Защитный слой бетона для арматуры: нормативные требования
Содержание
- Назначение предохранительного слоя
- Что влияет на размер бетонной прослойки
- Толщина пласта бетона для различных случаев
- Особенности реконструкции прослойки
- Нормативные требования
- Максимально возможные отклонения защитного ряда.
Защитный слой бетона — это расстояние от поверхности арматурного стержня до грани железобетонного изделия. Арматура любой железобетонной конструкции должна иметь защитный слой бетона, дабы обеспечивать её совместную работу с бетоном, при этом одновременно защищая стальной элемент от воздействия окружающей среды. Кроме того, данный защитный слой увеличивает огнестойкость металлического элемента.
В зависимости от вида конструкции и её месторасположения, диаметра арматуры, условий эксплуатации, назначения (продольная рабочая, поперечная, распределительная, конструктивная) и условий работы минимальное значение защитного слоя бетона может разниться.
Назначение предохранительного слоя
Точно выдержанная толщина прослойки обеспечивает долговечность и надежность строения.
Она рассчитана так, чтобы:
- исключить влияние на арматуру влаги, агрессивных сред и уберечь от коррозийных изменений и разрушения;
- гарантировать верную совместную работу составляющих железобетона. Возникшее в конструкции напряжение от нагрузки бетон будет передавать металлическому стержню без потери энергии;
- увеличить огнестойкость строений из железобетона;
- обеспечить анкеровку прутков в бетоне с возможностью создания стыков и выводов на другие уровни.
Что влияет на размер бетонной прослойки
Неподвижное, добротное и точное соединение раствора и арматурных стержней – залог прочности железобетонного сооружения. При недостаточной величине пласта бетона прутки начнут разрушаться и произойдут изменения во всей конструкции строения.
Большой слой – не лучший вариант. Стоимость сооружения неоправданно увеличится, появится вероятность смещения прутков, что в свою очередь снизит прочность объекта. При использовании специальных фиксирующих устройств сдвиг арматуры перестал быть проблемой.
От чего же зависит оптимально подходящая толщина защитного пласта? Эта величина подбирается с учетом:
- Типа конструкций. Строительные нормативы четко указывают размеры защитного пласта для стен, фундамента, колонны, балок и других элементов;
- Диаметра арматурного прутка. Чем выше его сечение, тем больше толщина бетонной прослойки;
- Роли металлических элементов в конструкциях. Это могут быть распределительные стержни или рабочие, воспринимающие основные нагрузки;
- Условий окружающей среды. Чем она агрессивнее для элемента сооружения, тем выше нормы величины слоя вплоть до максимально допустимых;
- Вида арматуры. Она может быть ненапрягаемой и напрягаемой, устанавливаемой в места наибольших нагрузок.
Толщина пласта бетона для различных случаев
Величина слоя для защиты в железобетонных конструкциях прописана в СП 63.13330.2012. С помощью этого документа можно узнать точное значение прослойки для того или иного случая.
Минимальный размер слоя для рабочей арматуры должен составлять:
- в фундаменте с устроенной бетонной подготовкой и в грунте – 40 мм;
- для конструкции, находящейся на открытом воздухе – 30 мм;
- для закрытых влажных помещений – 25 мм;
- для помещений с пониженной и нормальной влажностью – 10 мм.
При использовании распределительного стержня и сборных элементов эти значения уменьшаются на 5 мм, но в любом случае толщина прослойки не должна быть меньше диаметра арматурного стержня и как минимум равняться 10 мм.
Если для односложных конструкций применяется поризованная или легкая бетонная смесь класса В7,5 или ниже, то пласт бетона должен быть не меньше 20 мм. При использовании для таких конструкций ячеистого раствора он составляет 25 мм. Это же значение установлено для стеновых панелей, монтируемых снаружи и без фактурного слоя.
Для стержней в предварительно напряженных элементах толщина защитной прослойки должна быть не меньше 40 мм или равняться трем диаметрам, а при размещении арматурных канатов – не меньше 20 мм. Если напрягаемый продольный пруток натягивается на бетон и размещается в каналах, то потребуется заливка раствора слоем 40 мм и более. При этом пласт смеси должен быть не менее диаметра канала, а пространство по краям арматуры – половина такого расстояния.
При эксплуатации в агрессивных средах стеновых панелей, ребристых и плоских плит защитный пласт создают из легкого и тяжелого бетона. Независимо от выбранного класса стали для арматуры толщина раствора для слабо- и среднеагрессивной среды составляет 15 см.
При сильной негативной степени влияния – 20 мм. Нередко в таких случаях используют композитные неметаллические стержни. В этих случаях величина защитного слоя подбирается так, чтобы обеспечивалась совместная работа прутка с бетоном. Для монолитных конструкций указанную выше толщину прослойки увеличивают на 5 мм.
Особенности реконструкции прослойки
В процессе эксплуатации строительные конструкции испытывают жесткие природные воздействия. Самые опасные из них – колебания температур и периодическое увлажнение внешней поверхности бетона. Поэтому защитный пласт, даже верно подобранный, постепенно может начать разрушаться. Трещины и отслоения со временем приводят к оголению арматурных стержней. Чтобы армирование могло выполнять свои функции на таких конструкциях необходимо восстановить прослойку.
Работы по реконструкции объекта начинаются с тщательного осмотра повреждений и проверки толщины имеющегося защитного пласта. Она измеряется специальным устройством, работа которого построена на магнитном принципе. Также выявляются причины возникновения повреждения и их степень. Ведь если глубинные слои элементов строения будут затронуты, то потребуется глобальное усиление прочности.
В простых случаях необходимо основательно заделать отдельные раковины, сколы и подобные дефекты поверхности. Такие ремонтные работы не требуют много времени и сил. Поврежденные участки подготавливают, убирая пыль, грязь и отслоившиеся частички.
Затем зачищают трещины и щели сжатым воздухом, грунтуют подлежащую ремонту плоскость и все дефекты заполняются раствором. Серьезные трещины сшивают плоскими анкерами; они должны быть покрыты защитным слоем в 20 мм. Все работы проводят при благоприятных температурных режимах в сухую погоду.
При значительном отслоении защитной прослойки, изменении характеристик материалов и поражении арматурных прутков коррозией необходима полная замена пласта.
Реконструкцию проводят следующим образом:
- аккуратно удаляют старый слой;
- арматуру очищают химическим способом или аппаратами высокого давления;
- прутки покрывают антикоррозийными составами;
- при необходимости восстановить прочность конструкции устанавливают стальные анкеры;
- старое основание очищают от загрязнений, пыли и насыщают водой;
- ремонтный раствор наносят торкретированием или набрызгом.
При этом малейшие трещины, поры и впадины заполняются смесью. Толщина прослойки обычно составляет порядка 30 мм.
Если вертикальные участки незначительные, то используют нанесение смеси по принципу оштукатуривания. Горизонтальное основание восстанавливают методом обычной стяжки.
Нормативные требования
Перед началом строительства следует ознакомиться со всеми строительными нормами и придерживаться их в процессе производства. При определении оптимальной толщины защитного пласта нужно руководствоваться всеми действующими требованиями, а не использовать только расчет диаметра прутка. Он не учитывает различные факторы и бывает неточным.
Отступление от норм, прописанных в документах, может привести к проблемам не только после окончания строительства, но и во время него. Масштабные строения контролируются специальными органами, поэтому несоответствие требованиям строительных правил повлечет за собой существенные затраты. Кроме того, от верных действий зависит срок службы всего сооружения.
Максимально возможные отклонения защитного ряда.
В соответствии со Строительными нормами и правилами допускается отклонение толщины экранизирующего ряда бетона:
- при толщине слоя менее 1,5 см – 0,3 см;
- при толщине слоя свыше 1,5 см – 0,5 см;
- при толщине слоя до 20 см – 0,9 см;
- смещение прута арматуры в процессе установки и в каркасе – четверть диаметра арматурного прута, но
- не свыше 0,2 диаметра наибольшего прута;
- продольное размещение окончания или сгиба прута арматуры – 5 см.
В зависимости от сечения арматуры и бетонного сооружения отклонения от необходимой толщины бетонного слоя, согласно с проектом, могут колебаться в пределах 0,4-0,8 см в сторону его увеличения и 0,3-0,5 см в сторону уменьшения.
Источники:
https://omega-beton.ru/informatsiya/stati/zashitnyi_sloy_betona/
http://svoydomtoday.ru/poleznoe-razdela-1/599-zashitniy-sloy-betona-dlya-armaturi.html
https://prorab2.ru/fundament/armatura-dlya-fundamenta/zaschitnyy-sloy-betona-dlya-armatury-v-fundamente.html
Инженерный вестник Дона | Расчет оптимальной величины защитного слоя бетона колонн квадратного сечения
Аннотация
В.А. Мурадян
Дата поступления статьи: 25.09.2013
Предлагается подход к расчету оптимальных значений защитного слоя бетона продольно армированных колонн, работающих при центральном сжатии. Моделирование осуществлено с использованием МКЭ — пакета Ansys при реализации пространственной конструкции и плоской модели сечения колонны.
Ключевые слова: железобетонная колонна, продольная арматура, защитный слой бетона, метод конечных элементов, критическая нагрузка
05.23.01 — Строительные конструкции, здания и сооружения
Предлагается подход к расчету оптимальных значений защитного слоя бетона продольно армированных колонн, работающих при центральном сжатии. Моделирование осуществлено с использованием МКЭ — пакета Ansys при реализации пространственной конструкции и плоской модели сечения колонны.

Рассмотрим конечно-элементную модель плоского деформирования нормального сечения колонны в следующей постановке [8-10]:
, ,
где — область, занимаемая бетоном, — область арматуры (рис. 1),
— величина защитного слоя бетона.
На линиях задаются нормальные растягивающие распределенные усилия по закону и соответственно. На линиях , — условия симметрии деформирования сечения колонны:
, .
Рис. 1
В качестве физических параметров выбраны значения величин, представленных в таблице 1, и использованных как для пространственной, так и плоской моделей.
Таблица 1
Материал |
Свойства материала |
|||||||
Арматура, |
Модуль Юнга EА, МПа |
2. |
||||||
Коэффициент Пуассона |
0.3 |
|||||||
Расчетное сопротивление RA, МПа |
400 |
|||||||
Мультилинейная диаграмма деформирования |
||||||||
|
Деформация |
Напряжение , МПа |
||||||
точка 1 |
RA/EA |
RA |
||||||
точка 2 |
0. |
RA |
||||||
Бетон, элемент |
Модуль Юнга EB, МПа |
3.25e4 |
||||||
Коэффициент Пуассона |
0.2 |
|||||||
Расчетное сопротивление при сжатии RB , МПа |
22 |
|||||||
Расчетное сопротивление при растяжении RBt , МПа |
1. |
|||||||
Мультилинейная диаграмма деформирования |
||||||||
|
Деформация |
Напряжение , МПа |
||||||
Сжатие |
||||||||
точка1 |
0.6*RB/EB |
0.6 RB |
||||||
точка2 |
|
RB |
||||||
точка3 |
0. |
RB |
||||||
Растяжение |
||||||||
точка1 |
0.6* RBt /EB |
0.6 RBt |
||||||
точка2 |
0.002 |
RBt |
||||||
точка3 |
0.0035 |
RBt |
||||||
Бетон, элемент |
Модуль Юнга EB, МПа |
3. |
||||||
Коэффициент Пуассона |
0.2 |
|||||||
Расчетное сопротивление на сжатие RB , МПа |
22 |
|||||||
Расчетное сопротивление на растяжение RBt , МПа |
1.8 |
|||||||
Коэффициент передачи касательных напряжений для открытой трещины |
0.1 |
|||||||
Коэффициент передачи касательных напряжений для закрытой трещины |
0. |
|||||||
Предельная прочность при двухосном растяжении |
1.2 RB |
|||||||
Предельная прочность при двухосном сжатии, наложенном на гидростатическое напряжение |
1.45 RB |
|||||||
Предельная прочность при одноосном сжатии, наложенном на гидростатическое напряжение |
1.725 RB |
Для плоской модели сечения считаем уровень прикладываемых нагрузок соответствующим линейному участку деформирования среды без учета пластических деформаций и процессов трещинообразования.
Рис. 2 Сетка конечных элементов
Для выбора характера прикладываемой нагрузки рассмотрены перемещения в среднем сечении колонны пространственной модели при уровне вертикального сжимающего усилия 0.7 от критического. Модуль вектора перемещений в сечении близок аналогичной величине смещения при плоской деформации при равномерном распределении нагрузки . Близость диаграмм распределения перемещений по сечению позволила сделать вывод о возможности рассмотрения случая постоянных усилий .
Дальнейшее исследование по выбору оптимального положения арматуры по сечению колонны основывалось на анализе интенсивности напряжений в зависимости от величины защитного слоя бетона
.
В качестве основного варианта использован случай выбора геометрических параметров модели: м. Установлено, что основными влияющими факторами на распределение интенсивности напряжений в сечении являются: соотношение модулей упругости бетона и арматуры, а также коэффициент Пуассона бетона, в основном определяющий характер сжимаемости материала сечения.
Установлено, что наиболее чувствительной характеристикой к изменению положения арматуры является концентрация напряжений вблизи границы раздела арматуры и бетона. Величина , Па на поверхности арматуры от параметра , м выведена на рис. 3.
Рис. 3. Распределение , Па от параметра .
Отметим, что минимальное значение полученной характеристики соответствует значению м и по сути определяет максимальный уровень критического усилия, приводящего к разрушению конструкции. Полученное значение соответствует анализу задачи в пространственной постановке по расчету критических усилий при нелинейном деформировании среды с учетом явлений трещинообразования и дробления бетона.
- Мурадян В.А., Маилян Д.Р. Железобетонные стойки с заглубленными продольными стержнями без поперечного армирования // Расчет и проектирование железобетонных конструкций. — Ростов-на-Дону: РГСУ, 2009 – С. 94-95.
- Мурадян В.А., Маилян Д.Р. Устойчивость арматурных стержней в сжатой железобетонной колонне // Строительство 2010. Материалы научно-практической конференции. — Ростов-на-Дону: 2010 . – С.40-42.
- Кургин К.В., Маилян Д.Р. Работа керамзитофибробетонных колонн при повторных нагрузках [Электронный ресурс] // «Инженерный вестник Дона», 2012, №1. – Режим доступа: http://www.ivdon.ru/magazine/archive/n1y2012/738 (доступ свободный) – Загл. с экрана. – Яз. рус.
- Мурадян В.А., Маилян Д.Р. К методике расчета железобетонных внецентренно сжатых колонн // «Инженерный вестник Дона», 2012, №4. – Режим доступа: http://www.ivdon.ru/magazine/archive/n4p2y2012/1333 (доступ свободный) – Загл.
с экрана. – Яз. рус.
- Маилян Д.Р., Несветаев Г.В. О несущей способности колонн из высокопрочных самоуплотняющихся бетонов // Бетон и железобетон в третьем тысячелетии. Материалы научно-практической конференции. — Махачкала: 2010. – С.47-49.
- Маилян Д.Р., Резван И.В. Несущая способность бетонного ядра трубобетонных колонн // Вестник Майкопского государственного технического университета. -Майкоп: 2011. – С. 14-19.
- Шиляева О.В., Хунагов Р.А., Блягоз А.М. Моделирование устойчивости железобетонной панели // Новые технологии. — 2012. – Вып. 3. – С. 114-119.
- ANSYS, Inc. Theory Reference: ANSYS Release 9.0. – С.14-203.
- Mkrtchyan A., Akcenov V., Mailyan. Experimental study of the structural properties of high-strength concrete // 5th International Scientific Conference “European Applied Sciences: modern approaches in scientific researches”:Papers of the 5th International Scientific Conference. August 26–27. — Stuttgart, Germany.
– 2013. — 164 p.
- Mkrtchyan A., Akcenov V., Mailyan. Experimental study of reinforced concrete columns of high-strength concrete // “Applied Sciences and technologies in the United States and Europe: common challenges and scientific findings”: Papers of the 2nd International Scientific Conference (September 9–10, 2013). Cibunet Publishing. — New York, USA. — 2013. — 242 p.
Покрытия против карбонизации для бетонных зданий и сооружений
ЖБ Конструкции в экстремальных условиях подвергаются суровым условиям воздействия. Происходящая коррозия арматуры представляет собой сложный электрохимический процесс из-за проникновения либо влаги, ионов хлора, CO 2 , либо проникновения комбинированных вредных веществ через пористый бетон и ускоряется другими каталитическими факторами, такими как средняя температура, относительная влажность. и давление ветра. Таким образом, износ железобетонных конструкций становится очень быстрым, и для увеличения срока их службы требуется защита подходящим защитным покрытием. В этой статье основное внимание уделяется пригодности нанесения алифатического акрилового покрытия против карбонизации для обеспечения долговечности железобетонных конструкций в таких экстремальных условиях.
ВВЕДЕНИЕ
Бетонные конструкции со временем изнашиваются, и износ происходит намного быстрее в экстремальных условиях, связанных с высокой влажностью, хлоридами и CO 2 в атмосфере. Попадание влаги и вредных веществ, таких как ионы хлорида, CO 2 и других химических веществ, происходит через поры бетона в процессе диффузии и вызывает коррозию арматуры и последующее повреждение железобетонных конструкций.
Защита железобетонных конструкций подходящим защитным покрытием является общепринятым методом увеличения срока службы в таких экстремальных условиях. Без защитного покрытия деградация железобетонных конструкций становится очень быстрой из-за коррозии закладной стальной арматуры. Инфраструктурные проекты, такие как мосты, эстакады, подземные переходы и гаражи, подвержены проникновению CO 2 . Плотный уплотненный бетон с минеральными и химическими добавками с низким водоцементным коэффициентом сам по себе не может предотвратить такую коррозию. Следовательно, дополнительные меры защиты, такие как защитное покрытие, ингибиторы коррозии на основе нитрита кальция для новых конструкций и мигрирующий ингибитор коррозии для старых конструкций, а также коррозионностойкая сталь или антикоррозионная окраска стали, довольно часто необходимы для увеличения долговечности и срока службы. Новейшие технологии катодной защиты также больше подходят для дополнительной защиты таких конструкций, как мосты и эстакады.
РАЗЛОЖЕНИЕ В СВЯЗИ С КАРБОНИРОВАНИЕМ
Карбонизация представляет собой естественный процесс, при котором гидроксид кальция Ca(OH) 2 в гидратированном портландцементном тесте соединяется с диоксидом углерода (CO 2 ) в присутствии влаги и в последующем образует карбонат кальция. реакции, как показано в уравнениях ниже:
Растворение CO 2 в поровом растворе цементного теста:
CO 2 + 2 OH = CO 3 2- + H 2 O
Растворение Ca(OH) 2:
Ca(OH) 2 = Ca 2+ + 2 OH-
Разложение гидратированных силикатных и алюминатных фаз,
X CaO. SiO 2 (водн.) + z H 2 O = y Ca 2 + + 2y OH- + (x-y) CaO.SiO 2 (водн.)
Реакция с образованием карбоната:
Ca 2 + + CO 3 2- = Ca CO 3
После разрушения пассивирующего слоя вокруг стали из-за карбонизации дальнейшими требованиями для защиты от коррозии является достаточное количество влаги, чтобы служить электролитом с низким сопротивлением, и достаточное количество кислорода, чтобы поддерживать реакцию катодной коррозии. Следовательно, на скорость карбонизации сильно влияют прочность бетона, проницаемость, относительная влажность, глубина защитного слоя бетона, период отверждения во влажном состоянии и условия воздействия. Хороший непроницаемый бетон с большим защитным слоем защищает от проникновения CO 2 . Из-за образования угольного пористого раствора может быть снижение pH до 8,3 и, следовательно, большая вероятность усиленной коррозии арматуры. При рН менее 5 и влажности выше 50% возникает кислая среда, которая приводит к обширной коррозии арматуры. Но когда pH находится в диапазоне от 5,5 до 8,5, а влажность выше 50%, в это время в нейтральной среде начнется коррозия арматуры, которая является умеренной коррозией. Но если pH больше 8,5 и независимо от влажности, там, где арматура защищена, будет щелочная среда. Относительная влажность играет важную роль в диффузии CO 2 через бетон. Относительная влажность менее 50% и выше 80% не оказывает большого влияния на диффузию CO 2 , поскольку поры в бетоне становятся либо слишком сухими, либо почти насыщенными, соответственно, не создавая давления паров для процесса диффузии. Установлено, что критическая влажность для карбонизации бетона составляет 80 %. Точно так же оптимальными климатическими условиями для карбонизации являются относительная влажность в диапазоне от 50% до 70%, при этом циклы смачивания и сушки усиливают реакцию. Поскольку Мумбаи является прибрежным городом и имеет более высокую концентрацию хлоридов в атмосфере, комбинированное воздействие хлоридов вместе с CO 2 не рассматривался.
Тем не менее, в экстремальных условиях с комбинированным износом из-за карбонизации и хлоридов скорость коррозии становится очень высокой, как показано на рис.1. Таким образом, коррозия арматуры представляет собой чрезвычайно сложную электрохимическую реакцию, в которой железо соединяется с кислородом с образованием оксидов и гидроксидов железа, которые являются продуктами ржавчины. Эти продукты ржавчины расширяются в пять-восемь раз, в результате чего они занимают больший объем, чем некорродированная сталь, вызывая внутренние напряжения из-за удержания корродирующей стали. Эти внутренние напряжения приводят к растрескиванию бетонного покрытия. После этой фазы инициации коррозии эти трещины становятся источником дальнейшего проникновения вредных веществ для распространения в более крупные трещины, расслаивания и выкрашивания бетона, как показано на рис. 2.
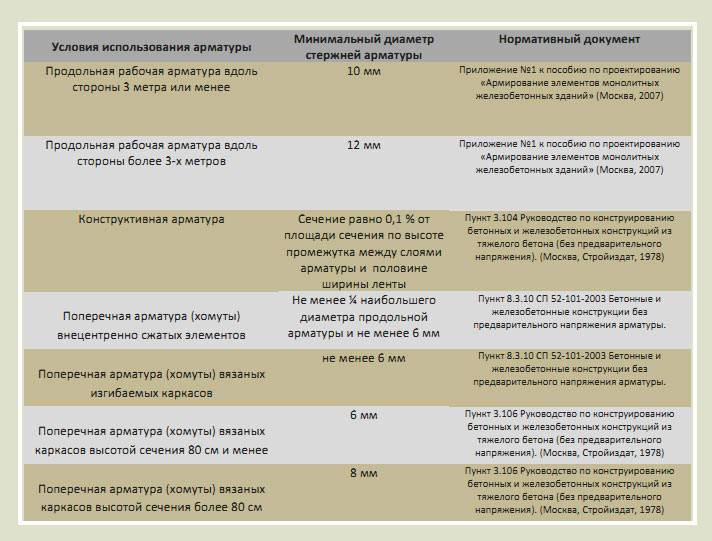
Уравнение Бре: d = k √t Где d — глубина карбонизации.
t – время экспозиции.
k — коэффициент.
Значения k, влияющие на скорость карбонизации, были установлены в исследовании Морено Е.И.: < 3 мм/год ½: Менее 3 мм – 6 мм/год ½: Умеренная > 6 мм/год ½:
Тяжелая Уравнение Брауна: d = k (√t/S)
Где d, t и k, как указано выше, и дополнительно S – прочность бетона на сжатие Из приведенных выше уравнений глубина карбонизации за 20 лет (мм) за 28 дней прочность на сжатие различных марок бетона приведены в таблице ниже:
РАСЧЕТНАЯ ГЛУБИНА КАРБОНИРОВАНИЯ
Расчетный срок службы 20 лет.![]() | 28 дней Прочность на сжатие (МПа) |
6 | 58 |
14 | 48 |
22 | 38 |
33 | 28 |
При проектировании любых железобетонных конструкций с конкретной маркой бетона глубина карбонизации рассчитывается по приведенным выше уравнениям без какого-либо защитного покрытия, и глубина защитного слоя обеспечивается соответственно с учетом минимальной глубины защитного слоя, как указано в сводах правил. Это также помогает обеспечить дополнительную защиту с помощью защитного покрытия, чтобы определить оптимальную глубину покрытия при проектировании долговечности конструкций.
Имеются также данные об увеличении прочности на сжатие и растяжение, иногда до 100% в карбонизированном режиме при испытании молотком на отскок. Потому что карбонизированный бетон становится очень твердым, что может дать ложные показания при испытании молотком с отскоком. Простой тест 1% раствора фенолфталеина должен быть распылен, чтобы проверить карбонизацию бетона, прежде чем нужно будет пройти тест на отскок. Если после распыления бетон из розового становится белым, то это карбонизированный бетон, в противном случае бетон негазированный.
ПОКРЫТИЯ В КАЧЕСТВЕ ЭКРАНОВ ДЛЯ ДИОКСИДА УГЛЕРОДА
Метод измерения сопротивления диффузии диоксида углерода любого покрытия может соответствовать стандарту ASTM E 96:2000, «Стандартный метод испытаний материалов на пропускание водяного пара», который в основном предназначен для измерения воды. паропроницаемость. Однако эту процедуру можно использовать, подвергая поверхность с покрытием воздействию среды, богатой CO 2 , и, таким образом, определяя устойчивость к диффузии CO 2 на основе прироста массы образца.
Защитное покрытие заполняет поверхностные поры и перекрывает мелкие трещины, образуя барьер для движения углекислого газа. Измеряется диффузией углекислого газа, которая определяется как способность покрытия сопротивляться проникновению углекислого газа и останавливать карбонизацию бетона. Сопротивление диффузии CO 2 (µ) указано в метрах эквивалентной толщины воздуха. Эти значения показывают, насколько более непроницаемым для CO 2 является покрытие по сравнению с воздухом. Коэффициент диффузии обычно составляет около 7x 10–8 см 2 /сек.
Эквивалентная толщина слоя воздуха (R) является произведением коэффициента диффузии CO 2 (µ) и толщины покрытия (S).
R = µ x S метров
Значение R, превышающее 50 м, обычно считается адекватным. Значение R, используемое при проектировании системы покрытия, предназначено для предотвращения фронта карбонизации, достигающего стальной арматуры в течение 60-летнего жизненного цикла, при условии, что защитный слой составляет не менее 25 мм, в противном случае для меньшего защитного слоя значения R необходимо увеличить. Также значение R остается одинаковым для старого и нового бетона марки М 45 и выше.
Другим способом выражения диффузии углекислого газа является эквивалентная толщина бетона (Sc) Sc = R/µ бетона,
Где µ бетона принимается равным 400, что является средним значением для бетона с прочностью 30 Н/мм2.
Sc дает эквивалентный бетонный слой, который имеет такое же сопротивление диффузии CO 2 , что и данная толщина покрытия. Как правило, высококачественная система защиты от карбонизации на основе растворителя размером 150 микрон будет иметь эквивалентную толщину бетона 700 мм. Следовательно, для диффузии углерода требуется минимальная толщина 150 мм.
ПОКРЫТИЯ, ПРЕДОТВРАЩАЮЩИЕ КАРБОНИРОВАНИЕ
Защита от карбонизации зависит от барьерных свойств покрытия, а также от проницаемости или сопротивления диффузии покрытия атмосферному CO 2 . Большинство покрытий, препятствующих карбонизации, представляют собой композицию акрилового раствора полимера на основе растворителя, правильно подобранных и градуированных инертных наполнителей, светостойких пигментов и добавок. Свойства такого антикарбонатного покрытия приведены в табл.
Покрытие против карбонизации также разработано для защиты армированного бетона и других цементных оснований кирпичной кладки, которые подвергаются непосредственному воздействию атмосферных условий, таких как УФ-излучение, высокая влажность, сильный дождь, промышленное загрязнение и карбонизация. Он проникает в пористую бетонную основу, образуя непроницаемое для наружной кладки покрытие. Различные типы усиленных силиконом, виниловых и полиуретановых покрытий также хорошо подходят для защиты от карбонизации. Покрытия на универсальной основе из полиэтилена, эпоксидной смолы, эпоксидной смолы, хлоркаучука, битумные, цементные, силиконовые и силикатные не подходят для антикарбонатных покрытий.
СПОСОБ ПРИМЕНЕНИЯ
- Подготовка поверхности для новых бетонных поверхностей
Новые бетонные/оштукатуренные поверхности должны сохнуть не менее 6–8 недель перед нанесением покрытия. Если не будет проведено достаточное отверждение, захваченная влага будет оказывать давление на мембрану покрытия. Все поверхности должны быть чистыми, сухими и свободными от рыхлого материала, масляной смазки; и т. д. В случае, если бетонная поверхность обеспечивает лучшую очистку и сцепление, следует выполнить легкую пескоструйную очистку. Бетонную поверхность необходимо тщательно промыть водой, чтобы удалить грязь и пыль, которые могут ухудшить декоративный эффект и сцепление покрытия. Любой предыдущий рост грибка и водорослей должен быть полностью удален энергичной чисткой проволочной щеткой и промывкой водой. Обработка подходящим раствором биоцида также должна быть проведена до нанесения, чтобы гарантировать полное удаление водорослей/грибков.
- Подготовка поверхности для ранее окрашенных поверхностей
Алкидная краска, если таковая имеется, должна быть тщательно отшлифована, чтобы полностью удалить все отслоившиеся частицы. Механические методы являются наиболее подходящими. Внешнюю поверхность, ранее покрытую цементной краской, следует очистить металлической щеткой, тщательно промыть водой и дать высохнуть. Обработка против роста водорослей/грибков остается такой же, как и для новой бетонной поверхности. Все трещины должны быть соответствующим образом обработаны с использованием эластомерного герметика или материалов для ремонта трещин.
- Грунтовка
Для лучшего сцепления и улучшения качества поверхности грунтовку следует наносить кистью или распылением, разбавляя минеральным скипидаром в пропорции 2:1. Перед нанесением финишного слоя необходимо дать высохнуть в течение 2-3 часов.
- Отделочное покрытие
Два аккуратных слоя антикарбонизирующего покрытия следует наносить без разбавления. Необходимо убедиться, что покрытие нанесено после того, как первый слой высохнет в течение 5-6 часов.
- Меры предосторожности и ограничения
Несмотря на то, что между двумя слоями может быть выдержан промежуток в 5-6 часов, в холодном/влажном климате время высыхания может увеличиться. Продукты покрытия следует хорошо перемешать перед использованием. Нанесение не следует проводить при температуре окружающей среды ниже 10 o C.
- Области применения
В качестве антикарбонатного, защитного и декоративного покрытия для мостов, эстакад, метро, подземных переходов, гаражей, туннелей, дымоходов, промышленных сооружений, стадионов и резервуаров для воды ЖБИ. Также оштукатуриваются все бетонные конструкции и цементные наружные каменные поверхности, подвергающиеся воздействию экстремальных атмосферных условий. Кроме того, все тонкие железобетонные конструкции с меньшим покрытием, такие как фасады, ребра, являются другими областями применения антикарбонатного покрытия.
ОСОБЕННОСТИ И ПРЕИМУЩЕСТВА
Карбонизация – Эти покрытия являются отличным барьером для проникновения и воздействия углекислого газа, воды, сульфатов и ионов хлора.
Защита – Покрытие защищает конструкции от неблагоприятной морской и прибрежной среды.
Адгезия – Обеспечивают превосходную адгезию к основанию с высокой пленкообразующей способностью. Устойчивость к микроорганизмам – они также обеспечивают превосходную устойчивость к водорослям и грибкам.
Простота нанесения – Поскольку они однокомпонентные, наносятся прямо из контейнера, кистью, валиком или распылением.
Долговечность. Обеспечивают прочное, гибкое и долговечное покрытие.
ВЫВОДЫ
Антикарбонатное покрытие позволяет создать защитный барьер на бетонных конструкциях не только от карбонизации, но и от проникновения хлоридов и влаги. Наиболее подходят для таких покрытий акриловые, усиленные силиконом, эпоксидные и полиуретановые. Учитывая экстремальные условия окружающей среды, все железобетонные конструкции должны быть защищены алифатическим акриловым покрытием для увеличения срока их службы.
Эр. Шамант Кумар М., управляющий директор Skanda Group of the ConstructionsРуководство по нанесению эпоксидного покрытия на бетон
Руководство по нанесению эпоксидного покрытия
Руководство по проектированию: эпоксидные покрытия
Эпоксидные покрытия с высокими эксплуатационными характеристиками используются для защиты бетона и стали от химического и механического воздействия во внутренних, наружных и морских условиях. 2K эпоксидные покрытия состоят из двух или более компонентов, которые при смешивании и нанесении в виде пленки вступают в химическую реакцию с образованием защитной пленки с высокой целостностью, отличной адгезией, прочностью и ударопрочностью без добавления растворителей или воды.
Эти покрытия наносятся в виде пленок толщиной от нескольких до более 150 мил. Покрытия обеспечивают защитный непроницаемый барьер для элементов, которые в противном случае могут воздействовать на подложку. Химический состав и плотность поперечных связей материала покрытия определяют его устойчивость к определенным химическим веществам, в то время как устойчивость к механическим нагрузкам, таким как истирание и удары, зависит от физических свойств и толщины пленки покрытия.
Покрытия на основе растворителей, как правило, имеют длительный срок жизнеспособности, они «тоньше» и, следовательно, их легче наносить. Толщина «сухой пленки» или пленки, остающейся после испарения растворителя, пропорциональна содержанию твердых веществ в материале покрытия и толщине нанесенной или «мокрой пленки». ChemCo не производит эпоксидные смолы на основе растворителей, поскольку мы стремимся производить покрытия только с нулевым содержанием летучих органических соединений.
Чтобы избежать провисаний или утечек, а также обеспечить надлежащее испарение растворителя, покрытия на основе растворителей наносятся в виде тонких пленок. Нанесение при низкой температуре или толстым слоем может привести к захвату растворителя, что приведет к образованию пузырей или отслоению.
Покрытия на основе растворителей особенно полезны в качестве грунтовок, герметиков, пенетрантов или там, где не требуется большая толщина пленки. В последние годы были разработаны эпоксидные покрытия, в которых в качестве носителя используется вода. Такие продукты содержат материалы покрытия в виде эмульсий или дисперсий, которые при нанесении и испарении воды сливаются, образуя защитную пленку.
Покрытия без растворителей («100% твердых веществ») не содержат летучих компонентов, поэтому конечная толщина отвержденного покрытия такая же, как и нанесенная толщина. Эта категория эпоксидных покрытий производится компанией ChemCo Systems. Преимущества лакокрасочных материалов, не содержащих растворителей, по сравнению с материалами для покрытий на основе растворителей:
- Для достижения желаемой толщины пленки требуется меньше слоев.
- Может быть достигнуто низкотемпературное отверждение.
- Требования к вентиляции снижаются во время нанесения и отверждения.
- Загрязнение воздуха и риск возгорания сведены к минимуму.
- 0 Сертификаты VOC и LEED, включая соответствие требованиям IEQ 4.1.
- Компоненты негорючие.
При использовании на полах и палубах эпоксидные покрытия могут быть защищены от скольжения путем добавления песка в поверхностный слой или усилены путем добавления стеклоткани. Наносимые шпателем лакокрасочные материалы нерастекающейся или мастичной консистенции применяются для нанесения толстых слоев на вертикальные и потолочные поверхности.
Некоторые высокоэффективные эпоксидные покрытия для стальных и бетонных поверхностей могут мелеть и обесцвечиваться под воздействием прямых солнечных лучей, из-за чего их покрытие тускнеет. Эти особенности следует учитывать при применении наружных архитектурных покрытий.
Защита от высокоагрессивных химикатов
Большинство применений, требующих высокой степени химической стойкости, встречаются в обрабатывающей и химической промышленности. Правильно составленные и нанесенные материалы покрытия могут остановить действие химических веществ, быстро разрушающих бетон и сталь. Области применения, требующие высокой химической стойкости, включают:
- Нефтеперерабатывающие заводы, гальванические заводы, химические заводы, помещения для обработки свинцово-кислотных аккумуляторов.
- Предприятия пищевой промышленности, мясокомбинаты, кожевенные и молочные заводы.
- Районы с высоким уровнем радиационного облучения.
- Производственные предприятия, в частности, где используются смазочно-охлаждающие жидкости.
Защита от умеренно агрессивных химикатов
Эпоксидные покрытия защищают бетон и сталь, которые подвергаются умеренному химическому воздействию таких источников, как кислотный туман, органические кислоты и вода, содержащая коррозионно-активные химические вещества. Бетонные поверхности часто пористые, подвержены размножению бактерий и их трудно чистить. Глянцевая, похожая на плитку, непроницаемая природа этих покрытий обеспечивает идеальную защиту в следующих областях:
- Институциональные и коммерческие кухни и прачечные.
- Резервуары и метантенки для очистки сточных вод и воды.
- Пивоваренные и винодельческие предприятия.
- Защита бетонных колонн, опор и устоев от проникновения противогололедных солей.
- Защита бетона и стали в морских сооружениях выше зоны заплеска.
- Защита бетона от эрозии под воздействием воды с высокой скоростью.
Обеспечение сопротивления скольжению на дорожном покрытии
Сопротивление скольжению бетонных, стальных и асфальтовых поверхностей можно улучшить путем нанесения противоскользящего покрытия. Он состоит из выбранного заполнителя, встроенного в покрытие. Заполнитель резко увеличивает коэффициент трения гладкого покрытия.
Области, подверженные сильному износу из-за высокой скорости и объема движения, требуют текстуры поверхности, которая не будет стираться или полироваться до гладкости. Противоскользящие покрытия используются для покрытия:
- Промышленные полы
- Парковочные площадки и пандусы
- Погрузочные доки
- Бетонные настилы мостов
- Пункты взимания платы
Покрытие морских конструкций
Эпоксидные покрытия используются для защиты бетонных и стальных морских конструкций, поскольку доступны составы для прилипания к влажным субстратам. Использование морских покрытий можно разделить на две области: нанесение в зоне брызг и нанесение под водой. Оба применения требуют способности материала покрытия быть пригодным для обработки, прилипать и отверждаться под водой; в зоне разбрызгивания материал должен противостоять воздействию волн во время нанесения и после отверждения. Типичные области применения для защиты морских сооружений включают:
- Покрытие свай, причалов, ограждений и устоев в зоне заплеска.
- Покрытие резервуаров для воды, рыбоходов, дамб и водосточных сооружений.
- Покрытие свай, причалов, дамб и устоев под водой.
Особенности дизайна
Влияние температуры
- Температура нанесения: Температура во время нанесения влияет на характеристики обработки материала, скорость испарения растворителя из пленки и характеристики отверждения покрытия. При наружном применении оптимальным временем для нанесения покрытия является период снижения температуры поверхности, чтобы свести к минимуму вероятность образования пузырей, вызванных проникновением водяного пара (см. 1.2.2).
- Рабочая температура: большинство физических свойств эпоксидных смол зависят от температуры. Важно определить диапазон рабочих температур для предлагаемого применения, чтобы можно было оценить рабочие характеристики продукта-кандидата.
Влажность
- Влажность поверхности: Хотя некоторые материалы будут прилипать к влажной поверхности, превосходная адгезия достигается в сухих условиях.
- Поднимающаяся влага: водяной пар проходит через пористое вещество, такое как бетон, из области с высокой влажностью в область с низкой влажностью. Когда поток этой влаги прерывается непроницаемым слоем, таким как эпоксидная смола, это может вызвать образование пузырей на неотвержденном материале. Влага, скапливающаяся под отвержденным верхним слоем, также может привести к отслаиванию в случае замерзания. Это условие особенно распространено с плитами на уровне без барьера влаги между почвой и плитой. Повышение влажности можно обнаружить, приклеив к полу полиэтиленовый лист площадью 3 фута. Через 24 часа, если бетон под листом становится темным или на нижней стороне листа образуется конденсат, это означает, что существует повышенная влажность, и перед нанесением покрытия следует оценить корректирующие меры. В индустрии напольных покрытий установлен минимальный стандарт водопроницаемости 3 фунта или меньше на тысячу квадратных футов в сутки. При подозрении на наличие влаги несколько тестовых наборов следует разместить через произвольные промежутки вокруг плиты перекрытия.
- Конденсирующая влага: когда температура плиты равна или ниже точки росы атмосферы, на ней будет конденсироваться влага. Чтобы облегчить это условие, температура плиты должна быть повышена на достаточную величину, чтобы температура поверхности оставалась выше температуры воздуха во время нанесения материала покрытия.
- Время простоя: область, на которую наносится покрытие, должна быть выведена из эксплуатации во время установки и отверждения. Рекомендуется реалистично оценить временной интервал, в течение которого данный участок может быть закрыт на ремонт.
Продукты питания и питьевая вода
- Контакт: Если продукты питания или питьевая вода могут вступить в контакт с покрытием, обычно применяется стандарт ANSI 61 с испытаниями, проводимыми NSF или UL.
- Запах: Химические вещества, связанные с некоторыми продуктами для покрытия, могут испортить вкус продуктов и напитков, находящихся на открытом воздухе; во время применения рекомендуются соответствующие меры предосторожности, включая удаление таких продуктов.
- Механическая нагрузка: Прочность покрытия препятствует истиранию, износу и ударам. Толщина покрытия способствует устойчивости к ударам.
- Химическое воздействие: характер и тяжесть химического воздействия зависят от химических соединений, их концентрации, продолжительности воздействия, частоты очистки или промывки, рабочей температуры окружающей среды и температуры раствора.
Сопротивление скольжению
- Тяговые силы, которым должны сопротивляться поверхности, подверженные пешеходному движению, создаются изношенной опорой. Относительная скользкость поверхности, влажной и сухой, измеряется как для кожи, так и для резины (см. раздел 6.5.1).
- Транспортное движение: Помимо текстуры поверхности, сопротивление скольжению транспортных средств зависит от скорости транспортного средства и уклона поверхности. Методы испытаний, учитывающие эти переменные, были разработаны и используются несколькими дорожными агентствами (см.
раздел 6.5.2). Под воздействием автомобильного движения текстура поверхности может изнашиваться и полироваться, что снижает сопротивление скольжению; поэтому сопротивление скольжению периодически контролируется, чтобы убедиться, что оно поддерживается в безопасных пределах.
- Архитектура: ультрафиолетовый компонент солнечного света может вызвать меление и обесцвечивание некоторых эпоксидных материалов при наружном применении. Эти изменения являются поверхностным явлением и не влияют на характеристики материала покрытия в агрессивных средах. Важно, чтобы проектировщик знал об этих возможных изменениях.
Материалы
Характеристики применения
- Покрытия на основе растворителей: Покрытия на основе растворителей лучше всего наносить с помощью воздушного распыления или обычного безвоздушного распыления, хотя также можно использовать кисть, валик или ракель. Толщина мокрой пленки не должна превышать максимальную, рекомендованную для отдельного продукта, чтобы избежать захвата растворителя или провисания.
- Покрытия, не содержащие растворителей: Покрытия, не содержащие растворителей, чаще всего наносятся кистью, валиком, ракелем или шпателем, но также могут наноситься с помощью оборудования для многокомпонентного, нагреваемого, дозированного смешивания, распыления воздухом или безвоздушного распыления.
- Характеристики отверждения: Отверждение эпоксидной смолы ускоряется при повышении и замедляется при понижении температуры. Скорость испарения растворителя также замедляется при понижении температуры.
- Жизнеспособность: Жизнеспособность представляет собой срок полезного использования смешанной эпоксидной системы в емкости для смешивания и зависит от температуры материала.
- Время нанесения следующего слоя: Последующие слои должны наноситься в пределах минимального и максимального пределов. Минимальное время перекрытия – это время, необходимое для того, чтобы покрытие стало нелипким. Максимальное время перекрытия – это время, по истечении которого последующий слой не будет прилипать к предыдущему слою без механической шероховатости отвержденной поверхности.
- Время высыхания: время, необходимое для того, чтобы покрытие стало достаточно твердым, чтобы выдерживать легкие нагрузки (например, пешеходное движение).
- Время полного отверждения: время, необходимое для того, чтобы покрытие полностью проявило свой механический и химический потенциал.
Характеристики отверждения
- Адгезия: Прочность сцепления покрытия зависит от подготовки поверхности, способности связывания материала покрытия с рассматриваемой подложкой и толщины покрытия. Подложка может быть влажным или сухим бетоном, сталью, бетоном с грунтовочным покрытием, сталью с грунтовочным покрытием и различными другими субстратами. Прочность сцепления можно определить с помощью подходящего тестера адгезии (см. раздел 6.3).
- Химическая стойкость: Устойчивость к химическим веществам зависит от внутренней устойчивости системы смола/отвердитель в составе покрытия и целостности покрытия. Приемлемые покрытия не имеют точечных отверстий, пропусков, трещин и других дефектов поверхности.
- Прочность: чтобы сохранить целостность при использовании, покрытия должны быть прочными и ударопрочными, чтобы противостоять выбоинам и сколам.
- Сопротивление скольжению: как заполнитель, так и материал покрытия вносят вклад в свойства сопротивления скольжению: количество заполнителя и его градация, износ, полировка и характеристики твердости влияют на степень и долговечность сопротивления скольжению. Толщина, когезия и прочность сцепления материала покрытия влияют на способность покрытия связывать заполнитель на месте.
Оценка количества
Когда известна требуемая толщина сухой пленки:
- Определите количество галлонов на квадратный фут для достижения требуемой толщины сухой пленки:
Галлоны на квадратный фут = милы сухой пленки
% твердых веществ по объему x 16,04
Умножьте это значение на количество квадратных футов, подлежащих покрытию, чтобы получить общее количество галлонов требуемого материала.
При использовании рекомендуемой производителем нормы укрывистости:
- Толщину сухой пленки на слой определяют по: мил сухой пленки = % твердых веществ по объему x 16,04 скорость распространения (кв. футов на галлон)
- Определите необходимое количество слоев, разделив требуемую толщину сухой пленки на милы сухой пленки на слой.
- Разделите рекомендуемую норму расхода (в квадратных футах на галлон) на общую площадь покрытия и умножьте на количество слоев, чтобы получить необходимые галлоны.
Подготовка поверхности
Подготовка поверхности
- Общие. Склеиваемые поверхности должны быть чистыми и прочными, что во всех случаях требует определенной подготовки.
- Оценка поверхности: Для оценки состояния поверхности и эффективности процедур подготовки поверхности можно использовать следующие тесты.
- Прочность: Прочность поверхности на растяжение при прямом растяжении может быть определена испытанием на отрыв заглушки трубы или имеющимся в продаже тестером адгезии.
Прочность бетонной связи должна быть не менее 200 фунтов на квадратный дюйм.
- Загрязнители: Присутствие жира, воска или масла можно определить, капнув на поверхность небольшое количество соляной кислоты. Отсутствие реакции указывает на присутствие загрязнителей. Если масло проникло в бетонную поверхность, это можно обнаружить, подняв температуру небольшого участка примерно до 150°F с помощью нагревательной лампы. О наличии загрязнения свидетельствует появление масла или участок становится «сальным» на ощупь.
Процедуры очистки
- Бетонные поверхности:
- Жировые, восковые и масляные загрязнения могут быть удалены путем очистки моющим средством промышленного класса или обезжиривающими составами с последующей механической очисткой.
- Слабый или испорченный бетон необходимо удалить до прочного бетона. Это может быть достигнуто с помощью бучардирования, пескоструйной обработки, дробеструйной обработки, скарификации, гидроструйной обработки или других подходящих механических средств.
- Грязь, пыль, цементное молоко и отвердители удаляются дробеструйной очисткой, пескоструйной обработкой, шлифованием или травлением 15%-ной соляной кислотой. Кислотное травление следует использовать только в том случае, если нет практической альтернативы. За этим следует чистка и промывка большим количеством чистой воды. Проверьте удаление кислоты с помощью влажной индикаторной бумаги. Чтение должно быть больше 10.
- За механической очисткой следует вакуумная очистка или безмасляная струйная очистка сухим воздухом.
- Стальные поверхности:
- Грязь, жир и масло удаляются с помощью подходящих чистящих и обезжиривающих составов промышленного класса.
- Ржавчина и прокатная окалина удаляются дробеструйной и пескоструйной обработкой до белого металла. За пескоструйной обработкой следует вакуумная или безмасляная сухая струйная очистка.
Общий
- Предварительное кондиционирование: Для облегчения смешивания и нанесения эпоксидных покрытий рекомендуется предварительное кондиционирование материала до комнатной температуры за 24 часа до использования.
- Смешивание: Как и другие лакокрасочные материалы, пигментированные эпоксидные покрытия необходимо перемешивать для повторного диспергирования пигментов и наполнителей, которые могли осесть во время хранения. Для обеспечения надлежащего отверждения важно, чтобы компоненты покрытия были тщательно отмерены и надлежащим образом смешаны. Тщательное перемешивание займет от 3 до 5 минут, в течение которых стенки и дно сосуда для смешивания следует очищать лопаткой для смешивания. Растворители следует добавлять только в том случае, если это рекомендовано производителем.
- Количество слоев: Требуемая общая толщина сухой пленки и тип материала покрытия определяют количество слоев. Для покрытия на основе растворителя потребуется несколько слоев для достижения той же конечной толщины, что и для одного слоя покрытия со 100%-ным содержанием твердых веществ.
- Методы нанесения: Жидкие покрытия можно наносить кистью, валиком, воздушным или безвоздушным распылением, а на горизонтальные поверхности можно использовать ракель.
Неусадочные покрытия можно наносить ракелем или кельмой. Выбор способа применения является вопросом экономики. 905:30 Щетка
для небольших участков с углами, краями и необычными формами, где маскировка от брызг не имеет смысла
Ролик
для больших площадей, где распыление потребует тщательной маскировки, вентиляции или может представлять опасность для здоровья или пожара
Воздушный спрей
когда области, подлежащие покрытию, обширны или имеют неравномерную форму, а время, необходимое для маскировки, может быть компенсировано более высокой производительностью
Безвоздушное распыление
где высокая стоимость оборудования по сравнению с воздушным распылением может быть компенсирована более высокой производительностью, меньшим временем маскирования и потерями при перераспылении.
Покрытия, препятствующие скольжению
- Поверхность для пешеходов и легковых автомобилей:
- Поверхности для движения транспортных средств: при использовании на автомагистралях или в других тяжелых условиях материал покрытия используется в качестве матрицы для нанесения чипсила.
Подходящий устойчивый к полировке заполнитель для чипсилинга включает оксид алюминия, наждак или кальцинированный боксит. Выбранный заполнитель должен иметь твердость по шкале Мооса 8 или выше и следующую градацию:
- Мастика или покрытия, препятствующие провисанию: Эта система используется там, где требуется толстое покрытие, чтобы противостоять истиранию и ударам или выравнивать неровности на вертикальной поверхности. Мастика наносится кельмой или ракелем. Песок в количестве, рекомендованном производителем, может быть смешан с мастикой для снижения стоимости материала. Используйте сортированный кварцевый песок; промыты, высушены и упакованы. Хорошей «пропускной» градацией для низкого содержания пустот является смесь по весу двух частей #12 или #16 меш и одной части #80 или #100 меш.
- Мастика или покрытия, препятствующие провисанию: Эта система используется там, где требуется толстое покрытие, чтобы противостоять истиранию и ударам или выравнивать неровности на вертикальной поверхности.
Мастика наносится кельмой или ракелем. Песок в количестве, рекомендованном производителем, может быть смешан с мастикой для снижения стоимости материала. Используйте сортированный кварцевый песок; промыты, высушены и упакованы. Хорошей «пропускной» градацией для низкого содержания пустот является смесь по весу двух частей #12 или #16 меш и одной части #80 или #100 меш.
Можно использовать два метода включения песка в покрытие для эксплуатации в зонах с пешеходным движением и движением легковых автомобилей. Там, где желательно увеличить толщину или добиться высокой степени агрессивности поверхности, в верхний слой покрытия в избытке вбрасывается песок. После высыхания покрытия излишки песка удаляются. Полученную в результате текстуру, похожую на наждачную бумагу, можно смягчить и облегчить очистку с помощью окончательного финишного слоя, нанесенного валиком. Для этого применения подходят встречающиеся в природе чистые, высушенные в печи кварцевые пески размером от 16 до 20 меш.
Для легких условий эксплуатации, когда желательны более тонкие слои или менее агрессивная поверхность вместо насыпной системы, в материал покрытия можно добавить мелкий заполнитель размером от 60 до 80 меш и распределить его ракелем в качестве окончательного слоя. Для этой цели можно использовать мелкий кварцевый песок или наждачную крошку.
Стандартное сито № | % Прохождение веса |
---|---|
1/4 | 100 |
6 | 97-100 |
8 | 55-75 |
16 | 0-3 |
Заполнитель должен быть равномерно распределен по поверхности и падать в вертикальном направлении, чтобы избежать смещения неотвержденного покрытия. Заполнитель следует распределять до избытка, пока поверхность не станет сухой.
Требуемое количество заполнителя зависит от толщины покрытия. Типичные нормы внесения от 28 до 30 квадратных футов на галлон требуют от 1,3 до 1,5 фунтов на квадратный фут фракционированного заполнителя.
После распределения заполнителя любое движение должно быть запрещено до тех пор, пока материал покрытия не затвердеет достаточно, чтобы выдерживать движение. Затем излишки заполнителя можно подмести и использовать повторно, если они все еще чистые и сухие.
Контроль качества
- Толщина мокрой пленки: Для измерения толщины мокрой пленки доступны датчики мокрой пленки. Измерение считывается сразу после нанесения покрытия (до того, как произойдет испарение), и окончательная толщина пленки рассчитывается на основе известного процентного содержания твердых веществ в материале покрытия.
- Толщина сухой пленки: Измерители сухой пленки доступны для измерения толщины пленки непроводящего материала на железной подложке.
- Испытание на адгезию к царапинам для стальных подложек: Инструмент с несколькими лезвиями проводят по покрытию, делая параллельные надрезы.
Под углом 900 к этим надрезам делается еще один набор надрезов, в результате чего получается множество маленьких квадратов. Затем на лоскутное одеяло наклеивается малярная лента и быстро удаляется. Количество удаленных квадратов является показателем качества адгезии.
Испытание на отрыв - для бетонных или стальных оснований: Алюминиевая или стальная «кукла» приклеивается к покрытию и снимается калиброванным тестером. Этот тест обычно проводят с помощью тестера адгезии Elcometer (ASTM D4547). Минимальная прочность на отрыв для бетонных поверхностей составляет 200 фунтов на квадратный дюйм. Более высокие значения получаются для стальных подложек. Для бетонных оснований разрушение должно происходить внутри бетона. Для стальных поверхностей разрушение должно происходить внутри покрытия или в месте соединения стали и покрытия. Прочность на отрыв будет зависеть от прочности покрытия и его толщины. Поэтому следует обращаться к технической информации для конкретного покрытия.
- Обнаружение точечных отверстий: Доступны устройства обнаружения точечных отверстий как для стальных, так и для бетонных поверхностей.
- Пешеходное движение. Распространенным методом измерения сопротивления скольжению при пешеходном движении является маятниковый тестер Сеглера. Он измеряет кинетический коэффициент трения и соответствует как «Федеральному стандарту метода испытаний № 501a, метод 7121», так и «Отчету Национального бюро стандартов BMS 100, «Относительная скользкость полов и поверхностей настила». Типичные значения кинетического коэффициента трения для напольных покрытий находятся в диапазоне от 0,46 до 0,7; меньшие значения представляют собой более скользкую поверхность.
- Транспортное движение: Для определения сопротивления скольжению автомобильных поверхностей используются два метода испытаний: AASHTO T242 и ASTM E247.
Адгезия
Сопротивление скольжению
Толщина нанесенного покрытия (1000 мил = 1 дюйм) | Покрытие на галлон США Система 100% твердых веществ |
---|---|
250 мил (1/4 дюйма) | 6,4 фут2 |
187,5 мил (3/16 дюйма) | 8,5 футов2 |
125 мил (1/8 дюйма) | 12,8 футов2 |
100 мил | 16 футов2 |
62,5 мил (1/16 дюйма) | 25,5 футов2 |
50 мил | 32 фут2 |
31,25 мил | 51 фут2 |
20 мил | 80 футов2 |
15,63 мил (1/64 дюйма) | 102 фут2 |
10 мил | 160 кв.![]() |