ВЫСОКОПРОЧНЫЕ БЕТОНЫ ДЛЯ ДОРОЖНОГО СТРОИТЕЛЬСТВА
УДК 691.328
А.М.Шейнин, С.В.Эккель
ОАО СоюздорНИИ
Цементобетонные покрытия автомобильных дорог и аэродромов являются наиболее долговечным видом покрытий. В России проектный срок службы цементобетонных покрытий составляет 20-25 лет (за рубежом – 40-50 лет), асфальтобетонных 10-15 лет. Поскольку реальный, фактический межремонтный срок службы асфальтобетонных покрытий, по ряду объективных и субъективных причин, намного ниже проектного (составляет по данным Росавтодора, в среднем, 3-5 лет или даже меньше), ещё более актуальным представляется строительство долговечных цементобетонных покрытий.
Часто отказ от строительства именно цементобетонных покрытий объясняют трудностью их ремонта. Однако, во-первых, следует обеспечивать требуемый срок службы покрытия или, по крайней мере, гарантийный срок строительства, для чего необходимо вести должный контроль качества проектирования, строительства и содержания автомобильных дорог. Во-вторых, в настоящее время многие организации предлагают различные варианты ремонта цементобетонных покрытий автомобильных дорог и аэродромов (с помощью мастик, сухих ремонтных смесей, полимерных пропиточных составов и пр.).
Наиболее перспективным в настоящее время является дорожный цементный бетон с прочностью на растяжение при изгибе, его расчётной характеристикой, соответствующей по величине классу не ниже Вtb4,8 (марок не ниже Рtb60). Эта величина прочности бетона определяет высокую несущую способность покрытий, их выносливость и трещиностойкость. Такая прочность дорожного бетона обеспечивается при использовании стандартных, выпускаемых отечественной промышленностью материалов за счёт снижения водоцементного отношения до величин 0,28-0,38 и использования комплексных химических добавок (воздухововлекающих добавок и суперпластификаторов). При этом прочность бетона на сжатие соответствует классам не ниже В35 (маркам не ниже М450), что, в свою очередь, определяет высокую износостойкость цементобетонного покрытия, стойкость против скалывания на кромках плит и к истиранию, ударную стойкость, готовность покрытия к нарезке деформационных швов в установленные технологическими правилами сроки, к раннему открытию движения автотранспорта и др. Такие бетоны по современной зарубежной классификации относятся к бетонам с высокими эксплуатационными характеристиками (High Performance Concrete – HPC).
В условиях России главным фактором агрессивного климатического воздействия на дорожный бетон, определяющим долговечность цементобетонных покрытий, является попеременное замораживание-оттаивание в присутствии водных растворов хлористых солей-антиобледенителей. Соответственно, для обеспечения высокой долговечности цементобетонных покрытий наиболее актуально получение бетона надёжной, гарантированной высокой морозостойкости.
Достигнутый в настоящее время уровень развития техники и технологии дорожного строительства позволяет обеспечить высокую долговечность цементобетонных покрытий [1]. Для этого необходимо выполнить комплекс соответствующих мер (таблица).
При этом малоподвижные бетонные смеси, уплотняемые с помощью вибрации (марок П1, Ж1), предпочтительнее с точки зрения морозостойкости, чем высокоподвижные и литые (марок П3-П5) или жёсткие (марки Ж4). Предпочтительнее также бетоны естественного твердения, чем пропаренные. Должны выполняться все предписанные нормативно-технической документацией (СНиП 3.06.03-85, ВСН 139-80 и др.) требования к режиму уплотнения бетонной смеси, к технологии ухода за свежеуложенным дорожным бетоном.
Многолетние обследования состояния монолитных цементобетонных покрытий автомобильных дорог и аэродромов, выполненные СоюздорНИИ, подтверждают, что при соблюдении всех вышеизложенных требований в течение всего срока службы в бетоне отсутствуют признаки морозного разрушения (шелушение, снижение прочности, трещины, отколы и др.), несмотря на активное применение различных химических методов борьбы с зимней скользкостью.
Следует особое внимание обратить на требование к содержанию вовлечённого воздуха в бетонной смеси для высокоморозостойкого дорожного бетона (бетона покрытий автомобильных дорог и аэродромов). Нормируемый объём вовлечённого и диспергированного (до размера пузырьков не более 200-300 мкм.) с помощью воздухововлекающих добавок (типа СНВ) воздуха в бетонной смеси необходим именно для обеспечения высокой морозостойкости бетона в присутствии хлористых солей-антиобледенителей.
По известной «гидравлической» теории, предложенной Пауэрсом почти 50 лет назад, бетон при циклическом замораживании разрушается под воздействием движущейся под большим давлением незамерзающей в «узких» капиллярах воды в сторону от замёрзших участков в «широких» капиллярах цементного камня. Равномерно распределённые воздушные пузырьки служат резервуаром, куда при замораживании отжимается движущаяся по капиллярам вода, что позволяет снять возникающие в цементном камне напряжения. Кроме того, при использовании воздухововлекающей добавки бетон становится более деформативным и трещиностойким, что также позволяет успешно выдерживать циклическое воздействие замораживания-оттаивания. При использовании солей-антиобледенителей повышается вязкость незамерзающей воды в цементном камне (по предположению А.М.Подвального), в результате чего величина возникающих при замораживании напряжений возрастает и ещё более актуальной становится необходимость защиты бетона от попеременного замораживания-оттаивания с помощью вовлечённого воздуха.
Пузырьки вовлечённого воздуха одновременно ослабляют структуру бетона и снижают его прочность. По нашим данным, увеличение объёма вовлечённого в бетонную смесь воздуха на 1% приводит к снижению прочности бетона на растяжение при изгибе, в среднем, на 2,5%, а на сжатие — на 6%. Соответственно, при обеспечении нормированного воздухововлечения (5% в бетонной смеси для бетона покрытий по ГОСТ 26633-91), прочность бетона на сжатие уменьшится на 30% по сравнению с бетоном без вовлечённого воздуха.
Необходимо подчеркнуть, что качество дорожного бетона и проектируемый срок службы покрытия (конструкции, изделия) обеспечивается не достижением каких-либо одного-двух его проектных показателей, например, прочности и морозостойкости, как самых важных, но соблюдением всех требований к материалам, составу бетона, свойствам бетонной смеси и технологии работ, установленных в нормативно-технических документах. Т.е., качество дорожного бетона обеспечивает только соблюдение всей системы нормативных требований.
Все эти требования взаимно дополняют, но не заменяют друг друга. Достижение проектной марки бетона по морозостойкости является необходимым, но недостаточным условием обеспечения нормативного срока службы покрытия — конечной цели проектирования и строительства. И не означает, что можно ослабить другие требования, требования к составу бетона, к качеству применяемых материалов, к технологии работ, ко всему, что относится к так называемой первичной защите бетона от внешних воздействий. Чаще всего на практике ревизии подвергается норма содержания вовлечённого воздуха в бетонной смеси (на месте укладки бетона), соблюдение которой требует определённой культуры производства и налаженной работы службы контроля качества.
Применение бетонных смесей с относительно низким водоцементным отношением для получения высокопрочных бетонов – известный технологический приём, ставший эффективным в широких масштабах за счёт использования добавок-суперпластификаторов.
При использовании суперпластификаторов, при умеренных расходах портландцемента, 400-500 кг/м3 (марки ПЦ 500-Д0-Н), реально, используя принятые технологии бетонных работ, получение высокопрочных бетонов с вовлечённым воздухом (бетонов дорожных покрытий) марок по прочности (на растяжение при изгибе/на сжатие) Р tb60/М450 – Рtb75/М600. Рис.1,2 иллюстрируют это для дорожного бетона с 5% вовлечённого воздуха в бетонной смеси, приготовленного на портландцементе марки ПЦ 500, гранитном щебне и кварцево-полевошпатовом песке. Здесь К – величина достоверности аппроксимации.
Из многочисленных видов добавок-суперпластификаторов, исследованных у нас в стране в 1980-1990-ые годы различными научно-исследовательскими институтами и лабораториями, наиболее доступным и освоенным отечественной химической промышленностью и строительным производством оказался суперпластификатор С-3. Суперпластификатор С-3 представляет собой водорастворимый сульфированный продукт на нафталинформальдегидной основе. В состав С-3 входит также некоторое количество пластификатора ЛСТ (технических лигносульфонатов) и сульфата натрия. Добавка С-3 выпускается в жидком виде, в виде водного раствора 33-39% концентрации, и в порошкообразном (выпуск С-3 в виде порошка освоен на Новомосковском заводе «Оргсинтез»). Порошок С-3 хорошо растворяется в воде, не требует для растворения подогрева. Поставляется в мешках различной ёмкости.
В СССР добавка С-3 выпускалась на 11 заводах-изготовителях. В настоящее время С-3 выпускают в России на 4 заводах, в г.г. Новомосковск, Россошь, Владимир, Первоуральск. Добавка С-3 остаётся сегодня самой эффективной отечественной пластифицирующей добавкой в цементные бетоны, сравнимой с зарубежными аналогами («Мельмент», «Майти», «Мапей», «Woerment» и др.).
Принцип действия добавки С-3 в бетоне, как и других пластификаторов, основывается на ослаблении коагуляционного взаимодействия новообразований в цементном тесте в первые минуты (часы) после затворения сухих составляющих бетонной смеси водой, на пептизирующем (диспергирующем) действии добавки в цементных системах. Добавки-суперпластификаторы, в отличие от обычных пластифицирующих добавок типа ЛСТ, можно применять в более высоких дозировках (в 2-5 раз), не опасаясь каких-либо отрицательных побочных действий на бетон, что является основой их более высокой эффективности.
Применение тонкомолотых (с удельной поверхностью 4500-5000 см2/г) многокомпонентных цементов (ТМЦ) или вяжущих низкой водопотребности (ВНВ) – ещё один способ повысить прочность бетона. Как показали проведенные в СоюздорНИИ исследования, применение ТМЦ и ВНВ взамен портландцемента марки ПЦ 500 позволяет повысить прочность дорожного бетона ещё, в среднем, на марку, и по сжатию, и по растяжению при изгибе. Однако их практическое использование в дорожном бетоне оказалось нерентабельным из-за высоких затрат на дополнительный помол цементного клинкера.
Кроме того, проведённые исследования выявили случаи снижения морозостойкости дорожного бетона при использовании таких вяжущих, несмотря на высокие абсолютные значения прочности бетона и использование воздухововлекающих добавок. Вероятно, повышение тонкости помола цемента выше определённой, оптимальной, величины отрицательно отражается на долговечности, в частности, на морозостойкости дорожного бетона
Подобные проблемы возникают и при использовании в дорожном бетоне высокодисперсных минеральных добавок, обладающих уплотняющим цементный камень действием и «пуццолановым» эффектом, повышающим степень гидратации цемента, таких, как золы-уноса (отход, попутный продукт работы теплоэлектростанций) и микрокремнезём («белая сажа», отход, попутный продукт ферросплавного производства).
При использовании микрокремнезёма (порядка 10% массы цемента) по существующей технологии легко можно получить бетоны марок по прочности на сжатие М600-М800 и марок Рtb70-Рtb80 по прочности на растяжение при изгибе или снизить расход портландцемента в бетоне на 80-120 кг/м3. Другими словами, за счёт применения микрокремнезёма можно повысить прочность бетона, в среднем, на 20% или на столько же снизить расход портландцемента в бетоне. В то же время, проведенные исследования выявили случаи заметного снижения морозостойкости дорожных бетонов при введении в их состав микрокремнезёма (2). При этом, указанное снижение морозостойкости происходит, несмотря на получаемую высокую прочность, низкую капиллярную пористость и существенную величину условно-закрытой пористости бетона, на наличие воздухововлекающей добавки и требуемого объёма вовлечённого воздуха в бетонной смеси. Вопрос эффективного применения микрокремнезёма в дорожном бетоне с точки зрения его морозостойкости в присутствии хлорида натрия требует дальнейшего изучения.
В последние годы появились предложения повысить водонепроницаемость, коррозионную стойкость и морозостойкость дорожного бетона с помощью «вторичной» защиты его поверхности. В качестве «вторичной» защиты предлагаются различные пропиточные составы на основе акриловых и эпоксидных смол, метилметакрилата, силиконовых композиций. Действительно, как показали проведённые исследования, легко с помощью пропитки бетона указанными составами снизить его водопоглощение до 0,1-0,2% (по массе), и, как правило, обеспечить стойкость поверхностных слоёв (глубиной пропитки 3-5 мм.) к шелушению при совместном действии мороза и хлористых солей-антиобледенителей (3).
Одновременно, «вторичная» защита достаточно морозостойкого дорожного бетона (бетона, состав и технология приготовления которого соответствует требованиям, указанным выше, в таблице) не повышает далее (дополнительно) его морозостойкость в присутствие хлористых солей-антиобледенителей по критерию прочности, не защищает от коррозии арматуру, находящуюся в бетоне. Поверхностная «вторичная» защита не повышает морозостойкость и недостаточно морозостойкого бетона. Под действием мороза и солей-антиобледенителей бетон в объёме конструкции может разрушаться под слоем (под коркой) материалов вторичной защиты.
В ряде случаев, не «вторичная» поверхностная защита, но глубокая, на всю толщину, пропитка неморозостойкого бетона полимером, которая, практически, превратила бетон в бетонополимер (при лакоёмкости бетона более 4% по массе), смогла повысить его морозостойкость.
В этой связи, морозостойкость дорожного бетона следует всегда обеспечивать мерами «первичной» защиты, включающими в себя обоснованный выбор состава бетона и технологии бетонных работ, требуемый контроль качества строительства.
Важно подчеркнуть, что получение на практике высокопрочного и высокоморозостойкого бетона и отмеченные выше преимущества цементобетонных покрытий автомобильных дорог в сравнении с асфальтобетонными (больший фактический и проектный срок службы, меньшие эксплуатационные и приведенные затраты, в частности, меньший расход топлива и др.), реализуются только при обеспечении требуемого качества строительства.
В общей проблеме обеспечения качества монолитного дорожного бетона с вовлечённым воздухом особое место занимают принципы применения статистических методов контроля прочности товарного бетона, когда готовая бетонная смесь транспортируется определённое время от завода-изготовителя к месту укладки бетона, и обеспечение сохраняемости свойств такой смеси. Очевидно, что все требуемые (правилами производства работ) свойства бетонной смеси должны обеспечиваться именно на месте укладки бетона.
Если не принимать специальных мер, бетонная смесь и бетон на стройплощадке могут существенно отличаться по качеству от смеси и бетона на цементобетонном заводе (ЦБЗ). Главным образом, это касается показателя удобоукладываемости (подвижности, жёсткости) и объёма вовлечённого воздуха из-за влияния времени и условий транспортирования бетонной смеси. Соответственно будут отличаться величины прочности и морозостойкости бетона. Для того, чтобы производитель бетонной смеси на ЦБЗ обеспечивал сохраняемость свойств бетонной смеси, необходимо оговаривать это специально потребителем (например, в техническом задании на подбор данного состава бетона, в договоре поставки или в иных документах). Более того, чтобы завод–изготовитель товарной бетонной смеси мог обеспечивать и отвечать за качество смеси на месте укладки бетона, он должен заранее быть готов к этому, должен предусмотреть соответствующие конкретным условиям строительства, условиям транспортирования, изменения в составе бетона на стадии его подбора (по ГОСТ 27006-86) по заданию потребителя. Например, должен предусмотреть большее содержание воды и цемента в бетоне, больший расход добавок, пластифицирующих и воздухововлекающих.
В общем случае, должна меняться и цена бетона: чем дольше транспортирование бетонной смеси – тем больше затрат на сохранение её свойств.
Важно отметить, что бетон на стройплощадке, в силу более низкой, как правило, однородности, должен иметь, в отличие от бетона на ЦБЗ, более высокую величину среднего уровня прочности, Rу, более высокую величину требуемой прочности, Rт, и соответственно подобранный состав. Необходимы технические решения, принимаемые на стадии подбора состава бетона или на стадии заключения договора на его поставку, направленные на учёт фактической однородности прочности дорожного бетона на стройплощадке. Например, при использовании статистических методов контроля прочности монолитного дорожного бетона, шагом вперёд в обеспечении его качества на стройплощадке будет назначение заранее величин Rу=Rт=1,41Внорм., соответствующих обычно принимаемому межпартионному коэффициенту вариации прочности бетона 13,5% и коэффициенту запаса 1,1 (ГОСТ 18105-86, п.4.1, п.4.4).
Возможно, положения ГОСТ 18105-86, ГОСТ 7473-94, ГОСТ 27006-86 следует пересмотреть для монолитных бетонных сооружений, особенно для бетона с вовлечённым воздухом.
Любая корректировка состава дорожного бетона должна производиться с учётом безусловного обеспечения его морозостойкости. При этом, наиболее достоверная информация о морозостойкости монолитного бетона в конструкции может быть получена при испытании на морозостойкость образцов бетона, формуемых на стройплощадке и твердеющих в условиях конструкции до достижения проектной прочности.
Выборочный контроль морозостойкости бетона дорожно-транспортных сооружений, проводимый Союздорнии, показал, что, как правило, на ЦБЗ (по образцам, отформованным и твердеющим в нормальных условиях) все показатели качества бетона, его прочность и морозостойкость, соответствуют предъявляемым проектом требованиям. В то же время часто образцы, отформованные и твердевшие в условиях стройплощадки, и керны, отобранные из конструкции, не выдерживают испытание на морозостойкость.
Это несовпадение результатов контроля качества бетона на ЦБЗ и на стройплощадке можно объяснить недостатками приёмочного контроля бетонной смеси, отсутствием отбраковки бетонной смеси на месте укладки при несоответствии её характеристик требуемым величинам. Главным образом, отсутствует выбраковка бетонной смеси по фактическому содержанию в ней вовлечённого воздуха, объём которого должен составлять 5-7% на месте укладки бетона, о чём говорилось выше. В связи с этим, представляется необходимым на стройплощадке вести приёмку и выбраковку бетонной смеси, в том числе, помашинно, не только по показателям её удобоукладываемости и плотности, но также по содержанию вовлечённого воздуха.
Следует особо подчеркнуть, что марка бетона по морозостойкости – это минимальный, проверочный критерий долговечности дорожного бетона. При определении марки бетона по морозостойкости (по ГОСТ 10060-95) бетон не доводится в обязательном порядке до критерия разрушения, как при испытании на прочность. Марка бетона на морозостойкость не связана однозначно со сроком службы покрытия (изделия). Нельзя утверждать, что бетон, соответствующий марке F300, прослужит дольше, и тем более, в два раза дольше, чем бетон марки F150. По нашему мнению, долговечность новых материалов и технологий, пересмотр существующих норм и т.п. должны обосновываться проведением сравнительных испытаний бетонов на морозостойкость при доведении их до разрушения, по крайней мере, до величины критериев морозостойкости по ГОСТ 10060-95, а не до конкретного числа циклов (например, 100 или 200). В этом случае испытание на морозостойкость, как и испытание на прочность, может характеризовать пределы стойкости бетона как материала. Иными словами, когда предполагается сравнить новый состав бетона (вариант технологии и т.п.) с наилучшим или типичным существующим, то сравнивать морозостойкость бетонов следует на основе сопоставления кинетики изменения прочности и массы бетонов при испытании. При этом испытание на морозостойкость следует проводить вплоть до полного разрушения (величина критерия в 5-10 раз больше, чем по ГОСТ 10060-95) сравниваемых бетонов, иначе не удастся получить данные о кинетике изменения их прочности и массы. Если же довести до разрушения бетоны не удаётся, то следует или ужесточить режим испытания (например, понизить температуру замораживания с минус 200С до минус 500С), или увеличить количество циклов при испытании (например, с 200-300 до 500-1000 циклов).
Именно такие исследования (испытания) дорожного бетона должны быть проведены в случаях, когда действующие стандарты допускают отклонение от представленных в них нормативных требований к качеству, предписывая проведение соответствующих обосновывающих исследований. При этом в стандартах не определено, как проводить те или иные указанные исследования, что на практике позволяет вместо исследований ограничиваться определением только проектной марки бетона на прочность и морозостойкость, что недостаточно для оценки долговечности дорожного бетона (срока службы покрытия или основания и др.).
Случаи необходимости проведения подобных исследований достаточно распространены. Например, ГОСТ 26633-91, п.1.6.2 допускает отклонение характеристик крупного и мелкого заполнителей от нормируемых величин при проведении обосновывающих исследований в бетонах. ГОСТ 10178-85 п.1.13 допускает применение технологических добавок в цементе (типа триэтаноламина и др.) также при подтверждении отсутствия отрицательных последствий в бетоне. Такие же исследования должны быть проведены при использовании в дорожном бетоне природных песков второго класса вместо первого по ГОСТ 8736-93, при изучении морозостойкости дорожного бетона (покрытий, бортового камня и пр.) из жёстких бетонных смесей без воздухововлекающих или газообразующих добавок, при обосновании необходимости вторичной защиты бетона и в других аналогичных случаях.
Библиографический список
1. Шейнин А.М., Эккель С.В. Высокопрочный бетон для дорожных и аэродромных покрытий // Бетон и железобетон.-1998.- №6.- с.7-9.
2. Шейнин А.М., Эккель С.В. Использование микрокремнезёма в дорожном бетоне // Наука и техника в дорожной отрасли. – 2005. — №2.-с.28-33.
3. Шейнин А.М., Эккель С.В. Эффективность вторичной защиты дорожного бетона // Наука и техника в дорожной отрасли. – 2004. — №1.- с.19-23.
Еще на сайте:
sbcmi.ru
ГОСТ 26633-2015, сфера использования, виды, марки
Дата: 11 января 2018
Просмотров: 1674
Коментариев: 0
ГОСТ 26633-2015. Бетоны тяжелые и мелкозернистые. Технические условия
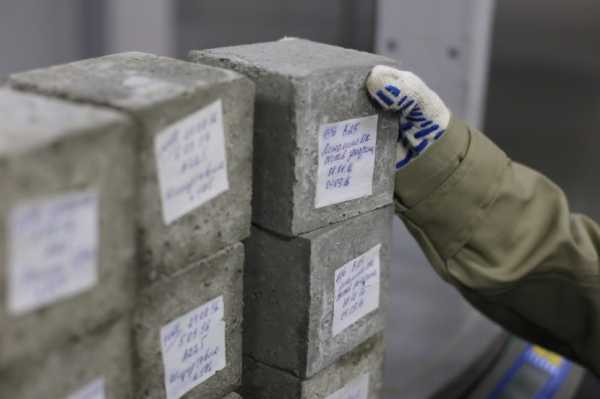
Для осуществления строительных мероприятий применяются различные материалы. Пользуется популярностью бетонная смесь, после твердения превращающаяся в монолит, и позволяющая решать широкий круг специальных задач. Повышенную прочность и долговечность объектов строительства обеспечивает изготовленный по специальной рецептуре бетон. ГОСТ 26633-2015 классифицирует бетонные составы в зависимости от области использования. Он содержит технические требования к применяемым ингредиентам. Ознакомимся с положениями действующего межгосударственного стандарта.
Какую информацию содержит ГОСТ на бетоны тяжелые и мелкозернистые
Действующий ГОСТ 26633-2015 на бетоны выпущен взамен прежних версий стандарта, изданных в 1991 и 2012 годах. Он распространяется на материалы со средним удельным весом, составляющим 2–2,5 т/м3, изготовленные на основе вяжущего вещества и заполнителя различной крупности. В официальном документе изложена техническая информация для определения характеристик монолита, а также требования к исходным компонентам.
Стандарт содержит основные разделы, описывающие:
- сферу использования;
- расшифровку специальных терминов;
- укрупненную классификацию с маркировкой;
- рекомендации по выбору исходного сырья;
- технологию приемки и правила контроля;
- особенности бетонов специального назначения.
Рассмотрим более детально главные положения стандарта.

Бетон — это искусственный камень, состоящий из четырех основных компонентов: воды, цемента, мелких и крупных заполнителей
ГОСТ на бетон – сфера использования
Требования документа распространяются на следующие виды бетонов:
- тяжелые;
- мелкозернистые.
Обе разновидности включают цемент, выполняющий функцию вяжущего вещества и наполнители повышенной плотности.
Составы, изготавливаемые согласно требованиям стандарта, используются:
- в любых климатических условиях;
- во всех сферах строительной отрасли.
Положения нормативного акта не распространяются на специальные составы:
- устойчивые к агрессивным средам;
- стойкие к воздействию повышенных температур;
- композитные составы с дисперсным усилением;
- обеспечивающие защиту от радиационного излучения;
- композиты с ячеистой структурой;
- специальные виды монолита с повышенной плотностью;
- смеси, предназначены для изготовления предварительно напряженных конструкций.

Прочность является самым важным свойством бетона
Тяжелый бетон по ГОСТ 26633-2015 применяется для различных областей:
- постройки жилых и производственных объектов;
- возведения гидротехнических объектов;
- сооружения покрытий автомагистралей;
- обустройства аэродромных покрытий;
- строительства транспортных развязок, эстакад и мостов.
Бетонный раствор – главный стройматериал, используемый в строительной сфере. Он применяется для решения различных задач:
- изготовления составных конструкций из предварительно изготовленных железобетонных изделий;
- бетонирования цельных бетонных конструкций непосредственно на объекте строительства.
Нормативный документ предусматривает расширенную область применения тяжелых бетонных составов.
ГОСТ на тяжелый бетон – используемая терминология
Стандарт использует специальную терминологию и дифференцированно подходит к различным бетонным составам. Он разделяет их на следующие виды:
- тяжелые. Характеризуются структурой повышенной плотности и удельным весом в интервале 2–2,5 т/м3. Изготавливаются на основе цемента и крупнофракционного или мелкодисперсного наполнителя с повышенной плотностью;
- мелкозернистые. Средняя плотность мелкозернистого монолита, а также структура материала соответствуют тяжелым составам. Главное отличие – применение мелкозернистого наполнителя, который смешивается с портландцементом при замесе.
Каждая разновидность бетонного раствора изготавливается согласно определенной рецептуре и после твердения образует искусственный камень.

Прочность бетона нарастает в результате физико-химических процессов взаимодействия цемента с водой, которые нормально проходят в теплых и влажных условиях
Регламентируемые ГОСТ марки бетона
По показателям, характеризующим качество монолита, он классифицируется по следующим критериям:
- прочностным характеристикам. Способность выдерживать сжимающие нагрузки обозначается буквой В и цифровой маркировкой в интервале от 3,5 до 120;
- стойкости к отрицательным температурам. Маркировка бетонных составов по морозостойкости производится латинской буквой F и цифрами от 50 до 500;
- способности препятствовать поглощению влаги. Водонепроницаемость характеризуется заглавной буквой W и цифровым индексом от 2 до 20;
- устойчивости к воздействию истирающих нагрузок. Истираемость монолита проверяется на специальном круге с присвоением маркировки G1–G3.
При определении прочностных свойств монолита проверяется:
- способность сохранять целостность под воздействием сжимающих усилий;
- устойчивость материала к растяжению в осевом направлении;
- стойкость к изгибающим моментам.
Каждому классу соответствует определенная марка. Например, изготавливаемый по ГОСТ бетон в15 соответствует марке М200. Заказывая на специализированном предприятии, выпускающем продукцию согласно ГОСТ, бетон тяжелый класс в15 (м200), всегда можно рассчитывать на гарантированные прочностные характеристики бетонной смеси. При выполнении проектных работ в документации указывается марка бетона по ГОСТ. Эксплуатационные характеристики бетонного состава достигаются по истечении 28 суток после бетонирования. Только после этого можно нагружать конструкции.
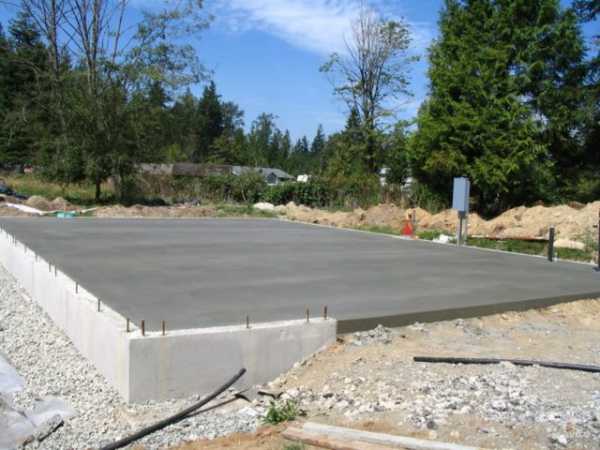
Бетон должен быть однородным — это важнейшее технологическое требование
Тяжелый бетон по ГОСТ – применяемые материалы
Рецептура бетонной смеси должна гарантировать получение монолита с определенными техническими характеристиками, соответствующими положениям стандарта.
Тяжелый бетон, изготовленный согласно ГОСТ 26633-2015, включает следующие ингредиенты:
- портландцемент. Он выполняет функцию связующего вещества и, впитывая влагу, стает твердым. Скорость протекания гидратации определяется маркой вяжущего компонента и его концентрацией;
- заполнитель. Стандарт предусматривает возможность применения в качестве наполнителя различных материалов, отличающихся гранулометрическим составом, прочностными свойствами, удельным весом и объемом примесей;
- воду. Она применяется для затворения приготовляемой смеси, вводится на этапе смешивания до необходимой консистенции раствора. Она также используется для подготовки растворов модифицирующих добавок;
- специальные модификаторы. При необходимости в бетонный раствор вводят добавки, ускоряющие твердение, влияющие на температурный порог замерзания, а также обеспечивающие стойкость монолита к проникновению влаги.
Эксплуатационные характеристики бетонного раствора после твердения достигаются соблюдением оптимальных пропорций и требований технологии.
Документ обязывает соблюдать следующие требования к вяжущим материалам:
- использовать портландцемент марки ПЦ500 и выше, не содержащий минеральных включений;
- соблюдать концентрацию цемента для конструкций с ненапряженной арматурой, составляющую на кубический метр смеси 150–180 кг;
- вводить портландцемент для армированных изделий с предварительно напряженными прутками в количестве 220–270 кг на метр кубический.
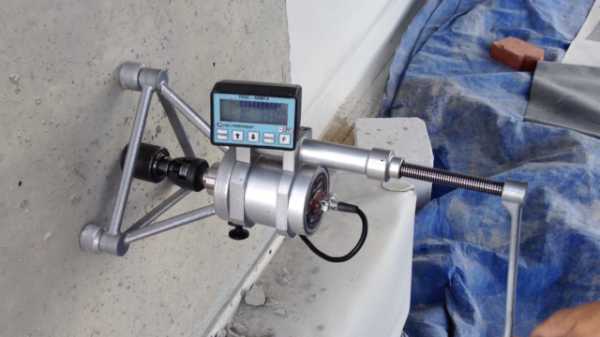
Для оценки однородности бетона данной марки используют результаты контрольных испытаний бетонных образцов за определенный период времени
Стандарт также содержит рекомендации по выбору заполнителей. В качестве мелкофракционного наполнителя допускается использовать следующие материалы:
- песок природного происхождения;
- песок, полученный в процессе дробления различных пород;
- шлаковый песок, применяемый в металлургической отрасли;
- смесь золы со шлаками.
Необходимо обращать внимание на следующие моменты:
- применение мелкого заполнителя с удельным весом 2–2,8 т/м3;
- предельную концентрацию пылеобразных частиц на уровне 3%;
- максимальное содержание глинистой фракции до 2%.
Документ указывает на возможность применения различных видов крупного наполнителя:
- гравия, полученного из плотных пород горного происхождения;
- щебня, просеянного из продуктов дробления;
- шлакового щебня из ферросплавных отходов;
- дробленой щебенки, произведенной из бывшего в употреблении монолита.
Главные требования к крупнофракционному заполнителю:
- плотность материала в интервале 2–3 т/м3;
- раздельная дозировка различных видов крупного наполнителя;
- содержание пылевидной и глинистой фракций не более 2%;
- предельное влагопоглощение материала – 2,5%.
В таблицах госта указана концентрация крупного заполнителя в зависимости от размера фракции.
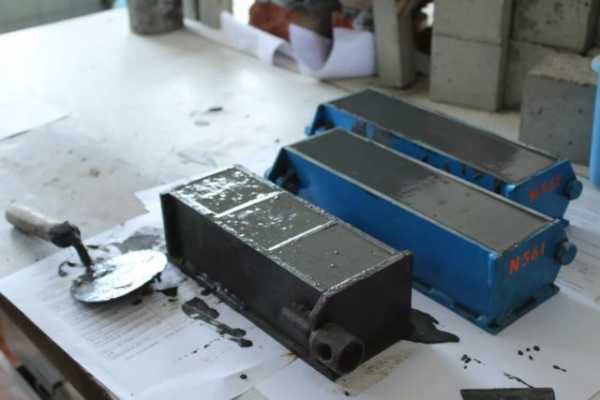
На плотность бетона оказывает существенное влияние наличие пор
Проверка качества
ГОСТ обязывает изготовителей бетонной и железобетонной продукции контролировать следующие основные показатели:
- прочностные свойства;
- морозоустойчивость;
- влагопоглощение;
- истираемость;
- усредненную плотность;
- трещиностойкость.
Контролю в лабораторных условиях подлежит каждая партия продукции.
Какие специальные требования к бетону регламентирует действующий ГОСТ
Документ содержит технические условия к материалам специального назначения:
- гидротехническим. Они изготавливаются из сульфатостойкого портландцемента, могут содержать наполнитель размером более 15 см;
- дорожным и аэродромным. Бетонные составы для покрытий автомагистралей и аэродромов характеризуются повышенной морозостойкостью;
- транспортным. Дорожные развязки, путепроводы и мосты изготавливаются из бетонного состава с увеличенным до 0,55 т/м3 содержанием цемента.
Детальная информация изложена в обязательном приложении к действующему стандарту.
Подводим итоги
ГОСТ на бетон содержит комплекс требований, выполнение которых гарантирует изготовление качественного монолита. Соблюдение положений стандарта позволит увеличить ресурс эксплуатации и прочность строительных конструкций.
pobetony.ru
Бетон гост 26633 2012: технические характеристики
Изготовление и состав тяжелых мелкозернистых бетонных смесей регулируется государственным стандартом № 26633 2012. Подробней о марках готовых смесей, а также физических свойствах тяжелого бетона и сферах его использования расскажет вам наша статья.
Рассмотрим состав и свойства.
Технические характеристики
Готовая бетонная смесь отличается высоким удельным весом, который составляет примерно 1800–2500 кг/м³. в составе находится большое количество цемента, крупного и мелкого наполнителя и вода. Остальные добавки зависят от производителя, но регламентируются инструкциями ГОСТ 26633 2012. В статье вы можете почитать о том, как считать удельный вес бетона.
О том каковы марки бетона и их применение можно узнать прочитав данную статью.
Подробнее главные характеристики сведены в таблицу. Различают пять основных типов бетонных смесей. Использование каждой из них целесообразно назначению повысить прочность конструкции и придаст ей необходимые свойства.
Каковы пропорции бетона в ведрах можно узнать из данной статьи.
Марки и характеристики готовых бетонных смесей:
№ п/п: | Обозначение бетонного раствора: | Марка используемого цемента: | Удельная масса (кг/м³): | Водонепроницаемость: | Морозостойкость: | Подвижность (влияет на удобство укладки): | Пропорции состава (на 1 м³): | |||
Цемент, кг: | Песок, кг: | Щебень, кг: | Вода, л: | |||||||
1. | В 15. | М 200. | 2400. | 6. | 200. | П 2. | 260. | 900. | 1086. | 155. |
2. | В 20. | М 250. | 2390. | 6. | 200. | П 3. | 320. | 860. | 1040. | 165. |
3. | В 22,5. | М 300. | 2400. | 8. | 300. | П 3. | 360. | 830. | 1040. | 165. |
4. | В 25, | М 350. | 2395. | 8. | 300. | П 4. | 420. | 795. | 1000. | 175. |
5. | БСГ В 30. | М 400. | 2410. | 10. | 300. | П 4. | 470. | 760. | 1000. | 175. |
Марка цемента играет немаловажную роль при создании качественного тяжелого бетона. Применяются все возможные вариации, начиная от М 100, для которой достижение необходимой прочности обеспечивается специальными примесями. Бетоны, выполненные с использованием цемента М 700 и выше, относятся к супертяжелым. Но самыми популярными и востребованными считаются бетонные смеси, приготовленные с использованием цемента М 200–350.
Каковы пропорция бетона для фундамента можно прочесть из статьи.
На видео – бетон гидротехнический гост 26633 2012:
Подробнее о составе тяжелого материала
Главный компонент — цемент марки М 200 и выше. От качества цемента будет зависеть свойства готового раствора. Существуют специальные добавки, которые повышаю прочность и крепость готового слоя, но не рекомендуется использовать заведомо «легкую» цементную смесь.
Каковы пропорции бетона для стяжки пола в гараже можно узнать из данной статьи.
Крупный наполнитель обычно представляет собой гравий, гранит, известняк или диабаз, а также другие представители горной породы. Самая подходящая фракция крупных элементов от 5 до 70 мм. Марка используемых компонентов также должна быть не ниже М 350 для известняковых и М 450 для гравийных включений.
В составе тяжелого бетона присутствуют и небольшие компоненты: кварцевый песок крупного и мелкого подбора. Преобладание мелкозернистых составляющих также характерно для этого типа бетонных смесей. Называются они мелкозернистые или пескобетон. Благодаря довольно большому удельному весу такие разновидности также относятся к разряду тяжелых бетонов, технические характеристики и состав будут регламентироваться государственным стандартом.
О том каково время застывания бетона в зависимости от температуры можно прочесть из статьи.
Специальные добавки каждый производитель может использовать по своему усмотрению. Различают перечень следующих рекомендуемых для включения в состав примесей.
Добавки для придания специфических свойств в бетонный состав:
- Пластификаторы служат для создания более пластичной и послушной массы. Оказывают комплексное воздействие, главными критериями готового раствора станет увеличение подвижности, прочности, водонепроницаемости и однородности. Предотвращает прилипания смеси к формовочным элементам, появление трещин и усадки готовой поверхности. Благодаря добавке снижается водопотребность раствора и расход сухого цемента без риска потери качества. Также имеют широкое применение среди других строительных материалов.
- Добавки – ускорители для сокращения сроков затвердения готовой смеси помогут быстрее получить качественное покрытие. Обычно бетонный раствор полностью готов к дальнейшей эксплуатации от 48 часов, в зависимости от площади и толщины заливаемого слоя. Использование специальных химических веществ ускоряет этот процесс примерно на 12 часов и позволит получить готовую плоскость за более короткое время без ущерба в качестве.
- Противоморозная добавка используется для понижения точки замерзания воды, благодаря чему можно производить заливку бетона даже при температуре -20º С. Выпускается в жидком виде и в сухом порошке.
О том, что такое марка бетона В 15 и как она используется, можно прочесть из статьи.
Лучше всего не выполнять подобные работы в столь экстремальных условиях, но при необходимости можно использовать дополнительное утепление, нагрев арматурных конструкций и эту специальную добавку.
- Гидродобавка для бетона помогает улучшить гидроизоляцию готового слоя. Большим преимуществом этого вещества будут способность «самозатягивания» мелких (до 0,4 мм толщиной) трещин на поверхности.
- Пеногаситель, в отличие от пенообразователя, используемого для насыщения бетонного раствора воздушными пузырьками, необходим для прямо противоположных целей. С его помощью из жидкого раствора быстро и эффективно удаляется воздух, а структура становится однородной и плотной. Для тяжелых бетонов это необходимый критерий, свидетельствующий о его качестве.
Каковы характеристики бетона 200 можно прочесть из статьи.
Благодаря пеногасителю застывшая поверхность будет иметь ровный вид без характерных «кратеров» и ямок.
Использование специальных добавок делает раствор более удобным в работе, избавляя от мелких недостатков и улучшая достоинства. Большинство строителей предпочитают работать именно с усовершенствованными бетонами. Это позволит существенно сэкономить время и силы, а также некоторые строительные материалы. Такие растворы легче в укладке, а готовая поверхность обладает хорошей прочностью и однородностью, без видимых дефектов и недостатков.
О том каков состав бетона М 400 на 1 м-2 можно прочесть в данной статье.
Область применения
Тяжелые бетонные растворы широко используются в бытовом и инженерном строительстве. Все несущие и силовые элементы зданий и сооружений целесообразней выполнять именно из тяжелого бетона. Если сфера применения легких смесей ограничивается возведением стен и перекрытий, то на долю тяжелого бетона приходится все остальное.
Каков состав бетона М 200 на 1 м-2 можно прочесть из статьи.
Для тяжелых бетонов характерна естественная усадка на протяжении 2–3 лет после установки, поэтому такой фактор в обязательном порядке учитывается.
Для жилых зданий, возведенных с использование тяжелых составов, например, бетон марки в25, так же может понадобиться дополнительная теплоизоляция, так как материал сам по себе обладает высоким показателем теплопроводности.
О том каковы пропорции бетона марки 200 можно узнать из данной статьи.
Производство железобетонных изделий, фундаменты различных типов, гидротехнические сооружения, плиты перекрытия, напольные стяжки, бетонная подушка для дорожных покрытий и изготовление бордюрного камня. Все это лишь краткий перечень возможностей использования тяжелого бетона.
resforbuild.ru