Разрушающие методы контроля — Энциклопедия по машиностроению XXL
Разрушающие методы контроля сварных соединений [c.152]Разрушающие методы контроля. Данные методы контроля являются выборочными. Их используют на стадии отладки технологических процессов, при освоении производства новых единиц продукции, при входном и текущим контроле и т. д. [c.211]
К разрушающим методам контроля сварных соединений относят механические испытания, которые производят в [c.212]
Выбор разрушающих методов контроля толщины покрытий [c.54]
Разрушающие методы контроля — такие, как испытание механических свойств, твердости, металлографический анализ, технологические пробы (например, испытание на осадку) и другие являются выборочными. Они приводят к порче одной или нескольких деталей в партии и не позволяют отделить в партии годные детали от бракованных.
Применение разрушающих методов контроля паяного изделия оговаривается техническими условиями на изделие. [c.360]
Разрушающие методы. При разрушающих методах контроля паяных изделий испытанию до разрушения подвергают непосредственно изделие, образцы, вырезанные из взятого от партии изделия, или образцы, вырезанные из свидетеля , т. е. паявшегося по той же технологии изделия, пред- [c.370]
Не разрушающие методы контроля [c.191]
К разрушающим методам контроля относят механические испытания, металлографию, коррозионные испытания, технологические пробы на свариваемость и др. РК обычно дает возможность получить количественные характеристики качества соединения (например, прочность соединения на растяжение) и точно определить вид (природу) дефекта. Недостатком РК является то, что испытания проводятся на образцах-свидетелях, моделях, реже на готовых изделиях, но не на тех объектах, которые в дальнейшем применяются в эксплуатации.
Механические испытания и изучение макро- и микроструктуры сварных соединений относятся к разрушающим методам контроля. Методика механических испытаний должна учитывать условия эксплуатации изделия. В ряде случаев механические испытания проводятся на стендах, имитирующих условия работы изделия. Однако чаще испытания проводятся на стандартных образцах. Это позволяет сравнить между собой результаты испытаний свойств соединений, полученных в различных условиях или различными сварщиками (например, при аттестации сварщиков). При механических испытаниях определяют предел прочности металла на растяжение, усталостную прочность при знакопеременных нагрузках, пластичность металла по предельному углу загиба и относительному удлинению образца при растяжении, ударную вязкость, твердость.
Статистические методы управления качеством и выборочный контроль не исключают применения разрушающих методов контроля, а, наоборот, базируются на статистическом материале, полученном этими методами. [c.554]
РАЗРУШАЮЩИЕ МЕТОДЫ КОНТРОЛЯ [c.378]
Методы контроля подразделяют на разрушающие и неразрушающие. Разрушающему контролю подвергают обычно опытные отливки для установления соответствия их качества ТУ и необходимости доработки технологии литья перед запуском в серийное производство, а также детали, технологический процесс изготовления которых изменился. Разрушающие методы контроля предусматривают определение химического состава материала отливок, механических свойств отдельно отлитых или вырезанных из тела отливки образцов, изучение ее макро- и микроструктуры, в том числе определение балла пористости и неметаллических включений.
Разрушающие методы контроля……………………………………….378 [c.394]
Технологические методы испытаний (табл. 4.55) основаны на доведении металла зоны термического влияния или шва сварных образцов до образования холодных трещин под действием остаточных сварочных напряжений. После сварки образцы выдерживают при нормальной температуре в течение 20 ч. Испытывают 3-5 образцов одного типа. Образование холодных трещин выявляют путем периодического визуального осмотра сварного соединения, а на образцах, не разрушившихся при испытаниях и не имеющих визуально наблюдаемых трещин, их выявляют с помощью не-разрушающихся методов контроля и металлографического исследования.
Замена громоздкого испытательного и вспомогательного оборудования, используемого для разрушающих методов контроля, малогабаритными приборами и АСК экономит производственные площади. Машины, собранные из деталей, прошедших контроль неразрушающими способами, гораздо реже выходят из строя и, соответственно, реже требуют ремонта, замены частей и деталей. Чтобы более наглядно представить себе, какую от этого выгоду получает народное хозяйство, скажем, что себестоимость запасных частей к тракторам составляет 80% стоимости самих тракторов. Применение неразрушающего контроля на тракторных заводах позволяет сократить эту цифру на 10—15%. Если мобилизовать усилия и средства на создание комплекса автоматических средств неразрушающего контроля качества всех материалов, выпускаемых промышленностью, то потенциал металлургической, хи-
[c.535]
Организация контроля сварных изделий. Проверка качества готовых сварных изделий может осуществляться разрушающими методами контроля сварных соединений и швов, неразрушающими методами контроля сварных швов и неразрушающими методами контроля сварного изделия в целом. [c.263]
К разрушающим методам контроля относятся механические испытания, технологические пробы, металлографические исследования, химический анализ, коррозионные испытания, испытания на свариваемость. Прочность и пластичность сварных соединений проверяют с помощью механических испытаний специально изготовленных образцов. ГОСТ 6995—54 предусматривает следующие виды механических испытаний испытание металла шва на растяжение на образцах Гагарина (рис. 259, а) испытание сварного соединения на растяжение (рис. 259, б) испытание металла шва и зоны термического влияния на ударный изгиб (рис. 259, е) испытания сварного соединения на изгиб (рис. 259, г) определение твердости сварного соединения.
К разрушающим методам контроля относятся технологическая проба, механические испытания, металлографические исследования, химический анализ, коррозионные испытания, испытания на свариваемость. [c.338]
Методы разрушающего контроля. Разрушающие испытания проводят обычно на контрольных образцах, реже на моделях и на самих изделиях. Контрольные образцы сваривают из того же материала и по той же технологии, что и сварные соединения изделий. К разрушающим методам контроля относятся механические испытания металлографические исследования химический анализ коррозионные испытания исследования на свариваемость.
К разрушающим методам контроля относятся механические испытания, металлографические исследования, а также специальные испытания с целью получения тех или иных характеристик (например, усталостной прочности, коррозионной стойкости). Эти испытания проводят на специальных образцах, вырезанных из сварных соединений. [c.438]
В настоящее время все большее признание приобретают не-разрушающие методы контроля изделий с помощью проникаю-ши.х излучений радиоактивных изотопов. [c.62]
Контроль качества сварных соединений разрушающими методами контроля производится путем определения соответствующих физико-механических характеристик. Методы определения большинства этих характеристик стандартизованы. Соответствующие ГОСТы и приборы для испытаний приведены в табл.
Механические испытания швов сварных соединений из пластмасс на растяжение, напряженный изгиб и ударный изгиб, т. е. разрушающие методы контроля, проводят в соответствии с ГОСТ 16971—71. [c.189]
Разрушающие методы контроля. При разрушающих методах контроля паяные соединения и паяные изделия испытывают на [c.249]
В настоящей статье описаны некоторые наиболее важные виды испытаний, применяемые для оценки покрытий. Сюда входят частные методы, не разрушающие методы контроля и испытания образцов в условиях, аналогичных эксплуатационным. Далеко не все эти методы используются организациями, занимающимися изучением покрытий. Здесь описаны только наиболее широко распространенные методы испытаний и наиболее известные их варианты. Специфические детали отдельных методов не рассмотрены. [c.230]
Решение этих проблем возможно при условии организации на постоянной основе сертификационных испытаний металла труб, используя для этого неразрушающие и разрушающие методы контроля.
[c.35]
СИР — спектрометрия ионного рассеяния ИНС — ионно-нейтрализационная спектроскопия ИМАР — ионный микрозонд с анализом рентгеновских лучей ПИР — рентгеновское излучение, создаваемое протонами. Ионные пучки вызывают наибольшие изменения в поверхностном слое [1, с. 60—101] это — разрушающий метод контроля. [c.154]
На рис. 10.9 показаны некоторые методы, основанные на ионном облучении. Помимо МСВИ, это СИР — спектрометрия ионного рассеяния, ИНС — ионно-нейтрализационная спектроскопия, ИМАР — ионный микрозонд с анализом рентгеновских лучей и ПИР — рентгеновское излучение, создаваемое протонами. Ионные пучки вызывают набольшие изменения в поверхностном слое 110.4] это — разрушающий метод контроля.
В последнее время много внимания уделялось вопросам механизации вспомогательных операций, сопутствующих сварке. Одним из важнейших узлов является узел гратосъема. Многие стыковые машины снабжаются специальными блоками и приборами контроля параметров процесса сварки, которые позволяют с большей достоверностью оценить качество сварных соединений без применения разрушающих методов контроля.
[c.187]
Заключительной операцией в технологическом процессе приформовки является контроль качества соединения. При визуальном контроле проверяют наличие складок в материале, смещений наружных слоев накладок, разрывов армирующих наполнителей, участков с неоднородной пропиткой связующим. С помощью разрушающих методов контроля определяют прочность соединения образцов при различных видах нагружения. [c.563]
Сбор сведений и контроль состояния сооружения может выполняться с помощью разрушающих и неразрушающих методов. При этом разрушающие методы контроля применяют в тех местах, где с помощью неразрушающих методов установлено опасное состояние сооружения. Одним из наиболее распространенных методов неразрущающего контт [c.172]
Лаборатории при монтажных управлениях, как правило, состоят из двух групп группы неразрушающих и группы разрушающих методов контроля. Первая занимается рентгено- и 7-дефектоскопией, ультразвуковым и магнитографическим контролем, а вторая — механическими испытаниями образцов, которые сварщики заваривают при дипломировании, и образцов из контрольных сварных соединений. Структура лабораторий при трестах зависит от характера работ, выполняемых монтажными организациями треста. Часть лабораторий, особенно в трестах, выполняющих санитарно-технические работы, по структуре аналогична лабораториям монтажных управлений. В лабораториях трестов, выполняющих механомонтажные работы, группа по механическим испытаниям обычно отсутствует, но иногда создаются группы по металлографическому исследованию и рентгеновскому контролю. Лаборатории при монтажных управлениях подчиняются непосредственно руководству мон-
[c.256]
К разрушающим методам контроля качества сварных соединений принято относить следующие испытания механические (на растяжение, изгиб, ударную вязкость и др.), металлографические, коррозионные, химические. Особо следует вьщелить так называемые безобраз-цовые испытания механических свойств металла. Например, на стыках труб действующих энергоблоков периодически в зоне сварного шва металл зачищают и осуществляют замер твёрдости, металлографические, рентгеноструктурные и другие испытания. При этом нарушают целостность материала, но не изделия в общем.
[c.221]
МЕТОДЫ КОНТРОЛЯ КАЧЕСТВА СВАРНЫХ СОЕДИНЕНИЙ
Что это такое?
Методы контроля качества сварных соединений — это совокупность способов оценки состояния сварных стыков газопроводов на пригодность к эксплуатации.
Для чего это нужно?
Контроль качества сварных соединений — это важная и обязательная часть сварочных работ и работ по оценке состояния газопроводов. Проверка состоятельности сварного шва входит в систему объективного контроля качества газовых магистралей и является эффективным способом оценки их надежности и безопасности.
СПРАВКА:
В Обществе при проведении текущего и капитального ремонта магистральных газопроводов в качестве основных методов неразрушающего контроля используются визуально-измерительный, радиографический и ультразвуковой.
В частности, после сварки стыков невооруженным глазом можно рассмотреть лишь часть дефектов, например, наружные трещины и поры, непровары, подрезы. Большая часть несовершенств может быть скрыта в глубине металла или иметь такие малые размеры, что обнаружить их можно только с использованием специальных приборов и материалов. Существуют разные методы контроля сварных швов, различающихся по принципу действия, способности к обнаружению тех или иных видов дефектов, техническому оснащению. Методы контроля сварных соединений подразделяются на разрушающие и неразрушающие. Последние являются наиболее широко используемыми в газовой отрасли.
Какие бывают методы?
Неразрушающий контроль представляет собой целый спектр методов, позволяющих определять недопустимые дефекты без нарушения целостности сварного соединения газопровода. На практике используют более десятка видов неразрушающего контроля: визуально-измерительный, радиационный, ультразвуковой, магнитный, акустико-эмиссионный, метод воздействия проникающими веществами (капиллярный и течеискание), вибродиагностический, тепловой, электрический, оптический, вихретоковый, метод напряженно-деформированного состояния. Применение определенного метода зависит от объекта контроля и категории ответственности участка.
Как это происходит?
Широкое распространение в газовой промышленности получили физико-технические методы неразрушающего контроля. Существует несколько эффективных способов проверки качества сварного соединения с применением специального оборудования.
Ультразвуковой метод основывается на избирательном отражении ультразвукового излучения от структур с разными акустическими характеристиками. Направленная аппаратом ультразвуковая волна, пересекая материал, отражается от его обратной поверхности и возвращается, где обнаруживается специальным датчиком. Если в толще металла присутствует дефект, то датчик уловит любое волновое искажение.
Сущность радиационного вида контроля заключается в поглощении и рассеивании рентгеновских лучей и гамма-излучения в местах наличия дефектов. Излучение подается с одной стороны при помощи специального источника, а на противоположной стороне устанавливается чувствительная пластина (пленка). Лучи, проходя через металл, облучают пленку, оставляя в местах дефектов более темные пятна из-за меньшего поглощения.
Магнитная дефектоскопия осуществляется с помощью дефектоскопов, формирующих электромагнитное поле внутри сваренных металлов. Контроль проводится двумя способами. При магнитопорошковом — наносится ферромагнитный порошок, который иллюстрирует магнитное поле со сгущением в местах дефектов. Более современный магнитографический метод подразумевает наложение ферромагнитной пленки, на которой проявляется полная картина магнитных линий.
Как у нас?
Специалисты ООО «Газпром трансгаз Ставрополь» используют многие методы разрушающего и неразрушающего контроля. Часть методов применяется при выполнении сварочно-монтажных работ на магистральных газопроводах при текущем и капитальном ремонте, часть — при диагностическом обследовании действующих объектов газовых магистралей.
Выполнение таких работ обеспечивают Лаборатория контроля качества сварки и диагностики на базе Невинномысского ЛПУМГ, а также служба диагностики технологического оборудования Инженерно-технического центра. Кроме того, в каждом филиале Общества трудятся аттестованные специалисты, ответственные за строительный контроль.
Служба по связям с общественностью и СМИ
ООО «Газпром трансгаз Ставрополь»
Методы и виды контроля качества сварных соединений
Методы и виды контроля качества сварных соединений
По своей сути, методы контроля качества сварных соединений можно разделить на две группы: методы разрушающего контроля и методы неразрушающего контроля сварных соединений.
Если виды контроля качества сварных соединений, называемые разрушающими, применяются только к контрольным образцам, для выяснения общих механических свойств, то неразрушающие методы контроля качества сварных соединений служат для массового контроля качества продукции. Так, пооперационный контроль качества сварных соединений производится в большинстве случаев только неразрушающими способами контроля качества соединений, а объем контроля сварных соединений визуально-измерительным методом составляет 100%.
Рассмотрим некоторые неразрушающие методы контроля сварных соединений. Все методы контроля сварных швов можно найти в ГОСТ 18353-79 «Контроль неразрушающий. Классификация видов и методов».
Контроль качества сварных швов и соединений начинается с визуально-измерительного метода. РД 03-606-03(статус: действующий) регламентирует порядок проведения контроля сварных швов. Контроль качества сварного шва ВИК обязателен, так как позволяет менее затратным способом выявить дефекты.
Магнитографический контроль сварных соединений основан на обнаружении полей рассеивания, образующихся в местах расположения дефектов при намагничивании контролируемых сварных соединений. Поля рассеивания фиксируются на эластичной магнитной ленте, плотно прижатой к поверхности шва. Запись производят на дефектоскопе. Дефектоскопия сварных швов магнитнопорошковым методом применяется только для проверки сварных соединений металлов и сплавов небольшой толщины, обладающих ферромагнитными свойствами.
К радиационной дефектоскопии относятся рентгенографический контроль сварных соединений и гаммаграфический контроль сварных соединений. Эти методы заключаются в получении на рентгеновской пленке или экране изображения сварного соединения, просвечиваемого рентгеновским или гамма-излучением.
Ультразвуковой контроль основан на способности ультразвуковых колебаний отражаться от поверхности, разделяющей среды с разными акустическими свойствами. УЗ контроль сварных швов относится к акустическим методам неразрушающего контроля. Ультразвуковая толщинометрия — одним из акустических методов, для определения технического состояния технологического оборудования. Приборы толщинометрии весьма разнообразны и подбираются индивидуально.
Капиллярная дефектоскопия сварных швов предназначена для выявления невидимых или слабо видимых дефектов. Основой для этого метода дефектоскопии сварных швов послужила способность жидкостей втягиваться и заполнять даже мельчайшие каналы.
Классификация методов контроля качества РЭСИ.

Министерство образования Республики Беларусь
Белорусский государственный университет информатики и
радиоэлектроники
кафедра РЭС
РЕФЕРАТ
на тему:
«Классификация методов контроля качества РЭСИ. Методы неразрушающего контроля РЭСИ»
МИНСК, 2008
Классификация методов контроля качества РЭСИ
Стандартом на термины и определения в области испытаний и контроля качества продукции понятие контроль формулируется как проверка соответствия качества продукции (изделия) установленным требованиям.
Проверка показателей
качества технических устройств (в том
числе изделий РЭСИ
или технологических процессов их
производства) техническим условиям
(ГОСТ 15504-81)
проводится подразделениями ОТК служб
управления качества радиоэлектронного
комплекса предприятий.
Технический контроль проводится с целью:
получения первичной информации о фактическом состоянии объекта и показателях его качества;
сопоставления первичной информации с заранее установленными в технической документации требованиями, критериями, нормами. Полученная таким образом информация об отклонении фактических показателей качества от заданных называется вторичной.
Вторичная информация используется для выработки управляющего решения и направлена на объект контроля. При этом решается главная задача управления качеством — совершенствование конструкции изделия и сведение к минимуму выявленных отклонений в технологическом процессе.
Объект контроля — это предметы
труда (материалы, РЭСИ, техническая
документация),
средства труда или технологическое и
общезаводское оборудование, технологическая
оснастка и инструмент, процессы создания
продукции, труд исполнителей, условия
труда и тд. Объект
контроля обладает
рядом определенных признаков (свойств),
по совокупности
которых оценивается его качество.
Контролируемые признаки (свойства),
как известно, в квалиметрии называются
показателями качества.
Методы контроля — это совокупность правил применения определенных принципов для осуществления контроля: технология проведения, количество контролируемых параметров, требуемая точность измерений.
Средства контроля — это изделия (контрольные и исполнительные стенды, измерительная и регастрирующая аппаратура и т.п.) и материалы, применяемые при контроле.
Классификационная группировка контроля по определенному признаку называется видом контроля. Классификация основных видов контроля качества продукции представлена в таблице 1 и схеме, показанной на рис. 1.
Таблица 1 – Виды контроля РЭСИ
Признак классификации | Вид контроля |
Стадия технического контроля | Контроль опытного образца, производственный контроль, контроль при эксплуатации |
Стадия производственного процесса | Входной, операционный, контроль качества готовой продукции, транспортирования, хранения |
Вид воздействия | Разрушающий, неразрушающий |
Объем контролируемой продукции | Сплошной, выборочный |
Цель контроля | Приемочный. |
Характер контроля | Инспекционный, летучий |
Принимаемое решение | Активный, пассивный |
Применение средств контроля | Органолептический, визуальный, инструментальный |
Характер поступления продукции на контроль | Партиями, непрерывный |
Контролируемый параметр | По количественному признаку, по качественному признаку, по альтернативному признаку |
Степень участия оператора в контроле | Ручной, автоматизированный |
В зависимости от
технической сложности контролируемых
изделий различают сплошной
контроль,
при котором контролируется каждая
единица продукции (например, проверка
качества функционирования бортовой
радиолокационной станции самолета,
компьютерной техники, систем управления
и т. п.), и выборочный,
при котором решение о качестве
контролируемой продукции принимается
по результатам проверки одной или
нескольких выборок из большой партии
продукции
(микросхем, резисторов, трансформаторов,
плат, приборных корпусов,
штампованных или пластмассовых литых
деталей и т.д.).
В зависимости от возможностей дальнейшего использования проконтролированной продукции методы контроля подразделяются на разрушающие и неразрушающие.
Разрушающий контроль применяется для оценки показателей качества материалов, деталей, сборочных единиц и изделий в целом. Этими методами пользуются, например, при испытаниях изделий РЭС на надежность (проверка причин отказов). После проведения разрушающего контроля продукция считается непригодной для дальнейшего использования по назначению.
Разрушающий контроль
Довольно часто необходимо гарантировать возможность эксплуатации конструкционного материала или соединения в заданных условиях. Наиболее надёжную информацию может обеспечить разрушающий контроль. Он представляет собой совокупность различных методов проведения измерений и выявления параметров, которые после своего завершения предполагают невозможность дальнейшей эксплуатации объектов исследования. Наша лаборатория разрушающего контроля готова предложить свои услуги для всех заинтересованных лиц. Проводится проверка нескольких образцов из партии, количество которых зависит от конкретной ситуации.
Разрушающие методы контроля
Когда осуществляются проверки, необходимо получить наиболее достоверный результат, что требует использования различных вариантов проведения испытаний. Следует выяснить важные параметры и установить пределы прочности, а также надёжности. Для этого используются следующие разрушающие методы контроля:
- Определение механических свойств. Оно предполагает различные условия проведения замеров. Например, характеристики будут серьёзно отличаться при исследовании в ходе изменения температуры.
Как правило, выполняется замер в нескольких вариантах на интервале от -80 градусов до 250. Диапазон может быть изменён для конкретной ситуации.
- Анализ химического состава. Как правило, он проводится с использованием спектрального метода. Стандартным параметром для выяснения является определение химического состава металлов.
- Динамические испытания. Разрушающий контроль конструкционных материалов, а также их соединений, выполняемый в рамках подобных испытаний, предполагает осуществление ударного воздействия при различных температурах: пониженной, завышенной и комнатной.
- Исследования склонности материала подвергаться воздействию коррозии. Как правило, разрушающий контроль данного типа предполагает использование методик, ускоряющих процессы ржавления.
Перечисленные виды разрушающего контроля предполагают, что после их проведения может быть выполнено специальное исследование. Его задачей является выявление факторов, послуживших причиной разрушения объекта или соединения. Такая информация позволяет выявить методы улучшения характеристик. Следует сказать о том, что выше были перечислены далеко не все разрушающие методы контроля сварных соединений. Наша компания использует и другие варианты, что зависит от конкретной ситуации.
Макроанализ и микроанализ
Данные типы мероприятий относятся к категории металлографических исследований. Когда реализуются разрушающие методы контроля качества, макроанализ предполагает выявление дефектов, определение неоднородностей структуры с химической точки зрения и в ходе использования термической обработки. Анализ на микроскопическом уровне использует электронный и оптический микроскоп. Он позволяет определять саму структуру сплава и узнать о способах предшествующей исследованию обработки.
Преимущества работы с нашей компанией
Довольно часто у заинтересованных в сотрудничестве лиц возникает вопрос о том, какие условия они получат при обращении в нашу компанию. Мы готовы предложить ряд преимуществ, если проводить сравнение с конкурентами на этом рынке услуг:
- Доступный уровень цен.
Стоимость проведения работ не является минимальной, но предполагает разумный показатель.
- Аттестация лаборатории разрушающего контроля проводится точно в установленные сроки.
- Профессиональный подход к выполнению поставленных задач. Специалисты являются мастерами своего дела и постоянно проходят курсы для повышения квалификации.
- Минимальные сроки проведения работ. Мы ценим время своих клиентов и выполняем все мероприятия оперативно, но без потери в качестве.
- Наша компания сотрудничает на постоянной основе с большим количеством организаций, работающих в самых разных сферах.
Когда разрушающие методы контроля сварных соединений осуществлены, а информация обработана, клиент получает на руки все необходимые документы.
Экспертиза промышленной безопасности
Неразрушающий контроль и механические испытания сварных швов в Екатеринбурге
С 2005 года в нашей организации действует лаборатория неразрушающего контроля. В Екатеринбурге это одна из опытнейших лабораторий, где работают квалифицированные и ответственные специалисты. Мы проводим техническую диагностику и освидетельствование технических устройств тех производственных объектов, где высока вероятность аварий. Это химические, нефтегазовые предприятия, трубопроводы и др. Экспертиза с применением традиционных и новейших методов неразрушающего контроля проводится как на стадии строительства объектов, так и в процессе их эксплуатации. ООО «Корпорация «Энергокомплекс» имеет свидетельство об аттестации лаборатории и отвечает требованиям Системы неразрушающего контроля.
Компания «Энергокомплекс» в Екатеринбурге проводит техническое диагностирование оборудования, материалов и сварных швов разрушающими и неразрушающими методами контроля при возведении, монтаже, ремонте либо реконструкции особо опасных производственных объектов.
Области проведения неразрушающего контроля качества сварки
- Газораспределение и газоснабжение
- Горнорудная промышленность
- Нефтегазовый сектор
- Металлургия
- Котлонадзор
- Химически опасные и взрывопожароопасные производства
- Ж/д транспорт
- Строительство
- Подъемные сооружения
Испытания проводятся непосредственно на базе нашей лаборатории неразрушающего контроля сварных соединений либо на территории заказчика.
Методы технической диагностики и неразрушающего контроля
- Визуально-измерительный метод контроля.
Первичная диагностика заготовок под сварку и сварных швов.
- Радиационный (радиографический) метод контроля.
Высокоточное выявление размеров и характера скрытых дефектов внутри шва при помощи рентгена за короткое время. При необходимости к документам прилагаются снимки проверенных сварных соединений.
- Ультразвуковой метод контроля.
Определение внутренних дефектов сварных швов и металлических конструкций с помощью ультразвука.
- Ультразвуковая толщинометрия.
Метод, применяющийся в условиях, когда невозможно обойтись одними лишь механическими измерительными инструментами. УЗТ позволяет получить данные о толщине стенки изделия, имея доступ к нему только с одной стороны.
- Магнитопорошковый метод контроля.
Выявление скрытых дефектов изделий из ферромагнитных сплавов. Метод основывается на принципе магнитного рассеяния, которое возникает над дефектом при намагничивании объекта.
- Контроль проникающими веществами.
Определение наружных дефектов путем нанесения специальных индикаторных веществ — пенетрантов.
- Вибрационно-диагностический метод контроля
Контроль техсостояния объектов в режиме постоянного либо периодического слежения за уровнем вибрации.
- Электрический метод контроля
Обнаружение дефектов различных материалов; замер толщины стенок, покрытий и слоев; распределение металлов по маркам; контроль диэлектрических или проводящих материалов
Разрушающий контроль конструкционных материалов и соединений
Наша лаборатория имеет большой опыт в области проведения испытаний методом разрушающего контроля. В настоящее время с его помощью можно получить наиболее полную и верную информацию о возможности эксплуатации материала или соединения в тех или иных условиях. Однако данный метод имеет недостаток: продукция, прошедшая испытания, становится непригодной для дальнейшего использования.
Для исследования берутся отдельные образцы объекта контроля, затем делаются выводы о качестве всей партии.
Методы разрушающего контроля
- Статические испытания (на сжатие/растяжение, изгиб)
- Динамические испытания (на ударный изгиб)
- Исследования на стойкость к коррозии
- Измерение твердости материала по Бринеллю
- Сплющивание и расплющивание
- Металлографический контроль сварных швов
- Стилоскопирование на наличие легирующих элементов
Все методы механических испытаний материалов регламентированы государственными стандартами.
Исследования позволяют проверить правильность выбранных материалов, режимов и технологий; соответствует ли сварное соединение ТУ и иным нормативам, принятым в данной области. По результатам механических испытаний также оценивают квалификацию сварщика.
Лаборатория разрушающего и неразрушающего контроля компании «Энергокомплекс» готова предложить свои услуги для всех заинтересованных лиц. Мы имеем достаточный опыт в проведении исследований с помощью данных методов и все необходимое оборудование.
Заявки на контроль можно отравить на naks-man@mail.ru
Для расчета стоимости и проведения контроля желательно предоставить следующие данные: количество и размеры объектов контроля (диаметр и/или толщина), чертежи или схемы объектов контроля, нормативные документы на оценку качества и методику проведения контроля.
Свидетельство об аттестации:
Методы испытаний неразрушающие — Справочник химика 21
И наконец, на помощь авиастроителям пришел новый, набирающий силу метод испытаний — неразрушающий контроль, пришло внутривидение, способное предусмотреть возможную аварию, провести исследование всех критических точек и компонент во время изго- [c.42] Применение тех или иных методов должно быть оговорено в технических условиях на ремонт насоса конкретного типоразмера или в рабочих чертежах. Последовательность применения методов определяется технологическим процессом ремонта, однако внешний осмотр должен предшествовать любому другому методу, а гидравлическое испытание — неразрушающему контролю. [c.127]
Характеристики старения двухосновных и смесевых твердых топлив различны. Что касается двухосновных топлив, то процессы старения в них связаны главным образом с ограниченной стабильностью. Раньше при хранении ракет, снаряженных такими зарядами, даже употреблялся термин время безопасного хранения , однако большие усилия, предпринятые с целью стабилизации свойств этих топлив, привели к практически полному исключению названного фактора. В смесевых топливах нарушения характеристик, вызванные старением, проявляются как твердение или размягчение, повышение хрупкости или изменение адгезионных свойств. Для диагностики ТРТ весьма важны неразрушающие методы испытаний, и многие такие методы уже применяются [36].
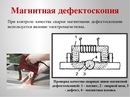
Основными документами, регламентирующими применение метода, являются ГОСТ 18442—80 Контроль неразрушающий. Капиллярные методы контроля , ГОСТ 23349—78 Дефектоскопы капиллярные. Общие технические требования и методы испытаний и ГОСТ 24522—80 Контроль неразрушающий капиллярный. Термины и определения . [c.55]
Контроль неразрушающий. Преобразователи ультразвуковые. Методы испытаний. [c.838]
При проведении люминесцентного капиллярного контроля руководствуются также ГОСТ 28369-89 Контроль неразрушающий. Облучатели ультрафиолетовые. Общие технические требования и методы испытаний . При использовании люминесцентных пенетрантов и систем для течеискания руководствуются ГОСТ 26182-84 Контроль неразрушающий. Люминесцентный метод течеискания . [c.733]
Книга предназначена для широкого круга работников топливно-энергетического комплекса и других отраслей народного хозяйства. Она может быть рекомендована студентам, аспирантам, инженерно-техническим и научным работникам, специализирующимся в области акустических и других физических методов исследования, испытаний, неразрушающего контроля и диагностики материалов и конструкций, в частности при подготовке к квалификационным экзаменам на право проведения акустического контроля. Возможно, читатель найдет применение идеям, изложенным в книге, там, где авторам не пришло в голову их искать. [c.7]
В качестве иллюстрации возможностей выборочного и сплошного технологического акустического контроля оболочек твэл с помощью описанного метода укажем на возможность оценки анизотропии предела текучести оболочек. При этом разрушающий метод заменяется неразрушающим, а производительность контроля по сравнению с обычными механическими испытаниями возрастает на два порядка. [c.256]
В связи с этим значительный практический интерес представляют неразрушающие методы испытаний, позволяющие снизить число образцов, например, по данным работы [213], в 40 раз. На рис. 3.17 показана блок-схема установки, применявшейся в этих испытаниях. [c.80]
В настоящей главе описываются основные методы испытания физических и физико-химических свойств клеев, определения статической и динамической прочности клеевых соединений, а также способов неразрушающего контроля их качества. [c.108]
ГОСТ 23702-90. Контроль неразрушающий. Преобразователи ультразвуковые. Методы испытаний. [c.21]
ГОСТ 28369-89. Контроль неразрушающий. Облучатели ультрафиолетовые. Общие технические требования и методы испытаний. [c.22]
Разработка ускоренных электрохимических неразрушающих методов испытания на МКК готовых изделий представляет собой важную задачу, в решении которой заинтересованы промышленные предприятия. [c.108]
Так как максимум сопротивления расслаиванию металлополимерных соединений связан с релаксационными свойствами полимеров, то для поиска условий его реализации (температура, скорость расслаивания, концентрация пластификатора и т.д.) можно воспользоваться методом релаксационной спектрометрии (механических потерь), т. е. неразрушающим методом испытаний. Сопоставление экспериментальных данных подтверждает, что характер влияния различных факторов на сопротивление расслаиванию соединений и механические потери одинаков. Например, максимум на температурной зависимости тангенса угла механических потерь вырождается при введении наполнителей [29] и увеличении степени кристалличности [30], смещается в область более низких температур при уменьшении скорости деформирования (частоты) и увеличении концентрации пластификаторов [22]. [c.26]
Новые клеи и выполненные на их основе клеевые соединения должны быть подвергнуты тщательному и всестороннему исследованию в условиях, максимально приближающихся к условиям эксплуатации. Для этого необходимо создание методов неразрушающего контроля клеевых соединений, экспресс-методов испытания клеев в процессе их получения, а также более подробное исследование влияния масштабного фактора на свойства клеевых соединений. [c.7]
Таким образом, связь между прочностными свойствами полимеров и их поведением при малых деформациях представляет большой интерес. В частности, измерения динамических свойств могут быть использованы в качестве неразрушающего метода испытаний при изучении прочностных свойств. [c.325]
Существуют разрушающие и неразрушающие методы испытаний клеевых соединений. Разрушающие испытания классифицируют по характеру напряженного состояния в соединении методы испытаний при неравномерном отрыве (испытания клеевых соединений жестких материалов испытания соединений, в которых один из субстратов гибкий или эластичный) [c.207]
Конструкция должна быть изготовлена под качественным контролем, так как окончательный продукт чувствителен к изменениям в исходных материалах и технологии. Для полного контроля процесса, от исходных материалов до контроля качества конечного продукта, необходим подбор методов испытаний, как разрушающих, так и неразрушающих. Стандартизация и использование широко признанных и надежных методов испытаний представляют конструктору полезные данные и критерий для максимального использования метода намотки. [c.24]
Методы диагностики технического состояния можно разделить на разрушающие и неразрушающие. К методам разрушающего контроля можно отнести предпусковое или периодическое гидравлическое испытание, а также механические испытания образцов, вырезанных из элементов. Неразрушающие методы предполагают применение физических методов контроля качества без нарушения работоспособности конструкции. [c.4]
Цель неразрушающих испытаний не сводится только лишь к обнаружению дефектов, а ставит задачи по контролю и оценке качества материала в исходном состоянии. Неразрушающие испытания служат инструментом для улучшения качества и контроля методов конструирования и технических процессов. [c.5]
Испытание отливок разрешается проводить после сборки и сварки в собранном узле или готовом сосуде пробным давлением, принятым для сосудов при условии 100% контроля отливок неразрушающими методами. [c.12]
Если по внешнему виду и результатам контроля неразрушающими методами швы контрольных стыков признаны удовлетворительными, то из стыков вырезают образцы для механических испытаний. [c.421]
Результат испытания металла заготовок на детали трубопроводов, аппаратов Результат проверки деталей машин, аппаратов, трубопроводов неразрушающими методами контроля [c.560]
По заданию групп технического надзора, ремонтных и других служб предприятия выполняет работы по механическим испытаниям, химическому и спектральному анализам металлов, металлографическому анализу, по неразрушающим методам контроля. [c.76]
Дефекты основного металла и сварных соединений приводят к образованию некогерентных границ зерен, коррозионно нестойких пленок, создают концентрацию макро- и микронапряжений, повышают термодинамическую неустойчивость дефектных участков поверхности и интенсифицируют их наводороживание и электрохимическое растворение. Поэтому для повышения надежности оборудования и коммуникаций, контактирующих с сероводородсодержащими средами, наряду с тщательным входным контролем соответствия материалов конструкций техническим условиям на их поставку и неразрушающим контролем монтажных сварных соединений, эффективными являются предпусковые гидроиспытания металлоконструкций давлением, создающим напряжения до 95% от минимального нормативного значения предела текучести металла [33, 34]. В ходе этих испытаний разрушаются участки основного металла и сварных соединений, содержащие потенциально опасные дефекты. Вокруг оставшихся неопасных дефектов образуются зоны остаточного сжатия, повышающего коррозионную стойкость сварных соединений. Кроме того, после гидравлических испытаний в 2-3 раза снижаются максимальные остаточные напряжения в зоне сварных соединений труб за счет пластического удлинения растянутых областей металла. Одновременно снижаются наиболее высокие монтажные напряжения в трубопроводах. Там, где по техническим причинам проведение гидроиспытаний не представляется возможным, для выявления недопустимых дефектов необходимо применять 100%-ный радиографический контроль сварных соединений и его 100%-ное дублирование ультразвуковым методом [25, 35]. [c.67]
Механические свойства основного металла и металла сварных соединений трубопроводов определяют путем испытаний на растяжение по ГОСТ 1497-84 и ГОСТ 6996-66 соответственно, а также на ударный изгиб на образцах Шарпи — по ГОСТ 9454-78 и ГОСТ 6996-66 соответственно. Предел текучести и временное сопротивление металла определяют также неразрушающим методом в зонах контроля сварных соединений с помощью переносных твердомеров по ГОСТ 22761-77 и ГОСТ 22762-77. Выполняют не менее пяти замеров и за искомую твердость принимают их среднее арифметическое значение [74]. [c.164]
Данная серия испытаний показала, что использованный энергетический критерий обнаружения существенного развития трещин не является однозначным и его можно применять только совместно с результатами локации источников и их идентификации другими методами и средствами. Погрешность определения положения источников акустической эмиссии оказалась соизмеримой с толщиной стенок сосудов. Обнаруженные в промышленных сосудах источники эмиссии представляли собой мелкие трещины, не фиксируемые другими методами неразрушающего контроля. Все испытанные аппараты были признаны пригодными к эксплуатации, В рассматриваемом случае метод АЭД оказался более консервативным. [c. 185]
Тепловые методы контроля качества ориентированы на применение универсальной теплоизмерительной или тепловизионной аппаратуры для получения и переработки информации о тепловом излучении контролируемого объекта. С помощью такой аппаратуры в зависимости от потребностей можно получать одномерную или двумерную информацию, причем ее обработка производится специализированными или универсальными ЭВМ. Стало возможным подавление самого сильного мешающего фактора — вариации коэффициента теплового излучения контролируемого объекта, определяемого состоянием его поверхности. Усилия ученых и инженеров направлены в первую очередь на улучшение эксплуатационных характеристик аппаратуры теплового контроля, в частности на создание первичных измерительных преобразователей с выходным сигналом большей величины, например, за счет эффектов накопления энергии излучения, а также на применении электрического охлаждения взамен неудобной заливки жидкого азота. Важную роль имеет разработка методик проведения контроля, обеспечивающих высокую достоверность испытаний для конкретных изделий, особенно сложной конструкции. В ближайшее время значение тепловых методов в неразрушающем контроле будет возрастать в связи с разработкой качественной универсальной аппаратуры контроля и пригодности этих методов для контролй самых разнообразных материалов, промышленной продукции и решения многих задач контроля качества. Значительные расстояния, на которых тепловыми методами могут обнаруживаться дефекты энерготрасс, промышленного оборудования и других объектов, а также быстрота анализа, в том числе и с помощью ЭВМ, делает их незаменимыми для оперативного контроля. [c.359]
Рассмотрены различные типы клеев на основе полимерных композиииГ5 и технологические приемы склеивания ими разнообразных материалов. Даны рекомендации по выбору клеев и оптимальных режимов склеивания. Особое внимание уделено контролю качества и ремонту клеевых соединений, методам испытания, в том числе неразрушающему контролю. Рассмотрены вопросы техники безопасности при работе с клеями. [c.2]
Технические требования на материалы можно также отнести к рекомендованным методам испытания, например В5 18 [18], В8 1639 [19], В8 131 [20], АЗТМ 393-66Л21]. Для материалов частных видов существуют специальные методы неразрушающих испытаний, например для поковок ВЗ 4214 [22] и АЗТМ А388-67 [23], для слитков ВЗ 4080 [24], для труб малого и среднего диаметров ВЗ 3889 [25]. [c.290]
В СТП по функции ведомственного контроля качества и испытаний про дукцни необходимо регламентировать порядок организации и методы испытаний продукции в процессе ее разработки организацию и техническое оснащение входного, операционного, приемочного контроля и испытаний продукции технологию контрольных операций и определение их мест в общем технологическом процессе применение статистического, неразрушающего и автоматического контроля порядок предъявления продукции на контроль порядок проведения летучего и инспекционного контроля порядок учета и анализа брака порядок разработки мероприятий по результатам ведомственных проверок качества продукции и т. д. [c.46]
Виброреометрия. Этот метод относится к динамическим неразрушающим методам испытаний резиновых смесей в процессе вулканизации. В виброреометрах, которые подразделяются на приборы роторной (метод А) и безроторной конструкции (метод Б), материал подвергается знакопеременному периодическому сдвиговому деформированию (вибровоздействию) при сравнительно малых амплитудах, чем достигается сохранение исходной надмолекулярной структуры образца (в отличие от испытаний в условиях стационарного сдвига). Наибольшее распространение в шинной и резинотехнической промышленности получили виброметр роторного типа Монсанто-100 и отечественные безроторные приборы типа РВС и РВМ. В приборе Монсанто-100 рабочий орган (биконический диск) совершает круговые колебания в закрытой рабочей камере с амплитудой Г, 3° и 5° при частоте 100 мин . Образец в рабочей камере находится под давлением и при заданной температуре (до 300 °С). [c.93]
Ползучесть при кратковременных нагружениях связана практически только с деформациями упрочнения. Методы испытаний, основан11ые на таком деформировании, имеют большое значение для оценки материалов по следующим причинам 1) испытания при кратковременном нагружении ироводятся очень быстро 2) в результате испытаний не происходит разрушения материала, поэтому их можно проводить непосредственно на изделиях (неразрушающие методы испытаний) 3) в процессе испытания, если деформации невелики, структура материала существенно не изменяется, т. е. результаты характеризуют исходную структуру материала, сильно зависящую от всей предыстории испытуемого объекта 4) методы кратковременных испытаний чрезвычайно чувствительны к малейшим различиям в материалах. [c.43]
Есть основания предполагать, что >в будущем наибольшее развитие получат неразрушающие методы испытаний, поскольку разрушающие методы обладают рядом существенных недостатков. Во-первых, процесс разрушения всегда носит локальный характер, поэтому используя его для оценки свойств материала, нельзя относить результаты измерений ко всей массе испытуемого образца. Во-вторых, разрушение всегда оценивается конечным результатом испытания, и если в процессе испытания структура материала изменяется, то неизвест-5Ю, к какому состоянию относить эти результаты к начальному или к конечному. И, наконец, в-третьих, часто важно иметь возможность оценить свойства материала в изделии, не разрушая его. [c.70]
Использование неразрушающих методов ограничивает применение разрушающих методов испытания, которые требуют много времени на подготовку, проведение и оценку полученных данных, а также больших материальных расходов. Неразру-шающне испытания можно проводить по ходу технологического процесса склеивания и в случае необходимости на каждом изделии. Однако при использовании неразрушающих методов капиталовложения, так же как требования к квалификации работников, выше. [c.217]
Пробою обычно предшествует частичный разряд в мельчайших порах внутри материала, поэтому усилия исследователей направлены на выявление очагов частичного разряда путем измерения tgo, воздействия таками высокой частоты или ультразвуковыми колебаниями. Установки и методы, применяемые в кабельной, электромашиностроительной, анпаратостроительной и конденсаторной промышленности, обнаруживают очаги ионизации только больших размеров. На международной конференции яо неразрушающим методам испытаний, происходившей в Токио в 1960 г., проф. Малецкий (Польша) сделал сообщение, касавшееся замены определения электрической прочности фарфора исследованием сравнительно больших очагов ионизации при помощи ультразвуковых импульсов. Промышленность пластических iMa интересует лроблема обнаружения мельчайших очагов ионизации величиной, измеряемой в микронах и долях микрона в тонких пленках эта проблема еще не разрешена. [c.233]
И 0,45 мкм. Фирма Майкрофилтрейшн Системе осуществляет проверку своих мембран с порами диаметром 0,1 мкм, используя культуру бактерий My oplasma laidlawii, клетки которых проходят сквозь поры размером 0,2 мкм. Фирма Пол компани испытывает свои мембраны с порами диаметром 0,1 мкм, используя один из штаммов бактерий, обнаруженных в воде и имеющих размеры в пределах 0,08—0,13 мкм. За исключением особых случаев, таких, как промышленное производство вакцин и инъекционных растворов, остается не ясным, следует ли столь трудоемкий метод испытания, как метод задержки бактерий, широко использовать на практике, за исключением изготовителей мембран, применяющих этот метод при контроле качества продукции в процессе ее производства. Целостность мембраны можно установить также и методом пузырька, описанным в разд. 4.2 этот метод позволяет осуществить неразрушающий контроль, в то время как мембрана, испытанная по методу задержки бактерий, очевидно, непригодна для дальнейшего использования. [c.101]
Контроль качества паяных пластинчатых теплообменников осуществляется неразрушающими методами. Пдотность паяных швов проверяется опрессовкой сжатым воздухом избыточным давлением 1,5 кгс/см . Теплообменник в сборе проходит гидравлические испытания. [c.196]
Дефектация. При проверке технического состояния (дефектации) составных частей насосов применяют один из следующих методов (или их сочетания) внещний осмотр и измерения гидравлическое испытание на плотность и прочность неразрушающий контроль (акустический, капиллярный, магнитный, электромагнитный и т. д.). [c.127]
Количество ежегодно испытываемых дефектных труб должно составлять 5% от числа ремонтируемых участков трубопровода. Необходимо проводить не менее одного гидроиспытания в год при осуществлении за этот период более десяти вырезок дефектных труб одного типоразмера и из одной марки стали. Для испытаний сосудов или участков трубопровода на герметичность и прочность, а также для гидроиспытаний поврежденных труб применяют неразрушающие методы контроля развития дефектов УЗК, метод натурной тензометрии с использованием отечественной и импортной (например, прибор типа 8ТКЕ55САЫ 500 С) аппаратуры. В случае обнаружения дефектов, повреждений элементов конструкций, которые требуют проведения дополнительных исследований методом акустической эмиссии (АЭК), диагностику технического состояния объекта осуществляют методом АЭК в соответствии с нормативно-техническими документами [83, 121]. [c.165]
Сравнение результатов оценки поврежденносги колонного аппарата методами неразрушающего (двухпараметрического) и разрушающего (испытание плоских образцов на растяжение) показывает, что двухпарамет рический методконтроля имеет вполне приемлемую точность при сущест венном снижении трудоемкости диагностирования. [c.78]
NDT (неразрушающий контроль): полное руководство
NDT означает неразрушающий контроль. Он относится к набору методов проверки, которые позволяют инспекторам оценивать и собирать данные о материале, системе или компоненте без их постоянного изменения.
NDT также может называться:
- NDE (неразрушающий контроль или оценка)
- НДИ (неразрушающий контроль)
В полевых условиях NDT часто используется как общий термин для обозначения методов неразрушающего контроля, инструментов контроля или даже всей области неразрушающего контроля.
Для коммерческого применения цель неразрушающего контроля — обеспечить надлежащее обслуживание критически важной инфраструктуры во избежание катастрофических аварий.
Хотя методы неразрушающего контроля обычно связаны со случаями промышленного использования, такими как проверка слабых мест в котле, используемом на нефтеперерабатывающем заводе, использование в медицине на самом деле является одним из наиболее распространенных. Например, беременная мать, проходящая ультразвуковое исследование для проверки здоровья ее ребенка, будет считаться вариантом использования неразрушающего контроля, как и получение рентгеновского снимка или МРТ, чтобы узнать больше о травме.
Но важно отметить, что неразрушающий контроль не обязательно требует использования специальных инструментов или каких-либо инструментов вообще.
Например, когда инспекторы на промышленных предприятиях осматривают внешнюю часть сосуда высокого давления невооруженным глазом, это подпадет под обозначение неразрушающего контроля, поскольку они собирают данные о состоянии котла, не повреждая его. С другой стороны, использование сложного инструмента, такого как ультразвуковой датчик, для поиска дефектов в определенном материале или активе также будет называться неразрушающим контролем.
Независимо от конкретного варианта использования, основная общность всех этих примеров — это сбор данных ненавязчивым образом.
Вот содержание, которое поможет вам ориентироваться во всей информации, относящейся к неразрушающему контролю, содержащейся в этой статье:
Что такое неразрушающий контроль — более детальный взгляд
Мы уже рассмотрели, что означает NDT и как эта фраза используется в полевых условиях. Теперь давайте углубимся и более внимательно рассмотрим некоторые детали, которые управляют миром неразрушающего контроля.
Разрушающий и неразрушающий контроль
Прежде чем идти дальше, мы должны пояснить, что есть некоторые методы, используемые для тестирования материалов, которые изменяют — или даже повреждают и разрушают — проверяемые материалы.
Использование этих методов называется разрушающим тестированием.
При разрушающем испытании кусок материала может быть соскребен для анализа или изменен каким-либо образом на месте.
Вот несколько примеров:
- Макрорезка. Макросрезы позволяют испытать небольшой участок сварного материала путем его полировки и травления для исследования.
- Испытание на растяжение. Также называемый испытанием на растяжение, это метод разрушающего испытания, в котором используется контролируемое натяжение, прикладываемое к материалу образца, чтобы увидеть, как он реагирует.
Напряжение можно применять для испытания определенных нагрузок или условий или для проверки точки разрушения материала.
- Испытание на трехточечный изгиб. При испытании на 3-точечный изгиб исследуется прочность и гибкость (или пластичность) материала путем взятия его образца, называемого купоном, и его изгиба в трех точках под заданным углом.
Прочтите наше руководство по разрушающему тестированию.
Коды и стандарты неразрушающего контроля
Методы неразрушающего контролямогут использоваться для всех видов проверок. Но одними из наиболее важных видов неразрушающего контроля являются такие активы, как котлы и сосуды под давлением, которые могут быть невероятно опасными, если не будут обслуживаться должным образом.
Поскольку надлежащее обслуживание этих активов так важно для безопасности тех, кто работает поблизости (или даже на расстоянии, когда дело доходит до атомных электростанций), в большинстве стран есть законы, требующие от компаний соблюдения определенных правил и стандартов инспекций при проведении инспекций. .
Эти стандарты и кодексы обычно требуют периодического проведения проверок в соответствии с конкретными инструкциями. Для большинства активов, представляющих наибольший риск, эти проверки должны проводиться сертифицированным инспектором и утверждаться сертифицированным свидетелем, работающим в официальном инспекционном органе.
Вот наиболее популярные в мире организации, создающие стандарты и нормы неразрушающего контроля:
- API (Американский институт нефти)
- ASME (Американское общество инженеров-механиков)
- ASTM (Американское общество испытаний и материалов)
- ASNT (Американское общество неразрушающего контроля)
- COFREND (Французский комитет по исследованиям неразрушающего контроля)
- Группа CSA (Канадская ассоциация стандартов )
- CGSB (Канадский совет по общим стандартам)
Вот основные причины, по которым неразрушающий контроль используется таким количеством компаний по всему миру:
- Экономия .
Наиболее очевидный ответ на этот вопрос заключается в том, что неразрушающий контроль более привлекателен, чем разрушающий контроль, потому что он позволяет исследуемому материалу или объекту пережить исследование без повреждений, тем самым экономя деньги и ресурсы.
- Безопасность . НК привлекателен еще и тем, что почти все методы неразрушающего контроля (кроме рентгенологического) безвредны для людей.
- Эффективность . Методы неразрушающего контроля позволяют проводить тщательную и относительно быструю оценку активов, что может иметь решающее значение для обеспечения постоянной безопасности и производительности на стройплощадке.
- Точность . Методы неразрушающего контроля доказали свою точность и предсказуемость — оба качества, которые вам нужны, когда речь идет о процедурах технического обслуживания, призванных обеспечить безопасность персонала и долговечность оборудования.
«Неразрушающий контроль — это жизненная сила хорошо управляемого объекта. Методы неразрушающего контроля и воспроизводимые результаты зависят от высококвалифицированных технических специалистов, обладающих опытом и добросовестностью. Промышленные методы неразрушающего контроля и интерпретация результатов выполняются сертифицированными профессионалами.Технический специалист не только должен быть сертифицирован по определенному методу неразрушающего контроля, но он также должен знать, как работать с оборудованием, используемым для сбора данных. Понимание возможностей и ограничений оборудования — это разница между принятием или отклонением решения ».
— Джейсон Ачерби, генеральный директор MFE Rentals, «Ваш универсальный источник для инспекций»
8 наиболее распространенных методов неразрушающего контроля
В неразрушающем контроле используется несколько методов для сбора различных типов данных, каждый из которых требует своего рода инструментов, обучения и подготовки.
Некоторые из этих методов могут позволить провести полный объемный контроль объекта, в то время как другие позволяют только поверхностный контроль. Аналогичным образом, некоторые методы неразрушающего контроля будут иметь разную степень успеха в зависимости от типа материала, на котором они используются, а некоторые методы, такие как, например, неразрушающий контроль магнитных частиц, будут работать только с определенными материалами (т. Е. С теми, которые может быть намагничен).
Вот восемь наиболее часто используемых методов неразрушающего контроля:
- Визуальный неразрушающий контроль (VT)
- Ультразвуковой неразрушающий контроль (UT)
- Рентгенографический неразрушающий контроль (RT)
- Вихретоковый неразрушающий контроль (ET)
- НК с магнитными частицами (MT)
- Акустико-эмиссионный неразрушающий контроль (AE)
- Пенетрант с красителем NDT (PT)
- Тестирование на герметичность (LT)
1.Визуальное тестирование (VT)
Определение : Визуальный неразрушающий контроль — это сбор визуальных данных о состоянии материала. Визуальное тестирование — это самый простой способ исследовать материал или объект без каких-либо изменений.
Как проводить визуальное тестирование
Визуальное тестирование может проводиться невооруженным глазом инспекторами, визуально просматривающими материал или актив. Для визуального тестирования в помещении инспекторы используют фонарики, чтобы добавить глубины исследуемому объекту.Визуальное тестирование также можно выполнить с помощью инструмента RVI (Remote Visual Inspection), такого как камера для осмотра. Чтобы поставить камеру на место, инспекторы по неразрушающему контролю могут использовать робота или дрон или просто повесить ее на веревке.
Прочтите наше руководство по визуальному тестированию.
2. Ультразвуковой контроль (UT) Определение : Ультразвуковой неразрушающий контроль — это процесс передачи высокочастотных звуковых волн в материал для выявления изменений свойств материала.
Как проводить ультразвуковые испытания
В общем, ультразвуковой контроль использует звуковые волны для обнаружения дефектов или изъянов на поверхности созданного материала.
Одним из наиболее распространенных методов ультразвукового контроля является импульсное эхо. С помощью этого метода инспекторы вводят звуки в материал и измеряют эхо (или звуковые отражения), создаваемые дефектами на поверхности материала, когда они возвращаются в приемник.
Вот еще несколько видов ультразвукового контроля:
Прочтите наше руководство по ультразвуковому контролю.
3. Рентгенологическое исследование (RT)Определение : Радиографический неразрушающий контроль — это действие гамма- или рентгеновского излучения на материалах для выявления дефектов.
Как проводить рентгенографический неразрушающий контроль
Radiography Testing направляет излучение радиоактивного изотопа или генератора рентгеновских лучей через проверяемый материал на пленку или какой-либо другой детектор. Показания детектора создают теневую диаграмму, которая выявляет основные аспекты исследуемого материала.
Радиография Испытания могут выявить аспекты материала, которые трудно обнаружить невооруженным глазом, например изменение его плотности.
Прочтите наше руководство по промышленной радиографии.
4. Вихретоковые (электромагнитные) испытания (ET)Определение : Вихретоковый неразрушающий контроль — это тип электромагнитного контроля, который использует измерения силы электрических токов (также называемых вихревыми токами) в магнитном поле, окружающем материал, для определения материала, который может указать местонахождение дефектов.
Как проводить вихретоковые испытания
Для проведения испытаний на вихревые токи инспекторы исследуют течение вихревых токов в магнитном поле, окружающем проводящий материал, для выявления прерываний, вызванных дефектами или несовершенствами материала.
Прочтите наше руководство по вихретоковым испытаниям.
5. Контроль магнитных частиц (MPI)Определение : Неразрушающий контроль магнитными частицами — это процесс выявления дефектов в материале путем изучения нарушений в потоке магнитного поля внутри материала.
Как проводить контроль магнитных частиц
Чтобы использовать контроль магнитных частиц, инспекторы сначала создают магнитное поле в материале, который очень чувствителен к намагничиванию. После создания магнитного поля поверхность материала покрывается частицами железа, которые обнаруживают нарушения в потоке магнитного поля. Эти нарушения создают визуальные индикаторы для определения местоположения недостатков в материале.
Прочтите наше руководство по магнитопорошковой инспекции.
6. Испытание на акустическую эмиссию (AE) Определение : Неразрушающий контроль акустической эмиссии — это акт использования акустической эмиссии для выявления возможных дефектов и дефектов в материале.
Как проводить испытания на акустическую эмиссию
Инспекторы, проводящие испытания на акустическую эмиссию, исследуют материалы на предмет выбросов акустической энергии, также называемых акустической эмиссией, которые вызваны дефектами материала.Можно исследовать интенсивность, местоположение и время поступления, чтобы выявить информацию о возможных дефектах в материале.
Прочтите наше руководство по тестированию.
7. Испытания на проникновение красителя (PT)Определение : Неразрушающий контроль проницаемости красителя (также называемый испытанием на проницаемость жидкости) относится к процессу использования жидкости для покрытия материала с последующим поиском разрывов в жидкости для выявления дефектов в материале.
Как проводить испытания на проникновение
Инспекторы, проводящие тест на проникновение, сначала покрывают тестируемый материал раствором, содержащим видимый или флуоресцентный краситель. Затем инспекторы удаляют лишний раствор с поверхности материала, оставляя раствор в дефектах, которые «ломают» поверхность материала. После этого инспекторы с помощью проявителя вытягивают раствор из дефектов, а затем используют ультрафиолет, чтобы выявить дефекты (для флуоресцентных красителей). Для обычных красок цвет проявляется в контрасте между пенетрантом и проявителем.
Прочтите наше руководство по тестированию на пенетрант красителя.
8. Тестирование на герметичность (LT)Определение : Неразрушающий контроль утечек относится к процессу изучения утечек в сосуде или конструкции с целью выявления в них дефектов.
Как проводить испытания на утечку
Инспекторымогут обнаруживать утечки внутри сосуда, используя, среди прочего, измерения, выполненные с помощью манометра, тестов с мыльным пузырем или электронных подслушивающих устройств.
Прочтите наше руководство по тестированию на герметичность.
Где используется неразрушающий контроль?
В зависимости от того, насколько широко вы определяете неразрушающий контроль, можно сказать, что он используется почти во всех отраслях в мире, поскольку визуальные проверки (формальные или случайные) проводятся почти на каждом рабочем месте в той или иной форме.
При этом есть определенные отрасли, которые требуют неразрушающего контроля и имеют формализованные процессы для его использования, как это кодифицировано перечисленными выше организациями, такими как API и ASME.
Эти отрасли включают:
- Нефть и газ
- Производство электроэнергии
- Химическая промышленность
- Горное дело
- Аэрокосмическая промышленность
- Автомобильная промышленность
- Морской
- Горное дело
Во всех этих отраслях существуют три различных метода, которые инспекторы используют для получения доступа к труднодоступным местам или местам на высоте:
- Строительные леса .
Использование строительных лесов требует, чтобы инспекторы работали на высоте лично для сбора данных инспекции.
- Веревочный доступ . Использование веревочного доступа также требует от инспекторов работы на высоте для сбора данных инспекции. Узнайте больше о веревочном доступе и о том, как он используется инспекторами, в этом руководстве.
- Дроны . Инспекторы могут использовать беспилотные летательные аппараты для удаленного сбора данных инспекции, что позволяет им безопасно оставаться вне замкнутых пространств или в безопасных местах на высоте.Прочтите следующий раздел, чтобы узнать больше о том, как дроны могут использоваться для неразрушающего контроля.
Как дроны могут помочь с неразрушающим контролем
За последние несколько лет дроны, оснащенные камерами, стали еще одним инструментом, широко используемым в неразрушающем контроле для сбора визуальных данных.
Из-за ограничений технологии в течение некоторого времени дроны могли предоставлять только дополнительные визуальные данные для инспекторов, но не могли заменить инспекторов, которые сами физически собирали визуальные данные.
[Связанное чтение: Можно ли использовать дрон в качестве инструмента официальной проверки? ]
Однако по мере совершенствования технологии дронов инспекторы могут все больше и больше использовать дроны в качестве инструментов RVI, в некоторых случаях полностью избавляя их от необходимости собирать визуальные данные вручную.
Вот два основных способа, которыми дроны сегодня помогают в неразрушающем контроле:
БезопасностьУстраняя необходимость для инспекторов входить в опасные замкнутые пространства для сбора визуальных данных, дроны помогают повысить безопасность на рабочем месте.
Для наружных проверок таких объектов, как линии электропередач или вышки, использование беспилотного летательного аппарата для сбора визуальных данных сокращает время, необходимое человеку для физического нахождения в воздухе на вышке или линии.
Для внутренних проверок оборудования, такого как сосуды под давлением или котлы, использование беспилотного летательного аппарата, такого как Elios 2, для сбора визуальных данных означает, что инспектору не нужно входить для этого в замкнутое пространство, что опять же помогает значительно снизить подверженность риску.
могут помочь компаниям повысить рентабельность инвестиций как в помещениях, так и на улице, но экономия особенно значительна при проверках внутри помещений.
Использование профессионального внутреннего беспилотника вместо отправки инспектора для сбора визуальных данных вручную означает, что компании экономят на том, что им не нужно строить и демонтировать строительные леса, и могут сократить время простоя, связанное с этими требованиями, в некоторых случаях на 1-2 дней.
Что дальше для дронов в неразрушающем контроле?
На сегодняшний день основным вариантом использования дронов в неразрушающем контроле был сбор визуальных данных.
Но в последние несколько лет тепловые датчики, прикрепленные к дронам, позволили инспекторам собирать тепловые данные с помощью дронов, и со временем вполне вероятно, что мы увидим новые датчики, разработанные для дронов, которые будут поддерживать еще больше методов неразрушающего контроля.
Прочтите о семи основных преимуществах неразрушающего контроля, которые дают дроны.
Практическое применение методов неразрушающего контроля
Тестирование — неотъемлемая часть обслуживания оборудования. Его необходимо проводить для оценки материалов, компонентов, конструкции или структуры механических компонентов. В зависимости от состояния тестируемого компонента после завершения тестирования используемые процедуры могут быть отнесены к категории разрушающих или неразрушающих испытаний.
Если компонент поврежден или разрушен в процессе тестирования, используемый метод тестирования описывается как разрушающий.Напротив, неразрушающий контроль проводится без повреждения испытуемого оборудования.
В этой статье мы сосредоточимся на различных применениях методов неразрушающего контроля.
Что такое неразрушающий контроль?
Методы испытаний, которые не нарушают структурную целостность испытываемых деталей, называются неразрушающими испытаниями (NDT) . При неразрушающем контроле используются различные методы контроля для оценки компонентов по отдельности или в совокупности.Он использует различные принципы в научных областях (физика, химия и математика) для проверки компонентов.
NDT также может называться неразрушающей оценкой / исследованием (NDE) или неразрушающим контролем (NDI).
Представим себе поршень, работающий внутри двигателя, который проверяется на наличие дефектов или разрушения материала. Поршень можно разрезать, чтобы проверить, нет ли внутри дефектов. Однако после проверки поршень больше не может использоваться в двигателе, даже если он не был признан неисправным. Это форма разрушающего контроля .
Поршень можно не разрезать, а проверить с помощью рентгенографии. Мы можем использовать ионизирующее излучение (рентгеновские лучи, гамма-лучи) для обнаружения дефектов или разрушения материала в компоненте. Если он пройдет проверку, компонент все равно можно будет использовать. Это форма неразрушающего контроля .
Где используется неразрушающий контроль?
NDT используется для проверки качества компонентов и состояния машины до или во время их активного использования.Неразрушающий контроль используется для оценки состояния и контроля качества в широком спектре отраслей, включая (но не ограничиваясь):
- Aerospace — испытание отливок
- Automotive — для проверки прочности поршневых головок
- Производство — для проверки качества компонентов перед их запуском в производство
- Изделия медицинские — для проверки прочности и состава стентов
- Военное дело и оборона — баллистические испытания и анализ
- Упаковка — для проверки конструкции и возможности утечки для упаковок
- Морская промышленность — для выявления коррозии
- Производство электроэнергии — для проверки дефектов, связанных со сваркой
- Управление отходами — для определения подлежащих выкупу металлов в отходах
- Нефтехимическая промышленность — для испытания трубопроводов, используемых для транспортировки нефти
Почему используется неразрушающий контроль?
Несомненным преимуществом неразрушающего контроля является возможность многократного использования протестированных компонентов. Вдобавок ко всему, неразрушающий контроль часто может применяться к компонентам, которые все еще находятся в эксплуатации. Устройства и испытательное оборудование, используемые для проведения большинства методов неразрушающего контроля, компактны и портативны. Это упрощает тестирование компонентов на работающей машине.
Дополнительные преимущества проведения неразрушающего контроля перечислены ниже:
- Проведение неразрушающего контроля обеспечивает безопасность рабочих компонентов . Компоненты изнашиваются, что неизбежно приводит к сбоям в работе и сбоям.НК помогает обнаружить ранние признаки деградации и помогает определить причины отказов оборудования. Группа обслуживания может использовать эту информацию для выполнения корректирующего обслуживания и корректировки своих усилий по профилактическому обслуживанию. Все это приводит к повышению надежности активов.
- Цели обеспечения качества. Методы неразрушающего контроля могут использоваться для обеспечения качества выпускаемой продукции.
Команда обеспечения качества сможет быстро проанализировать, находится ли продукт в пределах допуска.
- Оценка оставшегося срока полезного использования машин. Износ машин — естественный побочный продукт их работы. По истечении срока службы их необходимо заменить. Но не все машины из-за различных условий эксплуатации и других факторов деградируют с одинаковой скоростью. Проверка неразрушающего контроля может помочь оценить, как долго машины могут использоваться, прежде чем будет лучше закупить замену.
Все методы неразрушающего контроля имеют уникальные варианты использования и требования.Давайте обсудим это дальше.
Методы неразрушающего контроля
Существует множество вариантов неразрушающего контроля. Какой метод вы собираетесь использовать, зависит от типа тестируемого компонента и от того, что именно вы ищете.
Некоторые методы неразрушающего контроля применяются только в нишевых категориях. Ниже мы обсудим наиболее распространенные методы неразрушающего контроля, которые имеют более широкое применение.
1) Визуальный осмотр
Удаленный визуальный осмотр ( Источник изображения )
Визуальный контроль — это, безусловно, самый простой метод неразрушающего контроля.Это часто классифицируется как часть регулярного технического обслуживания. Специалисты по техническому обслуживанию используют его ежедневно для проверки общих признаков износа. В зависимости от области применения, он может или не может проводиться во время работы машины.
В сценариях, где прямой доступ к объекту испытаний недоступен, роботы и дроны, оснащенные камерами, могут использоваться для удаленного визуального осмотра.
В своем наиболее продвинутом приложении визуальное тестирование сочетается с алгоритмами машинного обучения.Это экономично только для тестирования качества продукции, когда необходимо проверить большой объем стандартизованных компонентов.
2) Ультразвуковой контроль
Ультразвуковой контроль ( Источник изображения )
Ультразвуковой контроль основан на принципе распространения и отражения высокочастотных звуковых волн. Его можно использовать для обнаружения / оценки дефектов, измерения размеров, определения характеристик материалов и т. Д.Тестирование проводится с помощью ультразвукового приемника и передатчика.
Ультразвуковые звуковые волны проходят через исследуемый материал. Звук распространяется через компонент и отражается от твердой поверхности, расположенной на противоположном конце передатчика. Измеряется время, необходимое для передачи и приема звуковых волн. Разница во времени на разных участках компонента может использоваться для выявления дефектов в материале.
Для выявления различных дефектов, полостей, порчи материала и т. Д. Можно использовать различные типы режимов ультразвукового контроля.Механические компоненты, которые работают с большими нагрузками, регулярно проходят ультразвуковые испытания. Хороший пример ультразвукового контроля — это испытание для выявления дефектов и деформаций колес и осей железнодорожных вагонов.
3) Анализ вибрации
Контроль вибрации ( Источник изображения )
Анализ вибрации — это широко используемый метод контроля состояния вращающихся компонентов в процессе работы. Основополагающий принцип анализа вибрации заключается в том, что разные материалы имеют разные сигнатуры вибрации.
Помимо устройства для измерения вибрации, существуют различные типы датчиков, которые могут быть установлены для измерения вибрации. Они предназначены для измерения смещения, скорости и ускорения, перекосов, неплотности и подобных неисправностей, с которыми может столкнуться вращающееся оборудование.
Анализ вибрации, как и любой другой метод, который мы обсуждаем здесь, предоставляет ценные данные, которые используются для мониторинга состояния и профилактического обслуживания.
4) Магнитопорошковое испытание
Магнитопорошковый контроль ( Источник изображения )
Магнитопорошковые испытания используются для обнаружения приповерхностных дефектов в ферромагнитных материалах. Образец для испытаний помещается между двумя полюсами электромагнита, и на образец для испытаний выливается суспензия магнитных частиц. Этот метод тестирования основан на воздействии магнитного поля на ферромагнитные материалы.
Дефекты на поверхности материала будут выделены скоплением магнитных частиц около дефектов и трещин.Для лучшей видимости дефекты используются в ультрафиолетовом свете.
Исследование магнитных частиц может выполняться с помощью влажного горизонтального аппарата MPI или портативных устройств, таких как магнитные ярмы. Инспекционный кодекс Национального совета (NBIC) указывает, что MT может использоваться для проверки таких предметов, как:
- внутренние и внешние поверхности котлов и сосудов под давлением
- деталей, поврежденных огнем
- паровоз и исторические котлы
- сушилки янки
- грузовые танки
- судов в службе сжиженного газа
- Ремонт сварных швов и переделка РПН
5) Пенетрантное тестирование
Испытание на проникновение жидкости ( Источник изображения )
Испытание на пенетрант может использоваться там, где невозможно испытание магнитными частицами. Для проведения пенетрантного тестирования требуется чистая рабочая поверхность.
Во время дефектоскопии жидкий краситель-пенетрант распыляется на исследуемую область и остается нетронутым на открытом воздухе. Время, необходимое для того, чтобы пенетрант подействовал (также известный как время выдержки) на поверхности, может составлять от 10 минут до часа. Это зависит от характеристик тестируемого материала.
Жидкий пенетрант удаляется с рабочей поверхности сухой безворсовой тканью. Легкое нанесение проявителя распыляется на тестируемую рабочую поверхность.Если на тестируемой поверхности есть дефекты, жидкий краситель будет выведен на поверхность после нанесения проявителя.
Испытание на проникновение жидкости обычно используется для испытания сварных поверхностей и работает по принципу капиллярного действия.
6) Вихретоковый контроль
Вихретоковый контроль ( Источник изображения )
Вихретоковый контроль — распространенный метод неразрушающего контроля, используемый как в ручных, так и в автоматических сценариях тестирования. В его основе лежит принцип электромагнитной индукции.
Когда на катушку подается электрическое напряжение, она создает сильное магнитное поле. Когда металл вводится внутрь катушки, магнитное поле колеблется, и ток, протекающий по цепи, увеличивается. Это связано с протеканием вихревых токов внутри металла.
При наличии дефекта или полости в материале потребление тока увеличивается. Вихревой ток должен проходить большее расстояние — увеличивая сопротивление, что проявляется в увеличении потребления тока.Разница в потреблении тока по разным поперечным сечениям материала может использоваться для определения местоположения и размеров дефекта.
Этот тип неразрушающего контроля выполняется с помощью оборудования для вихретокового контроля, которое может включать электромагнитные зонды, токовые дефектоскопы, измерители электропроводности ECT и другие аксессуары. Эти инструменты используются для выполнения различных типов электромагнитных проверок, таких как сканирование поверхности, подповерхностная проверка, проверка сварных швов, проверка отверстий под крепеж, проверка труб, проверка термообработки и сортировка по качеству металла.
7) Рентгенологический контроль и промышленная компьютерная томография
Промышленное КТ сканирование ( Источник изображения )
Рентгеновские лучи и другие методы томографии широко используются в медицине. Однако некоторые из тех же методов также используются в промышленных приложениях как часть неразрушающего контроля.
Рентгеновские снимки и компьютерная томография могут использоваться в промышленной радиографии для просмотра подробных изображений исследуемого материала.Рентгеновские лучи проходят через компоненты, и изображение может быть отпечатано на пленке или просмотрено в реальном времени с помощью компьютера.
Технология компьютерной томографии также может использовать цветовую кодировку различных объектов в соответствии с составными металлами или имеющимися полостями. Рентгеновские лучи можно направлять на тестовый объект под разными углами для получения изображений с более высокой детализацией. Рентгеновское обследование и компьютерная томография относятся к более широкой категории радиографических испытаний, в которых могут использоваться различные типы ионизирующего излучения.
8) Достойные упоминания
Семь типов неразрушающего контроля, описанные в предыдущих разделах, обычно используются в различных отраслях промышленности. Однако в научных лабораториях и промышленных предприятиях используется гораздо больше методов неразрушающего контроля, например:
- Волноводное тестирование : определение дефектов путем контролируемого возбуждения нескольких ультразвуковых волн, посылаемых в разных направлениях.
- Лазерное тестирование: лазерных луча используются для обнаружения дефектов в материалах.Используются три метода лазерного тестирования: голография, ширография и профилометрия.
- Проверка герметичности: проверка утечек с помощью различных методов, таких как тестирование пузырьков, изменение давления, галогенные диоды и масс-спектрометрические испытания.
- Рассеивание магнитного потока: определяет дефекты, связанные с изменением структуры магнитного потока в черных металлах.
- Нейтронный радиографический контроль: нейтрона низкой энергии отправляются через рабочую поверхность вместо рентгеновского излучения.
- Тепловое / инфракрасное тестирование: отображение температуры поверхности на основе испускаемого инфракрасного излучения.
Некоторое время назад мы составили полный список методов мониторинга состояния для журнала MRO, для тех, кто хочет узнать больше.
Кто выполняет неразрушающий контроль?
Как вы понимаете, разные методы неразрушающего контроля требуют технических специалистов с разными навыками и опытом.
Например, при небольшом обучении и хорошем контрольном списке PM некоторые визуальные осмотры могут быть выполнены даже начинающими техниками.Напротив, промышленная компьютерная томография требует технических специалистов со специальными знаниями в области радиологии и оборудования, используемого в процессе тестирования.
Кто проводит тестирование, также будет определяться тем, что тестируется — состоянием машин / компонентов или качеством продукции.
Когда необходимо проверить качество продукции производственной линии, группа обеспечения качества может нести ответственность за проведение неразрушающего контроля.
В большинстве других сценариев тестирование выполняется командой обслуживания.В некоторых случаях OEM-производители могут нести ответственность за проведение испытаний неразрушающего контроля в соответствии с заранее определенным графиком. В обоих сценариях организации могут использовать программное обеспечение CMMS для планирования интервалов тестирования и записи данных тестирования. Когда тестирование выполняется с помощью дооснащения машин датчиками, CMMS можно использовать для анализа входящих данных в реальном времени и автоматического запуска предупреждений при обнаружении любых признаков износа.
Американское общество неразрушающего контроля (ASNT) является пионером в предоставлении аккредитации квалифицированным техническим специалистам.Они предлагают различные учебные курсы по неразрушающему контролю, проводят экзамены, выдают сертификаты и аккредитуют разные организации.
Подробности представлены на сайте ASNT.
Будущее неразрушающего контроля
Огромное количество неразрушающих испытаний, разработанных за долгие годы, говорит о полезности этих методов. Проверка состояния машины без ее повреждения и без необходимости выключения — это два огромных преимущества, особенно в производственной среде.
По мере того, как распространение прогнозирующей и предписывающей аналитики продолжает расти, будет расти и использование неразрушающего контроля. Алгоритмам требуется большой объем точных данных о состоянии машины для прогнозирования отказов и предложения решений. Нет лучшего способа сделать это, чем с помощью датчиков мониторинга состояния и неразрушающего контроля.
Неразрушающие методы контроля качества в аддитивном производстве: исследование
Цель
В последние годы технология аддитивного производства (AM) была признана эффективным методом изготовления сложных геометрических объектов с широким спектром применений. Однако неточности размеров и наличие дефектов затрудняют широкую адаптацию процедур AM. Эти факторы вызывают озабоченность по поводу качества продукции, производимой с использованием AM, и использование методов контроля качества (QC) является обязательным условием для дальнейшей поддержки этой новой технологии. Этот документ направлен на то, чтобы помочь исследователям получить четкое представление о тенденциях и проверках в отношении методов контроля качества неразрушающего контроля (NDT) в AM. Дизайн / методология / подход
В этой статье был проведен обзор достижений в области неразрушающих процедур контроля качества, используемых в технологии AM.Документ организован следующим образом: в разделе 2 обсуждаются существующие методы неразрушающего контроля, применяемые для исследования исходного материала, то есть входной контроль качества (IQC). В разделе 3 описаны методы контроля качества на месте, а в разделе 4 представлены методы неразрушающего контроля, применяемые после производственного процесса, то есть методы исходящего контроля качества.
В разделе 5 описаны статистические методы контроля качества, используемые в технологиях AM. Будущие тенденции и проблемы включены в Раздел 6, а выводы сделаны в Разделе 7.Результаты
Основная цель исследования — представить доступные и надежные методы неразрушающего контроля, применяемые в каждой технологии AM и на всех этапах процесса. Большинство разработанных до сих пор методов сосредоточено в основном на контроле изготовленной детали во время и после процесса AM, по сравнению с проверкой до процедуры. Более того, экструзия материалов, прямое нанесение энергии и процессы порошкового слоя являются фокусом исследований методов неразрушающего контроля, применяемых в AM. Оригинальность / ценность
В этом обзоре литературы впервые собраны новейшие и наиболее совместимые методы оценки качества деталей, производимых в основных процессах AM до, во время и после производственной процедуры.
Insight NDT Equipment — Что такое неразрушающий контроль?
Неразрушающий
Тестирование (N. D.T.) является частью функции контроля качества и
дополняет другие давно зарекомендовавшие себя методы.
Автор определение неразрушающего контроля — это испытание материалов для поверхностные или внутренние дефекты или металлургическое состояние без нарушения каким-либо образом с целостностью материала или его пригодностью для услуга.
метод может применяться на выборочной основе для индивидуального исследования или может использоваться для 100% проверки материала на качество продукции система контроля.
Пока
будучи концепцией высоких технологий, эволюция оборудования сделала
он достаточно прочен для применения в любой производственной среде в любой
стадия производства — от производства стали до инспекции комплектующих на месте
уже в строю.Требуется определенная степень навыков для применения
методы правильно, чтобы получить максимальное количество информации
касательно продукта, с последующей обратной связью с производством.
Неразрушающий Тестирование — это не только метод отказа от некачественного материала; Это также гарантия того, что якобы хорошее — это хорошо. Техника использует множество принципов; нет единого метода, вокруг которого черный ящик может быть построен таким образом, чтобы удовлетворять всем требованиям при любых обстоятельствах.
Insight Оборудование для неразрушающего контроля производят с использованием следующих технологий:
Это информация взята из технического документа Insight NDT, озаглавленного «A Краткое объяснение методов неразрушающего контроля ». Копия Полный текст статьи в формате Adobe Acrobat доступен по щелчку здесь.
Разница между разрушающим и неразрушающим контролем
Зачем нужны испытания материалов? Испытания материалов могут предоставить много информации об испытанных материалах, прототипах или образцах продукции для различных целей.Инженеры, дизайнеры, руководители производства и другие могут извлечь большую пользу из данных, полученных во время тестирования, и окончательных результатов тестирования. Ниже приведены некоторые из причин, по которым испытания материалов имеют решающее значение:- Соответствие нормативным стандартам
- Выбор подходящих материалов и обработки для работы
- Оценка дизайна продукта или требований к усовершенствованию
- Проверка производственного процесса
Тестирование материалов позволяет нам определить, подходит ли определенный материал или обработка для данной области применения.Тестирование может помочь ограничить выбор наиболее приемлемым материалом и обработкой для предполагаемого использования, учитывая широкий спектр материалов и обработок, доступных на рынке.
В промышленности существует два типа процедур испытаний материалов: разрушающие и неразрушающие методы.
Что такое разрушающий контроль (ДТ)?Разрушающий контроль — это метод качественного анализа для определения свойств материала, таких как прочность на разрыв, свойство удлинения, значение твердости и ударная вязкость, среди прочего.
Вышеупомянутые качественные характеристики не обнаруживаются процедурами неразрушающего контроля. Потому что механические свойства материала должны определяться путем приложения к нему нагрузки. Материал деформируется в результате нагрузки, делая его бесполезным.
С другой стороны, методы неразрушающего контроля применяются таким образом, что материал может быть повторно использован после тестирования.
07 Примеры разрушающего контроля
- Испытание на растяжение
- Испытание на изгиб
- Испытание на разрушение
- Испытание на сплющивание
- Испытание на твердость
- Испытание на сдвиг
- Испытания на удар
Одним из самых основных и распространенных видов механических испытаний является испытание на растяжение, широко известное как испытание на растяжение.Испытание на растяжение включает приложение растягивающей (тянущей) силы к материалу и измерение реакции образца.
DT Test 02 — Испытание на изгибИспытание на изгиб — это простое и недорогое испытание на разрушение, которое может быть выполнено для определения пластичности и прочности материала. Его часто используют для контроля качества стыковых сварных соединений благодаря простоте испытательных образцов и оборудования.
DT Test 03 — испытание на разрушениеСпособность материала противостоять росту или распространению ранее существовавшего разлома измеряется испытаниями на вязкость разрушения.Усталостный излом, пустоты или любая другая аномалия в исследуемом материале может быть дефектом или дефектом. Испытания на вязкость разрушения проводят путем механической обработки испытательного образца с уже существующей трещиной и затем циклического приложения напряжений к каждой стороне трещины, чтобы вызвать ее расширение. Циклическая нагрузка прикладывается до тех пор, пока трещина в образце не расширится. Количество циклов до разрушения отслеживается и используется для оценки характеристик развития разрушения материала.
DT Test 04 — Испытание на сплющиваниеИспытания на сплющивание обычно проводят на образцах, вырезанных из трубчатых изделий, и включают в себя сплющивание колец из трубы или трубы между двумя параллельными плитами до определенной степени.Сплющивание трубы — это испытание типа «годен / не годен», которое определяет пластичность трубы после того, как она была сплющена.
DT Test 05 Тест на твердостьИспытание на твердость — это метод определения твердости материала. Устойчивость материала к стойкому вдавливанию измеряется твердостью.
Существует множество методов измерения твердости, и каждое из этих испытаний может выявить разные уровни твердости для одного и того же материала. В результате испытание на твердость как процедура может быть различным, и результаты каждого испытания должны быть помечены, чтобы установить тип используемого испытания на твердость.
Пять наиболее распространенных шкал твердости:
- Роквелл
- Бринелл
- Виккерс
- Берег
- Кнуп
Испытание на сдвиг отличается от испытаний на растяжение и сжатие тем, что прилагаемые силы параллельны верхней и нижней граням объекта. Материалы, работающие на сдвиг, ведут себя иначе, чем материалы на растяжение или сжатие, что приводит к другим значениям прочности и жесткости.Испытание на сдвиг включает приложение поперечной силы сдвига к образцу до тех пор, пока он не разрушится.
Сдвиг происходит на одной поверхности при одинарном сдвиге и на двух поверхностях при двойном сдвиге. При строительстве любых конструкций или компонентов машин понимание разрушения при сдвиге имеет решающее значение. Сила сдвига вызывает смещение поверхностей друг относительно друга, что приводит к разрушению материала.
DT Test 07 — Испытание на ударИспытание на удар используется для определения прочности продукта или его способности выдерживать энергию ударной нагрузки или динамического удара.После этого образцы исследуются на предмет признаков деформации, разрушения и разрыва с помощью этой процедуры испытаний.
Изод и Шарпи — две основные формы испытаний на удар с помощью маятника. Оба теста очень похожи, однако есть некоторые ключевые отличия:
- При испытании на удар по Изоду образец держат вертикально, выемка направлена к маятнику
- При испытании на удар по Шарпи образец держат горизонтально с выемкой, направленной в сторону от маятника.
Неразрушающий контроль — это метод, используемый в промышленности для проверки свойств материала, компонента, конструкции или системы на предмет типичных изменений, дефектов сварки и разрывов без повреждения исходной детали. Неразрушающий контроль — это разновидность неразрушающего контроля, который включает неразрушающий контроль (NDE), неразрушающий контроль (NDI) и неразрушающий контроль (NDE)
07 Примеры неразрушающего контроля- Визуальный осмотр
- Испытание магнитными частицами (MPT)
- Тест на проникновение красителя (DPT)
- Ультразвуковой контроль (UT)
- Вихретоковый контроль (ECT)
- Акустическая импульсная рефлектометрия (APR)
- Радиографический контроль (RT)
Визуальное тестирование — это метод анализа дефектов, видимых невооруженным глазом.В труднодоступных регионах также можно использовать увеличительные стекла, видеобороскопы или зеркала.
NDT Test 02- Испытание магнитными частицами (MPT)Испытание на магнитные частицы (MPT) или контроль магнитных частиц (MPI) используется для обнаружения дефектов на поверхности и вблизи поверхности. Этот подход применим только к ферромагнитным материалам (содержащим значительное количество Fe, Co или Ni) и не подходит для аустенитных сталей. Тем не менее, это чрезвычайно эффективный подход к обнаружению трещин.
NDT Test 03- Испытание на проникновение красителя (DPT)DPT — это метод обнаружения дефектов поверхности. Его можно использовать на любом материале, кроме пористых материалов и материалов с чрезвычайно жесткой обработкой поверхности. В этом подходе используется высококонтрастная матрица, которая усиливает капиллярное действие для проникновения в мелкие дефекты, в результате чего дефекты становятся очевидными во время нанесения сухого порошка на поверхность.
NDT Test 04 — Ультразвуковой контроль (UT)Ультразвуковой контроль использует высокочастотные звуковые волны, которые не слышны человеку.Неисправности обнаруживаются путем анализа возвращенных звуковых волн, которые появляются на экране машины в виде эха. Этот подход имеет широкий спектр применения и может использоваться для обнаружения внутренних дефектов практически любого материала.
NDT Test 05 — Вихретоковый контрольДля обнаружения неисправностей Eddy Current использует принцип электромагнитной индукции в проводящих материалах.
Любой разрыв вызывает сдвиг поля вихревых токов, а также сдвиг фазы и амплитуды записанного сигнала.
Вихретоковый контроль обычно используется для проверки дефектов поверхности и труб. Эти методы часто использовались в таких отраслях, как аэрокосмическая и нефтяная.
NDT Test 06 — Электромагнитные испытания (ET)Процесс создания электрического тока или магнитного поля, или того и другого, внутри тестового объекта и обнаружения электромагнитного отклика известен как электромагнитное тестирование. Неисправность внутри тестового объекта вызывает измеримый отклик, если тест правильно настроен.
NDT Test 07 — Радиографический контроль (RT)Радиографический контроль — это процедура неразрушающего контроля, при которой исследуется внутренняя структура произведенных компонентов с помощью рентгеновских или гамма-лучей для обнаружения каких-либо дефектов или дефектов.
Испытуемая часть располагается между источником излучения и пленкой при рентгенографическом контроле (или детекторе). Посредством процессов взаимодействия, включающих рассеяние и / или поглощение, расхождения плотности и толщины части исследуемого материала будут уменьшаться (т.е. нижний) проникающее излучение.
ЗАКЛЮЧЕНИЕ В определенном смысле разрушающий контроль является более надежной процедурой по сравнению с неразрушающим контролем. Однако неразрушающий контроль (NDT) имеет существенное преимущество перед разрушающим испытанием, так как он охватывает большую территорию и экономит деньги на материалах. Аналитики могут использовать неразрушающий контроль, чтобы не навредить активам, а также выявить больше слабых мест в процессе. Инспекторы должны повредить жизнеспособные материалы, которые могли быть использованы во время обычных операций, что делает разрушающие испытания более дорогостоящими и расточительными.Кроме того, испытание с использованием разрушающего средства менее эффективно, чем неразрушающий контроль, с точки зрения сроков проверки, требуя ручных действий, которые занимают больше времени и требуют больше работы, чем упрощенные методы неразрушающего контроля.
Связанная статья:
डेसट्रक्टिव टेस्टिंग और नॉन डेसट्रक्टिव टेस्टिंग के बीच अंतर (Статья на хинди)
Что такое многоуровневый аудит процессов? как реализовать многоуровневый аудит процессов?
6 наиболее важных методов испытания на трещинообразование при неразрушающем контроле материалов
6 наиболее важных методов испытания на трещинообразование при неразрушающем контроле материалов
Неразрушающий контроль материалов в последние годы прочно вошел в историю мониторинга процессов.Благодаря своей эффективной работе эта процедура проверки стала решающей для комплексного управления технологическим процессом. В то же время во многих отраслях промышленности уже недостаточно проверять только геометрические размеры компонента. Это связано с тем, что все более высокие требования предъявляются к тестированию компонентов параллельно с непрерывной работой. Поэтому необходимы более обширные испытания для подтверждения соответствующих свойств в течение срока службы.
Почему необходим неразрушающий контроль материалов?
Существует множество критически важных для безопасности приложений или серьезных косвенных экономических убытков, когда компоненты выходят из строя или не соответствуют их требованиям.Если, например, американские горки разобьются во время работы, человеческие жизни немедленно окажутся под угрозой. Если трубопровод здания выходит из строя, это может привести к значительному ущербу от воды с последующими высокими затратами на ремонт.
Соответственно, определены стандарты в автомобильном секторе и во многих других отраслях. Они обеспечивают постоянный и тщательный контроль компонентов, важных для безопасности, в процессе производства и перед установкой.
Какие дефекты можно найти в компонентах?
Каталог дефектов от заказчиков разнообразен.Например, решающими факторами влияния являются область применения компонента, материал, из которого он изготовлен, и его размеры. Наиболее распространенные типы дефектов, обнаруживаемые при осмотре поверхности:
- Трещины
- Полости
- Вмятины
- Горелка шлифовальная
- Жесткие пятна
- Мягкие пятна
- Магнитные включения (Remanences)
Классические дефекты деталей — это трещины на поверхности материала. Здесь обычно используется вихретоковый контроль.Это связано с тем, что даже самые маленькие трещины, которые изначально не представляют проблемы, могут увеличиваться и расширяться при постоянной нагрузке. В худшем случае это может привести к отказу компонентов. Представьте себе трещину в тормозном диске: есть вероятность, что после определенного периода эксплуатации тормозной диск сильно разорвется при замедлении. В дорожном движении такой неисправный компонент может быстро привести к опасным для жизни ситуациям.
По этой причине заказчики ожидают, что даже самые мелкие дефекты глубиной всего несколько микрометров будут обнаружены и надежно отображены в процессе проверки.Например, для проверки этого обычно используется испытательный прибор STATOGRAPH от FOERSTER. Размер дефекта, который можно устранить с помощью СТАТОГРАФА, зависит от компонента и его материала, а также от частоты испытаний и используемого датчика. Оптимальная конструкция позволяет обнаружить трещины глубиной всего 30 мкм.
Какие методы доступны для обнаружения трещин в литых деталях?
Существует несколько методов тестирования компонентов.Различают два классических подхода:
- Разрушающий контроль
- Неразрушающий контроль
Компоненты из партий, которые позже перепроданы и установлены, могут быть протестированы только случайным и разрушительным образом. По мере увеличения потребности в тестировании стоимость лома, оставшегося после тестирования, возрастает. В результате провести полную проверку методологически невозможно.
На этой заметке была развита область неразрушающего контроля. Исходя из этого, доступны разные методы в зависимости от задачи тестирования:
- Визуальный осмотр (VT)
- Испытание на проникновение красителя (PT)
- Вихретоковый контроль (ET)
- Термографические испытания (ТТ)
- Магнитопорошковые испытания (MT)
- Ультразвуковой контроль (UT)
В зависимости от области применения используются разные методы испытаний.Существенными влияющими факторами являются тестовый материал, размер, тип дефекта и тестовая задача, а также требуемое время цикла и доступный бюджет.
1. Испытание на трещинообразование с визуальным осмотром (VT)
Во время процедур визуального контроля качества поверхности, такие как отклонения формы, дефекты или состояние поверхности компонента, просматриваются и оцениваются невооруженным глазом или с помощью оптических устройств (например,увеличительные стекла, микроскопы или эндоскопы). Перед всеми другими методами разрушающего и неразрушающего контроля визуальный осмотр сначала проводится в виде комплексного испытания и используется для изделий различной формы в соответствии с указанными инструкциями по испытаниям.
Процедура испытания реализуется как прямой и косвенный визуальный осмотр в рамках производственного контроля, осмотра и расследования повреждений компонентов, систем или других объектов испытаний. Результаты тестирования сильно зависят от опыта и субъективной оценки тестировщика.Поэтому добиться сопоставимости сложно.
2. Испытание на трещинообразование с использованием пенетранта красителя (PT)
Испытание на проникновение красителя — еще один метод неразрушающего контроля поверхностей материала. В основе этого процесса лежит капиллярное действие. Процесс проплавления используется как визуальное свидетельство дефектов поверхности, таких как трещины или поры.
Этот процесс в основном используется для металлов. Если возможно, тест на проникновение красителя может также выявить дефекты в пластике и керамике.Как и в случае с визуальным осмотром, проверка на проникновение цвета является субъективным методом, который зависит от опыта инспектора.
3. Испытание на трещины с помощью вихретоковых приборов (ET)
Для контроля поверхности токопроводящих деталей вихретоковый метод (англ. «Вихретоковый контроль», сокращенно ECT) зарекомендовал себя как доминирующая технология. Системы вихретокового контроля состоят из испытательного прибора с соответствующим датчиком и, при необходимости, дополнительных программных модулей.Измерительный щуп содержит обмотку возбуждения (первичную обмотку) и дифференциальную обмотку (вторичную обмотку). Измерительный щуп подключается к испытательному прибору, например, STATOGRAPH CM для испытания на трещины.
Катушка возбуждения работает с переменным полем и индуцирует вторичное поле в дифференциальной катушке, которое изменяет амплитуду и фазу сигнала при изменении поверхности. Это изменение сигнала регистрируется испытательным прибором с очень высокой скоростью передачи данных.Эта информация позже передается на завод-изготовитель. В результате можно распознать и устранить неисправность.
В зависимости от характера неисправности и материала тестового объекта должна быть выбрана правильная конфигурация тестового прибора и тестового зонда. Существуют различные способы настройки параметров теста так, чтобы они максимально оптимально реагировали на определенные шаблоны ошибок. В то же время это способствует тому, что нерелевантные ошибки будут хуже обнаруживаться. Последующее программное обеспечение также может помочь в оценке данных испытаний.Одни и те же данные оцениваются с помощью разных методов фильтрации и, таким образом, оптимизируются для множественных шаблонов ошибок.
STATOVISION является примером такого программного обеспечения, работающего в нисходящем направлении, способного улучшить качество сигнала. После сбора необработанных данных программное обеспечение использует методы цифровой фильтрации. Это особенно необходимо, если требования к размеру обнаруживаемой ошибки очень высоки. Типичные глубины ошибок, которые, как ожидается, будут обнаружены с помощью вихретокового метода, находятся в диапазоне от 30 мкм до 1 мм.
Предпосылками для вихретокового контроля дефектов поверхности являются, с одной стороны, обычно токопроводящие компоненты, с другой — вращательная симметрия испытуемых объектов. Вращательная симметрия необходима для максимально эффективного проведения теста. Компонент вращается для тестирования, и зонд параллельно сканирует его поверхность. Если симметрии нет, возможно, придется использовать другой метод испытаний.
4. Испытание на трещинообразование с помощью термографического оборудования (ТТ)
Вихретоковый контроль всегда является полезным методом, когда речь идет о проводящих и осесимметричных материалах.Кроме того, эти компоненты должны иметь как можно более гладкую поверхность, чтобы их можно было сканировать зондом. Если эти условия не выполняются, используются дополнительные методы испытаний. Обнаружение трещин с помощью термографии неуклонно растет в промышленных приложениях. Термографическое испытание на растрескивание обычно проводится с использованием метода импульсной термографии или термографического метода Lock-In. Здесь компонент нагревается локально короткими импульсами с помощью источника энергии (например, индукционным путем, оптически с помощью ламп или лазера).Поверхность регистрируется термографической камерой. Трещины и другие локальные различия на поверхности по-разному реагируют на приложенное тепло. Трещина накапливает меньше тепла и четко выделяется на термографическом изображении.
Различные источники тепла также показывают разные эффекты. Если, например, проводящий компонент возбуждается индуктором, на концах трещины выделяется больше тепла, чем в других точках испытуемой детали. Здесь конденсируются вихревые токи, и тепловложение выше.Изображения, записанные с помощью термографической камеры, поступают в программу обработки данных. Для оценки изображения используются специальные алгоритмы обработки. Несколько изображений, сделанных последовательно, показывают, среди прочего, тепловой поток с течением времени и предоставляют дополнительную информацию. Основное преимущество термографического метода обнаружения трещин заключается в том, что компоненты могут иметь большую степень свободы по размеру и геометрии. Кроме того, этот метод может применяться к непроводящим компонентам. В этих случаях для ввода энергии обычно требуется оптический метод.
Кроме того, метод относительно устойчив к воздействиям окружающей среды. Однако проверяемая поверхность по возможности не должна быть загрязнена. Измененные свойства поверхности могут приводить к различным тепловым потокам, которые могут проявляться в оценке как псевдодефекты. Автоматизированные процессы с обработкой компонентов сегодня могут быть реализованы относительно легко. Сейчас доступны хорошие термографические камеры, поэтому этот процесс постепенно внедряется в производственные линии. Эта технология может заменить магнитопорошковый контроль, который все еще доминирует сегодня.
5. Испытание на трещины с использованием оборудования для испытания магнитных частиц (MT)
Вероятно, самый старый метод обнаружения трещин в материалах — это испытания магнитными частицами. Согласно этому методу ферромагнитные компоненты намагничиваются и напыляются магнитным порошком. Дефекты в исследуемой детали по-разному реагируют на намагничивание. В этот момент магнитное поле проявляется на поверхности сильнее. Соответственно, магнитный порошок лучше прилипает.При добавлении флуоресцентного материала к магнитному порошку дефекты «светятся» по-разному при определенных условиях освещения. Основным недостатком этой процедуры является то, что хорошая или плохая сортировка тестовой части происходит на основе субъективной оценки инженера-испытателя. Только опыт инспектора определяет, будет ли трещина оценена как большая или маленькая, или степень ошибки может быть оценена как плохая. Кроме того, очистка компонентов после испытания требует больших усилий, поскольку магнитный порошок прилипает к испытываемым деталям.Автоматизация систем контроля магнитных частиц может быть довольно сложной. Таким образом, процедура тестирования полезна только в том случае, если количество тестовых заданий не слишком велико.
6. Испытание трещин ультразвуковыми приборами (UT)
Вихретоковый контроль — это предпочтительный метод обнаружения открытых трещин в проводящих компонентах. Однако этот метод достигает своих пределов в случае трещин или аномалий материала, которые находятся внутри испытуемого образца. Это связано с тем, что глубина проникновения этого метода зависит от используемой частоты.Если это находится в диапазоне кГц, глубина проникновения относительно быстро уменьшается до нескольких миллиметров. Таким образом, еще один установленный метод испытаний — это испытание на трещину с помощью ультразвуковых устройств. Ультразвуковой метод подходит для тестирования компонентов на всю глубину. С помощью этого метода можно полностью «просвечивать» любой материал. Для этого на тестируемую часть помещается измерительная головка с ультразвуковым излучателем и приемником. Ультразвук, генерируемый измерительной головкой, переносится в испытуемую часть через соединительную среду, обычно это вода.Хорошая связь важна для эффективного тестирования.
Ультразвук проникает в образец, и эхо ультразвуковых волн создается отражениями от задней стенки. Дефекты, такие как трещины или включения, приводят к дополнительному отражению ультразвука. Они записываются в блоке поиска. Тип и размер отражений позволяют сделать выводы о том, где находится обнаруженная аномалия в образце. Производство ультразвуковых поисковых устройств очень сложно.Кроме того, замкнутые системы требуются из-за связующей среды. Кроме того, связующая среда должна быть как можно более свободной от примесей и образования пузырьков, поскольку они нарушают путь ультразвукового звука и действуют как дефект материала.
Какая трещина — какой процесс?
Подписи
A = наиболее подходящий
B = Вид нормального использования
C = Не очень хорошо
D = Совершенно не подходит
Заключение
Все представленные здесь методы неразрушающего контроля трещин оправданы.Соответствующий метод испытаний определяется в зависимости от типа ошибки и используемого материала. Также возможно использовать комбинацию различных методов тестирования, которые могут быть объединены вместе в одной тестовой линии.
Неразрушающие методы контроля качества отливок
Каждый этап литья под давлением выполняется с особой тщательностью, чтобы получить качественные продукты, которые не имеют проблем с отделкой поверхности, прочностью, механическими свойствами, а также конечными размерами. Тем не менее, даже тщательно отлитые детали должны проходить проверку в рамках мер контроля качества.Могут возникнуть небольшие проблемы, а некоторые детали, отлитые под давлением, имеют механические характеристики, которые могут быть нарушены из-за не так легко заметного дефекта. Благодаря инспекции литейщики и их клиенты получают больше уверенности в качестве конечного продукта.
Типы тестированияСуществует множество методов для тестирования и обнаружения проблем внутри отливки. Эти методы помогают убедиться, что он не выйдет из строя под нагрузкой. Двумя основными методами внутреннего контроля являются разрушающий и неразрушающий контроль.
Как следует из названия, разрушающий метод включает вскрытие отливки для тщательной проверки свойств металла. Проверяющий будет искать пористость, вкрапления и усадку. В отличие от этого другой метод не предусматривает разрезания отлитого объекта для проверки его внешней и внутренней прочности. Это делают рабочие литейного цеха, клиенты литейщиков, а также техники по неразрушающему контролю.
Конечно, неразрушающий контроль включает в себя визуальный осмотр. Есть и другие, более совершенные методы тестирования, не повреждающие отливку.
Методы неразрушающего контроля Контроль размеровЭто делается для того, чтобы убедиться, что литая под давлением деталь соответствует допускам / требованиям по размерам. Это можно сделать вручную или с помощью КИМ (координатно-измерительной машины). Это два основных способа выполнения контроля размеров. В оборудовании используются зонды для получения чрезвычайно точных измерений. Для этого также используются другие инструменты. Точность измерительных инструментов также способствует сохранению размеров и качества изготавливаемой детали.
Тестирование проникновения жидкого красителяЭтот метод, также известный как LPI (Liquid Penetrate Inspection), позволяет находить небольшие трещины, поры или другие дефекты на поверхности отливки, которые трудно обнаружить невооруженным глазом. Тестер сначала очищает компонент, чтобы избавиться от любых частиц пыли или песка, которые могут препятствовать попаданию жидкого красителя в трещины на металлической части. После того, как он станет чистым и сухим, отлитую под давлением деталь промывают пенетрантным раствором.
В различных типах LPI используются разные растворы, в том числе ярко окрашенное масло с низкой вязкостью и высокими капиллярами, что означает, что жидкий краситель будет свободно течь к трещинам на компоненте.Жидкую краску оставляют в том же положении, чтобы краска могла пробиться к любым невидимым трещинам.
По прошествии достаточного времени, чтобы позволить ему сделать то, для чего он предназначен, лишняя жидкость удаляется с поверхности детали. Обычно это выполняется путем аккуратного вытирания излишка жидкости влажной тканью, следя за тем, чтобы не затопить деталь, так как это может удалить краситель из трещин. Затем испытатель наносит на отливку специальный проявитель, и на отливке можно отчетливо увидеть его недостатки.
Контроль магнитных частицMPI также используется для поиска небольших отверстий и трещин на поверхности отливки или в ее неглубоких подповерхностях, и в этом смысле процесс аналогичен вышеупомянутому. Однако его можно использовать только для проверки компонентов, изготовленных из ферромагнитных металлов, которые могут создавать магнитные поля, таких как кобальт, никель, железо, а также некоторые сплавы. Литая деталь намагничивается, как правило, с помощью электромагнитов, чтобы начать испытание.
Магнитное поле в металле сильнее, чем в воздухе.Когда на отливке или на ее поверхности существуют неоднородности, такие как отверстия или трещины, индуцированное магнитное поле будет нарушено.
Чтобы найти сбои, литейщики опрыскивают отливку жидкостью или пылью, содержащей частицы оксида железа или другие вещества, которые вступают в реакцию в полевых условиях. Распыленные частицы затем собираются вблизи краев искажений, очерчивая области с низким магнитным потоком. В результате можно использовать магнитный порошок и магниты, чтобы показать искажения там, где воздух больше, чем металл, над любыми отверстиями или в любых трещинах.
Радиографический осмотр или рентгеновское исследованиеОн создает изображения, например, в медицинском учреждении, на которых видны переломы костей. Этот метод используется для выявления участков, где есть дефекты. Эти рентгеновские лучи помогают слесарю определить, ухудшаются ли механические свойства отливки из-за включений, отверстий или усадки, и можно ли их исправить до отправки продукта.