Технология производства цемента
Технология производства цементаСтроительный материал — бетон, знают все. Благодаря высокой прочности и универсальности его широко используют в строительстве. Однако, технология производства цемента требует значительных энергетических затрат и сопровождается большим выделением парниковых газов. Учёные всего мира ведут поиск новых технологий, позволяющих создавать новые строительные материалы, более безопасные для окружающей среды.
Цемент составляет от 7 до 15% от общей массы бетона по весу и производится прокаливанием в печах смеси известняка и глины, а затем перемалывается в порошок. Машины и оборудование цементного завода производят выбросы CO2. Технологический процесс производства цемента также связан с высвобождением двуокиси углерода при его нагревании. Сорок процентов выбросов СО2 цементного завода происходит от процесса сгорания топлива и шестьдесят процентов выбросов от процесса прокаливания.
Положительные результаты были достигнуты в снижении количества выбросов на одном производстве в Англии. Специалистам компании Novacem удалось создать цемент, в производстве которого используется силикат магния, не выделяющий СО2 при прокаливании. Этот процесс, также проходит при более низких температурах. Цемент поглощает гораздо больше СО2 во время затвердевания бетона компенсируя выбросы, образующиеся при производстве. Калифорнийская компания Калера утверждает, что разработан цементный технологический процесс с отрицательным выбросом углерода в атмосферу. Новая технология основана на исследованиях учёных коралловых рифов, для создания которых происходит фильтрация выбросов двуокиси углерода из морской воды.
На сегодняшний день реальность такова, что стоимость новой технологии изготовления цемента существенно выше традиционной. Значительное сокращение CO2 невозможно осуществить без субсидирования промышленности, особенно, в развивающихся странах, которые используют цемент наиболее интенсивно. Создание новых энергоэффективных и дешёвых технологий производства цемента является важнейшей задачей охраны окружающей среды завтрашнего дня.
myremdom.ru
Полная технологическая схема производства цемента
Учитывая, что строительный материал – цемент, разных марок, является строительным материалом, без которого невозможно ни одно строительство, многих застройщиков и покупателей интересует схема его производства и нюансы изготовления.
СодержаниеСвернуть
- Схема производства цемента
- Технологическая схема производства цемента
Схема производства цемента
Это отработанный многими десятилетиями процесс, который имеет несколько принципиально новых способов, состоящих из следующих основных этапов:
- Разработка, добыча, доставка и обогащение исходных материалов: известняковых и глиноземных пород для производства клинкера;
- Получение клинкера. Является одним самых энергозатратных, поэтому самых дорогостоящих этапов схемы производства цемента. В частности на осуществление этого этапа приходится до 75% затрат на производство цемента. В общем случае технология производства клинкера выглядит так: подготовленную смесь компонентов заливают водой, дают отстояться в течение определенного периода времени, после чего начинается термическая обработка в печах при температуре до 1 500 градусов Цельсия. При этом исходные компоненты клинкера спекаются в виде гранул определенной фракции;
- Измельчение клинкера. На этом этапе происходит мелкодисперсное измельчение гранул клинкера и введение присадок, которые определяют специальные свойства и марку цемента. По сути это конечный этап схемы изготовления цемента, который оканчивается фасовкой данного материала в мягкие контейнеры Биг-Бены, бумажные многослойные клапанные мешки или транспортировкой в силосы для последующей реализации «навалом».
Технологическая схема производства цемента
На данный момент времени цемент изготавливается по нескольким принципиально разным технологиям, имеющим свои принципиальные преимущества и недостатки.
- Так называемый мокрый способ производства цемента, широко использующийся отечественными цементными заводами. Является самой энергозатратной. Суть схемы заключается в загрузке компонентов цемента в специальное оборудование, в водную среду. После выдержки в воде компоненты цемента поступают в мельницу, которая измельчает их в порошок. Полученный таким образом полуфабрикат транспортируется в специальный бассейн, корректируется по составу и в дальнейшем обжигается в специальной печи с последующим охлаждением. После контроля качества, данный продукт следует на измельчение до состояния товарного цемента;
- Сухая технология. Принципиальное отличие от «мокрой схемы» заключается в том что после предварительного измельчения компоненты цемента направляются в осушительные барабаны, после чего перемешиваются и проходят дополнительное измельчение в мельнице. При этом на этапе измельчения в цемент вводятся добавки и присадки. Далее полученная масса направляется на обжиг, измельчение и упаковку. Одним из преимуществ этого способа получения портландцемента можно отметить возможность использования в качестве сырья зольную пыль и прочие отходы энергетического и металлургического производства. Сухая технология исключает: многоступенчатое дробление компонентов, снижает «добывающие» и транспортные затраты, а также расширяет выбор сырья для производства цемента;
- «Полусухая» схема производства цемента. Данная схема отличается габаритами гранул клинкера, влажностью материала и технологией обжига. В частности масса компонентов для изготовления цемента обжигается в специальных печах «ЛЕПОЛЬ», которые при всех прочих равных условиях обеспечивают уменьшение уровня карбонизации конечного продукта на 22-23%;
- Комбинированный способ производства цемента. В этом случает, происходит органичное сочетание нескольких технологий: «мокрой» и «сухой». С ответствующими преимуществами и недостатками.
В завершение данного повествования следует сказать, что цементные заводы, расположенные на территории Российской Федерации, по объективным причинам, используют исключительно «мокрую» схему производства цемента.
Применение передовых энергоэффективных технологий «сухого» производства цемента требует значительных капиталовложений и полного перевооружения действующего производства, невозможных в ближайшем обозримом будущем.
salecement.ru
Производство цемента — от добычи сырья до расфасовки + видео
Современное производство цемента, видео рассказ о котором дополняет нашу сегодняшнюю статью — полностью автоматизированный процесс. Существует четыре способа изготовления этого стройматериала, о каждом из которых мы расскажем подробно.
Технология производства цемента — от карьера до завода ↑
Видео ролик о производстве цементаПоскольку цемент, в отличие, к примеру, от песка, не имеет природного происхождения, процесс его производства начинается с добычи необходимых «ингредиентов». Для того чтобы в итоге получился знакомый каждому серый порошок, требуются такие компоненты, как:
- Известняк.
- Глина.
Эти два материала природного происхождения — основа цемента. В зависимости от того, какими именно характеристиками должен будет обладать цементный порошок в итоге, в него вводят различные добавки. Например, оксид алюминия при производстве глиноземистого или азотистый кальций для создания расширяющегося антикоррозийного цементов.
Как производят цемент, используя мокрый способ? ↑
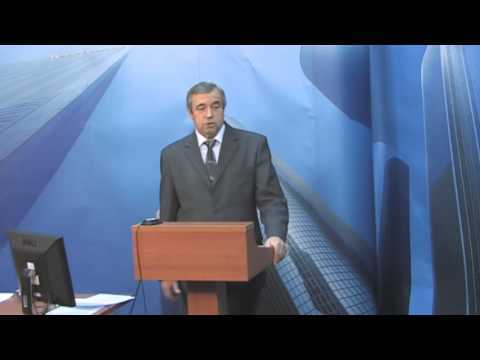
Первый из четырех способов получения цемента — мокрый. Процесс начинается с измельчения известняка. Большие куски породы (до одного метра в диаметре) перемалывают в несколько этапов, добиваясь того, чтобы отдельные «гранулы» были не больше сантиметра. Глину также измельчают в дробилках, а затем перемещают в специальные болтушки. Затем оба перемолотых компонента встречаются в сырьевой мельнице, где и подвергаются совместному перемалыванию.
Теперь пришло время отправить «полуфабрикат» (на профессиональном языке он называется шламом) в специальные вертикальные бассейны, в котором корректируют его состав в соответствии с нормами изготовителя. Затем порошок отправляют в другой бассейн — на сей раз горизонтальный, где происходит его постоянное перемешивание. При применении мокрого способа шлам примерно на треть состоит из воды. Следующий этап создания цемента — обжиг, на который порошок отправляется прямо из бассейна.
Температура в печи может достигать 1450 °С, она заставляют шлам избавляться от влаги, спекаться и превращаться в так называемый клинкер. Далее следует процесс охлаждения клинкера в холодильниках. Затем гранулы спекшегося клинкера нуждаются в измельчении — это делается в специальной мельнице, в которую также отправляют различные добавки, о которых мы говорили выше. На этом процесс изготовления цементного порошка заканчивается. Готовый цемент поступает на хранение в специальные силосы, где держится до того времени, как будут проведены все испытания на качество. Затем его расфасовывают в мешки или поставляют потребителю валом.
Как осуществляется производство цемента сухим способом? ↑
Процесс изготовления сухим способом также начинается с дробления известняка и глины. Полученную «заготовку» необходимо высушить — это делается в специальных сепараторах, где ее влажность доводится до одного процента. Современное производственное оборудование позволяет вместе не только сушить, но и одновременно и измельчать порошок, что позволяет добиться максимально возможной однородности состава.
Теперь пришло время отправить «полуфабрикат» в силос, в котором его доводят до нужной консистенции, одновременно перемешивая. В это же время порошок подвергается предварительному нагреву до 800 °С, благодаря чему он лишается остатков влаги. После этого будущий цемент переводят в печь, где он «томится» до образования клинкера, который затем перемалывается, отправляется на проверку, расфасовку и хранится на складе до момента отгрузки потребителю.
Другие способы производства цемента ↑
Существуют также полусухой и комбинированный способы изготовления цемента. При применении полусухого метода процесс изготовления цементного порошка до стадии обжига выглядит точно так же, как если бы его делали сухим способом. Однако перед тем, как превратить шлам в клинкер, его отправляют на гранулирование, и лишь затем — в печь. После этого гранулы отправляются на специальный конвейер, где декарбонизируются и полностью высушиваются. Теперь их еще раз отправляют в печь, где они окончательно превращаются в клинкер, который затем перемалывается.
Отличительная комбинированного способа особенность состоит в том, что все стадии производства вплоть до обжига, в точности повторяют этапы мокрого метода, а вот сам обжиг — стадии полусухого.
Мокрая схема производства цемента наиболее распространена на российских заводах, построенных в советские времена. Сухой же способ, считающийся на сегодняшний момент самым экономичным и эффективным, используют новые предприятия, созданные в последние годы.
mastter.ru
Технология производства цемента — n1.docx
Технология производства цементаДоступные файлы (1):
n1.docx
Федеральное агентство по образованиюГОУВПО «Удмуртский государственный университет»
Институт экономики и управления
Кафедра труда
РЕФЕРАТ
по дисциплине
«Технология»
на тему: «Технология производства цемента»
Выполнил: студент гр. З-2007-0661100-19
Алексеев Д.Н.
Проверил: д.к.т. Овчинников В.Ф.
СОДЕРЖАНИЕ
Введение……………………………………………………………………3
Описание технологического процесса производства цемента………….5
История цемента……………………………………………………………9
Заключение…………………………………………………………………10
Список литературы………………………………………………………..11
ВВЕДЕНИЕ
Цемент — связующее вещество в форме порошка, который отвердевает, будучи смешанным с водой. Цемент используется для производства бетона, представляющего собой совокупность цемента, песка и воды. Бетон – материал, используемый для строительства дорог, мостов, гаваней, жилых зданий, школ, больниц и т.д. Использование цемента внесло свой вклад в благосостояние общества и повышение экономических стандартов. По европейским стандартам для обычного проектирования используется список, включающий 27 различных видов цемента.
Цементная промышленность — энергоемкая промышленность, в которой расходы на энергоносители составляют 30-40 % издержек производства.
Первоначально топливом, используемым в данной промышленности, являлся уголь. Кроме того, использовался широкий диапазон других видов топлива, включая нефтяной кокс, природный газ и масло. На протяжении последних 10 лет цементная промышленность использует некоторые отходы производства как альтернативное топливо для цементных печей. Использование отходов как топлива в цементных печах экономит ископаемое топливо, глобально уменьшает эмиссию воздуха и устраняет потребность в избавлении от шлака и пепла.
Продукция цементной печи зависит, прежде всего, от протекания физических и химических реакций сырья, и уже потом — от сгорания топлива. Газы, выделяющиеся в процессе работы цементной печи — азот из поступающего в зону горения воздуха, CO2, выделяющийся в процессе прокаливания CaCO3 и сгорания топлива, вода, выделяющаяся в процессе горения и обработки сырья, и лишний кислород. В состав выделяющихся газов также входит небольшое количество (менее 1 %) пыли, диоксида серы, NOx и других веществ.
Цементная промышленность — капиталоемкая промышленность. Стоимость нового цементного завода эквивалентна приблизительно 3-летнему товарообороту, что ставит цементную промышленность в ряд наиболее капиталоемких отраслей промышленности. Поэтому проходит определенный период времени, прежде чем инвестиции будут возвращены, и модификации завода следует тщательно планировать, принимая во внимание долгосрочную природу данной отрасли промышленности.
Наличествующая конфигурация производства и оборудования завода отражает технический уровень того времени, когда завод был построен или изменен. Выгоды от применения определенного оборудования имеют место лишь до определенного момента, когда, с точки зрения экономики и конкурентоспособности, становится более выгодным заменить оборудование на новое, более совершенное. Та же самая ситуация имеет место, когда происходит дальнейшее совершенствование технологий.
ОПИСАНИЕ ТЕХНОЛОГИЧЕСКОГО ПРОЦЕССА
ПРОИЗВОДСТВА ЦЕМЕНТА
Главные процессы и подпроцессы
Существует четыре главных технологических способа производства — сухой, полусухой, полувлажный и мокрый процесс.
Обычно все эти процессы включают в себя следующие подпроцессы:
Карьерные работы
Подготовка сырья
Подготовка топлива
Горение клинкера
Подготовка минеральных добавок
Размол цемента
Отправка цемента
Карьерные работы
Природное («первичное») сырье, например, известняк/мел, известковая глина и глина/сланец добываются в карьерах, которые, в большинстве случаев, расположены поблизости от цементного завода. После добычи сырье дробится непосредственно в карьере и транспортируется на цементный завод для промежуточного хранения, гомогенизации и дальнейшей переработки.
«Корректирующие» материалы, такие как глинозем, железная руда или песок могут быть необходимы в химическом составе сырьевой смеси в соответствии с требованиями процесса и технических требований к продукту. Количество корректирующих материалов обычно очень мало по сравнению с общими объемами основного сырья.
В ограниченных объемах используется «вторичное» (или «альтернативное») сырье, получаемое от индустриальных источников, чтобы заменить природное сырье и коррективы. Таким же образом как традиционное сырье, они могут подаваться на дробилку карьера или непосредственно в процессе подготовки сырья на цементном заводе.
На сегодняшний день, современные методы обработки на компьютере позволяют оценить сырье и оптимизировать долгосрочные и краткосрочные производственные планы.
Подготовка сырья
После промежуточного хранения и догомогенизации сырье сушится и перетирается в определенных и хорошо контролируемых пропорциях в мельницах, в результате чего получается сырьевая мука для сухого (и полусухого) процесса. При влажном (и полувлажном) процессе сырье – катализированная суспензия, измельчается с определенным количеством воды для получения жидкого цементного теста.
В зависимости от технологического процесса может быть применена дополнительная ступень, например, подготовка «гранул» из сырьевой смеси – сухого тонко размолотого вещества (полусухой процесс), или получение «фильтрационного осадка» в процессе осушения жидкого раствора в фильтрующем прессе (полувлажный процесс).
Получающийся промежуточный продукт — то есть сырьевая мука или жидкое цементное тесто (или их производные) — сохраняется и далее гомогенизируется в бункерах сырьевой смеси или шламовых бассейнах, в результате чего достигается и поддерживается необходимый однородный химический состав перед отправлением в печь.
Как правило, приблизительно необходимо 1.5 — 1.6 тонны (сухого) сырья для производства одной тонны спекшегося материала — клинкера.
Подготовка топлива
Обычное (ископаемое) топливо, используемые в европейской цементной промышленности — главным образом уголь (гумат и каменный уголь), топливный мазут (продукт, получаемый в результате очистки сырой нефти) и необработанная нефть (“бункер C”). Природный газ редко используется из-за его высокой стоимости.
«Альтернативные» виды топлива — неорганические топлива, производимые из индустриальных отходов — широко используются в наши дни вместо традиционных видов ископаемого топлива.
Подготовка топлив — то есть измельчение, высыхание, размол, и гомогенизация – обычно производится на месте. Для этого нужны угольные мельницы, бункеры и помещения для хранения твердого топлива, резервуары для жидкого топлива и соответствующий транспорт и системы подачи к печам.
Потребление топлива в значительной степени зависит от основного технологического процесса, применяемого при спекании цементного клинкера.
Спекание цементного клинкера
Готовое сырье поступает в печи, где подвергается процессу тепловой обработки, состоящему из последовательных ступеней высыхания/подогрева, прокаливания (например при получении CO2 из известняка), и спекания (или “клинкеризации”, например при минерализации клинкера при температуре до 1450 ° C). Спекшийся продукт «клинкер» охлаждается потоком воздуха до 100-200 ° C и транспортируется к месту хранении.
Обычно применяются барабанные печи с или без так называемых циклонных теплообменников ( в более современных системах — «декарбонизатор») в зависимости от основного процесса избранного проекта. Сама барабанная печь представляет собой наклонную стальную трубу с соотношением длины и диаметра 10 х 40. Небольшой наклон (от 2.5 до 4.5 %) вместе с медленным вращением (0.5 — 4.5 оборотов в минуту), позволяют перемещать обрабатываемые материалы достаточно долго для достижения термической конверсии требуемых процессов.
Высокая температура в печи используется для сушки сырья, твердого горючего или минеральных добавок в мельнице. Отработанные газы проходят через электростатические осадители или системы мешочных фильтров прежде, чем выпускаются в атмосферу.
Размол цемента
Портландцемент производится путем совместного размола клинкерного цемента с небольшим количеством природного или индустриального гипса (или ангидрита) на цементном заводе. Цементы с добавками (или «смешанный» цемент) содержат другие элементы, например, раздробленный доменный шлак, природный или индустриальный туф (например, вулканические туфы или зола – отходы от тепловых электростанций), или инертные наполнители, такие как известняк.
Минеральные добавки вводятся при дроблении вместе с клинкером или размалываются отдельно и смешиваются с портландцементом.
Размалывающие установки могут быть расположены отдаленно от производства клинкера.
Различные типы цемента должны храниться отдельно в цементных бункерах до укладывания в мешки и отправки потребителю.
Подготовка минеральных добавок
Минеральные добавки из природных или индустриальных источников, которые будут использованы в цементе с добавками, должны быть вначале высушены, раздроблены или перетерты в отдельных сооружениях на месте. Отдельные “перемалывающие заводы”, где производятся минеральные добавки, могут быть расположены далеко от места производства клинкера.
Отправка цемента
Цемент может быть отправлен или насыпью, или упакованный в мешки и уложенный в штабеля для отправки. Использование видов транспортировки (то есть дорог, железных дорог, водных путей) зависит от местных условий и требований.
ИСТОРИЯ ЦЕМЕНТА
Цемент начали производить в прошлом столетии. В начале 20-х годов XIX в. Е. Делиев получил обжиговое вяжущее из смеси извести с глиной и опубликовал результаты своей работы в книге, изданной в Москве в 1825 г. В 1856 г. был пущен первый в России завод портландцемента. Цемент является одним из важнейших строительных материалов. Его применяют для изготовления бетонов, бетонных и железобетонных изделий, строительных растворов, асбестоцементных изделий. Изготовляют его на крупных механизированных и автоматизированных заводах.
В 1995 году в мире было произведено 1 420 миллионов тонн цемента. В Европейском союзе производство цемента составляло 172 миллиона тонн в 1995 году, в то время как потребление данного продукта промышленности — 168 миллионов тонн. Импорт составлял 23 миллиона тонн и экспорт — 27 миллионов тонн. Эти данные включают торговлю между странами ЕС. Потребление цемента на душу населения составляет 52 кг. С 1990 года потребление цемента в Европейском союзе снизилось приблизительно на 13 %, а производство — на 11 %. В 1973 году цементная промышленность в Европейском союзе производила 27 % от количества цемента, произведенного в мире, а в 1995 году — 12 %.
ЗАКЛЮЧЕНИЕ
Цемент не является природным материалом. Его изготовление — процесс дорогостоящий и энергоемкий, однако результат стоит того — на выходе получают один из самых популярных строительных материалов, который используется как самостоятельно, так и в качестве составляющего компонента других строительных материалов (например, бетона и железобетона).
Без цемента не обходится ни одно строительство, а это лучший показатель его высоких эксплуатационных характеристик.
СПИСОК ЛИТЕРАТУРЫ
Алексеев Б.В. Технология производства цемента –Москва: 1980г.
И.Ф. Пономарев, Е.Д. Вернг, В.С. Чекрынен, Г.М. Златокрылов. Технология производства цемента сухим и полусухим способами. – Киев: 1988.
Н.Н. Холина. Справочник по производству цемента. – Москва: Госстройиздат, 1963.
В.К. Классен. Обжиг цементного клинкера. – Красноярск: Стройиздат, 1994.
Ю.М. Бутт, С.Д. Сычев, М.М. Тимашев. Технология вяжущих веществ. – Москва: Высшая школа. 1965.
perviydoc.ru