Сухие реакционно-порошковые бетонные смеси (РПБ) — CemGid.ru
Ученые не перестают удивлять разработками революционных технологий, Смесь с улучшенными свойствами была получена не так давно – в начале 90-х годов 20-го века. В России ее использование при возведении зданий встречается не так часто, основное применение – изготовление наливных полов и декоративных изделий: столешниц, ажурных арок и перегородок.
Оглавление:
- Состав РПБ
- Технические параметры
- Область применения
- Расценки
Отличия от обычного бетона
Определить преимущества более качественного материала РПБ позволит рассмотрение параметров:
- Состав.
- Свойства.
- Сфера использования.
- Экономическое обоснование выгоды.
Бетон – стройматерил, формованный из уплотненной смеси различного состава:
1. Основа – вяжущее, «склеивающее» заполнитель вещество. Свойство надежно, в единое целое объединять компоненты обеспечивает главные требования сферы применения. Виды вяжущего:
- Цемент.
- Гипс.
- Известь.
- Жидкое стекло.
- Полимеры.
- Битум.
2. Заполнитель – составляющая, которая определяет плотность, вес, прочность. Виды и размер зерна:
- Песок – до 5 мм.
- Керамзит – до 40.
- Шлак – до 15.
- Щебень – до 40.
3. Добавки – модификаторы, улучшающие свойства, изменяющие процессы схватывания получаемой смеси. Виды:
- Пластифицирующие.
- Армирующие.
- Поризующие.
- Регулирующие морозостойкость и/или скорость схватывания.
4. Вода – компонент, вступающий в реакцию с вяжущим (не используется в битумных бетонах). Процентное соотношение жидкости к массе основы определяет пластичность и время схватывания, морозостойкость и прочность изделия.
Применение различных сочетаний основы, заполнителя, добавок, их соотношения, пропорций позволяет получать бетоны с разнообразными характеристиками.
Отличие РПБ от других видов материалов – мелкая фракция заполнителя.
Снижение процентного содержания цемента, его замена каменной мукой, микрокремнеземом позволило создать смеси с высокой текучестью, самоуплотняющиеся составы.
Сверхпрочные РПБ получают смешиванием воды (7-11 %) и реакционно-активного порошка. Пропорции (%):
- Портландцемент марки М500 серый или белый – 30~34.
- Микрокварц или каменная мука – 12-17 %.
- Микрокремнезем – 3.2~6.8.
- Тонкозернистый кварцевый песок (фракция 0.1~0.63 мм).
- Суперпластификатор на основе поликарбоксилатного эфира – 0,2~0,5.
- Ускоритель набора прочности – 0.2.
Технология получения:
- Компоненты подготавливают в соответствии с процентным содержанием.
- В смеситель подают воду и пластификатор. Начинается процесс перемешивания.
- Добавляют цемент, каменную муку, микрокремнезем.
- Для придания цвета допускается добавка красителей (железоокисные).
- Перемешивание 3 минуты.
- Дополняют песком и фиброй (для армированных бетонов).
- Процесс смешивания 2-3 минуты. В этом промежутке времени вводят ускоритель схватывания в процентном соотношении 0,2 от общей массы.
- Поверхность формы смачивают водой.
- Заливают смесь.
- Сбрызгивают водой поверхность раствора, распределившегося в форме.
- Накрывают литьевую емкость.
На все операции потребуется до 15 минут.
Свойства реакционно-порошковых бетонов
Положительные качества:
1. Применение микрокремнезема и каменной муки привело к снижению пропорции содержания цемента и дорогих суперпластификаторов в РПБ, что обусловило падение стоимости.
2. Получен состав самоуплотняющегося порошкового сверхпрочного бетона с высокой степенью текучести:
- Не обязательно применение вибростола.
- Лицевая поверхность получаемых изделий практически не требует механической доработки
- Возможность изготовления элементов с различной текстурой и шероховатостью поверхности.
3. Армирование стальной, целлюлозной фиброй, использование ажурно-тканевых каркасов повышает марку до М2000, прочность на сжатие – до 200 МПа.
4. Высокая устойчивость к карбонатной и сульфатной коррозии.
5. Применение порошковой реакционной смеси помогает создать сверхпрочные (˃40-50 Мпа), легкие конструкции (плотность 1400~1650 кг/м3). Снижение массы уменьшает нагрузку на фундамент сооружений. Прочность позволяет выполнять несущие элементы каркаса здания меньшей толщины – сокращается расход.
Характеристики
Инженеры на этапе проектирования проводят расчеты и составляют ряд рекомендаций и требований к строительным материалам и параметрам. Основные показатели:
- Марка бетона – число после буквы «М» (М100) в маркировке, указывает диапазон статической нагрузки на сжатие (кг/см2) после превышения которой наступает разрушение.
- Прочность: на сжатие – фиксированная опытным путем величина давления пресса на образец до его деформации, единица измерения: МПа. На изгиб – давление пресса на центр образца, установленного на две опоры.
- Плотность – масса изделия объемом 1 кубический метр, единица измерения: кг/м3.
- Морозостойкость – количество циклов замораживания и обратного процесса с разрушением образца менее 5 %.
- Коэффициент усадки – процентное уменьшение объема, линейных размеров конструкции по готовности.
- Водопоглощение – отношение массы или объем впитываемой образцом воды при погружении в сосуд с жидкостью. Характеризует открытую пористость бетона.
Марка | Прочность, МПа | Плотность, кг/м3 | Морозостойкость, кол-во циклов | Усадка, мм/м | Водопоглощение, % | |
сжатие | Растяжение (изгиб) | |||||
М1000 – М2000 | От 120 | 10 ~14 | От 2300 | 500 ~ 1000 | Менее 0.28 | 0.5 ~ 2.4 |
Сфера применения
Новая технология на основе реакционно-порошковой смеси позволяет создавать бетоны с улучшенными характеристиками и широкой областью использования:
- 1.
Наливные полы с высоким сопротивлением истиранию при минимальной толщине наносимого слоя.
- 2. Изготовление бордюрного камня с длительным сроком эксплуатации.
- 3. Различные в нужной пропорции добавки способны значительно снижать процесс водопоглощения, что позволяет применять материал при возведении морских нефтяных платформ.
- 4. В гражданском и промышленном строительстве.
- 5. Возведение мостов и тоннелей.
- 6. Для столешниц с высокой прочностью, поверхностью различной структуры и шероховатостью.
- 7. Декоративные панели.
- 8. Создание перегородок, художественных изделий из прозрачного бетона. При постепенной заливке в форму укладывают светочувствительные волокна.
- 9. Изготовление архитектурных тонкостенных деталей с помощью тканевого армирования.
- 10. Использование для прочных клеевых составов и ремонтных смесей.
- 11. Теплоизоляционный раствор с применением стеклосфер.
- 12. Высокопрочный бетон на гранитном щебне.
- 13. Барельефы, памятники.
- 14. Цветные бетоны.
Стоимость
Высокая цена вводит в заблуждение застройщиков относительно целесообразности использования. Снижение транспортных расходов, увеличение срока эксплуатации сооружений и наливных полов, другие позитивные свойства материала окупают финансовые вложения. Найти и купить РПБ довольно сложно. Проблема связана с пониженным спросом.
Цены, по которым можно приобрести РПБ в России:
Вид | Марка | Цена, руб/кг |
Сухая бетонная порошковая реакционная смесь, мешок, 30 кг | М1200 | 48 |
Высокопрочный промышленный наливной пол | М1500 | 54 |
Сухой ремонтный состав | В120 | 51 |
Сталефиброармированный самонивелирующийся бетон | В180 | 50 |
Бетон на гранитном щебне готовый (1 м3) | М1000 | 6000 |
К сожалению, сложно привести примеры объектов гражданского или промышленного назначения, возведенные на территории России с применением РПБ. Основное использование порошковых бетонов получило при изготовлении искусственного камня, столешниц, а также в качестве наливных полов и ремонтных составов.
Порошковый бетон: особенности состава, применение
Бетон — один из главных составляющих строительных конструкций. Не так давно на рынке появился новый вид — порошковый бетон. Этот тип материала обладает улучшенными свойствами и физико-техническими характеристиками. Он стал фаворитом для мастеров строительного дела. Его прочность и текучесть вышли на новый качественно лучший уровень.
Содержание
- Что собой представляют?
- Особенности состава
- Преимущества
- Применение
Что собой представляют?
Этот вид бетона получил название из-за особенностей состава. Он разработан учеными не так давно, но уже завоевал симпатию пользователей. Изготавливают такой вид бетона с реакционных материалов, которые очень тонко измельчены. Он обладает прочностью 200- 800 МПа. Это высокий показатель по сравнению с другими видами бетона. Изделия, изготовленные из материла, проходят тепловую и влажную обработки.
Особенности состава
Компоненты, из которых изготавливают бетон, такие:
Специфичность материала обеспечивается его уникальным составом.- вода;
- гиперпластификатор;
- цемент;
- микрокремнезем;
- каменная мука;
- песок фракционный;
- стальная фибра.
Каждый добавленный компонент материала должен быть тщательно размешан.Секрет процесса смешивания составляющих материалов заключается в правильной последовательности их введения в смесь.
Самостоятельное приготовление порошкового материала занимает 15—20 минут. Сначала в воду добавляется гиперпластификатор, компоненты перемешиваются до получения однородной массы. Затем добавляется цемент, микрокремнезем, каменная мука, песок и фибра. После введения в смесь каждого нового элемента обязательно перемешивать компоненты. Бетон готов, когда мастер получил материал с необходимой текучестью. Его сразу можно использовать по назначению.
Преимущества
Рассматриваемый вид пользуется высоким спросом у покупателей. Этому способствуют его положительный для строительства и облицовки свойства. Вот некоторые из них:
В данном случае нет необходимости добавлять в материал крупный заполнитель.- Изготовленные изделия имеют идеальную форму и гладкую поверхность.
- Крупный заполнитель не применяется в технологии его изготовления.
- Большое разнообразие форм и текстуры готовых изделий.
- Прочность материала при изгибе — Ptb100.
- Высокая прочность при сжатии.
- Готовые изделия могут быть украшены ажурными и тонкими составляющими, что было совершенно невозможно при использовании бетона старого образца.
- Материал просто сделать самостоятельно без использования специализированных промышленных агрегатов.
- Финальный этап изготовления элементов из материала быстрый и недорогой: обжечь при температуре 95—200 °С и увлажнить водой.
Применение
С помощью такого материала можно обустроить наливной пол.Высокопрочная порошковая смесь активно используется во всех этапах строительства и внутренних работах. Этот вид применяют для изготовления балок, столбов, смесей для уменьшения зазоров между конструкциями, ажурных заборов, наливных полов. Изделие используется для создания сложных архитектурных сооружений, которые выгодно отличаются наличием тонких вычурных элементов. Порошковая смесь идеально подходит по своим свойствам для изготовления плит разных форм и размеров. Это могут быть элементы для укладки на улице, например, тротуара, так и внутри здания — в качестве облицовки стен.
Рейтинг
( Пока оценок нет )
0 249 просмотров
Понравилась статья? Поделиться с друзьями:
Реактивный порошковый бетон — состав и преимущества
🕑 Время чтения: 1 минута
Содержание:
- Что такое реактивный порошковый бетон?
- Состав реакционно-порошкового бетона
- Функции компонентов реакционно-порошкового бетона
- 1.
Цемент
- 2. Песок
- 3. Кварцевый порошок
- 4. Кремнезем 900 08
- 5. Стальные волокна
- 6. Суперпластификатор
- 1.
- Преимущества реактивного порошкового бетона
- Ограничения реактивного порошкового бетона
Реактивный порошковый бетон (RPC) представляет собой бетон сверхвысокой прочности, приготовленный путем замены обычного заполнителя обычного бетона кварцевым порошком, микрокремнеземом, стальными волокнами и т. д. RPC обладает не только высокой прочностью, но и высокой пластичностью. Прочность на сжатие составляет от 200 МПа до 800 МПа.
Состав реактивного порошкового бетона Реактивный порошковый бетон содержит очень мелкие порошки, такие как цемент, мелкий песок, кварцевый порошок размером менее 300 микрон, микрокремнезем, стальные волокна длиной 1 см размером 180 микрон и суперпластификатор. Типичный состав ингредиентов реактивного порошкового бетона с давлением 200 МПа и 800 МПа приведен в таблице ниже.
Таблица 1: Типовой состав RPC 200 МПа
Компонент | Количество (кг/м |
OPC (тип V) | 955 |
Мелкий песок (150–400 микрон) | 1051 |
Диоксид кремния | 229 |
Осажденный диоксид кремния | 10 |
Суперпластификатор | 13 |
Стальные волокна | 191 |
Вода | 153 |
Рис. 1: Система бокового перехода показанного выше моста построена с использованием RPC
Таблица 2: Типичный состав RPC 800 МПа
Ингредиент | Количество (кг/м 3 ) |
OPC (тип V) | 1000 |
Мелкий песок (150–400 микрон) | 500 |
Порошок молотого кварца (4 микрона) | 390 |
Диоксид кремния | 230 |
Суперпластификатор | 18 |
Стальные волокна | 630 |
Вода | 180 |
Функции каждого из ингредиентов и параметры их выбора обсуждаются ниже. Ингредиенты реактивного порошкового бетона:
- Цемент
- Песок
- Кварцевый порошок
- Кремнеземный дым
- Стальные волокна
- Суперпластификаторы
- Портландцемент рядовой средней крупности пригоден для изготовления РПК. Размер частиц цемента должен быть от 1 микрона до 100 микрон.
- Функция цемента состоит в том, чтобы выступать в качестве вяжущего материала, а также создавать первичные гидранты из бетона.
- Оптимальное процентное содержание основных минералов или фиктивных соединений, необходимых для изготовления RPC, приведено в таблице ниже:
Таблица 3: Оптимальное процентное содержание основных минералов в цементе
Трехкальциевый силикат (C 3 S) | 60% |
Двухкальциевый силикат (C 2 S) | 22% |
Трехкальциевый алюминат (C 3 A) | 3,8% |
Тетракальциевый алюмоферрит (C 4 AF) | 7,4% |
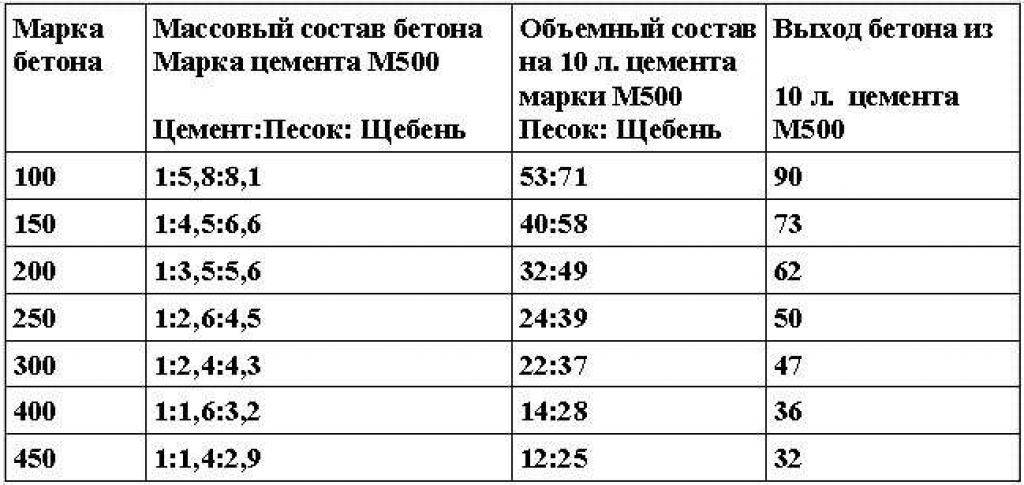
- Рекомендуется натуральный речной или дробленый песок с размером частиц от 150 до 600 микрон.
- Он должен иметь хорошую твердость и быть доступным по низкой цене.
- В реакционноспособном порошкообразном бетоне частицы песка имеют наибольший размер, поэтому их функция заключается в придании прочности бетонной смеси.
Рис. 2: Речной песок
3. Кварцевый порошок- Обычно кварцевый порошок доступен в кристаллической форме. Его выбирают исходя из его тонкости.
- Размер частиц должен быть от 5 микрон до 25 микрон.
- Основная функция кварца – придать бетону максимальную устойчивость к теплу.
Рис. 3: Порошок кварца
4. Микрокремнезем- Микрокремнезем обычно получают на предприятиях по производству ферросилиция. Его следует выбирать таким образом, чтобы в нем было меньше примесей.
- Размер частиц микрокремнезема составляет от 0,1 микрона до 1 микрона.
- Его функция заключается в заполнении небольших пустот, а также в улучшении текучести бетона.
- Также способствует образованию вторичных гидратов в бетоне.
Рис. 4: Силикатный дым
5. Стальные волокна- Стальные волокна длиной от 13 до 25 мм и диаметром от 0,15 до 0,2 мм выбираются для приготовления реактивного порошкового бетона.
- Повышает пластичность бетона.
Рис. 5: Стальные волокна
6. Суперпластификатор- Полиакрилат используется в качестве суперпластификатора в RPC.
- Основной функцией полиакрилата является снижение водоцементного отношения, а также улучшение удобоукладываемости бетона.
Ниже приведены преимущества реактивного порошкового бетона по сравнению с другими типами бетонов.
- Благодаря своей высокой пластичности он всегда конкурирует со сталью.
- Мелкие ингредиенты делают бетон непроницаемым для пустот, и не происходит утечки газа или жидкости.
- Уменьшение статической нагрузки на конструкцию из-за более высокой способности к сдвигу наряду с превосходной прочностью. Члены ПКР
- обладают большой устойчивостью к сейсмическим воздействиям.
Рис. 6: Транзитная станция легкорельсового транспорта, построенная с использованием реакционно-порошкового бетона
Ограничения реактивно-порошкового бетонаРеактивный порошковый бетон также имеет некоторые ограничения, а именно:
- Замещающие материалы, используемые в RPC, немного дороже, что увеличивает стоимость проекта.
- Оптимизация основных минералов в бетоне также увеличивает стоимость бетона.
- Долгосрочные свойства реактивного порошкового бетона неизвестны, так как он все еще находится в стадии разработки.
- Официальных кодов для рецептур реактивной порошковой бетонной смеси не существует.
Исследование свойств реактивного порошкового бетона – IJERT
Исследование свойств реактивного порошкового бетона
Сарика С.
Студент магистра технических наук, кафедра гражданского строительства MACE, Котамангалам, Эрнакулам, Керала, Индия
Д-р Элсон Джон Ассистент. Профессор,
Кафедра гражданского строительства MACE, Котамангалам Эрнакулам, Керала, Индия
Резюме – Термин реактивный порошковый бетон (RPC) использовался для описания армированной волокнами суперпластифицированной смеси кремнезема с цементом с очень низким содержанием воды. цементный коэффициент, характеризующийся наличием очень мелких заполнителей вместо обычного заполнителя. Он имеет прочность на сжатие около 150 МПа. Волокна включены в RPC, чтобы улучшить свойства разрушения композитного материала. Реактивный порошковый бетон признан революционным материалом, обеспечивающим сочетание сверхвысокой прочности и превосходной долговечности. Однако производство реактивного порошкового бетона пока недоступно из-за ограниченных исследований в этой области. В данной статье исследуются механические свойства реактивного порошкового бетона и свойства свежего бетона.
Ключевые слова Реактивный порошковый бетон, Прочность на сжатие, Удобоукладываемость.
ВВЕДЕНИЕ
Спрос на высокопрочные строительные материалы является движущей силой разработки реактивного порошкового бетона. Предварительно напряженный гибридный пешеходный мост в Шербруке в Канаде, показанный на рис. 1, завершенный в 1997 году, был первым инженерным сооружением с применением RPC. В 1997 и 1998 годах МПК были отлиты в балках электростанций Каттеном и Сиво в качестве первого промышленного применения. Первый автомобильный мост UHPC был спроектирован и построен в Бур-ле-Валанс во Франции в 2001 году [2]. Подготовка и эффективность UHPC были исследованы в других источниках [3-5].
Бетон со сверхвысокими характеристикамихарактеризуется в первую очередь высокой прочностью (> 150 МПа), а когда он армирован стальными волокнами, проявляет высокую пластичность.
, также известный как сверхвысококачественный бетон (UHPC), был разработан с помощью методов улучшения микроструктуры цементных материалов. Термин RPC использовался для описания армированной волокном сверхпластифицированной кремнеземисто-цементной смеси с очень низким водоцементным отношением, характеризующейся наличием очень мелких заполнителей вместо обычного заполнителя. По сути, это не бетон, так как в цементной смеси нет крупного заполнителя. Волокна включены в RPC, чтобы улучшить свойства разрушения композитного материала. К преимуществам Реактивно-порошкового бетона (РПБ) относятся более высокая долговечность, пластичность и прочность по сравнению с обычным бетоном и фибробетоном за счет его
чрезвычайно низкая пористость, плотная матрица, высокая прочность на растяжение/сжатие и пластичность при растяжении. Ожидается, что по сравнению с обычным сталежелезобетоном применение армированного бетона улучшит устойчивость зданий и инфраструктуры к экстремальным механическим и экологическим нагрузкам.
Реактивный порошковый бетон (RPC), который является UHPC, находится на переднем крае с точки зрения инноваций, эстетики и структурной эффективности. Этот новый тип бетона имеет прочность на сжатие 150-230 МПа в зависимости от типа и количества используемых волокон. RPC имеет сверхплотную микроструктуру, как бетон сверхвысокой прочности. Исследован РПК, основанный на теории плотнейшей упаковки с тепловым отверждением, и установлено, что он демонстрирует прочность на сжатие более 200 МПа при большой пластичности. Реактивные порошковые бетоны характеризуются высоким содержанием микрокремнезема и очень низким водоцементным отношением. Песок очень мелкого гранулометрического состава и термическая обработка оптимизированы для получения превосходных механических свойств и долговечности. Для повышения пластичности бетона и прочности на изгиб в него могут быть добавлены металлические волокна.
В настоящее время для достижения превосходных механических свойств при приготовлении RPC необходимо использовать некоторые специальные методы и сырье, в том числе:
Крупный заполнитель удаляется для повышения однородности бетона.
Металлическое волокно или стальная труба вводятся для улучшения пластичности композитов.
Добавлены высококачественный суперпластификатор и большое количество тонкодисперсного микрокремнезема и кварца для достижения низкого соотношения вода/связующее для снижения пористости и повышения прочности.
Давление может быть приложено до и во время схватывания для увеличения плотности бетона.
Высокоактивный микрокремнезем и/или осажденный кремнезем можно смешивать с вяжущими материалами для ускорения гидратации цемента и катализа сильного эффекта пуццолановой реакции.
Паровая отверждение может поставляться для повышения прочности.
Короче говоря, для достижения желаемой прочности UHPC обычно требуется правильно подобранное сырье и сложные технические процедуры.[2]
RPC обладает превосходными техническими характеристиками, в том числе пластичностью, прочностью и долговечностью, обеспечивая при этом легко формуемые изделия с высококачественным внешним видом поверхности.
Это инновационное, уникальное сочетание свойств позволяет проектировщикам создавать более тонкие секции и более длинные пролеты, которые легче, изящнее и инновационнее по геометрии и форме, обеспечивая при этом повышенную долговечность и непроницаемость для коррозии, истирания и ударов. Технология материала позволяет использовать его без пассивного армирования (армирования), а сокращение опалубки, трудозатрат и технического обслуживания еще больше способствует экономии. Отсутствие арматуры повышает безопасность, снижение веса ускоряет строительство, а повышенная долговечность снижает затраты на техническое обслуживание и продлевает срок службы. Было проведено множество исследований бетона с реактивным порошком, и в большинстве из них была сделана только характеристика материала. Основная цель настоящего исследования — выяснить, насколько эффективно RPC можно использовать для структурных приложений.
Рис. 1. Шербрукский мост
ОБЗОР ЛИТЕРАТУРЫ
Мохаммед Мансур и др.
(2014) [3] провели исследования характеристик реактивного порошкового бетона (RPC) при двух различных условиях отверждения: отверждение водой при 25°C и термообработка при 90°C и относительной влажности 95%. Они изучили влияние использования стальной фибры и термической обработки на образец плиты RPC. Плиты, свободно опертые по четырем краям, были концентрически нагружены квадратной плитой размером (70x70x25 мм). Было обнаружено, что использование стальных волокон и термическая обработка показали адекватное улучшение прочности на сжатие, прочности на косвенное растяжение, модуля упругости и прочности на изгиб. Экспериментальные результаты показали, что присутствие ультратонких стальных волокон обеспечивает повышенную жесткость, меньшую ширину трещин и распространение трещин. Стальные волокна обеспечивают достаточную прочность на растяжение и пластичность. Это позволяет уменьшить количество армирования, необходимого для сопротивления растяжению во многих конструкциях, и, таким образом, может снизиться собственный вес и стоимость.
Это позволяет проектировщику создавать более тонкие секции, более длинные пролеты и более высокие конструкции.
Р.Ю и др. (2014) [5] представляет состав смеси и оценку свойств бетона, армированного волокнами со сверхвысокими характеристиками (UHPFRC). Расчет бетонных смесей производится для получения плотно уплотненной цементной матрицы. Удобоукладываемость, пористость, содержание воздуха, прочность на сжатие и изгиб разработанного UHPFRC измеряются и анализируются. Результаты подтверждают конструкцию UHPFRC с относительно низким количеством связующего за счет использования
.улучшенная модель упаковки. Рассчитана степень гидратации цемента UHPFRC. И результаты показывают, что после 28 дней отверждения в матрице UHPFRC все еще остается большое количество негидратированного цемента, который можно дополнительно заменить наполнителями для улучшения удобоукладываемости и эффективности CST UHPFRC. Это исследование поддерживает использование добавок в UHPFRC.
H.M.
Al-Hassani et al. (2014) [1] исследовали некоторые механические свойства реактивного порошкового бетона (РПБ). Эти свойства включают прочность на сжатие, статический модуль упругости, прочность на растяжение (прямое, на расщепление и изгиб), способность на изгиб при нагрузке и ударную вязкость при изгибе. Переменные параметры в исследовании, где содержание микрокремнезема (SF) как частичная замена по массе цемента, объемная доля стального волокна и тип суперпластификатора. Влияние этих переменных на свойства RPC было тщательно изучено. Экспериментальные результаты показали, что увеличение содержания микрокремнезема (SF) от 0% до 30% приводит к значительному увеличению прочности на сжатие, в то время как увеличение прочности на растяжение относительно ниже. Включение стальной фибры приводит к значительному увеличению прочности на растяжение и лишь незначительному увеличению прочности на сжатие РПК, так как объемная доля фибры увеличивается с 0% до 3%. Увеличение объемной доли стального волокна и содержания микрокремнезема улучшило поведение при нагрузке и прогибе и привело к большей пластичности и вязкости разрушения RPC.
C.M.Tam et al. (2010) [2] исследовали механические свойства реактивного порошкового бетона и свежего бетона с целью достижения оптимальных условий для производства реактивного порошкового бетона с использованием местных материалов путем исследования состава материала, режимов отверждения и нагрева, а также микроструктуры реактивного порошкового бетона. По результатам экспериментов установлено, что реактивный порошковый бетон с водовяжущим отношением 0,2, дозировкой суперпластификатора 2,5%, кварцевым песком 150-600 микрон, отвержденным при 27°С в водной среде, обеспечивает наилучшие результаты по механическим и композиционным показателям. свойств, а также по практическим и экономическим причинам, хотя термическая обработка реактивного порошкового бетона может привести к значительному увеличению прочности на сжатие.
К.М.Нг и др. (2010) [4] попытка производства реактивного порошкового бетона с использованием местных материалов в лабораторных условиях. Проведены экспериментальные исследования и проведено сравнение бетона, изготовленного из реактивного порошкового бетона и высокопрочного бетона.
Результаты показывают, что прочность на сжатие, прочность на разрыв при расщеплении и статический модуль упругости оказываются значительно выше, чем у высокопрочного бетона с тем же соотношением воды и вяжущего. Отмечено, что скорость набора прочности образцов реактивного порошкового бетона больше, чем у высокопрочного бетона. Разница в силе в более позднем возрасте еще больше. Прочность на сжатие около 200 МПа могла быть достигнута даже за 3 дня для реактивных порошковых образцов бетона при термообработке образцов при температуре около 250°С в течение 16 ч, что можно объяснить образованием ксонотлита при исследовании методом сканирующей электронной микроскопии. .
Цемент:
СВОЙСТВА МАТЕРИАЛА
ТАБЛИЦА IV. ДЕТАЛИ ИЗ СТАЛЬНОЙ ВОЛОКНЫ
Для исследования использовали портландцементобыкновенный марки 53. Физические свойства используемого цемента приведены в таблице I.
ТАБЛИЦА I. ФИЗИЧЕСКИЕ СВОЙСТВА ЦЕМЕНТА
Длина
Диаметр
Соотношение сторон
Прочность на растяжение
20 мм
0,3 мм
66
>1100 МПа
ПРОПОРЦИЯ СМЕСИ
Соотношение смеси, принятое для смеси RPC, приведено в таблице V.
Удельный вес
3,14
Стандартная консистенция
35%
Время начальной настройки
76
Окончательное время схватывания
380
ТАБЛИЦА V. ПРОПОРЦИЯ СМЕСИ
Кремнезем:
Высокореактивный кремниевый пуццолан является важным компонентом реактивного порошкового бетона.
В исследовании использовали Microsilica 920D. Он соответствует обязательным требованиям соответствующих стандартов Американского общества испытаний и материалов (ASTM) и Европейского комитета по стандартизации. Химический состав материала приведен в таблице II
ТАБЛИЦА II. ХИМИЧЕСКИЙ СОСТАВ MICROSILICA 920D
Вода:
Для смешивания использовалась питьевая вода.
Суперпластификаторы (СП):
В работе использовали суперпластификатор на основе конденсата поликарбоксилатного эфира (ПКЭ).
В Таблице III показан технический паспорт суперпластификатора.
ТАБЛИЦА III. ТЕХНИЧЕСКИЕ ХАРАКТЕРИСТИКИ СУПЕРПЛАСТИКАТОРА.
Аспект
Светло-коричневая жидкость
Относительная плотность
1,08 ± 0,01 при 25°С
рН
6
Содержание ионов хлорида
< 0,2%
Кварцевый порошок
Для смесей RPC, предназначенных для температурного отверждения, включая автоклавирование при повышенном давлении, необходимо дополнительное количество кремнезема для изменения соотношения CaO/SiO в связующем. В этих случаях применяли порошкообразную кварцевую муку со средним размером частиц 10 15 мкм.
Мелкий заполнитель
RPC производится с использованием промышленного песка с размером частиц менее 2,36 мм.
Используются три различных градации, имеющие размер от 2,36 мм до 1,18 мм, от 1,18 мм до 600 микрон и от 600 до 0 микрон, в различных пропорциях.
Стальные волокна
Для повышения пластичности РПК были изготовлены смеси со стальной фиброй длиной 20 мм и диаметром 0,3 мм с минимальным пределом прочности на растяжение на проволоке более 1100 МПа. Детали стальной фибры показаны в таблице IV.
Материал
Пропорция смеси (кг/м3)
Цемент
1000
Микрокремнезем
225
Кварцевый порошок
252
ж/б
0,2
Вода
245
Стальная фибра
30,6
Суперпластификатор
49
Заполнитель (2,36–1,18 мм)
700
Заполнитель (1,18 мм-600 мкм)
150
Заполнитель (600 мкм-0)
100
ПРОЦЕДУРА СМЕШИВАНИЯ
Все материалы смешивают в сухом состоянии в течение 2 минут, затем добавляют 80% воды затворения и перемешивают в течение 3 минут, добавляют 15% воды и 70% суперпластификатора и снова перемешивают в течение 3 минут, после чего смеситель останавливают на 1 минута.
Теперь добавляют оставшуюся воду и суперпластификатор и перемешивание продолжают в течение 4 минут. Добавляют стальные волокна и перемешивают в течение 1 минуты для равномерного распределения. Общее время перемешивания составляет 14 минут.
ОТВЕРДЕНИЕ
Кубики размером 100 мм x 100 мм отливаются и отверждаются в воде в течение 28 дней.
СВОЙСТВА БЕТОНА
Свежие свойства бетона
Удобоукладываемость бетона
Испытание на текучестьпроводится для измерения удобоукладываемости бетона. В этом испытании форма заполняется РПЦ, и диаметр распределения РПЦ измеряется в двух ортогональных направлениях после подъема формы вертикально вверх. Среднее значение выражается как растекание бетона. Кровотечение и расслоение смеси можно проверить визуально. Растекание бетона показано на рис. 2.
Рис. 2. Испытание на подвижный поток
Механические свойства затвердевшего бетона
Прочность на сжатие затвердевшего бетона
Испытание на прочность на сжатие проводили на кубическом образце размером 100 мм на машине для испытания на сжатие мощностью 2000 кН в соответствии со спецификацией IS 516:1959.
Схема испытания на сжатие показана на рис. 3.
Рис. 3. Испытание на сжатие
РЕЗУЛЬТАТЫ И ОБСУЖДЕНИЕ
Удобоукладываемость бетона
260 мм
ТАБЛИЦА VI. ОБРАБАТЫВАЕМОСТЬ БЕТОНА
Бетонная смесь
Прочность на сжатие затвердевшего бетона
ТАБЛИЦА VII. ПРОЧНОСТЬ НА СЖАТИЕ
Прочность на сжатие (Н/мм2)
7 дней
28день
92
130
Рис. 4. Изменение прочности на сжатие
Прочность смеси через 28 дней 130 МПа. 70% прочности 28-го дня достигается на 7-й день.
ВЫВОДЫ
Результаты испытаний показывают, что производство RPC возможно при стандартном отверждении водой.
Из литературы ясно, что при температурном отверждении можно улучшить механические свойства.
Достигнута прочность бетона 130 МПа. Прочность смеси через 28 дней составляет 130 МПа. 70%
28-дневной прочности достигается на 7-й день.
Ширина бетона, полученного в результате испытаний на осадку, составляет 260 мм.
БЛАГОДАРНОСТЬ
Я хочу поблагодарить моего гида доктора Элсона Джона, доцента кафедры гражданского строительства, MACE, координатора PG доктора Ладжу Котталила, координатора PG, Департамента гражданского строительства, MACE, и доктора Джаясри Рамануджан. , начальника отдела, Департамент гражданского строительства, MACE за поддержку в проведении этого исследования и ELKEM South Asia PVT. LTD, Master Micron India и BASF Chemicals за предоставленные материалы.
ССЫЛКИ
Х. М. Аль Хассани, В. И. Халил, Л. С. Данха, Механические свойства реактивного порошкового бетона с различными стальными волокнами и содержанием кремнезема, Acta Technica Corviniensis, стр. 47-58, 2014.
Чонг Ван, Чанхуэй Ян, Фан Лю, Чаоцзюнь Ван, Синьчэн Пу, Приготовление бетона со сверхвысокими характеристиками с использованием обычных технологий и материалов, Цементные и бетонные композиты, Том: 34, стр.