Изготовление арболита своими руками: технология производства и самостоятельные работы
Поэтапная технология изготовления арболита предвидит подготовку основания, определения компонентов и состава блочного материала. В данной статье рассмотрим особенности производства своими руками с применением необходимого оборудования, расчета массы и заливки.
Оглавление:
- Преимущества и недостатки арболита
- Технология производства арболита
- Подготовка основания для работы
- Компоненты и состав арболита
- Процесс и принципы изготовления
- Оборудование: применение на практике
- Блочные формы для арболита
- Процесс производства своими руками
- Советы экспертов при изготовлении блоков своими руками
Преимущества и недостатки арболита
Для многих строителей арболитные блоки являются ценным и качественным материалом для возведения домов.
1. Прочность материала составляет 600-650 кг/м3, что по компонентной структуре не уступает иному строительному материалу. Главной особенностью является пластичность, что формируется в результате использования древесины, которая качественно армирует блоки. Таким образом, арболит не трескается под тяжестью иных материалов, а может только слегка деформироваться сохраняя общую систему конструкции.
2. Стойкость к низким температурам, что очень важно в процессе возведения дома и его эксплуатации. Дело в том, что если здание нагреется и замерзнет несколько раз, то это не повлияет на качество материала. Фактически дом из арболита может простоять минимум 50 лет в любые погодные условия. Конструкции из пеноблоков не имеют подобных свойств, ведь при постоянном замораживании они быстро потеряют свою функциональность.
3. Арболит не поддается воздействию углекислого газа, так что не стоит беспокоиться о карбонизации блоков, ведь их структура не позволит превратиться материалу в мел.
4. Теплопроводность блоков свидетельствует о популярности материала. Сравнивая показатели, стоит отметить, что стена из арболита в 30 см равняется 1 метру толщины кирпичной кладке. Структура материала позволяет сохранять тепло внутри помещения даже в самые холодные зимы, что весьма экономично при строительстве.
5. Звукоизоляционные свойства свидетельствуют о высоком коэффициенте поглощения арболита, который составляет от 0,7 до 0,6. Для сравнения древесина имеет показатели 0,06 -0,1, а кирпич немного больше около 0,04-0,06.
6. Легкость материала, что позволяет сэкономить средства на заливку фундамента.
7. Арболит является экологически чистым и долговечным строительным материалом, что определяет компонентный состав блоков. После возведения дома он не образует плесень и грибок на стенах.
8. Материал является безопасным, так он не воспламенятся.
9. Арболитные блоки легко применять в строительных работах, поскольку без труда в них можно забить гвозди, просверлить отверстие, использовать шурупы и так далее. Внешняя структура материала позволяет покрывать его штукатуркой без использования специальных сеток и дополнительных утеплителей.
Мы рассмотрели преимущества арболитных блоков, но для полного воссоздания картины о данном строительном материале приведем некоторые недостатки:
1. Стеновая панель может не выделяться точными геометрическими параметрами, от чего для восстановления ровности стены используют вагонку, сайдинг или гипсокартон, а сверху все отделяют штукатуркой.
2. Блоки не являются дешевым строительным материалом, ведь изготовление щепы для арболита требует некоторых затрат. Делая расчеты по сравнению из газобетоном, данный строительный материал обойдется только на 10-15 процентов дороже, что не формирует полное преимущество.
Технология производства арболита
Изготовление арболита требует следованию технологиям производства с расчетом состава и объема для одного блока. Арболитные блоки представляют собой строительный материал простой по компонентному составу, в который входят древесина, вода, опилки, цемент и другие предметы.
Главной основой для производства считается древесная щепа. Составная часть арболитового блока определяет его прочность и устойчивость к повреждениям, что высчитывается высшим уровнем, чем у пено- или газоблоков. Производство в домашних условиях осуществить не сложно, однако необходимо придерживаться распределения массы предмета и следовать инструкции.
Подготовка основания для работы
Основной составляющей для изготовления щепы для арболита является соотношение пропорций стружки и опилок – 1:2 или 1:1. Все предметы хорошо высушивают, для чего их помещают на 3 – 4 месяца на свежий воздух, время от времени обрабатывая известью и переворачивая.
Примерно на 1 кубический метр средства потребуется около 200 литров извести 15-ти процентной. В них помещают все щепы на четыре дня и перемешивают их от 2 до 4 раз на день. Все работы проводятся с целью убрать сахар с древесины, который может спровоцировать гниение блоков. Щепу приобретают в готовом виде, однако, с помощью щепорезов можно сделать самостоятельно.
Компоненты и состав арболита
Компонентный состав арболита является самым важным этапом технологии производства и требует внимательного соотношения всех материалов. При изготовлении блоков важно следить за качеством и разновидностью приобретаемых материалов, которые определяют готовый строительный материал. После процесса изготовления в щепу добавляют следующие материалы, такие как:
- известь гашеную;
- жидкое стекло растворимое;
- портландцемент;
- хлористый калий;
- алюминий и сернокислый кальций.
Производство арболита в пропорциях представлено в таблице 1. Стоит учесть, что для всех компонентов масса рассчитана на четыре процента доли цемента. Данная компоновка помогает сохранить огнеупорность предмета и придает пластичности.
Таблица 1. Состав арболита по объему
Марка арболита | Цемент (М400) | Кол-во извести | Кол-во песка | Кол-во опилок | Получаемая плотность (кг/м3) |
5 | 1 | 1,5 | — | 15 | 300-400 |
10 | 1 | 1 | 1,5 | 12 | 600-700 |
15 | 1 | 0,5 | 2,5 | 9 | 900-1000 |
25 | 1 | — | 3 | 6 | 1200-1300 |
Процесс и принципы изготовления
Оптимальные параметры блоков для технологии производства арболита составляют 25х25х50 сантиметров. Установленные размеры удобны при кладке стен домов, а также в процессе промышленности. Заливка блока состоит из трех рядов смеси и арболита, после каждого этапа необходимо уплотнять раствор молотком, отделанным жестью.
Излишняя масса свертывается при содействии шпателя. Выдерживается блок при температуре 18 градусов тепла на раскрытом воздухе. По истечении суток арболит выстукивается из формы на ровную поверхность, где он скрепляется на протяжении 10 дней.
Оборудование: применение на практике
Для производства необходимо разное снабжение, например, станки для изготовления арболита, которые выбираются в соответствии с объемом продукции и количества сырья. Технология промышленного процесса должна отвечать требованиям и критериям СН 549-82 и ГОСТу 19222-84. В качестве основного материала для выработки выступают хвойные деревья. Раздробление древесины происходит с помощью рубильных машин, таких как РРМ-5, ДУ-2, а более скрупулезное дробление осуществляется на оборудовании ДМ-1.
Арболитовую смесь подготавливают со смесителями и растворителями различного цикличного воздействия на материал. Подвозят большие объемы обработанной смеси к формам с помощью приспособления в качестве бетонораздатчиков или кюбелей. Подъем или опускание машины должно осуществляться при параметрах 15о по верхнему подъему и 10о по нижнему, а скорость оборудования рассчитывается в 1 м/с. Разлив арболитовой смеси по формам делают на высоте до 1 метра.
Уплотнения раствора производят с содействием вибропреса или ручной трамбовки. Для производства небольшого количества блоков нужно применить мини-станок. Изготовление своими руками арболита не представляет особых трудностей, однако на промышленных объектах применяется специальное оборудование по смешиванию, изготовления блоков. На некоторых заводах присутствуют тепловые камеры с ИК-излучением или ТЭНом, что позволяет определить нужную температуру для высыхания блоков.
Блочные формы для арболита
Существуют разные блочные формы для обработки арболита, а примерные величины могут составлять: 20х20х50 см или 30х20х50 см.
В зависимости от класса арболитовые блоки применяют в малоэтажном строительстве для возведения несущих стен, перегородок, а также для теплоизоляциии и звукоизоляции конструктивных элементов здания.
Процесс производства своими руками
Рассмотрев технологию изготовления состава арболита, можно приступать к выполнению работы самостоятельно. Для начала потребуются некоторые материалы и оборудование:
- специальный лоток для смеси;
- падающий и вибрирующий стол;
- стол с ударно-встряхивающим эффектом;
- разъемные формы и подставки;
- поддон из металла для форм.
Производить арболит своими руками очень сложно без использования необходимых инструментов, станков и оборудования. Как правило, на производстве потребуются некоторые приспособления:
1. Для получения качественного раствора необходимо применить бетономешалку. Разумеется, в процессе можно все сделать своими руками, однако придется, много времени потратить на получение раствора необходимой консистенции.
2. Для формирования структуры блоков важно приобрести формы соответствующих размеров. Как правило, арболит имеет прямоугольную форму, а в производстве используются пластиковые формы.
3. При помощи станка вы профессионально измельчите щепу.
4. Используя пресс можно получить хорошую плотность материала при трамбовке, при этом важно убрать воздух из консистенции. В качестве приспособлений применяется вибростол.
5. Обязательное наличие камеры для сушки арболита, что позволит его превратить в твердую однокомпонентную структуру.
6. В домашних условиях понадобится лопата для загрузки смеси в формы, а для скрепления блоков используют армирующую сетку.
При наличии выше перечисленных приспособлений можно производить в день около 350 – 450 м3 строительного раствора в месяц. Места для монтажа потребуется около 500 квадратных метров, а затрат на электроэнергию пойдет 15-45 кВт/ч. Для самостоятельного процесса органические средства заливаются водой, а также цементом до образования однородной смеси. Все пропорции и расчеты отображены в таблице 1, главное чтобы вышедшая смесь была сыпучей.
Перед заливкой раствора в формы, их обмазывают с внутренней стороны молочком известковым. После этого, средство скрупулезно и аккуратно укладывают и утрамбовывают специальными приспособлениями. Верхняя часть блока выравнивается с помощью шпателя или линейки и заливается раствором штукатурки на слой в 2 сантиметра.
После образованной формы арболита его потребуется тщательно уплотнить с помощью деревянной конструкции, оббитой железом. Прочными и надежными считаются блоки, которые выстоялись и схватились на протяжении десяти дней при температуре 15о. Чтобы арболит не пересох, рекомендуется периодически поливать его водой.
Технология изготовления арболита своими руками не представляет определенной сложности, а поэтому все работы провести легко при наличии необходимых инструментов и приспособлений. При соблюдении правил и критериев производства, правильного расчета компонентов строительный материал получится качественным и прочным для применения.
Советы экспертов при изготовлении блоков своими руками
Рекомендации специалистов по производству арболитных блоков основаны на практике их использования и применения. Чтобы достичь высокого качества продукции необходимо следовать некоторым факторам. В производстве рекомендуется применять не только большую щепу, но и использовать опилки, стружку из дерева. Обработка консистенции и выдавливание из него сахара позволяет избежать дальнейшего вспучивания строительного материала, что не приспускается при сооружении дома.
В процессе изготовления раствор следует тщательно перемешивать, чтобы все части оказались в цементе. Это важно для качественного и прочного скрепления древесины и иных материалов в блоке. В производстве не менее важным остается добавление следующих компонентов, таких как алюминий, гашеная известь и так далее. Весь состав образует дополнительные свойства арболита, например жидкое стекло не позволяет впитывать влагу блокам, а известь служит в качестве антисептика.
Хлористый калий способствует уничтожению микроорганизмов и других веществ, что не благотворно влияют на структуру. При добавлении всех компонентов стоит следить за таблицей пропорциональности, чтобы готовый раствор соответствовал требованиям производства арболитных блоков.
Изготовление арболита своими руками: технология производства и самостоятельные работы
Поэтапная технология изготовления арболита предвидит подготовку основания, определения компонентов и состава блочного материала. В данной статье рассмотрим особенности производства своими руками с применением необходимого оборудования, расчета массы и заливки.
Оглавление:
- Преимущества и недостатки арболита
- Технология производства арболита
- Подготовка основания для работы
- Компоненты и состав арболита
- Процесс и принципы изготовления
- Оборудование: применение на практике
- Блочные формы для арболита
- Процесс производства своими руками
- Советы экспертов при изготовлении блоков своими руками
Преимущества и недостатки арболита
Для многих строителей арболитные блоки являются ценным и качественным материалом для возведения домов. Главная особенность теплоизоляционных свойств позволяет из раствора производить напольные листы. Технология изготовления и принципы выдержки и сушки блоков предоставляют арболиту некоторые преимущества:
1. Прочность материала составляет 600-650 кг/м3, что по компонентной структуре не уступает иному строительному материалу. Главной особенностью является пластичность, что формируется в результате использования древесины, которая качественно армирует блоки. Таким образом, арболит не трескается под тяжестью иных материалов, а может только слегка деформироваться сохраняя общую систему конструкции.
2. Стойкость к низким температурам, что очень важно в процессе возведения дома и его эксплуатации. Дело в том, что если здание нагреется и замерзнет несколько раз, то это не повлияет на качество материала. Фактически дом из арболита может простоять минимум 50 лет в любые погодные условия. Конструкции из пеноблоков не имеют подобных свойств, ведь при постоянном замораживании они быстро потеряют свою функциональность.
3. Арболит не поддается воздействию углекислого газа, так что не стоит беспокоиться о карбонизации блоков, ведь их структура не позволит превратиться материалу в мел.
4. Теплопроводность блоков свидетельствует о популярности материала. Сравнивая показатели, стоит отметить, что стена из арболита в 30 см равняется 1 метру толщины кирпичной кладке. Структура материала позволяет сохранять тепло внутри помещения даже в самые холодные зимы, что весьма экономично при строительстве.
5. Звукоизоляционные свойства свидетельствуют о высоком коэффициенте поглощения арболита, который составляет от 0,7 до 0,6. Для сравнения древесина имеет показатели 0,06 -0,1, а кирпич немного больше около 0,04-0,06.
6. Легкость материала, что позволяет сэкономить средства на заливку фундамента.
7. Арболит является экологически чистым и долговечным строительным материалом, что определяет компонентный состав блоков. После возведения дома он не образует плесень и грибок на стенах.
8. Материал является безопасным, так он не воспламенятся.
9. Арболитные блоки легко применять в строительных работах, поскольку без труда в них можно забить гвозди, просверлить отверстие, использовать шурупы и так далее. Внешняя структура материала позволяет покрывать его штукатуркой без использования специальных сеток и дополнительных утеплителей.
Мы рассмотрели преимущества арболитных блоков, но для полного воссоздания картины о данном строительном материале приведем некоторые недостатки:
1. Стеновая панель может не выделяться точными геометрическими параметрами, от чего для восстановления ровности стены используют вагонку, сайдинг или гипсокартон, а сверху все отделяют штукатуркой.
2. Блоки не являются дешевым строительным материалом, ведь изготовление щепы для арболита требует некоторых затрат. Делая расчеты по сравнению из газобетоном, данный строительный материал обойдется только на 10-15 процентов дороже, что не формирует полное преимущество.
Технология производства арболита
Изготовление арболита требует следованию технологиям производства с расчетом состава и объема для одного блока. Арболитные блоки представляют собой строительный материал простой по компонентному составу, в который входят древесина, вода, опилки, цемент и другие предметы.
Главной основой для производства считается древесная щепа. Составная часть арболитового блока определяет его прочность и устойчивость к повреждениям, что высчитывается высшим уровнем, чем у пено- или газоблоков. Производство в домашних условиях осуществить не сложно, однако необходимо придерживаться распределения массы предмета и следовать инструкции.
Подготовка основания для работы
Основной составляющей для изготовления щепы для арболита является соотношение пропорций стружки и опилок – 1:2 или 1:1. Все предметы хорошо высушивают, для чего их помещают на 3 – 4 месяца на свежий воздух, время от времени обрабатывая известью и переворачивая.
Примерно на 1 кубический метр средства потребуется около 200 литров извести 15-ти процентной. В них помещают все щепы на четыре дня и перемешивают их от 2 до 4 раз на день. Все работы проводятся с целью убрать сахар с древесины, который может спровоцировать гниение блоков. Щепу приобретают в готовом виде, однако, с помощью щепорезов можно сделать самостоятельно.
Компоненты и состав арболита
Компонентный состав арболита является самым важным этапом технологии производства и требует внимательного соотношения всех материалов. При изготовлении блоков важно следить за качеством и разновидностью приобретаемых материалов, которые определяют готовый строительный материал. После процесса изготовления в щепу добавляют следующие материалы, такие как:
- известь гашеную;
- жидкое стекло растворимое;
- портландцемент;
- хлористый калий;
- алюминий и сернокислый кальций.
Производство арболита в пропорциях представлено в таблице 1. Стоит учесть, что для всех компонентов масса рассчитана на четыре процента доли цемента. Данная компоновка помогает сохранить огнеупорность предмета и придает пластичности.
Таблица 1. Состав арболита по объему
Марка арболита | Цемент (М400) | Кол-во извести | Кол-во песка | Кол-во опилок | Получаемая плотность (кг/м3) |
5 | 1 | 1,5 | — | 15 | 300-400 |
10 | 1 | 1 | 1,5 | 12 | 600-700 |
15 | 1 | 0,5 | 2,5 | 9 | 900-1000 |
25 | 1 | — | 3 | 6 | 1200-1300 |
Процесс и принципы изготовления
Оптимальные параметры блоков для технологии производства арболита составляют 25х25х50 сантиметров. Установленные размеры удобны при кладке стен домов, а также в процессе промышленности. Заливка блока состоит из трех рядов смеси и арболита, после каждого этапа необходимо уплотнять раствор молотком, отделанным жестью.
Излишняя масса свертывается при содействии шпателя. Выдерживается блок при температуре 18 градусов тепла на раскрытом воздухе. По истечении суток арболит выстукивается из формы на ровную поверхность, где он скрепляется на протяжении 10 дней.
Оборудование: применение на практике
Для производства необходимо разное снабжение, например, станки для изготовления арболита, которые выбираются в соответствии с объемом продукции и количества сырья. Технология промышленного процесса должна отвечать требованиям и критериям СН 549-82 и ГОСТу 19222-84. В качестве основного материала для выработки выступают хвойные деревья. Раздробление древесины происходит с помощью рубильных машин, таких как РРМ-5, ДУ-2, а более скрупулезное дробление осуществляется на оборудовании ДМ-1.
Арболитовую смесь подготавливают со смесителями и растворителями различного цикличного воздействия на материал. Подвозят большие объемы обработанной смеси к формам с помощью приспособления в качестве бетонораздатчиков или кюбелей. Подъем или опускание машины должно осуществляться при параметрах 15о по верхнему подъему и 10о по нижнему, а скорость оборудования рассчитывается в 1 м/с. Разлив арболитовой смеси по формам делают на высоте до 1 метра.
Уплотнения раствора производят с содействием вибропреса или ручной трамбовки. Для производства небольшого количества блоков нужно применить мини-станок. Изготовление своими руками арболита не представляет особых трудностей, однако на промышленных объектах применяется специальное оборудование по смешиванию, изготовления блоков. На некоторых заводах присутствуют тепловые камеры с ИК-излучением или ТЭНом, что позволяет определить нужную температуру для высыхания блоков.
Блочные формы для арболита
Существуют разные блочные формы для обработки арболита, а примерные величины могут составлять: 20х20х50 см или 30х20х50 см. Выпускаются предметы и прочих размеров, особенно для постройки вентиляционных систем, покрытий и так далее. Формы можно приобрести в строительных магазинах или же подготовить все своими руками. Для этого, используют доски толщиной в 2 сантиметра, которые скрепляют до образования определенной конструкции. Внешне форма отделывается фанерой, или пленкой.
В зависимости от класса арболитовые блоки применяют в малоэтажном строительстве для возведения несущих стен, перегородок, а также для теплоизоляциии и звукоизоляции конструктивных элементов здания.
Процесс производства своими руками
Рассмотрев технологию изготовления состава арболита, можно приступать к выполнению работы самостоятельно. Для начала потребуются некоторые материалы и оборудование:
- специальный лоток для смеси;
- падающий и вибрирующий стол;
- стол с ударно-встряхивающим эффектом;
- разъемные формы и подставки;
- поддон из металла для форм.
Производить арболит своими руками очень сложно без использования необходимых инструментов, станков и оборудования. Как правило, на производстве потребуются некоторые приспособления:
1. Для получения качественного раствора необходимо применить бетономешалку. Разумеется, в процессе можно все сделать своими руками, однако придется, много времени потратить на получение раствора необходимой консистенции.
2. Для формирования структуры блоков важно приобрести формы соответствующих размеров. Как правило, арболит имеет прямоугольную форму, а в производстве используются пластиковые формы.
3. При помощи станка вы профессионально измельчите щепу.
4. Используя пресс можно получить хорошую плотность материала при трамбовке, при этом важно убрать воздух из консистенции. В качестве приспособлений применяется вибростол.
5. Обязательное наличие камеры для сушки арболита, что позволит его превратить в твердую однокомпонентную структуру.
6. В домашних условиях понадобится лопата для загрузки смеси в формы, а для скрепления блоков используют армирующую сетку.
При наличии выше перечисленных приспособлений можно производить в день около 350 – 450 м3 строительного раствора в месяц. Места для монтажа потребуется около 500 квадратных метров, а затрат на электроэнергию пойдет 15-45 кВт/ч. Для самостоятельного процесса органические средства заливаются водой, а также цементом до образования однородной смеси. Все пропорции и расчеты отображены в таблице 1, главное чтобы вышедшая смесь была сыпучей.
Перед заливкой раствора в формы, их обмазывают с внутренней стороны молочком известковым. После этого, средство скрупулезно и аккуратно укладывают и утрамбовывают специальными приспособлениями. Верхняя часть блока выравнивается с помощью шпателя или линейки и заливается раствором штукатурки на слой в 2 сантиметра.
После образованной формы арболита его потребуется тщательно уплотнить с помощью деревянной конструкции, оббитой железом. Прочными и надежными считаются блоки, которые выстоялись и схватились на протяжении десяти дней при температуре 15о. Чтобы арболит не пересох, рекомендуется периодически поливать его водой.
Технология изготовления арболита своими руками не представляет определенной сложности, а поэтому все работы провести легко при наличии необходимых инструментов и приспособлений. При соблюдении правил и критериев производства, правильного расчета компонентов строительный материал получится качественным и прочным для применения.
Советы экспертов при изготовлении блоков своими руками
Рекомендации специалистов по производству арболитных блоков основаны на практике их использования и применения. Чтобы достичь высокого качества продукции необходимо следовать некоторым факторам. В производстве рекомендуется применять не только большую щепу, но и использовать опилки, стружку из дерева. Обработка консистенции и выдавливание из него сахара позволяет избежать дальнейшего вспучивания строительного материала, что не приспускается при сооружении дома.
В процессе изготовления раствор следует тщательно перемешивать, чтобы все части оказались в цементе. Это важно для качественного и прочного скрепления древесины и иных материалов в блоке. В производстве не менее важным остается добавление следующих компонентов, таких как алюминий, гашеная известь и так далее. Весь состав образует дополнительные свойства арболита, например жидкое стекло не позволяет впитывать влагу блокам, а известь служит в качестве антисептика.
Хлористый калий способствует уничтожению микроорганизмов и других веществ, что не благотворно влияют на структуру. При добавлении всех компонентов стоит следить за таблицей пропорциональности, чтобы готовый раствор соответствовал требованиям производства арболитных блоков.
Производство арболита от ЭкоДревПродукт в Москве и Иваново — ЭкоДревПродукт
«ЭкоДревПродукт» имеет крупнейшее производство арболита. За долгие годы работы накоплен огромный опыт в производстве и строительстве из
арболитовых блоков. У нас существует большое количество складов, с готовым стройматериалом, на всей европейской части России:
Клин, Вологда, Ярославль, Кострома, Иваново, Волгоград, Ростов-на-Дону, Тейково, Рыбинск, Липецк, Саратов, Краснодар.
В связи с большими объемами продаж по всей центральной части России изготовление арболита в компании ведется в промышленных масштабах на высокотехнологичном оборудовании.
Производственная база оснащена полуавтоматической линией для производства арболитовых блоков, позволяющей изготавливать большие объёмы продукции высокого качества в короткий срок.
Производительность линии до 1000 м3в месяц.
Одной из главных составляющих, отвечающих за долговечность
арболитового блока, является качество древесной щепы. Многие конкурирующие фирмы используют в качестве сырья для щепы кору деревьев, древесные отходы или горбыль. В отличие от них у нашей компании есть смежное предприятие, занимающееся утилизацией деревянных поддонов бывших в употреблении. Их мы и используем в качестве сырьевого материала для получения щепы. Это значит, что при производстве арболита применяется качественная древесная щепа из деловой древесины (без обзола).
Производство арболита. Наша технология.
Специалистами «ЭкоДревПродукт» была разработана уникальная технология производства арболита. Заявленная технология производства отвечает необходимым сертификатам и ГОСТам, с документацией вы можете ознакомиться в разделе сертификаты.
Главное отличие данной технологии в использовании масла минеральных сортов, не содержащее вредных примесей, с целью не прилипания блока к внутренним стенкам формы. Для достижения оптимальной геометрии блока используются металлические формы. Трамбуется арболитовая смесь с при помощи вибропресса, таким образом, блок получается идеально ровным. Во-первых, уменьшает образование «мостиков холода», а во-вторых, снижает расход цемента на строительство и отделку. Мостик холода – участок соединительного шва, который зимой будет значительно холоднее, чем вся остальная стена. Благодаря идеальной геометрии арболитового блока, количество таких участков резко уменьшается, а это значит, что в доме, построенном из таких блоков, будет всегда тепло.
При производстве очень важны размеры древесной щепы, оптимальной является щепа длиной 2—20 мм, шириной 2—5 мм и толщиной не более 5 мм. Если использовать щепу меньшего размера, то арболит будет крошиться и рассыпаться, а если большего – то незащищенные бетоном большие частицы щепы будут подвержены гниению и воздействию микроорганизмов. В процессе производства древесная щепа для нейтрализации сахаров подвергается воздействию сернокислого алюминия. Однако в дальнейшем, все химические добавки нейтрализуются и переходят в неактивное состояние, поэтому
наш арболит — экологически чистый.
На стойкость арболита к внешним факторам, существенно влияет время выдержки после изготовления. Блок выдерживается в форме до момента застывания структуры, что обеспечивает 100% геометрические параметры, тем самым увеличивается плотность, и, соответственно, теплоизоляционные характеристики.
Четкое соблюдение технологии на всех этапах производства, работа на современном оборудовании и квалифицированный персонал позволяют нам производить качественные арболитовые блоки, которые идеально подходят для строительства.
Этапы производства арболита
- Изготовление щепы. Преимущественно для этих целей используется древесина большинства видов деревьев хвойных пород, но можно применять и другие, характеризующиеся повышенной стойкостью к биологическому разрушению — осина, береза. Плохое качество готового арболита может быть обусловлено применением деревоматералов из бука, лиственницы.
- Минерализация щепы. Данная процедура необходима для придания этому компоненту повышенного уровня адгезии с портландцементом. Для этих целей применяется хлористый кальций, реже — сернокислый алюминий.
- Смешивание предварительно минерализованной щепы с остальными компонентами — цементной массой и связующим составом. После тщательного перемешивания полученную смесь заливают в предварительно подготовленные формы, затем оставляют для затвердевания. Длительность данного процесса зависит от многих условий, главным из которых является температурный режим. Летом либо в прогретом помещении готовый продукт можно получить гораздо быстрее, чем при низких температурах. Не рекомендуется осуществлять производство арболитных блоков при температуре, не превышающей пятнадцати градусов.
Производство арболита
Производство нашей продукции основано на проверенных технологиях и современной производственной базе, мы выпускаем только качественные арболитовые блоки.
Производство арболитовых блоков предполагает использование вибропресса, с его помощью смесь плотно утрамбовывается, равномерно распределяется по форме. В результате блок имеет идеально ровные поверхности, препятствующие образованию мостиков холода.
Наш производственный участок с установкой «Сфера-1»Высокая степень механизации производства позволяет нам снизить издержки и предложить клиенту низкую цену на арболит высокого качества.
Дробилка опилок Доктор АрболитДля получения качественных арболитовых блоков при производстве должны соблюдаться определенные условия. Так, например, важное значение имеет величина древесной щепы, мы используем щепу оптимальных размеров – длина от 10 до 40 мм, ширина от 5 до 10 мм, толщина не больше 5 мм.
При производстве арболита используется щепа из хвойной древесины. Сначала она измельчается на нашем оборудовании до необходимой фракции, затем обрабатывается сульфатом алюминия, это позволяет нейтрализовать сахара, содержащиеся в древесине и позволяет получить материал, который не боится разрушительного воздействия микроорганизмов
Для арболитовых блоков при производстве необходим цемент, мы используем высококлассный портландцемент. Данный вид цемента применяется также в промышленном строительстве при возведении ответственных конструкций, к которым предъявляются жесткие требования по таким качествам, как водостойкость, долговечность, морозоустойчивость.
Устойчивость арболита к внешнему воздействию зависит от того, насколько правильно было соблюдено время выдержки после изготовления блока. Изделие необходимо выдержать в форме сутки, за это время происходит застывание структуры, увеличивается плотность изделия, и соответственно его теплоизоляционные характеристики.
Вид на производственный участок с формами для выдержки блоков и партией свежей продукцииПолучить арболитовые блоки идеальной геометрической формы нам позволяет использование специальных форм из металла. Для того чтобы исключить прилипание смеси к стенкам формы, мы обрабатываем их минеральным маслом, не содержащим вредных примесей.
Арболитовые блоки от нашей компании отличаются идеальной геометрией и оптимальной плотностью – 650-700 кг на 1 м3. Добиться подобных результатов помогает тщательно выверенная технология изготовления.
Всё производство и хранение находится в отапливаемом помещении. Благодаря равномерной сушке наши арболитовые блоки имеют равномерную структуру и соответствуют требованиям стандартов.
Готовая продукция арболита на пандусе для погрузкиКаждая партия арболита изделий имеет сертификаты соответствия, протоколы испытаний, заключение санитарно-эпидемиологической службы.
Дерево — это новый бетон?
Стремясь найти новые способы удержания углерода, девелоперы, архитекторы и заинтересованные в чистом нулевом уровне компании задаются вопросом: «Является ли дерево новым бетоном?» Новая технология в производстве так называемой «массовой древесины» предлагает сокращающую углеродистость альтернативу бетону и стали в строительном секторе.
В дополнение к эстетическим преимуществам древесины как строительного материала, защитники говорят, что использование древесины может существенно снизить выбросы парниковых газов в строительном секторе. Его использование также может сократить отходы, загрязнение, затраты и время по сравнению с материалами, более широко используемыми сейчас.
«Массовая древесина — неподходящий материал навсегда, но на данный момент это подходящий материал», — говорит архитектор Майкл Грин, сторонник деревянного строительства из Ванкувера. «Если бы у нас были другие способы строительства с нулевым выбросом углерода, нам не понадобилась бы массивная древесина».
Новые методы обрезки, сушки и склеивания деревянных досок, включая древесные отходы, для создания больших «плит», массивная древесина используется для всего: от полов, стен и потолков до целых зданий и небоскребов — даже для городов.
Технический гигант Microsoft обновляет свой кампус в Кремниевой долине, используя древесину с учетом углеродных и других экологических преимуществ. Кампус площадью 644 000 квадратных футов станет крупнейшим лесопромышленным комплексом в Северной Америке.
Массовая древесина не всегда будет подходящим материалом, но на данный момент это подходящий материал.
«Использование массивной древесины является частью обязательства Microsoft по снижению выбросов углерода к 2030 году, включая сокращение выбросов Scope 3 на 55 процентов», — сказал Даррен Ломбарди, старший менеджер по недвижимости в Microsoft SVC.Объем 3 Выбросы — это выбросы от клиентов или активов, которые не принадлежат компании или не контролируются ею, но которые косвенно влияют на ее цепочку создания стоимости и выбросы. Microsoft использует данные из инструмента Embodied Carbon Calculator for Construction (EC3), который анализирует строительные материалы, для получения данных для принятия решений о строительстве, включая наиболее эффективные способы сокращения выбросов углерода.
В настоящее время самое высокое деревянное здание в мире находится в Норвегии, его высота составляет 18 этажей и 280 футов. Градостроители в Хельсинки, Финляндия, создают так называемый Лесной город, целый город, построенный из древесины в качестве основного строительного материала.
«Массовая древесина включает в себя набор строительных элементов, которые превращают относительно дешевое древесное сырье в конструкционные элементы, которые имеют более высокие показатели удельного веса к прочности, чем сталь или бетон», — говорит Кейт Круз, профессор Австралийского университета Квинсленда. По его словам, поддержка энергоэффективных зданий на протяжении всего их жизненного цикла может быть эффективным способом сократить долгосрочные выбросы углерода и приблизиться к нулю.
См. Нашу связанную историю: Каликс получает 17 долларов.7 миллионов инвестиций от Carbon Direct для улавливания углерода в бетоне.
Обычно массовая древесина изготавливается из быстрорастущих хвойных пород деревьев, таких как пихта, сосна и ель. Чтобы превратить его в прочный и адаптируемый строительный материал, используются различные методы, в том числе ламинированные дюбелями (DLT), клееные (Glulam или GLT) балки, клееный брус (LVL) и брус, клееный гвоздями (NLT). Наиболее перспективным для крупных строительных проектов является кросс-клееный брус (CLT).
«Это немного похоже на то, что IKEA сделала с мебелью», — говорит Крюс. «Все готово с очень высокими допусками, поставляется в плоской упаковке и собирается в конечный продукт».
Улавливание углеродаСогласно новому отчету Программы ООН по окружающей среде, выбросы в строительном секторе составляют почти 38 процентов от общего объема выбросов парниковых газов в мире и достигли рекордного уровня в 2019 году. Использование древесины вместо стали и бетона может значительно снизить углеродный след конструкции за счет предотвращения попадания углерода в атмосферу и его улавливания на протяжении всего срока службы здания.Поскольку древесина улавливает и хранит углерод посредством фотосинтеза, сторонники говорят, что массовая древесина действует как форма удаления углерода.
Выбросы в строительном секторе составили почти 38% от общих выбросов парниковых газов в мире и достигли рекордного уровня в 2019 году.
К 2050 году ООН ожидает, что 70 процентов населения мира будет жить в городах, что означает создание дополнительной инфраструктуры. Это не сулит ничего хорошего для борьбы с изменением климата. Сталь и бетон, которые в настоящее время являются двумя наиболее распространенными строительными материалами, используемыми во всем мире, производят примерно 8 процентов мировых выбросов углерода.
Уже ведутся работы по уменьшению углеродного следа бетона и стали с использованием технологий. Бетон можно использовать для улавливания углерода, когда рециркулируемый углекислый газ постоянно встраивается в цемент во время процесса смешивания. Зеленый водород, производимый с использованием возобновляемых источников энергии, выглядит наиболее многообещающим решением для снижения углеродного следа стали, если его можно производить в больших количествах и транспортировать.
Не новинка, не навсегда
Противники массового использования древесины говорят, что вырубка деревьев для строительства недопустима.Но Боди Кабийо, доктор философии. кандидат Калифорнийского университета в Беркли не согласен. По его словам, он не видит, что массовый спрос в ближайшее время станет проблемой, но устойчивое лесопользование имеет важное значение.
«Нам действительно нужно помнить о том, что мы не создадим всплеск спроса на массовую древесину без устойчивых методов ведения лесного хозяйства», — говорит он. «Мы не хотим рубить 1000-летние деревья ради массовой древесины».
«Потребители забывают, что мы уже вырубаем деревья для производства бумаги и пиломатериалов», — говорит Кабийо.Дерево используется для всего: от туалетной бумаги и записных книжек до декоров и мебели. По его словам, на самом деле деревья сажают и выращивают для того, чтобы их рубить для бесчисленных ежедневных нужд.
Массовая древесина может сыграть роль в создании экономики замкнутого цикла и обеспечить рабочие места в лесном хозяйстве, проектировании, строительстве и установке.
Строительство — это отрасль с оборотом 9 триллионов долларов, а массовое производство древесины — это растущее предприятие, которое недавно стало частью решения по борьбе с изменением климата. По оценкам, мировой рынок CLT, всего лишь одной из множества товаров массового производства из древесины, достигнет 3 долларов. 5 миллиардов к 2027 году.
Грин говорит, что необходимо постоянно наращивать инвестиции и инновации, чтобы найти способы улучшить строительство, а массовая древесина — это всего лишь ступенька к тому, что мы в конечном итоге можем сделать.
Некоторые мировые лидеры, использующие массовую древесину, включают Stora Enso в Финляндии, Mayr Melnhof Holz Holding AG в Австрии и Xlam Ltd. в Австралии и Новой Зеландии. Глобальный девелопер Lendlease построил несколько многоэтажных деревянных домов на своей родной базе в Австралии. Walmart даже начинает массовую игру в древесине и заключает контракт со Structurlam, ведущим поставщиком лесоматериалов в Северной Америке, на строительство новых офисов в кампусе.
Согласно отчету Forest Economic Advisors, массивная древесина может сыграть роль в создании экономики замкнутого цикла и обеспечить рабочие места в лесном хозяйстве, проектировании, строительстве и установке. По словам Боди, в идеальном мире мы бы использовали меньше древесины для производства целлюлозы и бумаги — за счет увеличения вторичной переработки и других средств — чтобы вместо этого можно было использовать ее для массового производства древесины.
«Переход от использования древесины с недолговечных продуктов к долгоживущим, таким как [здания], принесет огромные выгоды для климата», — сказал Боди.
Вновь открыт старый материал: дерево-бетон
Дерево и бетон — два материала, которые вряд ли могут быть более разными. У каждого есть свои качества, преимущества и недостатки по сравнению с другим, поэтому вопрос о том, строить ли с тем или с другим, в основном вопрос принципа. Но сейчас есть комбинации этих двух материалов, которые пользуются большой популярностью. Но их сочетание — дерево-бетон — встречается гораздо реже. До сих пор он в основном использовался для ненесущих компонентов, например, в дизайне интерьеров или фасада.Ученые из Национальной исследовательской программы Resource Wood в Швейцарии разработали композитный материал для несущих стен и потолков.
© iTEC / HTA-FR
В композитных материалах из дерева и цемента нет ничего нового. В 1930-х годах голландец Ричард Хандл запатентовал «метод производства легкого строительного материала из древесных отходов и цемента». Во время Второй мировой войны в Германии при строительстве жилых домов применялся арболит .Чтобы восполнить дефицит цемента, связанный с войной, использовались заменители, такие как бурый угольный шлак, но с ограниченным успехом из-за плохой защиты от влаги. В ГДР, напротив, хорошая тепло- и звукоизоляция была достигнута за счет ненесущих плит, изготовленных из более качественной древесно-бетонной смеси.
Современный арболит
Интерес к древесному бетону возродился в связи с общим повышением осведомленности об устойчивости в последние годы. С начала тысячелетия Мюнхенский технический университет исследовал деревянный легкий бетон .Основное внимание уделяется потенциалу противопожарной защиты и визуальному дизайну фасадов и интерьеров . В университете Баухаус в Веймаре в период с 2009 по 2010 год был построен экспериментальный паркетный дом green: house , который сочетал в себе положительные структурные и физические свойства дерева (например, способность к диффузии) и бетона (например, звукоизоляция), которая в то же время могла быть изготовлена заранее и обработана в каркасной конструкции, такой как дерево. Композиционный материал состоял исключительно из древесной стружки и цемента.
Инновация: экологичный древесный бетон
Уже построен первый полноценный деревянно-бетонный дом с использованием легких методов строительства. Но теперь ученые разработали несущий древесный бетон в рамках Национальной исследовательской программы (NRP 66) «Resource Wood» в Швейцарии, который даже может быть подходящим в качестве замены обычному бетону в бетонных конструкциях.Шлифованная древесина заменяет обычный гравий и песок. Исследователи экспериментировали с различными составами разного веса, которые все весят почти вдвое меньше обычного бетона. В самой легкой смеси объем древесины превышает 50 процентов, а вес арболита настолько мал, что он даже плавает на воде.
Помимо небольшого веса, новый арболит отличается повышенной огнестойкостью, и лучшей теплоизоляцией по сравнению с обычным бетоном. К тому же порция из дерева, конечно, тоже положительно сказывается с точки зрения экологии. И последнее, но не менее важное: древесина с песком и гравием имеет большое преимущество в том, что она возобновляемая. И, прежде всего, энергия все еще может быть получена из древесного бетона после сжигания на мусоросжигательном заводе.
Заключение
Этот очень интересный составной древесно-бетонный материал, который сочетает в себе преимущества двух очень разных материалов экологически безопасным способом, во многих случаях может в долгосрочной перспективе заменить обычный бетон.Но, вероятно, пройдет некоторое время, прежде чем вновь обнаруженный старый строительный материал действительно «войдет в строй» в строительной отрасли. На данный момент исследователи проекта NRP 66 все еще исследуют вопрос, какая смесь лучше всего подходит для каких целей.
Древесный цемент, обладающий высокой прочностью и многофункциональностью
Формирование и трехмерная архитектура из древесного цемента.
Природа часто вдохновляет на создание биомиметических искусственных материалов. В новом отчете, опубликованном в журнале « Advanced Science », Фахенг Ван и группа ученых в области передовых материалов, инженерии и науки в Китае разработали новые цементные материалы на основе однонаправленной пористой архитектуры, имитирующей конструкции из натурального дерева.Полученный древесно-подобный цементный материал показал более высокую прочность при одинаковой плотности, а также многофункциональные свойства для эффективной теплоизоляции, водопроницаемости и легкости регулирования отталкивания воды. Команда одновременно достигла высокой прочности и многофункциональности, что сделало древесный цемент новым многообещающим строительным материалом для создания древесно-имитирующих конструкций с высокими характеристиками. Они представили простую процедуру изготовления для повышения эффективности при массовом производстве с приложениями, подходящими для других систем материалов.
Разработка биоинспирированных древесных материалов
Пористые материалы на основе цемента обладают низкой теплопроводностью для теплоизоляции, высокой звукопоглощающей способностью, отличной проницаемостью для воздуха и воды при сохранении небольшого веса и огнестойкости. Тем не менее, ключевой задачей по-прежнему остается достижение одновременного улучшения как механических, так и многофункциональных свойств, включая механическую поддержку, эффективную транспортировку и хорошую теплоизоляцию.Поэтому крайне желательно создавать материалы с улучшенными механическими и многофункциональными свойствами, чтобы активно реализовывать принципы проектирования натурального дерева. В ходе экспериментов Wang et al. разработан древесный цемент с однонаправленной пористой структурой, сформированной методом двунаправленной обработки замораживанием. Процесс позволил сформировать мосты между составляющими конструкции, а затем команда оттаяла полностью замороженные тела, пока лед постепенно не растаял, а цемент не затвердел.Последующий процесс гидратации произвел новые минералы и гели в цементе, включая гидроксид кальция в форме шестиугольника, игольчатый эттрингит и гели силиката-гидрата кальция. Фазы в основном образовывались на цементных пластинах и перерастали в промежутки между ними в процессе оттаивания и отверждения для лучшей структурной целостности с улучшенными взаимосвязями ламелей во время образования пористого цемента. Затем с помощью рентгеновской томографии (XRT) команда выявила образование однонаправленных микропор в цементе с ледяной структурой.

Wang et al.использовали изображения сканирующей электронной микроскопии (СЭМ), чтобы выявить однонаправленные поры между пластинами в цементе с ледяной структурой, которые охватывают большое количество межсоединений, соединяющих ламели. Команда классифицировала взаимосвязи на три типа: (1) мосты и пересечения, образованные из-за частиц цемента, захваченных кристаллами льда в процессе замерзания, (2) гидроксид кальция шестиугольной формы и (3) игольчатый эттрингит. Последние минералы являются результатом реакций гидратации цемента во время процессов оттаивания и отверждения.Цементные ламели содержали обильные поры, образовавшиеся в процессе сушки цемента из-за обезвоживания гелей и удаления воды. Ученые классифицировали поры в древесном цементе на три типа, включая (1) межламеллярные открытые поры, (2) внутриламеллярные открытые поры и (3) внутриламеллярные закрытые поры. Межламеллярная пористость в основном определяется содержанием воды, которая играет роль порообразователя.
- c,d) Variations in the c) failure strain, d) energy absorption density, represented using the area under stress–strain curve until the peak stress, and specific strength (inset in panel (d)) as a function of the total porosity Ptotal. The general varying trends are indicated by the dashed curves for clarity. e) Dependence of the compressive strength on the relative density in the wood‐like cement. f) Interpretation of the strength according to the equivalent element approach by taking different types of pores into account. The data in panels (c)–(f) are obtained from at least three measurements for each set of samples and presented in form of mean ± standard deviation. Credit: Advanced Science, doi: 10.1002/advs.202000096″>
Механические свойства древесного цемента.a, b) Типичные кривые напряжения-деформации сжатия древесно-подобного цемента, изготовленного из суспензий с различным соотношением W / C а) без и б) с добавками SF. c, d) Вариации в c) деформации разрушения, d) плотности поглощения энергии, представленной с использованием площади под кривой зависимости напряжения от напряжения до пикового напряжения, и удельной прочности (вставка на панели (d)) в зависимости от общей пористости.


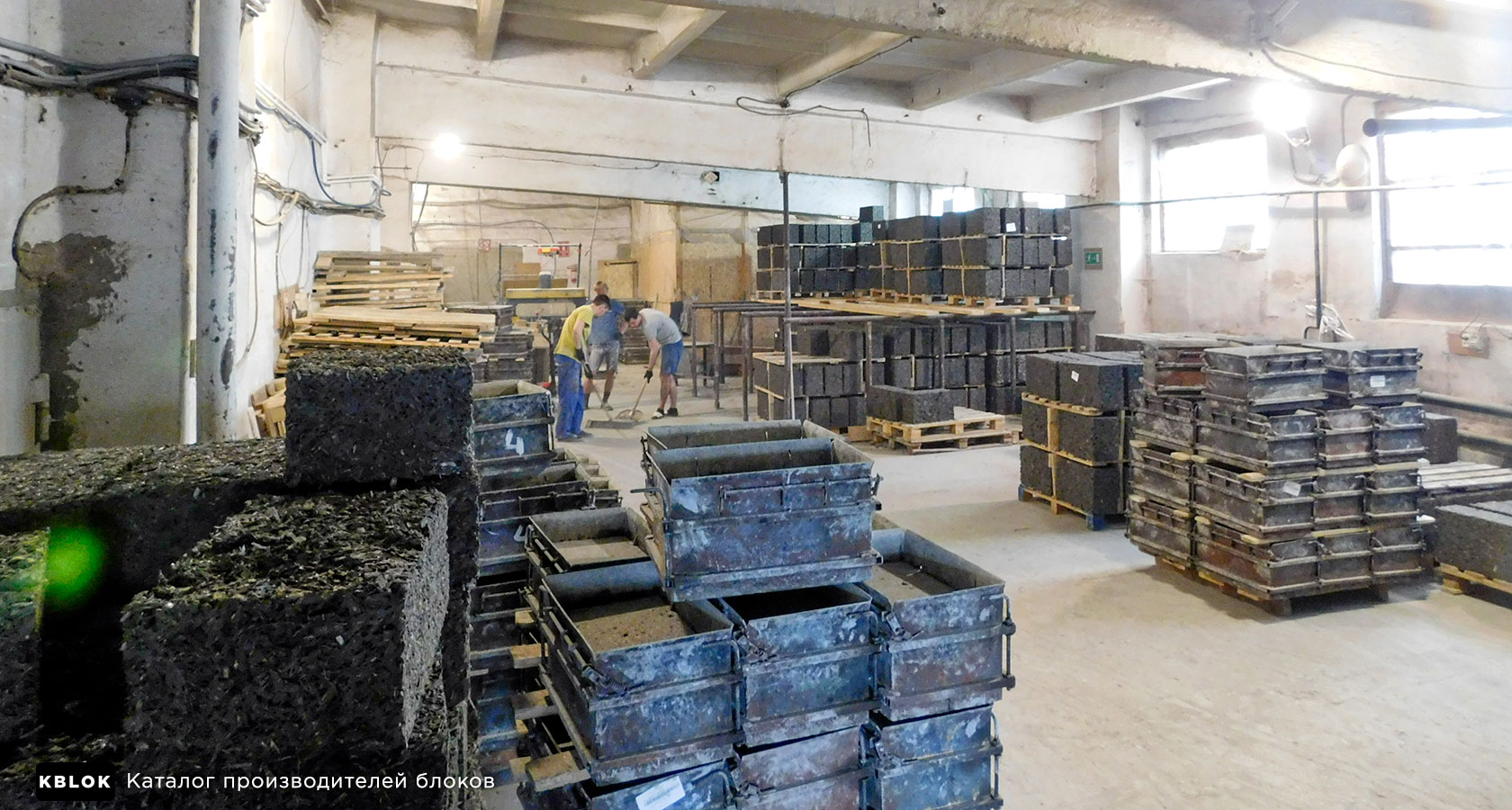
Механические и многофункциональные свойства материала
Команда получила характерные кривые напряжения-деформации сжатия древесного цемента с добавлением паров кремния или без них в его состав.Прочность на сжатие монотонно снижалась с увеличением соотношения вода / цемент в растворах, используемых для разработки материала, что в конечном итоге привело к увеличению пористости цемента. Поскольку деформация разрушения материала увеличивается с увеличением общей пористости, прочность пористого твердого тела может определяться по его пористости. Затем команда измерила коэффициент теплопроводности древесного цемента с ледяной структурой, чтобы показать уменьшение теплопроводности с увеличением пористости материала. Они также использовали инфракрасные (ИК) изображения для четкого наблюдения за прочными теплоизоляционными свойствами цементного материала с ледяной структурой. Для регулирования эффективности теплоизоляции Wang et al. регулировали твердую нагрузку в цементных растворах, увеличивая содержание воды / цемента. Полученный цементный материал впитывает воду из-за гидрофильного (водопривлекательного) характера его внутренних поверхностей. Напротив, они могут предотвратить проникновение воды в поры за счет гидроизоляции поверхностей кремнийорганическим агентом; такие усилия по гидрофобности могут даже заставить материал плавать на воде.Таким образом, этот метод может облегчить переключаемые применения в качестве проницаемых или водонепроницаемых конструкций, подходящих в качестве строительных материалов.
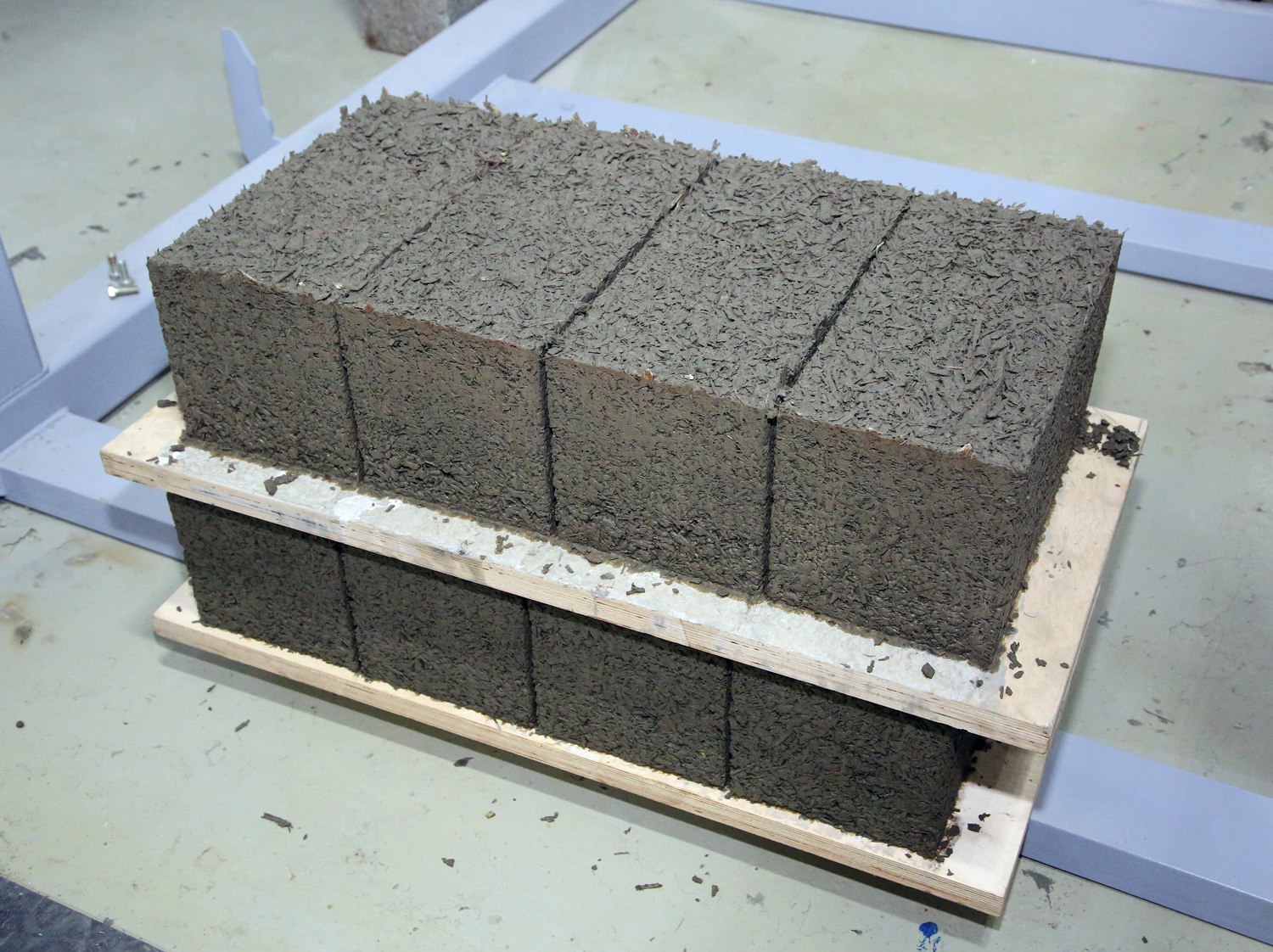
Перспективы древесных цементных материалов
Таким образом, Фахенг Ван и его коллеги представили технику создания ледяных шаблонов как жизнеспособный подход к созданию однонаправленных микропор для применения в керамике, полимерах, металлах и их композитах.Ученые разработали процесс обработки сублимационной сушкой, основанный на самоотвердевающем поведении цемента при контакте с реакциями гидратации. Полученная в результате архитектура из цемента, напоминающая древесину, содержала множество пор в открытой или закрытой форме и множество соединений, соединяющих их ламели. Когда пористость увеличивалась, прочность цемента снижалась. Древесный цемент также отличался более низкой теплопроводностью и хорошей водопроницаемостью. Команда могла изменить цементный материал на водоотталкивающий или водоотталкивающий с помощью гидрофобной или гидрофильной обработки соответственно.Простая и практичная стратегия разработки материалов в сочетании с самозатвердевающей природой его составляющих может значительно улучшить временную и экономическую эффективность метода ледового темперирования для формирования устойчивого бетона с потенциалом для переноса этого метода на другие системы материалов.
Цемент с применением наноинженерии перспективен для герметизации газовых скважин с утечками
Дополнительная информация: Ван Ф.
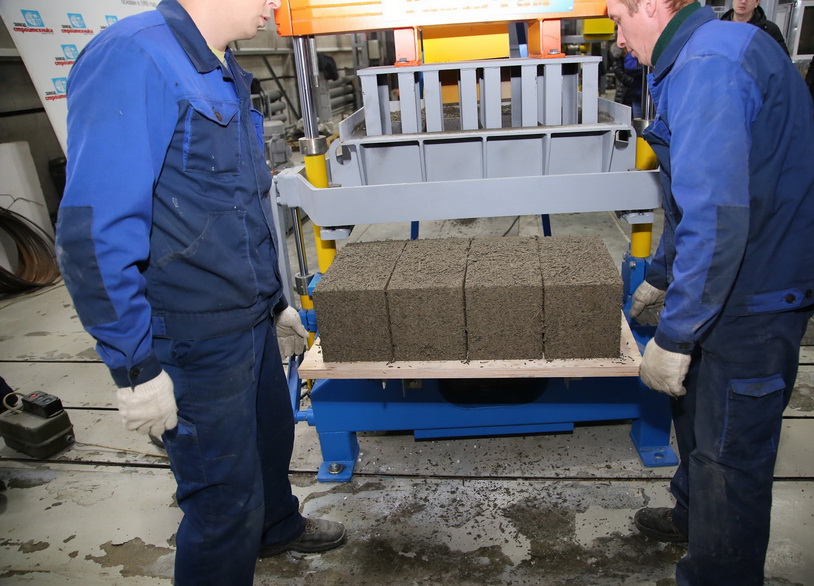
Монтейро П. и др. На пути к устойчивому бетону, Nature Materials , doi.org/10.1038/nmat4930
Рой Д. М. Новые прочные цементные материалы: химически связанная керамика, Science , 10.1126 / science.235.4789.651
© 2021 Сеть Science X
Ссылка :
Цемент на основе дерева, обладающий высокой прочностью и многофункциональностью (2021 г., 5 января)
получено 25 декабря 2021 г. с https: // физ.org / news / 2021-01-древесный-цемент-высокопрочный-многофункциональный.html
Этот документ защищен авторским правом. За исключением честных сделок с целью частного изучения или исследования, никакие часть может быть воспроизведена без письменного разрешения. Контент предоставляется только в информационных целях.
Бетон из дерева — ScienceDaily
Дома могут быть деревянными, как раньше, или бетонными, как сегодня.Чтобы построить завтрашний день, комбинируются два метода строительства: эти гибридные конструкции, содержащие как деревянные, так и бетонные элементы, становятся все более популярными в современной архитектуре.
В контексте Национальной ресурсной программы «Ресурс древесины» (NRP 66) швейцарские исследователи разработали еще более радикальный подход к объединению дерева и бетона: они производят несущий бетон, который сам состоит в основном из дерева. Во многих смесях объемная доля древесины превышает 50 процентов.
Изделия из древесины на цементной основе существуют уже более ста лет. Однако раньше они использовались только для ненесущих целей, например, для изоляции. Дайя Цвикки, руководитель Института строительных и экологических технологий Школы инженерии и архитектуры Фрибурга, задалась вопросом, не пришло ли время для более амбициозного использования деревянного бетона.
Плавающий бетон
Вместе со своей командой Цвикки экспериментировал с составом и зернистостью древесины, а также с различными добавками, а затем подверг различные смеси строгим испытаниям.Основное отличие от классического бетона в том, что щебень и песок заменены мелко измельченной древесиной. Другими словами, с цементом примешиваются не мелкие камни, а опилки. Благодаря высокому содержанию древесины новые строительные материалы обладают хорошей огнестойкостью и действуют как теплоизоляция. «Они весят не больше половины того, что весит нормальный бетон — самые легкие из них даже плавают!» — говорит Цвикки. Более того, поскольку материалы в основном основаны на возобновляемых ресурсах, после демонтажа их можно повторно использовать в качестве источника тепла и электроэнергии.Древесину можно сжигать при сжигании отходов, хотя для повседневного использования она соответствует стандартам противопожарной защиты.
Первоначальные стресс-тесты 1: 1 показывают, что новый бетон на древесной основе также подходит для плит и стеновых элементов и может выполнять несущие функции в строительстве. Этот процесс также подходит для сборных блоков. В этом контексте, в частности, группа Фрибург хотела бы углубить свой опыт с помощью более широкого спектра тестов. Исследователи хотят выяснить, какой древесно-бетонный композит лучше всего подходит для каких областей применения и как его можно эффективно производить.
«Пройдет несколько лет, прежде чем мы увидим первые здания, в которых легкий бетон, содержащий дерево, играет важную роль в строительстве», — говорит Цвикки. «Уровень знаний, необходимый для широкого применения, все еще слишком ограничен».
История Источник:
Материалы предоставлены Швейцарским национальным научным фондом (SNSF) . Примечание. Содержимое можно редактировать по стилю и длине.
«Дерево» Вы любите перерабатывать бетон? — ScienceDaily
Исследователи из Института промышленных наук, входящего в состав Токийского университета, разработали новую процедуру переработки бетона с добавлением выброшенной древесины.Они обнаружили, что правильная пропорция материалов может дать новый строительный материал с более высокой прочностью на изгиб, чем у исходного бетона. Это исследование может помочь резко снизить затраты на строительство, а также сократить выбросы углерода.
Бетон уже давно является предпочтительным материалом для строительства в нашем современном мире, используется в таких конструкциях, как небоскребы, мосты и дома — и это лишь некоторые из них. Однако, поскольку страны работают над ограничением выбросов парниковых газов, производство бетона подвергается все более пристальному вниманию.Бетон состоит из двух частей: заполнителя, который обычно состоит из гравия и щебня, и цемента. Именно производство цемента является причиной выброса большого количества углекислого газа в атмосферу.
«Простое повторное использование заполнителя из старого бетона нерационально, потому что именно производство нового цемента приводит к выбросам, связанным с изменением климата», — объясняет первый автор Ли Лян. Следовательно, необходим новый, экологически чистый подход, способствующий развитию замкнутой экономики бетона.Исследователи оптимизировали свой новый метод, отрегулировав пропорцию смеси, давление, температуру, продолжительность прессования и содержание воды. Выбор правильного соотношения бетона и переработанной древесины имел решающее значение для получения бетона максимальной прочности. Древесина приобретает жесткость за счет лигнина, который представляет собой сильно сшитый органический полимер. В этом случае лигнин заполняет зазоры в бетоне и действует как клей при смешивании с бетонным порошком и нагревании. Прочность также повысилась за счет более высоких температур и давлений во время прессования.
«Большая часть произведенных нами переработанных продуктов демонстрирует лучшую прочность на изгиб, чем у обычного бетона», — говорит старший автор, преподаватель Юя Сакаи. «Эти результаты могут способствовать переходу к более экологичной и экономичной строительной отрасли, которая не только сокращает запасы отходов бетона и древесины, но и помогает решить проблему изменения климата».
Рециклированный бетон, вероятно, будет даже биоразлагаемым, потому что бетонные отходы прикрепляются к деревянному компоненту. Этот метод также может быть расширен для переработки других типов выброшенных растительных материалов вместо древесины или даже нового бетона, сделанного из растений, песка и гравия.
История Источник:
Материалы предоставлены Институтом промышленных наук Токийского университета . Примечание. Содержимое можно редактировать по стилю и длине.
Конструкционные изделия из дерева — Системы формования бетона UFP
Передовые технологии, дизайн и инженерия позволяют производить изделия из дерева с превосходной структурой для различных применений в индустрии формования бетона.В продуктах EWP для использования в приложениях по формовке бетона используются материалы высочайшего качества, обеспечивающие высокие эксплуатационные характеристики и надежность. Компании Universal Forest Products производят изделия из дерева, такие как гальванические фермы, с 1955 года. Мы также занимаемся продажей изделий из LVL, LSL и двутавровых балок заводов-членов APA.
Engineered Wood Products специально созданы для использования в откидных конструкциях, настилах мостов, а также при вертикальной и горизонтальной формовке. Каждая деталь единообразна, удобна в использовании и рассчитана на работу даже при воздействии элементов с течением времени. Нет никакой сортировки, чтобы найти хорошие части или узлы и убытки, чтобы их обойти. Помимо этих преимуществ, ваши бригады должны будут обрабатывать меньше материала, чем создание того же проекта с использованием традиционных материалов.
Группа по опалубке UFP Concrete Forming Solutions может показать вам ценность работы с подобными продуктами EWP в вашем следующем проекте.
Фермы с покрытием
Являясь ведущим национальным производителем деревянных ферм для жилищного строительства и производства бетонных конструкций, мы освоили технологию изготовления деревянных ферм с покрытием.Некоторые преимущества наших деревянных ферм из гальванического покрытия:
- Разработано и спроектировано в точном соответствии со спецификациями
- Упростить формирование требований по заполнению / блокированию пустот
- Скошенные концы позволяют легко разобрать на палубе
- Простота обращения и установки в полевых условиях
LVL Профильная балка
Использование прочности и долговечности изделий из клееного бруса, произведенных на заводах-членах APA, дает нашей опалубочной группе и нашим клиентам уверенность в том, что они выбирают качественные продукты премиум-класса, которые обеспечат стабильность и долговечность в течение многих лет.
Балка LVL Form Beam защищена от длительного воздействия погодных условий высококачественным уплотнением кромок, что делает ее долгосрочным активом для вашей компании. Вы испытаете:
- Превосходные структурные характеристики по сравнению с традиционными размерными пиломатериалами
- Ровная поверхность забивания гвоздей без зазоров
- Самый высокий коэффициент повторного использования среди всех деревообрабатывающих элементов
- Удобство для плотников, в отличие от недревесных элементов конструкции
- Доступна прецизионная обрезка с допуском 1/16 дюйма
Бетонная опалубка
UFP Concrete Forming Solutions — ведущий дистрибьютор опалубочных плит на всей территории США.S .. Используя в вашем проекте строительства подъемно-откидного бруса или ламинированного шпона (LVL), или клееного бруса (LSL), вы быстро осознаете ценность, которую эта линейка продуктов может принести вашей компании, поскольку вы берете ее из одной работы.
к следующему. Есть три основных фактора, которые делают этот продукт EWP лучшим выбором для обрезки пиломатериалов с кромкой:
- 100% годный к употреблению продукт
- Всегда прямо
- Нет отверстий под натекание или сучки
- Не раскалывается и не деформируется, как традиционные размерные пиломатериалы
- Самый высокий коэффициент повторного использования любого изделия для обработки кромок из дерева
Бетонная опалубка двутавровая
Бетонные двутавровые балки UFP (CFI) не являются обычными двутавровыми балками.CFI производятся для работы в приложениях по формованию бетона, где нагрузки часто в 3-4 раза превышают величину, установленную в жилом проекте. Выбор CFI вместо жилой двутавровой балки имеет важное значение для безопасности бригад на рабочем месте.
- CFI доступны с глубиной от 9 ½ до 24 дюймов
- CFI не имеют предварительно перфорированных «выбивок», характерных для двутавровых балок жилых домов
- Выдерживает высокий уровень влажности и длительное воздействие погодных условий
- Возможность уменьшения количества опор, необходимых в случае больших пролетов
LVL Доска для строительных лесов
UFP Concrete Forming Solutions распространяет LVL Scaffold Plank, сертифицированный OSHA и имеющий тиснение с соответствующими товарными знаками APA.
Когда речь идет о безопасности, нет никаких компромиссов, поэтому мы ведем очень эксклюзивный и короткий список поставщиков для этого конкретного товара.
- Стандартные толщины — 1 ½ «, 1 5/8» и 1 ¾ «
- Стандартная ширина — 9 ¼ ”, 9 ½” 11 ¼ ”, 11 7/8”
- Доступна шлифованная поверхность
- Огнеупорная доска в наличии
Для получения дополнительной информации о продуктах EWP для бетонной формовочной промышленности, пожалуйста, ознакомьтесь с «Руководством по формованию — Технические данные для бетонной опалубки» Pacific Woodtech.
Бетон, сталь или дерево: поиск конструкционных материалов с нулевым содержанием углерода
Для продвижения своих проектов легких конструкций Бакминстер Фуллер спросил: «Сколько весит ваше здание?» Сегодня, когда архитекторы понимают, что необходимы как структурная, так и углеродная эффективность, возникает вопрос: «Сколько углерода содержит ваше здание?»
Многие архитекторы настаивают на сокращении или устранении воплощенных выбросов углерода, как это уже происходит с производственной энергией. Например, начиная с 2020 года, глобальная архитектурная и инженерная компания HOK планирует провести оценку жизненного цикла конструкций всех своих новых проектов целостного здания и «искать возможности для оптимизации наших спецификаций», — говорит Аника Ландрено, доц. . AIA, директор по устойчивому дизайну.
Действительно, строительная конструкция и подконструкция — хорошие места для охоты, потому что вместе они составляют более половины углеродного следа коммерческого здания. Более того, архитекторы и разработчики должны искать возможности для повторного использования и обновления существующих конструкций, чтобы не тратить впустую энергию, уже израсходованную (и уже выделенный углекислый газ), на их создание.Палитра углеродных интеллектуальных материалов в архитектуре 2030 и калькулятор воплощенного углерода в строительстве, или EC3, инструмент, разработанный Carbon Leadership Forum, C Change Labs и Skanska, — отличные места для изучения влияния выбора материалов как для проектов модернизации, так и для новых строительных проектов. .
При взвешивании вариантов стали, бетона или дерева необходимо учитывать такие факторы, как местоположение проекта, масштаб, ожидаемый срок службы, потенциал повторного использования и даже сравниваемые показатели материалов (см. «Как измерить воплощенный углерод»).По мере того, как растет осведомленность о воплощенном углероде, отрасли стремятся сделать свою продукцию более привлекательной. Сами по себе архитекторы не могут уменьшить воплощенный углерод в своих проектах, но они, скорее всего, будут прислушиваться к клиенту и могут повлиять на цепочку поставок через свои спецификации. Прежде чем принимать окончательные решения по материалам, воспользуйтесь все более удобными для пользователя инструментами сравнения и вовлеките в диалог строителей и поставщиков — чем раньше, тем лучше.
Мировой сталелитейный сектор имеет огромный углеродный след, на который приходится более 10% глобальных выбросов углекислого газа.«Крупные сталелитейные компании очень хорошо осведомлены о требованиях общества по сокращению выбросов и ищут способы отреагировать на это», — говорит Мэтью Венбан-Смит, исполнительный директор международной некоммерческой организации ResponsibleSteel. базируется в Вуллонгонге, Новый Южный Уэльс, Австралия.
Производство новой стали из железной руды энергоемко. В кислородных печах (кислородных конвертерах), являющихся нормой для большинства развивающихся стран, требуется кокс — очищенная версия угля — для извлечения железа из руды и легирования ее углеродом.Полученный чугун затем очищается до низкоуглеродистой стали, которая содержит около 25% переработанного железа и стального лома. Производители экспериментируют со способами замены угля и кокса не ископаемыми веществами, такими как водород и электролиз на конвертерных фабриках.
По оценкам Американского института стальных конструкций, 98% конструкционной стали из снесенных зданий восстанавливается и перерабатывается в новые стальные изделия.Таким образом, отечественная конструкционная сталь, которая производится на заводах с электродуговыми печами (EAF), может похвастаться содержанием вторичного сырья 93%, согласно утвержденной UL экологической декларации продукции (EPD), составленной AISC в 2016 году. стальную балку, транспортный контейнер или старый холодильник можно продать на металлолом и превратить в стальную балку с широкими полками, которая переходит в новый небоскреб », — говорит советник AISC Люк Джонсон.
Поскольку заводы из ДСП работают на электричестве, они в основном такие же экологически чистые, как и их источники энергии.В сентябре прошлого года сталелитейный завод в Колорадо XIX века, принадлежащий российскому конгломерату Evraz, заключил сделку с местной энергетической компанией о строительстве прилегающей солнечной батареи мощностью 240 мегаватт, которая будет обеспечивать значительную часть энергии комбината. Сталелитейная компания Nucor строит в Миссури завод стоимостью 250 миллионов долларов, который будет полностью работать за счет ветра. Другие похожие проекты находятся в разработке.
ResponsibleSteel недавно опубликовала первую версию своего одноименного стандарта, добровольного международного эталонного теста, разработанного для поддержки «ответственного поиска поставщиков и производства стали» и разработанного в рамках процесса с участием многих заинтересованных сторон с участием производителей, таких как ArcelorMittal, и групп по защите окружающей среды, таких как Могучая Земля.Сертификация основана на стороннем аудите и одобрении независимой комиссии.
Венбан-Смит, который помогал разработать стандарты устойчивого развития в лесном хозяйстве до того, как сосредоточился на стали, хочет сделать сталь одним из самых чистых материалов в мире: «Когда энергетический след для EAF становится нейтральным, мы можем думать о стали в полностью замкнутой экономике. ,» он говорит. Осуществление этой мечты, если возможно, скорее всего, произойдет сначала в развитых странах, где большое количество металлолома доступно для вторичной переработки.
Что спрашивать при указании стали
- Доступна ли сталь на электростанциях с электродуговыми печами и, в частности, на станах, работающих на возобновляемых источниках энергии?
- Можно ли в конструкции использовать скрепленные рамы вместо стойких к моменту рам, чтобы уменьшить требуемую массу стали?
- Можете ли вы закупить сталь, сертифицированную ResponsibleSteel?
Люди ненавидят бетон почти так же сильно, как любят его использовать. Как самый распространенный в мире строительный материал, на него приходится от 6% до 11% глобальных выбросов углекислого газа.Большая часть этих выбросов связана с производством связующего, портландцемента, который составляет в среднем около 10% бетонной смеси по весу. Производство заполнителя — песка и щебня, которые в среднем могут составлять от 70% до 80% смеси — также требует энергии, но в гораздо меньшей степени. Добыча песка может нанести ущерб речным и прибрежным экосистемам.
Почти половина выбросов углекислого газа цемента возникает в результате сжигания ископаемого топлива для нагрева цементных печей до примерно 2500 F. Достижения в области производства чистой энергии могут помочь сократить эти выбросы: прототипы цементных заводов на солнечных батареях в Калифорнии и Франции от Heliogen и Solpart соответственно, успешно нагрели печи до температуры около 1800 F с использованием огромных массивов зеркал.Однако большая часть выбросов углекислого газа происходит в результате химических реакций, присущих производству цемента: в процессе, называемом кальцинированием, известняк распадается на углекислый газ, который уходит в атмосферу, и негашеную известь, составляющую цемента.
Некоторые компании связали углекислый газ в бетон, в том числе компания CarbonCure в Дартмуте, Канада, и Blue Planet в Лос-Гатосе, Калифорния. Эти процессы остаются исключением и на сегодняшний день не полностью компенсируют выбросы углерода при производстве бетона.
В настоящее время наиболее простой способ уменьшить углеродный след бетона — это использовать меньше цемента, как ясно показывает палитра углеродных интеллектуальных материалов. Так называемые смешанные цементы используют некальцинированный известняк и другие дополнительные вяжущие материалы (SCM) вместо части клинкера — твердых гранул, полученных в печи, которые измельчаются и смешиваются с другими ингредиентами — при производстве цемента.Включая природные пуццоланы, такие как зола рисовой шелухи, и промышленные побочные продукты, такие как летучая зола, доменный шлак и микрокремнезем, SCM могут улучшить структурные характеристики бетона, а также снизить содержание в нем углерода.
Северная Америка отстает от Европы в использовании цементов с добавками, говорит Джули Баффенбаргер, старший научный сотрудник и директор по вопросам устойчивого развития компании Beton Consulting Engineers из Мендота-Хайтс, штат Миннесота. Спецификации — хороший способ сделать бетонное строительство более эффективным, отмечает она, но слишком строгие предписания могут привести к обратным результатам.Вместо того, чтобы диктовать пропорции ингредиентов в бетонной смеси, она предлагает проектным группам указать критерии эффективности с точки зрения измеримых пластичных и твердосплавных свойств, «чтобы производитель мог предоставить варианты в рамках ограничений». Имейте в виду, что SCM могут увеличивать время, необходимое для достижения требуемых показателей прочности.
Что спрашивать при указании бетона
- Можно ли уменьшить количество цемента в бетонной смеси?
- Можно ли уменьшить общую массу бетона в проекте?
- Какая цементная печь является наименее энергоемкой из имеющихся на местном уровне?
- Какие методы улавливания углерода агрегатами или смесями могут быть включены?
Инновации в области массового производства древесины, в частности, отечественное производство инженерных изделий, таких как древесина, клееная крест-накрест, клеем, гвоздями и дюбелями, подогревают надежды на то, что строительство с нулевым выбросом углерода станет возможным в больших масштабах. Согласно отраслевым исследованиям, деревья, срубленные и замененные для производства массивной древесины, могут улавливать больше углерода во время своего роста, чем то, что выбрасывается при производстве, транспортировке и строительстве. Повышенный спрос на древесину из экологически чистых источников может стимулировать лесовозобновление. «Мы должны заново покрыть часть этой планеты лесами», — говорит Ландрено из HOK. «Мы можем повлиять на это, выбрав деревянную конструкцию, где это возможно».
Спроектированные деревянные панели могут заменить стальные настилы и бетонные перекрытия в коммерческих структурах, а клееные колонны могут выдерживать нагрузку на среднеэтажные и высотные конструкции от своих стальных и бетонных аналогов.Эти изделия из дерева также могут быть огнестойкими и быстро монтируемыми. «В тот день, когда они будут установлены и подключены к несущей конструкции, они смогут нести полную проектную нагрузку», — говорит Кеннет Бланд, вице-президент American Wood Council.
Но оправдывает ли массовая древесина заявленную экологическую устойчивость?
По данным Министерства сельского хозяйства США, общий объем деревьев, произрастающих в лесах США, с 1953 года увеличился на 60%. По мере роста спроса на конструкционные изделия из древесины, лесами, производящими массовую древесину, необходимо будет рационально управлять с помощью повторной посадки деревьев. после сбора урожая.Различия в методах ведения лесного хозяйства приводят к большим различиям в количестве улавливаемого углерода, поэтому важно знать, где и как были произведены ваши лесоматериалы.
Требуются дополнительные исследования выбросов углерода при заготовке, переработке и транспортировке изделий из древесины. Новые средние отраслевые EPD для древесины и изделий из нее ожидаются в первом квартале 2020 года, но заявления конкретных производителей древесины будут еще более полезными. Помимо углерода, заключенного в самой древесине, существуют выбросы от воздействия почвы и леса, а также от производства смол и клеев, связывающих массивные слои древесины.
Наконец, преимущество массового хранения углерода в древесине сохраняется только в том случае, если балки и панели остаются в эксплуатации или не допускаются разложения, в результате чего углерод будет высвобождаться обратно в атмосферу. Чтобы деревянные конструкции были долговечными, они должны быть защищены от проникновения воды, насекомых или грибков, возможно, за счет использования герметиков в сочетании с продуманным дизайном и деталями ограждающей конструкции. Чтобы деревянные элементы можно было использовать повторно, они должны соединяться съемными застежками.
Что спрашивать при указании древесины
- Рекуперируется ли ваша деревянная продукция? Если нет, то происходит ли это из устойчивого лесного хозяйства?
- Можно ли собрать конструкцию с помощью съемных креплений, чтобы можно было повторно использовать элементы?
- Используются ли в проекте эффективные методы обрамления, позволяющие минимизировать требуемую массу древесины?
[Ознакомьтесь с этими советами и инструментами для измерения воплощенного углерода, а также посетите палитру углеродных интеллектуальных материалов. ]
Эта статья появилась в выпуске за январь 2020 года под названием «Проблема конструкционных материалов».
Проблема углерода
.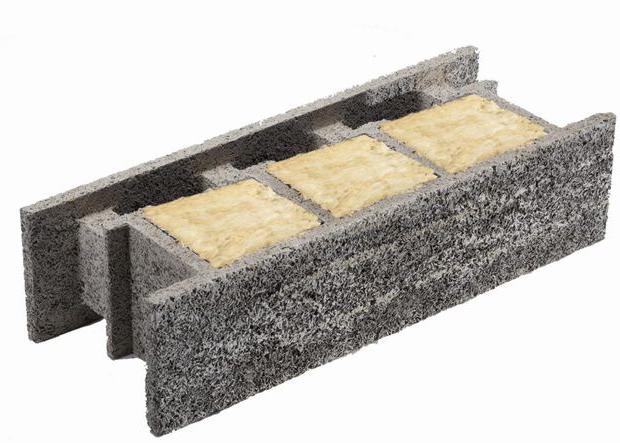