Технология производства цемента — материалы для производства, виды и способы производства, сырье, добавки, отходы
Дата публикации: 14.02.2019 11:08
Являясь одним из самых распространенных стройматериалов, цемент в современном строительстве применяется или самостоятельно, или как базовый компонент растворных, отделочных и бетонных смесей. Промышленная технология производства цемента позволяет получить гидравлически вяжущий материал, превращающийся в процессе затвердевания в камневидное тело с гарантированными прочностью, водостойкостью и долговечностью.
Основные материалы для производства цемента — клинкер и гипс. В зависимости от марки и предназначения стройматериала в сухую смесь могут также добавляться глина, доменный шлак, вулканические породы и другие компоненты, воздействующие на рабочие характеристики конечного продукта.
Оборудование, используемое в цементном производстве
Различные виды производства цемента требуют собственных технических средств. При этом к обязательным технологическим элементам производственной линии цементного завода следует отнести:
- барабанную печь;
- установку для предварительного нагрева исходного сырья;
- мельницу;
- вальцы, охладитель и сушилку;
- сепаратор и пылеуловитель;
- оборудование предварительной гомогенизации;
- дробилку.
В процессе массового производства материала также не обойтись без транспортера и машины для упаковки готового продукта.
Разновидности и марки цемента
В зависимости от того, какое используется для производства цемента сырье, равно как и какой набор добавок вводится в сухую смесь, описываемый стройматериал может относиться к одной из классификационных групп:
- Портландцемент.
Самая популярная общестроительная марка, включающая клинкер и гипс. Помол мелкий. - Белый цемент.
Производится из мелкомолотого клинкера без окислов железа. Служит для декоративных целей. - Шлаковый.
Включает измельченный доменный шлак, активаторы и минеральные добавки. Примечателен повышенной прочностью, благодаря чему используется в подземных/подводных конструкциях. - Глиноземистый.
Удобен при строительных работах в зимний период и при монтаже жаропрочных стройконструкций.
Из специальных марок материала применение находят расширяющийся, быстротвердеющий, гидрофобный, тампонажный (для заделки скважин) и пуццолановый (для водяных емкостей) цемент.
Марка материала определяется пределом прочности такового на сжатие, выраженным по старому ГОСТу в кг на см.кв.: М200-М600 или по обновленному стандарту — в МПа (мегапаскалях): 20-60 МПа соответственно.
Изготовление портландцемента
Производство материала разделяют на две укрупненных стадии, в свою очередь состоящие из отдельных этапов.
Первая стадия — получение клинкера, являющегося основой цементной смеси. После добычи желтовато-зеленого известняка в процессе разработки известняковых месторождений, первично раздробленное сырье проходит этапы сушки и смешивания с некоторыми составляющими. Подготовленный таким образом исходный материал подвергается обжигу, результатом которого является собственно портландцементный клинкер.
На второй стадии образовавшийся клинкер измельчается до порошкообразного вида, при этом в него вносятся гипс и другие необходимые для производства цемента добавки. В итоге образуется сыпучая однородная масса. Технология обеих стадий процесса для разных видов сырья и различных состояний такового может различаться. Исходя из этого, в промышленности используются сухой, мокрый и комбинированный способы производства цемента.
Сухой способ предполагает предварительное смешивание известняка и глины в машине для дробления/сушки и дальнейшее перемалывание компонентов в мельнице до однородного состояния сырьевой муки. После специального смешивания, называемого гомогенизацией, такая мука преобразуется в гомогенизационныйсилос, направляемый на обжиг. Прошедший обжиг силос вновь перемалывается с добавлением гипса. Готовый товарный продукт собирается в бункере для хранения или расфасовки.
При мокрой технологии сухие компоненты (известняк, глина, железосодержащие добавки) загружаются в дробилку, где смешиваются и дробятся до однородного состояния. После этого они поступают в мельницу, в которой после добавления воды проходят операцию мокрого помола с корректировкой в шламбассейне. Образовавшийся полуфабрикат (шлам) направляется на обжиг во вращающуюся печь. Дальнейшие этапы процесса аналогичны операциям при сухом способе. Ныне подобная мокрая технология считается устаревшей, поскольку сухой метод обеспечивает заметную экономию топлива, снижает трудовые затраты и дает более качественную продукцию.
Комбинированный способ не имеет жесткой технологической регламентации и зависит, прежде всего, от технических возможностей конкретного производителя. В одном случае сначала идет безводная стадия (при приготовлении смеси), затем — мокрая. В другом — сперва готовится водная суспензия, проходящая далее последовательные операции классического сухого метода.
Твердые отходы производства цемента, главным образом цементная пыль, относятся к группе неопасных для человека и допускаются к повторному использованию.
На что влияет технология производства цемента?
Цемент – уникальное сырье, которое уже много лет используется как самостоятельно, так и для создания разнообразных строительных смесей. Измельченный материал отличается по составу и стоимости, но создается с помощью давно известных технологий. Методов несколько, они меняются и комбинируются в зависимости от производственных целей. Но каждый вариант позволяет создать качественный цемент, который с успехом используется в строительстве.
Несмотря на десятки видов разнообразных цементных смесей, существуют базовые элементы, которые присутствуют в каждой из них. Основа материала – клинкер, который состоит из глиняных пород. Также в цементе присутствуют добавки, напрямую влияющие на свойства и характеристики раствора.
Технология производства тоже отражается на качестве. Способ производства может изменить:
- Уровень зернистости, что сказывается на прочности и скорости застывания;
- Степень пластичности, то есть особенности взаимодействия основы и пластифицирующих добавок;
- Скорость выделения тепла, то есть уровень тепловыделения при внесении определенных компонентов.
Даже при том, что производственная сфера развивается быстрыми шагами, методы изготовления цемента уже много лет остаются неизменными. Стандартные технологии полностью устраивают девелоперов и строителей, ведь смесь получается долговечной, прочной, качественной и сравнительно недорогой.
Основные производственные этапы
На начальном этапе производства выполняется изготовление клинкера, а также измельчение компонентов. Клинкер – основа цементной смеси, состоит из извести и глины, то есть имеет природный характер. Для некоторых видов цемента глину заменяют доломитом или пеплом, но в любом случае обжигают в печах.
Перед обжигом выполняется тщательное перемешивание клинкерных элементов, они вступают во взаимодействие друг с другом и образуют фракции размером с орех, а затем еще раз измельчаются.
Популярные технологии
Наиболее известны и востребованы три способа производства: сухой, мокрый и комбинированный. Подбор технологии осуществляется каждым предприятием в индивидуальном порядке, ведь производственное оборудование часто подразумевает использование только одного или двух способов, к примеру:
- сухого метода, который используется практически повсеместно, ведь считается самым выгодным.
Название говорит само за себя: все компоненты остаются сухими. Сырье высушивается, дробится до порошка, смешивается и приобретает однородный вид. После обжига смесь принято называть клинкер. Последний этап сухой технологии – внесение добавок и повторное измельчение;
- мокрого метода. В этом случае в смесь из карбонатного мела, силикатной глины и конверторного шлама добавляется жидкость. Это более трудозатратный вариант, поэтому используется нечасто. После измельчения состав приобретает влажность от 30 до 50 %, затем обжигается и измельчается в порошок повторно.
- Комбинированного метода, при котором измельченный состав принудительно увлажняется, а затем обезвоживается. Последний штрих – прогрев массы при постоянном помешивании.
Производство белого цемента требует применения отдельных технологий. В него входит мергель, известняк, песок и глина, а также мраморная крошка. Белый цвет после высыхания смеси придает мел и каолин. При изготовлении клинкер измельчается в мельницах со специфической облицовкой, а также проходит несколько этапов очистки.
Поделиться с друзьями
CEMEX и Coolbrook электрифицируют процесс производства цемента — корпоративный веб-сайт
Вернуться в отдел новостей
CEMEX и Coolbrook электрифицируют процесс производства цемента
17.05.2022
- CEMEX и финско-голландская компания Coolbrook подписывают меморандум о взаимопонимании, направленный на изучение инновационной технологии электрификации процесса нагрева цементной печи.
- Запатентованная технология Coolbrook заменяет ископаемое топливо в процессе производства цемента.
СЕМЕКС, С.А.Б. де К.В. («CEMEX») объявила сегодня, что планирует работать с Coolbrook для тестирования их запатентованной технологии, которая использует электричество вместо ископаемого топлива в процессе нагрева при производстве цемента. На ископаемые виды топлива, используемые для обогрева печей, приходится примерно 45% выбросов углерода при производстве цемента.
Технология Roto Dynamic Heater (RDH) компании Coolbrook призвана произвести революцию в производстве цемента путем замены ископаемого топлива, традиционно используемого для обогрева печей, электричеством. Прорыв технологии RDH заключается в том, что она способна, используя только электричество, нагревать печь до достаточно высокой температуры, около 1700 градусов Цельсия, необходимой для производства цемента из самых современных материалов. При питании от электроэнергии из возобновляемых источников эта технология устраняет выбросы CO
«Электрификация процесса нагрева и обжига при производстве цемента является важным шагом на пути к обезуглероживанию нашего цементного производства», — сказал Роберто Понгута, вице-президент CEMEX по глобальным операциям, техническим вопросам и энергетике. «В той мере, в какой мы можем использовать электричество из возобновляемых источников, мы можем исключить выбросы углерода, связанные с нагревом цементных печей. Мы постоянно ищем лучшие технологии и наиболее перспективные партнерские отношения для достижения наших целей в области борьбы с изменением климата. Наше сотрудничество с Coolbrook — еще один тому пример».0003
Илпо Куокканен, исполнительный председатель Coolbrook, сказал: «Coolbrook поставила перед собой цель создать всеобъемлющую экосистему вокруг своей революционной технологии и как можно быстрее протестировать ее использование во многих промышленных процессах. Вместе с CEMEX мы можем принести технологии для производства цемента и достижения значительного сокращения выбросов в одном из самых энергоемких и CO 2 промышленных процессов. Мы искренне рады начать эту работу с CEMEX, который является мировым лидером в области экологически чистых строительных материалов и решений».
Компании ожидают, что эта революционная технология будет готова к коммерческому использованию в промышленных масштабах в 2024 году. Компании рассчитывают совместно оценить лучшую производственную площадку для тестирования и разработки этой технологии. Эта инициатива является частью дорожной карты CEMEX по достижению амбициозных целей в области борьбы с изменением климата в рамках программы «Будущее в действии».
В рамках своей программы «Будущее в действии» CEMEX объявила о цели действий по борьбе с изменением климата по сокращению выбросов CO 2 на 40 % к 2030 году.%, от 55% к 2030 году. Эти цели являются самыми амбициозными в цементной промышленности и подтверждены Инициативой по научным целям (SBTi) по сценарию значительно ниже 2 ° C. CEMEX ожидает, что эти промежуточные цели помогут компании в достижении ее цели к 2050 году по полному нулевому выбросу углерода в бетоне.
О компании Coolbrook
Coolbrook Ltd. — финско-голландская технологическая и инжиниринговая компания, целью которой является обезуглероживание основных отраслей промышленности, таких как нефтехимия и химическая промышленность, металлургия и производство цемента. Революционная технология вращения Coolbrook сочетает в себе космическую науку, турбомашиностроение и химическую инженерию, чтобы заменить сжигание ископаемого топлива во всех основных отраслях промышленности. Эта технология имеет два основных применения: Roto Dynamic Reactor (RDR) для достижения 100% CO 2 производство свободных олефинов и Roto Dynamic Heater (RDH) для обеспечения безуглеродного технологического нагрева при производстве чугуна и стали, цемента и химикатов. Технология Coolbrook, поддерживаемая растущим числом правительств, технологических партнеров, промышленных производителей и природоохранных органов, должна стать новым мировым стандартом в промышленной электрификации.
Настоящий пресс-релиз содержит заявления прогнозного характера в соответствии с федеральным законодательством США о ценных бумагах. CEMEX предполагает, что на эти заявления прогнозного характера распространяются положения о безопасной гавани для заявлений прогнозного характера в федеральных законах США о ценных бумагах.
Эти заявления обязательно связаны с рисками, неопределенностями и допущениями, которые могут привести к тому, что фактические результаты будут существенно отличаться от ожиданий CEMEX, включая, помимо прочего, риски, неопределенности и допущения, обсуждаемые в последнем годовом отчете CEMEX и время от времени подробно описываемые в отчете CEMEX. другие документы, поданные в Комиссию по ценным бумагам и биржам, какие факторы включены в настоящий документ посредством ссылки, которые, если они материализуются, в конечном итоге могут привести к тому, что CEMEX, включая его бизнес Regenera, не достигнет результатов или не окажет последствий, указанных в этом пресс-релизе. Эти факторы могут быть пересмотрены или дополнены, но CEMEX не несет и прямо отказывается от каких-либо обязательств по обновлению или исправлению этого пресс-релиза или любого прогнозного заявления, содержащегося в нем, будь то в результате новой информации, будущих событий или иным образом.
Любые или все прогнозные заявления CEMEX могут оказаться неточными. Соответственно, не следует чрезмерно полагаться на прогнозные заявления, поскольку такие прогнозные заявления действительны только на даты, когда они были сделаны. Содержание этого пресс-релиза предназначено только для информационных целей, и вы не должны толковать любую такую информацию или другие материалы как юридические, налоговые, инвестиционные, финансовые или другие советы. CEMEX не несет ответственности за содержание любых сторонних веб-сайтов или веб-страниц, на которые есть ссылки или которые доступны в этом пресс-релизе.
Связанные новости
Контакты для СМИ
Связи со СМИ
Хорхе Перес
+52 (81) 8259-6666
[email protected] 90Analyst andInvestor
3 9000Investor 002 Скотт Поллак
+1 ( 212) 317-6011
Фабиан Орта
+52 (81) 8888-4327
Контакты для СМИ
3
ге Перес
+52 ( 81) 8259-6666
jorgeluis. [email protected]
Аналитик и специалист по связям с инвесторами
Альфредо Гарса
+52 (81) 8888-4327
Скотт 0 Поллак 12) 317-6011Политика конфиденциальности
Карта сайта
Контакты
+1-888-847-5016
©2023 CEMEX, S.A.B. де К.В. Все права защищены.
Политика конфиденциальности
Положения и условия
Карта сайта
Озеленение производства цемента
Цементная промышленность является одним из крупнейших в мире источников выбросов углекислого газа.© Michael Milner/Moment/Getty
Цементная промышленность ежегодно производит около 3,5 миллиардов тонн общего портландцемента, наиболее распространенной формы, при этом выбросы в этом секторе составляют около 7% от общих глобальных антропогенных выбросов ПГ. Если бы цементная промышленность была страной, она была бы третьим по величине источником выбросов углекислого газа в мире с годовым объемом производства до 2,8 млрд тонн.
Теперь группа под руководством Ан Джи Вана, директора флагманского центра минерализации углерода Корейского института геолого-геофизических исследований и минеральных ресурсов (KIGAM), разработала метод производства зеленого цемента, который частично заменяет известняк, основной компонент цемента. и сырье для выбросов углекислого газа с побочными промышленными продуктами. Кроме того, команда смогла производить этот цемент при температуре примерно на 200°C ниже отраслевого стандарта.
Проезжая мимо Портленда
Для производства портландцемента известняк смешивают с сырьем, таким как кремнистый камень и глина, и нагревают примерно до 1450 °C. В ходе этого процесса образуется промежуточный продукт, называемый «клинкер», и около 44 весовых процентов известняка выделяется в виде углекислого газа.
Новая технология производства сырого цемента, однако, синтезирует клинкер из сульфоалюмината кальция (CSA) путем смешивания части известняка с сырьем, таким как угольная зола и побочный глинозем, образующийся на тепловых электростанциях.
Тепловая энергия, необходимая для производства 1 кг сырого цементного клинкера, составляет около 570 килокалорий, что меньше, чем общая тепловая энергия портландцемента, составляющая около 720 килокалорий. «Это снижает потребление энергии на 20 % и выбросы углекислого газа на 2 %, — объясняет Ан.
«Кроме того, наш сырой цемент в два раза лучше портландцемента для высокопрочных бетонов (исходя из трехдневной прочности, прочность на сжатие портландцемента составила 12,5 МПа, тогда как сырой цемент — 25 МПа) и расширяемость (портландцемент — 25 МПа). содержание цемента составляло 0,01%, тогда как содержание сырого цемента составляло 0,03%), поэтому его можно применять в таких областях строительства, как здания и мосты. А благодаря своим улучшенным водоотталкивающим характеристикам зеленый цемент в будущем можно будет использовать в качестве наполнителя для заброшенных шахт, месторождений отработанных газов и месторождений отработанного масла», — добавляет она.
Совершенствование международных стандартов
В октябре 2021 года представители правительства Южной Кореи и лидеры почти 200 стран встретились на 26-м заседании Конференции сторон (COP26) РКИК ООН в Глазго, Великобритания. COP26 была предназначена для ускорения действий по достижению Парижского соглашения 2015 года, которое направлено на ограничение роста средней глобальной температуры ниже 2 ° C к 2050 году по сравнению с доиндустриальным уровнем. На встрече Южная Корея обязалась сократить выбросы парниковых газов не менее чем на 40 % к 2030 г. по сравнению с уровнем 2018 г. и обязалась достичь углеродной нейтральности к 2050 г.
Ан Чжи Ван, Корейский институт геолого-геофизических исследований и минеральных ресурсов (КИГАМ).© KIGAM
Технология зеленого цемента KIGAM не только снижает выбросы парниковых газов, но и отвечает одной из целей механизма устойчивого развития COP26 — сократить использование известняка, минерального природного ресурса, и преодолеть отклонения и вредность промышленных побочных продуктов. «Около 88,7% внутренних запасов полезных ископаемых составляют неметаллические руды, из которых почти 72% приходится на известняк, и большая часть этих полезных ископаемых используется в цементной промышленности», — объясняет Ан.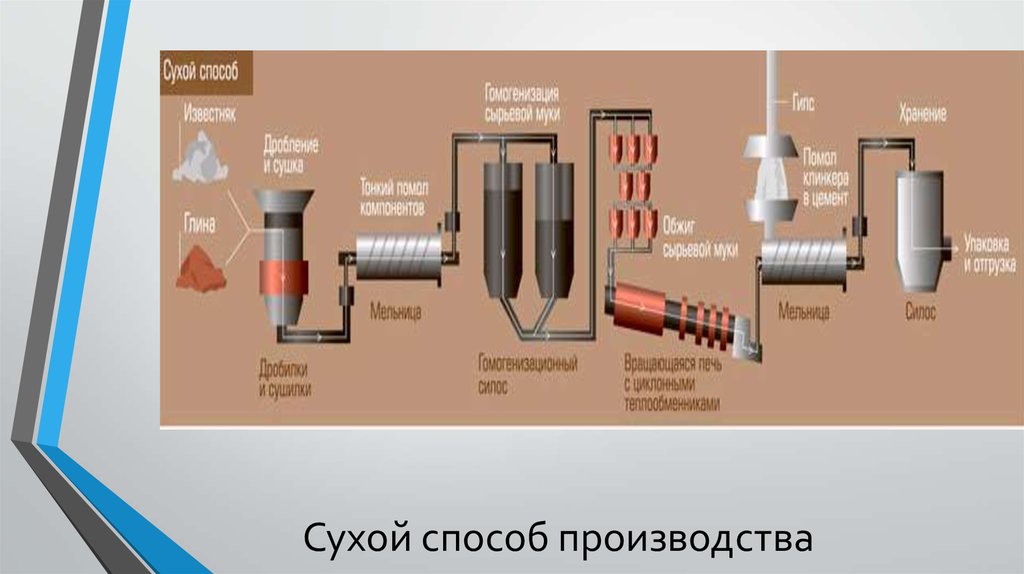
В дополнение к технологии зеленого цемента Ан разработал новую методологию Механизма чистого развития (CDM) для использования в цементной промышленности, которая имеет много ограничений на углеродные кредиты.
«Новая методология CDM является международным стандартом для оценки выбросов парниковых газов, которые сокращаются за счет конкретных видов деятельности, и необходимо сертифицировать эффективность сокращения выбросов парниковых газов нашей технологии производства зеленого цемента», — объясняет она.
Самым сложным аспектом регистрации технологии по методологии CDM была оценка количества двуокиси углерода, уменьшенного за счет технологии производства цемента, вспоминает Ан. По ее оценкам, цемент, разработанный с использованием этой технологии, выделяет на 0,281 тонны углекислого газа выбросы углекислого газа (тCO2) на тонну производимого цемента меньше, чем при производстве обычного портландцемента.
«Возьмите, к примеру, данные за 2019 год — если бы сырой цемент составлял 5% (2 912 710 тонн) от общего объема производства цемента в 2019 году, можно было бы сократить около 820 000 т CO2 от общего количества парниковых газов».