Доменный процесс печи — схема получения чугуна, химические процессы, физика и продукты
Сталями принято считать сплавы железа с углеродом с содержанием последнего до 2,14%. Все, что имеет более высокое содержание углерода – это чугуны. Получают стали на основе двух процессов — доменного (в результате получается передельный чугун) и собственно получения стали, когда из передельного чугуна путем выжигания углерода и добавки легирующих элементов получают стали и сплавы нужной марки и нужного состава.
Сырье
Основой для получения чугуна в доменном процессе служат железные руды. Поскольку железо обладает сравнительно большим сродством к кислороду, оно в чистом виде в земной коре не обнаруживается, а находится в виде соединений с кислородом и диоксидом углерода.
Основные руды железа, которые используются в металлургическом производстве – это окись-закись железа (Fe3O4 – магнетит, магнитный железняк), окись железа (Fe2O3 — красный железняк, 2Fe2O3 * 3H2O — бурый железняк) и карбонат железа FeCO Естественно, что в чистом виде данные вещества не встречаются, а имеют примеси других элементов (чаще всего серы и фосфора) и других веществ в виде сопутствующих пород, не образующих с целевым продуктом химических соединений (обычно SiO2, Al2O3, CaO, MgO).
Кроме того, в больших количествах в виде руд имеется железный колчедан FeS2, но он очень редко применяется в металлургии, так как выплавляемое из него железо получается очень низкого качества из-за большого содержания серы.
В результате проведения специальных технологий дробления руды и флотационного процесса значительную часть пустой породы удается отделить от целевого продукта, в результате чего в ряде случаев удается повысить содержание железа в руде до 63-67%, а иногда до 69-72%.
Однако полностью удалить пустую породу не удается, эта операция осуществляется в самом доменном процессе путем перевода пустой породы в шлаки, которые отделяются от чугуна.
Процесс и схемы
Процесс доменной плавки (процесс получения передельного чугуна) осуществляется в шахтных печах (домнах). Домна, схематический разрез которой дан на рис. 5.1, представляет из себя устройство в виде конуса в верхней части высотой в несколько десятков метров, обложенное изнутри огнеупорным кирпичом и снаружи стянутое железными обручами или окруженное сплошной железной оболочкой. Верхняя часть домны носит название шахты и заканчивается наверху отверстием — колошником, которое закрывается подвижной воронкой – колошниковым затвором. Самая широкая часть домны называется распаром. Нижняя часть домны образует горн. В горне имеются отверстия – фурмы, через которые в печь вдувается горячий воздух.
При запуске доменную печь загружают сначала углем (коксом), а потом послойно смесью руды с флюсом и углем и чистым углем. Нижние слои угля зажигают, после чего горение и необходимая для выплавки температура поддерживаются вдуванием в горн подогретого в рекуператорах тепла воздуха. Последний поступает в кольцевую трубу, расположенную вокруг нижней части печи, а из нее по распределительным трубкам через фурмы в горн.
Рис. 5.1. Схематическое изображение шахтной печи для получения чугуна (домны).
Рис. 5.2. Схема химических реакций, протекающих по высоте доменной печи.
В нижней части печи, как уже упоминалось, происходит горение кокса по реакции:
< C > + { O2 } = { CO2 }Здесь угловыми скобками обозначено твердое состояние, фигурными – газообразное.
Проходя вверх далее через слой раскаленного угля, СО2 превращается в оксид углерода:
{ CO2 } + < C > = 2 { CO }Монооксид углерода является сильным восстановителем и именно он восстанавливает железо из руд. Реакция идет постадийно, что и отображено на рисунке. В результате образуются крупинки твердого железа.
По мере сгорания угля это железо опускается вниз по печи в ее более горячую часть — распар, и здесь при температуре порядка 1200°С плавится при соприкосновении с углем, отчасти растворяя его и образуя заэвтектический чугун с содержанием углерода 4-4,5%. В то время как чистое железо плавится при 1535°С, чугун в точке эвтектики плавится при 1150°С, поэтому капли жидкого чугуна стекают в нижнюю часть горна. Для того, чтобы сэкономить тепловую энергию отходящих газов и возвратить ее в процесс, отходящие газы из домны направляются в т.н. «кауперы», где газы отдают часть тепла. Сначала эти газы направляются в один из кауперов, в то время как через второй продувается воздух для последующей подачи в домну, где он нагревается. Через определенные промежутки времени потоки меняются местами.
Одновременно с восстановлением железа происходят процессы отделения пустой породы от целевого продукта через образование шлака при взаимодействии примесей с флюсовыми добавками. Конечный шлак на 85-95% состоит из SiO2, Al2O3 и СаО; остальное — MgО (2-10%), FeO (0,2-0,6%), MnО (0,3-2%) и 1,5-2,5% серы в виде CaS. Стремятся создать наиболее легкоплавкий шлак, поэтому, в зависимости от типа примесей в используемой руде в шихту добавляют либо кислые (SiО 2), либо щелочные компоненты (оксиды кальция и магния).
Для выпуска жидких продуктов плавки используют раздельно чугунные и шлаковые летки.
Поскольку шлак – многокомпонентная система, кроме того, процесс перехода из твердого в жидкое состояние осуществляется в достаточно большом интервале температур, вязкость шлака определяется не только температурой, но и составом шлака, поэтому у каждого типа шихты свои особенности.
Еще одна проблема, которая наблюдается в доменном процессе и которую решают для каждого типа шихты по-разному – это проблема серы. Сера – вредный элемент, ухудшающий качество металла. Она является причиной красноломкости стали и ухудшает качество литейных чугунов, увеличивая вероятность образования раковин в отливках.
Хотя значительное количество серы удаляется при огневой обработке руд (агломерации и обжиге окатышей), очень много серы вносится в доменную печь с коксом и железорудными материалами в виде сернистого железа (пирита FeS2), барита BaSO4 и гипса CaSO4 * h3O.
Часть серы удаляется при проведении технологических процессов естественным путем через образование газов (SO2, H2S и др.), но это лишь небольшая часть, по оценке для обычного доменного процесса порядка 15%. Поэтому основное внимание обращается на перевод соединений серы, растворяющихся в чугуне, в соединения, в нем не растворяющихся, например, по реакции:
FeS + CaO = CaS + FeO
FeO + C = Fe + CO
FeS +CaO + C = CaS +Fe + CO
Существуют и другие способы десульфуризации, что позволяет в целом решать эту проблему при использовании самых различных руд.
Конечными продуктами доменной плавки являются чугун (целевой продукт) и шлак и доменные газы (побочные продукты производства). Нас в данном случае интересует только чугун, на нем и остановимся.
Чугун представляет собой многокомпонентный сплав железа с углеродом, кремнием, марганцем и серой. В зависимости от назначения чугуна в нем могут содержаться и другие вещества, содержание которых регламентируется соответствующими стандартами.
Основной вид чугуна, производимый в доменном производстве, — это передельный чугун (до 90% от всего выпускаемого чугуна), который затем используют для получения различных видов сталей.
Производство чугуна имеет и самостоятельное значение, поскольку некоторые виды используют для отливок. Для получения чугунных отливок используется и небольшая часть передельного чугуна. Некоторые типы чугунных изделий можно оцинковывать, но об этом мы поговорим позже.
В зависимости от назначения чугуна последний перевозится от доменных печей чугуновозами в жидком виде либо в сталеплавильные цехи, либо на разливочные машины (при выплавке товарного чугуна).
Таблицы DPVA.ru — Инженерный Справочник | Адрес этой страницы (вложенность) в справочнике dpva.ru: главная страница / / Техническая информация / / Химический справочник / / Водные растворы и смеси для обработки металлов — мытья, обезжиривания, нанесения покрытий, очистки и т.п. Составы для очистки и обезжиривания поверхности и нанесения покрытий. / / Обезжиривающие водные растворы и органические растворители.![]() Поделиться:
![]() | ||||||||||||||||||||||||||||||||||||||||||||||||||||||||||||||||||||||||||||||||||||||||
Если Вы не обнаружили себя в списке поставщиков, заметили ошибку, или у Вас есть дополнительные численные данные для коллег по теме, сообщите , пожалуйста. Вложите в письмо ссылку на страницу с ошибкой, пожалуйста. | |||||||||||||||||||||||||||||||||||||||||||||||||||||||||||||||||||||||||||||||||||||||||
Коды баннеров проекта DPVA.ru Начинка: KJR Publisiers Консультации и техническая | Проект является некоммерческим. Информация, представленная на сайте, не является официальной и предоставлена только в целях ознакомления. Владельцы сайта www.dpva.ru не несут никакой ответственности за риски, связанные с использованием информации, полученной с этого интернет-ресурса. Free xml sitemap generator |
1. Основные свойства сварки чугуна. Технология горячей сварки чугуна
Похожие главы из других работ:
Компоненты железоуглеродных сплавов
1.
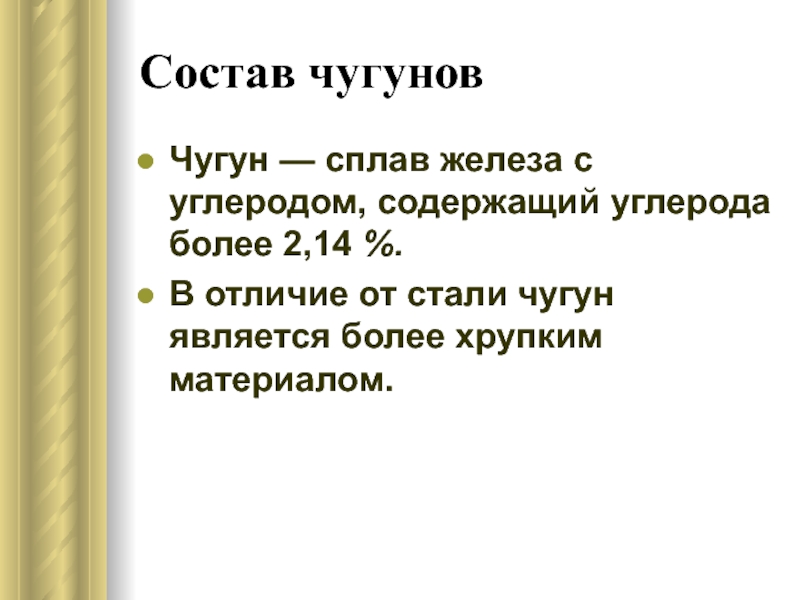
…
Лазерная сварка
1.1 Основные параметры режимов сварки
Нам были даны пластины из Стали45. Их нужно сварить однопроходной сквозной стыковой лазерной сваркой. Для выполнения данной задачи нужно подобрать параметры режима сварки: P- мощность излучения, Вт; Vсв — скорость сварки…
Ликвидация трещины в алюминиевом поддоне автомобиля
2. Основные трудности сварки алюминия и его сплавов
К ним относятся: 1. Наличие и возможность образования тугоплавкого окисла Al2O3 (Tпл = 2050єС) с плотностью больше, чем у алюминия, затрудняет сплавление кромок соединения и способствует загрязнению металла шва частичками этой пленки. 2…
Механические свойства древесины
2. Основные свойства древесины
…
Определение геометрических параметров графитовых включений в микроструктуре серых чугунов методом автоматического анализа изображений ImageExpertPro 3
4.
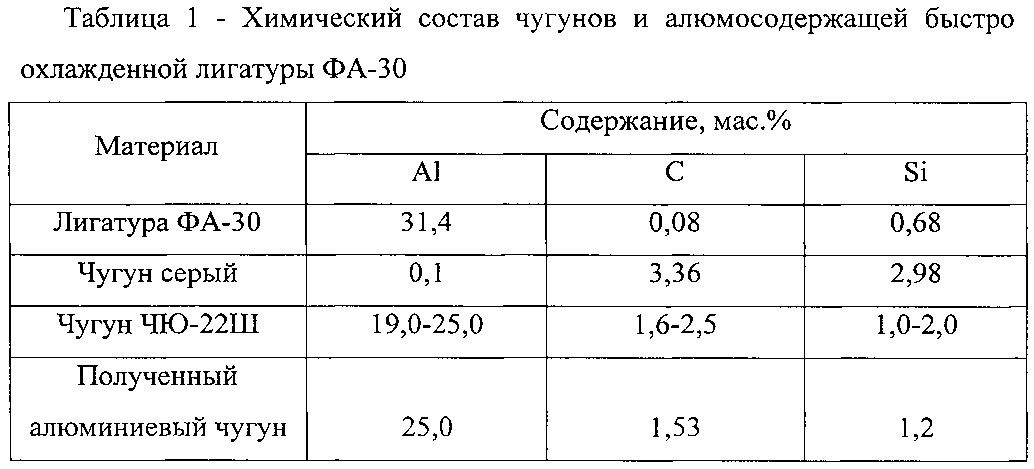
4.1 Графит. Его свойства и применение Графит (от греч. — пишу) — это минерал, наиболее устойчивый при нормальных условиях кристаллическая модификация углерода. Графит огнеупорен…
Очистка отходящих газов от паров органических растворителей
2.1 Основные свойства рабочих сред
2.1.1 Н-бутанол. Физико-химические свойства н-Бутанол — бесцветная жидкость со спиртовым запахом Химическая формула С4H9OH, эмпирическая формула С4h20O, молярная масса 74,12 г/моль, температура кипения 117,4оС, температура вспышки 34оС…
Проект камнеобрабатывающего цеха по производству облицовочных изделий из натурального камня
2.1 Основные свойства природного камня
Под основными свойствами камня понимается ряд физико-механических, технологических, эксплуатационных параметров, характеризующих поведение камня под воздействием соответствующих внешних воздействий…
Проект камнеобрабатывающего цеха по производству облицовочных изделий из натурального камня
Основные свойства природного камня
№ п/п Наименование характеристики Единица измерения ГОСТ, СТ СЭВ, организация — разработчик Европейский стандарт CEA (UNI, Италия) 1. Предел прочности (сопротивление) при сжатии МПа ГОСТ 8462-75 ГОСТ 9479-84 UNI 9724/3 2…
Проектирование состава конструкционно-теплоизоляционного керамзитобетона
4. Основные свойства проектируемого бетона
Легкие бетоны, в частности керамзитобетон, согласно ГОСТ 25820-83 характеризуются следующими показателями качества: — прочностью на сжатие, — средней плотностью, — морозостойкостью, — водонепроницаемостью, — теплопроводностью…
Проектирование судна-нефтесборщика для ликвидации разливов нефти в Финском заливе
1.5.1 Состав и основные свойства нефти
Нефть — горючая маслянистая жидкость, вязкая, темно-коричневого цвета со специфическим запахом, является важнейшим полезным ископаемым. К основным компонентам нефти относятся углеводороды(98%).Кроме того, в состав нефти входят их производные…
Производство передельного чугуна
3. Потребительские свойства передельного чугуна
Передельный чугун должен изготовляться в соответствии с требованиями ГОСТ 805-80 «Чугун передельный. Технические условия» по технологической документации, утвержденной в установленном порядке…
Разработка технологии сварки газопровода низкого давления из труб диаметром 219 мм
1.1 Основные понятия сварки трубопроводов
Сварные соединения являются неразъемными, т.е. не могут быть разобраны без поломки деталей. Это свидетельствует о монолитности (сплошности) сварных соединений. Такая монолитность может быть обеспечена…
Сварка пластмасс
2. Основные виды и особенности сварки пластмасс
Сварка пластмасс — это процесс неразъёмного соединения термопластов и реактопластов, в результате которого исчезает граница раздела между соединяемыми деталями. Соединение реактопластов осуществляют способом…
Технологический процесс изготовления ригеля сварного
1.9.3 Технология сварки и свойства сварных соединений
Технология сварки низколегированной стали 09Г2С, проектируется с учётом того…
Ультразвуковая сварка
Физическая сущность и основные способы сварки.
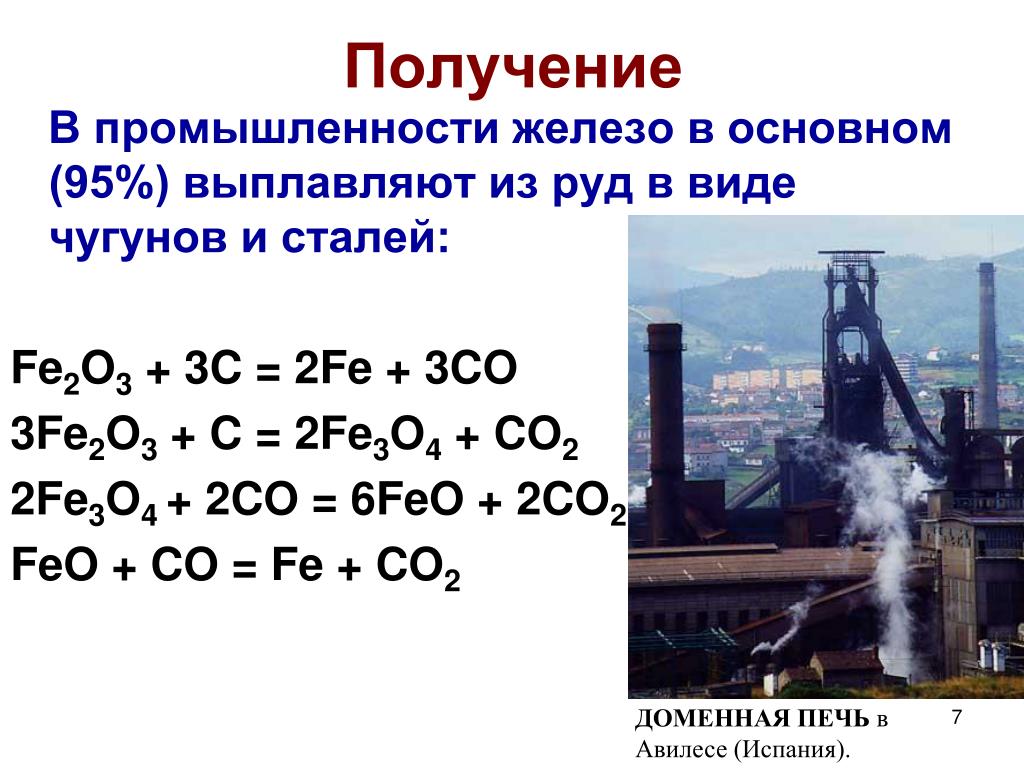
Сваркой называется технологический процесс получения неразъемных соединений посредством установления межатомных связей между свариваемыми частями при их местном или общем нагреве, или при пластическом деформировании…
Ржавчина
О ржавчине рассказывается на многих сайтах. Есть много фотографий, но только изделий или, в крайнем случае, макроструктура. Как выглядит ржавчина под микроскопом?
Ржавчиной, как правило, называют продукт коррозии только железа и его сплавов, таких, как сталь или чугун, хотя многие другие металлы тоже подвергаются коррозии.
Все знают красный налет на поверхности металлических материалов или изделий, которые находятся под воздействием влаги или некоторых реактивов. Этот налет — окислы, которые образуются при взаимодействии железа с кислородом. Химическая формула ржавчины Fe2O3nH2O (гидратированный оксид трехвалентного железа), а также метагидрооксид (FeO(OH), Fe(OH)3). На рис.1 показаны красные окислы железа – Fe2O3 и Fe3O4.
а | б |
Рисунок 1. Красные окислы железа: а — Fe2O3; б — Fe3O4.
Если поверхность железных изделий не защищать, то в конце концов изделие рассыплется в порошок. Красный окисел не пассивирует поверхность, т.е. не защищает ее от дальнейшего разрушения. (Кстати, концентрированная серная кислота пассивирует поверхность. При взаимодействии железа с кислотой на поверхности железа образуется сернокислое железо и окисление железа прекращается).
Окисление возможно и на воздухе, т.к. он в наших условиях содержит некоторое количество влаги. На рис. 2 показана ржавчина на изломе пластинки быстрорежущей стали Р6М5.
Рисунок 2. Излом стали Р6М5; окисление в комнатных условиях; светлопольное изображение
Ржавчина образуется и при коррозии металла в почве (рис. 3 и 4). На рис. 3 показан фрагмент детали сельхозтехники, пролежавшей несколько лет в поле. Это макроструктура, которая показывает расположение окисленных участков на поверхности. Более красивую и интересную картину дает микроструктура (рис. 4). Видны кристаллы красной ржавчины (рис. 4 а) и осадки другого типа (рис. 4 б), состав которых не определялся.
Рисунок 3. Фрагмент детали сельхозтехники; почвенная коррозия.
а | б |
Рисунок 4. Ржавчина и осадки на изломе детали; темнопольное изображение
Поскольку влага присутствует и в воздухе, окисляются и шлифы металлов и сплавов, хранящиеся не в специальных условиях. Окисление их усиливается еще и потому, что они протравлены. Нетравленные шлифы хранятся куда лучше. На рис. 5 показано окисление протравленных шлифов стали ШХ15. Ржавчина в основном располагается на матрице (мартенсит), карбиды (белая фаза) видны хорошо (рис. 5а). В структуре зернистого перлита (рис. 5 б) окисляется феррит, на изображении он имеет голубой и зеленый цвет; ржавчина сосредоточена в виде отельных пятен (до поры, пока не окислится весь образец).
а | б |
Рисунок 5. Окисление шлифов стали ШХ15 после травления и длительного хранения в комнатных условиях: а — закалка и отпуск, равномерное окисление поверхности; б – зернистый перлит, формирование островков окисной пленки.
На рис. 6а показано крупное скопление окислов. Некоторые из них имеют красный цвет, это ржавчина, другие – светлый (рис. 6 б). Состав их не анализировали; также это может быть и пыль, поскольку шлиф находился на открытом воздухе.
а | б |
Рисунок 6. Скопления окислов на поверхности шлифа: а – светлое поле, б- темное поле.
Если процесс зашел далеко, то практически вся поверхность покрыта ржавчиной (рис. 7). Участков чистого металла осталось мало.
Рисунок 7. Сплошной окисный слой на шлифе
Все, что содержит железо, может ржаветь. В том числе и метеориты (рис. 8).
Рисунок 8. Окислы железа на метеоритах
Урок в 9 классе. Чугун, его производство.
Тема: Производство чугуна и его применение
Класс: 9
Тип урока: изучение нового материала
Цель: ознакомление учащихся с чугуном, как сплавом железа и его применением.
Задачи:
закрепить знания, об основных месторождениях железа в России, полученные на уроках географии;
познакомить с доменным процессом выплавки чугуна;
познакомить с историей чугунного литья и применением чугуна в архитектуре.
формировать умения выбирать главное, работать по плану;
развивать кругозор.
развивать познавательный интерес, через межпредметные связи в обучении;
профориентационное воспитание.
Ход урока:
I. Организационный момент
1. Вводное слово учителя, актуализация
II. Новая тема
Постановка цели урока, изложение плана урока;
Изложение материала учащимися по первому этапу урока, работа с картой;
Изложение материала учителем и учащимися по второму этапу урока;
Изложение материала учителем и учащимися по третьему этапу урока;
Изложение материала учащимися по четвёртому этапу урока;
Решение расчётной задачи на практический выход продукта реакции.
III. Заключительное слово учителя, итог урока
IV. Рефлексия
V. Домашнее задание.
Средства обучения:
Мультимедийная установка;
Диски: «Неорганическая химия», с мультимедийной презентацией;
Коллекция минералов;
Алгоритм
Схема устройства доменной печи
Методы:
По источнику информации – наглядные
По способу познавательной деятельности – проблемный
По движению мысли от незнания к знанию — дедуктивный
Часы истории человечества стали отсчитывать время быстрее, когда в его жизнь вошли металлы и, что важнее всего, их сплавы. Вся история человечества в зависимости от материала и изготовления орудий труда делится на четыре больших эпохи. И в большинстве своем, именно металлы дали названия этим эпохам: каменный век — медный век — бронзовый век — железный век. Здесь мы видим прогресс развития человечества. Слайд 1
Давайте сразу перенесемся в эпоху железного века. Ведь железо сыграло большую роль в развитии человеческого общества и не потеряло своего значения в настоящее время: из всех металлов оно и его сплавы наиболее широко используются в современной промышленности.
Первобытный человек начал использовать железо за несколько тысячелетий до нашей эры. В те времена он еще не добывал железо из руд, а использовал упавшие из космоса на Землю метеориты. Отсюда и древнее название железа ваасперс, что обозначает в переводе с шумерского языка – это металл, “капнувший с неба, небесный”.
Получение железа из железных руд, приходится на середину II тыс. до н.э. Данный процесс был осуществлен египтянами. Начало металлургии железа на территории нашей страны приходится на рубеж II и I тыс. до н.э. Сегодня на уроке мы поговорим о сплаве железа.
И объектом нашего урока сегодня будет чугун.
Тема урока: «Производство чугуна и его применение». Исходя из темы, сформулируйте для себя задачи урока. Слайд 2
Предполагаемый ответ: выяснить химизм получения чугуна и познакомиться с отраслями его применения.
Чтобы реализовать поставленные вами задачи, необходим план урока. Я вам предлагаю план, по которому мы с вами будем сегодня работать. Найдите его на своих столах и положите посередине. Слайд 3
Сообщение учащегося, работа с картой Слайд 4 Железо один из самых распространенных в природе элементов. В земной коре его массовая доля составляет 5,1%, и оно уступает лишь кислороду, кремнию и алюминию. Железо входит в состав большинства горных пород в виде руд: магнетит, красный железняк, бурый железняк. Слайд 5 Демонстрация коллекции минералов. Железорудные месторождения имеются на территории всей России. Это Курская магнитная аномалия, на Урале, в Западной Сибири. Слайд 6
Слово учителя У нас на территории РХ тоже имеются железорудные месторождения, их более 130. А вы можете назвать какие-нибудь? Показать.
Добыча железной руды в Хакасии ведется двумя рудниками: Абаканском и Тейском. Кроме того, месторождение в Западном Саяне: Анзасское является резервным. Слайд 7
Чистое железо из железных руд можно получить химическим способом, однако мягкость чистого металла делает его применение нецелесообразным. В промышленности и технике используют железо в виде сплавов: чугуна и стали.
Первый чугун был произведен в Китае в VI в. до н.э. В Европе чугун начали получать в ХIV в. (когда появились первые доменные печи. В России первые доменные производства открылись в ХVI столетии).
Что же такое чугун? Для этого нам нужно ответить на следующие вопросы. Слайд 8 Что такое? Какой он? Из чего состоит? Чтобы ответить на эти вопросы, мы познакомимся сначала с его производством.
3. Получение чугуна осуществляется в доменных печах, или домнах. Давайте познакомимся с их устройством. Внимание на экран. Диск «Неорганическая химия», раздел «Железо и хром», параграф «Чугун и сталь» — п.3 – устройство доменной печи или слайд 9
Самостоятельная работа учащихся со схемой в тетрадях (3мин). У вас на столах имеются таблицы с изображением доменной печи. Сделайте на них обозначения, характеризующие устройство домны. Чтобы вам было легче справиться обратите внимание на следующие термины (записаны на доске). Проверьте, верно, ли вы сделали обозначения (отвечает один ученик, показывает на слайде). Проверим ещё раз. Диск «Неорганическая химия», раздел «Железо и хром», параграф «Чугун и сталь» — п.3 – устройство доменной печи включить повторно для проверки (отвечают учащиеся). Если есть неточности в ваших работах, исправьте их.
Через колошник происходит загрузка сырья для выплавки чугуна, а снизу подается воздух.
Давайте познакомимся с химизмом выплавки чугуна в доменных печах.
4. Самостоятельная работа учащихся по алгоритму (10мин). Представьте, что вы рабочие-металлурги и вам необходимо выплавить 1т чугуна. Для этого у вас есть 1800кг Fe2O3, 800кг кокса, 300кг флюсов в виде СаСО3. По предложенному вам алгоритму получите, пожалуйста, вашу первую тонну чугуна. Слайд 10
Давайте посмотрим, получили ли вы свою первую тонну чугуна. Кто желает выйти к доске и написать уравнения реакций процессов, которые идут в доменной печи. Запись на доске. Теперь проверим, верно, ли вы написали уравнения процессов и, следовательно, получили ли чугун. Внимание на экран. Диск «Неорганическая химия», раздел «Железо и хром», параграф «Чугун и сталь» — п.4,5.или слайд11,12 Такие процессы должны пройти в доменной печи. Чтобы глубже узнать профессию металлурга, у нас в г.Абакане есть филиал КГТУ, где вы можете приобрести данную профессию.
Мы познакомились с устройством доменной печи и процессами выплавки чугуна. Давайте теперь вернемся к нашим вопросам Что такое? Какой он? Из чего состоит? Слайд 13 и скажем, что же такое чугун. (ответы учащихся).
Чугун – определение в тетрадь. Слайд 14
Слово учителя Различают два вида чугуна: белый и серый. Белый чугун идет на производство стали, а серый используется для нужд человека.
5. Давайте выясним, где же чугун находит свое применение. Для этого слайд 15 из приведенного перечня выберите те области, в которых используются изделия из чугуна. И приведите примеры изделий из этого сплава. Работа учащихся над выбором отраслей применения чугуна.
В быту
Авиастроение
Мебельная промышленность
Водоснабжение
Коммунальное хозяйство
Искусство
Архитектура (ответы учащихся с примерами).
Слово учителя Но чугун используется и в искусстве, в архитектуре и скульптуре.
Сообщение учащегося об истории первых чугуноплавильных заводов на территории России.
Сообщения учащегося из Интернет-ресурсов о Каслинском литье, решётках Санкт-Петербурга, мостах и Исаакиевском соборе. Слайды по ходу сообщений 16-19
6. Решение задачи. Мы с вами сегодня выплавили в доменной печи чугун. Теперь давайте решим задачу стр.157, зад.4 и узнаем, сколько можно получить чугуна из 100т железной руды.
III. Итог Давайте вернемся к нашему плану и посмотрим, все ли пункты плана реализованы? (Ответ учащихся: все). Я согласна и тоже считаю что все. IV. Рефлексия Посмотрите на предложенные Вам вопросы и ответьте на них. Слайд 20 ответы и отзывы учащихся.
V. Домашнее задание стр. 157. зад.5, пар.56, вопр.5-10, более сильным учащимся индивидуальные карточки с заданиями в тетрадь
Спасибо за урок! Слайд 21. Я рада, что урок Вам понравился.
Используемая литература
Аликберова Л.
Ю. Занимательная химия: Книга для учащихся, учителей и родителей – М.: АСТ-ПРЕСС. 2002. – 560 с.
Бердоносов С. С., Менделеева Е. А. Химия. Новейший справочник. – М.: Махаон, 2006.
Ф.Г.Фельдман, Г.Е. Рудзитис Химия:Учеб. Для 9 кл. сред. Общеобразоват. Учеб. Заведений. – М.: Просвещение, 2008.
Химия. – 2-е изд., перераб./ред. Коллегия: М.Аксёнова, И.Леенсон, С.Мартынова и др. – М.: Мир энциклопедий Аванта+, Астрель, 2007.
Хомченко Г.П. Химия для поступающих в ВУЗы: учеб.пособие. – 2-е изд. – М.: высш. Шк., 1993.
Электронные издания
Диск «Неорганическая химия»
Диск Химия 9 класс «Просвещение»
Учащимися использовались Интернет-ресурсы
Свойства серого чугуна и химический состав
Свойства серого чугуна и химический состав | Литье в песчаные формы, литье по выплавляемым моделям и обработка с ЧПУ в Китае 30 июля 2010 г.
(отливки из серого чугуна) получил свое название из-за цвета излома.Он содержит 1,5-4,3% углерода и 0,3-5% кремния, а также марганец, серу и фосфор. Он хрупок с низкой прочностью на растяжение, но легко отливается.
Все данные в этом документе относятся к китайскому стандарту GB/T 9439-1988. Qingdao Casting Quality пишет все материалы из справочника.
www.castingquality.com
Наши услуги
Качество литья сосредоточено на производстве металлических деталей, мы предоставляем профессиональные услуги в области литья металлов.
Литье в песчаные формы— это популярный метод формовки металла, подходящий для всех материалов, таких как серый чугун, ковкий чугун, ковкий чугун, углеродистая сталь, нержавеющая сталь, алюминий и бронза.
просмотров: 3179
, также называемый прецизионным литьем по выплавляемым моделям, в основном подходит для деталей из углеродистой и нержавеющей стали.
Мы также поставляем детали из серого и ковкого чугуна, а также алюминия и бронзы методом литья по выплавляемым моделям. Он может добиться наилучшего внешнего вида с хорошей устойчивостью
просмотров: 3179
- Метод литья в оболочку
является хорошим вариантом для замены литья по выплавляемым моделям и литья в песчаные формы.качество лучше, чем детали для литья в песчаные формы, подходящие для массового производства.
просмотров: 3179
Фрезерование с ЧПУ, токарная обработка с ЧПУ с 5 xix центром с ЧПУ, мы обеспечиваем прецизионную обработку для всех отливок на основе чертежей заказчика.
просмотров: 3179
Услуги по механическому проектированию на основе требований клиентов, наше программное обеспечение — Solidworks и AutoCAD.
просмотров: 3179
Проектирование и производство пресс-форм будет обслуживаться для литья металлов и литья пластмасс под давлением.
Основываясь на нашем более чем 10-летнем опыте, мы поставляем профессиональные пресс-формы для наших клиентов в Европе и Северной Америке.
просмотров: 3179
Свойство серого чугуна
Прочность на растяжение образца одиночной отливки для серого чугуна
Серый чугун Марка | Отдельный образец Прочность на растяжение | Отливки из серого чугуна | |
Толщина стенки /мм | Прочность на растяжение σb≥/МПа | ||
НТ100 | 100 | >2.5~10 >10~20 >20~30 >30~40 | 130 100 90 80 |
HT150 | 150 | >2,5~10 >10~20 >20~30 >30~40 | 175 145 130 120 |
НТ200 | 200 | >2,5~10 >10~20 >20~30 >30~40 | 220 195 170 160 |
НТ250 | 250 | >4.![]() >10~20 >20~30 >30~50 | 270 240 220 200 |
НТ300 | 300 | >10~20 >20~30 >30~50 | 290 250 230 |
НТ350 | 350 | >10~20 >20~30 >30~50 | 340 290 260 |
www.castingquality.com
.com
Свойство прочности на растяжение прикрепленного образца отливок
Серый чугун Марка | Толщина стенки /мм | Прочность на растяжение σb≥/МПа | Прочность на растяжение (ссылка) σb≥/МПа | |||
Прилагаемый тестовый талон | Прикрепленный тестовый блок | |||||
Ø30 мм | Ø50 мм | R15мм | R25мм | |||
HT150 | >20~40 >40~80 >80~150 >150~300 | 130 115 – – | – (115) 105 100 | 120 110 – – | – – 100 90 | 120 105 90 80 |
НТ200 | >20~40 >40~80 >80~150 >150~300 | 180 160 – – | – (155) 145 135 | 170 150 – – | – – 140 130 | 165 145 130 120 |
НТ250 | >20~40 >40~80 >80~150 >150~300 | 220 200 – – | – (190) 180 165 | (210) 190 – – | – – 170 160 | 205 180 165 150 |
НТ300 | >20~40 >40~80 >80~150 >150~300 | 260 235 – – | – (230) 210 195 | (250) 225 – – | – – 200 185 | 245 215 195 180 |
НТ350 | >20~40 >40~80 >80~150 >150~300 | 300 270 – – | – (265) 240 215 | (290) 260 – – | – – 230 210 | 285 255 225 205 |
Другое механическое имущество отливок из серого чугуна
Марка | Прочность на сжатие σbc/МПа | Прочность на сдвиг τb/МПа | Испытание на удар αKV/(Дж/см2) | Безопасный диапазон напряжений σ-1/МПа | Модуль упругости Ε/ГПа |
HT150 | 500~700 | 150~250 | – | 60~90 | 70~90 |
НТ200 | 600~800 | 200~300 | 2~5 | 80~90 | 80~110 |
НТ250 | 800~1000 | 250~350 | 4~8 | 100~140 | 100~130 |
НТ300 | 1000~1200 | 300~450 | 7~10 | 120~160 | 120~140 |
НТ350 | 1100~1300 | 350~500 | 9~11 | 140~180 | 130~160 |
Отливки из серого чугуна Твердость
Серый чугун Марка | Класс твердости | Диапазон твердости HBS | Металлография |
НТ100 | х245 | ≤170 | Феррит |
HT150 | х275 | 150~200 | Феррит + Перлит |
НТ200 | х295 | 170~220 | Перлит |
НТ250 | х315 | 190~240 | Перлит |
НТ300 | х335 | 210~260 | Перлит (модифицированный чугун) |
НТ350 | х355 | 230~280 | Перлит (модифицированный чугун) |
Термообработка литья из серого чугуна
Масса отливки кг | Начальная температура /°C | Скорость нагрева /(°C/ч) | Температура консервации/°C | Время сохранения тепла /ч | Скорость охлаждения /(°C/ч) | Конечная температура /°C | |
Чугун | Низколегированный чугун | ||||||
Простые отливки | |||||||
<200 | ≤200 | ≤100 | 500~550 | 550~570 | 4~6 | 30 | 200 |
200~2500 | ≤200 | ≤80 | 500~550 | 550~570 | 6~8 | 30 | 200 |
>2500 | ≤200 | ≤60 | 500~550 | 550~570 | 8 | 30 | 200 |
Точное литье | |||||||
<200 | ≤200 | ≤100 | 500~550 | 550~570 | 4~6 | 20 | 200 |
200~2500 | ≤200 | ≤80 | 500~550 | 550~570 | 6~8 | 20 | 200 |
Литье из серого чугуна, ни в одном стандарте не упоминается химический состав, поэтому мы предлагаем только следующий химический состав, основанный на фактическом производстве.
Марка | Толщина стенки /мм | С | Си | Мн | Р ≤ | С ≤ |
НТ100 | – | 3,4~3,9 | 2,1~2,6 | 0,5~0,8 | 0,3 | 0,15 |
HT150 | <30 30~50 >50 | 3,3~3,5 3,2~3,5 3,2~3,5 | 2,0~2,4 1.9~2,3 1,8~2,2 | 0,5~0,8 0,5~0,8 0,6~0,9 | 0,2 0,2 0,2 | 0,12 0,12 0,12 |
НТ200 | <30 30~50 >50 | 3,2~3,5 3,1~3,4 3,0~3,3 | 1,6~2,0 1,5~1,8 1,4~1,6 | 1,7~0,9 0,8~1,0 0,8~1,0 | 0,15 0,15 0,15 | 0,12 0,12 0,12 |
НТ250 | <30 30~50 >50 | 3.0~3,3 2,9~3,2 2,8~3,1 | 1,4~1,7 1,3~1,6 1,2~1,5 | 0,8~1,0 0,9~1,1 1,0~1,2 | 0,15 0,15 0,15 | 0,12 0,12 0,12 |
НТ300 | <30 30~50 >50 | 2,9~3,2 2,9~3,2 2,8~3,1 | 1,4~1,7 1,2~1,5 1,1~1,4 | 0,8~1,0 0,9~1,1 1,0~1,2 | 0,15 0,15 0,15 | 0.![]() 0,10 0,10 |
Серый чугун Сравнить
Индекс | Страна | Серый чугун Марка | ||||||
1 | Китай | — | НТ350 | НТ300 | НТ250 | НТ200 | НТ150 | НТ100 |
2 | японский | — | ФК350 | FC300 | ФК250 | ФК200 | ФК150 | ФК100 |
3 | США | №.60 | № 50 | № 45 | № 35/ № 40 | № 30 | № 25 | № 20 |
4 | Россия | СЧ40 | СЧ35 | СЧ30 | СЧ24/СЧ25 | СЧ18/СЧ20/СЧ21 | СЧ15 | СЧ10 |
5 | Германия | ГГ40 | ГГ35 | ГГ30 | ГГ25 | ГГ20 | ГГ15 | ГГ10 |
6 | Италия | — | Г35 | Г30 | Г25 | Г20 | Г15 | Г10 |
7 | Франция | ФГЛ400 | ФГЛ350 | ФГЛ300 | ФГЛ250 | ФГЛ200 | ФГЛ150 | — |
8 | Англия | 400 | 350 | 300 | 260 | 180/220 | 150 | 100 |
9 | Польша | З140 | З135 | З130 | З125 | Z120 | З115 | — |
10 | Индия | ФГ400 | ФГ350 | ФГ300 | ФГ260 | ФГ200 | ФГ150 | — |
11 | Румыния | ФК400 | ФК350 | FC300 | ФК250 | ФК200 | ФК150 | — |
12 | Испанский | — | ФГ35 | ФГ30 | ФГ25 | ФГ20 | ФГ15 | — |
13 | Бельгия | ФГГ40 | ФГГ35 | ФГГ30 | ФГГ25 | ФГГ20 | ФГГ15 | ФГГ10 |
14 | Австралия | Т400 | Т350 | Т300 | Т260 | Т220 | Т150 | — |
15 | Швеция | О140 | О135 | О130 | О125 | О120 | О115 | О110 |
16 | Венгрия | ОВ40 | ОВ35 | ОВ30 | ОВ25 | ОВ20 | ОВ15 | — |
17 | Болгария | — | Вч45 | Вч40 | Вч35 | Вч30 | Вч25 | — |
18 | ИСО | — | 350 | 300 | 250 | 200 | 150 | 100 |
19 | КОПАНТ | ФГ400 | ФГ350 | ФГ300 | ФГ250 | ФГ200 | ФГ150 | ФГ100 |
20 | Тайвань (Китай) | — | — | FC300 | ФК250 | ФК200 | ФК150 | ФК100 |
21 | Голландия | — | ГГ35 | ГГ30 | ГГ25 | ГГ20 | ГГ15 | — |
22 | Люксембург | ФГГ40 | ФГГ35 | ФГГ30 | ФГГ25 | ФГГ20 | ФГГ15 | — |
23 | Австрия | — | ГГ35 | ГГ30 | ГГ25 | ГГ20 | ГГ15 | — |
24 | Европейский стандарт | EN-GJL-350 | EN-GJL-300 | EN-GJL-250 | EN-GJL-200 | EN-GJL-150 |
Отливки из серого чугуна
Чугунные колеса были изготовлены методом литья в песчаные формы, их также называют направляющими роликами или гусеничными роликами для железной дороги, фланцевыми гусеничными колесами, фланцевыми гусеничными роликами, промышленными гусеничными колесами, стальными рельсовыми колесами.
Корпус шпинделя из ковкого чугуна
Корпус шпинделя для вала, штока или подшипника. Производство: Литье в песчаные формы. Материал: ковкое чугунное литье GGG40, GGG50, GGG60, GGG70, GGG80. Качество литья. Промышленные поставки. Обработка с ЧПУ для отливки корпуса шпинделя в Китае. Просмотров: 452 Ключевые слова: литье из ВЧШГ
Чугунные гильзы цилиндров
Метод литья: литье в песчаные формы или центробежное литье Прецизионная обработка: токарная обработка и шлифование. Материал: серый чугун HT250; ГГ20; FC25 Гильза цилиндра — центральная рабочая часть Просмотров: 490 Ключевые слова: литье в песчаные формы, литье из серого чугуна, центробежное литье
Запасные части для направляющих устройств
Процесс литья в песчаные формы с ЧПУ; Литой серый чугун (серый чугун) материал HT200/GG20/GG25; Направляющая арматура насоса со статическим балансом, защищенная лакокрасочным покрытием Просмотров: 110 Ключевые слова: отливка из серого чугуна, отливка арматуры насоса
Чугунные отливки рабочих колес водяных насосов. Основным материалом является литой серый чугун GG20/HT200/HT300. Метод литья в песчаные формы с ЧПУ и статической балансировкой. Просмотров: 102 Ключевые слова: насосная арматура литье
Фитинги из ковкого чугуна, ниппель, материал — ковкий чугун 300-6. Черная поверхность или горячая поверхность (белая). Литье в песчаные формы, горячее погружение с резьбой. Стандарт: EN 10242, DIN 2950 Просмотров: 144 Ключевые слова: литье из ковкого чугуна
просмотров: 3179
13 апреля 2021 г.ошибка: Предупреждение: Спасибо за интерес, но статья защищена! Вы можете щелкнуть вверху справа по электронной почте!
Химический состав чугуна и литой стали
Почему важно контролировать химический состав металлических отливок?
Химические компоненты металлических отливок, включая обычный углерод
(C), кремний (Si), марганец (Mn), сера (S), фосфор (P) и
также включая многие компоненты сплава, такие как хром (Cr),
Молибден (Mo), никель (Ni), медь (Cu) и т. Д.
Различные химические компоненты выполняют разные функции, поэтому очень разные механические свойства, такие как увеличение их прочность на растяжение, твердость, абразивная стойкость и коррозионная стойкость сопротивление. Вот почему мы должны рассмотреть химический сочинение.
Химический состав чугуна, серого чугуна и ковкого чугуна
Что касается легированного чугуна, химический состав, особенно содержание сплава, очень важно.Будет большой риск или неисправность, если содержание сплава не соответствует требованиям.
Как и для обычного серого чугуна и ковкого чугуна, химический состав сравнительно не важен. Чугунолитейные заводы могли регулировать композиции в соответствии со своим опытом, пока они могли соответствовать физическим и механическим требованиям. Однако, по В принципе, Sulphur также следует контролировать в разумном диапазоне. большое количество серы приведет к хрупкости чугунных отливок.
Химический состав литой стали, углеродистой стали и легированной стали
Химический состав очень важен для стальных отливок, как для
большинство стальных отливок, пока химический состав
в требуемом диапазоне, то их механические свойства должны быть
квалифицированный. Потому что большая часть литой стали должна соответствовать некоторым особым требованиям.
свойствами, помимо прочности на растяжение и относительного удлинения, поэтому химические
состав будет самым важным осмотром.
Как проверить химический состав чугуна и литья стали?
1. Метод химического анализа (химический метод испытаний)
Подходит для материалов из чугуна, стального литья и легированной стали. Точность результата зависит от мастерства лаборатории техник.
Недостаток: Медленно, поэтому не может соответствовать требованиям для проверки до и во время производства. Наше литейное производство обычно использовало этот метод. исследовать химический состав чугунных материалов.
2. Спектрометр химического состава
Подходит как для чугуна, так и для стального литья, а также для легированной стали.
Точность и скорость очень высоки, поэтому хорошо подходит для проверки во время
производство.
Недостаток: если некоторые химические элементы очень высокие или очень низкие,
то результат не будет точным.
Дом | Другие статьи
Влияние Cr, Mo и Al на микроструктуру, абразивный износ и коррозионную стойкость Ni-Mn-Cu чугуна
Материалы (Базель).2019 ноябрь; 12(21): 3500.
Daniel Medyński
1 Факультет технических и экономических наук, Государственный университет прикладных наук им. Кафедра передовых технологий материалов, Вроцлавский политехнический университет, Смолуховского 25, 50-372 Вроцлав, Польша; [email protected]
1 Факультет технических и экономических наук, Государственный университет прикладных наук Вителон в Легнице, Sejmowa 5A, 59-220 Легница, Польша
3 Кафедра передовых технологий материалов, Вроцлав Технологический университет, Смолуховского 25, 50-372 Вроцлав, Польша; л.с[email protected]Поступила в редакцию 5 августа 2019 г.; Принято 23 октября 2019 г.
Лицензиат MDPI, Базель, Швейцария. Эта статья находится в открытом доступе и распространяется на условиях лицензии Creative Commons Attribution (CC BY) (http://creativecommons.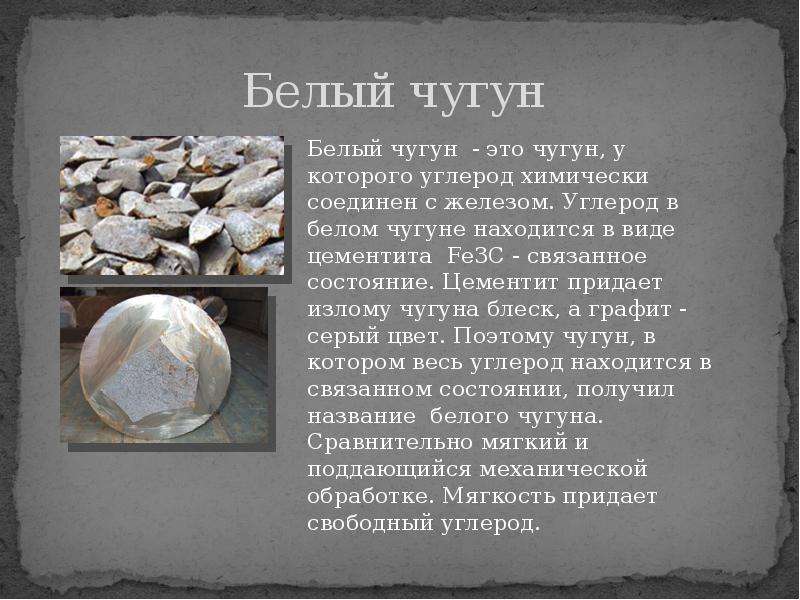
Abstract
Представлены результаты исследования влияния Cr, Mo и Al на микроструктуру, абразивный износ и коррозионную стойкость Ni-Mn-Cu чугуна в литом и термически обработанном состояниях.Из-за охлаждающего эффекта первых двух элементов (склонность к образованию твердых пятен) в сплавы добавляли графитизирующий алюминий с самой высокой концентрацией Cr и Mo. Все отливки в литом состоянии имели аустенитную матрицу, гарантирующую хорошую обрабатываемость. . Термическая обработка сырцовых отливок, заключающаяся в отжиге при 500 °С в течение 4 ч, привела к частичному превращению аустенита. В результате образовался пересыщенный углеродом игольчатый феррит, морфологически подобный бейнитному ферриту.Степень этого превращения увеличивалась с увеличением концентрации Cr и Mo, что последовательно снижало термодинамическую стабильность аустенита. Изменение структуры матрицы позволило значительно повысить твердость и абразивную износостойкость отливок. Наибольший прирост твердости и износостойкости показали отливки с наибольшим суммарным содержанием Cr и Mo с добавкой 0,4 % Al. Введение Cr и Mo также привело к повышению коррозионной стойкости.В термически обработанных образцах увеличение концентрации Cr и Mo приводило к последовательному уменьшению глубины коррозионных язв при одновременном увеличении их количества. Это очень выгодно с точки зрения коррозионной стойкости.
Ключевые слова: абразивный износ, аустенитный чугун, аустенитное превращение, коррозионная стойкость, Ni-Mn-Cu чугун аустенитный чугун [1,2].Однако это материал с низкой стойкостью к истиранию. Альтернативой является чугун Ni-Mn-Cu с радикально сниженным содержанием Ni по сравнению с чугуном Ni-Resist, при этом пониженное содержание Ni компенсируется добавлением аустенитизирующих элементов, таких как Mn и Cu [2].
Правильный подбор химического состава Ni-Mn-Cu чугуна позволяет получать отливки с аустенитной структурой, гарантирующей хорошую обрабатываемость [2]. В свою очередь правильный подбор параметров термической обработки, провоцирующий коренные изменения литейной матрицы, позволяет получить хорошие механические свойства и высокую абразивную износостойкость при сохранении повышенной коррозионной стойкости (высокий электрохимический потенциал легирующих элементов) [3, 4,5,6,7,8].Это позволяет использовать этот тип чугуна для отливки деталей машин, работающих в тяжелых условиях, например, в горнодобывающей промышленности.
Выбор химического состава в основном основывается на значении эквивалента никеля Equ Ni , которое указывает на термодинамическую стабильность аустенитной матрицы. Если эквивалентное значение, рассчитанное по уравнению (1) [9], меньше 16,0%, это приводит к частичному превращению аустенита в игольчатый феррит [4,5,8,9].
Equ Ni = 0,32⋅C + 0,13⋅Si + Ni + 2,48⋅Mn + 0,53⋅Cu
(1)
где Equ Ni — эквивалент никеля [мас. %], C, Si, Ni, Mn, Cu — концентрации элементов [мас. %].
Чем выше степень этого превращения, тем меньше значение никелевого эквивалента [4,5,8]. Это приводит к значительному повышению твердости отливок, что значительно затрудняет их механическую обработку.
В свою очередь, если значение Equ Ni не менее 16.0 % матричная структура сырцовых отливок состоит исключительно из аустенита [9]. Увеличение эквивалентного значения приводит к повышению стабильности аустенитной матрицы [8,10]. Это благоприятное явление с точки зрения возможности получения конструкции, устойчивой в широком диапазоне температур. Однако это ограничивает возможность получения путем термической обработки твердой и стойкой к истиранию структуры, по свойствам аналогичной аустенизированному ковкому чугуну (ADI) [11, 12, 13, 14, 15, 16, 17,18,19,20,21,22,23,24,25].
В этом отношении наиболее выгодно использовать чугун со значением Equ Ni ок. 16,0%. Это позволяет получать сырцовые отливки с аустенитной матрицей и изменять эту структуру технически несложной термической обработкой (выдержкой и охлаждением на воздухе) [6,7].
Представляется возможным повысить твердость, стойкость к абразивному износу и коррозионную стойкость Ni-Mn-Cu чугуна путем введения хрома и молибдена, элементов, обычно используемых с этой целью в других марках чугуна.Из-за охлаждающего действия этих элементов представляется целесообразным одновременно добавить небольшое количество алюминия. Поэтому целью работы было определить, в какой степени добавки Cr, Mo и Al повлияют на структуру, твердость, абразивную износостойкость и коррозионную стойкость термически обработанных отливок.
2. Материалы и методы
Были проведены исследования чугуна, полученного из девяти плавок (). При предполагаемой постоянной концентрации основных элементов: 3.4 ± 0,2% С; 1,8 ± 0,2 % Si; 4,2 ± 0,2 % марганца; 3,2 ± 0,2 % никеля; 1,8 ± 0,2 % Cu; 0,18 ± 0,2 % P и 0,01 % S, концентрации Cr и Mo изменялись от 0,4 до 1,8 % и от 0,2 до 0,5 % соответственно. Кроме того, в сплавы с более высокими концентрациями Cr и Mo добавляли 0,4% Al, чтобы компенсировать их охлаждающий эффект (склонность к образованию твердых пятен). Такой подбор химического состава, разработанный на основе ранее проведенных исследований и литературных данных [26], должен позволить получать чугуны, близкие к эвтектическим, с низкой термодинамической стабильностью аустенитной матрицы сырцовых отливок и с ограниченной склонностью к образованию твердые места.
Таблица 1
Химический состав сырых отливок, никелевый эквивалент Equ Ni и коэффициент эвтектического насыщения S C.
Сплав № | Химический состав [WT%] | S C [/] | EQU [WT%] | ||||||||||
---|---|---|---|---|---|---|---|---|---|---|---|---|---|
C | SI | MN | NI | CU | CR | Mo | Al | P | S | ||||
1 | 3.![]() | 1,9 | 4,3 | 3,3 | 1,9 | — | — | — | 0,19 | 0,01 | 1,02 | 16,3 | |
2 | 3,6 | 1,8 | 4,2 | 3.![]() | 2.0 | 0.4 | — | — | 0.19 | 0,01 | 1.03 | 16.1 | |
3 | |||||||||||||
3 | 3.4 | 1.7 | 4.4 | 2.9 | 1,7 | 0,7 | — | — | 0,20 | 0,01 | 0,95 | 16,0 | |
4 | 3,5 | 1,8 | 4,2 | 3,4 | 1,8 | 0,9 | — | 0,4 | 0,18 | 0,01 | 1.![]() | 16.1 | |
5 | |||||||||||||
5 | 3.4 | 2.0 | 4.1 | 3.4 | 2.0 | 1.8 | — | 0,4 | 0,17 | 0,01 | 0,99 | 16,0 | |
6 | 3,4 | 2,0 | 4,3 | 3,3 | 1,7 | 0,7 | 0,2 | — | 0,18 | 0.![]() | 0.01 | 16.2 | 16.2 |
7 | 3.6 | 1.9 | 4.3 | 3.1 | 1.8 | 1.0 | 0.2 | — | 0.16 | 0,01 | 1,01 | 16,1 | |
8 | 3,3 | 1,7 | 4,2 | 3,3 | 1,9 | 0,7 | 0,5 | 0,4 | 0,20 | 0,01 | 0,95 | 16,0 | |
9 | 3.![]() | 3.5 | 1.8 | 4.2 | 3.2 | 2.0 | 1.1 | 0.5 | 0,4 | 0,18 | 0,01 | 1.01 | 16,0 |
Чугун выплавляли в индукционной среднечастотной печи, в тигле SiC типа А35. Отливки из сплавов от 1 до 9 в виде диам. Валы размером 30 мм х 250 мм были отлиты в оболочковых формах. Затем каждую из полученных отливок разрезали на опытные образцы в виде валков толщиной 10 мм, которые подвергали металлографическим испытаниям. Испытывались образцы сырого чугуна и после термической обработки. Термическая обработка образцов заключалась в выдержке при 500°С в течение 4 ч (в печи сопротивления) с последующим охлаждением на воздухе.
От полученных отливок отбирали образцы для химического анализа, микроскопических наблюдений, измерения твердости, испытаний на стойкость к абразивному износу и испытания на коррозионную стойкость. Все результаты исследования представляют собой средние значения не менее чем из трех измерений.
Химический анализ проводили спектрально с использованием анализатора тлеющего разряда GDS 750 QDP (Leco, Лондон, Великобритания) и сканирующего электронного микроскопа Quanta 250 (FEI, Уолтем, Массачусетс, США), оснащенного детектором EDS. Результаты анализа, а также значения никелевого эквивалента Equ Ni (рассчитанного по уравнению (1)) и коэффициента эвтектического насыщения S C (показатель степени отклонения химического состава чугуна от его эвтектический состав) приведены в .
Микроскопические исследования проводились с использованием светового микроскопа MA200 (Nikon, Бангкок, Таиланд) и TM 3000 (Hitachi, Токио, Япония) и сканирующих электронных микроскопов FEI Quanta 250.
Твердость по Бринеллю измерена в соотв. в соответствии с EN ISO 6506-1:2014-12 на тестере Nexus (Innovatest, Маастрихт, Нидерланды) с шаром диам. 2,5 мм при 1838,75 Н. Микротвердость по Виккерсу измеряли в соотв. EN ISO 6507-1:2018-05 на приборе Nova от Innovatest (Innovatest, Маастрихт, Нидерланды) при нулевой нагрузке на индентор.01 Н и 0,1 Н.
Стойкость к абразивному износу определяли методом «штифт на диске» на машине (Struers, Токио, Япония). Измерения заключались в истирании образцов диам. 25 мм прижимали с усилием 30 Н к алмазному диску (размер зерен от 45 до 53 мкм), охлаждаемому водой. Измерения проводились в шести циклах. Каждый цикл длительностью 5 мин соответствовал скользящей дистанции 175 м. Поэтому каждый образец истирался в течение 30 мин на расстоянии 1050 м.
Коррозионную стойкость сплава определяли гравиметрическим и потенциодинамическим методами.В обоих случаях в качестве агрессивного раствора использовали 3% водный раствор NaCl при температуре окружающей среды [27]. При гравиметрических измерениях агрессивную среду аэрировали для повышения ее агрессивности [28].
Результаты гравиметрических испытаний представлены в виде потери массы в единицу времени на единицу площади образца V C [мг/(дм 2 ·сут)] и после пересчета по формуле (2) [29, 30], как скорость линейной коррозии V P :
где V P — линейная скорость коррозии [мм/год], V C — потеря массы образца во времени [мг/(дм 2 ·сут)], d — плотность металлического материала [г/ см 3 ].
Потенциодинамические измерения проводились в полностью автоматизированной трехэлектродной системе с использованием потенциостата (BioLogic, Seyssinet-Pariset, Франция). В качестве электрода сравнения использовали насыщенный каломельный электрод. Вспомогательным электродом служил платиновый электрод [31,32,33]. Поляризацию всех образцов начинали с потенциала ок. -900 мВ NEC , при 1 мВ/с в анодном направлении. Коррозионную стойкость определяли по потенциалу катодно-анодного перехода E K-A , стационарному потенциалу E’, плотности тока коррозии i corr и поляризационному сопротивлению R P .
3. Результаты и обсуждение
3.1. Наблюдения под микроскопом и измерения твердости необработанных отливок
Наблюдения под микроскопом, включая определение характеристик графита в соотв. EN ISO 945-1:2018-04, проводились на полированных срезах, непротравленных и протравленных ниталом, см. Результаты качественного анализа микроструктуры приведены в .
Микроструктуры необработанных отливок: ( а ) № 1 — графит ИА4; ( б ) № 1 – аустенит, графит; ( с ) №2 — графит ИЭ4; ( д )№. 2 — аустенит, графит; ( и ) № 5 — графит ИЭ6; ( ф ) № 5 – аустенит, графит, цементит; ( г ) №8 – графит ИД5; ( h ) № 8 – аустенит, графит, цементит; ( и ) № 9 — графит ИД4; ( j ) №9 – аустенит, графит, цементит. Полированные срезы слева не протравлены; те, что справа, выгравированы Ниталом.
Таблица 2
Состав микроструктуры и твердость необработанных отливок.
Сплав № | EUC NI [WT%] | MATRIX | High-Carbon Phas % Fe 3 C -% C GR * / Тип C GR / | HBS AVR 2.5 /187.5kg [/] (+/- 2) (+/- 2) | HV0.01N AVR Austenite [/] (+/- 2) | |
---|---|---|---|---|---|---|
1 | 16.![]() | Austenite | 0% Fe 3 C – 100%C г /IA4/ | 160 | 168 | |
2 | 16.1 | Austenite | 0% Fe 3 C — 100% C GR / IE4 / | 170 | 182 | |
3 | 16.0 | Austenite | 0% FE 3 C — 100% C GR / IE4 / | 185 | 192 | 192 |
4 | 16.![]() | Austenite | 10% FE 3 C — 90% C GR / IE5 / | 280 | 204 | |
5 | 16.0 | austenite | 95% Fe 3 C — 5% C GR / IE6 / | 380 | 230 | |
6 | 16.2 | Austenite | 45% FE 3 C — 55% C GR / ID5 / | 205 | 195 | 195 |
7 | 16.![]() | Austenite | 50% Fe 3 C — 50% C GR / ID5 / | 220 | 203 | |
8 | 16.0 | Austenite | 55% Fe 3 C — 45% C GR / ID5 / | 210 | 214 | |
9 | 16.0 | Austenite | 60% FE 3 C — 40%C г /ID4/ | 250 | 207 |
Введение дополнительных элементов в Ni-Mn-Cu чугун не повлияло на структуру матрицы исходных отливок. В каждом случае матрица состояла исключительно из аустенита, см. b, d, f, h, j.Однако характеристики и количества графита различались, см. a,c,e,g,i.
В сплаве №1 (без добавок Cr и Mo) обнаружен прямой графит типа А размера 4, см. а. Введение 0,4 % Cr в сплав № 2 привело к уменьшению количества и размера частиц графита. Появилась тенденция к междендритному расположению типа Е, см. c. Эти тенденции возрастали по мере увеличения концентрации хрома в последующих сплавах № 3–5. Начиная с 0,9 % Cr (сплав №4, а затем сплав № 5), несмотря на введение 0,4 % Al, в отливках появилось частичное отхолаживание, см. ф. Добавление молибдена, как и хрома, приводило к уменьшению количества и размера частиц графита и увеличивало склонность к закалке. Однако это влияние было менее интенсивным, чем влияние хрома. Вследствие этого наибольшая степень отбела обнаружена у сплава № 5 (наибольшее содержание Cr) и № 9 с наибольшим суммарным содержанием обоих элементов, см. е,к.
Введение дополнительных элементов и связанные с этим изменения микроструктуры привели к изменению твердости отливок по НВ. Основным фактором, определяющим твердость сырцовых отливок, была степень их закалки, строго связанная с общим содержанием в них Cr и Mo. С увеличением концентрации этих элементов твердость сплавов возрастала. Свою роль сыграла и HV-твердость аустенита, которая повышалась с увеличением концентрации хрома: от 160 HV0,01N в бесхромовом сплаве №1 до 230 ХВ0,01Н в сплаве №5 с наибольшей концентрацией Cr. В результате наименьшую твердость (160 HBS) показал бесхромистый сплав № 1, а наибольшую твердость (380 HBS) — безалюминиевый сплав № 5, содержащий 1,8 % Cr.
3.2. Микроскопические наблюдения и измерения твердости термообработанных отливок
Термическая обработка (выдержка при 500 °С в течение 4 ч с последующим охлаждением на воздухе) привела к изменению матричной структуры всех отливок. Аустенит частично трансформировался в игольчатый феррит, морфологически сопоставимый с ферритом, присутствующим в верхнем бейните.Степень превращения была различной в отдельных отливках, см. и .
Микроструктуры отливок после термической обработки: ( а ) № 1 — остаточный аустенит, игольчатый феррит; ( б ) № 2 – остаточный аустенит, игольчатый феррит; ( c ) № 5 – остаточный аустенит, игольчатый феррит, перлит; ( d ) № 7 – остаточный аустенит, игольчатый феррит; ( и ) № 8 — остаточный аустенит, игольчатый феррит; ( ф ) №8 – остаточный аустенит, игольчатый феррит.Травление Ниталом. РА — остаточный аустенит; AF – игольчатый феррит.
Таблица 3
Состав микроструктуры и твердость термически обработанных отливок.
Сплав № | EQU NI [WT%] | Компоненты матрицы * A — Fe M — P [% -% -%] | Форма углерода в эвтектической смеси ** | HBW AVR 2,5/187,5 [/] (+/−3) | Увеличение HBW 2. ![]() [/] | ||||||
---|---|---|---|---|---|---|---|---|---|---|---|
1 | 16.3 | 50 — 50 — 0 | C GR | 313 | 154 | ||||||
2 | 16.1 | 48 — 52 — 0 | C GR | 347 | 178 | 178 | |||||
3 | 16.![]() | 47 — 53 — 0 | C GR | 372 | 189 | ||||||
4 | 16.1 | 45 – 55 – 0 | C г + Fe 3 C | 411 | 129 | ||||||
5 | 16.0 | 45 — 25 — 30 | C GR + C | 492 | 492 | 112 | |||||
6 | |||||||||||
6 | 16.![]() | 45 — 55 — 0 | C гр + Fe 3 C | 362 | 362 | 157 | |||||
7 | 16.1 | 40 — 60 — 0 | C GR + C | 383 | 163 | ||||||
8 | 16.0 | 10 – 90 – 0 | C г + Fe 3 C | 441 | 230 | ||||||
6 1956 9 9000 | 15 – 85 – 0 | C гр + Fe 3 C | 454 | 205 |
Сплав № | Увеличение HBW 2,5/187,5 [/] | Скорость износа [мг/м∙10 4 ] | Снижение скорости износа по сравнению со сплавом №1 | Индекс поверхностной топографии [мкм] | |||||
---|---|---|---|---|---|---|---|---|---|
R PAVR (+/- 0,02) | R Vavr (+/ 0,02) | R Zavr (+/- 0,02 ) | R AAVR (+/- 0,02) | R qavr (+/- 0,02) | |||||
1 | |||||||||
1 | 154 | 2.![]() | — | 5.17 | 12.19 | 17,36 | 0,87 | 1,44 | |
2 | 178 | 1.62 | -0,57 4,18 | 10,88 15,06 | 0,54 0,85 | ||||
3 189 | 1,52 -0,67 | 4,19 10,83 15,02 | 0,56 0,87 | ||||||
4 | 129 | -0.![]() | -0.95 | -0,99 | 10.84 | 10.84 | 15.00 | 0.52 | 0.85 |
5 | 112 | 0.57 | -1,624,01 10,02 14,03 | 0,48 0,83 | |||||
6 157 | 1,14 -1,05 | 4,17 10,78 14,95 | 0,50 0,84 | ||||||
7 | 163 | 1.![]() | -1.14 | -1.14 | 4.14 | 10.74 | 14.88 | 0.49 | 0.83 |
8 | 230 | 0.85 | -1,33 4,05 | 10,53 14,58 | 0,45 0,81 | ||||
9 205 | 1,62 -1,29 | 4,09 10,68 14,77 | 0,44 0,84 |
Наибольшую скорость изнашивания, свидетельствующую о наименьшей абразивной износостойкости, продемонстрировал бесхромовый сплав № 1, лишенный твердых пятен и с наименьшей степенью превращения аустенита. Более низкая скорость изнашивания других сплавов обусловлена повышенной степенью закалки отливок и/или повышенной степенью превращения аустенита. По этой причине среди сплавов с сопоставимой исходной структурой, например сплавов № 2 и 3 или сплавов № 6 и 7, меньшую скорость изнашивания показали отливки с более высоким содержанием хрома. Наименьшую скорость изнашивания показал практически полностью закаленный сплав № 5, содержащий 1,8 % Cr. Однако наиболее выгодным решением с точки зрения возможности получения отливок с хорошей обрабатываемостью и высокой стойкостью к абразивному износу оказался сплав № 1.8 (без твердых пятен и с очень высокой степенью аустенитного превращения). Его скорость изнашивания была аналогична скорости изнашивания сплава № 5.
После испытаний на абразивный износ образцы подвергались наблюдению за топографией их поверхности с использованием метода визуализации СЭМ. Меньшее топографическое разнообразие поверхности, указывающее на равномерный износ, может указывать на более высокую устойчивость к истиранию. Значения показателей, определяющих топографию поверхности, определяли с помощью сканирующего электронного микроскопа.Индивидуальные индексы определяли при измерении длины ок. 30 мм. Были определены следующие средние параметры профиля: средний самый высокий пик (R pAVR ), средний самый низкий пик (R vAVR ) и среднее расстояние между этими двумя значениями (R zAVR = R pAVR + R ). vAVR ), среднее арифметическое отклонение профиля от средней линии, измеренное на испытательном участке (R aAVR ) и среднеквадратичное отклонение профиля от средней линии, измеренное на испытательном участке (R qAVR ).Результаты приведены в . Наименьшее топографическое разнообразие показали сплавы № 5 и № 8. В сплаве № 5 оно было вызвано практически полным отхолаживанием (около 95%), а в сплаве № 8 — очень высокой степенью аустенитного превращения (около 90%).
3.4. Испытания на коррозионную стойкость
Для получения достоверных результатов испытаний на коррозионную стойкость применялись два метода исследования: гравиметрический и потенциодинамический.
Гравиметрические измерения продолжались в течение 24 дней.Образцы взвешивали (после очистки) после следующих сроков выдержки в 3%-ном водном растворе NaCl: 1, 2, 5, 8, 13, 18 и 24 сут. Скорости коррозии в зависимости от времени определяли по формуле (2). Результаты представлены в .
Таблица 5
Скорость коррозии V P после выдержки образцов в 3-процентном растворе NaCl.
Сплав № | v p [мм / год] После воздействия на указанное время (дни) | ||||||||
---|---|---|---|---|---|---|---|---|---|
1 | 2 | 5 | 8 | 13 | 18 | 24 | |||
1 | как литой | 0.![]() | 0,58 | 0,56 | 0,52 | 0,48 | 0,44 | 0,39 | |
термообработке | 0,57 | 0,59 | 0,57 | 0,55 | 0,51 | 0,45 | 0,37 | ||
2 | AS CAST | 0.![]() | 0.57 | 0.54 | 0.51 | 60.51 | 0.46 | 0.42 | 0.37 |
0.56 | 0,59 | 0,55 | 0,53 | 0,47 | 0,44 | 0,38 | |||
3 | в литом | 0,53 | 0,55 | 0,54 | 0,50 | 0,44 | 0,42 | 0,35 | |
Теплообработанные | 0.![]() | 0.56 | 0.55 | 0.55 | 0.53 | 0.44 | 0.43 | 0.43 | 0.37 |
4 | As Chast | 0.52 | 0,53 | 0,52 | 0,51 | 0,43 | 0,43 | 0,33 | |
термообработке | 0,53 | 0,55 | 0,53 | 0,52 | 0,43 | 0,45 | 0,34 | ||
5 | AS CAST | 0.![]() | 0.51 | 0.51 | 0.48 | 0.44 | 60.44 | 0.41 | 0.30 |
0.50 | 0,52 | 0,50 | 0,48 | 0,46 | 0,42 | 0,31 | |||
6 | в литом | 0,53 | 0,54 | 0,54 | 0,51 | 0,43 | 0,42 | 0,35 | |
Теплообработанные | 0.![]() | 0.54 | 0.54 | 0.54 | 0.52 | 0.42 | 0.43 | 0.36 | |
7 | 97 | As Chast | 0.52 | 0,53 | 0,52 | 0,50 | 0,42 | 0,41 | 0,33 |
термообработке | 0,53 | 0,54 | 0,53 | 0,52 | 0,41 | 0,42 | 0,34 | ||
8 | AS CAST | 0.![]() | 0.53 | 0.50 | 0.49 | 0,42 | 0.41 | 60.41 | 0.31 |
0.52 | 0,53 | 0,51 | 0,50 | 0,41 | 0,43 | 0,31 | |||
9 | в литом | 0,50 | 0,51 | 0,50 | 0,49 | 0,43 | 0,42 | 0,30 | |
Термообработанные | 4 0.![]() | 0.52 | 0.52 | 0.50 | 0.51 | 0.41 | 0.42 | 0.31 |
Gravimetric Examinations показали небольшие различия в коррозионной стойкости между отдельными сплавами.Через 1 сут выдержки образцов в агрессивном растворе скорость коррозии сырых отливок колебалась в пределах 0,49–0,55 мм/год. Наибольшее его значение было измерено для сплава № 1 (не содержащего Cr), а наименьшее — для закаленного сплава № 5 (содержащего 1,8 % Cr). Увеличение времени выдержки до 2 суток привело к более высокой скорости коррозии всех сплавов. Выдержка образцов от 2 до 5 суток привела к последовательному снижению скорости коррозии всех сплавов. Это явление очень благоприятно с точки зрения коррозионной стойкости.После 24 дней воздействия снижение скорости коррозии прибл. Во всех случаях обнаружено отклонение от 30 до 40% по отношению к исходным значениям.
Скорость коррозии отливок после термической обработки была несколько ниже по сравнению со скоростью сырых отливок. После 1 сут выдержки скорость коррозии термообработанных образцов колебалась от 0,50 до 0,57 мм/год. Как и для сырцовых отливок, наибольшее его значение было у бесхромистого сплава № 1, а наименьшее — у отбеленного сплава № 5 с наибольшей концентрацией хрома.
С точки зрения возможности получения отливок, устойчивых как к абразивному износу, так и к коррозии, наиболее благоприятными свойствами обладает сплав № 8, содержащий Cr, Mo и Al. Скорость коррозии этого сплава была аналогична скорости коррозии самого коррозионностойкого сплава № 5. Элементом, наиболее эффективно повышавшим коррозионную стойкость, оказался хром.
Пропитка снижает сегрегацию элементов, а также может уменьшить глубину коррозионных язв [10], поэтому потенциодинамические испытания проводились только на термически обработанных сплавах, показавших повышенную стойкость к абразивному износу.
При потенциодинамических испытаниях образцы подвергали поляризации через 30 мин и через 48 ч выдержки в 3% водном растворе NaCl. Результаты приведены в .
Таблица 6
Электрохимические индикаторы, характеризующие процесс коррозии.
Сплав № | E ‘ [MV] | E KA [MV] | I Corr [мкА / см 2 ] | R P [Kω · CM 2 ] | |||||||
---|---|---|---|---|---|---|---|---|---|---|---|
30 мин | 48 мин | 30 минут | 30 мин | 30 мин | 30 минут | 30 мин | 48 H | ||||
1 | -565 | -524 | — 582 | −733 | 23.![]() | 2 98,8 | 1,2 0,3 | ||||
2 -569 | -535 -643 -739 | 20,1 92,3 | 1,2 0,2 | ||||||||
3 -572 | -538 | -621 | -753 | -753 9006 | 89.![]() | 1.3 | 0.3 | ||||
4 | -581 | -544 | -618 | -751 | 18 . | 7 84,5 | 1,3 0,3 | ||||
5 -589 | -548 -726 -790 | 18,9 79,5 | 1,5 0,5 | ||||||||
6 -568 | -533 | -635 | -758 | -758 | 94.![]() | 1,3 | 0.3 | ||||
7 | -572 | -539 | -669 | -773 | 19 . | 8 88,5 | 1,4 0,3 | ||||
8 -597 | -556 -659 -790 | 18,6 79,5 | 1,6 0,5 | ||||||||
9 -625 | -588 | -678 | -78 | -785 | -785 | 20.![]() | 94.3 | 1,4 | 0.3 | 0.3 |
Наибольшие значения стационарного потенциала E ‘, с указанием повышенной коррозионной стойкости, были обнаружены для сплава. Нет.1 как через 30 мин (-565 мВ), так и через 48 ч (-524 мВ), см. Этот сплав показал самую низкую степень трансформации своей аустенитной матрицы, стабилизированную наибольшим общим содержанием Ni, Mn и Cr (Equ Ni = 16,3%). Наименьшее значение E’ было установлено для сплава № 9 (–605 мВ через 30 мин и –558 мВ через 48 ч). Это сплав с наивысшей степенью превращения аустенита. Помимо Ni, Mn и Cu, он содержал также добавки Cr, Mo и Al. Более длительное время воздействия привело к более высоким значениям E’ для всех образцов. Это благоприятно с точки зрения коррозионной стойкости исследуемых сплавов.
Относительно большие различия значений потенциала катодно-анодного перехода Е КА (около 144 мВ после 30-минутной выдержки) для сплавов № 1 и № 5 свидетельствуют о разнообразии протекающих электродных процессов на металлической поверхности см. и . Это связано с разнообразием фазового состава исследованных сплавов. Более длительное время пребывания в агрессивном растворе привело к меньшим различиям между значениями E K-A для отдельных сплавов.
Поляризационная кривая для сплавов №1-№9 после 30-минутной ( а ) и 48-часовой ( б ) выдержки в 3-процентном водном растворе NaCl.
Значения плотности тока коррозии i корр и поляризационного сопротивления R p показали обратно пропорциональную зависимость, см. . Меньшие значения i соответствуют значениям и большие значения R p часто указывают на повышенную коррозионную стойкость. Однако полученные результаты не свидетельствуют о радикальных различиях этих величин между отдельными сплавами ( и ).После 30-минутной экспозиции значения i corr изменялись от 18,6 до 23,2 мкА/см 2 , а значения R p находились в пределах от 1,2 до 1,6 кОм·см 2 . В свою очередь, меньшее время экспозиции привело к небольшому увеличению значений i corr (от 79,5 до 98,8 мкА/см 2 ) и снижению значений R p (от 0,2 до 0,5 кОм·см 2 ).
Результаты потенциодинамических испытаний не показали радикальных различий между коррозионной стойкостью отдельных сплавов.Более длительное время выдержки образцов также не вызывало существенных изменений их коррозионной стойкости. Поэтому были проведены дополнительные наблюдения за топографией поверхности образцов после потенциодинамических испытаний и после 48-часовой выдержки в агрессивном растворе. Результаты приведены в .
Таблица 7
Показатели, характеризующие топографию поверхности образцов после потенциодинамических испытаний (после 48-часовой выдержки в 3-процентном водном растворе NaCl).
Сплав № | EQU NI [WT%] | CR [WT%] | MO [WT%] | AL [WT%] | Поверхностный топографический индекс [мкм] | ||||
---|---|---|---|---|---|---|---|---|---|
R Pavr (+/- 0,03) | R Vavr (+/- 0,03) | R Zavr (+/- 0,03) | |||||||
1 | 16.![]() | — | — | − | 5,01 | 34,64 | 39.65 | ||
2 | 16,1 | 0,4 | — | — | 4,98 | 33,35 | 38,33 | ||
3 | 16,0 | 0,7 | — | — | 4,85 | 32,21 | 37.![]() | ||
4 | 16.1 | 0.9 | — | — | 0.4 | 4,77 | 28.25 | 33.02 | |
5 | 16.0 | 1.8 | — | 0,4 | 4,73 | 21,14 | 25,87 | ||
6 | 16,2 | 0,7 | 0,2 | — | 4,86 | 24,17 | 29,03 | ||
7 | 16.![]() | 1.0 | 0.2 | — | 4.72 | 22.14 | 22.14 | 28.86 | |
8 | 16.0 | 0,7 | 0.5 | 0.4 | 4.61 | 19.08 | 19.![]() | 23.75 | |
9 | 16.0 | 1.1 | 0.5 | 0.4 | 4.58 | 19.14 | 23.66 |
Что касается различий между отдельными образцами, в сплаве нет .1 с наибольшим значением Equ Ni было обнаружено небольшое количество относительно глубоких ямок. Введение Cr, а также Mo (снижающего устойчивость аустенитной матрицы) приводило к последовательному уменьшению глубины ямок при одновременном увеличении их количества. Этот эффект благоприятен с точки зрения коррозионной стойкости. Наибольшее количество ямок наименьшей глубины обнаружено в сплавах с высоким суммарным содержанием Cr, Mo и Al, наибольшей степенью превращения аустенита и фрагментацией эвтектических колоний. Во всех сплавах коррозионные повреждения располагались в основном вблизи эвтектических колоний и границ фаз, см. и . Это было связано с различием электрохимических потенциалов между отдельными фазами.
Торцевые поверхности образцов после потенциодинамических испытаний, предварительно выдержанных в течение 48 ч в 3-процентном растворе NaCl: сплав №1 ( а ) и сплав № 8 ( б ). Нетронутый.
Поверхности поперечного сечения образцов после потенциодинамических испытаний, предварительно выдержанных в течение 48 ч в 3-процентном растворе NaCl: сплав № 1 ( а ) и сплав № 8 ( б ). Нетронутый.
Механизм коррозионного поражения типичен для точечной коррозии. Он был рассмотрен на примере сплава №1, что обусловлено наименьшей степенью превращения аустенита, а значит, и читабельностью анализа. После 30-минутной выдержки образцов в агрессивном растворе наибольшие коррозионные повреждения наблюдались преимущественно вблизи чешуек графита (а) Это было связано со значительными различиями электрохимических потенциалов между графитом (+0.372 В) и чугунной матрицей (-0,776 В) [26,27]. В результате большой разности потенциалов, которая составляла около 1 В, образовывались микроячейки, увеличивающие скорость коррозии. После выдержки образцов в коррозионном растворе в течение 48 ч было обнаружено углубление ямок вблизи графита. Кроме того, в матрице появились коррозионные повреждения, в основном по границам аустенитных зерен (б).
Торцевые поверхности образцов из сплава № 1 после потенциодинамических испытаний, выдержанных предварительно в 3% растворе NaCl в течение: 30 мин ( а ) и 48 ч ( б ).Нетронутый.
4. Выводы
Структура матрицы всех необработанных отливок состояла исключительно из аустенита. Принятые диапазоны концентраций Cr, Mo и Al не вызывали фазовых превращений, происходящих в случае слишком низкой термодинамической устойчивости аустенита. Однако было обнаружено, что твердость аустенита увеличивалась с увеличением содержания Cr и Mo.
С увеличением содержания в основном Cr и Mo количество и размер частиц графита уменьшались, а тенденция к их междендритному расположению возрастала.Эти элементы привели к более высокой восприимчивости сплава к закалке (созданию твердых пятен). Это привело к явно более высокой твердости необработанных отливок. Добавление 0,4% Al частично ограничивало эту тенденцию.
Термическая обработка привела к частичному превращению аустенита в пересыщенный углеродом твердый игольчатый феррит во всех отливках. Степень превращения увеличивалась с увеличением концентрации Cr и Mo, что свидетельствует о снижении термодинамической устойчивости обоих элементов аустенитной матрицы.
Наибольшие приросты твердости и сопротивления абразивному износу, вызванные термической обработкой, имели место у отливок с наибольшей степенью аустенитного превращения, т.е. у отливок с наибольшим содержанием Cr и Mo, и с добавкой 0,4 % Ал.
В то же время введение в чугун Cr и Mo (элементов с относительно высоким электрохимическим потенциалом) привело к повышению коррозионной стойкости. Увеличение содержания Cr и Mo (преимущественно Cr) приводило к снижению скорости коррозии сырых отливок, так как с увеличением общего содержания обоих элементов уменьшались количество и размеры графитовых чешуек (обычно вблизи них обнаруживались повреждения), проявлялась склонность к междендритному распределению усилилась фрагментация эвтектических колоний.Термическая обработка отливок привела к незначительному по сравнению с повышением стойкости к истиранию снижению коррозионной стойкости по отношению к сырым отливкам. Введение элементов Cr и Mo, снижающих устойчивость аустенитной матрицы, приводило к последовательному уменьшению глубины коррозионных язв, сопровождавшемуся увеличением их количества. С точки зрения коррозионной стойкости это явление желательно.
Вклад авторов
Концептуализация, Д.М. и Эй Джей; Формальный анализ, Д. М., Б.С.; Расследование, Д.М., Б.С. и Дж.К.; Методология, Д.М.; Надзор, AJ; Письмо — первоначальный вариант, Д.М.; Написание — обзор и редактирование, А.Дж. и J.C.
Финансирование
Это исследование не получило внешнего финансирования.
Конфликт интересов
Авторы заявляют об отсутствии конфликта интересов.
Литература
2. Янус А. Формирование структуры отливок из аустенитного чугуна Ni–Mn–Cu. Редакция Вроцлавского политехнического университета; Вроцлав, Польша: 2013 г.[Google Академия]3. Янус А., Гранат К. Износостойкий аустенитно-бейнитный чугун. Институт Машиностроения и Автоматизации Вроцлавского Технического Университета; Вроцлав, Польша: 2005 г. Отчет Института машиностроения и автоматизации Вроцлавского технологического университета; SPR 28. [Google Scholar]4. Мединьский Д., Янус А. Влияние химического состава на структуру и коррозионную стойкость Ni-Mn-Cu чугуна. Арка Литейный инж. 2016;16:59–62. doi: 10.1515/afe-2016-0050. [Перекрестная ссылка] [Академия Google]5.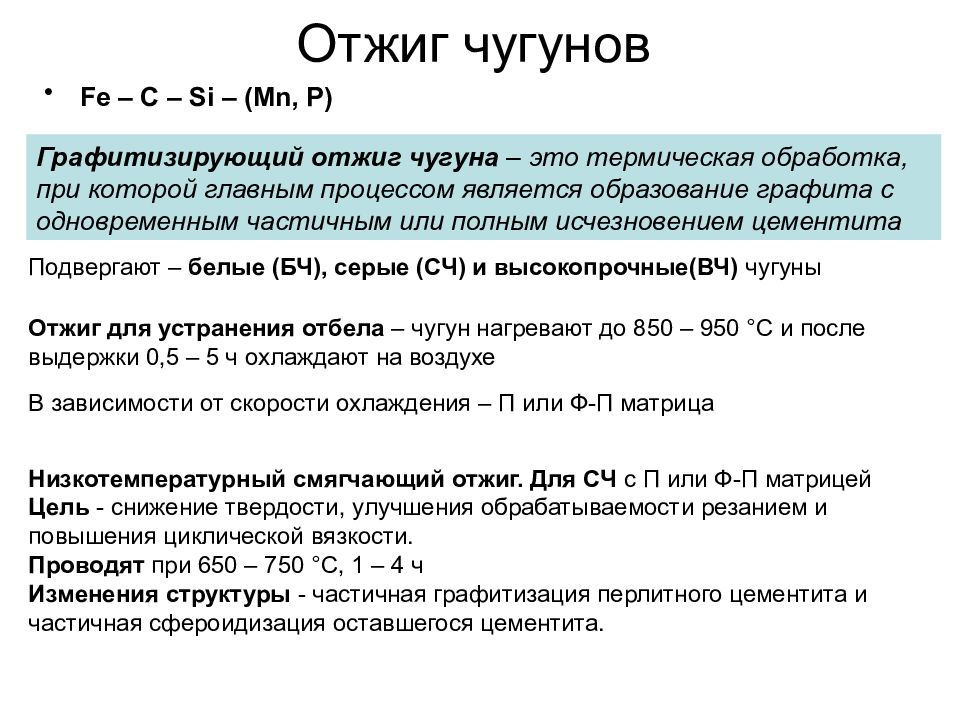


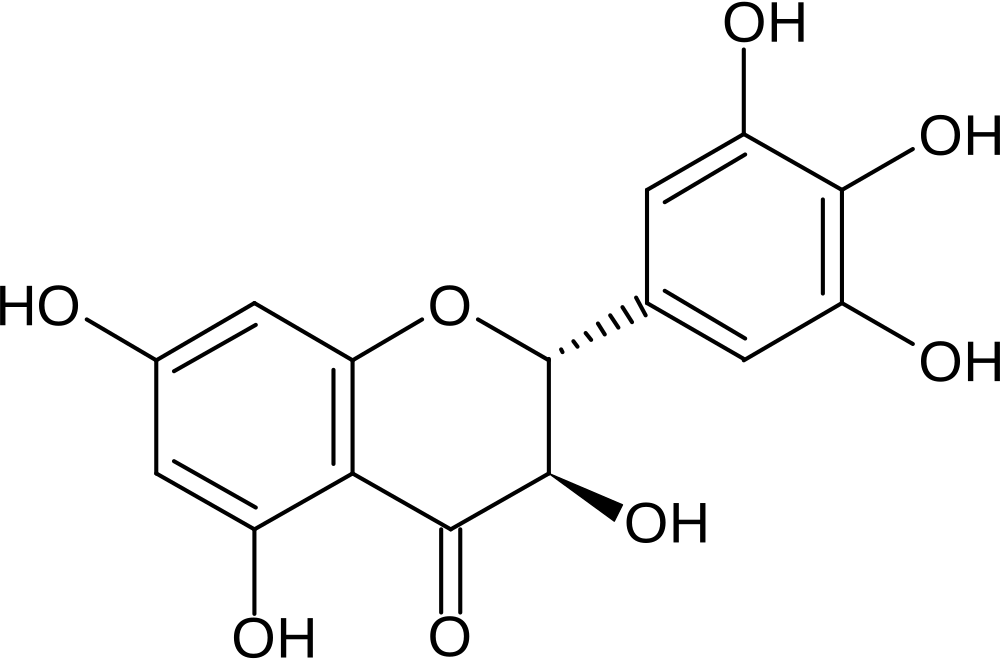



Чугун
Диаграмма состояния железа и углерода
В своей простейшей форме стали представляют собой сплавы железа (Fe) и углерода (C). Изучение состава и структуры железа и стали начинается с фазовой диаграммы железо-углерод. Это также является основой понимания термической обработки сталей.
В железоуглеродной системе присутствуют некоторые важные металлургические фазы и микрокомпоненты. На низкоуглеродистом конце находятся феррит (альфа-железо) и аустенит (гамма-железо). Феррит может растворить не более 0,028 мас.% С при 727°С, а аустенит (гамма-железо) может растворить 2,11 мас.% С при 1148°С. На богатой углеродом стороне находится цементит (Fe3C).
Между однофазными полями встречаются области со смесями двух фаз, таких как феррит и цементит, аустенит и цементит, феррит и аустенит.При самых высоких температурах можно обнаружить поле жидкой фазы, а под ним находятся поля двух фаз: жидкость и аустенит, жидкость и цементит и жидкость и феррит. При термообработке сталей всегда избегают жидкой фазы. Некоторым важным границам в однофазных полях даны специальные названия, облегчающие понимание диаграммы.
Основные микроструктуры железа и стали в равновесии:
1. Аустенитная или гамма-фаза. Аустенит является высокотемпературной фазой и имеет гранецентрированную кубическую (ГЦК) структуру (которая представляет собой плотноупакованную структуру).гамма-железо обладает хорошей прочностью и ударной вязкостью, но оно нестабильно при температурах ниже 723°C.
2. Ферритная или альфа-железная фаза – это относительно мягкая низкотемпературная фаза и стабильная равновесная фаза. Феррит является обычным компонентом сталей и имеет объемно-центрированную кубическую (ОЦК) структуру (которая менее плотно упакована, чем ГЦК). ?-железо мягкое, пластичное, имеет низкую прочность и хорошую ударную вязкость.
3. Цементит – Fe3C или карбид железа. Это промежуточное соединение Fe и C.Он имеет сложную орторомбическую структуру и является метастабильной фазой. Он твердый, хрупкий и имеет низкую прочность на растяжение, хорошую прочность на сжатие и низкую ударную вязкость
4. Перлит представляет собой смесь ферритно-цементитной фазы. Он имеет характерный внешний вид и может рассматриваться как микроструктурная единица или микрокомпонент. Он представляет собой совокупность чередующихся пластинок феррита и цементита, которая после длительной выдержки ниже 723°С вырождается («сфероидизируется» или «укрупняется») в частицы цементита, диспергированные с ферритовой матрицей. Это эвтектоид и имеет структуру ОЦК. Это частично растворимый раствор Fe и C. Обладает высокой прочностью и низкой ударной вязкостью.
В случае неравновесного затвердевания системы Fe-C могут образовываться следующие основные микроструктуры.
• Бейнит представляет собой фазу между перлитом и мартенситным участком. Это твердый метастабильный микрокомпонент; непластинчатая смесь феррита и цементита в очень мелком масштабе. Верхний бейнит образуется при более высоких температурах и имеет перистый вид.Нижний бейнит образуется при более низких температурах и имеет игольчатый вид. Твердость бейнита увеличивается с понижением температуры формования. Обладает хорошей прочностью и жесткостью.
• Мартенсит образуется при быстром охлаждении и является твердым и хрупким. Это пересыщенный раствор атомов С в феррите. Он имеет структуру ОЦТ и твердую метастабильную фазу. Он имеет решетчатую морфологию при 1,0 мас.% С и смеси промежуточных значений. Он имеет высокую прочность и твердость и низкую ударную вязкость.
• Сорбит / троостит
На диаграмме железа-C есть много температур и критических точек, которые важны как с базовой, так и с практической точки зрения.
• Температура А1, при которой происходит эвтектоидная реакция, равная 723 град. С на схеме. A1 называется эвтектоидной температурой и является минимальной температурой для аустенита.
• На более низкотемпературной границе аустенитной области при низком содержании углерода находится ?/? + ? граница.
• Acm – это граница соответствия для высокого содержания углерода, то есть ?/? + граница Fe3C (граница перлита). Содержание углерода, при котором достигается минимальная температура аустенита, называется эвтектоидным содержанием углерода (0,77 мас. % С).
• Температура A4, при которой аустенит превращается в β-железо, 1390 град. C в чистом железе, но эта температура увеличивается по мере добавления углерода.
• Температура A2 является точкой Кюри, когда железо переходит из ферро в парамагнитное состояние. Эта температура составляет 769 градусов. C для чистого железа, но без изменения кристаллической структуры.
• Accm – температура в заэвтектоидной стали, при которой растворение цементита в аустените завершается при нагреве.
• Ac1 – это температура, при которой во время нагревания начинается образование аустенита, где c происходит от французского chauffant.
• Ac3 – температура, при которой завершается превращение феррита в аустенит при нагреве.
• Aecm, Ae1, Ae3 – температуры фазовых переходов при равновесии.
• Arcm – это температура в заэвтектоидной стали, температура, при которой начинается осаждение цементита во время охлаждения, где r происходит от французского refroidissant.
• Ar1 – температура, при которой завершается превращение аустенита в феррит или в феррит плюс цементит во время охлаждения.
• Ar3 – это температура, при которой аустенит начинает превращаться в феррит при охлаждении.
• Ar4 – это температура, при которой дельта-феррит превращается в аустенит при охлаждении.
• Ms (или Ar”) – температура, при которой начинается превращение аустенита в мартенсит при охлаждении.
• Mf – температура, при которой заканчивается образование мартенсита при охлаждении.
Все изменения, кроме образования мартенсита, происходят при более низких температурах при охлаждении, чем при нагреве, и зависят от скорости изменения температуры.
Превращение аустенита в феррит
В равновесных условиях в сплавах железа с углеродом, содержащих до 0,2% образуется доэвтектоидный феррит.8 процентов углерода. Реакция происходит при 910 град. C в чистом железе, но имеет место между 910 град. С и 723 град. C в железоуглеродистых сплавах.
Однако при закалке из аустенитного состояния до температур ниже эвтектоидной температуры Ae1 феррит может образовываться при температурах до 600 град. C. Имеются выраженные морфологические изменения при понижении температуры превращения, которые, следует подчеркнуть, относятся в основном к гипо- и заэвтектоидным фазам, хотя в каждом случае будут вариации из-за точной кристаллографии вовлеченных фаз. Например, те же принципы применимы к образованию цементита из аустенита, но морфологически отличить феррит от цементита нетрудно.
Превращение аустенита в цементит
Классификация Дюба в равной степени применима к различным морфологиям цементита, образующегося при все более низких температурах превращения. Начальное развитие аллотриоморфов границ зерен очень похоже на развитие феррита, и рост боковых пластин или цементита видманстатена происходит по той же схеме.Пластинки цементита имеют более строго кристаллографическую форму, несмотря на то, что ориентационная связь с аустенитом более сложная.
Как и в случае с ферритом, большинство боковых пластин происходит из аллотриоморфов границ зерен, но в реакции цементита больше боковых пластин зарождается на границах двойников в аустените.
Реакция аустенита и перлита
Перлит является наиболее известной микроструктурной особенностью во всей металлографии.Он был обнаружен Сорби более века назад, который правильно предположил, что это пластинчатая смесь железа и карбида железа.
Перлит является очень распространенным компонентом многих сталей, где он вносит существенный вклад в прочность. Пластинчатые эвтектоидные структуры этого типа широко распространены в металлургии, и для их описания часто используется термин перлит.
Эти структуры имеют много общего с реакциями клеточной преципитации. Оба типа реакций происходят путем зародышеобразования и роста и, следовательно, контролируются диффузией.Зародыши перлита встречаются на границах аустенитных зерен, но ясно, что они также могут быть связаны как с доэвтектоидным ферритом, так и с цементитом. В промышленных сталях перлитные конкреции могут образовываться на включениях.
Можно видеть, что нормальная диаграмма равновесия железо-углерод представляет собой метастабильное равновесие между железом и карбидом железа. Цементит метастабилен, так как истинное равновесие находится между железом и графитом. Хотя графит широко встречается в чугунах (от 2 до 4 мас.% углерода), обычно трудно получить эту равновесную фазу в сталях (0. от 03 до 1,5 мас.% углерода). Поэтому обычно рассматривается метастабильное равновесие между железом и карбидом железа, поскольку оно имеет отношение к поведению различных сталей на практике.
При сравнении аустенита (гамма-железа) с ферритом (альфа-железом) замечено, что растворимость углерода больше в аустените с максимальным значением чуть более 2 мас.% при 1147 град. C. Эта высокая растворимость углерода в аустените чрезвычайно важна при термической обработке, когда обработка на твердый раствор в аустените с последующей быстрой закалкой до комнатной температуры позволяет образовать пересыщенный твердый раствор углерода в железе.
Ферритовая фаза ограничена максимальной растворимостью углерода 0,02 мас.% при 723 град. C. Поскольку диапазон содержания углерода в обычных сталях составляет от 0,05 до 1,5 мас.%, феррит обычно связан с цементитом в той или иной форме. Точно так же ?-фаза очень ограничена и находится в диапазоне температур от 1390 до 1534 градусов. C и полностью исчезает, когда содержание углерода достигает 0,5 мас. %.
Чугун с никелевым сопротивлением
Отливки из сплаваNi Resist могут быть изготовлены либо из материала на основе серого чугуна, либо из материала на основе чугуна с шаровидным графитом.Эти материалы были разработаны для обеспечения хорошей устойчивости к морской воде и щелочной коррозии, устойчивости к образованию накипи, тепловому расширению, фрикционному износу, окислению, структурной стабильности, криогенным применениям и эрозии.
Ni Resist также может использоваться в тех случаях, когда требуются ненамагничивающиеся свойства.
Преимущества нирезистивного чугуна:
Стоимость
По сравнению с отливками из нержавеющей стали, отливки из никелевого резиста могут предложить ценовые преимущества.Отливки из Ni Resist легче отливок из нержавеющей стали. Их можно отливать почти до окончательной формы
Обработка
Ni Resist легче обрабатывается, чем нержавеющая сталь. Припуски на механическую обработку отливок из никелевого резиста ниже по сравнению с нержавеющей сталью.
Возможность литья
Как и в случае с серым чугуном и чугуном с шаровидным графитом, отливки из нирезиста обладают всеми преимуществами конструкции, присущими отливкам из чугуна. Могут быть использованы сложные формы, будет достигнута превосходная отделка поверхности и могут быть выполнены сложные конструкции.
Спецификация нирезистаBS 3468 1986
Тип | Класс | Химический состав | ||||||||
С%макс. | Si% | Мн% | Ni% | Cu% | Кр% | Нб% | П%макс. | Мг% | ||
Чешуйчатый графит | Ф1 | 3.0 | 1,5 – 2,8 | 0,5 – 1,5 | 13,5 – 17,5 | 5,5 – 7,5 | 1,0 – 2,5 | – | 0,2 | – |
F2 | 3,0 | 1,5 – 2,8 | 0,5 – 1,5 | 18,0 – 22,0 | 0,5 макс.![]() | 1,5 – 2,5 | – | 0.2 | – | |
F3 | 2,5 | 1,5 – 2,8 | 0,5 – 1,5 | 28,0 – 32,0 | 0,5 макс. | 2,5 – 3,5 | – | 0,2 | – | |
Сфероидальный графит | С2 | 3,0 | 1,5 – 2,8 | 0,5 – 1,5 | 18.0 – 22,0 | 0,5 макс. | 1,5 – 2,5 | – | 0,08 | |
С2Б | 3,0 | 1,5 – 2,8 | 0,5 – 1,5 | 18,0 – 22,0 | 0,5 макс. | 2,5 – 3,5 | – | 0,08 | – | |
S2C | 3.0 | 1,5 – 2,8 | 1,5 – 2,5 | 21,0 – 24,0 | 0,5 макс. | 0,5 макс. | – | 0,08 | – | |
С2М | 3,0 | 1,5 – 2,5 | 4,0 – 4,5 | 21,0 – 24,0 | 0,5 макс.![]() | 0,2 макс. | – | 0.08 | – | |
S2W | 3,0 | 1,5 – 2,2 | 0,5 – 1,5 | 18,0 – 22,0 | 0,5 макс. | 1,5 – 2,2 | 0,12 – 0,2 | 0,05 | 0,06макс.* | |
С3 | 2,5 | 1,5 – 2,8 | 0,5 – 1,5 | 28,0 – 32.0 | 0,5 макс. | 2,5 – 3,5 | – | 0,08 | – | |
S5S | 2,2 | 4,8 – 5,4 | 1,0 макс. | 34,0 – 36,0 | 0,5 макс. | 1,5 – 2,5 | – | 0,08 | – | |
С6 | 3,0 | 1.5 – 2,8 | 6,0 – 7,0 | 12,0 – 14,0 | 0,5 макс. | 0,2 макс. | – | 0,08 | – |
Аустенитный чугун Спецификации в соответствии с BS 3468 1986
Тип | Класс | Прочность на растяжение (мин) Н/мм2 | 0,2% Proof Stress (только информация) | Удлинение, % (только информация) | V-образный вырез по Шарпи при 20°C (J) | Твердость по Бринеллю BHN | Типичные свойства/использование |
Чешуйчатый графит | Ф1 | 170 | – | 1 – 2 | – | 140 – 220 | Хорошая коррозионная и термостойкость в сочетании с хорошими свойствами подшипника.![]() |
F2 | 170 | – | 1 – 3 | – | 140 – 220 | Аналогичен F1, но обладает большей устойчивостью к щелочной коррозии. Для использования в насосах для производства мыла, продуктов питания и пластмасс. | |
F3 | 190 | – | 1 – 3 | – | 120 – 215 | Стойкость к эрозии во влажном паре и солевом шламе.Хорошая стойкость к тепловому удару до 800°С наряду с хорошей коррозионной стойкостью при высоких температурах. Область применения включает коллекторы выхлопных газов, корпуса турбонагнетателей, фильтры, насосы и клапаны. | |
Сфероидальный графит | С2 | 370 | 210 | 7 – 20 | 4 – 20 | 140 – 230 | Коррозионная и термостойкость аналогична F1, но с превосходными механическими свойствами.Типичные области применения включают выпускные коллекторы для использования до 750c, насосы, клапаны и детали турбонагнетателя.![]() |
С2Б | 370 | 210 | 7 – 20 | 4 – 10 | 140 – 230 | Лучшая коррозионная стойкость по сравнению с классом S2 благодаря присутствию хрома, но это более твердый сплав, обеспечивающий отсутствие пористости. Типичные области применения включают выпускные коллекторы для использования при температурах до 750°C, насосы, клапаны и детали турбонагнетателей. | |
S2C | 370 | 170 | 20 – 40 | 20 – 30 | 130 – 170 | Немагнитный материал с хорошими ударными характеристиками до -100°C. Более низкая коррозионная и термостойкость, чем у S1. Типичные области применения включают немагнитные компоненты для генераторных установок, фланцы изолятора и для умеренных криогенных применений. | |
С2М | 420 | 210 | 25 – 45 | 15 – 25 | 150 – 180 | Немагнитный материал с сохранением механических свойств до -150°С.![]() | |
S2W | 370 | 210 | 7 – 20 | 10 – 20 | 140 – 200 | Коррозионная и термостойкость аналогична F1, но с превосходными механическими свойствами. Типичные области применения включают выпускные коллекторы для использования до 750c, насосы, клапаны и детали турбонагнетателя. S2W имеет улучшенную свариваемость по сравнению с маркой S2. | |
С3 | 370 | 210 | 7 – 18 | 4 – 20 | 130 – 200 | Аналогичен марке F3, но с улучшенными механическими свойствами. Область применения включает коллекторы выхлопных газов, корпуса турбонагнетателей, фильтры, насосы и клапаны. | |
S5S | 370 | 210 | 7 – 20 | – | 130 – 180 | Очень хорошая устойчивость к росту и шелушению до 850°С в сочетании с хорошей термостойкостью.![]() | |
С6 | 390 | 200 | 15 – 25 | 15 – 25 | 130 – 170 | Немагнитный, используется для крышек воздуховодов и выводов турбогенераторных установок. |
Производитель отливок из специального сплава чугуна
S G Чугунные отливки (отливки из чугуна с шаровидным графитом / отливки из чугуна с шаровидным графитом)
Производитель и экспортер чугунных отливок SG. S G Чугун также известен как Чугун с шаровидным графитом, Чугун с шаровидным графитом, Чугун с шаровидным графитом, Чугун с шаровидным графитом, Чугун с шаровидным графитом. SG Iron представляет собой тип чугуна, который в расплавленном состоянии был обработан таким элементом, как магний или церий, чтобы вызвать образование свободного графита в виде узелков или сферолитов. Это придает отлитому металлу измеримую степень пластичности (которую легко манипулировать). Семейство ковких чугунов предлагает инженерам-конструкторам уникальное сочетание прочности, износостойкости, сопротивления усталости и ударной вязкости, а также превосходные характеристики пластичности.
S G Железо/ковкий чугун не является отдельным материалом, а является частью группы материалов, которые могут быть получены с широким спектром свойств за счет контроля микроструктуры. Общей определяющей характеристикой этой группы материалов является форма графита. В ковких чугунах графит имеет форму узелков , а не чешуек , как в сером чугуне. Острая форма чешуек графита создает точки концентрации напряжений в металлической матрице, а округлая форма конкреций в меньшей степени, таким образом препятствуя образованию трещин и обеспечивая повышенную пластичность, которая и дала название сплаву.
Эта узловатая графитовая структура препятствует образованию линейных трещин, что обеспечивает устойчивость к деформации.
Состав:
Типичный химический анализ этого материала:
- Углерод от 3,2 до 3,6%
- Кремний от 2,2 до 2,8 %
- Марганец от 0,1 до 0,5%
- Магний от 0,03 до 0,05 %
- Фосфор от 0,005 до 0,04%
- Сера от 0,005 до 0,02%
- Медь 0.40%
- Железные весы
Другие элементы, такие как медь или олово, могут быть добавлены для увеличения прочности на растяжение и предела текучести при одновременном снижении пластичности. Улучшение коррозионной стойкости может быть достигнуто путем замены от 15% до 30% железа в сплаве различными количествами никеля, меди или хрома.
Приложения:
Ковкий чугун особенно полезен во многих автомобильных компонентах, где требуется прочность выше, чем у алюминия, но не обязательно требуется сталь.К другим основным промышленным применениям относятся внедорожные дизельные грузовики, грузовики класса 8, сельскохозяйственные тракторы, насосы для нефтяных скважин и т. д.
Ковкий чугун также называют чугуном с шаровидным графитом или чугуном с шаровидным графитом. Его химические компоненты не имеют строгого диапазона для многих стандартов материалов, однако его диапазон должен быть полезен покупателям для оценки качества чугуна.
Поэтому мы заполнили некоторые нормальные стандарты, чтобы показать разумный диапазон для ковкого чугуна.Пожалуйста, помните, что химические компоненты являются только ссылкой, а не строгим стандартом для материала. Литейный завод может корректировать свои химические компоненты в соответствии со своим опытом, чтобы соответствовать физическим свойствам. Таким образом, физические свойства должны быть единственным стандартом для материалов.
Технические характеристики:
- ИС — 1865 — 1998 (третье издание)
- Сорта — SG — 350/22, SG — 400/15, SG — 450/10, SG — 500/7, SG — 600/3, SG — 700/2, СГ — 800/2 и СГ — 900/2.
- Все марки лучше Стойкость к коррозии, износу и жаре.
Продукты — Кривошипно-шатунный механизм, вкладыш корпуса сепаратора, барабаны лебедки, элеваторные блоки, рабочие колеса, клапаны, Hallow Cylinder и другие различные типы отливок из чугуна S G (отливки из чугуна с шаровидным графитом / отливки из чугуна с шаровидным графитом)
Химические компоненты ковкого чугунаСША | Германия | ИСО | С % | Si % | Мл % | П % | С % | Мг % | Cu % | Sn % |
60-40-18 | ГГГ40 | 400-18 | 3. | 2,80-2,85 | 0,2-0,5 | 0,03-0,06 | 0,02-0,035 | 0,020-0,060 | ||
65-45-12 | GGG40 | 450-10 | 3.30-3,80 | 2,40-2,90 | 0,2-0,5 | 0,03-0,06 | 0,02-0,040 | 0,020-0,060 | ||
70-50-05 | GGG50 | 500-7 | 3. | 2,30-2,90 | 0,4-0,6 | 0,03-0,06 | 0,02-0,040 | 0,030-0,055 | <0,4 | |
80-60-03 | GGG60 | 600-3 | 3.00-3.50 | 2,40-2,80 | 0,3-0,5 | 0,03-0,06 | 0,02-0,040 | 0,035-0,050 | 0,30-0,40 | |
100-70-03 | ГГГ70 | 700-2 | 3.65-3,90 | 1,70-1,90 | 0,3-0,5 | <0,06 | <0,03 | 0,035-0,050 | 0,30-0,40 | 0,03-0,06 |
120-90-02 | GGG80 | 800-2 | — | — | — | — | — | — | — | — |
Эквивалентные марки ковкого чугуна (чугун с шаровидным графитом/отливка из чугуна с шаровидным графитом)
Страна | Стандартный | Эквивалентные марки ковкого чугуна (чугун с шаровидным графитом, чугун с шаровидным графитом) | ||||||
ИСО | ИСО 1083 | 400-15 | 450-10 | 500-7 | 600-3 | 700-2 | 800-2 | 900-2 |
Китай | ГБ 1348 | QT400-18 | QT450-10 | QT500-7 | QT600-3 | QT700-2 | QT800-2 | QT900-2 |
США | АСТМ А536 | 60-40-18 | 60-42-10 | 70-50-05 | 80-55-06 | 100-70-03 | 120-90-02 | — |
Германия | DIN 1693 | ГГГ40 | — | GGG50 | GGG60 | ГГГ70 | GGG80 | — |
Европейский | EN 1563 | EN-GJS-400-15 | EN-GJS-450-10 | EN-GJS-500-7 | EN-GJS-600-3 | EN-GJS-700-2 | EN-GJS-800-2 | EN-GJS-900-2 |
Япония | ДЖИС Г5502 | FCD400 | FCD450 | FCD500 | FCD600 | FCD700 | FCD800 | — |
Италия | УНИ 4544 | GS370-17 | GS400-12 | GS500-7 | GS600-2 | GS700-2 | GS800-2 | — |
Франция | НФ А32-201 | ФГС370-17 | ФГС400-12 | ФГС500-7 | ФГС600-2 | ФГС700-2 | ФГС800-2 | — |
Великобритания | БС 2789 | 400/17 | 420/12 | 500/7 | 600/7 | 700/2 | 800/2 | 900/2 |
Индия | ИС 1865 | SG370/17 | СГ400/12 | SG500/7 | SG600/3 | SG700/2 | SG800/2 | — |
Испания | УНФ | ФГЭ38-17 | ФГЭ42-12 | FGE50-7 | ФГЭ60-2 | ФГЭ70-2 | ФГЭ80-2 | — |
Бельгия | НБН 830-02 | FNG38-17 | ФНГ42-12 | FNG50-7 | FNG60-2 | ФНГ70-2 | ФНГ80-2 | — |
Австралия | КАК 1831 | 300-17 | — | 500-7 | 600-3 | 700-2 | 800-2 | — |
Швеция | нерж. | 0717-02 | — | 0727-02 | 0732-03 | 0737-01 | 0864-03 | — |
Норвегия | NS11 301 | СЖК-400.3 | — | СЖК-500 | СЖК-600 | СЖК-700 | СЖК-800 | — |
Таблица марок ковкого чугуна
ASTM A536 1993 (США)
Марка | Прочность на растяжение | Предел текучести | Удлинение | |
ANSI/ASTM | УНС | |||
60-40-18 | F32800 | 414 | 276 | 18 |
65-45-12 | F33100 | 448 | 310 | 12 |
80-55-06 | F33800 | 552 | 379 | 6. |
100-70-03 | F34800 | 689 | 483 | 3,0 |
120-90-02 | F36200 | 827 | 621 | 2.0 |
Специальное назначение |
|
|
|
|
60-42-10 |
| 415 | 290 | 10 |
70-50-05 | 485 | 345 | 5. | |
80-60-03 | 555 | 415 | 3,0 |
ГБ/т 1348 1998 (Китай)
Марка | Прочность на растяжение σ b ≥/МПа | Предел текучести о 0.2 ≥/МПа | Удлинение δ 5 ≥( % ) | Твердость ОБД |
QT400-18 | 400 | 250 | 18 | 130~180 |
QT400-15 | 400 | 250 | 15 | 130~180 |
QT450-10 | 450 | 310 | 10 | 160~210 |
QT500-7 | 500 | 320 | 7 | 170~230 |
QT600-3 | 600 | 370 | 3 | 190~270 |
QT700-2 | 700 | 420 | 2 | 225~305 |
QT800-2 | 800 | 480 | 2 | 245~335 |
QT900-2 | 900 | 600 | 2 | 280~360 |
* Низкотемпературное испытание на удар с V-образным надрезом (-20±2 ℃ )
DIN 1693 1997 (Германия)Марка | Материал № W-Nr. | Прочность на растяжение σ b ≥/МПа | Предел текучести σ 0,2 ≥/МПа | Удлинение δ≥ (%) |
ГГГ-40 | 0.7040 | 400 | 250 | 15 |
ГГГ-50 | 0,7050 | 500 | 320 | 7 |
ГГГ-60 | 0. | 600 | 380 | 3 |
ГГГ-70 | 0,7070 | 700 | 400 | 2 |
ГГГ-80 | 0.7080 | 800 | 500 | 2 |
EN 1563 1997 (Европейский стандарт)
Марка | Прочность на растяжение | Предел текучести | Удлинение | |
Символ | Номер | |||
EN GJS 350-22 | EN JS1010 | 350 | 220 | 22 |
EN GJS 350-22-LT* | EN JS1015 | 350 | 220 | 22 |
EN GJS 400-18 | EN JS1020 | 400 | 250 | 18 |
EN GJS 400-18-LT* | EN JS1025 | 400 | 240 | 18 |
EN GJS 400-15 | EN JS1030 | 400 | 250 | 15 |
EN GJS 450-10 | EN JS1040 | 450 | 310 | 10 |
EN GJS 500-7 | EN JS1050 | 500 | 320 | 7 |
EN GJS 600-3 | EN JS1060 | 600 | 370 | 3 |
EN GJS 700-2 | EN JS1070 | 700 | 420 | 2 |
EN GJS 800-2 | EN JS1080 | 800 | 480 | 2 |
EN GJS 900-2 | EN JS1090 | 900 | 600 | 2 |
* Низкотемпературное испытание на удар с V-образным надрезом (-20±2 ℃ )
ISO 1083 1987 (международный)Марка | Прочность на растяжение σ b ≥/МПа | Предел текучести о 0. | Удлинение δ≥ ( % ) | Твердость ОБД |
900-2 | 900 | 600 | 2 | 280~360 |
800-2 | 800 | 480 | 2 | 245-335 |
700-2 | 700 | 420 | 2 | 225~305 |
600-3 | 600 | 370 | 3 | 190~270 |
500-7 | 500 | 320 | 7 | 170~230 |
450-10 | 450 | 320 | 10 | 160~210 |
400-15 | 400 | 250 | 15 | 130~180 |
400-18 | 400 | 250 | 18 | 130~180 |
350-22 | 350 | 220 | 22 | ≤150 |
* Низкотемпературное испытание на удар с V-образным надрезом (-20±2 ℃ )
мифов и заблуждений — коллекционер чугуна: информация для любителей винтажной посуды
Мифы и заблуждения о чугунной посуде
Несмотря на то, что такие ресурсы, как этот веб-сайт и другие, пытались информировать и просвещать об истории и правильном обращении с старинными коллекционными чугунными полыми изделиями, все еще распространяется много дезинформации как в Интернете, так и на рынке. Здесь в произвольном порядке представлены десять наиболее часто встречающихся примеров.
Убеждение №1 : Чугунная посуда практически не поддается разрушению.
Правда или ложь? : Ложь. Чугун прочный, но не небьющийся. Подобно стеклу, свойства, делающие чугун твердым, также делают его хрупким. Чугун, подвергнутый удару или силе скручивания, сломается до того, как согнется. Слишком быстрое нагревание пустой кастрюли или большой кастрюли над маленькой конфоркой также может привести к растрескиванию или необратимой деформации.
Происхождение : Скорее всего путаница между чугуном и кованым железом или сталью.
Убеждение № 2 : Лучший и самый простой способ очистить чугунную сковороду от нагара — сжечь ее на огне.
Правда или ложь? : Ложь. В то время как огонь, как правило, полностью удаляет отложения, сильный нагрев часто повреждает сковороду, либо деформируя или раскалывая ее, либо потенциально изменяя молекулярную структуру железа, делая его необратимо чешуйчатым.
Происхождение : Скорее всего, из лагерных поваров пограничной эпохи, у которых не было другого способа восстановить сильно покрытые коркой сковороды.
Убеждение №3 : Покрытие приправы на сковороде придает вкус приготовленной пище.
Правда или ложь? : Ложь. Термин «приправа», относящийся к чугунной посуде, относится к накоплению со временем полимеризованных и обугленных кулинарных жиров, что приводит к образованию антикоррозионного антипригарного покрытия, и не имеет ничего общего с пищевой приправой.В данном случае смысл сродни тому, чтобы называть опытного человека «бывалым ветераном» или правильно просушенные дрова «бывалым». Традиционные методы очистки не должны оставлять следов, которые могут повлиять на вкус продуктов, приготовленных впоследствии, хотя жирная рыба может быть нежелательным исключением.
Происхождение : Неизвестно. Это утверждение часто можно услышать от продавцов бывших в употреблении неотремонтированных сковородок, скорее всего, в ошибочной попытке сделать так, чтобы изделия с толстой коркой казались более ценными.
Убеждение № 4 : Большая цифра на дне сковороды или на верхней части ручки сковороды указывает ее диаметр в дюймах.
Правда или ложь? : Ложь. Цифры были ранним соглашением, используемым для обозначения того, какой размер проушины дровяной печи подходит для кастрюли. Размеры не обязательно были одинаковыми для всех брендов, поэтому сковорода № 8 одного производителя могла не соответствовать печной проушине № 8 другого производителя. Система нумерации продолжала использоваться некоторое время даже после появления газовых и электрических плит.
Происхождение : ошибочное предположение, сделанное теми, кто не знаком с ранними дровяными печами.
Убеждение № 5 : Маленькие буквы на чугунных сковородах указывают производителя.
Правда или ложь? : Ложь. Маленькие отдельные буквы, выгравированные на чугунных изделиях, являются идентификаторами узоров. Несколько шаблонов использовались для создания форм для нескольких деталей одновременно, поэтому был необходим какой-то способ отслеживания того, какой уникальный шаблон изготовил какую деталь, либо для контроля качества, либо для сдельной оплаты. Точно так же маленькие выпуклые буквы на днище сковороды обычно являются отметинами формовщика, отштампованными в песчаной форме непосредственно перед отливкой литейщиком, чтобы отслеживать его ежедневное производство.
Происхождение : Еще один случай дезинформированных продавцов, пытающихся увеличить стоимость предметов без маркировки, например, любая буква «G», увиденная как «код» для Griswold.
Убеждение № 6 : «Старая железная» руда, добываемая и используемая для изготовления чугунной посуды на рубеже веков (начало 1900-х годов), превосходила ту, которая использовалась в конце 20-го века.
Правда или ложь? : Ложь. Элементарное железо не существует в природе в чистом виде. Хотя существуют различия в составе железной руды, полученной из разных источников, процесс плавки, используемый для извлечения элементарного железа из руды, удалял бы большинство, если не все нежелательные примеси. Железо, используемое для создания чугуна, не используется «в расплавленном виде», а добавляются такие ингредиенты, как углерод и кремний, чтобы придать металлу желаемые свойства. И хотя более ранние литейные заводы вполне могли использовать исключительно первичную железную руду, любой переработанный лом, который мог быть добавлен отечественными производителями в конце 20-го века, соответствовал стандартам чистоты и проверялся перед использованием.
Происхождение : Старая чугунная посуда отливалась вручную с использованием более мелкозернистых песчаных форм, к которым применялась обработка для улучшения отделки. Создание пресс-форм вручную также позволило производить более тонкостенные и легкие отливки. В сочетании с прекращенной в настоящее время практикой полировки варочных поверхностей до гладкости старые процессы приводили к получению более тонкого литья и готового продукта. Таким образом, термин «старое железо», используемый для обозначения превосходства, более применим к самой посуде, а не к металлу, из которого она была сделана.
Убеждение № 7 : Треснувшую кастрюлю можно обнаружить, прислушиваясь к звуку, издаваемому постукиванием по ней.
Правда или ложь? : Верно, но с исключениями. Поговорка гласит: «Звенит, как колокольчик, если постучать деревянной ложкой». Неповрежденная кастрюля обычно издает определенный звенящий звук при постукивании, когда ее подвешивают или держат определенным образом. Та же кастрюля с трещиной имеет тенденцию издавать глухой или менее отчетливый звенящий звук. Однако этот метод практически бесполезен при попытке оценить корку на сковороде, поскольку наросты затрудняют визуальный осмотр и подавляют звуковые вибрации.Более толстые и тяжелые кастрюли также не дают такого заметного кольца, как более тонкие и легкие. Будучи в лучшем случае субъективным тестом, на него не следует полагаться вместо тщательного визуального осмотра чистой кастрюли при соответствующем освещении.
Происхождение : Неизвестно. Наблюдение, возможно, делалось достаточно часто, чтобы установить рубрику.
Убеждение № 8 : Миниатюрная посуда была изготовлена для продажи в качестве образцов продавцам.
Правда или ложь? : Ложь.Крошечная старинная чугунная и алюминиевая посуда, выпускаемая крупными и другими брендами, производилась в качестве детских игрушек. В большинстве случаев они изготавливались по тому же стандарту, что и полноразмерная посуда, и предназначались не только для игр, но и для приготовления пищи. Часто продаваемые наборами в коробках, каталоги той эпохи, а также отмеченные контейнеры подтверждают первоначальное назначение.
Происхождение : В то время как некоторая игрушечная посуда, возможно, была передана бизнес-клиентам, ошибочное представление может иметь корни в миниатюрных демонстрационных единицах, созданных, чтобы облегчить нагрузку путешествующих продавцов печей.
Убеждение №9 : Чугун почитается за его способность равномерно нагреваться.
Правда или ложь? : Это зависит от того, как вы определяете «равномерный нагрев». Если вы считаете, что тепло, подаваемое конфоркой, будет равномерно распределяться по кастрюле, то ответ «ложный». Чугун на самом деле является относительно плохим проводником тепла, а это означает, что область сковороды, к которой применяется тепло, будет повышаться, но с уменьшающимся эффектом по мере удаления от этой области.Однако его плотность позволяет ему сохранять больше тепла на фунт по сравнению с другими металлами.
Происхождение : Вероятно, существует путаница между способностью железа накапливать тепло и способностью нагреваться равномерно. Из-за низкой проводимости он медленно нагревается, но, будучи горячим, остается горячим дольше, что позволяет избежать внезапных скачков температуры. В этом смысле железо легче поддерживает постоянство температуры. Лучший способ равномерно разогреть чугунную сковороду — в духовке.
Убеждение №10 : Мытье чугунной сковороды с мылом испортит приправу.
Правда или ложь? : Ложь в большинстве случаев. Хорошо приправленная сковорода будет защищена достаточно прочным, почти пластичным слоем полимеризованного кулинарного жира и углерода, способным выдерживать температуру приготовления в несколько сотен градусов. Хотя обычно это не требуется, мытье теплой водой и обычным средством для мытья посуды с использованием неабразивной губки или щетки не окажет существенного влияния на хорошо зарекомендовавшую себя приправу. Однако чугунные сковороды не следует оставлять погруженными в воду, и, конечно же, их никогда не следует подвергать автоматической мойке в посудомоечной машине, независимо от того, насколько хорошо они приправлены.
Происхождение : Возможно использование щелочи или древесной золы в качестве ингредиента для производства мыла до 20-го века. Было обнаружено, что кипячение щелочи (гидроксида натрия) или древесной золы (для получения гидроксида калия) с животным жиром в чугунных горшках для создания мыла удаляет приправу. Виновником, однако, было не мыло, а щелочь, использованная при его изготовлении. Однако на очень простую начальную приправу, в которой используемый жир или масло не полностью полимеризованы, может повлиять энергичное мытье с мылом для посуды.
Убеждение №10½ : Кислые продукты никогда не следует готовить в чугунных кастрюлях.
Правда или ложь? : Оба. В то время как кислые продукты действительно вызывают попадание железа в них, хорошо зарекомендовавший себя слой приправы обеспечит барьер между кислотностью и железом. Однако то же самое может быть не так для только что приправленных сковородок.
Происхождение : Сковорода с недостаточно приготовленными приправами действительно может отдавать железо приготовленным в ней продуктам или реагировать с ними, особенно с кислыми продуктами, такими как помидоры, или жидкостями, такими как вино, уксус и т. д.Это может привести к металлическому привкусу пищи или даже обесцвечиванию таких продуктов, как бобы или шпинат.
Почетное упоминание
Есть несколько других заблуждений, с которыми вы будете время от времени сталкиваться, в том числе:
Маркировка чугунных сковородок выбита на них.
Ложь. Чугун, по крайней мере из того, что используется для посуды, недостаточно податлив, чтобы на нем можно было нанести отпечаток штамповкой. Маркировка могла быть выбита на шаблоне (обычно сделанном из алюминия), но они были отлиты в поддоне.То же самое относится и к деталям из кованого чугуна.
Этот чугун пористый.
Ложь. Многих заставили поверить, что чугун не только пористый, но и что эти поры расширяются и сужаются при изменении температуры, позволяя маслу или другим посторонним веществам не только прилипать, но и «поглощаться» или «запечатываться» в чугуне. . Хотя даже полированное железо не является полностью плоским, любые пустоты представляют собой просто микроскопические неровности, возникающие в результате удаления с поверхности кристаллического графита, углеродного компонента чугуна.
Приготовление пищи в чугуне является ценным источником пищевого железа.
Ложь. Как только сковорода хорошо приправлена, полимеризованное масляно-углеродное покрытие образует барьер между приготовляемой пищей и утюгом. Однако, если бы кто-то готовил пищу, особенно пищу с избытком влаги или кислоты, в кастрюле без приправ, железо переносилось бы в пищу. Обычно не готовят на чугунной сковороде без приправ. (Людям с гемохроматозом, нарушением перегрузки железом, тем не менее, вероятно, следует избегать пищи, приготовленной в любом чугуне.)
Чугунная сковорода после использования и мытья должна быть немедленно повторно приправлена.
Ложь. Мытье с использованием неабразивных губок и обычных бытовых средств для мытья посуды не удаляет слой полимеризованного жира и нагара, образующий приправу для чугунной сковороды. Поэтому не должно быть причин наносить и запекать еще одно ручное нанесение масла после каждого использования.
Цвет ржавчины на репродукции отличается от цвета подлинника.
Ложь. Ржавчина есть ржавчина. Оксид железа. Гидратированный оксид железа или оксид железа (III), химическая формула Fe2O3. Различия в цвете ржавчины связаны с тем, насколько она развита на конкретном предмете, или с уровнем содержащейся в нем влаги.
Многоразовая «форма» используется для изготовления чугунных изделий.
Ложь. Чугунные детали изготавливаются в разъемных формах, состоящих из смеси влажного мелкозернистого песка и других составов, которые плотно набиваются по многоразовой модели.Когда форма затвердевает, ее половинки разъединяются, выкройка снимается, форма снова собирается и в нее заливается расплавленное железо. Когда железо остывает и затвердевает, удаление песчаной формы из куска эффективно разрушает его.
Эти сковороды с маркировкой «ERIE» были изготовлены предшественником Griswold Mfg. Co.
Ложь. Слишком часто встречающийся термин «до Грисволда», используемый в отношении сковородок Эри, является неправильным. Их производил Griswold, сначала под эгидой Selden & Griswold Mfg.Co., а затем Griswold Mfg. Co.
В качестве приправы льняное масло превосходит другие масла или жиры.
Как зависит. Многие начинающие коллекционеры находят в онлайн-блогах статьи, в которых излагаются достоинства льняного масла как имеющие научное обоснование превосходства жира приправы.