Достоинства смазок под полиуретан для форм
Жидкий полиуретан для заливки форм повсеместно применяется для литья точных матриц под самые разные изделия. Без преувеличения, мастера по всему миру уже на протяжении многих лет активно используют этот материал и остаются довольны. Но, как мы писали ранее в наших статьях, при литье полиуретана есть свои нюансы. Есть в нашем багаже знаний на сайте одна статья, посвящённая адгезии, и там мы вскользь качаемся темы антиадгезионных разделителей и смазок. В данной же статье, мы хотим рассказать Вам о том, как важно использовать разделительные смазки, когда вы льёте жидкий полиуретан для форм.
В первую очередь перечислим главные достоинства смазок, которые прольют свет на факт необходимости их использования:
- 1. Обеспечивают антиадгезионное покрытие при литье.
- 2. Позволяют легко вынимать изделия из формы.
- 3. Создают защитную поверхность, обеспечивающую сохранность формы.
- 4. Предотвращают прилипание.
Как видите, у разделительных смазок имеется ряд важных для использования факторов, которые делают их незаменимыми при заливке форм из полиуретана или смесей в форму.
Как использовать разделители
Коротко о том, как правильно наносить разделительную смазку. Как правило, смазка наносится кистью. Даже если вы обладатель разделителя, фасованного в балончики, всё равно, после взбрызгивания смазки, её необходимо размазать по форме кистью. При нанесении смазки важно соблюсти золотую середину: её нельзя использовать слишком мало или слишком много. Два или три полных прохода тонким слоем кисти по всей поверхности взаимодействия будет достаточно. Если нанесёте слишком мало смазки — появится риск, что Ваше изделие слипнется при выемке, если нанесёте много смазки — появится возможность того, что ваш литьевой материал вступит в реакцию со смазкой ещё до схватывания, что тоже отразится на качестве итогового изделия.

Виды смазок
Смазок, которые используются в сфере литья полиуретанов, на данный момент на рынке имеется великое множество. Они разнятся по составу, качеству, таре, но все их условно можно разделить на следующие три категории:1. Смазки на восковой основе. Как не сложно догадаться, в основе таких смазок лежит такой материал как воск. Данные смазки весьма неприхотливы и дешевы, при том, что являются специализированными в полимерном производстве. Восковая смазка для литья будет несколько более густой, чем её аналоги, а главной её проблемой при использовании будет забивка фактуры формы. Спустя несколько циклов использования, рельефные неровности и впадины на вашей форме могут забиться данным разделителем. Поэтому, при использовании восковой смазки очень важно мыть и чистить формы после каждых 2-3 использований. Не забывайте сушить ваши формы!

2. Смазки на силиконовой основе. Являются более дорогими и более удобными в использовании, нежели восковые. Из названия следует, что в основе таких смазок лежит силикон. Благодаря этому, данные разделители не забивают фактуру и рельеф формы, в отличии от восковых смазок. В частных случаях одного нанесения восковой смазки может быть достаточно даже для нескольких отливок.
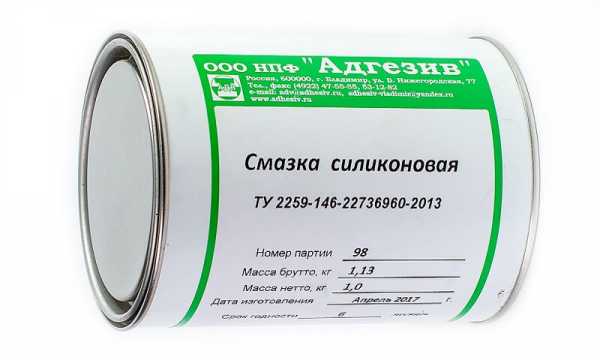
3. Самодельные смазки. Мы настоятельно не рекомендуем Вам пользоваться данными смазками, однако, если бы мы не упомянули об их существовании, то статья была бы не полной. Для самодельных смазок люди используют самые разнообразные материалы. Как по отдельности, так и смешивая. Этими материалами могут выступать всевозможные мыльные растворы, жиры, мазут и прочее. Некоторые мастера имеют свои рецепты. Мы же снова повторимся, что такие смазки опасно использовать, так как они могут повредить вашему изделию, либо негативно сказаться на его качестве.
kremen.ru
Изготовление полиуретановых форм своими руками
Недавно я писал статью про изготовление формы для искусственного декоративного камня из силикона, сегодня же хочу рассказать, как изготовить полиуретановую форму своими руками, т.к. процесс немного отличается. У меня при заливке форм из силикона, всегда получалось все гладко — формы получались без пузырей. С полиуретаном же все наоборот и прежде, чем начали получаться качественные формы я «закосячил» около 10 форм.
Что нужно для изготовления формы
Чтобы форма из полиуретана получилась качественной нужно сделать хорошую матрицу. Как собрать матрицу можно почитать тут. Также вам понадобится сам полиуретан для заливки форм, ведерко, палочка для замешивания (или шуруповерт с миксером), пластиковый шпатель (я его сделал из крышки пластикового ведерка), весы и смазка. В качестве смазки я использую восковую разделительную смазку ВС-М. Можно также взять мыльный раствор, растрясти его, чтобы получилась пенка и ею обработать матрицу, но лично мне, ВС-М мне нравится больше.
Ну и конечно же нужно помещение с пониженной влажностью и комнатной температурой. Хотя, честно признаюсь, я формы заливал всего при +5 градусов. Полиуретан не такой текучий при такой температуре, но других условий у меня не было.
Как сделать полиуретановую форму. Инструкция
В первую очередь матрицу нужно просушить, т.к. на ней может оставаться влага (которая никак не ощущается) и именно из-за этой влаги у меня было куча пузырей на тыльной стороне формы. Я беру фен строительный и в течении 3-5 минут просушиваю. Но нужно сушить так, чтобы камень слишком не нагревался, т.к. может нагреваться силикон на который он приклеен. После сушки, примерно через 5 минут, как камень примет комнатную температуру, можно наносить разделительную смазку. Я делаю в 2 слоя с интервалом в несколько минут. Беру ВС-М и на расстоянии 20-30 см распрыскиваю его во все участки матрицы, под разными углами. Одного баллончика мне хватает на 2 формы, площадью ~0,2 кв. метра. Далее нужно развести компаунд, но для начала определяем его количество.
Как узнать сколько нужно полиуретана?
Возьмите готовую матрицу с прикрученными брусками (желательно до обработки разделительной смазкой) и насыпьте в нее что-нибудь сыпучее. Я видел на ютубе как парень засыпает пшеницу и таким образом определяет объем компаунда. Я бы рекомендовал использовать, что-то более мелкое, например, рис, гречку или пшено. И он еще там говорит, что дно формы должно быть толщиной 1-1,5 см — это я считаю лишнее. Достаточно всего 5 мм, чтобы получилось нормальное изделие, а для своих форм я вообще делаю 3 мм — и этого вполне хватает.
Итак, находим самый высокий камень в матрице, замеряем его максимальную толщину (высоту), прибавляем 5 мм и делаем отметку сбоку на одном из брусков. Затем засыпаем пшено ровно по этой отметке и разравниваем. Затем пересыпаем все в какую нибудь тару и замеряем объем, именно объем, а не вес, т.к, например, у гречки и пшена вес будет разный. Для подсчета можно использовать мерные стаканчики или стеклянные банки по 0,5 литра. Допустим у вас получилось 2,5 литра — это и будет объем компаунда. У меня на форму 0,2 квадратных метра с толщиной камня около 1 см как раз получается 2,5 килограмма. Не забываем, что это примерный расчет и лучше перестраховаться, добавив 300-500 грамм полиуретана.
Также хочу сказать про расстояние между плитками в матрице. В идеале это 1 см, но в целях экономии можно делать меньше. Для тонких кирпичей я делаю по 6 мм между плитками и по 8 мм по периметру. Для более толстых 8 и 1 см соответственно.
Приступаем к заливке
Вначале медленно (что бы не было пузырьков воздуха) размешиваем оба компонента палочкой в течении 2-3-х минут. Затем берем чистое ведерко, отмеряем компонент А и наливаем нужное количество. В зависимости от марки полиуретана кол-во двух компонентов может быть разное, у некоторых делается 2 к 1, у других 1 к 1. Я использую Силагерм 5045 он разводится 2 к 1. Беру 2 части компонента А — 1666 грамм и 1 часть компонента Б — 833 грамма, итого 2500 грамм или 2,5 кг.
Затем добавляю компонент Б и начинаю замешивать до однородной массы в течении 2-3х- минут. Замешивать можно палочкой или дрелью с насадкой на небольших оборотах. Полиуретан нужно хорошо размешать, тщательно проходя по дну и стенкам.
Матрица должна стоять по уровню и после этого можно заливать нашу смесь. Заливку лучше производить в одну точку по центру, тонкой струйкой. Если температура компаунда и помещения 20-25 градусов, то компаунд сам растечется, если меньше, то можно помочь ему шпателем, как делаю я. Если полиуретан плохо растекается, то он скорее всего холодный. Компоненты можно предварительно разогреть, но только по отдельности. В смешанном состоянии этого делать категорически нельзя, т.к. высокая температура влияет на скорость отверждения.
Если вы хотите отблагодарить меня, за то, что я делюсь с вами своим опытом, то напишите комментарий к этой статье с любым вопросом или предложением. Возможно из вашего комментария я почерпну тему для одной из будущих статей.Написать комментарий
После того, как смесь выровнялась по матрице, а это примерно через 1-2 минуты, берем фен, включаем на максимум и на расстоянии 2-3 см от залитого компаунда проходим сверху всю поверхность — так мы максимально выгоним воздух. Жидкий полиуретан от фена будет «плыть» и будет выходить воздух.
Напоследок
На этом можно было и завершить написание инструкции, но бывает так, что в 1-2-х местах постоянно выходит воздух, шарик лопается, но снова надувается. Это может происходить из-за того, что либо под камнем, есть небольшая щель, либо в самом камне есть «раковинка». В таком случае, я беру обычную иглу, вставляю в то место откуда идет воздух и резко выдергиваю. При необходимости можно сделать несколько раз. Бывает помогает, бывает нет.
Лучше конечно при заливке использовать вакуумную камеру, чтобы избежать брака, но это дорогое удовольствие. И подходит только тем, кто делает формы на продажу. Ну и хочу дать один совет: если вы собираетесь сделать себе декоративный камень и встал вопрос с формами, покупать или сделать самому, то я бы рекомендовал купить, т.к. при изготовлении без вакуумной камеры высока вероятность брака. Если планируется производство и нужно много форм, то можно сделать самому, но я вас уверяю, брак будет 100%.
Читайте дальше: как сделать сушилку для декоративного камня
Статьи по теме
kamnedeloff.ru
SMOOTH-ON Полиуретан для форм VytaFlex 40 очень прочный для бетонных изделий
SMOOTH-ON Полиуретан для форм VytaFlex 40
Описание и применение. Полиуретан для форм VytaFlex от производителя полиуретановых резин № 1 в мире компании Smooth-on (USA, год основания 1895) обеспечивает превосходные физические и эксплуатационные свойства форм для литья бетона. Универсальная твердость по Шору 40A. Удобное соотношение при смешивании — один к одному по объему.
ВАЖНО! Работать только со смазкой для полиуретановых форм, так как полиуретан ко всему прилипает!
Особенно эффективны полиуретаны VytaFlex для литья пигментного/цветного бетона. Формы, изготовленные из полиуретана VytaFlex 40, позволят получать точные и однородные цветные отливки.
Внешний вид: часть Б – кремовая, часть А — прозрачно-желтоватая, средней вязкости, при смешивании становится кремовым — отличная индикация тщательности смешивания.
Расфасовка: ПЭ канистры (наш репак из заводской тары) — 0,45 кг + 0,45 кг = 0,9 кг.
Соотношение смешивания по объему | 1А: 1В |
Соотношение смешивания по весу | 1А: 1В |
Плотность, г/см3 | 1,03 |
Цвет | Кремовый |
Твердость по Шору А | 40 |
Предел прочности | 522 фунтов на квадратный дюйм |
Удлинение при разрыве, % | 660 |
Жизнеспособность, мин. (при 23°С) | 30 |
Время отверждения (при 23°С), часов | 16 — 24 |
Усадка, % | менее 0,3 |
Предел прочности на разрыв, МПа C | 3,60 |
Вязкость после смешивания, cps | 2000 |
Технология работы с полиуретановым компаундом VytaFlex 40
Хранить и использовать при комнатной температуре 23 °C. Этот продукт имеет ограниченный срок хранения и должен использоваться как можно скорее. Используйте в условиях низкой влажности (ниже 50% относительной влажности). Контейнеры для смешивания должны иметь прямые стороны и плоское дно. Смешивающие палочки должны быть плоскими и жесткими для очистки сторон и нижней части контейнера для смешивания.
Пористые поверхности (например, натуральные камни, гипсовые штукатурки, бетон, дерево, камень, глина, полистирол и т. д.) должны быть «запечатаны» перед нанесением разделительного агента. Все полиуретаны являются по своей сути клеями. Чтобы предотвратить адгезию между поверхностью резины и модели, модели должны быть «запечатаны» капсулятором (закрытие пор) SuperSeal ™ (он также есть у нас в продаже). Это быстросохнущий герметик, подходящий для герметизации пористых поверхностей, не портящий детализацию поверхности. Следует нанести герметик и оставить его полностью высохнуть перед нанесением разделительного агента.
Непористые поверхности. Металл, стекло, твердые пластмассы, требуют только разделительного агента.
Разделительная смазка обязательно необходима для демонтажа при литье, иначе неизбежно прилипание. Используйте разделительный агент, специально предназначенный для изготовления полиуретановых форм Universal Mold Release от Smooth-On (он также есть у нас в продаже). На все поверхности, которые будут контактировать с полиуретаном, должен быть нанесен защитный слой этого разделительного агента. Он на основе силикона, и его можно использовать только с полиуретановыми формами, с силиконовыми нельзя!
ВАЖНО: чтобы обеспечить полное покрытие, нанесите смазку мягкой щеткой на все поверхности модели. Дайте смазке высохнуть в течение 30 минут. Поскольку каждое применение всегда отличается друг от друга, рекомендуется всегда делать пробные отливки для определения пригодности для вашего проекта.
________________________________________
Дозирование и смешивание. Жидкие полиуретаны очень чувствительны к влаге и поглощают атмосферную влагу. Смесительные инструменты и контейнеры должны быть чистыми, сухими и изготовлены из металла или пластика. Материалы следует хранить и использовать в теплой среде (не ниже 23 °C).
ВАЖНО: тщательно перемешать часть Б (кремовую) перед дозированием. После дозирования равных количеств частей А и Б в емкость для смешивания тщательно перемешайте в течение как минимум 3 минут, убедившись, что вы несколько раз очищаете боковые стенки и днище смесительного контейнера.
Если смешиваете большие количества (от 1 кг или более) за один раз, используйте механический смеситель в течение 3 минут с последующим тщательным перемешиванием вручную в течение одной минуты.
Затем вылейте все количество в новый, чистый контейнер для смешивания и перемешайте снова и снова (техника двойного перемешивания).
Хотя этот продукт разработан для минимизации пузырьков воздуха в вашей отвержденной полиуретановой форме, вакуумная дегазация резины еще больше уменьшит захваченный воздух.
________________________________________
Заливка, отверждение, ресурс формы, хранение. Для достижения наилучших результатов, вылейте свою смесь в одном месте в самой нижней точке. Равномерный низкий поток поможет свести к минимуму захваченный воздух. Жидкая резина должна выровняться по крайней мере на 1,3 см над самой высокой точкой поверхности модели.
Отверждение происходит как минимум 24 часа при комнатной температуре (23 °C) перед извлечением из опалубки. Не отверждайте полиуретан при температуре ниже 18 °C.
Постотверждение необязательно, но после 16-24 ч. отверждения нагрев резины до 65 °C в течение 4-8 часов увеличит физические свойства и рабочие характеристики формы.
Ресурс и хранение. Полностью отвержденный полиуретан — прочный, долговечный и будет работать при правильном использовании и хранении. Физическая жизнь резины зависит от того, как вы ее используете. Храните в ровном нескрученном положении.
При тиражировании бетонных изделий для облегчения выемки и сохранности формы можно использовать густой мыльный раствор (нанести и просушить).
Делаем бетонную раковину в полиуретановой форме из VYTAFLEX 40
Смотрите видео о полиуретане VYTAFLEX 40 на сайте производителя SMOOTH-ON
VytaFlex™ 40 Product Information | Smooth-On, Inc.
elastoform24.ru
Разделительная смазка Universal Mold Release от Smooth-On для полиуретановых форм (70 г) под кисть
Universal Mold Release — разделительный состав для полиуретановых форм
Описание и применение. Universal Mold Release — разделительный состав в виде жидкости, разработанный специально для формовочных и литейных работ и применяемый как для облегчения снятия только что изготовленной формы с прототипа изделия, так и при тиражировании изделий, для облегчения выемки последних из эластичных полиуретановых форм.
Хорошо работает с большинством жидких резин (таких как полиуретаны и полисульфиды), жидких пластмасс, а также является отличным разделительным составом для эпоксидных и полиэфирных смол при формовке последних в эластичные полиуретановые формы. Universal Mold Release эффективен в широком температурном диапазоне от 21 °С до 260 °С.
ВАЖНО! Перед применением смазки может потребоваться герметизация пористых моделей (дерева, гипса, бетона) или некоторых модельных глин (содержащих воду или серу) с помощью Smooth-On SuperSeal.
Особенности
- Нельзя использовать Universal Mold Release с силиконовыми формами
- Universal Mold Release улучшает эффективность формования и продлевает срок службы вашей полиуретановой форме.
Применение смазки Universal Mold Release:
Хорошо взболтать перед использованием.
Этот продукт имеет ограниченный срок хранения и должен использоваться как можно скорее.
Используя мягкую щетку, нанесите смазку на все поверхности, где будет соприкосновение с полиуретановой формой.
Дать смазке высохнуть 5 минут.
Для ускорения высыхания можно использовать фен.
Повторите применение и дайте высохнуть (до 20 минут).
Теперь можно лить полиуретан для форм или делать отливки в отвержденную резиновую форму.
Поскольку каждое применение всегда отличается друг от друга, рекомендуется всегда делать пробные отливки для определения пригодности для вашего проекта.
elastoform24.ru
Как сделать полиуретановую форму для камня из Адваформ марка 40
В данной инструкции мы поэтапно разберём, как правильно изготовить матрицу под искусственный камень из жидкого полиуретана для форм Адваформ марка 40. Обращаем ваше внимание, что в данном руководстве не будет приведено способов дегазации смеси. Об этом можно почитать в другой нашей статье.

Подготовка опалубки
В первую очередь нам будет необходимо изготовить каркас для литья нашего материала — опалубку для будущей формы. Сделать её можно из обычных досок или листов ДСП, расположив их на ровной поверхности и надёжно скрепив их между собой любым доступным способом. Мастер модель, в качестве которой выступают оригиналы камней, которые мы собираемся копировать в форме, выкладываем на поверхность внутри опалубки. Обратите внимание, чтобы между стыками граней опалубки, а также между камнями и поверхностью не было зазоров и щелей, в которые при заливке сможет проникнуть наша литьевая смесь. Подробнее о том, как нужно делать опалубку, читайте в нашей статье.
Подготовка материалов.
Нам понадобится смазка на силиконовой или восковой основе и, конечно же, сам жидкий полиуретан для форм. Как правило, в руки к нам попадает полиуретан, будучи расфасованным в вёдра. Поскольку это сырьё двухкомпонентное, то и вёдер будет два — по одному под каждый компонент. Вскройте вёдра, открыв боковой замок и отогнув металлические лепестки, удерживающие крышку (для данного действия идельно подойдут пассатижи или щипцы с узким носом). Проверьте агрегатное состояние материала: Оба компонента должны быть жидкими, текучими. Компонент А — беловатая прозрачная жидкость, компонент Б — прозрачная жидкость с желтоватым оттенком, напоминающая растительное масло. При транспортировке и хранении в температурных условиях ниже 17 градусов по Цельсию, компонент Б может закристаллизоваться. Вернуть ему рабочее состояние можно путём разогрева материала до температурного диапазона в 60-70 градусов по Цельсию и сопутствующему перемешиванию компонента. Применимо воздействие исключительно сухого тепла (фен, обогреватель, тепловая пушка и т. п.), использовать горячую воду, водяной пар, водяную баню или горячий конденсат при разогреве полиуретана категорически запрещено. Любой контакт незатвердевшего материала с водой может сделать компаунд непригодным к использованию. Также, перед использованием, каждый компонент нужно перемешать отдельно, так как при долгом хранении некоторые части компонентов могут выпасть в осадок.
Помимо всего, перед началом литья будет необходимо обработать опалубку антиадгезионной смазкой. Это необходимо для лёгкого извлечения формы из опалубки после полимеризации. Смазка предотвратит прилипание материала к поверхностям соприкосновения полиуретана.
Приготовление литьевой смеси.
После того, как ёмкости с полиуретаном были вскрыты, мы готовим отдельную тару и смешиваем в ней компоненты между собой. Пропорции компонентов А к Б являются 1 к 1. После вливания материала в соблюдённых пропорциях, сырьё необходимо перемешать. Делать это рекомендуется с помощью специальной насадки на дрель, которая создана специально для перемешивания смесей, однако можно обойтись просто широкой доской или иным подходящим приспособлением. Перемешивать сырьё нужно активно, не взбалтывая, чтобы не образовать в компаунде пузырей воздуха. Продолжать перемешивание необходимо до тех пор, пока смесь не станет однородной по массе и цвету. Подробнее о том, как готовить полиуретан к литью, написано в этой статье.
Литьё полиуретана
После того как смесь будет приготовлена, стоит приступать к литью. Компаунд нужно лить не торопясь, в одну точку, чтобы он своей массой сам вытеснял лишний воздух. Количество смеси нужно брать в расчёт на то, чтобы камни скрылись под смесью примерно на 2 — 2.5 см. После того, как с литьём покончено, оставляем полиуретан полимеризоваться, т. е. затвердевать.
Расформовка.
По прошествии суток, после того, как полиуретан схватился и приобрёл должные свойства, форму можно вынимать из опалубки.
Вот и весь нехитрый процесс производства формы под искусственный камень.
kremen.ru
Полезная информация по полиуретану для форм
Жидкий литьевой полиуретан для форм — это двухкомпонентный компаунд, предназначенный для холодного литья самых разнообразных изделий: от гибких форм для камня, изделий из всевозможных литьевых смесей (гипса, бетона), до изделий технического характера и широкого круга направленности (например, втулок, прокладок, деталей и прочего).
Так как жидкий полиуретан состоит из двух частей, как правило, это изоцианат и полиол, итоговый материал, в котором воплощается форма, получается после смешивания этих компонентов. Что касается нашего полиуретана для форм линейки товаров Адваформ, принцип остаётся тем же: Вы смешиваете компоненты, заливаете их в опалубку или форму и получаете готовое изделие спустя некоторое время.
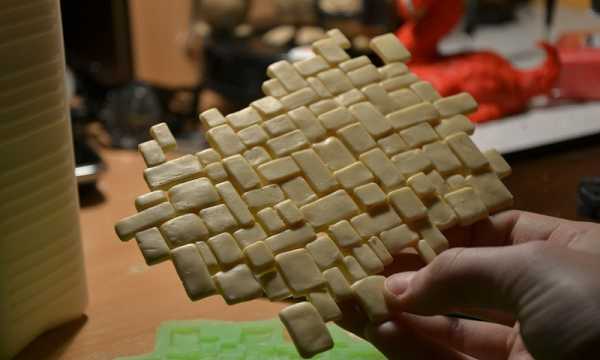
О том, как правильно изготовить опалубку под литьё, смешивать компоненты, использовать смесь и производить расформовку, можно почитать в разделе Статей на нашем сайте. Там мы собрали массу важной и полезной информации по всем этим вопросам.
Что касается самого полиуретана для форм, придерживайтесь самого важного правила: соблюдайте инструкцию! Небольшой мануал очень поможет вам в работе и исключит возможность изготовления некачественного изделия.
О том, как хранить и лить полиуретан
Ранее мы так же писали статьи о том, как правильно хранить материал, проводить его восстановление после негативных последствий окружающей среды, а также писали много инструкций по поводу его правильной эксплуатации. Важно помнить, что главным врагом жидкого полиуретана до того, как он вступил в процесс полимеризации, является вода. Она может испортить отдельные компоненты полиуретана или незатвердевшую смесь. Об этом также пишут в инструкциях.
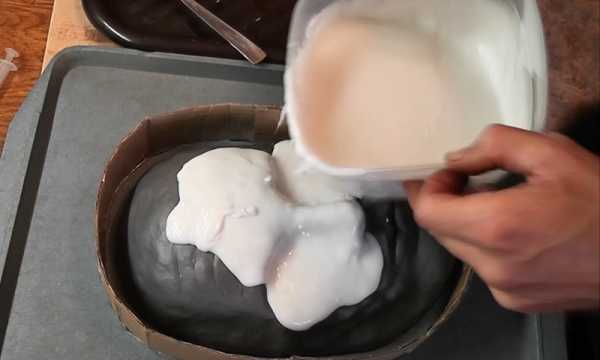
Помимо всего, непосредственно на нашем сайте, в карточке каждого товара имеется информация с описанием товара, действующими на него скидками, а также раздел с инструкцией. Консультацию и дополнительную информацию по товару, Вы также можете получить по телефону в шапке сайта.

Напоминаем, что доставка полиуретана происходит по всей территории СНГ, а в верхнем юзербаре нашего сайта можно найти разделы, которые помогут вам рассчитать стоимость доставки полиуретана для форм, а также габариты его вёдер и их итоговый вес.
kremen.ru
Термопластвинил как замена полиуретана для эластичных форм
Что такое термопластвинил TPV-45 для эластичных форм для вибролитья
Для изготовления гибких форм используются синтетический каучук (резина), ПВХ-смолы (пластизоли), ПВХ-гранулы (пластикаты), полиуретан холодной и горячей вулканизации, силиконовые компаунды.
Наиболее широкое применение при изготовлении форм для искусственного камня находит пластифицированный поливинилхлорид — пластикат. Он легко формуется и требуемое сочетание в нём прочности по Шорту, деформационной устойчивости и щелочестойкости достигается подбором соотношения пластификатора и наполнтелей (эластомеров).
Термопластвинил TPV-45 — это разработанный спецально для изготовления эластичных форм для искусственного камня и декоративной плитки термопласт на основе модифицированного пластиката ПВХ. Старое название такого материала — формопласт. Но с применением новых суперпластификаторов и наполнителей мы смогли существенно улучшить эксплуатационные характеристики пластиката ПВХ, увеличив срок службы материала, эластичность и снизив адгезию к цементной матрице и гипсу. Материал не теряет геометрию со временем, имеет высокую износостойкость. Формы не нуждаются в разделительной смазке.
Наши эластичные формы для камня и плитки универсальные, предназначены для заливки как цементом так и гипсом, не рвутся и служат долго, не менее 2000 отливок.
Преимущества термопластвинила в сравнении с полиуретаном и силиконом
Термопластвинил по своим характеристикам превосходит как полиуретановые формы для камня так и силиконовые. По точности передачи текстуры камня, в том числе с отрицательными углами, термопластвинил аналогичен полиуретановым и силиконовым формам но при этом обладает следующими преимуществами :
- Высокая щелочестойкость. В формы из термопластвинила можно заливать смеси на гипсе и на цементе (щелочная среда). Обычные силиконовые формы разрушаются под воздействием щелочи в составе цемента.
- Отсутствие адгезии к цементу и гипсу. Очень важное преимущество термопластвинила перед полиуретаном, особенно при работе с цементом. Без смазки полиуретановые формы имеют высокую адгезию к бетону и при передержке изделия при извлечении повреждается форма, а при недодержке — само изделие. Разделительная смазка для полиуретановых форм обязательна. Но смазка сама по себе это не только дополнительные расходы и время на ее нанесение, но и проблема с последующей окраской, особенно с применением кислотных красителей.
- Отсутствует усадка форм. Силиконовые и полиуретановые формы со временем теряют геометрию, у нашего материала такой проблеммы уже нет.
- Возможность передачи глянца. Структура полиуретана и силикона практически не позволяет передавать глянец на изделиях. Для термопластвинила такой проблемы нет и на наших формах можно изготавливать декоративную плитку и камень с глянцевой (полированной) поверхностью, особенно при использовании гипперпластификаторов для бетона Master Glenium (снижает В/Ц и уменьшает кол-во микропор и капиляров на поверхности бетона которые и снижают эффект глянца.
- Простота использования окраса пигментной маской. Поверхность формы хорошо удерживает пигменты, что позволяет использовать все техники окраса камня даже без использования специальной смазки.
При всех преимуществах термопластвинила наши формы дешевле форм из полиуретана и силикона благодаря меньшей стоимости сырья. Работа с пластикатом ПВХ (в отличие от полиуретана и силикона с которыми легко можно работать дома, изготавливая формы для камня своими руками) требует специального оборудования (нагреватели, экструдеры, термокамеры и.т.д) и многоступенчатого технологического процесса. Отлаженное производство и высокая производительность позволяет нам держать низкие цены на предлагаемые нами эластичные формы.
Характеристики термопластвинила
Термопластвинил TPV-45 — это без преувеличения лучший материал для изготовления эластичных форм для искуственного камня, заборов, тротуарной плитки, мыла и др. Термопласт предназначен для работы с бетоном, гипсом, полимерами и смолами.
- температура плавления: 160-195 °С.
- твёрдость: 45А по Шор
- высокая механическая прочность, износоустойчивость
- высокая химическая стойкость к агрессивным средам
- низкая воспламеняемость, самозатухание после изъятия из пламени
- физиологически безопасный материал
- превосходно сопротивляется трению, стойкий к образованию царапин
- температурный диапазон эксплуатации форм из TPV до +60 °C
legobeton.ru