огнеупорностью (не ниже 1580 °С) обладает высокоглиноземистый цемент с содержанием глинозема 65-80%; в сочетании с высокоогнеупорным заполнителем его применяют при температурах до 1700 °С.
Столь же высокой огнеупорности позволяют достигнуть фосфатные и алюмофосфатные связующие: фосфорная кислота Н3РО4, алюмофосфаты А1(Н2Р04)3 и магнийфосфаты Mg(h3P04)2. Жаростойкие бетоны на фосфатных связующих можно применять при температурах до 1700 °С, они имеют небольшую огневую усадку, термически стойки, хорошо сопротивляются истиранию.
Заполнитель для жаростойкого бетона должен быть не только стойким при высоких температурах, но и обладать равномерным температурным расширением.
Бескварцевые изверженные горные породы, как плотные (сиенит, диорит, диабаз, габбро), так и пористые (пемза, вулканические туфы, пеплы), можно использовать для жаростойкого бетона, применяемого при температурах до 700°С.
Для бетона, работающего при температурах 700-900°С, целесообразно применять бой обычного глиняного кирпича и доменные отвальные шлаки с модулем основности не более 1, не подверженные распаду.
При более высоких температурах заполнителем служат огнеупорные материалы, кусковой шамот, хромитовая руда, бой шамотных, хроммагнезитовых и других огнеупорных изделий.
Легкий жаростойкий бетон на пористом заполнителе имеет плотность менее 2100 кг/м3, его теплопроводность в 1,5-2 раза меньше, чем у тяжелого бетона. Применяют пористые заполнители, выдерживающие действие высоких температур (700-1000 °С): керамзит, вспученный перлит, вермикулит, вулканический туф.
Ячеистый жаростойкий бетон отличается небольшой массой (500-1200 кг/м3) и малой теплопроводностью.
Сборные элементы и монолитные конструкции из жаростойкого бетона широко применяют в различных отраслях промышленности: энергетической, черной и цветной металлургии, в химической и нефтеперерабатывающей, в производстве строительных материалов; используют взамен полукислых и шамотных изделий, предназначенных для температур 800-1400 °С, а также вместо высокоогнеупорных изделий при температуре выше 1400 °С.
Кислотоупорный бетон
Вяжущим для кислотоупорного бетона является жидкое стекло с полимерной добавкой. Для повышения плотности бетона вводят наполнители: кислотостойкие минеральные порошки, получаемые измельчением чистого кварцевого песка, андезита, базальта, диабаза и т. п. В качестве отвердителя используют кремнефтористый натрий (Na2SiF6), а в качестве заполнителя — кварцевый песок, щебень из гранита, кварцита, андезита и других стойких пород. После укладки с вибрированием бетон выдерживает не менее 10 сут на воздухе (без поливки) при 15-20 °С. После отвердевания рекомендуется поверхность бетона «окислить», т. е. смочить раствором серной или соляной кислот. Кислотоупорный бетон хорошо выдерживает действие концентрированных кислот; вода разрушает его за 5-10 лет, щелочные растворы разрушают быстрее. Кислотоупорный бетон применяют в качестве защитных слоев (футеровок) по железобетону и металлу.
Бетон для защиты от радиоактивного воздействия
Бетоны, применяемые для защиты от радиоактивных воздействий, должны иметь возможно большую плотность бетона и определенное содержание водорода — обычно в виде воды, связанной с вяжущим.
Вяжущим служит портландцемент или шлакопортландцемент, который выделяет при гидратации немного тепла и поэтому хорошо зарекомендовал себя в массивных защитных конструкциях.
В качестве заполнителей используют тяжелые природные или искусственные материалы. Для особо тяжелого бетона применяют в качестве заполнителя близкие по своим свойствам железные руды — магнетит (Fe304) и гематит (Fe203) с содержанием железа не менее 60%. Бурый железняк (лимонит) Fc203 nh30 позволяет значительно
293
повысить содержание связанной воды в гидратном бетоне. Баритовые руды (или барит), содержащие около 80% сульфата бария (BaS04), применяют как мелкий и крупный заполнитель.
Металлический крупный заполнитель получают из отходов металлообрабатывающих заводов, мелким заполнителем служит кварцевый или лимонитовый песок, а также чугунная дробь. Свинцовая дробь дорогая, и ее применяют при малой толщине защиты, для заделки отверстий в конструкциях, когда требуется бетон с повышенными защитными свойствами. Плотность бетона на металлическом заполнителе достигает 6000 кг/м3.
Бетон должен иметь заданную марку по прочности и относительно низкий модуль упругости, что позволяет снизить величину растягивающих напряжений во внешней зоне защиты, вызываемых односторонним нагревом. Кроме того, бетон, расположенный у активного корпуса реактора, должен обладать достаточной стойкостью к воздействию излучений, быть огнестойким и жаростойким даже при температурах, возможных при аварийном режиме реактора. Для массивных конструкций желательны меньшая теплота гидратации цемента и минимальная усадка бетона (для предотвращения температурных и усадочных трещин), а также небольшая величина коэффициента температурного расширения.
Механические свойства особо тяжелых магнетитового, гематитового, лимонитового и баритового бетонов близки. Особо тяжелый бетон имеет марки по прочности М100, М200 и М300, при этом марки на осевое растяжение составляют 10, 20.
В качестве дополнительной характеристики бетона, которую учитывают в расчете толщины защиты, подбирают количество связанной воды исходя из того, что она связывается цементом или входит в состав заполнителя (лимонита, серпентина).
Мелкозернистый бетон
Мелкозернистый бетон не содержит крупного заполнителя. Его применяют при изготовлении тонкостенных, в том числе армоце — ментных конструкций. Свойства мелкозернистого бетона характеризуются теми же факторами, что и обычный бетон. Однако из-за отсутствия крупного заполнителя увеличивается водопотребность бетонной смеси и, чтобы получить равнопрочный бетон и равноподвижную бетонную смесь, расход цемента увеличивают на 20-40% по сравнению с обычным бетоном. Снижение расхода цемента воз-
294
можно за счет применения высокопрочного песка, суперпластификатора, усиленного уплотнения.
Мелкозернистый бетон имеет повышенную прочность на изгиб, хорошую водонепроницаемость и морозостойкость. Повышение эффективности мелкозернистого бетона возможно за счет использования отходов зол ТЭС и основных шлаков литейного производства. Мелкозернистый бетон широко применяется при изготовлении силикатных изделий автоклавного твердения.
Серный бетон
Серный бетон представляет собой смесь сухих заполнителей — щебня, песка, минеральной муки, нагретых до 140-150 °С, и расплавленного серного вяжущего при температуре перемешивания 145-155 °С. Использование серы в строительстве известно с середины прошлого века: в виде растворов и мастик для заливки швов каменных кладок, для заделки металлических стоек перил лестничных маршей и заделки металлических связей каменных конструкций взамен расплавленного свинца.
Процесс получения серного бетона основан на свойстве серы изменять свою вязкость при различной температуре — при 119— 122 °С сера полностью переходит из кристаллического состояния в расплав. В качестве заполнителей используют кислотоупорный цемент, андезитовую или кварцевую муку, кварцевый песок и другие кислотостойкие минеральные наполнители. Во многих странах серный бетон применяют для изготовления свай, фундаментов, емкостей, покрытий дорог и химостойких полов.
Одним из факторов, сдерживающих широкое внедрение серного бетона в нашей стране, является его стоимость, которая выше, примерно в 2 раза стоимости бетона на портландцементе. Однако имеется много химических предприятий, располагающих отходами, содержащими от 25 до 80% технической серы. Также большое количество серосодержащих отходов образуется при добыче серы.
Использование серосодержащих отходов для серных бетонов, с одной стороны, позволит решить проблему сырья, а с другой — охраны окружающей среды.
Бетон на шлакощелочных вяжущих
Шлакощелочное вяжущее представляет собой гидравлическое вяжущее вещество, получаемое на основе шлаков черной или цветной металлургии, домолотых совместно с высокомодульными добавками феррохромового шлака, белитовых шламов, высококальциевых зол-уноса ТЭС (или без них), затворенных растворами щелочных металлов натрия или калия, дающих в водных растворах щелочную реакцию (жидкое стекло). Применяют заполнители из горных пород, а также техногенных твердых отходов. В отличие от цементного шлакощелочное вяжущее активно взаимодействует с минеральными заполнителями. По своим свойствам бетоны на шлакощелочных вяжущих не уступают цементным, но имеют повышенную жаро — и химическую стойкость.
Бетон, упрочненный волокнами
Дисперсно-армированный бетон (фибробетон) представляет собой композиционный материал, упрочненный волокнами. В нем невысокая прочность на растяжение и пластичность матрицы (бетона) сочетается с высокомодульным волокном, обладающим высокой прочностью на разрыв. Эффективность армирования короткими волокнами зависит от ориентации волокон к действию растягивающих усилий и при перпендикулярной ориентации составляет 40-50%, а при объемно-произвольной — лишь около 20% по отношению к параллельной ориентации. Волокна препятствуют развитию усадочных трещин, повышают прочность сцепления стержневой арматуры с бетоном примерно на 40%.
Волокна должны быть стойкими в щелочной среде цементного раствора или бетона. В зависимости от конструкций применяют волокна минеральные (стеклянные — из бесщелочного стекла, базальтовые, кварцевые и др.), металлические (преимущественно из обычной или нержавеющей стали), синтетические (пропиленовые, капроновые и др.).
Вопросы для самоконтроля
1. Бетон как композиционный материал. Влияние вида заполнителя на структуру и среднюю плотность бетона.
2. Связь реологических и технических свойств бетонной смеси; классификация смесей по показателям удобоукладывае
msd.com.ua
Жаростойкость бетона и жаростойкий бетон
Бетон используется в современном строительстве для осуществления практически всех этапов возведения. Причина столь высокой популярности заключается в сочетании некоторых факторов. В первую очередь, следует отметить высокие прочностные показатели. Дополнительно, нельзя забывать про разумную стоимость состава. Этот фактор особенно важен с учётом значительной потребности в бетоне при осуществлении строительных работ. Жаростойкость бетона – это только одна из его многочисленных характеристик. Она полностью определяется параметрами компонентов, составляющих смесь. Не меньшую роль играет такой момент, как пропорции материалов, используемых для создания. Жаростойкий бетон используется для промышленного строительства и в специальных тепловых агрегатах. Он применяется при создании фундаментов и нагревателей воздуха для домен, а также печей для переработки серного колчедана в химической промышленности. Из огнеупорного бетона изготавливаются туннельные печи для обжига кирпича, дымовые трубы и производится футеровка элементов сталеплавильных печей. Жаростойкость бетона играет важную роль только в том случае, когда происходит использование материала для решения специализированных задач. В иных вариантах развития событий, вовсе нет необходимости обеспечивать значительные эксплуатационные характеристики данного типа. Это приведёт только к излишнему перерасходу денежных средств. Жаростойкость бетона подразумевает, что чем выше данный параметр, тем эффективнее материал способен противостоять воздействию внешних факторов нагрева. При этом, высокая температура не является единственным негативным фактором, способным оказать своё влияние. Резкое изменение температуры, будь то нагрев или охлаждение, приводит к негативным последствиям. Линейные размеры блока способны уменьшиться или увеличиться, что вызовет растрескивания, в случае превышения некоторой предельной величины.
Классификация смесей происходит по максимально допустимой температуре:
-
Жаростойкие — до 1580 С. Жаростойкость бетона данного типа достаточно велика, что позволяет добиться высокой эффективности использования в специализированных направлениях современного строительства.
-
Огнеупорные — до 1770 С. Жаростойкость бетона наиболее высока и материал может применяться в тех местах, где на него будут оказывать воздействие постоянный жар или другие факторы данной категории.
При повышении температуры в обычном бетоне происходит обезвоживание кристаллогидратов, а гидроксид кальция разлагается с выделением СаО. Оксид кальция склонен гидратироваться, после чего начинается расширение и растрескивание покрытия. Для борьбы с этим явлением в жаростойкий бетон вводятся мелкодисперсные компоненты в состав которых входит активный кремнезем. Вяжущим является портландцемент с активными добавками: пемзой, золой, доменным гранулированным шлаком. Жаростойкость бетона, в таком случае, не снижается в процессе его эксплуатации. Это позволяет добиться некоторых преимуществ, к которым следует отнести значительный срок, в течение которого можно осуществлять использование блоков или других изделий монолитного типа. Жаростойкий бетон изготавливается из специальных компонентов. Заполнители получают дроблением тугоплавких и огнеупорных горных пород, а также искусственных материалов. В зависимости от удельного веса, такие смеси подразделяют на обычные и легкие. Масса кубического метра последних не превышает 1500 кг. Жаростойкость бетона, при этом, несколько снижается, поскольку не могут быть использованы материалы, обладающие высокими параметрами в данной сфере.
Шлакопортландцемент содержит добавку гранулированного шлака, что позволяет успешно применять его в температурном диапазоне до 700 градусов. Обычный портландцемент неприменим для жаростойких бетонов, которые подвергаются воздействию соединений кислот, например, сернистого ангидрида проходящего через дымовые трубы. В таких ситуациях используется состав, изготовленный на жидком стекле. Он не боится кислотной коррозии и может сохранять свои характеристики при температуре до 1000 С. Жаростойкость бетона существенно повышается, что позволяет говорить о расширении возможностей применения. Главной проблемой является то, что возрастает стоимость и материал становится достаточно дорогим. Дополнительно, имеются некоторые проблемы в вопросе планирования бюджета.
Высокоглиноземистые цементы, в которых содержание основной составляющей превышает 65%, могут эксплуатироваться при температурах до 1580 градусов, а если добавить высокоогнеупорные заполнители, то и до 1700. Жаростойкость бетона для подобных смесей считается максимальной, особенно, если сравнивать с другими вариантами вяжущих составов. Фосфатные связующие и алюмофосфаты позволяют добиться аналогичного результата. Бетоны, изготовленные на их основе, выдерживают 1700-градусный нагрев, обладают минимальной огневой усадкой и имеют высокую износостойкость. Заполнитель для жаростойких смесей должен помимо термоустойчивости иметь еще равномерное тепловое расширение. Здесь нашли применение бескварцевые горные породы, такие как диорит, диабаз, сиенит и габбро, а также пемза, вулканические пеплы и туфы. Эти компоненты чаще всего используются для создания материалов, работающих в температурном диапазоне до 700 градусов. Для материалов, которые должны выдерживать до 900 С, чаще всего используется бой глиняного кирпича и отвальные шлаки, модуль основности которых не превышает единицу. Жаростойкость бетона находится на среднем уровне, но появляется возможность снизить стоимость до разумных пределов.
Для более высоких температур в ход идут кусковой шамот, дробленые обломки из хромомагнезита и других огнеупорных материалов и хромитовая руда.
dombeton.ru