Оборудование для производства керамзитобетонных блоков. Технология, станки для производства
Сегодня на современных стройках все большего и большего значения находят керамзитобетонные стеновые блоки, у которых кроме выдающихся эксплуатационных качеств есть еще существенная экономия времени, затрачиваемого на строительство. В сжатых условиях осуществления строительства, производство керамзитобетонных блоков повышается, так как повышается потребность отрасли в них. НО стоит помнить, что экономия времени это еще далеко не все, и производство керамзитобетонных блоков никак бы не продвигалось такими стремительными темпами, если бы у этого материала не было необходимой легкости, прочности, звуко- и теплоизоляции.
Производство керамзитобетонных блоков выполняется из керамзита, что можно понять следуя из названия. Вообще керамзит является очень хорошим утеплителем, который надежно сохраняет тепло. Технологический процесс изготовления керамзитобетонных блоков имеет много отличий по сравнению с производством остальных строительных компонентов.
а) высокую прочность;
б) устойчивость к различным воздействиям;
в) высокую пористость.
Резкое нагревание, или же быстрое оплавление дают уникальные качества материалу, при недорогой технологии, что дает возможность выпускать качественный, современный товар по низкой себестоимости.
Несущие стеновые блоки, на сегодняшний день, с полной уверенностью можно назвать наиболее востребованным строительным материалом. В нашей стране широко распространены стеновые блоки с высокими показателями теплоизоляции. Скорее всего, растущий спрос на них обусловлен климатическими условиями. Изготавливается этот материал при помощи специализированного вибропресса, спроектированного с целью производства керамзитобетонных блоков. Такие блоки имеют массу положительных качеств и существенно отличаются от своего главного конкурента – керамического кирпича своей экономичностью.
Оборудование для блочного производства из керамзитобетона основано на использовании керамзита с фракцией от 5 до 10, а для заполнения пустот берется измельченный керамзит с фракцией от 0 – до 5. Дробленый керамзит выполняет так же и функцию теплоизоляции.
Еще одним положительным качеством керамзитобетонных блоков является их низкий вес, снижающий общую нагрузку на фундамент. По сравнению с тем же кирпичом, этот показатель снижается почти в два раза. При этом снижается и расход связующего состава. Надо заметить, что при легкости блоков, их износостойкость и прочность остается на высоком уровне. А высокая теплоизоляция позволит сэкономить запланированные расходы на получение тепла, как при строительстве, так и в дальнейшем, при эксплуатации объекта.
Исходя из вышесказанного, можно сделать вывод, что приобретение специального оборудования для производства блоков окупит все вложенные средства. Приобретение такой техники для обеспечения процесса строительства экономически обосновано: затраты на оборудование в результате окажутся намного меньше затрат на покупку готового материала. Рынок керамзитобетонных блоков сегодня предлагает изделия по ценам, намного превосходящим себестоимость материала. Поэтому, приобретя специально оборудование, работающее по методу вибропрессования, потребитель получит прочный, качественный и надежный стеновой блок по максимально низкой цене.
Часто читают…
- Производство блочного кирпича
Когда разговор поднимается о фабриках, обычно думают, что это: гектары с большими рабочими помещениями, тысячи рабочих, парк техники, множество технологических линий. Успешность хорошего…
- Мини производство кирпича глины станок для производства
Во время того, как заходит беседа о заводах, чаще всего думают, что это: множество устройств, множество машин, площади с большими рабочими помещениями, сотни.
..
- Производство лицевого керамического кирпича на закаменной видео
Когда речь заводится о производствах, большая часть людей воображают: множество рабочих, парк техники, множество различной техники, гектары с большими длинными…
Оборудование для производства керамзитоблоков
Одним из наиболее простых в технологическом отношении и одновременно прибыльных является выпуск керамзитобетонных блоков. Исходным сырьем для его получения являются песок, цемент и керамзит.
Этапы технологического процесса
Изготовление блоков из керамзитобетона выполняется полусухим вибропрессованием. Технологией производства продукции предусмотрено выполнение таких операций:
- подготовка бетонной смеси;
- доставка смеси бетонной к вибропрессу;
- наполнение смесью оснастки;
- складирование готовой продукции и выдержка до установленных прочностных показателей.
Оборудование для производства блоков
В соответствии с технологическим процессом для получения продукции необходимо следующее оборудование для производства керамзитоблоков, выпускаемое отечественными предприятиями и устанавливающими экономически обоснованные цены:
- смеситель бетона;
- конвейер, подающий полученную смесь в бункер приема вибропресса;
- вибропресс, который, исходя из степени механизации, может быть ручным либо гидравлическим.
Ручной пресс, прилагающий нагрузки на формируемое изделие с помощью рычага, обычно находит применение на небольших производственных участках. Отличается невысокой ценой, простотой конструктивного исполнения и довольно высокой производительностью – около тысячи блоков за смену.
Гидравлический вибропресс обеспечивает получение высококачественной продукции, отличается более высокой производительностью, позволяет выполнять переналадку на другую продукцию, более рационально использовать цемент.
Дополнительное оборудование
К оборудованию дополнительного назначения следует отнести:
- оснастку в виде комплекта матрица-пуансон, благодаря которым производятся керамзитовые блоки различных исполнений: полнотелые, пустотелые, стеновые, щелевые, перегородочные, фундаментные и др.
- деревянные поддоны для вибропресса.
Похожие материалы:
Оборудование для производства блоков — Мои статьи — Каталог статей
Stanki-Saratov — конструирует и изготавливает оборудование, станки для производства шлакоблоков, керамзитоблоков, опилкоблоков, деламитоблоков, опилкоблоков, арболитоблоков, сплиттерных, стеновых блоков
В современном мире бизнеса оборудование для производства строительных блоков очень востребовано. Производство стеновых блоков позволяет вести строительство более быстрыми темпами.
Приобретая, например, оборудование для производства керамзитобетонных блоков, даже малое предприятие не останется в проигрыше – продукция пользуется спросом. Используя необходимое оборудование для производства керамзитобетонных, можно получить и строительный и отделочный материал одновременно.
Станки для производства керамзитобетонных блоков имеет относительно невысокую стоимость и небольшой вес. При компактных размерах установок и оборудования можно организовать производство керамзитобетонных блоков даже на малых площадях. Оборудование для производства керамзитобетонных блоков не занимает много места, и при этом отличается хорошей производительностью.
Передвижные установки для производства керамзитобетонных блоков позволяют перемещать оборудование для производства строительных блоков по мере необходимости. Малогабаритное оборудование для изготовления блоков быстро окупается и удовлетворяет в полной мере потребности покупателя. Производство керамзитобетонных блоков не обязательно вести в «промышленных масштабах». Однако собственное оборудование для производства строительных блоков значительно уменьшает затраты на строительство. К тому же, производство керамзитобетонных блоков, позволяет решит вопрос и отделочных материалов.
Оборудование для изготовления блоков могут обслуживать 1-3 человека. Поэтому производство керамзитобетонных блоков — неплохой вариант для семейного бизнеса. Оборудование для изготовления блоков позволит создать практически с нуля настоящий производственный цех.
Паспорт с описание состава для блоков бесплатно прилагается в комплекте со станком.
http://stanki-saratov.ru
Вибростанки для блоков по самым лучшим ценам!
Оборудование для производства керамзитобетонных блоков, керамзитоблоков, керамзита и керамзитового гравия
Оборудование для производства керамзитобетонных блоков
Если вы задумали начать свой бизнес на строительном поприще, то вас, безусловно, должно было заинтересовать оборудование для производства керамзитобетонных блоков. Не зря такая деятельность считается прибыльной.
Керамзит, который считают по осени
Народная мудрость гласит о том, что цыплят считают именно по осени. Керамзит, конечно, глупо будет считать по временам года. Здесь смысл в другом. Лишь хорошее оборудование для производства керамзитоблоков сможет себя впоследствии оправдать, поднимая на ноги ваш молодой бизнес. Именно поэтому нужно с особой тщательностью выбирать оборудование для производства керамзита, помня, что от этого будет зависеть весь успех вашего еще пока зарождающегося дела. Не стоит в таких случаях делать акцент исключительно на ценовую политику, обратите внимание в первую очередь на технические характеристики аппаратов, их возможности, выносливость и мощностями, с какими они могут справляться. И только после этого смотрите на ярлычок с упоминанием цены.
Пусто или густо
Далее вам предстоит разобраться с тем, какой направленности будут ваши блоки. От этого будет зависеть, какое конкретно оборудование для производства керамзитных блоков окажется для вас самым актуальным. Все виды блоков имеют два основных подразделения: пустотелые и полнотелые.
А уже потом вы будете решать, что еще вам нужно от агрегатов. То ли это будет облицовочная плитка по итогу, то ли модная ныне – тротуарная плитка.
Наполнитель
Подобно любому распространенному строительному материалу, блоки подобного характера могут вмещать в себя разнообразные наполнители. На оборудование для производства керамзитового гравия это не особо влияет, но при этом важно помнить о том, что подобные машины могут быть многофункциональными (в разрезе наполнения).
Керамзит используется в большинстве случаев для изоляции жилья, но при этом установка, которая будет производить такие блоки, может справиться и с производством блоков из другого материала, например, из опилок или шлака. Все зависит от конкретного конечного употребления продукта. Некоторые установки успешно перерабатывают даже песок для создания блоков.
Возможно, вас заинтересует
Размер керамзитобетонных блоковГабариты в строительстве играют передовую роль, именно поэтому не обойтись здесь без тщательного просчета не только финансовых затрат, а и необходимого количества рабочей силы. ..
Вряд ли люди еще лет десять назад могли себе представить, что дома будут возводиться из не совсем обычных материалов, которые раньше даже за полноценный строительный элемент н…
Как сделать керамзитобетон своими рукамиВ строительстве используется все большее количество материалов, которые отличаются природными характеристиками. Они обладают идеальными свойствами, позволяющими их применять в…
оборудование для производства керамзитных блоков китаи
Производство керамзитобетонных блоков
Процесс производства керамзитобетонных блоков начинается с добычи сырья и производства керамзита Затем следует формовка и вибропрессование блоков, пропарка и , Соблюдается ли технология? ,, Вячеслав Китаев г.
Производство керамзитобетонных блоков:
9 май , Технические характеристики; Технология изготовления; Состав и , Готовая линия по производству керамзитобетонных блоков:.
Оборудование для производства шлакоблоков в
Хотите купить оборудование для производства шлакоблоков по цене от , Станок для производства шлакоблоков и керамзитовых блоков
Оборудование для керамзитобетонных блоков-производство-оборудование.
Мини-завод по производству керамзита
18 сен , Мини-заводы по производству керамзита из Китая nerudopt/.
О нас, о комнапии «Командор Техно»
, установок (станков) для изготовления шлакоблочных \ керамзитобетонных блоков , продажу бетоносмесительного оборудования (Россия, Китай).
Оборудование по производству керамзитобетонных
5 мар , Продается оборудование по производству керамзитобетонных блоков В комплект оборудования входят:
Основной изготовления керамзитобетонных блоков является профессиональное оборудование, позволяющее производить до 600 единиц продукции.
китай оборудование для производства керамзита
25 май , Для получения дополнительных сведений и ценообразования, общаться с агентом по продаже: оборудование для производства.
Производство керамзитобетонных блоков как бизнес
28 апр , Одна из них: производство керамзитобетонных блоков , собой керамзитобетонные блоки; 12 Необходимое оборудование и сырьё.
Оборудование для производства стеновых
Оборудование для производства тротуарной плитки, стеновых керамзитобетонных блоков, шлакоблоков Поставка оборудования, технологических.
Оборудование для производства керамзитоблоков и описание технологического процесса
Технология производства керамзитоблоков
Керамзитобетон – искусственный материал, изготовленный на основе цемента, воды и керамзита. Керамзит получают путем обжига легкоплавкой глины.
Он представляет собой округлые или овальные гранулы неправильной формы, которые имеют диаметр 4-8 мм. Более мелкие гранулы называют керамзитовым песком.
Гранула керамзита на изломе похожа по структуре на застывшую пену. Благодаря спекшейся оболочке, гранулы отличаются особой прочностью.
Линия по изготовлению блоков «под ключ» включает:
- вибропресс с пультом управления;
- бетономешалку;
- эстакаду для установки бетономешалки с приемным лотком;
- формообразующую оснастку;
- формовочные поддоны.
Технология изготовления керамзитоблоков значительно отличается от процесса производства пеноблоков. Это обусловливает тот факт, что керамзитобетон обладает лучшими техническими качествами. Он не нуждается в дополнительном утеплении, и при разнице температур не образуется конденсат.
Технологический процесс можно разделить на следующие этапы:
- приготовление смеси;
- формовка;
- затвердение с применением вибростанка;
- просушка изделий;
- транспортировка на склад.
Расчеты и технология строительства пристроек из керамзитоблока не отличается принципиально от строительства самого дома. Единственным условием является выполнение отдельно стоящего фундамента.
Приготовление смеси
На изготовление одного блока потребуется 0,01 м3 раствора. Как приготовить смесь и из чего определяется ГОСТом и ТУ и может несколько варьироваться.
При соблюдении таких пропорций получается крепкий материал, который имеет небольшой вес и отличается хорошей теплоизоляцией. Вес готового блока в сыром виде составляет 11 кг, в сухом – 9,5 кг.
Чтобы блоки были как можно крепче и прочнее, в керамзитную смесь необходимо добавлять больше цемента. Но следует учесть, что в этом случае теплопроводность материала возрастет, поэтому стены будут несколько холоднее.
Цемент для производства блоков должен быть свежим и идеально чистым. Желательно взять цемент марки М400 или М500. Керамзитового песка необходимо брать в 2 раза меньше, чем керамзита. Это позволит обеспечить оптимальную плотность материала.
Чтобы получить глянцевую поверхность, в раствор можно добавить клей для камня или плитки. Но при этом экологическая безопасность материала снижается. Также в раствор добавляют специальные воздухововлекающие добавки. Как правило, для этого используют древесную омыленную смолу.
Чтобы повысить прочность материала, в него добавляют пластификатор (около 5 г на 1 блок). Такой материал отличается более высокой водонепроницаемостью и морозостойкостью. Он более стойкий к образованию трещин и истиранию блоков.
Приготовление смеси для керамзитоблоков в бетономешалке типа «груша»:
Формовка
После смешивания компонентов раствор отправляют на формовку, где будущим блокам придается нужная форма и размер.
Затвердение с применением вибростанка
Для обеспечения твердения раствора используют вибростанок. Благодаря вибрациям, раствор в формах становится более плотным и приобретает требуемую структуру. Когда раствор достигает максимальной плотности, излишки смеси снимают с помощью стальной пластины.
Просушка изделий
Блоки отправляются на просушку прямо в формах. Она может производиться естественным путем или с помощью пропаривания в специальной камере.
Сушка продолжается около двух суток. Если в смесь был добавлен пластификатор, время сушки снижается до 6-8 часов.
Транспортировка на склад
Готовые блоки складируют в сухом помещении. После просушки они готовы к реализации и использованию.
как сделать керамзитоблоки
чем утеплить керамзитоблок снаружи
как обшить баню из керамзитоблоков внутри
Производство керамзита с использованием устройства вихревого слоя
Производство керамзита основано на гомогенизации и измельчении частиц глинистого сырья, формировании и дальнейшем обжиге гранул. Учитывая такие процессы, целесообразно использовать устройство вихревого слоя (АВС) из GlobeCore .
Актуальность производства керамзита
Керамзит — востребованный строительный материал, недорогой теплоизолятор, наполнитель, декоративное изделие.Выпускается в виде шариков, гравия, щебня, песка с толстой оболочкой и пористой внутренней структурой. Сырьем для керамзита служат легкоплавкие, вспучивающиеся глины, сланцы и суглинки.
Зерно получается в результате гомогенизации, смешивания шихты и обжига. Отличаются низкой теплопроводностью, инертностью к воздействию щелочей, кислот, долговечностью, экологичностью, звукопоглощающей способностью. Применяются в основном в строительстве и при производстве строительных материалов:
- Производство пористых бетонов
Наполнитель для легких, сверхлегких пористых бетонов, используемых в стяжках, монолитных стенах и конструкциях.
- Производство блоков из керамзита
Основной наполнитель стеновых блоков из керамзита. Они также содержат цемент, песок и воду. Конструктивные элементы применяются в малоэтажном строительстве при возведении стен и перегородок в домах.
- Теплоизоляция зданий, сооружений
Высокопористые разновидности керамзита применяются в качестве теплоизолятора полов, стен и межэтажных перекрытий.
- Строительство фундаментов
Используется для наполнения с целью предотвращения промерзания. Это позволяет снизить расход материала при возведении конструкций.
Является хорошей основой для чернового выравнивания пола. материал легкий; поэтому не оказывает нагрузки на межэтажные перекрытия. Повышает теплоизоляционные характеристики внутреннего пространства.
Материал относительно низкой пористости применяется в насыпях при строительстве дорог и водоотводов, при обработке и подготовке почвы.
- Теплоизоляция инженерных сетей
Трубы системы теплоснабжения, подведенные к домам и зданиям, покрыты гранулами. Они обеспечивают качественную теплоизоляцию и легкий доступ к системе.
Столь широкая сфера применения керамзита делает его востребованным на рынке строительных материалов, в промышленности, сельском хозяйстве. Перспективной и актуальной выглядит модернизированная технология производства керамзита с использованием устройства вихревого слоя.Но сначала обсудим, какими недостатками характеризуются существующие линии по производству этого материала.
Производство керамзита традиционными способами, недостатки этих способов
Практически на каждом современном заводе по производству керамзита в процессе смешивания и измельчения сырья используются глиносмесители, вальцы и кромкообрезные станки. Выпечка осуществляется в печных барабанах. Обработка гранул в устройстве занимает примерно 45 минут.
Однако обычное оборудование для подготовки, гомогенизации и диспергирования сырья не обеспечивает качественного измельчения и смешивания ингредиентов.Это отрицательно сказывается на прочности готового изделия.
При низкой степени гомогенизации и плохой диспергируемости частиц даже 3% карбонатных примесей во вспучивающихся легкоплавких глинах отрицательно сказываются на качестве материала. Гидратация СаО сопровождается деструкцией керамзита и потерей прочности при хранении.
Традиционное производство керамзита с использованием катков, бегунков и глиносмесителей также неактуально для обработки глинистых масс с высоким содержанием песка.При содержании в смеси 10–30 % свободного SiO2 невозможно изготовить из сырья качественный прочный продукт.
Обработка сырья в вихрепластовом аппарате помогает в решении этих задач классическими методами. Кроме того, появляется возможность производить качественный керамзит даже из изначально непригодных глиняных масс.
Кроме того, по традиционной технологии отсортированное сырье можно смешивать с веществами, улучшающими его набухание, — мазутом, соляркой.Применение АВС позволяет минимизировать использование добавок или отказаться от них, что дает положительный экономический эффект и влияет на чистоту и экологичность готового продукта.
Производство керамзита с помощью устройства вихревого слоя
Производство керамзита с помощью устройства вихревого слоя основано на обработке сырья в электромагнитном поле ферромагнитными частицами. Агрегат может работать как с сухими, так и с влажными влажными средами.В рабочей камере аппарата наблюдаются процессы диспергирования и перемешивания, сопровождающиеся активацией частиц. Это влияет на прочность готового изделия. Процессы происходят при воздействии электромагнитного поля, акустических колебаний, высокого локального давления, электролиза.
В вихревом слое ферромагнитные иглы превращаются в мешалки и дробилки. При этом они перемещаются по камере, вращаются, сталкиваются с обрабатываемым материалом, друг с другом и со стенками устройства.Все это способствует эффективному перемешиванию, измельчению и активации шихты и смеси.
Эффект обработки глинистого сырья на керамзит с помощью АВС описан и экспериментально изучен Д. Д. Логвиненко. В результате мы получаем материал с меньшим объемным весом и лучшими прочностными характеристиками. Результаты представлены в таблице 1.
Таблица 1 – Характеристики керамзита при переработке сырья в АВС
Эксперимент № | Характеристика сырья и продолжительность обработки в АВС | Характеристики керамзита | |||||
Переработка сырья в АВС | Переработка сырья без АВС | ||||||
Объемный вес (γ), г/см3 | Предел прочности на скалывание (σс*10-5), Па | Коэффициент прочности | Объемный вес (γ), г/см3 | Предел прочности на скалывание (σс*10-5), Па | Коэффициент прочности | ||
1 | Глина, содержащая 26 % свободного SiO2 (30 % от обработки шликера) | 0.![]() | 2,25 | 10,3 | 0,38 | 1,60 | 5,1 |
2 | Глина, содержащая 41% свободного SiO2 (30% от обработки шликера) | 0,34 | 2,45 | 7,8 | 0,84 | 3,24 | 4.1 |
3 | Монотермит (7 минут сухой обработки) | 0,85 | 29,4 | 36 | 1,6 | 9,81 | 6.5 |
4 | Глина, содержащая угольную золу в соотношении 50/50 (7 минут сухой обработки) | 0,57 | 10,7 | 18 | 0,58 | 4,32 | 8,4 |
5 | Глина, содержащая угольную золу в соотношении 50/50 при опыливании полуфабриката каолином (7 минут сухой обработки) | 0,74 | 27,9 | 32,0 |
Для сравнения обработан шликер глины, содержащий до 40 % свободного диоксида кремния. Производство керамзита с применением АВС отличается двукратным снижением объемной массы при одновременном повышении прочности материала. Прочностно-массовая характеристика изделия, полученного из шихты после обработки в вихреслойном устройстве, в два раза выше, чем у материала, изготовленного традиционным способом.
Этому результату способствует тщательная обработка сырья в вихревом слое с активацией входящего в состав смеси кварцевого песка.При обработке в АВС наблюдается разрыв силоксановой связи Si-O. Следовательно, на поверхности частиц появляются активные центры в виде свободных радикалов. Это стало причиной повышения качества конечного продукта. Песок активируется по тому же принципу, что и при диспергировании в дезинтеграторах на высоких скоростях.
В связи с активацией кварцевого песка происходят реакции стеклообразования и силикатообразования с участием диоксида кремния. После завершения производства керамзита обжигом изделия в нем отсутствуют крупные песчинки SiO2, в которых концентрировались бы напряжения. А в составе стекла кварцевый песок влияет на повышение прочности и термостойкости материала.
Кроме того, изучена сухая технология производства керамзита с использованием вихревого слоя. Для исследования был взят монотермит. Из сырья, обработанного в сухой среде с помощью АВС, получен наполнитель, прочность которого в три раза выше, чем у материала, изготовленного классическим способом. При этом объемная масса огнеупорного заполнителя была вдвое меньше, чем в образце.
Сухая обработка многокомпонентных шихт, состоящих более чем наполовину из зол тепловых электростанций (золы ТЭС), также показала положительный результат.
Полученные данные свидетельствуют о том, что технология производства керамзита с использованием вихревого слоя позволяет получать высокопрочный строительный материал даже из глин с высоким содержанием песчаных или карбонатных примесей.
Преимущества использования устройства вихревого слоя в производстве керамзита
Устройство вихревого слоя – передовое оборудование, которое можно использовать для оптимизации как компактного завода по производству керамзита, так и крупного предприятия по следующим причинам:
Готовый материал характеризуется повышенной прочностью и термостойкостью даже при высоком содержании песка и карбонатных примесей в глиняных массах. Также АВС позволяет использовать отходы энергетики, в том числе золу ТЭС, в производстве керамзита.
Оборудование отличается низким потреблением электроэнергии и преимуществами в несколько раз по сравнению с обычными установками. Потребляемая мощность моделей AVS-100 и AVS-150 составляет 4,5 кВт и 9,5 кВт соответственно.
Устройство компактное, простое в эксплуатации и может быть интегрировано в существующую производственную линию. При этом для этого оборудования нет необходимости делать тумбу или дополнительные конструкции.AVS без проблем перемещается по мастерской.
Таким образом, АВС из GlobeCore – это универсальное, удобное, высокопроизводительное оборудование, которое позволит расширить и оптимизировать производство высококачественного керамзита. Кроме того, снижаются требования к качеству сырья, а значит, появляется больше возможностей в части производства легкого заполнителя, на котором базируется производство керамзитоблоков, легких бетонов и т. д.Себестоимость материала можно снизить за счет повышения его эксплуатационных характеристик.
Для получения консультации и заказа моделей АВС-100 или АВС-150 для завода по производству керамзита обращайтесь к торговым представителям GlobeCore.
Машина для производства бетонных блоков Vess 12.2
Особенно в наши дни, если вы планируете производить какие-либо бетонные изделия, такие как бетонные пустотелые блоки, бетонные блоки для мощения, бордюры, полнотелые блоки, блоки для перекрытий или другие виды бетонных изделий, вам необходимо приобрести машину для производства бетонных блоков. .
Сегодня на промышленном рынке можно найти множество компаний, особенно производителей машин для производства бетонных блоков, некоторые из них производят эти машины с высоким качеством, а некоторые с низким качеством.
В основном такие станки для изготовления блоков некачественные, плохо работают. Их цена кажется в несколько раз дешевле, чем у качественного бетоноблока. Но, как мы всегда рекомендуем нашим клиентам, приобретайте станки для производства бетонных блоков качественно и по доступным ценам.
Сначала дешевые машины выглядят дешевле, но в будущем техническое обслуживание, замена сломанных деталей, низкое качество продукции и отказ производства будут стоить намного дороже, чем машина премиум-класса.
Машина для производства бетонных блоков Основное оборудование
Для получения качественных бетонных блоков важно обращать внимание на состав бетонной смеси и какие инертные материалы используются.
Обычно для изготовления раствора используют различные внутренние детали, основными материалами которых являются:
* Песок
* Вода
* Различные типы добавок
Для изготовления каждого вида бетонного блока необходимо использовать свою рецептуру и сырье. Если вы всегда делаете раствор из качественного сырья, вы можете производить качественные бетонные блоки с помощью машин.
Производство бетонных блоков
Специально для производства различных бетонных блоков, брусчатки и бордюров песок является одним из важнейших основных инертных материалов.По этой причине можно сказать, что основным инертным материалом для изготовления этих разнообразных бетонных блоков, брусчатки и бордюров является песок.
На самом деле песок очень тонкий материал. Когда цемент смешивается с другими инертными материалами, песок становится прочным, прилипая к частицам цемента и образуя однородную смесь. Если песок слишком тонкий, на этом этапе невозможно использовать мелкие бетонные изделия для полуавтоматической машины для производства бетонных блоков, автоматической машины для производства блоков или полностью автоматических машин для производства блоков.
Однако этот мелкий песок можно использовать для покрытия тротуарной плитки. Для этого вам понадобится машина с двойным бункером.
Для изготовления бетонных блоков выбор инертных материалов может быть самым различным: цемент, керамзит, шлак, перлит, опилки, песок, отсев каменного дробления, щебень мелких фракций, любой другой вид инертных материалов.
При использовании этих различных инертных материалов они могут влиять на технические характеристики готового бетонного блока, такие как прочность, вес, теплопроводность и другие.
Машина для производства бетонных блоков Vess 12.2 | |||
Бетонные пустотелые блоки: 12 000 шт. | Бетонные блоки для мощения: 1000 квадратных метров | Тумбы: 3850 шт. | Тип автоматизации: полностью автоматический |
Дополнительно: мини-система или полная система | Взаимосвязанные блоки для мощения: 1000 квадратных метров | Сила вибрации: 43.500 кг | Гарантия: 2 года |
Гидравлическое давление: 200 бар | Емкость бака гидравлического масла: 350 л | Мощность гидравлического двигателя: 45 кВт | Установка: бесплатно |
Бункеры: одинарные или двойные | Курс обучения операторов: бесплатно | Использованные материалы высшего качества | Достаточно одного человека для управления машиной |
Когда вы решаете купить машину для производства бетонных блоков, цена также является одним из наиболее важных вопросов, которые вам необходимо учитывать. В связи с этим всегда стоит оценить, что представляет собой машина для производства бетонных блоков и цена, и как она соотносится с качеством и техническими характеристиками оборудования.
Только в этом случае вы сможете подобрать оптимальное решение под свои нужды, особенно учитывая тот факт, что одни покупатели сегодня заинтересованы в более доступных товарах, а другие заинтересованы, в первую очередь, в долговечной и надежной машине.
В нашей компании мы предлагаем нашим клиентам различные варианты машин для производства бетонных блоков и детали цен на машины для производства блоков, вы можете связаться с нами в любое время для разговора и узнать, какая машина для производства блоков является лучшим вариантом в соответствии с вашим проектом.
Полностью автоматическая машина для производства бетонных блоков В наши дни вы можете найти множество производственных компаний, которые производят машины для производства бетонных блоков. В нашей компании, как правило, у нас есть три различных автомата для производства бетонных кирпичей в соответствии с вашим проектом.
Если вы только решили заняться этим бизнесом, в таком случае лучше приобрести полуавтоматический станок для изготовления блоков. Вы можете производить различные виды бетонных блоков.Достаточно будет сменить пресс-форму на станке. Сбор бетонных блоков производится вручную рабочими с ручными тележками на полуавтоматических машинах.
Если у вас есть опыт и вы хотите заменить свою старую машину для изготовления блоков, вы можете приобрести автоматическую машину для изготовления блоков.
Для этого вида автоматизации есть два робота с задней и передней стороны машины. Один из них загрузчик, другой разгрузчик.После производственного процесса приезжает вилочный погрузчик и забирает готовые бетонные блоки для перевозки на участок отверждения.
Также имеется полностью автоматическая автоматика. Эту автоматизацию могут выбрать опытные заказчики или компании. Ежедневная производительность этой автоматизации высока, и вся система может контролироваться компьютерной системой, также известной как ПЛК.
Вы можете ознакомиться с некоторыми особенностями полностью автоматических машин для производства бетонных блоков:
• Начальная суточная вместимость — 12.000 бетонных пустотелых блоков и 1000 квадратных брусчатки за день за восемь часов.
• Время производства бетонных блоков: Полностью автоматические машины могут производить продукцию быстрее с использованием новейших технологий, чем другие виды машин.
• Все производственные процессы могут выполняться с помощью полностью автоматической системы ПЛК немецкой марки.
• Количество персонала: В случае полностью автоматических машин для производства бетонных блоков вам нужен всего один человек для управления всей системой.
• У вас есть возможность добавлять или удалять оборудование, которое вам нужно или нет.
• С помощью наших машин вы можете изготовить любую понравившуюся вам форму высотой от 5 до 40 см.
Основываясь на этой информации, вы можете купить машину для производства бетонных блоков любого типа по хорошей цене. Для получения более подробной информации о цене и деталях бетонных блоков вы всегда можете связаться с нами.
Машина для производства бетонных блоков
Сегодня бетонные блоки для мощения самого высокого качества можно производить на машинах для производства бетонных блоков.С помощью высококачественных автоматических машин для производства брусчатки можно производить практически все виды бетонных изделий. Именно поэтому большинство покупателей предпочитают приобретать качественную прессованную брусчатку.
Брусчатка, произведенная по новейшей технологии, намного лучше по прочности и морозостойкости, кроме того, эта технология легко поддается автоматизации, а значит дешевле по себестоимости, так как требуется меньше рабочих рук.
Система дозирования этой машины является автоматической, как и дозировочная установка. поскольку эта машина является высокопроизводительной, лучше обсудить бетонную установку в отдельном разделе. если вам нужна дополнительная информация о системе дозирования, вы можете проверить основную статью «Бетоносмесительный завод», чтобы получить более подробную информацию.
Заключение
Машина для производства бетонных блоков Vess 12.2 является одной из наиболее подходящих машин для клиентов, которые хотят производить высококачественные бетонные пустотелые блоки, брусчатку, бордюрный камень и другие изделия с высокой производительностью.
По вашему запросу вы можете найти подходящий вариант машины для производства бетонных блоков, который вам нужен. Для других наших моделей, вы можете связаться с нами. Наши машины для производства блоков способны производить практически все бетонные блоки, достаточно лишь сменить форму.
Облегченная производственная линия заполнителя керамзита LECA, завод по производству песка керамзита
Легкий заполнитель из керамзита Производственная линия LECA План производства песка
Описание:
Легкий заполнитель из керамзита (производственная линия LECA) или керамзит (exclay) представляет собой легкий заполнитель, полученный путем нагревания глины примерно до 1200 °C (2190 ° F) во вращающейся печи.Выделяющиеся газы расширяют глину за счет тысяч маленьких пузырьков, образующихся при нагревании и образующих сотовую структуру. LECA имеет приблизительно круглую или картофельную форму из-за кругового движения в печи и доступен в различных размерах и плотности. LECA используется для изготовления изделий из легкого бетона и других целей.
ЭКА обычно производятся разных размеров и плотностей от 0,1 мм (0,0039 дюйма) до 25 мм (0,98 дюйма), обычно 0-4 мм, 4-10 мм, 10-25 мм и плотностью 250, 280, 330 , и 510 кг/м3. Валун LECA — это самый большой размер LECA размером 100–500 мм и плотностью 500 кг / м3.
Некоторые характеристики LECA (производственной линии LECA): легкость, теплоизоляция за счет низкого коэффициента проводимости (всего 0,097 Вт/мК[1]), звукоизоляция за счет высокого акустического сопротивления, влагонепроницаемость, несжимаемость при постоянном давлении и гравитационных нагрузках. , не разлагается в тяжелых условиях, огнестойкий, pH около 7, стойкость к замерзанию и плавлению, простота перемещения и транспортировки, легкая засыпка и отделка, снижение статической нагрузки конструкции и поперечной нагрузки при землетрясении, идеальная плодородная почва для растений, материал для дренажа и фильтрация.
Спецификация | Емкость (T / D) | Наклон тела (°) | скорость (R / min) | Главный мотор (кВт) | ||
Φ2 .![]() | 168 | 3.5 | 0.516-1.549 | 9016-1.549 9016-1.549|||
Φ3 * 48 | 700 | 3,5 | 0.726-3.63 | 110 | ||
Φ3.2 * 46 | 1000 | 3000 | 3.5 | 0.36-3.57 | 160 | |
1200 | 3.5 | 0.343-0.34 | 125 | |||
1300 | 3.5 | 0.576-3.38 | 160 | 160 | ||
Φ3.3 * 52 | 1300 | 3,5 | 0.266-2.66 | 125 | ||
Φ3.5 * 54 | 1500 | 3.5 | 0.55-3.4 | 220 | ||
Φ3.6 * 70 | 1800 | 3.5 | 0.25-1.25 | 125 | ||
Φ4 * 60 | 2500 | 3.5 | 0.59698 | 0.396-3.96 | 315 | 315 |
Облегченная производственная линия агрегата ЛЕКА расширенной глины, завод по производству песка керамзита Изображений |
Тепловые и механические исследования перлитобетонных обшивок дымоходов жилых зданий
.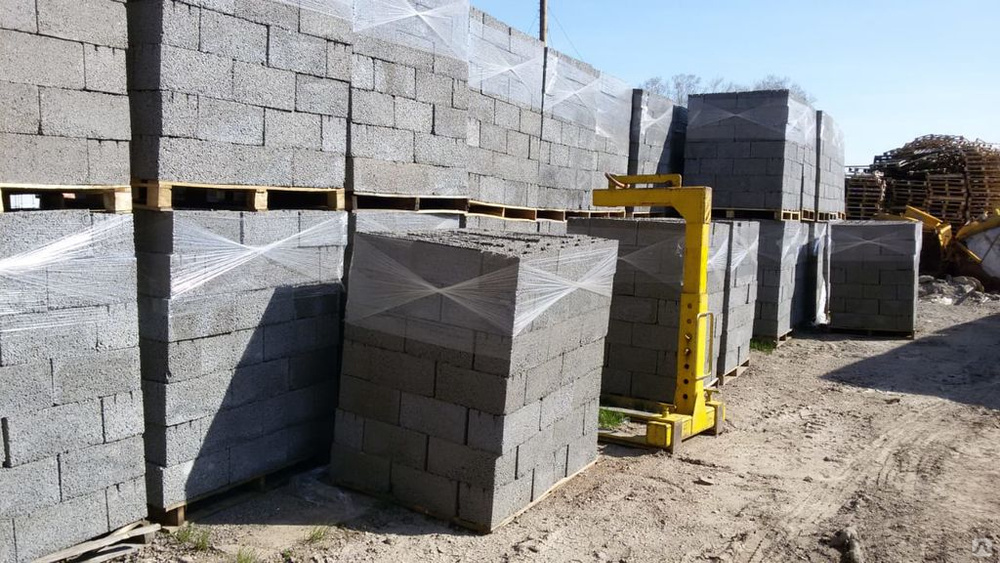
Принадлежности Расширять
принадлежность
- 1 Факультет строительства и архитектуры, Опольский технологический университет, улица Катовицка 48, 45-758 Ополе, Польша.
Элемент в буфере обмена
Кшиштоф Дроззол.
Материалы (Базель). .
Показать варианты
Формат АннотацияPubMedPMID
.2021 16 апреля; 14(8):2011. дои: 10.3390/ma14082011.принадлежность
- 1 Факультет строительства и архитектуры, Опольский технологический университет, улица Катовицка 48, 45-758 Ополе, Польша.
Элемент в буфере обмена
Полнотекстовые ссылки Параметры отображения цитированияПоказать варианты
Формат АннотацияPubMedPMID
Абстрактный
Дымоходы – это конструкции, предназначенные для отвода выхлопных газов от отопительных приборов наружу зданий. Материалы, из которых они изготовлены, оказывают большое влияние на их пожарную безопасность, а также на безопасность всего здания. Поскольку современные тенденции в строительной отрасли движутся в сторону улучшения воздействия на окружающую среду и пожарной безопасности, постоянно вносятся изменения в строительные материалы. Это также относится к развитию технологии дымоходов, поскольку по-прежнему существует признанная потребность в новых решениях, когда речь идет о материалах, используемых в производстве дымоходных систем. В данной статье представлены результаты испытаний дымохода из инновационных перлитобетонных блоков.Были проанализированы четыре различных перлитобетонных блока, различающихся объемной плотностью. Затем полученные результаты сравнивали с широко используемыми бетонными блоками из лека (легкий керамзитобетон). Результаты испытаний подтвердили высокие изоляционные свойства перлитобетонного блока, из которого изготовлен инновационный кожух дымохода. Уровень пожарной безопасности сохранялся даже при высоких температурах, возникающих при возгорании сажи (1000 °С).
Эти свойства сохранились, несмотря на отсутствие дополнительной изоляции дымохода.Несмотря на то, что термическая нагрузка снизила прочность на сжатие блоков дымохода, они все же показали достаточную среднюю прочность 4,03 МПа. Кроме того, результаты испытаний подтвердили возможность рекуперации тепла из дымохода с эффективностью 23-30%, что представляет собой значительное увеличение по сравнению с дымоходами из бетонных блоков.
Ключевые слова: дымовая труба; пожарная безопасность; рекуперация тепла; перлитобетон.
Заявление о конфликте интересов
Авторы заявляют об отсутствии конфликта интересов.
Цифры
Рисунок 1
Поперечное сечение слоев…
Рисунок 1
Сечение слоев анализируемой дымовой трубы (размеры в мм).
Рисунок 1Сечение слоев анализируемой дымовой трубы (размеры в мм).
Рисунок 2
Фотографии: ( a ) перлит (1), ( b ) бетонный блок leca…
фигура 2 Фотографии: ( a ) перлитовые (1), ( b ) бетонные блоки leca (2) и ( c ) перлитобетонные блоки (3–6) с различной насыпной плотностью.
Рисунок 3
Зависимость теплопроводности…
Рисунок 3
Зависимость коэффициента теплопроводности от насыпной плотности перлита и…
Рисунок 3Зависимость коэффициента теплопроводности от насыпной плотности перлитных и лекабетонных блоков; 2* значение определено на основе [33,34].
Рисунок 4
Тестовые фотографии: ( a ) вид на герметичный дымоход над крышей и…
Рисунок 4 Тестовые фотографии: ( a ) вид на герметичный дымоход над крышей и ( b ) отопительный прибор после установки.
Рисунок 5
Испытательный стенд (синий и красный…
Рисунок 5
Испытательный стенд (синяя и красная стрелки обозначают воздух и вытяжку соответственно).
Рисунок 5Испытательный стенд (синяя и красная стрелки обозначают воздух и вытяжку соответственно).
Рисунок 6
Схема стенда б/у…
Рисунок 6
Схема стенда для огневых испытаний дымоходов.
Схема стенда для огневых испытаний дымоходов.
Рисунок 7
Стенд для огневых испытаний:…
Рисунок 7
Стенд для огневых испытаний: ( a ) проверен дымоход на испытательных…
Рисунок 7Стенд для огневых испытаний: ( a ) проверенная дымовая труба на испытательной камере и ( b ) генератор горячего выхлопа.
Рисунок 8
Курс испытаний на прочность – сжатие…
Рисунок 8
Курс испытаний на прочность – сжатие блока в гидравлическом прессе.
Курс испытаний на прочность – сжатие блока в гидравлическом прессе.
Рисунок 9
Вид на ( a ) прозрачную контрольную точку на входе в…
Рисунок 9Вид ( a ) прозрачной контрольной точки на входе воздуха в печь, ( b ) цветной конструкции воздуховода (красный) и ( c ) цветного дымохода (синий).
Рисунок 10
Тепловой КПД дымохода…
Рисунок 10
Тепловой КПД дымохода из перлитобетонных блоков.
Тепловой КПД дымохода из перлитобетонных блоков.
Рисунок 11
Видимые повреждения, вызванные сжатием…
Рисунок 11
Видимые повреждения, вызванные сжимающей нагрузкой.
Рисунок 11Видимые повреждения, вызванные сжимающей нагрузкой.
Рисунок 12
Результаты испытаний на прочность при сжатии.
Рисунок 12
Результаты испытаний на прочность при сжатии.
Рисунок 12Результаты испытаний на прочность при сжатии.
Все фигурки (12)
Похожие статьи
- Свойства и распределение микроструктуры высокоэффективного теплоизоляционного бетона.
Мохаммад М., Масад Э., Сирс Т., Аль-Гамди С.Г. Мохаммад М. и др. Материалы (Базель).2020 1 мая; 13 (9): 2091. дои: 10.3390/ma13092091. Материалы (Базель). 2020. PMID: 32369971 Бесплатная статья ЧВК.
- Неразрушающий контроль технического состояния промышленных высотных железобетонных дымовых труб, подвергающихся воздействию высоких температур.
Май М, Убыш А, Хаммаде Х, Аскифи Ф. Май М и др. Материалы (Базель). 2019 24 июня; 12 (12): 2027. дои: 10.3390/ma12122027. Материалы (Базель).2019. PMID: 31238578 Бесплатная статья ЧВК.
- Легкий реактивный порошковый бетон, содержащий вспученный перлит.
Гжещик С, Янус Г. Гжещик С. и соавт. Материалы (Базель). 2021 17 июня; 14 (12): 3341. дои: 10.3390/ma14123341. Материалы (Базель). 2021. PMID: 34204260 Бесплатная статья ЧВК.
- Акустические свойства инновационных бетонов: обзор.
Федюк Р., Амран М., Ватин Н., Васильев Ю., Лесовик В., Озбаккалоглу Т. Федюк Р. и соавт. Материалы (Базель). 2021 14 января; 14 (2): 398. дои: 10.3390/ma14020398. Материалы (Базель). 2021. PMID: 33466943 Бесплатная статья ЧВК.
Обзор.
- Обзор литературы о способности бетона сохранять прочность после воздействия огня на основе коэффициента накопления тепла.
Паштетник М., Врублевски Р.Пастетник М. и соавт. Материалы (Базель). 2021 21 августа; 14 (16): 4719. дои: 10.3390/ma14164719. Материалы (Базель). 2021. PMID: 34443241 Бесплатная статья ЧВК. Обзор.
использованная литература
- Леппянен П., Инха Т., Пентти М. Экспериментальное исследование влияния расчетной температуры дымовых газов на пожаробезопасность дымоходов.Пожарная техника. 2014; 51:847–866. doi: 10.1007/s10694-014-0415-4. — DOI
- Леппянен П.
, Маласка М., Инха Т., Пентти М. Экспериментальное исследование пожарной безопасности дымоходов при реальном использовании и реальных условиях объекта. Дж. Билд. англ. 2017;14:41–54.doi: 10.1016/j.jobe.2017.09.014. — DOI
- Леппянен П.
- Леппянен П., Нери М., Мякинен Й. Выделение тепла при тлеющем горении вяжущего минеральной ваты. Дж. Структура. мех. 2015;48:68–82.
- Нери М., Лусьетти Д., Фиорентино А., Пилотелли М. Экспериментальный анализ дымоходов в деревянных крышах. Пожарная техника. 2016; 52:1939–1955. doi: 10.1007/s10694-015-0525-7. — DOI
- Нери М.
, Леппянен П., Бани С., Пентти М., Пилотелли М. Экспериментальное и расчетное исследование температурного поля вокруг прохода через крышу дымохода.Пожарная техника. 2016;52:1799–1823. doi: 10.1007/s10694-015-0540-8. — DOI
- Нери М.
Показать все 40 ссылок
LinkOut — больше ресурсов
Полнотекстовые источники
Прочие литературные источники
Материалы исследований
Блог
Бетонные блоки или цементные кирпичи являются строительным материалом, используемым для возведения стен в здании.Он также известен как блок бетонной кладки (CMU). Бетонные блоки являются одним из сборных железобетонных изделий, используемых в строительстве. Сборные блоки формируются и затвердевают до того, как они попадут на рабочую площадку. Существуют различные бетонные блоки, имеющие одну или несколько полых полостей, а сторона может быть отлита гладкой или с рисунком. Эти блоки укладываются на бетонный раствор, чтобы получилась стена.
Бетонный раствор впервые использовали римляне в 200 г. до н.э. для крепления фасонного камня в здании.При римском императоре Калигуле в 37-41 гг. н.э. небольшие блоки бетона использовались в качестве строительного материала в современном Неаполе, Италия. Бетонная технология, разработанная римлянами, утрачена с падением Римской империи в пятом веке. Английский каменщик Джозеф Аспдин разработал портландцемент в 1824 году.
Первый пустотелый бетонный блок был разработан Хармоном С. Палмером в 1890 году в Соединенных Штатах, и после 10 лет исследований и экспериментов он запатентовал конструкцию в 1900 году. Блок, разработанный Палмером, имел размеры 8 x 10 x 30 дюймов и был тяжелым, кран используется для перемещения.
За это время один человек изготовил в среднем 10 блоков и отлил их вручную. С современными машинами и передовыми технологиями это составляет 2000 блоков в час.
Какое сырье используется?Для изготовления бетонных кирпичей или блоков используется сырье, такое как смесь порошкообразного портландцемента, воды, песка и гравия. Вместе эти сырьевые материалы образуют блок светло-серого цвета с мелкой текстурой поверхности и высокой прочностью на сжатие.Вес типичного бетонного блока составляет от 38 до 43 фунтов (от 17,2 до 19,5 кг). Для блоков более высокий процент песка и более низкий процент гравия и воды. Получилась очень сухая, густая смесь, сохраняющая форму при извлечении из блочной формы.
Различные виды сырья Шлакоблок изготавливается из гранулированного угля или вулканического пепла. Это темно-серый блок с текстурой поверхности от средней до грубой, обладающий хорошей прочностью и хорошими звукоизоляционными свойствами с более высокой теплоизоляцией, чем бетонный блок. Типичный шлакоблок весит около 26-33 фунтов (11,8-15,0 кг).
При наличии гранулированного угля или вулканического пепла вместо песка и гравия с керамзитом, сланцем или сланцем изготавливается легкобетонный блок. Керамзит, сланец и сланец изготавливают с дроблением сырья и нагревом до 2000 o (1093 o ) . Материал раздувается или вздувается из-за быстрого образования газов, вызванного сгоранием мелких частиц органического материала внутри.Блок из легкого бетона весит около 22-28 фунтов (от 10,0 до 12,7 кг) и используется для возведения ненесущей несущей стены и других перегородок. Кроме того, для облегченных блоков используются доменный шлак и природные вулканические материалы, такие как пемза и шлак.
Наряду с основными компонентами для изготовления блоков используется бетонная смесь, содержащая химическое вещество, называемое добавкой, для изменения времени отверждения и повышения прочности на сжатие или для улучшения обрабатываемости. Пигменты добавляются в блоки для однородного цвета или делают поверхность блока однородной.Это также защищает поверхность блока от химических веществ. Глазурь на поверхности блока выполнена на термореактивной смолянистой связке, кварцевом песке и цветных пигментах.
Существуют стандартизированные формы и размеры обычных бетонных блоков для строительства зданий. Обычный размер блока 8 x 8 x 16, высота 8 дюймов, глубина 8 дюймов и ширина 16 дюймов. Это измерение включает в себя валик раствора, а размер блока составляет 7,63 дюйма (19.4 см) в высоту, 7,63 дюйма (19,4 см) в глубину и 15,63 дюйма (38,8 см) в ширину.
Многие производители блоков предлагают варианты блоков, чтобы они выглядели более эстетично для конкретных применений. Например, есть один производитель бетонных кирпичей или блоков, который проектирует блоки специально для водонепроницаемости через наружные стены. Блок с раздвоенной поверхностью с шероховатой каменной текстурой на одной стороне блока, затем гладкая поверхность. Эти бетонные кирпичи придают красивый эстетический вид.
Процесс производства бетонных кирпичей состоит из четырех этапов: смешивание, формование, отверждение и формирование кубов.Есть бетонные заводы, которые производят только бетонные блоки, в то время как другие производят различные сборные изделия, такие как блоки, плоская брусчатка, декоративные элементы, такие как окантовка газона, бетонные кирпичи и т. Д. С развитием технологий некоторые заводы по производству бетонных кирпичей могут производить 2000 блоков час.
1. Смешивание Песок и гравий хранятся в силосах снаружи, а затем при необходимости передаются по конвейерной ленте, а цемент хранится в силосах, чтобы защитить его от влаги.Когда смешивание началось, песок, гравий и цемент выходят из силосов через весовой дозатор, который взвешивает каждый материал. Сухие материалы поступают в смеситель, где они смешиваются в течение нескольких минут. В основном есть два типа миксеров, в которых используется планетарный или тарельчатый миксер, также известный как неглубокий лоток с крышкой. Смесительные лопасти прикреплены к вертикальному вращающемуся валу с мешалкой. Другой тип — горизонтальный барабанный смеситель. Это кофе, перевернутый на бок, с лопастями для смешивания, прикрепленными к горизонтальному вращающемуся валу внутри миксера.
После смешивания сухих материалов в смеситель добавляется небольшое количество воды. Теперь, если завод расположен в теплых местах, вода сначала проходит через нагреватель или чиллер для поддержания температуры. В это время добавляются смешивающие химикаты и цветные пигменты, и бетон перемешивается в течение шести-восьми минут.
2. Молдинг После смешивания бетон сбрасывается на ковшовый конвейер и транспортируется в приподнятый бункер, а цикл смешивания начинается после следующей загрузки.После этого он транспортируется в другие бункеры на блок-машине с регулируемой скоростью. Затем бетон снижают до расхода и заливают в формы. В формах есть внешняя коробка формы, в которой находятся другие вкладыши формы. Вкладыши имеют внешнюю форму блока и внутреннюю форму полостей блока. В зависимости от мощности машины за один раз формуется от 5 до 15 блоков.
После заполнения формы бетоном гидравлический пресс прессует бетон в форму. Сжатие осуществляется воздушным или гидравлическим давлением.Многие машины для производства бетонных кирпичей и бетонных блоков используют вибрацию для завершения процесса.
После этого блоки выталкиваются из формы на плоский стальной поддон. Поддон и блоки выталкиваются из машины на цепной конвейер. Некоторые из машин имеют функцию вращающейся щетки, которая удаляет рыхлый материал с верхней части блоков.
3. Отверждение Теперь поддоны блока транспортируются к автоматизированному укладчику или загрузчику, который помещает их в стеллаж для отверждения.На каждой стойке несколько сотен блоков. После заполнения стеллажа его закатывают на рельсы, а затем перемещают в сушильную печь.
Это помещение, вмещающее несколько стоек блоков одновременно. В основном используются два типа отверждения. Во-первых, это печь низкого давления, где блоки выдерживают от одного до трех часов при комнатной температуре для медленного затвердевания. Затем вводят пар с температурой 60°F (16°C в час) для повышения температуры закалки. Блоки стандартного веса отверждаются при 150-165° F (66-74° C), а легкие блоки отверждаются при 170-185° F (77-85° C).После достижения температуры пар отключают и блоки пропитывают горячим влажным воздухом в течение 12-18 часов. Процесс отверждения занимает около 24 часов.
Другой тип печи – паровая печь высокого давления, также известная как автоклав. Температура в этой печи составляет 300-375°F (149-191°C), а давление 80-185 фунтов на квадратный дюйм, примерно от 5,5 до 12,8 бар. Блоки выдерживают от 5 до 10 часов. Давление сбрасывается, и блоки выпускают влагу внутрь. Процесс отверждения в автоклаве потребляет больше энергии и является более дорогим, но он производит больше блоков за меньшее время.
Затем стеллажи с отвержденными блоками выкатывают из печи, а поддоны блоков раскладывают и размещают на цепном конвейере. После этого блоки сталкиваются со стальных поддонов, а пустые поддоны возвращаются в блок-машину для получения новых блоков.
Если есть блок с разъемной поверхностью, он сначала отформован как два соединенных блока. После завершения отверждения двойных блоков он проходит через рассекатель, и тяжелое лезвие ударяет между двумя половинками.
Бетонные кирпичи и блоки проходят через кубер, который выравнивает каждый блок и укладывает их в куб три блока по шесть блоков в глубину и три или четыре блока в высоту. Затем кубики выносятся на улицу вилочным погрузчиком и складируются для отправки.
Качество Производство бетонных блоков и кирпичей требует постоянного контроля за получением блоков требуемых свойств. Перед подачей в смеситель сырье взвешивается электронным способом. Содержание воды в песке и гравии измеряется ультразвуковыми датчиками, а количество воды требуется для автоматического измерения.В холодных и теплых условиях вода перед использованием должна пройти через охладитель или нагреватель.
После выхода из машины высота блока должна быть проверена с помощью лазерных датчиков, а в камере отверждения температура, давление и время цикла должны быть проверены должным образом и записаны автоматически, чтобы гарантировать, что блоки должны быть отверждены должным образом для достижения максимальной прочности.
Деятельность, связанная с производством строительных материалов – производство керамзитобетонных блоков
Керамзитовые блоки являются экологически чистым строительным материалом, так как для их изготовления используются натуральные компоненты – цемент, песок и керамзит.
Использование керамзитоблоков для кладки стен часто превышает использование керамического кирпича, т. к. последний уступает керамзитобетонным блокам по своим эксплуатационным свойствам.
Деятельность, связанная с производством строительных материалов – производство керамзитобетонных блоков
В частности, основными достоинствами керамзитоблоков являются легкость и, как следствие, возможность снижения веса конструкции на 40 % по сравнению с кирпичной кладкой, отсутствие усадки и трещин, хорошие показатели морозостойкости, хорошая теплоизоляция, более доступная цена.
Небольшие габариты (каждая единица по стандарту имеет размер 19х19х39 см) и вес обеспечивают удобство и экономию при транспортировке и хранении, простота установки не требует дополнительных приспособлений.
Этими факторами обусловлено широкое применение керамзитобетонных блоков в малоэтажном и бескаркасном строительстве, при кладке плит перекрытий в неотапливаемых помещениях, в сельском хозяйстве, судостроении, строительстве в шахтах, в качестве опор линий электропередач.
Для реализации бизнес-идеи по производству керамзитобетонных блоков в жизнь необходим небольшой стартовый капитал, сам процесс достаточно прост.
Конкуренция в этом сегменте еще достаточно низкая, а уже представленная на рынке продукция часто не отличается хорошим качеством, так как многие недобросовестные производители, стремясь снизить себестоимость, используют материалы, не соответствующие стандарту, например, не кварц или обогащенные песок, но дешевый речной или карьерный, что существенно влияет на прочностные и эксплуатационные свойства изделия.
Кроме того, важно, чтобы сырье, используемое для производства, не содержало радионуклидов, поэтому к выбору поставщика материала следует отнестись очень серьезно.Выпуск качественных керамзитоблоков обеспечит успех бизнесу, стабильный спрос и высокую прибыль.
Давайте немного пройдемся по цифрам.
Стоимость сырья
Мешок цемента марки М400/М 500 – 6,5-6,9$;
Песок – 6 у.е. за 1 тонну;
Керамзит — 30$ за 1 куб.м. м.;
Вода – по действующему тарифу.
Соблюдение пропорций, регламентированных ГОСТ и техническими условиями, необходимо для получения качественных, прочных блоков.
Технология производства
Где взять деньги на открытие собственного дела? Именно с этой проблемой сталкиваются 95% начинающих предпринимателей! В статье «Где взять деньги для бизнеса» мы раскрыли самые актуальные способы получения стартового капитала для предпринимателя. Также рекомендуем внимательно изучить результаты нашего эксперимента по биржевому заработку: «посмотреть результаты эксперимента»
Керамзитовые блоки получают объемным вибропрессованием. Технологический процесс состоит из 4 основных стадий: приготовление смеси, формование, передача на обработку вибропрессом, сушка.
Перечень оборудования и его стоимость
Основной узел – вибропресс. Для выполнения крупнообъемных заказов рациональнее сразу приобрести мощное оборудование, позволяющее производить до 800 единиц блоков в смену. Такой вибропресс обойдется минимум в 2000 долларов, это аппарат размерами 2,5 на 1,5 м, он позволяет производить керамзит, бетон, шлакоблоки.
Помимо вибропрессовой установки потребуется вибростол – от 930 у. е., бетономешалка – 3125 у.е., формовочные поддоны в количестве 3 шт. – 100 у.е./шт., гидростанция – от 3100 у.е.
Для обслуживания оборудования необходимо нанять 2-3 человека.
Также в продаже полностью укомплектованные готовые автоматические линии для производства керамзитобетонных блоков. Стоимость такой конвейерной установки составляет 45 000 долларов. Обслуживать его под силу 1 сотруднику. Необходимая площадь для установки 100 кв.м. Высота потолков – от 5,5 метров.
Комната
В зависимости от типа используемого оборудования, необходимая площадь под производство составит от 70 до 150 кв.м. м. Желательно наличие свободных площадей для хранения и сушки, допустимо расположение блоков на улице в поддонах под оборудованными навесами.Требования к помещению – ровный пол, высокие потолки, хорошее освещение, система отопления и производственной вентиляции.
Себестоимость, прибыль, срок окупаемости
Общая стоимость реализации бизнес-идеи составит от 19 тысяч долларов (в случае использования бюджетного варианта — сборное оборудование в виде отдельных узлов).