что выбрать для строительства дома и основные характеристики материалов
В последнее время в строительной среде распространилась сильная путаница по поводу названий блоков из ячеистого бетона. Часто разными словами называют один материал, а иногда объединяют под одним названием материалы совсем с разными свойствами. В этой статье разберемся, чем газобетон отличается от пеноблока, пенобетона, газосиликата и др.
Основные отличия пеноблока от газоблока
Для понимания вопроса нужно обратиться к нормативным документам, которые регулируют производство вышеупомянутых материалов.
Оба вида блоков имеют схожие свойства, похожи внешне и относятся к одному типу материалов – ячеистому бетону. Изделия из такого бетона имеют пористую структуру, что делает их более «теплыми» (низкая теплопроводность), но при этом они сохраняют достаточную прочность для строительства несущих стен.
Слова «пенобетон» и «газобетон» давно вошли в употребление, но фактически эти названия никак не отражают состав материала, потому что эти изделия не являются бетоном. Бетон – это составной материал, в состав которого входит заполнитель и вяжущее. Первая часть названия обычно обозначает заполнитель (железобетон). Части «пено-» и «газо-» тут обозначают способ порообразования. В одном случае — пена, в другом — газ.
Пенобетон
Производство этого материала регулируется двумя ГОСТами: «25820-2014 Бетоны легкие. Технические условия» (вступает в силу с 1 января 2020) и «25485-2012 Бетоны ячеистые. Общие технические условия». Из пенобетона изготавливаются пеноблоки, которые используют в качестве строительного стенового материала. Основные компоненты: цемент, вода, песок и пенообразователь.
Пенобетон от газобетона отличается по двум основным признакам.
По способу твердения – все ячеистые бетоны подразделяются на автоклавные и неавтоклавные. Пенобетон относится к последней категории, т.е. он твердеет естественным путем на воздухе (гидратационное твердение) в съемной опалубке. В некоторых случаях опалубка сразу разделяет материал на блоки, иногда пенобетон заливают одним большим блоком, а потом нарезают на части.
Автоклав – герметичная емкость для нагрева под давлением, на изделия внутри воздействует пар и высокая температура, поэтому газобетон сразу после производства получается влажным (влажность по массе у изделий низкой плотности может достигать 50%).
По способу пенообразования – пористой структуры в пенобетоне добиваются путем добавления специальных пенообразователей. В жидком виде материал вспенивают, а после затвердения у него остается пористая структура. В качестве пенообразователей могут использоваться костный клей, скрубберная паста и др.
В ГОСТе, который действовал до 2019 года пенообразователи нормировались, в новом нормативе пенообразователи не указываются.
Газобетон
Правильнее называть газобетон автоклавным ячеистым бетоном. Изготовление регулируется ГОСТом 31359-2007 «Бетон ячеистый автоклавного твердения. Технические условия». Газобетон делают из цемента, песка, воды, извести и газообразователя. Компоненты схожие, но остановимся на отличиях от пенобетона.
Песок измельчается до мелкой фракции (2000 – 3000 см.кв/кг), это необходимо для формирования единой с цементом массы. Песок для пенобетона не измельчают.
Материал нарезается еще до застывания, для этого не используется опалубка. Газоблоки продавливаются через стальные струны.
Застывание происходит за 12 часов в автоклаве. Благодаря этому порообразование происходит более предсказуемо, и блоки получаются более однородными.
Образование ячеек происходит при взаимодействии газообразователя (алюминиевая пудра ПАП-1 и ПАП-2) с известью и водой. В результате этого выделяется водород, который и формирует поры внутри материала.
Газобетон в некоторых регионах называют газосиликатом, но на самом деле это разные материалы. Когда производство ячеистых бетонов только началось, практиковались разные составы: на основе цемента, на основе извести и смешанные. Изделия на основе извести назывались газосиликатными блоками, сейчас такая рецептура практически не применяется.
Рассмотрим достоинства и недостатки каждого из материалов
Как понятно из описания процедуры производства, газобетонный блок изготовить кустарными методами практически невозможно, чего нельзя сказать о пенобетоне. Конечно, такие изделия имеют непредсказуемые физико-технические параметры, поэтому сравнивать их не имеет смысла. Для сравнения мы возьмем усредненные параметры пенобетона, который производится с соблюдением требований нормативов.
Что прочнее?
Марка прочности ячеистых бетонов обозначается буквой B (прочность на сжатие) и выражается в МПа (Н/м.кв). От этого параметра зависит усилие, после которого блок разрушится и потеряет свою несущую способность. Характеристика прочности обычно влияет на плотность. Повышение прочности приводит к повышению плотности, что снижает тепловые характеристики материала, поэтому прочность должна быть рассчитана в соответствии с требованиями конкретной конструкции.
Прочность пенобетона обычно не превышает B1,5, газобетон может иметь марку B1,5 – B7,5. Что позволяет использовать газобетон для более нагруженных конструкций, пенобетон можно использовать для ненагруженных конструкций (перегородки, хозяйственные конструкции) или в качестве теплоизоляционной прослойки.
По ГОСТам ячеистые бетоны подразделяются на теплоизоляционные, конструкционно-теплоизоляционные и конструкционные.
B0,5 – B1,5 – теплоизоляционные
B1 – B10 – конструкционно-теплоизоляционные
B7,5 – B12,5 – конструкционные
Это разделение достаточно условно, потому что выбор прочности должен быть продиктован расчетами для конкретного проекта. Раньше эта классификация была привязана к плотности материала, поэтому до сих пор ошибочно её продолжают приводить. В ГОСТе 2009 года для автоклавных газобетонов приводились только предельные значения по прочности, с 2020 года классификацию по прочности распространили на все ячеистые бетоны.
Что легче?
Газобетон имеет меньший вес за счет большего количества пустот и более однородной структуры (вес блока 300 мм – 18,5 кг). В пенобетоне (вес блока 300 мм от 35 кг) песок является заполнителем, который не участвует в синтезе, к тому же часто для кладки пенобетона нельзя использовать кладку с тонким швом. Увеличение шва способствует повышению веса всей конструкции.
Что теплее?
Низкая теплопроводность обусловлена количеством пор и их структурой. Плотный материал обладает более высокой теплопроводностью, соответственно постройки из него получаются менее «теплыми». Фактическая плотность пенобетона превышает марку D600, плотность газобетона D300 – D600. Это позволяет использовать последний для возведения однослойных стен с достаточно для средней полосы России тепловым сопротивлением.
Марка плотности блоков обозначается буквой D и цифровым значением (D200 – D700).
Порообразование в газобетоне происходит более равномерно, большинство пор получается закрытыми и маленькими. В пенобетоне больше открытых пор и они более крупные, а соответственно материал имеет более высокую теплопроводность.
Теплопроводность газобетона – 0,05 – 0,2 Вт/(м*С)
Теплопроводность пенобетона начинается от 0,18
Водопоглощение
Главная проблема газобетона заключается в изначально высокой влажности, после обработки в автоклаве она может достигать 50%. В процессе работы на строительной площадке и из раствора материал может дополнительно увлажняться. После возведения здания за 3 – 6 месяцев стены выходят на равновесную с окружающей средой влажностью (5%). До этого момент дом из газобетонных блоков не рекомендуется утеплять и отделывать.
Особенно важно выждать срок высушивания блоков при утеплении с помощью пенополистирола. В противном случае в стене может происходить влагонакопление с последующим разрушением стенового материала при пониженных температурах.
Когда влажность газоблоков выходит на 5 – 8%, то здание может эксплуатироваться в обычном режиме. Для влажных помещений (баня, отапливаемые помещения для домашних животных) на газобетонной стене надо сделать гидро- и пароизоляцию.
Пенобетон в этом отношении более практичен, так как он высыхает в процессе своего изготовления и увлажняется только осадками или раствором.
Что экологичнее?
Оба материала изготавливаются на основе минеральных компонентов (цемент, песок, известь). В изделиях не используются полимерные компоненты. Газобетон и пенобетон не вызывают аллергических реакций и не являются благоприятной средой для распространения плесени. Показатели радиоактивности у ячеистых бетонов тоже ниже, чем у других строительных материалов.
Какие размеры?
Газоблоки могут иметь различную форму и размеры. Максимальный размер крупного блока – 1500 мм, мелкого – 625 мм. Ширина соответственно – 600 и 400 мм, высота 1000 – 300 мм. Пеноблоки могут иметь схожие размеры, но встречаются и изделия большего размера.
Также пеноблоки и газоблоки могут иметь разнообразную форму. Например, из газобетона делают цельные перемычки для оконных и дверных проемов. По форме тычковой плоскости изделия подразделяют на блоки паз-паз, паз-гребень, плоскость-паз.
По этим параметрам пеноблоки и газоблоки находятся примерно на одном уровне, но пенобетонные изделия существенно проигрывают газобетону по точности размеров. Если у газоблоков первой категории отклонения от вертикалей и горизонталей обычно не превышают +-1 мм, то у пенобетонных блоков отклонения могут быть практически любыми.
Удобство в строительстве
Из прошлого пункта следует, что геометрия пеноблока хуже, чем у газоблока. Кладка с тонким швом (2-3 мм) при больших перепадах становится невозможной. Толстый растворный шов требует использования цементно-песчаных растворов, работа с ними требует определенного опыта каменщика.
Во вставке: Увеличение толщины шва ведет к снижению прочности кладки. С 10 мм до 20 на 20%, с 20 до 30 на 30%. Кладка с тонким швом прочнее на 20 – 30%.
Пенобетонные блоки нельзя класть на клей-пену из-за недостаточно ровной геометрии. Этот простой способ укладки, который используют при строительстве из газоблоков с тонким швом.
Еще одним негативным фактором является больший вес блоков. Из-за этого материал сложнее переносить, поднимать на объект. Это влияет на увеличение транспортных издержек.
Пенобетон более неоднородный, поэтому дает большую усадку 1-3 м/мм, усадка газобетона меньше и составляет 0,4 м/мм.
Вывод
По соотношению прочности и низкой плотности газобетон лучше пенобетона. Пенобетон больше подойдет для хозяйственных построек и зданий, в которых тепловое сопротивление стен не играет принципиальной роли.
В чем же разница между газобетоном и газоблоком
Каждый из этих материалов: газобетон и газоблок, обладает индивидуальными достоинствами и недостатками, которые следует учитывать при выборе. Чтобы помочь вам принять взвешенное решение, здесь мы обсудим различия между газобетоном и пенобетоном.
Каждый из этих материалов: газобетон и газоблок, обладает индивидуальными достоинствами и недостатками, которые следует учитывать при выборе. Чтобы помочь вам принять взвешенное решение, здесь мы обсудим различия между газобетоном и пенобетоном.
Газобетон изготавливается из цемента, смешанного с другими материалами, такими как песок или зола, которые затем соединяются с газообразователем (обычно алюминиевой пудрой). Эта комбинация создает внутри материала крошечные воздушные пузырьки, которые обеспечивают отличные теплоизоляционные свойства. С другой стороны, газобетон подвержен усадке со временем, если за ним не ухаживать должным образом, и с ним трудно работать из-за его хрупкости.
Пенобетон изготавливается из цемента, смешанного с различными пенообразователями и водой, в результате чего получается легкий материал, с которым легко работать и который обладает хорошими огнеупорными свойствами. Недостатком пенобетона является то, что он не обладает высокими теплоизоляционными свойствами по сравнению с газобетоном. Кроме того, у него низкая прочность на сжатие, поэтому он может не подойти для некоторых видов строительства.
В заключение следует отметить, что оба типа пористых строительных блоков имеют свои сильные и слабые стороны, когда речь идет о строительных проектах. Важно учитывать ваши конкретные потребности, прежде чем принимать решение о том, какой из них обеспечит наилучшие результаты для вашего проекта!
Газобетон — это вид легкого бетона, который создается путем соединения цемента с пористым веществом, таким как алюминиевая пудра. Он имеет высокое отношение прочности к весу и может использоваться для строительства зданий и других сооружений, требующих прочной опоры. Он однороден по всей плоскости, то есть имеет равномерную консистенцию по всему объему. Кроме того, газобетон лучше выдерживает сверление, бурение, забивание гвоздей и другие виды интенсивных нагрузок, которые могут привести к повреждению более слабых строительных материалов.
Газобетонные блоки изготавливаются из тех же материалов, что и обычный газобетон, но с меньшим количеством добавляемого воздуха, чтобы создать более крупные блоки для строительных целей. Хотя эти блоки все еще относительно легкие по сравнению с другими видами кладки или камней, используемых в строительстве, они не обладают таким же уровнем прочности, как их аналоги, поскольку не являются однородными во всей своей плоскости, как обычный газобетон. Кроме того, поскольку в их структуре больше воздушных карманов, чем в твердом материале, это может сделать их более восприимчивыми к повреждениям от определенных давлений, которые в противном случае не повлияли бы на твердые материалы, такие как обычные ячеистые бетоны.
В заключение, при сравнении газобетонов с их блочными вариантами очевидно, что в некоторых случаях одна форма превосходит другую, однако это зависит от того, для чего вы будете их использовать и какое давление, по вашим ожиданиям, будет испытывать ваша конструкция/здание с течением времени. Обычный газобетон обладает повышенной прочностью благодаря своей однородной консистенции по всей плоскости, в то время как газобетонные блоки имеют большие размеры для строительных целей, но ценой меньшей прочности из-за наличия воздушных карманов в структуре, что делает их более восприимчивыми к определенным повреждениям, которые в конечном итоге могут ослабить вашу конструкцию/здание со временем, что может дорого обойтись в долгосрочной перспективе, если не принять меры или не заметить, пока не станет слишком поздно!
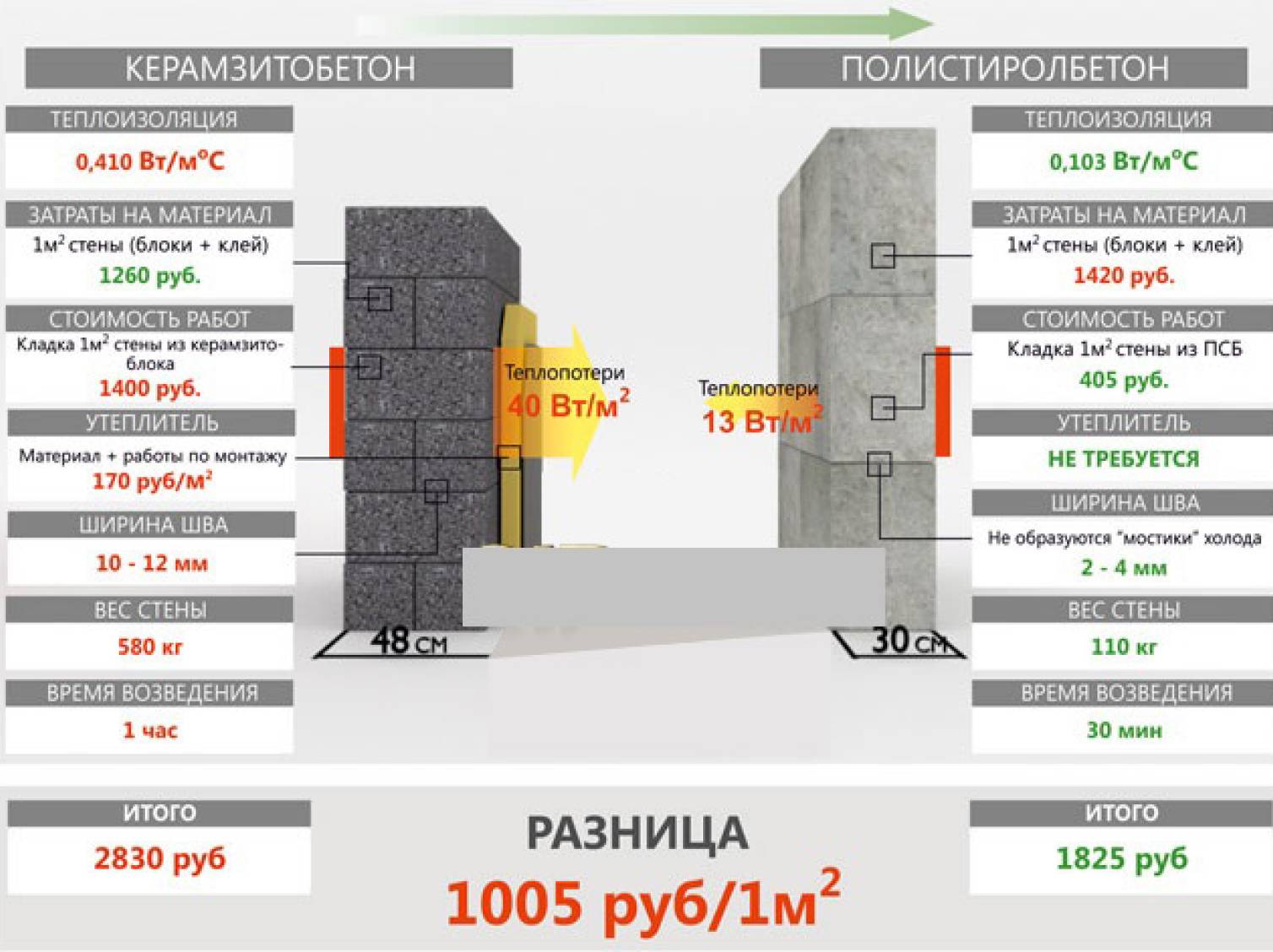
Пенобетон, также известный как ячеистый бетон, имеет более неоднородный состав, чем газобетон. Это дает ему большую скорость усадки — 1–3 м/мм по сравнению с 0,4 м/мм для газобетона. Однако, когда речь идет о прочности и низком коэффициенте плотности, газобетон превосходит пенобетон.
По этой причине пенобетон обычно считается более подходящим для проектов, где тепловое сопротивление не имеет большого значения — например, для сельскохозяйственных зданий или других сооружений в менее экстремальных климатических условиях. С другой стороны, газобетон обычно рекомендуется для более сложных условий, где термостойкость играет важную роль в прочности и долговечности конструкций.
В целом, как ячеистые, так и газобетоны обладают различными преимуществами, которые делают их подходящими для определенных типов проектов и применений. Понимая их уникальные характеристики, вы сможете принять обоснованное решение о том, какой материал лучше всего подходит для ваших конкретных нужд.
Газобетон входит в семейство ячеистых бетонов, к которому также относятся пенобетон и легкий газобетон. Характерной особенностью этих бетонов, отличающей их от традиционных бетонов, является их ячеистая структура. Пузырьки газа занимают до 85% объема материала, что приводит к значительному снижению общего объемного веса по сравнению с традиционными бетонами.
Пузырьки газа, присутствующие в газобетоне, придают ему легкие свойства, что делает его более простым в монтаже, чем традиционные виды, при сохранении прочности и долговечности. Кроме того, благодаря аэрации улучшаются теплоизоляционные свойства, а также повышается огнестойкость по сравнению с другими видами строительных материалов. Кроме того, благодаря своему уникальному составу, газобетон легко обрабатывается пилами и сверлами, как дерево, что является значительным преимуществом для строительных проектов, требующих сложных работ по резке или сверлению, таких как криволинейные стены или оконные проемы.
В общем, существует множество причин, по которым газобетон стал так популярен как среди строителей, так и среди дилеров — от повышения прочности и долговечности до улучшения теплоизоляционных свойств и простоты монтажа — и все это благодаря уникальной ячеистой структуре, состоящей в основном из пузырьков газа!
Свойства автоклавного газобетона в различных условиях твердения: обзор
Авторы: Джаякришнан К., Инду Сьюзан Радж, д-р Элсон Джон
Ссылка DOI: https://doi.org/10.22214/ijraset.2023.50704
Сертификат: Посмотреть сертификат
Abstract
Автоклавный газобетон (AAC) имеет много преимуществ для конструкций, таких как теплоизоляция, звукоизоляция, огнестойкость, уменьшенный собственный вес и многое другое. Продукты AAC включают блоки, стеновые панели, панели пола и крыши, а также перемычки. Помимо изоляционных свойств, одним из преимуществ газобетона в строительстве является его быстрая и простая установка, поскольку материал можно фрезеровать, шлифовать и резать по размеру на месте с помощью стандартных ленточных пил из углеродистой стали, ручных пил и сверл. Хотя газобетон производится уже много лет, все же есть некоторые моменты, требующие уточнения. Одним из таких моментов является влияние влажности на элементы AAC в районах с высоким уровнем относительной влажности, таких как средиземноморский климат. Поэтому необходимо проводить различные испытания, связанные с механическими и физическими свойствами бетона из газобетона, в частности испытание на прочность при сжатии для оценки прочности блоков из газобетона. Текущий проект предназначен для анализа физических и механических свойств блоков из ячеистого бетона автоклавного твердения при трех различных условиях отверждения с использованием резервуара для ускоренного отверждения, чтобы сравнить влияние отверждения на свойства газобетона.
Введение
I. ВВЕДЕНИЕ
Одним из важнейших направлений современного строительного материаловедения является разработка и внедрение новых эффективных теплоизоляционных материалов, что в основном связано с ростом тарифа на электроэнергию и себестоимости энергии, необходимой для обогрева зданий. Что касается энергоэффективности зданий, то следует отметить ужесточение требований к тепловому сопротивлению ограждающих конструкций и улучшению контролируемой среды в зданиях [1]. Легкий бетон с низкой плотностью является примером материала с эффективными тепловыми характеристиками и звукоизоляцией для конструкции. Легкие материалы могут повысить способность здания к захвату. Ниже приведены различные типы легкого бетона: (а) легкий заполнитель бетона; (b) газобетон, ячеистый, пено- или газобетон, который может быть изготовлен путем создания пузырьковых пустот в массе бетона или раствора с использованием подходящих воздухововлекающих добавок и обеспечивает большую однородность и распределение пустот в бетоне; и (c) Бетон без мелких частиц, который может быть изготовлен путем удаления мелких заполнителей из смеси, что не приводит к сегрегации мелких частиц. Его можно классифицировать как (а) конструкционный легкий бетон, (б) кирпичный бетон или (в) оба варианта, показанные на рисунке 1 [2]. Термический коэффициент изолирующего бетона должен быть менее приблизительно 0,3 Дж/м2 с °C/м. Различные типы пуццолановых материалов могут использоваться в качестве замены связующего в бетоне для снижения выбросов CO2, вызванных OPC. Вместо OPC использовались GGBFS, летучая зола и диоксид кремния, которые, согласно расчетам, обеспечивали лучшие физические свойства. В присутствии влаги пуццолановые материалы образуют гидраты силиката кальция после химической реакции с гидроксидом кальция.
Экологичные отходы можно использовать для частичной замены заполнителя в бетоне. Накопление отходов может оказать негативное воздействие на окружающую среду. Его также можно рассматривать как эффективный способ переработки отходов. Повторное использование или восстановление отходов имеет два основных преимущества. Он ограничивает использование обычных ресурсов и защищает использование свалок для материалов одноразового использования. Для улучшения связи между бетонной матрицей и отходами можно применять определенные методы предварительной обработки. Так, при добавлении поверхностно-модифицированных отходов наблюдалось увеличение прочности. Бетон, смешанный с цементом и пуццолановыми материалами, прочнее, чем бетон, смешанный только с цементом. Бетон, содержащий микрокремнезем, был испытан с различными пропорциями резиновых гранул. Сочетание резиновой крошки и микрокремнезема прочнее, чем сочетание резиновой крошки и цемента [3].
A. Газобетон
Газобетон — это новый легкий, высокоизолирующий и прочный строительный материал различных размеров и толщины. По сравнению с красным кирпичом газобетонные блоки имеют небольшой вес. Газобетонные блоки в два-три раза легче обычных бетонных блоков. Газобетон можно разделить на две марки в зависимости от процесса твердения. Автоклавный газобетон (AAC) и неавтоклавный газобетон (NAAC) [4]. Было проведено несколько исследований для изучения влияния соотношения смешивания, свойств тепловой инерции, отношения воды к твердой фазе, давления пара и времени отверждения на свойства автоклавного ячеистого бетона [5]. Количество добавляемой алюминиевой пудры влияет на плотность газобетона. Алюминиевая пудра является наиболее часто используемым воздухововлекающим материалом. Также можно использовать перекись водорода, хлорную известь и карбид кальция, но они выделяют соответственно водород, кислород и ацетилен [6]. Для получения точных физических свойств бетона необходимо определить пористость AAC. Реакции гидратации могут быть усилены паром высокого давления. Пар высокого давления также улучшает свойства бетона. Микроструктурные исследования газобетона показывают, что продукты гидратации заполняют поры бетона [7]. Блоки газобетона примерно на 85% легче красного кирпича, что может снизить вес конструкции. Другими словами, газобетонные блоки недороги и обладают приемлемой прочностью на сжатие [8].
Плотность газобетона снижается за счет летучей золы и ГГБФС [16]. GGBFS инициирует пуццолановые реакции с образованием гелей CSH при смешивании с цементом. Это делает GGBFS подходящей частичной заменой цемента. При GGBFS пуццолановая реакция возникает после определенного возраста. Значения прочности на сжатие увеличиваются по мере увеличения количества GGBFS до 30 % [9]. Замена цемента на ГГБФС и золу-уноса помогает газобетону достичь прочности 25 МПа. Исследования проводились на газобетоне с различными наполнителями. Резиновая пыль также может использоваться в качестве наполнителя в газобетоне. Обмен дает менее плотную смесь. Установлено, что оптимальная дозировка резинового порошка составляет 5 % [3]. Добавление наполнителей также влияет на удобоукладываемость бетона. Шлак индукционных печей может использоваться как полузаменитель мелочи. Однако удобоукладываемость бетона снижается при более чем 40-процентной замене мелкого заполнителя из-за его угловатой природы [10]. Удобоукладываемость также зависит от добавления различных минеральных добавок. Удобоукладываемость первоначально повышается при добавлении минеральных добавок, но снижается при более высоких скоростях замещения цемента [11]. Дозировка суперпластификатора должна быть оптимизирована на основе совместимости добавки с цементом и совместимости смеси с добавкой.
Удобоукладываемость бетона снижается при добавлении разжижителя [12].
Недавно было организовано исследование по использованию карьерной пыли в качестве заменителя природных заполнителей. Эксперименты проводятся с использованием традиционных методов заливки бетона. Карьерная пыль, которая образуется в больших количествах как на площадке, так и за ее пределами, является побочным продуктом резки, шлифования, просеивания и дробления камня и создает ряд экологических проблем. Это снижает потребление энергии и выбросы парниковых газов. Около 30% всех каменных отходов приходится на карьеры. Это огромное количество попадает на свалки [10]. Торговое издание исследовало использование отходов в качестве наполнителя в газобетоне, что наносит вред окружающей среде и благополучию человека. Замена гранитного порошка положительно влияет на удобоукладываемость, прочность и долговечность. Мраморная пудра заполняет поры, созданные алюминиевой пудрой, и увеличивает прочность газобетона. Энергоэффективность повышается за счет использования резины и резинотехнических изделий вместо летучей золы. Таким образом, использование отходов снижает затраты на утилизацию и площадь земли [13]. Лучшей концепцией является использование преимуществ легкого бетона при изготовлении каменных конструкций. Производство бетона для заливки кладочных блоков отличается от производства различных видов бетона для облегченных строительных блоков. Для снижения затрат и усадки следует использовать меньше цемента [14]. Обычные бетонные блоки обычно отливают с очень небольшим количеством воды и минимальной осадкой.
B. Пенобетон
Пенобетон производится либо методом предварительного вспенивания, либо методом смешанного вспенивания Метод предварительного вспенивания включает раздельное производство основной цементной смеси, раствора (цементного теста или раствора) и стабилизированного водного ( пенообразователь на водной основе), а затем тщательное вмешивание пены в базовую смесь [18]. При смешанном пенообразовании поверхностно-активное вещество смешивается с базовой смесью. В процессе смешивания добавление ингредиентов способствует образованию пенообразующих ячеистых структур в бетоне, как показано на рис. 2.
Готовая пена может быть влажной или сухой. Влажная пена получается путем распыления раствора пенообразователя на мелкоячеистую сетку, имеет размер пузырьков от 2 до 5 мм и относительно менее стабильна. Сухая пена получается путем проталкивания раствора пенообразователя через ряд ограничений высокой плотности и одновременного нагнетания сжатого воздуха в смесительную камеру. Пенообразователи используются для получения пенобетона. Он называется воздухововлекателем [19]. Наибольшее влияние на пенобетон оказывают пенообразователи. Когда пенообразователи добавляются в воду затворения, они создают отдельные пузырьковые полости, которые внедряются в цементное тесто. Свойства пенобетона сильно зависят от качества пены. Воздушные пустоты ограничиваются от 10% до 70% в газобетоне, создаваемом воздушными карманами. Эти воздушные карманы могут быть образованы пропеллентами на белковой или синтетической основе. Для создания таких воздушных карманов можно использовать различные методы [20]. Объемная доля предварительно сформированной пены может быть введена в цементное тесто методом, известным как процесс физического вспенивания. Воздухововлекающие агенты, такие как h3O2, мелкодисперсный алюминиевый или цинковый порошок, можно использовать для вовлечения воздуха в цементное тесто посредством химической реакции. Этот процесс известен как технология химической аэрации [21]. Эти два материала имеют разные механизмы воздухововлечения. Пенные концентраты на белковой основе образуют пузырьки воздуха в результате расщепления белка. Они генерируют устойчивые пузырьки газа за счет образования водородных связей между молекулярными группами [21,22]. Синтетические наполнители гидрофильны, поэтому они легко растворяются в воде и образуют пузырьки воздуха. Дренаж, коалесценция и непропорциональность могут повлиять на стабильность пены. Поэтому разные пенообразователи позволяют получать пенобетон с разными характеристиками [20]. Тип используемого пенообразователя оказывает существенное влияние на текучесть, прочность на сжатие, водопоглощение, усадку при высыхании и морозостойкость свежевспененного бетона [23,31].
Это также влияет на термическое сопротивление и коэффициент адсорбции пенобетона [24].
Дополнительные вяжущие материалы (SCM) являются побочным продуктом промышленных производственных процессов, которые можно использовать для повышения прочности и долговечности пенобетона благодаря его пуццолановому действию. Диоксид кремния, метакаолин, летучая зола и GGBFS являются одними из важных SCM. Эти СКМ могут использоваться как по отдельности, так и в качестве частичной замены цемента [26]. Несмотря на то, что они не вносят большого вклада в развитие ранней прочности, достигается значительное увеличение последующей прочности с учетом влияния типа наполнителя (зольная пыль) на пенобетон. Для эксперимента использовали местный пенообразователь, портландцемент марки 53, крупнозернистый речной песок и летучую золу класса F. Смеси, которые были приготовлены с золой-уносом в качестве наполнителя, показали лучшую консистенцию, повышенную прочность за счет увеличения крупности, более высокие характеристики текучести и улучшенное отношение прочности к плотности [28,32]. Однако с повышением плотности водопоглощение уменьшилось. Очень было проведено очень мало исследований по включению GGBFS в пенобетон. GGBFS является побочным продуктом производства железа, который при добавлении в бетон улучшает его свойства, такие как удобоукладываемость, прочность и долговечность [29].,30].
II. ПРОИЗВОДСТВО АВТОКЛАВИРОВАННОГО ГАЗОБЕТОНА
Смесь мелкомолотого песка, цемента, негашеной извести (гашеной), ангидрита или гипса и алюминиевой пудры или пасты (пенообразователя) ) смешивается с водой с образованием суспензии [6] . Затем суспензию заливают в стальные формы примерно на две трети объема формы. Затем происходит реакция между алюминием и водой в щелочной среде с образованием газообразного водорода (h3). Образуются небольшие пузырьки воздуха, и по мере затвердевания суспензии расширяющиеся пузырьки воздуха создают продукт, похожий на лепешку, который заполняет объем формы. При изготовлении армирующих элементов, таких как панели пола, стен и крыши, арматуру из коррозионностойкой стали помещают в форму либо до, либо сразу после заливки.
Во время так называемого процесса подъема кек выделяет тепло из-за диссипативной реакции обожженной извести. Это ускоряет реакцию затвердевания цемента, и «кек» приобретает достаточную прочность в сыром виде примерно через 2-4 часа. Затем пирог разрезают по горизонтали и вертикали на блоки или плиты с помощью режущего оборудования, такого как проволока высокого давления и формовочные ножи. Нарезанный пирог затем переносится в автоклав, где горячий насыщенный пар инициирует процесс отверждения материала AAC. Типичный диапазон давления составляет 1,1-1,3 МПа (160-190 фунтов на кв. дюйм, а диапазон температур составляет 190–205 °C (380–400 °F).
В процессе твердения мелкоизмельченный песок вступает в реакцию с известью и водой, образуя кристаллическую структуру гидратированного силиката кальция, известную как тоберморит (C5S6H5). Это природный минерал. Примерно через 12 часов готовый строительный материал готов к упаковке, транспортировке и сборке. После обработки в автоклаве материал еще больше затвердевает [7,18].
III. ХАРАКТЕРИСТИКИ ЯБЕТОНА
A. Удобоукладываемость
Удобоукладываемость измеряется с помощью блок-схемы. Удобоукладываемость цементного теста или раствора основана на текучести. Текучесть или технологичность увеличиваются по мере увеличения отношения воды к твердым веществам. Твёрдая паста не пригодна для производства газобетона [33].
B. Плотность
Водоцементное отношение является фактором, влияющим на скорость аэрации и, следовательно, на плотность бетона. Если он изготовлен из пуццоланового материала, учитывайте соотношение воды и твердой фазы, а не соотношение воды и цемента. Водоцементное отношение не должно быть слишком низким из-за плохой аэрации и не должно быть слишком высоким из-за образования полостей. Поэтому водоцементное отношение принимается исходя из консистенции бетона и нет смысла выбирать заданное.
C. Водопоглощение
По мере увеличения плотности бетона водопоглощение уменьшается. По данным водопоглощения при постоянной плотности снижается с повышением температуры отверждения. Сравнительная плотность с наименьшим водопоглощением имеет место при температуре 90 °С [34].
D. Микроструктура
Микроструктурные свойства газобетона – это бетон, в котором большое количество пустот распределено равномерно для снижения плотности. В данном исследовании сообщается об исследованиях структуры автоклавного газобетона (АГБ) на цементной основе и без него с песком или золой-уноса в качестве наполнителя. Изменение прочности на сжатие, прочности на изгиб и т. д. объясняется на основе микроструктуры, и анализ был основан на SEM и XRD. Микроструктура газобетона может изменяться в зависимости от условий твердения, изменения состава наполнителей и т. д. Процесс гидратации в автоклавном газобетоне на основе цемента будет происходить быстрее, чем в газобетоне, содержащем песок и зольную пыль в качестве наполнителя. Поскольку летучая зола будет окружена продуктами гидратации, образованными цементом, и замедлит процесс гидратации. Скорость гидратации также влияет на микроструктуру. Таким образом, микроструктура газобетона на основе цемента со временем будет стабильной. Продукты реакции в AAC будут лучше кристаллическими, а в не-AAC — плохо кристаллическими. Так, AAC обладает хорошей прочностью по сравнению с другими. На границе пустота-паста присутствует промежуточная зона. Пустоты действуют как агрегаты нулевой плотности. Переходная зона будет менее пористой и останется неограниченное пространство для гидратации и отвода сбрасываемой воды [6].
Заключение
Легкий газобетон отличается от обычного бетона некоторыми материалами и свойствами. Легкий газобетон не содержит крупнозернистого заполнителя и имеет множество преимуществ, в том числе низкую плотность при более высокой прочности по сравнению с обычным бетоном, улучшенную тепло- и звукоизоляцию, а также меньшую собственную нагрузку, что может быть обусловлено несколькими преимуществами, такими как уменьшение конструктивных элементов и снижение передают нагрузку на фундаменты и несущую способность. Пенобетон отличается в конце процесса образования воздушных пустот по сравнению с автоклавным газобетоном. Воздушные пустоты в пенобетоне образуются пенообразователями; эта операция является физической обработкой. Воздушные пустоты в автоклавном газобетоне образуются за счет добавления алюминиевой пудры к другим материалам и взаимодействия между ними; эта операция является химической обработкой. Воздушные пустоты равномерно распределены внутри легкого газобетона. Прочность на сжатие пенобетона может быть увеличена до конструкционной прочности по сравнению с автоклавным газобетоном. Ячеистый легкий бетон считается наиболее экономичным с точки зрения материалов, побочных продуктов потребления и отходов, таких как зола-уноса и ГГБС.
Ссылки
Wenyi Hu, Ronald D. Neufeld; Луис Э. Вальехо; «Прочностные свойства автоклавного ячеистого бетона с большим объемом летучей золы» ASCE.August, 1997.
[2] Экспериментальное исследование высокоэффективного автоклавного газобетона, изготовленного из переработанного древесного волокна и резинового порошка». Хе, Тиншу, Жуншэн и др. (2019), Журнал чистого производства 234: 559–67.
[3] Экспериментальное исследование автоклавного газобетона. Авадхут Бхосале1 ; Нихил П. Заде2 ; Робин Дэвис3. DOI: 10.1061/(ASCE)MT.1943-5533.0002762. © 2019 Американское общество инженеров-строителей.
[4] «Механические свойства и разработка легкого бетона с использованием автоклавного ячеистого бетона (AAC) с алюминиевой пудрой». Materials Today: Proceedings 56 (2022) 3734–3739 Абхишек Тхакур и Саурав Кумар. (2022):
[5] «Структура и свойства газобетона: обзор». Цементные и бетонные композиты 22 (2000): 321-329. Н. Нараянан, К. Рамамурти. (2000),
[6] Появляется новый кладочный продукт для дизайнера из США – газобетон автоклавного твердения. Джон Х. Мэттис, доктор философии, Американское общество инженеров-строителей, 2018 г.
[7] Реакция автоклавного ячеистого бетона и алюмината натрия в слабощелочных и кислых гидротермальных условиях: модель переработки газобетона. 10.1061/(АССЕ)МТ.1943-5533.0000392. © 2012 Американское общество инженеров-строителей.


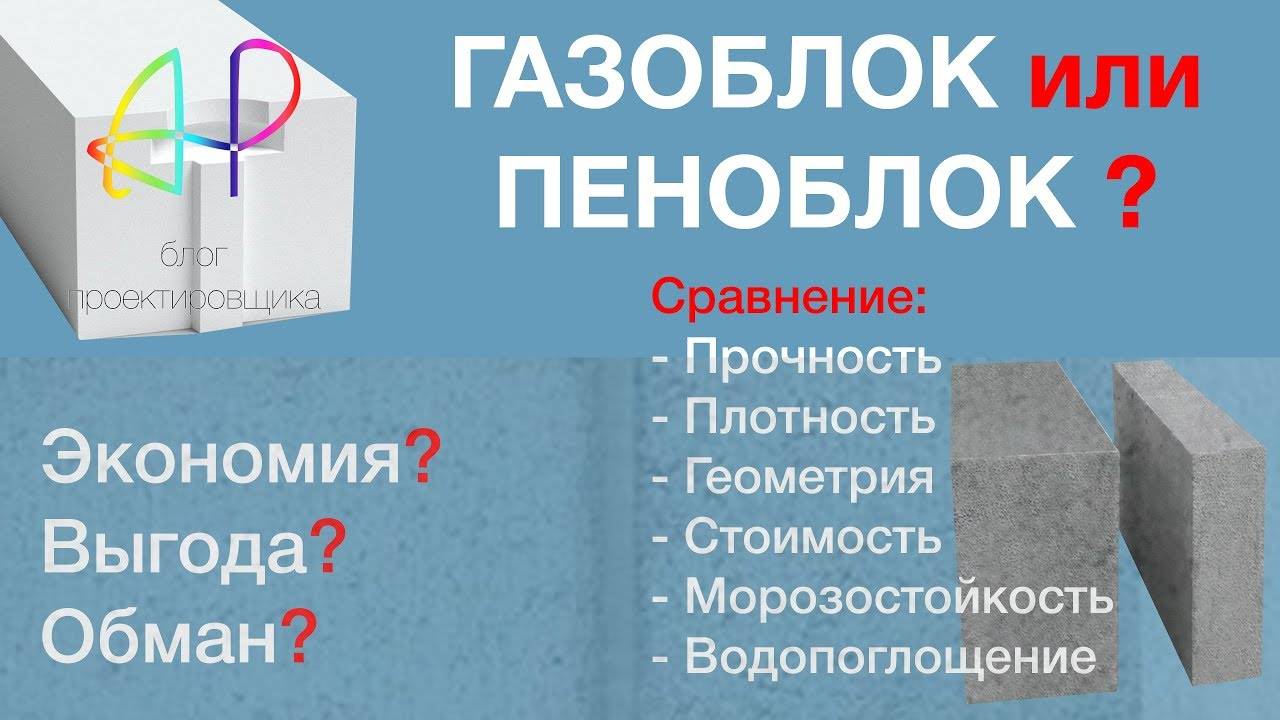

Радж, доктор Элсон Джон. Это статья с открытым доступом, распространяемая в соответствии с лицензией Creative Commons Attribution License, которая разрешает неограниченное использование, распространение и воспроизведение на любом носителе при условии надлежащего цитирования оригинальной работы.
Built Expressions Bangalore :: Ячеистый бетон с высокими эксплуатационными характеристиками
Ячеистый бетон с высокими эксплуатационными характеристиками
Существует два способа производства легкого бетона. Одним из способов является использование доступных в природе легких заполнителей горных пород, таких как пемза [наиболее широко используемый], шлак, вулканический пепел, туф и диатомит, или легких заполнителей, произведенных искусственными вращающимися печами, таких как керамзит, сланцы, шлак, перлит или сланцы. Ценосферы [полая сфера, состоящая в основном из кремнезема и оксида алюминия с полостями, заполненными инертными газами, такими как азот и углекислый газ] и переработанные стеклянные шарики являются дополнительными многофункциональными наполнителями. Эти заполнители с низкой плотностью могут хорошо функционировать; однако они экономически доступны только вблизи доменных печей и становятся все более дорогими из-за увеличения стоимости материалов, топлива и рабочей силы.
Рисунок 1: Схема производства пенобетона
Другой способ заключается во введении относительно большого количества воздуха, который может быть вовлечен в бетон без существенного снижения прочности конечной конструкции. Это можно сделать, используя новую усовершенствованную механическую воздухововлекающую добавку или бетон, содержащий воздушные ячейки или пустоты по всему объему. Такой бетон называется SDC: бетон с заданной плотностью или HPCC: высокоэффективный ячеистый бетон.
Рис. 2: Схематическое изображение газобетона
Ячеистый бетон
Ячеистый бетон представляет собой вяжущую массу из чистого цемента или цемента и мелкозернистого песка с множеством микро- и макрочастиц. скопические дискретные воздушные ячейки, равномерно распределенные по всему смесь для создания легкого бетона.
Обычно производится двумя разными способами.
- Первый метод заключается в смешивании предварительно приготовленной пены [ПАВ] или смеси пенообразователей с цементно-водной суспензией. По мере затвердевания бетона пузырьки распадаются, оставляя воздушные пустоты одинакового размера. В пеногенераторе вспенивают пенообразователь, состоящий из стабилизатора, растворителя, ПАВ, воды и щелочного полимера, смешанных в заданном порядке и пропорциях. Заданное количество вспененной пены вводят в бетонный раствор нормальной плотности в смесителе непрерывного действия.
После достаточного перемешивания вспененный ячеистый бетон готов к укладке. Производство пенобетона схематично представлено на Рисунок 1.
- Второй метод, известный как автоклавный газобетон [AAC], состоит из смеси извести, песка, цемента, воды и расширительного агента. На рис. 2 схематично показано изделие из газобетона. Пузырь образуется путем добавления в смесь расширительных агентов [алюминиевого порошка или перекиси водорода] в процессе смешивания. Это создает химическую реакцию, в результате которой выделяется газ в виде водорода или кислорода, образуя структуру газовых пузырьков внутри бетона. Затем материал формуется в формы. Каждая форма заполняется суспензией на половину ее глубины. Начинается процесс газификации, и смесь расширяется, чтобы заполнить форму выше верха. Похоже на выпечку торта. После начального отверждения он затем отверждается под воздействием пара под высоким давлением [от 180° до 210°C / 356° до 410°F] в течение определенного времени в «автоклаве» для получения окончательной микро/макроструктуры.
В последнее время рассматривается направление на бетонные композиции, приготовленные с использованием водных гелей [аквагелей] как всего или части заполнителя в бетонной смеси. Сферы, частицы или кусочки аквагеля формируются из желатинизированного крахмала и добавляются к матрице. Модифицированный или немодифицированный крахмал, такой как пшеничный, кукурузный, рисовый, картофельный, или комбинация модифицированного или немодифицированного крахмала являются примерами водных гелей. Модифицированный крахмал представляет собой крахмал, модифицированный путем гидролиза. Агар — еще один материал, который может создавать поры или ячейки в бетоне. В процессе отверждения, когда аквагель теряет влагу, он сжимается и в конечном итоге высыхает, образуя высушенные шарики или частицы, которые составляют часть размера исходного аквагеля в ячейке или поре в бетоне. В результате получается ячеистый легкий бетон.
Зола с высоким содержанием углерода, переработанные алюминиевые отходы и цеолитовые порошки являются дополнительными механическими структурами, подходящими для производства легкого ячеистого бетона. Эти клетки могут составлять до 80% от общего объема. Вес бетонных смесей колеблется от 220 кг на кубический метр [14 фунтов. кубический фут] до 1922 килограммов на кубический метр [120 фунтов. кубический фут], а прочность на сжатие варьируется от 0,34 мегапаскаля [50 фунтов на квадратный дюйм] до 20,7 мегапаскаля [3000 фунтов на квадратный дюйм].
Ячеистый бетон с высокими эксплуатационными характеристиками [HPCC]
Системы «умных» стен из устойчивой каменной кладки LWC
Высококачественный ячеистый бетон HPCC обладает всеми свойствами ячеистого бетона и может выдерживать давление 55,37 МПа [8000 фунтов на кв. дюйм]. Более высокие прочности могут быть получены с добавлением дополнительных вяжущих материалов. Плотность и прочность можно регулировать для удовлетворения конкретных конструктивных и неконструктивных требований к конструкции, в то время как в обычном ячеистом бетоне этого достичь невозможно.
Бетон с высокими эксплуатационными характеристиками определяется как «бетон, отвечающий особым требованиям к характеристикам и однородности, которые не всегда могут быть достигнуты при обычном использовании только обычных материалов и обычных методов смешивания, укладки и отверждения». Требования могут включать улучшение таких характеристик, как простота укладки и уплотнения без расслоения, долговременные механические свойства, плотность, объем, выносливость, стабильность или срок службы в суровых или агрессивных средах.
Плотность – лучшая характеристика ячеистого бетона. В то время как самые низкие плотности используются для заполнения и изоляции, более высокие плотности используются для конструкционных применений, что приводит к существенному снижению собственного веса конструкции. 0,028 кубических метра [один кубический фут] пены в матрице заменяет 28,30 кг [62,4 фунта] воды или 0,028 кубических метра [один твердый кубический фут] заполнителя весом 74,84 кг [165 фунтов]. за кубический фут].
HPCC обладает отличными изоляционными свойствами, что значительно снижает передачу тепла через бетонный элемент. Этот пузырь отвечает за превосходную стойкость к замораживанию и оттаиванию и теплопроводность, низкое водопоглощение, высокую прочность на растяжение, высокую огнестойкость и звукоизоляцию, а также устраняет недостатки песка, вызывающие кровотечение. Системы формования, транспортировки, укладки и отделки ячеистого бетона ничем не отличаются от существующих методов в строительной отрасли.
Преимущества пенобетона
- Снижение затрат на сырье. Добавляя воздух, можно увеличить объем бетона при очень низких затратах.
- Энергосбережение/экологичность-В отличие от автоклавного газобетона (газобетон/газобетон), воздух Это экономит до 9 м возможно отверждение пенобетона.3 газа для отверждения одного кубометра газобетона и, следовательно, защищает нашу окружающую среду .
- Уменьшение веса — требуется меньшее количество стальной арматуры.
- Снижение затрат на транспортировку и хранение. Меньше сырья, очень эффективно.
- Улучшенная теплоизоляция. Пенобетон может обеспечить те же результаты изоляции, что и обычный бетон, только с 20% веса и 10% сырья.
- Улучшенная противопожарная защита
- Простота использования/производства/управления
- Низкие инвестиции — требуется всего одна простая машина.
- Высокая текучесть. Может заполнять пустоты.
- Низкое водопоглощение — всего 10–15 %, при использовании специальных пенообразователей в сочетании с силиконовым маслом в цементном растворе степень водопоглощения может быть снижена всего до 1 %.
Процесс
Рис. Изготовление из пенообразователя, воды и сжатого воздуха.
Обычный ячеистый бетон, изготовленный из предварительно сформованной пенной смеси, производится путем подачи потока предварительно сформованной пены в смесительный узел на месте или транзитной загрузки смеси из песчано-цементного раствора или цементно-водного раствора. Эта пена [ПАВ] напоминает крем для бритья или пену, используемую для пожаротушения. Большинство пенообразователей представляют собой гидролизованные белки или синтетику и доступны через собственные источники. Примерами таких соединений являются амины и оксиды аминов, конденсаты нафталинсульфоната и формальдегида. Некоторые из этих продуктов могут содержать вещество или вещества, классифицированные как опасные или опасные для окружающей среды, при использовании этих продуктов следует соблюдать особую осторожность, особенно в отношении конденсатов формальдегида, бутилкарбитола и эфиров гликоля.
Гранулы вспенивающегося полистирола
В зависимости от области применения использование пены, полученной из поверхностно-активного вещества, обычно не является проблемой для окружающей среды. Однако в некоторых странах это может иметь религиозное значение. Это может иметь место при использовании поверхностно-активных веществ на основе гидролизованного белка, содержащих кератин или производные казеина.
Поверхностно-активные вещества или агенты [детергенты, смачивающие агенты, эмульгаторы], которые при добавлении к воде снижают поверхностное натяжение и увеличивают «смачивающую» способность воды, тем самым улучшая процесс смачивания и проникновения в эту поверхность или материал. При взбалтывании образует большую массу микро/макроскопических пузырьков.
В этом устройстве или процессе [HPCC] поверхностно-активное вещество [смачивающий агент] или пенообразователь разбавляется водой с образованием раствора пены. Затем этот раствор впрыскивается сжатым воздухом через смесительное устройство или пеногенератор. Количество пены, вводимой в пропорции смеси, находится в диапазоне от 0,07 до 0,40 на кубический метр [от 2 до 11 кубических футов на кубический ярд] бетона. Отношение вода/цемент [Вт/см] находится в диапазоне от 0,23 до 0,32, а пена микроскопических пузырьков, по крайней мере, большая часть которых находится в диапазоне от 25 мкм до 100 мкм [от 0,025 мм до 0,1 мм / от 0,001 дюйма до 0,004 дюйма ] в диаметре. * Обычный диапазон пузырьков ячеистого бетона составляет 0,3–0,8 мм [0,012–0,032 дюйма] в диаметре.
Бетон образуется путем смешивания жидкого цементного теста с заполнителем заданного качества. Заполнитель обычно состоит из среднего и крупного заполнителя или камня и мелкого заполнителя или песка. Или наполнители следующего поколения, которые являются искусственными или переработанными. К ним относятся натуральный/искусственный пуццолан, переработанное стекло, керамика, гранулы пенополистирола, пластик, органические или неорганические материалы.
В обычном бетоне процентное содержание песка в заполнителе составляет от 30% до 40%. Однако вспененный цемент этого способа/изобретения предпочтительно смешивают с заполнителем, имеющим более высокое содержание песка, предпочтительно в диапазоне от 40% до 50%. Это уменьшает или устраняет пустоты в бетонной смеси, поскольку промежутки между более крупными частицами породы могут быть заполнены комбинацией более мелких камней, песка и пузырьков воздуха. Чем меньше коэффициент зазора, тем прочнее будет бетон. Эти микроскопические пузырьки меньше, чем размер частиц песка, повышая пластичность или текучесть смеси.
По мере затвердевания бетона пузырьки разрушаются или трансформируются, высвобождая воду, которая впитается в цементную матрицу, тем самым способствуя процессу гидратации и оставляя воздушные пустоты одинакового размера. Таким образом, меньше необходимости смачивать бетон во время отверждения, как это обычно необходимо для обычного не вспененного бетона.
Воздухововлекающая добавка должна образовывать стабильные пузырьки воздуха, которые не будут сливаться с образованием более крупных пузырьков во время смешивания. Для данного содержания воздуха или объема воздуха, если пузырьки слишком велики, их будет недостаточно для надлежащей защиты пасты. Большие пузырьки также с большей вероятностью лопнут во время смешивания, транспортировки, укладки и вибрации бетона. Если во время этих операций теряется слишком много воздуха, оставшиеся воздушные пустоты могут не защитить затвердевший бетон в холодную погоду или из-за недостаточной теплопроводности. Чтобы предотвратить потерю воздуха, оболочка пузыря должна быть стабильной и достаточно прочной, чтобы сопротивляться разрушению и слипанию, а размер должен быть очень маленьким, крошечным или микроскопическим.
Сегрегация
Градация заполнителя существенно влияет на состав бетонной смеси и ее удобоукладываемость. Распределение размеров частиц, форма частиц и текстура поверхности являются важными элементами обеспечения качества и долговечности бетона. Вариации в сортировке материалов, будь то смешивание заполнителей выбранных размеров или корректировка пропорций бетонной смеси, требуют постоянного внимания для соответствия техническим требованиям.
При плохом распределении частиц в смеси или при недостатке промежуточных [средних] заполнителей механические свойства смеси, а также укладка и отделка приведут к получению некачественного продукта. В конце концов, механические и физические свойства бетона будут продолжать ухудшаться, создавая дополнительные проблемы.
Количество мелкого и крупного заполнителя в смеси должно быть в балансе друг с другом, чтобы создать распределение частиц по размерам для получения заданной накопленной плотности. Однако выбор заполнителей является, а иногда и не всегда последовательным. Доступность, экологические требования и стоимость импорта дополнительных натуральных или искусственных промежуточных заполнителей — это вопросы, которые необходимо решить, чтобы можно было производить максимально оптимизированный бетон с минимальными затратами для производительности, долговечности и методологии структурного строительства.
Легкие заполнители
Введение
Легкие заполнители определяются как заполнители низкой плотности, такие как: (a) вспученная или спеченная глина, сланцевый сланец, диатомовый сланец, перлит, вермикулит или шлак; (б) природная пемза, шлак, вулканический пепел, туф и диатомит; или (c) спеченная летучая зола или промышленные огарки, используемые в легком бетоне.
Определение
Бетон с легким заполнителем имеет существенно меньшую объемную плотность, чем бетон, изготовленный из гравия или щебня. Эта более низкая объемная плотность является результатом использования легких заполнителей, натуральных или искусственных. Многие виды заполнителей относятся к легким и используются для производства бетонов с широким диапазоном плотностей и прочности.
К ним относятся бетоны низкой плотности, конструкционные легкие бетоны и легкие бетоны средней прочности, каждый из которых обсуждается более подробно ниже вместе с типами заполнителей, обычно используемых при его производстве.
Бетоны низкой плотности
Бетоны низкой плотности, плотность которых редко превышает 800 кг/м3 (50 фунтов/фут3), используются главным образом в качестве изоляции. Хотя их теплоизоляционные свойства высоки, их прочность на сжатие низка и составляет примерно от 0,7 до 7,0 МПа (от 100 до 1000 фунтов на квадратный дюйм). Вермикулит и перлит являются наиболее распространенными заполнителями, используемыми в этом типе бетона. Вермикулит – слюдистый минерал. При нагревании слои объединенной воды в ламинарной структуре слюды превращаются в пар, и материал распадается, отслаиваясь на последовательные слои, каждый из которых набухает и раскрывается. Перлит представляет собой вулканическое стекло, содержащее достаточное количество связанной воды, так что при быстром нагревании образующийся внутри пар сильно расширяется и разбивает материал на мелкие расширенные частицы. Насыпная плотность вермикулита и перлита колеблется от 9от 6 до 192 кг/м3 (от 6 до 12 фунтов/фут3).
Конструкционный легкий бетон
Конструкционный легкий бетон имеет плотность от 1360 до 1920 кг/м3 и минимальную прочность на сжатие 17,0 МПа. Их изоляционная эффективность ниже, чем у бетонов с низкой плотностью, но значительно выше, чем у бетонов с нормальной массой. Наиболее распространенными заполнителями, используемыми в этом типе бетона, являются расширенные шлаки; керамзит, глина или летучая зола; и керамзит, глина или сланец из вращающейся печи.
В результате спекания могут быть получены дробленые или гранулированные заполнители. Измельченные заполнители производятся с использованием сырья, которое либо содержит органические вещества, которые могут служить топливом, либо смешаны с топливом, таким как мелкоизмельченный уголь или кокс. Сырье предварительно увлажняют и сжигают, при этом образуются газы, вызывающие расширение. Полученный клинкер затем охлаждают, измельчают и просеивают до требуемой градации. Готовый продукт имеет тенденцию быть острым и угловатым с пористой текстурой поверхности. Гранулированные заполнители производятся путем смешивания глины, пылевидного сланца или летучей золы с водой и топливом; гранулирование или экструдирование этой смеси; а потом сжечь. Полученные заполнители обычно имеют сферическую или цилиндрическую форму.
В процессе вращающейся печи сырье, такое как сланец, глина или сланец, вводится непрерывным потоком в верхнем конце вращающейся печи. Поскольку материал медленно движется к горелке на нижнем конце, тепло, наклон и медленное вращение печи заставляют материал размягчаться и улавливать образующиеся внутри газы во внутренней ячеистой структуре. В одном варианте этого процесса расширенный (вздутый) материал выгружается, охлаждается, а затем измельчается и просеивается до требуемой градации заполнителя. Полученные частицы обычно имеют кубическую или угловатую форму и имеют пористую текстуру поверхности. В качестве альтернативы перед подачей в печь сырье подвергается предварительному измельчению и просеиванию или гранулированию. Затем отдельные частицы раздуваются, не слипаясь. Они, как правило, имеют гладкую оболочку поверх клеточной внутренней части. Эти два варианта можно комбинировать для получения крупного заполнителя, состоящего в основном из недробленых частиц, полученных просеиванием, и мелких частиц, полученных дроблением продукта обжига.
Легкий бетон средней прочности
Легкие бетоны средней прочности имеют плотность и прочность примерно посередине между плотностью и прочностью бетонов низкой плотности и конструкционных бетонов, и иногда их называют заполняющими бетонами. Обычно их изготавливают из пемзы или шлака. Пемза представляет собой губчатую лаву, из которой вышел пар или газ, пока она была еще горячей, и имеет трубчатые, соединенные между собой пустотные поры. Шлак представляет собой вулканический пепел, пористая структура которого состоит в основном из изолированных пустот.
Свойства
Из-за их ячеистой структуры объемный удельный вес легких заполнителей ниже, чем у заполнителей нормальной массы. Объемный удельный вес легких заполнителей также варьируется в зависимости от размера частиц, будучи самым высоким для мелких частиц и самым низким для крупных частиц. Это связано с тем, что дробление разрушает более крупные пустоты, образуя более мелкие заполнители с меньшей пористостью. С помощью современных методов ASTM трудно точно определить объемную удельную плотность и абсорбцию для легких заполнителей из-за проблем с постоянным достижением насыщенного поверхностно-сухого состояния. Так, при проектировании бетонов с использованием легких заполнителей вместо объемного удельного веса используется коэффициент удельного веса. Этот коэффициент находится так же, как ранее описанный объемный удельный вес SSD, за исключением того, что Mass S – масса заполнителя при влажности склада, а масса образца в воде измеряется через определенное количество минут после погружения. Дополнительная информация о коэффициентах удельного веса легких заполнителей приведена в Приложении ACI 211.2.
Насыпная плотность конструкционного легкого крупнозернистого заполнителя обычно составляет от 480 до 1040 кг/м3 (от 30 до 65 фунтов/фут3), что значительно ниже, чем у заполнителей нормальной массы. Насыпная плотность конструкционного легкого мелкого заполнителя обычно составляет от 720 до 1120 кг/м3 (от 45 до 70 фунтов/фут3). Для заполнителей с такой же градацией и формой частиц насыпная плотность по существу пропорциональна удельному весу. Хотя заполнители обычно дозируются по массе, объемная доля заполнителя определяет конечный выход (объем получаемого бетона). По этой причине насыпная плотность легкого заполнителя обычно проверяется ежедневно. Колебания объемной плотности обычно связаны с изменениями гранулометрического состава или формы частиц и могут вызывать колебания выхода бетона.
Форма частиц и текстура поверхности могут значительно различаться для легких заполнителей, полученных разными способами. Частицы обычно имеют примерно сферическую форму, но могут быть и довольно угловатыми. Текстура поверхности может варьироваться от относительно гладкой с небольшими открытыми порами до неровной с небольшими или большими открытыми порами. Эти характеристики как мелких, так и крупных заполнителей влияют на удобоукладываемость, потребность в воде и содержание цемента в бетоне с легким заполнителем точно так же, как они влияют на бетон, изготовленный с заполнителями нормальной массы.
В целом требования к фракционированию легких заполнителей аналогичны требованиям для заполнителей нормальной массы. Однако для легких заполнителей требуется больший процент по массе материала, удерживаемого на мелких ситах, поскольку удельный вес увеличивается с уменьшением размера частиц.
Таким образом, чтобы получить достаточный объем более мелких частиц, необходимо увеличить массовую долю этих частиц. Требования к сортности для легких заполнителей приведены в ASTM C 330. Максимальные общедоступные обозначения фракций 19, 12,5 и 9,5 мм (3/4, 1/2 и 3/8 дюйма). Ситовой анализ проводят так же, как и для обычных заполнителей, за исключением того, что исследуемый образец мелкого заполнителя имеет меньшую массу, а время механического рассева составляет всего 5 минут. Эти модификации предназначены для предотвращения засорения мелких сит и предотвращения поломки более сыпучих частиц при просеивании. Для крупного заполнителя испытуемый образец должен иметь объем не менее 3 л (0,10 фут3).
Легкие заполнители благодаря своей ячеистой структуре могут поглощать больше воды, чем обычные заполнители. При 24-часовом испытании на абсорбцию они обычно поглощают от 5 до 20% по массе сухого заполнителя, в зависимости от пористой структуры заполнителя. Обычно в условиях хранения на открытом воздухе в складских запасах общая влажность не превышает двух третей этого значения. Это означает, что легкие заполнители обычно поглощают воду при добавлении в бетонную смесь, и результирующая скорость поглощения важна при дозировании легкого бетона. Для получения дополнительной информации о пропорциях легкого бетона читатель может обратиться к ACI 211.2, «Рекомендуемая практика выбора пропорций для конструкционного легкого бетона».
Максимальная прочность на сжатие, достижимая в бетоне, изготовленном с данным легким заполнителем, может зависеть от самого заполнителя. В этом отношении может оказаться полезным понятие «потолок прочности». Смесь близка к пределу прочности, когда аналогичные смеси, содержащие те же заполнители и с более высоким содержанием цемента, имеют лишь немного более высокую прочность. Потолок прочности представляет собой точку убывающей отдачи, за пределами которой увеличение содержания цемента не приводит к соразмерному увеличению прочности. На этот потолок влияет преимущественно крупный заполнитель. Потолок прочности может быть значительно повышен за счет уменьшения максимального размера крупного заполнителя для большинства легких заполнителей, особенно более слабых и рыхлых.