Ускорители твердения бетона. Их использование.
1 0 21 Октября 2016Строительные компании, а также те производства, которые занимаются изготовлением железобетонных конструкций и изделий, стремятся выполнять заказы максимально быстро, не допуская простоев и технологических перерывов в своей работе. Однако, для того, чтоб цементный камень был действительно крепким и прочным, необходимо не только приготовить раствор по установленным правилам, но и выдержать его в течение определенного времени для набора максимальной прочности.
Бетон может схватываться недостаточно быстро из-за неблагоприятных условий на стройплощадке или в цеху. Например, при достаточно низкой температуре окружающей среды схватывание бетона замедляется, а при замерзании и вовсе останавливается, из-за того, что жидкая составляющая раствора кристаллизуется. Сцепление ингредиентов строительной массы нарушается, а при оттаивании и последующем наборе прочности бетон теряет в качестве: он становится подвержен трещинообразованию, усадке и плохому уплотнению. Для того, чтобы заставить бетон схватываться быстрее, необходимо использовать специальные строительные добавки, которые называются ускорители твердения или схватывания бетонного состава.
Ускорители твердения в нашем магазине
- Код товара:
0002331
- Фасовка: {{option_item.option_name}}
- Тип материала:
сухой
- Бренд:
Полипласт
- Страна производитель:
Россия
- Код товара:
0009979
- Фасовка: {{option_item.option_name}}
- Тип материала:
жидкий
- Бренд:
Полипласт
- Страна производитель:
Россия
Ускорители твердения бетонного раствора для сокращения сроков строительства
Ускорители схватывания раствора представляют собой вещества в жидком или порошкообразном варианте, которые добавляют к бетонному составу непосредственно перед бетонированием. Данные вещества ускоряют процесс гидратации цемента. Происходит это благодаря тому, что ячейки ускорителей поглощают в достаточном количестве жидкую фазу, стимулируют быстрое схватывание раствора с заполнителем и последующее ускоренное упрочнение цементного камня.
Благодаря применению добавок-ускорителей можно добиться сокращения сроков производства, что, в конечном итоге, позволит существенно сэкономить время и денежные затраты. Именно применение ускорителей схватывания отдельно или в комплексе с другими модификаторами бетона позволяет начать получать выгоду от строительства и бетонирования, существенно сокращая трудозатраты и вложенные материальные средства.
Помимо сокращения сроков производства использование этого вида добавок позволяет бетону получить ряд дополнительных преимуществ перед раствором без добавок:
- Появляется возможность сократить время выдержки отформованных бетонных изделий в формах. Таким образом, для изготовления необходимого количества заготовок применяется меньшее количество форм, которые являются достаточно дорогостоящими.
- Для выдержки отформованных изделий не нужны большие площади, так как время выдержки каждой партии сокращается.
- Применение данных добавок возможно и в технологии железобетона и сборного бетона, подходит для бетонных растворов с плотными и пористыми заполнителями.
- Время, затраченное на тепло-влажностную обработку бетонных конструкций, существенно уменьшается, а значит, сокращаются и энергозатраты, что в промышленных масштабах играет немаловажную роль.
- Благодаря применению ускорителей твердения вы можете сэкономить и на количестве вводимого в состав цемента. Если ввести в состав ускоритель вместе с пластификатором, то можно добиться снижения количества цемента до 15 процентов.
- Ускорители твердения позволяют осуществлять бетонирование при резко отрицательных температурах в зимний период. Они ускоряют процесс гидратации цемента, а ускоренное твердение позволяет бетону набрать критический уровень прочности. Бетон, достигший уровня критической прочности, уже может сопротивляться давлению замерзающей воды.
Благодаря этим процессам структура цементного камня становится мелкопористой; количество свободной воды резко уменьшается и замерзание становится практически невозможным.
За счет введения таких добавок бетонный раствор твердеет на 25 процентов быстрее при температуре окружающей среды + 20 градусов. Твердение бетона в возрасте 24 часов должно составлять 20 процентов и выше. Именно это является критерием применения качественной добавки.
Виды веществ, ускоряющих схватывание бетона
Название добавки-ускорителя твердения | Описание добавки |
Поташ, представляющий собой карбонат калия | Кристаллический порошок белого цвета вводится в раствор в пропорции не более пяти процентов по отношению к количеству цемента. Схватывание бетонной смеси ускоряется, а структура бетона представляет собой крупные поры. Эта добавка считается противоморозной добавкой-антифризом, с которой строительство можно продолжать даже при очень низких минусовых температурах.![]() |
Нитрат кальция | Бесцветный порошок, который полностью растворяется в воде. |
Сульфат натрия | Кристаллообразный порошок белого цвета с оттенком желтого. Данное вещество плохо растворяется в воде |
Хлорид кальция | Порошок белого цвета, может быть представлен в виде водных растворов. |
Хлорид натрия | Белое кристаллическое порошкообразное вещество, которое следует вводить в железобетонные изделия с ограничениями, поскольку может произойти интенсивная коррозия арматуры. Приблизительное количество вводимой добавки не должно превышать 4 процентов от количества цемента. |
Алюминат натрия | Водный раствор, который следует готовить непосредственно перед введением в бетон. Дозировка алюмината натрия составляет 3 процента от общего количества цемента, вводимого в строительный состав. |
Существует и ряд других добавок, которые используются в строительстве в виде ускорителей схватывания бетонных масс. В интернет-магазине Триколор вы можете купить добавки, ускоряющие твердение, в порошкообразном и жидком виде, изготовленные российской компанией Полипласт, которая является опытным и надежным производителем-поставщиком добавок для бетонов
.
Ускорители твердения в нашем магазине
- Код товара:
0002331
- Фасовка: {{option_item.option_name}}
- Тип материала:
сухой
- Бренд:
Полипласт
- Страна производитель:
Россия
- Код товара:
0009979
- Фасовка: {{option_item.option_name}}
- Тип материала:
жидкий
- Бренд:
Полипласт
- Страна производитель:
Россия
Ускоритель 1 жидкий — Новые технологии и материалы
Ускоритель твердения и набора прочности бетонов и строительных растворов
Содержание сухих веществ не менее 34%, плотность при 20°С не менее 1,28 г/см3. Не содержит едких веществ, не вызывает коррозию арматуры. Соответствует требованиям ГОСТ 24211-2003.
Позволяет:
- · ускорить набор прочности бетона и цементных растворов в 2,0 -5,0 раз в возрасте 1-3 сутки (в зависимости от дозировки и состава бетона и цементных растворов), при нормальных и повышенных температурах;
- · ускорить оборот заливочных форм и распалубку конструкции;
- · произвести нормальную укладку и транспортировку бетонов и строительных растворов без сокращения времени схватывания и загущения;
- · увеличить водонепроницаемость бетона на три-четыре марки, т.е. 6-8 W;
- · увеличить морозостойкость на одну-три ступени, т.е. на 50-150 циклов;
- · увеличить конечную прочность бетонов и цементных растворов на 5-25%;
- · значительно сокращает время пропаривания.
Расход
10 — 30 мл жидкого ускорителя на 1 кг цемента. Например, для бетонов, содержащих 280-380 кг цемента, на 1 куб.м рекомендуется 2-8 литров добавки. В пересчёте на сухое вещество: 0,25 — 1,0% от массы цемента.
Технология применения:
Применяется на стадии приготовления бетонных и цементных растворов. Вводится в бетоносмеситель вместе с водой затворения, либо через дозатор жидких добавок вместо части воды затворения, либо в готовый бетон в миксере непосредственно на строительной площадке с дополнительным перемешиванием раствора.
Ускоритель совместим с другими добавками для бетонов, соответствующих ГОСТ 24211-2003.
Примечания:
Может сокращать время начала схватывания бетонного и строительного раствора на 10-30% в зависимости от состава бетона.
Рекомендуется использовать также при изготовлении железобетонных изделий – плит, блоков, труб, колонн, стяжек, дорожек, заливочных стен, тротуарной плитки, бордюров и т.д. – с целью сокращения технологического цикла и увеличения оборачиваемости форм.
Ускоритель-пластификатор АКТИВАТОР А10
Ускоритель-пластификатор АКТИВАТОР А10
Ускоритель набора прочности AKTIVATOR A10 — комплексная добавка для бетонных смесей.
Соответствует требованиям ГОСТ 24211
«Добавки для бетонов и строительных растворов. Общие технические условия».
Удовлетворяет требованиям ТУ 20.59.59-004-16918243-2018.
Приемущества
- Улучшает удобоукладываемость бетонных смесей.
- Ускоряет процесс твердения бетона и раствора, на 30% и более.
- Обеспечивает нормированное воздухововлечение – 2-4%.
- Повышает связность и уменьшает расслаиваемость бетонной смеси.
- Позволяет значительно увеличивать прочность бетона в 1 сутках твердения, за счет акти- визирующих и диспергирующих свойств.
- Увеличивает прочность бетона в 28 сутках твердения, % не менее: 40-50 (в сравнении с бетоном без добавок при одинаковой О.
К).
- Позволяет увеличить распалубочную прочность в условиях не отапливаемого цеха или в условиях полигона.
- Повышает марку бетона по морозостойкости и водонепроницаемости.
- Позволяет сократить время и энергетические затраты на тепловлажностную обработку бетона, а также затраты на вибрирование бетонной смеси.
Область применения
- Промышленное и гражданское строительство.
- Тяжелый бетон, за исключением бетонов с преднапрягаемой арматурой.
- Легкий бетон (пенобетон, газобетон, керамзитобетон и др.).
- Малые архитектурные формы (тротуарная плитка, бордюры, заборы, бетонные ограждения и др.).
- Кладочные растворы.
Технические характеристики
Вид добавки | Ускоритель-пластификатор |
---|---|
Наименование | AKTIVATOR A10 |
Контроль качества | ГОСТ 24211, ГОСТ 30459, ТУ 20.![]() |
Внешний вид | Светло-желтый порошок |
Насыпная плотность, кг/м³ | 700 — 1300 |
Водородный показатель pH | 4,0 — 9,0 |
≥97,0 | |
Оптимальная дозировка, в % в пересчете на сухой продукт от массы цемента | 0,4 — 0,7 |
Граничная дозировка, в % в пересчете на сухой продукт от массы цемента | 0,3 – 0,8 |
Срок хранения | 1 год со дня изготовления |
Форма поставки | Полипропиленовые мешки 30 кг |
Рекомендации по применению
Перед применением, сухой порошок рекомендуется растворить в воде, до концентрации не более 15 %. Для ускорения растворения, рекомендуется использовать подогретую воду, до 30-50°С. Не допускается использовать, водный раствор добавки, при наличии осадка. Готовый водный раствор добавки, вводится в бетонные смеси вместе с водой затворения.
Совместимость
При технико-экономическом обосновании для обеспечения показателей качества бетонных смесей, бетонов и сборных железобетонных изделий допускается применение добавок AKTIVATOR A10 в комплексе с другими добавками типа гидрофобизирующих, противомо- розных, и т.п. Введение добавок AKTIVATOR A10 в бетонную смесь рекомендуется производить отдельно от других добавок.
Требования по безопасности при работе с добавкой
Добавка AKTIVATOR A10 является веществом умеренно опасным и относится к 3-му классу опасности по ГОСТ 12.1.007. Добавка не образует токсичных соединений в воздушной среде и сточных водах. Введение добавки в бетонную смесь, не изменяет токсиколого-гигиенических характеристик бетона. Затвердевший бетон с добавкой, в воздушную среду, токсичных веществ не выделяет.
Добавка в бетоны Нитрат Кальция!!!
NITCAL (Нитрат кальция технического качества (CN)) специально разработанный качественный Нитрат Кальция, обладает свойствами, которые позволяют использовать продукт в создании бетонной смеси со следующими свойствами:
— Ускоренным набором прочности;
— Устойчивостью к трещинообразованию;
— Пролонгированным во времени набором прочности.
УСКОРИТЕЛЬ НАБОРА ПРОЧНОСТИ
Растущий интерес к коррозии арматурных стержней, внедренных в бетон из портландцемента, которая вызвана хлоридами, привел к появлению добавок, не содержащих хлориды. Особое внимание было уделено составам ускоряющих добавок, не содержащих хлориды, которые пришли на смену широко используемому ускорителю ? хлориду кальция.
Соль, которая удовлетворяла этим требованиям, был нитрат кальция. После пяти лет непрерывных исследований, было обнаружено, что нитрат кальция является также очень эффективным замедлителем коррозийных процессов в металлах, помещенных в бетон.
NITCAL в дозировке 0, 2 -1, 2% от массы цемента действует как ускоритель сроков схватывания при 20ºС и, таким образом, повышает прочность на ранней стадии (например, через 6-8 часов). Вследствие превращения небольшого количества аммония в Нитрате Кальция технического качества в амин в процессе реакции с эпоксидом, происходит превращение Нитрата Кальция из чистого ускорителя сроков схватывания еще и в ускоритель твердения. При небольших дозах (1- 2 %) вводится для долгосрочного повышения прочностных характеристик бетона.
В дозировке 0,5 — 1 % от массы цемента обеспечивает наилучшую водонепроницаемость бетона, интенсифицирует набор прочности и повышает конечную прочность на 20 — 30 %.
NITCAL уплотняет бетон. Это способствует его ускоренной самокальматации (самозакупоривании порового пространства карбонизирующейся на воздухе гидроокисью кальция) и предотвращает высолообразование на стадии эксплуатации.
Использование нитрата кальция как ускорителя для бетона:
Сокращение сроков схватывания при завершении работ, выравнивании плит для пола или при работе с готовыми элементами (заводского изготовления)
Повышенная скорость твердения для бетонов с низким показателем вода/цемент, с замедленными сроками схватывания при добавлении большого количества пластификаторов/ суперпластификаторов.
При транспортировке на большие расстояния или в условиях жаркого климата бетон с добавлением лигносульфоната можно привести в рабочее состояние на месте путем добавления нитрата кальция в барабан бетономешалки.
При зимнем бетонировании, ускоренное возрастание прочности предотвратит слишком быстрое затвердевание после выделения тепла вследствие гидратации.
Получение бетонов с высокой прочностью.
ЗАВИСИМОСТЬ ЭФФЕКТИВНОСТИ ОТ ТИПА ЦЕМЕНТА
Экспертиза эффективности NITCAL с 10 различными марками Портландцемента показала, что не было никакой корреляции между ускоренным набором прочности и содержанием С3А( трех кальциевый алюминат-целит). Однако, корреляция была найдена с С2S (двух кальциевый силикат-белит) содержанием. ЭффективностьNITCAL как ускорителя набора прочности уменьшается с увеличивающимся содержанием щелочи Na2O в бетонной смеси, тогда как гидроксиды и сульфаты ускорят активность кальция.
NITCAL используется для цементов с низким содержанием щелочи, используется для цементов как с низким, так и с высоким содержанием белита (C2S).
NITCAL ? наиболее эффективен, как ускоритель набора прочности для Портландцемента с высоким содержанием белита и низким содержанием щелочи.
Уменьшенный период индукции и время набора прочности могут использоваться несколькими способами:
? В зимний период для избегания переохлаждения свежего бетона до начала твердения.
? Производство готовых элементов (более быстрое повторное использование форм).
? Уменьшенный риск трещин из-за усадки бетонной смеси.
? Уменьшенное время до финишной обработки (заглаживание) бетонных полов.
? Увеличенная ранняя прочность бетона.
? Для активации бетонной смеси после долгой транспортировки или транспортировки в жарком климате.
СНИЖЕНИЕ РИСКА ТРЕЩИНООБРАЗОВАНИЯ
NITCAL может использоваться как добавка, снижающая риск трещинообразования из-за быстрой потери влаги в свежем бетоне. Наиболее вероятен эффект ускоренного набор прочности. При проведенных испытаниях бетонных смесей с w/c=0.45, с 2% NITCAL от массы цемента и без добавки. Бетонные кольца были подвергнуты высыханию в установке, со скорость ветра 4,5 м/с, при температуре 20ºС, относительной влажностью 43%. Бетон без добавки имел усадочные трещины, в то время как не наблюдалось ни одной трещины в бетоне с 2% NITCAL.
ИНГИБИТОР КОРРОЗИИ
NITCAL Препятствует коррозии арматуры, вызванной повышенным содержанием хлоридов. Дозировка 2 — 4 %.
В ходе проведения длительных испытаний было доказано, что нитрат кальция замедляет процесс коррозии арматурной стали, вызванный хлоридами как добавленными непосредственно в воду для затворения, так и добавленными позднее, а также превосходит нитрит кальция в испытаниях по коррозии. Механизм действия нитрата и нитрита как ингибиторов коррозии схожи в щелочных средах, таких как бетон. Кинетика действия нитрата медленнее, чем нитрита, но это важно только в краткосрочных испытаниях, поскольку на практике процесс коррозии ? это довольно длительный процесс. Как следует из теории, нитрат кальция обеспечивает больший резервный запас, чем нитрит кальция.
Противоморозная добавка
Добавка NITCAL в качестве ускорителя сроков схватывания цемента предназначена для производства бетонных смесей, в частности, рекомендована при низких температурах воздуха.
Введение добавки NITCAL в бетонную смесь при низкой температуре окружающей среды вызывает понижение температуры замерзания воды, что позволяет замешивать бетон при температуре воздуха — 10ºC без замедления процесса гидратации цемента. Эффективное влияние NITCAL на бетонную смесь достигается при температуре — 15?С окружающей среды, если добавляется больше 1-2% добавки от массы цемента.
Применение NITCAL имеет устойчивый рост в мировом масштабе, находит применение во многих серьезных строительных проектах.
Бетонная смесь с NITCAL использовалась на строительстве шахт в Северном море (высота 369 м), под нефтегазодобывающие платформы. Целесообразность использования NITCAL заключалась в том, что он противодействовал эффекту замедления твердения смеси при заливке высоких и массивных конструкций. Объем продаж по миру составляет более 1 млн. тонн в год.
Материал подготовлен по данным изготовителя YARA INDUSTRIAL и испытаний профессора Гарольда Джастнеса, SINTEF Гражданское строительство, моделирование условий эксплуатации, цементы и бетоны, Тронхейм, Норвегия.
Влияние ускорителей и замедлителей набора прочности бетона на основе низкотемпературного отверждаемого обычного портландцемента и смесей сульфоалюмината кальция
(Базель). 2020 апрель; 13(7): 1505.
Hyeonggil Choi
2 Школа архитектуры, Национальный университет Кёнпук, Бук-Гу, Тэгу 4566, Корея
2 Школа архитектуры, Национальный университет Кёнпук, Бук-Гу, Тэгу 4566, Корея
† Эти авторы внесли такой же вклад в эту работу, как и первый автор.
Поступила в редакцию 1 февраля 2020 г .; Принято 22 марта 2020 г.
Лицензиат MDPI, Базель, Швейцария. Эта статья находится в открытом доступе и распространяется в соответствии с условиями лицензии Creative Commons Attribution (CC BY) (http://creativecommons.org/licenses/by/4.0/). Эта статья цитировалась в других статьях в PMC. .Abstract
В этом исследовании были проведены эксперименты по применению строительных растворов и бетонов на основе вяжущих на основе сульфоалюмината кальция (CSA) для ускорения набора прочности обычного портландцемента (OPC) в условиях низких температур. Оптимальная смесь CSA была оценена для улучшения ранней прочности OPC, и было изучено влияние ускорителей и замедлителей схватывания на эту смесь, чтобы продемонстрировать применимость полученной бетонной смеси. Кроме того, применимость смеси была подтверждена производством бетона на заводе Remicon Batcher и проведением численного моделирования. Как было замечено, оптимальная степень замены CSA для достижения ранней прочности составляла 17% от общего количества вяжущего на единицу с соотношениями CaO/SO 3 и SO 3 /Al 2 O 3 , равными 1.9 и 1,25 соответственно. Очевидно, CSA в сочетании с Na 2 SO 4 в качестве ускорителя способствует ранней прочности бетона с OPC и обеспечивает его технологичность с помощью дополнительных замедлителей схватывания для контроля быстрого схватывания бетона. Кроме того, активация начальной гидратации при низких температурах позволила получить прочность на сжатие 5 МПа/12 ч и выше для полученной бетонной смеси.
Ключевые слова: низкотемпературный режим, портландцемент рядовой, ЦСА, ускоритель, замедлитель схватывания, ранняя прочность
1.Введение
Ввиду реакции с водой с образованием гидратов цемент подвергается упрочнению за счет конденсации с последующим отверждением [1,2,3,4,5]. Эта начальная реакция гидратации приводит к образованию эттрингита, и ионы Ca 2+ , присутствующие в жидкой фазе, непрерывно элюируются для увеличения производства Ca(OH) 2 [6]. Следовательно, наступает период акселерации, при котором происходит реактивация гидратации из мембраны C–S–H, окружающей частицы алита (C 3 S) и белита (C 2 S), которые подвергаются расширению и разрушению.В дальнейшем в фазе C–S–H образуются зародыши для ускорения роста и быстрого потребления Ca(OH) 2 , который активно производит гидратированные продукты. В период торможения эттрингитовая оболочка, окружающая частицы алюмината, разрушается до регидратации С 3 А, а прочность на сжатие выражается переходом в моносульфаты, от недостаточного количества гипса [2,6].
Обыкновенный портландцемент (OPC) имеет преимущество в том, что он обладает благоприятными физическими свойствами и прочностью благодаря своим стабильным химическим реакциям, что обеспечивает широкую область применения.Однако его зависимость от высоких температур снижает его реакционную способность в области низких температур [7], что ограничивает его раннее развитие прочности при нанесении на строительные растворы или бетоны.
Напротив, цементы на основе сульфоалюмината кальция (гауин минералы, CSA) имеют значительно более высокую скорость гидратации, чем OPC [8,9,10,11]; им уделяется постоянное внимание исследователей, поскольку их ранняя прочность может быть достигнута при замене на OPC в оптимальном соотношении из-за высоких температур, участвующих в начальной реакции гидратации [12, 13, 14, 15, 16, 17, 18, 19, 20].Кроме того, можно обеспечить формирование пассивирующей пленки арматурной стали в дополнение к стабильному объему благодаря отличной начальной прочности на ранней стадии, тем самым позволяя развить 28-дневную проектную норму ранней прочности [21]. ,22]. Таким образом, цементы CSA приобрели популярность для раннего набора прочности OPC.
Кляйн и Мета сообщили, что различные гидраты могут быть получены в зависимости от молярных соотношений Al 2 O 3 /SO 3 и CaO/SO 3 в CaO-Al 2 O 3 -SO 3 [23], где компонент с высоким содержанием Al 2 O 3 проявляет быстросхватываемость и раннюю прочность, компонент с высоким содержанием CaO проявляет расширяемость, а компонент с высоким содержанием SO 3 обладает высокими прочностными характеристиками [23]. 24].Ключевые факторы гидратации CSA-цементов варьируются в зависимости от ингредиентов и состава клинкеров Hauyne, реакционной способности внешнего гипса, типа смеси, а также условий смешивания и отверждения. Эти соединения CSA наносятся на строительные растворы или бетоны и способствуют расширению затвердевшего тела за счет давления роста, когда кристаллы эттрингита растут после образования затвердевших тканей. Однако, если расширенное давление превышает модуль упругости закаленного тела, это часто приводит к разрушению закаленного тела [23,25].Следовательно, для придания функциональности растворам или бетонам желательно разрабатывать материалы с характеристиками гидратов, таких как эттрингит, наряду с развитием всестороннего понимания и достаточного анализа заполнителей и поверхности раздела, смешивания с раствором и бетона для быть трудоустроенным. Хотя были проведены различные исследования набора прочности растворов и бетонов на основе OPC на ранней стадии, большинство из них было проведено на растворе, и было несколько ограничений из-за начальной высокой теплоты гидратации и свойств быстрого схватывания цементов CSA по сравнению с OPC. [26,27,28,29].
В этом исследовании проводятся эксперименты на строительном растворе и бетоне для разработки вяжущих для бетона с ранней прочностью с использованием вяжущих OPC и CSA при низких температурах. Кроме того, это исследование направлено на подтверждение применимости CSA в бетоне путем рассмотрения различных факторов, таких как оптимальное вяжущее, ускоритель и замедлитель схватывания, посредством экспериментов с раствором для раннего набора прочности.
2. Экспериментальная работа
2.1. Материалы
и представить физические характеристики материалов, использованных в этом исследовании.В качестве цемента использовали OPC (3150 кг/м 3 , крупность 330 м 2 /кг). В качестве связующих используют золу-уноса (плотность: 2140 кг/м 3 , крупность: 396 м 2 /кг), Шлак доменный молотый гранулированный (плотность: 2860 кг/м 3 , крупность: 430 м 2 /кг) и сульфоалюминат кальция (плотность: 2890 кг/м 3 , крупность: 466 м 2 /кг).
Таблица 1
Химический состав используемых связующих.
Материалы | Химические композиции (%) | 7 CAO | SiO 2 4 AL 2 O 3 Fe 4 Fe 2 O 3 4 MgO | K 2 O 4 | NA 2 O 2 O | 9 TIO 2 SO 3 | Loi | | |||||||||
---|---|---|---|---|---|---|---|---|---|---|---|---|---|---|---|---|---|
OPC (1) | 60.![]() | 21.6 | 21.6 | 5.15 | 5.15 | 3.30 | 0.99 | 0.99 | 0.53 | — | — | ||||||
GGB (2) | 44.![]() | 35.4 | 13.0 | 0.47 | 5.01 | 5.01 | 0.37 | — | — | 1.31 — | 0.31 | 0.69 | |||||
FA (3) | 4,00 | 57.![]() | 20.5 | 6.80 | 1.38 | 1.18 | 0,18 | 0,89 | — | — | |||||||
CSA 45.51 | 45.51 | 4.91 | 22.![]() | 1.74 | 1.57 | 0,17 | 0.43 | — | 22,63 | 1,90 |
Таблица 2
Физические свойства используемых материалов.
Материал | Недвижимость | ||
---|---|---|---|
ASTM Тип I Обычные Портленд Цемент Плотность: 3150 кг / м 3 , Тритант: 330 м 2 / кг | |||
FA | Fly Fly Плотность: 2140 кг / м 3 , Тритатура: 396 млн. ![]() | ||
GGBS | Гранулированный доводной ГГБС | Гранулированный Гранулированный шлак Плотность: 2860 кг / м 3 , Трикота: 430 M 2 / кг | |
CSA | CALSIUR Плотность: 2890 кг / м 3 , Тритатура: 466 млн. 2 / кг | ||
Прекрасный агрегат | S1 | ISO Стандартный песок, Размер: 2 мм Модуль крупности: 2. ![]() | |
S2 | Морской песок, Размер: 5 мм Модуль крупности: 2,01, плотность: 2600 кг/м 3 : 0.79% | ||
S3 | S3 | Разрешеный песок, размер: 5 мм Модуль тонкости: 3.29, плотность: 2570 кг / м 3 , поглощение: 0,87% | |
Грубый совокупность | Разрешеный гранитный агрегат, размер : 25 мм Модуль крупности: 6,94, плотность: 2600 кг/м 3 , абсорбция: 0.76% | ||
Химическая добавка | Группа поликарбоновой кислоты, плотность: 1260 кг / м 3 | ||
Материал ускорителя | NS | Na 2 SO 4 , плотность: 3350 кг / м 3 , Растворимость: 13,9 г / 100 мл (20 ° C) | |
AS | AL 2 (SO 4 ) 3 , плотность: 2672 кг / м 3 , растворимость: 36,4 г /100 мл (20 °C) | ||
CH | Ca(OH) 2 , плотность: 2211 кг/м 3 , растворимость: 17.![]() | ||
CN | Ca(NO 3 ) 2 , плотность: 2504 кг/м 3 , растворимость: 51,4 г/100 | ||
NC | Nahco 3 , плотность: 2200 кг / м 3 , растворимость: 9,6 г / 100 мл (20 ° C) | ||
Retarder | CA: Лимонная кислота, SG: глюконат натрия , BA: борная кислота, TA: винная кислота |
показывает результаты испытания просеивания заполнителей (ASTM C136) [30], использованных в настоящем документе, которое было проведено для анализа классификации мелких и крупных заполнителей.Для мелких заполнителей используется стандартный песок ISO (размер: 2 мм, модуль крупности: 2,99, плотность: 2620 кг/м 3 , SiO 2 : 99%, 0,08 мм, количество проходов: 0,04%) [31] В эксперименте с раствором использовали морской песок (размер: 5 мм, модуль крупности: 2,01, плотность: 2600 кг/м 3 , абсорбция: 0,79%) и дробленый песок (модуль крупности: 3,29, плотность: 2570 кг/м). m 3 , и поглощение: 0,87%), использовали для оценки их применимости в бетоне. Мелкие заполнители готовили путем смешивания морского песка и дробленого песка в соотношении 4:6 с модулем крупности 2.84.
Кривые ситового анализа для используемых здесь заполнителей: ( a ) Стандартный песок ISO; ( b ) мелкие заполнители; и ( c ) крупные заполнители.
В качестве крупных заполнителей использовались дробленые гранитные заполнители (размер: 25 мм, модуль крупности: 6,94, плотность: 2600 кг/м 3 , абсорбция: 0,76%).
Группа поликарбоновых кислот (плотность: 1260 кг/м 3 ) использовалась в качестве химической добавки. В качестве материалов-ускорителей, NS: Na 2 SO 4 , AS: Al 2 (SO 4 ) 3 , CH: Ca(OH) 2 , CN: Ca(NO ) 2 и NC: NaHCO 3 , а в качестве замедлителей схватывания использовали CA: лимонную кислоту, SG: глюконат натрия, BA: борную кислоту и TA: винную кислоту.
2.2. Схема эксперимента и пропорции смеси
показывает схему эксперимента для этого исследования. Для изучения оптимального метода набора ранней прочности бетона с использованием обычного цемента реакционную способность вяжущего CSA и количество дополнительных материалов контролировали на основе стехиометрических уравнений реакции по CaO/SO 3 и Al 2 O [23].Кроме того, оптимальное количество вяжущего CSA, которым можно заменить OPC, было определено путем оценки характеристик строительного раствора на основе количества используемого вяжущего CSA.
Таблица 3
(° C)
16, 17, 18
Прочность на компрессию
-12 ч, 24 ч
(B × 0.
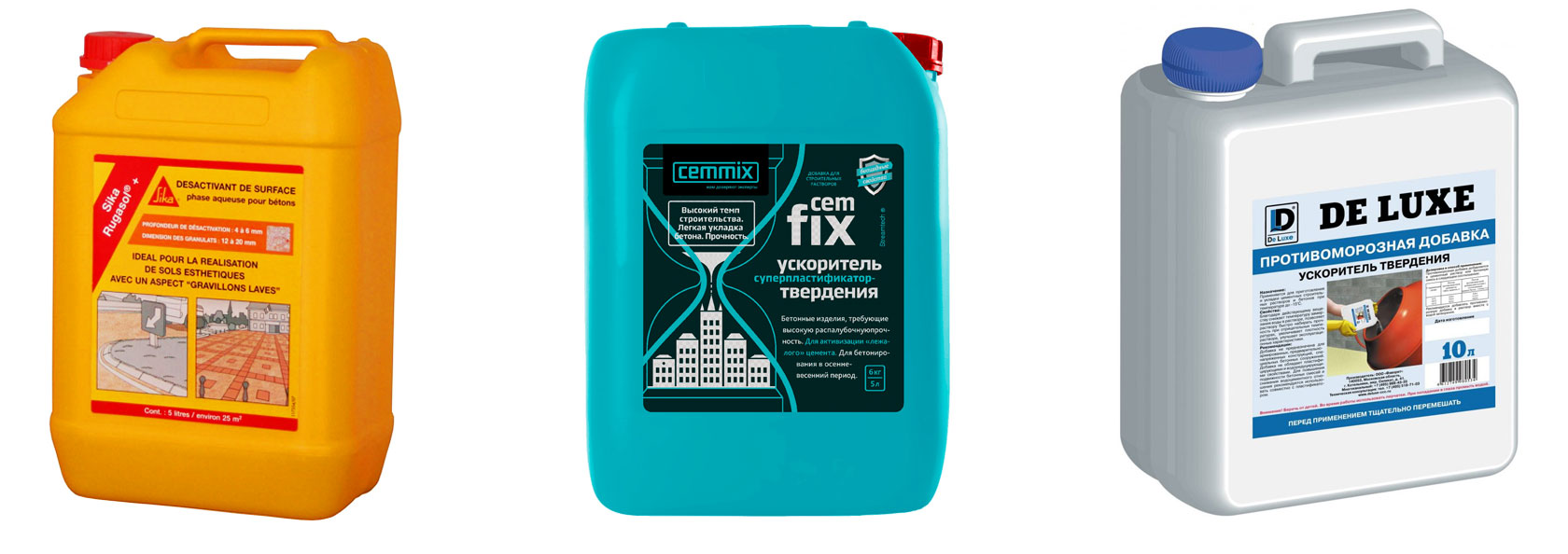
Прочность на сжатие
-12 ч, 24 ч, 72 ч
(B × 1%, 2%, 3%)
CA (B × 0,2%)
( Периодическая установка + макетный элемент)
Камера (13)
Комнатная температура (20)
(B × 3.
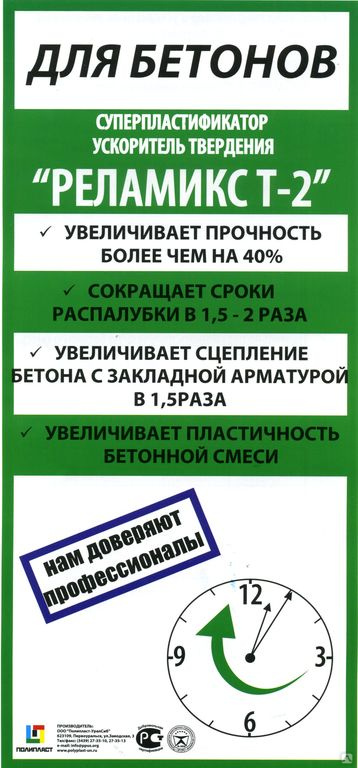
Прочность на сжатие — 12 ч, 24 ч, 72 ч
7 Д, 28 Д — Макет элемента: 12 ч, 24 ч, 72 ч
Возможность повышения начальной прочности раствора затем исследовали комбинирование связующего CSA и ускорителя; В качестве ускорителя использовали 0,5% от общего количества связующего. При использовании вяжущих CSA может происходить быстрое схватывание, поэтому был рассмотрен замедлитель схватывания, совместимый со вяжущим CSA. Добавлено пять типов замедлителей на уровне 0.2% c.f., связующее. Для приготовления образцов бетона использовалась комбинация ускорителя и замедлителя схватывания, и в каждом случае оценивались характеристики ранней прочности и способность предотвращать быстрое схватывание. Количество замедлителя было доведено до 0,2%, а три типа ускорителей использовались в количествах 1%, 2% и 3%.
Наконец, на основе количества CSA, ускорителя и замедлителя схватывания, полученного в результате вышеуказанных экспериментов, был разработан состав бетонной смеси. Применимость рассмотренных в настоящей работе вяжущих для бетона с ранней прочностью оценивалась в ходе макетных экспериментов производства на заводе Remicon Batcher.
и показать пропорции смешивания раствора и бетона, используемые в этом исследовании. Течение раствора составляло <200 мм в соответствии с ASTM C1437 [32]. Осадка бетона составила 210 ± 25 мм, содержание воздуха 4,5 ± 1,5 %.
Таблица 4
Пропорции основного раствора.
серии | W / C (%) | C: S (1) | Цемент (G) | Вода (G) | AD (2) (B ×%) |
---|---|---|---|---|---|
Ⅰ (Раствор) | 50 | 1:3 | 450 | 225 | 0.![]() |
Таблица 5
Пропорции смешивания бетона.
Series | W / B (%) | S / A (%) | Единица (кг / м 3 ) | AD (3) (B ×%) | AC (b ×%) | |||||||||
---|---|---|---|---|---|---|---|---|---|---|---|---|---|---|
W | C (1) | CSA | GGBS | FA | S (2) | (2)G | ||||||||
ⅱ ( Бетон) | Гладкая | 53.![]() | 49.0 | 175 | 175 | 215 | — | 66 | 50 | 8 | 9 | 0,7 | — | |
CA17 | 53.0 | 49,0 | 175 | 274 | 56 | — | — | 899 | 901 | — | 3.![]() |
2.3. Test Methods
показывает методы испытаний и соответствующие им элементы оценки для образцов строительного раствора и бетона.Различные процедуры тестирования описаны ниже.
Таблица 6
Методы испытаний и соответствующие им элементы оценки.
Серия | Элемент оценки | Метод испытаний | Размер (мм) |
---|---|---|---|
Ⅰ. Метчатый тест | Установка времени (h) | ASTM C403 / C403M [33] | — |
Прочность на компрессию (MPA) | ASTM C109 / C109M [34] | 40 × 40 × 160 | |
Ⅱ.![]() | Спад (мм) | ASTM C143 [35] | — |
Содержание воздуха (%) | ASTM C231 [36] | — | |
Прочность на компрессию (МПа) | ASTM C873 [37] | Ø100 × 200 | |
ASTM C39 [38] |
2.

Испытание на текучесть строительного раствора проводилось на основе ASTM C1437 [32], а испытание на схватывание строительного раствора проводилось на основе ASTM C403/C403M [33].Прочность раствора на сжатие была рассчитана путем измерения максимальной нагрузки с использованием 30-тонного UTM в течение запланированного времени в соответствии с ASTM C109/C109M [34]. Прочность бетона на сжатие рассчитывали как среднее значение, полученное на трех испытательных образцах.
2.3.2. Применение для бетона
На основании соотношения оптимального вяжущего и добавки, полученной в результате испытания раствора, оценивалась применимость к бетону. Бетон был произведен на заводе Remicon Batcher, а теплота гидратации и набор прочности были смоделированы путем изготовления макетов стен.и покажите детали макета и установки термопары соответственно. Моделирование макета было установлено на 200 мм × 600 мм × 1000 мм, а термопара типа K была встроена в центр макета.
Прикладные испытания бетона ранней прочности на дозаторном заводе.
Установка термопары и закладной двойной формы для испытания бетона.
Для оценки свойств свежего бетона было проведено испытание на осадку в соответствии с ASTM C143/C143M [35], а испытание на содержание воздуха было проведено в соответствии с ASTM C231/C231M-17a [36].Для оценки удобоукладываемости на площадке исследовали свойства свежего бетона после выдержки в автобетоносмесителе в течение 0, 60 и 90 мин. Для измерения прочности на сжатие бетона, подвергнутого гидратации, была установлена двойная форма в соответствии с ASTM C873 [37].
Прочность бетона на сжатие была рассчитана путем подготовки образца Ø100 мм × 200 мм в соответствии с ASTM C39/C39M [38] и измерения максимальной нагрузки с использованием 300-тонного UTM в течение определенных периодов времени.Прочность бетона на сжатие рассчитывали как среднее значение, полученное на трех образцах.
3. Результаты и обсуждение
3.

3.1.1. Влияние замены CSA
наи показывают время схватывания и результаты прочности на сжатие, соответственно, для образца раствора с заменой CSA, причем очевидно, что оба эти показателя увеличиваются с увеличением коэффициента замены CSA. При замещении CSA выше 17% наблюдалось небольшое изменение прочности на сжатие, поэтому это значение считалось оптимальным.Кроме того, прочность раствора на сжатие достигала максимума при 8,3 МПа через 12 ч при использовании в смеси 17 % CSA и при времени схватывания >75 мин.
Время схватывания раствора с заменой CSA.
Прочность раствора на сжатие с заменой CSA.
отображает тренды расчетных отношений CaO/SO 3 и Al 2 O 3 /SO 3 в соответствии с изменениями коэффициента замещения CSA, а также показывает оптимальный химический состав бетона ранней прочности.Хотя предыдущие исследования подтвердили, что химические свойства CSA способствовали гидратации цемента из-за высокого содержания SO 3 , этот эффект применим только в соответствующем диапазоне [39,40,41].
Относительные индексы CaO/SO 3 и Al 2 O 3 /SO 3 с заменой CSA.
Оптимальный химический состав для бетона ранней прочности.
Как указано в рамках данного исследования, оптимальное соотношение замещения для вяжущего CSA для ранней прочности составляет 17% при соотношениях CaO/SO 3 и Al 2 O 3 /SO 3 , равном 1.9 и 1,23 соответственно.
Кроме того, было обнаружено, что при нанесении на бетон комбинации вяжущего для ранней прочности, ускорителя и замедлителя схватывания достигается прочность на сжатие 5 МПа/12 ч при низких температурах. Однако это также требовало тщательного контроля за смешиванием бетона. Кроме того, следует отметить, что характеристики вяжущих с ранней прочностью должны быть проверены в ряде условий для обеспечения надежности.
3.1.2. Влияние ускорителя
и показать время схватывания и результаты прочности на сжатие для раствора с добавлением ускорителей. В отсутствие ускорителя время схватывания раствора составляло 90 мин, а в присутствии ускорителя оно быстро уменьшалось до 20–40 мин. Эти результаты показывают, что использование ускорителя способствует гидратации реактивных гауиновых минералов, и, поскольку это также влияет на прочность на сжатие, считается, что начальное производство эттрингита также увеличивается [19, 20].
Время схватывания раствора в присутствии различных ускорителей.
Различия в прочности раствора на сжатие в присутствии разных ускорителей.
В частности, Na 2 SO 4 и Al 2 (SO 4 ) 3 сульфатные ускорители оказались наиболее эффективными в улучшении начальной прочности на сжатие из-за более высокой скорости ионизации по сравнению с цементом. , а также потому, что первоначально элюированные ионы SO 4 2– выгодны для зародышеобразования гидрата эттрингита. Однако, хотя ускорители могут улучшить начальную прочность раствора, следует избегать использования одного ускорителя, так как это значительно сокращает время схватывания.
3.1.3. Влияние замедлителя и ускорителя схватывания
Изменение времени схватывания раствора в присутствии различных замедлителей схватывания показано в . Как указано, СА проявляет наибольший эффект замедления, за ним следуют БА, СК и ТА. Действительно, CA и SG широко используются в качестве замедлителей схватывания строительных растворов и бетона благодаря их превосходным экономическим характеристикам и характеристикам замедления схватывания. И CA, и SG состоят из шести атомов углерода, хотя CA содержит одну группу –OH и три группы –COOH, тогда как SG содержит пять групп –OH и одну группу –COOH.Таким образом, эти различия объясняют их различные характеристики в отношении замедления гидратации цемента. Следует отметить, что использование эквивалентного количества СА (т.е. с линейной молекулярной структурой) показало оптимальный эффект замедления.
Время схватывания раствора в присутствии различных замедлителей схватывания.
Кроме того, в случае времени схватывания раствора, за исключением случая СА, схватывание происходит в течение 2 часов, поэтому добавление СА необходимо для обеспечения достаточной технологичности. Однако видно, что прочность бетона на сжатие с использованием замедлителя схватывания была снижена. Таким образом, можно ускорить развитие силы на ранних этапах за счет комбинированного использования различных ускорителей.
Различия в прочности раствора на сжатие в присутствии различных замедлителей схватывания.
Изменение времени схватывания раствора и прочности на сжатие в присутствии как ускорителя (А), так и замедлителя (R) показаны на и . Как указано, время схватывания Plain R0A0 составляло 60 минут, а время схватывания R0.2А0, содержащем 0,2% замедлителя схватывания, составляло 135 мин, что указывает на задержку гидратации. Следовательно, начальная прочность на сжатие образца строительного раствора значительно снизилась до 57% от этого показателя простого образца [42].
Время схватывания раствора в присутствии ускорителей и замедлителей схватывания.
Различия в прочности строительных растворов на сжатие в присутствии ускорителей и замедлителей схватывания.
По сравнению с Обычным образцом (CSA17), в серии NS03_R0.2, где в качестве ускорителя использовался Na 2 SO 4 , время схватывания раствора немного уменьшилось, но прочность стабильно увеличилась в пределах 12 –24 ч, что дает значение 191.1–218,9%.
обобщает результаты времени схватывания и прочности на сжатие для образцов строительного раствора. Более конкретно, когда в цемент добавляли 17% CSA, было очевидно, что прочность раствора на сжатие улучшалась, а время схватывания уменьшалось. Кроме того, начальная прочность раствора, содержащего CSA, была увеличена, но скорость набора прочности снизилась через 24 часа, что указывает на то, что для обеспечения достаточной прочности раствора требуется ускоритель. Более того, при смешивании строительного раствора с Na 2 SO 4 в качестве ускорителя быстрое нарастание прочности было успешным, но время схватывания уменьшилось.Отсюда было сочтено, что использование дополнительного замедлителя необходимо для обеспечения стабильного рабочего времени.
Свойства раствора в присутствии CSA и примеси.
Кроме того, сообщалось, что использование замедлителей схватывания в строительных растворах на основе CSA является эффективным подходом к улучшению удобоукладываемости системы цементных смесей, которая довольно быстро отверждается без снижения конечной прочности [20,43].
3.2. Concrete Properties
показывает изменение осадки образца бетона во времени, где были изучены времена 60 и 90 минут с учетом времени между производством и доставкой на площадку.Для целей этого испытания бетон вращали на низкой скорости в автобетоносмесителе, и в каждый момент времени измеряли изменение осадки. Было обнаружено, что OPC и CSA17_NS03_R0.2 привели к незначительному снижению осадки, но полученные значения остались в пределах диапазона осадки, установленного в настоящем исследовании, что указывает на отсутствие проблем с точки зрения работоспособности в полевых условиях. Исходя из этого результата, использование связующего CSA может быть использовано для управления свойствами настройки.
Изменение осадки образца бетона со временем.
показывает изменение прочности бетона на сжатие в зависимости от температуры отверждения. В частности, в случае OPC измерение прочности бетона на сжатие через 12 часов было невозможно из-за задержки схватывания и твердения в условиях внешнего отверждения. Через 3 дня развивалась начальная прочность ≥5 МПа, а при повышении температуры время, необходимое для набора этой степени ранней прочности, имело тенденцию к уменьшению. Однако целевая прочность развивалась уже через 24 часа, даже при 20 °C.
Изменение прочности бетона на сжатие в зависимости от температуры отверждения.
В случае образца CSA17_NS03_R0.2 прочность на сжатие 5 МПа развивалась через 24 часа при низкой температуре <10 °C и через 12 часов при температуре выше 13 °C. Здесь следует отметить, что материалы типа ранней прочности развивают превосходную начальную прочность бетона из-за быстрой начальной реакции, но имеют тенденцию к задержке в долговременном наборе прочности. Кроме того, было обнаружено, что комбинация материалов с ранней прочностью, используемых в этом исследовании, приводит к превосходному набору прочности для образцов бетона даже через 28 дней.
Температурная история и зрелость [44] метода отверждения изображены на и соответственно. В этих экспериментах бетонная смесь отверждалась путем поддержания постоянной температуры 13 и 20 °С с использованием камер с постоянной температурой, а экспериментальная установка подвергалась воздействию наружного воздуха. В ходе макетного эксперимента наружная температура постепенно снижалась от исходного значения 7,9 °С, а средние значения температуры через 12 и 24 ч составили 4,3 и 9,4 °С соответственно.
Температурная история и зрелость в зависимости от метода отверждения.
Температурная история и зрелость образцов бетона в модельном эксперименте.
В целом, модельный эксперимент показал, что использование CSA17_NS03_R0.2 выгодно с точки зрения раннего набора прочности благодаря более высокой теплоте гидратации и более высокой зрелости по сравнению с OPC. показаны сканирующие электронные микрофотографии OPC и CSA17_NS03_R0.2, сделанные через 12 часов после отверждения при 13 °C. Как видно из этих изображений, в случае CSA17_NS03_R0.2, был получен и активирован продукт гидратации эттрингит. Однако для образца Plain OPC этого не наблюдалось.
Сканирующая электронная микроскопия образцов ( a ) Plain OPC и ( b ) CSA17_NS03_R0.2 через 12 часов и при температуре отверждения 13 °C.
4. Выводы
В этом исследовании изучалось развитие ранней прочности бетона на основе обычного портландцемента (OPC) и смесей сульфоалюмината кальция (CSA) при низкотемпературном отверждении.Время схватывания и начальная прочность раствора на сжатие оценивались путем корректировки количества CSA-содержащего OPC, и оптимальные характеристики наблюдались при использовании 17% CSA по отношению к общему вяжущему, в дополнение к CaO/SO 3 и SO 3 /Al 2 O 3 соотношения 1,9 и 1,25 соответственно. Кроме того, влияние ускорителя на развитие ранней прочности раствора на сжатие уменьшалось в порядке NS > AS > CH > NC > CN ≥ Plain.Время схватывания раствора Plain без добавления ускорителя составляло 90 минут, тогда как в присутствии ускорителя это время быстро уменьшалось до 20–40 минут, что позволяет предположить, что использование только ускорителя нежелательно. Кроме того, эксперименты с использованием связующих CSA показали, что наиболее эффективное замедление схватывания наблюдается в следующем порядке: лимонная кислота > борная кислота > глюконат натрия > винная кислота. Схватывание было замедлено максимум на 141 мин при использовании лимонной кислоты по сравнению с обычным образцом (CSA17).Комбинация ускорителя и замедлителя была эффективной для достижения ранней прочности образца строительного раствора, содержащего Na 2 SO 4 в качестве ускорителя. Однако время схватывания было сокращено, поэтому необходимо использовать дополнительный замедлитель схватывания, чтобы обеспечить достаточное рабочее время.
Кроме того, при комбинировании бетона с вяжущим для ранней прочности (т. е. CSA, ускорителем и замедлителем) наблюдалось незначительное изменение осадки в течение 90 минут, а прочность на сжатие >5 МПа/12 ч была подтверждена после начальной гидратации при низкотемпературные условия.Наконец, несмотря на то, что в этом исследовании наблюдалось развитие ранней прочности бетона при низких температурах, для облегчения получения качественно стабильной бетонной смеси необходимо изучить тонкую регулировку состава бетона и характеристики вяжущих с ранней прочностью в различных условиях эксплуатации.
Вклад авторов
Т.Л., Дж.Л. и Х.К. в равной степени способствовала концептуализации исследования и всех исследований, проведенных в его рамках. Закупкой ресурсов занимался Т.Л. и Дж.Л. Первоначальный проект рукописи был подготовлен Т.Л. и Дж.Л., тогда как окончательный вариант был рассмотрен и отредактирован Т.Л., Дж.Л. и Х.К. Все авторы прочитали и согласились с опубликованной версией рукописи.
Финансирование
Эта работа была поддержана грантом Национального исследовательского фонда Кореи (NRF), финансируемым правительством Кореи (MSIT; № NRF-2018R1A5A1025137). Кроме того, исследование было поддержано Программой фундаментальных научных исследований через Национальный исследовательский фонд Кореи (NRF), финансируемой Министерством образования (№ 1).2018R1D1A1B07049812).
Конфликт интересов
Авторы заявляют об отсутствии конфликта интересов. Спонсоры не участвовали в разработке исследования; при сборе, анализе или интерпретации данных; в написании рукописи или в решении опубликовать результаты.
Литература
1. Гартнер Э.М., Янг Дж.Ф., Дамидот Д.А., Джавед И. Состав цементных фаз. В: Бенстед Дж., Барнс П., редакторы. Структура и характеристики цементов. 2-е изд. КПР Пресс; Лондон, Великобритания: 2002.стр. 57–113. [Google Академия]2. Дахтар Дж., доктор философии. Тезис. Университет Шеффилда; Шеффилд, Великобритания: 2004. Цемент на основе сульфоалюмината кальция как вяжущее для конструкционного бетона.


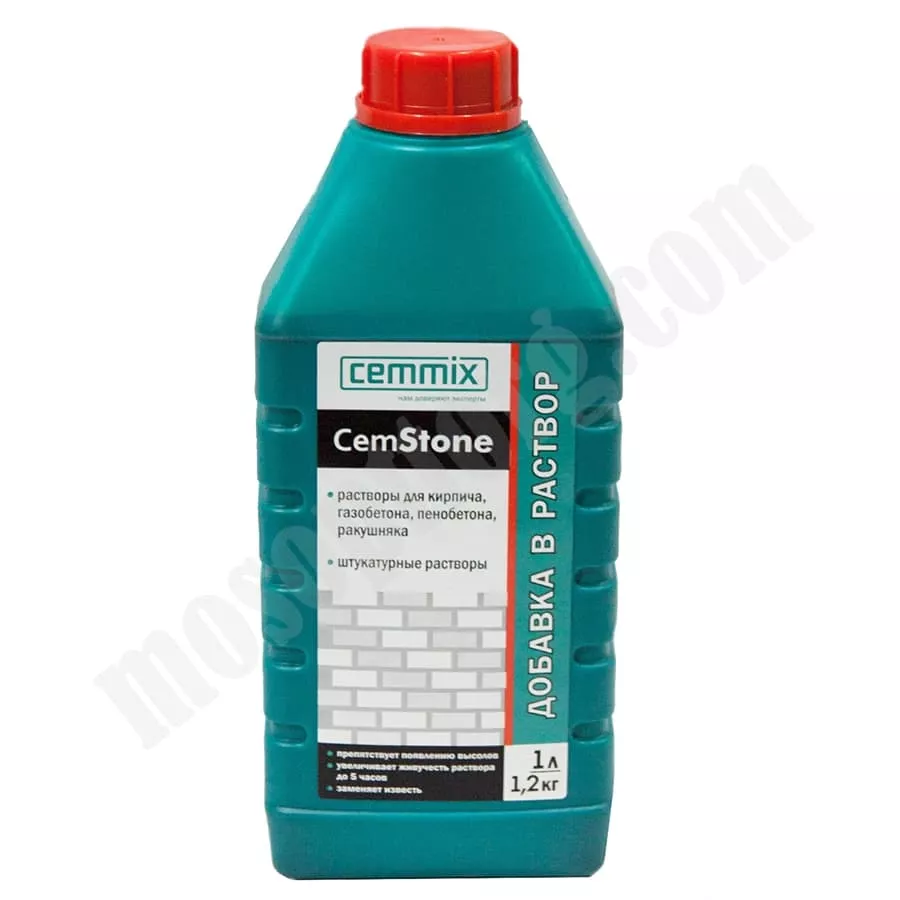
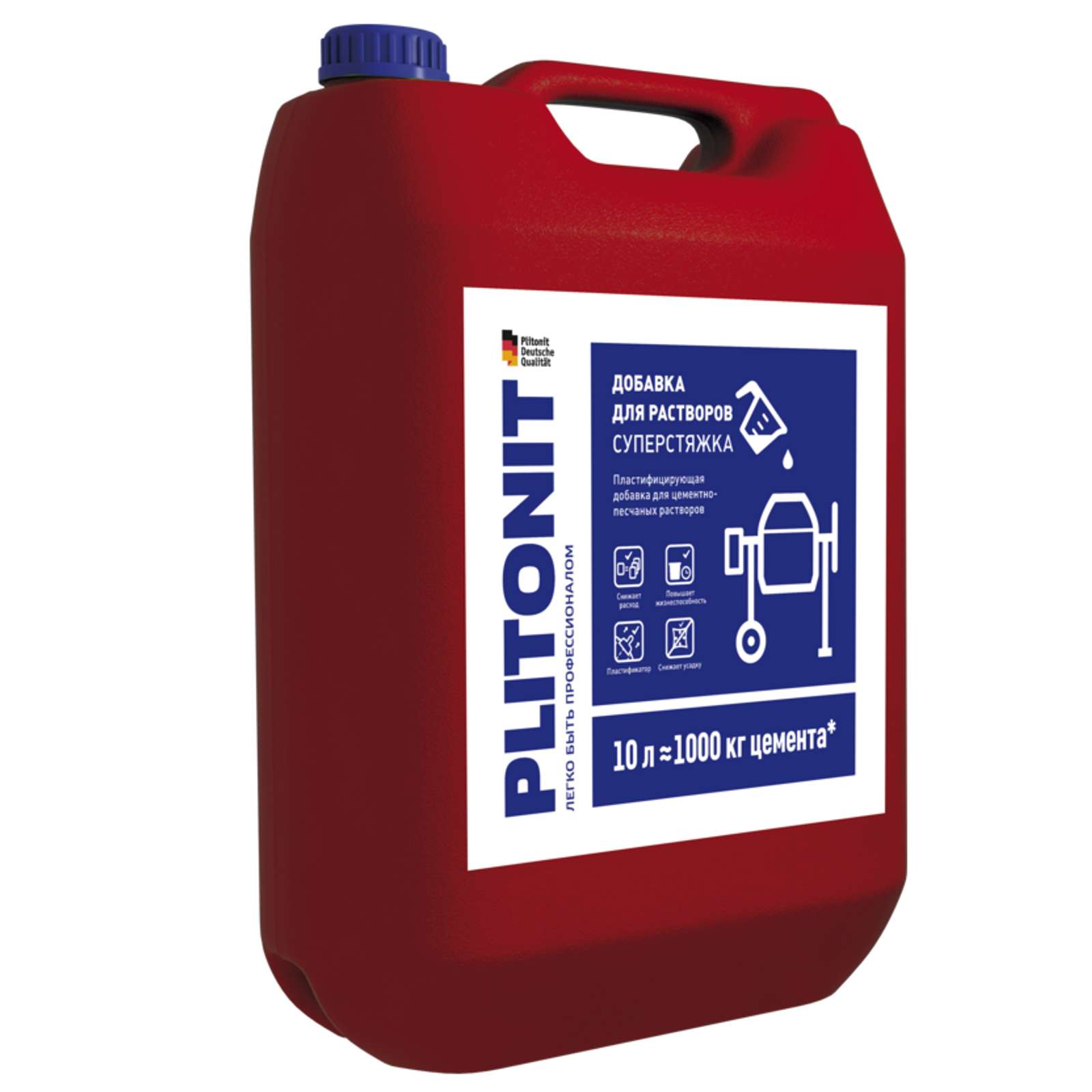




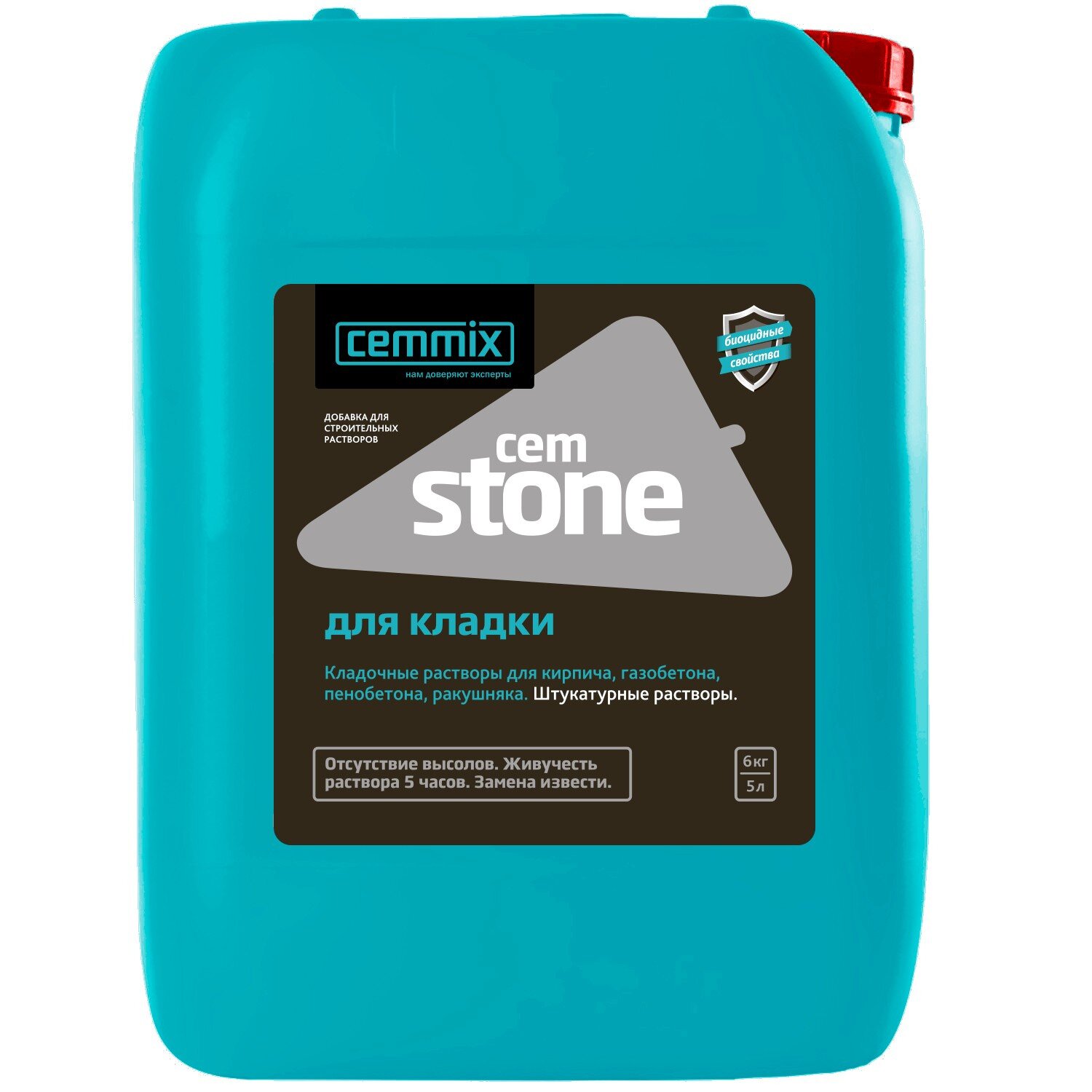
Влияние ускорителей и замедлителей на раннее развитие прочности бетона на основе низкотемпературных смесей обычного портландцемента и сульфоалюмината кальция
(Базель).2020 апрель; 13(7): 1505.
Hyeonggil Choi
2 Школа архитектуры, Национальный университет Кёнпук, Бук-Гу, Тэгу 4566, Корея
2 Школа архитектуры, Национальный университет Кёнпук, Бук-Гу, Тэгу 4566, Корея
† Эти авторы внесли такой же вклад в эту работу, как и первый автор.
Поступила в редакцию 1 февраля 2020 г .; Принято 22 марта 2020 г.
Лицензиат MDPI, Базель, Швейцария. Эта статья находится в открытом доступе и распространяется на условиях лицензии Creative Commons Attribution (CC BY) (http://creativecommons.
Abstract
В этом исследовании были проведены эксперименты по применению строительных растворов и бетонов на основе вяжущих на основе сульфоалюмината кальция (CSA) для ускорения набора прочности обычного портландцемента (OPC) в условиях низких температур. Оптимальная смесь CSA была оценена для улучшения ранней прочности OPC, и было изучено влияние ускорителей и замедлителей схватывания на эту смесь, чтобы продемонстрировать применимость полученной бетонной смеси.Кроме того, применимость смеси была подтверждена производством бетона на заводе Remicon Batcher и проведением численного моделирования. Как было замечено, оптимальная степень замены CSA для достижения ранней прочности составляла 17% от общего количества вяжущего на единицу с соотношениями CaO/SO 3 и SO 3 /Al 2 O 3 , равными 1,9 и 1,25. соответственно. Очевидно, CSA в сочетании с Na 2 SO 4 в качестве ускорителя способствует ранней прочности бетона с OPC и обеспечивает его технологичность с помощью дополнительных замедлителей схватывания для контроля быстрого схватывания бетона. Кроме того, активация начальной гидратации при низких температурах позволила получить прочность на сжатие 5 МПа/12 ч и выше для полученной бетонной смеси.
Ключевые слова: низкотемпературные условия, обычный портландцемент, CSA, ускоритель, замедлитель схватывания, ранняя прочность 1,2,3,4,5]. Эта начальная реакция гидратации приводит к образованию эттрингита, и ионы Ca 2+ , присутствующие в жидкой фазе, непрерывно элюируются для увеличения производства Ca(OH) 2 [6].Следовательно, наступает период акселерации, при котором происходит реактивация гидратации из мембраны C–S–H, окружающей частицы алита (C 3 S) и белита (C 2 S), которые подвергаются расширению и разрушению. В дальнейшем в фазе C–S–H образуются зародыши для ускорения роста и быстрого потребления Ca(OH) 2 , который активно производит гидратированные продукты. В период торможения эттрингитовая оболочка, окружающая частицы алюмината, разрушается до регидратации С 3 А, а прочность на сжатие выражается переходом в моносульфаты, от недостаточного количества гипса [2,6].
Обыкновенный портландцемент (OPC) имеет преимущество в том, что он обладает благоприятными физическими свойствами и прочностью благодаря своим стабильным химическим реакциям, что обеспечивает широкую область применения. Однако его зависимость от высоких температур снижает его реакционную способность в области низких температур [7], что ограничивает его раннее развитие прочности при нанесении на строительные растворы или бетоны.
Напротив, цементы на основе сульфоалюмината кальция (гауин минералы, CSA) имеют значительно более высокую скорость гидратации, чем OPC [8,9,10,11]; им уделяется постоянное внимание исследователей, поскольку их ранняя прочность может быть достигнута при замене на OPC в оптимальном соотношении из-за высоких температур, участвующих в начальной реакции гидратации [12, 13, 14, 15, 16, 17, 18, 19, 20].Кроме того, можно обеспечить формирование пассивирующей пленки арматурной стали в дополнение к стабильному объему благодаря отличной начальной прочности на ранней стадии, тем самым позволяя развить 28-дневную проектную норму ранней прочности [21]. ,22]. Таким образом, цементы CSA приобрели популярность для раннего набора прочности OPC.
Кляйн и Мета сообщили, что различные гидраты могут быть получены в зависимости от молярных соотношений Al 2 O 3 /SO 3 и CaO/SO 3 в CaO-Al 2 O 3 -SO 3 [23], где компонент с высоким содержанием Al 2 O 3 проявляет быстросхватываемость и раннюю прочность, компонент с высоким содержанием CaO проявляет расширяемость, а компонент с высоким содержанием SO 3 обладает высокими прочностными характеристиками [23]. 24].Ключевые факторы гидратации CSA-цементов варьируются в зависимости от ингредиентов и состава клинкеров Hauyne, реакционной способности внешнего гипса, типа смеси, а также условий смешивания и отверждения. Эти соединения CSA наносятся на строительные растворы или бетоны и способствуют расширению затвердевшего тела за счет давления роста, когда кристаллы эттрингита растут после образования затвердевших тканей. Однако, если расширенное давление превышает модуль упругости закаленного тела, это часто приводит к разрушению закаленного тела [23,25].Следовательно, для придания функциональности растворам или бетонам желательно разрабатывать материалы с характеристиками гидратов, таких как эттрингит, наряду с развитием всестороннего понимания и достаточного анализа заполнителей и поверхности раздела, смешивания с раствором и бетона для быть трудоустроенным. Хотя были проведены различные исследования набора прочности растворов и бетонов на основе OPC на ранней стадии, большинство из них было проведено на растворе, и было несколько ограничений из-за начальной высокой теплоты гидратации и свойств быстрого схватывания цементов CSA по сравнению с OPC. [26,27,28,29].
В этом исследовании проводятся эксперименты на строительном растворе и бетоне для разработки вяжущих для бетона с ранней прочностью с использованием вяжущих OPC и CSA при низких температурах. Кроме того, это исследование направлено на подтверждение применимости CSA в бетоне путем рассмотрения различных факторов, таких как оптимальное вяжущее, ускоритель и замедлитель схватывания, посредством экспериментов с раствором для раннего набора прочности.
2. Экспериментальная работа
2.1. Материалы
и представить физические характеристики материалов, использованных в этом исследовании.В качестве цемента использовали OPC (3150 кг/м 3 , крупность 330 м 2 /кг). В качестве связующих используют золу-уноса (плотность: 2140 кг/м 3 , крупность: 396 м 2 /кг), Шлак доменный молотый гранулированный (плотность: 2860 кг/м 3 , крупность: 430 м 2 /кг) и сульфоалюминат кальция (плотность: 2890 кг/м 3 , крупность: 466 м 2 /кг).
Таблица 1
Химический состав используемых связующих.
Материалы | Химические композиции (%) | 7 CAO | SiO 2 4 AL 2 O 3 Fe 4 Fe 2 O 3 4 MgO | K 2 O 4 | NA 2 O 2 O | 9 TIO 2 SO 3 | Loi | | |||||||||
---|---|---|---|---|---|---|---|---|---|---|---|---|---|---|---|---|---|
OPC (1) | 60.![]() | 21.6 | 21.6 | 5.15 | 5.15 | 3.30 | 0.99 | 0.99 | 0.53 | — | — | ||||||
GGB (2) | 44.![]() | 35.4 | 13.0 | 0.47 | 5.01 | 5.01 | 0.37 | — | — | 1.31 — | 0.31 | 0.69 | |||||
FA (3) | 4,00 | 57.![]() | 20.5 | 6.80 | 1.38 | 1.18 | 0,18 | 0,89 | — | — | |||||||
CSA 45.51 | 45.51 | 4.91 | 22.![]() | 1.74 | 1.57 | 0,17 | 0.43 | — | 22,63 | 1,90 |
Таблица 2
Физические свойства используемых материалов.
Материал | Недвижимость | ||
---|---|---|---|
ASTM Тип I Обычные Портленд Цемент Плотность: 3150 кг / м 3 , Тритант: 330 м 2 / кг | |||
FA | Fly Fly Плотность: 2140 кг / м 3 , Тритатура: 396 млн. ![]() | ||
GGBS | Гранулированный доводной ГГБС | Гранулированный Гранулированный шлак Плотность: 2860 кг / м 3 , Трикота: 430 M 2 / кг | |
CSA | CALSIUR Плотность: 2890 кг / м 3 , Тритатура: 466 млн. 2 / кг | ||
Прекрасный агрегат | S1 | ISO Стандартный песок, Размер: 2 мм Модуль крупности: 2. ![]() | |
S2 | Морской песок, Размер: 5 мм Модуль крупности: 2,01, плотность: 2600 кг/м 3 : 0.79% | ||
S3 | S3 | Разрешеный песок, размер: 5 мм Модуль тонкости: 3.29, плотность: 2570 кг / м 3 , поглощение: 0,87% | |
Грубый совокупность | Разрешеный гранитный агрегат, размер : 25 мм Модуль крупности: 6,94, плотность: 2600 кг/м 3 , абсорбция: 0.76% | ||
Химическая добавка | Группа поликарбоновой кислоты, плотность: 1260 кг / м 3 | ||
Материал ускорителя | NS | Na 2 SO 4 , плотность: 3350 кг / м 3 , Растворимость: 13,9 г / 100 мл (20 ° C) | |
AS | AL 2 (SO 4 ) 3 , плотность: 2672 кг / м 3 , растворимость: 36,4 г /100 мл (20 °C) | ||
CH | Ca(OH) 2 , плотность: 2211 кг/м 3 , растворимость: 17.![]() | ||
CN | Ca(NO 3 ) 2 , плотность: 2504 кг/м 3 , растворимость: 51,4 г/100 | ||
NC | Nahco 3 , плотность: 2200 кг / м 3 , растворимость: 9,6 г / 100 мл (20 ° C) | ||
Retarder | CA: Лимонная кислота, SG: глюконат натрия , BA: борная кислота, TA: винная кислота |
показывает результаты испытания просеивания заполнителей (ASTM C136) [30], использованных в настоящем документе, которое было проведено для анализа классификации мелких и крупных заполнителей.Для мелких заполнителей используется стандартный песок ISO (размер: 2 мм, модуль крупности: 2,99, плотность: 2620 кг/м 3 , SiO 2 : 99%, 0,08 мм, количество проходов: 0,04%) [31] В эксперименте с раствором использовали морской песок (размер: 5 мм, модуль крупности: 2,01, плотность: 2600 кг/м 3 , абсорбция: 0,79%) и дробленый песок (модуль крупности: 3,29, плотность: 2570 кг/м). m 3 , и поглощение: 0,87%), использовали для оценки их применимости в бетоне. Мелкие заполнители готовили путем смешивания морского песка и дробленого песка в соотношении 4:6 с модулем крупности 2.84.
Кривые ситового анализа для используемых здесь заполнителей: ( a ) Стандартный песок ISO; ( b ) мелкие заполнители; и ( c ) крупные заполнители.
В качестве крупных заполнителей использовались дробленые гранитные заполнители (размер: 25 мм, модуль крупности: 6,94, плотность: 2600 кг/м 3 , абсорбция: 0,76%).
Группа поликарбоновых кислот (плотность: 1260 кг/м 3 ) использовалась в качестве химической добавки. В качестве материалов-ускорителей, NS: Na 2 SO 4 , AS: Al 2 (SO 4 ) 3 , CH: Ca(OH) 2 , CN: Ca(NO ) 2 и NC: NaHCO 3 , а в качестве замедлителей схватывания использовали CA: лимонную кислоту, SG: глюконат натрия, BA: борную кислоту и TA: винную кислоту.
2.2. Схема эксперимента и пропорции смеси
показывает схему эксперимента для этого исследования. Для изучения оптимального метода набора ранней прочности бетона с использованием обычного цемента реакционную способность вяжущего CSA и количество дополнительных материалов контролировали на основе стехиометрических уравнений реакции по CaO/SO 3 и Al 2 O [23].Кроме того, оптимальное количество вяжущего CSA, которым можно заменить OPC, было определено путем оценки характеристик строительного раствора на основе количества используемого вяжущего CSA.
Таблица 3
(° C)
16, 17, 18
Прочность на компрессию
-12 ч, 24 ч
(B × 0.

Прочность на сжатие
-12 ч, 24 ч, 72 ч
(B × 1%, 2%, 3%)
CA (B × 0,2%)
( Периодическая установка + макетный элемент)
Камера (13)
Комнатная температура (20)
(B × 3.

Прочность на сжатие — 12 ч, 24 ч, 72 ч
7 Д, 28 Д — Макет элемента: 12 ч, 24 ч, 72 ч
Возможность повышения начальной прочности раствора затем исследовали комбинирование связующего CSA и ускорителя; В качестве ускорителя использовали 0,5% от общего количества связующего. При использовании вяжущих CSA может происходить быстрое схватывание, поэтому был рассмотрен замедлитель схватывания, совместимый со вяжущим CSA. Добавлено пять типов замедлителей на уровне 0.2% c.f., связующее. Для приготовления образцов бетона использовалась комбинация ускорителя и замедлителя схватывания, и в каждом случае оценивались характеристики ранней прочности и способность предотвращать быстрое схватывание. Количество замедлителя было доведено до 0,2%, а три типа ускорителей использовались в количествах 1%, 2% и 3%.
Наконец, на основе количества CSA, ускорителя и замедлителя схватывания, полученного в результате вышеуказанных экспериментов, был разработан состав бетонной смеси. Применимость рассмотренных в настоящей работе вяжущих для бетона с ранней прочностью оценивалась в ходе макетных экспериментов производства на заводе Remicon Batcher.
и показать пропорции смешивания раствора и бетона, используемые в этом исследовании. Течение раствора составляло <200 мм в соответствии с ASTM C1437 [32]. Осадка бетона составила 210 ± 25 мм, содержание воздуха 4,5 ± 1,5 %.
Таблица 4
Пропорции основного раствора.
серии | W / C (%) | C: S (1) | Цемент (G) | Вода (G) | AD (2) (B ×%) |
---|---|---|---|---|---|
Ⅰ (Раствор) | 50 | 1:3 | 450 | 225 | 0.![]() |
Таблица 5
Пропорции смешивания бетона.
Series | W / B (%) | S / A (%) | Единица (кг / м 3 ) | AD (3) (B ×%) | AC (b ×%) | |||||||||
---|---|---|---|---|---|---|---|---|---|---|---|---|---|---|
W | C (1) | CSA | GGBS | FA | S (2) | (2)G | ||||||||
ⅱ ( Бетон) | Гладкая | 53.![]() | 49.0 | 175 | 175 | 215 | — | 66 | 50 | 8 | 9 | 0,7 | — | |
CA17 | 53.0 | 49,0 | 175 | 274 | 56 | — | — | 899 | 901 | — | 3.![]() |
2.3. Test Methods
показывает методы испытаний и соответствующие им элементы оценки для образцов строительного раствора и бетона.Различные процедуры тестирования описаны ниже.
Таблица 6
Методы испытаний и соответствующие им элементы оценки.
Серия | Элемент оценки | Метод испытаний | Размер (мм) |
---|---|---|---|
Ⅰ. Метчатый тест | Установка времени (h) | ASTM C403 / C403M [33] | — |
Прочность на компрессию (MPA) | ASTM C109 / C109M [34] | 40 × 40 × 160 | |
Ⅱ.![]() | Спад (мм) | ASTM C143 [35] | — |
Содержание воздуха (%) | ASTM C231 [36] | — | |
Прочность на компрессию (МПа) | ASTM C873 [37] | Ø100 × 200 | |
ASTM C39 [38] |
2.

Испытание на текучесть строительного раствора проводилось на основе ASTM C1437 [32], а испытание на схватывание строительного раствора проводилось на основе ASTM C403/C403M [33].Прочность раствора на сжатие была рассчитана путем измерения максимальной нагрузки с использованием 30-тонного UTM в течение запланированного времени в соответствии с ASTM C109/C109M [34]. Прочность бетона на сжатие рассчитывали как среднее значение, полученное на трех испытательных образцах.
2.3.2. Применение для бетона
На основании соотношения оптимального вяжущего и добавки, полученной в результате испытания раствора, оценивалась применимость к бетону. Бетон был произведен на заводе Remicon Batcher, а теплота гидратации и набор прочности были смоделированы путем изготовления макетов стен.и покажите детали макета и установки термопары соответственно. Моделирование макета было установлено на 200 мм × 600 мм × 1000 мм, а термопара типа K была встроена в центр макета.
Прикладные испытания бетона ранней прочности на дозаторном заводе.
Установка термопары и закладной двойной формы для испытания бетона.
Для оценки свойств свежего бетона было проведено испытание на осадку в соответствии с ASTM C143/C143M [35], а испытание на содержание воздуха было проведено в соответствии с ASTM C231/C231M-17a [36].Для оценки удобоукладываемости на площадке исследовали свойства свежего бетона после выдержки в автобетоносмесителе в течение 0, 60 и 90 мин. Для измерения прочности на сжатие бетона, подвергнутого гидратации, была установлена двойная форма в соответствии с ASTM C873 [37].
Прочность бетона на сжатие была рассчитана путем подготовки образца Ø100 мм × 200 мм в соответствии с ASTM C39/C39M [38] и измерения максимальной нагрузки с использованием 300-тонного UTM в течение определенных периодов времени.Прочность бетона на сжатие рассчитывали как среднее значение, полученное на трех образцах.
3. Результаты и обсуждение
3.

3.1.1. Влияние замены CSA
наи показывают время схватывания и результаты прочности на сжатие, соответственно, для образца раствора с заменой CSA, причем очевидно, что оба эти показателя увеличиваются с увеличением коэффициента замены CSA. При замещении CSA выше 17% наблюдалось небольшое изменение прочности на сжатие, поэтому это значение считалось оптимальным.Кроме того, прочность раствора на сжатие достигала максимума при 8,3 МПа через 12 ч при использовании в смеси 17 % CSA и при времени схватывания >75 мин.
Время схватывания раствора с заменой CSA.
Прочность раствора на сжатие с заменой CSA.
отображает тренды расчетных отношений CaO/SO 3 и Al 2 O 3 /SO 3 в соответствии с изменениями коэффициента замещения CSA, а также показывает оптимальный химический состав бетона ранней прочности.Хотя предыдущие исследования подтвердили, что химические свойства CSA способствовали гидратации цемента из-за высокого содержания SO 3 , этот эффект применим только в соответствующем диапазоне [39,40,41].
Относительные индексы CaO/SO 3 и Al 2 O 3 /SO 3 с заменой CSA.
Оптимальный химический состав для бетона ранней прочности.
Как указано в рамках данного исследования, оптимальное соотношение замещения для вяжущего CSA для ранней прочности составляет 17% при соотношениях CaO/SO 3 и Al 2 O 3 /SO 3 , равном 1.9 и 1,23 соответственно.
Кроме того, было обнаружено, что при нанесении на бетон комбинации вяжущего для ранней прочности, ускорителя и замедлителя схватывания достигается прочность на сжатие 5 МПа/12 ч при низких температурах. Однако это также требовало тщательного контроля за смешиванием бетона. Кроме того, следует отметить, что характеристики вяжущих с ранней прочностью должны быть проверены в ряде условий для обеспечения надежности.
3.1.2. Влияние ускорителя
и показать время схватывания и результаты прочности на сжатие для раствора с добавлением ускорителей. В отсутствие ускорителя время схватывания раствора составляло 90 мин, а в присутствии ускорителя оно быстро уменьшалось до 20–40 мин. Эти результаты показывают, что использование ускорителя способствует гидратации реактивных гауиновых минералов, и, поскольку это также влияет на прочность на сжатие, считается, что начальное производство эттрингита также увеличивается [19, 20].
Время схватывания раствора в присутствии различных ускорителей.
Различия в прочности раствора на сжатие в присутствии разных ускорителей.
В частности, Na 2 SO 4 и Al 2 (SO 4 ) 3 сульфатные ускорители оказались наиболее эффективными в улучшении начальной прочности на сжатие из-за более высокой скорости ионизации по сравнению с цементом. , а также потому, что первоначально элюированные ионы SO 4 2– выгодны для зародышеобразования гидрата эттрингита. Однако, хотя ускорители могут улучшить начальную прочность раствора, следует избегать использования одного ускорителя, так как это значительно сокращает время схватывания.
3.1.3. Влияние замедлителя и ускорителя схватывания
Изменение времени схватывания раствора в присутствии различных замедлителей схватывания показано в . Как указано, СА проявляет наибольший эффект замедления, за ним следуют БА, СК и ТА. Действительно, CA и SG широко используются в качестве замедлителей схватывания строительных растворов и бетона благодаря их превосходным экономическим характеристикам и характеристикам замедления схватывания. И CA, и SG состоят из шести атомов углерода, хотя CA содержит одну группу –OH и три группы –COOH, тогда как SG содержит пять групп –OH и одну группу –COOH.Таким образом, эти различия объясняют их различные характеристики в отношении замедления гидратации цемента. Следует отметить, что использование эквивалентного количества СА (т.е. с линейной молекулярной структурой) показало оптимальный эффект замедления.
Время схватывания раствора в присутствии различных замедлителей схватывания.
Кроме того, в случае времени схватывания раствора, за исключением случая СА, схватывание происходит в течение 2 часов, поэтому добавление СА необходимо для обеспечения достаточной технологичности. Однако видно, что прочность бетона на сжатие с использованием замедлителя схватывания была снижена. Таким образом, можно ускорить развитие силы на ранних этапах за счет комбинированного использования различных ускорителей.
Различия в прочности раствора на сжатие в присутствии различных замедлителей схватывания.
Изменение времени схватывания раствора и прочности на сжатие в присутствии как ускорителя (А), так и замедлителя (R) показаны на и . Как указано, время схватывания Plain R0A0 составляло 60 минут, а время схватывания R0.2А0, содержащем 0,2% замедлителя схватывания, составляло 135 мин, что указывает на задержку гидратации. Следовательно, начальная прочность на сжатие образца строительного раствора значительно снизилась до 57% от этого показателя простого образца [42].
Время схватывания раствора в присутствии ускорителей и замедлителей схватывания.
Различия в прочности строительных растворов на сжатие в присутствии ускорителей и замедлителей схватывания.
По сравнению с Обычным образцом (CSA17), в серии NS03_R0.2, где в качестве ускорителя использовался Na 2 SO 4 , время схватывания раствора немного уменьшилось, но прочность стабильно увеличилась в пределах 12 –24 ч, что дает значение 191.1–218,9%.
обобщает результаты времени схватывания и прочности на сжатие для образцов строительного раствора. Более конкретно, когда в цемент добавляли 17% CSA, было очевидно, что прочность раствора на сжатие улучшалась, а время схватывания уменьшалось. Кроме того, начальная прочность раствора, содержащего CSA, была увеличена, но скорость набора прочности снизилась через 24 часа, что указывает на то, что для обеспечения достаточной прочности раствора требуется ускоритель. Более того, при смешивании строительного раствора с Na 2 SO 4 в качестве ускорителя быстрое нарастание прочности было успешным, но время схватывания уменьшилось.Отсюда было сочтено, что использование дополнительного замедлителя необходимо для обеспечения стабильного рабочего времени.
Свойства раствора в присутствии CSA и примеси.
Кроме того, сообщалось, что использование замедлителей схватывания в строительных растворах на основе CSA является эффективным подходом к улучшению удобоукладываемости системы цементных смесей, которая довольно быстро отверждается без снижения конечной прочности [20,43].
3.2. Concrete Properties
показывает изменение осадки образца бетона во времени, где были изучены времена 60 и 90 минут с учетом времени между производством и доставкой на площадку.Для целей этого испытания бетон вращали на низкой скорости в автобетоносмесителе, и в каждый момент времени измеряли изменение осадки. Было обнаружено, что OPC и CSA17_NS03_R0.2 привели к незначительному снижению осадки, но полученные значения остались в пределах диапазона осадки, установленного в настоящем исследовании, что указывает на отсутствие проблем с точки зрения работоспособности в полевых условиях. Исходя из этого результата, использование связующего CSA может быть использовано для управления свойствами настройки.
Изменение осадки образца бетона со временем.
показывает изменение прочности бетона на сжатие в зависимости от температуры отверждения. В частности, в случае OPC измерение прочности бетона на сжатие через 12 часов было невозможно из-за задержки схватывания и твердения в условиях внешнего отверждения. Через 3 дня развивалась начальная прочность ≥5 МПа, а при повышении температуры время, необходимое для набора этой степени ранней прочности, имело тенденцию к уменьшению. Однако целевая прочность развивалась уже через 24 часа, даже при 20 °C.
Изменение прочности бетона на сжатие в зависимости от температуры отверждения.
В случае образца CSA17_NS03_R0.2 прочность на сжатие 5 МПа развивалась через 24 часа при низкой температуре <10 °C и через 12 часов при температуре выше 13 °C. Здесь следует отметить, что материалы типа ранней прочности развивают превосходную начальную прочность бетона из-за быстрой начальной реакции, но имеют тенденцию к задержке в долговременном наборе прочности. Кроме того, было обнаружено, что комбинация материалов с ранней прочностью, используемых в этом исследовании, приводит к превосходному набору прочности для образцов бетона даже через 28 дней.
Температурная история и зрелость [44] метода отверждения изображены на и соответственно. В этих экспериментах бетонная смесь отверждалась путем поддержания постоянной температуры 13 и 20 °С с использованием камер с постоянной температурой, а экспериментальная установка подвергалась воздействию наружного воздуха. В ходе макетного эксперимента наружная температура постепенно снижалась от исходного значения 7,9 °С, а средние значения температуры через 12 и 24 ч составили 4,3 и 9,4 °С соответственно.
Температурная история и зрелость в зависимости от метода отверждения.
Температурная история и зрелость образцов бетона в модельном эксперименте.
В целом, модельный эксперимент показал, что использование CSA17_NS03_R0.2 выгодно с точки зрения раннего набора прочности благодаря более высокой теплоте гидратации и более высокой зрелости по сравнению с OPC. показаны сканирующие электронные микрофотографии OPC и CSA17_NS03_R0.2, сделанные через 12 часов после отверждения при 13 °C. Как видно из этих изображений, в случае CSA17_NS03_R0.2, был получен и активирован продукт гидратации эттрингит. Однако для образца Plain OPC этого не наблюдалось.
Сканирующая электронная микроскопия образцов ( a ) Plain OPC и ( b ) CSA17_NS03_R0.2 через 12 часов и при температуре отверждения 13 °C.
4. Выводы
В этом исследовании изучалось развитие ранней прочности бетона на основе обычного портландцемента (OPC) и смесей сульфоалюмината кальция (CSA) при низкотемпературном отверждении.Время схватывания и начальная прочность раствора на сжатие оценивались путем корректировки количества CSA-содержащего OPC, и оптимальные характеристики наблюдались при использовании 17% CSA по отношению к общему вяжущему, в дополнение к CaO/SO 3 и SO 3 /Al 2 O 3 соотношения 1,9 и 1,25 соответственно. Кроме того, влияние ускорителя на развитие ранней прочности раствора на сжатие уменьшалось в порядке NS > AS > CH > NC > CN ≥ Plain.Время схватывания раствора Plain без добавления ускорителя составляло 90 минут, тогда как в присутствии ускорителя это время быстро уменьшалось до 20–40 минут, что позволяет предположить, что использование только ускорителя нежелательно. Кроме того, эксперименты с использованием связующих CSA показали, что наиболее эффективное замедление схватывания наблюдается в следующем порядке: лимонная кислота > борная кислота > глюконат натрия > винная кислота. Схватывание было замедлено максимум на 141 мин при использовании лимонной кислоты по сравнению с обычным образцом (CSA17).Комбинация ускорителя и замедлителя была эффективной для достижения ранней прочности образца строительного раствора, содержащего Na 2 SO 4 в качестве ускорителя. Однако время схватывания было сокращено, поэтому необходимо использовать дополнительный замедлитель схватывания, чтобы обеспечить достаточное рабочее время.
Кроме того, при комбинировании бетона с вяжущим для ранней прочности (т. е. CSA, ускорителем и замедлителем) наблюдалось незначительное изменение осадки в течение 90 минут, а прочность на сжатие >5 МПа/12 ч была подтверждена после начальной гидратации при низкотемпературные условия.Наконец, несмотря на то, что в этом исследовании наблюдалось развитие ранней прочности бетона при низких температурах, для облегчения получения качественно стабильной бетонной смеси необходимо изучить тонкую регулировку состава бетона и характеристики вяжущих с ранней прочностью в различных условиях эксплуатации.
Вклад авторов
Т.Л., Дж.Л. и Х.К. в равной степени способствовала концептуализации исследования и всех исследований, проведенных в его рамках. Закупкой ресурсов занимался Т.Л. и Дж.Л. Первоначальный проект рукописи был подготовлен Т.Л. и Дж.Л., тогда как окончательный вариант был рассмотрен и отредактирован Т.Л., Дж.Л. и Х.К. Все авторы прочитали и согласились с опубликованной версией рукописи.
Финансирование
Эта работа была поддержана грантом Национального исследовательского фонда Кореи (NRF), финансируемым правительством Кореи (MSIT; № NRF-2018R1A5A1025137). Кроме того, исследование было поддержано Программой фундаментальных научных исследований через Национальный исследовательский фонд Кореи (NRF), финансируемой Министерством образования (№ 1).2018R1D1A1B07049812).
Конфликт интересов
Авторы заявляют об отсутствии конфликта интересов. Спонсоры не участвовали в разработке исследования; при сборе, анализе или интерпретации данных; в написании рукописи или в решении опубликовать результаты.
Литература
1. Гартнер Э.М., Янг Дж.Ф., Дамидот Д.А., Джавед И. Состав цементных фаз. В: Бенстед Дж., Барнс П., редакторы. Структура и характеристики цементов. 2-е изд. КПР Пресс; Лондон, Великобритания: 2002.стр. 57–113. [Google Академия]2. Дахтар Дж., доктор философии. Тезис. Университет Шеффилда; Шеффилд, Великобритания: 2004. Цемент на основе сульфоалюмината кальция как вяжущее для конструкционного бетона.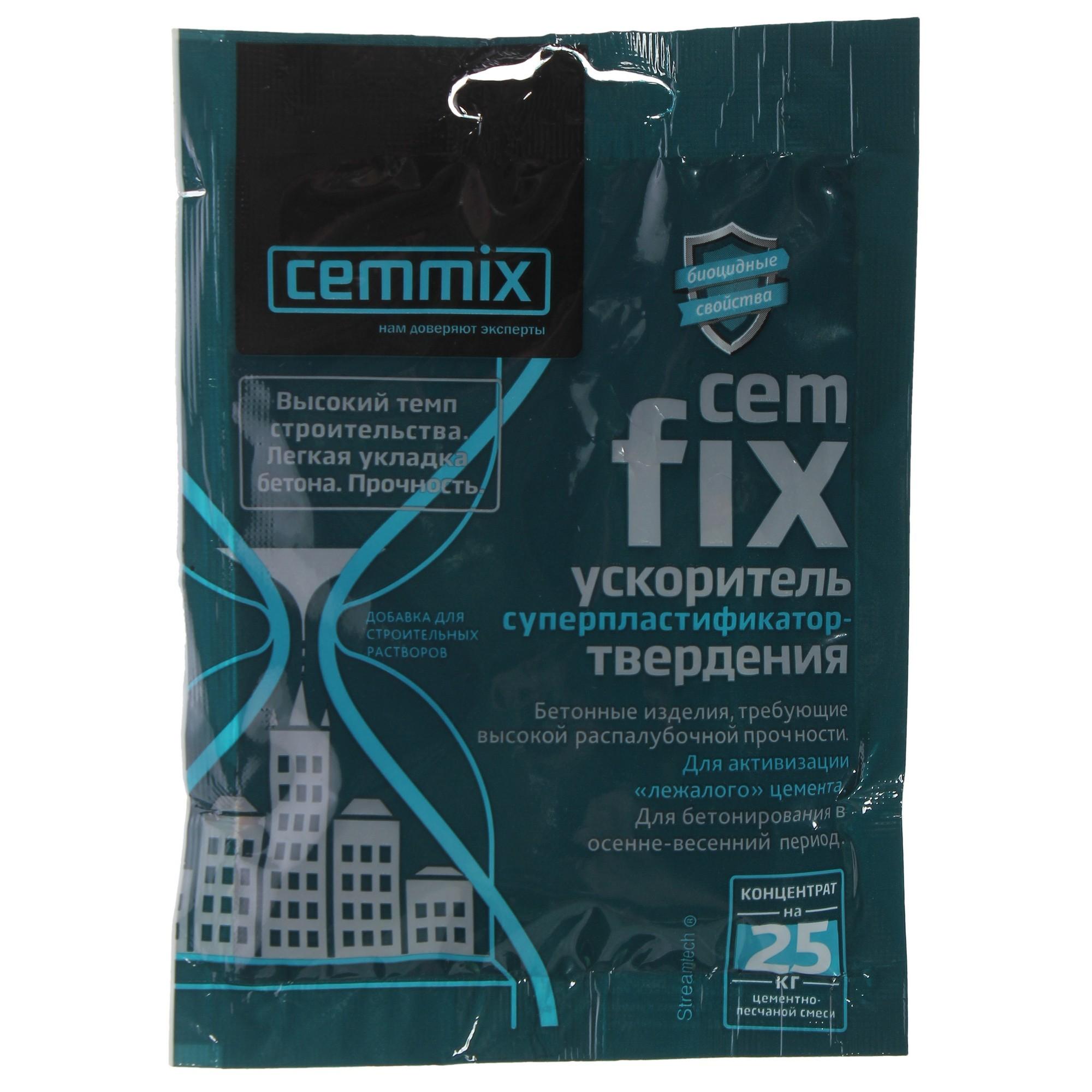


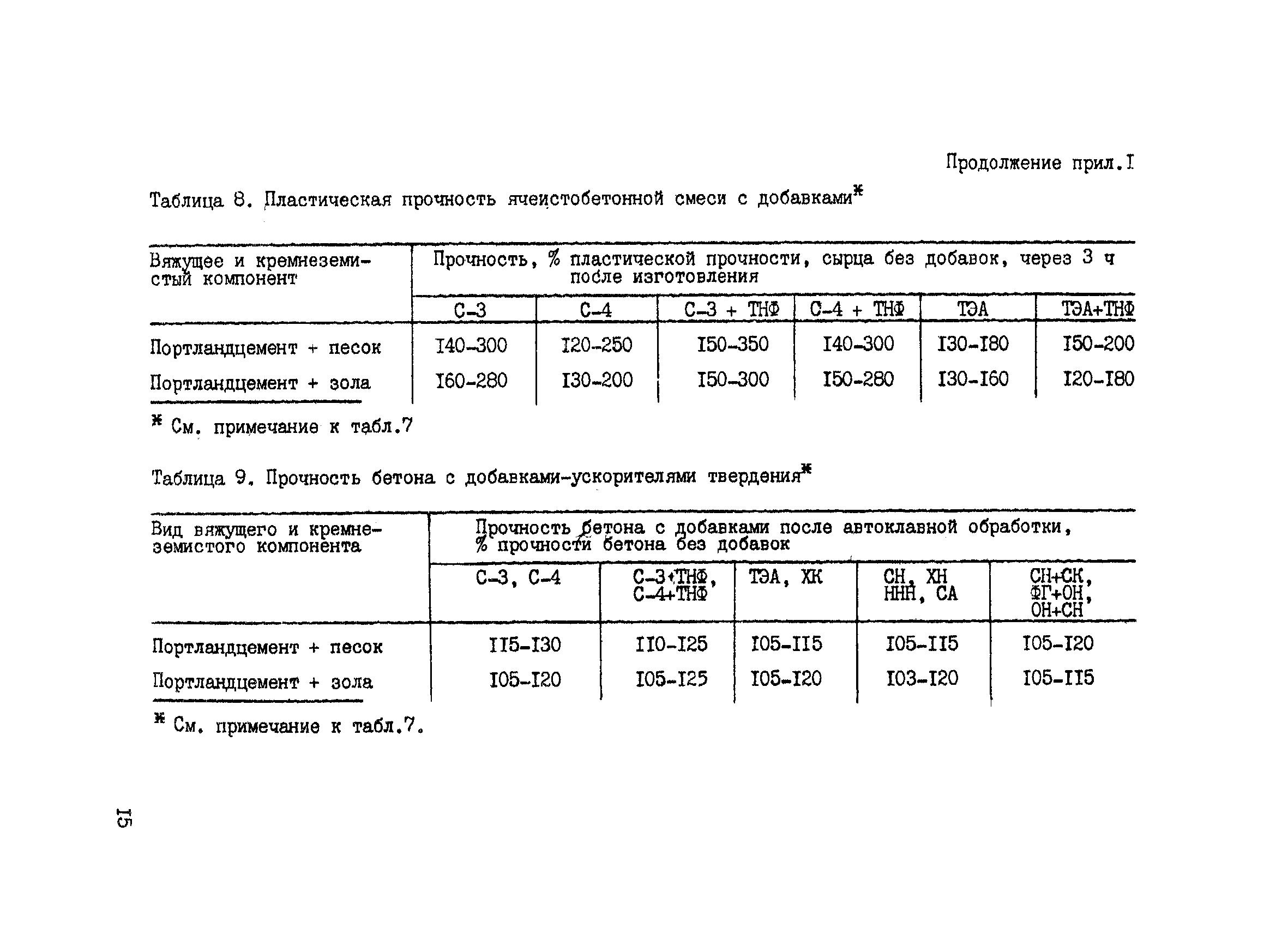



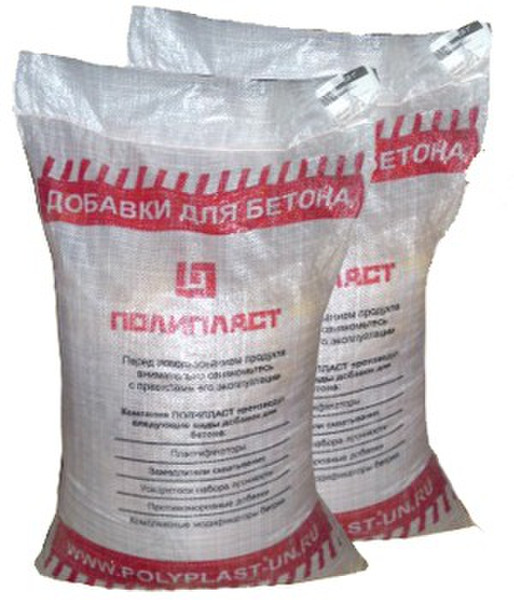


Влияние ускорителей и замедлителей на раннее развитие прочности бетона на основе низкотемпературных смесей обычного портландцемента и сульфоалюмината кальция
(Базель).2020 апрель; 13(7): 1505.
Hyeonggil Choi
2 Школа архитектуры, Национальный университет Кёнпук, Бук-Гу, Тэгу 4566, Корея
2 Школа архитектуры, Национальный университет Кёнпук, Бук-Гу, Тэгу 4566, Корея
† Эти авторы внесли такой же вклад в эту работу, как и первый автор.
Поступила в редакцию 1 февраля 2020 г .; Принято 22 марта 2020 г.
Лицензиат MDPI, Базель, Швейцария. Эта статья находится в открытом доступе и распространяется на условиях лицензии Creative Commons Attribution (CC BY) (http://creativecommons.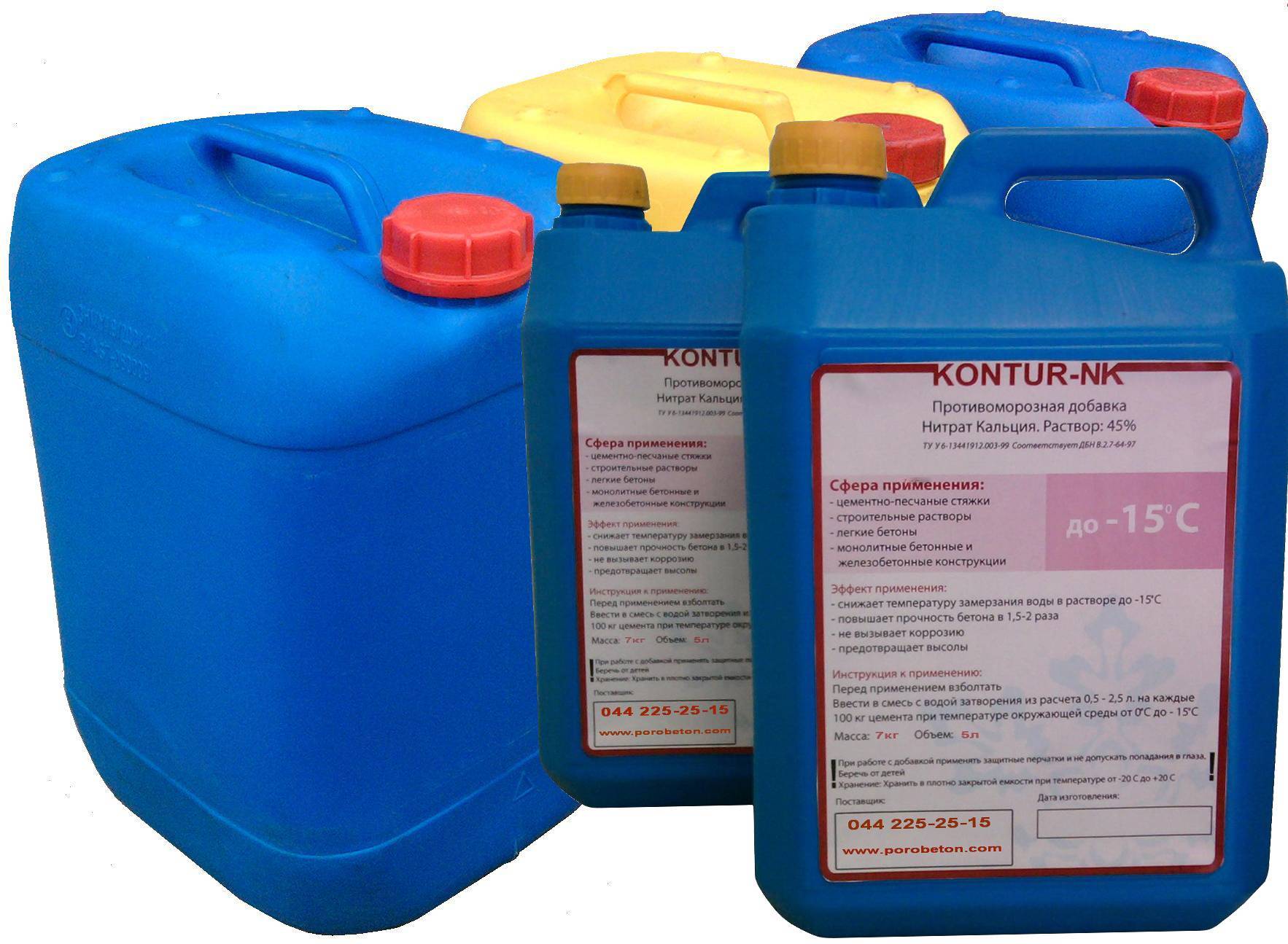
Abstract
В этом исследовании были проведены эксперименты по применению строительных растворов и бетонов на основе вяжущих на основе сульфоалюмината кальция (CSA) для ускорения набора прочности обычного портландцемента (OPC) в условиях низких температур. Оптимальная смесь CSA была оценена для улучшения ранней прочности OPC, и было изучено влияние ускорителей и замедлителей схватывания на эту смесь, чтобы продемонстрировать применимость полученной бетонной смеси.Кроме того, применимость смеси была подтверждена производством бетона на заводе Remicon Batcher и проведением численного моделирования. Как было замечено, оптимальная степень замены CSA для достижения ранней прочности составляла 17% от общего количества вяжущего на единицу с соотношениями CaO/SO 3 и SO 3 /Al 2 O 3 , равными 1,9 и 1,25. соответственно. Очевидно, CSA в сочетании с Na 2 SO 4 в качестве ускорителя способствует ранней прочности бетона с OPC и обеспечивает его технологичность с помощью дополнительных замедлителей схватывания для контроля быстрого схватывания бетона. Кроме того, активация начальной гидратации при низких температурах позволила получить прочность на сжатие 5 МПа/12 ч и выше для полученной бетонной смеси.
Ключевые слова: низкотемпературные условия, обычный портландцемент, CSA, ускоритель, замедлитель схватывания, ранняя прочность 1,2,3,4,5]. Эта начальная реакция гидратации приводит к образованию эттрингита, и ионы Ca 2+ , присутствующие в жидкой фазе, непрерывно элюируются для увеличения производства Ca(OH) 2 [6].Следовательно, наступает период акселерации, при котором происходит реактивация гидратации из мембраны C–S–H, окружающей частицы алита (C 3 S) и белита (C 2 S), которые подвергаются расширению и разрушению. В дальнейшем в фазе C–S–H образуются зародыши для ускорения роста и быстрого потребления Ca(OH) 2 , который активно производит гидратированные продукты. В период торможения эттрингитовая оболочка, окружающая частицы алюмината, разрушается до регидратации С 3 А, а прочность на сжатие выражается переходом в моносульфаты, от недостаточного количества гипса [2,6].
Обыкновенный портландцемент (OPC) имеет преимущество в том, что он обладает благоприятными физическими свойствами и прочностью благодаря своим стабильным химическим реакциям, что обеспечивает широкую область применения. Однако его зависимость от высоких температур снижает его реакционную способность в области низких температур [7], что ограничивает его раннее развитие прочности при нанесении на строительные растворы или бетоны.
Напротив, цементы на основе сульфоалюмината кальция (гауин минералы, CSA) имеют значительно более высокую скорость гидратации, чем OPC [8,9,10,11]; им уделяется постоянное внимание исследователей, поскольку их ранняя прочность может быть достигнута при замене на OPC в оптимальном соотношении из-за высоких температур, участвующих в начальной реакции гидратации [12, 13, 14, 15, 16, 17, 18, 19, 20].Кроме того, можно обеспечить формирование пассивирующей пленки арматурной стали в дополнение к стабильному объему благодаря отличной начальной прочности на ранней стадии, тем самым позволяя развить 28-дневную проектную норму ранней прочности [21]. ,22]. Таким образом, цементы CSA приобрели популярность для раннего набора прочности OPC.
Кляйн и Мета сообщили, что различные гидраты могут быть получены в зависимости от молярных соотношений Al 2 O 3 /SO 3 и CaO/SO 3 в CaO-Al 2 O 3 -SO 3 [23], где компонент с высоким содержанием Al 2 O 3 проявляет быстросхватываемость и раннюю прочность, компонент с высоким содержанием CaO проявляет расширяемость, а компонент с высоким содержанием SO 3 обладает высокими прочностными характеристиками [23]. 24].Ключевые факторы гидратации CSA-цементов варьируются в зависимости от ингредиентов и состава клинкеров Hauyne, реакционной способности внешнего гипса, типа смеси, а также условий смешивания и отверждения. Эти соединения CSA наносятся на строительные растворы или бетоны и способствуют расширению затвердевшего тела за счет давления роста, когда кристаллы эттрингита растут после образования затвердевших тканей. Однако, если расширенное давление превышает модуль упругости закаленного тела, это часто приводит к разрушению закаленного тела [23,25].Следовательно, для придания функциональности растворам или бетонам желательно разрабатывать материалы с характеристиками гидратов, таких как эттрингит, наряду с развитием всестороннего понимания и достаточного анализа заполнителей и поверхности раздела, смешивания с раствором и бетона для быть трудоустроенным. Хотя были проведены различные исследования набора прочности растворов и бетонов на основе OPC на ранней стадии, большинство из них было проведено на растворе, и было несколько ограничений из-за начальной высокой теплоты гидратации и свойств быстрого схватывания цементов CSA по сравнению с OPC. [26,27,28,29].
В этом исследовании проводятся эксперименты на строительном растворе и бетоне для разработки вяжущих для бетона с ранней прочностью с использованием вяжущих OPC и CSA при низких температурах. Кроме того, это исследование направлено на подтверждение применимости CSA в бетоне путем рассмотрения различных факторов, таких как оптимальное вяжущее, ускоритель и замедлитель схватывания, посредством экспериментов с раствором для раннего набора прочности.
2. Экспериментальная работа
2.1. Материалы
и представить физические характеристики материалов, использованных в этом исследовании.В качестве цемента использовали OPC (3150 кг/м 3 , крупность 330 м 2 /кг). В качестве связующих используют золу-уноса (плотность: 2140 кг/м 3 , крупность: 396 м 2 /кг), Шлак доменный молотый гранулированный (плотность: 2860 кг/м 3 , крупность: 430 м 2 /кг) и сульфоалюминат кальция (плотность: 2890 кг/м 3 , крупность: 466 м 2 /кг).
Таблица 1
Химический состав используемых связующих.
Материалы | Химические композиции (%) | 7 CAO | SiO 2 4 AL 2 O 3 Fe 4 Fe 2 O 3 4 MgO | K 2 O 4 | NA 2 O 2 O | 9 TIO 2 SO 3 | Loi | | |||||||||
---|---|---|---|---|---|---|---|---|---|---|---|---|---|---|---|---|---|
OPC (1) | 60.![]() | 21.6 | 21.6 | 5.15 | 5.15 | 3.30 | 0.99 | 0.99 | 0.53 | — | — | ||||||
GGB (2) | 44.![]() | 35.4 | 13.0 | 0.47 | 5.01 | 5.01 | 0.37 | — | — | 1.31 — | 0.31 | 0.69 | |||||
FA (3) | 4,00 | 57.![]() | 20.5 | 6.80 | 1.38 | 1.18 | 0,18 | 0,89 | — | — | |||||||
CSA 45.51 | 45.51 | 4.91 | 22.![]() | 1.74 | 1.57 | 0,17 | 0.43 | — | 22,63 | 1,90 |
Таблица 2
Физические свойства используемых материалов.
Материал | Недвижимость | ||
---|---|---|---|
ASTM Тип I Обычные Портленд Цемент Плотность: 3150 кг / м 3 , Тритант: 330 м 2 / кг | |||
FA | Fly Fly Плотность: 2140 кг / м 3 , Тритатура: 396 млн. ![]() | ||
GGBS | Гранулированный доводной ГГБС | Гранулированный Гранулированный шлак Плотность: 2860 кг / м 3 , Трикота: 430 M 2 / кг | |
CSA | CALSIUR Плотность: 2890 кг / м 3 , Тритатура: 466 млн. 2 / кг | ||
Прекрасный агрегат | S1 | ISO Стандартный песок, Размер: 2 мм Модуль крупности: 2. ![]() | |
S2 | Морской песок, Размер: 5 мм Модуль крупности: 2,01, плотность: 2600 кг/м 3 : 0.79% | ||
S3 | S3 | Разрешеный песок, размер: 5 мм Модуль тонкости: 3.29, плотность: 2570 кг / м 3 , поглощение: 0,87% | |
Грубый совокупность | Разрешеный гранитный агрегат, размер : 25 мм Модуль крупности: 6,94, плотность: 2600 кг/м 3 , абсорбция: 0.76% | ||
Химическая добавка | Группа поликарбоновой кислоты, плотность: 1260 кг / м 3 | ||
Материал ускорителя | NS | Na 2 SO 4 , плотность: 3350 кг / м 3 , Растворимость: 13,9 г / 100 мл (20 ° C) | |
AS | AL 2 (SO 4 ) 3 , плотность: 2672 кг / м 3 , растворимость: 36,4 г /100 мл (20 °C) | ||
CH | Ca(OH) 2 , плотность: 2211 кг/м 3 , растворимость: 17.![]() | ||
CN | Ca(NO 3 ) 2 , плотность: 2504 кг/м 3 , растворимость: 51,4 г/100 | ||
NC | Nahco 3 , плотность: 2200 кг / м 3 , растворимость: 9,6 г / 100 мл (20 ° C) | ||
Retarder | CA: Лимонная кислота, SG: глюконат натрия , BA: борная кислота, TA: винная кислота |
показывает результаты испытания просеивания заполнителей (ASTM C136) [30], использованных в настоящем документе, которое было проведено для анализа классификации мелких и крупных заполнителей.Для мелких заполнителей используется стандартный песок ISO (размер: 2 мм, модуль крупности: 2,99, плотность: 2620 кг/м 3 , SiO 2 : 99%, 0,08 мм, количество проходов: 0,04%) [31] В эксперименте с раствором использовали морской песок (размер: 5 мм, модуль крупности: 2,01, плотность: 2600 кг/м 3 , абсорбция: 0,79%) и дробленый песок (модуль крупности: 3,29, плотность: 2570 кг/м). m 3 , и поглощение: 0,87%), использовали для оценки их применимости в бетоне. Мелкие заполнители готовили путем смешивания морского песка и дробленого песка в соотношении 4:6 с модулем крупности 2.84.
Кривые ситового анализа для используемых здесь заполнителей: ( a ) Стандартный песок ISO; ( b ) мелкие заполнители; и ( c ) крупные заполнители.
В качестве крупных заполнителей использовались дробленые гранитные заполнители (размер: 25 мм, модуль крупности: 6,94, плотность: 2600 кг/м 3 , абсорбция: 0,76%).
Группа поликарбоновых кислот (плотность: 1260 кг/м 3 ) использовалась в качестве химической добавки. В качестве материалов-ускорителей, NS: Na 2 SO 4 , AS: Al 2 (SO 4 ) 3 , CH: Ca(OH) 2 , CN: Ca(NO ) 2 и NC: NaHCO 3 , а в качестве замедлителей схватывания использовали CA: лимонную кислоту, SG: глюконат натрия, BA: борную кислоту и TA: винную кислоту.
2.2. Схема эксперимента и пропорции смеси
показывает схему эксперимента для этого исследования. Для изучения оптимального метода набора ранней прочности бетона с использованием обычного цемента реакционную способность вяжущего CSA и количество дополнительных материалов контролировали на основе стехиометрических уравнений реакции по CaO/SO 3 и Al 2 O [23].Кроме того, оптимальное количество вяжущего CSA, которым можно заменить OPC, было определено путем оценки характеристик строительного раствора на основе количества используемого вяжущего CSA.
Таблица 3
(° C)
16, 17, 18
Прочность на компрессию
-12 ч, 24 ч
(B × 0.

Прочность на сжатие
-12 ч, 24 ч, 72 ч
(B × 1%, 2%, 3%)
CA (B × 0,2%)
( Периодическая установка + макетный элемент)
Камера (13)
Комнатная температура (20)
(B × 3.

Прочность на сжатие — 12 ч, 24 ч, 72 ч
7 Д, 28 Д — Макет элемента: 12 ч, 24 ч, 72 ч
Возможность повышения начальной прочности раствора затем исследовали комбинирование связующего CSA и ускорителя; В качестве ускорителя использовали 0,5% от общего количества связующего. При использовании вяжущих CSA может происходить быстрое схватывание, поэтому был рассмотрен замедлитель схватывания, совместимый со вяжущим CSA. Добавлено пять типов замедлителей на уровне 0.2% c.f., связующее. Для приготовления образцов бетона использовалась комбинация ускорителя и замедлителя схватывания, и в каждом случае оценивались характеристики ранней прочности и способность предотвращать быстрое схватывание. Количество замедлителя было доведено до 0,2%, а три типа ускорителей использовались в количествах 1%, 2% и 3%.
Наконец, на основе количества CSA, ускорителя и замедлителя схватывания, полученного в результате вышеуказанных экспериментов, был разработан состав бетонной смеси. Применимость рассмотренных в настоящей работе вяжущих для бетона с ранней прочностью оценивалась в ходе макетных экспериментов производства на заводе Remicon Batcher.
и показать пропорции смешивания раствора и бетона, используемые в этом исследовании. Течение раствора составляло <200 мм в соответствии с ASTM C1437 [32]. Осадка бетона составила 210 ± 25 мм, содержание воздуха 4,5 ± 1,5 %.
Таблица 4
Пропорции основного раствора.
серии | W / C (%) | C: S (1) | Цемент (G) | Вода (G) | AD (2) (B ×%) |
---|---|---|---|---|---|
Ⅰ (Раствор) | 50 | 1:3 | 450 | 225 | 0.![]() |
Таблица 5
Пропорции смешивания бетона.
Series | W / B (%) | S / A (%) | Единица (кг / м 3 ) | AD (3) (B ×%) | AC (b ×%) | |||||||||
---|---|---|---|---|---|---|---|---|---|---|---|---|---|---|
W | C (1) | CSA | GGBS | FA | S (2) | (2)G | ||||||||
ⅱ ( Бетон) | Гладкая | 53.![]() | 49.0 | 175 | 175 | 215 | — | 66 | 50 | 8 | 9 | 0,7 | — | |
CA17 | 53.0 | 49,0 | 175 | 274 | 56 | — | — | 899 | 901 | — | 3.![]() |
2.3. Test Methods
показывает методы испытаний и соответствующие им элементы оценки для образцов строительного раствора и бетона.Различные процедуры тестирования описаны ниже.
Таблица 6
Методы испытаний и соответствующие им элементы оценки.
Серия | Элемент оценки | Метод испытаний | Размер (мм) |
---|---|---|---|
Ⅰ. Метчатый тест | Установка времени (h) | ASTM C403 / C403M [33] | — |
Прочность на компрессию (MPA) | ASTM C109 / C109M [34] | 40 × 40 × 160 | |
Ⅱ.![]() | Спад (мм) | ASTM C143 [35] | — |
Содержание воздуха (%) | ASTM C231 [36] | — | |
Прочность на компрессию (МПа) | ASTM C873 [37] | Ø100 × 200 | |
ASTM C39 [38] |
2.

Испытание на текучесть строительного раствора проводилось на основе ASTM C1437 [32], а испытание на схватывание строительного раствора проводилось на основе ASTM C403/C403M [33].Прочность раствора на сжатие была рассчитана путем измерения максимальной нагрузки с использованием 30-тонного UTM в течение запланированного времени в соответствии с ASTM C109/C109M [34]. Прочность бетона на сжатие рассчитывали как среднее значение, полученное на трех испытательных образцах.
2.3.2. Применение для бетона
На основании соотношения оптимального вяжущего и добавки, полученной в результате испытания раствора, оценивалась применимость к бетону. Бетон был произведен на заводе Remicon Batcher, а теплота гидратации и набор прочности были смоделированы путем изготовления макетов стен.и покажите детали макета и установки термопары соответственно. Моделирование макета было установлено на 200 мм × 600 мм × 1000 мм, а термопара типа K была встроена в центр макета.
Прикладные испытания бетона ранней прочности на дозаторном заводе.
Установка термопары и закладной двойной формы для испытания бетона.
Для оценки свойств свежего бетона было проведено испытание на осадку в соответствии с ASTM C143/C143M [35], а испытание на содержание воздуха было проведено в соответствии с ASTM C231/C231M-17a [36].Для оценки удобоукладываемости на площадке исследовали свойства свежего бетона после выдержки в автобетоносмесителе в течение 0, 60 и 90 мин. Для измерения прочности на сжатие бетона, подвергнутого гидратации, была установлена двойная форма в соответствии с ASTM C873 [37].
Прочность бетона на сжатие была рассчитана путем подготовки образца Ø100 мм × 200 мм в соответствии с ASTM C39/C39M [38] и измерения максимальной нагрузки с использованием 300-тонного UTM в течение определенных периодов времени.Прочность бетона на сжатие рассчитывали как среднее значение, полученное на трех образцах.
3. Результаты и обсуждение
3.
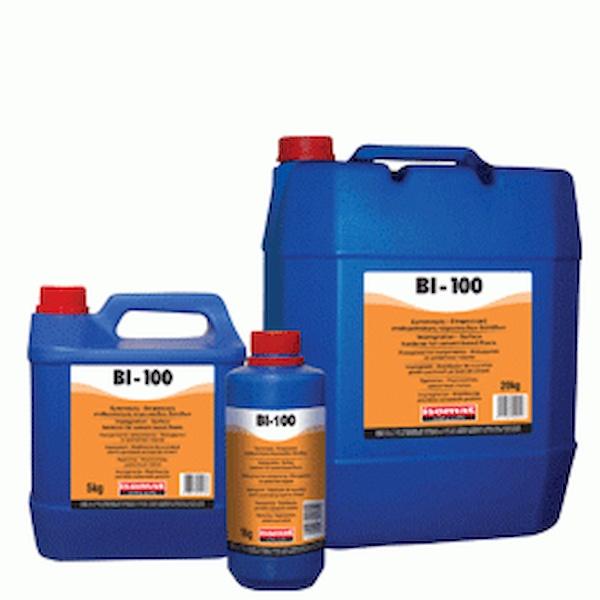
3.1.1. Влияние замены CSA
наи показывают время схватывания и результаты прочности на сжатие, соответственно, для образца раствора с заменой CSA, причем очевидно, что оба эти показателя увеличиваются с увеличением коэффициента замены CSA. При замещении CSA выше 17% наблюдалось небольшое изменение прочности на сжатие, поэтому это значение считалось оптимальным.Кроме того, прочность раствора на сжатие достигала максимума при 8,3 МПа через 12 ч при использовании в смеси 17 % CSA и при времени схватывания >75 мин.
Время схватывания раствора с заменой CSA.
Прочность раствора на сжатие с заменой CSA.
отображает тренды расчетных отношений CaO/SO 3 и Al 2 O 3 /SO 3 в соответствии с изменениями коэффициента замещения CSA, а также показывает оптимальный химический состав бетона ранней прочности.Хотя предыдущие исследования подтвердили, что химические свойства CSA способствовали гидратации цемента из-за высокого содержания SO 3 , этот эффект применим только в соответствующем диапазоне [39,40,41].
Относительные индексы CaO/SO 3 и Al 2 O 3 /SO 3 с заменой CSA.
Оптимальный химический состав для бетона ранней прочности.
Как указано в рамках данного исследования, оптимальное соотношение замещения для вяжущего CSA для ранней прочности составляет 17% при соотношениях CaO/SO 3 и Al 2 O 3 /SO 3 , равном 1.9 и 1,23 соответственно.
Кроме того, было обнаружено, что при нанесении на бетон комбинации вяжущего для ранней прочности, ускорителя и замедлителя схватывания достигается прочность на сжатие 5 МПа/12 ч при низких температурах. Однако это также требовало тщательного контроля за смешиванием бетона. Кроме того, следует отметить, что характеристики вяжущих с ранней прочностью должны быть проверены в ряде условий для обеспечения надежности.
3.1.2. Влияние ускорителя
и показать время схватывания и результаты прочности на сжатие для раствора с добавлением ускорителей. В отсутствие ускорителя время схватывания раствора составляло 90 мин, а в присутствии ускорителя оно быстро уменьшалось до 20–40 мин. Эти результаты показывают, что использование ускорителя способствует гидратации реактивных гауиновых минералов, и, поскольку это также влияет на прочность на сжатие, считается, что начальное производство эттрингита также увеличивается [19, 20].
Время схватывания раствора в присутствии различных ускорителей.
Различия в прочности раствора на сжатие в присутствии разных ускорителей.
В частности, Na 2 SO 4 и Al 2 (SO 4 ) 3 сульфатные ускорители оказались наиболее эффективными в улучшении начальной прочности на сжатие из-за более высокой скорости ионизации по сравнению с цементом. , а также потому, что первоначально элюированные ионы SO 4 2– выгодны для зародышеобразования гидрата эттрингита. Однако, хотя ускорители могут улучшить начальную прочность раствора, следует избегать использования одного ускорителя, так как это значительно сокращает время схватывания.
3.1.3. Влияние замедлителя и ускорителя схватывания
Изменение времени схватывания раствора в присутствии различных замедлителей схватывания показано в . Как указано, СА проявляет наибольший эффект замедления, за ним следуют БА, СК и ТА. Действительно, CA и SG широко используются в качестве замедлителей схватывания строительных растворов и бетона благодаря их превосходным экономическим характеристикам и характеристикам замедления схватывания. И CA, и SG состоят из шести атомов углерода, хотя CA содержит одну группу –OH и три группы –COOH, тогда как SG содержит пять групп –OH и одну группу –COOH.Таким образом, эти различия объясняют их различные характеристики в отношении замедления гидратации цемента. Следует отметить, что использование эквивалентного количества СА (т.е. с линейной молекулярной структурой) показало оптимальный эффект замедления.
Время схватывания раствора в присутствии различных замедлителей схватывания.
Кроме того, в случае времени схватывания раствора, за исключением случая СА, схватывание происходит в течение 2 часов, поэтому добавление СА необходимо для обеспечения достаточной технологичности. Однако видно, что прочность бетона на сжатие с использованием замедлителя схватывания была снижена. Таким образом, можно ускорить развитие силы на ранних этапах за счет комбинированного использования различных ускорителей.
Различия в прочности раствора на сжатие в присутствии различных замедлителей схватывания.
Изменение времени схватывания раствора и прочности на сжатие в присутствии как ускорителя (А), так и замедлителя (R) показаны на и . Как указано, время схватывания Plain R0A0 составляло 60 минут, а время схватывания R0.2А0, содержащем 0,2% замедлителя схватывания, составляло 135 мин, что указывает на задержку гидратации. Следовательно, начальная прочность на сжатие образца строительного раствора значительно снизилась до 57% от этого показателя простого образца [42].
Время схватывания раствора в присутствии ускорителей и замедлителей схватывания.
Различия в прочности строительных растворов на сжатие в присутствии ускорителей и замедлителей схватывания.
По сравнению с Обычным образцом (CSA17), в серии NS03_R0.2, где в качестве ускорителя использовался Na 2 SO 4 , время схватывания раствора немного уменьшилось, но прочность стабильно увеличилась в пределах 12 –24 ч, что дает значение 191.1–218,9%.
обобщает результаты времени схватывания и прочности на сжатие для образцов строительного раствора. Более конкретно, когда в цемент добавляли 17% CSA, было очевидно, что прочность раствора на сжатие улучшалась, а время схватывания уменьшалось. Кроме того, начальная прочность раствора, содержащего CSA, была увеличена, но скорость набора прочности снизилась через 24 часа, что указывает на то, что для обеспечения достаточной прочности раствора требуется ускоритель. Более того, при смешивании строительного раствора с Na 2 SO 4 в качестве ускорителя быстрое нарастание прочности было успешным, но время схватывания уменьшилось.Отсюда было сочтено, что использование дополнительного замедлителя необходимо для обеспечения стабильного рабочего времени.
Свойства раствора в присутствии CSA и примеси.
Кроме того, сообщалось, что использование замедлителей схватывания в строительных растворах на основе CSA является эффективным подходом к улучшению удобоукладываемости системы цементных смесей, которая довольно быстро отверждается без снижения конечной прочности [20,43].
3.2. Concrete Properties
показывает изменение осадки образца бетона во времени, где были изучены времена 60 и 90 минут с учетом времени между производством и доставкой на площадку.Для целей этого испытания бетон вращали на низкой скорости в автобетоносмесителе, и в каждый момент времени измеряли изменение осадки. Было обнаружено, что OPC и CSA17_NS03_R0.2 привели к незначительному снижению осадки, но полученные значения остались в пределах диапазона осадки, установленного в настоящем исследовании, что указывает на отсутствие проблем с точки зрения работоспособности в полевых условиях. Исходя из этого результата, использование связующего CSA может быть использовано для управления свойствами настройки.
Изменение осадки образца бетона со временем.
показывает изменение прочности бетона на сжатие в зависимости от температуры отверждения. В частности, в случае OPC измерение прочности бетона на сжатие через 12 часов было невозможно из-за задержки схватывания и твердения в условиях внешнего отверждения. Через 3 дня развивалась начальная прочность ≥5 МПа, а при повышении температуры время, необходимое для набора этой степени ранней прочности, имело тенденцию к уменьшению. Однако целевая прочность развивалась уже через 24 часа, даже при 20 °C.
Изменение прочности бетона на сжатие в зависимости от температуры отверждения.
В случае образца CSA17_NS03_R0.2 прочность на сжатие 5 МПа развивалась через 24 часа при низкой температуре <10 °C и через 12 часов при температуре выше 13 °C. Здесь следует отметить, что материалы типа ранней прочности развивают превосходную начальную прочность бетона из-за быстрой начальной реакции, но имеют тенденцию к задержке в долговременном наборе прочности. Кроме того, было обнаружено, что комбинация материалов с ранней прочностью, используемых в этом исследовании, приводит к превосходному набору прочности для образцов бетона даже через 28 дней.
Температурная история и зрелость [44] метода отверждения изображены на и соответственно. В этих экспериментах бетонная смесь отверждалась путем поддержания постоянной температуры 13 и 20 °С с использованием камер с постоянной температурой, а экспериментальная установка подвергалась воздействию наружного воздуха. В ходе макетного эксперимента наружная температура постепенно снижалась от исходного значения 7,9 °С, а средние значения температуры через 12 и 24 ч составили 4,3 и 9,4 °С соответственно.
Температурная история и зрелость в зависимости от метода отверждения.
Температурная история и зрелость образцов бетона в модельном эксперименте.
В целом, модельный эксперимент показал, что использование CSA17_NS03_R0.2 выгодно с точки зрения раннего набора прочности благодаря более высокой теплоте гидратации и более высокой зрелости по сравнению с OPC. показаны сканирующие электронные микрофотографии OPC и CSA17_NS03_R0.2, сделанные через 12 часов после отверждения при 13 °C. Как видно из этих изображений, в случае CSA17_NS03_R0.2, был получен и активирован продукт гидратации эттрингит. Однако для образца Plain OPC этого не наблюдалось.
Сканирующая электронная микроскопия образцов ( a ) Plain OPC и ( b ) CSA17_NS03_R0.2 через 12 часов и при температуре отверждения 13 °C.
4. Выводы
В этом исследовании изучалось развитие ранней прочности бетона на основе обычного портландцемента (OPC) и смесей сульфоалюмината кальция (CSA) при низкотемпературном отверждении.Время схватывания и начальная прочность раствора на сжатие оценивались путем корректировки количества CSA-содержащего OPC, и оптимальные характеристики наблюдались при использовании 17% CSA по отношению к общему вяжущему, в дополнение к CaO/SO 3 и SO 3 /Al 2 O 3 соотношения 1,9 и 1,25 соответственно. Кроме того, влияние ускорителя на развитие ранней прочности раствора на сжатие уменьшалось в порядке NS > AS > CH > NC > CN ≥ Plain.Время схватывания раствора Plain без добавления ускорителя составляло 90 минут, тогда как в присутствии ускорителя это время быстро уменьшалось до 20–40 минут, что позволяет предположить, что использование только ускорителя нежелательно. Кроме того, эксперименты с использованием связующих CSA показали, что наиболее эффективное замедление схватывания наблюдается в следующем порядке: лимонная кислота > борная кислота > глюконат натрия > винная кислота. Схватывание было замедлено максимум на 141 мин при использовании лимонной кислоты по сравнению с обычным образцом (CSA17).Комбинация ускорителя и замедлителя была эффективной для достижения ранней прочности образца строительного раствора, содержащего Na 2 SO 4 в качестве ускорителя. Однако время схватывания было сокращено, поэтому необходимо использовать дополнительный замедлитель схватывания, чтобы обеспечить достаточное рабочее время.
Кроме того, при комбинировании бетона с вяжущим для ранней прочности (т. е. CSA, ускорителем и замедлителем) наблюдалось незначительное изменение осадки в течение 90 минут, а прочность на сжатие >5 МПа/12 ч была подтверждена после начальной гидратации при низкотемпературные условия.Наконец, несмотря на то, что в этом исследовании наблюдалось развитие ранней прочности бетона при низких температурах, для облегчения получения качественно стабильной бетонной смеси необходимо изучить тонкую регулировку состава бетона и характеристики вяжущих с ранней прочностью в различных условиях эксплуатации.
Вклад авторов
Т.Л., Дж.Л. и Х.К. в равной степени способствовала концептуализации исследования и всех исследований, проведенных в его рамках. Закупкой ресурсов занимался Т.Л. и Дж.Л. Первоначальный проект рукописи был подготовлен Т.Л. и Дж.Л., тогда как окончательный вариант был рассмотрен и отредактирован Т.Л., Дж.Л. и Х.К. Все авторы прочитали и согласились с опубликованной версией рукописи.
Финансирование
Эта работа была поддержана грантом Национального исследовательского фонда Кореи (NRF), финансируемым правительством Кореи (MSIT; № NRF-2018R1A5A1025137). Кроме того, исследование было поддержано Программой фундаментальных научных исследований через Национальный исследовательский фонд Кореи (NRF), финансируемой Министерством образования (№ 1).2018R1D1A1B07049812).
Конфликт интересов
Авторы заявляют об отсутствии конфликта интересов. Спонсоры не участвовали в разработке исследования; при сборе, анализе или интерпретации данных; в написании рукописи или в решении опубликовать результаты.
Литература
1. Гартнер Э.М., Янг Дж.Ф., Дамидот Д.А., Джавед И. Состав цементных фаз. В: Бенстед Дж., Барнс П., редакторы. Структура и характеристики цементов. 2-е изд. КПР Пресс; Лондон, Великобритания: 2002.стр. 57–113. [Google Академия]2. Дахтар Дж., доктор философии. Тезис. Университет Шеффилда; Шеффилд, Великобритания: 2004. Цемент на основе сульфоалюмината кальция как вяжущее для конструкционного бетона.
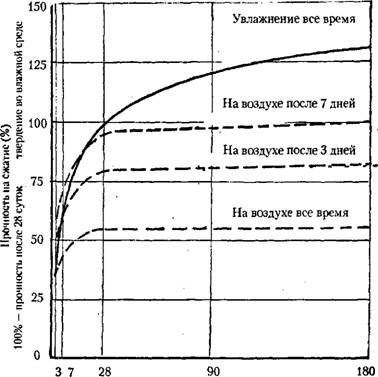

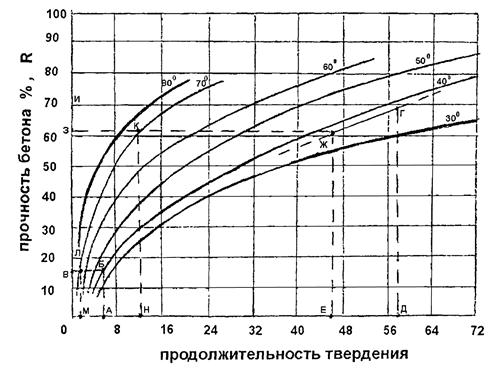

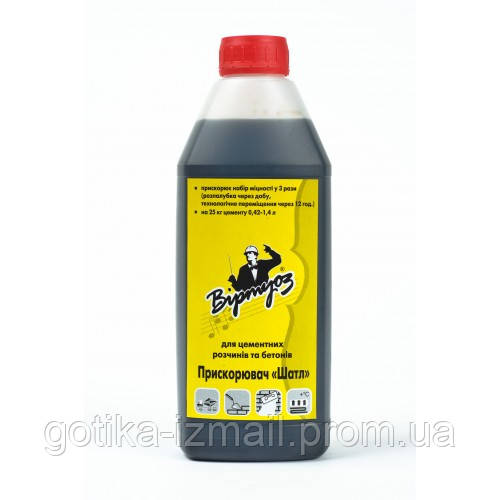
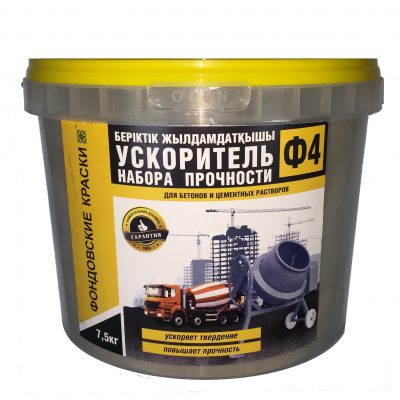



Влияние ускорителей и замедлителей на раннее развитие прочности бетона на основе низкотемпературных смесей обычного портландцемента и сульфоалюмината кальция
(Базель).2020 апрель; 13(7): 1505.
Hyeonggil Choi
2 Школа архитектуры, Национальный университет Кёнпук, Бук-Гу, Тэгу 4566, Корея
2 Школа архитектуры, Национальный университет Кёнпук, Бук-Гу, Тэгу 4566, Корея
† Эти авторы внесли такой же вклад в эту работу, как и первый автор.
Поступила в редакцию 1 февраля 2020 г .; Принято 22 марта 2020 г.
Лицензиат MDPI, Базель, Швейцария. Эта статья находится в открытом доступе и распространяется на условиях лицензии Creative Commons Attribution (CC BY) (http://creativecommons.
Abstract
В этом исследовании были проведены эксперименты по применению строительных растворов и бетонов на основе вяжущих на основе сульфоалюмината кальция (CSA) для ускорения набора прочности обычного портландцемента (OPC) в условиях низких температур. Оптимальная смесь CSA была оценена для улучшения ранней прочности OPC, и было изучено влияние ускорителей и замедлителей схватывания на эту смесь, чтобы продемонстрировать применимость полученной бетонной смеси.Кроме того, применимость смеси была подтверждена производством бетона на заводе Remicon Batcher и проведением численного моделирования. Как было замечено, оптимальная степень замены CSA для достижения ранней прочности составляла 17% от общего количества вяжущего на единицу с соотношениями CaO/SO 3 и SO 3 /Al 2 O 3 , равными 1,9 и 1,25. соответственно. Очевидно, CSA в сочетании с Na 2 SO 4 в качестве ускорителя способствует ранней прочности бетона с OPC и обеспечивает его технологичность с помощью дополнительных замедлителей схватывания для контроля быстрого схватывания бетона. Кроме того, активация начальной гидратации при низких температурах позволила получить прочность на сжатие 5 МПа/12 ч и выше для полученной бетонной смеси.
Ключевые слова: низкотемпературные условия, обычный портландцемент, CSA, ускоритель, замедлитель схватывания, ранняя прочность 1,2,3,4,5]. Эта начальная реакция гидратации приводит к образованию эттрингита, и ионы Ca 2+ , присутствующие в жидкой фазе, непрерывно элюируются для увеличения производства Ca(OH) 2 [6].Следовательно, наступает период акселерации, при котором происходит реактивация гидратации из мембраны C–S–H, окружающей частицы алита (C 3 S) и белита (C 2 S), которые подвергаются расширению и разрушению. В дальнейшем в фазе C–S–H образуются зародыши для ускорения роста и быстрого потребления Ca(OH) 2 , который активно производит гидратированные продукты. В период торможения эттрингитовая оболочка, окружающая частицы алюмината, разрушается до регидратации С 3 А, а прочность на сжатие выражается переходом в моносульфаты, от недостаточного количества гипса [2,6].
Обыкновенный портландцемент (OPC) имеет преимущество в том, что он обладает благоприятными физическими свойствами и прочностью благодаря своим стабильным химическим реакциям, что обеспечивает широкую область применения. Однако его зависимость от высоких температур снижает его реакционную способность в области низких температур [7], что ограничивает его раннее развитие прочности при нанесении на строительные растворы или бетоны.
Напротив, цементы на основе сульфоалюмината кальция (гауин минералы, CSA) имеют значительно более высокую скорость гидратации, чем OPC [8,9,10,11]; им уделяется постоянное внимание исследователей, поскольку их ранняя прочность может быть достигнута при замене на OPC в оптимальном соотношении из-за высоких температур, участвующих в начальной реакции гидратации [12, 13, 14, 15, 16, 17, 18, 19, 20].Кроме того, можно обеспечить формирование пассивирующей пленки арматурной стали в дополнение к стабильному объему благодаря отличной начальной прочности на ранней стадии, тем самым позволяя развить 28-дневную проектную норму ранней прочности [21]. ,22]. Таким образом, цементы CSA приобрели популярность для раннего набора прочности OPC.
Кляйн и Мета сообщили, что различные гидраты могут быть получены в зависимости от молярных соотношений Al 2 O 3 /SO 3 и CaO/SO 3 в CaO-Al 2 O 3 -SO 3 [23], где компонент с высоким содержанием Al 2 O 3 проявляет быстросхватываемость и раннюю прочность, компонент с высоким содержанием CaO проявляет расширяемость, а компонент с высоким содержанием SO 3 обладает высокими прочностными характеристиками [23]. 24].Ключевые факторы гидратации CSA-цементов варьируются в зависимости от ингредиентов и состава клинкеров Hauyne, реакционной способности внешнего гипса, типа смеси, а также условий смешивания и отверждения. Эти соединения CSA наносятся на строительные растворы или бетоны и способствуют расширению затвердевшего тела за счет давления роста, когда кристаллы эттрингита растут после образования затвердевших тканей. Однако, если расширенное давление превышает модуль упругости закаленного тела, это часто приводит к разрушению закаленного тела [23,25].Следовательно, для придания функциональности растворам или бетонам желательно разрабатывать материалы с характеристиками гидратов, таких как эттрингит, наряду с развитием всестороннего понимания и достаточного анализа заполнителей и поверхности раздела, смешивания с раствором и бетона для быть трудоустроенным. Хотя были проведены различные исследования набора прочности растворов и бетонов на основе OPC на ранней стадии, большинство из них было проведено на растворе, и было несколько ограничений из-за начальной высокой теплоты гидратации и свойств быстрого схватывания цементов CSA по сравнению с OPC. [26,27,28,29].
В этом исследовании проводятся эксперименты на строительном растворе и бетоне для разработки вяжущих для бетона с ранней прочностью с использованием вяжущих OPC и CSA при низких температурах. Кроме того, это исследование направлено на подтверждение применимости CSA в бетоне путем рассмотрения различных факторов, таких как оптимальное вяжущее, ускоритель и замедлитель схватывания, посредством экспериментов с раствором для раннего набора прочности.
2. Экспериментальная работа
2.1. Материалы
и представить физические характеристики материалов, использованных в этом исследовании.В качестве цемента использовали OPC (3150 кг/м 3 , крупность 330 м 2 /кг). В качестве связующих используют золу-уноса (плотность: 2140 кг/м 3 , крупность: 396 м 2 /кг), Шлак доменный молотый гранулированный (плотность: 2860 кг/м 3 , крупность: 430 м 2 /кг) и сульфоалюминат кальция (плотность: 2890 кг/м 3 , крупность: 466 м 2 /кг).
Таблица 1
Химический состав используемых связующих.
Материалы | Химические композиции (%) | 7 CAO | SiO 2 4 AL 2 O 3 Fe 4 Fe 2 O 3 4 MgO | K 2 O 4 | NA 2 O 2 O | 9 TIO 2 SO 3 | Loi | | |||||||||
---|---|---|---|---|---|---|---|---|---|---|---|---|---|---|---|---|---|
OPC (1) | 60.![]() | 21.6 | 21.6 | 5.15 | 5.15 | 3.30 | 0.99 | 0.99 | 0.53 | — | — | ||||||
GGB (2) | 44.![]() | 35.4 | 13.0 | 0.47 | 5.01 | 5.01 | 0.37 | — | — | 1.31 — | 0.31 | 0.69 | |||||
FA (3) | 4,00 | 57.![]() | 20.5 | 6.80 | 1.38 | 1.18 | 0,18 | 0,89 | — | — | |||||||
CSA 45.51 | 45.51 | 4.91 | 22.![]() | 1.74 | 1.57 | 0,17 | 0.43 | — | 22,63 | 1,90 |
Таблица 2
Физические свойства используемых материалов.
Материал | Недвижимость | ||
---|---|---|---|
ASTM Тип I Обычные Портленд Цемент Плотность: 3150 кг / м 3 , Тритант: 330 м 2 / кг | |||
FA | Fly Fly Плотность: 2140 кг / м 3 , Тритатура: 396 млн. ![]() | ||
GGBS | Гранулированный доводной ГГБС | Гранулированный Гранулированный шлак Плотность: 2860 кг / м 3 , Трикота: 430 M 2 / кг | |
CSA | CALSIUR Плотность: 2890 кг / м 3 , Тритатура: 466 млн. 2 / кг | ||
Прекрасный агрегат | S1 | ISO Стандартный песок, Размер: 2 мм Модуль крупности: 2. ![]() | |
S2 | Морской песок, Размер: 5 мм Модуль крупности: 2,01, плотность: 2600 кг/м 3 : 0.79% | ||
S3 | S3 | Разрешеный песок, размер: 5 мм Модуль тонкости: 3.29, плотность: 2570 кг / м 3 , поглощение: 0,87% | |
Грубый совокупность | Разрешеный гранитный агрегат, размер : 25 мм Модуль крупности: 6,94, плотность: 2600 кг/м 3 , абсорбция: 0.76% | ||
Химическая добавка | Группа поликарбоновой кислоты, плотность: 1260 кг / м 3 | ||
Материал ускорителя | NS | Na 2 SO 4 , плотность: 3350 кг / м 3 , Растворимость: 13,9 г / 100 мл (20 ° C) | |
AS | AL 2 (SO 4 ) 3 , плотность: 2672 кг / м 3 , растворимость: 36,4 г /100 мл (20 °C) | ||
CH | Ca(OH) 2 , плотность: 2211 кг/м 3 , растворимость: 17.3 г/100 мл (20 °C) | ||
CN | Ca(NO 3 ) 2 , плотность: 2504 кг/м 3 , растворимость: 51,4 г/100 | ||
NC | Nahco 3 , плотность: 2200 кг / м 3 , растворимость: 9,6 г / 100 мл (20 ° C) | ||
Retarder | CA: Лимонная кислота, SG: глюконат натрия , BA: борная кислота, TA: винная кислота |
показывает результаты испытания просеивания заполнителей (ASTM C136) [30], использованных в настоящем документе, которое было проведено для анализа классификации мелких и крупных заполнителей.Для мелких заполнителей используется стандартный песок ISO (размер: 2 мм, модуль крупности: 2,99, плотность: 2620 кг/м 3 , SiO 2 : 99%, 0,08 мм, количество проходов: 0,04%) [31] В эксперименте с раствором использовали морской песок (размер: 5 мм, модуль крупности: 2,01, плотность: 2600 кг/м 3 , абсорбция: 0,79%) и дробленый песок (модуль крупности: 3,29, плотность: 2570 кг/м). m 3 , и поглощение: 0,87%), использовали для оценки их применимости в бетоне. Мелкие заполнители готовили путем смешивания морского песка и дробленого песка в соотношении 4:6 с модулем крупности 2.84.
Кривые ситового анализа для используемых здесь заполнителей: ( a ) Стандартный песок ISO; ( b ) мелкие заполнители; и ( c ) крупные заполнители.
В качестве крупных заполнителей использовались дробленые гранитные заполнители (размер: 25 мм, модуль крупности: 6,94, плотность: 2600 кг/м 3 , абсорбция: 0,76%).
Группа поликарбоновых кислот (плотность: 1260 кг/м 3 ) использовалась в качестве химической добавки. В качестве материалов-ускорителей, NS: Na 2 SO 4 , AS: Al 2 (SO 4 ) 3 , CH: Ca(OH) 2 , CN: Ca(NO ) 2 и NC: NaHCO 3 , а в качестве замедлителей схватывания использовали CA: лимонную кислоту, SG: глюконат натрия, BA: борную кислоту и TA: винную кислоту.
2.2. Схема эксперимента и пропорции смеси
показывает схему эксперимента для этого исследования. Для изучения оптимального метода набора ранней прочности бетона с использованием обычного цемента реакционную способность вяжущего CSA и количество дополнительных материалов контролировали на основе стехиометрических уравнений реакции по CaO/SO 3 и Al 2 O [23].Кроме того, оптимальное количество вяжущего CSA, которым можно заменить OPC, было определено путем оценки характеристик строительного раствора на основе количества используемого вяжущего CSA.
Таблица 3
(° C)
16, 17, 18
Прочность на компрессию
-12 ч, 24 ч
(B × 0.5%)
Прочность на сжатие
-12 ч, 24 ч, 72 ч
(B × 1%, 2%, 3%)
CA (B × 0,2%)
( Периодическая установка + макетный элемент)
Камера (13)
Комнатная температура (20)
(B × 3.2)
Прочность на сжатие — 12 ч, 24 ч, 72 ч
7 Д, 28 Д — Макет элемента: 12 ч, 24 ч, 72 ч
Возможность повышения начальной прочности раствора затем исследовали комбинирование связующего CSA и ускорителя; В качестве ускорителя использовали 0,5% от общего количества связующего. При использовании вяжущих CSA может происходить быстрое схватывание, поэтому был рассмотрен замедлитель схватывания, совместимый со вяжущим CSA. Добавлено пять типов замедлителей на уровне 0.2% c.f., связующее. Для приготовления образцов бетона использовалась комбинация ускорителя и замедлителя схватывания, и в каждом случае оценивались характеристики ранней прочности и способность предотвращать быстрое схватывание. Количество замедлителя было доведено до 0,2%, а три типа ускорителей использовались в количествах 1%, 2% и 3%.
Наконец, на основе количества CSA, ускорителя и замедлителя схватывания, полученного в результате вышеуказанных экспериментов, был разработан состав бетонной смеси. Применимость рассмотренных в настоящей работе вяжущих для бетона с ранней прочностью оценивалась в ходе макетных экспериментов производства на заводе Remicon Batcher.
и показать пропорции смешивания раствора и бетона, используемые в этом исследовании. Течение раствора составляло <200 мм в соответствии с ASTM C1437 [32]. Осадка бетона составила 210 ± 25 мм, содержание воздуха 4,5 ± 1,5 %.
Таблица 4
Пропорции основного раствора.
серии | W / C (%) | C: S (1) | Цемент (G) | Вода (G) | AD (2) (B ×%) |
---|---|---|---|---|---|
Ⅰ (Раствор) | 50 | 1:3 | 450 | 225 | 0.7 |
Таблица 5
Пропорции смешивания бетона.
Series | W / B (%) | S / A (%) | Единица (кг / м 3 ) | AD (3) (B ×%) | AC (b ×%) | |||||||||
---|---|---|---|---|---|---|---|---|---|---|---|---|---|---|
W | C (1) | CSA | GGBS | FA | S (2) | (2)G | ||||||||
ⅱ ( Бетон) | Гладкая | 53.0 | 49.0 | 175 | 175 | 215 | — | 66 | 50 | 8 | 9 | 0,7 | — | |
CA17 | 53.0 | 49,0 | 175 | 274 | 56 | — | — | 899 | 901 | — | 3.1 |
2.3. Test Methods
показывает методы испытаний и соответствующие им элементы оценки для образцов строительного раствора и бетона.Различные процедуры тестирования описаны ниже.
Таблица 6
Методы испытаний и соответствующие им элементы оценки.
Серия | Элемент оценки | Метод испытаний | Размер (мм) |
---|---|---|---|
Ⅰ. Метчатый тест | Установка времени (h) | ASTM C403 / C403M [33] | — |
Прочность на компрессию (MPA) | ASTM C109 / C109M [34] | 40 × 40 × 160 | |
Ⅱ.Тест бетона | Спад (мм) | ASTM C143 [35] | — |
Содержание воздуха (%) | ASTM C231 [36] | — | |
Прочность на компрессию (МПа) | ASTM C873 [37] | Ø100 × 200 | |
ASTM C39 [38] |
2.3.1. Испытание строительного раствора
Испытание на текучесть строительного раствора проводилось на основе ASTM C1437 [32], а испытание на схватывание строительного раствора проводилось на основе ASTM C403/C403M [33].Прочность раствора на сжатие была рассчитана путем измерения максимальной нагрузки с использованием 30-тонного UTM в течение запланированного времени в соответствии с ASTM C109/C109M [34]. Прочность бетона на сжатие рассчитывали как среднее значение, полученное на трех испытательных образцах.
2.3.2. Применение для бетона
На основании соотношения оптимального вяжущего и добавки, полученной в результате испытания раствора, оценивалась применимость к бетону. Бетон был произведен на заводе Remicon Batcher, а теплота гидратации и набор прочности были смоделированы путем изготовления макетов стен.и покажите детали макета и установки термопары соответственно. Моделирование макета было установлено на 200 мм × 600 мм × 1000 мм, а термопара типа K была встроена в центр макета.
Прикладные испытания бетона ранней прочности на дозаторном заводе.
Установка термопары и закладной двойной формы для испытания бетона.
Для оценки свойств свежего бетона было проведено испытание на осадку в соответствии с ASTM C143/C143M [35], а испытание на содержание воздуха было проведено в соответствии с ASTM C231/C231M-17a [36].Для оценки удобоукладываемости на площадке исследовали свойства свежего бетона после выдержки в автобетоносмесителе в течение 0, 60 и 90 мин. Для измерения прочности на сжатие бетона, подвергнутого гидратации, была установлена двойная форма в соответствии с ASTM C873 [37].
Прочность бетона на сжатие была рассчитана путем подготовки образца Ø100 мм × 200 мм в соответствии с ASTM C39/C39M [38] и измерения максимальной нагрузки с использованием 300-тонного UTM в течение определенных периодов времени.Прочность бетона на сжатие рассчитывали как среднее значение, полученное на трех образцах.
3. Результаты и обсуждение
3.1. Свойства раствора
3.1.1. Влияние замены CSA
наи показывают время схватывания и результаты прочности на сжатие, соответственно, для образца раствора с заменой CSA, причем очевидно, что оба эти показателя увеличиваются с увеличением коэффициента замены CSA. При замещении CSA выше 17% наблюдалось небольшое изменение прочности на сжатие, поэтому это значение считалось оптимальным.Кроме того, прочность раствора на сжатие достигала максимума при 8,3 МПа через 12 ч при использовании в смеси 17 % CSA и при времени схватывания >75 мин.
Время схватывания раствора с заменой CSA.
Прочность раствора на сжатие с заменой CSA.
отображает тренды расчетных отношений CaO/SO 3 и Al 2 O 3 /SO 3 в соответствии с изменениями коэффициента замещения CSA, а также показывает оптимальный химический состав бетона ранней прочности.Хотя предыдущие исследования подтвердили, что химические свойства CSA способствовали гидратации цемента из-за высокого содержания SO 3 , этот эффект применим только в соответствующем диапазоне [39,40,41].
Относительные индексы CaO/SO 3 и Al 2 O 3 /SO 3 с заменой CSA.
Оптимальный химический состав для бетона ранней прочности.
Как указано в рамках данного исследования, оптимальное соотношение замещения для вяжущего CSA для ранней прочности составляет 17% при соотношениях CaO/SO 3 и Al 2 O 3 /SO 3 , равном 1.9 и 1,23 соответственно.
Кроме того, было обнаружено, что при нанесении на бетон комбинации вяжущего для ранней прочности, ускорителя и замедлителя схватывания достигается прочность на сжатие 5 МПа/12 ч при низких температурах. Однако это также требовало тщательного контроля за смешиванием бетона. Кроме того, следует отметить, что характеристики вяжущих с ранней прочностью должны быть проверены в ряде условий для обеспечения надежности.
3.1.2. Влияние ускорителя
и показать время схватывания и результаты прочности на сжатие для раствора с добавлением ускорителей.В отсутствие ускорителя время схватывания раствора составляло 90 мин, а в присутствии ускорителя оно быстро уменьшалось до 20–40 мин. Эти результаты показывают, что использование ускорителя способствует гидратации реактивных гауиновых минералов, и, поскольку это также влияет на прочность на сжатие, считается, что начальное производство эттрингита также увеличивается [19, 20].
Время схватывания раствора в присутствии различных ускорителей.
Различия в прочности раствора на сжатие в присутствии разных ускорителей.
В частности, Na 2 SO 4 и Al 2 (SO 4 ) 3 сульфатные ускорители оказались наиболее эффективными в улучшении начальной прочности на сжатие из-за более высокой скорости ионизации по сравнению с цементом. , а также потому, что первоначально элюированные ионы SO 4 2– выгодны для зародышеобразования гидрата эттрингита. Однако, хотя ускорители могут улучшить начальную прочность раствора, следует избегать использования одного ускорителя, так как это значительно сокращает время схватывания.
3.1.3. Влияние замедлителя и ускорителя схватывания
Изменение времени схватывания раствора в присутствии различных замедлителей схватывания показано в . Как указано, СА проявляет наибольший эффект замедления, за ним следуют БА, СК и ТА. Действительно, CA и SG широко используются в качестве замедлителей схватывания строительных растворов и бетона благодаря их превосходным экономическим характеристикам и характеристикам замедления схватывания. И CA, и SG состоят из шести атомов углерода, хотя CA содержит одну группу –OH и три группы –COOH, тогда как SG содержит пять групп –OH и одну группу –COOH.Таким образом, эти различия объясняют их различные характеристики в отношении замедления гидратации цемента. Следует отметить, что использование эквивалентного количества СА (т.е. с линейной молекулярной структурой) показало оптимальный эффект замедления.
Время схватывания раствора в присутствии различных замедлителей схватывания.
Кроме того, в случае времени схватывания раствора, за исключением случая СА, схватывание происходит в течение 2 часов, поэтому добавление СА необходимо для обеспечения достаточной технологичности.Однако видно, что прочность бетона на сжатие с использованием замедлителя схватывания была снижена. Таким образом, можно ускорить развитие силы на ранних этапах за счет комбинированного использования различных ускорителей.
Различия в прочности раствора на сжатие в присутствии различных замедлителей схватывания.
Изменение времени схватывания раствора и прочности на сжатие в присутствии как ускорителя (А), так и замедлителя (R) показаны на и . Как указано, время схватывания Plain R0A0 составляло 60 минут, а время схватывания R0.2А0, содержащем 0,2% замедлителя схватывания, составляло 135 мин, что указывает на задержку гидратации. Следовательно, начальная прочность на сжатие образца строительного раствора значительно снизилась до 57% от этого показателя простого образца [42].
Время схватывания раствора в присутствии ускорителей и замедлителей схватывания.
Различия в прочности строительных растворов на сжатие в присутствии ускорителей и замедлителей схватывания.
По сравнению с Обычным образцом (CSA17), в серии NS03_R0.2, где в качестве ускорителя использовался Na 2 SO 4 , время схватывания раствора немного уменьшилось, но прочность стабильно увеличилась в пределах 12 –24 ч, что дает значение 191.1–218,9%.
обобщает результаты времени схватывания и прочности на сжатие для образцов строительного раствора. Более конкретно, когда в цемент добавляли 17% CSA, было очевидно, что прочность раствора на сжатие улучшалась, а время схватывания уменьшалось. Кроме того, начальная прочность раствора, содержащего CSA, была увеличена, но скорость набора прочности снизилась через 24 часа, что указывает на то, что для обеспечения достаточной прочности раствора требуется ускоритель. Более того, при смешивании строительного раствора с Na 2 SO 4 в качестве ускорителя быстрое нарастание прочности было успешным, но время схватывания уменьшилось.Отсюда было сочтено, что использование дополнительного замедлителя необходимо для обеспечения стабильного рабочего времени.
Свойства раствора в присутствии CSA и примеси.
Кроме того, сообщалось, что использование замедлителей схватывания в строительных растворах на основе CSA является эффективным подходом к улучшению удобоукладываемости системы цементных смесей, которая довольно быстро отверждается без снижения конечной прочности [20,43].
3.2. Concrete Properties
показывает изменение осадки образца бетона во времени, где были изучены времена 60 и 90 минут с учетом времени между производством и доставкой на площадку.Для целей этого испытания бетон вращали на низкой скорости в автобетоносмесителе, и в каждый момент времени измеряли изменение осадки. Было обнаружено, что OPC и CSA17_NS03_R0.2 привели к незначительному снижению осадки, но полученные значения остались в пределах диапазона осадки, установленного в настоящем исследовании, что указывает на отсутствие проблем с точки зрения работоспособности в полевых условиях. Исходя из этого результата, использование связующего CSA может быть использовано для управления свойствами настройки.
Изменение осадки образца бетона со временем.
показывает изменение прочности бетона на сжатие в зависимости от температуры отверждения. В частности, в случае OPC измерение прочности бетона на сжатие через 12 часов было невозможно из-за задержки схватывания и твердения в условиях внешнего отверждения. Через 3 дня развивалась начальная прочность ≥5 МПа, а при повышении температуры время, необходимое для набора этой степени ранней прочности, имело тенденцию к уменьшению. Однако целевая прочность развивалась уже через 24 часа, даже при 20 °C.
Изменение прочности бетона на сжатие в зависимости от температуры отверждения.
В случае образца CSA17_NS03_R0.2 прочность на сжатие 5 МПа развивалась через 24 часа при низкой температуре <10 °C и через 12 часов при температуре выше 13 °C. Здесь следует отметить, что материалы типа ранней прочности развивают превосходную начальную прочность бетона из-за быстрой начальной реакции, но имеют тенденцию к задержке в долговременном наборе прочности. Кроме того, было обнаружено, что комбинация материалов с ранней прочностью, используемых в этом исследовании, приводит к превосходному набору прочности для образцов бетона даже через 28 дней.
Температурная история и зрелость [44] метода отверждения изображены на и соответственно. В этих экспериментах бетонная смесь отверждалась путем поддержания постоянной температуры 13 и 20 °С с использованием камер с постоянной температурой, а экспериментальная установка подвергалась воздействию наружного воздуха. В ходе макетного эксперимента наружная температура постепенно снижалась от исходного значения 7,9 °С, а средние значения температуры через 12 и 24 ч составили 4,3 и 9,4 °С соответственно.
Температурная история и зрелость в зависимости от метода отверждения.
Температурная история и зрелость образцов бетона в модельном эксперименте.
В целом, модельный эксперимент показал, что использование CSA17_NS03_R0.2 выгодно с точки зрения раннего набора прочности благодаря более высокой теплоте гидратации и более высокой зрелости по сравнению с OPC. показаны сканирующие электронные микрофотографии OPC и CSA17_NS03_R0.2, сделанные через 12 часов после отверждения при 13 °C. Как видно из этих изображений, в случае CSA17_NS03_R0.2, был получен и активирован продукт гидратации эттрингит. Однако для образца Plain OPC этого не наблюдалось.
Сканирующая электронная микроскопия образцов ( a ) Plain OPC и ( b ) CSA17_NS03_R0.2 через 12 часов и при температуре отверждения 13 °C.
4. Выводы
В этом исследовании изучалось развитие ранней прочности бетона на основе обычного портландцемента (OPC) и смесей сульфоалюмината кальция (CSA) при низкотемпературном отверждении.Время схватывания и начальная прочность раствора на сжатие оценивались путем корректировки количества CSA-содержащего OPC, и оптимальные характеристики наблюдались при использовании 17% CSA по отношению к общему вяжущему, в дополнение к CaO/SO 3 и SO 3 /Al 2 O 3 соотношения 1,9 и 1,25 соответственно. Кроме того, влияние ускорителя на развитие ранней прочности раствора на сжатие уменьшалось в порядке NS > AS > CH > NC > CN ≥ Plain.Время схватывания раствора Plain без добавления ускорителя составляло 90 минут, тогда как в присутствии ускорителя это время быстро уменьшалось до 20–40 минут, что позволяет предположить, что использование только ускорителя нежелательно. Кроме того, эксперименты с использованием связующих CSA показали, что наиболее эффективное замедление схватывания наблюдается в следующем порядке: лимонная кислота > борная кислота > глюконат натрия > винная кислота. Схватывание было замедлено максимум на 141 мин при использовании лимонной кислоты по сравнению с обычным образцом (CSA17).Комбинация ускорителя и замедлителя была эффективной для достижения ранней прочности образца строительного раствора, содержащего Na 2 SO 4 в качестве ускорителя. Однако время схватывания было сокращено, поэтому необходимо использовать дополнительный замедлитель схватывания, чтобы обеспечить достаточное рабочее время. Кроме того, при комбинировании бетона с вяжущим для ранней прочности (т. е. CSA, ускорителем и замедлителем) наблюдалось незначительное изменение осадки в течение 90 минут, а прочность на сжатие >5 МПа/12 ч была подтверждена после начальной гидратации при низкотемпературные условия.Наконец, несмотря на то, что в этом исследовании наблюдалось развитие ранней прочности бетона при низких температурах, для облегчения получения качественно стабильной бетонной смеси необходимо изучить тонкую регулировку состава бетона и характеристики вяжущих с ранней прочностью в различных условиях эксплуатации.
Вклад авторов
Т.Л., Дж.Л. и Х.К. в равной степени способствовала концептуализации исследования и всех исследований, проведенных в его рамках. Закупкой ресурсов занимался Т.Л. и Дж.Л. Первоначальный проект рукописи был подготовлен Т.Л. и Дж.Л., тогда как окончательный вариант был рассмотрен и отредактирован Т.Л., Дж.Л. и Х.К. Все авторы прочитали и согласились с опубликованной версией рукописи.
Финансирование
Эта работа была поддержана грантом Национального исследовательского фонда Кореи (NRF), финансируемым правительством Кореи (MSIT; № NRF-2018R1A5A1025137). Кроме того, исследование было поддержано Программой фундаментальных научных исследований через Национальный исследовательский фонд Кореи (NRF), финансируемой Министерством образования (№ 1).2018R1D1A1B07049812).
Конфликт интересов
Авторы заявляют об отсутствии конфликта интересов. Спонсоры не участвовали в разработке исследования; при сборе, анализе или интерпретации данных; в написании рукописи или в решении опубликовать результаты.
Литература
1. Гартнер Э.М., Янг Дж.Ф., Дамидот Д.А., Джавед И. Состав цементных фаз. В: Бенстед Дж., Барнс П., редакторы. Структура и характеристики цементов. 2-е изд. КПР Пресс; Лондон, Великобритания: 2002.стр. 57–113. [Google Академия]2. Дахтар Дж., доктор философии. Тезис. Университет Шеффилда; Шеффилд, Великобритания: 2004. Цемент на основе сульфоалюмината кальция как вяжущее для конструкционного бетона. [Google Академия]3. Барнс П., Бенстед Дж. Структура и свойства цемента. 2-е изд. КПР Пресс; Лондон, Великобритания: 2002. [Google Scholar]4. Тейлор Х.Ф.В. Химия цемента. 2-е изд. Издательство Томаса Телфорда; Лондон, Великобритания: 1997. [Google Scholar]5. Хьюлетт П., Лиска М. Химия цемента и бетона Ли. 5-е изд. Баттерворт-Хайнеманн; Оксфорд, Великобритания: 2019.[Google Академия]6. Джуилланд П., Галлуччи Э., Флэтт Р., Скривенер К. Теория растворения применительно к индукционному периоду гидратации алита. Цем. Конкр. Рез. 2010;40:831–844. doi: 10.1016/j.cemconres.2010.01.012. [Перекрестная ссылка] [Академия Google] 7. Мехта П.К., Монтейро П.Дж.М. Бетон: микроструктура, свойства и материалы. 3-е изд. Макгроу-Хилл; Нью-Йорк, штат Нью-Йорк, США: 2006. [Google Scholar]8. Чжан Л., Су М., Ван Ю. Развитие применения сульфо- и ферроалюминатных цементов в Китае. Доп. Цем. Рез. 1999; 11:15–21.doi: 10.1680/adcr.1999.11.1.15. [Перекрестная ссылка] [Академия Google]9. Мехта П.К. Исследования по энергосберегающим цементам. Всемирная цементная технология. 1980; 11: 166–177. [Google Академия] 10. Одлер И. Специальные неорганические цементы. КПР Пресс; Лондон, Великобритания: 2003. [Google Scholar]11. Юнгер М., Виннефельд Ф., Провис Дж., Идекер Дж. Достижения в области альтернативных цементных вяжущих. Цем. Конкр. Рез. 2011;41:1232–1243. doi: 10.1016/j.cemconres.2010.11.012. [Перекрестная ссылка] [Академия Google] 12. Попеску К., Мунтян М., Шарп Дж. Пробное промышленное производство низкоэнергетического белитового цемента.Цем. Конкр. Композиции 2003; 25: 689–693. doi: 10.1016/S0958-9465(02)00097-5. [Перекрестная ссылка] [Академия Google] 13. Gartner E. Промышленно интересные подходы к цементам с низким содержанием CO 2 . Цем. Конкр. Рез. 2004; 34:1489–1498. doi: 10.1016/j.cemconres.2004.01.021. [Перекрестная ссылка] [Академия Google] 14. Zajac M., Skocek J., Bullerjahn F., Haha M.B. Влияние замедлителей схватывания на раннюю гидратацию кальциево-сульфоалюминатных (CSA) цементов. Цем. Конкр. Рез. 2016; 84: 62–75. doi: 10.1016/j.cemconres.2016.02.014. [Перекрестная ссылка] [Академия Google] 15.Ван П., Ли Н., Сюй Л. Эволюция гидратации и прочность на сжатие цемента на основе сульфоалюмината кальция, постоянно отвержденного в диапазоне температур от 0 до 800 °C. Цем. Конкр Рез. 2017; 100: 203–213. doi: 10.1016/j.cemconres.2017.05.025. [Перекрестная ссылка] [Академия Google] 16. Trauchessec R., Mechling J.M., Lecomte A., Roux A., Le Rolland B. Гидратация смесей обычного портландцемента и сульфоалюмината кальция. Цем. Конкр. Композиции 2015;56:106–114. doi: 10.1016/j.cemconcomp.2014.11.005. [Перекрестная ссылка] [Академия Google] 17.Адамс М.П., Идекер Дж.Х. Влияние типа заполнителя на конверсию и прочность алюмокальциевого цементного бетона. Цем. Конкр. Рез. 2017; 100: 284–296. doi: 10.1016/j.cemconres.2017.07.007. [Перекрестная ссылка] [Академия Google] 18. Виннефельд Ф., Мартин Л.Х.Дж., Мюллер С.Дж., Лотенбах Б. Использование гипса для контроля кинетики гидратации цементов CSA. Констр. Строить. Матер. 2017; 155:154–163. doi: 10.1016/j.conbuildmat.2017.07.217. [Перекрестная ссылка] [Академия Google] 19. Чон Ю., Харгис К.В., Канг Х., Чун С., Мун Дж. Влияние повышенных температур отверждения на цементные растворы с высоким содержанием сульфоалюмината кальция из элимита.Материалы. 2019;12:1072. doi: 10.3390/ma12071072. [Бесплатная статья PMC] [PubMed] [CrossRef] [Google Scholar]20. Гвон С., Джанг С., Шин М. Совместное воздействие замедлителей схватывания и полимерного порошка на свойства цементных систем с добавлением сульфоалюмината кальция. Материалы. 2018;11:825. doi: 10.3390/ma11050825. [Бесплатная статья PMC] [PubMed] [CrossRef] [Google Scholar]21. Глассер Ф., Чжан Л. Высокоэффективные цементные матрицы на основе композиций сульфоалюмината кальция и белита. Цем. Конкр. Рез. 2001; 31: 1881–1886.doi: 10.1016/S0008-8846(01)00649-4. [Перекрестная ссылка] [Академия Google] 22. Пера Дж., Амбруаз Дж. Новые применения цемента на основе сульфоалюмината кальция. Цем. Конкр. Рез. 2003; 33: 371–676. doi: 10.1016/j.cemconres.2003.10.019. [Перекрестная ссылка] [Академия Google] 23. Мехта П.К., Кляйн А. Образование эттрингита путем гидратации системы, содержащей безводный сульфоалюминат кальция. Варенье. Керам. соц. 1965; 48: 435–436. doi: 10.1111/j.1151-2916.1965.tb14786.x. [Перекрестная ссылка] [Академия Google] 24. Ли П., Ма З., Чжан З., Ли С., Лу С., Хоу П., Ду П. Влияние гипса на гидратацию и свойства затвердевания модифицированного алитом цемента из сульфоалюмината кальция. Материалы. 2019;12:3131. doi: 10.3390/ma121Влияние ускорителей и компонентов смеси на свойства бетона с высокой начальной прочностью
Настоящее исследование было сосредоточено на свойствах бетона с высокой начальной прочностью, которые могут быть получены при значительной замене цемента летучей золой.Кроме того, определяется влияние добавления волокон на прирост прочности при сжатии и прирост прочности в раннем возрасте. Испытания проводились на различных образцах высокопрочного бетона, в которых золой-уносом заменяли цемент до 50%. Различные типы образцов бетона были отлиты и испытаны на различное соотношение мелкого и крупного заполнителя, содержание металлических волокон, соотношение цемента к общему заполнителю и дозировку ускорителя. Результаты испытаний показали, что бетон с высокой начальной прочностью (50,7 МПа через 7 дней) был получен при более высоком соотношении F/C, равном 0.8, соотношение C/TA 0,24 и более высокий уровень дозировки стальной фибры 1,5%.
1. Введение
Цементные материалы с высокой начальной прочностью имеют жизненно важное значение для современной расширяющейся гражданской инфраструктуры. Однако износ гражданской инфраструктуры во всем мире привел к осознанию необходимости улучшения вяжущих материалов с точки зрения их технических свойств и долговечности. Использование добавок, таких как летучая зола, мало влияет на пуццолановые свойства для улучшения технических свойств бетона, замещенного летучей золой.Прочность конструкционного бетона должна быть высокой, о чем свидетельствует водо-вяжущее отношение (В/В). Бетонная конструкция называется прочной, если она выдерживает условия, на которые рассчитана, без износа в течение всего срока службы [1–5]. Однако использование хлоридов может вызвать коррозию стальной арматуры и запрещено в некоторых странах, так что нитраты кальция потенциально могут использоваться для получения бетона с высокой начальной прочностью. Эти методы особенно полезны в производстве сборных конструкций, где высокая прочность на раннем этапе позволяет снимать опалубку в течение 24 часов, тем самым сокращая время цикла, что приводит к снижению затрат [6].Пуццолан увеличивает прочность бетона в более позднем возрасте, поскольку он вступает в реакцию с гидроксидом кальция и превращает его в гидраты силиката кальция (C-S-H). Однако портландцементы из пуццолана имеют более высокую энергию активации и, следовательно, скорость их гидратации ниже по сравнению с обычными портландцементами [7]. В аналогичном контексте добавление стальных волокон улучшает бетонную матрицу по всем механическим свойствам бетона, таким как прочность на сжатие, прочность на растяжение при растяжении, прочность на изгиб и ударная вязкость.Сталефибробетон изготавливается из композиционного материала на основе цемента, армированного хаотично распределенными по диаметру стальными волокнами. Он содержит пуццоланы и добавки, обычно используемые при строительстве дорожных покрытий в строительных работах [8]. В этой аналогичной области исследований из более ранних исследований можно наблюдать, что прочностные свойства бетона не ухудшаются в случае высокого прироста прочности бетона в раннем возрасте [9]. Также введение минеральных и химических добавок способствовало увеличению скорости набора прочности и показало улучшение 1-суточной прочности на сжатие до 30 МПа, что может быть достаточным для раннего снятия опалубки [10, 11].Можно отметить, что как прочность на сжатие, так и УПВ всех образцов увеличились, особенно для образцов, содержащих летучую золу. Для минеральных примесей зависимость между UPV и прочностью на сжатие оказалась экспоненциальной [12]. Неразрушающий контроль с использованием метода ультразвукового контроля был расширен для изучения цементных материалов, армированных стальной фиброй, для прогнозирования влияния объемной доли и геометрии волокон на технические свойства бетона. Настоящее исследование направлено на изучение прочностных характеристик вяжущих систем, содержащих стальные волокна, зольную пыль и ускоритель в различных дозировках.Кроме того, скорость затвердевания контролировали с помощью портативного ультразвукового измерителя скорости импульса.
2. Материалы и методы экспериментов
Использовали обычный портландцемент марки 53 с пределом прочности при сжатии через 28 суток 54,9 МПа, соответствующий требованиям ГОСТ 12269-1987. Удельный вес цемента оказался равным 3,12. Использовался мелкий заполнитель, полученный из местного речного песка, прошедшего через сито IS 4,75 мм, соответствующее II градационной зоне IS: 383-1978. Он имеет модуль крупности 2.60, удельный вес 2,69 и водопоглощение 0,97% за 24 часа. Использовался крупный заполнитель щебня из голубого гранита с максимальным размером 12,5 мм, соответствующий IS: 383-1978. Было обнаружено, что удельный вес составляет 2,75, модуль крупности 6,5 и водопоглощение 0,62% за 24 часа. В исследовании использовали суперпластификатор на основе сульфированного нафталина и формальдегида, который соответствует ASTM типа F и IS: 9103-1999. Удельный вес ОЯТ составил 1,20. Использовались волокна, соответствующие стандарту ASTM A820-01, стальные волокна с загнутыми концами использовались при уровне дозировки 0.5 и 1,5% по объемной доле бетона, диаметр стальной фибры 0,5 мм, длина 30 мм, соотношение размеров (l/d) 60, предел прочности при растяжении 900 МПа, модуль упругости 210 ГПа. Для получения бетона с высокой начальной прочностью использовали ускоритель при дозировке 1% от массы цемента. Пропорции бетонной смеси, использованные в исследовании, представлены в таблице 1. Всего 16 различных бетонных смесей были распределены на основе отношения цемента к общему заполнителю (C/TA), равного 0.24 и 0,26, водоцементное отношение (В/Ц) 0,3 и 0,4, мелкозернистое и крупнозернистое (Ф/Ц) 0,6 и 0,8. Бетонные смеси замешивали в 40-литровой емкости с опрокидывающейся мешалкой барабанного типа, а образцы отливали с использованием стальных форм, стандартных кубических форм (100 × 100 × 100 мм) и цилиндров (диаметр 100 мм × высота 200 мм) и уплотняется настольным вибратором. Из каждой смеси через 24 часа после заливки отливали не менее трех образцов и отверждали водой при 27±2°С до возраста испытаний 1, 3, 7, 14, 28 и 56 суток.Все образцы были отверждены в одном и том же резервуаре для отверждения, чтобы обеспечить равномерное отверждение для всех образцов.
результаты испытаний на сжатие различных бетонных смесей приведены в таблицах 2 и 3 и показаны на рисунках 1, 2, 3, 4 и 5. Можно заметить, что по сравнению с контрольным бетоном все бетонные композиты, содержащие металлическую фибру, показали более высокую прочность.Можно также отметить, что такие переменные, как отношение цемента к заполнителю и отношение мелкого к крупному заполнителю, сильно влияли на сжимающие свойства, когда отношение В/Ц составляло 0,3, как показано на рисунке 1. Аналогичным образом это видно из На рисунках 2 и 5 показано, что по сравнению с отношением 0,3 В/Ц, 0,4 В/Ц показало более высокую прочность из-за более высокого отношения фтор/цемент (0,8), тогда как отношение С/ТА (0,24) было ниже, чем при более низком соотношении В/Ц (0,3). ) соотношение. Кроме того, такая же тенденция наблюдалась для контролируемой бетонной смеси, что привело к незначительному увеличению прочности на сжатие для соотношения В/Ц и Ц/ТА.Также хорошо известно, что более высокое соотношение F/C, используемое в бетоне, приводит к более высокой прочности. Это можно обосновать тем фактом, что оба параметра C/TA и соотношение F/C оказывают существенное влияние на улучшение скорости прироста силы (как видно на рисунках 6, 7, 8 и 9). Это может привести к замедленному растрескиванию бетона при нагрузке. Расщепленные свойства при растяжении далее показали ту же тенденцию, что и прочность на сжатие. Результаты испытаний на раннее твердение через несколько часов после извлечения из формы образцов бетона были зарегистрированы и представлены в таблице 4.Значения результатов ультразвуковых испытаний показали, что прирост прочности через 1 день показал хорошее увеличение скорости пульса и удовлетворял требованиям IS 13311 (показано на рисунке 10). Это, по существу, показывает, что бетон хорошего качества был получен при гораздо более раннем периоде твердения с добавлением ускорителя и волокон.
4.ВыводыНа основании приведенного выше экспериментального исследования можно сделать следующие выводы. (i) Использование летучей золы класса F и ускорителя показало, что свойства бетона в раннем возрасте могут быть более полезными, когда требуется быстрое бетонирование с высокой скоростью. Кроме того, добавление металлических компонентов оказывает значительное влияние на свойства бетона при сжатии и растяжении. (ii) Тщательный выбор различных переменных, таких как отношение цемента к заполнителю и отношение мелкого к крупному заполнителю, оказал значительное влияние, а также отношение цемента к заполнителю, которое обеспечило большее улучшение механических свойств бетона.(iii) Совершенно очевидно, что раннее увеличение прочности бетона зависит от низкого водоцементного отношения, отношения F/C, дозировки ускорителя и отношения цемента к общему заполнителю. Замена цемента до 50% летучей золы показала прирост прочности в начале старения немного ниже, чем у бетона, изготовленного с 25% летучей золы. Следовательно, бетонные смеси, содержащие золу класса F, могут безопасно использоваться до 50% для производства бетона с высокой начальной прочностью для сборных изделий. (iv) По результатам испытаний было замечено, что более высокая прочность была получена при соотношении В/Ц, равном 0.3, отношение F/C 0,8 и отношение C/TA 0,24 с содержанием металлов 1,5%, из которых прочность на сжатие через 28 дней составила 54,9 МПа, и аналогичная тенденция была отмечена для более низкого отношения W/C 0,3, отношения F/C 0,6. , и отношение C/TA 0,26 с более высоким содержанием металлов 1,5%, из которого значение результата испытаний за 28 дней составило 53,4 МПа. Можно сделать вывод, что более высокое соотношение мелких и крупных заполнителей и содержание металлического волокна до 1,5% показали более высокую прочность. Добавление ускорителя оказывает прямое влияние на ранний прирост прочности и приводит к достижению 28 дней за короткий период в 7 дней. Авторские праваАвторские права © 2012 В. М. Сунтарараджан и А. Сивакумар. Это статья с открытым доступом, распространяемая в соответствии с лицензией Creative Commons Attribution License, которая разрешает неограниченное использование, распространение и воспроизведение на любом носителе при условии надлежащего цитирования оригинальной работы. Влияние ускорителя на набор прочности бетона, разрушение…Бетонные покрытия, демонстрирующие серьезные повреждения, требующие ремонта, обычно наблюдаются в бетонном покрытии в Небраске.Из-за требований открытия дорожного покрытия для движения транспорта после укладки материалов для быстрого ремонта важно, чтобы этот бетон достиг высокой ранней прочности. Чтобы гарантировать это, в настоящее время в материалах для быстрой заделки на основе портландцемента, разработанных Министерством транспорта штата Небраска (NDOT), используется высокое содержание цемента и ускорители на основе хлоридов. Помимо связанной с этим высокой стоимости, высокое содержание цемента приводит к менее стабильной смеси с высокой усадкой, высокой теплотой гидратации и высоким потенциалом образования трещин.Кроме того, использование ускорителей на основе хлоридов отрицательно влияет на долговечность бетона. Кроме того, влияние низкой температуры окружающей среды оказывает значительное влияние на прирост прочности и требует оценки для оценки открытия движения. Таким образом, в рамках этого проекта изучалась эффективность материалов для быстрого ремонта по трем различным аспектам: снижение содержания цемента за счет оптимизации градации заполнителя, замена обычного хлорида кальция бесхлористым ускорителем и частичная замена цемента типа I/II или типа III типом IP. цемент.Свежий, ранний возраст, механические характеристики, долговечность и технологичность оценивались для каждой из разработанных смесей. Также оценивались характеристики разработанных смесей при низкой температуре окружающей среды (50 и 60°F). В целом представляется, что при оптимизированной градации заполнителя смеси с пониженным содержанием цемента до 100 фунтов/ярд3 в совокупности обладают хорошей технологичностью и могут соответствовать общим требованиям, что было подтверждено оценкой ключевых параметров, включая прочность на сжатие в раннем возрасте. , модуль разрыва, прочность сцепления, удельное поверхностное сопротивление, усадка при высыхании и удельное сопротивление щелочно-кремнеземной реакции (ASR).Ускоритель, не основанный на хлоридах, показал многообещающее поведение в качестве альтернативного ускорителя. Разработанные смеси обладают удовлетворительными показателями прочности при сжатии в раннем возрасте и через 28 суток, модуля разрыва и прочности сцепления. Свободная усадка может быть уменьшена до 30% при более низком содержании цемента. Тенденцию к ухудшению ASR можно значительно уменьшить, заменив 50% цемента типа III цементом типа IP. Наконец, как и ожидалось, при низкой температуре окружающей среды рост прочности может быть задержан, и использование смесей PR3 будет более жизнеспособным вариантом для сокращения продолжительности закрытия движения. Ускоритель схватывания бетона | Набор ускоряющих добавокТРЕБОВАНИЕ: Высокая ранняя прочность, для раннего снятия опалубки, раннего использования бетонных конструкций и т. д. Также для больших заливок бетона полы, чтобы отделка следовала за укладкой.ПРОДУКТ ДЛЯ ИСПОЛЬЗОВАНИЯ: RAPIDARDКАК ОПРЕДЕЛИТЬ: Все бетоны (указать разделы) должны содержать высокораннюю добавку «Рапидард» из расчета от 3/4 до 2 литров на мешок цемента. ЭФФЕКТЫ: Обеспечивает нормальную прочность бетона за меньшее время следующим образом: (только приблизительные результаты – марки цемента несколько различаются)
Рапидард содержит специальные компоненты высокой ранней прочности, плюс хлористый кальций, плюс антикоррозийные факторы. Rapidard значительно увеличивает удобоукладываемость, и смесь может быть скорректирована, чтобы воспользоваться этим преимуществом, уменьшив содержание воды примерно на 1.5 литров на каждый использованный литр Rapidard. ВРЕМЯ НАСТРОЙКИ: Rapidard оказывает лишь ограниченное влияние на начальное время схватывания, поскольку рассчитан на достаточное время для работы и укладки, но при этом ускоряет набор прочности после схватывания. При 1 л/пакет, время схватывания уменьшится примерно на 30% при 2 литрах, примерно на 50%. При необходимости это можно исправить с помощью PLASTET No.2 для замедления набора. При использовании вместо воды Rapidard вызывает образование свежего чистого цемента. затвердеть за считанные минуты. ГДЕ РЕКОМЕНДУЕТСЯ: Бетон, который очень быстро обнажается после укладки.
ПРИМЕЧАНИЕ: Не рекомендуется для предварительно напряженного бетона или железобетона, подверженного воздействию влаги. |