Качество бетона: требования, показатели
При выполнении активных работ со строительными смесями приходится учиться определять их характеристики при помощи специальных приборов или по визуальным признакам. При надобности проверка качества бетона может быть произведена как в жидком, так и в уже затвердевшем состоянии, когда полностью готова конструкция.
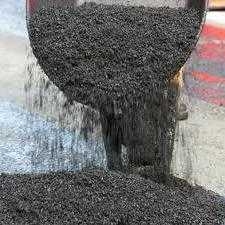
Как определить параметры смеси в жидком состоянии?
Хороший бетон, как правило, имеет серый цвет. Перед заливанием свежеприготовленного раствора нужно убедиться в том, что технологические свойства на высоком уровне, особенно если производитель не может внушить доверие или замес был произведен своими руками. Сделав самостоятельную проверку, можно много узнать о качественных характеристиках продукции. Параметры смеси в жидком состоянии можно узнать по лабораторным исследованиям.
Контроль затвердевшего материала
Более точную оценку качества бетона можно произвести после того, как он окончательно застынет, когда пройдет двадцать восемь суток от того момента, как была произведена заливка.
Контроль может быть неразрушающим и разрушающим. В первом случае проводится тестирование разными приборами, показания которых не особо точные, а во втором — производится непосредственно взятие образца.

Неразрушающие методы
Различают следующие виды:
- Отрывание дисковых элементов предполагает снятие напряжения, производимое при местном разрушении.
- Скол ребер, который может позволить определить характеристику линейной конструкции в виде колонн, свай и балок. Метод не может быть выполнен, если защитный слой не превышает двух сантиметров.
- Отрывание со сколом является единственным способом неразрушающего контроля, по которому официально все регламентировано, в том числе и градуировочная зависимость. При прохождении теста иногда можно увидеть высокую точность.
- Упругость отскока может предоставлять возможность измерения величины, на которую произойдет сдвижение ударника после воздействия на конструктивную поверхность. Испытания проводят пружинными молотками.
- Ударный импульс позволяет сделать регистрацию энергии совершившегося удара, образуемого при соприкосновении бойка с поверхностью. Подобные устройства могут отличаться компактностью в размерах.
- Пластическая деформация основана на измерении размера оставленного отпечатка от удара стальным шариком.
Проверка ультразвуком
Проверить качество бетона ультразвуковым методом можно с помощью волновых прохождений в виде сквозного и поверхностного прозвучивания. Разница заключается в том, как располагаются датчики.
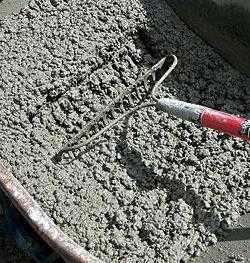
Разрушающие методы
Применяются следующие виды методов:
- вырезание образца из бетонированной конструкции исполняется особым оснащением УРБ-175, оборудованным разрезающим прибором типа алмазных дисков;
- выбуривание выполняется при помощи станков для сверления вида ИЭ 1806. Они обладают алмазным или твердосплавным сверлом.
Прежде чем приобрести готовый раствор у изготовителя, нужно выяснить, имеется ли у него паспорт качества на бетон. Это не обязательное условие, но оно дает представление о надежности компании.
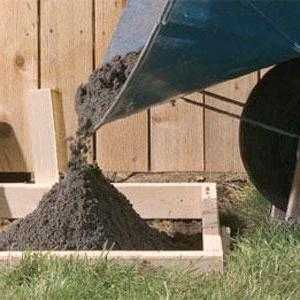
Особенности бетона
Одним из ключевых показателей качества бетона считается его удобоукладываемость (способность раствора наполнять форму бетонируемого изделия и трамбоваться в ней под воздействием силы тяжести либо вследствие внешнего механического воздействия). Эта особенность бетона оценивается показателями жесткости и подвижности. При бетонировании железобетонных монолитных конструкций используют чаще всего бетонные смеси.

Работники стройфирмы обязаны никак не реже двух раз осуществлять контроль подвижности смеси. Для бетона, у которого подвижность с нулевой осадкой конуса, в стройлаборатории определяют жесткость смеси в соответствии с методикой по применяемому стандарту. Жесткость характеризуется периодом вибрации, требуемым для выравнивания и уплотнения заранее отформованного конуса бетона в устройстве для определения жесткости.
Транспортирование бетонированной смеси
Правильно выполненная поставка смеси во многом определяет качество бетона ко времени её укладывания в конструкцию. При нарушении правил транспортировки и подачи смеси в бетонируемые системы бетонная смесь утрачивает свою однородность – расслаивается: более тяжелые составляющие (гравий, песок, щебень) оседают, а сверху на поверхности появляется цементное молоко. Поэтому заданная подвижность нарушается и уменьшается удобоукладываемость. Качество бетона достигается регулярным контролем за транспортированием и подачей смеси в конструкции.
Бригадир и мастер стройучастка обязаны регулярно контролировать качество уплотнения бетонной смеси. При укладке горизонтальными пластами следят за соответствием толщины всех уложенных слоев согласно требованиям проекта. Длительность вибрирования обеспечивает уплотнение бетона, главными свойствами которого считаются: окончание оседания смеси, возникновение цементного молока на её плоскости, прекращение отделения из нее пузырьков воздуха.
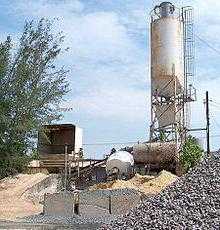
Возобновление бетонирования после паузы разрешается только лишь при набирании бетоном прочности на сжатие минимум 1,5 МПа. Длительность данных интервалов, как правило, не больше 2 часов.
Для прочности сцепления нового слоя раствора с уже затвердевшим его поверхность чистят от мусора, устраняют железными щетками цементную пленку, затем промывают струей воды под давлением. Оставшуюся воду из углублений устраняют. Перед самой укладкой нового слоя нужно на поверхность старого бетона положить слой цементного раствора, толщина которого 20 мм того же состава, что и в старом бетоне.
Что влияет на качество?
Качество бетона во многом зависит от условий, в которых состав находится уже после проведения его укладки. На интенсивность затвердевания оказывают большое влияние влажность и температура окружающей среды. Уложенный бетон содержат во влажном состоянии и оберегают от механических повреждений, тряски, резких скачков температуры и быстрого высыхания.
Что используют, чтобы сберечь влагу?
Для сбережения влаги в бетоне используют разжиженный битум, битумные и дегтевые и прочие эмульсии, способные быстро образовать на поверхности бетона непроницаемую для воды пленку.
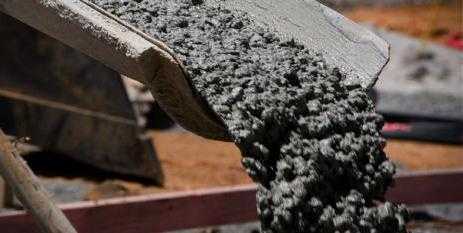
Показатели качества бетона
К самым важным показателям качества бетона относится прочность. Это один из самых важных показателей. Именно возможность бетона противостоять большой нагрузке и делает его практически незаменимым при строительных работах. Бетон имеет 3 типа прочности:
- на сжатие, по которому оценивают свойство бетона противостоять сжимающим нагрузкам;
- на растяжение при изгибе, по которой определяют свойство бетона противостоять изгибающей нагрузке;
- на осевое растяжение, по которой определяют способность бетона противостоять нагрузкам на растяжение по всей площади поперечного сечения.
Прочность определяют путем испытаний стандартных образцов бетона на разрывных машинах и прессах.
- Морозостойкость бетона. С помощью этого показателя оценивается способность бетона сохранять свои прочностные характеристики после попеременной заморозки и оттаивания. Морозостойкость является важным показателем для бетона, используемого в местах с суровым климатом и холодными зимами.
- Водонепроницаемость бетона. Данным показателем оценивают возможность бетона сопротивляться просачиванию воды. Его используют в местах, где имеется непосредственный контакт с водой.
- Коррозионная стойкость бетона. С помощью этого требования к качеству оценивают способность после воздействия агрессивной среды сохранять свои прочностные характеристики. Этот показатель важно учитывать при наличии риска контакта бетона при эксплуатации с агрессивными химическими веществами.
Качество бетона для фундамента или прочих строительных работ очень важно. Именно от него зависит продолжительность жизни постройки и безопасность ее эксплуатации.
fb.ru
Бетона качество
Качество бетона: требования, показатели
При выполнении активных работ со строительными смесями приходится учиться определять их характеристики при помощи специальных приборов или по визуальным признакам. При надобности проверка качества бетона может быть произведена как в жидком, так и в уже затвердевшем состоянии, когда полностью готова конструкция.
Как определить параметры смеси в жидком состоянии?
Хороший бетон, как правило, имеет серый цвет. Перед заливанием свежеприготовленного раствора нужно убедиться в том, что технологические свойства на высоком уровне, особенно если производитель не может внушить доверие или замес был произведен своими руками. Сделав самостоятельную проверку, можно много узнать о качественных характеристиках продукции. Параметры смеси в жидком состоянии можно узнать по лабораторным исследованиям.
Контроль затвердевшего материала
Более точную оценку качества бетона можно произвести после того, как он окончательно застынет, когда пройдет двадцать восемь суток от того момента, как была произведена заливка.
Контроль может быть неразрушающим и разрушающим. В первом случае проводится тестирование разными приборами, показания которых не особо точные, а во втором — производится непосредственно взятие образца.
Неразрушающие методы
Различают следующие виды:
- Отрывание дисковых элементов предполагает снятие напряжения, производимое при местном разрушении.
- Скол ребер, который может позволить определить характеристику линейной конструкции в виде колонн, свай и балок. Метод не может быть выполнен, если защитный слой не превышает двух сантиметров.
- Отрывание со сколом является единственным способом неразрушающего контроля, по которому официально все регламентировано, в том числе и градуировочная зависимость. При прохождении теста иногда можно увидеть высокую точность.
- Упругость отскока может предоставлять возможность измерения величины, на которую произойдет сдвижение ударника после воздействия на конструктивную поверхность. Испытания проводят пружинными молотками.
- Ударный импульс позволяет сделать регистрацию энергии совершившегося удара, образуемого при соприкосновении бойка с поверхностью. Подобные устройства могут отличаться компактностью в размерах.
- Пластическая деформация основана на измерении размера оставленного отпечатка от удара стальным шариком.
Проверка ультразвуком
Проверить качество бетона ультразвуковым методом можно с помощью волновых прохождений в виде сквозного и поверхностного прозвучивания. Разница заключается в том, как располагаются датчики.
Разрушающие методы
Применяются следующие виды методов:
- вырезание образца из бетонированной конструкции исполняется особым оснащением УРБ-175, оборудованным разрезающим прибором типа алмазных дисков;
- выбуривание выполняется при помощи станков для сверления вида ИЭ 1806. Они обладают алмазным или твердосплавным сверлом.
Прежде чем приобрести готовый раствор у изготовителя, нужно выяснить, имеется ли у него паспорт качества на бетон. Это не обязательное условие, но оно дает представление о надежности компании.
Особенности бетона
Одним из ключевых показателей качества бетона считается его удобоукладываемость (способность раствора наполнять форму бетонируемого изделия и трамбоваться в ней под воздействием силы тяжести либо вследствие внешнего механического воздействия). Эта особенность бетона оценивается показателями жесткости и подвижности. При бетонировании железобетонных монолитных конструкций используют чаще всего бетонные смеси.
Работники стройфирмы обязаны никак не реже двух раз осуществлять контроль подвижности смеси. Для бетона, у которого подвижность с нулевой осадкой конуса, в стройлаборатории определяют жесткость смеси в соответствии с методикой по применяемому стандарту. Жесткость характеризуется периодом вибрации, требуемым для выравнивания и уплотнения заранее отформованного конуса бетона в устройстве для определения жесткости.
Транспортирование бетонированной смеси
Правильно выполненная поставка смеси во многом определяет качество бетона ко времени её укладывания в конструкцию. При нарушении правил транспортировки и подачи смеси в бетонируемые системы бетонная смесь утрачивает свою однородность – расслаивается: более тяжелые составляющие (гравий, песок, щебень) оседают, а сверху на поверхности появляется цементное молоко. Поэтому заданная подвижность нарушается и уменьшается удобоукладываемость. Качество бетона достигается регулярным контролем за транспортированием и подачей смеси в конструкции.
Бригадир и мастер стройучастка обязаны регулярно контролировать качество уплотнения бетонной смеси. При укладке горизонтальными пластами следят за соответствием толщины всех уложенных слоев согласно требованиям проекта. Длительность вибрирования обеспечивает уплотнение бетона, главными свойствами которого считаются: окончание оседания смеси, возникновение цементного молока на её плоскости, прекращение отделения из нее пузырьков воздуха.
Возобновление бетонирования после паузы разрешается только лишь при набирании бетоном прочности на сжатие минимум 1,5 МПа. Длительность данных интервалов, как правило, не больше 2 часов.
Для прочности сцепления нового слоя раствора с уже затвердевшим его поверхность чистят от мусора, устраняют железными щетками цементную пленку, затем промывают струей воды под давлением. Оставшуюся воду из углублений устраняют. Перед самой укладкой нового слоя нужно на поверхность старого бетона положить слой цементного раствора, толщина которого 20 мм того же состава, что и в старом бетоне.
Что влияет на качество?
Качество бетона во многом зависит от условий, в которых состав находится уже после проведения его укладки. На интенсивность затвердевания оказывают большое влияние влажность и температура окружающей среды. Уложенный бетон содержат во влажном состоянии и оберегают от механических повреждений, тряски, резких скачков температуры и быстрого высыхания.
Что используют, чтобы сберечь влагу?
Для сбережения влаги в бетоне используют разжиженный битум, битумные и дегтевые и прочие эмульсии, способные быстро образовать на поверхности бетона непроницаемую для воды пленку.
Показатели качества бетона
К самым важным показателям качества бетона относится прочность. Это один из самых важных показателей. Именно возможность бетона противос
vest-beton.ru
Качество и свойства бетона — Материалы и свойства
Автор Admin На чтение 8 мин. Просмотров 34 Опубликовано
Качество и свойства бетона в значительной мере определяются свойствами бетонной смеси, основными из которых является удобоукладываемость и связность. Удобоукладываемость оценивается по показателям подвижности смеси или ее жесткости (ГОСТ 10181.1—81). Подвижностью (консистенцией) называется способность бетонной смеси растекаться под действием собственной массы. Степень подвижности смеси оценивается величиной осадки конуса, отформованного , из нее. Чем больше осадка конуса, тем более подвижна бетонная смесь. По величине осадки конуса (в сантиметрах) бетонные смеси подразделяются на жесткие (не дающие осадки конуса), малоподвижные (осадка I—3 см), подвижные (осадка 4—15 см) и литые (осадка более 15 см).
Жесткость бетонной смеси – способность ее растекаться и заполнять форму под действием вибрации. Степень жесткости измеряется временем вибрации (в секундах), в течение которого свежеотформованный бетонный конус займет горизонтальное положение в форме. Жесткость бетонной смеси (с максимальной крупностью заполнителя 40 мм) определяют с помощью технического вискозиметра. По степени жесткости смеси делятся на особо жесткие (более 200 с), жесткие (30—200 с) и малоподвижные (15—25 с).
Под связностью (пластичностью) понимается свойство бетонной смеси не расслаиваться при транспортировке, выгрузке и укладке. При отсутствии связности подвижная бетонная смесь расслаивается, теряет однородность и становится непригодной к укладке в форму.
Основные свойства бетона – прочность, плотность, водонепроницаемость и морозостойкость. Главный показатель механических свойств – прочность при сжатии (марка). Она определяется пределом прочности при сжатии стандартных образцов- кубов размером 150×150×150 мм, изготовленных из данной бетонной смеси и выдержанных до испытания в течение 28 суток в нормальных условиях, т. е. при температуре 15—20 °C и относительной влажности воздуха не менее 90 %, которые создают в специальных камерах. Марку бетона можно определить также на кубах с размерами ребер 100, 200 и 300 мм с помощью переводных коэффициентов, соответственно 0,91; 1,05 и 1,1 (приведенные к пределу прочности кубов с размером ребра 150 мм).
Для тяжелых бетонов установлено восемь марок: 100, 150, 200, 250, 300, 400, 500 и 600, что соответствует пределу прочности при сжатии 10, 15, 20, 25, 30, 40, 50 и 60 МПа. Прочность бетона при сжатии в основном зависит от активности цемента, водоцементного отношения В/Ц, прочности и качества заполнителей, их зернового состава, а также от температуры и влажности окружающей среды.
Плотность тяжелого бетона находится в пределах 2650—2800 кг/м3. С увеличением ее повышаются прочность, водонепроницаемость, морозостойкость и другие свойства бетона.
Водонепроницаемость бетона характеризуется степенью водонепроницаемости, т. е. величиной наименьшего давления воды, при котором она еще просачивается через бетонный образец. По этому показателю бетоны делятся на четыре марки: В2, В4, В6 и В8. Цифры в марках обозначают, что данные бетоны выдерживают давление воды соответственно не менее 0,2; 0,4; 0,6 и 0,8 МПа. Для повышения водонепроницаемости в состав бетона вводят кремнийорганические добавки и добавки, способствующие уплотнению цементного камня, например алюминат натрия.
По степени морозостойкости тяжелые бетоны делятся на пять марок: от Мрз 50 до Мрз 300. Цифры в марках показывают, сколько циклов замораживания и оттаивания выдерживает бетон без разрушения.
Процесс приготовления бетонной смеси состоит из дозирования цемента, воды, песка, гравия или щебня и перемешивания их до получения однородной массы. Приготовление смеси осуществляется в основном на автоматизированных бетонных заводах и в бетоносмесительных узлах предприятий по производству сборного железобетона. При небольших объемах работ ее приготовляют на приобъектных бетоносмесительных установках.
В бетонную смесь декоративного бетона также входят портландцемент, вода, мелкий и крупный заполнители. Портландцемент может быть обычным серым, белым или цветным. Цветной цемент разрешается получать введением в серый или белый цветостойких щелочеустойчивых по отношению к цементу пигментов, не снижающих физико-механические показатели декоративного бетона. ОСТ 20-40—84 «Блоки искусственные для распиливания на облицовочные плиты» (которые изготовляют из декоративного бетона) допускает использовать для окраски цемента следующие пигменты: сурик железный (ГОСТ 8135—74), двуоксид марганца (ГОСТ 4470—79*), оксид хрома (ГОСТ 2912—79). Содержание пигментов не должно превышать 5 % общей массы окрашиваемого цемента. Лучшей водой для затворения является питьевая вода. Можно применять и любую другую воду, не содержащую вредных примесей, которые препятствуют нормальному твердению бетона.
Заполнитель может быть получен дроблением горных пород любого происхождения при условии его соответствия ГОСТ 22856— .77 «Щебень и песок декоративные из природного камня». После дробления заполнитель необходимо разделить на фракции 6-2,5; 2,5—5; 5—10; 10—20; 20—40 мм. По согласованию с заказчиком можно использовать также фракции 40—70 и более 70 мм.
Для улучшения свойств бетонной смеси и бетона могут использоваться следующие поверхностно-активные добавки: сульфатно-дрожжевая бражка СДБ (ГОСТ8179—69), мылонафт (ГОСТ 13302—77) и нитрит- нитрат-хлорид кальция HHXK (ТУ-6 – 18 – 157—73).
Подбор оптимального состава декоративного бетона рекомендуется производить в следующем порядке: определение водоцементного отношения; расхода цемента и воды; расхода мелкого и крупного заполнителей; уточнение подобранного состава.
Расход цемента рекомендуется устанавливать эмпирическим путем (табл. 22).
Расход воды определяется опытным путем из условия заданной удобоукладываемости бетонной смеси при выбранной максимальной крупности щебня. Для бетонов с наибольшей степенью уплотнения подвижность должна составлять 1—2 см. Ориентировочный расход воды на 1 м3 бетона должен быть 170—180 л (при цементе марки 300) и 150—160 л (при цементе марки 400) с учетом применения материалов, высушенных до постоянной массы. Для заполнителей с естественной влажностью необходима корректировка, учитывающая содержание в них воды.
Таблица 22. Расход цемента, кг/м3, на приготовление бетонной смеси
Марка цемента | Марка бетона | |
200 | 300 | |
300 | 380/350 | |
400 | 330/300 | 410/420 |
Примечание. В числителе приведен расход для карбонатного песка, в знаменателе – для кварцевого.
Расход песка на 1 м3 бетона определяется как разность между абсолютным объемом бетона и суммой абсолютных объемов составляющих:
П = [1000 – (Ц / γц + В + Щ / γщ)] γп,
где Ц, В, Щ, П – расход соответственно цемента, воды, щебня и песка, кг; γ
Расход щебня на 1 м3 бетона определяется исходя из условия максимального насыщения образца уплотненной бетонной смеси крупным заполнителем с минимальной раздвижкой зерен цементно-песчаным раствором:
Щ = 1000 / (Vщ — α/ γ’щ + 1 / γщ)
где Vщ – Пустотность щебня в стандартном рыхлом состоянии, определяемая по ГОСТ 8269—76;
α – коэффициент раздвижки зерен (принимается равным 1,35 при расходе цемента до 350 кг/м3 и 1,43 при расходе цемента более 350 кг/м3;
γ’щ – насыпная средняя плотность щебня, кг/ дм3;
γщ – истинная плотность щебня, кг/ дм3.
После корректировки состава бетона (бетонной смеси) для определения фактического расхода материала пробными замесами вычисляется средняя плотность бетона γб (отклонение фактической величины расхода от расчетной допускается в пределах ±2 %):
γб = (G2 – G1) / V,
где G1 – масса формы, кг;
G2 – масса формы с бетоном, кг;
V – объем формы, дм3.
Зная объем полученной бетонной смеси, и расход материалов на пробные замесы, можно определить фактический расход материалов на 1 м3 бетона:
M = ∑ G/γф,
где ∑ G – суммарная масса материалов на пробный замес, кг; γф – фактическая средняя плотность уплотненной бетонной смеси, кг/ дм3.
Расход материалов на один замес бетономешалки определяется с учетом коэффициента выхода бетона
rб = 1000/ (Ц / γ’ц
+ П / γ’п
+ Щ / γ’щ) Kв,
где Ц. П, Щ – количество соответственно цемента, песка и щебня, требуемое на замес, кг; γ’ц γ’п γ’щ – насыпная средняя плотность соответственно цемента, песка и щебня, кг/дм3; Kв – коэффициент выхода бетона: Kв
= 0,67 – 0,68.
Таблица 23. Составы декоративного бетона и расход материалов в зависимости от вида мраморного щебня
Месторождение мрамора | Расход на 1 м3 бетона, кг | ||||||||
Цемент : песок:щебень (Ц:П:Щ) | Водоцементное отношение В/Ц | цемента | песка карбонатного фракции 0—5 мм | 5—10 | щебня фракций, мм 10—20 20—40 40—70 | Всего | |||
Коелгинское | 1:1,3:6,0 | 0,45—0,46 | 280 | 375 | 420 | 650 | 630 | 1700 | |
Кибик-Кордонское: розовый мрамор | 1:1,2:4,0 | 0,46—0,49 | 380 | 450 | 200 | 300 | 450 | 570 | 1520 |
серый мрамор | 1:1,14:4,55 | 0,46—0,49 | 350 | 400 | 200 | 300 | 450 | 640 | 1590 |
Иджеванское, Маймехское, Хорвирапское | 1:1,5:6,0 | 0,55—0,6 | 270 | 405 | 400 | 620 | 600 | 1620 |
Для иллюстрации определения состава бетона (бетонной смеси) по приведенным формулам рассмотрим следующий пример.
Пример. Требуется определить расход щебня и песка при заданном расходе цемента и соотношение этих материалов по массе, приняв расход цемента за единицу.
Задаемся подвижностью бетонной смеси 2—3 см, что соответствует расходу воды 170—180 л на 1 м3 смеси. Расход воды принимаем равным 175 л/м3, а водоцементное отношение (В / Ц) – 0,5. Тогда расход цемента составит 350 кг/м3.
Определяем расход щебня, приняв Vщ
= 0,46 :
Щ = 1000 / (0,46 · 1,35 / 2,66 + 1 / 2,68) = 1650 кг.
Определяем расход песка при известных расходах цемента, щебня и воды:
П = [ 1000 – (350 / 3,1 + 175 + 1650 / 2,68] × 2,68 = 258 кг.
Зная расходы песка и щебня и отнеся их к расходу цемента (равен 1), получаем следующее их соотношение:
Ц:П: Щ = 1 : 0,74:4,71.
Рассчитанный состав имеет чисто конструктивное значение и не может считаться оптимальным для декоративных бетонов.
Критериями оптимальности при выборе состава декоративного бетона следует считать внешний вид, удобоукладываемость (необходимое количество цементного теста для обволакивания камня и заполнения межзернового пространства), максимальное заполнение поверхности изделия камнем и отсутствие крупных пор. В соответствии с ГОСТ 24099—80 коэффициент камненасыщения, характеризуемый отношением площади, занимаемой природным камнем размером свыше 5 мм, к общей лицевой поверхности декоративных плит, должен составлять 0,75 или 0,80 в зависимости от категории качества плит.
Исследованиями и практикой установлено, что оптимальный состав декоративного бетона (бетонной смеси) и связанный с ним расход материалов зависят от физико-механических свойств и химического состава заполнителя – щебня, т. е. по физико-механическим и химическим показателям при разных заполнителях составы бетонов будут различными.
В качестве примера в табл. 23 приведены оптимальные составы и расход компонентов декоративного бетона с заполнителем из мраморов наиболее известных месторождений: Коелгинского, Кибик-Кордонского, Иджеванского, Маймехского и Хорвирапского.
arxipedia.ru
Качество бетона и стандартизация правил контроля его прочности
С.А. ПОДМАЗОВА, канд. техн. наук; Н.Н. КУПРИЯНОВ, канд. техн. наук; Б.А. КРЫЛОВ, доктор техн. наук; А.И. САГАЙДАК, канд. техн. наук Научно-исследовательский, проектно-конструкторский и технологический институт бетона и железобетона (НИИЖБ).
Рассматривается фактор комплексного подхода к изготовлению бетона. Только при соблюдении всех составляющих процесса, начиная с процедур контроля прочности бетона и заканчивая соблюдением правил ухода за ним в готовой конструкции, можно рассчитывать на обеспечение надлежащего качества железобетонных изделий.
В течение последних 10–15 лет в Москве и других регионах России бурно развивается монолитное строительство. Проверка поставляемых на строительный объекты бетонных смесей, контроль прочности бетона в монолитных конструкциях, анализ имеющихся дефектов в них указывают на серьезные проблемы с обеспечением качества в монолитном строительстве. Нередко строительным организациям приходится тратить время и средства на усиление и/или ремонт возведенных конструкций.
Для строительства жилых, общественных зданий и объектов транспортной инфраструктуры из монолитного бетона изготавливаются и поставляются на строительные площадки готовые бетонные смеси. По оценке специалистов, ежегодный объем таких поставок в масштабе страны составляет порядка 40 млн м3.
В строительной практике бетонные смеси, в зависимости от требований проекта или условий договора, поставляются с заданной проектной прочностью (обычно назначаемой как класс бетона по прочности на сжатие) и дополнительно, в зависимости от назначения объекта, заданной маркой бетона по водонепроницаемости и маркой по морозостойкости. Все эти показатели должны контролироваться согласно процедурам, указанным в соответствующих стандартах.
В настоящей статье речь будет идти о влиянии систем контроля прочности на качество бетона монолитных и сборных железобетонных конструкций.
Соответствующая идеология контроля прочности, как и любого другого показателя качества, направлена на обеспечение стабильности заданного показателя в рамках допустимого статистического разброса. Так, показатель прочности бетона должен соответствовать средней прочности для заданного класса бетона.
В период централизованного управления экономикой одним из концептуальных требований государственной политики в области строительства была экономия материалов. Практически все научные результаты в строительных НИИ, включая диссертационные работы, должны были заканчиваться показателями достигаемой экономии при применении этого результата на практике — «внедрении», как тогда было принято говорить.
Одним из важнейших фондируемых, т. е. распределяемых централизованно, материалов был цемент. Экономия цемента была одной из главных целей при разработке новых и пересмотре старых стандартов. Поскольку прочность бетона зависит, главным образом, от водоцементного отношения и зависимого от этого показателя расхода цемента на единицу объема, то одной из задач стандартизации была разработка процедур, которые вели бы к снижению расхода цемента. Иными словами, стандарт должен был разрешать легально снижение прочности бетона в конструкции. А иногда не просто разрешать, но и обязывать снизить прочность бетона. Этого подхода не избежали и СНиП «Типовые нормы расхода цемента» и, естественно, стандарты, определяющие правила контроля прочности.
Во всех строительных нормах, вплоть до ГОСТ 26633, регламентировалась минимальная типовая норма расхода цемента, например для армированных железобетонных изделий — 220 кг/м3в нормальных условиях.
Следующий и действующий в настоящее время СНиП 82-02-95 «Федеральные (типовые) элементные нормы расхода цемента при изготовлении бетонных и железобетонных конструкций» был разработан с позиции упрощения назначения теоретического расхода цемента на 1 м³ бетона. Нормы расхода цемента были разработаны из условия приготовления бетонов на портландцементе марки 400 и его разновидностей с определёнными фракцией щебня и модулем крупности песка. При применении других составляющих бетонной смеси следует пользоваться различными поправочными коэффициентами.
Применение химических добавок рекомендуется этим СНиП не для всех бетонов, а только для бетонов, к которым предъявляются требования по морозостойкости и водонепроницаемости. Ограничения по минимальным классам бетона по прочности на сжатие для обеспечения морозостойкости и водонепроницаемости в этом документе отсутствуют. Однако следует отметить, что отсутствие требований по назначению минимальной прочности бетонов, эксплуатирующихся в средах с агрессивным воздействием на конструкции, например дорожные и гидротехнические сооружения (ГОСТ 26633 «Бетоны тяжёлые и мелкозернистые. Технические условия»), частично компенсировались требованиями по обязательному воздухововлечению и ограничению максимального значения водоцементного отношения.
Сравнивая нормы расхода цемента, можно сказать, что за 30 лет рекомендуемые расходы цемента снизились в среднем на 1 7–20% для бетонов всех классов по прочности, морозостойкости и водонепроницаемости при фактически таком же качестве самого цемента.
Стандарт «Бетоны. Правила контроля прочности» насчитывает уже несколько десятилетий своей истории. Так, разработанный в 1972 г. стандарт устанавливал методы контроля прочности и однородности на заводах по производству готовых бетонных смесей и комбинатах по изготовлению сборных железобетонных конструкций. В этом документе указывалось, что контроль и оценка прочности и однородности бетона должны быть направлены на достижение постоянства показателей, принятых для данной марки бетона.
Оценка прочности бетона должна выполняться сопоставлением фактической средней прочности контрольных образцов бетона в партии с требуемой средней прочностью. Прочность бетона в партии признается отвечающей требуемой, если фактическая средняя прочность бетона в партии не менее требуемой средней партионной прочности. Требуемая прочность бетона определялась как величина, устанавливаемая лабораторией БСУ в процентах от нормируемой прочности с учетом фактической однородности бетона.
В ГОСТе 1980 г. в разделе «Правила приемки бетона по прочности» был сохранен такой же подход к контролю прочности бетона. Но при высокой однородности показателей прочности бетона уже требовалось назначать более низкую прочность, которая была равна или несколько выше требуемой прочности. Например, если за анализируемый предшествующий период на заводе был получен коэффициент вариации прочности Vn=7%, то было достаточно при проектной марке бетона М400, выпускаемой в данный момент (контролируемый период), обеспечить прочность, равную 340 кгс/см2.
В 1980-х годах нормирование бетона по прочности перешло от марок к классам.
В редакции ГОСТ 18105 1986 г. уже указаны классы бетона по прочности и принято, что показатели, которые близки к значению класса, считаются принадлежащими к этому классу. Так, марка бетона М400 примерно соответствует классу бетона В30 (средняя прочность класса 393 кгс/см2 при Vn=13,5%).
В соответствии с требованиями ГОСТ 18105–86, при получении коэффициента вариации прочности за анализируемый (т. е. предшествующий) период производства бетона, например 7%, требуемая средняя прочность класса бетона ВЗО в контролируемый (т. е. текущий) период должна быть равна 32,4 МПа.
Для того чтобы в следующий контролируемый период выпускать бетон с пониженной требуемой прочностью 32,4 МПа, следует разработать состав бетона с обеспечением среднего уровня его прочности, который должен быть выше требуемой всего на 4%. При этом результат по прочности подобранного состава бетона станет известен разработчику лишь через 28 суток.
Указанные 4% — это разрешённая поправка на предполагаемый разброс прочности бетона в серии и/или на возможную ошибку при дозировании составляющих бетонной смеси. Иными словами, стандарт разрешал разрабатывать составы бетона практически на минимально допустимое значение прочности.
Требуемая прочность, согласно этому стандарту, равна минимально допустимому значению фактической прочности бетона в партии, которая вычисляется на основании показателей однородности, полученных на предыдущем этапе процесса производства. Чем выше однородность показателей прочности бетона, тем ближе может быть средняя фактическая (т. е. требуемая) прочность к значению класса. И с такими значениями прочности поставку бетона на объекты строительства стандарт разрешает.
В 2008 г. была подготовлена новая редакция стандарта ГОСТ 18105, где требования к назначению фактической прочности класса не изменились.
Как может влиять на качество бетона монолитных конструкций разрешаемое прежним и только что утверждённым стандартом «вылизывание» всех возможных прочностных запасов бетона на стадии его приготовления? Основное положение ГОСТ 1972 г. говорит о том, что контроль и оценка однородности с применением статистических методов необходимы для достижения постоянства производственного процесса и принятых при расчете величин нормативных сопротивлений. В редакции ГОСТа 2008 г. о постоянстве производственного процесса уже не упоминается, основная цель — обеспечить значения заданного класса бетона по прочности. Например, класс бетона по прочности ВЗО, в зависимости от величины коэффициента вариации, полученного в предшествующий период производства, может быть обеспечен в диапазонах изменения прочности от 32,1 МПа до 42,9 МПа. Оба эти показателя прочности соответствуют значению класса бетона по прочности на сжатие ВЗО, только первый при коэффициенте вариации 7%, второй — 16%.
На предприятии с недостаточно налаженной технологией производства всегда присутствует соблазн указать пониженный коэффициент вариации по результатам заводского контроля прочности, с тем, чтобы подогнать полученную прочность под необходимый класс, согласно требованию заказчика на поставку бетона, при его пониженной фактической и средней прочности. Различные бетоносмесительные узлы могут поставлять на один и тот же объект бетонную смесь, спроектированную на получение прочности в готовой конструкции от 32,1 до 42,9 МПа, и этот бетон будет одного и того же класса по прочности.
Иными словами, при поставке бетонной смеси от нескольких заводов-изготовителей на объект (а это широко распространённая ситуация), величина средней прочности бетона одного и того же класса может существенно различаться. Укладка бетона одного заказанного класса, но с различной средней прочностью приведёт к увеличению разброса прочности бетона в готовой конструкции. Может даже получиться, что проектный класс бетона будет не обеспечен. В реальной практике ощутимые разбросы по прочности в пределах готовой конструкции являются массовым явлением.
Представим, что на объект поставили бетон с одинаковой заводской прочностью 31,2 МПа, что соответствует классу ВЗО при коэффициенте вариации 7%. Бетон уложен в опалубку, укрыт, выдержан в соответствии с правилами производства работ и через 28 суток, будучи проверен не-разрушающими методами, показывает прочность- как раз те самые 31,2 МПа, что были заданы на заводе. Согласно п. 7.4 того же ГОСТ 18105, для того чтобы определить условный класс, эту величину необходимо умножить на 0,8, следовательно, в конструкции условный класс бетона по прочности на сжатие будет равен не ВЗО, а В25, т. е. ниже проектного. Таким образом, минимизация требований по прочности приводит при определённых условиях к необеспечению проектного класса бетона в конструкции.
Выход видится в изменении требований ГОСТ 53231, а именно в том, чтобы изложить требования в стандарте в следующей редакции: состав бетона следует производить с обеспечением средней прочности класса, принятой из предположения, что коэффициент вариации равен 13,5% плюс запас в 10%. Этот подход позволяет быть уверенным в том, что требования к бетону по прочности будут обеспечены после доставки бетонной смеси на стройплощадку. Имеется в виду, что укладка, уплотнение и уход за бетоном в процессе набора прочности даёт дополнительный разброс по прочности бетона в конструкции. Зарубежный опыт монолитного строительства, существующая нормативная база подтверждает целесообразность такого подхода.
Есть ряд бетонно-смесительных узлов, которые уже сегодня выпускают бетон с обеспечением средней прочности класса, исходя из предположения, что коэффициент вариации Vn=13,5%. На объект строительства поставляется бетон с несколько завышенными показателями относительно требуемой прочности, но с большей вероятностью обеспечения проектных характеристик. По этому пути идут БСУ, поставляющие бетон на объекты транспортного строительства. По распоряжению Мостовой инспекции и центральной лаборатории «Мостотреста» номинальный состав бетона разрабатывается на среднюю прочность класса при Vn=13,5% и еще дополнительно 10%. При таком подходе обеспечивается средняя прочность в пределах средней прочности класса при Vn=13,5% и более высокая однородность бетона при всех равных условиях.
Теперь рассмотрим контроль качества бетона сборных конструкций. На ныне действующих предприятиях ЖБИ и ДСК при приемке партии готовых изделий ведется контроль прочности двух видов: при передаче напряжения с упоров форм или стендов на бетон (передаточная прочность) и отпуске продукции потребителю (отпускная прочность). Предприятие при всех условиях должно гарантировать достижение бетоном проектной прочности в возрасте 28 суток.
ГОСТ 1972 г. содержит таблицу 3, где указано, что следует снижать отпускную проектную прочность на 1 5%, если коэффициент вариации не превышает 5%, при испытании одной серии из 6 опытных образцов.
В аналогичном ГОСТе 1980 г. указано, что снижение отпускной или передаточной прочности ниже проектной допустимо, если ведется проверка выполнения технологических требований. В правилах приемки готовой продукции сказано, что если фактическая средняя прочность не ниже требуемой, т. е. если коэффициент вариации в партии равен 5% и ниже, то разрешается, в зависимости от количества испытанных образцов, снижение отпускной и передаточной прочности, соответственно, на 8–18%.
ГОСТ 1986 г. повторяет версию предыдущих стандартов, но дана таблица (приложение 4, справочное), согласно которой в зависимости от нормируемой величины отпускной прочности, от группы цементов по эффективности пропаривания, продолжительности тепловой обработки необходимо назначить отпускную прочность, увеличенную до 45%. В примечании к этой таблице указано, что следует применять следующие технологические приемы: удлинить цикл тепловой обработки, применять добавки-ускорители твердения или применять цементы только I группы эффективности при пропаривании. Все эти предложения практически невыполнимые. И в этом же стандарте, с другой стороны, предлагается при высокой однородности по прочности снижать отпускную или передаточную прочность.
Наконец, в упоминаемом выше ГОСТ 2008 г. «Бетоны. Правила контроля прочности» указаны такие же подходы к назначению отпускной или передаточной прочности. Все эти приёмы, направленные на экономию цемента, ведут к тому, что в конструкции на стадии строительства закладывается пониженный эксплуатационный ресурс. И не случайно обследование и разработка рекомендаций по усилению железобетонных конструкций как монолитных, так и сборных составляют сегодня весомую долю в объеме работ различных проектных и исследовательских организаций.
На основании вышеизложенного для повышения качества бетона конструкций, в первую очередь — показателей качества по прочности, необходимо пересмотреть уровень требований обеспечения прочности как отпускной и передаточной, так и проектной (соответственно классу бетона по прочности).
Анализ методов по определению прочности и назначению рабочего (номинального) состава в зависимости от уровня по лученной однородности по ГОСТ 18105 выпуска 1972, 1980, 1986 и 2008 гг. показывает, что следует разработать другие подходы по назначению рабочего (номинального) состава, а также уровня прочности при назначении отпускной, передаточной и проектной прочности в сборном железобетоне и бетоне, изготовленном из готовых бетонных смесей.
В сборном железобетоне отпускную, передаточную и проектную прочность следует обеспечивать на уровне проектных требований или выше вне зависимости от показателей однородности бетона по прочности, полученной за анализируемый период.
При производстве готовых бетонных смесей (товарного бетона) для монолитных конструкций необходимо в стандарте установить уровень средней прочности и поддерживать ее вне зависимости от показателя однородности бетона по прочности, полученного в анализируемом периоде. Кроме того, следует строго выдерживать правила ухода за бетоном после его укладки.
На заводах сборного железобетона и на бетонно-смесительных узлах контроль прочности с определением однородности бетона по прочности следует проводить с целью оценки стабильности показателей выпускаемой продукции.
Только при комплексном подходе к изготовлению бетона, начиная с процедур контроля его прочности и заканчивая соблюдением правил ухода за бетоном в готовой конструкции, можно рассчитывать на обеспечение надлежащего качества железобетонных конструкций.
Журнал «Технологии бетонов», №5, 2009.
Все публикации
Архив по годам: 2006; 2008; 2013; 2015; 2016; 2018; 2019;
www.stroypribor.com
Определение качества бетона и его показатели
Качество цемента определяется его маркой (М – 100, М – 200 и т.д.). Чем выше марка бетона, тем он прочнее и надёжнее. Тем не менее, в каждом строительном проекте заранее предусмотрено, цемент какой марки следует использовать в данном случае. Кроме того, при изготовлении бетонной смеси и её залитии следует точно соблюдать технологию, в противном случае качество готового изделия может сильно не совпадать с номинальной маркой.
Чтобы сохранить качество поставляемого бетона, следует уделить внимание способу поставки: только автобетоносмесители позволяют доставить на строительную площадку не расслоенную, качественную смесь (доставка бетона в самосвале недопустима).
Требуемая марка бетона на 28-й день | Бетоны | ||||||||
Жесткие, укладываемые с сильным уплотнением | Пластичные, требующие вибрирования или тщательной ручной укладки | Весьма пластичные, предполагают ручную укладку | |||||||
Усадка конуса | |||||||||
около 1 см | около 5 см | около 10 см | |||||||
Марка цемента | |||||||||
200 | 300 | 400 | 200 | 300 | 400 | 200 | 300 | 400 | |
50 | 1:3,4:5 | 1:3,8:6,5 | — | 1:3:5 | 1:3,7:5,8 | — | 1:2,8:4,4 | 1:3,5:4,9 | — |
75 | 1:2,3:5 | 1:2,8:5,5 | 1: 3,5:6 | 1:2,3:4 | 1:2,7:4,8 | 1: 3,2:5,2 | 1:2:3,5 | 1:2,5:4 | 1:3:4,4 |
100 | 1:2,1:4,3 | 1:2,5:5 | 1:3:5,5 | 1:1,9:3,6 | 1:2,5:4,3 | 1:2,8:4,9 | 1:1,8:3,1 | 1:2,1:3,6 | 1:2,6:4,2 |
150 | — | 1:1,9:4 | 1:2,3:4,5 | — | 1:1.7:3,3 | 1:2,2:4,2 | — | 1:1,6:3 | 1:2: 3,5 |
Самой распространенной ошибкой строителей на месте строительства является разбавление смеси дополнительной водой. Соотношение воды и цемента — принципиально важный показатель. Но часто смесь получается слишком густой, укладывать её неудобно и тяжело. Спасение от такой напасти находчивые российские рабочие нашли уже давно: «Добавь водички, он, глядишь, и сам растечётся как надо». В результате избыточная вода, не вступив в реакцию с цементом, испаряется из объёма заливки, оставляя поры и каверны. В будущем такая экономия сил обязательно скажется на качестве, и будет большой удачей, если никто при этом не пострадает.
Расход воды и содержание песка в смеси заполнителей для товарного бетона
Наибольший размер зерен щебня (мм) | Процентное содержание песка от общего количества заполнителей по абсолютному объему (%) | Расход воды на 1 м³ бетона (л) |
10-12 | 56 | 230 |
15 | 52 | 220 |
20 | 49 | 200 |
25 | 46 | 195 |
40 | 41 | 185 |
50 | 39 | 177 |
70 | 35 | 167 |
Также важно уделять внимание тщательному уплотнению бетонной смеси. В процессе перемешивания смеси в её объём вкрадываются микроскопические пузырьки воздуха. С этими образованиями можно бороться при помощи вибраторов на стадии залития бетона в форму.
Определением качества бетона занимаются специализированные лаборатории. Заказчик, сомневающийся в качестве поставляемого ему бетона, может провести самостоятельную оценку качества, залив часть раствора (с лотка смесителя) во влажную форму (желательно 10³ или 15³ см). При этом свежеотлитую заготовку следует «уплотнить» штыкованием. Отлитый пробный кубик следует выдержать 28 дней в прохладном и тёмном месте, после чего предоставить для исследования в любую независимую лабораторию. Там проведут исследования на прочность предоставленного образца и предоставят заключение о характеристиках данного бетонного изделия.
www.01beton.ru
Качество бетона, правильная приемка бетона
Качество обслуживания
Система М350 стремится удерживать самые высокие стандарты в обслуживании клиентов. Именно поэтому с помощью нашей системы:
Информацией о том, как определить некачественного поставщика, защитить свои риски и компенсировать возможные убытки можно воспользоваться вне зависимости от того, через систему «М350» осуществляется поставка или нет.
Помимо этого, на сайте системы представлен достаточно обширный раздел «Вопросы и ответы» с информацией по выбору марок бетона, прокачке бетона или раствора бетононасосами, миксерам (автобетоносмесителям), заливке в зимний период с использованием ПМД (противоморозных добавок) и другим разделам.
Также в разделе содержится перевод американского руководства по бетонированию «Concrete in Practice». Представлены резюме статей (если они есть), переводы отдельных руководств и оригиналы на английском языке.
В соответствии с требованиями стандарта ГОСТ Р ИСО 9001-2008 мы осуществляем сбор обратной связи о качестве своей работы. Отправить отзыв.
Качество товара (бетона, раствора)
Качество бетона — параметр, наряду с ценой интересующий каждого покупателя.
Чтобы не стать каналом продаж некачественного бетона, система «М350» со своей стороны уделяет отдельное внимание добросовестности поставщиков-участников системы.
При этом качество бетона обеспечивается не только работой изготовителя, но и правильной приемкой бетона на объекте — то есть, зависит и от покупателя тоже. Поэтому работа с покупателями и обеспечение правильной приемки также является важной частью работы системы.
Заводское качество бетона
Бетонная смесь (или раствор) с заданными свойствами (класс, водонепроницаемость, морозостойкость, подвижность или жесткость) не подлежит обязательной сертификации, но большинство уважающих себя заводов ее сертифицируют. Получение сертификата означает, что технология производства смеси данного поставщика обеспечивает достижение требуемых стандартами свойств смеси.
На каждую отгружаемую партию выдается паспорт качества — заводской документ, показывающий, какой марке и классу соответствует, поставленный бетон, и какие он имеет дополнительные свойства.
Если требуется изготовить бетон с заданными свойствами (например, повышенной водонепроницаемости), то при добавлении присадок он часто перестает быть сертифицированным, потому что сертификация каждой рецептуры бетона стоит отдельных денег, и не все заводы считают нужным себе это позволить.
Если при этом обязательно нужен сертифицированный бетон, можно заказать бетон повышенной марки (например, бетон В35 (М450) может иметь водонепроницаемость W12, в то время как бетон В25 (М350) — W6, что в два раза меньше) — правда, по деньгам это часто дороже, чем добавка гидрофобной присадки — но зато безопаснее с точки зрения соблюдения технологии производства.
На качество бетона влияет также правильная поставка. Согласно ГОСТ Р 7473-2010 «Смеси бетонные. Технические условия», по согласованию с потребителем допускается транспортировать смесь в самосвалах, но если поставщик предлагает доставку бетона в самосвалах — это прямой путь к дальнейшему расслоению смеси.
Скорость перемешивания задается производителем смесителя, поэтому на нее обращать особенное внимание не стоит.
Типовые признаки недоброкачественного поставщика
Приемка бетона
Самое распространенное и при этом губительное для качества бетона действие, происходящее при приемке — это добавление воды в смесь. Вода резко понижает прочность бетона, поэтому никогда не добавляйте воду в готовую бетонную смесь!
Кроме того, при добавлении воды в бетон производитель снимает с себя обязательства по обеспечению свойств, некоторые в случае добавлении воды на объекте не дают паспорт качества на бетон.
При заливке крупных ответственных объектов особенно важно руководствоваться нормами ГОСТ Р 18105-2010 «Бетоны. Правила контроля и оценки прочности».
Ответы на другие вопросы по приемке бетона читайте на странице «Вопросы и ответы».
m350.ru
Определяем качество бетона по внешнему виду
Ни для кого не будет сюрпризом, что в настоящее время некоторые производители бетона стараются разбогатеть на выпуске в продажу низкокачественного продукта, представляя его покупателям как отменный товар наивысшего качества. Проще всего получить плохой товар, если заказывать его относительно небольшими объемами. Отличный вариант не оплатить такой товар – проверить его реальное качество по внешнему виду. Как же правильно выбрать надёжный бетонный завод и как можно определить высококачественную смесь на вид?
Для начала, нужно насыпать смесь в небольшую емкость и взглядом оценить ее. Продукт хорошего качества не будет содержать в себе никаких примесей и зерен, которые не покрыты раствором. Затем сделайте небольшую проверочную опалубку. Если используемый бетон начнет выпадать кусками, или наоборот будет бежать как вода из крана, это будет означать, что качество продукта оставляет желать лучшего.
Так же стоит обратить внимание на количество присутствующей в бетоне воды. Ее излишки в составе бетона занижают его прочность, следовательно, прочность и сроки эксплуатации изготовленной из него конструкции значительно уменьшатся. Проверяют это довольно просто: наполняют раствором ведро и заливают на место фундамента. Если после того, как вы выльете бетон, он будет выглядеть однородной массой без трещин и без присутствия визуального расслоения, это будет означать, что присутствие воды находится в норме. Если вы увидите в налитой смеси скопление сгустков, это однозначно говорит о том, что продукт не качественный.
Важный фактор определения качества бетона по внешнему виду является его цвет. Идеальный продукт будет серый, цвета цемента (основного элемента, который применяют во время изготовления бетона).Если вы видите, что цвет стремится ближе к коричневому, знайте: в бетонную смесь добавили большое количество песка. Если цвет будет рыжеватым – это знак того, что при изготовлении были применены низкокачественные наполнители.
Помните главное: при визуальной оценке качества продукции, цвет смеси обязан быть однородным. Если в разных частях смеси цвет меняется – продукт однозначно низкого качества.
prom-beton.ru