состав, технические характеристики, соответствие требованиям ГОСТ, назначение и применение
В технологии современного строительства появился относительно молодой материал — полимербетон.
Благодаря своей универсальности и повышенным качественным характеристикам он уверено потеснил традиционные цементные смеси.
Весь секрет заключается в полимерном связующем в составе, который и определяет повышенные прочностные свойства полимербетонных изделий.
Интересной особенностью является возможность применения вторичных пластиков в производстве полимербетона, причем качество готового материала от этого не страдает.
В этой статье пойдет речь о сферах применения полимерцементного раствора и изделий из него.
Общее описание и отличие
У цементного раствора из обычных составляющих, как и у других растворов, в которых в качестве вяжущего вещества выступает минеральное вещество, есть ряд недостатков. Среди них особенно выделяется низкая прочность при растяжении или изгибе, низкая стойкость к ударам, малый процент деформации, низкая стойкость к истиранию и слабая адгезию по отношению к другим строительным веществам. Список недостатков достаточно велик, что сильно ограничивает применение обычного раствора. Для того чтобы как можно сильнее снизить влияние этих недостатков или же вовсе ликвидировать их влияние, в состав смеси вводят специальные полимеры в качестве добавки от 2 до 30 % от общей массы. Таким образом можно сказать, что состав полимерцементного раствора отличается от обычного лишь наличием этой самой добавки.
Полимербетонные полы
Покрытие из полимербетона используется там, где нагрузка на пол достаточно высокая. Причем не только механическая, но и химическая.
Входящий в состав полимер повышает стойкость к ударным нагрузкам, истиранию и образованию трещин.
Наливным полом оборудуют:
- гаражи и закрытые стоянки;
- производственные помещения;
- спортивные залы;
- складские терминалы;
- залы ожидания и помещения вокзалов и аэропортов;
- медицинские, образовательные, административные учреждения.
Сочетание свойств пластика и бетона придает покрытию полезные практические свойства. Причем толщина цементного слоя не ухудшает его эксплуатационные характеристики и может варьироваться от 7 до 50 мм. Если нужно, можно выровнять перепады по высоте до 200 мм без потери прочности основания.
Среди преимуществ полимербетонного пола выделяют следующее:
Связующим элементом полимерцементной стяжки для пола является полимерная смола. Используются разнообразные типы: эпоксидная, полиуретановая, акриловая и т.д. Из вторичного пластика можно получить стирольную смолу методом пиролиза.
Она хороша тем, что отверждается (полимеризуется) различными способами даже при простой термообработке.
Для повышения скорости реакции можно применять инициаторы, которые являются доступными и недорогими. Сырьем для производства стирольной смолы являются отходы из полистирола (одноразовая посуда, пенопласт, упаковка, формы для рассады и т. д.).
Введение полимера в смеси
Стоит сказать о том, что полимер, так или иначе, вводится в большое количество самых разных смесей. Чаще всего он предназначен лишь для улучшения пластификации, а также гидрофобизации. Кроме этого, наличие таких добавок составляет менее 1 % от общей массы. Это является основным отличием от полноценного полимерцементного раствора. В них полимер серьезно влияет на состав, изменяя его физико-химические свойства, на его структуру, а также входит в раствор, как самостоятельный элемент, а не обычная присадка.
Методы добавления полимеров могут отличаться. К примеру, можно добавлять его в виде водной смеси. В таких случаях обычно содержание его в цементе будет не более 3-5 % от общей массы. Намного чаще используется метод, в котором задействованы водные дисперсии, содержащие полимеры. Отличие состоит в том, что в дисперсии полимер не растворяется в воде, а значит, его количество может быть увеличено. Таким образом, удается ввести в цементную смесь примерно 10-20 % добавки от общей массы цемента.
Дополнительные элементы
Стоит отметить, что все характеристики полимерцементного раствора могут быть утеряны, если во время добавки полимерной дисперсии произойдет такой процесс, как коагуляция или же створаживание раствора. Чаще всего, чтобы избежать таких негативных последствий, применяются различные стабилизаторы. В качестве них обычно выбирают поверхностно-активные вещества (ПАВ) — ОП-7 или ОП-Ю. Возможно также заменить их небольшой группой электролитов, к примеру, жидким стеклом. Без добавки стабилизатора может обойтись лишь полимерцементный раствор, который был смешан на основе пластифицированной дисперсии ПВА.
Однако введение ПАВ не проходит бесследно. Чаще всего эти вещества выступают в роли мощных пенообразователей, а также они способны вовлекать воздух в растворную смесь. Если это происходит, то мельчайшие пузырьки воздуха, которые были вовлечены, могут достигать в объеме 30% от общей массы раствора.
Изменение свойств раствора
Наличие полимерных добавок в растворе помогает более равномерно распределить поры, а также сделать их объем куда более меньшим. Можно привести пример. В обычном цементном растворе, к примеру, поры могут быть до 1 мм в диаметре, а их основная часть отличается показателями в 0,2-0,5 мм в объеме. Если речь идет о полимерцементном составе, то максимальный объем снижается до 0,5 мм, а наибольшее количество, примерно 90-95 %, и вовсе не будут более 0,2 мм.
Это сказывает самым положительным образом, допустим, при сплошном выравнивании штукатурки стен полимерцементным раствором, где поры могли бы нарушить общую структуру. Также здесь стоит добавить, что те смеси, в которых имеется вовлеченный воздух, характеризуются большей пластичностью, а также лучше удобоукладываемостью при меньшем содержании жидкости. Как говорилось ранее, пластификации у таких составов также на более высоком уровне. Все это ведет к тому, что при добавлении воды очень важно учитывать процент вовлеченного воздуха и пластификацию полимерцементного раствора.
Правила нанесения акриловой штукатурки на стену
Сама по себе штукатурка эластичная, к тому же продается в готовом виде. Это означает, что новичку работать с ней будет легко. Все же, техника нанесения имеет свои нюансы. В целом работы выполняются так:
Подготовительный этап. Хоть акриловая штукатурка используется для ремонтных работ, но не для выравнивания. Ею можно скрыть мелкие изъяны и недочеты стен. Сам слой тонкий, поэтому стены требуется выровнять до идеального состояния. Тогда отделка будет выглядеть красиво. Отклонения по плоскости допустимы в районе 1-2 мм. С ними штукатурка справится. После выравнивания стену требуется затереть, очистить от пыли и грязи
Процесс грязный, поэтому важно защитить глаза и дыхательные пути. Грунтовка. Слой грунта позволит сделать стену идеальной для последующих манипуляций
Сцепление увеличится, а стена не будет впитывать много воды из смеси. Поэтому ее расход снизится. Грунтовка выполняется валиком и кистью. Требуется тщательно обработать все участки поверхности. Нанесение акриловой штукатурки. Это нужно делать после высыхания грунта. Перед началом работ, открытую смесь нужно перемешать. Технология нанесения и инструмент для работ зависит от выбранного состава. На упаковке есть подробная инструкция, как именно выполнять манипуляции. Финишная отделка. Готовую поверхность можно усовершенствовать. Для этого применяется акриловая краска, воск. Поверхность можно зашлифовать. Есть вариант двухслойного окрашивания.
При первичной работе со смесями, рекомендуется потренироваться с нанесением на незаметном участке стены.
Адгезионные свойства
У таких составов наблюдается повышенная адгезия, которая объясняется следующим образом. При нанесении смеси полимер концентрируется на границе раздела и играет роль клейкой основы между раствором и основанием. Что касается самой адгезии, то она напрямую зависит от вида добавленного полимера, а также от его концентрации. Далее стоит сказать о том, что это свойство проявляется только в том случае, когда происходит высушивание раствора в воздушно-сухих условиях. Поэтому, допустим, штукатурка с полимерцементным раствором, нанесенная на стены, будет отличной основой для укладки. Если затвердевание происходит в воде, то адгезия не будет проявлять себя так хорошо, даже при огромной концентрации полимера. Это обусловлено тем, что стабилизаторы растворяются в воде, а некоторые добавки и вовсе способны изменять свои свойства, если они находятся в жидкой среде.
Можно добавить, что высокий уровень адгезии сказывается не только на улучшенном сцеплении с другими материалами, а еще и на механических характеристиках самого раствора. Это особенно заметно при возникающих нагрузках при растяжении и изгибе. У смесей с присадками эти показатели выше примерно в 10 раз, чем у обычных. Это благодаря тому, что слои полимера связывают минеральные составляющие между собой. Есть также такая характеристика, как модуль упругости, который примерно в 10 раз ниже, чем у обычного. Благодаря этому факту можно смело утверждать, что полимерный состав более деформативен, чем обыкновенный.
Усадка и другие характеристики
Если в смесь вводится более 7-10 % полимера от общей массы цемента, то при ее затвердевании будет наблюдаться более существенная усадка. Однако так как вместе с этим сильно возрастает и деформативность раствора, то по такой характеристике, как устойчивость к трещинам, смесь ничем не уступает обычной, а в некоторых ситуациях может даже превышать. Еще одно отличие в параметрах — это отдача влаги. В полимерном растворе она проходит более медленно, что позитивно сказывается на процессе затвердевания, так как не наблюдается быстрое пересыхание, из-за чего могут возникать трещины.
Взаимодействие с другими материалами
Для чего используется полимерцементный раствор? Все выше указанные свойства и характеристика материала привели к тому, что он отлично подходит для крепления облицовочных материалов, так как может обеспечить более лучшее крепление. Здесь можно привести простое сравнение обычной смеси и смеси с добавкой полимера. Раствор на основе цемента и песка создает максимальную прочность крепления к 7-9 суткам после облицовки, а к 28 суткам этот показатель будет уменьшаться примерно в 5-6 раз. Если говорит о растворе с присадкой из полимеров, то максимальная прочность крепления будет достигнута чуть позже, на 9-10 сутки, однако при этом ее отсутствие в дальнейшем и вовсе не наблюдается. Благодаря этому качеству такие составы и стали максимально широко использоваться при облицовке.
Коротко о главном
Штукатурка на основе цемента применяется для работ снаружи и внутри помещения. Покрытие отличается высокой прочностью и стойкостью к влаге.
Из недостатков цементного состава выделяют сложность нанесения, большой вес и высокий риск появления трещин.
Смесь на основе гипса применима только для отделки внутри сухого проветриваемого и отапливаемого помещения. Характерными для покрытия свойствами являются быстрое высыхание, гладкость.
К минусам относят относительно низкую прочность на отрыв, хрупкость, неустойчивость к влаге. Также выделяется меньшая инертность к биологической активности и коррозии. Но состав является экологически более безопасным.
Перед нанесением раствора на основе цемента рекомендуется монтаж армирующей прослойки. При увеличении предельной толщины однослойного покрытия при использовании обеих смесей обязательно применение металлической или стекловолоконной штукатурной сетки.
Лучшие составы для работ и расход
При модификации обычного цементно-песчаного раствора пластификаторами и полимерами можно достичь сильного сокращения расхода. Полимерцементный раствор может наноситься максимально тонкими слоями и при этом быть качественным основанием для облицовочного материала. Это обусловлено тем, что дисперсия с полимерами не только серьезно увеличивает пластичность, но и вовлекает воздух от 8 до 12 %.
На сегодняшний день в этой сфере наиболее перспективным раствором считается тот, который сделан на основе гипсоцементно-пуццоланового вяжущего (ГЦПВ), а также водными дисперсиями полимеров. Использовать такой состав можно как при наружных работах, так и при внутреннем оштукатуривании. Однако наибольший эффект, как показала практика, достигает при применении его в декоративных растворах и мастичных смесей для обработки фасадов зданий.
Технология штукатурки стен
Теперь рассмотрим основные правила выравнивания стен цементным раствором:Стены предварительно обрабатывают грунтовкой для улучшения сцепления и тщательно просушивают;
Для создания плоскости на стене расставляются маяки – направляющие. На небольших площадях их можно заменить шлепками раствора, высоту которых выставляют по уровню.
В качестве маяков можно использовать специальный металлический профиль. Его крепят к стене на шпаклевку. Также можно сделать маяки из деревянных реек или брусков, их крепят на саморезы. Главное помнить, что расстояние между маяками должно быть на 10-20 см меньше ширины правила, которым будут разравнивать штукатурку.
Штукатурку набрасывают на стены мастерком, для создания слоя большей толщины можно воспользоваться ковшиком. Этот первый слой называется обрызг — основа для последующих слоев.
Наносить второй слой следует через пару часов после схватывания первого. Его кладут по направлению снизу вверх, полностью закрывая предыдущий. Оштукатуривать удобней небольшими участками по 1-1,5 метра. Затем штукатурку начинают протягивать и выравнивать правилом. Его плотно прижимают к маякам и поднимают вверх, при этом немного двигают правило из стороны в сторону. Излишки раствора с правила снимаются мастерком.
Таким образом оштукатуривают весь участок между двух маячков и переходят дальше.
Для выравнивания небольших дефектов маяки можно не использовать. Оштукатуривание в данном случае ведется по иной технологии. После обрызга раствор распределяют большим шпателем снизу вверх.
Более гладкую поверхность можно получить дополнительной накрывкой жидкой смесью (второй слой). Пропорция раствора в этом случае будет 1:1 или 1:3 (цемент, песок).
После схватывания, пока еще цементно-песчаная штукатурка не окрепла, ее затирают. Круговыми движениями теркой снимают мелкие неровности, бороздки и выступы.
Выровненная таким образом стена после высыхания будет готова к финишной отделке. Цементная штукатурка сохнет от 4 до 7 суток при нормальной влажности в помещении. На фасадных работах это время может увеличится до двух недель.
Требования к составу
На сегодняшний день имеется государственный документ, который регламентирует все требования, которые должны быть соблюдены при эксплуатации такого рода смеси. Ранее для полимерцементного раствора ГОСТ 28013-98 не был полностью подготовлен. Его действие распространялось лишь на обычные строительные растворы, без специальных добавок. Взамен данному и неполному ГОСТу был введен СП 82-101-98, которые распространялся на более полный перечень всех смесей. К примеру, в своде правил указанно, что специальные смеси могут готовиться лишь в специальных узлах — на растворных заводах, если они используются при строительстве государственных построек. Кроме того, для доставки такого строительного материала следует использоваться лишь специальные автосамосвалы или же растворовозы. Еще одним важным требованием стало то, что все составляющие компоненты, прежде чем приступить к их смешению, должны пройти все необходимые проверки на их пригодность и качество.
Ступени
Для изготовления и покрытия ступеней нужен материал с повышенной износостойкостью, в частности полимербетон, ведь обычные бетонные смеси слишком быстро истираются, края ступеней проседают и деформируются.
Выбирая определенный тип смолы, например, полиуретановый, можно получить стойкий материал, который
будет амортизировать ударную нагрузку.
Для упрощения системы и некоторого удешевления допустимо смешение полиуретана с более дешевым компонентом (эпоксидной, резорциновой и т.д. смолой).
Для облегчения конструкции допустимо вводить мелкие частицы армирующего пластика. Он усилит изделия из полимербетона и повысит их износостойкость.
Состав для полового покрытия
Наиболее весомое отличие обычного раствора с добавкой полимеров от того, который должен использоваться для полового покрытия, состоит в том, что он имеет более высокую устойчивость к истиранию, а также не образует пыли во время износа. Чаще всего для составления такой основы используют дисперсии ПВА или же бутадиенстирольные латексы. Если добавить латекс в количестве 15-20 %, то можно увеличить стойкость к истиранию в 4-5 раз, если добавить столько же дисперсии ПВА, то можно добиться увеличения этого параметра только в 3 раза.
Если делать вывод из всего вышесказанного, то можно с уверенностью сказать, что использование обычной смеси уже не так актуально. Наличие разнообразных добавок вполне оправдано, даже если это несколько повышает стоимость смеси.
состав, технические характеристики, соответствие требованиям ГОСТ, назначение и применение
Полимерцементный раствор — это одна из модификаций обычного песчано-цементного раствора. Также полимеры могут добавляться в смеси, которые используются при кладке штукатурки и другого облицовочного материала. Добавление этого вещества в состав помогает улучшить его характеристики.
Общее описание и отличие
У цементного раствора из обычных составляющих, как и у других растворов, в которых в качестве вяжущего вещества выступает минеральное вещество, есть ряд недостатков. Среди них особенно выделяется низкая прочность при растяжении или изгибе, низкая стойкость к ударам, малый процент деформации, низкая стойкость к истиранию и слабая адгезию по отношению к другим строительным веществам. Список недостатков достаточно велик, что сильно ограничивает применение обычного раствора. Для того чтобы как можно сильнее снизить влияние этих недостатков или же вовсе ликвидировать их влияние, в состав смеси вводят специальные полимеры в качестве добавки от 2 до 30 % от общей массы. Таким образом можно сказать, что состав полимерцементного раствора отличается от обычного лишь наличием этой самой добавки.
Введение полимера в смеси
Стоит сказать о том, что полимер, так или иначе, вводится в большое количество самых разных смесей. Чаще всего он предназначен лишь для улучшения пластификации, а также гидрофобизации. Кроме этого, наличие таких добавок составляет менее 1 % от общей массы. Это является основным отличием от полноценного полимерцементного раствора. В них полимер серьезно влияет на состав, изменяя его физико-химические свойства, на его структуру, а также входит в раствор, как самостоятельный элемент, а не обычная присадка.
Методы добавления полимеров могут отличаться. К примеру, можно добавлять его в виде водной смеси. В таких случаях обычно содержание его в цементе будет не более 3-5 % от общей массы. Намного чаще используется метод, в котором задействованы водные дисперсии, содержащие полимеры. Отличие состоит в том, что в дисперсии полимер не растворяется в воде, а значит, его количество может быть увеличено. Таким образом, удается ввести в цементную смесь примерно 10-20 % добавки от общей массы цемента.
Дополнительные элементы
Стоит отметить, что все характеристики полимерцементного раствора могут быть утеряны, если во время добавки полимерной дисперсии произойдет такой процесс, как коагуляция или же створаживание раствора. Чаще всего, чтобы избежать таких негативных последствий, применяются различные стабилизаторы. В качестве них обычно выбирают поверхностно-активные вещества (ПАВ) — ОП-7 или ОП-Ю. Возможно также заменить их небольшой группой электролитов, к примеру, жидким стеклом. Без добавки стабилизатора может обойтись лишь полимерцементный раствор, который был смешан на основе пластифицированной дисперсии ПВА.
Однако введение ПАВ не проходит бесследно. Чаще всего эти вещества выступают в роли мощных пенообразователей, а также они способны вовлекать воздух в растворную смесь. Если это происходит, то мельчайшие пузырьки воздуха, которые были вовлечены, могут достигать в объеме 30% от общей массы раствора.
Изменение свойств раствора
Наличие полимерных добавок в растворе помогает более равномерно распределить поры, а также сделать их объем куда более меньшим. Можно привести пример. В обычном цементном растворе, к примеру, поры могут быть до 1 мм в диаметре, а их основная часть отличается показателями в 0,2-0,5 мм в объеме. Если речь идет о полимерцементном составе, то максимальный объем снижается до 0,5 мм, а наибольшее количество, примерно 90-95 %, и вовсе не будут более 0,2 мм.
Это сказывает самым положительным образом, допустим, при сплошном выравнивании штукатурки стен полимерцементным раствором, где поры могли бы нарушить общую структуру. Также здесь стоит добавить, что те смеси, в которых имеется вовлеченный воздух, характеризуются большей пластичностью, а также лучше удобоукладываемостью при меньшем содержании жидкости. Как говорилось ранее, пластификации у таких составов также на более высоком уровне. Все это ведет к тому, что при добавлении воды очень важно учитывать процент вовлеченного воздуха и пластификацию полимерцементного раствора.
Адгезионные свойства
У таких составов наблюдается повышенная адгезия, которая объясняется следующим образом. При нанесении смеси полимер концентрируется на границе раздела и играет роль клейкой основы между раствором и основанием. Что касается самой адгезии, то она напрямую зависит от вида добавленного полимера, а также от его концентрации. Далее стоит сказать о том, что это свойство проявляется только в том случае, когда происходит высушивание раствора в воздушно-сухих условиях. Поэтому, допустим, штукатурка с полимерцементным раствором, нанесенная на стены, будет отличной основой для укладки. Если затвердевание происходит в воде, то адгезия не будет проявлять себя так хорошо, даже при огромной концентрации полимера. Это обусловлено тем, что стабилизаторы растворяются в воде, а некоторые добавки и вовсе способны изменять свои свойства, если они находятся в жидкой среде.
Можно добавить, что высокий уровень адгезии сказывается не только на улучшенном сцеплении с другими материалами, а еще и на механических характеристиках самого раствора. Это особенно заметно при возникающих нагрузках при растяжении и изгибе. У смесей с присадками эти показатели выше примерно в 10 раз, чем у обычных. Это благодаря тому, что слои полимера связывают минеральные составляющие между собой. Есть также такая характеристика, как модуль упругости, который примерно в 10 раз ниже, чем у обычного. Благодаря этому факту можно смело утверждать, что полимерный состав более деформативен, чем обыкновенный.
Усадка и другие характеристики
Если в смесь вводится более 7-10 % полимера от общей массы цемента, то при ее затвердевании будет наблюдаться более существенная усадка. Однако так как вместе с этим сильно возрастает и деформативность раствора, то по такой характеристике, как устойчивость к трещинам, смесь ничем не уступает обычной, а в некоторых ситуациях может даже превышать. Еще одно отличие в параметрах — это отдача влаги. В полимерном растворе она проходит более медленно, что позитивно сказывается на процессе затвердевания, так как не наблюдается быстрое пересыхание, из-за чего могут возникать трещины.
Взаимодействие с другими материалами
Для чего используется полимерцементный раствор? Все выше указанные свойства и характеристика материала привели к тому, что он отлично подходит для крепления облицовочных материалов, так как может обеспечить более лучшее крепление. Здесь можно привести простое сравнение обычной смеси и смеси с добавкой полимера. Раствор на основе цемента и песка создает максимальную прочность крепления к 7-9 суткам после облицовки, а к 28 суткам этот показатель будет уменьшаться примерно в 5-6 раз. Если говорит о растворе с присадкой из полимеров, то максимальная прочность крепления будет достигнута чуть позже, на 9-10 сутки, однако при этом ее отсутствие в дальнейшем и вовсе не наблюдается. Благодаря этому качеству такие составы и стали максимально широко использоваться при облицовке.
Лучшие составы для работ и расход
При модификации обычного цементно-песчаного раствора пластификаторами и полимерами можно достичь сильного сокращения расхода. Полимерцементный раствор может наноситься максимально тонкими слоями и при этом быть качественным основанием для облицовочного материала. Это обусловлено тем, что дисперсия с полимерами не только серьезно увеличивает пластичность, но и вовлекает воздух от 8 до 12 %.
На сегодняшний день в этой сфере наиболее перспективным раствором считается тот, который сделан на основе гипсоцементно-пуццоланового вяжущего (ГЦПВ), а также водными дисперсиями полимеров. Использовать такой состав можно как при наружных работах, так и при внутреннем оштукатуривании. Однако наибольший эффект, как показала практика, достигает при применении его в декоративных растворах и мастичных смесей для обработки фасадов зданий.
Требования к составу
На сегодняшний день имеется государственный документ, который регламентирует все требования, которые должны быть соблюдены при эксплуатации такого рода смеси. Ранее для полимерцементного раствора ГОСТ 28013-98 не был полностью подготовлен. Его действие распространялось лишь на обычные строительные растворы, без специальных добавок. Взамен данному и неполному ГОСТу был введен СП 82-101-98, которые распространялся на более полный перечень всех смесей. К примеру, в своде правил указанно, что специальные смеси могут готовиться лишь в специальных узлах — на растворных заводах, если они используются при строительстве государственных построек. Кроме того, для доставки такого строительного материала следует использоваться лишь специальные автосамосвалы или же растворовозы. Еще одним важным требованием стало то, что все составляющие компоненты, прежде чем приступить к их смешению, должны пройти все необходимые проверки на их пригодность и качество.
Состав для полового покрытия
Наиболее весомое отличие обычного раствора с добавкой полимеров от того, который должен использоваться для полового покрытия, состоит в том, что он имеет более высокую устойчивость к истиранию, а также не образует пыли во время износа. Чаще всего для составления такой основы используют дисперсии ПВА или же бутадиенстирольные латексы. Если добавить латекс в количестве 15-20 %, то можно увеличить стойкость к истиранию в 4-5 раз, если добавить столько же дисперсии ПВА, то можно добиться увеличения этого параметра только в 3 раза.
Если делать вывод из всего вышесказанного, то можно с уверенностью сказать, что использование обычной смеси уже не так актуально. Наличие разнообразных добавок вполне оправдано, даже если это несколько повышает стоимость смеси.
Почему полимерный раствор/бетон | Типы полимерного раствора/бетона
Полимерный бетон представляет собой комбинированный материал, в котором вяжущее полностью состоит из синтетических органических полимеров , также известных как бетон на искусственной смоле.
Полимерный бетон состоит из минерального наполнителя, например заполнителя, и полимерного связующего, который может быть термопластичным, но чаще представляет собой термореактивный полимер.
Песок используется в качестве наполнителя, а смесь называется полимерным раствором. Другие наполнители включают гравий, известняк, щебень, мел, конденсированный микрокремнезем (кремнеземная пыль, кварцевая мука), гранит, кварц, глину, вспененное стекло и металлические наполнители . Как правило, в качестве наполнителя можно использовать любой сухой невпитывающий твердый материал.
Важный момент
ПереключательПочему полимерный раствор?
Прежде всего нужно понять, что полимеры в основном используются для модификации строительных растворов (портландцемент + вода + песчаный заполнитель) , не для бетона (строительный раствор + более крупные заполнители, такие как гравий или камень) из-за относительной стоимости.
Основными исключениями являются бетон, модифицированный полимерами, для перекрытий настила мостов и ремонта дорог . В большинстве случаев применения модифицированного полимером цемента используется раствор толщиной не более одного или двух дюймов. Но давайте начнем с основ.
Также читайте: Что такое арматура | Зачем использовать армирование в бетоне | Типы стальной арматуры
Различные типы полимерных растворов/бетон;
Существует несколько типов мономеров, и форполимеры используются для производства полимербетона. Наиболее часто используемые полимеры зависят от основных пяти типов форполимеров и мономеров.
- Эпоксидная смола
- Карбамид (карбамид формальдегид)
- Акрил (метилметакрилат)
- Полиэстер
- Фуран (фурфуриловый спирт)
1. Эпоксидно-полимерный бетон;
Это связующее представляет собой термореактивный полимер; его можно отверждать различными отвердителями; наиболее частым содержанием являются полиамины. Использование полиаминовых отвердителей приводит к получению изделий из полимерных растворов с максимальной химической стойкостью. Другими отвердителями являются полиамиды и полисульфидный полимер . Изделия из эпоксидно-полимерного раствора, отвержденные полиамидами, обладают большей гибкостью, отличной термостойкостью и меньшей тенденцией к мелению при воздействии на открытом воздухе. Однако их стойкость к растворителям и химическим веществам ниже, чем у идентичных продуктов, отверждаемых полиаминами. Добавление полисульфидного полимера дает эпоксидно-полимерный раствор с большей гибкостью.
Из-за сравнительной дороговизны эпоксидные полимеры широко используются в качестве связующего в полимерных растворах.
Физическая прочность изделий зависит от количества смолы и наполнителя, используемых в химическом составе изготавливаемого эпоксидного полимербетона. Например, образец , содержащий 15 % смолы и 200 % наполнителя, показал высокую прочность на сжатие и прочность на изгиб. Предел прочности при растяжении был максимальным при 20% смолы и 200% наполнителя. При этом механическая прочность модифицированного полимербетона в 4-5 раз выше, чем у ПКК.
Также читайте: Разница между раствором и бетоном | Что такое раствор и бетон | Типы раствора и бетона
2. Карбаминдный полимерный бетон:
Эта смола получается реакцией поликонденсации мочевины и формальдегида в водной или водно-спиртовой среде. Смолы на основе карбамида малотоксичны, предпочтительнее в производстве. Однако содержание полимерной матрицы в этих полимерных растворах высокое максимум до 30%, и их физико-механические характеристики ниже, чем у других типов полимербетонов.
Эта смола содержит значительное количество древесной воды около 30-40% , что приводит к большей усадке при отверждении композиции. Иногда это приводило к растрескиванию материалов.
3. Акриловый полимерный бетон:
В основном используемый акриловый полимер представляет собой полиметилметакрилат, который получают путем полимеризации метила, он также известен как ММА. Полимербетон, изготовленный с использованием этого акрилового полимера в качестве связующего, представляет собой универсальный материал , который обладает отличной стойкостью к атмосферным воздействиям, хорошими гидроизоляционными свойствами, хорошей химической стойкостью и относительно низкой усадкой при отверждении. Он имеет очень низкую склонность к водопоглощению. Акриловый полимерный бетон имеет очень высокую морозостойкость. Низкая температура воспламенения мономера ММА является недостатком, но представляет собой проблему безопасности. Полимербетон ММА можно легко применять в любое время после грунтовка затвердела, что позволяет заранее подготовить многие области, что делает укладку более эффективной.
Также читайте: Соотношение бетонной смеси | Что такое соотношение бетонной смеси | Типы бетонной смеси Соотношение
4. Полиэфирный полимерный бетон:
Полиэфирные смолы, такие как эпоксидные, являются одним из видов термореактивных смол, получаемых поликонденсацией . Его вязкость низкая, а материалы на его основе обладают высокими механическими и электроизоляционными свойствами, высокой стойкостью к кислотам, маслам, бензину. Полиэфирные смолы токсичны, и при слабом перемешивании компонентов смеси велика вероятность расслоения и поэтапного отверждения состава .
5. Фурановый полимерный бетон:
Этот полимер основан на фурфуриловом спирте, полученном из сельскохозяйственных отходов , таких как рисовая шелуха, сахарный тростник, багасса, кукурузные початки, овсяная шелуха . Обычно его перекрестно связывают с фурфуриловым спиртом, фурфуральдегидом или формальдегидом, чтобы получить термореактивные полимеры, обладающие высокой устойчивостью к большинству водных кислот или кислот.0005 основные растворы и сильные растворители, такие как кетоны, ароматические соединения и хлорсодержащие соединения . Важным моментом в этом является способность храниться в течение длительного времени, примерно до 5 лет, даже при очень низких температурах.
Также читайте: Что такое сливовый бетон | Приложение | Микс-дизайн | Методология
Наиболее часто используемый метод улучшения полимерных растворов
Здесь мы рассматриваем метод ремонта полимербетона, метод заключается в следующем.
- Отверждение цемента
- Улучшение работоспособности
- Модифицированная адгезия
- Повышенная долговечность и прочность
Расскажите подробнее о способе улучшения полимербетона.
1. Отверждение цемента:
Широко распространенное отверждение цемента используется для модифицирования полимерного раствора . Прочность цемента/бетона зависит от правильного отверждения, химической реакции, известной как гидратация между водой и цементом, которая заставляет кристаллы расти и обволакивать компоненты смеси. На начальных стадиях отверждения (около пяти-семи дней) необходимо достаточное количество воды для поддержания процесса гидратации, иначе бетон не затвердеет должным образом .
Здесь полимеры конденсируют скорость испарения воды. Позволил кристаллической структуре продолжать расти и увеличивать прочность на этих критических ранних стадиях отверждения. Уменьшение испарения воды особенно важно для небольших применений, где площадь рассеиваемой поверхности больше по сравнению с объемом раствора.
2. Улучшение работоспособности.
Модификация заметно улучшает характеристики нанесения, делая раствор немного более водянистым, поэтому он легко обрабатывается и наносится. Есть некоторые полимеры, которые также продлевают период гидратации, что может увеличить время работы, жизненно важное свойство в жарких погодных условиях. Такого рода уловки используют подрядчики, чтобы меньше расходовать воды на технологичность. Полимер также действует как поглотитель воды, что в конечном итоге приводит к получению более прочного раствора с меньшим количеством пустот или слабых мест.
Также читайте: Что такое покрытие в бетоне | Прозрачное покрытие в балках, перекрытии, колонне, фундаменте
3. Модифицированная адгезия.
Полимерные модификаторы действуют как клей, облегчая нанесение модифицированного раствора на различные поверхности, такие как кирпичная кладка, бетон, кирпич, стекло, дерево, пенополиуретан, жесткий полистирол и металлы. Адгезия является жизненно важным свойством, особенно в тонкостенных покрытиях, таких как штукатурка, напыляемые покрытия и подложки, а также в приложениях с сильной вибрацией и в местах с интенсивным движением.
В некоторых особых случаях, таких как отвержденные модифицированные полимером строительные растворы, обычно улучшающие прочность на изгиб, сопротивление удару и истиранию, прочность на растяжение, водостойкость и химическую стойкость по сравнению с немодифицированными растворами — кроме того, полимер в растворе помогает контролировать распространение микротрещин, что в значительной степени повышает ударную вязкость раствора.
Также читайте: Что такое покрытие в бетоне | Прозрачное покрытие в балках, плите, колонне, фундаменте
Где это применимо?
Объединение всех характеристик, таких как улучшенная удобоукладываемость, характеристики отверждения, адгезия, позволяет использовать полимер-модифицированный раствор во многих областях, которые в противном случае были бы затруднены или невозможны. Одна вещь, которую обычно используют в большинстве этих применений, — это тонкий слой раствора. Обычно он может оставаться толщиной менее 1 или 2 (дюймов) или не превышать ее. Все они требуют одного или нескольких химических и механических свойств, упомянутых ранее.
Ремонтные растворы:
Затирки для ремонта трещин и расслаивания бетонных конструкций forex. Подъездные пути, тротуары и стены, Адгезия, сопротивление истиранию, прочность на растяжение и изгиб . Свежий раствор не будет идеально стыковаться со старой бетонной частью конструкции без модификации полимером.
Затирки и клеи:
Керамика, мрамор, камень, настенная и напольная плитка и т. д. Адгезия, прочность на изгиб, водо- и химическая стойкость . Это стандартное применение для растворов, модифицированных полимерами.
Используется для гидроизоляции:
В основном применяется в области септиктенков, подвалов, резервуаров для хранения наливной воды и бетонных стен, палуб кораблей, крыш. Водонепроницаемость для всей химической стойкости, другие свойства зависят от применения материала.
Напольные покрытия и тротуары:
Может использоваться в растворе или там, где тяжелые бетонные промышленные/коммерческие полы покрывают рецептуры. Вот несколько примеров: лестницы, гаражи, склады, фабрики, больницы, железнодорожные платформы, взлетно-посадочные полосы аэропортов, лестницы, гаражи и т. д. свойства сопротивления истиранию , химическая стойкость, сопротивление растяжению и водостойкости, прочность на изгиб и внешняя долговечность изменяются.
Горение и механические свойства цементного раствора, модифицированного полимерами, при высокой температуре необходимо понимать его свойства горения и механические свойства при высокой температуре. В этом исследовании оценивались характеристики горения при различных экспериментальных параметрах, таких как тип полимера, удельная доля полимера, соотношение полимер-цемент и толщина образца.
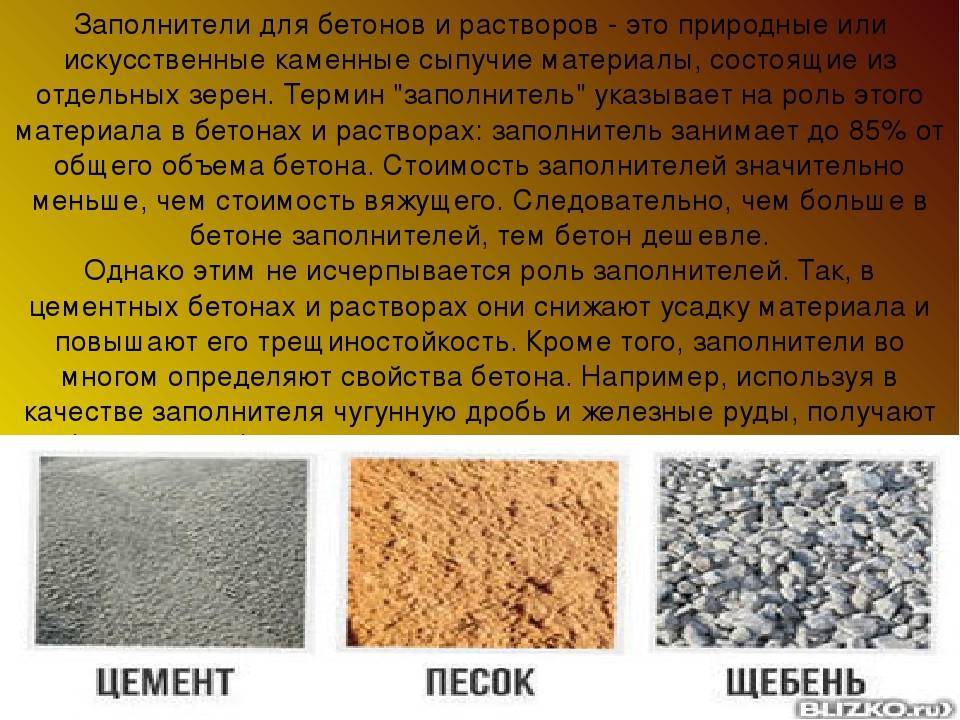
1. Введение
Ремонт и усиление необходимы для продления срока службы существующих зданий. Полимерно-модифицированный цементный раствор (ПЦМ) получил широкое применение при ремонтных работах, так как ПКМ обладает превосходными характеристиками как высокоэффективный материал, в частности, для отделочных и ремонтных работ в бетонных зданиях [1-4]. PCM также широко используются в гражданской инфраструктуре, мостах, растворе для изоляции наружных стен, самовыравнивающемся растворе и отремонтированных бетонных полях благодаря их превосходной прочности, защите от окружающей среды, адгезии, гидроизоляции, устойчивости к химическому воздействию и удобству обработки [5-8]. Кроме того, ПКМ обладает выдающимися характеристиками по сравнению с обычным раствором в качестве материалов для ремонта бетона в случае их нанесения на поврежденную железобетонную конструкцию [9].–12]. Однако выбор подходящих материалов для накладного ремонта очень затруднен из-за недостаточности экспериментальных данных по огнестойкости и безопасности ПКМ [12, 13]. С все более распространенным использованием ПКМ в зданиях возникли опасения относительно поведения этого материала в случае пожара, поскольку ПКМ, как правило, горюч и подвержен ухудшению механических и связующих свойств при повышенной температуре [12-14]. Поэтому необходимо уточнить его поведение при высокой температуре при воздействии огня; однако данных по этому поводу недостаточно [14–16].
Чтобы соответствовать требованиям огнестойкости, характеристики этих материалов при повышенных температурах необходимо понимать на основе оценки механических свойств [14]. Однако, когда требуется ремонт, очень сложно подобрать подходящие ремонтные материалы из-за недостаточности экспериментальных данных по огнестойкости и безопасности ПКМ [7–9].].
Поскольку ПКМ содержит органический полимер, необходимо понимать его свойства горения и механические свойства при высоких температурах, таких как те, которые возникают во время пожаров, для которых недостаточно доступных данных. Традиционные технологии и существующие исследования в основном сосредоточены на механических свойствах, таких как адгезия и прочность на сжатие, пропорции смеси ПКМ и долговечность при использовании до ремонта и после ремонта с использованием ПКМ в бетонной конструкции.
В этом исследовании оценивались характеристики горения ПХМ с помощью конусного калориметра, испытаний на негорючесть и воспламеняемость с различными экспериментальными параметрами, такими как тип полимера, удельная доля полимера, соотношение полимер-цемент и толщина образца. Влияние типа полимера, удельного содержания полимера и водоцементного отношения (В/Ц) оценивали по результатам вышеупомянутых испытаний. Кроме того, были проведены испытания на воспламенение и скорость выделения тепла для ПКМ различной толщины. Кроме того, механические свойства ПКМ оцениваются с помощью испытания на горячее прессование. Влияние типов полимера и единичного содержания полимера оценивают путем анализа прочности на сжатие и модуля упругости.
2. Экспериментальная процедура
В этом исследовании оценивались характеристики горения ПКМ с помощью конусного калориметра, испытаний на негорючесть и воспламеняемость с различными экспериментальными параметрами, такими как тип полимера, удельная доля полимера, соотношение полимер-цемент и толщина образца [15, 16]. В этом исследовании также оценивались прочность на сжатие и модуль упругости ПКМ, содержащих четыре типа полимеров (сополимер этилена и винилацетата (EVA), винилацетат-винилверсатат (VVA), стирол-бутадиеновый каучук (SBR) и полиакриловый эфир (PAE)) с акцентом на влияние типа полимера, удельного содержания полимера и соотношения полимер-цемент.
2.1. Горючесть PCM
2.1.1. Материалы и состав Портландцемент
и мелкий заполнитель (модуль крупности 2,97, плотность 2,63 г/см 3 и водопоглощение 1,81 %) были использованы для изготовления строительного раствора. В качестве модификаторов цемента использовали полимеры, указанные в JIS A 6203 (полимерные дисперсии и редиспергируемые полимерные порошки для модификаторов цемента), EVA, VVA, PAE и SBR. При этом к редиспергируемым полимерным порошкам добавляли 1% пенообразователя. 1% пенообразователя добавляли к полимерной дисперсии при различном общем соотношении твердых веществ. Для испытаний использовали шестьдесят композиций с фиксированным цементно-мелким заполнителем (массовое соотношение 1 : 3) и различными типами полимеров, количествами полимеров и значениями В/Ц. В этом исследовании количество полимера выражается как масса на единицу объема. Например, 10 кг/м 3 единицы массы полимера в составе ПКМ соответствует 2% соотношению полимер-цемент. Плоские образцы (100 × 100 × 10 (мм)) использовались для испытаний на скорость тепловыделения, а цилиндрические образцы (диаметром 44 × 50 (мм)) использовались для испытаний на негорючесть. Образец размером 100×100×400 (мм), использованный для испытания на воспламенение, был разрезан на три типа образцов: 100×100×10 (мм), 100×100×30 (мм) и 100×100×50 (мм) после отверждения в воде (20°C) в течение четырех недель. Физические свойства использованных полимеров представлены в табл. 1. В табл. 2 приведены состав ПКМ и экспериментальные параметры. Все образцы были отверждены в течение четырех недель в воде при 20°C, а затем подвергнуты отверждению на воздухе при 20°C и относительной влажности 60% в течение девяти недель. Наконец, образцы высушивали при 60°С и охлаждали до комнатной температуры в эксикаторе в течение трех дней перед испытанием. Два образца с водопоглощением 0,5–2,0 % были подвергнуты испытаниям на скорость тепловыделения и воспламенение. Три образца с водопоглощением 2,0–4,0 % были подвергнуты испытанию на негорючесть.
2.1.2. Методы испытаний
Испытание скорости тепловыделения проводилось в соответствии с ISO 5660-1 (Стандартный метод испытаний конусного калориметра) [17]. Источником воспламенения служила электрическая искра, генерируемая электродвигателем конусного типа. Количество тепловыделения и скорость тепловыделения измеряли с помощью калориметрии потребления кислорода [15–17]. Негорючий материал имеет общую теплотворную способность менее 8 МДж/м 2 в течение 20 мин после нагрева и максимальную скорость тепловыделения менее 200 кВт/м 2 на 10 с непрерывно. Кроме того, такой материал лишен трещин или отверстий на поверхности, что делает его опасным при использовании в качестве антипирена. Испытания на негорючесть проводились в соответствии со стандартом ISO 1182 (реакция на огнестойкость строительных изделий: испытание на негорючесть) [18]. Измеряли температуру нагревательной печи и изменение массы образца. В рамках процедуры испытаний цилиндрический образец помещали в нагревательную печь при температуре 750°C и измеряли повышение температуры внутри печи.
В качестве важного требования при испытании на негорючесть разница между температурой негорючего материала и максимальной температурой внутри печи должна составлять 20°С в течение 20 минут после начала нагрева, а средняя температура через 1 мин после прекращения нагрева должна быть менее 20°С при потере веса образца менее 30%.
Более того, поскольку строительный раствор содержит воду и, следовательно, не является однородным материалом, для стабилизации температуры внутри печи потребуется более 20 мин. В этом исследовании время нагрева было установлено равным 30 мин от предварительного эксперимента. Кроме того, некоторые образцы (удельное содержание полимера: более 50 кг/м 3 ), которые могут воспламеняться или растрескиваться, были испытаны в предварительном эксперименте по стандарту JIS A 9523 (теплоизоляционные материалы со свободным наполнителем) [19]. Температуру образца и внутренней части печи измеряли с помощью термоэлектрической пары типа К, установленной как внутри, так и снаружи образца. На рис. 1 показана установка для испытаний на воспламеняемость и измерение температуры.
2.2. Механические свойства ПКМ
2.2.1. Материалы и состав
Образец строительного раствора для испытания механических свойств содержал те же материалы, что и в таблице 1. Экспериментальные параметры и состав ПКМ были скорректированы на основе типа полимера, соотношения полимер-цемент и испытания на горячее прессование, как показано в таблице 3. Для испытаний использовались четыре пропорции с фиксированным водоцементным отношением, равным 50. В этом исследовании количество полимера представлено как масса на единицу объема, где 10 кг·м −3 единица массы полимера в составе ПКМ соответствует соотношению полимер-цемент 2%.
Образцы для испытания на прочность при сжатии и испытания на модуль упругости были цилиндрическими (100 мм в диаметре и 200 мм в высоту), и для каждого испытания было приготовлено более трех образцов. Представленные ниже результаты являются средними. Каждый образец отверждали в условиях относительной влажности 90% при 20°C в течение четырнадцати дней. Все образцы сушили в условиях относительной влажности 60% при 20°С в течение шестидесяти трех дней. Наконец, все образцы высушивали в сушильном шкафу при 60°С в течение семи дней и выдерживали в эксикаторе. Используя эти процедуры, скорость водопоглощения для каждого образца контролировали в диапазоне 1,5~2,0%.
2.2.2. Методы испытаний
Для оценки механических свойств ПКМ при повышенной температуре использовался метод испытаний на горячее прессование. Как показано на рисунке 2, в образец были помещены пять термопар для измерения изменений температуры. Каждый образец помещали в нагревательную печь для испытания на горячее прессование, как показано на рис. 3. На основании предыдущих данных скорость и количество тепла, выделяемого из ПКМ, зависели от содержания полимера независимо от В/Ц. В этом исследовании количество выделяемого тепла соответствовало порядку VVA < EVA < PAE < SBR. Это указывало на то, что ПКМ, модифицированный ВВА и ЭВА, при содержании полимера менее 75 кг·м -3 и ПКМ с ПАЭ при содержании полимера менее 30 кг·м -3 соответствуют требованиям к негорючим материалам.
При обычном методе испытаний при скорости нагрева 150°C·ч −1 образец выкрашивался после 3 ч нагрева со степенью водопоглощения 3%. В этом исследовании скорость водопоглощения контролировалась в диапазоне 1,5~2,0%, и все образцы нагревались со скоростью 100°С·ч -1 .
Диаметр испытательного образца, использованного в эксперименте, составляет 100 мм. Как показано на рис. 2(а), термопары были встроены в образец для проверки температуры поверхности, внутренней части и центра образца. Когда поверхность каждого образца достигала заданной температуры, температуру нагрева поддерживали до тех пор, пока центр образца не достигал заданной температуры. Время достижения одинаковой температуры внутри и снаружи PCM зависит от температуры и времени нагрева. Программа нагрева, используемая для печи, показана на рисунке 4. На рисунке 4 показано время, необходимое для достижения общей внутренней температуры образца в каждом диапазоне температур нагрева. В этом исследовании температуры нагрева были установлены на 200°C, 400°C, 600°C и 800°C. Температура поверхности каждого образца достигает 2, 4, 6 и 8 часов соответственно. После этого время, за которое центральная температура каждого образца достигает соответствующей температуры, составляет 3, 2, 2 и 1 час соответственно. В случае нагрева при 200°С время достижения внутренней и внешней температур до 200°С составило 5 часов, а при 800°С — 9 часов.часов, чтобы внутренняя и внешняя температура достигла 800°C.
Как показано на рис. 3, прочность на сжатие измерялась после того, как температура в центре образца достигла заданной температуры.
3. Результаты и анализ
3.1. Свойства горения
3.1.1. Результаты испытаний на скорость тепловыделения
Образец дымился в каждой серии SBR и серии EVA с содержанием полимера 40 кг/м 3 единиц полимера. ПКМ серии SBR с плотностью более 40 кг/м 9Содержимое полимера 0253 3 и серия EVA, содержащая 100 кг/м полимера 3 , подверглись воспламенению. Выкрашивание было особенно заметно в случае образцов серии ВВА с содержанием полимера 100 кг/м 3 . Эти наблюдения показывают, что дымообразование, состояние воспламенения и характеристики отслаивания ПКМ различаются в зависимости от типа полимера, содержания единичного полимера и В/Ц. Также было замечено, что образцы без выкрашивания не имели трещин или отверстий, независимо от присутствия полимера.
На рис. 5 показано общее количество тепловыделения ПКМ за 20 мин после начала нагрева. В случае серий ЭВА и ВВА, чем выше содержание полимера в единице, тем больше общее тепловыделение, независимо от разницы В/Ц. В случае образцов серии SBR с содержанием полимера более 40 кг/м 3 ед. общее количество тепловыделения увеличивалось с увеличением содержания полимера при воспламенении. Содержание полимера и скорость выделения превышали 40 кг/м 3 и 8 МДж/м 2 соответственно.
SBR разлагается на стирол и бутадиен-латекс при температуре около 200°C и испаряется путем пиролиза при температуре около 360°C. Температура в поверхностном слое образца превышала максимальную температуру разложения и испарения через 5 мин после начала нагрева. Считается, что быстрое увеличение количества выделяемого тепла и скорости выделения тепла связано с потреблением кислорода при воспламенении.
3.1.2. Результаты испытаний на негорючесть
В таблице 4 представлены результаты наблюдения за образцами во время испытаний. Выкрашивание произошло между 80 и 180 с; чем выше содержание единичного полимера в ПКМ, тем быстрее отслаивается. Воспламенение и образование дыма произошли между 90 и 320 с; опять же, чем выше содержание единичного полимера в ПКМ, тем быстрее воспламеняется образец. На рис. 6 также показана зависимость между содержанием полимера в ПКМ и изменением температуры внутри печи.
Изменение температуры указывает на разницу температур между максимальной температурой внутри печи через 30 мин после начала нагрева и средней температурой за 1 мин в конце нагрева. Образцы серии ЭВА с удельным содержанием полимера менее 50 кг/м 3 показал изменение температуры менее чем на 20°C, в то время как серия EVA с содержанием полимера 100 кг/м 3 показала изменение температуры более чем на 50°C. Серия ВВА с удельным содержанием полимера более 30 кг/м 3 и серия SBR с удельным содержанием полимера более 20 кг/м 3 показали изменение температуры более чем на 20°C. Чем выше содержание единичного полимера в ПКМ, тем больше изменение температуры. Однако серии ВВА и SBR с плотностью 100 кг/м 3 удельного содержания полимера показал такое же изменение температуры, как и серия с удельным содержанием полимера 50 кг/м 3 .
Масса каждого образца серии ПКМ без выкрашивания также измерялась после окончания нагрева. На рис. 7 показана зависимость между содержанием единичного полимера в ПКМ и скоростью потери массы после нагревания. Скорость потери массы показывает линейный рост с увеличением содержания единичного полимера.
Скорость потери массы ПКМ составляла менее 30%, независимо от типа полимера, содержания единичного полимера и В/Ц. Считается, что уменьшение массы ПКМ было вызвано свободной водой в образце, некоторым количеством связанной воды в цементной матрице и разложившимся полимером. Кроме того, считается, что увеличение потери массы с увеличением содержания полимера было вызвано разложением полимера.
При содержании полимера 10 кг/м 3 и изменении массы образца в диапазоне 0,4%–0,5% скорость потери массы серий SBR и VVA увеличивалась с увеличением единичного содержания полимера. Кроме того, результаты испытания на негорючесть показали, что характер разложения полимера различается в зависимости от типа полимера. В частности, считалось, что серия SBR подвергается горению легче, чем другие серии PCM, из-за сгорания полимера.
3.1.3. Оценка свойств горения на основе состава ПКМ и толщины образца
На рис. 8 представлена взаимосвязь между содержанием единичного полимера в ПКМ и общим тепловыделением. Воспламенение возникло в случае серии ПАЭ с содержанием полимера более 40 кг/м 3 ед. В случае образца ЭВА с содержанием полимера 3 ед. 100 кг/м произошло выкрашивание, в то время как в других образцах той же серии не было обнаружено ни трещин, ни отверстий.
Как показано на Рисунке 8, как серия PAE, так и серия SBR показывают пропорциональную зависимость от содержания единичного полимера. Необходимо учитывать воспламенение ПКМ из-за возможности воспламенения, особенно в серии SBR.
На рис. 9 представлена зависимость между толщиной образца и общим количеством тепловыделения. Воспламенение произошло в случае образцов толщиной 10 мм, в сериях SBR и EVA с содержанием полимера 50 кг/м 3 ед. Выкрашивание также наблюдалось для образцов серии ЭВА толщиной 30 и 50 мм при 50 кг/м 3 единиц содержания полимера. Чем толще образец, тем меньше общее количество тепловыделения, поскольку абсолютное содержание полимера увеличивается с увеличением толщины образца.
На рис. 10 показано изменение температуры для образцов серии EVA с содержанием полимера 20 кг/м 3 единиц полимера и различной толщины. Для толщины 10 мм температура поверхности увеличилась через 3 мин по сравнению с другими образцами; внутренняя температура образца увеличивалась при нагреве, возможно, из-за накопления тепла внутри образца вследствие непрерывного нагрева. В случае образцов толщиной 30 мм и 50 мм максимальная температура была менее 200°С.
3.2. Механические свойства
3.2.1. Механические свойства при комнатной температуре
Механические свойства ПКМ при комнатной температуре оценивались в зависимости от типа и содержания полимера. Прочность на сжатие ПКМ представлена на рисунке 11, а модуль упругости ПКМ показан на рисунке 12. Серия ПКМ, модифицированных ЭВА и ПАЭ, показала увеличение прочности на сжатие с увеличением содержания полимера, тогда как серия ПКМ, модифицированная ВВА, показала незначительное увеличение. С другой стороны, образцы, модифицированные ВВА и ПАЭ, показали снижение модуля упругости с увеличением содержания полимера. ПКМ с 10% ЭВА и серия ПАЭ показали хорошие механические свойства.
3.2.2. Механические свойства при высокой температуре
Механические свойства ПКМ также оценивались при повышенной температуре с изменением типа и содержания полимера. Прочность на сжатие серии ПКМ показана на рисунке 13, а модуль упругости ПКМ показан на рисунке 14. Как показано в таблице 4, ВВА имеет более высокий риск скалывания, чем другие полимеры. Испытание на прочность при сжатии показало, что серия ВВА имеет меньшую прочность. Согласно предыдущему исследованию, негорючесть PCM варьируется в зависимости от типа полимера и содержания единичного полимера. Прочность на сжатие снижается с увеличением содержания полимера. Серия PAE показала отличную огнестойкость в диапазоне температур 200~400°C. С другой стороны, серии EVA и VVA показали быстрое снижение прочности на сжатие, когда содержание полимера превышало 5%. Большинство образцов показали снижение модуля упругости с увеличением содержания полимера, за исключением видов с 5% EVA и 5% PAE. ПКМ с 5% ЭВА и серии ПАЭ показали хорошие механические свойства в диапазоне температур 200~400°С.
4. Выводы
Скорость и количество тепловыделения из ПКМ зависели от содержания полимера, независимо от В/Ц. В этом исследовании было обнаружено, что количество тепловыделения следует порядку VVA < EVA < PAE < SBR.
Образцы серий ВВА и ЭВА с содержанием полимера менее 75 кг/м 3 , а также образцы серии ПАЭ и SBR с содержанием полимера менее 30 кг/м 3 , удовлетворяли требованиям к негорючему материалу. Негорючесть ПКМ различалась в зависимости от типа полимера и содержания звена полимера. В этом исследовании негорючесть ПКМ располагалась в следующем порядке: SBR < VVA < EVA.
Ввиду недостаточности экспериментальных данных по огнестойкости и безопасности ПКМ были исследованы механические свойства ПКМ при повышенной температуре с использованием в качестве модификаторов трех типов полимеров: ЭВА, ВВА и ПАЭ.
Используемый метод испытаний связан с риском отслаивания из-за скорости нагрева и скорости водопоглощения PCM. В этом исследовании основное внимание уделялось степени водопоглощения 1,5–2,0% и соотношению полимер-цемент, необходимому для предотвращения выкрашивания. Испытание на горячее прессование показало, что ПКМ с 5% ЭВА и серии ПАЭ показали хорошие механические свойства в диапазоне температур 200~400°C.
Конфликт интересов
Авторы заявляют об отсутствии конфликта интересов в связи с публикацией данной статьи.
Благодарности
Это исследование было проведено при поддержке Программы исследований и разработок противопожарной безопасности и 119 спасательных технологий, финансируемой Министерством общественной безопасности (NEMA-Next Generation-2014-58).
Ссылки
Y. Ohama, «Добавки на полимерной основе»,
Комитет ACI 548, Отчет о современном состоянии бетона, модифицированного полимерами (548.
3R-95) , Фармингтон-Хиллз, Мичиган, США, Американский институт бетона.
Y. Ohama, Handbook of Polymer-Modified Concreth and Mortars, Properties and Process Technology , Noyes Publications, Park Ridge, NJ, USA, 1995.
K.P. Grosskurth and A. Коницко, «Структура и механическое поведение полимерцементного бетона», в с. 9.0411 Материалы 5-го Международного конгресса по полимерам в бетоне , стр. 171–174, 1987 г. , «Исследование механизма модифицированного полимерным латексом цемента», Construction and Building Materials , vol. 111, стр. 710–718, 2016.
Посмотреть по адресу: Сайт издателя | Google ScholarЛ. К. Аггарвал, П. К. Таплиял и С. Р. Караде, «Свойства модифицированных полимерами растворов с использованием эпоксидных и акриловых эмульсий», Строительство и строительные материалы , том. 21, нет. 2, стр. 379–383, 2007 г.
Посмотреть по адресу: Сайт издателя | Google ScholarД.
Посмотреть по адресу: Сайт издателя | Google ScholarПарк, Дж. Ан, С. О, Х. Сонг и Т. Ногучи, «Влияние высыхания полимер-модифицированного цемента для строительного раствора с заплатой на напряжение сжатия», Construction and Building Materials , vol. 23, нет. 1, стр. 434–447, 2009 г.
Д. Парк, С. Пак, Ю. Сео и Т. Ногучи, «Анализ водопоглощения и ограничивающего напряжения модифицированного полимером цементного раствора, используемого в качестве материала для ремонта заплат»,
Дж. Мирза, М. С. Мирза и Р. Лапойнт, «Лабораторные и эксплуатационные характеристики ремонтных растворов на основе цемента, модифицированного полимерами, в холодном климате», Construction and Building Materials , vol. 16, нет. 6, стр. 365–374, 2002.
Посмотреть по адресу: Сайт издателя | Google ScholarА.
Посмотреть по адресу: Сайт издателя | Google ScholarЯхия, «Загущение при сдвиге высокоэффективных цементных растворов — влияние на расчетные параметры смеси», Исследование цемента и бетона , vol. 41, нет. 3, стр. 230–235, 2011.
К. А. Анагностопулос, Г. Сапидис и Э. Папастергиадис, «Основные свойства цементных растворов, модифицированных эпоксидной смолой», Construction and Building Materials , vol. 125, стр. 184–195, 2016.
Посмотреть по адресу: Сайт издателя | Google ScholarЖ.-П. Вон, С.-В. Чой, К.-Г. Парк и К.-И. Джанг, «Высокопрочный модифицированный полимером ремонтный цементный композит для противопожарной защиты», Полимеры и полимерные композиты , vol. 15, нет. 5, стр. 379–388, 2007.
Посмотреть по адресу: Google ScholarJ.-P. Вон, Х.-Б. Канг, С.-Дж. Ли и Дж.-У. Канг, «Экологичные пожаробезопасные высокопрочные полимерные вяжущие композиты», Construction and Building Materials , vol.
Посмотреть по адресу: Сайт издателя | Google Scholar30, стр. 406–412, 2012.
Ю. Цяо, Дж. К. Деливала, С. С. Чакравартула и К. Конг, «Высокотемпературные свойства интеркалированного/расслоенного полимерного цемента при растяжении»,
Х. Хамасаки, Х. Дж. Ким и Т. Ногучи, «Исследование свойств тепловыделения полимер-модифицированного цементного раствора», в Труды части 1 Влияние веса единицы полимера и смешанной конструкции , стр. 435-436, 2009.
Посмотреть по адресу: Google ScholarХ. Дж. Ким, Х. Хамасаки и Т. Ногучи, «Исследование свойств тепловыделения полимер-модифицированного цементного раствора», в Материалы части 2 «Влияние на толщину образца» на ежегодной конференции Архитектурного института Японии , стр. 437–438, 2009 г. -1:2015 Испытания реакции на огонь.