Бетон из ПГС: что это такое, для чего используют и как изготовить самостоятельно. Смесь песчано бетонная
Пропорции бетонной смеси
Чтобы приготовить бетонную смесь важно знать ее пропорции. Соотношение основных компонентов бетона – цемента, песка, щебня и воды определяют его вид и целевое использование. По сути, бетон — это цемент с несколькими наполнителями. Основными наполнителями являются песок и щебень, реже – гравий, керамзит, скол камня. Иногда в состав смеси вводят пластификатор – специальную добавку.
Какой цемент выбрать
Для бетона важно подобрать соответствующий вид цемента. Цемент выбирают исходя из требований к бетону по морозостойкости, прочности, стойкости к воздействию химических веществ, водопроницаемости. Нужно учитывать особенности конструкции и способы изготовления железобетонных конструкций. Выбор марки цемента в зависимости от требуемой марки бетона по прочности на сжатие:Марка бетона | Марка цемента |
100 | 300 |
150 | 300 |
200 | 400 |
250 | 400-500 |
300 | 500 |
400 | 400-600 |
500 | 600 |
600 | 600 |
Например, используя наиболее распространенный цемент марки М-400, получают бетон марки М-250.
От качества и количества используемого песка и щебня в составе бетона зависит марка нужного цемента.
Для получения хорошего результата целесообразно брать для бетона наполнитель разной величины. Большое количество пустот увеличит расход цемента, и соответственно, денежные траты, так как цемент-самый дорогой компонент бетонной смеси. Разные по величине наполнители позволят уменьшить количество пустот.
По толщине бетонное покрытие для фундамента при укладке вручную должно быть в 3 раза превышать размер наполнителя максимального размера. Для расчета объема пустот нужно заполнить 10 литровое ведро наполнителем и налить туда воду до краев. Если расход воды составит 3,5 л, то 35% общего объема осталось для заполнения пустот цементом.
Какой щебень пригодится
Известняк имеет среднюю прочность, но низкую устойчивость к морозам. Получаемые виды бетона – до М-350.
- Щебень — прочность 800-1000, получаемые виды бетона – до М-450. Достаточно прочности и морозостойкости для частного строительства.
- Гранит — прочность 1000-1400, получаемые виды бетона – от М-450 и выше. Наиболее прочный, морозостойкий, для строительства дорог.
Зачем нужны добавки В бетон иногда добавляют различные добавки, но перед этим нужно определиться с тем, какие показатели они будут улучшать. В основном они нужны для того, чтобы сделать бетон более пластичным и удобным в укладке. Есть добавки, которые повышают прочность бетонного покрытия и регулируют степень адгезии и схватывания смеси, те, которые повышают морозостойкость и уменьшают влагопоглощение. При использовании добавок внимательно читайте инструкцию по применению. Количество требуемой воды при использовании специальных добавок уменьшается. Воду добавляйте небольшими порциями. Некоторые пластификаторы несовместимы с другими.Стандартные пропорции бетонной смеси
Непосредственный выбор пропорций
Выбирать пропорции бетонной смеси нужно проанализировав несколько моментов:
- Как будет укладываться бетонная смесь. Если вручную, то она должна быть пластичной. При механизированном способе укладки требуется смесь большей плотности. Добавляя воду, не забывайте добавлять цемент. Пластичность определяется не количеством воды, излишнее ее количество приведет к потере прочности конструкции, что при воздействии нагрузок или неблагоприятных условиях может привести к разрушению. Это особенно критично при возведении фундамента.
- ля чего она будет использоваться
- Компоненты какого качества будут входить в ее состав.
Как такового универсального рецепта для приготовления различных марок бетона нет. Из-за того, что компоненты разные по качеству можно лишь ориентировочно указать пропорции бетонной смеси разных марок.Некоторым стандартной пропорцией бетонной смеси есть соотношение 3:1 или 4:1 песка к цементу – в зависимости от качества наполнителей и целевого назначения бетона, нужное соотношение определяется опытным путем. От правильного соотношения воды и цемента напрямую зависит прочность бетона.
Обычную бетонную смесь разводят в таком соотношении: 1:2:4:1/2 цемент, песок, щебень, вода соответственно.
Например, для получения 1 м3 бетона понадобится:
- 330 кг цемента
- 180 л воды
- 1250 кг щебня
- 600 кг песка
Указанное количество воды может незначительно меняться. Жесткой воды добавляют меньше указанного количества, мягкой — больше. Цемент без наполнителей затвердевает, но не имеет необходимой прочности из-за трещин и дает большую усадку. Кроме того, наполнители еще уменьшают себестоимость бетона, так как по сравнению с песком и щебнем цена на цемент больше. Песок лучше брать крупный чистый речной без глины.
1)
- Цемент М-400 — 492 кг
- Вода — 205 л
- ПГС (песчано-гравийная смесь)- 661 кг
- Щебень- 1000 кг
2)
- Цемент М-300 — 384 кг
- Вода — 205 л
- ПГС (песчано-гравийная смесь)- 698 кг
- Щебень- 1055 кг
3)
- Цемент М-200 — 287 кг
- Вода — 185 л
- ПГС (песчано-гравийная смесь)- 751 кг
- Щебень- 1135 кг
4)
- Цемент М-100 — 206 кг,
- Вода — 185 л
- ПГС (песчано-гравийная смесь)- 780 кг
- Щебень- 1177 кг
При изготовлении бетонного раствора в домашних условиях составляющие бетона удобнее отмерять литрами или ведрами, а не килограммами. Полезно знать, что в мешке 50 кг находится 38 л цемента.
Если работу нужно выполнить срочно и времени на эксперименты нет, купите готовую сухую смесь
sevparitet.ru
: Гидроизоляция. Материалы и технологии :: BlogStroiki Default Default :: BlogStroiki
Бетоном называется искусственный камень, получаемый в результате твердения рационально подобранной смеси, состоящей из вяжущего вещества, воды и заполнителей: песка и щебня или гравия. Смесь этих материалов до затвердевания называется бетонной смесью.
Зерна песка и щебня составляют каменный остов в бетоне. Цементное тесто, образующееся после затворения бетонной смеси водой, обволакивает зерна песка и щебня, заполняет промежутки между ними и играет вначале роль смазки заполнителей, придающей подвижность (текучесть) бетонной смеси, а впоследствии, затвердевая, связывает зерна заполнителей.
Изготовленные из бетонной смеси камни должны иметь необходимую прочность. Этот параметр зависит от количества введенного в смесь вяжущего и соотношения между собой мелкой и крупной фракции заполнителя. Поэтому для получения необходимой прочности изделий смесь должна содержать вполне определенное количество вяжущего. Так, например, при изготовлении стеновых камней количество цемента марки 400 обычно составляет 200-230 кг/м 3 смеси, и производитель не может в широких пределах влиять на смесь, меняя содержание вяжущего. В его распоряжении остается только подбор правильного соотношения мелкой и крупной фракции заполнителя и количества воды.
Следует отметить, чем крупнее заполнитель, тем выше прочность изделия, поскольку крупный заполнитель образует внутри изделия жесткий пространственный скелет, который воспринимает основные эксплуатационные нагрузки изделия. Крупный заполнитель повышает прочность изделия на сжатие, увеличивает его долговечность, уменьшает ползучесть, усадку и расход цемента. Однако все эти положительные свойства крупного заполнителя могут проявиться только в том случае, если в смеси присутствует достаточное количество мелких частиц, роль которых заключается в заполнении пространства между крупными зернами и исключении их взаимного сдвига при сжатии изделия.
Однако следует учитывать, что избыток в смеси очень мелких частиц или пыли приводит к потере прочности изделия и к увеличению его себестоимости за счет вынужденного увеличения количества вяжущего (до 20-40%), необходимого для достижения заданной прочности изделий. Необходимость в увеличении содержания вяжущего объясняется следующим. Для получения прочного бетона вяжущее должно покрыть тонким слоем каждую частицу заполнителя. В процессе схватывания бетона покрытые вяжущим частицы срастаются друг с другом и образуют прочное монолитное изделие. Если количество мелкой фракции превышено или в ее составе много пыли, то общая площадь частиц заполнителя становится очень большой, поэтому обычной дозы цемента не хватает на обволакивание всех частиц заполнителя. В бетоне появляются участки, не содержащие цемента, поэтому прочность изделия снижается.
Однако при толщине слоя от 30 до50 ммжелательно использовать армирующую сетку с размером ячеек 100х100 мм. Это, как говорилось выше, связано с потерей прочности бетона при мелком заполнителе.
Таким образом, прочность и долговечность монолитных бетонных конструкций напрямую зависят не только от качества применяемых материалов, способа уплотнения бетонной смеси и условий выдерживания бетона, но, главным образом, и от рационального подбора состава бетонной смеси, то есть дозировки материалов на замес бетономешалки.
Добавлено: 23.05.2012 13:51
Смесь цементно бетонная
Бетонная смесь: характеристики основных компонентов и ключевые свойства
Из чего состоит бетонная смесь, знает, наверное, каждый: берем цемент, гравий, песок, замешиваем все с водой до однородной консистенции и заливаем в форму. Однако, как и в большинстве случаев, просто все только на первый взгляд. На самом деле в процессе приготовления раствора есть множество нюансов, потому соотношение основных компонентов зависит как от применяемых веществ, так и от назначения бетона.
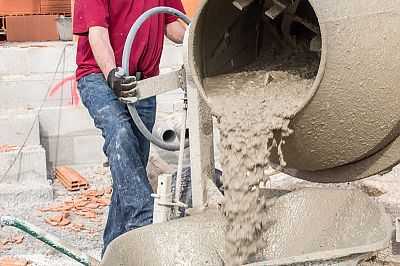
У процесса приготовления смеси есть множество нюансов
Типы составов
По назначению
Пропорции бетонной смеси не являются постоянными: в зависимости от того, что будет использоваться в качестве связующего и наполнителя, а также в каких условиях будет эксплуатироваться конструкция, они могут изменяться. Ниже мы рассмотрим классификацию бетонов по ряду параметров.
В зависимости от назначения составы делятся на такие группы:
- Обычные растворы. Применяются для формирования строительных блоков, а также для заливки монолитных конструкций. В большинстве случаев не содержат дополнительных компонентов за исключением модификаторов, улучшающих естественные свойства материала.
- Ячеистые материалы. Бетонная смесь для такого раствора обычно включает в себя порообразующий состав, который в процессе реакции с компонентами выделяет газ. Этот газ в виде мелких пузырьков распространяется в толще залитого бетона, обеспечивая повышение его эксплуатационных показателей.
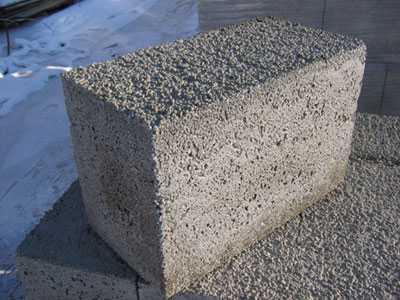
Пористые материалы достаточной плотности могут выступать и в качестве несущих конструкций
Обратите внимание! Часто в эту группу материалов относят растворы с теплоизоляционными наполнителями, такие как полистиролбетон, керамзитобетон, арболит. В зависимости от плотности данные композиты могут применяться как для возведения несущих конструкций с низкой теплопроводностью, так и для утепления уже построенных стен.
- Гидротехнические бетоны. Отличаются минимальной водопроницаемостью, длительное время не разрушаются при контакте с водой. Обычно применяются для облицовки плотин, мостовых ферм и т.д., но могут использоваться и в быту – например, для обустройства колодцев.
- Специальные составы. Предназначены для эксплуатации в экстремальных условиях. Включают в себя компоненты, способные длительное время противостоять эксплуатационным нагрузкам. Выделяют огнестойкие (цементно — бетонная смесь содержит глинозем, шлаки, бой шамотного кирпича), кислотостойкие, противорадиационные материалы и т.д.
- Отдельно стоит выделить вспомогательные растворы, к которым относится, например, пусковая смесь для бетононасоса. Этот состав готовится практически так же, как строительный цемент, но воды мы добавляем куда больше (около 150 литров на 2 мешка цемента). Жидкое «бетонное молоко» смачивает трубопроводы и предотвращает образование пробок.

Без пусковой смеси начать работу такой системы практически невозможно
- Наконец, отдельную группу составляют ремонтные составы. К ним относят текучие смеси (применяются для восстановления горизонтальных поверхностей) и тиксотропные материалы с малой усадкой (используются для устранения дефектов на вертикальных стенах). Главным достоинством этих средств является эффективная адгезия с уже полимеризованным бетоном.
По основному веществу
Вне зависимости от того, где будет применяться состав, он должен быть изготовлен на основе связующего – вещества, которое обеспечивает превращение смеси в монолит.
По этому параметру выделяются такие категории материалов:
- Состав на цементном связующем. Самая простая бетонная смесь по ГОСТу производится на основе портландцемента различной прочности. Также для строительства используется пуццолановый цемент и шлакопортландцемент. Данная разновидность является наиболее распространенной, и потому ниже мы будем ориентироваться в основном на ее характеристики.
Обратите внимание! К этой же категории относятся ремонтные составы с безусадочным цементом, а также огнеупорные смеси с высоким содержанием глинозема.
- Гипсовый раствор тоже включают в группу бетонов. Этот материал применяется для отделки потолков и возведения перегородок. Сочетание гипса с пуццолановым цементом обеспечивает высокий уровень водостойкости, потому такие смеси используются при ремонте санузлов.
- Шлакощелочной раствор. Производится путем воздействия щелочей на тонко размолотые шлаки. Используется при заливке фундаментов, производстве строительных блоков, возведении монолитных конструкций. Реакции, проходящие в растворе, позволяют эффективно связывать даже некачественные заполнители с высоким содержанием глинистой и пылеватой фракции.
- Полимер-цементные комплексы. Обычно содержат портландцемент в смеси с латексом, полиуретаном или эпоксидной смолой. После полимеризации на поверхности материала формируется пленка, закрывающая поры и предотвращающая проникновение влаги в толщу материала. Полимер-цемент используется при отделке полов, стен, садовых дорожек и т.д. Ключевой недостаток – достаточно высокая цена.
Наполнители
К параметрам, которыми характеризуется бетонная смесь, можно также отнести состав наполнителя. Без этого компонента в нашем распоряжении будет только цементно-песчаный раствор, который и стоит дороже, и по прочности уступает полноценному бетону.
В качестве наполнителя мы используем:
- Известняк. Дешев и прост в обработке, однако обладает сравнительно малой прочностью (до 600). В принципе, может применяться для приготовления фундаментных составов, однако низкая морозостойкость ограничивает географию использования.
Обратите внимание! Дробленый известняк обычно берется в качестве наполнителя для цемента не прочнее М300.
- Гравий (прочность 800-1000). Доступен, относительно д
vest-beton.ru
О ПЕСЧАНОМ БЕТОНЕ
технология ТИСЭ
Каждого, кто знакомился с технологией ТИСЭ, интересовал состав смеси, прочность стеновых блоков, какими теплоизолирующими характеристиками они обладают. Очень многих одолевали сомнения: неужели на такой простой оснастке и своими руками так легко можно отформовать блок, выдерживающий более 100 тонн, и который обладает высокой степенью морозостойкости.
Да, это так, что было подтверждено и теорией строительных материалов, и испытаниями, и немалым опытом строительства.
На начальных этапах освоения технологии ТИСЭ в качестве бетонного раствора предлагалось использовать смесь цемента и песка (1 : 3) с небольшим содержанием воды (жесткая смесь).
Идея использования такой смеси для формования стеновых блоков пришла автору при просмотре одной из книг по строительной технологии.
«Материаловедение для каменщиков, монтажников конструкций», К. Н. Попов, М., Высшая школа. 1991г.
«…Марку цемента определяют по прочности на изгиб и сжатие образцов — балочек, изготовленных из цементно — песчаного раствора с весовым соотношением 1 : 3, и твердевших в нормальных условиях 28 суток при температуре (20()С).
Для изготовления трех образцов отвешивают 500 г портландцемента и 1500 г стандартного песка (модуль крупности Мк=2,5…2,7). Смесь перемешивают и заливают 200 г воды (В/Ц=0,4) Тщательно перемешивают до получения однородной массы.
Приготовляемая растворная смесь не является кладочным или штукатурным раствором, а представляет собой как бы модель бетона, поэтому она значительно менее пластична, чем традиционная растворная смесь, которой пользуются каменщики и штукатуры. Создается жесткая смесь.
Теоретически, для твердения цемента, для протекания процесса его гидратации, требуется В/Ц = 0,2….0,25, но расход во-
А — испытание на изгиб; б — испытание на сжатие; 1 — половинка образца; 2 — плиты пресса; 3 — металлические накладки |
Ды увеличивают для повышения удобоукладываемости раствора.
Смесь закладывают в разъемную металлическую форму, предназначенную для формования трех образцов размерами 40 х 40 х 160 мм. Смесь уплотняется либо вибрацией на вибростоле в течение 3 минут, либо — послойным штыкованием (ручная трамбовка).
Прочность образцов — балочек определяют, испытывая их сначала на изгиб (рис. 6.9, а), а образовавшиеся половинки — на сжатие (рис. 6.9, б).
Предел прочности на сжатие Исж для образца вычисляют по формуле Исж = Р / F, где
Р — разрушающая нагрузка (кГ), F — площадь металлических накладок (см2).
. Предел прочности на сжатие цемента вычисляют по результатам шести испытаний, как среднее арифметическое четырех результатов (наибольший и наименьший не учитывают…)».
Величина Исж в (кГ/см2) и будет соответствовать марке цемента. Так цемент, образцы которого разрушились при давлении 400 кГ/см2, будет иметь марку 400.
Именно такой процесс формования смеси песка и цемента было решено использовать при изготовлении стеновых блоков. Такой подход позволил получить для стеновых блоков
Максимально возможные прочностные характеристики, которые можно создать с данным цементом.
Например, если площадь опоры стенового блока ТИСЭ-2 — около 600 см2, то при марке цемента 400, этот блок должен выдержать на сжатие около 240 т. Правда есть такой параметр, который показывает различие между результатами испытания образцов и уровнем предельных напряжений в реальных изделиях, изготовленных из тех же материалов и по той же технологии, что и образцы. Этот параметр зависит от геометрии изделия: чем меньше относительная толщина стенок реальной конструкции, тем меньше этот коэффициент. В среднем, проч-. ность изделий уменьшается в 0,4…0,6 раз по отношению к прочности образцов.
Таким образом, вполне реально, чтобы наш стеновой блок смог выдержать на сжатие около 120 тонн. Если стеновой блок, отформованный с модулем ТИСЭ, подвержен длительной эксплуатации в условиях замораживания и оттаивания (блоки, расположенные во влажном грунте), то его реальная прочность снижается ещё вдвое. Это — около 60 тонн.
Если стеновые блоки не находятся в грунте, не намокают, защищены от попадания влаги или они находятся под слоем теплозащиты и не подвержены замораживанию — оттаиванию, то их расчетная прочность сохраняется на уровне 120 тонн.
Тем не менее, и 60 тонн — достаточно высокая величина. Один пустотный стеновой блок, отформованный с модулем ТИСЭ-2, может выдержать вес небольшого каменного дома с бетонными перекрытиями (рис. 6.10).
При дальнейшем изучении материалов, касающихся разработанной технологии, автор получил много подтверждений выбранной позиции.
«Бетонныеработы», А. А. Афанасьев., М., Высшая школа., 1991г.
«..Жесткие бетоны при хорошем уплотнении обладают большей прочностью, чем подвижные, при одном и том же расходе цемента. Применение жестких бетонов позволяет экономить 10…20% цемента…».
«..Жесткая смесь имеет наименьшее водоцементное соот-
\ t / Рис. 6.10, Один стеновой блок, отформованный на модуле ТИСЭ-2, может выдержать вес среднего дома |
Ношение (В/Ц)…… Морозостойкость повышается при снижении В/Ц… В настоящее время созданы бетоны с морозостойкостью 600…800 циклов, например, бетоны на мелкозернистых заполнителях — песках.».
«…Особо жесткие смеси используют при изготовлении изделий по технологии, предусматривающей их немедленную распалубку…. Для повышения морозостойкости конструкций и увеличения их механических характеристик в дорожном строительстве применяют бетоны повышенной жесткости…».
«… Для уплотнения жестких бетонных смесей при устройстве покрытий небольшой толщины используется трамбование. Применяют пневматические или ручные трамбовки. Смеси уплотняют слоями толщиной 10…15 см».
Стройинформ., 2001г., «Песчаный бетон:родина — Россия», К. Львович, проф., НИИЖБ.
«… Известный уже более века песчаный бетон стал предметом систематических исследований с середины пятидесятых годов, что было связано, в первую очередь, с организацией производства железобетона в ‘регионах, где отсутствуют месторождения крупного заполнителя…».
«…Песчаный бетон, как правило, обладает высокими физико — механическими характеристиками по сравнению с бетоном на крупном заполнителе… «.
«…Бортовые камни из песчаного бетона, находившиеся 25 лет в эксплуатации, не имели следов разрушения, в то время, как бортовые камни из тяжелого крупнозернистого бетона, изготавливаемые по традиционной технологии, разрушились через 2-3 года от размораживания».
. «Песок — единственный заполнитель в песчаном бетоне, наиболее дешевый и повсеместно распространенный строительный материал, стоимость которого в России в 2 — 3 раза ниже стоимости щебня ив 6 — 8 раз — керамзитового гравия…».
Высокие показатели блоков, отформованных по технологии ТИСЭ, были подтверждены комплексными испытаниями в КТБ Мосоргстройматериалы, проведенными в начале 1995 г. Блоки, отформованные с опалубкой ТИСЭ-2 с использованием цемента марки 400, выдержали больше 100 т. При испытании на морозостойкость после 50 циклов их прочность снизилась на 10% (по СНиП допускается — 25%).
Применение жесткой пескобетонной смеси в индивидуальном строительстве пока не столь распространено. Для многих начинающих и даже профессиональных строителей это в новинку. Поэтому на составе применяемых жестких смесей придется остановиться более подробно.’
Для правильного подбора состава пескобетонной смеси и ухода за созревающим бетоном, необходимо знать как характеристики самих составляющих смеси, так и технологические особенности создания пескобетона.
Немент
Портландцемент — гидравлическое вяжущее, получаемое тонким измельчением портландцементного клинкера и небольшого количества гипса (1,5…3%).
Соотношение компонентов сырьевой смеси, необходимой для создания цемента, выбирают с тем расчетом, чтобы полученный при обжиге портландцементный клинкер имел следующий химический состав (%): СаО — 62…68, Si02 — 18…26, АІ203 — 4…9, Fe203 — 2…6. Для получения клинкера чаще всего используют известняк и глину (добываемые отдельно) в соотношении 3 :1 (по весу). Приготовленную смесь подают на обжиг во вращающуюся печь, где при температуре 1200..,1450°С происходит обжиг — образование цементного клинкера — твердых кусков размером в горошину или орех серого цвета. В шаровых мельницах куски клинкера тонко размалываются с гипсом и другими добавками (тонкость помола — менее 0,08 мм).
Обращаем внимание некоторых индивидуальных застройщиков, которые очень ревностно относятся к экологии жилья, что эти природные минеральные составляющие цемента — экологически нейтральны. Низкий уровень экологической безопасности бетонных домов — в гранитном щебне и малой воздухопроницаемости стен.
Свойства портландцемента зависят от его минерального состава и тонкости помола. Чем тоньше помол, тем цемент быстрее твердеет.
Насыпная плотность цемента — 1100 …1200 кг/м3, в уплотненном состоянии — до 1700 кг/м3.
Твердение цемента — химический процесс, который происходит при взаимодействии его с водой, сопровождающийся выделением тепла. Частицы цемента начинают растворяться, причем одновременно происходят гидролиз (разложение отдельных минералов водой) и гидратация (присоединение воды), образуется цементное тесто, из которого позднее выпадают твердые кристаллы высокой прочности.
Процесс твердения портландцемента — достаточно длительный процесс (месяцы и годы). Но с течением времени скорость нарастания прочности замедляется. Поэтому качество цемента принято оценивать по прочности, набираемой им в первые 28 суток твердения.
Срок схватывания — одна из основных характеристик твердения цемента. Он рассчитывается от момента затворения {соединение с водой). Начало схватывания должно быть не ранее чем через 45 минут, а конец — не позднее 10 часов. Такие сроки дают возможность транспортировать и укладывать бетонные смеси до начала схватывания. Эти показатели определяют при температуре 20° С. Если цемент затворяют горячей водой (более 40″ С), то может произойти очень быстрое схватывание.
При твердении бетона в естественных условиях 50% прочности достигается через 2-7 суток. Эти сроки значительно удлиняются при пониженных температурах. При повышении температуры до 80° С сроки созревания бетона сокращаются в 8 — 10 раз.
На производствах ЖБИ для ускорения набора прочности бетонными изделиями применяют пропарочные камеры, где бетонные изделия набирают прочность, достаточную для транспортировки изделий, за 5 — 10 часов.
Работая по технологии ТИСЭ, надо учитывать, что приготовленная смесь должна быть израсходована до начала момента схватывания (за 20 — 30 мин).
Противоморозные добавки
При температуре + 5° С бетонные смеси резко снижают скорость набора прочности. При температуре ниже 0° С химически несвязанная вода превращается в лед и увеличивается в объеме на 9%. В результате в бетоне возникают напряжения, разрушающие его структуру.
При оттаивании процесс гидратации цемента возобновляется, но из — за разрушенной структуры бетон не может набрать проектной прочности.
Экспериментами установлено, что если бетон до замерзания наберет 30 — 50% от проектной прочности, то дальнейшее воздействие низких температур не влияет на его физико — механические характеристики.
При внесении химических добавок процесс твердения бетона будет протекать и при температурах ниже 0°С, но несколько замедленно (это свойство используется при бетонировании столбов в условиях вечной мерзлоты). Скорость набора прочности бетоном зависит от температуры и химическо-
Табл. 6.1. Скорость набора прочности бетона с протнвоморознымн добавками % от R
|
Го состава противоморозных добавок. |
Если противоморозные добавки действуют до температуры — 15°С, то можно принять следующие параметры скорости набора прочности бетоном (табл. 6.4).
Добавки водят в видр, водных растворов в процесс приготовления бетонных смесей в количестве 2…10% от массы цемента.
В качестве противоморозной добавки может быть использована обычная пищевая соль, смесь её и хлорида кальция:
— 5% водный раствор пищевой соли (на 40л воды — 1 кг соли) замерзает при — 5°С;
— раствор 6% пищевой соли и 9% хлорид кальция (ХК) (на 100 литров воды — 2,5 кг соли и 4 кг хлорид кальция) замерзает при — 15°С.
В качестве противоморозных добавок применяют и другие соли: нитрит натрия (НН), нитрат кальция (НК), нитрит — нитрат кальция (ННК), поташ (П) и их соединения. Соли вводят в бетонную смесь только в виде водных растворов.
В настоящее время на рынке строительных материалов появилось достаточно много весьма эффективных отечественных противоморозных добавок в жидком и в сухом виде.
Заполнитель песчаного бетона — песок
Заполнители занимают в бетоне до 80% объема и существенно влияют на его прочность, долговечность и стоимость. В технологии ТИСЭ для формования стеновых блоков основной заполнитель — песок, но не любой.
Немедленная распалубка требует повышенной жесткости для раствора. Пластичные растворы, включающие мелкие
Фракции песка, — не подходят для этой цели. Мелкие и пыле — ватые пески идут только на штукатурку и на кладочный раствор, но не для формования стеновых блоков с немедленной распалубкой.
В случае, когда нет песка с крупной или средней фракцией, приходится брать мелкий песок. Бетонная смесь с таким песком требует очень тщательной дозировки воды. При незначительном избытке влаги, формуемые блоки после распалубки «плывут» (рис. 6.11). Именно в этом и состоит ограничение по выбору подходящего песка.
Основная цель заполнителя — образовать скелет, основу для сохранения формы после распалубки. Смесь мелкого песка с цементом и водой больше напоминает сметану, а смесь цемента с крупным песком — влажный грунт.
Мелкий песок не может создать достаточно жесткую пространственную структуру (рис. 6.12, а). Смесь крупного и мелкого песка — идеальный заполнитель для этой цели (рис. 6.12, б).
Б
Рис. 6.12. Структура песчаного бетона: а — мелкий песок; б — крупнозернистый песок |
Наилучший вариант, если песок представляет собой рыхлую смесь зерен, когда крупность зерен колеблется от 0,14 До 5мм. Количество мелких зерен, проходящих через сито 0,16мм в песчаных бетонах не должно быть более 10%.
Чем больше в песке мелких зерен, тем больше его удельная поверхность и тогда для соединения зерен песка в растворе или бетоне потребуется больше цемента.
По зерново, му составу пески подразделяются на группы, приведенные ниже (ГОСТ 8736 — 85) — табл. 6.2.
Водопотребностпъ песка — наибольшее количество воды, которое может быть принято сухим песком в весовом отношении.
Как видно из таблицы мелкий песок может принять влаги в 2 раза больше, чем крупный песок, благодаря большей поверхности смачивания зерен.
Для составления смеси важным параметром является плотность песка. Она изменяется с изменением его влажности своеобразным образом:
— совсем сухой песок имеет насыпную плотность 1500кг/м3;
— при влажности 5% она уменьшается до — 1300 кг/м3;
— при влажности 15% и более она увеличивается до 1900кг/м1
Именно поэтому, когда требуется уплотнить песок, его проливают водой.
Табл. 6.2. Зерновой состав песков различных групп
|
Используя песок, лежащий под открытым небом, в процессе приготовления цементной смеси необходимо учитывать как повышение его плотности от дождей, так и наличие самой влаги.
При указании состава смеси всегда подразумевают весовое соотношение сухого песка и цемента. Если же дозирование — объемное, то изменение плотности песка от степени его влажности — обязательно следует учитывать.
Пески делятся на природные, образовавшиеся в результате выветривания горных пород, и искусственные, получаемые в результате дробления твердых горных пород.
Горные (овражные) пески образуются в результате выверивания горных пород и последующего переноса продуктов выветривания ветром и ледниками. Угловатая форма и шероховатость поверхности зерен способствуют хорошему сцеплению их с вяжущим. Недостаток таких песков — загрязненность глиной и примесями.
Речные и морские пески более чистые, но их зерна, как правило, округлой формы в результате длительного воздействия движущейся воды. Наиболее вредная примесь в песке — глина, так как она препятствует сцеплению составляющих самой смеси.
Искусственные пески, используемые значительно реже, бывают тяжелые и легкие. Тяжелые пески получаются дроблением плотных горных пород (базальт, диабаз, мрамор, гранит). Легкие пески получают дроблением пористый пород (пемза, туф) или изготавливают специально (перлитовый и керамзитовый песок).
Присутствие в песке пылеватых и глинистых включений снижает прочность и морозостойкость бетона. В природном песке пылеватых и глинистых включений не должно быть больше 3% по массе, причем содержание собственно глины не должно превышать 0,5%.
Избавиться от загрязнений песка можно только его промывкой. Для этого песок помещают в деревянный ящик или металлическую ёмкость (бочку) и промывают его п
msd.com.ua
Песчано-бетонная смесь должна готовиться правильно
26.11.2013
Звоните!
+7 (961) 018-50-00
+7 (903) 630-01-02
+7 (4822) 57-77-48
Песчано-бетонная смесь обычно используется для устройства железобетонных конструкций, фундаментов и изготовления блоков. Для приготовления бетонной смеси, которая пойдет на устройство фундамента, берут щебень либо гравий, цемент воду и песок. Конечно, вяжущим компонентом выступает цемент, кстати, самым распространенным на сегодняшний день является портландцемент, его производители выпускают нескольких марок. Например, цемент марки 300 и 400 используют при замесе песчано-бетонной смеси для возведения небольших одноэтажных строений, а также для изготовления кладочных растворов и железобетонных конструкций.
Между прочим, замешанную смесь необходимо выработать в течение одного-двух часов, в противном случае раствор схватиться и его придется просто выбросить, а это — перерасход. Что касается цемента марки 500 и 600, то они обладают высокой прочностью и схватываются быстро, что крайне неудобно при строительстве небольших конструкций. Песчано-бетонная смесь, замешанная на цементе меньших марок, схватывается медленнее, чем смесь замешанная на более крупных, зато для строительства маленьких домов она прекрасно подходит, однако, в зимний период ее для бетонирования применять нежелательно.
На прочность песчано-бетонной смеси влияет не только цементный раствор, но и его заполнитель, то есть, качество песчано-щебеночной либо песчано-гравийной смеси. Гравий величиной до 80 мм применяется при замесе обычного раствора бетона, а для железобетона применяются зерна до 30 мм. Для изготовления фундамента в бетон кладут большие крепкие камни, что позволяет сэкономить бетонную смесь. Кроме того, песчано-бетонная смесь высокого качества получается только при использовании чистого песка. Для того чтобы определить наличие грязи и примеси в песке, нужно его засыпать в бутыль с чистой водой и хорошо потрясти, чтобы смесь тщательно перемешалась, после чего оставить на 24 часа. Если через данное время вода будет слегка мутная или чистая, то песок пригоден для песчано-бетонной смеси, а если на поверхности песка есть слой грязи, то от такого песка лучше отказаться.
Знайте, что бумажные мешки с цементом, не важно какого производителя и марки, при хранении необходимо складывать в сухом и закрытом помещении. Хранить его долго не стоит, потому как он способен впитывать влагу из воздуха и превращаться в камень, поэтому при недолгом хранении оберните мешки тщательно в пленку или сложите в полихлорвиниловые мешки. При этом имейте ввиду, если цемент хранится один месяц, то он теряет 10 процентов прочности, если в течение трех месяцев, то теряется 20 процентов, после 12 месяцев — 40, а после того как пройдет два года — он потеряет свои свойства на 50 процентов. Однако мастера используют в строительстве залежавшийся материал, если его комки легко рассыпаются. Конечно, какой строительный материал использовать при песчано-бетонной смеси решает заказчик, ведь он оплачивает строительство — соответственно и качество.
Песчано-бетонная смесь должна замешиваться на чистой воде, без содержания хлора и каких-либо агрессивных химических веществ, помимо того, если песчано-бетонную смесь готовят в летнее время, то в нее льют холодную воду, для того чтобы раствор не схватывался быстро. А в зимнее время лучше применять подогретую воду до 40 градусов, чтобы песчано-бетонная смесь схватилась прежде чем замерзнет. Вот такие хитрости специалисты используют в строительстве зданий, домов и других сооружений. Следует знать, что правильно замешанная песчано-бетонная смесь, сжатая в ладони, сохраняется в виде комка с остатком цементного молочка.
Смотрите также:
Все статьи
все новости
www.kgbi-6.ru
Приготовление бетонных смесей при производстве высокопрочных бетонов
Бетон является сложным композиционным материалом, потенциальные возможности которого до настоящего времени используются не в полном объеме. Производителей бетона и изделий на его основе прежде всего интересует проблема получения прочного бетона при минимальном расходе цемента, и для ее решения постоянно совершенствуются расчетно-экспериментальные методы подбора состава бетонной смеси, используются различные добавки, ускоряющие твердение цемента, суперпластификаторы, добавки микрокремнезема и многое другое. Вместе с тем сама технология изготовления бетона остается незыблемой и состоит из операций дозирования компонентов бетонной смеси, перемешивания их в бетоносмесителе и приготовления бетонной смеси, формования изделий и их тепловлажностной обработки.
Из всех этих операций наименее изученной является операция приготовления бетонной смеси, и на многих предприятиях ее осуществляют путем увлажнения и перемешивания смеси цемента, крупного и мелкого заполнителей в бетоносмесителях. Поэтому многие исследователи считают, что введение дополнительных операций предварительной обработки и подготовки таких компонентов бетонной смеси, как цемент и мелкий заполнитель перед окончательным перемешиванием позволит существенно повысить прочность бетона.
В научно-популярной литературе по бетоноведению изготовителями различных вихревых смесителей и измельчителей настойчиво пропагандируется идея по дополнительному помолу цемента с обязательством значительного увеличения марки бетона. Следует отметить, что такие утверждения базируются на весьма поверхностном понимании роли зернового состава цемента в бетоне, и предприятия, которые приобрели такие установки, убедились в бесперспективности их использования.
В патентной и технической литературе приводится большое количество новых способов приготовления бетонных смесей, которые можно разделить на две группы. К первой группе относятся способы, в которых предлагается изменять последовательность подачи компонентов смеси, добавок и воды в бетоносмеситель при его работе. Эти способы позволяют достичь повышения прочности бетона, но по сути они не отличаются от распространенного способа, а эффект повышения прочности достигается в основном за счет использования суперпластификаторов и других добавок. Ко второй группе относятся способы, включающие предварительно активацию цемента путем совместного помола его в шаровой мельнице с небольшим количеством сухого песка. Такие способы также не приводят к существенному увеличению прочности бетона, и повысить его эффективность можно только при совместном помоле всего расчетного количества песка и цемента. Однако при использовании в качестве помольного оборудования шаровых мельниц возникают проблемы сушки песка и увеличения энергозатрат на помол смеси.
Цель настоящего доклада — исследование способа приготовления бетонной смеси, по которому смешение компонентов осуществляется в следующей последовательности: сначала перемешиваются расчетные количества портландцемента и кварцевого песка с естественной влажностью 3–5 % в центробежном смесителе роторного типа в течение 1–2 мин, после чего полученная сыпучая цементно-песчаная смесь с конечной влажностью 5–8 % (дополнительное увлажнение) поступает в бетоносмеситель, в который подается крупный заполнитель и остальное количество воды для совместного перемешивания всех компонентов бетонной смеси расчетного состава в течение 3–4 мин.
Сущность этого способа заключается в том, что при поступлении цементно-песчаной смеси в смеситель формируются два взаимонаправленных потока смеси, движущихся в слое толщиной 10–20 см навстречу друг другу со скоростью 35–40 м/с, в котором частицы цемента и песка соударяются на скорости 70–80 м/с и измельчаются до более тонкого состояния. В составе цементно-песчаных смесей для рядовых бетонов соотношение между цементом (Ц) и песком (П) колеблется в пределах Ц : П = (26:74) ч (45:55) % (мас.) с преобладанием песка в смеси. Частицы кварцевого песка обладают более высокой твердостью, и поэтому при скоростном смешении цементно-песчаной смеси они выполняют роль абразивных мелющих тел.
Весьма важно, что при контактевлажного песка и цемента вода начинает интенсивно взаимодействовать с частицами цемента, образовывая в поверхностном слое цементных частиц первичные продукты гидратации — гидрооксид кальция, гидросиликаты и гидроалюминаты кальция. За счет этого взаимодействия происходят аморфизация и дополнительное диспергирование поверхностного слоя частиц цемента, который легко сдирается частицами песка и образует в цементно-песчаной смеси фракцию высокоактивных частиц нанодисперсного размера.
При интенсивном механическом воздействии на цементно-песчаную смесь происходит также удаление адсорбированного воздуха с поверхности частиц и замещение его пленкой воды толщиной в несколько молекул воды, особенно на свежеобразованных плоскостях разрушения частиц. На этих пленках происходит конденсация преимущественно нанодисперсных частиц продуктов гидратации цемента за счет адгезионного взаимодействия и достигается весьма равномерное распределение цемента и воды на поверхности частиц песка во всех микрообъемах цементно-песчаной смеси.
Проверку вышеизложенных подходов при приготовлении бетонной смеси проводили с использованием портландцемента Топкинского завода марки 500Д0 (ГОСТ 10178-85), гравия фракции 5–20 мм (ГОСТ 82690-97), песка для строительных работ с модулем крупности Мкр = 2,6 (ГОСТ 8736-93) и воды.
Компонентный состав бетона рассчитан на получение подвижной бетонной смеси с осадкой конуса ОК = 5–11 см и марки пескобетона 300.
Мелкий заполнитель с естественной влажностью 3,5 % (абс.) и портландцемент подавали в смеситель и перемешивали в течение 1 или 2 минут. В процессе перемешивания смесь дополнительно увлажнялась до 8 % с целью достижения наиболее полного смачивания всех частиц смеси пленкой воды. Увлажнение смеси более 8 % нежелательно, так как при этом уменьшается сыпучесть смеси и увеличивается ее налипание на рабочие органы смесителя.
Далее цементно-песчаная смесь подавалась в бетоносмеситель и перемешивалась с гравием и остаточным количеством воды в течение 3–5 мин до получения однородной бетонной смеси; из смеси формовали образцы-кубы размером 10Ч10Ч10 см, у которых определялась прочность при сжатии после пропариванияпо режиму 2 + 7 + 3 ч и после твердения в воздушно-влажных условиях в течение 28 суток.
Для объективности сравнения результатов готовилась бетонная смесь при одновременном смешении в бетоносмесителе всех компонентов, а также смесь с цементом, предварительно измельченным в присутствии 3 % кварцевого песка до удельной поверхности 4900 см2/г. Составы бетонных смесей и результаты испытаний, представленные в таблице, подтверждают целесообразность предварительного смешения влажного песка с цементом.
Интенсивное и концентрированное механическое воздействие на цементно-песчаную смесь, содержащую небольшое количество воды, сопровождается быстрым ростом температуры смеси до 45–50 °С
Таблица №1: Составы бетонных смесей и результаты испытаний бетона.
в течение одно– двухминутного перемешивания, что свидетельствует об интенсификации процессов гидратации цемента. Предварительное и равномерное распределение влаги в цементно-песчаной смеси увеличивает скорость смачивания и распространения оставшейся воды при перемешивании всех компонентов бетонной смеси и позволяет практически в два раза сократить время перемешивания в бетоносмесителе. Однородная, практически дегазированная цементно-песчаная смесь позволяет сформировать в процессе уплотнения плотную и прочную цементно-песчаную матрицу в составе бетона. Анализ поверхностей разрушения бетонных образцов показывает, что их разрушение происходит не только по цементно-песчаной матрице, но и по зернам крупного заполнителя. Использование более прочного заполнителя позволит увеличить прочность бетона. Из данных табл. 1 следует, что использование предварительного смешения влажного песка с цементом позволяет увеличить прочность рядового бетона на 59–77 % без применения каких-либо добавок.
Снижение расхода цемента на 15 % (состав 5) приводит к уменьшению прочности бетона, тем не менее она достаточно высока (44,3 МПа). Предварительное смешение цемента с песком позволит более эффективно использовать лежалые цементы.
Изготовление высокопрочных бетонов требует повышенного расхода цемента, который необходимо равномерно распределить в бетонной смеси. Предварительное смешение цемента с увлажненным песком позволяет наиболее эффективно решить эту проблему и приготовить пластичную однородную бетонную смесь без использования суперпластификаторов. Если же в состав бетонной смеси вводится суперпластификатор либо другие добавки в виде порошков или растворов солей, то все эти добавки лучше всего вводить при предварительном перемешивании песка и цемента.
Таким образом, предварительное смешение расчетных количеств цемента и песка с небольшой влажностью в интенсивном смесителе непосредственно перед приготовлением бетонной смеси открывает новые возможности в технологии бетонов, особенно высокопрочных.
См. далее по теме:
Применение пескобетона.
www.voscem.ru
Бетонная смесь – оптимальное соотношение песка и щебня. | Бетон и строительные технологии
Главная >> Производство бетонных работ >> бетонная смесь, песок щебень, соотношение песка и щебня в бетоне, коэффициент раздвижки зерен, соотношение песка и щебня
admin 06.09.2013
Уважаемые коллеги!
Пишу эту статью «Бетонная смесь – оптимальное соотношение песка и щебня» по многочисленным просьбам посетителей моего сайта. Те кто получил мою «Программу подбора состава бетона», у них нет в этом плане проблем, программа сама все считает при вводе исходных данных.
Обстоятельства бывают разные и иногда необходимо просто рассчитать соотношение песка и щебня в бетоне при производстве бетонной смеси. Должен сказать в этом вопросе и некоторые довольно опытные бетонщики допускают ошибки.
Вот об этом локальном но важном вопросе и поговорим.
[important] Это для Вас важно, скачайте файл +Файл со ссылками-Производство бетонных работ – «Производство бетонных работ» в нем активные ссылки на все мои статьи по этой тематике, их уже 20 и количество будет расти, сохраните где то у себя, будет удобнее пользоваться как пособием. [/important]
«А ларчик то открывается довольно просто», всего лишь надо вспомнить, метод абсолютных объемов и естественно не забыть применить коэффициент раздвижки зерен (об этом я Вам напомню и расскажу чуть ниже). Раньше мне это казалось сложной проблемой, а когда немного вник в теорию оказалось все довольно просто, недаром говорят «Все гениальное просто, но не все простое гениально», конечно ничего особенного гениального здесь нет, просто к слову пришлось.
Все буду рассказывать и делать расчет, на конкретных примерах, когда приготавливается бетонная смесь.
У нас есть песок щебень.
1 Определяем в заводской лаборатории следующие показатели (естественно все делаем по сухому веществу).
2 Истинная плотность щебня – Мист.щ = 2720,0 кг/куб
3 Насыпная плотность щебня – Мнас.щ = 1480,0 кг/куб
4 Истинная плотность песка – Мист.п = 1680,0 кг/куб
5 Насыпная плотность песка – Мнас.п = 1530,0 кг/куб
Все данные для расчетов у нас уже есть, кстати как определять эти показатели более просто можно почитать на моем сайте по этим ссылка, по щебню и по песку и на странице «Бетон пособие».
Двигаемся дальше. Вся «изюминка» определения оптимального соотношения П/Щ (песок щебень) заключается в том, что песок в насыпном состоянии должен заполнить пустоты между фракциями щебня, с учетом коэффициента раздвижки зерен щебня, только тогда бетонная смесь будет максимально уплотненной
3 Сначала определим пустотность щебня, он равен Пщ = 1-Мнас.щ/М ист.щ или Пщ=1-1480,0/2720,0=0,456, то есть проще говоря, если мы засыпем 1,0 куб щебня, межзерновые пустоты у него будут 0,456 куб, вот эту пустоту мы должны заполнить песком в насыпном виде.
[important] Но это очень важно, нужно учесть коэффициент раздвижки зерен щебня, кстати об этом более подробно можно узнать посмотрев мой 1 видео урок к «Программе подбора состава бетона» [/important]
Напомню, кто не знает, что такое Крз. – коэффициент раздвижки зерен щебня.
Этот показатель впервые ввел известный Советский ученый бетоновед Скрамтаев Б.Г., кстати более пдробно о нем можно прочесть на ресурсе Wikipedia по этой ссылке.
На фото показано: 1 — Цементно песчаная смесь, 2 — Частицы песка, 3 — Крупный заполнитель. Коэффициент раздвижки зерен щебня (Крз.) показывает избыток растворной части против необходимого ее количества для заполнения пустот в щебне или гравии. Его находят по таблицам в зависимости от объема цементного теста. Считается, что объем цементно песчаной смеси должен быть больше, чем необходимо для заполнения пустот между щебнем при расчете по методу абсолютных объемов.
Ниже привожу таблицы для определения Крз., в зависимости от расхода цемента и В/Ц (водоцементного отношения бетонной смеси).
Значение коэффициента раздвижки зерен Крз. – бетонная смесь подвижная.
Расход цемента, кг/м3 | Коэффициент Крз. при В/Ц | ||||
0,4 | 0,5 | 0,6 | 0,7 | 0,8 | |
250 | — | — | 1,26 | 1,32 | 1,38 |
300 | — | 1,30 | 1,36 | 1,42 | — |
350 | 1,32 | 1,38 | 1,44 | — | — |
400
| 1,40 | 1,46 | — | — | — |
500 | 1,50 | 1,56 | — | — | — |
Значение коэффициента раздвижки зерен Крз. – бетонная смесь жесткая
Расход цемента, кг/м3 | до 400 | 400…500 | 500…600 |
Коэффициент Крз. | 1,05…1,1 | 1,1…1,2 | 1,2…1,25 |
4 Проще говоря для жестких смесей Крз.=1,1, для подвижных В15 и выше Крз.=1,35, для наших расчетов примем Крз=1,35
5 Итак мы имеем для расчета оптимального соотношения П/Щ следующие данные:
Мист.щ = 2720,0 кг/куб, Мнас.щ = 1480,0 кг/куб, Мнас.п = 1530,0 кг/куб, Пщ=0,456, Крз=1,35
Делаем расчет, объем песка в насыпном состоянии должен равняться объему пустот щебня с учетом раздвижки зерен.
Соотношение песка и щебня определяется по формуле П/Щ = Пщ*Крз.*(Мнас.п/Мнас.щ), вставляем цифры получается П/Щ=0,456*1,35*(1530,0/1480,0) = 0,63.
То есть получается по этим расчетам, что песка должно быть равно 0,63 щебня или 63% от щебня, к примеру если щебня 1000,0 кг/куб, то песка 630 кг/куб.
Но на мой взгляд, как практика, такая бетонная смесь будет слишком «щебенистой» и пользуясь моей программой, все таки песочка получается больше, где то около 75%, так что советую пользуйтесь ею.
В этой статье я показал как правильно посчитать соотношение П/Щ исходя из тех произвольных данных, которые мы с Вами взяли.
[tip] Мой Вам совет протестируйте этот метод на своих параметрах песок щебень, которые Вы используете, сравните результаты, и напишите мне. [/tip]
Будут вопросы пишите, помогу и проконсультирую более подробно и конкретнее применительно к Вашим условиям и возможностям.
Ну вот вроде и все по этой теме, буду искренне рад если смог оказаться Вам полезен.
[help] Уважаемые коллеги, рекомендую Вам посмотреть на моем сайте другие материалы о некоторых уникальных, по своему, технологиях по производству строительных материалах:
1 Грунтоблоки, уникальная технология и оборудование для их производства.
2 Вспученный вермикулит и перлит — сегодня, это новые возможности для производства и бизнеса.
3 Серобетон и сероасфальт – уникальные технологии и оборудование для их производства.
4 Ячеистый бетон — что лучше? Выбираем оптимальный вариант. Лучший и недорогой вариант технологии и оборудования для производства строительных блоков из неавтоклавного газобетона
5 Полистиролбетонные негорючие блоки для строительства методом без опалубочного строительства.
6 Сухие строительные смеси – простой и недорогой способ приготовления.
7 Производите и используйте композитную арматуру для бетона — это выгодно!
8 Вата целлюлозная – производство и применение. [/help]
На этом все, кликните по этой ссылке, чтобы посмотреть другие интересные и полезные материалы моего сайта.
Желаю Вам успехов.
Творите, дерзайте и побеждайте!
С уважением, Николай Пастухов.
Рекомендую прочесть похожие посты!
www.helpbeton.ru