ΠΊΠ°ΠΊΠΎΠΉ ΠΊΠΈΡΠΏΠΈΡ Π»ΡΡΡΠ΅ Π²ΡΠ±ΡΠ°ΡΡ Π΄Π»Ρ ΡΠΎΠΊΠΎΠ»Ρ ΠΈ Π»Π΅Π½ΡΠΎΡΠ½ΠΎΠ³ΠΎ ΡΡΠ½Π΄Π°ΠΌΠ΅Π½ΡΠ° ΠΈ ΠΊΠ°ΠΊ Π΅Π³ΠΎ Π²ΡΠ»ΠΎΠΆΠΈΡΡ ΡΠ²ΠΎΠΈΠΌΠΈ ΡΡΠΊΠ°ΠΌΠΈ?
Π‘ΡΡΠ΅ΡΡΠ²Π΅Π½Π½ΡΠ΅ Π½Π°Π³ΡΡΠ·ΠΊΠΈ ΠΎΡ ΠΆΠΈΠ»ΠΎΠ³ΠΎ (ΠΈ Π½Π΅ ΡΠΎΠ»ΡΠΊΠΎ) ΡΡΡΠΎΠ΅Π½ΠΈΡ ΠΏΡΠΈΠ½ΠΈΠΌΠ°Π΅Ρ Π½Π° ΡΠ΅Π±Ρ Π½Π΅ ΡΠΎΠ»ΡΠΊΠΎ ΡΡΠ½Π΄Π°ΠΌΠ΅Π½Ρ, Π½ΠΎ ΠΈ ΡΠΎΠΊΠΎΠ»Ρ. ΠΡΠΎΠΌΠ΅ ΡΠΎΠ³ΠΎ, ΠΏΠΎΡΠ»Π΅Π΄Π½ΠΈΠΉ ΠΏΠΎΠ΄Π²Π΅ΡΠ³Π°Π΅ΡΡΡ Π½Π΅Π³Π°ΡΠΈΠ²Π½ΡΠΌ Π²Π½Π΅ΡΠ½ΠΈΠΌ ΡΠ°ΠΊΡΠΎΡΠ°ΠΌ Π²ΡΠΎΠ΄Π΅ Π°ΡΠΌΠΎΡΡΠ΅ΡΠ½ΡΡ ΠΎΡΠ°Π΄ΠΊΠΎΠ², ΠΊΠ°ΠΊ ΠΈ ΡΠ°ΡΠ°Π΄Π½Π°Ρ ΡΠ°ΡΡΡ Π²ΠΎΠ·Π²Π΅Π΄Π΅Π½ΠΈΡ. ΠΠΌΠ΅Π½Π½ΠΎ ΠΏΠΎΡΡΠΎΠΌΡ ΡΠ°ΠΊ Π²Π°ΠΆΠ½ΠΎ ΠΏΠΎΠ΄Π±ΠΈΡΠ°ΡΡ Π΄Π»Ρ ΡΠΎΠΊΠΎΠ»Ρ ΠΊΠ°ΡΠ΅ΡΡΠ²Π΅Π½Π½ΡΠ΅ ΠΈ Π΄ΠΎΠ»Π³ΠΎΠ²Π΅ΡΠ½ΡΠ΅ ΠΌΠ°ΡΠ΅ΡΠΈΠ°Π»Ρ, ΠΊΠΎΡΠΎΡΡΠ΅ Π±ΡΠ΄ΡΡ ΡΠ»ΡΠΆΠΈΡΡ ΠΌΠ½ΠΎΠ³ΠΎ Π»Π΅Ρ Π±Π΅Π· ΠΏΡΠΎΠ±Π»Π΅ΠΌ. Π‘Π΅Π³ΠΎΠ΄Π½Ρ ΠΌΡ ΠΏΠΎΠ·Π½Π°ΠΊΠΎΠΌΠΈΠΌΡΡ ΠΏΠΎΠ±Π»ΠΈΠΆΠ΅ Ρ ΡΠ°ΠΊΠΈΠΌ ΡΡΡΠΎΠΉΠΌΠ°ΡΠ΅ΡΠΈΠ°Π»ΠΎΠΌ, ΠΊΠ°ΠΊ ΡΠΎΠΊΠΎΠ»ΡΠ½ΡΠΉ ΠΊΠΈΡΠΏΠΈΡ, ΠΈ ΡΠ·Π½Π°Π΅ΠΌ, ΠΊΠ°ΠΊ Π΅Π³ΠΎ Π½Π°Π΄ΠΎ ΠΏΡΠ°Π²ΠΈΠ»ΡΠ½ΠΎ ΡΠΊΠ»Π°Π΄ΡΠ²Π°ΡΡ.
Π’ΡΠ΅Π±ΠΎΠ²Π°Π½ΠΈΡ
ΠΡΠ΅ΠΆΠ΄Π΅ ΡΠ΅ΠΌ ΡΠ°Π·ΡΡΠΊΠΈΠ²Π°ΡΡ ΠΊΠΎΠ½ΠΊΡΠ΅ΡΠ½ΡΠΉ Π²ΠΈΠ΄ ΠΊΠΈΡΠΏΠΈΡΠ° Π΄Π»Ρ ΡΡΡΠΎΠΈΡΠ΅Π»ΡΡΡΠ²Π° ΡΠΎΠΊΠΎΠ»Ρ, ΡΠ»Π΅Π΄ΡΠ΅Ρ ΡΠ·Π½Π°ΡΡ, ΠΊΠ°ΠΊΠΈΠΌ ΡΡΠ΅Π±ΠΎΠ²Π°Π½ΠΈΡΠΌ ΠΎΠ½ Π΄ΠΎΠ»ΠΆΠ΅Π½ ΠΎΡΠ²Π΅ΡΠ°ΡΡ.
- Π’Π°ΠΊΠΎΠΉ ΡΡΡΠΎΠΉΠΌΠ°ΡΠ΅ΡΠΈΠ°Π» Π΄ΠΎΠ»ΠΆΠ΅Π½ ΠΎΠ±Π»Π°Π΄Π°ΡΡ Π΄ΠΎΡΡΠ°ΡΠΎΡΠ½ΠΎΠΉ ΠΏΠ»ΠΎΡΠ½ΠΎΡΡΡΡ ΠΈ ΠΆΠ΅ΡΡΠΊΠΎΡΡΡΡ.
- ΠΠΈΡΠΏΠΈΡ Π΄Π»Ρ ΡΠΎΠΊΠΎΠ»Ρ ΠΎΠ±ΡΠ·Π°ΡΠ΅Π»ΡΠ½ΠΎ Π΄ΠΎΠ»ΠΆΠ΅Π½ Π±ΡΡΡ ΡΡΠΎΠΉΠΊΠΈΠΌ ΠΊ ΠΈΠ·Π½ΠΎΡΡ. ΠΠ½ Π½Π΅ Π΄ΠΎΠ»ΠΆΠ΅Π½ Β«Π±ΠΎΡΡΡΡΡΒ» Π°ΡΠΌΠΎΡΡΠ΅ΡΠ½ΡΡ ΠΎΡΠ°Π΄ΠΊΠΎΠ². ΠΡΠΎΠΌΠ΅ ΡΠΎΠ³ΠΎ, ΡΡΠΎΡ ΡΡΡΠΎΠΉΠΌΠ°ΡΠ΅ΡΠΈΠ°Π» Π΄ΠΎΠ»ΠΆΠ΅Π½ Π±ΡΡΡ Π²Π»Π°Π³ΠΎΡΡΠΎΠΉΠΊΠΈΠΌ. Π ΠΈΠ½ΠΎΠΌ ΡΠ»ΡΡΠ°Π΅ ΠΏΡΠΎΡΠ»ΡΠΆΠΈΡ ΠΎΠ½ ΡΠΎΠ²ΡΠ΅ΠΌ Π½Π΅Π΄ΠΎΠ»Π³ΠΎ ΠΈ Π±ΡΡΡΡΠΎ Π½Π°ΡΠ½Π΅Ρ ΡΠ°Π·ΡΡΡΠ°ΡΡΡΡ.
- ΠΠ°Π½Π½ΡΠ΅ ΡΡΡΠΎΠΉΠΌΠ°ΡΠ΅ΡΠΈΠ°Π»Ρ Π½Π΅ Π΄ΠΎΠ»ΠΆΠ½Ρ Π±ΠΎΡΡΡΡΡ Π½ΠΈΠ·ΠΊΠΈΡ ΡΠ΅ΠΆΠΈΠΌΠΎΠ² ΡΠ΅ΠΌΠΏΠ΅ΡΠ°ΡΡΡ ΠΈ ΠΌΠΎΡΠΎΠ·ΠΎΠ². ΠΠΎΠ΄ΠΎΠΏΠΎΠ³Π»ΠΎΡΠ΅Π½ΠΈΠ΅ ΡΠΎΠΊΠΎΠ»ΡΠ½ΠΎΠ³ΠΎ ΠΊΠΈΡΠΏΠΈΡΠ° Π΄ΠΎΠ»ΠΆΠ½ΠΎ Π±ΡΡΡ ΠΏΠΎ ΠΌΠ°ΠΊΡΠΈΠΌΡΠΌΡ Π½ΠΈΠ·ΠΊΠΈΠΌ. ΠΠ½Π°ΡΠ΅ ΡΡΡΠΎΠΉΠΌΠ°ΡΠ΅ΡΠΈΠ°Π» ΠΏΠΎΠΏΡΠΎΡΡΡ ΠΏΠΎΠΉΠ΄Π΅Ρ ΡΡΠ΅ΡΠΈΠ½Π°ΠΌΠΈ ΠΈ Π²ΡΠΉΠ΄Π΅Ρ ΠΈΠ· ΡΡΡΠΎΡ.
- Π‘ΡΡΠΎΠΉΠΌΠ°ΡΠ΅ΡΠΈΠ°Π» Π΄Π»Ρ ΡΠΎΠΊΠΎΠ»Ρ Π΄ΠΎΠ»ΠΆΠ΅Π½ ΠΈΠΌΠ΅ΡΡ ΡΡΠ°Π½Π΄Π°ΡΡΠ½ΡΠ΅ ΡΠ°Π·ΠΌΠ΅ΡΠ½ΡΠ΅ ΠΏΠ°ΡΠ°ΠΌΠ΅ΡΡΡ. ΠΡΠ»ΠΈ ΠΌΠ°ΡΠ΅ΡΠΈΠ°Π» ΠΎΡΠ²Π΅ΡΠ°Π΅Ρ ΡΡΠΎΠΌΡ ΡΡΠ΅Π±ΠΎΠ²Π°Π½ΠΈΡ, ΡΠΎ Π΅Π³ΠΎ ΡΠΊΠ»Π°Π΄ΠΊΠ° ΠΎΠΊΠ°ΠΆΠ΅ΡΡΡ ΠΏΡΠΎΡΡΠΎΠΉ ΠΈ Π±ΡΡΡΡΠΎΠΉ, Ρ Π½Π΅ΠΉ ΡΠΌΠΎΠΆΠ΅Ρ ΡΠΏΡΠ°Π²ΠΈΡΡΡΡ ΠΈ ΠΌΠ°Π»ΠΎΠΎΠΏΡΡΠ½ΡΠΉ Π΄ΠΎΠΌΠ°ΡΠ½ΠΈΠΉ ΠΌΠ°ΡΡΠ΅Ρ.
- ΠΠΈΡΠΏΠΈΡ Π΄Π»Ρ ΡΠΎΠΊΠΎΠ»Ρ ΠΎΠ±ΡΠ·Π°ΡΠ΅Π»ΡΠ½ΠΎ Π΄ΠΎΠ»ΠΆΠ΅Π½ ΠΎΡΠ»ΠΈΡΠ°ΡΡΡΡ Π΄ΠΎΡΡΠ°ΡΠΎΡΠ½ΠΎ Ρ ΠΎΡΠΎΡΠΈΠΌ ΠΈ Π½Π°Π΄Π΅ΠΆΠ½ΡΠΌ ΡΡΠ΅ΠΏΠ»Π΅Π½ΠΈΠ΅ΠΌ Ρ Π²ΡΠ±ΡΠ°Π½Π½ΡΠΌ Π΄Π»Ρ ΡΡΡΠΎΠΈΡΠ΅Π»ΡΠ½ΡΡ ΡΠ°Π±ΠΎΡ ΡΠ°ΡΡΠ²ΠΎΡΠΎΠΌ.
- ΠΡΠΎΠ΄ΡΠΊΡ ΠΎΠ±ΡΠ·Π°ΡΠ΅Π»ΡΠ½ΠΎ Π΄ΠΎΠ»ΠΆΠ΅Π½ Π±ΡΡΡ ΡΠΊΠΎΠ»ΠΎΠ³ΠΈΡΠ΅ΡΠΊΠΈ Π±Π΅Π·ΠΎΠΏΠ°ΡΠ½ΡΠΌ.
ΠΡΠΈΠΌΠ΅Π½Π΅Π½ΠΈΠ΅ ΡΠΎΠΊΡΠΈΡΠ½ΡΡ ΠΈΠ·Π΄Π΅Π»ΠΈΠΉ ΡΡΠ°Π½Π΅Ρ Π½Π΅ ΡΠ°ΠΌΡΠΌ Π»ΡΡΡΠΈΠΌ ΡΠ΅ΡΠ΅Π½ΠΈΠ΅ΠΌ.
- ΠΠ΅Ρ ΡΠΌΡΡΠ»Π° ΠΏΠΎΠΊΡΠΏΠ°ΡΡ ΡΠ΅ΡΠ΅ΡΡΡΡ Π΄ΠΎΡΠΎΠ³ΠΎΠΉ ΠΊΠΈΡΠΏΠΈΡ Π΄Π»Ρ ΡΠΎΠΊΠΎΠ»Ρ. ΠΡΠΎΡ ΡΡΡΠΎΠΉΠΌΠ°ΡΠ΅ΡΠΈΠ°Π» Π΄ΠΎΠ»ΠΆΠ΅Π½ ΠΈΠΌΠ΅ΡΡ Π°Π΄Π΅ΠΊΠ²Π°ΡΠ½ΡΡ ΡΠ΅Π½Ρ.
- ΠΠ°ΠΆΠ΅Π½ ΡΠ°ΠΊΠΆΠ΅ ΠΈ Π²ΠΈΠ΄ ΡΠΎΠΊΠΎΠ»ΡΠ½ΠΎΠ³ΠΎ ΠΊΠΈΡΠΏΠΈΡΠ°. ΠΠ½ Π΄ΠΎΠ»ΠΆΠ΅Π½ Π±ΡΡΡ ΡΡΡΠ΅ΡΠΈΡΠ½ΡΠΌ ΠΈ ΠΏΡΠΈΠ²Π»Π΅ΠΊΠ°ΡΠ΅Π»ΡΠ½ΡΠΌ.
ΠΠ°ΡΠ΅ΠΌ Π½ΡΠΆΠ΅Π½ ΡΠΎΠΊΠΎΠ»Ρ?
ΠΠΈΡΠΏΠΈΡΠ½ΡΠ΅ ΡΠΎΠΊΠΎΠ»ΡΠ½ΡΠ΅ ΠΊΠΎΠ½ΡΡΡΡΠΊΡΠΈΠΈ ΠΈΠ·Π³ΠΎΡΠ°Π²Π»ΠΈΠ²Π°ΡΡ Π΄Π»Ρ ΡΠΎΠ³ΠΎ, ΡΡΠΎΠ±Ρ:
- ΠΎΠ±Π΅ΡΠΏΠ΅ΡΠΈΡΡ ΠΏΠΎΠ»Π½ΠΎΡΠ΅Π½Π½ΡΡ Π·Π°ΡΠΈΡΡ ΡΡΠ΅Π½ΠΎΠ²ΡΡ ΠΎΡΠ½ΠΎΠ²Π°Π½ΠΈΠΉ ΠΎΡ ΠΏΠΎΠΏΠ°Π΄Π°Π½ΠΈΡ Π² ΠΈΡ ΡΡΡΡΠΊΡΡΡΡ Π½ΠΈΠ·ΠΊΠΈΡ ΡΠ΅ΠΌΠΏΠ΅ΡΠ°ΡΡΡ ΠΈ Π³ΡΠ±ΠΈΡΠ΅Π»ΡΠ½ΠΎΠΉ Π²Π»Π°Π³ΠΈ;
- ΡΠΎΡΠΌΠΈΡΠΎΠ²Π°ΡΡ ΠΏΡΠ°Π²ΠΈΠ»ΡΠ½ΡΡ Π³ΠΎΡΠΈΠ·ΠΎΠ½ΡΠ°Π»ΡΠ½ΡΡ ΠΏΠ»ΠΎΡΠΊΠΎΡΡΡ Π΄Π»Ρ ΠΏΠΎΡΠ»Π΅Π΄ΡΡΡΠ΅Π³ΠΎ Π²ΡΠΏΠΎΠ»Π½Π΅Π½ΠΈΡ ΠΊΠ»Π°Π΄ΠΊΠΈ;
- ΡΠ°Π²Π½ΠΎΠΌΠ΅ΡΠ½ΠΎ ΡΠ°ΡΠΏΡΠ΅Π΄Π΅Π»ΡΡΡ Π½Π°Π³ΡΡΠ·ΠΊΠΈ Π½Π° ΡΡΠ½Π΄Π°ΠΌΠ΅Π½ΡΠ½ΡΡ ΠΎΡΠ½ΠΎΠ²Ρ;
- ΠΎΠ±Π΅ΡΠΏΠ΅ΡΠΈΡΡ Π½Π΅ΠΎΠ±Ρ ΠΎΠ΄ΠΈΠΌΡΠΉ ΡΡΠΎΠ²Π΅Π½Ρ ΠΏΠΎΠ»Π° ΡΠ°ΠΌΠΎΠ³ΠΎ Π½ΠΈΠ·ΠΊΠΎΠ³ΠΎ ΡΡΠ°ΠΆΠ°;
- ΡΠ΄Π΅Π»Π°ΡΡ Π±ΠΎΠ»Π΅Π΅ Π²ΡΡΠΎΠΊΠΈΠΌ ΡΠ΅Ρ Π½ΠΈΡΠ΅ΡΠΊΠΎΠ΅ ΠΏΠΎΠ΄ΠΏΠΎΠ»ΡΠ΅;
- ΡΠ΄Π΅Π»Π°ΡΡ Π²ΠΎΠ·Π²Π΅Π΄Π΅Π½ΠΈΠ΅ Π±ΠΎΠ»Π΅Π΅ ΡΡΡΠ΅ΡΠΈΡΠ½ΡΠΌ ΠΈ ΡΠΎΠ»ΠΈΠ΄Π½ΡΠΌ.
ΠΠ· Π²ΡΠ΅Ρ Π²ΡΡΠ΅ΡΠΊΠ°Π·Π°Π½Π½ΡΡ Π·Π°Π΄Π°Ρ ΠΌΠΎΠΆΠ½ΠΎ ΡΠ΄Π΅Π»Π°ΡΡ Π²ΡΠ²ΠΎΠ΄, ΡΡΠΎ Π΄Π»Ρ ΡΡΡΠΎΠΈΡΠ΅Π»ΡΡΡΠ²Π° ΡΠΎΠΊΠΎΠ»Ρ Π½Π΅ΠΎΠ±Ρ ΠΎΠ΄ΠΈΠΌΠΎ ΠΏΠΎΠ΄Π±ΠΈΡΠ°ΡΡ ΡΠΎΠ»ΡΠΊΠΎ Π²ΡΡΠΎΠΊΠΎΠΊΠ°ΡΠ΅ΡΡΠ²Π΅Π½Π½ΡΠΉ ΠΊΠΈΡΠΏΠΈΡ, ΠΊΠΎΡΠΎΡΡΠΉ Π»Π΅Π³ΠΊΠΎ ΠΏΠ΅ΡΠ΅Π½Π΅ΡΠ΅Ρ Π±ΠΎΠ»ΡΡΠΈΠ΅ Π½Π°Π³ΡΡΠ·ΠΊΠΈ.
ΠΠΈΠ΄Ρ
ΠΠ»Ρ ΡΡΡΠΎΠΈΡΠ΅Π»ΡΡΡΠ²Π° ΡΠΎΠΊΠΎΠ»ΡΠ½ΠΎΠΉ ΠΊΠΎΠ½ΡΡΡΡΠΊΡΠΈΠΈ ΠΌΠΎΠΆΠ½ΠΎ ΠΈΡΠΏΠΎΠ»ΡΠ·ΠΎΠ²Π°ΡΡ ΡΠ°Π·Π½ΡΠ΅ Π²ΠΈΠ΄Ρ ΠΊΠΈΡΠΏΠΈΡΠ°. Π Π°ΡΡΠΌΠΎΡΡΠΈΠΌ Ρ Π°ΡΠ°ΠΊΡΠ΅ΡΠΈΡΡΠΈΠΊΠΈ Π½Π°ΠΈΠ±ΠΎΠ»Π΅Π΅ ΠΏΠΎΠΏΡΠ»ΡΡΠ½ΡΡ ΠΈ ΡΠ°ΡΡΠΎ Π²ΡΡΡΠ΅ΡΠ°ΡΡΠΈΡ ΡΡ Π²Π°ΡΠΈΠ°Π½ΡΠΎΠ².
Π‘ΠΈΠ»ΠΈΠΊΠ°ΡΠ½ΡΠΉ
ΠΡΠ΅Π½Ρ ΡΠ°ΡΡΠΎ ΠΏΡΠΈ ΠΊΠΎΠ½ΡΡΡΡΠΈΡΠΎΠ²Π°Π½ΠΈΠΈ ΡΠΎΠΊΠΎΠ»Ρ ΠΏΡΠΈΠΌΠ΅Π½ΡΠ΅ΡΡΡ ΠΈΠΌΠ΅Π½Π½ΠΎ ΡΠΈΠ»ΠΈΠΊΠ°ΡΠ½ΡΠΉ ΠΊΠΈΡΠΏΠΈΡ. ΠΠΎΠ΄ΠΎΠ±Π½ΡΠΉ ΡΡΡΠΎΠΉΠΌΠ°ΡΠ΅ΡΠΈΠ°Π» Ρ
Π°ΡΠ°ΠΊΡΠ΅ΡΠΈΠ·ΡΠ΅ΡΡΡ Π²ΡΡΠΎΠΊΠΎΠΉ ΠΏΡΠΎΡΠ½ΠΎΡΡΡΡ, Π½ΠΎ ΠΏΡΠΈ ΡΡΠΎΠΌ ΠΈΠΌΠ΅Π΅Ρ Π²Π½ΡΡΠΈΡΠ΅Π»ΡΠ½ΡΠΉ Π²Π΅Ρ, ΠΏΠΎΡΡΠΎΠΌΡ ΡΠ°Π±ΠΎΡΠ°ΡΡ Ρ Π½ΠΈΠΌ Π½Π΅ Π²ΡΠ΅Π³Π΄Π° Π±ΡΠ²Π°Π΅Ρ ΡΠ΄ΠΎΠ±Π½ΠΎ. Π£ΡΠΎΠ²Π΅Π½Ρ Π²ΠΎΠ΄ΠΎΠΏΠΎΠ³Π»ΠΎΡΠ΅Π½ΠΈΡ ΡΠΈΠ»ΠΈΠΊΠ°ΡΠ° ΡΠΎΡΡΠ°Π²Π»ΡΠ΅Ρ ΠΏΡΠΈΠΌΠ΅ΡΠ½ΠΎ 8-16%. Π’Π°ΠΊΠΈΠ΅ ΠΈΠ·Π΄Π΅Π»ΠΈΡ ΠΏΡΠΎΠΈΠ·Π²ΠΎΠ΄ΡΡΡΡ Π² ΡΠΎΠΎΡΠ²Π΅ΡΡΡΠ²ΠΈΠΈ Ρ ΡΠ΅Ρ
Π½ΠΎΠ»ΠΎΠ³ΠΈΠ΅ΠΉ ΠΏΡΠ΅ΡΡΠΎΠ²Π°Π½ΠΈΡ ΠΈΠ· ΡΠΏΠ΅ΡΠΈΠ°Π»ΡΠ½ΠΎΠ³ΠΎ ΡΠΎΡΡΠ°Π²Π°, ΠΏΠΎΠ΄Π³ΠΎΡΠΎΠ²Π»Π΅Π½Π½ΠΎΠ³ΠΎ ΠΈΠ· ΠΊΠ²Π°ΡΡΠ΅Π²ΠΎΠ³ΠΎ ΠΏΠ΅ΡΠΊΠ° ΠΈ ΠΈΠ·Π²Π΅ΡΡΠΈ. ΠΠ· ΠΏΠΎΠ΄ΠΎΠ±Π½ΡΡ
ΠΊΠΎΠΌΠΏΠΎΠ½Π΅Π½ΡΠΎΠ² ΠΏΠΎΠ»ΡΡΠ°ΡΡΡΡ ΠΎΡΠ΅Π½Ρ ΠΊΡΠ΅ΠΏΠΊΠΈΠ΅ ΠΈ Π΄ΠΎΠ»Π³ΠΎΠ²Π΅ΡΠ½ΡΠ΅ Π±Π»ΠΎΠΊΠΈ. ΠΠ΄Π½Π°ΠΊΠΎ Π΅ΡΡΡ Ρ Π½ΠΈΡ
ΠΈ ΠΎΠ΄ΠΈΠ½ ΡΠ΅ΡΡΠ΅Π·Π½ΡΠΉ ΠΌΠΈΠ½ΡΡ β ΠΎΠ½ΠΈ ΠΎΡΠ»ΠΈΡΠ°ΡΡΡΡ Π΄ΠΎΡΡΠ°ΡΠΎΡΠ½ΠΎ Π½ΠΈΠ·ΠΊΠΎΠΉ Π²ΠΎΠ΄ΠΎΡΡΠΎΠΉΠΊΠΎΡΡΡΡ.
ΠΠΎ ΡΠ»ΠΎΠ²Π°ΠΌ ΡΠΏΠ΅ΡΠΈΠ°Π»ΠΈΡΡΠΎΠ², Π΄Π»Ρ ΡΡΠ΅Π΄Π½Π΅ΠΉ ΠΏΠΎΠ»ΠΎΡΡ ΡΠΊΠ°Π·Π°Π½Π½ΡΠΉ ΡΡΡΠΎΠΉΠΌΠ°ΡΠ΅ΡΠΈΠ°Π» Π½Π΅ ΠΏΠΎΠ΄ΠΎΠΉΠ΄Π΅Ρ. ΠΠ°ΠΆΠ΅ Π΅ΡΠ»ΠΈ Π² ΠΏΠΎΠ΄ΠΎΠ±Π½ΡΡ ΠΎΠ±ΡΡΠΎΡΡΠ΅Π»ΡΡΡΠ²Π°Ρ ΡΡΠ΅Π½Ρ Π΄ΠΎΠΌΠ° ΠΈΠ·Π³ΠΎΡΠ°Π²Π»ΠΈΠ²Π°ΡΡΡΡ ΠΈΠ· Π½Π°Π΄Π΅ΠΆΠ½ΠΎΠ³ΠΎ ΡΠΈΠ»ΠΈΠΊΠ°ΡΠ½ΠΎΠ³ΠΎ ΠΊΠΈΡΠΏΠΈΡΠ°, ΡΠΎΠΊΠΎΠ»Ρ ΠΎΠ±ΡΡΠ½ΠΎ Π΄Π΅Π»Π°ΡΡ ΠΈΠ· Π±ΠΎΠ»Π΅Π΅ Π²ΠΎΠ΄ΠΎΡΡΠΎΠΉΠΊΠΈΡ ΠΌΠ°ΡΠ΅ΡΠΈΠ°Π»ΠΎΠ².
ΠΠ»ΠΈΠ½ΡΠ½ΡΠΉ
ΠΠ΅ΡΠ΅Π΄ΠΊΠΎ Π² ΡΡΡΠΎΠΈΡΠ΅Π»ΡΡΡΠ²Π΅ ΡΠΎΠΊΠΎΠ»ΡΠ½ΡΡ ΠΊΠΎΠ½ΡΡΡΡΠΊΡΠΈΠΉ ΠΌΠ°ΡΡΠ΅ΡΠ° ΠΎΠ±ΡΠ°ΡΠ°ΡΡΡΡ ΠΊ ΠΏΠΎΠΏΡΠ»ΡΡΠ½ΠΎΠΌΡ Π³Π»ΠΈΠ½ΡΠ½ΠΎΠΌΡ ΠΊΠΈΡΠΏΠΈΡΡ. ΠΡΠΎΡ ΡΡΡΠΎΠΉΠΌΠ°ΡΠ΅ΡΠΈΠ°Π» ΠΏΡΠΎΠΈΠ·Π²ΠΎΠ΄ΠΈΡΡΡ Ρ Π²ΠΎΠ²Π»Π΅ΡΠ΅Π½ΠΈΠ΅ΠΌ ΡΠ΅Ρ Π½ΠΎΠ»ΠΎΠ³ΠΈΠΈ ΡΠ΅ΡΠΌΠΎΠΎΠ±ΡΠ°Π±ΠΎΡΠΊΠΈ, ΡΠΎ Π΅ΡΡΡ Β«Π²ΡΠΏΠ΅ΠΊΠ°Π΅ΡΡΡΒ».
ΠΠ»ΠΈΠ½ΡΠ½ΡΠΉ ΠΊΠΈΡΠΏΠΈΡ Ρ
ΠΎΡΠΎΡ ΡΠ΅ΠΌ, ΡΡΠΎ ΡΠ²Π»ΡΠ΅ΡΡΡ Π±ΠΎΠ»Π΅Π΅ Π²ΠΎΠ΄ΠΎΡΡΠΎΠΉΠΊΠΈΠΌ, ΠΎΡΠΎΠ±Π΅Π½Π½ΠΎ Π΅ΡΠ»ΠΈ ΡΡΠ°Π²Π½ΠΈΠ²Π°ΡΡ Π΅Π³ΠΎ Ρ ΡΠΈΠ»ΠΈΠΊΠ°ΡΠ½ΡΠΌΠΈ ΠΈΠ·Π΄Π΅Π»ΠΈΡΠΌΠΈ. ΠΠΎ Π½Π°Π΄ΠΎ ΡΡΠΈΡΡΠ²Π°ΡΡ, ΡΡΠΎ ΡΠΎΠ²ΡΠ΅ΠΌ Π½Π΅Π²Π°ΠΆΠ½ΠΎ, ΠΏΠΎΠ»Π½ΠΎΡΠ΅Π»ΡΠΉ ΠΈΠ»ΠΈ ΠΏΡΡΡΠΎΡΠ΅Π»ΡΠΉ ΡΡΠΎΡ ΠΌΠ°ΡΠ΅ΡΠΈΠ°Π» β ΠΎΠ±Π° Π²Π°ΡΠΈΠ°Π½ΡΠ° Π±ΡΠ΄ΡΡ Π°ΠΊΡΠΈΠ²Π½ΠΎ Π²ΠΏΠΈΡΡΠ²Π°ΡΡ Π²Π»Π°Π³Ρ Π² ΡΠ²ΠΎΡ ΡΡΡΡΠΊΡΡΡΡ. ΠΡΠΎ ΠΊΠ°ΡΠ΅ΡΡΠ²ΠΎ ΠΎΠΊΠ°Π·ΡΠ²Π°Π΅Ρ Π²Π»ΠΈΡΠ½ΠΈΠ΅ Π½Π° ΠΌΠΎΡΠΎΠ·ΠΎΡΡΠΎΠΉΠΊΠΎΡΡΡ ΠΊΠΈΡΠΏΠΈΡΠ½ΡΡ
ΡΠΎΠΎΡΡΠΆΠ΅Π½ΠΈΠΉ. Π ΡΠ»ΡΡΠ°Π΅ ΠΏΡΠΎΠΌΠ΅ΡΠ·Π°Π½ΠΈΡ Π² ΠΏΠΎΡΠ°Ρ
Π²ΠΎΠ΄Π° Π½Π°ΡΠΈΠ½Π°Π΅Ρ ΡΠ°ΡΡΠΈΡΡΡΡΡΡ, Π° ΠΏΠΎΡΠΎΠΌΡ ΠΈ ΡΡΡΠΈΡΡ ΡΠ°ΠΌ ΠΌΠ°ΡΠ΅ΡΠΈΠ°Π».
ΠΡΠ»ΠΈ Π²Ρ ΠΏΠΎΠ΄Π±ΠΈΡΠ°Π΅ΡΠ΅ Π΄Π»Ρ ΠΈΠ·Π³ΠΎΡΠΎΠ²Π»Π΅Π½ΠΈΡ ΡΠΎΠΊΠΎΠ»Ρ ΠΈΠΌΠ΅Π½Π½ΠΎ Π³Π»ΠΈΠ½ΡΠ½ΡΠ΅ ΠΊΠΈΡΠΏΠΈΡΠΈΠΊΠΈ, ΡΠΎ Π²Π°ΠΌ Π»ΡΡΡΠ΅ ΠΎΠΏΠΈΡΠ°ΡΡΡΡ Π½Π° ΠΈΡ ΠΌΠ°ΡΠΊΡ. Π£ ΠΈΠ·Π΄Π΅Π»ΠΈΠΉ Ρ ΡΠ°Π·Π»ΠΈΡΠ½ΠΎΠΉ ΠΌΠ°ΡΠΊΠΈΡΠΎΠ²ΠΊΠΎΠΉ ΠΈ Ρ Π°ΡΠ°ΠΊΡΠ΅ΡΠΈΡΡΠΈΠΊΠΈ ΡΠ°Π·Π»ΠΈΡΠ°ΡΡΡΡ. Π ΠΏΡΠΈΠΌΠ΅ΡΡ, ΠΎΠ΄Π½ΠΈ ΠΌΠΎΠ΄Π΅Π»ΠΈ Π²ΡΠΏΡΡΠΊΠ°ΡΡΡΡ ΠΌΠΎΡΠΎΠ·ΠΎΡΡΠΎΠΉΠΊΠΈΠΌΠΈ, Π° Π΄ΡΡΠ³ΠΈΠ΅ ΠΊ Π½ΠΈΠ·ΠΊΠΈΠΌ ΡΠ΅ΠΌΠΏΠ΅ΡΠ°ΡΡΡΠ°ΠΌ Π½Π΅ ΠΏΠΎΠ΄Π³ΠΎΡΠΎΠ²Π»Π΅Π½Ρ. Π ΠΏΡΠΈΠΌΠ΅ΡΡ, ΠΊΠΈΡΠΏΠΈΡΠΈ ΠΌΠ°ΡΠΊΠΈ Π150 ΠΌΠΎΠ³ΡΡ Π±Π΅ΡΠΏΡΠΎΠ±Π»Π΅ΠΌΠ½ΠΎ ΠΏΠ΅ΡΠ΅Π½Π΅ΡΡΠΈ Π±ΠΎΠ»Π΅Π΅ 60 ΡΠΈΠΊΠ»ΠΎΠ² Π·Π°ΠΌΠΎΡΠΎΠ·ΠΊΠΈ ΠΈ ΠΎΡΡΠ°ΠΈΠ²Π°Π½ΠΈΡ. Π§Π΅ΠΌ Π²ΡΡΠ΅ Π½ΠΎΠΌΠ΅Ρ ΠΌΠ°ΡΠΊΠΈ, ΡΠ΅ΠΌ Π²ΡΡΠ΅ ΠΈ ΠΌΠΎΡΠΎΠ·ΠΎΡΡΠΎΠΉΠΊΠΎΡΡΡ.
ΠΠ΅ΡΠ°ΠΌΠΈΡΠ΅ΡΠΊΠΈΠΉ ΠΊΠΈΡΠ»ΠΎΡΡΡΠΎΠΉΡΠΈΠ²ΡΠΉ
ΠΡΠ΅ΠΊΡΠ°ΡΠ½ΡΠΌΠΈ ΡΠΊΡΠΏΠ»ΡΠ°ΡΠ°ΡΠΈΠΎΠ½Π½ΡΠΌΠΈ Ρ
Π°ΡΠ°ΠΊΡΠ΅ΡΠΈΡΡΠΈΠΊΠ°ΠΌΠΈ ΠΌΠΎΠΆΠ΅Ρ ΠΏΠΎΡ
Π²Π°ΡΡΠ°ΡΡΡΡ ΠΊΠ΅ΡΠ°ΠΌΠΈΡΠ΅ΡΠΊΠΈΠΉ ΠΊΠΈΡΠ»ΠΎΡΡΡΠΎΠΉΡΠΈΠ²ΡΠΉ ΠΊΠΈΡΠΏΠΈΡ.
- ΡΡΡΠΎΠΉΡΠΈΠ² ΠΊ Π²ΠΎΠ·Π΄Π΅ΠΉΡΡΠ²ΠΈΡ ΡΡΡΠΎΡΡΠΈ ΠΈ Π²Π»Π°Π³ΠΈ;
- Β«Π½Π΅ ΡΡΡΠ°ΡΠΈΡΡΡΒ» ΡΠ΅ΠΌΠΏΠ΅ΡΠ°ΡΡΡΠ½ΡΡ ΠΏΠ΅ΡΠ΅ΠΏΠ°Π΄ΠΎΠ²;
- ΡΠ²Π»ΡΠ΅ΡΡΡ ΠΌΠΎΡΠΎΠ·ΠΎΡΡΡΠΎΠΉΡΠΈΠ²ΡΠΌ;
- ΠΎΡΠ»ΠΈΡΠ°Π΅ΡΡΡ Π΄ΠΎΡΡΠ°ΡΠΎΡΠ½ΠΎ Π½ΠΈΠ·ΠΊΠΈΠΌ Π²ΠΎΠ΄ΠΎΠΏΠΎΠ³Π»ΠΎΡΠ΅Π½ΠΈΠ΅ΠΌ;
- ΠΈΠΌΠ΅Π΅Ρ Ρ ΠΎΡΠΎΡΠΈΠ΅ Π·Π²ΡΠΊΠΎΠΈΠ·ΠΎΠ»ΡΡΠΈΠΎΠ½Π½ΡΠ΅ ΠΊΠ°ΡΠ΅ΡΡΠ²Π°;
- ΠΎΡΠ»ΠΈΡΠ°Π΅ΡΡΡ Π½Π΅ΠΏΠ»ΠΎΡ ΠΎΠΉ ΡΠ΅ΠΏΠ»ΠΎΠΈΠ·ΠΎΠ»ΡΡΠΈΠ΅ΠΉ.
ΠΡΠΎΡ ΡΠ°ΡΠΏΡΠΎΡΡΡΠ°Π½Π΅Π½Π½ΡΠΉ ΡΡΡΠΎΠΈΡΠ΅Π»ΡΠ½ΡΠΉ ΠΌΠ°ΡΠ΅ΡΠΈΠ°Π» Ρ Π°ΡΠ°ΠΊΡΠ΅ΡΠΈΠ·ΡΠ΅ΡΡΡ Π²ΡΡΠΎΠΊΠΎΠΉ ΠΏΠ»ΠΎΡΠ½ΠΎΡΡΡΡ, Π±Π»Π°Π³ΠΎΠ΄Π°ΡΡ ΡΠ΅ΠΌΡ ΠΈΠ· Π½Π΅Π³ΠΎ Π΄ΠΎΠΏΡΡΡΠΈΠΌΠΎ ΡΡΡΠΎΠΈΡΡ Π΄Π°ΠΆΠ΅ ΠΌΠ½ΠΎΠ³ΠΎΡΡΠ°ΠΆΠ½ΡΠ΅ ΠΊΠΎΠ½ΡΡΡΡΠΊΡΠΈΠΈ. ΠΡΠ΅ ΠΎΠ΄Π½ΠΎΠΉ Π²Π°ΠΆΠ½ΠΎΠΉ ΠΎΡΠΎΠ±Π΅Π½Π½ΠΎΡΡΡΡ ΠΊΠ΅ΡΠ°ΠΌΠΈΡΠ΅ΡΠΊΠΎΠ³ΠΎ ΠΊΠΈΡΠΏΠΈΡΠ° ΡΠ²Π»ΡΠ΅ΡΡΡ Π΅Π³ΠΎ ΡΡΡΠΎΠΉΡΠΈΠ²ΠΎΡΡΡ ΠΊ ΠΎΠΏΠ°ΡΠ½ΡΠΌ ΡΡΠ΅Π΄Π°ΠΌ. ΠΡΠΎ ΠΊΠ°ΡΠ΅ΡΡΠ²ΠΎ Π²Π΅ΡΡΠΌΠ° Π°ΠΊΡΡΠ°Π»ΡΠ½ΠΎ Π΄Π»Ρ ΡΠΎΠΊΠΎΠ»Ρ, ΠΏΠΎΡΠΎΠΌΡ ΠΊΠ°ΠΊ ΠΈ Π² ΠΏΠΎΡΠ²Π΅, ΠΈ Π² Π°ΡΠΌΠΎΡΡΠ΅ΡΠ½ΡΡ ΠΎΡΠ°Π΄ΠΊΠ°Ρ ΠΈΠΌΠ΅ΡΡ ΠΌΠ΅ΡΡΠΎ ΡΠ°Π·Π»ΠΈΡΠ½ΡΠ΅ Ρ ΠΈΠΌΠΈΡΠ΅ΡΠΊΠΈ Π°ΠΊΡΠΈΠ²Π½ΡΠ΅ ΠΊΠΎΠΌΠΏΠΎΠ½Π΅Π½ΡΡ.
Π ΡΠΎΡΡΠ°Π²Π΅ ΠΏΠΎΠ΄ΠΎΠ±Π½ΡΡ ΠΈΠ·Π΄Π΅Π»ΠΈΠΉ ΠΏΡΠΈΡΡΡΡΡΠ²ΡΠ΅Ρ ΡΠ°ΠΊΠΎΠΉ Π½Π΅ΠΎΠ±Ρ ΠΎΠ΄ΠΈΠΌΡΠΉ ΠΊΠΎΠΌΠΏΠΎΠ½Π΅Π½Ρ, ΠΊΠ°ΠΊ Π³Π»ΠΈΠ½Π°, Π΄ΠΎΠΏΠΎΠ»Π½Π΅Π½Π½Π°Ρ Π΄ΡΠ½ΠΈΡΠΎΠΌ.
ΠΠ»ΠΈΠ½ΠΊΠ΅ΡΠ½ΡΠΉ
Π‘ΡΠ΅ΠΏΠ΅Π½Ρ Π²ΠΎΠ΄ΠΎΠΏΠΎΠ³Π»ΠΎΡΠ΅Π½ΠΈΡ ΠΊΠ»ΠΈΠ½ΠΊΠ΅ΡΠ½ΠΎΠ³ΠΎ ΠΊΠΈΡΠΏΠΈΡΠ° Π΄ΠΎΡΡΠΈΠ³Π°Π΅Ρ ΠΎΡΠΌΠ΅ΡΠΊΠΈ Π² 3-5%. ΠΠΎΠ΄ΠΎΠ±Π½ΠΎ ΠΏΠΎΠΏΡΠ»ΡΡΠ½ΠΎΠΉ ΠΊΠ»ΠΈΠ½ΠΊΠ΅ΡΠ½ΠΎΠΉ ΠΏΠ»ΠΈΡΠΊΠ΅, ΡΠ°ΠΊΠΎΠΉ ΡΡΡΠΎΠΉΠΌΠ°ΡΠ΅ΡΠΈΠ°Π» Π΄Π΅Π»Π°ΡΡ ΠΈΠ· ΠΎΡΠΎΠ±ΡΡ ΡΠΎΡΡΠΎΠ² Π³Π»ΠΈΠ½Ρ Π² ΡΠΎΠΎΡΠ²Π΅ΡΡΡΠ²ΠΈΠΈ Ρ ΡΠ΅Ρ Π½ΠΎΠ»ΠΎΠ³ΠΈΠ΅ΠΉ Π΅Π΄ΠΈΠ½ΠΈΡΠ½ΠΎΠ³ΠΎ ΠΎΠ±ΠΆΠΈΠ³Π° Π² ΠΎΠ±ΡΡΠ°Π½ΠΎΠ²ΠΊΠ΅ Π²ΡΡΠΎΠΊΠΈΡ ΡΠ΅ΠΌΠΏΠ΅ΡΠ°ΡΡΡ.
ΠΠ΅ΡΡΡΠ°Ρ ΡΠΏΠΎΡΠΎΠ±Π½ΠΎΡΡΡ Ρ ΠΊΠ»ΠΈΠ½ΠΊΠ΅ΡΠ½ΠΎΠ³ΠΎ ΠΊΠΈΡΠΏΠΈΡΠ° Π½Π°ΠΌΠ½ΠΎΠ³ΠΎ Π²ΡΡΠ΅, ΡΠ΅ΠΌ Ρ ΡΡΠ°Π½Π΄Π°ΡΡΠ½ΠΎΠ³ΠΎ ΠΊΡΠ°ΡΠ½ΠΎΠ³ΠΎ ΡΡΡΠΎΠΉΠΌΠ°ΡΠ΅ΡΠΈΠ°Π»Π°. ΠΡΠΎΠΌΠ΅ ΡΠΎΠ³ΠΎ, ΠΎΠ½ ΠΎΡΠ»ΠΈΡΠ°Π΅ΡΡΡ Π½Π΅ΠΏΠ»ΠΎΡ ΠΈΠΌΠΈ Π΄Π΅ΠΊΠΎΡΠ°ΡΠΈΠ²Π½ΡΠΌΠΈ ΠΊΠ°ΡΠ΅ΡΡΠ²Π°ΠΌΠΈ ΠΈ ΡΡΡΠΎΠΉΡΠΈΠ²ΠΎΡΡΡΡ ΠΎΠΊΡΠ°ΡΠ°. ΠΠ½ΠΎΠ³ΠΈΠ΅ ΡΠΈΡΠΌΡ ΠΏΡΠ΅Π΄ΠΎΡΡΠ°Π²Π»ΡΡΡ Π³Π°ΡΠ°Π½ΡΠΈΡ Π½Π° Π΄Π°Π½Π½ΡΡ ΠΏΡΠΎΠ΄ΡΠΊΡΠΈΡ Π΄ΠΎ 100 Π»Π΅Ρ. ΠΠ΄Π½Π°ΠΊΠΎ Π½Π°Π΄ΠΎ ΠΈΠΌΠ΅ΡΡ Π² Π²ΠΈΠ΄Ρ, ΡΡΠΎ ΡΡΠΎΠΈΡ ΠΏΠΎΠ΄ΠΎΠ±Π½Π°Ρ ΠΏΡΠΎΠ΄ΡΠΊΡΠΈΡ Π΄ΠΎΡΠΎΠΆΠ΅ ΠΏΡΠΎΡΠΈΡ Π²Π°ΡΠΈΠ°Π½ΡΠΎΠ².
ΠΡΠΈΡΠ΅ΡΠΈΠΈ Π²ΡΠ±ΠΎΡΠ°

- ΠΠ΄ΠΈΠ½Π°ΠΊΠΎΠ²ΡΠΉ ΡΠ²Π΅Ρ ΠΈ ΡΠΎΡΠΌΠ° ΠΊΠΈΡΠΏΠΈΡΠ΅ΠΉ Π² ΠΏΠ°ΡΡΠΈΠΈ. ΠΠ±ΡΠ·Π°ΡΠ΅Π»ΡΠ½ΠΎ ΠΎΠ±ΡΠ°ΡΠΈΡΠ΅ Π²Π½ΠΈΠΌΠ°Π½ΠΈΠ΅ Π½Π° ΡΡΠΈ ΠΏΠ°ΡΠ°ΠΌΠ΅ΡΡΡ. ΠΡΠ»ΠΈ ΠΎΡΠ΄Π΅Π»ΡΠ½ΡΠ΅ ΠΊΠΈΡΠΏΠΈΡΠΈΠΊΠΈ Π² ΡΠΏΠ°ΠΊΠΎΠ²ΠΊΠ΅ Π±ΡΠ΄ΡΡ ΡΠ°Π·Π»ΠΈΡΠ°ΡΡΡΡ ΠΏΠΎ ΡΠ²ΠΎΠ΅ΠΌΡ ΠΎΡΡΠ΅Π½ΠΊΡ, ΡΠΎ ΡΡΠΎ Π±ΡΠ΄Π΅Ρ ΡΡΠ°Π·Ρ Π±ΡΠΎΡΠ°ΡΡΡΡ Π² Π³Π»Π°Π·Π°. ΠΠΎΠ·Π²Π΅Π΄Π΅Π½ΠΈΠ΅ ΠΈΠ· ΠΏΠΎΠ΄ΠΎΠ±Π½ΡΡ ΠΌΠ°ΡΠ΅ΡΠΈΠ°Π»ΠΎΠ² ΡΡΠ°Π½Π΅Ρ Π²ΡΠ³Π»ΡΠ΄Π΅ΡΡ Π΄ΠΈΡΠ³Π°ΡΠΌΠΎΠ½ΠΈΡΠ½ΠΎ. ΠΡΠ»ΠΈ ΠΆΠ΅ ΠΊΠΈΡΠΏΠΈΡΠΈ Π±ΡΠ΄ΡΡ ΠΎΡΠ»ΠΈΡΠ°ΡΡΡΡ ΠΏΠΎ ΡΠΎΡΠΌΠ΅, ΡΠΎ ΠΏΠΎΡΡΡΠΎΠΈΡΡ ΠΈΠ· Π½ΠΈΡ ΠΏΡΠ°Π²ΠΈΠ»ΡΠ½ΠΎΠ΅ Π²ΠΎΠ·Π²Π΅Π΄Π΅Π½ΠΈΠ΅ Π±ΡΠ΄Π΅Ρ ΠΏΠΎΡΡΠΈ Π½Π΅Π²ΠΎΠ·ΠΌΠΎΠΆΠ½ΠΎ Π»ΠΈΠ±ΠΎ ΠΊΡΠ°ΠΉΠ½Π΅ ΡΡΡΠ΄Π½ΠΎ.
- ΠΠΎΠ²Π΅ΡΡ Π½ΠΎΡΡΡ. ΠΡΠΈΡΠΌΠΎΡΡΠΈΡΠ΅ΡΡ ΠΊ ΠΏΠΎΠ²Π΅ΡΡ Π½ΠΎΡΡΠΈ ΠΏΠΎΠ΄Π±ΠΈΡΠ°Π΅ΠΌΡΡ ΠΊΠΈΡΠΏΠΈΡΠ΅ΠΉ Π΄Π»Ρ ΡΡΡΠΎΠΈΡΠ΅Π»ΡΡΡΠ²Π° ΡΠΎΠΊΠΎΠ»Ρ. ΠΠ½Π° ΠΎΠ±ΡΠ·Π°ΡΠ΅Π»ΡΠ½ΠΎ Π΄ΠΎΠ»ΠΆΠ½Π° Π±ΡΡΡ ΠΈΠ΄Π΅Π°Π»ΡΠ½ΠΎ ΡΠΎΠ²Π½ΠΎΠΉ ΠΈ ΡΠ΅Π»ΠΎΠΉ β Π½Π° Π½Π΅ΠΉ Π½Π΅ Π΄ΠΎΠ»ΠΆΠ½Ρ ΠΏΡΠΎΡΠΌΠ°ΡΡΠΈΠ²Π°ΡΡΡΡ ΡΡΠ΅ΡΠΈΠ½ΠΊΠΈ ΠΈΠ»ΠΈ ΡΠΊΠΎΠ»Ρ. ΠΡΠ»ΠΈ ΡΠ°ΠΊΠΎΠ²ΡΠ΅ Π²ΡΠ΅-ΡΠ°ΠΊΠΈ Π½Π°Π±Π»ΡΠ΄Π°ΡΡΡΡ, ΡΠΎ ΠΎΡ ΠΏΠΎΠΊΡΠΏΠΊΠΈ ΠΏΠΎΠ΄ΠΎΠ±Π½ΡΡ ΠΈΠ·Π΄Π΅Π»ΠΈΠΉ Π»ΡΡΡΠ΅ ΠΎΡΠΊΠ°Π·Π°ΡΡΡΡ β Π²ΠΎΠ·ΠΌΠΎΠΆΠ½ΠΎ, Π΄ΠΎΠ»Π³ΠΎ ΠΎΠ½ΠΈ Π½Π΅ ΠΏΡΠΎΡΠ»ΡΠΆΠ°Ρ ΠΈ Π½Π΅ Π²ΡΠ΄Π΅ΡΠΆΠ°Ρ ΡΠ΅ΡΡΠ΅Π·Π½ΡΡ Π½Π°Π³ΡΡΠ·ΠΎΠΊ ΠΏΠΎΠ΄ Π²Π΅ΡΠΎΠΌ ΡΠΎΠ³ΠΎ ΠΆΠ΅ ΠΊΠΈΡΠΏΠΈΡΠ½ΠΎΠ³ΠΎ Π΄ΠΎΠΌΠ°.
- Π Π°ΡΡΠ²Π΅ΡΠΊΠ°.
ΠΠΎΡΠΌΠΎΡΡΠΈΡΠ΅ Π½Π° ΡΠ²Π΅Ρ ΠΊΠΈΡΠΏΠΈΡΠ΅ΠΉ. ΠΠ½ Π½Π΅ ΡΠΎΠ»ΡΠΊΠΎ Π΄ΠΎΠ»ΠΆΠ΅Π½ Π±ΡΡΡ ΠΎΠ΄ΠΈΠ½Π°ΠΊΠΎΠ²ΡΠΌ Ρ Π²ΡΠ΅Ρ ΠΊΠΈΡΠΏΠΈΡΠΈΠΊΠΎΠ². ΠΠΊΡΠ°Ρ ΡΡΠΈΡ ΡΡΡΠΎΠΉΠΌΠ°ΡΠ΅ΡΠΈΠ°Π»ΠΎΠ² Π΄ΠΎΠ»ΠΆΠ΅Π½ Π±ΡΡΡ Π΄ΠΎΡΡΠ°ΡΠΎΡΠ½ΠΎ ΡΡΠΊΠΈΠΌ ΠΈ ΡΠ°Π²Π½ΠΎΠΌΠ΅ΡΠ½ΡΠΌ. Π’ΡΡΠΊΠ»ΡΡ ΠΈ Π±Π΅Π»Π΅ΡΡΡ ΡΡΠ°ΡΡΠΊΠΎΠ² Π±ΡΡΡ Π½Π΅ Π΄ΠΎΠ»ΠΆΠ½ΠΎ.
- Π‘ΡΠΎΠΈΠΌΠΎΡΡΡ. Π Π°Π·ΡΠΌΠ΅Π΅ΡΡΡ, ΠΊΠ°ΠΆΠ΄ΡΠΉ ΠΏΠΎΡΡΠ΅Π±ΠΈΡΠ΅Π»Ρ ΠΆΠ΅Π»Π°Π΅Ρ ΡΡΠΊΠΎΠ½ΠΎΠΌΠΈΡΡ ΠΈ ΠΊΡΠΏΠΈΡΡ Π½Π΅ ΡΠΎΠ»ΡΠΊΠΎ ΠΊΠ°ΡΠ΅ΡΡΠ²Π΅Π½Π½ΡΠΉ, Π½ΠΎ ΠΈ Π½Π΅Π΄ΠΎΡΠΎΠ³ΠΎΠΉ ΠΊΠΈΡΠΏΠΈΡ. Π’ΡΡ ΡΡΠΎΠΈΡ Π±ΡΡΡ ΠΎΡΡΠΎΡΠΎΠΆΠ½ΡΠΌΠΈ. ΠΠ°ΡΠ΅ΡΠΈΠ°Π»Ρ Ρ ΠΏΠΎΠ΄ΠΎΠ·ΡΠΈΡΠ΅Π»ΡΠ½ΠΎ Π½ΠΈΠ·ΠΊΠΎΠΉ ΡΡΠΎΠΈΠΌΠΎΡΡΡΡ ΠΌΠΎΠ³ΡΡ ΠΎΠΊΠ°Π·Π°ΡΡΡΡ Π½ΠΈΠ·ΠΊΠΎΠΊΠ°ΡΠ΅ΡΡΠ²Π΅Π½Π½ΡΠΌΠΈ ΠΈ Π½Π΅ ΡΠ°ΡΡΡΠΈΡΠ°Π½Π½ΡΠΌΠΈ Π½Π° ΡΠ΅ΡΡΠ΅Π·Π½ΡΠ΅ Π½Π°Π³ΡΡΠ·ΠΊΠΈ.
- Π’ΠΎΡΠ³ΠΎΠ²Π°Ρ ΡΠΎΡΠΊΠ°. ΠΡΠΈΠΎΠ±ΡΠ΅ΡΠ°ΡΡ ΠΊΠΈΡΠΏΠΈΡ Π΄Π»Ρ ΡΠΎΠΎΡΡΠΆΠ΅Π½ΠΈΡ ΡΠΎΠΊΠΎΠ»Ρ Π½Π΅ΠΎΠ±Ρ ΠΎΠ΄ΠΈΠΌΠΎ Π² ΠΏΡΠΎΠ²Π΅ΡΠ΅Π½Π½ΡΡ ΡΠΎΡΠ³ΠΎΠ²ΡΡ ΡΠΎΡΠΊΠ°Ρ , ΠΈΠ·Π²Π΅ΡΡΠ½ΡΡ Π² Π²Π°ΡΠ΅ΠΌ Π³ΠΎΡΠΎΠ΄Π΅. ΠΡ Π±Π°Π·Π°ΡΠ½ΠΎΠΉ ΠΈ Π»Π°Π²ΠΎΡΠ½ΠΎΠΉ ΠΏΡΠΎΠ΄ΡΠΊΡΠΈΠΈ Π»ΡΡΡΠ΅ ΠΎΡΠΊΠ°Π·Π°ΡΡΡΡ β ΠΎΠ½Π° ΡΠ΅Π΄ΠΊΠΎ Π±ΡΠ²Π°Π΅Ρ Π΄Π΅ΠΉΡΡΠ²ΠΈΡΠ΅Π»ΡΠ½ΠΎ ΠΊΠ°ΡΠ΅ΡΡΠ²Π΅Π½Π½ΠΎΠΉ ΠΈ Π½Π°Π΄Π΅ΠΆΠ½ΠΎΠΉ. ΠΠ΅Π»Π°ΡΠ΅Π»ΡΠ½ΠΎ ΠΏΡΠΈ ΠΏΠΎΠΊΡΠΏΠΊΠ΅ Π·Π°ΠΏΡΠΎΡΠΈΡΡ Ρ ΠΏΡΠΎΠ΄Π°Π²ΡΠ° ΡΠ΅ΡΡΠΈΡΠΈΠΊΠ°Ρ ΠΊΠ°ΡΠ΅ΡΡΠ²Π°, Π½Π° ΠΊΠΎΡΠΎΡΠΎΠΌ Π±ΡΠ΄ΡΡ ΡΠΊΠ°Π·Π°Π½Ρ Π²ΡΠ΅ Ρ Π°ΡΠ°ΠΊΡΠ΅ΡΠΈΡΡΠΈΠΊΠΈ ΡΡΡΠΎΠΉΠΌΠ°ΡΠ΅ΡΠΈΠ°Π»Π°. ΠΡΠ»ΠΈ Π² ΠΏΡΠΎΡΡΠ±Π΅ Π²Π°ΠΌ Π±ΡΠ»ΠΎ ΠΎΡΠΊΠ°Π·Π°Π½ΠΎ, ΡΠΎ Π»ΡΡΡΠ΅ Π½Π΅ ΡΠΈΡΠΊΠΎΠ²Π°ΡΡ ΠΈ ΠΎΡΠΏΡΠ°Π²ΠΈΡΡΡΡ Π² Π΄ΡΡΠ³ΠΎΠΉ ΠΌΠ°Π³Π°Π·ΠΈΠ½.
ΠΠ°ΠΊ Π²ΡΠ»ΠΎΠΆΠΈΡΡ ΡΠ²ΠΎΠΈΠΌΠΈ ΡΡΠΊΠ°ΠΌΠΈ?
Π¦ΠΎΠΊΠΎΠ»ΡΠ½ΡΡ ΠΊΠΎΠ½ΡΡΡΡΠΊΡΠΈΡ ΠΈΠ· ΠΊΠΈΡΠΏΠΈΡΠ° Π²ΠΏΠΎΠ»Π½Π΅ Π²ΠΎΠ·ΠΌΠΎΠΆΠ½ΠΎ ΡΠΎΠΎΡΡΠ΄ΠΈΡΡ ΡΠ²ΠΎΠΈΠΌΠΈ ΡΡΠΊΠ°ΠΌΠΈ. ΠΠ»Π°Π²Π½ΠΎΠ΅, ΠΈΡΠΏΠΎΠ»ΡΠ·ΠΎΠ²Π°ΡΡ ΡΠΎΠ»ΡΠΊΠΎ Π²ΡΡΠΎΠΊΠΎΠΊΠ°ΡΠ΅ΡΡΠ²Π΅Π½Π½ΡΠ΅ ΡΡΡΠΎΠΉΠΌΠ°ΡΠ΅ΡΠΈΠ°Π»Ρ ΠΈ ΡΡΠΈΡΡΠ²Π°ΡΡ Π²ΡΠ΅ ΠΎΡΠΎΠ±Π΅Π½Π½ΠΎΡΡΠΈ ΠΏΡΠΎΠ²Π΅Π΄Π΅Π½ΠΈΡ ΠΏΠΎΠ΄ΠΎΠ±Π½ΡΡ
ΡΠ°Π±ΠΎΡ. ΠΠ·Π½Π°ΠΊΠΎΠΌΠΈΠΌΡΡ Ρ Π½ΠΈΠΌΠΈ.
- ΠΠ°ΠΆΠ½ΠΎ ΡΡΠΈΡΡΠ²Π°ΡΡ, ΡΡΠΎ ΡΠΎΠ»ΡΠΈΠ½Π° ΡΠΎΠΊΠΎΠ»ΡΠ½ΠΎΠΉ ΠΊΠΎΠ½ΡΡΡΡΠΊΡΠΈΠΈ Π²ΡΠ΅Π³Π΄Π° Π±ΡΠ΄Π΅Ρ Π·Π°Π²ΠΈΡΠ΅ΡΡ ΠΎΡ ΠΌΠ°ΡΠ΅ΡΠΈΠ°Π»ΠΎΠ², ΠΈΠ· ΠΊΠΎΡΠΎΡΡΡ ΠΈΠ·Π³ΠΎΡΠΎΠ²Π»Π΅Π½ ΡΠ°ΡΠ°Π΄. ΠΡΠ»ΠΈ ΠΎΠ½ ΡΠ΄Π΅Π»Π°Π½ ΠΈΠ· ΠΊΠΈΡΠΏΠΈΡΠ°, ΡΠΎ ΡΠΈΡΠΈΠ½Π° ΡΠΎΠΊΠΎΠ»Ρ Π΄ΠΎΠ»ΠΆΠ½Π° ΡΠΎΡΡΠ°Π²Π»ΡΡΡ Π½Π΅ ΠΌΠ΅Π½Π΅Π΅ 51 ΡΠΌ. ΠΡΠ»ΠΈ ΠΆΠ΅ ΡΠ΅ΡΡ ΠΈΠ΄Π΅Ρ ΠΎ Π±ΡΡΡΠΎΠ²ΠΎΠΌ Π΄ΠΎΠΌΠ΅, ΡΠΎ Π·Π΄Π΅ΡΡ Π²ΠΏΠΎΠ»Π½Π΅ Ρ Π²Π°ΡΠΈΡ ΡΠΎΠΊΠΎΠ»Ρ Π² 25 ΡΠΌ.
- ΠΠ°ΠΊ ΠΏΡΠ°Π²ΠΈΠ»ΠΎ, ΠΊΠ»Π°Π΄ΠΊΡ Π΄Π΅Π»Π°ΡΡ Π² 1,5 Π»ΠΈΠ±ΠΎ 2 ΠΊΠΈΡΠΏΠΈΡΠ° Π² ΡΠΈΡΠΈΠ½Ρ. ΠΠ°ΡΠ°ΠΌΠ΅ΡΡ ΠΎΠ±ΡΠ΅ΠΉ Π²ΡΡΠΎΡΡ ΡΠΎΠΊΠΎΠ»Ρ Π΄ΠΎΠ»ΠΆΠ΅Π½ ΡΠΎΡΡΠ°Π²Π»ΡΡΡ Π½Π΅ ΠΌΠ΅Π½Π΅Π΅ 30 ΡΠΌ.
- Π§ΡΠΎΠ±Ρ ΠΏΠΎΠ»ΠΎΠΆΠΈΡΡ ΠΊΠΈΡΠΏΠΈΡ Π²Π΅ΡΠ½ΠΎ ΠΈ Π½Π°Π΄Π΅ΠΆΠ½ΠΎ, ΡΠΎΠ²Π΅ΡΡΡΡ ΠΏΡΡΠΊΠ°ΡΡ Π² Π΄Π΅Π»ΠΎ ΡΠ°ΡΡΠ²ΠΎΡ ΡΠ΅ΠΌΠ΅Π½ΡΠ° Ρ ΠΌΠ°ΡΠΊΠΎΠΉ Π½Π΅ Π½ΠΈΠΆΠ΅ Π200 Ρ ΠΈΠ·Π²Π΅ΡΡΠΊΠΎΠΉ ΠΈ ΠΏΡΠΎΡΠ΅ΡΠ½Π½ΡΠΌ ΠΏΠ΅ΡΠΊΠΎΠΌ. ΠΡΠΎΠΏΠΎΡΡΠΈΠΈ Π΄ΠΎΠ»ΠΆΠ½Ρ Π±ΡΡΡ ΡΠ°ΠΊΠΈΠΌΠΈ: 1 ΡΠ°ΡΡΡ ΡΠ΅ΠΌΠ΅Π½ΡΠ° ΠΊ 6,7 ΠΏΠ΅ΡΠΊΠ°, Π° ΡΠ°ΠΊΠΆΠ΅ 0,7 Π³Π»ΠΈΠ½Ρ ΠΈΠ»ΠΈ ΠΈΠ·Π²Π΅ΡΡΠΈ.
- ΠΠ°ΠΆΠ½ΠΎ ΡΠ»Π΅Π΄ΠΈΡΡ Π·Π° ΠΊΠΎΠ½ΡΠΈΡΡΠ΅Π½ΡΠΈΠ΅ΠΉ ΡΠΎΡΡΠ°Π²Π°.
ΠΠ½Π° Π΄ΠΎΠ»ΠΆΠ½Π° Π±ΡΡΡ Π³ΡΡΡΠΎΠΉ, ΠΊΠ°ΠΊ ΡΠ΅ΡΡΠΎ. ΠΠ° 1 ΡΠ°ΡΡΡ ΡΠ΅ΠΌΠ΅Π½ΡΠ° ΠΎΠ±ΡΡΠ½ΠΎ Π±Π΅ΡΡΡ ΠΎΠΊΠΎΠ»ΠΎ 0,8 ΡΠ°ΡΡΠΈ Π²ΠΎΠ΄Ρ. ΠΠ°Π±Ρ ΡΠ΅ΡΠ΅ΡΡΡΡ ΠΆΠΈΠ΄ΠΊΠΈΠΉ ΡΠΎΡΡΠ°Π² ΡΠ΄Π΅Π»Π°ΡΡ Π±ΠΎΠ»Π΅Π΅ Π³ΡΡΡΡΠΌ, Π² Π½Π΅Π³ΠΎ Π΄ΠΎΠΏΡΡΡΠΈΠΌΠΎ ΠΏΠΎΠ΄ΠΌΠ΅ΡΠ°ΡΡ Π΅ΡΠ΅ ΠΈΠ·Π²Π΅ΡΡΠΈ ΠΈΠ»ΠΈ Π³Π»ΠΈΠ½Ρ. Π’Π°ΠΊΠΆΠ΅ ΡΠΏΠ΅ΡΠΈΠ°Π»ΠΈΡΡΡ ΡΠΎΠ²Π΅ΡΡΡΡ ΠΏΠΎΠ΄ΠΌΠ΅ΡΠΈΠ²Π°ΡΡ Π½Π΅Π±ΠΎΠ»ΡΡΡΡ ΡΠ°ΡΡΡ ΠΏΠ»Π°ΡΡΠΈΡΠΈΠΊΠ°ΡΠΎΡΠΎΠ² (Π² ΡΠΎΠ»ΠΈ ΡΡΠΈΡ ΠΊΠΎΠΌΠΏΠΎΠ½Π΅Π½ΡΠΎΠ² ΡΠ°Π·ΡΠ΅ΡΠ΅Π½ΠΎ ΠΏΡΠΈΠΌΠ΅Π½ΡΡΡ ΡΡΠΈΡΠ°Π»ΡΠ½ΡΠΉ ΠΏΠΎΡΠΎΡΠΎΠΊ).
- ΠΠ°Π±Ρ ΡΡΡΠ΅ΠΊΡΠΈΠ²Π½ΠΎ Π³ΠΈΠ΄ΡΠΎΠΈΠ·ΠΎΠ»ΠΈΡΠΎΠ²Π°ΡΡ ΡΠΎΠΊΠΎΠ»ΡΠ½ΡΡ ΠΊΠΎΠ½ΡΡΡΡΠΊΡΠΈΡ, ΠΌΠΎΠΆΠ½ΠΎ ΠΏΡΡΠΊΠ°ΡΡ Π² Ρ ΠΎΠ΄ Π»ΠΈΡΡΡ ΡΡΠ±Π΅ΡΠΎΠΈΠ΄Π° Π»ΠΈΠ±ΠΎ ΡΠΎΠ»Ρ. ΠΠΌΠΈ Π½Π°Π΄ΠΎ ΠΎΠ±Π»ΠΎΠΆΠΈΡΡ ΠΎΡΠ½ΠΎΠ²Ρ, ΠΏΠΎΠΊΡΡΡΡΡ Π±ΠΈΡΡΠΌΠ½ΠΎΠΉ ΠΌΠ°ΡΡΠΈΠΊΠΎΠΉ. Π£ΠΊΠ»Π°Π΄ΡΠ²Π°Π΅ΡΡΡ Π³ΠΈΠ΄ΡΠΎΠΈΠ·ΠΎΠ»ΡΡΠΈΡ Π² 2 ΡΠ»ΠΎΡ Ρ Π΄ΠΎΠΏΠΎΠ»Π½Π΅Π½ΠΈΠ΅ΠΌ Π² Π²ΠΈΠ΄Π΅ Π²ΡΠ΅ ΡΠΎΠΉ ΠΆΠ΅ ΠΌΠ°ΡΡΠΈΠΊΠΈ.
- ΠΠΈΡΠΏΠΈΡΠ½ΡΠΉ ΡΠΎΠΊΠΎΠ»Ρ ΠΎΠ±ΡΠ·Π°ΡΠ΅Π»ΡΠ½ΠΎ Π½ΡΠΆΠ½ΠΎ ΠΏΡΠ°Π²ΠΈΠ»ΡΠ½ΠΎ ΡΡΠ΅ΠΏΠ»ΠΈΡΡ ΠΏΠΎΠ΄Ρ ΠΎΠ΄ΡΡΠΈΠΌΠΈ ΠΏΠΎΠΊΡΡΡΠΈΡΠΌΠΈ.
- ΠΠ°Π±Ρ ΡΠ½Π°ΡΡΠΆΠΈ ΡΠΎΠΊΠΎΠ»Ρ Π±ΡΠ» Π½Π°Π΄Π΅ΠΆΠ½ΠΎ Π·Π°ΡΠΈΡΠ΅Π½ ΠΎΡ Π½Π΅Π±Π»Π°Π³ΠΎΠΏΡΠΈΡΡΠ½ΡΡ Π²Π½Π΅ΡΠ½ΠΈΡ ΡΠ°ΠΊΡΠΎΡΠΎΠ² ΠΈ Π°ΡΠΌΠΎΡΡΠ΅ΡΠ½ΡΡ ΠΎΡΠ°Π΄ΠΊΠΎΠ², Π΅Π³ΠΎ ΠΏΠΎΠ½Π°Π΄ΠΎΠ±ΠΈΡΡΡ Π·Π°Π²Π΅ΡΡΠΈΡΡ ΠΊΠ°ΡΠ΅ΡΡΠ²Π΅Π½Π½ΠΎΠΉ ΡΠΈΠ½ΠΈΡΠ½ΠΎΠΉ ΠΎΡΠ΄Π΅Π»ΠΊΠΎΠΉ. ΠΠ½Π° Π½Π΅ ΡΠΎΠ»ΡΠΊΠΎ Π±ΡΠ΄Π΅Ρ ΠΎΠ±Π΅ΡΠ΅Π³Π°ΡΡ ΠΊΠΎΠ½ΡΡΡΡΠΊΡΠΈΡ, Π½ΠΎ ΠΈ ΡΠ΄Π΅Π»Π°Π΅Ρ Π΅Π΅ Π±ΠΎΠ»Π΅Π΅ ΠΏΡΠΈΠ²Π»Π΅ΠΊΠ°ΡΠ΅Π»ΡΠ½ΠΎΠΉ ΠΈ ΡΡΡΠ΅ΡΠΈΡΠ½ΠΎΠΉ.
Π‘ΠΎΠ²Π΅ΡΡ
ΠΠ΅ΡΠ΅Π΄ Π½Π°ΡΠ°Π»ΠΎΠΌ ΡΡΡΠΎΠΈΡΠ΅Π»ΡΠ½ΡΡ
ΡΠ°Π±ΠΎΡ ΠΎΠ±ΡΠ·Π°ΡΠ΅Π»ΡΠ½ΠΎ Π½ΡΠΆΠ½ΠΎ ΡΠ±Π΅Π΄ΠΈΡΡΡΡ Π² Π³ΠΎΡΠΈΠ·ΠΎΠ½ΡΠ°Π»ΡΠ½ΠΎΡΡΠΈ ΡΡΠ½Π΄Π°ΠΌΠ΅Π½ΡΠ½ΠΎΠΉ ΠΎΡΠ½ΠΎΠ²Ρ. ΠΡΠΈΡΠ΅ΠΌ ΡΠΎΠ²ΡΠ΅ΠΌ Π½Π΅Π²Π°ΠΆΠ½ΠΎ, ΠΊΠ°ΠΊΠΎΠΉ ΡΡΠ½Π΄Π°ΠΌΠ΅Π½Ρ ΡΠΎΠΎΡΡΠΆΠ΅Π½ Π½Π° ΡΡΠ°ΡΡΠΊΠ΅ β Π»Π΅Π½ΡΠΎΡΠ½ΡΠΉ, ΡΡΠΎΠ»Π±ΡΠ°ΡΡΠΉ ΠΈΠ»ΠΈ Π»ΡΠ±ΠΎΠΉ Π΄ΡΡΠ³ΠΎΠΉ. Π Π΅Π³ΠΎ Π²Π΅ΡΠ½ΠΎΠΌ ΠΈΡΠΏΠΎΠ»Π½Π΅Π½ΠΈΠΈ ΠΏΠΎΠ½Π°Π΄ΠΎΠ±ΠΈΡΡΡ ΡΠ±Π΅Π΄ΠΈΡΡΡΡ Π² Π»ΡΠ±ΠΎΠΌ ΡΠ»ΡΡΠ°Π΅.
ΠΡΠ»ΠΈ Π΄Π»Ρ ΡΠΎΠΎΡΡΠΆΠ΅Π½ΠΈΡ ΡΠΎΠΊΠΎΠ»Ρ Π²Ρ Π²ΡΠ±ΡΠ°Π»ΠΈ ΡΠΈΠ»ΠΈΠΊΠ°ΡΠ½ΡΠΉ ΠΊΠΈΡΠΏΠΈΡ, ΡΠΎ Π²Π°ΠΌ ΡΠ»Π΅Π΄ΡΠ΅Ρ ΠΏΠΎΠΌΠ½ΠΈΡΡ ΠΎ ΡΠΎΠΌ, ΡΡΠΎ ΠΎΠ½ Ρ ΠΎΡΡ ΠΈ ΠΎΡΠ΅Π½Ρ ΠΏΡΠΎΡΠ½ΡΠΉ, Π½ΠΎ Π±ΡΡΡΡΠΎ Π²ΠΏΠΈΡΡΠ²Π°Π΅Ρ ΠΆΠΈΠ΄ΠΊΠΎΡΡΡ, ΠΏΠΎΡΠ»Π΅ ΡΠ΅Π³ΠΎ Π½Π°Π±ΡΡ Π°Π΅Ρ ΠΈ ΡΡΡΠ°ΡΠΈΠ²Π°Π΅Ρ ΡΠ²ΠΎΠΈ ΠΏΡΠΎΡΠ½ΠΎΡΡΠ½ΡΠ΅ ΠΊΠ°ΡΠ΅ΡΡΠ²Π°. Π ΡΡΠΎΠΌΡ ΡΡΡΠΎΠΉΠΌΠ°ΡΠ΅ΡΠΈΠ°Π»Ρ ΡΠ΅ΠΊΠΎΠΌΠ΅Π½Π΄ΡΡΡ ΠΎΠ±ΡΠ°ΡΠ°ΡΡΡΡ ΡΠΎΠ»ΡΠΊΠΎ Π² ΡΠΎΠΌ ΡΠ»ΡΡΠ°Π΅, Π΅ΡΠ»ΠΈ Π²Ρ ΠΏΡΠΎΠΆΠΈΠ²Π°Π΅ΡΠ΅ Π² ΡΠ΅Π³ΠΈΠΎΠ½Π΅ Ρ Π΄ΠΎΡΡΠ°ΡΠΎΡΠ½ΠΎ ΡΡΡ ΠΈΠΌ ΠΊΠ»ΠΈΠΌΠ°ΡΠΎΠΌ. ΠΡΠΈ ΡΡΠΎΠΌ ΠΏΠΎΠ½Π°Π΄ΠΎΠ±ΠΈΡΡΡ ΠΏΠΎΠ·Π°Π±ΠΎΡΠΈΡΡΡΡ ΠΎ Ρ ΠΎΡΠΎΡΠ΅ΠΉ Π³ΠΈΠ΄ΡΠΎΠΈΠ·ΠΎΠ»ΡΡΠΈΠΈ ΡΠΎΠΊΠΎΠ»ΡΠ½ΠΎΠΉ ΠΊΠΎΠ½ΡΡΡΡΠΊΡΠΈΠΈ.
ΠΡΠ»ΠΈ Π²Ρ ΡΠ°ΠΊ ΠΈ Π½Π΅ ΡΠΌΠΎΠ³Π»ΠΈ ΠΏΠΎΠ΄ΠΎΠ±ΡΠ°ΡΡ ΠΈΠ΄Π΅Π°Π»ΡΠ½ΡΠΉ ΠΊΠΈΡΠΏΠΈΡ Π΄Π»Ρ ΠΎΡΠ³Π°Π½ΠΈΠ·Π°ΡΠΈΠΈ ΡΠΎΠΊΠΎΠ»Ρ, ΡΠΎ Π΅Π³ΠΎ ΠΌΠΎΠΆΠ½ΠΎ ΡΠΎΠΎΡΡΠ΄ΠΈΡΡ ΠΈΠ· Π±Π΅ΡΠΎΠ½Π°.
ΠΡΠ΅ΠΆΠ΄Π΅ ΡΠ΅ΠΌ ΠΏΠ΅ΡΠ΅Ρ
ΠΎΠ΄ΠΈΡΡ Π½Π΅ΠΏΠΎΡΡΠ΅Π΄ΡΡΠ²Π΅Π½Π½ΠΎ ΠΊ ΠΌΠΎΠ½ΡΠ°ΠΆΠ½ΡΠΌ ΡΠ°Π±ΠΎΡΠ°ΠΌ, ΡΠ»Π΅Π΄ΡΠ΅Ρ ΡΠ°ΡΡΡΠΈΡΠ°ΡΡ, Π² ΠΊΠ°ΠΊΠΎΠΌ ΠΎΠ±ΡΠ΅ΠΌΠ΅ Π²Π°ΠΌ Π½ΡΠΆΠ½ΠΎ ΠΊΡΠΏΠΈΡΡ ΡΡΡΠΎΠΉΠΌΠ°ΡΠ΅ΡΠΈΠ°Π». ΠΠ»Ρ ΡΡΠΎΠ³ΠΎ Π΄ΠΎΠΏΡΡΡΠΈΠΌΠΎ ΠΈΡΠΏΠΎΠ»ΡΠ·ΠΎΠ²Π°ΡΡ ΠΎΠ½Π»Π°ΠΉΠ½-ΠΊΠ°Π»ΡΠΊΡΠ»ΡΡΠΎΡΡ ΠΈ ΡΠ΅ΡΠ²ΠΈΡΡ Π½Π° ΡΡΡΠΎΠΈΡΠ΅Π»ΡΠ½ΡΡ
ΠΏΠΎΡΡΠ°Π»Π°Ρ
Π»ΠΈΠ±ΠΎ ΠΏΠΎΠΏΡΡΠ°ΡΡΡΡ ΡΠ΄Π΅Π»Π°ΡΡ Π²ΡΠ΅ ΡΠ°ΡΡΠ΅ΡΡ ΡΠ°ΠΌΠΎΡΡΠΎΡΡΠ΅Π»ΡΠ½ΠΎ. ΠΠΎΠ½Π΅ΡΠ½ΠΎ, Π² Π±ΠΎΠ»ΡΡΠΈΠ½ΡΡΠ²Π΅ ΡΠ»ΡΡΠ°Π΅Π² Π»ΡΠ΄ΠΈ ΠΎΠ±ΡΠ°ΡΠ°ΡΡΡΡ ΠΊ ΠΏΠ΅ΡΠ²ΠΎΠΌΡ ΡΠΏΠΎΡΠΎΠ±Ρ, ΠΏΠΎΡΠΊΠΎΠ»ΡΠΊΡ ΡΠ°ΠΌ ΠΎΡΠΈΠ±ΠΈΡΡΡΡ Π½Π°ΠΌΠ½ΠΎΠ³ΠΎ ΡΡΡΠ΄Π½Π΅Π΅.
Π‘ΠΏΠ΅ΡΠΈΠ°Π»ΠΈΡΡΡ Π½Π°ΡΡΠΎΡΡΠ΅Π»ΡΠ½ΠΎ ΡΠ΅ΠΊΠΎΠΌΠ΅Π½Π΄ΡΡΡ ΠΏΡΠΈΠΎΠ±ΡΠ΅ΡΠ°ΡΡ ΠΊΠΈΡΠΏΠΈΡ Π΄Π»Ρ ΡΠΎΠΊΠΎΠ»Ρ Ρ Π½Π΅Π±ΠΎΠ»ΡΡΠΈΠΌ Π·Π°ΠΏΠ°ΡΠΎΠΌ, ΡΡΠΈΡΡΠ²Π°Ρ Π²ΠΎΠ·ΠΌΠΎΠΆΠ½ΠΎΡΡΡ ΡΡΠΎΠ»ΠΊΠ½ΠΎΠ²Π΅Π½ΠΈΡ Ρ Π±ΡΠ°ΠΊΠΎΠ²Π°Π½Π½ΡΠΌΠΈ Π΄Π΅ΡΠ°Π»ΡΠΌΠΈ ΠΈΠ»ΠΈ ΠΏΠΎΠ²ΡΠ΅ΠΆΠ΄Π΅Π½ΠΈΡΠΌΠΈ Π² ΠΏΡΠΎΡΠ΅ΡΡΠ΅ ΡΡΠ°Π½ΡΠΏΠΎΡΡΠΈΡΠΎΠ²ΠΊΠΈ.
Π¦ΠΎΠΊΠΎΠ»ΡΠ½ΡΠΉ ΠΊΠΈΡΠΏΠΈΡ Π·Π°ΡΠ°ΡΡΡΡ Π΄ΠΎΠΏΠΎΠ»Π½ΡΡΡ ΡΠ°Π·Π½ΠΎΠ³ΠΎ ΡΠΎΠ΄Π° ΠΎΠ±Π»ΠΈΡΠΎΠ²ΠΎΡΠ½ΡΠΌΠΈ ΠΌΠ°ΡΠ΅ΡΠΈΠ°Π»Π°ΠΌΠΈ. ΠΡΠΎΠ±Π΅Π½Π½ΠΎ ΠΏΠΎΠΏΡΠ»ΡΡΠ½Π° ΡΠ΅Π³ΠΎΠ΄Π½Ρ ΠΊΡΠ°ΡΠΈΠ²Π°Ρ ΠΊΠ°ΠΌΠ΅Π½Π½Π°Ρ ΠΊΠ»Π°Π΄ΠΊΠ°. ΠΠ½Π° ΡΠΌΠΎΡΡΠΈΡΡΡ Π³Π°ΡΠΌΠΎΠ½ΠΈΡΠ½ΠΎ Ρ Π±ΠΎΠ»ΡΡΠΈΠ½ΡΡΠ²ΠΎΠΌ ΡΡΡΠ΅ΡΡΠ²ΡΡΡΠΈΡ ΡΠ°ΡΠ°Π΄ΠΎΠ² ΡΠ°Π·Π½ΡΡ ΠΎΡΡΠ΅Π½ΠΊΠΎΠ². ΠΠ»Π°Π³ΠΎΠ΄Π°ΡΡ ΠΏΠΎΠ΄ΠΎΠ±Π½ΠΎΠΌΡ Π΄ΠΎΠΏΠΎΠ»Π½Π΅Π½ΠΈΡ ΠΆΠΈΠ»ΠΈΡΠ΅ Π±ΡΠ΄Π΅Ρ Π²ΡΠ³Π»ΡΠ΄Π΅ΡΡ Π½Π°ΠΌΠ½ΠΎΠ³ΠΎ ΠΈΠ½ΡΠ΅ΡΠ΅ΡΠ½Π΅Π΅.
Π Π°ΡΡΠ²ΠΎΡ Π΄Π»Ρ ΠΊΠ»Π°Π΄ΠΊΠΈ ΠΌΠΎΠΆΠ½ΠΎ ΠΊΡΠΏΠΈΡΡ Π½Π΅ ΡΠΎΠ»ΡΠΊΠΎ Π² Π³ΠΎΡΠΎΠ²ΠΎΠΌ ΡΠΎΡΡΠΎΡΠ½ΠΈΠΈ, Π½ΠΎ ΠΈ Π·Π°Π³ΠΎΡΠΎΠ²ΠΈΡΡ ΡΠ°ΠΌΠΎΡΡΠΎΡΡΠ΅Π»ΡΠ½ΠΎ. ΠΠ»Ρ ΡΡΠΎΠ³ΠΎ Π±Π΅ΡΠ΅ΡΡΡ ΡΠ΅ΠΌΠ΅Π½Ρ ΠΈ ΠΏΠ΅ΡΠΎΠΊ Π² ΡΠΎΠΎΡΠ½ΠΎΡΠ΅Π½ΠΈΠΈ 1 ΠΊ 3.
ΠΠ±ΡΡΡΡΠ°ΠΈΠ²Π°Ρ ΡΠΎΠΊΠΎΠ»ΡΠ½ΡΡ ΠΊΠΎΠ½ΡΡΡΡΠΊΡΠΈΡ ΠΈΠ· ΠΊΠΈΡΠΏΠΈΡΠ°, ΡΠ»Π΅Π΄ΡΠ΅Ρ ΡΠΊΠ»Π°Π΄ΡΠ²Π°ΡΡ ΡΠ°ΡΡΠ²ΠΎΡ Π² ΡΠΎΠ»ΡΠΈΠ½Ρ Π½Π΅ Π±ΠΎΠ»ΡΡΠ΅ 1 ΡΠΌ. Π‘ΠΎΠ±Π»ΡΠ΄Π°ΡΡ ΡΡΠΎ ΠΏΡΠ°Π²ΠΈΠ»ΠΎ ΠΎΡΠΎΠ±Π΅Π½Π½ΠΎ Π²Π°ΠΆΠ½ΠΎ, Π΅ΡΠ»ΠΈ ΡΡΠ½Π΄Π°ΠΌΠ΅Π½Ρ ΡΡΡΠΎΠ΅Π½ΠΈΡ ΠΈΠ·Π³ΠΎΡΠΎΠ²Π»Π΅Π½ ΠΈΠ· ΠΆΠ΅Π»Π΅Π·ΠΎΠ±Π΅ΡΠΎΠ½Π½ΡΡ Π±Π»ΠΎΠΊΠΎΠ².
ΠΠ½ΠΎΠ³ΠΈΠ΅ ΠΏΠΎΠ»ΡΠ·ΠΎΠ²Π°ΡΠ΅Π»ΠΈ ΠΈΠ½ΡΠ΅ΡΠ΅ΡΡΡΡΡΡ, Π΄ΠΎΠΏΡΡΡΠΈΠΌΠΎ Π»ΠΈ Π΄Π»Ρ ΠΎΡΠ³Π°Π½ΠΈΠ·Π°ΡΠΈΠΈ ΡΠΎΠΊΠΎΠ»Ρ ΠΈΡΠΏΠΎΠ»ΡΠ·ΠΎΠ²Π°ΡΡ ΠΊΠΈΡΠΏΠΈΡ, ΠΊΠΎΡΠΎΡΡΠΉ Π½Π΅ ΠΏΡΠΎΡ
ΠΎΠ΄ΠΈΠ» ΠΎΠ±ΠΆΠΈΠ³ Π² ΠΏΡΠΎΡΠ΅ΡΡΠ΅ ΠΈΠ·Π³ΠΎΡΠΎΠ²Π»Π΅Π½ΠΈΡ. ΠΠ°, ΠΏΡΠΈΠΌΠ΅Π½Π΅Π½ΠΈΠ΅ ΠΏΠΎΠ΄ΠΎΠ±Π½ΠΎΠ³ΠΎ ΡΡΡΠΎΠΉΠΌΠ°ΡΠ΅ΡΠΈΠ°Π»Π° ΡΠ°Π·ΡΠ΅ΡΠ°Π΅ΡΡΡ, Π½ΠΎ ΡΠΏΠ΅ΡΠΈΠ°Π»ΠΈΡΡΡ ΡΠΎΠ²Π΅ΡΡΡΡ ΠΎΡΠ΄Π°Π²Π°ΡΡ ΠΏΡΠ΅Π΄ΠΏΠΎΡΡΠ΅Π½ΠΈΠ΅ Π±Π»ΠΎΠΊΠ°ΠΌ, ΠΊΠΎΡΠΎΡΡΠ΅ Π²ΡΠ΅-ΡΠ°ΠΊΠΈ Π΄Π°Π½Π½ΡΡ ΠΏΡΠΎΡΠ΅Π΄ΡΡΡ ΠΏΠ΅ΡΠ΅Π½Π΅ΡΠ»ΠΈ. Π ΠΏΡΠΈΠΌΠ΅Π½Π΅Π½ΠΈΡ Π½Π΅ΠΎΠ±ΠΎΠΆΠΆΠ΅Π½Π½ΡΡ
ΠΊΠΈΡΠΏΠΈΡΠ΅ΠΉ ΡΠ΅ΠΊΠΎΠΌΠ΅Π½Π΄ΡΠ΅ΡΡΡ ΠΎΠ±ΡΠ°ΡΠ°ΡΡΡΡ ΡΠΎΠ»ΡΠΊΠΎ Π² ΡΠΎΠΌ ΡΠ»ΡΡΠ°Π΅, Π΅ΡΠ»ΠΈ Π½Π΅Ρ Π²ΠΎΠ·ΠΌΠΎΠΆΠ½ΠΎΡΡΠΈ Π·Π°ΠΊΡΠΏΠΈΡΡΡΡ ΠΈΠ½ΡΠΌΠΈ ΠΌΠ°ΡΠ΅ΡΠΈΠ°Π»Π°ΠΌΠΈ.
ΠΠ΅ Π·Π°Π±ΡΠ²Π°ΠΉΡΠ΅ ΠΎΠ± ΡΡΠ΅ΠΏΠ»Π΅Π½ΠΈΠΈ ΡΠΎΠΊΠΎΠ»Ρ, Π΅ΡΠ»ΠΈ Π²ΠΎΠ·Π²ΠΎΠ΄ΠΈΡΠ΅ ΠΆΠΈΠ»ΠΎΠ΅ ΡΡΡΠΎΠ΅Π½ΠΈΠ΅. Π’Π°ΠΊΠΆΠ΅ Π½Π°Π΄ΠΎ ΡΡΠ΅ΡΡΡ, ΡΡΠΎ ΡΠ°Π·Π»ΠΈΡΠ°ΡΡ ΡΡΠΈ ΡΠ°Π·Π½ΠΎΠ²ΠΈΠ΄Π½ΠΎΡΡΠΈ ΡΠΎΠΊΠΎΠ»ΡΠ½ΡΡ ΠΊΠΎΠ½ΡΡΡΡΠΊΡΠΈΠΉ β Π²Ρ ΠΎΠ΄ΡΡΡΡ, Π²ΡΡΡΠΊ Ρ Π²Π½Π΅ΡΠ½ΠΈΠΌΠΈ ΡΡΠ΅Π½Π°ΠΌΠΈ ΠΈ ΡΡΠΎΠΏΠ»Π΅Π½Π½ΡΡ. ΠΠΎΡΠ»Π΅Π΄Π½ΡΡ Π²ΡΠ΅Π³Π΄Π° ΡΠΎΠΎΡΡΠΆΠ°Π΅ΡΡΡ Π΄Π»Ρ ΠΆΠΈΠ»ΡΡ Π΄ΠΎΠΌΠΎΠ² Π½Π° Π³Π»ΡΠ±ΠΈΠ½Π΅ Π² 6 ΡΠΌ Π½ΠΈΠΆΠ΅ Π½Π°ΡΡΠΆΠ½ΡΡ ΡΡΠ΅Π½ΠΎΠ²ΡΡ ΠΎΡΠ½ΠΎΠ²Π°Π½ΠΈΠΉ.
Π ΡΠΎΠΌ, ΠΊΠ°ΠΊ Π²ΡΠ±ΡΠ°ΡΡ ΠΈ Π²ΡΠ»ΠΎΠΆΠΈΡΡ ΡΠΎΠΊΠΎΠ»ΡΠ½ΡΠΉ ΠΊΠΈΡΠΏΠΈΡ, ΡΠΌΠΎΡΡΠΈΡΠ΅ Π² ΡΠ»Π΅Π΄ΡΡΡΠ΅ΠΌ Π²ΠΈΠ΄Π΅ΠΎ.
ΠΠ°ΠΊΠΎΠΉ ΠΊΠΈΡΠΏΠΈΡ ΠΌΠΎΠΆΠ½ΠΎ ΠΈΡΠΏΠΎΠ»ΡΠ·ΠΎΠ²Π°ΡΡ Π΄Π»Ρ ΡΠΎΠΊΠΎΠ»Ρ Π΄ΠΎΠΌΠ°
ΠΡΠ»ΠΈ Π²Ρ ΡΠ΅ΡΠΈΠ»ΠΈ ΡΠ²ΠΎΠΈΠΌΠΈ ΡΡΠΊΠ°ΠΌΠΈ ΠΏΠΎΡΡΡΠΎΠΈΡΡ ΠΊΠΈΡΠΏΠΈΡΠ½ΡΠΉ Π³Π°ΡΠ°ΠΆ, ΡΠ°ΡΠ°ΠΉ ΠΈΠ»ΠΈ Π΄ΠΎΠΌ, ΡΠΎ Π½ΡΠΆΠ½ΠΎ ΡΠ·Π½Π°ΡΡ ΠΊΠ°ΠΊΠΎΠΉ ΠΊΠΈΡΠΏΠΈΡ ΠΌΠΎΠΆΠ½ΠΎ ΠΈΡΠΏΠΎΠ»ΡΠ·ΠΎΠ²Π°ΡΡ Π΄Π»Ρ ΡΠΎΠΊΠΎΠ»Ρ.
ΠΠ°ΠΊΠΎΠ΅ Π±Ρ Π·Π΄Π°Π½ΠΈΠ΅ Π²Ρ Π½ΠΈ ΡΡΡΠΎΠΈΠ»ΠΈ, ΠΎΡΠΎΠ±ΠΎΠ΅ Π²Π½ΠΈΠΌΠ°Π½ΠΈΠ΅ Π½ΡΠΆΠ½ΠΎ ΡΠ΄Π΅Π»ΠΈΡΡ ΡΠΎΠΊΠΎΠ»Ρ. ΠΠΎΡΠΊΠΎΠ»ΡΠΊΡ ΡΠΎΠΊΠΎΠ»Ρ β ΡΡΠΎ ΡΠΎΡ ΠΆΠ΅ ΡΡΠ½Π΄Π°ΠΌΠ΅Π½Ρ, Π΄Π»Ρ Π²ΠΎΠ·Π²Π΅Π΄Π΅Π½ΠΈΡ Π½Π΅ΡΡΡΠΈΡ ΡΡΠ΅Π½.
ΠΠ³ΠΎ ΡΠ΅Π»Ρ Π·Π°ΡΠΈΡΠΈΡΡ ΠΏΠΎΠΌΠ΅ΡΠ΅Π½ΠΈΠ΅ ΡΠ½Π°ΡΡΠΆΠΈ ΠΎΡ Ρ ΠΎΠ»ΠΎΠ΄Π½ΠΎΠ³ΠΎ Π²ΠΎΠ·Π΄ΡΡ Π° ΠΈ Π²ΠΎΠ΄Ρ. ΠΠΎΡΡΠΎΠΌΡΒ ΡΡΠΎΠ±Ρ ΠΌΠΈΠ½ΠΈΠΌΠΈΠ·ΠΈΡΠΎΠ²Π°ΡΡ ΠΏΡΠΎΠ±Π»Π΅ΠΌΡ ΠΏΡΠΈ ΡΠΊΡΠΏΠ»ΡΠ°ΡΠ°ΡΠΈΠΈ ΠΏΠΎΡΡΡΠΎΠΉΠΊΠΈ Π½Π΅ΠΎΠ±Ρ ΠΎΠ΄ΠΈΠΌΠΎ ΡΡΠ°ΡΠ΅Π»ΡΠ½ΠΎ Π²ΡΠ±ΡΠ°ΡΡ ΠΊΠΈΡΠΏΠΈΡ Π΄Π»Ρ ΠΎΡΠ½ΠΎΠ²Ρ Π±ΡΠ΄ΡΡΠ΅Π³ΠΎ Π·Π΄Π°Π½ΠΈΡ.
ΠΠ°ΠΊΠΎΠΉ ΠΊΠΈΡΠΏΠΈΡ ΠΈΡΠΏΠΎΠ»ΡΠ·ΠΎΠ²Π°ΡΡ Π΄Π»Ρ ΡΠΎΠΊΠΎΠ»Ρ
Π‘ΡΡΠΎΠ²ΡΠΉ ΠΊΠ»ΠΈΠΌΠ°Ρ, ΠΎΠΊΡΡΠΆΠ°ΡΡΠ°Ρ ΡΡΠ΅Π΄Π° ΠΏΠΎΡΡΠΎΡΠ½Π½ΠΎ Π²ΠΎΠ·Π΄Π΅ΠΉΡΡΠ²ΡΡΡ Π½Π° ΠΊΠΈΡΠΏΠΈΡΠΈ ΡΠΎΠΊΠΎΠ»Ρ. ΠΠ»Π°Π³Π° ΠΎΠΊΠ°Π·ΡΠ²Π°Π΅Ρ Π½Π΅Π³Π°ΡΠΈΠ²Π½ΠΎΠ΅ Π΄Π΅ΠΉΡΡΠ²ΠΈΠ΅ Π½Π΅ ΡΠΎΠ»ΡΠΊΠΎ Π² Π²ΠΈΠ΄Π΅ ΡΠ°Π»ΠΎΠΉ Π²ΠΎΠ΄Ρ ΠΈΠ»ΠΈ Π΄ΠΎΠΆΠ΄Ρ, Π½ΠΎ ΠΈ ΠΏΠΎΠ΄Π½ΠΈΠΌΠ°Π΅ΡΡΡ ΠΏΠΎ ΠΊΠ°ΠΏΠΈΠ»Π»ΡΡΠ°ΠΌ ΠΊ ΠΎΡΠ½ΠΎΠ²Π°Π½ΠΈΡ ΡΡΠ΅Π½Ρ. ΠΠΈΠΌΠΎΠΉ Π½Π° ΠΏΡΠΎΡΠ΅ΡΡ Π·Π°ΠΌΠ΅ΡΠ·Π°Π½ΠΈΡ, ΡΠ°ΡΡΠΈΡΠ΅Π½ΠΈΡ ΠΈ Π΄Π°Π»ΡΠ½Π΅ΠΉΡΠ΅Π΅ ΡΠ°Π·ΡΡΡΠ΅Π½ΠΈΠ΅, Π±ΡΠ΄Π΅Ρ Π²Π»ΠΈΡΡΡ Π½Π΅Π±ΠΎΠ»ΡΡΠΎΠ΅ ΠΊΠΎΠ»ΠΈΡΠ΅ΡΡΠ²ΠΎ Π²ΠΎΠ΄Ρ, Π½Π°ΠΊΠΎΠΏΠ»Π΅Π½Π½ΠΎΠ΅ Π²Π½ΡΡΡΠΈ ΡΡΡΡΠΊΡΡΡΡ ΠΌΠ°ΡΠ΅ΡΠΈΠ°Π»Π°.
Π§ΡΠΎΠ±Ρ ΡΠ²Π΅ΡΡΠΈ ΠΊ ΠΌΠΈΠ½ΠΈΠΌΡΠΌΡ Π²Π½ΡΡΡΠ΅Π½Π½Π΅Π΅ ΠΏΡΠΎΠ½ΠΈΠΊΠ½ΠΎΠ²Π΅Π½ΠΈΠ΅ ΠΈΒ Π½Π°ΠΊΠΎΠΏΠ»Π΅Π½ΠΈΠ΅ Π²Π»Π°Π³ΠΈ Π² ΡΠΎΠΊΠΎΠ»Π΅, Π½Π΅ΠΎΠ±Ρ ΠΎΠ΄ΠΈΠΌΠΎ Π·Π°ΡΠΈΡΠΈΡΡ ΠΊΠΎΠ½ΡΡΡΡΠΊΡΠΈΡ ΠΈΠ·Π½ΡΡΡΠΈ ΠΈ ΡΠ½Π°ΡΡΠΆΠΈ Ρ ΠΏΠΎΠΌΠΎΡΡΡ ΠΌΠ°ΡΠ΅ΡΠΈΠ°Π»ΠΎΠ² Π³ΠΈΠ΄ΡΠΎΠΈΠ·ΠΎΠ»ΡΡΠΈΠΈ ΠΈ ΡΠ΅ΠΏΠ»ΠΎΠΈΠ·ΠΎΠ»ΡΡΠΈΠΈ.
ΠΡΡΠΈΡΠ°ΡΠ΅Π»ΡΠ½ΠΎΠ΅ Π²ΠΎΠ·Π΄Π΅ΠΉΡΡΠ²ΠΈΠ΅ Π½Π° ΠΊΠΈΡΠΏΠΈΡ
ΠΡΠ΄Π΅Π»ΡΡΡ Π½Π΅ΡΠΊΠΎΠ»ΡΠΊΠΎ Π²Π°ΠΆΠ½ΡΡ ΡΠ°ΠΊΡΠΎΡΠΎΠ², ΠΎΠΊΠ°Π·ΡΠ²Π°ΡΡΠΈΡ ΠΎΡΡΠΈΡΠ°ΡΠ΅Π»ΡΠ½ΠΎΠ΅ Π²ΠΎΠ·Π΄Π΅ΠΉΡΡΠ²ΠΈΠ΅ Π½Π° ΡΠΎΠΊΠΎΠ»Ρ:
- ΠΠ΅ΠΏΠΎΡΡΠ΅Π΄ΡΡΠ²Π΅Π½Π½ΠΎΠ΅ ΡΠ°ΡΠΏΠΎΠ»ΠΎΠΆΠ΅Π½ΠΈΠ΅ Π½Π° ΠΏΠΎΠ²Π΅ΡΡ
Π½ΠΎΡΡΠΈ Π·Π΅ΠΌΠ»ΠΈ.
ΠΠΎΡΡΠΎΠΌΡ Π²ΠΎΠ·Π΄Π΅ΠΉΡΡΠ²ΠΈΠ΅ Π²Π»Π°Π³ΠΈ Π½Π° ΡΠΎΠΊΠΎΠ»Ρ Π·Π½Π°ΡΠΈΡΠ΅Π»ΡΠ½ΠΎ Π²ΡΡΠ΅, ΡΠ΅ΠΌ Π½Π° ΡΡΠ΅Π½Ρ. ΠΡΠ΅ΡΡΠΎΡΠΎΠ½Π½ΡΡ ΠΈΠ·ΠΎΠ»ΡΡΠΈΡ ΡΠΎΠΊΠΎΠ»Ρ Π½Π°ΡΠΈΠ½Π°Π΅ΡΡΡ Π½Π° ΡΡΠ°ΠΏΠ΅ ΡΡΡΠΎΠΈΡΠ΅Π»ΡΡΡΠ²Π° Π΄ΠΎΠΌΠ°.
- ΠΠ΅ΡΠΈΠΎΠ΄ΠΈΡΠ΅ΡΠΊΠΎΠ΅ ΠΏΠΎΠΏΠ°Π΄Π°Π½ΠΈΠ΅ Π²Π»Π°Π³ΠΈ ΡΠ΅ΡΠ΅Π· Π½Π΅ΠΊΠΎΡΠΎΡΠΎΠ΅ Π²ΡΠ΅ΠΌΡ ΠΏΡΠΈΠ²Π΅Π΄ΡΡ ΠΊ Π½Π°ΠΌΠΎΠΊΠ°Π½ΠΈΡ ΡΡΡΠΎΠΈΡΠ΅Π»ΡΠ½ΠΎΠ³ΠΎ ΠΌΠ°ΡΠ΅ΡΠΈΠ°Π»Π°, Π°, Π·Π½Π°ΡΠΈΡ, ΠΊ Π²ΠΏΠΈΡΡΠ²Π°Π½ΠΈΡ Π²Π»Π°Π³ΠΈ.
- ΠΠΎΠ»Π½ΠΎΠ΅ Π½Π°ΠΌΠΎΠΊΠ°Π½ΠΈΠ΅ ΠΊΠΎΠ½ΡΡΡΡΠΊΡΠΈΠΈ Π½Π°ΡΡΡΠΏΠ°Π΅Ρ Ρ ΠΏΡΠΈΡ ΠΎΠ΄ΠΎΠΌ ΡΠ΅ΠΏΠ»Π° ΠΏΠΎΡΠ»Π΅ Π·ΠΈΠΌΡ, ΠΊΠΎΠ³Π΄Π° Π²ΠΎΠΊΡΡΠ³ ΡΠΎΠΊΠΎΠ»Ρ Π½Π°ΡΠΈΠ½Π°Π΅ΡΡΡ ΡΠ°ΡΠ½ΠΈΠ΅ ΡΠ½Π΅Π³Π°. ΠΡΠΎ ΠΏΡΠΈΠ²ΠΎΠ΄ΠΈΡ ΠΊ ΠΏΠΎΠ»Π½ΠΎΠΌΡ Π½Π°ΠΌΠΎΠΊΠ°Π½ΠΈΡ ΡΡΠ½Π΄Π°ΠΌΠ΅Π½ΡΠ°.
- ΠΠ΅ΠΎΠ±Ρ ΠΎΠ΄ΠΈΠΌΠΎ ΡΠΎΠ·Π΄Π°ΡΡ ΠΏΠΎΠ²ΡΡΠ΅Π½Π½ΡΠΉ ΡΡΠΎΠ²Π΅Π½Ρ ΠΏΡΠΎΡΠ½ΠΎΡΡΠΈ Π΄Π»Ρ ΡΠΎΠΊΠΎΠ»Ρ, ΠΏΠΎΡΠΊΠΎΠ»ΡΠΊΡ ΡΡΠΎ ΡΠΎΠΏΡΡΠΆΠ΅Π½ΠΎ Ρ Π²ΠΎΠ·Π΄Π΅ΠΉΡΡΠ²ΠΈΠ΅ΠΌ Π²ΡΡΠΎΠΊΠΎΠΉ Π½Π°Π³ΡΡΠ·ΠΊΠΈ.
- ΠΠ΅ΡΡ ΡΠΎΠΊΠΎΠ»ΡΠ½ΡΠΉ ΡΡΠ°ΠΆ ΠΌΠΎΠΆΠ΅Ρ ΠΏΠΎΠ΄Π²Π΅ΡΠ³Π°ΡΡΡΡ ΠΎΠΏΠ°ΡΠ½ΠΎΡΡΠΈ ΠΈΠ·-Π·Π° Π΄Π°Π²Π»Π΅Π½ΠΈΡ ΡΠΎ ΡΡΠΎΡΠΎΠ½Ρ Π³ΡΡΠ½ΡΠ°.
- Π Ρ ΠΎΠ»ΠΎΠ΄Π½ΠΎΠ΅ Π²ΡΠ΅ΠΌΡ Π²ΠΎΠ΄Π°, ΠΏΡΠΎΠ½ΠΈΠΊΡΠ°Ρ Π² ΠΌΠ°ΡΠ΅ΡΠΈΠ°Π», ΠΏΡΠ΅Π²ΡΠ°ΡΠ°Π΅ΡΡΡ Π² Π»ΡΠ΄ ΠΈ ΡΠ°Π·ΡΡΡΠ°Π΅Ρ ΠΊΠΈΡΠΏΠΈΡ ΠΈΠ·Π½ΡΡΡΠΈ. ΠΡΠΎ ΡΠΌΠ΅Π½ΡΡΠΈΡ ΡΡΠΎΠΊ ΡΠΊΡΠΏΠ»ΡΠ°ΡΠ°ΡΠΈΠΈ ΡΡΠ½Π΄Π°ΠΌΠ΅Π½ΡΠ° ΠΈ ΠΏΡΠΈΠ±Π»ΠΈΠ·ΠΈΡ ΡΡΠΎΠΊ ΠΏΡΠΎΠ²Π΅Π΄Π΅Π½ΠΈΡ ΠΊΠ°ΠΏΠΈΡΠ°Π»ΡΠ½ΠΎΠ³ΠΎ ΡΠ΅ΠΌΠΎΠ½ΡΠ°, ΠΊΠΎΡΠΎΡΡΠΉ ΡΡΠ΅Π±ΡΠ΅Ρ Π±ΠΎΠ»ΡΡΠΈΡ ΡΠΈΠ½Π°Π½ΡΠΎΠ²ΡΡ Π·Π°ΡΡΠ°Ρ.
ΠΠΈΡΠΏΠΈΡ Π΄Π»Ρ ΡΠΎΠΊΠΎΠ»Ρ Π΄ΠΎΠ»ΠΆΠ΅Π½ ΡΠΎΠΎΡΠ²Π΅ΡΡΡΠ²ΠΎΠ²Π°ΡΡ ΡΡΠ΅Π±ΠΎΠ²Π°Π½ΠΈΡΠΌ,
ΠΏΠΎΠ·Π²ΠΎΠ»ΡΡΡΠΈΠΌ Π΅Π³ΠΎ ΠΈΡΠΏΠΎΠ»ΡΠ·ΠΎΠ²Π°ΡΡ ΠΏΡΠΈ Π²ΠΎΠ·Π΄Π΅ΠΉΡΡΠ²ΠΈΠΈ Π²ΡΡΠΎΠΊΠΈΡ
Π½Π°Π³ΡΡΠ·ΠΎΠΊ ΠΈ ΠΏΠΎΠ²ΡΡΠ΅Π½Π½ΠΎΠΉ
Π²Π»Π°ΠΆΠ½ΠΎΡΡΠΈ, Ρ ΡΡΡΡΠΎΠΌ Π²Π»ΠΈΡΠ½ΠΈΡ Π΄ΡΡΠ³ΠΈΡ
ΡΠ°ΠΊΡΠΎΡΠΎΠ², ΡΠ²ΠΎΠΉΡΡΠ²Π΅Π½Π½ΡΡ
ΡΠΏΠ΅ΡΠΈΡΠΈΡΠ΅ΡΠΊΠΈΠΌ
Ρ
Π°ΡΠ°ΠΊΡΠ΅ΡΠΈΡΡΠΈΠΊΠ°ΠΌ ΠΏΠΎΡΡΡΠΎΠΉΠΊΠΈ ΠΈ ΠΊΠ»ΠΈΠΌΠ°ΡΠΈΡΠ΅ΡΠΊΠΈΡ
ΡΡΠ»ΠΎΠ²ΠΈΠΉ.
ΠΡΠ°Π²ΠΈΠ»ΡΠ½ΡΠΉ Π²ΡΠ±ΠΎΡ ΠΊΠΈΡΠΏΠΈΡΠ°
ΠΠ΅ ΡΡΠΎΠΈΡ Π΄Π°ΠΆΠ΅ ΡΠ°ΡΡΠΌΠ°ΡΡΠΈΠ²Π°ΡΡ Π²Π°ΡΠΈΠ°Π½ΡΡ Π΄Π΅ΡΡΠ²ΡΡ ΠΈ Π½Π΅ΠΊΠ°ΡΠ΅ΡΡΠ²Π΅Π½Π½ΡΡ ΠΌΠ°ΡΠ΅ΡΠΈΠ°Π»ΠΎΠ². ΠΡΠΈ Π²ΡΠ±ΠΎΡΠ΅ ΠΊΠΈΡΠΏΠΈΡΠ° ΡΠ»Π΅Π΄ΡΠ΅Ρ ΠΎΡΠ΅Π½ΠΈΠ²Π°ΡΡ Π΅Π³ΠΎ ΡΠΊΡΠΏΠ»ΡΠ°ΡΠ°ΡΠΈΠΎΠ½Π½ΡΠ΅ ΠΏΠ°ΡΠ°ΠΌΠ΅ΡΡΡ, ΠΏΡΠΎΡΠ½ΠΎΡΡΡ ΠΈ ΡΡΡΠ΅ΡΠΈΡΠ½ΠΎΡΡΡ.
ΠΡΡΠΎΠΊΠΈΠ΅ Π½Π°Π³ΡΡΠ·ΠΊΠΈ ΠΈ ΠΊΠ»ΠΈΠΌΠ°ΡΠΈΡΠ΅ΡΠΊΠΈΠ΅ Π²ΠΎΠ·Π΄Π΅ΠΉΡΡΠ²ΠΈΡ Π΄ΠΎΠ»ΠΆΠ½Ρ Ρ Π»ΡΠ³ΠΊΠΎΡΡΡΡ Π²ΡΠ΄Π΅ΡΠΆΠΈΠ²Π°ΡΡΡΡ ΡΡΡΠΎΠΈΡΠ΅Π»ΡΠ½ΡΠΌ ΠΌΠ°ΡΠ΅ΡΠΈΠ°Π»ΠΎΠΌ ΠΈ ΠΊΠΎΠ½ΡΡΡΡΠΊΡΠΈΠ΅ΠΉ ΡΠΎΠΊΠΎΠ»Ρ. Π ΡΠ°ΠΊΠΆΠ΅, ΠΏΡΠΈ Π²ΡΠ±ΠΎΡΠ΅ ΡΡΠΎΠΈΡ ΡΡΠΈΡΡΠ²Π°ΡΡ ΠΈ Π²Π½Π΅ΡΠ½ΠΈΠΉ Π²ΠΈΠ΄ ΠΏΠΎΡΡΡΠΎΠΉΠΊΠΈ, ΡΡΠΎΠ±Ρ ΡΠΎΠΊΠΎΠ»Ρ Π² Π½Π΅Ρ Π³Π°ΡΠΌΠΎΠ½ΠΈΡΠ½ΠΎ Π²ΠΏΠΈΡΠ°Π»ΡΡ.
ΠΠΎΡΡΡΠΏΠ½ΠΎΡΡΡ ΠΈ ΠΌΠ½ΠΎΠ³ΠΎΡΡΠ½ΠΊΡΠΈΠΎΠ½Π°Π»ΡΠ½ΠΎΡΡΡ ΡΠ²Π»ΡΡΡΡΡ ΠΎΠΏΡΠ΅Π΄Π΅Π»ΡΡΡΠΈΠΌΠΈ ΡΠ°ΠΊΡΠΎΡΠ°ΠΌΠΈ ΠΏΡΠΈ Π²ΡΠ±ΠΎΡΠ΅ ΠΊΠΈΡΠΏΠΈΡΠ° Π² ΠΊΠ°ΡΠ΅ΡΡΠ²Π΅ ΡΡΡΠΎΠΈΡΠ΅Π»ΡΠ½ΠΎΠ³ΠΎ ΠΌΠ°ΡΠ΅ΡΠΈΠ°Π»Π° ΡΠΎΠΊΠΎΠ»Ρ. ΠΡΠ»ΠΈ ΠΈΡΠΏΠΎΠ»ΡΠ·ΠΎΠ²Π°ΡΡ ΡΡΠΎΡ ΠΌΠ°ΡΠ΅ΡΠΈΠ°Π», ΡΠΎ Π² Π΄Π°Π»ΡΠ½Π΅ΠΉΡΠ΅ΠΌ ΠΌΠΎΠΆΠ½ΠΎ Π½Π΅ ΠΏΡΠΈΠ±Π΅Π³Π°ΡΡ ΠΊ ΠΎΡΠ΄Π΅Π»ΠΎΡΠ½ΡΠΌ ΡΠ°Π±ΠΎΡΠ°ΠΌ.
Π Π°Π·Π½ΠΎΠ²ΠΈΠ΄Π½ΠΎΡΡΡ ΠΊΠΈΡΠΏΠΈΡΠ° Π΄Π»Ρ ΡΠΎΠΊΠΎΠ»Ρ, ΠΏΡΠ΅Π΄Π»Π°Π³Π°Π΅ΠΌΠ°Ρ ΠΏΡΠΎΠΈΠ·Π²ΠΎΠ΄ΠΈΡΠ΅Π»ΡΠΌΠΈ, ΠΏΠΎΠΌΠΈΠΌΠΎ Π±Π°Π·ΠΎΠ²ΡΡ ΠΏΠ°ΡΠ°ΠΌΠ΅ΡΡΠΎΠ² Π΅Π³ΠΎ ΠΌΠ°ΡΠΊΠΈ, Π΄ΠΎΠ»ΠΆΠ΅Π½ ΠΎΠ±Π»Π°Π΄Π°ΡΡ ΠΈ Π΄ΠΎΠΏΠΎΠ»Π½ΠΈΡΠ΅Π»ΡΠ½ΡΠΌΠΈ Ρ Π°ΡΠ°ΠΊΡΠ΅ΡΠΈΡΡΠΈΠΊΠ°ΠΌΠΈ ΠΏΠΎ Π²ΠΎΠ΄ΠΎΠΏΠΎΠ³Π»ΠΎΡΠ΅Π½ΠΈΡ ΠΈ ΠΌΠΎΡΠΎΠ·ΠΎΡΡΡΠΎΠΉΡΠΈΠ²ΠΎΡΡΠΈ.
ΠΡΠΈ Π²ΡΠ±ΠΎΡΠ΅ ΡΠ»Π΅Π΄ΡΠ΅Ρ ΡΡΠΈΡΡΠ²Π°ΡΡ ΡΠ»Π΅Π΄ΡΡΡΠΈΠ΅ ΠΏΠ°ΡΠ°ΠΌΠ΅ΡΡΡ ΠΊΠΈΡΠΏΠΈΡΠ°:
- Π‘ΡΠ°Π½Π΄Π°ΡΡΠ½ΡΠ΅ ΡΠ°Π·ΠΌΠ΅ΡΡ. Π Π·Π°Π²ΠΈΡΠΈΠΌΠΎΡΡΠΈ ΠΎΡ ΡΠΏΠΎΡΠΎΠ±Π° ΠΊΠ»Π°Π΄ΠΊΠΈ, ΡΡΠΎ ΠΏΠΎΠΌΠΎΠΆΠ΅Ρ ΠΎΠ±Π»Π΅Π³ΡΠΈΡΡ ΠΈ ΡΡΠΊΠΎΡΠΈΡΡ ΡΠΊΠ»Π°Π΄ΠΊΡ ΠΊΠΎΠ½ΡΡΡΡΠΊΡΠΈΠΈ.
- ΠΡΡΠΎΠΊΠΈΠΉ ΠΏΠΎΠΊΠ°Π·Π°ΡΠ΅Π»Ρ ΡΠΊΠΎΠ»ΠΎΠ³ΠΈΡΠ½ΠΎΡΡΠΈ. ΠΡΠΎ Π΄ΠΎΠΏΠΎΠ»Π½ΠΈΡΠ΅Π»ΡΠ½ΠΎ ΠΎΠ±Π΅Π·ΠΎΠΏΠ°ΡΠΈΡ ΠΎΠΊΡΡΠΆΠ°ΡΡΡΡ ΡΡΠ΅Π΄Ρ ΠΈ ΡΠ΅Π»ΠΎΠ²Π΅ΠΊΠ° ΠΎΡ Π²ΠΎΠ·Π΄Π΅ΠΉΡΡΠ²ΠΈΡ Π²ΡΠ΅Π΄Π½ΡΡ ΡΠ°ΠΊΡΠΎΡΠΎΠ².
- Π₯ΠΎΡΠΎΡΠΈΠΉ ΡΡΠΎΠ²Π΅Π½Ρ Π²Π»Π°Π³ΠΎΡΡΠΎΠΉΠΊΠΎΡΡΠΈ. ΠΠ±Π΅ΡΠΏΠ΅ΡΠΈΠ²Π°Π΅Ρ Π΄ΠΎΠ»Π³ΠΎΠ²Π΅ΡΠ½ΠΎΡΡΡ ΠΌΠ°ΡΠ΅ΡΠΈΠ°Π»Π° ΠΈ Π²ΡΠ΅ΠΉ ΠΊΠΎΠ½ΡΡΡΡΠΊΡΠΈΠΈ.
- ΠΡΡΠΎΠΊΠ°Ρ Π°Π΄Π³Π΅Π·ΠΈΡ Ρ ΡΠ°ΡΡΠ²ΠΎΡΠΎΠΌ. Π ΠΏΡΠΎΡΠ΅ΡΡΠ΅ ΡΠΊΡΠΏΠ»ΡΠ°ΡΠ°ΡΠΈΠΈ Π½Π΅ ΠΏΠΎΠ·Π²ΠΎΠ»ΡΠ΅Ρ ΠΎΠ±ΡΠ°Π·ΠΎΠ²ΡΠ²Π°ΡΡΡΡ ΡΡΠ΅ΡΠΈΠ½Π°ΠΌ ΠΈ Π΄Π΅ΡΠ΅ΠΊΡΠ°ΠΌ, ΠΏΠΎΠ΄Π²Π΅ΡΠΆΠ΅Π½Π½ΡΡ ΠΏΡΠΎΠ½ΠΈΠΊΠ½ΠΎΠ²Π΅Π½ΠΈΡ Ρ ΠΎΠ»ΠΎΠ΄Π½ΠΎΠ³ΠΎ Π²ΠΎΠ·Π΄ΡΡ Π°.
ΠΠΎΠ»ΡΡΠΎΠΉ ΠΏΠΎΠΏΡΠ»ΡΡΠ½ΠΎΡΡΡΡ ΠΏΠΎΠ»ΡΠ·ΡΡΡΡΡ ΡΠΈΠ»ΠΈΠΊΠ°ΡΠ½ΡΠΉ ΠΈ ΠΊΡΠ°ΡΠ½ΡΠΉ ΠΊΠΈΡΠΏΠΈΡΠΈ, Π° ΡΠ°ΠΊΠΆΠ΅ ΠΊΠ΅ΡΠ°ΠΌΠΈΡΠ΅ΡΠΊΠΈΠ΅. ΠΠΎΡΠ»Π΅Π΄Π½ΠΈΠΉ Π² Π±ΠΎΠ»ΡΡΠΎΠΌ ΡΠ°Π·Π½ΠΎΠΎΠ±ΡΠ°Π·ΠΈΠΈ ΠΏΡΠ΅Π΄ΡΡΠ°Π²Π»Π΅Π½ Π½Π° ΡΡΠ½ΠΊΠ΅.
ΠΠΈΡΠΏΠΈΡ ΡΠΈΠ»ΠΈΠΊΠ°ΡΠ½ΡΠΉ
ΠΠ»Ρ ΠΏΡΠΎΠΈΠ·Π²ΠΎΠ΄ΡΡΠ²Π° ΡΠΈΠ»ΠΈΠΊΠ°ΡΠ½ΠΎΠ³ΠΎ ΠΊΠΈΡΠΏΠΈΡΠ° ΠΈΡΠΏΠΎΠ»ΡΠ·ΡΡΡ ΡΠ΅Ρ Π½ΠΎΠ»ΠΎΠ³ΠΈΡ, ΠΊΠΎΡΠΎΡΠ°Ρ Π½Π΅ ΠΏΠΎΠ·Π²ΠΎΠ»ΡΠ΅Ρ ΠΈΡΠΏΠΎΠ»ΡΠ·ΠΎΠ²Π°ΡΡ Π΅Π³ΠΎ Π΄Π»Ρ ΡΠ°Π±ΠΎΡ Ρ ΠΏΠΎΠ²ΡΡΠ΅Π½Π½ΠΎΠΉ Π²Π»Π°ΠΆΠ½ΠΎΡΡΡΡ. Π Π°Π·Π±ΡΡ Π°Π½ΠΈΠ΅, ΡΡΡΠ°ΡΠ° ΡΠ°Π±ΠΎΡΠΈΡ ΠΏΠ°ΡΠ°ΠΌΠ΅ΡΡΠΎΠ², ΠΈ Π½Π΅ΠΈΠ·Π±Π΅ΠΆΠ½ΠΎΠ΅ ΡΠ°Π·ΡΡΡΠ΅Π½ΠΈΠ΅ ΡΠ΅ΡΠ΅Π· Π²ΡΠ΅ΠΌΡ ΠΏΡΠΎΠΈΡΡ ΠΎΠ΄ΠΈΡ ΠΏΡΠΈ Π΄Π»ΠΈΡΠ΅Π»ΡΠ½ΠΎΠΌ Π²ΠΎΠ·Π΄Π΅ΠΉΡΡΠ²ΠΈΠΈ Π½Π° ΠΌΠ°ΡΠ΅ΡΠΈΠ°Π» Π²Π»Π°Π³ΠΈ. ΠΠΎΠΏΡΡΡΠΈΠΌΠΎ ΠΈΡΠΏΠΎΠ»ΡΠ·ΠΎΠ²Π°Π½ΠΈΠ΅ ΡΡΠΎΠ³ΠΎ ΠΊΠΈΡΠΏΠΈΡΠ° ΡΠΎΠ»ΡΠΊΠΎ Π² ΡΡΠ»ΠΎΠ²ΠΈΡΡ Π·Π°ΡΡΡΠ»ΠΈΠ²ΠΎΠ³ΠΎ ΠΊΠ»ΠΈΠΌΠ°ΡΠ° Ρ ΠΌΠΈΠ½ΠΈΠΌΠ°Π»ΡΠ½ΡΠΌ ΠΊΠΎΠ»ΠΈΡΠ΅ΡΡΠ²ΠΎΠΌ ΠΎΡΠ°Π΄ΠΊΠΎΠ².
ΠΠΎΠΏΠΎΠ»Π½ΠΈΡΠ΅Π»ΡΠ½ΠΎΠΉ Π·Π°ΡΠΈΡΠΎΠΉ ΡΠΎΠΊΠΎΠ»Ρ ΠΈΠ· ΡΠΈΠ»ΠΈΠΊΠ°ΡΠ½ΠΎΠ³ΠΎ ΠΊΠΈΡΠΏΠΈΡΠ°
Π±ΡΠ΄Π΅Ρ ΡΠ»ΡΠΆΠΈΡΡ Π²ΡΡΠΎΠΊΠΎΠΊΠ°ΡΠ΅ΡΡΠ²Π΅Π½Π½Π°Ρ Π³ΠΈΠ΄ΡΠΎΠΈΠ·ΠΎΠ»ΡΡΠΈΡ. ΠΠ°Π΄ΡΠΆΠ½ΠΎΡΡΡ Π²ΡΠ΅ΠΉ ΠΏΠΎΡΡΡΠΎΠΉΠΊΠΈ Π±ΡΠ΄Π΅Ρ
ΠΎΠΏΡΠ΅Π΄Π΅Π»ΡΡΡΡΡ ΠΏΡΠΎΡΠ½ΠΎΡΡΡΡ ΠΌΠ°ΡΠΊΠΈ ΡΠΈΠ»ΠΈΠΊΠ°ΡΠ½ΠΎΠ³ΠΎ ΠΊΠΈΡΠΏΠΈΡΠ°.
ΠΡΠ±ΠΈΡΠ°Ρ ΡΡΠΎΡ ΠΌΠ°ΡΠ΅ΡΠΈΠ°Π» Π΄Π»Ρ Π²ΠΎΠ·Π²Π΅Π΄Π΅Π½ΠΈΡ ΡΠΎΠΊΠΎΠ»Ρ, Π² Π½Π΅ΠΊΠΎΡΠΎΡΠΎΠΉ ΡΡΠ΅ΠΏΠ΅Π½ΠΈ ΠΏΠΎΠ·Π²ΠΎΠ»ΡΠ΅Ρ ΡΠΌΠ΅Π½ΡΡΠΈΡΡ ΡΡΡΠ΄ΠΎΡΠΌΠΊΠΎΡΡΡ ΡΠ°Π±ΠΎΡ, ΡΡΡΡΠ°Π½ΠΈΡΡ Π½Π΅ΠΊΠΎΡΠΎΡΡΠ΅ ΠΏΡΠΎΠ±Π»Π΅ΠΌΡ Ρ ΠΏΡΠΈΠΌΠ΅Π½Π΅Π½ΠΈΠ΅ΠΌ ΡΡΠ°Π½Π΄Π°ΡΡΠ½ΡΡ ΡΠ΅ΠΏΠ»ΠΎ- ΠΈ Π³ΠΈΠ΄ΡΠΎΠΈΠ·ΠΎΠ»ΡΡΠΎΡΠΎΠ². ΠΠΎΠ²ΡΡΠ΅Π½Π½Π°Ρ Π²Π»Π°ΠΆΠ½ΠΎΡΡΡ ΠΌΠ΅ΡΡΠ½ΠΎΡΡΠΈ ΡΠ²Π»ΡΠ΅ΡΡΡ ΠΏΡΠΎΡΠΈΠ²ΠΎΠΏΠΎΠΊΠ°Π·Π°Π½ΠΈΠ΅ΠΌ Π΄Π»Ρ ΠΈΡΠΏΠΎΠ»ΡΠ·ΠΎΠ²Π°Π½ΠΈΡ ΡΡΠΎΠ³ΠΎ Π²ΠΈΠ΄Π° ΠΊΠΈΡΠΏΠΈΡΠ° Π΄Π»Ρ ΡΠΎΠΊΠΎΠ»ΡΠ½ΠΎΠΉ ΠΊΠΎΠ½ΡΡΡΡΠΊΡΠΈΠΈ.
ΠΡΠ°ΡΠ½ΡΠΉ Π³Π»ΠΈΠ½ΡΠ½ΡΠΉ ΠΊΠΈΡΠΏΠΈΡ
ΠΡΠΎΡ Π²ΠΈΠ΄ ΠΊΠΈΡΠΏΠΈΡΠ° ΡΠ²Π»ΡΠ΅ΡΡΡ ΡΠ°ΠΌΡΠΌ ΠΎΠΏΡΠΈΠΌΠ°Π»ΡΠ½ΡΠΌ. Π Π΅Π³ΠΎ ΡΠ΅Ρ Π½ΠΎΠ»ΠΎΠ³ΠΈΡΠ΅ΡΠΊΠΈΠ΅ ΠΏΠΎΠΊΠ°Π·Π°ΡΠ΅Π»ΠΈ ΠΎΠ±Π»Π°Π΄Π°ΡΡ Π² Π±ΠΎΠ»ΡΡΠ΅ΠΉ ΡΡΠ΅ΠΏΠ΅Π½ΠΈ ΠΏΠΎΠ΄Ρ ΠΎΠ΄ΡΡΠΈΠΌΠΈ Π΄Π»Ρ ΡΠΎΠΎΡΡΠΆΠ΅Π½ΠΈΡ ΡΠΎΠΊΠΎΠ»Ρ ΠΈ ΡΡΠ½Π΄Π°ΠΌΠ΅Π½ΡΠ°.
Π‘ΡΠΎΠΊ ΡΠ»ΡΠΆΠ±Ρ ΠΊΠΈΡΠΏΠΈΡΠ½ΠΎΠ³ΠΎ ΡΠΎΠΊΠΎΠ»Ρ Π΄ΠΎΠ²ΠΎΠ»ΡΠ½ΠΎ Π΄Π»ΠΈΡΠ΅Π»ΡΠ½ΡΠΉ, ΡΡΡΠΎΠΉΡΠΈΠ²ΡΠΉ ΠΊ Π²ΠΎΠ·Π΄Π΅ΠΉΡΡΠ²ΠΈΡ ΠΏΡΠΈΡΠΎΠ΄Π½ΡΡ ΠΊΠ»ΠΈΠΌΠ°ΡΠΈΡΠ΅ΡΠΊΠΈΡ ΡΠ°ΠΊΡΠΎΡΠΎΠ².
ΠΠΎ Π΄Π°ΠΆΠ΅ Π²ΡΡΠΎΠΊΠΎΠΊΠ°ΡΠ΅ΡΡΠ²Π΅Π½Π½ΡΠΉ ΠΊΠΈΡΠΏΠΈΡ Π²ΠΏΠΈΡΡΠ²Π°Π΅Ρ Π²Π»Π°Π³Ρ,
ΠΏΠΎΡΡΠΎΠΌΡ ΠΌΠ°ΡΠΊΠ° ΠΌΠ°ΡΠ΅ΡΠΈΠ°Π»Π° Π΄ΠΎΠ»ΠΆΠ½Π° ΠΌΠ°ΠΊΡΠΈΠΌΠ°Π»ΡΠ½ΠΎ ΡΠΎΠΎΡΠ²Π΅ΡΡΡΠ²ΠΎΠ²Π°ΡΡ ΡΡΠ»ΠΎΠ²ΠΈΡΠΌ ΠΏΠΎΡΡΡΠΎΠΉΠΊΠΈ ΠΈ
ΠΎΠΊΡΡΠΆΠ°ΡΡΠ΅ΠΉ ΡΡΠ΅Π΄Ρ. ΠΠ°ΠΌΠΎΡΠ°ΠΆΠΈΠ²Π°Π½ΠΈΠ΅ Π±ΠΎΠ»Π΅Π΅ 60 Π²ΡΠ΄Π΅ΡΠΆΠΈΠ²Π°Π΅Ρ ΠΌΠ°ΡΠΊΠ° Π-150. ΠΡΡΠ°Π½ΠΎΠ²ΠΈΡΡΡΡ
Π½Π° ΠΌΠ°ΡΠΊΠ΅ Π-250 ΡΠ»Π΅Π΄ΡΠ΅Ρ Π² ΡΠ΅Ρ
ΡΠ»ΡΡΠ°ΡΡ
, Π΅ΡΠ»ΠΈ ΠΌΠ΅ΡΡΠ½ΠΎΡΡΡΒ ΠΏΠΎΠ΄Π²Π΅ΡΠΆΠ΅Π½Π° ΠΏΠΎΠ²ΡΡΠ΅Π½Π½ΠΎΠΉ
Π²Π»Π°ΠΆΠ½ΠΎΡΡΠΈ ΠΈ ΡΠ΅Π³ΡΠ»ΡΡΠ½ΡΠΌ ΠΎΡΠ°Π΄ΠΊΠ°ΠΌ.
ΠΠ»Π°Π³ΠΎΡΡΠΎΠΉΠΊΠΎΡΡΡ ΠΈ ΠΏΡΠΎΡΠ½ΠΎΡΡΡ ΠΎΡΠ΅Π½Ρ Π²Π°ΠΆΠ½Ρ Π΄Π»Ρ ΡΠΈΠ»ΠΈΠΊΠ°ΡΠ½ΠΎΠ³ΠΎ ΠΈ ΠΊΡΠ°ΡΠ½ΠΎΠ³ΠΎ ΠΊΠΈΡΠΏΠΈΡΠ°, ΠΏΠΎΡΠΊΠΎΠ»ΡΠΊΡ Π²ΠΎΠ΄Π°, Π·Π°ΠΌΠ΅ΡΠ·Π°Ρ Π² ΡΡΠ΅ΡΠΈΠ½Π°Ρ , ΡΠ°ΡΡΠΈΡΡΠ΅ΡΡΡ ΠΈ ΡΠ°Π·ΡΡΡΠ°Π΅Ρ ΡΡΡΡΠΊΡΡΡΡ ΠΊΠΈΡΠΏΠΈΡΠ° ΠΈΠ·Π½ΡΡΡΠΈ. ΠΡΠ° ΠΎΡΠΎΠ±Π΅Π½Π½ΠΎΡΡΡ ΠΎΠΊΠ°Π·ΡΠ²Π°Π΅Ρ ΠΏΡΡΠΌΠΎΠ΅ Π²Π»ΠΈΡΠ½ΠΈΠ΅ Π½Π° Π²Π΅ΡΡ ΡΠΎΠΊΠΎΠ»ΡΠ½ΡΠΉ ΡΡΠ°ΠΆ.
ΠΡΠ»ΠΈ Π² ΡΡΠ»ΠΎΠ²ΠΈΡΡ ΡΡΡ ΠΎΠ³ΠΎ ΠΊΠ»ΠΈΠΌΠ°ΡΠ°, ΡΡΡΠΎΠΈΡΠ΅Π»ΡΡΡΠ²ΠΎ ΡΡΠ΅Π½ Π΄ΠΎΠΌΠ° ΠΏΡΠΎΠΈΠ·Π²ΠΎΠ΄ΠΈΡΡΡ ΠΈΠ· ΡΠΈΠ»ΠΈΠΊΠ°ΡΠ½ΠΎΠ³ΠΎ ΠΊΠΈΡΠΏΠΈΡΠ°, ΡΠΎ Π΄Π»Ρ ΡΠΎΠΊΠΎΠ»Ρ ΡΡΠ°Π΄ΠΈΡΠΈΠΎΠ½Π½ΡΠΉ Π³Π»ΠΈΠ½ΡΠ½ΡΠΉ ΠΊΠΈΡΠΏΠΈΡ ΡΠ²Π»ΡΠ΅ΡΡΡ ΠΎΠ±ΡΠ·Π°ΡΠ΅Π»ΡΠ½ΡΠΌ ΡΡΠ»ΠΎΠ²ΠΈΠ΅ΠΌ ΠΊΠ°ΡΠ΅ΡΡΠ²Π΅Π½Π½ΠΎΠΉ ΠΏΠΎΡΡΡΠΎΠΉΠΊΠΈ.
ΠΠΎ ΠΌΠ½ΠΎΠ³ΠΈΠΌ ΡΠΊΠΎΠ½ΠΎΠΌΠΈΡΠ΅ΡΠΊΠΈΠΌ ΡΠΎΠΎΠ±ΡΠ°ΠΆΠ΅Π½ΠΈΡΠΌ, ΠΊΡΠ°ΡΠ½ΡΠΉ ΠΊΠΈΡΠΏΠΈΡ ΡΠ²Π»ΡΠ΅ΡΡΡ ΡΡΠ°Π΄ΠΈΡΠΈΠΎΠ½Π½ΡΠΌ Π½Π΅Π΄ΠΎΡΠΎΠ³ΠΈΠΌ ΠΌΠ°ΡΠ΅ΡΠΈΠ°Π»ΠΎΠΌ Π΄Π»Ρ Π²ΠΎΠ·Π²Π΅Π΄Π΅Π½ΠΈΡ ΡΠΎΠΊΠΎΠ»Ρ. ΠΠΎ ΠΏΡΠ΅ΠΆΠ΄Π΅ ΡΠ΅ΠΌ ΡΠΎΠ²Π΅ΡΡΠΈΡΡ ΠΏΠΎΠΊΡΠΏΠΊΡ, ΡΠ΄ΠΎΡΡΠΎΠ²Π΅ΡΡΡΠ΅ΡΡ Π² ΠΊΠ°ΡΠ΅ΡΡΠ²Π΅ ΠΊΠΈΡΠΏΠΈΡΠ° ΠΈ ΠΏΠΎΠΏΡΠΎΡΠΈΡΠ΅ ΠΏΡΠΎΠ΄Π°Π²ΡΠ° ΠΏΡΠ΅Π΄ΠΎΡΡΠ°Π²ΠΈΡΡ, ΡΠΎΠΎΡΠ²Π΅ΡΡΡΠ²ΡΡΡΠΈΠ΅ Π΄ΠΎΠΊΡΠΌΠ΅Π½ΡΡ.
ΠΠ΅ΡΠ°ΠΌΠΈΡΠ΅ΡΠΊΠΈΠΉ ΠΌΠ°ΡΠ΅ΡΠΈΠ°Π»
Π ΡΡΠ°Π²Π½Π΅Π½ΠΈΠΈ Ρ Π΄ΡΡΠ³ΠΈΠΌΠΈ ΡΡΡΠΎΠΈΡΠ΅Π»ΡΠ½ΡΠΌΠΈ ΠΌΠ°ΡΠ΅ΡΠΈΠ°Π»Π°ΠΌΠΈ (ΠΊΡΠ°ΡΠ½ΡΠΉ ΠΈ ΡΠΈΠ»ΠΈΠΊΠ°ΡΠ½ΡΠΉ) Π΄Π»Ρ ΡΠΎΠΊΠΎΠ»Ρ, ΠΊΠ΅ΡΠ°ΠΌΠΈΡΠ΅ΡΠΊΠΈΠΉ ΠΎΡΠ»ΠΈΡΠ°Π΅ΡΡΡ ΠΌΠ°ΠΊΡΠΈΠΌΠ°Π»ΡΠ½ΠΎΠΉ Π΄ΠΎΠ»Π³ΠΎΠ²Π΅ΡΠ½ΠΎΡΡΡΡ.
ΠΠ½ΠΎΠ³ΠΈΠ΅ ΠΏΡΠΎΠΈΠ·Π²ΠΎΠ΄ΠΈΡΠ΅Π»ΠΈ ΠΏΡΠ΅Π΄Π»Π°Π³Π°ΡΡ ΡΠ°Π·Π½ΡΠ΅ Π²ΠΈΠ΄Ρ ΠΊΠ΅ΡΠ°ΠΌΠΈΡΠ΅ΡΠΊΠΈΡ
ΠΊΠΈΡΠΏΠΈΡΠ΅ΠΉ, Π² ΠΊΠΎΡΠΎΡΡΡ
ΠΏΠΎΡΠΎΠΉ ΠΌΠΎΠΆΠ½ΠΎ Π·Π°ΠΏΡΡΠ°ΡΡΡΡ. ΠΠ· ΠΊΠ»ΠΈΠ½ΠΊΠ΅ΡΠ½ΡΡ
ΠΊΠΈΡΠΏΠΈΡΠ΅ΠΉ ΠΌΠΎΠΆΠ½ΠΎ Π²ΠΎΠ·Π²ΠΎΠ΄ΠΈΡΡ ΠΊΠ°ΠΊ ΡΠ°ΠΌ ΡΠΎΠΊΠΎΠ»Ρ, ΡΠ°ΠΊ ΠΈ Π΄ΡΡΠ³ΠΈΠ΅ ΡΡΡΠΎΠ΅Π½ΠΈΡ Π² ΡΠ°Π·Π½ΡΡ
ΠΊΠ»ΠΈΠΌΠ°ΡΠΈΡΠ΅ΡΠΊΠΈΡ
Π·ΠΎΠ½Π°Ρ
.
ΠΠ»Ρ ΠΏΡΠΎΠΈΠ·Π²ΠΎΠ΄ΡΡΠ²Π° ΠΊΠ»ΠΈΠ½ΠΊΠ΅ΡΠ½ΠΎΠ³ΠΎ ΠΊΠΈΡΠΏΠΈΡΠ° ΠΈΡΠΏΠΎΠ»ΡΠ·ΡΡΡ ΡΠΏΠ΅ΡΠΈΠ°Π»ΡΠ½ΡΠΉ Π²ΠΈΠ΄ Π³Π»ΠΈΠ½Ρ, ΡΠΏΠ΅ΠΊΠ°Π½ΠΈΠ΅ ΠΊΠΎΡΠΎΡΠΎΠΉΒ ΠΏΡΠΎΠΈΡΡ ΠΎΠ΄ΠΈΡ ΡΠΎΠ»ΡΠΊΠΎ ΠΏΡΠΈ Π²ΡΡΠΎΠΊΠΈΡ ΡΠ΅ΠΌΠΏΠ΅ΡΠ°ΡΡΡΠ°Ρ . ΠΠ±Π»Π°Π΄Π°Π΅Ρ ΠΈΠ½Π΅ΡΡΠ½ΠΎΡΡΡΡ ΠΊ Π²Π»Π°Π³Π΅ ΠΈ Π² ΡΠΎ ΠΆΠ΅ Π²ΡΠ΅ΠΌΡ Ρ ΠΎΡΠΎΡΠΈΠΌΠΈ ΠΏΡΠΎΡΠ½ΠΎΡΡΠ½ΡΠΌΠΈ ΠΏΠΎΠΊΠ°Π·Π°ΡΠ΅Π»ΡΠΌΠΈ.
ΠΠ΅ΡΠ°ΠΌΠΈΡΠ΅ΡΠΊΠΈΠΉ ΠΊΠΈΡΠΏΠΈΡ ΠΌΠΎΠΆΠ½ΠΎ ΠΈΡΠΏΠΎΠ»ΡΠ·ΠΎΠ²Π°ΡΡ Π΄Π»Ρ Π΄ΡΡΠ³ΠΈΡ ΠΊΠΎΠ½ΡΡΡΡΠΊΡΠΈΠΉ Π½Π° ΡΡΠ°ΡΡΠΊΠ΅: Π±Π°Π½ΠΈ, ΡΠ°ΡΠ½Ρ, Π±Π΅ΡΠ΅Π΄ΠΊΠΈ, ΡΡΡΠΎΠ΅Π½ΠΈΡ, ΠΎΠ±Π»Π°Π΄Π°ΡΡΠΈΠ΅ Ρ ΠΎΡΠΎΡΠΈΠΌΠΈ ΡΠ°Π±ΠΎΡΠΈΠΌΠΈ ΠΏΠΎΠΊΠ°Π·Π°ΡΠ΅Π»ΡΠΌΠΈ.
ΠΠ°ΠΊΠΎΠΉ ΠΊΠΈΡΠΏΠΈΡ ΠΈΡΠΏΠΎΠ»ΡΠ·ΠΎΠ²Π°ΡΡ Π΄Π»Ρ ΡΠΎΠΊΠΎΠ»Ρ, Π²ΡΠ²ΠΎΠ΄
ΠΡΠ΅ΠΆΠ΄Π΅ ΡΠ΅ΠΌ ΠΎΡΡΠ°Π½ΠΎΠ²ΠΈΡΡΡΡ Π½Π° ΡΠΎΠΌ ΠΈΠ»ΠΈ ΠΈΠ½ΠΎΠΌ Π²ΠΈΠ΄Π΅ ΠΌΠ°ΡΠ΅ΡΠΈΠ°Π»ΠΎΠ² Π΄Π»Ρ ΡΠΎΠΊΠΎΠ»Ρ, Π½Π΅ΠΎΠ±Ρ ΠΎΠ΄ΠΈΠΌΠΎ Π΄ΠΎΠΏΠΎΠ»Π½ΠΈΡΠ΅Π»ΡΠ½ΠΎ ΠΏΡΠΎΠΊΠΎΠ½ΡΡΠ»ΡΡΠΈΡΠΎΠ²Π°ΡΡΡΡ ΡΠΎ ΡΠΏΠ΅ΡΠΈΠ°Π»ΠΈΡΡΠΎΠΌ. Π£ Π½Π΅Π³ΠΎ ΡΠ·Π½Π°ΡΡ ΡΠΏΠ΅ΡΠΈΡΠΈΠΊΡ ΡΠ΅ΠΏΠ»ΠΎΠΈΠ·ΠΎΠ»ΡΡΠΈΠΈ ΠΈ Π³ΠΈΠ΄ΡΠΎΠΈΠ·ΠΎΠ»ΡΡΠΈΠΈ ΡΠΎΠΊΠΎΠ»ΡΠ½ΠΎΠΉ ΠΊΠΎΠ½ΡΡΡΡΠΊΡΠΈΠΈ.
ΠΡΠ»ΠΈ Π² Π²Π°ΡΠ΅ΠΉ ΠΏΠΎΡΡΡΠΎΠΉΠΊΠ΅ ΠΏΡΠ΅Π΄ΡΡΠΌΠΎΡΡΠ΅Π½ ΠΏΠΎΠ΄Π²Π°Π», ΡΠΎ Π΅Π³ΠΎ ΠΏΠΎΠ» Π΄ΠΎΠ»ΠΆΠ΅Π½ Π±ΡΡΡ ΡΠΎΠΆΠ΅ Π½Π°Π΄ΡΠΆΠ½ΠΎ ΠΈΠ·ΠΎΠ»ΠΈΡΠΎΠ²Π°Π½, ΡΡΠΎΠ±Ρ Π½Π΅ ΠΏΠΎΠ΄Π²Π΅ΡΠ³Π°ΡΡ ΡΠΎΠΊΠΎΠ»Ρ Π΄ΠΎΠΏΠΎΠ»Π½ΠΈΡΠ΅Π»ΡΠ½ΠΎΠΌΡ Π²ΠΎΠ·Π΄Π΅ΠΉΡΡΠ²ΠΈΡ Π²Π»Π°Π³ΠΈ ΡΠ½ΠΈΠ·Ρ.
ΠΡΡ, Π΄Π»Ρ ΡΠΎΠΊΠΎΠ»Ρ Ρ ΠΎΡΠΎΡΠΎ ΠΏΠΎΠ΄ΠΎΠΉΠ΄ΡΡ Π½ΠΎΠ²Π΅ΠΉΡΠΈΠΉ Π²ΠΈΠ΄ ΡΡΡΠΎΠΈΡΠ΅Π»ΡΠ½ΠΎΠ³ΠΎ ΠΌΠ°ΡΠ΅ΡΠΈΠ°Π»Π° — ΡΠ΅Π΄ΡΡΠΈΡΠΎΠ²Π°Π½Π½ΡΠΉ ΠΊΠΈΡΠΏΠΈΡ.
ΠΠΈΠ΄Π° ΠΊΠΈΡΠΏΠΈΡΠ°:
- ΠΠΎΡΠΈΠ·ΠΎΠ²Π°Π½Π½ΡΠΉ ΠΊΠΈΡΠΏΠΈΡ, ΡΠ²ΠΎΠΉΡΡΠ²Π°, ΠΏΡΠΈΠΌΠ΅Π½Π΅Π½ΠΈΠ΅
- ΠΡΡΡΠΎΡΠ΅Π»ΡΠΉ ΠΊΠΈΡΠΏΠΈΡ: ΠΎΠΏΡΠ΅Π΄Π΅Π»Π΅Π½ΠΈΠ΅, Π²ΠΈΠ΄Ρ, ΠΈΠ·Π³ΠΎΡΠΎΠ²Π»Π΅Π½ΠΈΠ΅
- Π‘ΠΈΠ»ΠΈΠΊΠ°ΡΠ½ΡΠΉ ΠΊΠΈΡΠΏΠΈΡ, ΠΏΡΠ΅ΠΈΠΌΡΡΠ΅ΡΡΠ²Π° ΠΈ Π½Π΅Π΄ΠΎΡΡΠ°ΡΠΊΠΈ, ΠΏΡΠΈΠΌΠ΅Π½Π΅Π½ΠΈΠ΅
- Π‘ΡΡΠ΅Ρ ΠΊΠΈΡΠΏΠΈΡ, ΡΠ΅Ρ Π½ΠΎΠ»ΠΎΠ³ΠΈΡ ΠΈΠ·Π³ΠΎΡΠΎΠ²Π»Π΅Π½ΠΈΡ, ΠΎΡΠΎΠ±Π΅Π½Π½ΠΎΡΡΠΈ
- Π§Π΅ΠΌ ΠΎΡΠ»ΠΈΡΠ°Π΅ΡΡΡ ΡΡΠ΄ΠΎΠ²ΠΎΠΉ ΠΊΠΈΡΠΏΠΈΡ ΠΎΡ Π»ΠΈΡΠ΅Π²ΠΎΠ³ΠΎ, ΡΡΠ°Π²Π½Π΅Π½ΠΈΠ΅
- Π§ΡΠΎ ΠΆΠ΅ ΡΠ°ΠΊΠΎΠ΅ ΡΠ°ΠΌΠΎΡΠ½ΡΠΉ ΠΊΠΈΡΠΏΠΈΡ
- Π§ΡΠΎ Π»ΡΡΡΠ΅ ΠΊΠΈΡΠΏΠΈΡ ΠΈΠ»ΠΈ Π³Π°Π·ΠΎΠ±Π»ΠΎΠΊ, ΡΠΊΠΎΠ»ΡΠΊΠΎ ΠΊΠΈΡΠΏΠΈΡΠ΅ΠΉ Π·Π°ΠΌΠ΅Π½ΡΡ Π³Π°Π·ΠΎΠ±Π»ΠΎΠΊ
ΡΠ΅Ρ Π½ΠΈΡΠ΅ΡΠΊΠΈΠ΅ Ρ Π°ΡΠ°ΠΊΡΠ΅ΡΠΈΡΡΠΈΠΊΠΈ, ΡΠ°Π·ΠΌΠ΅ΡΡ, ΡΠ΅Π½Π° Π·Π° ΠΌ3
ΠΡΠΈ Π²ΠΎΠ·Π²Π΅Π΄Π΅Π½ΠΈΠΈ Π΄ΠΎΠΌΠ° ΡΠ°ΡΡΠΎ ΠΏΠ»Π°Π½ΠΈΡΡΠ΅ΡΡΡ ΡΠΎΠΊΠΎΠ»ΡΠ½ΡΠΉ ΡΡΠ°ΠΆ, Π½Π°ΠΏΡΠΈΠΌΠ΅Ρ, Π΄Π»Ρ ΠΎΠ±ΡΡΡΡΠΎΠΉΡΡΠ²Π° ΠΌΠ°ΡΡΠ΅ΡΡΠΊΠΈΡ
ΠΈΠ»ΠΈ ΠΏΠΎΠ΄Π²Π°Π»ΡΠ½ΡΡ
ΠΏΠΎΠΌΠ΅ΡΠ΅Π½ΠΈΠΉ. ΠΡΠΎΠΌΠ΅ ΠΈΡΠΊΠ»ΡΡΠΈΡΠ΅Π»ΡΠ½ΠΎ Π°ΡΡ
ΠΈΡΠ΅ΠΊΡΡΡΠ½ΡΡ
Π·Π°Π΄Π°Ρ ΠΊΠΈΡΠΏΠΈΡΠ½Π°Ρ ΠΊΠ»Π°Π΄ΠΊΠ° Π½Π΅ΡΠ΅Ρ ΠΈ ΡΡΠ½ΠΊΡΠΈΠΎΠ½Π°Π»ΡΠ½ΡΠ΅ Π½Π°Π³ΡΡΠ·ΠΊΠΈ β ΠΏΠΎΠ²ΡΡΠ°Π΅Ρ ΡΡΡΠΎΠΉΡΠΈΠ²ΠΎΡΡΡ ΡΡΠ΅Π½, ΠΏΡΠ΅Π΄ΠΎΡΠ²ΡΠ°ΡΠ°Π΅Ρ ΠΏΠΎΡΠ²Π»Π΅Π½ΠΈΠ΅ ΠΌΠΎΡΡΠΈΠΊΠΎΠ² Π²Π»Π°Π³ΠΈ ΠΈ ΡΡΡΠΎΡΡΠΈ, ΠΎΠΏΡΠΈΠΌΠΈΠ·ΠΈΡΡΠ΅Ρ ΡΡΠΈΠ»ΠΈΡ, ΠΏΠ΅ΡΠ΅Π΄Π°Π²Π°Π΅ΠΌΡΠ΅ ΡΡΠ½Π΄Π°ΠΌΠ΅Π½ΡΡ.
ΠΠ³Π»Π°Π²Π»Π΅Π½ΠΈΠ΅:
- ΠΠΈΠ΄Ρ ΠΈ ΠΎΠΏΠΈΡΠ°Π½ΠΈΠ΅
- Π‘ΡΠΎΠΈΠΌΠΎΡΡΡ
- Π’Π΅Ρ Π½ΠΎΠ»ΠΎΠ³ΠΈΡ ΠΌΠΎΠ½ΡΠ°ΠΆΠ°
Π Π°Π·Π½ΠΎΠ²ΠΈΠ΄Π½ΠΎΡΡΠΈ
ΠΠ»Ρ ΠΈΠ·Π³ΠΎΡΠΎΠ²Π»Π΅Π½ΠΈΡΒ ΠΏΠΎΠ΄Π±ΠΈΡΠ°ΡΡ ΡΠ»Π΅Π΄ΡΡΡΠΈΠ΅ ΠΌΠ°ΡΠ΅ΡΠΈΠ°Π»Ρ:
- ΠΠ΅ΡΠ°ΠΌΠΈΠΊΡ.
- ΠΠ±ΠΎΠΆΠΆΠ΅Π½Π½ΡΡ Π³Π»ΠΈΠ½Ρ (ΠΊΡΠ°ΡΠ½ΡΡ ΠΈΠ»ΠΈ Π±Π΅Π»ΡΡ).
- ΠΠ»ΠΈΠ½ΠΊΠ΅Ρ.
- ΠΡΠΊΡΡΡΡΠ²Π΅Π½Π½ΡΠΉ ΠΊΠ°ΠΌΠ΅Π½Ρ.
ΠΡΠ±ΠΎΡ ΠΎΠΏΡΠ΅Π΄Π΅Π»ΡΠ΅ΡΡΡ ΡΡΠ»ΠΎΠ²ΠΈΡΠΌΠΈ Π²ΠΎΠ·Π²Π΅Π΄Π΅Π½ΠΈΡ ΠΈ ΡΠΊΡΠΏΠ»ΡΠ°ΡΠ°ΡΠΈΠΈ Π΄ΠΎΠΌΠ°, ΡΡΡΠ΅ΡΠΈΡΠ΅ΡΠΊΠΈΠΌΠΈ ΡΠΎΠΎΠ±ΡΠ°ΠΆΠ΅Π½ΠΈΡΠΌΠΈ Π·Π°ΡΡΡΠΎΠΉΡΠΈΠΊΠ°, ΡΠ΅Π½ΠΎΠΉ.
ΠΠΊΡΠΏΠ»ΡΠ°ΡΠ°ΡΠΈΠΎΠ½Π½ΡΠΌΠΈ ΠΏΠΎΠΊΠ°Π·Π°ΡΠ΅Π»ΡΠΌΠΈ ΠΊΠΈΡΠΏΠΈΡΠ°, ΠΈΡΠΏΠΎΠ»ΡΠ·ΡΠ΅ΠΌΠΎΠ³ΠΎ Π΄Π»Ρ ΡΠΎΠΊΠΎΠ»Π΅ΠΉ, ΡΡΠΈΡΠ°ΡΡΡΡ:
- ΠΡΠΎΡΠ½ΠΎΡΡΡ (Π² ΡΠΎΠΌ ΡΠΈΡΠ»Π΅, ΠΈ ΠΏΡΠΈ ΡΠΈΠΊΠ»ΠΈΡΠ΅ΡΠΊΠΈΡ Π½Π°Π³ΡΡΠ·ΠΊΠ°Ρ ).
- ΠΠΎΡΠΎΠ·ΠΎΡΡΠΎΠΉΠΊΠΎΡΡΡ.
- ΠΠΎΡΠΈΡΡΠΎΡΡΡ.
- ΠΠΎΡΡΡΠΈΡΠΈΠ΅Π½Ρ ΡΠ΅ΠΌΠΏΠ΅ΡΠ°ΡΡΡΠ½ΠΎΠ³ΠΎ ΡΠ°ΡΡΠΈΡΠ΅Π½ΠΈΡ.
- Π£Π΄ΠΎΠ±ΠΎΡΠΊΠ»Π°Π΄ΡΠ²Π°Π΅ΠΌΠΎΡΡΡ.
- ΠΡΡΠ΅ΡΠΈΡΠ΅ΡΠΊΠΈΠ΅ ΡΠ°ΠΊΡΠΎΡΡ.
Π‘ΠΎΠΏΠΎΡΡΠ°Π²ΠΈΠΌ ΠΏΠΎ ΡΡΠΈΠΌ ΠΏΠΎΠ·ΠΈΡΠΈΡΠΌ ΠΏΠ°ΡΠ°ΠΌΠ΅ΡΡΡ Π²ΡΠ΅Ρ ΠΌΠ°ΡΠ΅ΡΠΈΠ°Π»ΠΎΠ², ΠΏΡΠΈΠ³ΠΎΠ΄Π½ΡΡ Π΄Π»Ρ ΠΊΠ»Π°Π΄ΠΊΠΈ ΡΠΎΠΊΠΎΠ»Ρ Π΄ΠΎΠΌΠ°.
1. ΠΠ΅ΡΠ°ΠΌΠΈΠΊΠ°.
ΠΠ·Π΄Π΅Π»ΠΈΡ, ΠΏΡΠΎΠΈΠ·Π²Π΅Π΄Π΅Π½Π½ΡΠ΅ ΠΈΠ· ΠΊΠ»ΠΈΠ½ΠΊΠ΅ΡΠ°, Ρ Π°ΡΠ°ΠΊΡΠ΅ΡΠΈΠ·ΡΡΡΡΡ Π½Π°ΠΈΠ±ΠΎΠ»ΡΡΠΈΠΌΠΈ ΠΏΠΎΠΊΠ°Π·Π°ΡΠ΅Π»ΡΠΌΠΈ ΡΡΠΎΠΉΠΊΠΎΡΡΠΈ, ΡΠ΅ΠΌΡ ΡΠΏΠΎΡΠΎΠ±ΡΡΠ²ΡΡΡ ΠΎΡΠΎΠ±ΡΠ΅ ΡΠ΅Ρ Π½ΠΎΠ»ΠΎΠ³ΠΈΠΈ ΠΎΠ±ΠΆΠΈΠ³Π° ΠΏΡΠΎΠ΄ΡΠΊΡΠΈΠΈ. ΠΡΠΎΡΠ½ΠΎΡΡΡ ΠΈ ΠΏΠ»ΠΎΡΠ½ΠΎΡΡΡ ΡΠ°ΠΊΠΎΠ³ΠΎ ΠΊΠΈΡΠΏΠΈΡΠ° Π²Π·Π°ΠΈΠΌΠΎΡΠ²ΡΠ·Π°Π½Ρ. Π Π°Π±ΠΎΡΡ ΠΎΠ±ΡΡΠ½ΠΎ Π΄ΠΎΠ²Π΅ΡΡΡΡ ΡΠΏΠ΅ΡΠΈΠ°Π»ΠΈΡΡΠ°ΠΌ Π²ΡΡΠΎΠΊΠΎΠΉ ΠΊΠ²Π°Π»ΠΈΡΠΈΠΊΠ°ΡΠΈΠΈ; Π»ΠΎΠ³ΠΈΡΠ½ΠΎ, ΡΡΠΎ ΠΎΠ±ΠΎΠΉΠ΄ΡΡΡΡ ΠΎΠ½ΠΈ Π΄ΠΎΡΠΎΠΆΠ΅. Π‘ ΠΏΡΠΈΠ²Π»Π΅ΠΊΠ°ΡΠ΅Π»ΡΠ½ΠΎΡΡΡΡ Ρ ΠΊΠ»ΠΈΠ½ΠΊΠ΅ΡΠ° ΡΠΎΠΆΠ΅ Π½Π΅ ΠΎΡΠ΅Π½Ρ β Π² Ρ ΠΎΠ΄Ρ ΠΏΡΠ΅ΠΈΠΌΡΡΠ΅ΡΡΠ²Π΅Π½Π½ΠΎ ΠΎΡΡΠ΅Π½ΠΊΠΈ ΠΎΡ ΠΊΠΎΡΠΈΡΠ½Π΅Π²ΠΎΠ³ΠΎ Π΄ΠΎ ΠΊΠΈΡΠΏΠΈΡΠ½ΠΎ-ΠΊΡΠ°ΡΠ½ΠΎΠ³ΠΎ, Π° ΠΌΠ°ΡΠ΅ΡΠΈΠ°Π» Π±ΠΎΠ»Π΅Π΅ ΡΠ²Π΅ΡΠ»ΡΡ ΡΠ°ΡΡΠ²Π΅ΡΠΎΠΊ Π²ΡΡΡΠ΅ΡΠ°Π΅ΡΡΡ ΡΠΎΠ»ΡΠΊΠΎ Π² ΠΈΠΌΠΏΠΎΡΡΠ½ΡΡ ΠΏΡΠ΅Π΄Π»ΠΎΠΆΠ΅Π½ΠΈΡΡ .
ΠΠ΅ΡΠ°ΠΌΠΈΡΠ΅ΡΠΊΠ°Ρ ΠΏΡΠΎΠ΄ΡΠΊΡΠΈΡ, ΠΈΠ·Π³ΠΎΡΠ°Π²Π»ΠΈΠ²Π°Π΅ΠΌΠ°Ρ Π½Π° ΠΎΡΠ½ΠΎΠ²Π΅ ΠΏΡΠΎΡΠΈΡ
ΠΊΠΎΠΌΠΏΠΎΠ·ΠΈΡΠΈΠΉ, ΠΎΡΠ»ΠΈΡΠ°Π΅ΡΡΡ ΠΎΠ΄Π½ΠΈΠΌ ΠΎΠ±ΡΠΈΠΌ ΠΎΠ³ΡΠ°Π½ΠΈΡΠ΅Π½ΠΈΠ΅ΠΌ β Π²ΡΠ΅ ΠΎΠ½ΠΈ Π°Π΄Π°ΠΏΡΠΈΡΠΎΠ²Π°Π½Ρ ΠΏΠΎΠ΄ ΠΏΡΠΈΠΌΠ΅Π½Π΅Π½ΠΈΠ΅ Π² ΡΡΠ»ΠΎΠ²ΠΈΡΡ
ΡΡΠ΅Π΄Π½Π΅ΠΉ ΠΈ Π²ΡΡΠΎΠΊΠΎΠΉ Π²Π»Π°ΠΆΠ½ΠΎΡΡΠΈ. ΠΡΠΎ ΠΎΠ±ΡΡΡΠ½ΡΠ΅ΡΡΡ ΡΠ΅Ρ
Π½ΠΎΠ»ΠΎΠ³ΠΈΠ΅ΠΉ ΠΈΠ·Π³ΠΎΡΠΎΠ²Π»Π΅Π½ΠΈΡ Π±ΠΎΠ»ΡΡΠΈΠ½ΡΡΠ²Π° ΡΠΎΡΡΠΎΠ². ΠΠ΅ΡΠ°ΠΌΠΈΠΊΠ° ΠΏΡΠΈΠ³ΠΎΠ΄Π½Π° Π΄Π»Ρ ΠΎΠ±ΡΡΡΡΠΎΠΉΡΡΠ²Π° Π»ΡΠ±ΠΎΠΉ ΡΠΎΠ»ΡΠΈΠ½Ρ ΠΊΠ»Π°Π΄ΠΊΠΈ, ΠΏΠΎΡΠΊΠΎΠ»ΡΠΊΡ Π΄ΠΎΡΡΡΠΏΠ½Π° Π² ΡΠΈΡΠΎΠΊΠΎΠΉ Π³Π°ΠΌΠΌΠ΅ ΡΠ°Π·ΠΌΠ΅ΡΠΎΠ² ΠΈ ΠΈΡΠΏΠΎΠ»Π½Π΅Π½ΠΈΠΉ.
ΠΡΠ»ΠΈ ΡΠΎΠΊΠΎΠ»Ρ Π²ΡΠ΅ΠΌΡ ΠΎΡ Π²ΡΠ΅ΠΌΠ΅Π½ΠΈ ΠΏΠΎΠ΄Π²Π΅ΡΠ³Π°Π΅ΡΡΡ ΠΈΠ·ΠΌΠ΅Π½Π΅Π½ΠΈΡ Π²Π½Π΅ΡΠ½ΠΈΡ Π½Π°Π³ΡΡΠ·ΠΎΠΊ, ΡΠΎ ΠΎΠ½ ΡΠ΅ΡΡΠ΅Ρ ΡΠ²ΠΎΡ ΡΠ΅Π»ΠΎΡΡΠ½ΠΎΡΡΡ ΠΈ ΡΠ°ΡΡΡΠ΅ΡΠΊΠΈΠ²Π°Π΅ΡΡΡ, ΠΏΠΎΡΡΠΎΠΌΡ Π½ΡΠΆΠ΄Π°Π΅ΡΡΡ Π² ΠΎΠ±ΡΡΡΡΠΎΠΉΡΡΠ²Π΅ ΠΏΠ΅ΡΠΈΠΎΠ΄ΠΈΡΠ΅ΡΠΊΠΈΠΌΠΈ Π²ΡΡΠ°Π²ΠΊΠ°ΠΌΠΈ, Π½Π°ΠΏΡΠΈΠΌΠ΅Ρ, ΠΈΠ· ΡΠΎΠ³ΠΎ ΠΆΠ΅ ΠΊΠ»ΠΈΠ½ΠΊΠ΅ΡΠ°. Π¦Π΅Π½Π° Π²ΠΎΠΏΡΠΎΡΠ° Π²ΠΎΠ·ΡΠ°ΡΡΠ΅Ρ, Π½ΠΎ Π½Π΅ ΡΡΠΎΠ»Ρ ΡΠΈΠ»ΡΠ½ΠΎ, ΠΊΠ°ΠΊ ΠΏΡΠΈ Π²ΡΠΏΠΎΠ»Π½Π΅Π½ΠΈΠΈ ΡΠ°Π±ΠΎΡ Ρ ΠΈΡΠΏΠΎΠ»ΡΠ·ΠΎΠ²Π°Π½ΠΈΠ΅ΠΌ ΡΠ»Π΅ΠΌΠ΅Π½ΡΠΎΠ² ΠΏΠΎΠ²ΡΡΠ΅Π½Π½ΠΎΠΉ ΠΏΠ»ΠΎΡΠ½ΠΎΡΡΠΈ.
ΠΠ½ΠΎΠ³ΠΈΡ ΠΏΠΎΠ»ΡΠ·ΠΎΠ²Π°ΡΠ΅Π»Π΅ΠΉ ΠΏΠΎΠ΄ΠΊΡΠΏΠ°Π΅Ρ ΠΌΡΠ»ΡΡΠΈΠ²Π°ΡΠΈΠ°Π½ΡΠ½ΠΎΡΡΡ ΠΊΠ΅ΡΠ°ΠΌΠΈΡΠ΅ΡΠΊΠΈΡ ΠΈΠ·Π΄Π΅Π»ΠΈΠΉ β ΠΎΠ½ΠΈ ΠΌΠΎΠ³ΡΡ Π±ΡΡΡ Π»ΡΠ±ΠΎΠΉ ΡΠΎΠ»ΡΠΈΠ½Ρ ΠΈ Π²ΡΡΠΎΡΡ, Π³Π»Π°Π΄ΠΊΠΈΠΌΠΈ, Ρ ΡΠΈΡΠ»Π΅Π½ΠΎΠΉ ΠΏΠΎΠ²Π΅ΡΡ Π½ΠΎΡΡΡΡ, Π΄Π΅ΠΊΠΎΡΠΈΡΡΠ΅ΠΌΡΠΌΠΈ ΠΏΠΎΠ΄ ΠΊΠ°ΠΌΠ΅Π½Ρ, ΡΠ°ΠΉΠ΄ΠΈΠ½Π³.
2. ΠΠ±ΠΎΠΆΠΆΠ΅Π½Π½Π°Ρ Π³Π»ΠΈΠ½Π°.
ΠΠ»Ρ ΠΊΠ»Π°Π΄ΠΊΠΈ ΠΏΡΠΈΠ³ΠΎΠ΄Π½Ρ ΡΠΈΠ»ΠΈΠΊΠ°ΡΠ½ΡΠΉ (Π±Π΅Π»ΡΠΉ) ΠΈ ΠΎΠ±ΡΡΠ½ΡΠΉ ΠΊΡΠ°ΡΠ½ΡΠΉ ΠΊΠΈΡΠΏΠΈΡ. ΠΠΎΡΠΊΠΎΠ»ΡΠΊΡ ΠΏΠΎΡΡΠ΅Π±ΠΈΡΠ΅Π»ΡΡΠΊΠΈΠ΅ ΡΠ²ΠΎΠΉΡΡΠ²Π° ΡΠ°ΠΊΠΎΠΉ ΠΏΡΠΎΠ΄ΡΠΊΡΠΈΠΈ Π½Π°Ρ
ΠΎΠ΄ΡΡΡΡ Π² ΡΡΠ΄Ρ ΡΡΠ΅Π΄Π½ΠΈΡ
, ΡΠΎ Ρ ΡΡΡΡΠΎΠΌ ΡΠΏΠ΅ΡΠΈΡΠΈΡΠ΅ΡΠΊΠΈΡ
ΠΎΡΠΎΠ±Π΅Π½Π½ΠΎΡΡΠ΅ΠΉ ΡΠΊΡΠΏΠ»ΡΠ°ΡΠ°ΡΠΈΠΈ ΠΈΠ·Π΄Π΅Π»ΠΈΡ Π½ΡΠΆΠ΄Π°ΡΡΡΡ Π² Π΄ΠΎΠΏΠΎΠ»Π½ΠΈΡΠ΅Π»ΡΠ½ΠΎΠΉ Π·Π°ΡΠΈΡΠ΅ ΠΎΡ Π½Π΅Π±Π»Π°Π³ΠΎΠΏΡΠΈΡΡΠ½ΡΡ
Π²Π½Π΅ΡΠ½ΠΈΡ
ΡΠ°ΠΊΡΠΎΡΠΎΠ². Π‘ΠΈΠ»ΠΈΠΊΠ°Ρ, Π² ΡΠ°ΡΡΠ½ΠΎΡΡΠΈ, ΠΏΡΠΈΠ³ΠΎΠ΄Π΅Π½ Π΄Π»Ρ ΠΎΠ±ΡΡΡΡΠΎΠΉΡΡΠ²Π° ΡΠΎΠΊΠΎΠ»Π΅ΠΉ Π½Π° ΠΌΠ°Π»ΠΎΠ²Π»Π°ΠΆΠ½ΡΡ
Π³ΡΡΠ½ΡΠ°Ρ
. Π‘ ΠΎΠ³ΠΎΠ²ΠΎΡΠΊΠΎΠΉ β ΠΏΡΠΈΠΌΠ΅Π½Π΅Π½ΠΈΠ΅ ΠΎΡΠΎΠ±ΠΎ Π½Π°Π΄ΡΠΆΠ½ΠΎΠΉ Π³ΠΈΠ΄ΡΠΎΠΈΠ·ΠΎΠ»ΡΡΠΈΠΈ β Π΅Π³ΠΎ ΠΌΠΎΠΆΠ½ΠΎ ΠΈΡΠΏΠΎΠ»ΡΠ·ΠΎΠ²Π°ΡΡ ΠΈ Π² ΠΈΠ½ΡΡ
ΡΠΈΡΡΠ°ΡΠΈΡΡ
, Π½ΠΎ ΠΊΠΎΠ½ΡΠΈΠ³ΡΡΠ°ΡΠΈΡ ΠΏΡΠ΅Π΄ΡΡΠΌΠ°ΡΡΠΈΠ²Π°Π΅ΡΡΡ ΡΡΡΠΎΠ³ΠΎ ΠΎΠΏΡΠ΅Π΄Π΅Π»Π΅Π½Π½ΠΎΠΉ. ΠΠ°ΠΏΡΠΈΠΌΠ΅Ρ, ΡΠΊΠ»ΠΎΠ½ Π²ΡΠΏΠΎΠ»Π½ΡΡΡ ΡΠΎΠ»ΡΠΊΠΎ ΠΏΠΎΠ»ΠΎΠΆΠΈΡΠ΅Π»ΡΠ½ΡΠΌ, ΠΈ Π½Π΅ ΠΌΠ΅Π½Π΅Π΅ 12-15Β° (ΡΠ°ΠΊ ΠΎΠ±Π΅ΡΠΏΠ΅ΡΠΈΠ²Π°Π΅ΡΡΡ Π΅ΡΡΠ΅ΡΡΠ²Π΅Π½Π½ΡΠΉ ΡΡΠΎΠΊ Π²Π»Π°Π³ΠΈ ΠΏΠΎ ΠΏΠΎΠ²Π΅ΡΡ
Π½ΠΎΡΡΠΈ ΡΠΈΠ»ΠΈΠΊΠ°ΡΠ½ΠΎΠ³ΠΎ ΡΠ»Π΅ΠΌΠ΅Π½ΡΠ°). ΠΠ΅Π΄ΠΎΠΏΡΡΡΠΈΠΌΡ ΠΊΠ°ΠΊΠΈΠ΅-Π»ΠΈΠ±ΠΎ ΠΊΠ°ΡΠΌΠ°Π½Ρ, ΠΏΠΎΠ΄Π½ΡΡΡΠ΅Π½ΠΈΡ, ΠΈ Π²ΠΎΠΎΠ±ΡΠ΅ Π²ΡΠ΅ ΡΠΎ, ΡΡΠΎ ΠΏΡΠΎΠ²ΠΎΡΠΈΡΡΠ΅Ρ Π΄Π»ΠΈΡΠ΅Π»ΡΠ½ΠΎΠ΅ Π½Π°ΠΊΠ°ΠΏΠ»ΠΈΠ²Π°Π½ΠΈΠ΅ Π°ΡΠΌΠΎΡΡΠ΅ΡΠ½ΡΡ
ΠΎΡΠ°Π΄ΠΊΠΎΠ².
Π―Π²Π½ΠΎΠ΅ ΠΏΡΠ΅ΠΈΠΌΡΡΠ΅ΡΡΠ²ΠΎ Π΄Π°Π½Π½ΠΎΠ³ΠΎ Π²Π°ΡΠΈΠ°Π½ΡΠ° ΠΏΠΎ ΡΡΠ°Π²Π½Π΅Π½ΠΈΡ Ρ ΠΊΠ΅ΡΠ°ΠΌΠΈΠΊΠΎΠΉ β ΠΌΠ΅Π½ΡΡΠ°Ρ ΡΠ΅Π½Π° ΠΊΠ°ΠΊ ΡΠ°ΠΌΠΎΠ³ΠΎ ΠΊΠΈΡΠΏΠΈΡΠ°, ΡΠ°ΠΊ ΠΈ ΡΠ°Π±ΠΎΡ ΠΏΠΎ Π΅Π³ΠΎ ΡΠΊΠ»Π°Π΄ΠΊΠ΅. ΠΠΎΡΡΠΎΠΌΡ, Π΅ΡΠ»ΠΈ Π²Π°Ρ Π΄ΠΎΠΌ ΡΠ°ΡΠΏΠΎΠ»ΠΎΠΆΠ΅Π½ Π½Π° Π²ΠΎΠ·Π²ΡΡΠ΅Π½ΠΈΠΈ ΠΈΠ»ΠΈ Ρ ΠΎΠ»ΠΌΠ΅, ΡΠΎ ΠΈΡΠΏΠΎΠ»ΡΠ·ΠΎΠ²Π°Π½ΠΈΠ΅ ΡΠΈΠ»ΠΈΠΊΠ°ΡΠ° β ΡΡΠΎ ΠΏΡΠ°Π²ΠΈΠ»ΡΠ½ΠΎΠ΅ ΡΠ΅ΡΠ΅Π½ΠΈΠ΅.
ΠΡΠ°ΡΠ½ΡΠΉ Π±Π»ΠΎΠΊ ΡΡΠΈΡΠ°Π΅ΡΡΡ Π½Π°ΠΈΠ±ΠΎΠ»Π΅Π΅ Π±ΡΠ΄ΠΆΠ΅ΡΠ½ΡΠΌ Π²Π°ΡΠΈΠ°Π½ΡΠΎΠΌ Π΄Π»Ρ ΠΎΠ±ΡΡΡΡΠΎΠΉΡΡΠ²Π° ΡΠΎΠΊΠΎΠ»Ρ. ΠΡΠ°Π΄Π°ΡΠΈΡ ΡΠ°Π·ΠΌΠ΅ΡΠΎΠ² β ΡΠ°ΠΌΠ°Ρ ΡΠΈΡΠΎΠΊΠ°Ρ, Π° ΡΠΊΡΠΏΠ»ΡΠ°ΡΠ°ΡΠΈΠΎΠ½Π½ΡΠ΅ ΠΏΠΎΠΊΠ°Π·Π°ΡΠ΅Π»ΠΈ Π΄Π°Π½Π½ΠΎΠ³ΠΎ ΠΌΠ°ΡΠ΅ΡΠΈΠ°Π»Π° Π²ΠΏΠΎΠ»Π½Π΅ ΡΠΌΠΎΠ³ΡΡ ΡΠΎΠΎΡΠ²Π΅ΡΡΡΠ²ΠΎΠ²Π°ΡΡ Π±ΠΎΠ»ΡΡΠΈΠ½ΡΡΠ²Ρ ΡΡΠ΅Π±ΠΎΠ²Π°Π½ΠΈΠΉ. ΠΠ΄Π΅ΡΡ ΠΎΡΠΎΠ±ΠΎ ΡΡΠ°ΡΠ΅Π»ΡΠ½ΠΎ Π½ΡΠΆΠ½ΠΎ Π²ΡΠ±ΠΈΡΠ°ΡΡ ΠΌΠ°ΡΠΊΡ. ΠΠ°ΠΏΡΠΈΠΌΠ΅Ρ, ΠΊΠΈΡΠΏΠΈΡ Π-150, Π΄Π»Ρ ΡΡΡΠΎΠΈΡΠ΅Π»ΡΡΡΠ²Π° Π½Π΅ ΠΏΠΎΠ΄ΠΎΠΉΠ΄Π΅Ρ, ΠΏΠΎΡΠΊΠΎΠ»ΡΠΊΡ Π½Π΅ Π³Π°ΡΠ°Π½ΡΠΈΡΡΠ΅Ρ Π²ΡΡΠΎΠΊΡΡ ΠΌΠΎΡΠΎΠ·ΠΎΡΡΠΎΠΉΠΊΠΎΡΡΡ. Π ΡΠ΅Π·ΡΠ»ΡΡΠ°ΡΠ΅ Π½Π΅ΠΊΠΎΡΠΎΡΡΠ΅ ΡΡΠ°ΡΡΠΊΠΈ ΠΏΠΎΡΠ»Π΅ Π³ΠΎΠ΄Π° ΡΠΊΡΠΏΠ»ΡΠ°ΡΠ°ΡΠΈΠΈ Π½Π°ΡΠ½ΡΡ ΡΠ°Π·ΡΡΡΠ°ΡΡΡΡ. ΠΠ»Ρ ΠΌΠ°ΡΠΊΠΈ ΠΎΡ Π-250 ΠΈ Π²ΡΡΠ΅ Π·Π° ΡΡΡΠΎΠΉΡΠΈΠ²ΠΎΡΡΡ ΠΈ ΡΠ΅Π»ΠΎΡΡΠ½ΠΎΡΡΡ ΠΌΠΎΠΆΠ½ΠΎ Π½Π΅ Π±Π΅ΡΠΏΠΎΠΊΠΎΠΈΡΡΡΡ. ΠΠΎΠΊΡΠΏΠ°ΡΡ ΠΏΡΠΎΠ΄ΡΠΊΡΠΈΡ Π½Π΅ΠΎΠ±Ρ
ΠΎΠ΄ΠΈΠΌΠΎ ΡΠΎΠ»ΡΠΊΠΎ Ρ ΡΠ΅ΡΡΠΈΡΠΈΡΠΈΡΠΎΠ²Π°Π½Π½ΡΡ
ΠΏΡΠΎΠΈΠ·Π²ΠΎΠ΄ΠΈΡΠ΅Π»Π΅ΠΉ: Π΅Π΅ ΡΠ΅Π½Π°, ΡΠ°Π·ΡΠΌΠ΅Π΅ΡΡΡ, Π±ΡΠ΄Π΅Ρ Π²ΡΡΠ΅, Π·Π°ΡΠΎ ΠΈ ΡΠ°Π²Π½ΠΎΠΌΠ΅ΡΠ½ΠΎΡΡΡ Ρ
Π°ΡΠ°ΠΊΡΠ΅ΡΠΈΡΡΠΈΠΊ Π² ΠΏΡΠ΅Π΄Π΅Π»Π°Ρ
Π²ΡΠ΅Ρ
Π·Π°ΠΊΠ°Π·Π°Π½Π½ΡΡ
ΠΏΠ°ΡΡΠΈΠΉ ΠΌΠΎΠΆΠ΅Ρ Π±ΡΡΡ Π³Π°ΡΠ°Π½ΡΠΈΡΠΎΠ²Π°Π½Π°.
3. ΠΡΠΊΡΡΡΡΠ²Π΅Π½Π½ΡΠΉ ΠΊΠ°ΠΌΠ΅Π½Ρ.
ΠΠΎΠ΄Π±ΠΈΡΠ°Ρ ΡΠΎΡΠΌΡ ΠΈ Π³Π°Π±Π°ΡΠΈΡΡ, ΠΌΠΎΠΆΠ½ΠΎ Π΅Π³ΠΎ ΠΈΡΠΏΠΎΠ»ΡΠ·ΠΎΠ²Π°ΡΡ ΠΊΠ°ΠΊ ΡΠ΅Π»ΠΎΡΡΠ½ΡΠΉ ΡΡΠ°Π³ΠΌΠ΅Π½Ρ Π΄ΠΎΠΌΠ°, Π·Π°Π±ΠΎΡΠ°, ΠΎΠ³ΡΠ°Π΄Ρ. ΠΡΠΊΡΡΡΡΠ²Π΅Π½Π½ΡΠ΅ ΠΌΠ°ΡΠ΅ΡΠΈΠ°Π»Ρ Ρ ΠΎΡΠΎΡΠΈ ΠΈ Π² ΠΊΠ°ΡΠ΅ΡΡΠ²Π΅ Π°Π»ΡΡΠ΅ΡΠ½Π°ΡΠΈΠ²Ρ ΡΠ°ΠΉΠ΄ΠΈΠ½Π³Ρ ΡΒ ΠΈΠΌΠΈΡΠ°ΡΠΈΠ΅ΠΉ ΠΊΠ»Π°Π΄ΠΊΠΈ. Π¦Π΅Π½Π° Π·Π°Π²Π΅Π΄ΠΎΠΌΠΎ ΠΎΠΊΠ°ΠΆΠ΅ΡΡΡ Π½ΠΈΠΆΠ΅ ΠΈΠ·-Π·Π° ΡΠ½ΠΈΠΆΠ΅Π½ΠΈΡ ΡΡΡΠ΄ΠΎΡΠΌΠΊΠΎΡΡΠΈ ΡΠ°Π±ΠΎΡ, Π²Π΅Π΄Ρ ΡΡΠ»ΠΎΠ²Π½ΡΠΉ ΡΠ°Π·ΠΌΠ΅Ρ ΠΊΠΈΡΠΏΠΈΡΠ° Π² Π΄Π°Π½Π½ΠΎΠΌ ΡΠ»ΡΡΠ°Π΅ Π±ΡΠ΄Π΅Ρ Π±ΠΎΠ»ΡΡΠ΅, Π° Π²ΡΡΠ°Π²ΠΎΠΊ ΠΈ ΠΏΠ΅ΡΠ΅Π²ΡΠ·ΠΎΠΊ ΠΎΠΆΠΈΠ΄Π°Π΅ΡΡΡ ΠΌΠ΅Π½ΡΡΠ΅.
ΠΠΊΡΠΏΠ»ΡΠ°ΡΠ°ΡΠΈΠΎΠ½Π½ΡΠ΅ Ρ
Π°ΡΠ°ΠΊΡΠ΅ΡΠΈΡΡΠΈΠΊΠΈ ΠΈΡΠΊΡΡΡΡΠ²Π΅Π½Π½ΠΎΠ³ΠΎ ΠΊΠ°ΠΌΠ½Ρ ΠΏΠΎ ΡΠ°ΠΊΠΈΠΌ ΠΏΠΎΠΊΠ°Π·Π°ΡΠ΅Π»ΡΠΌ ΠΊΠ°ΠΊ Π²Π»Π°Π³ΠΎ- ΠΈ ΠΌΠΎΡΠΎΠ·ΠΎΡΡΠΎΠΉΠΊΠΎΡΡΡ, ΠΏΠΎΡΠΈΡΡΠΎΡΡΡ ΠΈ ΠΏΡΠΎΡΠ½ΠΎΡΡΡ ΠΏΡΠ΅Π²ΠΎΡΡ
ΠΎΠ΄ΡΡ ΠΈΠ·Π΄Π΅Π»ΠΈΡ ΠΈΠ· ΠΎΠ±ΠΎΠΆΠΆΠ΅Π½Π½ΠΎΠΉ Π³Π»ΠΈΠ½Ρ, Π½ΠΎ ΡΡΡΡΠΏΠ°ΡΡ ΠΊΠ΅ΡΠ°ΠΌΠΈΠΊΠ΅ ΠΈ ΠΊΠ»ΠΈΠ½ΠΊΠ΅ΡΡ. ΠΠΎΡΠΊΠΎΠ»ΡΠΊΡ ΠΏΡΠΈ ΠΌΠΎΠ½ΡΠ°ΠΆΠ΅ ΡΠΎΠΊΠΎΠ»ΡΠ½ΠΎΠ³ΠΎ ΡΡΠ°ΠΆΠ° Π΅Π³ΠΎ Π³Π°Π±Π°ΡΠΈΡΡΒ ΡΠΆΠ΅ ΠΈΠ·Π²Π΅ΡΡΠ½Ρ, ΡΠΎ ΠΈ ΠΏΠ°ΡΠ°ΠΌΠ΅ΡΡΡ Π±Π»ΠΎΠΊΠΎΠ² Π»Π΅Π³ΠΊΠΎ ΠΌΠΎΠ³ΡΡ Π±ΡΡΡ ΡΠΎΠ³Π»Π°ΡΠΎΠ²Π°Π½Ρ. Π ΠΏΠΎΠ»ΡΠ·Ρ Π΄Π°Π½Π½ΠΎΠ³ΠΎ Π²Π°ΡΠΈΠ°Π½ΡΠ° Π³ΠΎΠ²ΠΎΡΠΈΡ ΠΈ ΡΠ°Π·Π½ΠΎΠΎΠ±ΡΠ°Π·ΠΈΠ΅Β ΡΠ°Π·ΠΌΠ΅ΡΠΎΠ², ΡΠ²Π΅ΡΠΎΠ² ΠΈ ΡΠ°ΠΊΡΡΡΡ ΠΈΡΠΊΡΡΡΡΠ²Π΅Π½Π½ΠΎΠ³ΠΎ ΠΊΠ°ΠΌΠ½Ρ.
Π Π°ΡΡΠ΅Π½ΠΊΠΈ
ΠΡΠΈΠ²Π΅Π΄Π΅ΠΌ ΡΠ²ΠΎΠ΄Π½ΡΡ ΡΠ°Π±Π»ΠΈΡΡ ΠΏΠΎΡΡΠ΅Π±ΠΈΡΠ΅Π»ΡΡΠΊΠΈΡ ΠΏΠ°ΡΠ°ΠΌΠ΅ΡΡΠΎΠ² ΠΌΠ°ΡΠ΅ΡΠΈΠ°Π»ΠΎΠ², ΠΊΠΎΡΠΎΡΡΠ΅ ΠΈΡΠΏΠΎΠ»ΡΠ·ΡΡΡΡΡ Π΄Π»Ρ ΡΠΎΠΎΡΡΠΆΠ΅Π½ΠΈΡ ΡΠΎΠΊΠΎΠ»ΡΠ½ΡΡ ΡΠ°ΡΡΠ΅ΠΉ Π·Π΄Π°Π½ΠΈΠΉ (ΡΠ΅Π½Ρ ΡΠΊΠ°Π·Π°Π½Ρ ΠΏΠΎ ΠΠΎΡΠΊΠ²Π΅):
ΠΠΈΠ΄ | ΠΡΠΎΡ-Π½ΠΎΡΡΡ, ΠΠΠ° | ΠΠΎΡΠΎΠ·ΠΎΡΡΠΎΠΉΠΊΠΎΡΡΡ. ΠΠ΅ ΠΌΠ΅Π½Π΅Π΅ ΡΠ΅ΠΏΠ»ΠΎΡΠΌΠ΅Π½ | ΠΠΎΡΠΈΡΡΠΎΡΡΡ, % | ΠΠ»ΠΎΡΠ½ΠΎΡΡΡ, Π³/ΡΠΌ3 | Π¦Π΅Π½Π° Π·Π° ΠΌ3, ΡΡΠ±Π»ΠΈ |
ΠΠ»ΠΈΠ½ΠΊΠ΅Ρ | 45-52 | 300 | 0,06-0,08 | 1,9-2,0 | 14000-18000 |
Π‘ΠΈΠ»ΠΈΠΊΠ°ΡΠ½ΡΠΉ ΠΊΠΈΡΠΏΠΈΡ (Π-250) | 25-35 | 75 | 0,08-0,12 | 1,6-1,8 | 4800-5200 |
ΠΡΠ°ΡΠ½ΡΠΉ (Π-250) | 24-32 | 200 | 0,08-0,12 | 1,7-1,9 | 3600-3800 |
ΠΠ΅ΡΠ°ΠΌΠΈΠΊΠ° | 25-30 | 250 | 0,06-0,10 | 1,5-1,9 | 2200-2400 |
ΠΡΠΊΡΡΡΡΠ²Π΅Π½Π½ΡΠΉ ΠΊΠ°ΠΌΠ΅Π½Ρ | 35-50 | 250 | 0,03-0,08 | 1,8-2,2 | 8700-12000 |
ΠΡΠ°Π²ΠΈΠ»Π° ΡΠΊΠ»Π°Π΄ΠΊΠΈ
ΠΠ»Ρ ΠΎΠ±Π΅ΡΠΏΠ΅ΡΠ΅Π½ΠΈΡ ΠΏΡΠΎΡΠ½ΠΎΡΡΠΈ ΠΈ Π΄ΠΎΠ»Π³ΠΎΠ²Π΅ΡΠ½ΠΎΡΡΠΈ ΡΠΎΠΊΠΎΠ»Ρ Π½Π΅ΠΎΠ±Ρ
ΠΎΠ΄ΠΈΠΌΠΎ Π²Π΅ΡΠ½ΠΎ ΡΡΡΠ°Π½ΠΎΠ²ΠΈΡΡ Π΅Π³ΠΎ ΡΠΈΡΠΈΠ½Ρ: ΡΠ°Π·ΠΌΠ΅ΡΠ΅Π½ΠΈΠ΅ Π΄ΠΎΠ»ΠΆΠ½Π° Π±ΡΡΡ Π² Π΄Π²Π° ΠΊΠΈΡΠΏΠΈΡΠ°, ΠΏΡΠΈ Π²ΡΡΠΎΡΠ΅ Π½Π΅ ΠΌΠ΅Π½Π΅Π΅ 400-450 ΠΌΠΌ. Π‘Π½Π°ΡΠ°Π»Π° ΠΎΠ±ΡΡΡΡΠ°ΠΈΠ²Π°ΡΡ ΡΠ³Π»ΠΎΠ²ΡΠ΅ ΡΠ»Π΅ΠΌΠ΅Π½ΡΡ, Π²ΡΠ²Π΅ΡΡΡ ΡΠ°Π·ΠΌΠ΅ΡΡ ΠΎΠ±ΡΠ°Π·ΡΡΡΠΈΡ
ΡΡ Π΄ΠΈΠ°Π³ΠΎΠ½Π°Π»Π΅ΠΉ ΠΈ ΡΠ»Π΅Π΄Ρ Π·Π° ΡΠ°Π²Π½ΠΎΠΌΠ΅ΡΠ½ΠΎΡΡΡΡ ΡΠ»ΠΎΠ΅Π². Π‘Π°ΠΌΠΎ Π²ΠΎΠ·Π²Π΅Π΄Π΅Π½ΠΈΠ΅ Π²ΡΠΏΠΎΠ»Π½ΡΡΡ Π½Π° ΠΎΠ±ΡΡΠ½ΠΎΠΌ ΡΠ΅ΠΌΠ΅Π½ΡΠ½ΠΎ-ΠΏΠ΅ΡΡΠ°Π½ΠΎΠΌ ΡΠ°ΡΡΠ²ΠΎΡΠ΅, ΠΎΠ΄Π½Π°ΠΊΠΎ ΠΏΠ΅ΡΠ΅Π²ΡΠ·ΠΊΡ ΠΏΡΠ΅Π΄ΡΡΠΌΠ°ΡΡΠΈΠ²Π°ΡΡ ΠΏΠΎ ΠΊΠ°ΠΆΠ΄ΠΎΠΌΡ ΡΡΠ΄Ρ, Π° ΠΌΠ°ΠΊΡΠΈΠΌΠ°Π»ΡΠ½ΡΡ ΡΠΈΡΠΈΠ½Ρ ΡΠ²ΠΎΠ² Π²ΡΠ΄Π΅ΡΠΆΠΈΠ²Π°ΡΡ Π½Π΅ Π±ΠΎΠ»Π΅Π΅ 8-12 ΠΌΠΌ. Π ΡΠ»ΡΡΠ°Π΅ ΡΠΈΠ»ΠΈΠΊΠ°ΡΠ° ΡΡΠΈΠ»ΠΈΡΡ ΠΎΡΠ½ΠΎΠ²Ρ ΠΌΠΎΠΆΠ½ΠΎ Π°ΡΠΌΠΈΡΠΎΠ²Π°Π½Π½ΠΎΠΉ ΡΠ΅ΡΠΊΠΎΠΉ ΠΈΠ· ΠΎΡΠΈΠ½ΠΊΠΎΠ²Π°Π½Π½ΠΎΠΉ ΠΏΡΠΎΠ²ΠΎΠ»ΠΎΠΊΠΈ.
Π Π·Π°Π²Π΅ΡΡΠ΅Π½ΠΈΠ΅ ΡΠ°Π±ΠΎΡ ΠΏΡΠΎΠΈΠ·Π²ΠΎΠ΄ΠΈΡΡΡ ΠΏΠΎΠΊΡΡΡΠΈΠ΅ Π³ΠΈΠ΄ΡΠΎΠΈΠ·ΠΎΠ»ΠΈΡΡΡΡΠ΅ΠΉ ΠΌΠ°ΡΡΠΈΠΊΠΎΠΉ ΠΈΠ»ΠΈ Π±ΠΈΡΡΠΌΠΎΠΌ, Π° Π² ΠΊΠ°ΡΠ΅ΡΡΠ²Π΅ ΡΠ΅ΠΏΠ»ΠΎΠΈΠ·ΠΎΠ»ΡΡΠΎΡΠ° ΠΏΡΠΈΠΌΠ΅Π½ΡΡΡ ΠΏΠ΅Π½ΠΎΠΏΠΎΠ»ΠΈΡΡΠΈΡΠΎΠ», ΠΏΠ΅ΡΠΈΠΎΠ΄ΠΈΡΠ΅ΡΠΊΠΈ ΠΎΠ±ΡΡΡΡΠ°ΠΈΠ²Π°ΡΡ Π²Π΅Π½ΡΠΈΠ»ΡΡΠΈΠΎΠ½Π½ΡΠ΅ ΠΎΡΠ²Π΅ΡΡΡΠΈΡ. Π¦ΠΎΠΊΠΎΠ»Ρ ΠΈΠ· ΡΠΈΠ»ΠΈΠΊΠ°ΡΠ½ΠΎΠ³ΠΎ/ΠΊΡΠ°ΡΠ½ΠΎΠ³ΠΎ ΠΊΠΈΡΠΏΠΈΡΠ° Π΄ΠΎΠΏΠΎΠ»Π½ΠΈΡΠ΅Π»ΡΠ½ΠΎ ΠΎΠ±ΡΠ°Π±Π°ΡΡΠ²Π°ΡΡ Π·Π°ΡΠΈΡΠ½ΡΠΌΠΈ ΡΠΈΠ»Π°Π½ΠΎ-ΠΊΡΠ΅ΠΌΠ½ΠΈΡΡΡΠΌΠΈ ΡΠΎΡΡΠ°Π²Π°ΠΌΠΈ ΡΡΠ΅Π±ΡΠ΅ΠΌΠΎΠΉ ΡΠ²Π΅ΡΠΎΠ²ΠΎΠΉ Π³Π°ΠΌΠΌΡ (ΡΠ΅Π½Π° Π·Π°Π²ΠΈΡΠΈΡ ΠΎΡ ΡΠΎΡΡΠ°Π²Π° ΠΊΡΠ°ΡΡΡΠΈΡ ΠΏΠΈΠ³ΠΌΠ΅Π½ΡΠΎΠ²), ΠΊΠ΅ΡΠ°ΠΌΠΈΠΊΠ° ΠΈ ΠΈΡΠΊΡΡΡΡΠ²Π΅Π½Π½ΡΠΉ ΠΊΠ°ΠΌΠ΅Π½Ρ Π² ΡΠ°ΠΊΠΎΠΉ ΠΎΠ±ΡΠ°Π±ΠΎΡΠΊΠ΅ Π½Π΅ Π½ΡΠΆΠ΄Π°ΡΡΡΡ.
Β
ΠΠ»Π°Π΄ΠΊΠ° ΡΠΎΠΊΠΎΠ»Ρ ΠΈΠ· ΠΊΠΈΡΠΏΠΈΡΠ° | Π‘ΡΡΠΎΠΈΡΠ΅Π»ΡΡΡΠ²ΠΎ Π±Π°Π½ΠΈ
Π¦ΠΎΠΊΠΎΠ»Ρ-ΡΡΠΎ Π½Π°Π΄Π·Π΅ΠΌΠ½Π°Ρ ΡΠ°ΡΡΡ Π΄ΠΎΠΌΠ° Π½Π°Π΄ ΡΡΠ½Π΄Π°ΠΌΠ΅Π½ΡΠΎΠΌ. ΠΠ³ΠΎ Π²Π΅ΡΡ
Π½ΡΡ ΠΎΡΠΌΠ΅ΡΠΊΠ°,ΠΎΠ±ΡΡΠ½ΠΎ,ΡΠ²Π»ΡΠ΅ΡΡΡ ΠΎΡΠΌΠ΅ΡΠΊΠΎΠΉ ΠΏΠΎΠ»Π° 1 ΡΡΠ°ΠΆΠ°. ΠΠΎΠ»ΡΡΠ°Π΅ΡΡΡ,ΡΡΠΎ ΡΠΎΠΊΠΎΠ»Ρ -ΡΡΠΎ ΡΠ°ΡΡΡ ΡΡΠ΅Π½Ρ Π΄ΠΎΠΌΠ°,ΠΊΠΎΡΠΎΡΠ°Ρ ΠΎΠ³ΡΠ°ΠΆΠ΄Π°Π΅Ρ ΠΏΠΎΠ΄ΠΏΠΎΠ»ΡΠ½ΠΎΠ΅ ΠΏΡΠΎΡΡΡΠ°Π½ΡΡΠ²ΠΎ.
Π‘ΠΎΠ΄Π΅ΡΠΆΠ°Π½ΠΈΠ΅:
ΠΠΎΠ΄ΠΏΠΎΠ»ΡΠ΅,ΠΏΠΎΠ΄Π²Π°Π» ΠΈΠ»ΠΈ ΡΠ΅Ρ ΡΡΠ°ΠΆ ΠΌΠΎΠΆΠ΅Ρ Π±ΡΡΡ Ρ ΠΎΠ»ΠΎΠ΄Π½ΡΠΌ ΠΈΠ»ΠΈ ΡΠ΅ΠΏΠ»ΡΠΌ. ΠΠ»Ρ ΡΠ°ΠΊ Π½Π°Π·ΡΠ²Π°Π΅ΠΌΠΎΠ³ΠΎ,ΡΠ΅ΠΏΠ»ΠΎΠ³ΠΎ ΠΏΠΎΠ΄ΠΏΠΎΠ»ΡΡ,Π½Π΅ΠΎΠ±Ρ ΠΎΠ΄ΠΈΠΌΠΎ ΡΠΎΠΊΠΎΠ»Ρ Π΄ΠΎΠΏΠΎΠ»Π½ΠΈΡΠ΅Π»ΡΠ½ΠΎ ΡΡΠ΅ΠΏΠ»ΡΡΡ. ΠΠΎ,Π² Π΄Π°Π½Π½ΠΎΠΉ ΡΡΠ°ΡΡΠ΅ Π±ΡΠ΄Π΅ΠΌ ΡΠ°ΡΡΠΌΠ°ΡΡΠΈΠ²Π°ΡΡ Ρ ΠΎΠ»ΠΎΠ΄Π½ΡΠΉ ΡΠΎΠΊΠΎΠ»Ρ,ΠΏΠΎΡΠΎΠΌΡ ΡΡΠΎ Π΄Π»Ρ ΠΏΡΠΎΡΡΠΎΠΉ,ΡΠ΅Π·ΠΎΠ½Π½ΠΎΠΉ Π±Π°Π½ΠΈ ΠΈΠ»ΠΈ Π΄ΠΎΠΌΠ° Π½Π° Π΄Π°ΡΠ΅,Π² ΡΠ΅ΠΏΠ»ΠΎΠΌ ΠΏΠΎΠ΄ΠΏΠΎΠ»ΡΠ΅ Π½Π΅ΠΎΠ±Ρ ΠΎΠ΄ΠΈΠΌΠΎΡΡΠΈ Π½Π΅Ρ.
ΠΠ°ΡΠ΅ΡΠΈΠ°Π» Π΄Π»Ρ ΡΠΎΠΊΠΎΠ»Ρ Β Π΄ΠΎΠΌΠ°
Π‘Π΅ΠΉΡΠ°Ρ ΡΡΡΠ΅ΡΡΠ²ΡΠ΅Ρ Π΄Π²Π° ΠΌΠ½Π΅Π½ΠΈΡ ΠΎ ΠΊΠΎΠ½ΡΡΡΡΠΊΡΠΈΠΈ ΡΠΎΠΊΠΎΠ»Ρ, ΠΊΠΎΠ³Π΄Π° Π²ΡΡΠ°Π΅Ρ Π²ΠΎΠΏΡΠΎΡ ΠΊΠ°ΠΊΠΎΠΉ Π²ΡΠ±ΡΠ°ΡΡ ΠΌΠ°ΡΠ΅ΡΠΈΠ°Π» Π΄Π»Ρ ΡΠΎΠΊΠΎΠ»Ρ Π΄ΠΎΠΌΠ°:
- ΡΠΎΠΊΠΎΠ»ΡΠ½Π°Ρ ΡΠ°ΡΡΡ Π΄Π΅Π»Π°Π΅ΡΡΡ Π±Π΅ΡΠΎΠ½Π½ΠΎΠΉ,ΠΊΠ°ΠΊ ΠΏΡΠΎΠ΄ΠΎΠ»ΠΆΠ΅Π½ΠΈΠ΅ ΠΌΠΎΠ½ΠΎΠ»ΠΈΡΠ½ΠΎΠ³ΠΎ ΡΡΠ½Π΄Π°ΠΌΠ΅Π½ΡΠ°
- ΡΠΎΠΊΠΎΠ»Ρ Π²ΡΠΊΠ»Π°Π΄ΡΠ²Π°Π΅ΡΡΡ ΠΈΠ· ΠΊΠΈΡΠΏΠΈΡΠ°
ΠΠ»Π°Π΄ΠΊΠ° ΠΊΠΈΡΠΏΠΈΡΠ½ΠΎΠ³ΠΎ ΡΠΎΠΊΠΎΠ»Ρ Π² ΠΏΡΠ΅ΠΆΠ½ΠΈΠ΅ Π²ΡΠ΅ΠΌΠ΅Π½Π° Π΄Π°ΠΆΠ΅ Π½Π΅ ΠΎΠ±ΡΡΠΆΠ΄Π°Π»Π°ΡΡ.Π¦ΠΎΠΊΠΎΠ»Ρ Π΄ΠΎΠ»ΠΆΠ΅Π½ Π±ΡΡΡ ΠΊΠΈΡΠΏΠΈΡΠ½ΡΠΌ ΠΈ ΡΠΎΡΠΊΠ°. ΠΡΠ΅ 10 Π»Π΅Ρ Π½Π°Π·Π°Π΄ Π½Π΅ Π±ΡΠ»ΠΎ ΡΠ°ΠΊΠΎΠΉ ΠΌΠΎΠ΄Ρ ΠΏΠΎΠ΄Π½ΠΈΠΌΠ°ΡΡ ΡΡΠ½Π΄Π°ΠΌΠ΅Π½Ρ Π²ΡΡΠ΅ 150ΠΌΠΌ Π½Π°Π΄ Π·Π΅ΠΌΠ»Π΅ΠΉ.
ΠΡΠ»ΠΈ ΡΡΠ°Π²Π½ΠΈΠ²Π°ΡΡ Π±Π΅ΡΠΎΠ½ ΠΈ ΠΊΠΈΡΠΏΠΈΡΠ½ΡΡ ΠΊΠ»Π°Π΄ΠΊΡ,ΡΠΎ ΠΏΠΎ ΡΠ΅ΠΏΠ»ΠΎΡΠ΅Ρ
Π½ΠΈΡΠ΅ΡΠΊΠΈΠΌ ΠΊΠ°ΡΠ΅ΡΡΠ²Π°ΠΌ,Π±Π΅Π· ΡΠΎΠΌΠ½Π΅Π½ΠΈΡ, ΠΊΠΈΡΠΏΠΈΡΠ½ΡΠΉ ΡΠΎΠΊΠΎΠ»Ρ Π²ΡΠΈΠ³ΡΡΠ²Π°Π΅Ρ. ΠΠΎΡΠΎΠΌΡ ΡΡΠΎ,Π΄Π»Ρ ΠΆΠΈΠ»ΠΎΠ³ΠΎ Π΄ΠΎΠΌΠ° Π²ΡΠΊΠ»Π°Π΄ΡΠ²Π°Π΅ΡΡΡ ΠΊΠΈΡΠΏΠΈΡΠ½ΡΠΉ ΡΠΎΠΊΠΎΠ»Ρ ΡΠΎΠ»ΡΠΈΠ½ΠΎΠΉ ΠΊΠ»Π°Π΄ΠΊΠΈ 510-640 ΠΌΠΌ. Π’Π°ΠΊΠ°Ρ ΡΠΎΠ»ΡΠΈΠ½Π° ΠΊΠΈΡΠΏΠΈΡΠ½ΠΎΠΉ ΡΡΠ΅Π½Ρ Π½Π΅ ΡΡΠ΅Π±ΡΠ΅Ρ Π΄ΠΎΠΏΠΎΠ»Π½ΠΈΡΠ΅Π»ΡΠ½ΠΎΠ³ΠΎ ΡΡΠ΅ΠΏΠ»Π΅Π½ΠΈΡ Π² ΡΠ½Π΅ΠΆΠ½ΡΡ
ΡΠ°ΠΉΠΎΠ½Π°Ρ
Π ΠΎΡΡΠΈΠΈ.
ΠΠΎ,Π²Π΅Π΄Ρ Π² ΠΏΠΎΡΠ»Π΅Π΄Π½Π΅Π΅ Π²ΡΠ΅ΠΌΡ Π² ΠΌΠΎΠ΄Ρ Π²ΠΎΡΠ»Π° ΡΠ΅Ρ Π½ΠΎΠ»ΠΎΠ³ΠΈΡ ΡΡΠ΅ΠΏΠ»Π΅Π½ΠΈΡ Π±Π΅ΡΠΎΠ½Π½ΡΡ ΡΡΠ΅Π½. Π ΡΡΠ° ΡΠ΅Ρ Π½ΠΎΠ»ΠΎΠ³ΠΈΡ ΡΠΎΠΊΠΎΠ»Ρ ΡΠ΅ΠΉΡΠ°Ρ ΠΏΡΠ΅Π΄ΠΏΠΎΡΡΠΈΡΠ΅Π»ΡΠ½Π΅Π΅ ΠΏΡΠΈ ΡΡΡΠΎΠΈΡΠ΅Π»ΡΡΡΠ²Π΅ ΠΊΠ°ΠΏΠΈΡΠ°Π»ΡΠ½ΠΎΠ³ΠΎ ΠΆΠΈΠ»ΠΎΠ³ΠΎ Π΄ΠΎΠΌΠ°,ΠΏΠΎΡΠΎΠΌΡ ΡΡΠΎ,ΠΎΠ΄Π½ΠΎΠ²ΡΠ΅ΠΌΠ΅Π½Π½ΠΎ Ρ ΡΡΠ΅ΠΏΠ»Π΅Π½ΠΈΠ΅ΠΌ ΡΠΎΠΊΠΎΠ»Ρ Π΄Π΅Π»Π°Π΅ΡΡΡ Π³ΠΎΡΠΈΠ·ΠΎΠ½ΡΠ°Π»ΡΠ½ΠΎΠ΅ ΡΡΠ΅ΠΏΠ»Π΅Π½ΠΈΠ΅ ΠΎΡΠΌΠΎΡΡΠΊΠΈ,ΡΡΠΎ Π΄Π°Π΅Ρ ΠΏΡΠ΅ΠΈΠΌΡΡΠ΅ΡΡΠ²ΠΎ Π² ΠΊΠ°ΡΠ΅ΡΡΠ²Π΅ Π·Π°ΡΠΈΡΠ½ΠΎΠ³ΠΎ ΠΌΠ΅ΡΠΎΠΏΡΠΈΡΡΠΈΡ Π΄Π»Ρ ΡΡΠ½Π΄Π°ΠΌΠ΅Π½ΡΠΎΠ² ΠΎΡ ΠΏΡΠΎΠΌΠ΅ΡΠ·Π°Π½ΠΈΡ.
ΠΡΠ»ΠΈ ΠΡ Π½Π΅ ΡΠΎΠ±ΠΈΡΠ°Π΅ΡΠ΅ΡΡ ΡΡΠ΅ΠΏΠ»ΡΡΡ Ρ Π½Π°ΡΡΠΆΠ½ΠΎΠΉ ΡΡΠΎΡΠΎΠ½Ρ Π΄ΠΎΠΌΠ° ΡΠΎΠΊΠΎΠ»ΡΠ½ΡΡ ΡΠ°ΡΡΡ ΡΡΠ΅Π½Ρ ΠΈ ΠΎΡΠΌΠΎΡΡΠΊΡ Π΄ΠΎΠΌΠ°,ΡΠΎ ΡΠΎΠ³Π΄Π° Π±Π΅Π· Π²Π°ΡΠΈΠ°Π½ΡΠΎΠ²,Π΄Π»Ρ Π²Π°Ρ ΠΏΠΎΠ΄ΠΎΠΉΠ΄Π΅Ρ ΠΊΠ»Π°Π΄ΠΊΠ° ΡΠΎΠΊΠΎΠ»Ρ ΠΈΠ· ΠΊΠΈΡΠΏΠΈΡΠ°:
- ΠΏΡΠΎΡΠ΅
- ΡΠ΅ΠΏΠ»Π΅Π΅
- Π΄Π΅ΡΠ΅Π²Π»Π΅
- Π½Π΅ ΡΡΠ΅Π±ΡΠ΅Ρ Π΄ΠΎΠΏΠΎΠ»Π½ΠΈΡΠ΅Π»ΡΠ½ΠΎΠΉ ΠΎΡΠ΄Π΅Π»ΠΊΠΈ
ΠΠΎ,ΡΡΠΎ ΡΡΠ±ΡΠ΅ΠΊΡΠΈΠ²Π½ΠΎΠ΅ ΠΌΠ½Π΅Π½ΠΈΠ΅.
ΠΡΠ»ΠΈ ΠΠ°ΠΌ ΠΏΡΠΎΡΠ΅ Π·Π°ΠΌΠΎΠ½ΠΎΠ»ΠΈΡΠΈΡΡ ΡΠΎΠΊΠΎΠ»Ρ, ΡΠΎ, ΠΊΠΎΠ½Π΅ΡΠ½ΠΎ, Π²ΡΠ±ΠΈΡΠ°ΠΉΡΠ΅ ΡΡΠΎΡ Π²Π°ΡΠΈΠ°Π½Ρ.ΠΠΎΡΠΎΠΌΡ ΡΡΠΎ ΠΈ Π² ΡΠΎΠΌ ΠΈ Π΄ΡΡΠ³ΠΎΠΌ Π²Π°ΡΠΈΠ°Π½ΡΠ΅,Π±Π°Π½Ρ -ΡΠΎΠΎΡΡΠΆΠ΅Π½ΠΈΠ΅,Π΄Π»Ρ ΠΊΠΎΡΠΎΡΠΎΠ³ΠΎ Π½Π΅ ΡΡΠ΅Π±ΡΠ΅ΡΡΡ Π²ΡΡΠΎΠΊΠΎΠ³ΠΎ ΠΏΠΎΠ΄ΠΏΠΎΠ»ΡΡ. Β ΠΠ°ΠΊΡΠΈΠΌΠ°Π»ΡΠ½Π°Ρ Π²ΡΡΠΎΡΠ° ΡΠΎΠΊΠΎΠ»Ρ Π΄Π»Ρ Π±Π°Π½ΠΈ 300-400ΠΌΠΌ.
Π Β Π² ΡΠ»ΡΡΠ°Π΅ Π²ΡΠ±ΠΎΡΠ° ΠΊΠΈΡΠΏΠΈΡΠ½ΠΎΠ³ΠΎ ΡΠΎΠΊΠΎΠ»Ρ Β Π΄Π»Ρ Π±Π°Π½ΠΈ ,Π²ΡΠ΅ ΡΠ°Π²Π½ΠΎ, Π΅Π³ΠΎ ΡΠΎΠ»ΡΠΈΠ½Π° Π±ΡΠ΄Π΅Ρ Π½Π΅ Π±ΠΎΠ»Π΅Π΅ 250ΠΌΠΌ(Π² ΠΊΠΈΡΠΏΠΈΡ),Π² ΡΠΈΠ»Ρ ΡΠΎΠ³ΠΎ,ΡΡΠΎ Π½Π΅ ΡΡΠ΅Π±ΡΠ΅ΡΡΡ Π΄Π΅Π»Π°ΡΡ ΡΠΈΡΠΎΠΊΠΎΠ³ΠΎ ΡΡΠ½Π΄Π°ΠΌΠ΅Π½ΡΠ° ΠΏΠΎΠ΄ ΡΡΡΠ± ΠΈΠ· Π±ΡΠ΅Π²Π΅Π½ 200-240ΠΌΠΌ. Π ΡΠ°ΠΊΠ°Ρ ΡΠΎΠ»ΡΠΈΠ½Π° ΠΊΠΈΡΠΏΠΈΡΠ½ΠΎΠΉ ΠΊΠ»Π°Π΄ΠΊΠΈ Π½Π΅ Π½Π°ΠΌΠ½ΠΎΠ³ΠΎ ΡΠ΅ΠΏΠ»Π΅Π΅ Π±Π΅ΡΠΎΠ½Π½ΠΎΠΉ ΡΡΠ΅Π½Ρ. Π ΠΏΡΠΈ ΡΠ΅Π·ΠΎΠ½Π½ΠΎΠΉ ΡΠΊΡΠΏΠ»ΡΠ°ΡΠ°ΡΠΈΠΈ (Π² Π»Π΅ΡΠ½ΠΈΠΉ ΠΏΠ΅ΡΠΈΠΎΠ΄) ΡΠ΅ΠΏΠ»ΡΠΉ ΠΌΠ°ΡΠ΅ΡΠΈΠ°Π» Π΄Π»Ρ ΡΠΎΠΊΠΎΠ»Ρ Π½Π΅ ΠΈΠΌΠ΅Π΅Ρ ΠΎΠ³ΡΠΎΠΌΠ½ΠΎΠ³ΠΎ Π·Π½Π°ΡΠ΅Π½ΠΈΡ ΠΏΡΠΈ ΠΏΠΎΠ»ΠΎΠΆΠΈΡΠ΅Π»ΡΠ½ΡΡ ΡΠ΅ΠΌΠΏΠ΅ΡΠ°ΡΡΡΠ°Ρ Π½Π°ΡΡΠΆΠ½ΠΎΠ³ΠΎ Π²ΠΎΠ·Π΄ΡΡ Π°.
ΠΡΠΆΠ΅Π½ Π»ΠΈ ΡΠΎΠΊΠΎΠ»Ρ ΠΈΠ· ΠΊΠΈΡΠΏΠΈΡΠ°
ΠΡΠΆΠ΅Π½ ΡΠΎΠΊΠΎΠ»Ρ ΠΈΠ· ΠΊΠΈΡΠΏΠΈΡΠ° -Π²ΠΎΠΏΡΠΎΡ,ΠΊΠΎΡΠΎΡΡΠΌ ΠΌΡΡΠ°Π΅ΡΡΡ ΠΊΠ°ΠΆΠ΄ΡΠΉ Π·Π°ΡΡΡΠΎΠΉΡΠΈΠΊ. Π§Π°ΡΡΠΈΡΠ½ΠΎ ΠΎΡΠ²Π΅Ρ Β Π½Π°ΠΉΠ΄Π΅ΡΠ΅ Β Π² ΠΏΡΠ΅Π΄ΡΠ΄ΡΡΠ΅ΠΌ ΡΠ°Π·Π΄Π΅Π»Π΅.
ΠΠΎ,Ρ ΡΠΎΠΊΠΎΠ»Ρ Π΅ΡΡΡ Π΅ΡΠ΅ ΠΎΠ΄Π½Π° ΡΡΠ½ΠΊΡΠΈΡ-Π·Π°ΡΠΈΡΠ½Π°Ρ. ΠΠ°ΠΊ ΠΈΠ·Π²Π΅ΡΡΠ½ΠΎ,ΡΡΠ½Π΄Π°ΠΌΠ΅Π½Ρ,Π½Π°Ρ ΠΎΠ΄ΡΡΠΈΠΉΡΡ Π² Π·Π΅ΠΌΠ»Π΅,Π²ΠΏΠΈΡΡΠ²Π°Π΅Ρ Π²Π»Π°Π³Ρ.ΠΡΠΎΠ±Π΅Π½Π½ΠΎ,Π΅ΡΠ»ΠΈ Π±Π΅ΡΠΎΠ½ Π³ΠΎΡΠΎΠ²ΠΈΠ»ΡΡ Π²ΡΡΡΠ½ΡΡ,ΡΠΎ Π΅Π³ΠΎ Π³ΠΈΠ³ΡΠΎΡΠΊΠΎΠΏΠΈΡΠ½ΠΎΡΡΡ ΠΎΡΡΠ°Π²Π»ΡΠ΅Ρ ΠΆΠ΅Π»Π°ΡΡ Π»ΡΡΡΠ΅Π³ΠΎ. ΠΠΎΡΡΠΎΠΌΡ ,Π²ΡΠ΅Π³Π΄Π° Π½ΡΠΆΠ½ΠΎ ΠΏΡΠΎΠΊΠ»Π°Π΄ΡΠ²Π°ΡΡ ΡΡΠ±Π΅ΡΠΎΠΈΠ΄ ΠΌΠ΅ΠΆΠ΄Ρ Π±Π΅ΡΠΎΠ½ΠΎΠΌ ΠΈ ΠΊΠΈΡΠΏΠΈΡΠ½ΠΎΠΉ ΠΊΠ»Π°Π΄ΠΊΠΎΠΉ ΡΠΎΠΊΠΎΠ»Ρ Π² ΠΊΠ°ΡΠ΅ΡΡΠ²Π΅ Π³ΠΈΠ΄ΡΠΎΠΈΠ·ΠΎΠ»ΡΡΠΈΠΎΠ½Π½ΠΎΠ³ΠΎ ΡΠ»ΠΎΡ,ΠΊΠΎΡΠΎΡΡΠΉ Π±ΡΠ΄Π΅Ρ ΠΏΡΠ΅Π΄ΠΎΡ ΡΠ°Π½ΡΡΡ ΠΊΠΈΡΠΏΠΈΡ ΠΎΡ Π²ΠΏΠΈΡΡΠ²Π°Π½ΠΈΡ Π³ΡΡΠ½ΡΠΎΠ²ΠΎΠΉ Π²Π»Π°Π³ΠΈ.
Π’Π°ΠΊ Π²ΠΎΡ,Π½ΡΠΆΠ½ΠΎ,ΡΡΠΎΠ±Ρ ΠΊΠΈΡΠΏΠΈΡΠ½Π°Ρ ΠΊΠ»Π°Π΄ΠΊΠ° ΡΠΎΠΊΠΎΠ»Ρ Π²ΡΡΡΡΠΏΠ°Π»Π° Π½Π° 20-50ΠΌΠΌ Π½Π°Π΄ ΡΡΠ½Π΄Π°ΠΌΠ΅Π½ΡΠΎΠΌ. ΠΡΠΎ Π΄Π΅Π»Π°Π΅ΡΡΡ Π΄Π»Ρ Π·Π°ΡΠΈΡΡ ΡΡΠ½Π΄Π°ΠΌΠ΅Π½ΡΠ° ΠΈ ΠΏΠΎΠΏΠ°Π΄Π°Π½ΠΈΡ Π°ΡΠΌΠΎΡΡΠ΅ΡΠ½ΡΡ
ΠΎΡΠ°Π΄ΠΊΠΎΠ² (Π΄ΠΎΠΆΠ΄Ρ,ΡΠ½Π΅Π³Π°) Π½Π° Π³ΠΈΠ΄ΡΠΎΠΈΠ·ΠΎΠ»ΡΡΠΈΠΎΠ½Π½ΡΠΉ ΡΠ»ΠΎΠΉ.
ΠΠ°ΠΏΡΠΈΠΌΠ΅Ρ, ΡΠΈΡΠΈΠ½Π° ΡΡΠ½Π΄Π°ΠΌΠ΅Π½ΡΠ° 300ΠΌ. ΠΠ½Π°ΡΠΈΡ ΠΊΠΈΡΠΏΠΈΡΠ½ΡΡ ΠΊΠ»Π°Π΄ΠΊΡ ΡΠΎΠΊΠΎΠ»Ρ Π½ΡΠΆΠ½ΠΎ Π΄Π΅Π»Π°ΡΡ ΡΠΈΡΠΈΠ½ΠΎΠΉ Π² 1.5 ΠΊΠΈΡΠΏΠΈΡΠ° (380 ΠΌΠΌ),ΠΠΎΠ»ΡΡΠ°Π΅ΡΡΡ ΠΏΠΎ 40ΠΌΠΌ ΡΠ²Π΅ΡΠ° Ρ ΠΊΠ°ΠΆΠ΄ΠΎΠΉ ΡΡΠΎΡΠΎΠ½Ρ ΡΡΠ½Π΄Π°ΠΌΠ΅Π½ΡΠ°.
ΠΡΠ»ΠΈ ΡΠΈΡΠΈΠ½Π° ΡΡΠ½Π΄Π°ΠΌΠ΅Π½ΡΠ° 400ΠΌ,ΡΠΎ ΡΠΎΠ²ΡΠ΅ΠΌ Π½Π΅ ΡΠΊΠΎΠ½ΠΎΠΌΠΈΡΠ½ΠΎ Π΄Π΅Π»Π°ΡΡ ΡΠΎΠΊΠΎΠ»Ρ ΡΠΈΡΠΈΠ½ΠΎΠΉ 500ΠΌΠΌ(Π² 2 ΠΊΠΈΡΠΏΠΈΡΠ°).ΠΠΎΠΆΠ½ΠΎ Β ΡΠ΄Π΅Π»Π°ΡΡ Π² 1.5 ΠΊΠΈΡΠΏΠΈΡΠ°(380ΠΌΠΌ) ΠΈ ΡΠΌΠ΅ΡΡΠΈΡΡ Π΅Π³ΠΎ Π½Π° 20ΠΌΠΌ Π½Π° Π²Π½Π΅ΡΠ½ΡΡ ΡΡΠΎΡΠΎΠ½Ρ.
ΠΠΎΠΆΠ½ΠΎ ΡΠ΄Π΅Π»Π°ΡΡ ΠΈ Π·Π°ΠΏΠ°Π΄Π°ΡΡΠΈΠΉ Π²Π°ΡΠΈΠ°Π½Ρ ΡΠΎΠΊΠΎΠ»Ρ,ΠΊΠΎΠ³Π΄Π° ΠΊΠΈΡΠΏΠΈΡΠ½Π°Ρ ΠΊΠ»Π°Π΄ΠΊΠ° Π²ΡΠΏΠΎΠ»Π½ΡΠ΅ΡΡΡ ΠΏΠΎΡΠ΅ΡΠ΅Π΄ΠΈΠ½Π΅ ΡΡΠ½Π΄Π°ΠΌΠ΅Π½ΡΠ½ΠΎΠΉ Π»Π΅Π½ΡΡ. ΠΠΎΠ»ΡΡΠ°Π΅ΡΡΡ,ΡΡΠΎ Β Π½Π° 20ΠΌΠΌ ΡΡΠ½Π΄Π°ΠΌΠ΅Π½Ρ Π±ΡΠ΄Π΅Ρ Π²ΡΡΡΡΠΏΠ°ΡΡ. Π ΡΡΠΎΠΌ ΡΠ»ΡΡΠ°Π΅,ΠΏΠΎΠΏΠ°Π΄Π°Π½ΠΈΠ΅ Π΄ΠΎΠΆΠ΄Π΅Π²ΠΎΠΉ Π²Π»Π°Π³ΠΈ Π½Π° Π³ΠΈΠ΄ΡΠΎΠΈΠ·ΠΎΠ»ΡΡΠΈΠΎΠ½Π½ΡΠΉ ΡΠ»ΠΎΠΉ Π½Π΅ΠΈΠ·Π±Π΅ΠΆΠ½ΠΎ.ΠΠΎΠ·ΠΌΠΎΠΆΠ½ΠΎ ΡΠΊΠΎΠΏΠ»Π΅Π½ΠΈΠ΅ Π²ΠΎΠ΄Ρ ΠΈ ΠΏΠΎΡΠ»Π΅Π΄ΡΡΡΠ΅Π΅ Π²ΠΏΠΈΡΡΠ²Π°Π½ΠΈΠ΅ ΠΊΠΈΡΠΏΠΈΡΠΎΠΌ. ΠΡΠΎΠ³ΠΎ ΠΌΠΎΠΆΠ½ΠΎ ΠΈΠ·Π±Π΅ΠΆΠ°ΡΡ,Π΅ΡΠ»ΠΈ ΡΠ΄Π΅Π»Π°ΡΡ Π·Π°ΡΠΈΡΡ ΠΊΠΈΡΠΏΠΈΡΠ½ΠΎΠΉ ΠΊΠ»Π°Π΄ΠΊΠΈ ΠΈ ΡΡΠ½Π΄Π°ΠΌΠ΅Π½ΡΠ° ΠΊΠ°ΡΠ½ΠΈΠ·Π½ΡΠΌΠΈ ΡΠ²Π΅ΡΠ°ΠΌΠΈ ΠΈΠ· ΠΎΡΠΈΠ½ΠΊΠΎΠ²Π°Π½Π½ΠΎΠΉ ΠΈΠ»ΠΈ ΠΊΡΠ°ΡΠ΅Π½Π½ΠΎΠΉ ΡΡΠ°Π»ΠΈ.
Π‘ΡΡΠ±,ΡΡΡΠ°Π½ΠΎΠ²Π»Π΅Π½Π½ΡΠΉ Π½Π° ΡΠΎΠΊΠΎΠ»Ρ,Π±ΡΠ΄Π΅Ρ Β Π·Π°ΡΠΈΡΠ΅Π½ ΠΎΡ Π³ΡΡΠ½ΡΠΎΠ²ΠΎΠΉ Π²Π»Π°Π³ΠΈ Π³ΠΈΠ΄ΡΠΎΠΈΠ·ΠΎΠ»ΡΡΠΈΠΎΠ½Π½ΡΠΌΠΈ ΡΠ»ΠΎΡΠΌΠΈ Π² Π΄Π²ΡΡ
ΠΌΠ΅ΡΡΠ°Ρ
( 1-ΠΌΠ΅ΠΆΠ΄Ρ ΡΡΠ½Π΄Π°ΠΌΠ΅Π½ΡΠΎΠΌ ΠΈ ΡΠΎΠΊΠΎΠ»Π΅ΠΌ, 2- ΠΌΠ΅ΠΆΠ΄Ρ ΡΠΎΠΊΠΎΠ»Π΅ΠΌ ΠΈ ΡΡΡΠ±ΠΎΠΌ),ΡΡΠΎ ΡΠ²Π΅Π»ΠΈΡΠΈΡ ΡΡΠΎΠΊ ΡΠ»ΡΠΆΠ±Ρ ΡΡΡΠ±Π°:ΠΊΠ°ΠΊ ΠΏΡΠ°Π²ΠΈΠ»ΠΎ, Β Π½ΠΈΠΆΠ½ΠΈΠ΅ Π²Π΅Π½ΡΡ ΡΡΡΠ±Π° Π² 90% ΡΠ»ΡΡΠ°Π΅Π² ΡΠ³Π½ΠΈΠ²Π°ΡΡ ΠΎΡ ΠΏΠΎΡΡΠΎΡΠ½Π½ΠΎΠ³ΠΎ ΠΏΠΎΠΏΠ°Π΄Π°Π½ΠΈΡ Π²Π»Π°Π³ΠΈ ΡΠ½ΠΈΠ·Ρ.
ΠΠΈΡΠΏΠΈΡ Π΄Π»Ρ ΡΠΎΠΊΠΎΠ»Ρ
ΠΠΈΡΠΏΠΈΡ Π΄Π»Ρ ΡΠΎΠΊΠΎΠ»Ρ Π΄ΠΎΠ»ΠΆΠ΅Π½ Π±ΡΡΡ ΠΏΠΎΠ»Π½ΠΎΡΠ΅Π»ΡΠΌ Π³Π»ΠΈΠ½ΡΠ½ΡΠΌ. ΠΠΈ Π² ΠΊΠΎΠ΅ΠΌ ΡΠ»ΡΡΠ°Π΅,Π½Π΅Π»ΡΠ·Ρ ΠΏΡΠΈΠΌΠ΅Π½ΡΡΡ ΠΏΡΡΡΠΎΡΠ΅Π»ΡΠΉ ΠΊΠΈΡΠΏΠΈΡ,Π΄Π°ΠΆΠ΅,Π΅ΡΠ»ΠΈ ΠΎΠ½ Π²ΡΡΠΎΠΊΠΎΠΉ ΠΌΠ°ΡΠΊΠΈ Π200. ΠΠΎΡΠΎΠΌΡ ΡΡΠΎ ΠΏΡΠΈ ΠΏΠ΅ΡΠ΅ΠΏΠ°Π΄Π΅ ΡΠ΅ΠΌΠΏΠ΅ΡΠ°ΡΡΡ Π² Π·ΠΈΠΌΠ½ΠΈΠΉ ΠΏΠ΅ΡΠΈΠΎΠ΄ Π²ΡΠ΅ΠΌΠ΅Π½ΠΈ,ΠΏΡΠΈ ΠΎΡΡΠ°ΠΈΠ²Π°Π½ΠΈΠΈ ΠΈ Π·Π°ΠΌΠ΅ΡΠ·Π°Π½ΠΈΠΈ Π² ΠΏΡΡΡΠΎΡΠ°Ρ ΠΊΠΈΡΠΏΠΈΡΠ° Π±ΡΠ΄Π΅Ρ ΠΊΠΎΠ½Π΄Π΅Π½ΡΠΈΡΠΎΠ²Π°ΡΡΡΡ Π²Π»Π°Π³Π°,ΠΊΠΎΡΠΎΡΠ°Ρ Π½ΠΈΠΊΡΠ΄Π° Π½Π΅ Π΄Π΅Π²Π°Π΅ΡΡΡ,Π° Π²ΠΏΠΈΡΡΠ²Π°Π΅ΡΡΡ ΠΊΠΈΡΠΏΠΈΡΠΎΠΌ.Π§ΡΠΎ,Π΅ΡΡΠ΅ΡΡΠ²Π΅Π½Π½ΠΎ ΠΏΡΠΈΠ²Π΅Π΄Π΅Ρ ΠΊ ΠΏΠΎΡΡΠ΅ΠΏΠ΅Π½Π½ΠΎΠΌΡ ΡΠ°Π·ΡΡΡΠ΅Π½ΠΈΡ ΠΊΠΈΡΠΏΠΈΡΠ°.
Π ΡΠΎΠΎΡΠ²Π΅ΡΡΡΠ²ΠΈΠΈ Ρ ΠΏΠΎΠ»ΠΎΠΆΠ΅Π½ΠΈΡΠΌΠΈ Π‘ΠΠΈΠΏ 3.03.01-87 Β«ΠΠ΅ΡΡΡΠΈΠ΅ ΠΈ ΠΎΠ³ΡΠ°ΠΆΠ΄Π°ΡΡΠΈΠ΅ ΠΊΠΎΠ½ΡΡΡΡΠΊΡΠΈΠΈΒ»:
7.3.Β ΠΠ»Π°Π΄ΠΊΡ ΠΊΠΈΡΠΏΠΈΡΠ½ΡΡ ΡΠΎΠΊΠΎΠ»Π΅ΠΉ Π·Π΄Π°Π½ΠΈΠΉ Π½Π΅ΠΎΠ±Ρ ΠΎΠ΄ΠΈΠΌΠΎ Π²ΡΠΏΠΎΠ»Π½ΡΡΡ ΠΈΠ· ΠΏΠΎΠ»Π½ΠΎΡΠ΅Π»ΠΎΠ³ΠΎ ΠΊΠ΅ΡΠ°ΠΌΠΈΡΠ΅ΡΠΊΠΎΠ³ΠΎ ΠΊΠΈΡΠΏΠΈΡΠ°. ΠΡΠΈΠΌΠ΅Π½Π΅Π½ΠΈΠ΅ Π΄Π»Ρ ΡΡΠΈΡ ΡΠ΅Π»Π΅ΠΉ ΡΠΈΠ»ΠΈΠΊΠ°ΡΠ½ΠΎΠ³ΠΎ ΠΊΠΈΡΠΏΠΈΡΠ° Π½Π΅ Π΄ΠΎΠΏΡΡΠΊΠ°Π΅ΡΡΡ.
ΠΠ°ΡΠΊΠ° ΠΊΠΈΡΠΏΠΈΡΠ° Π΄Π»Ρ ΡΠΎΠΊΠΎΠ»Ρ
ΠΠ°ΡΠΊΠ° ΠΊΠΈΡΠΏΠΈΡΠ° Π΄Π»Ρ ΡΠΎΠΊΠΎΠ»Ρ Π΄ΠΎΠ»ΠΆΠ½Π° Π±ΡΡΡ Π½Π΅ Π½ΠΈΠΆΠ΅ Π200 Π΄Π»Ρ ΠΊΠΈΡΠΏΠΈΡΠ½ΠΎΠ³ΠΎ Π΄ΠΎΠΌΠ° Π² Π½Π΅ΡΠΊΠΎΠ»ΡΠΊΠΎ ΡΡΠ°ΠΆΠ΅ΠΉ ΠΈ Π½Π΅ Π½ΠΈΠΆΠ΅ Π150 Π΄Π»Ρ Π΄ΡΡΠ³ΠΈΡ Π±ΠΎΠ»Π΅Π΅ Π»Π΅Π³ΠΊΠΈΡ ΠΊΠΎΠ½ΡΡΡΡΠΊΡΠΈΠΉ ΡΡΠ΅Π½ Π² 1 ΡΡΠ°ΠΆ. ΠΠΎΡΠ΅ΠΌΡ? ΠΠΎΡΠΎΠΌΡ ΡΡΠΎ ΡΠΎΠΊΠΎΠ»Ρ-ΡΡΠΎ ΡΠ°ΠΌΠ°Ρ Π½Π°Π³ΡΡΠΆΠ΅Π½Π½Π°Ρ ΠΊΠΎΠ½ΡΡΡΡΠΊΡΠΈΡ ΠΏΠΎΡΠ»Π΅ ΡΠ°ΠΌΠΎΠ³ΠΎ ΡΡΠ½Π΄Π°ΠΌΠ΅Π½ΡΠ°. Π¦ΠΎΠΊΠΎΠ»Ρ Π±ΡΠ΄Π΅Ρ Π½Π΅ΡΡΠΈ Π½Π° ΡΠ΅Π±Π΅ Π²ΡΠ΅,ΡΡΠΎ Π²ΡΡΠ΅ Π½Π΅Π³ΠΎ:
- ΡΡΠ΅Π½Ρ
- ΠΏΠ΅ΡΠ΅ΠΊΡΡΡΠΈΠ΅
- ΠΊΡΡΡΡ
- ΡΠ½Π΅Π³ Π½Π° ΠΊΡΡΡΠ΅
- ΠΌΠ΅Π±Π΅Π»Ρ ΠΈ Π»ΡΠ΄Π΅ΠΉ Π² Π΄ΠΎΠΌΠ΅
Π ΡΠΎΠΎΡΠ²Π΅ΡΡΡΠ²ΠΈΠΈ ΡΠΎ Π‘ΠΠΈΠ II-22-81 Β«ΠΠ°ΠΌΠ΅Π½Π½ΡΠ΅ ΠΈ Π°ΡΠΌΠΎΠΊΠ°ΠΌΠ΅Π½Π½ΡΠ΅ ΠΊΠΎΠ½ΡΡΡΡΠΊΡΠΈΠΈΒ»:
1.
3. ΠΡΠΈΠΌΠ΅Π½Π΅Π½ΠΈΠ΅ ΡΠΈΠ»ΠΈΠΊΠ°ΡΠ½ΡΡ ΠΊΠΈΡΠΏΠΈΡΠ°, ΠΊΠ°ΠΌΠ½Π΅ΠΉ ΠΈ Π±Π»ΠΎΠΊΠΎΠ²; ΠΊΠ°ΠΌΠ½Π΅ΠΉ ΠΈ Π±Π»ΠΎΠΊΠΎΠ² ΠΈΠ· ΡΡΠ΅ΠΈΡΡΡΡ Π±Π΅ΡΠΎΠ½ΠΎΠ²; ΠΏΡΡΡΠΎΡΠ΅Π»ΠΎΠ³ΠΎ ΠΊΠΈΡΠΏΠΈΡΠ° ΠΈ ΠΊΠ΅ΡΠ°ΠΌΠΈΡΠ΅ΡΠΊΠΈΡ ΠΊΠ°ΠΌΠ½Π΅ΠΉ; Π³Π»ΠΈΠ½ΡΠ½ΠΎΠ³ΠΎ ΠΊΠΈΡΠΏΠΈΡΠ° ΠΏΠΎΠ»ΡΡΡΡ ΠΎΠ³ΠΎ ΠΏΡΠ΅ΡΡΠΎΠ²Π°Π½ΠΈΡ Π΄ΠΎΠΏΡΡΠΊΠ°Π΅ΡΡΡ Π΄Π»Ρ Π½Π°ΡΡΠΆΠ½ΡΡ ΡΡΠ΅Π½ ΠΏΠΎΠΌΠ΅ΡΠ΅Π½ΠΈΠΉ Ρ Π²Π»Π°ΠΆΠ½ΡΠΌ ΡΠ΅ΠΆΠΈΠΌΠΎΠΌ ΠΏΡΠΈ ΡΡΠ»ΠΎΠ²ΠΈΠΈ Π½Π°Π½Π΅ΡΠ΅Π½ΠΈΡ Π½Π° ΠΈΡ Π²Π½ΡΡΡΠ΅Π½Π½ΠΈΠ΅ ΠΏΠΎΠ²Π΅ΡΡ Π½ΠΎΡΡΠΈ ΠΏΠ°ΡΠΎΠΈΠ·ΠΎΠ»ΡΡΠΈΠΎΠ½Π½ΠΎΠ³ΠΎ ΠΏΠΎΠΊΡΡΡΠΈΡ. ΠΡΠΈΠΌΠ΅Π½Π΅Π½ΠΈΠ΅ ΡΠΊΠ°Π·Π°Π½Π½ΡΡ ΠΌΠ°ΡΠ΅ΡΠΈΠ°Π»ΠΎΠ² Π΄Π»Ρ ΡΡΠ΅Π½ ΠΏΠΎΠΌΠ΅ΡΠ΅Π½ΠΈΠΉ Ρ ΠΌΠΎΠΊΡΡΠΌ ΡΠ΅ΠΆΠΈΠΌΠΎΠΌ, Π° ΡΠ°ΠΊΠΆΠ΅ Π΄Π»Ρ Π½Π°ΡΡΠΆΠ½ΡΡ ΡΡΠ΅Π½ ΠΏΠΎΠ΄Π²Π°Π»ΠΎΠ² ΠΈ ΡΠΎΠΊΠΎΠ»Π΅ΠΉ Π½Π΅ Π΄ΠΎΠΏΡΡΠΊΠ°Π΅ΡΡΡ.
Π Π΅ΠΊΠΎΠΌΠ΅Π½Π΄ΡΠ΅ΡΡΡ ΠΈΡΠΏΠΎΠ»ΡΠ·ΠΎΠ²Π°ΡΡ Π³Π»ΠΈΠ½ΡΠ½ΡΠΉ ΠΎΠ±ΠΎΠΆΠΆΠ΅Π½Π½ΡΠΉ ΠΊΠΈΡΠΏΠΈΡ ΠΏΠ»Π°ΡΡΠΈΡΠ½ΠΎΠ³ΠΎ ΡΠΎΡΠΌΠΈΡΠΎΠ²Π°Π½ΠΈΡ ΠΏΠΎ Β ΠΠΠ‘Π’ 530-2007 Β«ΠΠΈΡΠΏΠΈΡ ΠΈ ΠΊΠ°ΠΌΠ΅Π½Ρ ΠΊΠ΅ΡΠ°ΠΌΠΈΡΠ΅ΡΠΊΠΈΠ΅Β» Β Π-150 ΠΈ Π±ΠΎΠ»Π΅Π΅, F-50, Π³Π΄Π΅ :
- M β ΠΏΡΠΎΡΠ½ΠΎΡΡΡ ΠΈ ΡΡΠΎΠΉΠΊΠΎΡΡΡ Π½Π° ΠΈΠ·Π³ΠΈΠ±, ΡΠΆΠ°ΡΠΈΠ΅
- F β ΠΌΠΎΡΠΎΠ·ΠΎΡΡΠΎΠΉΠΊΠΎΡΡ (ΡΡΡΠΎΠΉΡΠΈΠ²ΠΎΡΡΡ ΠΏΡΠΎΡΠΈΠ² ΡΠ΅Π·ΠΊΠΎΠ³ΠΎ ΠΏΠ΅ΡΠ΅ΠΏΠ°Π΄Π° ΡΠ΅ΠΌΠΏΠ΅ΡΠ°ΡΡΡ)
Π Π°ΡΡΠ΅Ρ ΠΊΠΈΡΠΏΠΈΡΠ° Π½Π° ΡΠΎΠΊΠΎΠ»Ρ
Π Π°ΡΡΠ΅Ρ ΠΊΠΈΡΠΏΠΈΡΠ° Π½Π° ΡΠΎΠΊΠΎΠ»Ρ Π΄Π»Ρ Π΅Π³ΠΎ ΠΏΠΎΠΊΡΠΏΠΊΠΈ ΠΈ Π΄ΠΎΡΡΠ°Π²ΠΊΠΈ ΡΠ»Π΅Π΄ΡΡΡΠΈΠΉ:
- ΡΠ½Π°ΡΠ°Π»Π° ΠΏΠΎΠ΄ΡΡΠΈΡΡΠ²Π°Π΅ΡΡΡ ΠΎΠ±ΡΠ΅ΠΌ ΠΊΠΈΡΠΏΠΈΡΠ½ΠΎΠΉ ΠΊΠ»Π°Π΄ΠΊΠΈ.ΠΠ»Ρ ΡΡΠΎΠ³ΠΎ ΠΏΠ΅ΡΠΈΠΌΠ΅ΡΡ ΡΡΠ½Π΄Π°ΠΌΠ΅Π½ΡΠ° ΡΠΌΠ½ΠΎΠΆΠ°Π΅ΠΌ Π½Π° ΡΠΈΡΠΈΠ½Ρ ΠΊΠ»Π°Π΄ΠΊΠΈ ΠΈ Π΅Π΅ Π²ΡΡΠΎΡΡ.ΠΠ°ΠΏΡΠΈΠΌΠ΅Ρ, ΡΠ°Π·ΠΌΠ΅ΡΡ ΡΡΠ½Π΄Π°ΠΌΠ΅Π½ΡΠ° 4Ρ
3ΠΌ.
ΠΏΡΠΈ ΡΠΈΡΠΈΠ½Π΅ ΡΡΠ½Π΄Π°ΠΌΠ΅Π½ΡΠ° 300ΠΌΠΌ. ΠΠ΅ΡΠΈΠΌΠ΅ΡΡ ΡΠ°Π²Π΅Π½ 14ΠΌ.ΠΠ»Π°Π΄ΠΊΡ Π±ΡΠ΄Π΅ΠΌ Π²ΡΠΏΠΎΠ»Π½ΡΡΡ ΡΠΈΡΠΈΠ½ΠΎΠΉ Π² ΠΊΠΈΡΠΏΠΈΡ (250ΠΌΠΌ) ΠΈ Π²ΡΡΠΎΡΠΎΠΉ Π² 4 ΡΡΠ΄Π° (70*4=280ΠΌΠΌ). ΠΠΎΠ»ΡΡΠ°Π΅ΠΌ ΠΎΠ±ΡΠ΅ΠΌ Π±ΡΠ΄ΡΡΠ΅ΠΉ ΠΊΠ»Π°Π΄ΠΊΠΈ ΡΠ°Π²Π½ΡΠΌ : 14ΠΌ*0,25ΠΌ *0,28ΠΌ=0,98 ΠΌ3.
- Π 1 ΠΌ3 ΠΊΠΈΡΠΏΠΈΡΠ½ΠΎΠΉ ΠΊΠ»Π°Π΄ΠΊΠΈ ΡΡΡΠ΅Π΄Π½Π΅Π½Π½ΡΠΉ ΡΠ°ΡΡ ΠΎΠ΄ ΠΊΠΈΡΠΏΠΈΡΠ° ΡΠ°Π²Π΅Π½ 400ΡΡ. Π£ΠΌΠ½ΠΎΠΆΠ°Π΅ΠΌ Π½Π°Ρ ΠΎΠ±ΡΠ΅ΠΌ ΠΊΠ»Π°Π΄ΠΊΠΈ Π½Π° 400ΡΡ,ΠΏΠΎΠ»ΡΡΠ°Π΅ΠΌ: 0,98 ΠΌ*400ΡΡ=392ΡΡ.
Π ΠΏΠΎΠ΄Π΄ΠΎΠ½Π΅ 300-330 ΡΡ (Π² Π·Π°Π²ΠΈΡΠΈΠΌΠΎΡΡΠΈ ΠΎΡ Π·Π°Π²ΠΎΠ΄Π°-ΠΏΡΠΎΠΈΠ·Π²ΠΎΠ΄ΠΈΡΠ΅Π»Ρ).ΠΠ½Π°ΡΠΈΡ Π½ΡΠΆΠ½ΠΎ ΠΊΡΠΏΠΈΡΡ 2 ΠΏΠΎΠ΄Π΄ΠΎΠ½Π°. Π‘ Π·Π°ΠΏΠ°ΡΠΎΠΌ. ΠΠΈΡΠΏΠΈΡ ΠΎΡΡΠ°Π½Π΅ΡΡΡ,Π½ΠΎ ΠΎΠ½ Π»ΠΈΡΠ½ΠΈΠΌ ΠΏΡΠΈ ΡΡΡΠΎΠΈΡΠ΅Π»ΡΡΡΠ²Π΅ Π½ΠΈΠΊΠΎΠ³Π΄Π° Π½Π΅ Π±ΡΠ²Π°Π΅Ρ. ΠΠΎΠΆΠ½ΠΎ ,Π² Π΄Π°Π»ΡΠ½Π΅ΠΉΡΠ΅ΠΌ, ΡΠ΄Π΅Π»Π°ΡΡ ΠΏΡΠΎΡΡΠ΅Π½ΡΠΊΠΈΠΉ ΠΊΠΈΡΠΏΠΈΡΠ½ΡΠΉ ΠΌΠ°Π½Π³Π°Π».
ΠΠ°ΠΊ ΠΊΠ»Π°ΡΡΡ ΡΠΎΠΊΠΎΠ»Ρ ΠΈΠ· ΠΊΠΈΡΠΏΠΈΡΠ°
ΠΠ»Π°ΡΡΡ ΡΠΎΠΊΠΎΠ»Ρ ΠΈΠ· ΠΊΠΈΡΠΏΠΈΡΠ° Π½ΡΠΆΠ½ΠΎ ΠΏΠΎ Π³ΠΈΠ΄ΡΠΎΠΈΠ·ΠΎΠ»ΡΡΠΈΠΎΠ½Π½ΠΎΠΌΡ ΡΠ»ΠΎΡ ΠΈΠ· ΡΡΠ±Π΅ΡΠΎΠΈΠ΄Π°ΠΠ΅ΡΠΊΠΎΠ»ΡΠΊΠΎ ΡΠ΅ΠΊΠΎΠΌΠ΅Π½Π΄Π°ΡΠΈΠΉ ΠΊΠ°ΠΊ ΠΊΠ»Π°ΡΡΡ ΡΠΎΠΊΠΎΠ»Ρ ΠΈΠ· ΠΊΠΈΡΠΏΠΈΡΠ°:
- ΠΏΠ΅ΡΠ΅Π΄ ΠΊΠΈΡΠΏΠΈΡΠ½ΠΎΠΉ ΠΊΠ»Π°Π΄ΠΊΠΎΠΉ ΠΏΠΎ ΠΏΠΎΠ²Π΅ΡΡ
Π½ΠΎΡΡΠΈ ΡΡΠ½Π΄Π°ΠΌΠ΅Π½ΡΠ° Π½Π΅ΠΎΠ±Ρ
ΠΎΠ΄ΠΈΠΌΠΎ ΡΡΡΡΠΎΠΈΡΡ Π³ΠΎΡΠΈΠ·ΠΎΠ½ΡΠ°Π»ΡΠ½ΡΠΉ Π³ΠΈΠ΄ΡΠΎΠΈΠ·ΠΎΠ»ΡΡΠΈΠΎΠ½Π½ΡΠΉ ΡΠ»ΠΎΠΉ ΠΈΠ· ΡΡΠ±Π΅ΡΠΎΠΈΠ΄Π° Π΄Π»Ρ ΠΏΡΠ΅Π΄ΠΎΡΠ²ΡΠ°ΡΠ΅Π½ΠΈΡ ΠΏΡΠΎΠ½ΠΈΠΊΠ½ΠΎΠ²Π΅Π½ΠΈΡ Π²Π»Π°Π³ΠΈ ΡΠ½ΠΈΠ·Ρ.ΠΠΎ Π½ΠΎΡΠΌΠ°ΡΠΈΠ²Π½ΡΠΌ Π΄ΠΎΠΊΡΠΌΠ΅Π½ΡΠ°ΠΌ Π² ΡΡΡΠΎΠΈΡΠ΅Π»ΡΡΡΠ²Π΅ ΠΎΠ½ Π΄ΠΎΠ»ΠΆΠ΅Π½ Π±ΡΡΡ ΠΈΠ· 2 ΡΠ»ΠΎΠ΅Π² ΡΡΠ±Π΅ΡΠΎΠΈΠ΄Π° Ρ ΠΏΡΠΎΠΊΠ»Π΅ΠΉΠΊΠΎΠΉ ΠΊΠ°ΠΆΠ΄ΠΎΠ³ΠΎ ΠΌΠ°ΡΡΠΈΠΊΠΎΠΉ.
- ΠΡΠ»ΠΈ ΠΊΠΎΠ½ΡΡΡΡΠΊΡΠΈΡ ΡΠΎΠΊΠΎΠ»Ρ ΠΌΠ°ΡΡΠΈΠ²Π½Π°Ρ (ΠΏΠΎ ΡΠΈΡΠΈΠ½Π΅ ΠΈ Π²ΡΡΠΎΡΠ΅),ΡΠΎ ΠΏΠΎ Π³ΠΈΠ΄ΡΠΎΠΈΠ·ΠΎΠ»ΡΡΠΈΠΎΠ½Π½ΠΎΠΌΡ ΡΠ»ΠΎΡ Π½Π΅ΠΎΠ±Ρ ΠΎΠ΄ΠΈΠΌΠΎ ΡΠ΄Π΅Π»Π°ΡΡ Π²ΡΡΠ°Π²Π½ΠΈΠ²Π°ΡΡΡΡ ΡΡΡΠΆΠΊΡ ΠΈΠ· ΡΠ΅ΠΌΠ΅Π½ΡΠ½ΠΎ-ΠΏΠ΅ΡΡΠ°Π½Π½ΠΎΠ³ΠΎ ΡΠ°ΡΡΠ²ΠΎΡΠ° ΡΠΎΠ»ΡΠΈΠ½ΠΎΠΉ 20ΠΌΠΌ,Π½Π° ΠΊΠΎΡΠΎΡΡΠΉ ΡΠΊΠ»Π°Π΄ΡΠ²Π°Π΅ΡΡΡ ΠΊΠ»Π°Π΄ΠΎΡΠ½Π°Ρ ΡΠ΅ΡΠΊΠ° Ρ ΡΡΠ΅ΠΉΠΊΠ°ΠΌΠΈ 50Ρ 50ΠΌΠΌ ΠΈΠ· ΠΏΡΠΎΠ²ΠΎΠ»ΠΎΠΊΠΈ 4ΠΌΠΌ. ΠΠ°Π½Π½ΡΠΉ Π°ΡΠΌΠΈΡΡΡΡΠΈΠΉ ΡΠ»ΠΎΠΉ ΠΏΡΠΈΠ΄Π°ΡΡ Π΄ΠΎΠΏΠΎΠ»Π½ΠΈΡΠ΅Π»ΡΠ½ΡΡ ΠΆΠ΅ΡΡΠΊΠΎΡΡΡ ΠΈ ΠΏΡΠΎΡΠ½ΠΎΡΡΡ ΠΎΡΠ½ΠΎΠ²Π°Π½ΠΈΡ Π²ΡΡΠ΅Π»Π΅ΠΆΠ°ΡΠ΅ΠΌΡ ΠΊΠΈΡΠΏΠΈΡΠ½ΠΎΠΌΡ ΡΠΎΠΊΠΎΠ»Ρ.
- ΠΠ»Ρ ΡΡΠ±Π»Π΅Π½Π½ΠΎΠΉ Π±Π°Π½ΠΈ Π²ΡΡΠ΅ΡΠΊΠ°Π·Π°Π½Π½ΠΎΠ΅ ΡΡΠ»ΠΎΠ²ΠΈΠ΅ Π½Π΅ ΡΠ°ΠΊ Π²Π°ΠΆΠ½ΠΎ,ΠΏΠΎΡΠΎΠΌΡ ΡΡΠΎ ΡΡΡΠ± Π³ΠΎΡΠ°Π·Π΄ΠΎ Π»Π΅Π³ΡΠ΅ ΠΊΠΈΡΠΏΠΈΡΠ½ΡΡ ΡΡΠ΅Π½ Π΄ΠΎΠΌΠ° ΠΈ Π΄Π»Ρ Π±Π°Π½ΠΈ Π½Π΅ ΡΡΠ΅Π±ΡΠ΅ΡΡΡ Π²ΡΡΠΎΠΊΠΎΠ³ΠΎ ΡΠΎΠΊΠΎΠ»Ρ.
- ΠΠ΅ΡΠ²ΡΠΉ ΡΡΠ΄ ΠΊΠΈΡΠΏΠΈΡΠ½ΠΎΠΉ ΠΊΠ»Π°Π΄ΠΊΠΈ Π΄ΠΎΠ»ΠΆΠ΅Π½ Π±ΡΡΡ ΡΡΡΠΊΠΎΠ²ΡΠΉ
- Π½Π΅ΠΎΠ±Ρ ΠΎΠ΄ΠΈΠΌΠΎ ΡΡΠ°ΡΠ΅Π»ΡΠ½ΠΎ Π·Π°ΠΏΠΎΠ»Π½ΡΡΡ Π³ΠΎΡΠΈΠ·ΠΎΠ½ΡΠ°Π»ΡΠ½ΡΠ΅ ΠΈ Π²Π΅ΡΡΠΈΠΊΠ°Π»ΡΠ½ΡΠ΅ ΡΠ²Ρ ΡΠ°ΡΡΠ²ΠΎΡΠΎΠΌ,ΠΏΠΎΡΠΎΠΌΡ ΡΡΠΎ ΠΏΡΠΈ ΠΏΡΠΎΠ½ΠΈΠΊΠ½ΠΎΠ²Π΅Π½ΠΈΠΈ Π²Π»Π°Π³ΠΈ ΡΠ°ΡΡΠ²ΠΎΡ Π² ΡΠ²Π°Ρ ΡΠΎ Π²ΡΠ΅ΠΌΠ΅Π½Π΅ΠΌ Π½Π°ΡΠ½Π΅Ρ ΡΠ°Π·ΡΡΡΠ°ΡΡΡΡ.
- Π΅ΡΠ»ΠΈ ΡΠΎΠΊΠΎΠ»Ρ Π²ΡΡΠΎΠΊΠΈΠΉ,ΡΠΎ Π½ΡΠΆΠ½ΠΎ Π°ΡΠΌΠΈΡΠΎΠ²Π°ΡΡ ΠΊΠ»Π°Π΄ΠΊΡ ΡΠ΅ΡΠ΅Π· ΠΊΠ°ΠΆΠ΄ΡΠ΅ 3 ΠΈΠ»ΠΈ 5 ΡΡΠ΄ΠΎΠ².ΠΠ»ΠΈ Ρ ΠΎΡΡ Π±Ρ ΠΏΠΎ ΡΠ³Π»Π°ΠΌ.
- ΠΏΠΎΠ²Π΅ΡΡ Π²Π΅ΡΡ Π½Π΅Π³ΠΎ ΡΡΠ΄Π° ΠΊΠΈΡΠΏΠΈΡΠ½ΠΎΠΉ ΠΊΠ»Π°Π΄ΠΊΠΈ ΡΠΎΠΊΠΎΠ»Ρ Π²Π½ΠΎΠ²Ρ Π²ΡΠΏΠΎΠ»Π½ΡΠ΅ΡΡΡ Π³ΠΎΡΠΈΠ·ΠΎΠ½ΡΠ°Π»ΡΠ½Π°Ρ Π³ΠΈΠ΄ΡΠΎΠΈΠ·ΠΎΠ»ΡΡΠΈΡ ΠΈΠ· ΡΡΠ±Π΅ΡΠΎΠΈΠ΄Π°.
ΠΠΎΡΠΊΠΎΠ»ΡΠΊΡ ΠΊΠ»Π°Π΄ΠΊΠ° ΡΠΎΠΊΠΎΠ»Ρ ΠΈΠ· ΠΊΠΈΡΠΏΠΈΡΠ° -ΡΡΠ° ΡΠ° ΡΠ°ΡΡΡ ΡΡΠ΅Π½,ΠΊΠΎΡΠΎΡΠ°Ρ ΠΎΡΠΎΠ±Π΅Π½Π½ΠΎ ΠΏΠΎΠ΄Π²Π΅ΡΠΆΠ΅Π½Π° Π²Π»ΠΈΡΠ½ΠΈΡ Π°ΡΠΌΠΎΡΡΠ΅ΡΠ½ΡΡ
Π²ΠΎΠ·Π΄Π΅ΠΉΡΡΠ²ΠΈΠΉ (Π΄ΠΎΠΆΠ΄Ρ,ΡΠ½Π΅Π³,Π³ΡΡΠ½ΡΠΎΠ²Π°Ρ Π²Π»Π°Π³Π°) ΠΈ ΠΏΠΎΡΡΠΈ Π²ΡΠ΅ Π²ΡΠ΅ΠΌΡ ΡΠ°Π±ΠΎΡΠ°Π΅Ρ Π²ΠΎ Π²Π»Π°ΠΆΠ½ΠΎΡΡΠ½ΠΎΠΌ ΡΠ΅ΠΆΠΈΠΌΠ΅,ΡΠΎ Π΄Π»Ρ ΠΊΠ°ΠΏΠΈΡΠ°Π»ΡΠ½ΡΡ
ΡΡΡΠΎΠ΅Π½ΠΈΠΉ Π΅Π³ΠΎ Π½Π΅ΠΎΠ±Ρ
ΠΎΠ΄ΠΈΠΌΠΎ Π΄ΠΎΠΏΠΎΠ»Π½ΠΈΡΠ΅Π»ΡΠ½ΠΎ Π·Π°ΡΠΈΡΠ°ΡΡ. Π‘Π°ΠΌΠ°Ρ Π»ΡΡΡΠ°Ρ Π·Π°ΡΠΈΡΠ°-ΡΡΠΎ ΠΎΠ±Π»ΠΈΡΠΎΠ²ΠΊΠ° ΠΈΠ· ΠΏΡΠΈΡΠΎΠ΄Π½ΠΎΠ³ΠΎ ΠΊΠ°ΠΌΠ½Ρ. ΠΠΎΠ·ΠΌΠΎΠΆΠ½Ρ Π΄ΡΡΠ³ΠΈΠ΅ Π²Π°ΡΠΈΠ°Π½ΡΡ: ΠΊΠ΅ΡΠ°ΠΌΠΈΡΠ΅ΡΠΊΠ°Ρ ΠΏΠ»ΠΈΡΠΊΠ°,ΠΈΡΠΊΡΡΡΡΠ²Π΅Π½Π½ΡΠΉ ΠΊΠ°ΠΌΠ΅Π½Ρ,ΡΡΡΠΊΠ°ΡΡΡΠΊΠ°).
Π¦ΠΎΠΊΠΎΠ»Ρ ΠΈΠ· ΠΊΠΈΡΠΏΠΈΡΠ° Π½Π° Π»Π΅Π½ΡΠΎΡΠ½ΡΠΉ ΡΡΠ½Π΄Π°ΠΌΠ΅Π½Ρ: ΡΠ΅Ρ Π½ΠΎΠ»ΠΎΠ³ΠΈΡ ΠΊΠ»Π°Π΄ΠΊΠΈ
Π§ΡΠΎΠ±Ρ ΠΈΡΠΊΠ»ΡΡΠΈΡΡ ΡΠ°Π·Π²ΠΈΡΠΈΠ΅ ΠΏΠ»Π΅ΡΠ΅Π½ΠΈ ΠΈ Π³ΡΠΈΠ±ΠΊΠ°, Π²ΡΠ»Π΅Π΄ΡΡΠ²ΠΈΠ΅ ΠΏΠ°Π³ΡΠ±Π½ΠΎΠ³ΠΎ Π²ΠΎΠ·Π΄Π΅ΠΉΡΡΠ²ΠΈΡ Π²Π»Π°Π³ΠΈ, Π½ΡΠΆΠ½ΠΎ ΠΊΠ»Π°ΡΡΡ ΡΠΎΠΊΠΎΠ»Ρ ΠΈΠ· ΠΊΠΈΡΠΏΠΈΡΠ° Π½Π° Π»Π΅Π½ΡΠΎΡΠ½ΡΠΉ ΡΡΠ½Π΄Π°ΠΌΠ΅Π½Ρ. ΠΡΠ° ΡΠ°ΡΡΡ Π΄ΠΎΠ»ΠΆΠ½Π° Π±ΡΡΡ ΠΌΠ°ΠΊΡΠΈΠΌΠ°Π»ΡΠ½ΠΎ ΠΊΡΠ΅ΠΏΠΊΠΎΠΉ ΠΈ ΡΡΡΠΎΠΉΡΠΈΠ²ΠΎΠΉ ΠΏΠΎ ΠΏΡΠΈΡΠΈΠ½Π΅ ΡΠΎΠ³ΠΎ, ΡΡΠΎ ΠΈΠΌΠ΅Π½Π½ΠΎ Π½Π° ΡΠΎΠΊΠΎΠ»Π΅ ΡΠ°ΡΠΏΠΎΠ»Π°Π³Π°Π΅ΡΡΡ ΠΎΡΠ½ΠΎΠ²Π½Π°Ρ ΠΊΠΎΠ½ΡΡΡΡΠΊΡΠΈΡ. ΠΠ΅ ΡΠ΅ΠΊΠΎΠΌΠ΅Π½Π΄ΡΠ΅ΡΡΡ ΡΠΊΡΠΏΠΈΡΡΡΡ Π½Π° ΠΊΠ°ΡΠ΅ΡΡΠ²Π΅Π½Π½ΡΠ΅ ΠΌΠ°ΡΠ΅ΡΠΈΠ°Π»Ρ, ΡΠ°ΠΊ ΠΊΠ°ΠΊ ΠΎΠ½ΠΈ Π΄ΠΎΠ»ΠΆΠ½Ρ ΡΠΎΠΎΡΠ²Π΅ΡΡΡΠ²ΠΎΠ²Π°ΡΡ Π²ΡΠ΅ΠΌ ΠΏΠ°ΡΠ°ΠΌΠ΅ΡΡΠ°ΠΌ: ΠΏΠΎΠ²ΡΡΠ΅Π½Π½Π°Ρ ΡΡΠΎΠΉΠΊΠΎΡΡΡ ΠΊ ΠΌΠΎΡΠΎΠ·Ρ ΠΈ Π²Π»Π°Π³Π΅. ΠΡΠΈ ΡΠ°Π±ΠΎΡΠ΅ Π²Π°ΠΆΠ½Ρ Π²ΡΠ΅ ΠΌΠΎΠΌΠ΅Π½ΡΡ, ΠΊΠΎΡΠΎΡΡΠ΅ Π²ΠΊΠ»ΡΡΠ°ΡΡ ΡΠ΅Ρ Π½ΠΈΠΊΡ Π·Π°ΠΊΠ»Π°Π΄ΠΊΠΈ, ΡΠΎΡΡΠ°Π² ΡΠ°ΡΡΠ²ΠΎΡΠ° Π΄Π»Ρ ΡΠ°Π±ΠΎΡΡ, Π΄ΠΎΠΏΠΎΠ»Π½ΠΈΡΠ΅Π»ΡΠ½Π°Ρ ΡΠ΅ΠΏΠ»ΠΎ ΠΈ Π³ΠΈΠ΄ΡΠΎΠΈΠ·ΠΎΠ»ΡΡΠΈΡ.
ΠΠ°ΠΊΠΎΠΉ ΠΊΠΈΡΠΏΠΈΡ ΠΈΡΠΏΠΎΠ»ΡΠ·ΡΠ΅ΡΡΡ ΠΈ ΡΠΊΠΎΠ»ΡΠΊΠΎ?
ΠΠ΅ΡΠ΅Π΄ ΡΠ΅ΠΌ ΠΊΠ°ΠΊ Π½Π°ΡΠ°ΡΡ Π΄Π΅Π»Π°ΡΡ ΡΡΡΡΠΎΠΉΡΡΠ²ΠΎ, Π½Π΅ΠΎΠ±Ρ
ΠΎΠ΄ΠΈΠΌΠΎ ΠΏΠΎΠ·Π°Π±ΠΎΡΠΈΡΡΡΡ ΠΎ Π·Π°ΠΊΡΠΏΠΊΠ΅ ΠΌΠ°ΡΠ΅ΡΠΈΠ°Π»ΠΎΠ² Π΄Π»Ρ ΡΠ°Π±ΠΎΡΡ. ΠΠ°ΠΆΠ½ΠΎ ΠΏΡΠ°Π²ΠΈΠ»ΡΠ½ΠΎ ΡΠ°ΡΡΡΠΈΡΠ°ΡΡ ΠΊΠΎΠ»ΠΈΡΠ΅ΡΡΠ²ΠΎ ΠΊΡΠ°ΡΠ½ΠΎΠ³ΠΎ ΠΊΠΈΡΠΏΠΈΡΠ°. ΠΠ»Ρ ΡΡΠΎΠ³ΠΎ ΡΠΈΡΠΈΠ½Π° ΠΈ Π²ΡΡΠΎΡΠ° ΡΠ°ΡΠΊΠ»Π°Π΄ΠΊΠΈ ΡΠΌΠ½ΠΎΠΆΠ°Π΅ΡΡΡ Π½Π° ΠΏΠ΅ΡΠΈΠΌΠ΅ΡΡ ΡΡΠ½Π΄Π°ΠΌΠ΅Π½ΡΠ°, ΡΠ°ΠΊΠΈΠΌ ΠΎΠ±ΡΠ°Π·ΠΎΠΌ, ΡΠ°ΡΡΡΠΈΡΡΠ²Π°Π΅ΡΡΡ ΠΎΠ±ΡΠ΅ΠΌ. Π‘ΡΠ΅Π΄Π½ΠΈΠ΅ ΠΏΠΎΠΊΠ°Π·Π°ΡΠ΅Π»ΠΈ ΡΠ°ΡΡ
ΠΎΠ΄Π° ΠΌΠ°ΡΠ΅ΡΠΈΠ°Π»Π° β 400 ΠΊΠΈΡΠΏΠΈΡΠ΅ΠΉ Π½Π° 1 ΠΌΒ³ ΠΏΠΎΠ»ΡΡΠ΅Π½Π½ΠΎΠ³ΠΎ ΠΎΠ±ΡΠ΅ΠΌΠ°. ΠΠ΄Π½Π°ΠΊΠΎ ΡΡΠΎ ΠΏΡΠΈΠ±Π»ΠΈΠ·ΠΈΡΠ΅Π»ΡΠ½ΡΠ΅ ΠΏΠΎΠΊΠ°Π·Π°ΡΠ΅Π»ΠΈ, ΡΠΎΡΠ½ΠΎΠ΅ ΡΠΈΡΠ»ΠΎ Π·Π°Π²ΠΈΡΠΈΡ ΠΎΡ ΠΏΠ°ΡΠ°ΠΌΠ΅ΡΡΠΎΠ² ΠΈ ΡΠΈΠΏΠ° ΠΈΡΠΏΠΎΠ»ΡΠ·ΠΎΠ²Π°Π½Π½ΠΎΠ³ΠΎ ΠΌΠ°ΡΠ΅ΡΠΈΠ°Π»Π°.
ΠΡΠΈ ΠΏΠΎΠΊΡΠΏΠΊΠ΅ ΠΊΠΈΡΠΏΠΈΡΠ΅ΠΉ Π²Π°ΠΆΠ½ΠΎ ΡΡΠΈΡΡΠ²Π°ΡΡ ΠΏΡΠΎΡΠ΅Π½Ρ Π±ΠΎΡ, ΠΏΠΎΡΡΠΎΠΌΡ ΡΠ΅ΠΊΠΎΠΌΠ΅Π½Π΄ΡΠ΅ΡΡΡ ΠΏΡΠΈΠΎΠ±ΡΠ΅ΡΠ°ΡΡ Π½Π° 10β15% Π±ΠΎΠ»ΡΡΠ΅ ΡΠ°ΡΡΡΠΈΡΠ°Π½Π½ΠΎΠ³ΠΎ ΠΊΠΎΠ»ΠΈΡΠ΅ΡΡΠ²Π°.
Π§ΡΠΎΠ±Ρ Π·Π°Π»ΠΎΠΆΠΈΡΡ ΠΊΠΈΡΠΏΠΈΡΠ½ΡΠΉ ΡΠΎΠΊΠΎΠ»Ρ ΡΠ²ΠΎΠΈΠΌΠΈ ΡΡΠΊΠ°ΠΌΠΈ Π½Π΅ ΡΠ΅ΠΊΠΎΠΌΠ΅Π½Π΄ΡΠ΅ΡΡΡ ΠΈΡΠΏΠΎΠ»ΡΠ·ΠΎΠ²Π°ΡΡ Π² ΡΠ°Π±ΠΎΡΠ΅ ΡΠΈΠ»ΠΈΠΊΠ°ΡΠ½ΡΠΉ ΠΌΠ°ΡΠ΅ΡΠΈΠ°Π» ΠΈΠ»ΠΈ Π±Π΅ΡΠΎΠ½Π½ΡΠΉ Π±Π»ΠΎΠΊ. ΠΡΠΏΠΎΠ»ΡΠ·ΠΎΠ²Π°Π½ΠΈΠ΅ ΠΎΠΏΠ°ΡΠ½ΠΎ ΡΠ΅ΠΌ, ΡΡΠΎ ΡΠ°ΠΊΠΎΠΉ ΠΊΠΈΡΠΏΠΈΡ ΠΌΠ°ΠΊΡΠΈΠΌΠ°Π»ΡΠ½ΠΎ Π²ΠΏΠΈΡΡΠ²Π°Π΅Ρ Π²Π»Π°Π³Ρ ΠΈ Π²ΠΏΠΎΡΠ»Π΅Π΄ΡΡΠ²ΠΈΠΈ Π²Π»ΠΈΡΠ΅Ρ Π½Π° ΡΠ°Π·ΡΡΡΠ΅Π½ΠΈΠ΅ ΡΡΠ½Π΄Π°ΠΌΠ΅Π½ΡΠ° ΠΈ Π½Π΅ΡΡΡΠΈΡ ΡΡΠ΅Π½. ΠΠ»ΡΡ ΠΊΠΎ Π²ΡΠ΅ΠΌΡ ΡΡΡΠ°Π΄Π°Π΅Ρ ΠΏΠΎΠ²Π΅ΡΡ Π½ΠΎΡΡΡ ΠΊΠ»Π°Π΄ΠΊΠΈ, ΠΏΠ»ΠΎΡ ΠΎ Π»ΠΎΠΆΠΈΡΡΡ ΠΈ Π΄Π΅ΡΠΆΠΈΡΡΡ ΡΡΡΠΊΠ°ΡΡΡΠΊΠ°. ΠΠΏΡΠΈΠΌΠ°Π»ΡΠ½ΡΠΌΠΈ Π²Π°ΡΠΈΠ°Π½ΡΠ°ΠΌΠΈ Π²ΠΌΠ΅ΡΡΠΎ ΠΈΡΠΏΠΎΠ»ΡΠ·ΠΎΠ²Π°Π½ΠΈΡ ΡΠΈΠ»ΠΈΠΊΠ°ΡΠ½ΠΎΠ³ΠΎ Π² ΡΡΡΠΎΠΈΡΠ΅Π»ΡΠ½ΠΎΠΌ ΠΏΡΠΎΡΠ΅ΡΡΠ΅ ΡΠ²Π»ΡΠ΅ΡΡΡ ΠΏΡΠΈΠΌΠ΅Π½Π΅Π½ΠΈΠ΅ ΡΠ°ΠΊΠΈΡ Π²ΠΈΠ΄ΠΎΠ² ΠΊΠΈΡΠΏΠΈΡΠ΅ΠΉ:
ΠΠ»Ρ ΡΠ°Π±ΠΎΡΡ ΠΌΠΎΠΆΠ΅Ρ Π±ΡΡΡ ΠΈΡΠΏΠΎΠ»ΡΠ·ΠΎΠ²Π°Π½ Π³Π»ΠΈΠ½ΡΠ½ΡΠΉ ΠΊΠΈΡΠΏΠΈΡ.- ΠΊΠ»ΠΈΠ½ΠΊΠ΅ΡΠ½ΡΠΉ;
- ΡΡΡ ΠΎΠ³ΠΎ ΠΈΠ»ΠΈ ΠΏΠΎΠ»ΡΡΡΡ ΠΎΠ³ΠΎ ΠΏΡΠ΅ΡΡΠΎΠ²Π°Π½ΠΈΡ;
- ΠΏΠΎΡΠΈΠ·ΠΎΠ²Π°Π½Π½ΡΠΉ;
- ΠΊΠ΅ΡΠ°ΠΌΠΈΡΠ΅ΡΠΊΠΈΠΉ;
- Π³Π»ΠΈΠ½ΡΠ½ΡΠΉ.
ΠΡΡΠ³ΠΈΠ΅ ΠΌΠ°ΡΠ΅ΡΠΈΠ°Π»Ρ ΠΈ ΠΈΠ½ΡΡΡΡΠΌΠ΅Π½ΡΡ
ΠΠ»Ρ Π·Π°ΠΊΠ»Π°Π΄ΠΊΠΈ ΡΠΎΠΊΠΎΠ»ΡΠ½ΠΎΠ³ΠΎ ΠΎΡΠ½ΠΎΠ²Π°Π½ΠΈΡ, ΠΊΡΠΎΠΌΠ΅ ΠΊΠΈΡΠΏΠΈΡΠ΅ΠΉ, Π½Π΅ΠΎΠ±Ρ
ΠΎΠ΄ΠΈΠΌΠΎ ΠΈΡΠΏΠΎΠ»ΡΠ·ΠΎΠ²Π°ΡΡ ΠΈΠ½ΡΡΡΡΠΌΠ΅Π½ΡΡ. Π‘ΠΏΠΈΡΠΎΠΊ Π΄ΠΎΠΏΠΎΠ»Π½ΡΠ΅ΡΡΡ Π² Π·Π°Π²ΠΈΡΠΈΠΌΠΎΡΡΠΈ ΠΎΡ ΡΠ»ΠΎΠΆΠ½ΠΎΡΡΠΈ ΡΠ°Π±ΠΎΡ ΠΈ Ρ
Π°ΡΠ°ΠΊΡΠ΅ΡΠΈΡΡΠΈΠΊΠΈ ΠΈΡΠΏΠΎΠ»ΡΠ·ΠΎΠ²Π°Π½Π½ΠΎΠ³ΠΎ ΠΌΠ°ΡΠ΅ΡΠΈΠ°Π»Π°. Π‘ΡΡΠΎΠΈΡΠ΅Π»ΡΡΡΠ²ΠΎ ΠΏΠΎΠ΄ΡΠ°Π·ΡΠΌΠ΅Π²Π°Π΅Ρ ΠΏΡΠΈΠΌΠ΅Π½Π΅Π½ΠΈΠ΅ ΡΠ°ΠΊΠΎΠ³ΠΎ ΠΈΠ½Π²Π΅Π½ΡΠ°ΡΡ:
- ΠΊΠ΅Π»ΡΠΌΠ° ΡΡΠ°Π½Π΄Π°ΡΡΠ½ΠΎΠ³ΠΎ Π²ΠΈΠ΄Π°;
- ΡΡΡΠΎΠΈΡΠ΅Π»ΡΠ½ΡΠΉ ΡΡΠΎΠ²Π΅Π½Ρ;
- ΠΎΡΠ²Π΅Ρ;
- ΡΠ½ΡΡ;
- ΠΏΡΠΈΡΠ°Π»ΠΊΠ°;
- ΠΊΠΈΡΠΊΠ°.
Π ΠΏΡΠΎΡΠ΅ΡΡΠ΅ ΡΠ°Π±ΠΎΡΡ, Π²ΠΎΠ·ΠΌΠΎΠΆΠ½ΠΎ, ΠΏΡΠΈΠ΄Π΅ΡΡΡ ΠΏΡΠΎΠ²ΠΎΠ΄ΠΈΡΡ ΠΎΠ±Π»ΠΈΡΠΎΠ²ΠΊΡ ΠΊΠΈΡΠΏΠΈΡΠ΅ΠΉ. ΠΠ»Ρ ΡΡΠΎΠ³ΠΎ Π½Π΅ΠΎΠ±Ρ ΠΎΠ΄ΠΈΠΌΠΎ ΠΈΡΠΏΠΎΠ»ΡΠ·ΠΎΠ²Π°ΡΡ Π±ΠΎΠ»Π³Π°ΡΠΊΡ Π½Π° Π°Π»ΠΌΠ°Π·Π½ΡΡ Π΄ΠΈΡΠΊΠ°Ρ ΠΈΠ»ΠΈ ΠΊΠ°ΠΊ Π°Π»ΡΡΠ΅ΡΠ½Π°ΡΠΈΠ²Π° β ΠΎΡΠ½Π°ΡΡΠΊΡ ΠΏΠΎ ΠΊΠ°ΠΌΠ½ΡΠΌ. Π ΠΊΠ°ΡΠ΅ΡΡΠ²Π΅ ΠΈΠ·ΠΎΠ»ΡΡΠΈΠΎΠ½Π½ΠΎΠ³ΠΎ ΠΌΠ°ΡΠ΅ΡΠΈΠ°Π»Π° ΠΏΡΠΈΠΌΠ΅Π½ΡΡΡ ΡΡΠ±Π΅ΡΠΎΠΈΠ΄ ΠΈΠ»ΠΈ Π»ΠΈΡΡΡ ΠΌΠ΅ΡΠ°Π»Π»Π°. ΠΠ»Ρ Π·Π°ΠΌΠ΅ΡΠ° ΡΡΡΠΎΠΈΡΠ΅Π»ΡΠ½ΠΎΠ³ΠΎ ΡΠ°ΡΡΠ²ΠΎΡΠ° Π² ΠΎΠ±ΡΠ·Π°ΡΠ΅Π»ΡΠ½ΠΎΠΌ ΠΏΠΎΡΡΠ΄ΠΊΠ΅ ΠΏΠΎΡΡΠ΅Π±ΡΠ΅ΡΡΡ Π΅ΠΌΠΊΠΎΡΡΡ (Π²Π΅Π΄ΡΠΎ ΠΈΠ»ΠΈ ΡΠ°Π·), Π»ΠΎΠΏΠ°ΡΠ°, Π΄ΡΠ΅Π»Ρ Ρ ΠΌΠΈΠΊΡΠ΅ΡΠΎΠΌ.
ΠΠ΅ΡΠ½ΡΡΡΡΡ ΠΊ ΠΎΠ³Π»Π°Π²Π»Π΅Π½ΠΈΡΠΠ°ΠΊ ΡΠ΄Π΅Π»Π°ΡΡ ΡΠ°ΡΡΠ²ΠΎΡ Π΄Π»Ρ ΡΠΎΠΊΠΎΠ»Ρ ΠΈΠ· ΠΊΠΈΡΠΏΠΈΡΠ° Π½Π° Π»Π΅Π½ΡΠΎΡΠ½ΡΠΉ ΡΡΠ½Π΄Π°ΠΌΠ΅Π½Ρ?
ΠΠ»Ρ Π·Π°ΠΌΠ΅ΡΠ° ΡΠ°ΡΡΠ²ΠΎΡΠ° ΠΏΠΎΠ΄Ρ ΠΎΠ΄ΠΈΡ ΡΠ΅ΠΌΠ΅Π½Ρ ΠΏΠΎΡΡΠ»Π°Π½Π΄ 400.ΠΠΈΡΠΏΠΈΡΠ½Π°Ρ ΠΊΠ»Π°Π΄ΠΊΠ° ΡΠΎΠΊΠΎΠ»Ρ Π² 1 ΠΊΠΈΡΠΏΠΈΡ Π½Π°ΡΠΈΠ½Π°Π΅ΡΡΡ Ρ ΠΏΡΠΈΠ³ΠΎΡΠΎΠ²Π»Π΅Π½ΠΈΡ ΡΠΌΠ΅ΡΠΈ. ΠΠ΅Π· ΠΊΠ°ΡΠ΅ΡΡΠ²Π΅Π½Π½ΠΎΠ³ΠΎ ΡΠ°ΡΡΠ²ΠΎΡΠ° ΠΊΠΈΡΠΏΠΈΡΠΈ Π΄ΠΎΠ»ΠΆΠ½ΡΠΌ ΠΎΠ±ΡΠ°Π·ΠΎΠΌ Π½Π΅ ΡΠΊΡΠ΅ΠΏΡΡΡΡ, ΠΈ ΠΎΡΠ½ΠΎΠ²Π° Π±ΡΠ΄Π΅Ρ Π½Π΅ΡΡΡΠΎΠΉΡΠΈΠ²ΠΎΠΉ. Π’Π΅Ρ
Π½ΠΎΠ»ΠΎΠ³ΠΈΡ ΠΏΡΠΈΠ³ΠΎΡΠΎΠ²Π»Π΅Π½ΠΈΡ ΡΠ°ΡΡΠ²ΠΎΡΠ° Π±ΡΠ²Π°Π΅Ρ ΡΠ°Π·Π½ΠΎΠΉ, Π½ΠΎ Π² ΡΠ΅Π»ΠΎΠΌ ΠΌΠ°ΡΡΠ΅ΡΠ° ΡΠ΅ΠΊΠΎΠΌΠ΅Π½Π΄ΡΡΡ ΠΈΡΠΏΠΎΠ»ΡΠ·ΠΎΠ²Π°ΡΡ ΡΠ΅ΠΌΠ΅Π½Ρ (ΠΏΠΎΡΡΠ»Π°Π½Π΄) 300 ΠΈΠ»ΠΈ 400 ΠΌΠ°ΡΠΊΠΈ, Π° ΡΠ°ΠΊΠΆΠ΅ ΠΏΠ΅ΡΠΎΠΊ (ΠΌΠ΅Π»ΠΊΠΎΠ·Π΅ΡΠ½ΠΈΡΡΡΠΉ) ΠΈ Π³Π»ΠΈΠ½Ρ. Π‘ΡΡΡΠΊΡΡΡΠ° ΡΡΡΠΎΠΈΡΠ΅Π»ΡΠ½ΠΎΠΉ ΠΌΠ°ΡΡΡ Π΄ΠΎΠ»ΠΆΠ½Π° Π²ΡΠΉΡΠΈ ΠΎΠ΄Π½ΠΎΡΠΎΠ΄Π½ΠΎΠΉ, ΠΏΠ»Π°ΡΡΠΈΡΠ½ΠΎΠΉ. ΠΠ»Ρ Π΄ΠΎΡΡΠΈΠΆΠ΅Π½ΠΈΡ ΠΆΠ΅Π»Π°Π΅ΠΌΠΎΠΉ ΠΊΠΎΠ½ΡΠΈΡΡΠ΅Π½ΡΠΈΠΈ ΡΠΌΠ΅ΡΡ Π½Π΅ΠΎΠ±Ρ
ΠΎΠ΄ΠΈΠΌΠΎ ΠΏΡΠΎΡΠ΅ΡΡΡ ΡΠ΅ΡΠ΅Π· ΡΠΈΡΠΎ Ρ ΠΌΠ΅Π»ΠΊΠΈΠΌΠΈ ΡΡΠ΅ΠΉΠΊΠ°ΠΌΠΈ. ΠΠ°ΠΌΠ΅ΡΠΈΠ²Π°Π΅ΡΡΡ ΡΠ°ΡΡΠ²ΠΎΡ ΠΏΡΠΈ ΠΏΠΎΠΌΠΎΡΠΈ Π΄ΡΠ΅Π»ΠΈ, Π½Π° ΠΊΠΎΡΠΎΡΡΡ ΠΏΡΠ΅Π΄Π²Π°ΡΠΈΡΠ΅Π»ΡΠ½ΠΎ ΠΌΠΎΠ½ΡΠΈΡΡΡΡ ΡΠΏΠ΅ΡΠΈΠ°Π»ΡΠ½ΡΡ ΠΌΠΈΠΊΡΠ΅ΡΠ½ΡΡ Π½Π°ΡΠ°Π΄ΠΊΡ. ΠΠ°ΠΆΠ½ΡΠΌ ΠΌΠΎΠΌΠ΅Π½ΡΠΎΠΌ ΠΏΡΠΈ ΠΊΠ»Π°Π΄ΠΊΠ΅ Π½Π° Π±Π΅ΡΠΎΠ½Π½ΠΎΠΌ ΡΡΠ½Π΄Π°ΠΌΠ΅Π½ΡΠ΅ ΡΠ²Π»ΡΠ΅ΡΡΡ ΡΡΠ΅ΠΏΠ΅Π½Ρ Π²Π»Π°ΠΆΠ½ΠΎΡΡΠΈ ΠΏΠΎΡΠ²Ρ Π½Π° ΡΡΡΠΎΠΈΡΠ΅Π»ΡΠ½ΠΎΠΌ ΡΡΠ°ΡΡΠΊΠ΅. Π§ΡΠΎΠ±Ρ ΠΏΡΠ°Π²ΠΈΠ»ΡΠ½ΠΎ ΠΏΠΎΠ΄ΠΎΠ±ΡΠ°ΡΡ ΡΠΎΠΎΡΠ½ΠΎΡΠ΅Π½ΠΈΠ΅ ΠΌΠ°ΡΠ΅ΡΠΈΠ°Π»ΠΎΠ², ΡΠ΅ΠΊΠΎΠΌΠ΅Π½Π΄ΡΠ΅ΡΡΡ Π²ΠΎΡΠΏΠΎΠ»ΡΠ·ΠΎΠ²Π°ΡΡΡΡ ΡΠ°Π±Π»ΠΈΡΠ°ΠΌΠΈ, Π² ΠΊΠΎΡΠΎΡΡΡ
ΠΏΡΠΈΠ²Π΅Π΄Π΅Π½Ρ ΠΏΠΎΠΊΠ°Π·Π°ΡΠ΅Π»ΠΈ ΠΏΡΠΎΡΠ½ΠΎΡΡΠΈ.
Π’Π΅Ρ Π½ΠΎΠ»ΠΎΠ³ΠΈΡ ΠΊΠ»Π°Π΄ΠΊΠΈ
ΠΠΎΡΠ»Π΅ ΡΠΎΠ³ΠΎ ΠΊΠ°ΠΊ ΡΠ΅ΡΠΊΠ° ΠΈΠ· Π°ΡΠΌΠ°ΡΡΡΡ ΡΡΡΠ°Π½ΠΎΠ²Π»Π΅Π½Π° Π½Π° ΡΡΠ½Π΄Π°ΠΌΠ΅Π½ΡΠ΅ ΠΊΠΎΠ½ΡΡΡΡΠΊΡΠΈΠΈ, Π½ΡΠΆΠ½ΠΎ ΠΏΡΠΈΡΡΡΠΏΠΈΡΡ ΠΊ ΠΏΡΠΎΡΠ΅ΡΡΡ Π·Π°ΠΊΠ»Π°Π΄ΠΊΠΈ. ΠΡΠ»ΠΎΠΆΠΈΡΡ ΡΠΎΠΊΠΎΠ»ΡΠ½ΡΠΉ ΠΊΠ°ΡΠΊΠ°Ρ ΠΏΡΠΈΠ΄Π΅ΡΡΡ Ρ ΡΠ³Π»ΠΎΠ². ΠΡΠΈ ΡΡΠΎΠΌ ΠΏΠΎΡΠ»Π΅ ΡΠΎΠ³ΠΎ, ΠΊΠ°ΠΊ Π±ΡΠ΄Π΅Ρ ΠΎΡΠΎΡΠΌΠ»Π΅Π½ ΠΏΠ΅ΡΠ²ΡΠΉ ΡΡΠ΄, ΠΏΡΠΎΠ²Π΅ΡΡΡΡ ΡΠΎΠ²Π½ΠΎΡΡΡ ΠΊΠΎΠ½ΡΡΡΡΠΊΡΠΈΠΈ ΡΡΡΠΎΠΈΡΠ΅Π»ΡΠ½ΡΠΌ ΡΡΠΎΠ²Π½Π΅ΠΌ. ΠΠ»Π°Π΄ΠΊΠ° ΠΊΠΈΡΠΏΠΈΡΠ° Π½Π° ΡΡΠ½Π΄Π°ΠΌΠ΅Π½Ρ Π²ΡΠΏΠΎΠ»Π½ΡΠ΅ΡΡΡ ΡΡΡΠΎΠ³ΠΎ Π³ΠΎΡΠΈΠ·ΠΎΠ½ΡΠ°Π»ΡΠ½ΡΠΌΠΈ ΡΡΠ΄Π°ΠΌΠΈ Π² ΠΎΠ΄ΠΈΠ½ ΠΊΠΈΡΠΏΠΈΡ ΠΈΠ»ΠΈ Π² 1,5, ΡΠ΅ΠΆΠ΅ Π² 2 ΠΊΠΈΡΠΏΠΈΡΠ°. ΠΠ°ΠΆΠ΄ΡΠΉ ΡΡΠ°ΠΏ ΠΊΠ»Π°Π΄ΠΊΠΈ ΠΏΠΎΠΊΡΡΠ²Π°Π΅ΡΡΡ ΡΠ°ΡΡΠ²ΠΎΡΠΎΠΌ, ΡΠΎΠ»ΡΠΈΠ½Π° ΠΊΠΎΡΠΎΡΠΎΠ³ΠΎ ΠΏΡΠΈΠΌΠ΅ΡΠ½ΠΎ 2,5 ΡΠΌ. ΠΠΎΡΠ»Π΅ ΡΠΎΠ³ΠΎ ΠΊΠ°ΠΊ ΠΊΠΈΡΠΏΠΈΡΠ½ΡΠΉ ΡΡΠ½Π΄Π°ΠΌΠ΅Π½Ρ ΡΡΠ°Π½ΠΎΠ²ΠΈΡΡΡ Π²ΡΡΠΎΡΠΎΠΉ Π² ΡΠ΅ΡΡΡΠ΅ ΡΡΠ΄Π°, ΡΠ΅ΠΊΠΎΠΌΠ΅Π½Π΄ΡΠ΅ΡΡΡ Π½Π°ΡΠ°ΡΡ ΠΏΡΠΎΡΠ΅ΡΡ Π²ΠΎΠ·Π²Π΅Π΄Π΅Π½ΠΈΡ ΡΡΠ΅Π½. Π¦ΠΎΠΊΠΎΠ»ΡΠ½Π°Ρ ΠΏΠΎΠ²Π΅ΡΡ
Π½ΠΎΡΡΡ ΠΎΡΠ΄Π΅Π»ΡΠ²Π°Π΅ΡΡΡ ΠΏΡΠ΅ΠΈΠΌΡΡΠ΅ΡΡΠ²Π΅Π½Π½ΠΎ Π΄Π΅ΠΊΠΎΡΠ°ΡΠΈΠ²Π½ΡΠΌ ΠΊΠ°ΠΌΠ½Π΅ΠΌ. ΠΡΠ²Π°Π΅Ρ, ΡΡΠΎ Π² ΠΊΠ°ΡΠ΅ΡΡΠ²Π΅ ΠΎΡΠ΄Π΅Π»ΠΎΡΠ½ΠΎΠ³ΠΎ ΠΌΠ°ΡΠ΅ΡΠΈΠ°Π»Π° Π΄Π»Ρ Π·Π΄Π°Π½ΠΈΡ ΠΈΡΠΏΠΎΠ»ΡΠ·ΡΠ΅ΡΡΡ ΠΏΠ»ΠΈΡΠΊΠ°.
ΠΡΠ»ΠΈ Π² ΠΏΠΎΠΌΠ΅ΡΠ΅Π½ΠΈΠΈ ΠΏΠ»Π°Π½ΠΈΡΡΠ΅ΡΡΡ Π²ΠΎΠ·Π²Π΅ΡΡΠΈ ΡΠΎΠΊΠΎΠ»ΡΠ½ΡΠΉ ΡΡΠ°ΠΆ Π½Π° ΠΊΠΈΡΠΏΠΈΡΠ½ΡΠΉ ΡΡΠ½Π΄Π°ΠΌΠ΅Π½Ρ, ΡΡΠΎΠΈΡ ΠΏΠΎΠ·Π°Π±ΠΎΡΠΈΡΡΡΡ ΠΎΠ± ΡΡΡΠ°Π½ΠΎΠ²ΠΊΠΈ Π²Π΅Π½ΡΠΈΠ»ΡΡΠΈΠΎΠ½Π½ΠΎΠΉ ΡΠΈΡΡΠ΅ΠΌΡ. ΠΡΠ²Π΅ΡΡΡΠΈΡ Π΄Π»Ρ Π²Π΅Π½ΡΠΈΠ»ΡΡΠΈΠΈ Π»ΡΡΡΠ΅ ΠΏΠΎΠ»ΠΎΠΆΠΈΡΡ Π½Π° Π²ΡΡΠΎΡΠ΅ 15 ΡΠΌ ΠΎΡ ΡΡΠΎΠ²Π½Ρ Π·Π΅ΠΌΠ»ΠΈ. Π Π°Π·ΠΌΠ΅Ρ ΠΎΠΊΠΎΡΠΊΠ° Π·Π°Π²ΠΈΡΠΈΡ ΠΎΡ ΠΎΠ±ΡΠ΅Π³ΠΎ Π΄ΠΈΠ°ΠΌΠ΅ΡΡΠ° ΡΡΡΠ± Π΄Π»Ρ ΠΎΡΠ΄ΡΡΠΈΠ½. ΠΠ»Π°ΡΡΡ ΡΠΎΠΊΠΎΠ»Ρ Π½ΡΠΆΠ½ΠΎ Π½Π΅ Π½Π° Π·Π΅ΠΌΠ»Ρ, Ρ ΠΈΡΠΏΠΎΠ»ΡΠ·ΠΎΠ²Π°Π½ΠΈΠ΅ΠΌ Π³ΠΈΠ΄ΡΠΎΠΈΠ·ΠΎΠ»ΡΡΠΈΠΎΠ½Π½ΠΎΠ³ΠΎ ΡΠ»ΠΎΡ Π² Π²Π΅ΡΡ Π½Π΅ΠΉ ΡΠ°ΡΡΠΈ. ΠΠΎΡΡΠΎΠΌΡ ΠΏΠΎ Π·Π°Π²Π΅ΡΡΠ΅Π½ΠΈΠΈ ΡΡΡΠ°Π½ΠΎΠ²ΠΊΠΈ ΠΈΠ·ΠΎΠ»ΡΡΠΈΠΈ, ΠΏΡΠΎΠΊΠ»Π°Π΄ΡΠ²Π°ΡΡ ΠΏΠ»Π°ΡΡΡ ΡΡΠ±Π΅ΡΠΎΠΈΠ΄Π°.
ΠΠ΅ΡΠ½ΡΡΡΡΡ ΠΊ ΠΎΠ³Π»Π°Π²Π»Π΅Π½ΠΈΡΠΡΠ»ΠΈ Π² Π±ΡΠ΄ΡΡΠ΅ΠΌ ΠΏΠ»Π°Π½ΠΈΡΡΠ΅ΡΡΡ ΡΡΠ΅ΠΏΠ»Π΅Π½ΠΈΠ΅ ΠΊΠΎΠ½ΡΡΡΡΠΊΡΠΈΠΈ, ΡΠ°ΡΠΊΠ»Π°Π΄ΠΊΠ° Π²ΡΠΏΠΎΠ»Π½ΡΠ΅ΡΡΡ Π² ΠΏΠΎΠ»ΡΠΎΡΠ° ΠΊΠΈΡΠΏΠΈΡΠ°.
ΠΠΈΠ΄ΡΠΎ- ΠΈ ΡΠ΅ΠΏΠ»ΠΎΠΈΠ·ΠΎΠ»ΡΡΠΈΡ
ΠΡΠΎΠ±ΠΎΠ³ΠΎ Π²Π½ΠΈΠΌΠ°Π½ΠΈΡ Π² Π·Π΄Π°Π½ΠΈΠΈ Π·Π°ΡΠ»ΡΠΆΠΈΠ²Π°Π΅Ρ ΡΠΎΠΊΠΎΠ»ΡΠ½Π°Ρ ΠΈΠ·ΠΎΠ»ΡΡΠΈΡ. ΠΠ°ΡΡΠΆΠ½ΡΠΉ Π³ΡΡΠ½Ρ ΠΎΡ Π·Π΅ΠΌΠ»ΠΈ, ΠΊΠΎΡΠΎΡΠ°Ρ ΡΠ°ΡΠΏΠΎΠ»ΠΎΠΆΠ΅Π½Π° ΠΏΠΎΠ΄ ΠΊΠΎΠ½ΡΡΡΡΠΊΡΠΈΠ΅ΠΉ Π΄ΠΎΠΌΠ°, ΠΎΡΠ»ΠΈΡΠ°Π΅ΡΡΡ ΡΠ΅ΠΌ, ΡΡΠΎ Π²ΡΠΎΡΠ°Ρ Π½Π΅ Π·Π°ΠΌΠ΅ΡΠ·Π°Π΅Ρ Π΄Π°ΠΆΠ΅ ΠΏΡΠΈ Π½ΠΈΠ·ΠΊΠΈΡ
ΠΏΠΎΠΊΠ°Π·Π°ΡΠ΅Π»ΡΡ
ΡΠ΅ΠΌΠΏΠ΅ΡΠ°ΡΡΡΡ ΠΎΠΊΡΡΠΆΠ°ΡΡΠ΅ΠΉ ΡΡΠ΅Π΄Ρ. Π§ΡΠΎΠ±Ρ ΠΎΡΠ³Π°Π½ΠΈΠ·ΠΎΠ²Π°ΡΡ ΡΡΠΎΡ ΠΌΠΎΠΌΠ΅Π½Ρ, ΡΡΠ½Π΄Π°ΠΌΠ΅Π½Ρ ΠΎΡΠ³ΠΎΡΠ°ΠΆΠΈΠ²Π°Π΅ΡΡΡ ΠΎΡ ΠΏΠΎΡΠ²Ρ Π³ΠΈΠ΄ΡΠΎΠΈΠ·ΠΎΠ»ΡΡΠΈΠΎΠ½Π½ΡΠΌ ΡΠ»ΠΎΠ΅ΠΌ ΠΈΠ· ΡΡΠ±Π΅ΡΠΎΠΈΠ΄Π° ΠΈΠ»ΠΈ Π΄ΡΡΠ³ΠΎΠ³ΠΎ ΠΌΠ΅ΡΠ°Π»Π»Π°. ΠΠ»Ρ ΠΊΠ°ΡΠ΅ΡΡΠ²Π΅Π½Π½ΠΎΠΉ ΡΠΊΠ»Π°Π΄ΠΊΠΈ Π³ΠΈΠ΄ΡΠΎΠΈΠ·ΠΎΠ»ΡΡΠΈΠΈ Π½Π΅ΠΎΠ±Ρ
ΠΎΠ΄ΠΈΠΌΠΎ ΠΏΠΎΠ»ΠΎΠΆΠΈΡΡ Π΄Π²Π° ΡΠ»ΠΎΡ ΡΡΠ»ΠΎΠ½Π°, ΠΏΠ»Π΅Π½ΠΊΠΈ ΠΈΠ»ΠΈ ΠΌΠ΅ΠΌΠ±ΡΠ°Π½Ρ. ΠΠΎΠΊΠΎΠ²Π°Ρ ΡΠΎΠΊΠΎΠ»ΡΠ½Π°Ρ ΡΡΠ΅Π½Π° Π±Π΅ΡΠΎΠ½Π° ΡΠ°ΠΊΠΆΠ΅ ΠΎΠ±ΡΠ°Π±Π°ΡΡΠ²Π°Π΅ΡΡΡ Π·Π°ΡΠΈΡΠΎΠΉ ΠΎΡ ΡΠ°Π»ΡΡ
ΠΈ ΠΏΠΎΠ·Π΅ΠΌΠ½ΡΡ
Π²ΠΎΠ΄. ΠΠ΅ΡΡ
Π½ΡΡ ΡΠ°ΡΡΡ Π³ΠΈΠ΄ΡΠΎΠΈΠ·ΠΎΠ»ΡΡΠΈΠΈ Π½Π° Π±Π΅ΡΠΎΠ½Π½ΠΎΠΌ ΡΡΠ½Π΄Π°ΠΌΠ΅Π½ΡΠ΅ Π½Π°Π½ΠΎΡΠΈΡΡΡ Π²Π½Π°Ρ
Π»Π΅ΡΡ, ΠΏΡΠ΅ΠΈΠΌΡΡΠ΅ΡΡΠ²Π΅Π½Π½ΠΎ Π² ΠΎΠ±Π»Π°ΡΡΡΡ
ΡΡΡΠΊΠΎΠ² ΠΈ Π²ΡΡΡΡΠΏΠ°Π΅Ρ Π½Π° 2 ΡΠΌ Π·Π° ΠΏΠ΅ΡΠΈΠΌΠ΅ΡΡ.
ΠΠ΄Π½ΠΎΠΉ Π³ΠΈΠ΄ΡΠΎΠΈΠ·ΠΎΠ»ΡΡΠΈΠ΅ΠΉ ΡΠ°Π±ΠΎΡΠ° ΠΏΠΎ ΠΎΠ±ΡΡΡΡΠΎΠΉΡΡΠ²Ρ ΡΠΎΠΊΠΎΠ»Ρ Π΄ΠΎΠΌΠ° Π½Π΅ Π·Π°ΠΊΠ°Π½ΡΠΈΠ²Π°Π΅ΡΡΡ. ΠΠ»Ρ Π·Π΄Π°Π½ΠΈΠΉ ΡΠ°ΠΊΠΆΠ΅ Π½Π΅ΠΎΠ±Ρ
ΠΎΠ΄ΠΈΠΌΠΎ ΡΠ΄Π΅Π»Π°ΡΡ ΡΠ΅ΠΏΠ»ΠΎΠΈΠ·ΠΎΠ»ΡΡΠΈΡ. ΠΡΡΡΠΈΠΌ ΠΌΠ°ΡΠ΅ΡΠΈΠ°Π»ΠΎΠΌ Π΄Π»Ρ ΡΠ°ΡΠΊΠ»Π°Π΄ΠΊΠΈ ΡΠ²Π»ΡΠ΅ΡΡΡ ΠΏΠ΅Π½ΠΎΠ±Π»ΠΎΠΊ. Π’Π΅Ρ
Π½ΠΎΠ»ΠΎΠ³ΠΈΡ ΡΠ°Π±ΠΎΡΡ ΠΏΡΠ΅Π΄ΠΏΠΎΠ»Π°Π³Π°Π΅Ρ Π·Π°ΠΊΡΠ΅ΠΏΠ»Π΅Π½ΠΈΠ΅ ΠΊΠΎΠ½ΡΡΡΡΠΊΡΠΈΠΈ Π½Π° Π²Π½Π΅ΡΠ½Π΅ΠΉ ΡΠ°ΡΡΠΈ ΡΡΡΡΠΎΠΉΡΡΠ²Π° ΡΠΎΠΊΠΎΠ»Ρ. ΠΠ°ΠΆΠ½ΠΎ ΠΏΡΠΈ ΡΡΠΎΠΌ ΠΏΡΠ°Π²ΠΈΠ»ΡΠ½ΠΎ ΠΏΠΎΠ΄ΠΎΠ±ΡΠ°ΡΡ ΡΠΊΡΠ΅ΠΏΠ»ΡΡΡΠΈΠΉ ΠΌΠ°ΡΠ΅ΡΠΈΠ°Π». Π§ΡΠΎΠ±Ρ ΠΊΡΠ΅ΠΏΡΠ΅ ΡΡΠ΅ΠΏΠΈΡΡ ΠΏΠ΅Π½ΠΎΠ±Π»ΠΎΠΊΠΈ ΠΈΡΠΏΠΎΠ»ΡΠ·ΡΡΡ ΠΊΠ»Π΅ΠΉ ΠΈΠ»ΠΈ ΠΌΠ°ΡΡΠΈΠΊΡ. ΠΡΠΈ ΡΡΠΎΠΌ ΠΌΠ°ΡΠ΅ΡΠΈΠ°Π» Π½Π΅ Π΄ΠΎΠ»ΠΆΠ΅Π½ ΡΠΎΠ΄Π΅ΡΠΆΠ°ΡΡ Π² ΡΠΎΡΡΠ°Π²Π΅ ΡΠΎΠ»ΡΠ²Π΅Π½Ρ ΠΈΠ»ΠΈ Π°ΡΠ΅ΡΠΎΠ½, ΡΠ°ΡΡΠ²ΠΎΡΡΡΡΠΈΠ΅ ΠΏΠΎΠ²Π΅ΡΡ
Π½ΠΎΡΡΠΈ. ΠΠ΅ΡΠ΅Π΄ΠΊΠΎ ΡΠΎΠΊΠΎΠ»Ρ Π²ΠΎΠ·Π²ΠΎΠ΄ΡΡ Π½Π° Π³Π°Π·ΠΎΠ±Π΅ΡΠΎΠ½Π΅. ΠΡΠΎΡ ΠΌΠ°ΡΠ΅ΡΠΈΠ°Π» ΠΈΠΌΠ΅Π΅Ρ ΠΌΠ°ΡΡΡ ΠΏΡΠ΅ΠΈΠΌΡΡΠ΅ΡΡΠ². ΠΠΎ ΠΏΡΠΈ ΡΡΠΎΠΌ Π²Π°ΠΆΠ½ΠΎ ΡΡΠΈΡΡΠ²Π°ΡΡ ΡΠΈΠΏ Π³ΡΡΠ½ΡΠ° (Π½Π΅ ΡΠ΅ΠΊΠΎΠΌΠ΅Π½Π΄ΡΠ΅ΡΡΡ ΡΠΊΠ»Π°Π΄ΠΊΠ° Π½Π° ΡΠ»Π°Π±ΠΎΠΉ ΠΏΠΎΡΠ²Π΅) ΠΈ ΡΠ΅ΠΌΠΏΠ΅ΡΠ°ΡΡΡΡ ΠΌΠ΅ΡΡΠ½ΠΎΡΡΠΈ. ΠΡΠ»ΠΈ ΡΡΠΎΠ»Π±ΠΈΠΊ ΡΠ΅ΡΠΌΠΎΠΌΠ΅ΡΡΠ° ΠΎΠΏΡΡΠΊΠ°Π΅ΡΡΡ Π½ΠΈΠΆΠ΅ 10 Π³ΡΠ°Π΄ΡΡΠΎΠ² ΠΌΠΎΡΠΎΠ·Π°, ΠΈΡΠΏΠΎΠ»ΡΠ·ΠΎΠ²Π°ΡΡ Π³Π°Π·ΠΎΠ±Π΅ΡΠΎΠ½ Π½Π΅ ΡΠΎΠ²Π΅ΡΡΡΡ.
ΠΡΠΎΠΈΠ·Π²ΠΎΠ΄ΡΡΠ²ΠΎ ΡΠΈΠ»ΠΈΠΊΠ°ΡΠ½ΠΎΠ³ΠΎ ΠΊΠΈΡΠΏΠΈΡΠ° Π½Π° ΡΡΡΠ°Π½ΠΎΠ²ΠΊΠ΅ Π²ΠΈΡ ΡΠ΅Π²ΠΎΠ³ΠΎ ΡΠ»ΠΎΡ
ΠΡΠΎΠΈΠ·Π²ΠΎΠ΄ΡΡΠ²ΠΎ ΡΡΡΠΎΠΈΡΠ΅Π»ΡΠ½ΡΡ ΠΌΠ°ΡΠ΅ΡΠΈΠ°Π»ΠΎΠ² — ΠΎΠ΄Π½ΠΎ ΠΈΠ· ΠΎΡΠ½ΠΎΠ²Π½ΡΡ Π½Π°ΠΏΡΠ°Π²Π»Π΅Π½ΠΈΠΉ ΠΈΡΠΏΠΎΠ»ΡΠ·ΠΎΠ²Π°Π½ΠΈΡ Π£ΡΡΡΠΎΠΉΡΡΠ²ΠΎ Π²ΠΈΡ ΡΠ΅Π²ΠΎΠ³ΠΎ ΡΠ»ΠΎΡ (ΠΠΠ‘) . ΠΠ±ΠΎΡΡΠ΄ΠΎΠ²Π°Π½ΠΈΠ΅ ΠΏΠΎΠ·Π²ΠΎΠ»ΡΠ΅Ρ ΠΏΠΎΠ»ΡΡΠ°ΡΡ ΡΠΌΠ΅ΡΠΈ ΠΈ Π²Π΅ΡΠ΅ΡΡΠ²Π° Ρ Π²ΡΡΠΎΠΊΠΎΠΉ ΡΡΠ΅ΠΏΠ΅Π½ΡΡ Π°ΠΊΡΠΈΠ²Π°ΡΠΈΠΈ, ΡΡΠΎ Π² ΠΏΠΎΡΠ»Π΅Π΄ΡΡΠ²ΠΈΠΈ ΡΠΊΠ°Π·ΡΠ²Π°Π΅ΡΡΡ Π½Π° ΠΊΠ°ΡΠ΅ΡΡΠ²Π΅ ΠΏΡΠΎΠ΄ΡΠΊΡΠΈΠΈ. ΠΡΠΎΠΈΠ·Π²ΠΎΠ΄ΡΡΠ²ΠΎ ΡΠΈΠ»ΠΈΠΊΠ°ΡΠ½ΠΎΠ³ΠΎ ΠΊΠΈΡΠΏΠΈΡΠ° Π·Π°ΠΊΠ»ΡΡΠ°Π΅ΡΡΡ Π² ΡΠΎΡΠΌΠΈΡΠΎΠ²Π°Π½ΠΈΠΈ Π±Π»ΠΎΠΊΠΎΠ² ΠΈΠ· ΠΈΠ·Π²Π΅ΡΡΠΊΠΎΠ²ΠΎ-ΠΏΠ΅ΡΡΠ°Π½ΠΎΠΉ ΡΠΌΠ΅ΡΠΈ Π½Π° ΠΎΡΠ½ΠΎΠ²Π΅ ΠΊΠ²Π°ΡΡΠ΅Π²ΠΎΠ³ΠΎ ΠΏΠ΅ΡΠΊΠ° (92β95%) ΠΈ ΠΈΠ·Π²Π΅ΡΡΠΈ (5β8%). ΠΡΠ½ΠΎΠ²Π½Π°Ρ Ρ Π°ΡΠ°ΠΊΡΠ΅ΡΠΈΡΡΠΈΠΊΠ° ΡΡΠΎΠ³ΠΎ ΠΌΠ°ΡΠ΅ΡΠΈΠ°Π»Π° — ΠΏΡΠΎΡΠ½ΠΎΡΡΡ.ΠΡΠΎ Π²ΠΎ ΠΌΠ½ΠΎΠ³ΠΎΠΌ Π·Π°Π²ΠΈΡΠΈΡ ΠΎΡ ΡΠΎΡΡΠ°Π²Π° ΡΡΡΡΡ, ΡΠΎΠΎΡΠ½ΠΎΡΠ΅Π½ΠΈΡ ΠΈΠ½Π³ΡΠ΅Π΄ΠΈΠ΅Π½ΡΠΎΠ², ΡΡΠ΅ΠΏΠ΅Π½ΠΈ Π°ΠΊΡΠΈΠ²Π°ΡΠΈΠΈ ΡΠ°ΡΡΠΈΡ ΡΡΡ ΠΎΠΉ ΡΠΌΠ΅ΡΠΈ ΠΈ ΠΎΠ΄Π½ΠΎΡΠΎΠ΄Π½ΠΎΡΡΠΈ ΡΡΡ ΠΎΠΉ ΡΠΌΠ΅ΡΠΈ.
Π ΡΠ²ΡΠ·ΠΈ Ρ ΡΡΠΈΠΌ ΠΈΡΠΏΠΎΠ»ΡΠ·ΠΎΠ²Π°Π½ΠΈΠ΅ ΡΡΡΡΠΎΠΉΡΡΠ²Π° Π²ΠΈΡ
ΡΠ΅Π²ΠΎΠ³ΠΎ ΡΠ»ΠΎΡ ΡΡΠ°Π½ΠΎΠ²ΠΈΡΡΡ ΠΎΡΠΎΠ±Π΅Π½Π½ΠΎ Π²Π°ΠΆΠ½ΡΠΌ ΠΏΡΠΈ ΠΏΡΠΎΠΈΠ·Π²ΠΎΠ΄ΡΡΠ²Π΅ ΡΠΈΠ»ΠΈΠΊΠ°ΡΠ½ΠΎΠ³ΠΎ ΠΊΠΈΡΠΏΠΈΡΠ°. ΠΠ³ΡΠ΅Π³Π°Ρ ΠΏΡΠ΅Π΄ΡΡΠ°Π²Π»ΡΠ΅Ρ ΡΠΎΠ±ΠΎΠΉ ΠΎΠ΄Π½ΠΎΠ²ΡΠ΅ΠΌΠ΅Π½Π½ΠΎ ΡΡΡΠ΅ΠΊΡΠΈΠ²Π½ΡΠΉ Π΄ΠΈΡΠΏΠ΅ΡΠ³Π°ΡΠΎΡ ΠΈ ΡΠΌΠ΅ΡΠΈΡΠ΅Π»Ρ. ΠΠ° Π²ΡΡ
ΠΎΠ΄Π΅ ΠΌΡ ΠΏΠΎΠ»ΡΡΠ°Π΅ΠΌ ΠΎΠ΄Π½ΠΎΡΠΎΠ΄Π½ΡΡ ΡΠΌΠ΅ΡΡ Ρ Π²ΡΡΠΎΠΊΠΈΠΌ ΡΡΠΎΠ²Π½Π΅ΠΌ ΠΈΠ·ΠΌΠ΅Π»ΡΡΠ΅Π½ΠΈΡ ΠΈ Π°ΠΊΡΠΈΠ²Π°ΡΠΈΠΈ, ΠΈΠ· ΠΊΠΎΡΠΎΡΠΎΠΉ ΠΌΠΎΠΆΠ½ΠΎ ΠΈΠ·Π³ΠΎΡΠ°Π²Π»ΠΈΠ²Π°ΡΡ Π²ΡΡΠΎΠΊΠΎΠΊΠ°ΡΠ΅ΡΡΠ²Π΅Π½Π½ΡΠ΅ ΠΊΠΈΡΠΏΠΈΡΠ½ΡΠ΅ Π±Π»ΠΎΠΊΠΈ.
Π’ΡΠ΅Π±ΠΎΠ²Π°Π½ΠΈΡ ΠΊ ΡΡΡΡΡ Π΄Π»Ρ ΠΏΡΠΎΠΈΠ·Π²ΠΎΠ΄ΡΡΠ²Π° ΡΠΈΠ»ΠΈΠΊΠ°ΡΠ½ΠΎΠ³ΠΎ ΠΊΠΈΡΠΏΠΈΡΠ°
Π‘ΠΈΠ»ΠΈΠΊΠ°ΡΠ½ΡΠΉ ΠΊΠΈΡΠΏΠΈΡ ΠΈΠ·Π³ΠΎΡΠ°Π²Π»ΠΈΠ²Π°Π΅ΡΡΡ ΠΈΠ· ΠΊΠ²Π°ΡΡΠ΅Π²ΠΎΠ³ΠΎ ΠΏΠ΅ΡΠΊΠ° ΠΈ ΠΈΠ·Π²Π΅ΡΡΠΈ.Π ΡΠΎΡΡΠ°Π²Π΅ ΠΈΡΠΊΠ»ΡΡΠ°ΡΡΡΡ ΠΎΡΠ³Π°Π½ΠΈΡΠ΅ΡΠΊΠΈΠ΅ ΠΈ ΡΠ°ΡΡΠ²ΠΎΡΠΈΠΌΡΠ΅ Π²Π΅ΡΠ΅ΡΡΠ²Π°. Π ΡΠΎΡΡΠ°Π²Π΅ Π³Π»ΠΈΠ½Ρ ΠΌΠΎΠ³ΡΡ Π±ΡΡΡ Π²ΡΠΎΡΠΎΡΡΠ΅ΠΏΠ΅Π½Π½ΡΠ΅ ΠΈΠ½Π³ΡΠ΅Π΄ΠΈΠ΅Π½ΡΡ (Π½Π΅ Π±ΠΎΠ»Π΅Π΅ 8β10% ΠΎΡ ΠΌΠ°ΡΡΡ ΠΏΠ΅ΡΠΊΠ°). ΠΡΠΎ ΠΎΠ±Π΅ΡΠΏΠ΅ΡΠΈΠ²Π°Π΅Ρ Π³Π»Π°Π΄ΠΊΠΎΡΡΡ ΠΏΡΠΎΠ΄ΡΠΊΡΠΎΠ². Π’Π°ΠΊΠΆΠ΅ Π² ΡΠΌΠ΅ΡΡ Π΄ΠΎΠ±Π°Π²Π»Π΅Π½ ΠΏΠΈΠ³ΠΌΠ΅Π½Ρ. ΠΡΠΈΠ΄Π°Π΅Ρ ΡΠ²Π΅Ρ ΠΊΠΈΡΠΏΠΈΡΠ°ΠΌ.
ΠΡΠΈ ΠΏΡΠΎΠΈΠ·Π²ΠΎΠ΄ΡΡΠ²Π΅ ΡΠΈΠ»ΠΈΠΊΠ°ΡΠ½ΠΎΠ³ΠΎ ΠΊΠΈΡΠΏΠΈΡΠ° ΠΊ ΠΊΠ°ΡΠ΅ΡΡΠ²Ρ ΠΈΡΡ
ΠΎΠ΄Π½ΡΡ
ΠΈΠ½Π³ΡΠ΅Π΄ΠΈΠ΅Π½ΡΠΎΠ² ΠΏΡΠ΅Π΄ΡΡΠ²Π»ΡΡΡΡΡ Π²ΡΡΠΎΠΊΠΈΠ΅ ΡΡΠ΅Π±ΠΎΠ²Π°Π½ΠΈΡ. ΠΠ½ΠΈ Π΄ΠΎΠ»ΠΆΠ½Ρ Π±ΡΡΡ ΡΠΈΡΡΡΠΌΠΈ, Π±Π΅Π· ΠΏΡΠΈΠΌΠ΅ΡΠ΅ΠΉ, Π²ΡΡΠΎΠΊΠΎΠ°ΠΊΡΠΈΠ²Π½ΡΠΌΠΈ ΠΈ ΠΌΠ΅Π»ΠΊΠΎΠ΄ΠΈΡΠΏΠ΅ΡΡΠ½ΡΠΌΠΈ. Π ΡΡΠΎΠΌ ΡΠ»ΡΡΠ°Π΅ ΠΏΠ΅ΡΠΎΠΊ ΠΈΠ·ΠΌΠ΅Π»ΡΡΠ°Π΅ΡΡΡ Π΄ΠΎ ΡΡΠ°ΠΊΡΠΈΠΈ 2β¦ 0,2 ΠΌΠΌ.ΠΡΠΎ ΠΏΠΎΠ·Π²ΠΎΠ»ΡΠ΅Ρ Π΄ΠΎΠ±ΠΈΡΡΡΡ ΠΌΠ°ΠΊΡΠΈΠΌΠ°Π»ΡΠ½ΠΎΠΉ ΠΏΠ»ΠΎΡΠ½ΠΎΡΡΠΈ ΠΌΠ°ΡΠ΅ΡΠΈΠ°Π»Π°. ΠΡΠΎΠΌΠ΅ ΡΠΎΠ³ΠΎ, ΡΠ»Π΅Π΄ΡΠ΅Ρ Π°ΠΊΡΠΈΠ²ΠΈΡΠΎΠ²Π°ΡΡ ΠΏΠ΅ΡΠΎΠΊ ΠΈ ΠΈΠ·Π²Π΅ΡΡΡ, ΡΡΠΎ ΠΏΠΎΠ·Π²ΠΎΠ»ΠΈΡ ΠΈΠΌ ΡΡΡΠ΅ΠΊΡΠΈΠ²Π½ΠΎ Π²Π·Π°ΠΈΠΌΠΎΠ΄Π΅ΠΉΡΡΠ²ΠΎΠ²Π°ΡΡ Π΄ΡΡΠ³ Ρ Π΄ΡΡΠ³ΠΎΠΌ.
Π’Π°ΠΊΠΈΠ΅ ΡΠ²ΠΎΠΉΡΡΠ²Π° ΠΈ Ρ Π°ΡΠ°ΠΊΡΠ΅ΡΠΈΡΡΠΈΠΊΠΈ ΠΌΠ°ΡΠ΅ΡΠΈΠ°Π»Π° ΠΌΠΎΠΆΠ½ΠΎ ΠΎΠ±Π΅ΡΠΏΠ΅ΡΠΈΡΡ Π·Π° ΡΡΠ΅Ρ ΠΌΠ΅Ρ Π°Π½ΠΈΡΠ΅ΡΠΊΠΎΠΉ Π°ΠΊΡΠΈΠ²Π°ΡΠΈΠΈ. ΠΠ΄Π΅ΡΡ Π°ΠΊΡΡΠ°Π»ΡΠ½ΠΎΠΉ ΡΡΠ°Π½ΠΎΠ²ΠΈΡΡΡ ΠΏΠ΅ΡΠ΅ΡΠ°Π±ΠΎΡΠΊΠ° ΡΡΡΡΡ Π² Π΄ΠΈΡΠΏΠ΅ΡΠ³Π°ΡΠΎΡΠ°Ρ ΠΈ ΡΠΌΠ΅ΡΠΈΡΠ΅Π»ΡΡ . Π‘ ΠΈΡ ΠΏΠΎΠΌΠΎΡΡΡ ΠΌΠΎΠΆΠ½ΠΎ ΠΈΠ·ΠΌΠ΅Π»ΡΡΠΈΡΡ ΠΏΡΠΎΠ΄ΡΠΊΡ Π΄ΠΎ ΡΡΠ°ΠΊΡΠΈΠΈ ΠΆΠ΅Π»Π°Π΅ΠΌΠΎΠ³ΠΎ ΡΠ°Π·ΠΌΠ΅ΡΠ°, Π°ΠΊΡΠΈΠ²ΠΈΡΠΎΠ²Π°ΡΡ Π΅Π³ΠΎ ΠΈ ΠΏΠ΅ΡΠ΅ΠΌΠ΅ΡΠ°ΡΡ ΠΈΠ½Π³ΡΠ΅Π΄ΠΈΠ΅Π½ΡΡ Π΄ΠΎ ΠΎΠ΄Π½ΠΎΡΠΎΠ΄Π½ΠΎΠ³ΠΎ ΡΠΎΡΡΠΎΡΠ½ΠΈΡ.
Π ΡΠ΅Π»ΠΎΠΌ ΡΡΡΡΠ΅ Π΄Π»Ρ ΠΏΡΠΎΠΈΠ·Π²ΠΎΠ΄ΡΡΠ²Π° ΡΠΈΠ»ΠΈΠΊΠ°ΡΠ½ΠΎΠ³ΠΎ ΠΊΠΈΡΠΏΠΈΡΠ° ΠΎΡΠ΅Π½ΠΈΠ²Π°Π΅ΡΡΡ Π² ΡΠΎΠΎΡΠ²Π΅ΡΡΡΠ²ΠΈΠΈ Ρ ΠΎΡΠ½ΠΎΠ²Π½ΡΠΌΠΈ ΠΊΡΠΈΡΠ΅ΡΠΈΡΠΌΠΈ, ΠΈΠ·Π»ΠΎΠΆΠ΅Π½Π½ΡΠΌΠΈ Π½ΠΈΠΆΠ΅:
- ΡΡΠ΅ΠΏΠ΅Π½Ρ ΠΈΠ·ΠΌΠ΅Π»ΡΡΠ΅Π½ΠΈΡ ΡΠ°ΡΡΠΈΡ;
- ΡΡΠΎΠ²Π΅Π½Ρ Π°ΠΊΡΠΈΠ²Π°ΡΠΈΠΈ ΠΈΠ½Π³ΡΠ΅Π΄ΠΈΠ΅Π½ΡΠΎΠ²;
- ΠΎΠ΄Π½ΠΎΡΠΎΠ΄Π½ΠΎΡΡΡ ΠΈ ΡΠΈΡΡΠΎΡΠ° ΡΠΌΠ΅ΡΠΈ.
ΠΠ±ΠΎΡΡΠ΄ΠΎΠ²Π°Π½ΠΈΠ΅ Π΄Π»Ρ ΠΈΠ·ΠΌΠ΅Π»ΡΡΠ΅Π½ΠΈΡ ΠΈ ΡΠΌΠ΅ΡΠΈΠ²Π°Π½ΠΈΡ ΠΈΠ½Π³ΡΠ΅Π΄ΠΈΠ΅Π½ΡΠΎΠ² ΠΎΡΠ²Π΅ΡΠ°Π΅Ρ Π·Π° Π±ΠΎΠ»ΡΡΠΈΠ½ΡΡΠ²ΠΎ ΡΡΠΈΡ ΡΠ²ΠΎΠΉΡΡΠ². ΠΠΎΡΡΠΎΠΌΡ ΠΏΡΠΎΠΈΠ·Π²ΠΎΠ΄ΡΡΠ²ΠΎ ΡΠΈΠ»ΠΈΠΊΠ°ΡΠ½ΠΎΠ³ΠΎ ΠΊΠΈΡΠΏΠΈΡΠ° ΠΎΡΠ½ΠΎΠ²Π°Π½ΠΎ Π½Π° ΠΈΡΠΏΠΎΠ»ΡΠ·ΠΎΠ²Π°Π½ΠΈΠΈ ΡΠΌΠ΅ΡΠΈΡΠ΅Π»Π΅ΠΉ ΠΈ Π΄ΠΈΡΠΏΠ΅ΡΠ³Π°ΡΠΎΡΠΎΠ². ΠΠ½ΠΈ ΡΠΎΡΡΠ°Π²Π»ΡΡΡ Π½Π°ΠΈΠ±ΠΎΠ»Π΅Π΅ Π²Π°ΠΆΠ½ΡΡ ΡΠ°ΡΡΡ ΠΏΡΠΎΠΈΠ·Π²ΠΎΠ΄ΡΡΠ²Π΅Π½Π½ΠΎΠΉ ΡΠ΅ΠΏΠΎΡΠΊΠΈ.
ΠΡΠΎΠ΅ΠΊΡΠ½Π°Ρ ΡΡ Π΅ΠΌΠ° ΠΏΡΠΎΠΈΠ·Π²ΠΎΠ΄ΡΡΠ²Π° ΡΠΈΠ»ΠΈΠΊΠ°ΡΠ½ΠΎΠ³ΠΎ ΠΊΠΈΡΠΏΠΈΡΠ° ΠΎΠ±ΡΠΊΠ½ΠΎΠ²Π΅Π½Π½ΠΎΠ³ΠΎ
ΠΠ»Π°ΡΡΠΈΡΠ΅ΡΠΊΠ°Ρ ΡΠ΅Ρ Π½ΠΎΠ»ΠΎΠ³ΠΈΡ ΠΏΡΠΎΠΈΠ·Π²ΠΎΠ΄ΡΡΠ²Π° ΡΠΈΠ»ΠΈΠΊΠ°ΡΠ½ΠΎΠ³ΠΎ ΠΊΠΈΡΠΏΠΈΡΠ° Π²ΠΊΠ»ΡΡΠ°Π΅Ρ ΡΠ΅ΡΡΡΠ΅ ΡΡΠ°ΠΏΠ°:
- Π‘ΠΌΠ΅ΡΠΈΠ²Π°Π½ΠΈΠ΅ ΠΏΠ΅ΡΠΊΠ°, ΠΈΠ·Π²Π΅ΡΡΠΈ ΠΈ ΠΏΠΈΠ³ΠΌΠ΅Π½ΡΠ° Ρ Π²ΠΎΠ΄ΠΎΠΉ Π΄ΠΎ ΠΎΠ±ΡΠ°Π·ΠΎΠ²Π°Π½ΠΈΡ ΠΎΠ΄Π½ΠΎΡΠΎΠ΄Π½ΠΎΠΉ ΠΌΠ°ΡΡΡ.
- Π€ΠΎΡΠΌΠΎΠ²ΠΊΠ° Π±Π»ΠΎΠΊΠΎΠ² Π½Π° ΠΏΡΠ΅ΡΡΠ΅.
- ΠΠ±ΠΆΠΈΠ³ Π±Π»ΠΎΠΊΠΎΠ² Π² Π°Π²ΡΠΎΠΊΠ»Π°Π²Π΅.
- Π‘ΠΎΡΡΠΈΡΠΎΠ²ΠΊΠ°, ΡΠΏΠ°ΠΊΠΎΠ²ΠΊΠ°, ΡΠΊΠ»Π°Π΄ΠΈΡΠΎΠ²Π°Π½ΠΈΠ΅ ΠΊΠΈΡΠΏΠΈΡΠ°.
ΠΠ±ΡΠ°Π±ΠΎΡΠΊΠ° ΠΈΠ½Π³ΡΠ΅Π΄ΠΈΠ΅Π½ΡΠΎΠ² ΡΠ²Π»ΡΠ΅ΡΡΡ ΠΊΡΠΈΡΠΈΡΠ΅ΡΠΊΠΈΠΌ ΡΡΠ°ΠΏΠΎΠΌ, Π²Π»ΠΈΡΡΡΠΈΠΌ Π½Π° ΠΊΠ°ΡΠ΅ΡΡΠ²ΠΎ ΠΏΡΠΎΠ΄ΡΠΊΡΠ°. ΠΠ° ΡΡΠΎΠΌ ΡΡΠ°ΠΏΠ΅ Π²Π°ΠΆΠ½ΠΎ Π΄ΠΎΠ±ΠΈΡΡΡΡ Π²ΡΡΠΎΠΊΠΎΠΉ Π°ΠΊΡΠΈΠ²Π°ΡΠΈΠΈ ΠΌΠ°ΡΠ΅ΡΠΈΠ°Π»ΠΎΠ², ΡΡΠΎΠ±Ρ ΠΎΠ½ΠΈ Π²ΡΡΡΠΏΠ°Π»ΠΈ Π² ΡΠ²Π΅ΡΠ΄ΠΎΡΠ°Π·Π½ΡΠ΅ ΡΠ΅Π°ΠΊΡΠΈΠΈ. Π’Π°ΠΊΠΆΠ΅ ΡΡΠ΅Π±ΡΠ΅ΡΡΡ ΡΠ°Π·ΠΌΠ΅ΡΠ°ΡΡ ΡΠΌΠ΅ΡΡ Π΄ΠΎ ΠΎΠ΄Π½ΠΎΡΠΎΠ΄Π½ΠΎΠ³ΠΎ ΡΠΎΡΡΠΎΡΠ½ΠΈΡ.
ΠΠ»Π°ΡΡΠΈΡΠ΅ΡΠΊΠ°Ρ ΠΏΡΠΎΠ΅ΠΊΡΠ½Π°Ρ ΡΡ Π΅ΠΌΠ° ΠΏΡΠΎΠΈΠ·Π²ΠΎΠ΄ΡΡΠ²Π° ΡΠΈΠ»ΠΈΠΊΠ°ΡΠ½ΠΎΠ³ΠΎ ΠΊΠΈΡΠΏΠΈΡΠ° ΠΏΡΠ΅Π΄ΠΏΠΎΠ»Π°Π³Π°Π΅Ρ ΠΈΡΠΏΠΎΠ»ΡΠ·ΠΎΠ²Π°Π½ΠΈΠ΅ ΡΠ°ΡΠΎΠ²ΡΡ ΠΌΠ΅Π»ΡΠ½ΠΈΡ.Π‘ΠΌΠ΅ΡΡ ΠΌΠΎΠΆΠ½ΠΎ ΠΎΠ±ΡΠ°Π±Π°ΡΡΠ²Π°ΡΡ ΠΏΡΡΠ΅ΠΌ ΠΈΡΡΠΈΡΠ°Π½ΠΈΡ, ΠΈΠ·ΠΌΠ΅Π»ΡΡΠ΅Π½ΠΈΡ, ΡΠ°Π·Π»Π°ΠΌΡΠ²Π°Π½ΠΈΡ ΠΈ ΠΈΠ·ΠΌΠ΅Π»ΡΡΠ΅Π½ΠΈΡ ΠΈΠ½Π³ΡΠ΅Π΄ΠΈΠ΅Π½ΡΠΎΠ². ΠΠ°ΡΠ΅ΡΠΈΠ°Π»Ρ ΠΌΠΎΠΆΠ½ΠΎ ΠΎΠ±ΡΠ°Π±Π°ΡΡΠ²Π°ΡΡ ΠΎΡΠ΄Π΅Π»ΡΠ½ΠΎ, Π° Π·Π°ΡΠ΅ΠΌ ΡΠΌΠ΅ΡΠΈΠ²Π°ΡΡ, ΠΈΠ»ΠΈ ΠΏΠΎΠ΄Π²Π΅ΡΠ³Π°ΡΡ ΠΎΠ΄Π½ΠΎΠ²ΡΠ΅ΠΌΠ΅Π½Π½ΠΎΠΌΡ ΠΈΠ·ΠΌΠ΅Π»ΡΡΠ΅Π½ΠΈΡ ΠΈ Π³ΠΎΠΌΠΎΠ³Π΅Π½ΠΈΠ·Π°ΡΠΈΠΈ ΡΠΌΠ΅ΡΠΈ. ΠΠ»Π°ΡΡΠΈΡΠ΅ΡΠΊΠ°Ρ ΡΠ΅Ρ Π½ΠΎΠ»ΠΎΠ³ΠΈΡ Ρ ΠΎΡΡ ΠΈ ΠΏΠΎΠ·Π²ΠΎΠ»ΡΠ΅Ρ ΠΏΠΎΠ»ΡΡΠΈΡΡ ΠΊΠ°ΡΠ΅ΡΡΠ²Π΅Π½Π½ΡΠΉ ΠΏΡΠΎΠ΄ΡΠΊΡ, Π½ΠΎ ΠΎΡΠ»ΠΈΡΠ°Π΅ΡΡΡ Π±ΠΎΠ»ΡΡΠΈΠΌ ΡΠ°ΡΡ ΠΎΠ΄ΠΎΠΌ ΡΠ»Π΅ΠΊΡΡΠΎΡΠ½Π΅ΡΠ³ΠΈΠΈ, Π²ΡΠ΅ΠΌΠ΅Π½Π½ΡΠΌΠΈ Π·Π°ΡΡΠ°ΡΠ°ΠΌΠΈ ΠΈ ΡΠ»ΠΎΠΆΠ½ΠΎΡΡΡΡ. ΠΠ±ΠΎΡΡΠ΄ΠΎΠ²Π°Π½ΠΈΠ΅ Π³ΡΠΎΠΌΠΎΠ·Π΄ΠΊΠΎΠ΅, ΡΡΠΌΠ½ΠΎΠ΅, ΠΈΠ·Π½Π°ΡΠΈΠ²Π°Π΅ΠΌΠΎΠ΅, Π° Π΅Π³ΠΎ ΠΠΠ Π΄ΠΎΡΡΠΈΠ³Π°Π΅Ρ Π²ΡΠ΅Π³ΠΎ 20%.
ΠΡ Π½Π΅Π΄ΠΎΡΡΠ°ΡΠΊΠΎΠ² ΡΡΠ°Π΄ΠΈΡΠΈΠΎΠ½Π½ΠΎΠΉ ΡΡ
Π΅ΠΌΡ ΠΏΡΠΎΠ΅ΠΊΡΠΈΡΠΎΠ²Π°Π½ΠΈΡ ΠΌΠΎΠΆΠ½ΠΎ ΠΈΠ·Π±Π°Π²ΠΈΡΡΡΡ, ΠΈΡΠΏΠΎΠ»ΡΠ·ΡΡ ΡΡΡΡΠΎΠΉΡΡΠ²ΠΎ Π²ΠΈΡ
ΡΠ΅Π²ΠΎΠ³ΠΎ ΡΠ»ΠΎΡ ΠΎΡ GlobeCore . ΠΡΠΎ ΠΊΠΎΠΌΠΏΠ°ΠΊΡΠ½Π°Ρ, ΡΡΡΠ΅ΠΊΡΠΈΠ²Π½Π°Ρ ΠΈ ΡΠΊΠΎΠ½ΠΎΠΌΠΈΡΠ½Π°Ρ ΡΡΡΠ°Π½ΠΎΠ²ΠΊΠ°, ΠΏΡΠ΅Π΄Π½Π°Π·Π½Π°ΡΠ΅Π½Π½Π°Ρ Π΄Π»Ρ ΠΎΠ±ΡΠ°Π±ΠΎΡΠΊΠΈ ΡΡΡΡΡ Π΄Π»Ρ ΠΏΡΠΎΠΈΠ·Π²ΠΎΠ΄ΡΡΠ²Π° ΡΠΈΠ»ΠΈΠΊΠ°ΡΠ½ΠΎΠ³ΠΎ ΠΊΠΈΡΠΏΠΈΡΠ°.
Π’Π΅Ρ Π½ΠΎΠ»ΠΎΠ³ΠΈΡ ΠΏΡΠΎΠΈΠ·Π²ΠΎΠ΄ΡΡΠ²Π° ΡΠΈΠ»ΠΈΠΊΠ°ΡΠ½ΠΎΠ³ΠΎ ΠΊΠΈΡΠΏΠΈΡΠ° Π½Π° ΡΡΡΠ°Π½ΠΎΠ²ΠΊΠ΅ Π²ΠΈΡ ΡΠ΅Π²ΠΎΠ³ΠΎ ΡΠ»ΠΎΡ
ΠΡΠΎΠΈΠ·Π²ΠΎΠ΄ΡΡΠ²ΠΎ ΡΠΈΠ»ΠΈΠΊΠ°ΡΠ½ΠΎΠ³ΠΎ ΠΊΠΈΡΠΏΠΈΡΠ° Ρ ΠΈΡΠΏΠΎΠ»ΡΠ·ΠΎΠ²Π°Π½ΠΈΠ΅ΠΌ ΡΡΡΡΠΎΠΉΡΡΠ²Π° Π²ΠΈΡ ΡΠ΅Π²ΠΎΠ³ΠΎ ΡΠ»ΠΎΡ Π²ΠΊΠ»ΡΡΠ°Π΅Ρ ΠΎΠ±ΡΠ°Π±ΠΎΡΠΊΡ ΠΈΠ½Π³ΡΠ΅Π΄ΠΈΠ΅Π½ΡΠΎΠ² ΠΈ ΠΈΡ Π°ΠΊΡΠΈΠ²Π°ΡΠΈΡ Π² ΡΠ»Π΅ΠΊΡΡΠΎΠΌΠ°Π³Π½ΠΈΡΠ½ΠΎΠΌ ΠΏΠΎΠ»Π΅.
ΠΠ΅ΡΠΎΠΊ ΠΈ ΠΈΠ·Π²Π΅ΡΡΡ ΠΏΠΎΠ΄Π°ΡΡ Π² ΠΊΠ°ΠΌΠ΅ΡΡ, ΡΠΎΠ΄Π΅ΡΠΆΠ°ΡΡΡ ΡΠ΅ΡΡΠΎΠΌΠ°Π³Π½ΠΈΡΠ½ΡΠ΅ ΠΈΠ³Π»Ρ, ΠΊΠΎΡΠΎΡΡΠ΅ ΠΏΠΎΠ΄ Π΄Π΅ΠΉΡΡΠ²ΠΈΠ΅ΠΌ ΡΠ»Π΅ΠΊΡΡΠΎΠΌΠ°Π³Π½ΠΈΡΠ½ΠΎΠ³ΠΎ ΠΏΠΎΠ»Ρ ΠΏΡΠ΅Π²ΡΠ°ΡΠ°ΡΡΡΡ Π² ΠΌΠΈΠ½ΠΈΠ°ΡΡΡΠ½ΡΠ΅ ΡΠΌΠ΅ΡΠΈΡΠ΅Π»ΠΈ ΠΈ Π΄ΡΠΎΠ±ΠΈΠ»ΠΊΠΈ.ΠΠ½ΠΈ ΠΈΠ½ΡΠ΅Π½ΡΠΈΠ²Π½ΠΎ Π΄Π²ΠΈΠΆΡΡΡΡ ΠΏΠΎ ΡΠ°Π±ΠΎΡΠ΅ΠΉ ΠΊΠ°ΠΌΠ΅ΡΠ΅, ΡΠ΄Π°ΡΡΡΡΡΡ ΠΎ Π΅Π΅ ΡΡΠ΅Π½ΠΊΠΈ, ΡΡΠ°Π»ΠΊΠΈΠ²Π°ΡΡΡΡ Π΄ΡΡΠ³ Ρ Π΄ΡΡΠ³ΠΎΠΌ ΠΈ Ρ ΡΠ°ΡΡΠΈΡΠ°ΠΌΠΈ ΠΎΠ±ΡΠ°Π±Π°ΡΡΠ²Π°Π΅ΠΌΠΎΠ³ΠΎ ΠΌΠ°ΡΠ΅ΡΠΈΠ°Π»Π°.
Π ΡΠΎ ΠΆΠ΅ Π²ΡΠ΅ΠΌΡ Π·Π΄Π΅ΡΡ Π½Π°Π±Π»ΡΠ΄Π°ΡΡΡΡ ΠΏΡΠΎΡΠ΅ΡΡΡ ΠΏΠ΅ΡΠ΅ΠΌΠ΅ΡΠΈΠ²Π°Π½ΠΈΡ ΠΈ Π΄ΠΈΡΠΏΠ΅ΡΠ³ΠΈΡΠΎΠ²Π°Π½ΠΈΡ, Π²ΡΠ·Π²Π°Π½Π½ΡΠ΅ Π²ΡΡΠΎΠΊΠΈΠΌΠΈ Π»ΠΎΠΊΠ°Π»ΡΠ½ΡΠΌΠΈ Π΄Π°Π²Π»Π΅Π½ΠΈΡΠΌΠΈ, ΡΠ»Π΅ΠΊΡΡΠΎΠΌΠ°Π³Π½ΠΈΡΠ½ΡΠΌΠΈ ΠΏΠΎΠ»ΡΠΌΠΈ, Π°ΠΊΡΡΡΠΈΡΠ΅ΡΠΊΠΈΠΌΠΈ ΠΊΠΎΠ»Π΅Π±Π°Π½ΠΈΡΠΌΠΈ, Π° ΡΠ°ΠΊΠΆΠ΅ ΡΠ»Π΅ΠΊΡΡΠΎΠ»ΠΈΠ·ΠΎΠΌ ΠΏΡΠΈ ΡΠ°Π±ΠΎΡΠ΅ Ρ ΠΆΠΈΠ΄ΠΊΠΎΡΡΡΡ. Π ΡΡΠΎΠΉ ΡΡΠ΅Π΄Π΅ Π²Π΅ΡΠ΅ΡΡΠ²Π° ΠΈΠ½ΡΠ΅Π½ΡΠΈΠ²Π½ΠΎ ΠΏΠ΅ΡΠ΅ΠΌΠ΅ΡΠΈΠ²Π°ΡΡΡΡ ΠΈ Π°ΠΊΡΠΈΠ²ΠΈΡΡΡΡΡΡ, ΠΎΠ±ΡΠ°Π·ΡΡ ΠΊΠ°ΡΠ΅ΡΡΠ²Π΅Π½Π½ΡΡ ΡΠΌΠ΅ΡΡ.
ΠΠ»Ρ Π΄ΠΎΡΡΠΈΠΆΠ΅Π½ΠΈΡ ΡΠ΅Π·ΡΠ»ΡΡΠ°ΡΠ° ΡΡΠ΅Π±ΡΠ΅ΡΡΡ ΠΎΡ Π½Π΅ΡΠΊΠΎΠ»ΡΠΊΠΈΡ
ΡΠ΅ΠΊΡΠ½Π΄ Π΄ΠΎ 2β4 ΠΌΠΈΠ½ΡΡ. ΠΠ»Ρ ΡΠ΅Π³ΡΠ»ΠΈΡΠΎΠ²Π°Π½ΠΈΡ ΡΡΠ΅ΠΏΠ΅Π½ΠΈ Π°ΠΊΡΠΈΠ²Π°ΡΠΈΠΈ ΠΈ ΠΈΠ·ΠΌΠ΅Π»ΡΡΠ΅Π½ΠΈΡ ΠΈΠ½Π³ΡΠ΅Π΄ΠΈΠ΅Π½ΡΠΎΠ² Π΄ΠΎΡΡΠ°ΡΠΎΡΠ½ΠΎ ΠΈΠ·ΠΌΠ΅Π½ΠΈΡΡ Π²ΡΠ΅ΠΌΡ ΠΎΠ±ΡΠ°Π±ΠΎΡΠΊΠΈ ΠΌΠ°ΡΠ΅ΡΠΈΠ°Π»ΠΎΠ² Π² Π²ΠΈΡ
ΡΠ΅Π²ΠΎΠΌ ΡΠ»ΠΎΠ΅.
ΠΡΡΠ΅ΠΊΡΠΈΠ²Π½ΠΎΡΡΡ Π°ΠΊΡΠΈΠ²Π°ΡΠΈΠΈ ΡΠΌΠ΅ΡΠΈ Π² ΠΠΠ‘ ΠΏΡΠΈ ΠΏΡΠΎΠΈΠ·Π²ΠΎΠ΄ΡΡΠ²Π΅ ΡΠΈΠ»ΠΈΠΊΠ°ΡΠ½ΠΎΠ³ΠΎ ΠΊΠΈΡΠΏΠΈΡΠ°
ΠΡΠΈ ΠΎΠ±ΡΠ°Π±ΠΎΡΠΊΠ΅ ΠΏΠ΅ΡΠΊΠ° Π² ΡΡΡΡΠΎΠΉΡΡΠ²Π΅ Π²ΠΈΡ ΡΠ΅Π²ΠΎΠ³ΠΎ ΡΠ»ΠΎΡ ΠΎΠ½ ΠΏΠΎΠ΄Π²Π΅ΡΠ³Π°Π΅ΡΡΡ Π²ΡΡΠΎΠΊΠΎΠΉ ΡΡΠ΅ΠΏΠ΅Π½ΠΈ Π°ΠΊΡΠΈΠ²Π°ΡΠΈΠΈ. ΠΠ° Π·Π΅ΡΠ½Π°Ρ ΠΎΠ±ΡΠ°Π·ΡΠ΅ΡΡΡ ΠΌΠ½ΠΎΠ³ΠΎ Π½ΠΎΠ²ΠΎΠΉ ΠΏΠΎΠ²Π΅ΡΡ Π½ΠΎΡΡΠΈ Ρ Π²ΡΡΠΎΠΊΠΈΠΌ ΠΊΠΎΠ½ΡΠ°ΠΊΡΠΎΠΌ ΠΈΠ·-Π·Π° Π½Π°Π»ΠΈΡΠΈΡ Π°ΠΊΡΠΈΠ²Π½ΡΡ ΡΠ΅Π½ΡΡΠΎΠ², ΡΠ²ΠΎΠ±ΠΎΠ΄Π½ΡΡ ΡΠ°Π΄ΠΈΠΊΠ°Π»ΠΎΠ². Π ΡΡΠΎΡ ΠΌΠΎΠΌΠ΅Π½Ρ ΠΎΠ±ΡΠ°Π·ΡΠ΅ΡΡΡ ΠΈΠ·Π±ΡΡΠΎΡΠ½Π°Ρ ΠΏΠΎΠ²Π΅ΡΡ Π½ΠΎΡΡΠ½Π°Ρ ΡΠ½Π΅ΡΠ³ΠΈΡ, Π° Π²Π½ΡΡΡΠ΅Π½Π½ΡΡ ΡΠ½Π΅ΡΠ³ΠΈΡ, Π½Π°ΠΏΡΠΎΡΠΈΠ², ΡΠΌΠ΅Π½ΡΡΠ°Π΅ΡΡΡ.ΠΡΠΎ Π²ΡΠ·Π²Π°Π½ΠΎ ΡΠ°Π·ΡΡΠ²ΠΎΠΌ ΡΠΈΠ»ΠΎΠΊΡΠ°Π½ΠΎΠ²ΡΡ ΡΠ²ΡΠ·Π΅ΠΉ Si-O. Π ΡΡΠΎΠΌ ΡΠΎΡΡΠΎΡΠ½ΠΈΠΈ ΠΏΠ΅ΡΠΎΠΊ Π±ΡΡΡΡΠ΅Π΅ ΠΈ ΡΡΡΠ΅ΠΊΡΠΈΠ²Π½Π΅Π΅ Π²ΡΡΡΠΏΠ°Π΅Ρ Π² ΡΠ²Π΅ΡΠ΄ΠΎΡΠ°Π·Π½ΡΠ΅ ΡΠ΅Π°ΠΊΡΠΈΠΈ ΠΈ ΠΎΠ±Π»Π°Π΄Π°Π΅Ρ Π²ΡΡΠΎΠΊΠΈΠΌΠΈ ΡΡΡΡΠΊΡΡΡΠΎΠΎΠ±ΡΠ°Π·ΡΡΡΠΈΠΌΠΈ Ρ Π°ΡΠ°ΠΊΡΠ΅ΡΠΈΡΡΠΈΠΊΠ°ΠΌΠΈ. ΠΡΠΎΠΈΠ·Π²ΠΎΠ΄ΡΡΠ²ΠΎ ΡΠΈΠ»ΠΈΠΊΠ°ΡΠ½ΠΎΠ³ΠΎ ΠΊΠΈΡΠΏΠΈΡΠ° ΠΈΠ· ΡΠ°ΠΊΠΎΠ³ΠΎ ΡΡΡΡΡ ΠΏΠΎΠ·Π²ΠΎΠ»ΡΠ΅Ρ ΠΏΠΎΠ»ΡΡΠΈΡΡ ΠΌΠ°ΡΠ΅ΡΠΈΠ°Π» Ρ Π²ΡΡΠΎΠΊΠΈΠΌΠΈ ΠΏΠΎΠΊΠ°Π·Π°ΡΠ΅Π»ΡΠΌΠΈ ΠΏΡΠΎΡΠ½ΠΎΡΡΠΈ.
Π ΡΠΎ ΠΆΠ΅ Π²ΡΠ΅ΠΌΡ ΠΈΠ·Π²Π΅ΡΡΡ ΡΠ°ΠΊΠΆΠ΅ ΠΏΠΎΠ΄Π΄Π°Π΅ΡΡΡ Π°ΠΊΡΠΈΠ²Π°ΡΠΈΠΈ. Π’Π°ΠΊΠΆΠ΅ ΡΠ²Π΅Π»ΠΈΡΠΈΠ²Π°Π΅ΡΡΡ Π΅Π³ΠΎ ΡΠΏΠΎΡΠΎΠ±Π½ΠΎΡΡΡ Π²ΡΡΡΠΏΠ°ΡΡ Π² ΡΠ΅Π°ΠΊΡΠΈΡ Ρ ΠΏΠ΅ΡΠΊΠΎΠΌ, ΡΡΠΎ Π² ΠΊΠΎΠ½Π΅ΡΠ½ΠΎΠΌ ΠΈΡΠΎΠ³Π΅ ΡΠΊΠ°Π·ΡΠ²Π°Π΅ΡΡΡ Π½Π° ΠΏΡΠΎΡΠ½ΠΎΡΡΠ½ΡΡ
Ρ
Π°ΡΠ°ΠΊΡΠ΅ΡΠΈΡΡΠΈΠΊΠ°Ρ
ΠΈΠ·Π΄Π΅Π»ΠΈΠΉ.
ΠΠ»Ρ ΠΏΠΎΠ΄ΡΠ²Π΅ΡΠΆΠ΄Π΅Π½ΠΈΡ ΡΡΡΠ΅ΠΊΡΠΈΠ²Π½ΠΎΡΡΠΈ Π°ΠΊΡΠΈΠ²Π°ΡΠΈΠΈ ΠΈΠ·Π²Π΅ΡΡΠΊΠΎΠ²ΠΎ-ΠΏΠ΅ΡΡΠ°Π½ΠΎΠΉ ΡΠΌΠ΅ΡΠΈ Π² ΠΠΠ‘ Π±ΡΠ» ΠΏΡΠΎΠ²Π΅Π΄Π΅Π½ ΡΠΎΠΎΡΠ²Π΅ΡΡΡΠ²ΡΡΡΠΈΠΉ ΡΠΊΡΠΏΠ΅ΡΠΈΠΌΠ΅Π½Ρ ΠΏΠΎ ΠΊΡΠ°ΡΠΊΠΎΠ²ΡΠ΅ΠΌΠ΅Π½Π½ΠΎΠΉ ΠΏΠ΅ΡΠ΅ΡΠ°Π±ΠΎΡΠΊΠ΅ ΡΡΡΡΡ Π² Π²ΠΈΡ ΡΠ΅Π²ΠΎΠΌ ΡΠ»ΠΎΠ΅ Π·Π° Π΄ΠΎΠ»ΠΈ ΡΠ΅ΠΊΡΠ½Π΄Ρ.ΠΡΠΈ ΡΡΠΎΠΌ ΠΈΠ·ΠΌΠ΅Π»ΡΡΠ΅Π½ΠΈΡ ΠΌΠ°ΡΠ΅ΡΠΈΠ°Π»ΠΎΠ² ΠΏΡΠ°ΠΊΡΠΈΡΠ΅ΡΠΊΠΈ Π½Π΅ Π½Π°Π±Π»ΡΠ΄Π°Π»ΠΎΡΡ, Π½ΠΎ ΠΎΠ½ΠΈ Ρ ΠΎΡΠΎΡΠΎ ΠΏΠΎΠ΄Π΄Π°Π»ΠΈΡΡ Π°ΠΊΡΠΈΠ²Π°ΡΠΈΠΈ. Π‘ΠΌΠ΅ΡΡ ΠΏΡΠΎΠΏΡΡΠΊΠ°Π»ΠΈ ΡΠ΅ΡΠ΅Π· ΠΠΠ‘, ΠΈ ΡΠ²ΠΎΠΉΡΡΠ²Π° ΠΏΠΎΠ»ΡΡΠ΅Π½Π½ΠΎΠ³ΠΎ ΠΊΠΈΡΠΏΠΈΡΠ° Π°Π½Π°Π»ΠΈΠ·ΠΈΡΠΎΠ²Π°Π»ΠΈ ΠΏΡΠΈ ΡΠ°Π·Π»ΠΈΡΠ½ΡΡ ΡΡΠ»ΠΎΠ²ΠΈΡΡ ΠΎΠ±ΡΠ°Π±ΠΎΡΠΊΠΈ. Π Π΅Π·ΡΠ»ΡΡΠ°ΡΡ ΠΈΡΡΠ»Π΅Π΄ΠΎΠ²Π°Π½ΠΈΡ ΠΏΡΠ΅Π΄ΡΡΠ°Π²Π»Π΅Π½Ρ Π² ΡΠ°Π±Π»ΠΈΡΠ΅ 1:
.Π‘ΡΠΎΠ» 1
ΠΠ°ΡΠ°ΠΌΠ΅ΡΡΡ ΠΎΠ±ΡΠ°Π±ΠΎΡΠΊΠΈ ΠΈΠ·Π²Π΅ΡΡΠΊΠΎΠ²ΠΎ-ΠΏΠ΅ΡΡΠ°Π½ΠΎΠΉ ΡΠΌΠ΅ΡΠΈ | ΠΡΠ΅Π΄Π΅Π» ΠΏΡΠΎΡΠ½ΠΎΡΡΠΈ ΠΊΠΈΡΠΏΠΈΡΠ° Π½Π° ΡΠΆΠ°ΡΠΈΠ΅, ΟΡ * 10β5, ΠΠ° |
ΠΠ΅Π· ΠΎΠ±ΡΠ°Π±ΠΎΡΠΊΠΈ | 91.2 |
ΠΠ΄Π½ΠΎΠΊΡΠ°ΡΠ½ΠΎΠ΅ ΠΏΡΠΎΡΡΠΏΠ°Π½ΠΈΠ΅ ΡΠ΅ΡΠ΅Π· Π²ΠΈΡ ΡΠ΅Π²ΠΎΠΉ ΡΠ»ΠΎΠΉ | 239,5 |
ΠΠ²ΠΎΠΉΠ½ΠΎΠ΅ ΠΏΡΠΎΡΡΠΏΠ°Π½ΠΈΠ΅ ΡΠ΅ΡΠ΅Π· Π²ΠΈΡ ΡΠ΅Π²ΠΎΠΉ ΡΠ»ΠΎΠΉ | 324,5 |
Π’ΡΠΎΠΉΠ½ΠΎΠ΅ ΠΏΡΠΎΡΡΠΏΠ°Π½ΠΈΠ΅ ΡΠ΅ΡΠ΅Π· Π²ΠΈΡ ΡΠ΅Π²ΠΎΠΉ ΡΠ»ΠΎΠΉ | 328,1 |
ΠΠΈΠ΄Π½ΠΎ, ΡΡΠΎ Π΄Π°ΠΆΠ΅ ΠΏΡΠΈ ΠΊΡΠ°ΡΠΊΠΎΠ²ΡΠ΅ΠΌΠ΅Π½Π½ΠΎΠΉ ΠΎΠ±ΡΠ°Π±ΠΎΡΠΊΠ΅ ΡΡΡΡΡ Π² ΡΡΠ΅Π΄Π΅ Π²ΠΈΡ
ΡΠ΅Π²ΠΎΠ³ΠΎ ΡΠ»ΠΎΡ Π²ΠΎΠ·ΠΌΠΎΠΆΠ½ΠΎ ΠΏΠΎΠ»ΡΡΠ΅Π½ΠΈΠ΅ ΡΠΈΠ»ΠΈΠΊΠ°ΡΠ½ΠΎΠ³ΠΎ ΠΊΠΈΡΠΏΠΈΡΠ° ΠΏΡΠΎΡΠ½ΠΎΡΡΡΡ 3. Π 5 ΡΠ°Π· Π²ΡΡΠ΅, ΡΠ΅ΠΌ Π±Π΅Π· ΠΈΡΠΏΠΎΠ»ΡΠ·ΠΎΠ²Π°Π½ΠΈΡ AVS. ΠΠ»Ρ ΠΈΡΡΠ»Π΅Π΄ΠΎΠ²Π°Π½ΠΈΡ ΠΈΡΠΏΠΎΠ»ΡΠ·ΠΎΠ²Π°Π»Π°ΡΡ ΠΌΠΎΠ΄Π΅Π»Ρ ΡΡΡΡΠΎΠΉΡΡΠ²Π° Π²ΠΈΡ
ΡΠ΅Π²ΠΎΠ³ΠΎ ΡΠ»ΠΎΡ ΠΠΠ‘-100. ΠΠ°Π½Π½Π°Ρ ΡΡΡΠ°Π½ΠΎΠ²ΠΊΠ° ΠΏΡΠ΅Π΄ΡΡΠ°Π²Π»Π΅Π½Π° ββΠ² ΠΊΠ°ΡΠ°Π»ΠΎΠ³Π΅ GlobeCore .
ΠΡΠΎΠΌΠ΅ ΡΠΎΠ³ΠΎ, Π²ΡΡΠΎΠΊΠ°Ρ ΡΡΠ΅ΠΏΠ΅Π½Ρ Π³ΠΎΠΌΠΎΠ³Π΅Π½ΠΈΠ·Π°ΡΠΈΠΈ ΠΈΠ·Π²Π΅ΡΡΠΊΠΎΠ²ΠΎ-ΠΏΠ΅ΡΡΠ°Π½ΠΎΠΉ ΡΠΌΠ΅ΡΠΈ Π²Π»ΠΈΡΠ΅Ρ Π½Π° ΠΊΠ°ΡΠ΅ΡΡΠ²ΠΎ ΠΊΠΎΠ½Π΅ΡΠ½ΠΎΠ³ΠΎ ΠΏΡΠΎΠ΄ΡΠΊΡΠ°. ΠΠΎΠ΄ Π²ΠΎΠ·Π΄Π΅ΠΉΡΡΠ²ΠΈΠ΅ΠΌ ΠΌΠ½ΠΎΠΆΠ΅ΡΡΠ²Π° ΠΏΡΠΎΡΠ΅ΡΡΠΎΠ² Π² Π²ΠΈΡ ΡΠ΅Π²ΠΎΠΌ ΡΠ»ΠΎΠ΅ ΠΈΠ½Π³ΡΠ΅Π΄ΠΈΠ΅Π½ΡΡ Π°ΠΊΡΠΈΠ²Π½ΠΎ ΡΠΌΠ΅ΡΠΈΠ²Π°ΡΡΡΡ Π² ΠΠΠ‘, ΠΎΠ±ΡΠ°Π·ΡΡ ΠΎΠ΄Π½ΠΎΡΠΎΠ΄Π½ΡΡ ΡΠΌΠ΅ΡΡ. ΠΡΠΈ ΡΡΠΎΠΌ ΠΎΠ½ΠΈ ΠΏΠΎΠ΄Π²Π΅ΡΠ³Π°ΡΡΡΡ Π΄ΠΎΠΏΠΎΠ»Π½ΠΈΡΠ΅Π»ΡΠ½ΠΎΠΉ ΡΠ»ΠΈΡΠΎΠ²ΠΊΠ΅ ΠΈ Π°ΠΊΡΠΈΠ²Π°ΡΠΈΠΈ. Π ΡΡΠΎ ΠΎΠ΄ΠΈΠ½ ΠΈΠ· Π²Π°ΠΆΠ½Π΅ΠΉΡΠΈΡ ΡΠ°ΠΊΡΠΎΡΠΎΠ², Π²Π»ΠΈΡΡΡΠΈΡ Π½Π° ΠΊΠ°ΡΠ΅ΡΡΠ²ΠΎ ΠΊΠΈΡΠΏΠΈΡΠ°.
Π’Π°ΠΊΠ°Ρ ΠΎΠ±ΡΠ°Π±ΠΎΡΠΊΠ° ΠΈΠ·Π²Π΅ΡΡΠΊΠΎΠ²ΠΎ-Π·ΠΎΠ»ΡΠ½ΡΡ , ΠΈΠ·Π²Π΅ΡΡΠΊΠΎΠ²ΠΎ-ΠΊΡΠ΅ΠΌΠ½Π΅Π·Π΅ΠΌΠ½ΡΡ ΠΈ ΠΈΠ·Π²Π΅ΡΡΠΊΠΎΠ²ΠΎ-ΠΏΠ΅ΡΡΠ°Π½ΡΡ ΡΠΌΠ΅ΡΠ΅ΠΉ Π°ΠΊΡΡΠ°Π»ΡΠ½Π° ΠΈ ΠΏΡΠΈ ΠΏΡΠΎΠΈΠ·Π²ΠΎΠ΄ΡΡΠ²Π΅ ΡΠΈΠ»ΠΈΠΊΠ°ΡΠ½ΡΡ Π±Π΅ΡΠΎΠ½ΠΎΠ², ΡΠ°ΠΊ ΠΊΠ°ΠΊ ΠΏΡΠΈΠ²ΠΎΠ΄ΠΈΡ ΠΊ Π·Π½Π°ΡΠΈΡΠ΅Π»ΡΠ½ΠΎΠΌΡ ΡΠ»ΡΡΡΠ΅Π½ΠΈΡ ΠΌΠ΅Ρ Π°Π½ΠΈΡΠ΅ΡΠΊΠΈΡ Ρ Π°ΡΠ°ΠΊΡΠ΅ΡΠΈΡΡΠΈΠΊ ΠΌΠ°ΡΠ΅ΡΠΈΠ°Π»Π°.
ΠΡΠ΅ΠΈΠΌΡΡΠ΅ΡΡΠ²Π° ΠΏΡΠΎΠΈΠ·Π²ΠΎΠ΄ΡΡΠ²Π° ΡΠΈΠ»ΠΈΠΊΠ°ΡΠ½ΠΎΠ³ΠΎ ΠΊΠΈΡΠΏΠΈΡΠ° Π½Π° ΡΡΡΠ°Π½ΠΎΠ²ΠΊΠ΅ Π²ΠΈΡ ΡΠ΅Π²ΠΎΠ³ΠΎ ΡΠ»ΠΎΡ
ΠΡΡΠ΅ΠΊΡΠΈΠ²Π½ΠΎΡΡΡ ΡΡΡΡΠΎΠΉΡΡΠ²Π° Π²ΠΈΡ ΡΠ΅Π²ΠΎΠ³ΠΎ ΡΠ»ΠΎΡ ΠΏΡΠΈ ΠΏΡΠΎΠΈΠ·Π²ΠΎΠ΄ΡΡΠ²Π΅ ΡΠΈΠ»ΠΈΠΊΠ°ΡΠ½ΠΎΠ³ΠΎ ΠΊΠΈΡΠΏΠΈΡΠ° Π΄ΠΎΠΊΠ°Π·Π°Π½Π° Π½Π° ΠΏΡΠ°ΠΊΡΠΈΠΊΠ΅. Π ΡΠ΅Π»ΠΎΠΌ ΠΈΡΠΏΠΎΠ»ΡΠ·ΠΎΠ²Π°Π½ΠΈΠ΅ ΠΠΠ‘ Π΄Π»Ρ Π΄Π°Π½Π½ΠΎΠΉ ΠΎΠ±Π»Π°ΡΡΠΈ ΠΏΡΠΎΠΈΠ·Π²ΠΎΠ΄ΡΡΠ²Π° ΡΡΡΠΎΠΈΡΠ΅Π»ΡΠ½ΡΡ ΠΌΠ°ΡΠ΅ΡΠΈΠ°Π»ΠΎΠ² Π²ΡΠ³ΠΎΠ΄Π½ΠΎ ΠΈ Π°ΠΊΡΡΠ°Π»ΡΠ½ΠΎ ΠΏΠΎ ΡΠ»Π΅Π΄ΡΡΡΠΈΠΌ ΠΏΡΠΈΡΠΈΠ½Π°ΠΌ:
- Π‘ΠΈΠ»ΠΈΠΊΠ°ΡΠ½ΡΠΉ ΠΊΠΈΡΠΏΠΈΡ ΠΏΠΎΠ²ΡΡΠ΅Π½Π½ΠΎΠ³ΠΎ ΠΊΠ°ΡΠ΅ΡΡΠ²Π°
ΠΠ»Π°Π³ΠΎΠ΄Π°ΡΡ Π²ΡΡΠΎΠΊΠΎΠΌΡ ΡΡΠΎΠ²Π½Ρ Π°ΠΊΡΠΈΠ²Π°ΡΠΈΠΈ ΡΠ°ΡΡΠΈΡ ΠΌΡ ΠΏΠΎΠ»ΡΡΠ°Π΅ΠΌ ΠΏΡΠΎΠ΄ΡΠΊΡ Ρ Π²ΡΡΠΎΠΊΠΎΠΉ ΠΏΡΠΎΡΠ½ΠΎΡΡΡΡ Π½Π° ΡΠΆΠ°ΡΠΈΠ΅. ΠΠ°ΡΠ΅ΡΠΈΠ°Π» ΠΎΡΠ»ΠΈΡΠ°Π΅ΡΡΡ ΡΠ»ΡΡΡΠ΅Π½Π½ΡΠΌΠΈ Ρ
Π°ΡΠ°ΠΊΡΠ΅ΡΠΈΡΡΠΈΠΊΠ°ΠΌΠΈ ΠΈ ΠΈΠ·Π½ΠΎΡΠΎΡΡΠΎΠΉΠΊΠΎΡΡΡΡ, Π±Π»Π°Π³ΠΎΠ΄Π°ΡΡ ΡΠ΅ΠΌΡ ΠΏΡΠ°ΠΊΡΠΈΡΠ΅ΡΠΊΠΈ Π½Π΅ ΠΏΠΎΠ²ΡΠ΅ΠΆΠ΄Π°Π΅ΡΡΡ ΠΏΡΠΈ ΡΡΠ°Π½ΡΠΏΠΎΡΡΠΈΡΠΎΠ²ΠΊΠ΅, ΠΏΠΎΠ³ΡΡΠ·ΠΊΠ΅, ΡΠ°Π·Π³ΡΡΠ·ΠΊΠ΅, ΠΎΠ±Π΅ΡΠΏΠ΅ΡΠΈΠ²Π°Π΅Ρ Π½Π΅ΠΎΠ±Ρ
ΠΎΠ΄ΠΈΠΌΡΡ ΠΏΡΠΎΡΠ½ΠΎΡΡΡ Π·Π΄Π°Π½ΠΈΠΉ ΠΈ ΡΠΎΠΎΡΡΠΆΠ΅Π½ΠΈΠΉ.
ΠΡΠ΅Π³ΠΎ Π·Π° Π½Π΅ΡΠΊΠΎΠ»ΡΠΊΠΎ ΡΠ΅ΠΊΡΠ½Π΄ ΠΎΠ±ΡΠ°Π±ΠΎΡΠΊΠΈ ΡΡΡΡΡ ΠΌΠΎΠΆΠ½ΠΎ Π΄ΠΎΡΡΠΈΡΡ Π²ΡΡΠΎΠΊΠΎΠ³ΠΎ ΡΡΠΎΠ²Π½Ρ Π°ΠΊΡΠΈΠ²Π°ΡΠΈΠΈ ΠΈΠ½Π³ΡΠ΅Π΄ΠΈΠ΅Π½ΡΠΎΠ² ΠΈ ΠΎΠ΄Π½ΠΎΡΠΎΠ΄Π½ΠΎΡΡΠΈ ΡΠΌΠ΅ΡΠΈ. Π ΠΈΠ·ΠΌΠ΅Π»ΡΡΠ΅Π½ΠΈΠ΅ ΠΈΠ½Π³ΡΠ΅Π΄ΠΈΠ΅Π½ΡΠΎΠ² Π·Π°Π½ΠΈΠΌΠ°Π΅Ρ Π±ΡΠΊΠ²Π°Π»ΡΠ½ΠΎ 2β3 ΠΌΠΈΠ½ΡΡΡ. Π ΡΠ»ΡΡΠ°Π΅ ΠΎΠ±ΡΡΠ½ΡΡ ΡΠ΅Ρ Π½ΠΎΠ»ΠΎΠ³ΠΈΠΉ Π½Π° ΡΡΠΎ ΡΡ ΠΎΠ΄ΡΡ ΡΠ°ΡΡ.
ΠΠΎΡΡΠ΅Π±Π»ΡΠ΅ΠΌΠ°Ρ ΠΌΠΎΡΠ½ΠΎΡΡΡ ΡΡΡΡΠΎΠΉΡΡΠ² AVS-100 ΠΈ AVS-150 ΠΏΡΠΎΠΈΠ·Π²ΠΎΠ΄ΡΡΠ²Π° GlobeCore ΡΠΎΡΡΠ°Π²Π»ΡΠ΅Ρ 4.5 ΠΈ 9,5 ΠΊΠΡ ΡΠΎΠΎΡΠ²Π΅ΡΡΡΠ²Π΅Π½Π½ΠΎ. ΠΠ±ΠΎΡΡΠ΄ΠΎΠ²Π°Π½ΠΈΠ΅ ΠΏΠΎΠ·Π²ΠΎΠ»ΡΠ΅Ρ Π² Π½Π΅ΡΠΊΠΎΠ»ΡΠΊΠΎ ΡΠ°Π· ΡΠ½ΠΈΠ·ΠΈΡΡ ΠΏΠΎΡΡΠ΅Π±Π»Π΅Π½ΠΈΠ΅ ΡΠ»Π΅ΠΊΡΡΠΎΡΠ½Π΅ΡΠ³ΠΈΠΈ ΠΏΡΠΎΠΈΠ·Π²ΠΎΠ΄ΡΡΠ²Π΅Π½Π½ΠΎΠΉ Π»ΠΈΠ½ΠΈΠΈ. ΠΡΠΎΠΌΠ΅ ΡΠΎΠ³ΠΎ, ΡΡΠΎ ΡΠΎΠΊΡΠ°ΡΠ°Π΅Ρ Π²ΡΠ΅ΠΌΡ ΠΎΠ±ΡΠ°Π±ΠΎΡΠΊΠΈ ΠΌΠ°ΡΠ΅ΡΠΈΠ°Π»Π°, ΡΡΠΎ ΡΠ°ΠΊΠΆΠ΅ Π²ΡΠ³ΠΎΠ΄Π½ΠΎ Ρ ΡΠΎΡΠΊΠΈ Π·ΡΠ΅Π½ΠΈΡ ΡΠΊΠΎΠ½ΠΎΠΌΠΈΠΈ ΡΠ΅ΡΡΡΡΠΎΠ².
Π£ΡΡΠ°Π½ΠΎΠ²ΠΊΠ° Π±Π΅Π· ΡΡΡΠ΄Π° ΠΈΠ½ΡΠ΅Π³ΡΠΈΡΡΠ΅ΡΡΡ Π² ΡΡΡΠ΅ΡΡΠ²ΡΡΡΡΡ Π»ΠΈΠ½ΠΈΡ ΠΏΠΎ ΠΏΡΠΎΠΈΠ·Π²ΠΎΠ΄ΡΡΠ²Ρ ΡΠΈΠ»ΠΈΠΊΠ°ΡΠ½ΠΎΠ³ΠΎ ΠΊΠΈΡΠΏΠΈΡΠ°. ΠΠ΅ ΡΡΠ΅Π±ΡΠ΅Ρ Π΄Π»Ρ ΡΡΡΠ°Π½ΠΎΠ²ΠΊΠΈ ΠΏΠΎΡΡΠ°ΠΌΠ΅Π½ΡΠΎΠ² ΠΈ Π΄ΠΎΠΏΠΎΠ»Π½ΠΈΡΠ΅Π»ΡΠ½ΡΡ
ΠΊΠΎΠ½ΡΡΡΡΠΊΡΠΈΠΉ. ΠΠ½ ΠΎΡΠ»ΠΈΡΠ°Π΅ΡΡΡ ΠΊΠΎΠΌΠΏΠ°ΠΊΡΠ½ΠΎΡΡΡΡ ΠΈ Π»Π΅Π³ΠΊΠΎ ΠΏΠ΅ΡΠ΅ΠΌΠ΅ΡΠ°Π΅ΡΡΡ ΠΏΠΎ ΠΌΠ°ΡΡΠ΅ΡΡΠΊΠΎΠΉ.
Π£ΡΡΡΠΎΠΉΡΡΠ²ΠΎ Π²ΠΈΡ ΡΠ΅Π²ΠΎΠ³ΠΎ ΡΠ»ΠΎΡ ΠΏΠΎΠ΄Ρ ΠΎΠ΄ΠΈΡ ΠΊΠ°ΠΊ Π΄Π»Ρ ΠΊΡΡΠΏΠ½ΠΎΠ³ΠΎ ΠΏΡΠ΅Π΄ΠΏΡΠΈΡΡΠΈΡ ΠΏΠΎ ΠΏΡΠΎΠΈΠ·Π²ΠΎΠ΄ΡΡΠ²Ρ ΡΠΈΠ»ΠΈΠΊΠ°ΡΠ½ΠΎΠ³ΠΎ ΠΊΠΈΡΠΏΠΈΡΠ°, ΡΠ°ΠΊ ΠΈ Π΄Π»Ρ ΡΡΠ°Π²Π½ΠΈΡΠ΅Π»ΡΠ½ΠΎ Π½Π΅Π±ΠΎΠ»ΡΡΠΎΠ³ΠΎ ΡΠ΅Ρ Π°.ΠΡΠΎ ΠΏΠΎΠ·Π²ΠΎΠ»ΡΠ΅Ρ ΠΏΠΎΠ²ΡΡΠΈΡΡ ΡΡΡΠ΅ΠΊΡΠΈΠ²Π½ΠΎΡΡΡ ΠΏΡΠΎΠΈΠ·Π²ΠΎΠ΄ΡΡΠ²Π°, ΡΠ»ΡΡΡΠΈΡΡ ΠΊΠ°ΡΠ΅ΡΡΠ²ΠΎ Π²ΡΠΏΡΡΠΊΠ°Π΅ΠΌΠΎΠΉ ΠΏΡΠΎΠ΄ΡΠΊΡΠΈΠΈ ΠΈ ΠΎΠΏΡΠΈΠΌΠΈΠ·ΠΈΡΠΎΠ²Π°ΡΡ ΠΏΡΠΎΠΈΠ·Π²ΠΎΠ΄ΡΡΠ²Π΅Π½Π½ΡΠΉ ΠΏΡΠΎΡΠ΅ΡΡ. ΠΠ»Ρ Π·Π°ΠΊΠ°Π·Π° ΡΡΡΡΠΎΠΉΡΡΠ²Π° AVS ΠΈΠ»ΠΈ ΠΏΠΎΠ»ΡΡΠ΅Π½ΠΈΡ ΠΊΠΎΠ½ΡΡΠ»ΡΡΠ°ΡΠΈΠΈ ΠΎΠ±ΡΠ°ΡΠ°ΠΉΡΠ΅ΡΡ ΠΊ ΡΠΎΡΠ³ΠΎΠ²ΡΠΌ ΠΏΡΠ΅Π΄ΡΡΠ°Π²ΠΈΡΠ΅Π»ΡΠΌ GlobeCore .
Π·Π΄Π°Π½ΠΈΠΉ | ΠΠ΅ΡΠΏΠ»Π°ΡΠ½ΡΠΉ ΠΏΠΎΠ»Π½ΠΎΡΠ΅ΠΊΡΡΠΎΠ²ΡΠΉ | Π ΠΎΠ»Ρ ΡΡΠ΅ΠΊΠΎΠ»ΡΠ½ΡΡ ΡΠΌΠ΅ΡΠ΅ΠΉ Π² Π°Π²ΡΠΎΠΊΠ»Π°Π²Π½ΠΎΠΌ ΠΊΠΈΡΠΏΠΈΡΠ΅
Π‘ΡΡΠΎΠΈΡΠ΅Π»ΡΠ½Π°Ρ ΠΏΡΠΎΠΌΡΡΠ»Π΅Π½Π½ΠΎΡΡΡ ΠΎΠΊΠ°Π·ΡΠ²Π°Π΅Ρ ΠΎΡΠΎΠ±ΠΎΠ΅ Π²Π»ΠΈΡΠ½ΠΈΠ΅ Π½Π° Π»Π°Π½Π΄ΡΠ°ΡΡ ΠΈ ΠΈΠ·ΠΌΠ΅Π½Π΅Π½ΠΈΡ ΠΎΠΊΡΡΠΆΠ°ΡΡΠ΅ΠΉ ΡΡΠ΅Π΄Ρ Π² ΡΠ΅Ρ ΠΎΠ±Π»Π°ΡΡΡΡ , Π³Π΄Π΅ ΠΎΠ½Π° ΠΏΠΎΡΡΡΠΎΠ΅Π½Π°. ΠΡΠΎΠΈΠ·Π²ΠΎΠ΄ΡΡΠ²ΠΎ ΡΡΡΠΎΠΈΡΠ΅Π»ΡΠ½ΡΡ ΠΌΠ°ΡΠ΅ΡΠΈΠ°Π»ΠΎΠ² Π² Π½Π°ΡΡΠΎΡΡΠ΅Π΅ Π²ΡΠ΅ΠΌΡ Π½Π°ΠΏΡΠ°Π²Π»Π΅Π½ΠΎ Π½Π° Π²ΡΠΎΡΠΈΡΠ½ΡΡ ΠΏΠ΅ΡΠ΅ΡΠ°Π±ΠΎΡΠΊΡ ΠΈ ΡΡΡΠΎΠΉΡΠΈΠ²ΠΎΠ΅ ΡΠ°Π·Π²ΠΈΡΠΈΠ΅.ΠΡΠΎΡ ΡΡΠΈΠΌΡΠ» Π² Π·Π½Π°ΡΠΈΡΠ΅Π»ΡΠ½ΠΎΠΉ ΡΡΠ΅ΠΏΠ΅Π½ΠΈ ΡΠ²ΡΠ·Π°Π½ Ρ Π³Π»ΠΎΠ±Π°Π»ΡΠ½ΡΠΌΠΈ ΠΊΠ»ΠΈΠΌΠ°ΡΠΈΡΠ΅ΡΠΊΠΈΠΌΠΈ ΠΈΠ·ΠΌΠ΅Π½Π΅Π½ΠΈΡΠΌΠΈ, ΠΊΠΎΡΠΎΡΡΠ΅ ΡΡΠ°Π½ΠΎΠ²ΡΡΡΡ Π²ΡΠ΅ Π±ΠΎΠ»Π΅Π΅ Π·Π°ΠΌΠ΅ΡΠ½ΡΠΌΠΈ ΠΈ ΠΊΠΎΡΠΎΡΡΠ΅ Π±ΡΠ»ΠΈ ΡΠ΅ΡΠΊΠΎ Π²ΠΈΠ΄Π½Ρ Ρ Π½Π°ΡΠ°Π»Π° 2019 Π³ΠΎΠ΄Π° (ΡΠ°ΡΡΡΠ΅ ΠΏΠΎΠΆΠ°ΡΡ, Π΄ΠΎΠΆΠ΄ΠΈ, Π°Π½ΠΎΠΌΠ°Π»ΡΠ½ΡΠ΅ Π½Π°Π²ΠΎΠ΄Π½Π΅Π½ΠΈΡ ΠΈ Π·Π°ΡΡΡ ΠΈ Π² ΠΠ²ΡΠΎΠΏΠ΅, ΠΊΠΎΡΠΎΡΡΠ΅ ΡΠ²Π»ΡΡΡΡΡ ΡΠ΅Π·ΡΠ»ΡΡΠ°ΡΠΎΠΌ ΠΏΠΎΠ²ΡΡΠ΅Π½ΠΈΡ ΡΠ΅ΠΌΠΏΠ΅ΡΠ°ΡΡΡΡ ΠΈΠ·ΠΌΠ΅Π½Π΅Π½ΠΈΡ ΠΊΠ»ΠΈΠΌΠ°ΡΠ°) [1,2].




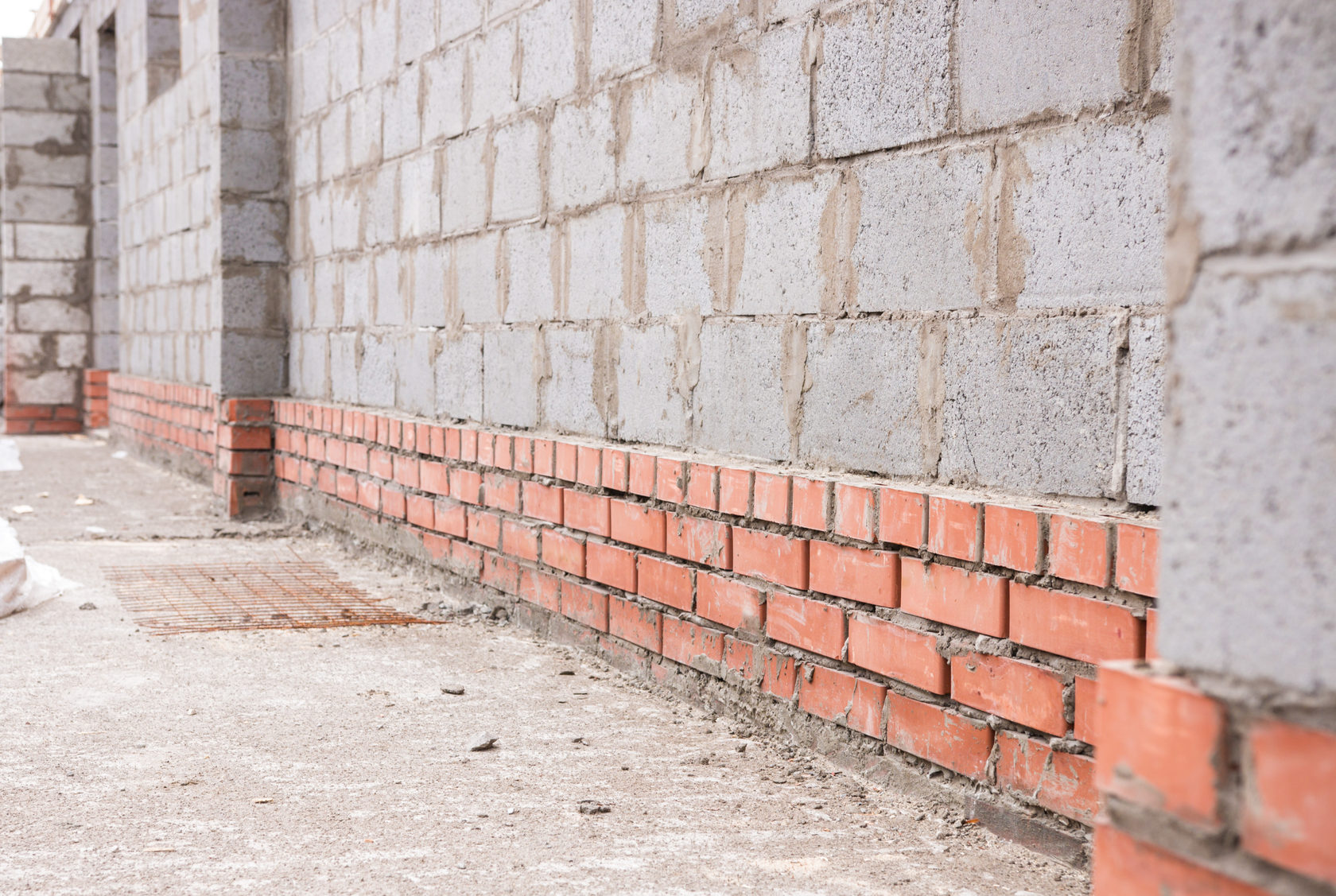

Calsi Bricks — ΠΠ°ΡΠ°Π»ΠΎ Π½ΠΎΠ²ΠΎΠ³ΠΎ ΠΏΡΠ΅Π΄ΠΏΡΠΈΡΡΠΈΡ Π² ΠΌΠΈΡΠ΅ ΠΌΠ°ΡΠΎΠ½ΡΡΠ²Π°. — ICE Student Chapter UET Lahore
Π ΠΊΠ°ΠΌΠ΅Π½Π½ΠΎΠΉ ΠΊΠ»Π°Π΄ΠΊΠ΅ ΠΈΡΠΏΠΎΠ»ΡΠ·ΡΡΡΡΡ ΡΠ°Π·Π»ΠΈΡΠ½ΡΠ΅ ΡΠΈΠΏΡ ΠΊΠΈΡΠΏΠΈΡΠ΅ΠΉ Π½Π° ΠΎΡΠ½ΠΎΠ²Π΅ ΡΠ°ΠΊΠΈΡ ΠΌΠ°ΡΠ΅ΡΠΈΠ°Π»ΠΎΠ², ΠΊΠ°ΠΊ Π³Π»ΠΈΠ½Π°, Π±Π΅ΡΠΎΠ½, ΠΈΠ·Π²Π΅ΡΡΡ, Π»Π΅ΡΡΡΠ°Ρ Π·ΠΎΠ»Π° ΠΈ Ρ. Π. Π ΡΠΎΠ²ΡΠ΅ΠΌΠ΅Π½Π½ΠΎΠΌ ΠΌΠΈΡΠ΅ Π²ΡΠ΅ΠΌ Π΄Π»Ρ Π²ΡΠΆΠΈΠ²Π°Π½ΠΈΡ Π½Π΅ΠΎΠ±Ρ ΠΎΠ΄ΠΈΠΌΠΎ ΡΠΊΡΡΡΠΈΠ΅, ΠΏΠΎΡΡΠΎΠΌΡ ΡΡΡΠ΅ΡΡΠ²ΡΠ΅Ρ Π°Π»ΡΡΠ΅ΡΠ½Π°ΡΠΈΠ²Π½ΡΠΉ ΠΌΠ΅ΡΠΎΠ΄ ΠΏΡΠΎΠΈΠ·Π²ΠΎΠ΄ΡΡΠ²Π° ΠΊΠΈΡΠΏΠΈΡΠ° Ρ ΠΈΡΠΏΠΎΠ»ΡΠ·ΠΎΠ²Π°Π½ΠΈΠ΅ΠΌ ΠΏΠ΅ΡΠΊΠ° ΠΈ ΠΈΠ·Π²Π΅ΡΡΠΈ.Π ΡΡΠΎΠΉ ΡΡΠ°ΡΡΠ΅ ΠΏΡΠ΅Π΄ΡΡΠ°Π²Π»Π΅Π½Ρ ΠΏΡΠΎΡΠ΅ΡΡ ΠΈΠ·Π³ΠΎΡΠΎΠ²Π»Π΅Π½ΠΈΡ, ΠΈΡΡΠΎΡΠΈΡ ΠΈ ΡΠ°Π·Π»ΠΈΡΠ½ΡΠ΅ ΠΈΡΠΏΡΡΠ°Π½ΠΈΡ ΡΠΈΠ»ΠΈΠΊΠ°ΡΠ½ΠΎΠ³ΠΎ ΠΊΠΈΡΠΏΠΈΡΠ° ΠΊΠ°Π»ΡΡΠΈΡ.
Π‘Π²Π΅ΠΆΠΈΠΉ ΠΊΠΈΡΠΏΠΈΡ ΠΠ°Π»ΡΠΈΠΡΡΠΎΡΠΈΡ
ΠΡΠΎΡΠ΅ΡΡ ΠΏΡΠΎΠΈΠ·Π²ΠΎΠ΄ΡΡΠ²Π° ΠΊΠΈΡΠΏΠΈΡΠ° Π·Π° ΠΏΠ΅ΡΠΊΠΎΠΌ Π±ΡΠ» ΠΎΡΠΊΡΡΡ ΠΈ Π·Π°ΠΏΠ°ΡΠ΅Π½ΡΠΎΠ²Π°Π½ Π΄ΠΎΠΊΡΠΎΡΠΎΠΌ Π£ΠΈΠ»ΡΡΠΌΠΎΠΌ ΠΠΈΡ
Π°ΡΠ»ΠΈΡΠΎΠΌ Π² 1880 Π³ΠΎΠ΄Ρ. ΠΡΠΎ ΠΏΡΠ°Π²Π΄Π°, ΡΡΠΎ Peppel 2 ΡΠ°ΡΠΏΠΎΠ·Π½Π°Π΅Ρ ΡΠΈΠ»ΠΈΠΊΠ°ΡΠ½ΡΠΉ ΠΊΠΈΡΠΏΠΈΡ, ΠΏΠΎΠ»ΡΡΠ΅Π½Π½ΡΠΉ Ρ ΠΏΠΎΠΌΠΎΡΡΡ Π΄ΡΡΠ³ΠΈΡ
ΠΏΡΠΎΡΠ΅ΡΡΠΎΠ², ΠΈ Π² Π»ΠΈΡΠ΅ΡΠ°ΡΡΡΠ΅ ΠΌΠΎΠΆΠ½ΠΎ Π½Π°ΠΉΡΠΈ ΠΌΠ½ΠΎΠ³ΠΎΡΠΈΡΠ»Π΅Π½Π½ΡΠ΅ ΡΡΠ²Π΅ΡΠΆΠ΄Π΅Π½ΠΈΡ, ΠΊΠ°ΡΠ°ΡΡΠΈΠ΅ΡΡ Β«ΠΏΠ΅ΡΠΊΠ°Β». ΡΠΈΠ»ΠΈΠΊΠ°ΡΠ½ΡΠΉ ΠΊΠΈΡΠΏΠΈΡ Β», ΠΈΠ·Π³ΠΎΡΠΎΠ²Π»Π΅Π½Π½ΡΠΉ Π² ΠΡΡ-ΠΠΆΠ΅ΡΡΠΈ ΠΎΠΊΠΎΠ»ΠΎ 1860 Π³ΠΎΠ΄Π°.ΠΠ° ΡΠ°ΠΌΠΎΠΌ Π΄Π΅Π»Π΅ ΡΡΠΎΡ ΠΌΠ°ΡΠ΅ΡΠΈΠ°Π» ΠΏΡΠ΅Π΄ΡΡΠ°Π²Π»ΡΠ» ΡΠΎΠ±ΠΎΠΉ ΡΡΡΠΎΠΈΡΠ΅Π»ΡΠ½ΡΠΉ ΠΊΠΈΡΠΏΠΈΡ, ΡΠΎΡΡΠΎΡΡΠΈΠΉ ΠΈΠ· ΠΎΠ±ΡΡΠ½ΠΎΠ³ΠΎ ΠΈΠ·Π²Π΅ΡΡΠΊΠΎΠ²ΠΎΠ³ΠΎ ΡΠ°ΡΡΠ²ΠΎΡΠ°, ΠΊΠΎΡΠΎΡΠΎΠΌΡ ΠΏΡΠΈΠ΄Π°Π½Π° ΡΠΎΡΠΌΠ° ΠΈ ΠΊΠΎΡΠΎΡΡΠΉ ΠΏΠΎΠ·Π²ΠΎΠ»ΠΈΠ» Π·Π°ΡΠ²Π΅ΡΠ΄Π΅ΡΡ. ΠΠ°ΡΠΊΠΎΠ»ΡΠΊΠΎ ΠΌΠΎΠΆΠ½ΠΎ ΡΠ·Π½Π°ΡΡ, Π½ΠΈ ΠΎΠ΄ΠΈΠ½ ΠΈΠ· ΡΡΠΈΡ
ΡΠ°Π½Π½ΠΈΡ
ΠΏΡΠΎΡΠ΅ΡΡΠΎΠ² Π½Π΅ ΠΎΠΊΠ°Π·Π°Π»ΡΡ ΠΊΠΎΠΌΠΌΠ΅ΡΡΠ΅ΡΠΊΠΈ ΡΡΠΏΠ΅ΡΠ½ΡΠΌ. ΠΡΠ΅ ΡΠΈΠ»ΠΈΠΊΠ°ΡΠ½ΡΠ΅ ΠΊΠΈΡΠΏΠΈΡΠΈ, ΠΊΠΎΡΠΎΡΡΠ΅ ΡΠ΅ΠΉΡΠ°Ρ ΠΏΡΠΎΠ΄Π°ΡΡΡΡ Π² ΠΌΠΈΡΠ΅, ΠΏΡΠΎΠΈΠ·Π²ΠΎΠ΄ΡΡΡΡ Π² ΡΠΎΠΎΡΠ²Π΅ΡΡΡΠ²ΠΈΠΈ Ρ ΠΎΡΠ½ΠΎΠ²Π½ΡΠΌΠΈ ΠΏΡΠΈΠ½ΡΠΈΠΏΠ°ΠΌΠΈ, Π·Π°ΠΊΡΠ΅ΠΏΠ»Π΅Π½Π½ΡΠΌΠΈ Π² ΠΎΡΠΈΠ³ΠΈΠ½Π°Π»ΡΠ½ΠΎΠΌ ΠΏΠ°ΡΠ΅Π½ΡΠ΅ ΠΠΈΡ
Π°ΡΠ»ΠΈΡΠ°. ΠΠ½ ΠΏΠΎΠ·Π²ΠΎΠ»ΠΈΠ» ΡΠ²ΠΎΠ΅ΠΌΡ ΠΏΠ°ΡΠ΅Π½ΡΡ ΠΈΡΡΠ΅ΡΡ Π±Π΅Π· ΠΈΡΠΏΠΎΠ»ΡΠ·ΠΎΠ²Π°Π½ΠΈΡ. ΠΡΠ°ΠΊΡΠΈΡΠ΅ΡΠΊΠΈ ΡΡΠ°Π·Ρ ΠΏΠΎΡΠ»Π΅Π΄ΠΎΠ²Π°Π»ΠΎ Π½Π΅ΡΠΊΠΎΠ»ΡΠΊΠΎ Π΄ΠΎΡΠ°Π±ΠΎΡΠΎΠΊ.
ΠΠΈΡΠΏΠΈΡ ΠΈΠ· ΡΠΈΠ»ΠΈΠΊΠ°ΡΠ° ΠΊΠ°Π»ΡΡΠΈΡΠΠ²Π΅Π΄Π΅Π½ΠΈΠ΅
ΠΏΠΎΠ΄Ρ
ΠΎΠ΄ΠΈΡ ΠΊΠ°ΠΊ Π΄Π»Ρ Π½Π°ΡΡΠΆΠ½ΡΡ
, ΡΠ°ΠΊ ΠΈ Π΄Π»Ρ Π²Π½ΡΡΡΠ΅Π½Π½ΠΈΡ
ΡΡΠ΅Π½.ΠΠ½ΠΈ Π΄ΠΎΡΡΡΠΏΠ½Ρ Π² Π²ΠΈΠ΄Π΅ ΠΎΠ±Π»ΠΈΡΠΎΠ²ΠΎΡΠ½ΠΎΠ³ΠΎ ΠΊΠΈΡΠΏΠΈΡΠ° ΠΈΠ»ΠΈ ΠΎΠ±ΡΠΊΠ½ΠΎΠ²Π΅Π½Π½ΠΎΠ³ΠΎ ΠΊΠΈΡΠΏΠΈΡΠ°. ΠΠΈΡΠΏΠΈΡΠΈ ΠΈΠ· ΡΠΈΠ»ΠΈΠΊΠ°ΡΠ° ΠΊΠ°Π»ΡΡΠΈΡ ΡΠΎΡΡΠΎΡΡ ΠΈΠ· ΠΏΠ΅ΡΠΊΠ°, ΠΈΠ·Π²Π΅ΡΡΠΈ Ρ Π²ΡΡΠΎΠΊΠΈΠΌ ΡΠΎΠ΄Π΅ΡΠΆΠ°Π½ΠΈΠ΅ΠΌ ΠΊΠ°Π»ΡΡΠΈΡ ΠΈ Π²ΠΎΠ΄Ρ, ΡΠΈΡΠΎΠΊΠΎ ΠΈΠ·Π²Π΅ΡΡΠ½ΠΎΠΉ ΠΊΠ°ΠΊ ΡΠΈΠ»ΠΈΠΊΠ°ΡΠ½ΡΠΉ ΠΊΠΈΡΠΏΠΈΡ. ΠΡΠΈ ΠΊΠΈΡΠΏΠΈΡΠΈ ΠΈΡΠΏΠΎΠ»ΡΠ·ΡΡΡΡΡ Π΄Π»Ρ ΡΠ°Π·Π»ΠΈΡΠ½ΡΡ
ΡΠ΅Π»Π΅ΠΉ Π² ΡΡΡΠΎΠΈΡΠ΅Π»ΡΠ½ΡΡ
ΠΎΡΡΠ°ΡΠ»ΡΡ
, ΡΠ°ΠΊΠΈΡ
ΠΊΠ°ΠΊ Π΄Π΅ΠΊΠΎΡΠ°ΡΠΈΠ²Π½ΡΠ΅ ΡΠ°Π±ΠΎΡΡ Π² Π·Π΄Π°Π½ΠΈΡΡ
, ΠΊΠ»Π°Π΄ΠΎΡΠ½ΡΠ΅ ΡΠ°Π±ΠΎΡΡ ΠΈ Ρ. Π.
Π‘ΠΈΠ»ΠΈΠΊΠ°ΡΠ½ΡΠΉ ΠΊΠΈΡΠΏΠΈΡ ΡΠΈΡΠΎΠΊΠΎ ΠΈΡΠΏΠΎΠ»ΡΠ·ΡΠ΅ΡΡΡ Π² ΡΡΡΠ°Π½Π°Ρ ΠΠ²ΡΠΎΠΏΡ, ΠΠ²ΡΡΡΠ°Π»ΠΈΠΈ ΠΈ ΠΡΡΠΈΠΊΠΈ. Π ΠΠ½Π΄ΠΈΠΈ ΡΡΠΈ ΠΊΠΈΡΠΏΠΈΡΠΈ ΡΠΈΡΠΎΠΊΠΎ ΠΈΡΠΏΠΎΠ»ΡΠ·ΡΡΡΡΡ Π² ΡΡΠ°ΡΠ΅ ΠΠ΅ΡΠ°Π»Π°, ΠΈ ΠΈΡ ΠΈΡΠΏΠΎΠ»ΡΠ·ΠΎΠ²Π°Π½ΠΈΠ΅ Π±ΡΡΡΡΠΎ ΡΠ°ΡΡΠ΅Ρ.
ΠΠ°ΡΡΠΈΡ ΠΏΠ΅ΡΠ΅ΡΠ°Π±ΠΎΡΠ°Π½Π½ΡΡ ΠΊΠΈΡΠΏΠΈΡΠ΅ΠΉ CalsiΠΠ°ΡΠ΅ΡΠΈΠ°Π»Ρ, ΠΈΡΠΏΠΎΠ»ΡΠ·ΡΠ΅ΠΌΡΠ΅ Π΄Π»Ρ ΡΠΈΠ»ΠΈΠΊΠ°ΡΠ½ΠΎΠ³ΠΎ ΠΊΠΈΡΠΏΠΈΡΠ°
ΠΠ΅ΡΠΎΠΊ ΠΈ Π³Π°ΡΠ΅Π½Π°Ρ ΠΈΠ·Π²Π΅ΡΡΡ — Π΄Π²Π° Π²ΠΈΠ΄Π° ΡΡΡΡΡ, ΠΊΠΎΡΠΎΡΡΠ΅ ΠΏΡΠΈΠΎΠ±ΡΠ΅Π»ΠΈ ΠΊΠΎΠΌΠΌΠ΅ΡΡΠ΅ΡΠΊΠΎΠ΅ Π·Π½Π°ΡΠ΅Π½ΠΈΠ΅ Π²ΠΎ Π²ΡΠ΅ΠΌ ΠΌΠΈΡΠ΅ ΠΏΡΠΈ ΠΏΡΠΎΠΈΠ·Π²ΠΎΠ΄ΡΡΠ²Π΅ ΠΊΠΈΡΠΏΠΈΡΠ΅ΠΉ Calsi.
ΠΠ΅ΡΠ΅ΡΠΈΡΠ»Π΅Π½Π½ΡΠ΅ Π½ΠΈΠΆΠ΅ ΠΌΠ°ΡΠ΅ΡΠΈΠ°Π»Ρ Π² ΠΎΡΠ½ΠΎΠ²Π½ΠΎΠΌ ΠΈΡΠΏΠΎΠ»ΡΠ·ΡΡΡΡΡ Π΄Π»Ρ ΠΏΡΠΎΠΈΠ·Π²ΠΎΠ΄ΡΡΠ²Π° ΠΊΠΈΡΠΏΠΈΡΠ΅ΠΉ Calsi.
ΠΈ. ΠΠ΅ΡΠΎΠΊ:
ΠΠ΅ΡΠΎΠΊ ΡΠ²Π»ΡΠ΅ΡΡΡ ΠΎΡΠ½ΠΎΠ²Π½ΡΠΌ ΠΊΠΎΠΌΠΏΠΎΠ½Π΅Π½ΡΠΎΠΌ ΠΊΠΈΡΠΏΠΈΡΠ΅ΠΉ ΠΈΠ· ΡΠΈΠ»ΠΈΠΊΠ°ΡΠ° ΠΊΠ°Π»ΡΡΠΈΡ. ΠΠ΅ΡΠΎΠΊ ΠΈΡΠΏΠΎΠ»ΡΠ·ΡΠ΅ΡΡΡ Π² Π΄Π²ΡΡ
ΠΏΡΠΎΠΏΠΎΡΡΠΈΡΡ
. Π§Π°ΡΡΡ Π΅Π³ΠΎ Π²ΡΡΡΠΏΠ°Π΅Ρ Π² ΡΠ΅Π°ΠΊΡΠΈΡ Ρ ΠΈΠ·Π²Π΅ΡΡΡΡ, ΠΎΠ±ΡΠ°Π·ΡΡ ΡΠ²ΡΠ·ΡΡΡΠΈΠΉ ΠΌΠ°ΡΠ΅ΡΠΈΠ°Π» ΠΈΠ· ΡΠΈΠ»ΠΈΠΊΠ°ΡΠ° ΠΊΠ°Π»ΡΡΠΈΡ. Π ΡΠΎ Π²ΡΠ΅ΠΌΡ ΠΊΠ°ΠΊ ΠΎΡΡΠ°Π»ΡΠ½ΡΠ΅ ΠΏΠ΅ΡΡΠΈΠ½ΠΊΠΈ ΡΠΎΡΡΠ°Π²Π»ΡΡΡ ΡΠΎΠ²ΠΎΠΊΡΠΏΠ½ΠΎΡΡΡ, ΠΊΠΎΡΠΎΡΠ°Ρ ΡΠ²ΡΠ·Π°Π½Π° Π²ΠΌΠ΅ΡΡΠ΅ ΠΈ ΠΎΠ±ΡΠ°Π·ΡΠ΅Ρ ΠΎΡΠ½ΠΎΠ²Π½ΡΡ ΡΠ°ΡΡΡ ΠΊΠΈΡΠΏΠΈΡΠ°. Π ΠΏΠ΅ΡΠ²ΠΎΠΉ ΠΏΡΠΎΠΏΠΎΡΡΠΈΠΈ ΠΎΡΠ΅Π½Ρ Π²Π°ΠΆΠ½ΠΎ, ΡΡΠΎΠ±Ρ ΠΏΠ΅ΡΠΎΠΊ Π±ΡΠ» ΠΊΠ°ΠΊ ΠΌΠΎΠΆΠ½ΠΎ Π±ΠΎΠ»Π΅Π΅ ΠΌΠ΅Π»ΠΊΠΈΠΌ. Π₯ΠΎΡΠΎΡΠΈΠΉ ΠΏΡΠ°ΠΊΡΠΈΡΠ΅ΡΠΊΠΈΠΉ ΠΏΠΎΠ΄Ρ
ΠΎΠ΄ ΡΠΎΡΡΠΎΠΈΡ Π² ΡΠΎΠΌ, ΡΡΠΎ ΠΎΠΊΠΎΠ»ΠΎ 15% ΠΏΠ΅ΡΠΊΠ° Π΄ΠΎΠ»ΠΆΠ½ΠΎ ΠΏΡΠΎΡ
ΠΎΠ΄ΠΈΡΡ ΡΠ΅ΡΠ΅Π· ΡΠΈΡΠΎ 100 ΠΌΠ΅Ρ. ΠΡΡΠ°Π²ΡΠΈΠ΅ΡΡ 85% ΠΏΠ΅ΡΠΊΠ° ΠΏΡΠ΅Π΄Π½Π°Π·Π½Π°ΡΠ΅Π½Ρ Π΄Π»Ρ ΠΎΠ±ΡΠ°Π·ΠΎΠ²Π°Π½ΠΈΡ ΠΈΠ½Π΅ΡΡΠ½ΠΎΠ³ΠΎ Π½Π°ΠΏΠΎΠ»Π½ΠΈΡΠ΅Π»Ρ ΠΈΠ»ΠΈ ΠΎΡΠ½ΠΎΠ²Π½ΠΎΠΉ ΠΌΠ°ΡΡΡ ΠΊΠΈΡΠΏΠΈΡΠ°. ΠΠΈΡΠΏΠΈΡΠΈ ΠΈΠ· ΡΠΈΠ»ΠΈΠΊΠ°ΡΠ° ΠΊΠ°Π»ΡΡΠΈΡ ΡΠΎΠ΄Π΅ΡΠΆΠ°Ρ Π±ΠΎΠ»ΡΡΠΎΠ΅ ΠΊΠΎΠ»ΠΈΡΠ΅ΡΡΠ²ΠΎ ΠΏΠ΅ΡΠΊΠ°, ΡΠΎ Π΅ΡΡΡ 88β92%. ΠΡΠΎ ΠΎΠ·Π½Π°ΡΠ°Π΅Ρ, ΡΡΠΎ ΡΠ²ΠΎΠΉΡΡΠ²Π° ΡΡΠΈΡ
ΠΊΠΈΡΠΏΠΈΡΠ΅ΠΉ Π·Π°Π²ΠΈΡΡΡ ΠΎΡ ΡΠ²ΠΎΠΉΡΡΠ² ΠΈΡΠΏΠΎΠ»ΡΠ·ΡΠ΅ΠΌΠΎΠ³ΠΎ ΠΏΠ΅ΡΠΊΠ°. Π’Π°ΠΊΠΈΠΌ ΠΎΠ±ΡΠ°Π·ΠΎΠΌ, ΠΈΡΠΏΠΎΠ»ΡΠ·ΡΠ΅ΠΌΡΠΉ ΠΏΠ΅ΡΠΎΠΊ Π΄ΠΎΠ»ΠΆΠ΅Π½ Π±ΡΡΡ Ρ
ΠΎΡΠΎΡΠΎ ΡΠ°ΡΡΠΎΡΡΠΈΡΠΎΠ²Π°Π½ ΠΈ Π½Π΅ Π΄ΠΎΠ»ΠΆΠ΅Π½ ΡΠΎΠ΄Π΅ΡΠΆΠ°ΡΡ Π½ΠΈΠΊΠ°ΠΊΠΈΡ
ΠΏΡΠΈΠΌΠ΅ΡΠ΅ΠΉ, ΡΠ°ΠΊΠΈΡ
ΠΊΠ°ΠΊ ΠΎΡΠ³Π°Π½ΠΈΡΠ΅ΡΠΊΠΈΠ΅ Π²Π΅ΡΠ΅ΡΡΠ²Π°, ΡΠ°ΡΡΠ²ΠΎΡΠΈΠΌΡΠ΅ ΡΠΎΠ»ΠΈ ΠΈ Ρ. Π. ΠΠΎΠΆΠ΅Ρ ΠΏΡΠΈΡΡΡΡΡΠ²ΠΎΠ²Π°ΡΡ ΠΌΠ΅Π»ΠΊΠΎΠ΄ΠΈΡΠΏΠ΅ΡΡΠ½Π°Ρ Π³Π»ΠΈΠ½Π°, Π½ΠΎ Π΅Π΅ ΡΠΎΠ»ΡΠΊΠΎ Π΄ΠΎ 4% ΡΠΏΠ»ΠΎΡΠ½ΡΠ΅Ρ ΠΊΠΈΡΠΏΠΈΡ ΠΈ ΠΎΠ±Π΅ΡΠΏΠ΅ΡΠΈΠ²Π°Π΅Ρ Π±ΠΎΠ»Π΅Π΅ Π³Π»Π°Π΄ΠΊΡΡ ΡΠ΅ΠΊΡΡΡΡΡ.ΠΠ»Ρ Π±ΠΎΠ»ΡΡΠ΅ΠΉ ΠΏΡΠΎΡΠ½ΠΎΡΡΠΈ ΠΆΠ΅Π»Π°ΡΠ΅Π»ΡΠ½ΠΎ ΠΏΠΎ Π²ΠΎΠ·ΠΌΠΎΠΆΠ½ΠΎΡΡΠΈ ΠΈΠΌΠ΅ΡΡ Π±ΠΎΠ»Π΅Π΅ ΠΊΡΡΠΏΠ½ΠΎΠ΅ Π·Π΅ΡΠ½ΠΎ.
ii. ΠΠ°ΠΉΠΌ:
ΠΠΎΠ»Ρ ΠΈΠ·Π²Π΅ΡΡΠΈ, ΠΈΡΠΏΠΎΠ»ΡΠ·ΡΠ΅ΠΌΠ°Ρ Π² ΠΊΠ°Π»ΡΡΠΈΠ΅Π²ΡΡ
ΠΊΠΈΡΠΏΠΈΡΠ°Ρ
, ΠΎΡΠ½ΠΎΡΠΈΡΠ΅Π»ΡΠ½ΠΎ Π½Π΅Π²Π΅Π»ΠΈΠΊΠ°, Π½ΠΎ, ΠΏΠΎΠΌΠΈΠΌΠΎ ΡΡΠΎΠ³ΠΎ, ΠΎΠ½ΠΈ ΠΈΠΌΠ΅ΡΡ ΠΏΠ΅ΡΠ²ΠΎΡΡΠ΅ΠΏΠ΅Π½Π½ΠΎΠ΅ Π·Π½Π°ΡΠ΅Π½ΠΈΠ΅. Π‘ΠΎΠ΄Π΅ΡΠΆΠ°Π½ΠΈΠ΅ ΠΈΠ·Π²Π΅ΡΡΠΈ Π² ΡΠΈΠ»ΠΈΠΊΠ°ΡΠ½ΠΎΠΌ ΡΠΈΠ»ΠΈΠΊΠ°ΡΠ½ΠΎΠΌ ΠΊΠΈΡΠΏΠΈΡΠ΅ ΡΠΎΡΡΠ°Π²Π»ΡΠ΅Ρ ΠΎΡ 8 Π΄ΠΎ 12%. ΠΡΠΏΠΎΠ»ΡΠ·ΡΠ΅ΠΌΠ°Ρ ΠΈΠ·Π²Π΅ΡΡΡ Π΄ΠΎΠ»ΠΆΠ½Π° Π±ΡΡΡ Ρ
ΠΎΡΠΎΡΠ΅Π³ΠΎ ΠΊΠ°ΡΠ΅ΡΡΠ²Π° Ρ Π²ΡΡΠΎΠΊΠΈΠΌ ΡΠΎΠ΄Π΅ΡΠΆΠ°Π½ΠΈΠ΅ΠΌ ΠΊΠ°Π»ΡΡΠΈΡ. ΠΠ΅ΡΠ΅Π΄ ΠΏΡΠ΅ΡΡΠΎΠ²Π°Π½ΠΈΠ΅ΠΌ ΠΊΠΈΡΠΏΠΈΡΠ΅ΠΉ ΠΈΠ·Π²Π΅ΡΡΡ Π΄ΠΎΠ»ΠΆΠ½Π° Π±ΡΡΡ ΠΈΠ΄Π΅Π°Π»ΡΠ½ΠΎ Π³ΠΈΠ΄ΡΠ°ΡΠΈΡΠΎΠ²Π°Π½Π°. Π ΠΏΡΠΎΡΠΈΠ²Π½ΠΎΠΌ ΡΠ»ΡΡΠ°Π΅ ΠΎΠ½ Π±ΡΠ΄Π΅Ρ ΡΠ°ΡΡΠΈΡΡΡΡΡΡ Π²ΠΎ Π²ΡΠ΅ΠΌΡ ΠΎΠ±ΡΠ°Π±ΠΎΡΠΊΠΈ ΠΏΠ°ΡΠΎΠΌ ΠΈ Π²ΡΠ·ΡΠ²Π°ΡΡ Π²Π½ΡΡΡΠ΅Π½Π½ΠΈΠ΅ Π΄Π΅ΡΠΎΡΠΌΠ°ΡΠΈΠΈ, ΠΊΠΎΡΠΎΡΡΡ
Π΄ΠΎΡΡΠ°ΡΠΎΡΠ½ΠΎ ΡΠ°ΡΡΠΎ, ΡΡΠΎΠ±Ρ ΡΠ°Π·ΡΡΡΠΈΡΡ ΠΊΠΈΡΠΏΠΈΡ.ΠΠ·Π²Π΅ΡΡΡ ΡΠ°ΠΊΠΆΠ΅ Π΄ΠΎΠ»ΠΆΠ½Π° Π±ΡΡΡ Π΄ΠΎΡΡΠ°ΡΠΎΡΠ½ΠΎ Π΅Π΄ΠΊΠΎΠΉ, ΡΡΠΎΠ±Ρ Π»Π΅Π³ΠΊΠΎ Π²ΡΡΡΠΏΠ°ΡΡ Π² ΠΊΠΎΠΌΠ±ΠΈΠ½Π°ΡΠΈΡ Ρ ΠΏΠ΅ΡΠΊΠΎΠΌ.
iii. ΠΠΎΠ΄Π°:
Π ΠΏΡΠΎΡΠ΅ΡΡΠ΅ ΠΏΡΠΎΠΈΠ·Π²ΠΎΠ΄ΡΡΠ²Π° ΡΠ»Π΅Π΄ΡΠ΅Ρ ΠΈΡΠΏΠΎΠ»ΡΠ·ΠΎΠ²Π°ΡΡ ΡΠΈΡΡΡΡ Π²ΠΎΠ΄Ρ. ΠΠΎΡΡΠΊΠ°Ρ Π²ΠΎΠ΄Π°, Π²ΠΎΠ΄Π°, ΡΠΎΠ΄Π΅ΡΠΆΠ°ΡΠ°Ρ ΡΠ°ΡΡΠ²ΠΎΡΠΈΠΌΡΠ΅ ΡΠΎΠ»ΠΈ ΠΈΠ»ΠΈ ΠΎΡΠ³Π°Π½ΠΈΡΠ΅ΡΠΊΠΈΠ΅ Π²Π΅ΡΠ΅ΡΡΠ²Π° Π±ΠΎΠ»Π΅Π΅ 0,25%, Π½Π΅ ΠΏΠΎΠ΄Ρ ΠΎΠ΄ΡΡ.
iv. ΠΠΈΠ³ΠΌΠ΅Π½Ρ:
ΠΠΈΠ³ΠΌΠ΅Π½ΡΡ ΠΎΠ±ΡΡΠ½ΠΎ ΠΈΡΠΏΠΎΠ»ΡΠ·ΡΡΡΡΡ Π΄Π»Ρ ΠΏΡΠΈΠ΄Π°Π½ΠΈΡ ΡΠ²Π΅ΡΠ° ΠΊΠΈΡΠΏΠΈΡΠ°ΠΌ. ΠΡ ΡΠΌΠ΅ΡΠ°Π»ΠΈ Ρ ΠΏΠ΅ΡΠΊΠΎΠΌ ΠΈ ΠΈΠ·Π²Π΅ΡΡΡΡ. ΠΠ±ΡΠΈΠΉ Π²Π΅Ρ ΠΊΠΈΡΠΏΠΈΡΠ° ΡΠΎΠ΄Π΅ΡΠΆΠΈΡ ΠΎΡ 0,2 Π΄ΠΎ 3% ΠΊΠΎΠ»ΠΈΡΠ΅ΡΡΠ²Π° ΠΏΠΈΠ³ΠΌΠ΅Π½ΡΠ°.Π Π°Π·Π»ΠΈΡΠ½ΡΠ΅ ΠΏΠΈΠ³ΠΌΠ΅Π½ΡΡ, ΠΈΡΠΏΠΎΠ»ΡΠ·ΡΠ΅ΠΌΡΠ΅ Π΄Π»Ρ ΠΏΠΎΠ»ΡΡΠ΅Π½ΠΈΡ ΡΠ°Π·Π½ΡΡ ΡΠ²Π΅ΡΠΎΠ², ΡΠΊΠ°Π·Π°Π½Ρ Π² ΡΠ°Π±Π»ΠΈΡΠ΅ Π½ΠΈΠΆΠ΅:
ΠΡΠΎΡΠ΅ΡΡ ΠΏΡΠΎΠΈΠ·Π²ΠΎΠ΄ΡΡΠ²Π° ΡΠΈΠ»ΠΈΠΊΠ°ΡΠ½ΠΎΠ³ΠΎ ΡΠΈΠ»ΠΈΠΊΠ°ΡΠ½ΠΎΠ³ΠΎ ΠΊΠΈΡΠΏΠΈΡΠ°
- ΠΠ° ΠΏΠ΅ΡΠ²ΠΎΠΌ ΡΡΠ°ΠΏΠ΅ ΠΏΠΎΠ΄Ρ
ΠΎΠ΄ΡΡΠΈΠ΅ ΠΏΡΠΎΠΏΠΎΡΡΠΈΠΈ ΠΏΠ΅ΡΠΊΠ°, ΠΈΠ·Π²Π΅ΡΡΠΈ ΠΈ ΠΏΠΈΠ³ΠΌΠ΅Π½ΡΠ° ΡΡΠ°ΡΠ΅Π»ΡΠ½ΠΎ ΡΠΌΠ΅ΡΠΈΠ²Π°ΡΡΡΡ Ρ 3-5% Π²ΠΎΠ΄Ρ.
ΠΠ±ΡΠ°Π·ΡΠ΅ΡΡΡ ΠΏΠ°ΡΡΠ° Ρ ΠΏΠ»Π°ΡΡΠΈΡΠ½ΠΎΠΉ ΠΏΠ»ΠΎΡΠ½ΠΎΡΡΡΡ.
- Π‘ΠΌΠ΅ΡΡ ΡΠΎΡΠΌΡΡΡ Π² ΠΊΠΈΡΠΏΠΈΡΠΈ Ρ ΠΏΠΎΠΌΠΎΡΡΡ ΠΏΡΠ΅ΡΡΠ° Ρ Π²ΡΠ°ΡΠ°ΡΡΠΈΠΌΡΡ ΡΡΠΎΠ»ΠΎΠΌ, ΠΊΠΎΡΠΎΡΡΠΉ ΠΈΡΠΏΠΎΠ»ΡΠ·ΡΠ΅Ρ ΠΌΠ΅Ρ Π°Π½ΠΈΡΠ΅ΡΠΊΠΎΠ΅ Π΄Π°Π²Π»Π΅Π½ΠΈΠ΅ Π΄Π»Ρ ΠΏΡΠ΅ΡΡΠΎΠ²Π°Π½ΠΈΡ ΠΊΠΈΡΠΏΠΈΡΠ΅ΠΉ. ΠΠ°Π²Π»Π΅Π½ΠΈΠ΅ ΠΏΡΠ΅ΡΡΠΎΠ²Π°Π½ΠΈΡ Π²Π°ΡΡΠΈΡΡΠ΅ΡΡΡ ΠΎΡ 31.ΠΡ 5 Π΄ΠΎ 63 Π / ΠΌΠΌ2.
- ΠΠ° Π·Π°ΠΊΠ»ΡΡΠΈΡΠ΅Π»ΡΠ½ΠΎΠΌ ΡΡΠ°ΠΏΠ΅ ΠΊΠΈΡΠΏΠΈΡΠΈ ΠΏΠΎΠΌΠ΅ΡΠ°ΡΡΡΡ Π² Π°Π²ΡΠΎΠΊΠ»Π°Π². ΠΠ²ΡΠΎΠΊΠ»Π°Π² ΠΏΡΠ΅Π΄ΡΡΠ°Π²Π»ΡΠ΅Ρ ΡΠΎΠ±ΠΎΠΉ ΡΡΠ°Π»ΡΠ½ΠΎΠΉ ΡΠΈΠ»ΠΈΠ½Π΄Ρ Ρ Π³Π΅ΡΠΌΠ΅ΡΠΈΡΠ½ΡΠΌΠΈ ΠΊΠΎΠ½ΡΠ°ΠΌΠΈ. ΠΠ²ΡΠΎΠΊΠ»Π°Π² ΠΈΠΌΠ΅Π΅Ρ Π΄Π»ΠΈΠ½Ρ ΠΎΠΊΠΎΠ»ΠΎ 20 ΠΌΠ΅ΡΡΠΎΠ² ΠΈ Π΄ΠΈΠ°ΠΌΠ΅ΡΡ 2 ΠΌΠ΅ΡΡΠ°.
- ΠΠΎΡΠ»Π΅ ΠΏΠΎΠΌΠ΅ΡΠ΅Π½ΠΈΡ ΠΊΠΈΡΠΏΠΈΡΠ΅ΠΉ Π² ΡΡΡ Π·Π°ΠΊΡΡΡΡΡ ΠΊΠ°ΠΌΠ΅ΡΡ Π΄Π°Π²Π»Π΅Π½ΠΈΠ΅ Π½Π°ΡΡΡΠ΅Π½Π½ΠΎΠ³ΠΎ ΠΏΠ°ΡΠ° ΡΠ±ΡΠ°ΡΡΠ²Π°Π΅ΡΡΡ, ΡΠΎΡΡΠ°Π²Π»ΡΡΡΠ΅Π΅ ΠΏΡΠΈΠΌΠ΅ΡΠ½ΠΎ 0,85β1,6 Π / ΠΌΠΌ2. Π’Π΅ΠΌΠΏΠ΅ΡΠ°ΡΡΡΠ° Π²Π½ΡΡΡΠΈ ΠΊΠ°ΠΌΠ΅ΡΡ ΠΏΠΎΠ²ΡΡΠ°Π΅ΡΡΡ, ΠΈ Π½Π°ΡΠΈΠ½Π°Π΅ΡΡΡ Ρ ΠΈΠΌΠΈΡΠ΅ΡΠΊΠ°Ρ ΡΠ΅Π°ΠΊΡΠΈΡ.
- Π‘ΠΎΠ΄Π΅ΡΠΆΠ°Π½ΠΈΠ΅ ΠΊΡΠ΅ΠΌΠ½Π΅Π·Π΅ΠΌΠ° Π² ΠΏΠ΅ΡΠΊΠ΅ ΠΈ ΡΠΎΠ΄Π΅ΡΠΆΠ°Π½ΠΈΠ΅ ΠΊΠ°Π»ΡΡΠΈΡ Π² ΠΈΠ·Π²Π΅ΡΡΠΈ Π²ΡΡΡΠΏΠ°ΡΡ Π² ΡΠ΅Π°ΠΊΡΠΈΡ Ρ ΠΎΠ±ΡΠ°Π·ΠΎΠ²Π°Π½ΠΈΠ΅ΠΌ ΠΊΡΠΈΡΡΠ°Π»Π»ΠΈΡΠ΅ΡΠΊΠΎΠ³ΠΎ ΡΠΎΠ΅Π΄ΠΈΠ½Π΅Π½ΠΈΡ, Π½Π°Π·ΡΠ²Π°Π΅ΠΌΠΎΠ³ΠΎ Π³ΠΈΠΏΠΎΡΠΈΠ»ΠΈΠΊΠ°ΡΠΎΠΌ ΠΊΠ°Π»ΡΡΠΈΡ.ΠΡΠΎΡ ΠΏΡΠΎΡΠ΅ΡΡ Π΄Π»ΠΈΡΡΡ ΠΎΡ 6 Π΄ΠΎ 12 ΡΠ°ΡΠΎΠ². ΠΠ°ΠΊΠΎΠ½Π΅Ρ, ΠΏΠΎΠ»ΡΡΠ΅Π½Π½ΡΠ΅ ΠΊΠΈΡΠΏΠΈΡΠΈ Π²ΡΠ²ΠΎΠ·ΡΡ Π½Π° ΡΠ°Π±ΠΎΡΠ΅Π΅ ΠΌΠ΅ΡΡΠΎ.
ΠΡΠΏΡΡΠ°Π½ΠΈΡ ΡΠΈΠ»ΠΈΠΊΠ°ΡΠ½ΠΎΠ³ΠΎ ΡΠΈΠ»ΠΈΠΊΠ°ΡΠ° ΠΊΠ°Π»ΡΡΠΈΡ
ΠΈ. ΠΡΠΎΡΠ½ΠΎΡΡΡ Π½Π° ΡΠ°Π·Π΄Π°Π²Π»ΠΈΠ²Π°Π½ΠΈΠ΅:
ΠΡΠΎΡΠ½ΠΎΡΡΡ ΠΊΠΈΡΠΏΠΈΡΠ° Π½Π° ΡΠ°Π·Π΄Π°Π²Π»ΠΈΠ²Π°Π½ΠΈΠ΅ ΠΈΠ·ΠΌΠ΅ΡΡΠ΅ΡΡΡ Π½Π°Π³ΡΡΠ·ΠΊΠΎΠΉ, ΠΊΠΎΡΠΎΡΡΡ ΠΎΠ½ ΠΌΠΎΠΆΠ΅Ρ Π²ΡΠ΄Π΅ΡΠΆΠ°ΡΡ, ΠΊΠΎΠ³Π΄Π° ΠΊΠ»Π°Π΄Π΅ΡΡΡ Π½Π° ΠΏΠ»ΠΎΡΠΊΡΡ ΠΏΠΎΠ²Π΅ΡΡ Π½ΠΎΡΡΡ ΠΈ Π½Π°Π³ΡΡΠ·ΠΊΠ° ΡΠ°Π²Π½ΠΎΠΌΠ΅ΡΠ½ΠΎ ΡΠ°ΡΠΏΡΠ΅Π΄Π΅Π»ΡΠ΅ΡΡΡ ΠΏΠΎ Π²Π΅ΡΡ Π½Π΅ΠΉ ΠΈ Π½ΠΈΠΆΠ½Π΅ΠΉ ΡΠ°ΡΡΠΈ. ΠΠΎΠ»ΡΡΠ΅Π½Π½ΡΠ΅ ΡΠ΅Π·ΡΠ»ΡΡΠ°ΡΡ Π±ΡΠ΄ΡΡ ΠΎΡΠ»ΠΈΡΠ°ΡΡΡΡ Π² Π·Π°Π²ΠΈΡΠΈΠΌΠΎΡΡΠΈ ΠΎΡ ΠΏΡΠΎΡΠ΅Π΄ΡΡΡ ΡΠ΅ΡΡΠΈΡΠΎΠ²Π°Π½ΠΈΡ, ΠΊΠΎΡΠΎΡΠ°Ρ ΠΌΠΎΠΆΠ΅Ρ ΠΎΡΠ»ΠΈΡΠ°ΡΡΡΡ.Π‘ΠΊΠΎΡΠΎΡΡΡ ΠΏΡΠΈΠ»ΠΎΠΆΠ΅Π½ΠΈΡ Π½Π°Π³ΡΡΠ·ΠΊΠΈ ΠΌΠΎΠΆΠ΅Ρ Π²ΡΠ·Π²Π°ΡΡ ΡΠ²Π½ΠΎΠ΅ ΠΈΠ·ΠΌΠ΅Π½Π΅Π½ΠΈΠ΅ ΠΈΠ·ΠΌΠ΅ΡΠ΅Π½Π½ΠΎΠΉ ΠΏΡΠΎΡΠ½ΠΎΡΡΠΈ Π½Π° ΡΠ°Π·Π΄Π°Π²Π»ΠΈΠ²Π°Π½ΠΈΠ΅. ΠΡΠ»ΠΈ Π½Π°Π³ΡΡΠ·ΠΊΠ° ΠΏΡΠΈΠΌΠ΅Π½ΡΠ΅ΡΡΡ ΡΠ΅Π·ΠΊΠΎ, ΡΠ΅Π·ΡΠ»ΡΡΠ°ΡΡ ΠΌΠΎΠ³ΡΡ Π±ΡΡΡ Π²ΡΡΠ΅, ΡΠ΅ΠΌ ΠΎΠ½ΠΈ Π΄ΠΎΠ»ΠΆΠ½Ρ Π±ΡΡΡ. ΠΠ΅ΠΌΠ΅ΡΠΊΠΈΠ΅ ΡΠΏΠ΅ΡΠΈΡΠΈΠΊΠ°ΡΠΈΠΈ Π΄Π»Ρ ΡΠΈΠ»ΠΈΠΊΠ°ΡΠ½ΠΎΠ³ΠΎ ΠΊΠΈΡΠΏΠΈΡΠ° ΡΡΠ΅Π±ΡΡΡ ΠΏΡΠΎΡΠ½ΠΎΡΡΠΈ Π½Π° ΡΠ°Π·Π΄Π°Π²Π»ΠΈΠ²Π°Π½ΠΈΠ΅ 140 ΠΊΠ³ / ΡΠΌ2 (2000 ΡΡΠ½ΡΠΎΠ² Π½Π° ΠΊΠ²Π°Π΄ΡΠ°ΡΠ½ΡΠΉ Π΄ΡΠΉΠΌ). Π‘ΡΡΠΎΠΈΡΠ΅Π»ΡΠ½ΡΠΉ ΠΊΠΎΠ΄Π΅ΠΊΡ, ΠΈΠ·Π΄Π°Π½Π½ΡΠΉ ΠΡΡ-ΠΠΎΡΠΊΠΎΠΌ Π² 1905 Π³ΠΎΠ΄Ρ, ΠΎΠΏΡΠ΅Π΄Π΅Π»ΡΠ΅Ρ, ΡΡΠΎ ΡΡΠ΅Π΄Π½ΡΡ ΠΏΡΠΎΡΠ½ΠΎΡΡΡ Π½Π° ΡΠ°Π·Π΄Π°Π²Π»ΠΈΠ²Π°Π½ΠΈΠ΅ Π΄Π»Ρ ΠΏΡΡΠΈ ΠΊΠΈΡΠΏΠΈΡΠ΅ΠΉ Π΄ΠΎΠ»ΠΆΠ½Π° Π±ΡΡΡ Π½Π΅ ΠΌΠ΅Π½Π΅Π΅ 3000 ΡΡΠ½ΡΠΎΠ² Π½Π° ΠΊΠ²Π°Π΄ΡΠ°ΡΠ½ΡΠΉ Π΄ΡΠΉΠΌ, Π½ΠΈ ΠΎΠ΄ΠΈΠ½ ΠΊΠΈΡΠΏΠΈΡ Π½Π΅ Π΄ΠΎΠ»ΠΆΠ΅Π½ ΠΏΠ°Π΄Π°ΡΡ Π½ΠΈΠΆΠ΅ 2500 ΡΡΠ½ΡΠΎΠ² Π½Π° ΠΊΠ²Π°Π΄ΡΠ°ΡΠ½ΡΠΉ Π΄ΡΠΉΠΌ.
ii.ΠΠΎΠΏΠ΅ΡΠ΅ΡΠ½Π°Ρ ΠΏΡΠΎΡΠ½ΠΎΡΡΡ:
ΠΠΎΠΏΠ΅ΡΠ΅ΡΠ½Π°Ρ ΠΏΡΠΎΡΠ½ΠΎΡΡΡ ΠΊΠΈΡΠΏΠΈΡΠ° ΠΈΠ·ΠΌΠ΅ΡΡΠ΅ΡΡΡ ΠΏΡΡΠ΅ΠΌ ΠΏΠΎΠ΄Π΄Π΅ΡΠΆΠΊΠΈ ΠΊΠΈΡΠΏΠΈΡΠ° Ρ ΠΎΠ±ΠΎΠΈΡ
ΠΊΠΎΠ½ΡΠΎΠ² ΠΈ ΠΏΡΠΈΠ»ΠΎΠΆΠ΅Π½ΠΈΡ Π½Π°Π³ΡΡΠ·ΠΊΠΈ ΠΊ ΡΠ΅ΡΠ΅Π΄ΠΈΠ½Π΅ Π΄ΠΎ ΡΠ°Π·ΡΡΠ²Π°. ΠΠ½ ΡΠΊΠ°Π·ΡΠ²Π°Π΅Ρ Π½Π° ΡΠΎΠΏΡΠΎΡΠΈΠ²Π»Π΅Π½ΠΈΠ΅, ΠΊΠΎΡΠΎΡΠΎΠ΅ ΠΊΠΈΡΠΏΠΈΡ ΠΌΠΎΠΆΠ΅Ρ ΠΎΠΊΠ°Π·Π°ΡΡ Π»ΡΠ±ΠΎΠΉ ΡΠΈΠ»Π΅, ΠΏΡΡΠ°ΡΡΠ΅ΠΉΡΡ Π΅Π³ΠΎ ΡΠΎΠ³Π½ΡΡΡ. ΠΠΊΡΠ°ΡΡΠ΅, ΠΎΠ½ ΡΠΎΡΡΠΎΠΈΡ ΠΈΠ· ΡΡΡΠ°Π½ΠΎΠ²ΠΊΠΈ ΠΊΠΈΡΠΏΠΈΡΠ° Π½Π° Π΄Π²ΡΡ
ΠΏΠ°ΡΠ°Π»Π»Π΅Π»ΡΠ½ΡΡ
ΠΎΠΏΠΎΡΠ°Ρ
Π½Π° ΡΠ°ΡΡΡΠΎΡΠ½ΠΈΠΈ 7 Π΄ΡΠΉΠΌΠΎΠ² Π΄ΡΡΠ³ ΠΎΡ Π΄ΡΡΠ³Π°. ΠΠ°Π³ΡΡΠ·ΠΊΠ° ΠΏΡΠΈΠΊΠ»Π°Π΄ΡΠ²Π°Π΅ΡΡΡ ΡΡΠΏΡΠΌ ΠΎΡΡΡΠΈΠ΅ΠΌ, ΠΊΠΎΡΠΎΡΠΎΠ΅ ΠΏΡΠΈΠΆΠΈΠΌΠ°Π΅ΡΡΡ ΠΊ ΠΊΠΈΡΠΏΠΈΡΡ Π½Π° ΠΏΠΎΠ»ΠΏΡΡΠΈ ΠΌΠ΅ΠΆΠ΄Ρ ΠΎΠΏΠΎΡΠ°ΠΌΠΈ ΠΈ ΠΏΠ°ΡΠ°Π»Π»Π΅Π»ΡΠ½ΠΎ ΠΈΠΌ. ΠΠΈΡΠΏΠΈΡ ΠΈΡΠΏΡΡΠ°Π½ ΡΠΎΠ²Π½ΡΠΌ.ΠΡΠ΅Π²ΠΈΠ΄Π½ΠΎ, ΡΡΠΎ Π½Π°Π³ΡΡΠ·ΠΊΠ°, Π½Π΅ΠΎΠ±Ρ
ΠΎΠ΄ΠΈΠΌΠ°Ρ Π΄Π»Ρ ΡΠ°Π·ΡΡΡΠ΅Π½ΠΈΡ ΠΊΠΈΡΠΏΠΈΡΠ°, Π±ΡΠ΄Π΅Ρ Π·Π°Π²ΠΈΡΠ΅ΡΡ ΠΎΡ ΡΠΈΡΠΈΠ½Ρ ΠΈ Π³Π»ΡΠ±ΠΈΠ½Ρ, Π° ΡΠ°ΠΊΠΆΠ΅ ΠΎΡ ΡΠ°ΡΡΡΠΎΡΠ½ΠΈΡ ΠΌΠ΅ΠΆΠ΄Ρ ΠΎΠΏΠΎΡΠ°ΠΌΠΈ. ΠΠΎΡΡΠΎΠΌΡ ΡΠ°Π·ΡΡΠ²Π½Π°Ρ Π½Π°Π³ΡΡΠ·ΠΊΠ° ΡΠΎΠΎΠ±ΡΠ°Π΅ΡΡΡ ΡΠ΅Π΄ΠΊΠΎ, ΠΏΠΎΡΠΊΠΎΠ»ΡΠΊΡ Π΄Π»Ρ ΡΡΠΎΠ³ΠΎ ΠΏΠΎΡΡΠ΅Π±ΡΠ΅ΡΡΡ ΠΏΠΎΠ΄ΡΠΎΠ±Π½ΠΎΠ΅ ΠΎΠΏΠΈΡΠ°Π½ΠΈΠ΅ ΠΈΡΠΏΡΡΠ°Π½ΠΈΡ. Π€Π°ΠΊΡΠΎΡΠΎΠΌ, ΠΊΠΎΡΠΎΡΡΠΉ Π²ΠΊΠ»ΡΡΠ°Π΅Ρ Π² ΡΠ΅Π±Ρ Π²ΡΠ΅ ΡΡΠΈ ΠΏΠ΅ΡΠ΅ΠΌΠ΅Π½Π½ΡΠ΅, ΡΠ²Π»ΡΠ΅ΡΡΡ ΠΌΠΎΠ΄ΡΠ»Ρ ΡΠ°Π·ΡΡΠ²Π° (MOR). ΠΡΠΎ ΡΠ°Π²Π½ΠΎ 1,5-ΠΊΡΠ°ΡΠ½ΠΎΠΉ ΡΠ°Π·ΡΡΠ²Π½ΠΎΠΉ Π½Π°Π³ΡΡΠ·ΠΊΠ΅, ΡΠΌΠ½ΠΎΠΆΠ΅Π½Π½ΠΎΠΉ Π½Π° ΡΠ°ΡΡΡΠΎΡΠ½ΠΈΠ΅ ΠΌΠ΅ΠΆΠ΄Ρ ΠΎΠΏΠΎΡΠ°ΠΌΠΈ ΠΈ ΡΠ°Π·Π΄Π΅Π»Π΅Π½Π½ΠΎΠΉ Π½Π° ΡΠΈΡΠΈΠ½Ρ ΠΊΠΈΡΠΏΠΈΡΠ°, ΡΠΌΠ½ΠΎΠΆΠ΅Π½Π½ΡΡ Π½Π° ΠΊΠ²Π°Π΄ΡΠ°Ρ Π΅Π³ΠΎ ΡΠΎΠ»ΡΠΈΠ½Ρ.
ΠΡΠ΅ΠΈΠΌΡΡΠ΅ΡΡΠ²Π° ΠΊΠ°Π»ΡΡΠΈΠ΅Π²ΠΎ-ΡΠΈΠ»ΠΈΠΊΠ°ΡΠ½ΠΎΠ³ΠΎ ΠΊΠΈΡΠΏΠΈΡΠ°
Π£ ΠΊΠ°Π»ΡΡΠΈΠ΅Π²ΠΎ-ΡΠΈΠ»ΠΈΠΊΠ°ΡΠ½ΠΎΠ³ΠΎ ΠΊΠΈΡΠΏΠΈΡΠ° ΠΌΠ½ΠΎΠ³ΠΎ ΠΏΡΠ΅ΠΈΠΌΡΡΠ΅ΡΡΠ² ΠΏΡΠΈ ΠΈΡΠΏΠΎΠ»ΡΠ·ΠΎΠ²Π°Π½ΠΈΠΈ Π² ΠΊΠ»Π°Π΄ΠΊΠ΅:
- ΠΠ»Ρ ΠΎΡΡΡΠΊΠ°ΡΡΡΠΈΠ²Π°Π½ΠΈΡ ΡΡΠ΅Π±ΡΠ΅ΡΡΡ Π½Π΅Π±ΠΎΠ»ΡΡΠΎΠ΅ ΠΊΠΎΠ»ΠΈΡΠ΅ΡΡΠ²ΠΎ ΡΠ°ΡΡΠ²ΠΎΡΠ°.
- ΠΡΠΈ ΠΊΠΈΡΠΏΠΈΡΠΈ ΠΎΠ±Π»Π°Π΄Π°ΡΡ Π½ΠΈΠ·ΠΊΠΎΠΉ ΡΠ΅ΠΏΠ»ΠΎΠΏΡΠΎΠ²ΠΎΠ΄Π½ΠΎΡΡΡΡ.
- ΠΡΠΈ ΠΊΠΈΡΠΏΠΈΡΠΈ ΠΎΠ΄Π½ΠΎΡΠΎΠ΄Π½Ρ ΠΏΠΎ ΡΠ²Π΅ΡΡ ΠΈ ΡΠ°ΠΊΡΡΡΠ΅.
- ΠΡΠΎΡΠ½ΠΎΡΡΡ Π½Π° ΡΠΆΠ°ΡΠΈΠ΅ ΡΠΈΠ»ΠΈΠΊΠ°ΡΠ½ΠΎΠ³ΠΎ ΠΊΠΈΡΠΏΠΈΡΠ° ΡΠΎΡΡΠ°Π²Π»ΡΠ΅Ρ ΠΎΠΊΠΎΠ»ΠΎ 10 Π / ΠΌΠΌ2. Π’Π°ΠΊ ΡΡΠΎ ΠΎΠ½ΠΈ Ρ ΠΎΡΠΎΡΠΎ ΠΏΠΎΠ΄Ρ ΠΎΠ΄ΡΡ Π΄Π»Ρ ΠΌΠ½ΠΎΠ³ΠΎΡΡΠ°ΠΆΠ½ΡΡ Π΄ΠΎΠΌΠΎΠ².
- Π ΡΠ»ΡΡΠ°Π΅ ΡΠΈΠ»ΠΈΠΊΠ°ΡΠ½ΠΎΠ³ΠΎ ΠΊΠΈΡΠΏΠΈΡΠ° ΠΏΡΠΎΠ±Π»Π΅ΠΌΠ° Π²ΡΡΡΡ Π°Π½ΠΈΡ Π½Π΅ Π²ΠΎΠ·Π½ΠΈΠΊΠ°Π΅Ρ.
- Π‘ΠΈΠ»ΠΈΠΊΠ°ΡΠ½ΡΠΉ ΠΊΠΈΡΠΏΠΈΡ ΠΎΠ±Π΅ΡΠΏΠ΅ΡΠΈΠ²Π°Π΅Ρ Π±ΠΎΠ»ΡΡΠΈΠΉ ΠΊΠΎΠΌΡΠΎΡΡ ΠΈ Π΄ΠΎΡΡΡΠΏΠ½ΠΎΡΡΡ Π΄Π»Ρ Π°ΡΡ ΠΈΡΠ΅ΠΊΡΠΎΡΠΎΠ², ΠΏΠΎΠ·Π²ΠΎΠ»ΡΡΡΠΈΡ Π΄ΠΎΡΡΠΈΡΡ ΠΆΠ΅Π»Π°Π΅ΠΌΡΡ ΡΠΎΡΠΌ ΠΈ Π΄ΠΈΠ·Π°ΠΉΠ½ΠΎΠ².
- ΠΡΠΈ ΠΊΠΈΡΠΏΠΈΡΠΈ ΠΈΠΌΠ΅ΡΡ ΡΠΎΡΠ½ΡΡ ΡΠΎΡΠΌΡ, ΡΠ°Π·ΠΌΠ΅Ρ Ρ ΠΏΡΡΠΌΡΠΌΠΈ ΠΊΡΠ°ΡΠΌΠΈ, Π° ΡΠ°ΠΊΠΆΠ΅ ΠΆΠ΅ΡΡΠΊΡΡ ΠΈ Π»Π΅Π³ΠΊΡΡ ΠΏΠ»ΠΎΡΠ½ΠΎΡΡΡ 250 ΠΊΠ³ / ΠΌ3.
- Π£ΠΌΠ΅Π½ΡΡΠ°Π΅ΡΡΡ Π²ΠΎΠ·Π΄Π΅ΠΉΡΡΠ²ΠΈΠ΅ ΡΠΎΠ»Π½Π΅ΡΠ½ΠΎΠ³ΠΎ ΡΠ΅ΠΏΠ»Π° Π½Π° ΠΎΡΠΊΡΡΡΡΠ΅ ΡΡΠ΅Π½Ρ ΠΈΠ· ΡΠΈΠ»ΠΈΠΊΠ°ΡΠ½ΠΎ-ΠΊΠ°Π»ΡΡΠΈΠ΅Π²ΠΎΠ³ΠΎ ΠΊΠΈΡΠΏΠΈΡΠ°.
- Π¦Π²Π΅ΡΠ½ΠΎΠΉ ΡΠΈΠ»ΠΈΠΊΠ°ΡΠ½ΡΠΉ ΠΊΠΈΡΠΏΠΈΡ Π½Π΅ ΡΡΠ΅Π±ΡΠ΅Ρ ΠΎΡΠ΄Π΅Π»ΠΊΠΈ ΡΡΠ΅Π½, ΡΡΠΎ ΡΠ½ΠΈΠΆΠ°Π΅Ρ Π΅Π³ΠΎ ΡΡΠΎΠΈΠΌΠΎΡΡΡ.
- ΠΡΠΈ ΠΊΠΈΡΠΏΠΈΡΠΈ ΠΎΠ±Π»Π°Π΄Π°ΡΡ ΠΎΡΠ»ΠΈΡΠ½ΠΎΠΉ ΠΎΠ³Π½Π΅ΡΡΠΎΠΉΠΊΠΎΡΡΡΡ ΠΈ Π²ΠΎΠ΄ΠΎΠΎΡΡΠ°Π»ΠΊΠΈΠ²Π°ΡΡΠΈΠΌΠΈ ΡΠ²ΠΎΠΉΡΡΠ²Π°ΠΌΠΈ.
- Π‘ΡΠ΅Π½Ρ ΠΈΠ· ΡΠΈΠ»ΠΈΠΊΠ°ΡΠ½ΠΎΠ³ΠΎ ΡΠΈΠ»ΠΈΠΊΠ°ΡΠ½ΠΎΠ³ΠΎ ΠΊΠΈΡΠΏΠΈΡΠ° ΡΡΡΠΎΠΉΡΠΈΠ²Ρ ΠΊ Π²Π½Π΅ΡΠ½Π΅ΠΌΡ ΡΡΠΌΡ.
- ΠΡΠΈ ΠΊΠΈΡΠΏΠΈΡΠΈ ΠΈΠΌΠ΅ΡΡ Π½ΠΈΠ·ΠΊΡΡ ΡΡΠ°Π΄ΠΊΡ ΠΈ Π½ΠΈΠ·ΠΊΡΡ ΡΠ΄Π΅Π»ΡΠ½ΡΡ ΡΠ΅ΠΏΠ»ΠΎΠ΅ΠΌΠΊΠΎΡΡΡ, Π½Π΅Π³ΠΎΡΡΡΠΈΠ΅ ΠΈ Π½Π΅Π°Π³ΡΠ΅ΡΡΠΈΠ²Π½ΡΠ΅ ΡΠ²ΠΎΠΉΡΡΠ²Π°.
- Π‘ΡΠΎΠΈΠΌΠΎΡΡΡ ΡΡΡΠΎΠΈΡΠ΅Π»ΡΡΡΠ²Π° ΡΠ½ΠΈΠΆΠ°Π΅ΡΡΡ ΠΏΡΠΈΠΌΠ΅ΡΠ½ΠΎ Π½Π° 40% ΠΎΡ ΠΎΠ±ΡΠ΅ΠΉ ΡΡΠΎΠΈΠΌΠΎΡΡΠΈ Π·Π° ΡΡΠ΅Ρ ΡΠ»Π΅Π΄ΡΡΡΠΈΡ ΡΠ°ΠΊΡΠΎΡΠΎΠ²:
a.ΠΠ°ΡΡΠ°ΡΡ ΡΠΈΠ»ΠΈΠΊΠ°ΡΠ½ΠΎ-ΠΊΠ°Π»ΡΡΠΈΠ΅Π²ΡΡ ΠΏΡΠΎΠ΄ΡΠΊΡΠΎΠ² ΠΎΡΠ΅Π½Ρ ΠΌΠ΅Π½ΡΡΠ΅.
Π³. Π’ΡΠ΅Π±ΡΠ΅ΡΡΡ ΠΌΠ΅Π½ΡΡΠ΅Π΅ ΠΊΠΎΠ»ΠΈΡΠ΅ΡΡΠ²ΠΎ ΡΠ°ΡΡΠ²ΠΎΡΠ°.
Π³. Π’ΠΎΠ»ΡΠΈΠ½Π° ΡΡΠ΅Π½ΠΊΠΈ ΠΌΠΎΠΆΠ΅Ρ Π±ΡΡΡ ΡΠΌΠ΅Π½ΡΡΠ΅Π½Π° Π·Π° ΡΡΠ΅Ρ Π²ΡΡΠΎΠΊΠΎΠΉ ΠΏΡΠΎΡΠ½ΠΎΡΡΠΈ Π½Π° ΡΠΆΠ°ΡΠΈΠ΅.
ΠΠ΅Π΄ΠΎΡΡΠ°ΡΠΊΠΈ ΠΊΠ°Π»ΡΡΠΈΠ΅Π²ΠΎ-ΡΠΈΠ»ΠΈΠΊΠ°ΡΠ½ΠΎΠ³ΠΎ ΠΊΠΈΡΠΏΠΈΡΠ°
Π Π½Π΅ΠΊΠΎΡΠΎΡΡΡ ΡΡΠ»ΠΎΠ²ΠΈΡΡ ΡΠΈΠ»ΠΈΠΊΠ°ΡΠ½ΡΠΉ ΠΊΠΈΡΠΏΠΈΡ Π½Π΅ ΠΏΠΎΠ΄Ρ ΠΎΠ΄ΠΈΡ, ΠΈ Π΅Π³ΠΎ Π½Π΅Π΄ΠΎΡΡΠ°ΡΠΊΠΈ ΡΠ°ΠΊΠΎΠ²Ρ:
- ΠΡΠΈ Π½Π°Π»ΠΈΡΠΈΠΈ Π±ΠΎΠ»ΡΡΠΎΠ³ΠΎ ΠΊΠΎΠ»ΠΈΡΠ΅ΡΡΠ²Π° Π³Π»ΠΈΠ½Ρ Π³Π»ΠΈΠ½ΡΠ½ΡΠ΅ ΠΊΠΈΡΠΏΠΈΡΠΈ Π±ΠΎΠ»Π΅Π΅ ΡΠΊΠΎΠ½ΠΎΠΌΠΈΡΠ½Ρ, ΡΠ΅ΠΌ ΠΊΠΈΡΠΏΠΈΡΠΈ ΠΈΠ· ΡΠΈΠ»ΠΈΠΊΠ°ΡΠ° ΠΊΠ°Π»ΡΡΠΈΡ.
- ΠΠ΅ ΠΏΠΎΠ΄Ρ ΠΎΠ΄ΡΡ Π΄Π»Ρ Π·Π°ΠΊΠ»Π°Π΄ΠΊΠΈ ΡΡΠ½Π΄Π°ΠΌΠ΅Π½ΡΠ°, ΡΠ°ΠΊ ΠΊΠ°ΠΊ Π½Π΅ ΠΌΠΎΠ³ΡΡ ΠΎΠ±Π΅ΡΠΏΠ΅ΡΠΈΡΡ Π²ΠΎΠ΄ΠΎΠ½Π΅ΠΏΡΠΎΠ½ΠΈΡΠ°Π΅ΠΌΠΎΡΡΡ Π² ΡΠ΅ΡΠ΅Π½ΠΈΠ΅ Π΄Π»ΠΈΡΠ΅Π»ΡΠ½ΠΎΠ³ΠΎ ΠΏΠ΅ΡΠΈΠΎΠ΄Π°.
- ΠΠ½ΠΈ Π½Π΅ ΠΌΠΎΠ³ΡΡ ΠΏΡΠΎΡΠΈΠ²ΠΎΡΡΠΎΡΡΡ ΠΎΠ³Π½Ρ Π² ΡΠ΅ΡΠ΅Π½ΠΈΠ΅ Π±ΠΎΠ»Π΅Π΅ Π΄Π»ΠΈΡΠ΅Π»ΡΠ½ΠΎΠ³ΠΎ ΠΏΠ΅ΡΠΈΠΎΠ΄Π° Π²ΡΠ΅ΠΌΠ΅Π½ΠΈ, ΡΠ»Π΅Π΄ΠΎΠ²Π°ΡΠ΅Π»ΡΠ½ΠΎ, ΠΎΠ½ΠΈ Π½Π΅ ΠΏΠΎΠ΄Ρ ΠΎΠ΄ΡΡ Π΄Π»Ρ ΡΡΡΠΎΠΈΡΠ΅Π»ΡΠ½ΡΡ ΠΏΠ΅ΡΠ΅ΠΉ ΠΈ Ρ. Π.
- Π‘ΡΠΎΠΉΠΊΠΎΡΡΡ ΠΊ ΠΈΡΡΠΈΡΠ°Π½ΠΈΡ Ρ ΡΡΠΈΡ
ΠΊΠΈΡΠΏΠΈΡΠ΅ΠΉ ΠΎΡΠ΅Π½Ρ Π½ΠΈΠ·ΠΊΠ°Ρ, ΠΏΠΎΡΡΠΎΠΌΡ ΠΈΡ
Π½Π΅Π»ΡΠ·Ρ ΠΈΡΠΏΠΎΠ»ΡΠ·ΠΎΠ²Π°ΡΡ Π΄Π»Ρ ΡΡΠΎΡΡΠ°ΡΠΎΠ².
ΠΠ²ΡΠΎΡ ΡΡΠ°ΡΡΠΈ:
ΠΡΡ Π°ΠΌΠΌΠ°Π΄ ΠΠ°ΡΡΠΊΠΈΠΉ
(PDF) ΠΠ²ΡΠΎΠΊΠ»Π°Π²Π½ΡΠΉ ΡΠΈΠ»ΠΈΠΊΠ°ΡΠ½ΡΠΉ ΠΊΠΈΡΠΏΠΈΡ Π½Π° ΠΎΡΠ½ΠΎΠ²Π΅ Π³ΡΠ°Π½ΡΠ»ΠΈΡΠΎΠ²Π°Π½Π½ΠΎΠ³ΠΎ ΡΠ»Π°ΠΊΠ°
ΠΠ±Π·ΠΎΡ ΡΡΠ°ΡΡΠΈ
Π’ΠΎΠΌ 8 ΠΡΠΏΡΡΠΊ 4 — ΠΈΡΠ½Ρ 2019
DOI: 10.19080 / CERJ.2019.08.555741
Civil Eng Res J
ΠΠ²ΡΠΎΡΡΠΊΠΈΠ΅ ΠΏΡΠ°Π²Π° Β© ΠΡΠ΅ ΠΏΡΠ°Π²Π° ΠΏΡΠΈΠ½Π°Π΄Π»Π΅ΠΆΠ°Ρ Nourredine Arabi
ΠΠ²ΡΠΎΠΊΠ»Π°Π² Π½Π° ΠΎΡΠ½ΠΎΠ²Π΅ Π³ΡΠ°Π½ΡΠ»ΠΈΡΠΎΠ²Π°Π½Π½ΠΎΠ³ΠΎ ΡΠ»Π°ΠΊΠ°
ΠΠ·Π²Π΅ΡΡΠΊΠΎΠ²ΠΎ-ΠΏΠ΅ΡΡΠ°Π½ΡΠ΅ ΠΊΠΈΡΠΏΠΈΡΠΈ
Nourredine Arabi *
ΠΠ°Π±ΠΎΡΠ°ΡΠΎΡΠΈΡ ΠΎΠΊΡΡΠΆΠ°ΡΡΠ΅ΠΉ ΡΡΠ΅Π΄Ρ ΠΈ ΠΎΠΊΡΡΠΆΠ°ΡΡΠ΅ΠΉ ΡΡΠ΅Π΄Ρ ΠΠ°Π΄ΠΆΠΈ ΠΠΎΡ ΡΠ°Ρ ΠΠ½Π½Π°Π±Π°, AlgΓ©rie
ΠΠ°ΡΠ° ΠΏΠΎΠ΄Π°ΡΠΈ: 27 ΠΌΠ°Ρ 2019 Π³ .; ΠΠΏΡΠ±Π»ΠΈΠΊΠΎΠ²Π°Π½ΠΎ: 25 ΠΈΡΠ½Ρ 2019 Π³.
* ΠΠ²ΡΠΎΡ, ΠΎΡΠ²Π΅ΡΡΡΠ²Π΅Π½Π½ΡΠΉ Π·Π° ΠΏΠ΅ΡΠ΅ΠΏΠΈΡΠΊΡ: Nourredine Arabi, Laboratoire MatΓ©riaux GΓ©omatΓ©riaux et Environnement, UniversitΓ© Badji Mokhtar Annaba, PB 12 Annaba
23000, AlgΓ©rie
ΠΠ²Π΅Π΄Π΅Π½ΠΈΠ΅
ΠΠ΄ΠΈΠ½ ΠΈΠ· ΡΠΈΠ»ΠΈΠΊΠ°ΡΠ½ΡΡ ΠΊΠΈΡΠΏΠΈΡΠ΅ΠΉ ΠΈΠ· ΠΊΠ°Π»ΡΡΠΈΡ ΡΡΠΈΡΠ°Π΅ΡΡΡ ΡΡΠΎΠ²Π΅ΡΡΠ΅Π½ΡΡΠ²ΠΎΠ²Π°Π½Π½ΡΠΌ.
ΡΡΡΠΎΠΈΡΠ΅Π»ΡΠ½ΡΡ
ΠΌΠ°ΡΠ΅ΡΠΈΠ°Π»ΠΎΠ² Π² ΠΌΠΈΡΠ΅ ΠΈ ΠΏΡΠΎΠΈΠ·Π²ΠΎΠ΄ΠΈΡΡΡ ΠΏΡΡΠ΅ΠΌ Π³ΠΈΠ΄ΡΠΎΡΠ΅ΡΠΌΠ°Π»ΡΠ½ΠΎΠΉ ΡΠ΅Π°ΠΊΡΠΈΠΈ ΠΌΠ΅ΠΆΠ΄Ρ ΠΏΠ΅ΡΠΊΠΎΠΌ ΠΈΠ»ΠΈ ΠΊΡΠ΅ΠΌΠ½ΠΈΡΡΡΠΌΠΈ ΠΌΠ°ΡΠ΅ΡΠΈΠ°Π»Π°ΠΌΠΈ ΠΈ ΠΈΠ·Π²Π΅ΡΡΡΡ. ΠΠ΅ΡΠΌΠΎΡΡΡ Π½Π° ΠΌΠ½ΠΎΠΆΠ΅ΡΡΠ²ΠΎ ΠΏΡΠ΅Π΄ΡΠ΅ΡΡΠ²ΡΡΡΠΈΡ
ΠΈΡΡΠ»Π΅Π΄ΠΎΠ²Π°Π½ΠΈΠΉ, Π½Π΅ΠΊΠΎΡΠΎΡΡΠ΅ Π°ΡΠΏΠ΅ΠΊΡΡ ΡΠ΅Π°ΠΊΡΠΈΠΈ Π΄ΠΎ ΡΠΈΡ ΠΏΠΎΡ Π½Π΅ Π΄ΠΎ ΠΊΠΎΠ½ΡΠ° ΠΏΠΎΠ½ΡΡΡ [1-3]. ΠΡΠΈ Π΄Π°Π²Π»Π΅Π½ΠΈΠΈ Π½Π°ΡΡΡΠ΅Π½Π½ΠΎΠ³ΠΎ ΠΏΠ°ΡΠ° ΠΈ
ξξ ξξξξξξξξξξξξ ξξξξξξξξ ξξξξξξξξ ξ³ξΉξ²ξ ξξξξ ξ΄ξ²ξ²ξ ξΉ ΠΠ²Π°ΡΡ
(Π½Π΅ΡΠ°ΡΡΠ²ΠΎΡΠΈΠΌΡΠΉ ΠΏΡΠΈ ΡΠ΅ΠΌΠΏΠ΅ΡΠ°ΡΡΡΠ΅ ΠΎΠΊΡΡΠΆΠ°ΡΡΠ΅ΠΉ ΡΡΠ΅Π΄Ρ) ΡΡΠ°Π½ΠΎΠ²ΠΈΡΡΡ Ρ ΠΈΠΌΠΈΡΠ΅ΡΠΊΠΈ Π°ΠΊΡΠΈΠ²Π½ΡΠΌ
ΠΈ Π²ΡΡΡΠΏΠ°Π΅Ρ Π² ΡΠ΅Π°ΠΊΡΠΈΡ Ρ Π³Π°ΡΠ΅Π½ΠΎΠΉ ΠΈΠ·Π²Π΅ΡΡΡΡ Β«Ca (OH) 2Β». ΠΡΠΎ
Π΄Π°Π΅Ρ Π³ΠΈΠ΄ΡΠ°ΡΠΈΡΠΎΠ²Π°Π½Π½ΡΠΉ ΡΠΈΠ»ΠΈΠΊΠ°Ρ ΠΊΠ°Π»ΡΡΠΈΡ, ΠΊΠΎΡΠΎΡΡΠΉ ΡΠ²Π»ΡΠ΅ΡΡΡ ΡΠ²Π΅ΡΠ΄ΡΠΌ, ΡΡΠΎΠΉΠΊΠΈΠΌ ΠΈ Π½Π΅ΡΠ°ΡΡΠ²ΠΎΡΠΈΠΌΡΠΌ Π² Π²ΠΎΠ΄Π΅ [4].ΠΡΠΈ ΡΠ°Π·Ρ ΡΠ°ΡΡΠΎ ΠΎΠ±ΡΠ΅Π΄ΠΈΠ½ΡΡΡΡΡ Π² Π½Π°ΠΈΠΌΠ΅Π½ΠΎΠ²Π°Π½ΠΈΠ΅ Π±Π΅ΡΠΌΠΎΡΠΈΡΠΎΠ² Π΄ΠΎ
. ΠΠ°ΠΈΠ±ΠΎΠ»Π΅Π΅ ΠΈΠ·Π²Π΅ΡΡΠ½Ρ ΡΠΎΠ±Π΅ΡΠΌΠΎΡΠΈΡ 14Γ , 11Γ ΠΈΠ»ΠΈ
9Γ ; Π½Π΅ΠΊΠΎΡΠΎΡΡΠ΅ ΠΈΠ· Π½ΠΈΡ Π½Π°Π·ΡΠ²Π°ΡΡΡΡ Β«Π½ΠΎΡΠΌΠ°Π»ΡΠ½ΡΠΌΠΈΒ», Π° Π΄ΡΡΠ³ΠΈΠ΅
Π½Π°Π·ΡΠ²Π°ΡΡΡΡ Β«Π°Π½ΠΎΠΌΠ°Π»ΡΠ½ΡΠΌΠΈΒ» Ρ ΡΠΎΠΎΡΠ½ΠΎΡΠ΅Π½ΠΈΠ΅ΠΌ Ca / Si 0,8β1,0 [5-7].
ΠΠ»Π°Π³ΠΎΠ΄Π°ΡΡ ΡΠ²ΠΎΠ΅ΠΌΡ Ρ ΠΈΠΌΠΈΡΠ΅ΡΠΊΠΎΠΌΡ ΡΠΎΡΡΠ°Π²Ρ, Π±Π»ΠΈΠ·ΠΊΠΎΠΌΡ ΠΊ
ΡΠ΅ΠΌΠ΅Π½ΡΠ°, Π΄ΠΎΠΌΠ΅Π½Π½ΡΠΉ ΡΠ»Π°ΠΊ ΡΠ°ΠΊΠΆΠ΅ ΠΌΠΎΠΆΠ΅Ρ ΠΈΡΠΏΠΎΠ»ΡΠ·ΠΎΠ²Π°ΡΡΡΡ Π²ΠΌΠ΅ΡΡΠΎ ΠΈΠ·Π²Π΅ΡΡΠΈ
Π² ΡΠΈΠ»ΠΈΠΊΠ°ΡΠ½ΡΡ ΠΌΠ°ΡΠ΅ΡΠΈΠ°Π»Π°Ρ . ΠΡΡΡΡΠΎΠ΅ ΠΎΡ Π»Π°ΠΆΠ΄Π΅Π½ΠΈΠ΅ ΡΠ»Π°ΠΊΠ° ΠΏΡΠΈΠ²ΠΎΠ΄ΠΈΡ ΠΊ ΠΎΠ±ΡΠ°Π·ΠΎΠ²Π°Π½ΠΈΡ ΠΌΠ΅ΡΠ°ΡΡΠ°Π±ΠΈΠ»ΡΠ½ΠΎΠΉ ΡΡΠ΅ΠΊΠ»ΠΎΠ²ΠΈΠ΄Π½ΠΎΠΉ ΡΡΡΡΠΊΡΡΡΡ
, ΠΊΠΎΡΠΎΡΠ°Ρ ΡΠΏΠΎΡΠΎΠ±ΡΡΠ²ΡΠ΅Ρ Π΅Π³ΠΎ ΡΠ΅Π°ΠΊΡΠΈΠΈ Ρ ΠΈΠ·Π²Π΅ΡΡΡΡ
ξξξξξξ ξξξξ ξξξξ ξ ξ ξξξξξξξξξξ ξξΊ ξξ€ξ ξξξξ ξξξξξξ ξξξξξξ ξξ ξξξξξ ξξξ ξξξξξξ
, ΡΡΠΎΠ±Ρ ΠΎΠ±Π»Π°Π΄Π°ΡΡ ΡΠΊΡΡΡΠΎΠΉ Π³ΠΈΠ΄ΡΠ°Π²Π»ΠΈΡΠ΅ΡΠΊΠΎΠΉ Π°ΠΊΡΠΈΠ²Π½ΠΎΡΡΡΡ; Ρ. Π΅. ΠΏΡΠΎΡΠ²Π»ΡΠ΅Ρ ΡΠ΅ΠΌΠ΅Π½ΡΠΈΡΡΡΡΠΈΠ΅ ΡΠ²ΠΎΠΉΡΡΠ²Π°
ΠΏΡΠΈ Π΄Π»ΠΈΡΠ΅Π»ΡΠ½ΠΎΠΌ ΠΊΠΎΠ½ΡΠ°ΠΊΡΠ΅ Ρ Π²ΠΎΠ΄ΠΎΠΉ
[9]. ΠΠ»Ρ Π½Π°ΡΠ°Π»Π° ΠΏΡΠΎΡΠ°ΡΡΠ°Π½ΠΈΡ Π½Π΅ΠΎΠ±Ρ ΠΎΠ΄ΠΈΠΌΠ° Ρ ΠΈΠΌΠΈΡΠ΅ΡΠΊΠ°Ρ Π°ΠΊΡΠΈΠ²Π°ΡΠΈΡ [10].
ΠΡΠΎΠΌΠ΅ ΡΠΎΠ³ΠΎ, ΡΠ»Π°ΠΊ ΡΠ°ΠΊΠΆΠ΅ ΠΌΠΎΠΆΠ΅Ρ ΡΠ΅Π°Π³ΠΈΡΠΎΠ²Π°ΡΡ ΠΏΡΡΠ΅ΠΌ ΡΠ΅ΡΠΌΠΈΡΠ΅ΡΠΊΠΎΠΉ Π°ΠΊΡΠΈΠ²Π°ΡΠΈΠΈ (Π² ΠΏΠ°ΡΠ½ΠΎΠΉ ΠΈ Π°Π²ΡΠΎΠΊΠ»Π°Π²Π΅
) [11].
ΠΠ°ΡΠ΅ΡΠΈΠ°Π»Ρ ΠΈ ΠΈΡΠΏΡΡΠ°Π½ΠΈΡ
ΠΠ°ΡΠ΅ΡΠΈΠ°Π»Ρ
ΠΡΠ°Π½ΡΠ»ΠΈΡΠΎΠ²Π°Π½Π½ΡΠΉ Π΄ΠΎΠΌΠ΅Π½Π½ΡΠΉ ΡΠ»Π°ΠΊ (GBFS): ΠΡΠ°Π½ΡΠ»ΠΈΡΠΎΠ²Π°Π½Π½ΡΠΉ Π΄ΠΎΠΌΠ΅Π½Π½ΡΠΉ ΡΠ»Π°ΠΊ
Π±ΡΠ» ΠΏΡΠ΅Π΄ΠΎΡΡΠ°Π²Π»Π΅Π½ ΡΡΠ°Π»Π΅Π»ΠΈΡΠ΅ΠΉΠ½ΡΠΌ Π·Π°Π²ΠΎΠ΄ΠΎΠΌ ArcelorMittal
(ΡΠ°ΡΠΏΠΎΠ»ΠΎΠΆΠ΅Π½ Π½Π° Π²ΠΎΡΡΠΎΠΊΠ΅ ΠΠ»ΠΆΠΈΡΠ°).Π₯ΠΈΠΌΠΈΡΠ΅ΡΠΊΠ°Ρ Ρ Π°ΡΠ°ΠΊΡΠ΅ΡΠΈΡΡΠΈΠΊΠ°
ξξξξξξξξξξξξξξξξξξξξξξξξ³ξ€ξ ξξξξ ξξξξξ ξξξξξξξξξ ξξξξξξξξξξξξξξξξξξξ
ΠΎΠΊΠΎΠ»ΠΎ 350 ΠΌ2 / ΠΊΠ³ (ΠΏΠΎ ΠΌΠ΅ΡΠΎΠ΄Ρ ΠΠ»Π΅ΠΉΠ½Π°) Π² Π»Π°Π±ΠΎΡΠ°ΡΠΎΡΠ½ΠΎΠΉ ΡΠ°ΡΠΎΠ²ΠΎΠΉ ΠΌΠ΅Π»ΡΠ½ΠΈΡΠ΅.
Π ΠΈΡΡΠ½ΠΎΠΊ 1 ΠΠΎΠΊΠ°Π·ΡΠ²Π°Π΅Ρ ΡΠ΅Π½ΡΠ³Π΅Π½ΠΎΠ³ΡΠ°ΠΌΠΌΡ ΠΈΡΠΏΠΎΠ»ΡΠ·ΡΠ΅ΠΌΠΎΠ³ΠΎ BFWS. ΠΡΠΈΡΡΠ°Π»Π»ΠΈΡΠ΅ΡΠΊΠ°Ρ ΡΡΡΡΠΊΡΡΡΠ° GBFS ΠΏΠΎΡΡΠΈ ΠΏΠΎΠ»Π½ΠΎΡΡΡΡ Π°ΠΌΠΎΡΡΠ½Π°, ΡΠ°ΠΊ ΠΊΠ°ΠΊ
ξξξξξξξξξξξξξξξξξξξξξξξξξξξξξξξξ€ξ ξξξξξξξξξξξξξξξξξξξξξξξξξξ΄ξ·ξΉξ
ξξξξξ΅ξ·ξΉξξξ΄ξ ξξξ ξξξξξ ξξξ ξξξξξξξξξξξ ξξξ ξξ ξξξξξξξξ ξξξξ ξξξξξξξξξξξξξξ
Π°ΠΌΠΎΡΡΠ½Π°Ρ ΡΡΡΡΠΊΡΡΡΠ° ( ΡΡΠ΅ΠΊΠ»ΠΎ).ΠΠ΄Π½Π°ΠΊΠΎ ΡΠ»Π΅Π΄Ρ ΠΌΠ΅Π»Π»ΠΈΠ»ΠΈΡΠ°, ΠΌΠ΅Ρ-
ξξξξξξξξξξξξξξξξξξξξξξξξξξ ξξξξξξξξξξ ξ΄ξ ξξ± β-
Π½Π° Π±ΠΎΠ»Π΅Π΅ ΠΊΡΠΈΡΡΠ°Π»Π»ΠΈΠ·ΠΎΠ²Π°Π½Π½ΡΡ
ΠΏΠΎΡΡΠΈΡΡ
Π³ΡΠ°Π½ΡΠ»ΠΈΡΠΎΠ²Π°Π½Π½ΠΎΠ³ΠΎ ΡΠ»Π°ΠΊΠ°. ΠΠ΅ΡΠΎΡΡΠ½ΠΎ
, ΡΡΠΎ Π½Π΅ΠΊΠΎΡΠΎΡΡΠ΅ Π°Π³Π»ΠΎΠΌΠ΅ΡΠ°ΡΡ ΡΠ»Π°ΠΊΠ° ΠΏΡΠ΅ΡΠ΅ΡΠΏΠ΅Π»ΠΈ ΡΠ°ΡΡΠΈΡΠ½ΡΡ ΠΊΡΠΈΡΡΠ°Π»Π»ΠΈΠ·Π°ΡΠΈΡ
Π² ΠΏΡΠΎΡΠ΅ΡΡΠ΅ ΠΎΡ Π»Π°ΠΆΠ΄Π΅Π½ΠΈΡ. ΠΠΎΠΌΠΈΠΌΠΎ ΡΡΠΈΡ ΠΌΠΈΠ½Π΅ΡΠ°Π»ΠΎΠ², ΠΏΡΠΈΡΡΡΡΡΠ²ΡΡΡ
ΡΠ»Π΅Π΄ΠΎΠ² ΠΊΠ²Π°ΡΡΠ°, ΠΊΠ°Π»ΡΡΠΈΡΠ° ΠΈ ΠΎΠΊΡΠΈΠ΄Π° ΠΆΠ΅Π»Π΅Π·Π° [12-14].
Π ΠΈΡ. 1. Π Π΅Π½ΡΠ³Π΅Π½ΠΎΠ³ΡΠ°ΠΌΠΌΠ° ΠΈΡΠΏΠΎΠ»ΡΠ·ΠΎΠ²Π°Π½Π½ΠΎΠ³ΠΎ Π΄ΠΎΠΌΠ΅Π½Π½ΠΎΠ³ΠΎ ΡΠ»Π°ΠΊΠ°.
ΠΠ°ΡΠ΅Π½Π°Ρ ΠΈΠ·Π²Π΅ΡΡΡ: Π½Π΅Π³Π°ΡΠ΅Π½Π°Ρ ΠΈΠ·Π²Π΅ΡΡΡ ΡΠ°ΠΊΠΆΠ΅ ΡΠΎΠ±ΠΈΡΠ°Π΅ΡΡΡ Π½Π° Π·Π°Π²ΠΎΠ΄Π΅
ArcelorMittal Steel.Π’ΡΡΠ΅Π½ΠΈΠ΅ ΠΈ ΠΈΠ·ΠΌΠ΅Π»ΡΡΠ΅Π½ΠΈΠ΅ ΠΏΡΠΎΠ²ΠΎΠ΄ΠΈΠ»ΠΈΡΡ
Π² ΠΡΡΠ»Π΅Π΄ΠΎΠ²Π°ΡΠ΅Π»ΡΡΠΊΠΎΠΉ Π»Π°Π±ΠΎΡΠ°ΡΠΎΡΠΈΠΈ Π³ΡΠ°ΠΆΠ΄Π°Π½ΡΠΊΠΎΠ³ΠΎ ΡΡΡΠΎΠΈΡΠ΅Π»ΡΡΡΠ²Π°, Annaba Uni-
Civil Eng Res J 8 (4): CERJ.MS.ID.555741 (2019) 001
Abstract
ΠΠ΅Ρ Π°Π½ΠΈΡΠ΅ΡΠΊΠΈΠ΅ ΡΠ²ΠΎΠΉΡΡΠ²Π° ΠΏΠ΅ΡΠΊΠ° -ΠΈΠ·Π²Π΅ΡΡΠΊΠΎΠ²ΡΠ΅ ΠΊΠΈΡΠΏΠΈΡΠΈ, ΠΏΠΎΠ»ΡΡΠ΅Π½Π½ΡΠ΅ Π°Π²ΡΠΎΠΊΠ»Π°Π²ΠΈΡΠΎΠ²Π°Π½ΠΈΠ΅ΠΌ Π² ΡΠ°Π·Π»ΠΈΡΠ½ΡΡ ΡΡΠ»ΠΎΠ²ΠΈΡΡ ΠΈ Π²Π²Π΅Π΄Π΅Π½ΠΈΠ΅ΠΌ Π³ΡΠ°Π½ΡΠ»ΠΈΡΠΎΠ²Π°Π½Π½ΠΎΠ³ΠΎ ΡΠ»Π°ΠΊΠ°
, Π±ΡΠ»ΠΈ ΠΈΡΡΠ»Π΅Π΄ΠΎΠ²Π°Π½Ρ ΡΠ°Π½Π΅Π΅. Π ΡΡΠΎΠΌ ΠΈΡΡΠ»Π΅Π΄ΠΎΠ²Π°Π½ΠΈΠΈ ΡΡΡΠ°Π½Π°Π²Π»ΠΈΠ²Π°Π΅ΡΡΡ Π²Π·Π°ΠΈΠΌΠΎΡΠ²ΡΠ·Ρ ΠΌΠ΅ΠΆΠ΄Ρ ΡΡΡΡΠΊΡΡΡΠΎΠΉ, ΡΡΠΎΡΠΌΠΈΡΠΎΠ²Π°Π½Π½ΡΠΌΠΈ ΡΠ°Π·Π°ΠΌΠΈ ΠΈ ΠΏΡΠΎΡΠ½ΠΎΡΡΡΡ.ΠΠ° ΠΎΡΠ½ΠΎΠ²Π΅ ΠΈΠ·Π²Π΅ΡΡΠΈ
ΠΈ Π³ΡΠ°Π½ΡΠ»ΠΈΡΠΎΠ²Π°Π½Π½ΠΎΠ³ΠΎ ΡΠ»Π°ΠΊΠ° ΡΠ°Π·ΡΠ°Π±ΠΎΡΠ°Π½ΠΎ Π½ΠΎΠ²ΠΎΠ΅ Π²ΡΠΆΡΡΠ΅Π΅. ΠΡΠΎ ΠΎΡΠ²Π΅ΡΠΆΠ΄Π°Π΅ΡΡΡ ΠΏΡΠΈ Π΄Π°Π²Π»Π΅Π½ΠΈΠΈ Π½Π°ΡΡΡΠ΅Π½Π½ΠΎΠ³ΠΎ ΠΏΠ°ΡΠ° 1,0 ΠΈ 1,8 ΠΠΠ°. Π Π΅Π·ΡΠ»ΡΡΠ°ΡΡ ΠΏΠΎΠΊΠ°Π·Π°Π»ΠΈ ΡΠ½ΠΈΠΆΠ΅Π½ΠΈΠ΅ ΠΏΡΠΎΡΠ½ΠΎΡΡΠΈ Π½Π° ΡΠΆΠ°ΡΠΈΠ΅ Π½Π°
ΠΈΠ·-Π·Π° Π·Π°ΠΌΠ΅Π½Ρ. ΠΠ½Π°Π»ΠΈΠ· ΠΌΠΈΠΊΡΠΎΡΡΡΡΠΊΡΡΡΡ ΠΏΠΎΠΊΠ°Π·Π°Π», ΡΡΠΎ ΠΏΡΠΎΠ΄ΡΠΊΡΡ ΡΠ΅Π°ΠΊΡΠΈΠΈ ΡΠΎΡΡΠΎΡΡ Π² ΠΎΡΠ½ΠΎΠ²Π½ΠΎΠΌ ΠΈΠ· ΡΠΎΠ±Π΅ΡΠΌΠΎΡΠΈΡΠ°
11Γ ΠΈ ΠΊΡΠΎΠ½ΠΎΡΠ»ΠΈΡΠ°. ΠΡΠΎΠΌΠ΅ ΡΠΎΠ³ΠΎ, ΠΏΠΎΠ²ΡΡΠ΅Π½ΠΈΠ΅ ΡΠ΅ΠΌΠΏΠ΅ΡΠ°ΡΡΡΡ Π°Π²ΡΠΎΠΊΠ»Π°Π²Π° ΠΏΡΠΈΠ²ΠΎΠ΄ΠΈΡ ΠΊ ΡΠ²Π΅Π»ΠΈΡΠ΅Π½ΠΈΡ ΡΠΎΠ΄Π΅ΡΠΆΠ°Π½ΠΈΡ ΠΊΡΠΎΠ½ΠΎΡΠ»ΠΈΡΠ° ΠΏΠΎ ΡΡΠ°Π²Π½Π΅Π½ΠΈΡ Ρ ΡΠΎΠ±Π΅ΡΠΌΠΎΡΠΈΡΠΎΠΌ. ΠΠ° ΡΠ΅Π½ΡΠ³Π΅Π½ΠΎΠ²ΡΠΊΠΈΡ Π΄ΠΈΡΡΠ°ΠΊΡΠΎΠ³ΡΠ°ΠΌΠΌΠ°Ρ
ΡΡΠΈΡ ΡΠ°Π· ΠΎΡΠ΅Π½Ρ ΠΌΠ°Π»ΠΎ, ΠΏΠΎΡΡΠΈ Π½Π΅ Π²ΠΈΠ΄Π½ΠΎ, ΠΎΠ½ΠΈ ΠΌΠ°ΡΠΊΠΈΡΡΡΡΡΡ Π½Π°Π»ΠΈΡΠΈΠ΅ΠΌ ΠΊΠ²Π°ΡΡΠ°.ΠΡ ΠΈΠ½ΡΠ΅Π½ΡΠΈΠ²Π½ΠΎΡΡΡ ΡΠ²Π΅Π»ΠΈΡΠΈΠ²Π°Π΅ΡΡΡ Ρ Π½Π°Π»ΠΈΡΠΈΠ΅ΠΌ ΡΠ»Π°ΠΊΠ°.
ΠΠ»ΡΡΠ΅Π²ΡΠ΅ ΡΠ»ΠΎΠ²Π°: ΡΠΈΠ»ΠΈΠΊΠ°ΡΠ½ΡΠΉ ΠΊΠΈΡΠΏΠΈΡ; ΠΠ²ΡΠΎΠΊΠ»Π°Π²ΠΈΡΠΎΠ²Π°Π½ΠΈΠ΅; ΠΡΠ°Π½ΡΠ»ΠΈΡΠΎΠ²Π°Π½Π½ΡΠΉ ΡΠ»Π°ΠΊ; Π’ΠΎΠ±Π΅ΡΠΌΠΎΡΠΈΡ; Xonotlite
ΠΡΡΡΠΈΠΉ ΠΏΠ΅ΡΠΎΠΊ Π΄Π»Ρ ΠΏΠΎΠ²ΡΠΎΡΠ½ΠΎΠ³ΠΎ Π½Π°Π½Π΅ΡΠ΅Π½ΠΈΡ Π½Π°ΡΡΡΠ°Π»ΡΠ½ΠΎΠΉ Π³ΠΈΠ΄ΡΠ°Π²Π»ΠΈΡΠ΅ΡΠΊΠΎΠΉ ΠΈΠ·Π²Π΅ΡΡΠΈ?
ΠΠ°ΠΊ Π²ΡΠ±ΡΠ°ΡΡ ΠΏΠ΅ΡΠΎΠΊ Π΄Π»Ρ Π½Π°ΡΡΡΠ°Π»ΡΠ½ΠΎΠΉ Π³ΠΈΠ΄ΡΠ°Π²Π»ΠΈΡΠ΅ΡΠΊΠΎΠΉ ΠΈΠ·Π²Π΅ΡΡΠΈ
ΠΠΎΡΠΎΡΠ΅ Π³ΠΎΠ²ΠΎΡΡβ¦. ΠΡΠ±ΠΈΡΠ°Ρ ΠΏΠ΅ΡΠΎΠΊ Π΄Π»Ρ Π½Π°ΡΡΡΠ°Π»ΡΠ½ΠΎΠΉ Π³ΠΈΠ΄ΡΠ°Π²Π»ΠΈΡΠ΅ΡΠΊΠΎΠΉ ΠΈΠ·Π²Π΅ΡΡΠΈ, ΡΠ±Π΅Π΄ΠΈΡΠ΅ΡΡ, ΡΡΠΎ ΠΏΠ΅ΡΠΎΠΊ ΡΠΎΠΎΡΠ²Π΅ΡΡΡΠ²ΡΠ΅Ρ ΡΡΠ°Π½Π΄Π°ΡΡΡ ASTM C-144. ΠΠΎ Π²Ρ ΠΌΠΎΠΆΠ΅ΡΠ΅ ΡΠΏΡΠΎΡΠΈΡΡ ΡΠ΅Π±Ρ, ΡΡΠΎ, ΡΠ΅ΡΡ Π²ΠΎΠ·ΡΠΌΠΈ, ΡΡΠΎ Π·Π½Π°ΡΠΈΡ? ASTM C-144 — ΡΡΠΎ ΡΡΠ°Π½Π΄Π°ΡΡΠ½Π°Ρ ΡΠΏΠ΅ΡΠΈΡΠΈΠΊΠ°ΡΠΈΡ Π·Π°ΠΏΠΎΠ»Π½ΠΈΡΠ΅Π»Ρ Π΄Π»Ρ ΠΊΠ»Π°Π΄ΠΎΡΠ½ΠΎΠ³ΠΎ ΡΠ°ΡΡΠ²ΠΎΡΠ°, ΠΏΡΠ΅Π΄ΡΡΠ°Π²Π»Π΅Π½Π½Π°Ρ ΠΠΌΠ΅ΡΠΈΠΊΠ°Π½ΡΠΊΠΈΠΌ ΠΎΠ±ΡΠ΅ΡΡΠ²ΠΎΠΌ ΠΈΡΠΏΡΡΠ°Π½ΠΈΠΉ ΠΌΠ°ΡΠ΅ΡΠΈΠ°Π»ΠΎΠ² (ASTM).ΠΠ»Ρ Π½Π°ΡΠ°Π»Π° ΠΌΠ½ΠΎΠ³ΠΈΠ΅ Π»ΡΠ΄ΠΈ Π±ΡΠ΄ΡΡ ΠΈΡΠΏΠΎΠ»ΡΠ·ΠΎΠ²Π°ΡΡ ΡΠ΅ΡΠΌΠΈΠ½ Β«Π·Π°ΠΏΠΎΠ»Π½ΠΈΡΠ΅Π»ΡΒ», Π° Π½Π΅ Β«ΠΏΠ΅ΡΠΎΠΊΒ». ΠΡΠΎ ΡΠ²ΡΠ·Π°Π½ΠΎ Ρ ΡΠ΅ΠΌ, ΡΡΠΎ Π·Π°ΠΏΠΎΠ»Π½ΠΈΡΠ΅Π»Ρ — ΡΡΠΎ Π±ΠΎΠ»Π΅Π΅ ΡΠΈΡΠΎΠΊΠΈΠΉ ΡΠ΅ΡΠΌΠΈΠ½, ΠΊΠΎΡΠΎΡΡΠΉ ΠΌΠΎΠΆΠ΅Ρ ΠΎΡΠ½ΠΎΡΠΈΡΡΡΡ ΠΊ ΠΏΠ΅ΡΠ΅ΡΠ°Π±ΠΎΡΠ°Π½Π½ΡΠΌ ΠΌΠ°ΡΠ΅ΡΠΈΠ°Π»Π°ΠΌ, ΠΊΠΎΡΠΎΡΡΠ΅ ΠΏΡΠΈ ΠΆΠ΅Π»Π°Π½ΠΈΠΈ ΠΌΠΎΠΆΠ½ΠΎ ΠΈΡΠΏΠΎΠ»ΡΠ·ΠΎΠ²Π°ΡΡ Π²ΠΌΠ΅ΡΡΠΎ ΠΏΠ΅ΡΠΊΠ°. Π ΡΠΏΠ΅ΡΠΈΡΠΈΠΊΠ°ΡΠΈΠΈ Π΅ΡΡΡ ΠΌΠ½ΠΎΠ³ΠΎ Ρ
ΠΎΡΠΎΡΠΈΡ
ΡΠ΅ΠΊΠΎΠΌΠ΅Π½Π΄Π°ΡΠΈΠΉ, ΠΊΠΎΡΠΎΡΡΠΌ Π½ΡΠΆΠ½ΠΎ ΡΠ»Π΅Π΄ΠΎΠ²Π°ΡΡ ΠΏΡΠΈ Π²ΡΠ±ΠΎΡΠ΅ ΠΏΠ΅ΡΠΊΠ°, ΡΠ°ΠΊΠΈΡ
ΠΊΠ°ΠΊ ΡΠΈΡΡΠΎΡΠ°, ΡΠΎΡΠΌΠ°, ΡΠΎΡΡΠ°Π² ΠΈ Π³ΡΠ°Π½ΡΠ»ΠΎΠΌΠ΅ΡΡΠΈΡΠ΅ΡΠΊΠΈΠΉ ΡΠΎΡΡΠ°Π².
Π₯ΠΎΡΠΎΡΠΈΠΉ, ΡΠΈΡΡΡΠΉ ΠΏΠ΅ΡΠΎΠΊ Π²Π°ΠΆΠ΅Π½. Π Π·Π°Π²ΠΈΡΠΈΠΌΠΎΡΡΠΈ ΠΎΡ ΡΠΎΠ³ΠΎ, Π³Π΄Π΅ Π²Ρ Π΄ΠΎΠ±ΡΠ²Π°Π΅ΡΠ΅ ΠΏΠ΅ΡΠΎΠΊ, ΠΌΠΎΠ³ΡΡ Π²ΠΎΠ·Π½ΠΈΠΊΠ½ΡΡΡ Π½Π΅ΠΊΠΎΡΠΎΡΡΠ΅ ΡΠ»ΠΎΠΆΠ½ΠΎΡΡΠΈ. ΠΡΠ»ΠΈ Π²Ρ ΠΏΠΎΠΊΡΠΏΠ°Π΅ΡΠ΅ ΠΏΠ΅ΡΠΎΠΊ Ρ Π΄ΠΈΡΡΡΠΈΠ±ΡΡΡΠΎΡΠ°, ΠΏΡΠ΅Π΄Π²Π°ΡΠΈΡΠ΅Π»ΡΠ½ΠΎ ΡΠ°ΡΡΠ°ΡΠΎΠ²Π°Π½Π½ΡΠΉ Π² ΠΌΠ΅ΡΠΊΠΈ ΠΏΠ΅ΡΠΎΠΊ ΠΎΡΠ΅Π½Ρ ΡΠΈΡΡΡΠΉ, ΠΏΠΎΡΠΊΠΎΠ»ΡΠΊΡ Π΅Π³ΠΎ ΠΎΠ±ΡΡΠ½ΠΎ ΠΌΠΎΡΡ ΠΈ ΡΡΡΠ°Ρ.ΠΠ΄Π½Π°ΠΊΠΎ Π½Π°ΡΡΠΏΠ½ΠΎΠΉ ΠΏΠ΅ΡΠΎΠΊ ΠΌΠΎΠΆΠ΅Ρ ΠΈΠΌΠ΅ΡΡ Π½Π΅ΠΊΠΎΡΠΎΡΡΠ΅ ΠΏΡΠΈΠΌΠ΅ΡΠΈ, ΡΡΠΎ ΠΌΠ°Π»ΠΎΠ²Π΅ΡΠΎΡΡΠ½ΠΎ, Π½ΠΎ ΡΠ»Π΅Π΄ΡΠ΅Ρ ΠΎΡΠΌΠ΅ΡΠΈΡΡ Π΄ΡΡΠ³ΠΈΠ΅ ΠΏΠΎΡΠ΅Π½ΡΠΈΠ°Π»ΡΠ½ΡΠ΅ ΠΏΡΠΎΠ±Π»Π΅ΠΌΡ, ΠΊΠΎΡΠΎΡΡΠ΅ Π±ΡΠ΄ΡΡ ΠΎΠ±ΡΡΠΆΠ΄Π°ΡΡΡΡ Π² Π±Π»ΠΈΠΆΠ°ΠΉΡΠ΅Π΅ Π²ΡΠ΅ΠΌΡ. ΠΡΠ»ΠΈ Π²Ρ ΡΠΎΠ±ΠΈΡΠ°Π΅ΡΠ΅ ΠΏΠ΅ΡΠΎΠΊ ΠΈΠ· Π±Π»ΠΈΠΆΠ°ΠΉΡΠ΅Π³ΠΎ ΡΡΡΡΡ ΠΈΠ»ΠΈ ΡΡΡΡΡ Π² ΠΈΡΡΠΎΡΠΈΡΠ΅ΡΠΊΠΈΡ
ΡΠ΅Π»ΡΡ
, Π±ΡΠ΄ΡΡΠ΅ ΠΎΡΡΠΎΡΠΎΠΆΠ½Ρ. ΠΠ°ΠΌ ΡΠ»Π΅Π΄ΡΠ΅Ρ ΠΏΡΠΎΠ²Π΅ΡΠΈΡΡ ΡΠ²ΠΎΠΈ ΠΌΠ΅ΡΡΠ½ΡΠ΅ Π·Π°ΠΊΠΎΠ½Ρ, ΡΡΠΎΠ±Ρ ΡΠ·Π½Π°ΡΡ, Π·Π°ΠΊΠΎΠ½Π½ΠΎ Π»ΠΈ ΡΡΠΎ Π²ΠΎΠΎΠ±ΡΠ΅, ΠΏΠΎΡΠΊΠΎΠ»ΡΠΊΡ ΡΡΠΎ ΠΌΠΎΠΆΠ΅Ρ ΠΈΠΌΠ΅ΡΡ ΠΏΠΎΡΠ»Π΅Π΄ΡΡΠ²ΠΈΡ Π΄Π»Ρ ΠΎΠΊΡΡΠΆΠ°ΡΡΠ΅ΠΉ ΡΡΠ΅Π΄Ρ. ΠΡΠΈ ΡΡΠΎΠΌ ΡΠ±Π΅Π΄ΠΈΡΠ΅ΡΡ, ΡΡΠΎ ΠΏΠ΅ΡΠΎΠΊ Π½Π΅ ΡΠΎΠ΄Π΅ΡΠΆΠΈΡ ΠΈΠ»Π° ΠΈ ΠΎΡΠ³Π°Π½ΠΈΡΠ΅ΡΠΊΠΈΡ
Π²Π΅ΡΠ΅ΡΡΠ². Π€ΠΎΡΠΌΠ° ΠΈΠ»ΠΈ ΡΠ΅Π·ΠΊΠΎΡΡΡ ΠΏΠ΅ΡΠΊΠ° ΠΏΠΎΠΌΠΎΠ³ΡΡ ΡΠ΄Π΅Π»Π°ΡΡ ΡΠΌΠ΅ΡΡ Π±ΠΎΠ»Π΅Π΅ ΠΏΠ»ΠΎΡΠ½ΠΎΠΉ ΠΈ Π² ΡΠ΅Π»ΠΎΠΌ ΡΠΎΠ·Π΄Π°ΡΡ Π±ΠΎΠ»Π΅Π΅ ΠΏΡΠΎΡΠ½ΡΠΉ ΡΠ°ΡΡΠ²ΠΎΡ.Π£Π³Π»ΠΎΠ²ΡΠ΅ Π·Π°ΠΏΠΎΠ»Π½ΠΈΡΠ΅Π»ΠΈ Π»ΡΡΡΠ΅ Π·Π°ΠΏΠΎΠ»Π½ΡΡΡ ΠΏΡΡΡΠΎΡΡ, ΡΠ΅ΠΌ ΠΎΠΊΠ°ΡΠ°Π½Π½ΡΠ΅ ΠΏΠ΅ΡΠΊΠΈ. Π₯ΠΎΡΠΎΡΠΈΠΉ Π½Π°Π³Π»ΡΠ΄Π½ΡΠΉ ΠΏΡΠΈΠΌΠ΅Ρ Π΄Π»Ρ ΡΡΠΎΠ³ΠΎ — ΠΏΠΎΠΏΡΡΠ°ΡΡΡΡ ΠΏΡΠ΅Π΄ΡΡΠ°Π²ΠΈΡΡ ΡΠ΅Π±Π΅ Π±ΡΡΡΠ»ΠΊΡ Π²ΠΎΠ΄Ρ Ρ ΠΊΡΡΠ³Π»ΡΠΌΠΈ Π±ΡΡΡΠ»ΠΊΠ°ΠΌΠΈ, Π° ΡΠ΅ΠΏΠ΅ΡΡ ΠΏΡΠ΅Π΄ΡΡΠ°Π²ΡΡΠ΅ ΡΠ΅ ΠΆΠ΅ ΡΠ°ΠΌΡΠ΅ Π±ΡΡΡΠ»ΠΊΠΈ, Π½ΠΎ ΠΊΠ²Π°Π΄ΡΠ°ΡΠ½ΡΠ΅. ΠΠ²Π°Π΄ΡΠ°ΡΠ½ΡΠ΅ Π±ΡΡΡΠ»ΠΊΠΈ Π±ΡΠ΄ΡΡ ΠΏΠ»ΠΎΡΠ½ΠΎ ΠΏΡΠΈΠ»Π΅Π³Π°ΡΡ Π΄ΡΡΠ³ ΠΊ Π΄ΡΡΠ³Ρ, Π² ΡΠΎ Π²ΡΠ΅ΠΌΡ ΠΊΠ°ΠΊ ΠΊΡΡΠ³Π»ΡΠ΅ Π±ΡΡΡΠ»ΠΊΠΈ ΡΠΎΠΏΡΠΈΠΊΠ°ΡΠ°ΡΡΡΡ ΡΠΎΠ»ΡΠΊΠΎ Π² ΡΠ΅ΡΡΡΠ΅Ρ
ΡΠΎΡΠΊΠ°Ρ
ΠΊΠΎΠ½ΡΠ°ΠΊΡΠ°, ΠΎΡΡΠ°Π²Π»ΡΡ ΠΏΡΡΡΠΎΡΡ.
Π‘ΠΎΡΡΠ°Π² Π·Π°ΠΏΠΎΠ»Π½ΠΈΡΠ΅Π»Ρ Π±ΡΠ΄Π΅Ρ ΠΎΠΏΡΠ΅Π΄Π΅Π»ΡΡΡ Π΄ΠΎΠ»Π³ΠΎΡΡΠΎΡΠ½ΠΎΠ΅ Π΄Π΅ΠΉΡΡΠ²ΠΈΠ΅ ΡΠ°ΡΡΠ²ΠΎΡΠ°. Π‘ΡΡΠ΅ΡΡΠ²ΡΡΡ Π°Π³ΡΠ΅Π³Π°ΡΡ, ΠΊΠΎΡΠΎΡΡΠ΅ ΠΌΠΎΠ³ΡΡ Π²ΡΠ·Π²Π°ΡΡ Π·Π°ΠΌΠ΅Π΄Π»Π΅Π½Π½ΠΎΠ΅ ΡΠ°ΡΡΠΈΡΠ΅Π½ΠΈΠ΅ ΠΈ ΡΠ°Π·ΡΡΡΠ΅Π½ΠΈΠ΅ ΡΡΡΠΎΠΈΡΠ΅Π»ΡΠ½ΠΎΠ³ΠΎ ΡΠ°ΡΡΠ²ΠΎΡΠ°.Π‘ΡΠΎΠΈΡ ΠΎΠ±ΡΠ°ΡΠΈΡΡ Π²Π½ΠΈΠΌΠ°Π½ΠΈΠ΅ Π½Π° Π΄ΠΎΠ»ΠΎΠΌΠΈΡΠΎΠ²ΡΠΉ ΡΠ΅Π±Π΅Π½Ρ. ΠΡΡΡ ΠΈ Π΄ΡΡΠ³ΠΈΠ΅, Π½ΠΎ Π΄Π»Ρ Π±ΠΎΠ»ΡΡΠΈΠ½ΡΡΠ²Π° ΡΠ΅ΡΡΠ°Π²ΡΠ°ΡΠΈΠΎΠ½Π½ΡΡ ΡΠ°Π±ΠΎΡ ΡΡΠΎ ΡΠ°ΠΌΡΠΉ ΡΠ°ΡΠΏΡΠΎΡΡΡΠ°Π½Π΅Π½Π½ΡΠΉ Π²ΠΈΠ΄. ΠΠ°Ρ ΠΌΠ΅ΡΡΠ½ΡΠΉ ΠΏΠΎΡΡΠ°Π²ΡΠΈΠΊ Π΄ΠΎΠ»ΠΆΠ΅Π½ Π·Π½Π°ΡΡ, Π΅ΡΡΡ Π»ΠΈ Ρ Π½ΠΈΡ ΡΡΠΎΡ ΡΠΈΠΏ, ΠΈ, ΡΠΊΠΎΡΠ΅Π΅ Π²ΡΠ΅Π³ΠΎ, Π½Π΅ Π±ΡΠ΄Π΅Ρ ΡΠ΅ΠΊΠΎΠΌΠ΅Π½Π΄ΠΎΠ²Π°ΡΡ Π΅Π³ΠΎ Π΄Π»Ρ Π»ΡΠ±ΠΎΠ³ΠΎ ΠΊΠ»Π°Π΄ΠΎΡΠ½ΠΎΠ³ΠΎ ΡΠ°ΡΡΠ²ΠΎΡΠ°.
ΠΡΠ°Π½ΡΠ»ΠΎΠΌΠ΅ΡΡΠΈΡΠ΅ΡΠΊΠΈΠΉ ΡΠΎΡΡΠ°Π² ΡΠ²Π»ΡΠ΅ΡΡΡ Π½Π°ΠΈΠ±ΠΎΠ»Π΅Π΅ Π²Π°ΠΆΠ½ΡΠΌ ΡΠ°ΠΊΡΠΎΡΠΎΠΌ ΠΏΡΠΈ Π²ΡΠ±ΠΎΡΠ΅ Π·Π°ΠΏΠΎΠ»Π½ΠΈΡΠ΅Π»Ρ. ΠΠ΄Π΅Π°Π»ΡΠ½ΡΠΉ ΠΏΠ΅ΡΠΎΠΊ Π΄ΠΎΠ»ΠΆΠ΅Π½ ΠΈΠΌΠ΅ΡΡ Π² ΡΠ²ΠΎΠ΅ΠΌ ΡΠΎΡΡΠ°Π²Π΅ ΡΠΈΡΠΎΠΊΠΈΠΉ Π΄ΠΈΠ°ΠΏΠ°Π·ΠΎΠ½ ΡΠ°Π·ΠΌΠ΅ΡΠΎΠ². Π₯ΠΎΡΠΎΡΠ΅Π΅ ΡΠ°ΡΠΏΡΠ΅Π΄Π΅Π»Π΅Π½ΠΈΠ΅ Π² Π·Π½Π°ΡΠΈΡΠ΅Π»ΡΠ½ΠΎΠΉ ΡΡΠ΅ΠΏΠ΅Π½ΠΈ Π²Π»ΠΈΡΠ΅Ρ Π½Π° ΡΠ΄ΠΎΠ±ΠΎΡΠΊΠ»Π°Π΄ΡΠ²Π°Π΅ΠΌΠΎΡΡΡ ΠΈ Π΄ΠΎΠ»Π³ΠΎΠ²Π΅ΡΠ½ΠΎΡΡΡ. ΠΡΠ»ΠΈ Π²Ρ ΠΌΠΎΠΆΠ΅ΡΠ΅ ΠΏΠΎΠ»ΡΡΠΈΡΡ Π΄ΠΎΡΡΡΠΏ ΠΊ ΡΠΈΡΠΎΠ²ΠΎΠΌΡ Π°Π½Π°Π»ΠΈΠ·Ρ, ΠΈΡΠΈΡΠ΅ ΠΊΠΎΠ»ΠΎΠΊΠΎΠ»ΠΎΠΎΠ±ΡΠ°Π·Π½ΡΡ ΠΊΡΠΈΠ²ΡΡ, ΠΊΠΎΠ³Π΄Π° ΡΠΈΡΠ»Π° Π½Π°Π½Π΅ΡΠ΅Π½Ρ Π½Π° Π³ΡΠ°ΡΠΈΠΊ.ΠΡΠΎ ΠΏΠΎΠΊΠ°Π·ΡΠ²Π°Π΅Ρ, ΡΡΠΎ Π΅ΡΡΡ Π½Π΅ΡΠΊΠΎΠ»ΡΠΊΠΎ Π±ΠΎΠ»ΡΡΠΈΡ
ΠΊΡΡΠΊΠΎΠ², ΡΠ²Π΅Π»ΠΈΡΠΈΠ²Π°ΡΡΠ΅Π΅ΡΡ ΠΊΠΎΠ»ΠΈΡΠ΅ΡΡΠ²ΠΎ ΡΡΠ΅Π΄Π½ΠΈΡ
ΡΠ°Π·ΠΌΠ΅ΡΠΎΠ² ΠΈ Π½Π΅Π±ΠΎΠ»ΡΡΠΎΠ΅ ΠΊΠΎΠ»ΠΈΡΠ΅ΡΡΠ²ΠΎ ΠΌΠ΅Π»ΠΊΠΈΡ
ΡΠ°ΡΡΠΈΡ ΠΈΠ»ΠΈ ΠΏΠΎΡΠΎΡΠΊΠ°. ΠΠ·Π±ΡΡΠΎΡΠ½Π°Ρ ΠΌΠ΅Π»ΠΎΡΡ Π² ΠΏΠ΅ΡΠΊΠ΅ ΠΏΡΠΈΠ²ΠΎΠ΄ΠΈΡ ΠΊ ΠΏΠ»ΠΎΡ
ΠΎΠΉ ΠΎΠ±ΡΠ°Π±Π°ΡΡΠ²Π°Π΅ΠΌΠΎΡΡΠΈ ΠΈ ΡΠ°ΡΡΠΎ ΡΡΡΡΠ°Π½ΡΠ΅ΡΡΡ ΠΈΠ·Π±ΡΡΠΎΡΠ½ΡΠΌ ΠΊΠΎΠ»ΠΈΡΠ΅ΡΡΠ²ΠΎΠΌ Π²ΠΎΠ΄Ρ, ΡΡΠΎ ΠΏΡΠΈΠ²ΠΎΠ΄ΠΈΡ ΠΊ ΠΏΠ»ΠΎΡ
ΠΎΠΉ Π΄ΠΎΠ»Π³ΠΎΠ²Π΅ΡΠ½ΠΎΡΡΠΈ.
Π₯ΠΎΡΠΎΡΠΈΠΉ ΡΠΈΡΡΡΠΉ ΠΈ ΡΡΡ ΠΎΠΉ ΠΏΠ΅ΡΠΎΠΊ Π±ΡΠ΄Π΅Ρ ΠΈΠΌΠ΅ΡΡ ΡΠ΅ΠΎΡΠ΅ΡΠΈΡΠ΅ΡΠΊΡΡ ΠΏΡΡΡΠΎΡΠ½ΠΎΡΡΡ 33%. ΠΡΡΠ³ΠΈΠΌΠΈ ΡΠ»ΠΎΠ²Π°ΠΌΠΈ, ΠΏΡΠΈ ΠΎΠΏΡΠ΅Π΄Π΅Π»Π΅Π½Π½ΠΎΠΌ ΠΎΠ±ΡΠ΅ΠΌΠ΅ ΠΏΠ΅ΡΠΊΠ° Π±ΡΠ΄Π΅Ρ ΠΈΠ΄Π΅Π°Π»ΡΠ½ΠΎΠ΅ Π²ΠΎΠ·Π΄ΡΡΠ½ΠΎΠ΅ ΠΏΡΠΎΡΡΡΠ°Π½ΡΡΠ²ΠΎ ΠΌΠ΅ΠΆΠ΄Ρ ΠΏΠ΅ΡΡΠΈΠ½ΠΊΠ°ΠΌΠΈ ΠΎΡ 33% Π΄ΠΎ 66%. Π ΡΡΠ°ΡΡΡΡ, Π΅ΡΡΡ ΠΏΡΠΎΡΡΠΎΠΉ ΡΠ΅ΡΡ, ΠΊΠΎΡΠΎΡΡΠΉ ΠΌΠΎΠΆΠ΅Ρ ΡΠ΄Π΅Π»Π°ΡΡ ΠΊΠ°ΠΆΠ΄ΡΠΉ, ΡΡΠΎΠ±Ρ ΡΠ·Π½Π°ΡΡ, ΠΊΠ°ΠΊΠΎΠ²ΠΎ ΡΠΎΠΎΡΠ½ΠΎΡΠ΅Π½ΠΈΠ΅ ΠΏΡΡΡΠΎΡΡ ΠΏΠ΅ΡΠΊΠ°.
Π‘Π½Π°ΡΠ°Π»Π° Π²ΠΎΠ·ΡΠΌΠΈΡΠ΅ Π΄Π²Π΅ ΠΏΡΠΎΠ·ΡΠ°ΡΠ½ΡΠ΅ Π΅ΠΌΠΊΠΎΡΡΠΈ, ΡΠ°Π·ΠΌΠ΅Ρ ΠΎΠ΄Π½ΠΎΠΉ ΠΈΠ· ΠΊΠΎΡΠΎΡΡΡ
ΠΊΠ°ΠΊ ΠΌΠΈΠ½ΠΈΠΌΡΠΌ Π² Π΄Π²Π° ΡΠ°Π·Π° Π±ΠΎΠ»ΡΡΠ΅, ΡΠ΅ΠΌ Π΄ΡΡΠ³ΠΎΠΉ, Π½Π°ΠΏΠΎΠ»Π½ΠΈΡΠ΅ ΠΌΠ°Π»ΡΡ Π΅ΠΌΠΊΠΎΡΡΡ Π²ΠΎΠ΄ΠΎΠΉ, Π½Π°Π»Π΅ΠΉΡΠ΅ Π΅Π΅ Π² Π±ΠΎΠ»ΡΡΡΡ Π΅ΠΌΠΊΠΎΡΡΡ ΠΈ ΡΠ΄Π΅Π»Π°ΠΉΡΠ΅ ΠΎΡΠΌΠ΅ΡΠΊΡ. ΠΠ°ΡΠ΅ΠΌ ΡΠ½ΠΎΠ²Π° Π½Π°ΠΏΠΎΠ»Π½ΠΈΡΠ΅ ΠΌΠ°Π»Π΅Π½ΡΠΊΡΡ Π΅ΠΌΠΊΠΎΡΡΡ ΠΈ Π²ΡΠ»Π΅ΠΉΡΠ΅ Π΅Π΅ Π² Π±ΠΎΠ»ΡΡΡΡ Π΅ΠΌΠΊΠΎΡΡΡ, ΡΠ»Π΅Π΄Ρ Π·Π° ΡΠ΅ΠΌ, ΡΡΠΎΠ±Ρ Π² Π΅ΠΌΠΊΠΎΡΡΠΈ ΠΎΡΡΠ°Π²Π°Π»Π°ΡΡ ΠΏΠ΅ΡΠ²Π°Ρ ΠΏΠΎΡΡΠΈΡ Π²ΠΎΠ΄Ρ. ΠΡΠΌΠ΅ΡΡΡΠ΅ ΡΡΠΎΠ²Π΅Π½Ρ Π²ΡΠΎΡΠΎΠΉ ΠΌΠ΅ΡΡ ΠΈ ΡΠ°Π²Π½ΠΎΠΌΠ΅ΡΠ½ΠΎ ΡΠ°ΡΠΏΡΠ΅Π΄Π΅Π»ΠΈΡΠ΅ 4 Π»ΠΈΠ½ΠΈΠΈ ΠΌΠ΅ΠΆΠ΄Ρ Π½ΠΈΠΌΠΈ, ΡΠΎΠ·Π΄Π°Π² Π² ΠΎΠ±ΡΠ΅ΠΉ ΡΠ»ΠΎΠΆΠ½ΠΎΡΡΠΈ ΡΠ΅ΡΡΡ ΠΎΡΠΌΠ΅ΡΠΎΠΊ Π½Π° Π±ΠΎΠ»ΡΡΠΎΠΌ ΠΊΠΎΠ½ΡΠ΅ΠΉΠ½Π΅ΡΠ΅. ΠΠΏΡΡΡΠΎΡΠΈΡΠ΅ Π±ΠΎΠ»ΡΡΡΡ Π΅ΠΌΠΊΠΎΡΡΡ ΠΈ Π½Π°ΠΏΠΎΠ»Π½ΠΈΡΠ΅ ΠΌΠ°Π»ΡΡ Π΅ΠΌΠΊΠΎΡΡΡ Π²ΠΎΠ΄ΠΎΠΉ.ΠΡΠ»Π΅ΠΉΡΠ΅ Π²ΠΎΠ΄Ρ ΠΈΠ· ΠΌΠ°Π»Π΅Π½ΡΠΊΠΎΠΉ Π΅ΠΌΠΊΠΎΡΡΠΈ Π² Π±ΠΎΠ»ΡΡΡΡ Π΅ΠΌΠΊΠΎΡΡΡ Π΄ΠΎ Π΄Π½Π° ΠΈΠ· ΡΠ΅ΡΡΠΈ Π»ΠΈΠ½ΠΈΠΉ. Π’Π΅ΠΏΠ΅ΡΡ Π·Π°ΠΏΠΎΠ»Π½ΠΈΡΠ΅ ΠΌΠ°Π»Π΅Π½ΡΠΊΡΡ ΡΡΡ
ΡΡ Π΅ΠΌΠΊΠΎΡΡΡ ΡΡΡ
ΠΈΠΌ ΠΏΠ΅ΡΠΊΠΎΠΌ ΠΈ ΠΏΠ΅ΡΠ΅Π»Π΅ΠΉΡΠ΅ Π΅Π΅ Π² Π±ΠΎΠ»ΡΡΡΡ Π΅ΠΌΠΊΠΎΡΡΡ. ΠΠΎΡΠ»Π΅ ΡΠΎΠ³ΠΎ, ΠΊΠ°ΠΊ Π²ΡΠ΅ ΡΠ»ΡΠΆΠ΅ΡΡΡ, Π²Ρ ΡΠΌΠΎΠΆΠ΅ΡΠ΅ ΡΠ²ΠΈΠ΄Π΅ΡΡ, ΡΠΊΠΎΠ»ΡΠΊΠΎ Π²ΠΎΠ΄Ρ Π±ΡΠ»ΠΎ Π²ΡΡΠ΅ΡΠ½Π΅Π½ΠΎ. ΠΠ°ΡΠΈΠ½Π°Ρ Ρ Π²Π΅ΡΡ
Π½Π΅ΠΉ ΡΡΡΠΎΠΊΠΈ, ΠΏΡΠ΅Π΄ΡΡΠ°Π²Π»ΡΡΡΠ΅ΠΉ 0%, ΠΊΠ°ΠΆΠ΄Π°Ρ Π»ΠΈΠ½ΠΈΡ, Π΄Π²ΠΈΠΆΡΡΠ°ΡΡΡ Π²Π½ΠΈΠ· ΠΏΠΎ Π±ΠΎΠ»ΡΡΠΎΠΌΡ ΠΊΠΎΠ½ΡΠ΅ΠΉΠ½Π΅ΡΡ, Π±ΡΠ΄Π΅Ρ ΠΏΡΠ΅Π΄ΡΡΠ°Π²Π»ΡΡΡ 20%. ΠΠΎΠ»ΡΡΠ΅Π½Π½ΡΠΉ ΠΏΡΠΎΡΠ΅Π½Ρ Π±ΡΠ΄Π΅Ρ ΠΏΡΠ΅Π΄ΡΡΠ°Π²Π»ΡΡΡ ΡΠΎΠ±ΠΎΠΉ ΠΊΠΎΡΡΡΠΈΡΠΈΠ΅Π½Ρ ΠΏΡΡΡΠΎΡΠ½ΠΎΡΡΠΈ ΠΈ ΠΏΡΠ΅Π΄ΡΡΠ°Π²Π»ΡΠ΅Ρ ΡΠΎΠ±ΠΎΠΉ ΠΌΠΈΠ½ΠΈΠΌΠ°Π»ΡΠ½ΠΎΠ΅ ΠΊΠΎΠ»ΠΈΡΠ΅ΡΡΠ²ΠΎ ΠΈΠ·Π²Π΅ΡΡΠΈ ΠΏΠΎ ΠΎΠ±ΡΠ΅ΠΌΡ, ΠΊΠΎΡΠΎΡΠΎΠ΅ Π²Ρ Π΄ΠΎΠ»ΠΆΠ½Ρ ΠΈΡΠΏΠΎΠ»ΡΠ·ΠΎΠ²Π°ΡΡ Π΄Π»Ρ ΠΏΡΠΈΠ³ΠΎΡΠΎΠ²Π»Π΅Π½ΠΈΡ Ρ
ΠΎΡΠΎΡΠ΅Π³ΠΎ ΡΠ°ΡΡΠ²ΠΎΡΠ°.
ΠΠ»ΠΎΡ
ΠΎΠΉ ΠΏΠ΅ΡΠΎΠΊ ΠΌΠΎΠΆΠ΅Ρ ΠΈΠΌΠ΅ΡΡ ΡΠΎΠΎΡΠ½ΠΎΡΠ΅Π½ΠΈΠ΅ Π²ΡΡΠ΅ 50% ΠΈ ΡΠ²Π΅Π»ΠΈΡΠΈΠ²Π°Π΅Ρ Π½Π΅ΠΎΠ±Ρ
ΠΎΠ΄ΠΈΠΌΠΎΠ΅ ΠΊΠΎΠ»ΠΈΡΠ΅ΡΡΠ²ΠΎ ΠΈΠ·Π²Π΅ΡΡΠΈ, ΡΡΠΎ ΠΏΡΠΈΠ²ΠΎΠ΄ΠΈΡ ΠΊ Π΄ΠΎΠΏΠΎΠ»Π½ΠΈΡΠ΅Π»ΡΠ½ΡΠΌ ΡΠ°ΡΡ
ΠΎΠ΄Π°ΠΌ Π΄Π»Ρ Π²Π°ΡΠ΅Π³ΠΎ ΠΏΡΠΎΠ΅ΠΊΡΠ°. ΠΠΎΡΡΠΎΠΌΡ, Π΅ΡΠ»ΠΈ Π²Ρ ΡΠΎΠΌΠ½Π΅Π²Π°Π΅ΡΠ΅ΡΡ, ΠΏΡΠΎΠ²Π΅Π΄ΠΈΡΠ΅ Π½Π΅Π±ΠΎΠ»ΡΡΠΎΠΉ ΡΠ΅ΡΡ Π½Π° Π΄ΠΎΡΡΡΠΏΠ½ΠΎΠΌ ΠΏΠ΅ΡΠΊΠ΅, Π²ΡΠ±Π΅ΡΠΈΡΠ΅ ΡΠΎΡ, ΠΊΠΎΡΠΎΡΡΠΉ ΠΈΠΌΠ΅Π΅Ρ ΠΊΠΎΡΡΡΠΈΡΠΈΠ΅Π½Ρ, Π±Π»ΠΈΠ·ΠΊΠΈΠΉ ΠΊ 33%, ΡΡΠΎΠ±Ρ ΡΡΠΊΠΎΠ½ΠΎΠΌΠΈΡΡ Π½Π° ΡΡΠ΅Π±ΡΠ΅ΠΌΠΎΠΌ ΠΊΠΎΠ»ΠΈΡΠ΅ΡΡΠ²Π΅ ΠΈΠ·Π²Π΅ΡΡΠΈ ΠΈ Π»Π΅Π³ΡΠ΅ ΡΠΏΠ°ΡΡ, Π·Π½Π°Ρ, ΡΡΠΎ Ρ Π²Π°Ρ ΠΏΡΠΈΠ»ΠΈΡΠ½ΡΠΉ ΠΏΠ΅ΡΠΎΠΊ.
ΠΠ΅ΡΠ²ΠΎΠ½Π°ΡΠ°Π»ΡΠ½ΠΎ Π½Π°ΠΏΠΈΡΠ°Π½ΠΎ: Randy Ruth
ΠΡΠ΅Π΄ΡΡΠ°Π²Π»Π΅Π½ΠΎ: LimeWorks.us
Π’Π΅Π»Π΅ΡΠΎΠ½: 215-536-6706
ΠΠΎΠΏΠΎΠ»Π½ΠΈΡΠ΅Π»ΡΠ½ΡΠ΅ ΠΏΠΎΠ»Π΅Π·Π½ΡΠ΅ ΡΡΡΠ»ΠΊΠΈ:
ΠΠ΅Π²Π΅ΡΠΎΡΡΠ½ΡΠΉ ΠΏΠΎΠ»Π½ΠΎΡΠ΅Π»ΡΠΉ ΡΠΈΠ»ΠΈΠΊΠ°ΡΠ½ΡΠΉ ΠΊΠΈΡΠΏΠΈΡ ΠΏΠΎ Π½ΠΈΠ·ΠΊΠΎΠΉ ΡΠ΅Π½Π΅ ΠΠ΅ΡΡΠ½ΠΎΠ΅ ΠΏΠΎΡΠ»Π΅ΠΏΡΠΎΠ΄Π°ΠΆΠ½ΠΎΠ΅ ΠΎΠ±ΡΠ»ΡΠΆΠΈΠ²Π°Π½ΠΈΠ΅
ΠΠΎΠ²ΡΡΡΡΠ΅ ΠΏΡΠΎΠΈΠ·Π²ΠΎΠ΄ΠΈΡΠ΅Π»ΡΠ½ΠΎΡΡΡ ΡΠ²ΠΎΠ΅Π³ΠΎ ΠΏΡΠΎΠΈΠ·Π²ΠΎΠ΄ΡΡΠ²Π° ΠΊΠΈΡΠΏΠΈΡΠ° Ρ ΠΏΠΎΠΌΠΎΡΡΡ ΡΡΠ΄Π΅ΡΠ½ΠΎΠ³ΠΎ ΠΏΠΎΠ»Π½ΠΎΡΠ΅Π»ΠΎΠ³ΠΎ ΡΠΈΠ»ΠΈΠΊΠ°ΡΠ½ΠΎΠ³ΠΎ ΠΊΠΈΡΠΏΠΈΡΠ° .ΠΠ½ΠΈ Π΄ΠΎΡΡΡΠΏΠ½Ρ Π½Π° Alibaba.com Π² Π²ΠΈΠ΄Π΅ Π·Π°ΠΌΠ°Π½ΡΠΈΠ²ΡΡ
ΠΏΡΠ΅Π΄Π»ΠΎΠΆΠ΅Π½ΠΈΠΉ, ΠΊΠΎΡΠΎΡΡΠ΅ Π½Π΅Π»ΡΠ·Ρ ΠΈΠ³Π½ΠΎΡΠΈΡΠΎΠ²Π°ΡΡ. ΠΠΎΠ»Π½ΠΎΡΠ΅Π»ΡΠΉ ΡΠΈΠ»ΠΈΠΊΠ°ΡΠ½ΡΠΉ ΠΊΠΈΡΠΏΠΈΡ ΠΏΡΠ΅ΠΌΠΈΡΠΌ-ΠΊΠ»Π°ΡΡΠ° ΠΎΠ±Π»Π°Π΄Π°Π΅Ρ Π½Π΅ΠΏΡΠ΅Π²Π·ΠΎΠΉΠ΄Π΅Π½Π½ΡΠΌΠΈ ΠΊΠ°ΡΠ΅ΡΡΠ²Π°ΠΌΠΈ, ΠΊΠΎΡΠΎΡΡΠ΅ Π±ΡΠ»ΠΈ Π΄ΠΎΡΡΠΈΠ³Π½ΡΡΡ Π±Π»Π°Π³ΠΎΠ΄Π°ΡΡ ΠΏΠ΅ΡΠ΅Π΄ΠΎΠ²ΡΠΌ ΡΠ΅Ρ
Π½ΠΎΠ»ΠΎΠ³ΠΈΡΠΌ ΠΈ ΠΈΠ·ΠΎΠ±ΡΠ΅ΡΠ΅Π½ΠΈΡΠΌ. ΠΠ½ΠΈ ΡΠ²Π΅Π»ΠΈΡΠΈΠ²Π°ΡΡ ΡΠΊΠΎΡΠΎΡΡΡ ΠΏΡΠΎΠΈΠ·Π²ΠΎΠ΄ΡΡΠ²Π° ΠΊΠΈΡΠΏΠΈΡΠ°, ΡΠ»Π΅Π΄ΠΎΠ²Π°ΡΠ΅Π»ΡΠ½ΠΎ, ΡΠΊΠΎΠ½ΠΎΠΌΡΡ Π²ΡΠ΅ΠΌΡ ΠΈ ΡΠ½Π΅ΡΠ³ΠΈΡ. Π ΠΏΡΠΎΠΈΠ·Π²ΠΎΠ΄ΡΡΠ²Π΅ ΡΠΈΠ»ΠΈΠΊΠ°ΡΠ½ΠΎΠ³ΠΎ ΠΊΠΈΡΠΏΠΈΡΠ° ΠΈΡΠΏΠΎΠ»ΡΠ·ΡΡΡΡΡ ΠΏΡΠΎΡΠ½ΡΠ΅ ΠΈ Π΄ΠΎΠ»Π³ΠΎΠ²Π΅ΡΠ½ΡΠ΅ ΠΌΠ°ΡΠ΅ΡΠΈΠ°Π»Ρ, ΠΎΠ±Π΅ΡΠΏΠ΅ΡΠΈΠ²Π°ΡΡΠΈΠ΅ Π΄ΠΎΠ»Π³ΠΈΠΉ ΡΡΠΎΠΊ ΡΠ»ΡΠΆΠ±Ρ ΠΈ Π½Π΅ΠΈΠ·ΠΌΠ΅Π½Π½ΠΎ Π±ΠΎΠ»Π΅Π΅ Π²ΡΡΠΎΠΊΡΡ ΠΏΡΠΎΠΈΠ·Π²ΠΎΠ΄ΠΈΡΠ΅Π»ΡΠ½ΠΎΡΡΡ.
Π‘ΡΡΠ΅ΡΡΠ²ΡΠ΅Ρ ΠΎΠ±ΡΠΈΡΠ½Π°Ρ ΠΊΠΎΠ»Π»Π΅ΠΊΡΠΈΡ ΠΈΠ· ΠΏΠΎΠ»Π½ΠΎΡΠ΅Π»ΠΎΠ³ΠΎ ΡΠΈΠ»ΠΈΠΊΠ°ΡΠ½ΠΎΠ³ΠΎ ΠΊΠΈΡΠΏΠΈΡΠ° , ΡΠΎΡΡΠΎΡΡΠ°Ρ ΠΈΠ· ΡΠ°Π·Π»ΠΈΡΠ½ΡΡ ΠΌΠΎΠ΄Π΅Π»Π΅ΠΉ, ΠΊΠΎΡΠΎΡΡΠ΅ ΡΡΠΈΡΡΠ²Π°ΡΡ ΡΠ°Π·Π»ΠΈΡΠ½ΡΠ΅ Π±ΠΈΠ·Π½Π΅Ρ-ΡΡΠ΅Π±ΠΎΠ²Π°Π½ΠΈΡ ΠΈ ΠΈΠ½Π΄ΠΈΠ²ΠΈΠ΄ΡΠ°Π»ΡΠ½ΡΠ΅ ΡΡΠ΅Π±ΠΎΠ²Π°Π½ΠΈΡ Π΄Π»Ρ Π²ΡΠ΅Ρ ΡΠΈΠΏΠΎΠ² ΡΡΡΠΎΠΈΡΠ΅Π»ΡΠ½ΡΡ ΡΠ°Π±ΠΎΡ.Alibaba.com ΡΡΡΠ΅ΠΌΠΈΡΡΡ ΡΠ±Π΅Π΄ΠΈΡΡ Π²ΡΠ΅Ρ ΠΏΠΎΠΊΡΠΏΠ°ΡΠ΅Π»Π΅ΠΉ, ΡΡΠΎ Π½Π° ΡΠ°ΠΉΡΠ΅ ΠΏΡΠΎΠ΄Π°Π΅ΡΡΡ ΡΠΎΠ»ΡΠΊΠΎ ΠΏΠΎΠ»Π½ΠΎΡΠ΅Π»ΡΠΉ ΡΠΈΠ»ΠΈΠΊΠ°ΡΠ½ΡΠΉ ΠΊΠΈΡΠΏΠΈΡ Π²ΡΡΡΠ΅Π³ΠΎ ΠΊΠ°ΡΠ΅ΡΡΠ²Π°. Π‘ΠΎΠΎΡΠ²Π΅ΡΡΡΠ²Π΅Π½Π½ΠΎ, ΠΏΠΎΡΡΠ°Π²ΡΠΈΠΊΠΈ Π½Π°Ρ ΠΎΠ΄ΡΡΡΡ ΠΏΠΎΠ΄ ΠΏΡΠΈΡΡΠ°Π»ΡΠ½ΡΠΌ Π½Π°Π±Π»ΡΠ΄Π΅Π½ΠΈΠ΅ΠΌ, ΡΡΠΎΠ±Ρ Π³Π°ΡΠ°Π½ΡΠΈΡΠΎΠ²Π°ΡΡ, ΡΡΠΎ ΠΎΠ½ΠΈ ΡΠΎΠ±Π»ΡΠ΄Π°ΡΡ Π²ΡΠ΅ Π½ΠΎΡΠΌΠ°ΡΠΈΠ²Π½ΡΠ΅ ΡΡΠ°Π½Π΄Π°ΡΡΡ. Π’Π°ΠΊΠΈΠΌ ΠΎΠ±ΡΠ°Π·ΠΎΠΌ, ΠΏΠΎΠΊΡΠΏΠ°ΡΠ΅Π»ΠΈ Π²ΡΠ΅Π³Π΄Π° ΠΏΠΎΠ»ΡΡΠ°ΡΡ ΠΏΠΎΠ»Π½ΠΎΡΠ΅Π»ΡΠΉ ΡΠΈΠ»ΠΈΠΊΠ°ΡΠ½ΡΠΉ ΠΊΠΈΡΠΏΠΈΡ , ΠΊΠΎΡΠΎΡΡΠΉ ΡΠΎΠΎΡΠ²Π΅ΡΡΡΠ²ΡΠ΅Ρ ΡΠ²ΠΎΠΈΠΌ ΠΎΠ±Π΅ΡΠ°Π½ΠΈΡΠΌ ΠΈ ΠΏΡΠ΅Π²ΠΎΡΡ ΠΎΠ΄ΠΈΡ ΠΈΡ .
ΠΠ»Π°Π³ΠΎΠ΄Π°ΡΡ ΠΏΠΎΡΡΠΎΡΠ½Π½ΠΎΠΌΡ ΡΠ΅Ρ
Π½ΠΎΠ»ΠΎΠ³ΠΈΡΠ΅ΡΠΊΠΎΠΌΡ ΠΏΡΠΎΠ³ΡΠ΅ΡΡΡ ΠΏΡΠΎΠΈΠ·Π²ΠΎΠ΄ΠΈΡΠ΅Π»ΠΈ Π²Π½Π΅Π΄ΡΠΈΠ»ΠΈ ΠΈΠ·ΠΎΠ±ΡΠ΅ΡΠ΅Π½ΠΈΡ, ΠΊΠΎΡΠΎΡΡΠ΅ ΡΠ½ΠΈΠΆΠ°ΡΡ ΠΏΠΎΡΡΠ΅Π±Π½ΠΎΡΡΡ Π² ΡΠ½Π΅ΡΠ³ΠΈΠΈ Ρ ΠΏΠΎΠΌΠΎΡΡΡ ΡΡΠΎΠ³ΠΎ ΠΏΠΎΠ»Π½ΠΎΡΠ΅Π»ΠΎΠ³ΠΎ ΡΠΈΠ»ΠΈΠΊΠ°ΡΠ½ΠΎΠ³ΠΎ ΠΊΠΈΡΠΏΠΈΡΠ° .Π ΡΠ΅Π·ΡΠ»ΡΡΠ°ΡΠ΅ Π²Ρ ΡΠΊΠΎΠ½ΠΎΠΌΠΈΡΠ΅ Π±ΠΎΠ»ΡΡΠ΅ Π΄Π΅Π½Π΅Π³ Π½Π° ΡΡΠ΅ΡΠ°Ρ
Π·Π° ΡΠΎΠΏΠ»ΠΈΠ²ΠΎ ΠΈ ΡΠ»Π΅ΠΊΡΡΠΎΡΠ½Π΅ΡΠ³ΠΈΡ. ΠΠΎΠ»Π½ΠΎΡΠ΅Π»ΡΠΉ ΡΠΈΠ»ΠΈΠΊΠ°ΡΠ½ΡΠΉ ΠΊΠΈΡΠΏΠΈΡ ΡΠ°ΠΊΠΆΠ΅ ΠΎΠ±Π»Π°Π΄Π°Π΅Ρ ΠΈΡΠΊΠ»ΡΡΠΈΡΠ΅Π»ΡΠ½ΡΠΌΠΈ Ρ
Π°ΡΠ°ΠΊΡΠ΅ΡΠΈΡΡΠΈΠΊΠ°ΠΌΠΈ Π±Π΅Π·ΠΎΠΏΠ°ΡΠ½ΠΎΡΡΠΈ, ΡΡΠΎΠ±Ρ Π³Π°ΡΠ°Π½ΡΠΈΡΠΎΠ²Π°ΡΡ ΠΌΠΈΠ½ΠΈΠΌΠ°Π»ΡΠ½ΡΠ΅ ΡΠΈΡΠΊΠΈ, ΡΠ²ΡΠ·Π°Π½Π½ΡΠ΅ Ρ ΠΏΡΠΎΠΈΠ·Π²ΠΎΠ΄ΡΡΠ²ΠΎΠΌ. ΠΠΎΠ»Π½ΠΎΡΠ΅Π»ΡΠΉ ΡΠΈΠ»ΠΈΠΊΠ°ΡΠ½ΡΠΉ ΠΊΠΈΡΠΏΠΈΡ ΠΎΡΠ»ΠΈΡΠ°Π΅ΡΡΡ ΠΎΡΠ½ΠΎΡΠΈΡΠ΅Π»ΡΠ½ΠΎ Π½ΠΈΠ·ΠΊΠΈΠΌΠΈ Π·Π°ΡΡΠ°ΡΠ°ΠΌΠΈ Π½Π° ΠΈΡ
ΠΏΡΠΈΠΎΠ±ΡΠ΅ΡΠ΅Π½ΠΈΠ΅ ΠΈ ΡΠ΅Ρ
Π½ΠΈΡΠ΅ΡΠΊΠΎΠ΅ ΠΎΠ±ΡΠ»ΡΠΆΠΈΠ²Π°Π½ΠΈΠ΅, ΠΏΠΎΡΡΠΎΠΌΡ ΠΎΠ½ΠΈ Π΄ΠΎΡΡΡΠΏΠ½Ρ ΠΏΠΎ ΡΠ°Π·ΡΠΌΠ½ΠΎΠΉ ΡΠ΅Π½Π΅ ΠΈ ΠΏΡΠ΅Π΄Π»Π°Π³Π°ΡΡ ΡΠΎΠΎΡΠ½ΠΎΡΠ΅Π½ΠΈΠ΅ ΡΠ΅Π½Ρ ΠΈ ΠΊΠ°ΡΠ΅ΡΡΠ²Π°.
ΠΡΠΎ Π²Π°ΡΠ΅ Π²ΡΠ΅ΠΌΡ, ΡΡΠΎΠ±Ρ ΡΡΠΊΠΎΠ½ΠΎΠΌΠΈΡΡ Π΄Π΅Π½ΡΠ³ΠΈ ΠΈ Π²ΡΠ΅ΠΌΡ, Π΄Π΅Π»Π°Ρ ΠΏΠΎΠΊΡΠΏΠΊΠΈ Π² ΠΠ½ΡΠ΅ΡΠ½Π΅ΡΠ΅ Π½Π° Alibaba.com. ΠΠ·ΡΡΠΈΡΠ΅ ΡΠ°Π·Π»ΠΈΡΠ½ΡΠΉ ΠΏΠΎΠ»Π½ΠΎΡΠ΅Π»ΡΠΉ ΡΠΈΠ»ΠΈΠΊΠ°ΡΠ½ΡΠΉ ΠΊΠΈΡΠΏΠΈΡ Π½Π° ΡΠ°ΠΉΡΠ΅ ΠΈ Π²ΡΠ±Π΅ΡΠΈΡΠ΅ Π½Π°ΠΈΠ±ΠΎΠ»Π΅Π΅ ΠΏΡΠΈΠ²Π»Π΅ΠΊΠ°ΡΠ΅Π»ΡΠ½ΡΠΉ ΠΈ ΠΏΠΎΠ΄Ρ ΠΎΠ΄ΡΡΠΈΠΉ Π΄Π»Ρ Π²Π°Ρ.ΠΡΠ»ΠΈ Π²Ρ ΠΈΡΠ΅ΡΠ΅ ΠΈΠ½Π΄ΠΈΠ²ΠΈΠ΄ΡΠ°Π»ΡΠ½ΡΡ Π½Π°ΡΡΡΠΎΠΉΠΊΡ Π² ΡΠΎΠΎΡΠ²Π΅ΡΡΡΠ²ΠΈΠΈ Ρ ΠΊΠΎΠ½ΠΊΡΠ΅ΡΠ½ΡΠΌΠΈ ΡΡΠ΅Π±ΠΎΠ²Π°Π½ΠΈΡΠΌΠΈ, ΠΈΡΠΈΡΠ΅ ΠΏΠΎΠ»Π½ΠΎΡΠ΅Π»ΡΠΉ ΡΠΈΠ»ΠΈΠΊΠ°ΡΠ½ΡΠΉ ΠΊΠΈΡΠΏΠΈΡ ΠΈ Π΄ΠΎΡΡΠΈΠ³Π½ΠΈΡΠ΅ ΡΠ²ΠΎΠΈΡ ΡΠ΅Π»Π΅ΠΉ. ΠΡΠΊΡΠΎΠΉΡΠ΅ Π΄Π»Ρ ΡΠ΅Π±Ρ Π΄ΠΎΡΡΡΠΏΠ½ΠΎΠ΅ ΠΊΠ°ΡΠ΅ΡΡΠ²ΠΎ Π½Π° ΡΠ°ΠΉΡΠ΅ ΡΠΆΠ΅ ΡΠ΅Π³ΠΎΠ΄Π½Ρ.
ΠΠΊΡΠΏΠ΅ΡΠΈΠΌΠ΅Π½ΡΠ°Π»ΡΠ½ΡΠ΅ ΠΈΡΡΠ»Π΅Π΄ΠΎΠ²Π°Π½ΠΈΡ ΠΊΠΈΡΠΏΠΈΡΠ΅ΠΉ ΠΈΠ· Π·ΠΎΠ»Ρ-ΡΠ½ΠΎΡΠ° Ρ Π΄ΠΎΠ±Π°Π²Π»Π΅Π½ΠΈΠ΅ΠΌ Π³ΠΈΠΏΡΠ°
ΠΠ»ΡΡΠ΅Π²ΡΠ΅ ΡΠ»ΠΎΠ²Π°: ΡΠ³ΠΎΠ»Ρ Π·ΠΎΠ»Π° ΡΠ½ΠΎΡΠ°, ΠΊΠΎΠ½ΡΡΡΡΠΊΡΠΈΠΎΠ½Π½ΡΠΉ ΠΊΠΈΡΠΏΠΈΡ, ΠΏΠ΅ΡΠΎΠΊ, Π³ΠΈΠΏΡ, ΠΌΠΈΠΊΡΠΎΡΡΡΡΠΊΡΡΡΠ°, ΡΠ²ΠΎΠΉΡΡΠ²Π°
ΠΠΌΠ΅ΡΠΈΠΊΠ°Π½ΡΠΊΠΈΠΉ ΠΆΡΡΠ½Π°Π» ΠΌΠ°ΡΠ΅ΡΠΈΠ°Π»ΠΎΠ²Π΅Π΄Π΅Π½ΠΈΡ ΠΈ ΡΠ΅Ρ
Π½ΠΎΠ»ΠΎΠ³ΠΈΠΉ , 2013 1 (3),
Π‘. 35-40.
DOI: 10.12691 / ΠΌΠ°ΡΠ΅ΡΠΈΠ°Π»Ρ-1-3-2
ΠΠΎΡΡΡΠΏΠΈΠ»ΠΎ 14.08.2013 Π³ .; ΠΡΡΠ΅Π΄Π°ΠΊΡΠΈΡΠΎΠ²Π°Π½ΠΎ 26 Π°Π²Π³ΡΡΡΠ° 2013 Π³ .; ΠΡΠΈΠ½ΡΡΠ° Π² ΠΏΠ΅ΡΠ°ΡΡ 28 Π°Π²Π³ΡΡΡΠ° 2013 Π³.
ΠΠ²ΡΠΎΡΡΠΊΠΈΠ΅ ΠΏΡΠ°Π²Π° Β© ΠΠ·Π΄Π°ΡΠ΅Π»ΡΡΡΠ²ΠΎ Β«ΠΠ°ΡΠΊΠ° ΠΈ ΠΎΠ±ΡΠ°Π·ΠΎΠ²Π°Π½ΠΈΠ΅Β», 2013. ΠΡΠ΅ ΠΏΡΠ°Π²Π° Π·Π°ΡΠΈΡΠ΅Π½Ρ.1. ΠΠ²Π΅Π΄Π΅Π½ΠΈΠ΅
ΠΡΠ»Π΅Π²ΠΈΠ΄Π½Π°Ρ Π·ΠΎΠ»Π°, ΡΠΈΡΠΎΠΊΠΎ ΠΈΠ·Π²Π΅ΡΡΠ½Π°Ρ ΠΊΠ°ΠΊ Π»Π΅ΡΡΡΠ°Ρ Π·ΠΎΠ»Π°, ΡΠ²Π»ΡΠ΅ΡΡΡ ΠΏΠΎΠ»Π΅Π·Π½ΡΠΌ ΠΏΠΎΠ±ΠΎΡΠ½ΡΠΌ ΠΏΡΠΎΠ΄ΡΠΊΡΠΎΠΌ ΡΠ΅ΠΏΠ»ΠΎΠ²ΡΡ
ΡΠ»Π΅ΠΊΡΡΠΎΡΡΠ°Π½ΡΠΈΠΉ, ΠΈΡΠΏΠΎΠ»ΡΠ·ΡΡΡΠΈΡ
ΠΏΡΠ»Π΅Π²ΠΈΠ΄Π½ΡΠΉ ΡΠ³ΠΎΠ»Ρ Π² ΠΊΠ°ΡΠ΅ΡΡΠ²Π΅ ΡΠΎΠΏΠ»ΠΈΠ²Π°.ΠΡΡΠΎΠΊΠ°Ρ ΡΠ΅ΠΌΠΏΠ΅ΡΠ°ΡΡΡΠ° Π³ΠΎΡΠ΅Π½ΠΈΡ ΡΠ³Π»Ρ ΠΏΡΠ΅Π²ΡΠ°ΡΠ°Π΅Ρ Π³Π»ΠΈΠ½ΠΈΡΡΡΠ΅ ΠΌΠΈΠ½Π΅ΡΠ°Π»Ρ, ΠΏΡΠΈΡΡΡΡΡΠ²ΡΡΡΠΈΠ΅ Π² ΡΠ³ΠΎΠ»ΡΠ½ΠΎΠΌ ΠΏΠΎΡΠΎΡΠΊΠ΅, Π² ΠΏΠ»Π°Π²Π»Π΅Π½ΡΠ΅ ΠΌΠ΅Π»ΠΊΠΈΠ΅ ΡΠ°ΡΡΠΈΡΡ, Π² ΠΎΡΠ½ΠΎΠ²Π½ΠΎΠΌ ΡΠΎΠ΄Π΅ΡΠΆΠ°ΡΠΈΠ΅ ΡΠΈΠ»ΠΈΠΊΠ°Ρ Π°Π»ΡΠΌΠΈΠ½ΠΈΡ. Π’Π°ΠΊΠΈΠΌ ΠΎΠ±ΡΠ°Π·ΠΎΠΌ, ΠΎΠ±ΡΠ°Π·ΡΡΡΠ°ΡΡΡ Π»Π΅ΡΡΡΠ°Ρ Π·ΠΎΠ»Π° ΠΎΠ±Π»Π°Π΄Π°Π΅Ρ ΠΊΠ°ΠΊ ΠΊΠ΅ΡΠ°ΠΌΠΈΡΠ΅ΡΠΊΠΈΠΌΠΈ, ΡΠ°ΠΊ ΠΈ ΠΏΡΡΡΠΎΠ»Π°Π½ΠΎΠ²ΡΠΌΠΈ ΡΠ²ΠΎΠΉΡΡΠ²Π°ΠΌΠΈ. ΠΠ΅ΡΡΡΠ°Ρ Π·ΠΎΠ»Π° — ΠΎΠΏΠ°ΡΠ½ΡΠ΅ ΠΎΡΡ
ΠΎΠ΄Ρ. ΠΡΠΎΠ±Π»Π΅ΠΌΠ° Ρ Π»Π΅ΡΡΡΠ΅ΠΉ Π·ΠΎΠ»ΠΎΠΉ Π·Π°ΠΊΠ»ΡΡΠ°Π΅ΡΡΡ Π½Π΅ ΡΠΎΠ»ΡΠΊΠΎ Π² ΡΠΎΠΌ, ΡΡΠΎ Π΄Π»Ρ Π΅Π΅ ΡΠ΄Π°Π»Π΅Π½ΠΈΡ ΡΡΠ΅Π±ΡΠ΅ΡΡΡ Π±ΠΎΠ»ΡΡΠΎΠ΅ ΠΊΠΎΠ»ΠΈΡΠ΅ΡΡΠ²ΠΎ Π·Π΅ΠΌΠ»ΠΈ, Π²ΠΎΠ΄Ρ ΠΈ ΡΠ½Π΅ΡΠ³ΠΈΠΈ, Π΅Π΅ ΠΌΠ΅Π»ΠΊΠΈΠ΅ ΡΠ°ΡΡΠΈΡΡ, Π΅ΡΠ»ΠΈ Ρ Π½ΠΈΠΌΠΈ Π½Π΅ ΡΠΏΡΠ°Π²ΠΈΡΡΡΡ Π΄ΠΎΠ»ΠΆΠ½ΡΠΌ ΠΎΠ±ΡΠ°Π·ΠΎΠΌ, Π² ΡΠΈΠ»Ρ ΡΠ²ΠΎΠ΅ΠΉ Π½Π΅Π²Π΅ΡΠΎΠΌΠΎΡΡΠΈ, ΠΌΠΎΠ³ΡΡ ΠΏΠΎΠΏΠ°ΡΡΡ Π² Π²ΠΎΠ·Π΄ΡΡ
. ΠΠ·Π²Π΅ΡΡΠ½ΠΎ, ΡΡΠΎ ΠΏΡΠΈ Π½Π΅ΠΏΡΠ°Π²ΠΈΠ»ΡΠ½ΠΎΠΉ ΡΡΠΈΠ»ΠΈΠ·Π°ΡΠΈΠΈ Π»Π΅ΡΡΡΠ°Ρ Π·ΠΎΠ»Π° Π·Π°Π³ΡΡΠ·Π½ΡΠ΅Ρ Π²ΠΎΠ·Π΄ΡΡ
ΠΈ Π²ΠΎΠ΄Ρ ΠΈ Π²ΡΠ·ΡΠ²Π°Π΅Ρ ΡΠ΅ΡΠΏΠΈΡΠ°ΡΠΎΡΠ½ΡΠ΅ ΠΏΡΠΎΠ±Π»Π΅ΠΌΡ ΠΏΡΠΈ Π²Π΄ΡΡ
Π°Π½ΠΈΠΈ.
ΠΠΎ Π²ΡΠ΅ΠΌ ΠΌΠΈΡΠ΅ ΠΎΠΊΠΎΠ»ΠΎ 20% Π»Π΅ΡΡΡΠ΅ΠΉ Π·ΠΎΠ»Ρ ΠΈΡΠΏΠΎΠ»ΡΠ·ΡΠ΅ΡΡΡ Π² ΠΏΡΠΈΠ»ΠΎΠΆΠ΅Π½ΠΈΡΡ
, ΡΠ²ΡΠ·Π°Π½Π½ΡΡ
Ρ Π±Π΅ΡΠΎΠ½ΠΎΠΌ. Π ΠΎΡΠ½ΠΎΠ²Π½ΠΎΠΌ CaO β SiO 2 βH 2 O ΠΈ CaO β Al 2 O 3 — SiO 2 βH 2 O-ΡΠ°Π·Ρ ΡΠΏΠΎΡΠΎΠ±ΡΡΠ²ΡΡΡ ΡΠΏΡΠΎΡΠ½Π΅Π½ΠΈΡ [1, 2] . ΠΠ΅ΡΡΡΠ°Ρ Π·ΠΎΠ»Π° ΡΠ°ΠΊΠΆΠ΅ ΠΈΡΠΏΠΎΠ»ΡΠ·ΡΠ΅ΡΡΡ Π²ΠΎ ΠΌΠ½ΠΎΠ³ΠΈΡ
ΡΠ°Π·Π»ΠΈΡΠ½ΡΡ
ΠΎΠ±Π»Π°ΡΡΡΡ
, ΡΠ°ΠΊΠΈΡ
ΠΊΠ°ΠΊ ΠΊΡΠ°ΡΠΊΠΈ, ΠΏΠ»Π°ΡΡΠΌΠ°ΡΡΡ ΠΈ Π² ΡΠ΅Π»ΡΡΠΊΠΎΠΌ Ρ
ΠΎΠ·ΡΠΉΡΡΠ²Π΅ [3, 4, 5, 6, 7] . Π ΠΠ°Π½Π³Π»Π°Π΄Π΅Ρ Π΅ΠΆΠ΅Π³ΠΎΠ΄Π½ΠΎ ΠΏΡΠΎΠΈΠ·Π²ΠΎΠ΄ΠΈΡΡΡ ΠΎΠΊΠΎΠ»ΠΎ 0,6 ΠΌΠΈΠ»Π»ΠΈΠΎΠ½Π° ΡΠΎΠ½Π½ Π»Π΅ΡΡΡΠ΅ΠΉ Π·ΠΎΠ»Ρ, ΠΈ Π΅Π΅ ΠΏΡΠΎΠΈΠ·Π²ΠΎΠ΄ΡΡΠ²ΠΎ, Π²Π΅ΡΠΎΡΡΠ½ΠΎ, Π·Π½Π°ΡΠΈΡΠ΅Π»ΡΠ½ΠΎ Π²ΠΎΠ·ΡΠ°ΡΡΠ΅Ρ, ΠΏΠΎΡΠΊΠΎΠ»ΡΠΊΡ Π±ΡΠ΄ΡΡΠΈΠ΅ ΡΠ»Π΅ΠΊΡΡΠΎΡΡΠ°Π½ΡΠΈΠΈ Π² ΠΠ°Π½Π³Π»Π°Π΄Π΅Ρ, Π²Π΅ΡΠΎΡΡΠ½ΠΎ, Π±ΡΠ΄ΡΡ ΡΠ°Π±ΠΎΡΠ°ΡΡ Π½Π° ΡΠ³Π»Π΅.Π‘ Π΄ΡΡΠ³ΠΎΠΉ ΡΡΠΎΡΠΎΠ½Ρ, ΠΈΡΠΏΠΎΠ»ΡΠ·ΠΎΠ²Π°Π½ΠΈΠ΅ Π»Π΅ΡΡΡΠ΅ΠΉ Π·ΠΎΠ»Ρ ΠΏΠΎΠΊΠ° Π½Π΅ ΠΏΠΎΠ»ΡΠ·ΡΠ΅ΡΡΡ ΠΏΠΎΠΏΡΠ»ΡΡΠ½ΠΎΡΡΡΡ. Π‘ΠΎΠΎΠ±ΡΠ°Π΅ΡΡΡ, ΡΡΠΎ Π½Π΅Π±ΠΎΠ»ΡΡΠΎΠ΅ ΠΊΠΎΠ»ΠΈΡΠ΅ΡΡΠ²ΠΎ ΠΈΠΌΠΏΠΎΡΡΠ½ΠΎΠΉ Π»Π΅ΡΡΡΠ΅ΠΉ Π·ΠΎΠ»Ρ ΠΈΡΠΏΠΎΠ»ΡΠ·ΡΠ΅ΡΡΡ ΠΏΡΠΈ ΠΏΡΠΎΠΈΠ·Π²ΠΎΠ΄ΡΡΠ²Π΅ ΡΠ΅ΠΌΠ΅Π½ΡΠ° Π² ΠΠ°Π½Π³Π»Π°Π΄Π΅Ρ. ΠΠΈΠ·Π½Π΅ΡΠΏΠΎΡΠΎΠ±Π½ΡΠΌ Π²Π°ΡΠΈΠ°Π½ΡΠΎΠΌ ΠΌΠ°ΡΡΠΎΠ²ΠΎΠ³ΠΎ ΠΈΡΠΏΠΎΠ»ΡΠ·ΠΎΠ²Π°Π½ΠΈΡ Π»Π΅ΡΡΡΠ΅ΠΉ Π·ΠΎΠ»Ρ ΠΌΠΎΠ³Π»ΠΎ Π±Ρ ΡΡΠ°ΡΡ ΠΏΡΠΎΠΈΠ·Π²ΠΎΠ΄ΡΡΠ²ΠΎ ΠΊΠΎΠ½ΡΡΡΡΠΊΡΠΈΠΎΠ½Π½ΠΎΠ³ΠΎ ΠΊΠΈΡΠΏΠΈΡΠ°, ΡΠΎΠ΄Π΅ΡΠΆΠ°ΡΠ΅Π³ΠΎ Π»Π΅ΡΡΡΡΡ Π·ΠΎΠ»Ρ Π² ΠΊΠ°ΡΠ΅ΡΡΠ²Π΅ ΠΎΡΠ½ΠΎΠ²Π½ΠΎΠ³ΠΎ ΠΈΠ½Π³ΡΠ΅Π΄ΠΈΠ΅Π½ΡΠ°. ΠΡΠΎΠΈΠ·Π²ΠΎΠ΄ΡΡΠ²ΠΎ ΠΎΠ±ΡΡΠ½ΡΡ
Π³Π»ΠΈΠ½ΡΠ½ΡΡ
ΠΊΠΈΡΠΏΠΈΡΠ΅ΠΉ ΠΏΡΠ΅Π΄ΠΏΠΎΠ»Π°Π³Π°Π΅Ρ ΠΏΠΎΡΡΠ΅Π±Π»Π΅Π½ΠΈΠ΅ Π±ΠΎΠ»ΡΡΠΎΠ³ΠΎ ΠΊΠΎΠ»ΠΈΡΠ΅ΡΡΠ²Π° Π³Π»ΠΈΠ½Ρ. ΠΡΠΎ ΠΈΡΡΠΎΡΠ°Π΅Ρ Π²Π΅ΡΡ
Π½ΠΈΠΉ ΡΠ»ΠΎΠΉ ΠΏΠΎΡΠ²Ρ ΠΈ Π²ΡΠ·ΡΠ²Π°Π΅Ρ Π΄Π΅Π³ΡΠ°Π΄Π°ΡΠΈΡ ΡΠ΅Π»ΡΡΠΊΠΎΡ
ΠΎΠ·ΡΠΉΡΡΠ²Π΅Π½Π½ΡΡ
Π·Π΅ΠΌΠ΅Π»Ρ. ΠΡΠ»ΠΈ ΠΌΠΎΠΆΠ½ΠΎ Π±ΡΠ΄Π΅Ρ ΠΏΡΠΎΠΈΠ·Π²ΠΎΠ΄ΠΈΡΡ ΠΊΠΈΡΠΏΠΈΡΠΈ ΠΈΠ· Π»Π΅ΡΡΡΠ΅ΠΉ Π·ΠΎΠ»Ρ, Π½Π΅ ΡΠΎΠ΄Π΅ΡΠΆΠ°ΡΠΈΠ΅ Π³Π»ΠΈΠ½Ρ, ΡΡΠΎ Π½Π΅ ΡΠΎΠ»ΡΠΊΠΎ ΠΏΠΎΠΌΠΎΠΆΠ΅Ρ ΡΠΎΡ
ΡΠ°Π½ΠΈΡΡ Π²Π΅ΡΡ
Π½ΠΈΠΉ ΡΠ»ΠΎΠΉ ΠΏΠΎΡΠ²Ρ, Π½ΠΎ ΠΈ ΡΠ½ΠΈΠ·ΠΈΡ ΡΠΊΠΎΠ»ΠΎΠ³ΠΈΡΠ΅ΡΠΊΠΈΠ΅ ΠΏΡΠΎΠ±Π»Π΅ΠΌΡ, Π²ΡΠ·Π²Π°Π½Π½ΡΠ΅ ΡΠ±ΡΠΎΡΠΎΠΌ Π»Π΅ΡΡΡΠ΅ΠΉ Π·ΠΎΠ»Ρ.
Π ΡΡΠΎΠΌ ΠΈΡΡΠ»Π΅Π΄ΠΎΠ²Π°Π½ΠΈΠΈ Π±ΡΠ»Π° ΠΏΡΠ΅Π΄ΠΏΡΠΈΠ½ΡΡΠ° ΠΏΠΎΠΏΡΡΠΊΠ° ΠΏΡΠΎΠΈΠ·Π²Π΅ΡΡΠΈ Π»Π΅Π³ΠΊΠΈΠ΅ ΠΊΠΈΡΠΏΠΈΡΠΈ Π΄Π»Ρ ΡΡΡΠΎΠΈΡΠ΅Π»ΡΠ½ΡΡ ΠΊΠΎΠ½ΡΡΡΡΠΊΡΠΈΠΉ Ρ ΠΈΡΠΏΠΎΠ»ΡΠ·ΠΎΠ²Π°Π½ΠΈΠ΅ΠΌ Π»Π΅ΡΡΡΠ΅ΠΉ Π·ΠΎΠ»Ρ, ΠΎΠ±ΡΠ°Π·ΡΡΡΠ΅ΠΉΡΡ Π½Π° Π’ΠΠ¦ ΠΠ°ΡΠ°ΠΏΡΠΊΡΡΠΈΡ.
2. ΠΠ°ΡΠ΅ΡΠΈΠ°Π»Ρ ΠΈ ΠΌΠ΅ΡΠΎΠ΄Ρ
ΠΠ»Ρ ΠΈΠ·Π³ΠΎΡΠΎΠ²Π»Π΅Π½ΠΈΡ ΠΊΠΈΡΠΏΠΈΡΠ° ΠΈΡΠΏΠΎΠ»ΡΠ·ΠΎΠ²Π°Π»ΠΈΡΡ ΡΠΌΠ΅ΡΠΈ Π»Π΅ΡΡΡΠ΅ΠΉ Π·ΠΎΠ»Ρ, ΠΏΠ΅ΡΠΊΠ° ΠΈ Π³Π°ΡΠ΅Π½ΠΎΠΉ ΠΈΠ·Π²Π΅ΡΡΠΈ Ρ Π³ΠΈΠΏΡΠΎΠΌ Π² ΠΊΠ°ΡΠ΅ΡΡΠ²Π΅ ΡΠ²ΡΠ·ΡΡΡΠ΅Π³ΠΎ. ΠΡΠ»ΠΈ ΠΎΠΏΡΠΈΠΌΠΈΠ·ΠΈΡΠΎΠ²Π°Π½Ρ ΡΠ°ΠΊΠΈΠ΅ ΠΏΠ°ΡΠ°ΠΌΠ΅ΡΡΡ ΠΏΡΠΎΡΠ΅ΡΡΠ°, ΠΊΠ°ΠΊ ΡΠΎΡΡΠ°Π² ΡΠΌΠ΅ΡΠΈ, Π΄Π°Π²Π»Π΅Π½ΠΈΠ΅, ΡΡΠ»ΠΎΠ²ΠΈΡ ΠΎΡΠ²Π΅ΡΠΆΠ΄Π΅Π½ΠΈΡ ΠΈ Ρ. Π. ΠΠ°ΠΊΠΎΠ½Π΅Ρ, Π±ΡΠ»ΠΈ ΠΎΠΏΡΠ΅Π΄Π΅Π»Π΅Π½Ρ ΡΠ²ΠΎΠΉΡΡΠ²Π° ΠΊΠΈΡΠΏΠΈΡΠ΅ΠΉ, ΠΏΡΠΎΠΈΠ·Π²Π΅Π΄Π΅Π½Π½ΡΡ Π² ΠΎΠΏΡΠΈΠΌΠ°Π»ΡΠ½ΡΡ ΡΡΠ»ΠΎΠ²ΠΈΡΡ .
ΠΠ΅ΡΡΡΠ°Ρ Π·ΠΎΠ»Π°, ΠΈΡΠΏΠΎΠ»ΡΠ·ΠΎΠ²Π°Π½Π½Π°Ρ Π² ΡΡΠΎΠΌ ΠΈΡΡΠ»Π΅Π΄ΠΎΠ²Π°Π½ΠΈΠΈ, Π±ΡΠ»Π° ΡΠΎΠ±ΡΠ°Π½Π° Π½Π° ΠΠ°ΡΠ°ΠΏΡΠΊΡΡΠΈΠΉΡΠΊΠΎΠΉ Π’ΠΠ‘. ΠΡΡΠ°Π»ΡΠ½ΡΠ΅ ΠΈΠ½Π³ΡΠ΅Π΄ΠΈΠ΅Π½ΡΡ — Π³Π°ΡΠ΅Π½Π°Ρ ΠΈΠ·Π²Π΅ΡΡΡ, ΠΏΠ΅ΡΠΎΠΊ ΠΈ Π³ΠΈΠΏΡ — Π±ΡΠ»ΠΈ ΡΠΎΠ±ΡΠ°Π½Ρ Π½Π° ΠΌΠ΅ΡΡΠ½ΠΎΠΌ ΡΡΠ½ΠΊΠ΅. ΠΡΠ½ΠΎΠ²Π½ΡΠ΅ ΠΈΠ½Π³ΡΠ΅Π΄ΠΈΠ΅Π½ΡΡ Π»Π΅ΡΡΡΠ΅ΠΉ Π·ΠΎΠ»Ρ ΠΏΡΠ΅Π΄ΡΡΠ°Π²Π»Π΅Π½Ρ Π² ΡΠ°Π±Π»ΠΈΡΠ΅ 1.
Π’Π°Π±Π»ΠΈΡΠ° 1. Π₯ΠΈΠΌΠΈΡΠ΅ΡΠΊΠΈΠΉ ΡΠΎΡΡΠ°Π² Π»Π΅ΡΡΡΠ΅ΠΉ Π·ΠΎΠ»Ρ ΠΠ°ΡΠ°ΠΏΡΠΊΡΡΠΈΠΈ Π’ΠΠ¦
ΠΠ±ΡΠ°Π·ΡΡ ΠΊΠΈΡΠΏΠΈΡΠ° Π±ΡΠ»ΠΈ ΠΈΠ·Π³ΠΎΡΠΎΠ²Π»Π΅Π½Ρ ΠΏΡΠΈ ΡΡΠ»ΠΎΠ²ΠΈΡΡ
, ΡΠΊΠ°Π·Π°Π½Π½ΡΡ
Π² ΡΠ°Π±Π»ΠΈΡΠ΅ 2. ΠΠΎ ΠΊΡΠ°ΠΉΠ½Π΅ΠΉ ΠΌΠ΅ΡΠ΅, ΠΏΡΡΡ ΠΊΠΈΡΠΏΠΈΡΠ΅ΠΉ Π±ΡΠ»ΠΈ ΠΈΠ·Π³ΠΎΡΠΎΠ²Π»Π΅Π½Ρ Π΄Π»Ρ ΠΊΠ°ΠΆΠ΄ΠΎΠ³ΠΎ ΡΠΈΠΏΠ° ΠΎΠ±ΡΠ°Π·ΡΠ°. ΠΠ΅ΡΠ΅Π΄ ΠΈΠ·Π³ΠΎΡΠΎΠ²Π»Π΅Π½ΠΈΠ΅ΠΌ ΠΊΠΈΡΠΏΠΈΡΠ° ΠΊΠ°ΠΆΠ΄ΡΠΉ ΠΈΠ½Π³ΡΠ΅Π΄ΠΈΠ΅Π½Ρ ΡΡΡΡΡ ΡΡΡΠΈΠ»ΠΈ Π² ΠΌΡΡΠ΅Π»ΡΠ½ΠΎΠΉ ΠΏΠ΅ΡΠΈ ΠΏΡΠΈ 110 β Π² ΡΠ΅ΡΠ΅Π½ΠΈΠ΅ 24 ΡΠ°ΡΠΎΠ².ΠΠ·Π²Π΅ΡΠΈΠ²Π°Π»ΠΈ Π½Π΅ΠΎΠ±Ρ
ΠΎΠ΄ΠΈΠΌΠΎΠ΅ ΠΊΠΎΠ»ΠΈΡΠ΅ΡΡΠ²ΠΎ ΠΊΠ°ΠΆΠ΄ΠΎΠ³ΠΎ ΠΈΠ½Π³ΡΠ΅Π΄ΠΈΠ΅Π½ΡΠ°, Π΄ΠΎΠ±Π°Π²Π»ΡΠ»ΠΈ 14% Π²Π»Π°Π³ΠΈ ΠΈ ΡΡΠ°ΡΠ΅Π»ΡΠ½ΠΎ ΠΏΠ΅ΡΠ΅ΠΌΠ΅ΡΠΈΠ²Π°Π»ΠΈ ΠΊΠΎΠΌΠΏΠΎΠ½Π΅Π½ΡΡ. Π§ΡΠΎΠ±Ρ ΠΎΠ±Π΅ΡΠΏΠ΅ΡΠΈΡΡ ΠΎΠ΄ΠΈΠ½Π°ΠΊΠΎΠ²ΡΠΉ ΡΠ°Π·ΠΌΠ΅Ρ ΠΊΠΈΡΠΏΠΈΡΠ΅ΠΉ, ΠΊΠ°ΠΆΠ΄ΡΠΉ ΡΠ°Π· Π΄Π»Ρ Π·Π°ΠΏΠΎΠ»Π½Π΅Π½ΠΈΡ ΠΏΠΎΠ»ΠΎΡΡΠΈ ΡΠΎΡΠΌΡ ΠΈΡΠΏΠΎΠ»ΡΠ·ΠΎΠ²Π°Π»Π°ΡΡ ΠΈΠ·Π²Π΅ΡΡΠ½Π°Ρ ΠΌΠ°ΡΡΠ° ΡΠΌΠ΅ΡΠΈ. Π Π°Π·ΠΌΠ΅Ρ ΠΎΡΠ²Π΅ΡΡΡΠΈΡ ΠΏΠΎΠ»ΠΎΡΡΠΈ ΡΠΎΡΠΌΡ ΡΠΎΡΡΠ°Π²Π»ΡΠ» 6 Ρ
3,5 ΡΠΌ. ΠΠΈΠ΄ΡΠ°Π²Π»ΠΈΡΠ΅ΡΠΊΠΈΠΉ ΠΏΡΠ΅ΡΡ ΠΈΡΠΏΠΎΠ»ΡΠ·ΠΎΠ²Π°Π»ΡΡ Π΄Π»Ρ ΠΏΡΠΈΠ»ΠΎΠΆΠ΅Π½ΠΈΡ Π΄Π°Π²Π»Π΅Π½ΠΈΡ Π² ΡΠ΅ΡΠ΅Π½ΠΈΠ΅ 15 ΡΠ΅ΠΊΡΠ½Π΄ (Π ΠΈΡΡΠ½ΠΎΠΊ 1). ΠΠ°ΡΠ΅ΠΌ ΠΊΠΈΡΠΏΠΈΡΠΈ (ΡΠΈΡ. 2) Π±ΡΠ»ΠΈ ΠΈΠ·Π²Π»Π΅ΡΠ΅Π½Ρ ΠΈ ΠΎΠΊΠΎΠ½ΡΠ°ΡΠ΅Π»ΡΠ½ΠΎ ΠΎΡΠ²Π΅ΡΠΆΠ΄Π΅Π½Ρ. ΠΡΠ²Π΅ΡΠΆΠ΄Π΅Π½ΠΈΠ΅ ΠΏΡΠΎΠΈΠ·Π²ΠΎΠ΄ΠΈΠ»ΠΎΡΡ Π½Π° Π²ΠΎΠ·Π΄ΡΡ
Π΅ Ρ ΠΈΡΠΏΠΎΠ»ΡΠ·ΠΎΠ²Π°Π½ΠΈΠ΅ΠΌ Π²ΠΎΠ΄Π½ΠΎΠ³ΠΎ ΡΠΏΡΠ΅Ρ, ΠΏΡΡΠ΅ΠΌ ΠΏΠΎΠΌΠ΅ΡΠ΅Π½ΠΈΡ ΠΊΠΈΡΠΏΠΈΡΠ΅ΠΉ ΠΏΠΎΠ΄ Π²Π»Π°ΠΆΠ½ΡΡ ΡΠΊΠ°Π½Ρ ΠΈ Π²ΡΠ΄Π΅ΡΠΆΠΈΠ²Π°Π½ΠΈΡ ΠΊΠΈΡΠΏΠΈΡΠ΅ΠΉ Π² Π²ΠΎΠ΄Π΅.ΠΠΈΡΠΏΠΈΡΠΈ, ΡΡΠΎΡΠΌΠΈΡΠΎΠ²Π°Π½Π½ΡΠ΅ ΠΏΠΎΠ΄ ΡΠ°Π·Π»ΠΈΡΠ½ΡΠΌ Π΄Π°Π²Π»Π΅Π½ΠΈΠ΅ΠΌ, ΡΠ°ΠΊΠΆΠ΅ ΠΏΠΎΠ΄Π²Π΅ΡΠ³Π°Π»ΠΈΡΡ ΠΎΡΠ²Π΅ΡΠΆΠ΄Π΅Π½ΠΈΡ Π² ΡΠ΅ΡΠ΅Π½ΠΈΠ΅ ΡΠ°Π·Π½ΡΡ
ΠΏΠ΅ΡΠΈΠΎΠ΄ΠΎΠ² Π²ΡΠ΅ΠΌΠ΅Π½ΠΈ Π² ΠΎΠΏΡΠΈΠΌΠ°Π»ΡΠ½ΡΡ
ΡΡΠ»ΠΎΠ²ΠΈΡΡ
ΠΎΡΠ²Π΅ΡΠΆΠ΄Π΅Π½ΠΈΡ.
Π ΠΈΡΡΠ½ΠΎΠΊ 1 . ΠΠΈΠ΄ΡΠ°Π²Π»ΠΈΡΠ΅ΡΠΊΠΈΠΉ ΠΏΡΠ΅ΡΡ
Π ΠΈΡΡΠ½ΠΎΠΊ 2 . ΠΠΈΡΠΏΠΈΡ Π·ΠΎΠ»ΡΠ½ΡΠΉ, ΡΠΈΠ»ΠΈΠΊΠ°ΡΠ½ΠΎ-ΠΈΠ·Π²Π΅ΡΡΠΊΠΎΠ²ΠΎ-Π³ΠΈΠΏΡΠΎΠ²ΡΠΉ
2.1. ΠΠ΅ΡΠΎΠ΄Ρ ΠΈΡΠΏΡΡΠ°Π½ΠΈΠΉ2.1.1. ΠΡΠΎΡΠ½ΠΎΡΡΡ Π½Π° ΡΠΆΠ°ΡΠΈΠ΅
ΠΡΠΎΡΠ½ΠΎΡΡΡ Π½Π° ΡΠΆΠ°ΡΠΈΠ΅ ΠΎΠΏΡΠ΅Π΄Π΅Π»ΡΠ»ΠΈ ΠΏΡΡΠ΅ΠΌ ΠΏΡΠΈΠ»ΠΎΠΆΠ΅Π½ΠΈΡ Π½Π°Π³ΡΡΠ·ΠΊΠΈ ΠΊ ΠΎΠ±ΡΠ°Π·ΡΡ Ρ ΠΈΡΠΏΠΎΠ»ΡΠ·ΠΎΠ²Π°Π½ΠΈΠ΅ΠΌ ΡΠ½ΠΈΠ²Π΅ΡΡΠ°Π»ΡΠ½ΠΎΠΉ ΠΈΡΠΏΡΡΠ°ΡΠ΅Π»ΡΠ½ΠΎΠΉ ΠΌΠ°ΡΠΈΠ½Ρ.ΠΠ°Π³ΡΡΠ·ΠΊΠ° Π±ΡΠ»Π° ΠΏΡΠΈΠ»ΠΎΠΆΠ΅Π½Π° ΠΊ ΠΏΠ»ΠΎΡΠ°Π΄ΠΈ ΡΠ°Π·ΠΌΠ΅ΡΠΎΠΌ 6 ΠΌΠΌ Ρ 3,5 ΠΌΠΌ [ΡΠ°Π·ΠΌΠ΅Ρ ΠΎΠ΄Π½ΠΎΠΉ ΡΡΠΎΡΠΎΠ½Ρ Π²ΡΠ΅Π³ΠΎ ΠΊΠΈΡΠΏΠΈΡΠ°].
2.1.2. ΠΠΈΠΊΡΠΎΡΡΡΡΠΊΡΡΡΠ°
ΠΠ±ΡΠ°Π·ΡΡ Π½Π°Π±Π»ΡΠ΄Π°Π»ΠΈ ΠΏΠΎΠ΄ ΠΎΠΏΡΠΈΡΠ΅ΡΠΊΠΈΠΌ ΠΌΠΈΠΊΡΠΎΡΠΊΠΎΠΏΠΎΠΌ (ΠΠ), Π° ΠΌΠΈΠΊΡΠΎΡΠΎΡΠΎΠ³ΡΠ°ΡΠΈΠΈ Π·Π°ΠΏΠΈΡΡΠ²Π°Π»ΠΈ Ρ ΠΏΠΎΠΌΠΎΡΡΡ ΡΠΈΡΡΠΎΠ²ΠΎΠΉ ΠΊΠ°ΠΌΠ΅ΡΡ (OPTIKA Microscope B-600 MET) Π΄Π»Ρ ΠΈΡΡΠ»Π΅Π΄ΠΎΠ²Π°Π½ΠΈΡ ΠΏΠΎΡΠΈΡΡΠΎΡΡΠΈ. ΠΠΎΠ΄Π³ΠΎΡΠΎΠ²ΠΊΠ° ΠΎΠ±ΡΠ°Π·ΡΠΎΠ² Π½Π΅ ΠΏΡΠΎΠΈΠ·Π²ΠΎΠ΄ΠΈΠ»Π°ΡΡ.
2.1.3. Π‘Π²ΠΎΠΉΡΡΠ²ΠΎ ΡΡΠ°Π΄ΠΊΠΈ
Π Π°Π·ΠΌΠ΅ΡΡ ΠΊΠΈΡΠΏΠΈΡΠ΅ΠΉ Π±ΡΠ»ΠΈ ΠΈΠ·ΠΌΠ΅ΡΠ΅Π½Ρ ΡΡΠ°Π·Ρ ΠΏΠΎΡΠ»Π΅ ΠΈΠ·Π³ΠΎΡΠΎΠ²Π»Π΅Π½ΠΈΡ ΠΊΠΈΡΠΏΠΈΡΠ΅ΠΉ, Π° ΡΠ°ΠΊΠΆΠ΅ ΠΏΠΎΡΠ»Π΅ ΠΎΡΠ²Π΅ΡΠΆΠ΄Π΅Π½ΠΈΡ, ΡΡΠΎΠ±Ρ ΠΎΠΏΡΠ΅Π΄Π΅Π»ΠΈΡΡ ΡΡΠ°Π΄ΠΊΡ ΠΊΠΈΡΠΏΠΈΡΠ΅ΠΉ.
2.1.4. ΠΠ±ΡΠ΅ΠΌΠ½ΡΠΉ Π²Π΅Ρ Π΅Π΄ΠΈΠ½ΠΈΡΡ
ΠΠΎΡΠ»Π΅ 7 Π΄Π½Π΅ΠΉ ΠΏΠ΅ΡΠΈΠΎΠ΄Π° ΠΎΡΠ²Π΅ΡΠΆΠ΄Π΅Π½ΠΈΡ ΠΊΠΈΡΠΏΠΈΡΠΈ ΡΡΡΠΈΠ»ΠΈ ΠΏΡΠΈ 110 β Π² ΡΠ΅ΡΠ΅Π½ΠΈΠ΅ 24 ΡΠ°ΡΠΎΠ², Π° Π·Π°ΡΠ΅ΠΌ Π΄Π°Π²Π°Π»ΠΈ ΠΎΡΡΡΡΡ Π΄ΠΎ ΠΊΠΎΠΌΠ½Π°ΡΠ½ΠΎΠΉ ΡΠ΅ΠΌΠΏΠ΅ΡΠ°ΡΡΡΡ. ΠΠ°ΡΠ΅ΠΌ ΠΈΠ·ΠΌΠ΅ΡΡΠ»ΠΈ ΡΡΡ
ΠΎΠΉ Π²Π΅Ρ D (Π³). ΠΠΎΡΠ»Π΅ ΡΡΠΎΠ³ΠΎ ΠΊΠΈΡΠΏΠΈΡΠΈ ΠΏΠΎΠ³ΡΡΠΆΠ°Π»ΠΈ Π½Π° 24 ΡΠ°ΡΠ° Π² Π²ΠΎΠ΄Ρ ΠΏΡΠΈ ΠΊΠΎΠΌΠ½Π°ΡΠ½ΠΎΠΉ ΡΠ΅ΠΌΠΏΠ΅ΡΠ°ΡΡΡΠ΅ ΠΈ ΠΈΠ·ΠΌΠ΅ΡΡΠ»ΠΈ Π²Π·Π²Π΅ΡΠ΅Π½Π½ΡΠΉ Π²Π΅Ρ S (Π³). ΠΠ°ΡΠ΅ΠΌ ΠΊΠΈΡΠΏΠΈΡΠΈ Π±ΡΠ»ΠΈ ΡΠ΄Π°Π»Π΅Π½Ρ, ΠΏΠΎΠ²Π΅ΡΡ
Π½ΠΎΡΡΠ½Π°Ρ Π²ΠΎΠ΄Π° Π±ΡΠ»Π° Π²ΡΡΠ΅ΡΡΠ° Π²Π»Π°ΠΆΠ½ΠΎΠΉ ΡΠΊΠ°Π½ΡΡ, ΠΈ Π² ΡΠ΅ΡΠ΅Π½ΠΈΠ΅ 5 ΠΌΠΈΠ½ΡΡ ΠΏΠΎΡΠ»Π΅ ΠΈΠ·Π²Π»Π΅ΡΠ΅Π½ΠΈΡ ΠΊΠΈΡΠΏΠΈΡΠ΅ΠΉ ΠΈΠ· Π²ΠΎΠ΄ΡΠ½ΠΎΠΉ Π±Π°Π½ΠΈ Π±ΡΠ» ΠΈΠ·ΠΌΠ΅ΡΠ΅Π½ Π½Π°ΡΡΡΠ΅Π½Π½ΡΠΉ Π²Π΅Ρ W (Π³).Π£Π΄Π΅Π»ΡΠ½ΡΠΉ ΠΎΠ±ΡΠ΅ΠΌΠ½ΡΠΉ Π²Π΅Ρ B, Π³ / ΡΠΌ 3 = D / V, Π³Π΄Π΅ ΡΠ°ΡΡΡΠΈΡΠ°Π½ ΠΎΠ±ΡΠ΅ΠΌ V, ΡΠΌ 3 = (W — S).
2.1.5. ΠΠ°ΡΠ°Π»ΡΠ½Π°Ρ ΡΠΊΠΎΡΠΎΡΡΡ Π°Π±ΡΠΎΡΠ±ΡΠΈΠΈ (IRA)
ΠΠΎΡΠ»Π΅ ΠΈΠ·ΠΌΠ΅ΡΠ΅Π½ΠΈΡ ΡΡΡ ΠΎΠΉ ΠΌΠ°ΡΡΡ D (Π³), ΠΊΠ°ΠΊ ΡΠΏΠΎΠΌΠΈΠ½Π°Π»ΠΎΡΡ ΡΠ°Π½Π΅Π΅, ΠΏΠΎΠ²Π΅ΡΡ Π½ΠΎΡΡΡ ΡΠ»ΠΎΡ ΠΊΠΈΡΠΏΠΈΡΠ° (ΠΏΠΎΠ²Π΅ΡΡ Π½ΠΎΡΡΡ ΡΠ°Π·ΠΌΠ΅ΡΠΎΠΌ 6 ΠΌΠΌ X 3,5 ΠΌΠΌ) Π·Π°ΡΡΠ°Π²Π»ΡΠ»ΠΈ Π°Π±ΡΠΎΡΠ±ΠΈΡΠΎΠ²Π°ΡΡ Π²ΠΎΠ΄Ρ Π² ΡΠ΅ΡΠ΅Π½ΠΈΠ΅ 1 ΠΌΠΈΠ½. ΠΠΎΠ΄Π° Π±ΡΠ»Π° ΠΏΠΎΠ»Π½ΠΎΡΡΡΡ ΡΠ΄Π°Π»Π΅Π½Π° Ρ ΠΏΠΎΠ²Π΅ΡΡ Π½ΠΎΡΡΠΈ ΠΊΠΈΡΠΏΠΈΡΠ° Π² ΡΠ΅ΡΠ΅Π½ΠΈΠ΅ 10 Ρ ΠΏΠΎΡΠ»Π΅ ΡΠ΄Π°Π»Π΅Π½ΠΈΡ ΠΎΡ ΠΊΠΎΠ½ΡΠ°ΠΊΡΠ° Ρ Π²ΠΎΠ΄ΠΎΠΉ, ΠΈ Π²Π΅Ρ D β(Π³) Π±ΡΠ» ΠΎΠΏΡΠ΅Π΄Π΅Π»Π΅Π½ Π² ΡΠ΅ΡΠ΅Π½ΠΈΠ΅ 2 ΠΌΠΈΠ½ΡΡ.ΠΠ°ΡΠ΅ΠΌ ΡΠ°ΡΡΡΠΈΡΡΠ²Π°Π»ΠΈ Π½Π°ΡΠ°Π»ΡΠ½ΡΡ ΡΠΊΠΎΡΠΎΡΡΡ Π°Π±ΡΠΎΡΠ±ΡΠΈΠΈ IRA,% = D β- D [ΠΠ±ΠΎΠ·Π½Π°ΡΠ΅Π½ΠΈΠ΅ C 67-00 ASTM].
2.1.6. ΠΠ±ΡΠΎΡΠ±ΡΠΈΠΎΠ½Π½Π°Ρ ΡΠΏΠΎΡΠΎΠ±Π½ΠΎΡΡΡ
ASTM ΠΠ±ΠΎΠ·Π½Π°ΡΠ΅Π½ΠΈΠ΅ C 67-00 ΠΈΡΠΏΠΎΠ»ΡΠ·ΠΎΠ²Π°Π»ΠΎΡΡ Π΄Π»Ρ ΠΈΠ·ΠΌΠ΅ΡΠ΅Π½ΠΈΡ Π°Π±ΡΠΎΡΠ±ΡΠΈΠΎΠ½Π½ΠΎΠΉ ΡΠΏΠΎΡΠΎΠ±Π½ΠΎΡΡΠΈ A,% = [(W — D) / D].
2.1.7. ΠΠ°ΠΆΡΡΠ°ΡΡΡ ΠΏΠΎΡΠΈΡΡΠΎΡΡΡ, ΠΎΡΠΊΡΡΡΡΠ΅ ΠΏΠΎΡΡ ΠΈ Π½Π΅ΠΏΡΠΎΠ½ΠΈΡΠ°Π΅ΠΌΡΠ΅ ΠΏΠΎΡΡ
ΠΠ±ΠΎΠ·Π½Π°ΡΠ΅Π½ΠΈΠ΅ ASTM C 67-00 ΠΈΡΠΏΠΎΠ»ΡΠ·ΠΎΠ²Π°Π»ΠΎΡΡ Π΄Π»Ρ ΠΎΠΏΡΠ΅Π΄Π΅Π»Π΅Π½ΠΈΡ ΠΊΠ°ΠΆΡΡΠ΅ΠΉΡΡ ΠΏΠΎΡΠΈΡΡΠΎΡΡΠΈ P,% = [(W — D) / V], ΠΎΠ±ΡΠ΅ΠΌ ΠΎΡΠΊΡΡΡΡΡ ΠΏΠΎΡ, ΡΠΌ 3 = W — D ΠΈ Π½Π΅ΠΏΡΠΎΠ½ΠΈΡΠ°Π΅ΠΌΡΠΉ ΠΎΠ±ΡΠ΅ΠΌ ΠΏΠΎΡ, ΡΠΌ 3 = D — S.
2.1.8. Π’Π΅ΡΡ Π½Π° Π²ΡΡΠ²Π΅ΡΠ°Π½ΠΈΠ΅
ΠΡΠΎΡ ΡΠ΅ΡΡ ΠΏΡΠΎΠ²ΠΎΠ΄ΠΈΠ»ΡΡ Π² ΡΠΎΠΎΡΠ²Π΅ΡΡΡΠ²ΠΈΠΈ Ρ ASTM C67-08. ΠΠ»Ρ ΡΡΠΎΠ³ΠΎ ΠΈΡΠΏΡΡΠ°Π½ΠΈΡ ΠΎΠ΄ΠΈΠ½ ΠΊΠΈΡΠΏΠΈΡ Π²Π΅ΡΡΠΈΠΊΠ°Π»ΡΠ½ΠΎ ΠΏΠΎΠΌΠ΅ΡΠ°Π»ΠΈ Π² Π²ΠΎΠ΄Ρ Ρ ΠΎΠ΄Π½ΠΈΠΌ ΠΏΠΎΠ³ΡΡΠΆΠ΅Π½Π½ΡΠΌ ΠΊΠΎΠ½ΡΠΎΠΌ, Π° Π΄ΡΡΠ³ΠΎΠΉ ΠΊΠΈΡΠΏΠΈΡ Ρ ΡΠ°Π½ΠΈΠ»ΠΈ Π² ΡΡΠ»ΠΎΠ²ΠΈΡΡ ΠΎΠΊΡΡΠΆΠ°ΡΡΠ΅ΠΉ ΡΡΠ΅Π΄Ρ. Π§Π΅ΡΠ΅Π· 7 Π΄Π½Π΅ΠΉ ΠΎΠ±Π° ΠΊΠΈΡΠΏΠΈΡΠ° ΡΡΡΠΈΠ»ΠΈ Π² ΠΏΠ΅ΡΠΈ ΠΏΡΠΈ 110 β Π² ΡΠ΅ΡΠ΅Π½ΠΈΠ΅ 24 ΡΠ°ΡΠΎΠ². ΠΠ°ΡΠ΅ΠΌ ΠΎΠ±Π° ΠΊΠΈΡΠΏΠΈΡΠ° Π½Π°Π±Π»ΡΠ΄Π°Π»ΠΈΡΡ Ρ ΡΠ°ΡΡΡΠΎΡΠ½ΠΈΡ 10 ΡΡΡΠΎΠ² ΠΏΠΎΠ΄ ΡΠ³Π»ΠΎΠΌ Π½Π΅ ΠΌΠ΅Π½Π΅Π΅ 50 ΡΡΡΠΎΠ² Ρ Π½ΠΎΡΠΌΠ°Π»ΡΠ½ΡΠΌ Π·ΡΠ΅Π½ΠΈΠ΅ΠΌ. ΠΡΠ»ΠΈ Π½Π°Π±Π»ΡΠ΄Π°Π΅ΡΡΡ ΠΊΠ°ΠΊΠΎΠ΅-Π»ΠΈΠ±ΠΎ ΡΠ°Π·Π»ΠΈΡΠΈΠ΅ ΠΈΠ·-Π·Π° Π½Π°Π»ΠΈΡΠΈΡ ΡΠΎΠ»Π΅Π²ΡΡ ΠΎΡΠ»ΠΎΠΆΠ΅Π½ΠΈΠΉ, ΡΠ΅ΠΉΡΠΈΠ½Π³ ΠΎΡΠΎΠ±ΡΠ°ΠΆΠ°Π΅ΡΡΡ ΠΊΠ°ΠΊ Β«Π²ΡΡΠΎΡ ΡΠΈΠΉΒ».ΠΡΠ»ΠΈ Π½ΠΈΠΊΠ°ΠΊΠΎΠΉ ΡΠ°Π·Π½ΠΈΡΡ Π½Π΅ Π½Π°Π±Π»ΡΠ΄Π°Π΅ΡΡΡ, ΡΠ΅ΠΉΡΠΈΠ½Π³ ΠΎΡΠΎΠ±ΡΠ°ΠΆΠ°Π΅ΡΡΡ ΠΊΠ°ΠΊ Β«Π½Π΅ Π²ΡΡΠΎΡ ΡΠΈΠΉΒ».
2.1.9. Π’Π΅ΡΡ Π½Π° ΡΠ°Π΄ΠΈΠΎΠ°ΠΊΡΠΈΠ²Π½ΠΎΡΡΡ
Π Π°Π΄ΠΈΠΎΠ°ΠΊΡΠΈΠ²Π½ΠΎΡΡΡ ΡΠΌΠ΅ΡΠΈ ΠΎΠΏΡΠΈΠΌΠ°Π»ΡΠ½ΠΎΠ³ΠΎ ΡΠΎΡΡΠ°Π²Π° Π±ΡΠ»Π° ΠΈΡΡΠ»Π΅Π΄ΠΎΠ²Π°Π½Π° ΠΡΠ΄Π΅Π»ΠΎΠΌ ΡΠΈΠ·ΠΈΠΊΠΈ Π·Π΄ΠΎΡΠΎΠ²ΡΡ ΠΠΎΠΌΠΈΡΡΠΈΠΈ ΠΏΠΎ Π°ΡΠΎΠΌΠ½ΠΎΠΉ ΡΠ½Π΅ΡΠ³ΠΈΠΈ ΠΠ°Π½Π³Π»Π°Π΄Π΅Ρ.
2.1.10. ΠΠ·ΠΌΠ΅Π½Π΅Π½ΠΈΠ΅ ΠΏΡΠΎΡΠ΅ΡΡΠ° ΠΈ Π²ΡΠ΅ΠΌΠ΅Π½ΠΈ ΠΎΡΠ²Π΅ΡΠΆΠ΄Π΅Π½ΠΈΡ
ΠΡΠ»ΠΎ ΠΈΡΡΠ»Π΅Π΄ΠΎΠ²Π°Π½ΠΎ Π²Π»ΠΈΡΠ½ΠΈΠ΅ ΡΠ΅ΡΡΡΠ΅Ρ ΡΠ°Π·Π»ΠΈΡΠ½ΡΡ ΠΏΡΠΎΡΠ΅ΡΡΠΎΠ² ΠΎΡΠ²Π΅ΡΠΆΠ΄Π΅Π½ΠΈΡ, Ρ. Π. ΠΠ° Π½Π΅ΠΏΠΎΠ΄Π²ΠΈΠΆΠ½ΠΎΠΌ Π²ΠΎΠ·Π΄ΡΡ Π΅, Ρ ΡΠ°Π·Π±ΡΡΠ·Π³ΠΈΠ²Π°Π½ΠΈΠ΅ΠΌ Π²ΠΎΠ΄Ρ Π΄Π²Π° ΡΠ°Π·Π° Π² Π΄Π΅Π½Ρ, Π²ΡΠ΄Π΅ΡΠΆΠΈΠ²Π°Π½ΠΈΠ΅ΠΌ ΠΎΠ±ΡΠ°Π·ΡΠ° ΠΏΠΎΠ΄ Π²Π»Π°ΠΆΠ½ΠΎΠΉ ΡΠΊΠ°Π½ΡΡ ΠΈ Π²ΡΠ΄Π΅ΡΠΆΠΈΠ²Π°Π½ΠΈΠ΅ΠΌ ΠΎΠ±ΡΠ°Π·ΡΠ° Π² Π²ΠΎΠ΄Π΅ Π² ΡΠ΅ΡΠ΅Π½ΠΈΠ΅ ΡΠ΅ΠΌΠΈ Π΄Π½Π΅ΠΉ.ΠΠ°ΠΊΠΎΠ½Π΅Ρ, Π±ΡΠ» ΠΈΠ·ΡΡΠ΅Π½ ΡΡΡΠ΅ΠΊΡ Π΄Π»ΠΈΡΠ΅Π»ΡΠ½ΠΎΠ³ΠΎ ΠΎΡΠ²Π΅ΡΠΆΠ΄Π΅Π½ΠΈΡ. ΠΠ»Ρ ΠΏΠΎΠ»ΡΡΠ΅Π½ΠΈΡ ΠΎΠΏΡΠΈΠΌΠ°Π»ΡΠ½ΠΎΠ³ΠΎ ΡΠΎΡΡΠ°Π²Π° ΠΈ ΡΠ°Π·Π½ΠΎΠ³ΠΎ Π΄Π°Π²Π»Π΅Π½ΠΈΡ ΡΠΏΠ»ΠΎΡΠ½Π΅Π½ΠΈΡ ΠΎΠ΄ΠΈΠ½ ΠΊΠΎΠΌΠΏΠ»Π΅ΠΊΡ ΠΊΠΈΡΠΏΠΈΡΠ΅ΠΉ Π²ΡΠ΄Π΅ΡΠΆΠΈΠ²Π°Π»ΠΈ Π½Π° Π²ΠΎΠ·Π΄ΡΡ Π΅ Π² ΡΠ΅ΡΠ΅Π½ΠΈΠ΅ ΠΏΡΡΠΈ Π½Π΅Π΄Π΅Π»Ρ. ΠΡΡΠ³ΠΎΠΉ Π½Π°Π±ΠΎΡ ΡΡΡΠΈΠ»ΠΈ Π½Π° Π²ΠΎΠ·Π΄ΡΡ Π΅ Π² ΡΠ΅ΡΠ΅Π½ΠΈΠ΅ ΠΎΠ΄Π½ΠΎΠΉ Π½Π΅Π΄Π΅Π»ΠΈ, Π° Π·Π°ΡΠ΅ΠΌ Π² ΡΠ΅ΡΠ΅Π½ΠΈΠ΅ ΡΠ΅ΡΡΡΠ΅Ρ Π½Π΅Π΄Π΅Π»Ρ ΠΏΠΎΠ΄ Π²ΠΎΠ΄ΠΎΠΉ. ΠΠ°ΡΠ΅ΠΌ ΡΡΠ°Π²Π½ΠΈΠ»ΠΈ ΠΈΡ ΠΏΡΠΎΡΠ½ΠΎΡΡΡ Π½Π° ΡΠΆΠ°ΡΠΈΠ΅. Π Π°Π·Π»ΠΈΡΠΈΠ΅ Π² ΠΏΡΠΎΡΠ½ΠΎΡΡΠΈ Π½Π° ΡΠΆΠ°ΡΠΈΠ΅ ΠΈΡΡΠ»Π΅Π΄ΠΎΠ²Π°Π»ΠΈ Ρ ΠΏΠΎΠΌΠΎΡΡΡ ΠΈΠ½ΡΡΠ°ΠΊΡΠ°ΡΠ½ΠΎΠΉ ΡΠΏΠ΅ΠΊΡΡΠΎΡΠΊΠΎΠΏΠΈΠΈ Ρ ΠΏΡΠ΅ΠΎΠ±ΡΠ°Π·ΠΎΠ²Π°Π½ΠΈΠ΅ΠΌ Π€ΡΡΡΠ΅ (FTIR).
3. Π Π΅Π·ΡΠ»ΡΡΠ°ΡΡ ΠΈ ΠΎΠ±ΡΡΠΆΠ΄Π΅Π½ΠΈΠ΅
3.1. ΠΠ»ΠΈΡΠ½ΠΈΠ΅ ΠΏΠ΅ΡΠΊΠ° Π½Π° ΠΏΡΠΎΡΠ½ΠΎΡΡΡ Π½Π° ΡΠΆΠ°ΡΠΈΠ΅ ΠΠ±ΡΠ°Π·ΡΡ T1 — T4 (ΡΠ°Π±Π»ΠΈΡΠ° 2) Π±ΡΠ»ΠΈ ΠΏΠΎΠ΄Π³ΠΎΡΠΎΠ²Π»Π΅Π½Ρ Π΄Π»Ρ ΠΎΠΏΡΠ΅Π΄Π΅Π»Π΅Π½ΠΈΡ Π²Π»ΠΈΡΠ½ΠΈΡ ΠΊΠΎΠ»ΠΈΡΠ΅ΡΡΠ²Π° ΠΏΠ΅ΡΠΊΠ° Π½Π° ΠΏΡΠΎΡΠ½ΠΎΡΡΡ Π½Π° ΡΠΆΠ°ΡΠΈΠ΅.ΠΡΠΎΡΠ½ΠΎΡΡΡ Π½Π° ΡΠΆΠ°ΡΠΈΠ΅ ΠΌΠΎΠΆΠ΅Ρ Π±ΡΡΡ ΡΠ²Π΅Π»ΠΈΡΠ΅Π½Π° Ρ 113,46 ΠΊΠ³ / ΡΠΌ 2 Π΄ΠΎ 165,57 ΠΊΠ³ / ΡΠΌ 2 Π·Π° ΡΡΠ΅Ρ ΡΠ²Π΅Π»ΠΈΡΠ΅Π½ΠΈΡ ΠΊΠΎΠ»ΠΈΡΠ΅ΡΡΠ²Π° ΠΏΠ΅ΡΠΊΠ° Ρ 10 Π΄ΠΎ 40% (Π ΠΈΡΡΠ½ΠΎΠΊ 3). ΠΠ°ΠΊΡΠΈΠΌΠ°Π»ΡΠ½Π°Ρ ΠΏΡΠΎΡΠ½ΠΎΡΡΡ Π±ΡΠ»Π° ΠΎΠ±Π½Π°ΡΡΠΆΠ΅Π½Π° Π΄Π»Ρ 40% ΠΏΠ΅ΡΠΊΠ° — 50% Π»Π΅ΡΡΡΠ΅ΠΉ Π·ΠΎΠ»Ρ — 10% ΠΈΠ·Π²Π΅ΡΡΠΊΠΎΠ²ΠΎΠ³ΠΎ ΠΊΠΈΡΠΏΠΈΡΠ° Ρ 2% Π³ΠΈΠΏΡΠ°. ΠΠΎΡΠΊΠΎΠ»ΡΠΊΡ ΠΎΡΠ½ΠΎΠ²Π½ΠΎΠΉ ΡΠ΅Π»ΡΡ Π΄Π°Π½Π½ΠΎΠ³ΠΎ ΠΈΡΡΠ»Π΅Π΄ΠΎΠ²Π°Π½ΠΈΡ Π±ΡΠ»ΠΎ ΠΌΠ°ΡΡΠΎΠ²ΠΎΠ΅ ΠΈΡΠΏΠΎΠ»ΡΠ·ΠΎΠ²Π°Π½ΠΈΠ΅ Π»Π΅ΡΡΡΠ΅ΠΉ Π·ΠΎΠ»Ρ, ΠΎΠΏΡΠΈΠΌΠ°Π»ΡΠ½ΠΎΠ΅ ΠΊΠΎΠ»ΠΈΡΠ΅ΡΡΠ²ΠΎ ΠΏΠ΅ΡΠΊΠ° Π±ΡΠ»ΠΎ ΠΏΡΠΈΠ½ΡΡΠΎ ΡΠ°Π²Π½ΡΠΌ 30%, ΡΡΠΎ Π΄Π°Π»ΠΎ ΠΏΡΠΎΡΠ½ΠΎΡΡΡ Π½Π° ΡΠΆΠ°ΡΠΈΠ΅ 155,20 ΠΊΠ³ / ΡΠΌ 2 . Π£Π»ΡΡΡΠ΅Π½ΠΈΠ΅ ΠΌΠ΅Ρ
Π°Π½ΠΈΡΠ΅ΡΠΊΠΎΠΉ ΠΏΡΠΎΡΠ½ΠΎΡΡΠΈ Ρ ΡΠ²Π΅Π»ΠΈΡΠ΅Π½ΠΈΠ΅ΠΌ ΡΠΎΠ΄Π΅ΡΠΆΠ°Π½ΠΈΡ ΠΏΠ΅ΡΠΊΠ° Π² Π±ΠΎΠ»ΡΡΠ΅ΠΉ ΡΡΠ΅ΠΏΠ΅Π½ΠΈ ΠΎΠ±ΡΡΡΠ½ΡΠ΅ΡΡΡ ΠΏΠΎΠ²ΡΡΠ΅Π½Π½ΡΠΌ ΠΊΠΎΠ»ΠΈΡΠ΅ΡΡΠ²ΠΎΠΌ ΡΠ²ΠΎΠ±ΠΎΠ΄Π½ΠΎΠ³ΠΎ SiO 2 , ΠΊΠΎΡΠΎΡΡΠΉ Π»Π΅Π³ΡΠ΅ ΡΠ΅Π°Π³ΠΈΡΡΠ΅Ρ Ρ ΠΈΠ·Π²Π΅ΡΡΡΡ, ΡΠ΅ΠΌ Π»Π΅ΡΡΡΠ°Ρ Π·ΠΎΠ»Π° [8] .
Π Π΅Π·ΡΠ»ΡΡΠ°ΡΡ ΠΈΡΠΏΡΡΠ°Π½ΠΈΠΉ Π½Π° ΠΏΡΠΎΡΠ½ΠΎΡΡΡ ΠΏΡΠΈ ΡΠΆΠ°ΡΠΈΠΈ, ΠΏΡΠΎΠ²Π΅Π΄Π΅Π½Π½ΡΠ΅ Π½Π° ΠΎΠ±ΡΠ°Π·ΡΠ°Ρ Π’5 — Π’9, ΠΏΠΎΠΊΠ°Π·Π°Π»ΠΈ, ΡΡΠΎ ΠΌΠ°ΠΊΡΠΈΠΌΠ°Π»ΡΠ½Π°Ρ ΠΏΡΠΎΡΠ½ΠΎΡΡΡ ΠΌΠΎΠΆΠ΅Ρ Π±ΡΡΡ ΠΏΠΎΠ»ΡΡΠ΅Π½Π° Ρ 15% ΠΈΠ·Π²Π΅ΡΡΠΈ ΠΈ 55% Π»Π΅ΡΡΡΠ΅ΠΉ Π·ΠΎΠ»Ρ (Π ΠΈΡΡΠ½ΠΎΠΊ 4). ΠΡΠ΅Π΄Π΅Π» ΠΏΡΠΎΡΠ½ΠΎΡΡΠΈ Π½Π° ΡΠΆΠ°ΡΠΈΠ΅ Π΄Π»Ρ ΡΡΠΎΠΉ ΠΊΠΎΠΌΠΏΠΎΠ·ΠΈΡΠΈΠΈ ΡΠΎΡΡΠ°Π²ΠΈΠ» 181,75 ΠΊΠ³ / ΡΠΌ 2 .
Π ΠΈΡΡΠ½ΠΎΠΊ 3 . ΠΠ»ΠΈΡΠ½ΠΈΠ΅ Π΄ΠΎΠ±Π°Π²ΠΊΠΈ ΠΏΠ΅ΡΠΊΠ° Π½Π° ΠΏΡΠΎΡΠ½ΠΎΡΡΡ Π½Π° ΡΠΆΠ°ΡΠΈΠ΅
Π ΠΈΡΡΠ½ΠΎΠΊ 4 . ΠΠ»ΠΈΡΠ½ΠΈΠ΅ Π΄ΠΎΠ±Π°Π²ΠΊΠΈ ΠΈΠ·Π²Π΅ΡΡΠΈ Π½Π° ΠΏΡΠΎΡΠ½ΠΎΡΡΡ Π½Π° ΡΠΆΠ°ΡΠΈΠ΅
ΠΠ·ΠΌΠ΅Π½Π΅Π½ΠΈΠ΅ ΠΏΡΠΎΡΠ½ΠΎΡΡΠΈ Π½Π° ΡΠΆΠ°ΡΠΈΠ΅ ΠΎΠ±ΡΠ°Π·ΡΠΎΠ² T10 — T13, ΡΠΎΠ΄Π΅ΡΠΆΠ°ΡΠΈΡ ΡΠ°Π·Π»ΠΈΡΠ½ΠΎΠ΅ ΠΊΠΎΠ»ΠΈΡΠ΅ΡΡΠ²ΠΎ Π³ΠΈΠΏΡΠ°, ΠΏΠΎΠΊΠ°Π·Π°Π½ΠΎ Π½Π° ΡΠΈΡΡΠ½ΠΊΠ΅ 5. ΠΠΎΠΆΠ½ΠΎ Π²ΠΈΠ΄Π΅ΡΡ, ΡΡΠΎ ΠΏΡΠΎΡΠ½ΠΎΡΡΡ Π½Π° ΡΠΆΠ°ΡΠΈΠ΅ ΡΠ²Π΅Π»ΠΈΡΠΈΠ»Π°ΡΡ Ρ 181,75 ΠΊΠ³ / ΡΠΌ 2 Π΄Π»Ρ 2-ΠΏΡΠΎΡΠ΅Π½ΡΠ½ΠΎΠ³ΠΎ Π³ΠΈΠΏΡΠ° Π΄ΠΎ 287,78 ΠΊΠ³ / ΡΠΌ 2 Π΄Π»Ρ ΠΎΠΏΡΠΈΠΌΠ°Π»ΡΠ½ΠΎΠ³ΠΎ ΡΠΎΠ΄Π΅ΡΠΆΠ°Π½ΠΈΡ Π³ΠΈΠΏΡΠ° 14%.
3,4. ΠΠ»ΠΈΡΠ½ΠΈΠ΅ Π΄Π°Π²Π»Π΅Π½ΠΈΡ ΡΠΎΡΠΌΠΎΠ²Π°Π½ΠΈΡ ΠΊΠΈΡΠΏΠΈΡΠ° Π½Π° ΠΏΡΠΎΡΠ½ΠΎΡΡΡ Π½Π° ΡΠΆΠ°ΡΠΈΠ΅ΠΡΠΏΡΡΠ°Π½ΠΈΡ Π½Π° ΠΏΡΠΎΡΠ½ΠΎΡΡΡ Π½Π° ΡΠΆΠ°ΡΠΈΠ΅ ΠΎΠ±ΡΠ°Π·ΡΠΎΠ² Π’14 — Π’16 ΠΏΠΎΠΊΠ°Π·Π°Π»ΠΈ, ΡΡΠΎ ΠΏΡΠΎΡΠ½ΠΎΡΡΡ Π½Π° ΡΠΆΠ°ΡΠΈΠ΅ ΡΠ²Π΅Π»ΠΈΡΠΈΠ²Π°Π΅ΡΡΡ Ρ ΡΠ²Π΅Π»ΠΈΡΠ΅Π½ΠΈΠ΅ΠΌ Π΄Π°Π²Π»Π΅Π½ΠΈΡ ΡΠΎΡΠΌΠΎΠ²Π°Π½ΠΈΡ ΠΊΠΈΡΠΏΠΈΡΠ° (ΡΠΈΡ. 6).ΠΠ±ΡΠ°Π·Π΅Ρ T16 ΠΏΠΎΠΊΠ°Π·Π°Π» ΠΌΠ°ΠΊΡΠΈΠΌΠ°Π»ΡΠ½ΡΡ ΠΏΡΠΎΡΠ½ΠΎΡΡΡ Π½Π° ΡΠΆΠ°ΡΠΈΠ΅ 417,96 ΠΊΠ³ / ΡΠΌ 2 Π΄Π»Ρ Π΄Π°Π²Π»Π΅Π½ΠΈΡ ΡΠΎΡΠΌΠΎΠ²Π°Π½ΠΈΡ ΠΊΠΈΡΠΏΠΈΡΠ° 3000 ΡΡΠ½ΡΠΎΠ² Π½Π° ΠΊΠ²Π°Π΄ΡΠ°ΡΠ½ΡΠΉ Π΄ΡΠΉΠΌ.
Π ΠΈΡΡΠ½ΠΎΠΊ 5 . ΠΠ»ΠΈΡΠ½ΠΈΠ΅ Π΄ΠΎΠ±Π°Π²ΠΊΠΈ Π³ΠΈΠΏΡΠ° Π½Π° ΠΏΡΠΎΡΠ½ΠΎΡΡΡ Π½Π° ΡΠΆΠ°ΡΠΈΠ΅
Π ΠΈΡΡΠ½ΠΎΠΊ 6 . ΠΠ»ΠΈΡΠ½ΠΈΠ΅ Π΄Π°Π²Π»Π΅Π½ΠΈΡ ΡΠΎΡΠΌΠΎΠ²Π°Π½ΠΈΡ ΠΊΠΈΡΠΏΠΈΡΠ° Π½Π° ΠΏΡΠΎΡΠ½ΠΎΡΡΡ Π½Π° ΡΠΆΠ°ΡΠΈΠ΅
3,5.
ΠΠ±ΡΠ°Π·ΡΡ Π’14, Π’15 ΠΈ Π’16 ΠΏΡΠ΅Π΄ΡΡΠ°Π²Π»ΡΡΡ ΡΠΎΠ±ΠΎΠΉ ΠΎΠ±ΡΠ°Π·ΡΡ Ρ ΠΎΠΏΡΠΈΠΌΠ°Π»ΡΠ½ΡΠΌ ΡΠΎΡΡΠ°Π²ΠΎΠΌ ΠΈ ΡΠ°Π·Π»ΠΈΡΠ½ΡΠΌΠΈ Π΄Π°Π²Π»Π΅Π½ΠΈΡΠΌΠΈ ΡΠΎΡΠΌΠΎΠ²Π°Π½ΠΈΡ ΠΊΠΈΡΠΏΠΈΡΠ°.ΠΠΈΠΊΡΠΎΡΡΡΡΠΊΡΡΡΠ° ΠΈ Π΄ΡΡΠ³ΠΈΠ΅ ΡΠ²ΠΎΠΉΡΡΠ²Π° ΠΏΠΎΠΌΠΈΠΌΠΎ ΠΏΡΠΎΡΠ½ΠΎΡΡΠΈ Π½Π° ΡΠΆΠ°ΡΠΈΠ΅ ΡΡΠΈΡ ΠΎΠ±ΡΠ°Π·ΡΠΎΠ² Π±ΡΠ»ΠΈ ΠΈΡΡΠ»Π΅Π΄ΠΎΠ²Π°Π½Ρ Π΄Π»Ρ ΠΎΠΏΡΠΈΠΌΠΈΠ·Π°ΡΠΈΠΈ Π΄Π°Π²Π»Π΅Π½ΠΈΡ ΡΠΎΡΠΌΠΎΠ²Π°Π½ΠΈΡ ΠΊΠΈΡΠΏΠΈΡΠ°. ΠΠ° ΡΠΈΡ. 7 ΠΏΠΎΠΊΠ°Π·Π°Π½ΠΎ, ΡΡΠΎ ΠΊΠ°ΠΊ ΠΈΠ½Π΄ΠΈΠ²ΠΈΠ΄ΡΠ°Π»ΡΠ½ΡΠΉ ΡΠ°Π·ΠΌΠ΅Ρ ΠΏΠΎΡ, ΡΠ°ΠΊ ΠΈ ΠΎΠ±ΡΠ°Ρ ΠΏΠΎΡΠΈΡΡΠΎΡΡΡ ΡΠΌΠ΅Π½ΡΡΠ°Π»ΠΈΡΡ Ρ ΡΠ²Π΅Π»ΠΈΡΠ΅Π½ΠΈΠ΅ΠΌ Π΄Π°Π²Π»Π΅Π½ΠΈΡ ΡΠΎΡΠΌΠΎΠ²Π°Π½ΠΈΡ ΠΊΠΈΡΠΏΠΈΡΠ°. ΠΡΠΎΠ³ΠΎ ΡΠ»Π΅Π΄ΠΎΠ²Π°Π»ΠΎ ΠΎΠΆΠΈΠ΄Π°ΡΡ.
Π ΠΈΡΡΠ½ΠΎΠΊ 7 . ΠΠΈΠΊΡΠΎΡΡΡΡΠΊΡΡΡΠ° ΠΊΠΈΡΠΏΠΈΡΠ΅ΠΉ, ΡΠΎΡΠΌΠΎΠ²Π°Π½Π½ΡΡ ΠΏΠΎΠ΄ Π΄Π°Π²Π»Π΅Π½ΠΈΠ΅ΠΌ (Π°) 1000 ΡΡΠ½ΡΠΎΠ² Π½Π° ΠΊΠ²Π°Π΄ΡΠ°ΡΠ½ΡΠΉ Π΄ΡΠΉΠΌ (Π±) 2000 ΡΡΠ½ΡΠΎΠ² Π½Π° ΠΊΠ²Π°Π΄ΡΠ°ΡΠ½ΡΠΉ Π΄ΡΠΉΠΌ (Π²) 3000 ΡΡΠ½ΡΠΎΠ² Π½Π° ΠΊΠ²Π°Π΄ΡΠ°ΡΠ½ΡΠΉ Π΄ΡΠΉΠΌ [ΠΡΠ΅ ΡΠ²Π΅Π»ΠΈΡΠ΅Π½ΠΈΡ 500X]
3,6. Π‘Π²ΠΎΠΉΡΡΠ²ΠΎ ΡΡΠ°Π΄ΠΊΠΈΠΠ°ΠΌΠ΅ΡΠ½ΠΎΠΉ ΡΡΠ°Π΄ΠΊΠΈ Π½Π΅ ΠΏΡΠΎΠΈΠ·ΠΎΡΠ»ΠΎ, ΠΊΠ°ΠΊ ΡΡΠΎ Π±ΡΠ»ΠΎ ΠΈΠ·ΠΌΠ΅ΡΠ΅Π½ΠΎ Π΄Π»Ρ ΠΎΠ±ΡΠ°Π·ΡΠΎΠ² T14, T15 ΠΈ T16.
3,7. ΠΠ±ΡΠ΅ΠΌΠ½ΡΠΉ Π²Π΅Ρ Π±Π»ΠΎΠΊΠ° Π‘ ΡΠ²Π΅Π»ΠΈΡΠ΅Π½ΠΈΠ΅ΠΌ Π΄Π°Π²Π»Π΅Π½ΠΈΡ ΡΠΎΡΠΌΠΎΠ²Π°Π½ΠΈΡ ΠΊΠΈΡΠΏΠΈΡΠ° ΠΎΠ±ΡΠ΅ΠΌΠ½ΡΠΉ Π²Π΅Ρ Π±Π»ΠΎΠΊΠ° ΡΠ²Π΅Π»ΠΈΡΠΈΠ²Π°Π»ΡΡ (ΡΠΈΡΡΠ½ΠΎΠΊ 8). ΠΠΎ Π²ΡΡΠ΅ 2000 ΡΡΠ½ΡΠΎΠ² Π½Π° ΠΊΠ²Π°Π΄ΡΠ°ΡΠ½ΡΠΉ Π΄ΡΠΉΠΌ ΠΈΠ·ΠΌΠ΅Π½Π΅Π½ΠΈΠ΅ ΠΏΠ»ΠΎΡΠ½ΠΎΡΡΠΈ Π±ΡΠ»ΠΎ Π½Π΅Π·Π½Π°ΡΠΈΡΠ΅Π»ΡΠ½ΡΠΌ. ΠΠ°ΠΊΡΠΈΠΌΠ°Π»ΡΠ½Π°Ρ ΠΏΠ»ΠΎΡΠ½ΠΎΡΡΡ 1,81 Π³ / ΠΊΡΠ±. ΡΠΌ Π±ΡΠ»Π° ΠΎΠ±Π½Π°ΡΡΠΆΠ΅Π½Π° Π΄Π»Ρ ΠΊΠΈΡΠΏΠΈΡΠ΅ΠΉ, ΡΡΠΎΡΠΌΠΈΡΠΎΠ²Π°Π½Π½ΡΡ
ΠΏΠΎΠ΄ Π΄Π°Π²Π»Π΅Π½ΠΈΠ΅ΠΌ 3000 ΡΡΠ½ΡΠΎΠ² Π½Π° ΠΊΠ²Π°Π΄ΡΠ°ΡΠ½ΡΠΉ Π΄ΡΠΉΠΌ, ΡΡΠΎ Π½Π°ΠΌΠ½ΠΎΠ³ΠΎ Π½ΠΈΠΆΠ΅, ΡΠ΅ΠΌ ΠΏΠ»ΠΎΡΠ½ΠΎΡΡΡ ΠΊΠΈΡΠΏΠΈΡΠ° Π½Π° ΠΎΡΠ½ΠΎΠ²Π΅ ΠΎΠ±ΠΎΠΆΠΆΠ΅Π½Π½ΠΎΠΉ Π³Π»ΠΈΠ½Ρ.
ΠΠ°ΡΠ°Π»ΡΠ½Π°Ρ ΡΠΊΠΎΡΠΎΡΡΡ Π°Π±ΡΠΎΡΠ±ΡΠΈΠΈ ΠΊΠΈΡΠΏΠΈΡΠ΅ΠΉ, ΠΈΠ·Π³ΠΎΡΠΎΠ²Π»Π΅Π½Π½ΡΡ ΠΏΠΎΠ΄ Π΄Π°Π²Π»Π΅Π½ΠΈΠ΅ΠΌ 1000 ΡΡΠ½ΡΠΎΠ² Π½Π° ΠΊΠ²Π°Π΄ΡΠ°ΡΠ½ΡΠΉ Π΄ΡΠΉΠΌ, ΠΏΡΠ΅Π²ΡΡΠ°Π΅Ρ 30 Π³, ΠΏΠΎΡΡΠΎΠΌΡ ΡΠΎΠ³Π»Π°ΡΠ½ΠΎ ASTM C 67-00 ΡΡΠΈ ΠΊΠΈΡΠΏΠΈΡΠΈ ΡΠ»Π΅Π΄ΡΠ΅Ρ ΡΠΌΠ°ΡΠΈΠ²Π°ΡΡ ΠΏΠ΅ΡΠ΅Π΄ ΡΠΊΠ»Π°Π΄ΠΊΠΎΠΉ (Π ΠΈΡΡΠ½ΠΎΠΊ 9).Π‘ ΡΠ²Π΅Π»ΠΈΡΠ΅Π½ΠΈΠ΅ΠΌ Π΄Π°Π²Π»Π΅Π½ΠΈΡ ΡΠΎΡΠΌΠΎΠ²Π°Π½ΠΈΡ ΠΊΠΈΡΠΏΠΈΡΠ° IRA ΡΠΏΠ°Π»ΠΎ Π½ΠΈΠΆΠ΅ 30 Π³ / ΠΌ2. Π‘Π°ΠΌΡΠΉ Π½ΠΈΠ·ΠΊΠΈΠΉ IRA 14,84 Π³ Π±ΡΠ» ΠΎΠ±Π½Π°ΡΡΠΆΠ΅Π½ Π΄Π»Ρ Π΄Π°Π²Π»Π΅Π½ΠΈΡ 3000 ΡΡΠ½ΡΠΎΠ² Π½Π° ΠΊΠ²Π°Π΄ΡΠ°ΡΠ½ΡΠΉ Π΄ΡΠΉΠΌ. Π’Π°ΠΊ ΡΡΠΎ ΡΡΠΈ ΠΊΠΈΡΠΏΠΈΡΠΈ Π½Π΅ Π½ΡΠΆΠ½ΠΎ ΡΠΌΠ°ΡΠΈΠ²Π°ΡΡ ΠΏΠ΅ΡΠ΅Π΄ ΠΊΠ»Π°Π΄ΠΊΠΎΠΉ.
3.9. ΠΠΏΠΈΡΡΠ²Π°ΡΡΠ°Ρ ΡΠΏΠΎΡΠΎΠ±Π½ΠΎΡΡΡ ΠΠ°ΠΊ ΠΏΠΎΠΊΠ°Π·Π°Π½ΠΎ Π½Π° Π ΠΈΡΡΠ½ΠΊΠ΅ 9, Π²ΠΏΠΈΡΡΠ²Π°ΡΡΠ°Ρ ΡΠΏΠΎΡΠΎΠ±Π½ΠΎΡΡΡ ΡΠΎΡΡΠ°Π²Π»ΡΠ»Π° 14,63% Π΄Π»Ρ Π΄Π°Π²Π»Π΅Π½ΠΈΡ ΡΠΎΡΠΌΠΎΠ²Π°Π½ΠΈΡ ΠΊΠΈΡΠΏΠΈΡΠ° 1000 ΡΡΠ½ΡΠΎΠ² Π½Π° ΠΊΠ²Π°Π΄ΡΠ°ΡΠ½ΡΠΉ Π΄ΡΠΉΠΌ. Π‘ ΡΠ²Π΅Π»ΠΈΡΠ΅Π½ΠΈΠ΅ΠΌ Π΄Π°Π²Π»Π΅Π½ΠΈΡ ΡΡΠΎ Π·Π½Π°ΡΠ΅Π½ΠΈΠ΅ ΡΠΏΠ°Π»ΠΎ Π΄ΠΎ 11,58% Π΄Π»Ρ Π΄Π°Π²Π»Π΅Π½ΠΈΡ 3000 ΡΡΠ½ΡΠΎΠ² Π½Π° ΠΊΠ²Π°Π΄ΡΠ°ΡΠ½ΡΠΉ Π΄ΡΠΉΠΌ. ΠΠ·ΠΌΠ΅Π½Π΅Π½ΠΈΠ΅ Π°Π±ΡΠΎΡΠ±ΡΠΈΠΎΠ½Π½ΠΎΠΉ ΡΠΏΠΎΡΠΎΠ±Π½ΠΎΡΡΠΈ ΠΏΡΠΈ Π΄Π°Π²Π»Π΅Π½ΠΈΠΈ Π²ΡΡΠ΅ 2000 ΡΡΠ½ΡΠΎΠ² Π½Π° ΠΊΠ²Π°Π΄ΡΠ°ΡΠ½ΡΠΉ Π΄ΡΠΉΠΌ Π±ΡΠ»ΠΎ Π½Π΅Π·Π½Π°ΡΠΈΡΠ΅Π»ΡΠ½ΡΠΌ.
Π ΠΈΡΡΠ½ΠΎΠΊ 8 . ΠΠ»ΠΈΡΠ½ΠΈΠ΅ Π΄Π°Π²Π»Π΅Π½ΠΈΡ ΡΠΎΡΠΌΠΎΠ²Π°Π½ΠΈΡ ΠΊΠΈΡΠΏΠΈΡΠ° Π½Π° ΠΎΠ±ΡΠ΅ΠΌΠ½ΡΡ ΠΌΠ°ΡΡΡ Π±Π»ΠΎΠΊΠ°
Π ΠΈΡΡΠ½ΠΎΠΊ 9 . ΠΠ»ΠΈΡΠ½ΠΈΠ΅ Π΄Π°Π²Π»Π΅Π½ΠΈΡ ΡΠΎΡΠΌΠΎΠ²Π°Π½ΠΈΡ ΠΊΠΈΡΠΏΠΈΡΠ° Π½Π° Π°Π±ΡΠΎΡΠ±ΡΠΈΠΎΠ½Π½ΡΡ ΡΠΏΠΎΡΠΎΠ±Π½ΠΎΡΡΡ ΠΈ IRA
3.10. ΠΠ°ΠΆΡΡΠ°ΡΡΡ ΠΏΠΎΡΠΈΡΡΠΎΡΡΡ, ΠΎΡΠΊΡΡΡΡΠ΅ ΠΏΠΎΡΡ ΠΈ Π½Π΅ΠΏΡΠΎΠ½ΠΈΡΠ°Π΅ΠΌΡΠ΅ ΠΏΠΎΡΡΠΠ»ΠΈΡΠ½ΠΈΠ΅ Π΄Π°Π²Π»Π΅Π½ΠΈΡ ΡΠΎΡΠΌΠΎΠ²Π°Π½ΠΈΡ ΠΊΠΈΡΠΏΠΈΡΠ° Π½Π° ΠΊΠ°ΠΆΡΡΡΡΡΡ ΠΏΠΎΡΠΈΡΡΠΎΡΡΡ, ΠΎΡΠΊΡΡΡΡΠ΅ ΠΏΠΎΡΡ ΠΈ ΠΎΠ±ΡΠ΅ΠΌ Π·Π°ΠΊΡΡΡΡΡ ΠΏΠΎΡ ΠΏΠΎΠΊΠ°Π·Π°Π½ΠΎ Π½Π° Π ΠΈΡΡΠ½ΠΊΠ΅ 10. ΠΠΈΠ΄ΠΈΠΌΠ°Ρ ΠΏΠΎΡΠΈΡΡΠΎΡΡΡ ΡΠΌΠ΅Π½ΡΡΠ°Π»Π°ΡΡ Ρ ΡΠ²Π΅Π»ΠΈΡΠ΅Π½ΠΈΠ΅ΠΌ Π΄Π°Π²Π»Π΅Π½ΠΈΡ. ΠΡΡΠ΅ 2000 ΡΡΠ½ΡΠΎΠ² Π½Π° ΠΊΠ²Π°Π΄ΡΠ°ΡΠ½ΡΠΉ Π΄ΡΠΉΠΌ ΠΈΠ·ΠΌΠ΅Π½Π΅Π½ΠΈΠ΅ Π±ΡΠ»ΠΎ Π½Π΅Π·Π½Π°ΡΠΈΡΠ΅Π»ΡΠ½ΡΠΌ.ΠΠ±ΡΠ΅ΠΌ ΠΎΡΠΊΡΡΡΡΡ ΠΏΠΎΡ ΡΠ°ΠΊΠΆΠ΅ ΡΠ»Π΅Π΄ΠΎΠ²Π°Π» ΡΠΎΠΉ ΠΆΠ΅ ΡΠ΅Π½Π΄Π΅Π½ΡΠΈΠΈ. ΠΠ°ΠΊ Π±Ρ ΡΠΎ Π½ΠΈ Π±ΡΠ»ΠΎ, Π½Π° ΠΎΠ±ΡΠ΅ΠΌ Π½Π΅ΠΏΡΠΎΠ½ΠΈΡΠ°Π΅ΠΌΡΡ ΠΏΠΎΡ Π½Π΅ ΠΏΠΎΠ²Π»ΠΈΡΠ»ΠΎ Π΄Π°Π²Π»Π΅Π½ΠΈΠ΅ ΡΠΎΡΠΌΠΎΠ²Π°Π½ΠΈΡ ΠΊΠΈΡΠΏΠΈΡΠ°. ΠΡΠΎΡ ΡΠ΅Π·ΡΠ»ΡΡΠ°Ρ ΡΠΊΠ°Π·ΡΠ²Π°Π΅Ρ Π½Π° ΡΠΎ, ΡΡΠΎ Π±ΠΎΠ»ΡΡΠ΅Π΅ ΡΠΏΠ»ΠΎΡΠ½Π΅Π½ΠΈΠ΅ ΠΏΡΠΈ ΡΠΎΠΌ ΠΆΠ΅ Π΄Π°Π²Π»Π΅Π½ΠΈΠΈ Π²ΠΎΠ·ΠΌΠΎΠΆΠ½ΠΎ, Π΅ΡΠ»ΠΈ Π·Π°ΠΊΡΡΡΡΠ΅ ΠΏΠΎΡΡ ΠΌΠΎΠ³ΡΡ Π±ΡΡΡ ΡΠΌΠ΅Π½ΡΡΠ΅Π½Ρ ΠΏΠΎΡΡΠ΅Π΄ΡΡΠ²ΠΎΠΌ ΠΊΠΎΠ½ΡΡΠΎΠ»Ρ ΡΠ°Π·ΠΌΠ΅ΡΠ° ΡΠ°ΡΡΠΈΡ.
Π ΠΈΡΡΠ½ΠΎΠΊ 10 . ΠΠ»ΠΈΡΠ½ΠΈΠ΅ Π΄Π°Π²Π»Π΅Π½ΠΈΡ ΡΠΎΡΠΌΠΎΠ²Π°Π½ΠΈΡ ΠΊΠΈΡΠΏΠΈΡΠ° Π½Π° ΠΊΠ°ΠΆΡΡΡΡΡΡ ΠΏΠΎΡΠΈΡΡΠΎΡΡΡ, ΠΎΡΠΊΡΡΡΡΠ΅ ΠΏΠΎΡΡ ΠΈ ΠΎΠ±ΡΠ΅ΠΌ Π½Π΅ΠΏΡΠΎΠ½ΠΈΡΠ°Π΅ΠΌΡΡ ΠΏΠΎΡ
3.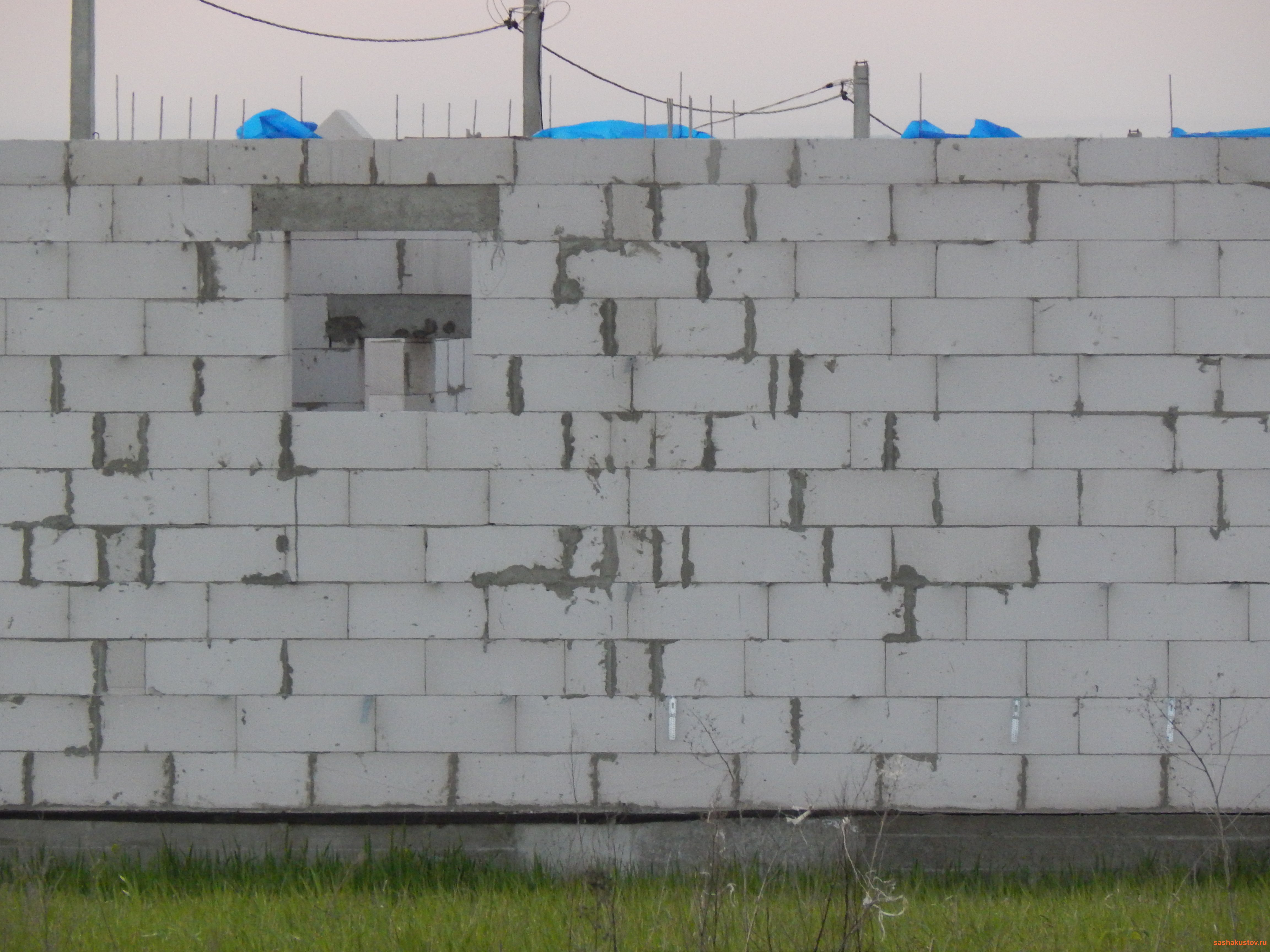
ΠΠΈΡΠΏΠΈΡΠΈ ΠΎΠΏΡΠΈΠΌΠ°Π»ΡΠ½ΠΎΠ³ΠΎ ΡΠΎΡΡΠ°Π²Π° ΠΎΠΊΠ°Π·Π°Π»ΠΈΡΡ Β«Π½Π΅ Π²ΡΡΠ²Π΅ΡΡΠΈΠΌΠΈΒ».ΠΠ°ΠΊ Π²ΠΈΠ΄Π½ΠΎ Π½Π° Π ΠΈΡΡΠ½ΠΊΠ΅ 11, Π½Π° ΠΏΠΎΠ²Π΅ΡΡ Π½ΠΎΡΡΠΈ ΠΈΡΠΏΡΡΠ°Π½Π½ΠΎΠ³ΠΎ ΠΊΠΈΡΠΏΠΈΡΠ° Π½Π΅ Π±ΡΠ»ΠΎ ΠΎΠ±Π½Π°ΡΡΠΆΠ΅Π½ΠΎ ΡΠΎΠ»ΠΈ.
Π ΠΈΡΡΠ½ΠΎΠΊ 11 . ΠΡΠΏΡΡΠ°Π½ΠΈΠ΅ Π²ΡΡΡΡ Π°Π½ΠΈΡ ΠΊΠΈΡΠΏΠΈΡΠ° ΠΎΠΏΡΠΈΠΌΠ°Π»ΡΠ½ΠΎΠ³ΠΎ ΡΠΎΡΡΠ°Π²Π°
3.12. Π Π°Π΄ΠΈΠΎΠ°ΠΊΡΠΈΠ²Π½ΠΎΡΡΡΠ Π°Π΄ΠΈΠΎΠ°ΠΊΡΠΈΠ²Π½ΠΎΡΡΡ ΡΠ΅Π·ΠΈΡ-137 Π±ΡΠ»Π° Π½ΠΈΠΆΠ΅ ΠΏΡΠ΅Π΄Π΅Π»Π° ΠΎΠ±Π½Π°ΡΡΠΆΠ΅Π½ΠΈΡ ΡΡΡΠ°Π½ΠΎΠ²ΠΊΠΈ, Ρ.Π΅. Π½ΠΈΠΆΠ΅ 1,54 ΠΠΊ / ΠΊΠ³. Π’Π°ΠΊ ΡΡΠΎ ΡΡΠΈ ΠΊΠΈΡΠΏΠΈΡΠΈ Π½Π΅ ΠΏΡΠ΅Π΄ΡΡΠ°Π²Π»ΡΡΡ ΠΎΠΏΠ°ΡΠ½ΠΎΡΡΠΈ ΠΊΠ°ΠΊ ΠΈΡΡΠΎΡΠ½ΠΈΠΊ ΡΠ°Π΄ΠΈΠΎΠ°ΠΊΡΠΈΠ²Π½ΠΎΡΡΠΈ.
3,13. ΠΠ»ΠΈΡΠ½ΠΈΠ΅ ΠΏΡΠΎΡΠ΅ΡΡΠ° ΠΎΡΠ²Π΅ΡΠΆΠ΄Π΅Π½ΠΈΡΠΠ±ΡΠ°Π·Π΅Ρ T17 Π±ΡΠ» ΠΎΡΠ²Π΅ΡΠΆΠ΄Π΅Π½ Π½Π° Π½Π΅ΠΏΠΎΠ΄Π²ΠΈΠΆΠ½ΠΎΠΌ Π²ΠΎΠ·Π΄ΡΡ Π΅. ΠΠ±ΡΠ°Π·ΡΡ Π’18, Π’19 ΠΈ Π’20 ΠΎΠ±ΡΠ°Π±Π°ΡΡΠ²Π°Π»ΠΈ Π²ΠΎΠ΄Π½ΡΠΌ ΡΠΏΡΠ΅Π΅ΠΌ Π΄Π²Π° ΡΠ°Π·Π° Π² Π΄Π΅Π½Ρ, Π΄Π΅ΡΠΆΠ° ΠΎΠ±ΡΠ°Π·Π΅Ρ ΠΏΠΎΠ΄ Π²Π»Π°ΠΆΠ½ΠΎΠΉ ΡΠΊΠ°Π½ΡΡ ΠΈ ΠΏΠΎΠ³ΡΡΠΆΠ°Ρ ΠΎΠ±ΡΠ°Π·Π΅Ρ ΠΏΠΎΠ΄ Π²ΠΎΠ΄Ρ ΡΠΎΠΎΡΠ²Π΅ΡΡΡΠ²Π΅Π½Π½ΠΎ.ΠΠ°ΠΊΡΠΈΠΌΠ°Π»ΡΠ½Π°Ρ ΠΏΡΠΎΡΠ½ΠΎΡΡΡ Π½Π° ΡΠΆΠ°ΡΠΈΠ΅ 442,96 ΠΊΠ³ / ΡΠΌ 2 Π±ΡΠ»Π° Π½Π°ΠΉΠ΄Π΅Π½Π° Π΄Π»Ρ ΠΎΠ±ΡΠ°Π·ΡΠ° T18 (ΡΠΈΡΡΠ½ΠΎΠΊ 12).
Π ΠΈΡΡΠ½ΠΎΠΊ 12 . ΠΠ»ΠΈΡΠ½ΠΈΠ΅ ΠΏΡΠΎΡΠ΅ΡΡΠ° ΠΎΡΠ²Π΅ΡΠΆΠ΄Π΅Π½ΠΈΡ Π½Π° ΠΏΡΠΎΡΠ½ΠΎΡΡΡ Π½Π° ΡΠΆΠ°ΡΠΈΠ΅
3,14. ΠΡΡΠ΅ΠΊΡ ΠΏΠ΅ΡΠΈΠΎΠ΄Π° ΠΎΡΠ²Π΅ΡΠΆΠ΄Π΅Π½ΠΈΡ ΠΠ΄ΠΈΠ½ ΠΊΠΎΠΌΠΏΠ»Π΅ΠΊΡ ΠΊΠΈΡΠΏΠΈΡΠ΅ΠΉ Π²ΡΠ΄Π΅ΡΠΆΠΈΠ²Π°Π»ΠΈ Π² ΡΠ΅ΡΠ΅Π½ΠΈΠ΅ ΡΠ΅ΠΌΠΈ Π΄Π½Π΅ΠΉ Π½Π° Π²ΠΎΠ·Π΄ΡΡ
Π΅; ΠΎΠ΄ΠΈΠ½ ΠΏΠΎΠ΄Ρ
ΠΎΠ΄ — ΠΏΡΡΡ Π½Π΅Π΄Π΅Π»Ρ Π½Π° Π²ΠΎΠ·Π΄ΡΡ
Π΅, Π΄ΡΡΠ³ΠΎΠΉ — ΠΏΠ΅ΡΠ²ΡΠ΅ ΡΠ΅ΡΡΡΠ΅ Π½Π΅Π΄Π΅Π»ΠΈ Π² Π²ΠΎΠ΄Π΅, Π° Π·Π°ΡΠ΅ΠΌ — ΠΎΠ΄Π½Π° Π½Π΅Π΄Π΅Π»Ρ Π½Π° Π²ΠΎΠ·Π΄ΡΡ
Π΅. ΠΠ°ΠΊΡΠΈΠΌΠ°Π»ΡΠ½Π°Ρ ΠΏΡΠΎΡΠ½ΠΎΡΡΡ 877,36 ΠΊΠ³ / ΡΠΌ 2 Π±ΡΠ»Π° ΠΎΠ±Π½Π°ΡΡΠΆΠ΅Π½Π° Π΄Π»Ρ ΠΊΠΈΡΠΏΠΈΡΠ΅ΠΉ, ΡΡΠΎΡΠΌΠΈΡΠΎΠ²Π°Π½Π½ΡΡ
ΠΏΠΎΠ΄ Π΄Π°Π²Π»Π΅Π½ΠΈΠ΅ΠΌ 3000 ΡΡΠ½ΡΠΎΠ² Π½Π° ΠΊΠ²Π°Π΄ΡΠ°ΡΠ½ΡΠΉ Π΄ΡΠΉΠΌ ΠΈ Π²ΡΠ΄Π΅ΡΠΆΠ°Π½Π½ΡΡ
Π² Π²ΠΎΠ΄Π΅ Π² ΡΠ΅ΡΠ΅Π½ΠΈΠ΅ ΡΠ΅ΡΡΡΠ΅Ρ
Π½Π΅Π΄Π΅Π»Ρ, Π° Π·Π°ΡΠ΅ΠΌ ΠΎΠ΄Π½ΠΎΠΉ Π½Π΅Π΄Π΅Π»ΠΈ Π½Π° Π²ΠΎΠ·Π΄ΡΡ
Π΅.FTIR-Π°Π½Π°Π»ΠΈΠ· ΠΏΠΎΠΊΠ°Π·Π°Π» (ΡΠΈΡ. 14), ΡΡΠΎ, ΠΊΠΎΠ³Π΄Π° ΠΊΠΈΡΠΏΠΈΡΠΈ Π²ΡΠ΄Π΅ΡΠΆΠΈΠ²Π°Π»ΠΈΡΡ Π² Π²ΠΎΠ΄Π΅ Π² ΡΠ΅ΡΠ΅Π½ΠΈΠ΅ ΡΠ΅ΡΡΡΠ΅Ρ
Π½Π΅Π΄Π΅Π»Ρ, Π° Π·Π°ΡΠ΅ΠΌ ΠΎΠ΄Π½Π° Π½Π΅Π΄Π΅Π»Ρ Π½Π° Π²ΠΎΠ·Π΄ΡΡ
Π΅ Π²ΠΌΠ΅ΡΡΠΎ ΠΏΡΡΠΈ Π½Π΅Π΄Π΅Π»Ρ Π½Π° Π²ΠΎΠ·Π΄ΡΡ
Π΅, Π±ΠΎΠ»Π΅Π΅ ΠΏΡΠΎΡΠ½Π°Ρ ΠΌΠ΅ΠΆΠΌΠΎΠ»Π΅ΠΊΡΠ»ΡΡΠ½Π°Ρ ΡΠ²ΡΠ·Ρ ΠΠ-Π ΡΡΠ°Π»Π° ΠΏΡΠ΅ΠΎΠ±Π»Π°Π΄Π°ΡΡΠ΅ΠΉ Π½Π°Π΄ Π±ΠΎΠ»Π΅Π΅ ΡΠ»Π°Π±ΠΎΠΉ Π²Π½ΡΡΡΠΈΠΌΠΎΠ»Π΅ΠΊΡΠ»ΡΡΠ½ΠΎΠΉ ΡΠ²ΡΠ·ΡΡ ΠΠ.
Π ΠΈΡΡΠ½ΠΎΠΊ 13 . ΠΠ»ΠΈΡΠ½ΠΈΠ΅ ΠΏΡΠΎΡΠ΅ΡΡΠ° ΠΎΡΠ²Π΅ΡΠΆΠ΄Π΅Π½ΠΈΡ Π½Π° ΠΏΡΠΎΡΠ½ΠΎΡΡΡ Π½Π° ΡΠΆΠ°ΡΠΈΠ΅
Π ΠΈΡΡΠ½ΠΎΠΊ 14 . FTIR-Π°Π½Π°Π»ΠΈΠ· ΠΊΠΈΡΠΏΠΈΡΠ΅ΠΉ, ΠΎΡΠ²Π΅ΡΠΆΠ΄Π΅Π½Π½ΡΡ ΠΏΡΠΈ ΡΠ°Π·Π»ΠΈΡΠ½ΡΡ ΡΡΠ»ΠΎΠ²ΠΈΡΡ ΠΎΡΠ²Π΅ΡΠΆΠ΄Π΅Π½ΠΈΡ
4.ΠΡΠ²ΠΎΠ΄Ρ
ΠΠ· ΡΡΠΎΠ³ΠΎ ΠΈΡΡΠ»Π΅Π΄ΠΎΠ²Π°Π½ΠΈΡ ΠΌΠΎΠΆΠ½ΠΎ ΡΠ΄Π΅Π»Π°ΡΡ ΡΠ»Π΅Π΄ΡΡΡΠΈΠ΅ ΠΎΡΠ½ΠΎΠ²Π½ΡΠ΅ Π²ΡΠ²ΠΎΠ΄Ρ:
β’ ΠΠΏΡΠΈΠΌΠ°Π»ΡΠ½ΡΠΌ ΡΠΎΡΡΠ°Π²ΠΎΠΌ Π½Π΅ΠΎΠ±ΠΎΠΆΠΆΠ΅Π½Π½ΡΡ
ΠΊΠΈΡΠΏΠΈΡΠ΅ΠΉ ΠΈΠ· Π·ΠΎΠ»Ρ-ΡΠ½ΠΎΡΠ°, ΡΠΈΠ»ΠΈΠΊΠ°ΡΠ°, ΠΈΠ·Π²Π΅ΡΡΠΈ ΠΈ Π³ΠΈΠΏΡΠ° Π±ΡΠ»ΠΎ 55 ΠΏΡΠΎΡΠ΅Π½ΡΠΎΠ² Π»Π΅ΡΡΡΠ΅ΠΉ Π·ΠΎΠ»Ρ, 30 ΠΏΡΠΎΡΠ΅Π½ΡΠΎΠ² ΠΏΠ΅ΡΠΊΠ°, 15 ΠΏΡΠΎΡΠ΅Π½ΡΠΎΠ² ΠΈΠ·Π²Π΅ΡΡΠΈ ΠΈ 14 ΠΏΡΠΎΡΠ΅Π½ΡΠΎΠ² Π³ΠΈΠΏΡΠ°, Π° ΠΎΠΏΡΠΈΠΌΠ°Π»ΡΠ½ΠΎΠ΅ Π΄Π°Π²Π»Π΅Π½ΠΈΠ΅ ΡΠΎΡΠΌΠΎΠ²Π°Π½ΠΈΡ ΠΊΠΈΡΠΏΠΈΡΠ° ΡΠΎΡΡΠ°Π²Π»ΡΠ»ΠΎ 3000 ΡΡΠ½ΡΠΎΠ² Π½Π° ΠΊΠ²Π°Π΄ΡΠ°ΡΠ½ΡΠΉ Π΄ΡΠΉΠΌ.
β’ ΠΠΎΠ²ΡΡΠ΅Π½ΠΈΠ΅ Π΄Π°Π²Π»Π΅Π½ΠΈΡ ΡΠΎΡΠΌΠΎΠ²Π°Π½ΠΈΡ ΠΊΠΈΡΠΏΠΈΡΠ° ΠΏΠΎΠΊΠ°Π·Π°Π»ΠΎ ΡΠ²Π΅Π»ΠΈΡΠ΅Π½ΠΈΠ΅ ΠΏΡΠΎΡΠ½ΠΎΡΡΠΈ Π½Π° ΡΠΆΠ°ΡΠΈΠ΅ ΠΈ ΡΠ΄Π΅Π»ΡΠ½ΠΎΠ³ΠΎ ΠΎΠ±ΡΠ΅ΠΌΠ½ΠΎΠ³ΠΎ Π²Π΅ΡΠ°, Π° ΡΠ°ΠΊΠΆΠ΅ ΡΠ½ΠΈΠΆΠ΅Π½ΠΈΠ΅ IRA, Π°Π±ΡΠΎΡΠ±ΡΠΈΠΎΠ½Π½ΠΎΠΉ ΡΠΏΠΎΡΠΎΠ±Π½ΠΎΡΡΠΈ, ΠΊΠ°ΠΆΡΡΠ΅ΠΉΡΡ Π΅ΠΌΠΊΠΎΡΡΠΈ ΠΈ ΠΎΠ±ΡΠ΅ΠΌΠ° ΠΎΡΠΊΡΡΡΡΡ ΠΏΠΎΡ. ΠΡΠ»ΠΎ ΠΎΠ±Π½Π°ΡΡΠΆΠ΅Π½ΠΎ, ΡΡΠΎ ΠΎΠ±ΡΠ΅ΠΌ Π½Π΅ΠΏΡΠΎΠ½ΠΈΡΠ°Π΅ΠΌΡΡ ΠΏΠΎΡ ΠΏΡΠ°ΠΊΡΠΈΡΠ΅ΡΠΊΠΈ Π½Π΅ Π·Π°Π²ΠΈΡΠΈΡ ΠΎΡ Π΄Π°Π²Π»Π΅Π½ΠΈΡ ΡΠΎΡΠΌΠΎΠ²Π°Π½ΠΈΡ ΠΊΠΈΡΠΏΠΈΡΠ°.
β’ ΠΠ»Ρ ΠΎΠΏΡΠΈΠΌΠ°Π»ΡΠ½ΠΎΠ³ΠΎ ΡΠΎΡΡΠ°Π²Π° ΠΈ Π΄Π°Π²Π»Π΅Π½ΠΈΡ ΠΊΠΈΡΠΏΠΈΡ ΠΎΠ±Π»Π°Π΄Π°Π΅Ρ ΡΠ»Π΅Π΄ΡΡΡΠΈΠΌΠΈ ΡΠ²ΠΎΠΉΡΡΠ²Π°ΠΌΠΈ:
1 ΠΠ΅Π· ΡΡΠ°Π΄ΠΊΠΈ.
2 ΠΠ±ΡΠ΅ΠΌΠ½ΡΠΉ Π²Π΅Ρ ΡΡΡΡΠΎΠΉΡΡΠ²Π°: 1,81 Π³ / ΡΠΌ 3 .
3 ΠΠ°ΡΠ°Π»ΡΠ½Π°Ρ ΡΠΊΠΎΡΠΎΡΡΡ Π°Π±ΡΠΎΡΠ±ΡΠΈΠΈ (IRA): 14,84 Π³. Π’Π°ΠΊ ΡΡΠΎ ΡΡΠΈ ΠΊΠΈΡΠΏΠΈΡΠΈ Π½Π΅ Π½ΡΠΆΠ½ΠΎ ΡΠΌΠ°ΡΠΈΠ²Π°ΡΡ ΠΏΠ΅ΡΠ΅Π΄ ΠΊΠ»Π°Π΄ΠΊΠΎΠΉ.
4 ΠΠΎΠ³Π»ΠΎΡΠ°ΡΡΠ°Ρ ΡΠΏΠΎΡΠΎΠ±Π½ΠΎΡΡΡ: 11,58%.
5 ΠΠΈΠ΄ΠΈΠΌΠ°Ρ ΠΏΠΎΡΠΈΡΡΠΎΡΡΡ: 20,99%.
6 ΠΠ±ΡΠ΅ΠΌ ΠΎΡΠΊΡΡΡΡΡ ΠΏΠΎΡ: 9,23 ΡΠΌ 3 .
7 ΠΠ±ΡΠ΅ΠΌ Π½Π΅ΠΏΡΠΎΠ½ΠΈΡΠ°Π΅ΠΌΡΡ ΠΏΠΎΡ: 34,74 ΡΠΌ 3 .
8 ΠΠ»Ρ ΠΎΠΏΡΠΈΠΌΠ°Π»ΡΠ½ΠΎΠ³ΠΎ ΡΠΎΡΡΠ°Π²Π° ΠΈ Π΄Π°Π²Π»Π΅Π½ΠΈΡ ΠΊΠΈΡΠΏΠΈΡΠΈ, ΠΎΡΠ²Π΅ΡΠΆΠ΄Π°Π΅ΠΌΡΠ΅ ΠΏΠΎΠ΄ ΡΡΡΡΠ΅ΠΉ Π²ΠΎΠ΄Ρ Π΄Π²Π° ΡΠ°Π·Π° Π² Π΄Π΅Π½Ρ, ΠΏΠΎΠΊΠ°Π·Π°Π»ΠΈ ΠΌΠ°ΠΊΡΠΈΠΌΠ°Π»ΡΠ½ΡΡ ΠΏΡΠΎΡΠ½ΠΎΡΡΡ Π½Π° ΡΠΆΠ°ΡΠΈΠ΅ 442,96 Π³ / ΡΠΌ 2 .
ΠΠ°ΠΊΠΎΠ½Π΅Ρ, ΠΊΠΈΡΠΏΠΈΡΠΈ, ΡΡΠΎΡΠΌΠΈΡΠΎΠ²Π°Π½Π½ΡΠ΅ ΠΏΠΎΠ΄ Π΄Π°Π²Π»Π΅Π½ΠΈΠ΅ΠΌ 3000 ΡΡΠ½ΡΠΎΠ² Π½Π° ΠΊΠ²Π°Π΄ΡΠ°ΡΠ½ΡΠΉ Π΄ΡΠΉΠΌ, ΠΏΠΎΠΊΠ°Π·Π°Π»ΠΈ ΠΌΠ°ΠΊΡΠΈΠΌΠ°Π»ΡΠ½ΡΡ ΠΏΡΠΎΡΠ½ΠΎΡΡΡ 877,36 ΠΊΠ³ / ΡΠΌ 2 ΠΏΡΠΈ ΠΎΡΠ²Π΅ΡΠΆΠ΄Π΅Π½ΠΈΠΈ Π² Π²ΠΎΠ΄Π΅ Π² ΡΠ΅ΡΠ΅Π½ΠΈΠ΅ ΡΠ΅ΡΡΡΠ΅Ρ
Π½Π΅Π΄Π΅Π»Ρ Ρ ΠΏΠΎΡΠ»Π΅Π΄ΡΡΡΠ΅ΠΉ Π½Π΅Π΄Π΅Π»Π΅ΠΉ Π½Π° Π²ΠΎΠ·Π΄ΡΡ
Π΅, Π° ΠΏΡΠΎΡΠ½ΠΎΡΡΡ ΠΎΠΏΡΠ΅Π΄Π΅Π»ΡΠ»Π°ΡΡ ΡΡΠ΅ΠΏΠ΅Π½ΡΡ ΠΌΠ΅ΠΆΠΌΠΎΠ»Π΅ΠΊΡΠ»ΡΡΠ½ΠΎΠΉ ΡΠ²ΡΠ·ΠΈ ΠΠ-Π.
ΠΠ΅ΡΠΌΠΎΡΡΡ Π½Π° ΡΠΎ, ΡΡΠΎ Π΄ΠΎ ΡΠΎΠ³ΠΎ, ΠΊΠ°ΠΊ Π±ΡΠ΄Π΅Ρ ΡΠ΄Π΅Π»Π°Π½ ΠΎΠΊΠΎΠ½ΡΠ°ΡΠ΅Π»ΡΠ½ΡΠΉ ΠΊΠΎΠΌΠΌΠ΅Π½ΡΠ°ΡΠΈΠΉ, ΠΏΠΎΡΡΠ΅Π±ΡΡΡΡΡ Π΄Π°Π»ΡΠ½Π΅ΠΉΡΠΈΠ΅ ΠΈΡΡΠ»Π΅Π΄ΠΎΠ²Π°Π½ΠΈΡ, ΠΊΠΈΡΠΏΠΈΡΠΈ ΠΈΠ· Π·ΠΎΠ»Ρ-ΡΠ½ΠΎΡΠ°, ΡΠΈΠ»ΠΈΠΊΠ°ΡΠ°, ΠΈΠ·Π²Π΅ΡΡΠ½ΡΠΊΠ° ΠΈ Π³ΠΈΠΏΡΠ°, ΠΏΡΠΎΠΈΠ·Π²Π΅Π΄Π΅Π½Π½ΡΠ΅ Π² ΡΡΠΎΠΌ ΠΈΡΡΠ»Π΅Π΄ΠΎΠ²Π°Π½ΠΈΠΈ, ΠΊΠ°ΠΆΡΡΡΡ ΠΏΠΎΠ΄Ρ ΠΎΠ΄ΡΡΠΈΠΌΠΈ Π΄Π»Ρ ΠΈΡΠΏΠΎΠ»ΡΠ·ΠΎΠ²Π°Π½ΠΈΡ Π² ΠΊΠ°ΡΠ΅ΡΡΠ²Π΅ ΡΡΡΠΎΠΈΡΠ΅Π»ΡΠ½ΠΎΠ³ΠΎ ΠΌΠ°ΡΠ΅ΡΠΈΠ°Π»Π°.ΠΡΠΎΠΈΠ·Π²ΠΎΠ΄ΡΡΠ²ΠΎ ΡΡΠΎΠ³ΠΎ ΡΠΈΠΏΠ° ΠΊΠΈΡΠΏΠΈΡΠ° (Π΅ΡΠ»ΠΈ ΡΡΠΎ ΡΠ΅Ρ Π½ΠΈΡΠ΅ΡΠΊΠΈ ΠΈ ΠΊΠΎΠΌΠΌΠ΅ΡΡΠ΅ΡΠΊΠΈ ΠΆΠΈΠ·Π½Π΅ΡΠΏΠΎΡΠΎΠ±Π½ΠΎ), Π±Π΅Π·ΡΡΠ»ΠΎΠ²Π½ΠΎ, Π±ΡΠ΄Π΅Ρ ΡΠΏΠΎΡΠΎΠ±ΡΡΠ²ΠΎΠ²Π°ΡΡ ΠΏΠ΅ΡΠ΅ΡΠ°Π±ΠΎΡΠΊΠ΅ Π»Π΅ΡΡΡΠ΅ΠΉ Π·ΠΎΠ»Ρ ΠΈ, ΡΠ»Π΅Π΄ΠΎΠ²Π°ΡΠ΅Π»ΡΠ½ΠΎ, ΠΌΠΈΠ½ΠΈΠΌΠΈΠ·ΠΈΡΠΎΠ²Π°ΡΡ Π½Π΅Π³Π°ΡΠΈΠ²Π½ΠΎΠ΅ Π²ΠΎΠ·Π΄Π΅ΠΉΡΡΠ²ΠΈΠ΅ Π½Π° ΠΎΠΊΡΡΠΆΠ°ΡΡΡΡ ΡΡΠ΅Π΄Ρ.
Π‘ΠΏΠΈΡΠΎΠΊ Π»ΠΈΡΠ΅ΡΠ°ΡΡΡΡ
[1] | Goni, S. Guerrero, A. Luxan, M.P. ΠΈ Macias, A. 2003. ΠΠΊΡΠΈΠ²Π°ΡΠΈΡ ΠΏΡΡΡΠΎΠ»ΠΎΠ½ΠΎΠ²ΠΎΠΉ ΡΠ΅Π°ΠΊΡΠΈΠΈ Π»Π΅ΡΡΡΠ΅ΠΉ Π·ΠΎΠ»Ρ Π² Π³ΠΈΠ΄ΡΠΎΡΠ΅ΡΠΌΠ°Π»ΡΠ½ΡΡ ΡΡΠ»ΠΎΠ²ΠΈΡΡ , Cem Concr Res , Vol. 33, ΡΡΡ 1399-405. | ||
Π Π°ΡΡΠΈΠΊΡΠ»Π΅ | CrossRef | ||
[2] | Klimesch, D.![]() | ||
Π ΡΡΠ°ΡΡΠ΅ | |||
[3] | ΠΠ°ΠΉΠΊΠ°Π» ΠΈ ΠΠΎΠ²Π΅Π½, Π.Π. 2000. Π£ΡΠΈΠ»ΠΈΠ·Π°ΡΠΈΡ Π»Π΅ΡΡΡΠ΅ΠΉ Π·ΠΎΠ»Ρ Π² ΠΏΡΠΎΡΠ΅ΡΡΠ΅ Π³ΡΠ°Π½ΡΠ»ΠΈΡΠΎΠ²Π°Π½ΠΈΡ; ΡΠ΅ΠΎΡΠΈΡ, ΠΎΠ±Π»Π°ΡΡΠΈ ΠΏΡΠΈΠΌΠ΅Π½Π΅Π½ΠΈΡ ΠΈ ΡΠ΅Π·ΡΠ»ΡΡΠ°ΡΡ ΠΈΡΡΠ»Π΅Π΄ΠΎΠ²Π°Π½ΠΈΠΉ, Resour Conserv Recy, Vol.30, Ρ. 59-77. | ||
Π ΡΡΠ°ΡΡΠ΅ | CrossRef | ||
[4] | Iyer, R.S. ΠΈ Π‘ΠΊΠΎΡΡ, ΠΠΆ. 2001. ΠΠ΅ΡΡΡΠ°Ρ Π·ΠΎΠ»Π° ΡΠ»Π΅ΠΊΡΡΠΎΡΡΠ°Π½ΡΠΈΠΈ — ΠΎΠ±Π·ΠΎΡ ΠΈΡΠΏΠΎΠ»ΡΠ·ΠΎΠ²Π°Π½ΠΈΡ Π΄ΠΎΠ±Π°Π²Π»Π΅Π½Π½ΠΎΠΉ ΡΡΠΎΠΈΠΌΠΎΡΡΠΈ Π²Π½Π΅ ΡΠ΅ΡΡΡΡΠΎΠ² ΡΡΡΠΎΠΈΡΠ΅Π»ΡΠ½ΠΎΠΉ ΠΈΠ½Π΄ΡΡΡΡΠΈΠΈ, Conserv Recy , Vol. 31, ΡΡΡ. 217-28. | ||
Π Π°ΡΡΠΈΠΊΡΠ»Π΅ | CrossRef | ||
[5] | ΠΠΈΠΌΡΠ°ΠΊΡΠ°, Π.![]() | ||
Π ΡΡΠ°ΡΡΠ΅ | |||
[6] | Poon, CS Kou, SC ΠΈ Lam, L. 2002. ΠΡΠΏΠΎΠ»ΡΠ·ΠΎΠ²Π°Π½ΠΈΠ΅ ΠΏΠ΅ΡΠ΅ΡΠ°Π±ΠΎΡΠ°Π½Π½ΡΡ Π·Π°ΠΏΠΎΠ»Π½ΠΈΡΠ΅Π»Π΅ΠΉ Π² ΡΠΎΡΠΌΠΎΠ²Π°Π½Π½ΡΡ Π±Π΅ΡΠΎΠ½Π½ΡΡ ΠΊΠΈΡΠΏΠΈΡΠ°Ρ ΠΈ Π±Π»ΠΎΠΊΠ°Ρ , Constr Build Mater , Vol.Π‘. 281-9. | ||
Π Π°ΡΡΠΈΠΊΡΠ»Π΅ | |||
[7] | Π’ΠΎΠΊΡΠ°ΠΉ, Π.Π‘. ΠΈ ΠΡΠΈΠ½, Π. 1991. ΠΠ΅Ρ Π°Π½ΠΈΡΠ΅ΡΠΊΠ°Ρ ΠΏΡΠΎΡΠ½ΠΎΡΡΡ ΠΈ Π²ΠΎΠ΄ΠΎΠΏΠΎΠ³Π»ΠΎΡΠ°ΡΡΠΈΠ΅ ΡΠ²ΠΎΠΉΡΡΠ²Π° Π°Π²ΡΠΎΠΊΠ»Π°Π²Π½ΠΎΠ³ΠΎ ΠΊΠΈΡΠΏΠΈΡΠ° ΠΈΠ· Π·ΠΎΠ»Ρ-ΡΠ½ΠΎΡΠ°, TMMOB, ΠΡΠ±Π»ΠΈΠΊΠ°ΡΠΈΡ ΠΠ°Π»Π°ΡΡ ΠΈΠ½ΠΆΠ΅Π½Π΅ΡΠΎΠ²-ΡΡΡΠΎΠΈΡΠ΅Π»Π΅ΠΉ , Vol. 1. Π‘. 385-394. | ||
Π ΡΡΠ°ΡΡΠ΅ | |||
[8] | Cicek, T.![]() |