название, что это такое, свойства и характеристики, противопоказания материала для строительства
Строительные материалы из бетона и древесных частиц – недорогой и практичный вариант, который применяют при возведении малоэтажных строений. Сырье может быть как утеплителем, так и прочным решением для перегородок. Чтобы подобрать нужный вид, надо разобраться в особенностях блоков из опилок и цемента.
Характеристики сырья
Строительный материал относят к разновидности легких крупноячеистых бетонов. В качестве наполнителя в сырье используют древесные остатки. Пиломатериалы соединяются вместе с цементом в крепкую монолитную конструкцию. Согласно ГОСТу блоки выпускают полнотелыми и пустотелыми, для утепления или возведения сооружений.
Строительный материал на поддонеИсточник surgut.blockexpert.ruХарактеристики строительного сырья зависят от компонентов, которые добавляют в состав. К основным ингредиентам относят 5 категорий:
- Древесина. Щепа или стружка увеличивает тепло- и звукоизоляционные свойства блоков из опилок, делает сырье легким.
- Цемент. Материал улучшает устойчивость изделия к износу. По технологии применяют марку М400.
- Песок. Усиливает прочность строительного сырья. Пропорции вещества влияют на параметры теплоизоляции и твердости.
- Добавки для изменения характеристик. Применяют для защиты от возгорания, от гниения и от паразитов (грызунов, насекомых).
- Вода. Жидкость без посторонних частиц добавляют для создания однородного раствора.
Готовый материал по паропроницаемости и звукоизоляции напоминает натуральное дерево, а по прочности – пенобетон. При производстве используют древесные остатки от пилорамы. Устойчивость сырья не привязана к размеру или форме исходных отходов, важнее однородность структуры. При создании применяют как щепки, так и опилки или муку.
Качество готового материала не зависит от сорта древесины. В производстве пользуются популярностью недорогие еловые и сосновые виды. Антисептические свойства смолы уменьшают процессы гниения в блоках, поэтому в состав добавляют меньше химии. Хорошо себя зарекомендовали береза, тополь и дуб.
В качестве вяжущего вещества применяют цемент. В древесном наполнителе содержится сахар, который уменьшает адгезию с жидким бетоном. Перед изготовлением сырье предварительно вымачивают в специальных растворах. Для минерализации используют кальция хлорид или жидкое стекло, глину или известковое молочко.
Легкий, крепкий материалИсточник poradu24.comПлотность стройматериала варьируется от 350 до 850 кг/м2. Форма и размер часто зависит от задач, которые должно выполнять изделие. Для возведения сооружений применяют блоки из опилок и цемента с параметрами 60*40*20 см. Для утепления подойдут как традиционные кирпичи, так и плиты.
Виды стройматериала
Характеристики бетонно-стружечного строительного материала можно кардинально изменить при разных пропорциях основных компонентов. Одни варианты подходят при выгонке малоэтажных зданий или возведении перегородок, другие – в качестве утеплителя. Выделяют 5 видов опилочно-цементных блоков.
Проекты и строительство домов из арболитовых блоков: плюсы и минусы технологии, проекты и цены
Арболит
Название сырья стало общим для всех разновидностей строительного материала из стружки. Для изготовления арболита используют много древесных щепок, цемента и песка. В качестве основного ингредиента берут отходы лиственных и хвойных пород. Иногда в виде заполнителя в блоках уместны измельченные:
- солома;
- хлопчатник;
- костра (конопляная, льняная).
Материал бывает теплоизоляционный и строительный. Плотность конструкционного арболита усилена за счет уменьшения в составе щепок и увеличения цемента с песком. Сырье отлично подходит для выгонки внутренних и наружных перегородок, создания стен, перекрытий потолка и пола.
Фибролит
Стружка и связующий раствор – основа строительного материала. В качестве наполнителя берут длинные древесные отходы, которые измельчают и потом минерализуют в хлористом калии. Влажное сырье под высоким давлением спрессовывают, придавая форму блока или толстой плиты.
Вариант из опилок и раствораИсточник drevplit.pro
Опилкобетон
Сырье очень напоминает арболит, свойства которого используют при возведении строений. Материал состоит из цементного раствора и опилок разной фракции, в смесь добавляют известь или глину. У блоков низкие характеристики теплоизоляции компенсируются высокой несущей способностью.
Параметры материала можно изменять, увеличивая пропорции песка или цемента в растворе. При одинаковой плотности прочность опилкобетона будет выше, чем у арболита. Нетребовательное к условиям эксплуатации, легкое и недорогое строительное сырье применяют при возведении невысоких зданий.
Опилкобетон для возведенияИсточник YouTube.comКсилолит
Материал делают из древесных остатков (опилок, муки), которые соединяют магнезиальным связывающим раствором. В составе присутствуют ингредиенты мелкой текстуры, обеспечивающие хорошую адгезию компонентам. Готовую массу спрессовывают под высоким давлением и температурой.
Полученный в итоге ксилолит используют при создании полов. Отличить от арболита можно по форме (плиты) и плотной, практически однородной текстуре на срезе. Строительный материал устойчив к ударным и механическим нагрузкам. Высокие тепло- и шумоизоляционные свойства применяют как в многоэтажке, так и в частном доме.
Ксилолит из опилок и бетонаИсточник midiltd.ruПлиты цементно-стружечные
Сырье создают из древесных отходов, которые смешивают с бетонным раствором и минеральными добавками. Готовую массу выливают в специальные плоские формы, прессуют и сушат при высокой температуре. Полученный строительный материал не горит, не разрушается от гнилей, бактерий и насекомых.
Изделие выдерживает многократные циклы заморозки-размораживания, что позволяет использовать плиты для утепления фасадов. Вид по весу чуть тяжелее, чем арболитовые блоки, состав которых подобен. Из-за низкой эластичности сырье в изгибах трескается, при этом имеет устойчивость к продольным изменениям.
Разрушаем стереотипы о домах из арболита – плюсы и минусы материала Современный материал для утепленияИсточник domokomplekt.pro
Плюсы и минусы
Высокие теплоизоляционные качества – основная положительная сторона материала из опилок и цемента. При использовании сырья в строительстве или утеплении внутри здания сохраняется тепло зимой и приятная прохлада летом. Пористая структура обеспечивает отличную паропроницаемость. Стена из блоков толщиной в 30 см по качеству не уступает метровой перегородке из кирпича.
Материал на основе древесных остатков долговечный. При использовании фибролита или арболита с его характеристиками здание служит очень долго. Сырье устойчиво к деформациям и ударным нагрузкам. Цемент и песок в составе раствора позволяет конструкции не гореть в течение 2 часов при +1200 С.
Материал по цене выходит дешевле, чем пеноблоки, кирпичи. Если самостоятельно сделать арболит, то можно сэкономить на сырье. Низкий вес составляющих снижает нагрузку на фундамент, поэтому уменьшает затраты на обустройство при строительстве.
Блоки из опилок и цемента легко пилить и резать, придавая нужный размер без использования сложного профессионального оборудования. В поверхность можно забить дюбель или вкрутить саморез. Объемный материал устойчив к образованию сколов и трещин.
Древесная щепа, опилки или стружка – чистое и безопасное сырье, которое редко вызывает аллергию. Технология производства позволяет комбинировать разные виды остатков. Если самостоятельно делать блоки, то владелец недвижимости контролирует состав арболита, пропорции и качество ингредиентов.
Плюсы и минусы материалаИсточник kaknadostroit.ruУ строительного материала слабая влагостойкость. Сырье из стружки или щепы активно впитывает жидкость, поэтому поверхность надо обязательно защищать. Шпаклевание уличных и внутренних перегородок оградит конструкцию от разрушительного влияния воды. При утеплении фасадов предусматривают водосточную систему с крыши и вылет карнизов на расстоянии 50 см.
Изготовление блоков из опилок и цемента – долгая и кропотливая процедура. После заливки в форму материал должен затвердеть в течение 3-3,5 месяцев. Во время сушки компоненты сжимаются, уменьшаются в размерах (до 1%). Если использовать «незрелое» сырье, то усыхание отразится на изменении параметров перегородок и появлении трещин в штукатурке.
Где используют
Теплопроводность арболита применяют при возведении малоэтажных строений. Из блоков можно построить гараж, дачу или помещение для животных. Из опилкобетона делают внутренние стены в бытовках и жилых комнатах. Устойчивое к плесени сырье не гниет и хорошо сохраняет прохладу, поэтому подойдет для обустройства погреба. Если защитить от влажности, то элементы часто применяют для ограды.
Опилочные блоки используют при возведении невысоких строений в регионах с низкими и умеренными температурами. Стройматериал устойчив к морозам и позволяет выгонять здание на любом типе грунта.
Плюсы и минусы бань из арболитовых блоков Где используют строительные блоки для сооруженийИсточник kupi-krasku.ru
На участках с высокой влажностью опилкобетон дополнительно защищают изоляцией, которая поглощает лишнюю жидкость. При армировании конструкции из щеп способны долго сберегать геометрию формы. Материал в стенах часто комбинируют с кирпичом или пеноблоками, увеличивая устойчивость к нагрузкам.
Как сделать самостоятельно
Точность пропорций и четкое соблюдение технологии – основное требование для изготовления арболитовых блоков. При правильном выполнении готовое сырье по качеству и внешнему виду не отличается от промышленных изделий. Для удобства профессионалы разделили процесс на 5 этапов.
Подготовка опилок
Для создания строительного материала в домашних условиях рекомендуем взять хвойные виды. У дуба и лиственницы длительный период набора прочности – от 100 дней и более, у ели и сосны – до 50. Сырье перед использованием измельчают в дробильной машине, просеивают, оставляя элементы размером до 50 мм.
Чтобы опилки не горели и не впитывали влагу, компоненты замачивают в известковом молоке. Обработанную заготовку сушат, после чего погружают в раствор жидкого стекла с кальцием хлористым. Древесные остатки оставляют подсыхать на открытом воздухе.
Пропорции
На 1 м3 блоков или плит понадобится 200 кг опилок (стружки, щепок). Плотность или теплопроводность для арболита зависит от правильных пропорций остальных ингредиентов. Соотношение цемента, песка и извести для утеплителя – 50*50*200 кг, для стен – 150*350*100 кг. Уменьшение или увеличение концентрации ведет к изменению характеристик.
Смешивание
Первыми соединяют сухие ингредиенты для раствора, потом добавляют известь и древесные остатки. Аккуратно вливают воду (15-25 С) с растворенными химическими улучшителями. По объему жидкости не должно быть больше бетона, иначе пострадает прочность блоков.
Компоненты удобнее соединять в бетономешалке. При отсутствии оборудования раствор можно перемешивать при помощи лопаты. Чтобы масса получилась однородной, в состав добавляют однопроцентный пластификатор. Готовое сырье не должно рассыпаться в руке и выделять жидкость.
Соединение компонентов для блоковИсточник stroy-podskazka.ruФормировка
Раствор выкладывают в формы лопатами. После заполнения полного объема с горкой утрамбовывают плотным брусом, прижимая отдельные участки. Чем хаотичней масса расположена внутри конструкции, тем крепче будут блоки. На вибростоле формировка и уплотнение проходит легче и быстрее, чем вручную.
Утрамбовка раствора в конструкцииИсточник krasnoyarsk.build2last.ruСушка
Заготовки накрывают полиэтиленом, оставляют твердеть 3-5 суток. Через несколько дней формы разбирают, а раствор должен сохнуть на свежем воздухе. Периодически сырье проверяют, предупреждая растрескивание влажным опрыскиванием. До готового состояния стройматериал доходит в течение 3-4 месяцев.
Арболит это теплоизоляционный и конструктивный материал для наружных стен
Заключение
Блоки из опилок – отличный вариант для строительных и ремонтных работ. Если есть доступ к древесным остаткам, то можно самостоятельно сделать недорогое сырье для возведения небольшого коттеджа, гаража или хозяйственного здания. Высокие параметры теплоизоляции и паропроницаемости используют при утеплении.
Изготовление опилкобетонных блоков своими руками
Опилкобетон является тем строительным материалом, который отличается пониженной плотностью.
Опилкобетон позволяет возводить крупные строения без строительства сложного фундамента, так как это очень легкий, но при этом прочный материал.
Изготовить опилкобетонные блоки своими руками не так сложно, как может показаться на первый взгляд, а популярность такой материал получил благодаря своим качествам:
- высокая степень экологической безопасности;
- пожароустойчивость;
- очень высокая прочность;
- высокие теплотехнические показатели;
- паропроницаемость;
- невысокая цена;
- устойчивость к морозам.
К тому же следует принять во внимание, что делать из опилок опилкобетонные блоки своими руками не трудно. Для этого понадобятся:
- бетономешалка или растворосмеситель.
- сито с ячейками 10 на 10 мм.
- полиэтиленовая пленка.
- шпатель.
Популярность материала
Состав блока опилкобетона.
Используются блоки из опилкобетона не только при возведении домов и коттеджей, но и во время утепления подвалов, при реконструкциях (не нужно усиливать фундамент, что является очень важны фактором, если дом строится своими руками). Надо отметить, что дом, при строительстве которого использовался такой материал, отличается легкостью: если площадь дома 250 кв. м, то весить он будет всего 50 т, так как опилкобетонные блоки отличаются легкостью. Этот фактор является очень важным, так как не нужно устанавливать сложный фундамент, что значительно сократит не только финансовые, но и временные расходы. Не следует упускать из внимания то, что такой материал обладает хорошей звукоизоляцией, сборка очень простая, срок эксплуатации долгий.
Что касается плотности блоков, то здесь все зависит от соотношения опилок и песка. Если песка ушло на много меньше на изготовление блоков, чем опилок, то будет меньше их плотность, теплотехнические характеристики при этом повышаются, но вот прочность уменьшается. Если добавить побольше песка и меньше опилок, то прочность значительно возрастает, водонипроницаемость и морозостойкость тоже возрастают.
Блоки из опилкобетона получаю все большее распространение не только, благодаря своим уникальным качествам, но и тем, что сделать их можно своими руками и компоненты, из которых они состоят, не нужно заготавливать заранее. Приобретение опилок не является трудным делом, их можно найти почти в любом магазине строительных материалов, но при этом нужно внимательно отнестись к выбору опилок, так как именно от них во многом зависит то, насколько вся дальнейшая работа будет качественной. Поэтому на приобретении опилок экономить не стоит, тем более, что стоят они не дорого. Все, что нужно для того, чтобы сделать блоки из опилкобетона, можно купить в большинстве строительных магазинов, так что начинать их заготовку можно буквально за день до того, как начнется строительство.
Изготовление блоков
Растворосмеситель значительно облегчит работу по изготовлению опилкобетонных блоков.
Для того чтобы сделать опилкобетон, желательно воспользоваться бетономешалкой или растворосмесителем, так как без этого оборудования процесс изготовления будет достаточно сложным и трудоемким. Начать следует с того, что хорошо просушенные опилки нужно просеять через сито (надо пользоваться таким ситом, где ячейки по размеру 10 на 10 мм), потом они смешиваются с цементом и песком. Теперь в готовую смесь из опилок , песка и цемента следует добавить заранее подготовленное тесто из глины или известняка и все как следует перемешать, налить воды, но не сразу, а постепенно, доливая ее из лейки. После того, как налили чуть-чуть воды, нужно все снова перемешать и снова добавить воды, все это делается своими руками, тогда можно быть уверенными в том, что все будет самого высокого качества.
Если полученную смесь сжать в кулаке и получится пластичный комок, на котором видны все вмятины от руки, то значит все сделано правильно и на высоком уровне. Не должны быть видны капельки воды, их наличие говорит о низком качестве. Если все в порядке, то можно лепить блоки из опилкобетона, однако следует помнить, что к этому процессу надо приступать не позднее, чем через 1,5-2 часа после того, как смесь была приготовлена, так как потом он будет твердеть. Когда смесь укладывается в форму, она должна хорошо утрамбовываться, чтобы там не было воздуха.
Опилкобетон можно сформировать в блоки любых размеров или даже панели – все зависит от проекта. Однако следует помнить – чем больше объем опилкобетона, тем больше времени уйдет на сушку.
Блоки из опилкобетона могут быть разных размеров, четких стандартов не существует. Размеры таких блоков могут зависеть от того, насколько толстые стены, проемы и простенки, какое расстояние от проемов до углов строения, нужно принимать во внимание и способ укладки. Чтобы строительные работы проходили с максимальным удобством, длина участков стены должны быть кратной блочным размерам.
Надо отметить, что в большинстве случаев толщина блоков из опилкобетона идентична толщине двух красных кирпичей, при этом нужно учитывать и уложенный между ними раствор, таким образом, получается в среднем 140 мм. Если блоки из опилкобетона делать большими, то нужно учитывать, что они сохнут достаточно долго, если есть необходимость в ускорении процесса, то рекомендуется сделать в них несколько отверстий. Благодаря этому блоки из опилкобетона будут сохнуть гораздо быстрее, а еще значительно улучшатся их теплозащитные свойства.
1%22%20viewBox%3D%220%200%2068%2048%22%20width%3D%22100%25%22%3E%3Cpath%20class%3D%22ytp-large-play-button-bg%22%20d%3D%22M66.52%2C7.74c-0.78-2.93-2.49-5.41-5.42-6.19C55.79%2C.13%2C34%2C0%2C34%2C0S12.21%2C.13%2C6.9%2C1.55%20C3.97%2C2.33%2C2.27%2C4.81%2C1.48%2C7.74C0.06%2C13.05%2C0%2C24%2C0%2C24s0.06%2C10.95%2C1.48%2C16.26c0.78%2C2.93%2C2.49%2C5.41%2C5.42%2C6.19%20C12.21%2C47.87%2C34%2C48%2C34%2C48s21.79-0.13%2C27.1-1.55c2.93-0.78%2C4.64-3.26%2C5.42-6.19C67.94%2C34.95%2C68%2C24%2C68%2C24S67.94%2C13.05%2C66.52%2C7.74z%22%20fill%3D%22%23f00%22%3E%3C%2Fpath%3E%3Cpath%20d%3D%22M%2045%2C24%2027%2C14%2027%2C34%22%20fill%3D%22%23fff%22%3E%3C%2Fpath%3E%3C%2Fsvg%3E%3C%2Fspan%3E%3C%2Fbody%3E%3C%2Fhtml%3E» allowtransparency=»true»/>
Изготовление форм
Рекомендуется строить стену, не используя опалубку, а применяя заранее подготовленные блоки. Однако перед тем как приступить к строительству, блоки из опилкобетона нужно высушивать не менее 3-х месяцев, только после этого срока они приобретают свою марочную твердость. Форму с такого блока не следует снимать сразу, надо подождать 3-5 дней, для того чтобы процесс был ускорен, рекомендуется сделать сразу 10-20 форм. Если поступить таким образом, то работа не будет прерываться и не будет тратиться время на ожидание высыхания блоков. Что касается количества форм, то тут все зависит от того, сколько их нужно приготовить за один раз.
Для больших блоков нужно приготовить разборные двойные или одинарные формы, они представляют собой сделанные из досок ящики. Такие формы разъемные, поэтому они быстро собираются и разбираются. При их изготовлении нужно использовать доски, толщина которых равняется 20 мм, скрепляются такие конструкции при помощи стальных стержней, на них следует накрутить барашковую гайку.
Если нужно сделать блоки небольшого размера, то они приготавливаются в сотовых формах, которые собраны из 20-миллиметровых досок. Нужно учитывать, что когда блоки высыхают, то становятся меньше (результат усушки), поэтому форму нужно делать несколько больших размеров, чем блоки, которые должны получиться, разница должна составлять около 10%.
1%22%20viewBox%3D%220%200%2068%2048%22%20width%3D%22100%25%22%3E%3Cpath%20class%3D%22ytp-large-play-button-bg%22%20d%3D%22M66.52%2C7.74c-0.78-2.93-2.49-5.41-5.42-6.19C55.79%2C.13%2C34%2C0%2C34%2C0S12.21%2C.13%2C6.9%2C1.55%20C3.97%2C2.33%2C2.27%2C4.81%2C1.48%2C7.74C0.06%2C13.05%2C0%2C24%2C0%2C24s0.06%2C10.95%2C1.48%2C16.26c0.78%2C2.93%2C2.49%2C5.41%2C5.42%2C6.19%20C12.21%2C47.87%2C34%2C48%2C34%2C48s21.79-0.13%2C27.1-1.55c2.93-0.78%2C4.64-3.26%2C5.42-6.19C67.94%2C34.95%2C68%2C24%2C68%2C24S67.94%2C13.05%2C66.52%2C7.74z%22%20fill%3D%22%23f00%22%3E%3C%2Fpath%3E%3Cpath%20d%3D%22M%2045%2C24%2027%2C14%2027%2C34%22%20fill%3D%22%23fff%22%3E%3C%2Fpath%3E%3C%2Fsvg%3E%3C%2Fspan%3E%3C%2Fbody%3E%3C%2Fhtml%3E» allowtransparency=»true»/>
Полезные рекомендации
Для окончательной просушки блоки опилкобетона укладывают так, чтобы между слоями оставались зазоры для свободной вентиляции блоков.
Перед тем, как залить опилкобетоновую смесь в деревянные формы, их нужно установить на поддоны (они могут быть сделаны из бетона или пластика) и посыпать тонким слоем опилок. Потом смесь следует максимально плотно уложить в форму, для этого можно воспользоваться ручной трамбовкой. После того, как этот процесс завершен, формы с опилкобетоном следует оставить на 3 дня, за это время блоки станут прочными.
Когда установленное время истекло нужно аккуратно вынуть толь и пробки, формы разобрать, а блоки следует оставить еще на 3 дня для того, чтобы они стали еще более прочными. Потом материал надо отнести под навес для дальнейшего высушивания. Для того чтобы блоки из опилкобетона были наилучшего качества, надо соблюдать некоторые рекомендации:
- во время сушки лучше всего их раскладывать на сквозняке, тогда процесс сушки будет осуществляться равномерно;
- когда блоки укладываются для просушивания, между ними нужно оставлять зазоры;
- нужно учитывать, что может пойти дождь, поэтому, если не имеется навеса, то строительный материал надо накрыть полиэтиленовой пленкой.
После того, как блоки просушатся окончательно из них надо сделать столбы. Для этого на заранее обожженные кирпичи укладываются 2 блока, поперек них укладываются еще 2, потом поперек еще 2 и так далее по аналогичному принципу. Теперь строительный материал просохнет и затвердеет быстрее. Для того чтобы блоки из опилкобетона просохли на 100%, нужно не менее 3-х месяцев, по истечению этого срока материал отличается твердостью, прочностью, на нем нет никаких трещин.
ytimg.com%2Fvi%2F35CQjUUYRSM%2Fsddefault.jpg%27%29%3Bbackground-position%3Acenter%3Bbackground-size%3Acover%3Bbackground-repeat%3Ano-repeat%3B%22%3E%3C%2Fa%3E%3Cspan%20style%3D%22position%3Aabsolute%3Bleft%3A50%25%3Btop%3A50%25%3Bwidth%3A68px%3Bheight%3A48px%3Bmargin-left%3A-34px%3Bmargin-top%3A-24px%3Bpointer-events%3Anone%3B%22%3E%3Csvg%20height%3D%22100%25%22%20version%3D%221.1%22%20viewBox%3D%220%200%2068%2048%22%20width%3D%22100%25%22%3E%3Cpath%20class%3D%22ytp-large-play-button-bg%22%20d%3D%22M66.52%2C7.74c-0.78-2.93-2.49-5.41-5.42-6.19C55.79%2C.13%2C34%2C0%2C34%2C0S12.21%2C.13%2C6.9%2C1.55%20C3.97%2C2.33%2C2.27%2C4.81%2C1.48%2C7.74C0.06%2C13.05%2C0%2C24%2C0%2C24s0.06%2C10.95%2C1.48%2C16.26c0.78%2C2.93%2C2.49%2C5.41%2C5.42%2C6.19%20C12.21%2C47.87%2C34%2C48%2C34%2C48s21.79-0.13%2C27.1-1.55c2.93-0.78%2C4.64-3.26%2C5.42-6.19C67.94%2C34.95%2C68%2C24%2C68%2C24S67.94%2C13.05%2C66.52%2C7.74z%22%20fill%3D%22%23f00%22%3E%3C%2Fpath%3E%3Cpath%20d%3D%22M%2045%2C24%2027%2C14%2027%2C34%22%20fill%3D%22%23fff%22%3E%3C%2Fpath%3E%3C%2Fsvg%3E%3C%2Fspan%3E%3C%2Fbody%3E%3C%2Fhtml%3E» allowtransparency=»true»/>
Для того чтобы узнать насколько прочен приготовленный материал, следует провести такое испытание: блок нужно сбросить с высоты не менее 1 м, если он останется целым, то качество хорошее. И тогда можно будет через короткое время справлять новоселье в новом, прочном, уютном доме, который был построен без больших материальных затрат.
Какова технология изготовления опилкобетонных блоков?
Опилкобетон, это легкий материал, который изготавливают с добавлением таких строительных материалов как: песок, цемент, опилки.
Опилкобетон, на сегодняшний день очень популярный строительный материал, благодаря которому изготавливают дома, коттеджи, гаражи, сараи.
Блоки из опилок имеют ряд преимуществ, например: имеют хорошую теплоизоляции, прочность, устойчивые перед морозами и перед огнём.
Один из главных минусов, это то, что этот материал хорошо впитывает влагу, но такая проблема легко решается, если обработать блоки из опилкобетона специальным средством, который отталкивает влагу.
Существует несколько типов опилкобетона М20, М5, М15, М10. Что касается прочности, то наиболее прочным опилкобетон есть марки типа М5.
Такой строительный материал применяется для строительства фундамента.
Если стоит сделать облицовку внутри помещения, то для этого отлично подойдёт такой тип как: М20 и М15.
Чтобы сделать опилкобетонные блоки понадобятся следующие материалы: опилки, бетономешалка, песок, цемент, глина, вода, доски, толь, стержни с резьбой, желательно чтобы они были стальные, барашковые гайки, листовая сталь, шпатель, гвозди, сито, формы для блоков. Если нужно делать блоки большими, то желательно, чтобы формы были разъемными.
Формы для блоков можно сделать из досок, внутри нужно покрыть форму листовой сталью.
Если формы внутри не покрыты листвой сталью, тогда блоки придётся увлажнять.
Если сделали опилкобетонные блоки, нельзя чтобы они пересыхали.
Во время изготовления блоков, стоит учесть то, что после высыхания, сушки блоков, становятся меньшими.
Если блоки имеют определенную ширину и толщину, тогда их стоит делать на 15-30 сантиметров больше.
В форму нужно положить свернутую в трубочку толи, это для того, если нужно, чтобы в опилкобетоне были отверстия. Тонким слоем опилок покрываются металлические поддоны, на которые будут ставиться деревянные формы.
Чтобы сделать опилкобетонные блоки, для этого стоит высушенные опилки пропустить через сито, потом опилки стоит перемешать с песком и цементом. Следующим этапом, стоит добавить слегка скомканную глину. Всё тщательно перемешиваем, а потом добавляем небольшой струей воду.
Чтобы приготовить раствор для опилкобетонных блоков, стоит учесть следующее, для какой цели будут изготавливаться блоки, если нужна низкая плотность, тогда стоит добавить 20 килограмм опилок, 5 килограмма песка и цемента, также, для изготовления блоков из высокой плотности понадобится: 20 килограмма опилок и цемента, 5 килограмма глины, добавляем 50 килограмма песка.
Для изготовления блоков средней плотности, для этого стоит взять опилок – 20 килограмм, глины – 10, а вот песка – 35, а цемента – 15.
Чтобы узнать качество раствора, то для этого стоит взять в руку подготовленную смесь, если во время сжатия появляется вода, то это говорит о неправильном приготовлении смеси. Если комок пластичный, при этом отбавляет следы от руки, можно смело приступать к изготовлению блоков.
Перед тем как делать опилкобетонные блоки, стоит сразу же определится с размерами, с толщиной стенок.
Стандартные размеры, это толщина материала равна двух кирпичей.
Чтобы блоки быстро высохли, то стоит сделать небольшие отверстия.
Перед тем как начинать делать блоки, то необходимо определиться с размером. Самый популярный размер, это толщина материала, равная толщине двух кирпичей. Чтобы ускорить процесс высыхания, в материале делаются отверстия.
Как только приготовили раствор, то начинать делать блоки нужно приблизительно в течение 1 часа. Подготовленную смесь нужно укладывать в формы, толщина должна быть приблизительно 20 сантиметров. Каждый слой нужно хорошо трамбовать, нужно стараться, чтобы не было воздуха.
Если сделали блоки, тогда их стоит оставить в покое на 2-3 дня. Перед тем как внимать блоки из формы их стоит проверить, для этого стоит взять обычный гвоздь и провести по блоку, если осталась царапина, то блок можно смело вынимать использовать по назначению.
Gale Apps — Технические трудности
Технические трудности
Приложение, к которому вы пытаетесь получить доступ, в настоящее время недоступно. Приносим свои извинения за доставленные неудобства. Повторите попытку через несколько секунд.
Если проблемы с доступом сохраняются, обратитесь за помощью в наш отдел технической поддержки по телефону 1-800-877-4253. Еще раз спасибо, что выбрали Gale, обучающую компанию Cengage.
org.springframework.remoting.RemoteAccessException: невозможно получить доступ к удаленной службе [authorizationService@theBLISAuthorizationService]; вложенным исключением является Ice.UnknownException
unknown = «java.lang.IndexOutOfBoundsException: индекс 0 выходит за границы для длины 0
в java.base/jdk. internal.util.Preconditions.outOfBounds(Preconditions.ява: 64)
в java.base/jdk.internal.util.Preconditions.outOfBoundsCheckIndex(Preconditions.java:70)
в java.base/jdk.internal.util.Preconditions.checkIndex(Preconditions.java:248)
в java.base/java.util.Objects.checkIndex(Objects.java:372)
в java.base/java.util.ArrayList.get(ArrayList.java:458)
на com.gale.blis.data.subscription.dao.LazyUserSessionDataLoaderStoredProcedure.populateSessionProperties(LazyUserSessionDataLoaderStoredProcedure.ява: 60)
в com.gale.blis.data.subscription.dao.LazyUserSessionDataLoaderStoredProcedure.reQuery(LazyUserSessionDataLoaderStoredProcedure.java:53)
в com.gale.blis.data.model.session.UserGroupEntitlementsManager.reinitializeUserGroupEntitlements(UserGroupEntitlementsManager.java:30)
в com.gale.blis.data.model.session.UserGroupSessionManager.getUserGroupEntitlements(UserGroupSessionManager.
java:17)
на com.gale.blis.api.authorize.contentmodulefetchers.CrossSearchProductContentModuleFetcher.getProductSubscriptionCriteria(CrossSearchProductContentModuleFetcher.java:244)
на com.gale.blis.api.authorize.contentmodulefetchers.CrossSearchProductContentModuleFetcher.getSubscribedCrossSearchProductsForUser(CrossSearchProductContentModuleFetcher.java:71)
на com.gale.blis.api.authorize.contentmodulefetchers.CrossSearchProductContentModuleFetcher.getAvailableContentModulesForProduct(CrossSearchProductContentModuleFetcher.java:52)
в ком.gale.blis.api.authorize.strategy.productentry.strategy.AbstractProductEntryAuthorizer.getContentModules(AbstractProductEntryAuthorizer.java:130)
на com.gale.blis.api.authorize.strategy.productentry.strategy.CrossSearchProductEntryAuthorizer.isAuthorized(CrossSearchProductEntryAuthorizer.java:82)
на com.gale.blis.api.authorize.strategy.productentry.strategy.CrossSearchProductEntryAuthorizer.
authorizeProductEntry(CrossSearchProductEntryAuthorizer.java:44)
в ком.gale.blis.api.authorize.strategy.ProductEntryAuthorizer.authorize(ProductEntryAuthorizer.java:31)
в com.gale.blis.api.BLISAuthorizationServiceImpl.authorize_aroundBody0(BLISAuthorizationServiceImpl.java:57)
на com.gale.blis.api.BLISAuthorizationServiceImpl.authorize_aroundBody1$advice(BLISAuthorizationServiceImpl.java:61)
на com.gale.blis.api.BLISAuthorizationServiceImpl.authorize(BLISAuthorizationServiceImpl.java:1)
на com.gale.blis.auth._AuthorizationServiceDisp._iceD_authorize(_AuthorizationServiceDisp.java:141)
в com.gale.blis.auth._AuthorizationServiceDisp._iceDispatch(_AuthorizationServiceDisp.java:359)
в IceInternal.Incoming.invoke(Incoming.java:209)
в Ice.ConnectionI.invokeAll(ConnectionI.java:2800)
в Ice.ConnectionI.dispatch(ConnectionI.java:1385)
в Ice.ConnectionI.
message(ConnectionI.java:1296)
в IceInternal.ThreadPool.запустить (ThreadPool.java: 396)
в IceInternal.ThreadPool.access$500(ThreadPool.java:7)
в IceInternal.ThreadPool$EventHandlerThread.run(ThreadPool.java:765)
в java.base/java.lang.Thread.run(Thread.java:834)
»
org.springframework.remoting.ice.IceClientInterceptor.convertIceAccessException(IceClientInterceptor.java:365) org.springframework.remoting.ice.IceClientInterceptor.вызывать (IceClientInterceptor.java:327) org.springframework.remoting.ice.MonitoringIceProxyFactoryBean.invoke(MonitoringIceProxyFactoryBean.java:71) org.springframework.aop.framework.ReflectiveMethodInvocation.proceed(ReflectiveMethodInvocation.java:186) org.springframework.aop.framework.JdkDynamicAopProxy.invoke(JdkDynamicAopProxy.java:212) com.sun.proxy.$Proxy130.authorize(Неизвестный источник) ком.gale.auth.service.BlisService.getAuthorizationResponse(BlisService.
java:61) com.gale.apps.service.impl.MetadataResolverService.resolveMetadata(MetadataResolverService.java:65) com.gale.apps.controllers.DiscoveryController.resolveDocument(DiscoveryController.java:57) com.gale.apps.controllers.DocumentController.redirectToDocument(DocumentController.java:22) jdk.internal.reflect.GeneratedMethodAccessor301.invoke (неизвестный источник) Ява.base/jdk.internal.reflect.DelegatingMethodAccessorImpl.invoke(DelegatingMethodAccessorImpl.java:43) java.base/java.lang.reflect.Method.invoke(Method.java:566) org.springframework.web.method.support.InvocableHandlerMethod.doInvoke(InvocableHandlerMethod.java:215) org.springframework.web.method.support.InvocableHandlerMethod.invokeForRequest(InvocableHandlerMethod.java:142) org.springframework.web.servlet.mvc.method.annotation.ServletInvocableHandlerMethod.invokeAndHandle(ServletInvocableHandlerMethod.java:102) org.springframework.web.servlet.mvc.method.annotation.RequestMappingHandlerAdapter.invokeHandlerMethod (RequestMappingHandlerAdapter.
java:895) org.springframework.web.servlet.mvc.method.annotation.RequestMappingHandlerAdapter.handleInternal (RequestMappingHandlerAdapter.java:800) org.springframework.web.servlet.mvc.method.AbstractHandlerMethodAdapter.дескриптор (AbstractHandlerMethodAdapter.java:87) org.springframework.web.servlet.DispatcherServlet.doDispatch(DispatcherServlet.java:1038) org.springframework.web.servlet.DispatcherServlet.doService(DispatcherServlet.java:942) org.springframework.web.servlet.FrameworkServlet.processRequest(FrameworkServlet.java:998) org.springframework.web.servlet.FrameworkServlet.doGet(FrameworkServlet.java:890) javax.servlet.http.HttpServlet.service(HttpServlet.java:626) org.springframework.web.servlet.FrameworkServlet.service(FrameworkServlet.java:875) javax.servlet.http.HttpServlet.service(HttpServlet.java:733) org.apache.catalina.core.ApplicationFilterChain.internalDoFilter(ApplicationFilterChain.java:227) org.apache.catalina.core.ApplicationFilterChain.doFilter(ApplicationFilterChain.
java:162) орг.apache.tomcat.websocket.server.WsFilter.doFilter(WsFilter.java:53) org.apache.catalina.core.ApplicationFilterChain.internalDoFilter(ApplicationFilterChain.java:189) org.apache.catalina.core.ApplicationFilterChain.doFilter(ApplicationFilterChain.java:162) org.apache.catalina.filters.HttpHeaderSecurityFilter.doFilter(HttpHeaderSecurityFilter.java:126) org.apache.catalina.core.ApplicationFilterChain.internalDoFilter(ApplicationFilterChain.ява: 189) org.apache.catalina.core.ApplicationFilterChain.doFilter(ApplicationFilterChain.java:162) org.springframework.web.servlet.resource.ResourceUrlEncodingFilter.doFilter(ResourceUrlEncodingFilter.java:63) org.apache.catalina.core.ApplicationFilterChain.internalDoFilter(ApplicationFilterChain.java:189) org.apache.catalina.core.ApplicationFilterChain.doFilter(ApplicationFilterChain.java:162) орг.springframework.web.filter.OncePerRequestFilter.doFilter(OncePerRequestFilter.java:101) org.apache.catalina.core.ApplicationFilterChain.
internalDoFilter(ApplicationFilterChain.java:189) org.apache.catalina.core.ApplicationFilterChain.doFilter(ApplicationFilterChain.java:162) org.springframework.web.filter.OncePerRequestFilter.doFilter(OncePerRequestFilter.java:101) org.apache.catalina.core.ApplicationFilterChain.внутреннийDoFilter(ApplicationFilterChain.java:189) org.apache.catalina.core.ApplicationFilterChain.doFilter(ApplicationFilterChain.java:162) org.springframework.web.filter.OncePerRequestFilter.doFilter(OncePerRequestFilter.java:101) org.apache.catalina.core.ApplicationFilterChain.internalDoFilter(ApplicationFilterChain.java:189) org.apache.catalina.core.ApplicationFilterChain.doFilter(ApplicationFilterChain.ява: 162) org.springframework.boot.web.servlet.support.ErrorPageFilter.doFilter(ErrorPageFilter.java:130) org.springframework.boot.web.servlet.support.ErrorPageFilter.access$000(ErrorPageFilter.java:66) org.springframework.boot.web.servlet.support.ErrorPageFilter$1.doFilterInternal(ErrorPageFilter.
java:105) org.springframework.web.filter.OncePerRequestFilter.doFilter(OncePerRequestFilter.java:107) орг.springframework.boot.web.servlet.support.ErrorPageFilter.doFilter(ErrorPageFilter.java:123) org.apache.catalina.core.ApplicationFilterChain.internalDoFilter(ApplicationFilterChain.java:189) org.apache.catalina.core.ApplicationFilterChain.doFilter(ApplicationFilterChain.java:162) org.springframework.boot.actuate.web.trace.servlet.HttpTraceFilter.doFilterInternal(HttpTraceFilter.java:90) org.springframework.web.filter.OncePerRequestFilter.doFilter(OncePerRequestFilter.java:107) org.apache.catalina.core.ApplicationFilterChain.internalDoFilter(ApplicationFilterChain.java:189) org.apache.catalina.core.ApplicationFilterChain.doFilter(ApplicationFilterChain.java:162) org.springframework.web.filter.RequestContextFilter.doFilterInternal (RequestContextFilter.java: 99) org.springframework.web.filter.OncePerRequestFilter.doFilter(OncePerRequestFilter.java:107) org.apache.catalina.core.
ApplicationFilterChain.internalDoFilter(ApplicationFilterChain.java:189) org.apache.catalina.core.ApplicationFilterChain.doFilter(ApplicationFilterChain.java:162) org.springframework.web.filter.FormContentFilter.doFilterInternal (FormContentFilter.java:92) org.springframework.web.filter.OncePerRequestFilter.doFilter(OncePerRequestFilter.java:107) орг.apache.catalina.core.ApplicationFilterChain.internalDoFilter(ApplicationFilterChain.java:189) org.apache.catalina.core.ApplicationFilterChain.doFilter(ApplicationFilterChain.java:162) org.springframework.web.filter.HiddenHttpMethodFilter.doFilterInternal (HiddenHttpMethodFilter.java:93) org.springframework.web.filter.OncePerRequestFilter.doFilter(OncePerRequestFilter.java:107) org.apache.catalina.core.ApplicationFilterChain.внутреннийDoFilter(ApplicationFilterChain.java:189) org.apache.catalina.core.ApplicationFilterChain.doFilter(ApplicationFilterChain.java:162) org.springframework.boot.actuate.metrics.web.servlet.WebMvcMetricsFilter.
filterAndRecordMetrics(WebMvcMetricsFilter.java:154) org.springframework.boot.actuate.metrics.web.servlet.WebMvcMetricsFilter.filterAndRecordMetrics(WebMvcMetricsFilter.java:122) org.springframework.boot.actuate.metrics.web.servlet.WebMvcMetricsFilter.doFilterInternal(WebMvcMetricsFilter.java:107) org.springframework.web.filter.OncePerRequestFilter.doFilter(OncePerRequestFilter.java:107) org.apache.catalina.core.ApplicationFilterChain.internalDoFilter(ApplicationFilterChain.java:189) org.apache.catalina.core.ApplicationFilterChain.doFilter(ApplicationFilterChain.java:162) org.springframework.web.filter.CharacterEncodingFilter.doFilterInternal (CharacterEncodingFilter.java:200) org.springframework.web.filter.OncePerRequestFilter.doFilter(OncePerRequestFilter.java:107) org.apache.catalina.core.ApplicationFilterChain.internalDoFilter(ApplicationFilterChain.java:189) org.apache.catalina.core.ApplicationFilterChain.doFilter(ApplicationFilterChain.java:162) org.apache.catalina.core.
StandardWrapperValve.invoke(StandardWrapperValve.ява: 202) org.apache.catalina.core.StandardContextValve.invoke(StandardContextValve.java:97) org.apache.catalina.authenticator.AuthenticatorBase.invoke(AuthenticatorBase.java:542) org.apache.catalina.core.StandardHostValve.invoke(StandardHostValve.java:143) org.apache.catalina.valves.ErrorReportValve.invoke(ErrorReportValve.java:92) org.apache.catalina.valves.AbstractAccessLogValve.invoke(AbstractAccessLogValve.ява: 687) org.apache.catalina.core.StandardEngineValve.invoke(StandardEngineValve.java:78) org.apache.catalina.connector.CoyoteAdapter.service(CoyoteAdapter.java:357) org.apache.coyote.http11.Http11Processor.service(Http11Processor.java:374) org.apache.coyote.AbstractProcessorLight.process(AbstractProcessorLight.java:65) org.apache.coyote.AbstractProtocol$ConnectionHandler.process(AbstractProtocol.ява: 893) org.apache.tomcat.util.net.NioEndpoint$SocketProcessor.doRun(NioEndpoint.java:1707) org.apache.tomcat.util.net.SocketProcessorBase.
run(SocketProcessorBase.java:49) java.base/java.util.concurrent.ThreadPoolExecutor.runWorker(ThreadPoolExecutor.java:1128) java.base/java.util.concurrent.ThreadPoolExecutor$Worker.run(ThreadPoolExecutor.java:628) org.apache.tomcat.util.threads.TaskThread$WrappingRunnable.запустить (TaskThread.java: 61) java.base/java.lang.Thread.run(Thread.java:834)
дизайнов | Бесплатный полнотекстовый | Влияние размеров частиц опилок на физико-механические свойства необожженных глиняных блоков. продукты.В этом контексте стала очевидной социальная, экономическая и экологическая устойчивость земляных строительных материалов, обогащенных сельскохозяйственными отходами/побочными продуктами. Эти материалы требуют меньше энергии для обработки и обладают хорошими техническими характеристиками. Опилки считаются отходами, которые являются побочным продуктом деревообрабатывающей промышленности и образуются при резке, распиловке или шлифовке древесины.

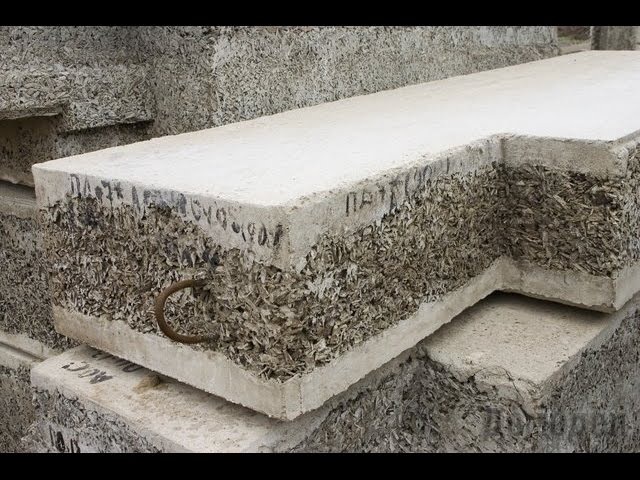
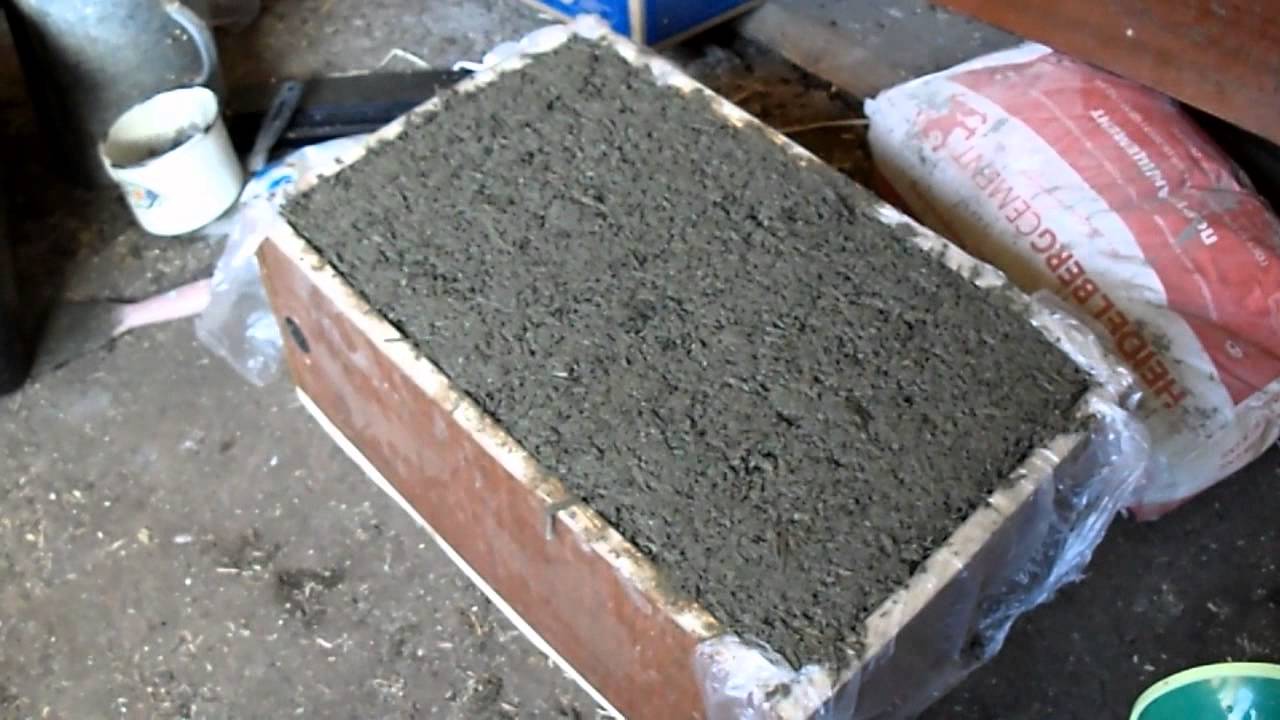


Выводы, сделанные на основе экспериментальных результатов, представленных в литературе, часто противоречивы. В результате необходимы дополнительные исследования, чтобы предложить всесторонние знания по этому вопросу. Таким образом, это исследование было направлено на изучение того, как три различных размера частиц опилок влияют на физические и механические характеристики необожженных глиняных блоков. Тесты включали плотность, линейную усадку, капиллярное водопоглощение, прочность на изгиб (FS) и прочность на сжатие (CS). Три группы образцов: SP-a (212 мкм < x < 300 мкм), SP-b (425 мкм < x < 600 мкм) и SP-c (1,18 мм < x < 2,00 мм) были приготовлены с разным процентным содержанием ( 0,25–10%) опилок. Результаты экспериментов были проанализированы и сопоставлены с эталонным образцом, чтобы сделать полезные выводы о влиянии размера и количества частиц на характеристики необожженных глиняных блоков.Результаты включения опилок с разным размером частиц дают интригующие дополнительные данные, которые помогут оценить потенциальное использование опилок при производстве необожженных глиняных блоков.
Обзор свойств, структурных характеристик и возможностей применения бетона, содержащего древесные отходы, в качестве частичной замены одного из составляющих его материалов
[1] ICE. (1975) Институт инженеров-строителей — Королевская хартия, подзаконные акты, положения и правила 1975 года;. https://www.ice.org.uk/ICEDevelopmentWebPortal/media/Documents/Royal-Charter-By-laws-Regulationsand-Rules-2015.pdf (оценка 19 февраля 2016 г.). Поиск в Google Scholar
[2 ] ЛЕД. Новый инженер-строитель 2017; http://www.newcivilengineer.com/confirmation?www.newcivilengineer.com%252fnew-definition-for-civil-engineering (оценка 17 февраля 2016 г.) Поиск в Google Scholar
[3] ASCE (2018) About Civil Инжиниринг. Американское общество инженеров-строителей, 2018 г.; http://www.asce.org/about_civil_engineering/ (по состоянию на 12 января 2018 г.) Поиск в Google Scholar
[4] RAE.(2017) http://www.raeng.org.uk/education/vps/sustdev.htm 2017 (оценка 6-10-2017). Поиск в Google Scholar
[5] MEHTA, P.K. (2002). Экологизация бетонной промышленности для устойчивого развития. Бетон Интернешнл Том. 24, № 7, стр. 23–28. Поиск в Google Scholar
[6] OCHSENDORF, J A. (2005) Устойчивое проектирование: будущее проектирования конструкций, Structures. ASCE http://www.ascelibrary. org/10.1061/40753(171)146Поиск в Google Scholar
[7] СУХЕНДРО, Б.(2014). К зеленому бетону для более устойчивой окружающей среды. Procedia Engineering Vol. 95, стр. 305 — 320.10.1016/j.proeng.2014.12.190Поиск в Google Scholar
[8] ШАФИГ П., МАХМУД Х. Б., ДЖУМААТ М. З., ЗАРГАР М. (2014). Отходы сельского хозяйства как заполнитель в бетонных смесях — обзор. Строительство и строительные материалы, Vol. 53, pp. 110 — 117.10.1016/j.conbuildmat.2013.11.074Search in Google Scholar
[9] DEMIRBOGA, R., GÜL, R. (2006) Производство высокопрочного бетона с использованием промышленных побочных продуктов.Строительная среда, Vol. 41, pp. 1124-1127.10.1016/j.buildenv.2005.04.023Search in Google Scholar
[10] DETWILER, RJ, FAPOHUNDA, C. A, NATALIE, J. (1994) Использование дополнительных вяжущих материалов для увеличения устойчивость к проникновению ионов хлора в бетон, отвержденный при повышенных температурах. Журналы материалов ACI, Vol. 91, № 1, стр. 63 — 66. Поиск в Google Scholar
[11] ЗЕЛЬКОВИЧ, М. (2009). Влияние метакаолина на долговечность бетона. Магистр Диссертация, Университет Торонто, Канада.Поиск в Google Scholar
[12] ИБРАГИМ, А. Г., ОКОЛИ, О. Г.. ДАХИРУ, Д. (2016). Сравнительное исследование свойств обычного бетона на портландцементе и бинарного бетона, содержащего метакаолин, полученный из канкарского каолина в Нигерии. Журнал экологических технологий ATBU, Vol. 9, № 2, стр. 53–59. Поиск в Google Scholar
[13] ТОМАС М. (2007). Оптимизация использования летучей золы в бетоне. Ассоциация портландцемента http://www.cement.org/docs/default-source/fc_concrete_technology/is548-optimizing-the-use-of-flyashash-concrete.pdf, (проверено 1–1–2017). Поиск в Google Scholar
[14] FOONG, K.Y., ALENGARAM, U.J., JUMAAT, M.Z.MO, K.H. (2015) Улучшение механических свойств легкого бетона из скорлупы масличной пальмы с использованием золы рисовой шелухи и промышленного песка. Журнал Чжэцзянского университета-НАУКА A (прикладная физика и инженерия), Vol. 16, No. 1, pp. 59 — 69.10.1631/jzus.A1400175Search in Google Scholar
[15] FAPOHUNDA, C., AKINBILE, B, SHITTU A. (2017) Структура и свойства раствора и бетона, содержащего рисовую шелуху зола как частичная замена обычного портландцемента — обзор.Международный журнал устойчивой застроенной среды (в печати). http://dx.doi.org/10.1016/j.ijsbe.2017.07.00410.1016/j.ijsbe.2017.07.004Открыть DOISsearch в Google Scholar
[16] GHORPADE, V.G. (2012). Влияние золы древесных отходов на прочностные характеристики бетона. Природа, окружающая среда и технологии загрязнения, Vol. 11, № 1, стр. 121–124. Поиск в Google Scholar
[17] ELINWA, AU MAMUDA AM (2014). Зола опилок как порошковый материал для самоуплотняющихся бетонов, содержащих нафталинсульфонат.Hindawi Publishing Corporation Advances in Civil Engineering, стр. 1–8. 2013). Переработанные бетонные заполнители: обзор. Международный журнал бетонных конструкций и материалов. Том. 7, № 1, с. 61-69, DOI 10.1007/s40069-013-0032-5.10.1007/s40069-013-0032-5Открыть DOIS Search в Google Scholar
[19] ALENGARAM. У. Дж., МУХИТ, Б. Дж., ДЖУМААТ, М. З. (2013). Использование легкого заполнителя скорлупы косточек масличной пальмы в бетоне — обзор.Строительство и строительные материалы, Vol. 38, pp. 161-172.10.1016/j.conbuildmat.2012.08.026Search in Google Scholar
[20] ФАПОХУНДА, К. А., АКИНСАНЯ, А. Ю., АДЕРОЮ, С. О. и ШИТТУ, К. А. (2016). Пригодность дробленой коровьей кости в качестве частичной замены мелких заполнителей для производства бетона. Вест-Индийский инженерный журнал, Vol. 39, № 1, стр. 25 — 31. Поиск в Google Scholar
[21] ФАПОХУНДА. С. А, ШИТТУ К. А, АДЕРОЮ., С. О. АКИНСАНЯ А.Ю. (2016). Прочностные характеристики бетона с щебнем в качестве частичной замены мелких заполнителей при различных водоцементных отношениях.Acta Technica Corniviensis — Инженерный бюллетень, Vol. 9, № 1, стр. 162–169. Поиск в Google Scholar
[22] GANIRON JR, TU (2014). Влияние опилок как мелкого заполнителя в бетонной смеси для строительства зданий. Международный журнал передовых наук и технологий, Vol. 63, стр. 73-82. http://dx.doi.org/10.14257/ijast.201 4.63.07Поиск в Google Scholar
[23] RAHEEM, A.A., OLASUNKANMI, B.S. FOLORUNSO, C.S. (2012). Зола опилок как частичная замена цемента в бетоне.Организация, технология и менеджмент в строительстве, Vol. 4, № 2, стр. 474–480.10.5592/otmcj.2012.2.3Поиск в Google Scholar
[24] ГАРСИЯ, М., СОУЗА-КОУТИНЬО, Дж. (2013). Прочность и долговечность цемента с зольным остатком лесных отходов. Строительство и строительные материалы, Vol. 41, с. Влияние зольных опилок (ЗДА) в качестве примеси в цементном тесте и бетоне. IJISET — Международный журнал инновационных наук, техники и технологий, Vol.1, № 10, стр. 736–743. Поиск в Google Scholar
[26] SUBBARAMAIAH, G. (2016) Исследования прочности и долговечности конструкционного бетона из древесных отходов. Кандидатская диссертация представлена в Технологическом университете им. Джавахарлала Неру в Анантапуре, Анантапураму, Индия. (http://shodhganga.inflibnet.ac.in/bitstream/.pdf оценка 6-10-2017). Поиск в Google Scholar
[27] CHEAH, C.B., RAMLI, M. (2014). Использование золы древесных отходов в качестве частичного заменителя цемента в производстве конструкционных бетонов и строительных растворов: обзор.Ресурс. Сохранить. Переработка, Том. 55, № 7, стр. 669-685. Поиск в Google Scholar
[28] ЧОУДХУРИ С., МИШРА М., СУГАНЯ О. (2014). Включение золы древесных отходов в качестве частичного замещающего материала для изготовления конструкционного бетона: обзор. Инженерный журнал Айн Шамс, том. 6, стр. 429–437. Поиск в Google Scholar
[29] ПРУСТИ, Дж. К., ПАТРО, С. К., БАСАРКАР, С. С. (2016). Бетон с использованием агроотходов в качестве мелкого заполнителя для устойчивой окружающей среды.t — Обзор.Международный журнал устойчивой застроенной среды Vol. 5, стр. 312–333.10.1016/j.ijsbe.2016.06.003Поиск в Google Scholar
[30] ДЖАХАНГИРИ Н., КОСЕОГЛУ К., ЧЕНГИЗЛЕР Х. (2017). Бетон с побочными продуктами и отходами в виде заполнителя или цемента. Журнал Института естественных и прикладных наук Университета Дикле, том 6, № 1, стр. 29–38. Поиск в Google Scholar
[31] АБДУЛЛАХИ, М. (2006). Характеристики бетона Wood ASH/OPC. Леонардо Электрон J Pract Technol Vol.8, pp. 9 — 16. Поиск в Google Scholar
[32] CHEAH, C.B, RAMLI, M. (2012). Механическая прочность, долговечность и усадка при высыхании конструкционного раствора, содержащего HCWA в качестве частичной замены цемента. Строительство и строительные материалы, Vol. 30, стр. 320-32910.1016/j.conbuildmat.2011.12.009Поиск в Google Scholar
[33] BERRA, M, MANGIALARDI, T, PAOLINI, A.E. (2015). Повторное использование летучей золы древесной биомассы в материалах на основе цемента. Строительство и строительные материалы, Vol. 76, с.286-296.10.1016/j.conbuildmat.2014.11.052Поиск в Google Scholar
[34] ETIEGNI, L, CAMPBELL, A.G. (1991). Физико-химические характеристики древесной золы. Биоресурсные технологии, Vol. 37, No. 2, pp. 173-17810.1016/0960-8524(91)
-ZSearch in Google Scholar [35] NAIK, T.R, KRAUS, R.N, SIDDIQUE, R. (2002) Демонстрация технология производства бетона и использование древесной золы из Висконсина, Департамент природных ресурсов штата Висконсин (Мэдисон, Висконсин) для проекта № 1-06 Отчет UWM №. CBU-2002-30, Центр утилизации побочных продуктов, Факультет гражданского строительства и механики, Университет Висконсин-Милуоки. Поиск в Google Scholar
[36] NAIK, T. R, KRAUS, R. N, SIDDIQUE, R (2003). CLSM, содержащий смесь угольной золы и нового пуццоланового материала. Журналы материалов ACI, Vol. 100, № 3, стр. 208-15. Поиск в Google Scholar
[37] UDOEYO, F. F, INYANG, H, YOUNG, D. T, OPARADU, E. E. (2006). Возможности использования отходов древесной золы в качестве добавки в бетон. Журнал материалов в области гражданского строительства, Vol.18, № 4, стр. 605-1110.1061/(ASCE)0899-1561(2006)18:4(605) Поиск в Google Scholar
[38] ETTU, LO, MBAJIORGU, MS W, NJOKU, F. C , AJOKU, C. A, NWACHUKWU, KC (2013) Изменение прочности композитов золы и опилок в зависимости от процентного содержания золы опилок. Гражданские и экологические исследования, Vol. 3, № 9, стр. 53–58. Поиск в Google Scholar
[39] ЧОУДХУРИ С., МАНИАР А., СУГАНЯ О. М. (2015). Развитие прочности бетона с добавлением цемента с добавлением древесной золы и использование моделей мягких вычислений для прогнозирования параметров прочности». Журнал перспективных исследований, Vol. 6, стр. 907-913.10.1016/j.jare.2014.08.006 Поиск в Google Scholar
[40] НАИК, Т. Р., КРАУС, Р. Н. (2003). Новый источник пуццолановых материалов. Concrete International, 55-62. Поиск в Google Scholar
[41] АБХИШЕК Д. С., КУМБАР П. К. (2017). Экспериментальное исследование аспектов долговечности бетона при частичной замене цемента золой опилок. Международный журнал научно-исследовательской организации Vol. 1, № 5, стр. 36 — 41. Поиск в Google Scholar
[42] CHEAH, C.Б, ЧАСТЬ, В.К., РАМЛИ, М. (2015). Гибридизация угольной летучей золы и древесной золы для изготовления низкощелочного геополимерного несущего блока, отверждаемого при температуре окружающей среды, Construction Building Material, Vol. 88, стр. 41-55. Поиск в Google Scholar
[43] АДАМУ, М., ТИФАСЭ, А.С., УЧЕ, О.А.У. (2017). Инженерные свойства золобетона из промышленных древесных отходов. Международный журнал достижений в области строительства, Vol. 1, № 1, стр. 1–10. Поиск в Google Scholar
[44] AWOLUSI, T.М., СОДЖОБИ, А.О., АФОЛЯН, Д.О.С.Д.А. (2017). и применение латерита в бетоне: перспективы и последствия повышенной температуры. Когент Инжиниринг. https://doi.org/10.1080/23311916.2017.1387954.10.1080/23311916.2017.1387954Открыть поиск DOIS в Google Scholar
[45] RAHEEM, A. A, ADEDOKUN, S. I, AJAYI, B. R, ADEDOYIN, O, АДЭГБОЙЕГА, БО (2017). Применение зольных опилок в качестве частичной замены цемента при производстве сцепляемой брусчатки. Международный журнал устойчивой инженерии и технологий строительства, Vol.8, № 1, стр. 1–11. Поиск в Google Scholar
[46] КУМАР, Т. Р. П., СУДХИШ, К., САСИ, К. С. (2015). Прочностные характеристики геополимерного бетона на основе зольных опилок. Международный журнал исследований ChemTech, Vol. 8, № 2, стр. 738-745. Поиск в Google Scholar
[47] MARTHONG, C. (2012). Зола опилок (ЗДА) как частичная замена цемента». Международный журнал инженерных исследований и приложений, Vol. 2, № 4, с. 1980-1985. Поиск в Google Scholar
[48] ТЯГЕР С., УЦЕВ Дж., АДАГБА Т.(2011). Пригодность зольно-известковой смеси опилок для производства пустотелых блоков Sandcrete. Нигерийский технологический журнал, Vol. 30, № 1, стр. 79-84Поиск в Google Scholar
[49] MAGESWARI, M, VIDIVELLI, B. (2009). Использование зольных опилок в качестве замены мелкого заполнителя в бетоне. Журнал экологических исследований и разработок, Vol. 3, № 3, стр. 720-726. Поиск в Google Scholar
[50] UDOEYO, F. F, DASHIBIL, P. U. (2002). Зола опилок как материал для бетона. Журнал материалов в области гражданского строительства, Vol.14, № 2, стр. 173-176.10.1061/(ASCE)0899-1561(2002)14:2(173) Поиск в Google Scholar
[51] ASTM C618-05 (2005). Стандартные технические условия на летучую угольную золу и необработанный или прокаленный природный пуццолан для использования в качестве минеральной добавки в бетон. Американское общество по испытаниям и материалам International West Conshohocken Philadelphia. Поиск в Google Scholar
[52] ВАСИЛЬЕВ С.В., БАКСТЕР Д., АНДЕРСЕН Л.К., ВАСИЛЕВА К.Г. (2010). Обзор химического состава биомассы. Топливо, Том.89, стр. 913-33.10.1016/j.fuel.2009.10.022Поиск в Google Scholar
[53] ЭЛИНВА А.У., МАХМУД, А.М. (2002). Зола из древесных отходов как заменитель цемента. Цементобетонные композиты, Vol. 24, 219-22.10.1016/S0958-9465(01)00039-7Поиск в Google Scholar
[54] ELINWA, AU, EJEH, S.P. (2004). Эффекты введения летучей золы от сжигания опилок в цементные пасты и строительные растворы. Журнал азиатской архитектуры, строительной техники, Vol. 3, № 1, с. 1-7.10.3130/jaabe.3.1Поиск в Google Scholar
[55] BS12. (1996). Британский институт стандартов — Спецификация портландцемента. Британский институт стандартов, ЛондонПоиск в Google Scholar
[56] РАДЖАММА, Р., БОЛЛ, Р. Дж., ТАРЕЛХО, Л. (2009). Характеристики и использование летучей золы биомассы в материалах на основе цемента. J Hazard Mater, Vol. 172, pp.1049-60.10.1016/j. jhazmat.2009.07.109Поиск в Google Scholar
[57] ДЕМИС С., ТАПАЛИ Т. Г., ПАПАДАКИС В.Г. (2014). Исследование эффективности использования золы биомассы в качестве пуццолановых материалов. Строительство и строительные материалы, Vol. 68, стр. 291-30010.1016/j.conbuildmat.2014.06.071Поиск в Google Scholar
[58] ПАПАДАКИС, В. Г., АНТИОХОС, С., ЦИМАС, С. (2002). Дополнительные вяжущие материалы в бетоне — Часть II: фундаментальная оценка коэффициента полезного действия. Цемент, бетон и исследования, Vol. 32, No. 10, pp. 1533 — 1538.10.1016/S0008-8846(02)00829-3Поиск в Google Scholar
[59] ANTIOHOS, S.К., ПАПАДАКИС, В.Г., ЧАНИОТАКИС, Э., ЦИМАС, С. (2007). Улучшение характеристик тройных смешанных цементов путем смешивания различных типов летучей золы. Cem Concr Res. Том. 37, No. 6, pp. 877-85.10.1016/j.cemconres.2007.02.017Search in Google Scholar
[60] RAMOS, T, MATOS, A.M., SOUSA-COUTINHO, J. (2013). Раствор с золой древесных отходов: механическая прочность, стойкость к карбонизации и расширению ASR. Строительство и строительные материалы, Vol. 49, стр. 343-35110.1016/j.conbuildmat.2013.08.026Поиск в Google Scholar
[61] MEHTA, P.К., МОНТЕЙРО, П.Дж.М. (2006). Конкретный. микроструктура, свойства и материалы McGraw-Hill, 3-е издание. Поиск в Google Scholar
[62] NEVILLE, AM (2011). Свойства бетона. Pearson Education Limited, Эдинбург, Англия, 5-е издание. http://www.pearsoned.co.uk. Поиск в Google Scholar
[63] MASSAZZA, F. (1998). LEA’S химия цемента и бетона. Питер С. Хьюлетт Арнольд, 4-е издание. Поиск в Google Scholar
[64] BS EN 196-1. (1995). Методы испытания цемента.Физические тесты. Испытания на прочность. Британский институт стандартов, Лондон. Поиск в Google Scholar
[65] SHETTY, MS (2009). Бетонная технология. S. Chand and Company Ltd, Нью-Дели, MultiColour Edition. Поиск в Google Scholar
[66] GAMBHIR, ML (2013). Технология бетона — теория и практика. McGraw Hill Education Private Limited, Нью-Дели, 5-е издание. Поиск в Google Scholar
[67] FALADE, F, IKPONMWOSA, E, AROGUNDADE, A. (2011). Исследование некоторых конструктивных свойств пенобетона.Журнал инженерных исследований, Vol. 16, стр. 67–80. Поиск в Google Scholar
[68] ELLINWA, A.U., EJEH, S.P., AKAPABIO, I.O. (2005). Использование метакаолина для улучшения опилкозольного бетона. Concrete International. Поиск в Google Scholar
[69] BS 811 0 (1997). Конструктивное использование бетона. Британский институт стандартов, Лондон. Поиск в Google Scholar
[70] MARTHONG, C. (2013). Исследование размерного эффекта опилкозолобетона при сжимающей нагрузке. Журнал IOSR по машиностроению и гражданскому строительству, Vol.1, № 5, стр. 27–32. Поиск в Google Scholar
[71] ETTU, L. O, EZEH, J. C, ANYA, U. C, NWACHUKWU, K. C, NJOKU, KO (2013) ). Прочность трехкомпонентного цементного бетона, содержащего золу рисовой шелухи афикпо и золу опилок. Международный журнал технических изобретений, Vol. 2, № 4, стр. 38 — 42. Поиск в Google Scholar
[72] ACI 318M-08 (2008). Требования строительных норм и правил к конструкционному бетону (ACI 318M-08) и комментарии. Американский институт бетона. Поиск в Google Scholar
[73] ASTM-C330 (2009).Стандартная спецификация для легких заполнителей для конструкционного бетона. American Society for Testing and Materials International, Филадельфия. Поиск в Google Scholar
[74] DAY, RL (1990). Использование пуццоланов в недорогом жилье — доклад о состоянии дел, подготовленный для Центра исследований международного развития в Оттаве, Канадский центр исследований в области международного развития, Оттава. Поиск в Google Scholar
[75] MHAISKAR, Y, NAIK, DD (2012 ). Исследования корреляции между прочностью на изгиб и прочностью бетона на сжатие, The Indian Concrete Journal, стр.1–6. Поиск в Google Scholar
[76] OLUOKUN, F.A. (1991). Прогноз прочности бетона на растяжение по его прочности на сжатие: оценка существующих отношений для нормального бетона. Журнал материалов ACI, Vol. 88, № 3, стр. 302–309. Поиск в Google Scholar
[77] ATIS, CD (2005). Прочностные свойства крупнообъемного бетона, уплотненного катком с летучей золой, и пригодного для обработки бетона, а также влияние условий отверждения. Исследования цемента и бетона, Vol. 35, стр. 1112 — 1121.10.1016/л.cemconres.2004.07.037Поиск в Google Scholar
[78] JSCE (2007). Стандартные спецификации для бетонных конструкций, материалов и конструкций. Японское общество инженеров-строителей, Vol. 7, стр. 10–11. Поиск в Google Scholar
[79] Комитет ACI (2011). Требования строительных норм и правил к конструкционному бетону. Американский институт бетона, Фармингтон-Хиллз, Мичиган. Поиск в Google Scholar
[80] JACKSON, N, DHIR, R.K. (1990). Материалы для гражданского строительства, Macmillan London, 4-е издание.Поиск в Google Scholar
[81] Патель В. Н. (209). Сорбционные испытания для оценки стойкости бетона к циклическому замораживанию-оттаиванию. Департамент гражданского строительства и прикладной механики, Университет Макгилла, Монреаль, Канада. Поиск в Google Scholar
[82] SIDDIQUE, R. (2013). Прочность на сжатие, водопоглощение, сорбционная способность, сопротивление истиранию и проницаемость самоуплотняющихся бетонов, содержащих золу угольного остатка. Констр. Строить. Матер. Том. 47, стр. 1444-1450.10.1016/л.conbuildmat.2013.06.081Поиск в Google Scholar
[83] ASTM C1567-11 (2011). Стандартный метод испытаний для определения потенциальной реакционной способности щелочно-кремнеземных комбинаций вяжущих материалов и заполнителя (метод ускоренного растворного стержня). Американское международное общество испытаний и материалов, Филадельфия. Поиск в Google Scholar
[84] WANG, S, BAXTER, L. (2007). Всестороннее исследование летучей золы биомассы в бетоне: прочность, микроскопия, кинетика и долговечность. Технология топливных процессов.88, стр. 1165-70.10.1016/j.fuproc.2007.06.016Поиск в Google Scholar
[85] CHANG, C. F, CHEN, JW (2006). Экспериментальное исследование глубины карбонизации бетона. Исследования цемента и бетона, Vol. 36, стр. 1760-1767.10.1016/j.cemconres.2004.07.025Поиск в Google Scholar
[86] WANG, S, LLAMAZOS, E, BAXTER, L, FONSECA, F. (2008). Долговечность бетона на основе летучей золы из биомассы: замораживание и оттаивание, а также экспресс-тесты на проницаемость для хлоридов. Топливо, Том. 87, стр. 359-64.10.1016/j.fuel.2007.05.027Поиск в Google Scholar
[87] ASTM C 1202 — 97 (1997). Стандартный метод испытаний для электрической индикации способности хлорида противостоять хлориду». American Society for Testing and Materials International, Philadelphia. Search in Google Scholar
[88] AMRUTHA, G, NAYAK, M, NARASIMHAN, C, RAJEEVA, S. V. (2089). Хлорид-ионная непроницаемость самоуплотняющихся крупнообъемных зольных бетонных смесей. Междунар. Дж. Гражданская среда. англ. Том. 11, № 4, стр. 29 — 35. Поиск в Google Scholar
[89] ACI 515.1 (1985). Руководство по использованию гидроизоляционных, гидроизоляционных, защитных и декоративных барьерных систем для бетона, Руководство ACI по бетонной кладке, Сборный бетон, Специальные процессы. Поиск в Google Scholar
[90] BDEIR, LMH (2012). Изучить некоторые механические свойства раствора с опилками как частичную замену песка. Анбарский журнал технических наук, Vol. 5, № 1, стр. 22–30. Поиск в Google Scholar
[91] КУМАР Д. , СИНГХ С., КУМАР Н., ГУПТА А.(2014). Недорогой строительный материал для бетона в виде опилок. Глобальный журнал инженерных исследований, Vol. 14, № 4, стр. 1–5. Поиск в Google Scholar
[92] OLUTOGE, F. A. (2010) Исследования опилок и скорлупы пальмовых ядер в качестве замены агрегата. Журнал инженерных и прикладных наук ARPN, Vol. 5, № 4, стр. 7–13Поиск в Google Scholar
[93] BOOB, T. N. (2014). Производительность опилок в недорогих песчано-бетонных блоках. Американский журнал инженерных исследований (AJER), Vol.3, № 4, стр. 197-206. Поиск в Google Scholar
[94] OSEI, D.Y., JACKSON, E.N. (2016). Прочность бетона на сжатие при использовании опилок в качестве заполнителя. Международный журнал научных и инженерных исследований, Vol. 7, № 4, стр. 1349–1353. Поиск в Google Scholar
[95] НАРАЯНАН А., ХЕМНАТ Г., САМПОЛ К., МЭРИ А. (2017). Замена мелкого заполнителя опилками. Международный журнал перспективных исследований в области фундаментальных инженерных наук и технологий, Vol. 3, № 35, с.206 — 210.Поиск в Google Scholar
[96] ОКОРОАФОР С.У., ИБЕАРУГБУЛАМ О.М., ОНУКВУГА Э.Р., АНЬЯОГУ Л., АДАХ Э.И. Структурные характеристики опилочно-песчано-цементного композита. Международный журнал достижений в области исследований и технологий, Vol. 6, № 1, стр. 173–180. Поиск в Google Scholar
[97] OYEDEPO, O.J., OLUWAJANA, S.D., AKANDE, S.P. (2014). Исследование свойств бетона с использованием опилок в качестве частичной замены песка. Гражданские и экологические исследования, Том, 6, №2, стр. 35–42. Поиск в Google Scholar
[98] АЛЬБЕРТ, М. Дж., ААЙЕНА, К. Дж., АНЮ, М. Р., БОБИНА, Э. Дж. (2016). Частичная замена мелкого заполнителя опилками на бетон. Международный журнал технологических исследований в области машиностроения Vo. 3, № 9, стр. 2439–2443. Поиск в Google Scholar
[99] THANDAVAMOURTHY, TS (2015). Древесные отходы как крупный заполнитель в производстве бетона. Европейский журнал экологического и гражданского строительства. http://dx. doi.org/10.1080/19648189.2015.101663110.1080/19648189.2015.1016631Открыть поиск в Google Scholar
[100] BUTT, W. A., GUPTA, K, JHA J. N. (2016) Прочностные характеристики глинистого грунта, стабилизированного золой из опилок. Международный журнал геоинженерии, Vol. 7, № 18, с. 2 — 9. Поиск в Google Scholar
[101] НИМЯТ, П. С, К К, Ю. (2013). Влияние зольных опилок (SDA) Pozzolana на характеристики бетона с добавлением цементного теста при высоких температурах. Гражданские и экологические исследования, Vo. 3, № 11, с.22 — 28.Поиск в Google Scholar
Влияние предварительной обработки и добавок на улучшение цементно-древесного композита: обзор :: Биоресурсы
Брахмиа, Ф.З., Хорват, П.Г., и Альпар, Т.Л. (2020). « Влияние предварительной обработки и добавок на улучшение цементно-древесного композита: обзор », « BioRes. 15(3), 7288-7308.Abstract
Древесно-цементные композиты (ЦДК) являются популярным строительным материалом. Легкие или панельные деревянные дома имеют растущий рынок в Центральной Европе.Требования и правила как на глобальном, так и на национальном уровне требуют постоянного развития. В данной статье обобщены результаты исследований по улучшению гигроскопических и механических свойств и сокращению времени производства ХБК за счет предварительной обработки и добавок. Кроме того, обсуждаются новые перспективы повышения его огнестойких свойств за счет применения антипиреновой предварительной обработки. ХБК без какой-либо предварительной обработки относится к категории огнестойкости B-s1, d0.Использование антипиренов может повысить его до категории А1, но антипирены не должны влиять на первичные свойства CWC. Существует ряд потенциальных антипиренов древесины, которые можно использовать, например, соединения фосфора, бора и магния.
Загрузить PDF
Полный текст статьи
Влияние предварительной обработки и добавок на улучшение качества цементно-древесного композита: обзор
Фатима З. Брахмиа*, Петер Дьердь Хорват и Тибор Л. Альпар
Цементно-древесные композиты (ЦДК) — популярный строительный материал.Легкие или панельные деревянные дома имеют растущий рынок в Центральной Европе. Требования и правила как на глобальном, так и на национальном уровне требуют постоянного развития. В этой статье обобщены результаты исследований по улучшению гигроскопических и механических свойств и сокращению времени производства CWC за счет предварительной обработки и добавок. Кроме того, обсуждаются новые перспективы повышения его огнестойких свойств за счет применения антипиреновой предварительной обработки.ХБК без какой-либо предварительной обработки относится к категории огнестойкости B-s1, d0. Использование антипиренов может повысить его до категории A 1 , но антипирены не должны влиять на основные свойства CWC. Существует ряд потенциальных антипиренов древесины, которые можно использовать, например, соединения фосфора, бора и магния.
Ключевые слова: Цемент; Древесина; отвердители; добавки; Уход; антипирены; Ингибиторы; Механические свойства
Контактная информация: Шопронский университет, Симони Карой Факультет инженерии, науки о древесине и прикладного искусства, Институт изделий и технологий на основе древесины, H-9400 Шопрон, Байчи-Зс. Евросоюз. 4.Венгрия; * Автор, ответственный за переписку : [email protected]
ВВЕДЕНИЕ
За прошедшие годы многие аспекты строительства зданий, от дизайна до строительных материалов, улучшились. Есть два известных вида строительства: деревянное строительство и бетонное строительство. Здания из дерева легкие и теплые зимой. Строительный материал обладает хорошей устойчивостью к растягивающим усилиям, но его сопротивление огню слабое (Deplazes 2005).Бетонные здания имеют тяжелую конструкцию и часто высокие (Косматка и др. 2008). Их стойкость к огню превосходна, но в отношении предела прочности на разрыв, который считается очень небольшим и в большинстве случаев им пренебрегают, верно обратное. Таким образом, стальная арматура используется в бетонных конструкциях для придания прочного сопротивления изгибу и растяжению, а также для защиты зданий от сейсмической активности (Zhang and Sun 2018). По прочности на сжатие бетон превосходен из-за содержащихся в нем заполнителей (Косматка и др. 2008). Проблема с бетоном заключается в том, что для достижения максимальной прочности требуется 28 дней, а вода вызывает коррозию арматурной стали (Zhang et al. 2017; Marcos-Meson et al. 2018), что со временем делает здания непрочными. Кроме того, распространенной проблемой в бетоне являются трещины (Hillerborg et al. 1976).
Текущие исследования сосредоточены на новом материале: цементно-деревянном композите (Frybort et al. 2008). Этот продукт имеет преимущества как бетона, так и дерева.Его огнестойкость лучше, чем у дерева. Он имеет лучшую прочность на растяжение и изгиб, чем бетон, а также легче (Deplazes 2005; Kosmatka et al . 2008). В цементно-древесных композитах цемент армирован древесными волокнами, частицами, чешуйками и древесной ватой различной формы и размера (Ferraz et al. 2012). Цементно-древесным композитам требуется 24 часа для отверждения и достижения максимальной прочности. Поскольку он легче бетона, этот тип материала прост в использовании, что означает экономию времени и денег. Эти композиты обычно используются в качестве изоляционного или строительного материала (Quiroga et al. 2016). В строительстве цементно-древесный композит используется в качестве панелей, а в некоторых недавних исследованиях цементно-древесные композиты использовались в основных конструктивных элементах зданий, таких как балки (Bejó and Takáts 2005; Frybort et al. 2008). Из-за прочностных свойств CWC он обычно используется для внутренних и наружных работ, а также для акустических свойств (, например, ., звуковые барьеры автомобильных дорог) (N и др. 2014). Гюндуз по адресу ул. (2018) указано, что цементно-стружечные плиты с композитной формой являются эффективным применением с точки зрения акустических барьеров от наружного шума.
Наиболее известными продуктами на основе цемента являются цементно-волокнистые плиты, цементно-стружечные плиты (ЦСП), древесно-волокнистые цементные плиты (ДВЦП) и строительные блоки (Vaickellionis и др. 2006). В качестве теплоизоляции используются плиты низкой плотности (Frybort и др. 2008). Наиболее важным аспектом изготовления изделий из цемента и дерева является соотношение используемых материалов, то есть соотношения древесины/цемента и цемента/воды (Phillips and Hse 1987). Совместимость древесины и цемента важна, поскольку древесина может содержать соединения, влияющие на отверждение цемента. Добавки отвердителя используются для решения этой проблемы и ускорения отверждения цемента.
В большинстве случаев используется портландцемент. Не все породы дерева хорошо сцепляются с цементом, потому что каждая порода имеет разную структуру и химический состав.Хотя вид древесины важен, место произрастания и возраст могут иметь значение (Wei et al. . 2000; Frybort et al. 2008; Alpár et al. . 2011). Вот почему в течение многих лет было проведено множество исследований по этой теме с различными породами древесины, видами цемента и добавками для отверждения для производства различных видов цементно-древесных композитов с улучшениями для различных целей.
Целью данной статьи является обобщение результатов исследований в области улучшения гигроскопических (таких как набухание по толщине и водопоглощение), механических свойств (таких как напряжение изгиба, напряжение растяжения, прочность на сжатие, модуль упругости и внутренняя связь) и сокращение времени производства CWC за счет предварительной обработки и добавок.Кроме того, открывается новая перспектива в отношении повышения его огнестойких свойств за счет использования антипиреновой предварительной обработки.
ДЕРЕВОЦЕМЕНТНЫЕ КОМПОЗИТЫ
Древесно-цементные композиты являются одной из категорий продуктов на минеральной связке. Материалы на неорганической связке впервые появились в начале 1900-х годов в виде древесно-стружечной плиты, скрепленной гипсом. В 1910 г. была произведена древесно-стружечная плита, связанная магнетитом, с приблизительной плотностью 400 кг/м 3 , а в 1914 г. она была разработана в Австрии.Такие плиты низкой плотности обычно используются в качестве изоляционных панелей. Цементно-древесные композиты появились в 1920 году путем производства древесно-волокнистых цементных плит (ДВЦП) плотностью 400 кг/м 3 . Вслед за этим в 1930 г. была разработана древесно-цементная плита плотностью 600 кг/м 3 , но в том году не было большого спроса на древесно-цементные панели для промышленного применения. В 1960 г. производилась грубая древесно-стружечная плита с диапазоном плотности от 500 до 700 кг/м 3 , а в 1970 г. была разработана цементно-стружечная плита (ЦДСП) с очень высокой плотностью от 1250 до 1400 кг/м 3 .Чтобы заменить асбестоцементные плиты в конструкционных целях, CPBP обычно использовался в Европе для изготовления фасадов, полов, огнестойкой и влагостойкой мебели (Stokke и др. 2013). Между 60-ми и 70-ми годами большинство исследователей сосредоточились на влиянии пропорции цемент/древесина на свойства WCP; результаты такой работы сильно различались из-за используемой геометрии частиц, обработки, породы дерева, плотности панели и многих других факторов (Moslemi and Pfister 1986).
В 1990 году изделия из цементно-древесноволокнистых плит получили дальнейшее развитие, и их плотность увеличилась до 900 кг/м 3 .С началом 21 века в 2000 г. выпускались древесно-стружечные цементные плиты (ДЦП) плотностью от 1000 до 1100 кг/м 3 (Stokke и др. 2013).
Форма используемой древесины, т. е. волокон, частиц, рубленых прядей, хлопьев или древесной шерсти влияет на механические свойства и использование изделий из цементно-древесного композита (Mohammed et al . 2016; Hannant et ал. . 2018). Существует несколько различных типов древесно-цементных композитов, как показано на рис.1.
Рис. 1. Схема различных типов цементно-древесных композитов (CWC)
Цементно-волокнистая древесно-цементная плита (CPB)
Цементно-волокнистая древесина и цементно-стружечная плита обычно изготавливаются из волокон и частиц древесины различных размеров и форм (Медведь и Резник, 2003). Эти виды плит имеют хорошие механические свойства и большой вес по сравнению с другими цементно-древесными композитами, поскольку они имеют более высокую плотность.В последние годы были предприняты обширные исследования возможности производства древесно-стружечных плит из древесных отходов. В нескольких исследованиях CO 2 использовался в качестве отвердителя для производства цементно-стружечных плит с использованием частиц строительных древесных отходов (Soroushian et al. 2013; Wang et al. 2017b). Ашори и др. . (2012a) производили плиты, используя древесные отходы железнодорожных шпал. Механические и физические характеристики картона улучшаются при использовании CaCl 2 или хлорида кальция.Ван и др. (2017b) использовали строительные древесные отходы для производства водостойких плит из магнезиально-фосфатного цемента с использованием красного шлама и глинозема. Результаты были удовлетворительными и показали, что красный шлам и древесные отходы являются возможными материалами для производства древесно-стружечных плит.
Исследовано производство цементно-стружечной плиты из переработанных древесных отходов, армированных фосфатом магния. Механические характеристики, тепловые свойства и водостойкость плиты улучшились (Wang et al. 2018).
Древесноволокнистые цементные плиты (WWCB)
Композиты на основе древесно-волокнистого цемента производятся из портландцемента и древесной шерсти (Koohestani и др. 2016). Производство древесно-волокнистых плит требует определенных размеров частиц. Длина колеблется от 25 до 500 мм, ширина от 0,5 до 5 мм, толщина от 0,03 до 0,64 мм (Мэллони, 1989) при плотности от 400 до 900 кг/м 3 . Этот продукт обладает впечатляющими механическими и химическими свойствами; однако трудно понять, почему его механические свойства настолько превосходны (Koohestani et al. 2016). Обычно для утепления используют древесно-волокнистые плиты. Альпар и др. (2011 г.) продемонстрировали усиление сцепления между портландцементом и древесиной, что улучшило качество продукта. Для изменения поверхности древесного волокна использовались добавки.
Строительные блоки
Эти виды продукции хорошо функционируют в качестве строительных строительных материалов. Строительные блоки были изготовлены с использованием цемента в качестве клея для древесных частиц. В Вашингтоне производились блоки толщиной 203 мм и размером 305 на 610 мм или 305 на 1280 мм; однако толщина и высота могут варьироваться.Самые большие блоки весили 45,5 кг (Мэллони, 1989). Строительные блоки обладают хорошей огнестойкостью и отличными изоляционными характеристиками. По плотности они похожи на мягкую древесину, поэтому их легко прибивать и шлифовать. Преимущество строительных блоков в том, что их легко изготовить (Мэллони, 1989).
ТЕХНОЛОГИЯ СОЗДАНИЯ ЦЕМЕНТНО-ДРЕВЕСНОЙ СМЕСИ
Для древесно-цементных композитов наиболее часто используемым цементом является портландцемент. Портландцемент представляет собой комбинацию материалов, нагреваемых в печи при определенной температуре, а затем измельчаемых с получением цементного порошка (Deplazes 2005; Kosmatka et al . 2008). Портландцемент состоит из 90% клинкера и небольшого количества гипса или дигидрата сульфата кальция (CaSO 4 .2H 2 O), оксида магния (магнезии) и других минералов, которые улучшают характеристики цемента и способствуют процессу гидратации. Состав каждого из пяти типов цемента разный (Kosmatka et al . 2008; Mohammed and Safiullah 2018).
При гидратации цемента он вступает в реакцию с водой, придавая цементу прочность и делая его твердым материалом (Bullard et al. 2011). Обычно под совместимостью цемента и дерева понимают степень схватывания цемента после смешивания его с деревом и водой. Наличие древесины влияет на химический процесс твердения цемента. Взаимодействие между цементом и древесиной снижает физические свойства цементных композитов. Эффект ингибитора обычно измеряют по уменьшению тепла, выделяющегося при отверждении цемента. Отношение количества теплоты, выделяемой от цементно-древесной смеси, а также теплоты, выделяемой на границах раздела цементно-древесная смесь, определяется как коэффициент C A и используется вместе с ( T max ), или период времени, необходимый для достижения максимальной температуры. На типичном графике температуры цементно-древесной смеси можно выделить три части. Он начинается с начального повышения температуры, за которым следует период покоя. На этой стадии температура почти постоянна, стагнирует или почти не снижается. Последней стадией является твердение цемента, во время которого температура быстро увеличивается. Совместимость цемента и дерева делится на три категории: совместимая, если C A > 68 %, умеренно совместимая, если 68 % > C A > 28 %, или несовместимая, если C A > 28 %.Однако причины несовместимости дерева и цемента неясны (Jorge et al. 2004)
Во время гидратации все минералы гидратируются одновременно, что усложняет процесс (Liang et al . 2014). Более того, это основная причина того, что полученная связка дерева и цемента очень прочная. Содержание и тип экстрактивных веществ в древесине действуют как ингибиторы отверждения цемента. Древесина содержит сахара, целлюлозы, гемицеллюлозы и лигнин (Frybort et al. 2008; Karade 2010).Эти вещества вызывают проблемы во время отверждения цемента, поскольку они растворяются вместе с цементными смесями, вызывая изменения, препятствующие процессу гидратации и удлиняющие его (Хорхе и др. 2004). Кохова и др. (2017) изучали влияние сахаридов на отверждение цемента. В цементную смесь добавляли различные органические соединения, включая фруктозу, глюкозу, лигнин, сахарозу и целлюлозу, присутствующие в лигноцеллюлозных волокнах. Также было добавлено волокно, обработанное фильтратом (жом, кокосовое волокно, пенька, масличная пальма, водяной гиацинт и еловая древесина).Результаты показали, что время схватывания увеличилось, а отверждение цемента заняло 2 дня из-за содержания глюкозы, маннозы и ксилозы в волокне, обработанном фильтратом.
ВЛИЯНИЕ ПОРОД ДРЕВЕСИНЫ
Правильный выбор породы дерева зависит от структуры древесины и вида производимых древесно-цементных композитов. Кроме того, древесина одной и той же породы может иметь разные характеристики из-за места произрастания, возраста и сезона рубки дерева. Содержание сахаров и экстрактивных веществ различается между породами древесины (Fan et al. 2012). Таким образом, важно выбрать правильную породу древесины, соотношение древесины и цемента и соотношение цемента и воды, поскольку количество сахаров и экстрактивных веществ влияет на процесс гидратации цемента (Phillips and Hse 1987). Наиболее распространенными породами древесины, используемыми в древесно-цементных композитах, являются тополь или Populus (Ашори и др. 2011; Альпар и др. 2012; Кирога и др. 2016) и ель. Ель — одна из лучших пород для древесно-цементных композитов, поскольку она содержит небольшое количество экстрактивных веществ (Мэллони, 1989).
Вентилятор и др. (2012 г.) создали цементные композиты из 15 тропических пород древесины для исследования их совместимости с портландцементом. Гемицеллюлозы и низкомолекулярные углеводы работали как ингибиторы гидратации цемента в цементно-древесной смеси. С увеличением доли древесины совместимость между цементом и древесиной ухудшалась с разной скоростью в зависимости от породы древесины. Породы в порядке убывания совместимости древесины и цемента могут быть перечислены как сапеле 97%, нкананг 85%, мвингуи 77%, падук 68%, ён 64%, тали 50%, ироко 22%, бете 21%, маоби 17%, и душси 10%.С увеличением растворимости тропической древесины коэффициент совместимости увеличивался. Гастро и др. (2019 г.) исследовали совместимость цемента со следующими породами древесины: Eshweilera coriaceae (Ec) , Swartzia reanva poepp (Sr) , Manilkara amazonica (Ma) и 2 Pouteria ganesis. Pouteria. Эти породы древесины подходят для производства CWC, поскольку они не оказывали ингибирующего действия на гидратацию цемента, а все породы древесины имели хороший коэффициент совместимости C A = 85 % для Ec, 74.4 % для Sr, 85 % для Ma и 76,4 % для Pg. Максимальных механических и физических свойств образцы CWC достигли через 28 сут. Антиви-Боасиако и др. (2018) изучали пригодность различных тропических пород древесины для CWC.
В производстве ХБК использовались опилки Triplochiton sclerosylon , Entandrophragma cylindricuim и Klainedosca gabonensis . На основании изучения химических компонентов, их состава и физико-механических свойств, Triplochiton sclerosylon имел самые низкие экстрактивные вещества — 6.12% от суммы экстрактивных веществ, 29,9% лигнина и 56,4% холоцеллюлозы. Он достиг самого высокого MOR среди используемых пород древесины с 696 Н/м 2 , имел значение влагопоглощения 8,8% и выдающиеся физико-механические свойства. Ван и Ю (2012) исследовали совместимость двух быстрорастущих пород, пихты китайской и тополя, с портландцементом. Результаты теста на гидратацию показали, что пихта китайская имеет лучшую совместимость с цементом, чем тополь с C A = 95%, в то время как у тополя C A = 24.3%.
Al-Mefarrej (2009) проверил совместимость пяти саудовских пород древесины: леббек, пуговица, советское дерево, левкаена, мадрасский трон и сосна обыкновенная с цементом. Выяснилось, что коэффициент совместимости C A отличался от одной породы дерева к другой. Результаты были следующими: 17,7% для леббека, 52,0% для пуговицы, 23,0% для советского дерева, 19,0% для левкаены, 19,9% для мадрастрона и 59,0% для сосны обыкновенной.
Papadopoulos (2009) исследовал CBPB из древесины граба.Испытания на гидратацию показали, что смесь цемента и древесины граба имела умеренное ингибирование при 39,15% C A и применялись два различных соотношения древесного цемента, 1:3 и 1:4. Исследование свойств плиты подтвердило, что, за исключением MOR, все свойства улучшились после увеличения отношения цемента к древесине. После воздействия на ЦСП различных грибков платы не пострадали.
Различия возникают даже при использовании одной и той же породы дерева. Кохова и др. (2020) изучали деградацию древесины и ее влияние на совместимость цемента с древесиной.Были использованы две практически идентичные партии древесно-волокнистой шерсти ели. Деревья были посажены, выращены и собраны в одних и тех же условиях. Было проведено сравнение двух пород древесины, и результаты показали, что их совместимость, механическая прочность и анатомическая структура различаются. Коэффициент C A для образца ели А составил 85%, а для образца В — 75%. Прочность на изгиб для А составила 4,5 МПа, а для В — 1,5 МПа. Процентное содержание экстрактивных веществ также было разным, так как один из видов имел больше экстрактивных веществ, чем другой, что приводило к его несовместимости с цементом и влияло на механические свойства.Кроме того, хранение древесины повлияло на совместимость цемента с древесиной, поскольку древесина может быть поражена синевой или другими грибками, что приводит к увеличению экстрактивных веществ древесины. Паска и др. (2010) изучали совместимость горного соснового жука и убитой сосны с портландцементом. В эксперименте участвовал ряд факторов, в том числе: время гибели дерева, синева заболони, белая гниль и бурая гниль.
Были измерены скорость нагрева, общее тепловыделение и гидратация цемента, и результаты не показали различий между свежей и мертвой горной сосной и сосной, убитой жуком.Коэффициент совместимости был между 78,9% и 81,8%. Единственная несовместимость возникла у образцов с белой гнилью, для которых С А составил 48,8%; во всех других случаях были обнаружены отличные физико-химические свойства. Смесь цемента и окрашенной в синий цвет заболони достигла наибольшей совместимости.
На основании приведенных результатов, касающихся совместимости пород древесины и цемента, можно сделать вывод, что породы древесины оказывают огромное влияние на качество CWC.Деревянные виды, разделенные на три категории в соответствии с их C C A : подходит как ESCWeilera Coraceae , Swartzia Reanva Poepp, Manilkara Amaanonica , и Poureeria Guianessaubl , Sapele, Nkanang, Mwingui, китайская ель , ель и горный сосновый лубоед погубили сосну-скворец. Умеренно подходящие (B) леса включали сосну обыкновенную, падук, йонг, тали, леббек, мадрасский трон и граб. К неподходящим лесам (C) относятся ироко, бете, маоби, доусси, пуговица, советское дерево, левкаена и тополь.
ВЛИЯНИЕ ПРЕДВАРИТЕЛЬНОЙ ОБРАБОТКИ НА СОВМЕСТИМОСТЬ ЦЕМЕНТА И ДРЕВЕСИНЫ
Поскольку экстрактивные вещества древесины препятствуют отверждению цемента, было проведено несколько исследований, чтобы найти предварительную обработку, которая уменьшает количество ингибиторов в древесине, что приводит к лучшей совместимости между древесиной и цементом. В большинстве случаев применяется предварительная обработка холодной и горячей водой.
Было проведено исследование совместимости портландцемента и жилок финиковой пальмы ( Phoenix dactylifera L).Древесные частицы подвергали обработке холодной и горячей водой для повышения их совместимости. Результаты показали, что необработанные древесные частицы не подходили для CBPB, но совместимость улучшалась при обработке. Обработка горячей водой была классифицирована как подходящая, и результаты также показали, что добавление 3% CaCl 2 улучшило совместимость цемента с древесиной в ограниченных условиях: T max = 54,2 °C и C A = 75,7% (Насер и Аль-Меффарей, 2011 г.).В 2014 году было проведено исследование совместимости портландцемента и предварительно обработанной древесины Eucalyptus benthamii . Использовали пять типов предварительной обработки: горячая вода, холодная вода, гидроксид натрия, CaCl 2 и гидроксид кальция. Результаты показали, что ингибирующий эффект видов уменьшился на 3% при использовании CaCl 2 , что было лучшим результатом.
Напротив, прочность на сжатие была увеличена за счет смешивания CaCl 2 с карбонизированными частицами через гидроксид кальция (Gastro et al. 2014). Исследование было проведено Quiroga et al. (2016) о влиянии обработки древесины на механические свойства WCC. В качестве материалов использовались портландцемент и Populus euroamericana , а в качестве обработки древесины использовались водная экстракция, разложение щелочным гидролизом и удержание ингибирующих веществ. Щелочной гидролиз оказался наиболее эффективным среди изученных способов подавления ингибиторов. Однако это привело к максимальному снижению механических свойств ВКК.
Ferraz и др. (2012) оценивали химическую совместимость портландцемента и кокосового волокна. В качестве предварительной обработки использовали холодную воду, горячую воду, гидроксид натрия и CaCl 2 . Лигнин и холоцеллюлоза были ингибиторами гидратации цемента, но добавление смеси NaOH и CaCl 2 снизило торможение. Цзян и др. (2015) исследовали влияние методов модификации на совместимость волокна из листьев тополя и цемента. Пять методов были использованы для повышения совместимости листьев.Совместимость листьев и цемента можно улучшить тремя способами: погрузить волокно листа в воду, опрыскать его силикатом натрия или эмульсией чистого акрилового полимера. Се и др. (2016) изучали влияние предварительной обработки рисовой соломы на отверждение цемента. Рисовую солому предварительно обрабатывали по-разному: необработанную, паровую, один раз отбеливали и дважды отбеливали. Предварительные обработки удаляют аморфную гемицеллюлозу и лигнин. Кроме того, они улучшают кристалличность цемента и повышают термическую стабильность волокна рисовой соломы.
Нассер и др. (2016) исследовали возможность изготовления высококачественных цементно-древесных композитов с использованием отходов обрезки деревьев. Были использованы различные породы древесины, в том числе Acacia salicina , Conocarpus erectus , Ficus altissima , Leucaena glauca , Pithecellobium dulce 2 aphyla 9×2 9×2 и 2 Tamari 9×2. Отходы обрезки древесины обрабатывали горячей и холодной водой и использовали CaCl 2 , Al 2 (SO 4 ) и MgCl 2 для ускорения отверждения цемента и улучшения совместимости. Результаты показали, что отходы могут быть введены в производство цементно-древесного композита в качестве альтернативы древесине, но с применением предварительной обработки и добавлением 3% добавок CaCl 2 , Al 2 (SO 4 ) и MgCl 2 .
Чехин и др. (2018) изучали совместимость между бамбуком мосо и портландцементом. Выбранные породы древесины подвергались различным предварительным обработкам, таким как холодная вода, горячая вода, гидроксид натрия, силикат натрия, силан и хлорид кальция.Результаты показали, что частицы бамбука мосо хорошо совместимы с цементом, что делает их пригодными для производства CWC. Механические свойства, совместимость и кристалличность произведенных плит были улучшены за счет предварительной обработки.
Гастро и др. (2018) провели исследования корреляции между химическим составом древесины и совместимостью цемента с древесиной. Для экспериментов использовали портландцемент II-Z и восемь различных тропических лиственных пород древесины из Амазонии. Корреляции между полярными и неполярными растворимыми экстрактивными веществами и ингибиторами схватывания цемента обнаружено не было, за исключением Swartzia recurva с содержанием арабинозы. Кроме того, была обнаружена корреляция между Larix с щелочным раствором и ингибиторами цемента. Лигнин и гемицеллюлоза создают большое количество расщепленных полисахаридов, которые вызывают ингибирование цемента. Пять из используемых пород древесины, Eschweilera coriacera, Inga paraensis, Ingalba, Pouteria guianensis и Byrsonima crispa , имели низкий ингибирующий эффект.
В таблице 1 представлены коэффициенты совместимости различных пород древесины с различными обычно используемыми предварительными обработками. Коэффициент C A был увеличен за счет использования предварительной обработки, повышающей качество древесины от непригодных до умеренно подходящих или подходящих, но в некоторых случаях, например, для пород древесины дусси, предварительная обработка не влияет на увеличение цементной древесины. совместимость. Предварительная обработка по-разному влияет на каждую породу древесины. В большинстве случаев было обнаружено, что горячая вода и MgCl 2 отличны для предварительной обработки, но это не повлияло на финиковую пальму.
Таблица 1. Влияние различных видов предварительной обработки на коэффициент совместимости C A (%) различных пород древесины
ВЛИЯНИЕ ДОБАВОК И СООТНОШЕНИЯ ДЕРЕВО/ЦЕМЕНТ НА СВОЙСТВА CWC
Поскольку цементно-древесные композиты являются широко используемыми строительными материалами, их свойства очень важны. Много усилий было направлено на улучшение свойств CWC. Соотношение древесины и цемента является одним из основных факторов, влияющих на CWC (Пападопулос, 2009 г.; Табарса и Ашори, 2011 г.; Ашори и др. 2012б; Абдельрахман и др. 2015; Боаду и др. 2018). Многие добавки также использовались в качестве ускорителей во время процесса гидратации (Frybort et al. 2008). Этот подход работает над склеиванием цемента и дерева, что приводит к улучшению свойств CWC. Наиболее часто используемыми добавками были жидкое стекло (Na 2 SiO 2 ), хлорид кальция (CaCl 2 ), силикат алюминия (Al 2 (So 4 ) 3 ) и хлорид магния или MgCl 2 (Alpár и др. 2011). Некоторые прошлые исследовательские работы были сосредоточены на закачке углекислого газа, который также использовался для улучшения сцепления цемента с древесиной.
Ашори и др. (2012b) провели исследование цементно-стружечной плиты, изготовленной из стружки тополя. Соотношение древесины влияло на механические и впитывающие свойства плит. Они становились прочнее и плотнее, когда изготавливались из 40% прядей тополя, а также достигали наилучшей прочности на изгиб. Механические и водопоглощающие свойства были улучшены добавлением 7% хлорида кальция (CaCl 2 ).
Сотаннде и др. (2012 г.) исследовал CBPB, изготовленный из Afzelia африканского дерева. Плиты изготавливались с использованием различных добавок, состава цемента и форм древесины, а именно: хлопьев, хлопьев с опилками и опилок. Увеличение содержания цемента в древесно-цементной смеси с 1:2 до 1:3,5 и добавление химических добавок уменьшило набухание по толщине примерно на 10%. 60% и водопоглощение также прибл. 71%. Плотность увеличилась примерно на 23%, прочность на сжатие увеличилась почти на 60%, а внутреннее склеивание плит в среднем на 38%.Только на MOR не влияло содержание цемента и добавок. Наилучшие результаты были достигнуты при добавлении 2% CaCl 2 . Форма древесных частиц оказывала влияние на механические свойства плит. Наилучшие результаты показали хлопья с опилками с IBS=0,50 Н/мм 2 , MOR= 11,6 Н/мм 2 и C s = 15,16 Н/мм 2 , а наихудшие результаты были достигнуты флеками, с IBS = 0,37 Н/мм 2 , MOR = 9.
57 Н/мм 2 и C с = 12,6 Н/мм 2 .
Боаду и др. (2018) исследовали плиту CWC, изготовленную из экстрагированных опилок различных тропических лиственных пород различной плотности: Triplochiton scleroxylon (низкая плотность), Entandrophragma cylindricum (средняя плотность) и Klainedoxa gabonensis (высокая плотность). Увеличение доли древесины вызывает увеличение механических и физических свойств (MOR, прочность на сдвиг и разбухание по толщине).Плиты, изготовленные из экстрагированных опилок, показали лучшие механические свойства и устойчивость к набуханию по толщине, чем плиты, изготовленные из обычных опилок. TS (%) была снижена по сравнению с контрольными образцами с TS = 1,5 и 2,9 для T. scleroxylon и E. cylindricum соответственно до TS = 0,42 и 0,95 соответственно при использовании горячей воды. Прочность на сдвиг была увеличена с 0,3 и 0 до 1,8 и 1 (Н/мм 2 ) для T. scleroxylon и E. cylindricum соответственно.MOR был увеличен с 1,8 и 1,1 до 4,1 и 2,4 (Н/мм 2 ) для T. scleroxylon и E. cylindricum соответственно при использовании экстрагированных опилок горячей водой. Плиты CWC, обладающие высокой размерной стабильностью и механическими свойствами, были изготовлены из экстрагированных древесных опилок выбранных пород.
Матоски и др. (2013) изучали влияние различных ускорителей на древесно-цементные панели. ВКП изготавливали из древесной пыли различных пород Pinus и портландцемента.Использовались различные добавки, в том числе хлорид кальция, хлорид магния, сульфат алюминия и силикат натрия. Результаты показали, что добавки хлорида смогли повысить механические свойства изготовленной панели до значений, превышающих требования следующих стандартов (EN 1058 и ASTM D 1037) с CS = 18,1 МПа, прочностью на изгиб (BS) = 4,72 МПа и IBS = 0,54 МПа для CaCl 2 , CS = 18,0 МПа, BS = 4,55 МПа и IBS = 0,57 МПа. Для испытания на водопоглощение было обнаружено, что сульфат алюминия показал наилучшие результаты с WA = 1.52% через 2 часа погружения в воду и 3,97% через 24 часа, создавая водонепроницаемую систему за счет увеличения количества ионов, реагирующих с трикальцийалюминатом, который является одним из компонентов цемента.
Было исследовано влияние предварительной обработки и соотношения цемент-древесина на цементный композит (Abdelrahman et al. 2015). Древесина Prosopis chilensis и портландцемент в дополнение к гипсу в качестве частичной замены цемента использовались для производства цементного композита.В качестве предварительной обработки использовали холодную воду, гидроксид натрия и хлорид кальция. ЦБК изготавливались с различным соотношением древесины и цемента: 2:1, 3:1, 4:1 и 5:1. Наилучшее соотношение древесины и цемента было 3:1, а добавление 10 % гипса в качестве частичной замены цемента улучшает прочность на сжатие с 51,6 % CS = 51,3 Н/мм 2 , в то время как для контрольных образцов CS = 24,8 Н/мм 2 . Однако добавление более 20% гипса отрицательно повлияло на прочность на сжатие.
Было проведено исследование характеристик гидратации ЦСПБ, изготовленного из цемента и смеси пшеничной соломы и тополя.Добавки MgCl 2 , CaCl 2 и Ca(OH) 2 использовались в разных пропорциях: 3%, 5% и 7% в расчете на массу цемента. Было показано, что соотношение соломы и древесины оказывает сильное влияние на физико-механические свойства ЦСП. Среди используемых добавок 7% CaCl 2 дала наилучшие результаты в целом для свойств с TS = 13,4%, IBS = 0,66 МПа и MOR = 16,87 МПа, а также сократила время схватывания (Nazerian and Sadeghiipanah 2013).Табарса и Ашори (2011) исследовали плиту из цементной древесной шерсти с использованием эвкалипта и тополя с портландцементом. Использовали соотношения 40:60 и 60:40 древесной шерсти и цемента, а в качестве обработки использовали CaCl 2 . Добавление 5% CaCl 2 повысило характеристики плат. Порода древесины – еще один фактор, определяющий свойства доски. Например, доски из эвкалипта имели более высокое водопоглощение и меньшее набухание при усадке. Цементный композит изготавливали из цемента и древесной шерсти келампиевой древесины ( Anthocephalus chinensis ).В качестве добавок использовались 3% формиат кальция, силикат натрия и хлорид магния для ускорения времени схватывания цементно-древесного композита. Добавки повысили прочность и механические свойства плит на ранней стадии (Mahzabin et al. 2013). Вульф и др. (2015) исследовали бетон, армированный минерализованными древесными частицами, в качестве элементов жесткости с возрастающей плотностью. Были приготовлены смеси портландцемента и частиц сосны обыкновенной и ели. Для минерализации древесины к древесным частицам применялись различные виды обработки.Древесный наполнитель, минерализованный жидким стеклом (силикатом натрия) и портландцементом, улучшал арболит только при использовании в качестве наполнителя 15% древесных частиц по массе.
Наблюдалось снижение плотности от 36 до 39%.
ПРОЦЕДУРЫ ДЛЯ УСКОРЕНИЯ ОТВЕРЖДЕНИЯ ЦЕМЕНТА
Сокращение времени отверждения цементно-древесных композитов было тщательно исследовано. Маковинг (2010) исследовал возможность сушки плит WCC в микроволновой печи без повреждения плит или снижения механических свойств.Результаты показали возможность сушки плит без ухудшения качества. В последние годы обработка CO 2 широко используется для сокращения времени отверждения древесно-цементного композита и одновременного улучшения его механических свойств.
Двуокись углерода (CO 2 )
При обычном производстве CBPB запрессовывают между стальными пластинами и оставляют сохнуть на 24 часа, что является временем, необходимым для того, чтобы стать самонесущим. Однако двуокись углерода (CO 2 ) упрочняла CBPB всего за 5 минут, что давало преимущества, в том числе снижение энергопотребления и повышение производительности (Alpár et al. 2003). Ци е т др. (2010) исследовали возможность ускорения твердения древесно-цементной смеси из красной сосны и портландцемента с использованием CO 2 . В первые минуты применения инъекций CO 2 началась реакция карбонизации. Через 30 мин примерно 43% содержания оксида кальция в цементе карбонизировалось. Быстрое затвердевание могло быть вызвано взаимодействием силикатов кальция в цементе с CO 2 . С другой стороны, никакой реакции между гидроксидом кальция и CO 2 не наблюдалось.Ван и др. (2017a) использовал отверждение CO 2 и армирование волокнами для ускорения отверждения цемента и улучшения физических свойств древесно-стружечных плит, изготовленных из цемента и древесных отходов. Результаты показали, что CO 2 способствует гидратации цемента, ускоряя превращение Ca(OH) 2 в CaCO 3 , что приводит к повышению прочности древесно-стружечной плиты. Кроме того, общая площадь пор 12,2 м 2 г -1 была уменьшена до 10.
3 м 2 г -1 и пористость от 34,8% до 29,7%. Все требования соответствующих международных стандартов были выполнены за счет улучшения механических свойств, стабильности размеров и связывания загрязняющих веществ. Сорушян и др. (2013) исследовали влияние ускоренного старения на прочность на изгиб; CO 2 помогает увеличить содержание CaCO 3 и снизить содержание Ca(OH) 2 , что приводит к повышению прочности на изгиб и жесткости.В результате старения содержание CaCO 3 увеличивается, а содержание Ca(OH) 2 уменьшается, что приводит к улучшению поверхности раздела волокнистой матрицы.
Повышение характеристик цементно-древесного композита с помощью CO 2 не всегда эффективно. Используемые породы дерева могут иметь важное значение. Таскиравати и др. (2019) оценивали характеристики цементно-древесной плиты, изготовленной из портландцемента и двух пород древесины: Acacia mangium (акация) и Arthophyllum diversifolium (Lento-lento). Плиты были изготовлены традиционным методом производства с использованием CaCl 2 в качестве добавки-ускорителя, а также плиты были изготовлены методом карбонизации с использованием впрыска CO 2 для ускорения отверждения и улучшения механических свойств. Результаты показали, что плиты из древесины ленто-ленто имели лучшие характеристики при использовании метода впрыска CO 2 , в то время как Acacia показала лучшие результаты при традиционном методе производства, тем самым показывая, что впрыск CO 2 не всегда лучше, чем при обычном производстве. методы, в зависимости от используемой породы дерева (Taskirawati et al. 2019).
Maail и др. (2013) изучали деградацию цементно-стружечной плиты из портландцемента и смеси древесных пород: кипариса японского ( Chamaecyparis obtusa Endl.) и кедра японского ( Cryptomeria japonica D. Don) под действием CO 2 в качестве ускорителя отверждения. Результаты показали влияние CO 2 на разложение CBPB. CO 2 помог плитам достичь максимальных механических свойств за короткое время за счет ускорения процесса отверждения цемента.CO 2 не только помог ускорить отверждение, но также улучшил механические свойства и стабильность размеров. Однако время обработки CO 2 оказало большое влияние на его эффективность. Лечение рекомендуется в течение короткого периода времени, не более 30 мин. Использование обработки CO 2 в течение от 60 минут до 10 дней оказало негативное влияние на механические свойства плит, поскольку более длительные периоды времени вызывают деградацию CBPB из-за влияния содержания карбоната кальция (Maail et al. 2011). Было проведено исследование цементно-древесных плит из портландцемента и финиковой пальмы с использованием ускорителя отверждения CO 2 . Выяснилось, что волокна финиковой пальмы несовместимы с цементом; однако с предварительной обработкой горячей водой совместимость волокон была повышена до подходящей.
Инъекция CO 2 снизила прочность на изгиб и улучшила матрицу и качество плиты (Hassan et al. 2016).
Кроме того, было проведено исследование CBPB, изготовленного из различных видов натуральных волокон с использованием впрыска CO 2 , чтобы повысить начальную совместимость между цементом и волокнами.Инъекция CO 2 успешно увеличила начальную прочность за счет ускорения отверждения цемента и связывания цемента и дерева. Эти плиты имели такие же механические свойства, как и плиты, изготовленные традиционным способом, и имели более низкое содержание цемента (Marteinsson and Gudmundsson 2018). Исследованы прочностные характеристики композитов из целлюлозного волокна и цемента. После обработки плит CO 2 результаты показали, что капиллярная пористость уменьшилась из-за отверждения CO 2 , а увеличение содержания CaCO 3 повысило совместимость между цементом и волокнами за счет улучшения матрицы на основе цемента. для целлюлозных волокон.Также были повышены долговечность и устойчивость к атмосферным воздействиям (Soroushian et al. 2012).
ОГНЕСТОЙКОСТЬ ЦЕМЕНТНО-ДРЕВЕСНОГО КОМПОЗИТА
Для строительных материалов промышленная огнестойкость является очень важным фактором. Материалы, изготовленные из изделий из магниевого цемента, считаются выдающимися огнезащитными материалами (Zuo et al. 2018). Как правило, цементно-древесные композиты представляют собой материалы с хорошей огнестойкостью. Саваль и др. (2014) исследовали воспламеняемость CBPB, изготовленного из цемента и отходов Oceanic Posidonia.Поскольку на CBPB не произошло распространения пламени, он не является горючим материалом. Согласно литературным данным, соотношение цемент-древесина влияет на огнестойкость композитов цемент-древесина. Было проведено исследование переработанных частиц китайской ели и цемента. Исследование проводили с помощью конусной калориметрии. Результаты показали, что отношение цемента к древесине повлияло на огнестойкость CBPB. При увеличении соотношения цемент-древесина с 0,5 до 2 время воспламенения увеличилось с 26 до 548 с, а скорость потери массы уменьшилась.
Был проведен ряд исследований CWC с целью улучшения его усадки и набухания, водопоглощения и механических свойств, а также сокращения времени его изготовления. Однако меньше исследований было направлено на огнестойкость CWC. Не проводилось исследований по предварительной обработке древесины для повышения огнестойкости CWC, как в случае снижения содержания ингибиторов древесины. Единственные исследования в этой области касались негорючести материала и влияния соотношения древесины на огнестойкость.Многие химические вещества могут быть использованы в качестве предварительной обработки для повышения огнестойкости древесины и, как следствие, повышения огнестойкости древесно-цементного композита. Силикат натрия известен как связующее и антипирен, который может улучшить свойства древесины, такие как механические свойства, стабильность размеров и огнестойкость (Medina and Schledjewski 2009; Mahzabin et al. 2013).
Антипирены по-разному воздействуют на разные материалы, потому что каждый материал имеет уникальную реакцию на огонь, основанную на ряде факторов.Например, следует учитывать легкость воспламенения материала, скорость горения и распространение пламени по поверхности. Кроме того, на огнестойкость материала влияет скорость, с которой пламя проникает в стену или преграду, скорость, с которой выделяется тепло, а также количество образующегося дыма и токсичного газа (Ayrilmis и др. ). 2009). Однако для начала важно разобраться в работе антипиренов, в чем различия между антипиренами и решить, какой из них лучше использовать в зависимости от ситуации.
Огнезащитные составы или антипирены созданы для снижения температуры материала. Когда происходит воспламенение, антипирены вызывают термическое разложение, увеличивая количество обугленных материалов и снижая воспламеняемость (LeVan et al. 1990). Антипирены имеют два вида действия: физическое и химическое.
Для физического действия существует множество способов отсрочить воспламенение. Охлаждение является одним из методов, и есть некоторые антипирены, которые могут снизить температуру материалов.Покрытие — это еще один способ отсрочить воспламенение, когда антипирены могут образовывать защитный слой, предотвращающий воспламенение основного материала. Разбавление — это третий способ выделения воды и углекислого газа из ингибиторов горения. Каждый антипирен лучше действует на определенный вид материала, поэтому выбор антипирена зависит от основания и его уникального набора характеристик.
Антипирены для предварительной обработки
Многие антипирены могут использоваться для предварительной обработки древесины при производстве ХБК, например соединения фосфора.Наиболее популярными фосфорсодержащими антипиренами являются фосфорная кислота и соли моно- и диаммонийфосфата. Кроме того, можно принимать во внимание фосфатно-азотные соли, содержащие органические соединения (Stevens et al. 2006). Поэтому в целом фосфорсодержащие антипирены делят на три категории: содержащие неорганические, органические и галогенные компоненты. Их механизм работает в большинстве случаев в твердой фазе горящего материала, но может действовать и в газовой фазе (Van der Veen and de Boer 2012).Соединения фосфора эффективны в качестве антипиренов, поскольку они уменьшают термическое разложение древесины (Jiang et al. 2010). Фосфорсодержащие химические вещества действуют как антипирены за счет образования кислот, которые снижают температуру древесины (Wu et al. 2002) и, как следствие, усиливают ее обезвоживание и обугливание (Liu 2001; Gao et al. 2006). Уголь действует как барьер для кислорода и летучих горючих компонентов (ЛОС).
Гидроксид магния представляет собой интересный антипирен и выделяется среди многих химических продуктов, поскольку он безопасен для окружающей среды, имеет низкую цену, низкую токсичность, коррозионную активность и способность подавлять дым (Zhang et al. 2016). При температуре около 300 °C гидроксид магния разлагается до гидроксида магния с выделением водяного пара, воздействующего на полимерную систему (Rothon and Hornsby 1996). В 2017 году было проведено новое исследование термического разложения гидроксида наномагния (Янг и др. 2017). Водяной пар высвобождается во время разложения, поэтому гидроксид магния действует как антипирен, поскольку создает слой, изолирующий материал от пламени (Zhu et al. 2016).
Бор, который можно отнести к классу экологически чистых материалов (El-Batal и др. 2019), используется в различных областях, таких как сельское хозяйство, производство стекловолокна или обработка материалов, но, что наиболее важно, для защиты от огня. (Саян и др. 2010). Соединения бора являются лучшим выбором в качестве антипиренов для целлюлозных материалов. На протяжении многих лет проводились исследования, показывающие эффективность соединений бора в качестве антипиренов. В большинстве случаев используются два вида: бура и борная кислота.Эти два соединения эффективны в качестве антипиренов на поверхности древесины. В большинстве случаев бура и борная кислота используются вместе, потому что они дополняют друг друга. Преимущество буры заключается в подавлении распространения пламени, а недостаток в том, что бура способствует тлению. С другой стороны, борная кислота является хорошим подавителем тления, но ее способность подавлять распространение пламени низкая (Baysal et al. 2007).
Поскольку каждая предварительная обработка антипиренами по-разному влияет на разные породы дерева, не только тип антипирена, но и его дозировка будут иметь большое влияние на результат.Брахмия и др. . (2020) изучали влияние различных антипиренов соединений бора и фосфора с разной концентрацией на тополь и сосну обыкновенную. Использовали буру с концентрацией 25 г/л, диаммонийгидрофосфат с концентрацией 25 г/л и 300 г/л и гидрофосфат динатрия с концентрацией 25 г/л и 77 г/л. Результаты показали, что соединения фосфора обладают лучшими характеристиками, чем бура, особенно при использовании с тополем. Концентрация оказывает большое влияние на характеристики огнестойкости, при этом более высокая концентрация обеспечивает более высокую огнестойкость.Рекомендуется использовать антипирены в высоких дозах для достижения лучших результатов, но в случае с цементно-древесными композитами необходима сбалансированная дозировка антипиренов, и необходимо учитывать их влияние на отверждение цементно-древесного материала.
ВЫВОДЫ
- Цементно-древесные композиты (CWC) — непредсказуемые строительные материалы, на которые влияет множество факторов. Наиболее важным фактором при производстве CWC является совместимость дерева и цемента. Порода древесины является наиболее важным фактором совместимости цемента с древесиной, потому что не все породы имеют одинаковый вид и количество экстрактивных веществ.Влияние оказывает не только порода древесины, но и время сбора, возраст и хранение, поскольку эти факторы могут влиять на экстрактивные вещества в древесине.
- Предварительная обработка древесины использовалась для снижения содержания экстрактивных веществ или ингибиторов цемента во многих исследованиях. Наиболее часто используемыми средствами предварительной обработки древесины были горячая и холодная вода, гидроксид натрия, гидроксид кальция, отбеливатель и щелочной гидролиз. Эти предварительные обработки могут изменить совместимость цементной древесины с несовместимой на подходящую.Из-за требований и правил CWC находится в постоянном развитии.
- Механические свойства и сокращение времени отверждения являются наиболее важными аспектами, на которых сосредоточились исследователи. Обычно механические свойства повышают с помощью различных добавок, таких как хлорид кальция и силикат натрия. Для уменьшения времени отверждения CWC широко используется углекислый газ (CO 2 ). Он не только используется для сокращения времени отверждения, но также улучшает механические свойства и водопоглощение.
- Несколько исследовательских проектов изучали огнестойкость CWC, и они в основном были сосредоточены на демонстрации того, что CWC с подходящим составом является негорючим материалом.
Исследования также показали влияние различных добавок на термическую стабильность материала. Тем не менее, огнестойкость CWC нуждается в повышении. Решением может быть предварительная обработка с использованием антипиренов. Однако используемые антипирены не должны влиять на первичные свойства, такие как механические характеристики.Кроме того, используемые антипирены должны быть экологически чистыми, чтобы не наносить вреда людям. Они также должны быть дешевыми, потому что CWC должны оставаться в рамках бюджета. Известные антипирены для древесины, которые, по-видимому, могут использоваться в качестве агентов для предварительной обработки, представляют собой соединения фосфора, бора и магния.
БЛАГОДАРНОСТИ
Авторы выражают благодарность профессору Ковачу Жолту за корректуру рукописи. Эта статья была подготовлена в рамках «EFOP-3.6.1-16-2016-00018 — Повышение роли исследований + разработок + инноваций в высшем образовании посредством институциональных разработок, способствующих интеллектуальной специализации в Шопроне и Сомбатхее.
Авторы также заявляют об отсутствии конфликта интересов.
ССЫЛКИ
Абдельрахман, А.Б., Парич, М.Т., Шах Уид, М., Абдул Самад, А.Р., и Ахмед Абдаллах, А.М. (2015). «Влияние предварительной обработки, соотношения древесины и цемента и частичной замены цемента гипсом на древесные композиты Prosopis chilensis », European Journal of Wood and Wood Products 73(4), 557-559. DOI: 10.1007/s00107-015-0909-x
Аль-Мефаррей, Х.А. (2009). «Испытание и повышение совместимости пяти саудовских пород древесины для производства цементно-стружечных плит», Alexandria Science Exchange Journal 30(3), 333-342.
Альпар, Л., Т., Павлекович, А.А., Чока, Л., и Хорват, Л. (2011). «Цементные плиты из древесной шерсти, изготовленные из наноминералов», Международная научная конференция по обработке твердой древесины (ISCHP2011) , 75-82.
Альпар, Л. Т., Сельмецци, Э., и Чока Л. (2012). «Расширенная совместимость древесного цемента с наноминералами», Международная научная конференция по устойчивому развитию и экологическому следу , 1–7.
Альпар, Л. Т., Такатс, П., и Хатано, Ю. (2003). «Пористость цементно-стружечных плит, отвержденных инъекцией CO 2 и отвержденных гидратацией», JARQ 37(4), 263-268.
Antiwi-Boasiako, C., Ofosuhene, L., и Boadu, K.B. (2018). «Пригодность опилок трех тропических пород древесины для древесно-цементных композитов», Journal of Sustainable Forestry 37(4), 414-428. DOI: 10.1080/10549811.2018.1427112
Ашори А., Табарса Т., Азизи Х.и Мирзабейги, Р. (2011). «Цементно-древесная плита с использованием смеси эвкалипта и тополя», Industrial Crops and Products 34(1), 1146-1149. DOI: 10.1016/j.indcrop.2011.03.033
Ашори, А., Табарса, Т., и Амоси, Ф. (2012a). «Оценка использования железнодорожных шпал из отходов древесины в древесно-цементных композиционных материалах», Строительные материалы 126-129. DOI: 10.1016/j.conbuildmat.2011.08.016.
Ашори, А., Табарса, Т., и Сепахванд, С. (2012b).«Цементно-композитные плиты из стружки тополя», Строительные материалы 26(1), 131-134. DOI: 10.1016/j.conbuildmat.2011.06.001
Айрилмис, Н., Дундар, Т., Кандан, З., и Акбулут, Т. (2009). «Смачиваемость обработанного антипиреном клееного бруса (LVL), изготовленного из шпона, высушенного при различных температурах», BioResources 4(4), 1536-1544. DOI: 10.15376/biores.4.4.1536-1544
Байсал Э., Ялинкилич М.К., Аалтинок М., Сонмез А., Пекер Х. и Чолак М. (2007). «Некоторые физические, биологические, механические и огнестойкие свойства древесно-полимерного композита (ДПК), предварительно обработанного смесью борной кислоты и буры», Construction and Building Materials 21(9), 1879-1885. DOI: 10.1016/j.conbuildmat.2006.05.026.
Бейо, Л., и Такац, П. (2005). «Разработка композитных балок на цементном основании», Acta Silvatica Et Lignaria Hungarica 1, 111–119.
Боаду, К.Б., Антви-Боасиако, К.и Офосухене, Л. (2018). «Экстракция растворителем ингибирующих веществ из трех твердых пород древесины разной плотности и их совместимость с цементом при производстве композитов», Journal of the Indian Academy of Wood Science 15(2), 140-148. DOI: 10.1007/s13196-018-0219-0.
Брахмиа, Ф. З., Альпар, Т., Хорват, П. Г., и Чиха, К. (2020). «Сравнительный анализ смачиваемости антипиренами тополя ( Populus сорта euramericana I214) и сосны обыкновенной ( Pinus sylvestris )», Surfaces and Interfaces 18, 100405.
Буллард, Дж. В., Дженнингс, Х. М., Ливингстон, Р. А., Нонат, А., Шерер, Г. В., Швейцер, Дж. С., Скривенер, К. Л., и Томас, Дж. Дж. (2011). «Механизмы гидратации цемента», Cement and Concrete Research 41(12), 1208-1223. DOI: 10.1016/j.cemconres.2010.09.011.
Чечин, Л., Матоски, А., Миранд а де Лима, А., Моник, А., и Бассо, Р. (2018). «Влияние обработки на высокую начальную прочность портландцемента и совместимость с бамбуковым мхом», Revista Ingenieria de Construction 33(2), 127-136.
Деплаз, А. (2005). «Построение архитектурных материалов обрабатывает структуры», Bikhauser-Publishers for Architecture , 60-112.
Эль-Батал, А. И., Эль-Сайяд, Г. С., Аль-Хазми, Н. Э., и Гобара, М. (2019). «Антибиопленочная и антимикробная активность наночастиц бора серебра, синтезированных полимером PVP и гамма-лучами, против патогенов мочевыводящих путей», Journal of Cluster Science , 30 (4), 947-964.
Фан, М., Надиконтар, М.К., Чжоу X. и Нгамвенг Дж. Н. (2012). «Цементные композиты из тропической древесины: совместимость дерева и цемента», Construction and Building Materials 36, 135-140. DOI: 10.1016/j.conbuildmat.2012.04.089.
Ферраз, Дж. М., Дель Менецци, Ч. Х. С., Сарза, М. Р., Окино, Э. Ю. А., и Мартинц, С. А. (2012). «Совместимость предварительно обработанных кокосовых волокон ( Cocos nucifera L.) с портландцементом для производства минеральных композитов», International Journal of Polymer Science 2012, 1-15.DOI: 10.1155/2012/2
Фрайборт, С., Мауртис, Р., Тейшингер, А., и Мюллер, У. (2008). «Композиты на цементной основе — механический обзор», BioResources 3(2), 602-626. DOI: 10.15376/biores.3.2.602-626
Гао, Ф., Тонг, Л. и Фанг, З. (2006). «Влияние нового вспучивающегося антипирена, содержащего фосфорсодержащий азот, на огнестойкость и тепловые характеристики поли(бутилентерефталата)», Polymer Degradation and Stability 91(6), 1295-1299.DOI: 10.1016/j.polymdegradstab.2005.08.013
Гастро В., Араужо Р. Д., Парчен К. и Ивакири С. (2014). «Оценка влияния предварительной обработки древесины эвкалипта бентами и камбаджа на степень совместимости с портландцементом», Revista Arvore 35(5), 935-942.
Гастро В., Да Роза Р., Замбуджа А., Била Н. Ф., Парчен С. Ф. А., Саассаки Г. И. и Ивкири С. (2018). «Взаимосвязь между химическим составом древесины тропических лиственных пород и совместимостью древесины и цемента», Journal of Wood Chemistry and Technology 38(1), 28-34.DOI: 10.1080/02773813.2017.1355390
Гастро, В., Замбуджа, Р. Д. Р., Парчен, К. Ф. А., и Ивакири, С. (2019). «Альтернативная вибродинамическая компрессионная обработка древесно-цементных композитов с использованием амазонской древесины», Acta Amazonia 49(1), 75-80.
Гундуз, Л., Калкан, С.О., и Искер, А.М. (2018). «Влияние использования цементно-стружечных плит с композитным компонентом на акустические характеристики в наружных шумозащитных экранах», Евразийские труды по науке, технологии, инженерии и математике, (4), 246–255.
Ханнант, Д. Дж., Венката, С. Б., Сивер и Шрикант, П. С. Р. (2018). «5.15 Композиты на основе цемента», Комплексные композитные материалы II 5, 379-420.
Хассан, М.С., Салих, С.А., и Али, И.М. (2016). «Оценка прочности цементных плит из целлюлозы, армированной волокнами финиковой пальмы, отвержденной CO2», Eng. и тех. Журнал 34, 1029-1046.
Hillerborg, A., Modéer, M., и Petersson, P.E. (1976). «Анализ образования и роста трещин в бетоне с помощью механики разрушения и конечных элементов», Cement and Concrete Research 6(6), 773-781.DOI: 10.1016/0008-8846(76)
-7. Цзян Д., Цуй С., Сюй Ф. и Туо Т. (2015). «Влияние методов модификации листовых волокон на совместимость между листовыми волокнами и материалами на основе цемента», Construction and Building Materials 94, 502-512. DOI: 10.1016/j.conbuildmat.2015.07.045
Цзян, Дж., Ли, Дж., Ху, Дж., и Фан, Д. (2010). «Влияние азотно-фосфорных антипиренов на термическое разложение древесины», Construction and Building Materials 24(12), 2633-2637.DOI: 10.1016/j.conbuildmat.2010.04.064
Хорхе, Ф. К., Перейра, К., и Феррейра, Дж. М. Ф. (2004). «Древесно-цементные композиты: обзор», Holz als Roh – und Werkstoff 62(5), 370-377. DOI: 10.1007/s00107-004-0501-2
Караде, С. Р. (2010). «Цементные композиты из лигноцеллюлозных отходов», Строительство и строительные материалы 24(8), 1323-1330. DOI: 10.1016/j.conbuildmat.2010.02.003
Кохова К., Капри В., Говен Ф. и Шольбах К.(2020). «Исследование локальной деградации древесных насаждений и ее влияния на цементно-древесные композиты», Construction and Building Materials 231, 117201. DOI: 10.1016/j.conbuildmat.2019.117201
Кохова, К., Шолльбах, К., Говен, Ф. , и Брауэрс, Х. Дж. Х. (2017). «Влияние сахаридов на гидратацию обычного портландцемента», Construction and Building Materials 150, 268-275. DOI: 10.1016/j.conbuildmat.2017.05.149
Кохестани, Б., Кубаа, А., Белем Т., Бюссьер Б. и Бузаза Х. (2016). «Экспериментальное исследование механических и микроструктурных свойств тампонажной закладки из цементной пасты, содержащей кленовый заполнитель», Строительные материалы 121, 222-228. DOI: 10.1016/j.conbuildmat.2016.05.118
Косматка, С. Х., Керхофф, Б. и Панарезе, В. К. (2008). «Конструкторское и контрольное проектирование и контроль бетонной смеси», Инженерный бюллетень 001, 1-228.
ЛеВан, С. Л., Росс, Р.Дж. и Винанди, Дж. Э. (1990). Влияние огнезащитных химикатов на свойства древесины при изгибе при повышенных температурах , Министерство сельского хозяйства США, Лаборатория лесных товаров, Мэдисон, Висконсин, США.
Лян, З. Ф., Ян, Б., Ван, Л., Чжан, С., Чжан, Л., и Хе, Н. (2014). «Разработка гибкой модели нейтрального дерева для процесса гидратации портландцемента», Advances in Swarn Intelligence 302-309.
Лю, Ю.Л. (2001). «Огнестойкие эпоксидные смолы из нового фосфорсодержащего новолака», Polymer 42(8), 3445-3454.DOI: 10.1016/S0032-3861(00)00717-5
Мааил, Р. С. (2013). «Анализ деградации при производстве цементно-стружечных плит с использованием сверхкритического CO 2 », Wood Research Journal 4(2), 76-82.
Мааил, Р. С., Умемура, К., Айзава, Х., и Канаи, С. (2011). «Процессы отверждения и разложения цементно-стружечной плиты с помощью сверхкритической обработки CO 2 », Journal of Wood Science 57(4), 302-307. DOI: 10.1007/s10086-011-1179-9
Махзабин, С., Хамид, Р., и Бадаруззаман, WH (2013). «Оценка свойств матрицы из древесноволокнистого цемента с включением химических веществ», Journal of Engineering Science and Technology 8(4), 385-398.
Маковинг, И. (2010). «Микроволновая сушка древесно-цементных композитов», Wood Research 55(2), 115-124.
Мэллони, Т. М. (1989). «Материалы для композиционных плит: свойства и испытания современных древесно-стружечных плит и плит для сухой обработки», Производство 120-128.
Маркос-Мезон, В., Мишель А., Солгаард А., Фишер Г., Эдвардсен К. и Сковхус Т.Л. (2018). «Коррозионная стойкость бетона, армированного стальной фиброй. Обзор литературы», Cement and Concrete Research 1-20. DOI: 10.1016/j.cemconres.2017.05.016
Мартейнссон, Б., и Гудмундссон, Э. (2018). «Цементно-стружечные плиты с различными типами натуральных волокон — с использованием впрыска углекислого газа для усиления начального сцепления», Open Journal of Composite Materials 8(1), 28-42.DOI: 10.4236/ojcm.2018.81003
Матоски, А., Хара, М.М., Ивакири, С., и Касаби, Дж.М. (2013). «Uso de aditivos aceleradores em painéis de cimento-madeira: Características e propridedes», Acta Scientiarum – Technology 35(4), 655-660. DOI: 10.4025/actascitechnol.v35i4.11261
Медина, Л. А., и Шледевски, Р. (2009). «Жидкое стекло в качестве гидрофобной и огнезащитной добавки для композитов, армированных натуральным волокном», Journal of Nanostructured Polymers and Nanocomposites 5(4), 107-114.
Медведь, С., и Резник, Дж. (2003). «Влияние размера частиц бука, используемого в поверхностном слое, на прочность при изгибе трехслойной ДСП», Сборник Госдарства в Лесарстве , 72, 197-207.
Мохаммед, А., Абдалла, А., и Ясин Абдельгадир, А. (2016). «Влияние соотношения цемент/древесина и размера частиц на некоторые свойства древесно-цементных заполнителей из акацинила», , Судан Сильва, 12(i), 41–52.
Мохаммед, С., и Сафиулла, О. (2018). «Оптимизация содержания SO 3 в алжирском портландцементе: исследование влияния различных количеств гипса на свойства цемента», Construction and Building Materials 164, 362-370.DOI: 10.1016/j.conbuildmat.2017. 12.218
Мослеми, А.А., и Пфистер, С.К. (1986). «Влияние соотношения цемент/древесина и типа цемента на прочность на изгиб и стабильность размеров древесно-цементных композитных панелей», Wood and Fiber Science 19(2), 165–175.
На Б., Ван З., Ван Х. и Лу Х. (2014). «Обзор совместимости древесины и цемента», Wood Research 59(5), 813-826.
Насер, Р. А., и Аль-Мефаррей, Х. А. (2011). «Средние части финиковой пальмы как сырье для производства древесно-цементных композитов в Саудовской Аравии», World Applied Science Journal 5(12), 1651-1658.
Насер, Р. А., Салем, М. З. М., Аль-Меферрей, Х. А., и Ареф, И. М. (2016). «Использование отходов обрезки деревьев для производства армированных древесиной цементных композитов», Цементные и бетонные композиты 72, 246-256. DOI: 10.1016/j.cemconcomp.2016.06.008
Назерян, М., и Садегиипанах, В. (2013). «Цементно-стружечная плита со смесью пшеничной соломы и древесины тополя», Journal of Forestry Research 24(2), 381-390. DOI: 10.1007/s11676-013-0363-8
Пападопулос, А.Н. (2009). «Физико-механические свойства и устойчивость к базидиомицетам древесно-стружечных плит, изготовленных из цемента и древесных частиц Carpinus betulus L.», Wood Research 54(2), 95-100.
Паска, С.А., Хартли, И.Д., Рид, М.Э., и Тринг, Р.В. (2010). «Оценка совместимости древесины сосны скрученной ( Pinus contorta var. Latifolia) с портландцементом», Materials 3(12), 5311-5319. DOI: 10.3390/ma3125311
Филлипс, Д.R. и Hse, C.Y., (1987). «Влияние соотношения цемент/древесина и условий хранения древесины на температуру гидратации, время гидратации и прочность на сжатие древесно-цементных смесей», Wood and Fiber Science 19(3), 262-268.
Ци, Х., Купер, П.А., и Хутон, Д. (2010). «Исследование основных процессов быстротвердеющей древесно-цементно-водной смеси с CO 2 », European Journal of Wood and Wood Products 68(1), 35-41. DOI: 10. 1007/s00107-009-0351-z
Кирога, А., Марзокки, В., и Ринтоул, И. (2016). «Влияние обработки древесины на механические свойства древесно-цементных композитов и древесных волокон Populus Euroamericana », Composites Part B: Engineering 84, 25-32. DOI: 10.1016/j.compositesb.2015.08.069
Ротон, Р. Н. и Хорнсби, П. Р. (1996). «Огнезащитные эффекты гидроксида магния», Polymer Degradation and Stability 54 (2-3 SPEC. ISS.), 383-385. DOI: 10.1016/s0141-3910(96)00067-5
Саваль, Дж.М., Лапуэнта Р., Наварро В. и Тенза-Абриль А. Дж. (2014). «Огнестойкость, физические и механические характеристики древесно-стружечных плит, содержащих отходы океанической Posidonia», Mater. Констр. 64, 314. DOI: 10.3989/mc.2014.01413
Саян П., Саргут С. Т. и Киран Б. (2010). «Влияние примесей на микротвердость декагидрата буры», Powder Technology 197(3), 254-259. DOI: 10.1016/j.powtec.2009.09.025
Сораушян, П., Ван, Дж. П. , и Хассан, М.(2012). «Характеристики долговечности композитов, армированных целлюлозным волокном, отвержденных CO 2 », Construction and Building Materials 34, 44-53. DOI: 10.1016/j.conbuildmat.2012.02.016
Сорушян, П., Вон, Дж. П., и Хассан, М. (2013). «Анализ долговечности и микроструктуры цементно-стружечной плиты, отвержденной углекислым газом», Cement and Concrete Composites 41, 34-44. DOI: 10.1016/j.cemconcomp.2013.04.014
Сотаннде А., Олввадаре А. О., Огедох О.и Адеогун, П.Ф. (2012). «Оценка цементно-стружечной плиты, изготовленной из древесных отходов Afzelia africana », Journal of Engineering Science and Technology 7(6), 732-743.
Стивенс, Р. ван Эс, Д.С., Беземер, Р.К., и Краненбарг, А. (2006). «Взаимосвязь структура-активность огнезащитных соединений фосфора в древесине», Polymer Degradation and Stability 91(4), 832-841. DOI: 10.1016/j.polymdegradstab.2005.06.014
Стокке, Д.Д., Ву, К., и Хан, Г. (2013). «Введение в композиты из древесины и натуральных волокон», серия Wiley в журнале «Возобновляемые ресурсы», Бельгия, стр. 225–226.
Табарса Т. и Ашори А. (2011). «Формомерная стабильность и водопоглощение древесных композитов на цементной основе», Journal of Polymers and the Environment 19(2), 518-521. DOI: 10.1007/s10924-011-0295-3
Таскирвати И., Сануси Д., Бахарудин Б., Агуссалим А. и Сухасман С. (2019). «Характеристики цементной плиты с добавлением CO 2 методом впрыскивания CaCl2 в качестве добавки с использованием двух пород древесины из общественных лесов», Серия конференций IOP: Науки о Земле и окружающей среде 270(1).DOI: 10.1088/1755-1315/270/1/012055
Вайкеллионис, Г., и Вайкельонис, Р. (2006). «Гидратация цемента в присутствии экстрактивных веществ древесины и минеральных добавок пуццолана», Ceramics-Silikáty 50(2), 115-122
Ван дер Вин, И. и де Бур, Дж. (2012). «Фосфорные антипирены: свойства, производство, присутствие в окружающей среде, токсичность и анализ», Chemosphere 88(10), 1119-1153. DOI: 10.1016/j.chemosphere.2012.03.067
Ван, Л., Чен, С.С., Цанг, Д. К. В., Пун, К. С., и Дай, Дж. Г. (2017a). «Отверждение CO2 и армирование волокнами для экологически чистой переработки загрязненной древесины в высокоэффективные цементно-стружечные плиты», Journal of CO 2 Utilization 18, 107–116. DOI: 10.1016/j.jcou.2017.01.018
Ван, Л., Ю, И.К.М., Цанг, Д.К.В., Ли, С., Ли, Дж., Пун, К.С., Ван, Ю.С., и Дай, Дж.Г. (2017b). «Преобразование древесных отходов в водостойкие плиты из магнезиально-фосфатного цемента, модифицированные глиноземом и красным шламом», Journal of Cleaner Production 452-462.DOI: 10.1016/j.jclepro.2017.09.038
Wang, L., Yu, IKM, Tsang, DCW, Yu, K., Li, S., Poon, CS, and Dai, JG (2018) «Вторичная переработка древесных отходов в армированные волокном плиты из фосфата магния». Строительство и строительные материалы 159, 54-63. DOI: 10.1016/j.conbuildmat.2017.10.107
Ван, X., и Ю, Y. (2012). «Совместимость двух распространенных быстрорастущих видов с портландцементом». Журнал Индийской академии наук о древесине , 9(2), 154–159.
Вэй, Ю.М., Гуан Чжоу, Ю., и Томита, Б. (2000). «Поведение гидратации композита на основе древесного цемента I: оценка влияния пород древесины на совместимость и прочность с обычным портландцементом», Journal of Wood Science 46(4), 296-302. DOI: 10.1007/BF00766220
Ву, К.С., Лю, Ю.Л. и Чиу, Ю.С. (2002). «Эпоксидные смолы, содержащие огнезащитные элементы из эпоксидных соединений с включением кремния, отвержденных фосфорсодержащими или азотсодержащими отвердителями», Polymer 43(15), 4277-4284.DOI: 10.1016/S0032-3861(02)00234-3
Вульф, Ф., Шульц, К., Брозель, Л., и Пфрим, А. (2015). «Armirani beton s mineraliziranim česticama drva kao element za ukrućenje smanjene gustoće», Drvna Industrija 66(1), 57-62. DOI: 10.5552/др.2015.1345
Се, X., Гоу, Г., Чжоу, З., Цзян, М., Сюй, X. , Ван, З. и Хуэй, Д. (2016). «Влияние предварительной обработки рисовой соломы на гидратацию композитов на основе цемента с наполнителем из соломы», Construction and Building Materials 113, 449-455.DOI: 10.1016/j.conbuildmat.2016.03.088
Ян В., Чжу З., Ши Дж., Чжао Б., Чен З. и Ву Ю. (2017). «Характеристика термического разложения гидроксида наномагния с помощью спектроскопии времени жизни аннигиляции позитронов», Powder Technology 311, 206-212. DOI: 10.1016/j.powtec.2017.01.059
Чжан, К., и Сунь, К. (2018). «Использование композита из проволочной сетки и полиуретанового цемента (WM-PUC) для усиления железобетонных тавровых балок при изгибе», Journal of Building Engineering 122-136.DOI: 10.1016/j.jobe.2017.11.008
Чжан Т., Лю В., Ван М., Лю П., Пан Ю. и Лю Д. (2016). «Синергетический эффект производного ароматической борной кислоты и гидроксида магния на огнестойкость эпоксидной смолы», Polymer Degradation and Stability 130, 257-263. DOI: 10.1016/j.polymdegradstab.2016.06.011
Чжан, X., Ван, Л., Чжан, Дж., Ма, Ю. и Луи., Ю. (2017). «Поведение скрепленных предварительно напряженных бетонных балок при изгибе при коррозии прядей», Nuclear Engineering and Design 313, 414-424.DOI: 10.1016/j.nucengdes.2017.01.004
Чжуа, Д., Ная, X., Лан, С., Биан, С., Лю, X., и Ли, В. (2016). «Модификация поверхности вискеров гидрата гидроксида сульфата магния с использованием силанового связующего агента сухим способом», Applied Surface Science 390, 25-30. DOI: 10.1016/j.apsusc.2016.08.033
Zuo, Y., Xiao, J., Wang, J., Liu, W., Li, X., and Wang, Y. (2018). «Приготовление и характеристика огнестойких композитов из соломы и магниевого цемента с органо-неорганической структурой металла», Construction and Building Materials 171, 404-413.DOI: 10.1016/j.conbuildmat.2018.03.111
Статья отправлена: 9 марта 2020 г.; Экспертная проверка завершена: 24 мая 2020 г.; Получена исправленная версия: 22 июня 2020 г. ; Принято: 27 июня 2020 г.; Опубликовано: 1 июля 2020 г.
DOI: 10.15376/biores.15.3.Brahmia
Top PDF Строительство здания из опилкобетона
Экспериментальное исследование прочностных свойств стальной фибровой стружки для бетонов марок М-25 и М-30
Обзор М30 с 0%, 0.25%, 0,5% и 0,75% по объему цемента. Они продемонстрировали результаты, что усиленный полипропиленовым волокном твердый материал обеспечивает более высокое качество изгиба при расширении 0,5% полипропиленового волокна по объему цемента. Саид Хесами, Саид Ахмади, Махди Нематзаде и др., Construction и Building Materials 53 (2014): 680-691. Существенно расширяется использование проницаемого твердого асфальта за счет уменьшения уличного стока и удержания волнения.В любом случае, этот вид асфальта не может быть использован для значительных перемещений из-за большого количества пустот и, следовательно, низкого качества проницаемого цемента. Зола рисовой шелухи (RHA) использовалась как часть заказа для усиления пуццоланового связующего клея и воздействия весовых норм 0%, 2%, 4%, 6%, 8%, 10% и 12% в качестве замены бетона . в твердых смесях на механические свойства. Кроме того, 0,2% Vf стекла (где Vf — объем волокна, добавляемый к объему цемента), 0.Для улучшения механических свойств проницаемого цемента использовались пряди из стали с содержанием Vf 5% и из полифениленсульфида (PPS) с содержанием Vf 0,3%. Wenjie Ge Jiwen Zhang (2015) В этой статье рассматриваются методы изгиба половинных и полутвердых стержней, усиленных стержнями BFRP (пластик, армированный базальтовым волокном), и стальными стержнями. Были проведены испытания на пластичность, стандартные испытания стержней из BFRP на вытяжку и статический анализ на изгиб пяти различных усиленных сплошных валов полукровки.Испытания показывают, что стержни из BFRP обладают высокой жесткостью и низким универсальным модулем по сравнению со стальными стержнями. Прочность сцепления между ребристыми стержнями из BFRP и бетоном аналогична прочности стальных стержней с резьбой того же диаметра, и, по-видимому, наблюдается хорошее сцепление.
Прочность соединения стальных стержней диаметром 8 мм немного выше, чем у стальных стержней диаметром 10 мм. Относительный коэффициент прочности связи VF стержней из BFRP можно считать равным 1,0. Предлагается использовать гибридные железобетонные балки в конструкциях с высокими требованиями к прочности на изгиб, но низкими требованиями к прогибу.Пластичность гибридных железобетонных балок может соответствовать требованиям при соответствующем управлении AF/AS.
7 Читать далее
Влияние добавки опилок на физико-механические свойства керамического кирпича для получения легкого строительного материала
Авторов: Башир Чемани, Халима Чемани
Резюме:
В статье исследуется применение различных опилочные материалы в производстве легкого теплоизоляционного кирпича.
Ключевые слова: Глиняный кирпич,
Пористость,
Опилки.
Цифровой идентификатор объекта (DOI): doi.org/10.5281/zenodo.1077395
Процессия АПА БибТекс Чикаго EndNote Гарвард JSON МДА РИС XML ISO 690 PDF Скачано 3872Каталожные номера:
[1] А.У. Элинва, Ю. А. Махмуд. «Зола от древесных отходов как материал-заменитель цемента», Цементно-бетонные композиты, т.24, н┬░. 2, стр. 219-222, 2002.
[2] Ф.Ф. Удойо, ПУ. Дашибиль, «Опилки золы как материал для бетона», ASCE, 0899-1561; vol.14, n┬░.2, pp. 173-176, 2002.
[3] Тургут П., Есилата Б. Физико-механические и тепловые характеристики недавно разработанные кирпичи с добавлением резины», «Энергия и здания», т. 40, стр. 679-688, 2008.
[4] П.Тургут, Х.М. Алгин, «Известняковая пыль и древесные опилки в виде кирпича». материал», Строительство и окружающая среда, т. 2, стр. 3399-3403, 2006.
[5] И. Демир, «Исследование производства строительного кирпича с чай из переработанных отходов», «Строительство и окружающая среда», т.

[6] О. Каяли, «Высокоэффективные кирпичи из летучей золы», Материалы Конференция «Мир угольной золы», Лексинтон, Кентукки, 2005 г.
. 7. Лин К.Л. Обоснование возможности применения кирпича из бытового массива. шлак зольной пыли мусоросжигательного завода «. Журнал опасных материалов, том 137, стр. 1810-1816, 2006.
[8] С. Вейсех, А. А. Юсефи, «Использование полистирола в легком кирпиче». производство», Иранский полимерный журнал, т. 12, № 4, стр. 324-329, 2003 г.
[9] Т.Баседжио, Ф. Берутти, А. Бернадес, К. П. Бергманн, «Экологический и технические аспекты утилизации шлама кожевенного производства в качестве сырья. материал для глиняных изделий», журнал Европейского керамического общества, том 22, стр. 2251-2259, 2002.
[10] М. Донди, М. Марсигли, Б. Фаббри, «Утилизация промышленных и городских отходы кирпичного производства» — обзор. Tile and Brick International 13 (1), 218-225. 1997.
[11] С. Хорисава, М. Сунагава, Ю. Тамаи, Ю.

[12] В. Дюкман, Т. Копар, «Опилки и шламы бумагоделательного производства как порообразователей для легкого глиняного кирпича. Керамика, вып. 21, н┬░. 2, стр. 81-86, 2001 г.
[13] R Sheyder, Les pÜótes et les glaúures Céramiques. Ecole Suisse de Керамик, 1970 г.
[14] Ж. Риго, «La cuisson des matières premières et des pÃótes céramiques», Industrie Céramique n┬░. 685, стр. 685-697. Джульетта 1975 г.
[15] М. Рэндалл. «Теория и практика спекания», John Willey and Sons, Inc.Нью-Йорк, 1996, стр. 209-213.
[16] J. Peyssou, «Industries céramique», n┬░. 661, стр. 255-261, 377-383, 1973.
Стоимость, плюсы и минусы и многое другое
Неудивительно, что столешницы из мясных блоков являются неотъемлемой частью как уютных загородных коттеджей, так и деревенских фермерских домов. Поверхность, состоящая из собранных деревянных досок, теплее и привлекательнее, чем другие материалы, и никогда не выйдет из моды. Взятый непосредственно из природы, мясной блок является биоразлагаемым и экологически чистым, и он привносит немного землистого элемента в любую кухню.
Поскольку древесина настолько нейтральна, многие домовладельцы смешивают ее с другими материалами: вы можете установить все столешницы из разделочных блоков, включить встроенную разделочную поверхность или вместо этого выбрать остров из разделочных блоков.
Но есть и недостатки. Мы расчистили опилки, чтобы раскрыть доступные варианты, а также цену, плюсы и минусы.
Фотография Донны Гриффит, дизайн Карен Бертелсен
Типы столешниц из мясных блоков
Существует множество вариантов столешниц из мясных блоков, начиная с различных пород дерева, включая клен, вишню, орех и дуб.
«Твердый клен имеет самую высокую плотность и представляет собой твердую древесину с закрытыми волокнами, что делает его предпочтительной поверхностью», — говорит Стив Плесс, менеджер по продажам национальных кухонных столешниц
в John Boos & Co. CountryLiving.com. К счастью, он также более доступен, чем его аналоги с закрытым зерном, вишня и орех, из которых также получаются отличные столешницы. А тут дуб. Плесс объясняет, что древесина дуба с открытыми волокнами не идеальна для непосредственного приготовления пищи. Однако в лакированном или лакированном виде материал вполне подходит для общих целей.
Клен хард-рок
· Самая легкая твердая древесина с закрытыми волокнами
· Самый прочный и плотный из всех видов клена
· Самая доступная кухонная столешница
Американская вишня
· Полутоновая твердая древесина с закрытыми волокнами
· Пользуется спросом благодаря привлекательному красному оттенку
· Дороже клена
Американский черный орех
· Темная твердая древесина с закрытыми волокнами
· Ценится за насыщенный глубокий оттенок
· Дороже, чем клен
Аппалачский красный дуб
· Древесина с открытыми волокнами с большим характером
· Текстура древесины более заметна, чем у других пород
· Не предназначен для приготовления пищи
Помимо типа древесины, вы также должны учитывать тип конструкции: кромка (при которой доски укладываются параллельно так, чтобы их «кромки» были видны), кромка (при которой небольшие квадратные кусочки выстраиваются вертикально с « концы») и смешанные (при которых разные длины соединяются без определенного узора).
Зерно кромки
· Полноразмерные сплошные рельсы
· Расположены рядом или параллельно и склеены
· Самый распространенный
Концевое зерно
· Небольшие квадратные деревянные бруски, стоящие на «конце»
· Расположены вертикально и склеены в шахматном порядке
· Обычно дороже
Смешанный
· Длины внутренних поручней с шиповым соединением и полноразмерных наружных поручней
· Отличается большим разнообразием цветов между светлым и темным деревом
Смешанный (морилка грецкого ореха)
Амазонка.ком
· Длина сращенных на шип внутренних перекладин и полноразмерных наружных перекладин
· Отличается большим разнообразием цветов между светлым и темным деревом
Что касается отделки, Плесс рекомендует домовладельцам подумать о том, как они видят себя, используя свои столешницы из разделочных блоков. Для зон приготовления пищи вам понадобится нанести (и периодически наносить повторно) масляное покрытие. Но если это просто общая или обеденная поверхность, выберите лаковое покрытие, так как масляное покрытие может сойти с одежды или бумаги.
Стоимость столешниц Butcher-Block
Цена, которую вы платите, зависит от вида и конструкции, а также района, в котором вы живете.
Энни Шлехтер
Но разделочный блок, как правило, довольно конкурентоспособен с другими материалами для столешницы, говорит Плесс, добавляя, что стандартная столешница из клена с кромкой продается по цене от 35 до 38 долларов за квадратный фут — дешевле, чем гранит, но дороже, чем ламинат.
Стоимость установки также зависит от местоположения, поэтому обращайтесь за консультацией.
«Я бы оценил один час на погонный фут как количество времени, которое потребуется для установки крышки», — советует Плесс. «Установка столешницы размером 60 x 30 дюймов займет примерно пять часов. Если оплата труда составляет 25 долларов в час, то установка будет стоить 125 долларов. Если установка составляет 65 долларов в час, установка будет стоить 325 долларов».
Нанимать ли вам профессионала для помощи или нет, зависит только от вас и, вероятно, от уровня сложности вашего проекта.
Плюсы и минусы столешниц Butcher-Block
Pro: Они так же удобны для ножей, как и для глаз. Единственная столешница, которую можно использовать в качестве разделочной поверхности, разделочная доска не затупит ваши ножи, как каменные или бетонные столешницы. Мягкая поверхность также делает кухню более тихой. А для тех, кто немного неуклюж, посуда с меньшей вероятностью разобьется при падении на дерево, а не на камень.
Макс Ким-Би
Con: Разделочный блок подвержен царапинам, вмятинам и пятнам. Если вы планируете резать прямо на столешнице, вам придется немного (или много) испачкать продукты. Тот стакан, который вы уронили, может просто оставить вмятину, а вино внутри может осесть в пятно.
Pro: Но они легко восстанавливаются. «Чтобы удалить зазубрины или выбоины после многих лет износа, просто отшлифуйте поверхность [мелкой наждачной бумагой] так же, как и зерна, и снова смажьте маслом», — говорит нам Мэнди Кук, другой представитель John Boos & Co. «Шлифование открывает совершенно новую режущую поверхность.» Или, чтобы сохранить разделочную доску без царапин, просто используйте разделочную доску, как и на любой другой столешнице.
Когда дело доходит до чистки, мыло и вода обычно должны помочь также служат дезинфицирующим средством и дезодорантом.Чтобы оттереть глубокие пятна, воспользуйтесь этим хитрым приемом очистки разделочной доски: разрежьте лимон пополам, окуните в соль и протрите пораженный участок.
Древесина высыхает.Чтобы он блестел, каждые несколько недель наносите на покрытые маслом столешницы безопасное для пищевых продуктов масло (например, стандартное пищевое минеральное масло). С другой стороны, столешницы из лакированного лака или покрытые полуматовым лаком не должны требовать много усилий. При необходимости вы можете обновить оба покрытия с помощью нетоксичного полиуретанового геля (например, EZ-DO).
Этот контент создается и поддерживается третьей стороной и импортируется на эту страницу, чтобы помочь пользователям указать свои адреса электронной почты.Вы можете найти дополнительную информацию об этом и подобном контенте на сайте piano.io.
.