Специальные методы бетонирования
Торкретирование — это нанесение на поверхность опалубки, бетона или железобетона под давлением сжатого воздуха одного или нескольких слоев цементно-песчаного раствора (торкрета). Его применяют для устройства гидроизоляции, защитного слоя предварительно напряженной навиваемой арматуры, укрепления тонкостенных конструкций, замоноличивания швов, при ремонтных работах и исправлении дефектов в бетоне и железобетоне.
Комплект оборудования для торкретирования:
1 – компрессор, 2 – воздушные шланги, 3 – воздушный фильтр, 4 – цемент-пушка, 5 – шланг для подачи сухой смеси, 6 – сопло, 7 – торкретируемая поверхность, 8 – шланг для воды. 9 – бак
Оборудование для торкретирования включает в себя цемент-пушку, компрессор, шланги для воды и воздуха, воздушный и водяной фильтры, сопла, бак для воды.
Сжатый воздух под давлением 0,2…0,25 МПа подается от компрессора 1 по воздушным шлангам 2 в воздушный фильтр 3, где очищается от пыли, масла и других включений.
Очищенный воздух подается в цемент-пушку 4, которую предварительно загружают сухой смесью песка и цемента.
Сухая смесь далее направляется по шлангу 5 в сопло 6 и одновременно вода из бака 9 под давлением 0,35…0,5 МПа также подается в сопло для увлажнения смеси.
Увлажненная смесь со скоростью 100 м/с вылетает из сопла в виде веерообразного факела.
Частицы песка, покрытые цементной пленкой, сталкиваются с опалубкой или железобетонной конструкцией и прилипают к ней.
Вследствие высоких скоростей движения смеси имеющийся избыток химически несвязанной воды в полете удаляется с частиц.
Таким образом на поверхности постепенно наращивается слой песчаного бетона, причем частицы песка проникают в ранее нанесенный слой и уплотняют его. Получается плотная структура бетона, которая обладает низкой водопроницаемостью и высокой прочностью.
За один цикл наносят торкретный слой толщиной 25…30 мм. При многослойном торкретировании время между нанесением каждого слоя определяют экспериментальным путем. Ранее нанесенный торкрет должен обладать достаточной прочностью и в то же время пластичностью для восприятия динамической нагрузки при нанесении последующего слоя.
Для торкретирования используют чистый песок влажностью не более 6% и модулем крупности 2,5…3.
Включения зерен размером более 8 мм не допускаются. В качестве вяжущего применяют цемент марки 500 и выше, а для создания водонепроницаемых оболочек и ремонта железобетонных конструкций — быстротвердеющие цементы.
Чтобы получить плотный слой торкрета равномерной толщины, сопло при нанесении держат на расстоянии 0,7… 1 м от торкретируемой поверхности (перемещают его круговыми движениями), а струю смеси направляют перпендикулярно ей.
На вертикальные, наклонные и криволинейные поверхности торкретный слой наносят снизу вверх, чтобы свеженанесенный торкрет не сползал с них. Регулируют вязкость смеси дозированием подачи воды.
Толщину наносимого слоя контролируют по маякам. Потолки и вертикальные поверхности торкретируют в несколько слоев, а полы — сразу на всю толщину.
Перед торкретированием поверхность очищают сжатым воздухом и увлажняют. Первый раз наносят слой торкрета снизу на высоту 1,3..1,5 м. При нанесении последующих слоев зоны их перекрытия должны быть не менее 20 см.
Вышележащие слои наносят с передвижных или стационарных подмостей. После нанесения первого слоя бетон выдерживают и при этом увлажняют. В жаркую погоду поверхность торкретного слоя накрывают брезентом или пленочным покрытием, исключающим быстрое испарение влаги. Когда бетон наберет необходимую прочность, наносят второй слой и т. д.
Пневмобетонирование — это нанесение на поверхность пластичных бетонных смесей на мелкозернистом заполнителе. Смеси, как правило, приготовляют централизованно на бетонном заводе или на строительной площадке в смесителе установки «Пневмобетон».
Таким способом бетонируют конструкции толщиной до 150 мм: тонкостенные покрытия куполов, оболочки, сооружения для хранения жидкостей (резервуары), плавательные бассейны, градирни, замоноличивают стыки сборных железобетонных конструкций, а также ремонтируют (восстанавливают) бетонные и железобетонные конструкции.
Уложенный этим способом бетон отличается высокими физико-механическими показателями (плотность, водонепроницаемость, морозостойкость и сцепление с различными поверхностями).
Схема установки «Пневмобетон»:
1 – скиповый подъемник, 2 – приемно-перемешивающее устройство, 3 – вибросито, 4 – растворонасос, 5 – шланг, 6 – сопло, 7 – поверхность бетонирования
Наносят бетонные смеси установкой, которая включает в себя приемно-перемешивающее устройство 2 со смесителем принудительного действия, питатель, вибросито 3 с ячейками 10×10 мм, шланги 5, воздушный трубопровод, сопло с гасителем 6 скорости движения смеси.
В качестве приемно-перемешивающего устройства 2 используют растворосмеситель СБ-97 или принудительного действия СБ-80, оборудованный скиповым подъемником 1. Транспортируют смесь растворонасосами С-683, С-684 или С-317Б с подачей 2,4…6 м3/ч, переоборудованными на прямоточную схему и снабженными дополнительной смесительной камерой.
Шланг 5 монтируют из отдельных секций с внутренним диаметром 50 или 63 мм. На конце шланга закреплено сопло. При вылете из сопла скорость смеси 70…90 м/с. Конфигурация и геометрические размеры сопла зависят от вида работ, применяемых материалов и положения сопла по отношению к бетонируемой поверхности. Расход сжатого воздуха давлением 0,7 МПа составляет 7…9 м 3/мин.
До начала работ подключают установку к электросети и водопроводу, монтируют леса или передвижные подмости так, чтобы расстояние между настилом и рабочей поверхностью было 1,2…1,5 м, а высота яруса 2 м.
Для вертикальных конструкций устанавливают опалубку облегченного типа. Щели шириной более 5 мм в опалубке не допускаются.
При нанесении смеси сопло держат перпендикулярно бетонируемой поверхности и на расстоянии 0,7…1,2 м от нее. Бетонную смесь на вертикальные поверхности наносят снизу вверх. Для получения равномерной толщины бетонируемой поверхности соплом совершают спиралеобразные поступательные движения.
Для создания нормальных условий твердения бетон предохраняют от воздействия ветра и прямых солнечных лучей, ударов, сотрясений и других механических воздействий, периодически его увлажняют.
7.2 Раздельное бетонирование
При возведении массивных монолитных конструкций сначала устанавливают опалубку, затем внутри нее монтируют арматурное заполнение и инъекционные трубки. Заполняют опалубку щебнем двух фракций: до 100 (50…60%) и до 20 мм (40…50%). При этом каждый слой вибрируют, чтобы получить более плотную структуру бетона. Подают щебень в опалубку бадьями.
По окончании укладки щебня к инъекционным трубкам поочередно подключают растворонасос, с помощью которого закачивают цементно-песчаный раствор.
Инъекционные трубки в нижней части на длине 0,25…0,5 м имеют перфорированные отверстия. Раствор под давлением 0,15… 0,2 МПа заполняет пространство между частицами щебня.
Схема раздельного бетонирования массивных фундаментов:
1 – опалубка фундамента, 2 – инъекционные трубы, 3 – щебеночная засыпка, 4 – область распространения раствора
Рассмотрим технологическую схему раздельного бетонирования массивных фундаментов.
Инъекционные трубки устанавливают на таком расстоянии друг от друга, которое обеспечивает взаимное пересечение зон их действия не менее чем на половину радиуса действия.
Раствор нагнетают непрерывно до полного заполнения пространства между щебнем, о чем свидетельствует появление в контрольных отверстиях, оставляемых в щитах опалубки, раствора. Затем трубы поднимают на высоту 1… 1,5 м и процесс нагнетания повторяют.
При возведении фундаментов большой высоты после бетонирования одного-двух ярусов инъекционные трубки укорачивают путем исключения их звеньев.
Технология бетонирования тонкостенных конструкций имеет свои особенности. Прежде всего в конструкции опалубки предусмотрено двустороннее расположение отверстий
Схема раздельного бетонирования тонкостенных конструкций:
1 – опалубка, 2 – арматурное заполнение, 3 – крупный заполнитель, 4 – отверстия для ннъекции раствора, 5 – инъектор, 6 – контрольное отверстие, 7 – металлическая спираль
Первоначально в опалубку 1 устанавливают арматурное заполнение 2 и одновременно укладывают крупный заполнитель 3 фракции 40…20 мм слоями и уплотняют его вибраторами. Высота каждого слоя должна быть на уровне отверстий для инъекции. После укладки очередного слоя крупного заполнителя устанавливают металлические спирали 7, которые служат направляющими при движении раствора от инъектора. Перед бетонированием крупный заполнитель смачивают водой.
Инъектор 5 направляют в отверстие 4 опалубки. Раствор под давлением 0,15…0,2 МПа распространяется сначала по спирали 7, а через пространство между ее витками — в заполнитель. Момент окончания нагнетания определяют по появлению раствора в контрольных отверстиях 6. Процесс бетонирования, как правило, ведут с двух сторон двумя инъекторами снизу вверх. Такой метод обеспечивает получение плотного водонепроницаемого бетона независимо от степени его армирования.
При раздельном бетонировании упрощается технологическая схема укладки бетона, снижаются транспортные расходы, повышается качество работ, но усложняется контроль качества работ и повышаются требования к конструкции опалубки (должна быть жесткой без щелей и неплотностей).
7.3 Подводное бетонирование
Подводное бетонирование — укладка бетонной смеси под водой без применения водоотлива — применяют при возведении подводных частей опор мостов, днищ опускных колодцев и других массивных сооружений на глубине 1,5…50 м. Бетонную смесь к месту укладки в основном подают двумя способами.
Способ вертикально перемещающихся труб (ВПТ) основан на непрерывной подаче бетонной смеси по вертикально расположенной трубе, которую по мере увеличения толщины бетонного слоя поднимают с помощью кранов и лебедок так, чтобы нижний конец трубы всегда находился в толще бетона.
Расстояние между трубами зависит от их диаметра, подвижности бетонной смеси и интенсивности бетонирования. В среднем для труб диаметром 200…300 мм их радиус бетонирования около 6 м. При этом расстояние между трубами должно быть 10…11 м.
Схема подводного бетонирования способом вертикально перемещающихся труб:
1 – опалубка, 2 – рабочий настил, 3 – звенья труб, 4 – загрузочная воронка, 5 – вибраторы, 6 – стойка, 7 – бетоновод, 8 – плавучий кран
При подводном бетонировании трубы 3 устанавливают с рабочего настила 2. Каждую трубу собирают из секций длиной 1…1,2 м.
Верхняя секция оканчивается загрузочной воронкой 4, на одну из сторон которой навешивают вибратор 5.
Смесь от бетононасоса по бетоноводу 7 поступает непрерывно и заполняет весь объем трубы.
Затем смесь под гидростатическим давлением вытекает из нижнего отверстия трубы.
Чтобы предотвратить размыв бетона, низ трубы должен быть погружен в бетон на глубину 0,5…0,8 м.
Таким образом, свежие порции бетона как бы вытесняют ранее уложенный и не контактируют с водой.
По мере роста толщины бетонной подушки трубу постепенно извлекают и лишние секции демонтируют. Бетонирование считается оконченным, когда уровень бетона дойдет до проектной отметки.
Бетон подают непрерывно. При перерывах, больших, чем время схватывания цемента, ухудшается монолитность конструкции.
Способ восходящего раствора (ВР) является разновидностью раздельного бетонирования. Он состоит в нагнетании с помощью растворонасосов 10 в каменную наброску или гравийно-щебеночную отсыпку 1 цементного раствора 2 с осадкой конуса 10…12 см. Для этой цели устанавливают решетчатые шахты 6, в которые пропускают трубы 7 для нагнетания по ним раствора. Радиус действия каждой трубы 2…3 м.
Схема подводного бетонирования способом восходящего раствора:
1 – каменно-щебеночная отсыпка, 2 – раствор, 3 – штунтовое ограждение (опалубка), 4 – ограждение, 5 – настил, 6 – шахта, 7 – труба, 8 – лебедка, 9 – рукав, 10 – растворонасос
При нагнетании раствор, выходя из нижнего конца трубы, поднимается вверх и, вытесняя из пустот воду, заполняет их. Так создается бетонный монолит. По мере повышения уровня раствора в шахте трубы поднимают, оставляя нижний конец трубы длиной 0,8…1 м в растворе.
Подводное бетонирование методом втрамбования
Втрамбовывание бетонной смеси начинают с создания бетонного островка в одном из углов бетонируемой конструкции при подаче смеси по трубе или в бадьях с открывающимся дном.
Островок должен возвышаться над поверхностью воды не менее чем на 30 см.
Для втрамбовывания применяют бетонную смесь подвижностью 5…7 см. Подводный откос островка, с которого начинают втрамбовывание, должен образовывать под водой угол 35…45° к горизонтали.
Новые порции бетонной смеси втрамбовывают в островок равномерно с интенсивностью, не нарушающей процесс твердения уложенного бетона, и не ближе 20…30 см от кромки воды. Этим приемом обеспечивается защита от соприкосновения с водой новых порций бетонной смеси.
Метод применяют при глубине воды до 1,5 м для конструкций больших площадей при классе бетона до В25.
Метод укладки кюбелями. Бетонную смесь опускают под воду на основание бетонируемого элемента в кюбелях (раскрывающихся ящиках, бадьях или грейферах) и разгружают через раскрытое дно или затвор.
Обычно применяют кюбели вместимостью от 0,2 до 3,0 м3, закрытые сверху и имеющие уплотнения по контуру раскрывания, которые препятствуют вытеканию цементного теста и проникновению воды внутрь кюбеля.
Бетонную смесь выпускают при минимальном отрыве дна кюбеля от поверхности уложенного бетона, исключая тем самым возможность свободного сбрасывания бетонной смеси через толщу воды.
Преимущество метода укладки кюбелями заключается в возможности бетонирования на любой глубине, в производстве работ без подмостей, в возможности укладки бетонной смеси на неровное основание с большими углублениями и возвышениями.
Однако при бетонировании кюбелями происходит частичный размыв смеси при разгрузке кюбеля и появляется некоторая слоистость укладки.
Этот метод применяют, если марка укладываемого бетона не выше 200.
Укладку бетонной смеси в мешках следует рассматривать как вспомогательный метод, который применяют при небольших объемах работ, для уплотнения щелей между дном и опалубкой, а также в аварийных случаях.
Бетонную смесь, укладываемую в мешках из редкой, но прочной ткани готовят на щебне с крупностью заполнителя 40 мм и осадкой конуса 2-5 см. объем смеси в одном мешке 10…20 л. Мешки со смесью укладывают водолазы, тщательно прижимая их один к другому.
7.4 Основы технологии полимерцементных бетонов и пластбетонов
Полимерцементным бетоном называют искусственный каменный материал, связующими которого являются полимер и цемент, заполнителями — песок и щебень.
В отличие от обычных бетонов с модифицирующими добавками (ГКЖ-94, винсол), которые из-за малых количеств практически не меняют структуру бетона, содержание полимера в полимерцементных бетонах достаточно велико.
Это позволяет получать материалы с новыми свойствами. Они имеют меньшую массу, морозостойки, обладают несколько большей прочностью по сравнению с обычными, повышенной износостойкостью.
Полимерцементные бетоны получают тремя способами:
— введением в бетон при смешивании водных дисперсий полимеров (поливинилацетата или синтетического каучука), распадающихся в бетонной смеси с выделением воды, при этом обезвоженный полимер выполняет роль дополнительного связующего;
— добавлением в воду затворения водорастворимых мономеров и полимеров (фуранового и поливинилового спиртов, эпоксидных, фенолформальдегидных смол и т. п.) с последующим их отверждением в бетоне нагревом или с помощью отвердителей;
— пропиткой бетона на необходимую глубину маловязкими полимерами (карбамидами, лаком «этиноль», стиролом), которые отверждаются непосредственно в бетоне.
Заполнителями для полимерцементных бетонов служат кварцевые или дробленые пески, а также щебень прочных и плотных горных пород крупностью не более 20 мм. Применяют также полимерцементные мелкозернистые растворы.
Оптимальное содержание полимера типа поливинилацетата составляет от 15 до 20% к массе цемента в пересчете на сухое вещество. При этом наилучшим образом используются свойства как цемента, так и полимера.
При такой дозировке в полимерцементном бетоне сохраняется сплошность цементного геля, а полимер, обволакивая цементные сростки и зерна заполнителя, дополнительно склеивает их.
При увеличении полимера сплошность цементных новообразований нарушается, из-за чего снижается прочность полимерцементных бетонов.
Оптимальное содержание водорастворимого карбамидного полимера С-89, а также эпоксидных полимеров ДЭГ-1 и ТЭГ-17 около 2% по отношению к массе цемента.
При этом водоцементное отношение бетонной смеси можно понизить до 0,29 — 0,30 без ущерба для ее удобоукладываемости, а также стойкости в агрессивных средах.
Применяя различные полимерные составляющие, можно получить полимерные бетоны, стойкие к действию нефтепродуктов, жиров и растворов солей.
Полимерцементные бетоны применяют для устройства износоустойчивых полов, аэродромных покрытий, резервуаров под нефтепродукты, а также монолитных конструкций для работы в агрессивных средах.
Для приготовления полимерцементных смесей применяют лопастные мешалки или вибросмесители. При механическом перемешивании смесь насыщается воздухом, в бетоне образуются мелкие поры, равномерно распределенные по объему.
Вследствие того, что полимерцементные бетоны применяют пока в небольших объемах, их смеси готовят в смесителях, расположенных вблизи места укладки.
Полимерцементные смеси обладают повышенной вязкостью, поэтому виброуплотнять их при низких частотах (3000 кол/мин) малоэффективно.
Воздух не удаляется из бетона, структура его получается чрезмерно пористой и рыхлой. Более целесообразно высокочастотное вибрирование, а для жестких смесей трамбование и вибропрессование.
Полимерцементные бетоны, приготовленные на водных дисперсиях полимеров, выдерживают в воздушно-сухих условиях, бетоны же с добавками эпоксидных и карбамидных полимеров быстро твердеют во влажных условиях.
Пластбетоны — искусственные конгломераты, получаемые целиком на органических полимерных связующих. Они являются, по существу, пластмассами с минеральными наполнителями различной крупности.
Связующими в пластбетонах служат маловязкие термореактивные полимеры (фенолформальдегидные, фурановые, полиэфирные и эпоксидные), которые при добавлении отвердителей и в определенных условиях твердеют, склеивая компоненты в прочный конгломерат. Обычно применяют пластбетоны составов 1:5-1:15 (полимер : наполнитель по массе).
Для отверждения полимеров применяют керосиновый контакт Петрова, сульфокислоты и минеральные кислоты, полиэтиленполиамин, диэтилентриамин и др.
В качестве наполнителей применяют чистые пески с крупностью зерен 0,6-2,5 мм и содержанием глинистых и пылеватых частиц не более 0,5%.
Щебень и гравий должны быть сухими и чистыми и иметь крупность не более 20 мм.
Помимо гранитного щебня в качестве наполнителей применяют андезитовый и баритовый, а также измельченный трепел и графит в зависимости от назначения пластбетона.
Прочностные свойства пластбетонов определяются свойствами связующего и наполнителя, а также адгезией между ними. Пластбетоны обладают высокой прочностью, особенно при растяжении и изгибе. Так, прочность при изгибе некоторых пластбетонов на эпоксидных полимерах достигает 350…450 кгс/см2.
Пластбетоны практически водонепроницаемы, морозостойки; они хорошо сопротивляются износу, стойки в агрессивных средах. Например, стойкость их против действия кислот в 10 раз выше, чем у обычных бетонов.
Пластбетоны целесообразно применять для гидроизоляционных и антикоррозионных облицовок. Их используют для получения износоустойчивых полов, в аэродромных покрытиях, а также для возведения частей зданий и сооружений, эксплуатируемых в агрессивных средах.
Пластбетонные смеси готовят в небольших объемах непосредственно у мест их укладки из-за быстрого их твердения.
В лопастный смеситель загружают наполнители, затем полимерные связующие. После 3…4 — минутного перемешивания и получения однообразной массы вводят отвердитель и перемешивают в течение 5…8 мин.
Приготовленную порцию смеси сразу же укладывают в дело. Уплотняют ее трамбованием или штыкованием.
Твердеют пластбетоны лучше в сухих условиях при 50…100° С.
Повышение относительной влажности выше 60% снижает прочность пластбетонов, особенно на полиэфирных полимерах.
Составы на эпоксидных полимерах менее чувствительны к повышенной влажности.
Время прогрева уложенных пластбетонов составляет 4…8 ч в зависимости от вида полимера и состава смеси.
При твердении пластбетонов происходит их усадка, величина которой зависит от вида и количества полимера.
perekos.net
земляные работы, приготовление и способы
Фундамент является неотъемлемой частью любого здания и сооружения. При его возведении важно не допустить технологических ошибок, ведь невнимательность и несоблюдение этапов строительства, способны привести к серьезным последствиям. Несмотря на серьезную ответственность, возведения фундаментов – это легкий процесс, с которым справится даже новичок. Бетонирование фундамента позволит получить прочную, надежную основу для зданий и сооружений, которая прослужит не один десяток лет. Но чтобы конструкция получилась с требуемыми прочностными характеристиками, следует обратить внимание на основные тонкости, которые присутствуют в процессе бетонирования.
Какие нужны материалы и инструменты?
Чтобы возвести бетонный фундамент, потребуются следующие инструменты и материалы:
- сварочный аппарат;
- терка;
- колышки;
- стальные прутья;
- бетономешалка или пустая емкость для приготовления раствора;
- лопата;
- веревка или шнур для разметки;
- тяпка;
- строительный уровень;
- цемент;
- песок;
- щебень;
- вода;
- брусья для возведения опалубки.
Земляные работы
Перед бетонированием подготавливают строительный участок и проводят комплекс мероприятий, необходимых для строительства фундамента. Первый этап включает в себя земляные работы. Для этого понадобятся колышки и веревка, которыми сделают разметку местности. После того как территория размечена, приступают к рытью траншеи. Глубину траншеи делают такой, чтобы она была больше глубины промерзания почвы на 30 сантиметров. Дно вырытой траншеи заполняют слоем песка или щебня.
Процесс возведения фундамента хоть и легкий, но все же требует определенных силовых нагрузок и времени, поэтому рекомендуют нанять еще несколько человек, которые помогут ускорить строительство. Облегчить работу можно, воспользовавшись услугами специальной техники. Трактор качественно и быстро выроет траншею даже в местах с твердым грунтом.
Вернуться к оглавлениюСоздание опалубки
В качестве основы под бетонную смесь устанавливают опалубку из деревянных досок или сборных щитов. При монтаже опалубки следует придерживаться следующих тонкостей:
- Части опалубки должны быть точно установлены и проверены строительным уровнем, который исключит перекосы и наклоны основы.
- Качество поверхности досок, а также наличие в возводимой конструкции щелей способны повлечь за собой ряд неприятных последствий. Поэтому возможные зазоры между досками устраняют еще до момента кладки рабочей смеси.
- Для достижения требуемой жесткости опалубки используют доски толщиной не меньше пяти сантиметров, которые способны выдержать большие нагрузки в процессе бетонирования конструкции.
- Чтобы придать опалубке повышенную жесткость, следует применять больше подкосов, располагая их с меньшим шагом.
- Перед тем как возводить опалубку, нужно вырыть траншею, засыпать ее и выровнять.
Установка опалубки начинается с забивки расположенных по всему периметру колышков в поверхность грунта. Далее приступают к крепежу досок с помощью гвоздей. Важно следить за ровностью возводимой конструкции, иначе перекосы отразятся на фундаменте. Демонтаж опалубки проводится после того как бетон полностью высохнет. Произойдет это через пару дней после кладки рабочей смеси.
Вернуться к оглавлениюПриготовление раствора
Чтобы обеспечить фундаменту высокую прочность, следует приготовить бетонный раствор с высокими качественными характеристиками. Цемент приобретают марки не ниже М-200. Для его приготовления понадобятся:
Для изготовления смеси нужно засыпать в бетономешалку сухие ингредиенты: три части песка, одну часть цемента и пять частей щебня. Сухие компоненты перемешивают и заливают водой, воды должно быть столько, чтобы получить раствор консистенции, напоминающей густую сметану. Перемешивание компонентов смеси в бетономешалке займет около пяти минут, если возможность приобретения такого оборудования отсутствует, тогда разводят рабочую смесь в емкости большого объема. Но тогда стоит учитывать, что приготовление раствора без специального оборудования займет много времени.
Вернуться к оглавлениюДелать бетонную смесь нужно непосредственно перед началом заливки фундамента.
Способы бетонирования
При бетонировании основы под здания и сооружения следует провести армирование стальными прутьями, диаметр которых 0,8-1,2 сантиметра. Из стальных прутьев конструируют сетку, соблюдая при этом размеры ячейки – 150х150 миллиметров. Бетонируем конструкцию только после того, как установлена армирующая сетка в полость опалубки. Кладка бетонного раствора может выполняться двумя способами:
- Ручной способ. Фундаменты, возведенные вручную, подразумевают заливку готового раствора несколькими людьми. В данном случае на строительной площадке должны находиться две бетономешалки, которые подают цемент с двух сторон.
- При помощи миксера. Кладка бетонной смеси с использованием миксера осуществляется в несколько раз быстрее ручного способа. Этот способ возведения фундамента является дорогостоящим, но с лучшим готовым результатом.
Ручной способ

Чтобы бетонировать небольшие сооружения, применяют ручной способ, для осуществления которого потребуется бригада из нескольких рабочих. При попытке бетонировать в одиночку, можно навредить строительному процессу и все труды будут напрасными.
Также следует приобрести две бетономешалки, которые устанавливают с двух сторон объекта бетонирования. На каждое оборудование назначается три человека. Процесс заливки раствора из песка, цемента и щебня должен осуществляться быстро, так как бетонный состав способен быстро набирать прочность. Бетонный раствор подают по всему периметру фундамента толщиной до 40 сантиметров.
После заливки смеси ее следует тщательно утрамбовать глубинным вибратором. Уплотнение позволит избавиться от пузырьков воздуха в смеси и распределить ее по всей глубине конструкции. Далее приступают к укладке последующего слоя бетонного раствора, который также следует уплотнить. Заливка каждого нового слоя осуществляется спустя два часа после того, как закончили бетонировать предыдущий. Заливка последнего слоя требует особой внимательности, а именно придание поверхности особой ровности. Сделать ровный слой можно с помощью строительного уровня или других специальных приспособлений для выравнивания массивной поверхности.
Залитый бетон достигнет своих прочностных характеристик спустя месяц, на протяжении которого важно обеспечить оптимальные условия для застывания бетонного раствора. Чтобы предотвратить воздействие прямых солнечных лучей и атмосферных осадков на бетон, следует накрыть его изолирующими материалами.
Вернуться к оглавлениюПри помощи миксера
Заливка фундамента с помощью миксера подразумевает использование транспортного средства, которое осуществит заливку бетонного раствора по всему периметру фундамента в короткие сроки. Такой способ более затратный, чем ручной, поэтому перед выбором способа бетонирования следует определить для себя приоритетные аспекты.
Заливка бетонного раствора с применением миксера включает в себя подачу бетона специальными желобами в опалубку. Стоит учитывать скорость подачи раствора и успевать выравнивать вибратором или тряпкой залитую поверхность.
Вернуться к оглавлениюУстройство рабочих швов
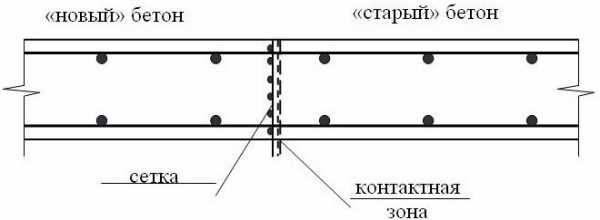
Заливку фундаментов бетонным раствором рекомендуется осуществлять без продолжительных перерывов. Укладка последующих слоев смеси не должна иметь перерыв более трех часов. Но зачастую придерживаться таких правил не получается и тогда нужно организовать устройство рабочих швов.
Рабочие швы являются границей между заливаемыми бетонными слоями, и при их изготовлении следует придерживаться технологического процесса. Если технология будет нарушена, то фундамент для зданий и сооружений не приобретет нужных качественных характеристик.
Устанавливая рабочие швы, важно добиться максимальной адгезии бетонных слоев со швами. Для этого затвердевшую поверхность следует подготовить для проведения последующих работ. Поверхность очищают от пыли, снега, мусора или воды. Далее удаляют цементное молочко, которое образуется на затвердевшем растворе. Цементное молочко образует пленку, которая имеет рыхлую непрочную структуру, что приводит к снижению адгезии раствора с затвердевшим слоем. Удаление пленки проводят с помощью водяной или воздушной струи, которую подают под высоким давлением. Таким образом, осуществляется удаление пленки с затвердевшей поверхности из бетона. Помимо удаления пленки струей с высоким давлением, используют фрезеровочные машинки. Разрушить цементную пленку можно кислотой, которую наносят на твердый слой и оставляют на несколько часов.
К укладке последующих слоев бетонного раствора приступают только после удаления пленки с застывшей поверхности. Далее проводят утепление и гидроизоляцию швов, что позволит предотвратить преждевременное разрушение основы зданий и сооружений.
Вернуться к оглавлениюЗаключение
Для качественного и прочного возведения фундамента следует придерживаться технологии производства и последовательности этапов. Соблюдение всех правил и рекомендаций по заливке бетонным раствором приведет к созданию надежного основания для зданий и сооружений, исключит необходимость в создании рабочих швов.
Но если все-таки создание швов неизбежно, тогда следует тщательно подготовить поверхность перед тем, как приступать к укладке бетонного раствора.
kladembeton.ru
Бетонирование
Бетонирование
Бетонирование – процесс возведения на строительной площадке предусмотренных проектом конструкций из бетона или железобетона. Самый ответственный этап строительства.
При бетонировании смесь заполняет все промежутки между стержнями арматуры, образует защитный слой требуемой толщины, подвергается уплотнению соответствующей заданной плотности и марке бетона и принимает форму конструкции опалубки.
Затвердевший бетон трудно поддается исправлению, поэтому надо строго соблюдать технологию бетонирования.
Технология бетонирования
Технология бетонирования состоит из подготовительных и проверочных операций, процесса укладки, содержащего операции по приему, распределению и уплотнению бетонной смеси бетонщиками, а также вспомогательных операций, осуществляемых по ходу бетонирования.
Этапы бетонирования
1. Подготовка к бетонированию естественного основания, выполнение гидроизоляционных работ, правильность установки арматуры и закладных деталей, анкеров, каналообразователей и т.п.
2. Геодезическими инструментами выверяют точность установки опалубки, наличие строительных подъемов в днищах коробов балок и арок, правильность установки клиньев или домкратов для раскружаливания и т. п.
3. Перед бетонированием опалубку очищают струёй воды или сжатого воздуха от загрязнений. Поверхность деревянной опалубки смачивают. Щели в опалубке толщиной больше 3 мм заделывают для предотвращения вытекания бетона. Поверхность опалубки покрывают смазкой, например отработанным маслом. Арматуру очищают от грязи и ржавчины. Одновременно выполняют работы по наладке механизмов, машин и приспособлений, используемых во всех взаимосвязанных операциях по бетонированию. На рабочем месте устанавливают нужный инвентарь, устраивают ограждения, предохранительные и защитные устройства, предусмотренные техникой безопасности. В необходимых случаях оборудуют телефонную, световую или звуковую сигнальную связь между рабочими местами по подаче, приему и укладке бетонной смеси.
4. Заливка бетона: бетонная смесь разливается в конструкцию опалубки. В зависимости от объёмов строительства бетонная смесь может быть приготовлена как на строительной площадке, так и на заводе, откуда она транспортируется на объект автобетоносмесителями (миксерами). Автобетоносмеситель, доставив бетонную смесь на объект, разливает её порциями в бункеры (бадьи), ящики для бетона и, при возможности подъезда, непосредственно в опалубку. Краном бункеры подаются к месту заливки.
5. Распределение и уплотнение бетонной смеси ведётся слоями в непрерывной последовательности. Каждый новый слой должен укладываться до схватывания предыдущего. За этим ответственным процессом нужен постоянный надзор технического персонала стройки. В журнале бетонных работ каждую смену записывают дату выполнения работ, их объемы, свойства бетонной смеси, дату изготовления бетонных контрольных образцов, их количество, температуру наружного воздуха и бетонной смеси, тип опалубки и дату распалубливания конструкций.
Во время укладки и распределения бетонной смеси следят за состоянием лесов и опалубки. При обнаружении смещений или деформаций опалубки бетонирование прекращают и принимают меры к исправлению дефектов.
Одновременно с бетонированием выполняют вспомогательные операции по установке и перемещению транспортных и грузоподъемных средств: виброжелобов, бункеров, бетоноводов, конвейеров и т. п.
В конце смены инвентарь, механизмы и приспособления очищают от наплывов бетона, промывают бетоноводы.
Вы смотрели: Бетонирование. Технология бетонирования
Поделиться ссылкой в социальных сетях
Оставить отзыв или комментарий
stroykaa.ru
ТЕХНОЛОГИЯ БЕТОНИРОВАНИЯ НАИБОЛЕЕ РАСПРОСТРАНЕННЫХ КОНСТРУКЦИЙ | Станки для шлакоблоков
• При выполнении бетонных и железобетонных работ следует руководствоваться положениями действующих строительных норм и правил (СНиП) и указаниями проекта производства работ (ППР), регламентирующими технологические требования к бетонированию данной конструкции или сооружения.
Перед началом бетонирования тщательно проверяют и оформляют актом соответствие проекту опалубки, арматуры, закладных деталей и других элементов конструкции, остающихся в не» после бетонирования. В частности, проверяют геометрические размеры формующего пространства опалубки, ее неизменяемость, прочность и устойчивость. Контролируют также соответствие проекту армирования закладных деталей, их установку и крепление, исключающие смещение при укладке бетонной смеси, правильность устройства каналов (при предварительно напряженном армировании), расположение отверстий, выпусков.
При бетонировании в скользящей опалубке проверяют наличие конусности опалубки, горизонтальность рабочего пола, правильность установки домкратов и т. д.
При применении несъемной опалубки следует обращать внимание на прочность крепления ее элементов, необходимую для восприятия распорного давления от свежеуложенной бетонной смеси, и іналичие выпусков или шероховатой фактуры на формующей поверхности.
При укладке бетона на естественное основание проверяют правильность устройства основания.
Непосредственно перед бетонированием опалубку очищакУг от грязи и строительного мусора. Деревянную опалубку примерно за 1 ч до укладки смеси обильно смачивают, а оставшиеся щели 3aJ конопачивают. В металлической опалубке зазоры заделывают алебастром. После вторичной проверки положения арматуры, а при необходимости — после очистки ее от грязи и попавшего раствора приступают к укладке бетонной смеси.
Технологические приемы бетонирования назначают в зависимости от типа конструкции.
При бетонировании подготовок под полы применяют тощую’ бетонную смесь с осадкой конуса 0…2 см. Площадь подготовок под
Х.45. Схема бетонирования полов
I — виброрейка; 2 — вибратор; З1 — самосвал; 4 — направляющая
Х..46. Бетонирование густоармированной железобетонной плиты с применением авто — бетоноиасоса
Ч
Х.47. Схема бетонирования фундаментов
1 — автобетоиосмеситель; 2 — автобетоио — яасос с распределительной стрелой; 3 — опалубка
1 2
«юлы разбивают іна так называемые карты бетонирования шириной 3…4 м. Через 6…8 м устраивают деформационные швы, снижающие температурные напряжения.
При бетонировании чистых полов на подготовке устанавливают маячные рейки, которые разделяют бетонируемую площадь пола
На полосы шириной 3…4 м. Верх маячной рейки соответствует проекной отметке пола. Бетонирование полос ведут через одну, вначале —нечетные полосы, а затем, после того как бетон затвердеет, удаляют маячные рейки и бетонируют четные полосы (рис. Х.45).
Бетонную смесь уплотняют поверхностными вибраторами или виброрейками, после чего поверхность пола выравнивают правйлом и заглаживают резиновой лентой.
• Свежеуложенный бетон заглаживают вручную или с помощью специальной машины, а через 30…40 мин после заглаживания полы железнят.
При бетонировании полов или оснований под полы на больших площадях можно применять специальные бетоноукладочные машина, которые, двигаясь, оставляют за собой готовую полосу пола.
В настоящее время при бетонировании полов успешно используют технологию, основанную на эффекте вибрации и вакуумирования.
При бетонировании массивных густоармированных плит под тяжелые фундаменты, днищ резервуаров и различного рода высотных сооружений основным технологическим требованием является: непрерывность укладки смеси на всю высоту плиты.
Плиты толщиной менее 0,5 м бетонируют картами шириной п» 3…4 м. При большей толщине плит их разбивают на карты шириной 5…10 м с разделительными полосами между ними 1…1.5 м.. Чтобы обеспечить непрерывную укладку смеси на всю высоту, плиту разбивают на блоки без разрезки арматуры, с ограждение^ блоков металлическими сетками. Бетонируют такие плиты с применением автобетоносмесителей, автобетоновозов или при больших объемах работ — автобетононасосов (рис. Х.46).
При бетонировании фундаментов и массивов (рис. Х.47) в зависимости от принятой технологической схемы бетонную смесь подают в опалубку непосредственно из транспортного средства с применением передвижного моста или эстакады либо вибропитателями и виброжелобами или бадьями с помощью кранов. При высоте разгрузки бетонной смеси более 3 м применяют хоботы.
Малоармированные -фундаменты и массивы бетонируют смесью с подвижностью по стандартному конусу 1…3 см и крупностью’ заполнителя не более трети наименьшего расстояния между стерж — .нями арматуры.
Бетонную смесь укладывают слоями 20…40 см. Наибольшая толщина слоя бетонной смеси не должна превышать 1,25 длины’ рабочей части вибратора. Более глубокое погружение вибратора’ может привести к нарушению структуры ранее’ уложенного слоя бетона.
При бетонировании фундаментов применяют глубинные вибраторы, а при устройстве крупных массивных фундаментов — вибрационные пакеты, подвешенные на стреле крана, или плоскостные1 виброизлучатели. При бетонировании крупных массивов используют мощное навесное вибрационное оборудование, устанавливаемое на малогабаритных самоходных устройствах.
При этом необходимо иметь їв виду, что строительные нормы и правила разрешают только минусовые допуски.
При бетонировании железобетонных фундаментов под металлические колонны в бетоне, в соответствии с проектом, устраивают шахты для анкерных болтов. При этом обращают особое внимаете на правильность расположения анкерных болтов, а при без-‘ выверочном монтаже металлических колонн — на точное соответствие верха опорной стальной плиты проектной отметке.
В последние годы применяют метод крепления оборудования на железобетонных и бетонных фундаментах с помощью анкерных болтов, которые устанавливают на эпоксидном клее в высверленные для этого в фундаменте отверстия, глубина которых доходит до 10 диаметров болта.
При бетонировании фундаментов, рассчитанных на восприятие’ динамических нагрузок (фундаменты под турбогенераторы, компрессоры, кузнечно-прессовое оборудование и т. д.), обязательным технологическим требованием является отсутствие рабочих швов, что обусловливает необходимость непрерывной укладки бетонной смеси.
ЦЯри сооружении фундаментов используют также метод безопалубочного бетонирования. Он заключается в том, что в построечных условиях изготовляют арматурно-опалубочные блоки с монолитной несъемной опалубкой. Готовый блок устанавливают краном в проектное положение и затем заполняют бетонной смесью.
Метод эффективен при возведении массивных конструкций, расположенных ниже уровня земли: подколонніиков, фундаментов «од оборудование, стен подземных сооружений и т. д.
Порядок возведения сооружений методом безопалубочного бетонирования следующий. Арматурный блок с закрепленными на яем закладными деталями и фиксаторами защитного слоя доставляют к специальному стенду, расположенному в непосредственной «близости от места установки. Стенд представляет собой площадку, выложенную железобетонными плитами, на которой из швеллеров устраивают ванну высотой и размерами в плане, несколько большими боковой грани блока. Арматурный блок устанавливают жраном в ванне и с помощью вибраторов, закрепленных на блоке, втапливают в бетон до тех пор, пока фиксаторы защитного блока не коснутся поверхности стенда. После того как бетон наберет необходимую прочность, блок извлекают из ванны и погружают « слой бетона следующей гранью. Готовый блок устанавливают в проектное положение, выполняют обратную засыпку грунта и бетонируют.
Данный метод по сравнению с традиционным методом бетонирования позволяет снизить трудовые затраты почти вдвое. При устройстве стен, расположенных ниже уровня грунтовых вод, он дает возможность получить более плотную структуру защитного слоя, так как способ его устройства обеспечивает более благоприятную ориентацию капилляров в бетоне по сравнению с другими способа-
Mflj
—При бетонировании тонких густоармированных стен и перегородок (рис. Х.48) бетонная смесь должна иметь осадку конуса 6 … 10 см, а для малоармированных стен толщиной более 0,5 м — 4…5 см.
Опалубку стен толщиной более 0,5 м можно возводить на всю высоту стены с подачей смеси сверху с помощью хоботов, а при тонких стенах опалубку устанавливают на всю высоту с одной стороны, а с другой наращивают по мере бетонирования. В последнем случае бетоніную смесь подают и уплотняют с низкой стороны опалубки.
При бетонировании стен резервуаров, опускных колодцев и других сооружений, к которым предъявляются особые требования к водопроницаемости, основным технологическим условием кроме точного выдерживания заданного проектом состава бетонной смеси является непрерывная укладка смеси равномерно по всему периметру сооружения.
При бетонировании колонн (рис. Х.49) нижнее отверстие в коробе опалубки, место примыкания колонны к фундаменту перед •укладкой бетонной смеси очищают от строительного мусора, после чего в опалубку укладывают слой цементного раствора состава 1:2… 1:3 или мелкозернистого бетона толщиной 5… 20 см. Этот буферный слой исключает образование раковин и неплотностей у основания колонны.
Колонны высотой до 5 м и с размером стороны сечения 40… 80 см бетонируют сразу на всю высоту до низа примыкающих прогонов, балок и капителей. При этом смесь подают бадьями и разгружают в приемный бункер хобота. Уплотняют бетонную смёсь внутренними вибраторами. Колонны высотой более 5 м бетонируют ярусами высотой до 2 м с ззгружением бетонной смеси и ее вибрированием через боковые окна в стенках короба.
Бетонирование балок и плит в ребристых перекрытиях производят одновременно. Балки высотой более 80 см можно бетонировать независимо от примыкаемых к ним плит. Бетонную смесь подают на перекрытия по бетоноводам или в бадьях, разгружаемых на весу.
Бетонирование прогонов, балок и плит следует начинать через 1 …2 ч после бетонирования колони и первоначальной осадки в них бетона.
Прогоны и балки высотой более 50 см бетонируют слоями 30… 40 см, при этом каждый слой в отдельности уплотняют глубинными вибраторами. Густоармированные прогоны и балки уплотняют вибраторами со специальными насадками. Последний слой бетонной смеси не доводят до нижней плоскости плиты на 3… 4 см.
Плиты перекрытия бетонируют сразу на всю ширину с’уплотне — лием поверхностными вибраторами.
Х.48. Схема бетонирования стен
А — послойное бетонирование; б — бето-
СГТ»,С0КИХ н густоармнрованных стен с нараіцнваннем опалубки — в — бетонирование через карманы; /-опалубні 2 ~ звенный хобот; 3 — бадья — 4 — разделительная опалубка в рабочем шве — 5 — арматурный каркас; 6 — карман ‘
А бетонирование колонн высотой до б м Т К°ЛОНН
ТУ1″°Й ®РМатУРой балок; 1 -арматура il. ба~я° У» ВЫС°Т0Й более 5 м: е-то же с хобот; 5-приемная воронка; 7 — съ^ый и^Тв’Л^ТгГЛ гн^кнГУбКа;
10 — арматура балки РР НМ ваЛ0М; 9 — карман;
Арки и своды пролетом, менее 15 м бетонируют непрерывно одновременно с двух сторон от пяты к замку. Своды пролетом более 15 м бетонируют отдельными участками. При этом бетонную смесь укладывают полосами одновременно на трех участках в замке и’ у пят. После этого бетонируют отдельные полосы, между которыми оставляют усадочные зазоры по 20… 30 см, которые заделывают малоподвижной бетонной смесью через 5… 7 дней после бетонирования полос. Затяжки сводов и арок перед бетонированием подтягивают.
При бетонировании арок и сводов рекомендуется применять малоподвижные бетонные смеси с осадкой конуса 1…3 см, что уменьшает опасность сползания смеси при укладке и уменьшает усадочние деформации.
На крутых участках1 арок или сводов, чтобы исключить сполза — яие бетонной смеси при вибрировании, бетонирование ведут в двусторонней опалубке, наружные щиты которой наращивают в процессе бетонирования.
Началу бетонирования должна предшествовать тщательная про верка (с составлением акта) геометрических размеров, устойчивости и прочности опалубки.
Технология возведения жилых и гражданских зданий из монолитного железобетона. Наряду с полносборным заводским домостроением в стране получает определенное развитие строительство зданий из монолитного железобетона. Этот вид строительства оказывается целесообразным:
При (необходимости решения градостроительных проблем за счет строительства нетиповых зданий башенной композиции;
При строительстве в районах высокой сейсмичности или на территории горных выработок, где предъявляются, повышенные требования к пространственной жесткости зданий;
При возведении зданий в районах, значительно удаленных от домостроительных предприятий.
Строительство зданий из монолитного железобетона можно считать индустриальным, когда работы ведут поточными методами, применяют унифицированные комплекты инвентарной опалубки, все процессы комплексно механизированы и в конечном счете обеспечиваются необходимое «качество работ и высокие технико-экономические показатели.
Практика показала, что при правильной организации и специализации строительных работ трудоемкость возведения зданий из монолитного железобетона может быть доведена до 2,5… 3 чел.-дней» на 1 м2 общей площади, что примерно соответствует уровню, достигнутому в заводском домостроении.
Из монолитного железобетона возводят цельномонолитные дома с преимущественным использованием бетонов на пористых заполнителях и оборно-монолитные дома, в том числе дома с монолитными поперечными стенами и перекрытиями и сборны — ми панелями наружных стен, здания с железобетонным каркасом, с монолитными диафрагмами и ядрами жесткости и т. д.
При прочих равных условиях предпочтительнее применять следующие типы опалубки:
Для зданий башенной композиции с однослойными стенами и простой планировочной структурой, а также для возведения ядер жесткости в зданиях сборно-монолитной конструкции — скользящую опалубку;
Для многоэтажных зданий большой протяженности с несущими поперечными стенами (сотовая структура) —объемно-переставную (туннельную) опалубку;
Для зданий со смешанным конструктивным решением (с наружными кирпичными стенами, монолитными перекрытиями и внутренними стенами и перегородками и др. ) —крупнощитовую и блочную опалубки.
Возведение зданий в скользящей опалубке. Технология возведения жилых зданий в скользящей опалубке в принципе идентична технологии, применяемой при строительстве в такой опалубке других сооружений, хотя ‘И имеет некоторые отличия, обусловленные более развитым периметром зданий, необходимостью устройства междуэтажных перекрытий и отделки наружных стен по ходу бетонирования, сложностью бетонирования наружных стен, имеющих слой утеплителя, и т. д. Существенно осложняет использование метода возведения зданий в скользящей опалубке наличие больших оконных проемов. В этом случае домкратные стержни и, следовательно, сами домкраты приходится группировать в простенках или местах пересечений стен. При этом утяжеляется опалубка, так как она должна иметь повышенную жесткость.
Перекрытия зданий, возводимых в скользящей опалубке, можно устраивать в процессе бетонирования стен монолитными или сборно-монолитными, выполнять с отставанием на 2 … 3 этажа или после сооружения стен коробки здания. Устройство монолитных перекрытий одновременно с бетонированием стен (рИс. Х.50) более технологично и повышает пространственную жесткость здаїния. При этом методе после окончания бетонирования стен очередного этажа скользящую опалубку поднимают с таким расчетом, чтобы низ внутренних щитов опалубки находился іна отметке верха будущего перекрытия. После этого устанавливают инвентарную опалубку, которая опирается на перекрытие нижерасположенного этажа, и производят армирование и бетонирование. После укладки бетонной смеси в перекрытие начинают бетонировать стены очередного этажа.
При бетонировании в скользящей опалубке жилых и гражданских зданий необходимо строго соблюдать технологические правила, обеспечивающие прочность возводимого сооружения и хорошее качество поверхностей.
При бетонировании в скользящей опалубке бетонная смесь должна иметь подвижность 8…10 см и распалубочную прочность0,2..<
Х.50. Схема устройства перекрытий одновременно с бетонированием стен в скользящей опалубке
1— внутренний щнт опалубки; 2 — поддомкратная рама; 3 —домкрат; 4 — домкратный стержень; 5 — стойка осветительного фонаря; б — ограждение; 7 — наружный щнт опалубки; 8 — подвесные подмости
Х.51. Схема бетонирования здания а скользящей опалубке с применением бетононасоса и автономной распределительной стрелы
/ — скользящая опалубка; 2 — положение стрелы; 3 — распределительная стрела; 4 — рукав — компенсатор длины бетоновода; 5 — постамент с полноповоротной платформой; 6 — бетоно — вод; 7 — бетононасос; 8 — автобетоносмеснтель
…0,3 МПа. С учетом этого скорость, необходимая для достижения. бетоном прочности, при которой исключено его оползание, составляет 250…і00 см в смену.
При вынужденных перерывах в бетонировании опалубке сообщают за счет реверсивного хода домкратов возвратно-поступательные движения, предотвращающие ее «примораживание» к поверхности бетонируемых стен.
При бетонировании многослойных стен проблема заключается в надежном закреплении утеплителя к арматуре, исключающем возможность его смещения при подъеме опалубки. К арматуре
Крепят также оконные и дверные коробки (или черновые, впоследствии извлекаемые коробки).
Отделку (наружных поверхностей возводимого здания ведут с
Наружных подвесных подмостей.
На уровень рабочего пола опалубки бетонную смесь можно подавать краном в бадье с устройством для равномерной выдачи смеси, при развитом периметре здания и достаточных объемах работ —с помощью бетононасосов в сочетании с автономной шар — нирно сочлененной распределительной стрелой (рис. Х.51). В этом случае бетононасос устанавливают рядом с возводимым зданием и смесь подают к распределительной стреле по стояку. Стрелу уста-‘ навливают на специальном постаменте, который поднимается вместе с опалубкой.
Метод бетонирования в объемно-переставной (туннельной) опалубке. Сущность метода заключается в бетонировании перекрытий и несущих поперечных стен с применением блоков туннельной опалубки, набираемых из инвентарных секций и переставляемых с этажа на этаж. В зависимости от фронта работ для бетонирования здания может быть применено несколько блоков опалубки.
Масса одной секции объемной опалубочной формы при шаге поперечных стен до 3,5 м и ширине секции 130 см — 800…1000 кг.
При возведении зданий в объемно-переставной опалубке бетонирование ведут поэтажно, причем каждый этаж делят на захватки, рассчитанные на суточный цикл работы. Работы выполняют в следующем порядке. Устанавливают вдоль продольных несущих стен монтажные подмости, монтируют секции блока опалубки, армируют стены и перекрытия и бетонируют. После набора бетоном распалубочной прочности секции поочередно с помощью ры — чажно-винтового механизма складывают в транспортное положе^ ние и выкатывают на наружные подмости, откуда краном переставляют на новую позицию для бетонирования очередного этажа или захватки. Секции опалубки можно переставлять и с помощью сбалансированной траверсы (рис. Х.52). Секции формы можно демонтировать и через проемы, оставляемые в перекрытии. Этот способ упрощает демонтаж опалубки, однако связан с необходимостью последующей заделки проемов.
При бетонировании в зимних условиях и для интенсификации работ в летних условиях может быть применена термоактивная’ объемно-переставная опалубка, оснащенная трубчатыми электрическими нагревателями (ТЭНами). Необходимая электрическая мощность для прогрева бетона в термоактивной опалубке 1,3… …1,5 кВт/м2. Опалубку снимают через 12… 14 ч после укладки смеси и ее прогревания.
Для этой же цели используют быстротвердеющие цементы rt химические добавки, ускоряющие процесс набора бетоном распалубочной прочности.
Разновидностью объемно-переставной опалубки является опа-
Х.52. Схема демонтажа секций опалубки помощью специальной траверсы |
X. S3. Строительство зданий из моиолитиого Жетона с применением объемной вертикальной извлекаемой опалубки
Лубка, соответствующая по своим размерам конструктивно-планировочной ячейке здания (рис. Х.53.). После окончания бетонирования эту опалубку извлекают краном вертикально, после чего устанавливают опалубку перекрытия и бетонируют его.
Бетонирование в крупнощитовой опалубке. Щиты опалубки размером иа комнату устанавливают на тщательно выверенную поверхность, обеспечивающую заданную отметку опирання вышерасположенного перекрытия. Щиты опалубки подают краном и с помощью винтовых домкратов приводят в проектное положение. Перед установкой противостоящих щитов монтируют дверные коробки, электропроводку и другие закладные элементы. Затем щиты раскрепляют между собой креплениями, воспринимающими давление свежеуложенного бетона. Опалубку. перекрытия устанавливают, как правило, после демонтажа опалубки стен. Перед армированием перекрытия опалубку с помощью винтовых домкратов в стойках точно выверяют с соблюдением заданной отметки и горизонтальности. Опалубку перекрытий при пролетах до 6 м снимают по достижении бетоном 70% проектной прочности. Трудо* емкость опалубочных работ при использовании крупнощитовой опалубки 0,2…0,3 чел.-ч/м2.
При бетонировании в зимних условиях или при необходимости ускорить процесс применяют термоактивную опалубку, оснащенную электронагревателями.
shlakoblok.com
concreting technology under extreme pressure «Eco-concrete»
concreting technology under extreme pressure «Eco-concrete».
concreting technology under extreme pressure «Eco-concrete» — is a fundamentally new technology, designed to create a high-density concrete structure with improved physical and mechanical properties. Technology «Eco-concrete» completely eliminates the use of traditional methods of concreting, special expensive formwork and vibrating machines. «Eco-concrete» as compaction process of concrete mix is based, and is directed to the use of the physical properties of, masses, inertia themselves solids concrete mix (crushed stone, sand and cement).
Description
Benefits
Schematic diagram of the concrete technology under high pressure
application
Description:
concreting technology under extreme pressure «Eco-concrete» — is a fundamentally new technology, designed to create a high-density concrete structure with improved physical and mechanical properties. Technology «Eco-concrete» completely eliminates the use of traditional methods of concreting, special expensive formwork and vibrating machines.
«Eco-concrete» as compaction process concrete based mixture and is directed to the use of the physical properties, masses, inertia themselves solids concrete mix (crushed stone, sand and cement).
concreting Technology under high pressure «Eco-concrete» includes preparation processes concrete the mixture in the sealed chamber speed concrete mixer, its transportation under high pressure (1,4 MPa at a rate 120-200 MS) and concreting in an aqueous medium in a pressurized aerosol closed system, eliminating dust emissions and bounces.
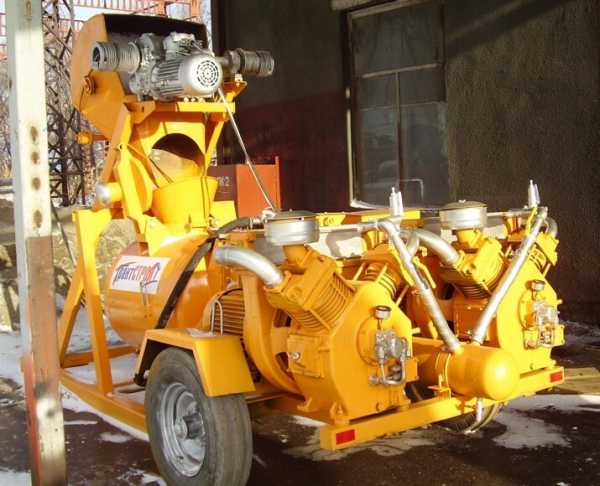
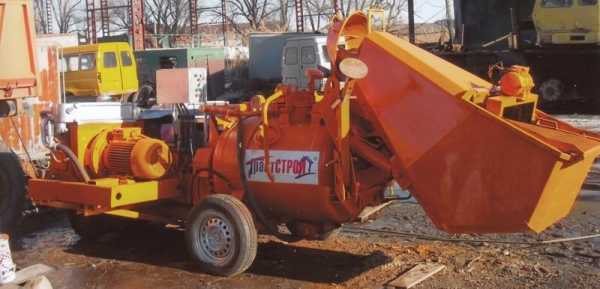
It uses a specially designed motorized complex, which implements these processes: preparation of a concrete mixture in the sealed chamber the mixer speed, transport it under very high pressure on the sleeve to the site of concrete and concreting in an aqueous medium in a pressurized aerosol closed system, eliminating dust emissions and bounces, special end device – nozzle.
Wherein, ultra high density concrete and reinforced concrete structures is achieved due to densification and displace the water and air from the concrete mix on the peripheral surface of concreting.
concreting technology under extreme pressure «Eco-Concrete»Provides strength of homogeneous single-layer concrete mix in the early stage before concreting 40%.
concreting technology under extreme pressure «Eco-concrete» provides for the reconstruction of buildings, structures, objects without interrupting the process and the production process, and no evictions.
«Eco-Concrete»High density, deposited under high pressure, It has enhanced operating properties: incl. improved resistance to abrasion and higher resistance to weathering and atmospheric agents.
In construction and reconstruction work waterworks (dams, hydropower plants, treatment facilities, tanks, retaining walls of channels of large and small rivers, and so forth.) this technology allows you to restore data without stopping.
Recovery engineering, water supply, sewer and storm water networks can produce inside, not exposing the water (etc.. network) and without making excavations.
Benefits:
– high economic efficiency. The technology eliminates the use of formwork and vibrating machines,
– It eliminates the use of traditional methods of concreting,
– high environmental cleanliness of workplaces and the environment, a sharp decrease in dust and technological rebounds with 30% to 2%,
– a significant reduction in construction costs,
– increase in performance of concrete work and concreting 10 time,
– increase in flexural strength, compressive strength, modulus of elasticity to the structures 20% and more,
– exception concrete shrinkage,
– It increases the safety of industrial operations due to a higher setting of the concrete in the early stages of work and set them strength,
– reduction of labor costs, consumption of materials and construction time (reconstruction),
– increased resistance to surface abrasion and its greater resistance to weathering and atmospheric agents,
– the strength of the homogeneous single-layer concrete mix in the early stage before concreting 40%,
– for the reconstruction of buildings, installations and facilities without interrupting the process and the production process, and no evictions.
Schematic diagram of the concrete technology under high pressure:
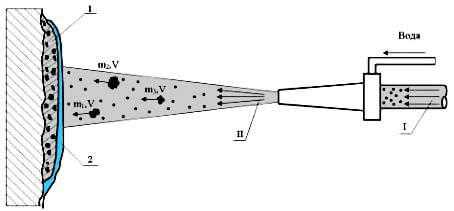
1 — high density concrete with a strength of up to 40%,
2 — displaced from the concrete water and air.
application:
– civil and industrial construction, including:
– construction and rehabilitation of hydraulic structures, dams, hydropower plants, treatment facilities, tanks, retaining walls of channels of large and small rivers,
– reinforcement of buildings and structures in areas of natural disasters from earthquakes, landslides and ground subsidence, floods and the impact of military operations,
– underground waterproofing of buildings and constructions from penetration of groundwater,
– protection and promotion of mountain mines, mines after working for ecological purity and stability of the environment,
– rehabilitation of metallurgical plants, melting, blast furnaces and other thermal units without stopping production,
– construction and erection of new fantastic lunar-space architecture with the use of computer graphics and inflatable inflatable formwork, reinforced structures or fibroarmirovannyh, and subsequent dismantling of inflatable formwork for reapplying,
– operated construction roofing systems.
Note: technology description on an example of concrete technology under high pressure «Eco-concrete».
RECOMMENDATIONS FOR THE USE OF TECHNOLOGY
CALL: +7-908-918-03-57
or use the search analogue technologies:
The unique technology SEARCH
or write to us here…
card site
To come in check in
Andrey-245Not quite clear. This battery can not be charged at all or something? How many volts it produces? Where to buy? And is it possible to connect such series-parallel, collecting a normal battery, eg, for electric vehicle?
2018-08-23 10:09:48SergeyShefgood afternoon! Interesting the above installation. How can it be ordered ? What are the terms of cooperation from the author?
2018-08-27 17:07:42Victor PotekhinSergei, throw a link here to install. Or e-mail me [email protected]
2018-08-27 18:52:14SergeyShefI have asked you, how and where it can be bought?
2018-08-27 21:07:41SergeyShefWho made the sample, that you in the photo and whether to make to order?
2018-08-27 21:10:05Victor Potekhincan not understand, that during installation. throw off the link here
2018-08-27 23:15:16Victor PotekhinWe do not possess such information
2018-08-28 21:45:17NPC-soundgood afternoon! SergeyShef product similar to, It is represented title, and in principle, any article of the LTCC technology can be made at our factory JSC «NPC «SpetsElektronSistemy». We are in g. Moscow. You can write me an email [email protected]
2018-08-29 18:41:34NPC-soundIn our production there are probably the most complete set of equipment in Russia, which allows 3D micro, including LTCC technology, in a closed loop, from incoming inspection of materials, all intermediate production processes …
2018-08-29 18:47:20JahanCryogels for plant growth and development under adverse conditions. who produce, how to find, to buy?
2018-08-30 23:48:23Victor Potekhinyou can buy from the manufacturer
2018-09-01 20:58:09Andrey-245Hello, Victor. I asked the question (2018-08-23) I meant about carbon battery, which serves as a 100 years old.
2018-09-18 12:15:33Victor Potekhinall information, that is, on the battery, It is written in the corresponding article.
2018-09-18 20:47:11Victor PotekhinTo get information about site technology manufacturers, write the bottom of the page — in FaceBook comments
2018-09-29 20:58:40DenssikAll the good days! I’m head of the center which developed the robot, on all matters concerning cooperation can write to the post office [email protected]
2018-10-03 17:19:46Victor PotekhinDenssik, Write pzhl about any work in question?
2018-10-03 19:10:33DS-SurferIf anyone there interested in «COMPLEX WATER BY hydrowave», I beg to contact me: [email protected] Sergei.
The settings are made and implemented.
good afternoon.
I am interested in the technology of processing of APG.
Please send your contact information to [email protected]
Welcome address to employees. site owners. And also to those who wrote an article about it where you can see and buy the generator tank gidrotoranny. Write on e-mail [email protected] sposibo
2019-01-22 20:57:09heardWho knows stellar battery on geteroelektrikah advertised in 2007 It was where and who’s producing. Where can I buy. If you do not produce, why not produce a promised two years reriyny release. What happened?
2019-01-22 21:00:39Victor Potekhinhave counterparts stellar battery
2019-01-23 08:10:34To post messages in the chat you need to login
technology winter concreting of foundations columns foundation slabs under columns in winter conditions
monolithic dry underwater concreting of roads in the winter I-bolt technology
floor concreting technology sprawled designs pile walls in the winter of monolithic structures monolithic slab yard
betonirovaniya technology platforms
concreting of the foundation plate technology
breakage concreting individual structures technology
concrete structures technology sprayed concrete bored piles concrete columns stripes in the winter of 3 meter base structures under water
concreting of the new technology of screw pile technology
concreting floors in industrial premises stripes technology
factor demand 300
comments powered by HyperCommentsxn--80aaafltebbc3auk2aepkhr3ewjpa.xn--p1ai
Технология бетонных работ ⋆ Прорабофф.рф
Технология проведения бетонных работ делится на три последовательных этапа:
- во-первых, подготовка площадки и опалубочные работы,
- во-вторых, подача и прием готовой бетонной смеси с последующим правильным уходом за поверхностью бетона,
- в-третьих, распалубочные работы после заливки бетона.
Каждый из этих этапов требует на его проведение определенного количества времени, соответствующих сил и профессиональных знаний. Все эти этапы проводятся в строгом порядке.
Подготовительные и опалубочные работы.
Во-первых, вам потребуется заказать бетон с завода, хотя вы можете сделать его и самостоятельно. Лучше всего остановить свой выбор на известном заводе по производству бетона, в этом вопросе вам помогут строители, которые постоянно контактируют с подобными организациями. Узнайте у них о качестве производимого бетона, способах его доставки, изучите цены на рынке. При заказе вам необходимо указать марку бетона, его морозоустойчивость и водонепроницаемость, так же может потребоваться указание на подвижность бетонной массы, качество фракций мелкого и крупного наполнителя. Самым важным показателем будет являться объем необходимого бетона и время его доставки. Пред монтажом опалубка необходимо убрать все крупногабаритные предметы с места, где будут проводиться бетонные работы, площадка для работы должна быть отчищена от строительного мусора и других посторонних предметов.
Опалубка для монтажа делится на два вида. Она бывает съемной конструкции или несъемной. Съемные конструкции подлежат повторному использованию при проведении дальнейших бетонных работ, несъемные опалубки остаются частью несущей конструкции.
Опалубок можно изготовить из 5 видов материала:
Деревянные опалубки получили наибольшее применение в частном строительстве, изготавливаются из различных пород хвойных деревьев. Толщина материала составляет более 20 мм.
Опалубки из фанеры изготавливаются из 12-слойной фанеры. Применяются для проведения бетонных работ с колоннами и лестницами.
Опалубки из древесностружечных плит имеют толщин до 20 мм. Применяются в той же сфере, что и фанерные конструкции.
Металлические опалубки изготавливаются из прокатного или листового металла. Чаще применяются в промышленных масштабах.
Опалубки из синтетических материалов. Наибольшее применение получили пенопласт, стеклоткань и стеклотекстолит.
Опалубки состоят из 3 основных частей: щитовой части (является плоскостью формирования поверхности будущей конструкции), крепежных и распорных элементов, поддерживающей стойки.
Второй этап – подача и прием бетонной смеси, уход за поверхностью бетона после заливки.
После установки опалубки монтируется арматурный каркас. Вам потребуется примерно 70-120 кг железной арматуры на 1 м³ заливаемого бетона. Только после установки арматуры можно приступать к самим бетонным работам.
Запомните, что при низких температурах бетонная смесь начнет расслаиваться, что приведет к потере ее свойств, при высоких температурах произойдет быстро отвердевание смеси. Именно по этой причине бетонная смесь заказывается только после изготовления и установки опалубка.
После заливки бетонной смеси и отвердевания бетона начинается последний этап – распалубочные работы.
Этот этап бетонных работ начинается после достижения бетоном 70-80% своей конструктивной прочности. В среднем этот процесс начинается через 7-10 суток после заливки бетона и достижении прочности бетона не менее 0,2-0,3 мПа. Показателями соответствующей прочности бетона в случае частного строительства будут следующие данные: светлая и твердая на ощупь поверхность.
xn--80ac1bcbgb9aa.xn--p1ai
Группа7 —
В статье будет рассказано о технологии бетонных работ, будет дана классификация бетонов для частного строительства и указаны важные аспекты производства бетонирования конструкций частного дома.
Почему так важно соблюдать технологию бетонных работ?
Именно этот вопрос и является основным для раскрытия в этой статье. Бетонные работы очень трудоемкий и сложный процесс. В частном строительстве он может занимать от 10% до 50% стоимости всех строительных работ, к ним можно отнести бетонирование фундаментов, ростверков, подвальных стен, балок, перекрытий, монолитных участков, перемычек и т. д. Не соблюдение строгих, но не сложных правил может привести к значительным дефектам бетонных конструкций:
уменьшение марки бетона по сравнению, с проектной
крошение бетона
недопустимые прогибы и крены конструкций
расслоение бетонной смеси
появление пор (дыр) в теле бетонной конструкции — образование концентраторов напряжений
сколы, отколы кусков бетона
уменьшение защитного слоя бетона
К примеру, кажется, что если не вибрировать бетон ничего страшного не будет, зато какая экономия времени и денег! А вот и нет, такая операция является неотъемлемой частью технологического процесса и пренебрежение ею может привести к неработоспособности фундамента и непредвиденным деформациям. Неверный уход при твердении бетона может привести к появлению низкокачественной и непригодной конструкции, даже если изначально вы брали качественный бетон высокого класса. Таким образом, стоит понять, что каждый пункт технологии, описанный ниже является обязательным к исполнению.
Классификация и виды бетона
Бетон получают смешиванием вяжущего вещества (обычно цемент), мелкого (песок) и крупного (щебень или гравий) заполнителя, воды и в случае необходимости специальных добавок. Плотность бетона в затвердевшем состоянии колеблется от 2200кг/куб.м до 2500кг/куб.м. При выборе вида, марки, класса бетона для конструкций инженер руководствуется расчетами, нормами и рекомендациями. Полный цикл набора прочности бетоном составляет 28 дней, при нормальных условиях — температура до 20 градусов и влажность не менее 80-90%.
Для того чтобы понять эти обозначения рассмотрим основные характеристики бетонных смесей:
Тяжелый (обычный) или легкий бетон. Основное отличие таких бетонов в заполнителе. В тяжелых бетонах крупный заполнитель — гравий или галька, В легких бетонах (газобетон, перлитобетон, пенобетон) доменный шлак (шлакобетон), заполнителем выступает относительно легкие материалы — керамзит, перлит, вспененный порошок. Тяжелые бетоны применимы для конструктивных элементов (фундаменты, балки, перекрытия), легкие применяются для конструктивных и теплоизолирующих элементов (стеновые блоки, облегченные перекрытия)
Виды фракций (размеров) крупного заполнителя. Крупнозернистый бетон – с заполнителем больше 10мм, мелкозернистый бетон в котором используют заполнитель меньше 10мм.
Прочность бетона — прочность затвердевшего бетона на сжатие. В зависимости от прочности бетона его разделяют на классы и марки: В3,5; В5; В7,5; В12; В15; В20; В25; В30; В35; В40; В45; В50; В55; В60. В частном строительстве наиболее применимы бетоны классов В3,5 и В7,5 (для неармированных конструкций, подливок, подбетонок, ступеней) и В15, В25 для устройства всех армированных конструкций.
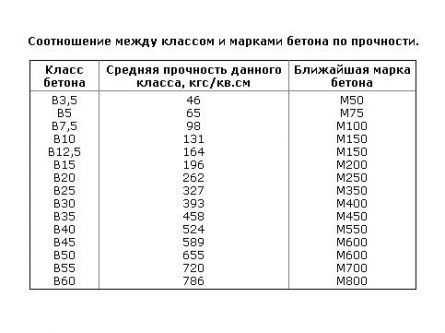
Соотношение класса и марки бетона
Плотность бетона — отношение массы бетона к его объему. Наиболее встречаемые в частном строительстве это тяжелые бетоны (1,8-2,5т/куб.м) и легкие (0,6-1,8т/куб.м)
Морозостойкость бетона — это способность бетона выдерживать попеременные циклы «замораживания-оттаивания», другими словами это насколько незащищенный бетон способен сохранять свою прочность под действием переменных температур. Марки бетона по морозостойкости: F25; F35; F50; F75; F100; F150; F200; F300; F400; F500, в частном строительстве применяют марки по морозостойкости от F35 до F150.
Водонепроницаемость бетона — сопротивляемость бетона просачиванию воды под давлением. Различают марки бетона по водонепроницаемости: W2, W4, W6, W8, W10, W12. В частном строительстве такая характеристика бетона может встретится при строительстве бассейнов или фундаментов в условиях высокого уровня грунтовых вод, наиболее применяемые марки W2-W6.
Жесткая или подвижная бетонная смесь. Подвижную смесь относительно легко перемешивать. Она плавно принимают форму опалубки под воздействием силы тяготения Земли. Жесткую смесь необходимо укладывать, прикладывая при этом силу.
Требования к подвижности бетона разных видов конструкций:
густоармированные конструкции, ригели, плиты, колонны 5-9 см
стены, стены подвала 1-4 см
бетонные набивные сваи 4-5 см
для неармированных и малоармированных фундаментов 1-3м
для массивных армированных фундаментов и плит 3-6 см
Эта характеристика имеет выражение в так называемой «осадке конуса», подсчитывается в сантиметрах. Общее время испытания с начала заполнения конуса бетонной смесью в установленном приборе при первом определении и до окончания определения жесткости при втором определении не должно превышать 15 мин. Чем больше осадка конуса (от 0см до 20см) тем более подвижная смесь.
Часто, частные застройщики прибегают к изготовлению бетона прямо на строительной площадке, обосновывая это дешевизной и удобством. Но не всегда таким образом можно достичь заявленной проектной марки бетона, однородности бетонной смеси, правильной подвижности бетона (удобоукладываемости). Ну а как по другому? Если бетон плохо сползает по коробу в опалубку, надо добавить воды? А вот и нет! Это изменит водоцементное соотношение бетона и понизит марку. Из этого можно сделать вывод, что лучше заказывать бетон на заводе, который хорошо себя зарекомендовал.
При этом вам обязаны предоставить паспорт на товарный бетон, где будут его характеристики. У вас будет документ, в случае не соответствия можно обратится с жалобой к производителю. Подвижность бетонной смеси определяется заводом изготовителем на основании разработанной технологии, в зависимости от количества армирования, воспринимаемых нагрузок, вида конструкции и т.д.
Технология бетонных работ и важные моменты
В целом технологию можно разделить на три больших этапа:
Подготовительные и опалубочные работы
Подача, прием бетонной смеси и уход за бетоном
Распалубливание, работы после бетонирования
Каждый из этапов требует определенное время, силы и знания на его выполнение, этапы будут описаны в хронологическом порядке, что даст возможность получить своеобразную «технологическую карту» производства бетонных работ.
Подготовительные и опалубочные работы
Прежде всего, необходимо сделать заказ бетона на заводе или сделать его самостоятельно. Выбирайте из известных заводов производителей или бетоно-растворных узлов (минизавод), посоветуйтесь со строителями, узнайте о качестве бетона, способах доставки, цене. Делая заказ, укажите марку, морозостойкость, водонепроницаемость, подвижность бетона, фракции мелкого и крупного заполнителя (зависит от назначения конструкции, типа армирования и способа бетонирования), объем и время доставки. Пред началом монтажа опалубки, все крупногабаритные грузы должны быть убраны с места монтажа, необходимо отчистить площадку от мусора и ненужных стройматериалов.
Опалубка по виду монтажа делится на съемную (которую можно использовать после бетонирования повторно) и несъемную (остается частью конструкции и повторное использование которой невозможно).
Перед началом опалубочных работ необходимо определится с видом опалубки, которую будете применять. Виды опалубки:
Дерево. Наиболее применяемый в частном строительстве вид опалубки, изготавливается из хвойных и реже лиственных пород деревьев, толщиной от 20мм. Применяют для всех видов конструкций.
Фанера. Применяют 12слойную фанеру для изготовления колонн, стен, лестниц. Также имеет широкое распространение в коттеджном строительстве.
Древесностружечные плиты. Толщиной 20мм, применяют также как и фанеру.
Металл. Применяют как прокатный металл, так и листовой (в виде несъемной и съемной опалубки). В частном домостроении применяют реже, из-за дороговизны материала.
Синтетические материалы. Номенклатура с каждым годом увеличивается, но наиболее применяемые — это пенопласт, стеклоткань, стеклотекстолит.
При строительстве коттеджа или частного дома самым применяемым видом опалубки является деревянная самодельная опалубка. Такая опалубка состоит из 3 частей:
1. Щитовая часть. Часть, которая примыкает непосредственно к бетону и является плоскостью формирования конструкции.
2. Крепежные, распорные элементы. Удерживают опалубку от деформаций под воздействием веса бетона.
3. Поддерживающие стойки. При бетонировании балок, перекрытий необходимый элемент временного крепления конструкции.
Щитовую часть делают из доски толщиной не менее 2-2.5см, ширина доски 150-200мм, из нее набирают требуемую поверхность и скрепляют поперечными брусковыми балками (сшивная планка), с шагом 0,5-1 метр, в зависимости от геометрических характеристик конструкции. Гвозди вбивают со стороны щита, обращенной к бетону. Гвозди необходимо подбирать на 10-20мм больше суммарной толщины доски и бруска. Если концы гвоздя выступают из внутренней поверхности опалубки их надо загнуть перепендикулярно. Доску обычно подбирают исходя из размеров конструкции, но при этом необходимо учитывать вес такой доски, ее должен быть в состоянии поднять и перенести рабочий. Опалубку монтируют согласно опалубочным чертежам, по осям и отметкам, указанным в проекте.
Бетон при твердении давит на поверхность опалубки своим весом, чтобы сохранить устойчивость щитов используют специальные элементы. В виде распорных и стяжечных элементов используют болты, арматуру, деревянные балочки, стяжки с шагом от 1,5 до 3м, в зависимости от вида и размеров конструкции.
Стойки выполняют из бруса сечением, определяемым расчетом, с уширением сверху. При расстановке стоек для перекрытий можно использовать шахматный порядок с шагом 1-2м. Понятное дело, что чем больше стоек, тем лучше и уменьшится вероятность неровности плоскостей перекрытия или балки.
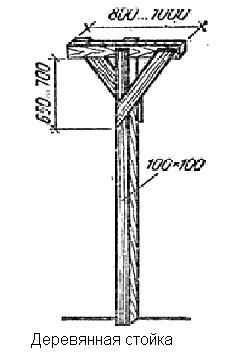
Важные моменты монтажа опалубки:
Перед бетонированием необходимо проверить жесткость и прочность опалубки, сверить все размеры опалубки с проектной документацией вертикальные и горизонтальные уровни.
Проверить наличие щелей и дыр в деревянной опалубке, в случае обнаружения щелей шириной более 3 мм и отверстия в деревянной опалубке заделывают, от 3 до 10 мм конопатят (скрученной в косичку) паклей, а более 10 мм — заделывают деревянными рейками. Забивают глиняным тестом, но это в прошлом, а сегодня пришла эра монтажной пены.
Внутренняя поверхность должна быть гладкой, если она не гладкая уложить по всему периметру полиэтиленовую пленку или картон, в итоге бетон будет гладким и цементное молоко останется в бетоне. Оно необходимо в цементе в виде связующего и его потеря может привести к уменьшению прочности бетона.
Непосредственно перед бетонированием необходимо отчистить опалубку от грязи, тряпок, кусков ненужной арматуры, деревяшек и т. д. Если бетонирование ведется зимой отчистить опалубку от снега.
Перед бетонированием внутреннюю часть опалубки необходимо смазать смазкой (состав вода-мыло-керосин, вода-мыло-масло) или увлажнить, для того чтобы после распалубливания опалубка снималась легче и ее можно было использовать повторно. Также используют отработанное масло, дизтопливо, эмульсол.
Подача, прием бетонной смеси и уход за бетоном.
Важно помнить, что переохлаждение бетонной смеси приведет к ее расслоению и потере свойств, перегрев — к быстрому твердению и невозможности укладки. Это процесс относится к зимним бетонным работам и это отдельная тема для статьи. Поэтому бетонную смесь стоит заказывать непосредственно на то время, когда по прикидочным расчетам будет готова опалубка и все подготовлено для бетонирования. Предельный допустимый срок доставки смеси от завода до площадки:
при 20 градусах Цельсия — 45 минут
10-19 градусах Цельсия — 60 минут
5-9 градусов Цельсия — 90 минут
В случае если время для доставки бетонной смеси больше чем 1,5 часа, в бетон добавляют замедлители схватывания и твердения, а также пластификаторы. Когда бетонную смесь привезли на стройплощадку нужно потребовать паспорт бетона, в нем уточнить марку (класс), время изготовления и дату, водонепроницаемость, морозостойкость и сравнить с теми данными, которые Вы заказали. Также нужно посмотреть не расслоился ли бетон? Как об этом можно узнать? Расслоение происходит, когда смесь перевозили неправильно (не перемешивая в бетоновозе). Тогда гравий и песок опускаются на дно, а цементное молоко и вода всплывают на поверхность. Этот процесс приводит к усложнению укладки бетонной смеси и в будущем к уменьшению класса. В случае расслоения бетонную смесь нужно тщательно перемешать перед бетонированием. Раньше перевозку осуществляли самосвалами, но в данный момент они почти не применяются.
В частном строительстве прием бетонной смеси в опалубку осуществляется в основном по специальным желобам из бетоновоза («миксера»), бетономешалки или непосредственно с бетоновоза, если есть возможность удобного подъезда.
Желоб выполняют из сбитых деревянных досок толщиной 50 мм и шириной от 150 мм, их укрепляют поперечными брусками с шагом 0,5-1м.
Бетонную смесь укладывают горизонтальными слоями одинаковой толщины (10-20 см) без разрывов, с последовательным направлением укладки в одну сторону во всех слоях. Следующий слой необходимо укладывать до начала схватывания предыдущего слоя. Желательно, чтобы бетон падал на поверхность опалубки с высоты не более 2 метра (для того чтобы не было расслоения бетона). При устройстве высоких монолитных конструкций можно использовать желоба или бетононасос. Во время укладки смеси его вибрируют глубинными вибраторами, это делается для того, чтобы из смеси вышли все поры воздуха (пузырьки) и бетон получился однородный. Под воздействием вибратора бетонная смесь становится более пластичной и попадает во все поры и не заполненные участки. При уплотнении бетонной смеси конец рабочей части вибратора должен погружаться в ранее уложенный слой. Переставлять вибратор надо на расстояние 25-50 см (зоны вибрирования должны немного перекрывать друг друга), вибрировать 0.5-2 минуты, в зависимости от вида бетонной смеси. При вибрировании нельзя дотрагиваться вибратором арматурных стержней, опалубки, подставок под арматуру. Вибрирование прекращают после того как не останется не провибрированных участков и когда обеспечено полное уплотнение бетонной смеси. На возможность окончания вибрирования указывает выделение раствора вдоль опалубки и погружение частиц крупного заполнителя в раствор.
После подачи бетонной смеси нужно начинать вести уход за ней, для того чтобы бетон приобрел требуемую прочность в назначенный срок. Нарастание прочности бетона происходит быстро и бетон (на портландцементе) через 7-10 дней после укладки набирает 60-70% своей 28-дневной прочности. Затем рост прочности замедляется. Нормальные условия твердения, описанные выше (t=20 C и влажность не менее 80%) особо важно поддерживать первые несколько дней. Уход за бетоном ведут обычно 3-5 дня.
Необходимый уход за бетоном:
поддерживать влажное состояние бетон — поливать водой до насыщения каждые 2-4 часа. Чем выше температура воздуха, тем больше испаряется воды, тем обильнее нужно поливать. При температуре ниже +5 градусов Цельсия поливку не производят.
не давать солнечным лучам напрямую воздействовать на бетон (укрытие бетона). Укрывают бетон влагоемким материалом (тканью, опилками, песком) и периодически смачивают его.
беречь бетон от ударов, сотрясений
беречь от резкой перемены температуры (день-ночь)
движение людей по забетонированным конструкциям разрешается только после 2-3 дней
Распалубливание.
Распалубочные работы начинают при достижении бетоном 70-80% проектной прочности, в нормальных условиях это наступает после 7-10 суток набора прочности бетоном. Прочность бетона незагруженных монолитных конструкций при распалубке должна быть не меньше 0,2-0,3 мПа. Как понять, что бетон набрал прочность? Необходимо провести испытание бетона на прочность, обычно это выполняется лабораторными методами с применением ударно-импульсных и ультразвуковых приборов.
Но в условиях частного строительства, при правильной технологии бетонирования и ухода за бетоном, показателем набора прочности бетона будут: бетонная поверхность станет светлее (не затвердевший бетон имеет темно-серый цвет) и на ощупь твердой. Важные момент при снятии опалубки:
Распалубочные работы необходимо проводить осторожно, с применением ломов, молотков, гвоздодеров для того чтобы можно было использовать опалубку повторно.
Желательно как можно меньше дотрагиваться к поверхности бетона инструментами для того чтобы не повредить структуру конструкции.
При загрязнении опалубочной поверхности бетонной смесью необходимо очистить поверхность металлическими щетками и скребками и смазать эмульсионным составом.
При образовании крупных раковин и сколов на поверхности бетона ее зачищают и затирают цементно-песчаным раствором.
Наплывы бетона на поверхности нужно удалить кельмой.
gruppa7.ru