Контроль прочности бетона
Каждый, кто работает на стройке, хоть раз видел как берутся пробы бетона для испытания его на прочность. Заливают бетонные кубы 100X100X100 миллиметров и отдают на растерзание лаборатории.
Когда спрашиваешь, зачем для испытания бетона не делают кубы другого размера, лишь недоумённо пожимают плечами. Чаще всего никто и не знает, что в отдельных случаях можно и нужно делать кубы большего размера. Например, с ребром 150, 200 и даже 300 мм.
Подождите читать дальше! Проявите свою инженерную смекалку и подумайте, отчего может зависеть размер кубиков для контрольных испытаний.
Знаете ответ? Ну можно тогда и не дочитывать. А для тех, кто поленился подумать немного расскажет о бетонных кубиках для контроля качества бетона.
Бетон, как известно, составной строительный материал, в его состав входят разные материалы, в числе которых щебень. Щебень бывает разных фракций (размера). В бетон кладут как щебёнку размером 5-20 мм, так и размером 20-40 мм и больше, в зависимости оттого, для каких целей мы производим прочный бетон. И вот представьте себе, какими окажутся результаты испытаний контрольных образцов бетона, если в этот маленький кубик с ребром 100 мм попадёт такой гранитный камушек длиной под 100 мм. А результат предсказуем: камень будет занимать большую часть объёма куба, и результаты испытаний окажутся неточными!
Вот специально для таких случаев контроля прочности бетона в ГОСТе 10180-90 «Бетоны. Методы определения прочности по контрольным образцам» и была определена зависимость размера бетонных кубиков для определение прочности бетона в зависимости от размера зерна наполнителя.
Как понятно из занимательной таблицы, зависимость размера кубиков от размера зерна наполнителя прямая при экспертизе бетона.
Однако это не вся полезная информация, которую можно почерпнуть, читая ГОСТ 10180-90.
Заглянем в примечания:
- Для испытания конструкционно-теплоизоляционного и теплоизоляционного бетонов класса В5 (М75) и менее на пористых заполнителях(независимо от наибольшей крупности заполнителя) следует применять образцы с наименьшим размером 150 мм.
- При изготовлении образцов из бетонной смеси должны быть удалены отдельные зёрна крупного заполнителя, размер которых превышает более чем в 1,5 раза наибольший номинальный размер заполнителя, указанный в табличке, а также все зёрна заполнителя размером более 100 мм.
Вот так друзья, знайте и любите нормативную документацию для испытания прочности бетона. В ней ещё много интересного.
Наибольший номинальный размер зерна заполнителя |
Наименьший размер образца (ребра куба, стороны поперечного сечения призмы или восьмёрки, диаметра и высоты цилиндра) |
20 мм и менее |
100 мм |
40 мм |
150 мм |
70 мм |
200 мм |
100 мм |
300 мм |
niola-td.ru
Испытание кубиков бетона
ПОЧЕМУ СУДЫ ОТКЛОНЯЮТ ЗАКЛЮЧЕНИЯ
Читать статью!
ВЫПОЛНЕННЫЕ РАБОТЫ
26.12.2018 г. — Проведена экспертиза для определения причин залива,по адресу: г.Москва, Есенинский бульвар.
24.12.2018 г. — Проведена экспертиза дома,по адресу: МО, г.Егорьевск.
23.12.2018 г. — Проведено тепловизионное обследование,по адресу: МО, Солнечногорский р-н, ул.Центральная.
23.12.2018 г. — Проведена экспертиза пригодности дома к проживанию,по адресу: МО, пос.Большие Вяземы.
22.12.2018 г. — Проведена экспертиза здания,по адресу: г.Москва, ул.Юннатов.
21.12.2018 г. — Проведена экспертиза качества ремонта,по адресу: г.Санкт-Петербург, ул.Большая Зеленина.
21.12.2018 г. — Проведена экспертиза фундамента,по адресу: МО, дер. Рязань.
20.12.2018 г. — Проведена экспертиза цоколя дома,по адресу: МО, с. Жаворонки.
20.12.2018 г. — Проведена экспертиза дома,по адресу: МО, пос. Тишково озеро.
18.12.2018 г. — Проведена экспертиза здания,по адресу: г.Александров.
СМОТРЕТЬ ЕЩЁ
*******
МЫ РАБОТАЕМ
БЕЗ ВЫХОДНЫХ
с 8-00 до 22-00
Ждем Ваших звонков не только в будние дни, а также в субботу и в воскресенье. Наши эксперты выезжают на экспертизу и обследование ежедневно и без выходных.
*******
СТРОИТЕЛЬНЫЙ АДВОКАТ
Бесплатная консультация нашего строительного юриста.
Анализ перспектив Вашего спора в суде или в досудебном порядке.
Юридические услуги оказывают юристы в области строительного права.
*******
ДОСТАВКА
курьером строительного заключения, актов приемки-сдачи, счетов-фактур.
*******
ОСТОРОЖНО!
В последнее время появилось большое количество мошенников и непрофессионалов.
Читать Проверка экспертной организации.
*******
ПЛАНЫ МНСЭ
В 2018 году
планируем открытие новых офисов МНСЭ
в следующих городах:
Севастополь
Минск
Астана
Киев
*******
ДОСТИЖЕНИЯ МНСЭ
ЗА 2017 г.:
698 проведенных строительных экспертиз;
267 проведенных обследований;
32 проведенных энергоаудита;
103 разработанных проектов.
*******
МНСЭ — участник и докладчик
2-го Всероссийского Симпозиума «Актуальные проблемы судебной экспертизы и контрольных процедур в строительстве», который прошел 16 апреля 2015 г. в Центральном Доме Архитектора в Москве.
*******
ПЛАГИАТ
Увидели у конкурентов похожий на наш сайт по структуре или по содержанию. Проверьте в интернете, кто является первоисточником. Ответ, который Вы получите — МЫ.
mnse.ru
Образцы бетона и испытание эталонных кубиков
Если рассматривать современные строительные материалы, то бетон занимает важное место и является незаменимым компонентом. Он используется практически повсеместно и может выдержать существенные нагрузки. Универсальность состава является одним из тех факторов, которые обеспечили привлекательные условия для применения на самых разных типах объектов. Таким образом, обеспечивается возможность реализовать сложные проекты, не тратя лишних денежных средств и не усложняя конструкцию. Следует сказать, что бетон состоит из трёх ключевых компонентов: заполнителя, вяжущего материала, а также воды. Для усиления различных эксплуатационных характеристик, в смесь могут вводиться различные добавки. Они позволяют добиться существенного улучшения ситуации при минимальном увеличении стоимости. Следует отметить, что введение добавок производится ещё на этапе смешивания и их общиё объём не должен превышать шести процентов от массы материала. Это важный фактор, поскольку в ином случае, результатом будет снижение прочностных свойств. Рекомендации по смешиванию добавок и состава можно прочесть в инструкциях, поставляемых вместе с данным изделием. Это позволяет обеспечить улучшенные характеристики, что весьма важно.
В зависимости от того, какие требования предъявляются к конкретной конструкции, различаются несколько вариантов её изготовления. Ключевую роль во всём этом играет создание необходимого типа состава. Он может существенно отличаться по своим прочностным, а также некоторым иным характеристикам, поскольку вводится определённая доля каждого составного компонента. Таким образом, различают несколько марок. Главной особенностью, в соответствии с которой проводится классификация, является прочность материала на сжатие. Для её измерения требуется использовать
образцы бетона, тестируемые на специальном оборудовании. Стоит рассмотреть этот момент детальнее, чтобы получить о нём необходимое представление.Испытание эталонных кубиков выполняется на специализированной машине, имеющей гидравлические компоненты. Они сжимаются, образуя значительное воздействие на заданный объект, помещённый в рабочую зону. При этом, прибор измеряет силу подобного влияния, что обеспечивает возможность классификации по соответствующему признаку.
Стоит рассмотреть не только то, как происходит испытание эталонных кубиков, то и такой немаловажный момент, как создаются образцы бетона. Подобная задача возлагается на изготовителей смеси. Все крупные заводы по производству данного вида строительного материала должны с каждой крупной партии брать несколько проб, чтобы выполнить испытание эталонных кубиков, а также ряд других процедур. Это важный момент по той причине, что образцы бетона позволяют установить соответствие смеси и заявленных параметров. Главным недостатком является невозможность оперативно сообщить результат. Испытание эталонных кубиков не может быть выполнено сразу после того, как образцы бетона были взяты. Требуется некоторое время для их застывания и набора номинального уровня прочности. Только в таком случае, достигается объёктивный результат, отражающий текущее положение вещей. Следует отметить, что образцы бетона должны твердеть именно таким образом, каким будет осуществляться набор прочности. В ином случае, достоверность полученных данных будет находиться под сомнением. Стоит детальнее описать этот момент. Когда состав продаётся потребителю, который будет использовать естественные методы твердения, образцы бетона
Когда проводится испытание эталонных кубиков, необходимо обеспечить их предварительное создание. Это довольно простой тип мероприятий, который начинается с изготовления опалубки. Прежде всего, следует определить габариты такого изделия, как образцы бетона. Размеры должны быть стандартизированы, чтобы результат всегда был на одном уровне. Только в таком случае можно добиться реального результата и минимального разброса параметров. Когда производится испытание эталонных кубиков, учитывается множество факторов. Согласно документации, используемой в данной сфере, размеры строго установлены. Куб из бетона должен обладать стороной в 15 сантиметров. Допускаются отклонения не более чем в несколько миллиметров. Если образцы бетона имеют отличные от этого размеры, то полученный результат нельзя считать достоверным. Подобные нестыковки повлияют на качество результата. Таким образом, создаётся опалубка из дерева, внутренний объём которой вычитается из расчёта, что каждая сторона имеет 15 сантиметров. Следует большое внимание уделить перпендикулярности всех плоскостей друг относительно друга. Если подобное требование не будет соблюдаться, велика вероятность возникновения проблем, когда произойдёт испытание эталонных кубиков.
Как брать образцы бетона и какие требования необходимо выполнить, при осуществлении подобных работ? Необходимо рассмотреть основные правила, чтобы испытание эталонных кубиков могло быть проведено максимально качественно и без проблем в дальнейшем. Следует уделить время тому варианту, когда машина с завода прибывает на строительную площадку. Не следует брать образцы бетона с верхней части смесителя. Причина заключается в том, что в ней скапливаются наименее плотные компоненты. Особенно, если смесь не подвергалась процессам смешивания. Подобные образцы бетона будут иметь несколько меньшие показатели, чем есть на самом деле. Дополнительно, в пути опрыскиватель создаёт водяной слой, препятствующий испарению влаги из состава. Если не учесть его присутствия и взять образцы бетона сразу, то испытание эталонных кубиков не даст соответствующего результата.
Укладка состава в специально подготовленную для него опалубку должна производиться по специальным правилам. Прежде всего, образец бетона заливается в конструкцию и проводится процесс штыкования. Это позволяет исключить возможность возникновения такого негативного явления, как воздушные полости, снижающие прочность смеси. Подобные мероприятия проводятся и для других типов бетонных конструкций. Как правило, используются вибраторы, поскольку они лучше подходят для обеспечения однородности при работе с большими объёмами. Состав укладывается в опалубку для дальнейшего испытания эталонных кубиков, в несколько слоёв. Все они трамбуются и создаётся однородная масса. Не допускается образования горки в верхней части опалубки. Выходящий за пределы конструкции цемент следует аккуратно снять шпателем или любым других инструментов. Если укладка произведена правильно, то усадки практически не будет и данный фактор не сможет оказать воздействия.
После того, как образцы бетона помещены в специальную опалубку, следует оставить их в месте с комнатной температурой и отсутствием прямого солнечного излучения. Дополнительным моментом, при обеспечении оптимальных условий хранения, является отсутствие различных механических воздействий, что негативно сказывается на целостности состава, а также его характеристиках, когда начинается испытание эталонных кубиков.
Поскольку состав заливается в специальную конструкцию – опалубку, стоит сказать пару слов о её демонтаже. Подобная задача не является сложной, если использован правильный материал. Не стоит помещать образцы бетона в конструкции со слишком гладкими или пористыми поверхностями. В обоих вариантах, это приведёт к некоторым неблагоприятным факторам. Образцы бетона следует извлекать из опалубки после 7-10 дней пребывания в ней, когда изделие набрало необходимый показатель прочности.
dombeton.ru
Испытания кубов и кернов бетона
Определение прочности бетона — важная процедура, которая предшествует возведение любого сооружения. Именно благодаря тестированию определяется сфера применения бетона: цементный раствор для стяжки, керамзитобетон для использования в суровых климатических условиях или мостовой бетон. В отличие от неразрушающего контроля бетона, чтобы провести испытание бетонного раствора, в данном случае необходимо взять кубы-образцы. В результате лабораторных исследований удаётся на практике установить, насколько прочный бетон, подходит ли он для применения в определенных задачах.
Порядок изготовления кубов-образцов следующий:
- подготовить изделия идеальной кубической формы с размерами ребер 100 (наиболее популярный вариант куба для тестирования), 150, 200 миллиметров;
- если подготавливать для тестирования еще меньшие образцы, с размером ребра 70 миллиметров, можно использовать заполнители, размер частиц которых составляет 2 сантиметра или меньше;
- в соответствии с ГОСТом 10181.0 взять пробу материала на объекте из бетоносмесителя;
- проследить за тем, чтобы форма кубов соответствовала стандартам;
- использовать для бетона тонкий слой смазки.
Пробу необходимо помещать в форму строго в течение 20 минут после взятия. Для уплотнения бетона в емкости формы — применять металлическую штыковку. Ее диаметр должен составлять 1.6 сантиметра.
Испытание кубов бетона на прочность
Как проходят исследования бетона
Дополнительная обработка смеси на виброплощадке применяется, чтобы максимально уплотнить ее, если раствор очень жесткий. Проводить распалубку образцов можно только через сутки после заливки в форму или позже. Перед применением формы для создания следующих образцов бетона ее необходимо аккуратно очистить, обработать смазкой.
Для твердения образцов бетона необходимо около 28 суток. Кубы помещают для этого в специальные камеры, в которых происходит формирование полноценного материала. По истечении рекомендованного срока твердения можно передать бетон в лабораторию для тестирования. Перед проведением испытаний на прессе образцы выдерживают 24 часа в идеальных условиях.
Существует несколько способов тестирования бетона: испытание на скручивание, прочность, устойчивости к морозу и влаге. После испытаний, осуществляемых в условиях, соответствующих тем или иным ГОСТам, им присваивают определенные характеристики.
Обратитесь в нашу лабораторию, чтобы заказать услуги по испытанию образцов бетона. Мы проводим все исследования при условиях, соответствующих государственным стандартам. Мы также даем рекомендации по правильной подготовке образцов, необходимой для максимально информативных результатов испытаний.
Вас интересует определение прочности образцов-кубов и «кернов»? Хотите узнать стоимость работ?
Закажите обратный звонок с сайта, мы перезвоним за 24 секунды и ответим на все вопросы!
ГОСТы, которые регламентируют определение прочности образцов-кубов и «кернов»
Образец протокола по испытанию кубов
Отбор кернов / испытание прочности бетона
- Здание ТРК по адресу: г. Москва, ул. Авиаконструктора Миля, Вл.7
- Многофункциональный центр «Променад», Московская область, г. Мытищи, микрорайон 17, кварталы 27-33
- ТЦ «Косино-Парк» ул. Святоозерская, вл. 5 ( Москва, ВАО, район: Косино-Ухтомский )
- ЖК «Пироговская Ривьера», МО, Мытищинский район, Городское поселение Пироговский, деревня Пирогово
- ТЦ «Юго-Запад», Проспект Вернадского, пересечение с ул. Покрышкина
- ТЦ «Курский», Варшавское шоссе, вл. 148
- ЖК «Эталон-сити», улица Старокрымская, вл. 13
- ЖК «Яуза Парк», Краснобогатырская улица, вл. 28
- ЖК «LIFE-Митинская Ecopark», ул. Митинская, вл. 22
- ЖК «Тушино», Москва, СЗАО, район Покровское-Стрешнево, Волоколамское шоссе, вл. 67
- Многофункциональный административно-деловой центр проспект Мира, вл. 127-129
- ЖК «Павелецкая II», Павелецкая наб., вл. 8
- ТЦ «Ашан Пролетарский», Пролетарский пр., 30, Москва
- ЖК «Версис», Нахимовский проспект, 69 (угол улицы Вавилова)
- Клубный дом, ул. Менжинского, вл. 30, стр. 1
fcc-msk.ru
Определение прочности бетона — методы проверки и приборы
Прочность бетона — важнейшая характеристика, которая применяется при проектировании и расчете конструкций для строительства различных сооружений. Она задается маркой М (в кг/см²) или классом В (в МПа) и выражает максимальное давление сжатия, которое выдерживает материал без разрушения.
При определении марочной прочности бетона строительные организации и изготовители конструкций должны руководствоваться требованиями нормативных документов — ГОСТ 22690-88, 28570, 18105-2010, 10180-2012. Они регламентируют методику проведения испытаний, обработку результатов.

Что влияет на прочность?
Затвердевшая в условиях строительной площадки бетонная смесь может давать отличные от лабораторных результаты. Помимо качества цемента и заполнителей на характеристику влияют:
- условия транспортировки;
- способ укладки в опалубку;
- размеры и форма конструкции;
- вид напряженного состояния;
- влажность, температура воздуха на всем протяжении твердения смеси;
- уход за монолитом после заливки.
Качество смеси и ее прочностные характеристики ухудшаются, если при производстве работ совершались грубые нарушения технологии:
- доставка производилась не в миксере;
- время в пути превысило допустимое;
- при заливке смесь не уплотнялась вибраторами или трамбовками;
- при монтаже была слишком низкая или высокая температура, ветер;
- после укладки в опалубку не поддерживались оптимальные условия твердения.
Неправильная транспортировка приводит к схватыванию, расслоению и потере подвижности смеси. Без уплотнения в толще конструкции остаются пузырьки воздуха, которые ухудшают качество монолита.
При температуре 15°-25°С и высокой влажности в первые 7-15 суток бетон достигает прочности 70%. Если условия не выдерживаются, то сроки затягиваются. Опасно как охлаждение смеси, так и ее пересушивание. Зимой опалубку утепляют или прогревают, летом поверхность монолита увлажняют, накрывают пленкой.
Читайте также: Прогрев бетона в зимнее время — способы и технологии
На заводах ЖБИ осуществляют пропаривание или автоклавную обработку конструкций, чтобы уменьшить время набора прочности. Процесс занимает от 8 до 12 часов.
Чтобы определить, насколько характеристики конструкции соответствуют проектным, а также при обследованиях и мониторинге технического состояния зданий проводят проверку прочности бетона. Она включает лабораторные испытания образцов, неразрушающие прямые и косвенные методы исследования объектов.
Факторы, влияющие на погрешность измерений при контроле и оценке прочности бетона:
- неравномерность состава;
- дефекты поверхности;
- влажность материала;
- армирование;
- коррозия, промасливание, карбонизация внешнего слоя;
- неисправности прибора — износ пружины, слабую зарядка аккумуляторной батареи.
Самый информативный способ проверки бетонных конструкций — изъятие образцов из тела монолита с последующим их испытанием. Такой метод сводит к минимуму ошибки, но достаточно дорог и трудоемок. Поэтому чаще пользуются более доступными исследованиями с помощью приборов, измеряющих зависимые от прочности характеристики — твердость, усилие на отрыв или скол, длину волны. Зная их, можно с помощью переходных формул вычислить искомую величину.

Требования к проверке
С точки зрения заказчика наиболее предпочтительно проводить испытания неразрушающими методами контроля фактической прочности бетона. Сегодня созданы приборы, которые позволяют быстро получить результаты без бурения, высверливания или вырубки образца, портящих целостность конструкции.
Для осуществления контроля и оценки прочности бетона рассматривают три показателя:
- точность измерений;
- стоимость оборудования;
- трудоемкость.
Наиболее дорогими являются испытания кернов на лабораторном прессе и отрыв со скалыванием. Исследования по величине ударного импульса, упругого отскока, пластических деформаций или с помощью ультразвука имеют меньшую затратную часть. Но применять их рекомендуется после установления градуировочной зависимости между косвенной характеристикой и фактической прочностью.
Параметры смеси могут существенно отличаться от тех, при которых была построена градуировочная зависимость. Чтобы определить достоверную прочность бетона на сжатие, проводят обязательные испытания кубиков на прессе или определяют усилие на отрыв со скалыванием.
Если пренебречь этой операцией, неизбежны большие погрешности при контроле и оценке прочности бетона. Ошибки могут достигать 15-75 %.
Целесообразно пользоваться косвенными методами при оценке технического состояния конструкции, когда необходимо выявить зоны неоднородности материала. Тогда правила контроля допускают применение неточного относительного показателя.
Как определить прочность бетона?
В производстве материалов и строительстве применяются методы для испытания бетона на прочность:
- разрушающие;
- неразрушающие прямые;
- неразрушающие косвенные.
Они позволяют с той или иной точностью проводить контроль и оценку фактической прочности бетона в лабораториях, на площадках или в уже построенных сооружениях.
Разрушающие методы
Из готовой смонтированной конструкции выпиливают или выбуривают образцы, которые затем разрушают на прессе. После каждого испытания фиксируют значения максимальных сжимающих усилий, выполняют статистическую обработку.
Этот метод, хотя и дает объективные сведения, часто не приемлем из-за дороговизны, трудоемкости и причинения локальных дефектов.
На производстве исследования проводят на сериях образцов, заготовленных с соблюдением требований ГОСТ 10180-2012 из рабочей бетонной смеси. Кубики или цилиндры выдерживают в условиях, максимально приближенным к заводским, затем испытывают на прессе.
Неразрушающие прямые
Неразрушающие методы контроля прочности бетона предполагают испытания материала без повреждений конструкции. Механическое взаимодействие прибора с поверхностью производится:
- при отрыве;
- отрыве со скалыванием;
- скалывании ребра.
При испытаниях методом отрыва на поверхность монолита приклеивают эпоксидным составом стальной диск. Затем специальным устройством (ПОС-50МГ4, ГПНВ-5, ПИВ и другими) отрывают его вместе с фрагментом конструкции. Полученная величина усилия переводится с помощью формул в искомый показатель.
При отрыве со скалыванием прибор крепится не к диску, а в полость бетона. В пробуренные шпуры вкладывают лепестковые анкеры, затем извлекают часть материала, фиксируют разрушающее усилие. Для определения марочной характеристики применяют переводные коэффициенты.
Метод скалывания ребра применим к конструкциям, имеющим внешние углы — балки, перекрытия, колонны. Прибор (ГПНС-4) закрепляют к выступающему сегменту при помощи анкера с дюбелем, плавно нагружают. В момент разрушения фиксируют усилие и глубину скола. Прочность находят по формуле, где учитывается крупность заполнителя.
Внимание! Способ не применяют при толщине защитного слоя менее 20 мм.
Неразрушающие косвенные методы
Уточнение марки материала неразрушающими косвенными методами проводится без внедрения приборов в тело конструкции, установки анкеров или других трудоемких операций. Применяют:
- исследование ультразвуком;
- метод ударного импульса;
- метод упругого отскока;
- пластической деформации.
При ультразвуковом методе определения прочности бетона сравнивают скорость распространения продольных волн в готовой конструкции и эталонном образце. Прибор УГВ-1 устанавливают на ровную поверхность без повреждений. Прозванивают участки согласно программе испытаний.
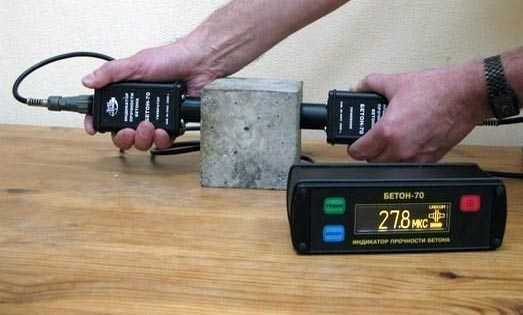
Данные обрабатывают, исключая выпадающие значения. Современные приборы оснащены электронными базами, проводящими первичные расчеты. Погрешность при акустических исследованиях при соблюдении требований ГОСТ 17624-2012 не превышает 5%.
При определении прочности методом ударного импульса используют энергию удара металлического бойка сферической формы о поверхность бетона. Пьезоэлектрическое или магнитострикционное устройство преобразует ее в электрический импульс, амплитуда и время которого функционально связаны с прочностью бетона.
Прибор компактен, прост в применении, выдает результаты в удобном виде — единицах измерения нужной характеристики.
При определении марки бетона методом обратного отскока прибор — склерометр — фиксирует величину обратного движения бойка после удара о поверхность конструкции или прижатой к ней металлической пластины. Таким образом устанавливается твердость материала, связанная с прочностью функциональной зависимостью.
Метод пластических деформаций предполагает измерение на бетоне размеров следа после удара металлическим шариком и сравнение его с эталонным отпечатком. Способ разработан давно. Наиболее часто на практике используется молоток Кашкарова, в корпус которого вставляют сменный стальной стержень с известными характеристиками.
По поверхности конструкции наносят серию ударов. Прочность материала определяется из соотношения полученных диаметров отпечатков на стержне и бетоне.
Заключение
Для контроля и оценки прочности бетона целесообразно пользоваться неразрушающими методами испытаний. Они более доступны и недороги по сравнению с лабораторными исследованиями образцов. Главное условие получения точных значений — построение градуировочной зависимости приборов. Необходимо также устранить факторы, искажающие результаты измерений.
betonpro100.ru
Как правильно забивать кубики бетона?
Перед внедрением в строительство либо после окончания монтажа бетонных конструкций (в редких случаях) бетонный раствор, согласно действующим строительным нормативам, необходимо подвергнуть тщательному контролю качества бетона. Для этих целей осуществляется отбор проб образцов бетона, которые в дальнейшем будут испытаны на прочность и на изгиб при помощи разрушающего метода. Данный метод подразумевает полную деструктуризацию испытуемых образцов и определения на ее основе его прочностных и других технических характеристик.
Проба бетонного раствора – это строго определенный объем испытуемого материала, который был отобран из единственного замеса, либо автоматического смесителя (отбор из нескольких осуществлять не рекомендуется, так как это препятствует точному определению марки и показателей отдельных образцов). Отбор проб образцов смеси раствора осуществляется строго из центральной зоны в замесе либо автобетоносмесителе.
В зависимости от типа бетонного раствора, отбор проб образцов осуществляется в следующих местах:
- при испытании образцов будущей железобетонной конструкции пробы забираются на месте ее формования;
- для испытания товарного раствора образцы берутся на месте загрузки смеси в транспортные емкости;
- при испытании бетона монолитной конструкции образцы берут на месте его заливки.
Независимо от того, какой объем будут иметь готовые для испытания кубики бетона, для их формования требуется брать смесь объемом в 2-2,5 раза больше готового образца. Это дает возможность изготовить несколько контрольных образцов и получить максимально точный результат на основе средних показателей испытаний. Как правило, для контроля качество формуется от 3 до 6 исследуемых образцов.
Как правильно «забивать» кубики бетона? Форма для изготовления опытных образцов бетона может иметь размеры 70х70х70 мм, 100х100х100 мм, 150х150х150 мм . Такая форма предварительно смазывается специальным составом (эмульсией) для последующего легкого изъятия. Форма заполняется бетонным раствором, по мере заполнения производится штыкование железным прутом для распределения плотности наполнителя (щебень, фибра, пр.) После наполнения снимается лишний слой по кромке формы. Через сутки образцы бетона извлекаются из форм и помещаются в место хранения, с температурой +18 ±2°С и относительной влажностью воздуха не менее 95%.
Для испытания на сжатие используется специальный пресс, генерирующий постепенно увеличивающуюся нагрузку. Испытуемый образец устанавливается на плоскую устойчивую платформу, и подвергается повышающемуся сжатию. Процедура происходит до полной потери целостности структуры бетонного кубика, которая, как правило, наступает в течение 20-30 секунд после начала испытания. Полученные данные вносятся в протокол исследования. Таким же образом обследуются остальные образцы бетонного раствора. На основе полученных данных выводится среднее значение прочности бетона из обследуемого замеса и определяется его марка.
Строительная лаборатория Verum предлагает вам квалифицированные услуги лучших профессионалов Украины в области контроля качества строительных материалов. К вашим услугам современная техническая база, укомплектованная новейшим высокоточным оборудованием и гарантирующая получение максимально точных результатов обследования. Заказчикам предоставляются все необходимые консультации касательно повышения качества испытуемого бетонного раствора. Также мы составляем весь перечень требуемой документации в строгом соответствии актуальным строительным нормативам и положениям закона. Заказывайте услуги нашей лаборатории, и лично убедитесь в этом!
verum.org.ua
Кубиковая прочность бетона: способы проверки, показатели прочности.
Содержание статьи:
Основным показателем прочности и способности к деформированию бетона является его устойчивость к осевому сжатию. Остальные характеристики прочности (стойкость к растяжению, местному сжатию и проч.) определяются прочностью бетон именно на осевое сжатие.
Простой способ проверки бетона на прочность
Самым простым способом оценить прочность бетона является помещение под пресс бетонных кубов, изготовленных в таких же условиях, что и конструкции в реальной жизни. Для испытаний берутся кубики с ребром 20 см (эталонный образец), а также большие и меньшие кубы.
Для испытания берутся кубики на 28-й день после затвердевания и испытываются в приближенных к нормальным условиях (температура воздуха 15-20 ℃, влажность воздуха 90-100%). Коэффициент сопротивления давлению и есть кубиковая прочность бетона.
С развитием современных технологий появляются новые методы оценки прочности бетона без физического воздействия. Бетон поддают действию ультразвука, просвечивают проникающими лучами и т. п.
Показатели кубиковой прочности
Лабораторные показатели кубиковой прочности бетона зависят от размера кубов. Так, опытным путем было установлено, что коэффициент прочности обратно пропорционален размеру кубов: чем он больше, тем меньше получается прочность. Прочность кубов с ребром 10 см на 10% выше, чем у эталонных образцов, а с ребром 30 см – на 11-13% ниже.
Такая разница в результатах обуславливается влиянием силы трения, которая возникает между гранями опытного куба и плитами пресса – чем больше грань, тем больше, соответственно, и сила трения. Также многое зависит от структуры бетона.
Важно! Если испытываются образцы размером больше или меньше эталонного, то полученные цифры предела прочности умножаются на соответствующий коэффициент.
Кубиковая прочность бетона, или иными словами предел сжатия, как уже говорилось выше, является предопределяющей характеристикой бетона устойчивости этого материала к другим видам воздействий, таким как и морозоустойчивость, к примеру, которые помогают определить бетон по классу и марке.
Показатели сжатия
Именно сжатию, давлению как правило подвергается бетон в реальных условиях. Показатели прочности при сжатии как правило в 8-20 раз выше, чем при растяжении.
За эталонный образец принято считать куб с длиной ребра 15 см, но вообще испытывают кубы и больше, и меньше. Также испытанию подвергают бетонные цилиндры разной величины.
Видео покажет, как на практике происходит испытание на прочность бетона.
dom-fundament.ru