Технология производства асфальтобетона | ООО «СДМ»
Одним из перспективных направлений деятельности в РФ является производство асфальтобетона, который используют для обустройства покрытия автомобильных дорог различного назначения. Асфальтобетон представляет собой строительный материал, который получают вследствие затвердевания смеси минеральных веществ с битумом. Технология получения асфальтобетона включает большой набор обязательных компонентов:
- Песок. Обеспечивает создание мелкозернистой основы, которая выполняет функции наполнителя мелких полостей и способствует распределению механического давления от поверхности дороги к грунту.
- Щебень. Создает требуемый уровень механической прочности, что является одной из главных характеристик асфальтобетонной смеси.
- Минеральные наполнители. В качестве этих компонентов используют измельченную горную породу (известняк, мел, песчаник). Эти наполнители позволяют асфальтобетонной смеси заполнять остаточные пустоты и значительно снижают себестоимость её производства.
- Битум. Является жидким связующим, которое склеивает все компоненты в единую монолитную смесь.
- Резина. Этот компонент вводится в виде измельченной крошки и предназначен для придания готовому асфальту высокой степени упругости, стойкости к воздействию влаги. Стоимость резины значительно увеличивает стоимость асфальта, поэтому её используют только для самых ответственных участков дороги с повышенной механической нагрузкой.
Правильное пропорциональное распределение всех этих компонентов позволяет получить асфальт, который будет обладать всеми необходимыми эксплуатационными параметрами.
Особенности производства асфальтобетона
Процесс производства асфальтобетона может выполняться при различных температурных режимах, что служит критерием для классификации асфальтной смеси на три различных категории:
- Холодные. Асфальтобетонный материал этого типа изготавливают с добавлением жидкого битума. Допускается длительное хранение и использование этой смеси при температуре не ниже +50С.
- Теплые. Асфальт этого типа изготавливают из жидкого битума и вязких связующих, поэтому температура их хранения должна составлять не менее 1000С.
- Горячие. Асфальтобетонная смесь изготавливается и укладывается при температуре не ниже 1200С.
В зависимости от фракции, используемых для изготовления асфальта компонентов, он подразделяется на три основных вида:
- Крупнозернистый. Данный материал отменно подходит для выполнения дорожного покрытия в нижних его слоях. Одним из основных компонентов этой смеси является щебень крупной и мелкой фракции.
- Мелкозернистый. Асфальтобетон этого типа применяют для обустройства верхнего покрытия у дорог общего пользования. В его состав входит щебень мелкой фракции, который может достигать величины 15 мм.
- Песчаный. Этот тип асфальта применяют для обустройства пешеходных дорожек и тротуаров. В состав этой асфальтной смеси вводят большое количество песка, битума и щебня с фракцией до 5,0 мм.
Технология изготовления смеси
Технология производства асфальтобетона состоит из нескольких основных этапов, которые включают все необходимые операции и работы:
- Входной контроль исходного сырья: минеральные добавки, битум, щебень, песок.
- Обработка инертных материалов: просеивание песка, разделение щебня по фракциям, разогрев битума.
- Доведение всех компонентов до требуемого уровня влажности и температуры нагрева.
- Перемешивание между собой всех составных компонентов асфальтобетонной смеси, что обеспечивает сцепление битума с песком, зернами щебня и минеральным наполнителем.
- Хранение готового асфальта в специальном бункере, где происходит поддержание требуемого температурного режима.
Забор готового продукта происходит непосредственно из бункера хранения, после чего его доставляют до места укладки с соблюдением всех технологических требований. Подобная технология изготовления асфальтобетона используется практически на всех отечественных заводах. Некоторые производители вводят в состав асфальта каучуковую крошку или латекс, что направлено на получение смеси с высокой степенью упругости.
Типы оборудования для производства
Оборудование для производства асфальтобетона в зависимости от технологических особенностей подразделяют на заводы непрерывного и циклического действия:
- Технологическая схема производства асфальтобетона на оборудовании непрерывного действия характеризуется отсутствием башни и грохота, которые необходимы для качественной сортировки исходного сырья.
Все ингредиенты непрерывно подают в приемные бункеры, после чего они доводятся до требуемого состояния готовности к перемешиванию. Отсутствие грохота делает возможным случаи попадания в готовую асфальтобетонную смесь щебня некондиционных размеров или посторонних включения. Основное преимущество подобных заводов – компактные размеры и высокая степень мобильности.
- Технология приготовления асфальтобетона на оборудовании циклического действия характеризуется наличием грохота и приемных башен. Благодаря этому вспомогательному оборудованию обеспечивается высокая степень подготовки исходного сырья еще до подачи в бункер для перемешивания. Асфальтный завод циклического действия располагают вблизи крупных городов, где регулярно есть потребность в небольшом объеме асфальтобетонной смеси. Главное преимущество подобных технологических схем: изменение рецептуры до нескольких раз в день, без ухудшения качества готового продукта, возможность готовить асфальт небольшими порциями, высокое качество подготовки сырья.
Главный недостаток подобных заводов – низкий уровень мобильности.
Приготовление асфальтобетона в заводских условиях требует наличия персонала соответствующего уровня квалификации, который будет уметь правильно снимать показания аппаратуры, знать все технологические особенности производства и быстро реагировать на отклонения от заданного технологического режима работы.
Производство асфальта (асфальтобетона): технология и описание
Перед тем, как мы начнем разговор о производстве асфальта, необходимо разобраться с терминологией.
В производстве используются два термина – асфальт и асфальтобетон (он же асфальтобетонная смесь, или АБС).
Их отличие состоит в следующем:
- Асфальт – это одна из разновидностей битума, минеральная смола
- Асфальтобетон – это строительный материал, широко востребованный в первую очередь при укладке дорог
Однако в быту термин «асфальт» обычно используется именно для обозначения асфальтобетонной смеси, а не смолы в ее составе.
- Производство асфальтобетона (асфальта)
- Технология производства асфальта
- Контроль исходного сырья
- Подготовка наполнителя и битума
- Смешивание
- Хранение и доставка до места укладки
- Из чего состоит асфальтовый (асфальтобетонный) завод
- Виды асфальтовых (асфальтобетонных) заводов (АБЗ)
- Циклические асфальтобетонные заводы
- Непрерывные асфальтобетонные заводы
- Мини-заводы
Асфальтобетон представляет из себя смесь двух компонентов: минерального наполнителя и вяжущего органического вещества – битума. В этом он схож с бетоном, который состоит из наполнителя и вяжущего цемента. Отсюда и название.
В качестве наполнителя асфальтобетонной смеси может выступать:
- Песок
- Смесь щебня и песка
- Смесь щебня, песка и минерального порошка
Наполнитель составляет большую часть смеси, тогда как на битум приходится около 6% от общего объема.
Теперь давайте поговорим о том, как изготавливается этот материал.
Технология производства асфальта
Необходимо отметить, что по способу производства и укладки выделяются четыре вида асфальтобетонных смесей:
- Горячий
- Теплый
- Холодный
- Литой
Основной принцип изготовления у них одинаковый, но есть кое-какие нюансы.
В целом же производство асфальта состоит из следующих этапов:
- Контроль исходного сырья
- Подготовка наполнителя
- Смешивание
- Хранение и доставка до места укладки
Собственно, разница между обозначенными видами асфальта проявляется на этапах смешивания и укладки (или хранения, если речь о холодном асфальте).
Давайте рассмотрим каждый из процессов производства немного подробнее.
Контроль исходного сырья
Это важный подготовительный шаг, от которого во многом зависит качество готовой смеси.
В состав асфальтобетонной установки входит своя лаборатория. Каждый раз, когда на завод поступает новая партия компонентов для смеси (щебень, песок, битум), она отправляется на дополнительную проверку.
Требования к сырью для производства асфальта установлены в ГОСТ 9128-2013.
Для наполнителя определяется:
- Гранулометрический состав щебня
Выбор щебня для асфальта зависит от зернистости смеси. Для крупнозернистых АБС берут материал с размером зерен до 40 мм. Его основу составляет фракция 20-40. В состав мелкозернистого асфальта входит щебень фракций 5-20 и 10-20. При необходимости сбалансировать зерновой состав в смесь также вносятся фракции 5-15, 10-15, 15-20. - Гранулометрический состав песка
В асфальтобетонных смесях обычно используется средне— или крупнозернистый песок с размером зерен от 0,63 до 5 мм. - Содержание глинистых частиц в песке
ГОСТ допускает наличие мельчайших глинистых частиц в природном песке, если оно не превышает 0,5% (для марок I-II) или 1% (для марки III) от общей массы материала. Для отсева этот показатель не нормируется. - Влажность песка (минерального порошка)
- Пористость
Эта характеристика наполнителя определяет показатель остаточной пористости готовой смеси. Для плотных асфальтов берется материал с пористостью в пределах 14-22%, а для пористых – 19-28%.
Для битума определяются следующие характеристики:
- Индекс пенетрации (глубина проникания иглы)
Как следует из названия, этот показатель определяется путем погружения в битум специальной иглы.Замеряется глубина, на которую кончик иглы погрузился за 5 секунд при температуре 25°C. Чем более «податливым» и плавким является битум, тем выше показатель. От этого зависит, до какой температуры будет разогреваться готовая асфальтобетонная смесь.
- Термостабильность
Этот показатель определяется температурами плавления и хрупкости битума. Температура плавления – это та температура, при которой битум переходит из твердого в жидкое состояние. Температура хрупкости же показывает, в какой момент материал перестает гнуться под воздействием внешней силы и начинает разрушаться. Обе эти характеристики имеют большое значение как при производстве, так и при дальнейшей эксплуатации асфальта.
Это показатели, которые во многом определяют качество и сферу применения готовой АБС. Например, от гранулометрического состава наполнителя – то есть соотношения зерен разных размеров – зависит, будет ли готовый асфальт крупнозернистым или мелкозернистым. А это уже существенно влияет на сферу его применения.
Конечно, сырье на асфальтобетонный завод поступает под заказ, с заранее заданными характеристиками. Но никто не может стопроцентно гарантировать добросовестность поставщика, не говоря уже об отсутствии банальных ошибок и просчетов. А поскольку асфальт производится непосредственно перед его укладкой, полагаться на удачу производитель не может. Если вдруг будет испорчена одна партия материала, встанет весь процесс ремонта или строительства.
Также на протяжении всего технологического процесса осуществляется текущий контроль.
Он включает в себя:
- Контроль дозирования материалов для АБС
- Контроль температурного режима
- Контроль качества перемешивания
- Контроль качества готовой АБС
Но переходить к замешиванию сразу после проведения контрольных мероприятий еще рано. Сначала нужно дополнительно подготовить компоненты смеси.
Подготовка наполнителя и битума
Минеральный наполнитель часто поступает на завод в увлажненном виде. Особенно это актуально для речного и намывного песков, которые добывается из водоемов. Однако влага в составе АБС – крайне нежелательная примесь. Она делает асфальт хрупким и ломким, из-за чего он быстро разрушается. Поэтому перед замешиванием наполнитель проходит обработку.
Подготовка минерального наполнителя подразумевает:
- Просушку (нагрев до 200°C)
- Дробление (при необходимости; например, если в исходном сырье содержится слишком много крупного щебня)
- Рассеивание на фракции (грохочение)
При этом просушка может быть как единовременной, так и сопровождать каждый из этапов подготовки. Это зависит от используемой технологии и особенностей сырья.
С битумом дела обстоят проще – он разогревается, становится жидким и пригодным для замешивания. Температура плавления зависит от разновидности материала и определяет вид готовой асфальтобетонной смеси.
Битум обычно разогревается до:
- 100-140°С – для теплого асфальта
- 160-200°С – для горячего и литого асфальта
При изготовлении холодного асфальта используются жидкие битумы, которые не требуют предварительного разогрева.
Подготовленное таким образом сырье отправляется на заключительный этап производства асфальта.
Смешивание
Минеральный наполнитель, просушенный при 200°C, остужается до нужной температуры. Как правило, это 160°C для горячего и 100°C для холодного асфальта – двух самых популярных разновидностей. А вот щебень и песок для литого асфальта, наоборот, разогреваются до 200-240°С.
Затем компоненты загружаются в специальный бункер, оснащенный смесительными лопатками. На каких-то заводах наполнитель сначала перемешивается до однородного состояния, и лишь потом, через отдельный рукав, к нему подается битум. Где-то все компоненты загружаются в смеситель одновременно. Это зависит от технологии, которой придерживается конкретный производитель.
Само замешивание с использованием специального оборудования занимает совсем немного времени – от 40 до 90 секунд.
На этом же этапе в асфальтобетонную смесь могут вносить добавки:
- Резиновую крошку
Прорезиненный асфальт имеет повышенные показатели водостойкости и шумопоглощения, отличается высокой прочностью.Производство такого материала более энергоемкое, чем у обычного асфальта, и цена получается соответствующая. Обратите внимание: многие люди путают термины «асфальт с резиновой крошкой» (прорезиненный асфальт) и «резиновый асфальт» (мягкий асфальт). Но это два принципиально разных материала. Первый – это высококачественная смесь для обустройства автомагистралей и трасс с высокой нагрузкой. Второй – дешевое покрытие на основе резиновой крошки и клея. Оно используется для застилания крылец, лестниц, детских и спортивных площадок.
- Пластик
Технология производства асфальтобетона с частичной заменой битума переработанным пластиком (до 8%) с начала 2000-х годов применяется в Индии, странах Западной Европы и Северной Америке. Такая добавка позволяет не только эффективно утилизировать пластиковый мусор, но и улучшает показатели прочности и долговечности дорожного покрытия. В России аналогичное производство пыталось наладить ОАО «Роснано», но массового применения материал пока не нашел.
Большинство разновидностей асфальта не пригодны для долгосрочного хранения. Сразу после изготовления они отправляются на место укладки.
Хранение и доставка до места укладки
Горячая АБС грузится в самосвалы или кохеры – транспорт, оборудованный специальными термосберегающими контейнерами. Они могут поддерживать температуру 150-180°С до четырех суток – на случай, если асфальт приходится перевозить на большие расстояния.
Смесь для литого асфальта при транспортировке требует постоянного перемешивания. Ведь она, по сути, представляет из себя суспензию. И в состоянии покоя наполнитель в ее составе быстро выпадет в осадок.
Готовый асфальт оперативно доставляется к месту проведения работ и выкладывается на подготовленный участок.
Технология укладки зависит от вида асфальта:
- Горячий и теплый асфальт распределяется по заданной территории, разравнивается и утрамбовывается катками или виброплитами.
- Холодный асфальт обычно используется для ремонта дорог.
Его засыпают в подготовленную яму и утрамбовывают виброплитами или вообще вручную. Специальной укатки такой материал не требует.
- Литой асфальт, как следует из названия, просто заливается на нужный участок дороги. Благодаря своей консистенции он растекается ровным слоем, который не требует трамбовки и укатки.
Холодный асфальт принципиально отличается от других разновидностей тем, что его необязательно укладывать сразу после изготовления. Такую смесь можно остудить, расфасовать в мешки и контейнеры и отправить на склад. Там он может храниться от 6 месяцев до года без потери качественных характеристик.
Итак, теперь вы имеете представление о том, как производятся различные виды асфальта. Теперь давайте подробнее поговорим о том, что из себя представляет стандартный асфальтобетонный завод.
Из чего состоит асфальтовый (асфальтобетонный) завод
Асфальтобетонные заводы (АБЗ) часто отличаются компактностью и мобильностью. Ведь, как мы уже отмечали, асфальт после изготовления нужно быстро уложить, иначе он остынет и станет хрупким. Поэтому производителям выгоднее иметь такой завод, который можно легко «упаковать» и перевезти туда, где в данный момент проводятся работы по строительству или ремонту дорог.
В состав стандартного АБЗ входят такие цеха и склады:
- Склад каменных материалов
Здесь хранятся компоненты наполнителя будущей смеси: щебень, песок, минеральный порошок (или сырье, из которого он изготавливается – известняк, песчаник и другие). - Дробильно-сортировочный цех
Здесь располагаются дробилки и грохоты для измельчения и последующей сортировки щебня. Наличие такого цеха характерно для циклических стационарных заводов (подробнее об этом читайте ниже). - Помольный цех
Он оборудуется в том случае, если минеральный порошок готовится на заводе, а не доставляется в готовом виде. - Сушильный цех
Он оборудуется сушильным барабаном, в котором минеральные компоненты асфальтобетонной смеси раскаляются до 200°С. - Цех битумного хозяйства
Он состоит из складов, на которых хранится битум, бункеров, в которых он разогревается до нужной температуры, и насосов для подачи жидкого вещества в смесители. - Смесительный цех
Сердце любого завода – это асфальтосмесительная установка, в которой и происходит смешивание минеральных компонентов с битумом. - Энергетическое хозяйство
Это комплекс машин и установок, обеспечивающих весь завод электричеством и теплом. Нетрудно догадаться, что любой АБЗ – это весьма энергоемкое предприятие. - Ремонтно-механические мастерские
Они располагаются на территории завода для максимально оперативного решения технических проблем и ремонта поломок, которые могут вызвать простой в работе цехов. - Лаборатория при отделе технического контроля качества
Здесь осуществляется проверка каждой новой партии сырья, а также текущий контроль в ходе производства асфальта.
Кроме того, на территории завода обязательно обустраиваются подъезды и стоянки для погрузчиков и самосвалов, которые доставляют сырье и развозят готовый асфальт до мест проведения работ.
Виды асфальтовых (асфальтобетонных) заводов (АБЗ)
Заводы по производству асфальтобетона используют разное сырье и имеют разные специализации. Например, прорезиненный асфальт часто изготавливается на отдельных предприятиях, а производители холодных смесей необязательно занимаются горячими разновидностями. Таким образом, каждый АБЗ в какой-то степени уникален.
Но все это разнообразие можно поделить на три типа:
- Заводы циклического производства
- Заводы непрерывного производства
- Мини-завод
Давайте рассмотрим их немного подробнее.
Циклические асфальтобетонные заводы
Производство асфальта на таких заводах осуществляется порционно, а производственные процессы протекают по очереди, один за другим. То есть пока щебень дробится и рассеивается по фракциям – асфальтосмесительная установка стоит.
Для чего это нужно? Такая схема производства позволяет менять рецептуру производимого асфальта хоть перед каждой новой партией. Можно, например, произвести определенный объем крупнозернистого асфальта, а после него – мелкозернистую смесь. Достаточно просто взять другую фракцию щебня-наполнителя.
Таким образом, циклические заводы обладают следующими преимуществами:
- Возможность быстро менять рецептуру производимого асфальта
- Более тщательный контроль за гранулометрическим составом наполнителя повышает качество смеси
Недостатки у них следующие:
- Стационарность (завод нельзя перевезти на другое место)
- Низкая производительность (по сравнению с непрерывными заводами)
- Высокая стоимость установки оборудования
Неудивительно, что заводы такого типа обычно строятся в городах, где часто требуется асфальт для широкого спектра строительных нужд и с разными характеристиками.
Непрерывные асфальтобетонные заводы
На таких заводах подача наполнителя на просушку и в смеситель осуществляется постоянно. Здесь не предусмотрена установка грохота, потому что нет необходимости разделять щебень на фракции.
АБЗ непрерывного производства имеют следующие достоинства:
- Мобильность – завод можно перевозить с места на места
- Высокая производительность
- Относительная дешевизна постройки
В то же время они обладают такими недостатками:
- Нельзя быстро изменить рецептуру асфальта (например, произвести мелкозернистую партию вместо крупнозернистой)
- Поскольку на заводе нет возможности дополнительно раздробить щебень и рассеять его по фракциям, качество асфальта очень сильно зависит от характеристик исходного сырья
Мобильность непрерывных АБЗ позволяет обустраивать их неподалеку от мелких населенных пунктов, в которых ведется активное строительство. Они также могут спокойно переезжать на новые площадки, когда спрос на асфальт на старом месте упадет.
Мини-заводы
С технической точки зрения это уже не завод, а просто передвижная установка для оперативного замешивания небольших партий асфальтобетонной смеси. Иными словами, это что-то вроде очень большой бетономешалки, только для асфальта.
Состоит она из:
- Бункера для хранения наполнителя и битума
- Горелки для нагрева компонентов смеси
- Асфальтосмесителя
- Бункера для хранения готовой смеси
Производительность одного мини-завода варьируется в пределах от 2 до 8 тонн материала в час.
Такая установка используется при проведении мелкомасштабных ремонтных работ и обустройстве небольших территорий, когда заказывать крупную партию высококачественного асфальта не очень выгодно. А с помощью подобного мобильного мини-завода можно хорошо сэкономить на лабораторных исследованиях и транспортировке готовой смеси.
Производство асфальта – процесс технологически достаточно простой. Он включает в себя подготовку компонентов смеси и их замешивание. При этом горячий, холодный и литой асфальты изготавливаются схожим образом. Разница заключается главным образом в температуре готовой смеси и особенностях ее укладки или хранения. Асфальт всех видов может производиться как на стационарном заводе циклического типа, так и на мобильной установке непрерывного действия.
Если вы хотите узнать больше о разновидностях асфальта, рекомендуем к прочтению следующие страницы:
- Виды асфальтобетона (асфальта)
Если вы хотите подробно прочитать о свойствах асфальтобетона, рекомендуем следующие страницы:
- Характеристики и свойства асфальтобетона
- Водно-физические свойства асфальтобетона
- Водопроницаемость асфальтобетона
- Водостойкость асфальтобетона
- Набухание асфальтобетона
- Водонасыщение асфальтобетона
- Класс опасности асфальтобетона
- Механические свойства асфальтобетона
- Деформативность асфальтобетона
- Колееобразование асфальтобетона
- Ползучесть асфальтобетона
- Прочность асфальтобетона
- Сдвигоустойчивость асфальтобетона
- Общефизические свойства асфальтобетона
- Плотность и масса асфальтобетона
- Пористость асфальтобетона
- Радиоактивность асфальтобетона
- Теплофизические свойства асфальтобетона
- Температурное расширение асфальта
- Теплоемкость асфальтобетона
- Теплопроводность асфальтобетона
- Технологические характеристики и свойства асфальтобетона
- Однородность асфальтобетонной смеси
- Сегрегируемость (разделимость) асфальтобетона
- Удобоукладываемость (подвижность) асфальтобетонной смеси
- Уплотняемость (формуемость) асфальтобетона
- Уплотнение асфальтобетона
- Химические свойства асфальтобетона
- Эксплуатационные свойства асфальтобетона
- Горючесть асфальтобетона
- Износостойкость асфальтобетона
- Морозостойкость асфальтобетона
- Срок службы асфальтового покрытия
- Трещиностойкость асфальтобетона
- Чем заделать трещины в асфальте
- Шероховатость асфальтобетонного покрытия
О том, как можно использовать асфальт и для каких работ он подходит, вы можете узнать на наших страницах:
- Применение асфальтобетона
- Асфальт для благоустройства территории
- Асфальт для детских и спортивных площадок
- Асфальт для дорожек и тротуаров
- Асфальт для парковки
- Асфальт для дорожных работ
- Асфальт для строительства дорог
- Асфальт для ямочного ремонта
- Стоимость строительства дороги из асфальта
- Асфальт для строительных работ
- Асфальт для отмостки
- Устройство отмостки из асфальта своими руками
- Асфальт для крыш
- Асфальт для пола
- Технология укладки срезки асфальта
- Технология укладки холодного асфальта
- Технология ямочного ремонта асфальта
- Укладка горячего асфальта
В компании Грунтовозов вы можете приобрести следующие виды асфальта:
- Горячий асфальт
- Холодный асфальт
Также у нас в продаже есть срезка асфальта (асфальтовая крошка).
Если вы хотите купить асфальт конкретной фракции:
- Крупнозернистый асфальт
- Мелкозернистый асфальт
Если вы хотите купить горячий асфальт, обратите внимание на следующие его разновидности:
- Горячий крупнозернистый асфальт
- Горячий мелкозернистый асфальт
Также у нас в продаже имеется холодный асфальт:
- Холодный мелкозернистый асфальт
Производство асфальта и переработка нефти – Pavement Interactive
Асфальт
Асфальт получают путем переработки нефти. Это вязкий клей, который вместе с заполнителем образует поверхности дорожного покрытия HMA.
В этой статье мы будем следить за тем, как сырая нефть покидает морской танкер на Морском терминале US Oil and Refining Company в Такоме, штат Вашингтон, и превращается в асфальт. Интересно, что большая часть информации о создании асфальта из сырой нефти получена в результате экспериментов. Результаты бесчисленных часов экспериментов будут максимально наглядно изложены в этой статье.
Сырая нефть
Сырая нефть представляет собой легковоспламеняющуюся жидкость, встречающуюся в природе. Он состоит из углеводородов, в основном состоящих из углеродных цепей или колец, с водородом в качестве другого основного компонента.
Количество любой конкретной молекулы углеводорода может широко варьироваться в сырой нефти. Это проявляется в различных классификациях сырой нефти. Легкая нефть может привести к увеличению количества бензина, керосина и нафты. Тяжелая нефть будет содержать больше газойля и мазута. Как правило, чем больше атомов углерода в углеводородном соединении, тем оно плотнее и имеет более высокую температуру кипения. Верно и обратное: меньшее количество углерода означает более легкое соединение и более низкую температуру кипения.
Сырая нефть также может быть классифицирована на основе содержания серы. Малосернистая нефть имеет содержание серы 0,5% или менее и имеет более высокую цену, чем высокосернистая нефть с содержанием серы 1,5% или более. Малосернистая нефть требует меньше переработки, чем сернистая, отсюда и благоприятная ценовая структура. Обозначение «сладкое» или «кислое» может показаться немного необычным, но в те дни, когда сырая нефть использовалась в первую очередь как ламповое масло, производители нефти поняли, что сырая нефть с высоким содержанием серы будет иметь неприятный запах при сжигании. Люди пробовали нефть на вкус — если бы в ней было много серы, она была бы кислой; в противном случае он был бы сладким.
Транспорт
На этот нефтеперерабатывающий завод суда с сырой нефтью прибывают каждые 10 дней и выгружают около 400 000 баррелей сырой нефти, которая перекачивается в большие резервуары для хранения. Значительное количество сырой нефти, перерабатываемой US Oil, поступает с Северного склона Аляски, которая отгружается в Валдезе.
На месторождении сырая нефть перекачивается из скважин в промысловый сепаратор, представляющий собой более широкий участок трубы. По мере того, как сырая нефть поступает в широкую трубу, давление внутри трубы падает. Более легкие газы (которые могут стать природным газом на отдельном газоперерабатывающем заводе) выделяются из сырой нефти. В этом месте также происходит отделение воды, которая сливается из трубопровода на промысловом сепараторе. Затем сырая нефть продолжает транспортироваться.
Сырая нефть доставляется на переработку разными способами – автомобильным, железнодорожным, по трубам или цистернами. В случае с US Oil and Refining Co. оптимальным видом транспорта является танкер. US Oil and Refining Co. имеет интегрированный морской терминал для приема танкеров.
Сырая нефть перекачивается с морского терминала US Oil and Refining на нефтеперерабатывающий завод по специальному 24-дюймовому трубопроводу, оборудованному станцией аварийной безопасности и автоматическим пробоотборником, который проверяет сырую нефть на исходное содержание воды.
Рисунок 3: «Полярное приключение» после разгрузки сырой нефти в порту. | Рисунок 4: Высокая белая труба предназначена для разгрузки сырой нефти. | Рис. 5: Крупный план разгрузочных рукавов в порту. |
The Polar Adventure
The Polar Adventure — это нефтевоз с двойным корпусом, который соответствует федеральному закону о загрязнении нефтью 1990 года. Он был построен в Новом Орлеане, штат Луизиана, в 2004 году.
Рисунок 6: «Полярное приключение» в доке, начинает покидать порт. | Рис. 7: Баржа подъезжает к причалу для погрузки. |
Рисунок 8: Сертифицировано для безопасного перемещения потенциально опасных грузов. | Рис. 9: «Полярное приключение» — танкер для сырой нефти с двойным корпусом. |
Это судно принадлежит Polar Tankers, Inc (подразделение ConocoPhillips). Он имеет дедвейт 125 000 тонн, 895 футов в длину и 152 фута в ширину и может перевозить более 1 миллиона баррелей сырой нефти.
Переработка
Сырая нефть может состоять из от тысячи до нескольких сотен тысяч различных углеводородных соединений. Каждый из них имеет различные характеристики, такие как вес, вязкость и температура кипения.
Сырая нефть кипит примерно при 150, 450, 750 и 900 градусах по Фаренгейту. Каждая фракция испаряется при этих приблизительных температурах, в то время как другие остаются позади. Когда контейнер с сырой нефтью нагревают до кипения и выдерживают при одной из температур кипения, часть сырой нефти испаряется. Это первое кипячение представляет собой самую легкую фракцию (которая может быть бутаном или другими легкими фракциями). Второе кипячение удалит бензин, третье удалит нафту и так далее. Этот процесс кипячения и повторного кипячения партии сырой нефти является простейшей формой очистки или дистилляции; это обычно называют периодической дистилляцией.
Однако этот процесс выпаривания фракций сырой нефти не является самым эффективным способом получения нефтепродуктов. В 1920-х годах была разработана фракционная дистилляция. В этом методе нефть нагревают, а затем подают в дистилляционную колонну или ректификационную колонну. Внутри башни или колонны расположены перфорированные тарелки, которые улавливают жидкие нефтепродукты на различных уровнях и сливают отделенные компоненты на хранение или дальнейшую переработку. Преимущества перегонки в градирнях включают повышение эффективности, сокращение трудозатрат и упрощение конструкции оборудования. На самом деле, перегонка сырой нефти наиболее эффективна и наименее затратна, когда осуществляется в два этапа: сначала фракционирование при атмосферном давлении, затем подача остатка из первой колонны в вакуумную колонну и повторная перегонка.
При выпаривании отдельных фракций сырой нефти можно построить кривую дистилляции. Это график зависимости температуры от процента испарения. Каждый тип сырой нефти будет иметь свою уникальную кривую дистилляции, которая поможет его описать. Как показано на следующем рисунке, кривая дистилляции может быть отмечена приблизительным расположением фракций, которые можно получить из сырой нефти.
Этот процесс будет рассмотрен более подробно в следующих разделах.
Рис. 11: Общий вид нефтяной и нефтеперерабатывающей компании США.Обессоливание
Когда сырая нефть поступает на нефтеперерабатывающий завод, вода и соли удаляются, чтобы упростить и удешевить переработку. Песок, ржавчина, минералы, соли и другие загрязняющие вещества загрязняют дистилляционную колонну. Многие из них оседают в резервуарах для сырой нефти и удаляются в виде донных отложений и воды, но некоторые остаются. Обессоливание также удаляет взвешенные твердые частицы в сырой нефти. Удаление взвешенных твердых частиц в процессе обессоливания должно составлять 60% или лучше – удаление частиц размером более 0,8 мкм должно составлять около 80%.
Если содержание соли в образце сырой нефти превышает десять фунтов на 1000 баррелей, необходимо обессоливать. Соль рассеяна по сырой нефти в виде крошечных капель воды, эмульсии воды и соли в нефти. Если его не удалить, он загрязнит дистилляционные колонны и вызовет коррозию металлических конструкций.
Чтобы удалить соль, в сырую нефть добавляется пресная вода, чтобы по существу вымыть соль. Могут быть добавлены химические вещества, помогающие разрушить эмульсию. Соль растворяется в пресной воде, а затем соленая вода опускается на дно резервуара, откуда ее можно удалить. Это осуществляется при температуре около 200-300 градусов по Фаренгейту. Добавляется около 3-10% объема воды.
В особо сложных случаях сырая нефть может быть пропущена через электрическое поле, где капли воды могут сливаться и оседать в сырой нефти.
Рис. 12. Вода удаляется из сырой нефти в процессе обессоливания в подобных емкостях.Перегонка
Нагнетательный насос перекачивает сырую нефть из резервуаров для хранения или обессоливания в систему. После обессоливания сырая нефть проходит через серию теплообменников для повышения ее температуры. Это доводит сырую нефть примерно до 550 градусов по Фаренгейту за счет теплообмена с потоками продукта и флегмы.
Печь дополнительно нагревает масло примерно до 700 градусов по Фаренгейту и направляется в одну из нескольких колонн фракционирования или дистилляторов. При этой температуре испаряется более половины сырой нефти. Внутри ректификационной колонны, которая может иметь от 30 до 50 тарелок, более тяжелые углеводороды (одной из них является асфальт) оседают на тарелках у дна, а более легкие (например, бутан) поднимаются вверх в виде пара или жидкости и удаляются.
Более легкие фракции поднимаются через перфорацию с тарелки на тарелку. Перфорация закрыта колпачком, который заставляет пар двигаться через жидкость, находящуюся в конкретном лотке. В этом процессе происходит передача тепла от пара к жидкости. Температура пара падает, и более тяжелые соединения, оставшиеся в паре, затем конденсируются на каждой тарелке, по мере того как более легкие фракции продолжают двигаться вверх по колонне.
Фракции удаляются по мере того, как лотки наполняются жидкостью через трубу, называемую боковым отводом. Метан и этан могут сжигаться в факелах. Более тяжелые смолоподобные углеводороды, которые оседают на дне ректификационной колонны, называются остатками.
Рис. 14. Более легкие углеводороды поднимаются наверх ректификационной колонны, а более тяжелые молекулы оседают на дно. Диапазон температур, при которых сырая нефть кипит, обозначает каждую фракцию. Эту дробь еще называют разрезом. Ключевые температуры, при которых происходит разделение каждого продукта, называются точкой разделения. Более низкая температура, указывающая на разрез, является начальной точкой кипения или IBP. Именно здесь нарезка или фракция только начинает закипать. Конечная точка, или EP, — это место, где эта конкретная фракция полностью испарилась.
Таблица 1: Некоторые общие точки отсечки
Рисунок 15: Эти колонны перегонки (или фракционирования) начинают отбирать более легкие компоненты сырой нефти, при этом обработка движется слева направо на этом изображении. Показанные башни работают при атмосферном давлении. Башня с ветроуказателем производит дизельное и реактивное топливо (по крайней мере, частично переработанное).Этот процесс может происходить в одной или нескольких колоннах, причем колонны могут находиться под атмосферным давлением или под давлением, в зависимости от продукта и нефтеперерабатывающего завода.
Вакуумное испарение или вакуумная перегонка
При температуре выше 900 градусов по Фаренгейту происходит растрескивание. Крекинг — это когда высокие температуры заставляют большие молекулы углеводородов расщепляться на более мелкие. Это нежелательно, поскольку не контролируется, если только это не происходит в процессе каталитического крекинга. Самые тяжелые точки разделения в дистилляционной колонне происходят при температуре около 750 градусов по Фаренгейту.
Можно продолжить разделение нескольких фракций, если температура кипения смеси понизится. Это происходит при снижении давления. Следовательно, более экономично перегонять при пониженном давлении, чтобы увеличить количество продуктов, которые может производить нефтеперерабатывающий завод. При вакуумном мгновенном испарении давление поддерживается на уровне 5% от атмосферного давления или ниже. Эта комбинация тепла и низкого давления эквивалентна перегонке при температуре около 1000 градусов по Фаренгейту.
Несмотря на то, что этот процесс происходит при высокой температуре и низком давлении, важно отметить, что вакуумное мгновенное испарение по-прежнему является процессом физического разделения, а не химической манипуляцией. Никаких реакций не происходит при перегонке или вакуумном мгновенном испарении. Однако можно разбить более крупные углеводороды на более мелкие и легкие молекулы — это называется крекингом, как упоминалось ранее.
Узел вакуумного промывания также содержит распределитель, флегму и вакуумный насос. Они помогают в разделении и захвате конечных продуктов. Когда жидкость и пар поступают в испаритель, большая часть жидкости падает на дно колонны, а остальная часть жидкости превращается в капли, которые поднимаются вместе с испарившейся частью остатка. Распределитель предназначен для улавливания этих капель. Распределитель представляет собой сетчатый экран или лоток из металлических колец толщиной в несколько дюймов. Они улавливают капли, которые затем сливаются и падают на дно.
Рефлюкс — это процесс, гарантирующий, что более тяжелые фракции не выйдут из верхней части дистилляционной колонны. Для этого часть пара охлаждается и снова подается на нижнюю тарелку. Все, что в этот момент еще остается паром, отправляется в качестве одного из конечных продуктов. Флегма в вакуумной испарительной камере обычно представляет собой распыленный спрей в верхней части колонны. Капли более тяжелого продукта способствуют конденсации пара на одной из тарелок.
Вакуумный насос поддерживает низкое давление внутри вакуумного мигающего устройства. Давление обычно поддерживается на уровне примерно от 25 мм рт. ст. до 40 мм рт. ст., что составляет примерно от 3 до 5% атмосферного давления. Вакуумный насос также откачивает еще не сконденсировавшийся пар, который обычно представляет собой смесь воды и некоторых углеводородов.
Для улучшения парообразования эффективное давление дополнительно снижается за счет добавления пара в колонну. Эффективное давление, которое можно определить как полное абсолютное давление за вычетом парциального давления пара, может составлять 10 мм рт. ст. или меньше. Небольшое снижение давления значительно снизит эксплуатационные расходы. Это связано с тем, что более низкое рабочее давление значительно увеличивает объем испаряемого пара на баррель, а это означает, что колонна вакуумной перегонки имеет больший диаметр, чем атмосферные колонны.
Рисунок 16: Вакуумная дистилляционная колонна значительно шире атмосферных колонн. Потоки, отводимые из верхней части вакуумного испарителя, называются верхними частями испарителя. Он состоит из легкого дистиллята мгновенного испарения и тяжелого дистиллята мгновенного испарения и обычно хранится отдельно. Однако оба они обычно отправляются в установку каталитического крекинга. Более тяжелая часть верхней части испарителя содержит большее количество загрязняющих веществ, которые отрицательно влияют на процесс каталитического крекинга. Раздельное хранение тяжелого и легкого дистиллята мгновенного испарения позволяет обрабатывать тяжелый дистиллят мгновенного испарения и способствовать более эффективному использованию установки каталитического крекинга в дальнейшем.
Последняя часть, отводимая от вакуумного испарителя, называется днищем испарителя. Эти жидкости стекают по трубе, которая немного охлаждается для охлаждения жидкости. Это предотвращает растрескивание, которое все еще может произойти при высокой температуре. Нижняя часть испарителя может стать асфальтом или может быть отправлена на смешивание, может быть расщеплена или, возможно, отправлена в печь для коксования.
Вакуумный испаритель для нефтеперерабатывающей промышленности США
Эта дистилляционная колонна, показанная на фотографиях, производит донный остаток, который соответствует PG 64-22. Он также производит верхние части испарителя, или легкий вакуумный газойль, и кубовые продукты испарителя, или тяжелый вакуумный газойль, которые отправляются на удаленную установку каталитического крекинга. Из этой башни асфальт перемещается в резервуары для хранения. Сырье для этой колонны было обработано с удалением таких компонентов, как нафта и дизельное топливо.
Рисунок 17: Легкий и тяжелый вакуумный газойль, или верхние и нижние слои фракционирования, удаляются в точках разреза, аннотированных на этом изображении. Refining Co.Жидкий каталитический крекинг
Если нефтеперерабатывающий завод оборудован для этого, более длинные углеводороды могут быть разбиты на более короткие с помощью флюид-каталитического крекинга или «кат-крекинга». Это делается при высоких температурах и давлениях с помощью катализатора, химического вещества, которое способствует протеканию реакции, но не расходуется в самой реакции. US Oil and Refining Co. заключает контракт с другим предприятием на выполнение этих операций.
Во-первых, может потребоваться обработка фракций для удаления примесей. Затем верхние и нижние части мигалки смешивают с катализатором в кошачьем крекере, чтобы создать более мелкие и более ценные молекулы. Это делается при температуре 650-1100 градусов по Фаренгейту. Кат-крекинг разрушает молекулы, но образует весь спектр углеводородов, а также кокс или чистый углерод. Затем их можно перегонять, как и в обычных операциях, для получения более широкого спектра углеводородов из тяжелых углеводородов, поступающих в результате прямой перегонки.
Наконец, различные фракции объединяются для создания конечного продукта. Другие добавки могут быть смешаны с фракциями в это время. При этом может производиться бензин с разным октановым числом или асфальт с разным PG.
Хранение битума и эмульсии
Рисунок 19: Резервуары битумной эмульсии CRS-2P и CSS-1. | Рисунок 20: Бак с маркировкой CRS-2P. |
Рисунок 21: Температура вяжущего CRS-2P в баке. | Рис. 22: Материалы, используемые при производстве битумной эмульсии. |
Рисунок 23: Резервуары используются при производстве битумной эмульсии. | Рисунок 24: Коллоидная мельница, используемая для производства битумной эмульсии. |
Некоторое дно испарителя, например, в US Oil and Refining Co., можно сразу же использовать в качестве асфальта. В этом случае остаток из вакуумной мигалки проходит испытания как ПГ 64-22, но это справедливо не для всех НПЗ. Остаток в этом случае представляет собой почти твердое вещество черного или темно-коричневого цвета.
На нефтеперерабатывающем заводе можно получить несколько сортов асфальта, создав заблокированные участки, что означает, что вакуумный распылитель работает с одним параметром для получения очень твердого асфальта. Затем настройки можно изменить для получения мягкого асфальта, которые можно смешивать для получения широкого спектра промежуточных асфальтов. Могут быть включены и другие добавки.
В зависимости от спецификации смеси к асфальту могут быть добавлены различные добавки. Некоторыми из наиболее распространенных добавок являются EVA, полимер, который делает смесь более пригодной для обработки, особенно в более холодных условиях, Sasobit, воск, который позволяет смешивать асфальт при более низких температурах, и SBS, термопластичный каучук, который обеспечивает прочность на растяжение и деформацию. восстановление.
Рисунок 25: Это три распространенные добавки к асфальту. | Рис. 26: Бункер для загрузки полимера (SBS) для добавления в битумное вяжущее. | Рис. 27: Смешивание полимера и асфальта в мельнице с большими сдвиговыми усилиями. |
Производство US Oil and Refining Company
НПЗ в настоящее время перерабатывает около 38 000 баррелей сырой нефти в день и работает 24 часа в сутки, 365 дней в году. В течение года US Oil производит:
- Около 3 различных битумных эмульсий
- Около 15 различных сортов полипропилена
- Наиболее часто используемая марка PG в US Oil — PG 64-22.
Бензин обычно содержит 10% этанола по объему, добавляемого во все смеси, которые, в свою очередь, продаются таким компаниям, как Exxon, Costco и т. д. Состав бензина меняется сезонно, 6 раз в год.
Асфальт состоит из более тяжелых и длинных углеводородных цепочек из сырой нефти. В US Oil and Refining Company самый распространенный сорт вяжущего PG, PG 64-22, поступает прямо из вакуумной колонны. Другие связующие PG могут быть изготовлены с простыми изменениями формулы, как отмечалось ранее.
Рис. 28: Этанол доставлен в US Oil по железной дороге. | Рисунок 29: Трубы для теплообмена. |
Топливные продукты в US Oil & Refining Co.
- Топливные продукты
- Все сорта неэтилированного бензина и E10.
- Дизельное топливо со сверхнизким содержанием серы
- Топливо для реактивных двигателей (JP-8 и Jet A)
- Все сорта неэтилированного бензина и E10.
- Изделия из асфальта
- Cutback MC-Cold Mix
- Эмульсии
- КМС-2
- КРС-2
- КРС-2П
- УС-1
- УС-1Н
- СТЭ-1
- Мощение
- AC 2,5, 5 или 7
- Арктика AC-5
- АР 2000
- ПБА-2, 5 или 6
- стр. 52-28
- ПГ 58-22, 28, 34, 40
- ПГ 64-10, 22, 28
- стр. 70-22
- стр. 76-22
Refinery Laboratory
US Oil and Refining Company проводит множество тестов, чтобы убедиться, что каждый из ее продуктов соответствует спецификациям для каждого продукта и его использования. Для этого у них есть большая лаборатория по тестированию асфальта, мазута и бензина. В оставшейся части этого раздела основное внимание будет уделено испытаниям и спецификациям асфальта.
Спецификации
Асфальт определяется его спецификациями. Эти критерии предсказывают реакцию асфальта в полевых условиях в различных температурных диапазонах. Наиболее популярной системой спецификаций является система вяжущего Superpave с оценкой производительности (PG). Оценка производительности Superpave основана на идее, что свойства битумного вяжущего HMA должны быть связаны с условиями, в которых оно используется. Для битумных вяжущих сюда относятся ожидаемые климатические условия, а также факторы старения. Таким образом, система PG использует общий набор тестов (как и более старые системы определения пенетрации и вязкости), но указывает, что конкретное битумное вяжущее должно пройти эти испытания при определенных температурах, которые зависят от конкретных климатических условий в районе использования.
Рис. 31: Спецификация для PG 64-22. | Рисунок 32: Спецификация для PG 64-28. |
Реометр динамического сдвига
Рисунок 33: Реометр динамического сдвига.Реометр динамического сдвига (DSR) используется для характеристики вязкости и эластичности битумных вяжущих при средних и высоких температурах. Эта характеристика используется в спецификации битумного вяжущего Superpave PG. Как и в случае других испытаний вяжущего Superpave, фактические температуры, ожидаемые в зоне, где будет укладываться асфальтовое вяжущее, определяют используемые температуры испытаний.
Обратите внимание, что в спецификациях измерение динамического сдвига указано для PG 64-22 как:
- @64°C = 1,00 кПа (мин)
- После RTFO
- при 64°C = 2,20 кПа (мин)
- После ПАВ 100°С
- при 25°C = 5000 кПа (макс.)
Кинематическая вязкость
Рисунок 34: Кинематическая вязкость при 135 градусах Цельсия. Кинематическая вязкость жидкости – это абсолютная (или динамическая) вязкость, деленная на плотность жидкости при температуре измерения. Температура измерения 135°C (275°F) была выбрана для имитации температур смешивания и укладки, обычно встречающихся при строительстве дорожного покрытия HMA.
Требования к вязкости для PG 64-22:
- Вязкость при 135°C = 3,0 Па-с (макс.)
- Тест выполняется на прямом цикле PG (без старения)
Температура вспышки PG 64-22
Рис. 35. Определение температуры вспышки для закрытого тигля Pensky MartensТипичное определение температуры вспышки включает нагревание небольшого образца битумного вяжущего в тестовом тигле. Температуру образца повышают и через определенные промежутки времени через чашу пропускают испытательное пламя. Температура вспышки – это самая низкая температура жидкости, при которой приложение испытательного пламени вызывает воспламенение паров образца. Испытание можно продолжать до точки воспламенения – точки, при которой испытательное пламя вызывает воспламенение образца и его горение в течение не менее 5 секунд.
Жесткость при ползучести для PG 64-22
Испытание реометром на изгиб балки (BBR) обеспечивает измерение низкотемпературной жесткости и релаксационных свойств битумных вяжущих. Эти параметры указывают на способность битумного вяжущего противостоять низкотемпературному растрескиванию. BBR используется в сочетании с DTT для определения низкотемпературного класса PG битумного вяжущего. Как и в случае других испытаний вяжущего Superpave, фактические температуры, ожидаемые в зоне, где будет укладываться асфальтовое вяжущее, определяют используемые температуры испытаний.
Жесткость при ползучести измеряется с помощью BBR:
- при -12°C, S = 300 МПа (макс.)
- @-12°C, М-значение = 0,300 (мин)
Сосуд старения под давлением
Рис. 37: Сосуд старения под давлением контролирует температуру и давление. | Рисунок 38: Обратите внимание на лотки в верхней части PAV, куда помещают образцы асфальта во время испытания. |
Сосуд старения под давлением (PAV) обеспечивает имитацию битумного вяжущего с длительным сроком старения для испытания физических свойств. Асфальтовое вяжущее подвергается воздействию тепла и давления для имитации старения в процессе эксплуатации в течение периода от 7 до 10 лет.
Каким будет будущее производства асфальта?
Отраслевые эксперты рассказывают о том, как может выглядеть асфальтовый завод завтрашнего дня
16 июня 2021 г.
Джессика Ломбардо
Десять лет назад журнал Asphalt Contractor поговорил с отраслевыми экспертами о том, как, по их мнению, будут выглядеть асфальтовые заводы в будущем. Перенесемся в 2021 год, и многие из их предсказаний сбылись; в то время как другие (например, крытые асфальтобетонные заводы) не совсем прижились в отрасли.
Разработки, касающиеся снижения энергопотребления, качества смеси и снижения себестоимости продукции, стали повседневной нормой на асфальтовых заводах, и спрос на них будет только расти. В связи с тем, что в ближайшие несколько лет в строительной отрасли, вероятно, произойдет много других изменений, мы снова поговорили с производителями асфальтобетонных заводов и производителями компонентов о том, что они ожидают в ближайшие 10 лет.
Устойчивое будущее
Ни для кого не секрет, что «устойчивое развитие» будет краеугольным камнем администрации Байдена. То, как асфальтовая промышленность адаптируется и как быстро, будет ключом к успеху.
В отрасли мы нашли способы уменьшить свой углеродный след за счет увеличения использования восстановленного асфальтового покрытия (RAP). В течение следующих 10 лет отрасли необходимо будет найти способы увеличить содержание вторичного сырья в наших смесях.
«Будет расширена возможность производства более экологически чистых смесей. Это означает больше RAP, а также теплых/низкотемпературных смесей», — Пол Лавенберг, региональный менеджер Ammann America в Северной Америке. «Интересно, что технология, возможно, уже существует, но внедрение смесей с более высоким содержанием РАП может быть не таким быстрым, как хотелось бы некоторым. Это вопрос наличия у производителей смесей возможности производить смеси с более высоким РАС… и все соглашаются с тем, что высокая RAP возможна. Новые методы тестирования, основанные на характеристиках смеси, также могут потребовать большего признания».
Экологически безопасные смеси станут нормой, прописанной в спецификациях заявок и законодательстве о финансировании, что еще больше подтолкнет производителей к поиску способов создания смесей с более высоким содержанием вторичного сырья.
«Общепринятые представления о том, как делать смеси с высоким содержанием RAP, развиваются и дают результаты», — говорит Лавенберг. «Одной из основных технологий, которые использует Ammann, является щадящий нагрев РАП отдельно от первичных заполнителей. Это сохраняет качество битума/АЦ за счет отсутствия термического напряжения при смешивании с перегретыми заполнителями. Это повышает качество, удобоукладываемость и снижает количество отходов».
Лавенберг добавляет, что специальные смесители также демонстрируют большие перспективы, когда речь идет о приготовлении однородных смесей – для поддержания температуры и дисперсии заполнителей. Это также имеет тенденцию быть очень эффективным для включения добавок в специальные смесители.
Превосходство эффективности
Экологичность не ограничивается созданием экологически чистых смесей. Асфальтобетонные заводы также должны будут адаптироваться, чтобы стать более эффективными, а эффективность завода начинается с расхода топлива. Стандартные виды топлива, используемые на заводе, включают природный газ, сжиженный газ, мазут, мазут и пылевидный лигнит. Многие горелки могут сжигать несколько видов топлива. Это позволяет клиентам перейти на топливо с наибольшими преимуществами — как экологическими, так и экономичными.
«Расширяется использование альтернативных видов топлива», — добавляет Лавенберг. «Мы часто встречаемся с нашими клиентами, чтобы обсудить и разработать идеальное решение для них. Заводы с крытым холодным питанием или бункерные бункеры идеально подходят для установок солнечных батарей. Это позволяет им покрывать свои потребности в энергии для хранения электрического битума. Неиспользованная энергия будет поставляться местным сообществам».
Асфальтовые заводы уже сегодня вынуждены проводить энергоаудит, чтобы увидеть, где они могут повысить эффективность и снизить потребление. ENERGY STAR работала с асфальтовыми заводами, чтобы наметить шаги, которые предприятия могут предпринять для проверки своего энергопотребления, и даже предоставила для предприятий карты сокровищ, которые они могут использовать, где они могут определить области на своем заводе, которые могут использовать слишком много энергии, и как они могут это исправить.
Поскольку в будущем могут появиться более строгие правила, воспользуйтесь возможностью прямо сейчас, чтобы увидеть, что можно улучшить в вашей компании.
Интеллектуальные системы
Асфальтовый завод будущего также должен будет адаптироваться, чтобы быть привлекательным для следующего поколения рабочих. Это означает, что системы должны быть более удобными для пользователя и управляемыми данными.
«Следующее поколение операторов также будет иметь гораздо больше технологических требований для своей работы и в качестве фонового интереса», — говорит Кристиансон из WEM. «Сейчас найм персонала стал такой проблемой, и эти заводы настолько экономичны, насколько это возможно по необходимости. множество датчиков ИТ-инфраструктуры и мобильных информационных платформ, которые уже доступны, но не получили широкого распространения».
Многие датчики теперь поставляются со встроенным веб-сервером, который может передавать состояние, предоставлять текущие значения, настраивать параметры или предлагать анализ. Наличие большего количества заводских датчиков улучшает контроль производственного процесса. Кристиансон добавляет, что это важно, поскольку будущие операторы будут более склонны к технике, в отличие от сегодняшних операторов, которые более склонны к механике.
«Будущие операторы выросли на технологиях, это заложено в их биологии», — добавляет он. «Им понадобятся инструменты для работы, которые позволят им получать обратную связь, которую они ищут. На заводе они будут искать свою диагностику в электронном виде, чтобы собирать информацию о том, как работает завод».
Это также соответствует обновленному виду диспетчерской.
«Пользовательский интерфейс, который мы видим на элементах управления заводом, станет более подробным, будет выглядеть более современно, будет иметь более интерактивную обратную связь и считывать данные, потому что это то, что оператор через 10 лет будет ожидать», — добавляет он. «Старая архаичная графика быстро потеряет интерес».
Мобильные приложения, которые могут управлять асфальтовыми заводами с телефонов и планшетов, также станут нормой для операторов. Кристансон говорит, что один оператор может управлять несколькими асфальтовыми заводами из одного центрального места.
Подготовка начинается сейчас
Адаптация к изменениям — это процесс. Лучший способ подготовить свой асфальтовый завод к успешному будущему — начать подготовку прямо сейчас. Уже существуют системы и технологии, доступные для асфальтовых заводов, которые обеспечивают более широкое использование RAP или более эффективную интеграцию данных. Асфальтовые заводы уже должны искать способы улучшить свою работу в будущем, тем более что борьба с изменением климата становится центральной темой разговоров в нашей стране.
«Каждая заинтересованная сторона (производитель, производитель растений, местная юрисдикция DOT, испытательные лаборатории, бригады по укладке и т. д.) играет роль в подготовке к потенциальным изменениям того, как климат повлияет на нашу отрасль», — Лавенберг. Производственные и технологические процессы ЗДЕСЬ СЕГОДНЯ, чтобы адаптироваться ко всему, что будет дальше».
Первые асфальтобетонные заводы
По данным Национальной ассоциации асфальтобетонных покрытий (NAPA), самые ранние установки по производству горячей асфальтобетонной смеси (HMA) состояли из неглубоких железных лотков, нагреваемых над открытым угольным огнем. Оператор сушил заполнитель на поддоне, сверху заливал горячим асфальтом и перемешивал смесь вручную. Качество смеси обычно зависело от мастерства и опыта оператора.
В 1870 г. компания Cummer открыла первые центральные предприятия по производству асфальтобетонного покрытия в США. К концу 19 в.90 451–90 452 века строители по обе стороны Атлантики производили миксеры и сушилки самых разных форм. Первый асфальтобетонный завод, содержащий практически все основные компоненты, которые у нас есть сегодня, был построен в 1901 году компанией Warren Brothers в Восточном Кембридже, штат Массачусетс. Не хватало только холодного питания и оборудования для очистки от загрязнений. №
Первыми барабанными смесителями и барабанными сушилками-смесителями, которые начали использоваться примерно в 1910 году, были бетоносмесители для портландцемента, адаптированные для использования с HMA. Механизация сделала еще один шаг вперед в 1920-х годов с усовершенствованием систем холодного питания для портативных и полупортативных систем. Вибрационные экраны и системы нагнетания давления были добавлены в 1930-х годах.
Асфальтобетонные заводы начала 50-х могли включать в себя сушилку, башню с выглаживающей плитой и смеситель. По словам NAPA, это были грязные и пыльные операции. Но к середине 60-х годов, когда загрязнение воздуха стало серьезной проблемой по всей стране, многие добавили мокрые скрубберы, а некоторые установили рукавные фильтры.
Другим важным изменением в середине-конце 60-х годов стало добавление бункеров-накопителей и бункеров для хранения. До этого все загружалось прямо с завода в грузовик.
Внутренние асфальтобетонные заводы?
10 лет назад д-р Дж. Дон Брок, в то время председатель Astec Industries, предсказал, что асфальтовые заводы завтрашнего дня, скорее всего, будут располагаться в здании.
Кроме того, что завод скрыт от глаз соседей, крытые здания помогают сохранить агрегаты более сухими. Чем суше материал, тем меньше топлива вы будете использовать для его сушки, что приводит к экономии энергии.
Это происходит уже глобально. Некоторые из самых передовых технологий и самых производительных заводов в Азии и Европе используют эту практику, чтобы быть хорошими соседями. Растения могут быть гораздо более привлекательными с визуальной точки зрения и могут помочь сдержать или уменьшить местное воздействие.
Кроме того, поскольку становится все сложнее строить новые заводы на существующих площадках, новых и заброшенных участках, у производителей есть установленные способы конфигурирования заводов в будущем для включения этих функций.
Увеличение производительности с помощью нагревателей песка ADM производительностью от 90 до 210 тонн в час0045
Как улучшить выбросы и эффективность асфальтобетонных заводов
3 важных выноса из NAPA Annual 2023
На ежегодном собрании Национальной ассоциации асфальтобетонного покрытия в этом году в Майами, Флорида, на различных заседаниях были выявлены некоторые общие темы: комитеты и встречи в течение пяти дней мероприятия South Beach.
2023 Состояние дорожно-строительной отрасли: зеленая мечта
Год действия IIJA и несколько месяцев после принятия Закона о снижении инфляции, отрасль все еще пытается решить проблемы с нехваткой рабочей силы, даже если цепочка поставок и материалы проблемы видели некоторые улучшения. Полный отчет читайте здесь!
Увеличьте производительность с помощью нагревателей песка ADM производительностью от 90 до 210 тонн в час
Нагреватели песка ADM эффективно нагревают песок для контроля температуры смеси, улучшения качества смеси и снижения затрат энергии и труда на производство зимнего бетона.
Профессионалы по асфальту и дорожному покрытию Загляните в NAPA, ConEXPO
И строителям дорог, и подрядчикам по техническому обслуживанию есть чем заняться в ближайшие месяцы. Ежегодная конференция NAPA и ConEXPO будут здесь, прежде чем вы это узнаете.
2023 Состояние дорожно-строительной отрасли: зеленая мечта
Год действия IIJA и несколько месяцев после принятия Закона о снижении инфляции, отрасль все еще пытается решить проблемы с нехваткой рабочей силы, несмотря на проблемы с цепочками поставок и материальными ресурсами. увидели некоторые улучшения. Полный отчет читайте здесь!
Как повысить энергопотребление вашего асфальтобетонного завода
Получите доступ к эффективным и чистым источникам тепла на вашем заводе.
Универсальность и производство для CA Langford
Производитель из Алабамы сотрудничает с ALmix в строительстве нового бетонного завода для удовлетворения потребностей клиентов.
Технология максимального использования рециклированного асфальта. следующий уровень.
Увеличьте производительность с помощью нагревателей песка ADM производительностью от 90 до 210 тонн в час
Нагреватели песка ADM эффективно нагревают песок для регулирования температуры смеси, улучшения качества смеси и снижения затрат энергии и труда на производство зимнего бетона.
Множество проблем и возможностей для производства асфальта на солнечной энергии
Norris Asphalt переводит свои заводы в Оттумве на солнечную энергию, экономя их деньги и настраивая их для будущих целей устойчивого развития
Earthwave позволяет отслеживать местоположение для асфальтовых загрузок отслеживает нагрузку с момента ее загрузки на асфальтобетонном заводе до ее выгрузки в асфальтоукладчик на стройплощадке.
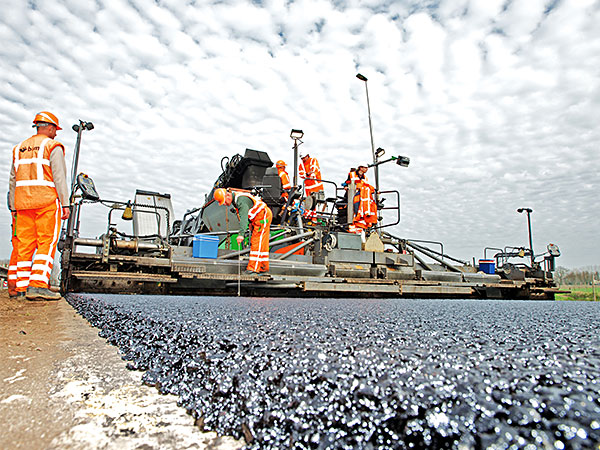