Как получают чугун | Справочник конструктора-машиностроителя
?Чугу?н — сплав железа с углеродом с содержанием более 2, 14 % ( точка предельной растворимости углерода в аустените на диаграмме состояний ).
Углерод в чугуне может содержаться в виде цементита и графита.
В зависимости от формы графита и количества цементита, выделяют : бледный, бесцветный, ковкий и высокопрочные чугуны.
Чугуны держат постоянные примеси ( Si, Mn, S, P ), а в отдельных событиях также легирующие элементы ( Cr, Ni, V, Al и др. ).
Обыкновенно, чугун хрупок.
Ковкий чугун получают длительным отжигом белого чугуна, в итоге которого образуется графит хлопьевидной формы.
Металлическая основа такого чугуна : феррит и реже перлит.
Ковкий чугун получил свое название из — за повышенной пластичности и вязкости ( при всем при том, что обработке давлением не подвергается ).
Ковкий чугун обладает повышенной крепостью при растяжении и рослым сопротивлением удару.
Из ковкого чугуна изготовляют детали непростой фигуры : картеры заднего моста машин, тормозные колодки, тройники, угольники и т. д.
Включенная в действие доменная печь функционирует непрерывно в течение нескольких лет.
Руду, кокс и флюсы периодически добавляют через верхнее отверстие ( колошник ) печи.
Также периодически производится выпуск из нее чугуна и шлака — через любые 4 — 6 ч.
При этом 99 — 99, 8% железа переходит в чугун и только 0, 2 — 1, 0% — в шлак.
Кроме углерода в составе чугуна присутствуют элементы кремния, марганца, серы, фосфора и пр.
По назначению доменные чугуны разделяют на литейный и передельный.
Литейный чугун переплавляют, и из него отливают чугунные изделия.
Из передельного чугуна получают сталь.
Он составляет около 90% всей выплавки

В нем содержится повышенное количество углерода, 0, 3 — 1, 2% Si, 0, 2 — 1, 0% Mn, 0, 2 — 1, 0% Р, 0, 02 — 0, 07% 5.
Белый Ч. представляет собой сплав, в котором избыточный углерод, не присутствующий в твёрдом растворе железа, присутствует в объединенном состоянии в виде карбидов железа Fe 3 C ( цементит ) или т. н. специальных карбидов ( в легированном Ч.
Кристаллизация белых Ч. происходит по метастабильной системе с образованием цементита и перлита.
Белый Ч. вследствие коротких механических характеристик и хрупкости располагает ограниченное применение для деталей простой конфигурации, действующих в обстановках повышенного абразивного износа.
Легирование белого Ч. карбидообразующими элементами ( Cr, W, Mo и др. ) повышает его износостойкость.
Белый чугун получают путем первичной кристаллизации из редкого сплава при быстрейшем охлаждении.
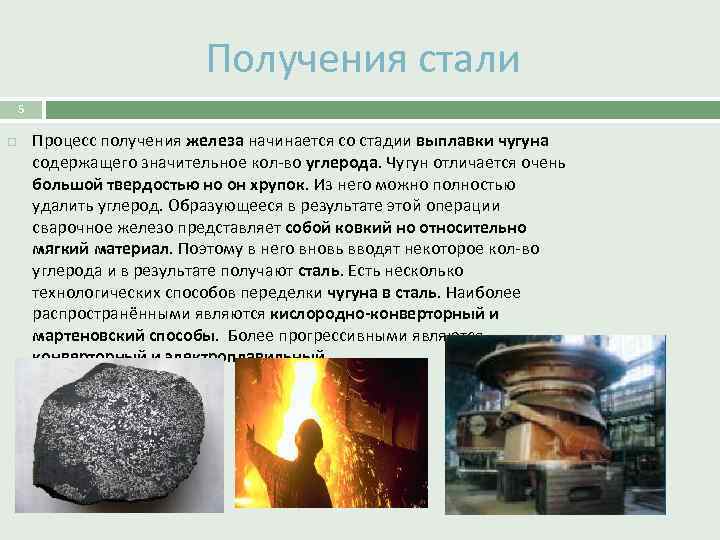
Белый чугун обладает высокой твердостью, хрупкостью и дурно обрабатывается, поэтому для изготовления деталей он не используется и применяется как передельный, т.е. идет на производство стали и иных паспортов чугуна.
Половинчатый чугун держит часть углерода в пустом состоянии в виде графита, а часть — в объединенном в виде карбидов.
Применяется в качестве фрикционного материала, действующего в условиях сухого трения ( тормозные колодки ), а также для изготовления деталей повышенной износостойкости ( прокатные, бумагоделательные, мукомольные валки ).
Механические свойства и рекомендуемый химический состав ковкого чугуна регламентирует ГОСТ 1215 — 79.
Ковкие чугуны маркируют буквами « К » — — ковкий, « Ч » _ ? угун и циферками.
Главная группа цифр показывает предел прочности чугуна при растяжении, другая — — сравнительное его удлинение при разрыве.
Например, КЧ 33 — 8 обозначает : ковкий чугун с лимитом крепости при растяжении 33 кг/мм 2 ( 330 МПа ) и относительным удлинением при разрыве 8 %.
В итоге длительной продувки воздухом из кусков руды получались почти без примесей кусочки настоящего железа, которые сваривались между собой кузнечным способом в зону, которые далее использовались для производства необходимых человеку изделий.
Это технически чистое железо держало весьма немного углерода и немного примесей ( настоящий древесный уголек и хорошая руда ), поэтому оно хорошо ковалось и сваривалось и практически не корродировало.
В итоге получалось ковкое ( рев ) железо.
Просуществовал этот способ до XIV века, а в несколько усовершенствованном облике до начала XX века, но был помалу вытеснен кричным переделом.
Серый чугун — наиболее широко применяемый вид чугуна ( машиностроение, сантехника, строительные конструкции ) — имеет включения графита пластинчатой формы.
Для подробностей из серого чугуна характерны небольшая чувствительность к действию внешних концентраторов напряжений при циклических нагружениях и более высокий коэффициент поглощения колебаний при вибрациях подробностей ( в 2 — 4 раза выше, чем у стали ).
Важная конструкционная особенность серого чугуна — выше, чем у стали, отношение предела текучести к пределу прочности на растяжение.
Наличие графита улучшает условия смазки при трении, что повышает антифрикционные свойства чугуна.
Свойства серого чугуна зависят от структуры металлической основы, фигуры, величины, числа и характера распределения включений графита.
Перлитный серый чугун имеет высокие прочностные свойства и применяется для цилиндров, втулок и др. нагруженных деталей двигателей, лафетов и т.д.
Для менее ответственных деталей используют серый чугун с ферритно — перлитной металлической основой.
Структура отливок определяется химическим составом чугуна и технологическими особенностями его термообработки.
Механические свойства серого чугуна зависят от свойств металлической матрицы, фигуры и размеров графитовых включений.
Свойства металлической матрицы чугунов близки к свойствам стали.
, который нельзя отменить невысокую прочность, снижает прочность чугуна.
Чем меньше графитовых включений и выше их дисперсность, тем больше прочность чугуна.
Графитовые включения вызывают сокращение предела прочности чугуна при растяжении.
На крепость при сжатии и твердость чугуна частицы графита почти не оказывают воздействия.
Свойство графита образовывать смазочные пленки обусловливает падение коэффициента трения и увеличение износостойкости изделий из серого чугуна.
Графит улучшает обрабатываемость резанием.
Великое значение для практики имеет свойство модификации ? — Fе растворять до 2, 14% углерода при температуре 1147°С с образованием твердого раствора и с внедрением атомов углерода в кристаллическую решетку.
При повышении и снижении температуры растворимость углерода в модификации ? — Fе уменьшается.
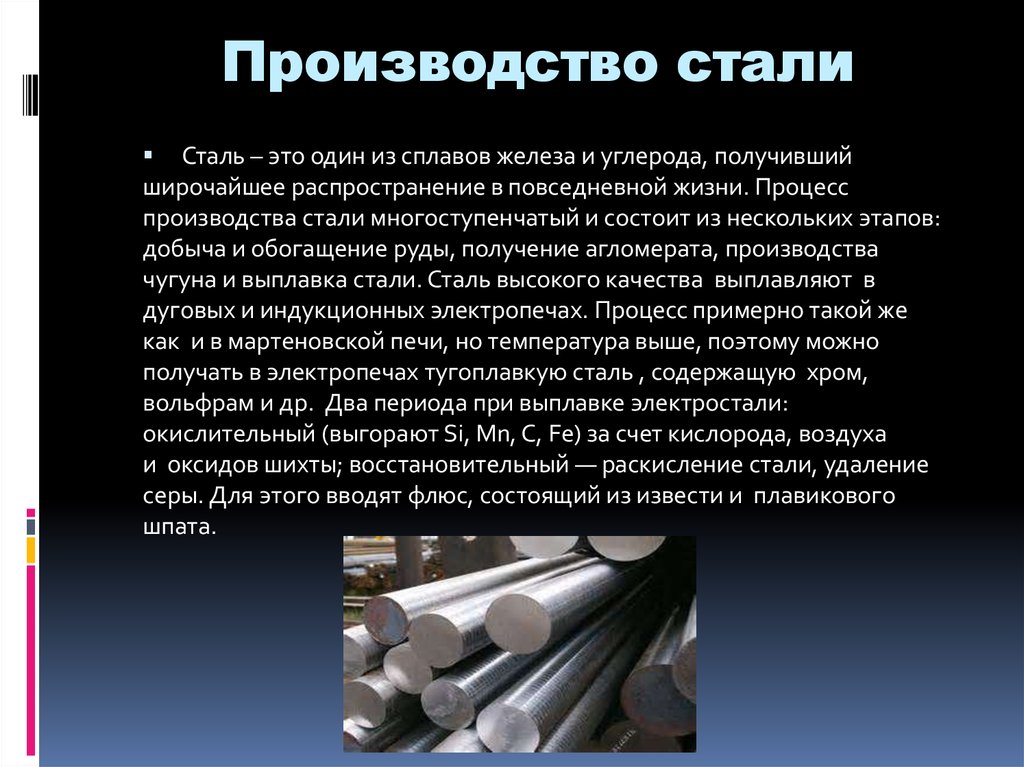
Химический состав и свойства высокопрочных чугунов регламентируются ГОСТ 7293 — 85 и маркируются буквами « В » — — высокопрочный, « Ч » — — чугун и количеством, означающим обыкновенное значение предела прочности чугуна при растяжении.
Например, ВЧ 100 — — высокопрочный чугун, лимит крепости при растяжении 1000 МПа ( или 100 кг/мм 2 ).
Термическая обработка чугуна :: Технология металлов
В машиностроении применяют отливки из серого, ковкого и высокопрочного чугуна. Эти чугуны отличаются от белого чугуна тем, что у них весь углерод или большая его часть находится в свободном состоянии в виде графита (а у белого чугуна весь углерод находится в виде цементита).
Структура указанных чугунов состоит из металлической основы аналогично стали (перлит, феррит) и неметаллических включений — графита.
Серый, ковкий и высокопрочный чугуны отличаются друг от друга в основном формой графитовых включений. Это и определяет различие механических свойств указанных чугунов.
У серого чугуна графит (при рассмотрении под микроскопом) имеет форму пластинок.
Графит обладает низкими механическими свойствами. Он нарушает сплошность металлической основы и действует как надрез или мелкая трещина. Чем крупнее и прямолинейнее формы графитовых включений, тем хуже механические свойства серого чугуна.
Основное отличие высокопрочного чугуна
заключается в том, что графит в нем имеет шаровидную (округленную) форму. Такая форма графита лучше пластинчатой, так как при этом значительно меньше нарушается сплошность металлической основы.Ковкий чугун получают длительным отжигом отливок из белого чугуна, в результате которого образуется графит хлопьевидной формы — углерод отжига.
Механические свойства рассматриваемых чугунов можно улучшить термической обработкой. При этом необходимо помнить, что в чугунах создаются значительные внутренние напряжения, поэтому нагревать чугунные отливки при термической обработке следует медленно, чтобы избежать образования трещин.
Отливки из чугуна подвергают следующим видам термической обработки.
Низкотемпературный отжиг. Чтобы снять внутренние напряжения и стабилизовать размеры чугунных отливок из серого чугуна, применяют естественное старение или низкотемпературный отжиг.
Более старым способом является естественное старение, при котором отливка после полного охлаждения претерпевает длительное вылеживание — от 3—5 месяцев до нескольких лет. Естественное старение применяют в том случае, когда нет требуемого оборудования для отжига. Этот способ в настоящее время почти не применяют; производят главным образом низкотемпературный отжиг. Для этого отливки после полного затвердевания укладывают в холодную печь (или печь с температурой 100—200° С) и вместе с ней медленно, со скоростью 75—100° С в час нагревают до 500— 550° С, при этой температуре их выдерживают 2—5 часов и охлаждают до 200° С со скоростью 30—50° в час, а затем на воздухе.
Графитизирующий отжиг.
При отливке изделий возможен частичный отбел серого чугуна с поверхности или даже по всему сечению. Чтобы устранить отбел и улучшить обрабатываемость чугуна, производится высокотемпературный графитизирующий отжиг с выдержкой при температуре 900—950° С в течение 1—4 часов и охлаждением изделий до 250—300° С вместе с печью, а затем на воздухе. При таком отжиге в отбеленных участках цементит Fe3Cраспадается на феррит и графит, вследствие чего белый или половинчатый чугун переходит в серый.
Нормализация.
Нормализации подвергают отливки простой формы и небольших сечений. Нормализация проводится при 850—900° С с выдержкой 1—3 часа и последующим охлаждением отливок на воздухе. При таком нагреве часть углерода-графита растворяется в аустените; после охлаждения на воздухе металлическая основа получает структуру трооститовидного перлита с более высокой твердостью и лучшей сопротивляемостью износу. Для серого чугуна нормализацию применяют сравнительно редко, более широко применяют закалку с отпуском.
Закалка.
Повысить прочность серого чугуна можно его закалкой. Она производится с нагревом до 850—900° С и охлаждением в воде. Закалке можно подвергать как перлитные, так и ферритные чугуны. Твердость чугуна после закалки достигает НВ 450—500. В структуре закаленного чугуна имеются мартенсит со значительным количеством остаточного аустенита и выделения графита. Эффективным методом повышения прочности и износоустойчивости серого чугуна является изотермическая закалка, которая производится аналогично закалке стали.
Высокопрочные чугуны с шаровидным графитом можно подвергать пламенной или высокочастотной поверхностной закалке. Чугунные детали после такой обработки имеют высокую поверхностную твердость, вязкую сердцевину и хорошо сопротивляются ударным нагрузкам и истиранию.
Легированные серые чугуны и высокопрочные магниевые чугуны иногда подвергают азотированию. Поверхностная твердость азотированных чугунных изделий достигает HV600—800° С; такие детали имеют высокую износоустойчивость. Хорошие результаты дает сульфидирование чугуна; так, например, сульфидированные поршневые кольца быстро прирабатываются, хорошо сопротивляются истиранию, и срок их службы повышается в несколько раз.
Отпуск.
Чтобы снять закалочные напряжения, после закалки производят отпуск. Детали, предназначенные для работы на истирание, проходят низкий отпуск при температуре 200—250° С. Чугунные отливки, не работающие на истирание, подвергаются высокому отпуску при 500—600° С. При отпуске закаленных чугунов твердость понижается значительно меньше, чем при отпуске стали. Это объясняется тем, что в структуре закаленного чугуна большое количество остаточного аустенита, а также тем, что в нем содержится большое количество кремния, который повышает отпускоустойчивость мартенсита.
Для отжига на ковкий чугун применяют белый чугун примерно следующего химического состава: 2,5—3,2% С; 0,6—0,9% Si; 0,3— 0,4% Μη; 0,1-0,2% Ρ и 0,06-0,1% S.
Существуют два способа отжига на ковкий чугун:
графитизирующий отжиг в нейтральной среде, основанный на разложении цементита на феррит и углерод отжига;
обезуглероживающий отжиг в окислительной среде, основанный на выжигании углерода.
Отжиг на ковкий чугун по второму способу занимает 5—6 суток, поэтому в настоящее время ковкий чугун получают главным образом графитизацией. Отливки, очищенные от песка и литников, упаковывают в металлические ящики либо укладывают на поддоне, а затем подвергают отжигу в методических, камерных и других отжигательных печах.
Процесс отжига состоит из двух стадий графитизации. Первая стадия заключается в равномерном нагреве отливок до 950—1000° С свыдержкой 10—25 часов; затем температуру понижают до 750— 720° С при скорости охлаждения 70—100° С в час. На второй стадии при температуре 750—720° С дается выдержка 15—30 часов, затем отливки охлаждаются вместе с печью до 500—400° С и при этой температуре извлекаются на воздух, где охлаждаются с произвольной скоростью. При таком ступенчатом отжиге в области температур 950—1000° С идет распад (графитизация) цементита. В результате отжига по такому режиму структура ковкого чугуна представляет собой зерна феррита с включениями гнезд углерода отжига — графита.
Перлитный ковкий чугун получается в результате неполного отжига: после графитизации при 950—1000° С чугун охлаждается вместе с печью. Структура перлитного ковкого чугуна состоит из перлита и углерода отжига.
Чтобы повысить вязкость, перлитный ковкий чугун подвергают сфероидизации при температуре 700—750° С, что создает структуру зернистого перлита.
Чтобы ускорить процесс отжига на ковкий чугун, изделия из белого чугуна подвергают закалке, затем проводят графитизацию при 1000—1100° С Ускорение графитизации закаленных чугунов при отжиге объясняется наличием большого количества центров графитизации, образовавшихся при закалке. Это дает возможность сократить время отжига закаленных отливок до 15—7 часов.
Термическая обработка ковкого чугуна.
Чтобы повысить прочность и износоустойчивость, ковкие чугуны подвергают нормализации или закалке с отпуском. Нормализация ковкого чугуна производится при 850—900° С с выдержкой при этой температуре 1—1,5 часа и охлаждением на воздухе. Если заготовки имеют повышенную твердость, их следует подвергать высокому отпуску при 650—680° С с выдержкой 1—2 часа.
Иногда ковкий чугун подвергают закалке, чтобы получить более высокую прочность и износоустойчивость за счет снижения пластичности. Температура нагрева под закалку, та же, что и при нормализации; охлаждение в воде или масле, а отпуск — в зависимости от требуемой твердости, обычно при температуре 650—680° С. Быстрое охлаждение может производиться непосредственно после первой стадии графитизации при достижении температуры 850—880° С с последующим высоким отпуском. Для ковкого чугуна применяют закалку токами высокой частоты или кислородо-ацетиленовым пламенем; при этом может быть достигнута высокая твердость поверхностного слоя при достаточной пластичности основной массы. Метод такой закалки тормозных колодок из ферритного ковкого чугуна заключается в нагреве деталей токами высокой частоты до 1000— 1100° С с выдержкой 1—2 минуты и последующим быстрым охлаждением.
Структура закаленного слоя состоит из мартенсита и углерода отжига HRC56—60.
Ковкий чугун по сравнению со сталью более дешевый материал; он обладает хорошими механическими свойствами и высокой коррозионной стойкостью (таблица). Поэтому детали из ковкого чугуна широко применяются в сельскохозяйственном машиностроении, автотракторной промышленности, станкостроении (для изготовления зубчатых колес, звеньев цепей, задних мостов, кронштейнов, тормозных колодок и пр.) и в других отраслях народного хозяйства.
Таблица
Механические свойства отливок из ковкого чугуна
Группы чугуна |
Марка чугуна | Механические свойства | ||
σb кГ/мм2
[Мн/мм2] не менее | δ % (образец диаметром 16 мм), не менее | твердость НВ | ||
Ферритные (черносердеч-ные) чугуны | КЧ 37—12 КЧ 35-10 КЧ 33-8 КЧ 30-6 | 37 [370] 35 [350] 33 [330] 30 [300] | 12 10 8 6 | 149 149 149 163 |
Перлитные (белосердечные) чугуны | КЧ 40—3 КЧ 35—4 КЧ 30—3 | 40 [400] 35 [350] 30 [300] | 3 4 3 | 201 201 201 |
Примечание. КЧ — означает ковкий чугун, первые две цифры — предел прочности при растяжении, вторые — относительное удлинение.
Источник:
Остапенко Н.Н.,Крапивницкий Н.Н. Технология металлов. М. Высшая школа,1970г.
Как делают чугун? (Отвечено) – Часто задаваемые вопросы о чугуне
Как получают чугун?
Процесс получения чугуна делится на две стадии:
На первой стадии чугун получают из чугуна.
При температуре 1100-1300 градусов Цельсия жидкий чугун заливают в ковш, где нагревают до 1200-1300 градусов Цельсия, затем корректируют состав жидкого металла добавлением сплавов (марганца и кремния) и заливкой примеси (шлак). Полученный расплав заливают в формы. Охлаждая формы, мы получаем прочный чугун.
Второй этап заключается в удалении литейных дефектов и примесей: песка, шлаков, газовых полостей (пламенной обработкой), усадочных полостей (сваркой или заполнением материалом с термическим расширением, близким к чугуну).
Сырье, используемое для производства чугуна, включает передельный чугун, стальной лом, известняк, уголь и кокс. Затем их плавят в печи при высокой температуре и разливают в формы для получения нужной формы. Весь процесс литья включает в себя переплавку чугуна, добавление к нему стального лома и переплавку снова и снова.
Как производят чугун?
При производстве чугуна железо плавится в печи (доменной или электродуговой) и разливается в формы для производства таких изделий, как детали машин и кухонная утварь. Расплавленное железо можно заливать прямо в формы или смешивать с ломом и загружать в электропечи.
Первым шагом в производстве чугуна является расплавление железной руды в печи. Затем расплавленный чугун смешивают со шлаком, обычно известняком и доломитом, который образует шлак, плавающий поверх жидкого чугуна. Чугун удаляется из печи и разбивается на более мелкие части с помощью машины, называемой дробилкой. После этого шага он готов к использованию в литье.
Как производится чугун?
Чугун – это твердый, хрупкий сплав железа и углерода, который легко отливается в форму и содержит больше углерода, чем сталь. Содержание углерода обычно колеблется от 1,7 до 4,5 процентов по весу, но чугуны с большим содержанием углерода считаются слишком хрупкими для большинства применений. Легирующие элементы, такие как кремний и марганец, также добавляются в небольших количествах для улучшения характеристик литья расплавленного металла.
Чугун производится путем плавки чугуна, который является продуктом плавки железной руды в доменной печи вместе с коксом и известняком. В Соединенных Штатах основным сырьем, используемым для производства чугуна, является таконит, низкосортная железная руда, в больших количествах встречающаяся в некоторых районах страны.
Процесс превращения чугуна в чугун называется ферросплавлением. Расплавленный чугун из доменной печи смешивают со стальным ломом и снова плавят, чтобы удалить большую часть содержащегося в нем углерода посредством окисления (процесс, называемый обезуглероживанием).
Степень обезуглероживания зависит от желаемых свойств конечного продукта, которые могут варьироваться в зависимости от его предполагаемого использования. Например, отливки, которые в течение срока службы будут подвергаться большим нагрузкам или напряжениям, требуют очень высоких
Из какого чугуна?
Чугун производится путем переплавки чугуна, часто вместе со значительным количеством железного лома и часто с добавлением других элементов, например стального лома.
Жидкое железо отливается или разливается и затвердевает в грубые слитки, называемые чушками, которые впоследствии переплавляются и отливаются в формы в литейном цехе для получения более подходящих размеров и форм железа.
Качество металла, используемого для этих изделий, зависит от состояния сырья, используемого при их изготовлении.
Литье в песчаные формы — Сборщик чугуна: информация для любителей винтажной посуды
Как это делается: литье в песчаные формы
Процесс начинается с создания шаблона. Выкройку можно считать оригиналом, с которого сделано множество дубликатов. Он во многом идентичен изделиям, для производства которых он был создан, за исключением размера. В контексте литья чугуна шаблон всегда делается немного больше, чем предполагаемый размер дубликатов, чтобы учесть тот факт, что расплавленное железо дает усадку при охлаждении и затвердевании.
Шаблон многократно используется для создания множества форм, каждая из которых в конечном итоге разрушается в процессе изготовления, как правило, одной формы. Форма состоит из влажной смеси на основе песка, упакованной вокруг узора в коробку, состоящую из двух частей, которую можно разделить для удаления узора после того, как песок затвердеет, а затем собрать вместе, оставив полость в форме узора. Затем расплавленный чугун заливается в полость формы через проход, созданный через уплотненный песок. Как только железо затвердевает, затвердевшая песчаная оболочка отрывается, чтобы освободить отливку, а любое лишнее железо, не являющееся частью готовой отливки, обрезается или сошлифовывается.
Это упрощенное объяснение. Фактический процесс современного литья немного сложнее, требуя соблюдения жестких производственных допусков и учета различий в том, как расплавленный чугун может течь в полость формы для определенной формы. Выкройки могут состоять из нескольких компонентов, используемых для создания половинок верхней и нижней формы по отдельности и с присоединенными литейными каналами. Состав и размер песка определяют текстуру поверхности отливки, а также препараты, наносимые на форму, которые также облегчают выход отливки из нее.
На уровне производства крупных литейных цехов для изготовления деталей с высоким спросом требовалось несколько рабочих схем. Для обеспечения согласованности будет создана ссылка, известная как мастер-шаблон. Первоначально вырезанный из дерева мастер-образец часто состоял из различных составных частей, возможно, для облегчения воспроизведения или для учета вариаций. Затем он будет отлит в латунной версии, к которой будут добавлены полозья и ворота. Из готового шаблона были отлиты алюминиевые версии, которые фактически использовались для изготовления песчаных форм.
Создание формы в деталях
Коробка, состоящая из двух частей, используемая для создания песчаной формы, известна на промышленном жаргоне как «опока». У коробки нет ни верха, ни низа. Нижняя половина, или «драг», укладывается на пол формовочного цеха и частично засыпается песком. Затем шаблон устанавливается вверх дном, и в него и вокруг него набивается больше песка, не оставляя пустот. Верхняя половина, или «вершина», располагается поверх перетаскивания, а песок продолжает заполняться вокруг оставшегося открытого рисунка. Инструмент для трамбовки используется для плотного уплотнения песка на протяжении всего процесса создания формы. Накладка и тяга имеют штифты и направляющие, чтобы удерживать их «в приводке» при изготовлении формы, а также для точной повторной сборки накладки и тяги после удаления выкройки перед отливкой. Будь «рука налита» поздним 19литейщика или отливки на современной автоматизированной линии по производству литья, это принципиально технология, по которой изготавливаются все изделия из чугуна.
Развивающиеся методики
Первые литейные заводы использовали очень примитивный метод введения расплавленного железа в песчаную форму. После того, как образец был упакован в песок, конический стержень использовался для создания канала или «литника» от верхней части формы до того места, которое должно было стать полостью формы. Железо также останется и затвердеет в литнике, и его нужно будет отпилить или отломить от отливки. Небольшие круглые дефекты, оставленные на дне таких отливок, известны как «следы литника» и обычно видны на отливках середины 19 века.го века и ранее.
Позже канал расширили, превратив его в щель, а не в маленькое отверстие. Это способствовало более быстрой заливке и лучшему распределению расплавленного чугуна в полости формы, что уменьшило количество бракованных отливок. Канал такого типа назывался «воротом», а леска оставляла на законченном забросе «метку ворот».
И литник, и литник соприкасаются с полостью формы в том месте, которое станет дном детали. Метка на литнике обычно была ненавязчивой, но иногда можно было увидеть, что метка на литнике сталкивалась с маркировкой производителя на днище кастрюль.
Литейная технология конца 19-го века преодолела недостатки методов литника и нижнего литника, переместив литник к тому месту, которое впоследствии станет внешним краем верхней кромки чаши. С помощью этого метода можно использовать несколько литников, соединенных желобами, для эффективного распределения расплавленного чугуна по полости формы, что значительно снижает количество дефектных отливок. Кастрюли, отлитые этим методом, известны как «боковые ворота». Затем лотки с боковыми литниками можно было обработать, перемещая лоток по столу станка с фиксированным шлифовальным кругом, чтобы удалить все или большую часть шероховатой кромки, оставшейся после отрыва лишнего металла литника от отливки.
Секреты мастерства
Хотя основы литья в песчаные формы могут распространяться даже на современную автоматизацию, бывают случаи, когда для реализации определенных конструктивных особенностей требуется значительная степень творчества. Ярким примером может служить литье крышек с петлевыми ручками.
Поскольку песок должен быть плотно упакован вокруг модели, чтобы создать форму, ручки-петли представляют собой уникальную проблему. В качестве фиксированной выступающей части шаблона петлевая ручка была бы невозможна, так как шаблон нельзя было удалить из формы для песка, не потревожив песок, упакованный вокруг него. Благодаря конструкциям ручек и артефактам литья можно наблюдать использование съемных или шарнирных секций при изготовлении крышек с петлевой ручкой.
Ранние ручки-петли обычно были шире в точках «прикрепления» и сужались посередине. Чтобы облегчить эту конструкцию, потребовались два съемных сегмента, по одному на каждую половину рукоятки, так как цельная деталь в этом случае все равно не позволяла бы снять ее, не нарушая уже тщательно уложенный вокруг нее песок. Это было достигнуто за счет того, что каждая половина ручки на выкройке была шарнирно закреплена, чтобы они могли высвободиться из песчаной формы при удалении выкройки, но не разрушив форму. О том, что использовались модели рукоятей, состоящих из двух частей, свидетельствует линия отливки, которую часто можно увидеть и почувствовать на вершине таких рукояток.