Цемент для кладки печей: какой лучше всего подойдет?
Цемент как связующий материал в силу своих свойств не может использоваться для кладки всех элементов отопительных печей. Обычно его применяют для приготовления раствора для строительства фундамента и дымохода печи – элементов, которые априори не работают при высоких температурах.
СодержаниеСвернуть
Как выбирают цемент для замешивания раствора кладки печей?
Цементный раствор как особо прочный связующий материал состоит из цемента, наполнителя (песка) и воды. В плане строительства отопительных печей цементный раствор используется для кладки фундаментов в сырых грунтах либо грунтах насыщенных влагой. А также его можно использовать для строительства дымоходов и боровов, которые не подвергаются влиянию высокой температуры печных газов.
При этом пропорциональный состав компонентов должен обеспечивать высокую прочность строительной конструкции. Поэтому состав кадочного раствора для кладки печи можно охарактеризовать как «крепкий» – 1 часть цемента М400 и 1 часть просеянного песка.
Изменять пропорции в сторону уменьшения количества цемента нет смысла, потому что в этом случае есть опасность столкнуться с малой долговечностью и необходимостью дорогостоящего ремонта.
Цемент для кладки печей используют для приготовления так называемых сложных растворов, состоящих из цемента М400, известкового молока и просеянного песка. При этом на одну часть цемента берется 1-3 части известкового теста и шесть частей просеянного песка. Данный рецепт пригоден к использованию при строительстве фундаментов и элементов печи которые не испытывают высокие температурные нагрузки (дымоходы, боровы дымоходов и фундаменты).
Жаростойкие цементные смеси
Жаростойкие цементные смеси применяют для строительства монолитных очагов открытого пламени (топок) либо блоков для кладки печей и их топок. При этом следует придерживаться следующих требований по составу компонентов от опытных мастеров по строительству печей:
Компоненты кладочного раствора | Количество в пропорциях |
Цемент марки М400-М50 | 1 |
Щебень из красного кирпича | 2-2,5 |
Шамотный песок | 0,35 |
Песок | 2-2,4 |
Жаростойкие цементные смеси для топки
Компоненты кладочного раствора | Количество в пропорциях |
Цемент М40-М500 | 1 |
Щебень из красного кирпича | 2 |
Песок | 2 |
Тонкосмолотый песок | 0,35 |
Специалисты по кладке печей и каминов, на основании богатого практического опыта настоятельно не рекомендуют использовать в строительстве печей и каминов цемент. Этот достаточно дорогостоящий материал, который с успехом и стопроцентной гарантией при всех прочих равных условиях заменяет дешевая и повсеместно доступная желтая или красная глина.
salecement.ru
Цементы для жаростойких бетонов
СПЕЦИАЛЬНЫЕ ЦЕМЕНТЫ
Жаростойкие бетоны состоят из твердеющей при нормальной температуре связующей части и огнеупорных заполнителей. Они способны длительно выдерживать воздействие высоких температур и не отличаются по своим свойствам от обычных огнеупоров. Для изготовления огнеупорных бетонов применяют портландцемент, глиноземистый цемент, жидкое стекло, бариевый цемент. Прежде всего следует отметить, что затвердевшие портландцемент, глиноземистый цемент и некоторые другие вяжущие, как известно, содержат воду различных видов: химически связанную (кристаллизационную), адсорбированную цементным гелем, капиллярную, свободную. Вода из гидросиликатов, гидроалюминатов, гидроксида кальция и др. удаляется в определенном интервале температур и практически полностью при высоких температурах. Дегидратация при быстром нагреве может вызвать нарушение структуры цементного камня.
Исследования К. Д. Некрасова и его сотрудников показали, что прочность бездобавочного портландцемента при дегидратации при температуре до 1173 К снизилась на 90% от первоначальной прочности, а у пуццолановых и шлакопортландцементов на 50—75%. Дальнейшее повышение температуры до 1523—1623 К ведет к образованию плотного спекшегося цементного камня.
Установлено, что для получения качественных бетонов на портландцементе в его состав вводят небольшое количество фосфорного ангидрида для стабилизации, C2S в p-форме и предупреждения его перехода в у-фор — му. Эффективность службы огнеупорного бетона повышается при введении в состав портландцемента тонкомолотой добавки, преимущественно огнеупорной, в виде хромита, магнезита, шамота обычно в количестве не более 10% массы цемента. Эта добавка при 873—■ 1273 К вступает в твердофазовую химическую реакцию с оксидом кальция, образовавшимся при дегидратации Са(ОН)2, а также с цементными дегидратированными и негидратированными соединениями. Реакции продолжаются при 1473—1573 К и протекают уже с участием появившейся жидкой фазы, которая способствует уплотнению структуры и повышению прочности бетона.
Для некоторых видов огнеупорного бетона можно применять шлакопортландцемент. При использовании глиноземистого цемента необходимость ввода в его состав тонкомолотой добавки отпадает, поскольку образующийся при гидратации цемента А1(ОН)3 и гидроалюминаты кальция постепенно дегидратируются и прочность бетона при этом снижается в меньшей степени. Применяются также высокоглиноземистый цемент, отличающийся повышенным (до 75%) содержанием глинозема, жидкое стекло с добавкой кремнефтористого натрия, тонкомолотого магнезитового кирпича, хромита, талька или шамота. Употребляют периклазовый цемент, получаемый путем затворегшя тонкоизмельченного магнезитового кирпича на растворе сернокислого магния. Топкомолотые добавки в его состав не вводят.
В огнеупорном бетоне вяжущим могут служить соединения бария. Они придают ему огнеупорность и делают устойчивым против радиоактивного излучения. Ортосиликаты бария и кальция образуют ряд твердых растворов, плотность которых достигает 5,2 г/см3. Орто — силикат бария 2Ba0-Si02 гидратируется с образованием гидроксида бария. Дегидратация этого соединения полностью заканчивается лишь при 1123 К.
Известны следующие соединения алюминатов бария, плавящиеся при высоких температурах без разложения:
3 Ва0-А1203 при 2023К;
ВаО-А120з » 2103К;
Ва0-6А1203 » 2173К (вяжущими свойствами не обладает) .
Возможно получение двухбариевого феррита, также обладающего вяжущими свойствами. Большой интерес для получения жаростойких бетонов представляет моноалюминат бария. Если в качестве заполнителя применяется шамот, хромомагнезит, муллит и корунд, то бетоны на бариево-алюминатной связке отличаются высокими техническими свойствами. Прочность бетонов на алюминатно-бариевом цементе не снижается при нагреве до 1473 К, а при 1623 К она возрастает примерно в 2 раза. Положительные результаты получены при испытании барийсодержащего портландцемента. Оксид бария (3—5%) в нем входит в виде твердого раствора преимущественно в состав белита. Жаростойкие бетоны, полученные на этом цементе, в состав которого вводилась тонкомолотая добавка шамота, характеризовались достаточной brneynopHocTbjo. Эффективным вяжущим для получения стойких бетонов является жидкое стекло.
Заполнителями бетона в этом случае должны быть преимущественно диабаз и андезит [92]. Наибольшей огнеупорностью обладают бетоны на высокоглиноземистых цементах, в состав которых введена тонкомолотая добавка корунда и особенно плавленого глинозема.
Важно отметить, что сушить и разогревать тепловые агрегаты из цементного бетона нужно очень медленно и осторожно, так как при быстром высушивании и разогреве в пусковой период работы агрегата возможно изменение структуры цементного камня, образование трещин в бетоне и даже его разрушение. Поэтому допустимы сушка и разогрев тепловых агрегатов из бетона на портландцементе только 7-суточного, а на других цементах только 3-суточного срока твердения. В зависимости от объема бетона общая продолжительность сушки и разогрева, включая подъем температуры от 973 К до рабочей, установлена в пределах 60—408 ч. Однако даже при соблюдении этих условий прочность бетона после сушки и разогрева снижается. Поэтому следует применять бетон самой высокой марки. Большую прочность бетона можно получить при минимальном значении ВЩ, без увеличения удельного расхода цемента.
По нормативным документам допустимая остаточная прочность после нагревания до 1073 К для бетона на портландцементе составляет 30—40%; на глиноземистом, высокоглиноземистом и периклазовом цементах— 30%; на жидком стекле — 50—90%. При применении барийсодержащего портландцемента с тонкомолотой добавкой шамота остаточная прочность достигает 43—68%.
Советская цементная промышленность по объему производства цемента занимает с’ 1962 г. первое место в мире. Выпуск цемента в СССР в 1982 г. составил 125 млн. т, а в США — …
В последние годы советские ученые М. М. Сычев, Н. Ф. Федоров, Л. Г. Судакас, Д. И. Чемоданов разрабатывают область науки о новых видах вяжущих, представляющих собой композиции из порошков металлов, …
‘ Современные строительные цементы, состоящие из силикатов, алюминатов и алюмоферритов кальция растворяются в кислотах, и поэтому их нельзя применять в условиях кислотной агрессии. В химической промышленности для связи (склеивания) штучных …
msd.com.ua
Жаростойкие свойства цемента.
Одним из важнейших показателей жаростойкости цементов является отношение цементного камня к воздействию повышенных температур. Процесс нагревания цементного камня сопровождается фазовыми превращениями, испарением воды, выделяющейся из кристаллогидратов, изменением пористости и, как следствие, снижением прочности. По степени снижения прочности, как правило, судят о жаростойкости цемента. В зависимости от температурных условий службы бетона используют различные цементы: портландцемент, глиноземистые цементы различного состава, жидкое стекло и т. д. Высокоглиноземистые цементы, обеспечивающие высокую огнеупорность бетона, являются наиболее перспективными.
Для организации производства высокоглиноземистого цемента на ОАО «Подольск-Цемент» была создана промышленная установка, состоящая из электродуговой печи — плазменного реактора и вспомогательного оборудования: сырьевых бункеров для различных видов специальных клинкеров, смесителя-утилизатора тепла, полых анода и катода, охладителя расплава для различных режимов охлаждения специальных клинкеров.
Плазменный реактор представляет собой металлический цилиндр, футерованный изнутри двумя слоями огнеупора (ШЦУи ВГЦ бетоном) и охлаждаемый снаружи циркуляционной водой. Днище и крышка плазменного реактора футерованы ВГЦ бетоном и охлаждаются через водяные кессоны циркуляционной водой. Средняя толщина футеровки подобрана экспериментально и составляет 250 мм.
Корпус плазменного реактора имеет ряд технологических отверстий для обеспечения загрузки шихты, слива расплава, отбора газов, розжига реактора, внутреннего осмотра реактора во время работы.
На созданной установке предприятие постоянно производит высокоглиноземистый цемент требуемого состава. Возможности установки велики — она способна выпускать любые высокоглиноземистые цементы от мономинерального до полиминерального состава с добавками различных веществ, повышающих огнеупорность цемента.
Для исследования был взят высокоглиноземистый цемент, характеризующийся следующим содержанием (мас. %): моноалюминаткальция СА — 32, диалюминат кальция СA2 — 60, другие примесные соединения — 8. В качестве добавки использовали микрокремнезем и органическую кислоту.
Известно, что при гидратации высокоглиноземистого цемента образуются метастабильные гидроалюминаты кальция САН10, С2АН8, перекристаллизовывающиеся затем в кубическую форму С3АН6. Для определения степени их влияния на изменение структуры и прочности цементного камня при его нагревании до высоких температур на первом этапе были приготовлены различные гидроалюминаты по методике, опубликованной в литературе.
При нагревании САН10 в пределах 100 °С потеря кристаллизационной воды составляет 3 мол., при 150–170 °С удаляется 1,5 молекулы Н20, при 260–280 °С — 5 мол. Н20, и оставшиеся 0,5 молекулы удаляется при 800–900 °С. Фазовый анализ, по данным РФА, соответственно представлен в начале аморфной массой, а затем СА и Аl203.
Таблица №1: Результаты испытаний исследуемого цемента.
При нагревании С2АН8 теряет воду: при 100 °С — 1 %, при 170 °С — 1,5 % и при 300–320 °С — 5,5 %. При этом происходит постепенное изменение фазы от С2АН7 до С2АН4, полностью разлагающихся и превращающихся в аморфную массу. При 600 °С обнаруживается появление минерала С12А7 (d = 0,480, 0,263 нм).
При нагревании С3АН6 основная часть воды (4,5 мол. Н20) удаляется при 310–320 °С. Оставшиеся 1,5 мол. Н20 отщепляются при 500 °С. Нагревание образца до 600 °С сопровождается образованием С12А7 и СаО. Наличие свободной извести в цементном камне нежелательно, поскольку при циклическом нагревании и охлаждении возможно превращение Са(ОН)2 СаО, что сопровождается деструкцией цементного камня, снижением прочности и даже, в определенных условиях, его разрушением.
Физико-химические исследования процесса гидратации и дегидратации высокоглиноземистого цемента с добавками и без добавок показали, что при 20 °С образуются в основном С2АН8 (бездобавочный ГЦ), перекристаллизовывающийся в С3АН6, в присутствии микрокремнезема — стерлингит С2АSH8, а органическая кислота способствует образованию САН10. При нагревании цементного камня до 200 °С степень гидратации всех цементов повышается за счет ускорения реакций взаимодействия компонентов с физически адсорбированной водой, находящейся в структуре цементного камня. Количество продуктов гидратации увеличивается, они заполняют поры в цементном камне, и прочность его повышается.
При этом состав продуктов гидратации в бездобавочном высокоглиноземистом цементе представлен кубическим гидроалюминатом кальция, в цементе с добавкой микрокремнезема — гидроалюмосиликатом кальция, а в цементе с добавкой органической кислоты — гексагональным гидроалюминатом кальция.
При дальнейшем повышении температуры нагрева происходит отщепление кристаллохимической воды из структуры гидратов, увеличение пористости и снижение прочности цементного камня. Степень снижения прочности зависит от состава цемента. Цементы с добавками показывают меньшую пористость и более высокую прочность по сравнению с бездобавочными.
Отмечено, что в присутствии добавок перекристаллизация первоначально образовавшихся гидро-алюминатов кальция замедляется и превалирует степень гидратации. Образующиеся гидраты заполняют поры и тем самым уменьшают снижение прочности цементного камня.
На основе проведенных исследований был изготовлен бетон с применением высокоглиноземистого цемента без и с добавкой указанных материалов. Как известно, свойства жаростойкого бетона зависят от природы заполнителя, который обеспечивает формирование контактной зоны между цементным тестом и заполнителем. Известны многочисленные исследования контактной зоны между заполнителем и цементным камнем. Согласно большинству из них, разрушение структуры бетона в основном зависит от степени сцепления заполнителя и цементного теста. В исследованиях показано, что главной составляющей контактной зоны является гидроксид кальция, который, главным образом, обусловливает связь «цемент–заполнитель». Эта связь обеспечивается за счет эпитаксиального роста кристаллов гидроксида кальция на поверхности заполнителя. Микроструктура контактной зоны, как правило, характеризуется большой пористостью и наличием крупных кристаллов гидроксида кальция. Однако эти данные характерны для бетонов на основе потландцемента. При гидратации высокоглиноземистого цемента, как показано выше, образуются гидроалюминаты кальция и гидроксид алюминия. Поэтому было целесообразно исследовать, как в этом случае формируется структура контактной зоны.
Для решения этой проблемы были проведены исследования с применением традиционного шамота как в качестве крупного, так и мелкого заполнителя. Для сравнения брали смесь, состоящую из шамота в качестве крупного компонента и микрокремнезем, как мелкий заполнитель. Образцы бетона нагревали при 100–1200 °С и затем исследовали методами РФА, ИКС и оптической микроскопии. Микроскопические исследования показали, что шамотные частицы окружены продуктами гидратации высокоглиноземистого цемента. Толщина контактной зоны составляет 10–15 мкм. Контактная зона образована благодаря эпитаксиальному росту кристаллов гидроалюминатов кальция на поверхности шамотных частиц. Контактная зона между микрокремнеземом и цементным тестом трудно просматривается из-за тонкого переплетения продуктов дегидратации цементных частиц. На поверхности частиц микрокремнезема наблюдается слой взаимных прорастаний продуктов его гидратации и цемента. При повышении температуры до 1200 °С, в результате реакции аморфизированных частиц, образовавшихся из дегидратированных компонентов высокоглиноземистого цемента и микрокремнезема, образуется муллит.
Исследования образцов, содержащих шамот в качестве заполнителя, показали, что микротрещины появляются вдоль зерен заполнителя, т. е. по контактной зоне. В случае образцов с микрокремнеземом формируется очень плотная контактная зона, простирающаяся как вдоль исходных негидратированных частиц, так и гидратированных фаз, что, видимо, является причиной высокой прочности бетона. Соответственно, пористость образцов очень низкая.
Таблица №2: Прочность бетонов при твердении в нормальных условиях и после нагревания.
Исследование образцов после их нагрева до 1200 °С показали значительно более высокуюостаточную прочность бетона со смесью шамота и микрокремнезема. Образцы имели высокую термостойкость — 30 циклов попеременного высушивания и увлажнения.
Таким образом, применение высокоглиноземистого цемента в сочетании с заполнителем, состоящим из шамота и микрокремнезема, весьма эффективно. Указанные высокоглиноземистый цемент и бетон на его основе рекомендуются для футеровки различных тепловых агрегатов.
www.voscem.ru
Огнеупорный цемент, описание, производители и цены на смеси ГЦ-40, ГЦ-60
Для тех, кто собирается построить камин, печь в доме или барбекю, предпочтительнее выбирать огнеупорный материал, которых сохраняет свои свойства даже при 1 750 °C. Найти его несложно, хотя в частном секторе используется редко, а применяется в основном при изготовлении бетона повышенной жаропрочности в промышленных печах. Уникальность раствора в том, что он быстро затвердевает и становится очень прочным.
В чем отличие от других видов
Почти каждый цемент горит, плавится и разрушается, при 250 °C он деформируется, а после 500 трескается и нарушается целостность структуры. Противостоят высоким температурам:
- Глиноземистые марки: гц-60-У, гц-60, гц-50, гц-40, вгц-2-25, СА-50, Исыдач-40, СА-50, GORKAL-70.
- Высокоглинозёмистые ВГКЦ 70-1, ВГКЦ 75-05, ВГЦ I, ВГЦ II, ВГЦ III.
Изготавливаются из сырья с использованием глинозема, методом запекания, плавки, измельчения до дисперсного вида. Отличие в том, что при нагревании жаростойкие цементы твердеют с появлением керамических сцеплений, а не гидравлических, что характерно для обычных марок.
Применение
Используется для получения жаростойких бетонных смесей в строительстве футеровок тепловых агрегатов, возведения сооружений, находящихся а минерализованных водах или подвергающихся действию сернистых газов, При установке разнообразных печей, дачных каминов, устройстве дымоходов. Он предпочтительнее кладки, так как она расширяется при нагревании, что требует предварительной обработки швов.
Характеристики
Одними из преимуществ глиноземистых марок являются быстрое отвердение в воде и обретение прочности в течение трех суток. Половину заявленной прочности смесь набирает в течение суток – это позволяет через 20 часов использовать сооружение. Необходимо знать, что для избежания перекристаллизации, цемент должен затвердевать при влажных температурах, которые выдерживаются в течение суток после заливания водой при 20 °C.
В процессе гидратации материал способен выделить за небольшой отрезок времени много тепла — до семидесяти процентов за несколько часов. Такая характеристика позволяет использовать его без подогрева для проведения работ зимой при — 10 °C. Момент схватывания – после 50 минут после контакта с жидкостью, не ранее, а окончание процесса — не позже десяти часов от начала схватывания.
Классификация
- По маркам: указываются в числах от 100 до 600, что показывает прочность при сжатии в 100 — 600 бар.
- По классам: в числах от 30 — 60, в зависимости от сжатия.
Отличие классов от марок — в расчете прочности, она выводится не по среднему показателю, а по обеспеченности не менее 95%. Это означает, что 95 образцов из 100 обязаны соответствовать требуемому классу.
Класс ГЦ-40
Свойства не теряются даже при эксплуатации до 1 700 °C. Совместно с огнеупорными и жаростойкими наполнителями — магнезитом, рудой хромитовой, шамотом, он используется при получении гидравлически затвердевающих растворов и бетона. Пользуется спросом огнеупорный глиноземистый цемент гц-40, ГОСТ 969-91, состав — известняк, известь или породы с большим содержанием глинозема. Они подразделяются на две группы: марки гц-40 и гц-50 (в конце первых суток прочность гц-50 выше).
Цены
Самые популярные: ВГКЦ-75-0.5, ВГКЦ-75-1 (ООО «Керамика Гжели»), гц-40, гц-50, гц-60 (Украина), «Ctembor» (Новгородская область), FireBarrier 135 (Франция), Gorkal 70 (Украина), Ciment Fondu (Франция).
Сравнительная таблица ценовых предложений поставщиков:
Название | Фасовка, мешок кг | Розничная цена в рублях |
глиноземистый гц-40 | 50 | 1 300 |
Gorkal 40 (Польша) | 50 | 1 300 |
ГГЦР (Россия) | 50 | 1 400 |
В зависимости от сезонного фактора цены на огнеупорный цемент могут меняться, например, летом с увеличением строительных работ они вырастают, а зимой значительно снижаются.
hardstones.ru
Цементы для жаростойких бетонов |
Цементы для жаростойких бетонов
Жаростойкие бетоны состоят из твердеющей при нормальной температуре связующей части и огнеупорных заполнителей. Они способны длительно выдерживать воздействие высоких температур и не отличаются по своим свойствам от обычных огнеупоров. Для изготовления огнеупорных бетонов применяют портландцемент, глиноземистый цемент, жидкое стекло, бариевый цемент. Прежде всего следует отметить, что затвердевшие портландцемент, глиноземистый цемент и некоторые другие вяжущие, как известно, содержат воду различных видов: химически связанную (кристаллизационную), адсорбированную цементным гелем, капиллярную, свободную. Вода из гидросиликатов, гидроалюминатов, гидроксида кальция и др. удаляется в определенном интервале температур и практически полностью при высоких температурах. Дегидратация при быстром нагреве может вызвать нарушение структуры цементного камня.
Исследования показали, что прочность бездобавочного портландцемента при дегидратации при температуре до 1173 К снизилась на 90% от первоначальной прочности, а у пуццолановых и шлакопортландцементов на 50—75%. Дальнейшее повышение температуры до 1523—1623 К ведет к образованию плотного спекшегося цементного камня.
Установлено, что для получения качественных бетонов на портландцементе в его состав вводят небольшое количество фосфорного ангидрида для стабилизации, C2S в р-форме и предупреждения его перехода в у-форму. Эффективность службы огнеупорного бетона повышается при введении в состав портландцемента тонкомолотой добавки, преимущественно огнеупорной, в виде хромита, магнезита, шамота обычно в количестве не более 10% массы цемента. Эта добавка при 873—1273 К вступает в твердофазовую химическую реакцию с оксидом кальция, образовавшимся при дегидратации Са(ОН)2, а также с цементными дегидратированными и негидратированными соединениями. Реакции продолжаются при 1473—1573 К и протекают уже с участием появившейся жидкой фазы, которая способствует уплотнению структуры и повышению прочности бетона. Для некоторых видов огнеупорного бетона можно применять шлакопортландцемент. При использовании глиноземистого цемента необходимость ввода в его состав тонкомолотой добавки отпадает, поскольку образующийся при гидратации цемента Аl(ОН)3 и гидроалюминаты кальция постепенно дегидратируются и прочность бетона при этом снижается в меньшей степени. Применяются также высокоглиноземистый цемент, отличающийся повышенным (до 75%) содержанием глинозема, жидкое стекло с добавкой кремнефтористого натрия, тонкомолотого магнезитового кирпича, хромита, талька или шамота. Употребляют периклазовый цемент, получаемый путем затворения тонкоизмельченного магнезитового кирпича на растворе сернокислого магния. Топкомолотые добавки в его состав не вводят.
В огнеупорном бетоне вяжущим могут служить соединения бария. Они придают ему огнеупорность и делают устойчивым против радиоактивного излучения. Ортосиликаты бария и кальция образуют ряд твердых растворов, плотность которых достигает 5,2 г/см3. Ортосиликат бария 2BaO-SiO2 гидратируется с образованием гидроксида бария. Дегидратация этого соединения полностью заканчивается лишь при 1123 К.
Возможно получение двухбариевого феррита, также обладающего вяжущими свойствами. Большой интерес для получения жаростойких бетонов представляет моноалюминат бария. Если в качестве заполнителя применяется шамот, хромомагнезит, муллит и корунд, то бетоны на бариево-алюминатной связке отличаются высокими техническими свойствами. Прочность бетонов на алюминатно-бариевом цементе не снижается при нагреве до 1473 К, а при 1623 К она возрастает примерно в 2 раза. Положительные результаты получены при испытании барийсодержащего портландцемента. Оксид бария (3—5%) в нем входит в виде твердого раствора преимущественно в состав белита. Жаростойкие бетоны, полученные на этом цементе, в состав которого вводилась тонкомолотая добавка шамота, характеризовались достаточной огнеупорностью. Эффективным вяжущим для получения стойких бетонов является жидкое стекло.
Заполнителями бетона в этом случае должны быть преимущественно диабаз и андезит. Наибольшей огнеупорностью обладают бетоны на высокоглипоземистых цементах, в состав которых введена топкомолотая добавка корунда и особенно плавленого глинозема.
Важно отметить, что сушить и разогревать тепловые агрегаты из цементного бетона нужно очень медленно и осторожно, так как при быстром высушивании и разогреве в пусковой период работы агрегата возможно изменение структуры цементного камня, образование трещин в бетоне и даже его разрушение. Поэтому допустимы сушка и разогрев тепловых агрегатов из бетона на портландцементе только 7-суточного, а на других цементах только 3-суточного срока твердения. В зависимости от объема бетона общая продолжительность сушки и разогрева, включая подъем температуры от 973 К до рабочей, установлена в пределах 60—408 ч. Однако даже при соблюдении этих условий прочность бетона после сушки и разогрева снижается. Поэтому следует применять бетон самой высокой марки. Большую прочность бетона можно получить при минимальном значении ВЩ, без увеличения удельного расхода цемента.
По нормативным документам допустимая остаточная прочность после нагревания до 1073 К для бетона на портландцементе составляет 30—40%; на глиноземистом, высокоглиноземистом и периклазовом цементах — 30%; на жидком стекле — 50—90%. При применении барийсодержащего портландцемента с тонкомолотой добавкой шамота остаточная прочность достигает 43—68%.
midas-beton.ru
Жаростойкий цемент на службе печного строительства cementiruem.ru
Испокон веков мастерство кладки каминов и печей было в почете, потому как этот очаг играл очень важную роль в доме, был источником тепла, местом отдыха и приготовления еды. От ловкости и умения строителя зависело то, как хорошо будет работать и греть этот источник тепла. Печи сооружали в основном из камня или красного кирпича, которые укладывались на глину, потому что только она могла переносить столь высокие температуры. Несмотря на отличные жаропрочные качества, глина плохо справлялась с большой нагрузкой, поэтому сооружать крупные и массивные печи из таких материалов не получалось. В таких случаях использовался жаростойкий цемент, который в отличие от простого цемента марок 500-400, хорошо переносил высокие температуры и обладал повышенной прочностью.
Современные марки огнеупорного цемента используются во всех сферах строительства: от домашней кладки каминов до сооружения промышленных дымоходных труб и ядерных реакторов. Отдельные марки жаростойкого цемента способны переносить воздействие температур вплоть до 3000 градусов Цельсия. Поскольку в домашних каминах и печах для обогрева температура редко превышает порог в 1500 градусов, для их сооружения вполне подойдет жаропрочный цемент марки ТМЦ-Ж. В его состав включены тонкомолотые огнеупорные добавки, которые и придают цементу жаростойкие качества. Сравнительно невысокая цена цемента этой марки позволяет использовать его в общестроительных работах, где необходимы такие свойства бетона, как высокая прочность и водостойкость. При своих достоинствах, марка ТМЦ-Ж имеет и некоторые недостатки: даже небольшое количество пыли и жира, попавшие в приготовленный бетон, могут полностью лишить его жаропрочных качеств, так что необходимо уделять особое внимание очистке и обезжириванию емкостей, в которых будет готовиться бетон.
cementiruem.ru
Особенности огнеупорного цемента
Общеизвестно, что противостоять огню крайне сложно. При воздействии высокими температурами практически все материалы горят, плавятся или разрушаются. Именно поэтому проблема жаростойкости строительных материалов так актуальна. При воздействии температуры в 250 градусов цемент начинает разрушаться, при 500 градусах – он начинает лопаться, что ведет к нарушению целостности конструкции.
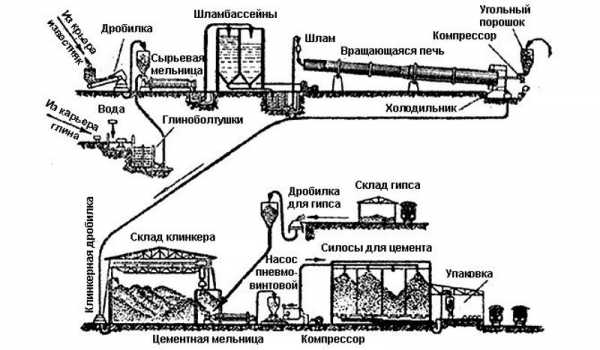
Схема производства
Именно для борьбы с высокими температурами и был разработан огнеупорный цемент.
Жаростойкий состав является разновидностью глиноземистых или высокоглиноземистых цементов. Изготовленный на его основе раствор достаточно быстро твердеет и становится прочным. Этот материал способен выдерживать температуру в среднем до 1750 градусов, что и объясняет его широкое применение.
Характеристики материала
Жаростойкий имеет свои достоинства и свои недостатки. Последних не очень много, но все-таки они есть. Итак, характеристика отрицательных свойств:
- Стоимость. Поскольку жаростойкий состав является специализированным, то и цена на него оказывается выше, чем на обычный материал. При покупке небольшого объема разница оказывается не такой уж и огромной, но при приобретении больших партий она становится ощутимой.
- Химический состав. Он не влияет ни на жизнедеятельность, ни на атмосферу, но при контакте с некоторыми элементами могут возникать реакции, способные ухудшить свойства раствора.
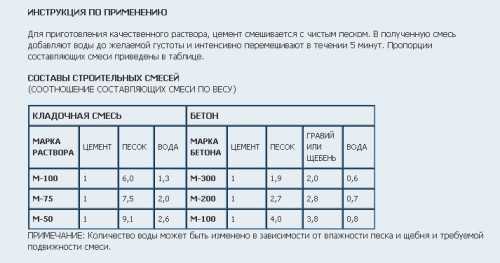
Таблица с инструкцией по приготовлению раствора.
Теперь рассмотрим положительные свойства специализированного цемента, которых оказывается гораздо больше:
- Жароустойчивость. В зависимости от вида и марки специализированного состава, температурный предел может колебаться в районе 2000 градусов, а некоторые разновидности, которые найти достаточно трудно, могут выдерживать даже 3500 градусов.
- Вязкость. По самым важным строительным параметрам, к каковым относится тягучесть, сцепляемость и другие, жаростойкий не уступает обычному.
- Простота приготовления. Для того чтобы смешать воду, песок и цемент, не нужно иметь соответствующего образования. А именно эти компоненты необходимы для приготовления раствора в домашних условиях.
Подготовительные работы
Перед тем, как начать строительные работы со специализированным составом, нужно провести подготовительные работы. Дело в том, что жаростойкий не любит пыли, сажи, жира, масляных пятен. Поэтому подготовительный этап заключается в обезжиривании и уборке рабочих поверхностей.
Необходимые инструменты для уборки:
- пылесос;
- влажная тряпка;
- спирт или любое другое чистящее обезжиривающее средство.
Жир необходимо оттереть спиртом или другой специальной жидкостью. Пыль нужно убрать с помощью пылесоса и влажной тряпки. Если на кирпичах имеется сажа, то их желательно отшлифовать, сняв при этом с поверхности 2 мм.
Для самой работы с раствором понадобятся следующие инструменты:
- дрель;
- миксер;
- бетономешалка;
- уровень;
- мастерок.
Работа с расвором
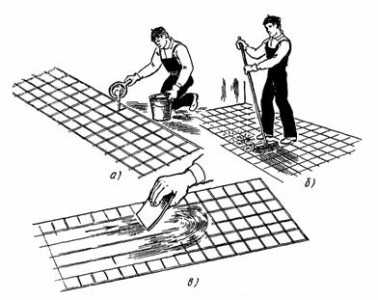
Схема отделки покрытий: а – заливка швов раствором; б – распределение раствора щеткой; в – выравнивание раствора шпателем.
После окончания подготовительных работ, можно приступать к заливке цемента. Сначала нужно развести необходимое количество смеси согласно прилагаемой инструкции. Приготовить состав можно либо в корыте, либо в бетономешалке, в зависимости от требуемого объема.
После приготовления, огнеупорный раствор выливается на рабочую поверхность и разглаживается мастерком. С помощью уровня время от времени проверяется ровность. При кладке кирпича с огнеупорным цементом, толщина наносимого слоя должна быть около 5 мм, на который кладется и плотно прижимается первый ряд кирпичей. Затем на эти кирпичи наносится еще один слой раствора и кладется второй ряд. Особое внимание при этом следует уделять нанесению раствора на стыки соседних кирпичей. По такому же принципу осуществляется и дальнейшая работа.
Важным моментом при работе с жаростойким цементом является тщательное заполнение цементом всех швов. Если следовать всем этим несложным правилам, данный материал прослужит не один десяток лет.
o-cemente.info