способы нанесения битумной мастики и цементной смеси Технониколь, ivsil vodostop
Гидроизоляция обмазочная или окрасочная – это самый простой способ восстановления гидрофобности ограждающих конструкций. Густые или жидкие составы, распределяемые по поверхности стен, цоколей, перекрытий, въедаются в их структуру и формируют практически непреодолимый барьер.
К тому же, устройство обмазочной гидроизоляции не вызовет затруднений даже у начинающих строителей или откровенно домашних «мастеров». Процесс очень похож на окрашивание очень густым составом.
И в данной статье мы рассмотрим типовые разновидности обмазочных материалов, делая упор на практику применения таких изоляторов.
Разновидности гидроизоляционных составов
Обмазочная технология предполагает использование составов с высокой плотностью и не менее высокой адгезией.
В итоге, основу обмазочных мембран составляет четыре типа веществ:
- Битумные мастики, которые характеризуются высокой адгезией, заметной гидрофобностью и не самым привлекательным внешним видом.
- Полимерные цементы, с помощью которых можно не только изолировать, но и усилить защищаемую поверхность.
- Вяжущие штукатурки, составляемые на базе гидрофобных безусадочных растворов.
- Полимерные мастики, характеризуемые очень долгим эксплуатационным периодом.
И каждый состав обладает своим набором достоинств и противопоказаний, которые ограничивают сферу применения мастик или штукатурных растворов. В итоге, обмазочная гидроизоляция фундамента не всегда подходит для гидроизоляции стен или перекрытий.
Поэтому далее по тексту мы рассмотрим каждый тип изоляционных составов, разбирая и процесс нанесения мастик или штукатурок, и достоинства и недостатки конкретных гидроизоляторов.
Обмазочная битумная гидроизоляция
Битумные составы используются как для наружного, так и для внутреннего «изолирования». Густая мастика, нанесенная на кирпичную или бетонную стену, защищает и от капиллярной, и от напорной влаги, удерживая давление до 0,2 МПа.
Битумные составы наносятся в несколько слоев с общей толщиной от 2 до 20 миллиметров. Причем на стену или перекрытие наносят только расплавленный битум.
После остывания мастики на защищаемой поверхности образуется эластичная корка без швов. Такое покрытие обеспечивает 100-процентную влагозащиту и не боится температурных деформаций.
Единственный недостаток битумного покрытия – малый срок службы. Незащищенный гидроизоляционный слой «проживет» не более шести лет. Причем основной враг такой гидроизоляции – это низкие температуры. Битумная мастика теряет свою эластичность уже при нуле, растрескиваясь практически до самого основания.
Поэтому такое покрытие, в наши дни, используют как клеящий или грунтовочный состав, наносимый под панели теплоизоляции. Причем пенопластовые или пенополистирольные панели можно наклеить прямо на битум.
Современные разновидности битумных мастик
Классические мастики на основе битума, состав которых регламентирован ГОСТ 30693-2000, не отличаются особой прочностью (особенно в замерзшем состоянии). Поэтому в современных обмазочных составах помимо битума встречается еще и минеральные присадки, полимеры и эпоксидные смолы.
Хороший пример такого состава – обмазочная гидроизоляция Технониколь (мастика). Такой «битум» не растрескается на морозе и проживет намного дольше шестилетнего эксплуатационного периода «классического» изолятора.
Мастики Технониколь наносятся на защищаемые поверхности, как горячим, так и холодным способом (окрашивание). Причем максимальная толщина слоя такой мастики – 1,5 миллиметра. Количество слоев почти не ограничено, а промежуток между нанесением равен 20-24 часам – за это время твердеет нижний слой.
Из фирменных составов бренда Технониколь можно выделить быстротвердеющую мастику №41, с помощью которых защищают канализационные колодцы, кровли и расположенные ниже нулевого уровня участки фундамента. Состав №21, распределяемый по поверхности методом налива, основу которого составляет микс из битума и синтетического каучука, связанный органическим растворителем. Бюджетный состав МБК-Г, в основе которого классический нефтяной битум, который распределяют по поверхности только в горячем состоянии.
Цементная обмазочная гидроизоляция
Гидроизоляционные покрытия на основе цемента отличаются от битумных мастик чуть более чем полностью:
- Во-первых, такие составы наносятся на защищаемую поверхность методом наброса с последующей правкой и выравниванием. То есть, такая гидроизоляция похожа не оштукатуривание, а не на окрашивание.
- Во-вторых, такие покрытия состоят из двух фракций (жидкой эмульсии и сухой смеси), которые «объединяются» только перед нанесением на горизонтальную или вертикальную поверхность.
- В-третьих, максимальная толщина изолирующего слоя, в данном случае – 5 сантиметров, а максимальная нагрузка, которую сможет выдержать такое покрытие рана 5-6 атмосферам.
Поэтому гидроизоляцию на основе цементных смесей и штукатурок практикуют при отделке бассейнов, сборных конструкций из железобетона, подземных тоннелей и прочего. Кроме того, на основе таких составов выполняется обмазочная гидроизоляция под плитку, как в интерьере, так в экстерьере строения.
В основе таких составов находится белый или серый портландцемент, объединяемый с различными минеральными массами неорганического происхождения. Кроме того, в составы вводятся полимеры, акриловые смолы и прочие присадки, улучшающие пластичность готовой мембраны.
К самым распространенным маркам «цементных составов» относятся обмазочная гидроизоляция ivsil vodostop (для бытового применения), Sika (для ремонтных работ в промышленных объемах) и так далее. Причем в открытой продаже можно встретить не только бытовые составы на основе полимеризируемого микроцемента, но и более сложные (и дорогие) изоляторы, на основе органических и неорганических связующих матриц.
Впрочем, существуют и более сильные составы, основанные на полимерных бетонах и рассчитанные на применение в паре с проблемными строительными материалами (пневмобетонами, газобетонами, вспененными батонами).
Ведь, если задействована стандартная гидроизоляционная смесь — из пневмобетона или газобетона гидрофобная поверхность уже не получится. У этих материалов слишком высокая паропроницаемость.
Поэтому в паре с пренвмобетонами «работают» составы с высокой адгезией и хорошей способностью к капиллярному проникновению.
Методика нанесения цементных гидроизоляционных растворов
Технология обмазочной гидроизоляции с помощью растворов на основе цемента похожа на классическое оштукатуривание поверхности.
На практике этот процесс выглядит следующим образом:
- С защищаемого участка удаляют всю грязь, высолы, пыль и следы старых покрытий.
- После этого участок напитывают влагой.
- Пока стена или перекрытие подсыхают можно приготовить раствор, соединив жидкую фракцию (акриловую или полимерную эмульсию) с сухой смесью (минеральным наполнителем).
- Дальнейшие действия зависят от типа технологии нанесения готового раствора на стену. И если состав наносится вручную, то наброс первичного слоя выполняется с помощью шпателя, а последующее выравнивание – с помощь правила. Гидроизоляция штукатурная методом торкретирования (механического наброса) предполагает использование на начальном этапе штукатурной машины, а финишное распределение слоя и его затирка осуществляются вручную. Причем торкретирование позволяет защитить до 1000 квадратных метров поверхности за одну рабочую смену.
По завершению ручного оштукатуривания или торкретирования гидроизолирующий слой оставляют в покое на 24 часа. За это время цементная основа схватывается с основным строительным материалом.
canalizator-pro.ru
Гидроизоляция обмазочная | Про гидроизоляцию.ру
Классическая обмазочная гидроизоляция до сих пор более чем востребована. Для проведения ремонтных работ, для точечной гидроизоляции труб (или восстановления изолирующего слоя) она просто идеальна – достаточно экономична, позволяет проводить работы точечно.
Содержание:
Обмазочная гидроизоляция отличается от других видов защиты помещений от влаги способом использования. При применении этого вида гидроизоляции поверхность, подверженную высокому уровню влажности, просто обмазывают специальным раствором.
Обмазочная изоляция по видам используемых материалов делится на два вида – битумная и штукатурные составы на основе цементно-песочного раствора. Второй вид отличается своей экологичностью, что ставит его на ступень выше первого вида. Такими составами могут обрабатывать даже питьевые резервуары, но в основном, его используют для обработки и защиты от влаги фундаментов. Обмазочная гидроизоляция наносится со стороны противоположной засыпке.
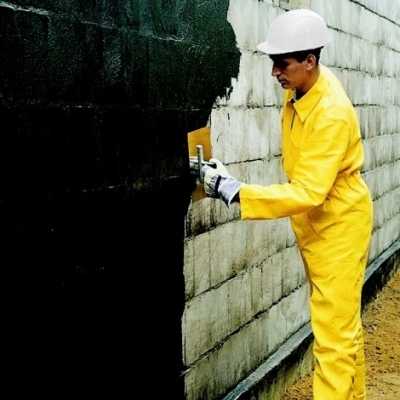
Фото: Нанесение обмазочной гидроизоляции
Из-за того, что срок действия обмазочной гидроизоляции ограничен и составляет всего 10 лет, ее используют в таких местах, где со временем можно будет повторить или восстановить ее функции.
Обмазочная гидроизоляция – это безшовное, влагоотталкивающее сплошное покрытие. Она призвана защитить строение изнутри и снаружи от почвенных вод и испарений.
Обмазочная гидроизоляция применяется в помещениях с повешенной влажностью. Для ее нанесения используются битумные и цементные мастики. Они легко и просто наносятся на любую поверхность.
Видео: Применение обмазочной гидроизоляции
Битумная мастика для создания гидроизоляции является самой популярной и востребованной. Наносится битумная мастика с помощью кисти либо валика. Она хорошо держится на всех видах поверхности и обладает высоким уровнем устойчивости к негативным внешним факторам. Во время производства в состав битумной мастики добавляют разные растворители и наполнители.
Для того чтобы закрепить действие обмазочной гидроизоляции, поверх нее обычно делают цементную стяжку, но эту стяжку обязательно нужно будет укрепить арматурой, так как самодельный цементно-песчаный раствор дает большую усадку. В случае, если выравнивание пола под битумную основу будет проводиться при помощи сухой смеси, то необходимо выбрать такую, которая содержит армирующие волокна.
Видео: Мастика битумная
В состав цементной мастики входит, непосредственно, цемент и дополнительные полимеры. Обычно, цементная гидроизоляция продается в виде сухой смеси, для приготовления которой нужно только добавить воды и перемешать. Цемент служит для укрепления материала на основе. Полимеры в составе цементной мастики отвечают за эластичность материала, а также являются главной водооттлакивающей и непроницаемой для влаги составляющей смеси. Встречается цементная мастика на основе латекса и цемента. После приготовления такой смеси получается материал похожий по консистенции на жидкий пластилин. Любая цементная мастика наносится в два слоя шпателем.
Примерный расход:
- 2,0 кг. на 1 м. кв. при толщине 1,5 мм. — в качестве покрытия
- 2,5 кг. на 1 м. кв. при толщине 2,0 мм. — в качестве покрытия
- 3,5 кг. на 1 м. кв. при толщине 2,5 мм. — в качестве покрытия
* точные характеристики материалов и способы использования уточняйте у производителя
progidroizoljacii.ru
Битумная мастика для гидроизоляции фундамента
Битумная мастика – надежный гидроизоляционный материал, который защитит фундамент от разрушительного воздействия грунтовых вод. С этим материалом легко работать, он недорогой и эффективный.
Что такое битумная мастика
Мастика состоит из нефтяных битумов с добавлением минеральных или полимерных наполнителей, которые улучшают характеристики выходного материала. Также обмазочная гидроизоляция может содержать антисептики, гербициды.
Положительные качества:
- Имеет высокую адгезию (сцепление) с основанием, на которое наноситься.
- Образует сплошное покрытие без швов, что препятствует проникновению воды и влаги.
- Обладает значительными гидрофобными свойствами.
- Не позволяет проникать и распространяться плесени, грибку.
- Устраняет мелкие дефекты фундамента, заполняя трещины, выбоины и даже поры бетона.
- Материал долговечен. Срок эксплуатации составляет больше 30 лет.
- Не изменяет своих свойств, не разрушается при воздействии низких температур.
- Используется независимо от погодных условий.
- Образовавшаяся пленка очень эластичная, она отлично справляется со всеми нагрузками.
- Небольшая стоимость и доступность.
- Несложная технология укладки.
Результат использования обмазочной гидроизоляции:
- Повышается долговечность здания.
- Надежность фундамента.
- Недопущение плесени и грибка в доме.
- Отсутствие повышенной влажности в помещениях.
- Уменьшение стоимости строительных работ.
Разновидности битумной мастики
В зависимости от вяжущего вещества:
- Битумная с минеральными наполнителями, такими как цемент, песок, доломит, минеральная вата и другие. Такое покрытие обладает прочностью и долговечностью. Допускается наносить гидроизоляцию поверх старого покрытия при модернизации фундамента, не проводя демонтажных работ.
- Битумно-резиновая с содержанием каучуковой крошки или дисперсной эмульсии. Предпочтительней используется для изоляции пола, где важно иметь эластичное основание. Также это будет идеальный материал при наличии подземных вод.
- Битумно-полимерная в своем составе имеет полимерные вещества – полиуретан, полистирол. Ее производят без использования органических растворителей, что позволит наносить их на пенополистирол. Также не выделяет вредных токсических веществ. Единственный минус этого покрытия – дороговизна.
- Битумно-эмульсионная (праймер) – представляет собой эмульсию, которая содержит мелкие битумные частицы. Используется для подготовки поверхности для нанесения основной гидроизоляции. Допускается покрывать стены подвалов как самостоятельный материал.
- Чистая битумная мастика без дополнительных вяжущих. Для ее нанесения нужен подогрев до температуры 300°С. Битум выгоден своей небольшой стоимостью. Применяется при больших объемах работ. Очень важно соблюдать правила охраны труда, пожарной безопасности, чтоб избежать травматизма.
Зависимо от способа нанесения:
- Холодный. Это самое простой метод, который применяется в частном строительстве и не требует специальных знаний и сложных технологических процессов. Также делится:
- на водной основе;
- на полиэфирной базе.
- Горячий. Используется редко в особых случаях, когда к фундаменту ставятся значительные требования к прочности и надежности. Использовать материал могут только профессионалы, используя специализированную технику. Материал нагревают до 300°С и покрывают поверхность фундамента. Если вы собираетесь проводить работы самостоятельно, выбирайте другой вариант.
От количества компонентов:
- Однокомпонентные. Сразу после покупки можно приступать к использованию.
- Двухкомпонентные. Требуется смешивать два сырья для получения изоляционного материала. Плюс этого вида – повышенный термин эксплуатации.
Стоимость материала
Она зависит от вида гидроизоляции, используемых компонентов. Цена одного килограмма мастики в среднем составляет:
- «ЮниПром» МБУ с растворителем на основе керосина –16,88 руб/кг;
- «ЮниПром» МБИ с масляным растворителем –18,75 руб/кг;
- «Грида» МЭБИС битумно-полимерная с латексом – 44,25 руб/кг;
- «Грида» МГХ-Г с органическими растворителями – 60 руб/кг;
- «Грида» МГХ-Т битумно-резиновая – 65 руб/кг;
- «Грида» МГХ-К битумно-резиновая с добавлением каучуковой крошки – 75 руб/кг;
- «ТехноНиколь» №33 водоэмульсионная – 100 руб/кг.
Расход мастики
- Чтоб рассчитать необходимое количество материала необходимо рассчитать площадь фундамента, знать с какого материала он изготовлен и в каком состоянии сейчас находится. Сколы, выбоины и небольшие трещины могут увеличить расход изоляции.
- Определитесь какую гидроизоляцию будете использовать, чтоб обеспечить проектируемую водонепроницаемость, твердость, морозостойкость и прочность фундамента.
- Если вы наносите битум, как клей для крепления рулонной гидроизоляции, тогда его расход будет минимальный 0,5-2 кг на 1 кв. м. Здесь будет достаточно 1 мм продукта.
- Как самостоятельное средство нужно наносить не меньше 3 мм в несколько слоев. Расход – 1-4 кг на 1 кв. м.
- Расход горячей мастики немного больше, чем холодной.
- На упаковке от гидроизоляции производитель всегда указывает рекомендуемый расход. Для расчета можете воспользоваться этими цифрами.
- Чтоб уменьшить количество материала подготовьте основание, прогрунтуйте поверхность.
Наносите каждый следующий слой битума после высыхания предыдущего. Это сэкономит вещество для изоляции.
Технология нанесения
Подготовка поверхности фундамента:
- Если на основании имеется много глубоких выбоин, ямок рекомендуется заделать их цементным раствором с мелким наполнителем. Это выровняет поверхность и позволит получить качественный изоляционный слой.
- Удалите острые выступы при помощи болгарки, используя специальную насадку.
- Закруглите углы фундамента (радиус 3-6 см).
- Позаботьтесь, чтоб все линии были плавными, а при переходе с вертикальной плоскости в горизонтальную оборудуйте галтели.
- Тщательно очистите фундамент от пыли, грязи, частичек бетона.
- Просушите основание при помощи строительного фена. Это позволит избежать последующего вздутия или расслоения материала.
Обработка поверхности грунтовкой:
- Нанесите на фундамент специальную грунтовку – праймер. Можете купить готовую смесь или сделать ее самостоятельно смешать битум с каким-либо растворителем в пропорции 1:3, 1:4.
- Обрабатывайте поверхность фундамента праймером при помощи кисточки или валика.
- Тип грунтовки должен соответствовать разновидности гидроизоляции.
- Наносите жидкость в один слой, а на стыках и участках, где находится цементный раствор, промазывайте два раза.
- Дайте грунтовке немного подсохнуть.
Нанесение битумной мастики:
- Обмазочная гидроизоляция должна находиться с внешней стороны фундамента.
- Мастику накладывайте при помощи шпателя, валика, кисти или наливом, параллельными полосами одинаковой толщины.
- Покрывайте фундамент движениями снизу вверх.
- Каждый следующий слой наносите только после полного высыхания предыдущего.
- Требуемая толщина мастики – 3-4 мм, количество слоев 2-4.
- Следите, чтоб в результате получить сплошной, равномерный слой покрытия.
- После завершения обработки фундамента мастикой обсыпьте последний слой грунтом. Это позволит повысить срок службы конструкции.
Армирования обмазочной гидроизоляции:
- Изоляционный слой армируют в участках, где возможное образование трещин или на месте швов.
- Для этого используется стекловолокно.
- Стекловолокно укладывается в первый слой мастики, придавливается при помощи валика или кисточки. После полного высыхания наноситься следующий слой.
- Накладывайте армирующий материал на 10 см больше в обе стороны от проблемного участка.
Блиц-советы
- При нанесении двух слоев толщина каждого должна составлять не больше 1,5 мм, а если предусмотрено 3-4 слоя накладывайте мастику не больше 1 мм.
- Если ваш дом находится в условиях повышенной влажности или с низким размещением грунтовых вод используйте двухкомпонентную битумно-полимерную мастику. Смешивать ингредиенты следует минимум 5 минут при помощи строительного миксера. Сразу после приготовления наносите средство. Его нужно использовать на протяжении 30 минут.
- Наносить мастику можно при помощи распылителя. Следите, чтобы давление в аппарате не превышало 150 бар.
- Мастика полностью застывает за 5-6 часов, зависимо от толщины слоя.
- На горизонтальных поверхностях расход мастики намного больше.
Понравилась статья? Поделиться с друзьями:
orcmaster.com
Растворы, бетоны, битумы, мастики
Растворы, используемые при сооружении любого здания, состоят из смеси связующего (цемента, глины, извести, гипса и т.д.), песка и воды.
Прочность раствора определяется его маркой, т.е. способностью выдерживать определенную нагрузку на сжатие, измеряемую в килограммах на квадратный сантиметр. Чтобы получить раствор одинакового состава, все входящие в него компоненты отмеривают определенными дозами. Различают тошие, нормальные и жирные растворы. В тощем много заполнителя, он неудобен в работе и не отличается надлежащей прочностью. Нормальный раствор содержит в достатке вяжущее вещество и заполнитель, в жирном же — избыток вяжущего, поэтому он трескается.
Жирность определяют в основном в глиняных и известковых растворах с помощью весла, которым его перемешивают. Если раствор не прилипает к веслу, а только пачкает его, — он тощий; если же прилипает отдельными сгустками — нормальный; когда раствор сильно обволакивает весло — он жирный.
В тощий раствор добавляют вяжущие вещества, в жирный — заполнитель.
Все материалы, используемые для приготовления раствора, предварительно просеивают на сите. При подготовке раствора для штукатурных работ используют сито с ячейками 5×5 мм, для каменных работ — с ячейками 10×10 мм.
Из глины или известкового теста раствор готовят сразу, а из цемента сначала готовят сухую смесь, а затем раствор. Составлять смесь можно в ящике, но лучше на бойке — деревянном щите размером 2×3 м.
Плохо перемешанный раствор неоднороден, и там, где он слабее, может начаться разрушение конструкций. Точное дозирование материалов обязательно. Сухие смеси, например, цемент с песком, лучше всего в виде грядки насыпать слоями, которые доводят до общей высоты 200-300 мм. Грядку перелопачивают лопатами несколько раз до однородности, а затем смесь просеивают через частое сито с ячейками не менее 3×3 мм.
Примечание: Составы растворов даны в объемных единицах.
Для приготовления раствора смесь и воду также отмеряют дозами и тщательно перемешивают.
Более жидкий раствор после высыхания менее прочный, чем густой раствор такого же состава.
Материалы и растворы для фундаментов и цоколей, находящихся в различных условиях эксплуатации, приведены в таблицах.
Для устройства фундаментов чаше всего применяют бутобетон. Заполнителем обычно служит камень из карьеров, крупный гравий, щебень, кирпичный бой и т. п.
Заполнитель укладывают слоями толщиной по 20— 25 см враспор по стенкам. Каждый слой поливают раствором и плотно трамбуют.
Цементно-известковый раствор готовят из цемента, известкового теста и песка. Известковое тесто разводят водой до густоты молока и процеживают на чистом сите. Из цемента и песка готовят сухую смесь, затворяют ее на известковом молоке и тщательно перемешивают. Добавление известкового молока повышает пластичность раствора.
Вместо известкового теста можно применять глиняное, которое берут в таком же количестве.
Составы (в объемных частях) и марки цементно-известковых и цементно-глиняных растворов приведены в таблицах.
И те, и другие растворы применяют как для кладки надземных стен, так и фундаментов в сухих грунтах.
Если подземная кладка ведется в маловлажном грунте, то на 1 м3 песка в цементно-известковых растворах берут не менее 75 кг цемента, в цементно-глиняных -100 кг; в очень влажных и насыщенных водой фунтах — 100 и 125кг.
Цементные растворы приготовляют в такой последовательности. Из цемента и песка предварительно готовят сухую смесь, причем на 1 часть цемента можно брать от 2,5 до 6 частей песка (в зависимости от марки цемента). Сухую смесь затворяют водой, перемешивают и употребляют в дело в течение 1 — 1,5 ч. Цементные растворы чаше всего используют для кладки фундаментов и других конструкций, которые находятся ниже уровня фунтовых вод. На этих же растворах можно класть и стены.
Они довольно прочные, но очень холодные. В зависимости от марки вяжущего материала и количества заполнителя, взятых в объемных частях, получают цементный раствор той или иной марки.
Потребность цемента определяют в зависимости от его марки и марки приготовляемого раствора.
Бетон состоит из смеси цемента, заполнителей разной крупности и воды.
Песок, гравий, используемые в бетоне, должны быть чистыми, так как загрязнения снижают его прочность. При необходимости материалы хорошо промывают.
Цемент применяют той марки, которая позволяет получить бетон нужной прочности. Вода тоже должна быть чистой.
Бетонная масса может быть разной консистенции — густоты. Жесткая (как бы влажная земля) при укладке требует сильного уплотнения; пластичная (относительно густая и более подвижная) нуждается в меньшем уплотнении; литая — это подвижная масса, почти самотеком заполняющая форму.
Консистенция бетонной массы зависит от количества воды, при избытке которой она расслаивается, а прочность бетона снижается. Если одновременно добавлять воду и цемент, не меняя соотношений между ними, то прочность бетона остается без изменения. Чем гуще масса и чем сильнее она уплотняется (трамбуется), тем выше прочность бетона, и наоборот.
Бетон прекрасно работает на сжатие, но имеет довольно низкую прочность на растяжение, вследствие чего может и ломаться. Для повышения прочности бетона его армируют металлическими стержнями. Прочность железобетона значительно выше, чему способствует близость коэффициента температурного расширения бетона и арматурных стержней и прочное их сцепление, обеспечивающее совместную работу как единого целого.
От правильной укладки арматурных стержней зависит несущая способность железобетона. В консольных конструкциях, защемленных с одной стороны, арматуру следует укладывать в верхней части бетонной массы. В конструкциях, защемленных с обеих сторон, арматурные стержни укладывают в нижних слоях. В наиболее ответственных конструкциях стальные стержни распределяют равномерно по всей массе бетона, сваривая (связывая) их в каркас. Но в любом случае арматура должна находиться в толще бетона, приближаясь к краям на расстояние не менее 5 см. При правильном соотношении вяжуших, заполнителей и арматуры получается мощная конструкция, способная выдержать очень большие нагрузки.
Желательно готовить и укладывать более густую массу с осадкой конуса 2-6 см. Однако уложить и хорошо уплотнить ее можно только в крупных конструкциях с редко расположенной арматурой. Чем тоньше конструкция и чем чаще расположена в ней арматура, тем пластичнее должна быть бетонная масса.
Нормы предусматривают следующую консистенцию бетонной массы с осадкой конуса в сантиметрах:
подготовка под фундаменты и полы — 2-3 см;
массивные конструкции без арматуры (фундаменты, стены) или с редко расположенной арматурой — 3-6 см;
обычные железобетонные конструкции (балки, колонны, плиты) с арматурой средней густоты — 8—12см;
тонкие стены, колонны и балки малых сечений, а также конструкции с густой арматурой— 12-14см.
Консистенцию бетонной массы измеряют специальным металлическим конусом с очень гладкой внутренней поверхностью (без швов). Высота конуса — 305 мм, ширина в нижнем основании — 203 мм, в верхнем — 102 мм. Сбоку конус имеет две ручки, внизу его укрепляют два упора в виде лапок или скоб, на которые надо встать ногами, прижимая конус к горизонтальной площадке (широкая доска, фанера, лист стали или пластмассы). Для проверки готовят бетонную массу, смачивают площадку водой, ставят на нее конус, прижимают ногами, наполняют его в три слоя по 10см бетонной массой, каждый слой протыкают 25 раз стержнем-штыком из круглой стали диаметром 15 мм. Такое уплотнение называется штыкованием. Наполнив конус, излишнюю бетонную массу срезают вровень с краями. После этого конус за ручки медленно поднимают вертикально. Освобожденная из него бетонная масса начинает медленно оседать, меняя свою форму. Как только бетонная масса прекратит оседать, рядом с ней ставят конус, кладут на его верхнее основание рейку и измеряют расстояние от нее до осевшей массы линейкой с сантиметровыми делениями. Чем жиже консистенция бетонной массы, тем больше она оседает, и наоборот.
Конус для определения бетонной массы
Примерная осадка бетонной массы: жесткой — от О до 2см, пластичной— от 6 до 14см, литой— от 17 до 22см. Бетонная масса не должна выделять воду и расслаиваться.
При подборе заполнителей надо стремиться к тому, чтобы гравий, щебень и песок имели зерна различной крупности. В этом случае между зернами почти не будет
пустот. Принято считать, что объем пустот в песке не должен превышать 37%, в гравии — 45, а в щебне — 50%. Чем меньше пустот в крупном заполнителе (гравии или щебне), тем меньше потребуется песка и сократится расход цемента.
Проверить пустотность в заполнителе можно довольно простым способом. Подобранную смесь или отдельно гравий, щебень, песок насыпают в 10-литровое ведро. Не уплотняя, сравнивают с краями, отмеривают воду и заливают ее тонкой струей в ведро до краев. По объему влитой воды определяют пустотность: если ее влито, например, 4,5л, то пустотность— 45%.
Состав заполнителя подбирают с помощью стандартных сит. Гравий или щебень просеивают через сито с ячейками диаметром 80, 40, 20,10 и 5 мм; песок — 5; 2,5; 0,5; 0,3 и 0,15 мм. Зерна, остающиеся на каждом из сит, называются фракцией заполнителя.
Рассмотрим два способа подбора заполнителя.
1. Наибольшая крупность заполнителя— 40мм. Просеивают гравий или щебень через сито с ячейками диаметром 40 мм. Остаток заполнителя на сите называется верхним остатком. Затем то, что прошло через сито 40мм, просеивают через сито 20мм. Остаток заполнителя на этом сите называется первой фракцией с зернами крупностью от 21 до 40мм. То, что прошло через сито 20мм и осталось на сите 10мм, является второй фракцией с зернами крупностью от 11 до 20 мм. То, что прошло через сито 10мм, просеивают через сито 5мм, остаток дает третью фракцию с зернами крупностью от 6 до 10 мм. То, что прошло сквозь сито 5 мм, называют нижним остатком.
Для приготовления крупнозернистой смеси часто берут по 5% верхнего и нижнего остатка и по 30% первой, второй и третьей фракций. Верхний остаток можно заменить первой фракцией в количестве 5%.
Крупнозернистую смесь такого состава можно приготовить из двух фракций: 50—65% — первой, 35-50% -третьей или из трех: 40-45%— первой фракции, 20-30% — второй и 25-30% — третьей.
2. Наибольшая крупность заполнителя— 20мм. Просевая заполнитель через сито 20 мм, а то, что прошло через него, — через сито 10мм, получают первую фракцию с крупностью зерен от 11 до 20 мм. Затем то, что прошло через сито 10 мм, просеивают через сито 5 мм и получают вторую фракцию с зернами крупностью от 6 до 10 мм. Наконец, то, что прошло через сито 5 мм, просеивают через сито 3 мм и получают третью фракцию с зернами от 4 до 5 мм. Песок сначала просеивают через сито 2,5 мм, а то, что прошло через него, — через сито 1,2 мм и получают первую фракцию. То, что прошло через сито 1,2мм, просеивают через сито 0,3мм и получают вторую фракцию. Для приготовления песчаной смеси берут 50% первой фракции, 50-80% — второй.
Таким образом подбирают зерновой состав гравия или щебня и песка. Отмерив нужное количество заполнителя разных фракций, их необходимо хорошо между собой перемешать, чтобы зерна равномерно распределились по всей своей массе.
Размеры крупного заполнителя должны быть не более 1/4-1/5 наименьшего размера конструкции детали. Для тонких плит наибольшая крупность заполнителя может достигать 1/3 и даже 1/2 толщины плиты. Для железобетонных конструкций с густой арматурой наибольшая крупность зерен должна быть не более 40, а иногда и 20мм. Размер зерен заполнителя не должен быть больше 3/4 расстояния между стержнями или прутьями арматуры.
Цемент надо применять такой марки, которая превышала бы заданную марку бетона в 2-3 раза (для портландцемента — в 2 раза, для других — в 3 раза).
Например, для бетона марки 160кгс/см2 следует применять цемент марки не менее 400 кгс/см2.
Избыток цемента в бетоне приводит к перерасходу последнего, а недостаток уменьшает его плотность, водопроницаемость, морозостойкость, приводит к ржавлению уложенной арматуры.
При приготовлении бетонной массы смесь заметно уменьшается в объеме. Из 1 м3 сухой смеси получается от 0,59 до 0,71м3 бетонной массы. Поэтому для приготовления 1 м3 бетонной массы следует брать гораздо больше сухих материалов. Например, для одного состава бетона требуется 0,445м3 песка, 0,87 гравия, 0,193м3 цемента (250 кг), 179 л воды; для другого — 0,395 м3 песка, 0,880 гравия, 0,198м3 цемента (260кг), 185л воды; для третьего — 0,445 м3 песка, 0,880 гравия, 0,204 м3 цемента (265 кг), 189л воды.
Таким образом, умелый подбор зернового состава заполнителя позволяет получить бетон одной и той же марки, но с разным содержанием цемента. Составы обычных бетонов приведены в таблицах 8-9. В последней из них не указывается количество воды, его подбирают в зависимости от требуемой консистенции бетонной массы.
Подобрав крупные заполнители, их отмеривают объемными частями и перемешивают. Соответствующий песок также отмеривают в нужном количестве и засыпают на боек (деревянный щит) ровным слоем в виде грядки. На грядку насыпают цемент, и все тщательно перемешивают (гарцуют) до получения однородной смеси. Затем цементно-песчаную смесь гарцуют с гравием или щебнем до полной однородности сперва в сухом виде, затем постепенно поливают из лейки отмеренной водой и многократно перелопачивают до получения совершенно однородной по составу и густоте бетонной массы, которую тут же используют в дело (не позднее часа, считая с минуты затворения водой).
Цементогрунт приготовляют из цемента, фунта и воды. Используют при строительстве монолитных и сборных фундаментов, стен, полов-тротуаров, оснований для дорог и облицовки траншей.
Берут цемент марки не ниже 300 или 400; грунт -лесс, лёссовидные супеси и суглинки, т. е. грунты, богатые соединениями кальция. Чем больше кальция в грунте, тем выше прочность цементогрунта. На 1 м3 жесткого грунта требуется в среднем от 120 до 180 кг цемента марки не ниже 300.
При тщательном смешивании и уплотнении получается материал, близкий к низким маркам бетона, а по стоимости он в 3—4 раза дешевле бетона или бутовой кладки. При расходе цемента от 250 до 300 кг на 1 м готовых изделий марка цементогрунта после пропаривания достигает прочности 100-200 кг/см2.
Цементогрунт морозостоек и водостоек; чем сильнее он утрамбован, тем выше его марка, которая к тому же возрастает со временем. Уплотнять цементогрунт следует тяжелой трамбовкой, отчего он уменьшается в тол-шине в 1,5—1,6 раза.
Насыпать смесь рекомендуется слоями по 20 см. В состав смеси может входить 60% суглинка, 40 — песка и 17% воды (к весу грунта), но бывают и другие соотношения частей.
Влажность готовой смеси определяется довольно просто: она считается нормальной, если при сжатии в руке не рассыпается и не оставляет следов на ладони. При недостатке воды смесь рассыпается, а при избытке прилипает к рукам.
Вынутый грунт может состоять из крупных и мелких комков. Его нужно размельчить и просеять через сито с отверстиями 3 и 5 мм. Из грунта делают смесь, к 1 м3 которой добавляют от 120 до 180кг цемента. Все это сначала перемешивают до однородного состояния, затем добавляют воды (270—320), еще раз все тщательно перемешивают, укладывают и трамбуют.
Для получения более прочного цементогрунта поступают так. Грунт сушат, хорошо измельчают, просеивают несколько раз через сито, т. е. делят его на разные фракции. Из этих фракций составляют смесь, которую берут в определенных процентах: фракции крупностью 0,25— 2 мм — 25-35%; фракции 0,25-0,05 мм — 20-30; фракции 0,05-0,005 мм — 20-40 и фракции менее 0,005 мм — 5-10%.
Фундаменты и стены из цементогрунта необходимо выдержать в течение 15-20 дней, поливая их водой по 3-5 раз в день. За это время цементогрунт наберет определенную прочность.
При нормальных условиях твердения цементогрунт, содержащий в 1 м3 120 кг цемента, через 7 дней достигает прочности 16 кг/см2, через 28 дней — 20 кг/см2.
Когда цемента содержится 180кг, то прочность цементогрунта повышается от 25 до 70%.
Мастики применяют для наклеивания рулонных материалов на различные поверхности и склеивания полос рулонных материалов при многослойных покрытиях. Используют и как обмазочные материалы, а также как защитные покрытия.
Различают битумные и дегтевые мастики. Битумные применяют для наклеивания пергамина и рубероида, дегтевые — толя и толя-кожи. Мастики могут быть также горячими и холодными разных марок: битумные кровельные горячие — МБК-Г-55, МБК-Г-65, МБК-Г-75, МБК-Г-85и МБК-Г-100; дегтевые- МДК-Г-50, МДК.-Г-60 и МДК-Г-70. Цифры указывают температуру плавления.
Готовят мастики из вяжущих (битума, дегтя, песка) и сухих наполнителей: торфяной крошки, мела, мелкого асбеста № 6 или № 7, молотого шлака или известняка древесной муки, просеянных через частое сито. Наполнители Снижают хрупкость мастики при низких температурах, повышают ее теплостойкость, уменьшают расход битума при пониженных температурах. Лучше всего применять волокнистые наполнители — асбест и древесную муку.
Для пожарной безопасности котел или бак, в котором готовится мастика, рекомендуется обмуровать кирпичом и укрепить над ними тяжелую плотно закрывающуюся крышку,
Посторонние примеси с расплавленного битума снимают сеткой, натянутой на проволоку, или консервной банкой с пробитыми в дне отверстиями и укрепленной на длинной ручке.
Для быстроты плавления битум и пек рекомендуется закладывать в бак мелкими кусками.
Приготовление битумной горячей мастики. Для приготовления 10 кг мастики требуется 8,5 кг битума нефтяного Н-70/30 (марки 4) и 1,5—1,7 кг наполнителя. Загруженный в посуду на 3/4 ее объема битум нагревают до плавления. Когда он начнет пениться, с его поверхности снимают всплывшие примеси. Нагревать битум надо до тех пор, пока он не перестанет пениться и не станет обезвоженным. Залив огонь водой, в битум добавляют сухой наполнитель и тщательно все перемешивают. Готовить мастику следует за 2-3 ч до начала работы и применять только в горячем состоянии.
Приготовление холодной мастики. Для приготовления 10кг мастики необходимо; 5кг битума БН-90/10 (марки 5), 3 кг зеленого масла или точно такое же количество керосина и 2 кг мелкого наполнителя (лучше асбеста № 6 или № 7). Готовят мастику следующим образом. В посуду загружают битум, плавят его, пока он не перестанет пениться, снимают посторонние примеси, заливают огонь водой и при постоянном помешивании вливают в битум небольшими порциями зеленое масло или керосин, а затем (также небольшими порциями) -наполнитель. Все это тщательно перемешивают. Приготовленную мастику сливают в герметически закрываемую посуду.
Приготовление дегтевой мастики. Для приготовления 10кг мастики необходимо: 5кг каменноугольного дегтя, 3 — каменноугольного песка и 2 кг наполнителя. В посуду загружают деготь, нагревают его и добавляют туда небольшими порциями каменноугольный пек. Все это плавят и перемешивают до тех пор, пока не прекратится вспенивание. Снимают всплывшие посторонние примеси, гасят огонь, добавляют небольшими порциями наполнитель, тщательно все перемешивая. Дегтевую мастику применяют только в горячем виде.
Грунтовки — это жидкие растворы битума нефтяного БН-50/50 и БН-70/30 (марки 3 или 4) или каменноугольного пека с температурой размягчения 70—90°С. Используют в основном для грунтовки цементных оснований перед наклейкой на них рулонного материала. Грунтовки более жидкие, чем мастики, легче проникают во все поры и шероховатости и тем самым прочнее сцепляются с основанием.
Грунтовать можно и деревянные основания, но при следующих условиях: если настил выполнен из сухих шпунтованных досок шириной не более 150мм или при двойном настиле, когда верхний из них выполнен из сухих реек шириной 53-70 мм. Конечно, все выступы на настиле должны быть застроганы.
В остальных случаях нижний слой рулонного ковра должен пришиваться к основанию толевыми гвоздями с широкими шляпками.
Различают два вида грунтовок: битумная — для битумной мастики, пековая — для дегтевой. Материалы для приготовления грунтовок берут в процентах по массе. Например:
Битум — 40%, соляровое либо зеленое масло (или керосин) — 60%.
Битум — 30%, бензин (или бензол) — 70%.
Пек каменноугольный — 30%, бензол — 70%.
Применяют грунтовки холодными. Готовят их так. Предварительно плавят вяжущее вещество (битум или пек), вливают его в герметически закрываемый сосуд. Порциями сначала по 2—Зл, затем по 5 л добавляют растворитель, постоянно все перемешивая.
Сушка грунтовок на отвердевших цементных стяжках — не более 10 ч, на свежеуложенных стяжках— от 12 до 48 ч.
Грунтоасфальт применяют для покрытия полов вспомогательных помещений, дорог невысокого класса и отмосток вокруг дома. Готовят из 8-12% битума БН-70/30 или БН-90/10 (марки 4 или 5) и 88-92% суглинка. Части берут в весовом соотношении. Суглинок хорошо размельчают, просеивают на сите с ячейками не более 5×5 мм и хорошо просушивают на солнце. Битум плавят и добавляют в него суглинок небольшими порциями при тщательном перемешивании. Применяют в горячем виде, разравнивают деревянным валиком (куском остроганной доски). Основание под грунтоасфальт может быть из песка, щебня, уплотненного грунта, бетона и т.д.
house.aggress.ru
Битум для фундамента: технология нанесения достоинства недостатки
Гидроизоляция дома – гарантия его долговечности, прочности и надежности. Применяя битум для фундамента, можно оградить постройку от вредного воздействия влаги и расшатывания основы. Хорошо заизолированная конструкция здания продлевает срок его эксплуатации. Битумная мастика наносится просто и доступна в финансовом плане.
Какие бывают виды битума
В качестве исходных материалов при изготовлении мастики для фундамента используются песок, цемент, минеральная вата, разбавленные нефтяным битумом. По разновидности связывающих компонентов их делят на:
- битумные в чистом виде;
- резинобитумные;
- битумно-полимерные.
Битум без добавок – самый экономичный вариант из всех видов, но не такой прочный и долговечный. Резинобитумные мастики – более дорогие, обладают отличными гидроизолирующими свойствами. Битумно-полимерные – требуют больше денежных средств, компенсируя затраты такими характеристиками как надежность, долговечность, влагоустойчивость.
По методу нанесения битум для гидроизоляции подразделяется на два вида:
- холодный;
- горячий.
Благодаря бесшовному покрытию подземной конструкции доступ влаги к ней не способствует разрушению фундамента, и воздействие на него оказывает минимальное. Легкость материала в работе позволяет выполнять гидроизоляцию своими руками, избавляя от необходимости расходовать дополнительные денежные средства на оплату труда наемных рабочих.
Вернуться к содержанию
Холодная мастика
Чаще всего используется при проведении строительных работ. Главное ее достоинство – это отсутствие необходимости применять специальные технические средства или иметь определенные навыки в данной отрасли.
Виды по составу | Диапазон рабочих температур, градусы | Особенности |
---|---|---|
Водная мастика | -10 — +40 | Сразу готова к употреблению. |
Битумная с полиэфирной основой | -15 — +40 | Дополнительно выполняет роль клея между подошвой фундамента и рулонных гидроизоляционных материалов. |
Битумно-полимерная | -40 и выше | Сохраняет полезные технические характеристики даже под влиянием низких температур. |
Для гидроизоляции фундамента в умеренных климатических условиях обычно применяют мастику на водной основе или полиэфирной. Для северных широт больше подойдет битумная группа с наличием полимерных компонентов, которую можно использовать даже при минусовых температурах. При этом качество гарантируют и зарубежные производители, и отечественные. Холодная мастика в зависимости от количества ингредиентов, входящих в ее состав бывает:
- однокомпонентная;
- двухкомпонентная.
Однокомпонентную мастику можно использовать сразу после предварительного размешивания. Но зато у нее рабочее время дольше, чем у другой группы. После окончания одного из этапов работ достаточно просто закрыть емкость с битумом до следующего момента применения.
С двухкомпонентным материалом дело обстоит сложнее. Он требует досконального перемешивания и мгновенного нанесения на рабочую поверхность, потому что застывает практически сразу. Среди достоинств материала – длительный срок хранения и прочность.
Вернуться к содержанию
Горячая разновидность битума
Гидроизоляция фундамента горячим битумом применяется в исключительных случаях, когда нужно придать основанию максимальную прочность. Сложность работы с горячим продуктом состоит в необходимости предварительного разогрева до 300 градусов. Этот процесс требует привлечения профессиональных рабочих и использования особенной техники.
При этом важно соблюдать технику безопасности и не игнорировать правила. Если опыта обращения с горячим битумом не имеется, а инструментарий тоже отсутствует, обращайтесь к специалистам или выбирайте вариант холодной мастики.
Вернуться к содержанию
Плюсы и минусы использования для фундамента
Используя битумную мастику для гидроизоляции фундамента, стоит ознакомиться с ее отличительными свойствами и их роли в процессе построения здания.
Достоинства | Недостатки |
---|---|
|
|
Благодаря исключительным свойствам битума по всей площади фундамента создается надежная и не пропускающая воду пленка. Она не только закупоривает трещины, заполняет поры, но и предотвращает появление грибкового налета, а также плесени на поверхности. Хорошая адгезия свидетельствует о готовности взаимодействовать с любым материалом основания под монолитными стенами.
Благополучно переносит перепады температур – выдерживает колебания в диапазоне от -70 градусов до +1200. Это позволяет проводить строительные работы с использованием битумной мастики в любое время года. После окончательного высыхания она обволакивает фундамент мембраной, выдерживающей значительные механические воздействия извне благодаря прочности и эластичности.
Проявляет устойчивость к агрессивной химической среде и в то же время отличается не токсичностью технологии нанесения и легкостью процесса монтажа. Для этого не нужно обладать специальными навыками или иметь в наличии дополнительное оборудование – исключение составляет лишь использование горячего битума на полимерной основе. Цена при этом остается приемлемой.
Битумная мастика удобна в транспортировке, а работать с ней можно быстро, так как существуют готовые смеси, которые не нужно разводить и перемешивать. Покрытие не вздувается, не растрескивается под влиянием воды.
В период работы с большими площадями покрытия возрастает трудоемкость процесса. Необходимо потратить время на полимеризацию слоя, но это не столь существенные недостатки по сравнению с имеющейся массой преимуществ.
Вернуться к содержанию
Как правильно наносить битум
Процесс обработки основы битумной мастикой не слишком сложен, но у него есть некоторые нюансы, которые необходимо учитывать – определенные расчеты и соблюдение последовательности действий.
Для того, чтобы определить расход битума на 1 м2, нужно предварительно определиться с его предназначением. От этого зависит количество материала, необходимого для строительных работ. При вычислении расхода состава на гидроизоляцию следует площадь обрабатываемой поверхности умножить на два – именно столько килограмм битума понадобится для 1 м2.
Если битум используется как обмазка, расход его на 1 м2 составит 2-3 кг при толщине покрытия 2-3 см. Следует учитывать и расположение основы – при нанесении состава на вертикальную поверхность расход будет в 2-3 раза выше по сравнению с горизонтальной плоскостью.
Планируя выполнить работу своими руками, стоит ознакомиться с техническими требованиями, а также правилами, которые помогут выполнить гидроизоляцию качественно. Делятся они на основные этапы:
- подготовительные работы;
- грунтование поверхности;
- нанесение материала.
Битумный состав сразу готов к использованию, поэтому не придется тратить время на его растворение и размешивание. Годится он исключительно для наружных работ!
Пошаговая инструкция по нанесению:
- Одевается специальная одежда из плотной ткани, строительные очки для защиты от едких испарений.
- Если в работе используется горячая мастика для фундамента, рекомендуется надеть респиратор – открытых участков на теле быть не должно, даже когда на улице слишком жарко.
- Проводится осмотр фундамента на предмет обнаружения трещин или ямочных впадин – в случае их наличия замешивается цементный раствор для заделки имеющихся дефектов.
- С помощью болгарки удаляются острые выступы на гранях основы, углы закругляются.
- Поверхность очищается от пыли и грязи, затем обезжиривается, просушивается при помощи строительного фена, чтобы предотвратить вздутие и отслоение.
- Проверяется степень влажности – кусок полиэтиленовой пленки укладывается на основание, оставляется в одном положении на сутки. Если конденсат под ним не появляется – готовность покрытия к дальнейшей работе подтверждается.
- После того, как рабочая поверхность окончательно подсохнет, проводится обработка грунтовым составом.
- Перед применением материал перемешивается или встряхивается в закрытой емкости до полной однородности материала.
- Наносится грунтовка одним слоем с помощью валика, кисти или специального пульверизатора при сухих погодных условиях и в отдалении от источников огня.
- Когда грунтовой состав высохнет полностью, можно приступать к раскатке гидроизолятора сплошным слоем, чтобы не было разрывов. Для этого используется валик или грубая щетка, можно применять и метод налива.
- Каждый из последующих слоев накладывается после просушки предыдущего – долгие перерывы тут не нужны.
- В местах возможного появления трещин гидроизоляция армируется стеклотканью.
- По окончании работы проводится осмотр инструментов, их очистка с использованием мыла и воды или растворителя.
Период высыхания может колебаться в зависимости от сезонности, влажности воздуха или оттого, какова толщина изолятора. В нормальных условиях высыхание происходит в течение суток. Грамотно сделанная гидроизоляция основания будет оберегать здание от протечки и распространения грибка или плесени. От этого зависит также и долговечность дома.
Ознакомившись с классификацией битумной мастики, ее достоинствами и недостатками, технологией нанесения, можно смело начинать процесс гидроизоляции здания своими руками. Возможность самостоятельно осуществить расчет необходимого материала поможет избежать лишних затрат. Удачного строительства!
Не нашли ответов в статье? Больше информации по теме:
dachaorg.ru
Битумная мастика для гидроизоляции фундамента
«…Хотя в мире нет предмета, который был бы слабее и нежнее воды, но она может разрушить самый твердый предмет.» (Лао-Цзы)
Почему нужна гидроизоляция фундамента?
Гидроизоляция фундамента предназначена для предотвращения коррозии бетона. В бетонных конструкциях корродирует материал бетона и стальная арматура, обеспечивающая прочность на изгиб. Чаще всего разрушается цемент, малостойкие наполнители – щебень, бут, технологические добавки в бетон и т. п. Начинается массовая коррозия с поверхности и в зонах трещин, капилляров, воздушных включений, оставшихся при недостаточном или неправильном уплотнении бетона. Вода растворяет гидраты оксидов кальция, сульфиды и т. п. составные части цементного камня и выносит их из фундамента. Плотность бетона уменьшается по прогрессивному закону. Вода, содержащая соли, ускоряет процесс в несколько раз.
Борьба с коррозией:
- применение материалов высокой стойкости – цементов, арматуры, наполнителей;
- уменьшение пустот – трамбовка, виброуплотнение, послойная укладка;
- добавки в бетон – пластификаторы, водоотталкиватели, полимерные пропитки и пр;
- разные способы гидроизоляции бетонных фундаментов.
В 90-х годах в низинке одного из дачных участков на двух фундаментных блоках типа ФБС заводского изготовления была установлена бытовка строителей. В 2013 г. эти блоки выглядят так.
Виды битумных мастик для гидроизоляции и их цена
Мастики, в т. ч. и битумные, относятся к бесшовным материалам. При их нанесении образуется сплошной слой гидроизоляционного материала. Его может разрушить только внешнее механическое воздействие, например, строительный мусор, которым засыпается фундамент, возведенный в котловане.
В состав битумных мастик для гидроизоляции фундамента основным компонентом входит битум. В дополнение к битуму идут тонкоразмолотые наполнители, модификаторы, растворители и т. п.
Готовая к нанесению мастика имеет жидкую или сметанообразную консистенцию однородного состава. После затвердевания образует плотное, герметичное покрытие.
При снижении температуры ниже минус 18 – 20 град. С – мастики могут иметь повышенную хрупкость.
Для понижения хрупкости в состав битумных мастик добавляют компоненты, не дающие растрескиваться битуму: латексы, минеральные масла, эластомерные композиции и пр. Как наполнители применяют мел, известь, минеральную вату, фиброванные (измельченные до длины 10 – 40 мм) волоконные материалы, молотый кварц, золу электростанций, асбест и пр. Их используют для повышения механических свойств: износостойкости, твердости, уменьшения растрескиваемости и уменьшения расхода основного вещества.
Гидроизоляционные битумные мастики бывают:
А. Битумные.
- Горячего применения – разогреваются при перемешивании до температуры + 130 град. С – гудрокамовые и дегтевые и до 180 – битумные и битумно-резиновые. Разогрев идет в специальных нагревательных устройствах с механическими или ручными мешалками. Источником тепла может быть электроэнергия, дрова или жидкое топливо. При разогреве обязательно соблюдение правил пожарной безопасности.
Работать с горячими мастиками необходимо в защитной одежде и обуви.
- Холодного применения – полностью готовый состав. Продаются в ведрах, наносятся на защищаемую поверхность кистью или валиком. После высыхания (испарения растворителя) покрытие готово. Для увеличения стойкости увеличивают толщину и вводят армирование сеткой с мелкими ячейками из высокопрочных видов волокна или нетканого материала.
Загустевший состав разводят растворителем.
Нанесение на поверхности осуществляется до температуры не ниже + 5 град.С.
Если такую мастику разогреть до 60 – 70 град., возможна работа при температуре воздуха минус 20 град. С.
Если прогревать защищаемые поверхности, например, газовыми или инфракрасными горелками, то работы можно проводить при минус 30 град.С.
Б. Битумно-полимерные. Применяются в таких видах:
- Однокомпонентные. Имеют вид готовых смесей, хранящихся в герметичной таре. После нанесения вступают с водой бетона и водяным паром воздуха в реакцию полимеризации, в результате происходит твердение состава и образование гидроизоляционной пленки.
Наносят состав распылением, кистями или валиком. Время затвердевания от нескольких часов до нескольких суток. После распечатывания тары все ее содержимое должно быть выработано за короткое время. Невыработанный остаток придется выбросить.
- Двухкомпонентные. На стройплощадку доставляются в раздельной таре. Перед использованием их соединяют и тщательно перемешивают.
В этих видах мастик используются разные полимерные составы:
— полиуретановые составы;
— акриловые смеси;
— силиконовые смеси;
— смеси на основе MS-полимеров и т. п.
Мастики на основе полиуретановых или каучуковых композиций очень эластичны. При нагружении могут удлиняться в 10 – 15 раз, не разрываясь.
Так как большое количество рулонных, плитных (ЭППС) утеплителей для фундамента по технологическому процессу их применения нуждаются в приклеивании к поверхности, то чаще и проще всего использовать для этого разные виды мастик на основе битума. При этом мастичный слой обеспечивает и приклеивание и гидроизоляцию.
Из всех битумных мастик самую меньшую цену имеют битумные мастики горячего применения.
Процедура нанесения гидроизоляции и расход битумных мастик
Правила нанесения в основном определяются производителем материала и описаны в инструкции по его применению.
Расход битумной мастики для гидроизоляции фундамента определяется величиной «сухого остатка». Это то количество, которое остается после испарения растворителя или воды. У мастик эта величина колеблется в пределах 20 – 70 %. Она и определяет расход готового состава. Более «густые» составы выгоднее, т. к. уменьшается стоимость и трудоемкость процессов нанесения.
При нанесении гидроизоляционных слоев битумной мастики используют:
- распылители – воздушные, разбрызгивающие жидкую мастику потоком сжатого воздуха и безвоздушные, работающие при высоком давлении распыляемой мастики, выпускаемой через форсунку;
- кисти и/или валики – нанесение вручную растиранием или раскатыванием;
- шпателем, мастерком и т. п. – используется при густых составах и невозможности их разбавить.
После прошедшего дождя работы можно продолжать не ранее чем через 3 – 4 часа, т. е. после полного высыхания поверхности.
Перед нанесением мастики поверхность должна быть очищена, удалены выступы арматуры, затуплены острые края и т. п.
При нанесении толстых слоев необходимо контролировать их толщину металлическим щупом сразу после нанесения.
При нанесении мастик на водно-полимерной основе защищенную поверхность нужно закрыть от возможного дождя и солнца. Через сутки защитный материал снимают.
Показатели | Битумные мастики | ||||
---|---|---|---|---|---|
холодная, на основе растворителей | холодная, на основе воды | горячая мастика | |||
толщина 1-го слоя, мм | 1,0 | 0,5-1,0 | 1,0 | 0,5-1,0 | 2,0 |
расход на слой кг/м2 | 1,0-2,0 | 1,0-1,5 | 1,5 | 1,0-1,5 | 2,0 |
время твердения слоя, ч, (при + 20 град.С и 50 % влажности) | 24 | 5 | 4 | ||
температура нанесения, °С | минус 10 – +40 | +5 – +40 | не ниже минус 10 | ||
Влажность обрабатываемой поверхности, не более, % | 4 | 8 | 4 |
stroynedvizhka.ru
Приготовление клеящих мастик
Поверхности, которые имеют ровное основание (к примеру, крупнопанельные щиты), облицовываются с применением мастик. Мастика – пластичная смесь, состоящая из тонкомолотого, вяжущего наполнителя и разных добавок. От вида вяжущего материала будет зависеть и наименование мастики (канифольная, поливинилацетатная, битумная, перхлорвиниловая и т. д.). Мастика на синтетическом связующем обеспечивает надежное и прочное сцепление и достаточную морозо- и водостойкость. Токсических веществ в нем не содержатся.
Требования, предъявляемые к мастикам:
- должны соответствовать своим физико-механическим свойствам;
- приклеиваемые материалы на вертикальную поверхность не должны требовать пригрузки, т. е. дополнительной фиксации;
- быть стойкими, когда воздействуют органические растворители;
- быть однородными;
- прочность склейки должна нарастать быстро;
- в процессе укладки должны сохранять свои физические и механические свойства;
- легко наноситься тонким слоем;
- если на них воздействует температура до 60 градусов, то их свойства не должны изменяться;
- должны обладать неплохими адгезионными свойствами.
Поливинилацетатная мастика
Поливинилацетатная мастика состоит из (части по весу) одной части поливинилацетатной пластифицированной дисперсии, двух-трех частей воды, 100-ой марки цементно-песчаной смеси (до требуемой консистенции).
Канифольная мастика
Канифольная мастика состоит (проценты по массе) из канифоля (17%), скипидара либо денатурированного спирта (11%), оксольной олифы (7%), белого портландцемента или известняковой муки (65%). Мастику применяем для облицовки поверхности полистирольными плитками.
Изготовление
Чтобы приготовить мастику, в металлическую емкость заливаем растворитель (скипидар, денатурированный спирт или этиловый технический спирт с крепостью денатурированного спирта). После в емкость засыпаем измельченную канифоль и, время от времени перемешивая, выдерживаем раствор один-два часа, канифоль должна раствориться полностью. Если мы хотим, чтобы канифоль растворился быстрее, емкость с раствором подогреваем до 50-65 градусов.
Растворив канифоль, добавляем пластификатор (оксольную олифу) и смесь снова перемешиваем до однотонного цвета. Далее смесь заливаем в барабан растворосмесителя, засыпаем, перемешивая, сухой наполнитель (белый портландцемент либо известняковая мука) в дозированном количестве. Изготовленную на летучем растворителе мастику фасуем в герметично закрытую тару. В закрытой таре она хранится до 30 дней, в открытой – 1-2 дня. Область использования канифольной мастики ограничена в связи с ее медленным твердением и небольшой прочностью.
Перхлорвиниловая мастика
При облицовке стен полистирольными плитками и при укладке стеклянными плитками используем перхлорвиниловую мастику. Ее приготовляем в двухвальной мешалке либо жерновой краскотерке, перемешивая эмаль (или перхлорвиниловый лак) с известняковой мукой (или с белым портландцементом) в равных частях по весу, при этом соблюдаем меры предосторожности, т. к. эмаль и лак огнеопасны. Мастику храним в герметично закрытой таре. Если сравнить прочность сцепления канифольной и перхлорвиниловой мастики, то у последней она несколько выше.
Глинобитная мастика
Глинобитная мастика включает в себя следующие ингредиенты: битум БН-90/10, жирная глина и вода в равных частях по весу. Ее используем при укладке стеклянных плиток. Размельченную глину замачиваем в воде, полученное тесто нагреваем до 80-90 градусов. В других емкостях разогреваем битум до 100-120 градусов и отдельно кипятим воду. После в подогретое глиняное тесто при постоянном перемешивании малыми порциями добавляем воду и битум до образования однородной массы. Применяем мастику в холодном состоянии.
Карбинольная мастика
Карбинольная мастика состоит из (части по весу) одной части карбинольного сиропа, 0,02-ой части перекиси бензола, десяти частей 400-ой марки портландцемента.
Карбинольную мастику готовим при температуре 10-25 градусах. Просушенную перекись бензола растираем в ступке до состояния в виде пыли. Затем порошок перемешиваем с карбинольным сиропом на протяжении 20 минут, должна образоваться однородная смесь. Далее даем ей отстояться один-два часа, затем смешиваем с цементом до тех пор, пока не сформируется пластичная однородная масса. Пригодность мастики, приготовленной таким способом, определяем так. На стеклянную плитку (тыльная сторона) наносим слой этой мастики толщиной 1,5 мм. Если слой не стекает, а изделия, которые притерты к стене, не сползают, значит, мастика приготовлена качественно. Срок ее годности – от 6 до 8 часов.
Битумная мастика
В битумную мастику входят (части по массе): кислотоупорный цемент – одна часть, битум БН-70/30 – одна часть, асбест (сорт 6-й или 7-й) – одна десятая часть. Мастику используем как прослойку при устройстве кислотостойкого пола.
Изготовление
Мастику готовим так. В котел, который заполнен расплавленным битумом, засыпаем, помешивая, заранее подсушенную смесь асбеста и цемента. Смесь разогреваем до 200 градусов, иначе ценные масла, имеющиеся в битуме, улетучиваются. Это приводит к снижению склеивающей способности мастики. Появившийся дым над котлом говорит о том, что мастика перегревается.
Готовность битумной мастики проверяем таким способом. Из котла берем пробу, даем ей остыть, после застывшую твердую пробу ломаем, если в изломе она имеет черный цвет, значит, мастика готова к применению. Если на строительном объекте намечается большой объем работы, то битумную мастику привозим автогудронаторами и сливаем в термос-котел. Для работ мастику берем из термос-котла и при необходимости подогреваем.
Мастика «Биски»
Мастика «Биски» (битумно-скипидарная) – раствор битума в скипидаре с добавками и наполнителями. Мастику «Биски» применяем для приклеивания линолеума с тканевой подосновой и поливинилхлоридных плиток. На объект мастику доставляют в готовом виде в металлических бидонах, закрытых плотно. Перед употреблением мастику тщательно перемешиваем. Тару с загустевшей мастикой подогреваем в ванне, куда заранее наливаем горячую воду до температуры 30-40 градусов. Срок хранения мастики – до 6 месяцев.
Мастики КН-2, КН-3
Клеящими каучуковыми мастиками КН-2, КН-3 наклеиваем поливинилхлоридный линолеум, различные покрытия на основе каучука, крупноразмерные древесноволокнистые плиты. На объект мастика поступает в металлической таре, закрытой герметично, готовой к употреблению. Срок хранения мастик КН-2, КН-3 – 2 месяца.
moscowsad.ru