виды и особенности, правила монтажа, цены
Потребность использования специальных дюбелей для газобетона обусловлена его пористой структурой и низкими способностями к удерживанию крепежей. Данная группа включает изделия из металла или пластика с разными размерами, формами фиксирующих ребер, способами установки и ценами. Продукция реализуется многими отечественными и зарубежными производителями, к лучшим относят HPD, Hilti, Quattro, Mungo, Sormat, GB, Fischer, Креп-Комп (описание популярных марок дюбелей вы найдете здесь).
Оглавление:
- Классификация дюбелей
- Инструкция по монтажу
- Стоимость популярных марок
Виды и особенности крепежей
В зависимости от материала разделяются на металлические (стальные нержавеющие или покрытые антикоррозионными составами, из латуни или сплавов цинка и алюминия) и пластиковые (нейлоновые, полиэтиленовые или полипропиленовые). Первые считаются более надежными и подходят для сложного и сквозного монтажа, их единственным недостатком является способность к окислению при длительном воздействии влаги.
Пластиковые крепежи ценятся за легкость, стойкость к коррозии и многофункциональность. Лучшие прочностные характеристики имеют нейлоновые (полиамидные), их советуют приобрести для радиаторов, раковин, карнизов и полок, они позволяют безопасно пользоваться кухонной мебелью. Полипропиленовые не уступают им в чистоте и стойкости к агрессивным средам, но плохо переносят низкие температуры и не подходят для применения снаружи.
В зависимости от способа монтажа все механические дюбеля для стен из газобетона разделяются на вбиваемые и вкручиваемые без предварительного сверления блоков или фиксирующиеся с помощью резьбы в подготовленном отверстии. В большинстве случаев выбирают завинчивающиеся, считающиеся более надежными и удобными.
Исходя из типа резьбы или фиксирующих элементов различают стандартные втулки с винтовой спиралью с одинаковым сечением по всей длине, конусообразные метизы с расходящимися в стороны в процессе вкручивания лопастями и другие, расширяющиеся при распоре конструкции. Отдельной группой являются химические анкера, фиксирующиеся в блоках путем полимеризации специальных составов. Ими удобно пользоваться (достаточно заложить в подготовленное отверстие капсулу с болтом внутри и дождаться отвердевания), но в плане стоимости они в разы проигрывают обычным вариантам из металла и пластика.
Металлический дюбель-гвоздь предназначен для более плотных марок бетона, но ими можно пользоваться при фиксировании к газоблоку каркасов под гипсокартон и других строительных конструкций (для этих целей выбирают конусообразные виды, забиваемые без предварительного сверления и укрепляемые шурупом, подходящие метизы предлагают FMD, Fischer, MEF и Mungo). В остальных случаях ориентируются на следующие рекомендации:
- При креплении тяжелой мебели и техники, систем коммуникации и чугунных радиаторов предпочтение отдается металлическим вариантам.
- При размещении на стенах из газоблоков светильников, легких полок или зеркал достаточно пластика – нейлоновых с диаметром около 12 мм. Для фоторамок, крючков и небольших картин вполне хватает полипропиленовых на 8 мм.
- При работе с фасадными системами используются специализированные, устойчивые к температурным перепадам и влаге разновидности с удлиненной зоной раскрытия.
- Для размещения оконных и дверных коробок или направляющих для встраиваемой мебели следует применять рамные типы (выпускаемые как из металла, так и из пластика).
- Для укладки теплоизоляционных материалов (например, листов пенополистирола) покупаются дюбеля с тарельчатыми шляпками.
К учитываемым критериям относят тип конструкции рабочего основания, вид используемого крепежа, величину расчетной нагрузки, направление вектора воздействия и способ монтажа. Приводимые производителями значения не являются экстремальными и разрушающими, как правило, они указываются с учетом коэффициента безопасности. Нейлоновые пластиковые элементы выдерживают нагрузку от 0,3 до 0,6 кН, металлические – от 0,6. Зная вес радиаторов, раковин или навесной мебели и допустимые значения на вырыв, несложно найти вариант нужного диаметра.
Нюансы монтажа
Для исключения ошибки придерживаются следующей последовательности:
- С помощью дрели или перфоратора, работающего в безударном режиме, в газобетоне подготавливается отверстие с глубиной на 10 мм больше длины самого анкера. При установке разновидностей из пластика рекомендуется использовать сверло с диаметром на 1 мм меньше, при вкручивании металлических – на 2.
- Полость продувается и очищается от строительного мусора.
- Крепеж аккуратно вкручивается отверткой или установочным инструментом или забивается молотком. На этом этапе избегают перекосов, дюбеля и анкера обычно расположены перпендикулярно основанию.
- Окончательная фиксация с помощью шурупов или саморезов. Для обеспечения максимальной надежности кончик крепежа должен слегка выступать за края дюбеля, но при необходимости их можно затягивать на любую нужную глубину. Для расширения изделия внутри газосиликата не рекомендуется применять мощные электроинструменты, чересчур интенсивное воздействие просто проворачивает резьбу, сминая пористую структуру.
Дюбеля под газобетонные блоки закручиваются и закрепляются вручную. При большом объеме работ целесообразно использовать специальный установочный инструмент (в идеале – рекомендуемый производителем). Для подготовки посадочных отверстий оптимальным вариантом будет дрель с мягким режимом вращения: чем сильнее ударная нагрузка, тем выше риск повреждения ячеистых материалов.
На всех этапах проверяется целостность газоблоков, при необходимости они очищаются от пыли. К важным нюансам относят выбор правильной глубины бурения, она полностью зависит от типа дюбеля и длины установочной части, обязательно указываемых изготовителем.
Стоимость дюбелей
Тип и материал | Производитель | Длина, мм | Диаметр, мм | Фасовка, шт | Цена, рубли |
Пластиковый | Креп-Комп | 80 | 14 | 100 | 700 |
Нейлоновый SX | Fischer | 50 | 10 | 25 | 150 |
Металлический, с антикоррозийным покрытием | Креп-Комп | 32 | 6 | 30 | 120 |
Стальной анкер FPX I с внутренней резьбой, для предварительного и сквозного монтажа. | Fischer | 75 | 10 | 1 | 180 |
Рамный дюбель КАТ N, пластик | Sormat | 160 | 50 | 1240 |
Кладка газобетона в два блока: виды кладки
Качественный автоклавный газобетон плотностью D400 и D500 довольно хорошо удерживает тепло, и его несущей способности хватает для возведения двухэтажного здания. Поэтому, в подавляющем большинстве случаев, дома из него строят толщиной в один блок.
Но бывают случаи, когда требуется кладка газобетона толщиной в два блока. К примеру, если мы не хотим перегружать спину строителя. Ведь если по проекту дома требуется толщина стены в 375 мм из блоков плотностью D500, то вес таких блоков составит больше 40 кг. Как вы понимаете, один такой блок просто поднять трудновато, не говоря уже про точную укладку, переноску тысячи таких блоков для дома. Потому, приходится вести кладку вдвоем, или же кладку в два блока.
Также кладка в два блока необходима, если толщина стен планируется больше 40 см. Ведь газоблоки большей толщины не выпускаются.
Теперь разберем саму кладку блоков, варианты перевязки блоков, проклейку швов, и армирование кладки.
Рассмотрим три основных способа кладки: плашковая перевязка, когда используются блоки разной толщины; тычковая перевязка; кладка в прислонку.
Кладка в прислонку особенно хороша в плане, когда внутренний, более толстый слой, является несущим, а внешний слой работает как утеплитель. Важным достоинством такой кладки является то, что блоки не нужно подрезать для перевязки, что сэкономит много времени. Хорошим вариантом такой стены является внутренний слой 300 мм из D500 или D600, а внешний из D300/D200 толщиной 200 мм. Внешний слой можно сделать с горизонтальным смещением, что обеспечит закрытие швов внутреннего слоя.
Кладка блоков производится строго на клей, и все швы нужно промазывать.
Армирование кладки в два блока
Как и в обычной кладке, армировать нужно первый и каждый четвертый ряд, подоконный ряд, и места опирания перемычек.
Для тычковой и плашковой перевязки, достаточным будет армирование двумя прутками арматуры по ряду. Для кладки в прислонку, когда основной слой несущий, а второй теплоизоляционный, нужно несущий слой армировать двумя прутками арматуры, а внешний слой одним прутком.
Кладка газобетона толщиной в два блока
Газоблок, его тех характеристика и виды.
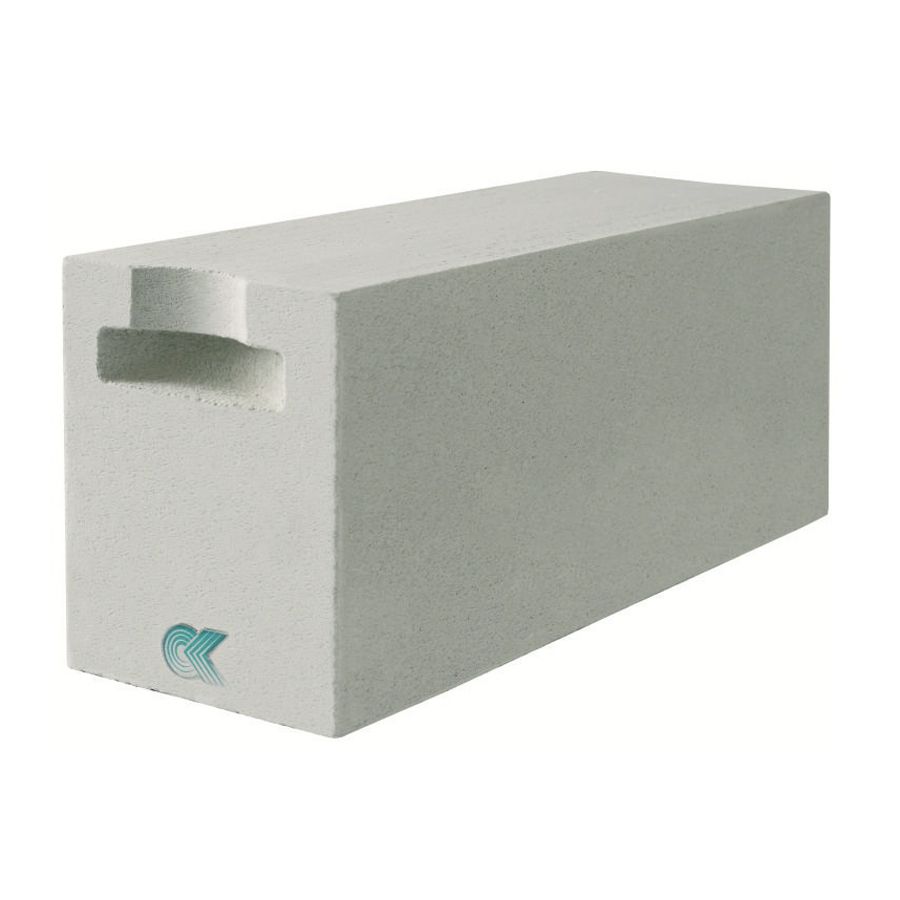
Газоблок — это искусственный пористый камень, разновидность ячеистого бетона который изготавливается из цементного раствора, кварцевого песка, газообразователя, иногда с добавлением промышленных отходов и других строительных сыпучих смесей.
В современном строительстве газобетон один из самых востребованных стеновых материалов, который используется как для возведения коробок домов, так и для организации внутреннего пространства зданий. Находит применение в разных сферах строительства, так в малоэтажном, частном строительстве из таких блоков полностью возводят дома, а в многоэтажной застройке газоблок, зачастую, служит базовым стеновым материалом, который заполняет монолитный каркас конструкции как внутри таки снаружи. Кроме реализации конструктивных решений, материал точечно используется как способ дополнительной шумоизоляции и теплоизоляции.
Газобетон относительно не молодой материал, однако широкое применение в развивающихся странах получил недавно. Корни создания газобетона уходят в 1889 год, в котором чешские химики – изобретатели, определили, что добавив в бетон соли и углекислый газ, получится эффект образования воздушных полостей в процессе высыхания материала. Такая структура значительно облегчила бетон и положительно отразилась на его теплопроводности. Доработали данную технологию уже в 1914 году американские ученые-химики, решив добавить в раствор бетонного блока порошки алюминия и цинка, это позволило увеличить объемы воздушных полостей, появляющихся в блоке в момент застывания.
Современный состав и вид газоблок, получил в 1929 году, в результате работы шведского ученого Ю. Эрикссона, которому удалось увеличить предел прочности и теплопроводности, а так же существенно снизить вес блока. В странах СНГ или бывшего СССР, газоблоки нашли свое применение лишь в 80 – х годах, и позволили решить задачи сокращения сроков ускоренного строительства и снизить финансовые затраты. Множество универсальных свойств газобетона, о которых мы рассказываем в настоящей статье, сохраняют и увеличивают потребности, как частного так и массового застройщика в данном материале.
Размеры блоков
Габариты газоблоков могут самыми разнообразными и выполняться даже по заказу, под каждого конкретного застройщика. В масштабном строительстве (промышленном и многоэтажном) имеются определенные стандартные размеры блоков. Однако каждый характеризуются точностью геометрии и формы. Вот почему материал монтируют на клей, а не на цементный раствор.
Плотность блока
В отличие от других искусственных камней, таких как кирпич и шлакоблок газоблок не отличается высокой плотностью, существенно уступает в данном свойстве из-за своей пористости. Поэтому зачастую используется как стеновой материал и только отдельные виды могут использоваться в малоэтажном строительстве для возведения несущих конструкций. На плотности блока отражается высокая ячеистость структуры, более пористые блоки, соответственно мене плотные и меньше весят. Таким образом, уровень плотности можно определить по весу кубометра.
Вес газоблока
Как отмечалось выше, вес блока напрямую зависит от плотности ячеек, блоки с малой пористостью меньше весят и менее прочны. Весовой показатель маркируется заглавной буквой D с указанием веса 1 ( одного) кубического метра материала. Например, маркировка D400 сообщает, что вес одного кубометра газобетона составляет 400 килограмм. Самые практичные блоки производится весом от 400 до 600 кг.
Вес разных видов газоблока в зависимости от размеров и марки прочностиТеплопроводность
Весь газобетон благодаря ячеистой структуре характеризуется повышенной шумоизоляцией и низким коэффициентом теплопроводности. Чем более пористый материал, тем эффективней отмеченные показатели. Таким образом, блоки марки D300 и 400 лучше сохранят тепло и оградят от шума в сравнении с блоками D 500.
Средний коэффициент теплопроводности блоков разной марки колеблется от 0,072 Вт/м*К до 0,140 Вт/м*К. Такие свойства значительно превосходят кирпич, бетон и иные популярные виды строительного камня.
Звукоизоляция
Индекс шумоизоляции газобетона зависит от нескольких параметров, потому один общий для всего материала коэффициент вывести нельзя. На способность защиты от шума виляет пористость материала то есть его плотность и толщина самого блока. Дополнительно усиливается данное свойство отделочными материалами такими как штукатурка и прочие. Ниже приведена таблица индексов звукопоглощения разных марок:
Паропроницаемость
Представляет собой способность материала накапливать и отдавать влажность в окружающую среду. Газобетон как пористый материал с однородной структурой, имеет один из самых высоких показателей поглощения влажности и такой же высокий показатель ее отдачи, при условии прямого взаимодействия с внешней средой (без отделочных материалов сверху).
Коэффициент паропроницаемости варьируется от 0,18 мг/м – ч-Па до 0,23 мг/м – ч-Па. Данный коэффициент показывает объем жидкости в виде пара в миллиграммах, которую поглощает 1 метр кубический материала за 1 час
Сравнительная таблица паропроницаемости газоблока и других стеновых материалов
Прочность
Имеет один из самых слабых показателей на прочность и сжатие, что так же обусловлено пористостью. Показатель прочности на сжатие блока обозначается буквой «В» и цифровым значением. Например В2,4 говорит о том, что материал выдерживает нагрузку в 2,4 Ньютона, то есть 24 кг на один сантиметр квадратный.
Морозостойкость
Количество циклов замерзания и оттаивания газоблока от 15 до 25, в зависимости от толщины и марки по плотности. Более морозостойкие используются для кладки внешних стен зданий, с низкой морозостойкостью в качестве стеновых перегородок. Маркируется показатель морозостойкости буковой «F» и цифровым указанием количества циклов замерзания, например F20.
Пожаростойкость
Газоблоки изготавливаются из негорючего сырья и потому не поддерживает горение и не воспламеняется. При длительном воздействии открытого огня начинает терять прочность структуры через 2 часа.
Усадка
Имеет незначительный показатель усадки от 0,5 мм до 2 мм в зависимости от вида, с абсолютным сохранением геометрии. По такому показателю можно практически исключить возможность возникновения усадки блоков.
Водопоглощение
Является достаточно гигроскопичным материалом из-за своей пористости. При прямом и длительном воздействии жидкости газоблок пропитывается до 2-3 см в глубину, быстро накапливает влажность, но и также быстро отдает ее при благоприятных погодных условиях. Это одна из причин, того что при кладке блоков не используется цементный раствор на водной основе.
Уровень микрокапиллярного подсоса влажности у газобетона низкий. Намокает непосредственно зона прямого воздействия жидкости на отмеченную выше глубину и не более. Строительные камни, с высокой плотностью, такие как кирпич и шлакоблок не могут похвастаться такими показателями и втягивают в себя жидкость на значительно большую глубину, а иногда и полностью пропитывается.
Сравнительная таблица тех свойств газоблока с другими стеновыми материалами
Виды газоблоковСуществует несколько практических классификаций газобетона, каждая из которых основывается на определенном свойстве материала, рассмотрим основные из них.
По марке плотности блока
Самая популярная классификация, которая обозначает уровень плотности воздушных пор в блоке и соответственно вес и прочность. Наиболее прочные используются для кладки внешних стен, а иногда и для монтажа части несущих конструкции дома.
По плотности производят марки от D200 до D1200, однако самый популярные которые производятся в промышленных масштабах это марки D300, D400, D500 и D600. Цифровой показатель сообщает нагрузку в килограммах, которую способна выдержать площадь блока в 1 см кв. . Марка с более высоким цифровым показателем самая плотная и менее пористая, имеет больший вес.
По назначению газоблоки можно классифицировать на:
Теплоизоляционные – с наибольшей пористостью и классом прочностью до D 300 -400 соответственно. Их рекомендуется использовать только для кладки межкомнатных перегородок, в целях утепления, а так же для монтажа внешних стен в доме с отдельным монолитным каркасом.
Конструкционно-теплоизоляционные – имеют большую плотность и прочность. Это уже блоки марки от D500 до D800, которые могут использоваться для формирования опорного конструктива небольших придомовых строений, хозяйственных построек с малой нагрузкой на стены. Такой материал одновременно выполняет функцию сохранения температуры внутри помещения и несущую функцию.
Конструкционные – марка плотности таких блоков от D900 до D1200. Как правило, в промышленных масштабах не производятся, а только под крупные заказы для крупного застройщика. Основным назначением материала является кладка опорного конструктива здания, теплоизоляционные свойства такого бетона не существенны. В сравнении с иными видами стенового искусственного камня имеет меньший вес, что является его существенным преимуществом.
Виды газоблоков по размеру и назначению
Блоки производятся различной длины, ширины и формы. Размеры определяются целями, в которых будет использоваться пористый бетон. Имеются размеры определенные нормами ГОСТа, но это не исключает возможность изготовления блоков под конкретный строительный проект.
- Классические стеновые — используются для кладки несущих стен, со стандартными размерами 600х250 мм по длине и высоте соответственно, ширина варьируется от 200 мм до 500 мм.
- Перегородочные блоки — применяются как материал для стеновых перегородок, также по длине и высоте имеет размеры 600х250, с меньшей толщиной до 150 мм.
- Каркасные блоки. Изготавливаются в форме буквы U, с пустотностью внутри для закладки бетонного аромопояса и оконных перемычек.
Длина таких изделий отличается и составляет от 1500 до 2000 мм, стандартной высотой 250 мм и шириной до 150 мм. Подобная разновидность блоков может изготавливаться по замковому типу «шип-паз», однако такое соединение не зарекомендовало себя с положительной стороны при эксплуатации здания, а также увеличивает стоимость конструкции и не пользуются популярностью. Потому рекомендуется выполнять классическую кладку блоков.
Плюсы стен из газоблока
Дополнительная звукоизоляция
Пустотная ячеистость структуры, является основной большинства шумоизоляционных материалов. Блоки с низкой плотностью особенно хорошо оградят от внешних звуков помещение, поглотят или существенно снизят звуки исходящие изнутри комнаты. В настоящее время, газоблок широко используется как основной материал для кладки межквартирных стен в новостройках. Таким образом, удается получить более качественную шумоизоляцию между изолированными жилым помещении, где ее уровень не должен быть ниже 52 Гц, если сравнивать кирпичные или даже гипсовые кладки старых домов. Оштукатуривание таких стен еще более усилит шумоизоляцию.
Высокая влагоотдача и паропроницаемость
Находящийся в условия большой влажности газоблок достаточно хорошо впитывает жидкость, однако также быстро ее и отдает. Высыхает с сохранением своей прочности, такое свойство проявляется благодаря все той же пористости. Это говорит и о том что материал «дышащий», не создает вакуумного эффекта и влажность в нем не застаивается. В сравнении с такими стеновыми материалами как дерево или герметичные сип- панели
газобетон не пропитывается водой полностью, в отличие от аналогичных строительных камнейОгнестойкость
Имеет один из самых высоких пределов огнестойкости среди стеновых материалов. Не возгорается и не поддерживает огонь при прямом его воздействии. Без изменения технических свойств выдерживает температуру до 700 Сº, после 900 Сº появляются микротрещины и повторное использование блоков не рекомендуется. Структура начинает терять свою целостность после 3 часов непрерывного воздействия открытого пламени.
Морозостойкость
Среднее количество раз заморозки и оттаивания составляет 35. Такая морозостойкость является оптимальной и является признаком долговечного материала для внешней стены. Данный срок рассчитан при условии прямого воздействия низких температур на влажный газоблок и без защитно-облицовочного материала. Данный коэффициент морозостойкости значительно увеличивается, когда наружные стены утепляются пенополистиролом или минеральной ватой с облицовочной кирпичной кладкой. При этом, смещается место образования конденсата – точка росы, в сторону улицы, в прослойку утеплителя между газоблоком и кирпичом, что исключает вероятность замерзания жидкости в самом газоблоке. Что бы получить такой эффект необходимо грамотно спланировать пирог внешней стены. Подробнее про точку росы и ее расчет в статье: (ССЫЛКА) « Точка росы в строительстве. Расчет точки росы и ее вред для стены дома»»
Теплопроводность
Заполненные воздухом поры, существенно увеличивают теплоизоляционные свойства бетона. Газоблок хорошо сохраняет тепло внутри помещения и ограждает его от холодного воздуха снаружи. Средний коэффициент теплопроводности составляет 0,14 Вт/м*С, и меняется в зависимости от марки. На теплопроводность газобетона может влиять влажность климата, в стабильно влажных условиях это показатель приближается к нулю и требует увеличение толщины стены, согласно техническим расчетам. Для создания теплоэффективного климата внутри помещения достаточной толщиной блока является от 20 до 30 см.
сравнение толщины стеновых материалов при одинаковом уровне теплопроводностиПолностью не пропитывается жидкостью
При постоянном воздействии жидкости на поверхность промокает максимум на глубину 15 см и не втягивает жидкость во все тело. В отличие от кирпича, который втягивает жидкость на толщину всей стены вплоть до нескольких метров.
Прост в раскройке и монтаже
Легко режется обычной пилой, благодаря легкому весу кладка и передвижение материала на объекте может выполняться самостоятельно, что снижает затраты на работу. Имеет ровную геометрию, что упрощает кладку в единой плоскости. Сроки возведения стен, так же существенно снижаются из-за больших размеров блоков.
Демонтаж газоблочной стены, с целью перепланировки, так же выполняется намного легче в отличие от любых других стеновых материалов. С помощью специальной пилы и молотка, кладка сравнительно быстро демонтируется, без лишнего мусора. А благодаря легкому весу и большим объемам блоков, легче и быстрее транспортируется с объекта.
Совместим со всеми видами материалами внутренней отделки стен.
газоблок достаточно легко режетсяСтоимость
Один кубометр газоблока в ценовой категории, вместе с затратами на дополнительные кладочные материалы обходится в несколько раз дешевле монтажа той же квадратуры из кирпича, дерева и даже шлакоблока с керамзитобетоном. Подробнее про керамзитобетон в статье : « Керамзитобетон, свойства и виды. Как выбрать »
Долговечность
При использовании для монтажа наружных стен, срок эксплуатации газобетона заявляется производителем от 60 лет. При использовании в качестве внутридомовых перегородок, газобетонная стена прослужит несколько поколений, так как не подвержена сезонным изменениям окружающей среды.
старый дом из газобетонаЛегкий вес и незначительная усадка
Такое достоинство особенно актуально для малоэтажного частного строительства, где от общего веса коробки дома зависит массивность фундамента и соответственно затраты на него. Если же планируется монтаж дополнительных стеновых перегородок, весовая нагрузка которых не была учтена при планировании фундамента дома, то такие стены не будут создавать критичного воздействия на конструкцию, как частном так и в многоквартирном домах.
Важным свойством является минимальная усадка или практически ее отсутствие. Усадка свежего и не полностью просохшего блока может составлять 0,5 мм на 1 метр, это крайне незначительны показатель для каменной стены. Но все же после кладки рекомендуется сразу не проводить отделочные работы, а дать в течении 2-6 месяцев, испариться лишней влажности из пористого газобетона. В ином случае, может возникнуть риск появления мелких трещин на поверхности материала, они не разрушают структуру стены, но их придется дополнительно устранять.
дом из газобетона практически не дает усадку
Устойчивость к плесени и грибку
Стены не накапливают сырость, на время достаточное для образования разного рода паразитических организмов на стене. Кроме того, для плесени и бытовых грибков сырье материала – неблагоприятная среда.
Безопасен для здоровья
При температурных изменениях газоблок не выделяет токсичных веществ и каких-либо запахов. Материал спокойно переносят люди с любыми видам аллергии. Сырье из которого изготавливаются блоки – это производные горных пород ( известь, песок , цемент, вода) В состав так же входят, алюминиевая паста, зола и шлак, однако их содержание на столько минимально, что не приходится говорить о возможности возникновения радиационного фона, накопления радиации и прочих негативных воздействий.
Низкая прочность на сжатие и ее риски
Это отрицательная сторона высокой пористости материала, которая в свою очередь нивелируются такими положительными характеристиками как малый вес, хорошая шумо- и теплоизоляция, а так же легкость в работе. Имеющейся плотности достаточно для монтажа практичных стеновых перегородок и внешних стен здания с монолитным каркасом, но не достаточно для возведения несущих конструкций.
Некоторые частные строители «для себя» а иногда и для «других» используют газоблок, как несущий материал. Возводят из него капитальные придомовые строения и даже жилые помещения. При этом, закладывают только межэтажный или предчердачный армопояс, чем только создают дополнительную нагрузку на, и без того, слабые блоки. Для таких домов обязательно следует закладывать полноценный монолитный каркас, состоящий из вертикальных балок, которые берут на себя несущую нагрузку и стягиваются ж/б поясом в верхней части и фундаментом у основания. В ином случае, такие конструкции представляют опасность для жизни и здоровья их владельцев в виду слабой прочности.
Впитывает влагу
Как отмечалось выше в статье, поверхность блока способна хорошо впитывать влажность при длительном и обильном ее воздействии, но глубоко ее не втягивает, а лишь до 2- максимум 3 см. После чего, сравнительно за коротки срок, газобетон отдает влажность наружу и не накапливает ее. Поэтому, после кладки стен из свежего газоблока, рекомендуется их просушить в течении 2 месяцев, и затем уже закрывать структуру стены отделочными материалами.
Наличие избыточной влаги в блоке может вызвать ее замерзание при отрицательных температурах воздуха, увеличение объемов и соответственно растрескивание.
Кроме того, высокая гигроскопичность создает некоторые трудности в оштукатуривании стены, так как блок быстро впитывает жидкость и гипсовая смесь на стене может не успеть набрать прочность и отслоится. Чтобы избежать таких последствий, рекомендуется не мене двух раз прогрунтовать поверхность блоков и уже после полного высыхания, смонтировать армировочную сетку, приступать к штукатурным работам.
высокая гигроскопичность создает трудности при оштукатуриванииРиск возникновения трещин при усадке основания ( фундамента)
Сам блок практически не подвержен усадке, однако нестабильный, не осевший до конца фундамент, который еще находится и на пучинистом грунте. Может спровоцировать появление как мелких, так и крупных сквозных трещин в слабом на сжатие газоблоке.
Мягкость и хрупкость
Мягкость проявляется при ударном воздействии твердых предметов, при этом блок находящейся в структуре стены не трескается, а в нем образуется вмятина, которая устраняется гипсовой смесью. Если, таким же ударным способом воздействовать на отдельный блок, то он расколется. Поэтому важно аккуратно транспортировать хрупкий газоблок и проверять его на сколы перед получением у продавца.
Мягкость материала позволяет осуществлять раскройку с помощью специальной пилы, однако это не значит, что с улицы можно проникнуть в помещение путем легкого демонтажа части стены. Для этого необходимо выполнить значительный объем трудоемких и шумных работ, сопоставимый с разрушением кирпичной кладки, кроме того внешняя часть стены всегда отделана облицовочным материалом. Потому можно быть уверенным в безопасности своего имущества в газобетонном доме.
блоки хрупкие при неосторожном обращении , могут появляться сколы и трещиныИспользование специальных крепежей для стены
Твердость структуры любой каменной или бетонной стены предполагает использование специальных пробок и крепежей, не исключением является и газбоетон. Даже не имея такую прочность как кирпич, чтобы закрепить на блочной стене тяжелый предмет мебели необходимо использовать специальные дюбеля, которые в настоящее время можно приобрести в любом строительном магазине по доступной стоимости. На таком крепеже стена выдерживает статическую нагрузку до 400 кг.
Технические характеристики современных газобетонных блоков, все их достоинства и недостатки позволяют сделать вывод, что материал имеет гараздо больше преимуществ, как в капитальном строительстве так и эффективно используется при организации внутреннего пространства для последующей отделки помещений. Доступная стоимость, практичность и долговечность газобетона, с соблюдением простой технологии монтажа, позволяют построить собственное, надежное жилье, высокого качества, с гараздо меньшими затратами, за сравнительно короткие сроки.
дом из газоблока дом из газоблокавиды, характеристики, плюсы и минусы
Газобетонные блоки
Газобетон изготавливается из кварцевого песка и цемента с использованием методики газообразования. В результате получается искусственный камень с пористой структурой. Именно наличие внутренних ячеек с воздухом обеспечивает этому строительному материалу столь высокие показатели энергосбережения, теплоизоляции, а также небольшой вес.
Рассказываем, какими плюсами и минусами обладают газобетонные блоки.
Классификация материала
Существуют следующие виды газобетонных блоков:
По типу базового вяжущего элемента:
-
Известковые. Такие блоки на 50% состоят из извести-кипелки. В их состав входят также гипс и шлак или цемент.
-
Цементные. До половины массы таких газобетонных блоков приходится на портландцемент.
-
Шлаковые. Этот материал включает в свой состав смесь шлака с гипсом, известью или щелочью (свыше 50%).
-
Зольные. Блоки этого типа изготавливаются на основе высокоосновных зол. Этого компонента в их составе – более 50%.
-
Смешанные. Они производятся из шлака и извести (либо их смеси) с добавлением 15 — 50% портландцемента.
По типу кремнеземистого элемента:
-
С применением природных песков.
Как правило, этот вид газобетонных блоков производится с применением кварцевого песка.
-
С применением вторичного сырья. В данном варианте используются отходы ферросплавной отрасли, золы-уноса с тепловых электростанций и т.д.
По условиям вторичного твердения материала:
-
Автоклавные. Газобетонные блоки этого вида затвердевают в автоклавных печах в условиях повышенного давления и насыщенного пара.
-
Неавтоклавные. В этом случае материал твердеет тоже во влажной среде, но при атмосферном давлении или с применением метода электроподогрева.
Основные характеристики газобетонных блоков
Прочность этого материала варьируется от 10-12 кгс/кв. см (у неавтоклавного газобетона) до 28-40 кгс/кв. см (у блоков автоклавного типа). Максимальная прочность материала достигается путем обработки в условиях повышенного давления.
Объемный вес может составлять от 200 кг/куб. м до 600 кг/куб. м. Самый легкий газобетон используется в качестве теплоизоляционного материала. Более тяжелый применяется в малоэтажном строительстве.
Теплопроводность блоков зависит от их плотности и составляет в среднем 0,12 Вт/мГрад. Это оптимальный показатель в соответствии с современными требованиями по сопротивлению теплопередаче конструкций.
Морозоустойчивость газобетонных блоков – F100. Для сравнения, у керамического кирпича М50 этот показатель соответствует уровню F25, а у газосиликатного блока D500 – F35.
Звуконепроницаемость. Эта характеристика газобетонных блоков определяется плотностью материала и составляет в среднем 50 Дб.
Усадка автоклавных газобетонных блоков – 0,2-0,5 мм/м. У материала неавтоклавного производства этот параметр несколько выше – от 2 до 5 мм/м.
Водопоглощение достаточно высокое – порядка 20%. У кирпича этот коэффициент в 1,5-2 раза ниже. Поэтому стены из газоблоков требуют облицовки.
Огнестойкость – до 7 часов. Газобетонные блоки состоят из минеральных веществ, которые не горят и не плавятся.
Плюсы и минусы газобетонных блоков
В список основных достоинств этого строительного материала входят следующие:
-
Газоблоки в 3-5 раз легче силикатного кирпича. Дома из таких блоков возводятся в среднем на 20% быстрее, чем кирпичные строения аналогичных размеров.
-
Пористый газобетон отлично сохраняет тепло внутри здания. Теплопроводность газоблоков в 2-3 раза ниже, чем теплопроводность обычного кирпича.
-
Этот материал легко пилится, сверлится и строгается без необходимости в применении специального инструмента.
-
Еще один плюс газобетонных блоков – высокая огнестойкость. Этот материал не горит и не выделяет опасных газов при воздействии открытого огня.
-
Благодаря пористой структуре, газобетон хорошо пропускает воздух. Стены из этого материала «дышат», и в доме создается комфортный микроклимат.
-
По уровню экологичности газоблоки уступают лишь древесине.
Среди недостатков этого материала можно отметить:
-
Гигроскопичность. Газобетон хорошо впитывает влагу.
-
Усадка. Особенно сильную усадку дают блоки неавтоклавного типа.
-
Недостаточная прочность. Из этого материала строят дома высотой не более 3 этажей.
Учитывая все вышеперечисленные характеристики газобетонных блоков, можно с уверенностью сказать, что это оптимальный материал для малоэтажного строительства в любых регионах России. Купить газоблоки по выгодной цене можно в компании «Керамик Групп». Для оформления заказа звоните по телефону +7 495 125-30-45.
особенности внутренней штукатурки, как и чем шкурить?
Наиболее часто в последнее время строительные работы выполняются из газоблоков. Такой выбор обусловлен возможностью строить как несущие стены, так и различного рода перегородки, а также скоростью выполнения работ. После возведения такие конструкции требуют оштукатуривания.
Штукатурка для газобетона представляет собой отделочный материал, с помощью которого улучшаются технические показатели конструкции, а также обеспечивается долговременная прочность стен как со стороны фасада, так и внутри здания. Она предназначена для защиты газобетонных поверхностей от растрескивания и последующего полного разрушения под влиянием внешних факторов.
Внутренние отделочные работы обычно производятся гипсовыми растворами, которые имеют достаточный уровень паропроницаемости. Наличие этого качества говорит о том, что штукатурку можно использовать в качестве подложки перед оклейкой обоев. При этом есть еще ряд преимуществ такого вида раствора, а именно:
- максимальная защита от проникновения влаги;
- хорошая пропускная способность воздушных масс;
- возможность выбора структуры;
- обеспечение звукоизоляции конструкции;
- позволяют по желанию менять структурную составляющую и цветовую гамму фактуры, независимо от временного периода по завершении строительных работ.
Также следует придерживаться следующей последовательности внутренней отделки стен:
- устранить все неровности и сколы на всех сторонах стены;
- устранить имеющуюся пыль;
- нанести штукатурку начальным слоем;
- произвести установку сетки, обеспечивающей армирование;
- нанести второй слой смеси;
- дать полностью высохнуть;
- наклеить обои или покрасить.
По желанию в штукатурку можно ввести различные добавки, что сделает ее более декоративной, или окрасить в любой колер. Необходимо также помнить, что всем действиям, связанным с работой по распределению штукатурной смеси для газобетона, обязательно предшествует грунтовка стен. Если придерживаться последовательности действий, несложно обеспечить безупречный результат, который продержится максимально длительное время.
Основные требования к штукатурке
Использование штукатурок, изготовленных на песчаной основе и разработанных для конструкций, возведенных из газобетона, профессионалы не рекомендуют. Это обусловлено тем, что традиционные песчаные растворы характеризуются большой плотностью. Это негативно влияет на адгезию при нанесении на поверхности, вследствие чего за короткий период времени можно обнаружить трещины.
Отдавать предпочтение следует строительным смесям с паропроницаемым основанием. Благодаря такому выбору будет обеспечена защита стен от проникновения влаги, а также это позволит сохранить благоприятный температурный режим помещений. Игнорирование уровня паропроницаемости приведет к скапливанию пара внутри перегородок, что повлечет за собой процесс начала разрушения конструкции в целом.
Штукатурки должны отвечать следующим требованиям; это:
- максимальная устойчивость к влиянию атмосферных явлений;
- высокие показатели адгезии;
- реакция на изменение температурного режима;
- высокий коэффициент прочности;
- достаточная паропроницаемость;
- плотность, которая не должна превышать необходимые пределы;
- повышение теплоизоляционных характеристик;
- эстетичный вид.
Штукатурки для газобетона и используемые для этого инструменты
Штукатурка для газобетона очень проста в использовании. Мастера, обладающие опытом работы, без труда приведут в порядок как внутренние поверхности, так и внешние. При этом здание будет иметь индивидуальный вид, который способны придумать хозяева, путем добавления различных декоративных компонентов в раствор.
Штукатурка относится к отделочным строительным материалам, которую наносят мастера; при этом используют специальные инструменты и оборудование. Необходимый набор таких приспособлений подходит для нанесения материала как на внутренние, так и на внешние поверхности. Чаще всего этот перечень состоит из такого набора, как:
- емкость для замешивания раствора;
- киянка для отбивания лишних частиц с поверхности и нанесения насечек;
- щетка для грунтования;
- строительный уровень;
- штроборез или перфоратор;
- специальная лопатка для набрасывания раствора;
- правило, с помощью которого определяется достаточность слоя и выравнивание его по всей поверхности;
- гладилка для идеального выравнивания.
Виды штукатурок, используемых для газобетонных блоков
Приступая к выбору отделочных материалов, необходимо определиться, где будут проводиться работы – снаружи или внутри. Штукатурки для газобетона могут отличаться по назначению:
- внутренние – влагостойкость имеет значение только при отделке санузла; стоимость материала гораздо ниже;
- внешние – обладают более высокими показателями влагостойкости, теплоизоляции и прочности, обеспечивают надежную защиту конструкции.
Выбор в пользу определенных материалов непосредственно зависит от места проведения работ. Штукатурки также подразделяются по типу состава:
- Известково-цементные растворы.
В таких растворах вместо песка используется известь, которая обеспечивает прочность и паропроницаемость. Они имеют низкие показатели эластичности, водостойкости и выбор цветовой гаммы, что легко устраняется при помощи специальных добавок;
- Штукатурка акриловая.
Используется только при качественной изоляции стен. Выполняется чаще всего в качестве прочной и надежной декоративной отделки, так как имеет плохую паропроницаемость.
- Штукатурка силикатная.
За основу в этом виде взято жидкое стекло. Отделка данным материалом имеет эстетичный вид и устойчива к загрязнениям. Обладает высокими показателями влагостойкости, паропроницаемости и прочности. Легко наносится. Штукатурки этого вида имеют недостаток выбора цветовой гаммы.
- Штукатурка на основе силикона.
Достаточно надежна. Благодаря возможности выбора цвета и специальным добавкам отличается декоративностью и возможностью придать фасаду оригинальности. Смеси на силиконовой основе выделяются эластичностью, которую сохраняют в течение выполнения всех работ.
В качестве штукатурок для газобетона не стоит использовать обычные смеси с песчаной основой. Они ненадежны, имеют низкую степень адгезии и за короткий промежуток времени начинают трескаться.
Наружная штукатурка стен из газобетона
Отделка конструкции из газобетона включает в себя наружные и внутренние работы. Наружная штукатурка газобетона может производиться по таким технологиям отделки стен:
- толстослойная – штукатурку наносят одним толстым слоем;
- тонкослойная – накладывается несколько тонких слоев.
Такая отделка дома, кроме защиты материала, из которых построено здание, обеспечивает и такие параметры, как:
- усиление шумоизоляции и теплоизоляции стен;
- устранение излишней влаги;
- защита от перепадов температурного режима;
- придание конструкции индивидуальности.
Распределение штукатурки на дом из газобетона необходимо выполнять поэтапно, а именно:
- подготовить и выровнять поверхности стен;
- провести грунтовку;
- нанести первичный слой для установки сетки;
- произвести армирование для исключения появления трещин;
- выровнять первый слой;
- нанести второй слой раствора;
- закрепить финальным слоем;
- затереть.
Особенности оштукатуривания стен из газоблоков
Штукатурка газобетона внутренняя и внешняя выполняется в зависимости от особенностей строительного материала, а именно:
- газобетонные блоки могут иметь отличия по текстуре;
- учитывая степень паропроницаемости, отделывать необходимо сначала внутренние, а затем фасадные стены;
- внутри отделка должна быть толще, чем внешняя.
У пиленых газоблоков открытое строение, поэтому они не требуют предварительной подготовки перед отделкой стен. Формированные – с закрытой, их нужно обработать с целью повышения сцепления. Для этого требуется отшлифовать газобетон щеткой из металла.
И немаловажной особенностью является то, что начинать штукатурить газобетон необходимо только после полного высыхания возведенной конструкции, так как в стенах во время выполнения строительных работ могла накопиться излишняя влага, от которой обязательно нужно избавиться.
Предпочтительные условия нанесения штукатурки
Штукатурка для газобетона обладает определенными особенностями, поэтому рекомендуется наносить ее внутри в весенний сезон, а на фасад – в летний; максимально допустимая температура не должна превышать +30 градусов. Штукатурка может наноситься и при низкой температуре воздуха, но в случае крайней необходимости. Тогда следует обязательно применять для грунтования раствор глубокого проникновения, чтобы избежать дефектов, приводящих к растрескиванию конструкции.
Проводя отделочные работы необходимо избегать:
- попадания прямых ультрафиолетовых лучей;
- выполнения отделки газобетона при высокой температуре воздуха;
- излишнего пропитывания материала влагой;
- выполнение работы в ветреную погоду.
Штукатурка внешней поверхности здания из газобетона должна проводиться следующим этапом, когда будут выполнены все внутренние работы, имеющие довольно высокий показатель влажности. Чтобы избежать нарушения сцепления материалов и обрушения слоев отделки и фасада, необходимо следить также за показателем влажности главных стен, который должен быть минимален. Если соблюдать эти элементарные правила, качественный результат гарантирован.
Приобретение строительных материалов
Штукатурки разного вида, как и строительные материалы другого предназначения, предлагает своим клиентам компания Poritep. Длительный период времени работаем на строительном рынке, предлагая огромный ассортимент соответствующих товаров и услуг. Обращайтесь, и мы поможем эффективно решить каждую задачу, предложим оптимальные материалы, проконсультируем по интересующим вопросам.
Индивидуально подходим к каждому клиенту, гарантируя высокое качество предлагаемой продукции и демократичную ценовую политику. Профессиональность наших сотрудников приятно удивит. За дополнительной информацией можно обратиться к консультантам, позвонив по телефону. Также они готовы ответить на все интересующие вопросы онлайн. Выбирайте сотрудничество, которое будет плодотворным и обоюдно выгодным. Мы готовы поставить материалы в любых необходимых количествах. Вам остается выбрать удобный способ заказа и оплаты товара. Всегда к вашим услугам!
Штукатурка для отделки газобетона
Дома из газобетонных блоков отличаются специфическими эксплуатационными характеристиками (паропроницаемостью, гидрофобностью и т. д.), что накладывает определенные ограничения на выбор отделочных материалов. Штукатурка для внутренних работ для аэрированного бетона представляет собой сухую смесь на основе естественных компонентов с добавлением синтетических присадок, предназначенную специально для обработки поверхностей из данного материала. Составы этого типа характеризуются высокой степенью адгезии к газосиликатам, эластичностью, стойкостью к перепадам температур и механическим воздействиям. Специфика смесей подразумевает значительный уровень паропроницаемости, что позволяет организовать оптимальный воздухообмен в помещениях даже при условии использования дополнительного утеплителя стен.
Параметры
При выборе состава для отделки поверхностей из аэрированного бетона рекомендуется обращать внимание на следующие параметры.
- Степень адгезии. Данный показатель указывает на качество сцепления материала с поверхностью. Оптимальным считается значение 0,5 мПа.
- Пропорции приготовления. Различные составы предполагают использование различного количества воды для замешивания. Оптимальным расходом считается 0,6–0,7 л/кг.
- Допустимая толщина слоя. В зависимости от свойств конкретного состава различается наибольшая и наименьшая толщина наносимого за один раз пласта. Качественная штукатурка допускает наложение слоя от 2 мм и более.
- Период использования.
Хорошая штукатурка для отделки газоблоков пригодна к нанесению в течение 2–2,5 часов после замешивания. Это позволяет работать с оптимальной скоростью, не отвлекаясь на подготовку новой небольшой порции.
Специфика использования
Смеси данного типа могут применяться для отделки помещений как с нормальным, так и с повышенным уровнем влажности. Рекомендуемая температура окружающей среды во время проведения работ составляет +5…+30 °C. Технология нанесения подразумевает наложение нескольких слоев смеси на поверхности. Вначале укладывается первый пласт и оставляется до частичного высыхания (в пределах 60 минут). По истечении этого срока поверхность стены выравнивается и оставляется до полного высыхания. После отвердевания первого слоя штукатурка увлажняется и разглаживается. На завершающем этапе отделки на стену наносится финишный слой смеси.
Види і характеристики газоблоків | ibud.ua
Ще на етапі проектних робіт слід замислитися про стінновий матеріал. Одним із сучасних і досить популярних на будівельному ринку матеріалів є газобетонний блок. Спочатку розберемося, що таке газоблоки.
Газоблоки за своєю структурою нагадують пористу бетонну губку, оскільки весь об’єм блоку складається з комірок (бульбашок діаметром 1-3 мм). Завдяки цьому такий блок має невелику вагу при великому розмірі, легко ріжеться і добре зберігає тепло.
Знаючи характеристики газоблоку, легко вибрати блоки з оптимальними параметрами, які підійдуть для будівництва стін, підвалів та інших приміщень.
Переваги та недоліки газоблоків
З газобетону будують будинки, котеджі, лазні та інші споруди. Сировиною для виготовлення газоблоків служить кварцовий пісок, вапно, цемент, вода, алюмінієва пудра. Всі компоненти перемішують у певному співвідношенні, після чого відбувається їх спінювання (вступ у реакцію високодисперсного алюмінію з лужним розчином), завдяки чому утворюється пориста структура. Суміш збільшується в об’ємі, схоплюється, потім її виймають з форми і роблять заготовки. Потім їх відправляють в автоклав для обробки парою при високому тиску, або висушують класичним способом.
Виділяють наступні види газоблоків:
- автоклавний;
- неавтоклавний.
Автоклавний газобетон – це пористі блоки автоклавного твердіння. Неавтоклавний газобетон виробляють шляхом зволоження та сушіння в природних умовах.
Блоки газобетону мають свої переваги та недоліки, які слід врахувати ще до початку будівництва. До переваг газобетону можна віднести такі властивості:
- низька вартість;
- добра теплоізоляція;
- зручність в роботі, можливість легко монтувати, перевозити, різати і шліфувати газоблоки;
- паропроникність, при якій забезпечується вихід водяної пари з опалювального будинку назовні;
- мала вага;
- вогнестійкість;
- екологічність і безпека для здоров’я.
Незважаючи на позитивні якості, необхідно врахувати і те, які є недоліки газобетону. До них можна віднести:
- підвищену крихкість при невеликій щільності;
- теплопровідність;
- високе поглинання вологи;
- низьку міцність на стискання (у блоків з низьким коефіцієнтом теплопровідності).
Виробники пропонують газобетон, розміри блоків якого відповідають певним стандартам. Ось основні розміри і різновиди газоблоків:
1. Газоблоки стінові бувають звичайної прямокутної форми з виїмками для захоплення руками.
Ширина (мм) | Висота (мм) | Довжина (мм) |
200 | 200 | 600 |
250 | 200 | 600 |
280 | 200 | 600 |
300 | 200 | 600 |
360 | 200 | 600 |
400 | 200 | 600 |
500 | 200 | 600 |
2. Газоблоки перегородкові являють собою блоки з плоскими гранями. Вони мають меншу товщину і вага.
Ширина (мм) | Висота (мм) | Довжина (мм) |
75 | 200 | 600 |
100 | 200 | 600 |
120 | 200 | 600 |
150 | 200 | 600 |
3. U-образні блоки для перемичок використовують для встановлення прихованих елементів будівництва (перемичок і монолітних поясів).
Ширина (мм) | Висота (мм) | Довжина (мм) |
250 | 200 | 500 |
300 | 200 | 500 |
360 | 200 | 500 |
Класифікація газоблоків за марками в залежності від щільності
Газоблоки класифікуються за щільностю. Його типи маркуються латинською літерою D з певними цифрами. Чим більше значення, тим вище щільність, а блок – міцніше. В залежності від марки газобетону характеристики будуть відрізнятися. За щільностю виділяють наступні його види:
- теплоізоляційний (D300 і D400) – застосовується лише в цілях збереження енергії та має пористість більше 75% від всього об’єму виробу;
- конструкційно-теплоізоляційний (від D500 до D900) – використовується для монолітних і малоповерхових споруд, пористість 55-75%;
- конструкційний (від D1000 до В1200) – призначається для зведення будівель, що піддаються великим навантаженням, пористість 40-55%.
Щільність ніздрюватого бетону марки D300 говорить про те, що 1 м³ газобетонного блоку вміщує в себе 300 кг твердих речовин, а весь інший простір займають повітряні пори. Чим вище щільність бетону, тим нижче його теплоізоляційні властивості.
Конструкційні блоки мають високу щільність. Теплоізоляційні газоблоки – більш тендітні, але краще зберігають температуру. Конструкційно-теплоізоляційні марки поєднують у собі всі перелічені вище якості, тому вони підходять для будівництва теплих стін.
Газоблок d300 може бути використаний тільки як утеплювач. Це досить рідкісна марка, що пов’язано з її крихкістю. Міцність знаходиться в межах 0,7-1,0 МПа, а теплопровідність становить 0,08-0,09 Вт/(мК).
Газоблок d400 популярний в приватному будівництві. Такі блоки використовуються для теплоізоляції прорізів. При високій міцності він володіє великими теплоізоляційними властивостями. Ці показники знаходяться в межах 1 МПа до 1,5 МПа (міцність), 0,10-0,11 Вт/(мК) (теплопровідність).
Газоблок d500 застосовують при спорудженні будинків (до 3-х поверхів). Його параметри 2-3 МПа (міцність) і 0,12-0,13 Вт/(мК) (теплопровідність).
Марка Д600 використовується для будівництва опорних стін будівель високої поверховості. Газоблок 600 відрізняється міцністю газобетону в 2,5-4,5 МПа і має показник теплопровідності 0,14-0,15 Вт/(мК).
Основні технічні характеристики газобетону:
Пористість, % | Щільність, кг/м³ | Міцність на стискання, МПа | Теплопровідність, Вт/(мК) |
50 | 1100-1200 | 10-15 | 0,33-0,40 |
60 | 900-1000 | 5-12 | 0,24-0,30 |
70 | 700-800 | 2,5-5 | 0,17-0,22 |
80 | 400-600 | 1,2-4 | 0,10-0,14 |
90 | 200-300 | 0,7-1,2 | 0,06-0,08 |
95 | 200 | 0,4-0,7 | 0,06 |
Теплоізоляційні властивості
Будівництво з автоклавного газобетону дуже вигідне завдяки його унікальним теплоізоляційним властивостям. Зовнішні стіни товщиною 30 см без додаткових ізоляційних матеріалів досягають коефіцієнта теплопередачі стінки К=0,34 Вт/м²К. Термічний опір огороджувальних конструкцій з ніздрюватого бетону в 3 рази вище, ніж з глиняної цегли і в 8 разів вище, ніж з важкого бетону.
Автоклавний газобетон не тільки утримує тепло, але й акумулює його. Тому приміщення вночі остигає повільно, а вранці швидко нагрівається. Одночасно газобетон забеспечує ефективний захист від зовнішнього тепла. Навіть при високій атмосферній температурі приміщення залишаються прохолодними, тоскільки стіни дуже повільно пропускають тепло в приміщення. Це знижує витрати на опалення на 25-30% без застосування додаткових теплоізоляційних матеріалів.
Будинки, побудовані з газоблоків, протягом усього року матимуть сприятливий мікроклімат. Стіни завжди теплі, оскільки прогріваються дуже швидко. В нормальному стані коефіцієнт теплопровідності становить близько 0,13 Вт/(мК).
Більш докладно характеристики теплопровідності газобетону наведені в таблиці.
Марка по щільності | D500 | D600 |
Нормована густина, кг/м³ | 500 | 600 |
Клас по міцності на стискання | B2,5 | B3,5 |
Коефіцієнт теплопровідності в сухому стані, [λ] | 0,12 | 0,14 |
Коефіцієнт теплопровідності при вологості 4%,[λ] | 0,141 | 0,16 |
Коефіцієнт теплопровідності при вологості 5%, [λ] | 0,147 | 0,183 |
З таблиці видно, що здатність газобетону зберігати тепло знижується в міру зволоження.
Виходячи зі значення коефіцієнта теплопровідності, можна зробити висновок, що газобетон з низькою щільністю утримує тепло набагато краще, ніж за високою. Стіна з газобетонних блоків з маркою щільністю D500 тепліша за D600 на 15-17%.
Звукоізоляційні властивості
Звукоізоляційні властивості – це здатність матеріалу до гасіння звуків. Вона залежить від товщини стін, марки і середньої густоти газобетону, а також від технології зведення стін.
Газобетон має коефіцієнт звукоізоляції на 2 дБ більше в порівнянні з іншими будівельними матеріалами, що є його безперечною перевагою.
У відповідності зі СНиП II-12-77 «Захист від шуму», нормативні індекси ізоляції повітряного шуму огороджувальних конструкцій складають:
Найменування та розміщення огороджувальної конструкції | Індекс ізоляції шуму, дБ |
Стіни і перегородки між квартирами, між приміщеннями квартири і сходовими клітинами, холами, коридорами, вестибюлями | 50 |
Стіни між приміщеннями квартири та магазинами | 55 |
Стіни між приміщеннями квартири та ресторанами, спортивними залами, кафе та іншими подібними закладами | 60 |
Перегородки без дверей між кімнатами, між кухнею і кімнатою в квартирі | 41 |
Перегородки між кімнатами однієї квартири | 45 |
Для різних марок газоблоку індекс ізоляції шуму наведено в таблиці:
Марка газобетону | Індекс ізоляції шуму, дБ при товщині огороджувальної конструкції, мм | ||||
120 | 180 | 240 | 300 | 360 | |
D500 | 36 | 41 | 44 | 46 | 48 |
D600 | 38 | 43 | 46 | 48 | 50 |
Вогнестійкість
Газобетон – це негорючий матеріал з високим класом вогнестійкості, який захищає від розповсюдження вогню. Згідно європейським стандартам газобетон відносять до класу «Євро клас А1». Згідно ДБН Ст. 1.1-7-2002 «Пожежна безпека об’єктів будівництва», будинки з несучими та огороджувальними конструкціями з газобетону характеризуються найбільш високими I і II ступенями вогнестійкості.
Оскільки для виготовлення газобетону використовується лише природна мінеральна сировина, то немає і небезпеки загоряння. Газобетон, будучи неорганічним і негорючим матеріалом, витримує односторонню дію вогню протягом 3–7 год. Це матеріал, який здатний захистити металеві конструкції від прямої дії вогню. Газобетон застосовується для всіх класів протипожежної безпеки. Він не руйнується під впливом високих температур і перешкоджає поширенню вогню. Дослідження показали, що при підвищенні температури до +4000 °C міцність газобетону збільшується на 85%.
Автоклавний газобетон забезпечує найвищій захист від вогню і відповідає всім вимогам пожежної безпеки. Через мінеральний склад, газобетон класифікується як негорючий будівельний матеріал. Він стійкий до вогню до 1200°C, є термостійким.
Неавтоклавний газобетон – незаймистий матеріал. Це зумовлено невисоким значенням теплопровідності і малої рівноважної вологістю. Він підходить для захисту будь-яких конструкцій від впливу полум’я. Всі конструкційні елементи з цього матеріалу, теж володіють вогнестійкістю.
Вироби з неавтоклавного газобетону використовується:
- для зведення протипожежних стін;
- підвищення вогнестійкості стін;
- для теплоізоляції обладнання;
- для захисту сталевої арматури.
Порівняльна таблиця вогнестійкості різних марок газобетону.
Марка щільності газобетону | Вогнестійкість при товщині 175 мм, годину |
D600 | 4,0 |
D700 | 4,0-5,0 |
D800 | 5,0 |
Усадка
Газобетонні блоки автоклавного твердіння отримують додаткову міцність матеріалу, завдяки термообробці. При автоклавуванні пористу структуру газобетону під впливом температури в 200°C проникають молекули мікрокристалічного з’єднання тоберморіта (Ca5Si6H5), які створюють стійкість до усадкових процесів на 25%. Відбувається микрокристаллизация газобетону, що підвищує загальний показник міцності на стискання і знижує рівень усадки.
На швидкість усадкової деформації впливають атмосферні зміни. Підвищена атмосферна вологість уповільнює усадку газобетону. В стандартних умовах при зменшенні вологості газоблоку від 35% до 5%, усадка, може доходити до 0,3 мм/м
Усадка будинку з газобетону може тривати близько двох років після здачі об’єкта в експлуатацію. Висихання автоклавного ніздрюватого бетону до рівня 2% вологості каталізує усадку. Вона може складати 2 мм/м.
Будівництво будинків з газоблоків ведеться з урахуванням того, що він, як і всі будматеріали, в основі яких зв’язка з цементу, схильні до усадки. Для газобетону ще на стадії розробки діє стандарт усадки, яка відбувається під час сушіння сформованих ніздрюватих блоків.
Для автоклавного газобетону, що має в своїй основі пісок, усадка не повинна перевищити показник 0,55 мм/м, а для блоків, які виготовляються способом класичного сушіння, стандарт встановлений на рівні 3,0 мм/м.
Щоб захистити газобетон від усадки, потрібно протидіяти його швидкому висиханню. Рекомендується обприскувати газосилікатні блоки водою перед їх кладкою. Рівномірне висихання здійснюється через встановлення газоблоків на ребро в процесі сушіння. Просушити газобетон рівномірно можливо 2 способами:
- досягти висихання внутрішнього ядра;
- призупинити висушування зовнішньої частини газобетону.
не Можна допускати нерівномірне зволоження або просушування сторін блоку з різною інтенсивністю. Повне висихання газоблоків залежить від його складових, ступеня пористості, вологості, температури. Забороняється тримати газобетон на відкритому сонці, протязі, піддавати постійному впливу атмосферних опадів.
Усадка в газобетонних блоках – це природний процес, який відбувається внаслідок випаровування води з основи. У автоклавного газобетону, який проходить сушку при високих температурах, усадка буде проявлятися менше, ніж у бетону, висушеного класичним способом.
Рівень стиснення газоблоку залежить і того, на основі якого матеріалу він зроблений:
- цемент;
- пісок;
- сланцева зола;
- вапно.
Дотримуючись будівельних норм, можна отримати чудовий будинок з газобетону, не турбуючись про його усадки.
Морозостійкість
Морозостійкість газобетону пояснюється наявністю резервних пор, в які при замерзанні витісняється лід і вода. Сам матеріал при цьому не руйнується. При дотриманні технології будівництва, морозостійкість матеріалу перевищує 200 циклів. При низькій об’ємній масі (наприклад, 500 кг/м³) газобетон має високу міцність на стиск – 28-40 кгс/см³ за рахунок автоклавної обробки. Для порівняння: пінобетон – 10-15 кгс/см³.
Газобетон стійкий до впливу морозу і не руйнується під впливом циклічного заморожування. На морозостійкість позитивно впливає структура газобетону – пори газобетону неподвержены повного насичення водою.
Завдяки пористій структурі газобетону, кожна повітряна раковина в ньому огороджена від інших тілом твердого матеріалу, основою якого є цемент і пісок. Потрібні особливі умови, щоб рідина проникла в газовий блок.
Надмірну кількість замороженої води перерозподіляється в сухі серединні пори. Вони служать буферними ємностями, де збирається зайва волога. В результаті, газобетон може витримати безліч циклів повторного замерзання, що робить його значно більше морозостійким, ніж важкі бетони.
Питання довговічності газобетону заслуговує особливої уваги. Заявлений виробниками термін служби будинків з газоблоку становить близько 100 років, за умови капітального ремонту після 60 років експлуатації. Але це може бути справедливо лише в разі, якщо витримані всі будівельні нормативи, правильно розраховані несучі конструкції і дотримана технологія зведення будівлі.
Прикладные науки | Бесплатный полнотекстовый | Производство пенобетона с промышленными отходами из сектора драгоценных камней и драгоценных камней Риу-Гранди-ду-Сул, Бразилия
1.



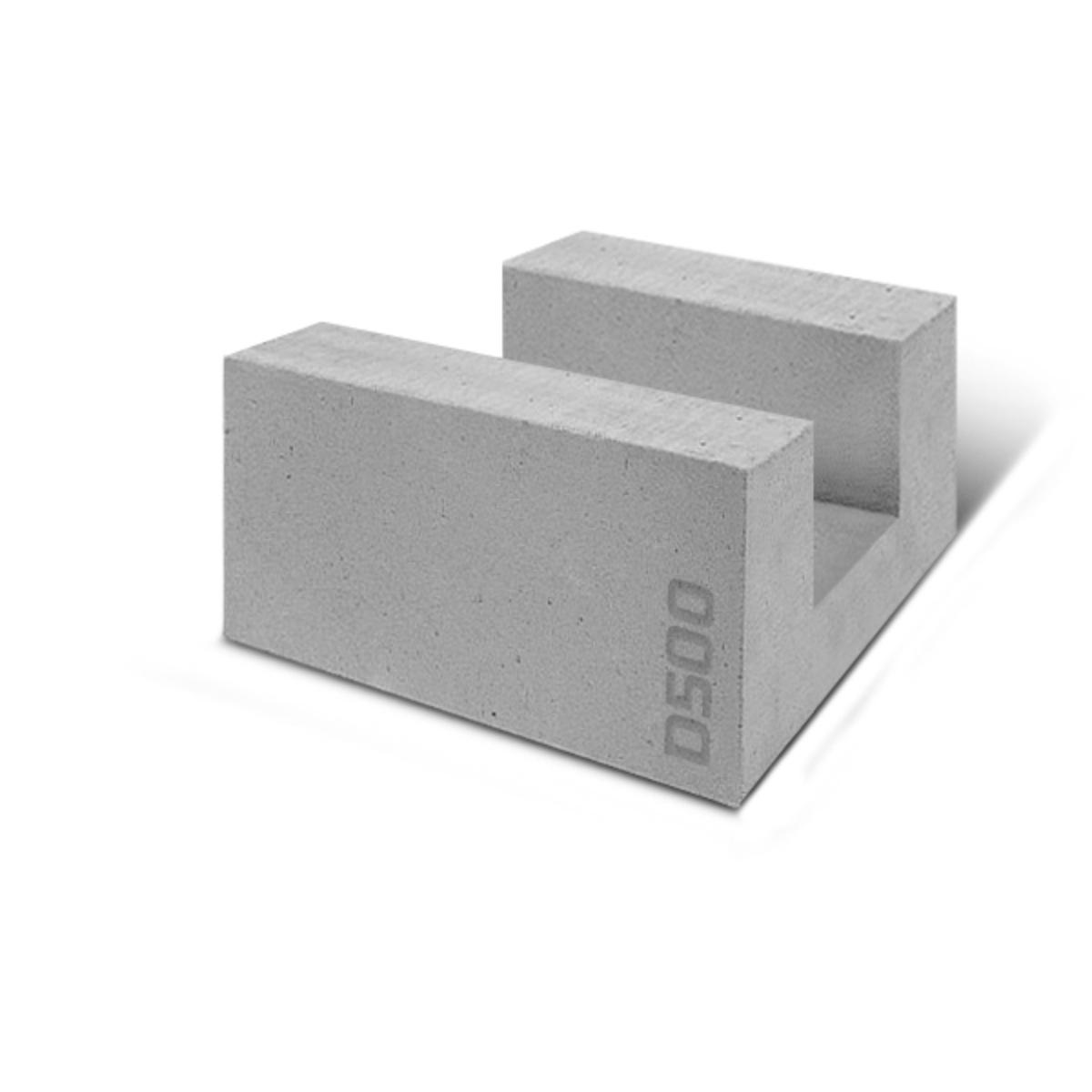




Основная цель данной статьи заключалась в оценке использования RP, полной замены природного песка в производстве AFCB пенообразователем, полученным из жирной кислоты кокосового ореха.Также было проведено краткое экономическое и экологическое обсуждение использования агатовых отходов.
2. Материалы и методы В качестве агрегата использовали
RP. Его собирали на предприятии по переработке проката агата в муниципалитете Соледад-Риу-Гранди-ду-Сул, Бразилия. Портландцемент (ПК) (Cimpasso, Passo Fundo, RS, Бразилия), используемый V-ARI, соответствует бразильским стандартам NBR 5733 [39] и NBR 5737 [40], цементам начальной высокой прочности и устойчивости к сульфатам, соответственно.
Пену получали механическим перемешиванием. Плотность образовавшейся пены составляла 75 кг / м 3 .
Раствор был приготовлен путем смешивания RP, воды, цемента и предварительно сформированной пены.

Образцы извлекали из формы через 24 часа, упаковывали в пластиковую пленку и выдерживали при температуре 20 ± 2 ° C в течение 28 дней в течение времени отверждения.
Плотность блоков и удельную массу RP определяли согласно ASTM C138 / C138M-16a [45]. Испытания на прочность при сжатии AFCB проводились в соответствии с ASTM C495-99a [34] с использованием универсальной испытательной машины (EMIC-PC200C, Instron, Норвуд, Массачусетс, США). Оценка распределения воздушных пустот и формы частицы получали методом вторичной электронной визуализации в сканирующем электронном микроскопе (SEM) «Тескан» при 30 кВ (Tescan, Kohoutovice, Чешская Республика). Для измерения пузырьков образцы были приготовлены в соответствии с ASTM C457 / C457M-12 [46] и запломбированы золотом.Полученные изображения обрабатывали и оценивали с помощью программного обеспечения ImageJ. Наконец, было выполнено сравнение прочности на сжатие и плотности коммерческих блоков (AFCB и AACB) и AFCB, разработанных с de RP. Для сравнения были использованы данные, предоставленные производителями. Также была кратко описана экономическая жизнеспособность.
Экспериментальное исследование сверхлегкого (
Тип сверхлегкого (<300 кг / м 3 ) пенобетона (FC), который может использоваться как новый энергосберегающий и защищающий окружающую среду строительный материал и особенно подходит для выполнена теплоизоляция наружных стен здания.Сообщалось о влиянии различных смешанных количеств летучей золы, активатора летучей золы, соотношения WC (WC) и пенообразователя (FA) на прочность на сжатие FC. Экспериментальное исследование показало, что (1) добавление летучей золы снижает прочность FC и что соответствующее количество смешиваемой золы в этой сверхлегкой системе FC не должно превышать 45%; (2) с увеличением количества активатора летучей золы прочность образца FC заметно увеличивается, и подходящее количество активатора летучей золы для смешивания составляет 2.5%; (3) оптимизированная пропорция WC составляет 0,45, и FC, произведенный в соответствии с этой пропорцией, имеет относительно высокую прочность на сжатие; (4) при увеличении смешиваемого количества FA прочность на сжатие FC заметно снижается, и оптимальное количество смешиваемой FA в этом эксперименте составляет 3,5%.
1. Введение
Пенобетон (ПБ) относится к более широкой категории ячеистых бетонов, в которых воздушные пустоты задерживаются в матрице раствора с помощью подходящего аэрирующего агента [1–4].Он легкий, имеет влагозащиту, противопожарную, звукоизоляцию и хорошую теплоизоляцию; Таким образом, он успешно применялся в проектах по цементированию нефтяных скважин, использовался в качестве материала обратной засыпки в проектах земляных работ и использовался для звуко- и теплоизоляции строительных панелей, противопожарных стен, энергопоглощающих прокладок на дорогах, дорожных оснований, строительных конструкций. насыпь, фундаменты, геотехнические и шахтные приложения [5–7].
Исследователи успешно создали ФК в диапазоне плотностей 300–1800 кг / м 3 3 [2–4, 8, 9], как тип основных материалов; Способы получения пены и свойства FC широко изучены.Ниже приведены некоторые примеры.
(i) Составляющие базовой смеси . В дополнение к обычному портландцементу, в быстротвердеющем портландцементе использовались высокоглиноземистый и сульфоалюминат кальция для сокращения времени схватывания и улучшения ранней прочности пенобетона. В дополнение к цементу, многие типы материалов, такие как летучая зола кремнезема, известковый мел, дробленый бетон, зола мусоросжигательного завода, переработанное стекло, формовочный песок, карьерный мелкозернистый материал, пенополистирол, скорлупа масличной пальмы и мелочь Lytag, были использованы для уменьшения количества пыли. плотность пенобетона и / или использовать отходы / вторсырье [3, 5, 6, 10, 11].
(ii) Способы производства пены . Были использованы химическое расширение и механическое вспенивание. При химическом вспенивании вспенивающий агент (FA), такой как алюминиевый порошок, CaH 2 , TiH 2 или MgH 2 , смешивается с ингредиентами базовой смеси, и в процессе смешивания пена образуется из химические реакции, образующие ячеистую структуру бетона. При механическом вспенивании пена готовится заранее с помощью специального устройства — пеногенератора, где вода и химическая примесь смешиваются в определенной пропорции, а предварительно полученная пена механически смешивается с бетонной смесью. После формования бетон затвердевает при нормальных атмосферных условиях [3, 12, 13].
(iii) Свойства FC . Физические свойства (усадка при высыхании, плотность, пористость, система воздушных пустот и сорбция), механические свойства (прочность на сжатие, предел прочности, модуль упругости и прогнозные модели), долговечность и функциональные характеристики (теплопроводность, акустические свойства и огнестойкость) широко обсуждались [5, 6, 14–19].
Во многих вышеупомянутых исследованиях FC использовался цемент в качестве одного из основных материалов. Однако цемент — это строительный материал с высоким энергопотреблением и серьезным загрязнением окружающей среды. Таким образом, традиционный производимый продукт FC противоречит методам разработки экологически чистых строительных материалов, хотя многие экспериментальные и теоретические исследования проводились путем добавления определенного количества промышленных отходов, таких как летучая зола и шлак, в цемент; например, Nambiar и Ramamurthy [10] использовали летучую золу для производства FC с плотностями 1000, 1250 и 1500 кг / м 3 . Kearsley и Wainwright [5, 6, 17] пришли к выводу, что долговременные свойства FC можно улучшить, заменив 75% цемента летучей золой. До сих пор было проведено мало экспериментальных исследований влияния высокого содержания золы на сжатие сверхлегкого (<300 кг / м 3 ) FC. Однако по мере того, как сфера применения FC становится все шире и шире, требуется все больше и больше сверхлегких (<300 кг / м 3 ) FC, например, теплоизоляционный материал для строительства наружных стен, засыпной материал для теплосохраняющих труб, фундамент. для автомобильных дорог и тд.В этих приложениях требования к прочности на сжатие не очень высоки; обычно достаточно 0,3 ~ 0,5 МПа.
В этом исследовании был произведен тип сверхлегкого (<300 кг / м 3 ) FC, который может быть использован в качестве нового энергосберегающего и экологически безопасного строительного материала и особенно подходит для теплоизоляции. возведения наружных стен. Сообщалось о влиянии различных смешанных количеств летучей золы, активатора летучей золы, соотношения WC и FA на прочность на сжатие FC.
2. Экспериментальные программы
2.1. Материалы
(i) Цемент . Цемент, использованный в этом исследовании, был стандартным китайским портландцементом 425 [20]. Его плотность составляет 3100 кг / м 3 , а его химический состав приведен в таблице 1.
|

(iii) Пенообразователь (FA) . Концентрация перекиси водорода составляет 27,5%; он реагирует с катализатором (MnO 2 ) с образованием газообразного кислорода в процессе производства FC.Уравнение реакции следующее:
(iv) Стабилизатор пены . Это белый порошок собственного производства. Он состоит из триэтаноламина (20%), полиакриламида (40%) и гидроксипропилметилцеллюлозы (40%), его количество в смеси составляет 1% FA, и его основная функция заключается в улучшении вязкости суспензии.
(v) Активатор летучей золы . Самодельная; основным компонентом является белый порошок CaO (80%), а другие компоненты включают NaOH (8%) и Na 2 SO 4 (12%).Принцип активации CaO заключается в следующем: химическая активность летучей золы обусловлена растворимыми SiO 2 и Al 2 O 3 в стекловидном теле, и они могут реагировать с CaO в присутствии воды, образуя гидратированный силикат кальция, и после этого появится прочность. Уравнения реакции следующие: Функция NaOH заключается в переводе раствора в щелочную среду, которая может стать основой для реакции золы. OH — вызовет разрыв связи Si – O, Al – O, что увеличит скорость гидратации.Функция Na 2 SO 4 заключается в основном в увеличении скорости и повышении уровня активации возбуждения летучей золы. Это потому, что он может реагировать с AlO 2-, когда существует Ca 2+ , с образованием гидратированного алюмината кальция. Он может покрывать частицы летучей золы и образовывать волокнистый слой, причем в близкой степени он меньше, чем C – S – H, что более выгодно для диффузии Ca 2+ в частицы летучей золы.
(vi) Катализатор. Представляет собой порошок диоксида марганца (MnO 2 ); его молекулярная масса 86.94 (г / моль).
2.2. Испытательное оборудование
(i) Высокоскоростной смеситель: автоконтроль со скоростью вращения 0 ~ 1200 об / мин. (Ii) Стандартный прибор для проверки консистенции и времени схватывания цемента (Vicat Apparatus) . (Iii) Воронка консистенции цементного раствора: производства Hebei Guanghua Weiye Construction Instrument Factory, вместимостью 1725 мл. (Iv) Многофункциональная машина для испытаний на механику горных пород (RMT): в нашем институте была разработана серия систем RMT. Машина имеет уникальный многофункциональный дизайн и технологию управления; он может проводить много типов испытаний, таких как одноосное сжатие, трехосное сжатие, растяжение, сдвиг и усталостные испытания.Максимальная нагрузка составляет 1 МН, а максимальное ограничивающее давление — 50 МПа. (V) Сушильная печь с электротермическим выдувом типа OL-103. (Vi) Камера для отверждения при постоянной температуре и влажности: Северный экспериментальный аппарат Beijing Huachuang. Co., Ltd.
2.3. Приготовление FC
(i) Добавьте воду в другие материалы, такие как цемент, летучая зола, стабилизатор пены и активатор летучей золы, кроме FA, и равномерно перемешайте, поддерживая температуру суспензии приблизительно 45 ° C. Обычно этот процесс длится примерно 5 минут.(ii) При перемешивании на высокой скорости быстро добавьте FA и продолжайте перемешивание в течение примерно 30 секунд. (iii) вылейте равномерно перемешанную суспензию в форму размером 1200 мм × 900 мм × 350 мм и подождите, пока она не вспенится; процесс вспенивания показан на рисунке 1. (iv) Разобрать форму через 2 часа и держать ее в камере для отверждения с постоянной температурой и влажностью до окончания периода испытаний. Для проведения теста используйте образец размером 100 мм × 100 мм × 100 мм; структура пор показана на рисунке 2.
Весь процесс приготовления FC с использованием химического вспенивания можно резюмировать как процесс динамического баланса.В процессе разработки эксперимента необходимо тщательно учитывать плотность суспензии, скорость вспенивания, скорость конденсации суспензии, добавляемое количество FA и другие факторы, влияющие на получение относительно высококачественного продукта. Ключом к формированию структуры FC с использованием химического вспенивания является обеспечение соответствия скорости вспенивания скорости схватывания и затвердевания суспензии.
3. Результаты и обсуждение
3.1. Влияние количества золы в смеси на прочность на сжатие
Прочность FC напрямую зависит от доли загущенного материала.Большие пропорции бетона в загущенном материале соответствуют более высокой прочности продукта. В системе цементно-летучая зола массовое использование летучей золы резко снижает прочность бетона, что особенно очевидно в сверхлегких ТЭ на основе цементно-летучей золы [5, 6, 18]. Поэтому количество летучей золы в сверхлегких продуктах FC значительно ограничено. Тем не менее, умеренное количество активатора летучей золы может эффективно улучшить начальную прочность продуктов [22], что также полезно для сокращения времени очистки продуктов и повышения эффективности производства.Для FC с фиксированным количеством смешиваемой золы-уноса-активатора 2,5% и насыпной плотностью в сухом состоянии 290 кг / м 3 прочность продуктов 28 d уменьшается по мере увеличения содержания золы-уноса, как показано на Рисунке 3.
Когда содержание летучей золы меньше 45%, тенденция к снижению прочности продукта является умеренной: когда количество смеси изменяется с 30% до 45%, прочность снижается на 0,14 МПа. Однако, когда содержание летучей золы превышает 45%, тенденция к снижению прочности продукта усиливается: когда количество смеси изменяется с 45% до 55%, прочность снижается на 0.37 МПа, а прочность продукта составляла всего 0,15 МПа при содержании летучей золы 55%. Следовательно, для практической осуществимости соответствующее количество летучей золы в этой сверхлегкой системе FC не должно превышать 45%.
3.2. Влияние количества активатора золы-уноса в смеси на прочность на сжатие. 25].В этом исследовании активатор золы-уноса изготовлен самостоятельно, и его основным компонентом является CaO. Механизм активации летучей золы СаО можно объяснить следующим образом. Вещество в извести, которое в конечном итоге влияет на активность летучей золы, — это Ca (OH)
2 ; Ca (OH) 2 может обеспечить OH — для раскрытия химических связей между Si – O и Al – O и Ca 2+ для создания гидравлических цементирующих материалов путем гидратации летучей золы.
Влияние смешиваемого количества активатора золы-уноса на прочность на сжатие FC, который имеет фиксированное содержание золы-уноса с внутренними присадками 45% и насыпную плотность в сухом состоянии 290 кг / м 3 , показано на рисунке 4. Как показано на рисунке 4, прочность образца FC заметно увеличивается с увеличением количества активатора летучей золы. При смешивании количества активатора летучей золы более 2.5% увеличение прочности FC имеет тенденцию к выравниванию, что означает, что смешиваемое количество активатора летучей золы имеет оптимальное значение. В этой сверхлегкой системе FC соответствующее количество активатора летучей золы составляет 2,5%.
3.

Отношение WC — еще один важный фактор, который может влиять на характеристики FC [5, 6]. При приготовлении FC путем химического вспенивания скорость загустевания и скорость вспенивания суспензии должны в высокой степени совпадать, что указывает на то, что вспенивание и статическое поддержание суспензии синхронизированы.В процессе приготовления FC соотношение WC существенно влияет на всю технологию приготовления: когда соотношение WC слишком низкое, а суспензия слишком густая, это препятствует полному диспергированию FA и приводит к частичному усилению пенообразования и образованию больших пузырей; кроме того, время начального схватывания суспензии заметно короткое, если соотношение WC низкое. Если суспензия затвердеет до завершения процедуры вспенивания FA, продукты будут перенапряжены внутри и появятся дефекты. Когда соотношение WC чрезмерно велико, а плотность суспензии чрезмерно низкая, конденсация и повышение жесткости суспензии отстают от вспенивания FA, что приведет к разрушению FC на более поздней стадии. Влияние соотношения WC на прочность на сжатие FC показано на рисунке 5. Когда соотношение WC увеличивается с 0,40 до 0,50, прочность на сжатие образца сначала увеличивается, а затем уменьшается, потому что в этом диапазоне соотношения WC консистенция жижа умеренная, а газы равномерно разбрасываются в жиже; таким образом, FA полностью вспенивается, и объем суспензии неуклонно увеличивается. Между тем, структура пор хорошо закреплена, поскольку начальная скорость схватывания суспензии соответствует скорости вспенивания FA.Таким образом, прочность на сжатие образца относительно высока. Когда соотношение WC увеличивается с 0,45 до 0,50, плотность суспензии слишком мала, и газ очень легко вырывается с поверхности образца и оставляет трещины и сквозные отверстия в образце, что снижает прочность образца. Кроме того, поскольку соотношение WC слишком велико, время коагуляции больше, чем время вспенивания везиканта; на более поздней стадии вспенивания части пор сливаются, что снижает равномерность и значительно снижает прочность пористой структуры в образце.
Поэтому в эксперименте оптимальное соотношение WC составляет 0,45. FC, который был произведен с таким соотношением WC, имеет относительно высокую прочность на сжатие.
3.4. Влияние ТВС на прочность на сжатие
ТВС является одним из основных сырьевых материалов для получения ТЭ. FA вызывает химические реакции в равномерно перемешиваемой суспензии, в результате которых образуется много газа. Газ рассеивается внутри раствора и постепенно фиксируется в затвердевшем бетоне по мере его конденсации; наконец, газ образует ровную и устойчивую везикулярную структуру.На рис. 6 показано влияние количества смеси FA на 28-дневную прочность FC на сжатие. Из рисунка 6 видно, что прочность на сжатие FC уменьшается по мере увеличения количества смеси FA, поскольку количество воздушных отверстий внутри FC также увеличивается, и стенки воздушных отверстий становятся тоньше. Следовательно, объемная плотность в сухом состоянии FC уменьшается, а вместе с ним и прочность. Наблюдается, что стенка поры образца с добавкой 3% H 2 O 2 является самой толстой и почти не имеет переплетенных пор; таким образом, этот образец имеет максимальную прочность на сжатие. Стенка поры образца с содержанием смеси 4,5% H 2 O 2 является самой тонкой с множеством взаимосвязанных пор; таким образом, он имеет минимальную прочность. Для образца, который был изготовлен с использованием ТВС с содержанием примеси H 2 O 2 3,5%, толщина стенки пор и структура пор являются относительно подходящими, а прочность также квалифицируется с требованием сохранения тепла внешняя стена. Следовательно, оптимальное количество примеси ЖК в данном эксперименте — 3.5%.
4. Выводы
Изготовлен тип сверхлегкого (<300 кг / м 3 ) ТЭ. Экспериментально изучалось влияние различных смешиваемых количеств летучей золы, активатора летучей золы, соотношения WC и FA на прочность на сжатие FC, и их можно резюмировать следующим образом. (1) Плотность суспензии, скорость вспенивания, конденсация скорость суспензии, добавляемое количество FA и другие влияющие факторы необходимо тщательно учитывать, чтобы приготовить относительно высококачественный продукт. При формировании структур FC с использованием химического вспенивания скорость вспенивания должна соответствовать скорости схватывания и твердения суспензии. (2) Когда содержание летучей золы меньше 45%, прочность продукта умеренно снижается, тогда как при содержании летучей золы больше 45%, прочность продукта быстро снижается. Для практической осуществимости соответствующее количество смешиваемой золы-уноса в этой сверхлегкой системе FC не должно превышать 45%. (3) С увеличением количества активатора золы-уноса прочность образца FC заметно увеличивается.Когда количество активатора летучей золы в смеси превышает 2,5%, увеличение прочности FC имеет тенденцию к выравниванию. В этой сверхлегкой системе FC соответствующее количество активатора летучей золы в смеси составляет 2,5%. (4) В эксперименте оптимизированная пропорция WC составляет 0,45. FC, который был произведен с этой пропорцией, имеет относительно высокую прочность на сжатие. (5) С увеличением количества добавки FA, прочность на сжатие FC заметно уменьшается.
Толщина стенки пор и структура пор образца, полученного с использованием ТВС с добавкой 3 H 2 O 2 .5% являются относительно подходящими, а прочность также удовлетворяет требованию сохранения тепла наружной стены. Поэтому оптимальное количество примеси ЖК в данном эксперименте составляет 3,5%.
Конфликт интересов
Авторы заявляют об отсутствии конфликта интересов в отношении публикации данной статьи.
Благодарности
Эта работа была поддержана Национальной программой по проекту ключевых фундаментальных исследований (программа 973) (грант № 2013CB036006), Национальным фондом естественных наук Китая (гранты №№.51208499, 41102193 и 51109207), Постдокторский научный фонд Китая (2014M550365) и Национальный научный фонд для выдающихся молодых ученых Китая (грант № 51225902).
Свойства и долговечность блоков кладки из автоклавного газобетона
Свойства и долговечность блоков из автоклавного газобетона9
А. Чайпанич2, П. Чиндапрасирт2 1 Университет Чиангмая, Чиангмай, Таиланд; 2 Университет Кхон Каен, Кхон Каен, Таиланд
9.1
Введение
В этой главе описываются различные свойства и долговечность кирпичных блоков из автоклавного ячеистого бетона (AAC) и содержатся следующие разделы: типы легкого бетона, история, использование, производство, механизм AAC, физические свойства, механические свойства. свойства, микроструктура, характеристики, теплопроводность и долговечность AAC. Раздел «Типы легкого бетона» описывает различные типы легкого бетона и различные производственные процессы, используемые при изготовлении легкого бетона, такого как пенобетон и пенобетон, с особым вниманием к AAC.Также упоминается использование AAC в качестве кирпичных блоков. Механизм, участвующий в производстве AAC, в зависимости от используемого метода порообразования и гидратации AAC, описан в разделе, посвященном механизму. В разделе физических свойств описывается объемная плотность AAC и его отношение к воздушным пустотам. Раздел механических свойств описывает прочность на сжатие и изгиб AAC, взаимосвязь с физическими свойствами и продуктами гидратации. Раздел микроструктуры описывает размер сформированных пор и морфологию микроструктуры AAC, охарактеризованную с помощью сканирующей электронной микроскопии (SEM), в то время как другой раздел характеризации включает использование методов дифракции рентгеновских лучей и термогравиметрического анализа.В этой главе также обсуждается теплопроводность. В разделе «Долговечность» этой главы описывается сопротивление замораживанию-оттаиванию AAC.
9,2
Типы легкого бетона
Легкий бетон можно классифицировать по его удельному весу или плотности, которая обычно составляет от 320 до 1920 кг / м3, в соответствии с Руководством Комитета 213 ACI по конструкционным легким заполненным бетоном (ACI 213). , 2001). По диапазону прочности существует три различных типа легкого бетона, которые представляют собой бетоны с низкой плотностью (0.7e2,0 МПа), бетоны средней прочности (7e14 МПа) и конструкционные бетоны (17e63 МПа). Плотность этих бетонов находится в диапазоне 300e800 кг / м3, 800e1350 кг / м3 и 1350ez1920 кг / м3 соответственно. С начала 1900-х годов в Соединенных Штатах Америки используется легкий бетон, экологически чистые кирпичи и блоки для каменной кладки. http://dx.doi.org/10.1016/B978-1-78242-305-8.00009-7 Авторские права © 2015 Elsevier Ltd. Все права защищены.
216
Экологичные кирпичи и блоки для каменной кладки
и легкий бетон использовались в многоэтажных зданиях, длиннопролетных мостах, морских платформах и крупных сооружениях (Mindess, Young, & Darwin, 2003).Ряд преимуществ использования легкого бетона низкой плотности в строительстве обусловлен его низкой плотностью, низкой теплопроводностью, низкой усадкой и высокой термостойкостью, а также снижением статической нагрузки, более низкой стоимостью перевозки и более быстрым темпом строительства (Wongkeo, Thongsanitgarn , Pimraksa, & Chaipanich, 2012). Для производства легкого бетона можно использовать несколько способов, в основном с использованием легкого заполнителя или легкой матрицы. Легкий заполнитель, который можно использовать, варьируется от натурального заполнителя пемзы до искусственного агломерированного заполнителя, такого как спеченная зола (Mindess et al., 2003). Обсуждение облегченного заполнителя выходит за рамки этой главы и не будет обсуждаться более подробно. В центре внимания будет легкая цементная матрица, заполненная воздухом, которую иногда называют газобетоном или пенобетоном. Джаст и Миддендорф (2009) упростили классификацию различного пенобетона или пенобетона, который может производиться, и сделав это пенобетоном AAC или пенобетоном с воздушным отверждением. Поэтому в основном газобетон бывает двух видов: пенобетон и пенобетон.В качестве вспенивающих агентов можно использовать различные виды моющих средств, смолистого мыла, клеящих смол или белков, таких как кератин (Narayanan & Ramamurthy, 2000a). Пену можно добавлять механическими или физическими методами, как сообщают Just & Middendorf (2009). Пена, образованная механически, использует метод взбивания пенообразователя вместе, в то время как физический метод относится к добавлению уже вспененного раствора непосредственно в процессе смешивания.
Было обнаружено, что последний метод дает более регулярные и стабильные поры, чем первый, который создает поры неправильной формы (Just & Middendorf, 2009).Этот пенобетон обычно отверждается на воздухе. AAC — это класс легкого бетона, который сначала создается путем создания пузырьков газа в свежем бетоне, а затем отверждается паром под высоким давлением, известным как автоклавирование. Автоклавный метод вентиляции обычно используется при производстве блоков из кирпичной кладки. Это связано с тем, что пенобетон, иногда известный как ячеистый бетон, полученный этим методом, имеет равномерно сформированную ячеистую структуру из воздушных пустот размером 0,1-1 мм, образующихся в цементном тесте или растворах (Mindess et al., 2003).
9,3
Автоклавный газобетон (AAC) История и использование в качестве кирпичных блоков
Первое коммерческое производство AAC было в 1923 году в Швеции. С тех пор он используется более чем в 40 странах Европы, Америки, Австралии, Ближнего и Дальнего Востока. Современное использование AAC в Соединенных Штатах началось в 1990 году для жилых и коммерческих зданий (журнал Masonry, 2008; Kocí, Madera, & Cerný, 2012; Radhi, 2011). Кладочные блоки из AAC могут быть изготовлены в виде сборных строительных блоков и используются в жилищном строительстве, больницах, офисных зданиях и университетских помещениях (Hess, Kincl, Amasay, & Wolfe, 2010.). Каменные блоки из AAC имеют много преимуществ по сравнению с обычным бетоном: меньший вес (обычно весит от одной шестой до одной трети обычного бетона), более низкие затраты на строительство и обеспечивают тепловую и звукоизоляцию (Hendry, 2001; Hess et al., 2010; Клингнер, 2008). Теплоизоляция
Свойства и долговечность блоков из автоклавного газобетона
217
Рисунок 9.1 Примеры стандартного блока AAC.
собственности AAC сделало бы здания более энергоэффективными, как сообщалось в тематическом исследовании в Объединенных Арабских Эмиратах, где было обнаружено, что использование AAC снижает потребление энергии в жилом секторе примерно на 7% (Radhi, 2011). Благодаря высокой пористой структуре с содержанием воздуха 60–70%, AAC обладает способностью гасить энергию механической вибрации, обеспечивая отличную звукоизоляцию, поэтому использование AAC было бы очень подходящим для таких мест, как школы, отели и квартиры (Краткий обзор технологий, 2010 г.) . Конструкция и технические характеристики блоков для каменной кладки AAC регулируются Кодексом Объединенного комитета по стандартам кладки и стандартом ASTM C1386. Стандартный размер кирпичного блока AAC больше по сравнению с блоком бетонного блока (CMU); длина кирпичного блока AAC составляет 610 мм по сравнению с длиной 410 мм блока CMU (Hess et al., 2010). Хотя он больше по размеру, он легче, поэтому большой размер блока AAC сопоставим с блоком CMU среднего размера с точки зрения веса (Hess et al., 2010). Стандартный блок имеет толщину 50–375 мм, высоту 200 мм и длину 610 мм (Klingner, 2008). Стандартный блок AAC показан на рисунке 9.1. В целом, благодаря этим желаемым свойствам AAC, особенно его легким, тепловым и акустическим свойствам, каменный блок AAC является идеальным строительным материалом для стен во многих жилых и офисных зданиях.
9,4
Производство и механизм автоклавного ячеистого бетона
AAC обычно изготавливается из кварцевого песка, извести, цемента и алюминиевого порошка (Kurama, Topcu, & Karakurt, 2009). Гипс и зола также могут использоваться при производстве газобетонных смесей (Klingner, 2008). Алюминиевый порошок используется как воздухововлекающий (аэрирующий) или порообразующий агент и является наиболее часто используемым агентом (Narayanan & Ramamurthy, 2000a). Он основан на реакции алюминия с растворимыми щелочами в цементе с образованием небольших пузырьков водорода, как в уравнении (8.1) (Mindess et al., 2003). Это заставляет материал подниматься в форме, и после отверждения
218
Эко-эффективных кирпичей и блоков
в течение 45 минут изделия нарезаются проволокой на кусочки необходимого размера (Technology Brief, 2010). Al þ 2OH þ 2h3 O / AlðOHÞ 4 þ h3
(8.1)
Гидрат алюмината кальция (C3AH6) также может быть образован с газообразным водородом в результате реакции алюминиевого порошка с гидроксидом кальция, как можно увидеть в уравнении (8. 2). ) (Курама и др., 2009). После этого газобетон автоклавировали в течение 8–12 часов (Technology Brief, 2010). 2AlðSÞ þ 3CaðOHÞ2 ðSÞ þ 6h3 O / 3CaO: Al2 O3: 6h3 O þ h3 ðgÞ
(8.2)
Автоклавное отверждение паром под высоким давлением используется для повышения прочности газобетона на сжатие. Продукты AAC готовы к использованию в течение 24 часов (прочность обычно эквивалентна 28 дням отверждения при комнатной температуре). Было обнаружено, что структура фаз C-S-H изменяется под воздействием высокой температуры и давления при отверждении в автоклаве.В портландцементе вместо аморфного гидрата силиката кальция (C-S-H) образуется гидрат адикальция силиката (a-C2SH), что приводит к снижению прочности (Mindess et al., 2003). Однако в присутствии кремнезема a-C2SH превращается в тоберморит (C5S6H5) при продолжительном нагревании (Mindess et al., 2003; Yazici, 2007). Дополнительный диоксид кремния может быть доступен за счет использования пуццоланового материала в качестве дополнительного вяжущего материала. Фаза тоберморита имеет больший объем структуры, чем фаза a-C2SH, что вызывает уменьшение пористости и, как следствие, увеличение прочности на сжатие.Образование тоберморита при высокотемпературном отверждении будет зависеть от соотношения CaO / SiO2, а также от температуры, как сообщили Меллер, Кирицис и Холл (2009) и Тейлор (1997). Типичные условия, ранее использовавшиеся для AAC, находятся в диапазоне продолжительности 8–16 часов и давлении в диапазоне 4–16 МПа (Narayanan & Ramamurthy, 2000a; RILEM, 1993). h3 O
C3 S þ C2 SÞ / C-S-H þ CH þ S
Кремнезем
Портландцемент h3 O
CH þ S / C-S-H þ / C5 S6 H5
(8.3)
(8,4)
Тоберморит
9,5
Физические свойства газобетона в автоклаве
Объемная плотность образцов AAC зольного цемента (BA) сообщается Wongkeo et al. (2012) путем сравнения добавления алюминиевого порошка. Насыпная плотность автоклавного легкого бетона без замены БА снизилась до 23,47% при добавлении алюминия (Al). Таким образом, было обнаружено, что добавка алюминия оказывает значительное влияние на объемную плотность автоклавного бетона.Более того, насыпная плотность зольного остатка AAC по сравнению с портландцементом AAC увеличилась с 2% до 7%, когда
Свойства и долговечность блоков из автоклавного газобетона
219
BA использовались для замены портландцемента на 10% и 30% соответственно. Увеличение объемной плотности шлакового шлака связано с образованием фазы тоберморита при использовании БА. Wongkeo & Chaipanich (2010) сообщают об объемах проницаемых пустот, полученных при использовании всех трехкомпонентных дымовых газов из портландцемента и золы кремнезема.Было обнаружено, что объем проницаемых пустот во всех образцах шлакового зольного остатка (BA) AAC уменьшался с увеличением содержания BA и добавления микрокремнезема (SF) из-за уменьшения газообразного водорода. Удельный вес БА ААК увеличивался с увеличением содержания БА. Когда SF был добавлен в количестве 2,5% и 5%, удельный вес BA AAC с SF увеличился. Таким образом, показано, что объем проницаемых пустот напрямую влияет на удельную массу всего шлакового зольного остатка.
9,6 9,6,1
Механические свойства газобетона в автоклаве Прочность на сжатие
Известно, что на прочность на сжатие влияет ряд факторов, таких как внешние и внутренние факторы.Внешние факторы — это условия испытаний и отверждения, в то время как внутренние факторы включают смесь, такие как содержание воды, используемый цемент и тип заполнителя, а также их содержание, а также используемые аэрированные агенты. Пористость в результате создается этими вовлеченными факторами и напрямую влияет на результат прочности на сжатие. Следовательно, плотность продукта напрямую связана с прочностью на сжатие. Сообщается, что уменьшение плотности за счет образования крупных микропор вызывает значительное падение прочности на сжатие (CEB, 1977).Сообщается, что прочность на сжатие находится в диапазоне 3,9–8,5 МПа при плотности AAC 700 кг / м3, но снижается до 1,3–2,8 МПа при плотности 400 кг / м3 (CEB, 1977; Narayanan & Ramamurthy, 2000а). Прочность на сжатие бетона AAC, по данным Huang, Ni, Cui, Wang и Zhu (2012), составляет 4,0 МПа при плотности 610 кг / м3. В то время как Серхат Баспинар, Демир, Кахраман и Горхан (2014) сообщили о прочности на сжатие AAC в диапазоне 1,91–5,10 МПа, когда диапазон плотности составлял 590–780 кг / м3, Albayrak et al.(2007) обнаружили, что прочность на сжатие AAC находится в диапазоне от 1,1 до 5,0 МПа и в диапазоне плотности от 270 до 500 кг / м3, что свидетельствует об увеличении прочности с увеличением плотности. Хотя условия в автоклаве были разными для каждого используемого метода, в целом можно увидеть, что прочность на сжатие снижается с уменьшением плотности AAC, и, по-видимому, существует прямая связь между прочностью на сжатие AAC с его плотностью. Таблица 9.1 суммирует результаты прочности на сжатие и условия автоклавирования из предыдущих опубликованных работ.Метод автоклавирования существенно влияет на прочность на сжатие, когда при более высоких температурах и давлении достигается стабильная форма тоберморита (Narayanan & Ramamurthy, 2000a).
Используемые типы цемента приводят к разной прочности на сжатие (Mindess et al., 2003). Обычный портландцемент типа I даст более слабый силикат кальция
220
Таблица 9.1
Обзор результатов прочности на сжатие Метод условий Плотность (кг / м3)
Связующее
Температура (C)
Давление (МПа)
Время (ч)
Мостафа (2005)
1.1e3.0 1.8e3.7 1.9e3.6 2.0e3.6
NA NA NA NA
C, L, AS
183
1
2 6 12 24
Albayrak et al. (2007)
1.25e3.25
270e533
Ze
200
1,5
12
Huang et al. (2012)
4,0
610,2
C, SCT, BFS, G
NA
1,35
8
Keriene et al. (2013)
2,24
451
C, L
176
0.8
20
Серхат Баспинар и др. (2014)
1.9e3.7
590e650
C, L, FA
NA
0,4
8
3.9e5.1
740e780
C, L, FA, SF
NA
0,8
8
Цемент, Lelime, AS Шлак с воздушным охлаждением, цезеолит, медные хвосты SCTeskarn, доменный шлак BFS, гегипс, зола FAe, дым SF-кремнезема, NA Нет в наличии.
Экологичные кирпичи и блоки для кладки
Прочность на сжатие (МПа)
Авторы
Свойства и долговечность кладочных блоков из автоклавного газобетона
221
Прочность на сжатие (МПа)
14
12
10
8 0
10 20 Зольность шламов (%)
30
Рисунок 9.2 Прочность на сжатие золы автоклавного газобетона. По материалам Wongkeo et al. (2012).
гидрат (a-C2SH), что привело к снижению прочности. Но когда присутствует дополнительный диоксид кремния, a-C2SH превращается в тоберморит (C5S6H5), что увеличивает прочность на сжатие AAC (Taylor, 1997; Yazici, 2007). Следовательно, химический состав используемого аморфного связующего оказывает значительное влияние на прочность на сжатие AAC. Было обнаружено, что прочность на сжатие шлакового зольного остатка с содержанием БА до 30% возрастает с увеличением содержания БА (Wongkeo et al., 2012), как показано на Рисунке 9.2. Повышенная прочность на сжатие является результатом образования фазы тоберморита в условиях автоклава, когда тоберморит образовывался при высокой температуре (выше 100 ° C) с CaO / SiO2 в диапазоне 0,8–1,0 (Meller et al. , 2009; Taylor , 1997). Дополнительное содержание кремнезема было получено из BA, что привело к изменению соотношения CaO / SiO2, таким образом достигнув подходящего соотношения CaO / SiO2 для образования тоберморита. Фаза тоберморита имеет больший объем структуры, чем фаза a-C2SH, что вызывает уменьшение пористости и увеличение прочности на сжатие по сравнению с контрольным портландцементом AAC (Richardson, 2008; Yazici, 2007).AAC с использованием тройного цемента, состоящего из портландцемента, зольного остатка и микрокремнезема, исследовали на прочность при сжатии. Было обнаружено, что прочность на сжатие всего AAC шлака увеличивается с увеличением содержания BA и SF (Wongkeo & Chaipanich, 2010). Как правило, можно увидеть, что удельный вес имеет прямую связь с прочностью на сжатие. При добавлении SF происходит более сильная пуццолановая реакция, которая приводит к увеличению плотности зольного остатка AAC.Следовательно, ранняя прочность на сжатие шлакового зольного остатка с SF была значительно улучшена.
Более того, когда Wongkeo & Chaipanich (2010) сравнили результаты прочности на сжатие образцов, отвержденных на воздухе и в автоклаве, было обнаружено, что прочность на сжатие шлакового остатка AAC с добавлением SF и отвержденного в автоклаве выше прочности, чем у соответствующих 7- и 14-дневных образцов, отвержденных на воздухе. зольный бетон. Преимущество заключается в лучшей пуццолановой реакции при автоклавировании, что привело к образованию фаз тоберморита.Было обнаружено, что прочность на сжатие, отвержденная на воздухе в течение 28 дней, аналогична прочности на сжатие из шлакового остатка, подвергнутого автоклавированию в течение шести часов. Был сделан вывод, что одним из основных факторов, влияющих на рост прочности, являются воздушные пустоты в бетоне. Как правило, прочность на сжатие AAC через 24 часа может достигать такой же прочности, как и у бетона с нормальным отверждением через 28 дней (Mindess et al., 2003). Прочность на сжатие AAC после 8 и 12 часов автоклавирования, о которых сообщают Narayanan & Ramamurthy (2000b), оказалась выше, чем у соответствующих бетонных смесей, по сравнению с таковыми в условиях влажного отверждения через 28, 90 и 150 дней.
9.6.2
Прочность на изгиб
Сообщается, что изгибная прочность бетона AAC находится в диапазоне 0,15e0,35 (Valore, 1954). Однако, казалось бы, соотношение будет варьироваться в зависимости от материалов и условий испытаний. Например, Wongkeo et al. (2012) сообщили, что изгибная прочность находится в диапазоне 2,7-3,2 МПа, а отношение изгибной прочности к прочности на сжатие составляет от 0,24 до 0,27 в зависимости от смеси (будь то только портландцемент или пуццолан, например поскольку зольный остаток используется в качестве дополнительного вяжущего материала).
9,7
Микроструктура газобетона в автоклаве
Микроструктура AAC состоит из макропор и микропор и находится под влиянием метода порообразования (Narayanan & Ramamurthy, 2000a). Размеры пор, которые первоначально образуются в результате реакции алюминия со щелочами цемента, несколько больше по размеру, как правило, в диапазоне 0,1–1,0 мм (Ioannou, Hamilton, & Hall, 2008; Mindess et al. , 2003). . Размеры пор, создаваемых химически прореагировавшим агентом, таким как алюминий, или методами вспенивания, поэтому достаточно велики, чтобы их можно было увидеть и легко увидеть.Сообщается, что образование макропор происходит в процессе аэрации, в то время как микропоры появляются в стенке макропор (Alexanderson, 1979). Петров и Шлегель (1994) суммировали размер макропор и микропор как более 60 мм для первого и 50 нм или менее для последнего (Alexanderson, 1979). Также сообщалось о размерах макропор 50-500 мм (0,05-0,5 мм), образовавшихся во время аэрации (Alexanderson, 1979). Было обнаружено, что микроструктура AAC, охарактеризованная с помощью SEM, показывает, что AAC состоит из этих двух различных типов пор.Крупные поры, наблюдаемые и сообщаемые в нескольких опубликованных работах, обычно имеют круглую форму и поэтому могут иметь размер в диапазоне 0,05–1,0 мм (Alexanderson, 1979; Ionnou et al., 2008; Mindess et al., 2003; Нараянан и Рамамурти, 2000а). Между продуктами гидратации видны микропоры, которые образуются между стенками.
СЭМ-микрофотографии также показывают форму таких продуктов гидратации, которые образуются после автоклавирования. Более распространенные пластинки тоберморита обычно обнаруживаются, когда в смеси достаточно кремнезема.Микроструктура AAC также будет зависеть от образующихся продуктов гидратации, которые, следовательно, во многом зависят от используемых типов и методов цемента.
Свойства и долговечность блоков из автоклавного газобетона
223
Отношение CaO / SiO2 0,83 является оптимальным для получения тоберморита 1,1 нм (Meller et al., 2009; Richardson, 2008). Было обнаружено, что портландцемент с BA и SF в зольной пыли AAC приводит к увеличению содержания реактивного SiO2 в системе и способствует образованию тоберморита (Wongkeo & Chaipanich, 2010).Образующаяся структура тоберморита придаст более плотную микроструктуру всей матрице, чем слабокристаллическое волокно, подобное C-S-H, которое в противном случае образовалось бы в нормальном портландцементе AAC.
9,8 9. 8.1
Характеристики автоклавного газобетона Дифракция рентгеновских лучей
Основным продуктом реакции ААС было обнаружено и подтверждено методом дифракции рентгеновских лучей (XRD), что это группа тоберморита (Matsui et al. др., 2011; Нараянан и Рамамурти, 2000b; Вонгкео и др., 2012). Образование тоберморита будет зависеть от цементных композиций с подходящим количеством диоксида кремния и условий автоклавирования, таких как температура, как сообщают Taylor (1997) и Meller et al. (2009). Wongkeo et al. Сообщили о рентгеновских дифрактограммах зольного остатка и AAC портландцемента. (2012). Таким образом, можно наблюдать сравнение рентгеновских дифрактограмм зольного цемента AAC и портландцемента AAC, показывая различные фазы, представленные в каждом бетоне. Следы XRD портландцемента и зольного цемента AAC показали некоторые незначительные пики C3S и C2S, которые представляют собой фазы дегидратированного силиката кальция из портландцемента.Более того, тоберморит (xCaOSiO2. zh3O) можно обнаружить только в зольном остатке AAC, но не был обнаружен в портландцементе, где вместо него были обнаружены фазы Ca (OH) 2 и a-C2SH (Ca2SiO4,3h3O). Кроме того, было обнаружено, что интенсивность пиков Ca (OH) 2 снижается с увеличением содержания БА. Это связано с пуццолановой реакцией и эффектом разбавления. Сообщалось также о других гидратированных фазах, таких как эттрингит, гидрогранат и C2SH, в дополнение к CSH, Ca (OH) 2 и тобермориту, обнаруженным в цементно-песчаном и цементно-зольном пепле AAC (Narayanan & Ramamurthy, 2000b).Кус и Карлссон (2003) провели рентгеноструктурный анализ ААС, подвергшегося естественному и искусственному выветриванию, и обнаружили фазы, поскольку основными пиками в связующем (если рассматривать только его часть) являются кальцит, ангидрит и тоберморит. Пик кальцита со временем увеличивается. Это вызвано карбонизацией, при которой Ca (OH) 2 превращается в карбонат кальция. Хотя тоберморит и кальцит обычно присутствуют в системе CaO и SiO2, при наличии Al и SO3 также могут быть обнаружены другие второстепенные фазы, такие как моносульфат и каотит (Matsui et al.
, 2011).
9.8.2
Термогравиметрический анализ
Результаты термогравиметрического анализа (ТГА) цементного остатка золы наносятся в виде производных термогравиметрических кривых (ДТГ) для идентификации обнаруженных фаз Wongkeo et al. (2012). Обнаруженные фазы представляют собой гидрат силиката кальция (C-S-H) при температуре
224
Эко-эффективные кирпичи и блоки для каменной кладки
z71e86 C, гидроксид кальция (Ca (OH) 2) при z446e476 C и карбонат кальция (CaCO3) при z697e708 C.Было обнаружено, что интенсивность кривых C-S-H увеличивается с увеличением содержания БА. Это связано с увеличением присутствия фазы тоберморита, образующейся при увеличении содержания БА, что соответствует повышенной прочности образцов на сжатие. Кроме того, можно увидеть, что Ca (OH) 2 уменьшается с увеличением содержания BA из-за пуццолановой реакции, которая использовалась в реакции образования тоберморита, а также из-за эффекта разбавления, когда было использовано использование дополнительных вяжущих материалов, таких как зольный остаток. используется для замены части портландцемента.Результаты TGA для тройного цемента AAC-бетона из портландцемента, зольной пыли и микрокремнезема были опубликованы Wongkeo & Chaipanich (2010). Результаты были нанесены на график как производные, показывающие кривые DTG для трехкомпонентного цементного бетона AAC по сравнению с образцами, отвержденными на воздухе в течение 28 дней. В трехкомпонентном цементном растворе AAC кривые DTG показали наличие фаз C-S-H (фаза тоберморита), Ca (OH) 2 и CaCO3. Потеря веса фазы тоберморита была приписана дегидратации слабосвязанной молекулярной межслоевой воды (Alarcon-Ruiz, Platret, Massieu, & Ehrlacher, 2005).Считается, что эттрингит и C2ASH8 не образовывались в бетоне AAC из-за замещения Al на Si в тетраэдрическом участке тоберморита (Wongkeo & Chaipanich, 2010). Сообщалось, что это оказывает значительное влияние на химическое поведение цементного теста, включая поведение катионного и анионного обмена, растворимость и реакции, которые могут привести к задержке образования эттрингита (Shaw, Henderson, & Komanschek, 2000).
Кроме того, образование групп C-A-S-H (гидрогранат) не будет происходить при температуре ниже 200 ° C, но вместо этого будет образовываться тоберморит, при котором кристаллизация тоберморита будет ускоряться, а стабильность тоберморита возрастает, когда доступен оксид алюминия (Meller et al., 2009; Мостафа, 2005). Тоберморитовая фаза автоклавного шлака увеличивалась с увеличением содержания БА до 20%. Было обнаружено, что фаза Ca (OH) 2 уменьшается с увеличением содержания БА из-за усиления пуццолановой реакции БА и SF и эффекта разбавления.
9,9
Теплопроводность шлакового цемента автоклавного газобетона
Теплопроводность бетона AAC находится в прямой зависимости от его физических свойств. Сообщается, что теплопроводность зольного цемента AAC несколько увеличивается при использовании зольного остатка в качестве дополнительного вяжущего материала в бетоне (Рисунок 9.3), поскольку содержание БА увеличило общую удельную массу или объемную плотность бетона (Wongkeo & Chaipanich, 2010; Wongkeo et al. , 2012). Пористая структура легких заполнителей, плотность бетона и цементная матрица влияют на теплопроводность бетона (Corinaldesi et al., 2011; Topcu & Uygunoglu, 2007). Таким образом, теплопроводность BLWC имела тенденцию к увеличению из-за уменьшения объема проницаемых пустот с увеличением содержания BA (Wongkeo & Chaipanich, 2010).Albayrak et al. (2007) сообщили, что прочность на сжатие и теплопроводность бетона AAC снижаются с уменьшением.
Свойства и долговечность блоков из автоклавного газобетона
225
Теплопроводность (Вт / мК)
0,70
0,65
0,60
0,55
0,50 0
10 20 Зольность шлака (%)
30
Рисунок 9.3 Теплопроводность шлакового газобетона автоклавного твердения.По материалам Wongkeo et al. (2012).
насыпной плотности. Albayrak et al. (2007) обнаружили теплопроводность AAC в диапазоне 1,1e5,0 МПа и диапазоне плотности 270e500 кг / м3, показывая увеличение прочности с увеличением плотности. Несколько других исследователей (Blanco, Garcia, Mateos, & Ayala, 2000; Demirboga, 2003, 2007; Demirboga & Gul, 2003) также сообщили, что снижение теплопроводности связано с уменьшением плотности бетона. Jerman, Keppert, Vyborny, & Cerny (2013) показали, что теплопроводность зависит от плотности AAC, а также от содержания влаги (Рисунок 9.4), где увеличение влажности и плотности приводит к увеличению теплопроводности. Следовательно, известно, что теплопроводность увеличивается с увеличением плотности как обычного бетона, так и бетона AAC. Теплопроводность AAC может составлять всего 0,08 Вт / м · К при 25 С. Однако, как следствие, прочность на сжатие составляет 1,0
300 кг / м3
Теплопроводность [Вт / м · К]
0,9
y = 0,1414e1,2666x R2 = 0,9174
0,8
500 кг / м3 350 кг / м3
0.7 0,6 0,5
y = 0,2811x + 0,0878 R2 = 0,972
0,4 0,3
y = 0,1049e0,6911x R2 = 0,9404
0,2 0,1 0,0 0
0,5
1 1,5 Влагосодержание [кг / кг]
2
2,5
Рисунок 9. 4 Зависимость теплопроводности автоклавного газобетона от влажности. Джерман и др. (2013) напечатано с разрешения Elsevier.
226
Экологичные кирпичи и блоки для каменной кладки
очень низкий (2.05 МПа) (Jerman et al., 2013). Когда AAC с зольным остатком используется в качестве дополнительного вяжущего материала, теплопроводность находится в диапазоне 0,58–0,61 Вт / м · К (Wongkeo et al., 2012). С другой стороны, когда зольный остаток используется в качестве заполнителя, теплопроводность бетона AAC, как сообщается, находится в пределах 0,220–0,361 Вт / м · К и, как было обнаружено, уменьшается с увеличением содержания BA, используемого в качестве замены песка (Kurama et al. др., 2009). Было обнаружено, что теплопроводность всего зольного бетона AAC с SF выше, чем у контрольного бетона с портландцементом, и увеличивается с увеличением SF (Wongkeo & Chaipanich, 2010).Это связано с уменьшением объема проницаемых пустот и плотности микроструктуры в матрице цементного теста. Сообщается, что небольшие изменения теплопроводности тройного портландцемента, зольной пыли и микрокремнезема аналогичны в диапазоне 0,61–0,65 Вт / м К. Таким образом, наблюдается прямая зависимость между теплопроводностью. и объемная плотность бетона AAC.
9,10
Долговечность газобетона в автоклаве
Поскольку в АБК есть пустоты, большие из-за образования начальной реакции на аэрацию, ожидается, что он будет морозоустойчивым (Mindess et al., 2003). Однако степень насыщения важна для реакций замораживания-оттаивания (Roulet, 1983), поскольку газобетон подвержен проникновению жидкости и газа из-за своей высокой пористости, которая может вызвать повреждение бетона (Narayanan & Ramamurthy, 2000a; RILEM, 1993). Сообщается, что максимальная степень насыщения находится в диапазоне 20-40%. При более высокой степени насыщения бетон станет хрупким и полностью расколется (Roulet, 1983). Джерман и др. (2013) сообщили о морозостойкости AAC с использованием метода масштабирования, при котором образцы должны были пройти 25 и 50 циклов замораживания по 8 часов при 15 ° C и оттаивания в течение 8 часов при 20 ° C. Они тестировали образцы в различных условиях, принимая во внимание характер различных сред, таких как сухость, влажность 10% и полное насыщение. Были протестированы условия сухости и влажности 10%, так как они лучше подходят для реалистичных условий эксплуатации здания по сравнению с полностью насыщенными условиями. Потеря массы и потеря прочности на сжатие образцов, испытанных в этих условиях, нанесены на график, как показано на рисунках 9.5 и 9.6. Интересно, что сухие образцы не показывают признаков потери массы или потери прочности на сжатие после 25 циклов.Более высокий процент потери массы был обнаружен в образцах с влажностью 10% и в образцах, насыщенных капиллярной водой. С другой стороны, результаты для сухих образцов после 50 циклов показали некоторую потерю массы (0,36–0,50%) и незначительную потерю прочности на сжатие (макс. 0,10%). В образцах с содержанием влаги 10% потеря массы находится в диапазоне 1,3–1,5%, в то время как потеря прочности на сжатие выше у образца P1,8-300 (16,3%), но кажется приемлемой при 6–8%.
для образцов П2-350 и П4-500. Для образцов, насыщенных капиллярами, потеря прочности на сжатие и потеря массы намного более серьезны после 50 циклов замораживания / оттаивания, особенно в P1.8-300 и P2-350, у которых потеря прочности на сжатие составляет 46,0% и 45,7% соответственно. Эти образцы, однако, имеют очень низкую прочность на сжатие первоначально 2,05 и 2,24 МПа (Jerman et al., 2013). Модель
Свойства и долговечность блоков кладки из автоклавного газобетона
Потеря массы (%)
20 15
(a)
Сухой образец (без потерь) Образец с содержанием влаги 10% Капиллярно-водонасыщенный образец
10 5
25 Потеря прочности на сжатие (%)
25
20 15
227
(б)
Сухой образец (без потерь) Образец с содержанием влаги 10% Капиллярно-водонасыщенный образец
10 5 0
0 P1.8–300
P2–350
P1.8–300
P4–500
P2–350
P4–500
Автоклавный газобетон
Автоклавный газобетон
25
Потеря массы (%)
20 15
(a)
Сухой образец Образец с содержанием влаги 10% Капиллярно-водонасыщенный образец
10 5
Потеря прочности на сжатие (%)
Рисунок 9. 5 (a) Потеря массы и (b) прочность на сжатие потеря ACC при 25 циклах.По материалам Jerman et al. (2013).
70 60 50
(б)
Сухой образец (без потерь) Образец с влажностью 10% Капиллярно-водонасыщенный образец
40 30 20 10 0
0 P1.8-300
P2-350
P4-500
Автоклавный газобетон
P1.8-300
P2-350
P4-500
Автоклавный газобетон
Рисунок 9.6 (a) Потеря массы и (b) потеря прочности на сжатие ACC при 50 циклы.По материалам Jerman et al. (2013).
P4-500 имеет прочность на сжатие 4,0, что дает меньшую потерю массы на 1,5% и меньшую потерю прочности на сжатие на 16,6%. В обеих сериях испытаний при 25 и 50 циклах результаты показывают, что степень водонасыщения оказывает значительное влияние на сопротивление замораживанию-оттаиванию бетона из AAC. Был сделан вывод, что для сухих и 10% -ных образцов замораживание-оттаивание допустимо в диапазоне прочности на сжатие 1,8–4,0 МПа (Jerman et al. , 2013). Это, по-видимому, согласуется с работой Тикальского, Посписила и Макдональда (2004) по достижению хорошей морозостойкости при содержании влаги менее 16% в бетоне AAC с объемной плотностью в диапазоне 500-600 кг / м3 и прочностью на сжатие. 1e2 МПа.Следовательно, при рассмотрении сопротивления замораживанию-оттаиванию бетона AAC решающими факторами, которые могут существенно повлиять на характеристики AAC, являются наличие воздушных пустот, степень насыщения и прочность на сжатие.
9,11
Выводы и будущие тенденции
Хотя в этой главе основное внимание уделяется свойствам и долговечности AAC, которая представляет собой обзор прошлых и недавних исследований по данной теме, будущие тенденции
228
Eco -эффективные кирпичи и блоки для каменной кладки
с использованием AAC во многом будут зависеть от применения AAC и спецификаций, требуемых строительной отраслью, а также тех, которые установлены стандартами.Исследования будут в значительной степени сосредоточены на новых науках и технологиях, ведущих к созданию инновационных продуктов AAC, с учетом требований спецификации, применения, экономических и экологических аспектов. Таким образом, при производстве AAC следует использовать новые технологии и новые материалы. Например, можно использовать другой и более подходящий источник диоксида кремния, и, если он является экологически чистым и экономичным, тем лучше. Вероятно, это причина того, почему исследования пуццолановых материалов были столь успешными и привлекли множество интересов.Следует также обратить внимание на новое рентабельное производство, не в последнюю очередь на новые материалы, такие как наноразмерные или новые отходы и побочные продукты, которые могут улучшить механические свойства и долговечность AAC.
9.12
Источники дополнительной информации и советов
Narayanan & Ramamurthy (2000a) рассмотрели работы по AAC, в которых описан ряд свойств AAC. Wongkeo и Chaipanich (2010) и Wongkeo et al. (2012) сообщили о работах по использованию пуццоланов в качестве бинарных и тройных смешанных цементов, а также о результатах механических свойств AAC.Бетон Миндесс и др. (2003) — также полезная книга для чтения, чтобы дать общее представление о легком бетоне в целом и классификации легкого бетона. Опубликованные работы Meller et al. (2009), Taylor (1997) и Richardson (2008) — другие полезные источники для чтения по гидратации силиката кальция и продуктов гидратации при различных температурах и давлении.
Ссылки ACI Committer 213. (2001). Руководство для конструкционного легкого заполнителя бетона. Фармингтон-Хиллз: Американский институт бетона.Аларкон-Руис, Л., Платре, Г., Масье, Э., и Эрлахер, А. (2005). Использование термического анализа для оценки влияния температуры на цементное тесто. Исследование цемента и бетона, 35, 609e613. Албайрак, М., Йорукоглу, А., Карахан, С., Атлихан, С., Арунтас, Х. Ю., и Гиргин, И. (2007). Влияние цеолитовой добавки на свойства автоклавного газобетона. Строительство и окружающая среда, 42, 3161e3165. Александерсон, Дж. (1979). Связь структуры и механических свойств автоклавного газобетона.Исследование цемента и бетона, 9, 507e514. Баспинар, С.М., Демир, И., Кахраман, Э., и Горхан, Г. (2014). Потенциал использования золы вместе с микрокремнеземом в производстве автоклавного газобетона. KSCE Journal of Civil Engineering, 18, 47e52. Бланко, Ф., Гарсия, П., Матеос, П., и Аяла, Дж. (2000). Характеристика и свойства легкого бетона, изготовленного из ценосфер. Исследование цемента и бетона, 30, 1715e1722. CEB. (1977). Автоклавный газобетон. Пособие по дизайну и технологии.Строительная пресса.
Свойства и долговечность блоков из автоклавного газобетона
229
Коринальдези В., Маццоли А. и Морикони Г. (2011). Механические свойства и теплопроводность растворов, содержащих частицы отработанной резины. Материалы и дизайн, 32, 1646e1650. Демирбога Р., Гуль Р. (2003). Влияние вспученного перлита, микрокремнезема, летучей золы на теплопроводность легкого бетона. Исследование цемента и бетона, 33, 723e727.Демирбога Р. (2003). Влияние минеральных добавок на теплопроводность и прочность раствора на сжатие. Энергетика и строительство, 35, 189e192. Демирбога Р. (2007). Теплопроводность и прочность на сжатие бетонной заделки с минеральными добавками. Строительство и окружающая среда, 42, 2467e2471. Хендри, А. В. (2001). Кладка стен: материалы и конструкции. Строительные и строительные материалы, 15, 323e330. Гесс, Дж. А., Кинкл, Л., Амасай, Т., и Вулф, П. (2010). Эргономическая оценка каменщиков кладки бетонных блоков и автоклавного газобетона.Прикладная эргономика, 41, 477e483. Хуанг, X., Ni, W., Cui, W., Wang, Z., & Zhu, L. (2012). Приготовление автоклавного газобетона из медных хвостов и доменного шлака. Строительные и строительные материалы, 27, 1e5. Иоанну И., Гамильтон А. и Холл К. (2008). Капиллярное поглощение воды и н-декана автоклавным газобетоном. Исследование цемента и бетона, 38, 766e771. Джерман, М., Кепперт, М., Выборный, Дж., И Черни, Р. (2013). Гигрические, термические и прочностные свойства автоклавного газобетона.Строительные и строительные материалы, 41, 352e359. Just, A., & Middendorf, B. (2009). Микроструктура высокопрочного пенобетона. Характеристики материалов, 60, 741e748. Кериене Дж., Клигис М., Лаукайтис А., Яковлев Г., Спокаускас А. и Алекневичюс М. (2013).
Влияние добавки многослойных углеродных нанотрубок на свойства неавтоклавированных и автоклавных газобетонов. Строительные и строительные материалы, 49, 527e535. Клингнер, Р. Э. (2008). Правильно использовать автоклавный газобетон.Журнал MASONRY: голос масонской индустрии. http://www.masonrymagazine.com/6-08/autoclaved. html. Коси В., Мадера Дж. И Черны Р. (2012). Системы наружной теплоизоляции для ограждающих конструкций зданий AAC: расчетный анализ, направленный на увеличение срока службы. Энергетика и строительство, 47, 84e90. Курама, Х., Топчу, И. Б., и Каракурт, К. (2009). Свойства автоклавного газобетона, полученного из зольного остатка. Журнал технологий обработки материалов, 209, 767e773. Кус, Х., И Карлссон, Т. (2003). Микроструктурные исследования автоклавного газобетона, подвергшегося естественному и искусственному выветриванию. Исследование цемента и бетона, 33, 1423e1432. Мацуи К., Кикума Дж., Цунашима М., Исикава Т., Мацуно С., Огава А. и др. (2011). Дифракция рентгеновских лучей с временным разрешением на месте образования тоберморита в автоклавном газобетоне: влияние реакционной способности источника кремнезема и добавления алюминия.
Исследование цемента и бетона, 41, 510e519. Меллер, Н., Кирицис, К., и Холл, К. (2009).Минералогия гидрокерамической системы CaOeAl2O3eSiO2eh3O (CASH) от 200 до 350 C. Исследования цемента и бетона, 39, 45e53. Миндесс, С., Янг, Дж. Ф. и Дарвин, Д. (2003). Конкретный. США: Pearson Education. Мостафа, Н. Ю. (2005). Влияние воздушно-охлаждаемого шлака на физико-химические свойства автоклавного газобетона. Исследование цемента и бетона, 35, 1349e1357.
230
Экологичные кирпичи и блоки для каменной кладки
Нараянан, Н., и Рамамурти, К. (2000a). Структура и свойства газобетона: обзор.Цемент и бетонные композиты, 22, 321e329. Нараянан, Н., и Рамамурти, К. (2000b). Микроструктурные исследования ячеистого бетона. Исследование цемента и бетона, 30, 457e464. Петров И. и Шлегель Э. (1994). Применение автоматического анализа изображений для исследования конструкции автоклавного газобетона. Исследование цемента и бетона, 24, 830e840. Радхи, Х. (2011). Жизнеспособность стен из автоклавного пенобетона для жилого сектора в Объединенных Арабских Эмиратах. Энергетика и строительство, 43, 2086e2092.Ричардсон, И. Г. (2008). Силикат кальция гидраты. Исследование цемента и бетона, 38, 137e158. Рекомендуемая практика RILEM. (1993). Автоклавный газобетон — свойства, испытания и проектирование. E&FN SPON. Руле, К. А. (1983). Расширение газобетона от мороза — определение критического насыщения. В Ф. Х. Виттманне (ред.), Протоколы автоклавного газобетона, влажности и свойств (стр. 157e169). Амстердам: Эльзевир. Шоу, С., Хендерсон, К. М. Б., и Команшек, Б. У. (2000).Механизмы дегидратации / перекристаллизации, энергия и кинетика гидратированных минералов силиката кальция: исследование in situ TGA / DSC и синхротронного излучения SAXS / WAXS. Химическая геология, 167, 141e159. Тейлор, Х. Ф. У. (1997). Цементная химия. Нью-Йорк: Краткий технологический обзор Тейлора и Томаса Телфорд Сервисез Лтд. (2010). Кирпичные блоки из автоклавного газобетона. Информация о ресурсах от Международного института масонства. Доступно по адресу: http://www.imiweb.org/design_ tools / tech_briefs / 01.
02% 20AAC% 20MASONRY% 20UNITS.pdf Дата обращения 14.04.2014. Тикальский П. Дж., Посписил Дж. И Макдональд В. (2004). Метод оценки морозостойкости выполненного пенобетона. Исследование цемента и бетона, 34, 889e893. Топчу, И. Б., & Уйгуноглу, Т. (2007). Свойства автоклавного бетона на легком заполнителе. Строительство и окружающая среда, 42, 4108e4116. Валор Р. К. (1954). Ячеистый бетон. Физические свойства. Журнал Американского института бетона, 25, 817e836. Вонгкео, В., и Чайпанич, А.(2010). Прочность на сжатие, микроструктура и термический анализ легкого конструкционного бетона, подвергнутого автоклавному и воздушному отверждению, на основе зольного остатка угля и микрокремнезема. Материаловедение и инженерия A, 527, 3676e3684. Wongkeo, W., Thongsanitgarn, P., Pimraksa, K., & Chaipanich, A. (2012). Прочность на сжатие, изгибная прочность и теплопроводность автоклавного бетонного блока, изготовленного с использованием золы в качестве заменителя цемента. Материалы и дизайн, 35, 434e439.
Язычи, Х. (2007).Влияние условий твердения на прочность на сжатие сверхвысокопрочного бетона с большим объемом минеральных добавок. Здания и окружающая среда, 42, 2083e2089.
Конструкционный легкий газобетон
Ячеистый бетон — это тип легкого бетона, состоящий только из цемента, воды и
песок с 20-процентным содержанием воздуха по объему или более, вовлеченным в бетон. Два
методы, используемые для воздухововлечения в ячеистом бетоне: (1) использование воздухововлекающего
агент (AEA) и (2) использование предварительно сформированной пены.Если для улавливания воздуха используется предварительно сформированная пена
в бетон, бетон называется пенобетоном, и если используется AEA, бетон
называется газобетон. В зависимости от типа применения, структурное или неструктурное,
ячеистый бетон может иметь плотность в диапазоне 400
до 1800 кг / м3. Применение ячеистого бетона в неструктурных целях включает заполнение пустот и траншей,
тепло- и звукоизоляция. Структурные применения ячеистого бетона включают сборный бетон. такие элементы, как бетонные кирпичи, перегородки, плиты крыши и т. д.Из-за высокого уровня воздуха в
из ячеистого бетона сложно обеспечить прочность на сжатие, достаточную для
классифицируют бетон как конструктивно полезный, когда используются неавтоклавные условия отверждения.
Процесс автоклавирования сочетает в себе высокую температуру и давление в процессе формования,
что приводит к повышению прочности и снижению усадки. Этот процесс также ограничен
сборные блоки. Условия неавтоклавного отверждения включают влажное отверждение, сухое отверждение и т. Д.
обертывание бетона пластиком и т. д.Однако теперь, когда мир движется в энергетике
эффективное направление, ищутся способы исключения энергоемкого автоклавирования. Это было для
Было обнаружено, что использование больших объемов летучей золы в ячеистом бетоне приводит к
к более высокой прочности, которая позволяет классифицировать бетон как конструктивно полезный.
Теперь, когда наблюдается возобновление интереса к конструкционным применениям бетона, конструкция
Необходимо найти методологию использования произвольного воздухововлекающего агента.
Исследование
сообщается в этой диссертации, поэтому пытается найти такую методологию и производить газированные
бетон с заданной плотностью и прочностью, который можно отнести к конструктивно полезным.
Для методологии проектирования смеси исследуются следующие факторы: потребность в воде
смеси, потребности в воде компонентов смеси и количества AEA, необходимого для производства
газобетон с определенной плотностью. Потребность в воде зависит от смеси.
составляющих, и поэтому предлагается метод расчета водопотребления смеси
составляющих на основе таблицы изменения потока ASTM.Из-за сложной природы воздуха
вовлечение в бетон, количество воздуха, вовлеченного в бетонную смесь, неизвестно
заранее, поэтому пришлось разработать метод проб и ошибок. Пробные смеси
проводились в небольшом миксере для выпечки. Расчетные дозировки AEA из пробных смесей
были найдены и разработаны бетонные смеси на их основе. Факторы, влияющие на состав смеси и прочность ячеистого бетона, включают:
Соотношение наполнитель / цемент (f / c), соотношение летучая зола / цемент (a / c) и расчетная целевая плотность.
Дополнительные факторы
на прочность газобетона влияют размер и форма образца, твердость и
конкретный возраст. Было обнаружено, что тип песка и соотношение f / c влияют на потребность воды в воде.
бетонная смесь. Тип песка и соотношение f / c также влияют на прочность на сжатие, с более высокой
прочность для более мелкого песка и более низких соотношений f / c. Однако плотность бетона является фактором
это больше всего влияет на силу.
Автоклавный пенобетон (AAC) — точка назначения
Автоклавный газобетон (AAC) — это сборный легкий пенобетонный строительный материал, который можно использовать для изготовления бетонных блоков (CMU).В 1920-х годах шведский архитектор впервые смешал традиционную бетонную смесь из цемента, извести, воды и песка с небольшим количеством алюминиевой пудры. AAC, который был изобретен более 800 лет назад, обеспечивает структуру, изоляцию, а также огнестойкость и устойчивость к плесени одновременно. Блоки, стеновые панели, напольные и кровельные панели, облицовочные (фасадные) панели и перемычки являются примерами типов.
Бетон AAC обычно формуют в блоки или плиты и используют для создания цементных стен так же, как и обычные бетонные блоки.Интенсивность блоков обычно составляет от 3 до 9 Нмм-2 (при испытании). Плотность колеблется от 460 до 750 кг м-3; Для сравнения, бетонные блоки средней плотности имеют типичный диапазон плотности 1350-1500 кг м-3, а плотные бетонные блоки — 2300-2500 кг м-3. Продукция AAC может использоваться как для внутреннего, так и для наружного строительства, и они могут быть покрыты сайдингом, таким как облицованный кирпич или виниловый сайдинг, или окрашены или покрыты штукатуркой или штукатурным составом, чтобы защитить их от элементов.
Ячеистый бетон занимается поиском промышленного материала с характеристиками, идентичными дереву с момента его открытия в 1920 году. Он был легким, его можно было разрезать или перфорировать, и он не имел некоторых недостатков, таких как водопоглощение и требования к уходу. Продукты ACC можно фрезеровать, отшлифовать или разрезать по размеру на месте с помощью обычных электроинструментов и фрез из углеродистой стали, помимо того, что они просты и удобны в установке. Блоки из автоклавного газобетона (AAC) теперь широко доступны благодаря таким компаниям, как Hebel и Retak, которые разрабатывают простой и эффективный метод строительства.
Блоки из автоклавного газобетона (AAC) используются для придания формы внутреннему листу полой стены и являются отличными теплоизоляторами. Они часто используются в фундаменте и на внешней стороне листа, где обычно визуализируются. Стены, полы с железобетонными балками, потолки и крыша могут быть построены из газобетона в автоклаве. Автоклавный газобетон можно быстро разрезать до любой формы. Aircrete продается под различными торговыми марками, как и другие изделия из каменной кладки.Aircrete обладает хорошими акустическими свойствами и долговечностью, с хорошей устойчивостью к воздействию сульфатов, огню и морозу.
В отличие от большинства других бетонных смесей, AAC производится только с использованием песка в качестве заполнителя. Связующие вещества включают кварцевый песок, кальцинированный гипс, известь (минеральную) и / или цемент, а также воду. Пузырьки воздуха попадают в материал, поскольку алюминий используется в качестве расширителя, в результате чего получается легкий материал с низкой плотностью. Мокрый бетон формуют в формы с помощью шаблонов, затем удаляют частично высохшие плиты и блоки.Алюминиевый порошок используется в концентрации 0,05–0,08% по объему (в зависимости от заданной плотности). Летучая зола угольных электростанций с содержанием кремнезема 50–65 процентов используется в некоторых странах в качестве агрегата. С бетонными блоками AAC легко работать, их можно резать и просверливать обычными деревообрабатывающими инструментами, включая ленточные пилы и дрели. Бетон должен быть измерен на прочность на сжатие, содержание влаги, объемный вес и усадку, поскольку он легкий и имеет низкую плотность.
При производстве газобетона автоклав обычно представляет собой стальную трубу диаметром 3 метра и длиной 45 метров. Пар подается в автоклав под высоким давлением, обычно 800 кПа и 180 ° C. При смешивании и разливке AAC происходит несколько химических реакций, что придает ему легкий вес (20% от веса бетона) и термические свойства. Из-за низкой температуры блоки AAC классифицируются как устройство для кладки из легкого бетона, а не обожженного кирпича.
Стены, полы, кровельные панели, блоки и перемычки могут быть изготовлены из автоклавного ячеистого бетона (AAC).Панели бывают толщиной от 8 до 12 дюймов, шириной от 24 дюймов и длиной до 20 футов. Доступны блоки длиной 24, 32 и 48 дюймов, а также толщиной от 4 до 16 дюймов и высотой 8 дюймов.
Из-за своей низкой плотности AAC имеет низкую структурную степень сжатия. Его прочность на сжатие составляет до 8 мегапаскалей (1200 фунтов на квадратный дюйм), что примерно вдвое меньше, чем у стандартного бетона. Первый завод по производству материалов AAC, LCC SIPOREX — Lightweight Construction Company, открылся в государстве Персидский залив в Саудовской Аравии в 1978 году, поставляя в страны Персидского залива пеноблоки и панели.Затвердевшие блоки или панели из пенобетона в автоклаве соединяются тонким слоем раствора с использованием тех же методов, что и обычные бетонные блоки. Стены могут быть усилены сталью или другими конструктивными элементами, которые проходят вертикально через щели в блоках для дополнительной прочности.
Как по способу изготовления, так и по составу готового продукта автоклавный газобетон (AAC) отличается от плотного бетона (также известного как «натуральный бетон»). С 1980 года во всем мире наблюдается рост использования материалов AAC.Австралия, Бахрейн, Китай, Восточная Европа, Индия и США строят новые производственные мощности. AAC становится все более распространенным среди девелоперов, архитекторов и строителей домов по всему миру. Из-за своего легкого веса бетон AAC можно использовать для стен, полов и крыш, что делает его более универсальным, чем обычный бетон. Материал прочный и огнестойкий, а также обеспечивает отличную звуко- и теплоизоляцию. AAC должен быть покрыт нанесенной отделкой, такой как модифицированная полимером штукатурка, натуральный или искусственный камень или сайдинг, чтобы быть долговечным.
Автоклавный газобетон, напротив, имеет гораздо меньшую плотность, чем плотный бетон. Химические реакции, образующие продукты гидратации, почти завершаются во время автоклавирования, поэтому блоки готовы к использованию после извлечения из автоклава и охлаждения. Наружная поверхность стен AAC должна быть покрыта толстым слоем водонепроницаемого материала или мембраны, если они используются в подвалах. Поверхности AAC, которые подвергаются воздействию элементов или влажности почвы, будут повреждены. В нем нет агрегата; все основные материалы смеси, включая измельченный песок, являются химически активными.Из-за высокой температуры и давления в автоклаве песок, который инертен при использовании в плотном бетоне, ведет себя как пуццолан.
Показатели собственной изоляции AAC довольно умеренные: от R-10 для стены толщиной 8 дюймов до R-12,5 для стены толщиной 10 дюймов. На каждый дюйм толщины материала AAC имеет значение R около 1,25. Его производственный процесс незначительно отличается в зависимости от производственного предприятия, но концепции остаются неизменными. AAC имеет высокую тепловую массу, что задерживает передачу тепловой энергии, значительно снижая затраты на нагрев и охлаждение.Чтобы свести к минимуму потери энергии из-за утечки воздуха, конструкции можно сделать чрезвычайно герметичными. AAC также хорошо работает в качестве звукоизоляционного экрана.
Источники информации:
- thebalancesmb.com
- standing-cement.com
- archdaily.com
- wikipedia
Газобетон и его свойства
Автоклавный газобетон (AAC) — это легкий конструкционный материал из сборного железобетона.Он сделан из кварцевого песка, кальцинированного гипса, известкового цемента, воды и алюминиевой пудры. Алюминиевый порошок используется в количестве от 0,05% до 0,08% по объему (в зависимости от заданной толщины).
Элементы AAC утилизируются в автоклаве в условиях тепла и веса. К разным типам AAC относятся блоки, разделительные панели, панели пола и крыши, панели облицовки и перемычки. Блоки из автоклавного газобетона (AAC) используются как при внутренних, так и при наружных строительных работах.
AAC придают конструкции огнестойкость и изоляцию.Материалы ACC представляют собой стандартные аппараты для нарезки и формования для использования. Он настоятельно рекомендовал использовать термозащитный материал как внутри, так и снаружи.
Достопримечательности AAC :
1. Самая большая свобода действий AAC — это его более низкий естественный эффект.
2. Улучшенное умение отапливать снижает тепловую и охлаждающую нагрузку на конструкции.
3. Великолепный звукоизоляционный материал и акустический протектор.
4. Исключительно пожаробезопасный и термитный.
5. Выпускается в ассортименте конструкции и размеров.
6. Снижает стоимость предприятия.
7. AAC поглощает влагу из воздуха и выделяет влагу.
8. Монтаж электрических и сантехнических линий прост.
9. Почтовая оплата становится все более доступной.
10. AAC — прочный материал.
11. AAC требует меньшего количества стали и бетона для простых людей.
12. Кладка выполняется быстрее из-за огромного размера блока.
13. В отличие от обычного, экологически чистого бетона образует до 30% твердых отходов.№
14. Точность панелей и блоков из автоклавного газобетона заданных размеров и формы перед отправкой с завода.
15. Блоки AAC ассимилируют сырость и сырость разряда, создавая прекрасное окружение.
16. Улучшение тепла в достаточной мере снижает охлаждение и потепление в зданиях.
Ущерб :
№ 1. Установка AAC в штормовых климатических условиях приводит к нарушению формы после укладки, что снижает качество раствора.
2. Будьте осторожны при обращении с глиняными кирпичами, чтобы избежать потерь.
